Modèle ·T· (Soft V16.3x) CNC 8035 Ref. 1106 MANUEL DE PROGRAMMATION Tous droits réservés. La reproduction totale ou partielle de cette documentation est interdite, de même que sa transmission, transcription, traduction ou son enregistrement dans un système de récupération de données sans autorisation expresse de Fagor Automation. Toute copie ou utilisation, totale ou partielle, non autorisée du logiciel est interdite. L'information contenue dans ce manuel peut être sujette à des variations dues à des modifications techniques. Fagor Automation se réserve le droit de modifier le contenu du manuel sans être tenue à en communiquer les changements. Toutes les marques enregistrées ou commerciales figurant dans le manuel appartiennent à leurs propriétaires respectifs. L’utilisation de ces marques par des tiers pour leurs propres fins peut aller à l’encontre des droits des propriétaires. La CNC peut réaliser d’autres fonctions que celles figurant dans la documentation associée, mais Fagor Automation ne garantit pas la validité de ces applications. En conséquence, sauf autorisation expresse de Fagor Automation, toute application de la CNC ne figurant pas dans la documentation doit être considérée comme "impossible". En tous cas, Fagor Automation n'assume aucune responsabilité en cas de blessures, dommages physiques ou matériels, subis ou provoqués par la CNC, si celle-ci est utilisée de manière différente de celle expliquée dans la documentation concernée. Le contenu de ce manuel et sa validité pour le produit décrit ont été vérifiés. Même ainsi, il se peut qu'une erreur involontaire ait été commise et c'est pour cela que la coïncidence absolue n'est pas garantie. De toute façon, on vérifie régulièrement l'information contenue dans le document et on effectue les corrections nécessaires qui seront comprises dans une édition ultérieure. Nous vous remercions de vos suggestions d’amélioration. Les exemples décrits dans ce manuel sont orientés à l'apprentissage. Avant de les utiliser dans des applications industrielles, ils doivent être convenablement adaptés et il faut s'assurer aussi que les normes de sécurité sont respectées. Dans ce produit, le code source suivant est utilisé, assujetti aux termes de la licence GPL. Les applications busybox V0.60.2; dosfstools V2.9; linux-ftpd V0.17; ppp V2.4.0; utelnet V0.1.1. La bibliothèque grx V2.4.4. Le kernel de linux V2.4.4. Le chargeur de linux ppcboot V1.1.3. Pour recevoir une copie de ce code source sur CD, envoyer 10 euros à Fagor Automation, au titre de frais de préparation et d’envoi. Manuel de programmation INDEX Au sujet du produit ................................................................................................................ 9 Déclaration de conformité ................................................................................................... 11 Historique de versions (T) ................................................................................................... 13 Conditions de sécurité......................................................................................................... 19 Conditions de garantie ........................................................................................................ 23 Conditions de ré-expédition................................................................................................. 25 Notes complémentaires....................................................................................................... 27 Documentation Fagor.......................................................................................................... 29 CHAPITRE 1 GÉNÉRALITÉS 1.1 1.2 1.3 CHAPITRE 2 CONSTRUCTION D'UN PROGRAMME 2.1 2.1.1 2.1.2 2.1.3 CHAPITRE 3 Nomenclature des axes........................................................................................... 44 Sélection de plans (G16,G17,G18,G19).................................................................. 45 Cotation de la pièce. Millimètres (G71) ou pouces (G70)........................................ 46 Programmation absolue/incrémentale (G90, G91) .................................................. 47 Programmation en rayons ou en diamètres (G152, G151) ..................................... 48 Programmation de cotes ......................................................................................... 49 Coordonnées cartésiennes.................................................................................. 50 Coordonnées polaires.......................................................................................... 51 Angle et une coordonnée cartésienne ................................................................. 53 Axes tournants......................................................................................................... 54 Zones de travail ....................................................................................................... 55 Définition des zones de travail............................................................................. 56 Utilisation des zones de travail ............................................................................ 57 SYSTÈMES DE RÉFÉRENCE 4.1 4.2 4.3 4.4 4.4.1 4.4.2 4.5 CHAPITRE 5 Structure d’un programme dans la CNC ................................................................. 38 En-tête de bloc..................................................................................................... 39 Bloc de programme ............................................................................................. 40 Fin de bloc ........................................................................................................... 41 AXES ET SYSTÈMES DE COORDONNÉES 3.1 3.2 3.3 3.4 3.5 3.6 3.6.1 3.6.2 3.6.3 3.7 3.8 3.8.1 3.8.2 CHAPITRE 4 Programmes pièce .................................................................................................. 32 Ligne DNC ............................................................................................................... 34 Protocole de communication via DNC ou périphérique........................................... 35 points de référence.................................................................................................. 59 Recherche de référence machine (G74) ................................................................. 60 Programmation par rapport au zéro machine (G53)................................................ 61 Présélection des coordonnées et décalages d’origine ............................................ 62 Présélection de coordonnées et limitation de la valeur de S (G92)..................... 63 Décalages d'origine (G54..G59 et G159)............................................................. 64 Présélection de l'origine polaire (G93)..................................................................... 66 PROGRAMMATION SUIVANT CODE ISO 5.1 5.2 5.2.1 5.2.2 5.3 5.3.1 5.3.2 5.4 Fonctions préparatoires........................................................................................... 68 Vitesse d'avance F .................................................................................................. 70 Avance en mm/min ou pouces/minute (G94) ...................................................... 71 Avance en mm/tour ou pouces/tour (G95)........................................................... 72 Vitesse de rotation de la broche (S) ........................................................................ 73 Vitesse de coupe constante (G96) ...................................................................... 74 Vitesse de rotation de la broche en t/min. (G97) ................................................. 75 Numéro d'outil (T) et correcteur (D)......................................................................... 76 CNC 8035 MODÈLE ·T· (SOFT V16.3X) ·5· Manuel de programmation 5.5 Fonction auxiliaire (M) ............................................................................................. 78 5.5.1 M00. Arrêt de programme ................................................................................... 79 5.5.2 M01. Arrêt conditionnel du programme ............................................................... 80 5.5.3 M02. Fin de programme ...................................................................................... 81 5.5.4 M30. Fin de programme avec retour au début .................................................... 82 5.5.5 M03. Démarrage de la broche à droite (sens horaire)......................................... 83 5.5.6 M04. Démarrage de la broche à gauche (sens anti-horaire) ............................... 84 5.5.7 M05. Arrêt de la broche ....................................................................................... 85 5.5.8 M06. Code de changement d'outil ....................................................................... 86 5.5.9 M19. Arrêt orienté de la broche ........................................................................... 87 5.5.10 M41, M42, M43, M44. Changement de gammes de la broche. .......................... 88 CHAPITRE 6 COMMANDE DE LA TRAJECTOIRE 6.1 6.2 6.3 6.4 6.5 6.6 6.7 6.8 6.9 6.10 6.11 6.12 6.13 6.14 6.15 CHAPITRE 7 FONCTIONS PRÉPARATOIRES SUPPLÉMENTAIRES 7.1 7.1.1 7.2 7.3 7.3.1 7.3.2 7.3.3 7.4 7.4.1 7.4.2 7.4.3 7.5 7.6 7.6.1 7.6.2 CHAPITRE 8 CHAPITRE 9 MODÈLE ·T· (SOFT V16.3X) ·6· Interrompre la préparation de blocs (G04) ............................................................ 113 G04 K0: Interruption de la préparation de blocs et actualisation de cotes ........ 115 Temporisation (G04 K) .......................................................................................... 116 Travail sur arête vive (G07) et arrondie (G05,G50)............................................... 117 Arête vive (G07) ................................................................................................ 117 Arête arrondie (G05).......................................................................................... 118 Arête arrondie commandée (G50) ..................................................................... 119 Analyse par anticipation ("Look-ahead") (G51) .................................................... 120 Algorithme avancé de look-ahead (intégrant des filtres Fagor) ......................... 122 Fonctionnement de look-ahead avec des filtres Fagor actifs. ........................... 123 Adoucissement de la vitesse d'usinage............................................................. 124 Image miroir (G11, G12, G13, G10, G14) ............................................................. 125 Facteur d'échelle (G72) ......................................................................................... 126 Facteur d’échelle appliqué à tous les axes........................................................ 127 Facteur d'échelle appliqué à un ou plusieurs axes............................................ 128 COMPENSATION D'OUTILS 8.1 8.2 8.2.1 8.2.2 8.2.3 8.2.4 8.2.5 8.2.6 8.2.7 8.2.8 8.2.9 8.3 CNC 8035 Positionnement rapide (G00) .................................................................................. 90 Interpolation linéaire (G01) ...................................................................................... 91 Interpolation circulaire (G02/G03) ........................................................................... 92 Interpolation circulaire avec programmation du centre de l’arc en coordonnées absolues (G06) ........................................................................................................ 96 Trajectoire circulaire tangente a la trajectoire précédente (G08) ............................ 97 Trajectoire circulaire définie avec trois points (G09) ............................................... 98 Entrée tangentielle au début de l'usinage (G37) ..................................................... 99 Sortie tangentielle à la fin de l'usinage (G38)........................................................ 101 Arrondissement commandé d'arêtes (G36)........................................................... 102 Chanfreinage (G39)............................................................................................... 103 Filetage électronique (G33) ................................................................................... 104 Retrait des axes face à un arrêt lors du taraudage (G233) ................................... 107 Filets à pas variable (G34) .................................................................................... 109 Déplacement contre butée (G52) .......................................................................... 110 Avance F comme fonction inverse du temps (G32) .............................................. 111 La compensation de longueur ............................................................................... 131 La compensation de rayon .................................................................................... 132 Le facteur de forme de l'outil ............................................................................. 133 Travail sans compensation de rayon d’outil ...................................................... 136 Travail avec compensation de rayon d’outil ...................................................... 138 Début de compensation de rayon de l'outil (G41, G42)..................................... 139 Segments de compensation de rayon d'outil..................................................... 142 Annulation de compensation de rayon d’outil (G40).......................................... 143 Annulation temporaire de la compensation avec G00....................................... 147 Changement du type de compensation de rayon pendant l'usinage................. 149 Compensation d’outil sur n’importe quel plan.................................................... 150 Détection de collisions (G41 N, G42 N)................................................................. 151 CYCLES FIXES 9.1 9.1.1 9.1.2 9.2 9.2.1 9.2.2 G66. Cycle fixe de poursuite de profil.................................................................... 154 Fonctionnement de base ................................................................................... 157 Syntaxe de programmation de profils ................................................................ 159 G68. Cycle fixe d'ébauchage sur l'axe X ............................................................... 160 Fonctionnement de base ................................................................................... 163 Syntaxe de programmation de profils ................................................................ 166 Manuel de programmation 9.3 9.3.1 9.3.2 9.4 9.4.1 9.5 9.5.1 9.6 9.6.1 9.7 9.7.1 9.8 9.8.1 9.9 9.9.1 9.10 9.10.1 9.11 9.11.1 9.12 9.12.1 CHAPITRE 10 TRAVAIL AVEC PALPEUR 10.1 CHAPITRE 11 G69. Cycle fixe d'ébauchage sur l'axe Z ............................................................... 167 Fonctionnement de base ................................................................................... 171 Syntaxe de programmation de profils ................................................................ 174 G81. Cycle fixe de tournage de segments droits................................................... 175 Fonctionnement de base ................................................................................... 177 G82. Cycle fixe de dressage de segments droits .................................................. 179 Fonctionnement de base ................................................................................... 181 G83. Cycle fixe de perçage axial / taraudage........................................................ 183 Fonctionnement de base ................................................................................... 185 G84. Cycle fixe de tournage de segments courbes............................................... 186 Fonctionnement de base ................................................................................... 189 G85. Cycle fixe de dressage de segments courbes .............................................. 191 Fonctionnement de base ................................................................................... 194 G86. Cycle fixe de filetage longitudinal ................................................................. 196 Fonctionnement de base ................................................................................... 200 G87. Cycle fixe de filetage frontal.......................................................................... 201 Fonctionnement de base ................................................................................... 206 G88. Cycle fixe de rainurage sur l'axe X ............................................................... 207 Fonctionnement de base ................................................................................... 208 G89. Cycle fixe de rainurage sur l'axe Z................................................................ 209 Fonctionnement de base ................................................................................... 210 Déplacement avec palpeur (G75, G76)................................................................. 212 PROGRAMMATION EN LANGAGE DE HAUT NIVEAU 11.1 Description lexique ................................................................................................ 213 11.2 Variables................................................................................................................ 215 11.2.1 Paramètres ou variables de caractère général.................................................. 217 11.2.2 Variables associées aux outils........................................................................... 219 11.2.3 Variables associées aux décalages d’origine .................................................... 222 11.2.4 Variables associées aux paramètres machine .................................................. 224 11.2.5 Variables associées aux zones de travail.......................................................... 225 11.2.6 Variables associées aux avances...................................................................... 227 11.2.7 Variables associées aux cotes .......................................................................... 229 11.2.8 Variables associées aux manivelles électroniques............................................ 231 11.2.9 Variables associées à la mesure ....................................................................... 233 11.2.10 Variables associées à la broche principale........................................................ 234 11.2.11 Variables associées à l’automate ...................................................................... 237 11.2.12 Variables associées aux paramètres locaux ..................................................... 239 11.2.13 Variables associées au mode de fonctionnement ............................................. 240 11.2.14 Autres variables ................................................................................................. 242 11.3 Constantes ............................................................................................................ 246 11.4 Opérateurs............................................................................................................. 247 11.5 Expressions ........................................................................................................... 249 11.5.1 Expressions arithmétiques................................................................................. 250 11.5.2 Expressions relationnelles ................................................................................. 251 CHAPITRE 12 INSTRUCTIONS DE CONTRÔLE DES PROGRAMMES 12.1 12.2 12.3 12.4 12.5 12.6 12.7 12.8 CHAPITRE 13 Instructions d’affectation........................................................................................ 254 Instructions d'affichage .......................................................................................... 255 Instructions de validation-invalidation.................................................................... 256 Instructions de contrôle de flux.............................................................................. 257 Instructions de sous-routines................................................................................. 259 Instructions de sous-routines d'interruption. .......................................................... 263 Instructions de programmes .................................................................................. 264 Instructions de personnalisation ............................................................................ 267 TRANSFORMATION ANGULAIRE DE L'AXE INCLINÉ 13.1 13.2 Activation et désactivation de la transformation angulaire .................................... 275 Blocage de la transformation angulaire ................................................................. 276 A B C D E Programmation en code ISO ................................................................................. 279 Instructions de contrôle des programmes ............................................................. 281 Résumé des variables internes de la CNC............................................................ 283 Code de touches ................................................................................................... 287 Maintenance .......................................................................................................... 289 CNC 8035 ANNEXES MODÈLE ·T· (SOFT V16.3X) ·7· Manuel de programmation CNC 8035 MODÈLE ·T· (SOFT V16.3X) ·8· AU SUJET DU PRODUIT Caractéristiques de base. Mémoire RAM 256 Kb Temps de cycle du PLC 3 ms / 1000 instructions Liaison série RS232 Standard DNC (à travers RS232) Standard Entrées de palpeur 5V ou 24V 2 Entrées et sorties numériques 40 I / 24 O Entrées de mesure pour axes et broche 4 entrées TTL / 1Vpp Entrées de mesure pour manivelles 2 entrées TTL Options de logiciel. Modèle M-MON M-MON-R M-COL M-COL-R T-MON T-COL Nombre d'axes 3 3 3 3 2 2 Disque dur Opt Opt Opt Opt Opt Opt Filetage électronique Stand Stand Stand Stand Stand Stand Gestion du magasin d'outils Stand Stand Stand Stand Stand Stand Cycles fixes d'usinage Stand Stand Stand Stand Stand Stand Usinages multiples Stand Stand Stand Stand ----- ----- Taraudage rigide Stand Stand Stand Stand Stand Stand DNC (Commande Numérique Directe) Stand Stand Stand Stand Stand Stand Compensation radiale Stand Stand Stand Stand Stand Stand Fonction Retracing ----- Stand ----- Stand ----- ----- Moniteur couleur ----- ----- Stand Stand ----- Stand Avant la mise en marche, vérifier que la machine où est installée la CNC remplit la Directive 89/392/CEE. CNC 8035 ·9· DÉCLARATION DE CONFORMITÉ Le fabricant: Fagor Automation, S. Coop. Barrio de San Andrés Nº 19, C.P. 20500, Mondragón -Guipúzcoa- (ESPAGNE). Déclare: Sous sa seule responsabilité la conformité du produit: COMMANDE NUMÉRIQUE 8035 Elle est composée des modules et accessoires suivants: 8035-M, 8035-T Note. Certains caractères supplémentaires peuvent suivre les références des modèles susmentionnés. Tous les modèles remplissent les Directives nommées. Néanmoins, l’accomplissement peut être vérifié sur l’étiquette de l'équipement. référée a cette déclaration, avec les normes suivantes. Normes de basse tension. EN 60204-1: 2006 Équipements électriques sur des machines — Partie 1. Prescriptions générales. Normes de compatibilité électromagnétique. EN 61131-2: 2007 Automates programmables — Par tie 2. Prescr iptions et essais d’équipements. Conformément aux dispositions des Directives Communautaires Basse Tension 2006/95/EC et Compatibilité Électromagnétique 2004/108/EC et leurs actualisations. À Mondragón le 27 juillet 2010. CNC 8035 ·11· HISTORIQUE DE VERSIONS (T) (modèle tour) Ci-après la liste des performances ajoutées dans chaque version de logiciel et les manuels où elles sont décrites. Dans l'historique de versions on a utilisé les abréviations suivantes : INST Manuel d'Installation PRG Manuel de programmation OPT Manuel d'utilisation Logiciel V08.1x juillet 2003 Première version. Logiciel V10.0x février 2004 Liste de prestations Axe incliné. Paramètres machine. Manuel INST / PRG INST TOOLTYPE (P167): Arrêter la préparation des blocs lors de l'exécution de "T" TOOLTYPE (P167): Exécuter le signal de stop après avoir terminé le changement de "T". FEEDTYPE (P169): Sélectionner le fonctionnement de l’avance pour F0. TYPCROSS (P135): Sur les axes Gantry, la compensation croisée s'applique aussi à l'axe esclave. RAPIDEN (P130): Touche de rapide commandée par PLC. Paramètres généraux modifiables depuis sous-routine/programme OEM: CODISET. Paramètres d'axes modifiables depuis sous-routine/programme OEM: MAXFLWE1, MAXFLWE2. Marques de PLC. INST Dénommer les entrées et sorties logiques avec le nom de l'axe. BLOABOR: Terminer l'exécution d'un bloc avec la marque de PLC (canal principal). BLOABORP: Terminer l'exécution d'un bloc avec la marque de PLC (canal de PLC). ELIMIS: Stationner la broche. Pendant la compilation du programme de PLC, les sorties se remettent à zéro. Variables. INST / PRG SELPRO : Variable pour sélectionner l'entrée active du palpeur. DIAM: Variable pour sélectionner le mode de programmation, les rayons ou les diamètres. G2/G3. Il n'est pas nécessaire de programmer les cotes du centre si leur valeur est zéro. M41-M44: Ces fonctions admettent des sous-routines lorsque le changement de gamme est automatique. PRG PRG CNC 8035 ·13· Logiciel V10.1x décembre 2004 Liste de prestations Calcul de la dissipation de chaleur de l’unité centrale. Nouvelle carte "Axes2". Auto-identification du type de clavier. Filtres de fréquence pour les axes et les broches. Paramètres machine. Manuel INST INST INST INST INST Historique de versions (T) COMPMODE (P175). Nouvelles méthodes de compensation de rayon. Paramètres d'axes modifiables depuis sous-routine/programme OEM: REFVALUE, REFDIREC, FLIMIT. Paramètres de broche modifiables depuis sous-routine/programme OEM: REFVALUE, REFDIREC, SLIMIT. Variables. INST / PRG DNCSTA: État de la communication DNC. TIMEG: État de comptage du temporisateur programmée avec G4. HANDSE: Bouton de sélection de la manivelle appuyé. ANAI(n): Valeur des entrées analogiques. APOS(X-C): Cote réelle de la base de l’outil, référée au zéro pièce. ATPOS(X-C): Cote théorique de la base de l’outil, référée au zéro pièce. Fonction retracing. INST Avec RETRACAC=2 la fonction retracing ne s'arrête pas dans les fonctions M. Le paramètre RETRACAC s'initialise avec [SHIFT][RESET]. Le nombre de blocs à reculer augmente jusqu'à 75. Activer la compensation de rayon dans le premier bloc de déplacement, même s'il n'y a pas de déplacement des axes du plan. Intervention manuelle avec manivelle additionnelle. G46. Maintenir G46 si aucun axe de la transformation angulaire n'intervient dans la recherche de référence machine. G151-G152. Programmation en diamètres ou en rayons. MEXEC. Exécuter un programme modal. Le nombre de fonctions G disponibles passe à 319. Les simulations sans déplacement des axes ne prennent pas en compte G4. Maintenir l’avance sélectionnée en simulation. Logiciel V10.12 INST INST / OPT INST / PRG PRG PRG PRG OPT OPT février 2005 Liste de prestations Look-ahead. Manuel INST / PRG Logiciel V10.13 avril 2005 Liste de prestations Pas de l’axe Hirth paramétrable en degrés. Axe de positionnement rollover. Déplacement en G53 par le chemin le plus court. Manuel INST INST CNC 8035 Logiciel V10.15 juin 2005 Liste de prestations Régulation CAN. ·14· Manuel INST Août 2005 Liste de prestations Manuel La CNC supporte Memkey Card + Compact Flash ou KeyCF. Explorateur de fichiers pour présenter le contenu des dispositifs de stockage. Chargement de version depuis la Memkey Card ou depuis le disque dur. Nouvelle façon de réaliser la recherche d’I0 sélectionnable avec le p.m.g. I0TYPE=3. Amélioration de la recherche de bloc. Pas de la simulation à l'exécution. Nouveau mode de repositionnement s’activant en mettant le p.m.g. REPOSTY=1. Rampes type sinus carré sur broche en boucle ouverte. Numérotation des entrées/sorties locales des modules d’expansion avec des paramètres machine de plc. Valeur par défaut des paramètres machine d’axe et de broche ACFGAIN = YES. Paramétrage des paramètres machine d’axes FFGAIN et FFGAIN2 avec deux décimales. Augmentation du nombre de symboles (DEF) disponibles dans le PLC à 400. Nouvelle variable HTOR indiquant la valeur du rayon de l’outil utilisé par la CNC. Override de la broche sur tout le cycle de filetage à 100%. OPT INST / OPT OPT INST INST / OPT INST/PRG/OPT INST INST Logiciel V12.11 INST INST INST INST / PRG PRG Février 2006 Liste de prestations Mesure de manivelle menée à un connecteur de mesure libre. Nouvelles variables RIP, GGSE, GGSF, GGSG, GGSH, GGSI, GGSJ, GGSK, GGSL, GGSM, PRGSP et PRBMOD. G04 K0. Interruption de la préparation de blocs et actualisation de cotes. Historique de versions (T) Logiciel V12.01 Manuel INST INST PRG Logiciel V12.13 Juin 2006 Liste de prestations Arrêt doux sur la référence des axes, sélectionnable avec le p.m.a. I0TYPE. Manuel INST Logiciel V12.14 Août 2006 Liste de prestations Sélection de la manivelle additionnelle comme manivelle associée à l’axe. Manuel INST Logiciel V12.18 Juin 2007 Liste de prestations Copier et exécuter des programmes sur le Disque Dur (KeyCF) Manuel CNC 8035 OPT ·15· Logiciel V14.01 décembre 2006 Historique de versions (T) Liste de prestations Affichage des messages de PLC ou CNC en Russe et en Chinois. Nouveaux filtres FAGOR. Compensation de jeu de vis. Critère de coupe de pointe de compensation. Recherche de I0 dans les axes Gantry (gestion de deux micros). Recherche automatique de I0 de la broche avec la première M3/M4. Permettre que deux axes "commutés" disposent de réductions différentes. Look-Ahead. Angle sous lequel l'arête vive est usinée. Teach-in. Exécution du bloc édité. Améliorations à l'oscilloscope et accès direct, depuis les modes: manuel et d'exécution. Édition dans le disque dur (KeyCF) Copie de sécurité des données. Backup - Restore. Nouvelle gamme de gains et d'accélérations. MSGFILE: Nombre de messages et d'erreurs de PLC, amplifiées à 255 et 128 respectivement. Taraudage rigide plus rapide sans passer Ms au PLC. Retrait des axes face à un arrêt lors du taraudage. Variation de l'Override de la broche au cours du filetage. Taraudage sur des filets borgnes (sans sortie de filet). Déplacements manuels sur G95. Logiciel V16.01 Manuel INST INST INST INST OPT INST PRG OPT OPT OPT OPT INST INST / OPT INST INST / PRG INST / PRG OPT / PRG PRG mai 2007 Liste de prestations Ne pas exécuter un programme envoyé par DNC avant d’avoir tapé sur START. Sélectionner la gamme de gains et d’accélérations à utiliser dans la recherche d’I0. Éviter que les blocs sans mouvement ne fassent arête vive. Élargissement du nombre de décalages d’origine. Nombre de chiffres des étiquettes amplifié à 8. Édition dans le disque dur (KeyCF) sur CNCs sans expansion de mémoire. Logiciel V16.11 Manuel INST INST INST / PRG PRG PRG OPT mars 2008 Liste de prestations Recherche d’I0 de la broche au tour suivant à la détection de pas par micro. Démarrage de la CNC avec des filtres actifs FAGOR. Augmentation du format numérique de la définition du centre de l’arc G2/G3 Surveillance de déphasage en taraudage rigide entre la broche et l’axe longitudinal Hystérésis dans l'ordre de compensation dans les inversions. Changement de la valeur par défaut du p.m.a. INPOSW2 (P51). Personnalisation de la CNC en Turc. G86/G87. Cycles de filetage à pas variable. Logiciel V16.12 Manuel INST INST PRG INST / OPT INST INST INST PRG mai 2008 CNC 8035 Liste de prestations Améliorations de la fonction Look-Ahead: • Algorithme avancé de look-ahead (intégrant des filtres FAGOR). • Fonctionnement de look-ahead avec des filtres FAGOR actifs. • Adoucissement de la vitesse d'usinage. ·16· Manuel INST / PRG janvier 2009 Liste de prestations Enregistrer les 10 dernières instructions de MDI. Activation de la fonction retracing avec Look-Ahead. Surveillance de la différence entre la première et la deuxième mesure. Améliorations à la sécurité avec mesure absolue. Améliorations au changeur d'outils. Gestion de réductions sur les axes et la broche. Filetage sans arrêt orienté de broche. Surveillance de PLC en langage de contacts. Éditeur de profils: Coordonnés polaires et incrémentales. Logiciel V16.32 Manuel OPT INST INST INST INST INST PRG OPT OPT juillet 2009 Liste de prestations Variable DISBLO: Distance totale programmée dans des blocs avec Look-Ahead. Logiciel V16.33 Manuel INST Historique de versions (T) Logiciel V16.31 mai 2010 Liste de prestations Incompatibilités dans le changement d’outil. Mode rainurage en zigzag. Manuel INST OPT-TC CNC 8035 ·17· CNC 8035 ·18· Historique de versions (T) CONDITIONS DE SÉCURITÉ Lire les mesures de sécurité suivantes dans le but d'éviter les accidents personnels et les dommages à cet appareil et aux appareils qui y sont connectés. L'appareil ne pourra être réparé que par du personnel autorisé par Fagor Automation. Fagor Automation n'assume aucune responsabilité en cas d'accident personnel ou de dommage matériel découlant du non-respect de ces normes de sécurité de base. Précautions face aux accidents personnels Interconnexions de modules Utiliser les câbles d'union fournis avec l'appareil. Utiliser les câbles de secteur appropriés. N’utilisez que des câbles de secteur spécifiquement recommandés pour cet appareil en vue d’éviter des risques. Éviter les surcharges électriques Pour éviter les décharges électriques et les risques d'incendie, ne pas appliquer de tension électrique hors du rang sélectionné dans la partie postérieure de l'Unité Centrale de l'appareil. Connexions à terre. Dans le but d'éviter les décharges électriques, brancher les bornes de terre de tous les modules au point central de branchement à terre. Par ailleurs, avant effectuer le branchement des entrées et sorties de cet appareil, s'assurer que le branchement à terre est effectué. Avant la mise sous tension de l’appareil, vérifiez que vous l’avez mis à la terre. En vue d’éviter des décharges électriques, vérifiez que vous avez procédé à la prise de terre. Ne pas travailler dans des ambiances humides Pour d'éviter les décharges électriques, travailler toujours dans des ambiances avec une humidité relative inférieure à 90% sans condensation à 45°C. Ne pas travailler dans des ambiances explosives Dans le but de prévenir les risques d'accident et de dommages, ne pas travailler dans des ambiances explosives. Précautions face aux dommages à l'appareil Ambiance de travail Cet appareil a été conçu pour être utilisé dans des ambiances industrielles remplissant les directives et normes en vigueur dans l'Union Européenne. Fagor Automation ne se responsabilise pas des accidents et dommages pouvant être causés par une utilisation de l'appareil dans des conditions différentes (ambiances résidentielles ou domestiques). CNC 8035 ·19· Installer l'appareil dans un lieu adéquat. Il est recommandé d'installer dans la mesure du possible la Commande Numérique dans un endroit loin du stockage de réfrigérants et autres produits chimiques et à l'abri des situations et éléments pouvant l'endommager. L'appareil remplit les directives européennes de compatibilité électromagnétique. À l'écart des sources de perturbation électromagnétique, telles que: • Les charges puissantes branchées au même réseau que l'équipement. • Les émetteurs portables (Radiotéléphones, émetteurs de radio amateurs). • Les émetteurs de radio/TV. Conditions de sécurité • Les machines à souder à l'arc. • Les lignes de haute tension. • Etc. Enveloppes Le fabricant est responsable de garantir que l'enveloppe où a été monté l'équipement remplit toutes les directives en vigueur de l'Union Européenne. Éviter les interférences en provenance de la machine-outil Tous les éléments générant des interférences (bobines des relais, contacteurs, moteurs, etc.)devront être découplés de la machine. • Bobines de relais à courant continu. Diode type 1N4000. • Bobines de relais à courant alternatif. RC connectée le plus près possible des bobines, avec des valeurs approximatives de R=220 1 W et C=0,2 µF / 600 V. • Moteurs à courant alternatif. RC branchées entre phases, avec des valeurs R=300 / 6 W et C=0,47 µF / 600 V. Utiliser la source d'alimentation adéquate Pour l'alimentation des entrées et sorties utiliser une source d'alimentation extérieure stabilisée de 24 V DC. Branchements à terre de la source d'alimentation. Le point de zéro volts de la source d'alimentation externe devra être branché au point principal de terre de la machine. Connexions des entrées et sorties analogiques. Il est recommandé d'effectuer la connexion avec des câbles blindés, en connectant toutes les mailles au terminal correspondant. Conditions de l’environnement La température ambiante en régime de fonctionnement doit être comprise entre +5 ºC et +40 ºC, avec une moyenne inférieure à +35 ºC. La température ambiante en régime de non fonctionnement doit être comprise entre -25 ºC et +70 ºC. Habitacle de l'unité Centrale (CNC 8055i) Garantir les distances requises entre l'unité centrale et chaque paroi de l'habitacle. Utiliser un ventilateur de courant continu pour améliorer l'aération de l'habitacle. Dispositif de sectionnement de l'alimentation Le dispositif de sectionnement de l'alimentation doit être situé dans un endroit facilement accessible et à une distance du sol comprise entre 0,7 et 1,7 m. CNC 8035 ·20· Protections de l'appareil Unité centrale Comporte 1 fusible extérieur rapide (F) de 4 A 250 V. OUT IN X1 FUSIBLE FUSIBLE +24V 0V X9 X10 X11 X12 X2 X3 X4 X5 X6 Conditions de sécurité X8 X7 Entrées-Sorties Toutes les entrées-sorties numériques disposent d'un isolement galvanique au moyen d'optocoupleurs entre la circuiterie de la CNC et l'extérieur. Précautions pendant les réparations Ne pas manipuler l'intérieur de l'appareil. Seul le personnel autorisé de Fagor Automation peut manipuler l'intérieur de l'appareil. . Ne pas manipuler les connecteurs, lorsque l'appareil est branché au réseau électrique. Avant de manipuler les connecteurs (entrées/sorties, mesure, etc..), vérifier que l'appareil n'est pas branché au réseau électrique. . Symboles de sécurité Symboles pouvant figurer dans le manuel. Symbole de danger ou d'interdiction. Indique les actions ou opérations pouvant provoquer des accidents personnels ou des dommages aux appareils. Symbole d'avertissement ou de précautions. Indique des situations pouvant dériver de certaines opérations de même que les actions à réaliser pour les éviter. CNC 8035 Symbole d'obligation. Indique les actions et opérations à réaliser obligatoirement. i Symbole d'information. Indique des notes, avis et conseils. ·21· CNC 8035 ·22· Conditions de sécurité CONDITIONS DE GARANTIE Garantie initiale. Tout produit fabriqué ou commercialisé par FAGOR est couvert par une garantie de 12 mois pour l’usager final, qui pourront être contrôlés par le réseau de service à travers le système de contrôle de garantie mis en place par FAGOR à cet effet. Pour que le délai entre la sortie d’un produit de nos magasins et son arrivée chez le client final n’affecte pas ces 12 mois de garantie, FAGOR a établi un système de contrôle de garantie basé sur la communication par le fabricant ou intermédiaire à FAGOR de la destination, l’identification et la date d’installation en usine, sur le document accompagnant chaque produit dans l’enveloppe de garantie. En plus d’assurer un an de garantie à l’usager, ce système permet d’informer les centres de service du réseau sur les équipements FAGOR rentrant dans leur domaine de responsabilité et provenant d’autres pays. La garantie prendra effet à la date d’installation figurant dans ledit document. FAGOR accorde un délai de 12 mois au fabricant ou à l’intermédiaire pour l’installation et la vente du produit, de façon à ce que la garantie puisse démarrer jusqu’à un an après la sortie du produit de nos magasins, à condition que la feuille de contrôle de la garantie nous ait été remise. Cela signifie de fait l’étendue de la garantie à deux ans depuis la sortie du produit des magasins de Fagor. Si cette feuille n’a pas été envoyée, la période de garantie terminera 15 mois après la sortie du produit de nos magasins. Cette garantie couvre tous les frais de matériels et de main d’œuvre chez Fagor pour la réparation d’anomalies de fonctionnement des équipements. FAGOR s'engage à réparer ou à remplacer ses produits dans la période comprise entre la date de fabrication et jusqu'au terme du délai de 8 ans à partir de la date où le produit a été rayé du catalogue. Il appartient exclusivement à FAGOR de déterminer si la réparation rentre dans les termes de la garantie. Clauses d'exclusion de garantie La réparation sera effectuée dans nos installations, par conséquent, tous les frais de déplacement du personnel technique pouvant surgir lors de la réparation, même durant la période de garantie, sont exclus de cette garantie. Cette garantie sera appliquée à condition que les équipements aient été installés en suivant les instructions, qu'ils n'aient pas subis de mauvais traitements ni de dommages pour causes d'accident ou de négligence ou du fait d'avoir été démontés ou réparés par du personnel non autorisé par FAGOR. Si après l'assistance ou la réparation, il apparaît que la cause de la panne n'est pas attribuable aux éléments concernés, le client devra assumer tous les frais occasionnés, suivant les tarifs en vigueur. D'autres garanties implicites ou explicites ne sont pas couvertes et FAGOR AUTOMATION se dégage de toute responsabilité pour d'autres dommages ou préjudices pouvant avoir lieu. Garantie sur les réparations CNC 8035 Comme pour la garantie de départ, FAGOR offre une garantie standard sur ses réparations dans les termes suivants : PÉRIODE 12 mois. CONCEPT Couvre les pièces et la main d’œuvre sur les éléments réparés (ou remplacés) dans les locaux du réseau propre. C L AU S E S D'EXCLUSION DE GARANTIE Les mêmes qui sont appliquées sur le chapitre de garantie de départ. Si la réparation est effectuée dans la période de garantie, le report de la garantie n’a pas d’effet. ·23· Si la réparation a été faite sur devis, c’est-à-dire en ne réparant que la partie défaillante, la garantie couvrira les pièces remplacées et aura une durée de 12 mois. Les pièces de rechange fournies séparément ont une garantie de 12 mois. Contrats de maintenance Conditions de garantie Un CONTRAT DE SERVICE est mis à la disposition du distributeur ou du fabricant qui achète et installe nos systèmes CNC. CNC 8035 ·24· CONDITIONS DE RÉ-EXPÉDITION Pour expédier l'Unité Centrale ou les modules à distance, utiliser leur emballage en carton et le matériel d'emballage original. Sinon, emballer les éléments de la manière suivante: 1. Se procurer une caisse en cartons dont les 3 dimensions internes soient au mois 15 cm (6 pouces) plus grandes que celles de l'appareil. Le carton utilisé devra avoir une résistance de 170 kgs. (375 livres). 2. Joindre une étiquette en indiquant le nom et l'adresse du propriétaire, la personne à contacter ainsi que le type et le numéro de série de l'appareil. 3. En cas de panne, veuillez en indiquer les symptômes et la décrire brièvement. 4. Envelopper l'appareil avec un film de polyéthylène ou similaire pour le protéger. 5. En cas d'expédition de l'Unité Centrale, protéger tout particulièrement l'écran. 6. Protéger l'appareil dans la caisse en carton à l'aide d'un rembourrage de mousse de polyuréthanne sur tous les côtés. 7. Fermer la caisse en carton avec du ruban adhésif ou des agrafes industrielles. CNC 8035 ·25· CNC 8035 ·26· Conditions de ré-expédition NOTES COMPLÉMENTAIRES Situer la CNC à l'écart du stockage de réfrigérants et autres produits chimiques et à l'abri des situations et éléments pouvant l'endommager. Avant de mettre l'appareil sous tension vérifier que les branchements à terre ont été effectués correctement. En cas de mauvais fonctionnement ou de panne de l'appareil, le débrancher et appeler le service d'assistance technique. Ne pas manipuler l'intérieur de l'appareil. CNC 8035 ·27· CNC 8035 ·28· Notes complémentaires DOCUMENTATION FAGOR Manuel OEM Adressé au fabricant de la machine ou à la personne chargée d'effectuer l'installation et la mise au point de la Commande Numérique. Manuel USER-M Adressé à l'utilisateur final. Indique la manière de travailler et de programmer sous le mode M. Manuel USER-T Adressé à l'utilisateur final. Indique la manière de travailler et de programmer sous le mode T. Manuel USER-TC Adressé à l'utilisateur final. Indique la manière de travailler et de programmer sous le mode ISO et conversationnel Fagor (TC). CNC 8035 ·29· CNC 8035 ·30· Documentation Fagor GÉNÉRALITÉS 1 La CNC peut être programmée aussi bien à la volée (depuis le panneau avant) que depuis des périphériques extérieurs (lecteur de bandes, lecteur/enregistreur de cassettes, ordinateur, etc.). La capacité de mémoire dont dispose l’utilisateur pour la réalisation des programmes pièce est de 1 Mbyte. Les programmes pièce et les valeurs des tables dont dispose la CNC peuvent être introduits depuis le panneau avant, depuis un ordinateur (DNC) ou depuis un périphérique. Introduction de programmes et de tables depuis le panneau avant. Après sélection du mode d’édition ou de la table désirée, la CNC permet l’introduction des données au moyen du clavier. Introduction de programmes et de tables depuis un ordinateur (DNC) ou Périphérique. La CNC permet de réaliser l'échange d'information avec un ordinateur ou un périphérique en utilisant pour cela la liaison série RS232C. Si ces communications sont contrôlées depuis la CNC, il est nécessaire de sélectionner au préalable la table correspondante ou le répertoire de programmes pièce (utilités) avec lesquels les communications sont établies. Selon le type de communications choisi, on doit personnaliser le paramètre machine des lignes série "PROTOCOL" comme suit: "PROTOCOL" = 0 Pour des communications avec un périphérique. "PROTOCOL" = 1 Pour des communications via DNC. CNC 8035 MODÈLE ·T· (SOFT V16.3X) ·31· Manuel de programmation 1.1 Programmes pièce Les différents modes de fonctionnement sont décrits dans le manuel de fonctionnement. Pour obtenir plus d'information, consulter ce manuel. Édition d'un programme pièce 1. GÉNÉRALITÉS Programmes pièce Pour créer un programme pièce il faut accéder au mode d’opération –Éditer–. Le nouveau programme pièce édité est emmagasiné dans la mémoire RAM de la CNC. Il est possible de sauvegarder une copie des programmes pièce sur un PC connecté à travers la liaison série. Le processus de transmission d'un programme à un PC connecté à travers la liaison série est le suivant : 1. Exécuter dans le PC l’application "Fagor50.exe" o "WinDNC.exe". 2. Activer la communication DNC dans la CNC. 3. Sélectionner le répertoire de travail dans la CNC. La sélection se réalise depuis le mode de fonctionnement –Utilités–, option Répertoire \L.Série \Changer répertoire. Le mode d’opération –Éditer– permet aussi de modifier les programmes pièce qu’il y a dans la mémoire RAM de la CNC. Si l'on veut modifier un programme emmagasiné dans un PC, il faut d'abord le copier dans la mémoire RAM. Exécution et simulation d'un programme pièce On peut exécuter ou simuler des programmes pièce emmagasinés dans n’importe quel endroit. La simulation s'effectue depuis le mode de fonctionnement –Simuler– alors que l'exécution s'effectue depuis le mode de fonctionnement –Automatique–. À l'heure d'exécuter ou de simuler un programme pièce les points suivants doivent être pris en compte : • On ne peut exécuter que des sous-routines existant dans la mémoire RAM de la CNC. Pour cela, si l'on souhaite exécuter une sous-routine emmagasinée dans un PC, il faut la copier dans la mémoire RAM de la CNC. • Les déclarations GOTO et RPT ne peuvent pas être utilisées dans des programmes exécutés depuis un PC raccordé à travers d’une des lignes série. • Depuis un programme pièce en exécution, avec l'instruction EXEC on peut exécuter n'importe quel autre programme pièce installé dans la mémoire RAM ou sur un PC. Les programmes de personnalisation d’utilisateur doivent être dans la mémoire RAM pour que la CNC les exécute. Mode de fonctionnement –Utilités– CNC 8035 MODÈLE ·T· (SOFT V16.3X) ·32· Le mode de fonctionnement –Utilités– permet également d'afficher le répertoire de programmes pièce de tous les dispositifs, d'effectuer des copies, supprimer, de renommer et même de fixer leurs protections. Manuel de programmation Opérations que l’on peut effectuer avec des programmes pièce: DNC Oui Oui Consulter le répertoire de sous-routines de ... Oui Non Créer un répertoire de travail de ... Non Non Changer le répertoire de travail de ... Non Oui Éditer un programme de ... Oui Non Modifier un programme de ... Oui Non Effacer un programme de ... Oui Oui Copier de/à mémoire RAM à/de ... Oui Oui Copier de/à DNC à/de ... Oui Oui Changer le nom à un programme de ... Oui Non Changer le commentaire à un programme de ... Oui Non Changer les protections à un programme de ... Oui Non Exécuter un programme pièce de ... Oui Oui Exécuter un programme d'utilisateur de ... Oui Non Exécuter le programme de PLC de ... Oui Non Exécuter des programmes avec des instructions GOTO ou RPT depuis ... Oui Non Exécuter des sous-routines existantes dans ... Oui Non Exécuter des programmes, avec l'instruction EXEC, en RAM depuis ... Oui Oui Exécuter des programmes, avec l'instruction EXEC, en DNC depuis ... Oui Non Ouvrir des programmes, avec l'instruction OPEN, en RAM depuis ... Oui Oui Ouvrir des programmes, avec l'instruction OPEN, en DNC depuis ... Oui Non 1. Programmes pièce Consulter le répertoire de programmes de ... GÉNÉRALITÉS RAM (*) Si elle n'est pas en mémoire RAM, elle génère un code exécutable en RAM et l'exécute. CNC 8035 MODÈLE ·T· (SOFT V16.3X) ·33· Manuel de programmation 1.2 Ligne DNC La CNC offre la possibilité de travailler en mode DNC (Distributed Numerical Control ou Commande Numérique Directe), ce qui permet les communications entre la CNC et un ordinateur pour exécuter les fonctions suivantes. • Commandes de répertoire et effacement. • Transfert de programmes et de tables entre la CNC et un ordinateur. • Commande à distance de la machine. 1. Ligne DNC GÉNÉRALITÉS • Possibilité de supervision de l’état de systèmes DNC évolués. CNC 8035 MODÈLE ·T· (SOFT V16.3X) ·34· Manuel de programmation Protocole de communication via DNC ou périphérique Ce type de communications autorise les commandes de transfert de programmes et de tables ainsi que la gestion des répertoires de la CNC et de l’ordinateur pour la copie et l’effacement de programmes, etc. indistinctement depuis la CNC o l’ordinateur. Pour transférer des fichiers, on procédera comme suit: • On utilisera le symbole "%" comme commencement de fichier, suivi optionnellement du commentaire de programme, qui pourra avoir jusqu'à 20 caractères. Pour terminer l’en-tête du fichier, on enverra le caractère RT (RETURN) ou LF, (LINE FEED) séparé du précédent par ",". Exemple: %Fagor Automation, MX, RT • Après l'en-tête, on programmera les blocs du fichier. Tous sont programmés suivant les normes de programmation indiquées dans ce manuel. Pour séparer chaque bloc du bloc suivant, on utilisera le caractère RT (RETURN) ou LF (LINE FEED). Exemple: N20 G90 G01 X100 Y200 F2000 LF (RPT N10, N20) N3 LF Dans le cas des communications avec un périphérique, la commande de fin de fichier doit être émise. Cette commande est sélectionnée au moyen du paramètre machine des liaisons série "EOFCHR", et il peut s’agir de l’un des caractères suivants: ESC ESCAPE EOT END OF TRANSMISSION SUB SUBSTITUTE EXT END OF TRANSMISSION 1. Protocole de communication via DNC ou périphérique On indiquera ensuite, en les séparant par une virgule ",", les protections (attributs) affectées à ce fichier: lecture, écriture, etc. Ces protections sont optionnelles et leur programmation n’est pas obligatoire. GÉNÉRALITÉS 1.3 CNC 8035 MODÈLE ·T· (SOFT V16.3X) ·35· Manuel de programmation GÉNÉRALITÉS Protocole de communication via DNC ou périphérique 1. CNC 8035 MODÈLE ·T· (SOFT V16.3X) ·36· CONSTRUCTION D'UN PROGRAMME 2 Un programme de commande numérique se compose d’un ensemble de blocs ou instructions. Ces blocs ou instructions sont constitués de mots composés de lettres majuscules et d’un format numérique. Le format numérique dont dispose la CNC est composé de: • Signes . (point), + (plus), - (moins). • Chiffres 0 1 2 3 4 5 6 7 8 9. La programmation admet des espaces entre les lettres, les chiffres et les symboles et permet d’ignorer le format numérique s’il est d’une valeur zéro ou le signe s’il est positif. Le format numérique d'un mot peut être remplacé par un paramètre arithmétique dans la programmation. Plus tard, pendant l'exécution de base, le contrôle remplacera le paramètre arithmétique par sa valeur. Par exemple, si on a programmé XP3, pendant l'exécution la CNC remplacera P3 par sa valeur numérique, en obtenant des résultats comme X20, X20.567, X-0.003, etc. CNC 8035 MODÈLE ·T· (SOFT V16.3X) ·37· Manuel de programmation 2.1 Structure d’un programme dans la CNC Tous les blocs constituant le programme auront la structure suivante: En-tête de bloc + bloc de programme + fin de bloc Structure d’un programme dans la CNC CONSTRUCTION D'UN PROGRAMME 2. CNC 8035 MODÈLE ·T· (SOFT V16.3X) ·38· Manuel de programmation En-tête de bloc L’en-tête d’un bloc est optionnelle, peut être constituée d’une ou plusieurs conditions de saut de bloc et de l’étiquette ou numéro de bloc. Les deux options doivent être programmées dans cet ordre. Condition de saut de bloc. "/", "/1", "/2", "/3". Étant donné que "/" et "/1" sont équivalentes, ces trois conditions de saut de bloc seront commandées par les marques BLKSKIP1, BLKSKIP2 et BLKSKIP3 du PLC. Si l’une de ces marques est active, la CNC n’exécute par le(s) bloc(s) où elle a été programmée et passe à l’exécution du bloc suivant. La commande lit 20 blocs en avant du bloc en cours d’exécution, afin de pouvoir calculer à l’avance la trajectoire à parcourir. La condition de saut de bloc sera analysée au moment de la lecture du bloc, soit 20 blocs avant son exécution. Pour analyser le bloc au moment de l’exécution, il est nécessaire d’interrompre la préparation des blocs, en programmant G4 dans le bloc précédent. Etiquette ou numéro de bloc. N(0-99999999). L’étiquette ou le numéro de bloc permettent d’identifier le bloc et ne sont utilisés que lors de la réalisation de références ou de saut à un bloc. Ils seront représentés avec la lettre "N" suivie d'un maximum de 8 chiffres (0-99999999). Structure d’un programme dans la CNC Il est possible de programmer jusqu’à 3 conditions de saut dans un seul bloc; elles seront évaluées l’une après l’autre selon l’ordre dans lequel elles ont été programmées. 2. CONSTRUCTION D'UN PROGRAMME 2.1.1 Il n'est pas nécessaire de suivre un certain ordre et on peut sauter des numéros. Si un programme comporte deux ou plusieurs blocs avec le même numéro d’étiquette, la CNC prendra toujours le premier. Bien que leur programmation ne soit pas nécessaire, la CNC permet, par l’intermédiaire d’une softkey, la programmation automatique d’étiquettes dont le nombre initial et le pas peuvent être sélectionnés par le programmeur. Restrictions: • Affichage du numéro de bloc actif, dans la fenêtre supérieure de l’écran. En exécutant un programme en mode ISO, lorsque le numéro d’étiquette est supérieur à 9999, le système affiche N****. Sur l’écran "AFFICHER / SOUS-ROUTINES ", en affichant un RPT ayant une étiquette supérieure à 9999, il sera affiché avec ****. • L’édition des cycles fixes G66, G68 et G69, n’admet que des étiquettes à 4 chiffres. CNC 8035 MODÈLE ·T· (SOFT V16.3X) ·39· Manuel de programmation 2.1.2 Bloc de programme Le bloc de programme se compose de commandes en langage ISO ou en langage à Haut Niveau. Pour l’élaboration d’un programme, des blocs écrits dans les deux langages sont utilisés, mais chacun d’eux doit être édité au moyen de commandes appartenant à un seul langage. Langage ISO. Ce langage est spécialement conçu pour contrôler le déplacement des axes, car il fournit des informations et des conditions de déplacement ainsi que des indications sur l’avance. Dispose des types suivants des fonctions. Structure d’un programme dans la CNC CONSTRUCTION D'UN PROGRAMME 2. • Fonctions préparatoires de déplacements, qui permettent de déterminer la géométrie et les conditions de travail telles que les interpolations linéaire et circulaire, les filetages, etc. • Fonctions de contrôle des avances des axes et des vitesses de broche. • Fonctions de contrôle des outils. • Fonctions complémentaires, qui contiennent des indications technologiques. Langage à Haut Niveau. Ce langage permet d’accéder à des variables de caractère général ainsi qu’aux tables et aux variables du système. Fournit à l'utilisateur un ensemble d'instructions de contrôle ressemblant à la terminologie utilisée par d'autres langages, tels que IF, GOTO, CALL, etc. Il permet également l’emploi de tout type d’expression: arithmétique, relationnelle ou logique. Il dispose également d’instructions permettant la construction de boucles, ainsi que de sousroutines à variables locales. Le terme variable locale désigne une variable connue de la seule sousroutine dans laquelle elle a été définie. Il permet aussi de créer des bibliothèques en regroupant des sous-routines comprenant des fonctions utiles et éprouvées accessibles depuis n’importe quel programme. CNC 8035 MODÈLE ·T· (SOFT V16.3X) ·40· Manuel de programmation Fin de bloc La fin d'un bloc est optionnelle et pourra être formée par l'indicatif de nombre de répétitions du bloc et par le commentaire du bloc. Les deux peuvent être programmés dans cet ordre. Nombre de répétitions du bloc. N(0-9999) Indique le nombre de fois que l'exécution du bloc sera répétée. Le nombre de répétitions est représenté par la lettre "N" suivie de 4 chiffres maximum (0-9999). Si NON est programmé, l’usinage actif n’est pas exécuté. Seul le déplacement programmé dans le bloc est exécuté. Commentaire de bloc La CNC permet d’associer tout type d’information à tous les blocs sous forme de commentaire. Le commentaire se programmera à la fin du bloc et devra commencer par le caractère ";" (point et virgule). Si un bloc commence par ";" tout son contenu est considéré comme un commentaire, et il n’est pas exécuté. Les blocs vides ne sont pas autorisés; ils doivent comporter au moins un commentaire. 2. Structure d’un programme dans la CNC Seuls les blocs de déplacement sous l’influence d’un cycle fixe ou d’une sous-routine modale lors de leur exécution peuvent être répétés. Dans ces cas, la CNC exécute le déplacement programmé ainsi que l’usinage actif (cycle fixe ou sous-routine modale) le nombre de répétitions indiqué. CONSTRUCTION D'UN PROGRAMME 2.1.3 CNC 8035 MODÈLE ·T· (SOFT V16.3X) ·41· Manuel de programmation Structure d’un programme dans la CNC CONSTRUCTION D'UN PROGRAMME 2. CNC 8035 MODÈLE ·T· (SOFT V16.3X) ·42· AXES ET SYSTÈMES DE COORDONNÉES 3 Étant donné que le but de la Commande Numérique est le contrôle du déplacement et du positionnement des axes, il est nécessaire de déterminer la position du point à atteindre, grâce à ses coordonnées. La CNC permet l’emploi de coordonnées absolues et de coordonnées relatives ou incrémentales dans l’ensemble d’un programme donné. CNC 8035 MODÈLE ·T· (SOFT V16.3X) ·43· Manuel de programmation 3.1 Nomenclature des axes Les noms des axes répondent à la norme DIN 66217. Nomenclature des axes AXES ET SYSTÈMES DE COORDONNÉES 3. Caractéristiques du système d’axes : X et Y déplacements principaux d’avance sur le plan de travail principal de la machine. Z parallèle à l’axe principal de la machine, perpendiculaire au plan principal XY. U, V, W axes auxiliaires parallèles à X, Y, Z, respectivement. A, B, C axes rotatifs sur chacun des axes X, Y, Z. La figure suivante illustre un exemple de la dénomination des axes sur un tour parallèle. CNC 8035 MODÈLE ·T· (SOFT V16.3X) ·44· Manuel de programmation Sélection de plans (G16,G17,G18,G19) La sélection de plan s’applique dans les cas suivants: • Interpolations circulaires. • Arrondissement commandé des arêtes. • Entrée et sortie tangentielle. • Chanfreinage. • Rotation du système de coordonnées. • Compensation de rayon d’outil. • Compensation de longueur d’outil. Les fonctions "G" permettant de sélectionner les plans de travail sont les suivantes: G16 axe1 axe2. Permet de sélectionner le plan de travail désiré ainsi que le sens de G02 G03 (interpolation circulaire), l'axe1 étant programmé comme axe des abscisses, et l'axe2 comme axe des ordonnées. G17. Sélectionne le plan XY G18. Sélectionne le plan ZX G19. Sélectionne le plan YZ Sélection de plans (G16,G17,G18,G19) 3. • Programmation de cotes en coordonnées polaires. AXES ET SYSTÈMES DE COORDONNÉES 3.2 Les fonctions G16, G17, G18 et G19 sont modales et incompatibles entre elles, la fonction G16 devant être programmée seule dans un bloc. CNC 8035 MODÈLE ·T· (SOFT V16.3X) A la mise sous tension, après l’exécution de M02, M30 ou après un ARRÊT D'URGENCE ou une RAZ, la CNC prendra comme plan de travail celui défini par le paramètre machine général "IPLANE". ·45· Manuel de programmation 3.3 Cotation de la pièce. Millimètres (G71) ou pouces (G70) La CNC permet l’introduction des unités de mesure au moment de la programmation, en millimètres ou en pouces. Dispose du paramètre machine général "INCHES", pour définir les unités de mesure de la CNC. Ces unités peuvent cependant être changées à tout moment dans le programme, grâce aux fonctions: 3. • G70. Programmation en pouces. AXES ET SYSTÈMES DE COORDONNÉES Cotation de la pièce. Millimètres (G71) ou pouces (G70) • G71. Programmation en millimètres. CNC 8035 MODÈLE ·T· (SOFT V16.3X) ·46· Selon que G70 ou G71 a été programmé, la CNC applique le système d’unités correspondant dans tous les blocs programmés suivants. Les fonctions G70/G71 sont modales et incompatibles entre elles. La CNC permet de programmer des chiffres de 0.00001 à 99999.9999 signés ou non en cas de programmation en millimètres (G71) (format ±5.4) ou de 0.00001 à 3937.00787 signés ou non en cas de programmation en pouces (G70), (format ±4.5). Toutefois, pour simplifier les explications, on peut dire que la CNC admet le format ±5.5, pour indiquer qu’elle admet ±5.4 en millimètres et ±4.5 en pouces. A la mise sous tension, après l’exécution de M02, M30 ou après un ARRÊT D'URGENCE ou un RESET, la CNC prendra comme système d’unités celui défini par le paramètre machine général "INCHES". Manuel de programmation Programmation absolue/incrémentale (G90, G91) La CNC permet la programmation des coordonnées d’un point en mode absolu G90 ou en mode incrémental G91. Dans le cas des coordonnées absolues (G90), les coordonnées du point sont établies par rapport à une origine des coordonnées définie, qui est souvent le point d’origine de la pièce. Dans le cas des coordonnées incrémentales (G91), la valeur numérique programmée correspond aux informations de déplacement sur le trajet à parcourir à partir de la position actuelle de l’outil. Le signe précédant la valeur indique le sens du déplacement. Exemple de programmation de l'axe X en diamètres. Programmation absolue/incrémentale (G90, G91) Les fonctions G90/G91 sont modales et incompatibles entre elles. 3. AXES ET SYSTÈMES DE COORDONNÉES 3.4 Coordonnées absolues: G90 X200 Z60 ; Point P0 X160 Z60 ; Point P1 X80 Z100 ; Point P2 X80 Z120 ; Point P3 Coordonnées incrémentales: G90 X200 G91 X-40 X-80 Z20 Z60 ; Point P0 ; Point P1 Z40 ; Point P2 ; Point P3 A la mise sous tension, après l’exécution de M02, M30 ou après un ARRÊT D'URGENCE ou une RAZ, la CNC prendra en compte G90 ou G91 selon la définition faite par le paramètre machine général "ISYSTEM". CNC 8035 MODÈLE ·T· (SOFT V16.3X) ·47· Manuel de programmation 3.5 Programmation en rayons ou en diamètres (G152, G151) La CNC admet que les cotes de l’axe X puissent être programmées en rayons ou en diamètres. Pour cela on dispose des fonctions suivantes. • G151. Programmation des cotes de l’axe X en diamètres. • G152. Programmation des cotes de l’axe X en rayons. Ces fonctions peuvent être programmées dans n'importe quelle partie du programme, et il n'est pas nécessaire qu'elles aillent seules dans le bloc. A partir de l'exécution d'une de ces fonctions, la CNC assume la modalité de programmation correspondante pour les blocs programmés par la suite. AXES ET SYSTÈMES DE COORDONNÉES Programmation en rayons ou en diamètres (G152, G151) 3. CNC 8035 MODÈLE ·T· (SOFT V16.3X) ·48· Le changement d'unités est tenu en compte dans les cas suivants. • Affichage de la valeur réelle de l'axe X dans le système de coordonnées de la pièce. • Lecture de la variable PPOSX (cote programmée). Les fonctions G151 et G152 sont modales et incompatibles entre-elles. A la mise sous tension, après l’exécution de M02, M30 ou après un ARRÊT D'URGENCE ou une RAZ, la CNC prendra en compte G151 ou G152 selon la définition faite par le paramètre machine "DFORMAT" de l'axe X. Manuel de programmation Programmation de cotes La CNC permet de sélectionner jusqu’à 2 axes parmi les 9 axes possibles X, Y, Z, U, V, W, A, B, C. Chaque axe peut être linéaire, linéaire de positionnement, rotatif normal, rotatif de positionnement ou rotatif à denture Hirth (positionnement par degrés entiers) selon les spécifications du paramètre machine de chaque axe "AXISTYPE". Pour pouvoir sélectionner à tout moment le système de programmation de coordonnées le mieux adapté, la CNC dispose des types suivants: • Coordonnées polaires • Angle et une coordonnée cartésienne Programmation de cotes 3. • Coordonnées cartésiennes AXES ET SYSTÈMES DE COORDONNÉES 3.6 CNC 8035 MODÈLE ·T· (SOFT V16.3X) ·49· Manuel de programmation 3.6.1 Coordonnées cartésiennes Le Système de Coordonnées Cartésiennes est défini par deux axes sur le plan, et par trois axes ou plus dans l’espace. L’origine de tous ces axes qui, dans le cas des axes X Y Z coïncide avec le point d’intersection, est appelée Origine Cartésienne ou Point Zéro du Système de Coordonnées. La position des différents points de la machine est exprimée au moyen des coordonnées des axes avec deux, trois, quatre ou cinq coordonnées. Programmation de cotes AXES ET SYSTÈMES DE COORDONNÉES 3. CNC 8035 MODÈLE ·T· (SOFT V16.3X) ·50· Les coordonnées des axes sont programmées grâce à la lettre de l’axe (X, Y, Z, U, V, W, A, B, C, toujours dans cet ordre) suivie de la valeur de la cote. Les valeurs des coordonnées seront absolues ou incrémentales, selon que l’on travaille en G90 ou en G91, et leur format de programmation sera ±5.5. Manuel de programmation Coordonnées polaires En cas de présence d’éléments circulaires ou de dimensions angulaires, il peut s’avérer plus commode d’exprimer les coordonnées des différents points sur le plan (2 axes à la fois) en Coordonnées polaires. Le point de référence porte le nom d’Origine Polaire et constituera l’origine du Système de Coordonnées Polaires. Un point de ce système sera défini par: • RAYON (R), qui sera la distance entre l’origine polaire et le point. • L’ANGLE (Q) qui sera l’angle formé par l’axe des abscisses et la ligne unissant l’origine polaire au point. (En degrés). Les valeurs de R et Q G90 sont absolues ou incrémentales selon que l’on travaille en G90 ou G91, et leur format de programmation est R +/- 5.5 Q +/- 5.5. La valeur affectée au rayon doit toujours être positive. Programmation de cotes 3. AXES ET SYSTÈMES DE COORDONNÉES 3.6.2 Les valeurs de R et Q sont incrémentales lorsqu'on travaille en G91 et leur format de programmation est R±5.5 Q±5.5. Les valeurs de R peuvent être négatives dans le cas de la programmation en relatif, mais la valeur résultante affectée au rayon doit toujours être positive. Si une valeur de Q supérieure à 360º est programmée, le module sera pris après une division par 360. Ainsi, Q420 est équivalent à Q60, et Q-420 est équivalent à Q-60. CNC 8035 MODÈLE ·T· (SOFT V16.3X) ·51· Manuel de programmation Exemple de programmation, en supposant que l’Origine Polaire est située sur l’Origine des Coordonnées. Programmation de cotes AXES ET SYSTÈMES DE COORDONNÉES 3. Coordonnées absolues: G90 R430 G03 Q0 ; Point P0 Q33.7 ; Point P1, en arc (G03) G01 R340 Q45 ; Point P2, en ligne droite (G01) G01 R290 Q33.7 ; Point P3, en ligne droite (G01) G01 R230 Q45 ; Point P4, en ligne droite (G01) G01 R360 Q63.4 ; Point P5, en ligne droite (G01) Q90 ; Point P6, en arc (G03) G03 Coordonnées incrémentales: G90 R430 G91 G03 Q0 ; Point 0 Q33.7 ; Point P1, en arc (G03) G01 R-90 Q11.3 ; Point P2, en ligne droite (G01) G01 R-50 Q-11.3 ; Point P3, en ligne droite (G01) G01 R-60 Q11.3 ; Point P4, en ligne droite (G01) G01 R130 Q18.4 ; Point P5, en ligne droite (G01) Q26.6 ; Point P6, en arc (G03) G03 L’origine polaire peut non seulement être présélectionnée par la fonction G93, décrite plus loin, mais également modifiée dans les cas suivants: • A la mise sous tension, après l’exécution de M02, M30 ou après un ARRÈT D'URGENCE ou une RAZ, la CNC prendra comme origine polaire l’origine des coordonnées du plan de travail définie par le paramètre machine général "IPLANE". • A chaque changement de plan de travail (G16, G17, G18 ou G19), la CNC prend comme origine polaire l’origine des coordonnées du nouveau plan de travail sélectionné. CNC 8035 MODÈLE ·T· (SOFT V16.3X) ·52· • Lors de l’exécution d’une interpolation circulaire (G02 ou G03), et si le paramètre machine général "PORGMOVE" a la valeur 1, le centre de l’arc devient la nouvelle origine polaire. Manuel de programmation Angle et une coordonnée cartésienne Sur le plan principal, il est possible de définir un point grâce à une de ses coordonnées cartésiennes et à l’angle de sortie de la trajectoire précédente. Exemple de programmation de l'axe X en rayons. X0 Z160 ; Point P0 Q90 X30 ; Point P1 Q149 Z110 ; Point P2 Q180 Z80 ; Point P3 Q146.3 Z50 ; Point P4 Q90 X100 ; Point P0 Programmation de cotes 3. AXES ET SYSTÈMES DE COORDONNÉES 3.6.3 Pour représenter un point dans l’espace, le reste des coordonnées pourra être programmé en coordonnées cartésiennes. CNC 8035 MODÈLE ·T· (SOFT V16.3X) ·53· Manuel de programmation 3.7 Axes tournants Les axes rotatifs disponibles sont: Axe rotatif normal. Axe rotatif de positionnement seulement. Axe rotatif hirth. De plus, chacun d’eux se subdivise en: 3. Lorsque son affichage se réalise entre 0º et 360º. Non-Rollover Lorsque l'affichage peut s'effectuer entre -99999º et 99999º. Axes tournants AXES ET SYSTÈMES DE COORDONNÉES Rollover Tous sont programmés en degrés, et donc leurs coordonnées ne seront pas influencées par le changement d’unités millimètres/pouces. Axes rotatifs normaux Ce sont ceux pouvant interpoler avec des axes linéaires. Déplacement: Sur G00 et G01. Programmation axe Rollover. G90 Le signe indique le sens de rotation et la cote la position finale (entre 0 et 359.9999). G91 Le signe indique le sens de rotation. Si le déplacement programmé est supérieur à 360°, l’axe fera plus d’un tour avant de se positionner sur le point désiré. Programmation axe Non Rollover. Sur G90 et G91 comme un axe linéaire. Axe rotatif de positionnement seulement. Ne peuvent pas interpoler avec des axes linéaires. Déplacement: Toujours sur G00, et n’admettent pas de compensation de rayon (G41, G42). Programmation axe Rollover. G90 Toujours positif et par le chemin le plus court. Cote finale entre 0 et 359.9999. G91 Le signe indique le sens de rotation. Si le déplacement programmé est supérieur à 360°, l’axe fera plus d’un tour avant de se positionner sur le point désiré. Programmation axe Non Rollover. Sur G90 et G91 comme un axe linéaire. Axe rotatif Hirth Son fonctionnement et sa programmation sont identiques à ceux de l’axe de positionnement seul, sauf que les axes rotatifs Hirth n’admettent pas de chiffres décimaux; on sélectionnera exclusivement des positions en degrés entiers. La CNC permet de disposer de plus d’un axe Hirth, mais n’admet pas de déplacements faisant intervenir plus d’un axe Hirth à la fois. CNC 8035 MODÈLE ·T· (SOFT V16.3X) ·54· Manuel de programmation Zones de travail La CNC permet de disposer de 4 zones de travail et de limiter les déplacements de l’outil dans chacune d’elles. Zones de travail 3. AXES ET SYSTÈMES DE COORDONNÉES 3.8 CNC 8035 MODÈLE ·T· (SOFT V16.3X) ·55· Manuel de programmation 3.8.1 Définition des zones de travail Dans chaque zone de travail, la CNC permet de limiter le déplacement de l’outil sur chacun des axes, les limites supérieure et inférieure étant définies sur chaque axe. G20: Définit les limites inférieures de la zone désirée. G21: Définit les limites supérieures de la zone désirée. Le format de programmation de ces fonctions est le suivant: G20 K X...C±5.5 3. Zones de travail AXES ET SYSTÈMES DE COORDONNÉES G21 K X...C±5.5 Oú: K Indique la zone de travail à définir (1, 2, 3 ou 4). X...C Indiquent les coordonnées (supérieures ou inférieures) servant à limiter les axes. Ces coordonnées sont exprimées en rayons et programmées par rapport au zéro machine. Il n’est pas nécessaire de programmer tous les axes; on limitera seulement les axes définis. G20 K1 X20 Z20 G21 K1 X100 Z100 CNC 8035 MODÈLE ·T· (SOFT V16.3X) ·56· Manuel de programmation Utilisation des zones de travail A l’intérieur de chaque zone de travail, la CNC permet de restreindre le déplacement de l’outil, soit en lui interdisant de sortir de la zone programmée (zone interdite à la sortie) ou de pénétrer dans cette zone (zone interdite à l’entrée). S= 1 Zona interdite à l’entrée S= 2 Zone interdite à la sortie La CNC tiendra compte en permanence des dimensions de l’outil (table de correcteurs) pour éviter tout franchissement des limites programmées. Les zones de travail sont personnalisées grâce à la fonction G22, dont le format de programmation est: G22 K S Oú: K Indique la zone de travail à personnaliser (1, 2, 3 ou 4). S Indique la validation-invalidation de la zone de travail. Zones de travail 3. AXES ET SYSTÈMES DE COORDONNÉES 3.8.2 S=0 Invalidation. S=1 Validation comme zone interdite à l’entrée. S=2 Validation comme zone interdite à la sortie. A la mise sous tension, la CNC invalide toutes les zones de travail, mais sans toucher aux limites supérieures et inférieures, qui peuvent être validées à nouveau grâce à la fonction G22. CNC 8035 MODÈLE ·T· (SOFT V16.3X) ·57· Manuel de programmation Zones de travail AXES ET SYSTÈMES DE COORDONNÉES 3. CNC 8035 MODÈLE ·T· (SOFT V16.3X) ·58· SYSTÈMES DE RÉFÉRENCE 4.1 4 points de référence Pour une machine à CNC, les points d’origine et de référence suivants doivent être définis: • Zéro machine ou point d’origine de la machine. Il est défini par le constructeur comme origine du système de coordonnées de la machine. • Zéro pièce ou point d’origine de la pièce. Il s’agit du point d’origine défini pour la programmation des cotes de la pièce, et son choix est laissé à l’appréciation du programmeur. Sa valeur par rapport au zéro machine peut être définie par un décalage d’origine. • Point de référence. Il s’agit d’un point de la machine défini par le constructeur et servant à la synchronisation du système. La commande se positionne sur ce point plutôt que de se déplacer jusqu’à l’origine de la machine, et elle prend alors les coordonnées de référence définies par l’intermédiaire du paramètre machine des axes "REFVALUE". M Zéro machine W Zéro pièce R Point de référence machine XMW, YMW, ZMW... Coordonnées du zéro pièce XMR, YMR, ZMR... C o o r d o n n é e s d u p o i n t d e r é f é r e n c e m a c h i n e ("REFVALUE") CNC 8035 MODÈLE ·T· (SOFT V16.3X) ·59· Manuel de programmation 4.2 Recherche de référence machine (G74) La CNC permet de programmer la recherche de la référence machine de deux manières: • Recherche de référence machine d'un ou plusieurs axes dans un certain ordre. On programmera G74 suivi des axes dans lesquels on désire effectuer une recherche de référence. Par exemple: G74 X Z. La CNC commence à déplacer tous les axes sélectionnés comportant un contact de référence machine (paramètre machine d’axes "DECINPUT"), dans le sens indiqué par le paramètre machine des axes "REFDIREC", SYSTÈMES DE RÉFÉRENCE Recherche de référence machine (G74) 4. Ce déplacement s’effectue selon l’avance indiquée dans le paramètre machine des axes "REFEED1", jusqu’au déclenchement du contact. Ensuite, la recherche de la référence machine de tous les axes commence dans l’ordre où ils ont été programmés. Ce second déplacement est exécuté pour un axe à la fois selon l’avance indiquée par le paramètre machine des axes "REFEED2", jusqu’à ce que le point de référence machine soit atteint. • Recherche de référence machine en utilisant la sous-routine associée. On programmera la fonction G74 seule dans le bloc, et la CNC exécutera automatiquement la sous-routine dont le numéro est indiqué dans le paramètre machine général "REFPSUB". Dans cette sous-routine, il est possible de programmer les recherches de référence machine désirées ainsi que l’ordre souhaité. Aucune autre fonction préparatoire ne doit être programmée dans le bloc contenant G74. Si la recherche de référence machine est exécutée en mode manuel, le zéro pièce sélectionné est perdu, et les coordonnées du point de référence machine indiquées dans le paramètre machine des axes "REFVALUE" sont affichées. Dans tous les autres cas, le zéro pièce sélectionné est conservé: les coordonnées affichées sont donc référencées par rapport à ce zéro pièce. Si la commande G74 est exécutée en mode MDI, l'affichage des coordonnées dépendra du mode d’exécution de cette commande: Manuel, Exécution ou Simulation. CNC 8035 MODÈLE ·T· (SOFT V16.3X) ·60· Manuel de programmation Programmation par rapport au zéro machine (G53) La fonction G53 peut être ajoutée à tout bloc contenant des fonctions de contrôle de trajectoire. Elle sera utilisée pour programmer les coordonnées du bloc par rapport au zéro machine; ces coordonnées devront être exprimées en millimètres ou en pouces, selon la définition du paramètre machine général "INCHES". Si la fonction G53 est programmée sans information de déplacement, le décalage de zéro actif actuel est annulé, qu’il soit le résultat de l’exécution de G54-G59 ou d’une présélection (G92). Cette présélection d’origine est décrite plus loin. Cette fonction annule temporairement la compensation de rayon et de longueur d’outil. Exemple de programmation de l'axe X en diamètres. M Zéro machine W Zéro pièce Programmation par rapport au zéro machine (G53) La fonction G53 est non-modale, ce qui signifie qu’elle devra être programmée chaque fois que l’on désirera indiquer les coordonnées par rapport au zéro machine. 4. SYSTÈMES DE RÉFÉRENCE 4.3 CNC 8035 MODÈLE ·T· (SOFT V16.3X) ·61· Manuel de programmation 4.4 Présélection des coordonnées et décalages d’origine La CNC permet d’exécuter des décalages d’origine dans le but d’utiliser les coordonnées relatives au plan de la pièce sans avoir à modifier les coordonnées des différents points de la pièce au moment de la programmation. On définit comme décalage d’origine la distance entre le zéro pièce (point d’origine de la pièce) et le zéro machine (point d’origine de la machine). SYSTÈMES DE RÉFÉRENCE Présélection des coordonnées et décalages d’origine 4. M Zéro machine W Zéro pièce Ce décalage d’origine peut être obtenu de deux façons: • Par la fonction G92 (présélection de coordonnées), la CNC acceptant les coordonnées des axes programmés après G92, comme nouvelles valeurs des axes. • À travers l’utilisation de décalages d’origine (G54… G59, G159N1 ... G159N20), la CNC acceptant comme nouveau zéro pièce le point situé par rapport au zéro machine à la distance indiquée par la ou les tables sélectionnées. Ces deux fonctions sont modales et incompatibles entre elles; si l’une est sélectionnée, l’autre est désactivée. Il existe également un autre décalage d’origine sous la commande du PLC, qui s’ajoute toujours au décalage d’origine sélectionné et qui permet, entre autres, de corriger les écarts dus aux dilatations, etc. ORG*(54) ORG*(55) ORG*(56) ORG*(57) G54 G55 G56 G57 ORG*(58) G58 G92 ORG*(59) CNC 8035 ORG* PLCOF* Offset du PLC MODÈLE ·T· (SOFT V16.3X) ·62· Décalage d’origine G59 Manuel de programmation Présélection de coordonnées et limitation de la valeur de S (G92) La fonction G92 permet de présélectionner n’importe quelle valeur dans les axes de la CNC et de limiter la vitesse maximum de la broche. • Présélections de coordonnées. Lorsqu’un décalage d’origine est exécuté par la fonction G92, la CNC prend en compte les coordonnées des axes programmés après G92 comme nouvelles valeurs des axes. Aucune autre fonction ne peut être programmée dans le bloc contenant G92, et le format de programmation est le suivant: Les valeurs affectées aux axes seront programmées en rayons ou en diamètres, suivant la personnalisation du paramètre machine d’axes "DFORMAT". ; Positionnement en P0 Présélection des coordonnées et décalages d’origine 4. G92 X...C ±5.5 SYSTÈMES DE RÉFÉRENCE 4.4.1 G90 X0 Z200 ; Présélectionner P0 en tant qu’origine pièce G92 X0 Y0 ; Programmation selon les cotes de la pièce G91 X30 Z-30 Z -30 X20 X20 Z-40 Z -30 • Limitation de la vitesse de la broche. En programmant G92 S5.4, on limite la vitesse de la broche à la valeur fixée avec S5.4. Cela signifie qu’à partir de ce bloc, la CNC n’acceptera pas la programmation de valeurs de S, supérieures au maximum défini. Il en sera de même pour les valeurs introduites depuis le clavier du panneau avant. CNC 8035 MODÈLE ·T· (SOFT V16.3X) ·63· Manuel de programmation 4.4.2 Décalages d'origine (G54..G59 et G159) La CNC dispose d’une table de décalages d’origine permettant de sélectionner différents décalages d’origine afin de générer certains zéros pièce indépendamment des zéros pièces actifs à un moment donné. Les valeurs de la table sont exprimées en rayons. L’accès à la table est possible depuis le panneau avant de la CNC dans les conditions indiquées dans le Manuel d’Utilisation ou par programme au moyen de commandes en langage évolué. Il existe deux types de décalage d’origine: 4. SYSTÈMES DE RÉFÉRENCE Présélection des coordonnées et décalages d’origine • Décalages d'origine absolus (G54 ... G57, G159N1 ... G159N20), qui doivent être référés au zéro machine. • Décalages d’origine incrémentaux (G58, G59). Les fonctions G54, G55, G56, G57, G58 et G59 doivent être programmées seules dans un bloc et leur fonctionnement est le suivant: Lors de l’exécution des fonctions G54, G55, G56 ou G57, la CNC applique le décalage d’origine programmé par rapport au zéro machine en annulant les éventuels décalages de zéro actifs. Si on exécute l'un des décalages incrémentaux G58 ou G59, la CNC ajoutera ses valeurs au décalage d'origine absolue valable à ce moment. En annulant au préalable l'éventuel décalage incrémental actif. On observera dans l’exemple suivant les décalages d’origine appliqués lors de l’exécution du programme: G54 Applique le décalage d’origine G54 ==> G54 G58 Ajoute le décalage d'origine G58 ==> G54+G58 G59 Annule le G58 et ajoute le G59 ==> G54+G59 G55 Annule tout décalage et applique G55 ==> G55 Lorsqu’un décalage d’origine a été sélectionné, il reste actif jusqu’à la sélection d’un autre décalage ou jusqu’à l’exécution d’une recherche de référence machine (G74) en mode manuel. Le décalage d’origine sélectionne reste actif, même après une mise hors/sous tension de la CNC. Ce type de décalages d’origine défini par programme est très utile en cas d’usinages répétés en divers points de la machine. Exemple: La table de décalages d’origine est initialisée avec les valeurs suivantes: CNC 8035 MODÈLE ·T· (SOFT V16.3X) ·64· G54: X0 Z330 G55: X0 Z240 G56: X0 Z150 G58: X0 Z-900 G59: X0 Z-180 Manuel de programmation Au moyen des décalages d’origine absolus: G54 ; Applique le décalage G54 Exécution du profil ; Exécute profil A1 G55 ; Applique le décalage G55 Exécution du profil ; Exécute profil A2 G56 ; Applique le décalage G56 Exécution du profil ; Exécute profil A3 G54 ; Applique le décalage G54 Exécution du profil ; Exécute profil A1 G58 ; Applique les décalages G54+G58 Exécution du profil ; Exécute profil A2 G59 ; Applique les décalages G54+G59 Exécution du profil ; Exécute profil A3 Fonction G159 Cette fonction permet d’appliquer n’importe quel décalage d’origine défini dans la table. Les six premiers décalages d’origine équivalent à programmer G54 à G59, avec la seule différence que les valeurs correspondant à G58 et G59 s’appliquent d’une manière absolue. Ceci est dû au fait que la fonction G159 annule les fonctions G54-G57, c’est pourquoi il n’y a aucun décalage actif auquel on puisse lui ajouter celui correspondant à G58 ou G59. Présélection des coordonnées et décalages d’origine Au moyen des décalages d’origine incrémentaux: SYSTÈMES DE RÉFÉRENCE 4. La façon de programmer la fonction G159 est la suivante: G159 Nn n étant un numéro de 1 à 20 indiquant le décalage d’origine appliqué. La fonction G159 est modale, se programme seule dans le bloc et incompatible avec les fonctions G53, G54, G55, G56, G57, G58, G59 et G92. À la mise sous tension, la CNC assume le décalage d’origine qui était actif au moment de la mise hors tension. De plus, le décalage d’origine n’est pas affecté par les fonctions M02, M03 ni par la RAZ. Cette fonction est affichée dans l’historique du mode G159Nn, n indiquant le décalage d’origine actif. Exemples: G159 N1 On applique le premier décalage d’origine. Équivaut à programmer G54. G159 N6 On applique le sixième décalage d’origine. Équivaut à programmer G59, mais s'applique de façon absolue. G159 N20 On applique le vingtième décalage d’origine. CNC 8035 MODÈLE ·T· (SOFT V16.3X) ·65· Manuel de programmation 4.5 Présélection de l'origine polaire (G93) La fonction G93 permet de présélectionner tout point du plan de travail en tant que nouvelle origine des coordonnées polaires. Cette fonction doit être programmée seule dans un bloc et son format est le suivant: G93 I±5.5 J±5.5 Les paramètres I et J définissent l'abscisse (I) et l'ordonnée (J) par rapport au zéro pièce, où l'on veut situer la nouvelle origine de coordonnées polaires. SYSTÈMES DE RÉFÉRENCE Présélection de l'origine polaire (G93) 4. Les valeurs affectées à ces paramètres seront programmées en rayons ou en diamètres suivant la personnalisation du paramètre machine d’axes "DFORMAT". Exemple de programmation de l'axe X en diamètres. G90 X180 Z50 ; Point P0. G01 X160 ; Point P1, en ligne droite (G01). G93 I90 J160 ; Présélectionne P5 comme origine polaire. G03 Q270 ; Point P2, en arc (G03). G01 Z130 ; Point P3, en ligne droite (G01). G93 I130 J0 ; Présélectionne P6 comme origine polaire. G02 Q0 ; Point P4, en arc (G02). Si seul G93 est programmé dans un bloc, le point où se trouve la machine à ce moment devient l’origine polaire. A la mise sous tension, après l’exécution de M02, M30 ou après un ARRÊT D'URGENCE ou une RAZ, la CNC prend le zéro pièce sélectionné comme nouvelle origine polaire. Lorsqu’un nouveau plan de travail est sélectionné (G16, G17, G18, G19) la CNC prend le zéro pièce de ce plan comme nouvelle origine polaire. i CNC 8035 MODÈLE ·T· (SOFT V16.3X) ·66· La CNC ne modifie pas l’origine polaire lorsqu’un nouveau zéro pièce est défini, mais elle modifie les valeurs des variables "PORGF" et "PORGS". Si, alors que le paramètre machine général "PORGMOVE" est sélectionné, une interpolation circulaire (G02 ou G03) est programmée, la CNC prend le centre de l’arc comme nouvelle origine polaire. PROGRAMMATION SUIVANT CODE ISO 5 Un bloc programmé en langage ISO peut se composer de: • Fonctions préparatoires (G) • Cotes des axes (X..C) • Vitesse d'avance (F) • Vitesse de la broche (S) • Nº d’outil (T) • Nº de correcteur (D) • Fonctions auxiliaires (M) Cet ordre doit être conservé dans chaque bloc, mais il n’est pas nécessaire que chaque bloc contienne toutes les informations. La CNC permet de programmer des chiffres de 0.00001 à 99999.9999 signés ou non en cas de programmation en millimètres (G71) (format ±5.4) ou de 0.00001 à 3937.00787 signés ou non en cas de programmation en pouces (G70), (format ±4.5). Toutefois, pour simplifier les explications, on peut dire que la CNC admet le format ±5.5, pour indiquer qu’elle admet ±5.4 en millimètres et ±4.5 en pouces. Toute fonction avec paramètres peut également être programmée dans un bloc, à l’exception du numéro de l’étiquette ou du bloc. Ainsi, lors de l’exécution du bloc, la CNC remplace le paramètre arithmétique par sa valeur active à ce moment. CNC 8035 MODÈLE ·T· (SOFT V16.3X) ·67· Manuel de programmation 5.1 Fonctions préparatoires Les fonctions préparatoires sont programmées avec la lettre G suivie d'un maximum de trois chiffres (G0 - G319). Elles sont toujours programmées au début du corps du bloc et permettent de déterminer la géométrie et les conditions de travail de la CNC. Table des fonctions G utilisées dans la CNC: Fonctions préparatoires PROGRAMMATION SUIVANT CODE ISO 5. CNC 8035 MODÈLE ·T· (SOFT V16.3X) ·68· Fonction M D V G00 G01 G02 G03 G04 G05 G06 G07 G08 G09 G10 G11 G12 G13 G14 G16 G17 G18 G19 G20 G21 G22 G32 G33 G34 G36 G37 G38 G39 G40 G41 G41 N G42 G42 N G50 G51 G52 G53 G54 G55 G56 G57 G58 G59 G66 G68 G69 G70 G71 G72 G74 * * * * ? ? * * * * * ? * * * ? * * * * * * * * * * * * ? ? * * * * * * * * * * * * * * * * * * * * * * * * * * * * * * * * * * ? ? * * * * * * * * * * * * * * * * * * * * Signification Positionnement rapide Interpolation linéaire Interpolation circulaire à droite Interpolation circulaire à gauche Temporisation/Suspension de la préparation de blocs Arête arrondie Centre de circonférence en coordonnées absolues Arête vive Circonférence tangente à la trajectoire antérieure Circonférence par trois points Annulation d'image miroir Image miroir sur X Image miroir sur Y Image miroir sur Z Image miroir dans les directions programmées Sélection de plan principal dans deux sens Plan principal X-Y et longitudinal Z Plan principal Z-X et longitudinal Y Plan principal Y-Z et longitudinal X Définition des limites inférieures des zones de travail Définition des limites supérieures des zones de travail Validation/invalidation des zones de travail Avance F comme fonction inverse du temps Filetage électronique Filetage à pas variable Arrondissement d'arêtes Entrée tangentielle Entrée tangentielle Chanfreinage Annulation de compensation radiale Compensation radiale d’outil à gauche Détection de collisions Compensation radiale d'outil à droite Détection de collisions Arête arrondie commandée Look-Ahead Déplacement vers butée Programmation par rapport au zéro machine Transfert d'origine absolu 1 Transfert d'origine absolu 2 Transfert d'origine absolu 3 Transfert d'origine absolu 4 Décalage d’origine additionnel 1 Décalage d’origine additionnel 2 Cycle fixe de poursuite de profil Cycle fixe d'ébauchage sur l'axe X Cycle fixe d'ébauchage sur l'axe Z Programmation en pouces Programmation en millimètres Facteurs d’échelle général et particulier Recherche de référence machine Point 6.1 6.2 6.3 6.3 7.1 / 7.2 7.3.2 6.4 7.3.1 6.5 6.6 7.5 7.5 7.5 7.5 7.5 3.2 3.2 3.2 3.2 3.8.1 3.8.1 3.8.2 6.15 6.11 6.13 6.9 6.7 6.8 6.10 8.2.6 8.2.3 8.3 8.2.3 8.3 7.3.3 7.4 6.14 4.3 4.4.2 4.4.2 4.4.2 4.4.2 4.4.2 4.4.2 9.1 9.2 9.3 3.3 3.3 7.6 4.2 Manuel de programmation D V Signification Point Déplacement avec palpeur jusqu’au contact Déplacement avec palpeur jusqu’à l’interruption du contact Cycle fixe de tournage de segments droits Cycle fixe de dressage de segments droits Cycle fixe de perçage Cycle fixe de tournage de segments courbes Cycle fixe de dressage de segments courbes Cycle fixe de filetage longitudinal Cycle fixe de filetage frontal Cycle fixe de rainurage sur l'axe X Cycle fixe de rainurage sur l'axe Z Programmation absolue * Programmation incrémentale Présélection de coordonnées / Limitation de vitesse de broche Présélection de l'origine polaire Avance en millimètres (pouces) par minute * Avance en millimètres (pouces) par tour * Vitesse de coupe constante Vitesse de rotation de la broche en T/MIN Programmation des cotes de l’axe X en diamètres. Programmation des cotes de l’axe X en rayons. Décalages d'origine absolus Retrait des axes face à un arrêt lors du taraudage. 10.1 10.1 9.4 9.5 9.6 9.7 9.8 9.9 9.10 9.11 9.12 3.4 3.4 4.4.1 4.5 5.2.1 5.2.2 5.3.1 5.3.2 3.5 3.5 4.4.2 6.12 * * * * * * * * * * * * * ? ? * * * * * * * * ? ? * ? ? La lettre M signifie MODAL, c'est-à-dire, qu'elle restera active une fois programmée à condition que l'on ne programme pas une fonction G incompatible, que l'on n'exécute pas M02 ou M30, qu'il n'y ait pas d'ARRÊT D'URGENCE, de RAZ ou une mise hors/sous tension de la CNC. 5. Fonctions préparatoires G75 G76 G81 G82 G83 G84 G85 G86 G87 G88 G89 G90 G91 G92 G93 G94 G95 G96 G97 G151 G152 G159 G233 M PROGRAMMATION SUIVANT CODE ISO Fonction La lettre D signifie PAR DEFAUT, c’est-à-dire que ces fonctions sont prises en compte par la CNC, à la mise sous tension, après l’exécution de M02, M30 ou à la suite d’un ARRÊT D'URGENCE ou d’une RAZ. Dans les cas indiqués par ? on devra comprendre que l’état PAR DEFAUT de ces fonctions G dépend de la personnalisation des paramètres machine généraux de la CNC. La lettre V signifie que le code G est affiché à côté des conditions d’usinage actuelles dans les modes exécution et simulation. CNC 8035 MODÈLE ·T· (SOFT V16.3X) ·69· Manuel de programmation 5.2 Vitesse d'avance F La vitesse d’avance en usinage peut être définie par programme, et elle reste active tant qu’une autre vitesse n’est pas programmée. La vitesse d’avance est repérée par la lettre F et, selon que G94 ou G95 est actif, elle est programmée en mm/minute (pouces/minute) ou en mm/tour (pouces/ tour). Son format de programmation est 5.5, soit 5.4 si elle est programmée en millimètres et 4.5 si elle est programmée en pouces. 5. Vitesse d'avance F PROGRAMMATION SUIVANT CODE ISO L’avance de travail maximum de la machine, limitée sur chaque axe par le paramètre machine d’axes "MAXFEED", peut être programmée par le code F0 ou en affectant la valeur adéquate à la lettre F. CNC 8035 MODÈLE ·T· (SOFT V16.3X) ·70· L’avance F programmée est effective lorsque la machine travaille en interpolation linéaire (G01) ou circulaire (G02, G03). Si la fonction F n’est pas programmée, la CNC prend en compte l’avance F0. Si la machine travaille en positionnement (G00), elle se déplacera selon l’avance rapide indiquée par le paramètre machine d’axes "G00FEED", indépendante de l’avance F programmée. L’avance F programmée peut varier entre 0% et 255% par l’intermédiaire du PLC, via DNC ou entre 0% et 120% grâce au sélecteur situé sur le Panneau de Commande de la CNC. La CNC dispose toutefois du paramètre machine général "MAXFOVR" pour limiter la variation maximum de l’avance. Si la machine travaille en positionnement (G00), l’avance rapide est fixée à 100% ou elle peut varier entre 0% et 100% selon l’état du paramètre machine "RAPIDOVR". Lorsqu'on exécute les fonctions G33 (filetage électronique), G34 (filetage à pas variable), G86 (cycle fixe de filetage longitudinal) ou G87 (cycle fixe de filetage frontal), on ne peut pas modifier l'avance, en travaillant à 100% de F programmée. Manuel de programmation Avance en mm/min ou pouces/minute (G94) Dès que le code G94 est programmé, la commande "sait" que les avances programmées par F5.5, sont en mm/minute ou en pouces/minute. Si le déplacement correspond à un axe tournant, la CNC assumera que l'avance est programmée en degrés/minute. Si une interpolation est réalisée entre un axe rotatif et un axe linéaire, l’avance programmée est prise en mm/minute ou en pouces/minute et le déplacement de l’axe rotatif, qui a été programmé en degrés, sera considéré comme programmé en millimètres ou en pouces. Avance F x Déplacement de l’axe Composante d'avance = Déplacement résultant programmé Exemple: Sur une machine à axes X Z linéaires et à axe C rotatif, situés tous au point X0 Z0 C0, le déplacement suivant est programmé: G1 G90 X100 Z20 C270 F10000 On a: 10000 100 F x = -----------------------------------------------= 3464 7946 Fx = ----------------------------------------------------------2 2 2 100 2 + 20 2 + 270 2 x + z + c 5. Vitesse d'avance F Le rapport entre la composante avance de l’axe et l’avance F programmée sera identique à celui existant entre le déplacement de l’axe et le déplacement résultant programmé. PROGRAMMATION SUIVANT CODE ISO 5.2.1 F z 10000 20 Fz = ----------------------------------------------------------= -----------------------------------------------= 692 9589 x 2 + z 2 + c 2 100 2 + 20 2 + 270 2 F c 10000 270 Fc = ----------------------------------------------------------= -----------------------------------------------= 9354 9455 2 2 2 x + z + c 100 2 + 20 2 + 270 2 La fonction G94 est modale, c’est-à-dire que dès qu’elle est programmée, elle reste active jusqu’à la programmation de G95. A la mise sous tension, après exécution de M02, M30 ou après un ARRÊT D'URGENCE ou une RAZ, la CNC prend en compte la fonction G94 ou G95 selon la personnalisation du paramètre machine général "IFEED". CNC 8035 MODÈLE ·T· (SOFT V16.3X) ·71· Manuel de programmation 5.2.2 Avance en mm/tour ou pouces/tour (G95) Dès que le code G95 est programmé, la commande suppose que les avances programmées par F5.5 sont en mm/tour ou en pouces/tour. Cette fonction n’affecte pas les déplacements rapides (G00), qui s’effectuent toujours en mm/minute ou en pouces/minute. Elle n’affectera pas non plus les déplacements en mode manuel, pendant le contrôle de l’outil, etc. La fonction G95 est modale, c’est-à-dire que dès qu’elle est programmée, elle reste active jusqu’à la programmation de G94. Vitesse d'avance F PROGRAMMATION SUIVANT CODE ISO 5. CNC 8035 MODÈLE ·T· (SOFT V16.3X) ·72· A la mise sous tension, après exécution de M02, M30 ou après un ARRÊT D'URGENCE ou une RAZ, la CNC prend en compte la fonction G94 ou G95 selon la personnalisation du paramètre machine général "IFEED". Déplacements manuels sur G95 Si l’axe à déplacer en JOG n’appartient pas au plan actif, le déplacement se réalisera en mm/minute, c’est pourquoi il ne sera pas nécessaire de programmer une S sur la broche. De plus, si l’un des axes du plan est l’axe Y, il ne sera pas non plus nécessaire de programmer la S pour réaliser des déplacements en JOG sur n’importe quel axe, qu’il soit du plan ou non. Ceci est particulièrement intéressant avec des axes auxiliaires, des lunettes et des contre-pointes, car dans ces cas la S n’a pas d’influence. Manuel de programmation Vitesse de rotation de la broche (S) Avec le code S5.4 on programme directement la vitesse de rotation de la broche en tours/minute (G97) ou en mètres/minute (pieds/minute si on travaille en pouce) si on est dans la modalité de vitesse de coupe constante (G96). La valeur maximum est limitée par les paramètres machine de la broche "MAXGEAR1, MAXGEAR2, MAXGEAR3 et MAXGEAR4", qui dépendent dans chaque cas de la gamme de vitesses de broche sélectionnée. La vitesse de rotation S programmée peut être modifiée par l’intermédiaire du PLC ou de la ligne DNC ou au moyen des touches SPINDLE "+" et "-" du Panneau de Commande de la CNC. La vitesse varie entre les valeurs maximum et minimum fixées par les paramètres machine de broche "MINSOVR" et "MAXSOVR". Le pas incrémental associé aux touches SPINDLE "+" et "-" du Panneau de Commande de la CNC permettant de modifier la vitesse S programmée est fixé par le paramètre machine de broche "SOVRSTEP". Lorsqu'on exécute les fonctions G33 (filetage électronique), G34 (filetage à pas variable), G86 (cycle fixe de filetage longitudinal) ou G87 (cycle fixe de filetage frontal), on ne peut pas modifier la vitesse programmée, en travaillant à 100% de S programmée. Vitesse de rotation de la broche (S) 5. Cette valeur maximum peut également être limitée par programme au moyen de la fonction G92 S5.4. PROGRAMMATION SUIVANT CODE ISO 5.3 CNC 8035 MODÈLE ·T· (SOFT V16.3X) ·73· Manuel de programmation 5.3.1 Vitesse de coupe constante (G96) En programmant G96, la CNC assume que la vitesse de broche programmée avec S5.4 est en mètres/minute ou pieds/minute et le tour commence à travailler dans la modalité de vitesse de coupe constante. Il est recommandé de programmer la vitesse de la broche S5.4 dans le même bloc où est programmée la fonction G96, et sélectionner pour cela la gamme de broche correspondante (M41, M42, M43, M44) dans le même bloc ou dans un bloc précédent. Vitesse de rotation de la broche (S) PROGRAMMATION SUIVANT CODE ISO 5. CNC 8035 MODÈLE ·T· (SOFT V16.3X) ·74· Si dans le bloc où est programmée la fonction G96 on ne programme pas la vitesse de broche S5.4, la CNC assume comme vitesse de broche la dernière vitesse de travail, dans la modalité de vitesse de coupe constante. Si on ne programme pas la vitesse de la broche et s’il n’y en a aucune préalable ou si la gamme de broche correspondante est sélectionnée, la CNC affichera l’erreur correspondante. La fonction G96 est modale, c’est-à-dire que dès qu’elle est programmée, elle reste active jusqu’à la programmation de G97. A la mise sous tension, après exécution de M02, M30 ou après un ARRÊT D'URGENCE ou une RAZ, la CNC prend en compte la fonction G97. Manuel de programmation Vitesse de rotation de la broche en t/min. (G97) En programmant G97, la CNC assume que la vitesse de broche programmée avec S5.4 est en tours/ minute. Si dans un bloc où l'on programme G97, la vitesse de broche S5.4 n'est pas programmée, la CNC assume comme vitesse programmée la vitesse de rotation actuelle de broche. La fonction G97 est modale, c’est-à-dire que dès qu’elle est programmée, elle reste active jusqu’à la programmation de G96. 5. Vitesse de rotation de la broche (S) A la mise sous tension, après exécution de M02, M30 ou après un ARRÊT D'URGENCE ou une RAZ, la CNC prend en compte la fonction G97. PROGRAMMATION SUIVANT CODE ISO 5.3.2 CNC 8035 MODÈLE ·T· (SOFT V16.3X) ·75· Manuel de programmation 5.4 Numéro d'outil (T) et correcteur (D) La fonction T permet de sélectionner l'outil et la fonction D permet de sélectionner le correcteur qui lui est associé. Lorsqu'on définit les deux paramètres, l'ordre de programmation est T D. Par exemple T6 D17. 5. Numéro d'outil (T) et correcteur (D) PROGRAMMATION SUIVANT CODE ISO Magasin? NON Si la machine dispose d’un magasin d’outils la CNC consulte la "Table du magasin d’outils" pour savoir la position qu’occupe l’outil désiré et la sélectionne. OUI Sélection de l'outil OUI D? NON Si la fonction D n’a pas été définie, elle consulte la "Table d’outils" pour savoir le numéro de correcteur (D) associé à celle-ci. La CNC prend D associée à T dans la table d'outils La CNC prend les dimensions définies pour D dans la table de correcteurs Examine la "Table de Correcteurs" et assume les dimensions de l’outil, correspondants au correcteur D. Analyse la "Table de Géométrie" pour connaître la géométrie de la plaquette (largeur, angle et angle de coupe). La "Table de Géométrie est associée à T ou à D suivant le critère du fabricant, le paramètre machine général "GEOMTYPE (P123)". Pour accéder, consulter et définir ces tables, consulter le manuel de fonctionnement. Utilisation des fonctions T et D • Les fonctions T et D peuvent être programmées seules ou ensemble, comme l’indique cet exemple : T5 D18 Elle sélectionne l’outil 5 et assume les dimensions du correcteur 18 D22 L’outil 5 continue à être sélectionné et les dimensions du correcteur 22 sont assumées. T3 Elle sélectionne l’outil 3 et assume les dimensions du correcteur associé à cet outil. • Avec une tourelle porte-outils, le nombre d’outils que l’on peut utiliser est supérieur au nombre de positions que possède la tourelle. C’est pourquoi une même position de la tourelle doit être utilisée par plus d’un outil. Dans ces cas, il faut programmer les fonctions "T" et "D". La fonction "T" fait référence à la position de la tourelle et la fonction "D" aux dimensions de l’outil placé sur cette position. CNC 8035 Ainsi, par exemple, programmer T5 D23 signifie que l’on veut sélectionner l’outil qui est sur la tourelle 5 et que la CNC doit prendre en compte les dimensions indiquées dans les tables des correcteurs et géométries pour le correcteur 23. • Lorsqu’on dispose d’un bras porte-outils avec 2 plaquettes, il faut aussi programmer les fonctions "T" et "D". MODÈLE ·T· (SOFT V16.3X) ·76· La fonction "T" fait référence au bras et la fonction "D" aux dimensions de la plaquette. On pourra ainsi programmer T1 D1 ou T1 D2, en fonction de la plaquette avec laquelle on veut travailler. Manuel de programmation Compensation longitudinale et compensation radiale de l’outil. La CNC examine la "Table de Correcteurs" et assume les dimensions de l’outil correspondant au correcteur D actif. La compensation longitudinale s’applique à tout moment alors que la compensation radiale doit être sélectionnée par l’usager avec les fonctions G40, G41, G42. S’il n’y a pas d’outil sélectionné ou si D0 est définie on n’applique pas de compensation longitudinale ni de compensation radiale. PROGRAMMATION SUIVANT CODE ISO Numéro d'outil (T) et correcteur (D) 5. Pour plus information consulter le chapitre 8 "Compensation d’outils" de ce même manuel. CNC 8035 MODÈLE ·T· (SOFT V16.3X) ·77· Manuel de programmation 5.5 Fonction auxiliaire (M) Les fonctions auxiliaires sont programmées par le code M4; il est possible de programmer jusqu’à 7 fonctions auxiliaires dans le même bloc. Si plus d’une fonction auxiliaire a été programmée dans un bloc, la CNC les exécute dans l’ordre où elles ont été programmées. La CNC dispose d’une table de fonctions M avec "NMISCFUN" (paramètre machine général) composants, les éléments suivants étant spécifiés: 5. • Le numéro de la sous-routine à associer à cette fonction auxiliaire. Fonction auxiliaire (M) PROGRAMMATION SUIVANT CODE ISO • Le numéro (0-9999) de la fonction auxiliaire M définie. • Un indicateur qui définit si la fonction M est exécutée avant ou après le bloc de déplacement dans lequel elle est programmée. • Un indicateur qui définit si l’exécution de la fonction M interrompt ou non la préparation des blocs. • Un indicateur qui définit si la fonction M est exécutée ou non après l’exécution de la sous-routine associée. • Un indicateur qui définit si la CNC doit ou non attendre le signal AUX END (signal de M exécutée émis par le PLC), avant de poursuivre l’exécution du programme. Si, lors de l’exécution de la fonction auxiliaire M, celle-ci n’est pas définie dans la table de fonctions M, la fonction programmée est exécutée au début du bloc, et la CNC attend le signal AUX END avant de poursuivre l’exécution du programme. Certaines fonctions auxiliaires ont une signification particulière interne dans la CNC. Si, pendant l’exécution de la sous-routine associée d’une fonction auxiliaire "M", un bloc contenant la même fonction "M" est rencontré, il sera exécuté mais la sous-routine associée n’est pas exécutée. i Toutes les fonctions auxiliaires "M" auxquelles une sous-routine est associée doivent être programmées seules dans un bloc. Dans le cas des fonctions M41 à M44 avec sous-routine associée, la S qui génère le changement de gamme doit être programmée seule dans le bloc. Dans le cas contraire, la CNC affiche l'erreur 1031. CNC 8035 MODÈLE ·T· (SOFT V16.3X) ·78· Manuel de programmation M00. Arrêt de programme Lorsque la CNC lit le code M00 dans un bloc, elle interrompt le programme. Pour redémarrer, frapper à nouveau la touche DEPART CYCLE. Il est recommandé de définir cette fonction dans la table de fonctions M, de façon qu’elle soit exécutée à la fin du bloc dans lequel elle est programmée. Fonction auxiliaire (M) 5. PROGRAMMATION SUIVANT CODE ISO 5.5.1 CNC 8035 MODÈLE ·T· (SOFT V16.3X) ·79· Manuel de programmation 5.5.2 M01. Arrêt conditionnel du programme Cette fonction est identique à M00, sauf que la CNC ne la prend en compte que si le signal M01 STOP émis par le PLC est actif (niveau logique "1"). Fonction auxiliaire (M) PROGRAMMATION SUIVANT CODE ISO 5. CNC 8035 MODÈLE ·T· (SOFT V16.3X) ·80· Manuel de programmation M02. Fin de programme Ce code indique la fin du programme et réalise une fonction de "Reset général" de la CNC (Retour à l’état initial). Il exécute également la fonction M05. Il est recommandé de définir cette fonction dans la table de fonctions M, de façon qu’elle soit exécutée à la fin du bloc dans lequel elle est programmée. Fonction auxiliaire (M) 5. PROGRAMMATION SUIVANT CODE ISO 5.5.3 CNC 8035 MODÈLE ·T· (SOFT V16.3X) ·81· Manuel de programmation 5.5.4 M30. Fin de programme avec retour au début Identique à la fonction M02, sauf que la CNC revient au premier bloc du programme. Fonction auxiliaire (M) PROGRAMMATION SUIVANT CODE ISO 5. CNC 8035 MODÈLE ·T· (SOFT V16.3X) ·82· Manuel de programmation M03. Démarrage de la broche à droite (sens horaire) Ce code signale le démarrage de la broche dans le sens horaire. Il est recommandé de définir cette fonction dans la table de fonctions M, de façon qu’elle soit exécutée au début du bloc dans lequel elle est programmée. Fonction auxiliaire (M) 5. PROGRAMMATION SUIVANT CODE ISO 5.5.5 CNC 8035 MODÈLE ·T· (SOFT V16.3X) ·83· Manuel de programmation 5.5.6 M04. Démarrage de la broche à gauche (sens anti-horaire) Ce code signale le démarrage de la broche à gauche. Il est recommandé de définir cette fonction dans la table de fonctions M, de façon qu’elle soit exécutée au début du bloc dans lequel elle est programmée. Fonction auxiliaire (M) PROGRAMMATION SUIVANT CODE ISO 5. CNC 8035 MODÈLE ·T· (SOFT V16.3X) ·84· Manuel de programmation M05. Arrêt de la broche Il est recommandé de définir cette fonction dans la table de fonctions M, de façon qu’elle soit exécutée à la fin du bloc dans lequel elle est programmée. Fonction auxiliaire (M) 5. PROGRAMMATION SUIVANT CODE ISO 5.5.7 CNC 8035 MODÈLE ·T· (SOFT V16.3X) ·85· Manuel de programmation 5.5.8 M06. Code de changement d'outil Si le paramètre machine général "TOFFM06" (indicatif du centre d’usinage) est actif, la CNC gère le changeur d’outil et met à jour la table correspondant au magasin d’outils. Il est recommandé de définir cette fonction dans la table de fonctions M, de façon que la sous-routine correspondant au changeur d’outil installé dans la machine soit exécuté. Fonction auxiliaire (M) PROGRAMMATION SUIVANT CODE ISO 5. CNC 8035 MODÈLE ·T· (SOFT V16.3X) ·86· Manuel de programmation M19. Arrêt orienté de la broche La CNC permet de travailler avec la broche en boucle ouverte (M3, M4) et en boucle fermée (M19). Pour travailler en boucle fermée, il est nécessaire de disposer d’un capteur rotatif (codeur) couplé à la broche de la machine. La fonction M19 ou M19 S±5.5 permet de passer de la boucle ouverte à la boucle fermée. La CNC agit comme suit: • Si la broche dispose d’un contact de référence, elle recherche le contact de référence machine à la vitesse de rotation indiquée par le paramètre machine de broche "REFEED1". Enfin, elle se positionne sur le point défini par S±5.5. • Si la broche ne dispose pas de contact de référence, elle recherche le signal Io du capteur, à la vitesse de rotation indiquée par le paramètre machine de broche "REFEED2". Ensuite, elle se positionne sur le point défini par S±5.5. Si seule la fonction auxiliaire M19 est exécutée, la broche se positionne sur S0 après avoir réalisé la recherche du micro de référence. Pour indexer la broche sur une autre position, il est nécessaire d’exécuter la fonction M19 S±5.5. La CNC n’effectue pas de recherche de la référence, car elle est déjà en boucle fermée et positionne la broche sur la position indiquée (S±5.5). Le code S±5.5 indique la position d’indexage de la broche en degrés à partir de la position de l’impulsion de marquage du codeur. 5. Fonction auxiliaire (M) Ensuite, elle recherche le signal Io du capteur, à la vitesse de rotation indiquée par le paramètre de machine de broche "REFEED2". PROGRAMMATION SUIVANT CODE ISO 5.5.9 Le signe indique le sens du comptage, et la valeur 5.5 est toujours considérée comme une valeur absolue, quel que soit le type d’unités sélectionné. Exemple: S1000 M3 Broche en boucle ouverte. M19 S100 La broche passe en boucle fermée. Recherche de référence et positionnement sur 100º. M19 S -30 La broche se déplace, en passant par 0º, jusqu'à -30º. M19 S400 La broche effectue une rotation et se positionne sur 40°. CNC 8035 MODÈLE ·T· (SOFT V16.3X) ·87· Manuel de programmation 5.5.10 M41, M42, M43, M44. Changement de gammes de la broche. La CNC dispose de 4 gammes de broche, M41, M42, M43 et M44, dont les vitesses maximum respectives sont limitées par les paramètres machine de broche "MAXGEAR1", "MAXGEAR2", "MAXGEAR3" et "MAXGEAR4". Si le paramètre machine de broche "AUTOGEAR" est défini de façon que la CNC exécute automatiquement le changement de gamme, la CNC émet automatiquement les fonctions M41, M42, M43 et M44, sans qu’il soit nécessaire de les programmer. Fonction auxiliaire (M) PROGRAMMATION SUIVANT CODE ISO 5. CNC 8035 MODÈLE ·T· (SOFT V16.3X) ·88· Dans le cas contraire, il appartient au programmeur de choisir la gamme correspondante, en tenant compte du fait que chaque gamme fournira la consigne définie par le paramètre machine de broche "MAXVOLT" pour la vitesse maximum spécifiée dans chaque gamme (paramètres machine de broche "MAXGEAR1", "MAXGEAR2", "MAXGEAR3" et "MAXGEAR4"). Indépendamment du fait que le changement de gamme est automatique ou non, les fonctions M41 à M44 peuvent avoir une sous-routine associée. Si on programme la fonction M41 à M44 puis une S qui correspond à cette gamme, le changement automatique de gamme n'a pas lieu et la sousroutine associée ne s'exécute pas. COMMANDE DE LA TRAJECTOIRE 6 La CNC permet de programmer les déplacements d’un ou de plusieurs axes simultanément. Seuls les axes intervenant dans le déplacement désiré sont programmés. L’ordre de programmation des axes est le suivant: X, Y, Z, U, V, W, A, B, C Les cotes de chaque axe seront programmées en rayons ou en diamètres, suivant la personnalisation du paramètre machine d’axes "DFORMAT". CNC 8035 MODÈLE ·T· (SOFT V16.3X) ·89· Manuel de programmation 6.1 Positionnement rapide (G00) Les déplacements programmés après G00 sont exécutés selon l’avance rapide indiquée dans le paramètre machine d’axes "G00FEED". Quel que soit le nombre d’axes déplacés, la trajectoire résultante est toujours une droite entre le point de départ et le point d’arrivée. Exemple de programmation de l'axe X en rayons. Positionnement rapide (G00) COMMANDE DE LA TRAJECTOIRE 6. X100 Z100; Point de départ G00 G90 X300 Z400; Trajectoire programmée Le paramètre machine général "RAPIDOVR", permet de définir si, en G00, le sélecteur de pourcentage de correction d’avance permettra la correction entre 0 et 100% ou si ce pourcentage restera fixé à 100%. Lors de la programmation de G00, le dernier code F programmé n’est pas annulé, c’est-à-dire que, lorsque G01, G02 ou G03 est programmé à nouveau, ce code F est rétabli. La fonction G00 est modale et incompatible avec G01, G02, G03, G33, G34 et G75. La fonction G00 peut être programmée sous la forme G ou G0. Au moment de la mise sous tension, après avoir exécuté M02, M30 ou après un ARRÊT D'URGENCE ou une RAZ, la CNC assume le code G00 ou le code G01 en fonction de la personnalisation du paramètre machine général "IMOVE" CNC 8035 MODÈLE ·T· (SOFT V16.3X) ·90· Manuel de programmation Interpolation linéaire (G01) Les déplacements programmés après G01 sont exécutés suivant une droite et selon l’avance F programmée. En cas de déplacement de deux ou trois axes simultanément, la trajectoire résultante est une droite entre le point de départ et le point d’arrivée. La machine se déplace suivant cette trajectoire et selon l’avance F programmée. La CNC calcule les avances de chaque axe afin que la trajectoire produite soit l’avance F programmée. 6. Interpolation linéaire (G01) Exemple de programmation de l'axe X en diamètres. COMMANDE DE LA TRAJECTOIRE 6.2 G01 G90 X800 Z650 F150 L'avance F programmée peut être fixée entre 0% et 120% grâce au sélecteur situé sur le Panneau de Commande de la CNC ou sélectionnée entre 0% et 255% depuis le PLC, la ligne DNC ou par programme. La CNC dispose toutefois du paramètre machine général "MAXFOVR" pour limiter la variation maximum de l’avance. La CNC permet de programmer des axes de positionnement seul, en blocs d’interpolation linéaire. La CNC calculera la vitesse d'avance correspondante à l’axe ou aux axes de positionnement seul, de façon à ce qu’ils arrivent au point final en même temps que les autres axes. La fonction G01 est modale et incompatible avec G00, G02, G03, G33 et G34. La fonction G01 peut être programmée sous la forme G1. Au moment de la mise sous tension, après avoir exécuté M02, M30 ou après un ARRÊT D'URGENCE ou une RAZ, la CNC assume le code G00 ou le code G01 en fonction de la personnalisation du paramètre machine général "IMOVE" CNC 8035 MODÈLE ·T· (SOFT V16.3X) ·91· Manuel de programmation 6.3 Interpolation circulaire (G02/G03) L’interpolation circulaire peut être réalisée de deux façons: G02: Interpolation circulaire à droite (Sens horaire). G03: Interpolation circulaire à gauche (Sens antihoraire). Les déplacements programmés après G02 et G03 sont exécutés sous forme de trajectoire circulaire et selon l’avance F programmée. 6. Interpolation circulaire (G02/G03) COMMANDE DE LA TRAJECTOIRE L’exemple suivant indique le sens de G02 et G03 sur différentes machines. Observer comment se maintient la position relative de l’outil par rapport aux axes. • Tours horizontaux: • Tours verticaux: L'interpolation circulaire ne peut être exécutée sur le plan. La façon de définir l'interpolation circulaire est la suivante : CNC 8035 MODÈLE ·T· (SOFT V16.3X) ·92· Manuel de programmation Coordonnées cartésiennes Les coordonnées du point de fin de l’arc et la position du centre par rapport au point de début sont définies d’après les axes du plan de travail. Les coordonnées du centre seront définies en rayons et avec les lettres I, J ou K, chacune étant associée aux axes de la façon suivante. Si on ne définit pas les coordonnées du centre, la CNC interprète que leur valeur est zéro. I Axes Y, V, B ==> J Axes Z, W, C ==> K Format de programmation : Plan XY: G02(G03) X±5.5 Y±5.5 I±6.5 J±6.5 Plan ZX: G02(G03) X±5.5 Z±5.5 I±6.5 K±6.5 Plan YZ: G02(G03) Y±5.5 Z±5.5 J±6.5 K±6.5 Interpolation circulaire (G02/G03) ==> COMMANDE DE LA TRAJECTOIRE 6. Axes X, U, A L’ordre de programmation des axes et des coordonnées au centre correspondantes est toujours le même, quel que soit le plan sélectionné. Plan AY: G02(G03) Y±5.5 A±5.5 J±6.5 I±6.5 Plan XU: G02(G03) X±5.5 U±5.5 I±6.5 I±6.5 Coordonnées polaires Il est nécessaire de définir l’angle de déplacement Q et la distance à partir du point de départ au centre (optionnel) d’après les axes du plan de travail. Les cotes du centre seront définies en rayons et avec les lettres I, J ou K, chacune étant associée aux axes de la façon suivante: Axes X, U, A ==> I Axes Y, V, B ==> J Axes Z, W, C ==> K Si le centre de l’arc n’est pas défini, la CNC considère qu’il coïncide avec l’origine polaire actuelle. Format de programmation : Plan XY: G02(G03) Q±5.5 I±6.5 J±6.5 Plan ZX: G02(G03) Q±5.5 I±6.5 K±6.5 Plan YZ: G02(G03) Q±5.5 J±6.5 K±6.5 CNC 8035 MODÈLE ·T· (SOFT V16.3X) ·93· Manuel de programmation Coordonnées cartésiennes avec programmation de rayon Les coordonnées du point d’arrivée de l’arc et le rayon R doivent être définis. Format de programmation : Interpolation circulaire (G02/G03) COMMANDE DE LA TRAJECTOIRE 6. Plan XY: G02(G03) X±5.5 Y±5.5 R±6.5 Plan ZX: G02(G03) X±5.5 Z±5.5 R±6.5 Plan YZ: G02(G03) Y±5.5 Z±5.5 R±6.5 Si, en programmant le rayon, un cercle complet est programmé, la CNC affichera l’erreur correspondante, en raison du nombre infini de solutions. Si l’arc est inférieur à 180º, le rayon est programmé avec un signe positif; s’il est supérieur à 180º, le signe sera négatif. Si P0 est le point de départ et P1 le point d’arrivée, le nombre d’arcs de rayon identique passant par ces deux points est de 4. L’arc nécessaire est défini en fonction de l’interpolation circulaire G02 ou G03 et du signe du rayon. Ainsi, le format de programmation des arcs de la figure sera le suivant: Arc 1 G02 X.. Z.. R- .. Arc 2 G02 X.. Z.. R+.. Arc 3 G03 X.. Z.. R+.. Arc 4 G03 X.. Z.. R- .. Exécution de l'interpolation circulaire CNC 8035 La CNC calculera, selon l’arc programmé, les rayons du point de départ et du point d’arrivée. Bien que, théoriquement, ces deux rayons doivent être parfaitement identiques, la CNC permet de sélectionner la différence maximum admissible entre ces deux rayons au moyen du paramètre machine général "CIRRINERR". Si la valeur définie est dépassée, la CNC affiche l’erreur correspondante. Dans tous les cas de programmation, la CNC vérifie que les coordonnées du centre ou du rayon ne dépassent pas 214748.3647mm. Dans le cas contraire, la CNC affichera l'erreur correspondante. MODÈLE ·T· (SOFT V16.3X) ·94· L'avance F programmée peut être fixée entre 0% et 120% grâce au sélecteur situé sur le Panneau de Commande de la CNC ou sélectionnée entre 0% et 255% depuis le PLC, la ligne DNC ou par programme. Manuel de programmation La CNC dispose toutefois du paramètre machine général "MAXFOVR" pour limiter la variation maximum de l’avance. Si une interpolation circulaire (G02 ou G03) est programmée après la sélection du paramètre machine général "PORGMOVE", la CNC prendra le centre de l’arc comme nouvelle origine polaire. Les fonctions G02 et G03 sont modales et incompatibles entre-elles, et avec G00, G01, G33 et G34. Les fonctions G02 et G03 peuvent être programmées sous la forme G2 et G3. Par ailleurs, les fonctions G74 (recherche de zéro) et G75 (déplacement avec palpeur) annulent les fonctions G02 et G03. Exemple de programmation de l'axe X en rayons. Interpolation circulaire (G02/G03) Exemples de programmation 6. COMMANDE DE LA TRAJECTOIRE Au moment de la mise sous tension, après avoir exécuté M02, M30 ou après un ARRÊT D'URGENCE ou une RAZ, la CNC assume le code G00 ou le code G01 en fonction de la personnalisation du paramètre machine général "IMOVE" Plusieurs modes de programmation sont analysés ci-dessous, avec X40 Z60 comme point de départ. Coordonnées cartésiennes: G90 G03 X90 Z110 I50 K0 X40 Z160 I10 K50 Coordonnées polaires: G90 G03 Q0 I50 K0 Q-90 I0 K50 Ou: G93 I90 J60 ; Définit un centre polaire G03 Q0 G93 I90 J160 ; Il définit le nouveau centre polaire. Q-90 Coordonnées cartésiennes avec programmation de rayon: G90 G03 X90 Z110 R50 CNC 8035 X40 Z160 R50 MODÈLE ·T· (SOFT V16.3X) ·95· Manuel de programmation 6.4 Interpolation circulaire avec programmation du centre de l’arc en coordonnées absolues (G06) L’ajout de la fonction G06 dans un bloc d’interpolation circulaire permet de programmer les coordonnées du centre de l’arc (I, J ou K) en mode absolu, c’est-à-dire par rapport au zéro d’origine, et non au début de l’arc. Les cotes du centre seront programmées en rayons ou en diamètres, en fonction des unités de programmation sélectionnées avec le paramètre machine d’axes "DFORMAT". COMMANDE DE LA TRAJECTOIRE Interpolation circulaire avec programmation du centre de l’arc en coordonnées absolues (G06) 6. La fonction G06 est non-modale, et doit donc être programmée chaque fois que les coordonnées du centre de l’arc doivent être indiquées en absolu. La fonction G06 peut être programmée sous la forme G6. Exemple de programmation de l'axe X en rayons. Plusieurs modes de programmation sont analysés ci-dessous, avec X40 Z60 comme point de départ. Coordonnées cartésiennes: G90 G06 G03 X90 Z110 I90 K60 G06 X40 Z160 Y40 I90 K160 Coordonnées polaires: G90 G06 G03 Q0 I90 K60 G06 Q-90 I90 K160 CNC 8035 MODÈLE ·T· (SOFT V16.3X) ·96· Manuel de programmation Trajectoire circulaire tangente a la trajectoire précédente (G08) La fonction G08 permet de programmer une trajectoire circulaire tangente à la trajectoire précédente, sans avoir à programmer les coordonnées (I, J ou K) du centre. On ne définira que les coordonnées du point final de l'arc, bien en coordonnées polaires, ou bien en coordonnées cartésiennes, suivant les axes du plan de travail. G90 G01 X0 Z270 X50 Z250 G08 X60 Z180 ;Arc tangent à la trajectoire précédente. G08 X50 Z130 ;Arc tangent à la trajectoire précédente. G08 X60 Z100 ;Arc tangent à la trajectoire précédente. G01 X60 Z40 Trajectoire circulaire tangente a la trajectoire précédente (G08) 6. Exemple de programmation de l'axe X en rayons. COMMANDE DE LA TRAJECTOIRE 6.5 La fonction G08 n'est pas modale, par conséquent il faut la programmer chaque fois que l'on veut exécuter un arc tangent à la trajectoire précédente. La fonction G08 peut être programmée sous la forme G8. La fonction G08 autorise une droite ou un arc comme trajectoire précédente et elle ne modifie pas son historique, restant active après la fin du bloc la même fonction G01, G02 ou G03. Lorsque la fonction G08 est utilisée, il est impossible d’exécuter un cercle complet en raison du nombre infini de solutions. La CNC affichera le code d’erreur correspondant. CNC 8035 MODÈLE ·T· (SOFT V16.3X) ·97· Manuel de programmation 6.6 Trajectoire circulaire définie avec trois points (G09) Avec la fonction G09 on peut définir une trajectoire circulaire (arc), en programmant le point final et un point intermédiaire (le point initial de l'arc est le point de départ du mouvement). C'est-à-dire, au lieu de programmer les coordonnées du centre, on programme n'importe quel point intermédiaire. Le point d’arrivée de l’arc est défini en coordonnées cartésiennes ou polaires, tandis que le point intermédiaire est toujours défini en coordonnées cartésiennes par les lettres I, J ou K. Chaque lettre est associée aux axes comme suit: COMMANDE DE LA TRAJECTOIRE Trajectoire circulaire définie avec trois points (G09) 6. Axes X, U, A ==> I Axes Y, V, B ==> J Axes Z, W, C ==> K En coordonnées cartésiennes: G18 G09 X±5.5 Z±5.5 I±5.5 K±5.5 R±5.5 Q±5.5 I±5.5 K±5.5 En coordonnées polaires: G18 G09 Exemple: Exemple avec P0 comme point initial. Programmation de l'axe X en rayons. G09 X60 Z20 I30 K50 Programmation de l'axe X en diamètres. G09 X120 Z20 I60 K50 La fonction G09 n'est pas modale, par conséquent il faut la programmer chaque fois que l'on veut exécuter une trajectoire circulaire définie par trois points. La fonction G09 peut être programmée comme G9. En programmant G09 il n'est pas nécessaire de programmer le sens de déplacement (G02 ou G03). CNC 8035 MODÈLE ·T· (SOFT V16.3X) ·98· La fonction G09 no modifie pas l’historique du programme. La même fonction G01, G02 ou G03 reste active après la fin du bloc. En utilisant la fonction G09 on ne peut pas exécuter un cercle complet, étant donné qu'il faut programmer trois points différents. La CNC affichera le code d’erreur correspondant. Manuel de programmation Entrée tangentielle au début de l'usinage (G37) La fonction G37 permet le raccordement tangentiel de deux trajectoires sans avoir à calculer les points d’intersection. La fonction G37 est non-modale et doit donc être toujours programmée pour lancer une opération d’usinage avec entrée tangentielle. Exemple de programmation de l'axe X en rayons. Si le point de départ est X20 Z60 et si l’on désire usiner un arc de circonférence avec une approche en ligne droite, on programmera: Entrée tangentielle au début de l'usinage (G37) 6. COMMANDE DE LA TRAJECTOIRE 6.7 G90 G01 X20 Z30 G03 X40 Z10 R20 CNC 8035 MODÈLE ·T· (SOFT V16.3X) ·99· Manuel de programmation Dans ce même exemple, pour que l’entrée de l’outil sur la pièce à usiner soit tangente à la trajectoire en décrivant un rayon de 5 mm, on devra programmer: COMMANDE DE LA TRAJECTOIRE Entrée tangentielle au début de l'usinage (G37) 6. G90 G01 G37 R5 R5 X20 Z30 G03 X40 Z10 R20 Comme on peut le voir sur la figure, la CNC modifie la trajectoire afin que l’outil commence l’usinage avec une entrée tangentielle sur la pièce. La fonction G37 et la valeur R doivent être programmées dans le bloc contenant la trajectoire à modifier. La valeur de R5.5 doit toujours apparaître après G37; elle indique le rayon de l’arc que la CNC introduit pour obtenir une entrée tangentielle sur la pièce. Cette valeur de R doit toujours être positive. La fonction G37 ne peut être programmée que dans un bloc comportant un déplacement linéaire (G00 ou G01). Si elle est programmée dans un bloc comportant un déplacement circulaire (G02 ou G03), la CNC affiche l’erreur correspondante. CNC 8035 MODÈLE ·T· (SOFT V16.3X) ·100· Manuel de programmation Sortie tangentielle à la fin de l'usinage (G38) La fonction G38 permet de terminer une opération d’usinage par une sortie tangentielle de l’outil. La trajectoire suivante doit être une droite (G00 ou G01). Dans le cas contraire, la CNC affiche l’erreur correspondante. La fonction G38 est non-modale et doit donc être programmée pour chaque sortie tangentielle de l’outil. Exemple de programmation de l'axe X en rayons. Sortie tangentielle à la fin de l'usinage (G38) 6. La valeur de R5.5 doit toujours apparaître après G38; elle indique le rayon de l’arc que la CNC introduit pour obtenir une sortie tangentielle de la pièce. Cette valeur de R doit toujours être positive. COMMANDE DE LA TRAJECTOIRE 6.8 Si le point de départ est X10 Z50 et si l’on désire usiner un arc de circonférence avec une approche en ligne droite, on programmera: G90 G02 X30 Z30 R20 G01 X30 Z10 Dans ce même exemple, pour que la sortie d’usinage soit tangente à la trajectoire et décrive un rayon de 5 mm, on devra programmer: G90 G02 G38 R5 X30 Z30 R20 G00 X30 Z10 CNC 8035 MODÈLE ·T· (SOFT V16.3X) ·101· Manuel de programmation 6.9 Arrondissement commandé d'arêtes (G36) La fonction G36 permet d'arrondir une arête avec un rayon déterminé, sans avoir à calculer le centre ni les points initial et final de l'arc. La fonction G36 est non-modale et doit donc être programmée pour chaque arrondi des arêtes. Cette fonction doit être programmée dans le bloc définissant le déplacement pour lequel on désire un arrondi au point d’arrivée. 6. COMMANDE DE LA TRAJECTOIRE Arrondissement commandé d'arêtes (G36) La valeur de R5.5 doit toujours figurer après G36; elle indique le rayon que la CNC introduit pour obtenir l’arrondi désiré aux arêtes. Cette valeur de R doit toujours être positive. Exemple de programmation de l'axe X en diamètres. G90 G01 X20 Z60 G01 G36 R10 X80 Z10 G90 X20 Z60 G01 G36 R10 X80 G02 X60 Z10 I20 K-30 G90 X60 Z90 G02 G36 R10 X60 Z50 R28 X60 Z10 R28 CNC 8035 MODÈLE ·T· (SOFT V16.3X) ·102· Manuel de programmation Chanfreinage (G39) Dans les opérations d’usinage, la fonction G39 permet de chanfreiner des arêtes entre deux droites, sans avoir à calculer les points d’intersection. La fonction G39 est non-modale et doit donc être programmée pour chaque chanfrein d'une arête. Cette fonction doit être programmée dans le bloc contenant le déplacement dont le point d’arrivée doit être chanfreiné. Exemple de programmation de l'axe X en diamètres. G90 G01 X20 Z80 G01 G39 R10 X80 Z60 X100 Z10 Chanfreinage (G39) 6. La valeur de R5.5 doit toujours figurer après G39; elle indique la distance entre la fin du déplacement programmé et le point où le chanfrein doit être exécuté. Cette valeur de R doit toujours être positive. COMMANDE DE LA TRAJECTOIRE 6.10 CNC 8035 MODÈLE ·T· (SOFT V16.3X) ·103· Manuel de programmation 6.11 Filetage électronique (G33) Si la broche de la machine est pourvue d’un capteur rotatif, on peut réaliser des filets à pointe de lame avec la fonction G33. Même si souvent ce type de filetage se réalise le long d'un axe, la CNC permet de réaliser le filetage en interpolant plus d'un axe en même temps. Format de programmation : 6. Filetage électronique (G33) COMMANDE DE LA TRAJECTOIRE G33 X.....C L Q X...C ±5.5 Point final du filet L 5,5 Pas du filet Q ±3.5 Optionnel. Indique la position angulaire de la broche (±359.9999) correspondant au point initial du filet. Cela permet d'effectuer des filets aux multiples entrées. Si on ne le programme pas, on prend la valeur 0. Considérations Chaque fois que la fonction G33 est exécutée, si le p.m.b. M19TYPE (P43) =0, avant de réaliser le filetage électronique, la CNC effectue une recherche de référence machine de la broche. Pour pouvoir programmer le paramètre Q (position angulaire de la broche), il faut définir le paramètre machine de broche M19TYPE (P43) =1. Si on exécute la fonction G33 Q (p.m.b. M19TYPE (P43) =1), avant d’exécuter le filetage, il fallait avoir effectué une recherche de référence machine de broche après la dernière mise sous tension. Si on exécute la fonction G33 Q (p.m.b. M19TYPE (P43) =1) et le p.m.b. DECINPUT (P31) =NON, il n’est pas nécessaire de réaliser la recherche de référence machine de la broche car après la mise sous tension, la première fois que l’on fait tourner la broche en M3 ou M4, la CNC réalise automatiquement la recherche. Cette recherche sera effectuée à la vitesse définie par le p.m.b. REFEED2 (P35). Après avoir trouvé l’I0, la broche accélère ou décélère jusqu’à atteindre la vitesse programmée sans arrêter la broche. Si la broche dispose de système de mesure du moteur avec un codeur SINCOS (sans I0 de référence), la recherche s’effectuera directement à la vitesse programmée S, sans passer par la vitesse définie par le p.m.b. REFEED2. Si après la mise sous tension on exécute une M19 avant une M3 ou M4, cette M19 sera exécutée sans effectuer la recherche de zéro de la broche en exécutant la première M3 ou M4. Si le système de mesure n’a pas d’I0 synchronisé, la recherche d’I0 en M3 pourra ne pas coïncider avec la recherche en M4. Cela n'a pas lieu avec le système de mesure FAGOR. Si on travaille en arête arrondie (G05), on peut unir différents filets de façon continue dans une même pièce. Lorsque des raccords de filets sont réalisés, seul le premier filet pourra avoir un angle d’entrée (Q). Alors que la fonction G33 est active, on ne peut pas varier l'avance F programmée ni la vitesse de broche S programmée, les deux fonctions étant fixes à 100%. L’override de la broche est ignoré aussi bien dans l’usinage que dans le recul. La fonction G33 est modale et incompatible avec G00, G01, G02, G03, et G34. CNC 8035 MODÈLE ·T· (SOFT V16.3X) ·104· Au moment de la mise sous tension, après avoir exécuté M02, M30 ou après un ARRÊT D'URGENCE ou une RAZ, la CNC assume le code G00 ou le code G01 en fonction de la personnalisation du paramètre machine général "IMOVE" Manuel de programmation Exemples de programmation Dans les exemples suivants, l'axe X est programmé en diamètres. Filetage longitudinal On veut réaliser d'une seule passe un filet cylindrique de 2 mm de profondeur et 5 mm de pas. G90 G00 X200 Z190 X116 Z180 G33 Z40 L5 Filetage électronique (G33) COMMANDE DE LA TRAJECTOIRE 6. ; Filetage. G00 X200 Z190 Filetage longitudinal multiple On veut réaliser un filet cylindrique à deux entrées. Les filets sont déphasés 180º et ont chacun 2 mm de profondeur et un pas de 5 mm. G90 G00 X200 Z190 X116 Z180 G33 Z40 L5 Q0 ; Premier filet. G00 X200 CNC 8035 Z190 X116 Z180 G33 Z40 L5 Q180 G00 X200 ; Deuxième filet. MODÈLE ·T· (SOFT V16.3X) Z190 ·105· Manuel de programmation Filetage conique On veut réaliser d'une seule passe un filet conique de 2 mm de profondeur et 5 mm de pas. Filetage électronique (G33) COMMANDE DE LA TRAJECTOIRE 6. G90 G00 X200 Z190 X84 G33 X140 Z50 L5 ; Premier filet. G00 X200 Z190 Union de filets Il s'agit de joindre un filetage longitudinal et un filetage conique de 2 mm de profondeur et de 5 mm de pas. G90 G00 G05 X220 Z230 X96 G33 Z120 L5 ; Filetage longitudinal. Z160 Z60 L5 ; Filetage conique. G00 X200 CNC 8035 MODÈLE ·T· (SOFT V16.3X) ·106· Z230 Manuel de programmation Retrait des axes face à un arrêt lors du taraudage (G233) La fonction G233 permet de programmer la distance de sécurité à laquelle se retirent les axes en cas d’interruption d’un taraudage (G33), que ce soit en tapant sur [STOP] ou sur feedhold. Cette fonction est une fonction modale programmée seule dans le bloc et affichée dans l’historique. Cette fonction établit la sortie de filet pour tous les filetages programmés ensuite. S’il y a plusieurs fonctions G33 de suite et que l’on veut réaliser un retrait différent dans chacune d’elles, il faut programmer la fonction G233 correspondante avant chaque fonction G33. En tapant sur la touche [STOP] pendant l’exécution d’un taraudage alors que la fonction G233 est active, les axes se retirent suivant les distances programmées dans cette fonction. S’il y a un DSTOP actif après le retrait, les blocs suivants du programme continueront à être exécutés jusqu’à trouver un ESTOP. Format de programmation G233 X....C X...C +/-5.5 Distances de sortie du filet. Exemple: X: Distance incrémentale positive ou négative, lors du déplacement sur l'axe de sortie du filet (axe X). Z: Distance incrémentale, lors du déplacement sur l'axe du filet (axe Z). Retrait des axes face à un arrêt lors du taraudage (G233) 6. La fonction G233 peut être désactivée en la programmant seule dans le bloc ou en programmant toutes les cotes à zéro. Dans le deux cas, G233 disparaît de l'historique. COMMANDE DE LA TRAJECTOIRE 6.12 Point de sortie du filet. X Point final Point d'arrêt du cycle X STOP Z Point initial Z CNC 8035 MODÈLE ·T· (SOFT V16.3X) ·107· Manuel de programmation Exemple de programmation Programmation avec G33 et G233 d'un filet. N10 G90 G18 S500 M3 N20 G0 X20 N30 Z0 N40 X10 COMMANDE DE LA TRAJECTOIRE Retrait des axes face à un arrêt lors du taraudage (G233) 6. CNC 8035 MODÈLE ·T· (SOFT V16.3X) ·108· N50 G233 X5 Z-20 ;Bloc d'activation de retrait de filet (5mm sur X et -20mm en Z). N60 G33 Z-30 L5 ;Bloc de taraudage pouvant être interrompu avec STOP. N70 G33 X15 Z-50 L5 ;Bloc de sortie du filetage antérieur. Retrait des axes face à un arrêt dans les cycles fixes de taraudage (G86, G87) Dans les cycles fixes de taraudage (G86, G87), avec programmation de sortie de filet, il n'est pas nécessaire de programmer G233. Les distances de retrait seront celles indiquées dans les paramètres D et J de ce cycle. Dans l’exécution de ces cycles, en tapant sur la touche [STOP] ou sur feedhold, après s’être retiré, l’outil revient au point de départ du cycle. Après cela, la machine reste à l’arrêt en attente de l’ordre [START] pour répéter la passe interrompue. Manuel de programmation Filets à pas variable (G34) Pour effectuer des filets à pas variable, la broche de la machine doit disposer d'un capteur rotatif. Même si souvent ce type de filetage se réalise le long d'un axe, la CNC permet de réaliser le filetage en interpolant plus d'un axe en même temps. Format de programmation : G34 X.....C L Q K Point final du filet L 5,5 Pas du filet Q ±3.5 Optionnel. Indique la position angulaire de la broche (±359.9999) correspondant au point initial du filet. Si on ne le programme pas, on prend la valeur 0. K ±5.5 Incrément ou décrément de pas de filet par tour de la broche. Considérations À chaque exécution de la fonction G34 et avant de réaliser le filetage électronique, la CNC effectue une recherche de référence machine de la broche et situe celle-ci sur la position angulaire indiquée par le paramètre Q. Le paramètre "Q" est disponible quand on a défini le paramètre machine de broche "M19TYPE=1". 6. Filets à pas variable (G34) X...C ±5.5 COMMANDE DE LA TRAJECTOIRE 6.13 Si on travaille en arête arrondie (G05), on peut unir différents filets de façon continue dans une même pièce. Alors que la fonction G34 est active, on ne peut pas varier l'avance F programmée ni la vitesse de broche S programmée, les deux fonctions étant fixes à 100%. La fonction G34 est modale et incompatible avec G00, G01, G02, G03, et G33. Au moment de la mise sous tension, après avoir exécuté M02, M30 ou après un ARRÊT D'URGENCE ou une RAZ, la CNC assume le code G00 ou le code G01 en fonction de la personnalisation du paramètre machine général "IMOVE" Union d'un filetage à pas fixe (G33) avec un filetage à pas variable (G34). Le pas de filet initial (L) de G34 doit coïncider avec le pas de filet de la G33. L'incrément de pas dans le premier tour de broche en pas variable sera d'un demi-incrément (K/ 2) et pour les tours suivant, il sera l'incrément complet K. Union d'un filetage à pas variable (G34) avec un filetage à pas fixe. S'utilise pour terminer un filetage à pas variable (G34) avec un bout de filet gardant le pas final du filetage précédent. Le filetage à pas fixe ne se programme pas avec G33 mais avec G34 … L0 K0. Raccord de deux filets à pas variable (G34). On ne peut pas unir deux filetages à pas variable (G34). CNC 8035 MODÈLE ·T· (SOFT V16.3X) ·109· Manuel de programmation 6.14 Déplacement contre butée (G52) La fonction G52 permet de programmer le déplacement d’un axe jusqu’à une butée mécanique. Cette possibilité peut s’avérer intéressante pour les machines à cintrer, les contre-pointes motorisées, les dispositifs d’alimentation de barres, etc. Le format de programmation est: G52 X..C ±5.5 6. Déplacement contre butée (G52) COMMANDE DE LA TRAJECTOIRE Après la fonction G52, on programmera l’axe désiré ainsi que la coordonnée du point d’arrivée du déplacement. CNC 8035 MODÈLE ·T· (SOFT V16.3X) ·110· L’axe se déplace jusqu’au point programmé, jusqu’à ce qu’il parvienne à la butée. S’il parvient au point programmé sans que la butée soit atteinte, la CNC stoppe le déplacement. La fonction G52 est non-modale, et doit donc être programmée à chaque exécution d’un déplacement jusqu’à une butée. L’exécution de cette fonction suppose que les fonctions G01 et G40 soient actives, ce qui change l’historique du programme. C'est incompatible avec les fonctions G00, G02, G03, G33, G34, G41, G42, G75 et G76. Manuel de programmation Avance F comme fonction inverse du temps (G32) Parfois il est plus simple de définir le temps que les différents axes de la machine ont besoin pour effectuer le déplacement, que de fixer une vitesse d'avance commune pour tous. Un cas typique se produit quand on veut effectuer de manière conjointe le déplacement des axes linéaires de la machine X, Z et le déplacement d'un axe rotatif programmé en degrés. La fonction G32 indique que les fonctions "F" programmées à continuation fixent le temps avec le quel le déplacement doit être effectué. Unités de "F": 1/min Exemple: G32 X22 F4 Indique que le mouvement doit être exécuté en ¼ de minute, c'est-à-dire, en 0.25 minutes. La fonction G32 est modale et incompatible avec G94 et G95. Au moment de la mise sous tension, après avoir exécuté M02, M30 ou après un arrêt d'urgence ou un Reset, la CNC assumera le code G94 ou G95 en fonction de la personnalisation du paramètre machine général "IFEED". Considérations La CNC affichera dans la variable PRGFIN l'avance en fonction inverse du temps qui a été programmée, et dans la variable FEED l'avance résultante en mm/min. ou pouce/min. Si l'avance résultante d'un axe quelconque dépasse le maximum fixé dans le paramètre machine général "MAXFEED", la CNC applique ce maximum. 6. Avance F comme fonction inverse du temps (G32) Dans le but qu'un numéro plus grand de "F" indique une vitesse d'avance plus grande, la valeur affectée à "F" est définie comme "Fonction inverse du temps" et est interprétée comme activation de l'avance en fonction inverse du temps. COMMANDE DE LA TRAJECTOIRE 6.15 Dans les déplacements en G00 on ne tient pas compte de la "F" programmée. Tous les déplacements s'effectuent avec l'avance indiquée dans le paramètre machine d'axes "G00FEED". Si on programme "F0" le déplacement s'effectue avec l'avance indiquée dans le paramètre machine d'axes "MAXFEED". La fonction G32 peut être programmée et exécutée dans le canal de PLC. La fonction G32 se désactive en mode JOG. CNC 8035 MODÈLE ·T· (SOFT V16.3X) ·111· ·112· COMMANDE DE LA TRAJECTOIRE Avance F comme fonction inverse du temps (G32) Manuel de programmation 6. CNC 8035 MODÈLE ·T· (SOFT V16.3X) FONCTIONS PRÉPARATOIRES SUPPLÉMENTAIRES 7.1 7 Interrompre la préparation de blocs (G04) La CNC peut lire jusqu’à 20 blocs en avant du bloc en cours d’exécution, afin de calculer à l’avance la trajectoire à parcourir. Chaque bloc est évalué (en son absence) lors de sa lecture, mais la fonction G04 permet son évaluation au moment de son exécution. Cette fonction interrompt la préparation des blocs et attend l’exécution d’un bloc donné avant de reprendre cette préparation. Un cas de ce type est l’évaluation de la "condition de saut de bloc", qui est définie dans l’en-tête du bloc. Exemple: . . G04 /1 G01 X10 Z20 ; Interruption de la préparation de blocs ; Condition de saut "/1" . . La fonction G04 est non-modale et doit donc être programmée à chaque interruption de la préparation de blocs. Elle doit être programmée seule dans le bloc précédant celui où doit s’effectuer l’évaluation pendant l’exécution. La fonction G04 peut être programmée sous la forme G4. Chaque programmation de G04 annule temporairement la compensation et de longueur actives. Pour cette raison, on n’utilisera cette fonction qu’avec précautions car, si elle est insérée entre des blocs d’usinage travaillant en compensation, des formes indésirables pourraient être produites. CNC 8035 MODÈLE ·T· (SOFT V16.3X) ·113· Manuel de programmation Exemple: Les blocs de programme suivants sont exécutés dans une section comportant une compensation G41. ... N10 X80 Z50 N15 G04 /1 N17 M10 N20 X50 Z50 N30 X50 Z80 7. Interrompre la préparation de blocs (G04) FONCTIONS PRÉPARATOIRES SUPPLÉMENTAIRES ... Le bloc N15 interrompt la préparation des blocs; l’exécution du bloc N10 se terminera donc au point A. Lorsque l’exécution du bloc N15 est terminée, la CNC reprend la préparation des blocs à partir du bloc N17. Comme le point suivant correspondant à la trajectoire compensée est le point "B", la CNC déplacera l’outil jusqu’à ce point, en exécutant la trajectoire "A-B". Comme on peut le constater, la trajectoire obtenue n’est pas celle désirée; il est donc recommandé d’éviter d’utiliser la fonction G04 dans des sections travaillant en compensation. CNC 8035 MODÈLE ·T· (SOFT V16.3X) ·114· Manuel de programmation G04 K0: Interruption de la préparation de blocs et actualisation de cotes Avec la fonctionnalité associée à G04 K0, il est possible, après certaines manœuvres de PLC, d’actualiser les cotes des axes du canal. Les manœuvres de PLC demandant une actualisation des cotes des axes du canal sont les suivantes : • Manœuvre du PLC avec les marques SWITCH*. Fonctionnement de G04. Fonction Description G04 Interrompt la préparation des blocs. G04 K50 Exécute une temporisation de 50 centièmes de seconde. G04 K0 ou G04 K Interrompt la préparation de blocs et l’actualisation des cotes de la CNC à la position actuelle. (G4 K0 fonctionne dans le canal de CNC et PLC). Interrompre la préparation de blocs (G04) 7. • Manœuvres de PLC dans lesquelles un axe devient axe de référence, puis redevient axe normal pendant l’exécution de programmes pièce. FONCTIONS PRÉPARATOIRES SUPPLÉMENTAIRES 7.1.1 CNC 8035 MODÈLE ·T· (SOFT V16.3X) ·115· Manuel de programmation 7.2 Temporisation (G04 K) La fonction G04 K permet de programmer une temporisation. La valeur de la temporisation est programmée en centièmes de seconde selon le format K5 (1..99999). Exemple: Temporisation (G04 K) FONCTIONS PRÉPARATOIRES SUPPLÉMENTAIRES 7. CNC 8035 MODÈLE ·T· (SOFT V16.3X) ·116· G04 K50 ; Temporisation de 50 centièmes de seconde (0.5 secondes) G04 K200 ; Temporisation de 200 centièmes de seconde (2 secondes) La fonction G04 K est non-modale, et doit donc être programmée à chaque temporisation. La fonction G04 K peut être programmée sous la forme G4 K. La temporisation est exécutée au début du bloc dans lequel elle est programmée. Note: Si on programme G04 K0 ou G04 K, au lieu de la temporisation, il se produira une interruption de préparation de blocs et une actualisation de cotes. Voir "7.1.1 G04 K0: Interruption de la préparation de blocs et actualisation de cotes" à la page 115. Manuel de programmation 7.3 Travail sur arête vive (G07) et arrondie (G05,G50) 7.3.1 Arête vive (G07) Dans le cas du travail en G07 (arête vive), la CNC ne commence pas l’exécution du bloc de programme suivant tant que la position programmée dans le bloc en cours n’a pas été atteinte. La CNC considère que la position programmée a été atteinte quand l’axe se situe à une distance inférieure à "INPOSW" (fenêtre d'arrêt) par rapport à la position programmée. -120 Les profils théorique et réel coïncident et permettent d’obtenir des arêtes vives comme le montre la figure. La fonction G07 est modale et incompatible avec G05, G50 et G51. La fonction G07 peut être programmée sous la forme G7. Travail sur arête vive (G07) et arrondie (G05,G50) Z FONCTIONS PRÉPARATOIRES SUPPLÉMENTAIRES G91 G01 G07 X100 F100 7. A la mise sous tension, après exécution de M02, M30 ou après un ARRÊT D'URGENCE ou une RAZ, la CNC prend en compte le code G05 ou G07 selon l’état du paramètre machine général "ICORNER" CNC 8035 MODÈLE ·T· (SOFT V16.3X) ·117· Manuel de programmation 7.3.2 Arête arrondie (G05) Lorsqu'on travaille en G05 (arête arrondie), la CNC démarre l'exécution du bloc suivant du programme, une fois achevée l'interpolation théorique du bloc actuel. N'attend pas à ce que les axes soient en position. La distance entre la position programmée et celle où commence l’exécution du bloc suivant dépend de la vitesse d’avance des axes. Travail sur arête vive (G07) et arrondie (G05,G50) FONCTIONS PRÉPARATOIRES SUPPLÉMENTAIRES 7. CNC 8035 MODÈLE ·T· (SOFT V16.3X) ·118· G91 G01 G05 X100 F100 Z -120 Cette fonction permet d’obtenir des arrondis aux angles, comme le montre la figure. La différence entre les profils théorique et réel dépend de la valeur de l’avance F programmée. Plus l’avance est grande, plus la différence entre les deux profils est importante. La fonction G05 est modale et incompatible avec G07, G50 et G51. La fonction G05 peut être programmée sous la forme G5. A la mise sous tension, après exécution de M02, M30 ou après un ARRÊT D'URGENCE ou une RAZ, la CNC prend en compte le code G05 ou G07 selon l’état du paramètre machine général "ICORNER" Manuel de programmation Arête arrondie commandée (G50) Dans le cas du travail en G50 (arête arrondie commandée), la CNC attend, après la fin de l’interpolation théorique du bloc actuel, que l’axe pénètre dans la zone définie par le paramètre machine "INPOSW2" avant de poursuivre l’exécution du bloc suivant. Z -120 La fonction G50 s’assure que la différence entre les profils théorique et réel reste inférieure à celle définie par le paramètre machine "INPOSW2". Au contraire, si l’on travaille avec la fonction G05, cette différence dépend de la valeur de l’avance F programmée. Plus l’avance est grande, plus la différence entre les deux profils est importante. La fonction G50 est modale et incompatible avec G07, G05 et G51. A la mise sous tension, après exécution de M02, M30 ou après un ARRÊT D'URGENCE ou une RAZ, la CNC prend en compte le code G05 ou G07 selon l’état du paramètre machine général "ICORNER" Travail sur arête vive (G07) et arrondie (G05,G50) 7. G91 G01 G50 X100 F100 FONCTIONS PRÉPARATOIRES SUPPLÉMENTAIRES 7.3.3 CNC 8035 MODÈLE ·T· (SOFT V16.3X) ·119· Manuel de programmation 7.4 Analyse par anticipation ("Look-ahead") (G51) L'exécution de programmes formés par des blocs avec des déplacements très petits (CAM, etc.) peuvent avoir tendance à ralentir. La fonction look-ahead permet d'atteindre une vitesse d'usinage élevée dans l'exécution de ces programmes. La fonction look-ahead analyse à l'avance la trajectoire à usiner (jusqu'à 75 blocs) pour calculer l'avance maximum dans chaque segment. Cette fonction permet d'obtenir un usinage doux et rapide dans des programmes avec des déplacements très petits, même de l'ordre de microns. 7. Analyse par anticipation ("Look-ahead") (G51) FONCTIONS PRÉPARATOIRES SUPPLÉMENTAIRES Il est conseillé de disposer de l'option CPU-TURBO lorsqu'on utilise la fonction look-ahead. Lorsque la fonction "Look-Ahead" est activée, il est judicieux de régler les axes de façon que leur erreur de poursuite soit la plus faible possible car l’erreur de l’usinage de contour est au moins égale à l’erreur de poursuite minimum. Format de programmation. Le format de programmation est: G51 [A] E B A (0-255) Il est optionnel et définit le pourcentage d’accélération à appliquer. S’il n’est pas programmé ou programmé avec une valeur "0", la CNC prend la valeur d’accélération définie par le paramètre machine pour chaque axe. E (5.5) Erreur de contour permis. Plus ce paramètre sera petit, plus l'avance d'usinage sera petite. B (0-180) Il permet d'usiner les angles comme arête vive, avec la fonction Look-ahead. Il indique la valeur angulaire (en degrés) des angles programmés, en dessous de laquelle l’usinage est réalisé comme arête vive. Bloc I Bloc I+1 B Le paramètre "A" permet l’application d’une accélération de travail standard et d’une autre accélération utilisable avec l’analyse par anticipation. Si le paramètre "B" n'est pas programmé, la gestion d’arête vive dans les angles est annulée. La gestion d’arête vive dans les angles est valide, aussi bien pour l’algorithme de Look-ahead avec gestion de jerk que pour l’algorithme de Look-ahead sans gestion de jerk. Considérations sur l'exécution. À l'heure de calculer l'avance, la CNC tient compte de ceci : • L’avance programmée. • Le rayon de courbure et les angles. • L'avance maximum des axes. CNC 8035 MODÈLE ·T· (SOFT V16.3X) ·120· • Les accélérations maximales. • Le jerk. Manuel de programmation Si, pendant l’exécution avec l’analyse par anticipation active, il se produit l’un des évènements cidessous, la CNC ralentit la vitesse appliquée au bloc précédent jusqu’à "0" et reprend les conditions d’usinage en "analyse par anticipation" dans le bloc à déplacement suivant. • Bloc sans déplacement. • Exécution de fonctions auxiliaires (M, S, T). • Exécution bloc par bloc. • Mode MDI. • Mode d'inspection d'outil. Propriétés de la fonction. La fonction G51 est modale et incompatible avec G05, G07 et G50. Si l’une de ces fonctions est programmée, la fonction G51 est annulée et la nouvelle fonction sélectionnée est activée. La fonction G51 doit être programmée seule dans un bloc; aucune autre information n’est admise. A la mise sous tension, après l’exécution de M02, M30 ou après un ARRÊT D'URGENCE ou une RAZ, la CNC annule G51 si elle était active et elle prend G05 ou G07 en fonction du réglage du paramètre machine général ‘ICORNER". La CNC émet l’erreur 7 (fonctions G incompatibles) si l’une des fonctions suivantes est programmée pendant que la fonction G51 est active. G33 Filetage électronique. G34 Filetage à pas variable G52 Déplacement contre butée. G95 Avance par tour. Analyse par anticipation ("Look-ahead") (G51) Pour éviter que les blocs sans déplacement ne provoquent un effet d’arête vive, modifier le bit 0 du paramètre machine général MANTFCON (P189). 7. FONCTIONS PRÉPARATOIRES SUPPLÉMENTAIRES Si "Stop", "Feed Hold", etc... se produisent pendant l’exécution en mode "Par anticipation", la machine risque de ne pas stopper sur le bloc actuel, et plusieurs blocs seront nécessaires avant d’obtenir l’arrêt selon la décélération autorisée. CNC 8035 MODÈLE ·T· (SOFT V16.3X) ·121· Manuel de programmation 7.4.1 Algorithme avancé de look-ahead (intégrant des filtres Fagor) Ce mode est indiqué lorsqu’on veut de la précision dans l’usinage, en particulier s’il y a des filtres Fagor définis par paramètre machine sur les axes. L'algorithme avancé de la fonction look-ahead, exécute le calcul des vitesses des angles, de façon à prendre en compte l'effet des filtres Fagor actifs sur ces vitesses. En programmant G51 E, les erreurs de contour dans les usinages des angles s’ajusteront à la valeur programmée en G51, en fonction des filtres. 7. Analyse par anticipation ("Look-ahead") (G51) FONCTIONS PRÉPARATOIRES SUPPLÉMENTAIRES Pour activer l'algorithme avancé de look-ahead, utiliser le bit 15 du p.m.g. LOOKATYP (P160). Considérations • S’il n’y a pas de filtres Fagor définis avec des paramètres machine sur les axes du canal principal, en activant l'algorithme avancé de look-ahead, des filtres Fagor d’ordre 5 et de fréquence 30Hz s’activent internement sur tous les axes du canal. • Si des filtres Fagor sont définis avec des paramètres machine, en activant l'algorithme avancé de look-ahead, les valeurs de ces filtres seront conservées à condition que leur fréquence ne dépasse pas 30Hz. Au cas où sa fréquence dépasserait 30Hz, les valeurs d’ordre 5 et de fréquence 30Hz seront prises. S’il y a plusieurs filtres définis sur les axes du canal, c’est celui avec la fréquence la plus basse qui sera pris, à condition que la fréquence de 30Hz ne soit pas dépassée. • Même si l'algorithme avancé de look-ahead (en utilisant des filtres Fagor) est actif avec le bit 15 du p.m.g. LOOKATYP (P160), il n’entrera pas en fonctionnement dans les cas suivants Si le p.m.g. IPOTIME (P73) = 1. Si l’un des axes du canal principal au p.m.a. SMOTIME (P58) différent de 0. Si l’un des axes du canal principal a un filtre défini par paramètre et dont le type n’est pas Fagor, p.m.a. TYPE (P71) différent de 2. Dans ces cas, en activant la G51, la CNC affichera l’erreur correspondante. CNC 8035 MODÈLE ·T· (SOFT V16.3X) ·122· Manuel de programmation Fonctionnement de look-ahead avec des filtres Fagor actifs. Cette option permet d’utiliser des filtres Fagor avec la fonction look-ahead (algorithme de lookahead non avancé). Ne sera prise en compte que si l’algorithme avancé de look-ahead est désactivé, c’est-à-dire, si le bit 15 du p.m.g. LOOKATYP (P-160)=0. Pour activer/désactiver cette position, utiliser le bit 15 du p.m.g. LOOKATYP (P160). Dans l’usinage de cercles, en utilisant la fonction Fagor, l’erreur sera inférieure que si on n’utilise pas ces filtres. Déplacement programmé. Déplacement réel en utilisant des filtres Fagor. Déplacement réel sans utiliser des filtres Fagor. Analyse par anticipation ("Look-ahead") (G51) 7. Effet des filtres Fagor dans l’usinage de cercles. FONCTIONS PRÉPARATOIRES SUPPLÉMENTAIRES 7.4.2 CNC 8035 MODÈLE ·T· (SOFT V16.3X) ·123· Manuel de programmation 7.4.3 Adoucissement de la vitesse d'usinage. En fonction de la puissance de processus de la CNC (qui dépend du modèle et du paramétrage) et en fonction aussi du type de pièce usinée, la gestion de l’adoucissement de F (vitesse d’avance d’usinage) s’active pour parvenir à maintenir celle-ci stable. On obtient ainsi plus de douceur d’usinage dans des programmes exigeants en capacité de calcul (programmes avec petits blocs et haute vitesse programmée). Cette option est valide pour n’importe quel algorithme de look-ahead. Pour activer cette option on utilisera le bit 14 du paramètre machine général LOOKATYP (P160). Analyse par anticipation ("Look-ahead") (G51) FONCTIONS PRÉPARATOIRES SUPPLÉMENTAIRES 7. CNC 8035 MODÈLE ·T· (SOFT V16.3X) ·124· i Si on active cette option avec l’algorithme de look-ahead avec gestion de jerk, (bit 0 du p.m.g. LOOKATYP (P160)=1), il n’est pas nécessaire de régler le paramètre machine général TLOOK (P161). Manuel de programmation Image miroir (G11, G12, G13, G10, G14) Les fonctions pour activer l'image miroir sont les suivantes. Annulation image miroir. G11: Image miroir sur l’axe X. G12: Image miroir sur l’axe Y. G13: Image miroir sur l’axe Z. G14: Image miroir sur n’importe quel axe (X..C) ou sur plusieurs à la fois. 7. Exemples: G14 W G14 X Z A B Lorsque la fonction image miroir est activée, la CNC exécute les déplacements programmés sur les axes pour lesquels l’image miroir est active, en changeant le signe. La sous-routine suivante définit l’usinage de la pièce "A". Image miroir (G11, G12, G13, G10, G14) G10: FONCTIONS PRÉPARATOIRES SUPPLÉMENTAIRES 7.5 G90 G00 X40 Z150 G02 X80 Z110 R60 G01 Z60 X120 Z0 La programmation de l’ensemble des pièces sera: Exécution de la sous-routine; Usine "A". G13 Image miroir sur l'axe Z. Exécution de la sous-routine; Usine "B". M30 ; Fin de programme Les fonctions G11, G12, G13 et G14 sont modales et incompatibles avec G10. G11, G12 et G13 peuvent être programmées dans le même bloc, puisqu’elles ne sont pas incompatibles entre elles. La fonction G14 doit être programmée seule dans un bloc, aucune information ne pouvant plus exister dans ce bloc. Si une nouvelle origine de coordonnées est présélectionnée par G92 pendant que l’une des fonctions miroir (G11, G12, G13, G14) est active, cette nouvelle origine n’est pas affectée par la fonction image miroir. A la mise sous tension, après exécution de M02, M30 ou après un ARRÊT D'URGENCE ou une RAZ, la CNC prendra en compte le code G10. CNC 8035 MODÈLE ·T· (SOFT V16.3X) ·125· Manuel de programmation 7.6 Facteur d'échelle (G72) La fonction G72 permet d’agrandir ou de réduire les pièces programmées. Ainsi, avec un seul programme on peut réaliser ainsi des familles de pièces semblables mais avec des dimensions différentes. La fonction G72 doit être programmée seule dans un bloc. Deux formats de programmation de la fonction G72 sont disponibles: 7. • Facteur d’échelle appliqué à tous les axes. Facteur d'échelle (G72) FONCTIONS PRÉPARATOIRES SUPPLÉMENTAIRES • Facteur d’échelle appliqué à un ou plusieurs axes. CNC 8035 MODÈLE ·T· (SOFT V16.3X) ·126· Manuel de programmation Facteur d’échelle appliqué à tous les axes. Le format de programmation est: G72 S5.5 Toutes les coordonnées programmées après G72 sont multipliées par la valeur du facteur d’échelle défini par S, jusqu’à la lecture d’une nouvelle définition de facteur d’échelle G72 ou jusqu’à son annulation. La sous-routine suivante définit l'usinage basique. G90 X200 Z0 G01 X200 Z30 F150 Facteur d'échelle (G72) 7. Exemple de programmation de l'axe X en diamètres. FONCTIONS PRÉPARATOIRES SUPPLÉMENTAIRES 7.6.1 G01 X160 Z40 G03 X160 Z60 I0 J10 G02 X160 Z80 I0 J10 G03 X160 Z100 I0 J10 G02 X160 Z120 I0 J10 La programmation des deux pièces sera: Exécution de la sous-routine. Usine "A1". G92 Z0 ; Présélection de cotes (décalage d'origine de coordonnées) G72 S0.5 ; Application du facteur d’échelle 2. Exécution de la sous-routine. Usine "A2". G72 S1 ; Annulation du facteur d’échelle M30 ; Fin de programme La fonction G72 est modale, et sera annulée par la programmation d’un autre facteur d’échelle S1, à la mise sous tension, après exécution de M02, M30 ou après un ARRÊT D'URGENCE ou une RAZ. CNC 8035 MODÈLE ·T· (SOFT V16.3X) ·127· Manuel de programmation 7.6.2 Facteur d'échelle appliqué à un ou plusieurs axes Le format de programmation est: G72 X...C 5.5 Le ou les axes et le facteur d’échelle désirés sont programmés après G72. Tous les blocs programmés après G72 sont traités comme suit par la CNC: 1. La CNC calcule les déplacements de tous les axes en fonction de la trajectoire et de la compensation programmées. Facteur d'échelle (G72) FONCTIONS PRÉPARATOIRES SUPPLÉMENTAIRES 7. 2. Ensuite, elle applique le facteur d’échelle indiqué au déplacement calculé du ou des axes correspondants. Si le facteur d’échelle est appliqué à un ou plusieurs axes, la CNC appliquera le facteur d’échelle indiqué à la fois au déplacement et à l’avance du ou des axes correspondants. Si, dans le même programme, les deux types de facteurs d’échelle sont appliqués (celui s’adressant à tous les axes et celui s’adressant à un ou plusieurs axes), la CNC applique à l’axe ou aux axes concernés par les deux types un facteur égal au produit des deux facteurs programmés pour cet axe. La fonction G72 est modale et sera annulée par la programmation d’un autre facteur d’échelle, à la mise sous tension, après exécution de M02, M30 ou après un ARRÊT D'URGENCE ou une RAZ. i En réalisant des simulations sans déplacement d'axes ce type de facteur d'échelle est ignoré. Application du facteur d’échelle de l'axe Z, lorsqu'on travaille en compensation radiale de l'outil. Comme on peut le constater, la trajectoire de l’outil ne coïncide pas avec la trajectoire désirée, en raison de l’application du facteur d’échelle au déplacement calculé. CNC 8035 MODÈLE ·T· (SOFT V16.3X) ·128· Manuel de programmation Si un facteur d’échelle égal à 360/2R est appliqué à un axe rotatif, R étant le rayon du cylindre sur lequel l’usinage est exécuté, cet axe peut être considéré comme linéaire, et il est possible de programmer n’importe quelle forme avec compensation de rayon sur la surface cylindrique. Exemple avec programmation de l’axe X en diamètres, en présumant que le rayon pour réaliser la rainure sur le cylindre est R20. Facteur d'échelle à appliquer = 360/(2R) = 2.86 Facteur d'échelle (G72) FONCTIONS PRÉPARATOIRES SUPPLÉMENTAIRES 7. G16 ZC G90 G42 G01 Z70 C0 ; Positionnement sur le point initial G91 X-4 ; Pénétration G72 C2.86 ; Facteur d'échelle G90 G36 R5 C45 G36 R5 Z130 C90 G36 R5 C112.5 G36 R5 Z190 C157.5 G36 R5 C202.5 G36 R5 Z130 C247.5 G36 R5 C270 G36 R5 Z70 C315 G36 R5 C360 G91 X4 ; Retrait G72 C1 ; Annule le facteur d'échelle M30 CNC 8035 MODÈLE ·T· (SOFT V16.3X) ·129· Manuel de programmation Facteur d'échelle (G72) FONCTIONS PRÉPARATOIRES SUPPLÉMENTAIRES 7. CNC 8035 MODÈLE ·T· (SOFT V16.3X) ·130· COMPENSATION D'OUTILS 8.1 8 La compensation de longueur Elle s’applique toujours pour compenser la différence de longueur entre les différents outils programmés. En sélectionnant un nouvel outil, la CNC prend compte de ses dimensions, qui sont définies dans le correcteur correspondant, et déplace la tourelle porte-outils pour que la pointe du nouvel outil occupe la même position (cote) que la précédente. CNC 8035 MODÈLE ·T· (SOFT V16.3X) ·131· Manuel de programmation 8.2 La compensation de rayon Il faut la programmer. La CNC assume comme pointe théorique (P) la résultante des faces utilisées dans le calibrage de l’outil (figure de gauche). Sans compensation de rayon, la pointe théorique (P) parcourt la trajectoire programmée (figure centrale) en laissant des surépaisseurs d’usinage. Avec compensation de rayon il faut tenir compte du rayon de la pointe et du facteur de forme ou type d’outil et on obtient les dimensions correctes de la pièce programmée (figure de droite). La compensation de rayon COMPENSATION D'OUTILS 8. La CNC indique toujours la position de la pointe théorique. Par cela, en travaillant avec compensation de rayon, les cotes et la représentation graphique ne coïncident pas toujours avec le parcours programmé. Parcours programmé. Compensation de rayon. La CNC tient compte du rayon de l’outil pour obtenir les dimensions correctes de la pièce programmée. La CNC n’affiche pas le parcours du centre de l’outil mais affiche la position qu’occupe la pointe théorique. Le parcours de la pointe théorique coïncide en partie avec le profil programmé dans les chariotages et surfaçages, mais ne coïncide jamais avec les segments inclinés et courbes. CNC 8035 MODÈLE ·T· (SOFT V16.3X) ·132· Manuel de programmation Le facteur de forme de l'outil Le facteur de forme indique le type d’outil et les faces qui ont été utilisées pour le calibrage. Il dépend de la position de l'outil et de l'orientation des axes de la machine. L’exemple suivant indique le facteur de forme F3 sur différentes machines. Observer comment se maintient la position relative de l’outil par rapport aux axes. Tours horizontaux La compensation de rayon 8. COMPENSATION D'OUTILS 8.2.1 Tours verticaux CNC 8035 MODÈLE ·T· (SOFT V16.3X) ·133· Manuel de programmation Ensuite sont affichés les facteurs de forme disponibles sur les tours horizontaux les plus communs. La compensation de rayon COMPENSATION D'OUTILS 8. CNC 8035 MODÈLE ·T· (SOFT V16.3X) ·134· Manuel de programmation La compensation de rayon COMPENSATION D'OUTILS 8. CNC 8035 MODÈLE ·T· (SOFT V16.3X) ·135· Manuel de programmation 8.2.2 Travail sans compensation de rayon d’outil Il existe certaines limitations pour travailler sans compensation de rayon. Facteur de forme de l'outil. On ne doit utiliser que des outils qui ont été calibrés en touchant leurs deux faces, facteurs de forme F1, F3, F5, F7, etc. L’usinage avec les autres outils n’est pas recommandable étant donné que la pointe théorique de l’outil parcourt la trajectoire programmée (la zone sombre sur figure de droite est supprimée). La compensation de rayon COMPENSATION D'OUTILS 8. Segments d'usinage On ne peut réaliser que des chariotages de faces avec diamètre constant (figure de gauche) ou des surfaçages de parois droites (figure de droite). Il y a des problèmes sur des segments inclinés (figure de gauche) et sur des faces arrondies (figure de droite). CNC 8035 MODÈLE ·T· (SOFT V16.3X) ·136· Manuel de programmation Surfaçage de parois droites. Pour effectuer un surfaçage jusqu’à la cote 0 (par exemple, de la cote 40 à la cote 0) la pointe théorique de l’outil arrive jusqu'à la cote 0, mais à cause de l’arrondissement de la pointe, il reste une partie saillante sur la pièce. Pour résoudre ce problème, réaliser le surfaçage jusqu’à la cote négative (par exemple de la cote 40 à la cote -3). La compensation de rayon COMPENSATION D'OUTILS 8. CNC 8035 MODÈLE ·T· (SOFT V16.3X) ·137· Manuel de programmation 8.2.3 Travail avec compensation de rayon d’outil En travaillant avec compensation de rayon, le rayon de la pointe et le facteur de forme emmagasinés dans la table de correcteurs correspondant à l’outil sont pris en compte pour obtenir les dimensions correctes de la pièce programmée. Tous les outils ont un correcteur associé (dans la table d’outils). Pour sélectionner un autre correcteur utiliser le code "D". Si aucun correcteur n’a été programmé, la CNC applique le correcteur D0, avec X=0, Z=0, F=0, R=0, I=0 et K=0. 8. La compensation de rayon COMPENSATION D'OUTILS On peut aussi définir les dimensions de l’outil avec les variables TOX, TOZ, TOF, TOR, TOI, TOK. Trois fonctions préparatoires sont disponibles pour la compensation de rayon d’outil: G40 Annulation de la compensation de rayon d’outil. G41 Compensation de rayon d’outil à gauche. G42 Compensation de rayon d’outil à droite. Les fonctions G41 et G42 sont modales et incompatibles entre elles. Elles sont annulées par G40, G04 (interruption de la préparation des blocs), G53 (programmation par rapport au zéro machine), G74 (recherche du zéro), G66, G68, G69, G83 (cycles fixes d’usinage), ainsi qu’à la mise sous tension, après exécution de M02, M30 ou après un arrêt d'urgence ou une RAZ. Tours horizontaux Tours verticaux CNC 8035 MODÈLE ·T· (SOFT V16.3X) ·138· Manuel de programmation Début de compensation de rayon de l'outil (G41, G42) Après avoir sélectionné le plan dans lequel on désire appliquer la compensation de rayon d'outil, on doit utiliser les fonctions G41 ou G42 pour initier cette compensation. Compensation de rayon d’outil à gauche. G42 Compensation de rayon d’outil à droite. Dans le bloc contenant G41 ou G42 (ou dans un bloc précédent), les fonctions T et D ou T seule doivent être programmées pour sélectionner, dans la table de correcteurs, la valeur de la correction à appliquer. Si aucun correcteur n’est sélectionné, la CNC prendra D0 avec les valeurs X0 Z0 F0 R0 I0 K0. Lorsque la fonction M06 est associée au nouvel outil et qu’une sous-routine est associée à M06, la CNC active la compensation de rayon d’outil au premier bloc de cette sous-routine comportant un déplacement. Si dans cette sous-routine on exécute un bloc dans lequel la fonction G53 est programmée, (programmation en cotes machine), dans ce bloc on annule temporairement la fonction G41 ou G42 sélectionnée préalablement. La sélection de la compensation de rayon d’outil (G41 ou G42) n’est possible que lorsque les fonctions G00 ou G01 sont actives (déplacements rectilignes). Si la compensation est sélectionnée alors que la fonction G02 ou G03 est active, la CNC affiche l’erreur correspondante. 8. La compensation de rayon G41 COMPENSATION D'OUTILS 8.2.4 Ensuite sont affichés plusieurs cas d’activation de compensation de rayon d’outil, dans lesquels la trajectoire programmée figure en traits pleins, tandis que la trajectoire du centre de l'outil est en trait discontinu. Début de la compensation sans déplacement programmé Après avoir activé la compensation, il se peut que les axes du plan n'interviennent pas dans le premier bloc de déplacement, bien parce qu'ils n'ont pas été programmés, parce qu'on a programmé le même point où se trouve l'outil ou bien parce qu'on a programmé un déplacement incrémental nul. Dans ce cas, la compensation s'effectue au point où se trouve l'outil en fonction du premier déplacement programmé sur le plan, l'outil se déplace perpendiculairement à la trajectoire sur son point initial. Le premier déplacement programmé dans le plan pourra être linéaire ou circulaire. Y X Y X ··· G90 G01 Y40 G91 G40 Y0 Z10 G02 X20 Y20 I20 J0 ··· (X0 Y0) ··· G90 G01 X-30 Y30 G01 G41 X-30 Y30 Z10 G01 X25 ··· (X0 Y0) CNC 8035 MODÈLE ·T· (SOFT V16.3X) ·139· Manuel de programmation Trajectoire DROITE - DROITE La compensation de rayon COMPENSATION D'OUTILS 8. CNC 8035 MODÈLE ·T· (SOFT V16.3X) ·140· Manuel de programmation Trajectoire DROITE-COURBE La compensation de rayon COMPENSATION D'OUTILS 8. CNC 8035 MODÈLE ·T· (SOFT V16.3X) ·141· Manuel de programmation 8.2.5 Segments de compensation de rayon d'outil La CNC peut lire jusqu’à 50 blocs en avant du bloc en cours d’exécution, afin de calculer à l’avance la trajectoire à parcourir. Lorsque la CNC travaille en compensation de rayon, elle doit connaître le déplacement programmé suivant, afin de calculer la trajectoire à parcourir. En conséquence, on ne doit pas programmer plus de 48 blocs successifs ou plus sans déplacement. Les schémas suivants montrent les différentes trajectoires décrites par un outil contrôlé par une CNC programmée avec une compensation de rayon d’outil. La trajectoire programmée est représentée avec un trait continu et la trajectoire compensée avec un trait discontinu. La compensation de rayon COMPENSATION D'OUTILS 8. La façon dont sont reliées les différentes trajectoires dépend de la personnalisation du paramètre machine COMPMODE. • S'il a été personnalisé avec valeur ·0·, la méthode de compensation dépend de l'angle entre trajectoires. Avec un angle entre trajectoires maximum de 300º, les deux trajectoires s'unissent avec des segments droits. Dans les autres cas, les deux trajectoires s'unissent avec des segments circulaires. • Si la longueur a été personnalisée avec valeur ·1·, les deux trajectoires s'unissent avec des segments circulaires. CNC 8035 • S'il a été personnalisé avec valeur ·2·, la méthode de compensation dépend de l'angle entre trajectoires. Avec un angle entre trajectoires maximum de 300º, on calcule l'intersection. Dans les autres cas, est compensé comme COMPMODE = 0. MODÈLE ·T· (SOFT V16.3X) ·142· Manuel de programmation Annulation de compensation de rayon d’outil (G40) La compensation de rayon d’outil est annulée par la fonction G40. Ne pas oublier que l’annulation de compensation de rayon d’outil (G40) n’est possible que dans un bloc dans lequel un déplacement rectiligne est programmé (G00 ou G01). Si G40 est programmé alors que les fonctions G02 ou G03 sont actives, la CNC affiche l’erreur correspondante. Ensuite sont affichés plusieurs cas d’activation de compensation de rayon d’outil, dans lesquels la trajectoire programmée figure en traits pleins, tandis que la trajectoire du centre de l'outil est en trait discontinu. Après avoir annulé la compensation, il se peut que les axes du plan n'interviennent pas dans le premier bloc de déplacement, bien parce qu'ils n'ont pas été programmés, parce qu'on a programmé le même point où se trouve l'outil ou bien parce qu'on a programmé un déplacement incrémental nul. Dans ce cas, la compensation s'annule au point où se trouve l'outil en fonction du dernier déplacement exécuté sur le plan, l'outil se déplace au point final sans compenser la trajectoire programmée. 8. La compensation de rayon Fin de la compensation sans déplacement programmé COMPENSATION D'OUTILS 8.2.6 (X0 Y0) (X0 Y0) Y Y X X ··· G90 G01 X-30 G01 G40 X-30 G01 X25 Y-25 ··· ··· G90 G03 X-20 Y-20 I0 J-20 G91 G40 Y0 G01 X-20 ··· CNC 8035 MODÈLE ·T· (SOFT V16.3X) ·143· Manuel de programmation Trajectoire DROITE - DROITE La compensation de rayon COMPENSATION D'OUTILS 8. CNC 8035 MODÈLE ·T· (SOFT V16.3X) ·144· Manuel de programmation Trajectoire ARC-DROITE La compensation de rayon COMPENSATION D'OUTILS 8. CNC 8035 MODÈLE ·T· (SOFT V16.3X) ·145· Manuel de programmation Exemple de programmation La compensation de rayon COMPENSATION D'OUTILS 8. T1 D1 G0 G90 X110 Z100 Positionnement au point de départ. G1 G42 X10 Z60 Active la compensation et le déplacement au point initial. X70 Z40 X70 Z20 CNC 8035 MODÈLE ·T· (SOFT V16.3X) ·146· X90 Z20 Déplacement au point final (compensation active). G40 X110 Z100 Il désactive la compensation et le déplacement su point de départ. Manuel de programmation Annulation temporaire de la compensation avec G00 Lorsqu’un un pas de G01, G02, G03, G33 ou G34 a G00 est détecté, la CNC annule temporairement la compensation de rayon, l’outil restant tangent à la perpendiculaire, sur l’extrémité du déplacement programmé dans le bloc de G01, G02, G03, G33 ou G34. Lorsqu’un pas de G00 à G01, G02, G03, G33 ou G34 est détecté, le nouveau bloc reçoit le traitement correspondant au premier point compensé, la compensation radiale reprenant normalement. Cas spécial: Si la commande n’a pas assez d’information pour compenser, mais le mouvement est en G00, s’exécutera sans compensation radiale. La compensation de rayon 8. COMPENSATION D'OUTILS 8.2.7 Exemple de programmation Exemple erroné de programmation. La compensation est supprimée dans le dernier bloc du profil et l’usinage ne coïncide pas avec celui souhaité parce que la CNC compense tout le segment défini. En compensant le dernier segment, l’outil s’introduit dans la face surfacée. T1 D1 G0 G90 X110 Z100 Positionnement au point de départ G1 G42 X10 Z60 Active la compensation et le déplacement au point initial X70 Z40 CNC 8035 X70 Z20 G40 X110 Z100 Il désactive la compensation et le déplacement su point de départ MODÈLE ·T· (SOFT V16.3X) ·147· Manuel de programmation Ce problème peut être résolu avec la fonction G00, comme il est indiqué ci-après. La compensation de rayon COMPENSATION D'OUTILS 8. T1 D1 G0 G90 X110 Z100 Positionnement au point de départ G1 G42 X10 Z60 Active la compensation et le déplacement au point initial X70 Z40 X70 Z20 G40 G0 X110 Z100 CNC 8035 MODÈLE ·T· (SOFT V16.3X) ·148· Il désactive la compensation et le déplacement su point de départ Manuel de programmation Changement du type de compensation de rayon pendant l'usinage On peut changer la compensation de G41 à G42 ou vice versa sans avoir à l'annuler avec G40. Le changement peut être réalisé dans n'importe quel bloc de déplacement et même dans un bloc à déplacement nul; c'est-à-dire, sans déplacement sur les axes du plan ou en programmant deux fois le même point. Le dernier déplacement avant le changement et le premier déplacement après le changement se compensent indépendamment. Pour réaliser le changement de type de compensation, les différents cas se résolvent en suivant les critères ci-dessous: Chaque trajectoire programmée se compense du côté lui correspondant. Le changement de côté se produit au point de coupe entre les deux trajectoires. B. Les trajectoires compensées ne se coupent pas. On introduit un segment supplémentaire entre les deux trajectoires. Depuis le point perpendiculaire à la première trajectoire au point final jusqu'au point perpendiculaire à la seconde trajectoire au point de départ. Les deux points sont situés à une distance R de la trajectoire programmée. Ci-dessous est exposé un résumé des différents cas: Trajectoire droite - droite: A La compensation de rayon 8. A. Les trajectoires compensées se coupent. COMPENSATION D'OUTILS 8.2.8 B Trajectoire droite - arc: A B Trajectoire arc - droite: A B Trajectoire arc - arc: CNC 8035 A B MODÈLE ·T· (SOFT V16.3X) ·149· Manuel de programmation 8.2.9 Compensation d’outil sur n’importe quel plan Le paramètre machine général "PLACOMP" permet de travailler avec compensation d’outil sur tous les plans ou uniquement sur le plan ZX. Si on a personnalisé "PLACOMP=1" pour travailler avec compensation d’outil sur tous les plans, la CNC interprète la table d’outils de la manière suivante : La compensation de rayon COMPENSATION D'OUTILS 8. CNC 8035 MODÈLE ·T· (SOFT V16.3X) ·150· Plan ZX Plan WX Plan AB Paramètres Z et K. Axe d'abscisses. axe Z axe W axe A Paramètres X et I. Axe d'ordonnées. axe X axe X axe B Manuel de programmation Détection de collisions (G41 N, G42 N) Avec cette option, la CNC analyse à l'avance les blocs à exécuter dans le but de détecter des boucles (intersections du profil avec lui-même) ou des collisions dans le profil programmé. Le nombre de blocs à analyser peut être défini par l'usager, avec la possibilité d'analyser jusqu'à 50 blocs. L'exemple montre des erreurs d'usinage (E) dues à une collision dans le profil programmé. Ce type d'erreurs peut être évité avec la détection de collisions. Détection de collisions (G41 N, G42 N) 8. COMPENSATION D'OUTILS 8.3 Si on détecte une boucle ou une collision, les blocs qui en sont à l'origine ne seront pas exécutés et un avis sera affiché pour chaque boucle ou collision éliminée. Cas possibles : échelon en trajectoire droite, échelon en trajectoire circulaire et rayon de compensation trop grande. L'information contenue dans les blocs éliminés, et qui ne soit pas le mouvement dans le plan actif, sera exécutée (y compris les mouvements des autres axes). La détection de blocs se définit et s'active avec les fonctions de compensation de rayon, G41 et G42. Un nouveau paramètre N (G41 N et G42 N) est inclus pour activer la performance et définir le nombre de blocs à analyser. Valeurs possibles de N3 à N50. Sans "N" ou avec N0 , N1 et N2 agissent comme dans les versions précédentes. Dans les programmes générés via CAD qui sont formés par de nombreux blocs d'une longueur très petite, il est recommandé d'utiliser des valeurs de N basses (de l'ordre de 5) si on ne veut pas pénaliser le temps de processus de bloc. Quand cette fonction est active, G41 N ou G42 N apparaissent dans l'historique de fonctions G activas. CNC 8035 MODÈLE ·T· (SOFT V16.3X) ·151· Manuel de programmation COMPENSATION D'OUTILS Détection de collisions (G41 N, G42 N) 8. CNC 8035 MODÈLE ·T· (SOFT V16.3X) ·152· CYCLES FIXES 9 La CNC dispose des cycles fixes d'usinage suivants: G66 Cycle fixe de poursuite de profil. G68 Cycle fixe d'ébauchage sur l'axe X. G69 Cycle fixe d'ébauchage sur l'axe Z. G81 Cycle fixe de tournage de segments droits. G82 Cycle fixe de dressage de segments droits. G83 Cycle fixe de perçage. G84 Cycle fixe de tournage de segments courbes. G85 Cycle fixe de dressage de segments courbes. G86 Cycle fixe de filetage longitudinal. G87 Cycle fixe de filetage frontal. G88 Cycle fixe de rainurage sur l'axe X. G89 Cycle fixe de rainurage sur l'axe Z. Un cycle fixe est défini par la fonction G indicative du cycle fixe et par les paramètres correspondants au cycle désiré. Un cycle fixe peut être défini dans n'importe quelle partie du programme, c'està-dire qu'il peut être défini aussi bien dans le programme principal que dans une sous-routine. En travaillant avec un plan de travail différent de ZX, par exemple G16 WX, la CNC interprète les paramètres du cycle fixe de la façon suivante: Plan ZX Plan WX Plan AB Le paramètre Z et tous ceux en rapport avec lui, avec l'axe d'abscisses. axe Z axe W axe A Le paramètre Z et tous ceux en rapport avec lui, avec l'axe d'ordonnées. axe X axe X axe B CNC 8035 MODÈLE ·T· (SOFT V16.3X) ·153· Manuel de programmation 9.1 G66. Cycle fixe de poursuite de profil Ce cycle usine le profil programmé en conservant le pas spécifié entre les passes d'usinage successives. Ce cycle permet d'utiliser des outils triangulaires, ronds et carrés. La structure de base du bloc est la suivante: G66 X Z I C A L M H S E Q CYCLES FIXES G66. Cycle fixe de poursuite de profil 9. X±5.5 Il définit la cote du point initial du profil suivant l'axe X. Programmation en cotes absolues et suivant les unités actives, rayons ou diamètres. Z±5.5 Il définit la cote du point initial du profil suivant l'axe Z. Programmation en cotes absolues. I5.5 Il définit le surplus de matière, c'est-à-dire la quantité à enlever de la pièce origine. La définition est faite en rayons et en fonction de la valeur affectée au paramètre "A" cette valeur sera interprétée, comme surplus sur X ou sur Z. Si sa valeur n'est pas supérieure à la surépaisseur pour la finition (L ou M), seule la passe de finition est exécutée, si H est différent de zéro. C5.5 Il définit le pas d'usinage. Toutes les passes d'usinage s'effectuent avec ce pas, sauf la dernière, qui éliminera le surplus de matière. La définition est faite en rayons et en fonction de la valeur affectée au paramètre "A" cette valeur sera interprétée, comme "I", comme un pas sur X ou sur Z. Si on fait la programmation avec valeur 0, la CNC affichera l'erreur correspondante. CNC 8035 MODÈLE ·T· (SOFT V16.3X) ·154· Manuel de programmation A1 Il définit l'axe principal d'usinage. • Si on programme A0, l'axe principal sera l'axe Z. La valeur de "I" est prise comme surplus de matière sur X et la valeur de "C" comme pas sur X. • Si on programme A1, l'axe principal sera l'axe X. La valeur de "I" est prise comme surplus de matière sur Z et la valeur de "C" comme pas sur Z. Si le paramètre A n'est pas programmé, la valeur de "I" et de "C" dépend des dimensions de l'outil. • Si la longueur de l'outil sur X est supérieure à la longueur sur Z, la valeur de "I" est prise comme surplus de matière sur X et la valeur de "C" comme pas sur X. • Si la longueur de l'outil sur X est inférieure à la longueur sur Z, la valeur de "I" est prise comme surplus de matière sur Z et la valeur de "C" comme pas sur Z. G66. Cycle fixe de poursuite de profil CYCLES FIXES 9. L±5.5 Il définit la surépaisseur que l'on laissera sur X pour effectuer la finition. La surépaisseur est définie en rayons et si on ne la programme pas, la valeur 0 sera prise. M±5.5 Il définit la surépaisseur que l'on laissera sur Z pour effectuer la finition. Si on programme "L" ou "M" avec une valeur négative, la passe de finition se réalise en arête arrondie (G5). Lorsque les deux paramètres sont programmés avec une valeur positive, la passe de finition se réalisera en arête vive (G07). Si on ne programme pas le paramètre "M", la surépaisseur sur X et Z sera celle indiquée dans le paramètre "L" et les passes d'ébauchage seront équidistantes, en maintenant la distance "C" entre 2 passes consécutives. CNC 8035 H5.5 Il définit la vitesse d'avance de la passe de finition. Si on ne la programme pas ou si on la programme avec valeur 0, il est entendu qu'on ne désire pas la passe de finition. MODÈLE ·T· (SOFT V16.3X) S4 Il définit le numéro d'étiquette du bloc où commence la description géométrique du profil. ·155· Manuel de programmation E4 Il définit le numéro d'étiquette du bloc où finit la description géométrique du profil. Q6 Il définit le numéro du programme contenant la description géométrique du profil. Ce paramètre est optionnel et s’il n’est pas défini, la CNC assume que le profil est défini dans le même programme contenant l’appel au cycle. CYCLES FIXES G66. Cycle fixe de poursuite de profil 9. Considérations Les conditions d'usinage (vitesse d'avance, vitesse de rotation de broche, etc.), doivent être programmées avant l'appel au cycle. Le point d'appel au cycle sera situé hors de la pièce à usiner et à une distance supérieure à celle définie comme surplus de matière (I) du profil plus extérieur de la pièce. Si la position de l'outil n'est pas correcte pour exécuter le cycle, la CNC affiche l'erreur correspondante. Dès que le cycle fixe est achevé, l'avance active sera la dernière avance programmée, celle correspondant à l'opération d'ébauchage (F) ou de finition (H). Par ailleurs, la CNC assumera les fonctions G00, G40 et G90. Optimisation de l'usinage Si on définit uniquement le profil souhaité, la CNC suppose que la pièce brute est cylindrique et effectue l'usinage comme indiqué à gauche. CNC 8035 MODÈLE ·T· (SOFT V16.3X) ·156· Si on connaît le profil de la pièce brute, il est conseillé de définir les deux profils: le profil de la pièce brute et le profil final souhaité. L'usinage est plus rapide car seule la matière délimitée par les deux profils est éliminée. Manuel de programmation Fonctionnement de base Chacune des passes se réalise de la façon suivante : 1. Le déplacement d'approche "1-2" se réalise en avance rapide (G00). 2. Le déplacement "2-3" se réalise à l'avance programmée (F). 3. Le déplacement de retour "3-1" se réalise en avance rapide (G00). S'il existe la possibilité de collision avec la pièce, ce déplacement se réalisera avec deux déplacements en G00 ("3-4" et "4-1"), comme indiqué sur la figure suivante. G66. Cycle fixe de poursuite de profil 9. CYCLES FIXES 9.1.1 4. Le cycle fixe finira toujours sur le point où il a été appelé. Les passes d’usinage Après avoir calculé le profil à exécuter, on calculera toutes les passes nécessaires pour éliminer le surplus de matière (I) programmé. L'usinage s'exécutera en conservant le travail en arête vive (G07) ou en arête arrondie (G05) qui est sélectionné au moment de l'appel au cycle. Si le paramètre "M" n'est pas programmé, les passes sont équidistantes, en maintenant la distance "C" entre 2 passes consécutives. De plus, si le dernier segment du profil est un segment courbe ou un plan incliné, la CNC calculera les différentes passes sans dépasser la cote maximale programmée. CNC 8035 MODÈLE ·T· (SOFT V16.3X) ·157· Manuel de programmation Le profil et l'outil Après avoir analysé le profil programmé et en fonction de l’outil utilisé, c’est ce profil qui sera exécuté ou à défaut le profil le plus proche de celui-ci. Dans les cas où l'on ne peut pas usiner le profil programmé (gorges) avec l'outil sélectionné, un message est affiché au début de l'exécution du cycle. L'opérateur pourra arrêter l'exécution et sélectionner l'outil approprié. S'il ne le fait pas, on calcule un nouveau profil dans les zones qui ne sont pas accessibles à l'outil sélectionné et on usine tout ce qui est possible. Le message est affiché pendant tout l’usinage. CYCLES FIXES G66. Cycle fixe de poursuite de profil 9. CNC 8035 MODÈLE ·T· (SOFT V16.3X) ·158· Manuel de programmation Syntaxe de programmation de profils Dans la définition du profil il n'est pas nécessaire de programmer le point initial, étant donné qu'il est spécifié avec les paramètres X, Z de définition du cycle fixe. Si on définit 2 profils, il faut d'abord définir le profil final et puis le profil de la pièce brute. Le premier bloc de définition du profil et le dernier (où finit le ou les profils), devront disposer de numéro d'étiquette de bloc. Ces numéros d'étiquette seront ceux qui indiqueront au cycle fixe le commencement et la fin de la description géométrique du profil. • Elle peut être programmée avec des cotes absolues et incrémentales et être formé d'éléments géométriques simples tels que droites, arcs, arrondissements et chanfreins, en suivant pour sa programmation les normes de syntaxe définies pour ceux-ci. • La fonction G00 indique que la définition du profil final a terminé et que la définition du profil de la pièce brute commence dans ce bloc. Programmer G01, G02 ou G03 dans le bloc suivant, étant donné que G00 est modal, en évitant ainsi que la CNC affiche le message d'erreur correspondant. • Dans la description du profil on ne peut pas programmer d'images miroir, de changements d'échelle, de rotation du système de coordonnées ou de décalages d'origine. • On ne peut pas non plus programmer de blocs en langage de haut niveau, comme les sauts, les appels aux sous-routines ou la programmation paramétrique. • On ne peut pas programmer d'autres cycles fixes. G66. Cycle fixe de poursuite de profil 9. La syntaxe de programmation du profil doit remplir les normes suivantes : CYCLES FIXES 9.1.2 Pour la définition du profil on peut utiliser les fonctions suivantes : G01 Interpolation linéaire. G02 Interpolation circulaire à droite. G03 Interpolation circulaire à gauche. G06 Centre de circonférence en coordonnées absolues. G08 Circonférence tangente à la trajectoire antérieure. G09 Circonférence par trois points. G36 Arrondissement d'arêtes. G39 Chanfreinage. G53 Programmation par rapport au zéro machine. G70 Programmation en pouces. G71 Programmation en millimètres. G90 Programmation absolue. G91 Programmation incrémentale. G93 Présélection de l'origine polaire. On peut programmer les fonctions suivantes, même si elles sont ignorées par le cycle. G05 Arête arrondie. G07 Arête vive. G50 Arête arrondie contrôlée. Fonctions F, S, T, D ou M. CNC 8035 MODÈLE ·T· (SOFT V16.3X) ·159· Manuel de programmation 9.2 G68. Cycle fixe d'ébauchage sur l'axe X Ce cycle usine le profil programmé en conservant le pas spécifié entre les passes d'usinage successives. Ce cycle permet des outils triangulaires, ronds et carrés. La structure de base du bloc est la suivante: G68 X Z C D L M K F H S E Q CYCLES FIXES G68. Cycle fixe d'ébauchage sur l'axe X 9. X±5.5 Il définit la cote du point initial du profil suivant l'axe X. Programmation en cotes absolues et suivant les unités actives, rayons ou diamètres. Z±5.5 Il définit la cote du point initial du profil suivant l'axe Z. Programmation en cotes absolues. C5.5 Il définit le pas d'usinage et sera programmé avec une valeur positive exprimée en rayons. Si on le programme avec une valeur 0, la CNC affiche l'erreur correspondante. Toutes les passes d'usinage s'effectuent avec ce pas, sauf la dernière, qui éliminera le surplus de matière. D 5.5 Il définit la distance de sécurité à laquelle s'effectue le retour de l'outil à chaque passe. CNC 8035 MODÈLE ·T· (SOFT V16.3X) Si on programme D avec une valeur différente de 0, la plaquette réalise un mouvement de retrait à 45° jusqu'à atteindre la distance de sécurité (figure à gauche). Si on programme D avec la valeur 0, la trajectoire de sortie coïncide avec la trajectoire d'entrée. Cela peut être intéressant pour rainurer des profils complexes, pour utiliser ces cycles sur des machines à rectifier cylindriques, etc. ·160· Manuel de programmation Si le paramètre D n'est pas programmé, le retrait de l'outil s'effectue en suivant le profil jusqu'à la passe précédente, distance C (figure à droite). Quand on ne programme pas le paramètre D, il faut tenir compte que le temps d'exécution du cycle est supérieur, mais la quantité de matière à enlever dans la passe de finition est inférieure. L±5.5 Il définit la surépaisseur que l'on laissera sur X pour effectuer la finition. La surépaisseur est définie en rayons et si on ne la programme pas, la valeur 0 sera prise. Si on programme "L" ou "M" avec une valeur négative, la passe de finition se réalise en arête arrondie (G5). Lorsque les deux paramètres sont programmés avec une valeur positive, la passe de finition se réalisera en arête vive (G07). Si on ne programme pas le paramètre "M", la surépaisseur aura la valeur indiquée dans le paramètre "L" et sera constante sur tout le profil. CYCLES FIXES Il définit la surépaisseur que l'on laissera sur Z pour effectuer la finition. G68. Cycle fixe d'ébauchage sur l'axe X 9. M±5.5 K5.5 Il définit la vitesse d'avance de pénétration de l'outil dans les gorges. Si on ne la programme pas ou si on la programme avec une valeur 0, assume la vitesse d'avance de l'usinage (celle programmée avant l'appel au cycle). F5.5 Il définit la vitesse d'avance de la passe finale d'ébauchage. Si on ne la programme pas ou si on la programme avec valeur 0, il est entendu qu'on ne désire pas la passe finale d'ébauchage. CNC 8035 H5.5 MODÈLE ·T· (SOFT V16.3X) Il définit la vitesse d'avance de la passe de finition. Si on ne la programme pas ou si on la programme avec valeur 0, il est entendu qu'on ne désire pas la passe de finition. ·161· Manuel de programmation S4 Il définit le numéro d'étiquette du bloc où commence la description géométrique du profil. E4 Il définit le numéro d'étiquette du bloc où finit la description géométrique du profil. Q6 9. CYCLES FIXES G68. Cycle fixe d'ébauchage sur l'axe X Il définit le numéro du programme contenant la description géométrique du profil. Ce paramètre est optionnel et s’il n’est pas défini, la CNC assume que le profil est défini dans le même programme contenant l’appel au cycle. Considérations Les conditions d'usinage (vitesse d'avance, vitesse de rotation de broche, etc.), doivent être programmées avant l'appel au cycle. Le point d'appel au cycle sera situé hors de la pièce à usiner et à une distance supérieure à celle définie comme surépaisseur de matière (L, M), suivant les axes (X, Z). Si la position de l'outil n'est pas correcte pour exécuter le cycle, la CNC affiche l'erreur correspondante. Dès que le cycle fixe est achevé, l'avance active sera la dernière avance programmée, celle correspondant à l'opération d'ébauchage (F) ou de finition (H). Par ailleurs, la CNC assumera les fonctions G00, G40 et G90. Optimisation de l'usinage Si on définit uniquement le profil souhaité, la CNC suppose que la pièce brute est cylindrique et effectue l'usinage comme indiqué à gauche. CNC 8035 MODÈLE ·T· (SOFT V16.3X) Si on connaît le profil de la pièce brute, il est conseillé de définir les deux profils: le profil de la pièce brute et le profil final souhaité. L'usinage est plus rapide car seule la matière délimitée par les deux profils est éliminée. ·162· Manuel de programmation Fonctionnement de base Les passes d’usinage Une fois les passes d’ébauchage nécessaires calculées, le nouveau profil résultant sera usiné. L'usinage s'exécutera en conservant le travail en arête vive (G07) ou en arête arrondie (G05) qui est sélectionné au moment de l'appel au cycle. D’autre part, le même pas est maintenu pendant tout l’usinage. Après avoir analysé le profil programmé et en fonction de l’outil utilisé, c’est ce profil qui sera exécuté ou à défaut le profil le plus proche de celui-ci. Dans les cas où l'on ne peut pas usiner le profil programmé (gorges) avec l'outil sélectionné, un message est affiché au début de l'exécution du cycle. L'opérateur pourra arrêter l'exécution et sélectionner l'outil approprié. S'il ne le fait pas, on calcule un nouveau profil dans les zones qui ne sont pas accessibles à l'outil sélectionné et on usine tout ce qui est possible. Le message est affiché pendant tout l’usinage. G68. Cycle fixe d'ébauchage sur l'axe X 9. Le profil et l'outil CYCLES FIXES 9.2.1 Usinage de canaux Si en exécutant l'une des passes d'ébauchage on détecte l'existence d'un canal, la CNC continuera l'exécution du reste du profil sans tenir compte de ce canal. Le nombre de canaux dont peut disposer un profil est illimité. CNC 8035 MODÈLE ·T· (SOFT V16.3X) ·163· Manuel de programmation Dès que le profil en trop est terminé, l'exécution des canaux détectés commence. CYCLES FIXES G68. Cycle fixe d'ébauchage sur l'axe X 9. Pour cela on retournera en G00 au point où l'usinage du profil a été interrompu. 1. À partir de ce point on suivra en G01 le contour programmé, en conservant la surépaisseur de finition, jusqu'à atteindre la profondeur de passe "C" sélectionnée. Segment 1-2. 2. Sur la nouvelle passe d'ébauchage, le déplacement "2-3" se réalise en G01 à l'avance programmée (F). 3. En ayant programmé le paramètre "D", le déplacement "3-4" se réalise en avance rapide (G00), mais si "D" n'a pas été programmé, le déplacement "3-4" s'effectue en suivant le contour programmé et en G01 à l'avance programmée (F). 4. Le déplacement de retour "4-5" se réalise en avance rapide (G00). Si en exécutant un canal on détecte des canaux internes à celui-ci, on suivra la même procédure que celle expliquée auparavant. La passe finale d’ébauchage Si on a sélectionné une passe finale de d'ébauchage, s'effectuera une passe parallèle au profil, tout en maintenant la surépaisseur "L", avec l'avance "F" indiquée. Cette passe finale d'ébauchage élimine les surépaisseurs ayant resté après l'ébauchage. Dès que l'ébauchage du profil est terminé, l'outil retourne au point d'appel au cycle. CNC 8035 MODÈLE ·T· (SOFT V16.3X) ·164· Manuel de programmation La passe finale de finition Si on a sélectionné une passe de finition, la machine réalisera une passe du profil calculé avec compensation de rayon d'outil et avec l'avance "H" indiquée. Ce profil pourra coïncider avec le profil programmé ou être un profil proche si on dispose de zones qui ne sont pas accessibles pour l'outil sélectionné. Dès que la passe de finition est terminée, l'outil retourne au point d'appel au cycle. G68. Cycle fixe d'ébauchage sur l'axe X CYCLES FIXES 9. CNC 8035 MODÈLE ·T· (SOFT V16.3X) ·165· Manuel de programmation 9.2.2 Syntaxe de programmation de profils Dans la définition du profil il n'est pas nécessaire de programmer le point initial, étant donné qu'il est spécifié avec les paramètres X, Z de définition du cycle fixe. Si on définit 2 profils, il faut d'abord définir le profil final et puis le profil de la pièce brute. Le premier bloc de définition du profil et le dernier (où finit le ou les profils), devront disposer de numéro d'étiquette de bloc. Ces numéros d'étiquette seront ceux qui indiqueront au cycle fixe le commencement et la fin de la description géométrique du profil. 9. CYCLES FIXES G68. Cycle fixe d'ébauchage sur l'axe X La syntaxe de programmation du profil doit remplir les normes suivantes : • Elle peut être programmée avec des cotes absolues et incrémentales et être formé d'éléments géométriques simples tels que droites, arcs, arrondissements et chanfreins, en suivant pour sa programmation les normes de syntaxe définies pour ceux-ci. • La fonction G00 indique que la définition du profil final a terminé et que la définition du profil de la pièce brute commence dans ce bloc. Programmer G01, G02 ou G03 dans le bloc suivant, étant donné que G00 est modal, en évitant ainsi que la CNC affiche le message d'erreur correspondant. • Dans la description du profil on ne peut pas programmer d'images miroir, de changements d'échelle, de rotation du système de coordonnées ou de décalages d'origine. • On ne peut pas non plus programmer de blocs en langage de haut niveau, comme les sauts, les appels aux sous-routines ou la programmation paramétrique. • On ne peut pas programmer d'autres cycles fixes. Pour la définition du profil on peut utiliser les fonctions suivantes : G01 Interpolation linéaire. G02 Interpolation circulaire à droite. G03 Interpolation circulaire à gauche. G06 Centre de circonférence en coordonnées absolues. G08 Circonférence tangente à la trajectoire antérieure. G09 Circonférence par trois points. G36 Arrondissement d'arêtes. G39 Chanfreinage. G53 Programmation par rapport au zéro machine. G70 Programmation en pouces. G71 Programmation en millimètres. G90 Programmation absolue. G91 Programmation incrémentale. G93 Présélection de l'origine polaire. On peut programmer les fonctions suivantes, même si elles sont ignorées par le cycle. G05 Arête arrondie. G07 Arête vive. G50 Arête arrondie contrôlée. Fonctions F, S, T, D ou M. CNC 8035 MODÈLE ·T· (SOFT V16.3X) ·166· Manuel de programmation G69. Cycle fixe d'ébauchage sur l'axe Z Ce cycle usine le profil programmé en conservant le pas spécifié entre les passes d'usinage successives. Ce cycle permet des outils triangulaires, ronds et carrés. La structure de base du bloc est la suivante: G69X Z C D L M K F H S E Q G69. Cycle fixe d'ébauchage sur l'axe Z 9. CYCLES FIXES 9.3 X±5.5 Il définit la cote du point initial du profil suivant l'axe X. Programmation en cotes absolues et suivant les unités actives, rayons ou diamètres. Z±5.5 Il définit la cote du point initial du profil suivant l'axe Z. Programmation en cotes absolues. C5.5 Il définit le pas d'usinage. Si on le programme avec une valeur 0, la CNC affiche l'erreur correspondante. Toutes les passes d'usinage s'effectuent avec ce pas, sauf la dernière, qui éliminera le surplus de matière. D 5.5 Il définit la distance de sécurité à laquelle s'effectue le retour de l'outil à chaque passe. CNC 8035 Si on programme D avec une valeur différente de 0, la plaquette réalise un mouvement de retrait à 45° jusqu'à atteindre la distance de sécurité (figure à gauche). MODÈLE ·T· (SOFT V16.3X) Si on programme D avec la valeur 0, la trajectoire de sortie coïncide avec la trajectoire d'entrée. Cela peut être intéressant pour rainurer des profils complexes, pour utiliser ces cycles sur des machines à rectifier cylindriques, etc. ·167· Manuel de programmation Si le paramètre D n'est pas programmé, le retrait de l'outil s'effectue en suivant le profil jusqu'à la passe précédente, distance C (figure à droite). Quand on ne programme pas le paramètre D, il faut tenir compte que le temps d'exécution du cycle est supérieur, mais la quantité de matière à enlever dans la passe de finition est inférieure. L±5.5 Il définit la surépaisseur que l'on laissera sur X pour effectuer la finition. La surépaisseur est définie en rayons et si on ne la programme pas, la valeur 0 sera prise. 9. CYCLES FIXES G69. Cycle fixe d'ébauchage sur l'axe Z M±5.5 Il définit la surépaisseur que l'on laissera sur Z pour effectuer la finition. Si on programme "L" ou "M" avec une valeur négative, la passe de finition se réalise en arête arrondie (G5). Lorsque les deux paramètres sont programmés avec une valeur positive, la passe de finition se réalisera en arête vive (G07). Si on ne programme pas le paramètre "M", la surépaisseur aura la valeur indiquée dans le paramètre "L" et sera constante sur tout le profil. K5.5 Il définit la vitesse d'avance de pénétration de l'outil dans les gorges. Si on ne la programme pas ou si on la programme avec une valeur 0, assume la vitesse d'avance de l'usinage (celle programmée avant l'appel au cycle). F5.5 Il définit la vitesse d'avance de la passe finale d'ébauchage. Si on ne la programme pas ou si on la programme avec valeur 0, il est entendu qu'on ne désire pas la passe finale d'ébauchage. CNC 8035 MODÈLE ·T· (SOFT V16.3X) H5.5 Il définit la vitesse d'avance de la passe de finition. Si on ne la programme pas ou si on la programme avec valeur 0, il est entendu qu'on ne désire pas la passe de finition. ·168· Manuel de programmation S4 Il définit le numéro d'étiquette du bloc où commence la description géométrique du profil. E4 Il définit le numéro d'étiquette du bloc où finit la description géométrique du profil. Q6 Considérations Les conditions d'usinage (vitesse d'avance, vitesse de rotation de broche, etc.), doivent être programmées avant l'appel au cycle. Le point d'appel au cycle sera situé hors de la pièce à usiner et à une distance supérieure à celle définie comme surépaisseur de matière (L, M), suivant les axes (X, Z). CYCLES FIXES Ce paramètre est optionnel et s’il n’est pas défini, la CNC assume que le profil est défini dans le même programme contenant l’appel au cycle. G69. Cycle fixe d'ébauchage sur l'axe Z 9. Il définit le numéro du programme contenant la description géométrique du profil. Si la position de l'outil n'est pas correcte pour exécuter le cycle, la CNC affiche l'erreur correspondante. Dès que le cycle fixe est achevé, l'avance active sera la dernière avance programmée, celle correspondant à l'opération d'ébauchage (F) ou de finition (H). Par ailleurs, la CNC assumera les fonctions G00, G40 et G90. CNC 8035 MODÈLE ·T· (SOFT V16.3X) ·169· Manuel de programmation Optimisation de l'usinage Si on définit uniquement le profil souhaité, la CNC suppose que la pièce brute est cylindrique et effectue l'usinage comme indiqué à gauche. CYCLES FIXES G69. Cycle fixe d'ébauchage sur l'axe Z 9. CNC 8035 MODÈLE ·T· (SOFT V16.3X) ·170· Si on connaît le profil de la pièce brute, il est conseillé de définir les deux profils: le profil de la pièce brute et le profil final souhaité. L'usinage est plus rapide car seule la matière délimitée par les deux profils est éliminée. Manuel de programmation Fonctionnement de base Les passes d’usinage Une fois les passes d’ébauchage nécessaires calculées, le nouveau profil résultant sera usiné. L'usinage s'exécutera en conservant le travail en arête vive (G07) ou en arête arrondie (G05) qui est sélectionné au moment de l'appel au cycle. D’autre part, le même pas est maintenu pendant tout l’usinage. Après avoir analysé le profil programmé et en fonction de l’outil utilisé, c’est ce profil qui sera exécuté ou à défaut le profil le plus proche de celui-ci. Dans les cas où l'on ne peut pas usiner le profil programmé (gorges) avec l'outil sélectionné, un message est affiché au début de l'exécution du cycle. L'opérateur pourra arrêter l'exécution et sélectionner l'outil approprié. S'il ne le fait pas, on calcule un nouveau profil dans les zones qui ne sont pas accessibles à l'outil sélectionné et on usine tout ce qui est possible. Le message est affiché pendant tout l’usinage. G69. Cycle fixe d'ébauchage sur l'axe Z 9. Le profil et l'outil CYCLES FIXES 9.3.1 Usinage de canaux Si en exécutant l'une des passes d'ébauchage on détecte l'existence d'un canal, la CNC continuera l'exécution du reste du profil sans tenir compte de ce canal. Le nombre de canaux dont peut disposer un profil est illimité. CNC 8035 MODÈLE ·T· (SOFT V16.3X) ·171· Manuel de programmation Dès que le profil en trop est terminé, l'exécution des canaux détectés commence. CYCLES FIXES G69. Cycle fixe d'ébauchage sur l'axe Z 9. Pour cela on retournera en G00 au point où l'usinage du profil a été interrompu. 1. À partir de ce point on suivra en G01 le contour programmé, en conservant la surépaisseur de finition, jusqu'à atteindre la profondeur de passe "C" sélectionnée. Segment 1-2. 2. Sur la nouvelle passe d'ébauchage, le déplacement "2-3" se réalise en G01 à l'avance programmée (F). 3. En ayant programmé le paramètre "D", le déplacement "3-4" se réalise en avance rapide (G00), mais si "D" n'a pas été programmé, le déplacement "3-4" s'effectue en suivant le contour programmé et en G01 à l'avance programmée (F). 4. Le déplacement de retour "4-5" se réalise en avance rapide (G00). Si en exécutant un canal on détecte des canaux internes à celui-ci, on suivra la même procédure que celle expliquée auparavant. La passe finale d’ébauchage Si on a sélectionné une passe finale de d'ébauchage, s'effectuera une passe parallèle au profil, tout en maintenant la surépaisseur "L", avec l'avance "F" indiquée. Cette passe finale d'ébauchage élimine les surépaisseurs ayant resté après l'ébauchage. Dès que l'ébauchage du profil est terminé, l'outil retourne au point d'appel au cycle. CNC 8035 MODÈLE ·T· (SOFT V16.3X) ·172· Manuel de programmation La passe finale de finition Si on a sélectionné une passe de finition, la machine réalisera une passe du profil calculé avec compensation de rayon d'outil et avec l'avance "H" indiquée. Ce profil pourra coïncider avec le profil programmé ou être un profil proche si on dispose de zones qui ne sont pas accessibles pour l'outil sélectionné. Dès que la passe de finition est terminée, l'outil retourne au point d'appel au cycle. G69. Cycle fixe d'ébauchage sur l'axe Z CYCLES FIXES 9. CNC 8035 MODÈLE ·T· (SOFT V16.3X) ·173· Manuel de programmation 9.3.2 Syntaxe de programmation de profils Dans la définition du profil il n'est pas nécessaire de programmer le point initial, étant donné qu'il est spécifié avec les paramètres X, Z de définition du cycle fixe. Si on définit 2 profils, il faut d'abord définir le profil final et puis le profil de la pièce brute. Le premier bloc de définition du profil et le dernier (où finit le ou les profils), devront disposer de numéro d'étiquette de bloc. Ces numéros d'étiquette seront ceux qui indiqueront au cycle fixe le commencement et la fin de la description géométrique du profil. 9. CYCLES FIXES G69. Cycle fixe d'ébauchage sur l'axe Z La syntaxe de programmation du profil doit remplir les normes suivantes : • Elle peut être programmée avec des cotes absolues et incrémentales et être formé d'éléments géométriques simples tels que droites, arcs, arrondissements et chanfreins, en suivant pour sa programmation les normes de syntaxe définies pour ceux-ci. • La fonction G00 indique que la définition du profil final a terminé et que la définition du profil de la pièce brute commence dans ce bloc. Programmer G01, G02 ou G03 dans le bloc suivant, étant donné que G00 est modal, en évitant ainsi que la CNC affiche le message d'erreur correspondant. • Dans la description du profil on ne peut pas programmer d'images miroir, de changements d'échelle, de rotation du système de coordonnées ou de décalages d'origine. • On ne peut pas non plus programmer de blocs en langage de haut niveau, comme les sauts, les appels aux sous-routines ou la programmation paramétrique. • On ne peut pas programmer d'autres cycles fixes. Pour la définition du profil on peut utiliser les fonctions suivantes : G01 Interpolation linéaire. G02 Interpolation circulaire à droite. G03 Interpolation circulaire à gauche. G06 Centre de circonférence en coordonnées absolues. G08 Circonférence tangente à la trajectoire antérieure. G09 Circonférence par trois points. G36 Arrondissement d'arêtes. G39 Chanfreinage. G53 Programmation par rapport au zéro machine. G70 Programmation en pouces. G71 Programmation en millimètres. G90 Programmation absolue. G91 Programmation incrémentale. G93 Présélection de l'origine polaire. On peut programmer les fonctions suivantes, même si elles sont ignorées par le cycle. G05 Arête arrondie. G07 Arête vive. G50 Arête arrondie contrôlée. Fonctions F, S, T, D ou M. CNC 8035 MODÈLE ·T· (SOFT V16.3X) ·174· Manuel de programmation G81. Cycle fixe de tournage de segments droits Ce cycle réalise le tournage du segment programmé en conservant le pas spécifié entre les passes successives de tournage. Le cycle permet de sélectionner si on effectue ou non une passe de finition dès que le tournage programmé est terminé. La structure de base du bloc est la suivante: G81 X Z Q R C D L M F H X±5.5 Il définit la cote du point initial du profil suivant l'axe X. Programmation en cotes absolues et suivant les unités actives, rayons ou diamètres. G81. Cycle fixe de tournage de segments droits 9. CYCLES FIXES 9.4 Z±5.5 Il définit la cote du point initial du profil suivant l'axe Z. Programmation en cotes absolues. Q±5.5 Il définit la cote, suivant l'axe X, du point final du profil. Programmation en cotes absolues et suivant les unités actives, rayons ou diamètres. R±5.5 Il définit la cote, suivant l'axe Z, du point final du profil. C5.5 Il définit le pas de tournage et sera programmé avec une valeur positive exprimée en rayons. Si on le programme avec une valeur 0, la CNC affiche l'erreur correspondante. Tout le tournage se réalise avec le même pas, celui-ci étant égal ou inférieur à celui programmé (C). D 5.5 Il définit la distance de sécurité à laquelle s'effectue le retour de l'outil à chaque passe. CNC 8035 MODÈLE ·T· (SOFT V16.3X) Si on programme D avec une valeur différente de 0, la plaquette réalise un mouvement de retrait à 45° jusqu'à atteindre la distance de sécurité (figure à gauche). Si on programme D avec la valeur 0, la trajectoire de sortie coïncide avec la trajectoire d'entrée. ·175· Manuel de programmation Si le paramètre D n'est pas programmé, le retrait de l'outil s'effectue en suivant le profil jusqu'à la passe précédente, distance C (figure à droite). Quand on ne programme pas le paramètre D, il faut tenir compte que le temps d'exécution du cycle est supérieur, mais la quantité de matière à enlever dans la passe de finition est inférieure. L5.5 Il définit la surépaisseur pour la finition suivant l'axe X et sera programmé en rayons. 9. Si on ne la programme pas, la valeur 0 est prise. CYCLES FIXES G81. Cycle fixe de tournage de segments droits M5.5 Il définit la surépaisseur pour la finition suivant l'axe Z. Si on ne la programme pas, la valeur 0 est prise. F5.5 Il définit la vitesse d'avance de la passe finale d'ébauchage. Si on ne la programme pas ou si on la programme avec valeur 0, il est entendu qu'on ne désire pas la passe finale d'ébauchage. H5.5 Il définit la vitesse d'avance de la passe de finition. Si on ne la programme pas ou si on la programme avec valeur 0, il est entendu qu'on ne désire pas la passe de finition. CNC 8035 MODÈLE ·T· (SOFT V16.3X) ·176· Manuel de programmation Fonctionnement de base Le cycle fixe analysera le profil programmé en effectuant, au besoin, un tournage horizontal jusqu'à atteindre le profil défini. Tout le tournage se réalise avec le même pas, celui-ci étant égal ou inférieur à celui programmé (C). Chaque pas de tournage se réalise de la façon suivante : • Le déplacement "1-2" se réalise en avance rapide (G00). • Le déplacement "2-3" se réalise en G01 à l'avance programmée (F). • En ayant programmé le paramètre "D", le déplacement "3-4" se réalise en avance rapide (G00), mais si "D" n'a pas été programmé, le déplacement "3-4" s'effectue en suivant le contour programmé et en G01 à l'avance programmée (F). • Le déplacement de retour "4-5" se réalise en avance rapide (G00). Si on a sélectionné une passe finale de d'ébauchage, s'effectuera une passe parallèle au profil, tout en maintenant les surépaisseurs "L" et "M", avec l'avance "F" indiquée. Cette passe finale d'ébauchage élimine les surépaisseurs ayant resté après l'ébauchage. G81. Cycle fixe de tournage de segments droits 9. CYCLES FIXES 9.4.1 Après avoir effectué le tournage (avec ou sans passe de finition), le cycle terminera toujours au point d'appel au cycle. CNC 8035 MODÈLE ·T· (SOFT V16.3X) ·177· Manuel de programmation Considérations Les conditions d'usinage (vitesse d'avance, vitesse de rotation de broche, etc.), ainsi que la compensation de rayon d'outil (G41, G42), doivent être programmées avant l'appel au cycle. Dès que le cycle fixe est achevé, le programme continue avec la même avance F et les mêmes fonctions G qu'il disposait au moment de l'appel au cycle. La distance entre le point de départ et le point final (R, Q), suivant l’axe X, doit être égal ou supérieur à L. La distance entre le point de départ et le point initial (X, Z), suivant l’axe Z, doit être égal ou supérieur à M. CYCLES FIXES G81. Cycle fixe de tournage de segments droits 9. CNC 8035 MODÈLE ·T· (SOFT V16.3X) ·178· Si la position de l'outil n'est pas correcte pour exécuter le cycle, la CNC affiche l'erreur correspondante. Manuel de programmation G82. Cycle fixe de dressage de segments droits Ce cycle réalise le dressage du segment programmé en conservant le pas spécifié entre les passes successives de dressage. Le cycle permet de sélectionner si on effectue ou non une passe de finition dès que le dressage programmé est terminé. La structure de base du bloc est la suivante: G82 X Z Q R C D L M F H X±5.5 Il définit la cote du point initial du profil suivant l'axe X. Programmation en cotes absolues et suivant les unités actives, rayons ou diamètres. G82. Cycle fixe de dressage de segments droits 9. CYCLES FIXES 9.5 Z±5.5 Il définit la cote du point initial du profil suivant l'axe Z. Programmation en cotes absolues. Q±5.5 Il définit la cote, suivant l'axe X, du point final du profil. Programmation en cotes absolues et suivant les unités actives, rayons ou diamètres. R±5.5 Il définit la cote, suivant l'axe Z, du point final du profil. C5.5 Il définit le pas de dressage. Tout le dressage se réalise avec le même pas, celui-ci étant égal ou inférieur à celui programmé (C). Si on le programme avec une valeur 0, la CNC affiche l'erreur correspondante. D 5.5 Il définit la distance de sécurité à laquelle s'effectue le retour de l'outil à chaque passe. CNC 8035 MODÈLE ·T· (SOFT V16.3X) Si on programme D avec une valeur différente de 0, la plaquette réalise un mouvement de retrait à 45° jusqu'à atteindre la distance de sécurité (figure à gauche). ·179· Manuel de programmation Si on programme D avec la valeur 0, la trajectoire de sortie coïncide avec la trajectoire d'entrée. Si le paramètre D n'est pas programmé, le retrait de l'outil s'effectue en suivant le profil jusqu'à la passe précédente, distance C (figure à droite). Quand on ne programme pas le paramètre D, il faut tenir compte que le temps d'exécution du cycle est supérieur, mais la quantité de matière à enlever dans la passe de finition est inférieure. L5.5 9. Il définit la surépaisseur pour la finition suivant l'axe X et sera programmé en rayons. CYCLES FIXES G82. Cycle fixe de dressage de segments droits Si on ne la programme pas, la valeur 0 est prise. M5.5 Il définit la surépaisseur pour la finition suivant l'axe Z. Si on ne la programme pas, la valeur 0 est prise. F5.5 Il définit la vitesse d'avance de la passe finale d'ébauchage. Si on ne la programme pas ou si on la programme avec valeur 0, il est entendu qu'on ne désire pas la passe finale d'ébauchage. H5.5 Il définit la vitesse d'avance de la passe de finition. Si on ne la programme pas ou si on la programme avec valeur 0, il est entendu qu'on ne désire pas la passe de finition. CNC 8035 MODÈLE ·T· (SOFT V16.3X) ·180· Manuel de programmation Fonctionnement de base Le cycle fixe analysera le profil programmé en effectuant, au besoin, un dressage vertical jusqu'à atteindre le profil défini. Tout le dressage se réalise avec le même pas, celui-ci étant égal ou inférieur à celui programmé (C). Chaque pas de dressage se réalise de la façon suivante : • Le déplacement "1-2" se réalise en avance rapide (G00). • Le déplacement "2-3" se réalise en G01 à l'avance programmée (F). • En ayant programmé le paramètre "D", le déplacement "3-4" se réalise en avance rapide (G00), mais si "D" n'a pas été programmé, le déplacement "3-4" s'effectue en suivant le contour programmé et en G01 à l'avance programmée (F). • Le déplacement de retour "4-5" se réalise en avance rapide (G00). Si on a sélectionné une passe finale de d'ébauchage, s'effectuera une passe parallèle au profil, tout en maintenant les surépaisseurs "L" et "M", avec l'avance "F" indiquée. Cette passe finale d'ébauchage élimine les surépaisseurs ayant resté après l'ébauchage. G82. Cycle fixe de dressage de segments droits 9. CYCLES FIXES 9.5.1 Après avoir effectué le dressage (avec ou sans passe de finition), le cycle terminera toujours au point d'appel au cycle. CNC 8035 MODÈLE ·T· (SOFT V16.3X) ·181· Manuel de programmation Considérations Les conditions d'usinage (vitesse d'avance, vitesse de rotation de broche, etc.), ainsi que la compensation de rayon d'outil (G41, G42), doivent être programmées avant l'appel au cycle. Dès que le cycle fixe est achevé, le programme continue avec la même avance F et les mêmes fonctions G qu'il disposait au moment de l'appel au cycle. La distance entre le point de départ et le point initial (X, Z), suivant l’axe X, doit être égal ou supérieur à L. La distance entre le point de départ et le point final (R, Q), suivant l’axe Z, doit être égal ou supérieur à M. CYCLES FIXES G82. Cycle fixe de dressage de segments droits 9. CNC 8035 MODÈLE ·T· (SOFT V16.3X) ·182· Si la position de l'outil n'est pas correcte pour exécuter le cycle, la CNC affiche l'erreur correspondante. Manuel de programmation 9.6 G83. Cycle fixe de perçage axial / taraudage Ce cycle permet d'effectuer un perçage axial ou un taraudage axial. L'exécution d'une opération ou d'une autre dépend du format de programmation utilisé. Si le paramètre "B=0" est défini, s'effectue un taraudage axial et si on définit "B>0" s'effectue un perçage axial. La structure basique du bloc dans chaque cas est : Taraudage axial G83 X Z I B0 D K R 9. X±5.5 Il définit la cote suivant l'axe X, où l'on veut exécuter le cycle. Programmation en cotes absolues et suivant les unités actives, rayons ou diamètres. G83. Cycle fixe de perçage axial / taraudage G83 X Z I B D K H C L R CYCLES FIXES Perçage axial Z±5.5 Il définit la cote suivant l'axe Z, où l'on veut exécuter le cycle. Programmation en cotes absolues. I±5.5 Il définit la profondeur. Il se rapportera au point de départ (X, Z), et donc aura une valeur positive si le perçage ou le filetage est réalisé dans le sens négatif suivant l'axe Z et une valeur négative si le perçage ou le filetage est réalisé dans le sens contraire. Si on le programme avec une valeur 0, la CNC affiche l'erreur correspondante. B5.5 Il définit le type d'opération que l'on veut exécuter. • Si on programme B=0, s'effectuera un taraudage axial. • Si on programme B>0 s'effectuera un perçage axial et la valeur de B indique le pas de perçage. D5.5 Il définit la distance de sécurité et indique à quelle distance du point de départ (Z, X) l'outil se positionne dans le mouvement d'approche. Si on ne la programme pas, la valeur 0 est prise. K5 Il définit le temps d'attente, en centièmes de seconde, au fond de l'alésage, jusqu'à ce que le retour commence. Si on ne la programme pas, la valeur 0 est prise. CNC 8035 H5.5 Il définit la distance de retour en rapide (G00) après chaque perçage. Si on programme la distance ou si on la programme avec valeur 0, retournera jusqu'au point d'approche. MODÈLE ·T· (SOFT V16.3X) ·183· Manuel de programmation C5.5 Il définit jusqu'à quelle distance du pas de perçage précédent, l'axe Z se déplacera en rapide (G00) dans son approche de la pièce pour réaliser un nouveau pas de perçage. Si on ne la programme pas, sera prise la valeur 1. L5.5 Optionnel. Sur le cycle de perçage il définit le pas minimum que peut prendre le pas de perçage. Il s'utilise avec des valeurs de "R" différentes de 1. 9. CYCLES FIXES G83. Cycle fixe de perçage axial / taraudage Si on ne la programme pas, la valeur 0 est prise. R5.5 Dans le cycle de perçage indique le facteur qui réduit le pas de perçage "B". Si on ne le programme pas ou si on le programme avec valeur 0, on prendra la valeur 1. • Avec R=1, tous les pas de perçage seront égaux et de la valeur programmée "B". • Si R n'est pas égal à 1, le premier pas de perçage sera "B", le deuxième "R B", le troisième "R (RB)", et ainsi de suite, c'est-à-dire qu'à partir du deuxième pas, le nouveau pas sera le produit du facteur R par le pas précédent. Le cycle de filetage définit le type de filetage que l'on veut effectuer. Si on ne le programme pas, on prend la valeur 0, taraudage. • Avec R0, taraudage. • Avec R1, taraudage rigide. La CNC arrête l'outil avec M19 et l'oriente pour commencer le filetage. • Avec R2, taraudage rigide. Si l’outil tourne en M3 ou M4, la CNC ne l’arrête ni l’oriente pas pour commencer le filetage. Cette option ne permet pas de repasser le filetage même si la pièce n'a pas été libérée, car l'entrée du filet ne coïncidera pas avec celui usiné auparavant. Pour pouvoir effectuer un taraudage rigide il faut que la broche correspondante (principale ou secondaire) soit prête à travailler en boucle, autrement dit qu'elle dispose d'un système moteurasservissement et de codeur de broche. CNC 8035 MODÈLE ·T· (SOFT V16.3X) ·184· Manuel de programmation Fonctionnement de base Perçage 1. Déplacement en rapide jusqu'au point d'approche, situé à une distance de sécurité "D" du point de perçage. 2. Première pénétration de perçage. Déplacement en avance de travail de l'axe longitudinal jusqu'à la profondeur incrémentale programmée en "D+B". D'abord, recule en rapide (G00) la quantité indiquée (H) ou jusqu'au point d'approche. Approche en rapide (G00) jusqu'à une distance "C" du pas de perçage précédent. Nouvelle passe de perçage. Déplacement en avance de travail (G01) jusqu'à la prochaine pénétration incrémentale suivant "B" et "R". 4. Temps d'attente K en centièmes de seconde, au fond du perçage, s'il a été programmé. 5. Retour en rapide (G00) jusqu'au point d'approche. Taraudage 1. Déplacement en rapide jusqu'au point d'approche, situé à une distance de sécurité "D" du point de taraudage. 2. Filetage. Déplacement en avance de travail de l'axe longitudinal jusqu'à la profondeur incrémentale programmée en "D+B". 9. G83. Cycle fixe de perçage axial / taraudage 3. Boucle de perçage. Les pas suivants seront répétés jusqu'à atteindre la cote de profondeur programmée en "I". CYCLES FIXES 9.6.1 3. Inversion du sens de rotation de la broche. Si on a programmé K, la broche s'arrête et après l'écoulement du temps programmé la broche redémarre dans le sens contraire. 4. Retour en avance de travail jusqu'au point d'approche. Taraudage rigide 1. Le filetage s'effectue au centre de la pièce (X0). Déplacement en rapide jusqu'au point d'approche, situé à une distance de sécurité "D" du point de taraudage. 2. Filetage. Déplacement jusqu'à la profondeur incrémentale programmée en "D+B". Il se réalise en interpolant la broche principale (qui est en train de tourner) avec l'axe Z. On ne peut pas arrêter le taraudage sans modifier les conditions d'usinage. Il s'effectue à 100% de S et F programmées. 3. Inversion du sens de rotation de la broche. Si on a programmé K, la broche s'arrête et après l'écoulement du temps programmé la broche redémarre dans le sens contraire. 4. Retour en avance de travail jusqu'au point d'approche. Pour la représentation graphique du taraudage rigide on utilise la couleur de "sans compensation". À la fin du cycle la broche s'arrête (M5). Considérations CNC 8035 Les conditions d'usinage (vitesse d'avance, vitesse de rotation de broche, etc.), doivent être programmées avant l'appel au cycle. Quand il s'agit d'un taraudage (rigide ou taraudage) la sortie logique générale "TAPPING" (M5517) reste active pendant l'exécution du cycle. MODÈLE ·T· (SOFT V16.3X) Dès que le cycle fixe est achevé, le programme continue avec la même avance F et les mêmes fonctions G qu'il disposait au moment de l'appel au cycle. Seule la compensation de rayon d'outil sera annulée, si elle était active, l'exécution du programme continuant avec la fonction G40. ·185· Manuel de programmation 9.7 G84. Cycle fixe de tournage de segments courbes Ce cycle réalise le tournage du segment programmé en conservant le pas spécifié entre les passes successives de tournage. Le cycle permet de sélectionner si on effectue ou non une passe de finition dès que le tournage programmé est terminé. La structure de base du bloc est la suivante: G84 X Z Q R C D L M F H I K CYCLES FIXES G84. Cycle fixe de tournage de segments courbes 9. X±5.5 Il définit la cote du point initial du profil suivant l'axe X. Programmation en cotes absolues et suivant les unités actives, rayons ou diamètres. Z±5.5 Il définit la cote du point initial du profil suivant l'axe Z. Programmation en cotes absolues. Q±5.5 Il définit la cote, suivant l'axe X, du point final du profil. Programmation en cotes absolues et suivant les unités actives, rayons ou diamètres. R±5.5 Il définit la cote, suivant l'axe Z, du point final du profil. C5.5 Il définit le pas de tournage et sera programmé avec une valeur positive exprimée en rayons. Si on le programme avec une valeur 0, la CNC affiche l'erreur correspondante. Tout le tournage se réalise avec le même pas, celui-ci étant égal ou inférieur à celui programmé (C). CNC 8035 MODÈLE ·T· (SOFT V16.3X) ·186· Manuel de programmation D 5.5 Il définit la distance de sécurité à laquelle s'effectue le retour de l'outil à chaque passe. • Si on programme D avec une valeur différente de 0, la plaquette réalise un mouvement de retrait à 45° jusqu'à atteindre la distance de sécurité (figure à gauche). • Si on programme D avec la valeur 0, la trajectoire de sortie coïncide avec la trajectoire d'entrée. • Si le paramètre D n'est pas programmé, le retrait de l'outil s'effectue en suivant le profil jusqu'à la passe précédente, distance C (figure à droite). Quand on ne programme pas le paramètre D, il faut tenir compte que le temps d'exécution du cycle est supérieur, mais la quantité de matière à enlever dans la passe de finition est inférieure. L5.5 Il définit la surépaisseur pour la finition suivant l'axe X et sera programmé en rayons. Si on ne la programme pas, la valeur 0 est prise. M5.5 Il définit la surépaisseur pour la finition suivant l'axe Z. G84. Cycle fixe de tournage de segments courbes CYCLES FIXES 9. Si on ne la programme pas, la valeur 0 est prise. F5.5 Il définit la vitesse d'avance de la passe finale d'ébauchage. Si on ne la programme pas ou si on la programme avec valeur 0, il est entendu qu'on ne désire pas la passe finale d'ébauchage. H5.5 Il définit la vitesse d'avance de la passe de finition. Si on ne la programme pas ou si on la programme avec valeur 0, il est entendu qu'on ne désire pas la passe de finition. CNC 8035 I±5.5 Il définit en rayons la distance depuis le point de départ (X, Z) au centre de l'arc, suivant l'axe X. Il est programmé en cotes incrémentales par rapport au point de départ, comme I en interpolations circulaires (G02, G03). MODÈLE ·T· (SOFT V16.3X) ·187· Manuel de programmation K±5.5 Il définit la distance depuis le point de départ (X, Z) au centre de l'arc, suivant l'axe Z. Il est programmé en cotes incrémentales par rapport au point de départ, comme K en interpolations circulaires (G02, G03). CYCLES FIXES G84. Cycle fixe de tournage de segments courbes 9. CNC 8035 MODÈLE ·T· (SOFT V16.3X) ·188· Manuel de programmation Fonctionnement de base Le cycle fixe analysera le profil programmé en effectuant, au besoin, un tournage horizontal jusqu'à atteindre le profil défini. Tout le tournage se réalise avec le même pas, celui-ci étant égal ou inférieur à celui programmé (C). Chaque pas de tournage se réalise de la façon suivante : • Le déplacement "1-2" se réalise en avance rapide (G00). • Le déplacement "2-3" se réalise en G01 à l'avance programmée (F). • En ayant programmé le paramètre "D", le déplacement "3-4" se réalise en avance rapide (G00), mais si "D" n'a pas été programmé, le déplacement "3-4" s'effectue en suivant le contour programmé et en G01 à l'avance programmée (F). • Le déplacement de retour "4-5" se réalise en avance rapide (G00). Si on a sélectionné une passe finale de d'ébauchage, s'effectuera une passe parallèle au profil, tout en maintenant les surépaisseurs "L" et "M", avec l'avance "F" indiquée. Cette passe finale d'ébauchage élimine les surépaisseurs ayant resté après l'ébauchage. G84. Cycle fixe de tournage de segments courbes 9. CYCLES FIXES 9.7.1 Après avoir effectué le tournage (avec ou sans passe de finition), le cycle terminera toujours au point d'appel au cycle. CNC 8035 MODÈLE ·T· (SOFT V16.3X) ·189· Manuel de programmation Considérations Les conditions d'usinage (vitesse d'avance, vitesse de rotation de broche, etc.), ainsi que la compensation de rayon d'outil (G41, G42), doivent être programmées avant l'appel au cycle. Dès que le cycle fixe est achevé, le programme continue avec la même avance F et les mêmes fonctions G qu'il disposait au moment de l'appel au cycle. La distance entre le point de départ et le point final (R, Q), suivant l’axe X, doit être égal ou supérieur à L. La distance entre le point de départ et le point initial (X, Z), suivant l’axe Z, doit être égal ou supérieur à M. CYCLES FIXES G84. Cycle fixe de tournage de segments courbes 9. CNC 8035 MODÈLE ·T· (SOFT V16.3X) ·190· Si la position de l'outil n'est pas correcte pour exécuter le cycle, la CNC affiche l'erreur correspondante. Manuel de programmation G85. Cycle fixe de dressage de segments courbes Ce cycle réalise le dressage du segment programmé en conservant le pas spécifié entre les passes successives de dressage. Le cycle permet de sélectionner si on effectue ou non une passe de finition dès que le dressage programmé est terminé. La structure de base du bloc est la suivante: G85 X Z Q R C D L M F H I K X±5.5 Il définit la cote du point initial du profil suivant l'axe X. Programmation en cotes absolues et suivant les unités actives, rayons ou diamètres. G85. Cycle fixe de dressage de segments courbes 9. CYCLES FIXES 9.8 Z±5.5 Il définit la cote du point initial du profil suivant l'axe Z. Programmation en cotes absolues. Q±5.5 Il définit la cote, suivant l'axe X, du point final du profil. Programmation en cotes absolues et suivant les unités actives, rayons ou diamètres. R±5.5 Il définit la cote, suivant l'axe Z, du point final du profil. C5.5 Il définit le pas de dressage. Tout le dressage se réalise avec le même pas, celui-ci étant égal ou inférieur à celui programmé (C). Si on le programme avec une valeur 0, la CNC affiche l'erreur correspondante. CNC 8035 MODÈLE ·T· (SOFT V16.3X) ·191· Manuel de programmation D 5.5 Il définit la distance de sécurité à laquelle s'effectue le retour de l'outil à chaque passe. • Si on programme D avec une valeur différente de 0, la plaquette réalise un mouvement de retrait à 45° jusqu'à atteindre la distance de sécurité (figure à gauche). • Si on programme D avec la valeur 0, la trajectoire de sortie coïncide avec la trajectoire d'entrée. • Si le paramètre D n'est pas programmé, le retrait de l'outil s'effectue en suivant le profil jusqu'à la passe précédente, distance C (figure à droite). CYCLES FIXES G85. Cycle fixe de dressage de segments courbes 9. Quand on ne programme pas le paramètre D, il faut tenir compte que le temps d'exécution du cycle est supérieur, mais la quantité de matière à enlever dans la passe de finition est inférieure. L5.5 Il définit la surépaisseur pour la finition suivant l'axe X et sera programmé en rayons. Si on ne la programme pas, la valeur 0 est prise. M5.5 Il définit la surépaisseur pour la finition suivant l'axe Z. Si on ne la programme pas, la valeur 0 est prise. F5.5 Il définit la vitesse d'avance de la passe finale d'ébauchage. Si on ne la programme pas ou si on la programme avec valeur 0, il est entendu qu'on ne désire pas la passe finale d'ébauchage. H5.5 CNC 8035 Il définit la vitesse d'avance de la passe de finition. Si on ne la programme pas ou si on la programme avec valeur 0, il est entendu qu'on ne désire pas la passe de finition. I±5.5 MODÈLE ·T· (SOFT V16.3X) ·192· Il définit en rayons la distance depuis le point de départ (X, Z) au centre de l'arc, suivant l'axe X. Il est programmé en cotes incrémentales par rapport au point de départ, comme I en interpolations circulaires (G02, G03). Manuel de programmation K±5.5 Il définit la distance depuis le point de départ (X, Z) au centre de l'arc, suivant l'axe Z. Il est programmé en cotes incrémentales par rapport au point de départ, comme K en interpolations circulaires (G02, G03). G85. Cycle fixe de dressage de segments courbes CYCLES FIXES 9. CNC 8035 MODÈLE ·T· (SOFT V16.3X) ·193· Manuel de programmation 9.8.1 Fonctionnement de base Le cycle fixe analysera le profil programmé en effectuant, au besoin, un dressage vertical jusqu'à atteindre le profil défini. Tout le dressage se réalise avec le même pas, celui-ci étant égal ou inférieur à celui programmé (C). Chaque pas de dressage se réalise de la façon suivante : CYCLES FIXES G85. Cycle fixe de dressage de segments courbes 9. • Le déplacement "1-2" se réalise en avance rapide (G00). • Le déplacement "2-3" se réalise en G01 à l'avance programmée (F). • En ayant programmé le paramètre "D", le déplacement "3-4" se réalise en avance rapide (G00), mais si "D" n'a pas été programmé, le déplacement "3-4" s'effectue en suivant le contour programmé et en G01 à l'avance programmée (F). • Le déplacement de retour "4-5" se réalise en avance rapide (G00). Si on a sélectionné une passe finale de d'ébauchage, s'effectuera une passe parallèle au profil, tout en maintenant les surépaisseurs "L" et "M", avec l'avance "F" indiquée. Cette passe finale d'ébauchage élimine les surépaisseurs ayant resté après l'ébauchage. Après avoir effectué le dressage (avec ou sans passe de finition), le cycle terminera toujours au point d'appel au cycle. CNC 8035 MODÈLE ·T· (SOFT V16.3X) ·194· Manuel de programmation Considérations Les conditions d'usinage (vitesse d'avance, vitesse de rotation de broche, etc.), ainsi que la compensation de rayon d'outil (G41, G42), doivent être programmées avant l'appel au cycle. Dès que le cycle fixe est achevé, le programme continue avec la même avance F et les mêmes fonctions G qu'il disposait au moment de l'appel au cycle. La distance entre le point de départ et le point initial (X, Z), suivant l’axe X, doit être égal ou supérieur à L. La distance entre le point de départ et le point final (R, Q), suivant l’axe Z, doit être égal ou supérieur à M. Si la position de l'outil n'est pas correcte pour exécuter le cycle, la CNC affiche l'erreur correspondante. G85. Cycle fixe de dressage de segments courbes CYCLES FIXES 9. CNC 8035 MODÈLE ·T· (SOFT V16.3X) ·195· Manuel de programmation 9.9 G86. Cycle fixe de filetage longitudinal Ce cycle permet de tailler des filets extérieurs ou intérieurs sur des corps coniques ou cylindriques. Les filets à droite ou à gauche seront programmés en indiquant le sens de rotation de la broche M03 ou M04. La structure de base du bloc est la suivante: G86 X Z Q R K I B E D L C J A W V M CYCLES FIXES G86. Cycle fixe de filetage longitudinal 9. X±5.5 Il définit la cote, suivant l'axe X, du point initial du filet. Programmation en cotes absolues et suivant les unités actives, rayons ou diamètres. Z±5.5 Il définit la cote, suivant l'axe Z, du point initial du filet. Programmation en cotes absolues. Q±5.5 Il définit la cote, suivant l'axe X, du point final du filet. Programmation en cotes absolues et suivant les unités actives, rayons ou diamètres. R±5.5 Il définit la cote, suivant l'axe Z, du point final du filet. K±5.5 Optionnel. Il s'utilise, en même temps que le paramètre "W", pour le repassage de filets. Il définit la cote, suivant l'axe Z, du point où s'effectue la mesure du filet. C'est normalement un point intermédiaire du filet. I±5.5 Il définit la profondeur du filet et sera programmé en rayons. Il aura une valeur positive pour les filets extérieurs et négative pour les filets intérieurs. Si on le programme avec une valeur 0, la CNC affiche l'erreur correspondante. CNC 8035 MODÈLE ·T· (SOFT V16.3X) ·196· Manuel de programmation B±5.5 Il définit la profondeur des passes de filetage et sera programmé en rayons. Ainsi, les pénétrations suivant l'axe X sont: B ,B 2 ,B 3 ,B 4 ,B n • Si la programmation est faite avec une valeur négative, l'incrément de la pénétration reste constant entre passes, avec une valeur égale à celle programmée (B). Ainsi, les pénétrations suivant l'axe X sont: B ,2B ,3B ,4B ,nB • Si on le programme avec une valeur 0, la CNC affiche l'erreur correspondante. Indépendamment du signe affecté à "B", lorsque la dernière passe d'ébauchage (avant la finition) est inférieure à la quantité programmée, le cycle fixe réalisera une passe égale au surplus de matière. G86. Cycle fixe de filetage longitudinal • Si on fait la programmation avec une valeur positive, la profondeur de chaque passe sera en fonction du numéro de passe correspondant. CYCLES FIXES 9. E±5.5 Il est en rapport avec le paramètre B. Il indique la valeur minimum que peut atteindre le pas de pénétration lorsqu'on a programmé le paramètre B avec une valeur positive. Si on ne le programme pas, la valeur 0 est prise. D±5.5 Il définit la distance de sécurité et indique à quelle distance, sur l'axe X, du point de départ du filet, l'outil se positionne dans le mouvement d'approche. La distance sera programmée en rayons. Le retour au point de départ, après chaque passe de filetage se réalise en maintenant cette même distance (D) du segment programmé. • Si la valeur programmée est positive, ce mouvement de retour se réalise en arête arrondie (G05) et si la valeur est négative, en arête vive (G07). • Si on ne la programme pas, la valeur 0 est prise. L±5.5 Il définit la surépaisseur pour la finition et sera programmé en rayons. • Si on fait la programmation avec une valeur positive, la passe de finition se réalise en maintenant le même angle d'entrée "A" que les autres passes. CNC 8035 MODÈLE ·T· (SOFT V16.3X) • Si on fait la programmation avec une valeur négative, la passe de finition se réalise avec entrée radiale. • Si on fait la programmation avec une valeur 0, la passe précédente est répétée. ·197· Manuel de programmation C5.5 Il définit le pas de filet. • Avec signe positif si on programme le pas suivant l'inclinaison du cône. • Avec signe négatif si on programme le pas suivant l'axe associé. CYCLES FIXES G86. Cycle fixe de filetage longitudinal 9. Si on le programme avec une valeur 0, la CNC affiche l'erreur correspondante. J5.5 Sortie du filet. Il définit à quelle distance, suivant l'axe Z, du point final du filet (R, Q) commence la sortie de celui-ci. • Si on le programme avec une valeur positive, l'outil se déplace directement du point "J" à la distance de sécurité Xs, Zs. • Si on fait la programmation avec une valeur négative, l'outil se déplace du point "J" au point final du filet (R, Q), puis à la distance de sécurité Xs. • S'il n'est pas programmé, la valeur 0 est prise (filet borgne). Pour améliorer le réglage et l’usinage de la sortie des filets borgnes, on pourra utiliser la troisième gamme de gains et d’accélérations pour les axes et la broche. Si le parcours de la sortie de filet est petit, on pourra utiliser n’importe quelle gamme d’accélérations et même supprimer l’accélération sans que l’erreur "accélération insuffisante pendant le filetage" ne soit affichée. Il est recommandé d'utiliser des accélérations basses ou nulles. J>0 J<0 A±5.5 Il définit l'angle de pénétration de l'outil. Il se rapportera à l'axe X et si on ne le programme pas, la valeur 30º sera attribuée. • Si on programme A=0, le filet se réalisera avec pénétration radiale. • Si la valeur affectée au paramètre "A" est la moitié de l'angle de l'outil, la pénétration se réalise en frôlant le flanc du filet. CNC 8035 MODÈLE ·T· (SOFT V16.3X) ·198· • Si on programme A avec une valeur négative, la pénétration se réalisera en zigzag, en alternant à chaque passe le flanc du filet. Manuel de programmation W±5.5 Optionnel. La signification dépend du paramètre "K". • Lorsque le paramètre "K" est défini, il s'agit d'un repassage de filets. Il indique la position angulaire de la broche correspondant au point où s'effectue la mesure du filet. L'exemple suivant indique comment effectuer un filet à 3 entrées. Pour cela, on programmera 3 cycles fixes de filetage avec les mêmes valeurs, sauf la valeur affectée au paramètre "W". G86 X Z Q R K I B E D L C J A W0 G86 X Z Q R K I B E D L C J A W120 G86 X Z Q R K I B E D L C J A W240 V±5.5 G86. Cycle fixe de filetage longitudinal • Si le paramètre "K" n'a pas été défini, il indique la position angulaire de la broche correspondant au point de départ du filet. Cela permet d'effectuer des filets aux multiples entrées sans utiliser le paramètre "V". CYCLES FIXES 9. Optionnel. Il définit le nombre d'entrées de filet que l'on veut effectuer. Si on ne le programme pas ou si on le programme avec valeur 0, le filet aura une seule entrée. M±5.5 Définit l’incrément (M positif) ou le décrément (M négatif) du pas du filet pour chaque tour de la broche. Ce paramètre est incompatible avec le paramètre K (repassage de filets), et donc si on programme les deux paramètres ensemble, la CNC affichera l’erreur correspondante. Il faut tenir compte qu’en programmant un décrément du pas de filet et si le pas arrive à la valeur 0 avant de terminer l’usinage, la CNC affichera l’erreur correspondante. CNC 8035 MODÈLE ·T· (SOFT V16.3X) ·199· Manuel de programmation 9.9.1 Fonctionnement de base 1. Déplacement en rapide jusqu'au point d'approche, situé à une distance de sécurité "D" du point de départ (X, Z). 2. Boucle de filetage. Les pas suivants seront répétés jusqu'à atteindre la cote de finition, profondeur programmée dans "I" moins la surépaisseur de finition "L". ·1· Déplacement en rapide (G00) jusqu'à la cote de profondeur programmée avec "B". Ce déplacement se réalisera suivant l'angle de pénétration de l'outil (A) sélectionné. CYCLES FIXES G86. Cycle fixe de filetage longitudinal 9. ·2· Il effectue le filetage du segment programmé et avec la sortie de filet (J) sélectionnée. Pendant le filetage, on ne peut pas changer la vitesse d’avance F avec le commutateur FEED-OVERRIDE, dont la valeur restera fixe à 100%. Sur les grands tours, au commencement de l’usinage, en réalisant des filetages longs, pour éviter que la pièce commence à "cintrer ", on peut changer l’override de la broche pendant les premières passes. ·3· Retour en rapide (G00) jusqu'au point d'approche. 3. Finition du filet. Déplacement en rapide (G00) jusqu'à la cote de profondeur programmée en "I". Ce déplacement se réalisera radialement ou suivant l'angle de pénétration d'outil (A), en fonction du signe appliqué au paramètre "L". 4. Il effectue le filetage du segment programmé et avec la sortie de filet (J) sélectionnée. Pendant le filetage, on ne peut pas changer la vitesse d’avance F avec le commutateur FEEDOVERRIDE, dont la valeur restera fixe à 100%. Lors de la dernière passe du filetage on ne peut pas changer l’override, celui-ci étant réglé à la valeur qui serait imposée sur la passe précédente. 5. Retour en rapide (G00) jusqu'au point d'approche. Repassage de filets Pour effectuer le repassage de filets, suivre les pas suivants: 1. Effectuer la recherche de référence machine de la broche. 2. Effectuer la mesure angulaire du filet (gorge), paramètres K W. 3. Définir le cycle G87 pour le repassage de filet. 4. Exécuter le cycle fixe. Considérations Les conditions d'usinage (vitesse d'avance, vitesse de rotation de broche, etc.), doivent être programmées avant l'appel au cycle. Dès que le cycle fixe est achevé, le programme continue avec la même avance F et les mêmes fonctions G qu'il disposait au moment de l'appel au cycle. Seule la compensation de rayon d'outil sera annulée, si elle était active, l'exécution du programme continuant avec la fonction G40. CNC 8035 MODÈLE ·T· (SOFT V16.3X) ·200· Manuel de programmation G87. Cycle fixe de filetage frontal Ce cycle permet de tailler des filets extérieurs ou intérieurs sur la face avant de la pièce. Les filets à droite ou à gauche seront programmés en indiquant le sens de rotation de la broche M03 ou M04. La structure de base du bloc est la suivante: G87 X Z Q R K I B E D L C J A W V M G87. Cycle fixe de filetage frontal 9. CYCLES FIXES 9.10 X±5.5 Il définit la cote, suivant l'axe X, du point initial du filet. Programmation en cotes absolues et suivant les unités actives, rayons ou diamètres. Z±5.5 Il définit la cote, suivant l'axe Z, du point initial du filet. Programmation en cotes absolues. Q±5.5 Il définit la cote, suivant l'axe X, du point final du filet. Programmation en cotes absolues et suivant les unités actives, rayons ou diamètres. R±5.5 Il définit la cote, suivant l'axe Z, du point final du filet. K±5.5 Optionnel. Il s'utilise, en même temps que le paramètre "W", pour le repassage de filets. Il définit la cote, suivant l'axe X, du point où s'effectue la mesure du filet. C'est normalement un point intermédiaire du filet. I±5.5 Il définit la profondeur du filet. Aura une valeur positive si on usine dans le sens négatif, suivant l'axe Z et une valeur négative, si on usine dans le sens contraire. Si on le programme avec une valeur 0, la CNC affiche l'erreur correspondante. CNC 8035 MODÈLE ·T· (SOFT V16.3X) ·201· Manuel de programmation B±5.5 Il définit la profondeur des passes de filet. CYCLES FIXES G87. Cycle fixe de filetage frontal 9. • Si on fait la programmation avec une valeur positive, la profondeur de chaque passe sera en fonction du numéro de passe correspondant. Ainsi, les pénétrations suivant l'axe X sont: B ,B 2 ,B 3 ,B 4 ,B n • Si la programmation est faite avec une valeur négative, l'incrément de la pénétration reste constant entre passes, avec une valeur égale à celle programmée (B). Ainsi, les pénétrations suivant l'axe X sont: B ,2B ,3B ,4B ,nB • Si on le programme avec une valeur 0, la CNC affiche l'erreur correspondante. Indépendamment du signe affecté à "B", lorsque la dernière passe d'ébauchage (avant la finition) est inférieure à la quantité programmée, le cycle fixe réalisera une passe égale au surplus de matière. E±5.5 Il est en rapport avec le paramètre B. Il indique la valeur minimum que peut atteindre le pas de pénétration lorsqu'on a programmé le paramètre B avec une valeur positive. Si on ne le programme pas, la valeur 0 est prise. D±5.5 Il définit la distance de sécurité et indique à quelle distance, sur l'axe Z, du point de départ du filet, l'outil se positionne dans le mouvement d'approche. Le retour au point de départ, après chaque passe de filetage se réalise en maintenant cette même distance (D) du segment programmé. CNC 8035 MODÈLE ·T· (SOFT V16.3X) ·202· • Si la valeur programmée est positive, ce mouvement de retour se réalise en arête arrondie (G05) et si la valeur est négative, en arête vive (G07). • Si on ne la programme pas, la valeur 0 est prise. Manuel de programmation L±5.5 Il définit la surépaisseur pour la finition. • Si on fait la programmation avec une valeur positive, la passe de finition se réalise en maintenant le même angle d'entrée "A" que les autres passes. • Si on fait la programmation avec une valeur 0, la passe précédente est répétée. C5.5 Il définit le pas de filet. G87. Cycle fixe de filetage frontal • Si on fait la programmation avec une valeur négative, la passe de finition se réalise avec entrée radiale. CYCLES FIXES 9. • Avec signe positif si on programme le pas suivant l'inclinaison du cône. • Avec signe négatif si on programme le pas suivant l'axe associé. Si on le programme avec une valeur 0, la CNC affiche l'erreur correspondante. J5.5 Sortie du filet. Il définit à quelle distance, suivant l'axe Z, du point final du filet (R, Q) commence la sortie de celui-ci. • Si on le programme avec une valeur positive, l'outil se déplace directement du point "J" à la distance de sécurité Xs, Zs. • Si on fait la programmation avec une valeur négative, l'outil se déplace du point "J" au point final du filet (R, Q), puis à la distance de sécurité Xs. • S'il n'est pas programmé, la valeur 0 est prise (filet borgne). Pour améliorer le réglage et l’usinage de la sortie des filets borgnes, on pourra utiliser la troisième gamme de gains et d’accélérations pour les axes et la broche. Si le parcours de la sortie de filet est petit, on pourra utiliser n’importe quelle gamme d’accélérations et même supprimer l’accélération sans que l’erreur "accélération insuffisante pendant le filetage" ne soit affichée. CNC 8035 MODÈLE ·T· (SOFT V16.3X) ·203· Manuel de programmation Il est recommandé d'utiliser des accélérations basses ou nulles. (R,Q) (R,Q) (Xs,Zs) Z CYCLES FIXES J>0 G87. Cycle fixe de filetage frontal (Xs,Zs) J J 9. D X D X Z J<0 A±5.5 Il définit l'angle de pénétration de l'outil. Il se rapportera à l'axe X et si on ne le programme pas, la valeur 30º sera attribuée. • Si on programme A=0, le filet se réalisera avec pénétration radiale. • Si la valeur affectée au paramètre "A" est la moitié de l'angle de l'outil, la pénétration se réalise en frôlant le flanc du filet. • Si on programme A avec une valeur négative, la pénétration se réalisera en zigzag, en alternant à chaque passe le flanc du filet. W±5.5 Optionnel. La signification dépend du paramètre "K". • Lorsque le paramètre "K" est défini, il s'agit d'un repassage de filets. Il indique la position angulaire de la broche correspondant au point où s'effectue la mesure du filet. • Si le paramètre "K" n'a pas été défini, il indique la position angulaire de la broche correspondant au point de départ du filet. Cela permet d'effectuer des filets aux multiples entrées sans utiliser le paramètre "V". L'exemple suivant indique comment effectuer un filet à 3 entrées. Pour cela, on programmera 3 cycles fixes de filetage avec les mêmes valeurs, sauf la valeur affectée au paramètre "W". G86 X Z Q R K I B E D L C J A W0 CNC 8035 G86 X Z Q R K I B E D L C J A W120 G86 X Z Q R K I B E D L C J A W240 V±5.5 MODÈLE ·T· (SOFT V16.3X) Optionnel. Il définit le nombre d'entrées de filet que l'on veut effectuer. Si on ne le programme pas ou si on le programme avec valeur 0, le filet aura une seule entrée. ·204· Manuel de programmation M±5.5 Définit l’incrément (M positif) ou le décrément (M négatif) du pas du filet pour chaque tour de la broche. Ce paramètre est incompatible avec le paramètre K (repassage de filets), et donc si on programme les deux paramètres ensemble, la CNC affichera l’erreur correspondante. Il faut tenir compte qu’en programmant un décrément du pas de filet et si le pas arrive à la valeur 0 avant de terminer l’usinage, la CNC affichera l’erreur correspondante. G87. Cycle fixe de filetage frontal CYCLES FIXES 9. CNC 8035 MODÈLE ·T· (SOFT V16.3X) ·205· Manuel de programmation 9.10.1 Fonctionnement de base 1. Déplacement en rapide jusqu'au point d'approche, situé à une distance de sécurité "D" du point de départ (X, Z). 2. Boucle de filetage. Les pas suivants seront répétés jusqu'à atteindre la cote de finition, profondeur programmée dans "I" moins la surépaisseur de finition "L". ·1· Déplacement en rapide (G00) jusqu'à la cote de profondeur programmée avec "B". Ce déplacement se réalisera suivant l'angle de pénétration de l'outil (A) sélectionné. CYCLES FIXES G87. Cycle fixe de filetage frontal 9. ·2· Il effectue le filetage du segment programmé et avec la sortie de filet (J) sélectionnée. Pendant le filetage, on ne peut pas changer la vitesse d’avance F avec le commutateur FEED-OVERRIDE, dont la valeur restera fixe à 100%. Sur les grands tours, au commencement de l’usinage, en réalisant des filetages longs, pour éviter que la pièce commence à "cintrer ", on peut changer l’override de la broche pendant les premières passes. ·3· Retour en rapide (G00) jusqu'au point d'approche. 3. Finition du filet. Déplacement en rapide (G00) jusqu'à la cote de profondeur programmée en "I". Ce déplacement se réalisera radialement ou suivant l'angle de pénétration d'outil (A), en fonction du signe appliqué au paramètre "L". 4. Il effectue le filetage du segment programmé et avec la sortie de filet (J) sélectionnée. Pendant le filetage, on ne peut pas changer la vitesse d’avance F avec le commutateur FEEDOVERRIDE, dont la valeur restera fixe à 100%. Lors de la dernière passe du filetage on ne peut pas changer l’override, celui-ci étant réglé à la valeur qui serait imposée sur la passe précédente. 5. Retour en rapide (G00) jusqu'au point d'approche. Repassage de filets Pour effectuer le repassage de filets, suivre les pas suivants: 1. Effectuer la recherche de référence machine de la broche. 2. Effectuer la mesure angulaire du filet (gorge), paramètres K W. 3. Définir le cycle G87 pour le repassage de filet. 4. Exécuter le cycle fixe. Considérations Les conditions d'usinage (vitesse d'avance, vitesse de rotation de broche, etc.), doivent être programmées avant l'appel au cycle. Dès que le cycle fixe est achevé, le programme continue avec la même avance F et les mêmes fonctions G qu'il disposait au moment de l'appel au cycle. Seule la compensation de rayon d'outil sera annulée, si elle était active, l'exécution du programme continuant avec la fonction G40. CNC 8035 MODÈLE ·T· (SOFT V16.3X) ·206· Manuel de programmation 9.11 G88. Cycle fixe de rainurage sur l'axe X Ce cycle réalise le rainurage sur l'axe X en conservant le même pas entre les passes successives, le pas étant égal ou inférieur à celui programmé. La structure de base du bloc est la suivante: G88 X Z Q R C D K G88. Cycle fixe de rainurage sur l'axe X CYCLES FIXES 9. X±5.5 Il définit la cote, suivant l'axe X, du point initial de la rainure. Programmation en cotes absolues et suivant les unités actives, rayons ou diamètres. Z±5.5 Il définit la cote, suivant l'axe Z, du point initial de la rainure. Programmation en cotes absolues. Q±5.5 Il définit la cote, suivant l'axe X, du point final de la rainure. Programmation en cotes absolues et suivant les unités actives, rayons ou diamètres. R±5.5 Il définit la cote, suivant l'axe Z, du point final de la rainure. C5.5 Il définit le pas de rainurage. Si on ne le programme pas, on prendra la valeur de la largeur de la plaquette (NOSEW) de l'outil actif, et si on le programme avec la valeur 0, la CNC affichera l'erreur correspondante. D5.5 Il définit la distance de sécurité et sera programmé avec une valeur positive exprimée en rayons. K5 CNC 8035 Il définit le temps d'attente, en centièmes de seconde, après chaque pénétration, jusqu'à ce que le retour commence. Si on ne la programme pas, la valeur 0 est prise. MODÈLE ·T· (SOFT V16.3X) ·207· Manuel de programmation 9.11.1 Fonctionnement de base Tout le rainurage se réalise avec le même pas, celui-ci étant égal ou inférieur à "C". Chaque pas de rainurage se réalise de la façon suivante : • Le déplacement de pénétration se réalise à l'avance programmée (F). • Le déplacement de retour et le déplacement au prochain point de pénétration se réalisent à l'avance rapide (G00). Après avoir effectué le rainurage, le cycle fixe terminera toujours au point d'appel au cycle. CYCLES FIXES G88. Cycle fixe de rainurage sur l'axe X 9. CNC 8035 MODÈLE ·T· (SOFT V16.3X) ·208· Considérations Les conditions d'usinage (vitesse d'avance, vitesse de rotation de broche, etc.), doivent être programmées avant l'appel au cycle. Dès que le cycle fixe est achevé, le programme continue avec la même avance F et les mêmes fonctions G qu'il disposait au moment de l'appel au cycle. Seule la compensation de rayon d'outil sera annulée, si elle était active, l'exécution du programme continuant avec la fonction G40. L’outil doit être situé par rapport à la pièce à une distance, sur l’axe X, supérieure ou égale à celle indiquée dans le paramètre "D" (distance de sécurité) de définition du cycle fixe. Si la profondeur de la rainure est nulle, la CNC affiche l'erreur correspondante. Si la largeur de la rainure est inférieure à la largeur de la plaquette (NOSEW), la CNC affiche l'erreur correspondante. Manuel de programmation 9.12 G89. Cycle fixe de rainurage sur l'axe Z Ce cycle réalise le rainurage sur l'axe Z en conservant le même pas entre les passes successives, le pas étant égal ou inférieur à celui programmé. La structure de base du bloc est la suivante: G89 X Z Q R C D K G89. Cycle fixe de rainurage sur l'axe Z CYCLES FIXES 9. X±5.5 Il définit la cote, suivant l'axe X, du point initial de la rainure. Programmation en cotes absolues et suivant les unités actives, rayons ou diamètres. Z±5.5 Il définit la cote, suivant l'axe Z, du point initial de la rainure. Programmation en cotes absolues. Q±5.5 Il définit la cote, suivant l'axe X, du point final de la rainure. Programmation en cotes absolues et suivant les unités actives, rayons ou diamètres. R±5.5 Il définit la cote, suivant l'axe Z, du point final de la rainure. C5.5 Il définit le pas de rainurage. La distance sera programmée en rayons. Si on ne le programme pas, on prendra la valeur de la largeur de la plaquette (NOSEW) de l'outil actif, et si on le programme avec la valeur 0, la CNC affichera l'erreur correspondante. D5.5 Définit la distance de sécurité. Si on ne la programme pas, la valeur 0 est prise. CNC 8035 K5 Il définit le temps d'attente, en centièmes de seconde, après chaque pénétration, jusqu'à ce que le retour commence. MODÈLE ·T· (SOFT V16.3X) Si on ne la programme pas, la valeur 0 est prise. ·209· Manuel de programmation 9.12.1 Fonctionnement de base Tout le rainurage se réalise avec le même pas, celui-ci étant égal ou inférieur à "C". Chaque pas de rainurage se réalise de la façon suivante : • Le déplacement de pénétration se réalise à l'avance programmée (F). • Le déplacement de retour et le déplacement au prochain point de pénétration se réalisent à l'avance rapide (G00) Après avoir effectué le rainurage, le cycle fixe terminera toujours au point d'appel au cycle. CYCLES FIXES G89. Cycle fixe de rainurage sur l'axe Z 9. CNC 8035 MODÈLE ·T· (SOFT V16.3X) ·210· Considérations Les conditions d'usinage (vitesse d'avance, vitesse de rotation de broche, etc.), doivent être programmées avant l'appel au cycle. Dès que le cycle fixe est achevé, le programme continue avec la même avance F et les mêmes fonctions G qu'il disposait au moment de l'appel au cycle. Seule la compensation de rayon d'outil sera annulée, si elle était active, l'exécution du programme continuant avec la fonction G40. L’outil doit être situé par rapport à la pièce à une distance, sur l’axe Z, supérieure ou égale à celle indiquée dans le paramètre "D" (distance de sécurité) de définition du cycle fixe. Si la profondeur de la rainure est nulle, la CNC affiche l'erreur correspondante. Si la largeur de la rainure est inférieure à la largeur de la plaquette (NOSEW), la CNC affiche l'erreur correspondante. TRAVAIL AVEC PALPEUR 10 La CNC dispose de deux entrées de palpeur pour des signaux 5 V DC du type TTL et pour signaux 24 V DC. La connexion des différents types de palpeurs à ces entrées est expliquée dans les appendices du manuel d'installation. CNC 8035 MODÈLE ·T· (SOFT V16.3X) ·211· Manuel de programmation 10.1 Déplacement avec palpeur (G75, G76) La fonction G75 permet de programmer des déplacements qui termineront après que la CNC aura reçu le signal du palpeur de mesure utilisé. La fonction G76 permet de programmer des déplacements qui se terminent dès que la CNC ne reçoit plus le signal émis par le palpeur de mesure utilisé. Le format de définition des deux fonctions est: TRAVAIL AVEC PALPEUR Déplacement avec palpeur (G75, G76) 10. G75 X..C ±5.5 G76 X..C ±5.5 A la suite de la fonction désirée G75 ou G76, on programmera le ou les axes désirés, ainsi que les coordonnées de ces axes, qui définiront le point final du déplacement programmé. La machine se déplacera selon la trajectoire programmée, jusqu’à ce qu’elle reçoive (G75) ou cesse de recevoir (G76) le signal du palpeur; à ce moment, la CNC considère que le bloc est terminé, et prend comme position théorique des axes la position réelle qu’ils occupent à ce moment. Si les axes atteignent la position programmée avant de recevoir ou de cesser de recevoir le signal externe du palpeur, la CNC interrompt le déplacement des axes. Ce type de bloc de déplacement avec palpeur est très utile pour mettre au point des programmes de mesure ou de vérification d’outils et de pièces. Les fonctions G75 et G76 sont non-modales et doivent donc être programmées pour chaque déplacement avec palpeur. Les fonctions G75 et G76 sont incompatibles entre elles et avec les fonctions G00, G02, G03, G33, G41 et G42. En outre, dès que l’une d’elles a été exécutée, la CNC suppose la présence des fonctions G01 et G40. Pendant les déplacements en G75 ou G76, le fonctionnement du commutateur feedrate override dépend de la façon dont le fabricant a personnalisé le paramètre machine FOVRG75. CNC 8035 MODÈLE ·T· (SOFT V16.3X) ·212· PROGRAMMATION EN LANGAGE DE HAUT NIVEAU 11.1 11 Description lexique Tous les mots constituant le langage à haut niveau de la commande numérique doivent être écrits en majuscules, à l’exception des textes associés, qui peuvent être écrits en majuscules et en minuscules. Les éléments disponibles pour la programmation en haut niveau sont: • Mots réservés. • Constantes numériques. • Symboles. Mots réservés Les mots réservés sont les mots que la CNC utilise dans la programmation à haut niveau pour dénommer les variables du système, les opérateurs, les instructions de contrôle, etc. Les lettres de l'alphabet A-Z sont aussi des mots réservés car elles peuvent former un mot du langage à haut niveau lorsqu'elles sont seules. Constantes numériques Les blocs programmés en langage à haut niveau permettent des nombres en format décimal et des nombres en format hexadécimal. • Les nombres en format décimal ne doivent pas dépasser le format ±6.5 (6 chiffres entiers et 5 décimales). • Les nombres en format hexadécimal doivent être précédés du symbole $ et doivent avoir un maximum de 8 chiffres. L’affectation à une variable d’une constante supérieure au format ±6.5, s’effectuera au moyen de paramètres arithmétiques, d’expressions arithmétiques ou de constantes en format hexadécimal. Pour affecter la valeur 100000000 à la variable "TIMER" , on peut procéder des façons suivantes: (TIMER = $5F5E100) (TIMER = 10000 * 10000) (P100 = 10000 * 10000) (TIMER = P100) CNC 8035 Si la commande travaille en système métrique (millimètres), la résolution est en dixième de micron, les chiffres étant programmés sous format ±5.4 (positif ou négatif, avec 5 chiffres entiers et 4 décimales). Si la commande travaille en pouces, la résolution est de cent millièmes de pouce, les chiffres étant programmés sous format ±4.5 (positif ou négatif, avec 4 chiffres entiers et 5 décimales). MODÈLE ·T· (SOFT V16.3X) ·213· Manuel de programmation Pour faciliter le travail du programmeur, cette commande admet toujours le format ±5.5 (positif ou négatif, avec 5 chiffres entiers et 5 décimales), et elle ajuste selon besoins chaque nombre en fonction des unités de travail au moment de l’utilisation. Symboles Les symboles utilisés dans le langage à haut niveau sont: Description lexique PROGRAMMATION EN LANGAGE DE HAUT NIVEAU 11. CNC 8035 MODÈLE ·T· (SOFT V16.3X) ·214· ( ) “ = + - * / , Manuel de programmation Variables La CNC dispose d’une série de variables internes accessibles depuis le programme utilisateur, depuis le programme du PLC ou via DNC. Suivant leur utilisation, ces variables sont des variables de lecture ou des variables de lecture-écriture. L’accès à ces variables depuis le programme utilisateur est obtenu au moyen de commandes à haut niveau. Chacune de ces variables sera référencée avec sa mnémonique, qui doit être écrite en majuscules. ORG(X-C) -> ORGX ORGY ORGZ ORGU ORGV ORGW ORGA ORGB ORGC • Les mnémoniques terminant en n indiquent que les variables sont regroupées en tables. Pour accéder à un élément de l'une de ces tables, il faut indiquer le champ de la table souhaitée avec la mnémonique correspondant suivi de l'élément en question. TORn -> TOR1 TOR3 TOR11 Les variables et la préparation de blocs Les variables accédant à des valeurs réelles de la CNC arrêtent la préparation de blocs. La CNC attend à ce que cette commande soit exécutée pour recommencer la préparation de blocs. vbEn conséquence, ce type de variable ne doit être utilisé qu’avec précautions car, si elles sont insérées entre des blocs d’usinage travaillant avec compensation, des profils indésirables risquent d’être produits. Exemple: Lecture d'une variable qui arrête la préparation de blocs. Variables 11. • Les mnémoniques terminant en(X-C) indiquent un ensemble de 9 éléments formés par la racine correspondante suivie de X, Y, Z, U, V, W, A, B et C. PROGRAMMATION EN LANGAGE DE HAUT NIVEAU 11.2 Les blocs de programme suivants sont exécutés dans une section comportant une compensation G41. ... N10 X80 Z50 N15 (P100 = POSX); Affecte au paramètre P100 la valeur de la cote réelle sur X. N20 X50 Z50 N30 X50 Z80 ... Le bloc N15 interrompt la préparation des blocs; l’exécution du bloc N10 se terminera donc au point A. Lorsque l’exécution du bloc N15 est terminée, la CNC reprend la préparation des blocs à partir du bloc N20. CNC 8035 MODÈLE ·T· (SOFT V16.3X) ·215· Manuel de programmation Comme le point suivant correspondant à la trajectoire compensée est le point "B", la CNC déplacera l’outil jusqu’à ce point, en exécutant la trajectoire "A-B". Comme on peut le voir, la trajectoire produite n’est pas la trajectoire désirée; il est donc recommandé d’éviter l’utilisation de ce type de variable dans les sections comportant une compensation. Variables PROGRAMMATION EN LANGAGE DE HAUT NIVEAU 11. CNC 8035 MODÈLE ·T· (SOFT V16.3X) ·216· Manuel de programmation 11.2.1 Paramètres ou variables de caractère général Les variables d'usage général sont référencées avec la lettre "P" suivie d'un nombre entier. La CNC dispose de quatre types de variables d'usage général. Paramètres locaux P0-P25 Paramètres globaux P100-P299 Paramètres d'utilisateur P1000-P1255 Paramètres OEM (de fabricant) P2000 - P2255 Dans les blocs programmés en code ISO, on peut associer des paramètres à tous les champs G F S T D M et cotes des axes. Le numéro d'étiquette de bloc sera défini avec une valeur numérique. Si des paramètres sont utilisés dans des blocs programmés en langage à haut niveau, ils pourront être programmés dans n’importe quelle expression. Le programmeur pourra utiliser des variables de caractère général lorsqu’il éditera ses propres programmes. Ensuite, et pendant l’exécution, la CNC remplacera ces variables par les valeurs qui leur sont affectées à un moment donné. Dans la programmation... Dans l'exécution... GP0 XP1 Z100 G1 X-12.5 Z100 (IF (P100 * P101 EQ P102) GOTO N100) (IF (2 * 5 EQ 12) GOTO N100) L’utilisation de ces variables de caractère général dépendra du type de bloc dans lequel elles seront programmées et du canal d’exécution. Les programmes exécutés dans le canal d'utilisateur pourront contenir n'importe quel paramètre global, d'utilisateur ou de fabricant mais ne pourront pas utiliser de paramètres locaux. 11. Variables Rang PROGRAMMATION EN LANGAGE DE HAUT NIVEAU Type de paramètre Types de paramètres arithmétiques Paramètres locaux Les paramètres locaux ne sont accessibles que depuis le programme ou la sous-routine dans laquelle ils ont été programmés. Il existe sept groupes de paramètres. Les paramètres locaux utilisés en langage à haut niveau pourront être définis, soit comme indiqué précédemment, soit au moyen des lettres A-Z, à l’exception de Ñ, de telle sorte que A est égal à P0 et Z à P25. L’exemple suivant présente ces 2 méthodes de définition: (IF ((P0+P1)* P2/P3 EQ P4) GOTO N100) (IF ((A+B)* C/D EQ E) GOTO N100) Si un nom de paramètre local est utilisé pour lui affecter une valeur (A au lieu de P0 par exemple), et si l’expression arithmétique est une constante numérique, l'instruction peut être abrégée comme suit: (P0=13.7) ==> (A=13.7) ==> (A13.7) On n’utilisera les parenthèses qu’avec précautions, car M30 ne signifie pas la même chose que (M30). La CNC interprète (M30) comme une instruction et comme M est une autre façon de définir le paramètre P12, cette instruction sera lue comme (P12=30), et la valeur 30 sera affectée au paramètre P12. CNC 8035 Paramètres globaux Les paramètres globaux sont accessibles depuis n'importe quel programme et sous-routine appelée depuis le programme. MODÈLE ·T· (SOFT V16.3X) Les paramètres globaux peuvent être utilisés par l'utilisateur, par le fabricant et par les cycles de la CNC. ·217· Manuel de programmation Paramètres d'utilisateur Ces paramètres sont une prolongation des paramètres globaux, avec la seule différence qu'ils ne sont pas utilisés par les cycles de la CNC. Paramètres OEM (de fabricant) Les paramètres OEM et les sous-routines avec des paramètres OEM ne peuvent être utilisés que dans les programmes propres du fabricant; ceux définis avec l'attribut [O]. Le code fabricant est sollicité pour modifier l'un de ces paramètres dans les tables. Variables PROGRAMMATION EN LANGAGE DE HAUT NIVEAU 11. Utilisation des paramètres arithmétiques par les cycles Les usinages multiples (G60 à G65) et les cycles fixes d'usinage (G69, G81 à G89) utilisent le sixième niveau d'imbrication de paramètres locaux lorsqu'ils sont actifs. Les cycles fixes d’usinage utilisent le paramètre global P299 pour leurs calculs internes, tandis que les cycles fixes de palpeur emploient les paramètres globaux P294 à P299. Actualisation des tables de paramètres arithmétiques La CNC mettra à jour la table de paramètres après avoir traité les opérations indiquées dans le bloc en préparation. Cette opération est toujours réalisée avant l’exécution du bloc; pour cette raison, il n’est pas obligatoire que les valeurs indiquées dans la table correspondent à celles du bloc en cours d’exécution. Si le mode exécution est abandonné après une interruption d’exécution du programme, la CNC met à jour les tables de paramètres avec les valeurs correspondant au bloc qui se trouvait en cours d’exécution. Lorsqu’on accède à la table de paramètres locaux et de paramètres globaux, la valeur affectée à chaque paramètre peut être exprimée en notation décimale (4127.423) ou scientifique (0.23476 E3). Paramètres arithmétiques dans les sous-routines La CNC dispose des instructions à haut niveau permettant de définir et d’utiliser des sous-routines pouvant être appelées depuis un programme principal ou une autre sous-routine qui peut en appeler une seconde, la seconde pouvant en appeler une troisième, etc.... La CNC limite le nombre d’appels, le nombre de niveaux d’imbrication étant limité à 15. On peut affecter 26 paramètres locaux (P0-P25) à une sous-routine. Ces paramètres, qui ne seront pas connus pour les blocs externes à la sous-routine, pourront être référencés par les blocs formant celle-ci. La CNC permet d’affecter des paramètres locaux à plus d’une sous-routine, le nombre maximum possible de niveaux d’imbrications de paramètres locaux étant de 6 à l’intérieur des 15 niveaux d’imbrication de sous-routines. CNC 8035 MODÈLE ·T· (SOFT V16.3X) ·218· Manuel de programmation 11.2.2 Variables associées aux outils. Ces variables sont associées la table de correcteurs, à la table d’outils et à la table de magasin d’outils; les valeurs affectées ou lues dans ces champs devront respecter les formats définis pour ces tables. Table des correcteurs La valeur du rayon (R), longueur (L) et correcteurs d'usure (I, K) de l'outil sont indiqués dans les unités actives. Si l'axe rotatif est en degrés (entre ±99999.9999). La valeur du facteur de forme (F) sera un nombre entier entre 0 et 9. Table d'outils Le numéro de correcteur sera un nombre entier entre 0 et 255. Le nombre maximum de correcteurs est limité par le p.m.g. NTOFFSET. Le code de famille sera un numéro entre 0 et 255. 0 a 199 s'il s'agit d'un outil normal. 200 à 255 s'il s'agit d'un outil spécial. La durée de vie nominale sera exprimée en minutes ou en opérations (0··65535). La durée de vie réelle sera exprimée en centièmes de minute (0··9999999) ou en opérations (0··999999). L’angle de la plaquette sera exprimé en dix-millièmes de degré (0··359999). PROGRAMMATION EN LANGAGE DE HAUT NIVEAU Si G71, en millimètres (entre ±99999,9999). Variables 11. Si G70, en pouces (entre ±3937.00787). La largeur de la plaquette est exprimée en unités actives. Si G70, en pouces (entre ±3937.00787). Si G71, en millimètres (entre ±99999,9999). Si l'axe rotatif est en degrés (entre ±99999.9999). L’angle de coupe sera exprimé en dix-millièmes de degré (0··359999). Table du magasin d’outils Chaque position du magasin est représentée de la façon suivante. 1··255 Numéro d'outil. 0 La position du magasin est vide. -1 La position du magasin a été annulée. La position de l'outil dans le magasin est représentée de la façon suivante. 1··255 Numéro de position. 0 L'outil est sur la broche. -1 Outil non trouvé. -2 L'outil est sur la position de changement. CNC 8035 Variables de lecture TOOL Donne le numéro de l’outil actif. MODÈLE ·T· (SOFT V16.3X) (P100=TOOL) Affecte au paramètre P100 le numéro d'outil actif. ·219· Manuel de programmation TOD Donne le numéro du correcteur actif. NXTOOL Donne le numéro de l’outil suivant, sélectionné mais en attente de l’exécution de M06 pour être actif. NXTOD Donne le numéro du correcteur correspondant à l’outil suivant, sélectionné mais en attente de l’exécution de M06 pour être actif. Variables PROGRAMMATION EN LANGAGE DE HAUT NIVEAU 11. TMZPn Donne la position occupée par l’outil indiqué (n) dans le magasin d’outils. Variables de lecture et d’écriture TOXn Cette variable permet de lire ou de modifier, dans la table de correcteurs, la valeur affectée à la longueur suivant l'axe X du correcteur indiqué (n). (P110=TOX3) Affecte au paramètre P110 la valeur X du Correcteur ·3·. (TOX3=P111) Affecte à la valeur X du correcteur ·3· la valeur du paramètre P111. TOZn Cette variable permet de lire ou de modifier, dans la table de correcteurs, la valeur affectée à la longueur suivant l'axe Z du correcteur indiqué (n). TOFn Cette variable permet de lire ou de modifier dans la table de correcteurs, la valeur affectée au code de forme (F) du correcteur indiqué (n). TORn Cette variable permet de lire ou de modifier, dans la table de correcteurs la valeur affectée au rayon (R) du correcteur indiqué (n). TOIn Cette variable permet de lire ou de modifier dans la table de correcteurs, la valeur affectée à l'usure de longueur suivant l'axe X (I) du correcteur indiqué (n). TOKn Cette variable permet de lire ou de modifier dans la table de correcteurs, la valeur affectée à l'usure de longueur suivant l'axe Z (K) du correcteur indiqué (n). CNC 8035 NOSEAn Cette variable permet de lire ou de modifier, dans la table d’outils, la valeur affectée à l'angle de la plaquette de l’outil indiqué (n). NOSEWn MODÈLE ·T· (SOFT V16.3X) ·220· Cette variable permet de lire ou de modifier, dans la table d’outils, la valeur affectée à la largeur de la plaquette de l’outil indiqué (n). Manuel de programmation CUTAn Cette variable permet de lire ou de modifier, dans la table d’outils, la valeur affectée à l'angle de coupe de l’outil indiqué (n). TLFDn Cette variable permet de lire ou de modifier, dans la table d’outils, le numéro du correcteur de l’outil indiqué (n). TLFNn Cette variable permet de lire ou de modifier, dans la table d’outils, la valeur affectée comme vie nominale de l’outil indiqué (n). TLFRn Cette variable permet de lire ou de modifier, dans la table d’outils, la valeur de la vie réelle de l’outil indiqué (n). TMZTn Cette variable permet de lire ou de modifier, dans la table du magasin d’outils, le contenu du logement indiqué (n). HTOR La variable HTOR indique la valeur du rayon d’outil utilisée par la CNC pour effectuer les calculs. Du fait d’être une variable de lecture et d’écriture depuis la CNC et de lecture depuis le PLC et la DNC, sa valeur peut être différente de celle assignée dans la table (TOR). PROGRAMMATION EN LANGAGE DE HAUT NIVEAU Cette variable permet de lire ou de modifier, dans la table d’outils, le code de famille de l’outil indiqué (n). Variables 11. TLFFn À la mise sous tension, après avoir programmé une fonction T, après une RAZ ou une autre fonction M30, elle prend la valeur de la table (TOR). Exemple d'application Si on veut usiner un profil avec un surépaisseur de 0,5 mm en réalisant des passes de 0,1 mm avec un outil de 10 mm de rayon. Assigner au rayon d’outil la valeur: 10,5 mm dans la table et exécuter le profil. 10,4 mm dans la table et exécuter le profil. 10,3 mm dans la table et exécuter le profil. 10,2 mm dans la table et exécuter le profil. 10,1 mm dans la table et exécuter le profil. 10,0 mm dans la table et exécuter le profil. Mais si le programme est interrompu pendant l’usinage ou en cas de RAZ, la table assume la valeur du rayon assignée à ce moment (par ex. : 10,2 mm). Sa valeur a été modifiée. Pour éviter cela, au lieu de modifier le rayon de l’outil dans la table (TOR), on dispose de la variable (HTOR) où on modifiera la valeur du rayon de l’outil, utilisé par la CNC pour réaliser les calculs. CNC 8035 En cas d’interruption de programme, la valeur du rayon de l’outil assigné au départ dans la table (TOR), sera la bonne car elle n’aura pas été modifiée. MODÈLE ·T· (SOFT V16.3X) ·221· Manuel de programmation 11.2.3 Variables associées aux décalages d’origine Ces variables sont associées aux décalages d’origine, et peuvent correspondre aux valeurs de la table ou aux valeurs actuelles sélectionnées par la fonction G92 ou par présélection manuelle en mode JOG. Les décalages d’origine possibles, en plus du décalage additionnel indiqué par le PLC, sont G54, G55, G56, G57, G58 et G59. Variables PROGRAMMATION EN LANGAGE DE HAUT NIVEAU 11. Les valeurs de chaque axe s’expriment en unités actives: Si G70, en pouces (entre ±3937.00787). Si G71, en millimètres (entre ±99999,9999). Si l'axe rotatif est en degrés (entre ±99999.9999). Bien qu’il existe des variables liées à chaque axe, la CNC n’autorise que celles associées aux axes sélectionnés dans la CNC. Ainsi, si la CNC commande les axes X, Z, elle n'admet, dans le cas de ORG(X-C), que les variables ORGX et ORGZ. Variables de lecture ORG(X-C) Donne la valeur du décalage d’origine actif pour l’axe sélectionné. Cette valeur n'inclut pas le décalage additionnel indiqué par le PLC ou par la manivelle supplémentaire. (P100=ORGX) Affecte au paramètre P100 la valeur du décalage d’origine actif pour l’axe X. Cette valeur a pu être sélectionnée manuellement, par la fonction G92 ou par la variable "ORG(X-C)n". PORGF Donne la coordonnée, par rapport à l’origine des coordonnées cartésiennes, de l’origine des coordonnées polaires selon l’axe des abscisses. Cette variable est exprimée en rayons ou en diamètres, suivant si le paramètre machine d’axes "DFORMAT" est personnalisé. PORGS Donne la coordonnée, par rapport à l’origine des coordonnées cartésiennes, de l’origine des coordonnées polaires selon l’axe des ordonnées. Cette variable est exprimée en rayons ou en diamètres, suivant si le paramètre machine d’axes "DFORMAT" est personnalisé. ADIOF(X-C) Affiche la valeur du décalage d'origine généré par la manivelle supplémentaire sur l'axe sélectionné. CNC 8035 MODÈLE ·T· (SOFT V16.3X) ·222· Manuel de programmation Variables de lecture et d’écriture ORG(X-C)n Cette variable permet de lire ou de modifier la valeur de l’axe sélectionnée dans la table correspondant au décalage d’origine indiqué (n). (P110=ORGX 55) Affecte au paramètre P110 la valeur de l’axe X dans la table correspondant au décalage d’origine G55. PLCOF(X-C) Cette variable permet de lire ou de modifier la valeur de l’axe sélectionnée dans la table de décalages d’origine indiquée par le PLC. L’accès à l’une des variables PLCOF(X-C) entraîne l’interruption de la préparation des blocs et l’attente de l’exécution de cette commande avant la reprise de la préparation des blocs. PROGRAMMATION EN LANGAGE DE HAUT NIVEAU Affecte à l'axe Z dans la table correspondant au décalage d'origine G54 le paramètre P111. Variables 11. (ORGZ 54=P111) CNC 8035 MODÈLE ·T· (SOFT V16.3X) ·223· Manuel de programmation 11.2.4 Variables associées aux paramètres machine Ces variables, associées aux paramètres machine, sont des variables de lecture. Ces variables pourront être de lecture et d'écriture lorsqu'elles sont exécutées dans un programme ou une sousroutine de fabricant. Pour connaître le format des valeurs données, on consultera le manuel d’installation et de mise en service. Les valeurs 1/0 correspondent aux paramètres définis par YES/NO, +/- et ON/OFF. Les valeurs relatives aux coordonnées et aux avances sont exprimées en unités actives: Si G70, en pouces (entre ±3937.00787). Si G71, en millimètres (entre ±99999,9999). Variables PROGRAMMATION EN LANGAGE DE HAUT NIVEAU 11. Si l'axe rotatif est en degrés (entre ±99999.9999). Modifier les paramètres machine depuis un programme/sous-routine de fabricant Ces variables pourront être de lecture et d'écriture lorsqu'elles sont exécutées dans un programme ou une sous-routine de fabricant. Dans ce cas, avec ces variables on peut modifier la valeur de certains paramètres machine. Consulter la liste des paramètres machine que l'on peut modifier dans le manuel d'installation. Pour pouvoir modifier ces paramètres depuis le PLC, il faut exécuter avec l'instruction CNCEX une sous-routine de fabricant avec les variables correspondantes. Variables de lecture MPGn Donne la valeur qui avait été affectée au paramètre machine général (n). (P110=MPG8) Affecte au paramètre P110 la valeur du paramètre machine général P8 "INCHES"; si millimètres P110=0 et si pouces P110=1. MP(X-C)n Donne la valeur qui avait été affectée au paramètre machine (n) de l’axe indiquée (X-C). (P110=MPY 1) Affecte au paramètre P110 la valeur du paramètre machine P1 de l'axe Y "DFORMAT". MPSn Donne la valeur qui avait été affectée au paramètre machine (n) de la broche principale. MPLCn Donne la valeur qui avait été affectée au paramètre machine (n) du PLC. CNC 8035 MODÈLE ·T· (SOFT V16.3X) ·224· Manuel de programmation 11.2.5 Variables associées aux zones de travail Ces variables associées aux zones de travail sont des variables à lecture seulement. Les valeurs des limites sont exprimées en unités actives: Si G70, en pouces (entre ±3937.00787). Si G71, en millimètres (entre ±99999,9999). Si l'axe rotatif est en degrés (entre ±99999.9999). 1 = Validée comme zone interdite à l’entrée. 2 = Validée comme zone interdite à la sortie. Variables de lecture FZONE Donne l’état de la zone de travail 1. FZLO(X-C) Limite inférieure de la zone 1 selon l’axe sélectionné (X-C). FZUP(X-C) Limite inférieure de la zone 1 selon l’axe sélectionné (X-C). (P100=FZONE) ; Affecte au paramètre P100 l’état de la zone de travail 1. (P101=FZOLOX) ; Affecte au paramètre P101 la limite inférieure de la zone 1. (P102=FZUPZ) ; Affecte au paramètre P102 la limite supérieure de la zone 1. PROGRAMMATION EN LANGAGE DE HAUT NIVEAU 0 = Invalidée. Variables 11. L’état des zones de travail est défini par le code suivant: SZONE État de la zone de travail 2. SZLO(X-C) Limite inférieure de la zone 2 selon l’axe sélectionné (X-C). SZUP(X-C) Limite inférieure de la zone 2 selon l’axe sélectionné (X-C). TZONE État de la zone de travail 3. TZLO(X-C) Limite inférieure de la zone 3 selon l’axe sélectionné (X-C). TZUP(X-C) CNC 8035 Limite inférieure de la zone 3 selon l’axe sélectionné (X-C). FOZONE État de la zone de travail 4. FOZLO(X-C) MODÈLE ·T· (SOFT V16.3X) Limite inférieure de la zone 4 selon l’axe sélectionné (X-C). ·225· Manuel de programmation FOZUP(X-C) Limite inférieure de la zone 4 selon l’axe sélectionné (X-C). FIZONE État de la zone de travail 5. FIZLO(X-C) Variables PROGRAMMATION EN LANGAGE DE HAUT NIVEAU 11. CNC 8035 MODÈLE ·T· (SOFT V16.3X) ·226· Limite inférieure de la zone 5 selon l’axe sélectionné (X-C). FIZUP(X-C) Limite inférieure de la zone 5 selon l’axe sélectionné (X-C). Manuel de programmation 11.2.6 Variables associées aux avances Variables de lecture associées à l’avance réelle FREAL Donne l'avance réelle de la CNC. En mm/minute ou pouces/minute. FREAL(X-C) Donne l'avance réelle de la CNC sur l'axe sélectionné. FTEO(X-C) Donne l'avance théorique de la CNC sur l'axe sélectionné. Variables de lecture associées à la fonction G94 FEED Donne l'avance sélectionnée dans la CNC avec la fonction G94. En mm/minute ou pouces/minute. Cette avance peut être définie par programme, par le PLC ou par DNC, le choix étant fait par la CNC; la plus prioritaire est celle définie par DNC, et la moins prioritaire celle définie par programme. DNCF PROGRAMMATION EN LANGAGE DE HAUT NIVEAU Affecte au paramètre P100 l'avance réelle de la CNC. Variables 11. (P100=FREAL) Donne l’avance, en mm/minute ou pouces/minute, sélectionnée par DNC. Une valeur 0 signifie que cette avance n’est pas sélectionnée. PLCF Donne l’avance, en mm/minute ou pouces/minute, sélectionnée par le PLC. Une valeur 0 signifie que cette avance n’est pas sélectionnée. PRGF Donne l’avance, en mm/minute ou pouces/minute, sélectionnée par programme. Variables de lecture associées à la fonction G95 FPREV Donne l'avance sélectionnée dans la CNC avec la fonction G95. En mm./tour ou pouces/tour. Cette avance peut être définie par programme, par le PLC ou par DNC, le choix étant fait par la CNC; la plus prioritaire est celle définie par DNC, et la moins prioritaire celle définie par programme. DNCFPR CNC 8035 Donne l’avance, en mm/tour ou pouces/tour, sélectionnée par DNC. Une valeur 0 signifie que cette avance n’est pas sélectionnée. PLCFPR MODÈLE ·T· (SOFT V16.3X) Donne l’avance, en mm/tour ou pouces/tour, sélectionnée par le PLC. Une valeur 0 signifie que cette avance n’est pas sélectionnée. ·227· Manuel de programmation PRGFPR Donne l’avance, en mm/tour ou pouces/tour, sélectionnée par programme. Variables de lecture associées à la fonction G32 PRGFIN De même, la CNC affichera dans la variable FEED, associée à la fonction G94, l’avance résultante en mm/min. ou pouces/minute. Variables PROGRAMMATION EN LANGAGE DE HAUT NIVEAU 11. Donne l’avance, en 1/min, sélectionné par programme. Variables de lecture associées à l’override FRO Donne l'(Override (%)) d’avance sélectionnée dans la CNC. Elle est indiquée par un nombre entier entre 0 et "MAXFOVR" (maximum:255) Ce pourcentage de l’avance peut être défini par programme, par le PLC, par DNC ou depuis le panneau avant; il est sélectionné par la CNC, l’ordre de priorité (du plus au moins prioritaire) étant: par programme, par DNC, par le PLC et depuis le sélecteur. DNCFRO Donne le pourcentage d’avance sélectionné par DNC. Une valeur 0 signifie que cette avance n’est pas sélectionnée. PLCFRO Donne le pourcentage d’avance sélectionné par PLC. Une valeur 0 signifie que cette avance n’est pas sélectionnée. CNCFRO Donne le pourcentage d’avance défini par le sélecteur. PLCCFR Donne le pourcentage d’avance défini par le canal d'exécution du PLC. Variables de lecture et d'écriture associées à l'override PRGFRO Cette variable permet de lire ou de modifier le pourcentage d’avance sélectionné par programme. Elle est indiquée par un nombre entier entre 0 et "MAXFOVR" (maximum:255) Une valeur 0 signifie que cette avance n’est pas sélectionnée. (P110=PRGFRO) CNC 8035 Affecte au paramètre P110 le pourcentage de l'avance qui est sélectionné par programme. (PRGFRO=P111) Affecte au pourcentage de l'avance sélectionné par programme la valeur du paramètre P111. MODÈLE ·T· (SOFT V16.3X) ·228· Manuel de programmation 11.2.7 Variables associées aux cotes Les valeurs des coordonnées de chaque axe sont exprimées en unités actives: Si G70, en pouces (entre ±3937.00787). Si G71, en millimètres (entre ±99999,9999). Si l'axe rotatif est en degrés (entre ±99999.9999). Les cotes fournies par les variables PPOS(X-C), POS(X-C), TPOS(X-C), APOS(X-C) et ATPOS(XC) seront exprimées suivant le système d’unités (rayons ou en diamètres) actif. Pour connaître le système d’unités actif, consulter la variable DIAM. PPOS(X-C) Donne la coordonnée théorique programmée de l’axe sélectionné. (P110=PPOSX) Affecte au paramètre P100 la cote théorique programmée de l'axe X. POS(X-C) Donne la cote réelle de la base de l'outil, référée au zéro machine, de l'axe sélectionné. Dans les axes rotatifs sans limites cette variable tient compte de la valeur du décalage actif. Les valeurs de la variable sont comprises entre le décalage actif et ±360º (ORG* ± 360º). Si ORG* = 20º affiche entre 20º et 380º / affiche entre -340º et 20º. Si ORG* = -60º 60º affiche entre -60º et 300º / affiche entre -420º et -60º. PROGRAMMATION EN LANGAGE DE HAUT NIVEAU L’accès à l’une des variables POS(X-C), TPOS(X-C), APOS(X-C), ATPOS(X-C) ou FLWE(X-C) entraîne l’interruption de la préparation des blocs et l’attente de l’exécution de cette commande, avant la reprise de la préparation des blocs. Variables 11. Variables de lecture TPOS(X-C) Donne la cote théorique (cote réelle + erreur de poursuite) de la base de l'outil, référée au zéro machine, de l'axe sélectionné. Dans les axes rotatifs sans limites cette variable tient compte de la valeur du décalage actif. Les valeurs de la variable sont comprises entre le décalage actif et ±360º (ORG* ± 360º). Si ORG* = 20º affiche entre 20º et 380º / affiche entre -340º et 20º. Si ORG* = -60º 60º affiche entre -60º et 300º / affiche entre -420º et -60º. APOS(X-C) Donne la cote réelle de la base de l'outil, référée au zéro pièce, de l'axe sélectionné. ATPOS(X-C) Donne la cote théorique (cote réelle + erreur de poursuite) de la base de l'outil, référée au zéro pièce, de l'axe sélectionné. FLWE(X-C) CNC 8035 Donne l’erreur de poursuite de l’axe sélectionné. DPLY(X-C) Donne la cote représentée sur écran pour l'axe sélectionné. MODÈLE ·T· (SOFT V16.3X) ·229· Manuel de programmation GPOS(X-C)n p Cote programmée pour un certain axe, dans le bloc (n) du programme (p) indiqué. (P80=GPOSX N99 P100) Affecte au paramètre P88 la valeur de la cote programmée pour l'axe X dans le bloc avec étiquette N99 et se trouvant dans le programme P100. Variables PROGRAMMATION EN LANGAGE DE HAUT NIVEAU 11. On ne peut consulter que des programmes se trouvant dans la mémoire RAM de la CNC. Si le programme ou le bloc défini n'existe pas, l'erreur correspondante sera affichée. Si dans le bloc l'axe sollicité n'est pas programmé, la valeur 100000.0000 est restituée. Variables de lecture et d’écriture DIST(X-C) Ces variables permettent de lire ou de modifier la distance parcourue par l’axe sélectionné. Cette valeur est accumulative et très utile si l’on désire réaliser une opération dépendant de la distance parcourue par les axes, comme par exemple leur graissage. (P110=DISTX) Affecte au paramètre P110 la distance parcourue par l'axe X. (DISTX=P111) Initialise la variable qui indique la distance parcourue par l'axe Z avec la valeur du paramètre P111. L’accès à l’une des variables DIST(X-C) entraîne l’interruption de la préparation des blocs et l’attente de l’exécution de cette commande avant la reprise de la préparation des blocs. LIMPL(X-C) LIMMI(X-C) Ces variables permettent de fixer une seconde limite de parcours pour chacun des axes, LIMPL pour le supérieur et LIMMI pour l’inférieur. Comme l’activation et la désactivation des deuxièmes limites sont réalisées par le PLC, au moyen de l’entrée logique générale ACTLIM2 (M5052), en plus de définir les limites il faut exécuter une fonction auxiliaire M pour le lui communiquer. Il est recommandé aussi d’exécuter la fonction G4 après le changement pour que la CNC exécute les blocs suivants avec les nouvelles limites. Le seconde limite de parcours sera prise en compte quand la première aura été définie, avec les paramètres machine d’axes LIMIT+ (P5) et LIMIT- (P6). CNC 8035 MODÈLE ·T· (SOFT V16.3X) ·230· Manuel de programmation 11.2.8 Variables associées aux manivelles électroniques. Variables de lecture HANPS HANPT HANPFO Donnent les impulsions de la première (HANPF), la deuxième (HANPS), la troisième (HANPT) ou la quatrième (HANPFO) manivelle qui ont été reçues depuis la mise sous tension de la CNC. 11. Sur les manivelles avec bouton sélecteur d'axes, indique si ce bouton a été tapé. Avec la valeur ·0·, signifie qu'il n'a pas été tapé. HANFCT Donne le facteur de multiplication fixé depuis le PLC pour chaque manivelle. On doit l’utiliser quand on dispose de plusieurs manivelles électroniques ou en ne disposant que d’une seule manivelle on veut appliquer différents facteurs de multiplication (x1, x10, x100) à chaque axe. C B A W V U Z Y X c b a c b a c b a c b a c b a c b a c b a c b a c b a lsb Une fois le sélecteur positionné sur l’une des positions de la manivelle, la CNC consulte cette variable et en fonction des valeurs affectées aux bits (c b a) de chaque axe elle applique le facteur multiplicateur sélectionné pour chacun d’eux c b a 0 0 0 Ce qui est indiqué dans le sélecteur du panneau de commande ou clavier 0 0 1 Facteur x1 0 1 0 Facteur x10 1 0 0 Facteur x100 PROGRAMMATION EN LANGAGE DE HAUT NIVEAU HANDSE Variables HANPF S’il y a plus d’un bit à 1 sur axe, on considère le bit moins significatif. Ainsi: c b a 1 1 1 Facteur x1 1 1 0 Facteur x10 i L’écran affiche toujours la valeur sélectionnée dans le sélecteur. HBEVAR À utiliser quand on dispose de la manivelle Fagor HBE. Indique si le comptage de la manivelle HBE est activé, l’axe que l’on veut déplacer et le facteur de multiplication (x1, x10, x100). C * ^ B A W V U Z Y X CNC 8035 c b a c b a c b a c b a c b a c b a c b a c b a c b a lsb (*) Indique si le comptage de la manivelle HBE est pris en compte en mode manuel. 0 = Il n'est pas pris en compte. 1 = Il est pris en compte. MODÈLE ·T· (SOFT V16.3X) (^) Quand la machine dispose d'une manivelle générale et de manivelles individuelles (associés à un axe), indique quelle manivelle a préférence quand les deux manivelles se déplacent en même temps. ·231· Manuel de programmation 0 = La manivelle individuelle a préférence. L'axe correspondant ne tient pas compte des impulsions de la manivelle générale, les autres axes oui. 1 = La manivelle générale a préférence. Ne tient pas compte des impulsions de la manivelle individuelle. (a, b, c) Indiquent l'axe que l'on veut déplacer et le facteur multiplicateur sélectionné. Variables PROGRAMMATION EN LANGAGE DE HAUT NIVEAU 11. c b a 0 0 0 Ce qui est indiqué dans le sélecteur du panneau de commande ou clavier 0 0 1 Facteur x1 0 1 0 Facteur x10 1 0 0 Facteur x100 S’il y a plusieurs axes sélectionnés on considérera l’ordre de priorité suivant: X, Y, Z, U, V, W, A, B, C. S’il y a plus d’un bit à 1 sur axe, on considère le bit moins significatif. Ainsi: c b a 1 1 1 Facteur x1 1 1 0 Facteur x10 La manivelle HBE a priorité. C’est-à-dire, indépendamment du mode du mode sélectionné dans le sélecteur de la CNC (JOG continu, incrémental, manivelle) on définit HBEVER différent à 0, la CNC travaille alors en mode manivelle. Elle affiche l’axe sélectionné en mode inverse et le facteur multiplicateur sélectionné par PLC. Quand la variable HBEVER se met à 0, elle affiche à nouveau le mode sélectionné dans le sélecteur. Variables de lecture et d’écriture MASLAN On doit l'utiliser lorsque la manivelle trajectoire ou le jog trajectoire sont sélectionnés. Indique l’angle de la trajectoire linéaire. MASCFI MASCSE On doit l'utiliser lorsque la manivelle trajectoire ou le jog trajectoire sont sélectionnés. Dans les trajectoires en arc, elles indiquent les cotes du centre de l’arc. CNC 8035 MODÈLE ·T· (SOFT V16.3X) ·232· Manuel de programmation 11.2.9 Variables associées à la mesure ASIN(X-C) Signal A de la mesure sinusoïdale de la CNC pour l'axe X-C. BSIN(X-C) Signal B de la mesure sinusoïdale de la CNC pour l'axe X-C. BSINS Signal B de la mesure sinusoïdale de la CNC pour la broche. PROGRAMMATION EN LANGAGE DE HAUT NIVEAU Signal A de la mesure sinusoïdale de la CNC pour la broche. Variables 11. ASINS CNC 8035 MODÈLE ·T· (SOFT V16.3X) ·233· Manuel de programmation 11.2.10 Variables associées à la broche principale Dans ces variables associées à la broche principale, les valeurs des vitesses sont données en tours par minute et les valeurs de l’override de la broche principale sont données par nombres entiers entre 0 et 255. Certaines variables arrêtent la préparation de blocs (cela est indiqué dans chacune) et on attend à ce que cette commande s’exécute pour recommencer la préparation de blocs. Variables PROGRAMMATION EN LANGAGE DE HAUT NIVEAU 11. Variables de lecture SREAL Donne la vitesse de rotation réelle de la broche principale en tours/minute. Arrête la préparation de blocs. (P100=SREAL) Affecte au paramètre P100 la vitesse de rotation réelle de la broche principale. FTEOS Donne la vitesse de rotation théorique de la broche principale. SPEED Donne, en tours par minute, la vitesse de rotation de la broche principale qui est sélectionnée dans la CNC. Cette vitesse de rotation peut être définie par programme, par le PLC ou par DNC, le choix étant fait par la CNC; la plus prioritaire est celle définie par DNC, et la moins prioritaire celle définie par programme. DNCS Donne la vitesse de rotation, en tours/minute, sélectionnée par DNC. Une valeur 0 signifie que cette avance n’est pas sélectionnée. PLCS Donne la vitesse de rotation, en tours/minute, sélectionnée par le PLC. Une valeur 0 signifie que cette avance n’est pas sélectionnée. PRGS Restitue la vitesse de rotation, en tours/minute, sélectionnée par programme. CSS Donne la vitesse de coupe constante sélectionnée dans la CNC. Sa valeur est donnée dans les unités actives (en pieds/minute ou en mètres/minute). Cette vitesse de coupe constante peut être indiquée par programme, par le PLC ou par DNC, le choix étant fait par la CNC; la plus prioritaire est celle définie par DNC, et la moins prioritaire celle définie par programme. CNC 8035 DNCCSS Donne la vitesse de coupe constante sélectionnée par DNC. Sa valeur est donnée en mètres/minute ou en pieds/minute et si elle a la valeur 0, cela signifie qu’elle n’est pas sélectionnée. PLCCSS MODÈLE ·T· (SOFT V16.3X) ·234· Donne la vitesse de coupe constante sélectionnée par PLC. Sa valeur est donnée en mètres/minute ou pieds/minute. Manuel de programmation PRGCSS Donne la vitesse de coupe constante sélectionnée par programme. Sa valeur est donnée en mètres/ minute ou pieds/minute. SSO Donne la Correction (Override (%)) de vitesse de rotation de la broche principale sélectionnée dans la CNC. Elle est indiquée par un nombre entier entre 0 et "MAXSOVR" (maximum:255) Ce pourcentage de vitesse de rotation de la broche principale peut être défini par programme, par le PLC, par DNC ou depuis le panneau avant; il est sélectionné par la CNC, l’ordre de priorité (du plus au moins prioritaire) étant: par programme, par DNC, par PLC et depuis le panneau avant. PLCSSO Donne le pourcentage de la vitesse de rotation de la broche principale qui est sélectionné par DNC. Une valeur 0 signifie que cette avance n’est pas sélectionnée. CNCSSO Donne le pourcentage de la vitesse de rotation de la broche principale qui est sélectionnée depuis le panneau avant. SLIMIT Donne, en tours par minute, la valeur à laquelle est fixée la limite de la vitesse de rotation de la broche principale dans la CNC. Cette limite peut être définie par programme, par le PLC ou par DNC, le choix étant fait par la CNC; la plus prioritaire est celle définie par DNC, et la moins prioritaire celle définie par programme. Variables Donne le pourcentage de la vitesse de rotation de la broche principale qui est sélectionné par DNC. Une valeur 0 signifie que cette avance n’est pas sélectionnée. PROGRAMMATION EN LANGAGE DE HAUT NIVEAU DNCSSO 11. DNCSL Donne, en tours/minute, la limite de vitesse de rotation de la broche principale sélectionnée par DNC. Une valeur 0 signifie que cette avance n’est pas sélectionnée. PLCSL Donne, en tours/minute, la limite de vitesse de rotation de la broche principale sélectionnée par PLC. Une valeur 0 signifie que cette avance n’est pas sélectionnée. PRGSL Donne, en tours/minute, la limite de vitesse de rotation de la broche principale sélectionnée par programme. MDISL Vitesse maximum de la broche pour l’usinage. Cette variable s'actualise aussi lorsqu'on programme la fonction G92 depuis MDI. POSS Donne la position réelle de la broche principale. Sa valeur est donnée entre ±99999.9999°. Arrête la préparation de blocs. CNC 8035 RPOSS Donne la position réelle de la broche principale dans le module 360°. Sa valeur est donnée entre 0 et 360°. Arrête la préparation de blocs. MODÈLE ·T· (SOFT V16.3X) ·235· Manuel de programmation TPOSS Donne la position théorique de la broche principale (cote réelle + erreur de poursuite). Sa valeur est donnée entre ±99999.9999º. Arrête la préparation de blocs. RTPOSS Donne la position théorique de la broche principale (cote réelle + erreur de poursuite) dans le module 360º. Sa valeur est donnée entre 0 et 360°. Arrête la préparation de blocs. Variables PROGRAMMATION EN LANGAGE DE HAUT NIVEAU 11. PRGSP Position programmée en M19 par programme pour la broche principal. Cette variable est de lecture depuis la CNC, le PLC et la DNC. FLWES Donne en degrés (entre ±99999.9999) l'erreur de poursuite de la broche principale. Arrête la préparation de blocs. Variables de lecture et d’écriture PRGSSO Cette variable permet de lire ou de modifier le pourcentage de vitesse de rotation de la broche principale sélectionné par programme. Elle est indiquée par un nombre entier entre 0 et "MAXSOVR" (maximum:255) Une valeur 0 signifie que cette avance n’est pas sélectionnée. (P110=PRGSSO) Affecte au paramètre P110 le pourcentage de la vitesse de rotation de la broche principale qui est sélectionné par programme. (PRGSSO=P111) Affecte au pourcentage de la vitesse de rotation de la broche principale sélectionné par programme la valeur du paramètre P111. CNC 8035 MODÈLE ·T· (SOFT V16.3X) ·236· Manuel de programmation 11.2.11 Variables associées à l’automate On tiendra compte du fait que l’automate dispose des ressources suivantes: (O1 à O256) Sorties. (M1 à M5957) Marques. (R1 à R499) Registres de 32 bits chacun. (T1 à T256) Temporisateurs avec comptage du temporisateur en 32 bits. (C1 à C256) Compteurs avec comptage du compteur en 32 bits. 11. L’accès à une variable quelconque permettant de lire ou de modifier l’état d’une ressource du PLC (I, O, M, R, T, C), entraîne l’interruption de la préparation des blocs et l’attente de l’exécution de cette commande avant la reprise de la préparation des blocs. Variables de lecture PLCMSG Donne le numéro du message d’automate le plus prioritaire actif, qui coïncidera avec celui affiché à l’écran (1··128). En l’absence de message, la variable est à 0. (P110=PLCMSG) Donne le numéro de message d'automate le plus prioritaire qui est actif. Variables de lecture et d’écriture Variables Entrées. PROGRAMMATION EN LANGAGE DE HAUT NIVEAU (I1 à I256) PLCIn Cette variable permet de lire ou de modifier 32 entrées de l’automate à partir de l’entrée indiquée (n) La valeur des entrées utilisées par l’armoire électrique ne peut pas être modifiée, car elle est imposée par cette armoire. L’état du reste des entrées peut être modifié. PLCOn Cette variable permet de lire ou de modifier 32 sorties de l’automate à partir de la sortie indiquée (n) (P110=PLCO 22) Affecte au paramètre P110 la valeur des sorties O22 a O53 (32 sorties) du PLC. (PLCO 22=$F) Affecte la valeur 1 aux sorties O22 à O25 et la valeur 0 aux sorties O26 à O53. Bit Sortie 31 30 29 28 27 26 25 24 23 22 ... 5 4 3 2 1 0 0 0 0 0 0 0 0 0 0 0 .... 0 0 1 1 1 1 53 52 51 50 49 48 47 46 45 44 .... 27 26 25 24 23 22 PLCMn CNC 8035 Cette variable permet de lire ou de modifier 32 marques de l’automate à partir de la marque indiquée (n) PLCRn Cette variable permet de lire ou de modifier l’état des 32 bits du registre indiqué (n). MODÈLE ·T· (SOFT V16.3X) PLCTn Cette variable permet de lire ou de modifier le comptage du temporisateur indiqué (n). ·237· Manuel de programmation PLCCn Cette variable permet de lire ou de modifier le comptage du compteur indiqué (n). PLCMMn Cette variable permet de lire ou de modifier la marque (n) de l'automate. (PLMM4=1) Variables PROGRAMMATION EN LANGAGE DE HAUT NIVEAU 11. CNC 8035 MODÈLE ·T· (SOFT V16.3X) ·238· Met à ·1· la marque M4 et laisse le reste comme il est. (PLCM4=1) Met à ·1· la marque M4 et à 0 les 31 suivantes (M5 à M35). Manuel de programmation 11.2.12 Variables associées aux paramètres locaux La CNC permet d’affecter 26 paramètres locaux (P0-P25) à une sous-routine grâce aux instructions PCALL et MCALL. Ces instructions permettent l’exécution de la sous-routine désirée ainsi que l’initialisation de ses paramètres locaux. Variables de lecture Les informations sont données par les 26 bits les moins significatifs (bits 0.25), chacun correspondant au paramètre local portant le même numéro; ainsi, le bit 12 correspond à P12. Chaque bit indiquera si le paramètre local a été défini (=1) ou non (=0). Bit 31 30 29 28 27 26 25 24 23 22 ... 5 4 3 2 1 0 0 0 0 0 0 0 * * * * ... * * * * * * Exemple: ; Appel à la sous-routine 20. (PCALL 20, P0=20, P2=3, P3=5) ... ... ; Début de la sous-routine 20. (SUB 20) PROGRAMMATION EN LANGAGE DE HAUT NIVEAU Permet de savoir quels paramètres locaux ont été définis et ceux qui ne l’ont pas été dans l’appel de sous-routine par l'instruction PCALL ou MCALL. Variables 11. CALLP (P100 = CALLP) ... ... Dans le paramètre P100, on obtiendra: 0000 0000 0000 0000 0000 0000 0000 1101 LSB CNC 8035 MODÈLE ·T· (SOFT V16.3X) ·239· Manuel de programmation 11.2.13 Variables associées au mode de fonctionnement Variables de lecture en rapport avec le mode standard OPMODE Donne le code correspondant au mode de fonctionnement sélectionné. Variables PROGRAMMATION EN LANGAGE DE HAUT NIVEAU 11. 0 = Menu principal. 10 = Exécution en automatique. 11 = Exécution bloc par bloc. 12 = MDI en EXÉCUTION. 13 = Inspection d'outil. 14 = Repositionnement. 15 = Recherche de bloc en exécutant G. 16 = Recherche de bloc en exécutant G, M, S et T. 20 = Simulation du parcours théorique. 21 = Simulation des fonctions G. 22 = Simulation des fonctions G, M, S et T. 23 = Simulation avec déplacement sur le plan principal. 24 = Simulation avec déplacement en rapide. 25 = Simulation en rapide avec S=0. 30 =Édition normale. 31 = Edition utilisateur. 32 = Edition en TEACH-IN. 33 = Éditeur Interactif. 40 = Déplacement en JOG continu. 41 = Déplacement en JOG incrémental. 42 = Déplacement avec manivelle électronique. 43 = Recherche du zéro en MANUEL. 44 = Présélection en MANUEL. 45 = Mesure d’outil. 46 = MDI en MANUEL. 47 = Fonctionnement MANUEL de l'utilisateur. 50 = Table d'origines. 51 = Table de correcteurs. 52 = Table d'outils. CNC 8035 53 = Table de magasin d'outils. 54 = Table de paramètres globaux. 55 = Tables de paramètres locaux. 56 = Table de paramètres d'utilisateur. 57 = Table de paramètres OEM. MODÈLE ·T· (SOFT V16.3X) 60 = Utilités. 70 = État DNC. ·240· Manuel de programmation 71 = État CNC. 80 = Edition des fichiers du PLC. 81 = Compilation du programme du PLC. 82 = Surveillance du PLC. 83 = Messages actifs du PLC. 84 = Pages actives du PLC. 85 = Sauver le programme du PLC. 88 = Statistiques du PLC. 90 = Personnalisation. 100 = Table des paramètres machine généraux. 101 = Tables de paramètres machine des axes. 102 = Table des paramètres machine de la broche. 103 = Tables des paramètres machine de la liaison série. 104 = Table des paramètres machine du PLC. 105 = Table de fonctions M. 106 = Tables de compensation de vis. 110 = Diagnostic: configuration. 111 = Diagnostic: test de hardware. 112 = Diagnostic: test de mémoire RAM. PROGRAMMATION EN LANGAGE DE HAUT NIVEAU 87 = Ressources du PLC utilisées. Variables 11. 86 = Restaurer le programme du PLC. 113 = Diagnostic: test de mémoire flash. 114 = Diagnostic d'utilisateur. CNC 8035 MODÈLE ·T· (SOFT V16.3X) ·241· Manuel de programmation 11.2.14 Autres variables Variables de lecture NBTOOL Indique le numéro d’outil en train d’être géré. On ne peut utiliser cette variable que dans la sousroutine de changement d'outil. Exemple: On dispose d’un changeur manuel d’outils. L’outil T1 est sélectionné et l’utilisateur sollicite l’outil T5. Variables PROGRAMMATION EN LANGAGE DE HAUT NIVEAU 11. La sous-routine associée aux outils peut contenir les instructions suivantes: (P103 = NBTOOL) (MSG "SÉLECTIONNER T?P103 ET TAPER SUR DÉPART") L’instruction (P103 = NBTOOL) affecte au paramètre P103 le numéro d’outil en train d’être géré, c’est-à-dire, celui que l’on désire sélectionner. Donc P103=5. Le message affiché par la CNC sera "SÉLECTIONNER T5 ET TAPER SUR DÉPART". PRGN Donne le numéro de programme en cours d’exécution. Si aucun programme n’est sélectionné, cette variable donne la valeur -1. BLKN Donne le numéro d’étiquette du dernier bloc exécuté. GSn Donne l’état de la fonction G indiquée (n). Un 1 indique une fonction active, un 0 indique une fonction inactive. (P120=GS17) Affecte au paramètre P120 la valeur 1 si la fonction G17 est active et 0 dans le cas contraire. MSn Donne l’état de la fonction M indiquée (n). Un 1 indique une fonction active, un 0 indique une fonction inactive. Cette variable donne l’état des fonctions M00, M01, M02, M03, M04, M05, M06, M08, M09, M19, M30, M41, M42, M43, M44 et M45. PLANE Donne sur 32 bits et codées les informations sur l’axe des abscisses (bits 4 à 7) et de l’axe des ordonnées (bits 0 à 3) du plan actif. ... CNC 8035 ... ... ... ... ... Axe d’abscisses 7654 3210 lsb Axe d'ordonnées Les axes sont codés en 4 bits et indiquent le numéro d’axe suivant l’ordre de programmation. MODÈLE ·T· (SOFT V16.3X) ·242· Manuel de programmation Exemple: Si la CNC commande les axes X Z et le plan ZX (G18) est sélectionné. (P122 = PLANE) affecte la valeur $31 au paramètre P122. 0000 0000 0000 0000 0000 0000 0011 0001 LSB = 3 (0011) => Axe Z Axe d'ordonnées = 1 (0001) => Axe X MIRROR Bit 8 Bit 7 Bit 6 Bit 5 Bit 4 Bit 3 Bit 2 Bit 1 Bit 0 Axe 2 Axe 1 LSB Le nom de l’axe correspond à l’ordre de programmation de ceux-ci. Exemple: Si la CNC commande les axes X, Z on a axe1=X, axe2=Z. SCALE Donne le facteur d’échelle général appliqué. SCALE(X-C) Donne le facteur d’échelle particulier de l’axe indiqué (X-C). PRBST Donne l’état du palpeur. 0 = le palpeur n’est pas en contact avec la pièce. 11. PROGRAMMATION EN LANGAGE DE HAUT NIVEAU Donne sur les bits moins significatifs d’un groupe de 32 bits l’état de l’image miroir de chaque axe, un 1 s’il est actif et un 0 dans le cas contraire. Variables Axe d'abscisses 1 = le palpeur est en contact avec la pièce. L’accès à cette variable entraîne l’interruption de la préparation des blocs et l’attente de l’exécution de cette commande avant la reprise de la préparation des blocs. CLOCK Donne, en secondes, l’heure indiquée par l’horloge système. Valeurs possibles 0··4294967295. L’accès à cette variable entraîne l’interruption de la préparation des blocs et l’attente de l’exécution de cette commande avant la reprise de la préparation des blocs. TIME Donne l’heure dans le format heures-minutes-secondes. (P150=TIME) Affecte hh-mm-ss au paramètre P150. Par exemple, s’il est 18h 22m. 34sec. on aura 182234 dans P150. L’accès à cette variable entraîne l’interruption de la préparation des blocs et l’attente de l’exécution de cette commande avant la reprise de la préparation des blocs. CNC 8035 DATE Donne la date dans le format année-mois-jour. (P151=DATE) Affecte au paramètre P151 année-mois-jour. Pour le 25 avril 1992, on aura 920425 dans P151. MODÈLE ·T· (SOFT V16.3X) L’accès à cette variable entraîne l’interruption de la préparation des blocs et l’attente de l’exécution de cette commande avant la reprise de la préparation des blocs. ·243· Manuel de programmation CYTIME Donne, en centièmes de seconde, la durée d’exécution écoulée de la pièce. Le temps que l'exécution ait pu être arrêtée n'est pas comptabilisé. Valeurs possibles 0··4294967295. L’accès à cette variable entraîne l’interruption de la préparation des blocs et l’attente de l’exécution de cette commande avant la reprise de la préparation des blocs. FIRST Indique s’il s’agit de la première exécution d’un programme. Cette variable est à 1 si c'est la première exécution et à 0 par la suite. On considère première exécution celle qui a lieu: Variables PROGRAMMATION EN LANGAGE DE HAUT NIVEAU 11. • Après la mise sous tension de la CNC. • Après avoir tapé sur les touches [SHIFT]+[RAZ]. • Chaque fois qu’un nouveau programme est sélectionné. ANAIn Donne en volts et dans le format ±1.4 (valeurs ±5 volts), l’état de l’entrée analogique indiquée (n), le choix étant possible parmi l’une des huit (1··8) entrées analogiques. L’accès à cette variable entraîne l’interruption de la préparation des blocs et l’attente de l’exécution de cette commande avant la reprise de la préparation des blocs. TIMEG Affiche l'état de comptage du temporisateur programmé avec G4 K, dans le canal de CNC. Cette variable donne le temps qui manque pour terminer le bloc de temporisation, en centièmes de seconde. RIP Vitesse théorique linéaire résultante de la boucle suivante (en mm/min). Le calcul de la vitesse résultante ne prend pas en compte les axes rotatifs, les axes esclaves (gantry, accouplés et synchronisés) ni les compteurs numériques. Variables de lecture et d’écriture TIMER Cette variable permet de lire ou de modifier le temps, en secondes, indiqué par l’horloge validée par le PLC. Valeurs possibles 0··4294967295. L’accès à cette variable entraîne l’interruption de la préparation des blocs et l’attente de l’exécution de cette commande avant la reprise de la préparation des blocs. PARTC La CNC dispose d'un compteur de pièces qui s'incrémente, dans tous les modes sauf celui de Simulation, chaque fois que l'on exécute M30 ou M02 et cette variable permet de lire ou de modifier sa valeur, qui sera donnée par un numéro entre 0 et 4294967295. L’accès à cette variable entraîne l’interruption de la préparation des blocs et l’attente de l’exécution de cette commande avant la reprise de la préparation des blocs. CNC 8035 KEY Permet de lire le code de la dernière touche acceptée par la CNC. MODÈLE ·T· (SOFT V16.3X) Cette variable peut être utilisée comme variable d’écriture exclusivement, dans un programme de personnalisation (canal utilisateur). L’accès à cette variable entraîne l’interruption de la préparation des blocs et l’attente de l’exécution de cette commande avant la reprise de la préparation des blocs. ·244· Manuel de programmation KEYSRC Cette variable permet de lire ou de modifier la provenance des touches, les valeurs possibles étant les suivantes: 0 = Clavier. 1 = PLC. 2 = DNC. La CNC n’autorise la modification du contenu de cette variable que si elle est à 0. Les sorties analogiques libres parmi les huit (1··8) dont dispose la CNC peuvent être modifiées, et le code d’erreur correspondant apparaîtra en cas de tentative d’écriture dans une sortie occupée. L’accès à cette variable entraîne l’interruption de la préparation des blocs et l’attente de l’exécution de cette commande avant la reprise de la préparation des blocs. SELPRO Lorsqu'on dispose de deux entrées de palpeur, on permet de sélectionner l'entrée active. Au démarrage, elle assume la valeur 1, la première entrée du palpeur étant sélectionnée. Pour sélectionner la deuxième entrée du palpeur on doit lui affecter la valeur ·2·. L'accès à cette variable depuis la CNC arrête la préparation de blocs. DIAM Change le mode de programmation pour les coordonnées de l'axe X entre rayons et diamètres. Lorsqu'on change la valeur de cette variable, la CNC assume le nouveau mode de programmation pour les blocs programmés ensuite. PROGRAMMATION EN LANGAGE DE HAUT NIVEAU Cette variable permet de lire ou de modifier la sortie analogique désirée (n). Sa valeur est exprimée en volts et dans le format ±2.4 (±10 volts). Variables 11. ANAOn Lorsque la variable prend la valeur ·1·, les cotes programmées sont assumées en diamètres; lorsqu'elle prend la valeur ·0·, les cotes programmées sont assumées en rayons. Cette variable affecte l'affichage de la valeur réelle de l'axe X dans le système de coordonnées de la pièce et la lecture de variables PPOSX, TPOSX et POSX. A la mise sous tension, après avoir exécuté M02 ou M30 et après un arrêt d'urgence ou une RAZ, la variable s'initialise suivant la valeur du paramètre DFORMAT de l'axe X. Si ce paramètre a une valeur supérieure ou égale à 4, la variable prend la valeur ·1·; dans le cas contraire, on prend la valeur ·0·. PRBMOD Indique s’il faut afficher ou non une erreur de palpage dans les cas suivants, même si le paramètre général PROBERR (P119) = YES. • Lorsque termine un déplacement de palpage G75 et que le palpeur n’a pas touché la pièce. • Lorsque termine un déplacement de palpage G76 et que le palpeur n’a pas cessé de toucher la pièce. La variable PRBMOD prend les valeurs suivantes. Valeur Signification 0 Il se produit une erreur. 1 L'erreur ne se produit pas. CNC 8035 Valeur par défaut 0. La variable PRBMOD est de lecture et d'écriture depuis la CNC et le PLC et de lecture seulement depuis la DNC. MODÈLE ·T· (SOFT V16.3X) ·245· Manuel de programmation 11.3 Constantes Sont définies comme constantes toutes les valeurs fixes ne pouvant pas être modifiées par programme. Sont considérés comme constantes: • Les nombres exprimés en système décimal. • Les nombres hexadécimaux. • La constante PI. Constantes PROGRAMMATION EN LANGAGE DE HAUT NIVEAU 11. CNC 8035 MODÈLE ·T· (SOFT V16.3X) ·246· • Les tables et les variables de lecture seule, car leur valeur ne peut pas être modifiée à l’intérieur d’un programme. Manuel de programmation Opérateurs Un opérateur est un symbole qui indique les manipulations mathématiques ou logiques à réaliser. La CNC dispose d’opérateurs arithmétiques, relationnels, logiques, binaires, trigonométriques et d’opérateurs spéciaux. Opérateurs arithmétiques. addition. P1=3 + 4 P1=7 - soustraction, également moins unaire. P2=5 - 2 P3= -(2 * 3) P2=3 P3 = -6 * multiplication. P4=2 * 3 P4=6 / division. P5=9 / 2 P5=4.5 MOD module ou reste de la division. P6=7 MOD 4 P6=3 EXP exponentiel. P7=2 EXP 3 P7=8 Opérateurs relationnels. EQ égal. NE non-égal. GT supérieur à. GE supérieur ou égal à. LT inférieur à. LE inférieur ou égal à. 11. Opérateurs + PROGRAMMATION EN LANGAGE DE HAUT NIVEAU 11.4 Opérateurs logiques et binaires. NOT, OR, AND, XOR: Ils agissent comme des opérateurs logiques entres les conditions, et comme des opérateurs binaires entres les variables et les constantes. IF (FIRST AND GS1 EQ 1) GOTO N100 P5 = (P1 AND (NOT P2 OR P3)) Fonctions trigonométriques. SIN sinus. P1=SIN 30 P1=0.5 COS cosinus. P2=COS 30 P2=0.8660 TAN tangente. P3=TAN 30 P3=0.5773 ASIN sinus d'arc. P4=ASIN 1 P4=90 ACOS cosinus d’arc. P5=ACOS 1 P5=0 ATAN tangente d’arc. P6=ATAN 1 P6=45 ARG ARG(x,y) tangente d'arc y/x. P7=ARG(-1,-2) P7=243.4349 Deux fonctions permettent de calculer la tangente d’arc: ATAN qui donne le résultat entre ± 90º et ARG qui la donne entre 0 et 360º. CNC 8035 MODÈLE ·T· (SOFT V16.3X) ·247· Manuel de programmation Autres fonctions. Opérateurs PROGRAMMATION EN LANGAGE DE HAUT NIVEAU 11. CNC 8035 MODÈLE ·T· (SOFT V16.3X) ·248· ABS valeur absolue. P1=ABS -8 P1=8 LOG logarithme décimal. P2=LOG 100 P2=2 SQRT racine carrée. P3=SQRT 16 P3=4 ROUND arrondi a un entier. P4=ROUND 5.83 P4=6 FIX partie entière. P5=FIX 5.423 P5=5 FUP si nombre entier, prend la partie entière. P6=FUP 7 si non, prend la partie entière plus un. P6=FUP 5.423 P6=7 P6=6 BCD convertit le numéro donné en BCD. P7=564 P7=BCD 234 0010 BIN convertit le numéro donné en binaire. P8=BIN $AB 0011 0100 P8=171 1010 1011 Les conversions en binaire et en BCD s’effectueront sur 32 bits, le nombre 156 pouvant être représenté dans les formats suivants : Décimal 156 Hexadécimal 9C Binaire 0000 0000 0000 0000 0000 0000 1001 1100 BCD 0000 0000 0000 0000 0000 0001 0101 0110 Manuel de programmation Expressions Une expression est toute combinaison valide entre opérateurs, constantes et variables. Toutes les expressions doivent être placées entre parenthèses, qui peuvent être omises si l’expression se réduit à un nombre entier. Expressions 11. PROGRAMMATION EN LANGAGE DE HAUT NIVEAU 11.5 CNC 8035 MODÈLE ·T· (SOFT V16.3X) ·249· Manuel de programmation 11.5.1 Expressions arithmétiques Les expressions arithmétiques sont formées en combinant des fonctions et des opérateurs arithmétiques, binaires et trigonométriques avec les constantes et les variables du langage. Le mode de fonctionnement avec ces expressions est défini par les priorités des opérateurs et leur associativité: Expressions PROGRAMMATION EN LANGAGE DE HAUT NIVEAU 11. Priorité du plus grand au plus petit Associativité NOT, fonctions, - (unaire) de droite à gauche. EXP, MOD de gauche à droite. *,/ de gauche à droite. +,- (addition, soustraction) de gauche à droite. opérateurs relationnels de gauche à droite. AND, XOR de gauche à droite. OR de gauche à droite. Il est conseillé d’utiliser des parenthèses pour clarifier l’ordre dans lequel s’évalue l’expression. (P3 = P4/P5 - P6 * P7 - P8/P9 ) (P3 = (P4/P5)-(P6 * P7)-(P8/P9)) L’emploi de parenthèses redondantes ou supplémentaires n’entraîne pas d’erreurs et ne réduit pas la vitesse d’exécution. L’emploi de parenthèses est obligatoire avec les fonctions, sauf si elles s’appliquent à une constante numérique; dans ce cas, elles sont optionnelles. (SIN 45) (SIN (45)) les deux sont valables et équivalentes. (SIN 10+5) équivaut à ((SIN 10)+5). Les expressions peuvent également être utilisées pour référencer les paramètres et les tables: (P100 = P9) (P100 = P(P7)) (P100 = P(P8 + SIN(P8 * 20))) (P100 = ORGX 55) (P100 = ORGX (12+P9)) (PLCM5008 = PLCM5008 OR 1) ; Sélectionne l'exécution bloc par bloc (M5008=1) (PLCM5010 = PLCM5010 AND $FFFFFFFE) ; Libère l'override de l’avance (M5010=0) CNC 8035 MODÈLE ·T· (SOFT V16.3X) ·250· Manuel de programmation 11.5.2 Expressions relationnelles Il s’agit d’expressions arithmétiques réunies par des opérateurs relationnels. (IF (P8 EQ 12.8) ; Analyse si la valeur de P8 est égale à 12.8 (IF (ABS(SIN(P24)) GT SPEED) ; Analyse si le sinus est supérieur à la vitesse de broche. A leur tour, ces conditions peuvent être réunies par des opérateurs logiques. (IF ((P8 EQ 12.8) OR (ABS(SIN(P24)) GT SPEED)) AND (CLOCK LT (P9 * 10.99)) ... Le résultat de ces expressions est vrai ou faux. PROGRAMMATION EN LANGAGE DE HAUT NIVEAU ; Analyse si le comptage de l’horloge est inférieur à (P9*10.99) Expressions 11. (IF (CLOCK LT (P9 * 10.99)) CNC 8035 MODÈLE ·T· (SOFT V16.3X) ·251· Manuel de programmation Expressions PROGRAMMATION EN LANGAGE DE HAUT NIVEAU 11. CNC 8035 MODÈLE ·T· (SOFT V16.3X) ·252· INSTRUCTIONS DE CONTRÔLE DES PROGRAMMES 12 Les instructions de contrôle que dispose la programmation en langage à haut niveau peuvent être regroupées de la façon suivante. • Instructions d’affectation. • Sentences d'affichage. • Instructions de validation-invalidation. • Instructions de contrôle de flux. • Sentences de sous-routines. • Instructions de sous-routines d'interruption. • Instructions de programmes. • Instructions de personnalisation. Une seule instruction devra être programmée par bloc, aucune autre information supplémentaire n’étant autorisée. CNC 8035 MODÈLE ·T· (SOFT V16.3X) ·253· Manuel de programmation 12.1 Instructions d’affectation Il s’agit du type d'instruction le plus simple, qui peut être défini comme: ( destination = expression arithmétique ) Le destinataire choisi peut être un paramètre local ou global ou une variable de lecture et d’écriture. L’expression arithmétique peut être aussi complexe que nécessaire ou une simple constante numérique. Instructions d’affectation INSTRUCTIONS DE CONTRÔLE DES PROGRAMMES 12. CNC 8035 MODÈLE ·T· (SOFT V16.3X) ·254· (P102 = FZLOX) (ORGX 55 = (ORGX 54 + P100)) Dans le cas particulier de l’affectation à un paramètre local au moyen de son nom (A au lieu de P0 par exemple) et si l’expression arithmétique est une constante numérique, l'instruction peut être abrégée comme suit: (P0=13.7) ==> (A=13.7) ==> (A13.7) Il est possible de réaliser jusqu’à 26 affectations à divers destinataires dans un seul bloc, l’ensemble d’affectations vers un seul et même destinataire étant interprété comme une affectation unique. (P1=P1+P2, P1=P1+P3, P1=P1*P4, P1=P1/P5) Cela revient à (P1=(P1+P2+P3)*P4/P5). Les différentes affectations réalisées dans un bloc donné sont séparées par des virgules ",". Manuel de programmation Instructions d'affichage (ERREUR nombre entier, "texte d'erreur") Cette instruction interrompt l’exécution du programme et affiche l’erreur indiquée, cette erreur pouvant être sélectionnée comme suit: (ERREUR nombre entier) Affichera le numéro d’erreur indiqué et le texte associé à ce numéro selon le code d’erreurs de la CNC (s’il existe). Affichera le numéro et le texte de l’erreur indiqués, le texte devant s’écrire entre guillemets. (ERREUR "texte d'erreur") Affichera exclusivement le texte d’erreur indiqué. Le numéro de l’erreur peut être défini par une constante numérique ou par un paramètre. Si un paramètre local est employé, on devra utiliser sa forme numérique (P0-P25). Exemples de programmation: (ERREUR 5) (ERREUR P100) (ERREUR "Erreur utilisateur") (ERREUR 3, "Erreur utilisateur") (ERREUR P120, "Erreur utilisateur") ( MSG "message") Cette instruction affiche le message figurant entre guillemets. L’écran de la CNC comporte une zone d'affichage des messages DNC ou du programme de l’utilisateur, qui affiche toujours le dernier message reçu, indépendamment de sa provenance. Instructions d'affichage 12. (ERREUR nombre entier, "texte d'erreur") INSTRUCTIONS DE CONTRÔLE DES PROGRAMMES 12.2 Exemple: (MSG "Vérifier outil") ( DGWZ expression 1, expression 2, expression 3, expression 4 ) L'instruction DGWZ (Define Graphic Work Zone) permet de définir la zone de représentation graphique. Chacune des expressions composant la syntaxe de l’instruction correspond à une des limites et toutes doivent être définies en millimètres ou en pouces. expression 1 Z minimum expression 2 Z maximum expression 3 Rayon intérieur ou diamètre intérieur. expresión 4 Rayon extérieur ou diamètre extérieur. CNC 8035 MODÈLE ·T· (SOFT V16.3X) ·255· Manuel de programmation 12.3 Instructions de validation-invalidation ( ESBLK et DSBLK ) A partir de l’exécution de l'instruction ESBLK, la CNC exécute tous les blocs suivants comme s’il s’agissait d’un bloc unique. Ce traitement en bloc unique reste actif jusqu’à son annulation par l’exécution de l'instruction DSBLK. Instructions de validation-invalidation INSTRUCTIONS DE CONTRÔLE DES PROGRAMMES 12. De cette façon, si le programme est exécuté en mode BLOC à BLOC, le groupe de blocs se trouvant entre les instructions ESBLK et DSBLK s’exécutera en continu; autrement dit, l’exécution ne s’interrompt pas à la fin d’un bloc, mais passe au bloc suivant. G01 X30 Z10 F1000 T1 D1 (ESBLK) ; Début du bloc unique G01 X20 Z10 G01 X20 Z20 G02 X10 Z30 I-10 K0 (DSBLK) ; Annulation du bloc unique G01 X10 Z40 M30 ( ESTOP et DSTOP ) A partir de l’exécution de l'instruction DSTOP, la CNC invalide la touche Stop ainsi que le signal de Stop provenant de la PLC. Cette invalidation reste active jusqu’à ce que la touche soit validée à nouveau par l'instruction ESTOP. ( EFHOLD et DFHOLD ) A partir de l’exécution de l'instruction DFHOLD, la CNC invalide l’entrée de Feed-Hold provenant du PLC. Cette invalidation reste active jusqu’à ce que l’entrée soit validée à nouveau par l'instruction EFHOLD. CNC 8035 MODÈLE ·T· (SOFT V16.3X) ·256· Manuel de programmation 12.4 Instructions de contrôle de flux. Les déclarations GOTO et RPT ne peuvent pas être utilisées dans des programmes exécutés depuis un PC raccordé à travers d’une des lignes série. ( GOTO N(expression) ) L'instruction GOTO provoque, à l’intérieur d’un programme donné, un saut au bloc défini au moyen de l’étiquette N(expression). L’exécution du programme continuera après le saut, à partir du bloc indiqué. X30 Z20 N22 (GOTO N22) ; Instruction de saut X20 Z20 ; Pas d’exécution X20 Z10 ; Pas d’exécution G01 X10 Z10 F1000 ; L’exécution continue dans ce bloc. G02 X0 Z40 I-105 K0 ... (RPT N(expression), N(expression), P(expression) ) L'instruction RPT exécute la partie de programme existant entre les deux blocs définis avec les étiquettes N(expression). Les blocs à exécuter pourront être dans le programme en exécution ou dans un programme de la mémoire RAM. L'étiquette P(expression) indique le numéro de programme où se trouvent les blocs à exécuter. S'il n'est pas défini, il est entendu que la partie que l'on veut répéter se trouve dans le même programme. Instructions de contrôle de flux. G00 X30 Z10 T2 D4 12. INSTRUCTIONS DE CONTRÔLE DES PROGRAMMES L’étiquette de saut peut être adressée au moyen d’un numéro ou de toute expression dont le résultat est un nombre. Toutes les étiquettes peuvent être indiquées par un nombre ou par toute expression dont le résultat est un nombre. La partie de programme sélectionnée grâce aux deux étiquettes doit appartenir au même programme, le bloc initial étant défini en premier, le bloc final ensuite. L’exécution du programme se poursuit par le bloc suivant celui dans lequel l'instruction RPT a été programmée, après exécution de la partie de programme sélectionnée. N10 G00 X10 Z20 G01 X5 G00 Z0 N20 X0 N30 (RPT N10, N20) N3 N40 G01 X20 M30 En arrivant au bloc N30, le programme exécutera 3 fois la section N10-N20. A la fin de l’exécution, il passera au bloc N40. i Comme l’instruction RPT n'arrête pas la préparation de blocs et n'interrompt pas la compensation d'outil, on peut l'utiliser avec l’instruction EXEC et lorsqu'il faut maintenir la compensation. CNC 8035 MODÈLE ·T· (SOFT V16.3X) ·257· Manuel de programmation ( IF condition <action1> ELSE <action2> ) Cette instruction analyse la condition donnée, qui devra être une expression relationnelle. Si la condition est certaine (résultat égal à 1), l' <action1> sera exécutée; dans le cas contraire (résultat égal à 0), sera exécutée l' <action2>. Exemple: (IF (P8 EQ 12.8) CALL 3 ELSE PCALL 5, A2, B5, D8) Si P8 =12.8 exécute l’instruction (CALL3) Instructions de contrôle de flux. INSTRUCTIONS DE CONTRÔLE DES PROGRAMMES 12. CNC 8035 MODÈLE ·T· (SOFT V16.3X) ·258· Si P8<>12.8 exécute l’instruction (PCALL 5, A2, B5, D8) ELSE peut être omis dans l’instruction, c’est-à-dire qu’il suffira de programmer IF condition <action1>. Exemple: (IF (P8 EQ 12.8) CALL 3) <action1> et <action2> peuvent être des expressions ou des instructions, à l’exception des instructions IF et SUB. Comme, dans un bloc à haut niveau, les paramètres locaux peuvent être nommés au moyen de lettres, des expressions du type ci-dessous peuvent être obtenues: (IF (E EQ 10) M10) Si la condition selon laquelle le paramètre P5 (E) a une valeur 10 est remplie, la fonction auxiliaire M10 n’est pas exécutée car un bloc à haut niveau ne peut pas disposer de commandes en code ISO. Dans ce cas, M10 représente l’affectation de la valeur 10 au paramètre P12, c’est-à-dire que l’on peut programmer: (IF (E EQ 10) M10) ou (IF (P5 EQ 10) P12=10) Manuel de programmation Instructions de sous-routines Une sous-routine est une partie de programme qui, lorsqu’elle est correctement identifiée, peut être appelée depuis n’importe quel point d’un programme pour être exécutée. Une sous-routine peut être chargée dans la mémoire de la CNC comme un programme indépendant ou comme une partie d’un programme, puis être appelée une ou plusieurs fois depuis différents points d’un programme ou depuis différents programmes. Si la sous-routine est trop grande pour la passer à la mémoire RAM, la convertir en programme et utiliser l'instructions EXEC. ( SUB nombre entier ) L'instruction SUB définit comme sous-routine l'ensemble de blocs de programme qui sont programmés ensuite, jusqu'à atteindre la sous-routine RET. La sous-routine est identifiée avec un nombre entier, qui définit aussi le type de sous-routine; sous-routine générale ou sous-routine OEM (de fabricant). Rang de sous-routines générales SUB 0001 - SUB 9999 Rang de sous-routines OEM (de fabricant) SUB 10000 - SUB 20000 Les sous-routines de fabricant ont le même traitement que les sous-routines générales, mais avec les restrictions suivantes. • On ne peut définir dans les programmes propres du fabricant, que ceux définis avec l'attribut [O]. Dans le cas contraire, l'erreur correspondante sera affichée. Erreur 63 : Programmer numéro de sous-routine de 1 à 9999. Instructions de sous-routines 12. On ne peut exécuter que des sous-routines existant dans la mémoire RAM de la CNC. Pour cela, si on veut exécuter une sous-routine emmagasinée dans un PC connecté à travers une des liaisons série, on doit la copier dans la mémoire RAM de la CNC. INSTRUCTIONS DE CONTRÔLE DES PROGRAMMES 12.5 • Pour exécuter une sous-routine OEM avec CALL, PCALL ou MCALL, celle-ci doit être dans un programme propre du fabricant. Dans le cas contraire, l'erreur correspondante sera affichée. Erreur 1255 : Sous-routine restreinte au programme OEM. Deux sous-routines portant le même numéro d’identification ne peuvent pas cohabiter dans la mémoire de la CNC, même si elles appartiennent à des programmes différents. ( RET ) L'instruction RET indique que la sous-routine définie grâce à SUB se termine dans ce bloc. (SUB 12) ; Définition de la sous-routine 12 G91 G01 XP0 F5000 ZP1 XP0 ZP1 ( RET ) ; Fin de sous-routine ( CALL (expression) ) L'instruction CALL appelle la sous-routine indiquée au moyen d’un nombre ou de toute expression dont le résultat est un nombre. CNC 8035 MODÈLE ·T· (SOFT V16.3X) ·259· Manuel de programmation Comme il est possible d’appeler une sous-routine depuis un programme principal ou une sousroutine, puis une seconde sous-routine depuis la première et une troisième depuis la seconde, etc..., la CNC limite les appels à un maximum de 15 niveaux d’imbrications, chaque niveau pouvant être répété 9999 fois. Instructions de sous-routines INSTRUCTIONS DE CONTRÔLE DES PROGRAMMES 12. Exemple de programmation. G90 G01 X100 Z330 (CALL 10) G90 G01 X100 Z240 (CALL 10) G90 G01 X100 Z150 M30 (SUB 10) G91 G01 Z -10 X40 Z-10 G03 X0 Z-20 I0 K-10 G01 X-20 G02 X0 Z-20 I0 K-10 G01 X40 Z-10 Z ( RET ) CNC 8035 MODÈLE ·T· (SOFT V16.3X) ·260· -20 Manuel de programmation ( PCALL (expression), (instruction d'affectation), (instruction d'affectation), ... ) L'instruction PCALL appelle la sous-routine indiquée au moyen d’un nombre ou de toute expression dont le résultat est un nombre. Elle permet également d’initialiser jusqu’à 26 paramètres locaux de cette sous-routine. Ces paramètres sont initialisés au moyen des instructions d’affectation. Exemple: (PCALL 52, A3, B5, C4, P10=20) Dans ce cas, un nouveau niveau d’imbrication de paramètres locaux est généré en plus d’un nouveau niveau d’imbrication de sous-routines, avec un maximum de 6 niveaux d’imbrication de paramètres locaux à l’intérieur des 15 niveaux d’imbrication de sous-routines. L’axe X se programme en diamètres. G90 G01 X80 Z330 (PCALL 10, P0=20, P1=-10) Instructions de sous-routines Exemple de programmation. INSTRUCTIONS DE CONTRÔLE DES PROGRAMMES Le programme principal et chaque sous-routine se trouvant à un niveau d’imbrication de paramètres disposeront de 26 paramètres locaux (P0-P25). 12. ; Également (PCALL 10, A20, B-10) G90 G01 X80 Z260 (PCALL 10, P0=20, P1=-10) ; Également (PCALL 10, A20, B-10) G90 G01 X200 Z200 (PCALL 10, P0=30, P1=-15) ; Aussi (PCALL 10, A30, B-15) G90 G01 X200 Z115 (PCALL 10, P0=30, P1=-15) ; Aussi (PCALL 10, A30, B-15) M30 (SUB 10) G91 G01 ZP1 XP0 ZP1 XP0 ZP1 ( RET ) CNC 8035 MODÈLE ·T· (SOFT V16.3X) ·261· Manuel de programmation (MCALL (expression), (instruction d'affectation), (instruction d'affectation), ... ) L'instruction MCALL permet de conférer le statut de cycle fixe à toute sous-routine définie par l’utilisateur (SUB nombre entier). L’exécution de cette instruction est identique à celle de PCALL, mais l’appel est modal, c’est-à-dire que si un bloc comportant un déplacement des axes est programmé à la suite de ce bloc, la sousroutine indiquée s’exécutera après ce déplacement avec les mêmes paramètres d’appel. Instructions de sous-routines INSTRUCTIONS DE CONTRÔLE DES PROGRAMMES 12. Si un bloc comportant un déplacement avec un nombre de répétitions tel que X10 N3 est exécuté alors qu’une sous-routine modale est sélectionnée, la CNC exécutera le déplacement (X10) une seule fois, et exécutera ensuite la sous-routine modale autant de fois qu’indiqué par le nombre de répétitions. Si des répétitions de bloc sont sélectionnées, la première exécution de la sous-routine modale sera exécutée avec les paramètres d’appel mis à jour, mais les autres répétitions s’effectueront avec les valeurs actuelles de ces paramètres. Si un bloc contenant la mnémonique MCALL est exécuté alors qu’une sous-routine est sélectionnée comme modale, la sous-routine actuelle perdra sa modalité et la nouvelle sous-routine sélectionnée deviendra modale. (MDOFF) l'instruction MDOFF indique que la modalité qu'avait acquis une sous-routine avec l'instruction MCALL ou un programme pièce avec MEXEC, termine dans ce bloc. L’utilisation de sous-routines modales simplifie la programmation. Exemple de programmation. L’axe X se programme en diamètres. (P100=20, P101=-10) G90 G01 X80 Z330 (MCALL 10) G90 G01 X80 Z260 (P100=30, P101=-15) G90 G01 X200 Z200 G90 G01 X200 Z115 (MDOFF) M30 CNC 8035 (SUB 10) G91 G01 ZP101 XP100 ZP101 XP100 MODÈLE ·T· (SOFT V16.3X) ZP101 ( RET ) ·262· Manuel de programmation Instructions de sous-routines d'interruption. Chaque fois que l’une des entrées logiques générales d’interruption "INT1" (M5024), "INT2" (M5025), "INT3" (M5026) ou "INT4" (M5027) est activée, la CNC suspend provisoirement l’exécution du programme en cours et passe à l’exécution de la sous-routine d’interruption dont le numéro est indiqué dans le paramètre machine général correspondant. Avec INT1 (M5024) celle indiquée par le paramètre INT1SUB (P35) Avec INT2 (M5025) celle indiquée par le paramètre INT2SUB (P36) Avec INT4 (M5027) celle indiquée par le paramètre INT4SUB (P38) Les sous-routines d’interruption sont définies comme n’importe quelle autre sous-routine, en utilisant les instructions "(SUB nombre entier)" et "(RET)". Les sous-routines d’interruption ne changent pas le niveau des paramètres locaux; en conséquence, seuls les paramètres globaux peuvent être utilisés dans ces sous-routines. Dans une sous-routine d’interruption, il est possible d’utiliser l’instruction "(REPOS X, Y, Z, ....)" décrite plus loin. Dès la fin de l’exécution de la sous-routine, la CNC poursuit l’exécution du programme en cours. ( REPOS X, Y, Z, ... ) L’instruction REPOS doit toujours être utilisée dans les sous-routines d’interruption, et elle facilite le repositionnement de la machine au point d’interruption. Lorsque cette instruction est exécutée, la CNC déplace les axes jusqu’au point où l’exécution du programme a été interrompue. A l’intérieur de l’instruction REPOS, on devra indiquer l’ordre dans lequel des axes doivent être déplacés jusqu’au point d’interruption. Instructions de sous-routines d'interruption. 12. Avec INT3 (M5026) celle indiquée par le paramètre INT3SUB (P37) INSTRUCTIONS DE CONTRÔLE DES PROGRAMMES 12.6 • Les axes sont déplacés un à la fois. • Seuls les axes à repositionner doivent être définis. • Les axes composant le plan principal de la machine sont déplacés ensemble. Il est inutile de définir les deux axes, puisque la CNC les déplace avec le premier. Le déplacement n’est pas répété lors de la définition du second axe, il est ignoré. Si, pendant l’exécution d’une sous-routine qui n’a pas été activée par l’une des entrées d’interruption, l’instruction REPOS est détectée, la CNC affiche le code d’erreur correspondant. CNC 8035 MODÈLE ·T· (SOFT V16.3X) ·263· Manuel de programmation 12.7 Instructions de programmes Depuis un programme en exécution la CNC permet: • D'exécuter un autre programme. Instruction (EXEC P.....) • D'exécuter un autre programme de façon modale. Instruction (MEXEC P.....) • De générer un nouveau programme. Instruction (OPEN P.....) • D'ajouter des blocs à un programme déjà existant. Instruction (WRITE P.....) Instructions de programmes INSTRUCTIONS DE CONTRÔLE DES PROGRAMMES 12. ( EXEC P(expression), (répertoire) ) L'instruction EXEC P exécute le programme pièce du répertoire indiqué. Le programme pièce peut être défini avec un numéro ou n’importe quelle expression ayant comme résultat un nombre. La CNC entend par défaut que le programme pièce est dans la mémoire RAM de la CNC. S’il se trouve dans un autre dispositif, l’indiquer dans le (répertoire). DNC dans un PC branché à travers la liaison série. ( MEXEC P (expression), (répertoire) ) L'instruction MEXEC exécute le programme pièce du répertoire indiqué et acquiert également la catégorie de modale; c'est-à-dire, si après ce bloc on en programme un autre avec déplacement des axes, après ce déplacement, le programme indiqué sera exécuté de nouveau. Le programme pièce peut être défini avec un nombre ou avec une expression dont le résultat est un nombre. La CNC entend par défaut que le programme pièce est dans la mémoire RAM de la CNC. S’il se trouve dans un autre dispositif, l’indiquer dans le (répertoire). DNC dans un PC branché à travers la liaison série. Le programme pièce modal étant sélectionné, si on exécute un bloc de mouvement avec un nombre de répétitions (par exemple X10 N3), la CNC omet le nombre de répétitions et exécute une seule fois le déplacement et le programme pièce modal. Un programme pièce étant sélectionné comme modal, si on exécute depuis le programme principal un bloc contenant l'instruction MEXEC, le programme pièce actuel perd sa condition de modal et le programme pièce appelé avec MEXEC devient modal. Si on essaie d'exécuter un bloc avec l'instruction MEXEC dans le programme pièce modal, l'erreur correspondante s'affichera. 1064: Le programme ne peut pas être exécuté. (MDOFF) l'instruction MDOFF indique que la modalité qu'avait acquis une sous-routine avec l'instruction MCALL ou un programme pièce avec MEXEC, termine dans ce bloc. CNC 8035 MODÈLE ·T· (SOFT V16.3X) ·264· Manuel de programmation (OPEN P (expression), (répertoire destination), A/D, "commentaire de programme") L'instruction OPEN entame l’édition d’un programme pièce. Le numéro de ce programme sera indiqué par un numéro ou n’importe quelle expression ayant comme résultat un nombre. Le nouveau programme pièce édité sera mémorisé par défaut dans la mémoire RAM de la CNC. Pour l’emmagasiner dans un autre dispositif l’indiquer dans le (répertoire destination). dans un PC branché à travers la liaison série. Le paramètre A/D s’utilisera quand le programme que l’on veut éditer existe déjà. La CNC ajoute les nouveaux blocs après les blocs déjà existants. D La CNC efface le programme existant et commence l’édition d’un nouveau. On a aussi la possibilité de lui associer un commentaire de programme qui ensuite sera affiché à côté de celui-ci dans le répertoire de programmes. L'instruction OPEN permet de générer depuis un programme en exécution un autre programme, qui pourra être en fonction des valeurs acquises par programme en exécution. Pour éditer les blocs on doit utiliser l’instruction WRITE décrite ci-après. Notes: Si le programme que l’on veut éditer existe et n’est pas définit dans les paramètres A/D, la CNC affichera un message d’erreur en exécutant le bloc. Le programme ouvert avec l’instruction OPEN se ferme en exécutant M30, une autre instruction OPEN et après avec un Arrêt d’Urgence ou une RAZ . ( WRITE <texte du bloc> ) L'instruction WRITE ajoute à la suite du dernier bloc de programme dont l’édition a été commencée au moyen de l’instruction OPEN P, les informations contenues dans <texte de bloc>comme un nouveau bloc de programme. 12. INSTRUCTIONS DE CONTRÔLE DES PROGRAMMES A Instructions de programmes DNC S’il s’agit d’un bloc paramétrique édité en code ISO tous les paramètres (globaux et locaux) sont remplacés par la valeur numérique qu’ils ont à ce moment. (WRITE G1 XP100 ZP101 F100) => G1 X10 Z20 F100 Lorsqu’il s’agit d’un bloc paramétrique édité en haut niveau, il faut indiquer avec le caractère ? que l’on veut remplacer le paramètre par la valeur numérique qu’il a à ce moment. (WRITE (SUB P102)) => (SUB P102) (WRITE (SUB ?P102)) => (SUB 55) (WRITE (ORGX54=P103)) => (ORGX54=P103) (WRITE (ORGX54=?P103)) => (ORGX54=222) (WRITE (PCALL P104)) => (PCALL P104) (WRITE (PCALL ?P104)) => (PCALL 25) Si l'instruction WRITE est programmée sans avoir programmé au préalable l'instruction OPEN, la CNC affiche le code d’erreur correspondant, sauf en cas d’édition d’un programme de personnalisation de l’utilisateur; dans ce cas, un nouveau bloc est ajouté au programme à éditer. CNC 8035 MODÈLE ·T· (SOFT V16.3X) ·265· Manuel de programmation Exemple de création d'un programme contenant divers points d'une trajectoire parabolique. Z = -K * X**2 Instructions de programmes INSTRUCTIONS DE CONTRÔLE DES PROGRAMMES 12. La programmation de l'axe X est en diamètres et on utilise la sous-routine numéro 2, dont les paramètres ont la signification suivante: Paramètres d'appel: A ou P0 Valeur de la constante K. B ou P1 Cote X initiale. C ou P2 Cote X finale. D ou P3 Incrément ou pas sur X. Paramètres calculés: E ou P4 Cote X. F ou P5 Cote Z. L’un des modes utilisation de cet exemple pourrait être: G00 X0 Z0 (PCALL 2, A0.01, B0, C100, D1) M30 Sous-routine de génération du programme. (SUB 2) (OPEN P12345) ; Commence l’édition du programme P12345 (P4=P1) N100 (IF (P4+P3 GE P2) P4=P2 ELSE P4=P4+P3) (P5=-(P0 * P4 * P4)) (WRITE G01 XP4 ZP5) ; Bloc de déplacement (IF (P4 NE P2) GOTO N100) CNC 8035 MODÈLE ·T· (SOFT V16.3X) ·266· (WRITE M30) ; Bloc de fin de programme ( RET ) ; Fin de sous-routine Manuel de programmation Instructions de personnalisation Las instructions de personnalisation ne peuvent être utilisées que dans les programmes de personnalisation réalisés par l’utilisateur. Ces programmes de personnalisation doivent être mémorisés dans la mémoire RAM de la CNC et peuvent utiliser les "Instructions de Programmation" ils seront exécutés dans le canal spécial réservé à cet effet; le programme sélectionné dans chaque cas sera indiqué dans les paramètres machine généraux suivants. "USEREDIT" indiquera le programme à exécuter dans le Mode Edition. "USERMAN" indiquera le programme à exécuter dans le Mode Manuel. "USERDIAG" indiquera le programme à exécuter dans le Mode Diagnostic. En plus du niveau actuel, les programmes de personnalisation peuvent disposer de cinq autres niveaux d’imbrication. En outre, les instructions de personnalisation n’admettent pas les paramètres locaux; il est toutefois possible d’utiliser tous les paramètres globaux pour les définir. ( PAGE (expression) ) L'instruction PAGE affiche à l’écran le numéro de page indiqué au moyen d’un nombre ou de toute expression dont le résultat est un nombre. Les pages définies par l’utilisateur sont comprises entre la page 0 et la page 255, et elles sont définies depuis le clavier de la CNC dans le mode personnalisation comme indiqué dans le Manuel d'Utilisation. Les pages du système sont définies par un nombre supérieur à 1000. Voir l’annexe correspondante. Instructions de personnalisation 12. "USERDPLY" indiquera le programme à exécuter dans le Mode Exécution. INSTRUCTIONS DE CONTRÔLE DES PROGRAMMES 12.8 ( SYMBOL (expression 1), (expression 2), (expression 3)) L'instruction SYMBOL affiche à l’écran le symbole dont le numéro est indiqué par la valeur de l’expression 1 dès qu’elle est évaluée. Par ailleurs, sa position à l’écran est définie par l’expression 2 (colonne) et par l’expression 3 (rangée). Expression 1, comme expression 2 et expression 3 pourront contenir un nombre ou toute expression dont le résultat est un nombre. La CNC permet d'afficher tout symbole défini par l’utilisateur (0-255) depuis le clavier de la CNC dans le mode personnalisation comme indiqué dans le Manuel d'Utilisation. Pour le positionner dans la zone d'affichage, il convient de définir les pixels de cette dernière, soit 0-639 pour les colonnes (expression 2) et 0-335 pour les rangées (expression 3). CNC 8035 MODÈLE ·T· (SOFT V16.3X) ·267· Manuel de programmation (IB (expression) = INPUT "texte", format) La CNC dispose de 26 variables d’entrée de données (IB0-IB25). L'instruction IB affiche, dans la fenêtre d’entrée de données, le texte indiqué et stocke la donnée introduite par l’utilisateur dans la variable d’entrée au moyen d’un nombre ou de toute expression dont le résultat est un nombre. L’introduction des données ne comporte une attente que si le format des données demandées est programmé. Ce format pourra avoir un signe, une partie entière et une partie décimale. Instructions de personnalisation INSTRUCTIONS DE CONTRÔLE DES PROGRAMMES 12. Si le format comporte le signe "-" , il admettra des valeurs positives et négatives; dans le cas contraire, il n’admet que des valeurs positives. La partie entière indique le nombre maximum de chiffres entiers (0-6) désirés. La partie entière indique le nombre maximum de chiffres décimaux (0-5) désirés. Si l'instruction est programmée sans format numérique, comme par exemple (IB1 = INPUT "texte"), l'instruction affiche le texte indiqué sans attendre l’introduction des données. ( ODW (expression 1), (expression 2), (expression 3) ) L'instruction ODW définit et dessine à l’écran une fenêtre blanche de dimensions fixes (1 rangée x 14 colonnes). A chaque fenêtre est associé un numéro indiqué par la valeur de l’expression 1 dès qu’elle est évaluée. En outre, sa position sur l’écran est définie par l’expression 2 (rangée) et l’expression 3 (colonne). Expression 1, comme expression 2 et expression 3 pourront contenir un nombre ou toute expression dont le résultat est un nombre. La CNC permet de définir 26 fenêtres (0-25) et de les positionner dans la zone de visualisation; pour ce faire, elle dispose de 21 rangées (0-20) et de 80 colonnes (0-79). ( DW (expression 1) = (expression 2), DW (expression 3) = (expression 4),...) ) L'instruction DW affiche sur la fenêtre indiquée par la valeur de l’expression 1, expression 3, .. dès qu’elle est évaluée les données numériques indiquées par l’expression 2, expression 4, .... Expression 1, expression 2, expression 3, .... pourront contenir un nombre ou toute expression dont le résultat est un nombre. L’exemple suivant montre une visualisation dynamique de variables: (ODW 1, 6, 33) ; Définit la fenêtre de données 1 (ODW 2, 14, 33) ; Définit la fenêtre de données 2 N10 (DW1=DATE, DW2=TIME) ; Affiche la date dans la fenêtre 1 et l’heure dans la 2 (GOTO N10) CNC 8035 La CNC permet d'afficher les données en format décimal, hexadécimal et binaire, grâce aux instructions suivantes: (DW1 = 100) Format décimal. Affiche sur la fenêtre 1 la valeur "100". (DWH2 = 100) MODÈLE ·T· (SOFT V16.3X) Format hexadécimal. Affiche sur la fenêtre 2 la valeur "64". (DWB3 = 100) Format binaire. Affiche sur la fenêtre 3 la valeur "01100100". ·268· Manuel de programmation En cas d’emploi de la représentation en binaire (DWB), la visualisation se limite à 8 caractères; la valeur "11111111" s’affiche pour les valeurs supérieures à 255, tandis que la valeur "10000000" s’affiche pour les valeurs inférieures à -127. La CNC permet en outre d'afficher sur la fenêtre demandée le nombre chargé dans l’une des 26 variables d’entrée de données (IB0-IB25). L’exemple suivant montre une demande et une visualisation ultérieure de l’avance des axes: (ODW 3, 4, 60) ; Affiche l’avance dans la fenêtre 3. ( SK (expression 1) = "texte 1", (expression 2) = "texte 2", .... ) L'instruction SK définit et affiche le nouveau menu de softkeys indiqué. Chacune des expressions indiquera le numéro de softkey - touche logiciel - à modifier (1-7, en commençant par la gauche) et les textes à écrire dans ces touches. Expression 1, expression 2, expression 3, .... pourront contenir un nombre ou toute expression dont le résultat est un nombre. Chaque texte autorise un maximum de 20 caractères sur deux lignes de 10 caractères chacune. Si le texte sélectionné comporte moins de 10 caractères, la CNC le centre sur la ligne supérieure, mais s’il a plus de 10 caractères, le centrage doit être réalisé par le programmeur. Exemples: INSTRUCTIONS DE CONTRÔLE DES PROGRAMMES ; Demande de l’avance des axes. (DW3=IB1) Instructions de personnalisation 12. ; Définit la fenêtre de données 3. (IB1=INPUT "Avance des axes: ", 5.4) (SK 1="HELP", SK 2="MAXIMUN POINT") HELP MAXIMUN POINT (SK 1="FEED", SK 2=" _ _MAXIMUN_ _ _POINT") FEED MAXIMUN POINT Si une ou plusieurs touches logiciel sont sélectionnées au moyen de l’expression à haut niveau "SK" pendant qu’un menu par touches logiciel CNC standard est actif, la CNC efface toutes les touches logiciel existantes et n’affiche que les touches sélectionnées. Si une ou plusieurs touches logiciel sont sélectionnées au moyen de l’expression à haut niveau "SK" pendant qu’un menu par touches logiciel utilisateur est actif, la CNC ne remplace que les touches logiciel sélectionnées en laissant les autres sans changement. ( WKEY ) L'instruction WKEY interrompt l’exécution du programme jusqu’à la frappe d’une touche. La touche tapée sera enregistrée dans la variable KEY. CNC 8035 ... ( WKEY ) ; Attente d’une touche (IF KEY EQ $FC00 GOTO N1000) ; Si F1 a été tapée, poursuite en N1000 ... MODÈLE ·T· (SOFT V16.3X) ·269· Manuel de programmation ( WBUF "texte", (expression) ) L'instruction WBUF n’est utilisable que dans le programme de personnalisation devant être exécuté dans le Mode Edition. Cette instruction peut être programmée de deux façons et, dans chaque cas, elle permet: • ( WBUF "texte", (expression) ) Elle ajoute au bloc en cours d’édition et dans la fenêtre d’entrée de données, le texte et la valeur de l’expression dès qu’elle est évaluée. La programmation de l’expression est optionnelle, mais le texte doit obligatoirement être défini. Si aucun texte n’est souhaité, on programmera "". Instructions de personnalisation INSTRUCTIONS DE CONTRÔLE DES PROGRAMMES 12. (Expression) pourra contenir un nombre ou toute expression dont le résultat est un nombre. Exemples pour P100=10: (WBUF "X", P100) => X10 (WBUF "X P100") => X P100 • ( WBUF ) Introduit en mémoire, en ajoutant au programme en cours d’édition et derrière l’emplacement du curseur, le bloc en cours d’édition (écrit au préalable avec les instructions "(WBUF "texte", (expression))"). Par ailleurs, efface la mémoire-tampon d’édition, en l’initialisant pour une nouvelle édition de bloc. Ceci permet à l’utilisateur d’éditer un programme complet sans avoir à quitter le mode édition utilisateur après chaque bloc et à taper sur [ENTER] pour le charger en mémoire. (WBUF "(PCALL 25, ") ; Ajoute au bloc en cours d’édition "(PCALL 25,", (IB1=INPUT "Paramètre A:",-5.4) ; Demande du paramètre A. (WBUF "A=", IB1) ; Ajoute au bloc en cours d’édition "A = (valeur introduite)". (IB2=INPUT "Paramètre B: ", -5.4) ; Demande du paramètre B. (WBUF ", B=", IB2) ; Ajoute au bloc en cours d’édition "B=(valeur introduite)" (WBUF ")") ; Ajoute au bloc en cours d’édition ")". ( WBUF ) ; Introduit en mémoire le bloc édité. ... Après l’exécution de ce programme, on dispose en mémoire d’un bloc de ce type: (PCALL 25, A=23.5, B=-2.25) ( SYSTEM ) l'instruction SYSTEM met fin à l’exécution du programme de personnalisation utilisateur et renvoie au menu standard correspondant de la CNC. Exemple d’un programme de personnalisation: CNC 8035 Le programme de personnalisation suivant doit être sélectionné comme programme utilisateur associé au mode Editeur. Après sélection du Mode Editeur et frappe de la touche logiciel UTILISATEUR, ce programme commence à s’exécuter et permet de réaliser une édition assistée des deux cycles utilisateur autorisés. Cette édition est réalisée cycle par cycle et autant de fois que l'on désire. MODÈLE ·T· (SOFT V16.3X) Affiche la page d’édition initiale N0 ·270· (PAGE 10) Manuel de programmation Personnalise les touches logiciel d’accès aux divers modes et demande une option (SK 1="CYCLE 1",SK 2="CYCLE 2",SK 7="SORTIR") ;Demander une touche (IF KEY EQ $FC00 GOTO N10) ; Cycle 1 (IF KEY EQ $FC01 GOTO N20) ; Cycle 2 (IF KEY EQ $FC06 SYSTEM ELSE GOTO N5) ; Sortir ou demander une touche CYCLE 1 ; Affiche la page 11 et définit 2 fenêtres de données N10 (PAGE 11) (ODW 1,10,60) (ODW 2,15,60) ;Edition (WBUF "(PCALL 1, ") ; Ajoute au bloc en cours d’édition "(PCALL 1,", (IB 1=INPUT "X:",-6.5) ; Demande de la valeur de X. (DW 1=IB1) ; Affiche sur la fenêtre 1, la valeur introduite. (WBUF "X",IB1) ; Ajoute au bloc en cours d’édition X (valeur introduite). (WBUF ",") ; Ajoute au bloc en cours d’édition ",". (IB 2=INPUT "Y:",-6.5) ; Demande de la valeur de Y. (DW 2=IB2) ; Affiche sur la fenêtre 2, la valeur introduite. (WBUF "Y",IB2) ; Ajoute au bloc en cours d’édition Y (valeur introduite). (WBUF ")") ; Ajoute au bloc en cours d’édition ")". ( WBUF ) ; Introduit en mémoire le bloc édité. ; Par exemple: (PCALL 1, X2, Y3) 12. Instructions de personnalisation ( WKEY ) INSTRUCTIONS DE CONTRÔLE DES PROGRAMMES N5 (GOTO N0) CNC 8035 MODÈLE ·T· (SOFT V16.3X) ·271· Manuel de programmation CYCLE 2 ; Affiche la page 12 et définit 3 fenêtres de données N20 (PAGE 12) (ODW 1,10,60) (ODW 2,13,60) Instructions de personnalisation INSTRUCTIONS DE CONTRÔLE DES PROGRAMMES 12. (ODW 3,16,60) ;Edition (WBUF "(PCALL 2, ") ; Ajoute au bloc en cours d’édition "(PCALL 2,", (IB 1=INPUT "A:",-6.5) ; Demande de la valeur de A. (DW 1=IB1) ; Affiche sur la fenêtre 1, la valeur introduite. (WBUF "A",IB1) ; Ajoute au bloc en cours d’édition A (valeur introduite). (WBUF ",") ; Ajoute au bloc en cours d’édition ",". (IB 2=INPUT "B:",-6.5) ; Demande de la valeur de B. (DW 2=IB2) ; Affiche sur la fenêtre 2, la valeur introduite. (WBUF "B",IB2) ; Ajoute au bloc en cours d’édition B (valeur introduite). (WBUF ",") ; Ajoute au bloc en cours d’édition ",". (IB 3=INPUT "C:",-6.5) ; Demande de la valeur de C. (DW 3=IB3) ; Affiche sur la fenêtre 3, la valeur introduite. (WBUF "C",IB3) ; Ajoute au bloc en cours d’édition C (valeur introduite). (WBUF ")") ; Ajoute au bloc en cours d’édition ")". ( WBUF ) ; Introduit en mémoire le bloc édité. Par exemple: (PCALL 2, A3, B1, C3). (GOTO N0) CNC 8035 MODÈLE ·T· (SOFT V16.3X) ·272· TRANSFORMATION ANGULAIRE DE L'AXE INCLINÉ 13 Avec la transformation angulaire d'axe incliné on réussit à effectuer des déplacements le long d'un axe qui n'est pas à 90º par rapport à un autre. Les déplacements sont programmés dans le système cartésien et pour réaliser les déplacements ils se transforment en déplacements sur les axes réels. Sur certaines machines les axes ne sont pas configurés en mode cartésien, mais forment des angles différents de 90º entre eux. Un cas typique est l'axe X de tour, qui pour des raisons de robustesse ne forme pas 90º avec l'axe Z, mais possède une autre valeur. X X' X Axe cartésien. X' Axe angulaire. Z Axe orthogonal. Z Pour pouvoir programmer dans le système cartésien (Z-X), il faut activer une transformation d'axe incliné qui convertit les déplacements aux axes réels non perpendiculaires (Z-X'). Ainsi, un déplacement programmé sur l'axe X se transforme en déplacements sur les axes Z-X'; c'est-à-dire, on effectue maintenant des déplacements le long de l'axe Z et de l'axe angulaire X'. Activer et désactiver la transformation angulaire. La CNC n'assume aucune transformation après la mise sous tension; l'activation des transformations angulaires se réalise depuis le programme pièce avec la fonction G46. La désactivation des transformations angulaires se réalise depuis le programme pièce avec la fonction G46. Optionnellement, aussi on pourra "bloquer" une transformation pour déplacer l'axe angulaire en programmant en cotes cartésiennes. Influence de la RAZ, de la mise hors tension et de la fonction M30. La transformation angulaire de l'axe incliné est maintenue active, après une RAZ, M30 et même après une mise hors/sous tension de la CNC. CNC 8035 MODÈLE ·T· (SOFT V16.3X) ·273· Manuel de programmation Considérations sur la transformation angulaire de l'axe incliné. Les axes qui configurent la transformation angulaire doivent être linéaires. Les deux axes peuvent avoir des axes Gantry associés. Si la transformation angulaire est active, les cotes affichées seront celles du système cartésien. Dans le cas contraire, les cotes des axes réels seront affichées. Avec la transformation active on peut réaliser les opérations suivantes: TRANSFORMATION ANGULAIRE DE L'AXE INCLINÉ 13. CNC 8035 MODÈLE ·T· (SOFT V16.3X) ·274· • Transferts d'origine. • Présélection de cotes. • Déplacements en Jog continu, Jog incrémental et manivelles. Avec la transformation active, on ne peut pas réaliser des mouvements contre-butée. Recherche de référence machine La fonction G46 se désactive lorsqu'on effectue la recherche de référence d'un des axes faisant partie de la transformation angulaire (paramètres machine ANGAXNA et ORTAXNA). Lorsqu'on fait la recherche de référence d'axes qui n'interviennent dans la transformation angulaire, la fonction G46 reste active. Pendant la recherche de référence machine, les déplacements se réalisent sur les axes réels. Déplacements en mode manuel (jog et manivelles). Les déplacements en mode manuel pourront être réalisés sur les axes réels ou sur les axes cartésiens, en fonction de comment ils aient été définis par le fabricant. La sélection se réalise depuis le PLC (MACHMOVE) et peut être disponible, par exemple, depuis une touche d'utilisateur. Manuel de programmation Activation angulaire et désactivation de la transformation Activation de la transformation angulaire Avec la transformation active, les déplacements sont programmés dans le système cartésien et pour les effectuer la CNC les transforme en déplacements sur les axes réels. Les cotes affichées à l'écran seront celles du système cartésien. G46 S1 Cette instruction active à nouveau une transformation angulaire bloquée. Voir "13.2 Blocage de la transformation angulaire" à la page 276. Désactivation de la transformation angulaire Sans la transformation active, les déplacements sont programmés et exécutés dans le système d'axes réels. Les cotes affichées à l'écran seront celles des axes réels. La désactivation de la transformation angulaire se réalise avec la fonction G46, le format de programmation étant le suivant. G46 S0 G46 La transformation angulaire de l'axe incliné est maintenue active, après une RAZ, M30 et même après une mise hors/sous tension de la CNC. 13. Activation et désactivation de la transformation angulaire L'activation de la transformation angulaire se réalise avec la fonction G46, le format de programmation étant le suivant. TRANSFORMATION ANGULAIRE DE L'AXE INCLINÉ 13.1 CNC 8035 MODÈLE ·T· (SOFT V16.3X) ·275· Manuel de programmation 13.2 Blocage de la transformation angulaire Le blocage de la transformation angulaire est un mode spécial pour réaliser des déplacements le long de l'axe angulaire, mais en programmant la cote dans le système cartésien. Pendant les déplacements en mode manuel le blocage de la transformation angulaire n'est pas appliqué. Le blocage de la transformation angulaire s'active avec la fonction G46, le format de programmation étant le suivant. Blocage de la transformation angulaire TRANSFORMATION ANGULAIRE DE L'AXE INCLINÉ 13. G46 S2 Programmation des déplacements après le blocage de la transformation angulaire. Avec une transformation angulaire bloquée, il ne faut programmer que la cote de l'axe angulaire dans le bloc de déplacement. Si on programme la cote de l'axe orthogonal, le déplacement se réalise suivant la transformation angulaire normale. Désactiver le blocage d'une transformation. Le blocage d'une transformation angulaire se désactive après une RAZ ou M30. L'activation de la transformation (G46 S1) désactive aussi le blocage. X' X P2 P1 N20 N40 N70 N60 P3 P4 Z N10 G46 S1 N20 G1 Z(P2) N30 G46 S2 Blocage de la transformation. N40 X(P3) Déplacement en programmant la cote dans le système cartésien ZX. N50 G46 S1 Activation du mode normal. N60 Z(P4) N70 X(P1) CNC 8035 MODÈLE ·T· (SOFT V16.3X) ·276· Manuel de programmation ANNEXES A. Programmation en code ISO ........................................................................279 B. Instructions de contrôle des programmes..................................................281 C. Résumé des variables internes de la CNC ..................................................283 D. Code de touches............................................................................................287 E. Maintenance ...................................................................................................289 CNC 8035 MODÈLE ·T· (SOFT V16.3X) ·277· Manuel de programmation PROGRAMMATION EN CODE ISO D V Signification Point G00 G01 G02 G03 G04 G05 G06 G07 G08 G09 G10 G11 G12 G13 G14 G16 G17 G18 G19 G20 G21 G22 G32 G33 G34 G36 G37 G38 G39 G40 G41 G41 N G42 G42 N G50 G51 G52 G53 G54 G55 G56 G57 G58 G59 G66 G68 G69 G70 G71 G72 G74 G75 G76 G81 G82 G83 * * * * ? ? * * * * * ? * ? Positionnement rapide Interpolation linéaire Interpolation circulaire à droite Interpolation circulaire à gauche Temporisation/Suspension de la préparation de blocs Arête arrondie Centre de circonférence en coordonnées absolues Arête vive Circonférence tangente à la trajectoire antérieure Circonférence par trois points Annulation d'image miroir Image miroir sur X Image miroir sur Y Image miroir sur Z Image miroir dans les directions programmées Sélection de plan principal dans deux sens Plan principal X-Y et longitudinal Z Plan principal Z-X et longitudinal Y Plan principal Y-Z et longitudinal X Définition des limites inférieures des zones de travail Définition des limites supérieures des zones de travail Validation/invalidation des zones de travail Avance F comme fonction inverse du temps Filetage électronique Filetage à pas variable Arrondissement d'arêtes Entrée tangentielle Entrée tangentielle Chanfreinage Annulation de compensation radiale Compensation radiale d’outil à gauche Détection de collisions Compensation radiale d'outil à droite Détection de collisions Arête arrondie commandée Look-Ahead Déplacement vers butée Programmation par rapport au zéro machine Transfert d'origine absolu 1 Transfert d'origine absolu 2 Transfert d'origine absolu 3 Transfert d'origine absolu 4 Décalage d’origine additionnel 1 Décalage d’origine additionnel 2 Cycle fixe de poursuite de profil Cycle fixe d'ébauchage sur l'axe X Cycle fixe d'ébauchage sur l'axe Z Programmation en pouces Programmation en millimètres Facteurs d’échelle général et particulier Recherche de référence machine Déplacement avec palpeur jusqu’au contact Déplacement avec palpeur jusqu’à l’interruption du contact Cycle fixe de tournage de segments droits Cycle fixe de dressage de segments droits Cycle fixe de perçage 6.1 6.2 6.3 6.3 7.1 / 7.2 7.3.2 6.4 7.3.1 6.5 6.6 7.5 7.5 7.5 7.5 7.5 3.2 3.2 3.2 3.2 3.8.1 3.8.1 3.8.2 6.15 6.11 6.13 6.9 6.7 6.8 6.10 8.2.6 8.2.3 8.3 8.2.3 8.3 7.3.3 7.4 6.14 4.3 4.4.2 4.4.2 4.4.2 4.4.2 4.4.2 4.4.2 9.1 9.2 9.3 3.3 3.3 7.6 4.2 10.1 10.1 9.4 9.5 9.6 * * * * * * * * * * * * * * ? ? * * * * * * * * * * * * * * * * * * * * * * * * * * * * * * * * * * ? ? * * * * * * * * * * * * * * * * * * * * * * * * * A. Programmation en code ISO M ANNEXES Fonction CNC 8035 MODÈLE ·T· (SOFT V16.3X) ·279· Manuel de programmation Fonction ANNEXES Programmation en code ISO A. G84 G85 G86 G87 G88 G89 G90 G91 G92 G93 G94 G95 G96 G97 G151 G152 M D V Signification Point Cycle fixe de tournage de segments courbes Cycle fixe de dressage de segments courbes Cycle fixe de filetage longitudinal Cycle fixe de filetage frontal Cycle fixe de rainurage sur l'axe X Cycle fixe de rainurage sur l'axe Z Programmation absolue * Programmation incrémentale Présélection de coordonnées / Limitation de vitesse de broche Présélection de l'origine polaire Avance en millimètres (pouces) par minute * Avance en millimètres (pouces) par tour * Vitesse de coupe constante Vitesse de rotation de la broche en T/MIN Programmation des cotes de l’axe X en diamètres. Programmation des cotes de l’axe X en rayons. 9.7 9.8 9.9 9.10 9.11 9.12 3.4 3.4 4.4.1 4.5 5.2.1 5.2.2 5.3.1 5.3.2 3.5 3.5 * * * * * * * * ? ? * * * * * * ? ? * ? ? La lettre M signifie MODAL, c'est-à-dire, qu'elle restera active une fois programmée à condition que l'on ne programme pas une fonction G incompatible, que l'on n'exécute pas M02 ou M30, qu'il n'y ait pas d'ARRÊT D'URGENCE, de RAZ ou une mise hors/sous tension de la CNC. La lettre D signifie PAR DEFAUT, c’est-à-dire que ces fonctions sont prises en compte par la CNC, à la mise sous tension, après l’exécution de M02, M30 ou à la suite d’un ARRÊT D'URGENCE ou d’une RAZ. Dans les cas indiqués par ? on devra comprendre que l’état PAR DEFAUT de ces fonctions G dépend de la personnalisation des paramètres machine généraux de la CNC. La lettre V signifie que le code G est affiché à côté des conditions d’usinage actuelles dans les modes exécution et simulation. CNC 8035 MODÈLE ·T· (SOFT V16.3X) ·280· Manuel de programmation INSTRUCTIONS DE CONTRÔLE DES PROGRAMMES Sentences d'affichage. ( section 12.2 ) (ERREUR nombre entier, "texte d'erreur") Arrête l'exécution du programme et affiche l'erreur indiquée. ANNEXES (DGWZ expression 1, ..... expression 4) Définir la zone de représentation graphique. Sentences d'activation et de désactivation. ( section 12.3 ) ( ESBLK et DSBLK ) La CNC exécute tous les blocs entre ESBLK et DSBLK comme s'il s'agissait d'un seul bloc. ( ESTOP et DSTOP ) Validation (ESTOP) et invalidation (DSTOP) de la touche Stop et du signal de Stop externe (PLC). ( EFHOLD et DFHOLD ) Validation (EFHOLD) et invalidation (DFHOLD) de l'entrée de Feed-Hold (PLC). Instructions de contrôle des programmes B. ( MSG "message") Affiche le message indiqué. Instructions de contrôle de flux. ( section 12.4 ) ( GOTO N(expression) ) Provoque un saut dans le programme, au bloc défini avec l'étiquette N(expression). (RPT N(expression), N(expression), P(expression) ) Répète l'exécution de la partie de programme existant entre les deux blocs définis avec les étiquettes N(expression). ( IF condition <action1> ELSE <action2> ) Analyse la condition donnée, qui devra être une expression relationnelle. Si la condition est certaine (résultat égal à 1), l' <action1> sera exécutée; dans le cas contraire (résultat égal à 0), sera exécutée l' <action2>. Sentences de sous-routines. ( section 12.5 ) ( SUB nombre entier ) Définition de sous-routine. ( RET ) Fin de sous-routine. ( CALL (expression) ) Appel à une sous-routine. ( PCALL (expression), (instruction d'affectation), (instruction d'affectation), ... ) Appel à une sous-routine. Elle permet aussi d'initialiser, avec les instructions d'affectation, un maximum de 26 paramètres locaux de cette sous-routine. CNC 8035 (MCALL (expression), (instruction d'affectation), (instruction d'affectation), ... ) Égale à l'instruction PCALL, mais en convertissant la sous-routine indiquée en sous-routine modale. (MDOFF) Annulation de sous-routine modale. MODÈLE ·T· (SOFT V16.3X) ·281· Manuel de programmation Instructions de sous-routines d'interruption. ( section 12.6 ) ( REPOS X, Y, Z, ... ) On doit toujours l'utiliser dans des sous-routines d'interruption et elle facilite le repositionnement de la machine au point d'interruption. Instructions de programmes. ( section 12.7 ) Instructions de contrôle des programmes ANNEXES B. ( EXEC P(expression), (répertoire) ) Démarre l'exécution du programme ( MEXEC P (expression), (répertoire) ) Démarre l'exécution du programme de façon modale. (OPEN P (expression), (répertoire destination), A/D, "commentaire de programme") Commence l'édition d'un nouveau programme et permet de lui associer un commentaire au programme. ( WRITE <texte du bloc> ) Ajoute après le dernier bloc du programme, dont l’édition a été commencée avec l'instruction OPEN P, l'information contenue dans <texte du bloc> comme un nouveau bloc du programme. Instructions de personnalisation. ( section 12.8 ) ( PAGE (expression) ) Affiche sur l'écran le numéro de page d'utilisateur (0-255) ou de système (1000) indiqué. ( SYMBOL (expression 1), (expression 2), (expression 3)) Affiche sur l'écran le symbole (0-255) indiqué avec expression 1. Sa position sur l'écran est définie par l'expression 2 (rangée, 0-639) et par l'expression 3 (colonne 0-335). (IB (expression) = INPUT "texte", format) Affiche le texte indiqué dans la fenêtre d'entrée de données et emmagasine la donnée introduite par l'utilisateur dans la variable d'entrée (IBn) . ( ODW (expression 1), (expression 2), (expression 3) ) Définit et dessine une fenêtre en blanc sur l'écran (1 rangée x 14 colonnes). Sa position sur l’écran est définie par l’expression 2 (rangée) et l’expression 3 (colonne). ( DW (expression 1) = (expression 2), DW (expression 3) = (expression 4),...) ) Affiche sur les fenêtres indiquées par la valeur de l'expression 1,3,.. , la donnée numérique indiquée par l'expression 2,4 ( SK (expression 1) = "texte 1", (expression 2) = "texte 2", .... ) Définit et affiche le nouveau menu de softkeys indiqué. ( WKEY ) Arrête l'exécution du programme jusqu'à ce que l'on tape sur une touche. ( WBUF "texte", (expression) ) Elle ajoute au bloc en cours d’édition et dans la fenêtre d’entrée de données, le texte et la valeur de l’expression dès qu’elle est évaluée. CNC 8035 MODÈLE ·T· (SOFT V16.3X) ·282· ( WBUF ) Introduit en mémoire le bloc qui se trouve en édition. On ne peut l'utiliser que dans le programme de personnalisation que l'on veut exécuter dans le Mode d'Édition. ( SYSTEM ) Achève l'exécution du programme de personnalisation d'utilisateur et revient au menu standard correspondant de la CNC. Manuel de programmation RÉSUMÉ DES VARIABLES INTERNES DE LA CNC • Le symbole R indique que l'on peut lire la variable correspondante. • Le symbole W indique que l'on peut modifier la variable correspondante. Variables associées aux outils. R R R R R R/W R/W R/W R/W R/W R/W R/W R/W R/W R/W R/W R/W R/W R/W R/W R R R R R R/W R/W R/W R/W R/W R R/W R/W R/W R/W R/W R/W R/W R/W R/W R R R R R - C. ( section 11.2.2 ) Numéro de l’outil actif. Numéro du correcteur actif. Numéro de l'outil suivant, en attente de M06. Numéro de correcteur de l'outil suivant. Position qu'occupe l'outil (n) dans le magasin. Numéro de correcteur de l'outil (n). Code de famille de l'outil (n). Valeur affectée comme durée de vie nominale de l'outil (n). Valeur de durée de vie réelle de l'outil (n). Contenu de la position de magasin (n). Valeur du rayon d’outil utilisé par la CNC pour réaliser les calculs. Longueur du correcteur (n) suivant l'axe X. Longueur du correcteur (n) suivant l'axe Z. Code de forme du correcteur (n). Rayon du correcteur (n). Usure de longueur du correcteur (n) suivant l'axe X. Usure de longueur du correcteur (n) suivant l'axe Z. Angle de la plaquette de l'outil indiqué. Largeur de l’outil indiqué. Angle de coupe de l'outil indiqué. Résumé des variables internes de la CNC CNC PLC DNC TOOL TOD NXTOOL NXTOD TMZPn TLFDn TLFFn TLFNn TLFRn TMZTn HTOR TOXn TOZn TOFn TORn TOIn TOKn NOSEAn NOSEWn CUTAn ANNEXES Variable Variables associées aux décalages d’origine. Variable ( section 11.2.3 ) CNC PLC DNC ORG(X-C) R R - PORGF PORGS ORG(X-C)n PLCOF(X-C) ADIOF(X-C) R R R/W R/W R R/W R/W R R R R R R Décalage d'origine active sur l'axe sélectionné. Le décalage additionnel indiqué par le PLC n'est pas inclus. Cote suivant l'axe d'abscisses de l'origine de coordonnées polaires. Cote suivant l'axe d'ordonnées de l'origine de coordonnées polaires. Valeur pour l'axe sélectionné du décalage d'origine (n). Valeur pour l'axe sélectionné du décalage d'origine additionnel (PLC). Valeur pour l'axe sélectionné du décalage d'origine avec manivelle additionnelle. Variables associées aux paramètres machine Variable MPGn MP(X-C)n MPSn MPLCn ( section 11.2.4 ) CNC PLC DNC R R R R R R R R - Valeur affectée au paramètre machine général (n). Valeur affectée au paramètre machine (n) de l'axe (X-C). Valeur affectée au paramètre machine (n) de la broche principale. Valeur affectée au paramètre machine (n) du PLC. Variables associées aux zones de travail Variable FZONE FZLO(X-C) FZUP(X-C) SZONE SZLO(X-C) SZUP(X-C) TZONE TZLO(X-C) TZUP(X-C) FOZONE FOZLO(X-C) FOZUP(X-C) FIZONE FIZLO(X-C) FIZUP(X-C) ( section 11.2.5 ) CNC PLC DNC R R R R R R R R R R R R R R R R/W R/W R/W R/W R/W R/W R/W R/W R/W R/W R/W R/W R/W R/W R/W R R R R R R R R R R R R R R R État de la zone de travail 1. Zone de travail 1. Limite inférieure suivant l'axe sélectionné (X- C). Zone de travail 1. Limite supérieure suivant l'axe sélectionné (X- C). État de la zone de travail 2. Zone de travail 2. Limite inférieure suivant l'axe sélectionné (X- C). Zone de travail 2. Limite supérieure suivant l'axe sélectionné (X- C). État de la zone de travail 3. Zone de travail 3. Limite inférieure suivant l'axe sélectionné (X- C). Zone de travail 3. Limite supérieure suivant l'axe sélectionné (X- C). État de la zone de travail 4. Zone de travail 4. Limite inférieure suivant l'axe sélectionné (X- C). Zone de travail 4. Limite supérieure suivant l'axe sélectionné (X- C). État de la zone de travail 5. Zone de travail 5. Limite inférieure suivant l'axe sélectionné (X- C). Zone de travail 5. Limite supérieure suivant l'axe sélectionné (X- C). Variables associées aux avances. Variable FREAL FREAL(X-C) FTEO/X-C) CNC PLC DNC R R R R R R R R R CNC 8035 MODÈLE ·T· (SOFT V16.3X) ( section 11.2.6 ) Avance réelle de la CNC, en mm/min ou pouces/min. Avance réelle de la CNC sur l'axe sélectionné. Avance théorique de la CNC sur l'axe sélectionné. ·283· Manuel de programmation Variables associées à la fonction G94. FEED DNCF PLCF PRGF R R R R R R R/W R R R/W R R Avance active dans la CNC, en mm/min ou pouces/min. Avance sélectionnée par DNC. Avance sélectionnée par PLC. Avance sélectionnée par programme. Variables associées à la fonction G95. FPREV DNCFPR PLCFPR PRGFPR R R R/W R R R/W R R Avance active dans la CNC, en mm/tour ou en pouces/tour Avance sélectionnée par DNC. Avance sélectionnée par PLC. Avance sélectionnée par programme. Variables associées à la fonction G32. Résumé des variables internes de la CNC ANNEXES C. R R R R PRGFIN R R R Avance sélectionnée par programme en 1/mm. Variables associées à l'override (%). FRO PRGFRO DNCFRO PLCFRO CNCFRO PLCCFR R R/W R R R R R R R R/W R R/W R R R/W R R R Override (%) de l'avance active dans la CNC. Override (%) sélectionné par programme. Override (%) sélectionné par DNC. Override (%) sélectionné par PLC. Override (%) sélectionné depuis le commutateur. Override (%) du canal d'exécution du PLC. Variables associées aux coordonnées. Variable CNC PLC DNC PPOS(X-C) POS(X-C) TPOS(X-C) APOS(X-C) ATPOS(X-C) FLWE(X-C) DIST(X-C) LIMPL(X-C) LIMMI(X-C) DPLY(X-C) GPOS(X-C)n p R R R R R R R/W R/W R/W R R R R R R R R/W R/W R/W R - R R R R R R R R R - ( section 11.2.7 ) Cote théorique programmée. Cotes machine. Cote réelle de la base de l'outil. Cotes machine. Cote théorique de la base de l'outil. Cotes pièce. Cote réelle de la base de l'outil. Cotes pièce. Cote théorique de la base de l'outil. Erreur de poursuite de l'axe sélectionné. Distance parcourue par l'axe sélectionné. Deuxième limite supérieure de parcours. Deuxième limite inférieure de parcours. Cote représentée sur l'écran, pour l'axe sélectionné. Cote de l'axe sélectionné, programmée dans le bloc (n) du programme (p). Variables associées aux manivelles électroniques. Variable ( section 11.2.8 ) CNC PLC DNC HANPF R R HANPS R R HANPT R R HANPFO R R HANDSE HANFCT R R R R/W HBEVAR R R/W MASLAN R/W R/W MASCFI R/W R/W MASCSE R/W R/W - Impulsions reçues de la 1ère manivelle depuis la mise sous tension de la CNC. Impulsions reçues de la 2ème manivelle depuis la mise sous tension de la CNC. Impulsions reçues de la 3ème manivelle depuis la mise sous tension de la CNC. Impulsions reçues de la 4ème manivelle depuis la mise sous tension de la CNC. Sur les manivelles avec bouton sélecteur, indique si ce bouton a été appuyé. R Facteur de multiplication différent pour chaque manivelle (s'il y en a plusieurs). R Manivelle HBE. Comptage activé, axe à déplacer et facteur de multiplication (x1, x10, x100). R/W Angle de la trajectoire linéaire avec "Manivelle trajectoire" ou "Jog trajectoire". R/W Coordonnées du centre de l'arc avec "Manivelle trajectoire" ou "Jog trajectoire". R/W Coordonnées du centre de l'arc avec "Manivelle trajectoire" ou "Jog trajectoire". Variables associées à la mesure. CNC 8035 Variable ASIN(X-C) BSIN(X-C) ASINS BSINS MODÈLE ·T· (SOFT V16.3X) R R R R R R R R R R R R Signal A de la mesure sinusoïdale de la CNC pour l'axe sélectionné. Signal B de la mesure sinusoïdale de la CNC pour l'axe sélectionné. Signal A de la mesure sinusoïdale de la CNC pour la broche. Signal B de la mesure sinusoïdale de la CNC pour la broche. Variables associées à la broche principale. Variable SREAL FTEOS ·284· ( section 11.2.9 ) CNC PLC DNC ( section 11.2.10 ) CNC PLC DNC R R R R R R Vitesse de rotation réelle de la broche. Vitesse théorique de rotation de la broche. Manuel de programmation Variables associées à la vitesse de rotation. SPEED DNCS PLCS PRGS R R R R R R R/W R R Vitesse de rotation de broche active dans la CNC. R/W Vitesse de rotation sélectionnée par DNC. R Vitesse de rotation sélectionnée par PLC. R Vitesse de rotation sélectionnée par programme. Variables associées à la vitesse de coupe constante. R R R R R R R/W R R Vitesse de coupe constante active sur la CNC. R/W Vitesse de coupe constante sélectionnée par DNC. R Vitesse de coupe constante sélectionnée par PLC. R Vitesse de coupe constante sélectionnée par programme. C. SSO PRGSSO DNCSSO PLCSSO CNCSSO R R/W R R R R R R R/W R R Override (%) de la vitesse de rotation de broche active dans la CNC. R Override (%) sélectionné par programme. R/W Override (%) sélectionné par DNC. R Override (%) sélectionné par PLC. R Override (%) sélectionné depuis le panneau avant. Variables associées aux limites de vitesse. SLIMIT DNCSL PLCSL PRGSL MDISL R R R R R R R R/W R R/W R Limite de la vitesse de rotation active dans la CNC. R/W Limite de la vitesse de rotation sélectionnée par DNC. R Limite de la vitesse de rotation sélectionnée par PLC. R Limite de la vitesse de rotation sélectionnée par programme. R Vitesse maximum de la broche pour l’usinage. Variables associées à la position. POSS R RPOSS TPOSS RTPOSS PRGSP R R R R R R R R R R Position réelle de la broche. R Lecture depuis le PLC en dix millièmes de degré (entre ±999999999) et depuis la CNC en degrés (entre ±99999.9999). Position réelle de la broche. R Lecture depuis le PLC en dix millièmes de degré (entre 0 et 3600000) et depuis la CNC en degrés (entre 0 et 360). Position théorique de la broche. R Lecture depuis le PLC en dix millièmes de degré (entre ±999999999) et depuis la CNC en degrés (entre ±99999.9999). Position théorique de la broche. R Lecture depuis le PLC en dix millièmes de degré (entre 0 et 3600000) et depuis la CNC en degrés (entre 0 et 360). Position programmée en M19 par programme pour la broche principal. ANNEXES Variables associées au spindle override. Résumé des variables internes de la CNC CSS DNCCSS PLCCSS PRGCSS Variables associées à l'erreur de poursuite. FLWES R R R Erreur de poursuite de la broche. Variables associées à l'automate. Variable CNC PLC DNC PLCMSG PLCIn PLCOn PLCMn PLCRn PLCTn PLCCn PLCMMn R R/W R/W R/W R/W R/W R/W R/W - R - ( section 11.2.11 ) Numéro du message de l'automate le plus prioritaire qui est actif. 32 entrées de l'automate à partir de la (n). 32 sorties de l'automate à partir de la (n). 32 marques de l'automate à partir de la (n). Registre (n). Comptage du temporisateur (n). Comptage du compteur (n). Modifie la marque (n) de l'automate. Variables associées aux paramètres locaux et globaux. Variable GUP n LUP (a,b) CALLP ( section 11.2.12 ) CNC PLC DNC R R/W R/W - - Paramètre global (P100-P299) (n). Paramètre local (P0-P25) indiqué (b), du niveau d'imbrication (a). Il indique quels paramètres locaux ont été définis et ceux qui ne l’ont pas été dans l’appel de sous-routine par l'instruction PCALL ou MCALL. CNC 8035 Variables associées au mode de fonctionnement. Variable OPMODE ( section 11.2.13 ) CNC PLC DNC R R R Mode de fonctionnement. MODÈLE ·T· (SOFT V16.3X) ·285· Manuel de programmation Autres variables. Variable ANNEXES Résumé des variables internes de la CNC C. CNC PLC DNC NBTOOL PRGN BLKN GSn GGSA GGSB GGSC GGSD MSn GMS PLANE LONGAX MIRROR SCALE SCALE(X-C) R R R R R R R R R R R R R R R R R R R R R R R R R R R R R R R R R R ORGROT PRBST CLOCK TIME DATE TIMER CYTIME PARTC FIRST KEY KEYSRC ANAIn ANAOn CNCERR PLCERR DNCERR DNCSTA TIMEG R R R R R R/W R R/W R R/W R/W R R/W R R R R R R R/W R R/W R R/W R/W R R/W R R R R R R R R/W R/W R/W R R/W R R/W R/W R R/W R R R SELPRO DIAM R/W R/W R/W R/W R R PRBMOD RIP R/W R R/W R R R ( section 11.2.14 ) Numéro d'outil en train d'être géré. Numéro de programme en exécution. Numéro d'étiquette du dernier bloc exécuté. État de la fonction G (n). État des fonctions G00 à G24. État des fonctions G25 à G49. État des fonctions G50 à G74. État des fonctions G75 à G99. État de la fonction M (n). État des fonctions M (0..6, 8, 9, 19, 30, 41..44). Axes des abscisses et des ordonnées du plan actif. Axe sur lequel est appliquée la compensation longitudinale (G15). Images miroir actives. Facteur d'échelle général appliqué. Lecture depuis le PLC en dix-millièmes. Facteur d'échelle particulier de l'axe indiqué. Lecture depuis le PLC en dixmillièmes. Angle de rotation du système de coordonnées (G73). Donne l’état du palpeur. Horloge du système, en secondes. Heure en format heures-minutes-secondes. Date en format année-mois-jour. Horloge activée par le PLC, en secondes. Temps d'exécution d'une pièce, en centièmes de seconde. Compteur de pièces de la CNC. Première fois que l'on exécute un programme Code de touche. Provenance des touches. Tension en volts de l'entrée analogique (n). Tension en volts à appliquer à la sortie analogique (n). Numéro d'erreur active dans la CNC. Numéro d'erreur active dans le PLC. Numéro d'erreur qui s'est produite dans la communication via DNC. État de la transmission DNC. Temps restant pour terminer le bloc de temporisation (en centièmes de seconde) Lorsqu'on dispose de deux entrées de palpeur, il sélectionne l'entrée active. Change le mode de programmation pour les coordonnées de l'axe X entre rayons et diamètres. Indique s’il faut afficher ou non une erreur de palpage. Vitesse théorique linéaire résultante de la boucle suivante (en mm/min). La variable "KEY" dans la CNC est d'écriture (W) uniquement dans le canal d'utilisateur. La variable "NBTOOL" ne peut être utilisée que dans la sous-routine de changement d'outil. CNC 8035 MODÈLE ·T· (SOFT V16.3X) ·286· Manuel de programmation CODE DE TOUCHES Panneau de Commande alphanumérique (modèles M-T) c e 101 f j k 107 l o 111 p q 112 113 u 117 v 118 w 119 i 103 h 104 105 106 m 109 n 110 ñ 164 r s 115 t 116 y z 122 g 114 x 120 121 99 d 100 98 102 65 66 67 68 69 70 108 71 72 73 74 75 76 77 78 79 80 81 82 83 84 85 86 87 88 89 90 91 32 65454 65456 64512 65522 64513 64514 65524 64515 027 64516 64517 61446 65453 65445 65460 65462 64518 65458 65455 013 61447 61452 35 40 61 37 93 33 60 53 45 61443 65523 54 44 50 59 43 57 38 34 49 42 62 56 52 47 36 41 55 91 63 D. Code de touches b 97 ANNEXES a 51 58 48 46 65521 65520 CNC 8035 MODÈLE ·T· (SOFT V16.3X) ·287· Manuel de programmation ANNEXES Code de touches D. CNC 8035 MODÈLE ·T· (SOFT V16.3X) ·288· Manuel de programmation MAINTENANCE Nettoyage L’accumulation de saletés dans l’appareil peut agir comme écran empêchant la dissipation correcte de la chaleur dégagée par les circuits électroniques internes, ce qui pourrait provoquer un risque de surchauffe et des pannes sur la Commande Numérique. Maintenance Pour le nettoyage du panneau de commandes et du moniteur il est conseillé d'utiliser un chiffon doux humidifié à l'eau désionisée et/ou un détergent vaisselle habituel non abrasif (liquides, jamais en poudre) ou bien avec de l'alcool à 75%. E. ANNEXES La saleté accumulée peut aussi dans certains cas, donner un cheminement conducteur à l’électricité qui pourrait provoquer des pannes dans les circuits internes de l’appareil, particulièrement sous des conditions de forte humidité. Ne pas utiliser d’air comprimé à haute pression pour le nettoyage de l’appareil, cela pourrait provoquer une accumulation de charges qui pourrait donner lieu à des décharges électrostatiques. Les plastiques utilisés dans la partie frontale des appareils sont résistants à: • Graisses et huiles minérales. • Bases et eaux de Javel. • Détergents dissous. • L’alcool. Fagor Automation se dégage de toute responsabilité en cas de dommage matériel ou physique pouvant découler du non-respect de ces exigences de base de sécurité. Pour vérifier les fusibles, débrancher d'abord l'alimentation. Si la CNC ne se met pas sous tension avec l'interrupteur de mise en marche, vérifier que les fusibles sont les adéquats et en parfait état. Éviter les dissolvants. L'action des dissolvants comme les chlorhydrocarbures, le benzol, les esters et éthers peuvent endommager les plastiques composant le frontal de l'appareil Ne pas manipuler l'intérieur de l'appareil. Seul le personnel autorisé de Fagor Automation peut manipuler l'intérieur de l'appareil. . Ne pas manipuler les connecteurs, lorsque l'appareil est branché au réseau électrique. Avant de manipuler les connecteurs (entrées/sorties, mesure, etc..), vérifier que l'appareil n'est pas branché au réseau électrique. . CNC 8035 MODÈLE ·T· (SOFT V16.3X) ·289· Manuel de programmation ANNEXES E. CNC 8035 MODÈLE ·T· (SOFT V16.3X) ·290· Manuel de programmation E. CNC 8035 MODÈLE ·T· (SOFT V16.3X) ·291· Manuel de programmation E. CNC 8035 MODÈLE ·T· (SOFT V16.3X) ·292· ">
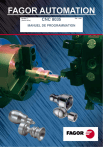
Lien public mis à jour
Le lien public vers votre chat a été mis à jour.