▼
Scroll to page 2
of
76
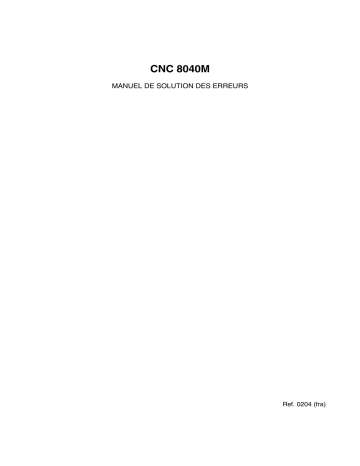
CNC 8040M MANUEL DE SOLUTION DES ERREURS Ref. 0204 (fra) INDEX Erreurs de programmation ..................................................... 1 (0001-0255) Erreurs de preparation et execution ................................... 34 (1000-1238) Erreurs de hardware ............................................................. 52 (2000-2028) Erreurs de PLC ...................................................................... 55 (3000-3004) Erreurs de regulation............................................................ 56 (4000-4025) Erreurs dans les donnees des tables ................................. 58 Erreurs du mode de travail 8040MC .................................... 61 Index alphabétique ............................................................... 71 CNC 8040M ERREURS DE PROGRAMMATION 0001 ‘Ligne vide.’ DETECTION Durant l’édition (durant l’exécution en programmes transmis par DNC). CAUSE/S Les différentes causes sont les suivantes: 1.-Lorsqu’on tente de s’introduire dans le programme ou d’exécuter un bloc dans lequel aucune information n’est éditée, ou seule l’étiquette apparaît (numéro de bloc). 2.-Dans le «Cycle fixe de poche avec îlots (G66)», lorsque le paramètre “S” (début du profil) est plus grand que le paramètre “E” (fin du profil). SOLUTION La solution à chacune des causes est la suivante: 1.-La CNC ne peut introduire dans le programme, ni exécuter une ligne vide. Si on désire introduire une ligne ne contenant pas d’information dans le programme, il faut utiliser le symbole «;» au début du bloc. La CNC ne tiendra pas compte de ce qui sera édité ensuite dans ce bloc. 2.-La valeur du paramètre “S” (bloc où commence la définition du profil) devra être inférieure à la valeur du paramètre “E” (bloc où termine la définition du profil). 0002 ‘Valeur inadaptée.’ DETECTION Lors de l’édition (durant l’exécution en programmes transmis par DNC). CAUSE/S Les différentes causes sont les suivantes: 1.-Lorsqu’on édite une coordonnée de l’axe après les conditions de coupe (F, S, T ou D) ou des fonctions «M». 2.-Lorsque les marques de blocs conditionnels (/1, /2 ou /3) ne sont pas au début du bloc. 3.-Lorsqu’en programmant en code ISO, on programme une étiquette (numéro de bloc) plus grande que 9999. 4.-lorsque durant l’opération de finition (G68) dans le «Cycle fixe de poche avec îlots», on a tenté de définir les coordonnées du point où on désire commencer l’usinage. 5.-En programmant en langage de haut niveau, on a programmé dans la commande RPT un nombre de répétitions supérieur à 9999. SOLUTION La solution à chacune des causes est: 1/2.- Se rappeler que l’ordre de programmation est: 1.- Bloc conditionnel (/1, /2 ou /3). 2.- Etiquette (N). 3.- Fonctions «G». 4.- Coordonnées des axes (X, Y, Z…). 5.- Conditions de coupe (F, S, T, D). 6.- Fonctions «M». Il n’est pas nécessaire de programmer toutes les valeurs. 3.-Corriger la syntaxe du bloc. Programmer les étiquettes dans l’intervalle 0-9999 4.-On ne peut programmer aucun point dans la définition du cycle de finition (G68) pour le «Cycle de poche avec îlots». La CNC choisit le point où l’usinage commencera. Le format de programmation est: G68 B— L— Q— I— R— K— V— Et ensuite, les conditions de coupe. 5.-Corriger la syntaxe du bloc. Programmer un nombre de répétitions dans l’intervalle 0-9999. 0003 ‘Ordre des valeurs incorrect.’ DETECTION Durant l’édition (durant l’exécution en programmes transmis par DNC). CAUSE L’ordre dans lequel les conditions de coupe ou les valeurs de l’outil ont été programmées n’est pas correct. SOLUTION Se rappeler que l’ordre de programmation est: … F— S— T— D— … Il n’est pas nécessaire de programmer toutes les valeurs. MANUEL DE SOLUTION DES ERREURS 1 CNC 8040M 0004 ‘Le bloc n’admet pas d’autre information.’ DETECTION Durant l’édition (durant l’exécution en programmes transmis par DNC). CAUSE/S Les différentes causes sont: 1.-Lorsqu’on édite une fonction «G» après une coordonnée d’axe. 2.-Lorsqu’on tente d’éditer quelque information après une fonction «G» (ou ses paramètres associés) et qu’elle doit être seule dans le bloc (ou qui n’admet que ses propres valeurs associées). 3.-Lorsqu’on assigne une valeur numérique à un paramètre qui n’en a pas besoin. SOLUTION La solution à chacune des causes est: 1.-Se rappeler que l’ordre de programmation est: 1.- Bloc conditionnel (/1, /2 ou /3). 2.- Etiquette (N). 3.- Fonctions «G». 4.- Coordonnées des axes (X, Y, Z…). 5.- Conditions de coupe (F, S, T, D). 6.- Fonctions «M». Il n’est pas nécessaire de programmer toutes les valeurs. 2.-Il y a quelques fonctions «G» qui comportent une information associée dans le bloc. Il est probable que ce type de fonctions ne permette pas la programmation d’autre information consécutive à ses paramètres associés. La programmation de conditions de coupe (F, S), les valeurs de l’outil (T, D) ou fonctions «M» ne sera pas non plus permise. 3.-Il y a des fonctions «G» qui comprennent des paramètres associés qui ne requièrent pas d’être définis par des valeurs. 0005 ‘Information répétée.’ DETECTION Durant l’édition (durant l’exécution en programmes transmis par DNC). CAUSE La même valeur a été introduite deux fois dans un bloc. SOLUTION Corriger la syntaxe du bloc. On ne peut définir deux fois la même valeur dans un bloc. 0006 ‘Format de la valeur inadapté.’ DETECTION Durant l’édition (durant l’exécution en programmes transmis par DNC). CAUSE Durant la définition des paramètres d’un cycle fixe d’usinage, une valeur négative a été assignée à un paramètre qui n’admet que des valeurs positives. SOLUTION Vérifier le format du cycle fixe. Dans certains cycles fixes, il y a des paramètres qui n’admettent que des valeurs positives. 0007 ‘Fonctions G incompatibles.’ DETECTION Durant l’édition (durant l’exécution en programmes transmis par DNC). 2 CAUSE/S Les différentes causes sont les suivantes: 1.-Lorsque dans un même bloc, on programme deux fonctions «G» contraires entre elles. 2.-Lorsqu’on tente de définir un cycle fixe dans un bloc qui contient un déplacement non linéaire (G02, G03, G08, G09, G33). SOLUTION La solution à chacune des causes est: 1.-Il y a de groupes de fonctions «G» qui ne peuvent aller ensemble dans un même bloc, car elles représentent des actions contraires entre elles. Par exemple: G01/G02: Interpolation linéaire et circulaire. G41/G42: Compensation du rayon à droite et à gauche. Ce type de fonctions doit être programmé dans des blocs différents. 2.-La définition d’un cycle fixe doit être réalisée dans un bloc qui contienne un mouvement linéaire. C’est à dire que pour définir un cycle fixe il faut que la fonction “G00” ou “G01” soit activée. La définition de mouvements non linéaires (G02, G03, G08 y G09)peut être réalisée dans les blocs qui suivent la définition du profil. MANUEL DE SOLUTION DES ERREURS CNC 8040M 0008 ‘Fonction G inexistante.’ DETECTION Durant l’édition (durant l’exécution en programmes transmis par DNC). CAUSE Une fonction «G» qui n’existe pas a été programmée. SOLUTION Réviser la syntaxe du bloc et vérifier qu’on ne tente pas d’éditer une fonction «G» différente par erreur. 0009 ‘Il n’est plus admis de fonctions G.’ DETECTION Durant l’édition (durant l’exécution en programmes transmis par DNC). CAUSE Une fonction «G» a été programmée après les conditions de coupe ou les valeurs de l’outil. SOLUTION Rappeler que l’ordre de programmation est : 1.- Bloc conditionnel (/1, /2 ou /3). 2.- Etiquette (N). 3.- Fonctions «G». 4.- Coordonnées des axes . (X,Y,Z…). 5.- Conditions de coupe (F, S, T, D). 6.- Fonctions «M». Il n’est pas nécessaire de programmer toutes les valeurs. 0010 ‘Il n’est plus admis de fonctions M.’ DETECTION Durant l’édition (durant l’exécution en programmes transmis par DNC). CAUSE Plus de 7 fonctions ont été programmées dans un même bloc. SOLUTION La CNC ne permet pas de programmer plus de 7 fonctions «M» dans un même bloc. Si on désire exécuter quelque fonction de plus, il faut l’éditer dans un bloc à part. Les fonctions «M» peuvent être seules dans le bloc. 0011 ‘La fonction G/M doit être seule.’ DETECTION Durant l’édition (durant l’exécution en programmes transmis par DNC). CAUSE Dans le bloc, il y a une fonction «G» ou «M» qui doit être seule dans un bloc. SOLUTION Placer la fonction seule dans un bloc. 0012 ‘Programmer F,S,T,D avant les fonctions M.’ DETECTION Durant l’édition (durant l’exécution en programmes transmis par DNC). CAUSE Quelques conditions de coupe (F, S) ou valeur de l’outil (T, D) ont été programmées après les fonctions «M». SOLUTION Se rappeler que l’ordre de programmation est : … F— S— T— D— M— On peut programmer plusieurs fonctions «M» (jusqu’à 7). Il n’est pas obligatoire de définir toutes les données. 0014 ‘Ne pas programmer d’étiquette avec paramètre.’ DETECTION Durant l’édition (durant l’exécution en programmes transmis par DNC). CAUSE Une étiquette (numéro de bloc) a été définie avec un paramètre. SOLUTION La programmation du numéro de bloc est optionnelle, mais il n’est pas permis de le définir avec un paramètre. On ne peut le définir que moyennant un numéro entre 0-9999. 0015 ‘Nombre de répétitions impossible.’ DETECTION Durant l’édition (durant l’exécution en programmes transmis par DNC). CAUSE Une répétition a été programmée de façon incorrecte, ou le bloc n’admet pas de répétitions. SOLUTION Les instructions de haut niveau n’admettent pas de nombre de répétitions à la fin d bloc. Pour réaliser une répétition, assigner une étiquette au bloc à répéter (numéro de bloc), et utiliser l’instruction RPT. MANUEL DE SOLUTION DES ERREURS 3 CNC 8040M 0016 ‘Programmer: G15 axe.’ DETECTION Durant l’édition (durant l’exécution en programmes transmis par DNC). CAUSE Dans la fonction «Sélection de l’axe longitudinal (G15)» le paramètre correspondant à l’axe n’a pas été programmé. SOLUTION Réviser la syntaxe du bloc. Dans la définition de la fonction “G15”, il faut obligatoirement programmer le nom du nouvel axe longitudinal. 0017 ‘Programmer: G16 axe-axe.’ DETECTION Durant l’édition (durant l’exécution en programmes transmis par DNC). CAUSE Dans la fonction «Sélection du plan principal en deux directions (G16)» un des deux paramètres correspondant aux axes n’a pas été programmé. SOLUTION Réviser la syntaxe du bloc. Dans la définition de la fonction “G16”, il faut obligatoirement programmer le nom des deux axes qui définissent le nouveau plan de travail. 0018 ‘Programmer: G22 K(1/2/3/4) S(0/1/2).’ DETECTION Durant l’édition (durant l’exécution en programmes transmis par DNC). CAUSE Dans la fonction «Habilitation/déshabilitation zones de travail (G22)» le type d’habilitation ou de déshabilitation de la zone de travail n’a pas été défini, ou une valeur non correcte lui a été assignée. SOLUTION Le paramètre d’habilitation ou de déshabilitation des zones de travail “S” doit obligatoirement être programmé et il peut prendre les valeurs suivantes: - S=0: La zone de travail est déshabilitée . - S=1: Elle est habilitée comme zone de non entrée . - S=2: Elle est habilitée comme zone de non sortie. 0019 ‘Programmer zone K1, K2, K3 o K4.’ DETECTION Durant l'édition (durant l'exécution en programmes transmis par DNC). CAUSE/S Les différentes causes sont les suivantes: 1.-Une fonction “G20”, “G21” ou “G22”a été programmée et la zone de travail K1, K2, K3 o K4 n’a pas été définie. 2.-La zone de travail programmée est inférieure à 0 ou supérieure à 4. SOLUTION La solution à chacune des causes est la suivante: 1.-Le format de programmation des fonctions “G20”, “G21” et “G22” est: G20 K— X...C±5.5 (Définition des limites inférieures des zones de travail). G21 K— X...C±5.5 (Définition des limites supérieures des zones de travail ). G22 K— S—(Habilitation/déshabilitation des zones de travail). Où: -K : Est la zone de travail. - X...C : Sont les axes dans lesquels les limites sont définies. -S : Est le type d’habilitation de la zone de travail. 2.-La zone de travail “K” ne peut prendre que les valeurs K1, K2, K3 ou K4. 0020 ‘Programmer G36-G39 avec R+5.5.’ DETECTION Durant l'édition (durant l'exécution en programmes transmis par DNC). 4 CAUSE Dans la fonction “G36” ou “G39”, le paramètre “R” n’a pas été programmé, ou il lui a été assignée une valeur négative . SOLUTION Pour définir la fonction “G36” ou “G39”, il faut définir le paramètre “R” (toujours avec une valeur positive ). G36: R= Rayon d’arrondissage. G39: R= Distance depuis la fin du parcours programmée jusqu’au point où l’on désire réaliser le chanfrein . MANUEL DE SOLUTION DES ERREURS CNC 8040M 0021 ‘Programmer: G72 S5.5 ou axe(s).’ DETECTION Durant l'édition (durant l'exécution en programmes transmis par DNC). CAUSE/S Les différentes causes sont les suivantes: 1.-Lorsqu’on programme un facteur d’échelle générale (G72) et le facteur de l’échelle à appliquer n’est pas défini. 2.-Lorsqu’on programme un facteur d’échelle particulière (G72) à plusieurs axes, et l’ordre dans lequel les axes ont été définis n’est pas correct. SOLUTION Se rappeler que le format de programmation de cette fonction est: - “G72 S5.5” Lorsqu’on applique le facteur d’échelle générale (à tous les axes). - “G72 X…C5.5” Lorsqu’on applique le facteur d’échelle particulière à un ou plusieurs axes. 0022 ‘Programmer: G73 Q (angle) I J (centre).’ DETECTION Durant l'édition (durant l'exécution en programmes transmis par DNC). CAUSE/S Les paramètres de la fonction «Rotation du système de coordonnées (G73) n’ont pas été correctement programmés. Les causes peuvent en être les suivantes: 1.-L’angle de rotation n’a pas été défini. 2.-Seule a été définie une coordonnée du centre de rotation. 3.-L’ordre dans lequel les coordonnées du centre de rotation ont été définies n’est pas correct. SOLUTION Le format de programmation de cette fonction est: G73 Q (angle) [I J] (centre) Il faut obligatoirement programmer la valeur de “Q”. Les valeurs “I”, “J” sont optionnelles, mais si on les programme, alors il faut programmer les deux. 0023 ‘Bloc incompatible avec définition de profil.’ DETECTION Durant l'édition (durant l'exécution en programmes transmis par DNC). CAUSE Dans l’ensemble de blocs qui définit le profil d’une poche, il y a un bloc qui contient une fonction «G» qui ne peut faire partie de la définition du profil . SOLUTION Les fonctions “G” disponibles dans la définition du profil d’une poche sont: G00: Début de profil. G01: Interpolation linéaire. G02/G03: Interpolation circulaire à droite/gauche. G06: Centre de circonférence en coordonnées absolues. G08: Circonférence tangente à la trajectoire antérieure. G09: Circonférence par trois points. G36: Arrondissage des arêtes. G39: Chanfreinage. G53: Programmation par rapport au zéro machine. G70/G71: Programmation en pouces/millimètres. G90/G91: Programmation en coordonnées absolues/accroissantes. G93: Présélection de l’origine polaire. Et de plus, dans le profil d’une poche 3D: G16: Sélection plan principal par deux directions. G17: Plan principal X-Y et longitudinal Z. G18: Plan principal Z-X et longitudinal Y. G19: Plan principal Y-Z et longitudinal X. 0024 ‘Blocs de haut niveau non permis en définition de profil.’ DETECTION Durant l'édition (durant l'exécution en programmes transmis par DNC). CAUSE Dans l’ensemble des blocs qui définit le profil d’une poche, un bloc a été programmé en langage de haut niveau. SOLUTION La définition du profil d’une poche doit être réalisée en code ISO. Les instructions de haut niveau ne sont pas admises (GOTO, MSG, RPT ...). MANUEL DE SOLUTION DES ERREURS 5 CNC 8040M 0025 ‘Programmer: G77 axes (de 2 à 6).’ DETECTION Durant l'édition (durant l'exécution en programmes transmis par DNC). CAUSE Dans la fonction «Accouplement électronique des axes (G77)» les paramètres correspondant aux axes n’ont pas été programmés. SOLUTION Dans la programmation de la fonction “G77”, il faut programmer au moins deux axes. 0026 ‘Programmer: G93 I J.’ DETECTION Durant l'édition (durant l'exécution en programmes transmis par DNC). CAUSE Dans la fonction «Présélection de l’origine polaire (G93)» un des deux paramètres correspondant aux coordonnées de la nouvelle origine polaire n’a pas été programmé. SOLUTION Se rappeler que le format de programmation de cette fonction est: G93 I— J— Les valeurs “I”, “J” sont optionnelles, mais si on les programmes, il faut alors programmer les deux et elles indiquent la position de la nouvelle origine polaire. 0027 ‘G49 T X Y Z S, X Y Z A B C , ou, X Y Z Q R S.’ DETECTION Durant l'édition (durant l'exécution en programmes transmis par DNC). CAUSE Dans la fonction «Définition du plan incliné (G49)» la programmation d’un paramètre s’est répétée. SOLUTION Réviser la syntaxe du bloc. Les formats de programmation sont: TXYZS XYZABC XYZQRS 0028 ‘Ne pas programmer un cycle fixe avec G2/G3.’ DETECTION Durant l'édition (durant l'exécution en programmes transmis par DNC). CAUSE On a tenté d’exécuter un cycle fixe, tout étant activées les fonctions “G02”, “G03” o “G33”. SOLUTION Pour exécuter un cycle fixe“G00” ou “G01” doit être active. Il se peut que dans l’histoire du programme, une fonction “G02” ou “G03” ait été activée. Vérifier que ces fonctions ne soient pas actives dans la définition du cycle fixe. 0029 ‘G60: [A] /X I K/(2) [P Q R S T U V].’ DETECTION Durant l'édition (durant l'exécution en programmes transmis par DNC). 6 CAUSE Les paramètres du cycle «Usinage multiple en ligne droite (G60)» n’ont pas été correctement programmés. Les causes peuvent être diverses: 1.- Il reste à programmer un ou plusieurs paramètre obligatoire. 2.- Les paramètres du cycle n’ont pas été édités dans l’ordre correct. 3.- Il se peut qu’il y ait une donnée de trop. SOLUTION Dans ce type d’usinage, la programmation de deux des paramètres suivants est obligatoire: X : Longueur de la trajectoire. I : Pas entre les usinages . K : Nombre d’usinages. Les autres paramètres sont optionnels. Les paramètres doivent être édités dans l’ordre indiqué dans le message d’erreur. MANUEL DE SOLUTION DES ERREURS CNC 8040M 0030 ‘G61-2: [A B] /X I J/(2) Y J D (2)/ [P Q R S T U V].’ DETECTION Durant l'édition (durant l'exécution en programmes transmis par DNC). CAUSE Les paramètres du cycle «Usinage multiple formant un parallélogramme (G61)» ou «Usinage multiple en grille(G62)» n’ont pas été correctement programmés. Les causes peuvent être diverses: 1.- Il reste à programmer un ou plusieurs paramètres obligatoires. 2.- Les paramètres du cycle n’ont pas été édités dans l’ordre correct. 3.- Il se peut qu’il y ait une valeur de trop. SOLUTION Dans ce type d’usinage, la programmation de deux paramètres de chaque groupe (X, I, K) et (Y, J, D) est obligatoire. X/Y : Longueur de la trajectoire. I/J : Pas entre les usinages. K /D : Nombre d’usinages. Les autres paramètres sont optionnels. Les paramètres doivent être édités dans l’ordre indiqué dans le message d’erreur. 0031 ‘G63: X Y /I K/(1) [C P][P Q R S T U V].’ DETECTION Durant l'édition (durant l'exécution en programmes transmis par DNC). CAUSE Les paramètres du cycle «Usinage multiple formant un circonférence (G63)» n’ont pas été correctement programmés. Les causes peuvent être diverses: 1.- Il reste à programmer un ou plusieurs paramètres obligatoire. 2.- Les paramètres du cycle n’ont pas été édités dans l’ordre correct. 3.- Il se peut qu’il y ait une valeur de trop. SOLUTION Dans ce type d’usinage, il faut obligatoirement programmer: X/Y : Distance du centre au premier trou. Et une des valeurs suivantes: I : Pas angulaire entre usinages. K : Nombre d’usinages. Les autres paramètres sont optionnels. Les paramètres doivent être édités dans l’ordre indiqué dans le message d’erreur. 0032 ‘G64: X Y /I K/(1) [C P][P Q R S T U V].’ DETECTION Durant l'édition (durant l'exécution en programmes transmis par DNC). CAUSE Les paramètres du cycle «Usinage multiple formant un arc (G64)» n’ont pas été correctement programmés. Les causes peuvent être diverses: 1.- Il reste à programmer un ou plusieurs paramètres obligatoire. 2.- Les paramètres du cycle n’ont pas été édités dans l’ordre correct. 3.- Il se peut qu’il y ait une valeur de trop. SOLUTION Dans ce type d’usinage, il faut obligatoirement programmer: X/Y : Distance du centre au premier trou. B : Parcours angulaire de la trajectoire. Et une des valeurs suivantes : I : Pas angulaire entre usinages. K : Nombre d’usinages. Les autres paramètres sont optionnels. Les paramètres doivent être édités dans l’ordre indiqué dans le message d’erreur. MANUEL DE SOLUTION DES ERREURS 7 CNC 8040M 0033 ‘G65: X Y /A I/(1) [C P].’ DETECTION Durant l'édition (durant l'exécution en programmes transmis par DNC). CAUSE SOLUTION 0034 Les paramètres du cycle «Usinage programmé moyennant une corde en arc (G65)» n’ont pas été correctement programmés. Les causes peuvent être diverses: 1.- Il reste à programmer un ou plusieurs paramètres obligatoire. 2.- Les paramètres du cycle n’ont pas été édités dans l’ordre correct. 3.- Il se peut qu’il y ait une valeur de trop. Dans ce type d’usinage, il faut obligatoirement programmer: X/Y : Distance du centre au premier trou. Et une des valeurs suivantes: A : Angle de la médiatrice de la corde avec l’axe des abscisses (en degrés). I : Longueur de la corde. Les autres paramètres sont optionnels. Les paramètres doivent être édités dans l’ordre indiqué dans le message d’erreur. ‘G66: [D H][R I][C J][F K] S E [Q].’ DETECTION Durant l'édition (durant l'exécution en programmes transmis par DNC). CAUSE SOLUTION 0035 Les paramètres du «Cycle fixe de poche avec îlots (G66)» . n’ont pas été correctement programmés. Les causes peuvent être diverses: 1.- Un paramètre qui ne correspond pas au format d’appel a été programmé. 2.- Il reste à programmer un ou plusieurs paramètres obligatoire. 3.- Les paramètres du cycle n’ont pas été édités dans l’ordre correct. Dans ce cycle d’usinage, il faut obligatoirement programmer: S : Bloc où commence la description géométrique des profils qui composent la poche. E : Bloc où termine la description géométrique des profils qui composent la poche. Les autres paramètres sont optionnels. Les paramètres doivent être édités dans l’ordre indiqué dans le message d’erreur. De plus, on ne pourra définir le paramètre: H si D n’a pas été défini. I si R n’a pas été défini. J si C n’a pas été défini. K si F n’a pas été défini. Les autres paramètres sont optionnels. Les paramètres doivent être édités dans l’ordre indiqué dans le message d’erreur. La programmation de la position (X...C) n’est pas non plus permise là ou se réalise l’usinage. ‘G67: [A] B [C] [I] [R] [K] [V].’ DETECTION Durant l'édition (durant l'exécution en programmes transmis par DNC). 8 CAUSE Les paramètres de l’opération d’ébauchage (poche 2D/3D) ou semi-finition (poche 3D) dans le «Cycle fixe de poche avec îlots» n’ont pas été correctement programmés. Les causes peuvent être diverses: 1.- Un paramètre qui ne correspond pas au format d’appel a été programmé. 2.- Il reste à programmer un ou plusieurs paramètres obligatoire. 3.- Les paramètres du cycle n’ont pas été édités dans l’ordre correct. SOLUTION Dans ce cycle d’usinage, il faut obligatoirement programmer: OPÉRATION D’ÉBAUCHAGE (Poches 2D o 3D) B : Profondeur de passe. I : Profondeur totale de la poche. R : Cote du plan de référence. OPÉRATION DE SEMI-FINITION (Poches 3D) B : Profondeur de passe. I : Profondeur totale de la poche (s’il n’a pas été défini d’opération d’ébauchage). R : Cote du plan de référence (s’il n’a pas été défini d’opération d’ébauchage). Les autres paramètres sont optionnels. Les paramètres doivent être édités dans l’ordre indiqué dans le message d’erreur. Dans ce cycle fixe, la programmation de la position (X...C) n’est pas permise là ou se réalise l’usinage. MANUEL DE SOLUTION DES ERREURS CNC 8040M 0036 ‘G68: [B] [L] [Q] [J] [I] [R] [K].’ DETECTION Durant l'édition (durant l'exécution en programmes transmis par DNC). CAUSE Les paramètres de l’opération de finition (poches 2D/3D) dans le «Cycle fixe de poche avec îlots» n’ont pas été correctement programmés. Las causes peuvent êtres diverses: 1.- Un paramètre qui ne correspond pas au format d’appel a été programmé. 2.- Il reste à programmer un ou plusieurs paramètres obligatoire. 3.- Les paramètres du cycle n’ont pas été édités dans l’ordre correct. SOLUTION Dans ce cycle d’usinage, il faut obligatoirement programmer: Poches 2D B : Profondeur de passe (s’il n’a pas été défini d’opération d’ébauchage). I : Profondeur totale de la poche (s’il n’a pas été défini d’opération d’ébauchage). R : Cote du plan de référence (s’il n’a pas été défini d’opération d’ébauchage). Poches 3D B : Profondeur de passe. I : Profondeur totale de la poche (s’il n’a pas été défini d’opération d’ébauchage ni de semifinition ). R : Cote du plan de référence (s’il n’a pas été défini d’opération d’ébauchage ni de semifinition). Les autres paramètres sont optionnels. Les paramètres doivent être édités dans l’ordre indiqué dans le message d’erreur. Dans ce cycle fixe, la programmation de la position (X...C) n’est pas permise là ou se réalise l’usinage. 0037 ‘G69: I B [C D H J K L R].’ DETECTION Durant l'édition (durant l'exécution en programmes transmis par DNC). CAUSE Les paramètres dans le «Cycle fixe de perçage profond à pas variable (G69)» n’ont pas été programmés correctement. Les causes peuvent être diverses: 2.- Il reste à programmer un ou plusieurs paramètres obligatoire. 3.- Les paramètres du cycle n’ont pas été édités dans l’ordre correct. SOLUTION Dans ce cycle d’usinage, il faut obligatoirement programmer: I : Profondeur de l’usinage. B : Pas de perçage. Les autres paramètres sont optionnels. Les paramètres doivent être édités dans l’ordre indiqué dans le message d’erreur, la position (X...C) pouvant se définir là où se réalise l’usinage. 0038 ‘G81-84-85-86-89: I [K].’ DETECTION Durant l'édition (durant l'exécution en programmes transmis par DNC). CAUSE Les paramètres dans les cycles de perçage (G81), taraudage (G84), alésage (G85) ou alésage à mandrin (G86/G89) n’ont pas été correctement programmés. La cause peut en être, que le paramètre “I: Profondeur de l’usinage” reste à programmer dans le cycle fixe édité. SOLUTION Dans ce type d’usinage, il faut programmer obligatoirement: I : Profondeur d’usinage. Les autres paramètres sont optionnels. Les paramètres doivent être édités dans l’ordre indiqué dans le message d’erreur, la position (X...C) pouvant se définir là où se réalise l’usinage. 0039 ‘G82: I K.’ DETECCION Durant l'édition (durant l'exécution en programmes transmis par DNC). CAUSE Les paramètres dans le «Cycle fixe de perçage à temporisation (G82)» n’ont pas été programmés correctement. La cause peut en être qu’il reste à programmer un paramètre. SOLUTION Dans ce type d’usinage, la programmation des deux paramètres est obligatoire: I : Profondeur d’usinage. K: Temporisation dans le fond . Pour programmer un perçage sans temporisation dans le fond, il faut utiliser la fonction G81. Les paramètres doivent être édités dans l’ordre indiqué dans le message d’erreur, la position (X...C) pouvant être définie là où l’usinage se réalise. MANUEL DE SOLUTION DES ERREURS 9 CNC 8040M 0040 ‘G83: I J.’ DETECTION Durant l'édition (durant l'exécution en programmes transmis par DNC). CAUSE Les paramètres dans le «Cycle fixe de perçage profond à pas constant (G83)» n’ont pas été correctement programmés. La cause peut être qu’il reste à programmer un paramètre. SOLUTION Dans ce type d’usinage, il faut obligatoirement programmer: I : Profondeur d’usinage. J : Nombre de pas. Les paramètres doivent être édités dans l’ordre indiqué dans le message d’erreur, la position (X...C) pouvant être définie là où se réalise l’usinage. 0041 ‘G87: I J K B [C] [D] [H] [L] [V].’ DETECTION Durant l'édition (durant l'exécution en programmes transmis par DNC). CAUSE Les paramètres dans le «Cycle fixe de poche rectangulaire» n’ont pas été correctement programmés. Les causes peuvent être diverses: 1.- Il reste à programmer un ou plusieurs paramètres obligatoire. 2.- Les paramètres du cycle n’ont pas été édités dans l’ordre correct. SOLUTION Dans ce cycle d’usinage, il faut obligatoirement programmer: I : Profondeur de la poche. J : Distance depuis le centre au bord de la poche, suivant l’axe des abscisses. K : Distance depuis le centre au bord de la poche, suivant l’axe des ordonnées. B : Définition du pas de pénétration suivant l’axe longitudinal. Les autres paramètres sont optionnels. Les paramètres doivent être édités dans l’ordre indiqué dans le message d’erreur, la position (X...C) pouvant être définie là où se réalise l’usinage. 0042 ‘G88: I J B [C] [D] [H] [L] [V].’ DETECTION Durant l'édition (durant l'exécution en programmes transmis par DNC). CAUSE Les paramètres dans le «Cycle fixe de poche circulaire (G88)» n’ont pas été correctement programmés. Les causes peuvent être diverses: 1.- Il reste à programmer un ou plusieurs paramètres obligatoire. 2.- Les paramètres du cycle n’ont pas été édités dans l’ordre correct. SOLUTION Dans ce cycle d’usinage, il faut obligatoirement programmer: I : Profondeur de la poche. J : Rayon de la poche. B : Définition du pas de pénétration suivant l’axe longitudinal. Les autres paramètres sont optionnels. Les paramètres doivent être édités dans l’ordre indiqué dans le message d’erreur, la position (X...C) pouvant être définie là où se réalise l’usinage. 0043 ‘Coordonnées incomplètes.’ DETECTION Durant l'édition (durant l'exécution en programmes transmis par DNC). CAUSE/S Les différentes causes sont: 1.-Durant la simulation ou l’exécution, lorsqu’une fonction «Interpolation circulaire (G02/G03)» étant active, on a tenté d’exécuter un déplacement défini seulement par une coordonnée du point final, ou sans définir le rayon de l’arc. 2.-Durant l’édition, lorsqu’on édite un déplacement circulaire (G02/G03) et seule une coordonnée du point final est définie, ou le rayon de l’arc n’est pas défini. SOLUTION La solution à chacune des causes est la suivante: 1.-Il se peut que dans l’histoire du programme, une fonction “G02” ou “G03” ait été activée. Dans ce cas, pour réaliser un déplacement, il faut définir les deux coordonnées du point final et le rayon de l’arc. Pour réaliser un déplacement linéaire, programmer “G01”. 2.-Pour réaliser un déplacement circulaire (G02/G03), il faut définir les deux coordonnées du point final et le rayon de l’arc. 10 MANUEL DE SOLUTION DES ERREURS CNC 8040M 0044 ‘Coordonnées incorrectes.’ DETECTION Durant l'édition (durant l'exécution en programmes transmis par DNC). CAUSE Dans la définition des paramètres d’un cycle fixe d’usinage (G81-G89) le paramètre “I: Profondeur d’usinage” n’a pas été défini. SOLUTION Dans ce type d’usinage, il faut obligatoirement programmer: I : Profondeur d’usinage. Les autres paramètres sont optionnels. Les paramètres doivent être édités dans l’ordre indiqué dans le message d’erreur, la position (X...C) pouvant être définie là où se réalise l’usinage. 0045 ‘Coordonnées polaires non admises.’ DETECTION Durant l'édition (durant l'exécution en programmes transmis par DNC). CAUSE Dans la fonction «Programmation par rapport au zéro machine (G53)» les cotes du point final ont été définies en coordonnées polaires, cylindriques ou en coordonnées cartésiennes avec angle. SOLUTION Programmer par rapport au zéro machine, seules les cotes en coordonnées cartésiennes peuvent être programmées. 0046 ‘Axe inexistant.’ DETECTION Durant l'édition (durant l'exécution en programmes transmis par DNC). CAUSE/S Las différentes causes sont les suivantes: 1.-Lorsqu’on édite un bloc dont l’exécution implique le déplacement d’un axe qui n’existe pas. 2.-Quelquefois cette erreur se produit, durant l’édition dans un bloc, due à l’omission d’un paramètre dans la fonction «G» définie dans ledit bloc. Ceci est dû à ce que quelques paramètres ayant un nom d’axe, ont un sens spécial dans certaines fonctions «G». Par exemple: G69 I— B—. Dans ce cas, le paramètre “B” a un sens spécial derrière le paramètre “I”, la CNC interprète le paramètre “B” comme étant la position où va se réaliser l’usinage dans cet axe. Si cet axe n’existe pas, cette erreur apparaîtra. SOLUTION 0047 La solution pour chacune des causes est la suivante: 1.-Vérifier que le nom de l’axe édité est correct. 2.-Réviser la syntaxe du bloc et vérifier que tous les paramètres obligatoires aient été édités. ‘Programmer axe(s).’ DETECTION Durant l'édition (durant l'exécution en programmes transmis par DNC). CAUSE Aucun axe n’a été programmé dans une fonction où la programmation d’un axe est nécessaire. SOLUTION Il y a certaines instructions (REPOS, G14, G20, G21…) pour lesquelles la programmation d’axes est obligatoire. 0048 ‘Ordre des axes incorrect.’ DETECTION Durant l'édition (durant l'exécution en programmes transmis par DNC). CAUSE Les coordonnées des axes n’ont pas été programmées dans l’ordre correct, ou un axe a été programmé deux fois dans le même bloc. SOLUTION Se rappeler que l’ordre de programmation est le suivant: X— Y— Z— U— V— W— A— B— C— Il n’est pas nécessaire de programmer tous les axes. MANUEL DE SOLUTION DES ERREURS 11 CNC 8040M 0049 ‘Point incompatible avec le plan actif.’ DETECTION Durant l'édition (durant l'exécution en programmes transmis par DNC). CAUSE/S Les différentes causes sont les suivantes: 1.-Lorsqu’on a tenté de réaliser une interpolation circulaire et que le point final n’est pas contenu dans le plan actif. 2.-Lorsqu’on a tenté de réaliser une sortie tangentielle dans une trajectoire qui n’est pas contenue dans le plan actif. SOLUTION La solution à chacune des causes est la suivante: 1.-Il se peut qu’un plan ait été défini moyennant “G16”, “G17”, “G18” ou “G19”. Dans ce cas, on ne peut réaliser les interpolations circulaires que dans les axes principaux qui définissent ce plan. Si on désire définir une interpolation circulaire dans un autre plan, il faudra le sélectionner au préalable. 2.-Il se peut qu’un plan ait été défini moyennant “G16”, “G17”, “G18” ou “G19”. Dans ce cas, on ne peut réaliser que des arrondis, chanfreins et entrées/sorties tangentielles en trajectoires qui sont comprises dans les axes principaux qui définissent ce plan. Si on désire les réaliser dans un autre plan, il faudra le sélectionner au préalable. 0053 ‘Programmer pas.’ DETECTION Durant l'édition (durant l'exécution en programmes transmis par DNC). CAUSE Dans la fonction «Filetage électronique (G33)» le paramètre correspondant au pas de filetage n’a pas été programmé. SOLUTION Se rappeler que le format de programmation de cette fonction est: G33 X...C— L— Où: L : est le pas de filetage. 0054 ‘Pas mal programmé.’ DETECTION Durant l'édition ou l'exécution (durant l'exécution en programmes transmis par DNC). CAUSE Une interpolation hélicoïdale a été programmée et la valeur du paramètre correspondant au pas d’hélice n’est pas correcte ou est négative. SOLUTION Se rappeler que le format de programmation est: G02/G03 X— Y— I— J— Z— K— Où: K : C’est le pas d’hélice (valeur toujours positive). 0057 ‘Ne pas programmer un axe accouplé.’ DETECTION Durant l'édition (durant l'exécution en programmes transmis par DNC). CAUSE Les différentes causes sont : 1.- Lorsqu’on a tenté de déplacer individuellement un axe qui se trouve accouplé à un autre. 2.- Lorsque moyennant la fonction «Accouplement électronique des axes (G77)» on a tenté d’accoupler un axe qui se trouve déjà accouplé. SOLUTION La solution à chacune des causes est: 1.-Un axe accouplé ne peut être déplacé individuellement. Pour déplacer un axe accouplé, il faut déplacer l’axe auquel il se trouve accouplé. Les axes se déplaceront en même temps. Exemple: Si on accouple l’axe Y à l’axe X, il faudra programmer un déplacement en X pour déplacer Y (en même temps que X). Pour découpler les axes, programmer les axes “G78”. 2.-Un axe ne peut être accouplé simultanément à deux axes. Pour découpler les axes, programmer “G78”. 12 MANUEL DE SOLUTION DES ERREURS CNC 8040M 0058 ‘Ne pas programmer un axe GANTRY.’ DETECTION Durant l'édition (durant l'exécution en programmes transmis par DNC). CAUSE/S Les différentes causes sont les suivantes: 1.-Lorsqu’on tente de déplacer un axe qui se trouve associé comme GANTRY à un autre. 2.-Lorsqu’une opération est définie sur un axe qui est défini comme GANTRY. (Définition de limites de travail, définition de plans…). SOLUTION La solution pour chacune des causes est : 1.-Un axe qui forme GANTRY avec un autre ne peut pas être déplacer individuellement. Pour déplacer un axe associé comme GANTRY à un autre, il faut déplacer l’axe auquel il se trouve associé. Les axes se déplaceront en même temps. Exemple: Si on associe comme GANTRY l’axe Y à l’axe X, il faudra programmer un déplacement en X pour déplacer Y (en même temps que X). Les axes GANTRY sont définis depuis paramètre machine. 2.-Les axes définis comme GANTRY ne peuvent pas être utilisés dans la définition d’opérations ou de déplacements. Ces opérations seront définies avec l’axe auquel est associé l’axe GANTRY. 0059 ‘Axe HIRTH: programmer des valeurs entières.’ DETECTION Durant l'édition (durant l'exécution en programmes transmis par DNC). CAUSE Une rotation dans l’axe HIRTH a été programmée, et l’angle de rotation n’est pas un nombre entier (il a des décimaux). SOLUTION Les axes HIRTH n’admettent pas de chiffres décimaux. Toutes les rotations doivent être réalisées en degrés entiers. 0061 ‘ELSE non associé à IF.’ DETECTION Durant l'édition (durant l'exécution en programmes transmis par DNC). CAUSE/S Les différentes causes sont: 1.-Lorsqu’en programmant en langage de haut niveau on édite en un bloc l’instruction “ELSE” mais on n’a pas édité un “IF” auparavant. 2.-Lorsqu’en programmant en langage de haut niveau, on édite l’instruction “IF” et on ne lui associe pas d’action après la condition. SOLUTION Se rappeler que les formats de programmation de cette instruction sont: (IF (condition) <action1>) (IF (condition) <action1> ELSE <action2>) Si la condition est vraie, <action1> s’exécute, dans le cas contraire c’est <action2> qui s’exécute. 0062 ‘Programmer étiquette N(0-9999).’ DETECTION Durant l'édition (durant l'exécution en programmes transmis par DNC). CAUSE En programmant en langage de haut niveau, une étiquette (numéro de bloc) qui n’est pas dans l’intervalle (0-9999) a été éditée dans l’instruction “RPT” ou “GOTO” . SOLUTION Se rappeler que le format de programmation de ces instructions est: (RPT N(nº étiquette), N(nº étiquette)) (GOTO N(nº étiquette)) Le numéro d’étiquette (numéro de bloc) doit être dans l’intervalle (0-9999). 0063 ‘Programmer numéro de sousroutine de 1 à 9999.’ DETECTION Durant l'édition (durant l'exécution en programmes transmis par DNC). CAUSE En programmant en langage de haut niveau, un numéro de sousroutine qui n’est pas dans l’intervalle (1-9999) a été édité dans l’instruction “SUB”. SOLUTION Se rappeler que le format de programmation de cette instruction est: (SUB (nº entier)) Le numéro de sousroutine doit être dans l’intervalle (1-9999). MANUEL DE SOLUTION DES ERREURS 13 CNC 8040M 0064 ‘Sousroutine répétée.’ DETECTION Durant l'édition (durant l'exécution en programmes transmis par DNC). CAUSE On a tenté de définir une sousroutine qui existe déjà dans un autre programme de la mémoire. SOLUTION Dans la mémoire de la CNC, il ne peut y avoir deux sousroutines avec le même numéro d’identification, bien qu’elles appartiennent à deux programmes différents. 0065 ‘Ne pas définir sousrout. dans progr. principal.’ DETECTION Durant l'exécution (durant l'exécution en programmes transmis par DNC). CAUSE/S Les différentes causes sont: 1.- On a tenté de définir une sousroutine depuis le mode d’exécution MDI. 2.- Une sousroutine a été définie dans le programme principal. SOLUTION La solution à chacune des causes est: 1.-On ne peut pas définir de sousroutines depuis l’option du menu “Exécution MDI”. 2.-Les sousroutines doivent être définies depuis le programme principal ou dans un programme à part. Elles ne peuvent être définies ni avant, ni dans le programme principal. 0066 ‘Message attendu.’ DETECTION Durant l'édition (durant l'exécution en programmes transmis par DNC). CAUSE En programmant en langage de haut niveau, l’instruction “MSG” ou “ERREUR” a été éditée mais le texte du message d’erreur qu’elle doit montrer n’a pas été défini. SOLUTION Se rappeler que le format de programmation de ces instructions est: (MSG “message”) (ERREUR nº entier, “texte erreur”) Bien qu’il existe aussi l’option de programmer: (ERREUR nº entier) (ERREUR “texte erreur”) 0067 ‘OPEN non réalisé.’ DETECTION Durant l'exécution (durant l'exécution en programmes transmis par DNC). CAUSE En programmant en langage de haut niveau, une instruction “WRITE” a été éditée mais, au préalable, il n’a pas été indiqué où exécuter cet ordre moyennant l’instruction “OPEN”. SOLUTION Avant l’instruction “WRITE”, il faut éditer une instruction “OPEN” pour indiquer à la CNC où (dans quel programme) l’instruction “WRITE” doit être exécutée. 0069 ‘Le programme n’existe pas.’ DETECTION Durant l'exécution (durant l'exécution en programmes transmis par DNC). CAUSE Dans le «Cycle fixe de poche avec îlots (G66)», on a programmé que les profils qui définissent la poche avec îlots se trouvent dans un autre programme (paramètre “Q”), et le programme n’existe pas. SOLUTION Le paramètre “Q” définit dans quel programme se trouvent définis les profils qui définissent la poche avec îlots. Si ce paramètre est programmé, ce numéro de programme doit exister, et de plus, contenir les étiquettes définies aux paramètres “S” et “E”. 0070 ‘Le programme existe.’ DETECTION Durant l'exécution (durant l'exécution en programmes transmis par DNC). CAUSE Cette erreur se produit durant l'exécution, quand en programmant en langage de haut niveau, on a tenté de créer à l’aide de l’instruction “OPEN” un programme qui existe déjà. SOLUTION Changer le numéro de programme ou utiliser les paramètres A/D dans l’instruction “OPEN”: (OPEN P———,A/D,… ) Où: - A: Ajoute de nouveaux blocs à la suite de ceux existants déjà. - D: Efface le programme existant et l’ouvre comme un nouveau programme. 14 MANUEL DE SOLUTION DES ERREURS CNC 8040M 0071 ‘Un paramètre est attendu.’ DETECTION Durant l'édition (durant l'exécution en programmes transmis par DNC). CAUSE/S Les différentes causes sont les suivantes: 1.-Dans la définition de la fonction «Modification de paramètres d’un cycle fixe(G79)» le paramètre à modifier n’a pas été indiqué. 2.-Durant l’édition des tables de paramètres machine, un numéro de paramètre non correct a été introduit (il manque probablement le caractère “P”), ou on tente de réaliser une autre action (se déplacer dans la table) avant d’abandonner le mode d’édition de tables. SOLUTION La solution à chacune des causes est: 1.-Pour définir la fonction “G79” il faut obligatoirement programmer le numéro de cycle que l’on désire modifier, ainsi que sa nouvelle valeur. 2.-Introduire le numéro du paramètre à éditer, ou taper [ESC] pour abandonner ce mode. 0072 ‘Paramètre inexistant’ DETECTION Durant l'édition (durant l'exécution en programmes transmis par DNC). CAUSE En programmant en langage de haut niveau, l’instruction “ERREUR” a été éditée et le numéro d’erreur qu’elle doit montrer lui a été assigné moyennant un paramètre local supérieur à 25 ou un paramètre global supérieur à 299. SOLUTION Les paramètres que la CNC utilise sont: - Locaux: 0-25 -Globaux: 100-299 0075 ‘Variable de lecture uniquement.’ DETECTION Durant l'édition (durant l'exécution en programmes transmis par DNC). CAUSE On a tenté d’assigner une valeur à une variable qui est uniquement de lecture. SOLUTION On ne peut assigner aucune valeur moyennant la programmation aux variables uniquement de lecture. Cependant, sa valeur, elle, peut être assignée à un paramètre. 0077 ‘Sortie analogique non disponible.’ DETECTION Durant l'édition (durant l'exécution en programmes transmis par DNC). CAUSE On a tenté d’écrire une sortie d’analogie qui est utilisée para la CNC. SOLUTION Il se peut que la sortie analogique choisie soit utilisée par un axe ou une broche. Choisir une autre sortie analogique entre 1-8. 0078 ‘Programmer canal 0(CNC), 1(PLC), 2(DNC).’ DETECTION Durant l'édition (durant l'exécution en programmes transmis par DNC). CAUSE En programmant en langage de haut niveau, l’instruction en langage de haut niveau, “KEYSRC” a été programmée, mais la provenance des touches n’a pas été définie. SOLUTION Lorsqu’on programme l’instruction “KEYSCR”, il faut obligatoirement programmer le paramètre correspondant à la provenance des touches: (KEYSCR=0) : Clavier de la CNC. (KEYSCR=1) : PLC (KEYSCR=2) : DNC La CNC permet uniquement de modifier le contenu de cette variable si celle-ci se trouve à zéro. MANUEL DE SOLUTION DES ERREURS 15 CNC 8040M 0079 ‘Programmer le numéro d’erreur de 0 à 9999.’ DETECTION Durant l'édition (durant l'exécution en programmes transmis par DNC). CAUSE En programmant en langage de haut niveau, l’instruction “ERREUR” a été éditée mais le numéro d’erreur qu’elle doit montrer n’a pas été défini. SOLUTION Se rappeler que le format de programmation de cette instruction est: (ERREUR nº entier, “texte erreur”) Bien qu’il existe aussi l’option de programmer: (ERREUR nº entier) (ERREUR “texte erreur”) 0081 ‘Expression erronée.’ DETECTION Durant l'édition (durant l'exécution en programmes transmis par DNC). CAUSE En programmant en langage de haut niveau, une expression dont le format n’est pas correct a été éditée. SOLUTION Corriger la syntaxe du bloc. 0082 ‘Opération incorrecte.’ DETECTION Durant l'édition (durant l'exécution en programmes transmis par DNC). CAUSE/S Les différentes causes sont: 1.-En programmant en langage de haut niveau, l’assignation d’une valeur à un paramètre est incomplète. 2.-En programmant en langage de haut niveau, l’appel à une sousroutine est incomplet. SOLUTION Corriger (compléter) le format d’assignation d’une valeur à un paramètre, ou d’appel à une sousroutine. 0083 ‘Opération incomplète.’ DETECTION Durant l'édition (durant l'exécution en programmes transmis par DNC). CAUSE/S Las différentes causes sont: 1.-En programmant en langage de haut niveau, l’instruction “IF” a été édité et la condition n’a pas été programmée entre parenthèse. 2.-En programmant en langage de haut niveau, l’instruction “DIGIT” a été éditée et aucune valeur n’a été assignée à un paramètre édité. SOLUTION La solution à chacune des causes est: 1.-Se rappeler que les formats de programmation de cette instructions sont les suivants: (IF (condition) <action1>) (IF (condition) <action1> ELSE <action2>) Si la condition est vraie, <action1> s’exécute , dans le cas contraire c’est <action 2> qui s’exécute. 2.-Corriger la syntaxe du bloc. Tous les paramètres qui sont définis dans une instruction “DIGIT” doivent être associés à une valeur. 0084 ‘Attente de “=”.’ DETECTION Durant l'édition (durant l'exécution en programmes transmis par DNC). CAUSE En programmant en langage de haut niveau, un symbole ou une donnée qui ne correspond pas à la syntaxe du bloc a été introduit. SOLUTION Introduire le symbole “=” à l’endroit correspondant. 0085 ‘Attente de “)”.’ DETECTION Durant l'édition (durant l'exécution en programmes transmis par DNC). CAUSE En programmant en langage de haut niveau, un symbole ou une donnée qui ne correspondant pas à la syntaxe du bloc a été introduit. SOLUTION Introduire le symbole “)” à l’endroit correspondant. 16 MANUEL DE SOLUTION DES ERREURS CNC 8040M 0086 ‘Attente de “(”.’ DETECTION Durant l'édition (durant l'exécution en programmes transmis par DNC). CAUSE En programmant en langage de haut niveau, un symbole ou une donnée qui ne correspondant pas à la syntaxe du bloc a été introduit. SOLUTION Introduire le symbole “(” à l’endroit correspondant . 0087 ‘Attente de “,”.’ DETECTION Durant l'édition (durant l'exécution en programmes transmis par DNC). CAUSE/S Les différentes causes sont: 1.-En programmant en langage de haut niveau, un symbole ou une donnée qui ne correspondant pas à la syntaxe du bloc a été introduit. 2.-En programmant en langage de haut niveau, une instruction a été programmée en code ISO. 3.-En programmant en langage de haut niveau, une opération a été assignée à un paramètre local supérieur à 25 ou un paramètre global supérieur à 299. SOLUTION La solution à chacune des causes est: 1.-Introduire le symbole “,” à l’endroit correspondant. 2.-Dans un bloc, il ne peut y avoir d’instructions en langage de haut niveau et en code ISO à la fois. 3.-Les paramètres que la CNC utilise sont: - Locaux: 0-25. - Globaux: 100-299. Dans les opérations on ne peut utiliser d’autres paramètres qui ne soient pas dans ce rang. 0089 ‘Logarithme de nombre négatif ou nul.’ DETECTION Durant l'édition ou l'exécution (durant l'exécution en programmes transmis par DNC). CAUSE Une opération dont l’exécution implique de calculer le logarithme d’un numéro négatif ou zéro a été programmée. SOLUTION On ne peut calculer que les logarithmes de nombres supérieurs à zéro. Si on travaille avec des paramètres, il se peut, que dans l’histoire du programme, ce paramètre ait acquis une valeur négative ou zéro. Vérifier que le paramètre n’arrive pas à l’opération avec cette valeur. 0090 ‘Racine de nombre négatif.’ DETECTION Durant l'édition ou l'exécution (durant l'exécution en programmes transmis par DNC). CAUSE Une opération dont l’exécution implique le calcul de la racine d’un nombre négatif a été programmée. SOLUTION On ne peut calculer que les racines de nombres supérieurs ou égaux à zéro. Si on travaille avec des paramètres, il se peut, que dans l’histoire du programme, ce paramètre ait acquis une valeur négative. Vérifier que le paramètre n’arrive pas à l’opération avec cette valeur. 0091 ‘Division par zéro.’ DETECTION Durant l'édition ou l'exécution (durant l'exécution en programmes transmis par DNC). CAUSE Une opération dont l’exécution implique la réalisation d’une division par zéro a été programmée. SOLUTION On ne peut réaliser de divisions que par de nombres différents de zéro. Si on travaille avec des paramètres, il se peut, que dans l’histoire du programme, ce paramètre ait acquis une valeur zéro. Vérifier que le paramètre n’arrive pas à l’opération avec cette valeur. 0092 ‘Base zéro et exposant non positif.’ DETECTION Durant l'édition ou l'exécution (durant l'exécution en programmes transmis par DNC). CAUSE Une opération dont l’exécution implique d’élever zéro à une puissance négative (ou zéro) a été programmée. SOLUTION On ne peut élever le nombre zéro qu’à des puissance positives supérieures à zéro. Si on travaille avec des paramètres, il se peut, que dans l’histoire du programme, ce paramètre ait acquis les valeurs citées. Vérifier que le paramètre n’arrive pas à l’opération avec ces valeurs. MANUEL DE SOLUTION DES ERREURS 17 CNC 8040M 0093 ‘Base négative et exposant non entier.’ DETECTION Durant l'édition ou l'exécution (durant l'exécution en programmes transmis par DNC). CAUSE Une opération dont l’exécution implique d’élever un nombre négatif à une puissance non entière a été programmée. SOLUTION On ne peut pas élever de nombres négatifs à des puissances entières. Si on travaille avec des paramètres, il se peut, que dans l’histoire du programme, ce paramètre ait acquis les valeurs citées. Vérifier que le paramètre n’arrive pas à l’opération avec ces valeurs. 0094 ‘Rang ASIN/ACOS dépassé.’ DETECTION Durant l'édition ou l'exécution (durant l'exécution en programmes transmis par DNC). CAUSE Une opération dont l’exécution implique de calculer l’arcosinus ou l’arcocosinus d’un nombre qui n’est pas compris entre ±1. SOLUTION On ne peut calculer l’arcosinus (ASIN) ou l’arcocosinus (ACOS) de nombres qui sont compris entre ±1. Si on travaille avec des paramètres, il se peut, que dans l’histoire du programme, ce paramètre ait acquis les valeurs hors des valeurs citées. Vérifier que le paramètre n’arrive pas à l’opération avec ces valeurs. 0095 ‘Programmer numéro de file.’ DETECTION Durant l'édition (durant l'exécution en programmes transmis par DNC). CAUSE Durant l’édition d’un programme de personnalisation, une fenêtre a été définie moyennant l’expression et la position verticale qu’elle occupe sur l’écran, n’a pas été programmée. SOLUTION La position verticale qu’une fenêtre occupe sur l’écran est définie en files. (0-25). 0096 ‘Programmer le numéro de colonne.’ DETECTION Durant l'édition (durant l'exécution en programmes transmis par DNC). CAUSE Durant l’édition d’un programme de personnalisation, une fenêtre a été définie moyennant l’expression ODW, et la position horizontale qu’elle occupe sur l’écran a été programmée. SOLUTION La position horizontale qu’une fenêtre occupe sur l’écran est définie en colonnes (0-79). 0097 ‘Programmer une autre softkey.’ DETECTION Durant l'édition (durant l'exécution en programmes transmis par DNC). CAUSE Durant l’édition d’un programme de personnalisation, le format de programmation de l 'expression “SK” n’a pas été respecté. SOLUTION Corriger la syntaxe du bloc. Le format de programmation est: (SK1=(texte 1), SK2=(texte 2)…) Si on introduit le caractère “,” après un (texte), la CNC attend le nom d’une autre softkey. 0098 ‘Programmer soft_keys de 1 à 7.’ DETECTION Durant l'exécution en canal d’utilisateur. CAUSE Dans la syntaxe du bloc une softkey a été programmée qui ne se trouve pas dans l’intervalle 1 à 7. SOLUTION On ne peut programmer les softkeys que dans l’intervalle 1 à 7. 0099 ‘Programmer autre fenêtre.’ DETECTION Durant l'édition (durant l'exécution en programmes transmis par DNC). CAUSE Durant l’édition d’un programme de personnalisation, le format de programmation de l'expression “DW” n’a pas été respecté. SOLUTION Corriger la syntaxe du bloc. Le format de programmation est: (DW1=(assignation), DW2=(assignation)…) Si on introduit le caractère “,” après une assignation, la CNC attend le nom de l’autre fenêtre. 18 MANUEL DE SOLUTION DES ERREURS CNC 8040M 0100 ‘Programmer fenêtres de 0 à 25.’ DETECTION Durant l'exécution en canal d’utilisateur. CAUSE Dans la syntaxe du bloc, une fenêtre qui n’est pas dans l’intervalle de 0 à 25 a été programmée. SOLUTION On ne peut programmer des fenêtres que dans l’intervalle 0 à 25. 0101 ‘Programmer files de 0 à 20.’ DETECTION Durant l'exécution en canal d’utilisateur. CAUSE Dans la syntaxe du bloc, on a programmé une file qui n’est pas dans l’intervalle 0 à 20. SOLUTION On ne peut programmer des files que dans l’intervalle 0 à 20. 0102 ‘Programmer colonnes de 0 à 79.’ DETECTION Durant l'exécution en canal d'utilisateur. CAUSE Dans la syntaxe du bloc, on a programmé une colonne qui n’est pas dans l’intervalle 0 à 79. SOLUTION On ne peut programmer des colonnes que dans l’intervalle 0 à 79. 0103 ‘Programmer pages de 0 à 255.’ DETECTION Durant l'exécution en canal d'utilisateur. CAUSE Dans la syntaxe du bloc on a programmé une page qui n’est pas dans l’intervalle 0 à 255. SOLUTION On ne peut programmer des pages que dans l’intervalle 0 à 255. 0104 ‘Programmer INPUT.’ DETECTION Durant l'édition (durant l'exécution en programmes transmis par DNC). CAUSE En programmant en langage de haut niveau, on a édité l'expression “IB” mais on ne lui a pas associé d’ “INPUT”. SOLUTION Se rappeler que les formats de programmation de cette instruction sont: (IB (expression) = INPUT “texte”, format) (IB (expression) = INPUT “texte”) 0105 ‘Programmer entrées de 0 à 25.’ DETECTION Durant l'exécution en canal d'utilisateur. CAUSE Dans la syntaxe du bloc, on a programmé une entrée qui n’est pas dans l’intervalle 0 à 25. SOLUTION On ne peut programmer d’entrées que dans l’intervalle 0 à 25. 0106 ‘Programmer format numérique.’ DETECTION Durant l'édition (durant l'exécution en programmes transmis par DNC). CAUSE En programmant en langage de haut niveau, on a édité l’expression “IB” en format non numérique. SOLUTION Se rappeler que le format de programmation de cette instruction est: (IB (expression) = INPUT “texte”, format) Où “format” doit être un nombre avec un signe et au maximum 6 chiffres entiers et 5 décimaux. Si on introduit le caractère “,” après le texte, la CNC attend le format. 0107 ‘Ne pas programmer formats supérieurs à 6.5.’ DETECTION Durant l'exécution en canal d'utilisateur. CAUSE En programmant en langage de haut niveau, on a édité une expression “IB” en un format qui a plus de 6 chiffres entiers ou plus de 5 chiffres décimaux. SOLUTION Se rappeler que le format de programmation de cette instruction est: (IB (expression) = INPUT “texte”, format) Où “format” doit être un nombre avec un signe et 6 chiffres entiers maximum et 5 décimaux. MANUEL DE SOLUTION DES ERREURS 19 CNC 8040M 0108 ‘Commande exécutable canal utilisateur seulement.’ DETECTION Durant l'exécution. CAUSE On a tenté d’exécuté un bloc qui contient une information exécutable seulement du canal d'utilisateur. SOLUTION Il y a des expressions spécifiques aux programmes de personnalisation qui ne peuvent être exécuter que dans le programme d'utilisateur. 0109 ‘C. utilis.: ne pas programmer aides géométriques, comp. ou cycles.’ DETECTION Durant l'exécution en canal d'utilisateur. CAUSE On a tenté d’exécuter un bloc qui contient des aides géométriques, compensation de rayon/longueur , ou cycles fixes d’usinage. SOLUTION Dans le programme de personnalisation on ne peut pas programmer: - D’aides géométriques ni de déplacements. - Compensation de rayon ou de longueur. - Cycles fixes. 0110 ‘Paramètres locaux non admis.’ DETECTION Durant l'édition (durant l'exécution en programmes transmis par DNC). CAUSE Quelques fonctions n’admettent que la programmation avec des paramètre globaux. SOLUTION Les paramètres globaux sont ceux qui sont inclus dans le rang 100-299. 0111 ‘Bloc non exécutable avec un autre programme en exécution’ DETECTION Durant l'exécution en modo MDI. CAUSE On a tenté d’exécuter une instruction de personnalisation depuis le mode MDI, tandis que le programme du canal d’utilisateur s’exécute. SOLUTION Les instructions de personnalisation ne peuvent s’exécuter que depuis le canal d'utilisateur. 0112 ‘WBUF seulement en canal utilisateur d’édition.’ DETECTION Durant l'exécution ou exécution en canal d'utilisateur. CAUSE On tenté d’exécuter l’instruction “WBUF”. SOLUTION L’instruction “WBUF” n’est pas exécutable. On ne peut l’utiliser dans la phase d’édition que de l’entrée d'utilisateur. 0113 ‘Limites de la table dépassées.’ DETECTION Durant l'édition de tables. CAUSE/S Les différentes causes sont: 1.-Dans la table de correcteurs d’outils, on a tenté de définir un correcteur avec un numéro supérieur à ceux permis par le fabricant. 2.-Dans les tables de paramètres, on a tenté de définir un paramètre qui n’existe pas. SOLUTION Le numéro de correcteur doit être inférieur au maximum permis par le fabricant. 0114 ‘Correcteur: D3 R L I K.’ DETECTION Durant l'édition de tables. CAUSE Dans la table de correcteurs d’outils, l’ordre d’édition des paramètres n’a pas été respecté. SOLUTION Introduire les paramètres de la table dans l’ordre correct. 0115 ‘Outil: T4 D3 F3 N5 R5(.2).’ DETECTION Durant l'édition de tables. CAUSE Dans la table d’outils, l’ordre d’édition des paramètres n’a pas été respecté. SOLUTION Introduire les paramètres de la table dans l’ordre correct. 20 MANUEL DE SOLUTION DES ERREURS CNC 8040M 0116 ‘Origine: G54-59 axes (1-5).’ DETECTION Durant l'édition de tables. CAUSE Dans les tables d’origines, l’origine (G54-G59) à définir n’a pas été choisie. SOLUTION Introduire les paramètre de la table dans l’ordre correct. Pour remplir la table d’origines, choisir d’abord quelle origine (G54-G59) va être définie et ensuite, la position de l’origine dans chaque axe. 0117 ‘Fonction: M4 S4 bits(8).’ DETECTION Durant l'édition de tables. CAUSE Dans la table de fonctions «M», l’ordre d’édition des paramètres n’a pas été respecté. SOLUTION Editer la table suivant le format: M1234 (sousroutine associée) 0118 (bits de personnalisation) ‘G51 [A] E’ DETECTION Durant l'exécution (durant l'exécution en programmes transmis par DNC). CAUSE Dans la fonction «Look-Ahead (G51)» le paramètre correspondant à l’erreur de contour permis n’a pas été programmé. SOLUTION Dans ce type d’usinage, il faut obligatoirement programmer: E : Erreur de contour permis. Les autres paramètres sont optionnels. Les paramètres doivent être édités dans l’ordre indiqué dans le message d’erreur. 0119 ‘Vis: Cote-erreur.’ DETECTION Durant l'édition de tables. CAUSE Dans les tables de compensation de vis, l’ordre d’édition des paramètres n’a pas été respecté. SOLUTION Introduire les paramètres de la table dans l’ordre correct. P123 (position de l ‘axe à compenser) (erreur de vis dans ce point) 0120 ‘Axe incorrect.’ DETECTION Durant l'édition de table. CAUSE Dans les tables de compensation de vis, on a tenté d’éditer un axe différent de celui qui correspond à cette table. SOLUTION Chaque axe a une table propre pour la compensation de vis. Dans la table de chaque axe, seules les positions correspondantes à cet axe peuvent apparaître. 0121 ‘Programmer P3 = valeur.’ DETECTION Durant l'édition de table. CAUSE Dans la table de paramètre machine, le format de l’édition n’a pas été respecté. SOLUTION Introduire les paramètres de la table dans l’ordre correct. P123 = (valeur du paramètre) 0122 ‘Magasin: P(1-255) = T(1-9999).’ DETECTION Durant l'édition de table. CAUSE Dans le magasin des outils, le format d’édition n’a pas été respecté, ou il reste une donnée à programmer . SOLUTION Introduire les paramètres de la table dans l’ordre correct. MANUEL DE SOLUTION DES ERREURS 21 CNC 8040M 0123 ‘L’outil T=0 n’existe pas.’ DETECTION Durant l'édition de tables. CAUSE Dans la table d’outils, on a tenté d’éditer un outil avec un numéro T0. SOLUTION On ne peut pas éditer un outil avec un numéro T0. Le premier outil doit être T1. 0124 ‘Le correcteur D=0 n’existe pas.’ DETECTION Durant l'édition de tables. CAUSE Dans la table de correcteurs d’outil, on a tenté d’éditer un correcteur d’outil avec un numéro . SOLUTION On ne peut pas éditer un correcteur d’outil avec un numéro D0. Le premier correcteur doit être D1. 0125 ‘Ne pas modifier l’outil actif ou le suivant.’ DETECTION Durant l'exécution. CAUSE Dans la table du magasin des outils, on a tenté de changer l’outil actif ou le suivant. SOLUTION Durant l'exécution on ne peut pas changer l’outil actif ou le suivant. 0126 ‘Outil non défini.’ DETECTION Durant l'édition des tables. CAUSE Dans la table de magasin des outils, on a tenté d’assigner un outil qui n’est pas défini dans le magasin des outils à une position du magasin. SOLUTION Définir l’outil dans la table des outils. 0127 ‘Le magasin n’est pas RANDOM.’ DETECTION Durant l'édition de tables. CAUSE On ne dispose pas de magasin RANDOM, et dans la table de magasin des outils, le numéro de l’outil ne coïncide pas avec le numéro de la position dans le magasin. SOLUTION Quand le magasin des outils n’est pas RANDOM, le numéro de l’outil doit être égal au numéro de position dans le magasin. 0128 ‘La position d’un outil spécial est fixe.’ DETECTION Durant l'édition de tables. CAUSE Dans la table du magasin des outils, on a tenté de placer un outil dans une position du magasin réservée à un outil spécial. SOLUTION Quand un outil spécial occupe plus d’une position dans le magasin, celles-ci sont réservée dans le magasin. Aucun autre outil ne pourra être placé dans ces positions. 0129 ‘Outil suivant possible en centre d’usinage seulement.’ DETECTION Durant l'exécution. CAUSE Un changement d’outil a été programmé avec M06 et la machine n’est pas un centre d’usinage. (il n’y a pas d’outil suivant en attente). SOLUTION Quand la machine n’est pas un centre d’usinage, le changement d’outil se réalise automatiquement en programmant le numéro d’outil «T». 0130 ‘Ecrire 0/1.’ DETECTION Durant l’édition des paramètres de la table de paramètres machine. CAUSE On a tenté d’assigner à un paramètre une valeur non valable. SOLUTION Le paramètre n’admet que les valeurs 0 ou 1. 22 MANUEL DE SOLUTION DES ERREURS CNC 8040M 0131 ‘Ecrire +/-.’ DETECTION Durant l’édition des paramètres de la table de paramètres machine. CAUSE On a tenté d’assigner à un paramètre une valeur non valable. SOLUTION Le paramètre n’admet que les valeurs + ou -. 0132 ‘Ecrire YES/NO.’ DETECTION Durant l’édition des paramètres de la table de paramètres machine. CAUSE On a tenté d’assigner à un paramètre une valeur non valable. SOLUTION Le paramètre n’admet que les valeurs YES ou NO. 0133 ‘Ecrire ON/OFF.’ DETECTION Durant l’édition des paramètres de la table de paramètres machine. CAUSE On a tenté d’assigner à un paramètre une valeur non valable. SOLUTION Le paramètre n’admet que les valeurs ON ou OFF. 0134 ‘Valeurs entre 0-2.’ DETECTION Durant l’édition des paramètres de la table de paramètres machine. CAUSE On a tenté d’assigner à un paramètre une valeur non valable. SOLUTION Le paramètre n’admet que les valeurs 0 et 2. 0135 ‘Valeurs entre 0-3.’ DETECTION Durant l’édition des paramètres de la table de paramètres machine. CAUSE On a tenté d’assigner à un paramètre une valeur non valable. SOLUTION Le paramètre n’admet que les valeurs entre 0 et 3. 0136 ‘Valeurs entre 0-4.’ DETECTION Durant l’édition des paramètres de la table de paramètres machine. CAUSE On a tenté d’assigner à un paramètre une valeur non valable. SOLUTION Le paramètre n’admet que les valeurs entre 0 et 4. 0137 ‘Valeurs entre 0-9.’ DETECTION Durant l’édition des paramètres de la table de paramètres machine. CAUSE On a tenté d’assigner à un paramètre une valeur non valable. SOLUTION Le paramètre n’admet que les valeurs 0 et 9. 0139 ‘Valeurs entre 0-100.’ DETECTION Durant l’édition des paramètres de la table de paramètres machine. CAUSE On a tenté d’assigner à un paramètre une valeur non valable. SOLUTION Le paramètre n’admet que les valeurs 0 et 100. 0140 ‘Valeurs entre 0-255.’ DETECTION Durant l’édition des paramètres de la table de paramètres machine. CAUSE On a tenté d’assigner à un paramètre une valeur non valable. SOLUTION Le paramètre n’admet que les valeurs 0 et 255. MANUEL DE SOLUTION DES ERREURS 23 CNC 8040M 0141 ‘Valeurs entre 0-9999.’ DETECTION Durant l’édition des paramètres de la table de paramètres machine. CAUSE/S Las différentes causes sont : 1.-On a tenté d’assigner à un paramètre une valeur non valable. 2.-Durant l'exécution, quand dans le programme un appel a une sousroutine (MCALL, PCALL) supérieure à 9999 a été réalisé. SOLUTION La solution à chacune des causes est: 1.-Le paramètre n’admet que des valeurs entre 0 et 9999. 2.-Le numéro de sousroutine doit être compris entre 1 et 9999. 0142 ‘Valeurs entre 0-32767.’ DETECTION Durant l’édition des paramètres de la table de paramètres machine. CAUSE On a tenté d’assigner à un paramètre une valeur non valable. SOLUTION Le paramètre n’admet que les valeurs 0 et 32767. 0144 ‘Valeurs entre 0-65535.’ DETECTION Durant l’édition des paramètres de la table de paramètres machine. CAUSE On a tenté d’assigner à un paramètre une valeur non valable. SOLUTION Le paramètre n’admet que les valeurs 0 et 65535. 0145 ‘Format +/- 5.5.’ DETECTION Durant l’édition des paramètres de la table de paramètres machine. CAUSE On a tenté d’assigner à un paramètre une valeur non valable. SOLUTION Le paramètre n’admet que les valeurs sous le format ±5.5. 0147 ‘Format numérique dépassé.’ DETECTION Durant l'édition (durant l'exécution en programmes transmis par DNC). CAUSE On a assigné à une donnée ou paramètre une valeur supérieure au format établi. SOLUTION Corriger la syntaxe du bloc. Dans la plupart des cas, le format numérique correct sera 5.4 (5 chiffres entiers et 4 décimaux). 0148 ‘Texte trop long.’ DETECTION Durant l'édition (durant l'exécution en programmes transmis par DNC). CAUSE En programmant en langage de haut niveau, on a assigné aux instructions “ERREUR” ou “MSG” un texte de plus de 59 caractères. SOLUTION Corriger la syntaxe du bloc. On ne peut pas assigner de textes de plus de 59 caractères aux instructions “ERREUR” et “MSG”. 0149 ‘Message incorrect.’ DETECTION Durant l'édition (durant l'exécution en programmes transmis par DNC). CAUSE En programmant en langage de haut niveau, dans les instructions “ERREUR” ou “MSG” on a édité de façon non correcte le texte qui leur est associé. SOLUTION Corriger la syntaxe du bloc. Le format de programmation est: (MSG “message”) (ERREUR numéro, “message”) Le message doit être entre guillemets. 24 MANUEL DE SOLUTION DES ERREURS CNC 8040M 0150 ‘Nombre incorrect de bits.’ DETECTION Durant l'édition de tables CAUSE/S Les différentes causes sont: 1.-Dans la table de fonctions «M», dans le point correspondant aux bits de personnalisation: - On n’introduit pas un nombre de 8 bits. - EL nombre n’est pas formé de 0 et 1. 2.-Dans la table de paramètres machine, on a tenté d’assigner une valeur de bits non valable à un paramètre. SOLUTION La solution à chacune des causes est: 1.-Les bits de personnalisation doivent former un nombre à 8 chiffres composé de 0 et 1. 2.- Le paramètre n’admet que des nombres de 8 ou 16 bits. 0152 ‘Programmation paramétrique erronée.’ DETECTION Durant l'exécution. CAUSE Le paramètre a une valeur incompatible avec la fonction à laquelle il a été assigné. SOLUTION Dans l’histoire du programme, il se peut que ce paramètre ait pris une valeur erronée. Corriger le programme pour que ce paramètre n’arrive pas à la fonction avec cette valeur. 0154 ‘Mémoire insuffisante.’ DETECTION Durant l'exécution. CAUSE La CNC ne dispose pas de mémoire suffisante pour réaliser les calculs internes des trajectoires. SOLUTION Quelquefois cette erreur peut être résolue en variant les conditions de coupe. 0156 ‘Ne pas programmer G33, G95 ou M19 S sans codeur broche.’ DETECTION Durant l'édition (durant l'exécution en programmes transmis par DNC). CAUSE On a programmé une des fonctions “G33”, “G95” ou “M19 S” et on ne dispose pas de codeur sur la broche. SOLUTION Si on ne dispose pas de codeur sur la broche, on ne peut pas programmer les fonctions “M19 S”, “G33” ou “G95”. Si on dispose de codeur sur la broche, le paramètre machine de la broche “NPULSES (P13)” indique le nombre d’impulsions par tour du codeur. . 0157 ‘G79 n’est pas admis s’il n’y a pas un cycle actif.’ DETECTION Durant l'exécution. CAUSE On a tenté d’exécuter la fonction «Modification de paramètres d’un cycle fixe (G79)» mais il n’y a pas de cycle fixe actif. SOLUTION La fonction “G79” modifie les valeurs d’un cycle fixe, donc, il doit y avoir un cycle fixe actif et la fonction “G79” doit être programmée dans la zone d’influence de ce cycle fixe. 0158 ‘Il est obligatoire de programmer l’outil T avec G67 et G68.’ DETECTION Durant l'édition (durant l'exécution en programmes transmis par DNC). CAUSE Dans le «Cycle fixe de poche avec îlots (G66)», il n’a pas été défini avec quel outil l’ébauchage allait être effectué. “G67” (poches 2D/3D), semi-finition “G67” (poche 3D) ou finition “G68” (poche 2D/3D). SOLUTION Dans le cycle fixe de poche avec îlots, il faut obligatoirement programmer avec quel outil s’effectuera l’ébauchage “G67” (poches 2D/3D), semi-finition “G67” (poche 3D) et finition “G68” (poche 2D/3D). 0159 ‘Limite de programmation en pouces dépassée.’ DETECTION Durant l'exécution. CAUSE On a tenté d’exécuter en pouces un programme édité en millimètres. SOLUTION Introduire au début du programme la fonction «Programmation en pouces (G70)» ou «Programmation en millimètres (G71)». MANUEL DE SOLUTION DES ERREURS 25 CNC 8040M 0161 ‘ G67-G68 ne sont pas admis sans programmer avant G66.’ DETECTION Durant l'exécution. CAUSE Les opérations d’ébauchage “G67” (poches 2D/3D), semi-finition “G67” (poche 3D) ou finition “G68” (poches 2D/3D) ont été définies sans programmer auparavant l’appel au «Cycle fixe de poche avec îlots (G66)». SOLUTION Lorsqu’on travaille sur les poches avec îlots, avant de programmer les opérations d’ébauchage “G67”(poches 2D/3D), semi-finition “G67” (poche 3D) ou finition “G68” (poches 2D/3D), il faut programmer l’appel au «Cycle fixe de poche avec îlots (G66)». 0162 ‘Rayon négatif non admis en coordonnées absolues.’ DETECTION Durant l'exécution. CAUSE En travaillant en coordonnées polaires absolues, on a programmé un déplacement avec un rayon négatif. SOLUTION En programmant en coordonnées polaires absolues, la programmation de rayons négatifs n’est pas permise. 0163 ‘L’axe programmé n’est pas longitudinal .’ DETECTION Durant l'exécution. CAUSE On a tenté de modifier les coordonnées du point où l’on désire exécuter le cycle fixe moyennant la fonction «Modification de paramètres du cycle fixe (G79)». SOLUTION Moyennant la fonction “G79” on peut varier les paramètres qui définissent un cycle fixe, excepté les coordonnées du point où l’on veut exécuter. Pour changer les coordonnées du point, programmer seulement les nouvelles coordonnées. 0164 ‘Nom de password incorrect.’ DETECTION Durant l’assignation de protections. CAUSE On a tapé [ENTER] avant de choisir le type de code auquel on veut assigner un password. SOLUTION Choisir moyennant les softkeys, le type de code auquel on veut assigner un password. 0165 ‘Password: utiliser lettres (majuscules ou minuscules) ou chiffres.’ DETECTION Durant l’assignation de protections. CAUSE On a introduit un caractère non valable dans le password. SOLUTION Le password ne peut être composé que de lettres (majuscules ou minuscules) ou chiffres. 0166 ‘On n’admet pas plus d’un axe HIRTH par bloc.’ DETECTION Durant l'édition (durant l'exécution en programmes transmis par DNC). CAUSE On a programmé un déplacement qui implique de déplacer deux axes HIRTH à la fois. SOLUTION La CNC n’admet pas de déplacements dans lesquels interviennent plusieurs axes à la fois. Les différents déplacements des axes HIRTH doivent être réalisés un à un. 0167 ‘Axe rot. position.: valeurs absolues (G90) entre 0-359.9999.’ DETECTION Durant l'exécution. CAUSE On a programmé un déplacement sur un axe défini comme rotatif de positionnement. Le déplacement a été programmé en coordonnées absolues (G90) et la cote finale de déplacement n’est pas dans l’intervalle 0-359.9999. SOLUTION Axes rotatifs de positionnement: En coordonnées absolues, les déplacements ne sont admis que dans l’intervalle 0-359.9999. 26 MANUEL DE SOLUTION DES ERREURS CNC 8040M 0168 ‘Axe rotatif: valeurs absolues (G90) entre +/-359.9999.’ DETECTION Durant l'exécution. CAUSE On a programmé un déplacement sur un axe défini comme rotatif de positionnement. Le déplacement a été programmé en coordonnées absolues (G90) et la cote finale de déplacement n’est pas dans l’intervalle 0-359.9999. SOLUTION Axes rotatifs de positionnement: En coordonnées absolues, les déplacements ne sont admis que dans l’intervalle +/-359.9999. 0169 ‘Ne pas programmer des sousroutines modales.’ DETECTION Durant l'exécution en modo MDI. CAUSE On a tenté d’appeler une sousroutine modale (MCALL). SOLUTION On ne peut pas exécuter de sousroutines modales (MCALL) depuis l’option de menu “Exécution MDI”. 0171 ‘La fenêtre n’a pas été définie.’ DETECTION Durant l'exécution ou exécution en canal d'utilisateur. CAUSE On a tenté d’écrire dans une fenêtre (DW) qui n’a pas été définie (ODW) auparavant. SOLUTION On ne peut pas écrire dans une fenêtre qui n’a pas été définie. Vérifier que la fenêtre dans laquelle on désire écrire (DW) ait été définie. 0172 ‘Le programme n’est pas accessible’ DETECTION Durant l'exécution. CAUSE On a tenté d’exécuter un programme qui n’est pas exécutable. SOLUTION Il se peut que le programme soit protégé de l’exécution. Pour savoir si un programme est exécutable, vérifier dans la colonne des attributs si le caractère «X» apparaît. Si ce caractère n’apparaît pas, le programme ne pourra pas être exécuté. 0174 ‘Interpolation hélicoïdale non permise.’ DETECTION Durant l'exécution. CAUSE On a tenté d’exécuter une interpolation hélicoïdale tout étant active la fonction «LOOK-AHEAD (G51)». SOLUTION On ne peut pas réaliser d’interpolations hélicoïdales la fonction «LOOK-AHEAD (G51)» étant active. 0175 ‘Entrées analogiques: ANAI(1-8) = +/-5 Volts.’ DETECTION Durant l'exécution. CAUSE Une entrée analogique a pris une valeur qui n’est pas dans l’intervalle ±5 volts. SOLUTION Les entrées analogiquesne peuvent prendre que des valeurs entre ±5 volts. 0176 ‘Sorties analogiques: ANAO(1-8) = +/-10 Volts.’ DETECTION Durant l'exécution. CAUSE On a assigné une valeur qui n’est pas dans l’intervalle ±10 volts à une sortie analogique. SOLUTION Les sorties analogiques ne peuvent prendre que des valeurs entre ±10 volts. 0178 ‘ G96 non admis si la broche n’est pas à vitesse continue’ DETECTION Durant l'exécution . CAUSE On a programmé la fonction “G96” et la broche n’est pas contrôlée en vitesse ou ne dispose pas de codeur. SOLUTION Pour travailler avec la fonction “G96” il faut que la broche soit contrôlée en vitesse (SPDLTYPE(P0)=0), et disposer d’un codeur sur la broche. (NPULSES(P13) différent de zéro). MANUEL DE SOLUTION DES ERREURS 27 CNC 8040M 0180 ‘Programmer DNC1/2, HD ou CARD A (optionnel).’ DETECTION Durant l'édition ou l'exécution. CAUSE En programmant en langage de haut niveau, dans les instructions “OPEN” et “EXEC”, on a tenté de programmer un paramètre différent de DNC1/2, HD u CARD A, ou on a assigné une valeur différente de 1 ou 2 au paramètre DNC. SOLUTION Réviser la syntaxe du bloc. 0181 ‘Programmer A (ajouter) ou D (effacer).’ DETECTION Durant l'édition (durant l'exécution en programmes transmis par DNC). CAUSE Il reste à programmer le paramètre A/D dans l’instruction “OPEN”. SOLUTION Réviser la syntaxe du bloc. Le format de programmation est: (OPEN P———,A/D,… ) Où: - A : Ajoute de nouveaux blocs à la suite de ceux qui existent déjà. - D : Efface le programme qui existe et l’ouvre comme programme nouveau. 0182 ‘Option non disponible.’ DETECTION Durant l'édition (durant l'exécution en programmes transmis par DNC). CAUSE 0183 On a défini une fonction «G» que ni n’est pas dans les options de software. ‘Cycle inexistant.’ DETECTION Durant l'édition (durant l'exécution en programmes transmis par DNC). CAUSE SOLUTION 0185 Dans l’instruction “DIGIT”, on a défini un cycle de digitalisation qui n’est pas disponible. L’instruction “DIGIT” n’admet que 2 types de cycle de digitalisation: (DIGIT 1,…) : Cycle de digitalisation en grille. (DIGIT 2,…) : Cycle de digitalisation en arc. ‘Correcteur inexistant.’ DETECTION Durant l'édition (durant l'exécution en programmes transmis par DNC). CAUSE Dans la syntaxe du bloc, on réalise un appel à un correcteur d’outil supérieur à ceux permis par le fabricant. SOLUTION Programmer un numéro de correcteur d’outil inférieur. 0188 ‘Fonction non permise depuis PLC.’ DETECTION Durant l'exécution. CAUSE Depuis le canal du PLC on a tenté d’exécuter une fonction incompatible avec le canal d’exécution du PLC moyennant l’instruction “CNCEX” SOLUTION Une liste des fonctions et instructions permises dans le canal d’exécution du PLC est disponible dans le “Manuel d’Installation” (Chapitre 11.1.2). 0190 ‘Programmation non autorisée en mode copiage .’ DETECTION Durant l'exécution. CAUSE Dans l’ensemble des blocs qui définissent les «Cycles fixes de copiage et digitalisation (TRACE)», il y a un bloc qui contient un fonction «G» qui ne peut pas faire partie de la définition du profil. SOLUTION Les fonctions «G» disponibles dans la définition des profils sont: G00 G01 G02 G03 G06 G08 G09 G36 G39 G53 G70 G71 G90 G91 G93 28 MANUEL DE SOLUTION DES ERREURS CNC 8040M 0191 ‘Ne pas programmer des axes de copiage.’ DETECTION Durant l'exécution . CAUSE On a tenté de déplacer un axe qui a été défini comme axe de copiage moyennant la fonction “G23”. SOLUTION Les axes de copiages sont contrôlés par la CNC. Pour désactiver les axes de copiages, utiliser la fonction “G25”. 0192 ‘Plan et axe longitudinal actifs incorrects.’ DETECTION Durant l'exécution. CAUSE En programmant en langage de haut niveau, on a tenté d’exécuter un cycle de palpation moyennant l’expression “PROBE”, et l’axe longitudinal est compris dans le plan actif. SOLUTION Les cycles fixes de palpation “PROBE” sont exécutés sur les axes X, Y, Z, le plan de travail étant formé par deux desdits axes. L’autre axe, qui doit être perpendiculaire audit plan, devra être sélectionner comme axe longitudinal. 0193 ‘ G23 n’a pas été programmé.’ DETECTION Durant l'exécution. CAUSE La digitalisation “G24” a été activée ou on a programmé un contour de copiage “G27”, mais on n’a pas activé auparavant le copiage “G23”. SOLUTION Pour réaliser une digitalisation ou pour travailler avec un contour, il faut activer auparavant le copiage. 0194 ‘Repositionnement non permis.’ DETECTION Durant l'exécution. CAUSE On ne peut pas repositionner les axes moyennant l’expression “REPOS” car la sousroutine n’a pas été activée par une des entrées d’interruption. SOLUTION Afin de pouvoir exécuter l’expression “REPOS”, il faut, auparavant, avoir activé une des entrées d’interruption. 0195 ‘Axes X Y ou Z accouplés ou synchronisés.’ DETECTION Durant l'exécution. CAUSE En programmant en langage de haut niveau, on a tenté d’exécuter un cycle de palpation moyennant l’expression “PROBE”, et un des axes X Y ou Z se trouve accouplé ou synchronisé. SOLUTION Pour exécuter l’expression “PROBE”¨, les axes X, Y, Z ne doivent pas être accouplés ni synchronisés. Pour découpler les axes, programmer “G78”. 0196 ‘Axes X, Y y Z doivent exister.’ DETECTION Durant l'édition (durant l'exécution en programmes transmis par DNC). CAUSE En programmant en langage de haut niveau, on a tenté d’éditer l’expression “PROBE¨ et un des axes X, Y ou Z n’existe pas. SOLUTION Afin de pouvoir travailler avec l’expression “PROBE”, il faut que les axes X, Y, Z soient définis. 0198 ‘Déflexion hors limite.’ DETECTION Durant l'exécution. CAUSE Dans le cycle de copiage “G23” on a défini une déflexion nominale du palpeur supérieure à celle autorisée moyennant le paramètre machine. SOLUTION Programmer une déflexion nominale du palpeur inférieure. MANUEL DE SOLUTION DES ERREURS 29 CNC 8040M 0199 ‘Présélection d’axes rotatifs: valeurs entre 0-359.9999.’ DETECTION Durant la présélection de cotes. CAUSE On a tenté de réaliser une présélection de cotes sur un axe rotatif, et la valeur de présélection n’est pas dans l’intervalle 0-359.9999. SOLUTION La valeur de la présélection de cotes dans un axe rotatif doit se trouver dans l’intervalle 0-359.9999. 0200 ‘Programmer: G52 axe +/-5.5’ DETECTION Durant l'édition (durant l'exécution en programmes transmis par DNC). CAUSE En programmant la fonction «Mouvement contre butée (G52)» on n’a pas programmé l’axe que l’on veut déplacer ou on a programmé plusieurs axes. SOLUTION Dans la programmation de la fonction “G52”, il faut obligatoirement programmer l’axe qu’on désire déplacer. On ne peut programmer qu’un axe à la fois. 0202 ‘Ne programmer G27 qu’en copiage de profil.’ DETECTION Durant l'exécution. CAUSE On a défini un contour (G27) et la fonction de copiage n’est pas bidimensionnelle ni tridimensionnelle. SOLUTION La fonction «Définition du contour de copiage (G27)» ne doit être définie que lorsqu’on réalise des copiages (ou digitalisations) bidimensionnelles ou tridimensionnelles. 0204 ‘Mode de copiage incorrect.’ DETECTION Durant l'exécution. CAUSE Durant l'exécution d’un copiage manuel “G23”, on a tenté de déplacer à l’aide des touches de JOG ou volants d’un axe sélectionné comme repérage. SOLUTION En exécutant un copiage manuel, les axes sélectionnés comme repérage se déplace manuellement. Le reste des axes peuvent être déplacés avec les touches de JOG ou avec des volants. 0205 ‘Mode de digitalisation incorrect.’ DETECTION Durant l'exécution. CAUSE On a défini une digitalisation point par point, et on ne se trouve pas en mode manuel (on se trouve en simulation ou en exécution). SOLUTION Pour exécuter une digitalisation point à point, il faut être en mode manuel. 0206 ‘Valeurs entre 0-6.’ DETECTION Durant l’édition des paramètres de la table de paramètres machine. CAUSE On a tenté d’assigner une valeur non valable à un paramètre. SOLUTION Le paramètre n’admet que des valeurs entre 0 et 6. 0207 ‘Table complète.’ DETECTION Durant l'édition de tables. CAUSE Dans les tables de fonctions «M», outils ou correcteurs, on a tenté de définir plus de données que celles permises par le fabricant moyennant les paramètres machine. Lorsqu’on charge une table via DNC, la CNC n’efface pas la table précédente, elle remplace les valeurs existantes et copient les nouvelles données dans les positions libres de la table. SOLUTION Le nombre maximum de données qui peut être défini est limité par les paramètres machine : - Nombre maximum de fonctions «M» : NMISCFUN(P29). - Nombre maximum d’Outils : NTOOL(P23). - Nombre maximum de correcteurs : NTOFFSET(P27). - Nombre maximum de positions en magasin : NPOCKET(P25). Si on désire charger une nouvelle table (via DNC), il est recommandé d’effacer la table précédente. 30 MANUEL DE SOLUTION DES ERREURS CNC 8040M 0208 ‘Programmer A entre 0 et 255.’ DETECTION Durant l'exécution. CAUSE Dans la fonction «LOOK-AHEAD (G51)» on a programmé le paramètre “A” (Pourcentage d’accélération à utiliser) avec une valeur supérieure à 255. SOLUTION Le paramètre “A” est optionnel, mais si on le programme, il doit avoir une valeur entre 0 et 255. 0209 ‘Imbriquement de programmes interdit.’ DETECTION Durant l'exécution. CAUSE D’un programme en exécution, on a tenté d’exécuter un autre programme moyennant l’instruction “EXEC”, qui comprend aussi une instruction “EXEC”. SOLUTION Du programme qui s’exécute moyennant l’expression de programme “EXEC” on ne peut pas réaliser un appel à un autre programme. 0210 ‘Compensation non admise.’ DETECTION Durant l'édition (durant l'exécution en programmes transmis par DNC). CAUSE On a tenté d’activer ou de désactiver la compensation de rayon (G41, G42, G40) en un bloc qui contient un mouvement non linéaire. SOLUTION La compensation de rayon doit être activer/désactiver dans un mouvement linéaire (G00, G01). 0211 ‘Ne pas programmer une nouvelle translation sans annuler l’antérieure.’ DETECTION Durant l'exécution. CAUSE Au moyen de la fonction «Définition du plan incliné (G49)», on a tenté de définir un plan incliné, tout en ayant un autre plan défini auparavant. SOLUTION Pour définir un nouveau plan incliné, il faut d’abord annuler le plan défini auparavant. Pour annuler un plan incliné, programmer “G49” sans paramètres. 0212 ‘Programmation non permise avec G48-G49 actives.’ DETECTION Durant l'exécution . CAUSE En programmant en langage de haut niveau, on a tenté d’exécuter un cycle de palpation moyennant l’expression “PROBE” la fonction “G48” ou “G49” étant active. SOLUTION Les cycles de digitalisation “PROBE” sont effectués sur les axes X, Y, Z. C’est pourquoi, afin de pouvoir les exécuter, les fonctions “G48” ni “G49” ne peuvent pas être actives. 0213 ‘Pour G28 ou G29 on a besoin d’une deuxième broche.’ DETECTION Durant l'édition (durant l'exécution en programmes transmis par DNC). CAUSE On a tenté de sélectionner la broche de travail moyennant “G28/G29”, mais la machine ne dispose que d’une broche de travail. SOLUTION Si la machine ne dispose que d’une broche de travail, on ne pourra pas programmer les fonctions “G28/ G29”. 0214 ‘Fonction G non permise en sélection de profil.’ DETECTION Durant la récupération d’un profil. CAUSE Dans l’ensemble des blocs choisis pour la récupération du profil, il y a un bloc qui contient une fonction «G» qui ne peut pas faire partie de la définition du profil. SOLUTION Les fonctions «G» disponibles dans la définition d’un profil sont: G00 G01 G02 G03 G06 G08 G09 G36 G37 G38 G39 G90 G91 G93 MANUEL DE SOLUTION DES ERREURS 31 CNC 8040M 0215 ‘Fonction G non permise après le point initial du profil’ DETECTION Durant la récupération d’un profil. CAUSE Dans l’ensemble des blocs choisis pour la récupération du profil et depuis le point initial d’un profil, il y a un bloc qui contient une fonction «G» qui ne peut pas faire partie de la définition du profil. SOLUTION Les fonctions «G» disponibles dans la définition d’un profil sont: G00 G01 G02 G03 G06 G08 G09 G36 G37 G38 G39 G90 G91 G93 0216 ‘Assignation non paramétrique après le point initial du profil.’ DETECTION Durant la récupération d’un profil. CAUSE Dans l’ensemble des blocs choisis pour la récupération du profil et après le point initial d’un profil, on a programmé en langage de haut niveau une assignation qui n’est pas paramétrique (à paramètre local ou global). SOLUTION Les seules instruction en langage de haut niveau qui peuvent être éditées sont les assignations à paramètres locaux (P0 a P25) et globaux (P100 a P299). 0217 ‘On ne peut pas programmer le bloc après le point initial du profil.’ DETECTION Durant la récupération d’un profil. CAUSE Dans l’ensemble des blocs choisis pour la récupération du profil, et après le point initial du profil, il y a un bloc en langage de haut niveau qui n’est pas une assignation. SOLUTION Les seules instructions en langage de haut niveau qui peuvent être éditées sont les assignations à paramètres locaux (P0 a P25) et globaux (P100 a P299). 0218 ‘On ne peut pas programmé l’axe après le point initial du profil.’ DETECTION Durant la récupération d’un profil. CAUSE Dans l’ensemble des blocs choisis pour la récupération du profil, on a défini une position sur un axe qui ne fait pas partie du plan actif. Il se peut qu’une cote de surface après le point initial d’un profil ait été défini. SOLUTION La cote de surface des profils ne peut être définie que dans le bloc initial du premier profil, correspondant au point initial du profil extérieur. 0219 ‘Point initial mal programmé en sélection profil’ DETECTION Durant la sélection d’un profil. CAUSE Le point initial d’un profil est mal programmé. Il reste à définir une des deux coordonnées qui définissent sa position. SOLUTION Le point initial d’un profil doit être défini dans les deux axes qui forment le plan actif. 0226 ‘Avec G48, il n’est pas possible de programmer un outil.’ DETECTION Durant l'exécution. CAUSE On a programmé un changement d’outil, la fonction «Transformation TCP (G48)» étant active. SOLUTION Il est impossible de réaliser un changement d’outil, la transformation TCP étant active. Pour réaliser un changement d’outil, il faut d’abord annuler la transformation TCP . 0227 ‘Programmer Q entre +/-359.9999.’ DETECTION Durant l'édition (durant l'exécution en programmes transmis par DNC). CAUSE Dans la fonction «Filetage électronique (G33)» on a programmé l’angle d’entrée “Q” avec une valeur se trouvant hors des limites ±359.9999. SOLUTION Programmer un angle d’entrée de l’intervalle +/-359.9999. 32 MANUEL DE SOLUTION DES ERREURS CNC 8040M 0228 ‘Ne pas programmer Q avec le paramètre M19TYPE=0.’ DETECTION Durant l'édition (durant l'exécution en programmes transmis par DNC). CAUSE Dans la fonction ««Filetage électronique (G33)» on a programmé l’angle d’entrée “Q”, mais le type d’arrêt orientée de la broche disponible ne permet pas de réaliser cette opération. SOLUTION Pour définir un angle d’entrée, il faut définir le paramètre machine de la broche M19TYPE(P43)=1. 0229 0230 0231 0232 0233 ‘Programmer ‘Programmer ‘Programmer ‘Programmer ‘Programmer X Y Y Z Z maximum’ minimum’ maximum’ minimum’ maximum’ DETECTION Durant l'édition (durant l'exécution en programmes transmis par DNC). CAUSE En programmant en langage de haut niveau, dans l’instruction “DGWZ” il reste à programmer la limite indiquée (ou elle a été définie avec une données qui n’a pas de valeur numérique). SOLUTION Réviser la syntaxe du bloc. 0234 ‘Limites graphiques erronées’ DETECTION Durant l'exécution. CAUSE Une des limites inférieures définies moyennant l’instruction “DGWZ” est supérieure à celle de sa limite supérieure. SOLUTION Programmer les limites supérieures de la zone graphique à visualiser supérieures aux limites inférieures. MANUEL DE SOLUTION DES ERREURS 33 CNC 8040M ERREURS DE PREPARATION ET EXECUTION 1000 ‘Information sur trajectoire insuffisante.’ DETECTION Durant l'exécution. CAUSE Dans le programme il y a trop de blocs suivis sans information sur la trajectoire afin de pouvoir réaliser la compensation de rayon, arrondi, chanfrein ou entrées ou sortie tangentielle. SOLUTION Afin de pouvoir réaliser ces opérations la CNC doit connaître à l’avance la trajectoire à parcourir, il ne peut donc y avoir plus de 48 blocs suivis sans information sur la trajectoire à parcourir. 1001 ‘Changement de plan en arrondi/chanfrein.’ DETECTION Durant l'exécution. CAUSE On a programmé un changement de plan dans la trajectoire qui suit la définition d’un «Arrondi contrôlé d’arêtes (G36)» ou «Chanfrein (G39)». SOLUTION On ne peut pas changer de plan durant l'exécution d'un arrondi ou chanfrein. La trajectoire qui suit la définition d'un arrondi ou chanfrein, doit être dans le même plan que l’arrondi ou chanfrein. 1002 ‘Rayon d’arrondi trop grand.’ DETECTION Durant l'exécution. CAUSE Dans la fonction «Arrondi d'arêtes (G36)» on a programmé un rayon d’arrondi supérieur à une des trajectoires dans lesquelles il est défini. SOLUTION Le rayon d’arrondi doit être inférieur aux trajectoires qui le définissent. 1003 ‘Arrondi en bloc final.’ DETECTION Durant l'exécution. CAUSE Un «Arrondi contrôlé d’arêtes (G36)» ou «Chanfrein (G39)» a été défini dans la dernière trajectoire du programme, ou lorsque la CNC ne trouve pas d’information de la trajectoire qui suit la définition de l'arrondi ou chanfrein. SOLUTION Un arrondi ou chanfrein doit être défini entre deux trajectoires. 1004 ‘Sortie tangentielle mal programmée’ DETECTION Durant l'exécution. CAUSE Le déplacement suivant la définition d’une sortie tangentielle (G38) est une trajectoire circulaire. SOLUTION Le déplacement suivant la définition d’une sortie tangentielle doit être une trajectoire droite. 1005 ‘Chanfrein mal programmé.’ DETECTION Durant l'exécution. CAUSE Le déplacement suivant la définition d’un «Chanfrein (G39)» est une trajectoire circulaire. SOLUTION Le déplacement suivant la définition d’un chanfrein doit être une trajectoire droite. 1006 ‘Valeur de chanfrein trop grande.’ DETECTION Durant l'exécution. CAUSE Dans la fonction «Chanfrein (G39)» on a programmé une dimension de chanfrein supérieure à une des trajectoires dans lesquelles il est défini. SOLUTION La dimension de chanfrein doit être inférieure aux trajectoires qui le définissent. 34 MANUEL DE SOLUTION DES ERREURS CNC 8040M 1007 ‘G8 mal défini.’ DETECTION Durant l'exécution. CAUSE/S Les différentes causes sont les suivantes: 1.-Lorsqu’on a programmé une circonférence complète moyennant la fonction «Circonférence tangentielle à trajectoire précédente (G08)» 2.-Quand la trajectoire tangentielle termine en un point de la trajectoire précédente, ou en son prolongement (en ligne droite). 3.-Travaillant avec le cycle fixe de poche avec îlots, lorsqu’on programme la fonction “G08” dans le bloc suivant la définition de début de profil (G00). SOLUTION La solution à chacune des causes est la suivante: 1.-La fonction “G08” ne permet pas la programmation de circonférences complètes. 2.-La trajectoire tangentielle ne peut pas terminer en un point de la trajectoire précédente, ou en son prolongement (en ligne droite). 3.-La CNC ne dispose pas d’information sur la trajectoire précédente, et ne peut pas exécuter un arc tangentiel. 1008 ‘Pas d’informations sur la trajectoire précédente’ DETECTION Durant l'exécution CAUSE On a programmé moyennant la fonction “G08” une circonférence tangentielle à la trajectoire précédente, mais il n’y pas d’information sur la trajectoire précédente. SOLUTION Pour réaliser une trajectoire tangentielle à la trajectoire précédente, il doit exister des informations sur la trajectoire précédente et elles doivent être dans les 48 blocs précédents à la trajectoire tangentielle. 1009 ‘Pas d’information pour arc tangent en poche avec îlot.’ DETECTION Durant l'exécution. CAUSE Dans l’ensemble des blocs qui définissent le profil d’une poche avec îlots, on a programmé un arc tangent mais il reste à définir une valeur, ou il n’y a pas d’information suffisante sur la trajectoire précédente. SOLUTION Réviser les valeurs de la définition du profil. 1010 ‘Plan erroné en trajectoire tangente.’ DETECTION Durant l'exécution CAUSE On a programmé un changement de plan entre la définition de la fonction «Trajectoire circulaire tangente à la trajectoire précédente (G08)», et la trajectoire précédente. SOLUTION Le changement de plan ne peut pas être réalisé à plat entre les deux trajectoires. 1011 ‘Mouvement en JOG hors des limites.’ DETECTION Durant l'exécution CAUSE Après avoir défini un plan incliné l’outil est positionné en un point hors des limites de travail, et moyennant JOG on tente de déplacer un axe qui ne positionne pas l’outil dans la zone définie par les limites de travail. SOLUTION Déplacer, moyennant JOG, l’axe qui permettra de positionner l’outil dans les limites de travail. 1012 ‘On ne peut pas programmer G48 avec G43 actif’ DETECTION Durant l'exécution CAUSE On a tenté d'activer la transformation TCP (G48), la compensation de longueur (G43) étant active. SOLUTION Pour activer la transformation TCP (G48), la compensation de longueur doit être désactivée car la TCP en elle-même implique une compensation de longueur spécifique. 1013 ‘On ne peut pas programmer G43 avec G48 actif’ DETECTION Durant l'exécution CAUSE On a tenté d'activer la compensation de longueur (G43), la transformation TCP (G48) étant active. SOLUTION La transformation TCP (G48) étant active, on ne peut pas activer la compensation de longueur (G43), car la TCP en elle-même implique une compensation de longueur spécifique. MANUEL DE SOLUTION DES ERREURS 35 CNC 8040M 1015 ‘Outil non défini dans la table des outils’ DETECTION Durant l'exécution CAUSE Un changement d'outil a été défini, et le nouvel outil n’est pas défini dans la table des outils. SOLUTION Définir le nouvel outil dans la table des outils. 1016 ‘L’outil n’est pas dans le magasin’ DETECTION Durant l'exécution. CAUSE Un changement d'outil a été défini, et le nouvel outil n’est défini dans aucune position dans la table du magasin des outils. SOLUTION Définir le nouvel outil dans la table du magasin des outils. 1017 ‘Il n’y a pas d’emplacement dans le magasin’ DETECTION Durant l'exécution. CAUSE Un changement d'outil a été défini et il n’y a pas d’emplacement dans le magasin pour placer l’outil qui se trouve actuellement dans la broche. SOLUTION Il se peut que le nouvel outil soit défini dans la table des outils comme outil spécial et qu’il ait plus d’une position réservée dans le magasin. Dans ce cas, cette position est fixe pour cet outil et aucun autre outil ne peut l’occuper. Afin d’éviter cette erreur, il convient de laisser une position libre dans le magasin des outils. 1018 ‘Changement d’outil programmé sans M06’ DETECTION Durant l'exécution. CAUSE Après avoir cherché un outil, et avant de réaliser la recherche suivante, on n’a pas programmé M06. SOLUTION Cette erreur se produit quand on dispose d’un centre d’usinage (paramètre machine générale TOFFM06(P28)=YES) qui dispose de changeur cyclique (paramètre machine générale CYCATC(P61)=YES). Dans ce cas, après avoir cherché un outil, et avant de chercher le suivant, il faut réaliser le changement d’outil moyennant M06. 1019 ‘Pas d’outil de la même famille pour remplacer.’ DETECTION Durant l'exécution. CAUSE La vie réelle de l’outil sollicité surpasse la vie nominale. La CNC a tenté de le remplacer par un autre de la même famille et elle n’en a trouvé aucun. SOLUTION Remplacer l’outil, ou définir un autre outil de la même famille. 1020 ‘Changement outil actif, suivant impossible en haut niveau.’ DETECTION Durant l'exécution CAUSE En programmant en langage de haut niveau, moyennant la variable “TMZT”, on a tenté d’assigner l’outil actif, ou le suivant, à une position dans le magasin. SOLUTION Pour changer l’outil actif, ou le suivant, utiliser la fonction «T». On ne peut pas déplacer l’outil actif, ou le suivant , au magasin moyennant la variable “TMZT”. 1021 ‘Pas de correcteur programmé en cycle fixe.’ DETECTION Durant l'exécution CAUSE On a programmé le cycle fixe de palpation “PROBE” correspondant au calibrage de l’outil, et aucun correcteur d’outil n’est sélectionné. SOLUTION Pour exécuter le «Cycle fixe de calibrage d’outil (PROBE)» le correcteur d’outil où va être gardée l’information du cycle de palpation doit être sélectionné. 36 MANUEL DE SOLUTION DES ERREURS CNC 8040M 1023 ‘G67. Rayon de l’outil trop grand.’ DETECTION Durant l'exécution CAUSE Dans le «Cycle fixe de poche avec îlots (G66)», un outil d’un rayon trop grand a été sélectionné pour l’opération d’ébauche “G67” (poche 2D). L’outil n’entre dans aucun point de la poche. SOLUTION Sélectionner un outil d’un rayon inférieur. 1024 ‘G68. Rayon de l’outil trop grand.’ DETECTION Durant l'exécution CAUSE Dans le «Cycle fixe de poche avec îlots (G66)», un outil d’un rayon trop grand a été sélectionné pour l’opération de finition “G68” (poche 2D). En un point d’usinage, la distance entre le profil extérieur et le profil d’un îlot est inférieur au diamètre de l’outil. SOLUTION Sélectionner un outil d’un rayon inférieur. 1025 ‘On a programmé un outil de rayon nul’ DETECTION Durant l'exécution CAUSE Dans le «Cycle fixe de poche avec îlots (G66)», une opération (G67/G68) avec un outil zéro a été programmé. SOLUTION Corriger dans la table d'outils la définition de l'outil, ou sélectionner un autre outil pour cette opération. 1026 ‘On a programmé un pas plus grand que le diamètre de l’outil’ DETECTION Durant l'exécution CAUSE Dans le «Cycle fixe de poche rectangulaire (G87)», dans le «Cycle fixe de poche circulaire (G88)» ou dans une des opérations du «Cycle fixe de poche avec îlots (G66)», on a programmé le paramètre “C” avec une valeur supérieure au diamètre de l’outil avec laquelle cette opération va être réalisée. SOLUTION Corriger la syntaxe du bloc. Le pas d’usinage “C” doit être inférieur ou égal au diamètre de l’outil. 1027 ‘Avec G48 actif, il n’est pas possible de programmer un outil.’ DETECTION Durant l'exécution CAUSE On a programmé un changement d'outil, la fonction «Transformation TCP (G48)» étant active. SOLUTION Il est impossible de réaliser un changement d'outil, la transformation TCP étant active. Afin de réaliser un changement d'outil, il faut d’abord annuler la transformation TCP. 1028 ‘Ne pas commuter ni décommuter des axes avec G15, G23, G48 ou G49 actives’ DETECTION Durant l'exécution CAUSE On a tenté de commuter ou décommuter (G28/G29) un axe, les fonctions “G15”, “G23”, “G48” ou “G49” étant actives. SOLUTION On ne peut pas commuter ni décommuter des axes, lorsque les fonctions “G15”, “G23”, “G48”, “G49” sont actives. 1029 ‘Ne pas commuter des axes déjà commutés.’ DETECTION Durant l'exécution. CAUSE On a tenté de commuter (G28) un axe qui se trouve déjà commuté à un autre. SOLUTION Un axe commuté à un autre ne peut pas être commuté directement à un troisième. Il faut le décommuter avant (G29 axe). MANUEL DE SOLUTION DES ERREURS 37 CNC 8040M 1030 ‘M du changement automatique de gamme impossible’ DETECTION Durant l'exécution CAUSE Le changement automatique de gamme est disponible, et dans un bloc 7 fonctions «M» et la fonction «S» qui suppose le changement de gamme sont programmées. Dans ce cas la CNC ne peut pas comprendre la fonction «M» du changement automatique dans ce bloc. SOLUTION Programmer une fonction «M» ou la fonction «S» dans un bloc à part. 1031 ‘Sousroutine avec changement gamme non admise.’ DETECTION Durant l'exécution CAUSE Dans les machines qui disposent de changement automatique de gamme, quand on programme une vitesse de rotation «S» qui implique un changement de gamme, et la fonction «M» du changement automatique de gamme a une sousroutine associée. SOLUTION Lorsque le changement automatique est disponible, les fonctions «M» correspondantes au changement de gamme ne peuvent avoir aucune sousroutine associée. 1032 ‘Gamme de broche non définie pour M19.’ DETECTION Durant l'exécution CAUSE On a programmé “M19” et aucune des fonctions de changement de gamme “M41”, “M42”, “M43”, “M44” est active. SOLUTION Après la mise en marche, la CNC ne prend en charge aucune gamme, donc, si la fonction de changement de gamme ne se produit pas automatiquement (paramètre de la broche AUTOGEAR(P6)=NO), il faut programmer les fonctions auxiliaires de changement de gamme (“M41”, “M42”, “M43” ou “M44”). 1033 ‘Changement de gamme incorrect.’ DETECTION Durant l'exécution. CAUSE/S Les différentes causes sont les suivantes: 1.-Lorsqu’on tente de réaliser un changement de gamme, et les paramètres machine des gammes (MAXGEAR1, MAXGEAR2, MAXGEAR3, ou MAXGEAR4) sont mal définis. Toutes les gammes n’ont pas été utilisées, et on a assigné la vitesse maximum zéro aux gammes non utilisées. 2.-Lorsqu’on a programmé un changement de gamme (“M41”, “M42”, “M43” ou “M44”) et le PLC n’a pas répondu par le signal de gamme active correspondant (GEAR1, GEAR2, GEAR3 ou GEAR4). SOLUTION La solution à chacune des causes est la suivante: 1.-Lorsque les quatre gammes ne sont pas utilisées, il faut employer les gammes inférieures, en commençant par “MAXGEAR1”, et on assignera aux gammes qui ne sont pas utilisées la même valeur que celle assignée à la gamme supérieure des gammes utilisées. 2.-Vérifier le programme du PLC. 1034 ‘S programmée sans gamme active.’ DETECTION Durant l'exécution. CAUSE On a tenté de mettre en marche la broche et il n’y a aucune gamme sélectionnée. SOLUTION Après la mise en marche, la CNC ne prend en charge aucune gamme, donc, si la fonction de changement de gamme ne se produit pas automatiquement (paramètre de la broche AUTOGEAR(P6)=NO), il faut programmer les fonctions auxiliaires de changement de gamme (“M41”, “M42”, “M43” ou “M44”). 1035 ‘S programmée trop grande’ DETECTION Durant l'exécution. CAUSE On a programmé une “S” supérieure à la valeur maximum permise par la dernière gamme active. SOLUTION Programmer une vitesse de rotation “S” inférieure. 38 MANUEL DE SOLUTION DES ERREURS CNC 8040M 1036 ‘S non programmée en G95 ou filetage’ DETECTION Durant l'exécution. CAUSE On a programmé la fonction «Avance en millimètres (pouces) par révolution (G95)» ou la fonction «Filetage électronique (G33)», mais il n’y a pas de vitesse de rotation sélectionnée. SOLUTION Afin de travailler avec l’avance en millimètres par révolution (G95) ou pour réaliser un filetage électronique (G33), il doit y avoir une vitesse de rotation “S” programmée. 1040 ‘Cycle fixe inexistant’ DETECTION Durant l'exécution en mode MDI. CAUSE Après avoir interrompu un programme durant l'exécution d’un cycle fixe (G8x), et par la suite réalisé un changement de plan, on tente d’exécuter un cycle fixe (G8x). SOLUTION Ne pas interrompre le programme durant l'exécution d’un cycle fixe. 1041 ‘Un paramètre obligatoire n’a pas été programmé dans le cycle fixe’ DETECTION Durant l'exécution CAUSE/S Les différentes causes sont les suivantes: 1.-Dans le «Cycle fixe de poche avec îlots» il reste à programmer un paramètre. POCHES 2D - Dans la opération d'ébauchage “G67”, un des paramètres “I”, “R” n’a pas été programmé. - Il n’y a pas d’opération d’ébauchage, et dans l’opération de finition “G68” un des paramètres “I”, “R” n’a pas été programmé. POCHES 3D - Dans l’opération d'ébauchage “G67”, un des paramètres “I”, “R” n’a pas été programmé. - Il n’y a pas d’opération d'ébauchage, et dans l’opération de semi-finition “G67” un des paramètres “I”, “R” n’a pas été programmé. - Il n’y a pas d’opération d'ébauchage ni de semi-finition, et dans l’opération de finition “G68” un des paramètres “I”, “R” n’a pas été programmé. - Dans l’opération de finition “G68”, le paramètre “B” n’a pas été programmé. 2.-Dans le cycle fixe de digitalisation il reste à programmer un paramètre. SOLUTION Corriger la définition des paramètres. Poche avec îlots (opération de finition) Dans le cycle fixe de poche avec îlots la programmation des paramètres “I” et “R” dans l’opération d'ébauchage est obligatoire. S’il n’y a pas d’opération d'ébauchage, ils doivent être définis dans l’opération de finition (2D) ou dans celle de semi-finition (3D). S’il n’y a pas de semi-finition (3D), ils doivent être définis dans l’opération de finition. Dans la poche 3D, il faut obligatoirement définir le paramètre “B” dans l’opération de finition. Cycles de digitalisation Réviser la syntaxe du bloc. Les formats de programmation sont les suivants: (DIGIT 1,X,Y,Z,I,J,K,B,C,D,F) (DIGIT 2,X,Y,Z,I,J,K,A,B,C,F) MANUEL DE SOLUTION DES ERREURS 39 CNC 8040M 1042 ‘Valeur de paramètre non valable en cycle fixe’ DETECTION Durant l'exécution CAUSE/S Les différentes causes sont les suivantes: 1.-Dans le «Cycle fixe de poche avec îlots», lorsqu’au cours de l’opération de finition “G68” il a été défini un paramètre avec une valeur non valable. Il se peut qu’une valeur négative (ou zéro) ait été assignée à un paramètre qui n’admet que des valeurs positives. 2.-Dans le «Cycle fixe de poche avec îlots», lorsque dans l’opération de perçage (G69) “B”, “C” ou “H” a été défini avec la valeur zéro. 3.-Dans les cycles fixes de poche rectangulaire (G87) ou circulaire (G88), le paramètre “C” a été défini, ou une dimension de la poche, avec la valeur zéro. 4.-Dans le «Cycle fixe de perçage profond à pas variable (G69)», le paramètre “C” a été défini avec la valeur zéro. 5.-Dans le cycle fixe de digitalisation, une valeur non correcte a été assignée à un paramètre. Il se peut qu’une valeur négative (ou zéro) ait été assignée à un paramètre qui n’admet que des valeurs positives. SOLUTION Corriger la définition des paramètres. Poche avec îlots (opération de finition) Paramètre “Q”: N’admet que les valeurs 0, 1 ou 2. Paramètre “B”: N’admet que des valeurs différentes de zéro. Paramètre “J”: Doit être inférieur au rayon de l’outil avec lequel cette opération va être réalisée. Digitalisation en GRILLE Paramètre “B”: N’admet que des valeurs positives supérieures à zéro. Paramètre “C”: N’admet que des valeurs positives différentes de 0. Paramètre “D”: N’admet que les valeurs 0 ou 1. Digitalisation en ARC Paramètre “J” et “C”: N’admettent que des valeurs positives supérieures à zéro. Paramètre “K”, “A” et “B”: N’admettent que des valeurs positives. 1043 ‘Profil de profondeur non valable en poches avec îlots.’ DETECTION Durant l'exécution. CAUSE Dans le «Cycle fixe de poche avec îlots» (3D): - Les profils de profondeur de deux sections d’un même contour (simple ou composé) s’entrecroisent. - Il est impossible de réaliser la finition d’un contour avec l’outil programmé (la trajectoire sphérique avec outil non sphérique). SOLUTION Les profils de profondeurs des deux sections d’un même profil ne peuvent pas s’entrecroiser. De plus, le profil de profondeur doit être défini juste après le profil dans le plan et il faut utiliser le même point initial dans les deux profils. Vérifier que la pointe choisie de l’outil est la plus appropriée au profil de profondeur programmé. 1044 ‘Profil du plan qui se coupe lui même en poches avec îlots’ DETECTION Durant l'exécution. CAUSE Dans l'ensemble des profils qui définit une poche avec îlots, il y a un profil qui se recoupe lui-même. SOLUTION Réviser la définition des profils. Le profil d’une poche avec îlots ne peut se recouper lui-même. 1045 ‘Erreur de programmation perçage de poche avec îlots.’ DETECTION Durant l'exécution CAUSE Dans le «Cycle fixe de poche avec îlots (G66)», on a programmé un cycle fixe qui n’est pas de perçage. SOLUTION Dans l’opération de perçage seuls les cycles fixes “G81”, “G82”, “G83” ou “G69” peuvent être définis. 1046 ‘Position d’outil non valable avant le cycle fixe’ DETECTION Durant l'exécution. CAUSE Au moment de l’appel à un cycle fixe, l’outil se trouve positionné entre la coordonnée du plan de référence et la coordonnée de profondeur finale d’une des opérations. SOLUTION Lorsqu’on réalise un appel à un cycle fixe, l’outil doit être positionné au-dessus du plan de référence. 40 MANUEL DE SOLUTION DES ERREURS CNC 8040M 1047 ‘Profil du plan ouvert en poches avec îlots’ DETECTION Durant l'exécution. CAUSE Dans l'ensemble des profils qui définit une poche avec îlots, il y a un profil qui ne commence ni termine au même point. SOLUTION Réviser la définition des profils. Les profils qui définissent les poches avec îlots doivent être fermés. L’erreur peut être due à ce que “G01” n’a pas été programmée après le début, avec “G00”, d’un des profils. 1048 ‘On n’a pas programmé la coordonnée de la surface de la pièce en poche avec îlots’ DETECTION Durant l'exécution. CAUSE On n’a pas programmé la coordonnée de la surface de la poche au premier point de la définition de la géométrie. SOLUTION La valeur correspondante à la coordonnée de la surface doit être définie dans le premier bloc de définition du profil de la poche (en coordonnées absolues). 1049 ‘Coordonnée du plan de référence non valable en cycle fixe’ DETECTION Durant l'exécution. CAUSE Dans une des opérations du «Cycle fixe de poche avec îlots (G66)», la coordonnée du plan de référence se trouve entre la coordonnée de la surface de la pièce et la coordonnée de profondeur finale d’une des opérations. SOLUTION Le plan de référence doit être situé au dessus de la surface de la pièce. Quelquefois cette erreur se produit suite à la programmation de la coordonnée de surface de la pièce en coordonnée accroissante. (La valeur de la surface de la poche doit être programmée en coordonnées absolues). 1050 ‘Valeur erronée pour donner à une variable’ DETECTION Durant l'exécution. CAUSE Moyennant des paramètres, une valeur trop élevée a été assignée à une variable. SOLUTION Réviser l'histoire du programme, afin que ce paramètre n’arrive pas avec cette valeur au bloc où l’assignation est réalisée. 1051 ‘Accès aux variables du PLC erroné.’ DETECTION Durant l'exécution CAUSE 1052 Depuis la CNC on a tenté de lire une variable du PLC qui n’est pas définie dans le programme du PLC. ‘Accès aux variables avec indice non permis’ DETECTION Durant l'édition CAUSE En programmant en langage de haut niveau, une opération avec un paramètre local supérieur à 25 ou avec un paramètre global supérieur à 299 est réalisée. SOLUTION Les paramètres que la CNC utilise sont les suivants: - Locaux: 0-25. - Globaux: 100-299. On ne peut pas utiliser dans les opérations d’autres paramètres qui ne soient pas dans ces rangs. 1053 ‘Paramètres locaux non accessibles’ DETECTION Durant l'exécution en canal d’utilisateur CAUSE On a tenté d’exécuter un bloc où une opération est réalisée avec des paramètres locaux . SOLUTION Le programme qui est exécuté dans le canal d’utilisateur ne permet pas de réaliser d’opérations avec des paramètres locaux (P0 à P25). MANUEL DE SOLUTION DES ERREURS 41 CNC 8040M 1054 ‘Limite des paramètres locaux dépassée’ DETECTION Durant l'exécution. CAUSE En programmant en langage de haut niveau, plus de 6 niveaux d’imbriquement ont été réalisés moyennant l’expression “PCALL”. Plus de 6 appels ont été réalisés moyennant l’expression “PCALL” dans la même boucle. SOLUTION Seuls six niveaux d’imbriquement de paramètres locaux sont permis, dans les 15 nivaux d’imbriquement de sousroutines. Chaque fois qu’un appel est réalisé moyennant l’expression “PCALL”, un nouveau niveau d’imbriquement de paramètres locaux est produit (et de plus, il se produit aussi un nouveau niveau d’imbriquement de sousroutines). 1055 ‘Imbriquement dépassé.’ DETECTION Durant l'exécution. CAUSE En programmant en langage de haut niveau, plus de 15 niveaux d’imbriquement ont été réalisés moyennant les expressions “CALL”, “PCALL” ou “MCALL”. Plus de 15 appels ont été réalisés moyennant les expressions “CALL”, “PCALL” ou “MCALL” dans la même boucle. SOLUTION Seuls 15 niveaux d’imbriquement de paramètres locaux sont permis. Chaque fois qu’un appel est réalisé moyennant les expressions “CALL”, “PCALL” ou “MCALL”, un nouveau niveau d’imbriquement est produit. 1056 ‘RET non associé à sousroutine’ DETECTION Durant l'exécution. CAUSE L’instruction “RET” a été éditée mais l’instruction “SUB” n’a pas été éditée auparavant. SOLUTION Afin d’utiliser l’instruction “RET” (fin de sousroutine), il faut avoir initié auparavant l’édition d’une sousroutine moyennant l’instruction “SUB (nº sousroutine)”. 1057 ‘Sousroutine non définie’ DETECTION Durant l'exécution. CAUSE Un appel (CALL, PCALL…) a été réalisé à une sousroutine qui n’est pas définie dans la mémoire de la CNC. SOLUTION Vérifier que le nom de la sousroutine est correct, et que la sousroutine existe dans la mémoire de la CNC (pas nécessairement dans le même programmé où l’appel est réalisé). 1059 ‘Saut à étiquette non définie’ DETECTION Durant l'exécution. CAUSE En programmant en langage de haut niveau, on a programmé l’instruction “GOTO N—” mais le numéro du bloc (N) programmé n’est existe pas. SOLUTION Lorsqu’on programme l’instruction “GOTO N—”, le bloc auquel elle fait référence doit être défini dans le même programme. 1060 ‘Etiquette non définie’ DETECTION Durant l'exécution. CAUSE/S Les différentes causes sont les suivantes: 1.-En programmant en langage de haut niveau, on a programmé l’instruction “RPT N—, N—”, mais un des numéros du bloc (N) programmé n’est existe pas. 2.-Lorsque dans le «Cycle fixe de poche avec îlots (G66)» on a programmé “G66 … S–– E––” et une des valeurs qui définit le début ou la fin des profils n’existe pas. SOLUTION La solution à chacune des causes est la suivante: 1.-Lorsqu’on programme l’instruction “RPT N—, N—”, les blocs auxquels elle fait référence doivent être définis dans le même programme. 2.-Réviser le programme. Placer l’étiquette correspondante au paramètre “S” au début de la définition des profils et l’étiquette correspondante au paramètre “E” à la fin de la définition des profils. 42 MANUEL DE SOLUTION DES ERREURS CNC 8040M 1061 ‘On ne peut pas chercher une étiquette’ DETECTION Durant l'exécution en mode MDI. CAUSE En programmant en langage de haut niveau, une instruction “RPT N—, N—” ou “GOTO N—” a été définie. SOLUTION En travaillant en mode MDI, des instructions du type “RPT” ou “GOTO” ne peuvent pas être programmées. 1062 ‘Sousroutine en programme non disponible.’ DETECTION Durant l'exécution CAUSE On a réalisé un appel à une sousroutine qui se trouve dans un programme qui est utilisé par la DNC. SOLUTION Attendre à ce que la DNC termine d’utiliser le programme. Si la sousroutine va être utilisée habituellement, il est recommandé la placer dans un programme à part. 1063 ‘On ne peut pas ouvrir le programme.’ DETECTION Durant l'exécution. CAUSE Un programme est exécuté en mode infini et depuis ce programme, on tente de exécuter un autre programme infini moyennant l’instruction “EXEC”. SOLUTION On ne peut pas exécuter plus d’un programme infini simultanément. 1064 ‘Le programme ne peut pas être exécuté’ DETECTION Durant l'exécution. CAUSE On a tenté d’exécuter un programme depuis un autre avec l’instruction “EXEC”, et le programme n’existe pas ou il est protégé de l’exécution. SOLUTION Le programme que l’on désire exécuter moyennant l’instruction “EXEC” doit exister dans la mémoire de la CNC et il doit être exécutable. 1065 ‘Début de compensation sans trajectoire droite’ DETECTION Durant l'exécution. CAUSE Le premier déplacement dans le plan de travail après avoir activé la compensation de rayon (G41/ G42) n’est pas un déplacement linéaire. SOLUTION Le premier déplacement après avoir activé la compensation de rayon (G41/G42) doit être linéaire. 1066 ‘Fin de compensation sans trajectoire droite’ DETECTION Durant l'exécution. CAUSE Le premier déplacement dans le plan de travail après avoir désactivé la compensation de rayon (G40) n’est pas un déplacement linéaire. SOLUTION Le premier déplacement après avoir désactivé la compensation de rayon (G40) doit être linéaire. 1067 ‘Rayon de compensation trop grand’ DETECTION Durant l'exécution. CAUSE On travail avec compensation de rayon (G41/G42) et on a programmé un arc intérieur de rayon inférieur au rayon de l'outil. SOLUTION Utiliser un outil de rayon inférieur. Si on travaille avec compensation de rayon, le rayon d’arc doit être supérieur au rayon de l'outil. Dans le cas contraire, l’outil ne peut pas usiner la trajectoire programmée. MANUEL DE SOLUTION DES ERREURS 43 CNC 8040M 1068 ‘Pas en trajectoire droite’ DETECTION Durant l'exécution. CAUSE On travail avec compensation de rayon (G41/G42), et le profil a une section droite qui ne peut être usinée étant donné que le diamètre de l’outil est trop grand. SOLUTION Utiliser un outil de rayon inférieur. 1070 ‘Pas en trajectoire circulaire’ DETECTION Durant l'exécution. CAUSE On travaille avec compensation de rayon (G41/G42), et le profil a une section droite qui ne peut être usinée, étant donné que le diamètre de l’outil est trop grand. SOLUTION Utiliser un outil de rayon inférieur. 1071 ‘Changement de plan en compensation’ DETECTION Durant l'exécution. CAUSE On travaille avec compensation de rayon (G41/G42), et un autre plan de travail a été sélectionné. SOLUTION Afin de changer le plan de travail, la compensation de rayon doit être désactivée (G40). 1072 ‘Compensation radiale non admise avec axe rotatif de positionnement.’ DETECTION Durant l'exécution CAUSE On a tenté d’exécuter un mouvement avec compensation de rayon (G41/G42) dans un axe rotatif de positionnement. SOLUTION Les axes rotatifs de positionnement n’admettent pas de compensation de rayon. Afin de désactiver la compensation de rayon, utiliser la fonction “G40”. 1076 ‘Programmation mauvaise angle cote.’ DETECTION Durant l'exécution CAUSE En programmant avec le format angle-cote, on a programmé un déplacement dans un axe avec un angle perpendiculaire à cet axe. (Par exemple, le plan principal est formé par las axes XY, et un déplacement dans l’axe X avec un angle à 90º est programmé). SOLUTION Vérifier et corriger dans le programme la définition du mouvement. Si on travaille avec des paramètres, vérifier que les paramètres arrivent avec les valeurs correctes à la définition du mouvement. 1077 ‘Arc programmé avec rayon trop petit ou cercle complet’ DETECTION Durant l'exécution CAUSE/S Les différentes causes sont les suivantes: 1.-Lorsqu’on programme une circonférence complète avec le format “G02/G03 X Y R”. 2.-Lorsqu’on programme avec le format “G02/G03 X Y R”, et la distance au point final d’arc est supérieur au diamètre de la circonférence programmée. SOLUTION La solution à chacune des causes est la suivante: 1.-On ne peut pas réaliser de circonférences complètes avec ce format. Programmer les coordonnées du point final différentes de celles du point initial. 2.-Le diamètre de la circonférence doit être supérieur à la distance au point final d’arc. 1078 ‘Rayon négatif en polaires’ DETECTION Durant l'exécution CAUSE En travaillant en cotes polaires accroissantes, on exécute un bloc dans lequel est obtenue une position finale de rayon négative. SOLUTION En programmant en cotes polaires accroissantes, la programmation de rayons négatifs est permise, mais la position finale (absolue) du rayon doit être positive. 44 MANUEL DE SOLUTION DES ERREURS CNC 8040M 1079 ‘Pas de sousroutine associée à G74’ DETECTION Durant l'exécution de la recherche de zéros. CAUSE/S Les différentes causes sont: 1.-Lorsqu’on a tenté de réaliser la recherche des zéros (tous les axes) manuellement, mais il n’y a pas de sousroutine associée où dans que l’ordre dans lequel les recherches doivent être réalisées soit indiqué. 2.-On a programmé la fonction “G74”, mais il n’y a pas de souroutine associée où l’ordre dans lequel les recherches doivent être réalisées soit indiqué. SOLUTION La solution à chacune des causes est la suivante: 1.-Afin d’exécuter la fonction “G74” il faut que la sousroutine associée soit définie. 2.-Si on va exécuter la fonction “G74” depuis un programme, on peut définir l’ordre de recherche des axes. 1080 ‘Changement de plan en inspection’ DETECTION Durant l'exécution de l'option “Inspection d'outil“. CAUSE Le plan de travail a été changé, et l’original n’a pas été restitué avant de reprendre l’exécution. SOLUTION Avant de reprendre l’exécution, il faut rétablir le plan qui était actif avant de réaliser l’“Inspection d'outil”. 1081 ‘Bloc non permis en MDI ou inspection d’outil.’ DETECTION Durant l'exécution de l'option “Inspection d'outil“. CAUSE On a tenté d’exécuter l’instruction “RET”. SOLUTION Dans l'option “Inspection d'outil”, on ne peut pas exécuter cette instruction. 1082 ‘Signal du palpeur non reçu.’ DETECTION Durant l'exécution CAUSE/S Les différentes causes sont les suivantes: 1.-On a programmé un cycle fixe de palpation “PROBE”, et le palpeur a parcouru la distance de sécurité maximum du cycle sans recevoir le signal du palpeur. 2.-Lorsqu’on a programmé la fonction “G75”, on est arrivé à la coordonnée finale sans que le signal du palpeur n’ait été reçu. (Seulement quand le paramètre machine générale PROBERR(P119)=YES). SOLUTION La solution à chacune des causes est la suivante: 1.-Vérifier que le palpeur est bien connecté. Le parcours du palpeur (dans les cycles PROBE) est une fonction de la distance de sécurité “B”. Afin d’augmenter le parcours, augmenter la distance de sécurité. 2.-Si PROBERR(P119)=NO, cette erreur n’apparaîtra pas quand la coordonnée finale sera atteinte sans avoir reçu de signal du palpeur (seulement avec la fonction “G75”). 1083 ‘Rang dépassé.’ DETECTION Durant l'exécution CAUSE La distance à parcourir par les axes est très longue, et la vitesse d’avance programmée pour réaliser le déplacement est très basse. SOLUTION Programmer une vitesse plus grande pour ce déplacement. MANUEL DE SOLUTION DES ERREURS 45 CNC 8040M 1084 ‘Trajectoire circulaire mal programmée’ DETECTION Durant l'exécution. CAUSE/S Les différentes causes sont les suivantes: 1.- En programmant un arc avec le format “G02/G03 X Y I J”, on ne peut pas réaliser d’arc de circonférence avec le rayon programmé, qui termine au point final défini. 2.- En programmant un arc avec le format “G09 X Y I J”, les trois points de la circonférence sont en ligne, ou il y a deux points égaux. 3.- Lorsqu’on a tenté de réaliser un arrondi ou une entrée tangentielle en une trajectoire que n’est pas comprise dans le plan actif. 4.- Lorsqu’on a programmé une sortie tangentielle, et la trajectoire suivante est tangentielle (et elle est sur le prolongement en ligne droite) à la trajectoire précédente à la sortie tangentielle. Si l’erreur s’est produite dans le bloc d’appel au «Cycle fixe de poche avec îlots», c’est parce que dans l’ensemble des blocs qui définissent les profils d’une poche avec îlots, nous nous trouvons dans un des cas mentionnés précédemment. SOLUTION La solution à chacune des causes est la suivante: 1.-Corriger la syntaxe du bloc. Les coordonnées du point final, ou du rayon, sont mal définies. 2.-Les trois points utilisés pour définir un arc de circonférence doivent être différents et ils ne peuvent pas être alignés. 3.-Il se peut qu’un plan ait été défini moyennant “G16”, “G17”, “G18” ou “G19”. Dans ce cas, on ne peut réaliser que des arrondis, chanfreins et entrées/sorties tangentielles en trajectoires qui soient contenus dans les axes principaux qui définissent ce plan. Si on désire les réaliser dans un autre plan, il faudra le sélectionner auparavant. 4.- La trajectoire suivante à une sortie tangentielle, peut être tangentielle, mais elle ne peut se trouver sur le prolongement (en ligne droite) de la trajectoire précédente. 1085 ‘Trajectoire hélicoïdale mal programmée’ DETECTION Durant l'exécution CAUSE En programmant un arc avec le format “G02/G03 X Y I J Z K” la trajectoire hélicoïdale programmée ne peut être réalisée. On ne peut pas atteindre la hauteur désirée avec le pas d’hélice programmé. SOLUTION Corriger la syntaxe du bloc. La hauteur de l’interpolation doit être en rapport avec les coordonnées du point final dans le plan, en tenant du pas d’hélice. 1086 ‘On ne peut pas référencer la broche. CAUSE 1087 Le paramètre machine de la broche REFEED1(P34) est égal à zéro. ‘Circonférence de rayon nul’ DETECTION Durant l'exécution CAUSE/S Les différentes causes sont les suivantes: 1.-En programmant un arc avec le format “G02/G03 X Y I J” on a programmé une interpolation circulaire de rayon zéro. 2.-En travaillant avec compensation de rayon, on a programmé un arc intérieur de rayon égal au diamètre de l’outil. SOLUTION La solution à chacune des causes est la suivante: 1.-On ne peut pas réaliser des arcs de rayon zéro. Programmer un rayon différent de zéro. 2.-Si on travaille avec compensation de rayon, le rayon de l'arc doit être supérieur au rayon de l'outil. Dans le cas contraire, l’outil ne peut pas usiner la trajectoire programmée (car pour usiner l’arc, l’outil devrait réaliser un arc de rayon zéro). 1088 ‘Rang dépassé en translation d’origine.’ DETECTION Durant l'exécution CAUSE On a programmé une translation d’origine et la position finale a une valeur trop haute. SOLUTION Vérifier que les valeurs assignées aux translations d’origine (G54-G59) sont correctes. Si on a assigné les valeurs aux origines depuis le programme moyennant des paramètres, vérifier que les valeurs des paramètres sont correctes. Si on a programmé une translation d’origine absolue (G54-G57) et une accroissante (G58-G59), vérifier que la somme de deux ne dépasse pas les limites de la machine. 46 MANUEL DE SOLUTION DES ERREURS CNC 8040M 1089 ‘Rang dépassé en limite de zone.’ DETECTION Durant l'exécution CAUSE On a programmé des limites de zone “G20” ou “G21” moyennant des paramètres, et la valeur du paramètre est supérieure à la valeur maximum permise par cette fonction. SOLUTION Réviser l'histoire du programme, pour que ce paramètre n’arrive pas avec cette valeur au bloc où on a programmé la définition des limites. 1090 ‘Point dans la zone prohibée 1.’ DETECTION Durant l'exécution CAUSE On a tenté de déplacer un axe à un point situé dans la zone de travail 1, qui est définie comme zone de “non entrée”. SOLUTION Dans l'histoire du programme, la zone de travail 1 a été habilitée (définie moyennant G20/G21) comme zone de “non entrée” (G22 K1 S1). Pour déshabiliter cette zone de travail, programmer “G22 K1 S0”. 1091 ‘Point dans la zone prohibée 2.’ DETECTION Durant l'exécution CAUSE On a tenté de déplacer un axe à un point situé dans la zone de travail 2, qui est définie comme zone de “non entrée”. SOLUTION Dans l'histoire du programme, la zone de travail 2 a été habilitée (définie moyennant G20/G21) comme zone de “non entrée” (G22 K2 S1). Pour déshabiliter cette zone de travail, programmer “G22 K2 S0”. 1092 ‘Accélération insuffisante pour la vitesse programmée en filetage.’ DETECTION Durant l'exécution CAUSE On a programmé un filetage et il n’y a pas suffisamment d’espace pour accélérer et désaccélérer. SOLUTION Programmer une vitesse inférieure. 1095 ‘Palpeur mal aligné.’ DETECTION Durant le processus de calibrage du palpeur. CAUSE Un axe a été déplacé en touchant le cube et un des axes qui n’a pas été déplacé présente une déflexion supérieure à celle qui est permise dans le paramètre machine MINDEFLE(P66). Cela est dû à ce que les axes du palpeur ne sont pas suffisamment parallèles aux axes de la machine. SOLUTION Corriger l’erreur de parallélisme entre les axes du palpeur et les axes de la machine. 1096 ‘Point dans la zone prohibée 3.’ DETECTION Durant l'exécution CAUSE On a tenté de déplacer un axe à un point situé dans la zone de travail 3, qui est définie comme zone de “non entrée”. SOLUTION Dans l'histoire du programme, la zone de travail 3 a été habilitée (définie moyennant G20/G21) comme zone de “non entrée” (G22 K3 S1). Pour déshabiliter cette zone de travail, programmer “G22 K3 S0”. 1097 ‘Point dans la zone prohibée 4.’ DETECTION Durant l'exécution CAUSE On a tenté de déplacer un axe à un point situé dans la zone de travail 4, qui est définie comme zone de “non entrée”. SOLUTION Dans l'histoire du programme, la zone de travail 4 a été habilitée (définie moyennant G20/G21) comme zone de “non entrée” (G22 K4 S1). Pour déshabiliter cette zone de travail, programmer “G22 K4 S0”. MANUEL DE SOLUTION DES ERREURS 47 CNC 8040M 1098 ‘Limites des zones de travail erronées.’ DETECTION Durant l'exécution. CAUSE Les limites supérieures définies (G21) de la zone de travail, sont égales ou inférieures aux limites inférieures (G20) de la même zone de travail. SOLUTION Programmer les limites supérieures (G21) de la zone de travail plus grandes que les limites inférieures (G20). 1099 ‘Ne pas programmer un axe accouplé.’ DETECTION Durant l'exécution. CAUSE En travaillant en coordonnées polaires, on a programmé un déplacement qui implique déplacer un axe qui se trouve accouplé à un autre. SOLUTION Les déplacements en coordonnées polaires sont réalisés dans les axes principaux du plan de travail, donc, les axes qui définissent le plan de travail ne peuvent pas être accouplés entre eux, ni à un troisième axe. Afin de désaccoupler les axes programmer “G78”. 1100 ‘Limites de courses de la broche dépassées’ DETECTION Durant l'exécution. CAUSE 1101 On a tenté de dépasser les limites physiques de rotation de la broche. En conséquence, le PLC active les marques “LIMIT+S” ou “LIMIT-S” de la broche. (“LIMIT+S2” ou “LIMIT-S2” si on travaille avec la seconde broche). ‘Broche bloquée’ DETECTION Durant l'exécution. CAUSE 1102 La CNC tente d’obtenir une consigne du régulateur lorsque l’entrée de la broche SERVOSON est encore au niveau bas. L’erreur peut être due à une erreur dans le programme du PLC dans lequel ce signal n’est pas traité correctement, ou à ce que la valeur du paramètre de broche DWELL(P17) n’a pas une valeur suffisamment haute. ‘Erreur de poursuite de la broche hors limite’ DETECTION Durant l'exécution. CAUSE La broche travaillant en boucle fermée (M19), l’erreur de poursuite de celle-ci est supérieure aux valeurs indiquées dans les paramètres de la broche MAXFLWE1(P21) ou MAXFLE2(P22). Les causes qui peuvent provoquer cette erreur sont les suivantes: DEFAILLANCE DANS LE REGULATEUR DEFAILLANCE DANS LE MOTEUR Régulateur en panne. Il manque des signaux d’habilitation. Il y a manque d’alimentation de puissance. Ajustement du régulateur incorrect. Le signal de consigne de vitesse n’arrive pas. DEFAILLANCE DE CAPTATION Moteur en panne. Câblage de puissance. DEFAILLANCE DANS LA CNC Capteur en panne. Câble de captation endommagé. CNC en panne. Ajustement des paramètres incorrect. DEFAILLANCE MECANIQUE Duretés mécaniques. Broche mécaniquement bloquée. 1110-1118 ‘Rang de l’axe * dépassé’ DETECTION Durant l'exécution. CAUSE On a défini un déplacement moyennant des paramètres, et la valeur du paramètre est supérieure à la distance maximum que l’axe peut parcourir. SOLUTION Réviser l'histoire du programme, pour que ce paramètre n’arrive pas avec cette valeur au bloc où on a programmé le déplacement. 48 MANUEL DE SOLUTION DES ERREURS CNC 8040M 1119-1127 ‘On ne peut pas synchroniser l’axe *’ DETECTION Durant l'exécution CAUSE/S 1128-1136 Les différentes causes sont les suivantes: 1.-Lorsqu’on a tenté de synchroniser un axe à un autre depuis le PLC, et l’axe se trouve déjà accouplé à un autre axe moyennant la fonction “G77”. 2.- Lorsqu’on programme ou on tente de déplacer un axe qui est synchronisé à un autre. ‘Vitesse maximale de l’axe * dépassée’ DETECTION Durant l'exécution CAUSE 1137-1145 La vitesse qui résulte d’un des axes après avoir appliqué un facteur d’échelle particulière dépasse la valeur maximum indiquée par le paramètre machine d’axe MAXFEED (P42). ‘Paramètre de vitesse de l’axe * incorrect’ DETECTION Durant l'exécution CAUSE 1146-1154 On a programmé “G00” avec le paramètre G00FEED(P38)=0, ou on a programmé “G1 F00” avec le paramètre d’axe MAXFEED(P42) = 0. ‘Axe * bloqué’ DETECTION Durant l'exécution CAUSE 1155-1163 La CNC tente d’obtenir une consigne du régulateur lorsque l’entrée de la broche SERVO(n)ON est encore au niveau bas. L’erreur peut être due à une erreur dans le programme du PLC dans lequel ce signal n’est pas traité correctement, ou à ce que la valeur du paramètre de broche DWELL(P17) n’a pas une valeur suffisamment haute. ‘Limites software de l’axe * dépassées’ DETECTION Durant l'exécution CAUSE 1164-1172 On a programmé une coordonnée qui se trouve hors des limites définies dans les paramètres d’axes LIMIT+(P5) et LIMIT-(P6). ‘Zone de travail 1 de l’axe * dépassée’ DETECTION Durant l'exécution CAUSE On a tenté de déplacer un axe à un point situé hors de la zone de travail 1, définie comme zone de “non sortie”. SOLUTION Dans l'histoire du programme, la zone de travail 1 a été habilitée (définie moyennant G20/G21) comme zone de “non sortie” (G22 K1 S2). Pour déshabiliter cette zone de travail, programmer “G22 K1 S0”. 1173-1181 ‘Zone de travail 2 de l’axe * dépassée’ DETECTION Durant l'exécution CAUSE On a tenté de déplacer un axe à un point situé hors de la zone de travail 2, définie comme zone de “non sortie”. SOLUTION Dans l'histoire du programme, la zone de travail 2 a été habilitée (définie moyennant G20/G21) comme zone de “non sortie” (G22 K2 S2). Pour déshabiliter cette zone de travail, programmer “G22 K2 S0”. MANUEL DE SOLUTION DES ERREURS 49 CNC 8040M 1182-1190 ‘Erreur de poursuite de l’axe * hors limites’ DETECTION Durant l'exécution. CAUSE L’erreur de poursuite de l’axe est supérieure aux valeurs indiquées dans les paramètres de la broche MAXFLWE1(P21) ou MAXFLE2(P22). Les causes qui peuvent provoquer cette erreur sont les suivantes: DEFAILLANCE DANS LE REGULATEUR DEFAILLANCE DANS LE MOTEUR Régulateur en panne. Moteur en panne. Il manque des signaux d’habilitation. Câblage de puissance. Il y a manque d’alimentation de puissance. Ajustement du régulateur incorrect. Le signal de consigne de vitesse n’arrive pas. DEFAILLANCE DE CAPTATION DEFAILLANCE DANS LA CNC Capteur en panne. Câble de captation endommagé. CNC en panne. Ajustement des paramètres incorrect. DEFAILLANCE MECANIQUE Duretés mécaniques. Broche mécaniquement bloquée. 1191-1199 CAUSE 1200-1208 ‘Différence d’erreurs poursuite de l’axe accouplé * trop grande’ L’axe “n” est accouplé électroniquement à un autre, ou il forme Gantry comme axe esclave, et la différence entre les erreurs de poursuite de l’axe “n” et celle de l’axe auquel il est accouplé est supérieure à l’erreur définie dans le paramètre machine de l’axe “n” MAXCOUPE(P45). ‘Limites de course de l’axe * dépassées’ DETECTION Durant l'exécution CAUSE 1209-1217 CAUSE 1218-1226 On a tenté de dépasser les limites physiques de course. En conséquence, le PLC active les marques “LIMIT+1” ou “LIMIT-1” de l’axe. ‘Erreur servo axe *’ La vitesse réelle de l’axe, une fois écoulé le temps indiqué dans le paramètre de l’axe FBALTIME(P12), est en dessous de 50% ou au dessus de 200% du paramètre programmé. ‘Zone de travail 3 de l’axe * dépassée’ DETECTION Durant l'exécution CAUSE On a tenté de déplacer un axe à un point situé hors d'une zone de travail 3, définie comme zone de “non sortie”. SOLUTION Dans l'histoire du programme, la zone de travail 3 a été habilitée (définie moyennant G20/G21) comme zone de “non sortie” (G22 K3 S2). Pour déshabiliter cette zone de travail, programmer “G22 K3 S0”. 1227 ‘Intersection des profils non valable en poche avec îlots’ DETECTION Durant l'exécution. CAUSE Dans le «Cycle fixe de poche avec îlots (G66)», il y a deux profils dans le plan qui ont le point initial ou une section en commun. SOLUTION Définir à nouveau les profils. Deux profils dans le plan ne peuvent pas commencer au même point ni avoir de sections communes. 50 MANUEL DE SOLUTION DES ERREURS CNC 8040M 1228-1236 ‘Zone de travail 4 de l’axe * dépassée’ DETECTION Durant l'exécution CAUSE On a tenté de déplacer un axe à un point situé hors d'une zone de travail 4, définie comme zone de “non sortie”. SOLUTION Dans l'histoire du programme, la zone de travail 4 a été habilitée (définie moyennant G20/G21) comme zone de “non sortie” (G22 K4 S2). Pour déshabiliter cette zone de travail, programmer “G22 K4 S0”. 1238 ‘Rang de paramètres protégés en écriture . P297, P298’ DETECTION Durant l'exécution CAUSE On tente d’exécuter la fonction «Définition de plan incliné (G49)» et les paramètres P297 et P298 se trouvent protégés de l’écriture moyennant les paramètres machine ROPARMIN(P51) et ROPARMAX(P52). SOLUTION Durant la définition d’un plan incliné, la CNC actualise les paramètres P297 et P298. Donc, ces deux paramètres ne peuvent pas être protégés de l’écriture. MANUEL DE SOLUTION DES ERREURS 51 CNC 8040M ERREURS DE HARDWARE 2000 ‘Urgence externe activée.’ DETECTION Durant l'exécution. CAUSE L'entrée I1 du PLC a été mise à zéro (bouton d’urgence possible) ou la marque M5000(/EMERGEN) du PLC a été mise à zéro. SOLUTION Vérifier dans le PLC pourquoi les entrée sont à zéro. (manque de puissance possible). 2001-2009 ‘Erreur de mesure sur l’axe *’ DETECTION Durant l'exécution. CAUSE Le signal des axes n’arrive pas à la CNC. SOLUTION Vérifier que les connections sont bien réalisées. NOTE: Cette erreur se produit dans les axes différentiels DIFFBACK(P14)=YES, et dans les axes sinusoïdaux SINMAGNI(P10) différents de zéro, lorsque le paramètre FBACKAL(P15)=ON. En positionnant le paramètre FBACKAL(P15)=OFF, la sortie de l’erreur est évitée, mais cette solution est seulement provisionnelle. 2010 ‘Erreur de mesure sur la broche’ DETECTION Durant l'exécution. CAUSE Le signal de la broche n’arrive pas à la CNC. SOLUTION Vérifier que les connections sont bien réalisées NOTE: Cette erreur se produit dans les axes différentiels DIFFBACK(P14)=YES, lorsque le paramètre FBACKAL(P15)=ON. En positionnant le paramètre FBACKAL(P15)=OFF, la sortie de l’erreur est évitée, mais cette solution est seulement provisionnelle. 2011 ‘Température maximale dépassée’ DETECTION À tout moment. CAUSE La température interne maximale de la CNC a été dépassée. Les causes peuvent être les suivantes: - Armoire électrique mal ventilée. - Carte des axes avec un composant défectueux. SOLUTION Eteindre la CNC et attendre qu’elle refroidisse. Si l’erreur persiste, il se peut qu’un composant de la carte soit défectueux. Dan ce cas il faudra changer la carte. Se mettre en rapport avec le SAT. 2012 ‘Pas de tension sur carte des axes’ DETECTION Durant l'exécution. CAUSE Il n y a pas 24v dans la alimentation des sorties de la carte des axes. Il se peut que le fusible se soit grillé. SOLUTION Alimenter les sorties de la carte d’axes (24v). Si le fusible s’est grillé, le remplacer. 2013 ‘Pas de tension sur carte des I/O 1.’ 2014 ‘Pas de tension sur carte des I/O 2.’ 2015 ‘Pas de tension sur carte des I/O 3.’ DETECTION Durant l'exécution. CAUSE Il n y a pas 24v dans la alimentation des sorties de la carte de I/O correspondante. Il se peut que le fusible se soit grillé. SOLUTION Alimenter les sorties de la carte de I/O (24v) correspondante. Si le fusible s’est grillé, le remplacer. 52 MANUEL DE SOLUTION DES ERREURS CNC 8040M 2016 ‘Le PLC n’est pas prêt.’ DETECTION Durant l'exécution. CAUSE Le programme du PLC n’est pas en marche. Les causes peuvent être diverses: - Il n’existe pas de programme de PLC. - Erreur de WATCHDOG. - Le programme a été arrêté depuis la monitorisation. SOLUTION Mettre en marche le programme de PLC. (En réinitiant le PLC). 2017 ‘Erreur de mémoire RAM de la CNC.’ DETECTION Durant le démarrage de la CNC ou durant la diagnose. CAUSE Un défaut a été trouvé dans la mémoire RAM de la CNC. SOLUTION Changer la carte CPU. Prendre contact avec le SAT. 2018 ‘Erreur de mémoire EPROM de la CNC.’ DETECTION Durant le démarrage de la CNC ou durant la diagnose. CAUSE Un défaut a été détecté dans la mémoire EPROM de la CNC. SOLUTION Changer la EPROM. Se mettre en contact avec le SAT. 2019 ‘Erreur de mémoire RAM du PLC.’ DETECTION Durant le démarrage de la CNC ou durant la diagnose. CAUSE Un défaut a été trouvé dans la mémoire RAM du PLC. SOLUTION Changer la carte PLC. Se mettre en contact avec le SAT. 2020 ‘Erreur de mémoire EPROM du PLC.’ DETECTION Durant le démarrage de la CNC ou durant la diagnose. CAUSE Un défaut a été trouvé dans la mémoire EPROM du PLC. SOLUTION Changer la EPROM. Se mettre en contact avec le SAT. 2021 ‘Erreur mémoire RAM utilisateur de la CNC. Taper une touche.’ DETECTION Durant le démarrage de la CNC ou durant la diagnose. CAUSE Un défaut a été trouvé dans la mémoire RAM d’utilisateur de la CNC. SOLUTION Se mettre en contact avec le SAT. 2022 ‘Erreur mémoire RAM du système de la CNC. Taper une touche.’ DETECTION Durant le démarrage de la CNC ou durant la diagnose. CAUSE Un défaut a été trouvé dans la mémoire RAM du système de la CNC. SOLUTION Se mettre en contact avec le SAT. 2023 ‘Erreur mémoire RAM du PLC. Taper une touche.’ DETECTION Durant le démarrage de la CNC ou durant la diagnose. CAUSE Un défaut a été trouvé dans la mémoire RAM du PLC. SOLUTION Se mettre en contact avec le SAT. MANUEL DE SOLUTION DES ERREURS 53 CNC 8040M 2024 ‘Pas de tension sur le module copiage’ DETECTION Durant l'exécution. CAUSE Il n y a pas 24v dans la alimentation des sorties de la carte de copiage. Il se peut que le fusible se soit grillé. SOLUTION Alimenter les sorties de la carte de copiage. Si le fusible s’est grillé, le remplacer. 2025 ‘Erreur de mesure du palpeur.’ DETECTION Durant l'exécution. CAUSE La sonde de copiage n’est pas connectée, ou un de ces câbles est mal connecté. SOLUTION Vérifier que la sonde est bien connectée. 2026 ‘Course maximale du palpeur dépassée.’ DETECTION Durant l'exécution. CAUSE Le palpeur a dépassé la déflexion maximale permise par le paramètre machine. SOLUTION Diminuer l’avance et vérifier que le palpeur n’ait pas souffert de dommages. 2027 ‘Erreur dans la RAM du chip SERCOS. Taper une touche.’ DETECTION Durant le démarrage de la CNC ou durant la diagnose. CAUSE Un défaut a été trouvé dans la mémoire RAM du chip SERCOS. SOLUTION Changer la carte SERCOS. Se mettre en contact avec le SAT. 2028 ‘Erreur de Version du chip SERCOS. Taper une touche.’ DETECTION Durant le démarrage de la CNC. CAUSE La version du chip SERCOS est ancienne. SOLUTION Changer le chip SERCOS. Se mettre en contact avec le SAT. 54 MANUEL DE SOLUTION DES ERREURS CNC 8040M ERREURS DE PLC 3000 ‘ (PLC_ERR sans description) ’ DETECTION Durant l'exécution. CAUSE Les marques ERR1 à ERR64 se sont mises à 1. SOLUTION Vérifier dans le PLC pourquoi les marques sont à un, et agir en conséquence. 3001 ‘WATCHDOG en Module Principal (PRG).’ DETECTION À tout moment. CAUSE/S Les différentes causes sont les suivantes: 1.-L'exécution du programme principal du PLC a dépassée le temps écrit en paramètre de PLC WAGPRG(P0). 2.-Le programme est resté dans une boucle infinie. SOLUTION Augmenter le temps du paramètre du PLC WAGPRG(P0), ou augmenter la vitesse du PLC. • Mettre CPU TURBO. • Changer le paramètre du PLC CPUTIME(P26) ou le paramètre général LOOPTIME(P72). 3002 ‘WATCHDOG en Module Périodique (PE).’ DETECTION À tout moment. CAUSE/S Les différentes causes sont les suivantes: 1.-L'exécution du programme périodique du PLC a dépassée le temps écrit en paramètre de PLC WAGPER(P1). 2.-Le programme est resté dans une boucle infinie. SOLUTION Augmenter le temps du paramètre du PLC WAGPER(P1), ou augmenter la vitesse du PLC. • Mettre CPU TURBO. • Changer le paramètre du PLC CPUTIME(P26) ou le paramètre général LOOPTIME(P72). 3003 ‘Division par ZERO en PLC’ DETECTION À tout moment. CAUSE Dans le programme du PLC il y a une ligne dont l’exécution implique de réaliser une division par zéro. SOLUTION Si on travaille avec des registres, il se peut que, dans l’histoire du programme, ce registre ait acquis la valeur zéro. Vérifier que le registre n’arrive pas à l’opération avec cette valeur. 3004 ‘Erreur en PLC -> ’ DETECTION À tout moment. CAUSE Une erreur a été détectée dans la carte PLC. SOLUTION Changer la carte PLC. Se mettre en contact avec le SAT. MANUEL DE SOLUTION DES ERREURS 55 CNC 8040M ERREURS DE REGULATION 4000 ‘Erreur dans l’anneau SERCOS’ DETECTION Durant l'exécution. CAUSE La communication SERCOS a été interrompue. Les causes peuvent être une interruption dans l’anneau des connections (fibre déconnectée ou cassée) ou une configuration erronée: 1.- La roue d’identification ne coïncide pas avec le sercosid. 2.- Paramètre P120 (SERSPD) ne coïncide pas avec la vitesse de transmission. 3.- La version du régulateur n’est pas compatible avec la CNC. 4.- Il y a une erreur dans la carte SERCOS. 5.- La vitesse de transmission est différente dans le régulateur et dans la CNC. SOLUTION Afin de vérifier que l’anneau des connections n’est pas interrompu, vérifier que la lumière arrive à travers la fibre. Si cela est dû à une configuration erronée, se mettre en contact avec le SAT. 4002 4003 4004 4005 4006 4007 4008 4009 4010 4011 ‘Surcharge dans le régulateur ( 201 )’ ‘Surtempérature dans le régulateur ( 107 )’ ‘Surtempérature dans le moteur ( 108 )’ ‘Surtempérature dans le radiateur ( 106 )’ ‘Erreur de contrôle de tension (100...105)’ ‘Erreur de mesure ( 600...606 )’ ‘Erreur dans bus de puissance ( 213...215 )’ ‘Surcourant ( 212 )’ ‘Surtension dans le bus de puissance ( 304/306 )’ ‘Sous-tension dans le bus de puissance ( 307 )’ DETECTION Durant l'exécution. CAUSE Une erreur s’est produite dans le régulateur. Le numéro entre parenthèse indique le numéro d’erreur standard du régulateur. Consulter le manuel du régulateur pour plus ample information. SOLUTION Ces types d’erreur sont accompagnés par les messages 4019, 4021, 4022 ou 4023, qui indiquent dans quel régulateur d’axe ou broche l’erreur s’est produite. Consulter dans le manuel du régulateur quel est l’erreur qui s’est produite (numéro entre parenthèse), et agir en conséquence. 4016 ‘Erreur classe 1 non définie’ DETECTION Durant l'exécution. CAUSE Le régulateur a détecté une erreur mais il ne peut pas l’identifier. SOLUTION Se mettre en contact avec le SAT. 4017 ‘Erreur dans le régulateur’ DETECTION Durant l'exécution. CAUSE Une erreur s’est produite dans le régulateur qui ne corresponde pas aux standards de SERCOS. SOLUTION Ces types d’erreur sont accompagnés par les messages 4019, 4021, 4022 ou 4023, qui indiquent dans quel régulateur d’axe ou broche l’erreur s’est produite. Consulter dans le manuel du régulateur quel est l’erreur qui s’est produite (numéro entre parenthèse), et agir en conséquence. 56 MANUEL DE SOLUTION DES ERREURS CNC 8040M 4018 ‘Erreur en accès à variable SERCOS’ DETECTION Durant l'exécution. CAUSE On a tenté de lire (ou écrire) depuis la CNC une variable SERCOS et: 1.- Cette variable n’existe pas. 2.- Les valeurs maximum/minimum ont été dépassées 3.- La variable SERCOS est de longueur variable. 4.- On a tenté d’écrire une variable uniquement de lecture. SOLUTION Vérifier que la variable à laquelle on a tenté d’associer l’action, est appropriée. 4019 ‘Erreur régulateur : Axe ’ DETECTION Durant l'exécution. CAUSE 4021 4022 4023 Ces messages accompagnent les erreurs 4002 - 4011. Lorsqu’une des erreurs citées s’est produite, ils indiquent dans quel axe cette erreur s’est produite. ‘Erreur régulateur broche’ ‘Erreur régulateur broche 2’ ‘Erreur régulateur broche auxiliaire’ DETECTION Durant l'exécution. CAUSE 4024 Ces messages accompagnent les erreurs 4002 - 4011. Lorsqu’une des erreurs citées s’est produite, ils indiquent dans quel axe cette erreur s’est produite. ‘Erreur SERCOS dans la recherche de zéro’ DETECTION Durant l'exécution. CAUSE 4025 La commande de recherche de zéro du SERCOS a été exécuté incorrectement. ‘Erreur 1 dans l’anneau SERCOS’ DETECTION Durant l'exécution. CAUSE Le temps nécessaire pour calculer la vitesse de l’axe est supérieur au temps de cycle établi de transmission au régulateur. SOLUTION Se mettre en contact avec le SAT. MANUEL DE SOLUTION DES ERREURS 57 CNC 8040M ERREURS DANS LES DONNEES DES TABLES echk_gen echk_cab echk_cab2 echk_cax echk_rs1 echk_rs2 echk_plc ‘ERREUR:CHECKSUM PARAMETRES GENERAUX Initialiser?(ENTER/ESC)’ ‘ERREUR:CHECKSUM PARAMETRES BROCHE Initialiser?(ENTER/ESC)’ ‘ERREUR:CHECKSUM PARAMETRES BROCHE 2Initialiser?(ENTER/ESC)’ ‘ERREUR:CHECKSUM PARAMETRES BROCHE AUX. Initialiser?(ENTER/ESC)’ ‘ERREUR:CHECKSUM PARAMETRES LIGNE SERIE 1 Initialiser?(ENTER/ESC)’ ‘ERREUR:CHECKSUM PARAMETRES LIGNE SERIE 2 Initialiser?(ENTER/ESC)’ ‘ERREUR:CHECKSUM PARAMETRES PLC Initialiser?(ENTER/ESC)’ DETECTION Durant le démarrage du CNC. CAUSE Il s’est produit une perte des données introduites dans les tables. Possible erreur de RAM. SOLUTION En tapent [ENTER] des valeur que la CNC a par défaut sont chargées dans les table. Si l’erreur persiste, se mettre en contact avec le SAT. echk_org echk_psw ‘ERREUR:CHECKSUM TABLE DE ORIGINES Initialiser?(ENTER/ESC)’ ‘ERREUR:CHECKSUM TABLE DE CODES Initialiser?(ENTER/ESC)’ DETECTION Durant le démarrage de la CNC. CAUSE Il s’est produit une perte des données introduites dans les tables. Possible erreur de RAM. SOLUTION En tapant [ENTER], les valeurs par défaut de la CNC sont chargées dans les tables. Si l’erreur persiste, se mettre en contact avec le SAT. echk_ejex echk_ejey echk_ejez echk_ejeu echk_ejev echk_ejew echk_ejea echk_ejeb echk_ejec ‘ERREUR:CHECKSUM ‘ERREUR:CHECKSUM ‘ERREUR:CHECKSUM ‘ERREUR:CHECKSUM ‘ERREUR:CHECKSUM ‘ERREUR:CHECKSUM ‘ERREUR:CHECKSUM ‘ERREUR:CHECKSUM ‘ERREUR:CHECKSUM PARAMETRES PARAMETRES PARAMETRES PARAMETRES PARAMETRES PARAMETRES PARAMETRES PARAMETRES PARAMETRES AXE AXE AXE AXE AXE AXE AXE AXE AXE X Y Z U V W A B C Initialiser?(ENTER/ESC)’ Initialiser?(ENTER/ESC)’ Initialiser?(ENTER/ESC)’ Initialiser?(ENTER/ESC)’ Initialiser?(ENTER/ESC)’ Initialiser?(ENTER/ESC)’ Initialiser?(ENTER/ESC)’ Initialiser?(ENTER/ESC)’ Initialiser?(ENTER/ESC)’ DETECTION Durant le démarrage de la CNC. CAUSE Il s’est produit une perte des données introduites dans les tables. Possible erreur de RAM. SOLUTION En tapant [ENTER], les valeurs par défaut de la CNC sont chargées dans les tables. Si l’erreur persiste, se mettre en contact avec le SAT. 58 MANUEL DE SOLUTION DES ERREURS CNC 8040M echk_herr ‘ERREUR:CHECKSUM TABLE OUTILS Initialiser?(ENTER/ESC)’ echk_corr ‘ERREUR:CHECKSUM TABLE CORRECTEURS Initialiser?(ENTER/ESC)’ echk_alm ‘ERREUR:CHECKSUM TABLE MAGASIN Initialiser?(ENTER/ESC)’ echk_aux ‘ERREUR:CHECKSUM TABLE FONCTIONS M Initialiser?(ENTER/ESC)’ echk_husx ‘ERREUR:CHECKSUM TABLE COMP. VIS AXE X Initialiser?(ENTER/ESC)’ echk_husy ‘ERREUR:CHECKSUM TABLE COMP. VIS AXE Y Initialiser?(ENTER/ESC)’ echk_husz ‘ERREUR:CHECKSUM TABLE COMP. VIS AXE Z Initialiser?(ENTER/ESC)’ echk_husu ‘ERREUR:CHECKSUM TABLE COMP. VIS AXE U Initialiser?(ENTER/ESC)’ echk_husv ‘ERREUR:CHECKSUM TABLE COMP. VIS AXE V Initialiser?(ENTER/ESC)’ echk_husw ‘ERREUR:CHECKSUM TABLE COMP. VIS AXE W Initialiser?(ENTER/ESC)’ echk_husa ‘ERREUR:CHECKSUM TABLE COMP. VIS AXE A Initialiser?(ENTER/ESC)’ echk_husb ‘ERREUR:CHECKSUM TABLE COMP. VIS AXE B Initialiser?(ENTER/ESC)’ echk_husc ‘ERREUR:CHECKSUM TABLE COMP. VIS AXE C Initialiser?(ENTER/ESC)’ echk_cru1 ‘ERREUR:CHECKSUM TABLE COMP. CROISEE 1 Initialiser?(ENTER/ESC)’ echk_cru2 ‘ERREUR:CHECKSUM TABLE COMP. CROISEE 2 Initialiser?(ENTER/ESC)’ echk_cru3 ‘ERREUR:CHECKSUM TABLE COMP. CROISEE 3 Initialiser?(ENTER/ESC)’ DETECTION Durant le démarrage de la CNC. CAUSE Il s’est produit une perte des données introduites dans les tables. Possible erreur de RAM. SOLUTION En tapant [ENTER], les valeurs par défaut de la CNC sont chargées dans les tables. Si l’eerreur persiste, se mettre en contact avec le SAT. eincx eincy eincz eincu eincv eincw einca eincb eincc ‘Table ‘Table ‘Table ‘Table ‘Table ‘Table ‘Table ‘Table ‘Table de de de de de de de de de vis vis vis vis vis vis vis vis vis X Y Z U V W A B C incorrecte.Taper incorrecte.Taper incorrecte.Taper incorrecte.Taper incorrecte.Taper incorrecte.Taper incorrecte.Taper incorrecte.Taper incorrecte.Taper touche’ touche’ touche’ touche’ touche’ touche’ touche’ touche’ touche’ DETECTION Durant le démarrage de la CNC. CAUSE Il y a une donné incorrecte dans les paramètres de la table de compensation de vis. SOLUTION La définition des points de la table doit remplir les exigences suivantes: - Les points de la table doivent être ordonnés suivant leur position dans l’axe, la table devant partir du point le plus négatif ou le moins positif qui va être compensé. - Le point de référence machine doit avoir l’erreur 0. - Il ne peut y avoir de différence d’erreur entre points supérieure à la distance entre les deux. einx1 einx2 einx3 ‘Table 1 de compensation croisée incorrecte’ ‘Table 2 de compensation croisée incorrecte’ ‘Table 3 de compensation croisée incorrecte’ DETECTION Durant le démarrage de la CNC. CAUSE Il y a une donné incorrecte dans les paramètres de la table de compensation croisée. SOLUTION La définition des points de la table doit remplir les exigences suivantes: - Les points de la table doivent être ordonnés suivant leur position dans l’axe, la table devant partir du point le plus négatif ou le moins positif qui va être compensé. - Le point de référence machine doit avoir l’erreur 0. - Il ne peut y avoir de différence d’erreur entre points supérieure à la distance entre les deux. MANUEL DE SOLUTION DES ERREURS 59 CNC 8040M einxx ‘Paramétres de la table de compensation croisée incorrects’ DETECTION Durant le démarrage de la CNC. CAUSE Les paramètres qui indiquent les axes qui agissent dans la compensation croisée sont mal définis. SOLUTION Il se peut qu’un axe qui n’existe pas ait été défini, ou que l’axe qu’on désire être compensé et duquel il dépend soit le même. esercos ‘Paramétres sercosid des axes et de broche incorrects’ DETECTION Durant le démarrage de la CNC. CAUSE Les paramètres du sercosid n’a pas été introduits correctement. SOLUTION Les normes que suivent les paramètres du sercosid sont: - Ils doivent partir du numéro1. - Ils doivent être consécutifs. - Il ne doit pas y avoir de paramètres répétés. (Sauf pour le tour avec l’axe C. La broche et l’axe C peuvent partager le même sercosid) 60 MANUEL DE SOLUTION DES ERREURS CNC 8040M ERREURS DU MODE DE TRAVAIL 8040MC Erreurs dans l’opération de surfaçage. ‘SURFAÇAGE: F=0’ DETECTION Durant l’exécution. CAUSE La vitesse d’avance «F» a été définie par une valeur non correcte . SOLUTION Programmer une vitesse d’avance «F» positive et différente de zéro. ‘SURFAÇAGE: S=0’ DETECTION Durant l’exécution. CAUSE La vitesse de rotation «S» a été définie par une valeur non correcte. SOLUTION Programmer une vitesse de rotation «S» positive et différente de zéro. ‘SURFAÇAGE: T=0’ DETECTION Durant l’exécution. CAUSE Le numéro de l’outil «T» n’a pas été défini. SOLUTION le numéro de l’outil «T» devra être différent de zéro. ‘SURFAÇAGE: P=0’ DETECTION Durant l’exécution. CAUSE La profondeur du surfaçage «P» n’a pas été définie. SOLUTION La profondeur du surfaçage «P» doit être différente de zéro. Erreurs dans l’opération de fraisage de profil 1. ‘FRAISAGE PROFIL 1: F=0’ DETECTION Durant l’exécution. CAUSE La vitesse d’avance «F» a été défini par une valeur non correcte SOLUTION Programmer une vitesse d’avance «F» positive et différente de zéro. ‘FRAISAGE PROFIL 1: S=0’ DETECTION Durant l’exécution. CAUSE La vitesse de rotation «S»a été définie par une valeur non correcte. SOLUTION Programmer une vitesse de rotation «S» positive et différente de zéro. ‘FRAISAGE PROFIL 1: T=0’ DETECTION Durant l’exécution. CAUSE Le numéro de l’outil «T» n’a pas été défini. SOLUTION Le numéro de l’outil «T» doit être différent de zéro. ‘FRAISAGE PROFIL 1: P=0’ DETECTION Durant l’exécution. CAUSE La profondeur de fraisage «P» n’a pas été définie. SOLUTION La profondeur de fraisage «P» doit être différente de zéro. ‘FRAISAGE PROFIL 1: Profil nul’ DETECTION Durant l’exécution. CAUSE Le profil à usiner n’a pas été défini. SOLUTION Le profil doit être formé au moins par deux points, outre celui d’entrée et de sortie. Erreurs dans l’opération de fraisage de profil 2. ‘FRAISAGE PROFIL 2: T=0’ DETECTION Durant l’exécution. CAUSE Le numéro de l’outil «T» n’a pas été défini. SOLUTION Le numéro de l’outil «T» doit être différent de zéro. MANUEL DE SOLUTION DES ERREURS 61 CNC 8040M ‘FRAISAGE PROFIL 2: F=0’ DETECTION Durant l’exécution. CAUSE La vitesse d’avance «F» a été définie par une valeur non correcte. SOLUTION Programmer une vitesse d’avance «F» positive et différente de zéro. ‘FRAISAGE PROFIL 2: S=0’ DETECTION Durant l’exécution. CAUSE La vitesse de rotation «S» a été définie par une valeur non correcte. SOLUTION Programmer une vitesse de rotation «S» positive et différente de zéro. ‘FRAISAGE PROFIL 2: P=0’ DETECTION Durant l’exécution. CAUSE La profondeur de fraisage «P» n’a pas été définie. SOLUTION La profondeur de fraisage «P» doit être différente de zéro. Erreurs dans l’opération de poche profil . ‘POCHE PROFIL: F=0’ DETECTION Durant l’exécution. CAUSE La vitesse d’avance «F» a été définie par une valeur non correcte. SOLUTION Programmer une vitesse d’avance «F» positive et différente de zéro. ‘POCHE PROFIL: S=0’ DETECTION Durant l’exécution. CAUSE La vitesse de rotation «S» a été définie par une valeur non correcte. SOLUTION Programmer une vitesse de rotation «S» positive et différente de zéro. ‘POCHE PROFIL: P=0’ DETECTION Durant l’exécution. CAUSE La profondeur de la poche «P» n’a pas été définie. SOLUTION La profondeur de la poche «P» doit être différente de zéro. ‘POCHE PROFIL: Angle de pénétration non valide’ DETECTION Durant l’exécution. CAUSE Un angle de pénétration inférieur à 0º ou supérieur à 90º a été programmé SOLUTION Programmer un angle de pénétration «β» et «Θ» compris dans l’intervalle 0º à 90º. ‘POCHE PROFIL: Diamètre outil plus petit que ∆ ’ DETECTION Durant l’exécution. CAUSE Le pas de fraisage «∆» programmé est supérieur au diamètre de l’outil . SOLUTION Programmer un pas de fraisage «∆» inférieur au diamètre de l’outil, ou choisir un outil de diamètre supérieur. ‘POCHE PROFIL: Diamètre outil FINITION plus petit que δ ’ DETECTION Durant l’exécution. CAUSE La surépaisseur pour la finition «δ» programmée est supérieure au diamètre de l’outil. SOLUTION Programmer une surépaisseur pour la finition «δ» inférieure au diamètre de l’outil, ou choisir un outil de diamètre supérieur . Erreurs dans l’opération de poche profil 3D. ‘POCHE PROFIL 3D: F=0’ DETECTION Durant l’exécution. CAUSE La vitesse d’avance «F» a été définie par une valeur non correcte. SOLUTION Programmer une vitesse d’avance «F» positive et différente de zéro. ‘POCHE PROFIL 3D: S=0’ DETECTION Durant l’exécution. CAUSE La vitesse de rotation «S» a été définie par une valeur non correcte. SOLUTION Programmer une vitesse de rotation «S» positive et différente de zéro ‘POCHE PROFIL 3D: P=0’ DETECTION Durant l’exécution. CAUSE La profondeur de la poche «P» n’a pas été définie. SOLUTION La profondeur de la poche «P» doit être différente de zéro 62 MANUEL DE SOLUTION DES ERREURS CNC 8040M ‘POCHE PROFIL 3D: Angle de pénétration non valide’ DETECTION Durant l’exécution. CAUSE Un angle de pénétration inférieur à 0º ou supérieur à 90º a été programmé. SOLUTION Programmer un angle de pénétration «β» et «Θ» compris dans l’intervalle 0º à 90º. ‘POCHE PROFIL 3D: Diamètre outil plus petit que ∆ ’ DETECTION Durant l’exécution. CAUSE Le pas de fraisage «∆» programmé est supérieur au diamètre de l’outil. SOLUTION Programmer un pas de fraisage «∆» inférieur au diamètre de l’outil, ou choisir un outil de diamètre supérieur. ‘POCHE PROFIL 3D: Diamètre outil FINITION plus petit que δ ’ DETECTION Durant l’exécution . CAUSE La surépaisseur pour la finition «δ» programmée est supérieur au diamètre de l’outil. SOLUTION Programmer une surépaisseur pour la finition «δ» inférieur au diamètre de l’outil, ou choisir un outil de diamètre supérieur. Erreurs dans l’opération de poche rectangulaire 1. ‘POCHE RECTANGULAIRE 1: F=0’ DETECTION Durant l’exécution. CAUSE La vitesse d’avance «F» a été définie par une valeur non correcte. SOLUTION Programmer une vitesse d’avance «F» positive et différente de zéro. ‘POCHE RECTANGULAIRE 1: S=0’ DETECTION Durant l’exécution. CAUSE La vitesse de rotation «S» a été définie par une valeur non correcte. SOLUTION Programmer une vitesse de rotation «S» positive et différente de zéro. ‘POCHE RECTANGULAIRE 1: T=0’ DETECTION Durant l’exécution. CAUSE Le numéro d’outil «T» n’a pas été définie. SOLUTION Le numéro d’outil «T» doit être différent de zéro. ‘POCHE RECTANGULAIRE 1: P=0’ DETECTION Durant l’exécution. CAUSE La profondeur de la poche «P» n’a pas été définie. SOLUTION La profondeur de la poche «P» doit être différente de zéro. ‘POCHE RECTANGULAIRE 1: Diamètre outil plus petit que ∆ ’ DETECTION Durant l’exécution. CAUSE Le pas de fraisage «∆» programmé est supérieur au diamètre de l’outil . SOLUTION Programmer un pas de fraisage «∆» inférieur au diamètre de l’outil, ou choisir un outil de diamètre supérieur. ‘POCHE RECTANGULAIRE 1: Diamètre outil plus grand que poche’ DETECTION Durant l’exécution. CAUSE Le diamètre de l’outil est supérieur à certaines des dimensions «H» ou «L» de la poche. SOLUTION Choisir un outil de diamètre inférieur pour réaliser la poche. ‘POCHE RECTANGULAIRE 1: Diamètre outil FINITION plus petit que δ ’ DETECTION Durant l’exécution. CAUSE La surépaisseur pour la finition «δ» programmée est supérieure au diamètre de l’outil. SOLUTION Programmer une surépaisseur pour la finition «δ» inférieure au diamètre de l’outil, ou choisir un outil de diamètre supérieur. Erreurs dans l’opération de poche rectangulaire 2. ‘POCHE RECTANGULAIRE 2: F=0’ DETECTION Durant l’exécution. CAUSE La vitesse d’avance «F» a été définie par une valeur non correcte. SOLUTION Programmer une vitesse d’avance «F» positive et différente de zéro. MANUEL DE SOLUTION DES ERREURS 63 CNC 8040M ‘POCHE RECTANGULAIRE 2: S=0’ DETECTION Durant l’exécution CAUSE La vitesse de rotation «S» a été définie par une valeur non correcte. SOLUTION Programmer une vitesse de rotation «S» positive et différente de zéro. ‘POCHE RECTANGULAIRE 2: P=0’ DETECTION Durant l’exécution. CAUSE La profondeur de la poche «P» n’a pas été définie. SOLUTION La profondeur de la poche «P» doit être différente de zéro. ‘POCHE RECTANGULAIRE 2: Angle de pénétration non valide’ DETECTION Durant l’exécution . CAUSE Un angle de pénétration inférieur à 0º ou supérieur à 90º a été programmé. SOLUTION Programmer un angle de pénétration «β» et «Θ» compris dans l’intervalle 0º à 90º. ‘POCHE RECTANGULAIRE 2: Diamètre outil plus petit que ∆ ’ DETECTION Durant l’exécution. CAUSE Le pas de fraisage «∆» programmé est supérieur au diamètre de l’outil . SOLUTION Programmer un pas de fraisage «∆» inférieur au diamètre de l’outil, ou choisir un outil de diamètre supérieur. ‘POCHE RECTANGULAIRE 2: Diamètre outil plus grand que poche’ DETECTION Durant l’exécution . CAUSE Le diamètre de l’outil est supérieur à certaines des dimensions «H» ou «L» de la poche. SOLUTION Choisir un outil de diamètre inférieur pour réaliser la poche. ‘POCHE RECTANGULAIRE 2: Diamètre outil FINITION plus petit que δ ’ DETECTION Durant l’exécution. CAUSE La surépaisseur pour la finition «δ» programmée est supérieure au diamètre de l’outil. SOLUTION Programmer une surépaisseur pour la finition «δ» inférieure au diamètre de l’outil, ou choisir un outil de diamètre supérieur. Erreurs dans l’opération de poche circulaire. ‘POCHE CIRCULAIRE: F=0’ DETECTION Durant l’exécution. CAUSE La vitesse d’avance «F» a été définie par une valeur non correcte . SOLUTION Programmer une vitesse d’avance «F» positive et différente de zéro. ‘POCHE CIRCULAIRE: S=0’ DETECTION Durant l’exécution CAUSE La vitesse de rotation «S» a été définie par une valeur non correcte. SOLUTION Programmer une vitesse de rotation «S» positive et différente de zéro. ‘POCHE CIRCULAIRE: P=0’ DETECTION Durant l’exécution. CAUSE La profondeur de la poche «P» n’a pas été définie. SOLUTION La profondeur de la poche «P» doit être différente de zéro. ‘POCHE CIRCULAIRE: Angle de pénétration non valide’ DETECTION Durant l’exécution. CAUSE Un angle de pénétration inférieur à 0º ou supérieur à 90º a été programmé. SOLUTION Programmer un angle de pénétration «β» et «Θ» compris dans l’intervalle 0º à 90º. ‘POCHE CIRCULAIRE: Diamètre outil plus petit que ∆ ’ DETECTION Durant l’exécution. CAUSE Le pas de fraisage «∆» programmé est supérieur au diamètre de l’outil . SOLUTION Programmer un pas de fraisage «∆» inférieur au diamètre de l’outil, ou choisir un outil de diamètre supérieur. ‘POCHE CIRCULAIRE: Diamètre outil plus grand que poche’ DETECTION Durant l’exécution . CAUSE Le diamètre de l’outil est supérieur à certaines des dimensions «H» ou «L» de la poche. SOLUTION Choisir un outil de diamètre inférieur pour réaliser la poche 64 MANUEL DE SOLUTION DES ERREURS CNC 8040M ‘POCHE CIRCULAIRE: Diamètre outil FINITION plus petite que d’ DETECTION Durant l’exécution. CAUSE La surépaisseur pour la finition «δ» programmée est supérieure au diamètre de l’outil. SOLUTION Programmer une surépaisseur pour la finition «δ» inférieure au diamètre de l’outil , ou choisir un outil de diamètre supérieur. Erreurs dans l’opération de moyeu rectangulaire ‘MOYEU RECTANGULAIRE: F=0’ DETECTION Durant l’exécution. CAUSE La vitesse d’avance «F» a été définie par une valeur non correcte. SOLUTION Programmer une vitesse d’avance «F» positive et différente de zéro. ‘MOYEU RECTANGULAIRE: S=0’ DETECTION Durant l’exécution. CAUSE La vitesse de rotation «S» a été définie par une valeur non correcte. SOLUTION Programmer une vitesse de rotation «S» positive et différente de zéro. ‘MOYEU RECTANGULAIRE: P=0’ DETECTION Durant l’exécution . CAUSE La hauteur du moyeu «P» n’a pas été définie . SOLUTION La hauteur du moyeu «P» doit être différente de zéro. ‘MOYEU RECTANGULAIRE: Diamètre outil plus petit que ∆ ’. DETECTION Durant l’exécution . CAUSE Le pas de fraisage «∆» programmé est supérieur au diamètre de l’outil . SOLUTION Programmer un pas de fraisage «∆» inférieur au diamètre de l’outil ou choisir un outil de diamètre supérieur . ‘MOYEU RECTANGULAIRE: Diamètre outil FINITION plus petit que δ ’ DETECTION Durant l’exécution. CAUSE La surépaisseur pour la finition «δ» programmée est supérieure au diamètre de l’outil . SOLUTION Programmer une surépaisseur pour la finition «δ» inférieur au diamètre de l’outil ou choisir un outil de diamètre supérieur. Erreurs dans l’opération de moyeu circulaire. ‘MOYEU CIRCULAIRE: F=0’ DETECTION Durant l’exécution. CAUSE La vitesse d’avance «F» a été définie par une valeur non correcte. SOLUTION Programmer une vitesse d’avance «F» positive et différente de zéro. ‘MOYEU CIRCULAIRE: S=0’ DETECTION Durant l’exécution. CAUSE La vitesse de rotation «S» a été définie par une valeur non correcte. SOLUTION Programmer une vitesse de rotation «S» positive et différente de zéro. ‘MOYEU CIRCULAIRE: P=0’ DETECTION Durant l’exécution . CAUSE La hauteur du moyeu «P» n’a pas été définie . SOLUTION La hauteur du moyeu «P» doit être différente de zéro. ‘MOYEU CIRCULAIRE: Diamètre outil plus petit que ∆ ’. DETECTION Durant l’exécution . CAUSE Le pas de fraisage «∆» programmé est supérieur au diamètre de l’outil . SOLUTION Programmer un pas de fraisage «∆» inférieur au diamètre de l’outil ou choisir un outil de diamètre supérieur . ‘MOYEU CIRCULAIRE: Diamètre outil FINITION plus petit que δ ’ DETECTION Durant l’exécution. CAUSE La surépaisseur pour la finition «δ» programmée est supérieure au diamètre de l’outil . SOLUTION Programmer une surépaisseur pour la finition «δ» inférieur au diamètre de l’outil ou choisir un outil de diamètre supérieur. MANUEL DE SOLUTION DES ERREURS 65 CNC 8040M Erreurs dans l’opération de pointage . ‘POINTAGE: F=0’ DETECTION Durant l’exécution. CAUSE La vitesse d’avance «F» a été définie par une valeur non correcte. SOLUTION Programmer une vitesse d’avance «F» positive et différente de zéro. ‘POINTAGE: S=0’ DETECTION Durant l’exécution. CAUSE La vitesse de rotation «S» a été définie par une valeur non correcte. SOLUTION Programmer une vitesse de rotation «S» positive et différente de zéro ‘POINTAGE: T=0’ DETECTION Durant l’exécution. CAUSE Le numéro de l’outil «T» n’a pas été défini. SOLUTION Le numéro de l’outil «T» doit être différent de zéro. ‘POINTAGE: P=0’ DETECTION Durant l’exécution. CAUSE La profondeur du pointage «P» n’a pas été définie. SOLUTION La profondeur du pointage «P» doit être différent de zéro . ‘POINTAGE: ø=0’ DETECTION Durant l’exécution. CAUSE Le diamètre du point «ø» n’a pas été défini. SOLUTION Le diamètre du point «ø» doit être positif et différent de zéro . ‘POINTAGE: α =0’ DETECTION Durant l’exécution. CAUSE L’angle de la pointe du foret «α» n’a pas été défini. SOLUTION L’angle de la pointe du foret «α» doit être positif et différent de zéro. Erreurs dans l’opération de perçage 1. ‘PERÇAGE 1: F=0’ DETECTION Durant l’exécution. CAUSE La vitesse d’avance «F» a été définie par une valeur non correcte . SOLUTION Programmer une vitesse d’avance «F» positive et différente de zéro. ‘PERÇAGE 1: S=0’ DETECTION Durant l’exécution. CAUSE La vitesse de rotation «S» a été définie par une valeur non correcte. SOLUTION Programmer une vitesse de rotation «S» positive et différente de zéro ‘PERÇAGE 1: T=0’ DETECTION Durant l’exécution. CAUSE Le numéro de l’outil «T» n’a pas été défini. SOLUTION Le numéro de l’outil «T» doit être différent de zéro. ‘PERÇAGE 1: P=0’ DETECTION Durant l’exécution. CAUSE La profondeur du perçage «P» n’a pas été définie. SOLUTION La profondeur du perçage «P» doit être différent de zéro. Erreurs dans l’opération de perçage 2 ‘PERÇAGE 2: F=0’ DETECTION Durant l’exécution. CAUSE La vitesse d’avance «F» a été définie par une valeur non correcte. SOLUTION Programmer une vitesse d’avance «F» positive et différente de zéro. ‘PERÇAGE 2: S=0’ DETECTION Durant l’exécution. CAUSE La vitesse de rotation «S» a été définie par une valeur non correcte. SOLUTION Programmer une vitesse de rotation «S» positive et différente de zéro. 66 MANUEL DE SOLUTION DES ERREURS CNC 8040M ‘PERÇAGE 2: T=0’ DETECTION Durant l’exécution. CAUSE Le numéro de l’outil «T» n’a pas été défini. SOLUTION Le numéro de l’outil «T» doit être différent de zéro. ‘PERÇAGE 2: P=0’ DETECTION Durant l’exécution. CAUSE La profondeur du perçage «P» n’a pas été définie. SOLUTION La profondeur du perçage «P» doit être différent de zéro. ‘PERÇAGE 2: B=0’ DETECTION Durant l’exécution. CAUSE La distance de retour après chaque pénétration «B» n’a pas été définie. SOLUTION La distance de retour après chaque pénétration «B» doit être différente de zéro. Erreurs dans l’opération de filetage. ‘FILETAGE : F=0’ DETECTION Durant l’exécution. CAUSE La vitesse d’avance «F» a été définie par une valeur non correcte . SOLUTION Programmer une vitesse d’avance «F» positive et différente de zéro. ‘FILETAGE : S=0’ DETECTION Durant l’exécution. CAUSE La vitesse de rotation «S» a été définie par une valeur non correcte. SOLUTION Programmer une vitesse de rotation «S» positive et différente de zéro. ‘FILETAGE: T=0’ DETECTION Durant l’exécution. CAUSE Le numéro de l’outil «T» n’a pas été défini. SOLUTION Le numéro de l’outil «T» doit être différent de zéro. ‘FILETAGE: P=0’ DETECTION Durant l’exécution. CAUSE La profondeur du filetage «P» n’a pas été définie. SOLUTION La profondeur du filetage «P» doit être différent de zéro. Erreurs dans l’opération d’alésage. ‘ALÉSAGE : F=0’ DETECTION Durant l’exécution. CAUSE La vitesse d’avance «F» a été définie par une valeur non correcte . SOLUTION Programmer une vitesse d’avance «F» positive et différente de zéro. ‘ALÉSAGE : S=0’ DETECTION Durant l’exécution. CAUSE La vitesse de rotation «S» a été définie par une valeur non correcte. SOLUTION Programmer une vitesse de rotation «S» positive et différente de zéro. ‘ALÉSAGE: T=0’ DETECTION Durant l’exécution. CAUSE Le numéro de l’outil «T» n’a pas été défini. SOLUTION Le numéro de l’outil «T» doit être différent de zéro. ‘ALÉSAGE: P=0’ DETECTION Durant l’exécution. CAUSE La profondeur de l’alésage «P» n’a pas été définie. SOLUTION La profondeur de l’alésage «P» doit être différent de zéro. Erreurs dans l’opération d’alésage grain. ‘ALÉSAGE GRAIN :F=0’ DETECTION CAUSE SOLUTION Durant l’exécution. La vitesse d’avance «F» a été définie par une valeur non correcte . Programmer une vitesse d’avance «F» positive et différente de zéro MANUEL DE SOLUTION DES ERREURS 67 CNC 8040M ‘ALÉSAGE GRAIN: S=0’ DETECTION CAUSE SOLUTION Durant l’exécution. La vitesse de rotation «S» a été définie par une valeur non correcte. Programmer une vitesse de rotation «S» positive et différente de zéro. ‘ALÉSAGE GRAIN: T=0’ DETECTION CAUSE SOLUTION Durant l’exécution. Le numéro de l’outil «T» n’a pas été défini. Le numéro de l’outil «T» doit être différent de zéro. ‘ALÉSAGE GRAIN: P=0’ DETECTION CAUSE SOLUTION Durant l’exécution. La profondeur de l’alésage grain «P» n’a pas été définie. La profondeur de l’alésage grain «P» doit être différent de zéro. Erreurs dans les opérations de positionnement . ‘POSITIONNEMENT EN LIGNE: I non valable’ DETECTION Durant l’exécution. CAUSE La distance entre positionnements «I» a été définie par une valeur non correcte qui ne permet pas de réaliser un nombre entier d’usinages. SOLUTION Vérifier que les valeurs introduites soient correctes. ‘POSITIONNEMENT EN ARC: ß non valable’ DETECTION Durant l’exécution. CAUSE La distance angulaire entre positionnements «I» a été définie par une valeur non correcte qui ne permet pas de réaliser un nombre entier d’usinages. SOLUTION Vérifier que les valeurs introduites soient correctes. ‘POSITIONNEMENT EN RECTANGLE: Ix/Iy non valable’ DETECTION Durant l’exécution . CAUSE Une des distances entre positionnements «Ix/Iy» a été définie par une valeur non correcte qui ne permet pas de réaliser un nombre entier d’usinages. SOLUTION Vérifier que les valeurs introduites soient correctes. ‘POSITIONNEMENT EN GRILLE: Ix/Iy non valable’ DETECTION Durant l’exécution . CAUSE Une des distances entre positionnements «Ix/Iy» a été définie par une valeur non correcte qui ne permet pas de réaliser un nombre entier d’usinages. SOLUTION Vérifier que les valeurs introduites soient correctes. 68 MANUEL DE SOLUTION DES ERREURS CNC 8040M FEUILLE DE NOTES MANUEL DE SOLUTION DES ERREURS 69 CNC 8040M FEUILLE DE NOTES 70 MANUEL DE SOLUTION DES ERREURS CNC 8040M INDEX ALPHABÉTIQUE Changement d’outil programmé sans M06 ................................ 36 Changement outil actif, suivant impossible en haut niveau ...... 36 A Accélération insuffisante pour la vitesse programmée en filetage .................................................................................. 47 Accès aux variables avec indice non permis ............................. 41 Accès aux variables du PLC erroné ........................................... 41 ALÉSAGE : F=0 ........................................................................ 67 ALÉSAGE : S=0 ........................................................................ 67 ALÉSAGE GRAIN :F=0 .............................................................. 67 ALÉSAGE GRAIN: P=0 .............................................................. 68 ALÉSAGE GRAIN: S=0 .............................................................. 68 ALÉSAGE GRAIN: T=0 .............................................................. 68 ALÉSAGE: P=0 ........................................................................ 67 ALÉSAGE: T=0 ........................................................................ 67 Arc programmé avec rayon trop petit ou cercle complet ........... 44 Arrondi en bloc final .................................................................... 34 Assignation non paramétrique après le point initial du profil ..... 32 Attente de “,” ............................................................................... 17 Attente de “(” ............................................................................... 17 Attente de “)” ............................................................................... 16 Attente de “=” .............................................................................. 16 Avec G48 actif, il n’est pas possible de programmer un outil ... 37 Avec G48, il n’est pas possible de programmer un outil ........... 32 Axe * bloqué ............................................................................... 49 Axe HIRTH: programmer des valeurs entières .......................... 13 Axe incorrect ............................................................................... 21 Axe inexistant ............................................................................. 11 Axe rot. position.: valeurs absolues (G90) entre 0-359.9999 .... 26 Axe rotatif: valeurs absolues (G90) entre +/-359.9999 .............. 27 Axes X Y ou Z accouplés ou synchronisés ............................... 29 Axes X, Y y Z doivent exister ..................................................... 29 B Base négative et exposant non entier ....................................... 18 Base zéro et exposant non positif .............................................. 17 Bloc incompatible avec définition de profil ................................... 5 Bloc non exécutable avec un autre programme en exécution .. 20 Bloc non permis en MDI ou inspection d’outil ............................ 45 Blocs de haut niveau non permis en définition de profil .............. 5 Broche bloquée .......................................................................... 48 C C. utilis.: ne pas programmer aides géométriques, comp. ou cycles .............................................................................. 20 Circonférence de rayon nul ........................................................ 46 Commande exécutable canal utilisateur seulement .................. 20 Compensation non admise ........................................................ 31 Compensation radiale non admise avec axe rotatif de positionnement ..................................................................... 44 Coordonnée du plan de référence non valable en cycle fixe ..... 41 Coordonnées incomplètes ......................................................... 10 Coordonnées incorrectes ........................................................... 11 Coordonnées polaires non admises .......................................... 11 Correcteur inexistant .................................................................. 28 Correcteur: D3 R L I K ................................................................ 20 Course maximale du palpeur dépassée .................................... 54 Cycle fixe inexistant .................................................................... 39 Cycle inexistant .......................................................................... 28 CH Chanfrein mal programmé ......................................................... 34 Changement de gamme incorrect .............................................. 38 Changement de plan en arrondi/chanfrein ................................. 34 Changement de plan en compensation ..................................... 44 D Début de compensation sans trajectoire droite ......................... 43 Déflexion hors limite ................................................................... 29 Différence d’erreurs poursuite de l’axe accouplé * trop grande 50 Division par zéro ......................................................................... 17 Division par ZERO en PLC ......................................................... 55 E Ecrire +/- ..................................................................................... 23 Ecrire 0/1 .................................................................................... 22 Ecrire ON/OFF ............................................................................ 23 Ecrire YES/NO ............................................................................ 23 ELSE non associé à IF ............................................................... 13 Erreur 1 dans l’anneau SERCOS ............................................... 57 Erreur classe 1 non définie ........................................................ 56 Erreur dans bus de puissance ( 213...215 ) ............................... 56 Erreur dans la RAM du chip SERCOS. Taper une touche ........ 54 Erreur dans l’anneau SERCOS .................................................. 56 Erreur dans le régulateur ............................................................ 56 Erreur de contrôle de tension (100...105) .................................. 56 Erreur de mémoire EPROM de la CNC ..................................... 53 Erreur de mémoire EPROM du PLC .......................................... 53 Erreur de mémoire RAM de la CNC .......................................... 53 Erreur de mémoire RAM du PLC ............................................... 53 Erreur de mesure ( 600...606 ) ................................................... 56 Erreur de mesure du palpeur ..................................................... 54 Erreur de mesure sur la broche ................................................. 52 Erreur de mesure sur l’axe * ...................................................... 52 Erreur de poursuite de la broche hors limite .............................. 48 Erreur de poursuite de l’axe * hors limites ................................. 50 Erreur de programmation perçage de poche avec îlots ............ 40 Erreur de Version du chip SERCOS. Taper une touche ............ 54 Erreur en accès à variable SERCOS ......................................... 57 Erreur en PLC ............................................................................. 55 Erreur mémoire RAM du PLC. Taper une touche ...................... 53 Erreur mémoire RAM du système de la CNC. Taper une touche ................................................................................... 53 Erreur mémoire RAM utilisateur de la CNC. Taper une touche 53 Erreur régulateur : Axe ............................................................... 57 Erreur régulateur broche ............................................................ 57 Erreur régulateur broche 2 ......................................................... 57 Erreur régulateur broche auxiliaire ............................................. 57 Erreur SERCOS dans la recherche de zéro .............................. 57 Erreur servo axe * ....................................................................... 50 ERREUR:CHECKSUM PARAMETRES AXE * .......................... 58 ERREUR:CHECKSUM PARAMETRES BROCHE .................... 58 ERREUR:CHECKSUM PARAMETRES BROCHE 2 ................. 58 ERREUR:CHECKSUM PARAMETRES BROCHE AUX. ........... 58 ERREUR:CHECKSUM PARAMETRES GENERAUX ............... 58 ERREUR:CHECKSUM PARAMETRES LIGNE SERIE 1 .......... 58 ERREUR:CHECKSUM PARAMETRES LIGNE SERIE 2 .......... 58 ERREUR:CHECKSUM PARAMETRES PLC ............................. 58 ERREUR:CHECKSUM TABLE COMP. CROISEE 1 ................. 59 ERREUR:CHECKSUM TABLE COMP. CROISEE 2 ................. 59 ERREUR:CHECKSUM TABLE COMP. CROISEE 3 ................. 59 ERREUR:CHECKSUM TABLE COMP. VIS AXE * .................... 59 ERREUR:CHECKSUM TABLE CORRECTEURS ..................... 59 ERREUR:CHECKSUM TABLE DE CODES .............................. 58 ERREUR:CHECKSUM TABLE DE ORIGINES ......................... 58 ERREUR:CHECKSUM TABLE FONCTIONS M ........................ 59 ERREUR:CHECKSUM TABLE MAGASIN ................................. 59 ERREUR:CHECKSUM TABLE OUTILS .................................... 59 MANUEL DE SOLUTION DES ERREURS 71 CNC 8040M Etiquette non définie ................................................................... 42 Expression erronée .................................................................... 16 F FILETAGE : F=0 ......................................................................... 67 FILETAGE : S=0 ......................................................................... 67 FILETAGE: P=0 ......................................................................... 67 FILETAGE: T=0 ......................................................................... 67 Fin de compensation sans trajectoire droite .............................. 43 Fonction G inexistante .................................................................. 3 Fonction G non permise après le point initial du profil .............. 32 Fonction G non permise en sélection de profil .......................... 31 Fonction non permise depuis PLC ............................................. 28 Fonction: M4 S4 bits(8) ........................................................... 21 Fonctions G incompatibles ........................................................... 2 Format +/- 5.5 ............................................................................. 24 Format de la valeur inadapté ....................................................... 2 Format numérique dépassé ....................................................... 24 FRAISAGE PROFIL 1: F=0 ........................................................ 61 FRAISAGE PROFIL 1: P=0 ....................................................... 61 FRAISAGE PROFIL 1: Profil nul ................................................ 61 FRAISAGE PROFIL 1: S=0 ....................................................... 61 FRAISAGE PROFIL 1: T=0 ........................................................ 61 FRAISAGE PROFIL 2: F=0 ........................................................ 62 FRAISAGE PROFIL 2: P=0 ....................................................... 62 FRAISAGE PROFIL 2: S=0 ....................................................... 62 FRAISAGE PROFIL 2: T=0 ........................................................ 61 G G23 n’a pas été programmé ...................................................... 29 G49 T X Y Z S, X Y Z A B C , ou, X Y Z Q R S .......................... 6 G51 [A] E .................................................................................... 21 G60: [A] /X I K/(2) [P Q R S T U V] .............................................. 6 G61-2: [A B] /X I J/(2) Y J D (2)/ [P Q R S T U V] ....................... 7 G63: X Y /I K/(1) [C P][P Q R S T U V] ........................................ 7 G64: X Y /I K/(1) [C P][P Q R S T U V] ........................................ 7 G65: X Y /A I/(1) [C P] .................................................................. 8 G66: [D H][R I][C J][F K] S E [Q] ................................................. 8 G67-G68 ne sont pas admis sans programmer avant G66 ...... 26 G67. Rayon de l’outil trop grand ................................................ 37 G67: [A] B [C] [I] [R] [K] [V] .......................................................... 8 G68. Rayon de l’outil trop grand ................................................ 37 G68: [B] [L] [Q] [J] [I] [R] [K] ......................................................... 9 G69: I B [C D H J K L R] .............................................................. 9 G79 n’est pas admis s’il n’y a pas un cycle actif ....................... 25 G8 mal défini .............................................................................. 35 G81-84-85-86-89: I [K] ................................................................. 9 G82: I K ......................................................................................... 9 G83: I J ....................................................................................... 10 G87: I J K B [C] [D] [H] [L] [V] .................................................... 10 G88: I J B [C] [D] [H] [L] [V] ........................................................ 10 G96 non admis si la broche n’est pas à vitesse continue ......... 27 Gamme de broche non définie pour M19 .................................. 38 I Il est obligatoire de programmer l’outil T avec G67 et G68 ...... 25 Il n’est plus admis de fonctions G ................................................ 3 Il n’est plus admis de fonctions M ................................................ 3 Il n’y a pas d’emplacement dans le magasin ............................. 36 Imbriquement de programmes interdit ....................................... 31 Imbriquement dépassé ............................................................... 42 Information répétée ...................................................................... 2 Information sur trajectoire insuffisante ....................................... 34 Interpolation hélicoïdale non permise ........................................ 27 Intersection des profils non valable en poche avec îlots ........... 50 L La fenêtre n’a pas été définie ..................................................... 27 La fonction G/M doit être seule .................................................... 3 La position d’un outil spécial est fixe ......................................... 22 72 L’axe programmé n’est pas longitudinal ..................................... 26 Le bloc n’admet pas d’autre information ...................................... 2 Le correcteur D=0 n’existe pas ................................................. 22 Le magasin n’est pas RANDOM ................................................ 22 Le PLC n’est pas prêt ................................................................. 53 Le programme existe .................................................................. 14 Le programme ne peut pas être exécuté ................................... 43 Le programme n’est pas accessible .......................................... 27 Le programme n’existe pas ........................................................ 14 Ligne vide ..................................................................................... 1 Limite de programmation en pouces dépassée ......................... 25 Limite des paramètres locaux dépassée ................................... 42 Limites de course de l’axe * dépassées .................................... 50 Limites de courses de la broche dépassées ............................. 48 Limites de la table dépassées .................................................... 20 Limites des zones de travail erronées ....................................... 48 Limites graphiques erronées ...................................................... 33 Limites software de l’axe * dépassées ....................................... 49 Logarithme de nombre négatif ou nul ........................................ 17 L’outil n’est pas dans le magasin ............................................... 36 L’outil T=0 n’existe pas ............................................................... 22 M M du changement automatique de gamme impossible ............. 38 Magasin: P(1-255) = T(1-9999) .................................................. 21 Mémoire insuffisante .................................................................. 25 Message attendu ........................................................................ 14 Message incorrect ...................................................................... 24 Mode de copiage incorrect ......................................................... 30 Mode de digitalisation incorrect .................................................. 30 Mouvement en JOG hors des limites ......................................... 35 MOYEU CIRCULAIRE: Diamètre outil FINITION plus petit que δ ............................................................................................. 65 MOYEU CIRCULAIRE: Diamètre outil plus petit que ∆ .............. 65 MOYEU CIRCULAIRE: F=0 ....................................................... 65 MOYEU CIRCULAIRE: P=0 ....................................................... 65 MOYEU CIRCULAIRE: S=0 ....................................................... 65 MOYEU RECTANGULAIRE: Diamètre outil FINITION plus petit que δ ................................................................................. 65 MOYEU RECTANGULAIRE: Diamètre outil plus petit que ∆ .... 65 MOYEU RECTANGULAIRE: F=0 .............................................. 65 MOYEU RECTANGULAIRE: P=0 .............................................. 65 MOYEU RECTANGULAIRE: S=0 .............................................. 65 N Ne pas programmer un cycle fixe avec G2/G3 ........................... 6 Ne pas commuter des axes déjà commutés ............................. 37 Ne pas commuter ni décommuter des axes avec G15, G23, G48 ou G49 actives .................................................... 37 Ne pas définir sousrout. dans progr. principal ........................... 14 Ne pas modifier l’outil actif ou le suivant ................................... 22 Ne pas programmer Q avec le paramètre M19TYPE=0 ......... 33 Ne pas programmer des axes de copiage ................................. 29 Ne pas programmer des sousroutines modales ........................ 27 Ne pas programmer d’étiquette avec paramètre ......................... 3 Ne pas programmer formats supérieurs à 6.5 ........................... 19 Ne pas programmer G33, G95 ou M19 S sans codeur broche . 25 Ne pas programmer un axe accouplé ................................. 12, 48 Ne pas programmer un axe GANTRY ....................................... 13 Ne pas programmer une nouvelle translation sans an .............. 31 Ne programmer G27 qu’en copiage de profil ............................. 30 Nom de password incorrect ....................................................... 26 Nombre de répétitions impossible ................................................ 3 Nombre incorrect de bits ............................................................ 25 O On a programmé un outil de rayon nul ...................................... 37 On a programmé un pas plus grand que le diamètre de l’outil . 37 On n’a pas programmé la coordonnée de la surface de la pièce en poche avec îlot ...................................................... 41 On n’admet pas plus d’un axe HIRTH par bloc ......................... 26 MANUEL DE SOLUTION DES ERREURS CNC 8040M On ne peut pas chercher une étiquette ..................................... 43 On ne peut pas ouvrir le programme ......................................... 43 On ne peut pas programmé l’axe après le point initial du profil ...................................................................................... 32 On ne peut pas programmer G43 avec G48 actif ...................... 35 On ne peut pas programmer G48 avec G43 actif ...................... 35 On ne peut pas programmer le bloc après le point initial du profil ...................................................................................... 32 On ne peut pas référencer la broche ......................................... 46 On ne peut pas synchroniser l’axe * .......................................... 49 OPEN non réalisé ....................................................................... 14 Opération incomplète ................................................................. 16 Opération incorrecte ................................................................... 16 Option non disponible ................................................................. 28 Ordre des axes incorrect ............................................................ 11 Ordre des valeurs incorrect .......................................................... 1 Origine: G54-59 axes (1-5) ......................................................... 21 Outil non défini ............................................................................ 22 Outil non défini dans la table des outils ..................................... 36 Outil suivant possible en centre d’usinage seulement .............. 22 Outil: T4 D3 F3 N5 R5(.2) .......................................................... 20 P Palpeur mal aligné ...................................................................... 47 Paramètre de vitesse de l’axe * incorrect .................................. 49 Paramètre inexistant .................................................................. 15 Paramétres de la table de compensation croisée incorrects .... 60 Paramètres locaux non accessibles .......................................... 41 Paramètres locaux non admis .................................................... 20 Paramétres sercosid des axes et de broche incorrects ............ 60 Pas de correcteur programmé en cycle fixe .............................. 36 Pas de sousroutine associée à G74 .......................................... 45 Pas de tension sur carte des axes ............................................. 52 Pas de tension sur carte des I/O 1 ............................................ 52 Pas de tension sur carte des I/O 2 ............................................ 52 Pas de tension sur carte des I/O 3 ............................................ 52 Pas de tension sur le module copiage ....................................... 54 Pas d’information pour arc tangent en poche avec îlot ............. 35 Pas d’informations sur la trajectoire précédente ....................... 35 Pas d’outil de la même famille pour remplacer ......................... 36 Pas en trajectoire circulaire ........................................................ 44 Pas en trajectoire droite ............................................................. 44 Pas mal programmé ................................................................... 12 Password: utiliser lettres (majuscules ou minuscules) ou chiffres .................................................................................. 26 PERÇAGE 1: F=0 ....................................................................... 66 PERÇAGE 1: P=0 ...................................................................... 66 PERÇAGE 1: S=0 ...................................................................... 66 PERÇAGE 1: T=0 ....................................................................... 66 PERÇAGE 2: B=0 ..................................................................... 67 PERÇAGE 2: F=0 ....................................................................... 66 PERÇAGE 2: P=0 ...................................................................... 67 PERÇAGE 2: S=0 ...................................................................... 66 PERÇAGE 2: T=0 ....................................................................... 67 Plan erroné en trajectoire tangente ............................................ 35 Plan et axe longitudinal actifs incorrects .................................... 29 PLC_ERR sans description ........................................................ 55 POCHE CIRCULAIRE: Angle de pénétration non valide .......... 64 POCHE CIRCULAIRE: Diamètre outil FINITION plus petit que δ ............................................................................................. 65 POCHE CIRCULAIRE: Diamètre outil plus grand que poche ... 64 POCHE CIRCULAIRE: Diamètre outil plus petit que ∆ .............. 64 POCHE CIRCULAIRE: F=0 ....................................................... 64 POCHE CIRCULAIRE: P=0 ....................................................... 64 POCHE CIRCULAIRE: S=0 ....................................................... 64 POCHE PROFIL 3D: Angle de pénétration non valide .............. 63 POCHE PROFIL 3D: Diamètre outil FINITION plus petit que δ 63 POCHE PROFIL 3D: Diamètre outil plus petit que ∆ .................. 63 POCHE PROFIL 3D: F=0 ........................................................... 62 POCHE PROFIL 3D: P=0 .......................................................... 62 POCHE PROFIL 3D: S=0 .......................................................... 62 POCHE PROFIL: Angle de pénétration non valide ................... 62 POCHE PROFIL: Diamètre outil FINITION plus petit que δ ...... 62 POCHE PROFIL: Diamètre outil plus petit que ∆ ........................ 62 POCHE PROFIL: F=0 ................................................................ 62 POCHE PROFIL: P=0 ................................................................ 62 POCHE PROFIL: S=0 ................................................................ 62 POCHE RECTANGULAIRE 1: Diamètre outil FINITION plus petit que δ .................................................................................... 63 POCHE RECTANGULAIRE 1: Diamètre outil plus grand que poche .................................................................................... 63 POCHE RECTANGULAIRE 1: Diamètre outil plus petit que ∆ . 63 POCHE RECTANGULAIRE 1: F=0 ............................................ 63 POCHE RECTANGULAIRE 1: P=0 ........................................... 63 POCHE RECTANGULAIRE 1: S=0 ........................................... 63 POCHE RECTANGULAIRE 1: T=0 ............................................ 63 POCHE RECTANGULAIRE 2: Angle de pénétration non valide .................................................................................... 64 POCHE RECTANGULAIRE 2: Diamètre outil FINITION plus petit que δ .................................................................................... 64 POCHE RECTANGULAIRE 2: Diamètre outil plus grand que poche .................................................................................... 64 POCHE RECTANGULAIRE 2: Diamètre outil plus petit que ∆ . 64 POCHE RECTANGULAIRE 2: F=0 ............................................ 63 POCHE RECTANGULAIRE 2: P=0 ........................................... 64 POCHE RECTANGULAIRE 2: S=0 ........................................... 64 Point dans la zone prohibée 1 .................................................... 47 Point dans la zone prohibée 2 .................................................... 47 Point dans la zone prohibée 3 .................................................... 47 Point dans la zone prohibée 4 .................................................... 47 Point incompatible avec le plan actif .......................................... 12 Point initial mal programmé en sélection profil .......................... 32 POINTAGE: α=0 ......................................................................... 66 POINTAGE: F=0 ......................................................................... 66 POINTAGE: ø=0 ......................................................................... 66 POINTAGE: P=0 ......................................................................... 66 POINTAGE: S=0 ......................................................................... 66 POINTAGE: T=0 ......................................................................... 66 Position d’outil non valable avant le cycle fixe ........................... 40 POSITIONNEMENT EN ARC: ß non valable ............................ 68 POSITIONNEMENT EN GRILLE: Ix/Iy non valable ................... 68 POSITIONNEMENT EN LIGNE: I non valable .......................... 68 POSITIONNEMENT EN RECTANGLE: Ix/Iy non valable .......... 68 Pour G28 ou G29 on a besoin d’une deuxième broche ........... 31 Présélection d’axes rotatifs: valeurs entre 0-359.9999 .............. 30 Profil de profondeur non valable en poches avec îlots .............. 40 Profil du plan ouvert en poches avec îlots ................................. 41 Profil du plan qui se coupe lui même en poches avec îlots ...... 40 Programmation mauvaise angle cote ........................................ 44 Programmation non autorisée en mode copiage ....................... 28 Programmation non permise avec G48-G49 actives ................ 31 Programmation paramétrique erronée ....................................... 25 Programmer A (ajouter) ou D (effacer) ...................................... 28 Programmer A entre 0 et 255 .................................................... 31 Programmer autre fenêtre .......................................................... 18 Programmer axe(s) ..................................................................... 11 Programmer canal 0(CNC), 1(PLC), 2(DNC) ............................. 15 Programmer DNC1/2, HD ou CARD A (optionnel) .................... 28 Programmer entrées de 0 à 25 ................................................. 19 Programmer étiquette N(0-9999) ............................................... 13 Programmer fenêtres de 0 à 25 ................................................ 19 Programmer files de 0 à 20 ........................................................ 19 Programmer format numérique .................................................. 19 Programmer F,S,T,D avant les fonctions M ................................. 3 Programmer G36-G39 avec R+5.5 .............................................. 4 Programmer INPUT .................................................................... 19 Programmer le numéro de colonne ........................................... 18 Programmer le numéro d’erreur de 0 à 9999 ............................ 16 Programmer numéro de file ....................................................... 18 Programmer numéro de sousroutine de 1 à 9999 ..................... 13 Programmer P3 = valeur ............................................................ 21 Programmer pages de 0 à 255 .................................................. 19 Programmer pas ......................................................................... 12 Programmer Q entre +/-359.9999 .............................................. 32 Programmer soft_keys de 1 à 7 ................................................. 18 Programmer une autre softkey .................................................. 18 Programmer X maximum ........................................................... 33 MANUEL DE SOLUTION DES ERREURS 73 CNC 8040M Programmer Y maximum ........................................................... 33 Programmer Y minimum ............................................................ 33 Programmer Z maximum ........................................................... 33 Programmer Z minimum ............................................................ 33 Programmer zone K1, K2, K3 o K4 ............................................. 4 Programmer: G15 axe .................................................................. 4 Programmer: G16 axe-axe ........................................................... 4 Programmer: G22 K(1/2/3/4) S(0/1/2) ......................................... 4 Programmer: G52 axe +/-5.5 ..................................................... 30 Programmer: G72 S5.5 ou axe(s) ................................................ 5 Programmer: G73 Q (angle) I J (centre) ...................................... 5 Programmer: G77 axes (de 2 à 6) ............................................... 6 Programmer: G93 I J .................................................................... 6 Surtempérature dans le régulateur ( 107 ) ................................. 56 Surtension dans le bus de puissance ( 304/306 ) ..................... 56 T Table 1 de compensation croisée incorrecte ............................. 59 Table 2 de compensation croisée incorrecte ............................. 59 Table 3 de compensation croisée incorrecte ............................. 59 Table complète ........................................................................... 30 Table de vis * incorrecte.Taper touche ....................................... 59 Température maximale dépassée .............................................. 52 Texte trop long ............................................................................ 24 Trajectoire circulaire mal programmée ...................................... 46 Trajectoire hélicoïdale mal programmée .................................... 46 R Racine de nombre négatif .......................................................... 17 Rang ASIN/ACOS dépassé ....................................................... 18 Rang de l’axe * dépassé ............................................................ 48 Rang de paramètres protégés en écriture . P297, P298 ........... 51 Rang dépassé ............................................................................ 45 Rang dépassé en limite de zone ................................................ 47 Rang dépassé en translation d’origine ....................................... 46 Rayon d’arrondi trop grand ......................................................... 34 Rayon de compensation trop grand ........................................... 43 Rayon négatif en polaires ........................................................... 44 Rayon négatif non admis en coordonnées absolues ................. 26 Repositionnement non permis ................................................... 29 RET non associé à sousroutine ................................................. 42 S S non programmée en G95 ou filetage ...................................... 39 S programmée sans gamme active ........................................... 38 S programmée trop grande ........................................................ 38 Saut à étiquette non définie ....................................................... 42 Signal du palpeur non reçu ........................................................ 45 Sortie analogique non disponible ............................................... 15 Sortie tangentielle mal programmée .......................................... 34 Sorties analogiques: ANAO(1-8) = +/-10 Volts .......................... 27 Sous-tension dans le bus de puissance ( 307 ) ......................... 56 Sousroutine avec changement gamme non admise ................. 38 Sousroutine en programme non disponible ............................... 43 Sousroutine non définie .............................................................. 42 Sousroutine répétée ................................................................... 14 Surcourant ( 212 ) ....................................................................... 56 Surcharge dans le régulateur ( 201 ) ......................................... 56 SURFAÇAGE: F=0 ..................................................................... 61 SURFAÇAGE: P=0 ..................................................................... 61 SURFAÇAGE: S=0 ..................................................................... 61 SURFAÇAGE: T=0 ..................................................................... 61 Surtempérature dans le moteur ( 108 ) ...................................... 56 Surtempérature dans le radiateur ( 106 ) ................................... 56 74 U Un paramètre est attendu .......................................................... 15 Un paramètre obligatoire n’a pas été programmé dan .............. 39 Urgence externe activée ............................................................ 52 V Valeur de chanfrein trop grande ................................................. 34 Valeur de paramètre non valable en cycle fixe .......................... 40 Valeur erronée pour donner à une variable ................................ 41 Valeur inadaptée ........................................................................... 1 Valeurs entre 0-100 .................................................................... 23 Valeurs entre 0-2 ........................................................................ 23 Valeurs entre 0-255 .................................................................... 23 Valeurs entre 0-3 ........................................................................ 23 Valeurs entre 0-32767 ................................................................ 24 Valeurs entre 0-4 ........................................................................ 23 Valeurs entre 0-6 ........................................................................ 30 Valeurs entre 0-65535 ................................................................ 24 Valeurs entre 0-9 ........................................................................ 23 Valeurs entre 0-9999 .................................................................. 24 Variable de lecture uniquement .................................................. 15 Vis: Cote-erreur .......................................................................... 21 Vitesse maximale de l’axe * dépassée ...................................... 49 W WATCHDOG en Module Périodique (PE) .................................. 55 WATCHDOG en Module Principal (PRG) .................................. 55 WBUF seulement en canal utilisateur d’édition ......................... 20 Z Zone de travail 1 de l’axe * dépassée ........................................ 49 Zone de travail 2 de l’axe * dépassée ........................................ 49 Zone de travail 3 de l’axe * dépassée ........................................ 50 Zone de travail 4 de l’axe * dépassée ........................................ 51 MANUEL DE SOLUTION DES ERREURS