FAGOR CNC 8050 M MANUEL D’UTILISATION Ref. 9701 (fra) FAGOR AUTOMATION S. Coop. Ltda. informe périodiquement tous les clients qui en font la demande sur les nouvelles possibilités mises en oeuvre dans la CNC FAGOR 8050. De cette façon, le client peut demander la ou les nouvelles fonctionnalités qu’il désire incorporer à sa machine. Pour obtenir ces informations, il vous suffit de nous communiquer l’adresse complète de votre société, ainsi que la référence (modèle et numéro de série) des différents modèles de Commandes Numériques que vous utilisez. Il convient de tenir compte du fait que certaines des fonctions décrites dans ce manuel peuvent être absentes de la version du logiciel que vous venez d’acquérir. Les fonctions dépendant des options du logiciel sont les suivantes: Gestion de durée de vie des outils Cycles de palpeur DNC Editeur de profils Logiciel pour 4 ou 6 axes Poches quelconques (avec ilôts) Digitalisation Graphiques solides Taraudage rigide Recopie Les informations données dans ce manuel pourront varier en fonction des modifications techniques. FAGOR AUTOMATION, S. Coop. Ltda. se reserve le droit de modifier le contenu de ce manuel sans être tenu d’en signaler les variations. Si vous venez d’acquérir le MODELE CNC FAGOR 8050 GP, nous recommandons de tenir compte des considérations suivantes: * Ce modèle est basé sur le modèle CNC 8050 de Fraiseuse. * Il ne dispose pas de certaines des fonctions dont bénéficie le modèle CNC 8050 de Fraiseuse La liste des fonctions non disponibles par rapport au modèle pour fraiseuse et les options de logiciel disponibles avec le modèle présenté figurent ci-dessous. Fonctions non disponibles Options de logiciel Filetage electronique (G33) Gestion du magasin d’outils Cycles fixes d’usinage (G8x) Usinages multiples (G6x) Cycles fixes de palpeur Gestion de durée de vie des outils Poches quelconques (avec ilôts) Digitalisation Graphiques Recopie Logiciel pour 4 ou 6 axes DNC Taraudage rigide (G84) Compensation de rayon d’outil (G40, G41, G42) Editeur de profils SOMMAIRE Section Page Nouvelles caractéristiques et modifications INTRODUCTION Règles de sécurité .......................................................................................................... 3 Conditions de retour du materiel .................................................................................. 5 Documentation Fagor pour la CNC 8050 .................................................................... 6 Sommaire ........................................................................................................................ 7 Chapitre 1 GENERALITES 1.1 1.2 1.3 Disposition des informations sur le moniteur ............................................................. 2 Disposition du clavier ................................................................................................... 4 Disposition du pupitre opérateur .................................................................................. 6 Chapitre 2 MODES DE FONCTIONNEMENT 2.1 Systèmes d’aide .............................................................................................................. 3 Chapitre 3 EXECUTION / SIMULATION 3.1 3.2 3.2.1 3.2.2 3.2.3 3.2.4 3.2.5 3.2.6 3.2.7 3.3 3.4 3.5 3.5.1 3.5.2 3.5.3 3.5.4 3.5.5 3.5.6 3.5.7 3.5.8 3.6 Sélection du bloc et condition d’arrêt ......................................................................... 4 Visualiser ........................................................................................................................ 7 Mode de visualisation standard .................................................................................... 9 Mode de visualisation de position ............................................................................... 10 Visualisation du programme pièce ............................................................................... 10 Mode de visualisation de sous-routines ...................................................................... 11 Mode de visualisation de l’erreur de poursuite .......................................................... 14 Mode de visualisation utilisateur ................................................................................. 14 Mode de visualisation des temps d’exécution ............................................................ 15 MDI ................................................................................................................................. 17 Inspection des outils ...................................................................................................... 18 Graphiques ...................................................................................................................... 20 Type de graphique ......................................................................................................... 21 Zone à visualiser ............................................................................................................ 27 Zoom ............................................................................................................................... 28 Point de vue .................................................................................................................... 30 Paramètres graphiques ................................................................................................... 31 Effacer l’écran ................................................................................................................ 33 Désactiver les graphiques .............................................................................................. 33 Mesure ............................................................................................................................. 34 Bloc à bloc ...................................................................................................................... 35 Section Page Chapitre 4 EDITION 4.1 4.1.1 4.1.2 4.1.3 4.1.4 4.1.4.1 4.1.4.2 4.1.5 4.2 4.3 4.4 4.5 4.6 4.7 4.8 4.9 4.10 4.10.1 4.10.2 Editer ............................................................................................................................... 2 Edition en langage CNC ............................................................................................... 2 Edition en TEACH-IN .................................................................................................... 3 Editeur Interactif ............................................................................................................ 4 Editeur de profils ........................................................................................................... 5 Mode d’utilisation de l’éditeur de profils ................................................................... 6 Exemple de définition d’un profil ................................................................................ 13 Utilisateur ....................................................................................................................... 14 Modifier .......................................................................................................................... 15 Chercher .......................................................................................................................... 16 Remplacer ....................................................................................................................... 17 Effacer un bloc ............................................................................................................... 18 Déplacer un bloc ............................................................................................................ 19 Copier un bloc ................................................................................................................ 20 Copier dans un programme ........................................................................................... 21 Inclure un programme .................................................................................................... 22 Paramètres éditeur .......................................................................................................... 23 Autonumération ............................................................................................................. 23 Selection des axes pour édition en TEACH-IN ........................................................... 24 Chapitre 5 MANUEL 5.1 5.1.1 5.1.2 5.1.3 5.2 Déplacement Déplacement Déplacement Déplacement Déplacement manuel de la machine ............................................................................. 9 en continu ................................................................................................ 9 incrémental .............................................................................................. 10 par manivelle électronique .................................................................... 11 manuel de la broche de la machine ....................................................... 12 Chapitre 6 TABLES 6.1 6.2 6.3 6.4 6.5 Table des origines .......................................................................................................... 2 Table de correcteurs ....................................................................................................... 6 Table d’outils ................................................................................................................. 11 Table de magasin d’outils ............................................................................................. 17 Tables de paramètres globaux et locaux ...................................................................... 22 Chapitre 7 UTILITAIRES 7.1 7.1.1 7.1.2 7.1.3 7.2 7.2.1 7.2.2 Répertoire ....................................................................................................................... 2 Répertoire de programmes ............................................................................................. 2 Répertoire de sous-programmes .................................................................................... 4 Répertoire de la ligne série (DNC) ............................................................................... 4 Copier ............................................................................................................................. 5 Copier un programme dans un autre programme ........................................................ 5 Envoyer le contenu de la EEPROM au programmateur .............................................. 6 Section 7.3 7.4 7.5 7.5.1 7.5.2 7.5.3 7.6 7.7 7.8 7.8.1 7.8.2 Page Effacer ............................................................................................................................. 7 Renommer ....................................................................................................................... 8 Protections ...................................................................................................................... 9 Autorisations données à l’utilisateur ........................................................................... 10 Autorisations données au fabricant .............................................................................. 10 Codes d’accès ................................................................................................................. 11 Compacter ....................................................................................................................... 13 Changer la date .............................................................................................................. 13 Opérations avec la mémoire EEPROM ......................................................................... 14 Déplacer un programme a la mémoire EEPROM ......................................................... 14 Déplacer un programme de la mémoire EEPROM ....................................................... 14 Chapitre 8 DNC 8.1 Modes de fonctionnement avec les lignes série .......................................................... 3 Chapitre 9 PLC 9.1 9.2 9.3 9.3.1 9.4 9.5 9.6 9.7 9.8 9.9 9.10 9.10.1 9.10.2 9.10.2.1 9.10.2.2 9.10.2.3 9.10.3 9.10.3.1 9.10.3.2 9.10.3.3 9.10.4 Editer ............................................................................................................................... 3 Compiler ......................................................................................................................... 10 Contrôle .......................................................................................................................... 11 Contrôle avec le PLC en service et le PLC stoppé ...................................................... 18 Messages actifs ............................................................................................................... 20 Pages actives .................................................................................................................. 20 Sauvegarder le programme ............................................................................................ 20 Restaurer le programme ................................................................................................. 21 Ressources utilisables .................................................................................................... 21 Statistiques ..................................................................................................................... 22 Analyseur logique .......................................................................................................... 24 Description de l’écran de travail ................................................................................... 24 Selection des variables et des conditions de déclenchement .................................... 27 Selectionner les variables .............................................................................................. 27 Selectionner la condition de déclenchement .............................................................. 29 Selectionner la base de temps ....................................................................................... 31 Exécuter tracé ................................................................................................................. 32 Saisie de données ........................................................................................................... 33 Modes de fonctionnement ............................................................................................. 34 Représentation du tracé ................................................................................................. 35 Analyser tracé ................................................................................................................. 36 Chapitre 10 PERSONNALISATION 10.1 10.2 10.3 10.4 10.5 Utilitaires ........................................................................................................................ 3 Edition de pages et symboles personnalisés ............................................................... 6 Eléments graphiques ...................................................................................................... 11 Textes .............................................................................................................................. 16 Modifications ................................................................................................................. 19 Section Page Chapitre 11 PARAMETRES MACHINE 11.1 11.2 11.3 11.4 11.5 Tables de paramètres machine ...................................................................................... 2 Table des fonctions auxiliaires “M” ............................................................................ 3 Tables de compensation de vis ..................................................................................... 4 Tables de compensation croisée ................................................................................... 5 Fonctionnement avec les tables de paramètres ........................................................... 6 Chapitre 12 DIAGNOSTICS 12.1 12.1.1 12.1.2 12.2 12.3 12.4 12.5 12.6 Configuration du système ............................................................................................. 2 Configuration hardware ................................................................................................. 2 Configuration software .................................................................................................. 4 Test hardware .................................................................................................................. 5 Test memoire .................................................................................................................. 7 Test EPROM ................................................................................................................... 9 Utilisateur ....................................................................................................................... 11 Notes utiles ..................................................................................................................... 12 NOUVELLES CARACTERISTIQUES ET MODIFICATIONS (Fraiseuse) Date: Juin 1992 Version du logiciel: 7.01 et suivants CARACTERISTIQUE MANUEL ET CHAPITRES CONCERNES Modèle GP Tous les manuels Réception de dessins sous Autocad Manuel spécifique, remis avec le logiciel Broche secondaire/outil motorisé Manuel d’installation Chap. 3, 9, Annexe Manuel de programmation Chap. 5, 13 Recopie Manuel d’installation Chap. 1, Chap. 13 Manuel de programmation Chap. 5, 14, 16, Annexe Editeur de profils Manuel d’utilisation Chap. 4 Editeur interactif Manuel d’utilisation Chap. 4 Editeur d’apprentissage (TEACH-IN) Manuel d’utilisation Chap. 4 Logiciel pour 4 ou 6 axes Manuel d’installation Chap. 4, 9, 10, Annexe Manuel de programmation Chap. 3, 13 Contrôle des axes depuis le PLC Manuel d’installation Chap. 3, Chap. 11 Chargement du contenu de la mémoire EEPROM dans une mémoire EPROM Manuel d’utilisation Chap. 7 Etalonnage des outils avec palpeur en mode manuel Manuel d’installation Manuel d’utilisation Chap. 3 Chap. 5 Sous-programmes d’interruption (4 entrées) Manuel d’installation Chap. 3, 9,Annexe AC-forward Manuel d’installation Chap. 3 Contrôle du PLC en mode JOG Manuel d’utilisation Chap. 5 Estimation des temps d’exécution Manuel d’utilisation Chap. 3 Chargement de programmes pièce en mémoire EEPROM Manuel d’installation Manuel d’utilisation Chap. 3 Chap. 7, 12 Trois tables de compensation croisée Manuel d’installation Manuel d’utilisation Chap. 3, Annexe Chap. 11 Déplacement des axes en manuel lors de la définition des tables de vis et de compensation croisée Manuel d’utilisation Chap. 11 Sous-programme associé aux outils Manuel d’installation Chap. 3 Possibilité de CHERCHER TEXTE dans l’option SELECTION DE BLOC Manuel d’utilisation Chap. 3 Plus de caractères de taille double et triple Manuel d’utilisation Chap. 10 Programmation de l’instruction ERREUR par paramètre Manuel de programmation Chap 14 Variables d’accès au centre de rotation: ROTPF et ROTPS Manuel de programmation Chap 13, Annexe Page 1 Nouvelles caractéristiques (M) - 1 CARACTERISTIQUE MANUEL ET CHAPITRES CONCERNES Variables d’accès au palpeur de recopie: DEFLEX, DEFLEY et DEFLEZ Manuel d’installation Chap. 10, Annexe Manuel de programmation Chap. 13, Annexe Sortie logique générale indiquant l’état de la boucle de positionnement d’axes: LOPEN Manuel d’installation Chap. 9, Annexe PLC: initialiser un bloc de registres Manuel d’utilisation Chap. 9 PLC: nouvelles directives Manuel d’installation Chap. 7 PLC: 200 symboles Manuel d’installation Chap. 7 Nouvelles possibilités dans les cycles fixes de poche avec ilôts Manuel de programmation Chap. 11 Connecteur X7 du module AXES Manuel d’installation Chap. 1 Support d’unité de disquettes FAGOR Manuel d’installation Chap. 1, 3 Assouplissement du cycle de changement d’outil Manuel d’installation Chap. 3 Traitement amélioré des erreurs Manuel d’utilisation Chap. 1 Date: Avril 1993 CARACTERISTIQUE Version du logiciel: 7.06 et suivants MANUEL ET CHAPITRES CONCERNES Axes rotatifs sans limites Manuel d’installation Axes de positionnement en G01 Manuel de programmation Chap. 6 Déplacement du point de référence Manuel d’installation Variables de zones de travail (R/W) depuis le PLC Manuel d’installation Chap. 10, Annexe Manuel de programmation Annexe Possibilité d’interrompre le canal utilisateur Manuel d’installation Mouvement jusqu’à la butée Manuel d’installation Chap. 3, 11 Manuel de programmation Chap. 6, Annexe Graphiques d’aléseuse Manuel d’installation Programmation de “WBUF” sans paramètres Manuel de programmation Chap. 14 Date: Juillet 1993 CARACTERISTIQUE Chap. 3 Chap. 3, 4 Chap. 9, Annexe Chap. 3 Version du logiciel: 7.07 et suivants MANUEL ET CHAPITRES CONCERNES Le modèle GP offre la compensation de rayon d’outil en option (G40, G41, G42) Sorties logiques d’état de touches 2 - Nouvelles caractéristiques (M) Manuel d’installation Chap. 9 Date: Janvier 1994 Version du logiciel: 9.01 et suivants CARACTERISTIQUE MANUEL ET CHAPITRES CONCERNES Visualisation de la pointe ou de la base de l’outil Manuel d’installation Chap. 3 Possibilité de mesure dans les graphiques avec un curseur Manuel d’utilisation Chap. 3 Permettre l’étalonnage de l’outil en manuel et par palpeur Manuel d’utilisation Chap. 5 Traitement des signaux Io codés Manuel d’installation Chap. 3 Possibilité de mémoriser sur EEPROM les messages et erreurs du PLC Manuel d’installation Manuel d’utilisation Chap. 3 Chap. 7 Indicateur “Programme en EEPROM” Manuel d’utilisation Chap. 7 Indicateur “programme en cours d’exécution” Manuel d’utilisation Chap. 7 G50. Arrondi aux angles contrôlé Manuel d’installation Chap. 3, 11 Manuel de programmation Chap. 5, 7, Annexe Avance par tour (G95) pour les axes contrôlés par l’intermédiaire du PLC Manuel d’installation Ebauche concentrique de poches avec ilôts Manuel de programmation Chap. 11 G93 en définition de profil de poche avec ilôts Manuel de programmation Chap. 11 Recopie et digitalisation manuelle, en 1, 2 et 3 dimensions Manuel d’installation Chap. 9, Annexe Manuel de programmation Chap. 5, 16, Annexe Nouveaux cycles de recopie/digitalisation Manuel de programmation Chap. 16 Visualisation de la déflexion et des facteurs de correction du palpeur de recopie Manuel d’utilisation Chap. 3, 5 Exécution de programme infinie depuis le PC Manuel d’utilisation Chap. 8 Programme infini multi-disquettes dans l’unité de disquettes Manuel d’utilisation Chap. 8 Digitalisation multi-disquettes dans l’unité de disquettes Manuel d’utilisation Chap. 8 Date: Mai 1994 CARACTERISTIQUE Chap. 11 Version du logiciel: 9.03 et suivants MANUEL ET CHAPITRES CONCERNES Temps d’anticipation pour poinçonneuses Manuel d’installation Chap. 3, 9, Annexe Variables TPOS(X-C), TPOSS, FLWES Manuel d’installation Chap. 10, Annexe Modification de la vitesse de M19 depuis le PLC Manuel d’installation Chap. 9, Annexe Déplacements en G75 et G76 à 100% de F Manuel de programmation Chap. 10 Nouvelles caractéristiques (M) - 3 Date: Décembre 1994 Version du logiciel: 9.06 et suivantes CARACTERISTIQUE MANUEL ET CHAPITRES CONCERNES Troisième zone de travail Manuel d’installation Chap. 10, Annexe Manuel de programmation Chap. 3, 13, Annexe Pour faciliter le fonctionnement sans moniteur, les valeurs par défaut des paramètres: PROTOCOL (1) et POWDNC (oui) ont été changées Manuel d’installation Date: Février 1995 Chap. 3 Version du logiciel: 9.07 et suivantes CARACTERISTIQUE MANUEL ET CHAPITRES CONCERNES Si, pendant la recherche de “zéros” codifiés, le signal DECEL* de l’axe passe à “1”, le sens du mouvement est inversé et la recherche se déroule en sens contraire. Manuel d’installation Chap. 4 Une fonction “T” avec un sous-programme associé peut être programmée dans un bloc comportant un mouvement. Manuel d’installation Chap. 3 Le paramètre “TAFTERS” indique si la fonction “T” est exécutée avant ou après son sous-programme associé. Manuel d’installation Chap. 3 La fonction G53 sans information de déplacement annule le décalage du zéro actif. Manuel de programmation Chap. 4 La table de fonctions “M” permet d’interrompre la préparation des blocs jusqu’au début ou la fin de la fonction “M”. Manuel d’installation Manuel d’utilisation Date: Octobre 1995 Chap. 3 Chap. 11 Version du logiciel: 9.09 et suivantes CARACTERISTIQUE MANUEL ET CHAPITRES CONCERNES M19 TYPE (paramètre de broche) indique si la broche recherche le zéro à chaque passage du mode boucle ouverte à boucle fermée. Manuel d’installation Les variables POSS et TPOSS sont toujours actives (que la boucle soit ouverte ou fermée) Manuel d’installation Chap. 10 Manuel de programmation Chap. 13 Les tables de compensation de vis autorisent des pentes pouvant atteindre ±45° Manuel d’installation Manuel d’utilisation Date: Avril 1996 Chap. 3 Chap. 3 Chap. 11 Version du logiciel: 9.10 et suivantes CARACTERISTIQUE MANUEL ET CHAPITRES CONCERNES Nouvelles variables RPOSS et RTPOSS associées à la broche Manuel d’installation Chap. 10 et Annexe Manuel de programmation Chap. 13 et Annexe 4 - Nouvelles caractéristiques (M) Date: Juillet 1996 Version du logiciel: 9.11 et suivantes CARACTERISTIQUE MANUEL ET CHAPITRES CONCERNES Paramètre machine EXTMULT à utiliser lorsque le signal Io du système de réalimentation est codifié Manuel d’installation Date: Mai 1996 Chap. 3 Version du logiciel: 11.01 et suivantes CARACTERISTIQUE MANUEL ET CHAPITRES CONCERNES CPU TURBO Manuel d’installation Analyse par anticipation Manuel de programmation Chap. 5, 7 et Annexe Poches quelconques en 3D (avec ilôts) Manuel de programmation Chap. 11 Possibilité de choix du type de début/fin de compensation de rayon Manuel d’installation Chap. 3 Manuel de programmation Chap. 8 Signal d’anticipation pour chaque axe Manuel d’installation Chap. 3, 9 et Annexe Exécution de bloc de haut niveau depuis l’automate Manuel d’installation Chap. 11 Possibilité d’axes rotatifs sans “rollover” (rebouclage) Manuel d’installation Chap. 3 Chap. 1 et 3 Graphiques en ligne dans le modèle GP Editeur de profils optionnel sur modèles GP Nouvelles caractéristiques (M) - 5 INTRODUCTION Introduction - 1 Introduction - 2 REGLES DE SECURITE Une lecture attentive des règles de sécurité suivantes est recommandée afin d’éviter tous dommages au personnel, au produit présenté dans ce manuel ainsi qu’aux éléments qui lui sont raccordés. Les réparations devant être effectuées sur cet appareil ne seront confiées qu’à un personnel dûment habilité par Fagor Automation. Fagor Automation ne pourra être tenu pour responsable d’aucun dommage corporel ou matériel découlant du non-respect de ces règles fondamentales de sécurité. Précautions contre les dommages corporels Avant de mettre l’appareil sous tension, s’assurer qu’il est correctement mis à la terre Pour éviter toutes décharges électriques, vérifier que tous les raccordements à la terre ont été réalisés. Ne pas travailler dans des environnements humides Pour éviter toutes décharges électriques, travailler sous une humidité relative de 90% maximum (sans condensation) et une température ne dépassant pas 45°C. Ne pas travailler dans des environnements explosifs Afin d’éviter tous dangers et accidents, ne pas travailler dans des environnements explosifs. Précautions contre les dommages au produit Environnement de travail Cet appareil est livré prêt à fonctionner dans les Environnements Industriels tels qu’ils ont été définis dans les directives et les normes en vigueur dans l’Union Européenne. Fagor Automation ne pourra êre tenu pour responsable de tout dommage provoqué ou subi en cas d’installation dans d’autres environnements (zones d’habitation). Installer le produit dans un emplacement adéquat Dans toute la mesure du possible, on veillera à installer la CNC loin des sources de liquides de refroidissement et de produits chimiques ainsi qu’à l’abri des chocs susceptibles de l’endommager. Cet appareil est conforme aux directives Européennes sur la compatibilité électromagnétique. Il est toutefois recommandé d’éviter la proximité des sources de parasites électromagnétiques tels que: - Charges puissantes reliées à la même source C.A. que l’appareil décrit ici, - Emetteurs portables (radiotéléphones, radio-amateurs, etc...), - Emetteurs radio/TV, - Machines à souder à l’arc, - Lignes haute tension, - etc... Environnement La température de travail doit être maintenue entre +5°C et +45°C La température de stockage doit être maintenue entre -25°C et +70°C. Introduction - 3 Protection de l’appareil proprement dit Module d’alimentation électrique Ce module comporte deux fusibles rapides de 3,15 A/250 V protégeant la ligne C.A. réseau Module d’axes Toutes les entrées/sorties digitales comportent une isolation galvanique par optocoupleurs entre les circuits de la CNC et l’extérieur. Une protection par fusible externe rapide (F) de 3,15 A/250 V contre l’inversion de phases de la source de courant est également prévue. Module d’entrées/sorties Toutes les entrées/sorties digitales comportent une isolation galvanique par optocoupleurs entre les circuits de la CNC et l’extérieur. Une protection par fusible externe rapide (F) de 3,15 A/250 V contre les surtensions (supérieures à 33 Vcc) et l’inversion de phases de la source de courant est également prévue. Module d’entrées/sorties et de recopie Toutes les entrées/sorties digitales comportent une isolation galvanique par optocoupleurs entre les circuits de la CNC et l’extérieur. Une protection par fusible externe rapide (F) de 3,15 A/250 V contre les surtensions (supérieures à 33 Vcc) et l’inversion de phases de la source de courant est également prévue. Module ventilateur Ce module comporte 1 ou 2 fusibles externes rapides de 0,4 A / 250 V, selon le modèle de ventilateur. Moniteur Le type de protection dépend du type de moniteur. Se reporter à la plaquette d’identification de l’appareil concerné. Précautions pendant les réparations Ne pas intervenir à l’intérieur de l’appareil Seul le personnel Fagor Automation habilité est autorisé à intervenir à l’intérieur de l’appareil. Ne pas manipuler les connecteurs lorsque l’appareil est sous tension Avant de manipuler les connecteurs (entrées/sorties, réalimentation, etc.), s’assurer que l’appareil n’est pas sous tension. Symboles de sécurité Symboles pouvant apparaître dans le manuel Symbole “ATTENTION” Un texte accompagne ce symbole pour indiquer les actions ou les opérations risquant de provoquer des blessures au personnel ou des dommages au produit. Symboles pouvant apparaître sur l’appareil Symbole “ATTENTION” Un texte accompagne ce symbole pour indiquer les actions ou les opérations risquant de provoquer des blessures au personnel ou des dommages au produit. Symbole “CHOC ELECTRIQUE” Ce symbole indique que le point signalé peut être sous tension. Symbole “TERRE DE PROTECTION” Ce symbole indique que ce point doit être relié au point de terre central de la machine afin d’assurer la protection du personnel et des appareils. Introduction - 4 CONDITIONS DE RETOUR DU MATERIEL En cas de retour du moniteur ou de l’UC, le carton et le matériau d’origine devront être réutilisés. En cas d’impossibilité, on procèdera comme suit: 1 Utiliser un carton dont les trois dimensions intérieures seront supérieures d’au moins 15 cm à celles de l’appareil. Le carton utilisé devra résister à une charge de 170 kg. 2 Lors du retour aux ateliers de Fagor Automation, fixer une étiquette indiquant le propriétaire de l’appareil, son adresse, le nom de la personne à contacter, le type d’appareil, le numéro de série, les symptômes et une courte description du problème. 3 Enrouler l’appareil dans un film de polyéthylène ou toute autre protection similaire. Lors de l’envoi du moniteur, prévoir une protection spéciale pour l’écran. 4 Caler l’appareil à l’intérieur du carton au moyen de blocs en mousse de polyurethane sur toutes ses faces. 5 Fermer le carton à l’aide de ruban adhésif ou d’agrafes industrielles. Introduction - 5 DOCUMENTATION FAGOR POUR LA CNC 8050 Manuel CNC 8050 OEM Il s’adresse au constructeur de la machine ou à la personne chargée de l’installation et de la mise en service de la CNC. Il est commun aux modèles de CNC 8050-M et 8050-T, et comprend le manuel d’installation. Manuel d’utilisation de la CNC 8050-M Il s’adresse à l’utilisateur final, c’est-à-dire à l’opérateur chargé de l’exploitation de la CNC. Il comprend deux manuels: Manuel d’utilisation Manuel de programmation Manuel d’utilisation de la CNC 8050-T Il s’adresse à l’utilisateur final, c’est-à-dire à l’opérateur chargé de l’exploitation de la CNC. Il comprend deux manuels: Manuel d’utilisation Manuel de programmation Manuel du logiciel DNC 8050 Manuel du protocole DNC 8050 qui explique comment utiliser la CNC qui explique comment programmer la CNC qui explique comment utiliser la CNC qui explique comment programmer la CNC Il s’adresse aux personnels utilisant le logiciel de communications DNC 8050 en option. Il s’adresse aux personnes désirant concevoir leur propre logiciel de communications DNC afin de communiquer avec la CNC 8050. Manuel AUTOCAD 8050 Il s’adresse aux personnes désirant concevoir leurs pages d’écran CNC et symboles “personnalisés” sur AUTOCAD. Ce manuel explique comment organiser leur programme Autocad de façon que la CNC interprète correctement les pages et symboles conçus. Manuel FLOPPY DISK Il s’adresse aux personnes utilisant l’unité de disquettes FAGOR et explique son mode d’utilisation. Introduction - 6 SOMMAIRE Le Manuel de l’Utilisateur de la CNC pour Fraiseuse comprend les chapitres suivants: Index Nouvelles fonctionnalités et modifications apportées au modèle pour fraiseuse. Introduction Résumé des règles de sécurité Conditions de retour Documentation Fagor pour la CNC 8050 Sommaire du manuel Chapitre 1 Généralités Décrit l’aménagement du clavier, du pupitre opérateur, et donne des informations sur le moniteur. Chapitre 2 Modes de fonctionnement Décrit les différents modes de fonctionnement de la CNC. Chapitre 3 Exécution/Simulation Indique comment exploiter la CNC dans les modes “Exécution” et “Simulation”. Les deux opérations peuvent être exécutées en mode automatique ou bloc à bloc. Chapitre 4 Edition Description du mode de fonctionnement “Edition”. Les différentes méthodes d’édition d’un programme pièce sont: en langage CNC, en mode Apprentissage (“Teach-in”), avec l’éditeur interactif et l’éditeur de profils. Chapitre 5 Manuel (JOG) Description du mode de fonctionnement manuel (JOG). Il s’agit du mode d’exploitation à utiliser chaque fois que la machine doit être contrôlée manuellement, soit pour déplacer les axes de la machine, soit pour la commande de broche. Chapitre 6 Tables Description du mode de fonctionnement “Tables”. Il permet d’accéder aux différentes tables de données de la CNC: tables des origines, table des correcteurs d’outils, tables d’outils, tables de magasins d’outils et tables de paramètres globaux et locaux. Chapitre 7 Utilitaires Description du mode de fonctionnement “Utilitaires”. Il permet d’accéder au répertoire des programmes pièce, aux sous-programmes et au répertoire de programmes pièce du PC ou d’un périphérique relié à la CNC. Il est également possible de copier, supprimer, déplacer ou renommer les programmes pièce. Il indique les protections pouvant être affectées à un programme pièce. Il montre les différentes méthodes d’exploitation avec la mémoire EEPROM. Chapitre 8 DNC Description du mode de fonctionnement “DNC” Il indique comment travailler par l’intermédiaire des lignes série. Chapitre 9 PLC Description du mode de fonctionnement “PLC” (automate programmable). Il indique comment éditer et compiler le programme de l’automate programmable (PLC). Il permet de vérifier le mode de finctionnelent du PLC et l’état de l’ensemble de ses variables. Il indique la date de l’édition du programme de l’automate, la mémoire qu’il utilise, et les temps d’exécution (temps de cycle) de ses divers modules. Il présente une description détaillée de l’analyseur logique. Introduction - 7 Chapitre 10 Editeur graphique Description du mode de fonctionnement “Editeur Graphique”. Il indique comment créer des pages définies par l’utilisateur (pages d’écran) et des symboles utilisables pour créer ces pages. Il montre comment utiliser les pages utilisateur dans les programmes de personnalisation, comment afficher une page utilisateur à la mise sous tension et comment activer ces pages utilisateur à partir de l’automate. Chapitre 11 Paramètres machine Description du mode de fonctionnement “Paramètres machine”. Il permet d’accéder aux tables de : Paramètres machine, fonctions “M” auxiliaires, compensation d’erreur de vis et de compensation croisée, et de travailler avec ces tables. Chapitre 12 Diagnostic Description du mode de fonctionnement “Diagnostic”. Il permet de connaître la configuration de la CNC, et de réaliser un essai du système. Introduction - 8 1. GENERALITES Ce manuel explique comment exploiter la CNC FAGOR 8050 à l’aide de son ensemble Moniteur-Clavier et du pupitre Opérateur. L’ensemble Moniteur-Clavier est composé des éléments suivants: * Un Moniteur ou écran CRT, utilisé pour afficher les informations nécessaires au système. * Un Clavier, qui permet de communiquer avec la CNC et de demander des informations au moyen de commandes; il permet également de modifier l’état de la CNC grâce à l’émission de nouvelles instructions. Chapitre: 1 GENERALITES Section: Page 1 1.1 DISPOSITION DES INFORMATIONS SUR LE MONITEUR Le moniteur de la CNC est divisé en plusieurs zones ou fenêtres d’affichage comme indiqué ci-dessous: 1 MENU PRINCIPAL DNC P...... N...... 14 : 47 : 16 3 2 4 5 6 Mercredi 27 Mars 1991 14 : 40 : 39 CAP INS 7 EXECUTER F1 SIMULER F2 EDITER MANUEL F3 F4 TABLES F5 UTILITAIRES F6 + 8 9 F7 1.- Cette fenêtre indique le mode de fonctionnement sélectionné, le numéro du programme et le nombre de blocs actifs. Elle indique aussi l’état du programme (en cours ou interrompu) et si le DNC est actif. 2.- Cette fenêtre indique l’heure selon le format "heures : minutes : secondes". 3.- Cette fenêtre visualise les Messages envoyés à l’opérateur depuis le programme pièce ou par l’intermédiaire du DNC. Le dernier message reçu est affiché, quelle que soit sa provenance. 4.- Cette fenêtre affiche les messages émanant du PLC. Si le PLC active deux messages ou plus, la CNC affiche toujours le plus prioritaire, c’est-à-dire celui portant le numéro le plus faible. Par exemple, MSG1 est le plus prioritaire et MSG128 le moins prioritaire. Page 2 Chapitre: 1 GENERALITES Section: DISPOSITION DES INFORMATIONS SUR LE MONITEUR Dans ce cas, la CNC affiche le caractère + (signe plus), pour indiquer la présence d’autres messages activés par le PLC, qui peuvent être visualisés grâce à l’option MESSAGES ACTIFS du mode PLC. Dans cette même fenêtre, la CNC affiche le caractère * (astérisque), pour signaler qu’au moins une des 256 pages d’écran définies par l’utilisateur est active. Les pages d’écran actives peuvent être visualisées une par une grâce à l’option PAGES ACTIVES du mode PLC. 5.- Fenêtre principale. Selon le mode de fonctionnement, la CNC affiche dans cette fenêtre toutes les informations nécessaires. Si une erreur se produit dans la CNC ou le PLC, le système l’affiche dans une fenêtre horizontale superposée à la principale. La CNC visualise toujours l’erreur la plus grave et affiche: * La touche “flèche vers le bas” pour indiquer la présence d’une autre erreur moins grave, et que cette touche doit être frappée pour accéder à cette erreur. * La touche “flèche vers le haut” pour indiquer la présence d’une autre erreur plus grave, et que cette touche doit être frappée pour accéder à cette erreur. 6.- Fenêtre d’édition. Dans certains modes de fonctionnement, les quatre dernières lignes de la fenêtre principale sont utilisées comme zone d’édition. 7.- Fenêtre de communications de la CNC. (erreurs détectées en édition, programme inexistant, etc...) 8.- Cette fenêtre affiche les informations suivantes: SHF Indique la frappe de la touche SHIFT pour activer la seconde fonction des touches. Par exemple, si après la touche SHIFT l’opérateur frappe la touche la CNC comprendra que le caractère "$" est demandé. CAP Signale les lettres majuscules (touche CAPS). La CNC comprendra que des majuscules sont demandées chaque fois que CAP est actif. INS/REP Indique si le système est en mode insertion (INS) ou remplacement (REP). la sélection se fait par la touche INS. MM/INCH Indique le système d’unités (millimètres ou pouces) sélectionné pour la visualisation. 9.- Affiche les différentes options sélectionnables par les touches F1 à F7 (appelées touches de fonctions). Chapitre: 1 GENERALITES Section: DISPOSITION DES INFORMATIONS SUR LE MONITEUR Page 3 1.2 DISPOSITION DU CLAVIER En fonction de l’utilisation affectée aux différentes touches, on peut considérer que le clavier de la CNC se divise comme suit: 1 2 4 3 1.- Clavier alphanumérique pour introduction de données en mémoire, sélection des axes, compensation d’outils, etc... 2.- Touches pour déplacement des informations affichées à l’écran vers l’avant ou arrière, page par page ou ligne par ligne et pour déplacement du curseur sur l’écran. La touche CL permet d’effacer le caractère sur lequel se trouve le curseur ou le dernier caractère introduit si le curseur se situe à la fin de la ligne. La touche INS permet le choix entre les modes insertion et remplacement. Page 4 Chapitre: 1 GENERALITES Section: DISPOSITION DU CLAVIER 3.- Groupe de touches qui, compte tenu de leurs caractéristiques et de leur importance, sont détaillées ci-après: ENTER Valide les commandes de CNC et de PLC générées dans la fenêtre Edition. HELP Permet d’accéder à l’Aide dans tous les modes de fonctionnement. RESET Permet d’initialiser l’historique du programme en cours d’exécution en lui affectant les valeurs définies par paramètres machine. La CNC n’accepte cette touche que si le programme est stoppé. ESC Permet de repasser à l’option de fonctionnement précédente affichée sur le moniteur. MAIN MENU La frappe de cette touche donne un accès direct au menu principal de la CNC. 4.- SOFT KEYS, ou touches de fonction qui permettent le choix entre les différentes options affichées sur le moniteur: Les séquences de touches spéciales suivantes sont également disponibles: SHIFT RESET Cette séquence équivaut à une mise hors tension de la CNC suivie d’une remise sous tension. On utilisera cette option après toute modification des paramètres machine de la CNC pour les rendre effectifs. SHIFT CL Cette séquence entraîne la disparition de l’affichage de l’écran. Pour revenir à l’état normal de l’écran, il suffit de frapper n’importe quelle touche. Si, pendant que l’écran est éteint, une erreur se produit ou si le PLC ou la CNC envoie un message, l’écran repasse à son état normal. SHIFT Permet de visualiser, dans la partie droite de l’écran, la position des axes et l’état du programme en cours. Cette séquence peut être utilisée dans tout mode de fonctionnement. Pour repasser à l’affichage précédent, on frappera la même séquence de touches. Chapitre: 1 GENERALITES Section: DISPOSITION DU CLAVIER Page 5 1.3 DISPOSITION DU PUPITRE OPERATEUR En fonction de l’utilité des différentes parties, on peut considérer que le Pupitre Opérateur de la CNC se décompose comme suit: 1 2 3 4 5 1.- Emplacement du bouton-poussoir d’urgence ou de la manivelle électronique. 2.- Bloc de touches pour déplacement manuel des axes. 3.- Sélecteur exécutant les fonctions suivantes: Sélection du multiplicateur de nombre d’impulsions de la manivelle électronique (1, 10 ou 100). Sélection de la valeur de l’incrément appliqué au déplacement des axes en mode "MANUEL". Modification de l’avance programmée des axes, entre 0% et 120%. 4.- Bloc de touches de commande de broche, qui permet sa mise en rotation dans le sens désiré, son arrêt et la modification de la vitesse de rotation programmée entre les pourcentages fixés par les paramètres machine de la broche "MINSOVR" et "MAXOVR", selon un incrément défini par le paramètre machine de broche "SOVRSTEP". 5.- Touches MARCHE et ARRET du bloc ou du programme à exécuter. Page 6 Chapitre: 1 GENERALITES Section: DISPOSITION DU PUPITRE OPERATEUR 2. MODES DE FONCTIONNEMENT Dès la mise sous tension de la CNC ou la frappe des touches SHIFT-RESET, le logo FAGOR apparaît dans la fenêtre principale, ou la page d’écran définie précédemment en tant que page 0 grâce aux outils de PERSONNALISATION s’affiche. Si la CNC affiche Initialis? (ENTER / ESC) , ne pas oublier que la frappe de ENTER provoque l’effacement de toutes les informations en mémoire et que les paramètres machine sont initialisés avec les valeurs par défaut, qui figurent dans le manuel d’installation. La partie inférieure de l’écran affiche le menu principal de la CNC, et les différents modes de fonctionnement peuvent être sélectionnés au moyen des touches de fonction (F1 à F7). Lorsque le menu de la CNC comporte un nombre d’options supérieur au nombre de touches de fonction (7), le caractère + apparaît sur la touche F7. Si cette touche est actionnée, la CNC affiche le reste des options disponibles. Les options affichées par le menu principal de la CNC à la mise sous tension, après la frappe de SHIFT-RESET ou de la touche “MAIN MENU” sont les suivantes: EXECUTER Permet l’exécution de programmes pièce en mode automatique ou bloc à bloc. SIMULER Permet la simulation des programmes pièces dans différents modes. EDITER Permet l’édition de programmes pièce nouveaux ou existants. MANUEL Permet le contrôle manuel des déplacements de la machine au moyen des touches du Pupitre Opérateur. TABLES Permet la manipulation des tables de la CNC liées aux programmes pièce (Origines, Correcteurs, Outils, Magasin d’outils et paramètres globaux ou locaux). UTILITAIRES Permet la manipulation des programmes (copier, effacer, renommer, etc...). DNC Permet l’activation et la désactivation des communications avec un ordinateur par l’intermédiaire du DNC. PLC Permet le fonctionnement avec le PLC (éditer le programme, contrôler, modifier l’état de ses variables, accéder à la page de messages ou d’erreurs en cours, etc...). Chapitre: 2 MODES DE FONCTIONNEMENT Section: Page 1 PERSONNALISATION Permet, grâce à un simple éditeur graphique, la création de pages d’écran définies par l’utilisateur et qui peuvent ensuite être activées depuis le PLC, utilisées dans les programmes de personnalisation ou affichées à la mise sous tension (page 0). PARAMETRES MACHINE Permet de personnaliser les paramètres machine afin d’adapter la CNC à la machine. DIAGNOSTIC Réalise un test de la CNC. La CNC permet, pendant l’exécution ou la simulation d’un programme pièce, d’accéder à tout autre mode de fonctionnement sans stopper l’exécution du programme. Il est donc possible d’éditer un programme pendant l’exécution ou la simulation d’un autre programme. Il n’est pas possible d’éditer le programme en cours d’exécution ou de simulation, et deux programmes pièce ne peuvent pas être exécutés ni simulés en même temps. Page 2 Chapitre: 2 MODES DE FONCTIONNEMENT Section: 2.1 SYSTEMES D’AIDE La CNC FAGOR 8050 permet à tout moment (menu principal, mode de fonctionnement, édition de commandes, etc...) d’accéder au système d’aide. Pour accéder à l’aide, frapper la touche HELP : la fenêtre principale de l’écran affiche la page d’aide correspondante. Si l’aide comporte plus d’une page, le symbole permet de passer à la page suivante et le symbole permet d’accéder à la page précédente Les aides suivantes sont disponibles: * AIDE AU FONCTIONNEMENT L’accès à cette aide est possible depuis le menu des modes de fonctionnement ou, si un mode a été activé, avant de sélectionner l’une des options affichées. Dans tous les cas, les touches de fonction sont à fond bleu. L’Aide donne des informations sur le mode de fonctionnement ou l’option correspondante . Tant que ces informations sont visibles à l’écran, la CNC ne peut pas être commandée par les touches de fonction; la touche HELP doit être actionnée à nouveau pour repasser aux informations qui étaient affichées dans la fenêtre principale avant la demande d’aide et pour reprendre l’exploitation de la CNC. La frappe de la touche ESC ou MAIN MENU permet également de sortir de l’Aide. * AIDE A L’EDITION L’accès à cette aide est possible après sélection d’une des options d’édition (programme pièce, programme PLC, tables, paramètres machine, etc...). Dans tous les cas, les touches de fonction sont à fond blanc. Cette aide donne des informations sur l’option correspondante. Pendant l’affichage de ces informations, la CNC peut continuer à fonctionner. Si la touche HELP est frappée à nouveau, la CNC vérifie si la même page d’aide s’applique ou non à l’état en cours de l’édition. Si une autre page est nécessaire, la CNC l’affiche à la place de la précédente, sinon elle rappelle les informations affichées dans la fenêtre principale avant la demande d’aide. Pour sortir du menu Aide et revenir à l’option de fonctionnement précédente, frapper ESC; pour repasser au menu principal, frapper la touche MAIN MENU. Chapitre: 2 Section: MODES DE FONCTIONNEMENT SYSTEMES D’AIDE Page 3 * AIDE A L’EDITION DE CYCLES FIXES L’accès à cette aide est possible pendant l’édition d’un cycle fixe. Cette aide donne des informations sur le cycle fixe correspondant; à partir de cet instant, l’opérateur dispose d’une aide à l’édition pour le cycle fixe sélectionné. Une aide à l’édition similaire est possible pour les cycles propres à l’utilisateur grâce à un programme utilisateur, qui doit être mis au point au moyen d’instructions de personnalisation. Lorsque tous les champs ou paramètres du cycle fixe ont été définis, la CNC affiche les informations existantes dans la fenêtre principale avant la demande d’aide. Le cycle fixe programmé grâce à l’édition assistée s’affiche dans la fenêtre d’édition et l’opérateur peut modifier ou compléter ce bloc avant de le charger en mémoire par la frappe de la touche ENTER. Il est possible de sortir à tout moment de l’édition assistée en frappant la touche HELP. La CNC affiche les informations présentées dans la fenêtre principale avant la demande d’aide et permet de poursuivre la programmation du cycle fixe dans la fenêtre d’édition. Pour sortir du menu Aide et revenir à l’option de fonctionnement précédente, frapper ESC; pour repasser au menu principal, frapper la touche MAIN MENU. Page 4 Chapitre: 2 MODES DE FONCTIONNEMENT Section: SYSTEMES D’AIDE 3. EXECUTER / SIMULER Le mode de fonctionnement EXECUTER permet d’exécuter des programmes pièce en mode automatique ou bloc à bloc. Le mode de fonctionnement SIMULER permet de simuler des programmes pièce en mode automatique ou bloc à bloc. Lorsque l’un de ces deux modes est activé, la CNC affiche: * Le répertoire de programmes pièce de la CNC Le numéro du programme peut être introduit directement depuis le clavier ou sélectionné dans le répertoire de programmes pièce affiché grâce au curseur. Lorsque le programme à exécuter ou à simuler a été sélectionné, frapper la touche ENTER. * Les touches de fonction [LIGNE SERIE 1 (DNC)] et [LIGNE SERIE 2 (DNC)] si elles ont été validées par un paramètre machine. Si l’une de ces touches est frappée, la CNC affiche le répertoire de programmes de l’appareil correspondant, soit l’ordinateur soit le lecteur de disquettes FAGOR. Le numéro du programme doit être introduit directement depuis le clavier. Pour exécuter le programme plusieurs fois, frapper la touche de fonction [n¦ fois] et indiquer le nombre de répétitions. Après sélection du programme pièce à exécuter ou à simuler, frapper la touche ENTER. Dans les deux cas, la CNC affiche le programme sélectionné, dans lequel le curseur peut se déplacer. Si, après l’exécution ou la simulation du programme sélectionné (ou d’une partie), l’opérateur désire passer au mode “MANUEL”, la CNC conserve les conditions d’usinage (type de déplacement, avances, etc...) sélectionnées pendant l’exécution ou la simulation. Chapitre: 3 EXECUTER / SIMULER Section: Page 1 Si l’opérateur désire SIMULER un programme pièce, la CNC demande le type de simulation souhaité, et l’une des options suivantes doit être choisie par touche de fonction: COURSE THEORIQUE Cette option simule l’exécution du programme sélectionné, mais sans déplacement des axes de la machine (les consignes et les signaux de validation sont ignorés) et sans tenir compte de la compensation de rayon de l’outil; les fonctions auxiliaires M, S, T ne sont pas exécutées. FONCTIONS G Cette option simule l’exécution du programme sélectionné, sans déplacement des axes de la machine (les consignes et les signaux de validation sont ignorés), avec exécution des fonctions G programmées mais sans exécution des fonctions auxiliaires M, S, T. FONCTIONS G, M, S, T Cette option simule l’exécution du programme sélectionné, sans déplacement des axes de la machine (les consignes et les signaux de validation sont ignorés), avec exécution des fonctions G et des fonctions auxiliaires M, S, T programmées. PLAN PRINCIPAL Cette option exécute le programme pièce sélectionné en contrôlant uniquement les mouvements correspondant aux axes formant le plan principal; elle exécute également les fonctions G et les fonctions auxiliaires M, S, T programmées. Les déplacements des axes s’effectuent selon l’avance maximum autorisée F0, indépendamment de l’avance F programmée; l’avance peut être modifiée grâce au sélecteur FEEDRATE OVERRIDE (Correcteur des avances). RAPIDE Cette option exécute le programme pièce sélectionné en contrôlant tous les mouvements des axes programmés; elle exécute les fonctions G ainsi que les fonctions auxiliaires M, S, T programmées. Les déplacements des axes s’effectuent selon l’avance maximum autorisée F0, indépendamment de l’avance F programmée; l’avance peut être modifiée grâce au sélecteur FEEDRATE OVERRIDE (Correcteur des avances). Page 2 Chapitre: 3 EXECUTER / SIMULER Section: Après sélection du programme désiré dans le mode EXECUTION ou du programme pièce et du type de SIMULATION désirés, frapper la touche du Pupitre Opérateur pour que la CNC exécute ou simule ce programme. Toutefois, avant l’exécution ou la simulation du programme pièce, la CNC permet de sélectionner l’une des options suivantes: SELECTION BLOC Cette option permet de sélectionner le bloc dans lequel on souhaite commencer l’exécution ou la simulation du programme. CONDITION D’ARRET Cette option permet de sélectionner le bloc dans lequel on souhaite stopper l’exécution ou la simulation du programme. VISUALISER Cette option permet de sélectionner l’un des modes de visualisation disponibles. MDI Cette option permet d’éditer tout type de bloc (ISO ou haut niveau) en fournissant grâce aux touches de fonction les informations nécessaires sur le format correspondant. Après l’édition du bloc et la frappe de la touche sans quitter ce mode de fonctionnement. la CNC exécutera ce bloc INSPECTION OUTIL Cette option permet, après interruption de l’exécution du programme, d’inspecter l’outil et de le changer si nécessaire. GRAPHIQUES Cette option réalise une représentation graphique de la pièce pendant l’exécution ou la simulation du programme pièce sélectionné. Elle permet également de sélectionner le type de graphique, la zone à visualiser, le point de vue et les paramètres graphiques désirés dans ce mode. BLOC A BLOC Cette option permet d’exécuter ou de simuler le programme en bloc a bloc ou en continu. Chapitre: 3 EXECUTER / SIMULER Section: Page 3 3.1 SELECTION DU BLOC ET CONDITION D’ARRET L’exécution ou la simulation du programme pièce sélectionné commence à la première ligne du programme et se termine après l’exécution d’une des fonctions spécifiques de fin de programme M02 ou M30. Toutefois, la CNC permet, grâce à l’option "SELECTION BLOC" d’indiquer le bloc de début de l’exécution ou de la simulation du programme, tandis que l’option "CONDITION D’ARRET" indique le bloc de fin correspondant. SELECTION BLOC Cette option permet d’indiquer le bloc de début de l’exécution ou de la simulation du programme, et n’est pas utilisable pendant que la CNC exécute ou simule le programme pièce sélectionné. Quand cette option est activée, la CNC affiche le programme sélectionné car le bloc de début doit toujours appartenir au programme que l’on désire exécuter ou simuler. L’opérateur doit sélectionner avec le curseur le bloc de programme où l’exécution doit commencer. Pour ce faire, il déplace le curseur sur l’écran une ligne à la fois grâce aux touches "flèche vers le haut et flèche vers le bas", ou une page à la fois grâce aux touches "page vers le haut et page vers le bas". Par ailleurs, des touches permettent les fonctions de recherche suivantes: DEBUT La frappe de cette touche positionne le curseur sur la première ligne du programme. FIN La frappe de cette touche positionne le curseur sur la dernière ligne du programme. TEXTE Cette fonction permet de chercher un texte ou une série de caractères à partir du bloc pointé par le curseur. Quand cette touche est frappée, la CNC demande quelle est la série de caractères à rechercher. Après définition du texte, frapper la touche "FIN TEXTE": le curseur se positionnera sur la première série de caractères rencontrée. La recherche commence par le bloc pointé par le curseur et s’effectue y compris dans le bloc lui-même. Le texte rencontré apparaît en surbrillance; la recherhe peut continuer dans tout le programme ou être abandonnée. Pour continuer la recherche, frapper ENTER. La CNC exécute la recherche à partir du dernier texte rencontré et l’affiche en surbrillance. Page 4 Chapitre: 3 EXECUTER / SIMULER Section: SELECTION DU BLOC ET CONDITION D’ARRET Cette opération peut être répétée autant de fois que désiré. Lorsqu’elle atteint la fin du programme, la CNC reprend la recherche depuis le début. Pour quitter l’option de recherche, frapper la touche de fonction "ARRETER" ou la touche ESC. La CNC affichera le curseur sur la ligne où le texte recherché a été rencontré pour la dernière fois. NUMERO DE LIGNE Si cette touche est frappée, la CNC demande le numéro de la ligne ou du bloc recherchés. Après l’entrée de ce numéro et la frappe de ENTER, le curseur se positionne sur la ligne demandée. Quand le bloc de début a été défini, frapper ENTER pour le valider. CONDITION D’ARRET Cette option permet d’indiquer le bloc où s’chèvera l’exécution ou la simulation du programme; elle n’est pas utilisable pendant que la CNC exécute ou simule le programme pièce sélectionné. Quand cette option est activée, la CNC affiche les fonctions suivantes: SELECTION PROGRAMME Cette fonction est utilisée quand le bloc où doit se terminer l’exécution ou la simulation du programme pièce appartient à un sous-programme défini dans un autre programme. Quand cette option est sélectionnée, la CNC affiche le répertoire de programmes pièce; après sélection du programme désiré grâce au curseur, frapper ENTER. Lorsque ce programme a été sélectionné, la CNC repasse à l’affichage du programme à exécuter, et l’option SELECTION BLOC doit être activée pour que la CNC affiche le programme sélectionné. SELECTION BLOC Lorsque cette fonction est activée, la CNC affiche le programme sélectionné comme fin d’exécution ou de simulation. Par défaut, la CNC affiche le programme à exécuter ou à simuler, sauf si un autre programme a été sélectionné auparavant par l’option SELECTION PROGRAMME. L’opérateur devra sélectionner, au moyen du curseur, le bloc de programme où doit s’achever l’exécution ou la simulation du programme. Pour ce faire, il déplace le curseur sur l’écran une ligne à la fois grâce aux touches "flèche vers le haut et flèche vers le bas", ou une page à la fois grâce aux touches "page vers le haut et page vers le bas". Chapitre: 3 EXECUTER / SIMULER Section: SELECTION DU BLOC ET CONDITION D’ARRET Page 5 Par ailleurs, des touches permettent les fonctions de recherche suivantes: DEBUT La frappe de cette touche positionne le curseur sur la première ligne du programme. FIN La frappe de cette touche positionne le curseur sur la dernière ligne du programme. NUMERO DE LIGNE Si cette touche est frappée, la CNC demande le numéro de la ligne ou du bloc recherchés. Après l’entrée de ce numéro et la frappe de ENTER, le curseur se positionne sur la ligne demandée. Quand le bloc de fin d’exécution ou de simulation a été défini, frapper ENTER pour le valider. NOMBRE DE FOIS Cette fonction est utilisée pour indiquer que l’exécution ou la simulation du programe pièce doit s’achever après plusieurs exécutions du bloc de fin de programme. Lorsque cette fonction est activée, la CNC demande le nombre d’exécutions de ce bloc avant que l’exécution ou la simulation du programme stoppe. Si un cycle fixe ou un appel de sous-programme a été choisi comme bloc de fin de programme, ne pas oublier que la CNC considère le bloc comme terminé lorsque l’ensemble du programme ou du sous-programme a été exécuté. Lorsque le bloc sélectionné comporte un nombre de répétitions, la CNC considère que le bloc est terminé lorsque toutes les répétitions indiquées ont été exécutées. Page 6 Chapitre: 3 EXECUTER / SIMULER Section: SELECTION DU BLOC ET CONDITION D’ARRET 3.2 VISUALISER Cette option, qui peut être activée à tout moment, y compris pendant l’exécution ou la simulation du programme pièce, permet de sélectionner le mode de visualisation le mieux adapté à chaque situation. Les modes de visualisation disponibles par touches de fonction sont les suivants: Mode Visualisation STANDARD Mode Visualisation de POSITION Visualisation du PROGRAMME pièce Mode Visualisation de SOUS-ROUTINES Mode Visualisation de l’ERREUR DE POURSUITE Mode Visualisation UTILISATEUR Mode Visualisation des TEMPS D’EXECUTION Tous ces modes de visualisation disposent d’une fenêtre d’informations au bas de l’écran pour afficher les conditions de l’usinage. Ces informations sont les suivantes: F et % Vitesse d’avance programmée (F) et CORRECTION ou pourcentage (%) d’avance sélectionné. S et % Vitesse de broche programmée et pourcentage de correction (OVERRIDE %) de vitesse de broche sélectionné. T Numéro de l’outil actif. D Numéro du correcteur d’outil actif. NT Numéro de l’outil suivant. Ce champ s’affiche dans le cas d’un centre d’usinage et visualise l’outil sélectionné, mais en attente d’exécution de M06 pour être actif. ND Numéro du correcteur correspondant à l’outil suivant. Ce champ s’affiche dans le cas d’un centre d’usinage et visualise l’outil sélectionné, mais en attente d’exécution de M06 pour être actif. S RPM Vitese de rotation réelle de broche, en tours/minute. En cas de travail en M19, ce champ indique la position de la broche en degrés. G Ce champ affiche toutes les fonctions G visualisables actuellement actives. M Ce champ affiche toutes les fonctions auxiliaires M actuellement sélectionnées. Chapitre: 3 Section: EXECUTER / SIMULER VISUALISER Page 7 PARTC Compteur de pièces. Indique le nombre de pièces consécutives exécutées avec un programme donné. A chaque sélection d’un nouveau programme, cette variable prend la valeur 0. La CNC dispose de la variable “PARTC”, qui permet de lire ou de modifier ce compteur depuis le programme du PLC, de programme CNC ou par le DNC. CYTIME Indique le temps écoulé pendant l’exécution de la pièce, dans le format "heures : minutes : secondes : centièmes". A chaque début d’exécution d’un programme, même répétitif, cette variable prend la valeur 0. TIMER Indique l’heure affichée par l’horloge activée par le PLC, selon le format "heures : minutes : secondes". Page 8 Chapitre: 3 EXECUTER / SIMULER Section: VISUALISER 3.2.1 MODE VISUALISATION STANDARD Ce mode est le mode par défaut de la CNC à la mise sous tension et à chaque frappe de SHIFT-RESET. Il affiche les champs ou fenêtres suivants: EXECUTION P000662 N..... 11 : 50 : 14 G54 G0 G17 G90 X0 Y0 Z10 T2 D2 (TOR3=2,TOR4=1) G72 S0.2 G72 Z1 M6 G66 D100 R200 F300 S400 E500 M30 ; N100 G81 G98 Z5 I-1 F400 ACTUEL COMMANDE RESTE X 00172.871 X 00172.871 X 00000.000 Y 00153.133 Y 00153.133 Y 00000.000 Z 00004.269 Z 00004.269 Z 00000.000 U 00071.029 U 00071.029 U 00000.000 V 00011.755 V 00011.755 V 00000.000 F00000.0000 %120 S00000.0000 %100 T0000 D000 NT0000 ND000 S 0000 RPM G00 G17 G54 PARTC=000000 CYTIME=00:00:00:00 TIMER=000000:00:00 CAP INS SELECTION BLOC F1 CONDITION D'ARRET VISUALISER F2 F3 MDI F4 INSPECTION OUTIL F5 GRAPHIQUES F6 BLOC A BLOC F7 * Un groupe de blocs de programme, le premier étant le bloc en cours d’exécution. * Les cotes correspondant aux axes de la machine. Le format de visualisation de chaque axe est indiqué par le paramètre machine "DFORMAT", et les valeurs affichées seront les valeurs réelles ou théoriques de chaque axe, selon le réglage du paramètre machine général "THEODPLY". Chaque axe dispose des champs suivants: Ce champ indique la cote programmée, c’est-à-dire la position COMMANDE que doit atteindre l’axe. ACTUEL Ce champ indique la cote ou la position réelle de l’axe. RESTE Ce champ indique la distance que l’axe doit encore parcourir pour atteindre la cote programmée. Chapitre: 3 Section: EXECUTER / SIMULER VISUALISER Page 9 3.2.2 MODE VISUALISATION DE POSITION Ce mode de visualisation affiche les cotes de position des axes de la machine. Il affiche les champs ou fenêtres suivants: EXECUTION P000662 N..... 11 : 50 : 14 ZERO PIECE X Y Z U V ZERO MACHINE 00100.000 00150.000 00004.269 00071.029 00011.755 X 00172.871 Y 00153.133 Z 00004.269 U 00071.029 V 00011.755 F00000.0000 %120 S00000.0000 %100 T0000 D000 NT0000 ND000 S 0000 RPM G00 G17 G54 PARTC=000000 CYTIME=00:00:00:00 TIMER=000000:00:00 CAP INS SELECTION BLOC F1 * CONDITION D'ARRET F2 VISUALISER F3 MDI F4 INSPECTION OUTIL F5 GRAPHIQUES F6 BLOC A BLOC F7 Les cotes réelles des axes, qui indiquent la position actuelle de la machine. Le format de visualisation de chaque axe est indiqué par le paramètre machine "DFORMAT", et les valeurs affichées seront les valeurs réelles ou théoriques de chaque axe, selon le réglage du paramètre machine général "THEODPLY". Chaque axe dispose des champs suivants: ZERO PIECE Ce champ indique la cote réelle de l’axe par rapport au zéro pièce sélectionné. ZERO MACHINE Ce champ indique la cote réelle de l’axe par rapport au zéro machine. 3.2.3 VISUALISATION DU PROGRAMME PIECE Ce mode affiche une page de blocs du programme, le bloc en cours d’exécution étant en surbrillance. Page 10 Chapitre: 3 EXECUTER / SIMULER Section: VISUALISER 3.2.4 MODE VISUALISATION DE SOUS-ROUTINES Ce mode donne des informations sur les commandes suivantes: (RPT N10,N20) Cette fonction exécute la partie du programme comprise entre les blocs N10 et N20, ces 2 blocs compris. (CALL 25) Cette fonction exécute le sous-programme 25. G87 ... Cette fonction exécute le cycle fixe correspondant. (PCALL 30) Cette fonction exécute le sous-programme 30 à un niveau de paramètres locaux. Si ce mode est activé, on tiendra compte des points suivants: La CNC FAGOR 8050 permet de définir et d’utiliser des sous-programmes pouvant être appelés depuis un programme principal ou un autre sous-programme, qui peut à son tour en appeler un second, qui en appelle un troisième, etc... La CNC limite le nombre de niveaux d’imbrication à 15. La CNC génère un nouveau niveau d’imbrication de paramètres locaux chaque fois que des paramètres sont affectés à un sous-programme. Le nombre de niveaux d’imbrication de paramètres locaux est limité à 6. Les cycles fixes d’usinage G66, G68, G69, G81, G82, G83, G84, G85, G86, G87, G88 et G89 utilisent le sixième niveau d’imbrication de paramètres locaux quand ils sont actifs. Chapitre: 3 Section: EXECUTER / SIMULER VISUALISER Page 11 Ce mode affiche les champs ou fenêtres suivants: EXECUTION P000662 NS NP SOUSROUT. REPET M PROG 07 06 05 04 03 02 01 06 05 04 03 02 01 00 PCALL PCALL PCALL PCALL PCALL PCALL CALL 0006 0005 0004 0003 0002 0001 0101 0001 0001 0001 0001 0001 0001 0001 N..... 11 : 50 : 14 NS NP SOUSROUT. REPET M PROG 000002 000002 000002 000002 000002 000002 000002 ACTUEL COMMANDE RESTE X 00172.871 X 00172.871 X 00000.000 Y 00153.133 Y 00153.133 Y 00000.000 Z 00004.269 Z 00004.269 Z 00000.000 U 00071.029 U 00071.029 U 00000.000 V 00011.755 V 00011.755 V 00000.000 F00000.0000 %120 S00000.0000 %100 T0000 D000 NT0000 ND000 S 0000 RPM G00 G17 G54 PARTC=000000 CYTIME=00:00:00:00 TIMER=000000:00:00 CAP INS SELECTION BLOC F1 * CONDITION D'ARRET F2 VISUALISER F3 MDI F4 INSPECTION OUTIL F5 GRAPHIQUES F6 BLOC A BLOC F7 Une zone de visualisation, qui affiche les informations suivantes au sujet des sousprogrammes actifs. NS Indique le niveau d’imbrication (1-15) occupé par le sousprogramme. NP Indique le niveau de paramètres locaux (1-6) dans lequel le sousprogramme est en cours d’exécution. SOUSROUTINE Indique le type de bloc ayant provoqué un nouveau niveau d’imbrication. Exemples: (RPT N10,N20) (CALL 25) (PCALL 30) G87 REPT Indique le nombre d’exécutions de commandes restant. Par exemple si (RPT N10, N20) N4 a été programmé, et s’il s’agit de la première exécution, ce paramètre affichera la valeur 4. Page 12 M Un astérisque (*) signale qu’un sous-programme modal est actif à ce niveau d’imbrication et qu’il est exécuté après chaque déplacement. PROG Indique le numéro du programme dans lequel est défini le sousprogramme. Chapitre: 3 EXECUTER / SIMULER Section: VISUALISER * Les cotes correspondant aux axes de la machine. Le format de visualisation de chaque axe est indiqué par le paramètre machine "DFORMAT", et les valeurs affichées seront les valeurs réelles ou théoriques de chaque axe, selon le réglage du paramètre machine général "THEODPLY". Chaque axe dispose des champs suivants: Ce champ indique la cote programmée, c’est-à-dire la position COMMANDE que doit atteindre l’axe. ACTUEL Ce champ indique la cote ou la position réelle de l’axe. RESTE Ce champ indique la distance que l’axe doit encore parcourir pour atteindre la cote programmée. Chapitre: 3 Section: EXECUTER / SIMULER VISUALISER Page 13 3.2.5 MODE VISUALISATION DE L’ERREUR DE POURSUITE Ce mode affiche l’erreur de poursuite (différence entre les valeurs de position théorique et réelle) de chaque axe et de la broche. En outre, lorsque l’option recopie est disponible, ce mode affiche les valeurs correspondant au palpeur de recopie dans un cadre situé dans la partie droite de l’écran. EXECUTION P000662 N..... 11 : 50 : 14 ERREUR DE POURSUITE DEVIATIONS FACTEURS F03000.0000 %100 S00000.0000 %100 T0000 D000 NT0000 ND000 S 0000 RPM G00 G17 G54 PARTC=000000 CYTIME=00:00:00:00 TIMER=000000:00:00 DEPLACEMENT MANUEL EN CONTINU SELECTION BLOC F1 CONDITION D'ARRET F2 VISUALISER F3 MDI F4 CAP INS INSPECTION OUTIL F5 GRAPHIQUES F6 BLOC A BLOC F7 Le format de visualisation de chaque axe est indiqué par le paramètre machine d’axes "DFORMAT". Les facteurs de correction du palpeur sont indépendants des unités de travail. Le format de visualisation des déviations du palpeur sur chaque axe (X, Y, Z) et de la déviation totale D est indiqué par le paramètre machine d’axes "DFORMAT". 3.2.6 MODE VISUALISATION UTILISATEUR Si cette option est activée, la CNC exécutera dans le canal utilisateur le programme sélectionné par le paramètre machine général "USERDPLY". Pour sortir de ce mode et repasser au menu précédent, frapper ESC. Page 14 Chapitre: 3 EXECUTER / SIMULER Section: VISUALISER 3.2.7 MODE VISUALISATION DES TEMPS D’EXECUTION Ce mode de visualisation est disponible pendant la simulation du programme et affiche les champs ou fenêtres suivants: EXECUTION OUTL T.POSIT P000662 T.USINA N..... OUTL T.POSIT TEMPS TOTAL 00:00:00 11 : 50 : 14 T.USINA OUTL T.POSIT FONCTIONS M 0038 CHANG. D'OUTIL 0 ACTUEL COMMANDE T.USINA RESTE X 00172.871 X 00172.871 X 00000.000 Y 00153.133 Y 00153.133 Y 00000.000 Z 00004.269 Z 00004.269 Z 00000.000 U 00071.029 U 00071.029 U 00000.000 V 00011.755 V 00011.755 V 00000.000 F00000.0000 %120 S00000.0000 %100 T0000 D000 NT0000 ND000 S 0000 RPM G00 G17 G54 PARTC=000000 CYTIME=00:00:00:00 TIMER=000000:00:00 CAP INS SELECTION BLOC F1 * CONDITION D'ARRET VISUALISER F2 F3 MDI F4 INSPECTION OUTIL F5 GRAPHIQUES F6 BLOC A BLOC F7 Une zone d’affichage, qui présente une estimation du temps nécessaire pour exécuter le programme à 100% de l’avance programmée. Cette zone présente les informations suivantes: Le temps mis par chaque outil (OUTL) pour exécuter les déplacements de positionnement (T.POSIT) et d’usinage (T.USINA) indiqués dans le programme. Le “TEMPS TOTAL” nécessaire pour exécuter le programme indiqué. Le nombre de “FONCTIONS M” exécutées sur l’ensemble du programme. Le nombre de “CHANGEMENTS D’OUTIL” effectués pendant l’exécution du programme. * Les cotes correspondant aux axes de la machine. Le format de visualisation de chaque axe est indiqué par le paramètre machine "DFORMAT", et les valeurs affichées seront les valeurs réelles ou théoriques de chaque axe, selon le réglage du paramètre machine général "THEODPLY". Chapitre: 3 Section: EXECUTER / SIMULER VISUALISER Page 15 Chaque axe dispose des champs suivants: Ce champ indique la cote programmée, c’est-à-dire la position COMMANDE que doit atteindre l’axe. ACTUEL Ce champ indique la cote ou la position réelle de l’axe. RESTE Ce champ indique la distance que l’axe doit encore parcourir pour atteindre la cote programmée. Page 16 Chapitre: 3 EXECUTER / SIMULER Section: VISUALISER 3.3 MDI Cette fonction n’est pas accessible dans le mode “Simulation de programmes”. En outre, si un programme est en cours d’exécution, elle n’est accessible qu’après interruption de l’exécution. Elle permet d’éditer tout type de bloc (ISO ou haut niveau) et donne, grâce aux touches de fonctions, les informations nécessaires sur le format correspondant. Après édition du bloc et frappe de la touche quitter ce mode de fonctionnement. la CNC exécutera ce bloc sans Chapitre: 3 Section: EXECUTER / SIMULER MDI Page 17 3.4 INSPECTION DES OUTILS Cette fonction n’est pas accessible dans le mode “Simulation de programmes”. En outre, si un programme est en cours d’exécution, elle n’est accessible qu’après interruption de l’exécution. Quand cette fonction est activée, il est possible de contrôler manuellement tous les déplacements la machine grâce aux touches de contrôle des axes du Pupitre Opérateur (X+, X-, Z+, Z-, 3+, 3-, 4+, 4-). En outre, la CNC affiche les touches de fonction permettant d’accéder aux tables de la CNC, de générer et d’exécuter des commandes en mode MDI et de positionner les axes de la machine au point d’appel de cette fonction. L’une des méthodes de changement d’outil est la suivante: * Déplacement de l’outil au point où s’effectuera le changement. Ce déplacement peut être manuel par les touches de commande des axes du Pupitre Opérateur ou par la génération et l’exécution de commandes en mode MDI. * Accès aux tables de la CNC (outils, correcteurs, etc...) afin de trouver l’outil similaire à celui à remplacer. * Sélection, en MDI, du nouvel outil en tant qu’outil actif. * Changement de l’outil. L’exécution de cette opération dépend du type de changeur d’outil utilisé. Pendant cette phase, il est possible de générer et d’exécuter des commandes en MDI. * Retour au point de début d’inspection de l’outil au moyen de l’option REPOSITIONNEMENT. * Poursuite de l’exécution du programme ( ) Les options disponibles par touches de fonction sont les suivantes: MDI Cette option permet d’éditer des blocs en code ISO ou de haut niveau (sauf ceux associés aux sous-programmes) en donnant par touches de fonction les informations nécessaires sur le format correspondant. Après édition du bloc et frappe de la touche sans quitter ce mode de fonctionnement. Page 18 Chapitre: 3 EXECUTER / SIMULER la CNC exécutera ce bloc Section: INSPECTION DES OUTILS TABLES Cette option permet d’accéder à toute table de la CNC (Origines, Correcteurs, Outils, Magasin d’outils et Paramètres). Dès sélection de la table désirée, toutes les commandes d’édition sont disponibles pour permettre son analyse ou sa modification. Pour repasser au menu précédent (Inspection des outils), frapper ESC. REPOSITIONNEMENT Si cette option est activée, la CNC repositionne les axes de la machine au point de début d’inspection des outils. Dès que cette option est activée, la CNC affiche les axes à repositionner et demande dans quel ordre ils doivent être déplacés. Pour les déplacements dans le plan principal, la touche de fonction "PLAN" s’affiche, tandis qu’une autre touche s’affiche pour chacun des autres axes de la machine à déplacer. L’ordre suivi par la CNC pour le repositionnement des axes est celui indiqué lors de la sélection des axes à déplacer. Après sélection de tous les axes, frapper la touche exécuter leur repositionnement. afin que la CNC puisse Chapitre: 3 Section: EXECUTER / SIMULER INSPECTION DES OUTILS Page 19 3.5 GRAPHIQUES Cette fonction permet de sélectionner le type de graphique désiré et de définir tous les paramètres de représentation graphique correspondants. Pour pouvoir activer cette fonction, aucun programme pièce ne doit être en cours d’exécution ou de simulation; dans le cas contraire, l’exécution ou la simulation doit être interrompue. Après sélection du type de graphique et définition des paramètres nécessaires, cette fonction est accessible y compris pendant l’exécution ou la simulation du programme. Dans ce cas, la CNC affiche la représentation graphique correspondant à la pièce en cours d’exécution ou de simulation. L’exécution du programme doit être interrompue pour changer de type de graphique ou modifier un paramètre graphique. Dès que cette fonction est activée, la CNC affiche les options suivantes disponibles par touches de fonction: * * * * * * * Type de graphique Zone à visualiser Zoom Point de vue. Paramètres graphiques Effacer écran Désactiver graphiques L’une des méthodes de définition des graphiques est la suivante: 1.- Définir la ZONE A VISUALISER. Elle dépend des dimensions de la pièce et ses cotes sont prises par rapport au zéro pièce en cours à ce moment. 2.- Sélectionner le TYPE DE GRAPHIQUE désiré. 3.- Définir le POINT DE VUE désiré. Cette option est disponible dans les types de graphiques en 3D et SOLIDE. 4.- Sélectionner les couleurs désirées au moyen de l’option PARAMETRES GRAPHIQUES. Après le démarrage de l’exécution ou de la simulation de la pièce, il est possible de l’interrompre et de définir un autre TYPE DE GRAPHIQUE ou de sélectionner une autre zone de représentation graphique grâce à l’option ZOOM. Page 20 Chapitre: 3 EXECUTER / SIMULER Section: GRAPHIQUES 3.5.1 TYPE DE GRAPHIQUE La CNC FAGOR 8050M offre deux types de graphiques: des graphiques à lignes et des graphiques à solides. Ces deux types sont totalement indépendants: une exécution ou simulation dans l’un de ces types n’affecte pas l’autre. La CNC affiche toutes les options disponibles par touches de fonction; une option doit être sélectionnée. Le type de graphique sélectionné reste actif jusqu’à la sélection d’un autre type, la désactivation des graphiques (par l’option "DESACTIVER") ou la mise hors tension de la CNC. Chaque fois qu’un type de graphique est sélectionné, toutes les conditions sélectionnées avec le dernier type de graphique utilisé (zoom, paramètres graphiques et zone à visualiser) sont rétablies. Ces conditions sont sauvegardées, même en cas de mise hors/ sous tension de la CNC. Le type de graphique choisi affichera les informations suivantes dans la partie droite de l’écran: EXECUTION P000662 N..... 11 : 50 : 14 X Y Z 00172.871 00153.133 00004.269 F S T D 03000.000 0000.000 0000 000 Z X Y CAP INS TYPE DE GRAPHIQUE F1 ZONE A VISUALISER ZOOM F2 F3 POINT DE VUE F4 PARAMETRES GRAPHIQUES F5 EFFACER ECRAN F6 DESACTIVER GRAPHIQUES F7 Chapitre: 3 Section: EXECUTER / SIMULER GRAPHIQUES Page 21 * Les cotes réelles des axes, qui indiquent la position en cours de la machine. Les cotes correspondant à l’outil indiqueront la position de la pointe de l’outil. * La vitesse d’avance des axes (F) et la vitesse de broche (S) sélectionnées. * L’outil (T) et le correcteur (D) actifs. * Le point de vue utilisé dans la représentation graphique. Il est défini par les axes X, Y, Z et peut être modifié grâce à l’option "POINT DE VUE". * Deux cubes ou deux rectangles selon le type de point de vue utilisé. Le cube dont les faces sont colorées indique la zone sélectionnée pour la représentation graphique, et le cube représenté uniquement pas ses arêtes montre la taille de la zone choisie comme zone de visualisation. Lorsque le point de vue utilisé affiche une seule surface du cube ou quand le type de graphique sélectionné correspond à l’un des plans XY, XZ ou YZ, la CNC affiche deux rectangles pour signaler la zone de représentation graphique (rectangle coloré) et la zone de visualisation (rectangle non coloré). Page 22 Chapitre: 3 EXECUTER / SIMULER Section: GRAPHIQUES La CNC FAGOR 8050M représentera tous les usinages réalisés avec l’outil selon les axes X, Y, Z, sauf lorsque l’outil se trouve en Z et que l’usinage est exécuté sur la face négative de la pièce (sens de "-Z" à "+Z"). L -L -L L L Z X Y Lors de la simulation d’un programme pièce, la CNC analyse la valeur affectée à la longueur de l’outil "L" dans le correcteur correspondant. Si cette valeur est positive, la représentation graphique s’effectue par la face positive de la pièce (sens "+" à "-"); si la valeur est négative l’usinage est exécuté par la face négative de la pièce (sens "-" à "+"). Ne pas oublier que la CNC interprète "L0" comme une valeur positive. Par ailleurs, si aucun outil n’est sélectionné pendant la simulation du programme pièce, la CNC prend par défaut les valeurs L0 et R0. Chapitre: 3 Section: EXECUTER / SIMULER GRAPHIQUES Page 23 GRAPHIQUES A LIGNES Ce type de graphique réalise une représentation graphique dans le(s) plan(s) sélectionné(s) (XY, XZ, YZ) et décrit le mouvement de l’outil au moyen de lignes de couleur. Les types de graphiques à lignes disponibles sont les suivants: 3D Cette option réalise une représentation tridimensionnelle de la pièce. XY, XZ, YZ Ces options réalisent une représentation graphique dans le plan sélectionné. CONJOINT Cette option divise l’écran en quatre quadrants et exécute la représentation graphique correspondant à chaque plan XY, XZ, YZ, ainsi que la représentation tridimensionnelle (3D). Le graphique généré après l’exécution ou la simulation d’un programme est perdu dans les cas suivants: * En cas d’effacement de l’écran (touche EFFACER ECRAN). * En cas de désactivation des graphiques (touche DESACTIVER GRAPHIQUES). * En cas de sélection d’un autre type de graphique (3D, XY, XZ, YZ, Conjoint, Plan ou Solide). Ne pas oublier qu’en cas d’exécution d’un ZOOM, de changement de point de vue ou d’exécution/simulation d’un programme différent du programme actuel, le nouveau graphique est dessiné sur le graphique existant. Il est toutefois possible d’effacer l’écran grâce à la touche EFFACER ECRAN. GRAPHIQUES SOLIDES Ce type de graphique présente les mêmes informations de deux manières différentes: comme un solide tridimensionnel (SOLIDE) o une vue en plan (PLAN). Si une exécution ou une simulation est effectuée dans l’un de ces modes, le graphique peut être représenté dans les deux modes. Normalement, une simulation en mode PLAN est plus rapide qu’en mode SOLIDE. Il est donc recommandé d’exécuter le programme en mode PLAN et d’examiner le graphique en mode SOLIDE. Le résultat est identique. Page 24 Chapitre: 3 EXECUTER / SIMULER Section: GRAPHIQUES PLAN Cette option permet d’afficher une vue en plan (plan XY) avec différents niveaux de gris qui indiquent la profondeur de la pièce. Les sections XZ et YZ correspondant aux zones signalées par les lignes-repère dans la vue en plan (plan XY) sont également visualisées. Pour permettre la sélection d’autres sections de la pièce, les touches "flèche vers le haut, flèche vers le bas, flèche à droite et flèche à gauche" de la CNC autorisent le déplacement de ces lignes qui, dans la vue en plan (plan XY), indiquent les emplacements où s’effectue le sectionnement. Les lignes peuvent être déplacées à tout moment, y compris pendant l’exécutionou la simulation d’un programme pièce. La CNC réalise un affichage dynamique de la nouvelle section sélectionnée. Dès la fin ou l’interruption de l’exécution ou de la simulation, la vue en plan est redessinnée afin d’optimiser les niveaux de couleur et de donner une meilleure sensation de profondeur. Ce type de représentation ne montre pas les usinages réalisés au moyen d’un outil positionné en X ou en Y, mais ceux exécutés avec un outil positionné en Z. Si le type SOLIDE est sélectionné ensuite, tous les usinages réalisés sont visualisés. SOLIDE Cette option affiche un bloc tridimensionnel, et la pièce otenue par exécution ou simulation du programme est visualisée. Si aucun outil n’est sélectionné pendant l’exécution ou la simulation d’un programme, la CNC suppose qu’un correcteur de valeur R0 et L0 a été sélectionné. En conséquence, elle n’affiche que la trajectoire programmée et la pièce n’est pas usinée puisque l’outil est supposé à rayon “0”. Dans ce mode, le rafraîchissement de l’écran s’effectue périodiquement, en fonction de la vitesse de simulation choisie et de gauche à droite indépendamment du sens de déplacement de l’outil. Ne pas oublier qu’en cas d’exécution ou de simulation d’un programme différent du programme actuel, le nouvel usinage est exécuté sur le solide existant. Il est toutefois possible d’effacer l’écran grâce à la touche EFFACER ECRAN. Chapitre: 3 Section: EXECUTER / SIMULER GRAPHIQUES Page 25 Le graphique produit après exécution ou simulation en modes PLAN ou SOLIDE est perdu (retour à son état d’origine sans usinage) dans les cas suivants: * En cas d’effacement de l’écran (touche de fonction EFFACER ECRAN). * En cas de désactivation des graphiques (touche de fonction DESACTIVER GRAPHIQUES). * En cas de redéfinition de la pièce (touche de fonction ZONE A VISUALISER). * En cas de redéfinition de la nouvelle zone de visualisation par exécution d’une fonction. Toutefois, si aucune des opérations ci-dessus n’a lieu, la représentation graphique de la pièce est conservée. Par exemple, si un programme est exécuté en mode solide et si un autre programme est exécuté ensuite en mode graphique à lignes, le graphique solide mémorisé est conservé et l’exécution en mode graphique à lignes est ignorée. Page 26 Chapitre: 3 EXECUTER / SIMULER Section: GRAPHIQUES 3.5.2 ZONE A VISUALISER Cette fonction n’est utilisable que si aucun programme n’est en cours d’exécution ou de simulation par la CNC. Dans le cas contraire, l’exécution doit être interrompue. Deux cubes ou deux rectangles apparaissent dans l’angle inférieur droit de l’écran, selon le point de vue utilisé. Le cube dont les faces sont colorées indique la zone sélectionnée pour la représentation graphique, tandis que le cube représenté uniquement par ses arêtes indique la taille de la zone choisie comme zone de visualisation. Quand le point de vue utilisé montre une seule face du cube ou quand le type de graphique sélectionné correspond à l’un des plans XY, XZ ou YZ, la CNC représente deux rectangles pour indiquer la zone de représentation graphique (rectangle coloré) et la zone de visualisation (rectangle non coloré). Cette option permet de modifier la zone de visualisation, qui doit être définie au moyen des coordonnées maximum et minimum de chaque axe, par rapport au zéro pièce. Pour permettre la définition après sélection de cette option, la CNC affiche dans la partie droite de l’écran une serie de fenêtres où doivent figurer les cotes affectées actuelles. Pour modifier une valeur, sélectionner la fenêtre concernée grâce aux touches "flèche vers le haut et flèche vers le bas", et introduire la valeur désirée depuis le clavier. Quand toutes les cotes de la zone de visualisation ont été définies, frapper ENTER pour les valider. Pour quitter cette fonction sans modifier les valeurs précédentes, frapper ESC. Lorsque le graphique en PLAN ou SOLIDE est sélectionné, ne pas oublier que, si une nouvelle zone de visualisation est définie, la CNC démarre la représentation graphique et la ramène à son état initial “non usiné”. Chapitre: 3 Section: EXECUTER / SIMULER GRAPHIQUES Page 27 3.5.3 ZOOM Cette fonction n’est utilisable que si aucun programme n’est en cours d’exécution ou de simulation par la CNC. Dans le cas contraire, l’exécution doit être interrompue. Cette fonction n’est pas utilisable avec les types de graphique CONJOINT et PLAN. Deux cubes ou deux rectangles apparaissent dans l’angle inférieur droit de l’écran, selon le point de vue utilisé. Le cube dont les faces sont colorées indique la zone sélectionnée pour la représentation graphique, tandis que le cube représenté uniquement par ses arêtes indique la taille de la zone choisie comme zone de visualisation. Quand le point de vue utilisé montre une seule face du cube ou quand le type de graphique sélectionné correspond à l’un des plans XY, XZ ou YZ, la CNC représente deux rectangles pour indiquer la zone de représentation graphique (rectangle coloré) et la zone de visualisation (rectangle non coloré). Cette fonction permet d’agrandir ou de réduire la zone de représentation graphique. Si cette option est activée, la CNC affiche une fenêtre qui se superpose sur le graphique représenté, et une autre sur le dessin figurant dans l’angle inférieur droit de l’écran. Ces fenêtres indiquent la nouvelle zone d’affichage sélectionnée. Les touches "+" et "-" permettent d’agrandir ou de réduire la taille de ces fenêtres et les touches "flèche vers le haut, vers le bas, vers la droite et vers la gauche" permettent de déplacer le cadre de zoom vers l’emplacement désiré. Pour repasser à la valeur permettant de visualiser la totalité de la zone d’affichage (sélectionnée par la touche "ZONE A VISUALISER")” pendant la sélection de la nouvelle zone d’affichage, frapper la touche "VALEUR INITIALE". La CNC affiche cette valeur sans quitter la fonction ZOOM. Pour quitter cette fonction sans changer les valeurs initiales, frapper ESC. Quand la nouvelle zone d’affichage a été définie, frapper ENTER pour valider les changements. Le moniteur conserve l’affichage graphique actuel. Si la touche est frappée, la CNC commence ou continue l’exécution du programme sélectionné; selon le type de graphique sélectionné à ce moment, la CNC réagit comme suit: Page 28 Chapitre: 3 EXECUTER / SIMULER Section: GRAPHIQUES SOLIDE La CNC réinitialise la représentation graphique en affichant un bloc tridimensionnel “non usiné”. Le dessin visible dans l’angle inférieur droit de l’écran apparaît changé et le cube dont les faces sont colorées représente la nouvelle zone graphique sélectionnée. La nouvelle zone sélectionnée reste active jusqu’à la définition d’un autre ZOOM SOLIDE ou à la redéfinition de la ZONE A VISUALISER. 3D Le dessin visible dans l’angle inférieur droit de l’écran a changé, avec une fenêtre rectangulaire superposée. Cette fenêtre indique la nouvelle zone graphique sélectionnée pour ce type de graphique et reste active tant que le point de vue de la pièce n’est pas modifié. Les types CONJOINT, PLAN ou SOLIDE peuvent être sélectionnés sans modifier la zone graphique définie puisqu’ils utilisent tous le même point de vue. La zone graphique sélectionnée est désactivée dans les cas suivants: * * * * Lorsqu’un des types XY, XZ ou YZ est sélectionné. Lorsqu’un nouveau POINT DE VUE de la pièce est sélectionné. Lorsqu’un nouveau ZOOM est exécuté dans ce mode. Lorsqu’un ZOOM est exécuté dans le mode SOLIDE. Ne pas oublier que la nouvelle opération d’usinage figurera sur la représentation graphique existante. Pour exécuter cette opération sur une pièce “non-usinée”, frapper la touche EFFACER ECRAN. XY, XZ, YZ Le dessin visible dans l’angle inférieur droit de l’écran a changé, avec une fenêtre rectangulaire superposée. Cette fenêtre indique la nouvelle zone graphique sélectionnée pour ce type de graphique et elle est désactivée dans les cas suivants: * En cas de choix d’un autre type de graphique. * Lorsqu’un nouveau ZOOM est exécuté dans ce mode. Ne pas oublier que la nouvelle opération d’usinage figurera sur la représentation graphique existante. Pour exécuter cette opération sur une pièce “non-usinée”, frapper la touche EFFACER ECRAN. Chapitre: 3 Section: EXECUTER / SIMULER GRAPHIQUES Page 29 3.5.4 POINT DE VUE Cette fonction n’est utilisable que si aucun programme n’est en cours d’exécution ou de simulation par la CNC. Dans le cas contraire, l’exécution doit être interrompue. Cette fonction est utilisable avec tout graphique tridimensionnel (3D, CONJOINT et SOLIDE), et permet de sélectionner le point de vue de la pièce en orientant les axes X, Y, Z. Quand cette option est activée, la CNC affiche en surbrillance le point de vue actuel dans la partie droite de l’écran. Les touches "flèche à droite et flèche à gauche" permettent une rotation de 360° afin d’orienter le plan XY. Les touches "flèche vers le haut et flèche vers le base" permettent une rotation de l’axe vertical de 90° afin d’orienter l’axe Z. Lorsque la nouvelle orientation des axes a été définie, frapper ENTER pour valider les changements. Si le type SOLIDE est déjà sélectionné ou s’il est sélectionné à nouveau, la CNC rafraîchit l’écran et affiche la même pièce que précédemment, mais en appliquant le nouveau point de vue. Si le type 3D ou CONJOINT est sélectionné, le moniteur conserve le graphique affiché en cours. Le nouveau point de vue sera appliqué aux blocs suivants exécutés. Ces blocs seront dessinés sur le graphique existant. Toutefois, l’écran peut être effacé grâce à la touche EFFACER ECRAN afin de démarrer le dessin avec une pièce “non-usinée”. Pour quitter cette option sans modifier le point de vue existant, frapper ESC. Page 30 Chapitre: 3 EXECUTER / SIMULER Section: GRAPHIQUES 3.5.5 PARAMETRES GRAPHIQUES Cette fonction est utilisable à tout moment, même pendant l’exécution ou la simulation d’un programme. Elle permet de modifier la vitesse de simulation, les couleurs utilisées pour le tracé des trajectoires d’outil et les couleurs du solide. Les modifications apportées aux paramètres graphiques sont immédiatement prises en compte par la CNC et peuvent être changées pendant l’exécution ou la simulation. La CNC affiche les options suivantes de paramètres graphiques disponibles par touche de fonction: VITESSE SIMULATION Cette option permet de modifier le pourcentage de vitesse utilisé par la CNC pour exécuter le programme dans les modes simulation. Pour définir cette vitesse, la CNC affiche dans l’angle supérieur droit de l’écran une fenêtre indiquant le pourcentage de vitesse de simulation actuel. Cette valeur peut être modifiée grâce aux touches "flèche à droite et flèche à gauche". Lorsque le pourcentage désiré a été défini, frapper ENTER pour valider la nouvelle valeur. Pour sortir de cette option sans modifier la valeur précédente, frapper ESC. COULEURS TRAJECT. Cette option permet de modifier les couleurs utilisées pour tracer les diverses trajectoires d’outil dans les modes exécution et simulation. Elles ne peuvent être utilisées que dans les graphiques à lignes (3D, XY, XZ, YZ et CONJOINT). Les paramètres suivants sont disponibles: Couleur représentant l’avance rapide. Couleur représentant la trajectoire sans compensation. Couleur représentant la trajectoire avec compensation. Couleur représentant le filetage. Couleur représentant les cycles fixes. Pour définir les couleurs après activation de cette option, la CNC affiche dans la partie droite de l’écran une série de fenêtres dans lesquelles figureront les couleurs actuelles sélectionnées. Parmi les couleurs disponibles, figure la couleur "transparente", qui est visualisée en noir comme le fond. Si cette couleur est sélectionnée, la CNC n’affiche pas la trajectoire correspondant au déplacement programmé. Chapitre: 3 Section: EXECUTER / SIMULER GRAPHIQUES Page 31 Pour modifier l’une de ces couleurs, sélectionner la fenêtre concernée grâce aux touches "flèche vers le haut et flèche vers le bas" avant de la modifier grâce aux touches "flèche à droite et flèche à gauche". Quand toutes les couleurs désirées ont été sélectionnées, frapper ENTER pour valider les nouveaux choix. Pour quitter cette option sans modifier les paramètres existants, frapper ESC. COULEURS DU SOLIDE Cette option permet de modifier les couleurs utilisées dans la représentation graphique du solide tridimensionnel. Ces valeurs seront prises en compte dans les modes exécution et simulation, et employées exclusivement dans le mode graphique SOLIDE. Les paramètres suivants sont disponibles: Couleur représentant la face X externe. Couleur représentant la face Y externe. Couleur représentant la face Z externe. Couleur représentant la face X interne, face usinée. Couleur représentant la face Y interne, face usinée. Couleur représentant la face Z interne, face usinée. Pour définir les couleurs après activation de cette option, la CNC affiche dans la partie droite de l’écran une série de fenêtres dans lesquelles figureront les couleurs actuelles sélectionnées. Parmi les couleurs disponibles, figure la couleur "noire". Si cette couleur est sélectionnée pour une face externe ou interne, la CNC n’affiche aucune des opérations d’usinage exécutées. Pour modifier l’une de ces couleurs, sélectionner la fenêtre concernée grâce aux touches "flèche vers le haut et flèche vers le bas" avant de la modifier grâce aux touches "flèche à droite et flèche à gauche". Quand toutes les couleurs désirées ont été sélectionnées, frapper ENTER pour valider les nouveaux choix. Pour quitter cette option sans modifier les paramètres existants, frapper ESC. Page 32 Chapitre: 3 EXECUTER / SIMULER Section: GRAPHIQUES 3.5.6 EFFACER ECRAN Cette fonction n’est utilisable que si aucun programme n’est en cours d’exécution ou de simulation par la CNC. Dans le cas contraire, l’exécution doit être interrompue. Cette fonction permet d’effacer l’écran ou la représentation graphique affichée. Si le mode Graphique Solide est sélectionné, la représentation graphique est “remise à zéro” et affiche la pièce non usinée. 3.5.7 DESACTIVER GRAPHIQUES Cette fonction est utilisable à tout moment, même pendant l’exécution ou la simulation d’un programme. Elle permet de désactiver la représentation graphique. Pour réactiver cette fonction, frapper à nouveau la touche de fonction "GRAPHIQUES". Pour ce faire, aucun programme pièce ne doit être en cours d’exécution ou de simulation par la CNC. Dans le cas contraire, l’exécution doit être interrompue. Par ailleurs, toutes les conditions antérieures (type de graphique, zoom, paramètres graphiques et zone à visualiser) sélectionnées avant la désactivation de ce mode sont récupérées. Chapitre: 3 Section: EXECUTER / SIMULER GRAPHIQUES Page 33 3.5.8 MESURE Cette fonction n’est utilisable qu’après sélection d’un “Graphique à lignes” (plans XY, XZ ou YZ) et à la condition que la CNC n’exécute ou ne simule pas le programme pièce. Dans le cas contraire, l’exécution doit être interrompue. Quand cette fonction a été activée, la CNC affiche sur l’écran: La partie centrale de l’écran affiche la section à mesurer au moyen de deux curseurs et d’un trait en pointillés. En outre, la partie droite de l’écran montre: * Les coordonnées des deux curseurs par rapport au zéro pièce. * La distance entre les deux points en ligne droite “D” et les composants de cette distance selon les axes du plan sélectionné “ X” et “ Y”. * Le pas du curseur “ “ correspondant la zone d’affichage sélectionnée. Il est exprimé en unités de travail, millimètres ou pouces. La CNC affiche le curseur sélectionné et ses coordonnées en rouge. Pour sélectionner un autre curseur, frapper la touche "+" ou "-". La CNC affiche le nouveau curseur sélectionné et ses coordonnées en rouge. Le curseur sélectionné peut être déplacé grâce aux touches “flèche vers le haut, flèche vers le bas, flèche à droite et flèche à gauche”. Les séquences de touches “Shift-flèche vers le haut, Shift-flèche vers le bas, Shiftflèche à droite et Shift-flèche à gauche” permettent de déplacer le curseur jusqu’à l’extrêmité indiquée. Page 34 Chapitre: 3 EXECUTER / SIMULER Section: GRAPHIQUES Pour sortir de cette fonction et repasser au menu graphiques, frapper [ESC]. Egalement, si la touche repasse au menu graphiques. 3.6 est frappée, la CNC quitte ce mode de travail et BLOC A BLOC Chaque fois que cette option est activée, la CNC change de mode de fonctionnement entre “bloc à bloc” et “en continu”. Ce changement est possible même pendant l’exécution ou la simulation d’un programme pièce. Si le mode bloc à bloc est sélectionné, la CNC n’exécute qu’une ligne du programme à chaque frappe de la touche . La fenêtre supérieure de la page d’écran affiche le mode sélectionné. En cas d’exécution en continu, aucun message n’apparaît; si le mode bloc à bloc est actif, la mention BLOC A BLOC s’affiche. Chapitre: 3 Section: EXECUTER / SIMULER BLOC A BLOC Page 35 4. EDITER Ce mode de fonctionnement est utilisé pour éditer, modifier ou voir le contenu d’un programme pièce. Lorsque ce mode a été activé, la CNC demande l’introduction du numéro du programme (6 chiffres maximum) à éditer ou à modifier, depuis le clavier ou au moyen du curseur pointant le programme désiré dans le répertoire, avant de frapper la touche ENTER. Le curseur peut être déplacé sur l’écran ligne par ligne grâce aux touches “flèche vers le haut et flèche vers le bas”, ou évoluer d’une page a la fois grâce aux touches “page vers le haut et page vers le bas”. Ce mode de fonctionnement offre plusieurs options décrites plus loin. Lorsqu’une de ces options a été activée, l’opérateur dispose d’une zone d’écran pour l’édition, dans laquelle le curseur peut évoluer grâce aux touches “flèche à droite et flèche à gauche”. En outre, la touche “flèche vers le haut” permet de placer le curseur sur le premier caractère de la zone d’édition, tandis que la “flèche vers le bas” le positionne sur le dernier caractère. Chapitre: 4 EDITER Section: Page 1 4.1 EDITER Cette option permet d’éditer de nouvelles lignes ou de nouveaux blocs du programme sélectionné. Pour ce faire, l’opérateur dispose de plusieurs options décrites plus loin et sélectionnables par touches de fonction. Avant de frapper l’une de ces touches, on sélectionnera grâce au curseur le bloc à partir duquel on désire introduire le(s) nouveau(x) bloc(s) à éditer. 4.1.1 EDITION EN LANGAGE CNC L’édition s’effectue bloc par bloc, chacun d’eux pouvant être écrit en code ISO ou en langage de haut niveau; il peut aussi s’agir simplement d’un commentaire de programme. Dès la sélection d’une option, les touches de fonction changent de couleur et apparaissent sur fond blanc; elles affichent les informations correspondant au type d’édition réalisable. Il est également possible, à tout moment, de demander plus de détails sur les commandes d’édition en frappant la touche HELP. Pour quitter ce mode, il suffit de frapper à nouveau la touche HELP. La frappe de la touche ESC pendant l’édition d’un bloc permet de quitter le mode Edition et le bloc en cours d’édition n’est pas ajouté au programme. A la fin de l’édition, frapper ENTER. Le nouveau bloc édité est ajouté au programme après le bloc pointé par le curseur. Le curseur se positionne sur le nouveau bloc édité et la zone d’édition s’efface, ce qui permet de passer à l’édition de nouveaux blocs. Pour quitter le mode édition de blocs, frapper ESC ou MAIN MENU. Page 2 Chapitre: 4 EDITER Section: EDITION EN LANGAGE CNC 4.1.2 EDITION EN TEACH-IN Cette option est fondamentalement identique à l’option précédente (édition en langage CNC), sauf en ce qui concerne la programmation des valeurs des coordonnées de position. Cette option affiche les cotes de chaque axe de la machine. Elle permet d’introduire les cotes des axes depuis le clavier de la CNC (comme pour l’édition en langage CNC) ou d’utiliser le format d’édition TEACH-IN comme indiqué ci-dessous. * Déplacement de la machine grâce aux touches JOG ou à la manivelle électronique jusqu’à la position désirée. * Frappe de la touche de fonction correspondant à l’axe à définir. * La CNC affectera à cet axe la position atteinte par la machine en tant que cote de position du programme. Les deux modes de définition des valeurs de position sont utilisables indistinctement, y compris pendant la définition d’un bloc. Quand le bloc en cours d’édition ne contient aucune information (zone d’édition vide), la touche ENTER peut être frappée: la CNC génère alors un nouveau bloc avec les cotes dont disposent à ce moment tous les axes de la machine. Ce bloc, qui est ajouté automatiquement au programme, est inséré après le bloc pointé par le curseur. Le curseur se positionne sur le nouveau bloc édité et la zone d’édition s’efface, ce qui permet de passer à l’édition de nouveaux blocs. Si l’on ne désire pas que les valeurs de position de tous les axes soient introduites dans les blocs édités de cette façon, la CNC permet de sélectionner les axes désirés. Ceci est possible grâce à la touche “AXES TEACH-IN” de l’option “PARAMETRES EDITEUR” de ce mode de fonctionnement. Chapitre: 4 EDITER Section: EDITION EN TEACH-IN Page 3 4.1.3 EDITEUR INTERACTIF L’éditeur interactif est un mode de programmation dans lequel l’opérateur est “piloté” par la CNC sur la base d’un dialogue. Ce type d’édition présente les avantages suivants: * Aucune connaissance du langage de programmation de la CNC n’est nécessaire. * La CNC n’autorise que l’entrée de données en réponse à ses questions, ce qui supprime toute erreur. * Le programmeur dispose en permanence de pages d’écran ou de messages d’aide à la programmation. Dès que cette option est activée, la CNC affiche dans la fenêtre principale une série d’options graphiques sélectionnables par touches de fonctions. Si l’option choisie dispose de menus supplémentaires, la CNC continue à afficher de nouvelles options graphiques jusqu’à la sélection de l’option désirée. A partir de ce moment, la fenêtre principale affiche les informations correspondant à cette option, et elle commence à demander les données nécessaires pour sa programmation. Au fur et à mesure de l’introduction des données demandées, la fenêtre d’édition affiche en langage CNC le bloc en cours d’édition. La CNC génèrera tous les blocs nécessaires et les ajoutera au programme dès la fin de l’édition de l’option sélectionnée, puis elle mes insèrera après le bloc pointé par le curseur. Les options graphiques correspondant au menu initial réapparaissent dans la fenêtre principale, ce qui permet de continuer l’édition du programme. Page 4 Chapitre: 4 EDITER Section: EDITEUR INTERACTIF 4.1.4 EDITEUR DE PROFILS Quand cette option est sélectionnée, la CNC affiche les champs ou fenêtres suivants: EDITION: P000001 P..... N..... 11 : 50 : 14 ZONE A VISUALISER X: -100 Y: -1000 2500 500 X1: 50.000 Y1: 60.000 1 3 Et: Er: Ni: Nr: 2 CAP INS MM X Y F1 VALIDER F2 F3 F4 F5 F6 F7 1.- Fenêtre affichant la représentation graphique du profil à éditer. 2.- Fenêtre d’édition affichant le nouveau bloc généré en langage CNC. 3.- Zone d’informations supplémentaires affichant: ZONE A VISUALISER Elle indique la zone du plan présentée dans la zone de représentation graphique du profil. Elle est définie par les valeurs de position maximum et minimum de chaque axe. DROITE, ARC HORAIRE, ARC ANTIHORAIRE Elle indique le type de section de profil sélectionné pour édition ou modification. Les informations affichées dans chaque dépendent du type de section choisi. Et, Er, Ni, Nr Il s’agit d’une série de paramètres internes dont la signification est la suivante: Et Er Ni Nr : : : : Eléments totaux dont dispose le profil Eléments achevés Nombre de données introduites Nombre de données demandées Chapitre: 4 Section: EDITER EDITEUR DE PROFILS Page 5 4.1.4.1 MODE D’UTILISATION DE L’EDITEUR DE PROFILS Pour éditer un profil, on procèdera comme suit: * Sélection d’un point du profil comme point de début de ce profil. * Découpage du profil en sections droites et courbes. Si le profil comporte des congés, chanfreins, entrées ou sorties tangentielles, on procèdera de l’une des façons suivantes: - Les traiter comme des sections individuelles si les informations disponibles sont suffisantes pour les définir. - Les ignorer pendant la définition du profil et, dès que sa définition est achevée, sélectionner les angles présentant ces caractéristiques avant d’introduire la valeur du rayon correspondant. * Introduire les textes complémentaires désirés. Ils peuvent être introduits dans tout bloc généré en langage CNC par l’éditeur de profils. Dès la sélection de l’option “Editeur de profils”, la CNC demande l’ABCISSE et l’ORDONNEE correspondant au point de début du profil. Pour définir ces valeurs, frapper chaque touche de fonction correspondant aux axes formant le plan de travail, introduire la valeur désirée et frapper “ENTER”. La valeur de l’ABCISSE et de l’ORDONNEE peut être définie par une constante numérique ou toute autre expression. Exemples: X 100 X 10 * cos 45 X 20 + 30 * sin 30 X 2 * (20 + 30 * sin 30) Dès que les deux valeurs sont définies (si l’une d’entre elles n’est pas définie, la CNC affecte une valeur de 0), frapper la touche “VALIDER”. La CNC affichera un cercle plein dans la zone d’affichage graphique pour indiquer le point défini comme point de début du profil. Par ailleurs, les options suivantes sont affichées au moyen de touches de fonction: Page 6 Chapitre: 4 EDITER Section: EDITEUR DE PROFILS PARAMETRES Cette option est utilisée quand le plan contenant le profil à définir ne coïncide pas avec le plan sélectionné actuel, ou pour modifier la zone utilisée pour la représentation graphique du profil. Sélection du plan correspondant au graphique Cette option est utilisée quand le plan contenant le profil à définir ne coïncide pas avec le plan sélectionné actuel. Deux touches de fonction sont disponibles pour sélectionner un nouvel “AXE D’ABCISSES” et un nouvel “AXE D’ORDONNEES” formant le plan qui contient le profil. A partir de ce moment, la CNC utilisera cette nomenclature d’axes pour représenter toutes les valeurs de position correspondant aux divers profils. Dans la description ci-dessous, “X” est pris comme axe d’abcisses et “Y” comne axe d’ordonnées. Modification de la zone de représentation graphique La frappe de la touche “ZONE A VISUALISER” donne accès à un mode permettant de sélectionner la zone de représentation graphique désirée. - La touche “flèche vers le haut” déplace la zone visualisée vers le haut. - La touche “flèche vers le bas” déplace la zone visualisée vers le bas. - La touche “flèche à gauche” déplace la zone visualisée vers la gauche. - La touche “flèche à droite” déplace la zone visualisée vers la droite. - La touche “+” agrandit le profil. - La touche “-” réduit le profil. - Quand la touche “ZONE OPTIMALE” est frappée, la CNC calcule tous les points du profil et affiche le profil complet sur l’écran. Chaque modification de la zone de représentation graphique entraîne la mise à jour des valeurs indiquées dans la ZONE VISUALISEE, telles que les valeurs de position maximum et minimum de chaque axe. Chapitre: 4 Section: EDITER EDITEUR DE PROFILS Page 7 DROITE Quand cette option est activée, la CNC affiche dans la zone d’informations supplémentaires le cadre présenté ci-contre. Les valeurs de position X1, Y1 correspondent au point de début de la droite et sont fixées par la CNC, puisqu’elles coïncident avec le dernier point de la section précédente. ZONE VISUALIZEE X:-100 Y:-1000 2500 500 DROITE Les valeurs de position X2, Y2 définissent le point de fin de la droite et le symbole indique l’angle formé entre la droite et l’axe des abcisses. X1: 50.000 Y1: 60.000 X2: Y2: Le paramètre TANGENCE indique si la droite à dessiner est tangente ou non à la section précédente. Il est inutile de définir tous ces paramètres, mais il est recommandé de définir tous les paramètres connus. TANGENCE Pour définir un paramètre, frapper la touche de fonction correspondante, introduire la valeur désirée, puis frapper “ENTER”. Et: Ec: Ni: Nr: Quand tous les paramètres connus ont été définis, frapper la touche “VALIDER” : la CNC affiche, si c’est possible, la section définie. La valeur peut être définie par une constante numérique ou par toute autre expression. Exemples: X 100 X 10 * cos 45 X 20 + 30 * sin 30 X 2 * (20 + 30 * sin 30) S’il existe plus d’une possibilité, toutes les options possibles s’afficheront et l’option désirée (en rouge) devra être sélectionnée grâce aux touches “flèche à gauche” et “flèche à droite”. Les touches “flèche vers le haut” et “flèche vers le bas” permettent de choisir d’afficher toutes les possibilités ou seulement celle indiquée en rouge. Dès la sélection de l’option désirée, frapper “ENTER” pour que la CNC la prenne en compte. Page 8 Chapitre: 4 EDITER Section: EDITEUR DE PROFILS ARC HORAIRE et ARC ANTIHORAIRE Quand une de ces options est activée, la CNC affiche dans la zone d’informations supplémentaires le cadre présenté ci-contre. ZONE VISUALIZEE Les valeurs de position X1, Y1 correspondent au point de début de l’arc et sont fixées par la CNC, puisqu’elles coïncident avec le dernier point de la section précédente. X:-100 Y:-1000 Les valeurs de position X2, Y2 définissent le point de fin de l’arc, tandis que les valeurs XC, YC corresponden au centre de l’arc et que le paramètre RA indique le rayon de l’arc. Le paramètre TANGENCE indique si l’arc à dessiner est tangent ou non à la section précédente. X1: 50.000 Y1: 60.000 X2: Y2: XC: YC: RA: Il est inutile de définir tous ces paramètres, mais il est recommandé de définir tous les paramètres connus. TANGENCE Pour définir un paramètre, frapper la touche de fonction correspondante, introduire la valeur désirée, puis frapper “ENTER”. Quand tous les paramètres connus ont été définis, frapper la touche “VALIDER” : la CNC affiche, si c’est possible, la section définie. 2500 500 ARC HORAIRE Et: Ec: Ni: Nr: La valeur peut être définie par une constante numérique ou par toute autre expression. Exemples: X 100 X 10 * cos 45 X 20 + 30 * sin 30 X 2 * (20 + 30 * sin 30) S’il existe plus d’une possibilité, toutes les options possibles s’afficheront et l’option désirée (en rouge) devra être sélectionnée grâce aux touches “flèche à gauche” et “flèche à droite”. Les touches “flèche vers le haut” et “flèche vers le bas” permettent de choisir d’afficher toutes les possibilités ou seulement celle indiquée en rouge. Dès la sélection de l’option désirée, frapper “ENTER” pour que la CNC la prenne en compte. Chapitre: 4 Section: EDITER EDITEUR DE PROFILS Page 9 MODIFIER Cette option affiche une série de touches permettant d’exécuter les opérations suivantes: * Ajout d’un arrondi aux angles, d’un chanfrein, d’une entrée ou d’une sortie tangentielles à l’un des angles valides, c’est-à-dire à ceux qui, en plus d’être complets, permettent d’exécuter l’une de ces opérations. Pour ce faire, frapper la touche de fonction correspondante “ARRONDI”, “CHANFREIN”, “ENTREE TANGENTIELLE” ou “SORTIE TANGENTIELLE”. La CNC présentera en surbrillance dans la zone de représentation graphique le premier angle valide. En outre, la zone d’informations complémentaires affichera la valeur des paramètres ayant permis de définir la trajectoire, la zone d’édition affichant le bloc en langage CNC correspondant à cette trajectoire. La trajectoire affichée est celle correspondant à celle en langage CNC qui comprendra plus tard l’arrondi, le chanfrein, l’entrée tangentielle ou la sortie tangentielle désirés. Les touches “flèche vers le haut” et “flèche vers le bas” permettent de passer d’un angle à l’autre le long du profil. Dès que l’angle à modifier a été sélectionné, frapper “ENTER”. La CNC demandera la valeur du rayon correspondant, qui devra être introduite depuis le clavier alphanumérique. Dès que cette opération est terminée, frapper “ENTER”: la CNC redessinera le nouveau profil sélectionné. * Ajout d’un texte supplémentaire à l’une des trajectoires déjà achevées. Frapper la touche “TEXTE ADDITIONN.”. La CNC affichera dans la zone d’édition le bloc en langage CNC correspondant à la première trajectoire achevée. Cette section apparaîtra en surbrillance dans la zone de représentation graphique du profil, la zone d’informations supplémentaires affichant la valeur des paramètres utilisés pour la définition. Les touches “flèche vers le haut” et “flèche vers le bas” permettent de passer aux diverses sections de l’ensemble du profil. Après sélection de la section où doit être inscrit le texte supplémentaire, frapper “ENTER”. Le curseur se positionne à la fin du bloc en langage CNC se trouvant dans la zone d’édition. Le texte supplémentaire est introduit depuis le clavier alphanumérique comme en édition en langage CNC; à la fin de cette opération, frapper “ENTER”. Page 10 Chapitre: 4 EDITER Section: EDITEUR DE PROFILS * Modification de la dernière section définie. Pour réaliser cette opération, frapper la touche “MODIFIER DERNIER”. La CNC affichera la section concernée et, si l’un de ses paramètres est sélectionné, la valeur correspondant à ce paramètre s’affichera en surbrillance dans la “zone d’informations supplémentaires”. Pour supprimer cette valeur, frapper “ESC”; pour la modifier, introduire la valeur désirée. * Modification d’une section précédente. Pour pouvoir modifier une section précédente, il est nécessaire d’effacer toutes les sections postérieures grâce à la touche “EFFACER DERNIER”. Toutes les sections s’effacent une à une en commençant par la dernière. Dès que la section à modifier a été sélectionnée, frapper la touche “EFFACER DERNIER” et procéder comme indiqué dans le paragraphe précédent. Toutes les sections effacées par la touche “EFFACER DERNIER” doivent être introduites à nouveau. Chapitre: 4 EDITER Section: EDITEUR DE PROFILS Page 11 TERMINER Cette touche doit être actionnée lorsque toutes les sections du profil ont été définies. La CNC tentera de calculer le profil demandé après avoir résolu toutes les inconnues. Si, lors du calcul du profil, certaines sections offrent plus d’une possibilité, la CNC affiche toutes les options possibles pour chaque section. Les touches “flèche à gauche” et “flèche à droite” permettent de choisir l’option désirée (indiquée en rouge). Les touches “flèche vers le haut” et “flèche vers le bas” permettent de sélectionner l’affichage de toutes les options possibles ou seulement de celle indiquée en rouge. Lorsque tout le profil a été calculé, la CNC inclut dans le programme sélectionné, après le bloc dans lequel l’éditeur de profil a été appelé, tous les blocs nécessaires en langage CNC pour définir ce profil. En outre, un premier bloc de déplacement au point initial en G00 est généré. Ces blocs sont précédés d’une ligne de commentaire “***** START****” et se terminent par la ligne de commentaire “***** END ****”. Si le profil ne peut être calculé par manque de données, la CNC affiche le message correspondant. Page 12 Chapitre: 4 EDITER Section: EDITEUR DE PROFILS 4.1.4.2 EXEMPLE DE DEFINITION D’UN PROFIL Le point (0,68) est pris comme point initial du profil. Lors de la définition du profil, les arrondis aux angles sont ignorés en raison des informations insuffisantes. Lorsque le profil a été défini, il est modifié pour introduire les arrondis correspondants. Définition du profil sans arrondis: Point initial Section 1 Droite Section 2 Droite Section 3 Droite Section 4 Arc horaire Section 5 Droite Section 6 Droite Section 7 Droite Section 8 Arc antihor. Section 9 Arc horaire Section 10 Arc antihor. Section 11 Droite X1=0 X1=30 X=0 Y1=0 Y1=0 Y=68 Angle=90 Ra=12 X1=80 Y1=0 X1=140 Y1=0 Angle=-35 Tangente=Oui Tangente=Oui Angle=120 Ra=25 Xc=85 Ra=15 X1=0 Yc=50 Ra=20 Y1=68 Angle=180 Tangente=Oui Tangente=Oui Tangente=Oui Tangente=Oui Lorsque le profil sans arrondis a été défini, frapper “MODIFIER” pour introduire les arrondis correspondants. Chapitre: 4 Section: EDITER EDITEUR DE PROFILS Page 13 Définition des arrondis: Pointe A Pointe B Pointe C Pointe D Rayon=10 Rayon=5 Rayon=20 Rayon=8 Lorsque l’introduction des données est achevée, frapper la touche “TERMINER”. La CNC inclura dans le programme sélectionné, après le bloc depuis lequel l’éditeur de profils a été appelé, les blocs suivants: ; ***************** START *********** G00 X0 Y68 G01 G36 R10 X0 Y0 G01 G36 R5 X30 Y0 G01 X30 Y11.9586 G02 X48.8829 Y21.7884 I12 J0 G01 G36 R20 X80 Y0 G01 G36 R8 X140 Y0 G01 X127.0682 Y 22.3986 G03 X94.0745 Y32.1771 I-21.6506 J-12.5 G02 X65.0736 Y51.7143 I-9.0745 J17.8229 G03 X50.1288 Y68 I-14.9448 J1.2857 G01 X0 Y68 ; ***************** END *********** 4.1.5 UTILISATEUR Si cette option est sélectionnée, la CNC exécute dans le canal utilisateur le programme de personnalisation sélectionné au moyen du paramètre machine général USEREDIT. Pour abandonner l’exécution et revenir au menu précédent, frapper ESC. Page 14 Chapitre: 4 EDITER Section: EDITEUR DE PROFILS UTILISATEUR 4.2 MODIFIER Cette option permet de modifier une ligne ou un bloc du programme sélectionné. Avant de frapper cette touche, on sélectionnera le bloc à modifier au moyen du curseur. Dès que cette option est activée, les touches de fonction changent de couleur et affichent sur fond blanc les informations relatives au type d’édition à utiliser dans le bloc à modifier. En outre, des informations supplémentaires sur les commandes d’édition peuvent être obtenues en frappant la touche HELP. Pour quitter le mode Aide, frapper la touche HELP une seconde fois. La frappe de la touche ESC permet d’effacer les informations figurant dans la zone d’édition correspondant au bloc à modifier. A partir de ce moment, le contenu de ce bloc peut être édité à nouveau. Pour quitter le mode modification de bloc, frapper CL ou ESC afin d’effacer les informations figurant dans la zone d’édition avant de frapper ESC. De cette façon, le bloc sélectionné ne sera pas modifié. Quand la modification du bloc est terminée, frapper ENTER. Le nouveau bloc édité remplacera le précédent. Chapitre: 4 Section: EDITER MODIFIER Page 15 4.3 CHERCHER Cette option permet d’exécuter une recherche dans le programme sélectionné. Lorsque cette option est activée, les touches de fonction affichent les options suivantes: DEBUT Cette touche positionne le curseur sur la première ligne du programme, qui est ainsi sélectionnée, et la CNC sort de l’option “chercher”. FIN Cette touche positionne le curseur sur la dernière ligne du programme, qui est ainsi sélectionnée, et la CNC sort de l’option “chercher”. TEXTE Cette fonction permet la recherche d’un texte ou d’une séquence de caractères à partir du bloc pointé par le curseur. Si cette touche est actionnée, la CNC demande la séquence de caractères à chercher. Lorsque le texte a été défini, frapper la touche “FIN TEXTE”; le curseur se positionnera sur la première séquence de caractères rencontrée. La recherche est exécutée à partir du bloc pointé par le curseur, y compris dans le bloc lui-même. Le texte rencontré apparaît en surbrillance et la recherche peut être poursuivie dans tout le texte ou abandonnée. Pour continuer la recherche dans tout le programme, frapper ENTER. La CNC exécutera la recherche à partir du dernier texte rencontré et l’affichera en surbrillance. La recherche peut être exécutée autant de fois que désiré; quand la fin du programme est atteinte, la recherche reprend au début du programme. Pour quitter l’option de recherche, frapper la touche “ARRETER” ou ESC. La CNC positionne le curseur sur la ligne où le texte recherché a été rencontré pour la dernière fois. N° LIGNE Si cette touche est frappée, la CNC demande le numéro de la ligne ou du bloc recherchés. Après l’introduction de ce numéro et la frappe de ENTER, le curseur se positionne sur la ligne demandée, qui est ainsi sélectionnée, et la CNC quitte l’option de recherche. Page 16 Chapitre: 4 EDITER Section: CHERCHER 4.4 REMPLACER Cette option permet de remplacer, dans le programme sélectionné et autant de fois que désiré, une séquence de caractères par une autre. Si cette option est activée, la CNC demande la séquence de caractères à remplacer. Lorsque le texte à remplacer a été défini, frapper la touche “PAR”: la CNC demande la séquence de caractères de remplacement. Lorsque ce texte a été défini, frapper la touche “FIN TEXTE”: le curseur se positionne sur la première séquence de caractères rencontrée. La recherche est exécutée à partir du bloc pointé par le curseur, y compris dans le bloc lui-même. Le texte rencontré apparaît en surbrillance et les touches de fonction affichent les options suivantes: Remplace le texte en surbrillance et continue la recherche REMPLACER jusqu’à la fin du programme. Si aucun autre texte à remplacer n’est rencontré, la CNC quitte l’option “remplacer”. Si un autre texte est rencontré, il est mis en surbrillance et les mêmes options “remplacer” et “ne pas remplacer” sont proposées. Ne remplace pas le texte en surbrillance et continue la NE PAS REMPLACER recherche jusqu’à la fin du programme. Si aucun autre texte à remplacer n’est rencontré, la CNC quitte l’option “remplacer”. Si un autre texte est rencontré, il est mis en surbrillance et les mêmes options “remplacer” et “ne pas remplacer” sont proposées. Cette option exécute une recherche et un remplacement du JUSQU’A LA FIN texte sélectionné, du texte en surbrillance à la fin du programme. Cette option ne remplace pas le texte en surbrillance et met fin ARRETER à l’option “chercher et remplacer”. Chapitre: 4 Section: EDITER REMPLACER Page 17 4.5 EFFACER BLOC Cette option permet d’effacer un bloc ou un groupe de blocs. Pour effacer un seul bloc, il suffit de positionner le curseur sur le bloc à effacer et de frapper ENTER. Pour effacer un groupe de blocs, on indiquera le premier et le dernier bloc à effacer. On procèdera comme suit: * Positionner le curseur sur le premier bloc à effacer et frapper la touche “DEBUT BLOC”. * Positionner le curseur sur le dernier bloc à effacer et frapper la touche “FIN BLOC”. Si le dernier bloc à effacer est aussi le dernier bloc du programme, ce bloc peut être sélectionné par la frappe de la touche “JUSQU’A LA FIN”. * Page 18 Après sélection du premier et du dernier bloc à effacer, la CNC met en surbrillance les blocs sélectionnés et demande confirmation avant de les effacer. Chapitre: 4 EDITER Section: EFFACER BLOC 4.6 DEPLACER BLOC Cette option permet de déplacer un ou plusieurs blocs, après avoir indiqué le premier et le dernier bloc à déplacer. Procéder comme suit: * Positionner le curseur sur le premier bloc à déplacer et frapper la touche “DEBUT BLOC”. * Positionner le curseur sur le dernier bloc à déplacer et frapper la touche “FIN BLOC”. Si le dernier bloc à déplacer est aussi le dernier bloc du programme, ce bloc peut être sélectionné par la frappe de la touche “JUSQU’A LA FIN”. Si le déplacement porte sur un seul bloc, le premier et le dernier seront les mêmes. * Après sélection du premier et du dernier bloc à déplacer, la CNC met en surbrillance les blocs sélectionnés. On signalera ensuite avec le curseur le bloc derrière lequel le ou les blocs sélectionnés devront être placés. * Après sélection du bloc, frapper la touche “DEBUT OPERATION” pour que la CNC exécute la commande. Chapitre: 4 Section: EDITER DEPLACER BLOC Page 19 4.7 COPIER UN BLOC Cette option permet de copier un ou plusieurs blocs, après avoir indiqué le premier et le dernier bloc à copier. Procéder comme suit: * Positionner le curseur sur le premier bloc à copier et frapper la touche “DEBUT BLOC”. * Positionner le curseur sur le dernier bloc à copier et frapper la touche “FIN BLOC”. Si le dernier bloc à copier est aussi le dernier bloc du programme, ce bloc peut être sélectionné par la frappe de la touche “JUSQU’A LA FIN”. Si la copie porte sur un seul bloc, le premier et le dernier seront les mêmes. Après sélection du premier et du dernier bloc à copier, la CNC met en surbrillance les blocs sélectionnés. On signalera ensuite avec le curseur le bloc derrière lequel le ou les blocs sélectionnés devront être copiés. Après sélection du bloc, frapper la touche “DEBUT OPERATION” pour que la CNC exécute la commande. Page 20 Chapitre: 4 EDITER Section: COPIER UN BLOC 4.8 COPIER A PROGRAMME Cette option permet de copier un ou plusieurs blocs d’un programme dans un autre programme. Lorsque cette option est activée, la CNC demande le numéro du programme où le ou les blocs doivent être copiés. Après l’introduction du numéro, frapper ENTER. Indiquer ensuite le premier et le dernier bloc à copier. Procéder comme suit: * Positionner le curseur sur le premier bloc à copier et frapper la touche “DEBUT BLOC”. * Positionner le curseur sur le dernier bloc à copier et frapper la touche “FIN BLOC”. Si le dernier bloc à copier est aussi le dernier bloc du programme, ce bloc peut être sélectionné par la frappe de la touche “JUSQU’A LA FIN”. Si la copie porte sur un seul bloc, le premier et le dernier seront les mêmes. Après sélection du premier et du dernier bloc à copier, la CNC met en surbrillance les blocs sélectionnés et exécute la commande. Si le programme destinataire de la copie existe déjà, la CNC affiche les options suivantes: * Ecraser le programme. La CNC effacera tous les blocs du programme destinataire et les remplacera par les blocs copiés. * Ajouter les blocs sélectionnés après ceux appartenant au programme destinataire. * Interrompre la commande sans exécuter la copie demandée. Chapitre: 4 Section: EDITER COPIER A PROGRAMME Page 21 4.9 INCLURE PROGRAMME Cette option permet d’inclure le contenu d’un programme dans un programme sélectionné. Lorsque cette option a été activée, la CNC demande le numéro du programme dont le contenu est à inclure. Après introduction de ce numéro, frapper ENTER. On signalera ensuite avec le curseur le bloc derrière lequel le programme considéré est à inclure. Lorsque le bloc a été sélectionné, frapper la touche “DEBUT OPERATION” pour que la CNC exécute la commande. Page 22 Chapitre: 4 EDITER Section: INCLURE PROGRAMME 4.10 PARAMETRES EDITEUR Cette option permet de sélectionner les paramètres d’édition utilisés dans ce mode de fonctionnement. Les options ou paramètres disponibles sont décrits ci-dessous et peuvent être sélectionnés par touches de fonction. 4.10.1 AUTONUMERATION Cette option permet de numéroter automatiquement tous les nouveaux blocs de programme venant après le bloc édité. Lorsque cette option a été activée, la CNC affiche les touches ON et OFF pour permettre l’activation (ON) ou la désactivation (OFF) de cette fonction. Dès que cette fonction est activée, les touches de fonction affichent les options suivantes: Après la frappe de cette touche, la CNC demande le numéro à affecter au DEBUT prochain bloc à éditer. Par défaut, la CNC affecte la valeur 0. Après la frappe de cette touche, la CNC demande le pas à conserver entre PAS blocs consécutifs. Lorsque le pas a été défini, la CNC permet également de choisir le numéro à affecter au prochain bloc à éditer. Pour ce faire, la touche DEBUT doit être actionnée. Après définition du pas et du début, frapper ENTER pour que la CNC prenne en compte cette ou ces valeurs. Par défaut, la CNC affecte la valeur 10 à ce paramètre (PAS). Attention: Cette opération ne réalise pas l’autonumération des blocs de programme existants. Chapitre: 4 EDITER Section: PARAMETRES EDITEUR Page 23 4.10.2 SELECTION DES AXES POUR EDITION EN TEACH-IN . On notera que, dans le mode édition en TEACH-IN, la caractéristique suivante est disponible: Quand le bloc en cours d’édition ne contient aucune information (zone d’édition vide), la touche ENTER peut être actionnée. Dans ce cas, la CNC génère un nouveau bloc avec les valeurs de position des axes. L’option décrite ici permet de sélectionner les axes dont les valeurs se trouveront dans ces blocs de position. Après frappe de la touche “AXES TEACH-IN”, la CNC visualise tous les axes dont dispose la machine. L’opérateur doit éliminer le ou les axes non désirés en frappant les touches de fonction correspondantes. Chaque fois qu’une touche est frappée, la CNC supprime l’axe concerné de l’écran et ne conserve que les axes sélectionnés restants. Pour mettre fin à cette opération, frapper “ENTER”. La CNC prendra désormais en compte les axes qui ont été sélectionnés chaque fois qu’une édition en TEACH-IN sera exécutée. Pour apporter des changements, il est nécessaire d’activer à nouveau cette option et de sélectionner les nouveaux axes. Page 24 Chapitre: 4 EDITER Section: PARAMETRES EDITEUR 5. MANUEL Ce mode de fonctionnement est utilisé chaque fois que la machine doit être déplacée manuellement. Lorsque ce mode a été activé, la CNC autorise le déplacement de tous les axes de la machine au moyen des touches de contrôle d’axes (X+, X-, Y+, Y-, Z+, Z-, 4+, 4-, etc.) situées sur le Pupitre Opérateur ou de la manivelle électronique (si elle est installée). De plus, la CNC valide les touches situées sur le Pupitre Opérateur, qui permettent de contrôler le déplacement de la broche. L’option “MDI” permet de modifier les conditions d’usinage (type de déplacement, avances, etc...) sélectionnées. En outre, la CNC conservera les conditions d’usinage sélectionnées dans ce mode en cas de passage aux modes de fonctionnement “EXECUTER” o “SIMULER”. Ce mode de fonctionnement offre les options suivantes, sélectionnables par touches: RECHERCHE ZERO Chapitre: 5 Section: MANUEL HOME SEARCH Page 1 Cette option permet la recherche de la référence machine sur le ou les axes désirés. La CNC FAGOR 8050 propose deux méthodes de recherche: * Utilisation du sous-programme associé à la fonction G74 et dont le numéro est défini par le paramètre machine général "REFPSUB". * Sélection du ou des axes sur lesquels la recherche doit être exécutée. Dès que l’option Recherche Zéro a été activée, la CNC affiche une touche pour chaque axe de la machine et la touche "TOUS". Si la touche "TOUS" est frappée, la CNC affiche le nom de tous les axes en vidéo inverse et, après frappe de la touche elle exécute le sous-programme associé à la fonction G74. Pour exécuter la recherche sur un ou plusieurs axes à la fois (sans exécution du sous-programme associé), on actionnera les touches correspondant aux axes concernés. Lorsque chaque touche est actionnée, la CNC affiche le nom du ou des axes concernés en vidéo inverse. Si un axe non désiré a été sélectionné, frapper "ESC" et activer à nouveau l’option "RECHERCHE ZERO". Lorsque tous les axes désirés ont été sélectionnés, frapper La CNC commence la recherche de la référence machine en déplaçant tous les axes à la fois jusqu’à ce qu’ils actionnent le contact de référence machine. Ensuite, elle exécute la recherche de référence machine un axe à la fois. Attention: Lors de la recherche du zéro machine au moyen de la touche programmable “TOUS”, la CNC conserve le zéro pièce ou le décalage de zéro actifs à cet instant. Toutefois, si les axes ont été sélectionnés individuellement, la CNC prend comme nouveau zéro pièce la position occupée par le zéro machine. PRESELECTION Cette option permet de présélectionner la valeur de position de l’axe désiré. Dès que cette option a été activée, la CNC affiche une touche pour chaque axe de la machine. Lorsque la touche correspondant à l’axe à présélectionner a été frappée, la CNC demande la valeur de présélection à appliquer. Quand cette valeur a été introduite, frapper "ENTER" afin qu’elle soit prise en compte par la CNC. Page 2 Chapitre: 5 MANUEL Section: RECHERCHE ZERO ET PRESELECTION MESURE Cette fonction permet d’étalonner la longueur de l’outil sélectionné, en utilisant pour ce faire une pièce de dimensions connues. Avant de frapper cette touche, on choisira l’outil et le correcteur à étalonner. L’étalonnage de l’outil s’effectuera sur l’axe sélectionné, grâce à la fonction G15 en tant qu’axe longitudinal (axe Z par défaut). Lorsqu’un palpeur est disponible pour cette opération, les paramètres machine généraux “PRBXMIN”, “PRBXMAX”, “PRBYMIN”, “PRBYMAX”, “PRBZMIN”, “PRBZMAX” et “PRBMOVE” doivent être personnalisés correctement. Mesure sans palpeur Prodéder comme suit: * Frapper la touche correspondant à l’axe longitudinal. * La CNC demandera la valeur de position de la pièce étalon au point où doit s’effectuer l’étalonnage. Après l’introduction de cette valeur, frapper "ENTER" afin qu’elle soit prise en compte par la CNC. * Déplacer l’outil au moyen des touches JOG (X+, X-, Y+, Y-, Z+, Z-, 4+, 4) jusqu’à ce qu’il entre en contact avec la pièce. * Frapper la touche CHARGER correspondant à cet axe. La CNC effectuera les calculs nécessaires et affectera sa nouvelle longueur au correcteur sélectionné. Mesure avec palpeur Cette opération peut s’effectuer de deux manières, soit comme décrit sous “Mesure sans palpeur”, soit comme indiqué ci-dessous: * Frapper la touche indiquant le sens de l’étalonnage de l’outil selon l’axe longitudinal. * La CNC déplacera l’outil selon l’avance indiquée par le paramètre machine pour cet axe “PRBFEED”, jusqu’à ce que l’outil touche le palpeur. Le déplacement maximum de l’outil est limité par la valeur affectée au paramètre machine général “PRBMOVE”. * Quand l’outil entre en contact avec le palpeur, la CNC stoppe l’axe et, après avoir effectué les calculs nécessaires, elle affecte sa nouvelle longueur au correcteur sélectionné. Chapitre: 5 Section: MANUEL MESURE Page 3 MDI Cette fonction permet d’éditer tout type de bloc (ISO ou haut niveau), en donnant les informations nécessaires sur le format correspondant au moyen de touches de fonction. Après édition du bloc et frappe de la touche quitter ce mode de fonctionnement. la CNC exécute ce bloc sans Attention: Lors de la recherche du zéro machine, “G74”, la CNC conserve le zéro pièce ou le décalage de zéro actifs à cet instant. UTILISATEUR Si cette option est activée, la CNC exécute dans le canal utilisateur le programme de personnalisation sélectionné et indiqué par le paramètre machine général "USERMAN". Pour quitter cette option et revenir au menu précédent, frapper ESC. Page 4 Chapitre: 5 MANUEL Section: MDI / UTILISATEUR VISUALISER Après frappe de la touche “PLC”, ce mode permet d’accéder au mode contrôle du PLC. Dans ce mode, on procèdera comme indiqué dans le chapitre relatif au contrôle du PLC. Ce mode permet en outre de sélectionner, grâce à la touche correspondante, un des modes suivants de représentation des valeurs de position (coordonnées): ACTUEL Si cette option est activée, la CNC affiche la position actuelle des axes par rapport au zéro pièce. MANUEL P..... N..... 11 : 50 : 14 ACTUEL X Y Z U V 00100.000 00150.000 00004.269 00071.029 00011.755 F03000.0000 %100 S00000.0000 %100 T0000 D000 NT0000 ND000 S 0000 RPM G00 G17 G54 PARTC=000000 CYTIME=00:00:00:00 TIMER=000000:00:00 CAP INS MM DEPLACEMENT MANUEL EN CONTINU RECHERCE ZERO PRESELECTION F1 F2 MESURE F3 MDI F4 UTILISATEUR F5 VISUALISER F6 MM/ POUCES F7 Chapitre: 5 Section: MANUEL VISUALISER Page 5 ERREUR DE POURSUITE Si cette option est activée, la CNC affiche l’erreur de poursuite (différence entre les positions théorique et réelle) de chaque axe et de la broche. En outre, si l’option recopie est disponible, ce mode affiche dans un cadre situé dans la partie droite de l’écran les valeurs relatives au palpeur de recopie. MANUEL P000662 N..... 11 : 50 : 14 ERREUR DE POURSUITE DEVIATIONS FACTEURS F03000.0000 %100 S00000.0000 %100 T0000 D000 NT0000 ND000 S 0000 RPM G00 G17 G54 PARTC=000000 CYTIME=00:00:00:00 TIMER=000000:00:00 DEPLACEMENT MANUEL EN CONTINU RECHERCE ZERO F1 PRESELECTION MESURE F2 F3 MDI F4 CAP INS UTILISATEUR VISUALISER F5 F6 MM/ POUCES F7 Le format d’affichage de chaque axe est indiqué par le paramètre machine "DFORMAT". Les facteurs de correction du palpeur sont indépendants des unités de travail. Le format d’affichage des déviations du palpeur sur chaque axe (X, Y, Z) et de la déviation totale D est indiqué dans le paramètre machine "DFORMAT". Page 6 Chapitre: 5 MANUEL Section: VISUALISER ACTUEL ET ERREUR DE POURSUITE Si cette option est activée, la CNC affiche la position actuelle et l’erreur de poursuite (différence entre les positions théorique et réelle) de chaque axe. MANUEL P..... N..... ACTUEL X Y Z U V 11 : 50 : 14 ERREUR DE POURSUITE 00100.000 00150.000 00004.269 00071.029 00011.755 X 00000.002 Y-00000.003 Z 00000.003 U 00000.001 V -00000.002 F03000.0000 %100 S00000.0000 %100 T0000 D000 NT0000 ND000 S 0000 RPM G00 G17 G54 PARTC=000000 CYTIME=00:00:00:00 TIMER=000000:00:00 DEPLACEMENT MANUEL EN CONTINU RECHERCE ZERO PRESELECTION F1 F2 MESURE MDI F3 F4 CAP INS MM UTILISATEUR F5 VISUALISER F6 Chapitre: 5 Section: MANUEL VISUALISER MM/ POUCES F7 Page 7 MM/POUCES Chaque fois que cette option est activée, la CNC change les unités indiquant les positions des axes linéaires. Les unités (mm ou pouces) sélectionnées sont inscrites dans la fenêtre située dans l’angle inférieur droit. On notera que ce changement n’affecte pas les axes rotatifs, qui sont représentés en degrés. Page 8 Chapitre: 5 MANUEL Section: MM/POUCES 5.1 DEPLACEMENT MANUEL DE LA MACHINE 5.1.1 DEPLACEMENT EN CONTINU Lorsque le pourcentage (0 à 120%) de l’avance en MANUEL indiqué dans le paramètre machines "JOGFEED" a été sélectionné grâce au sélecteur situé sur le Pupitre Opérateur, frapper la touche MANUEL correspondant à l’axe et au sens de déplacement de la machine désirés (X+, X-, Y+, Y-, Z+, Z-, 4+, 4-, etc...). Les axes sont déplacés un par un et en fonction de l’état de l’entrée logique générale "LATCHM" comme suit: * Si le PLC met cette entrée à “0” les axes ne se déplacent que si la touche MANUEL correspondante est maintenue. * Si le PLC met cette entrée à “1”, les axes se déplacent dès la frappe de la touche MANUEL correspondante et jusqu’à la frappe de la touche ou d’une autre touche MANUEL; dans ce cas, le déplacement affecte l’axe concerné par la nouvelle touche frappée. Si, pendant le déplacement demandé, la touche est frappée, ce déplacement est exécuté selon l’avance indiquée par le paramètre machine "G00FEED". Cette avance est appliquée tant que cette touche est maintenue et elle reprend la valeur (0% a 120%) définie dans le paramètre machine "JOGFEED" dès que la touche est relâchée. Chapitre: 5 MANUEL Section: DEPLACEMENT EN CONTINU Page 9 5.1.2 DEPLACEMENT INCREMENTAL Ce mode permet le déplacement manuel de l’axe désiré dans le sens défini, selon la valeur sélectionnée par une des positions du sélecteur situé sur le Pupitre Opérateur et à la vitesse d’avance indiquée dans le paramètre machine "JOGFEED", Les positions disponibles sont 1, 10, 100, 1000 et 10000, correspondant aux unités de résolution d’affichage. Exemple: Format d’affichage : 5.3 en mm ou 4.4 en pouces Position du sélecteur 1 10 100 1000 10000 Déplacement 0.001 mm ou 0.0001 pouce 0.010 mm ou 0.0010 pouce 0.100 mm ou 0.0100 pouce 1.000 mm ou 0.1000 pouce 10.000 mm ou 1.0000 pouce Le déplacement maximum est limité à 10 mm ou à 1 pouce, quel que soit le format d’affichage (exemple: 5,2 en mm ou 4,3 en pouces). Selon le positionnement du sélecteur, la machine se déplace de la valeur définie à chaque frappe de la touche MANUEL, qui indique l’axe concerné et le sens du déplacement (X+, X-, Y+, Y-, Z+, Z-, 4+, 4-, etc...). Si pendant le déplacement d’un axe, la touche est frappée, ce déplacement s’effectue selon la vitesse d’avance indiquée par le paramètre machine "G00FEED". Cette avance est appliquée tant que cette touche est maintenue et elle reprend la valeur (0% a 120%) définie dans le paramètre machine "JOGFEED", dès que la touche est relâchée. Page 10 Chapitre: 5 MANUEL Section: DEPLACEMENT INCREMENTAL 5.1.3 DEPLACEMENT PAR MANIVELLE ELECTRONIQUE Cette option permet le contrôle des déplacements de la machine par manivelle électronique. On sélectionnera d’abord sur le sélecteur du Pupitre Opérateur une des positions relatives à la manivelle électronique Les positions disponibles sont 1, 10 et 100, qui indiquent toutes le multiplicateur appliqué aux impulsions délivrées par la manivelle. Le produit du multiplicateur par le nombre d’impulsions délivrées par la manivelle donne les unités de déplacement de l’axe. Ces unités correspondent aux unités de résolution d’affichage. Exemple: Format d’affichage Résolution de la manivelle : 5.3 en mm ou 4.4 en pouces : 250 impulsions/tour Position du sélecteur Déplacement par tour 1 10 100 0.250 mm ou 0.0250 pouce 2.500 mm ou 0.2500 pouce 25.000 mm ou 2.5000 pouces Frapper ensuite l’une des touches MANUEL correspondant à l’axe à déplacer (X+, X-, Y+, Y-, Z+, Z-, 4+, 4-, etc...). L’axe sélectionné apparaît en surbrillance. Si une manivelle électronique FAGOR à BP sélecteur d’axe est disponible, l’axe à déplacer peut aussi être choisi comme suit: * Actionner le BP situé à l’arrière de la manivelle. La CNC sélectionne le premier axe et l’affiche en surbrillance. * Chaque nouvelle frappe du BP entraîne la sélection de l’axe suivant jusqu’au dernier, puis la sélection reprend au premier, etc... * Si le BP est maintenu pendant plus de 2 secondes, la CNC annule la sélection de l’axe considéré. La machine déplace l’axe sélectionné pendant la manoeuvre et selon le sens de la manivelle. Il est possible qu’en fonction de la vitesse de rotation de la manivelle et de la position du sélecteur, le déplacement demandé à la CNC se caractérise par une vitesse d’avance supérieure à celle indiquée par le paramètre machine "G00FEED". Dans ce cas, l’axe se déplace de la distance indiquée, mais la vitesse d’avance est limitée à la valeur définie par le paramètre. Chapitre: 5 MANUEL Section: MANIVELLE ELECTRONIQUE Page 11 5.2 COMMANDE MANUELLE DE LA BROCHE Les touches suivantes du Pupitre Opérateur permettent de contrôler la broche sans qu’il soit nécessaire d’exécuter M3, M4 ou M5. Equivaut à l’exécution de M03 et permet de démarrer la broche dans le sens horaire ainsi que d’afficher M03 dans l’historique des conditions d’usinage. Equivaut à l’exécution de M04 et permet de démarrer la broche dans le sens antihoraire ainsi que d’afficher M04 dans l’historique des conditions d’usinage. Equivaut à l’exécution de M05 et permet de stopper la rotation de la broche. et Permettent de faire varier la vitesse de rotation programmée entre les pourcentages définis par les paramètres machine de broche "MINSOVR" et "MAXOVR", selon un pas incremental défini par le paramètre machine de broche "SOVRSTEP". Il est recommandé de définir la vitesse de rotation de broche AVANT de choisir le sens de rotation afin d’éviter un démarrage brutal. Page 12 Chapitre: 5 MANUEL Section: DEPLACEMENT DE LA BROCHE 6. TABLES Un nouvel outil, un nouveau correcteur ou un nouveau zéro pièce ne peut être sélectionné que s’il a été chargé au préalable dans la CNC. Les tables disponibles dans la CNC sont les suivantes: * * * * * Table d’Origines Table de Correcteurs Table d’Outils Table de Magasin d’outils Table de Paramètres globaux et locaux Chapitre: 6 TABLES Section: Page 1 6.1 TABLE D’ORIGINES Cette table contient les valeurs affectées à chaque zéro pièce nécessaire pendant l’exécution de la pièce. Chaque champ de cette table représente un décalage du zéro, c’est-à-dire les coordonnées correspondant au nouveau zéro pièce à sélectionner. Ces coordonnées concernent chaque axe de la machine et sont prises par rapport au zéro machine. TABLE D'ORIGINES P..... N..... 11 : 50 : 14 ORIGINE PLC X 0.0000 Y 0.0000 Z 0.0000 U 0.0000 V 0.0000 G54 X 0.0000 Y 0.0000 Z 0.0000 U 0.0000 V 0.0000 G55 X 0.0000 Y 0.0000 Z 0.0000 U 0.0000 V 0.0000 G56 X 0.0000 Y 0.0000 Z 0.0000 U 0.0000 V 0.0000 G57 X 0.0000 Y 0.0000 Z 0.0000 U 0.0000 V 0.0000 G58 X 0.0000 Y 0.0000 Z 0.0000 U 0.0000 V 0.0000 G59 X 0.0000 Y 0.0000 Z 0.0000 U 0.0000 V 0.0000 CAP INS MM EDITER F1 MODIFIER F2 CHERCHER F3 EFFACER F4 CHARGER F5 SAUVER F6 MM/POUCES F7 Cette table comprend les champs ou décalages du zéro suivants: * Décalage d’origine supplémentaire défini par le PLC. Il est utilisé, entre autres, pour corriger des déviations dûes aux dilatations de la machine. Il peut être contrôlé par l’automate et depuis le programme pièce, grâce à la variable "PLCOF(X-C)". Chaque fois que la valeur affectée à ce décalage est différente de zéro, la CNC ajoute cette valeur au décalage d’origine sélectionné en cours. * Décalages d’origine absolus G54 à G57. Ces décalages d’origine peuvent être édités ou modifiés dans ce mode de fonctionnement depuis le clavier. Ils peuvent aussi être modifiés depuis l’automate et le programme pièce, grâce à la variable de niveau haut "ORG(X-C)". Pour activer l’un de ces décalages d’origine, il doit être sélectionné au niveau de la CNC par la fonction correspondante (G54 à G57). Page 2 Chapitre: 6 TABLES Section: TABLE D’ORIGINES * Décalages d’origine incrémentaux G58 et G59. Ces décalages d’origine peuvent être édités ou modifiés dans ce mode de fonctionnement depuis le clavier. Ils peuvent aussi être modifiés depuis l’automate et le programme pièce, grâce à la variable de niveau haut "ORG(X-C)". Pour activer un décalage d’origine incrémental, on exécutera la fonction correspondante (G58 ou G59). Le nouveau décalage d’origine incrémental s’ajoutera au décalage d’origine absolu sélectionné actif. Après sélection de la table d’origines, l’opérateur peut déplacer le curseur une ligne à la fois grâce aux touches "flèche vers le haut et flèche vers le bas". Plusieurs autres options disponibles sont décrites ci-dessous. Si l’une de ces options est activée, l’opérateur dispose d’une zone d’édition à l’écran, dans laquelle le curseur peut être déplacé grâce aux touches "flèche à droite et flèche à gauche". Les touches "flèche vers le haut et flèche vers le bas" permettent de positionner le curseur sur le premier et le dernier caractères de la zone d’édition respectivement. EDITER Cette option permet d’éditer un décalage d’origine. Dès que cette option est activée, les touches changent de couleur et affichent le type d’édition offert sur fond blanc. Par ailleurs, il est possible d’obtenir à tout moment des informations supplémentaires sur les commandes d’édition grâce à la touche HELP. Pour sortir du mode Aide, frapper HELP une seconde fois. La frappe de ESC permet de sortir du mode édition sans toucher aux valeurs de la table. Quand le décalage d’origine sélectionné a été édité, frapper ENTER. Les valeurs affectées à ce décalage sont chargées dans la table. Chapitre: 6 TABLES Section: TABLE D’ORIGINES Page 3 MODIFIER Cette option permet de modifier les valeurs affectées à un décalage d’origine. Avant de frapper cette touche, on pointera au moyen du curseur le décalage d’origine à modifier. Dès que cette option est activée, les touches changent de couleur et affichent sur fond blanc le type d’option de modification qu’elles offrent. Par ailleurs, il est possible d’obtenir à tout moment des informations supplémentaires sur les commandes d’édition grâce à la touche HELP. Pour sortir du mode Aide, frapper HELP une seconde fois. La frappe de ESC efface les informations affichées dans la zone d’édition correspondant au décalage sélectionné. A partir de ce moment, ce décalage peut être édité à nouveau. Pour sortir de l’option “modifier”, frapper CL ou ESC afin d’effacer les informations affichées dans la zone d’édition, puis frapper ESC à nouveau. La table conserve ses anciennes valeurs. Quand le décalage d’origine sélectionné a été modifié, frapper ENTER. Les nouvelles valeurs affectées à ce décalage sont chargées dans la table. CHERCHER Cette option permet d’effectuer une recherche dans une table. Dès que cette option est activée, les touches affichent les options suivantes: DEBUT Cette touche positionne le curseur sur le premier décalage d’origine pouvant être édité ou modifié dans ce mode, soit G54. FINCette touche positionne le curseur sur le dernier décalage d’origine pouvant être édité ou modifié dans ce mode et permet de sortir du mode “chercher”. ORIGINE Cette fonction permet de rechercher le décalage d’origine désiré et de positionner le curseur sur ce décalage. Quand cette touche est actionnée, la CNC demande le numéro du décalage d’origine recherché. Après introduction de ce numéro, frapper ENTER. Page 4 Chapitre: 6 TABLES Section: TABLE D’ORIGINES EFFACER Cette option permet d’effacer un ou plusieurs décalages d’origine de la table. Quand un décalage d’origine est effacé, la CNC met tous ses champs à “0”. Pour effacer un décalage d’origine, on indiquera son numéro avant de frapper ENTER. Pour effacer plusieurs décalages d’origine, indiquer le premier, frapper la touche "JUSQU’A", indiquer le numéro du dernier décalage à effacer et frapper ENTER. Pour effacer tous les décalages d’origine, frapper la touche "TOUT". La CNC demande confirmation; après la frappe de ENTER, elle efface les décalages G54 à G59. CHARGER Cette option permet de charger les valeurs reçues par l’intermédiaire d’une ligne série (RS232C ou RS422) dans tous les décalages d’origine de la table. Pour ce faire, frapper la touche correspondant à la ligne série utilisée pour la transmission. La transmission commence dès la frappe de cette touche. Pour interrompre une transmission en cours, frapper la touche "ARRETER". SAUVER Cette option permet d’envoyer tous les décalages d’origine de la table vers un périphérique ou un ordinateur. Pour ce faire, frapper la touche correspondant à la ligne série utilisée pour la transmission. La transmission commence dès la frappe de cette touche. Le récepteur doit donc être prêt avant le début de la transmission. Pour interrompre une transmission en cours, frapper la touche "ARRETER". MM/POUCES Chaque fois que cette option est activée, la CNC change les unités indiquant les positions des axes linéaires. Les unités (mm ou pouces) sélectionnées sont inscrites dans la fenêtre située dans l’angle inférieur droit. On notera que ce changement n’affecte pas les axes rotatifs, qui sont représentés en degrés. Chapitre: 6 Section: TABLES TABLE D’ORIGINES Page 5 6.2 TABLE DE CORRECTEURS Cette table contient les valeurs affectées à chaque correcteur d’outil, c’est-à-dire les dimensions de chaque outil qui sera utilisé pour l’usinage. TABLE DE CORRECTEURS CORRECTEUR D001 D002 D003 D004 D005 D006 D007 D008 D009 D010 D011 D012 D013 D014 D015 D016 D017 D018 D019 D020 R R R R R R R R R R R R R R R R R R R R P..... RAYON 8.0000 3.0000 0.0000 0.0000 0.0000 0.0000 0.0000 0.0000 0.0000 0.0000 0.0000 0.0000 0.0000 0.0000 0.0000 0.0000 0.0000 0.0000 0.0000 0.0000 N..... LONGUEUR L 50.0000 L 50.0000 L 0.0000 L 0.0000 L 0.0000 L 0.0000 L 0.0000 L 0.0000 L 0.0000 L 0.0000 L 0.0000 L 0.0000 L 0.0000 L 0.0000 L 0.0000 L 0.0000 L 0.0000 L 0.0000 L 0.0000 L 0.0000 11 : 50 : 14 USURE DU RAYON I 0.0000 I 0.0000 I 0.0000 I 0.0000 I 0.0000 I 0.0000 I 0.0000 I 0.0000 I 0.0000 I 0.0000 I 0.0000 I 0.0000 I 0.0000 I 0.0000 I 0.0000 I 0.0000 I 0.0000 I 0.0000 I 0.0000 I 0.0000 USURE DE LONG. K 0.0000 K 0.0000 K 0.0000 K 0.0000 K 0.0000 K 0.0000 K 0.0000 K 0.0000 K 0.0000 K 0.0000 K 0.0000 K 0.0000 K 0.0000 K 0.0000 K 0.0000 K 0.0000 K 0.0000 K 0.0000 K 0.0000 K 0.0000 CAP INS MM EDITER F1 MODIFIER F2 CHERCHER F3 EFFACER F4 CHARGER F5 SAUVER F6 MM/POUCES F7 La taille de cette table (nombre de correcteurs) est définie dans le paramètre machine général "NTOFFSET". Page 6 Chapitre: 6 TABLES Section: TABLE DE CORRECTEURS Chaque correcteur dispose d’une série de champs où sont définies les dimensions de l’outil. Ces champs sont: * Rayon de l’outil. Il est donné par les unités de travail indiquées par le paramètre général "INCHES", et son format est: R ±5.5 * Longueur de l’outil. Elle est donnée par les unités de travail indiquées par le paramètre général "INCHES", et son format est: L ±5.5 * Correcteur d’usure du rayon d’outil. Il est donné par les unités de travail indiquées par le paramètre général "INCHES", et son format est: I ±5.5 La CNC ajoutera cette valeur au rayon nominal pour calculer le rayon réel (R+I) de l’outil. * Correcteur d’usure de longueur d’outil. Il est donné par les unités de travail indiquées par le paramètre général "INCHES", et son format est: K ±5.5 La CNC ajoutera cette valeur àla longueur nominale pour calculer la longueur réelle (Z+K) de l’outil. Dès que la table de correcteurs est activée, l’opérateur peut déplacer le curseur sur l’écran une ligne à la fois grâce aux touches "flèche vers le haut et flèche vers le bas", ou page par page grâce aux touches "page avant et page arrière". Les valeurs de chaque correcteur peuvent être éditées ou modifiées depuis le clavier, l’automate et le programme pièce, grâce aux variables de niveau haut associées aux outils. Pour éditer ou modifier les valeurs de cette table, les options suivantes sont disponibles. Dès qu’une de ces options est activée, l’opérateur dispose d’une zone d’édition sur l’écran et peut déplacer le curseur dans cette zone grâce aux touches "flèche à droite et flèche à gauche". Les touches "flèche vers le haut et flèche vers le bas" permettent de positionner le curseur sur le premier et le dernier caractère respectivement. EDITER Chapitre: 6 Section: TABLES TABLE DE CORRECTEURS Page 7 Cette option permet d’éditer le correcteur désiré. Dès que cette option est activée, les touches changent de couleur et affichent le type d’édition offert sur fond blanc. Par ailleurs, il est possible d’obtenir à tout moment des informations supplémentaires sur les commandes d’édition grâce à la touche HELP. Pour sortir du mode Aide, frapper HELP une seconde fois. La frappe de ESC permet de sortir du mode édition sans toucher aux valeurs de la table. Quand le correcteur sélectionné a été édité, frapper ENTER. Les valeurs affectées à ce correcteur sont chargées dans la table. MODIFIER Cette option permet de modifier les valeurs affectées à un correcteur. Avant de frapper cette touche, on pointera au moyen du curseur le correcteur à modifier. Dès que cette option est activée, les touches changent de couleur et affichent sur fond blanc le type d’option de modification qu’elles offrent. Par ailleurs, il est possible d’obtenir à tout moment des informations supplémentaires sur les commandes d’édition grâce à la touche HELP. Pour sortir du mode Aide, frapper HELP une seconde fois. La frappe de ESC efface les informations affichées dans la zone d’édition correspondant au correcteur sélectionné. A partir de ce moment, ce correcteur peut être édité à nouveau. Pour sortir de l’option “modifier”, frapper CL ou ESC afin d’effacer les informations affichées dans la zone d’édition, puis frapper ESC à nouveau. La table conserve ses anciennes valeurs. Quand le correcteur sélectionné a été modifié, frapper ENTER. Les nouvelles valeurs affectées à ce correcteur sont chargées dans la table. Page 8 Chapitre: 6 TABLES Section: TABLE DE CORRECTEURS CHERCHER Cette option permet d’effectuer une recherche dans une table. Dès que cette option est activée, les touches affichent les options suivantes: DEBUT Cette touche positionne le curseur sur le premier correcteur de la table pouvant être édité ou modifié dans ce mode et permet de sortir du mode “chercher”. FINCette touche positionne le curseur sur le dernier correcteur pouvant être édité ou modifié dans ce mode et permet de sortir du mode “chercher”. CORRECTEUR Cette fonction permet de rechercher le correcteur désiré et de positionner le curseur sur ce correcteur. Quand cette touche est actionnée, la CNC demande le numéro du correcteur recherché. Après introduction de ce numéro, frapper ENTER. EFFACER Cette option permet d’effacer un ou plusieurs correcteurs de la table. Quand un correcteur est effacé, la CNC met tous ses champs à “0”. Pour effacer un correcteur, on indiquera son numéro avant de frapper ENTER. Pour effacer plusieurs correcteurs, indiquer le premier, frapper la touche "JUSQU’A", indiquer le numéro du dernier correcteur à effacer et frapper ENTER. Pour effacer tous les correcteurs, frapper la touche "TOUT". La CNC demande confirmation; après la frappe de ENTER, elle efface les correcteurs. Chapitre: 6 Section: TABLES TABLE DE CORRECTEURS Page 9 CHARGER Cette option permet de charger les valeurs reçues par l’intermédiaire d’une ligne série (RS232C ou RS422) dans la table de correcteurs. Pour ce faire, frapper la touche correspondant à la ligne série utilisée pour la transmission. La transmission commence dès la frappe de cette touche. Pour interrompre une transmission en cours, frapper la touche "ARRETER". Lorsque la taille de la table reçue ne coïncide pas avec celle de la table en cours (paramètre machine général "NTOFFSET"), la CNC réagit comme suit: * La table reçue est plus courte que la table actuelle. Les correcteurs reçus sont modifiés et les correcteurs restants conservent leurs valeurs d’origine. * La table reçue est plus longue que la table actuelle. Toutes les valeurs actuelles sont modifiées, et quand la CNC détecte qu’il n’y a plus de place, elle émet le message d’erreur correspondant. SAUVER Cette option permet d’envoyer la table de correcteurs vers un périphérique ou un ordinateur. Pour ce faire, frapper la touche correspondant à la ligne série utilisée pour la transmission. La transmission commence dès la frappe de cette touche. Le récepteur doit donc être prêt avant le début de la transmission. Pour interrompre une transmission en cours, frapper la touche "ARRETER". MM/POUCES Chaque fois que cette option est activée, la CNC change les unités indiquant les dimensions de l’outil. Les unités (mm ou pouces) sélectionnées sont inscrites dans la fenêtre située dans l’angle inférieur droit. Page 10 Chapitre: 6 TABLES Section: TABLE DE CORRECTEURS 6.3 TABLE D’OUTILS Cette table contient les informations relatives aux outils disponibles et indique le type de correcteur associé aux outils, la famille à laquelle ils appartiennent, etc... TABLE D'OUTILS OUTIL T0001 T0002 T0003 T???? T???? T???? T???? T???? T???? T???? T???? T???? T???? T???? T???? T???? T???? T???? T???? T???? P..... CORRECTEUR D001 D002 D003 D000 D000 D000 D000 D000 D000 D000 D000 D000 D000 D000 D000 D000 D000 D000 D000 D000 FAMILLE F001 F002 F000 F000 F000 F000 F000 F000 F000 F000 F000 F000 F000 F000 F000 F000 F000 F000 F000 F000 N..... V. NOMINALE N00000 N00000 N00000 N00000 N00000 N00000 N00000 N00000 N00000 N00000 N00000 N00000 N00000 N00000 N00000 N00000 N00000 N00000 N00000 N00000 11 : 50 : 14 VIE REELLE R 0000.00 R 0000.00 R 0000.00 R 0000.00 R 0000.00 R 0000.00 R 0000.00 R 0000.00 R 0000.00 R 0000.00 R 0000.00 R 0000.00 R 0000.00 R 0000.00 R 0000.00 R 0000.00 R 0000.00 R 0000.00 R 0000.00 R 0000.00 ETAT N N N N N N N N N N N N N N N N A A A A A A A A A A A A A A A A CAP INS MM EDITER F1 MODIFIER F2 CHERCHER F3 EFFACER F4 CHARGER F5 SAUVER F6 F7 La taille de cette table (nombre d’outils) est définie dans le paramètre machine général "NTOOL". Chapitre: 6 Section: TABLES TABLE D’OUTILS Page 11 Chaque outil comporte les champs suivants: * Numéro du correcteur associé à l’outil. Chaque fois qu’un outil est sélectionné, la CNC considère que ses dimensions sont définies dans la table de correcteurs et qu’elles correspondent à celles spécifiées dans le correcteur indiqué. * Code de famille. Ce code doit être utilisé lorsqu’un changeur automatique d’outils est installé: il permet de remplacer un outil usé par un autre de mêmes caractéristiques. Il existe deux types de famille: * Celles correspondant aux outils normaux, dont les codes sont compris entre 0 et 199. * Celles correspondant aux outils spéciaux (et qui occupent plus d’une poche dans le magasin), dont les codes sont compris entre 200 et 255. Chaque fois qu’un nouvel outil est sélectionné, la CNC vérifie s’il est usé ("vie réelle" supérieure à "vie nominale"). Si elle décèle une usure, elle ne le sélectionne pas et prend à sa place l’outil suivant de la table appartenant à la même famille. Si, pendant l’usinage d’une pièce, l’automate demande à la CNC d’abandonner l’outil en cours (en activant l’entrée logique "TREJECT"), la CNC place l’indicateur de rejet dans le champ "ETAT" et le remplace par l’outil suivant de latable appartenant à la même famille. Le changement intervient lors du choix suivant de cet outil. Page 12 Chapitre: 6 TABLES Section: TABLE D’OUTILS * Vie nominale de l’outil. Indique le temps d’usinage (en minutes) ou le nombre d’opérations restantes possibles de cet outil. Les unités de mesure de la vie nominale et de la vie réelle des outils sont définies dans le paramètre machine général "TOOLMONI". * Vie réelle de l’outil. Indique la durée effective d’usinage de l’outil (en minutes) ou le nombre d’opérations qu’il a exécutées. Les unités de mesure de la vie nominale et de la vie réelle des outils sont définies dans le paramètre machine général "TOOLMONI". * Etat de l’outil. Indique la taille de l’outil et son état: La taille de l’outil dépend du nombre de poches qu’il occupe dans le magasin et il se définit comme suit: N = Normale (famille 0-199) S = Spéciale (famille 200-255) L’état de l’outil est défini comme suit: A = Disponible E = Usé ("vie réelle" supérieure à "vie nominale") R = Rejeté par le PLC Dès que la table d’outils est activée, l’opérateur peut déplacer le curseur sur l’écran une ligne à la fois grâce aux touches "flèche vers le haut et flèche vers le bas", ou page par page grâce aux touches "page avant et page arrière". Les champs de chaque outil peuvent être édités ou modifiés dans ce mode de travail depuis le clavier grâce aux options décrites ci-dessous. Dès qu’une de ces options est activée, l’opérateur dispose d’une zone d’édition sur l’écran et peut déplacer le curseur dans cette zone grâce aux touches "flèche à droite et flèche à gauche". Les touches "flèche vers le haut et flèche vers le bas" permettent de positionner le curseur sur le premier et le dernier caractère respectivement. Chapitre: 6 Section: TABLES TABLE D’OUTILS Page 13 EDITER Cette option permet d’éditer l’outil désiré. Dès que cette option est activée, les touches changent de couleur et affichent le type d’édition offert sur fond blanc. Par ailleurs, il est possible d’obtenir à tout moment des informations supplémentaires sur les commandes d’édition grâce à la touche HELP. Pour sortir du mode Aide, frapper HELP une seconde fois. La frappe de ESC permet de sortir du mode édition sans toucher aux valeurs de la table. Quand l’outil sélectionné a été édité, frapper ENTER. Les valeurs affectées à ce correcteur sont chargées dans la table. MODIFIER Cette option permet de modifier les valeurs affectées à un outil. Avant de frapper cette touche, on pointera au moyen du curseur l’outil à modifier. Dès que cette option est activée, les touches changent de couleur et affichent sur fond blanc le type d’option de modification qu’elles offrent. Par ailleurs, il est possible d’obtenir à tout moment des informations supplémentaires sur les commandes d’édition grâce à la touche HELP. Pour sortir du mode Aide, frapper HELP une seconde fois. La frappe de ESC efface les informations affichées dans la zone d’édition correspondant à l’outil sélectionné. A partir de ce moment, cet outil peut être édité à nouveau. Pour sortir de l’option “modifier”, frapper CL ou ESC afin d’effacer les informations affichées dans la zone d’édition, puis frapper ESC à nouveau. La table conserve ses anciennes valeurs. Quand l’outil sélectionné a été modifié, frapper ENTER. Les nouvelles valeurs affectées à cet outil sont chargées dans la table. Page 14 Chapitre: 6 TABLES Section: TABLE D’OUTILS CHERCHER Cette option permet d’effectuer une recherche dans une table. Dès que cette option est activée, les touches affichent les options suivantes: DEBUT Cette touche positionne le curseur sur le premier outil de la table pouvant être édité ou modifié dans ce mode et permet de sortir du mode “chercher”. FINCette touche positionne le curseur sur le dernier outil pouvant être édité ou modifié dans ce mode et permet de sortir du mode “chercher”. OUTIL Cette fonction permet de rechercher l’outil désiré et de positionner le curseur sur cet outil. Quand cette touche est actionnée, la CNC demande le numéro de l’outil recherché. Après introduction de ce numéro, frapper ENTER. EFFACER Cette option permet d’effacer un ou plusieurs outils de la table. Quand un outil est effacé, la CNC met tous ses champs à “0”. Pour effacer un outil, on indiquera son numéro avant de frapper ENTER. Pour effacer plusieurs outils, indiquer le premier, frapper la touche "JUSQU’A", indiquer le numéro du dernier outil à effacer et frapper ENTER. Pour effacer tous les outils, frapper la touche "TOUT". La CNC demande confirmation; après la frappe de ENTER, elle efface les outils. Chapitre: 6 Section: TABLES TABLE D’OUTILS Page 15 CHARGER Cette option permet de charger les valeurs reçues par l’intermédiaire d’une ligne série (RS232C ou RS422) dans la table d’outils. Pour ce faire, frapper la touche correspondant à la ligne série utilisée pour la transmission. La transmission commence dès la frappe de cette touche. Pour interrompre une transmission en cours, frapper la touche "ARRETER". Lorsque la taille de la table reçue ne coïncide pas avec celle de la table en cours (paramètre machine général "NTOOOL"), la CNC réagit comme suit: * La table reçue est plus courte que la table actuelle. Les outils reçus sont modifiés et les outils restants conservent leurs valeurs d’origine. * La table reçue est plus longue que la table actuelle. Toutes les valeurs actuelles sont modifiées, et quand la CNC détecte qu’il n’y a plus de place, elle émet le message d’erreur correspondant. SAUVER Cette option permet d’envoyer la table d’outils vers un périphérique ou un ordinateur. Pour ce faire, frapper la touche correspondant à la ligne série utilisée pour la transmission. La transmission commence dès la frappe de cette touche. Le récepteur doit donc être prêt avant le début de la transmission. Pour interrompre une transmission en cours, frapper la touche "ARRETER". Page 16 Chapitre: 6 TABLES Section: TABLE D’OUTILS 6.4 TABLE DE MAGASIN D’OUTILS Cette table contient des informations sur le magasin d’outils et indique les outils disponibles ainsi que le logement qu’occupe chacun d’eux. Elle indique également l’outil actif ainsi que le prochain à utiliser. Cet outil sera mis en place sur la broche après exécution de la fonction auxiliaire M06. P..... TABLE DE MAGASIN D'OUTILS POSITION MAGASIN OUTIL ACTIF OUTIL SUIVANT P001 P002 P003 P004 P005 P006 P007 P008 P009 P010 P011 P012 P013 P014 P015 P016 P017 P018 N..... 11 : 50 : 14 ETAT OUTIL T T T0001 T0002 T T T T T T T T T T T T T T T T N N A A CAP INS MM EDITER MODIFIER F1 F2 CHERCHER F3 EFFACER F4 CHARGER F5 SAUVER F6 F7 La taille de cette table (nombre de logements d’outil dans le magasin) est définie dans le paramètre machine général "NPOCKET". Chapitre: 6 TABLES Section: TABLE DE MAGASIN D’OUTILS Page 17 Chaque logement du magasin est défini par les champs suivants: * Le contenu de chaque logement, qui peut être: Un emplacement vide, signalé par la lettre "T". Un emplacement occupé par un outil, signalé par la lettre "T" suivie du numéro de l’outil correspondant. Un emplacement annulé, signalé par les caractères "T****". * L’état de l’outil occupant ce logement; il est défini par la taille et l’état de l’outil. La taille de l’outil dépend du nombre de logements qu’il occupe dans le magasin et elle se définit comme suit: N = Normale (famille 0-199) S = Spéciale (famille 200-255) L’état de l’outil se définit comme suit: A = Disponible E = Usé ("vie réelle" supérieure à "vie nominale") R = Rejeté par le PLC Dès que la table du magasin d’outils est activée, l’opérateur peut déplacer le curseur sur l’écran une ligne à la fois grâce aux touches "flèche vers le haut et flèche vers le bas", ou page par page grâce aux touches "page avant et page arrière". Les champs de chaque logement du magasin peuvent être édités ou modifiés dans ce mode de travail depuis le clavier grâce aux options décrites ci-dessous. Dès qu’une de ces options est activée, l’opérateur dispose d’une zone d’édition sur l’écran et peut déplacer le curseur dans cette zone grâce aux touches "flèche à droite et flèche à gauche". Les touches "flèche vers le haut et flèche vers le bas" permettent de positionner le curseur sur le premier et le dernier caractère respectivement. Page 18 Chapitre: 6 TABLES Section: TABLE DE MAGASIN D’OUTILS EDITER Cette option permet d’éditer le logement de magasin désiré. Dès que cette option est activée, les touches changent de couleur et affichent le type d’édition offert sur fond blanc. Par ailleurs, il est possible d’obtenir à tout moment des informations supplémentaires sur les commandes d’édition grâce à la touche HELP. Pour sortir du mode Aide, frapper HELP une seconde fois. La frappe de ESC permet de sortir du mode édition sans toucher aux valeurs de la table. Quand le logement de magasin sélectionné a été édité, frapper ENTER. Les valeurs affectées à ce logement sont chargées dans la table. MODIFIER Cette option permet de modifier les valeurs affectées à un logement d’outil. Avant de frapper cette touche, on pointera au moyen du curseur le logement d’outil à modifier. Dès que cette option est activée, les touches changent de couleur et affichent sur fond blanc le type d’option de modification qu’elles offrent. Par ailleurs, il est possible d’obtenir à tout moment des informations supplémentaires sur les commandes d’édition grâce à la touche HELP. Pour sortir du mode Aide, frapper HELP une seconde fois. La frappe de ESC efface les informations affichées dans la zone d’édition correspondant au logement d’outil sélectionné. A partir de ce moment, ce logement peut être édité à nouveau. Pour sortir de l’option “modifier”, frapper CL ou ESC afin d’effacer les informations affichées dans la zone d’édition, puis frapper ESC à nouveau. La table conserve ses anciennes valeurs. Quand le logement d’outil sélectionné a été modifié, frapper ENTER. Les nouvelles valeurs affectées à ce logement sont chargées dans la table. Chapitre: 6 TABLES Section: TABLE DE MAGASIN D’OUTILS Page 19 CHERCHER Cette option permet d’effectuer une recherche dans une table. Dès que cette option est activée, les touches affichent les options suivantes: DEBUT Cette touche positionne le curseur sur le premier logement de la table pouvant être édité ou modifié dans ce mode et permet de sortir du mode “chercher”. FINCette touche positionne le curseur sur le dernier logement de la table pouvant être édité ou modifié dans ce mode et permet de sortir du mode “chercher”. POSITION Cette fonction permet de rechercher le logement de magasin désiré et de positionner le curseur sur ce logement. Quand cette touche est actionnée, la CNC demande le numéro du logement de magasin recherché. Après introduction de ce numéro, frapper ENTER. OUTIL Cette fonction permet de rechercher l’outil désiré et de positionner le curseur sur le logement du magasin dans lequel se trouve l’outil. Quand cette touche est actionnée, la CNC demande le numéro de l’outil recherché. Après introduction de ce numéro, frapper ENTER. EFFACER Cette option permet d’effacer un ou plusieurs logements de magasin. Un logement de magasin effacé par la CNC apparaît comme “vide” et repéré par la lettre "T". Pour effacer un logement de magasin, on indiquera son numéro avant de frapper ENTER. Pour effacer plusieurs logements du magasin, indiquer le premier, frapper la touche "JUSQU’A", indiquer le numéro du dernier logement à effacer et frapper ENTER. Pour effacer tous les logements du magasin, frapper la touche "TOUT". La CNC demande confirmation; après la frappe de ENTER, elle efface les logements. Page 20 Chapitre: 6 TABLES Section: TABLE DE MAGASIN D’OUTILS CHARGER Cette option permet de charger les valeurs reçues par l’intermédiaire d’une ligne série (RS232C ou RS422) dans la table du magasin d’outils. Pour ce faire, frapper la touche correspondant à la ligne série utilisée pour la transmission. La transmission commence dès la frappe de cette touche. Pour interrompre une transmission en cours, frapper la touche "ARRETER". Lorsque la taille de la table reçue ne coïncide pas avec celle de la table en cours (paramètre machine général "NPOCKET"), la CNC réagit comme suit: * La table reçue est plus courte que la table actuelle. Les logements de magasins reçus sont modifiés et les logements restants conservent leurs valeurs d’origine. * La table reçue est plus longue que la table actuelle. Tous les emplacements de magasin actuels sont modifiés, et quand la CNC détecte qu’il n’y a plus de place, elle émet le message d’erreur correspondant. SAUVER Cette option permet d’envoyer la table du magasin d’outils vers un périphérique ou un ordinateur. Pour ce faire, frapper la touche correspondant à la ligne série utilisée pour la transmission. La transmission commence dès la frappe de cette touche. Le récepteur doit donc être prêt avant le début de la transmission. Pour interrompre une transmission en cours, frapper la touche "ARRETER". Chapitre: 6 TABLES Section: TABLE DE MAGASIN D’OUTILS Page 21 6.5 TABLES DE PARAMETRES GLOBAUX ET LOCAUX La CNC FAGOR 8050 dispose de deux types de variables générales: les paramètres locaux P0-P25 (7 niveaux) et les paramètres globaux P100-P299. La CNC met à jour les tables de paramètres après exécution des opérations indiquées dans le bloc en cours de “préparation” (lecture). Cette opération a toujours lieu avant l’exécution du bloc: les valeurs figurant dans la table risquent d’être différentes de celles du bloc en cours d’exécution. La CNC lit (prépare) 20 blocs en avance par rapport au bloc en cours d’exécution. Si le Mode d’Exécution est quitté après interruption de l’exécution du programme, la CNC met à jour les tables de paramètres avec les valeurs correspondant au bloc qui était en cours d’exécution. La valeur des paramètres des tables de paramètres locaux et globaux peut être affichée en notation décimale (4127.423) ou scientifique (0.23476 E-3). La CNC génère un nouveau niveau d’imbrication de paramètres locaux à chaque affectation de paramètres à un sous-programme. Le nombre de niveaux d’imbrication des paramètres locaux est de 6 au maximum. Les cycles fixes d’usinage G66, G68, G69, G81, G82, G83, G84, G85, G86, G87, G88 et G89 utilisent le sixième niveau d’imbrication de paramètres locaux quand ils sont actifs. Pour accéder aux différentes tables de paramètres locaux, on indiquera d’abord le niveau correspondant (Niveau 0 a niveau 6). Lors de la programmation en langage de niveau haut, il est possible de référencer les paramètres locaux par P0 à P25 ou au moyen des lettres A à Z (à l’exception de la lettre Ñ) de telle sorte que A corresponde à P0 et Z à P25. Pour cette raison, les tables de paramètres locaux montrent également les lettres associées (entre parenthèses) à côté de leurs numéros. Toutefois, lors de l’édition des tables, les lettres asosciées ne doivent pas être utilisées. Dès que la table de paramètres est activée, l’opérateur peut déplacer le curseur sur l’écran une ligne à la fois grâce aux touches "flèche vers le haut et flèche vers le bas", ou page par page grâce aux touches "page avant et page arrière". Pour éditer ou modifier les valeurs de cette table, plusieurs options sont disponibles et décrites ci-dessous. Dès qu’une de ces options est activée, l’opérateur dispose d’une zone d’édition sur l’écran et peut déplacer le curseur dans cette zone grâce aux touches "flèche à droite et flèche à gauche". Les touches "flèche vers le haut et flèche vers le bas" permettent de positionner le curseur sur le premier et le dernier caractère respectivement. Page 22 Chapitre: 6 TABLES Section: TABLES DE PARAMETRES GLOBAUX ET LOCAUX EDITER Cette option permet d’éditer le paramètre désiré. Dès que cette option est activée, les touches changent de couleur et affichent le type d’édition offert sur fond blanc. Par ailleurs, il est possible d’obtenir à tout moment des informations supplémentaires sur les commandes d’édition grâce à la touche HELP. Pour sortir du mode Aide, frapper HELP une seconde fois. La frappe de ESC permet de sortir du mode édition sans toucher aux valeurs de la table. Quand le paramètre sélectionné a été édité, frapper ENTER. Les valeurs affectées à ce paramètre sont chargées dans la table. CHERCHER Cette option permet d’effectuer une recherche dans une table. Dès que cette option est activée, les touches affichent les options suivantes: DEBUT Cette touche positionne le curseur sur le premier paramètre de la table pouvant être édité ou modifié dans ce mode et permet de sortir du mode “chercher”. FIN Cette touche positionne le curseur sur le dernier paramètre de la table pouvant être édité ou modifié dans ce mode et permet de sortir du mode “chercher”. PARAMETRE Cette fonction permet de rechercher le paramètre désiré et de positionner le curseur sur ce paramètre. Quand cette touche est actionnée, la CNC demande le numéro du paramètre recherché. Après introduction de ce numéro, frapper ENTER. INITIALISER Cette option permet d’initialiser tous les paramètres de la table, en affectant la valeur “0” à chacun d’eux. Si cette option est activée, la CNC demande confirmation de la commande; après la frappe de ENTER, elle l’exécute. Chapitre: 6 TABLES Section: TABLES DE PARAMETRES GLOBAUX ET LOCAUX Page 23 CHARGER Cette option permet de charger les valeurs reçues par l’intermédiaire d’une ligne série (RS232C ou RS422) dans la table de paramètres sélectionnée. Pour ce faire, frapper la touche correspondant à la ligne série utilisée pour la transmission. La transmission commence dès la frappe de cette touche. Pour interrompre une transmission en cours, frapper la touche "ARRETER". SAUVER Cette option permet d’envoyer la table de paramètres sélectionnée vers un périphérique ou un ordinateur. Pour ce faire, frapper la touche correspondant à la ligne série utilisée pour la transmission. La transmission commence dès la frappe de cette touche. Le récepteur doit donc être prêt avant le début de la transmission. Pour interrompre une transmission en cours, frapper la touche "ARRETER". Page 24 Chapitre: 6 TABLES Section: TABLES DE PARAMETRES GLOBAUX ET LOCAUX 7. UTILITAIRES Le passage à ce mode de fonctionnement entraîne l’affichage par la CNC du répertoire de programmes, qui présente: Les programmes pièce et de personnalisation visibles Le programme de PLC (PLC_PRG), s’il est visible Le fichier d’erreurs PLC (PLC_ERR), s’il est visible Le fichier de messages PLC (PLC_MSG), s’il est visible L’opérateur peut déplacer le curseur sur l’écran une ligne à la fois grâce aux touches "flèche vers le haut et flèche vers le bas", ou une page à la fois grâce aux touches "page avant et page arrière". Plusieurs options sont disponibles et décrites plus loin. Dès qu’une de ces options est activée, l’opérateur dispose d’une zone d’édition sur l’écran et peut déplacer le curseur dans cette zone grâce aux touches "flèche à droite et flèche à gauche". Les touches "flèche vers le haut et flèche vers le bas" permettent de positionner le curseur sur le premier et le dernier caractère respectivement. Chapitre: 7 UTILITAIRES Section: Page 1 7.1 REPERTOIRE Dès la frappe de la touche Répertoire, la CNC affiche les options suivantes par touches de fonction: * * * 7.1.1 Visualiser le répertoire de programmes Visualiser le répertoire de sous-programmes Visualiser le répertoire de programmes d’un périphérique ou d’un ordinateur. REPERTOIRE DE PROGRAMMES UTILITAIRES PROGRAM. P000001 P000002 P000003 P000010 P000012 P000111 P000112 P000200 P000662 P009999 P022463 PLC_ERR PLC_MSG PLC_PRG P...... N.... COMMENTAIRE <MOULD 1> <CNC SUBROUTINES> <MOULD 3> <CANNED CYCLE> <> <> <> <> <USER-EDITING> <USER-EXECUTION> <> <> <> <> TAILLE 000217 023705 000009 000208 000029 000869 000981 002759 000801 009389 000039 000026 000026 020634 11 : 50 : 14 DATE 09/04/91 10/04/91 10/04/91 10/04/91 09/04/91 10/04/91 10/04/91 10/04/91 09/04/91 10/04/91 10/04/91 10/04/91 10/04/91 10/04/91 HEURE ATTRIBUT 14:27:43 14:32:26 11:21:13 15:24:15 16:02:22 11:16:29 14:01:02 15:36:49 15:19:17 14:29:18 15:25:11 11:17:23 11:17:24 17:13:52 O -MX -MX -MX -MX * -MX -MX -MX -MX -MX -MX -MX O -MX O -MX -MX 14 programmes 062800 octets libres CAP INS REPERTOIRE F1 COPIER EFFACER F2 F3 RENOMMER F4 PROTECTIONS F5 COMPACTER F6 CHANGER LA DATE F7 Cette option affiche tous les programmes visibles par l’utilisateur et chargés en mémoire de la CNC. Ce répertoire peut donc contenir: Les programmes pièce Les programmes de personnalisation Le programme de PLC (PLC_PRG) Le fichier d’erreurs PLC (PLC_ERR) Le fichier de messages PLC (PLC_MSG) Le répertoire de programmes comporte les champs de définition suivants: * Nom ou numéro du programme. Il est défini par le numéro du programme dans le cas d’un programme pièce ou d’un programme de personnalisation, ou par la mnémonique correspondante dans le cas d’un programme de PLC, du fichier d’erreurs du PLC ou du fichier de messages du PLC. Page 2 Chapitre: 7 UTILITAIRES Section: REPERTOIRE DE PROGRAMMES * Commentaire associé au programme. Pour faciliter l’identification des programmes, un commentaire peut être associé à chaque programme. Ces commentaires doivent se composer de caractères alphanumériques et sont introduits dans ce mode de fonctionnement par l’option RENOMMER comme décrit plus loin. * Taille du programme. Elle est exprimée en octets et indique la taille du texte du programme. On notera que la taille réelle du programme est légèrement supérieure car ce champ ne tient pas compte de l’espace occupé par certaines variables internes (en-tête, etc.). * Date et heure de la dernière édition (modification) du programme. * Attributs Les attributs de chaque programme donnent des informations sur sa provenance et son usage, dans les champs suivants: Indique que le programme est chargé en mémoire EEPROM. * Indique que le programme est en cours d’exécution, parce qu’il s’agit du programme principal ou qu’il contient un sous-programme appelé depuis le programme ou un autre sous-programme. O Indique un programme réalisé par le fabricant de la machine. H Indique que le programme est caché, c’est-à-dire qu’il ne peut être visualisé dans aucun répertoire. Comme un programme caché peut être effacé ou modifié si son numéro est connu, il est recommandé de ne pas sélectionner l’attribut “Modifiable” lorsque l’on “cache” un programme afin d’interdire à l’opérateur de le modifier ou de l’effacer. M Indique que le programme est modifiable, c’est-à-dire qu’il peut être édité, copié, etc... Un programme dépourvu de cet attribut peut être exécuté et visualisé dans le répertoire de programmes si les attributs correspondants le permettent, mais son contenu ne peut pas être modifié par l’utilisateur. X Indique que le programme est exécutable. Un programme dépourvu de cet attribut ne peut pas être exécuté par l’opérateur. En ce qui concerne les attributs de chaque programme, seules les lettres des champs sélectionnés sont affichées. Les champs non sélectionnés sont signalés par "-". Exemple O-X Indique que le programme a été réalisé par le fabricant, qu’il sera affiché Chapitre: 7 UTILITAIRES Section: REPERTOIRE DE PROGRAMMES Page 3 7.1.2 REPERTOIRE DE SOUS-PROGRAMMES P...... N.... 11 : 50 : 14 UTILITAIRES SOUSR 0001 0005 0015 0101 0105 0109 PROG SOUSR P000002 P000002 P000002 P000002 P000002 P000002 0002 0006 0016 0102 0106 0110 PROG SOUSR P000002 P000002 P000002 P000002 P000002 P000002 0003 0013 0017 0103 0107 PROG SOUSR P000002 P000002 P000002 P000002 P000002 0004 0014 0018 0104 0108 PROG P000002 P000002 P000002 P000002 P000002 0022 SOUS ROUTINES CAP INS REPERTOIRE F1 COPIER EFFACER F2 RENOMMER F3 F4 PROTECTIONS F5 COMPACTER F6 CHANGER LA DATE F7 Cette option permet d’afficher de manière ordonnée, du plus petit au plus grand, tous les sous-programmes définis dans les programmes pièce de la CNC. En outre, le numéro du programme où est défini le sous-programme figure à côté de chaque sous-programme localisé. Si l’attribut de programme invisible est associé au programme contenant le sous-programme, ce programme s’affiche sous la forme P??????. 7.1.3 REPERTOIRE DE LA LIGNE SERIE (DNC) Si ce mode de fonctionnement est activé, la CNC visualise le répertoire des programmes pièce de l’ordinateur en format DOS. Page 4 Chapitre: 7 UTILITAIRES Section: REPERTOIRE DE SOUSPROGRAMMES 7.2 COPIER Cette option permet de copier un programme dans un autre programme ou d’envoyer les données chargées dans la EEPROM à un programmateur de EEPROM. 7.2.1 COPIER UN PROGRAMME DANS UN AUTRE PROGRAMME Pour copier un programme dans un autre programme, on choisira grâce à la touche correspondante le type de programme à copier. Les options suivantes sont disponibles: Un programme pièce Un programme de personnalisation Le programme du PLC Le fichier de messages du PLC Le fichier d’erreurs du PLC Un programme de la ligne série 1 Un programme de la ligne série 2 Si le type sélectionné correspond à un programme pièce ou à un programme de personnalisation, la CNC demande le numéro du programme à copier. Lorsque ce numéro a été introduit, frapper la touche "EN". En cas de sélection d’un programme de la ligne série 1 ou 2, la CNC “comprend” que le programme à copier est celui reçu par l’intermédiaire de cette ligne. Lorsque le programme à copier a été défini, la CNC demande quel est le programme destinataire de la copie et indique par des touches les types autorisés dans chaque cas. Si le type sélectionné correspond à un programme pièce, indiquer son numéro et frapper ENTER. Exemple: Pour copier le programme 12 dans le programme 14, frapper: COPIER PROGRAMME 12 DANS PROGRAMME 14 ENTER Si le programme destinataire de la copie existe, la CNC affiche un avis et autorise la poursuite de l’opération (effacement du programme précédent) ou l’annulation de la copie moyennant la frappe de ENTER ou ESC respectivement. Le dernier programme exécuté par la CNC ne peut pas être sélectionné comme destinataire. Un programme contenant un sous-programme ne doit pas être copié car un sous-programme ne peut pas être défini dans plus d’un programme. Cette opération est toutefois possible à condition de changer le bloc de définition de sous-programme (SUB13) en commentaire ;(SUB13) et, après la copie, de changer le numéro du sous-programme ;(SUB14) avant de transformer à nouveau le bloc de définition en bloc normal (SUB14). Chapitre: 7 Section: UTILITAIRES COPIER Page 5 7.2.2 ENVOYER LE CONTENU DE LA EEPROM A UN PROGRAMMATEUR Pour envoyer le contenu d’une EEPROM à un programmateur de EEPROM, frapper la touche “EEPROM A PROGRAMMATEUR”. La CNC enverra toutes les données en mémoire EEPROM (pages et symboles de personnalisation, programmes pièce et programme du PLC) au programmateur de EPROM. Les données sont transférées en format “MOTOROLA S3” par la ligne série RS232C. Page 6 Chapitre: 7 UTILITAIRES Section: COPIER 7.3 EFFACER Cette option permet d’effacer un ou plusieurs programmes de la CNC ou du périphérique sélectionné. Quand cette option a été activée, on indiquera par la touche de fonction correspondante le type de programme à effacer, soit: Un programme pièce Un programme de personnalisation Le programme du PLC Le fichier de messages du PLC Le fichier d’erreurs du PLC La mémoire complète de la CNC Un programme de la ligne série 1 en cas de fonctionnement en mode DNC Un programme de la ligne série 2 en cas de fonctionnement en mode DNC Si le type sélectionné correspond à un programme pièce ou à un programme de personnalisation, la CNC demande le numéro du programme à effacer. Lorsque ce numéro a été introduit, frapper la touche "ENTER". De la même façon, si le type sélectionné correspond à un programme d’une des lignes série, la CNC demande le numéro du programme à effacer. Lorsque ce numéro a été introduit, frapper la touche "ENTER". Si l’option effacement de la mémoire complète de la CNC est activée, seuls les programmes comportant l’attribut “M” (modifiable) seront effacés. Chapitre: 7 Section: UTILITAIRES EFFACER Page 7 7.4 RENOMMER Cette option permet d’affecter un nouveau nom ou commentaire au programme sélectionné. Le type de programme à renommer doit être sélectionné par la touche correspondante, parmi les choix suivants possibles: Un programme pièce Un programme de personnalisation Le programme du PLC Le fichier de messages du PLC Le fichier d’erreurs du PLC Si le type sélectionné correspond à un programme pièce ou à un programme de personnalisation, la CNC demande le numéro du programme à renommer. Lorsque ce numéro a été introduit, frapper la touche "A". Sélectionner ensuite par touches de fonction le champ à renommer. * Nouveau numéro. Cette option permet d’affecter un nouveau nom au programme sélectionné. Frapper le nouveau numéro à affecter comme nom de programme, puis ENTER. Le numéro de programme correspondant au programme du PLC ainsi qu’au fichier de messages ou d’erreurs du PLC ne doit pas être changé car le nom de ces programmes doit se composer uniquement de leur mnémonique associée. Si le nouveau numéro de programme existe déjà, la CNC affiche un avis et autorise la poursuite de l’opération (effacement du programme précédent) ou l’annulation de la copie moyennant la frappe de ENTER ou ESC respectivement. * Nouveau commentaire. Cette option permet d’affecter un commentaire au programme sélectionné. Frapper le nouveau commentaire, puis la touche "FIN TEXTE". Exemple: Pour définir comme commentaire du programme 14 le texte "ENGRENAGE", procéder comme suit: RENOMMER PROGRAMME 14 EN NOUVEAU COMMENTAIRE ENGRENAGE FIN TEXTE Page 8 Chapitre: 7 UTILITAIRES Section: RENOMMER 7.5 PROTECTIONS Pour éviter toute intrusion dans certains programmes et limiter l’accès de l’opérateur à certaines commandes de la CNC, les protections suivantes ont été prévues et sont activées par touches: * AUTORISAT. UTILISATR. Cette option permet d’afficher les programmes CNC réalisés par l’utilisateur et de sélectionner leurs attributs. * AUTORISAT. FABRICANT. Cette option permet d’afficher tous les programmes chargés dans la CNC réalisés par l’utilisateur et le fabricant, et de sélectionner leurs attributs. * Codes d’accès. Cette option permet de définir les codes que l’utilisateur devra entrer avant d’accéder aux diverses commandes de la CNC. Les attributs de chaque programme donnent des informations sur leur provenance et leur usage. Les champs affichés sont les suivants: O Indique que le programme a été réalisé par le constructeur de la machine. H Indique que le programme est caché et qu’il ne peut donc être affiché dans aucun répertoire. Comme un programme caché peut être effacé ou modifié si son numéro est connu, il est recommandé de ne pas sélectionner l’attribut “Modifiable” lorsque l’on “cache” un programme afin d’interdire à l’opérateur de le modifier ou de l’effacer. M Indique que le programme est modifiable, c’est-à-dire qu’il peut être édité, copié, etc... Un programme dépourvu de cet attribut peut être exécuté et visualisé dans le répertoire de programmes si les attributs correspondants le permettent, mais son contenu ne peut pas être modifié par l’utilisateur. X Indique que le programme est exécutable. Un programme dépourvu de cet attribut ne peut pas être exécuté par l’opérateur. En ce qui concerne les attributs de chaque programme, seules les lettres des champs sélectionnés sont affichées. Les champs non sélectionnés sont signalés par "-". Exemple: O-X Indique que le programme a été réalisé par le fabricant, qu’il sera affiché dans les répertoires, qu’il n’est pas modifiable et qu’il est exécutable. Chapitre: 7 Section: UTILITAIRES PROTECTIONS Page 9 7.5.1 AUTORISATIONS UTILISATEUR Dès que cette option a été activée, la CNC affiche les options suivantes par touches: * Répertoire. Permet d’accéder au répertoire de programmes de la CNC en affichant, outre les programmes pièce, de personnalisation et PLC visibles, tous les programmes Utilisateur cachés (attribut H). * Programme. Cette option permet de sélectionner un programme utilisateur et de lui affecter les attributs correspondants. Pour ce faire, introduire le numéro du programme désiré et frapper ENTER. Dès que le programme a été sélectionné, la CNC permet de modifier par touches les attributs "H" (invisible), "M" (modifiable) et "X" (exécutable). Lorsque les nouveaux attributs ont été définis, frapper ENTER pour les valider. 7.5.2 AUTORISATIONS FABRICANT Dès que cette option a été activée, la CNC affiche les options suivantes par touches: * Répertoire. Permet d’accéder au répertoire de tous les programmes de la CNC, et de visualiser les programmes constructeur et utilisateur, qu’ils soient visibles ou invisibles. * Programme. Cette option permet de sélectionner un programme quelconque de la CNC et de lui affecter les attributs correspondants. Pour ce faire, introduire le numéro du programme désiré et frapper ENTER. Dès que le programme a été sélectionné, la CNC permet de modifier par touches les attributs "O" (fabricant), "H" (invisible), "M" (modifiable) et "X" (exécutable). Lorsque les nouveaux attributs ont été définis, frapper ENTER pour les valider. * Programme PLC, Mesages PLC, Erreurs PLC. Ces options permettent de sélectionner le programme automate désiré et de lui affecter les attributs correspondants. Dès que le programme a été sélectionné, la CNC permet de modifier par touches les attributs "O" (fabricant), "H" (invisible), "M" (modifiable) et "X" (exécutable). Lorsque les nouveaux attributs ont été définis, frapper ENTER pour les valider. Page 10 Chapitre: 7 UTILITAIRES Section: AUTORISATIONS UTILISATEUR/FABRICANT 7.5.3 CODES D’ACCES. Quand cette option est activée, la CNC affiche tous les codes d’accès disponibles, le code défini et la mnémonique correspondante. A chaque tentative d’accès à une table ou un mode auxquels un code d’accès a été affecté, la CNC affiche une fenêtre demandant l’introduction de ce code. Dès l’introduction du code, frapper ENTER. Les codes utilisables sont les suivants: Code d’accès général (MASTERPSW) Ce code est demandé par la CNC à chaque tentative d’accès à cette option de codes d’accès (Mode UTILITAIRES / PROTECTIONS/CODES D’ACCES). Code d’accès FABRICANT (OEMPSW) Ce code est demandé par la CNC à chaque tentative d’accès aux autorisations fabricant (Mode UTILITAIRES / PROTECTIONS/AUTORISATIONS FABRICANT). Code d’accès UTILISATEUR (USERPSW) Ce code est demandé par la CNC à chaque tentative d’accès aux autorisations utilisateur (Mode UTILITAIRES / PROTECTIONS/AUTORISATIONS UTILISATEUR). Code d’accès PLC (PLCPSW) Ce code est demandé par la CNC à chaque tentative d’édition du programme PLC, ainsi que les programmes de messages et d’erreurs PLC. Il est également demandé avant toute compilation du programme PLC. La CNC permet de visualiser le programme PLC (s’il n’est pas affecté de l’attribut "H"), ainsi que les valeurs des ressources n’exigeant pas de code d’accès. Aucun code n’est demandé pour accéder aux messages et aux pages actifs, au plan d’utilisation et aux statistiques du PLC. En revanche, un code d’accès sera toujours exigé pour modifier l’état d’une ressource quelconque ou pour exécuter une commande de contrôle d’exécution du programme. Un code d’accès est également nécessaire pour sauvegarder ou restaurer le programme PLC dans la mémoire EEPROM. Chapitre: 7 Section: UTILITAIRES CODES D’ACCES Page 11 Code d’accès de personnalisation (CUSTOMPSW) Ce code est demandé par la CNC à chaque tentative d’accès au mode PERSONNALISATION. Code d’accès aux paramètres machine (SETUPPSW) La CNC permet de visualiser toutes les tables de paramètres machine sans code d’accès. Ce code est demandé par la CNC à chaque tentative d’accès aux options supposant une modification des valeurs des tables (EDITER, MODIFIER, INITIALISER, EFFACER et CHARGER), sauf pour les tables des lignes série déprotégées. Dès l’activation de l’option "Codes d’accès", la CNC affiche les options suivantes par touches: * Changer le code. Sélectionner le code à changer el introduire le nouveau. * Effacer le code. Cette option permet d’effacer (supprimer) un ou plusieurs codes de la table. Pour effacer un code, indiquer son numéro et frapper ENTER. Pour effacer plusieurs codes (obligatoirement consécutifs), indiquer le numéro du premier code à effacer, frapper la touche "JUSQU’A", indiquer le numéro du dernier code à effacer et frapper ENTER. * Effacer tous. Cette option permet d’effacer tous les codes d’accès. La CNC demande confirmation de la commande et les efface après la frappe de ENTER. Page 12 Chapitre: 7 UTILITAIRES Section: CODES D’ACCES 7.6 COMPACTER Cette option est disponible dans les CNC à 128 Kb de RAM Utilisateur afin de mémoriser les programmes pièce. Elle permet de compacter la mémoire de la CNC afin d’utiliser au maximum l’espace inutilisé. Aucun programme CNC ne doit être en cours d’exécution, de simulation ou de transfert lors du compactage de la mémoire. 7.7 CHANGER LA DATE Cette option permet de modifier la date et l’heure du système. En premier lieu, la date s’affiche selon le format jour/mois/année (12/04/1992). Après l’introduction de la nouvelle date, frapper ENTER pour la valider, ou ESC pour renoncer à l’opération. Ensuite, l’heure s’affiche selon le format heures/minutes/secondes (08/30/00). Après l’introduction de la nouvelle heure, frapper ENTER pour la valider, ou ESC pour renoncer à l’opération. Chapitre: 7 UTILITAIRES Section: COMPACTER CHANGER LA DATE Page 13 7.8 OPERATIONS AVEC LA MEMOIRE EEPROM La CNC dispose de deux options permettant de travailler avec la mémoire EEPROM. Elles sont activées par touches et présentées ci-dessous. 7.8.1 DEPLACER UN PROGRAMME A LA MEMOIRE EEPROM Pour transférer un programme à la mémoire EEPROM, frapper “DEPLACER A EEPROM”. La CNC affiche les options suivantes, accessibles par touches de fonction: PROGRAMME Cette option permet de déplacer un programme à la mémoire EEPROM. Introduire le numéro du programme désiré et frapper “ENTER”. MESSAGES PLC Si cette option est activée, la CNC charge dans la mémoire EEPROM le fichier de messages du PLC (PLC_MSG). ERREURS PLC Si cette option est activée, la CNC charge dans la mémoire EEPROM le fichier d’erreurs du PLC (PLC_ERR). Le programme sélectionné passe de la mémoire interne de la CNC à la mémoire EEPROM; il continuera toutefois à apparaître dans le répertoire de programmes pièce de la CNC comme n’importe quel autre programme, mais avec l’attribut La CNC autorise l’exécution de ce programme; il est également possible de l’effacer de la mémoire EEPROM. Toutefois, il doit être ramené à la mémoire de la CNC (par la touche “DEPLACER DE EEPROM”) pour toute opération d’édition, de modification, de copie, etc... Les programmes chargés dans la EEPROM conservent tous leurs attributs de protection (O, H, M, X); l’introduction de codes d’accès demeure donc nécessaire pour accéder à ces programmes. 7.8.2 DEPLACER UN PROGRAMME DE LA MEMOIRE EEPROM Pour déplacer un programme de la mémoire EEPROM à la mémoire interne de la CNC, frapper la touche “DEPLACER DE EEPROM”. La CNC affiche les options suivantes, accessibles par touches de fonction: PROGRAMME Cette option permet de déplacer un programme de la mémoire EEPROM. Introduire le numéro du programme désiré et frapper “ENTER”. MESSAGES PLC Si cette option est activée, la CNC extrait de la mémoire EEPROM le fichier de messages du PLC (PLC_MSG). ERREURS PLC Si cette option est activée, la CNC extrait de la mémoire EEPROM le fichier d’erreurs du PLC (PLC_ERR). Le programme sélectionné passe de la mémoire EEPROM à la mémoire interne de la CNC, et il est à nouveau traité comme n’importe quel autre programme CNC. Page 14 Chapitre: 7 UTILITAIRES Section: OPERATIONS AVEC LA MEMOIRE EEPROM 8. DNC La CNC permet d’accéder à ce mode de fonctionnement quand au moins une ligne série (RS232C ou RS422) est configurée pour travailler en mode DNC ou pour communiquer avec l’unité de disquettes FAGOR. Paramètre machine pour lignes série: “PROTOCOLE” autre que 0. Lorsque l’on accède à ce mode, la CNC affiche les informations suivantes: DISQUE 1 Etat: Actif Operation Etat: Actif Operation Erreur dernière transmission Erreur dernière transmission Nouvelle tentative dernière transmission Erreur dernière transmission Nouvelle tentative dernière transmission Erreur dernière transmission Operation Operation ACTIVER DNC 1 DESACTIVER DNC 1 ACTIVER DNC 2 DESACTIVER DNC 2 La partie gauche de l’écran correspond à la ligne série 1, et la droite à la ligne série 2. Dans l’exemple ci-dessus, la ligne série 1 est utilisée pour communiquer avec une unité de disquettes Fagor, paramètre “PROTOCOL=2” et la ligne série 2 pour communiquer par l’intermédiaire du mode DNC, paramètre “PROTOCOLE=1”. La zone supérieure, 1, indique: * L’état de la ligne série. Actif / Inactif * Le type d’opération en cours: Envoi programme / Réception programme / Envoi répertoire / Réception répertoire / etc La zone inférieure, 2, indique la dernière opération exécutée et le type d’erreur éventuelle. Chapitre: 8 DNC Section: Page 1 La partie inférieure de l’écran présente, pour chaque ligne série activée, les options suivantes accessibles par touches de fonction: ACTIVER DNC Active la ligne série correspondante. DESACTIVER DNC Désactive la ligne série correspondante. L’activation/désactivation de ce mode s’effectue dynamiquement; en conséquence, si une transmission est en cours par ce canal lors de la désactivation du mode DNC, la CNC interrompt la transmission et désactive le mode DNC. Indépendamment de ce mode de fonctionnement, le paramètre machine des lignes série “PWONDNC” permet de définir si le mode DNC sera actif ou inactif à la mise sous tension dans le canal série correspondant (RS232C ou RS422). Page 2 Chapitre: 8 DNC Section: 8.1 MODES DE FONCTIONNEMENT AVEC LES LIGNES SERIE Par l’intermédiaire des lignes série, les opérations suivantes sont possibles depuis la CNC: * Affichage, sur l’écran de la CNC, du répertoire de programmes du PC ou de l’unité de disquettes Fagor. Sélectionner le mode de fonctionnement “Utilitaires” et frapper les touches programmables suivantes: REPERTOIRE * SERIE L.* Copie de programmes dans la mémoire de la CNC depuis un PC ou une unité de disquettes. Sélectionner le mode de fonctionnement “Utilitaires” et frapper les touches programmables suivantes: REPERTOIRE SERIE L.* La CNC affiche le répertoire du périphérique. Ensuite, frapper les touches suivantes dans l’ordre: COPIER * SERIE L.* DANS PROGRAMME N° programme ENTER Copie d’un programme pièce CNC dans le PC ou une unité de disquettes Fagor. Sélectionner le mode de fonctionnement “Utilitaires” et frapper les touches programmables suivantes: REPERTOIRE SERIE L.* La CNC affiche le répertoire du périphérique. Ensuite, frapper les touches suivantes dans l’ordre: COPIER * PROGRAMME N° programme DANS SERIE L.* ENTER Exécution ou simulation d’un programme se trouvant sur un PC ou dans une unité de disquettes Fagor. Sélectionner le mode de fonctionnement “Exécution” et frapper la touche programmable SERIE L.* La CNC affiche le répertoire du périphérique. Ensuite, frapper les touches suivantes dans l’ordre: N° programme ENTER Quand la taille du programme sur PC à exécuter dépasse la capacité de mémoire disponible dans la CNC pour transmission de données, l’opération porte le nom de “exécution de programme infini”. La CNC demandera des informations au PC au fur et à mesure de l’exécution du programme. Si le programme à exécuter se trouve sur plusieurs disquettes, l’opération porte le nom de “exécution de programme infini multi-disquettes”. La CNC demandera l’introduction de nouvelles disquettes au fur et à mesure de l’exécution du programme. * Digitalisation d’une pièce et génération du programme correspondant dans un PC ou une unité de disquettes Fagor. Dans le cas de l’utilisation d’une unité de disquettes Fagor et si la disquette est pleine, la CNC demande l’introduction d’une nouvelle disquette. L’unité de disquettes comporte une mémoire RAM permettant le stockage des données pendant le changement de disquette afin d’éviter d’interrompre la digitalisation. Chapitre: 8 DNC Section: Page 3 Par l’intermédiaire des lignes série, il est possible d’exécuter les opérations suivantes depuis un PC: * Affichage, sur l’écran du PC, du répertoire de programmes de la CNC. * Copie de programmes du PC à la mémoire de la CNC. * Copie de programmes pièce de la CNC au PC. * Exécution ou simulation d’un programme se trouvant dans la CNC ou le PC. Quand la taille du programme sur PC à exécuter dépasse la capacité de mémoire disponible dans la CNC pour transmission de données, l’opération porte le nom de “exécution de programme infini”. La CNC demandera des informations au PC au fur et à mesure de l’exécution du programme. Page 4 Chapitre: 8 DNC Section: 9. PLC Ce mode permet d’accéder à l’automate pour vérifier son fonctionnement ou l’état des différentes variables du PLC. Il permet également d’éditer ou d’analyser le programme du PLC ou les fichiers de messages et d’erreurs de l’automate. Les programmes accessibles associés au PLC sont: Le programme automate (PLC_PRG) Le fichier d’erreurs de l’automate (PLC_ERR) Le fichiers de messages de l’automate (PLC_MSG) Le programme d’automate (PLC_PRG) peut être édité depuis le panneau avant au moyen des commandes correspondantes, ou chargé depuis un ordinateur ou un périphérique par l’intermédiaire d’un des ports série RS-232C ou RS-422. Le programme PLC est chargé dans la mémoire interne de la CNC avec les programmes pièce; il est visualisé dans le répertoire de programmes (utilitaires) avec ces programmes. Pour que l’automate puisse exécuter son programme, le programme source édité (PLC_PRG) doit être COMPILE. Cette opération génère un code exécutable qui sera stocké dans la mémoire interne de l’automate. Lorsque le programme a été compilé, il est inutile de conserver en mémoire le programme source (PLC_PRG); chaque fois que le programme automate doit être exécuté, c’est le programme objet qui sera exécuté. Après vérification du fonctionnement du programme automate, il est conseillé de le sauvegarder dans la EEPROM par la commande "SAUVER". En cas de perte du programme exécutable du PLC, le programme source pourra être récupéré et compilé. Dès la mise sous tension de la CNC, l’automate démarre l’exécution du programme objet. Si ce programme n’est pas disponible, l’automate le génère automatiquement en compilant le programme source "PLC_PRG" existant en mémoire. Si aucun programme "PLC_PRG" ne se trouve en mémoire, la CNC le cherchera dans la EEPROM; après compilation, elle demandera s’il doit être exécuté. Si le programme "PLC_PRG" est introuvable dans la EEPROM, la CNC affiche le code d’erreur correspondant. Chapitre: 9 PLC Section: Page 1 Oui Programme objet Non Programme source “PLCPRG” Oui Non Programme en EEPROM Oui Non Génère un programme objet Message d’ERREUR EXECUTION Le PLC exécutera toujours le programme objet présent en mémoire, qui ne correspondra pas nécessairement au programme source actuel "PLC_PRG"; il est même possible que le programme source de l’automate soit absent du répertoire de la CNC. Page 2 Chapitre: 9 PLC Section: 9.1 EDITER Dès que cette option a été activée, on indiquera par la touche correspondante le programme automate à éditer Le programme automate (PLC_PRG) Le fichier d’erreurs de l’automate (PLC_ERR) Le fichier de messages de l’automate (PLC_MSG) Après sélection du programme, la CNC affiche son contenu et l’opérateur peut déplacer le curseur sur l’écran une ligne à la fois grâce aux touches "flèche vers le haut et flèche vers le bas", ou page par page grâce aux touches "page avant et page arrière". La position ou le numéro de la ligne pointée par le curseur apparaît sur fond blanc dans la fenêtre de communications de la CNC, à côté de la fenêtre indicative CAP/INS. Plusieurs options d’édition décrites ci-dessous sont également disponibles. Dès qu’une de ces options est activée, l’opérateur dispose d’une zone d’édition sur l’écran et peut déplacer le curseur dans cette zone grâce aux touches "flèche à droite et flèche à gauche". Les touches "flèche vers le haut et flèche vers le bas" permettent de positionner le curseur sur le premier et le dernier caractère respectivement. EDITER Cette option permet d’éditer de nouveaux blocs ou lignes dans le programme sélectionné. Avant de frapper cette touche, pointer au moyen du curseur le bloc derrière lequel le nouveau bloc édité doit être inséré. Dès que cette option est activée, les touches changent de couleur et affichent sur fond blanc le type d’édition offert. La frappe de ESC efface le bloc en cours d’édition et permet de recommencer l’édition de ce bloc. Lorsque le bloc a été édité, frapper ENTER. Le nouveau bloc édité est ajouté au programme derrière le bloc pointé par le curseur. Le curseur se positionnera sur le nouveau bloc édité et la zone d’édition s’effacera, ce qui permet d’éditer d’autres blocs. On ne peut quitter cette option que lorsque la zone d’édition est vide. Dans le cas contraire, frapper ESC pour effacer les données présentes, et ESC une seconde fois pour sortir de l’option. Chapitre: 9 Section: PLC EDITER Page 3 MODIFIER Cette option permet de modifier une ligne ou un bloc du programme sélectionné. Avant de frapper cette touche, on pointera au moyen du curseur le bloc à modifier. Dès que cette option est activée, les touches changent de couleur et affichent sur fond blanc le type d’option d’édition à appliquer au bloc à modifier. La frappe de ESC efface les données affichées dans la zone d’édition pour le bloc à modifier. A partir de ce moment, le contenu du bloc peut être édité à nouveau. Pour quitter l’option "modifier", frapper la touche CL ou ESC afin d’effacer les données affichées dans la zone d’édition, puis la touche ESC à nouveau. Le bloc sélectionné ne sera pas modifié. Lorsque le bloc est modifié, frapper ENTER. Le nouveau bloc édité remplace le précédent. Page 4 Chapitre: 9 PLC Section: EDITER CHERCHER Cette option permet d’effectuer une recherche dans le programme sélectionné. Dès que cette option est activée, les touches affichent les options suivantes: DEBUT Cette touche positionne le curseur sur la première ligne du programme, qui se trouve sélectionnée, et permet de sortir du mode "chercher". FIN Cette touche positionne le curseur sur la dernière ligne du programme, qui se trouve sélectionnée, et permet de sortir du mode "chercher". TEXTE Cette fonction permet de rechercher un texte ou une série de caractères à partir du bloc pointé par le curseur. Quand cette touche est actionnée, la CNC demande la série de caractères recherchée. Lorsque ce texte a été défini, frapper la touche "FIN DE TEXTE"; le curseur se positionne sur la première série de caractères rencontrée. La recherche s’effectue à partir du bloc pointé par le curseur, y compris dans ce bloc. Le texte rencontré apparaît en surbrillance et la recherche peut continuer dans tout le programme ou être stoppée. Pour continuer la recherche, frapper ENTER. La CNC exécute la recherche à partir du dernier texte rencontré et le met en surbrillance. La recherche peut être exécutée autant de fois que désiré. Quand la CNC atteint la fin du programme, elle revient au début. Pour quitter l’option de recherche, frapper la touche "ARRETER" ou ESC. La CNC positionne le curseur sur la ligne où le texte recherché a été rencontré pour la dernière fois. N° LIGNE Si cette touche est frappée, la CNC demande le numéro de la ligne ou du bloc recherchés. Après l’introduction de ce numéro et la frappe de ENTER, le curseur se positionne sur la ligne demandée, qui est ainsi sélectionnée, et la CNC quitte l’option de recherche. Chapitre: 9 PLC Section: EDITER Page 5 REMPLACER Cette option permet de remplacer, dans le programme sélectionné et autant de fois que désiré, une séquence de caractères par une autre. Si cette option est activée, la CNC demande la séquence de caractères à remplacer. Lorsque le texte à remplacer a été défini, frapper la touche "PAR": la CNC demande la séquence de caractères de remplacement. Lorsque ce texte a été défini, frapper la touche "FIN TEXTE": le curseur se positionne sur la première séquence de caractères rencontrée. La recherche est exécutée à partir du bloc pointé par le curseur, y compris dans le bloc lui-même. Le texte rencontré apparaît en surbrillance et les touches de fonction affichent les options suivantes: REMPLACER Remplace le texte en surbrillance et continue la recherche jusqu’à la fin du programme. Si aucun autre texte à remplacer n’est rencontré, la CNC quitte l’option "remplacer". Si un autre texte est rencontré, il est mis en surbrillance et les mêmes options "remplacer" et "ne pas remplacer" sont proposées. Ne remplace pas le texte en surbrillance et continue la NE PAS REMPLACER recherche jusqu’à la fin du programme. Si aucun autre texte à remplacer n’est rencontré, la CNC quitte l’option "remplacer". Si un autre texte est rencontré, il est mis en surbrillance et les mêmes options "remplacer" et "ne pas remplacer" sont proposées. Cette option exécute une recherche et un remplacement du JUSQU’A LA FIN texte sélectionné, du texte en surbrillance à la fin du programme. Esta búsqueda y sustitución comenzará en el texto mostrado en forma resaltada y continuará hasta el final del programa. Cette option ne remplace pas le texte en surbrillance et met fin à ARRETER l’option "chercher et remplacer". Page 6 Chapitre: 9 PLC Section: EDITER EFFACER BLOC Cette option permet d’effacer un bloc ou un groupe de blocs. Pour effacer un seul bloc, il suffit de positionner le curseur sur le bloc à effacer et de frapper ENTER. Pour effacer un groupe de blocs, on indiquera le premier et le dernier bloc à effacer. On procèdera comme suit: * Positionner le curseur sur le premier bloc à effacer et frapper la touche "DEBUT BLOC". * Positionner le curseur sur le dernier bloc à effacer et frapper la touche "FIN BLOC". Si le dernier bloc à effacer est aussi le dernier bloc du programme, ce bloc peut être sélectionné par la frappe de la touche "JUSQU’A LA FIN". * Après sélection du premier et du dernier bloc à effacer, la CNC met en surbrillance les blocs sélectionnés et demande confirmation avant de les effacer. DEPLACER BLOC Cette option permet de déplacer un ou plusieurs blocs, après avoir indiqué le premier et le dernier bloc à déplacer. Procéder comme suit: * Positionner le curseur sur le premier bloc à déplacer et frapper la touche "DEBUT BLOC". * Positionner le curseur sur le dernier bloc à déplacer et frapper la touche "FIN BLOC". Si le dernier bloc à déplacer est aussi le dernier bloc du programme, ce bloc peut être sélectionné par la frappe de la touche "JUSQU’A LA FIN". Si le déplacement porte sur un seul bloc, le premier et le dernier seront les mêmes. Après sélection du premier et du dernier bloc à déplacer, la CNC met en surbrillance les blocs sélectionnés. On signalera ensuite avec le curseur le bloc derrière lequel le ou les blocs sélectionnés devront être placés. Après sélection du bloc, frapper la touche "DEBUT OPERATION" pour que la CNC exécute la commande. Chapitre: 9 Section: PLC EDITER Page 7 COPIER UN BLOC Cette option permet de copier un ou plusieurs blocs, après avoir indiqué le premier et le dernier bloc à copier. Procéder comme suit: * Positionner le curseur sur le premier bloc à copier et frapper la touche "DEBUT BLOC". * Positionner le curseur sur le dernier bloc à copier et frapper la touche "FIN BLOC". Si le dernier bloc à copier est aussi le dernier bloc du programme, ce bloc peut être sélectionné par la frappe de la touche "JUSQU’A LA FIN". Si la copie porte sur un seul bloc, le premier et le dernier seront les mêmes. Après sélection du premier et du dernier bloc à copier, la CNC met en surbrillance les blocs sélectionnés. On signalera ensuite avec le curseur le bloc derrière lequel le ou les blocs sélectionnés devront être copiés. Après sélection du bloc, frapper la touche "DEBUT OPERATION" pour que la CNC exécute la commande. Page 8 Chapitre: 9 PLC Section: EDITER COPIER A PROGRAMME Cette option permet de copier un ou plusieurs blocs d’un programme dans un autre programme. Lorsque cette option est activée, la CNC demande le numéro du programme où le ou les blocs doivent être copiés. Après l’introduction du numéro, frapper ENTER. Indiquer ensuite le premier et le dernier bloc à copier. Procéder comme suit: * Positionner le curseur sur le premier bloc à copier et frapper la touche "DEBUT BLOC". * Positionner le curseur sur le dernier bloc à copier et frapper la touche "FIN BLOC". Si le dernier bloc à copier est aussi le dernier bloc du programme, ce bloc peut être sélectionné par la frappe de la touche "JUSQU’A LA FIN". Si la copie porte sur un seul bloc, le premier et le dernier seront les mêmes. Après sélection du premier et du dernier bloc à copier, la CNC met en surbrillance les blocs sélectionnés et exécute la commande. Si le programme destinataire de la copie existe déjà, la CNC affiche les options suivantes: * Ecraser le programme. Tous les blocs concernés du programme destinataire sont effacés et remplacés par les blocs copiés. * Ajouter les blocs sélectionnés après ceux appartenant au programme destinataire. * Interrompre la commande sans exécuter la copie demandée. INCLURE PROGRAMME Cette option permet d’inclure le contenu d’un programme dans un programme sélectionné. Lorsque cette option a été activée, la CNC demande le numéro du programme dont le contenu est à inclure. Après introduction de ce numéro, frapper ENTER. On signalera ensuite avec le curseur le bloc derrière lequel le programme considéré est à inclure. Lorsque le bloc a été sélectionné, frapper la touche "DEBUT OPERATION" pour que la CNC exécute la commande. Chapitre: 9 Section: PLC EDITER Page 9 9.2 COMPILER Cette option permet de compiler le programme source de l’automate "PLC_PRG". La compilation n’est possible que si le programme automate est stoppé; sinon, la CNC demande à l’opérateur s’il désire le stopper. Quand le programme source a été compilé, la CNC génère le programme exécutable de l’automate. Si des erreurs sont détectées pendant la compilation du programme source, la CNC ne génère pas le programme objet et les erreurs détectées (15 au maximum) sont affichées. Si des défauts sans conséquence sur l’exécution sont détectées (étiquettes non référencées, etc...), la CNC affiche les messages correspondants, mais génère le programme objet. Si la compilation est correcte, la CNC demande si le programme automate doit être lancé. Page 10 Chapitre: 9 PLC Section: COMPILER 9.3 MONITORISATION Cette option permet de visualiser le programme automate et d’analyser l’état des différentes ressources et variables de l’automate. Dès que cette option est activée, la CNC affiche le programme source correspondant au programme exécutable, même si le programme source a été effacé ou modifié au niveau de la CNC. En outre, la CNC affiche en surbrillance, y compris dans les lignes non exécutées, toutes les consultations au niveau logique "1" et les actions dont les conditions sont réunies. Pour visualiser le programme à partir d’une ligne donnée, frapper la touche "L", introduire le numéro de la ligne où doit commencer la visualisation, et frapper ENTER. L’opérateur peut déplacer le curseur sur l’écran une ligne à la fois grâce aux touches "flèche vers le haut et flèche vers le bas", ou page par page grâce aux touches "page avant et page arrière". Plusieurs options de contrôle disponibles sont décrites ci-dessous. Dès qu’une de ces options est activée, l’opérateur dispose d’une zone d’édition sur l’écran et peut déplacer le curseur dans cette zone grâce aux touches "flèche à droite et flèche à gauche". Les touches "flèche vers le haut et flèche vers le bas" permettent de positionner le curseur sur le premier et le dernier caractère respectivement. MODIFIER L’ETAT DES RESSOURCES La CNC dipose des instructions suivantes permettant de modifier l’état des différentes ressources de l’automate. I 1/256 = 0/1 Change l’état (0/1) de l’entrée indiquée. Par exemple I120 = 0 met à 0 l’entrée I120. I 1/256.1/256 = 0/1 Change l’état (0/1) du groupe d’entrées indiqué. Par exemple, I100.103 = 1 met à 1 les entrées I100, I101, I102, I103. O 1/256 = 0/1 Change l’état (0/1) de la sortie indiquée. Par exemple O20 = 0 met à 0 la sortie O20. O 1/256.1/256 = 0/1 Change l’état (0/1) du groupe de sorties indiqué. Par exemple, O22.25 = 1 met à 1 les sorties O22, O23, O24, O25. M 1/5957 = 0/1 Change l’état (0/1) de la marque indiquée. Par exemple, M33O = 0 met à 0 la marque M330. M 1/5957.1/5957 = 0/1 Change l’état (0/1) du groupe de marques indiqué. Par exemple, M400.403 = 1 met à 1 les marques M400, M401, M402, M403. Chapitre: 9 Section: PLC MONITORISATION Page 11 TEN 1/256 = 0/1 Change l’état (0/1) de l’entrée Enable du temporisateur indiqué. Par exemple, TEN12 = 1 met à 1 l’entrée Enable du temporisateur T12. TRS 1/256 = 0/1 Change l’état (0/1) de l’entrée Reset du temporisateur. Par exemple, TRS2 = 0 met à 0 l’entrée Reset du temporisateur T2. TGn 1/256 n = 0/1 Change l’état (0/1) de la porte de déclenchement "TGn" du temporisateur indiqué (1/256), en lui affectant la constante de temps désirée (n). Par exemple, TG1 22 1000 = 1, met à 1 la porte de déclenchement 1 du temporisateur T22 et lui affecte une constante de temps de 1000. CUP 1/256 = 0/1 Change l’état (0/1) de l’entrée de comptage (UP) du compteur indiqué. Par exemple, CUP 33 = 0 met à 0 l’entrée de comptage du compteur C33. CDW 1/256 = 0/1 Change l’état (0/1) de l’entrée de décomptage (DW) du compteur indiqué. Par exemple, CDW 32 = 1 met à 1 l’entrée de décomptage du compteur C32. CEN 1/256 = 0/1 Change l’état (0/1) de l’entrée Enable du compteur indiqué. Par exemple, CEN 12 = 0, met à 0 l’entrée Enable du compteur C12. CPR 1/256 n = 0/1 Change l’état (0/1) de l’entrée de Présélection du compteur indiqué (1/256). Une valeur de présélection (n) sera affectée au compteur si cette instruction génère un front montant sur cette entrée. Par exemple: CPR 10 1000 = 1 met à 1 l’entrée de présélection du compteur C10. En outre, si un changement d’état est intervenu sur cette entrée (précédemment à 0) le compteur est présélectionné avec la valeur 1000. Page 12 C 1/256 = n Affecte la valeur indiquée (n) au nombre compté par le compteur spécifié. Par exemple, C 42 = 1200, affecte 1200 à la valeur comptée par le compteur C42. B 0/31 R 1/559 = 0/1 Change l’état (0/1) du Bit (0/31) correspondant au Registre (1/559) indiqué. Par exemple, B5 R200 = 0, met à 0 le bit 5 du registre R200. R 1/559 = n Affecte la valeur (n) au registre spécifié. Par exemple, R 303 = 1200 affecte la valeur 1200 au registre R303. R 1/559.1/559 = n Affecte la valeur (n) au groupe de registres indiqué. Par exemple, R234.236 = 120, affecte la valeur 120 aux registres R234, R235, R236. Chapitre: 9 PLC Section: MONITORISATION Lorsqu’il est fait référence à une ressource unique, on notera qu’elle peut être référencée par sa mnémonique correspondante. Par exemple: /STOP=1 est interprêté par la CNC comme M5001=1 CREER FENETRE La CNC permet de créer une série de fenêtres afin de visualiser l’état des diverses ressources de l’automate. Ces fenêtres se superposent au programme automate et les informations qu’elles présentent sont mises à jour dynamiquement. Les options "MODIFIER FENETRE", "FENETRE ACTIVE" et "ACTIVER SYMBOLES" permttent de manipuler ces fenêtres. Chaque fois qu’une nouvelle fenêtre est créée, la CNC lui affecte 2 lignes d’information permettant de visualiser l’état des ressources désirées. Deux types de fenêtre sélectionnables par touches sont disponibles. FENETRE DE VISUALISATION DE TEMPORISATEURS ET REGISTRES Cette fenêtre est divisée en deux parties, une pour les Temporisateurs, l’autre pour les Registres. Temporisateur. Affiche un temporisateur par ligne avec les champs d’information suivants: TG M Indique l’état logique de l’entrée de déclenchement active. Indique l’état ou mode de travail du temporisateurr: "S" pour arrêt, "T" pour temporisation et "D" pour désactivé. TEN Indique l’état logique de l’entrée Enable. TRS Indique l’état logique de l’entrée Reset. T Indique l’état logique de la sortie d’état du temporisateur. ET Indique le temps écoulé. TO Indique le temps restant. Pour demander des informations à un ou plusieurs temporisateurs, frapper la commande T 1/256 ou T 1/256.1/256, puis ENTER. Registre. Affiche un registre par ligne avec les champs d’information suivants: HEX Indique la valeur de son contenu en format hexadécimal. DEC Indique la valeur de son contenu en format décimal (signé). Pour demander des informations à un ou plusieurs registres, frapper la commande R 1/559 ou R 1/559.1/559, puis ENTER. Chapitre: 9 Section: PLC MONITORISATION Page 13 FENETRE DE VISUALISATION DE COMPTEURS ET DE DONNEES BINAIRES Cette fenêtre est divisée en deux parties, une pour les Compteurs, l’autre pour les Données Binaires. Compteur. Affiche un compteur par ligne avec les champs d’information suivants: CEN CUP CDW CPR S C Indique l’état logique de l’entrée Enable. Indique l’état logique de l’entrée de Comptage. Indique l’état logique de l’entrée de Décomptage. Indique l’état logique de l’entrée de Présélection. Indique l’état du compteur, soit "1" quand sa valeur interne comptée est de "0", et 0 dans les autres cas. Indique la valeur comptée. Pour demander des informations à un ou plusieurs compteurs, frapper la commande C 1/256 ou C 1256.1/256, puis ENTER. Données binaires. Affiche une ligne d’informations pour chaque ressource ou groupe de ressources demandé. Les instructions disponibles pour demander des informations aux diverses ressources sont: I 1/256 ou I 1/256.1/256 Montre l’état de l’entrée ou du groupe d’entrées indiqué. O 1/256 ou O 1/256.1/256 Montre l’état de la sortie ou du groupe de sorties indiqué. M 1/5957 ou M 1/5957.1/5957 Montre l’état de la marque ou du groupe de marques indiqué. B 0/31 R 1/559 Montre l’état du bit de registre indiqué. Si l’état d’une ou plusieurs entrées, sorties, ou marques est demandé, la CNC affiche des lignes d’information complètes, même si tous leurs éléments n’ont pas été demandés. Quand les noms génériques (I / O / M) sont employés pour afficher les ressources, la CNC en affiche toujours 20 par ligne et, quand leur mnémonique associée est employée, elle en affiche 3 par ligne. Dans ce dernier cas, le nom générique est affiché si aucune mnémonique n’est associée à la ressource. Si l’état d’un bit de registre est demandé, la CNC n’affiche que le bit demandé dans la ligne correspondante. Page 14 Chapitre: 9 PLC Section: MONITORISATION MODIFIER FENETRE Cette option permet de manipuler la fenêtre active (la fenêtre sélectionnée), de modifier sa taille, d’effacer son contenu et même de la supprimer (fermer). Pour ce faire, les options suivantes sont disponibles par touches logicielles: AUGMENTER Permet d’augmenter la taille de la fenêtre active, avec une ligne d’informations en plus à chaque frappe de cette touche. DIMINUER Permet de réduire la taille de la fenêtre active, avec une ligne d’informations en moins à chaque frappe de cette touche (minimum : 2 lignes). EFFACER Permet d’effacer la fenêtre active, en annulant toutes les informations. FERMER Permet de fermer la fenêtre active. Quand une fenêtre êst fermée, la CNC cesse de l’afficher. FENETRE ACTIVE Cette option permet de choisir entre le programme automate et chaque fenêtre affichée (temporisateurs, registres, compteurs et données binaires) afin de pouvoir les exploiter. On notera que les manipulations ne sont possibles que sur la fenêtre active. Dès que la fenêtre active a été sélectionnée, il est possible de: Déplacer le curseur (si le programme automate est actif) ou la zone d’affichage grâce aux touches "flèche vers le haut et flèche vers le bas". Exécuter toute commande de l’option "MODIFIER FENETRE". Chapitre: 9 Section: PLC MONITORISATION Page 15 CHERCHER Cette option, exécutable quelle que soit la fenêtre active, permet une recherche dans le programme automate et offre les options de recherche suivantes: DEBUT Cette touche positionne le curseur sur la première ligne du programme, qui se trouve sélectionnée, et permet de sortir du mode "chercher". FIN Cette touche positionne le curseur sur la dernière ligne du programme, qui se trouve sélectionnée, et permet de sortir du mode "chercher". TEXTE Cette fonction permet de rechercher un texte ou une série de caractères à partir du bloc pointé par le curseur. Quand cette touche est actionnée, la CNC demande la série de caractères recherchée. La CNC considère la recherche comme réussie dès que la série de caractères cherchée est trouvée entre espaces ou séparateurs. Ainsi, si les entrées I1, I12 et I123 sont utilisées dans le programme automate et si le texte I1 est recherché, la seule entrée remplissant ces conditions est l’entrée I1. Lorsque ce texte a été défini, frapper la touche "FIN DE TEXTE"; le curseur se positionne sur la première série de caractères rencontrée. La recherche s’effectue à partir du bloc pointé par le curseur, y compris dans ce bloc. Le texte rencontré apparaît en surbrillance et la recherche peut continuer dans tout le programme ou être stoppée. Pour continuer la recherche, frapper ENTER. La CNC exécute la recherche à partir du dernier texte rencontré et le met en surbrillance. La recherche peut être exécutée autant de fois que désiré. Quand la CNC atteint la fin du programme, elle revient au début. Pour quitter l’option de recherche, frapper la touche "ARRETER" ou ESC. Page 16 Chapitre: 9 PLC Section: MONITORISATION ACTIVER / DESACTIVER SYMBOLES Cette option permet de sélectionner le mode de représentation des différentes ressources dans toutes les fenêtres disponibles. Les noms des ressources peuvent être représentés par leurs noms génériques (I / O / M / T / C / R), ou en activant les mnémoniques associées à ces noms. Si aucune mnémonique n’est associée à une ressource, c’est son nom générique qui sera affiché. Cette touche indique toujours l’option disponible et permet de passer de l’une à l’autre ("ACTIVER SYMBOLES" o "DESACTIVER SYMBOLES"). MARCHE PLC Lorsque cette option est activée, la CNC commence l’exécution du programme automate depuis le début, y compris le cycle CY1. La CNC ignorera cette commande lorsque le programme automate est en cours d’exécution. CYCLE INITIAL Lorsque cette option est activée, la CNC n’exécute que le cycle initial (CY1) du programme automate. La CNC ignorera cette commande lorsque le programme automate est en cours d’exécution. CYCLE UNIQUE Lorsque cette option est activée, la CNC exécute le cycle principal du programme automate (PRG) une seule fois. La CNC ignorera cette commande lorsque le programme automate est en cours d’exécution. ARRET PLC Lorsque cette option est activée, la CNC interrompt l’exécution du programme automate. CONTINUER Lorsque cette option est activée, la CNC interrompt l’exécution du programme automate. Chapitre: 9 Section: PLC MONITORISATION Page 17 9.3.1 MONITORISATION AVEC LE PLC EN MARCHE ET LE PLC A L’ARRET Ne pas oublier que la CNC initialise toutes ses sorties physiques et les ressources propres du PLC à la mise sous tension, après la frappe de SHIFT-RESET et en cas d’erreur de WATCHDOG dans le PLC. On notera que la CNC initialise toutes les sorties et ressources à "0", sauf celles actives à l’état 0; dans ce cas, elles sont mises à "1". Pendant la monitorisation du programme et des diverses ressources de l’automate, la CNC affiche toujours les valeurs réelles des ressources. Si le PLC est en service, on notera que le traitement cyclique du programme se déroule comme suit: * Mise à jour par le PLC des valeurs réelles des entrées après lecture des entrées physiques (depuis l’armoire électrique). * Mise à jour des ressources M5000/5957 et R500/559 avec les valeurs des sorties logiques de la CNC (variables internes). * Exécution du cycle de programme. * Mise à jour des entrées logiques de la CNC (variables internes) avec les valeurs réelles des ressources M5000/5957 et R500/559. * Affectation des valeurs réelles des ressources "0" correspondantes aux sorties physiques (armoire électrique). * Copie des valeurs réelles des ressources I, O, M dans leurs propres images. Page 18 Chapitre: 9 PLC Section: MONITORISATION: PLC EN MARCHE ET PLC A L’ARRET E. PHYSIQUES E. REELLES SORTIES LOGIQUES CNC M 5000/5957 R 500/559 PROGRAMME FIN M 5000/5957 R 500/559 ENTREES LOGIQUES CNC S. REELLES SORTIES PHYSIQUES E. REELLE S. REELLE M. REELLE E. IMAGE S. IMAGE M. IMAGE Si le PLC est à l’arrêt, son fonctionnement sera le suivant: * Les valeurs réelles des ressources I correspondant aux entrées physiques seront mises à jour toutes les 10 millisecondes. * Les sorties physiques seront mises à jour toutes les 10 millisecondes avec les valeurs réelles de ressources O correspondantes. * Le PLC traitera toutes les demandes et modifications de ses variables internes. Chapitre: 9 Section: PLC MONITORISATION: PLC EN MARCHE ET PLC A L’ARRET Page 19 9.4 MESSAGES ACTIFS Lorsque cette option est activée, la CNC affiche une page où sont visualisés dynamiquement tous les messages actifs générés par l’automate. Ces messages sont classés par ordre de priorité, en commençant toujours par celui portant le plus petit numéro (le plus prioritaire). L’opérateur peut déplacer le curseur sur l’écran une ligne à la fois grâce aux touches "flèche vers le haut et flèche vers le bas", ou page par page grâce aux touches "page avant et page arrière". Pour effacer un ou plusieurs messages affichés, sélectionner le(s) message(s) concerné avec le curseur et frapper la touche EFFACER MESSAGE. On notera que les messages actifs sont mis à jour dynamiquement par la CNC. 9.5 PAGES ACTIVES Lorsque cette option est activée, la CNC affiche la page active portant le plus petit numéro. Pour effacer une page ou accéder au reste des pages actives, la CNC affiche les options suivantes: PAGE SUIVANTE Cette option permet de visualiser la page active suivante. PAGE PRECEDENTE Cette option permet de visualiser la page active précédente. EFFACER PAGE Cette option permet de désactiver la page affichée. On notera que les pages actives sont mises à jour dynamiquement par la CNC. 9.6 SAUVER PROGRAMME Lorsque cette option est activée, la CNC sauvegarde le programme automate dans la mémoire EEPROM. Avant d’exécuter cette opération, le programme automate doit être stoppé; s’il est en cours d’exécution, la CNC demande s’il doit être stoppé. De plus, ce programme doit être compilé avant d’exécuter cette opération. Quand le programme a été sauvegardé dans la mémoire EEPROM, la CNC demande s’il doit ou non être exécuté. Page 20 Chapitre: 9 PLC Section: OPTIONS 9.7 RESTAURER PROGRAMME Lorsque cette option est activée, la CNC restaure (récupère) le programme automate dans la mémoire EEPROM, où il avait été sauvegardé précédemment. Pour pouvoir exécuter cette opération, aucun programme ne doit être en cours d’exécution par l’automate; dans le cas contraire, la CNC demande s’il peut être stoppé. Après exécution de cette instruction, le nouveau programme source restauré remplacera le programme source précédent dont disposait l’automate. Ce programme devra être compilé et lancé pour pouvoir être exécuté par l’automate. 9.8 VARIABLES UTILISEES Lorsque cette option est activée, la CNC permet de sélectionner par touches logiciel la table de ressources utilisées dans le programme de l’automate. Les tables de ressources suivantes sont disponibles: ENTREES (I) SORTIES (O) MARQUES (M) REGISTRES (R) TEMPORISATEURS (T) COMPTEURS (C) Chapitre: 9 PLC Section: OPTIONS Page 21 9.9 STATISTIQUES Cette option affiche l’aménagement de la mémoire utilisée par le PLC, les temps d’exécution des différents modules du PLC, l’état du programme automate et la date de son édition. PLC ARRETE P...... N.... * MEMOIRE RAM (bytes) * CYCLE GENERAL - TEMPS (ms) - Cycle Minimal Cycle Maximal Cycle Medium Watchdog - Installée - Libre - Programme Objet - Date - Taille 2 6 2 65535 * MODULE PERIODIQUE - TEMPS (ms) - 11 : 50 : 14 Cycle Minimum Cycle Maximum Cycle Medium Périodicité Watchdog 65536 44654 11/04/1991 16034 * MEMOIRE EEPROM (bytes) ***** ***** ***** ***** ***** - Installée - Libre - Programme Sauvé - Date - Taille * ETAT 16384 16270 09/04/1991 102 * SOURCE PROGRAMME - Exécution - Compilé - PLC integré en CPU-CNC ARRET OUI (1/32) - Date - Taille 11/04/1991 20789 CAP INS F1 F2 F3 F4 F5 F6 F7 CYCLE GENERAL Cette section affiche le temps (maximum, minimum et moyen) mis par le PLC pour exécuter un cycle de programme. On notera que ce temps comprend: * La mise à jour des ressources avec les valeurs des entrées physiques et des variables internes de la CNC. * L’exécution du cycle principal et du module périodique s’il est exécuté pendant le cycle. * La mise à jour des variables internes de la CNC et des sorties physiques avec les valeurs des ressources. * Les copies des ressources dans leurs images correspondantes. Cette section affiche également le temps de watchdog sélectionné par le paramètre machine de l’automate "WDGPRG". Page 22 Chapitre: 9 PLC Section: STATISTIQUES MODULE PERIODIQUE Cette section affiche le temps (maximum, minimum et moyen) mis par le PLC pour exécuter le module périodique. Elle affiche également la périodicité affectée à ce module par la directive "PE t". Cette périodicité indique selon quelle fréquence le module périodique sera exécuté. Elle affiche enfin le temps de watchdog du module périodique sélectionné par le paramètre machine de l’automate "WDGPER". ETAT Cette section donne des informations sur l’état du programme automate, en indiquant s’il est compilé ou non, en cours d’exécution ou stoppé. Lorsque l’automate ne dispose pas de sa propre UC (intégrée dans l’UC de la CNC), elle indique également le temps que l’UC de la CNC affecte à l’automate. Cette valeur sera définie par le paramètre machine “CPUTIME” de l’automate. MEMOIRE RAM Cette section indique la mémoire RAM du système disponible pour l’usage exclusif du PLC (installée), ainsi que la mémoire libre disponible. Le programme objet (exécutable) s’obtient par compilation du programme source, et c’est celui exécuté par le PLC. Cette section affiche la date de sa création et l’espace mémoire RAM qu’il occupe. MEMOIRE EEPROM Cette section indique la mémoire RAM du système disponible pour l’usage exclusif du PLC (installée), ainsi que la mémoire libre disponible. A chaque exécution de la commande SAUVER PROGRAMME, la CNC charge le programme automate dans cette mémoire EEPROM (dans un pseudo-code). Cette section indique la date de sa sauvegarde et sa taille. PROGRAMME SOURCE Cette section indique la date de la dernière édition du programme source ainsi que sa taille. Le programme source du PLC est stocké dans la mémoire RAM de la CNC. Chapitre: 9 PLC Section: STATISTIQUES Page 23 9.10 ANALYSEUR LOGIQUE L’analyseur logique est particulièrement indiqué pour réaliser la mise au point de la machine et déterminer des erreurs et situations critiques dans le comportement des signaux. Cette option permet d’analyser le comportement des signaux logiques du PLC en fonction d’une base de temps et de certaines conditions de déclenchement fixées par l’utilisateur. Il est possible d’analyser jusqu’à 8 signaux à la fois. Les résultats sont affichés au moyen d’une interface graphique facilitant l’interprétation des données. 9.10.1 DESCRIPTION DE L’ECRAN DE TRAVAIL La page d’écran de l’analyseur logique comporte les zones ou fenêtres d’affichage suivantes: PLC IN EXECUTION P...... N.... 12 : 16 : 37 M 2009 M 2010 T1 M 2011 C 10 MSTROBE /ALARM I5 Cycles TRIGGER: NOT/ALARM Base Temps: 300 ms Etat Trace: COMPLETE Offset Curseur: Type Trigger: CENTRE CAP INS SELECTION VARIABLES CONDITION TRIGGER F1 1.- F2 BASE TEMPS EXECUTER TRACE F3 F4 ANALYZER TRACE F5 F6 F7 Fenêtre d’états Elle affiche sous forme graphique l’état de chaque signal sélectionné. Elle comporte deux zones: une zone de variables et une zone d’états. * Page 24 La zone de variables affiche les noms ou symboles des signaux logiques à analyser. Chapitre: 9 PLC Section: ANALYSEUR LOGIQUE * La zone d’états affiche l’état de chaque variable sous forme d’ondes carrées. La ligne correspondant à l’état logique 0 est en gras. Elle affiche également une ligne verticale rouge pour indiquer le point TRIGGER ou de déclenchement et une autre ligne verticale verte pour indiquer la position du curseur. La ligne verticale verte peut être déplacée sur le tracé et permet de mesurer les temps entre deux points de ce tracé. La zone d’états est divisée en plusieurs bandes verticales, chacune représentant l’espace de temps défini par la constante de temps "Base de temps". La constante "Base de temps" définit la résolution des signaux logiques et, une fois définie par l’utilisateur, elle peut être modifiée autant de fois que désiré. Le rapport entre la "Base de temps" et la résolution des signaux est inversement proportionnelle: plus la "base de temps" est faible, plus la résolution des signaux est grande, et vice-versa. 2.- Fenêtre de cycles Cette fenêtre affiche une série de traits verticaux "¦". Chaque trait signale le moment où commence l’exécution d’un nouveau cycle de programme de PLC. Elle permet de maintenir un rapport entre le flux de signaux logiques et la durée de chaque cycle d’exécution du PLC. 3.- Fenêtre d’informations Cette fenêtre donne des informations générales sur tracé en cours d’affichage. Il s’agit des informations suivantes: Trigger Affiche la condition de déclenchcment fixée par l’utilisateur pour réaliser le tracé. Base Temps Indique la base de temps définie par l’utilisateur et employée pour afficher le tracé actuel. Etat tracé Indique l’état actuel du tracé. Les textes affichés et leurs significations sont les suivants: Vide Capture Complet Pas de tracé calculé. Tracé en cours. Un tracé est disponible en mémoire. Chapitre: 9 Section: PLC ANALYSEUR LOGIQUE Page 25 Offset Curseur Indique la distance, en millisecondes, entre l’emplacement du curseur (trait vert) et la position de déclenchement (trait rouge). Type Trigger Indique le type de déclenchement choisi. Les textes affichés et leurs significations sont les suivants: Avant Après Centre Defaut 4.- Le Trigger est placé au début du tracé. Le Trigger est placé à la fin du tracé. Le Trigger est placé au centre du tracé. Aucune condition de déclenchement n’a été fixée. Fenêtre d’édition Il s’agit de la fenêtre d’édition standard de la CNC, utilisée pour tous les processus exigeant une entrée de données. 5.- Fenêtre de messages La CNC utilise cette fenêtre pour afficher un message d’avertissement ou d’erreur. Page 26 Chapitre: 9 PLC Section: ANALYSEUR LOGIQUE 9.10.2 SELECTION DES VARIABLES ET DES CONDITIONS DE DECLENCHEMENT Avant de demander un tracé, il est nécessaire de définir les variables à analyser, le type et les conditions de déclenchement ainsi que la base de temps à employer pour afficher les données saisies. Pour ce faire, les options "SELECTION VARIABLES", "CONDITION TRIGGER" et "BASE DE TEMPS", affichées par touches logicielles sont disponibles. 9.10.2.1 SELECTION VARIABLES Cette option permet de sélectionner jusqu’à 8 variables pour analyse ultérieure. Elle affiche un curseur sur la zone de variables, qui peut être déplacé grâce aux touches "flèche vers le haut" et "flèche vers le bas". En outre, les options suivantes sont affichées par touches logicielles: EDITION Cette option permet d’éditer une nouvelle variable ou de modifier l’une des variables actuelles. Avant de frapper cette touche, on pointera grâce au curseur l’emplacement où cette variable sera affichée. Dès que cette option est activée, les touches changent de couleur et affichent sur fond blanc le type d’option d’édition possible. Tout signal logique du PLC (I3, B1R120, TEN 3, CDW 4, DFU M200, etc...) peut être analysé, et référencé par son nom ou son symbole associé. Il est également possible d’analyser des expressions logiques composées d’une ou plusieurs consultations deant respecter la syntaxe et les normes appliquées pour l’écriture des équations du PLC. M100 AND (NOT I15 OR I5) AND CPS C1 EQU 100 Même s’il semble difficile de comprendre le traitement des consultations et expressions au niveau d’un analyseur logique, on notera que cet utilitaire peut se révéler très utile si l’on désire connaître l’état de la totalité d’une expression. Il est interdit d’utiliser plus de 16 instructions de détection de fronts (DFU et DFD) dans l’ensemble des définitions de variables et condition de trigger sélectionnées. La frappe de ESC efface la variable en cours d’édition. A partir de ce moment, cette variable peut être éditée à nouveau. Chapitre: 9 Section: PLC ANALYSEUR LOGIQUE Page 27 Quand cette variable a été éditée, frapper ENTER. La nouvelle variable éditée s’affiche à l’emplacement occupé par le curseur dans la zone de variables. Seuls les 8 premiers caractères de la variable sélectionnée s’affichent, même si la variable ou l’expression utilisée pour définir cette variable en comporte plus. Le curseur se positionne sur l’emplacement de la variable suivante, qui s’affiche dans la zone d’édition; il est ainsi possible de poursuivre l’édition de nouvelles variables. Pour quitter cette option, la zone d’édition doit être vide. Frapper ESC pour effacer son contenu, puis ESC une seconde fois pour sortir de l’option. EFACER Cette option permet d’effacer une variable. Avant de frapper cette touche, sélectionner la variable à effacer au moyen du curseur. Répéter ces opérations pour chaque variable à effacer. EFFACER TOUS Cette option efface toutes les variables de la fenêtre d’états. Page 28 Chapitre: 9 PLC Section: ANALYSEUR LOGIQUE 9.10.2.2 SELECTION DE LA CONDITION TRIGGER La condition de déclenchement, ou Trigger est définie comme la condition autour de laquelle la saisie de données doit avoir lieu. La saisie peut intervenir avant, après, ou avant et après que la condition de déclenchement (trigger) sélectionnée a été remplie. Cette option permet de sélectionner le type et la condition de déclenchement de l’analyseur logique. Pour ce faire, les options suivantes sont disponibles par touches logiciel: EDITION Cette option permet d’éditer ou modifier la condition de trigger (ou déclenchement) autour de laquelle la saisie des données à analyser doit avoir lieu. Dès que cette option est activée, les touches changent de couleur et affichent sur fond blanc le type d’édition offert. Il est possible d’analyser toute expression logique, qui peut être composée d’une ou plusieurs consultations devant respecter la syntaxe et les règles utilisées pour écrire les équations de PLC. Exemples d’expressions et de conditions du déclenchement: M100 NOT M100 CPS R100 EQ 1 NOT I20 AND I5 Le déclenchement a lieu quand M100 = 1 Le déclenchement a lieu quand M100 = 0 Le déclenchement a lieu quand R100 = 1 Le déclenchement a lieu quand l’expression est vraie Il est interdit d’utiliser plus de 16 instructions de détection de fronts (DFU et DFD) dans l’ensemble des définitions de variables et condition de trigger sélectionnées. La frappe de ESC efface la condition de "trigger" en cours d’édition. A partir de ce moment, cette condition peut être éditée à nouveau. Quand "trigger" a été édité, frapper ENTER. La nouvelle condition éditée s’affiche dans la fenêtre d’informations. Si aucune condition de déclenchement n’a été spécifiée, le système considère qu’il s’agit d’un trigger par défaut et il affiche le message "Type Trigger: DEFAUT" dans la fenêtre d’informations. En outre, il interdit la sélection de toute condition de déclenchement possible (trigger avant, trigger centre, trigger après). TRIGGER AVANT La CNC commence la saisie des données dès que la condition de déclenchement choisie est remplie. Ensuite, dès que le tracé est exécuté, le trigger (trait vertical rouge) s’affiche au début du tracé. Chapitre: 9 Section: PLC ANALYSEUR LOGIQUE Page 29 TRIGGER APRES La CNC commence la saisie des données dès que l’opérateur a activé l’option d’exécution du tracé (avant que la condition de "trigger" soit remplie). Le tracé est considéré comme terminé dès que la condition de déclenchement choisie est remplie. Le système affiche le "trigger" (trait vertical rouge) à la fin du tracé. TRIGGER AU CENTRE La CNC commence la saisie des données dès que l’opérateur a activé l’option d’exécution du tracé. Lorsque le tracé est terminé, le "trigger" (trait vertical rouge) s’affiche au centre du tracé. Page 30 Chapitre: 9 PLC Section: ANALYSEUR LOGIQUE 9.10.2.3 SELECTION DE LA BASE DE TEMPS Grâce à ce paramètre, l’utilisateur spécifie la durée représentée par chaque bande verticale. Comme la largeur de ces bandes est fixe, la résolution des signaux sera définie par cette base de temps. Ainsi, plus la base de temps est faible, plus la résolution des signaux est grande. Exemple: Marque changeant d’état toutes les 2 millisecondes. Sa représentation avec une base de temps de 10 millisecondes sera: Sa représentation avec une base de temps de 20 millisecondes sera: Sa représentation avec une base de temps de 4 millisecondes sera: La base de temps est définie en millisecondes et la valeur sélectionnée s’affiche dans la fenêtre d’informations. Par défaut, la CNC fixe une base de temps de 10 millisecondes. En principe, il est possible de fixer une base de temps s’adaptant à la fréquence des signaux à traiter. Ensuite, pendant l’analyse du tracé, il sera possible de changer de base de temps, ce qui permet d’obtenir une résolution du signal plus fine. Chapitre: 9 Section: PLC ANALYSEUR LOGIQUE Page 31 9.10.3 EXECUTER TRACE Lorsque les variables et les conditions de déclenchement désirées ont été sélectionnées, frapper la touche logiciel "EXECUTER TRACE" afin que la CNC puisse commencer à saisir les données. Quand la condition de déclenchement sélectionnée est remplie, la ligne de trigger affichée dans la fenêtre d’informations change de couleur. Pendant l’exécution du tracé, la fenêtre d’informations affiche le message "Etat tracé: CAPTURE". Le tracé s’achève quand la mémoire-tampon interne affectée à cette fonction est pleine ou en cas d’interruption de la fonction par la touche "ARRETER TRACE". A partir de ce moment, la fenêtre d’informations affiche le message "Etat tracé: COMPLET". Page 32 Chapitre: 9 PLC Section: ANALYSEUR LOGIQUE 9.10.3.1 SAISIE DE DONNEES La saisie des données intervient au début de chaque cycle (PRG et PE), après lecture des entrées physiques et mise à jour des marques correspondant aux sorties logiques de la CNC ou juste avant le début de l’exécution du programme. Pour réaliser la saisie de données pendant l’exécution du cycle de PLC, utiliser la directive "TRACE". Cette directive permet la saisie de données de signaux dont la fréquence de changement est supérieure au temps de cycle, ainsi que de données changeant d’état pendant l’exécution du cycle, mais dont l’état est identique au début et à la fin du cycle. Exemple d’utilisation de la directive "TRACE": PRG ——————————TRACE ——————————TRACE ——————————TRACE ——————————FIN PE 5 —————TRACE —————END ; Saisie de données ; Saisie de données ; Saisie de données ; Saisie de données La saisie de données pendant l’exécution du tracé, dabs ce programme, se produit: - Au début de chaque cycle PRG A chaque exécution du module périodique (toutes les 5 millisecondes) A 3 reprises pendant l’exécution du module PRG Une fois pendant l’exécution du module PE De cette façon, grâce à la directive "TRACE", il est possible d’augmenter la fréquence de saisie de données, en particulier aux points du programme jugés les plus critiques. La directive "TRACE" ne doit être utilisée que lors du déverminage du programme automate; elle ne doit plus être utilisée dès que le déverminage est terminé. Chapitre: 9 Section: PLC ANALYSEUR LOGIQUE Page 33 9.10.3.2 MODES DE FONCTIONNEMENT Le mode de saisie de données dépend du type de trigger sélectionné. Les divers types de déclenchement (trigger) et le mode de saisie de données dans chaque cas sont décrits cidessous: Trigger Avant La saisie de données commence dès que la condition de déclenchement sélectionnée est remplie, soit lorsque la ligne de trigger affichée dans la fenêtre d’informations change de couleur. Le tracé est considéré comme terminé quand la mémoire-tampon de tracé est pleine ou quand l’opérateur force l’arrêt du tracé (touche "ARRETER TRACE"). En cas d’arrêt forcé du tracé (touche "ARRETER TRACE") avant que "trigger" se produise, le tracé sera vide. Trigger Après La saisie de données commence dès que l’opérateur frappe la touche "EXECUTER TRACE". Le tracé est considéré comme terminé quand la condition de déclenchement sélectionnée est remplie ou quand l’opérateur force l’arrêt du tracé (touche "ARRETER TRACE"). En cas d’arrêt forcé du tracé avant que "trigger" se produise, le tracé s’affiche avec des données mais sans position de déclenchement (ligne verticale rouge). Trigger Centre La saisie de données commence dès que l’opérateur frappe la touche "EXECUTER TRACE". La CNC validera une moitié de la mémoire-tampon du tracé pour stocker les données correspondant au tracé antérieur au "trigger" et l’autre moitié pour les données correspondant au tracé postérieur au "trigger". Le tracé est considéré comme terminé quand la mémoire-tampon de tracé est pleine ou quand l’opérateur force l’arrêt du tracé (touche "ARRETER TRACE"). En cas d’arrêt forcé du tracé avant que "trigger" se produise, le tracé s’affiche avec des données mais sans position de déclenchement (ligne verticale rouge). Trigger par Défaut La CNC réalise ce type de tracé quand aucune condition de déclenchement n’est spécifiée. La saisie de données commence dès que l’opérateur frappe la touche "EXECUTER TRACE". Le tracé est considéré comme terminé quand l’opérateur force l’arrêt du tracé (touche "ARRETER TRACE"), et le tracé s’affiche avec des données mais sans position de déclenchement (ligne verticale rouge). Page 34 Chapitre: 9 PLC Section: ANALYSEUR LOGIQUE 9.10.3.3 REPRESENTATION DU TRACE Lorsque la saisie de données est terminée, la CNC affiche dans la fenêtre d’états et sous forme graphique les signaux basés sur le tracé calculé pour les variables analysées. En outre, un trait vertical rouge indiquant le point où s’est produit le "trigger" et un trait vertical vert indiquant la position du curseur se superposent au tracé. La position du curseur (ligne verticale verte) peut être déplacée sur toute la longueur du tracé grâce aux touches suivantes: Flèche à gauche Déplace le curseur d’un pixel à gauche. Si cette touche est maintenue, le curseur avance d’un pixel à la fois, sa vitesse augmentant avec le temps. Si le curseur se trouve complètement à gauche, le tracé affiché se déplacera vers la droite sans que le curseur change de position. Flèche à droite Déplace le curseur d’un pixel à droite. Si cette touche est maintenue, le curseur avance d’un pixel à la fois, sa vitesse augmentant avec le temps. Si le curseur se trouve complètement à droite, le tracé affiché se déplacera vers la gauche sans que le curseur change de position. Page précédente Déplace le curseur d’une page d’écran à gauche. Page suivante Déplace le curseur d’une page d’écran à droite. La CNC affichera en permanence dans la fenêtre d’informations la position du curseur (trait vertical vert) par rapport à la position de déclenchement (trait vertical rouge). Cette donnée est affichée en tant que "Offset Curseur" et en millisecondes. Chapitre: 9 Section: PLC ANALYSEUR LOGIQUE Page 35 9.10.4 ANALYSER TRACE Lorsque la saisie de données est terminée, la CNC affiche le tracé dans la fenêtre d’états et valide la touche "ANALYSER TRACE". Cette option permet de positionner le curseur (trait vertical vert) au début du tracé, à sa fin ou en un point donné de ce tracé. Elle permet également de modifier la base de temps utilisée pour représenter le tracé ou de calculer l’intervalle de temps entre deux points du tracé. Pour ce faire, les options suivantes sont disponibles par touches logiciel: Chercher Début Affiche le début du tracé, avec le curseur positionné au début du tracé. Chercher Fin Affiche la dernière partie du tracé, avec le curseur positionné à la fin du tracé. Chercher Trigger Affiche la zone du tracé correspondant à la zone de déclenchement. Le point où s’est produit le "trigger" est signalé par un trait vertical rouge qui se superpose au tracé. La CNC exécute cette option quand un "trigger" se produit pendant l’analyse du tracé. Chercher Temps Lorsque cette touche est frappée, la CNC demande la position que doit occuper le curseur par rapport au point de déclenchement. Cette valeur est exprimée en millisecondes. Exemple: Si une "Recherche de Temps" de -1000 millisecondes a été sélectionnée, la CNC affichera la partie du tracé correspondant à 1 seconde avant le moment du "trigger". Si aucun "trigger" ne s’est produit pendant l’analyse du tracé, la CNC supposera que la position indiquée est référencée par rapport au début du tracé. Page 36 Chapitre: 9 PLC Section: ANALYSEUR LOGIQUE Calculer Temps Cette option permet de connaître l’intervalle de temps entre deux points du tracé. Procéder comme suit pour définir les points de début et de fin du calcul. Positionner le curseur sur le point de début du calcul et frapper la touche "MARQUER DEPART" pour le valider. Le déplacement du curseur est commandé par les touches "Flèche à gauche", "Flèche à droite", "Page précédente" et "Page suivante". Positionner le curseur sur le point final du calcul et frapper la touche "MARQUER FINAL" pour le valider. La CNC affiche l’intervalle de temps (en millisecondes) entre ces deux points dans la fenêtre de messages. Cette possibilité peut s’avérer très utile pour calculer avec précision les temps de montée et de descente du front des signaux, le temps entre le déclenchement de deux signaux, le temps entre le déclenchement d’un signal et le début du cycle, etc... Modifier Base Cette option permet de modifier la "Base de temps". La zone d’états est divisée en plusieurs bandes verticales, chacune représentant l’intervalle de temps défini par la constante "Base de temps". Le rapport entre la "Base de temps" et la résolution des signaux est inversement proportionnelle, c’est-à-dire que, plus la "base de temps" est faible, plus la résolution du signal est grande, et vice-versa. Lorsque cette touche est actionnée, la CNC demande la nouvelle valeur à affecter à la base de temps. Cette valeur est exprimée en millisecondes. Chapitre: 9 Section: PLC ANALYSEUR LOGIQUE Page 37 10. PERSONNALISATION Ce mode de fonctionnement permet de créer jusqu’à 256 PAGES définies par l’utilisateur, et qui sont stockées dans la mémoire EEPROM. Il permet également de créer jusqu’à 256 SYMBOLES utilisés pour créer les pages d’écran personnalisées de l’utilisateur. Ces symboles sont également stockés dans la mémoire EEPROM. Les informations contenues dans une page ou un symbole ne doivent pas occuper plus de 4 Ko de mémoire; dans le cas contraire, la CNC émet le message d’erreur correspondant. La mémoire EEPROM disponible pour stocker des pages et symboles de l’utilisateur est indiquée dans le mode de fonctionnement DIAGNOSTIC / Configuration du Système comme une des Ressources de la CNC. Les pages d’écran utilisateur chargées en EEPROM peuvent être: * Utilisées dans les programmes de personnalisation, comme décrit plus loin. * Affichées à la mise sous tension (pahe 0) en remplacement du logo FAGOR. * Activées depuis le PLC. Le PLC dispose de 256 marques avec leur mnémonique correspondante pour sélectionner les pages d’écran utilisateur. Ces marques sont: M4700 M4701 M4702 ----M4953 M4954 M4955 PIC0 PIC1 PIC2 ------PIC253 PIC254 PIC255 Lorsqu’une de ces marques est mise à "1", la page correspondante est activée. * Utilisées pour compléter le système d’aide des fonctions M (pages 250-255). A chaque demande d’informations d’aide lors de la programmation des fonctions auxiliaires "M" (frappe de HELP), la CNC affiche la page interne correspondante. Chapitre: 10 PERSONNALISATION Section: Page 1 Lorsque la page utilisateur 250 est définie, ces informations sont complétées par le symbole pour indiquer la présence de pages d’informations supplémentaires. Si cette touche est actionnée, la CNC affiche la page utilisateur 250. La CNC continue à afficher ce symbole tant que d’autres pages d’aide définies par l’utilisateur sont définies (250-255). Ces pages doivent être définies en ordre séquentiel, en commençant toujours par la page 250. Si elle constate qu’une des pages n’est pas définie, la CNC supposera qu’il n’existe plus de page disponible. Les pages utilisateur activées depuis le PLC peuvent être affichées avec l’option PAGES ACTIVES du PLC. Les diverses options disponibles dans ce mode de fonctionnement sont: * UTILITAIRES Permet la manipulation de symboles et pages utilisateur (éditer, copier, effacer, etc...). * ELEMENTS GRAPHIQUES Permet d’inclure des éléments graphiques dans le symbole ou la page sélectionnés. * TEXTES Permet d’inclure des textes dans le symbole ou la page sélectionnés. * MODIFICATIONS Permet de modifier le symbole ou la page sélectionnés. Page 2 Chapitre: 10 PERSONNALISATION Section: 10.1 UTILITAIRES Les diverses options disponibles dans ce mode sont: REPERTOIRE Cette option permet de visualiser le répertoire de pages utilisateur ou de symboles de l’utilisateur. Le répertoire de pages affiche les pages utilisateur chargées en mémoire EEPROM et la taille de chacune d’elles (en bytes). Le répertoire de symboles affiche les symboles chargés en mémoire EEPROM et la taille de chacun d’eux (en bytes). Dans les deux cas, le nombre total de pages ou de symboles ainsi que l’espace mémoire EEPROM libre sont indiqués. COPIER Cette option permet de copier une page ou un symbole. On procèdera comme suit: * Par la touche correspondante, sélectionner l’origine de la page ou du symbole à copier. Répertoire de PAGES, répertoire de SYMBOLES ou une des deux lignes série dont dispose le système. * Si PAGE ou SYMBOLE est sélectionné, on indiquera leur numéro avant de frapper la touche "EN". * Indiquer ensuite, par la touche correspondante, le destinataire de la copie. Une page de la CNC peut être copiée dans une autre page ou dans l’une des deux lignes série dont dispose le système. Un symbole de la CNC peut être copié dans un autre symbole ou dans l’une des deux lignes série dont dispose le système. Un fichier reçu par l’intermédiaire d’un des deux ports série du système peut être copié dans une page ou un symbole de la CNC, selon le type de fiochier reçu. * Frapper ENTER pour valider l’instruction de copie. Si la page ou le symbole destinataires de la copie existent déjà, la CNC permet d’annuler la commande ou de remplacer la page ou le symbole existants par la page ou le symbole copiés. Chapitre: 10 Section: PERSONNALISATION UTILITAIRES Page 3 Exemple: pour copier la page 22 dans la page 34, frapper les touches suivantes: COPIER PAGE 22 A PAGE 34 ENTER EFFACER Cette option permet d’effacer une page ou un symbole. On procèdera comme suit: * Par la touche correspondante, sélectionner le type de fichier à effacer, soit "PAGE" ou "SYMBOLE". * Indiquer leur numéro et frapper ENTER. La CNC demandera confirmation de la commande. RENOMMER Cette option permet d’affecter un nouveau numéro ou un nouveau commentaire à une page ou à un symbole. Par la touche correspondante, sélectionner le type de fichier à renommer, soit "PAGE" ou "SYMBOLE". La CNC demandera le numéro de page ou de symbole à renommer. Après l’introduction de ce numéro, frapper la touche "A". Sélectionner ensuite par touche le champ à renommer. * Nouveau numéro. Cette option permet d’affecter un nouveau numéro à la page ou au symbole sélectionnés. Introduire le numéro à affecter et frapper ENTER. Si le nouveau numéro existe déjà, la CNC affiche un message d’avertissement et donne la possibilité de continuer l’opération (en effaçant le numéro précédent) ou d’annuler l’opération en frappant les touches ENTER ou ESC respectivement. * Nouveau commentaire. Cette option permet d’affecter un commentaire à la page ou au symbole sélectionnés. Introduire le nouveau texte à affecter comme commentaire et frapper la touche "FIN TEXTE". Page 4 Chapitre: 10 PERSONNALISATION Section: UTILITAIRES Exemples: * Pour renommer le symbole 14 en symbole 33. RENOMMER SYMBOLE 14 * A NOUVEAU NUMERO 33 ENTER Pour modifier le commentaire de la page 44. RENOMMER PAGE 44 A NOUVEAU COMMENTAIRE GRAISSAGE FIN TEXTE EDITER Cette option permet de sélectionner une page ou un symbole utilisateur pour édition, modification ou sauvegarde. Si la page ou le symbole sélectionnés existent déjà, ils se trouvent dans la mémoire EEPROM, sont copiés dans la mémoire d’édition et leur contenu est affiché dans la zone d’édition Si la page ou le symbole sélectionnés n’existent pas, la zone d’édition affiche une page blanche. Dès qu’une page ou un symbole utilisateur ont été sélectionnés, ils peuvent être édités ou modifiés puis sauvegardés et restent actifs jusqu’à: * Leur sauvegarde (touche SAUVER) * La sortie du mode PERSONNALISATION. En cas de changements, la CNC demande si la page ou le symbole doivent être sauvegardés avant de sélectionner une nouvelle page ou un nouveau symbole. * La sélection d’une autre page ou d’un autre symbole avec cette même option. En cas de changements, la CNC demande si la page ou le symbole doivent être sauvegardés avant de sélectionner une nouvelle page ou un nouveau symbole. SAUVER Cette option permet de stocker en mémoire EEPROM le symbole ou la page utilisateur affichés en tant que symbole ou page actifs. Chapitre: 10 Section: PERSONNALISATION UTILITAIRES Page 5 10.2 EDITION DE PAGES ET SYMBOLES UTILISATEUR Avant d’éditer une page ou un symbole utilisateur, ils doivent être sélectionnés grâce à l’option EDITER du mode de fonctionnement UTILITAIRES. L’édition ou la modification d’une page ou d’un symbole utilisateur sont possibles grâce aux options ELEMENTS GRAPHIQUES, TEXTES et MODIFICATIONS. Les informations contenues dans une page ou un symbole ne doivent pas occuper plus de Ko; dans le cas contraire, la CNC affiche le message d’erreur correspondant. Lorsque la page ou le symbole ont été sélectionnés, la CNC affiche une page d’écran de ce type: P...... N.... PAGE : 0 1 8 16 11 : 50 : 14 24 X : 320 Y : 160 CAP INS LIGNE F1 RECTANGLE CERCLE F2 F3 ARC F4 POLYLIGNE F5 SYMBOL F6 + F7 * La partie supérieure gauche indique le numéro de la page ou du symbole en cours d’édition. * La fenêtre principale affiche la page ou le symbole sélectionnés. Dans le cas d’une page ou d’un symbole nouveaux, la fenêtre principale est "vide" (sur fond bleu). * Par ailleurs, une fenêtre au bas de l’écran affiche les divers paramètres d’édition disponibles et présente en surbrillance les valeurs sélectionnées. Page 6 Chapitre: 10 PERSONNALISATION Section: EDITION DE PAGES ET SYMBOLES UTILISATEUR Les divers paramètres disponibles sont les suivants: * Le type de tracé utilisé pour définir les éléments graphiques. * L’avance appliquée aux déplacements du curseur (en nombre de pixels). * La taille de caractères utilisée pour créer les textes à insérer dans les pages et les symboles. * La couleur de fond utilisée pour la création de la page et la couleur correspondant au tracé représentant les éléments graphiques et les textes. Parmi tous les rectangles de couleur affichés, l’un contient un autre rectangle. Le rectangle intérieur et le rectangle extérieur indiquent respectivement la couleur principale et la couleur de fond sélectionnées. Cette même fenêtre affiche en plus les coordonnées du curseur en pixels, la position horizontale étant définie par la cote en X (1 à 638), et la position verticale par la cote en Y (0 à 334). Après le choix d’une des options ELEMENTS GRAPHIQUES, TEXTES ou MODIFICATIONS, la CNC permet à tout moment, y compris pendant la définition des éléments graphiques et des textes, de modifier les paramètres d’édition. De cette façon, il est possible d’éditer des formes de couleur et de tracé différents, ainsi que des textes de différentes tailles. Pour accéder à ce menu, frapper INS. Dès l’entrée dans ce mode, la CNC affiche par touches logiciel les différentes options décrites ci-dessous et permettant de modifier ces paramètres. Pour quitter ce mode et revenir au menu précédent, frapper INS à nouveau. AVANCE CURSEUR Cette option permet de sélectionner l’avance, ou pas (1, 8, 16, 24), en pixels, de déplacement du curseur. Après la frappe de cette touche, la sélection s’effectue comme suit: 1.- Grâce aux touches "flèche à gauche" et "flèche à droite", sélectionner l’avance ou pas désiré. La CNC affichera en permanence et en surbrillance l’avance sélectionnée. 2.- Frapper ENTER pour valider l’avance sélectionnée, ou ESC pour quitter cette option sans effectuer aucun changement. Quand une nouvelle page ou un nouveau symbole est sélectionné, la CNC affiche la valeur 8 à ce paramètre. Chapitre: 10 PERSONNALISATION Section: EDITION DE PAGES ET SYMBOLES UTILISATEUR Page 7 TYPE DE LIGNE Cette option permet de sélectionner le type de ligne à utiliser pour définir les éléments graphiques. Après la frappe de cette touche, la sélection s’effectue comme suit: 1.- Grâce aux touches "flèche à gauche" et "flèche à droite", sélectionner le type de ligne ou trait désiré. La CNC affichera en permanence et en surbrillance le type de ligne sélectionné. 2.- Frapper ENTER pour valider le type de ligne sélectionné, ou ESC pour quitter cette option sans effectuer aucun changement. Quand une nouvelle page ou un nouveau symbole est sélectionné, la CNC affecte par défaut un "Trait continu fin". Ne pas utiliser de traits épais pour représenter des polylignes et des polygones; on utilisera toujours un trait fin. TAILLE TEXTE Cette option permet de sélectionner la taille des lettres utilisées pour écrire les textes à insérer dans les pages et les symboles. Trois tailles sont disponibles: * Taille normale. Cette taille sera utilisée pour représenter toutes les lettres, majuscules et minuscules, ainsi que tous les chiffres et signes disponibles sur le clavier de la CNC. * Taille double et taille triple. Ces tailles seront utilisées pour représenter les majuscules "A ... Z", les chiffres "0 ... 9", les signes "*", "+", "-", ".", ":", "#", "%", "/", "<", ">", "?", et les caractères spéciaux "Ç", "Ä", "Ö", "Ü", "ß". Si des minuscules sont choisies dans l’une de ces tailles, la CNC les transforme automatiquement en majuscules. Pour sélectionner une des tailles de lettre, procéder comme suit: 1.- Grâce aux touches "flèche à gauche" et "flèche à droite", sélectionner la taille de lettre désirée. La CNC affichera en permanence et en surbrillance la taille de lettre sélectionnée. 2.- Frapper ENTER pour valider la taille de lettre sélectionnée, ou ESC pour quitter cette option sans effectuer aucun changement. Quand une nouvelle page ou un nouveau symbole est sélectionné, la CNC affecte par défaut la taille de lettre normale. Page 8 Chapitre: 10 PERSONNALISATION Section: EDITION DE PAGES ET SYMBOLES UTILISATEUR COULEUR DU FOND Cette option permet de sélectionner la couleur de fond désirée, sur lequel seront édités les éléments graphiques et les textes. Lors d’une édition ou modification d’un symbole, la couleur du fond ne doit pas être changée, car il s’agit d’un attribut de la page et non du symbole. Si un fond BLANC est désiré, l’emploi d’une autre couleur de fond est conseillé pendant l’insertion d’éléments graphiques et de textes, car le curseur est de couleur blanche. Dès que la page a été créée, on pourra choisir la couleur de fond désirée. Parmi tous les rectangles de couleur affichés, l’un contient un autre rectangle. Le rectangle intérieur et le rectangle extérieur indiquent respectivement la couleur principale et la couleur de fond sélectionnées. Pour sélectionner la couleur du fond, procéder comme suit: 1.- Grâce aux touches "flèche à gauche", "flèche à droite", "flèche vers le haut" et "flèche vers le bas", sélectionner la couleur de fond désirée parmi les 16 couleurs affichées. La CNC affiche en permanence et grâce au rectangle intérieur la couleur de fond sélectionnée. 2.- Frapper ENTER pour valider la couleur de fond sélectionnée, ou ESC pour quitter cette option sans effectuer aucun changement. Quand une nouvelle page ou un nouveau symbole est sélectionné, la CNC affecte la couleur bleue à ce paramètre. Chapitre: 10 PERSONNALISATION Section: EDITION DE PAGES ET SYMBOLES UTILISATEUR Page 9 COULEUR PRINCIPALE Cette option permet de sélectionner la couleur de trait à utiliser pour représenter les éléments graphiques et les textes. Parmi tous les rectangles de couleur affichés, l’un contient un autre rectangle. Le rectangle intérieur et le rectangle extérieur indiquent respectivement la couleur principale et la couleur de fond sélectionnées. Pour sélectionner la couleur principale, procéder comme suit: 1.- Grâce aux touches "flèche à gauche", "flèche à droite", "flèche vers le haut" et "flèche vers le bas", sélectionner la couleur de fond désirée parmi les 16 couleurs affichées. La CNC affiche en permanence et grâce au rectangle intérieur blanc la couleur principale sélectionnée. Le rectangle contenant les deux couleurs sélectionnées (fond et principale) est également affiché. 2.- Frapper ENTER pour valider la couleur principale sélectionnée, ou ESC pour quitter cette option sans effectuer aucun changement. Quand une nouvelle page ou un nouveau symbole est sélectionné, la CNC affecte la couleur blanche à ce paramètre. GRILLE Cette option permet de visualiser à l’écran une grille constituée d’un réticule de points distants de 16 pixels les uns des autres. La grille est de couleur blanche quand le fond est de l’une des 8 couleurs représentées dans les rectangles supérieurs, et de couleur noire quand il est de l’une des 8 couleurs représentées dans les rectangles inférieurs. Pour supprimer la grille, frapper cette touche logiciel à nouveau. Chaque fois que la grille est affichée, la CNC initialise le paramètre d’avance ou de pas du curseur avec 16 pixels. Si cette valeur coïncide avec la distance entre points de la grille, tous les déplacements du curseur seront exécutés sur des points de la grille. Il est toutefois possible de modifier cette valeur ultérieurement grâce à la touche logiciel AVANCE CURSEUR. Page 10 Chapitre: 10 PERSONNALISATION Section: EDITION DE PAGES ET SYMBOLES UTILISATEUR 10.3 ELEMENTS GRAPHIQUES L’accès à cette option exige d’abord de sélectionner le symbole ou la page à éditer ou modifier, grâce à l’option EDITER du mode de fonctionnement UTILITAIRES. Cette option permet d’inclure des éléments graphiques dans le symbole ou la page sélectionnés. Pour ce faire, la CNC affichera une page d’écran de 80 colonnes et 21 rangées soit 640 pixels (coordonnée en X) x 336 pixels (coordonnée en Y). S’il s’agit d’une page nouvelle, la CNC affichera le curseur au centre de l’écran; dans le cas d’un symbole nouveau, le curseur se situe dans l’angle supérieur gauche. Le curseur apparaît toujours en blanc et, après sélection d’un des éléments graphiques, il peut être déplacé sur tout l’écran grâce aux touches "flèche à gauche", "flèche à droite", "flèche vers le haut" et "flèche vers le bas". Le curseur peut aussi être déplacé grâce aux combinaisons de touches suivantes: SHIFT Positionne le curseur sur la dernière colonne (X638) SHIFT Positionne le curseur sur la première colonne (X1) SHIFT Positionne le curseur sur la première rangée (Y0). SHIFT Positionne le curseur sur la dernière rangée (Y334). Il est également possible de frapper les coordonnées (X, Y) du point où l’on désire positionner le curseur. Procéder comme suit: * Frapper "X" ou "Y". La CNC affiche en surbrillance et dans la zone de visualisation des paramètres d’édition la valeur correspondant aux coordonnées de l’axe sélectionné. * Introduire la valeur de position correspondant au point où l’on désire positionner le curseur sur cet axe. La position horizontale est définie par la cote en X (1 à 638) et la position verticale par la cote en Y (0 à 334). Après l’introduction de la valeur désirée, frapper ENTER. La CNC amène le curseur à la position indiquée. Dès que cette option est activée, la CNC permet à tout moment, y compris pendant la définition des éléments graphiques, de modifier les paramètres d’édition. De cette façon, il est possible d’éditer des formes de couleurs et de tracés différents. Pour accéder à ce menu, frapper INS. Dans ce mode, actionner les touches logiciel correspondant aux diverses options permettant de modifier ces paramètres. Pour quitter ce mode et revenir au menu précédent, frapper à nouveau la touche INS. Chapitre: 10 PERSONNALISATION Section: ELEMENTS GRAPHIQUES Page 11 Les éléments graphiques pouvant être inclus dans une page ou un symbole sont sélectionnés par touches; il s’agit des éléments suivants: LIGNE Après la frappe de cette touche, procéder comme suit: 1.- Positionner le curseur au point de départ de la ligne et frapper ENTER pour le valider. 2.- Déplacer le curseur jusqu’à la fin de la ligne (la CNC affichera en permanence la ligne en cours de programmation). 3.- Frapper ENTER pour valider la ligne ou ESC pour l’annuler. Répéter les opérations ci-dessus pour tracer d’autres lignes. Dans le cas contraire, frapper ESC pour revenir au menu précédent. RECTANGLE Après la frappe de cette touche, procéder comme suit: 1.- Positionner le curseur sur un des angles du rectangle et frapper ENTER pour le valider. 2.- Amener le curseur sur l’angle opposé (la CNC affichera en permanence le rectangle en cours de programmation). 3.- Frapper ENTER pour valider le rectangle ou ESC pour l’annuler. Répéter les opérations ci-dessus pour dessiner d’autres rectangles. Dans le cas contraire, frapper ESC pour revenir au menu précédent. CERCLE Après la frappe de cette touche, procéder comme suit: 1.- Positionner le curseur au centre du cercle et frapper ENTER pour le valider. 2.- Déplacer le curseur afin de définir le rayon. Pendant le déplacement du curseur, la CNC affichera le cercle en cours de programmation. 3.- Frapper ENTER pour valider le cercle ou ESC pour l’annuler. Dès la validation du cercle, le curseur se positionne en son centre pour faciliter le dessin de cercles concentriques. Répéter les opérations ci-dessus pour dessiner d’autres cercles. Dans le cas contraire, frapper ESC pour revenir au menu précédent. Page 12 Chapitre: 10 PERSONNALISATION Section: ELEMENTS GRAPHIQUES ARC Après la frappe de cette touche, procéder comme suit: 1.- Positionner le curseur sur l’une des extrêmités de l’arc et frapper ENTER pour le valider. 2.- Amener le curseur sur l’autre extrêmité de l’arc (la CNC affichera la droite réunissant les deux points), et frapper ENTER pour le valider. Après la validation des deux extrêmités de l’arc, le curseur se positionne au centre de la droite qui les réunit. 3.- Déplacer le curseur pour définir la courbure (la droite affichée se transforme en un arc passant par les trois points indiqués). 4.- Frapper ENTER pour valider l’arc ou ESC pour l’annuler. Répéter les opérations ci-dessus pour dessiner d’autres arcs. Dans le cas contraire, frapper ESC pour revenir au menu précédent. POLYLIGNE Une polyligne se compose d’un ensemble de lignes, dans lequel le point d’arrivée de l’une coïncide avec le point de départ de la suivante. Après la frappe de cette touche, procéder comme suit: 1.- Positionner le curseur sur l’une des extrêmités de la polyligne et frapper ENTER pour le valider. 2.- Amener le curseur sur la première pointe de la polyligne (fin de la première ligne et début de la suivante); la CNC affiche en permanence la ligne en cours de programmation. Frapper ENTER pour valider la nouvelle ligne, ou ESC pour quitter cette option (la polyligne entière s’efface). 3.- Répéter les opérations 1 et 2 pour le reste des lignes. On notera que le nombre maximum de lignes d’une polyligne est limité à 127. Lorsque toute la polyligne a été dessinée, frapper à nouveau ENTER pour la valider, ou ESC pour quitter cette option (la polyligne entière s’efface). Répéter les opérations ci-dessus pour dessiner d’autres polylignes. Dans le cas contraire, frapper ESC pour revenir au menu précédent. Chapitre: 10 Section: PERSONNALISATION ELEMENTS GRAPHIQUES Page 13 SYMBOLE Cette option permet d’inclure un symbole déjà dessiné dans une page ou un symbole en cours d’édition. Pour pouvoir inclure un symbole à l’endroit désiré, procéder comme suit: 1.- Introduire le numéro du symbole à inclure dans la page ou le symbole en cours d’édition et frapper ENTER pour le valider. La CNC affichera ce symbole. Le curseur sera situé au point de référence correspondant à ce symbole (angle supérieur gauche du symbole). 2.- Amener le curseur au point où le symbole doit être placé. Seul le curseur se déplace. 3.- Quand le curseur a atteint le point désiré, frapper ENTER pour que la CNC positionne le symbole à l’endroit sélectionné. Pour renoncer à cette opération, frapper ESC: la CNC quittera cette option. 4.- La CNC permet d’inclure le symbole sélectionné en plusieurs points. Pour ce faire, déplacer à nouveau le curseur et frapper ENTER. 5.- Pour quitter cette option et revenir au menu précédent, frapper ESC. Pour inclure plusieurs symboles distincts dans la page ou le symbole sélectionnés, activer l’option "SYMBOLE" à chaque insertion d’un nouveau symbole. Un symbole ne peut pas être inclus en lui-même, c’est-à-dire que si le symbole 4 est en cours d’édition, la CNC permet d’inclure tout symbole sauf le symbole 4. Attention: Si un symbole est supprimé par l’option SUPPRIMER du menu UTILITAIRES, il disparaît de la mémoire EEPROM, mais tous les appels de ce symbole (pages ou symboles dans lesquels il est inclus) restent actifs. En conséquence, lorsqu’une page ou un symbole appelant un symbole inexistant (supprimé ou non défini) sont affichés, cette partie de la page apparaît vide. Toutefois, si ce symbole est édité plus tard, la nouvelle représentation affectée au symbole apparaîtra dans toutes les pages et symboles dans lesquels il a été inclus. Page 14 Chapitre: 10 PERSONNALISATION Section: ELEMENTS GRAPHIQUES POLYGONE Un polygone est une polyligne fermée dont les points de début et de fin coïncident. Pour représenter un polygone, procéder comme suit: 1.- Positionner le curseur sur une des pointes du polygone et frapper ENTER pour le valider. 2.- Amener le curseur sur la pointe suivante du polygone (la CNC affichera en permanence la ligne en cours de programmation). Frapper ENTER pour valider la nouvelle ligne, ou ESC pour quitter cette option (le polygone entier s’efface). 3.- Répéter l’opération 2 pour le reste des pointes. Quand toutes les pointes ont été définies, frapper à nouveau ENTER. La CNC terminera le polygone, en affichant la ligne qui unit les pointes de début et de fin. Répéter les opérations ci-dessus pour dessiner d’autres polygones. Dans le cas contraire, frapper ESC pour revenir au menu précédent. POLYGONE PLEIN Pour dessiner un polygone plein, on se reportera aux indications données avec l’option "POLYGONE". Lorsque le polygone a été défini, la CNC affiche son intérieur rempli avec la couleur utilisée pour sa définition. CERCLE PLEIN Pour dessiner un cercle plein, on se reportera aux indications données avec l’option "CERCLE". Lorsque le cercle a été défini, la CNC affiche son intérieur rempli avec la couleur utilisée pour sa définition. RECTANGLE PLEIN Pour dessiner un rectangle plein, on se reportera aux indications données avec l’option "RECTANGLE". Lorsque le rectangle a été défini, la CNC affiche son intérieur rempli avec la couleur utilisée pour sa définition. Chapitre: 10 Section: PERSONNALISATION ELEMENTS GRAPHIQUES Page 15 10.4 TEXTES L’accès à cette option exige d’abord de sélectionner le symbole ou la page à éditer ou modifier, grâce à l’option EDITER du mode de fonctionnement UTILITAIRES. Cette option permet d’introduire des textes dans le symbole ou la page sélectionnés. Pour ce faire, la CNC affichera une page d’écran de 80 colonnes et 21 rangées soit 640 pixels (coordonnée en X) x 336 pixels (coordonnée en Y). S’il s’agit d’une page nouvelle, la CNC affichera le curseur au centre de l’écran; dans le cas d’un symbole nouveau, le curseur se situe dans l’angle supérieur gauche. Le curseur apparaît toujours en blanc et, après sélection du texte à inclure, il peut être déplacé sur tout l’écran grâce aux touches "flèche à gauche", "flèche à droite", "flèche vers le haut" et "flèche vers le bas". Le curseur peut aussi être déplacé grâce aux combinaisons de touches suivantes: SHIFT Positionne le curseur sur la dernière colonne (X638) SHIFT Positionne le curseur sur la première colonne (X1) SHIFT Positionne le curseur sur la première rangée (Y0). SHIFT Positionne le curseur sur la dernière rangée (Y334). Il est également possible de frapper les coordonnées (X, Y) du point où l’on désire positionner le curseur. Procéder comme suit: * Frapper "X" ou "Y". La CNC affiche en surbrillance et dans la zone de visualisation des paramètres d’édition la valeur correspondant aux coordonnées de l’axe sélectionné. * Introduire la valeur de position correspondant au point où l’on désire positionner le curseur sur cet axe. La position horizontale est définie par la cote en X (1 à 638) et la position verticale par la cote en Y (0 à 334). Après l’introduction de la valeur désirée, frapper ENTER. La CNC amène le curseur à la position indiquée. Dès que cette option est activée, la CNC permet à tout moment, y compris pendant la définition des textes, de modifier les paramètres d’édition. De cette façon, il est possible d’insérer des textes de couleurs et de tracés différents. Pour accéder à ce menu, frapper INS. Dans ce mode, actionner les touches logiciel correspondant aux diverses options permettant de modifier ces paramètres. Pour quitter ce mode et revenir au menu précédent, frapper à nouveau la touche INS. Il est possible d’insérer un des textes disponibles au niveau de la CNC ou un texte introduit précédemment par l’utilisateur. Pour ce faire, les options suivantes sont disponibles par touches logicielles: Page 16 Chapitre: 10 PERSONNALISATION Section: TEXTES TEXTE DEFINI PAR L’UTILISATEUR Pour insérer le texte désiré, procéder comme suit: 1.- Frapper ENTER. La CNC affiche une zone d’écran pour édition du texte: le curseur peut être déplacé dans cette zone grâce aux touches "flèche à gauche" et "flèche à droite". 2.- Au moyen du clavier, définir le texte à insérer. Au fur et à mesure de l’introduction du texte dans la zone d’édition, un rectangle est généré dans la fenêtre principale de la CNC pour indiquer l’espace que ce texte occupera sur l’écran. Pour quitter cette option, frapper ESC: la CNC affiche le menu précédent. 3.- Lorsque le texte a été correctement défini, frapper ENTER. Le texte édité reste dans la zone d’édition, et le curseur se positionne sur le rectangle situé dans la fenêtre principale de la CNC. 4.- Déplacer le rectangle suivant besoins au moyen du curseur. 5.- Frapper ENTER pour valider la commande. La CNC remplace le rectangle par le texte indiqué. On notera que la taille et la couleur du texte introduit ne peuvent pas être changées. En conséquence, toute modification de ces paramètres doit être effectuée avant de frapper ENTER. Chapitre: 10 Section: PERSONNALISATION TEXTES Page 17 NUMERO DE TEXTE Cette option permet de sélectionner un texte utilisé par la CNC dans les divers modes de travail et de l’introduire dans la page ou le symbole actifs. Pour insérer l’un de ces textes, procéder comme suit: 1.- Frapper la touche logiciel correspondante. La CNC affiche une zone d’écran permettant d’indiquer le numéro du texte: le curseur affiché peut être déplacé dans cette zone grâce aux touches "flèche à gauche" et "flèche à droite". 2.- Au moyen du clavier, définir le numéro du texte à insérer et frapper ENTER. La CNC affiche le texte sélectionné et indique, dans un rectangle de la fenêtre principale, l’espace occupé par ce texte. Si l’opérateur ne désire plus utiliser ce texte, il peut frapper un autre numéro, puis la touche ENTER. Pour quitter cette option, frapper ESC : la CNC affiche le menu précédent. 3.- Lorsque le texte désiré a été sélectionné, frapper ENTER. Le texte sélectionné reste dans la zone d’édition, et le curseur se positionne sur le rectangle situé dans la fenêtre principale de la CNC. 4.- Déplacer le rectangle suivant besoins au moyen du curseur. 5.- Frapper ENTER pour valider la commande. La CNC remplace le rectangle par le texte indiqué. On notera que la taille et la couleur du texte introduit ne peuvent pas être changées. En conséquence, toute modification de ces paramètres doit être effectuée avant de frapper ENTER. Attention: Cette application peut être utile lorsque les pages ou les symboles à éditer doivent apparaître dans d’autres langues, car la CNC les traduira dans la langue choisie. En général, lorsque les textes ne doivent apparaître qu’en une seule langue, il est plus commode de les écrire simplement au lieu de les rechercher dans une liste de plus de 1500 messages prédéfinis. Toutefois, l’utilisateur désirant un tirage de ces textes préfinis peut en faire la demande auprès de Fagor Automation. Page 18 Chapitre: 10 PERSONNALISATION Section: TEXTES 10.5 MODIFICATIONS L’accès à cette option exige d’abord de sélectionner le symbole ou la page à éditer ou modifier, grâce à l’option EDITER du mode de fonctionnement UTILITAIRES. Le curseur apparaît toujours en blanc et, après sélection d’une des options de modification, il peut être déplacé sur tout l’écran grâce aux touches "flèche à gauche", "flèche à droite", "flèche vers le haut" et "flèche vers le bas". Le curseur peut aussi être déplacé grâce aux combinaisons de touches suivantes: SHIFT Positionne le curseur sur la dernière colonne (X638) SHIFT Positionne le curseur sur la première colonne (X1) SHIFT Positionne le curseur sur la première rangée (Y0). SHIFT Positionne le curseur sur la dernière rangée (Y334). Il est également possible de frapper les coordonnées (X, Y) du point où l’on désire positionner le curseur. Procéder comme suit: * Frapper "X" ou "Y". La CNC affiche en surbrillance et dans la zone de visualisation des paramètres d’édition la valeur correspondant aux coordonnées de l’axe sélectionné. * Introduire la valeur de position correspondant au point où l’on désire positionner le curseur sur cet axe. La position horizontale est définie par la cote en X (1 à 638) et la position verticale par la cote en Y (0 à 334). Après l’introduction de la valeur désirée, frapper ENTER. La CNC amène le curseur à la position indiquée. Les options permettant de modifier une page ou un symbole sont: EFFACER PAGE Cette option permet d’effacer la page ou le symbole sélectionnés. Lorsque cette touche a été frappée, la CNC demande confirmation avant d’exécuter l’opération indiquée. Si cette opération est exécutée, la CNC ne supprime la page ou le symbole que dans la zone d’édition, et elle conserve en mémoire EEPROM le contenu de cette page ou de ce symbole tel qu’il était après l’exécution de la dernière commande "SAUVER". Chapitre: 10 PERSONNALISATION Section: MODIFICATIONS Page 19 EFFACER ELEMENTS Cette option permet d’effacer l’un des éléments représentés dans la page ou le symbole sélectionnés. Pour ce faire, procéder comme suit: 1.- Positionner le curseur sur l’élément à effacer et frapper la touche ENTER. La CNC analysera une zone comprise entre ± 8 pixels par rapport à la position indiquée. Dans le cas d’un symbole, le curseur doit se situer sur la croix signalant son point de référence. Pour effacer un cercle ou un polygone plein, positionner le curseur sur un point de la circonférence ou sur l’une des lignes constituant le polygone extérieur. 2.- Si un élément graphique ou un texte est présent dans cette zone, la CNC l’affiche en surbrillance et demande s’il doit être effacé. Pour effacer cet élément, frapper ENTER; sinon, frapper ESC. Si la CNC détecte plusieurs éléments dans la zone indiquée, elle les affiche un par un en surbrillance et demande confirmation de l’effacement de chaque élément. DEPLACER ECRAN Cette option permet de déplacer l’ensemble des éléments graphiques et textes de l’écran sélectionné, grâce aux touches "flèche à gauche, à droite, vers le haut et vers le bas. Cette option ne s’applique qu’aux pages complètes, et non aux symboles individuels. Lorsque cette option est activée, la CNC positionne le curseur au centre de l’écran, qui est pris comme point de référence de l’écran. Pour déplacer l’écran, procéder comme suit: 1.- Amener le curseur à l’emplacement où doit se situer le point de référence de la page. 2.- Frapper ENTER pour valider la commande. La CNC déplace l’ensemble des éléments graphiques et textes de l’écran au point indiqué. Frapper ESC pour quitter cette option; la CNC affiche le menu précédent. Répéter les opérations ci-dessus pour exécuter d’autres déplacements de l’écran. Dans le cas contraire, frapper ESC pour revenir au menu précédent. Page 20 Chapitre: 10 PERSONNALISATION Section: MODIFICATIONS 11. PARAMETRES MACHINE Pour que la machine-outil puisse exécuter correctement les instructions programmées, la CNC doit connaître les données spécifiques de la machine telles que : avances, accélérations, réalimentations, changement automatique d’outils, etc... Ces données sont définies par le constructeur de la machine et peuvent être introduites grâce au clavier ou à la ligne série, par les commandes de personnalisation des paramètres machine. La CNC FAGOR 8050 dispose des groupes de paramètres machine suivants: * * * * * * * * Paramètres généraux de la machine Paramètres des axes (une table par axe) Paramètres de broche Paramètres de configuration des lignes série, RS-422 et RS-232-C. Paramètres du PLC Fonctions auxiliairesM Compensation d’erreur de vis (une table par axe) Compensations croisées entre axes (par exemple: Fléchissement du bélier). On personnalisera les paramètres machine généraux en premier, car ils permettent de définir les axes de la machine, et donc les tables de paramètres des axes. On décidera également si la machine disposera ou non de la compensation croisée et entre quels axes elle s’appliquera, la CNC générant la table de compensation croisée correspondante. Les paramètres machine généraux permettent également de définir les tailles des tables du Magasin d’outils, d’Outils, de Correcteurs et de la table de Fonctions auxiliaires M. Les paramètres d’axes permettent de définir si l’axe disposera ou non de la compensation de vis, et la taille de la table correspondante. Lorsque les paramètres généraux ont été définis, frapper SHIFT - RESET afin que la CNC valide les tables nécessaires. Chapitre: 11 PARAMETRES MACHINE Section: Page 1 11.1 TABLES DE PARAMETRES MACHINE Les tables de Paramètres Généraux, de Paramètres d’axes, de Paramètres de broche, de Paramètres des lignes série et de Paramètres de PLC ont la structure suivante: PARAMETRES GENERAUX P..... PARAMETRE N..... 11 : 50 : 14 NOM VALEUR AXIS1 AXIS2 AXIS3 AXIS4 AXIS5 AXIS6 AXIS7 AXIS8 INCHES IMOVE ICORNER IPLANE ILCOMP ISYSTEM IFEED THEODPLY GRAPHICS RAPIDOVR MAXFOVR CIRINLIM 01 02 03 04 05 10 11 00 0 0 0 0 0 0 0 1 000 YES 120 00000 P000 P001 P002 P003 P004 P005 P006 P007 P008 P009 P010 P011 P012 P013 P014 P015 P016 P017 P018 P019 CAP INS MM EDITER F1 MODIFIER F2 CHERCHER F3 INITIALIS. F4 CHARGER F5 SAUVER F6 MM/POUCES F7 Où sont indiqués le numéro du paramètre, la valeur qui lui est affectée et le nom ou la mnémonique associée à ce paramètre. Page 2 Chapitre: 11 PARAMETRES MACHINE Section: TABLES DE PARAMETRES MACHINE 11.2 TABLE DES FONCTIONS AUXILIAIRES "M" La table des fonctions auxiliaires M a la structure suivante: TABLE DES FONCTIONS M P..... N..... Sous routine Fonction auxiliaire M???? M???? M???? M???? M???? M???? M???? M???? M???? M???? M???? M???? M???? M???? M???? M???? M???? M???? M???? M???? 11 : 50 : 14 Bits de personnalisation S0000 S0000 S0000 S0000 S0000 S0000 S0000 S0000 S0000 S0000 S0000 S0000 S0000 S0000 S0000 S0000 S0000 S0000 S0000 S0000 00000000 00000000 00000000 00000000 00000000 00000000 00000000 00000000 00000000 00000000 00000000 00000000 00000000 00000000 00000000 00000000 00000000 00000000 00000000 00000000 CAP INS EDITER MODIFIER F1 CHERCHER F2 F3 INITIALIS. CHARGER F4 F5 SAUVER F6 F7 Le nombre de fonctions M de la table est défini par le paramètre machine général "NMISCFUN". Pour chaque fonction, les éléments suivants sont définis: * Le numéro (0-9999) de la fonction auxiliaire M définie. Si une fonction M n’est pas définie, la CNC affichera M????. * Le numéro du sous-programme devant être associé à cette fonction auxiliaire. * 8 bits de personnalisation x x x x x x x x 7) 6) 5) 4) 3) 2) 1) 0) Bit 0 Indique si la CNC doit (=0) ou non (=1) attendre le signal AUXEND (signal de "M" exécutée) avant de poursuivre l’exécution du programme. Bit 1 Indique si la fonction M est exécutée avant (=0) ou après (=1) le déplacement du bloc dans lequel elle est programmée. Bit 2 Indique si l’exécution de la fonction M interrompt (=1) ou non (=0) la préparation des blocs. Bit 3 Indique si la fonction M est exécutée après l’appel du sous-programme associé (=0) ou si seul le sous-programme associé est exécuté (=1). Bit 4 Lorsque le bit 2 est mis à “1”, il indique si la préparation du bloc doit être interrompue jusqu’à ce que l’exécution de la fonction “M” commence (= 0 ) ou se termine ( = 1 ). Les autres bits sont inutilisés actuellement. Chapitre: 11 PARAMETRES MACHINE Section: TABLE DES FONCTIONS AUXILIAIRES “M” Page 3 11.3 TABLES DE COMPENSATION DE VIS Les tables correspondant à la compensation de vis ont la structure suivante: COMPENSATION AXE X P..... POINT N..... 11 : 50 : 14 ERREUR POSITION X X X X X X X X X X X X X X X X X X X X P001 P002 P003 P004 P005 P006 P007 P008 P009 P010 P011 P012 P013 P014 P015 P016 P017 P018 P019 P020 EX EX EX EX EX EX EX EX EX EX EX EX EX EX EX EX EX EX EX EX 0.0000 0.0000 0.0000 0.0000 0.0000 0.0000 0.0000 0.0000 0.0000 0.0000 0.0000 0.0000 0.0000 0.0000 0.0000 0.0000 0.0000 0.0000 0.0000 0.0000 0.0000 0.0000 0.0000 0.0000 0.0000 0.0000 0.0000 0.0000 0.0000 0.0000 0.0000 0.0000 0.0000 0.0000 0.0000 0.0000 0.0000 0.0000 0.0000 0.0000 CAP INS MM EDITER F1 MODIFIER F2 CHERCHER F3 INITIALIS. F4 CHARGER F5 SAUVER F6 MM/POUCES F7 Le nombre de points de chaque table est défini grâce au paramètre machine d’axes "NPOINTS". Pour chaque point, les éléments suivants sont définis: * La position de l’axe à compenser. * L’erreur de cet axe à ce point. En outre, la position en cours de l’axe sélectionné est affichée, et mise à jour dès que cet axe se déplace. Page 4 Chapitre: 11 PARAMETRES MACHINE Section: TABLES DE COMPENSATION DE VIS 11.4 TABLES DE COMPENSATION CROISEE Les tables correspondant aux compensations croisées ont la structure suivante: TABLE DE COMP. CROISEE P..... POINT N..... 11 : 50 : 14 ERREUR POSITION X X X X X X X X X X X X X X X X X X X X P001 P002 P003 P004 P005 P006 P007 P008 P009 P010 P011 P012 P013 P014 P015 P016 P017 P018 P019 P020 EY EY EY EY EY EY EY EY EY EY EY EY EY EY EY EY EY EY EY EY 0.0000 0.0000 0.0000 0.0000 0.0000 0.0000 0.0000 0.0000 0.0000 0.0000 0.0000 0.0000 0.0000 0.0000 0.0000 0.0000 0.0000 0.0000 0.0000 0.0000 0.0000 0.0000 0.0000 0.0000 0.0000 0.0000 0.0000 0.0000 0.0000 0.0000 0.0000 0.0000 0.0000 0.0000 0.0000 0.0000 0.0000 0.0000 0.0000 0.0000 CAP INS MM EDITER MODIFIER F1 F2 CHERCHER F3 INITIALIS. F4 CHARGER F5 SAUVER F6 MM/POUCES F7 Le nombre de points de chaque table est défini par le paramètre machine général "NPCROSS", "NPCROSS2" et "NPCROSS3". Lorsqu’un de ces paramètres est mis à "0", ceci signifie que la table correspondante n’est pas utilisée. La CNC ne l’affiche pas. Un axe ne doit pas dépendre du déplacement de plusieurs axes à la fois (par exemple: A -> C et B -> C), mais le déplacement d’un axe peut affecter le positionnement de plusieurs axes (par exemple: A -> B y A -> C). Chaque table définit: * La position de l’axe entraînant l’erreur. Cet axe est défini par le paramètre machine général "MOVAXIS", “MOVAXIS2” et "MOVAXIS3". * L’erreur subie par l’axe à compenser au point considéré. Cet axe est défini par le paramètre machine général "COMPAXIS", "COMAXIS2" et "COMAXIS3". En outre, la position en cours de l’axe sélectionné est affichée, et mise à jour dès que cet axe se déplace. Chapitre: 11 PARAMETRES MACHINE Section: TABLES DE COMPENSATION CROISEE Page 5 11.5 FONCTIONNEMENT AVEC LES TABLES DE PARAMETRES Dès que la table désirée a été sélectionnée, la CNC affiche son contenu, et l’opérateur peut déplacer le curseur une ligne à la fois grâce aux touches "flèche vers le haut et flèche vers le bas", ou page par page grâce aux touches "page avant et page arrière". En outre, plusieurs options permettent de manipuler ces tables. Ces options sont accessibles par touches logiciel et sont décrites ci-dessous. Dès qu’une de ces options est activée, l’opérateur dispose d’une zone d’édition sur l’écran et peut déplacer le curseur dans cette zone grâce aux touches "flèche à droite et flèche à gauche". Les touches "flèche vers le haut et flèche vers le bas" permettent de positionner le curseur sur le premier et le dernier caractère respectivement. EDITER Cette option permet d’éditer le paramètre désiré. Dès que cette option est activée, les touches changent de couleur et affichent le type d’édition offert sur fond blanc. Dans les tables correspondant à la compensation de vis et à la compensation croisée, les valeurs de position de l’axe doivent être éditées comme suit: * Déplacement de l’axe et, quand l’importance de l’erreur justifie sa prise en compte, frappe de la touche logiciel ou de la touche correspondant à l’axe. * La CNC inclut dans la zone d’édition le nom de l’axe suivi des coordonnées correspondant à ce point. Cette valeur peut être modifiée si désiré. * Frappe de la touche correspondant à l’erreur, et introduction de sa valeur. Quand le paramètre a été édité, frapper ENTER. Ce nouveau paramètre est incorporé à la table et le curseur se positionne sur ce paramètre. La zone d’édition s’efface, ce qui permet d’éditer d’autres paramètres. Pour sortir de cette option, frapper ESC. Page 6 Chapitre: 11 PARAMETRES MACHINE Section: FONCTIONNEMENT AVEC LES TABLES DE PARAMETRES MODIFIER Cette option permet de modifier le paramètre sélectionné. Avant de frapper cette touche, on pointera au moyen du curseur le paramètre à modifier. Dès que cette option est activée, les touches changent de couleur et affichent sur fond blanc le type d’option d’édition qu’elles offrent pour modifier le paramètre. La frappe de ESC efface les informations affichées dans la zone d’édition correspondant au paramètre à modifier. A partir de ce moment, ce paramètre peut être édité à nouveau. Pour sortir de l’option "modifier", frapper CL ou ESC afin d’effacer les informations affichées dans la zone d’édition, puis frapper ESC à nouveau. Le paramètre sélectionné n’est pas modifié. Quand le paramètre a été modifié, frapper ENTER. Le nouveau paramètre édité remplace le précédent. CHERCHER Cette option permet d’effectuer une recherche dans la table sélectionnée. Dès que cette option est activée, les touches affichent les options suivantes: DEBUT Cette touche positionne le curseur sur le premier paramètre de la table et permet de sortir du mode "chercher". Cette touche positionne le curseur sur le dernier paramètre de la table mode FIN et permet de sortir du mode "chercher". PARAMETRE Lorsque cette touche est actionnée, la CNC demande le numéro du paramètre à chercher. Introduire ce numéro et frapper ENTER : le curseur se positionne sur le paramètre demandé et il est possible de sortir de l’option. INITIALISER Cette option permet d’initialiser tous les paramètres de la table sélectionnée avec les valeurs par défaut définies par la CNC. Ces valeurs sont définies dans le chapitre traitant des paramètres machine dans le manuel d’installation. Chapitre: 11 Section: PARAMETRES MACHINE FONCTIONNEMENT AVEC LES TABLES DE PARAMETRES Page 7 CHARGER Cette option permet de charger les valeurs reçues par l’intermédiaire d’une ligne série (RS232C ou RS422) dans tous les paramètres de latable sélectionnée. Pour ce faire, frapper la touche correspondant à la ligne série utilisée pour la transmission. La transmission commence dès la frappe de cette touche. Pour interrompre une transmission en cours, frapper la touche "ARRETER". Lorsque la taille de la table reçue ne coïncide pas avec celle de la table sélectionnée, la CNC réagit comme suit: * La table reçue est plus courte que la table actuelle. Les paramètres reçus sont modifiés et les paramètres restants conservent leurs valeurs d’origine. * La table reçue est plus longue que la table actuelle. Tous les paramètres de la table actuelle sont modifiés, et quand la CNC détecte qu’il n’y a plus de place, elle émet le message d’erreur correspondant. SAUVER Cette option permet d’envoyer tous les paramètres de la table sélectionnée vers un périphérique ou un ordinateur. Pour ce faire, frapper la touche correspondant à la ligne série utilisée pour la transmission. La transmission commence dès la frappe de cette touche. Le récepteur doit donc être prêt avant le début de la transmission. Pour interrompre une transmission en cours, frapper la touche "ARRETER". MM/POUCES Chaque fois que cette option est activée, la CNC change les unités représentant les paramètres dépendant de ces unités. Les unités (mm ou pouces) sélectionnées sont inscrites dans la fenêtre située dans l’angle inférieur droit. On notera que ce changement n’affecte pas le paramètre machine général "INCHES", qui signale le système d’unités par défaut. Page 8 Chapitre: 11 PARAMETRES MACHINE Section: FONCTIONNEMENT AVEC LES TABLES DE PARAMETRES 12. DIAGNOSTICS Ce mode de fonctionnement permet de connaître la configuration de la CNC et de tester le système. La CNC offre les options suivantes par touches logiciel: Configuration du système Test du matériel Test de mémoire Test de EPROM Utilisateur Chapitre: 12 DIAGNOSTICS Section: Page 1 12.1 CONFIGURATION DU SYSTEME Cette option affiche la configuration en cours du système Dès que cette option est activée, deux nouvelles touches s’affichent et permettent de sélectionner la configuration matériel du système. 12.1.1 CONFIGURATION HARDWARE Cette option affiche la configuration "matériel" du système et présente les informations suivantes: DIAGNOSTICS P...... N.... 11 : 50 : 14 CONFIGURATION UNITE CENTRALE CNC8050 - Alimentation. Module CPU - CNC. Module Axes. CPU - PLC. Module Entrées/Sorties 1 Module Entrées/Sorties 2 Module Entrées/Sorties 3 * VARIABLES CNC ( 02 ) ( 01 ) ( 03 ) ( 04 ) ( 05 ) * VARIABLES PLC - Memoire RAM (Kb) - Utilisateur 128 - Système 384 - Memoire EEPROM (Kb) - Utilisateur 8 - Système 8 - Memoire RAM (Kb) - Memoire EEPROM (Kb) 64 16 CAP INS CONFIGURATION F1 TEST HARDWARE F2 TEST MEMOIRE F3 TEST EPROM F4 UTILISATEUR F5 F6 F7 CONFIGURATION DE L’UNITE CENTRALE Cette rubrique indique les modules composant la configuration en cours de l’unité centrale de la CNC. Elle donne également la liste des options disponibles (CPU PLC et CPU SERVO). Les chiffres entre parenthèses à la suite de certains modules et options indiquent l’adresse logique affectée à chacun d’eux. Page 2 Chapitre: 12 DIAGNOSTICS Section: CONFIGURATION DU SYSTEME RESSOURCES CNC Cette rubrique indique l’espace mémoire RAM utilisé par le système et celui accessible à l’utilisateur. Les valeurs sont données en Kb. Elle indique également la partie de la mémoire EEPROM partagée avec le PLC et disponible pour stocker les programmes pièce de la CNC ainsi que les pages de personnalisation utilisateur. Les valeurs sont données en Kb. Le paramètre machine général "PAGESMEM" indique le pourcentage de mémoire EEPROM destiné au stockage des pages de personnalisation utilisateur, tandis que le paramètre machine du PLC "PLCMEM" indique le pourcentage de mémoire EEPROM destiné au stockage du programme automate. La mémoire EEPROM restante sert au stockage des programmes pièce de la CNC. RESSOURCES PLC Si le système comporte un automate intégré, une mention indique que le PLC est contrôlé par l’UC de la CNC. Au contraire, si l’automate dispose de sa propre UC, la mémoire RAM dont il dispose sera indiquée, en Kb. Elle indique également la partie de la mémoire EEPROM partagée avec la CNC et disponible pour stocker les programmes automate. Les valeurs sont données en Kb. Chapitre: 12 DIAGNOSTICS Section: CONFIGURATION DU SYSTEME Page 3 12.1.2 CONFIGURATION SOFTWARE Cete option indique les options software disponibles, la version installée et le code d’identification de l’appareil. OPTIONS INSTALLEES Cette rubrique indique la configuration software du système et affiche les informations suivantes: * Nombre maximum d’axes interpolables avec la version du CNC installée. * Toutes les options software disponibles. VERSION DE SOFTWARE Cette rubrique indique les versions de software correspondant à la CNC et au PLC disponibles. IDENTIFICATION Cette rubrique affiche le code d’identification de la CNC. L’utilisation de ce code est réservée aux Services d’Assistance technique. Page 4 Chapitre: 12 DIAGNOSTICS Section: CONFIGURATION DU SYSTEME 12.2 TEST HARDWARE Cette option vérifie les tensions d’alimentation du système, les tensions délivrées aux cartes, et la température intérieure de l’UC. Elle affiche les informations suivantes: DIAGNOSTICS P...... N.... 11 : 50 : 14 TEST DE HARDWARE * * * * * * * TENSIONS +5 [ -5 [ +15 [ -15 [ Pile [ GND [ GNDA [ D'ALIMENTATION ( volts ) +4.40 / +5.60 ] -4.40 / -5.60 ] +13.40 / +16.80] -13.40 / -16.80 ] +3.00 / +3.90 ] ] ] 5.06 - 4.98 14.75 -15.04 3.59 0.00 0.00 TENSIONS DE CARTES ( 24 volts ) * Axes * Entrées / Sorties 1 * Entrées / Sorties 2 * Entrées / Sorties 3 Correct **Erreur** **Erreur** **Erreur** - TEMPERATURE INTERIEURE [ 0 / 55 ] 23 ºC CAP INS CONFIGURATION TEST HARDWARE F1 F2 TEST MEMOIRE F3 TEST EPROM F4 UTILISATEUR F5 F6 F7 TENSIONS D’ALIMENTATION Cette rubrique indique la tension correspondant à la pile au lithium et les tensions délivrées par le Module d’Alimentation. Les tensions délivrées par le Module d’Alimentation pour utilisation interne par la CNC sont: +5V, -5V, +15V, -15V, GND (0V logique), GNDA (0V analogique) Chaque valeur est suivie de la marge de variations (valeurs maximum et minimum) que la CNC considère comme correcte. En outre, la valeur réelle de chaque alimentation est indiquée. Si une tension mesurée est hors de la plage autorisée, le message "** Erreur **" s’affiche. Chapitre: 12 Section: DIAGNOSTICS TEST HARDWARE Page 5 TENSIONS DELIVREES AUX CARTES Cette rubrique indique si le module d’AXES, le module de recopie (I/O TRACING) et les modules d’E/S sont alimentés en 24 V. Dans le cas contraire, le message "** Erreur **" s’affiche. L’absence du 24 V peut être dûe au défaut d’alimentation des connecteurs ou au claquage du fusible de protection de la carte concernée. TEMPERATURE INTERNE Cette rubrique indique la température interne de l’UC de la CNC, ainsi que la marge de variations (valeurs maximum et minimum) que la CNC considère comme correcte. Page 6 Chapitre: 12 DIAGNOSTICS Section: TEST HARDWARE 12.3 TEST MEMOIRE Cette option vérifie l’état de la mémoire interne de la CNC. Cette vérification n’est possible que si le programme automate est stoppé. Dans le cas contraire, la CNC demande à l’opérateur s’il désire interrompre l’exécution. Dès que cette option est activée, la page d’écran ci-dessous s’affiche: DIAGNOSTICS P...... N.... 11 : 50 : 14 TEST MEMOIRE CNC - Memoire RAM (Kb) -> Utilisateur -> Système 128 384 - Memoire EEPROM (Kb) Correct Correct 16 Correct PLC - Memoire RAM (Kb) - Memoire EEPROM (Kb) 64 Correct 16 Correct CAP INS CONFIGURATION TEST HARDWARE F1 F2 TEST MEMOIRE F3 TEST EPROM F4 UTILISATEUR F5 F6 F7 CNC Cette rubrique indique l’état de la mémoire RAM utilisée par le système et l’espace disponible pour l’utilisateur, en Kb. Elle indique également la partie de la mémoire EEPROM partagée avec le PLC et disponible pour stocker les programmes pièce de la CNC ainsi que les pages de personnalisation utilisateur. Les valeurs sont données en Kb. Le paramètre machine général "PAGESMEM" indique le pourcentage de mémoire EEPROM destiné au stockage des pages de personnalisation utilisateur, tandis que le paramètre machine du PLC "PLCMEM" indique le pourcentage de mémoire EEPROM destiné au stockage du programme automate. La mémoire EEPROM restante sert au stockage des programmes pièce de la CNC, des messages et des erreurs de l’automate. Après le test de l’ensemble de la mémoire, le résultat obtenu s’affiche face à chaque valeur, soit ("Correct", soit "** Erreur **"). Chapitre: 12 Section: DIAGNOSTICS TEST MEMOIRE Page 7 PLC Cette rubrique indique l’état de la mémoire RAM disponible pour l’automate; la taille est exprimée en Kb. Ici aussi, la partie de la mémoire EEPROM partagée avec la CNC et celle disponible pour stockage du programme de l’automate sont indiquées et exprimées en Kb. Après le test de l’ensemble de la mémoire, le résultat obtenu s’affiche face à chaque valeur, soit ("Correct", soit "** Erreur **"). Page 8 Chapitre: 12 DIAGNOSTICS Section: TEST MEMOIRE 12.4 TEST EPROM Cette option vérifie l’état de la mémoire EPROM de la CNC. Ces mémoires contiennent la version du logiciel de la CNC et de l’automate. Cette vérification n’est possible que si le programme automate est stoppé. Dans le cas contraire, la CNC demande à l’opérateur s’il désire interrompre l’exécution. Dès que cette option est activée, la page d’écran ci-dessous s’affiche: DIAGNOSTICS P...... N.... 11 : 50 : 14 TEST CHECKSUM EPROM CNC BANC 1 EPROM 1 EPROM 2 EPROM 3 EPROM 4 3C15 34C4 00FE C13A 3C15 34C4 00FE C13A BANC 2 Correct Correct Correct Correct D3F9 7A21 355E A7A8 D3F9 7A21 355E A7A8 LANGUE Correct Correct Correct Correct 5C35 5C35 Correct PLC BANC 1 EPROM1 EPROM 2 0388 44F0 0388 44F0 IDENTIFICATION Correct Correct 9E8A8D9496 999E98908D CAP INS CONFIGURATION F1 TEST HARDWARE F2 TEST MEMOIRE F3 TEST EPROM F4 UTILISATEUR F5 F6 F7 CNC Cette rubrique indique les sommes de contrôle correspondant à la version du logiciel CNC installée. La somme de contrôle correspondant à la version installée figurera face à chaque EPROM. A la fin de la vérification, la CNC affiche la nouvelle somme de contrôle calculée et ajoute à la suite le message correspondant au résultat obtenu, soit ("Correct", soit "** Erreur **"). Chapitre: 12 Section: DIAGNOSTICS TEST EPROM Page 9 PLC Cette rubrique indique les sommes de contrôle correspondant à la version du logiciel de PLC installée. La somme de contrôle correspondant à la version installée figurera face à chaque EPROM. A la fin de la vérification, la CNC affiche la nouvelle somme de contrôle calculée et ajoute à la suite le message correspondant au résultat obtenu, soit ("Correct", soit "** Erreur **"). Page 10 Chapitre: 12 DIAGNOSTICS Section: TEST EPROM 12.5 UTILISATEUR Si cette option est activée, la CNC exécute, dans le canal utilisateur, le programme de personnalisation sélectionné avec le paramètre machine général "USERDIAG". Pour interrompre l’exécution et revenir au menu principal, frapper ESC. Chapitre: 12 Section: DIAGNOSTICS UTILISATEUR Page 11 12.6 NOTES UTILES La CNC exécute une série de vérifications internes séquentielles. Si le résultat obtenu n’est pas le résultat souhaité, la CNC peut stopper l’avance des axes et la rotation de broche (en annulant toutes les sorties analogiques et en supprimant les signaux Enable); elle peut aussi stopper l’exécution du programme automate ou activer la sortie URGENCE externe (O1). Le tableau ci-dessous montre les tests exécutés par la CNC, indique leur fréquence d’exécution et les actions réalisées par la CNC lorsque le résultat obtenu n’est pas celui escompté. Type de TEST Exécution pendant Mémoire RAM de la CNC Mémoire EEPROM de la CNC Mémoire RAM du PLC Mémoire EEPROM du PLC Urgence externe (I1 ou M5000) Tension des cartes d’AXES, E/S et Recopie E/S PLC non prêt Température Pile déchargée (MESSAGE D’AVERTISSEMENT) WATCHDOG du PLC Erreurs utilisateur PLC Page 12 Démarrage CNC Démarrage CNC Démarrage CNC Démarrage CNC EXEC./SIMUL. EXEC./SIMUL. EXEC./SIMUL. Toujours Toujours Si “PLC RUN” EXEC./SIMUL. Chapitre: 12 DIAGNOSTICS Stoppe Axes et Broche OUI OUI OUI OUI OUI OUI OUI OUI NON OUI OUI Stoppe le PLC NON NON OUI OUI NON NON --NON NON OUI NON Active la sortie URGENCE OUI OUI OUI OUI NON OUI OUI OUI NON OUI NON Section: NOTES UTILES CNC FAGOR 8050 M MANUEL DE PROGRAMMATION Ref. 9701 (fra) FAGOR AUTOMATION S. Coop. Ltda. informe périodiquement tous les clients qui en font la demande sur les nouvelles possibilités mises en oeuvre dans la CNC FAGOR 8050. De cette façon, le client peut demander la ou les nouvelles fonctionnalités qu’il désire incorporer à sa machine. Pour obtenir ces informations, il vous suffit de nous communiquer l’adresse complète de votre société, ainsi que la référence (modèle et numéro de série) des différents modèles de Commandes Numériques que vous utilisez. Il convient de tenir compte du fait que certaines des fonctions décrites dans ce manuel peuvent être absentes de la version du logiciel que vous venez d’acquérir. Les fonctions dépendant des options du logiciel sont les suivantes: Gestion de durée de vie des outils Cycles de palpeur DNC Editeur de profils Logiciel pour 4 ou 6 axes Poches quelconques (avec ilôts) Digitalisation Graphiques solides Taraudage rigide Recopie Les informations données dans ce manuel pourront varier en fonction des modifications techniques. FAGOR AUTOMATION, S. Coop. Ltda. se reserve le droit de modifier le contenu de ce manuel sans être tenu d’en signaler les variations. Si vous venez d’acquérir le MODELE CNC FAGOR 8050 GP, nous recommandons de tenir compte des considérations suivantes: * Fraiseuse. Ce modèle est basé sur le modèle CNC 8050 de * bénéficie le modèle CNC 8050 de Fraiseuse Il ne dispose pas de certaines des fonctions dont La liste des fonctions non disponibles par rapport au modèle pour fraiseuse et les options de logiciel disponibles avec le modèle présenté figurent ci-dessous. Fonctions non disponibles Options de logiciel Filetage electronique (G33) Gestion du magasin d’outils Cycles fixes d’usinage (G8x) Usinages multiples (G6x) Cycles fixes de palpeur Gestion de durée de vie des outils Poches quelconques (avec ilôts) Digitalisation Graphiques Recopie Logiciel pour 4 ou 6 axes DNC Taraudage rigide (G84) Compensation de rayon d’outil (G40, G41, G42) Editeur de profils SOMMAIRE Section Page Nouvelles fonctionnalités et modifications .................................................................... INTRODUCTION Règles de sécurité ............................................................................................................ 3 Conditions de retour du materiel ..................................................................................... 5 Documentation Fagor pour la CNC 8050 ........................................................................ 6 Sommaire ......................................................................................................................... 7 Chapitre 1 1.1 1.2 Ligne DNC ....................................................................................................................... 1 Protocole de communications par DNC ou un périphérique ........................................... 2 Chapitre 2 2.1 2.1.1 2.1.2 2.1.2.1 2.1.2.2 2.1.3 CONSTRUCTION D’UN PROGRAMME Structure d’un programme dans la CNC .......................................................................... 1 En-tête de bloc ................................................................................................................. 2 Bloc de programme ......................................................................................................... 3 Langage ISO .................................................................................................................... 3 Langage de haut niveau .................................................................................................. 3 Fin de bloc ....................................................................................................................... 4 Chapitre 3 3.1 3.1.1 3.2 3.3 3.4 3.5 3.5.1. 3.5.2 3.5.3 3.5.4 3.6 3.7 3.7.1 3.7.2 GENERALITES AXES ET SYSTEMES DE COORDONNEES Nomenclature des axes .................................................................................................... 1 Sélection des axes ............................................................................................................ 2 Sélection de plans (G16,G17,G18,G19) .......................................................................... 3 Cotation de la pièce. Millimètres ou pouces (G70,G71) ................................................. 5 Programmation absolue/incrémentale (G90,G91) ........................................................... 6 Programmation des cotes ................................................................................................. 7 Coordonnées cartésiennes ............................................................................................... 7 Coordonnées polaires ...................................................................................................... 8 Coordonnées cylindriques .............................................................................................. 10 Angle et une coordonnée cartésienne ............................................................................. 11 Axes rotatifs ..................................................................................................................... 12 Zones de travail ............................................................................................................... 13 Définition des zones de travail ........................................................................................ 13 Utilisation des zones de travail ....................................................................................... 14 Section Page Chapitre 4 4.1 4.2 4.3 4.4 4.4.1 4.4.2 4.5 Points de référence ........................................................................................................... 1 Recherche de la référence machine (G74) ....................................................................... 2 Programmation par rapport au zéro machine (G53) ......................................................... 3 Présélection des coordonnées et décalages d’origine ..................................................... 4 Présélection de coordonnées et limitation de la valeur de S (G92) ................................. 6 Décalages d’origine (G54..G59) ...................................................................................... 7 Présélection de l’origine polaire (G93) ........................................................................... 9 Chapitre 5 5.1 5.2 5.2.1 5.2.2 5.3 5.3.1 5.3.2 5.4 5.4.1 5.4.2 5.4.3 5.4.4 5.4.5 5.4.5.1 5.4.5.2 5.4.5.3 5.4.5.4 5.4.5.5. 5.4.5.6 5.4.5.7 5.4.5.8 5.4.5.9 5.4.5.10 5.4.5.11 6.5 6.6 6.7 6.8 6.9 6.10 6.11 6.12 6.13 PROGRAMMATION EN CODE ISO Fonctions préparatoires ................................................................................................... 2 Fonctions d’avance (G94,G95) ........................................................................................ 4 Avance en mm/minute ou en pouces/minute (G94) ........................................................ 4 Avance en mm/tour ou en pouces/tour (G95) .................................................................. 5 Fonctions à vitesse constante (G96,G97) ........................................................................ 6 Vitesse de surface constante (G96) .................................................................................. 6 Vitesse constante du centre de l’outil (G97) ................................................................... 6 Fonctions complémentaires ............................................................................................. 7 Vitesse d’avance F ........................................................................................................... 7 Vitesse de rotation de broche et arrêt indexé de broche (S) ............................................ 8 Numéro d’outil (T) ........................................................................................................... 9 Numéro de correcteur (D) ................................................................................................. 10 Fonction auxiliaire (M) ................................................................................................... 11 M00. Arrêt du programme ............................................................................................... 12 M01. Arrêt conditionnel du programme .......................................................................... 12 M02. Fin de programme .................................................................................................. 12 M30. Fin de programme avec retour au premier bloc ...................................................... 12 M03. Rotation de la broche à droite (sens horaire) ......................................................... 12 M04. Rotation de la broche à gauche (sens anti-horaire) ................................................ 12 M05. Arrêt de broche ....................................................................................................... 12 M06. Code de changement d’outil .................................................................................. 13 M19. Arrêt indexé de broche ........................................................................................... 13 M41, M42, M43, M44. Changement de gammes de vitesse de broche .......................... 14 M45. Broche auxiliaire / Outil motorisé ......................................................................... 14 Chapitre 6 6.1 6.2 6.3 6.4 SYSTEMES DE REFERENCE CONTROLE DES TRAJECTOIRES Transversal rapide (G00) ................................................................................................. 1 Interpolation linéaire (G01) ............................................................................................. 2 Interpolation circulaire (G02,G03) .................................................................................. 3 Interpolation circulaire avec programmation du centre de l’arc en coordonnées absolues (G06) ........................................................................................... 9 Trajectoire circulaire tangente à la trajectoire précédente (G08) .................................... 10 Trajectoire circulaire définie par 3 points (G09) ............................................................. 11 Interpolation hélicoïdale ................................................................................................. 12 Entrée tangentielle au début de l’usinage (G37) ............................................................. 14 Sortie tangentielle à la fin de l’usinage (G38) ................................................................. 16 Arrondi automatique aux angles (G36) ........................................................................... 18 Chanfrein (G39) ............................................................................................................... 19 Filetage (G33) .................................................................................................................. 20 Déplacement jusqu’à une butée mécanique (G52) .......................................................... 21 Section Page Chapitre 7 7.1 7.2 7.3 7.3.1 7.3.2 7.3.3 7.4 7.5 7.6 7.6.1 7.6.2 7.7 7.8 7.8.1 7.8.2 Interruption de la préparation de blocs (G04) ................................................................. 1 Temporisation (G04K) ..................................................................................................... 3 Travail sur angle vif (G07) et arrondi (G05,G50) ............................................................ 4 Angle vif (G07) ................................................................................................................ 4 Arrondi aux angles (G05) ................................................................................................ 5 Arrondi aux angles contrôlé (G50) .................................................................................. 6 Analyse par anticipation ................................................................................................. 7 Image-miroir (G10,G11,G12,G13,G14) ........................................................................... 9 Facteur d’échelle (G72) ................................................................................................... 11 Facteur d’échelle appliqué à tous les axes ...................................................................... 12 Facteur d’échelle appliqué à un ou plusieurs axes .......................................................... 14 Rotation du système de coordonnées (G73) ................................................................... 16 Couplage/découplage électronique des axes .................................................................. 18 Couplage électronique des axes (G77) ............................................................................ 19 Annulation du couplage électronique des axes (G78) .................................................... 20 Chapitre 8 8.1 8.1.1 8.1.2 8.1.3 8.2 COMPENSATION D’OUTILS Compensation de rayon d’outil (G40,G41,G42) ............................................................. 2 Activation de la compensation de rayon d’outil ............................................................. 3 Sections de compensation de rayon d’outil .................................................................... 6 Annulation de la compensation de rayon d’outil ............................................................ 9 Compensation de longueur d’outil (G43,G44,G15) ........................................................ 15 Chapitre 9 9.1 9.2 9.2.1 9.3 9.4 9.5 9.5.1 9.5.2 9.5.3 9.5.4 9.5.5 9.5.6 9.5.7 9.5.8 9.5.9 9.5.10 FONCTIONS PREPARATOIRES SUPPLEMENTAIRES CYCLES FIXES Définition du cycle fixe ................................................................................................... 1 Zone d’influence du cycle fixe ........................................................................................ 2 G79. Modification des paramètres du cycle fixe ............................................................. 2 Annulation du cycle fixe ................................................................................................. 4 Considérations générales ................................................................................................. 5 Cycles fixes d’usinage ..................................................................................................... 6 G69. Cycle fixe de perçage profond à pas variable ......................................................... 8 G81. Cycle fixe de perçage .............................................................................................. 12 G82. Cycle fixe de perçage avec temporisartion ............................................................. 14 G83. Cycle fixe de perçage profond à pas constant ........................................................ 16 G84. Cycle fixe de taraudage .......................................................................................... 19 G85. Cycle fixe d’alésage de précision ........................................................................... 22 G86. Cycle fixe d’alésage avec retrait en rapide (G00) ................................................... 24 G87. Cycle fixe de poche rectangulaire .......................................................................... 26 G88. Cycle fixe de poche circulaire ................................................................................ 34 G89. Cycle fixe d’alésage avec retrait en avance de travail (G01) .................................. 41 Section Page Chapitre 10 10.1 10.2 10.3 10.4 10.5 10.6 G60: Usinage multiple selon une droite .......................................................................... 2 G61: Usinage multiple selon un parallélogramme .......................................................... 5 G62: Usinage multiple selon une grille ........................................................................... 8 G63: Usinage multiple selon une circonférence ............................................................. 11 G64: Usinage multiple selon selon un arc ....................................................................... 14 G65: Usinage programmé au moyen d’une corde d’arc .................................................. 17 Chapitre 11 11.1 11.1.1 11.1.2 11.1.3 11.1.4 11.1.5 11.1.5.1 11.1.5.2 11.1.5.3 11.1.6 11.1.7 11.1.8 11.2 11.2.1 11.2.2 11.2.3 11.2.4 11.2.5 11.2.5.1 11.2.6 11.2.6.1 11.2.7 11.2.8 11.2.9 11.2.10 CYCLE FIXE DE POCHE AVEC ILOTS Poches en 2D ................................................................................................................... 2 Operation de percage ....................................................................................................... 5 Operation d’ebauche ....................................................................................................... 6 Operation de finition ....................................................................................................... 9 Regles de programmation des profils .............................................................................. 12 Intersection de profils ...................................................................................................... 13 Intersection de profils de base (k=0) ................................................................................ 13 Intersection de profils evoluee (k=1) ............................................................................... 14 Profil resultant ................................................................................................................. 16 Syntaxe de la programmation de profils .......................................................................... 17 Erreurs .............................................................................................................................. 19 Exemples de programmation ........................................................................................... 21 Poches en 3D ................................................................................................................... 25 Operation d’ebauche ....................................................................................................... 29 Operation de semi-finition .............................................................................................. 32 Operation de finition ....................................................................................................... 34 Geometrie des contours ou profils ................................................................................... 36 Regles de programmation des profils .............................................................................. 37 Exemples de programmation .......................................................................................... 39 Profils composes .............................................................................................................. 42 Exemple de poche composee en 3d ................................................................................ 45 Profils superposes ............................................................................................................ 47 Syntaxe de programmation des profils ............................................................................ 48 Exemples ......................................................................................................................... 50 Erreurs .............................................................................................................................. 61 Chapitre 12 12.1 12.2 12.3 12.4 12.5 12.6 12.7 12.8 12.9 12.10 12.11 USINAGES MULTIPLES UTILISATION D’UN PALPEUR Déplacement avec palpeur (G75,G76) ............................................................................. 2 Cycles fixes de palpage ................................................................................................... 3 Cycle fixe d’étalonnage de longueur d’outil .................................................................. 4 Cycle fixe d’étalonnage de palpeur ................................................................................ 7 Cycle fixe de mesure de surface ...................................................................................... 11 Cycle fixe de mesure de coin extérieur ........................................................................... 15 Cycle fixe de mesure de coin intérieur ............................................................................ 18 Cycle fixe de mesure d’angle .......................................................................................... 21 Cycle fixe de mesure de coin extérieur et d’angle .......................................................... 24 Cycle fixe de mesure de trou ........................................................................................... 28 Cycle fixe de mesure de moyeu ....................................................................................... 32 Section Page Chapitre 13 13.1 13.1.1 13.1.2 13.1.3 13.2 13.2.1 13.2.2 13.2.3 13.2.4 13.2.5 13.2.6 13.2.7 13.2.8 13.2.9 13.2.10 13.2.11 13.3 13.4 13.5 13.5.1 13.5.2 Description lexique ......................................................................................................... 1 Mots réservés ................................................................................................................... 2 Constantes numériques.................................................................................................... 3 Symboles ......................................................................................................................... 3 Variables .......................................................................................................................... 4 Paramètres ou variables de caractère général .................................................................. 6 Variables associées aux outils ......................................................................................... 8 Variables associées aux décalages d’origine ................................................................... 10 Variables associées aux paramètres machine .................................................................. 11 Variables associées aux zones de travail ......................................................................... 12 Variables associées aux avances ...................................................................................... 13 Variables associées aux coordonnées .............................................................................. 15 Variables associées à la broche ........................................................................................ 16 Variables associées à l’automate ..................................................................................... 18 Variables associées aux paramètres locaux ..................................................................... 19 Autres variables ............................................................................................................... 20 Constantes ....................................................................................................................... 26 Opérateurs ........................................................................................................................ 26 Expressions ...................................................................................................................... 28 Expressions arithmétiques ............................................................................................... 28 Expressions relationnelles ............................................................................................... 29 Chapitre 14 14.1 14.2 14.3 14.4 14.5 14.5.1 14.6 14.7 DECLARATIONS DE CONTROLE DES PROGRAMMES Déclarations d’affectation ............................................................................................... 1 Déclarations de visualisation .......................................................................................... 2 Déclarations de validation/invalidation ......................................................................... 3 Déclarations de contrôle de flux ...................................................................................... 4 Déclarations de sous-routines .......................................................................................... 6 Déclarations de sous-routines d’interruption .................................................................. 12 Déclarations permetant de générer des programmes ....................................................... 13 Déclarations de personnalisation .................................................................................... 15 Chapitre 15 15.1 15.2 PROGRAMMATION EN LANGAGE DE HAUT NIVEAU CYCLES DE NUMERISATION Cycle fixe de numérisation suivant une grille ................................................................ 2 Cycle fixe de numérisation suivant un arc ...................................................................... 5 Section Page Chapitre 16 16.1 16.1.1 16.2 16.3 16.3.1 16.3.2 16.3.3 16.3.4 16.4 16.5 16.6 16.7 16.7.1 16.7.2 16.7.3 16.7.4 16.7.5 16.7.5.1 16.7.5.2 COPIE ET NUMERISATION Introduction ..................................................................................................................... 1 Considérations générales ................................................................................................. 7 G26. Etalonnage de la sonde de copie ............................................................................ 9 G23. Activation de la copie ............................................................................................. 11 G23. Activation de la copie manuelle ............................................................................. 12 G23. Activation de la copie unidimensionnelle ............................................................. 14 G23. Activation de la copie bidimensionnelle ................................................................ 16 G23. Activation de la copie tridimensionnelle ............................................................... 18 G27. Définition du contour de copie ............................................................................... 20 G25. Désactivation de la copie ........................................................................................ 24 G24. Activation de la numérisation ................................................................................ 25 Cycles fixes de copie et de numérisation ........................................................................ 28 Cycle fixe de copie suivant un grille .............................................................................. 29 Cycle fixe de copie suivant un arc .................................................................................. 34 Cycle fixe de profil dans le plan ...................................................................................... 40 Cycle fixe de profil dans l’espace ................................................................................... 45 Cycle fixe de copie par balayage de polygone ............................................................... 50 Règles de programmation des profils .............................................................................. 55 Syntaxe de programmation des profils ............................................................................ 56 ANNEXES A. B. C. D. E. Programmation en code ISO ............................................................................................ 2 Variables internes de la CNC ........................................................................................... 4 Programmation de haut niveau ........................................................................................ 9 Codes créés par touches ................................................................................................... 11 Pages du système d’aide à la programmation .................................................................. 16 NOUVELLES CARACTERISTIQUES ET MODIFICATIONS (Fraiseuse) Date: Juin 1992 Version du logiciel: 7.01 et suivants CARACTERISTIQUE MANUEL ET CHAPITRES CONCERNES Modèle GP Tous les manuels Réception de dessins sous Autocad Manuel spécifique, remis avec le logiciel Broche secondaire/outil motorisé Manuel d’installation Chap. 3, 9, Annexe Manuel de programmation Chap. 5, 13 Recopie Manuel d’installation Chap. 1, Chap. 13 Manuel de programmation Chap. 5, 14, 16, Annexe Editeur de profils Manuel d’utilisation Chap. 4 Editeur interactif Manuel d’utilisation Chap. 4 Editeur d’apprentissage (TEACH-IN) Manuel d’utilisation Chap. 4 Logiciel pour 4 ou 6 axes Manuel d’installation Chap. 4, 9, 10, Annexe Manuel de programmation Chap. 3, 13 Contrôle des axes depuis le PLC Manuel d’installation Chap. 3, Chap. 11 Chargement du contenu de la mémoire EEPROM dans une mémoire EPROM Manuel d’utilisation Chap. 7 Etalonnage des outils avec palpeur en mode manuel Manuel d’installation Manuel d’utilisation Chap. 3 Chap. 5 Sous-programmes d’interruption (4 entrées) Manuel d’installation Chap. 3, 9,Annexe AC-forward Manuel d’installation Chap. 3 Contrôle du PLC en mode JOG Manuel d’utilisation Chap. 5 Estimation des temps d’exécution Manuel d’utilisation Chap. 3 Chargement de programmes pièce en mémoire EEPROM Manuel d’installation Manuel d’utilisation Chap. 3 Chap. 7, 12 Trois tables de compensation croisée Manuel d’installation Manuel d’utilisation Chap. 3, Annexe Chap. 11 Déplacement des axes en manuel lors de la définition des tables de vis et de compensation croisée Manuel d’utilisation Chap. 11 Sous-programme associé aux outils Manuel d’installation Chap. 3 Possibilité de CHERCHER TEXTE dans l’option SELECTION DE BLOC Manuel d’utilisation Chap. 3 Plus de caractères de taille double et triple Manuel d’utilisation Chap. 10 Programmation de l’instruction ERREUR par paramètre Manuel de programmation Chap 14 Variables d’accès au centre de rotation: ROTPF et ROTPS Manuel de programmation Chap 13, Annexe Page 1 Nouvelles caractéristiques (M) - 1 CARACTERISTIQUE MANUEL ET CHAPITRES CONCERNES Variables d’accès au palpeur de recopie: DEFLEX, DEFLEY et DEFLEZ Manuel d’installation Chap. 10, Annexe Manuel de programmation Chap. 13, Annexe Sortie logique générale indiquant l’état de la boucle de positionnement d’axes: LOPEN Manuel d’installation Chap. 9, Annexe PLC: initialiser un bloc de registres Manuel d’utilisation Chap. 9 PLC: nouvelles directives Manuel d’installation Chap. 7 PLC: 200 symboles Manuel d’installation Chap. 7 Nouvelles possibilités dans les cycles fixes de poche avec ilôts Manuel de programmation Chap. 11 Connecteur X7 du module AXES Manuel d’installation Chap. 1 Support d’unité de disquettes FAGOR Manuel d’installation Chap. 1, 3 Assouplissement du cycle de changement d’outil Manuel d’installation Chap. 3 Traitement amélioré des erreurs Manuel d’utilisation Chap. 1 Date: Avril 1993 CARACTERISTIQUE Version du logiciel: 7.06 et suivants MANUEL ET CHAPITRES CONCERNES Axes rotatifs sans limites Manuel d’installation Axes de positionnement en G01 Manuel de programmation Chap. 6 Déplacement du point de référence Manuel d’installation Variables de zones de travail (R/W) depuis le PLC Manuel d’installation Chap. 10, Annexe Manuel de programmation Annexe Possibilité d’interrompre le canal utilisateur Manuel d’installation Mouvement jusqu’à la butée Manuel d’installation Chap. 3, 11 Manuel de programmation Chap. 6, Annexe Graphiques d’aléseuse Manuel d’installation Programmation de “WBUF” sans paramètres Manuel de programmation Chap. 14 Date: Juillet 1993 CARACTERISTIQUE Chap. 3 Chap. 3, 4 Chap. 9, Annexe Chap. 3 Version du logiciel: 7.07 et suivants MANUEL ET CHAPITRES CONCERNES Le modèle GP offre la compensation de rayon d’outil en option (G40, G41, G42) Sorties logiques d’état de touches 2 - Nouvelles caractéristiques (M) Manuel d’installation Chap. 9 Date: Janvier 1994 Version du logiciel: 9.01 et suivants CARACTERISTIQUE MANUEL ET CHAPITRES CONCERNES Visualisation de la pointe ou de la base de l’outil Manuel d’installation Chap. 3 Possibilité de mesure dans les graphiques avec un curseur Manuel d’utilisation Chap. 3 Permettre l’étalonnage de l’outil en manuel et par palpeur Manuel d’utilisation Chap. 5 Traitement des signaux Io codés Manuel d’installation Chap. 3 Possibilité de mémoriser sur EEPROM les messages et erreurs du PLC Manuel d’installation Manuel d’utilisation Chap. 3 Chap. 7 Indicateur “Programme en EEPROM” Manuel d’utilisation Chap. 7 Indicateur “programme en cours d’exécution” Manuel d’utilisation Chap. 7 G50. Arrondi aux angles contrôlé Manuel d’installation Chap. 3, 11 Manuel de programmation Chap. 5, 7, Annexe Avance par tour (G95) pour les axes contrôlés par l’intermédiaire du PLC Manuel d’installation Ebauche concentrique de poches avec ilôts Manuel de programmation Chap. 11 G93 en définition de profil de poche avec ilôts Manuel de programmation Chap. 11 Recopie et digitalisation manuelle, en 1, 2 et 3 dimensions Manuel d’installation Chap. 9, Annexe Manuel de programmation Chap. 5, 16, Annexe Nouveaux cycles de recopie/digitalisation Manuel de programmation Chap. 16 Visualisation de la déflexion et des facteurs de correction du palpeur de recopie Manuel d’utilisation Chap. 3, 5 Exécution de programme infinie depuis le PC Manuel d’utilisation Chap. 8 Programme infini multi-disquettes dans l’unité de disquettes Manuel d’utilisation Chap. 8 Digitalisation multi-disquettes dans l’unité de disquettes Manuel d’utilisation Chap. 8 Date: Mai 1994 CARACTERISTIQUE Chap. 11 Version du logiciel: 9.03 et suivants MANUEL ET CHAPITRES CONCERNES Temps d’anticipation pour poinçonneuses Manuel d’installation Chap. 3, 9, Annexe Variables TPOS(X-C), TPOSS, FLWES Manuel d’installation Chap. 10, Annexe Modification de la vitesse de M19 depuis le PLC Manuel d’installation Chap. 9, Annexe Déplacements en G75 et G76 à 100% de F Manuel de programmation Chap. 10 Nouvelles caractéristiques (M) - 3 Date: Décembre 1994 Version du logiciel: 9.06 et suivantes CARACTERISTIQUE MANUEL ET CHAPITRES CONCERNES Troisième zone de travail Manuel d’installation Chap. 10, Annexe Manuel de programmation Chap. 3, 13, Annexe Pour faciliter le fonctionnement sans moniteur, les valeurs par défaut des paramètres: PROTOCOL (1) et POWDNC (oui) ont été changées Manuel d’installation Date: Février 1995 Chap. 3 Version du logiciel: 9.07 et suivantes CARACTERISTIQUE MANUEL ET CHAPITRES CONCERNES Si, pendant la recherche de “zéros” codifiés, le signal DECEL* de l’axe passe à “1”, le sens du mouvement est inversé et la recherche se déroule en sens contraire. Manuel d’installation Chap. 4 Une fonction “T” avec un sous-programme associé peut être programmée dans un bloc comportant un mouvement. Manuel d’installation Chap. 3 Le paramètre “TAFTERS” indique si la fonction “T” est exécutée avant ou après son sous-programme associé. Manuel d’installation Chap. 3 La fonction G53 sans information de déplacement annule le décalage du zéro actif. Manuel de programmation Chap. 4 La table de fonctions “M” permet d’interrompre la préparation des blocs jusqu’au début ou la fin de la fonction “M”. Manuel d’installation Manuel d’utilisation Date: Octobre 1995 Chap. 3 Chap. 11 Version du logiciel: 9.09 et suivantes CARACTERISTIQUE MANUEL ET CHAPITRES CONCERNES M19 TYPE (paramètre de broche) indique si la broche recherche le zéro à chaque passage du mode boucle ouverte à boucle fermée. Manuel d’installation Les variables POSS et TPOSS sont toujours actives (que la boucle soit ouverte ou fermée) Manuel d’installation Chap. 10 Manuel de programmation Chap. 13 Les tables de compensation de vis autorisent des pentes pouvant atteindre ±45° Manuel d’installation Manuel d’utilisation Date: Avril 1996 Chap. 3 Chap. 3 Chap. 11 Version du logiciel: 9.10 et suivantes CARACTERISTIQUE MANUEL ET CHAPITRES CONCERNES Nouvelles variables RPOSS et RTPOSS associées à la broche Manuel d’installation Chap. 10 et Annexe Manuel de programmation Chap. 13 et Annexe 4 - Nouvelles caractéristiques (M) Date: Juillet 1996 Version du logiciel: 9.11 et suivantes CARACTERISTIQUE MANUEL ET CHAPITRES CONCERNES Paramètre machine EXTMULT à utiliser lorsque le signal Io du système de réalimentation est codifié Manuel d’installation Date: Mai 1996 Chap. 3 Version du logiciel: 11.01 et suivantes CARACTERISTIQUE MANUEL ET CHAPITRES CONCERNES CPU TURBO Manuel d’installation Analyse par anticipation Manuel de programmation Chap. 5, 7 et Annexe Poches quelconques en 3D (avec ilôts) Manuel de programmation Chap. 11 Possibilité de choix du type de début/fin de compensation de rayon Manuel d’installation Chap. 3 Manuel de programmation Chap. 8 Signal d’anticipation pour chaque axe Manuel d’installation Chap. 3, 9 et Annexe Exécution de bloc de haut niveau depuis l’automate Manuel d’installation Chap. 11 Possibilité d’axes rotatifs sans “rollover” (rebouclage) Manuel d’installation Chap. 3 Chap. 1 et 3 Graphiques en ligne dans le modèle GP Editeur de profils optionnel sur modèles GP Nouvelles caractéristiques (M) - 5 INTRODUCTION Introduction - 1 Introduction - 2 REGLES DE SECURITE Une lecture attentive des règles de sécurité suivantes est recommandée afin d’éviter tous dommages au personnel, au produit présenté dans ce manuel ainsi qu’aux éléments qui lui sont raccordés. Les réparations devant être effectuées sur cet appareil ne seront confiées qu’à un personnel dûment habilité par Fagor Automation. Fagor Automation ne pourra être tenu pour responsable d’aucun dommage corporel ou matériel découlant du non-respect de ces règles fondamentales de sécurité. Précautions contre les dommages corporels Avant de mettre l’appareil sous tension, s’assurer qu’il est correctement mis à la terre Pour éviter toutes décharges électriques, vérifier que tous les raccordements à la terre ont été réalisés. Ne pas travailler dans des environnements humides Pour éviter toutes décharges électriques, travailler sous une humidité relative de 90% maximum (sans condensation) et une température ne dépassant pas 45°C. Ne pas travailler dans des environnements explosifs Afin d’éviter tous dangers et accidents, ne pas travailler dans des environnements explosifs. Précautions contre les dommages au produit Environnement de travail Cet appareil est livré prêt à fonctionner dans les Environnements Industriels tels qu’ils ont été définis dans les directives et les normes en vigueur dans l’Union Européenne. Fagor Automation ne pourra êre tenu pour responsable de tout dommage provoqué ou subi en cas d’installation dans d’autres environnements (zones d’habitation). Installer le produit dans un emplacement adéquat Dans toute la mesure du possible, on veillera à installer la CNC loin des sources de liquides de refroidissement et de produits chimiques ainsi qu’à l’abri des chocs susceptibles de l’endommager. Cet appareil est conforme aux directives Européennes sur la compatibilité électromagnétique. Il est toutefois recommandé d’éviter la proximité des sources de parasites électromagnétiques tels que: - Charges puissantes reliées à la même source C.A. que l’appareil décrit ici, - Emetteurs portables (radiotéléphones, radio-amateurs, etc...), - Emetteurs radio/TV, - Machines à souder à l’arc, - Lignes haute tension, - etc... Environnement La température de travail doit être maintenue entre +5°C et +45°C La température de stockage doit être maintenue entre -25°C et +70°C. Introduction - 3 Protection de l’appareil proprement dit Module d’alimentation électrique Ce module comporte deux fusibles rapides de 3,15 A/250 V protégeant la ligne C.A. réseau Module d’axes Toutes les entrées/sorties digitales comportent une isolation galvanique par optocoupleurs entre les circuits de la CNC et l’extérieur. Une protection par fusible externe rapide (F) de 3,15 A/250 V contre l’inversion de phases de la source de courant est également prévue. Module d’entrées/sorties Toutes les entrées/sorties digitales comportent une isolation galvanique par optocoupleurs entre les circuits de la CNC et l’extérieur. Une protection par fusible externe rapide (F) de 3,15 A/250 V contre les surtensions (supérieures à 33 Vcc) et l’inversion de phases de la source de courant est également prévue. Module d’entrées/sorties et de recopie Toutes les entrées/sorties digitales comportent une isolation galvanique par optocoupleurs entre les circuits de la CNC et l’extérieur. Une protection par fusible externe rapide (F) de 3,15 A/250 V contre les surtensions (supérieures à 33 Vcc) et l’inversion de phases de la source de courant est également prévue. Module ventilateur Ce module comporte 1 ou 2 fusibles externes rapides de 0,4 A / 250 V, selon le modèle de ventilateur. Moniteur Le type de protection dépend du type de moniteur. Se reporter à la plaquette d’identification de l’appareil concerné. Précautions pendant les réparations Ne pas intervenir à l’intérieur de l’appareil Seul le personnel Fagor Automation habilité est autorisé à intervenir à l’intérieur de l’appareil. Ne pas manipuler les connecteurs lorsque l’appareil est sous tension Avant de manipuler les connecteurs (entrées/sorties, réalimentation, etc.), s’assurer que l’appareil n’est pas sous tension. Symboles de sécurité Symboles pouvant apparaître dans le manuel Symbole “ATTENTION” Un texte accompagne ce symbole pour indiquer les actions ou les opérations risquant de provoquer des blessures au personnel ou des dommages au produit. Symboles pouvant apparaître sur l’appareil Symbole “ATTENTION” Un texte accompagne ce symbole pour indiquer les actions ou les opérations risquant de provoquer des blessures au personnel ou des dommages au produit. Symbole “CHOC ELECTRIQUE” Ce symbole indique que le point signalé peut être sous tension. Symbole “TERRE DE PROTECTION” Ce symbole indique que ce point doit être relié au point de terre central de la machine afin d’assurer la protection du personnel et des appareils. Introduction - 4 CONDITIONS DE RETOUR DU MATERIEL En cas de retour du moniteur ou de l’UC, le carton et le matériau d’origine devront être réutilisés. En cas d’impossibilité, on procèdera comme suit: 1 Utiliser un carton dont les trois dimensions intérieures seront supérieures d’au moins 15 cm à celles de l’appareil. Le carton utilisé devra résister à une charge de 170 kg. 2 Lors du retour aux ateliers de Fagor Automation, fixer une étiquette indiquant le propriétaire de l’appareil, son adresse, le nom de la personne à contacter, le type d’appareil, le numéro de série, les symptômes et une courte description du problème. 3 Enrouler l’appareil dans un film de polyéthylène ou toute autre protection similaire. Lors de l’envoi du moniteur, prévoir une protection spéciale pour l’écran. 4 Caler l’appareil à l’intérieur du carton au moyen de blocs en mousse de polyurethane sur toutes ses faces. 5 Fermer le carton à l’aide de ruban adhésif ou d’agrafes industrielles. Introduction - 5 DOCUMENTATION FAGOR POUR LA CNC 8050 Manuel CNC 8050 OEM Il s’adresse au constructeur de la machine ou à la personne chargée de l’installation et de la mise en service de la CNC. Il est commun aux modèles de CNC 8050-M et 8050-T, et comprend le manuel d’installation. Manuel d’utilisation de la CNC 8050-M Il s’adresse à l’utilisateur final, c’est-à-dire à l’opérateur chargé de l’exploitation de la CNC. Il comprend deux manuels: Manuel d’utilisation Manuel de programmation Manuel d’utilisation de la CNC 8050-T Il s’adresse à l’utilisateur final, c’est-à-dire à l’opérateur chargé de l’exploitation de la CNC. Il comprend deux manuels: Manuel d’utilisation Manuel de programmation Manuel du logiciel DNC 8050 Manuel du protocole DNC 8050 qui explique comment utiliser la CNC qui explique comment programmer la CNC qui explique comment utiliser la CNC qui explique comment programmer la CNC Il s’adresse aux personnels utilisant le logiciel de communications DNC 8050 en option. Il s’adresse aux personnes désirant concevoir leur propre logiciel de communications DNC afin de communiquer avec la CNC 8050. Manuel AUTOCAD 8050 Il s’adresse aux personnes désirant concevoir leurs pages d’écran CNC et symboles “personnalisés” sur AUTOCAD. Ce manuel explique comment organiser leur programme Autocad de façon que la CNC interprète correctement les pages et symboles conçus. Manuel FLOPPY DISK Il s’adresse aux personnes utilisant l’unité de disquettes FAGOR et explique son mode d’utilisation. Introduction - 6 SOMMAIRE DU MANUEL Le Manuel de programmation de la CNC pour Fraiseuse comprend les chapitres suivants: Index Nouvelles fonctionnalités et modifications apportées au modèle pour Fraiseuse. Introduction Résumé des règles de sécurité Conditions de retour Documentation Fagor pour la CNC 8050 Sommaire du manuel Chapitre 1 Généralités Indique comment charger les programmes pièce depuis le clavier ou par ligne DNC. Présente le protocole à appliquer pour les communications par DNC. Chapitre 2 Création d’un programme Indique la structure d’un programme pièce et de tous ses blocs. Présente les langages pouvant être utilisés pour programmer les pièces: codes ISO et langages de haut niveau. Chapitre 3 Axes et systèmes de coordonnées Indique la nomenclature des axes et comment les sélectionner. Précise comment sélectionner les plans de travail, les unités de travail, le type de système de programmation (absolu/incrémental) Décrit les systèmes de coordonnées pouvant être utilisés pour la programmation: Cartésiennes, polaires, cylindriques, angulaires plus cartésiennes. Indique comment opérer avec les axes rotatifs et comment définir et utiliser les zones de travail. Chapitre 4 Systèmes de référence Indique les références machine (zéro) et les points d’origine devant être définis dans la CNC. Précise comment programmer une recherche du point de référence machine, les coordonnées par rapport au zéro machine, comment présélectionner des coordonnées, les décalages du zéro et les origines polaires. Chapitre 5 Programmation ISO Indique comment programmer les fonctions préparatoires d’avance et de vitesse constante, ainsi que les fonctions auxiliaires telles que “F, S, T, D et M”. Chapitre 6 Contrôle de trajectoire Indique comment programmer le déplacement en rapide, l’interpolation linéaire, circulaire et hélicoïdale. Indique comment programmer les entrées et les sorties tangentielles ainsi que les arrondis aux angles et les chanfreins. Indique comment programmer le filetage électronique et les déplacements sur butée matériel. Chapitre 7 Fonctions préparatoires supplémentaires Indique comment interrompre la préparation des blocs et programmer une temporisation. Indique comment programmer une arête vive, un coin ou un rayon contrôlé aux angles. Décrit le mode de programmation des fonctions analyse par anticipation, image miroir, facteur d’échelle, rotation de modèle et couplage/découplage électronique des axes. Chapitre 8 Compensation d’outils Indique comment programmer la compensation de rayon et de longueur d’outil. Chapitre 9 Cycles fixes Indique comment programmer les différents cycles fixes d’usinage. Chapitre 10 Usinages multiples Indique comment programmer les différents cycles d’usinages multiples. Introduction - 7 Chapitre 11 Cycles fixes de poches quelconques (avec ilôts) Indique comment programmer les différents cycles fixes de poches avec ilôts en 2D et 3D. Chapitre 12 Travail avec palpeur Indique comment exécuter des déplacements avec palpeur et programmer les cycles fixes de palpage. Chapitre 13 Programmation en langage de haut niveau Montre toutes les variables, les symboles, opérateurs, etc... à utiliser en cas de programmation en langage de haut niveau. Chapitre 14 Déclarations de contrôle des programmes Présente les séquences de contrôle utilisables en langage de haut niveau. Les instructions disponibles sont pour: affectation, activation/désactivation de la visualisation, contrôle de débit, sous-programmes, génération de programmes et personnalisation. Chapitre 15 Cycles de digitalisation Indique comment programmer les divers cycles de digitalisation. Chapitre 16 Recopie et digitalisation Indique comment programmer les divers cycles de recopie et de digitalisation. Annexes Introduction - 8 A B C D E Programmation en codes ISO Variables internes de la CNC Programmation en langage de haut niveau Codes clavier Pages du système d’aide à la programmation 1. GENERALITES La CNC FAGOR 8050 peut être programmée aussi bien à la volée (depuis le panneau avant) que depuis des périphériques extérieurs (lecteur de bandes, lecteur/enregistreur de cassettes, ordinateur, etc.). La taille de mémoire dont dispose l’utilisateur pour la réalisation des programmes pièce est de 128 Kb., extensible a 512 Kb. Les programmes pièce et les valeurs des tables dont dispose la CNC peuvent être introduits comme suit: * Depuis le panneau avant. Après sélection du mode d’édition ou de la table désirée, la CNC permet l’introduction des données au moyen du clavier. * Depuis un ordinateur (DNC) ou un Périphérique. La CNC permet l’échange d’informations avec un ordinateur ou un périphérique, au moyen des lignes série RS232C et RS422. Si ces communications sont contrôlées depuis la CNC, il est nécessaire de sélectionner au préalable la table correspondante ou le répertoire de programmes pièce (utilitaires) avec lesquels les communications sont établies. Selon le type de communications choisi, on sélectionnera le paramètre machine des lignes série "PROTOCOL" comme suit: "PROTOCOL" = 0 Pour des communications avec un périphérique. "PROTOCOL" = 1 Pour des communications par ligne DNC. 1.1 LIGNE DNC La CNC offre la possibilité de travailler en mode DNC (Distributed Numerical Control, ou Commande Numérique Déportée), ce qui permet les communications entre la CNC et un ordinateur pour exécuter les fonctions suivantes: * Commandes de répertoire et effacement. * Transfert de programmes et de tables entre la CNC et un ordinateur. * Commande à distance de la machine. * Possibilité de supervision de l’état de systèmes DNC évolués. Chapitre: 1 GENERALITES Section: Page 1 1.2 PROTOCOLE DE COMMUNICATIONS PAR DNC OU UN PERIPHERIQUE Ce type de communications autorise les commandes de transfert de programmes et de tables ainsi que la gestion des répertoires de la CNC et de l’ordinateur pour la copie et l’effacement de programmes, etc. indistinctement depuis la CNC o l’ordinateur. Pour transférer des fichiers, on procèdera comme suit: * Le fichier devra commencer par le symbole "%", suivi du commentaire de programme, qui est optionnel et qui peut comporter jusqu’à 20 caractères. On indiquera ensuite, en les séparant par une virgule ",", les protections (attributs) affectées à ce fichier: lecture, écriture, etc. Ces protections sont optionnelles et leur programmation n’est pas obligatoire. Pour terminer l’en-tête du fichier, on enverra le caractère RETURN (RT) ou LINE FEED (LF), séparé du précédent par ",". Exemple: %Fagor Automation, MX, RT * A la suite de l’en-tête, on programmera les blocs de fichier, qui sont tous programmés selon les règles de programmation exposées dans ce manuel. Pour séparer chaque bloc du bloc suivant, on utilisera le caractère RETURN (RT) ou LINE FEED (LF). Exemple: N20 G90 G01 X100 Y200 F2000 LF (RPT N10, N20) N3 LF Dans le cas des communications avec un périphérique, la commande de fin de fichier doit être émise. Cette commande est sélectionnée au moyen du paramètre machine des lignes série "EOFCHR", et il peut s’agir de l’un des caractères suivants: ESC EOT SUB EXT Page 2 ESCAPE END OF TRANSMISSION SUBSTITUTE END OF TRANSMISSION Chapitre: 1 GENERALITES Section: 2. CONSTRUCTION D’UN PROGRAMME Un programme de commande numérique se compose d’un ensemble de blocs ou instructions. Ces blocs ou instructions sont constitués de mots composés de lettres majuscules et d’un format numérique. Le format numérique dont dispose la CNC comprend: - les signes . + - les chiffres 0 1 2 3 4 5 6 7 8 9 La programmation admet des espaces entre les lettres, les chiffres et les symboles et permet d’ignorer le format numérique s’il est d’une valeur zéro, ou le signe s’il est positif. Le format numérique d’une lettre peut être remplacé par un paramètre arithmétique dans la programmation. Plus tard et pendant l’exécution de base, la commande remplacera le paramètre arithmétique par sa valeur. Exemple: Si XP3 est programmé, la CNC remplacera P3 par sa valeur numérique pendant l’exécution, le résultat obtenu étant X20, X20.567, X-0.003, etc. 2.1 STRUCTURE D’UN PROGRAMME DANS LA CNC Tous les blocs constituant le programme auront la structure suivante: En-tête de bloc + bloc de programme + fin de bloc Chapitre: 2 CONSTRUCTIOND’UNPROGRAMME Section: Page 1 2.1.1 EN-TETE DE BLOC L’en-tête d’un bloc est optionnelle et peut être constituée d’une ou plusieurs conditions de saut de bloc et de l’étiquette ou numéro de bloc. Les deux peuvent être programmés dans cet ordre. CONDITION DE SAUT DE BLOC, /, /1, /2, /3. Ces trois conditions de saut de bloc, puisque "/" est équivalent à "/1" , seront régies par les marques BLKSKIP1, BLKSKIP2 et BLKSKIP3 du PLC. Si l’une de ces marques est active, la CNC n’exécute par le(s) bloc(s) où elle a été programmée. Elle passe à l’exécution du bloc suivant. Il est possible de programmer jusqu’à 3 conditions de saut dans un seul bloc; elles seront évaluées l’une après l’autre selon l’ordre dans lequel elles ont été programmées. La commande lit 20 blocs en avant du bloc en cours d’exécution, afin de pouvoir calculer à l’avance la trajectoire à parcourir. La condition de saut de bloc sera analysée au moment de la lecture du bloc, soit 20 blocs avant son exécution. Pour analyser le bloc au moment de l’exécution, il est nécessaire d’interrompre la préparation des blocs, en programmant G4 dans le bloc précédent. ETIQUETTE OU NUMERO DE BLOC. N(0-9999) L’étiquette ou le numéro de bloc permettent d’identifier le bloc et ne sont utilisés que lors de la réalisation de références ou de saut à un bloc. Ils sont représentés par la lettre N suivie de 4 chiffres maximum (0-9999); il n’est pas obligatoire de suivre un ordre donné et que ces chiffres soient consécutifs. Si un programme comporte deux ou plusieurs blocs avec le même numéro d’étiquette, la CNC prendra toujours le premier. Bien que leur programmation ne soit pas nécessaire, la CNC permet, par l’intermédiaire d’une SOFTKEY, la programmation automatique d’étiquettes dont le nombre initial et le pas peuvent être sélectionnés par le programmeur. Page 2 Chapitre: 2 CONSTRUCTIOND’UNPROGRAMME Section: 2.1.2 BLOC DE PROGRAMME Le bloc de programme se compose de commandes en langage ISO ou en langage Evolué. Pour l’élaboration d’un programme, des blocs écrits dans les deux langages sont utilisés, mais chacun d’eux doit être édité au moyen de commandes appartenant à un seul langage. 2.1.2.1 LANGAGE ISO Ce langage est spécialement conçu pour contrôler le déplacement des axes, car il fournit des informations et des conditions de déplacement ainsi que des indications sur l’avance. Il dispose de : * Fonctions préparatoires de déplacements, qui permettent de déterminer la géométrie et les conditions de travail telles que les interpolations linéaire et circulaire, les filetages, etc. * Fonctions de contrôle des avances des axes et des vitesses de broche. * Fonctions de contrôle des outils. * Fonctions complémentaires, qui contiennent des instructions de nature technologique. 2.1.2.2 LANGAGE DE HAUT NIVEAU Ce langage permet d’accéder à des variables de caractère général ainsi qu’aux tables et aux variables du système. Il offre à l’utilisateur un ensemble de phrases de commande semblables à la terminologie utilisée par d’autres langages, telles que: IF, GOTO, CALL, etc. Il permet également l’emploi de tout type d’expression: arithmétique, relationnelle ou logique. Il dispose également d’instructions permettant la construction de boucles, ainsi que de sousroutines à variables locales. Le terme variable locale désigne une variable connue de la seule sous-routine dans laquelle elle a été définie. Il permet aussi de créer des bibliothèques en regroupant des sous-routines comprenant des fonctions utiles et éprouvées accessibles depuis n’importe quel programme. Chapitre: 2 CONSTRUCTIOND’UNPROGRAMME Section: Page 3 2.1.3 FIN DE BLOC La fin de bloc est optionnelle et peut être constituée de l’indication nombre de répétitions du bloc ainsi que du commentaire de bloc, qui doivent être programmés dans cet ordre. NOMBRE DE REPETITIONS DU BLOC, N(0-9999) Indique combien de fois l’exécution du bloc sera répétée. Seuls les blocs de déplacement sous l’influence d’un cycle fixe ou d’une sousroutine modale lors de leur exécution peuvent être répétés. Dans ces cas, la CNC exécute le déplacement programmé ainsi que l’usinage actif (cycle fixe ou sous-routine modale) le nombre de fois indiqué. Le nombre de répétitions est représenté par la lettre N suivie de 4 chiffres maximum (0-9999). Si NON est programmé, l’usinage actif n’est pas exécuté. Seul le déplacement programmé dans le bloc est exécuté. COMMENTAIRE DE BLOC La CNC permet d’associer tout type d’information à tous les blocs sous forme de commentaire. Le commentaire doit être programmé à la fin du bloc, et commencer par le caractère ";". Si un bloc commence par ";" , tout son contenu est considéré comme un commentaire, et il n’est pas exécuté. Les blocs vides ne sont pas autorisés; ils doivent comporter au moins un commentaire. Page 4 Chapitre: 2 CONSTRUCTIOND’UNPROGRAMME Section: 3. AXES ET SYSTEMES DE COORDONNEES Etant donné que le but de la Commande Numérique est le contrôle du déplacement et du positionnement des axes, il est nécessaire de déterminer la position du point à atteindre, grâce à ses coordonnées. La CNC 8050 permet l’emploi de coordonnées absolues et de coordonnées relatives ou incrémentales dans l’ensemble d’un programme donné. 3.1 NOMENCLATURE DES AXES Les noms des axes répondent à la norme DIN 66217. Z C Y W V B U A X Caractéristiques du système d’axes : * X et Y déplacements principaux d’avance dans le plan de travail principal de la machine. * Z parallèle à l’axe principal de la machine, perpendiculaire au plan principal XY * U,V,W axes auxiliaires parallèles à X,Y,Z, respectivement. * A,B,C axes rotatifs sur chacun des axes X,Y,Z Chapitre: 3 AXES ET SYSTEMES DE COORDONNEES Section: NOMENCLATURE DES AXES Page 1 La figure suivante montre un exemple de désignation des axes dans une fraiseuse-profileuse à table inclinée. Z X Y W Z A C X Y 3.1.1 SELECTION DES AXES Parmi les 9 axes existants possibles, la CNC FAGOR 8050 permet au fabricant d’en sélectionner jusqu’à 6. Lorsque 6 axes sont sélectionnés, l’un d’entre eux au moins doit être du type GANTRY ou un axe commandé depuis le PLC. En outre, tous les axes doivent être définis correctement en tant qu’axes linéaires, rotatifs etc., au moyen des paramètres machine des axes mentionnés dans le Manuel d’Installation et de mise en service. La programmation des axes n’est limitée en aucune manière, et l’interpolation est possible pour jusqu’à 5 axes simultanemént. Page 2 Chapitre: 3 AXES ET SYSTEMES DE COORDONNEES Section: NOMENCLATURE DES AXES 3.2 SELECTION DE PLANS (G16,G17,G18,G19) La sélection de plan s’applique dans les cas suivants: - Interpolations circulaires. - Arrondi aux angles contrôlé. - Entrée et sortie tangentielle. - Chanfrein. - Cycles fixes d’usinage. - Rotation du système de coordonnées. - Compensation de rayon d’outil. - Compensation de longueur d’outil. Les fonctions "G" permettant de sélectionner les plans de travail sont les suivantes: * G16 axe1 axe2. Permet de sélectionner le plan de travail désiré ainsi que le sens de G02 G03 (interpolation circulaire), axe1 étant programmé comme axe des abcisses, et axe2 comme axe des ordonnées. W Y G2 G2 Q Q X G16 XW U G16 UY * G17. Sélectionne le plan XY * G18. Sélectionne le plan ZX * G19. Sélectionne le plan YZ Chapitre: 3 AXES ET SYSTEMES DE COORDONNEES Section: SELECTION DE PLANS (G16,G17,G18,G19) Page 3 Les fonctions G16, G17, G18 et G19 sont modales et incompatibles entre elles, la fonction G16 devant être programmée seule dans un bloc. Z Y Z Les fonctions G17, G18 et G19 définissent deux des trois axes principaux X, Y, Z, comme appartenant au plan de travail, et le troisième comme axe perpendiculaire au plan de travail. Lorsque la compensation de rayon est exécutée sur le plan de travail, et la compensation de longueur sur l’axe perpendiculaire, la CNC n’autorise pas les fonctions G17, G18 et G19 si l’un des axes X, Y ou Z n’est pas sélectionné comme axe contrôlé par la CNC. A la mise sous tension, après l’exécution de M02, M30 ou après une URGENCE ou un RESET, la CNC prendra comme plan de travail celui défini par le paramètre machine général "IPLANE". Page 4 Chapitre: 3 AXES ET SYSTEMES DE COORDONNEES Section: SELECTION DE PLANS (G16,G17,G18,G19) 3.3 COTATION DE LA PIECE. MILLIMETRES (G71) OU POUCES (G70) La CNC permet l’introduction des unités de mesure au moment de la programmation, en millimètres ou en pouces. Elle dispose du paramètre machine général "INCHES", pour définir les unités de mesure de la CNC. Ces unités peuvent cependant être changées à tout moment dans le programme, grâce aux fonctions: * G70. Programmation en pouces. * G71. Programmation en millimètres. Selon que G70 ou G71 a été programmé, la CNC applique le système d’unités correspondant dans tous les blocs programmés suivants. Les fonctions G70/G71 sont modales et incompatibles entre elles. La CNC FAGOR 8050 permet de programmer d’une part des valeurs comprises entre 0.0001 et 99999.9999, signées ou non, et en millimètres (G71): le format porte alors le nom de format ±5.4, et d’autre part des valeurs de 0.00001 à 3937.00787 signées ou non et en pouces (G70): le format porte alors de nom de format ±4.5. Toutefois, pour simplifier les explications, on peut dire que la CNC admet le format ±5.5, pour indiquer qu’elle admet ±5.4 en millimètres et ±4.5 en pouces. A la mise sous tension, après l’exécution de M02, M30 ou après une URGENCE ou un RESET, la CNC prendra comme système d’unités celui défini par le paramètre machine général "INCHES" Chapitre: 3 AXES ET SYSTEMES DE COORDONNEES Section: MILLIMETRES (G71) / POUCES (G70) Page 5 3.4 PROGRAMMATION ABSOLUE/INCREMENTALE (G90,G91) La CNC permet la programmation des coordonnées d’un point en mode absolu G90, ou en mode incrémental G91. Dans le cas des coordonnées absolues (G90), les coordonnées du point sont établies par rapport à une origine des coordonnées définie, qui est souvent le point d’origine (zéro) pièce. Dans le cas des coordonnées incrémentales (G91), la valeur numérique programmée correspond aux informations de déplacement sur le trajet à parcourir à partir de la position actuelle de l’outil. Le signe précédant la valeur indique le sens du déplacement. Les fonctions G90/G91 sont modales et incompatibles entre elles. Exemple: Y P1 200 P2 X P0 150,5 300 Cotes absolues G90 X0 Y0 X150.5 Y200 X300 X0 Y0 ; Point P0 ; Point P1 ; Point P2 ; Point P0 Cotes incrémentales G90 G91 X0 Y0 X150.5 Y200 X149.5 X-300 Y-200 ; ; ; ; Point P0 Point P1 Point P2 Point P0 A la mise sous tension, après l’exécution de M02, M30 ou après une URGENCE ou un RESET, la CNC prendra en compte G90 ou G91 selon la définition faite par le paramètre machine général "ISYSTEM". Page 6 Chapitre: 3 AXES ET SYSTEMES DE COORDONNEES Section: ABSOLUE (G90) / INCREMENTALE(G91) 3.5 PROGRAMMATION DES COTES La CNC FAGOR 8050 permet de sélectionner jusqu’à 6 axes parmi les 9 axes possibles X, Y, Z, U, V, W, A, B, C. Chaque axe peut être linéaire, linéaire de positionnement, rotatif normal, rotatif de positionnement ou rotatif à denture Hirth (positionnement par degrés entiers) selon les spécifications du paramètre machine de chaque axe "AXISTYPE". Pour pouvoir sélectionner à tout moment le système de programmation de coordonnées le mieux adapté, la CNC dispose des types suivants: * Coordonnées cartésiennes * Coordonnées polaires * Coordonnées cylindriques * Angle et une coordonnée cartésienne 3.5.1 COORDONNEES CARTESIENNES Le système de coordonnées cartésiennes est défini par deux axes dans le plan et par trois, quatre ou cinq axes dans l’espace. L’origine de tous ces axes qui, dans le cas des axes X Y Z coïncide avec le point d’intersection, est appelée Origine Cartésienne ou Point Zéro du Système de Coordonnées. La position des différents points de la machine est exprimée au moyen des cooordonnées des axes avec deux, trois, quatre ou cinq coordonnées. Les coordonnées des axes sont programmées grâce à la lettre de l’axe (X, Y, Z, U, V, W, A, B, C, toujours dans cet ordre) suivie de la valeur de la cooordonnée. Les valeurs des coordonnées seront absolues ou incrémentales, selon que l’on travaille en G90 ou en G91, et leur format de programmation sera ±5.5 Y 50 Z X40 Y50 Y 40 X100 Y30 Z40 30 X 40 100 X Chapitre: 3 AXES ET SYSTEMES DE COORDONNEES Section: PROGRAMMATION DES COTES Page 7 3.5.2 COORDONNEES POLAIRES En cas de présence d’éléments circulaires ou de cotes angulaires, il peut s’avérer plus commode d’exprimer les coordonnées des différents points sur le plan (2 axes à la fois) en coordonnées polaires. Le point de référence porte le nom d’Origine Polaire et constituera l’origine du Système de Coordonnées Polaires. Un point de ce système sera défini par: Y R Q X - Le RAYON (R), qui sera la distance entre l’origine polaire et le point. - L’ANGLE (Q) qui sera l’angle formé par l’axe des abcisses et la ligne unissant l’origine polaire au point. (En degrés) Les valeurs de R et Q sont absolues ou incrémentales selon que l’on travaille en G90 ou G91, et leur format de programmation est R +/- 5.5 Q +/- 5.5. Les valeurs de R peuvent être négatives dans le cas de la programmation en relatif, mais la valeur résultante afectée au rayon doit toujours être positive. Si une valeur de Q supérieure à 360º est programmée, le module sera pris après une division par 360. Ainsi, Q420 est équivalent à Q60, et Q-420 est équivalent à Q-60. Page 8 Chapitre: 3 AXES ET SYSTEMES DE COORDONNEES Section: PROGRAMMATION DES COTES Exemple de programmation, en supposant que l’Origine Polaire est située sur l’Origine des Coordonnées. P6 P5 60 P2 P4 30 50 P3 100 P1 P0 Coordonnées absolues G90 G01 G03 G01 G03 G01 G03 G01 X0 Y0 ; R100 Q0 ; Q30 ; R50 Q30 ; Q60 ; R100 Q60 ; Q90 ; R0 Q90 ; Point P0 Point P1, en ligne droite (G01) Point P2, en arc (G03) Point P3, en ligne droite (G01) Point P4, en arc (G03) Point P5, en ligne droite (G01) Point P6, en arc (G03) Point P0, en ligne droite (G01) Coordonnées incrémentales G90 X0 Y0 G91 G01 R100 Q0 G03 Q30 G01 R-50 Q0 G03 Q30 G01 R50 Q0 G03 Q30 G01 R-100 Q0 ; ; ; ; ; ; ; ; Point P0 Point P1, en ligne droite (G01) Point P2, en arc (G03) Point P3, en ligne droite (G01) Point P4, en arc (G03) Point P5, en ligne droite (G01) Point P6, en arc (G03) Point P0, en ligne droite (G01) L’origine polaire peut non seulement être présélectionnée par la fonction G93, décrite plus loin, mais également modifiée dans les cas suivants: * A la mise sous tension, après l’exécution de M02, M30 ou après une URGENCE ou un RESET, la CNC 8050 prendra comme origine polaire l’origine des coordonnées du plan de travail définie par le paramètre machine général "IPLANE". * A chaque changement de plan de travail (G16, G17, G18 ou G19), la CNC 8050 prend comme origine polaire l’origine des coordonnées du nouveau plan de travail sélectionné. * Lors de l’exécution d’une interpolation circulaire (G02 ou G03), et si le paramètre machine général "PORGMOVE" a la valeur 1, le centre de l’arc devient la nouvelle origine polaire. Chapitre: 3 AXES ET SYSTEMES DE COORDONNEES Section: PROGRAMMATION DES COTES Page 9 3.5.3 COORDONNEES CYLINDRIQUES Pour définir un point dans l’espace, il est possible d’utiliser le système de coordonnées cylindriques en plus du système de coordonnées cartésiennes. Un point dans un tel système est défini par: Z Y Z P R Q X * La projection de ce point sur le plan principal, qui devra être défini en coordonnées polaires (R Q). * Le reste de axes en coordonnées cartésiennes. Exemples: R30 Q10 Z100, R20 Q45 Z10 V30 A20 Page 10 Chapitre: 3 AXES ET SYSTEMES DE COORDONNEES Section: PROGRAMMATION DES COTES 3.5.4 ANGLE ET UNE COORDONNEE CARTESIENNE Dans le plan principal, il est possible de définir un point grâce à une de ses coordonnées cartésiennes et à l’angle de sortie de la trajectoire précédente. Exemple de programmation, en supposant que le plan principal est le plan XY: Y P2 60 45 o P1 90 o P3 135 o 45 o 20 X10 Q45 Q90 Q-45 Q-135 Q180 180 o P0 P4 10 30 Y20 X30 Y60 X50 Y20 X10 X 50 ; Point P0, point de début ; Point P1 ; Point P2 ; Point P3 ; Point P4 ; Point P0 Pour représenter un point dans l’espace, le reste des coordonnées pourra être programmé en coordonnées cartésiennes. Chapitre: 3 AXES ET SYSTEMES DE COORDONNEES Section: PROGRAMMATION DES COTES Page 11 3.6 AXES ROTATIFS La CNC permet, grâce au paramètre machine d’axes "AXISTYPE", de sélectionner le type d’axe rotatif désiré, qui peut être: Un axe rotatif normal. Un axe rotatif de positionnement exclusivement. Un axe rotatif Hirth. Les coordonnées sont visualisées entre 0 et 359.9999 degrés. Le nombre de chiffres décimaux à représenter dans la visualisation de l’axe est sélectionné grâce au paramètre machine d’axe "DFORMAT". En cas de programmation en degrés, le passage aux millimètres ou aux pouces n’a aucune influence sur les coordonnées. Axes rotatifs normaux Dans le cas de la programmation en coordonnées absolues (G90), le signe indiquera le sens de rotation, et la coordonnée finale sera définie par des valeurs comprises entre 0 et 359.9999. Dans le cas de la programmation en coordonnées incrémentales (G91), sa programmation sera identique à celle d’un axe linéaire et il admettra toute valeur, signée ou non. Si le déplacement programmé est supérieur à 360, l’axe décrira plus d’un tour avant de se positionner sur le point désiré. Axe rotatif de positionnement exclusivement Ces axes sont toujours déplacés en G00, et ils n’admettent pas de compensation de rayon (G41, G42). Dans le cas de la programmation en coordonnées absolues (G90), leur programmation admet des valeurs entre 0 et 359.9999 degrés (non signées), et le déplacement s’effectue par le chemin le plus court. Dans le cas de la programmation en coordonnées incrémentales (G91), le signe indiquera le sens de rotation et la coordonnée finale sera définie par toute valeur. Si le déplacement programmé est supérieur à 360, l’axe décrira plus d’un tour avant de se positionner sur le point désiré. Axe rotatif Hirth Son fonctionnement et sa programmation sont identiques à ceux de l’axe de positionnement seul, sauf que les axes rotatifs Hirth n’admettent pas de chiffres décimaux; on sélectionnera exclusivement des positions en degrés entiers. La CNC permet de disposer de plus d’un axe Hirth, mais n’admet pas de déplacements faisant intervenir plus d’un axe Hirth à la fois. Page 12 Chapitre: 3 AXES ET SYSTEMES DE COORDONNEES Section: AXES ROTATIFS 3.7 ZONES DE TRAVAIL La CNC FAGOR 8050 permet de disposer de trois zones de travail et de limiter les déplacements de l’outil dans chacune d’elles. 3.7.1 DEFINITION DES ZONES DE TRAVAIL A l’intérieur de chaque zone de travail, la CNC permet de limiter le déplacement de l’outil selon les 5 axes, et définit des limites supérieures et inférieures pour chaque axe. G20: Définit les limites inférieures de la zone désirée. G21: Définit les limites supérieures de la zone désirée. Le format de programmation de ces fonctions est le suivant: G20 K X...C±5.5 G21 K X...C±5.5 Où: * K Indique la zone de travail à définir (1, 2 ou 3) * X...C Indiquent les coordonnées (supérieures ou inférieures) servant à limiter les axes. Ces coordonnées sont programmées par rapport au zéro machine. Il n’est pas nécessaire de programmer tous les axes; on limitera seulement les axes définis. Exemple: Y 50 20 100 20 X G20 K1 X20 Y20 G21 K1 X100 Y50 Chapitre: 3 AXES ET SYSTEMES DE COORDONNEES Section: ZONES DE TRAVAIL Page 13 3.7.2 UTILISATION DES ZONES DE TRAVAIL A l’intérieur de chaque zone de travail, la CNC permet de restreindre le déplacement de l’outil, soit en lui interdisant de sortir de la zone programmée (zone interdite à la sortie) ou de pénétrer dans cette zone (zone interdite à l’entrée). S= 1 Zona interdite à l’entrée S= 2 Zone interdite à la sortie La CNC tiendra compte en permanence des dimensions de l’outil (table de correcteurs) pour éviter tout franchissement des limites programmées. Les zones de travail sont personnalisées grâce à la fonction G22, dont le format de programmation est: G22 K S Où: * K Indique la zone de travail à personnaliser (1, 2 ou 3) * S Indique la validation-invalidation de la zone de travail: - S= 0 Invalidation. - S= 1 Validation comme zone interdite à l’entrée. - S= 2 Validation comme zone interdite à la sortie. A la mise sous tension, la CNC 8050 invalide toutes les zones de travail, mais sans toucher aux limites supérieures et inférieures, qui peuvent être validées à nouveau grâce à la fonction G22. Page 14 Chapitre: 3 AXES ET SYSTEMES DE COORDONNEES Section: ZONES DE TRAVAIL 4. 4.1 SYSTEMES DE REFERENCE POINTS DE REFERENCE Pour une machine à CN, les points d’origine et de référence suivants doivent être définis: * Zéro machine ou point d’origine de la machine. Il est défini par le constructeur comme origine du système de coordonnées de la machine. * Zéro pièce ou point d’origine de la pièce. Il s’agit du point d’origine défini pour la programmation des cotes de la pièce, et son choix est laissé à l’appréciation du programmeur. Sa valeur par rapport au zéro machine peut être définie par un décalage d’origine. * Point de référence. Il s’agit d’un point de la machine défini par le constructeur et servant à la synchronisation du système. La commande se positionne sur ce point plutôt que de se déplacer jusqu’à l’origine de la machine, et elle prend alors les coordonnées de référence définies par l’intermédiaire du paramètre machine des axes "REFVALUE". Z R ZMR W ZMW X M XMR XMW M W R XMW,YMW,ZMW,etc XMR,YMR,ZMR,etc Chapitre: 4 SYSTEMESDEREFERENCE Zéro Machine Zéro Pièce Point de référence machine Coordonnées du zéro pièce Coordonnées du point de référence machine ("REFVALUE") Section: Page 1 4.2 RECHERCHE DE LA REFERENCE MACHINE (G74) La CNC FAGOR 8050 permet de programmer la recherche de la référence machine de deux manières: * RECHERCHE DE REFERENCE MACHINE D’UN OU DE PLUSIEURS AXES DANS UN ORDRE DETERMINE On programmera G74 suivi des axes dans lesquels on désire effectuer une recherche de référence. Exemple: G74 X Z C Y La CNC commence à déplacer tous les axes sélectionnés comportant un contact de référence machine (paramètre machine d’axes "DECINPUT"), dans le sens indiqué par le paramètre machine des axes "REFDIREC", Ce déplacement s’effectue selon l’avance indiquée dans le paramètre machine des axes "REFEED1", jusqu’au déclenchement du contact. Ensuite, la recherche de la référence machine de tous les axes commence dans l’ordre où ils ont été programmés. Ce second déplacement est exécuté pour un axe à la fois selon l’avance indiquée par le paramètre machine des axes "REFEED2", jusqu’à ce que le point de référence machine soit atteint. * RECHERCHE DE REFERENCE MACHINE AU MOYEN DE LA SOUSROUTINE ASSOCIEE On programmera la fonction G74 seule dans le bloc, et la CNC exécutera automatiquement la sous-routine dont le numéro est indiqué dans le paramètre machine général "REFPSUB". Dans cette sous-routine, il est possible de programmer les recherches de référence machine désirées ainsi que l’ordre souhaité. Aucune autre fonction préparatoire ne doit être programmée dans le bloc contenant G74. Si la recherche de référence machine est exécutée en mode manuel, le zéro pièce sélectionné est perdu, et les coordonnées du point de référence machine indiquées dans le paramètre machine des axes "REFVALUE" sont affichées. Dans tous les autres cas, le zéro pièce sélectionné est conservé: les coordonnées visualisées sont donc référencées par rapport à ce zéro pièce. Si la commande G74 est exécutée en mode MDI, la visualisation des coordonnées dépendra du mode d’exécution de cette commande: Manuel, Exécution ou Simulation. Page 2 Chapitre: 4 SYSTEMESDEREFERENCE Section: 4.3 PROGRAMMATION PAR RAPPORT AU ZERO MACHINE (G53) La fonction G53 peut être ajoutée à tout bloc contenant des fonctions de contrôle de trajectoire. Elle sera utilisée seulement pour programmer les coordonnées du bloc par rapport au zéro machine; ces coordonnées devront être exprimées en millimètres ou en pouces, selon la définition du paramètre machine général "INCHES". Si la fonction G53 est programmée seule (sans information de déplacement), le décalage de zéro actif actuel est annulé, qu’il soit le résultat de l’exécution de G54-G59 ou d’une présélection (G92). Cette présélection d’origine G92 est décrite plus loin. Dès qu’un décalage du zéro a été défini, il reste actif jusqu’au choix du suivant ou jusqu’à l’exécution d’une recherche d’origine (G74). Le décalage du zéro n’est pas annulé par un coupure de courant de la CNC. La fonction G53 est non-modale, ce qui signifie qu’elle devra être programmée chaque fois que l’on désirera indiquer les coordonnées par rapport au zéro machine. Cette fonction annule temporairement la compensation de rayon et de longueur d’outil. Exemple: M Zéro machine (origine) W Zéro pièce Chapitre: 4 SYSTEMESDEREFERENCE Section: Page 3 4.4 PRESELECTION DES COORDONNEES ET DECALAGES D’ORIGINE La CNC permet d’exécuter des décalages d’origine dans le but d’utiliser les coordonnées relatives au plan de la pièce sans avoir à modifier les coordonnées des différents points de la pièce au moment de la programmation. On définit comme décalage d’origine la distance entre le zéro pièce (point d’origine de la pièce) et le zéro machine (point d’origine de la machine). Z Z Y W X Y X M M Zéro Machine W Zéro Pièce Ce décalage d’origine peut être obtenu de deux façons: * Par la fonction G92 (présélection de coordonnées), la CNC acceptant les coordonnées des axes programmés après G92, comme nouvelles valeurs des axes. * Par l’application de décalages d’origine (G54, G55, G56, G57, G58, G59), la CNC acceptant comme nouveau zéro pièce le point situé, par rapport au zéro machine, à la distance indiquée par la ou les tables sélectionnées. Ces deux fonctions sont modales et incompatibles entre elles; si l’une est sélectionnée, l’autre est désactivée. Il existe également un autre décalage d’origine sous la commande du PLC, qui s’ajoute toujours au décalage d’origine sélectionné et qui permet (entre autres) de corriger les écarts dûs aux dilatations, etc. Page 4 Chapitre: 4 SYSTEMESDEREFERENCE Section: ORG *(54) ORG G54 *(55) ORG G55 *(56) ORG G56 *(57) G57 ORG *(58) G58 + G92 + ORG *(59) G59 ORG + * PLCOF * Décalage d’origine sous la commande du PLC + Décalage d’origine Chapitre: 4 SYSTEMESDEREFERENCE Section: Page 5 4.4.1 PRESELECTION DE COORDONNEES ET LIMITATION DE LA VALEUR DE S (G92) La fonction G92 permet de présélectionner n’importe qquelle valeur dans les axes de la CNC et de limiter la vitesse maximum de la broche. * PRESELECTION DE COORDONNEES Lorsqu’un décalage d’origine est exécuté par la fonction G92, la CNC prend en compte les coordonnées des axes programmés après G92 comme nouvelles valeurs des axes. Aucune autre fonction ne peut être programmée dans le bloc contenant G92, et le format de programmation est le suivant: G92 X...C ±5.5 Exemple: G90 G92 G91 X50 X0 X30 X20 X-20 X-30 Y40 Y0 ; ; ; Positionnement en P0 Présélectionner P0 en tant qu’origine pièce Programmation selon les cotes de la pièce Y20 Y20 Y-40 * LIMITATION DE LA VITESSE DE BROCHE La programmation de G92 S5.4 permet de limiter la vitesse de broche à la valeur fixée au moyen de S5.4. Ceci signifie que la CNC n’acceptera pas, à partir de ce bloc, la programmation de valeurs de S supérieures au maximum défini. Il en sera de même pour les valeurs introduites depuis le clavier du panneau avant. Page 6 Chapitre: 4 SYSTEMESDEREFERENCE Section: 4.4.2 DECALAGES D’ORIGINE (G54..G59) La CNC FAGOR 8050 dispose d’une table de décalages d’origine permettant de sélectionner différents décalages d’origine afin de générer certains zéros pièce indépendamment des zéros pièces actifs à un moment donné. L’accès à la table est possible depuis le panneau avant de la CNC dans les conditions indiquées dans le Manuel d’Utilisation ou par programme au moyen de commandes en langage évolué. Il existe deux types de décalage d’origine: Décalages d’origine absolus (G54, G55, G56 et G57), qui doivent être référencés par rapport au zéro machine. Décalages d’origine incrémentaux (G58, G59). Les fonctions G54, G55, G56, G57, G58 et G59 doivent être programmées seules dans un bloc et leur fonctionnement est le suivant: Lors de l’exécution des fonctions G54, G55, G56 ou G57, la CNC applique le décalage d’origine programmé par rapport au zéro machine en annulant les éventuels décalages de zéro actifs. Si l’un des décalages incrémentaux G58 ou G59 est exécuté, la CNC ajoute ses valeurs au décalage d’origine absolu actif à ce moment en annulant au préalable un éventuel décalage incrémental actif. On observera dans l’exemple suivant les décalages d’origine appliqués lors de l’exécution du programme: G54 G58 G59 G55 Applique le décalage d’origine G54 -------------- > G54 Ajoute le décalage d’origine G58 ----------------- > G54+G58 Annule G58 et ajoute G59 --------------------- > G54+G59 Annule tout décalage et applique G55 ------------ > G55 Lorsqu’un décalage d’origine a été sélectionné, il reste actif jusqu’à la sélection d’un autre décalage ou jusqu’à l’exécution d’une recherche de référence machine (G74) en mode manuel. Le décalage d’origine sélectionne reste actif, même après une mise hors/sous tension de la CNC. Ce type de décalages d’origine défini par programme est très utile en cas d’usinages répétés en divers points de la machine. Chapitre: 4 SYSTEMESDEREFERENCE Section: Page 7 Exemple: Supposons la table de décalages d’origine initialisée avec les valeurs suivantes: G54: X0 Y0 G55: X160 Y 60 G56: X170 Y110 G58: X-40 Y-40 G59: X-30 Y10 Au moyen des décalages d’origine absolus: G54 ; Applique un décalage G54 Exécution du profil ; Exécute le profil A1 G55 ; Applique un décalage G55 Exécution du profil ; Exécute le profil A2 G56 ; Applique un décalage G56 Exécution du profil ; Exécute le profil A3 Au moyen des décalages d’origine incrémentaux G54 Exécution du profil G58 Exécution du profil G59 Exécution du profil Page 8 ; Applique un décalage G54 ; Exécute le profil A1 ; Applique les décalages G54 + G58 ; Exécute le profil A2 ; Applique les décalages G54 + G59 ; Exécute le profil A3 Chapitre: 4 SYSTEMESDEREFERENCE Section: 4.5 PRESELECTION DE L’ORIGINE POLAIRE (G93) La fonction G93 permet de présélectionner tout point du plan de travail en tant que nouvelle origine des coordonnées polaires. Cette fonction doit être programmée seule dans un bloc et son format est le suivant: G93 I±5.5 J±5.5 Les paramètres I et J définissent respectivement l’abcisse et l’ordonnée de la nouvelle origine des coordonnées polaires. Exemple: Supposons que l’outil se trouve en X0 Y0 P2 25 30 P3 P0 P1 35 G93 I35 J30 G90 G01 R25 Q0 G03 Q90 G01 X0 Y0 ; ; ; ; Présélectionner P3 en tant qu’origine polaire Point P1, en ligne droite (G01) Point P2, en arc (G03) Point P0, en ligne droite (G01) Si seul G93 est programmé dans un bloc, le point où se trouve la machine à ce moment devient l’origine polaire. Attention: La CNC ne modifie pas l’origine polaire lorsqu’un nouveau zéro pièce est défini, mais elle modifie les valeurs des variables “PORGF” et “PORGS”. Si, alors que le paramètre machine général "PORGMOVE" est sélectionné, une interpolation circulaire (G02 ou G03) est programmée, la CNC prend le centre de l’arc comme nouvelle origine polaire. A la mise sous tension, après l’exécution de M02, M30 ou après une URGENCE ou un RESET, la CNC prend le zéro pièce sélectionné comme nouvelle origine polaire. Lorsqu’un nouveau plan de travail est sélectionné (G16, G17, G18, G19) la CNC prend le zéro pièce de ce plan comme nouvelle origine polaire. Chapitre: 4 SYSTEMESDEREFERENCE Section: Page 9 5. PROGRAMMATION EN CODE ISO Un bloc programmé en langage ISO peut se composer de: Fonctions préparatoires (G) Cotes des axes (X..C) Vitesse d’avance (F) Vitesse de broche (S) Nº d’outil (T) Nº de correcteur (D) Fonctions auxiliaires (M) Cet ordre doit être conservé dans chaque bloc, mais il n’est pas nécessaire que chaque bloc contienne toutes les informations. La CNC FAGOR 8050 permet de programmer des chiffres de 0.00001 à 99999.9999 signés ou non en cas de programmation en millimètres (G71) (format ±5.4) ou de 0.00001 à 3937.00787 signés ou non en cas de programmation en pouces (G70), (format ±4.5). Toutefois, pour simplifier les explications, on peut dire que la CNC admet le format ±5.5, pour indiquer qu’elle admet ±5.4 en millimètres et ±4.5 en pouces. Toute fonction avec paramètres peut également être programmée dans un bloc, à l’exception du numéro de l’étiquette ou du bloc. Ainsi, lors de l’exécution du bloc, la CNC remplace le paramètre arithmétique par sa valeur active à ce moment. Chapitre: 5 PROGRAMMATION EN CODE ISO Section: Page 1 5.1 FONCTIONS PREPARATOIRES Les fonctions préparatoires sont programmées par la lettre G suivie de deux chiffres. Elles sont toujours programmées au début du corps du bloc et permettent de déterminer la géométrie et les conditions de travail de la CNC. Table des fonctions G utilisées dans la CNC: Fonction G00 G01 G02 G03 G04 G05 G06 G07 G08 G09 G10 G11 G12 G13 G14 G15 G16 G17 G18 G19 G20 G21 G22 G23 G24 G25 G26 G27 G33 G36 G37 G38 G39 G40 G41 G42 G43 G44 G50 G51 G52 G53 G54 G55 G56 G57 G58 G59 G60 G61 G62 Page 2 M D V * * * * ? ? * * * * * ? * * * ? * * Positionnement rapide Interpolation linéaire Interpolation circulaire (hélicoïdale) à droite Interpolation circulaire (hélicoïdale) à gauche Temporisation/Suspension de la préparation de blocs Arrondi aux angles Centre de circonférence en coordonnées absolues Arête vive Circonférence tangente à la trajectoire précédente Circonférence par trois points Annulation d’image miroir Image miroir en X Image miroir en Y Image miroir en Z Image miroir selon les directions programmées Sélection de l’axe longitudinal Sélection de plan principal dans deux directions Plan principal X-Y Plan principal Z-X Plan principal Y-Z Définition des limites inférieures de zone de travail Définition des limites supérieures de zone de travail Validation/Invalidation des zones de travail Activation de recopie Activation de la digitalisation Désactivation de recopie/ digitalisation Etalonnage de sonde de recopie Définition du profil de recopie * Filetage électronique * * * * Rayon congé Entrée tangentielle Sortie tangentielle Chanfrein Annulation de compensation de rayon Compensation de rayon d’outil à gauche Compensation de rayon à droite Compensation de longueur d’outil Annulation de compensation de longueur d’outil * * * * * * * * * * * * * ? ? * * * * * * * * * * * * * * * * * * * * * * * * * * * ? ? Signification * * * * * * * * * * * * * * * * Arrondi aux angles contrôlé Analyse par anticipation Déplacement vers butée Programmation par rapport au zéro machine Décalage d’origine absolue 1 Décalage d’origine absolue 2 Décalage d’origine absolue 3 Décalage d’origine absolue 4 Décalage d’origine incrémental 1 Décalage d’origine incrémental 2 Usinage multi-pièces en ligne droite Usinage multi-pièces formant un parallélogramme Usinage multi-pièces en grille Chapitre: 5 PROGRAMMATION EN CODE ISO Section: FONCTIONS PREPARATOIRES Fonction G63 G64 G65 G66 G67 G68 G69 G70 G71 G72 G73 G74 G75 G76 G77 G78 G79 G80 G81 G82 G83 G84 G85 G86 G87 G88 G89 G90 G91 G92 G93 G94 G95 G96 G97 G98 G99 M * * * * * * * D ? ? V Signification * * * * * * * * Usinage multi-pièces formant une circonférence Usinage multi-pièces formant un arc Usinage programmé par corde d’arc Cycle fixe de poches avec ilôts Ebauche de poches avec ilôts Finition de poches avec ilôts Cycle fixe de perçage profond à pas variable Programmation en pouces Programmation en millimètres Facteurs d’échelle général et particulier Rotation du système de coordonnées Recherche de référence machine Déplacement avec palpeur jusqu’au contact Déplacement avec palpeur jusqu’à l’interruption du contact Couplage électronique des axes Annulation du couplage électronique * * * * * * * * * * * * * * * * * * * * * * * * * * ? ? Modification des paramètres d’un cycle fixe Annulation de cycle fixe Cycle fixe de perçage Cycle fixe de perçage avec temporisation Cycle fixe de perçage profond à pas constant Cycle fixe de taraudage Cycle fixe d’alésage de précision Cycle fixe d’alésage en tirant en G00 Cycle fixe de poche rectangulaire Cycle fixe de poche circulaire Cycle fixe d’alésage en tirant en G01 Programmation absolue Programmation incrémentale Présélection de coordonnées / Limitation de vitesse de broche Présélection de l’origine polaire Avance en millimètres (pouces) par minute Avance en millimètres (pouces) par tour Vitesse constante de surface de coupe Vitesse constante du centre de l’outil Retour au plan initial à la fin du cycle fixe Retour au plan de référence à la fin du cycle fixe * * * * * * * * * ? ? * * * * * * La lettre M signifie MODAL, c’est-à-dire qu’une fois programmée, la fonction G reste active tant qu’une autre fonction G incompatible n’est pas programmée. La lettre D signifie PAR DEFAUT, c’est-à-dire que ces fonctions sont prises en compte par la CNC à la mise sous tension, après l’exécution de M02, M30 ou à la suite d’une URGENCE ou d’un RESET. Dans les cas indiqués par ? on devra comprendre que l’état PAR DEFAUT de ces fonctions G dépend de la personnalisation des paramètres machine généraux de la CNC. La lettre V signifie que le code G est visualisé à côté des conditions d’usinage actuelles dans les modes exécution et simulation. Chapitre: 5 PROGRAMMATION EN CODE ISO Section: FONCTIONS PREPARATOIRES Page 3 5.2 FONCTIONS D’AVANCE (G94,G95) La CNC FAGOR 8050 permet de programmer l’avance des axes en mm/minute et en mm/ tour si l’unité choisie est le mm, ou en pouces/minute et en pouces/tour si l’unité choisie est le pouce. 5.2.1 AVANCE EN mm/min. ou pouces/minute (G94) Dès que le code G94 est programmé, la commande “sait” que les avances programmées par F5.5, sont en mm/minute ou en pouces/minute. Si le déplacement concerne un axe rotatif, la CNC interprètera que l’avance est programmée en degrés/minute. Si une interpolation est réalisée entre un axe rotatif et un axe linéaire, l’avance programmée est prise en mm/minute ou en pouces/minute et le déplacement de l’axe rotatif, qui a été programmé en degrés, sera considéré comme programmé en millimètres ou en pouces. Le rapport entre la composante avance de l’axe et l’avance F programmée sera identique à celui existant entre le déplacement de l’axe et le déplacement résultant programmé. Avance F x Déplacement de l’axe Composante de avance = Déplacement résultant programmé Exemple: Dans une machine à axes X Y linéaires et à axe C rotatif situés tous au point X0 Y0 C0, le déplacement suivant est programmé: G1 G90 X100 Y20 C270 F10000 On a: Fx = Fy = Fc = Page 4 F ∆∗x = (∆x) + (∆y) + (∆c)2 2 2 10000 x 100 = 3464.7946 1002 + 202 + 2702 F ∆y = (∆x)2 + (∆y)2 + (∆c)2 10000 x 20 F ∆c 10000 x 270 = (∆x)2 + (∆y)2 + (∆c)2 2 2 = 692.9589 100 + 20 + 270 2 1002 + 202 + 2702 Chapitre: 5 PROGRAMMATION EN CODE ISO = 9354.9455 Section: FONCTIONS D’AVANCE (G94,G95) La fonction G94 est modale, c’est-à-dire que dès qu’elle est programmée, elle reste active jusqu’à la programmation de G95. A la mise sous tension, après exécution de M02, M30 ou après une URGENCE ou un RESET, la CNC prend en compte la fonction G94 ou G95 selon la personnalisation du paramètre machine général "IFEED". 5.2.2 AVANCE EN mm/tour ou en pouces/tour (G95) Dès que le code G95 est programmé, la commande suppose que les avances programmées par F5.5 sont en mm/tour ou en pouces/tour. Cette fonction n’affecte pas les déplacements rapides (G00), qui s’effectuent toujours en mm/minute ou en pouces/minute. Elle n’affectera pas non plus les déplacements en mode manuel, pendant le contrôle de l’outil, etc. La fonction G95 est modale, c’est-à-dire que, dès qu’elle est active, elle reste active jusqu’à la programmation de G94. A la mise sous tension, après exécution de M02, M30 ou après une URGENCE ou un RESET, la CNC prend en compte la fonction G94 ou G95 selon la personnalisation du paramètre machine général "IFEED". Chapitre: 5 PROGRAMMATION EN CODE ISO Section: FONCTIONS D’AVANCE (G94,G95) Page 5 5.3 FONCTIONS A VITESSE CONSTANTE (G96,G97) La CNC FAGOR 8050 permet, grâce aux fonctions G96 et G97, de sélectionner une vitesse constante soit pour le centre soit pour le point de coupe de l’outil. 5.3.1 VITESSE DE SURFACE CONSTANTE (G96) Lorsque G96 est programmé, la CNC “comprend” que l’avance F5.5 programmée correspond à l’avance du point de coupe de l’outil sur la pièce. Cette fonction permet d’obtenir une surface finie uniforme dans les sections courbes. De cette façon, grâce à la fonction G96, la vitesse du centre de l’outil varie dans les courbes intérieures ou extérieures afin de maintenir constante la vitesse du point de coupe. La fonction G96 est modale, c’est-à-dire que, dès qu’elle est active, elle reste active jusqu’à la programmation de G97. A la mise sous tension, après exécution de M02, M30 ou après une URGENCE ou un RESET, la CNC prend en compte la fonction G97. 5.3.2 VITESSE CONSTANTE DU CENTRE DE L’OUTIL (G97) La programmation de G97 indique à la CNC que l’avance F5.5 programmée correspond à l’avance de la trajectoire du centre de l’outil. De cette façon, grâce à la fonction G97, la vitesse du point de coupe diminue dans les courbes intérieures ou extérieures afin de maintenir constante la vitesse du centre de l’outil. La fonction G97 est modale, c’est-à-dire que, dès qu’elle est active, elle reste active jusqu’à la programmation de G96. A la mise sous tension, après exécution de M02, M30 ou après une URGENCE ou un RESET, la CNC prend en compte la fonction G97. Page 6 Chapitre: 5 PROGRAMMATION EN CODE ISO Section: FONCTIONS A VITESSE CONSTANTE (G96,G97) 5.4 FONCTIONS COMPLEMENTAIRES La CNC FAGOR 8050 dispose des fonctions complémentaires suivantes: Vitesse d’avance F Vitesse de rotation de broche S Numéro d’outil T Numéro de correcteur D Fonction auxiliaire M Cet ordre doit être conservé dans chaque bloc, mais il n’est pas nécessaire que chaque bloc contienne toutes les informations. 5.4.1 VITESSE D’AVANCE F La vitesse d’avance en usinage peut être définie par programme, et elle reste active tant qu’une autre vitesse n’est pas programmée. La vitesse d’avance est repérée par la lettre F et, selon que G94 ou G95 est actif, elle est programmée en mm/minute (pouces/minute) ou en mm/tour (pouces/tour). Son format de programmation est 5.5, soit 5.4 si elle est programmée en millimètres et 4.5 si elle est programmée en pouces. L’avance de travail maximum de la machine, limitée sur chaque axe par le paramètre machine d’axes "MAXFEED", peut être programmée par le code F0 ou en affectant la valeur adéquate à la lettre F. L’avance F programmée est effective lorsque la machine travaille en interpolation linéaire (G01) ou circulaire (G02, G03). Si la fonction F n’est pas programmée, la CNC prend en compte l’avance F0. Si la machine travaille en positionnement (G00), elle se déplacera selon l’avance rapide indiquée par le paramètre machine d’axes "G00FEED", indépendante de l’avance F programmée. L’avance F programmée peut varier entre 0% et 255% par l’intermédiaire du PLC ou de la ligne DNC, ou entre 0% et 120% grâce au sélecteur situé sur le pupitre de l’opérateur de la CNC. La CNC dispose toutefois du paramètre machine général "MAXFOVR" pour limiter la variation maximum de l’avance. Si la machine travaille en positionnement (G00), l’avance rapide est fixée à 100%, ou elle peut varier entre 0% et 100% selon l’état du paramètre machine "RAPIDOVR". Pendant l’exécution des fonctions G33 (filetage électronique) ou G84 (cycle fixe de taraudage), l’avance ne peut pas être modifiée; elle est fixée à 100% de l’avance F programmée. Chapitre: 5 PROGRAMMATION EN CODE ISO Section: FONCTIONS COMPLEMENTAIRES F,S,T,D,M Page 7 5.4.2 VITESSE DE ROTATION DE BROCHE ET ARRET INDEXE DE BROCHE (S) Le code S a 2 significations: a) VITESSE DE ROTATION DE BROCHE Le code S5.4 permet de programmer directement la vitesse de rotation de la broche en tours/minute. La valeur maximum est limitée par les paramètres machine de la broche "MAXGEAR1, MAXGEAR2, MAXGEAR3 et MAXGEAR4", qui dépendent dans chaque cas de la gamme de vitesses de broche sélectionnée. Cette valeur maximum peut également être limitée par programme au moyen de la fonction G92 S5.4. La vitesse de rotation S programmée peut être modifiée par l’intermédiaire du PLC ou de la ligne DNC, ou au moyen des touches SPINDLE "+" et "-" du pupitre de commande de la CNC. La vitesse varie entre les valeurs maximum et minimum fixées par les paramètres machine de broche "MINSOVR et MAXSOVR". Le pas incrémental associé aux touches SPINDLE "+" et "-" du pupitre opérateur de la CNC permettant de modifier la vitesse S programmée est fixé par le paramètre machine de broche "SOVRSTEP". Pendant l’exécution des fonctions G33 (filetage électronique) ou G84 (cycle fixe de taraudage), la vitesse ne peut pas être modifiée; elle est fixée à 100% de la valeur de S programmée. b) ARRET INDEXE DE BROCHE Si S±5.5 est programmé après M19, le code S±5.5 indique la position d’arrêt indexé de la broche en degrés à partir de l’impulsion de référence machine délivrée par le codeur. Pour exécuter cette fonction, il est nécessaire de disposer d’un codeur rotatif couplé à la broche de la machine. Si la machine ne dispose pas d’un contact de référence, la broche se déplacera à la vitesse de rotation indiquée par le paramètre de broche "REFEED1", jusqu’à ce qu’elle parvienne au point défini par S±5.5. Si la machine dispose d’un contact de référence, la broche se déplacera à la vitesse de rotation indiquée par le paramètre machine de broche "REFEED1", jusqu’à ce qu’elle atteigne ce contact, puis à celle indiquée par le paramètre machine de broche "REFEED2", jusqu’à ce qu’elle atteigne le point défini par S±5.5. Le déplacement en "REFEED1" jusqu’au contact de référence est toujours exécuté si M19 est programmé après le fonctionnement de la broche en boucle ouverte (M3, M4, M5). Aucun déplacement n’est exécuté entre deux M19 consécutifs. Page 8 Chapitre: 5 PROGRAMMATION EN CODE ISO Section: FONCTIONS COMPLEMENTAIRES F,S,T,D,M 5.4.3 NUMERO D’OUTIL (T) La CNC FAGOR 8050 permet de sélectionner le ou les outils nécessaires pour chaque opération d’usinage grâce à la fonction T4. Une table de magasin d’outils est disponible, dont le nombre de composants est défini par "NPOCKET" (paramètre machine général). Pour chaque composant, les éléments suivants sont spécifiés: * Le contenu du logement, avec indication du numéro de l’outil ou si le logement est vide ou annulé. * Taille de l’outil, soit N pour un outil normal et S pour un outil spécial. * Etat de l’outil, soit A pour un outil disponible, E s’il est usé ou R s’il est rejeté. Une table d’outils est également disponible. Le nombre de composants de cette table est fixé par "NTOOL" (paramètre machine général), et les éléments suivants sont spécifiés pour chaque composant: * Le numéro de correcteur associé à chaque outil (le correcteur indiquera les dimensions de l’outil) * Le code de famille à laquelle appartient cet outil, soit: code de famille 0 < n < 200 code de famille 200 < n < 255 -—> —-> outil normal. outil spécial. * Durée de vie nominale calculée pour cet outil, définie en minutes d’usinage ou en nombre d’opérations à exécuter, le choix s’effectuant grâce au paramètre machine général "TOOLMONI". * Durée de vie réelle pour cet outil, définie en minutes d’usinage ou en nombre d’opérations exécutées, le choix s’effectuant grâce au paramètre machine général "TOOLMONI". * Taille de l’outil, soit N pour un outil normal et S pour un outil spécial. * Etat de l’outil, soit "A" pour un outil disponible, "E" s’il est usé ou "R" s’il a été rejeté par le PLC. Chapitre: 5 PROGRAMMATION EN CODE ISO Section: FONCTIONS COMPLEMENTAIRES F,S,T,D,M Page 9 5.4.4 NUMERO DE CORRECTEUR (D) La CNC FAGOR 8050 permet, grâce à la fonction D4, d’associer le correcteur désiré à l’outil sélectionné. Pour ce faire, on programmera T4 D4, après sélection de l’outil et du correcteur désirés. Si seul T4 est programmé, la CNC prendra le correcteur indiqué pour l’outil considéré dans la table d’outils. La CNC dispose d’une table de correcteurs avec "NTOFFSET" (paramètre machine général) composants, les éléments suivants étant spécifiés pour chaque correcteur: * Rayon nominal de l’outil dans les unités de mesure indiquées par le paramètre général "INCHES", au format R±5.5 * Longueur nominale de l’outil, dans les unités de mesure indiquées par le paramètre général "INCHES", au format L±5.5 * Usure du rayon de l’outil, dans les unités de mesure indiquées par le paramètre général "INCHES", au format I±5.5. La CNC ajoutera cette valeur au rayon nominal (R) pour calculer le rayon réel (R+I). * Usure de la longueur de l’outil, dans les unités de mesure indiquées par le paramètre général "INCHES", au format K±5.5. La CNC ajoutera cette valeur à la longueur nominale (L) pour calculer la longueur réelle (L+K). Si une compensation de rayon d’outil est nécessaire (G41 ou G42), la CNC applique comme valeur de compensation de rayon la somme des valeurs R+I du correcteur sélectionné. Si une compensation de longueur d’outil est nécessaire (G43), la CNC applique comme valeur de compensation de longueur la somme des valeurs L+K du correcteur sélectionné. Si aucun correcteur n’et défini, la CNC applique le correcteur D0, avec R=0, L=0, I=0 et K=0. Page 10 Chapitre: 5 PROGRAMMATION EN CODE ISO Section: FONCTIONS COMPLEMENTAIRES F,S,T,D,M 5.4.5 FONCTIONS AUXILIAIRES (M) Les fonctions auxiliaires sont programmées par le code M4; il est possible de programmer jusqu’à 7 fonctions auxiliaires dans le même bloc. Si plus d’une fonction auxiliaire a été programmée dans un bloc, la CNC les exécute dans l’ordre où elles ont été programmées. La CNC dispose d’une table de fonctions M avec "NMISCFUN" (paramètre machine général) composants, les éléments suivants étant spécifiés: * Le numéro (0-9999) de la fonction auxiliaire M définie. * Le numéro de la sous-routine à associer à cette fonction auxiliaire. * Un indicateur qui définit si la fonction M est exécutée avant ou après le bloc de déplacement dans lequel elle est programmée. * Un indicateur qui définit si l’exécution de la fonction M interrompt ou non la préparation des blocs. * Un indicateur qui définit si la fonction M est exécutée ou non après l’exécution de la sous-routine associée. * Un indicateur qui définit si la CNC doit ou non attendre le signal AUX END (signal de M exécutée émis par le PLC), avant de poursuivre l’exécution du programme. Si, lors de l’exécution de la fonction auxiliaire M, celle-ci n’est pas définie dans la table de fonctions M, la fonction programmée est exécutée au début du bloc, et la CNC attend le signal AUX END avant de poursuivre l’exécution du programme. Certaines fonctions auxiliaires ont une signification particulière interne dans la CNC. Si, pendant l’exécution de la sous-routine associée d’une fonction auxiliaire "M", un bloc contenant la même fonction "M" est rencontré, il sera exécuté mais la sous-routine associée n’est pas exécutée. Attention: Toutes les fonctions auxiliaires "M" auxquelles une sous-routine est associée doivent être programmées seules dans un bloc. Chapitre: 5 PROGRAMMATION EN CODE ISO Section: FONCTIONS COMPLEMENTAIRES F,S,T,D,M Page 11 5.4.5.1 M00. ARRET DU PROGRAMME Lorsque la CNC lit le code M00 dans un bloc, elle interrompt le programme. Pour redémarrer, frapper à nouveau la touche DEPART CYCLE. Il est recommandé de définir cette fonction dans la table de fonctions M, de façon qu’elle soit exécutée à la fin du bloc dans lequel elle est programmée. 5.4.5.2 M01. ARRET CONDITIONNEL DU PROGRAMME Cette fonction est identique à M00, sauf que la CNC ne la prend en compte que si le signal M01 STOP émis par le PLC est actif (niveau logique “1”). 5.4.5.3 M02. FIN DE PROGRAMME Ce code indique la fin du programme et réalise une fonction de "Reset général" de la CNC (Retour à l’état initial). Elle exécute également la fonction M05. Il est recommandé de définir cette fonction dans la table de fonctions M, de façon qu’elle soit exécutée à la fin du bloc dans lequel elle est programmée. 5.4.5.4 M30. FIN DE PROGRAMME AVEC RETOUR AU PREMIER BLOC Identique à la fonction M02, sauf que la CNC revient au premier bloc du programme. 5.4.5.5 M03. ROTATION DE LA BROCHE A DROITE (SENS HORAIRE) Ce code signale le démarrage de la broche dans le sens horaire. Comme expliqué dans la section correspondante, la CNC exécute ce code automatiquement dans les cycles fixes d’usinage. Il est recommandé de définir cette fonction dans la table de fonctions M, de façon qu’elle soit exécutée au début du bloc dans lequel elle est programmée. 5.4.5.6 M04. ROTATION DE LA BROCHE A GAUCHE (SENS ANTIHORAIRE) Ce code signale le démarrage de la broche à gauche. Il est recommandé de définir cette fonction dans la table de fonctions M, de façon qu’elle soit exécutée au début du bloc dans lequel elle est programmée. 5.4.5.7 M05. ARRET DE BROCHE Il est recommandé de définir cette fonction dans la table de fonctions M, de façon qu’elle soit exécutée à la fin du bloc dans lequel elle est programmée. Page 12 Chapitre: 5 PROGRAMMATION EN CODE ISO Section: FONCTIONS COMPLEMENTAIRES F,S,T,D,M 5.4.5.8 M06. CODE DE CHANGEMENT D’OUTIL Si le paramètre machine général "TOFFM06" (indicatif du centre d’usinage) est actif, la CNC gère le changeur d’outil et met à jour la table correspondant au magasin d’outils. Il est recommandé de définir cette fonction dans la table de fonctions M, de façon que la sous-routine correspondant au changeur d’outil installé dans la machine soit exécuté. 5.4.5.9 M19. ARRET INDEXE DE BROCHE La CNC permet de travailler avec la broche en boucle ouverte (M3, M4) et en boucle fermée (M19). Pour travailler en boucle fermée, il est nécessaire de disposer d’un capteur rotatif (codeur) couplé à la broche de la machine. La fonction M19 ou M19 S±5.5 permet de passer de la boucle ouverte à la boucle fermée. La CNC agit comme suit: * Si la broche dispose d’un contact de référence, elle recherche le contact de référence machine à la vitesse de rotation indiquée par le paramètre machine de broche “REFEED1”. Ensuite, elle recherche le signal Io du capteur, à la vitesse de rotation indiquée par le paramètre de machine de broche “REFEED2”. Enfin, elle se positionne sur le point défini par S±5.5. * Si la broche ne dispose pas de contact de référence, elle recherche le signal Io du capteur, à la vitesse de rotation indiquée par le paramètre machine de broche “REFEED2”. Ensuite, elle se positionne sur le point défini par S±5.5. Si seule la fonction auxiliaire M19 est exécutée, la broche se positionne en S0. Pour indexer la broche sur une autre position, il est nécessaire d’exécuter la fonction M19 S±5.5. La CNC n’effectue pas de recherche de la référence, car elle est déjà en boucle fermée. Elle indexe la broche sur la position indiquée (S±5.5). Le code S±5.5 indique la position d’indexage de la broche en degrés à partir de la position de l’impulsion de marquage du codeur (S0). Le signe indique le sens du comptage, et la valeur 5.5 est toujours considérée comme une valeur absolue, quel que soit le type d’unités sélectionné. Exemple: S1000 M3 M19 S100 M19 S -30 M19 S400 Broche en boucle ouverte La broche passe en boucle fermée. Recherche de référence et positionnement sur 100° La broche se déplace jusqu’à -30° en passant par 0°. La broche effectue une rotation et se positionne sur 40°. Chapitre: 5 PROGRAMMATION EN CODE ISO Section: FONCTIONS COMPLEMENTAIRES F,S,T,D,M Page 13 5.4.5.10 M41, M42, M43, M44. CHANGEMENT DE GAMMES DE VITESSE DE BROCHE La CNC FAGOR 8050 dispose de 4 gammes de broche, M41, M42, M43 et M44, dont les vitesses maximum respectives sont limitées par les paramètres machine de broche "MAXGEAR1", "MAXGEAR2", "MAXGEAR3" et "MAXGEAR4". Si le paramètre machine de broche "AUTOGEAR" est défini de façon que la CNC exécute automatiquement le changement de gamme, la CNC émet automatiquement les fonctions M41, M42, M43 et M44, sans qu’il soit nécessaire de les programmer. Dans le cas contraire, il appartient au programmeur de choisir la gamme correspondante, en tenant compte du fait que chaque gamme fournira la consigne définie par le paramètre machine de broche "MAXVOLT" ppur la vitesse maximum spécifiée dans chaque gamme (paramètres machine de broche "MAXGEAR1", "MAXGEAR2", "MAXGEAR3" et "MAXGEAR4"). 5.4.5.11 M45. BROCHE AUXILIAIRE / OUTIL MOTORISE Pour pouvoir utiliser cette fonction auxiliaire, il est nécessaire de définir l’un des axes de la machine en tant que broche auxiliaire/outil motorisé (paramètre machine général P0 à P7). Pour utiliser la broche auxiliaire ou l’outil motorisé, on exécutera la commande M45 S±5.5, où S indique la vitesse de rotation en tours/mn et où le signe indique le sens de rotation désiré. La CNC émet la tension analogique correspondant à la vitesse de rotation choisie en fonction de la valeur affectée au paramètre machine de broche auxiliaire “MAXSPEED”. Pour stopper la rotation de la broche auxiliaire, on programmera M45 ou M45 S0. Chaque fois que la broche auxiliaire ou l’outil motorisé sont actifs, la CNC informe le PLC en activant la sortie logique générale “DM45” (M5548). Il est également possible de définir le paramètre machine de broche auxiliaire “SPDLOVR” de façon que les touches “Override” du panneau de commande puissent modifier la vitesse de rotation active actuelle de la broche auxiliaire. Page 14 Chapitre: 5 PROGRAMMATION EN CODE ISO Section: FONCTIONS COMPLEMENTAIRES F,S,T,D,M 6. CONTROLE DES TRAJECTOIRES La CNC FAGOR 8050 permet de programmer les déplacements d’un ou de plusieurs axes simultanément. Seuls les axes intervenant dans le déplacement désiré sont programmés. L’ordre de programmation des axes est le suivant: X, Y, Z, U, V, W, A, B, C 6.1 TRANSVERSAL RAPIDE (G00) Les déplacements programmés après G00 sont exécutés selon l’avance rapide indiquée dans le paramètre machine d’axes "G00FEED". Quel que soit le nombre d’axes déplacés, la trajectoire résultante est toujours une droite entre le point de départ et le point d’arrivée. Exemple: Y 300 100 X 400 100 X100 G00 G90 X400 Y100 ; Y300 ; Point de départ Trajectoire programmée Le paramètre machine général "RAPIDOVR", permet de définir si, en G00, le sélecteur de pourcentage de correction d’avance permettra la correction entre 0 et 100%, ou si ce pourcentage restera fixé à 100%. Lors de la programmation de G00, le dernier code F programmé n’est pas annulé, c’est-àdire que, lorsque G01, G02 ou G03 est programmé à nouveau, ce code F est rétabli. La fonction G00 est modale et incompatible avec G01, G02, G03, G33 et G75. La fonction G00 peut être programmée sous la forme G ou G0. A la mise sous tension, après exécution de M02, M30 ou après une URGENCE ou un RESET, la CNC prend en compte le code G00 ou G01 selon l’état du paramètre machine général "IMOVE". Chapitre: 6 CONTROLE DES TRAJECTOIRES Section: TRANSVERSAL RAPIDE (G00) Page 1 6.2 INTERPOLATION LINEAIRE (G01) Les déplacements programmés après G01 sont exécutés suivant une droite et selon l’avance F programmée. En cas de déplacement de deux ou trois axes simultanément, la trajectoire résultante est une droite entre le point de départ et le point d’arrivée. La machine se déplace suivant cette trajectoire et selon l’avance F programmée. La CNC calcule les avances de chaque axe afin que la trajectoire produite soit l’avance F programmée. Exemple: Y 400 150mm/min 150 150 X 650 G01 G90 X650 Y400 F150 La valeur de l’avance F programmée peut être fixée entre 0% et 120% grâce au sélecteur situé sur le panneau de commande de la CNC, ou sélectionnée entre 0% et 255% par le PLC, la ligne DNC ou par programme. La CNC dispose toutefois du paramètre machine général "MAXFOVR", qui permet de limiter la variation maximum de l’avance. La CNC permet, à partir de la version 706 du software, de programmer un axe de positionnement exclusivement dans un bloc d’interpolation linéaire. La CNC calculera l’avance de cet axe de façon qu’il atteigne la coordonnée souhaitée en même temps que les axes d’interpolation. La fonction G01 est modale et incompatible avec G00, G02, G03 et G33. La fonction G01 peut être programmée sous la forme G1. A la mise sous tension, après exécution de M02, M30 ou après une URGENCE ou un RESET, la CNC prendra en compte le code G00 ou G01 selon l’état du paramètre machine général "IMOVE". Page 2 Chapitre: 6 CONTROLE DES TRAJECTOIRES Section: INTERPOLATION LINEAIRE(G01) 6.3 INTERPOLATION CIRCULAIRE (G02,G03) L’interpolation circulaire peut être réalisée de deux façons: G02: Interpolation circulaire à droite (sens horaire). G03: Interpolation circulaire à gauche (sens anti-horaire) Les déplacements programmés après G02 et G03 sont exécutés sous forme de trajectoire circulaire et selon l’avance F programmée. Les notions de sens horaire (G02) et anti-horaire (G03) sont définies d’après le système de coordonnées présenté ci-dessous. Z G02 Y G03 G03 G02 G02 G03 X Ce système de coordonnées s’applique au déplacement de l’outil sur la pièce. L’interpolation circulaire ne peut être exécutée que dans un plan, et elle se définit de la façon suivante: Chapitre: 6 CONTROLE DES TRAJECTOIRES Section: INTERPOLATIONCIRCULAIRE (G02,G03) Page 3 a) COORDONNEES CARTESIENNES Les coordonnées du point de fin de l’arc et la position du centre par rapport au point de début sont définies d’après les axes du plan de travail. Les coordonnées du centre, qui doivent toujours être programmées même avec une valeur “0”, sont définies par les lettres I, J ou K, qui sont associées aux axes comme suit: Axes X, U, A --> Axes Y, V, B --> Axes Z, W, C --> I J K Format de programmation: Plan XY: G02(G03) X±5.5 Y±5.5 I±5.5 J±5.5 Plan ZX: G02(G03) X±5.5 Z±5.5 I±5.5 K±5.5 Plan YZ: G02(G03) Y±5.5 Z±5.5 J±5.5 K±5.5 L’ordre de programmation des axes et des coordonnées au centre correspondantes est toujours le même, quel que soit le plan sélectionné. Plan AY: Plan XU: G02(G03) Y±5.5 A±5.5 J±5.5 I±5.5 G02(G03) X±5.5 U±5.5 I±5.5 I±5.5 b) COORDONNEES POLAIRES Il est nécessaire de définir l’angle de déplacement Q et la distance à partir du point de départ au centre (optionnel) d’après les axes du plan de travail. Les coordonnées du centre sont définies par les lettres I, J ou K, qui sont associées aux axes comme suit: Axes X, U, A Axes Y, V, B Axes Z, W, C -> -> -> I J K Si le centre de l’arc n’est pas défini, la CNC considère qu’il coïncide avec l’origine polaire actuelle. Format de programmation: Plan XY: Plan ZX: Plan YZ: Page 4 G02(G03) Q±5.5 I±5.5 J±5.5 G02(G03) Q±5.5 I±5.5 K±5.5 G02(G03) Q±5.5 J±5.5 K±5.5 Chapitre: 6 CONTROLE DES TRAJECTOIRES Section: INTERPOLATIONCIRCULAIRE (G02,G03) c) COORDONNEES CARTESIENNES AVEC PROGRAMMATION DE RAYON Les coordonnées du point d’arrivée de l’arc et le rayon R doivent être définis. Format de programmation: Plan XY: Plan ZX: Plan YZ: G02(G03) X±5.5 Y±5.5 R±5.5 G02(G03) X±5.5 Z±5.5 R±5.5 G02(G03) Y±5.5 Z±5.5 R±5.5 Si, en programmation de rayon, un cercle complet est programmé, la CNC visualisera l’erreur correspondante, en raison du nombre infini solutions. Si l’arc est inférieur à 180º, le rayon est programmé avec un signe positif; s’il est supérieur à 180º, le signe sera négatif. Y 1 P1 (XY) 2 3 P0 4 X Si P0 est le point de départ et P1 le point d’arrivée, le nombre d’arcs de rayon identique passant par ces deux points est de 4. L’arc nécessaire est défini en fonction de l’interpolation circulaire G02 ou G03 et du signe du rayon. Le format de programmation des arcs de la figure sera le suivant: Arc 1 Arc 2 Arc 3 Arc 4 Chapitre: G02 X.. Y.. R G02 X.. Y.. R G03 X.. Y.. R G03 X.. Y.. R 6 CONTROLE DES TRAJECTOIRES - .. +.. +.. - .. Section: INTERPOLATIONCIRCULAIRE (G02,G03) Page 5 Exemple de programmation: Y 90 40 X 60 160 110 Plusieurs modes de programmation sont analysés ci-dessous, avec X60 Y40 comme point de départ. Coordonnées cartésiennes: G90 G17 G03 X110 Y90 I0 J50 X160 Y40 I50 J0 Coordonnées polaires: G90 G17 G03 Q0 Q-90 I0 J50 I50 J0 ou: G93 I60 J90 ; Définit un centre polaire G03 Q0 G93 I160 J90 ; Définit un nouveau centre polaire Q-90 Coordonnées cartésiennes avec programmation de rayon: G90 G17 G03 X110 Y90 R50 X160 Y40 R50 Page 6 Chapitre: 6 CONTROLE DES TRAJECTOIRES Section: INTERPOLATIONCIRCULAIRE (G02,G03) Exemple: Programmation d’un cercle (complet) en un seul bloc: Y 80 X 170 120 Plusieurs modes de programmation sont analysés ci-dessous, avec X170 Y80 comme point de départ Coordonnées cartésiennes: G90 G17 G02 X170 Y80 I-50 J0 ou: G90 G17 G02 I-50 J0 Coordonnées polaires: G90 G17 G02 Q360 I-50 J0 ou: G93 I120 J80 ; Définit un centre polaire G02 Q360 Coordonnées cartésiennes avec programmation de rayon: Il est impossible de programmer une circonférence complète en raison du nombre infini de solutions. Chapitre: 6 CONTROLE DES TRAJECTOIRES Section: INTERPOLATIONCIRCULAIRE (G02,G03) Page 7 La CNC calculera, selon l’arc programmé, les rayons du point de départ et du point d’arrivée. Bien que, théoriquement, ces deux rayons doivent être parfaitement identiques, la CNC permet de sélectionner la différence maximum admissible entre ces deux rayons au moyen du paramètre machine général "CIRRINERR". Si la valeur définie est dépassée, la CNC affiche l’erreur correspondante. La valeur de l’avance F programmée peut être fixée entre 0% et 120% grâce au sélecteur situé sur le panneau de commande de la CNC, ou sélectionnée entre 0% et 255% par le PLC, la ligne DNC ou par programme. La CNC dispose toutefois du paramètre machine général "MAXFOVR", qui permet de limiter la variation maximum de l’avance. Si une interpolation circulaire (G02 ou G03) est programmée après la sélection du paramètre machine général "PORGMOVE", la CNC prendra le centre de l’arc comme nouvelle origine polaire. Les fonctions G02 et 03 sont modales et incompatibles entre elles ainsi qu’avec G00, G01 et G33. Les fonctions G02 et G03 peuvent être programmées sous la forme G2 et G3. Par ailleurs, les fonctions G74 (recherche de zéro) et G75 (déplacement avec palpeur) annulent les fonctions G02 et G03. A la mise sous tension, après exécution de M02, M30 ou après une URGENCE ou un RESET, la CNC prendra en compte le code G00 ou G01 selon l’état du paramètre machine général "IMOVE". Page 8 Chapitre: 6 CONTROLE DES TRAJECTOIRES Section: INTERPOLATIONCIRCULAIRE (G02,G03) 6.4 INTERPOLATION CIRCULAIRE AVEC PROGRAMMATION DU CENTRE DE L’ARC EN COORDONNEES ABSOLUES (G06) L’ajout de la fonction G06 dans un bloc d’interpolation circulaire permet de programmer les coordonnées du centre de l’arc (I, J ou K) en mode absolu, c’est-à-dire par rapport au zéro d’origine, et non au début de l’arc. La fonction G06 est non-modale, et doit donc être programmée chaque fois que les coordonnées du centre de l’arc doivent être indiquées en absolu. La fonction G06 peut être programmée sous la forme G6. Exemple: Y 90 40 X 60 110 160 Plusieurs modes de programmation sont analysés ci-dessous, avec X60 Y40 comme point de départ Coordonnées cartésiennes : G90 G17 G06 G03 X110 Y90 I60 J90 G06 X160 Y40 I160 J90 Coordonnées polaires: G90 G17 G06 G03 Q0 I60 J90 G06 Q-90 I160 J90 Chapitre: 6 CONTROLE DES TRAJECTOIRES Section: CENTREDEL’ARCEN COORDONNEES ABSOLUES Page 9 6.5 TRAJECTOIRE CIRCULAIRE TANGENTE A LA TRAJECTOIRE PRECEDENTE (G08) La fonction G08 permet de programmer une trajectoire circulaire tangente à la trajectoire précédente, sans avoir à programmer les coordonnées (I, J ou K) du centre. Il suffit de définir les coordonnées du point d’arrivée de l’arc en coordonnées polaires ou cartésiennes en fonction des axes du plan de travail. Exemple: Supposons que le point de départ soit X0 Y40, et que l’on souhaite programmer une droite, puis un arc tangent à la droite, et un arc tangent à l’arc précédent. Y 60 40 70 G90 90 110 X G01 X70 G08 X90 Y60 ; Arc tangent à la trajectoire précédente G08 X110 Y60 ; Arc tangent à la trajectoire précédente La fonction G08 est non-modale, et doit donc être programmée pour chaque exécution d’un arc tangent à la trajectoire précédente. La fonction G08 peut être programmée sous la forme G8. La fonction G08 autorise une droite ou un arc comme trajectoire précédente et elle ne modifie pas son historique. La même fonction G01, G02 ou G03 reste active après la fin du bloc. Attention: Lorsque la fonction G08 est utilisée, il est impossible d’exécuter un cercle complet en raison du nombre infini de solutions. La CNC visualisera le code d’erreur correspondant. Page 10 Chapitre: 6 CONTROLE DES TRAJECTOIRES Section: ARC TANGENT A LA TRAJECTOIREPRECEDENTE 6.6 TRAJECTOIRE CIRCULAIRE DEFINIE PAR TROIS POINTS (G09) La fonction G09 permet de définir une trajectoire circulaire (arc) en programmant le point d’arrivée et un point intermédiaire (le point de départ de l’arc est le point de départ du déplacement). En d’autres termes, au lieu de programmer les coordonnées du centre, il suffit de programmer n’importe quel point intermédiaire. Le point d’arrivée de l’arc est défini en coordonnées cartésiennes ou polaires, tandis que le point intermédiaire est toujours défini en coordonnées cartésiennes par les lettres I, J ou K. Chaque lettre est associée aux axes comme suit: Axes X, U, A Axes Y, V, B Axes Z, W, C -> -> -> I J K En coordonnées cartésiennes: G17 G09 X±5.5 Y±5.5 I±5.5 J±5.5 En coordonnées polaires: G17 G09 R±5.5 Q±5.5 I±5.5 J±5.5 Exemple: Y Le point de départ est X-50 Y0. 25 20 -15 -50 35 X G09 X35 Y20 I-15 J25 La fonction G09 est non-modale, et doit donc être programmée pour chaque exécution d’une trajectoire circulaire définie par trois points. La fonction G09 peut être programmée sous la forme G9. Lors de la programmation de G09, il est inutile de programmer le sens de déplacement (G02 ou G03). La fonction G09 no modifie pas l’historique du programme. La même fonction G01, G02 ou G03 reste active après la fin du bloc. Attention: Lorsque la fonction G09 est utilisée, il est impossible d’exécuter un cercle complet, puisque trois points distincts doivent être programmés. La CNC visualisera le code d’erreur correspondant. Chapitre: 6 CONTROLE DES TRAJECTOIRES Section: ARC DEFINI PAR TROIS POINTS (G09) Page 11 6.7 INTERPOLATION HELICOIDALE La réalisation d’une interpolation hélicoïdale suppose l’exécution d’une interpolation circulaire dans le plan de travail en même temps qu’un déplacement linéaire synchronisé sur l’un quelconque des autres axes. L’interpolation circulaire peut être programmée en coordonnées cartésiennes ou polaires, ou grâce aux fonctions d’aide géométriques G08 ou G09. L’autre axe sélectionné, qui indique le point final du déplacement linéaire, doit être programmé en coordonnées cartésiennes. Le pas de l’hélice sera programmé (option) selon le format 5.5 avec les lettres I, J ou K. Chaque lettre sera associée aux axes comme suit: Axes X, U, A Axes Y, V, B Axes Z, W, C -> -> -> I J K Si le pas de l’hélice n’est pas programmé, la CNC calcule le pas nécessaire pour pouvoir effectuer la rotation correspondant à l’arc programmé. La CNC calcule également (d’après l’interpolation circulaire et le pas d’hélice programmés) la coordonnée finale correspondant à l’axe linéaire programmé. Bien que, théoriquement, cette coordonnée doive coïncider avec la coordonnée programmée, la CNC permet de sélectionner la différence maximum entre les deux coordonnées au moyen du paramètre machine général "CIRINERR". Si cette valeur est dépassée, la CNC affiche l’erreur correspondante. L’interpolation hélicoïdale est programmée dans un bloc, et quelques formats possibles, dans le plan XY, sont présentés ci-dessous: G02 X±5.5 Y±5.5 I±5.5 J±5.5 Z±5.5 K5.5 G02 X±5.5 Y±5.5 R±5.5 Z±5.5 K5.5 G03 Q±5.5 I±5.5 J±5.5 Z±5.5 K5.5 G08 X±5.5 Y±5.5 Z±5.5 K5.5 G09 X±5.5 Y±5.5 I±5.5 J±5.5 Z±5.5 K5.5 Page 12 Chapitre: 6 CONTROLE DES TRAJECTOIRES Section: INTERPOLATION HELICOIDALE Exemple: Programmation en coordonnées cartésiennes et polaires, avec X0 Y0 Z0 comme point de départ. Z Y 50 K=5 X 15 Coordonnées cartésiennes: G03 X0 Y0 I15 J0 Z50 K5 Coordonnées polaires: G03 Q180 I15 J0 Z50 K5 Chapitre: 6 CONTROLE DES TRAJECTOIRES Section: INTERPOLATION HELICOIDALE Page 13 6.8 ENTREE TANGENTIELLE AU DEBUT DE L’USINAGE (G37) La fonction G37 permet le raccordmeent tangentiel de deux trajectoires sans avoir à calculer les points d’intersection. La fonction G37 est non-modale et doit donc être toujours programmée pour lancer une opération d’usinage avec entrée tangentielle. Exemple: Y 50 30 10 X 40 60 80 Si le point de départ est X0 Y30 et si l’on désire usiner un arc (avec une approche en ligne droite), on programmera: G90 G01 X40 G02 X60 Y10 I20 J0 Page 14 Chapitre: 6 CONTROLE DES TRAJECTOIRES Section: ENTREETANGENTIELLE(G37) Dans ce même exemple, pour que l’entrée de l’outil sur la pièce à usiner soit tangente à la trajectoire et décrive un rayon de 5 mm, on devra programmer: G90 G01 G37 R5 X40 G02 X60 Y10 I20 J0 Y 50 R=5 30 25 10 30 40 60 80 X Comme on peut le voir sur la figure, la CNC modifie la trajectoire afin que l’outil commence l’usinage avec une entrée tangentielle sur la pièce. La fonction G37 et la valeur R doivent être programmées dans le bloc contenant la trajectoire à modifier. La valeur de R5.5 doit toujours apparaître après G37; elle indique le rayon de l’arc que la CNC introduit pour obtenir une entrée tangentielle sur la pièce. Cette valeur de R doit toujours être positive. La fonction G37 ne peut être programmée que dans un bloc comportant un déplacement linéaire (G00 ou G01). Si elle est programmée dans un bloc comportant un déplacement circulaire (G02 ou G03), la CNC affiche l’erreur correspondante. Chapitre: 6 CONTROLE DES TRAJECTOIRES Section: ENTREETANGENTIELLE(G37) Page 15 6.9 SORTIE TANGENTIELLE A LA FIN DE L’USINAGE (G38) La fonction G38 permet de terminer une opération d’usinage par une sortie tangentielle de l’outil. La trajectoire suivante doit être une droite (G00 ou G01). Dans le cas contraire, la CNC affiche l’erreur correspondante. La fonction G38 est non-modale et doit donc être programmée pour chaque sortie tangentielle de l’outil. La valeur de R5.5 doit toujours apparaître après G38; elle indique le rayon de l’arc que la CNC introduit pour obtenir une sortie tangentielle de la pièce. Cette valeur de R doit toujours être positive. Exemple: Y 50 30 40 60 80 120 X Pour usiner un arc avec X0 Y30 comme point de départ et des trajectoires d’approche et de sortie rectilignes, on programmera: G90 Page 16 G01 X40 G02 X80 I20 J0 G00 X120 Chapitre: 6 CONTROLE DES TRAJECTOIRES Section: SORTIETANGENTIELLE(G38) Dans ce même exemple, pour que la sortie d’usinage soit tangente à la trajectoire et décrive un rayon de 5 mm, on devra programmer: G90 G01 X40 G02 G38 R5 X80 I20 J0 G00 X120 Y 50 30 40 Chapitre: 6 CONTROLE DES TRAJECTOIRES 60 80 120 Section: SORTIETANGENTIELLE(G38) X Page 17 6.10 ARRONDI AUTOMATIQUE AUX ANGLES (G36) Dans les opérations de fraisage, la fonction G36 permet d’exécuter des arrondis aux angles selon un rayon donné, sans avoir à calculer le centre ni les points de départ et d’arrivée de l’arc. La fonction G36 est non-modale et doit donc être programmée pour chaque arrondi aux angles. Cette fonction doit être programmée dans le bloc définissant le déplacement pour lequel on désire un arrondi au point d’arrivée. La valeur de R5.5 doit toujours figurer après G36; elle indique le rayon que la CNC introduit pour obtenir l’arrondi au angles désiré. Cette valeur de R doit toujours être positive. Exemples: Y 60 20 20 35 X 50 G90 G01 G36 R5 X35 Y60 X50 Y0 Y 50 20 20 50 X G90 G03 G36 R5 X50 Y50 I0 J30 G01 X50 Y0 Page 18 Chapitre: 6 CONTROLE DES TRAJECTOIRES Section: ARRONDIAUTOMATIQUEAUX ANGLES (G36) 6.11 CHANFREIN (G39) Dans les opérations d’usinage, la fonction G39 permet de chanfreiner des angles entre deux droites, sans avoir à calculer les points d’intersection. La fonction G39 est non-modale et doit donc être programmée pour chaque chanfrein. Cette fonction doit être programmée dans le bloc contenant le déplacement dont le point d’arrivée doit être chanfreiné. La valeur de R5.5 doit toujours figurer après G39; elle indique la distance entre la fin du déplacement programmé et le point où le chanfrein doit être exécuté. Cette valeur de R doit toujours être positive. Exemple: Y 60 20 20 35 50 X G90 G01 G39 R15 X35 Y60 X50 Y0 Chapitre: 6 CONTROLE DES TRAJECTOIRES Section: CHANFREIN (G39) Page 19 6.12 FILETAGE (G33) Si la broche de la machine est équipée d’un codeur rotatif, la fonction G33 permet le filetage au grain. Bien que ce type de filetage soit souvent exécuté sur toute la longueur d’un axe, la CNC FAGOR 8050 permet le filetage en interpolant plus d’un axe à la fois (jusqu’à 5 axes). Dans le format de programmation, le point d’arrivée du filet (X...C±5.5) et le pas du filetage L5.5 doivent être définis Exemple: Exécution, en X0 Y0 Z0 et en une passe unique, d’un filet de 100 mm de profondeur et de 5 mm de pas au moyen d’un outil à fileter situé en Z10. Z X Y G90 G33 Z-100 L5 M19 G00 X3 Z30 ; ; ; ; Filetage programmé Arrêt indexé de la broche Retrait de l’outil Recul (sortie du trou fileté) Pendant que la fonction G33 est active, il est impossible de modifier l’avance F programmée ni la vitesse de broche S programmée, qui sont toutes deux fixées à 100%. La fonction G33 est modale et incompatible avec G00, G01, G02, G03 et G75. A la mise sous tension, après exécution de M02, M30 ou après une URGENCE ou un RESET, la CNC prendra en compte G00 ou G01, en fonction de l’état du paramètre machine général "IMOVE" Page 20 Chapitre: 6 CONTROLE DES TRAJECTOIRES Section: FILETAGE(G33) 6.13 DEPLACEMENT JUSQU’A UNE BUTEE MECANIQUE (G52) La fonction G52 permet de programmer le déplacement d’un axe jusqu’à une butée mécanique. Cette possibilité peut s’avérer intéressante pour les machines à cintrer, les poupées mobiles motorisées, les dispositifs d’alimentation de barres, etc. Le format de programmation est: G52 X..C ±5.5 Après G52, on programmera l’axe désiré ainsi que la coordonnée du point d’arrivée du déplacement. L’axe se déplace jusqu’au point programmé, jusqu’à ce qu’il parvienne à la butée. S’il parvient au point programmé sans que la butée soit atteinte, la CNC stoppe le déplacement. La fonction G52 est non-modale, et doit donc être programmée à chaque exécution d’un déplacement jusqu’à une butée. L’exécution de cette fonction suppose que les fonctions G01 et G40 soient actives, ce qui change l’historique du programme. Elle est incompatible avec les fonctions G00, G02, G03, G33, G41, G42, G75 et G76. Chapitre: 6 CONTROLE DES TRAJECTOIRES Section: DEPLACEMENTJUSQU’AUNE BUTEEMECANIQUE Page 21 7. 7.1 FONCTIONS PREPARATOIRES SUPPLEMENTAIRES INTERRUPTION DE LA PREPARATION DE BLOCS (G04) La CNC FAGOR 8050 peut lire jusqu’à 20 blocs en avant du bloc en cours d’exécution, afin de calculer à l’avance la trajectoire à parcourir. Chaque bloc est évalué (en son absence) lors de sa lecture, mais la fonction G04 permet son évaluation au moment de son exécution. Cette fonction interrompt la préparation des blocs et attend l’exécution d’un bloc donné avant de reprendre cette préparation. Un cas de ce type est l’évaluation de la "condition de saut de bloc", qui est définie dans l’en-tête du bloc. Exemple: . . . G04 ; Interrompt la préparation des blocs /1 G01 X10 Y20 ; Condition de saut "/1" . . La fonction G04 est non-modale et doit donc être programmée à chaque interruption de la préparation de blocs. Elle doit être programmée seule dans le bloc précédant celui où doit s’effectuer l’évaluation pendant l’exécution . La fonction G04 peut être programmée sous la forme G4. Chaque programmation de G04 annule temporairement la compensation et de longueur actives. Pour cette raison, on n’utilisera cette fonction qu’avec précautions car, si elle est insérée entre des blocs d’usinage travaillant en compensation, des formes indésirables pourraient être produites. Chapitre: 7 FONCTIONSPREPARATOIRESSUPPLEMENTAIRES Section: G04 ET G04K Page 1 Exemple: Les blocs de programme suivants sont exécutés dans une section avec la compensation G41. ........... ........... N10 X50 Y80 N15 G04 /1 N17 M10 N20 X50 Y50 N30 X80 Y50 ........... ........... Le bloc N15 interrompt la préparation des blocs, de façon que l’exécution du bloc N10 s’achève au point A. Y A 80 N10 N20 50 N30 50 80 X Lorsque l’exécution du bloc N15 est terminée, la CNC reprend la préparation des blocs à partir du bloc N17. Page 2 Chapitre: 7 FONCTIONSPREPARATOIRESSUPPLEMENTAIRES Section: G04 ET G04K Comme le point suivant appartenant à la trajectoire compensée est le point "B", la CNC déplace l’outil jusqu’à ce point, en exécutant la trajectoire "A-B". Y A 80 N10 N20 B 50 N30 X 50 80 Comme on peut le constater, la trajectoire obtenue n’est pas celle désirée; il est donc recommandé d’éviter d’utiliser la fonction G04 dans des sections travaillant en compensation. 7.2 TEMPORISATION (G04 K) La fonction G04 K permet de programmer une temporisation. La valeur de la temporisation est programmée en centièmes de seconde selon le format K5 (0 .. 99999). Exemple: G04 K50 ; Temporisation de 50 centièmes de seconde (0.5 seconde) G04 K200 ; Temporisation de 200 centièmes de seconde (2 secondes) La fonction G04 K est non-modale, et doit donc être programmée à chaque temporisation. La fonction G04 K peut être programmée sous la forme G4 K. La temporisation est exécutée au début du bloc dans lequel elle est programmée. Chapitre: 7 FONCTIONSPREPARATOIRESSUPPLEMENTAIRES Section: G04 ET G04K Page 3 7.3 TRAVAIL SUR ANGLE VIF (G07) ET ARRONDI (G05,G50) 7.3.1 ANGLE VIF (G07) Dans le cas du travail en G07 (angle vif), la CNC ne commence pas l’exécution du bloc de programme suivant tant que la position programmée dans le bloc en cours n’a pas été atteinte. La CNC considère que la position programmée a été atteinte quand l’axe se situe à une distance inférieure à “INPOSW” (zone “en-position”) par rapport à la position programmée. Exemple: G91 G01 G07 Y70 F100 X90 Les profils théorique et réel coïncident et permettent d’obtenir des arêtes vives comme le montre la figure. La fonction G07 est modale et incompatible avec G05, G50 et G51. La fonction G07 peut être programmée sous la forme G7. A la mise sous tension, après exécution de M02, M30 ou après une URGENCE ou un RESET, la CNC prend en compte le code G05 ou G07 selon l’état du paramètre machine général "ICORNER" Page 4 Chapitre: 7 FONCTIONSPREPARATOIRESSUPPLEMENTAIRES Section: ANGLE VIF (G07) ANGLE ARRONDI (G05,G50) 7.3.2 ARRONDI AUX ANGLES (G05) Dans le cas du travail en G05 (arrondi aux angles), la CNC commence l’exécution du bloc suivant du programme dès la fin de l’interpolation théorique du bloc actuel, sans attendre que les axes soient en position. La distance entre la position programmée et celle où commence l’exécution du bloc suivant dépend de la vitesse d’avance des axes. Exemple: G91 G01 G05 Y70 F100 X90 Cette fonction permet d’obtenir des arrondis aux angles, comme le montre la figure. La différence entre les profils théorique et réel dépend de la valeur de l’avance F programmée. Plus l’avance est grande, plus la différence entre les deux profils est importante. La fonction G05 est modale et incompatible avec G07, G50 et G51. La fonction G05 peut être programmée sous la forme G5. A la mise sous tension, après exécution de M02, M30 ou après une URGENCE ou un RESET, la CNC prend en compte le code G05 ou G07 selon l’état du paramètre machine général "ICORNER". Chapitre: 7 FONCTIONSPREPARATOIRESSUPPLEMENTAIRES Section: ANGLE VIF (G07) ANGLE ARRONDI (G05,G50) Page 5 7.3.3 ARRONDI AUX ANGLES CONTROLE (G50) Dans le cas du travail en G50 (arrondi aux angles contrôlé), la CNC attend, après la fin de l’interpolation théorique du bloc actuel, que l’axe pénètre dans la zone définie par le paramètre machine “INPOSW2” avant de poursuivre l’exécution du bloc suivant. Exemple: G91 G01 G50 Y70 F100 X90 La fonction G50 s’assure que la différence entre les profils théorique et réel reste inférieure à celle définie par le paramètre machine “INPOSW2”. Au contraire, si l’on travaille avec la fonction G05, cette différence dépend de la valeur de l’avance F programmée. Plus l’avance est grande, plus la différence entre les deux profils est importante. La fonction G50 est modale et incompatible avec G07, G05 et G51. A la mise sous tension, après exécution de M02, M30 ou après une URGENCE ou un RESET, la CNC prend en compte le code G05 ou G07 selon l’état du paramètre machine général "ICORNER". Page 6 Chapitre: 7 FONCTIONSPREPARATOIRESSUPPLEMENTAIRES Section: ANGLE VIF (G07) ANGLE ARRONDI (G05,G50) 7.4 ANALYSE PAR ANTICIPATION (“LOOK-AHEAD”) (G51) Généralement, l’exécution d’un programme composé de blocs à déplacement très faible (CAM, digitalisation, etc..) est très lente. Cette fonctionnalité permet l’usinage à grande vitesse pour ce type de programmes. Il est recommandé de disposer de l’option CPU-TURBO lorsque la fonction “Analyse par anticipation” est utilisée car la CNC doit analyser la trajectoire d’usinage à l’avance (jusqu’à 50 blocs) afin de calculer la vitesse maximale sur chaque tronçon de la trajectoire. Le format de programmation est: G51 [A] E A (0-255) Il est optionnel et définit le pourcentage d’accélération à appliquer. Sil n’est pas programmé ou programmé avec une valeur “0”, la CNC prend la valeur d’accélération définie par le paramètre machine pour chaque axe. E (5.5) Erreur de contournage maximum admise. Le paramètre “A” permet l’application d’une accélération de travail standard et d’une autre accélération utilisable avec l’analyse par anticipation. Plus la valeur du paramètre “E” est faible, plus l’avance d’usinage est réduite. Lorsque la fonction “Analyse par anticipation” est activée, il est judicieux de régler les axes de façon que leur erreur de poursuite soit la plus faible possible car l’erreur de l’usinage de contour est au moins égale à l’erreur de poursuite minimum. Lors du calcul de la vitesse d’avance de l’axe, la CNC prend en compte les éléments suivants: * * * * L’avance programmée. Le rayon de courbure et les angles. Les vitesses maximales des axes. Les accélérations maximales. Si, pendant l’exécution avec l’analyse par anticipation active, il se produit l’un des évènements ci-dessous, la CNC ralentit la vitesse appliquée au bloc précédent jusqu’à “0” et reprend les conditions d’usinage en “analyse par anticipation” dans le bloc à déplacement suivant. * * * * * Bloc sans déplacement. Exécution de fonctions auxiliaires (M, S, T). Mode bloc à bloc. Mode MDI. Mode CONTROLE D’OUTILS Si “Stop”, “Feed Hold”, etc... se produisent pendant l’exécution en mode “Par anticipation”, la machine risque de ne pas stopper sur le bloc actuel, et plusieurs blocs sront nécessaires avant d’obtenir l’arrêt selon la décélération autorisée. La fonction G51 est modale et incompatible avec G05, G07 et G50. Si l’une de ces fonctions est programmée, la fonction G51 est annulée et la nouvelle fonction sélectionnée est activée. Chapitre: 7 FONCTIONSPREPARATOIRESSUPPLEMENTAIRES Section: ANALYSE PAR ANTICIPATION (G51) Page 7 Par ailleurs, la CNC émet l’erreur 7 (fonctions G incompatibles) si l’une des fonctions suivantes est programmée pendant que G51 est actif. * * * * * * G23, G26, G27 Recopie G33 Filetage électronique G52 Déplacement jusqu’à une butée matériel G74 Recherche du zéro G75, G76 Cycles de palpeur G95 Avance par tour La fonction G51 doit être programmée seule dans un bloc; aucune autre information n’est admise. A la mise sous tension, après l’exécution de M02, M30 ou après un arrêt en URGENCE ou un RESET, la CNC annule G51 si elle était active et elle prend G05 ou G07 en fonction du réglage du paramètre machine général ‘ICORNER”. Page 8 Chapitre: 7 FONCTIONSPREPARATOIRESSUPPLEMENTAIRES Section: ANALYSE PAR ANTICIPATION (G51) 7.5 IMAGE MIROIR (G10,G11,G12,G13,G14) G10: G11: G12: G13: G14: Annulation de l’image miroir Image miroir sur l’axe X. Image miroir sur l’axe Y. Image miroir sur l’axe Z. Image miroir sur un axe quelconque (X..C), ou sur plusieurs axes à la fois (5 max.); Exemples: G14 W G14 X Z A B Lorsque la fonction image miroir est activée, la CNC exécute les déplacements programmés sur les axes pour lesquels l’image miroir est active, en changeant le signe. Exemple: Y 90 b a 70 30 -90 -50 -30 30 50 90 X -30 -70 d c -90 La sous-routine suivante définit l’usinage de la pièce "a". G91 G01 X30 Y30 F100 Y60 X20 Y-20 X40 G02 X0 Y-40 I0 J-20 G01 X-60 X-30 Y-30 Chapitre: 7 FONCTIONSPREPARATOIRESSUPPLEMENTAIRES Section: IMAGEMIROIR (G10,G11,G12,G13,G14) Page 9 La programmation de l’ensemble des pièces sera: Exécution de la sous-routine ; G11 ; Exécution de la sous-routine ; G10 G12 ; Exécution de la sous-routine ; G11 ; Exécution de la sous-routine ; M30 ; Usine "a". Image miroir sur l’axe X. Usine "b". Image miroir sur l’axe Y. Usine "c". Image miroir sur les axes X et Y. Usine "d". Fin de programme Les fonctions G11, G12, G13 et G14 sont modales et incompatibles avec G10. G11, G12 et G13 peuvent être programmées dans le même bloc, puisqu’elles ne sont pas incompatibles entre elles. La fonction G14 doit être programmée seule dans un bloc. Si la fonction G73 (rotation du système de coordonnées) est activée dans un programme comportant des fonctions image miroir, la CNC applique d’abord la fonction image miroir, puis la rotation. Si une nouvelle origine de coordonnées (zéro pièce) est présélectionnée par G92 pendant que l’une des fonctions miroir (G11, G12, G13, G14) est active, cette nouvelle origine n’est pas affectée par la fonction image miroir. A la mise sous tension, après exécution de M02, M30 ou après une URGENCE ou un RESET, la CNC prendra en compte le code G10. Page 10 Chapitre: 7 FONCTIONSPREPARATOIRESSUPPLEMENTAIRES Section: IMAGEMIROIR (G10,G11,G12,G13,G14) 7.6 FACTEUR D’ECHELLE (G72) La fonction G72 permet d’agrandir ou de réduire les pièces programmées. Ainsi, il est possible de réaliser des familles de pièces de forme semblable, mais de dimensions différentes avec un seul programme. La fonction G72 doit être programmée seule dans un bloc. Deux formats de programmation sont disponibles: Facteur d’échelle appliqué à tous les axes. Facteur d’échelle appliqué à un ou plusieurs axes. Chapitre: 7 FONCTIONSPREPARATOIRESSUPPLEMENTAIRES Section: FACTEURD’ECHELLE(G72) Page 11 7.6.1 FACTEUR D’ECHELLE APPLIQUE A TOUS LES AXES Le format de programmation est: G72 S5.5 Toutes les coordonnées programmées après G72 sont multipliées par la valeur du facteur d’échelle défini par S, jusqu’à la lecture d’une nouvelle définition de facteur d’échelle G72 ou jusqu’à son annulation. Exemple de programmation, avec X-30 Y10 comme point de départ. Y' Y b X' a X -30 La sous-routine suivante définit l’usinage de la pièce. G90 X-19 G01 G02 G01 Y0 X0 Y10 F150 X0 Y-10 I0 J-10 X-19 Y0 La programmation des deux pièces sera: Exécution de la sous-routine G92 X-79 Y-30 G72 S2 Exécution de la sous-routine G72 S1 M30 Page 12 ; Usine "a" ; Présélection de coordonnées (décalage du zéro) ; Application du facteur d’échelle 2. ; Usine "b". ; Annulation du facteur d’échelle ; Fin de programme Chapitre: 7 FONCTIONSPREPARATOIRESSUPPLEMENTAIRES Section: FACTEURD’ECHELLE(G72) Exemples d’application du facteur d’échelle. Y Y 20 20 10 10 10 N10 N20 G90 G91 G00 X0 Y0 G01 X20 Y10 Y10 X-10 X-10 Y-20 G72 S0.5 (RPT N10,20) M30 20 X 10 20 X G90 N10 G91 G00 X20 Y20 G01 X-10 X-10 Y-20 X20 Y10 N20 Y10 G72 S0.5 ;Facteur d’échelle (RPT N10,20) ;Répétition du bloc 10 au bloc 20 M30 La fonction G72 est modale, et sera annulée par la programmation d’un autre facteur d’échelle S1, à la mise sous tension, après exécution de M02, M30 ou après une URGENCE ou un RESET. Chapitre: 7 FONCTIONSPREPARATOIRESSUPPLEMENTAIRES Section: FACTEURD’ECHELLE(G72) Page 13 7.6.2 FACTEUR D’ECHELLE APPLIQUE A UN OU PLUSIEURS AXES Le format de programmation est: G72 X...C 5.5 Le ou les axes et le facteur d’échelle désirés sont programmés après G72. Tous les blocs programmés après G72 sont traités comme suit par la CNC: La CNC calcule les déplacements de tous les axes en fonction de la trajectoire et de la compensation programmées. Ensuite, elle applique le facteur d’échelle indiqué au déplacement calculé du ou des axes correspondants. Si le facteur d’échelle est appliqué à un ou plusieurs axes, la CNC appliquera le facteur d’échelle indiqué à la fois au déplacement et à l’avance du ou des axes correspondants. Si, dans le même programme, les deux types de facteurs d’échelle sont appliqués (celui s’adressant à tous les axes et celui s’adressant à un ou plusieurs axes), la CNC applique à l’axe ou aux axes concernés par les deux types un facteur égal au produit des deux facteurs programmés pour cet axe. La fonction G72 est modale et sera annulée par la programmation d’un autre facteur d’échelle, à la mise sous tension, après exécution de M02, M30 ou après une URGENCE ou un RESET. Exemple: Application du facteur d’échelle à un axe du plan, en compensation de rayon d’outil. 16 20 16 20 Comme on peut le constater, la trajectoire de l’outil ne coïncide pas avec la trajectoire désirée, en raison de l’application du facteur d’échelle au déplacement calculé. Page 14 Chapitre: 7 FONCTIONSPREPARATOIRESSUPPLEMENTAIRES Section: FACTEURD’ECHELLE(G72) Toutefois, si un facteur d’échelle égal à 360/2R est appliqué à un axe rotatif, R étant le rayon du cylindre sur lequel l’usinage est exécuté, cet axe peut être considéré comme linéaire, et il est possible de programmer n’importe quelle forme avec compensation de rayon sur la surface cylindrique. Chapitre: 7 FONCTIONSPREPARATOIRESSUPPLEMENTAIRES Section: FACTEURD’ECHELLE(G72) Page 15 7.7 ROTATION DU SYSTEME DE COORDONNEES (G73) La fonction G73 permet la rotation du système de coordonnées en prenant l’origine des coordonnées ou le centre de rotation programmé comme centre de rotation. Le format définissant la rotation est le suivant: G73 Q+/5.5 I±5.5 J±5.5 Où: Q : Indique l’angle de rotation en degrés I, J : Sont optionnels et définissent respectivement l’abscisse et l’ordonnée du centre de rotation. S’ils ne sont pas définis, c’est l’origine des coordonnées qui est prise comme centre de rotation. Les valeurs I et J seront définies en coordonnées absolues par rapport à l’origine des coordonnées du plan de travail. Ces coordonnées sont affectées par le facteur d’échelle et les images miroir actifs. Q 30 Q 20 G73 Q90 G73 Q90 I20 J30 Il convient de tenir compte du fait que la fonction G73 est incrémentale, c’est-à-dire que les diverses valeurs de Q programmées s’ajoutent. Q Page 16 Chapitre: 7 FONCTIONSPREPARATOIRESSUPPLEMENTAIRES Section: ROTATIONDUSYSTEMEDE COORDONNEES (G73) La fonction G73 doit être programmée seule dans un bloc. Exemple: Y Y' X' 45 o 45 o X 21 10 10 En supposant que le point de départ est X0 Y0, on a: N10 G01 X21 Y0 F300 G02 Q0 I5 J0 G03 Q0 I5 J0 Q180 I-10 J0 N20 G73 Q45 (RPT N10, N20) N7 M30 ; Positionnement sur le point de départ ; Rotation des coordonnées ; 7 répétitions des blocs 10 à 20 ; Fin de programme Dans un programme comportant une rotation du système de coordonnées, si une fonction image miroir est également active, la CNC applique d’abord cette dernière, puis la rotation. La fonction rotation du système de coordonnées peut être annulée par la programmation de G73 (seule sans la valeur de l’angle), par G16, G17, G18, G19, par la mise sous tension, après exécution de M02, M30 ou après une URGENCE ou un RESET. Chapitre: 7 Section: FONCTIONSPREPARATOIRESSUPPLEMENTAIRES ROTATIONDUSYSTEMEDE COORDONNEES (G73) Page 17 7.8 COUPLAGE/DECOUPLAGE ELECTRONIQUE DES AXES La CNC FAGOR 8050 permet de coupler deux axes ou plus ensemble. Leur déplacement est subordonné au déplacement de l’axe auquel ils ont été couplés. Trois modes de couplage sont disponibles: Couplage mécanique des axes. Il est imposé par le constructeur de la machine, et sélectionné par le paramètre machine d’axes "GANTRY". Par PLC. Chaque axe peut être couplé et découplé au moyen des entrées logiques de la CNC “SYNCHRO1”, “SYNCHRO2”, “SYNCHRO3”, “SYNCHRO4” et “SYNCHRO5”. Chaque axe est couplé à l’axe indiqué dans le paramètre machine des axes “SYNCHRO”. Par programme. Deux axes ou plus peuvent être couplés et découplés électroniquement grâce aux fonctions G77 et G78. Page 18 Chapitre: 7 FONCTIONSPREPARATOIRESSUPPLEMENTAIRES Section: COUPLAGE/DECOUPLAGE ELECTRONIQUEDESAXES 7.8.1 COUPLAGE ELECTRONIQUE DES AXES (G77) La fonction G77 permet de sélectionner aussi bien les axes maîtres que les axes esclaves. Le format de programmation est le suivant: G77 < Axe 1 > < Axe 2 > < Axe 3 > < Axe 4 > < Axe 5 > Où <Axe 2>, <Axe 3>, <Axe 4> et <Axe 5> indiqueront les axes à coupler à l’axe maître <Axe 1>. La définition de <Axe1> et <Axe2> est obligatoire, tandis que la programmation du reste des axes est optionnelle. Exemple: G77 X Y U ; Couple les axes Y et U à l’axe X Le couplage électronique des axes doit s’effectuer selon les règles suivantes: Un ou deux couplages électroniques distincts sont disponibles. G77 X Y U ; Couple les axes Y et U à l’axe X G77 V Z ; Couple l’axe Z à l’axe V Il n’est pas possible de coupler un axe à deux autres axes à la fois. G77 V Y G77 X Y ; Couple l’axe Y à l’axe V ; Produit un signal d’erreur, puisque l’axe Y est couplé à l’axe V Il est possible de coupler plusieurs axes à un seul par phases successives. G77 X Z G77 X U G77 X Y ; Couple l’axe Z à l’axe X ; Couple l’axe U à l’axe X -> Z U couplés à l’axe X ; Couple l’axe Y à l’axe X -> Y Z U couplés à l’axe X Deux axes déjà couplés entre eux ne peuvent pas être couplés à un autre axe. G77 Y U G77 X Y ; Couple l’axe U à l’axe Y ; Produit un signal d’erreur, puisque l’axe Y est couplé à l’axe U. Chapitre: 7 FONCTIONSPREPARATOIRESSUPPLEMENTAIRES Section: COUPLAGE/DECOUPLAGE ELECTRONIQUEDESAXES Page 19 7.8.2 ANNULATION DU COUPLAGE ELECTRONIQUE DES AXES (G78) La fonction G78 permet de découpler tous les axes couplés, ou de ne découpler que les axes indiqués. G78 Découple tous les axes couplés. G78 <Axe1> <Axe2> <Axe3> <Axe4> Ne découple que les axes indiqués Exemple: Page 20 G77 X Y U G77 V Z G78 Y ; ; ; G78 ; Couple les axes Y et U à l’axe X Couple l’axe Z à l’axe V Découple l’axe Y, mais l’axe U reste couplé à l’axe X, et l’axe Z à l’axe V Découple tous les axes Chapitre: 7 FONCTIONSPREPARATOIRESSUPPLEMENTAIRES Section: COUPLAGE/DECOUPLAGE ELECTRONIQUEDESAXES 8. COMPENSATION D’OUTILS La CNC FAGOR 8050 dispose d’une table de correcteurs, dont la taille est définie par le paramètre machine général "NTOFFSET". Pour chaque correcteur, on spécifiera: * Le rayon de l’outil, en unités de travail, au format R±5.5 * La longueur de l’outil, en unités de travail, au format L±5.5 * L’usure du rayon de l’outil, en unités de travail, au format I±5.5. La CNC ajoutera cette valeur au rayon théorique (R) pour calculer le rayon réel (R+I). * L’usure de la longueur de l’outil, en unités de travail, au format K±5.5. La CNC ajoutera cette valeur à la longueur théorique (L) pour calculer la longueur réelle (L+K). Si une compensation de rayon d’outil est nécessaire (G41 ou G42), la CNC applique comme valeur de compensation de rayon la somme des valeurs R+I du correcteur sélectionné. Si une compensation de longueur d’outil est nécessaire (G43), la CNC applique comme valeur de compensation de longueur la somme des valeurs L+K du correcteur sélectionné. Chapitre: 8 COMPENSATIOND’OUTILS Section: Page 1 8.1 COMPENSATION DE RAYON D’OUTIL (G40,G41,G42) Dans les opérations classiques de fraisage, la trajectoire de l’outil doit être calculée et définie en tenant compte de son rayon, de façon à obtenir les dimensions requises pour la pièce. La compensation de rayon d’outil permet de programmer directement le profil de la pièce et le rayon de l’outil sans tenir compte des dimensions de l’outil. La CNC calcule automatiquement la trajectoire que l’outil doit suivre, sur la base du profil de la pièce et de la valeur du rayon de l’outil chargés dans la table de correcteurs. Trois fonctions préparatoires sont disponibles pour la compensation de rayon d’outil: G40 Annulation de la compensation de rayon d’outil. G41 Compensation de rayon d’outil à gauche. G42 Compensation de rayon d’outil à droite. G42 G41 G41. L’outil est à la gauche de l’outil suivant le sens de l’usinage. G42. L’outil est à la droite de l’outil suivant le sens de l’usinage. Les valeurs de l’outil R, L, I, K, doivent être chargées dans la table de correcteurs avant le début des opérations d’usinage, ou au début du programme par affectations aux variables TOR, TOL, TOI, TOK. Lorsque le plan sur lequel portera la compensation a été défini grâce aux codes G16, G17, G18 ou G19, cette compensation est appliquée par G41 ou G42, sur la base de la valeur du correcteur sélectionné par le code D, ou en son absence, du correcteur indiqué dans la table d’outils pour l’outil T selectionné. Les fonctions G41 et G42 sont modales et incompatibles entre elles. Elles sont annulées par G40, G04 (interruption de la préparation des blocs), G53 (programmation par rapport au zéro machine), G74 (recherche du zéro), cycles fixes d’usinage (G81, G82, G83, G84, G85, G86, G87, G88, G89), ainsi qu’à la mise sous tension, après exécution de M02, M30 ou après une URGENCE ou un RESET. Page 2 Chapitre: 8 COMPENSATIOND’OUTILS Section: COMPENSATION DE RAYON D’OUTIL (G40,G41,G42) 8.1.1 ACTIVATION DE LA COMPENSATION DE RAYON D’OUTIL Lorsque le plan dans lequel la compensation doit être appliquée a été choisi par G16, G17, G18 ou G19, les codes G41 ou G42 permettent d’activer cette compensation. G41 Compensation de rayon d’outil à gauche. G42 Compensation de rayon d’outil à droite. Dans le bloc contenant G41 ou G42 (ou dans un bloc précédent), les fonctions T et D, ou T seule doivent être programmées pour sélectionner, dans la table de correcteurs, la valeur de la correction à appliquer. Si aucun correcteur n’est sélectionné, la CNC prendra D0 avec les valeurs R0 L0 I0 K0. Lorsque la fonction M06 est associée au nouvel outil et qu’une sous-routine est associée à M06, la CNC active la compensation de rayon d’outil au premier bloc de cette sousroutine comportant un déplacement. Si G53 est programmé dans un bloc de cette sous-routine (programmation en coordonnées machine), la CNC annule toute sélection antérieure de compensation de rayon par G41 ou G42. La sélection de la compensation de rayon d’outil (G41 ou G42) n’est possible que lorsque les fonctions G00 ou G01 sont actives (déplacements selon des droites). Si la compensation est sélectionnée alors que la fonction G02 ou G03 est active, la CNC affiche l’erreur correspondante. Les pages suivantes montrent plusieurs cas d’activation de compensation de rayon d’outil, dans lesquels la trajectoire programmée figure en traits pleins, tandis que la trajectoire compensée est en pointillés. Chapitre: 8 COMPENSATIOND’OUTILS Section: COMPENSATION DE RAYON D’OUTIL (G40,G41,G42) Page 3 Trajectoire DROITE-DROITE Page 4 Chapitre: 8 COMPENSATIOND’OUTILS Section: COMPENSATION DE RAYON D’OUTIL (G40,G41,G42) Trajectoire DROITE-ARC Chapitre: 8 COMPENSATIOND’OUTILS Section: COMPENSATION DE RAYON D’OUTIL (G40,G41,G42) Page 5 8.1.2 SECTIONS DE COMPENSATION DE RAYON D’OUTIL Les schémas suivants montrent les différentes trajectoires décrites par un outil contrôlé par une CNC programmée avec une compensation de rayon d’outil. La trajectoire programmée figure en trait plein, tandis que la trajectoire compensée est en pointillés. R R R R R R R R R R R R Page 6 Chapitre: 8 COMPENSATIOND’OUTILS Section: COMPENSATION DE RAYON D’OUTIL (G40,G41,G42) R R R R R R R Chapitre: 8 COMPENSATIOND’OUTILS R Section: COMPENSATION DE RAYON D’OUTIL (G40,G41,G42) Page 7 R R R R R R R R R R Page 8 Chapitre: 8 COMPENSATIOND’OUTILS Section: COMPENSATION DE RAYON D’OUTIL (G40,G41,G42) La CNC FAGOR 8050 lit jusqu’à 20 blocs en avant du bloc en cours d’exécution, afin de calculer à l’avance la trajectoire à décrire. Lorsqu’elle travaille en compensation, la CNC doit connaître le déplacement programmé suivant afin de calculer la trajectoire à décrire. En conséquence, on ne doit pas programmer plus de 18 blocs successifs ou plus sans déplacement. 8.1.3 ANNULATION DE COMPENSATION DE RAYON D’OUTIL La compensation de rayon d’outil est annulée par la fonction G40. Ne pas oublier que l’annulation de compensation de rayon d’outil (G40) n’est possible que dans un bloc dans lequel un déplacement rectiligne est programmé (G00 ou G01). Si G40 est programmé alors que les fonctions G02 ou G03 sont actives, la CNC affiche l’erreur correspondante. Les pages suivantes montrent plusieurs cas d’annulation de compensation de rayon d’outil, dans lesquels la trajectoire programmée figure en traits pleins, tandis que la trajectoire compensée est en pointillés. Chapitre: 8 COMPENSATIOND’OUTILS Section: COMPENSATION DE RAYON D’OUTIL (G40,G41,G42) Page 9 Trajectoire DROITE-DROITE Page 10 Chapitre: 8 COMPENSATIOND’OUTILS Section: COMPENSATION DE RAYON D’OUTIL (G40,G41,G42) Trajectoire ARC-DROITE Chapitre: 8 COMPENSATIOND’OUTILS Section: COMPENSATION DE RAYON D’OUTIL (G40,G41,G42) Page 11 Exemple d’usinage avec compensation de rayon Y 70 30 X 90 40 La trajectoire programmée apparaît en trait plein, alors que la trajectoire compensée est en pointillés. Rayon de l’outil Numéro de l’outil Numéro du correcteur : 10 mm. : T1 : D1 G92 X0 Y0 Z0 ; Présélection G90 G17 S100 T1 D1 M03 ; Outil,correcteur,démarrage de broche à S100 G41 G01 X40 Y30 F125 ; Activation de compensation Y70 X90 Y30 X40 G40 G00 X0 Y0 ; Annulation de compensation M30 Page 12 Chapitre: 8 COMPENSATIOND’OUTILS Section: COMPENSATION DE RAYON D’OUTIL (G40,G41,G42) Exemple d’usinage avec compensation de rayon Y 70 60 R 40 R 30 30 50 80 100 120 140 X La trajectoire programmée apparaît en trait plein, alors que la trajectoire compensée est en pointillés. Rayon de l’outil Numéro de l’outil Numéro du correcteur : 10 mm. : T1 : D1 G92 X0 Y0 Z0 ; G90 G17 G01 F150 S100 T1 D1 M03 ; G42 X30 Y30 ; X50 Y60 X80 X100 Y40 X140 X120 Y70 X30 Y30 G40 G00 X0 Y0 ; M30 Chapitre: 8 COMPENSATIOND’OUTILS Présélection Outil, correcteur, ... Activation de compensation Annulation de compensation Section: COMPENSATION DE RAYON D’OUTIL (G40,G41,G42) Page 13 Exemple d’usinage avec compensation de rayon Y R R 70 60 R 45 30 20 R R 20 25 50 55 70 85 100 X La trajectoire programmée apparaît en trait plein, alors que la trajectoire compensée est en pointillés. Rayon de l’outil Numéro de l’outil Numéro du correcteur G92 X0 Y0 Z0 G90 G17 G01 F150 G42 X20 Y20 X50 Y30 X70 G03 X85 Y45 I0 G02 X100 Y60 I15 G01 Y70 X55 G02 X25 Y70 I-15 G01 X20 Y20 G40 G00 X0 Y0 M30 Page 14 : 10 mm. : T1 : D1 S100 T1 D1 M03 ; Présélection ; Outil, correcteur, ... ; Activation de compensation J15 J0 J0 M5 Chapitre: 8 COMPENSATIOND’OUTILS ; Annulation de compensación Section: COMPENSATION DE RAYON D’OUTIL (G40,G41,G42) 8.2 COMPENSATION DE LONGUEUR D’OUTIL (G43,G44,G15) La compensation de longueur permet de compenser d’éventuelles différences de longueur entre l’outil programmé et l’outil qui va être utilisé. La compensation de longueur s’applique à l’axe indiqué par la fonction G15 ou, en son absence, à l’axe perpendiculaire au plan principal. Si G17, la compensation de longueur s’applique à l’axe Z Si G18, la compensation de longueur s’applique à l’axe Y Si G19, la compensation de longueur s’applique à l’axe X Chaque fois que l’une des fonctions G17, G18 ou G19 est programmée, la CNC prend comme nouvel axe longitudinal (celui sur lequel portera la compensation de longueur) l’axe perpendiculaire au plan sélectionné. En revanche, si la fonction G15 est exécutée pendant que l’une des fonctions G17, G18 ou G19 est active, le nouvel axe longitudinal sélectionné par G15 remplace le précédent. Les codes des fonctions utilisées en compensation de longueur sont: G43 Compensation de longueur d’outil. G44 Annulation de compensation de longueur d’outil. La fonction G43 indique seulement que la compensation de longueur doit être appliquée. La CNC applique cette compensation dès le début du déplacement de l’axe longitudinal. Exemple: G92 X0 Y0 Z50 G90 G17 G01 F150 S100 T1 D1 M03 G43 X20 Y20 X70 Z30 ; Présélection ; Outil, correcteur, ... ; Sélection de la compensation ; Application de la compensation La CNC compense la longueur selon la valeur du correcteur sélectionné grâce au code D ou, en son absence, selon le correcteur indiqué dans la table d’outils pour l’outil T sélectionné. Les valeurs de l’outil R, L, I, K, doivent être chargées dans la table de correcteurs avant le début de l’usinage, ou être chargées au début du programme au moyen d’affectations aux variables TOR, TOL, TOI, TOK. Si aucun correcteur n’est sélectionné, la CNC prend D0 avec les valeurs R0 L0 I0 K0. La fonction G43 est modale et peut être annulée par G44 et G74 (recherche du zéro). Si le paramètre machine général “ILCOMP=0”, il est également annulé à la mise sous tension, après l’exécution de M02, M30, ou après un arrêt d’URGENCE ou un RESET. G53 (programmation par rapport au zéro machine) annule temporairement G43, mais seulement pendant l’exécution d’un bloc contenant G53. La compensation de longueur peut être utilisée avec les cycles fixes mais, dans ce cas, on veillera à appliquer cette compensation avant le début du cycle. Chapitre: 8 COMPENSATIOND’OUTILS Section: COMPENSATION DE LONGUEUR (G43,G44,G15) Page 15 Exemple d’usinage avec compensation de longueur Y 55 35 15 X 30 90 50 120 4 mm 25 mm Z 2 mm 10 mm 15 mm Supposons que l’outil utilisé est plus court de 4 mm que l’outil programmé. Longueur de l’outil Numéro de l’outil Numéro du correcteur : - 4 mm. : T1 : D1 G92 X0 Y0 Z0 ; Présélection G91 G00 G05 X50 Y35 S500 M03 G43 Z-25 T1 D1 ; Activation de compensation G01 G07 Z-12 F100 G00 Z12 X40 G01 Z-17 G00 G05 G44 Z42 M05 ; Annulation de compensation G90 G07 X0 Y0 M30 Page 16 Chapitre: 8 COMPENSATIOND’OUTILS Section: COMPENSATION DE LONGUEUR (G43,G44,G15) 9. CYCLES FIXES Les cycles fixes sont exécutables dans n’importe quel plan, la pénétration en profondeur s’effectuant selon l’axe sélectionné comme axe longitudinal par G15 ou, en son absence, selon l’axe perpendiculaire à ce plan. Les fonctions dont dispose la CNC pour définir les cycles fixes d’usinage sont: G69 G81 G82 G83 G84 G85 G86 G87 G88 G89 Cycle fixe de perçage profond à pas variable. Cycle fixe de perçage. Cycle fixe de perçage avec temporisation. Cycle fixe de perçage profond à pas constant. Cycle fixe de taraudage. Cycle fixe d’alésage fin. Cycle fixe d’alésage avec retrait en avance rapide G00. Cycle fixe de poche rectangulaire. Cycle fixe de poche circulaire. Cycle fixe d’alésage avec retrait en avance de travail G01. Elle dispose également des fonctions suivantes, utilisables avec les cycles fixes d’usinage: G79 Modification des paramètres du cycle fixe G98 Retour au plan de départ après exécution du cycle fixe. G99 Retour au plan de référence, après exécution du cycle fixe. 9.1 DEFINITION DU CYCLE FIXE Un cycle fixe est défini par la fonction G indicative du cycle fixe et par les paramètres correspondants au cycle désiré. Un cycle fixe ne peut pas être défini dans un bloc comportant des déplacements nonlinéaires (G02, G03, G08, G09 ou G33). De même, l’exécution d’un cycle fixe est interdite lorsque les fonctions G02, G03 ou G33 sont actives. La CNC émet alors le message d’erreur correspondant. Toutefois, lorsqu’un cycle fixe a été défini dans un bloc et les blocs suivants, les fonctions G02, G03, G08 ou G09 peuvent être programmées. Chapitre: 9 CYCLESFIXES Section: Page 1 9.2 ZONE D’INFLUENCE DU CYCLE FIXE Dès qu’un cycle fixe est défini, il reste actif et tous les blocs programmés à la suite restent sous l’influence de ce cycle fixe tant qu’il n’est pas annulé. Autrement dit, chaque fois qu’un bloc dans lequel un déplacement d’axe a été programmé est exécuté, la CNC exécute, après le déplacement programmé, l’usinage correspondant au cycle fixe actif. Si le nombre de répétitions d’un bloc (N) est programmé à la fin d’un bloc comportant un déplacement et sous l’influence d’un cycle fixe, la CNC exécute, après le déplacement programmé, l’usinage correspondant au cycle fixe actif et autant de fois qu’indiqué. Si le “nombre de répétitions” programmé est N0, la CNC n’exécute pas l’usinage correspondant au cycle fixe actif. Elle n’exécute que le déplacement programmé. Si un bloc sans déplacement se trouve dans la zone d’influence d’un cycle fixe, l’usinage correspondant au cycle fixe défini n’est pas exécuté, sauf dans le bloc d’appel. G81 ............ G90 G1 X100 G91 X10 N3 G91 X20 N0 9.2.1 Définition et exécution du cycle fixe (perçage) L’axe X se déplace jusqu’en X100, où un autre perçage est exécuté La CNC exécute 3 fois l’opération suivante: * Déplacement incrémental X10 * Exécution du cycle fixe défini Déplacement incrémental X20 exclusivement, sans perçage G79. MODIFICATION DES PARAMETRES DU CYCLE FIXE La CNC permet, à l’intérieur de la zone d’influence du cycle fixe, de modifier un ou plusieurs paramètres d’un cycle fixe actif grâce à la fonction G79, sans qu’il soit nécessaire de redéfinir ce cycle fixe. La CNC maintient le cycle fixe actif, et exécute les opérations d’usinage du cycle fixe avec les paramètres mis à jour. La fonction G79 doit être programmée seule dans un bloc, qui ne doit pas contenir d’autres informations. Deux exemples de programmation sont présentés ci-dessous, en supposant que le plan de travail est constitué des axes X et Y, et que l’axe longitudinal est l’axe Z. Page 2 Chapitre: 9 CYCLESFIXES Section: ZONED’INFLUENCEDUCYCLE FIXE Z Z=-28 60 C 50 40 A 30 I=-14 D B E F 20 10 X 10 50 30 T1 M6 G00 G90 X0 Y0 Z60 G81 G99 G91 X15 Y25 Z-28 I-14 G98 G90 X25 G79 Z52 G99 X35 G98 X45 G79 Z32 G99 X55 G98 X65 M30 Z 70 ; Point de départ ; Définit un cycle de perçage. Exécute le perçage en A ; Exécute le perçage en B ; Modifie le plan de référence et la profondeur d’usinage ; Exécute le perçage en C ; Exécute le perçage en D ; Modifie le plan de référence et la profondeur d’usinage ; Exécute le perçage en E ; Exécute le perçage en F 60 C 50 D 40 30 A B E F 20 10 10 T1 M6 G00 G90 X0 Y0 Z60 G81 G99 X15 Y25 Z32 I18 G98 X25 G79 Z52 G99 X35 G98 X45 G79 Z32 G99 X55 G98 X65 M30 Chapitre: 9 CYCLESFIXES 30 50 X 70 ; Point de départ ; Définit le cycle de perçage. Exécute le perçage en A ; Exécute le perçage en B ; Modifie le plan de référence ; Exécute le perçage en C ; Exécute le perçage en D ; Modifie le plan de référence ; Exécute le perçage en E ; Exécute le perçage en F Section: ZONED’INFLUENCEDUCYCLE FIXE Page 3 9.3 ANNULATION DE CYCLE FIXE Un cycle fixe peut être annulé: - Par la fonction G80, qui peut être programmée dans n’importe quel bloc. - Par la définition d’un nouveau cycle fixe, qui annule et remplace tout autre cycle fixe actif. - Après l’exécution de M02, M30 ou après une URGENCE ou un RESET. - Par une recherche du zéro au moyen de la fonction G74. - Par sélection d’un nouveau plan de travail au moyen des fonctions G16, G17, G18 ou G19. Page 4 Chapitre: 9 CYCLESFIXES Section: ANNULATION DECYCLEFIXE 9.4 CONSIDERATIONS GENERALES 1.- Un cycle fixe peut être défini en tout point du programme, c’est-à-dire aussi bien dans le programme principal que dans une sous-routine. 2.- Les appels de sous-routines peuvent être effectués depuis un bloc placé sous l’influence d’un cycle fixe, sans impliquer l’annulation du cycle fixe. 3.- L’exécution d’un cycle fixe ne modifie pas l’historique des fonctions "G" antérieures. 4.- Le sens de rotation de la broche n’est pas non plus modifié. Il est possible d’entrer dans un cycle fixe quel que soit son sens de rotation (M03 ou M04), et d’en sortir suivant le même sens. En cas d’entrée dans un cycle fixe avec la broche à l’arrêt, elle démarrera dans le sens horaire (M03), et conservera ce sens après la fin du cycle. 5.- Si un facteur d’échelle doit être appliqué pendant le travail avec des cycles fixes, il est recommandé d’utiliser un facteur commun pour tous les axes concernés. 6.- L’exécution d’un cycle fixe annule la compensation de rayon (G41 et G42). Elle équivaut à G40. 7.- Pour appliquer la compensation de longueur d’outil (G43), on programmera cette fonction dans le même bloc ou dans le bloc précédant la définition du cycle fixe. Comme la CNC applique la compensation de longueur dès le début du déplacement de l’axe longitudinal, il est recommandé de positionner l’outil hors de la zone d’exécution du cycle fixe lorsque la fonction G43 est définie pour le cycle fixe. 8.- L’exécution de tout cycle fixe modifie la valeur du Paramètre Global P299. Chapitre: 9 CYCLESFIXES Section: CONSIDERATIONS GENERALES Page 5 9.5 CYCLES FIXES D’USINAGE Dans tous les cycles d’usinage, il existe trois coordonnées sur l’axe longitudinal, dont l’importance justifie une présentation détaillée: Coordonnée du plan de départ. Cette coordonnée est donnée par la position occupée par l’outil par rapport au zéro machine au moment de l’activation du cycle. Coordonnée du plan de référence. Elle est programmée dans le bloc de définition du cycle, et représente une coordonnée d’approche vers la pièce. Elle peut être programmée en absolu ou en incrémental; dans ce cas, elle est prise par rapport au plan de départ. Coordonnée de profondeur d’usinage. Elle est programmée dans le bloc de définition du cycle, en absolu ou en incrémental; dans ce cas, elle est prise par rapport au plan de référence. Deux fonctions permettent de sélectionner le retrait de l’axe longitudinal après l’usinage. G98 Sélectionne le retrait de l’outil jusqu’au plan de départ, après l’exécution de l’usinage indiqué. G99 Sélectionne le retrait de l’outil jusqu’au plan de référence, après l’exécution de l’usinage indiqué. Ces fonctions peuvent être utilisées dans le bloc de définition du cycle et dans les blocs se trouvant sous l’influence du cycle fixe. Le plan de départ correspond à la position occupée par l’outil au moment de la définition du cycle. La structure d’un bloc de définition de cycle fixe est la suivante: G** Point de départ Paramètres FSTDM N**** Le point de départ peut être programmé dans le bloc de définition de cycle fixe (à l’exception de l’axe longitudinal), en coordonnées polaires et en coordonnées cartésiennes. Après la définition du point où le cycle fixe doit être réalisé (optionnel), on définira la fonction et les paramètres correspondant au cycle fixe. Ensuite, on programmera si nécessaire les fonctions complémentaires F S T D M. Si un nombre de répétitions du bloc est programmé, la CNC répètera les positionnements programmés et les opérations d’usinage du cycle fixe le nombre de fois indiqué. Lorsque le “nombre de répétitions du bloc” (N) est programmé à la fin du bloc, la CNC exécute le déplacement programmé et l’opération d’usinage correspondant au cycle fixe actif le nombre de fois indiqué. Si un “nombre de répétitions” N0 est programmé, l’opération d’usinage correspondant au cycle fixe n’est pas exécuté. La CNC exécute seulement le déplacement programmé. Page 6 Chapitre: 9 CYCLESFIXES Section: Le fonctionnement général de tous les cycles est le suivant: * Si la broche était en marche, le sens de rotation est conservé. Si elle était à l’arrêt, elle démarrera à droite (M03). * Positionnement (s’il a été programmé) au point de départ du cycle programmé. * Déplacement, en rapide, de l’axe longitudinal du plan de départ au plan de référence. * Exécution du cycle d’usinage programmé. * Retrait, en rapide, de l’axe longitudinal jusqu’au plan de départ ou au plan de référence selon que G98 ou G99 a été programmé. Les cycles fixes d’usinage sont expliqués en détail dans les pages suivantes; dans tous ces exemples, le plan de travail est supposé être formé par les axes X et Y, et l’axe longitudinal est supposé être l’axe Z. Chapitre: 9 CYCLESFIXES Section: Page 7 9.5.1 G69. CYCLE FIXE DE PERÇAGE PROFOND A PAS VARIABLE Ce cycle exécute des passes de perçage successives jusqu’à ce que la coordonnée finale programmée soit atteinte. L’outil recule d’une valeur fixe après chaque perçage, et il est possible de décider que l’outil reculera jusqu’au plan de référence tous les J perçages. Il est également possible de programmer une temporisation après chaque perçage. Si on travaille en coordonnées cartésiennes, la structure de base du bloc est la suivante: G69 G98/G99 X Y Z I B C D H J K L R G00 G01 M03 M04 G98 G99 D I H C K K G98 Retrait de l’outil jusqu’au Plan de Départ, dès que le trou a été percé. G99 Retrait de l’outil jusqu’au Plan de Référence, dès que le trou a été percé. XY±5.5 Elles sont optionnelles et définissent le déplacement des axes du plan principal pour positionner l’outil sur le point d’usinage. Ce point pourra être programmé en coordonnées cartésiennes ou polaires, et les coordonnées pourront être absolues ou incrémentales selon que l’on travaille en G90 ou en G91. Z±5.5 Définit la coordonnée du plan de référence et peut être programmé en absolu ou en incrémental. Dans ce cas, il est référencé par rapport au plan de départ. S’il n’est pas programmé, la CNC prend comme plan de référence la position qu’occupe l’outil à cet instant. Page 8 Chapitre: 9 CYCLESFIXES Section: PERÇAGE PROFOND A PAS VARIABLE (G69) I±5.5 Définit la profondeur totale du perçage. Il pourra être programmé en absolu ou en incrémental. Dans ce cas, il est référencé par rapport au plan de référence. B5.5 Définit le pas de perçage selon l’axe longitudinal par rapport au plan principal. C5.5 Définit la distance de déplacement de l’axe longitudinal en avance rapide (G00) par rapport au pas de perçage précédent en approche vers la pièce pour exécuter une autre passe de perçage. Si ce paramètre n’est pas programmé, 1 mm est pris par défaut. Si une valeur 0 est programmée, la CNC affiche le message d’erreur correspondant. D5.5 Définit la distance entre le plan de référence et la surface de la pièce où le perçage doit être exécuté. Pour la première pénétration, cette valeur s’ajoute à la passe de perçage "B". Si ce paramètre n’est pas programmé, 0 est pris par défaut. H5.5 Distance de recul de l’axe longitudinal en rapide (G00) après chaque passe de perçage. Si ce paramètre n’est pas programmé, l’axe longitudinal retourne au plan de référence. Si une valeur 0 est programmée, la CNC affiche le message d’erreur correspondant. J4 Fixe le nombre de passes de perçage au-delà duquel l’outil retourne au plan de référence en G00. Il est possible de programmer une valeur de 0 à 9999. Si ce paramètre n’est pas programmé ou s’il est programmé avec une valeur 0, une valeur de 1 est prise par défaut: l’outil repassera au plan de référence après chaque passe de perçage. K5 Définit la temporisation en centièmes de seconde entre la fin de chaque passe de perçage et le début du retrait. Si ce paramètre n’est pas programmé, la CNC prendra la valeur K0. L5.5 Définit la valeur minimum que peut prendre la passe de perçage. Ce paramètre est utilisé avec des valeurs de R différentes de 1 mm. Si ce paramètre n’est pas programmé ou s’il est programmé avec une valeur 0, une valeur de 1 mm est prise par défaut. R5.5 Facteur réduisant la passe de perçage "B". Si ce paramètre n’est pas programmé ou s’il est programmé avec une valeur 0, une valeur de 1 est prise par défaut. Si R est égal à 1, toutes les passes de perçage seront identiques et de la valeur programmée "B". Si R n’est pas égal à 1, la première passe de perçage sera "B", la seconde "R B", la troisième "R (RB)", et ainsi de suite, c’est-à-dire qu’à partir de la seconde passe, la nouvelle passe sera le produit du facteur R par la passe précédente. Si une valeur de R autre que 1 est sélectionnée, la CNC n’autorise pas les passes inférieures à celles programmées en L. Chapitre: 9 CYCLESFIXES Section: PERÇAGE PROFOND A PAS VARIABLE (G69) Page 9 Fonctionnement de base: G98 J=3 G99 D B H C K RB H C K R(RB) C K R(RRB) H C K R(RRRB) K Page 10 Chapitre: 9 CYCLESFIXES Section: PERÇAGE PROFOND A PAS VARIABLE (G69) 1.- Si la broche était en marche, le sens de rotation est conservé. Si elle était à l’arrêt, elle démarrera à droite (M03). 2.- Déplacement, en rapide, de l’axe longitudinal du plan de départ au plan de référence. 3.- Première pénétration de perçage. Déplacement, en avance de travail, de l’axe longitudinal jusqu’à la profondeur incrémentale programmée en "B + D". 4.- Boucle de perçage. Les phases suivantes sont répétées jusqu’à ce que la coordonnée de profondeur de perçage programmée en I soit atteinte. 4.1.- Temporisation K en centièmes de seconde, si elle a été programmée. 4.2.- Recul de l’axe longitudinal en rapide (G00) jusqu’au plan de référence si le nombre de plongées programmées en J a été effectué. Dans le cas contraire, le recul s’effectue selon la distance programmée en "H". 4.3.- Approche de l’axe longitudinal en rapide (G00) jusqu’à une distance "C" de la passe de perçage précédente. 4.4.- Nouvelle passe de perçage. Déplacement de l’axe longitudinal en avance de travail (G01) jusqu’à la plongée incrémentale suivante selon "B et R". 5.- Temporisation K en centièmes de seconde, si elle a été programmée. 6.- Retrait, en avance rapide (G00), de l’axe longitudinal jusqu’au plan de départ ou au plan de référence, selon que G98 ou G99 a été programmé. Si un facteur d’échelle est appliqué à ce cycle, ne pas oublier que ce facteur n’affectera que les coordonnées du plan de référence et la profondeur de perçage. Par conséquent, et compte tenu du fait que le paramètre "D" n’est pas affecté par le facteur d’échelle, la coordonnée de surface de la pièce ne sera pas proportionnelle au cycle programmé. Exemple de programmation, en supposant que le plan de travail est celui formé par les axes X et Y, que l’axe longitudinal est l’axe Z et que le point de début est X0 Y0 Z0. T1 M6 G0 G90 X0 Y0 Z0 ..................................................... ; Point de début G69 G98 G91 X100 Y25 Z-98 I-52 B12 C2 D2 H5 J2 K150 L3 R0.8 F100 S500 M8 ...... ; Definition du cycle fixe G80 ............................................................................. ; Annulation du cycle fixe G90 X0 Y0 ................................................................. ; Positionnement M30 ............................................................................ ; Fin du programe Chapitre: 9 CYCLESFIXES Section: PERÇAGE PROFOND A PAS VARIABLE (G69) Page 11 9.5.2 G81. CYCLE FIXE DE PERÇAGE Ce cyle exécute un perçage au point indiqué, jusqu’à ce que la coordonnée finale programmée soit atteinte. Il est possible de programmer une temporisation en fond de trou. Si on travaille en coordonnées cartésiennes, la structure de base du bloc est la suivante: G81 G98/G99 X Y Z I K G98 Retrait de l’outil jusqu’au Plan de Départ, dès que le trou a été percé. G99 Retrait de l’outil jusqu’au Plan de Référence, dès que le trou a été percé. XY±5.5 Elles sont optionnelles et définissent le déplacement des axes du plan principal pour positionner l’outil sur le point d’usinage. Ce point pourra être programmé en coordonnées cartésiennes ou polaires, et les coordonnées pourront être absolues ou incrémentales selon que l’on travaille en G90 ou en G91. Z±5.5 Définit la coordonnée du plan de référence et peut être programmé en absolu ou en incrémental. Dans ce cas, il est référencé par rapport au plan de départ. S’il n’est pas programmé, la CNC prend comme plan de référence la position qu’occupe l’outil à cet instant. I±5.5 Définit la profondeur totale du perçage. Il pourra être programmé en absolu ou en incrémental. Dans ce cas, il est référencé par rapport au plan de référence. K5 Définit la temporisation en centièmes de seconde entre la fin de chaque passe de perçage et le début du retrait. Si ce paramètre n’est pas programmé, la CNC prendra la valeur K0. G00 G01 M03 M04 G98 G99 I K Page 12 Chapitre: 9 CYCLESFIXES Section: PERÇAGE(G81) Fonctionnement de base: 1.- Si la broche était en marche, le sens de rotation est conservé. Si elle était à l’arrêt, elle démarrera à droite (M03). 2.- Déplacement, en rapide, de l’axe longitudinal du plan de départ au plan de référence. 3.- Perçage du trou. Déplacement, en avance de travail, de l’axe longitudinal jusqu’au fond de trou programmé en I. 4.- Temporisation K en centièmes de seconde, si elle a été programmée. 5.- Retrait, en avance rapide (G00), de l’axe longitudinal jusqu’au plan de départ ou au plan de référence, selon que G98 ou G99 a été programmé. Exemple de programmation, en supposant que le plan de travail est le plan formé par les axes X et Y, que l’axe longitudinal est l’axe Z et que le point de départ est X0 Y0 Z0: T1 M6 G0 G90 X0 Y0 Z0 G81 G98 G00 G91 X250 Y350 Z-98 I-22 F100 S500 G93 I250 J250 Q-45 N3 G80 G90 X0 Y0 M30 Chapitre: 9 CYCLESFIXES ; Point de début ; Positionnement et définition de cycle fixe ; Définit l’origine des coordonnées polaires ; Rotation et cycle fixe 3 fois ; Annule le cycle fixe ; Positionnement ; Fin de programme Section: PERÇAGE(G81) Page 13 9.5.3 G82. CYCLE FIXE DE PERÇAGE AVEC TEMPORISATION Ce cyle exécute un perçage au point indiqué, jusqu’à ce que la coordonnée finale programmée soit atteinte. Ensuite, il applique une temporisation en fond de trou. Si on travaille en coordonnées cartésiennes, la structure de base du bloc est la suivante: G82 G98/G99 X Y Z I K G98 Retrait de l’outil jusqu’au Plan de Départ, dès que le trou a été percé. G99 Retrait de l’outil jusqu’au Plan de Référence, dès que le trou a été percé. XY±5.5 Elles sont optionnelles et définissent le déplacement des axes du plan principal pour positionner l’outil sur le point d’usinage. Ce point pourra être programmé en coordonnées cartésiennes ou polaires, et les coordonnées pourront être absolues ou incrémentales selon que l’on travaille en G90 ou en G91. Z±5.5 Définit la coordonnée du plan de référence et peut être programmé en absolu ou en incrémental. Dans ce cas, il est référencé par rapport au plan de départ. S’il n’est pas programmé, la CNC prend comme plan de référence la position qu’occupe l’outil à cet instant. I±5.5 Définit la profondeur totale du perçage. Il pourra être programmé en absolu ou en incrémental. Dans ce cas, il est référencé par rapport au plan de référence. K5 Définit la temporisation en centièmes de seconde entre la fin de chaque passe de perçage et le début du retrait. Sa définition est obligatoire; si aucune temporisation n’est désirée, on programmera K0. G00 G01 M03 M04 G98 G99 I K Page 14 Chapitre: 9 CYCLESFIXES Section: PERÇAGEAVEC TEMPORISATION (G82) Fonctionnement de base: 1.- Si la broche était en marche, le sens de rotation est conservé. Si elle était à l’arrêt, elle démarrera à droite (M03). 2.- Déplacement, en rapide, de l’axe longitudinal du plan de départ au plan de référence. 3.- Perçage du trou. Déplacement, en avance de travail, de l’axe longitudinal jusqu’au fond de trou programmé en I. 4.- Temporisation K en centièmes de seconde. 5.- Retrait, en avance rapide (G00), de l’axe longitudinal jusqu’au plan de départ ou au plan de référence, selon que G98 ou G99 a été programmé. Exemple de programmation, en supposant que le plan de travail est le plan formé par les axes X et Y, que l’axe longitudinal est l’axe Z et que le point de départ est X0 Y0 Z0: Y 500 150 100 50 X 50 100 150 500 Z=0 98 mm 2 mm 20 mm K=15 K=15 K=15 K=15 T1 M6 G0 G90 X0 Y0 Z0 G82 G99 G00 G91 X50 Y50 Z-98 I-22 K150 F100 S500 N3 G98 G90 G00 X500 Y500 G80 G90 X0 Y0 M30 Chapitre: 9 CYCLESFIXES Z ; Point de début ; 3 positionnements avec usinage ; Positionnement et cycle fixe ; Annule le cycle fixe ; Positionnement ; Fin de programme Section: PERÇAGEAVEC TEMPORISATION (G82) Page 15 9.5.4 G83. CYCLE FIXE DE PERCAGE PROFOND A PAS CONSTANT Ce cycle exécute des passes de perçage successives jusqu’à ce que la coordonnée finale programmée soit atteinte. L’outil recule jusqu’au plan de référence après chaque passe de perçage. Si on travaille en coordonnées cartésiennes, la structure de base du bloc est la suivante: G83 G98/G99 X Y Z I J G00 G01 M03 M04 G98 G99 I G98 Retrait de l’outil jusqu’au Plan de Départ, dès que le trou a été percé. G99 Retrait de l’outil jusqu’au Plan de Référence, dès que le trou a été percé. XY±5.5 Elles sont optionnelles et définissent le déplacement des axes du plan principal pour positionner l’outil sur le point d’usinage. Ce point pourra être programmé en coordonnées cartésiennes ou polaires, et les coordonnées pourront être absolues ou incrémentales selon que l’on travaille en G90 ou en G91. Z±5.5 Définit la coordonnée du plan de référence et peut être programmé en absolu ou en incrémental. Dans ce cas, il est référencé par rapport au plan de départ. S’il n’est pas programmé, la CNC prend comme plan de référence la position qu’occupe l’outil à cet instant. Page 16 Chapitre: 9 CYCLESFIXES Section: PERCAGE PROFOND A PAS CONSTANT (G83) I±5.5 Définit la valeur de chaque passe de perçage selon l’axe longitudinal. J4 Définit le nombre de passes de perçage. Il est possible de programmer une valeur comprise entre 1 et 9999. I 1 mm I 1 mm I Fonctionnement de base: 1.- Si la broche était en marche, le sens de rotation est conservé. Si elle était à l’arrêt, elle démarrera à droite (M03). 2.- Déplacement, en rapide, de l’axe longitudinal du plan de départ au plan de référence. 3.- Première pénétration de perçage. Déplacement, en avance de travail, de l’axe longitudinal jusqu’à la profondeur incrémentale programmée en "I". 4.- Boucle de perçage. Les passes suivantes se répéteront "J-1" fois, puisque la première pénétration programmée a été exécutée dans la passe précédente. 4.1.- Retrait, en avance rapide (G00), de l’axe longitudinal jusqu’au plan de référence. 4.2.- Approche de l’axe longitudinal, en rapide (G00), jusqu’à 1 mm. de la passe de perçage précédente. 4.3.- Nouvelle passe de perçage. Déplacement de l’axe longitudinal, en avance de travail (G01), de la profondeur incrémentale programmée en "I". 5.- Retrait, en avance rapide (G00), de l’axe longitudinal jusqu’au plan de départ ou au plan de référence, selon que G98 ou G99 a été programmé. Chapitre: 9 CYCLESFIXES Section: PERCAGE PROFOND A PAS CONSTANT (G83) Page 17 Si un facteur d’échelle est appliqué à ce cycle, le perçage sera proportionnel au perçage programmé avec le même pas "I" programmé, mais en faisant varier le nombre de passes "J". Exemple de programmation, en supposant que le plan de travail est le plan formé par les axes X et Y, que l’axe longitudinal est l’axe Z et que le point de départ est X0 Y0 Z0: T1 M6 G0 G90 X0 Y0 Z0 G83 G99 G00 G90 X50 Y50 Z-98 I-22 J3 F100 S500 M4 G98 G00 G91 X500 Y500 G80 G90 X0 Y0 M30 Page 18 Chapitre: 9 CYCLESFIXES ; Point de début ; Positionnement et définition de cycle fixe ; Positionnement et cycle fixe. ; Annule le cycle fixe ; Positionnemento ; Fin de programme Section: PERCAGE PROFOND A PAS CONSTANT (G83) 9.5.5 G84. CYCLE FIXE DE TARAUDAGE Ce cycle réalise un taraudage au point indiqué, jusqu’à ce que la coordonnée finale programmée soit atteinte. La sortie générale “TAPPING” (M5517) reste active pendant toute l’exécution de ce cycle. Etant donné que le taraud tourne dans les deux sens (un pour le taraudage, l’autre pour la sortie du filetage), le paramètre machine de broche "SREVM05" permet de définir si l’inversion du sens de rotation s’effectuera avec arrêt de broche intermédiaire ou directement. Une temporisation peut être programmée avant chaque inversion de broche, c’est-à-dire au fond du filetage et lors du retour au plan de référence. Si on travaille en coordonnées cartésiennes, la structure de base du bloc est la suivante: G84 G98/G99 X Y Z I K R G98 Retrait de l’outil jusqu’au Plan de Départ, dès que le trou a été taraudé. G99 Retrait de l’outil jusqu’au Plan de Référence, dès que le trou a été taraudé. XY±5.5 Elles sont optionnelles et définissent le déplacement des axes du plan principal pour positionner l’outil sur le point d’usinage. Ce point pourra être programmé en coordonnées cartésiennes ou polaires, et les coordonnées pourront être absolues ou incrémentales selon que l’on travaille en G90 ou en G91. Z±5.5 Définit la coordonnée du plan de référence et peut être programmé en absolu ou en incrémental. Dans ce cas, il est référencé par rapport au plan de départ. S’il n’est pas programmé, la CNC prend comme plan de référence la position qu’occupe l’outil à cet instant. I±5.5 Définit la profondeur du taraudage. Peut être programmé en absolu ou en incrémental. Dans ce cas, il est référencé par rapport au plan de référence. K5 Définit la temporisation en centièmes de seconde entre la fin de chaque passe de taraudage et le début du retrait. Si aucune temporisation n’est programmée, la CNC prendra la valeur K0. R Définit le type de taraudage à exécuter: "R0" programme un taraudage normal, alors que "R1" programme un taraudage rigide. Pour pouvoir exécuter un taraudage rigide, la broche doit être prête à travailler en boucle, c’est-à-dire disposer d’un moto-variateur et d’un codeur. Lorsqu’elle exécute un taraudage rigide, la CNC interpole le déplacement de l’axe avec la rotation de la broche. Exemple de programmation, en supposant que le plan de travail est le plan formé par les axes X et Y, que l’axe longitudinal est l’axe Z et que le point de départ est X0 Y0 Z0: Chapitre: 9 CYCLESFIXES Section: CYCLEFIXEDETARAUDAGE (G84) Page 19 G00 G01 M03 M04 G98 K G99 I K M04 M03 Fonctionnement de base: 1.- Si la broche était en marche, le sens de rotation est conservé. Si elle était à l’arrêt, elle démarrera à droite (M03). 2.- Déplacement, en rapide, de l’axe longitudinal du plan de départ au plan de référence. 3.- Déplacement de l’axe longitudinal et en avance de travail jusqu’au fond de la section usinée, avec taraudage du trou. Le cycle fixe exécutera ce déplacement et tous les suivants à 100% de l’avance F et de la vitesse S programmées. Si le taraudage rigide est sélectionné (paramètre R=1), la CNC active la sortie logique générale "RIGID" (M5521) pour indiquer au PLC qu’un bloc de taraudage rigide est en cours d’exécution. 4.- Arrêt de la broche (M05), qui n’est exécuté que si le paramètre machine de broche "SREVM05" est sélectionné et si une valeur autre que 0 a été affectée au paramètre “K”. 5.- Temporisation, si elle a été programmée dans le paramètre "K". 6.- Inversion du sens de rotation de la broche. 7.- Retrait, en avance de travail, de l’axe longitudinal jusqu’au plan de référence. Dès que cette coordonnéée est atteinte, le cycle fixe prend en compte les paramètres FEEDRATE OVERRIDE et SPINDLE OVERRIDE selectionnés. Si le taraudage rigide est sélectionné (paramètre R=1), la CNC active la sortie logique générale "RIGID" (M5521) pour indiquer au PLC qu’un bloc de taraudage rigide est en cours d’exécution. 8.- Arrêt de la broche (M05), qui n’est exécuté que si le paramètre machine de broche "SREVM05" est sélectionné. 9.- Temporisation, si elle a été programmée dans le paramètre "K". 10.- Inversion du sens de rotation de la broche, avec retour au sens initial. 11.- Retrait, en avance rapide (G00), de l’axe longitudinal jusqu’au plan de départ si G98 a été programmé. Page 20 Chapitre: 9 CYCLESFIXES Section: CYCLEFIXEDETARAUDAGE (G84) Y 500 150 100 50 X 50 100 150 500 Z=0 Z 98 mm 2 mm 20 mm K=15 K=15 K=15 T1 M6 G0 G90 X0 Y0 Z0 G84 G99 G00 G91 X50 Y50 Z-98 I-22 K150 F350 S500 N3 G98 G00 G90 X500 Y500 G80 G90 X0 Y0 M30 Chapitre: 9 CYCLESFIXES K=15 ; Point de début ; 3 positionnements avec usinage ; Positionnement et cycle fixe. ; Annule le cycle fixe ; Positionnement ; Fin de programme Section: CYCLEFIXEDETARAUDAGE (G84) Page 21 9.5.6 G85. CYCLE FIXE D’ALESAGE DE PRECISION Ce cycle exécute un alésage de précision au point indiqué jusqu’à ce que la coordonnée finale programmée soit atteinte. Il est possible de programmer une temporisation en fond de trou. Si on travaille en coordonnées cartésiennes, la structure de base du bloc est la suivante: G85 G98/G99 X Y Z I K G98 Retrait de l’outil jusqu’au Plan de Départ, dès que le trou a été alésé. G99 Retrait de l’outil jusqu’au Plan de Référence, dès que le trou a été alésé. XY±5.5 Elles sont optionnelles et définissent le déplacement des axes du plan principal pour positionner l’outil sur le point d’usinage. Ce point pourra être programmé en coordonnées cartésiennes ou polaires, et les coordonnées pourront être absolues ou incrémentales selon que l’on travaille en G90 ou en G91. Z±5.5 Définit la coordonnée du plan de référence et peut être programmé en absolu ou en incrémental. Dans ce cas, il est référencé par rapport au plan de départ. S’il n’est pas programmé, la CNC prend comme plan de référence la position qu’occupe l’outil à cet instant. I±5.5 Définit la profondeur de l’alésage. Peut être programmé en absolu ou en incrémental. Dans ce cas, il est référencé par rapport au plan de référence. K5 Définit la temporisation en centièmes de seconde entre la fin de chaque passe d’alésage et le début du retrait. Si aucune temporisation n’est programmée, la CNC prendra la valeur K0. G00 G01 M03 M04 G98 G99 I K Page 22 Chapitre: 9 CYCLESFIXES Section: ALESAGE DE PRECISION (G85) Fonctionnement de base: 1.- Si la broche était en marche, le sens de rotation est conservé. Si elle était à l’arrêt, elle démarrera à droite (M03). 2.- Déplacement, en rapide, de l’axe longitudinal du plan de départ au plan de référence. 3.- Déplacement de l’axe longitudinal et en avance de travail (G01) jusqu’au fond de la section usinée, avec alésage du trou. 4.- Temporisation, si elle a été programmée dans le paramètre "K". 5.- Retrait, en avance de travail, de l’axe longitudinal jusqu’au plan de référence. 6.- Retrait, en avance rapide (G00), de l’axe longitudinal jusqu’au plan de départ si G98 a été programmé. Exemple de programmation, en supposant que le plan de travail est celui formé par les axes X et Y, que l’axe longitudinal est l’axe Z et que le point de début est X0 Y0 Z0. T1 M6 G0 G90 X0 Y0 Z0 ......................................................... G85 G98 G91 X250 Y350 Z-98 I-22 F100 S500 .......... G80 ................................................................................. G90 X0 Y0 ..................................................................... M30 ................................................................................ Chapitre: 9 CYCLESFIXES ;Point de début ;Définition du cycle fixe ;Annulation du cycle fixe ;Positionnement ;Fin du programe Section: ALESAGE DE PRECISION (G85) Page 23 9.5.7 G86. CYCLE FIXE D’ALESAGE AVEC RETRAIT EN RAPIDE (G00) Ce cycle exécute un alésage au point indiqué jusqu’à ce que la coordonnée finale programmée soit atteinte. Il est possible de programmer une temporisation en fond de trou. Si on travaille en coordonnées cartésiennes, la structure de base du bloc est la suivante: G86 G98/G99 X Y Z I K G98 Retrait de l’outil jusqu’au Plan de Départ, dès que le trou a été alésé. G99 Retrait de l’outil jusqu’au Plan de Référence, dès que le trou a été alésé. XY±5.5 Elles sont optionnelles et définissent le déplacement des axes du plan principal pour positionner l’outil sur le point d’usinage. Ce point pourra être programmé en coordonnées cartésiennes ou polaires, et les coordonnées pourront être absolues ou incrémentales selon que l’on travaille en G90 ou en G91. Z±5.5 Définit la coordonnée du plan de référence et peut être programmé en absolu ou en incrémental. Dans ce cas, il est référencé par rapport au plan de départ. S’il n’est pas programmé, la CNC prend comme plan de référence la position qu’occupe l’outil à cet instant. I±5.5 Définit la profondeur de l’alésage. Peut être programmé en absolu ou en incrémental. Dans ce cas, il est référencé par rapport au plan de référence. K5 Définit la temporisation en centièmes de seconde entre la fin de chaque passe d’alésage et le début du retrait. Si aucune temporisation n’est programmée, la CNC prendra la valeur K0. G00 G01 M03 M04 M03 M04 G98 G99 I K M05 Page 24 Chapitre: 9 CYCLESFIXES Section: ALESAGEAVECRETRAITEN RAPIDE (G86) Fonctionnement de base: 1.- Si la broche était en marche, le sens de rotation est conservé. Si elle était à l’arrêt, elle démarrera à droite (M03). 2.- Déplacement, en rapide, de l’axe longitudinal du plan de départ au plan de référence. 3.- Déplacement de l’axe longitudinal et en avance de travail (G01) jusqu’au fond du trou, avec alésage. 4.- Arrêt de broche (M05). 5.- Temporisation, si elle a été programmée dans le paramètre "K". 6.- Retrait, en avance rapide (G00), de l’axe longitudinal jusqu’au plan de départ ou au plan de référence, selon que G98 ou G99 a été programmé. 7.- A la fin du retrait, la broche démarre dans le même sens que précédemment. Exemple de programmation, en supposant que le plan de travail est celui formé par les axes X et Y, que l’axe longitudinal est l’axe Z et que le point de début est X0 Y0 Z0. T1 M6 G0 G90 X0 Y0 Z0 ......................................................... G86 G98 G91 X250 Y350 Z-98 I-22 K20 F100 S500 .. G80 ................................................................................. G90 X0 Y0 ..................................................................... M30 ................................................................................ Chapitre: 9 CYCLESFIXES ;Point de début ;Définition du cycle fixe ;Annulation du cycle fixe ;Positionnement ;Fin du programe Section: ALESAGEAVECRETRAITEN RAPIDE (G86) Page 25 9.5.8 G87. CYCLE FIXE DE POCHE RECTANGULAIRE Ce cycle exécute une poche rectangulaire au point indiqué jusqu’à ce que la coordonnée finale programmée soit atteinte. Il permet de programmer, en plus de la passe et de l’avance de fraisage, une dernière passe de finition avec son avance de fraisage correspondante. Pour permettre d’obtenir un fini satisfaisant des parois de la poche, la CNC appliquera à chaque pénétration une entrée et une sortie tangentielles à la dernière passe de fraisage. Si on travaille en coordonnées cartésiennes, la structure de base du bloc est la suivante: G87 G98/G99 X Y Z I J K B C D H L G00 K G01(F) C L G01(H) J G99 D I G98 B G98 Retrait de l’outil jusqu’au Plan de Départ, dès que la poche a été exécutée. G99 Retrait de l’outil jusqu’au Plan de Référence, dès que la poche a été exécutée. XY±5.5 Elles sont optionnelles et définissent le déplacement des axes du plan principal pour positionner l’outil sur le point d’usinage. Ce point pourra être programmé en coordonnées cartésiennes ou polaires, et les coordonnées pourront être absolues ou incrémentales selon que l’on travaille en G90 ou en G91. Z±5.5 Définit la coordonnée du plan de référence. Si elle est programmée en absolu, elle est référencée par rapport au zéro pièce; si elle est programmée en incrémental, elle est référencée par rapport au plan de départ. Page 26 Chapitre: 9 CYCLESFIXES Section: POCHERECTANGULAIRE(G87) Si elle n’est pas programmée, la CNC prend comme plan de référence la position occupée par l’outil à cet instant. Autrement dit, les plans de départ (P.P.) et de référence (P.R.) seront identiques. I±5.5 Définit la profondeur de l’usinage. Si elle est programmée en absolu, elle est référencée par rapport au zéro pièce; si elle est programmée en incrémental, elle est référencée par rapport au plan de départ (P.P.). J±5.5 Définit la distance entre le centre et le bord de la poche suivant l’axe des abscisses. Le signe indique le sens de l’usinage de la poche. J J J avec signe "+" K5.5 J avec signe "-" Définit la distance entre le centre et le bord de la poche suivant l’axe des ordonnées. K Chapitre: 9 CYCLESFIXES Section: POCHERECTANGULAIRE(G87) Page 27 B±5.5 Définit le pas de pénétration selon l’axe longitudinal . - S’il est programmé avec un signe positif, l’ensemble du cycle est exécuté selon la même passe d’usinage, inférieure ou égale à la passe programmée. - S’il est programmé avec un signe négatif, la totalité de la poche est exécutée selon la passe prévue, à l’exception de la dernière, qui usinera la fin. B C±5.5 Définit le pas de fraisage selon le plan principal. - Si la valeur est positive, l’ensemble du cycle est exécuté selon le même pas de fraisage, inférieur ou égal au pas programmé. - Si la valeur est négative, la totalité de la poche est exécutée selon le pas prévu, sauf le dernier pas, qui usine le reste. C Si le pas n’est pas programmé, la valeur prise sera égale à 3/4 du diamètre de l’outil sélectionné. S’il est programmé avec une valeur supérieure au diamètre de l’outil, la CNC affiche l’erreur correspondante. S’il est programmé avec une valeur 0, la CNC affiche le message d’erreur correspondant. Page 28 Chapitre: 9 CYCLESFIXES Section: POCHERECTANGULAIRE(G87) D5.5 Définit la distance entre le plan de référence et la surface de la pièce, où sera exécutée la poche. Lors de la première pénétration, cette valeur s’ajoutera à la profondeur incrémentale "B". Si aucune valeur n’est programmée, la valeur 0 est prise par défaut. H.5.5 Définit l’avance de travail pendant la passe de finition. Si elle n’est pas programmée ou si elle est programmée avec une valeur 0, c’est la valeur de l’avance de travail en usinage qui sera prise en compte. L±5.5 Définit la valeur de la passe de finition, selon le plan principal. - Si la valeur est positive, la passe de finition est exécutée sur une arête vive (G07). - Si la valeur est négative, la passe de finition est exécutée sur un arrondi aux angles (G05). L Si la passe de finition n’est pas programmée ou si elle est programmée avec une valeur 0, elle n’est pas exécutée. Chapitre: 9 CYCLESFIXES Section: POCHERECTANGULAIRE(G87) Page 29 Fonctionnement de base: 1.- Si la broche était en marche, le sens de rotation est conservé. Si elle était à l’arrêt, elle démarrera à droite (M03). 2.- Déplacement, en rapide (G00), de l’axe longitudinal du plan de départ au plan de référence. 3.- Première pénétration. Déplacement de l’axe longitudinal à 50% de l’avance de travail (G01), jusqu’à la profondeur incrémentale programmée en "B + D". 4.- Fraisage, en avance de travail, de la surface de la poche suivant des pas définis par "C" jusqu’à une distance "L" (passe de finition), de la paroi de la poche. 5.- Fraisage de la passe de finition "L" selon l’avance de travail définie en "H". 6.- Dès la fin de la passe de finition, l’outil recule en avance rapide (G00) jusqu’au centre de la poche, et l’axe longitudinal s’écarte de 1 mm de la surface usinée. 1mm 7- Nouvelles surfaces de fraisage jusqu’à ce que la profondeur totale de la poche soit atteinte. - Déplacement de l’axe longitudinal à 50% de l’avance de travail, jusqu’à une distance "B" de la surface précédente. - Fraisage de la nouvelle surface comme indiqué aux points 4, 5 et 6. Page 30 Chapitre: 9 CYCLESFIXES Section: POCHERECTANGULAIRE(G87) 8.- Retrait, en avance rapide (G00), de l’axe longitudinal jusqu’au plan de départ ou au plan de référence, selon que G98 ou G99 a été programmé. G98 Z G99 D B I(G90) B 1mm I(G91) B 1mm 1mm Chapitre: 9 CYCLESFIXES Section: POCHERECTANGULAIRE(G87) Page 31 Exemple de programmation, en supposant que le plan de travail est le plan formé par les axes X et Y, que l’axe longitudinal est l’axe Z et que le point de départ est X0 Y0 Z0: Z Z=0 Z=48 D=2 D+B=14 B=12 B=12 X J Y K C 60 L 90 (TOR1=6) T1 D1 M6 G0 G90 X0 Y0 Z0 ................................................................... ; G87 G98 G00 G90 X90 Y60 Z-48 I-90 J52.5 K37.5 B12 C10 D2 H100 L5 F300 S1000 T1 D1 M03 ............. ; G80 ................................................................................. ; G90 X0 Y0 .............................................................................. ; M30 ................................................................................. ; Page 32 Chapitre: 9 CYCLESFIXES X Point de début Définition du cycle fixe Annulation du cycle fixe Positionnement Fin du programe Section: POCHERECTANGULAIRE(G87) Exemple de programmation, en supposant que le point de départ est X0 Y0 Z0: X Z (TOR1=6) T1 D1 M6 G0 G90 X0 Y0 Z0 .............................................................. ; Point de début G18 .................................................................................... ; Plan principal Z-X N10 G87 G98 G00 G90 X200 Y-48 Z0 I-90 J52.5 K37.5 B12 C10 D2 H100 L5 F300 ...................................................... ; Définition du cycle fixe N20 G73 Q45 ............................................................................ ; Rotation (RPT N10, N20) N7 ........................................................... ; 7 répétitions G80 .................................................................................... ; Annulation du cycle fixe G90 X0 Y0 ......................................................................... ; Positionnement M30 ................................................................................... ; Fin du programme Chapitre: 9 CYCLESFIXES Section: POCHERECTANGULAIRE(G87) Page 33 9.5.9 G88. CYCLE FIXE DE POCHE CIRCULAIRE Ce cycle exécute une poche circulaire au point indiqué jusqu’à ce que la coordonnée finale programmée soit atteinte. Il permet de programmer, en plus de la passe et de l’avance de fraisage, une dernière passe de finition avec son avance de fraisage correspondante. Si on travaille en coordonnées cartésiennes, la structure de base du bloc est la suivante: G88 G98/G99 X Y Z I J B C D H L J C G00 G01(F) G01(H) L G98 D I G99 B 1mm G98 Retrait de l’outil jusqu’au Plan de Départ, dès que la poche a été exécutée. G99 Retrait de l’outil jusqu’au Plan de Référence, dès que la poche a été exécutée. XY±5.5 Elles sont optionnelles et définissent le déplacement des axes du plan principal pour positionner l’outil sur le point d’usinage. Ce point pourra être programmé en coordonnées cartésiennes ou polaires, et les coordonnées pourront être absolues ou incrémentales selon que l’on travaille en G90 ou en G91. Page 34 Chapitre: 9 CYCLESFIXES Section: POCHECIRCULAIRE(G88) Z±5.5 Définit la coordonnée du plan de référence et peut être programmé en absolu ou en incrémental. Dans ce cas, il est référencé par rapport au plan de départ. S’il n’est pas programmé, la CNC prend comme plan de référence la position qu’occupe l’outil à cet instant. I±5.5 Définit la profondeur de l’usinage. Peut être programmé en absolu ou en incrémental. Dans ce cas, il est référencé par rapport au plan de référence. J±5.5 Définit le rayon de la poche. Le signe indique le sens d’usinage de la poche. J J J avec signe "+" B±5.5 J avec signe "-" Définit le pas de pénétration selon l’axe longitudinal par rapport au plan principal. - Si la valeur est positive, la totalité de la poche est exécutée avec un pas identique, inférieur ou égal au pas programmé. - Si la valeur est négative, la totalité de la poche est exécutée selon la passe fixée, sauf la dernière qui usine le reste. ............................................................................ B Chapitre: 9 CYCLESFIXES Section: Page POCHECIRCULAIRE(G88) 35 C±5.5 Définit le pas de fraisage selon le plan principal. - Si la valeur est positive, l’ensemble du cycle est exécuté selon le même pas de fraisage, inférieur ou égal au pas programmé. - Si la valeur est négative, la totalité de la poche est exécutée selon le pas prévu, sauf le dernier pas, qui usine le reste. C Si le pas n’est pas programmé, la valeur prise sera égale à 3/4 du diamètre de l’outil sélectionné. S’il est programmé avec une valeur supérieure au diamètre de l’outil, la CNC affiche l’erreur correspondante. S’il est programmé avec une valeur 0, la CNC affiche le message d’erreur correspondant. D5.5 Définit la distance entre le plan de référence et la surface de la pièce, où sera exécutée la poche. Lors de la première pénétration, cette valeur s’ajoutera à la profondeur incrémentale "B". Si aucune valeur n’est programmée, la valeur 0 est prise par défaut. D H5.5 Définit l’avance de travail pendant la passe de finition. Si elle n’est pas programmée ou si elle est programmée avec une valeur 0, c’est la valeur de l’avance de travail en usinage qui sera prise en compte. Page 36 Chapitre: 9 CYCLESFIXES Section: POCHECIRCULAIRE(G88) L5.5 Définit la valeur de la passe de finition, selon le plan principal. L Si la passe de finition n’est pas programmée ou si elle est programmée avec une valeur 0, elle n’est pas exécutée. Chapitre: 9 CYCLESFIXES Section: POCHECIRCULAIRE(G88) Page 37 G98 Z G99 D B I(G90) B 1mm I(G91) B 1mm 1mm J L Page 38 C Chapitre: 9 CYCLESFIXES Section: POCHECIRCULAIRE(G88) Fonctionnement de base: 1.- Si la broche était en marche, le sens de rotation est conservé. Si elle était à l’arrêt, elle démarrera à droite (M03). 2.- Déplacement, en rapide (G00), de l’axe longitudinal du plan de départ au plan de référence. 3.- Première pénétration. Déplacement de l’axe longitudinal à 50% de l’avance de travail (G01), jusqu’à la profondeur incrémentale programmée en "B + D". 4.- Fraisage, en avance de travail, de la surface de la poche suivant des pas définis par "C" jusqu’à une distance "L" (passe de finition), de la paroi de la poche. 5.- Fraisage de la passe de finition "L" selon l’avance de travail définie en "H". 6.- Dès la fin de la passe de finition, l’outil recule en avance rapide (G00) jusqu’au centre de la poche, et l’axe longitudinal s’écarte de 1 mm de la surface usinée. 1mm 7.- Nouvelles surfaces de fraisage jusqu’à ce que la profondeur totale de la poche soit atteinte. - Déplacement de l’axe longitudinal à 50% de l’avance de travail, jusqu’à une distance "B" de la surface précédente. - Fraisage de la nouvelle surface comme indiqué aux points 4, 5 et 6. 8.- Retrait, en avance rapide (G00), de l’axe longitudinal jusqu’au plan de départ ou au plan de référence, selon que G98 ou G99 a été programmé. Chapitre: 9 CYCLESFIXES Section: POCHECIRCULAIRE(G88) Page 39 Exemple de programmation, en supposant que le plan de travail est le plan formé par les axes X et Y, que l’axe longitudinal est l’axe Z et que le point de départ est X0 Y0 Z0: (TOR1=6) T1 D1 M6 G0 G90 X0 Y0 Z0 ........................................................................... G88 G98 G00 G90 X90 Y80 Z-48 I-90 J70 B12 C10 D2 H100 L5 F300 S1000 T1 D1 M03 .................................. G80 ............................................................................................... G90 X0 Y0 ...................................................................................... M30 ............................................................................................... Page 40 Chapitre: 9 CYCLESFIXES ; Point de début ; ; ; ; Définition du cycle fixe Annulation du cycle fixe Positionnement Fin du programe Section: POCHECIRCULAIRE(G88) 9.5.10 G89. CYCLE FIXE D’ALESAGE AVEC RETRAIT EN AVANCE DE TRAVAIL (G01) Ce cycle exécute un alésage au point indiqué jusqu’à ce que la coordonnée finale programmée soit atteinte. Il est possible de programmer une temporisation en fond de trou. Si on travaille en coordonnées cartésiennes, la structure de base du bloc est la suivante: G89 G98/G99 X Y Z I K G98 Retrait de l’outil jusqu’au Plan de Départ, dès que le trou a été alésé. G99 Retrait de l’outil jusqu’au Plan de Référence, dès que le trou a été alésé. XY±5.5 Elles sont optionnelles et définissent le déplacement des axes du plan principal pour positionner l’outil sur le point d’usinage. Ce point pourra être programmé en coordonnées cartésiennes ou polaires, et les coordonnées pourront être absolues ou incrémentales selon que l’on travaille en G90 ou en G91. Z±5.5 Définit la coordonnée du plan de référence et peut être programmé en absolu ou en incrémental. Dans ce cas, il est référencé par rapport au plan de départ. S’il n’est pas programmé, la CNC prend comme plan de référence la position qu’occupe l’outil à cet instant. I±5.5 Définit la profondeur de l’alésage. Peut être programmé en absolu ou en incrémental. Dans ce cas, il est référencé par rapport au plan de référence. K5 Définit la temporisation en centièmes de seconde entre la fin de l’lésage et le début du retrait. Si aucune temporisation n’est programmée, la CNC prendra la valeur K0. G00 G01 M03 M04 G98 G99 I K Chapitre: 9 CYCLESFIXES Section: Page ALESAGE AVEC RETRAIT EN AVANCE DE TRAVAIL (G89) 41 Fonctionnement de base: 1.- Si la broche était en marche, le sens de rotation est conservé. Si elle était à l’arrêt, elle démarrera à droite (M03). 2.- Déplacement, en rapide, de l’axe longitudinal du plan de départ au plan de référence. 3.- Déplacement de l’axe longitudinal et en avance de travail (G01) jusqu’au fond du trou, avec alésage. 4.- Arrêt de la broche (M05). 5.- Temporisation, si elle a été programmée dans le paramètre "K". 6.- Retrait, en avance de travail, de l’axe longitudinal jusqu’au plan de référence. 7.- Retrait, en avance rapide (G00), de l’axe longitudinal jusqu’au plan de départ si G98 a été programmé. 8.- A la fin du retrait, la broche démarre dans le même sens que précédemment. Exemple de programmation, en supposant que le plan de travail est celui formé par les axes X et Y, que l’axe longitudinal est l’axe Z et que le point de début est X0 Y0 Z0. T1 M6 G0 G90 X0 Y0 Z0 ......................................................... G89 G98 G91 X250 Y350 Z-98 I-22 K20 F100 S500 .. G80 ................................................................................. G90 X0 Y0 ..................................................................... M30 ................................................................................ Page 42 Chapitre: 9 CYCLESFIXES ;Point de début ;Définition du cycle fixe ;Annulation du cycle fixe ;Positionnement ;Fin du programe Section: ALESAGE AVEC RETRAIT EN AVANCE DE TRAVAIL (G89) 10. USINAGES MULTIPLES Sont définis comme Usinages Multiples une série de fonctions permettant de reproduire une opération d’usinage sur une trajectoire donnée. Le type d’usinage est sélectionné par le programmeur, et il peut s’agir d’un cycle fixe ou d’une sous-routine définie par l’utilisateur, et qui doit être programmée comme une sous-routine modale. Les trajectoires d’usinage sont définies par les fonctions suivantes: G60: usinage multiple sur une droite. G61: usinage multiple selon un parallélogramme. G62: usinage multiple selon une grille. G63: usinage multiple selon une circonférence. G64: usinage multiple selon un arc. G65: usinage programmé au moyen d’une corde d’arc. Ces fonctions peuvent être utilisées dans tout plan de travail, mais devront être définies à chaque utilisation, puisqu’elles ne sont pas modales. Il est indispensable que l’usinage à reproduire soit actif. En d’autres termes, ces fonctions n’ont un sens que si elles sont sous l’influence d’un cycle fixe ou d’une sousroutine modale. Pour exécuter un usinage multiple, procéder come suit: 1. Amener l’outil jusqu’au premier point où doit s’effectuer l’usinage multiple 2. Définir le cycle fixe ou le sous-programme modal à répéter à tous les points. 3. Définir l’usinage multiple à exécuter. Tous les usinages programmés grâce à ces fonctions sont exécutés dans les mêmes conditions de travail (T, D, F, S) que celles fixées lors de la définition du cycle fixe ou de la sous-routine modale. Après l’exécution de l’usinage multiple programmé, le programme retrouve les conditions qui étaient les siennes avant le début de l’usinage ci-dessus, et même le cycle fixe ou la sous-routine modale restent actifs. Dorénavant, l’avance F est celle programmée pour le cycle fixe ou la sous-routine modale. En outre, l’outil reste positionné sur le dernier point où a été exécuté l’usinage programmé. Si l’usinage multiple d’une sous-routine modale est exécuté en bloc à bloc, cette sousroutine est exécutée dans son ensemble (et non par blocs) après chaque déplacement programmé. Les usinages multiples sont expliqués en détail ci-dessous, le plan de travail étant supposé formé par les axes X et y dans tous les cas. Chapitre: 10 USINAGESMULTIPLES Section: Page 1 10.1 G60: USINAGE MULTIPLE SELON UNE DROITE Le format de programmation de ce cycle est le suivant: G60 A X I P Q R S T U V XK I K 4 3 I X 2 1 P0 A A (±5.5) Définit l’angle formé par la trajectoire d’usinage avec l’axe des abscisses. Il est exprimé en degrés et, s’il n’est pas programmé, la valeur A=0 est prise par défaut. X (5.5) Définit la longueur de la trajectoire d’usinage. I (5.5) Définit le pas entre usinages. K (5) Définit le nombre d’usinages total de la section, y compris celui du point de définition de l’usinage. Comme deux paramètres quelconques du groupe X I K suffisent pour définir l’usinage, la CNC permet les combinaisons de définition suivantes: XI, XK, IK. Cependant si le format XI est sélectionné, on prendra soin de définir un nombre entier d’usinages; dans le cas contraire, la CNC affiche le code d’erreur correspondant. Page 2 Chapitre: 10 USINAGESMULTIPLES Section: SELON UNE DROITE (G60) P,Q,R,S,T,U,V Ces paramètres sont optionnels et permettent d’indiquer sur quels points ou entre quels points programmés l’usinage ne doit pas être exécuté. Par exemple, la programmation de P7 indique que l’usinage ne doit pas être exécuté au point 7, tandis que la programmation de Q10.013 indique qu’aucun usinage ne doit être exécuté entre les points 10 à 13 ou, autrement dit, aux points 10, 11, 12 et 13. Si l’opérateur désire définir un groupe de points (Q10.013), il devra veiller à définir un point de fin au moyen de 3 chiffres car, s’il programme Q10.13, l’usinage multiple suppose Q10.130. Ces paramètres doivent être programmés dans l’ordre P Q R S T U V, et la numérotation des points affectés a chaque paramètre devra suivre la même règle, c’est-à-dire que la numérotation des points affectés à Q devra être supérieure à celle des points affectés à P et inférieure à celle des points affectés à R. Exemple: Programmation correcte Programmation incorrecte P5.006 Q12.015 R20.022 P5.006 Q20.022 R12.015 Si ces paramètres ne sont pas programmés, la CNC suppose que l’usinage doit être effectué sur tous les points de la trajectoire programmée. Fonctionnement de base: 1.- L’usinage multiple calcule le point suivant programmé sur lequel l’usinage doit être exécuté. 2.- Déplacement en avance rapide (G00) jusqu’à ce point. 3.- L’usinage multiple exécutera, après le déplacement, le cycle fixe ou la sousroutine modale sélectionnée. 4.- La CNC repète les phases 1-2-3 jusqu’à la fin de la trajectoire programmée. Après la fin de l’usinage multiple, l’outil reste positionné sur le dernier point de la trajectoire programmée sur lequel l’usinage a été exécuté. Chapitre: 10 USINAGESMULTIPLES Section: SELON UNE DROITE (G60) Page 3 Exemple de programmation, en supposant que le plan de travail est le plan formé par les axes X et Y, que l’axe longitudinal est l’axe Z et que le point de départ est X0 Y0 Z0: Y 1 2 3 4 5 6 7 8 9 10 11 12 300 X 200 G81 G98 G00 G91 X200 Y300 Z-8 I-22 F100 S500 G60 A30 X1200 I100 P2.003 Q6 R12 G80 G90 X0 Y0 M30 ; Positionnement et définition de cycle fixe ; Définit l’usinage multiple ; Annule le cycle fixe ; Positionnement ; Fin de programme Le bloc de définition d’usinage multiple peut également s’écrire comme suit: G60 A30 X1200 K13 P2.003 Q6 R12 G60 A30 I100 K13 P2.003 Q6 R12 Page 4 Chapitre: 10 USINAGESMULTIPLES Section: SELON UNE DROITE (G60) 10.2 G61: USINAGE MULTIPLE SELON UN PARALLELOGRAMME Le format de programmation de ce cycle est le suivant: G61 A B X I Y J P Q R S T U V XK YD I K JD Y 6 X 5 7 4 8 3 I 9 2 10 J 1 11 B A P0 A(±5.5) Définit l’angle formé par la trajectoire d’usinage et l’axe des abscisses. S’exprime en degrés et, s’il n’est pas programmé, la valeur A=0 est prise par défaut. B(±5.5) Définit l’angle formé par les deux trajectoires d’usinage. S’exprime en degrés et, s’il n’est pas programmé, la valeur B=90 est prise par défaut. X(5.5) Définit la longueur de la trajectoire d’usinage selon l’axe des abscisses. I (5.5) Définit le pas entre usinages selon l’axe des abscisses. K (5) Définit le nombre d’usinages total sur l’axe des abscisses, y compris celui du point de définition de l’usinage. Comme deux paramètres quelconques du groupe X I K suffisent pour définir l’usinage selon l’axe des abscisses, la CNC permet les combinaisons de définition suivantes: XI, XK, IK. Cependant si le format XI est sélectionné, on prendra soin de définir un nombre entier d’usinages; dans le cas contraire, la CNC affiche le code d’erreur correspondant. Y (5.5) Définit la longueur de la trajectoire d’usinage selon l’axe des ordonnées. J (5.5) Définit le pas entre usinages selon l’axe des ordonnées. Chapitre: 10 USINAGESMULTIPLES Section: SELONUN PARALLELOGRAMME(G61) Page 5 D (5) Définit le nombre d’usinages total sur l’axe des ordonnées, y compris celui du point de définition de l’usinage. Comme deux paramètres quelconques du groupe Y J D suffisent pour définir l’usinage selon l’axe des ordonnées, la CNC permet les combinaisons de définition suivantes: YJ, YD, JD. Cependant, si le format YJ est sélectionné, on prendra soin de définir un nombre entier d’usinages; dans le cas contraire, la CNC affiche le code d’erreur correspondant. P,Q,R,S,T,U,V Ces paramètres sont optionnels et permettent d’indiquer sur quels points ou entre quels points programmés l’usinage ne doit pas être exécuté. Par exemple, la programmation de P7 indique que l’usinage ne doit pas être exécuté au point 7, tandis que la programmation de Q10.013 indique qu’aucun usinage ne doit être exécuté entre les points 10 à 13 ou, autrement dit, aux points 10, 11, 12 et 13. Si l’opérateur désire définir un groupe de points (Q10.013), il devra veiller à définir un point de fin au moyen de 3 chiffres car, s’il programme Q10.13, l’usinage multiple suppose Q10.130. Ces paramètres doivent être programmés dans l’ordre P Q R S T U V, et la numérotation des points affectés a chaque paramètre devra suivre la même règle, c’est-à-dire que la numérotation des points affectés à Q devra être supérieure à celle des points affectés à P et inférieure à celle des points affectés à R. Exemple: Programmation correcte Programmation incorrecte P5.006 Q12.015 R20.022 P5.006 Q20.022 R12.015 Si ces paramètres ne sont pas programmés, la CNC suppose que l’usinage doit être effectué sur tous les points de la trajectoire programmée. Fonctionnement de base: 1.- L’usinage multiple calcule le point suivant programmé sur lequel l’usinage doit être exécuté. 2.- Déplacement en avance rapide (G00) jusqu’à ce point. 3.- L’usinage multiple exécutera, après le déplacement, le cycle fixe ou la sousroutine modale sélectionnée. 4.- La CNC repète les phases 1-2-3 jusqu’à la fin de la trajectoire programmée. Après la fin de l’usinage multiple, l’outil reste positionné sur le dernier point de la trajectoire programmée sur lequel l’usinage a été exécuté. Page 6 Chapitre: 10 USINAGESMULTIPLES Section: SELONUN PARALLELOGRAMME(G61) Exemple de programmation, en supposant que le plan de travail est le plan formé par les axes X et Y, que l’axe longitudinal est l’axe Z et que le point de départ est X0 Y0 Z0: Y 17 16 15 14 13 12 11 10 18 9 19 8 150 1 2 3 4 6 5 7 X 100 G81 G98 G00 G91 X100 Y150 Z-8 I-22 F100 S500 G61 X700 I100 Y180 J60 P2.005 Q9.011 G80 G90 X0 Y0 M30 ; Positionnement et définition de cycle fixe ; Définit l’usinage multiple ; Annule le cycle fixe ; Positionnement ; Fin de programme Le bloc de définition d’usinage multiple peut également s’écrire comme suit: G61 X700 K8 J60 D4 P2.005 Q9.011 G61 I100 K8 Y180 D4 P2.005 Q9.011 Chapitre: 10 USINAGESMULTIPLES Section: SELONUN PARALLELOGRAMME(G61) Page 7 10.3 G62: USINAGE MULTIPLE SELON UN GRILLE Le format de programmation de ce cycle est le suivant: G62 A B X I Y J P Q R S T U V XK YD I K JD 14 Y 13 5 X 12 6 4 11 7 I 10 J 3 8 9 2 1 B A P0 A(±5.5) Définit l’angle formé par la trajectoire d’usinage et l’axe des abscisses. S’exprime en degrés et, s’il n’est pas programmé, la valeur A=0 est prise par défaut. B(±5.5) Définit l’angle formé par les deux trajectoires d’usinage. S’exprime en degrés et, s’il n’est pas programmé, la valeur B=90 est prise par défaut. X(5.5) Définit la longueur de la trajectoire d’usinage selon l’axe des abscisses. I(5.5) Définit le pas entre usinages selon l’axe des abscisses. K(5) Définit le nombre d’usinages total sur l’axe des abscisses, y compris celui du point de définition de l’usinage. Comme deux paramètres quelconques du groupe X I K suffisent pour définir l’usinage selon l’axe des abscisses, la CNC permet les combinaisons de définition suivantes: XI, XK, IK. Cependant si le format XI est sélectionné, on prendra soin de définir un nombre entier d’usinages; dans le cas contraire, la CNC affiche le code d’erreur correspondant. Y(5.5) Définit la longueur de la trajectoire d’usinage selon l’axe des ordonnées. J(5.5) Définit le pas entre usinages selon l’axe des ordonnées. Page 8 Chapitre: 10 USINAGESMULTIPLES Section: SELON UN GRILLE (G62) D(5) Définit le nombre d’usinages total sur l’axe des ordonnées, y compris celui du point de définition de l’usinage. Comme deux paramètres quelconques du groupe Y J D suffisent pour définir l’usinage selon l’axe des ordonnées, la CNC permet les combinaisons de définition suivantes: YJ, YD, JD. Cependant, si le format YJ est sélectionné, on prendra soin de définir un nombre entier d’usinages; dans le cas contraire, la CNC affiche le code d’erreur correspondant. P,Q,R,S,T,U,V Ces paramètres sont optionnels et permettent d’indiquer sur quels points ou entre quels points programmés l’usinage ne doit pas être exécuté. Par exemple, la programmation de P7 indique que l’usinage ne doit pas être exécuté au point 7, tandis que la programmation de Q10.013 indique qu’aucun usinage ne doit être exécuté entre les points 10 à 13 ou, autrement dit, aux points 10, 11, 12 et 13. Si l’opérateur désire définir un groupe de points (Q10.013), il devra veiller à définir un point de fin au moyen de 3 chiffres car, s’il programme Q10.13, l’usinage multiple suppose Q10.130. Ces paramètres doivent être programmés dans l’ordre P Q R S T U V, et la numérotation des points affectés a chaque paramètre devra suivre la même règle, c’est-à-dire que la numérotation des points affectés à Q devra être supérieure à celle des points affectés à P et inférieure à celle des points affectés à R. Exemple: Programmation correcte Programmation incorrecte P5.006 Q12.015 R20.022 P5.006 Q20.022 R12.015 Si ces paramètres ne sont pas programmés, la CNC suppose que l’usinage doit être effectué sur tous les points de la trajectoire programmée. Fonctionnement de base: 1.- L’usinage multiple calcule le point suivant programmé sur lequel l’usinage doit être exécuté. 2.- Déplacement en avance rapide (G00) jusqu’à ce point. 3.- L’usinage multiple exécutera, après le déplacement, le cycle fixe ou la sousroutine modale sélectionnée. 4.- La CNC repète les phases 1-2-3 jusqu’à la fin de la trajectoire programmée. Après la fin de l’usinage multiple, l’outil reste positionné sur le dernier point de la trajectoire programmée sur lequel l’usinage a été exécuté. Chapitre: 10 USINAGESMULTIPLES Section: SELON UN GRILLE (G62) Page 9 Exemple de programmation, en supposant que le plan de travail est le plan formé par les axes X et Y, que l’axe longitudinal est l’axe Z et que le point de départ est X0 Y0 Z0: Y 30 29 28 27 16 17 18 19 20 15 14 13 12 11 2 3 31 26 25 21 22 24 23 10 9 8 5 6 7 150 1 4 X 100 G81 G98 G00 G91 X100 Y150 Z-8 I-22 F100 S500 ; Positionnement et définition de cycle fixe G62 X700 I100 Y180 J60 P2.005 Q9.011 R15.019 ; Définit l’usinage multiple G80 ; Annule le cycle fixe G90 X0 Y0 ; Positionnement M30 ; Fin de programme Le bloc de définition d’usinage multiple peut également s’écrire comme suit: G62 X700 K8 J60 D4 P2.005 Q9.011 R15.019 G62 I100 K8 Y180 D4 P2.005 Q9.011 R15.019 Page 10 Chapitre: 10 USINAGESMULTIPLES Section: SELON UN GRILLE (G62) 10.4 G63: USINAGE MULTIPLE SELON UNE CIRCONFERENCE Le format de programmation de ce cycle est le suivant: G63 X Y I CFPQRSTUV K 2 3 1 P0 I Y 7 4 6 5 X X (±5.5) Définit la distance entre le point de départ et le centre, selon l’axe des abscisses. Y (±5.5) Définit la distance entre le point de départ et le centre, selon l’axe des ordonnées. Les paramètres X et Y définissent le centre de la circonférence, comme le font I et J dans les interpolations circulaires (G02, G03). I (±5.5) Définit le pas angulaire entre les usinages. Lorsque le déplacement entre points s’effectue en G00 ou en G01, le signe indique le sens, soit”+” pour le sens anti-horaire et “-” pour le sens horaire. K (5) Définit le nombre d’usinages totaux sur la circonférence, y compris celui sur le point de définition de l’usinage. Il suffira de programmer I ou K dans le bloc de définition de l’usinage multiple. Toutefois, si K est programmé dans un usinage multiple dans lequel le déplacement entre les points s’effectue en G00 ou en G01, l’usinage est exécuté dans le sens anti-horaire. Chapitre: 10 USINAGESMULTIPLES Section: SELONUNECIRCONFERENCE (G63) Page 11 C Indique le mode de déplacement entre les points d’usinage. Si aucune valeur n’est programmée, la valeur C=0 est prise par défaut. C=0: C=1: C=2: C=3: F (5.5) Déplacement en avance rapide (G00). Déplacement en interpolation linéaire (G01). Déplacement en interpolation circulaire, sens horaire (G02). Déplacement en interpolation circulaire, sens anti-horaire (G03). Définit l’avance selon laquelle s’effectue le déplacement entre les points. Ce paramètre ne s’applique évidemment que pour des valeurs de "C" différentes de zéro. Si aucune valeur n’est programmée, c’est la valeur F0, qui correspond à l’avance maximum sélectionnée par le paramètre machine d’axess "MAXFEED" qui est prise par défaut. P,Q,R,S,T,U,V Ces paramètres sont optionnels et permettent d’indiquer sur quels points ou entre quels points programmés l’usinage ne doit pas être exécuté. Par exemple, la programmation de P7 indique que l’usinage ne doit pas être exécuté au point 7, tandis que la programmation de Q10.013 indique qu’aucun usinage ne doit être exécuté entre les points 10 à 13 ou, autrement dit, aux points 10, 11, 12 et 13. Si l’opérateur désire définir un groupe de points (Q10.013), il devra veiller à définir un point de fin au moyen de 3 chiffres car, s’il programme Q10.13, l’usinage multiple suppose Q10.130. Ces paramètres doivent être programmés dans l’ordre P Q R S T U V, et la numérotation des points affectés a chaque paramètre devra suivre la même règle, c’est-à-dire que la numérotation des points affectés à Q devra être supérieure à celle des points affectés à P et inférieure à celle des points affectés à R. Exemple: Programmation correcte Programmation incorrecte P5.006 Q12.015 R20.022 P5.006 Q20.022 R12.015 Si ces paramètres ne sont pas programmés, la CNC suppose que l’usinage doit être effectué sur tous les points de la trajectoire programmée. Page 12 Chapitre: 10 USINAGESMULTIPLES Section: SELONUNECIRCONFERENCE (G63) Fonctionnement de base: 1.- L’usinage multiple calcule le point suivant programmé sur lequel l’usinage doit être exécuté. 2.- Déplacement selon l’avance programmée par "C" (G00, G01, G02 ou G03) jusqu’au point ci-dessus. 3.- L’usinage multiple exécutera, après le déplacement, le cycle fixe ou la sousroutine modale sélectionnée. 4.- La CNC repète les phases 1-2-3 jusqu’à la fin de la trajectoire programmée. Après la fin de l’usinage multiple, l’outil reste positionné sur le dernier point de la trajectoire programmée sur lequel l’usinage a été exécuté. Exemple de programmation, en supposant que le plan de travail est le plan formé par les axes X et Y, que l’axe longitudinal est l’axe Z et que le point de départ est X0 Y0 Z0: Y 7 8 9 6 10 5 330 11 4 30 o 130 3 1 280 2 X 480 G81 G98 G01 G91 X280 Y130 Z-8 I-22 F100 S500 G63 X200 Y200 I30 C1 F200 P2.004 Q8 G80 G90 X0 Y0 M30 ; Positionnement et définition de cycle fixe ; Définit l’usinage multiple ; Annule le cycle fixe ; Positionnement ; Fin de programme Le bloc de définition d’usinage multiple peut également s’écrire comme suit: G63 X200 Y200 K12 C1 F200 P2.004 Q8 Chapitre: 10 USINAGESMULTIPLES Section: SELONUNECIRCONFERENCE (G63) Page 13 10.5 G64: USINAGE MULTIPLE SELON UN ARC Le format de programmation de ce cycle est le suivant: G64 X Y B I CFPQRSTUV K 2 3 1 B I P0 Y X X (±5.5) Définit la distance entre le point de départ et le centre, selon l’axe des abscisses. Y (±5.5) Définit la distance entre le point de départ et le centre, selon l’axe des ordonnées. Les paramètres X et Y définissent le centre de la circonférence, comme le font I et J dans les interpolations circulaires (G02, G03). B (5.5) Définit le déplacement angulaire de la trajectoire d’usinage et s’exprime en degrés. I (±5.5) Définit le pas angulaire entre les usinages. Lorsque le déplacement entre points s’effectue en G00 ou en G01, le signe indique le sens, soit”+” pour le sens anti-horaire et “-” pour le sens horaire. K (5) Définit le nombre d’usinages totaux sur la circonférence, y compris celui sur le point de définition de l’usinage. Il suffira de programmer I ou K dans le bloc de définition de l’usinage multiple. Toutefois, si K est programmé dans un usinage multiple dans lequel le déplacement entre les points s’effectue en G00 ou en G01, l’usinage est exécuté dans le sens anti-horaire. Page 14 Chapitre: 10 USINAGESMULTIPLES Section: SELON UN ARC (G64) C Indique le mode de déplacement entre les points d’usinage. Si aucune valeur n’est programmée, la valeur C=0 est prise par défaut. C=0: C=1: C=2: C=3: F (5.5) Déplacement en avance rapide (G00). Déplacement en interpolation linéaire (G01). Déplacement en interpolation circulaire, sens horaire (G02). Déplacement en interpolation circulaire, sens anti-horaire (G03). Définit l’avance selon laquelle s’effectue le déplacement entre les points. Ce paramètre ne s’applique évidemment que pour des valeurs de "C" différentes de zéro. Si aucune valeur n’est programmée, c’est la valeur F0, qui correspond à l’avance maximum sélectionnée par le paramètre machine d’axess "MAXFEED" qui est prise par défaut. P,Q,R,S,T,U,V Ces paramètres sont optionnels et permettent d’indiquer sur quels points ou entre quels points programmés l’usinage ne doit pas être exécuté. Par exemple, la programmation de P7 indique que l’usinage ne doit pas être exécuté au point 7, tandis que la programmation de Q10.013 indique qu’aucun usinage ne doit être exécuté entre les points 10 à 13 ou, autrement dit, aux points 10, 11, 12 et 13. Si l’opérateur désire définir un groupe de points (Q10.013), il devra veiller à définir un point de fin au moyen de 3 chiffres car, s’il programme Q10.13, l’usinage multiple suppose Q10.130. Ces paramètres doivent être programmés dans l’ordre P Q R S T U V, et la numérotation des points affectés a chaque paramètre devra suivre la même règle, c’est-à-dire que la numérotation des points affectés à Q devra être supérieure à celle des points affectés à P et inférieure à celle des points affectés à R. Exemple: Programmation correcte Programmation incorrecte P5.006 Q12.015 R20.022 P5.006 Q20.022 R12.015 Si ces paramètres ne sont pas programmés, la CNC suppose que l’usinage doit être effectué sur tous les points de la trajectoire programmée. Chapitre: 10 USINAGESMULTIPLES Section: SELON UN ARC (G64) Page 15 Fonctionnement de base: 1.- L’usinage multiple calcule le point suivant programmé sur lequel l’usinage doit être exécuté. 2.- Déplacement selon l’avance programmée par "C" (G00, G01, G02 ou G03) jusqu’au point ci-dessus. 3.- L’usinage multiple exécutera, après le déplacement, le cycle fixe ou la sousroutine modale sélectionnée. 4.- La CNC repète les phases 1-2-3 jusqu’à la fin de la trajectoire programmée. Après la fin de l’usinage multiple, l’outil reste positionné sur le dernier point de la trajectoire programmée sur lequel l’usinage a été exécuté. Exemple de programmation, en supposant que le plan de travail est le plan formé par les axes X et Y, que l’axe longitudinal est l’axe Z et que le point de départ est X0 Y0 Z0: Y 5 4 3 330 225 o 45 o 130 2 1 280 480 X G81 G98 G01 G91 X280 Y130 Z-8 I-22 F100 S500 ; Positionnement et définition de cycle fixe G64 X200 Y200 B225 I45 C3 F200 P2 ; Définit l’usinage multiple G80 ; Annule le cycle fixe G90 X0 Y0 ; Positionnement M30 ; Fin de programme Le bloc de définition d’usinage multiple peut également s’écrire comme suit: G64 X200 Y200 B225 K6 C3 F200 P2 Page 16 Chapitre: 10 USINAGESMULTIPLES Section: SELON UN ARC (G64) 10.6 G65: USINAGE PROGRAMME AU MOYEN D’UNE CORDE D’ARC Cette fonction permet d’exécuter l’usinage actif en un point programmé au moyen d’une corde d’arc. Un seul usinage est exécuté, dont le format de programmation est le suivant: G65 X Y A C F I I A Y P0 X X(±5.5) Définit la distance entre le point de départ et le centre, selon l’axe des abscisses. Y(±5.5) Définit la distance entre le point de départ et le centre, selon l’axe des ordonnées. Les paramètres X et Y définissent le centre de la circonférence, comme le font I et J dans les interpolations circulaires (G02, G03) A(±5.5) Définit l’angle formé par la médiatrice de la corde avec l’axe des abscisses, et s’exprime en degrés. I(±5.5) Définit la longueur de la corde. Si le déplacement s’effectue en G00, G01, le signe indique le sens: “+” = anti-horaire, “-” = horaire. C Indique le mode de déplacement entre les points d’usinage. Si aucune valeur n’est programmée, la valeur C=0 est prise par défaut. C=0: C=1: C=2: C=3: F(5.5) Déplacement en avance rapide (G00). Déplacement en interpolation linéaire (G01). Déplacement en interpolation circulaire, sens horaire (G02). Déplacement en interpolation circulaire, sens anti-horaire (G03). Définit l’avance selon laquelle s’effectue le déplacement entre les points. Ce paramètre ne s’applique évidemment que pour des valeurs de "C" différentes de zéro. Si aucune valeur n’est programmée, c’est la valeur F0, qui correspond à l’avance maximum sélectionnée par le paramètre machine d’axess "MAXFEED" qui est prise par défaut. Chapitre: 10 USINAGESMULTIPLES Section: AUMOYEND’UNECORDE D’ARC (G65) Page 17 Fonctionnement de base: 1.- L’usinage multiple calcule le point programmé sur lequel l’usinage doit être exécuté. 2.- Déplacement selon l’avance programmée par "C" (G00, G01, G02 ou G03) jusqu’au point ci-dessus. 3.- L’usinage multiple exécutera, après le déplacement, le cycle fixe ou la sousroutine modale sélectionnée. Après la fin de l’usinage multiple, l’outil reste positionné sur le point programmé. Exemple de programmation, en supposant que le plan de travail est le plan formé par les axes X et Y, que l’axe longitudinal est l’axe Z et que le point de départ est X0 Y0 Z0: 430 500 60 o 460 610 890 G81 G98 G01 G91 X890 Y500 Z-8 I-22 F100 S500 ; Positionnement et définition de cycle fixe G65 X-280 Y-40 A60 C1 F200 ; Définit l’usinage multiple G80 ; Annule le cycle fixe G90 X0 Y0 ; Positionnement M30 ; Fin de programme Le bloc de définition d’usinage multiple peut également s’écrire comme suit: G65 X-280 Y-40 I430 C1 F200 Page 18 Chapitre: 10 USINAGESMULTIPLES Section: AUMOYEND’UNECORDE D’ARC (G65) 11. CYCLE FIXE DE POCHE AVEC ILOTS Une poche se compose d’un contour ou profil extérieur (1) et d’une série de contours ou profils intérieurs (2). Ces derniers portent le nom d’ilôts. Ce cycle fixe de poches permet d’usiner des poches en 2D et en 3D. Poches en 2D (figure en haut à gauche) Les parois intérieures et extérieures sont verticales. La programmation est décrite en détail dans la première partie de ce chapitre. Pour définir les contours d’une poche en 2D, il est nécessaire de définir le profil dans le plan de tous les contours. Poches en 3D (figure en haut à droite) Ici, une ou plusieurs parois des profils intérieurs ou extérieurs et/ou des ilôts ne sont pas verticales. La programmation est décrite en détail dans la seconde partie de ce chapitre. Pour définir les contours d’une poche en 3D, il est nécessaire de définir le profil dans le plan (3) et le profil de profondeur (4) de tous les contours (même s’ils sont verticaux). La fonction d’appel de cycle fixe de poche quelconque en 2D ou en 3D est G66. L’usinage d’une poche peut comporter les opérations suivantes: Perçage avant usinage .............................................. Ebauche ...................................................................... Semi-finition ............................................................... Finition ........................................................................ Chapitre: 11 POCHES EN 2D ET 3D Poches Poches Poches Poches Section: en en en en 2D 2D 3D 2D seules et en 3D seules et en 3D Page 1 11.1 POCHES EN 2D La fonction G66 n’est pas modale, et doit donc être programmée chaque fois qu’une poche en 2D doit être exécutée. Dans un bloc contenant un cycle fixe de poche quelconque, aucune autre fonction ne doit être programmée; sa structure de définition est la suivante: G66 D R F S E D(0-9999) Définit le numéro d’étiquette du bloc dans lequel l’opération de perçage est programmée. Sa programmation est optionnelle. Si elle n’est pas programmée, l’opération n’a pas lieu. R(0-9999) Définit le numéro d’étiquette du bloc dans lequel l’opération d’ébauche est programmée. Sa programmation est optionnelle. Si elle n’est pas programmée, l’opération n’a pas lieu. F(0-9999) Définit le numéro d’étiquette du bloc dans lequel l’opération de finition est programmée. Sa programmation est optionnelle. Si elle n’est pas programmée, l’opération n’a pas lieu. S(0-9999) Définit le numéro d’étiquette du bloc dans lequel commence la description géométrique des profils composant la poche. E(0-9999) Définit le numéro d’étiquette du bloc dans lequel finit la description géométrique des profils composant la poche. Exemple de programmation: G00 G90 X100 Y200 Z50 F5000 T1 D2 M06 G66 D100 R200 F300 S400 E500 M30 ;Positionnement initial N100 G81 ......... N200 G67 ......... N300 G68 ......... N400 G0 G90 X300 Y50 Z3 ........ ........ N500 G2 G6 X300 Y50 I150 J0 ;Définit l’opération de perçage ;Définit l’opération d’ébauche ;Définit l’opération de finition ;Début de la description géométrique Page 2 ;Définition du cycle fixe de poche quelconque ;Fin du programme ;Fin de la description géométrique Chapitre: 11 POCHES EN 2D ET 3D Section: POCHES EN 2D Fonctionnement de base 1. Opération de perçage. Seulement si elle a été programmée. Après analyse de la géométrie de la poche à ilôts, du rayon de l’outil et de l’angle de la trajectoire programmée dans l’opération d’ébauche, la CNC calcule les coordonnées du point où l’opération de perçage choisie doit être exécutée. 2. Opération d’ébauche. Seulement si elle a été programmée. Elle se compose de plusieurs passes de fraisage de surface, jusqu’à ce que la profondeur programmée soit atteinte. Lors de chaque passe, on suivra les étapes suivantes en fonction du type d’usinage programmé. Cas A: Les trajectoires d’usinage sont linéaires et conservent un certain angle par rapport à l’axe des abscisses. * Exécution du contournage initial du profil extérieur de la pièce en premier. Si une opération de finition a été sélectionnée lors de l’appel du cycle, ce contournage est exécuté en laissant la surépaisseur programmée pour la finition. * Ensuite, le fraisage est exécuté selon l’avance et le pas programmés. Si, pendant le fraisage, un ilôt est atteint pour la première fois, son contournage est exécuté. Après le contournage de l’ilôt et pendant le reste des opérations, l’outil passe audessus des ilôts, son retrait s’effectue selon l’axe longitudinal jusqu’au plan de référence et l’usinage se poursuit dès l’achèvement de l’ilôt. Chapitre: 11 POCHES EN 2D ET 3D Section: POCHES EN 2D Page 3 Cas B: Les trajectoires d’usinage sont concentriques * L’ébauche s’effectue selon des trajectoires concentriques par rapport au profil. L’usinage est exécuté le plus rapidement possible en évitant (si possible) le passage au-dessus des ilôts. 3. Opération de finition. Seulement si elle a été programmée. Cette opération peut être exécutée en une ou plusieurs passes ainsi qu’en suivant les profils dans le sens programmé ou en sens contraire. La CNC usinera le profil extérieur et les ilôts selon des entrées et sorties tangentielles et avec une vitesse de coupe constante. Attention: Si la broche était à l’arrêt et si aucun sens de rotation n’a été programmé, elle tournera dans le sens horaire (M03). Dans le cycle fixe de poches avec ilôts, on rencontre quatre coordonnées le long de l’axe longitudinal (qui est normalement l’axe perpendiculaire au plan sélectionné par G15) dont l’importance mérite d’être détaillée ci-dessous: 1. Cote du plan de début. Cette cote est donnée par la position qu’occupe l’outil lors de l’appel du cycle. 2. Cote du plan de référence. Elle doit être programmée en absolu et représente une cote d’approche de la pièce. 3. Cote de la surface de la pièce. Elle est programmée en coordonnées absolues et dans le premier bloc de définition de profil. 4. Cote de profondeur d’usinage. Elle est programmée en coordonnées absolues. Conditions après la fin du cycle A la fin du cycle fixe, l’avance active est la dernière avance programmée, celle correspondant à l’opération d’ébauche ou de finition. De même, la CNC prend en compte les fonctions G00, G07, G40 et G90. Page 4 Chapitre: 11 POCHES EN 2D ET 3D Section: POCHES EN 2D 11.1.1 OPERATION DE PERCAGE Cette opération est optionnelle, et ne peut être exécutée par la CNC que si une ébauche est également programmée. Elle est utilisée principalement lorsque l’outil programmé dans l’opération d’ébauche n’exécute pas l’usinage selon l’axe longitudinal, et elle permet l’accès de cet outil à la surface à ébaucher. Elle sera programmée dans un bloc qui devra porter un numéro d’étiquette permettant d’indiquer au cycle fixe le bloc dans lequel l’opération de perçage est définie. Exemple: G66 D100 R200 F300 S400 E500 N100 G81 ....... ; Définition du cycle de poche quelconque avec ilôts ; Définition de l’opération de perçage Les cycles fixes de perçage programmables sont: - G69 - G81 - G82 - G83 Cycle fixe de perçage profond selon un pas variable. Cycle fixe de perçage. Cycle fixe de perçage avec temporisation. Cycle fixe de perçage profond selon un pas constant. Lors de la définition de l’opération de perçage, les paramètres de définition correspondant à la fonction désirée devront être programmés avec cette fonction. Aucun point de positionnement (X, Y) n’est à définir car c’est le cycle fixe lui-même qui calculera, en fonction du profil programmé et de l’angle d’ébauche de l’usinage, la cote du ou des points où le perçage sera exécuté. Après les paramètres de définition, il est possible de programmer les fonctions auxiliaires F S T D M si besoin. Aucune fonction M ne peut être programmée si un sous-programme lui est associé. Dans ce bloc, il est possible de programmer la fonction M06 de changement d’outil, à la condition qu’aucune sous-routine ne lui soit associée. Dans le cas contraire, l’outil de perçage doit être sélectionné avant d’appeler ce cycle. Exemples: N100 G69 G98 G91 Z-4 I-90 B1.5 C0.5 D2 H2 J4 K100 F500 S3000 M3 N120 G81 G99 G91 Z-5 I-30 F400 S2000 T3 D3 M3 N220 G82 G99 G91 Z-5 I-30 K100 F400 S2000 T2 D2 M6 N200 G83 G98 G91 Z-4 I-5 J6 T2 D4 Chapitre: 11 POCHES EN 2D ET 3D Section: POCHES EN 2D (PERCAGE) Page 5 11.1.2 OPERATION D’EBAUCHE Il s’agit de l’opération principale de l’usinage de poches avec ilôts, dont la programmation est optionnelle. Pendant cette opération, le travail sélectionné, soit en arête vive (G07) soit avec arrondi aux angles (G05) est conservé. Toutefois, le cycle fixe affectera le format G07 aux déplacements nécessaires. Elle sera programmée dans un bloc qui devra porter un numéro d’étiquette permettant d’indiquer au cycle fixe le bloc dans lequel l’opération d’ébauche est définie. Exemple: G66 D100 R200 F300 S400 E500 N200 G67 ....... ; Définition du cycle de poche quelconque avec ilôts ; Définition de l’opération d’ébauche L’ébauche est définie par la fonction G67 et son format de programmation est le suivant: G67 A B C I R K F S T D M A (±5.5) Définit l’angle formé par la trajectoire d’ébauche avec l’axe des abscisses. A Si le paramètre “A” n’est pas programmé, l’ébauche est exécutée selon des trajectoires concentriques au profil. L’usinage s’effectue le plus rapidement possible en évitant de passer au-dessus des ilôts. Page 6 Chapitre: 11 POCHES EN 2D ET 3D Section: POCHES EN 2D (EBAUCHE) B (±5.5) Définit la passe d’usinage selon l’axe longitudinal (profondeur de passe d’ébauche). Sa définition est obligatoire, et il doit être programmé avec une valeur différente de 0; dans le cas contraire, l’opération d’ébauche est annulée. - S’il est programmé avec un signe positif, la totalité de l’ébauche est exécutée avec le même pas d’usinage, le cycle fixe calculant une passe inférieure ou égale à la passe programmée. - S’il est programmé avec un signe négatif, la totalité de l’ébauche est exécutée selon la passe programmée, le cycle fixe ajustant la dernière passe de façon à atteindre la profondeur totale programmée. C(_5.5) Définit la passe de fraisage en ébauche selon le plan principal, la totalité de la poche étant exécutée suivant la passe définie, et le cycle fixe ajuste la dernière passe de fraisage. Si elle n’est pas programmée ou si elle est programmée avec une valeur “0”, une valeur égale à _ du diamètre de l’outil sélectionné est prise par défaut. Si elle est programmée avec une valeur supérieure au diamètre de l’outil, la CNC émet l’erreur correspondante. I(_5.5) Définit la profondeur totale de la poche; elle est programmée en coordonnées absolues. Sa programmation est obligatoire. R (±5.5) Définit la coordonnée du plan de référence, en absolu. Sa programmation est obligatoire. R Chapitre: 11 POCHES EN 2D ET 3D Section: POCHES EN 2D (EBAUCHE) Page 7 K (1) Définit le type d’intersection de profils désiré. 0 = Intersection de profils de base. 1 = Intersection de profils évoluée. S’il n’est pas programmé, la valeur “0” est prise par défaut. Les deux types d’intersection sont décrits en détail plus loin. T (4) Définit l’outil utilisé pour l’opération d’ébauche. Sa programmation est obligatoire. Dans le même bloc, il est possible de programmer les fonctions auxiliaires F S D et jusqu’à 7 fonctions auxiliaires M. Cette opération permet de définir M06 avec une sous-routine associée, le changement d’outil indiqué s’effectuant avant le début de l’opération d’ébauche. Page 8 Chapitre: 11 POCHES EN 2D ET 3D Section: POCHES EN 2D (EBAUCHE) 11.1.3 OPERATION DE FINITION Cette opération est la dernière de l’usinage d’une poche quelconque, et sa programmation est optionnelle. Elle sera programmée dans un bloc qui devra porter un numéro d’étiquette permettant d’indiquer au cycle fixe le bloc dans lequel l’opération de finition est définie. Exemple: G66 D100 R200 F300 S400 E500 N300 G68 ....... ; Définition du cycle de poche quelconque avec ilôts ; Définition de l’opération de finition La finition est définie par la fonction G68 et son format de programmation est le suivant: G68 B L Q I R K F S T D M B (±5.5) Définit la passe d’usinage selon l’axe longitudinal (profondeur de passe de finition). - S’il n’est pas programmé ou s’il est programmé avec une valeur 0, la CNC exécutera une passe de finition unique de la profondeur totale de la poche. - S’il est programmé avec un signe positif, la totalité de la finition est exécutée avec le même pas d’usinage, le cycle fixe calculant une passe inférieure ou égale à la passe programmée. - S’il est programmé avec un signe négatif, la totalité de la finition est exécutée selon la passe programmée, le cycle fixe ajustant la dernière passe de façon à atteindre la profondeur totale programmée. L (±5.5) Définit la surépaisseur dont disposent les parois latérales de la poche avant le début de l’opération de finition. - Si une valeur positive est programmée, la passe de finition est exécutée en G7 (arête vive). Chapitre: 11 POCHES EN 2D ET 3D Section: POCHES EN 2D (FINITION) Page 9 - Si une valeur négative est programmée, la passe de finition est exécutée en G5 (arrondi aux angles). - S’il n’est pas programmé ou s’il est programmé avec une valeur 0, le cycle n’exécute pas la passe de finition. Q Indique le sens de la passe de finition. - S’il est programmé avec une valeur de 1, la passe de finition est exécutée dans le sens opposé à celui programmé pour le profil extérieur. - S’il n’est pas programmé ou s’il est programmé avec une valeur différente de 1, la passe de finition est exécutée dans le même sens que celui programmé pour le profil extérieur. I (±5.5) Définit la profondeur totale de la poche; il est programmé en absolu. - Si la poche comporte une opération d’ébauche, il est inutile de définir ce paramètre, car il est programmé dans cette opération. Toutefois, s’il est programmé dans les deux opérations, le cycle fixe prendra en compte la profondeur indiquée dans chaque opération. - Si la poche ne comporte pas d’opération d’ébauche, ce paramètre doit être défini. R (±5.5) Définit la coordonnée du plan de référence; il est programmé en absolu. - Si la poche comporte une opération d’ébauche, il est inutile de définir ce paramètre, car il est programmé dans cette opération. Toutefois, s’il est programmé dans les deux opérations, le cycle fixe prendra en compte la profondeur indiquée dans chaque opération. - Si la poche ne comporte pas d’opération d’ébauche, ce paramètre doit être défini. R K (1) Définit le type d’intersection de profils désiré. 0 = Intersection de profils de base. 1 = Intersection de profils évoluée. Page 10 Chapitre: 11 POCHES EN 2D ET 3D Section: POCHES EN 2D (FINITION) Si la poche comporte une opération d’ébauche, il est inutile de définir ce paramètre, car il est programmé dans cette opération. Toutefois, s’il est programmé dans les deux opérations, le cycle fixe prendra en compte le type d’intersection défini dans l’opération d’ébauche. Si l’opération d’ébauche n’a pas été définie et si ce paramètre n’est pas programmé, le cycle fixe prendra en compte la valeur K0 par défaut. Les deux types d’intersection sont définis plus loin. T (4) Définit l’outil utilisé pour la finition. Sa programmation est obligatoire. Dans le même bloc, il est possible de programmer les fonctions auxiliaires F S D et jusqu’à 7 fonctions auxiliaires M. Cette opération permet de définir M06 avec une sous-routine associée, le changement d’outil indiqué s’effectuant avant le début de l’opération de finition. Chapitre: 11 POCHES EN 2D ET 3D Section: POCHES EN 2D (FINITION) Page 11 11.1.4 REGLES DE PROGRAMMATION DES PROFILS La programmation des profils extérieurs et intérieurs d’une poche avec ilôts doit respecter les règles suivantes de programmation: 1.- Tous les types de profils programmés doivent être fermés. Les exemples suivants entraînent une erreur de géométrie. 2.- Un profil ne doit pas se recouper. mismo. Les exemples suivants entraînent une erreur de géométrie. 3.- Lorsque plusieurs profils extérieurs sont programmés, le cycle fixe prend en compte celui occupant la plus grande surface. 4.- La programmation de profils intérieurs n’est pas obligatoire. S’ils sont programmés, ils doivent être partiellement ou totalement intérieurs au profil extérieur. Quelques exemples sont présentés ci-dessous. 5.- La définition d’un profil intérieur compris en entier dans un autre profil intérieur est interdite. Dans ce cas, seul le profil le plus à l’extérieur sera pris en considération. Le cycle fixe vérifie toutes ces règles avant de commencer l’exécution de la poche, adapte le profil de la poche en fonction de ces règles et visualise les messages d’erreur en cas de besoin. Page 12 Chapitre: 11 POCHES EN 2D ET 3D Section: POCHES EN 2D (PROFILS) 11.1.5 INTERSECTION DE PROFILS Afin de faciliter la programmation des profils, le cycle fixe permet l’intersection des profils intérieurs entre eux, et entre eux et le profil extérieur. Il est possible de sélectionner deux types d’intersection grâce au paramètre “K”. 11.1.5.1 INTERSECTION DE PROFILS DE BASE (K=0) Lorsque ce type est sélectionné, les règles suivantes d’intersection de profils sont adoptées: 1.- L’intersection de profils intérieurs génère un nouveau profil intérieur, qui constitue leur union Booléenne. Exemple: 2.- L’intersection entre un profil intérieur et un profil extérieur génère un nouveau profil extérieur, qui est le résultat de la différence entre le profil extérieur et le profil intérieur. Exemple: 3.- Si un profil intérieur présente une intersection avec un autre profil intérieur et le profil extérieur, le cycle fixe réalise d’abord l’intersection entre les profils intérieurs, puis l’intersection avec le profil extérieur. 4.- Le résultat de l’intersection des profils intérieurs avec le profil extérieur est une poche unique, qui correspond à celle dont le profil extérieur présente la plus grande surface. Les autres seront ignorées. 5.- Si l’opération de finition a été programmée, le profil de la poche résultante devra respecter toutes les règles de compensation d’outil, car si un profil impossible à usiner par l’outil de finition programmé est programmé, la CNC affiche le code d’erreur correspondant. Chapitre: 11 POCHES EN 2D ET 3D Section: POCHES EN 2D (PROFILS) Page 13 11.1.5.2 INTERSECTION DE PROFILS EVOLUEE (K=1) Lorsque ce type est sélectionné, les règles suivantes d’intersection de profils sont adoptées: 1.- Le point de départ de chaque contour détermine la section de contour à sélectionner. Dans une intersection de profils, chaque contour est divisé en plusieurs lignes pouvant être regroupées en tant que: - Lignes extérieures à l’autre contour - Lignes intérieures à l’autre contour Ce type d’intersection de profils sélectionne dans chaque contour le groupe de lignes incluant le point de définition du profil. L’exemple suivant montre le processus de sélection exposé, dans lequel les traits pleins représentent les lignes extérieures à l’autre contour, et les pointillés les lignes intérieures. Le point de départ de chaque contour est indiqué par le signe “x”. Exemples d’intersection de profils: Addition Booléenne Soustraction Booléenne Page 14 Chapitre: 11 POCHES EN 2D ET 3D Section: POCHES EN 2D (PROFILS) Intersection Booléenne 2.- L’ordre de programmation des différents profils est déterminant dans le cas de l’intersection de 3 profils ou plus. Le processus d’intersection des profils s’exécute selon l’ordre dans lequel les profils ont été programmés. De cette façon, après l’intersection des deux premiers profils programmés, l’intersection entre le profil résultant des deux premiers et le troisième a lieu et ainsi de suite. Le point de départ des profils résultants coïncide toujours avec le point de départ utilisé pour la définition du premier profil. Exemples: Chapitre: 11 POCHES EN 2D ET 3D Section: POCHES EN 2D (PROFILS) Page 15 11.1.5.3 PROFIL RESULTANT Après l’obtention des profils de la poche et des ilôts, le cycle fixe calcule les décalages correspondant aux profils résultants, en fonction du rayon de l’outil d’ébauche à utiliser et de la surépaisseur programmée. Au cours de ce processus, il est possible que des intersections n’apparaissant pas dans les profils programmés soient obtenues. Exemple: S’il existe une zone ne permettant pas le passage de l’outil d’ébauche, plusieurs poches seront produites du fait de l’intersection entre les décalages des profils, et toutes ces poches seront usinées. Exemple: Page 16 Chapitre: 11 POCHES EN 2D ET 3D Section: POCHES EN 2D (PROFILS) 11.1.6 SYNTAXE DE LA PROGRAMMATION DE PROFILS Le profil extérieur et les profils intérieurs ou ilôts programmés doivent être définis par des éléments géométriques simples (segments de droites et arcs). Le premier bloc de définition (où commence le premier profil) et le dernier (où se termine le dernier profil défini) devront comporter un numéro d’étiquette de bloc. Ces numéros d’étiquette indiquent au cycle fixe le début et la fin de la description géométrique des profils composant la poche. Exemple: G66 D100 R200 F300 S400 E500 ; Définition du cycle de poche quelconque avec ilôts N400 G0 G90 X300 Y50 Z3 ; Début de la description géométrique ——— —— —— —N500 G2 G6 X300 Y50 I150 J0 ; Fin de la description géométrique La syntaxe de programmation de profils doit répondre aux normes suivantes: 1.- Le premier profil doit commencer dans le premier bloc de définition de la description géométrique des profils de la pièce. Un numéro d’étiquette est affecté à ce bloc, afin d’indiquer au cycle fixe G66 le début de la description géométrique. 2.- La coordonnée de la surface de la pièce sera également programmée dans ce bloc. 3.- Tous les profils désirés peuvent être programmés l’un après l’autre; chacun doit commencer dans un bloc contenant la fonction G00 (indicatif de début du profil). Attention: On prendra soin de programmer G01, G02 ou G03 dans le bloc suivant celui où est défini le début car G00 est modal; on évite ainsi que la CNC interprète les blocs suivants comme le début d’un nouveau profil. 4.- Lorsque la définition des profils est terminée, un numéro d’étiquette doit être affecté au dernier bloc programmé, afin d’indiquer au cycle fixe G66 la fin de la description géométrique. Exemple: G0 G17 G90 X-350 Y0 Z50 G66 D100 R200 F300 S400 E500 G0 G90 X0 Y0 Z50 M30 N400 G0 X-260 Y-190 Z4.5 .......... .......... G0 X230 Y170 G1........ ......... G0 X-120 Y90 G2........ .......... N500 G1 X-120 Y90 Chapitre: 11 POCHES EN 2D ET 3D ; Description du cycle ; Début du premier profil ; Début d’un autre profil ; Début d’un autre profil ; Fin de la description géométrique Section: POCHES EN 2D (PROFILS) Page 17 5.- Les profils sont décrits comme des trajectoires programmées, qui peuvent comporter des arrondis, des chanfreins, etc... et qui doivent être programmées selon les règles de syntaxe définies. 6.- Dans la description de profils, la programmation d’images-miroir, de changements d’échelle, de rotation du système de coordonnées, de décalages d’origine, etc... est interdite. 7.- Il est également interdit de programmer des blocs en langage évolué tels que sauts, appels de sous-programmes ou programmation paramétrée. 8.- La programmation d’autres cycles fixes n’est pas autorisée. En plus de la fonction G00, qui a une signification spéciale, le cycle fixe de poche avec ilôts permet, pour la définition des profils, l’utilisation des fonctions suivantes: G01 G02 G03 G06 G08 G09 G36 G39 G53 G70 G71 G90 G91 G93 Page 18 Interpolation linéaire Interpolation circulaire à droite Interpolation circulaire à gauche Centre de circonférence en coordonnées absolues Circonférence tangente à la trajectoire précédente Circonférence par trois points Arrondi aux angles Chanfrein Programmation par rapport au zéro machine Programmation en pouces Programmation en millimètres Programmation absolue Programmation incrémentale Présélection de l’origine polaire Chapitre: 11 POCHES EN 2D ET 3D Section: POCHES EN 2D (PROFILS) 11.1.7 ERREURS Le cycle fixe pourra visualiser les erreurs suivantes: ERREUR 1023: G67. Rayon d’outil excessif Un outil d’ébauche incorrect a été sélectionné. ERREUR 1024: G68. Rayon d’outil excessif Un outil de finition incorrect a été sélectionné. ERREUR 1025: Un outil de rayon nul a été programmé Un des outils utilisés pour l’usinage d’une poche a été défini avec un rayon “0”. ERREUR 1026: Un pas supérieur au diamètre de l’outil a été programmé Le paramètre “C” de l’opération d’ébauche est supérieur au diamètre de l’outil d’ébauche. ERREUR 1041: Un paramètre obligatoire dans le cycle fixe n’a pas été programmé Cette erreur peut se produire dans les cas suivants: - Lorsque les paramètres “I” et “R” n’ont pas été programmés dans l’opération d’ébauche. - Absence d’opération d’ébauche, et non-programmation des paramètres “I” et “R” pour la finition. ERREUR 1042: Valeur de paramètre invalide dans le cycle fixe Cette erreur peut se produire dans les cas suivants: - Lorsque le paramètre “Q” de l’opération de finition a été programmé avec une valeur erronée. - Lorsque le paramètre “B” de l’opération de finition a été programmé avec une valeur nulle. - Lorsque le paramètre “J” de l’opération de finition a été programmé avec une valeur supérieure au rayon de l’outil de finition. ERREUR 1044: Le profil du plan se coupe lui-même dans un cycle de poche quelconque avec ilôts Cette erreur est émise lorsque l’un des profils du plan des contours programmés se coupe lui-même. ERREUR 1046: Position d’outil erronée avant le cycle fixe Cette erreur est émise en cas d’appel du cycle G66 si l’outil se trouve entre la cote du plan de référence et la cote de profondeur finale (fond) dans l’une quelconque des opérations. ERREUR 1047: Profil dans le plan ouvert dans un cycle de poche quelconque avec ilôts Cette erreur est émise lorsqu’un des contours programmés ne commence et ne finit pas au même point. La cause peut être la non-programmation de G1 après le début, avec G0, de l’un des profils. ERREUR 1048: La cote de surface de la pièce (sommet) n’a pas été programmée dans un cycle de poche quelconque avec ilôts Cette erreur est émise lorsque la cote de la surface de la poche n’a pas été programmée dans le premier point de définition de la géométrie. ERREUR 1049: Cote du plan de référence erronée pour le cycle fixe Cette erreur est émise lorsque la cote du plan de référence se situe entre le “haut” et le “bas” de la pièce dans l’une quelconque des opérations. Chapitre: 11 POCHES EN 2D ET 3D Section: POCHES EN 2D (ERREURS) Page 19 ERREUR 1084: Programmation d’une trajectoire circulaire erronée Cette erreur est émise lorsque l’une des trajectoires programmées en définition de géométrie de la poche est erronée. ERREUR 1227: Intersection de profils erronée dans un cycle de poche quelconque avec ilôts Cette erreur peut se produire dans les cas suivants: - Lorsque deux profils dans le plan présentent une section commune (dessin de gauche) - Lorsque les points de début de deux profils du plan principal sont confondus (dessin de droite) Page 20 Chapitre: 11 POCHES EN 2D ET 3D Section: POCHES EN 2D (ERREURS) 11.1.8 EXEMPLES DE PROGRAMMATION Exemples de programmation, sans changeur automatique d’outils: Y 200 100 X -200 -100 100 200 300 -100 -200 (TOR1=5, TOI1=0, TOL1=25, TOK1=0) (TOR2=3, TOI2=0, TOL2=20, TOK2=0) (TOR3=5, TOI3=0, TOL3=25, TOK3=0) G0 G17 G43 G90 X0 Y0 Z25 S800 G66 D100 R200 F300 S400 E500 M30 ;Dimensions de l’outil 1 ;Dimensions de l’outil 2 ;Dimensions de l’outil 3 ;Positionnement initial ;Programmation de poche avec ilôts ;Fin de programme N100 N200 N300 G81 Z5 I-40 T3 D3 M6 G67 B20 C8 I-40 R5 K0 F500 T1 D1 M6 G68 B0 L0.5 Q0 F300 T2 D2 M6 ;Définition de l’opération de perçage ;Définition de l’opération d’ébauche ;Définition de l’opération de finition N400 G0 G90 X-260 Y-190 Z0 G1 X-200 Y30 X-200 Y210 G2 G6 X-120 Y290 I-120 J210 G1 X100 Y170 G3 G6 X220 Y290 I100 J290 G1 X360 Y290 G1 X360 Y-10 G2 G6 X300 Y-70 I300 J-10 G3 G6 X180 Y-190 I300 J-190 G1 X-260 Y-190 ;Définition des contours de la poche ; (Contour extérieur) G0 X230 Y170 G1 X290 Y170 G1 X230 Y50 G1 X150 Y90 G3 G6 X230 Y170 I150 J170 ;Définition du contour du premier ilôt G0 X-120 Y90 G1 X20 Y90 G1 X20 Y-50 G1 X-120 Y-50 G1 X-120 Y90 ;Définition du contour du second ilôt N500 Chapitre: 11 POCHES EN 2D ET 3D ;Fin de la définition du contour Section: POCHES EN 2D (EXEMPLES) Page 21 Exemple de programmation, avec changeur automatique d’outils. Les “x” de la figure indiquent les points de début de chaque profil: Y 200 100 -300 -200 -100 100 200 300 X -100 -200 (TOR1=9, TOI1=0, TOL1=25, TOK1=0) (TOR2=3.6, TOI2=0, TOL2=20, TOK2=0) (TOR3=9, TOI3=0, TOL3=25, TOK3=0) G0 G17 G43 G90 X0 Y0 Z25 S800 G66 D100 R200 F300 S400 E500 M30 ;Dimensions de l’outil 1 ;Dimensions de l’outil 2 ;Dimensions de l’outil 3 ;Positionnement initial ;Programmation de poche avec ilôts N100 N200 N300 G81 Z5 I-40 T3 D3 M6 G67 B10 C5 I-40 R5 K1 F500 T1 D1 M6 G68 B0 L0.5 Q1 F300 T2 D2 M6 ;Définition de l’opération de perçage ;Définition de l’opération d’ébauche ;Définition de l’opération de finition N400 G0 G90 X-300 Y50 Z3 G1 Y190 G2 G6 X-270 Y220 I-270 J190 G1 X170 X300 Y150 Y50 G3 G6 X300 Y-50 I300 J0 G1 G36 R50 Y-220 X-30 G39 R50 X-100 Y-150 X-170 Y-220 X-270 G2 G6 X-300 Y-190 I-270 J-190 G1 Y-50 X-240 Y50 X-300 ;Définition des contours de la poche ; (Contour extérieur) G0 X-120 Y80 G2 G6 X-80 Y80 I-100 J80 G1 Y-80 G2 G6 X-120 Y-80 I-100 J-80 G1 Y80 ;Définition du contour du premier ilôt ; (Contour a) Page 22 Chapitre: 11 POCHES EN 2D ET 3D Section: POCHES EN 2D (EXEMPLES) N500 G0 X-40 Y0 G2 G6 X-40 Y0 I-100 J0 G0 X-180 Y20 G1 X-20 G2 G6 X-20 Y-20 I-20 J0 G1 X-180 G2 G6 X-180 Y20 I-180 J0 ; (Contour b) G0 X150 Y140 G1 X170 Y110 Y-110 X150 Y-140 X130 Y-110 Y110 X150 Y140 G0 X110 Y0 G2 G6 X110 Y0 I150 J0 ;Définition du contour du second ilôt ; (Contour d) Chapitre: 11 POCHES EN 2D ET 3D ; (Contour c) ; (Contour e) ;Fin de la définition du contour Section: POCHES EN 2D (EXEMPLES) Page 23 11.2 POCHES EN 3D La foncion G66 d’appel de cycle n’est pas modale; elle doit donc être programmée chaque fois qu’une poche en 3D doit être exécutée. Un bloc contenant une fonction G66 ne doit pas en comporter d’autre. Son format est le suivant: G66 R C F S E La fonction G66 n’est pas modale et doit donc être programmée chaque fois qu’une poche en 2D doit être exécutée. R(0-9999) Définit le numéro d’étiquette du bloc dans lequel l’opération d’ébauche est programmée. Elle est optionnelle et, lorsqu’elle n’est pas programmée, elle n’est pas exécutée. C(0-9999) Définit le numéro d’étiquette du bloc dans lequel l’opération de semifinition est programmée. Elle est optionnelle et, lorsqu’elle n’est pas programmée, elle n’est pas exécutée. F(0-9999) Définit le numéro d’étiquette du bloc dans lequel l’opération de finition est programmée. Elle est optionnelle et, lorsqu’elle n’est pas programmée, elle n’est pas exécutée. S(0-9999) Indique le numéro d’étiquette du bloc dans lequel commence la description géométrique des profils composant la poche. E(0-9999) Indique le numéro d’étiquette du bloc dans lequel finit la description géométrique des profils composant la poche. Exemple de programmation: G00 G90 X100 Y200 Z50 F5000 T1 D2 M06 G66 R100 C200 F300 S400 E500 M30 ;Positionnement initial N100 G67 ......... N200 G67 ......... N300 G68 ......... N400 G0 G90 X300 Y50 Z3 ........ ........ N500 G2 G6 X300 Y50 I150 J0 ;Définit l’opération d’ébauche ;Définit l’opération de semi-finition ;Définit l’opération de finition ;Début de la description géométrique Chapitre: 11 POCHES EN 2D ET 3D ;Définition du cycle fixe de poche en 3D ;Fin du programme ;Fin de la description géométrique Section: POCHES EN 3D Page 25 Fonctionnement de base: 1. Opération d’ébauche. Seulement si elle a été programmée. Elle se compose de plusieurs passes de fraisage de surface, jusqu’à ce que la profondeur programmée totale soit atteinte. Lors de chaque passe, on suivra les étapes suivantes en fonction du type d’usinage programmé. Cas A: Les trajectoires d’usinage sont linéaires et conservent un certain angle par rapport à l’axe des abscisses. * Exécution du contournage initial du profil extérieur de la pièce en premier. Si une opération de finition a été sélectionnée lors de l’appel du cycle, ce contournage est exécuté en laissant la surépaisseur programmée pour la finition. * Ensuite, le fraisage est exécuté selon l’avance et le pas programmés. Si, pendant le fraisage, un ilôt est atteint pour la première fois, son contournage est exécuté. Après le contournage de l’ilôt et pendant le reste des opérations, l’outil passe audessus des ilôts, son retrait s’effectue selon l’axe longitudinal jusqu’au plan de référence et l’usinage se poursuit dès l’achèvement de l’ilôt. Page 26 Chapitre: 11 POCHES EN 2D ET 3D Section: POCHES EN 3D Cas B: Les trajectoires d’usinage sont concentriques * L’ébauche s’effectue selon des trajectoires concentriques par rapport au profil. L’usinage est exécuté le plus rapidement possible en évitant (si possible) le passage au-dessus des ilôts. 2. Opération de semi-finition. Seulement si elle a été programmée. Après l’ébauche, certains gradins apparaissent sur le profil extérieur et sur les ilôts, comme montré dans la figure ci-dessous. L’opération de semi-finition permet de réduire ces gradins en exécutant plusieurs passes de contournage à différentes profondeurs. 3. Opération de finition. Seulement si elle a été programmée. Cette opération exécute plusieurs passes de finition en 3D. Elle peut s’effectuer, selon soit le sens de l’usinage des trajectoires , soit de l’extérieur de la poche vers la profondeur finale, de l’intérieur vers l’extérieur ou dans les deux sens alternativement. La CNC usinera le profil extérieur et les ilôts selon des entrées et sorties tangentielles et avec une vitesse de coupe constante. Attention: Si la broche était à l’arrêt et si aucun sens de rotation n’a été programmé, elle tournera dans le sens horaire (M03). Chapitre: 11 POCHES EN 2D ET 3D Section: POCHES EN 3D Page 27 Conditions après la fin du cycle A la fin du cycle fixe, l’avance active est la dernière avance programmée, celle correspondant à l’opération d’ébauche ou de finition. De même, la CNC prend en compte les fonctions G00, G40 et G90. Cotes de référence Dans le cycle fixe de poches quelconques avec ilôts, on rencontre quatre coordonnées le long de l’axe longitudinal (qui est normalement l’axe perpendiculaire au plan sélectionné par G15) dont l’importance mérite d’être détaillée ci-dessous: Page 28 1. Cote du plan de début. Cette cote est donnée par la position qu’occupe l’outil lors de l’appel du cycle. 2. Cote du plan de référence. Elle doit être programmée en absolu et représente une cote d’approche de la pièce. 3. Cote de la surface de la pièce. Elle est programmée en coordonnées absolues et dans le premier bloc de définition de profil. 4. Cote de profondeur d’usinage. Elle est programmée en coordonnées absolues. Chapitre: 11 POCHES EN 2D ET 3D Section: POCHES EN 3D 11.2.1 OPERATION D’EBAUCHE Il s’agit de l’opération principale de l’usinage d’une poche quelconque, et sa programmation est optionnelle. Elle sera programmée dans un bloc qui devra porter un numéro d’étiquette permettant d’indiquer au cycle fixe le bloc dans lequel l’opération d’ébauche est définie. Exemple: G66 R100 C200 F300 S400 E500 N100 G67 ....... ; Définition du cycle de poche quelconque avec ilôts ; Définition de l’opération d’ébauche L’ébauche est définie par la fonction G67 et elle ne peut pas être exécutée indépendamment de G66. Son format de programmation est: G67 A B C I R K F S T D M A(±5.5) Définit l’angle formé par la trajectoire d’ébauche et l’axe des abscisses. Si le paramètre “A” n’est pas programmé, l’opération d’ébauche est exécutée selon des trajectoires concentriques. L’usinage s’effectue le plus rapidement possible; en évitant de passer au-dessus des ilôts. Chapitre: 11 POCHES EN 2D ET 3D Section: POCHES EN 3D (EBAUCHE) Page 29 B(±5.5) Définit la passe d’usinage selon l’axe longitudinal (profondeur de la passe d’ébauche). Sa définition est obligatoire et la valeur programmée doit être différente de “0”; dans le cas contraire, l’opération d’ébauche est annulée. - Si elle est programmée avec le signe “+”, le cycle fixe calcule un pas égal ou inférieur au pas programmé afin d’exécuter une passe de fraisage à chaque cote de profondeur des surfaces des ilôts. - Si elle est programmée avec le signe “-”, l’ensemble de l’opération d’ébauche est effectué selon le pas programmé et le cycle fixe ajustera la dernière passe afin d’obtenir la profondeur totale programmée. - Si elle est effectuée avec B (+), les gradins n’apparaissent que sur les parois de la poche; si elle est exécutée avec B (-), ils risquent d’apparaître également sur les parois des ilôts. C(±5.5) Définit la passe de fraisage en ébauche selon le plan principal, la totalité de la poche étant exécutée suivant la passe définie, et le cycle fixe ajuste la dernière passe de fraisage. Si elle n’est pas programmée ou si elle est programmée avec une valeur “0”, une valeur égale à _ du diamètre de l’outil sélectionné est prise par défaut. Si elle est programmée avec une valeur supérieure au diamètre de l’outil, la CNC émet l’erreur correspondante. I(±5.5) Page 30 Définit la profondeur totale de la poche; elle est programmée en coordonnées absolues. Sa programmation est obligatoire. Chapitre: 11 POCHES EN 2D ET 3D Section: POCHES EN 3D (EBAUCHE) R(±5.5) Définit la cote du plan de référence; elle est programée en coordonnées absolues. Sa programation est obligatoire. T (4) Définit l’outil d’ébauche à utiliser. Sa programmation est obligatoire. F, S, D, M Les fonctions auxiliaires F S D et un maximum de 7 fonctions auxiliaires M peuvent être programmées. Elles sont optionnelles et seront exécutées au début de l’opération d’ébauche. Cette opération permet la définition de M06 avec le sous-programme associé, et le changement d’outil s’effectue avant le début de l’opération d’ébauche. Chapitre: 11 POCHES EN 2D ET 3D Section: POCHES EN 3D (EBAUCHE) Page 31 11.2.2 OPERATION DE SEMI-FINITI0N Cette opération est optionnelle. Elle sera programmée dans un bloc qui devra porter un numéro d’étiquette permettant d’indiquer au cycle fixe le bloc dans lequel l’opération d’ébauche est définie. Exemple: G66 R100 C200 F300 S400 E500 ; Définition du cycle de poche quelconque avec ilôts N200 G67 ....... ; Définition de l’opération de semi-finition La semi-finition est définie par la fonction G67 et elle ne doit pas être exécutée indépendamment de G66. Les opérations d’ébauche et de semi-finition sont définies par la fonction G67, mais dans des blocs distincts. Elles sont identifiées par la fonction G66 grâce aux paramètres “R” et “C”. Son format de programmation est: B(±5.5) G67 B I R F S T D M Définit la passe d’usinage selon l’axe longitudinal (profondeur de la passe de semi-finition). Sa définition est obligatoire et la valeur programmée doit être différente de “0”; dans le cas contraire, l’opération de semifinition est annulée. - Si elle est programmée avec le signe “+”, l’ensemble de l’opération de semi-finition est exécuté selon le même pas d’usinage, et le cycle fixe calcule un pas égal ou inférieur au pas programmé. - Si elle est programmée avec le signe “-”, l’ensemble de l’opération de semi-finition est effectué selon le pas programmé et le cycle fixe ajustera la dernière passe afin d’obtenir la profondeur totale programmée. I(±5.5) Définit la profondeur totale de la poche; elle est programmée en coordonnées absolues. Si une opération d’ébauche est présente et n’est pas programmée, la CNC prend la valeur définie pour l’opération d’ébauche. Si aucune opération d’ébauche n’est présente, elle doit être programmée. R(±5.5) Définit la cote du plan de référence; elle est programée en coordonnées absolues. Si une opération d’ébauche est présente et n’est pas programmée, la CNC prend la valeur définie pour l’opération d’ébauche. Si aucune opération d’ébauche n’est présente, elle doit être programmée. T (4) Page 32 Définit l’outil de semi-finition à utiliser. Sa programmation est obligatoire. Chapitre: 11 POCHES EN 2D ET 3D Section: POCHES EN 3D (SEMI-FINITION) F, S, D, M Les fonctions auxiliaires F S D et un maximum de 7 fonctions auxiliaires M peuvent être programmées. Elles sont optionnelles et seront exécutées au début de l’opération de semi-finition. Cette opération permet la définition de M06 avec le sous-programme associé, et le changement d’outil s’effectue avant le début de l’opération de semi-finition. Chapitre: 11 POCHES EN 2D ET 3D Section: POCHES EN 3D (SEMI-FINITION) Page 33 11.2.3 OPERATION DE FINITI0N Cette opération est optionnelle. Elle sera programmée dans un bloc qui devra porter un numéro d’étiquette permettant d’indiquer au cycle fixe le bloc dans lequel l’opération de finition est définie. Exemple: G66 R100 C200 F300 S400 E500 ; Définition du cycle de poche quelconque avec ilôts N300 G68 ....... ; Définition de l’opération de finition La finition est définie par la fonction G68 et elle ne peut pas être exécutée indépendamment de G66. Son format de programmation est: G68 B L Q J I R F S T D M B(±5.5) Définit la passe dans le plan compris entre deux trajectoires 3D de l’opération de finition. Il doit être défini avec une valeur différente de “0”. L(±5.5) Définit la valeur de la surépaisseur de finition laissée par les opérations d’ébauche et de semi-finition sur les parois latérales de la poche. Aucune surépaisseur n’est présente au sommet des ilôts ni dans le fond de la poche. Si aucune valeur n’est programmée, le cycle prend la valeur “L0”. Q Indique le sens de la passe de finition. Q = 1 Toutes les trajectoires se dirigent du sommet vers le fond de la poche. Q = 2 Toutes les trajectoires se dirigent du fond vers le sommet de la poche. Q = 0 Le sens est alternatif toutes les 2 trajectoires consécutives. Toute autre valeur génèrera l’erreur correspondante. Si le paramètre “Q” n’est pas programmé, le cycle prend “Q0” par défaut. J (5.5) Page 34 Indique le rayon de la pointe de l’outil et, par conséquent, le type d’outil de finition à utiliser. Chapitre: 11 POCHES EN 2D ET 3D Section: POCHES EN 3D (FINITION) En fonction du rayon affecté à l’outil dans la table de correcteurs (variables “TOR” + “TOI” de la CNC) et de la valeur affectée à ce paramètre, il est possible de définir trois types d’outils. PLAT ............................................... Si J n’est pas programmé ou si J = SPHERIQUE ................................... Si J = R TORIQUE (arrondi aux angles) .... Si J <> R et J < R I(±5.5) Définit la profondeur totale de la poche; elle est programmée en coordonnées absolues. - Si elle est définie, le cycle la prend en compte pendant l’opération de finition. - Si elle n’est pas définie et si la poche comporte une opération d’ébauche, le cycle prend par défaut la valeur définie dans l’opération d’ébauche. - Si elle n’est pas définie et si la poche ne comporte pas d’opération d’ébauche mais une opération de semi-finition, le cycle prend par défaut la valeur définie dans l’opération de semi-finition. - Si la poche ne comporte ni ébauche ni semi-finition, ce paramètre doit être défini. R(±5.5) Définit la cote du plan de référence; elle doit être programée en coordonnées absolues. - Si elle est définie, le cycle la prend en compte pendant l’opération de finition. - Si elle n’est pas définie et si la poche comporte une opération d’ébauche, le cycle prend par défaut la valeur définie dans l’opération d’ébauche. - Si elle n’est pas définie et si la poche ne comporte pas d’opération d’ébauche mais une opération de semi-finition, le cycle prend par défaut la valeur définie dans l’opération de semi-finition. - Si la poche ne comporte ni ébauche ni semi-finition, ce paramètre doit être défini. T (4) Définit l’outil de finition. Sa programmation est obligatoire. F, S, D, M Les fonctions auxiliaires F S D et un maximum de 7 fonctions auxiliaires “M” peuvent être programmées. Elles sont optionnelles et seront exécutées au début de l’opération de finition. Cette opération permet la définition de M06 avec le sous-programme associé, et le changement d’outil s’effectue avant le début de l’opération de finition. Chapitre: 11 POCHES EN 2D ET 3D Section: POCHES EN 3D (FINITION) Page 35 11.2.4 GEOMETRIE DES CONTOURS OU PROFILS Pour définir les contours ou profils d’une poche en 3D, il est nécessaire de spécifier le profil dans le plan ou section transversale (3) ainsi que le profil de profondeur ou section verticale (4) de tous les contours (même s’ils sont verticaux). Comme le cycle fixe applique le même profil de profondeur à l’ensemble du contour, on devra utiliser le même point de début pour définir le profil dans le plan et le profil de profondeur. Exemple de poche en 3D: Des contours en 3D à plus d’un profil de profondeur peuvent également être définis. Ces contours portent le nom de “profils 3D composés” et seront décrits plus loin. Page 36 Chapitre: 11 POCHES EN 2D ET 3D Section: POCHES EN 3D (GEOMETRIE) 11.2.5 REGLES DE PROGRAMMATION DES PROFILS La programmation de contours ou de profils extérieurs et intérieurs d’une poche quelconque en 3D (avec ilôts) doit suivre les règles suivantes: 1. Le profil dans le plan principal indique la forme du contour. Comme un contour en 3D comporte un nombre infini de profils différents (1 pour chaque cote de profondeur), on programmera: * Pour le contour extérieur de la poche: celui correspondant à la cote de la surface ou sommet de la pièce (1). * Pour les contours intérieurs: celui correspondant à la base ou fond (2). 2. Le profil dans le plan doit être fermé (points de début et de fin confondus) et il ne doit pas se recouper lui-même. Exemples: Les exemples ci-dessous entraînent une erreur de géométrie: 3. Le profil de profondeur (section verticale) doit être programmé avec l’un quelconque des axes du plan actif. Si le plan actif est le plan XY et si l’axe perpendiculaire est l’axe Z, on programmera G16XZ ou G16YZ. Tous les profils, profils du plan et de profondeur, doivent commencer par la définition du plan qui les contient. Exemple: G16 XY ........................... Début de la définition du profil extérieur —— définition du profil dans le plan ——G16 XZ —— définition du profil de profondeur ——G16 XY ........................... Début de la définition de l’ilôt —— définition du profil dans le plan ——G16 XZ —— définition du profil de profondeur ——- Chapitre: 11 POCHES EN 2D ET 3D Section: POCHES EN 3D (REGLES DE PROGRAMMATION) Page 37 4. Le profil de profondeur doit être défini après le profil dans le plan. Les points de début du profil dans le plan et du profil de profondeur doivent être identiques. Toutefois, le profil de profondeur doit être programmé: * Pour le contour extérieur de la poche, en commençant par la cote de surface (1). * Pour les contours intérieurs et les ilôts, en commençant par la cote de fond (2). 5. Le profil de profondeur doit être ouvert et sans changements de direction sur son trajet. Autrement dit, les zig-zag sont interdits. Exemples: Les exemples ci-dessous provoquent des erreurs de géométrie. Page 38 Chapitre: 11 POCHES EN 2D ET 3D Section: POCHES EN 3D (REGLES DE PROGRAMMATION) 11.2.5.1 EXEMPLES DE PROGRAMMATION Exemple de poche sans ilôts: (TOR1=2.5,TOL1=20,TOI1=0,TOK1=0) G17 G0 G43 G90 Z50 S1000 M4 G5 G66 R200 C250 F300 S400 E500 ...................... ;Définition de poche 3D M30 N200 G67 B5 C4 I-25 R5 F400 T1D1 M6 .................. ;Opération d’ébauche N250 G67 B2 I-23 R5 F550 T2D1 M6 ........................ ;Opération de semi-finition N300 G68 B1.5 L0.75 Q0 I-25 R2 F275 T3D1 M6 .... ;Opération de finition N400 G17 ...................................................................... G90 G0 X10 Y30 Z0 .......................................... G1 Y50 X70 Y10 X10 Y30 G16 XZ ............................................................... G0 X10 Z0 N500 G3 X40 Z-30 I30 K0 ........................................ Chapitre: 11 POCHES EN 2D ET 3D ;Début de définition de géométrie de poche ;Profil dans le plan (section horizontale) ;Profil de profondeur (section verticale) ;Fin de définition de géométrie de poche Section: POCHES EN 3D (EXEMPLES) Page 39 Exemples de définition de profils Ilôt pyramidal Profil dans le plan G17 G0 G90 X17 Y4 G1 X30 G1 Y30 G1 X4 G1 Y4 G1 X17 Profil de profondeur G16 YZ G0 G90 Y4 Z4 G1 Y17 Z35 Ilôt cônique Profil dans le plan G17 G0 G90 X35 Y8 G2 X35 Y8 I0 J27 Profil de profondeur G16 YZ G0 G90 Y8 Z14 G1 Y35 Z55 Ilôt hémisphérique Profil dans le plan G17 G0 G90 X35 Y8 G2 X35 Y8 I0 J27 Profil de profondeur G16 YZ G0 G90 Y8 Z14 G2 Y35 Z41 R27 Page 40 Chapitre: 11 POCHES EN 2D ET 3D Section: POCHES EN 3D (EXEMPLES) Exemple di una tasca 3D con isole: (TOR1=2.5,TOL1=20,TOI1=0,TOK1=0) G17 G0 G43 G90 Z50 S1000 M4 G5 G66 R200 C250 F300 S400 E500 ...................... ;Définition de poche 3D M30 N200 G67 B5 C4 I-25 R5 F400 T1D1 M6 .................. ;Opération d’ébauche N250 G67 B2 I-23 R5 F550 T2D1 M6 ........................ ;Opération de semi-finition N300 G68 B1.5 L0.75 Q0 I-25 R2 F275 T3D1 M6 .... ;Opération de finition N400 G17 ...................................................................... ;Début de définition de géométrie de poche G90 G0 X10 Y30 Z24 ........................................ ;Contour extérieur (profil dans le plan) G1 Y50 X70 Y10 X10 Y30 G16 XZ ............................................................... ;Profil de profondeur G0 X10 Z24 G1 X15 Z9 G17 ..................................................................... G90 G0 X30 Y30 ................................................ G2 X30 Y30 I10 K0 G16 XZ ............................................................... G90 G0 X30 Z9 N500 G1 X35 Z20 ...................................................... Chapitre: 11 POCHES EN 2D ET 3D ;Définition de l’ilôt ;Profil dans le plan ;Profil de profondeur ;Fin de définition de géométrie de poche Section: POCHES EN 3D (EXEMPLES) Page 41 11.2.6 PROFILS COMPOSES Un profil composé en 3D est un profil en 3D comportant plus d’un profil de profondeur. Il est défini par l’intersection de plusieurs contours. Le profil dans le plan est formé par l’intersection des profils dans le plan de chaque élément. Le profil de profondeur de chaque paroi du profil produit doit être défini. Pour définir le profil dans le plan, il est nécessaire de définir le profil correspondant à la surface la plus étendue de chaque élément (celle de la base), tout en respectant les règles d’intersection suivantes: 1. A l’intersection des profils, chaque contour est divisé en plusieurs lignes que l’on peut regrouper comme suit: - Lignes extérieures à l’autre contour. - Lignes intérieures à l’autre contour. Le point de début de chaque contour détermine le groupe de lignes à sélectionner. Page 42 Chapitre: 11 POCHES EN 2D ET 3D Section: POCHES EN 3D (PROFILS COMPOSES) L’exemple ci-dessous présente le processus de sélection, en traits pleins pour les lignes externes à l’autre contour et en pointillés pour les lignes internes. Le point de début de chaque contour est signalé par un “x”. Exemples d’intersection de profils: Addition Booléenne Soustraction Booléenne Intersection Booléenne 2. L’ordre de programmation des divers profils est un facteur déterminant en cas d’intersection de 3 profils ou plus. Le processus d’intersection de profils est réalisé selon l’ordre suivi lors de la programmation des profils. De cette façon, après l’intersection des deux profils programmés en premier, le profil résultant coupera le troisième et ainsi de suite. Chapitre: 11 POCHES EN 2D ET 3D Section: POCHES EN 3D (PROFILS COMPOSES) Page 43 Le point de début des profils résultants coïncide toujours avec le point de début utilisé pour définir le premier profil. Exemples: Page 44 Chapitre: 11 POCHES EN 2D ET 3D Section: POCHES EN 3D (PROFILS COMPOSES) 11.2.6.1 EXEMPLE DE POCHE COMPOSEE EN 3D Dans cet exemple, les faces qui définissent le profil dans le plan disposent de deux types de profil de profondeur. Les faces “A” et “C” présentent le même profil vertical, tandis que les faces “B” et “D” ont le même profil courbe. Il est possible de définir un contour pour chaque face, ou de regrouper les faces présentant le même profil. Définition d’un contour pour chaque face Lorsqu’un contour est défini pour chaque face, les conditions suivantes doivent être remplies: * Chaque profil dans le plan doit contenir les faces correspondantes en totalité. * Le profil dans le plan et le profil de profondeur doivent commencer au même point (A, B, C, D) Définition de contours regroupant des faces présentant le même profil Lorsque des faces présentant le même profil de profondeur sont regroupées, les conditions suivantes doivent être remplies: * Chaque profil dans le plan doit contenir les faces correspondantes en totalité. * Un seul profil de profondeur doit être défini pour chaque contour. * Les profils dans le plan et le profil de profondeur du contour regroupant plusieurs faces doivent commencer au même point. Les figures suivantes, celle de gauche et celle de droite, sont définies par deux contours regroupant les faces “A-C” et “B-D”. Chapitre: 11 POCHES EN 2D ET 3D Section: POCHES EN 3D (EXEMPLES DE PROFIL) Page 45 Les figures suivantes sont définies par 3 contours. Celle de gauche ne regroupe que des faces “B-D” et celle de droite des faces “A-C”. Page 46 Chapitre: 11 POCHES EN 2D ET 3D Section: POCHES EN 3D (EXEMPLES DE PROFIL) 11.2.7 PROFILS SUPERPOSES Lorsque 2 profils ou plus se superposent, on doit tenir compte des considérations suivantes: Pour plus de clarté, voir le croquis de droite, qui se compose de 2 profils superposés: 1 et 2. La cote correspondant à la base du profil supérieur (2) doit coïncider avec la cote de la surface du profil inférieur (1). Si un espace sépare les 2 profils, le cycle considèrera qu’il s’agit de 2 profils différents et il éliminera le profil supérieur pendant l’exécution du profil inférieur. Si les 2 profils se mélangent, le cycle fixe exécute une gorge autour du profil supérieur lors de la passe de finition. 47 Chapitre: 11 POCHES EN 2D ET 3D Section: POCHES EN 3D (PROFILS SUPERPOSES) Page 47 11.2.8 SYNTAXE DE PROGRAMMATION DES PROFILS Le profil extérieur et les profils intérieurs ou ilôts programmés doivent être définis par des éléments géométriques simples tels que des droites ou des arcs. Le premier bloc de définition (celui où commence le profil extérieur) et le dernier (celui où se termine le dernier profil défini) doivent porter un numéro d’étiquette de bloc. Ces numéros sont ceux qui indiquent au cycle fixe le début et la fin de la description géométrique des profils composant la poche. Exemple: G66 R100 C200 F300 S400 E500 ; Définition de cycle de poche quelconque avec ilôts N400 G17 ; Début de la description géométrique ——— —— —— —N500 G2 Y50 Z-15 I10 K0 ; Fin de la description géométrique La syntaxe de programmation des profils doit respecter les règles suivantes: 1. Le premier bloc de définition du profil doit porter un numéro de bloc pour indiquer au cycle fixe G66 le début de la description géométrique. 2. Le contour extérieur de la poche doit être défini en premier, avant le contour de chaque ilôt. 3. Lorsqu’un contour comporte plus d’un profil de profondeur, les contours doivent être définis un par un avec indication, pour chacun d’eux, du profil dans le plan puis du profil de profondeur. 4. Le premier bloc de définition du profil, qu’il s’agisse du profil dans le plan ou du profil de profondeur, doit contenir la fonction G00 (indiquant le début du profil). On veillera à programmer G01, G02 ou G03 dans le bloc suivant le bloc de définition du début car G00 est modal; ceci évite que la CNC n’interprète les blocs suivants comme les début d’un nouveau profil. 5. Le dernier bloc de définition du profil doit porter un numéro de bloc pour indiquer au cycle fixe G66 la fin de la description géométrique Exemple: G66 R200 C250 F300 S400 E500 ....... ;Définition de poche 3D N400 G17 .............................................. G0 G90 X5 Y-26 Z0 .......................... --- ---- ---- ------ ---- ---- ---G16 XZ ............................................... G0 --- ---- ---- ------ ---- ---- ---G17 ..................................................... G0 X30 Y-6 ........................................ --- ---- ---- ------ ---- ---- ---G16 XZ ............................................... G0 --- ---- ---- ------ ---- ---- ---N500 G3 Y-21 Z0 J-5 K0 ...................... Page 48 ;Début de définition de géométrie de poche ;Contour extérieur (profil dans le plan) ;Profil de profondeur ;Ilôt ;Profil dans le plan ;Profil de profondeur ;Fin de définition de géométrie de poche Chapitre: 11 POCHES EN 2D ET 3D Section: POCHES EN 3D (SYNTAXE) 6. Les profils sont décrits comme des trajectoires programmées, et il est possible d’inclure des arrondis aux angles, chanfreins, etc... en respectant les règles de syntaxe définies à cet effet. 7. La programmation d’images miroir, de changements de facteur d’échelle, de la rotation du système de coordonnées, de décalages d’origine, etc... est interdite dans la description des profils. 8. Il n’est pas non plus autorisé de programmer des blocs en langage de haut niveau tels que sauts, appels de sous-programmes ou programmation paramétrée. 9. La programmation d’autres cycles fixes est interdite. En plus de la fonction G00, qui a une signification spéciale, le cycle fixe de poche quelconque avec ilôts permet d’utiliser les fonctions suivantes pour définir les profils: G01 G02 G03 G06 G08 G09 G16 G17 G18 G19 G36 G39 G53 G70 G71 G90 G91 G93 Interpolation linéaire Interpolation circulaire horaire Interpolation circulaire anti-horaire Arc au centre en coordonnées absolues Arc tangent à la trajectoire précédente Arc défini par trois points Sélection de plan principal dans deux sens Plan principal X-Y et longitudinal Z (perpendiculaire) Plan principal Z-X et longitudinal Y (perpendiculaire) Plan principal Y-Z et longitudinal X (perpendiculaire) Arrondi aux angles Chanfrein Programmation par rapport au zéro machine Programmation en pouces Programmation en millimètres Programmation absolue Programmation incrémentale Présélection d’origine polaire Chapitre: 11 POCHES EN 2D ET 3D Section: POCHES EN 3D (SYNTAXE) Page 49 11.2.9 EXEMPLES Exemple 1, Poche sans ilôts Dans cet exemple, l’ilôt comporte 3 types de profil de profondeur: A, B et C. Pour définir l’ilôt, 3 contours sont utilisés: les types A, B et C. Page 50 Chapitre: 11 POCHES EN 2D ET 3D Section: POCHES EN 3D (EXEMPLES) (TOR1=2.5,TOL1=20,TOI1=0,TOK1=0) G17 G0 G43 G90 Z50 S1000 M4 G5 G66 R200 C250 F300 S400 E500 ...................... ;Définition de poche 3D M30 N200 G67 B5 C4 I-20 R5 F400 T1D1 M6 .................. ;Opération d'ébauche N250 G67 B2 I-18 R5 F550 T2D1 M6 ........................ ;Opération de semi-finition N300 G68 B1.5 L0.75 Q0 I-20 R2 F275 T3D1 M6 .... ;Opération de finition N400 G17 .................................... ;Début de définition de géométrie de poche G0 G90 X50 Y90 Z0 ......... ;Contour type A (profil dans le plan) G1 X0 Y10 X100 Y90 X50 G16 YZ .............................. ;Profil de profondeur G0 G90 Y90 Z0 G1 Z-20 G17 .................................... ;Contour type B G0 G90 X10 Y50 .............. ;Profil dans le plan G1 Y100 X-10 Y0 X10 Y50 G16 XZ .............................. ;Profil de profondeur G0 G90 X10 Z0 G1 X20 Z-20 G17 .................................... G0 G90 X90 Y50 .............. G1 Y100 X110 Y0 X90 Y50 G16 XZ .............................. G0 G90 X90 Z0 N500 G2 X70 Z-20 I-20 K0 ....... ;Contour type C ;Profil dans le plan ;Profil de profondeur ;Fin de définition de géométrie de poche Chapitre: 11 POCHES EN 2D ET 3D Section: POCHES EN 3D (EXEMPLES) Page 51 Exemple 2: Dans cet exemple, l’ilôt comporte 3 types de profil de profondeur: A, B et C. Pour définir l’ilôt, 3 contours sont utilisés: les types A, B et C. (TOR1=7.5,TOI1=0,TOR2=5,TOI2=0,TOR3=2.5,TOI3=0) G17 G0 G43 G90 Z50 S1000 M4 G5 G66 R200 C250 F300 S400 E500 ...................... ;Définition de poche 3D M30 N200 G67 B7 C14 I-25 R3 F500 T1D1 M6 ................ ;Opération d'ébauche N250 G67 B3 I-22 R3 F625 T2D2 M6 ........................ ;Opération de semi-finition N300 G68 B1 L1 Q0 J0 I-25 R3 F350 T3D3 M6 ........ ;Opération de finition Page 52 Chapitre: 11 POCHES EN 2D ET 3D Section: POCHES EN 3D (EXEMPLES) N400 G17 .................................... ;Début de définition de géométrie de poche G0 G90 X0 Y0 Z0 ............. ;Contour extérieur (profil dans le plan) G1 X150 Y100 X0 Y0 G16 XZ .............................. ;Profil de profondeur G0 G90 X0 Z0 G1 X10 Z-10 Z-25 G17 .................................... ;Contour type A G0 G90 X50 Y30 .............. ;Profil dans le plan G1 X70 Y70 X35 Y30 X50 G16 YZ .............................. ;Profil de profondeur G0 G90 Y30 Z-25 G2 Y50 Z-5 I20 K0 G17 .................................... ;Contour type B G0 G90 X40 Y50 .............. ;Profil dans le plan G1 Y25 X65 Y75 X40 Y50 G16 XZ .............................. ;Profil de profondeur G0 G90 X40 Z-25 G1 Z-5 G17 .................................... G0 G90 X80 Y40 .............. G1 X96 Y60 X60 Y40 X80 G16 YZ .............................. G0 G90 Y40 Z-25 N500 G2 Y50 Z-15 J10 K0 ........ ;Contour type C ;Profil dans le plan ;Profil de profondeur ;Fin de définition de géométrie de poche Chapitre: 11 POCHES EN 2D ET 3D Section: POCHES EN 3D (EXEMPLES) Page 53 Exemple 3: Dans cet exemple, l’ilôt comporte 3 types de profil de profondeur: A, B et C. Pour définir l’ilôt, 3 contours sont utilisés: les types A, B et C. Page 54 Chapitre: 11 POCHES EN 2D ET 3D Section: POCHES EN 3D (EXEMPLES) (TOR1=4,TOI1=0,TOR2=2.5,TOI2=0) G17 G0 G43 G90 Z25 S1000 M3 G66 R200 C250 F300 S400 E500 ...................... ;Définition de poche 3D M30 N200 G67 B5 C4 I-20 R5 F700 T1D1 M6 .................. ;Opération d'ébauche N250 G67 B2 I-18 R5 F850 T1D1 M6 ........................ ;Opération de semi-finition N300 G68 B1.5 L0.25 Q0 I-20 R5 F500 T2D2 M6 .... ;Opération de finition ; N400 G17 .................................... ;Début de définition de géométrie de poche G0 G90 X0 Y0 Z0 ............ ;Contour extérieur (profil dans le plan) G1 X105 Y62 X0 Y0 G16 XZ .............................. ;Profil de profondeur G0 X0 Z0 G2 X5 Z-5 I0 K-5 G1 X7.5 Z-20 G17 .................................... G90 G0 X37 Y19 .............. G2 I0 J12 G16 YZ .............................. G0 Y19 Z-20 G1 Z-16 G2 Y31 Z-4 R12 ................ ;Contour type A ;Profil dans le plan ;Profil de profondeur ;Fin de définition de géométrie de poche G17 .................................... ;Contour type B G90 G0 X60 Y37 .............. ;Profil dans le plan G1 X75 Y25 X40 Y37 X60 G16 YZ .............................. ;Profil de profondeur G0 Y37 Z-20 G1 Z-13 G3 Y34 Z-10 J-3 K0 G17 .................................... G0 X70 Y31 ...................... G1 Y40 X75 Y20 X70 Y31 G16 XZ .............................. G0 X70 Z-20 N500 G1 X65 Z-10 ..................... ;Contour type C ;Profil dans le plan ;Profil de profondeur ;Fin de définition de géométrie de poche Chapitre: 11 POCHES EN 2D ET 3D Section: POCHES EN 3D (EXEMPLES) Page 55 Exemple 4: Dans cet exemple, l’ilôt comporte 5 types de profil de profondeur: A, B, C, D et E. Pour définir l’ilôt, 3 contours sont utilisés: les types A, B, C, D et E. Page 56 Chapitre: 11 POCHES EN 2D ET 3D Section: POCHES EN 3D (EXEMPLES) (TOR1=4,TOI1=0,TOR2=2.5,TOI2=0) G17 G0 G43 G90 Z25 S1000 M3 G66 R200 C250 F300 S400 E500 ...................... ;Définition de poche 3D M30 N200 G67 B5 C7 I-30 R5 F700 T1D1 M6 .................... ;Opération d'ébauche N250 G67 B2.5 I-28 R5 F850 T1D1 M6 ...................... ;Opération de semi-finition N300 G68 B1.5 L0.75 Q0 I-30 R5 F500 T2D2 M6 ...... ;Opération de finition N400 G17 ...................................................................... ;Début de définition de géométrie de poche G90 G0 X0 Y0 Z0 .............................................. ;Contour extérieur (profil dans le plan) G1 X140 Y110 X0 Y0 G17 ..................................................................... ;Contour type A G90 G0 X30 Y95 ................................................ ;Profil dans le plan G1 X130 Y35 X10 Y95 X30 G16 YZ ................................................................ ;Profil de profondeur G90 G0 Y95 Z-30 G3 Y65 Z0 J-30 K0 G17 ..................................................................... ;Contour type B G90 G0 X12.5 Y65 ............................................. ;Profil dans le plan G1 Y120 X127.5 Y30 X97.5 Y100 X42.5 Y30 Chapitre: 11 POCHES EN 2D ET 3D Section: POCHES EN 3D (EXEMPLES) Page 57 X12.5 Y65 G16 XZ ................................................................ ;Profil de profondeur G90 G0 X12.5 Z-30 G1 Z0 G17 ..................................................................... ;Contour type C G90 G0 X70 Y90 ................................................ ;Profil dans le plan G1 X 105 Y40 X35 Y90 X-70 G16 YZ ................................................................ ;Profil de profondeur G90 G0 Y90 Z-30 G3 Y65 Z-5 J-25 K0 G17 ..................................................................... ;Contour type E G90 G0 X40 Y20 ................................................ ;Profil dans le plan G1 Y45 X100 Y10 X40 Y20 G16 XZ ................................................................ ;Profil de profondeur G90 G0 X40 Z-30 G2 X70 Z0 I30 K0 G17 ..................................................................... ;Contour type D G90 G0 X70 Y15 ................................................ ;Profil dans le plan G1 X105 Y5 X35 Y15 X70 G16 YZ ................................................................ ;Profil de profondeur G90 G0 Y15 Z-30 N500 G1 Z0 ................................................................. ;Fin de définition de géométrie de poche Page 58 Chapitre: 11 POCHES EN 2D ET 3D Section: POCHES EN 3D (EXEMPLES) Exemple 5: Dans cet exemple, l’ilôt comporte 2 types de profil de profondeur: A et B. Pour définir l’ilôt, 3 contours sont utilisés: les types A et B. (TOR1=2.5,TOL1=20,TOI1=0,TOK1=0) G17 G0 G43 G90 Z50 S1000 M4 G5 G66 R200 C250 F300 S400 E500 ...................... ;Définition de poche 3D M30 N200 G67 B5 C4 I-25 R5 F400 T1D1 M6 .................. ;Opération d'ébauche N250 G67 B2 I-23 R5 F550 T2D1 M6 ........................ ;Opération de semi-finition N300 G68 B1.5 L0.75 Q0 I-25 R2 F275 T3D1 M6 .... ;Opération de finition Chapitre: 11 POCHES EN 2D ET 3D Section: POCHES EN 3D (EXEMPLES) Page 59 N400 G17 ........................................................... ;Début de définition de géométrie de poche G90 G0 X5 Y-26 Z0 ................................ ;Contour extérieur (profil dans le plan) G1 Y25 X160 Y-75 X5 Y-26 G17 .......................................................... ;Contour bas (type A) G90 G0 X30 Y-6 ...................................... ;Profil dans le plan G1 Y-46 X130 Y-6 X30 G16 XZ ..................................................... ;Profil de profondeur G0 X30 Z-25 G1 Z-20 G2 X39 Z-11 I9 K0 G17 .......................................................... ;Contour haut (type B) G90 G0 X80 Y-16 .................................... ;Profil dans le plan G2 I0 J-10 G16 YZ ..................................................... ;Profil de profondeur G0 Y-16 Z-11 G1 Y-16 Z-5 N500 G3 Y-21 Z0 J-5 K0 ................................ ;Fin de définition de géométrie de poche Page 60 Chapitre: 11 POCHES EN 2D ET 3D Section: POCHES EN 3D (EXEMPLES) 11.2.10 ERREURS La CNC émettra les erreurs suivantes: ERREUR 1025: Un outil de rayon nul a été programmé Un des outils utilisés pour l’usinage d’une poche a été défini avec un rayon “0”. ERREUR 1026: Un pas supérieur au diamètre de l’outil a été programmé Le paramètre “C” de l’opération d’ébauche est supérieur au diamètre de l’outil d’ébauche. ERREUR 1041: Un paramètre obligatoire dans le cycle fixe n’a pas été programmé Cette erreur peut se produire dans les cas suivants: - Lorsque les paramètres “I” et “R” n’ont pas été programmés dans l’opération d’ébauche. - Absence d’opération d’ébauche, et non-programmation des paramètres “I” et “R” pour la semi-finition. - Absence d’opération de semi-finition et non-programmation des paramètres “I” et “R” pour la finition. - Lorsque le paramètre “B” n’a pas été programmé pour la finition. ERREUR 1042: Valeur de paramètre invalide dans le cycle fixe Cette erreur peut se produire dans les cas suivants: - Lorsque le paramètre “Q” de l’opération de finition a été programmé avec une valeur erronée. - Lorsque le paramètre “B” de l’opération de finition a été programmé avec une valeur nulle. - Lorsque le paramètre “J” de l’opération de finition a été programmé avec une valeur supérieure au rayon de l’outil de finition. ERREUR 1043: Profil de profondeur erroné dans un cycle de poche quelconque avec ilôts Cette erreur peut se produire dans les cas suivants: - Lorsque les profils de profondeur de 2 sections du même contour (simple ou composé) se coupent. - Lorsque la finition ne peut pas être exécutée avec l’outil programmé. Un cas typique est le moule sphérique avec un outil non-sphérique (paramètre “J” non égal au rayon). ERREUR 1044: Le profil du plan se coupe lui-même dans un cycle de poche quelconque avec ilôts Cette erreur est émise lorsque l’un des profils du plan des contours programmés se coupe lui-même. ERREUR 1046: Position d’outil erronée avant le cycle fixe Cette erreur est émise en cas d’appel du cycle G66 si l’outil se trouve entre la cote du plan de référence et la cote de profondeur finale (fond) dans l’une quelconque des opérations. ERREUR 1047: Profil dans le plan ouvert dans un cycle de poche quelconque avec ilôts Cette erreur est émise lorsqu’un des contours programmés ne commence et ne finit pas au même point. La cause peut être la non-programmation de G1 après le début, avec G0, de l’un des profils. Chapitre: 11 POCHES EN 2D ET 3D Section: POCHES EN 3D (ERREURS) Page 61 ERREUR 1048: La cote de surface de la pièce (sommet) n’a pas été programmée dans un cycle de poche quelconque avec ilôts Cette erreur est émise lorsque la cote de la surface de la poche n’a pas été programmée dans le premier point de définition de la géométrie. ERREUR 1049: Cote du plan de référence erronée pour le cycle fixe Cette erreur est émise lorsque la cote du plan de référence se situe entre le “haut” et le “bas” de la pièce dans l’une quelconque des opérations. ERREUR 1084: Programmation d’une trajectoire circulaire erronée Cette erreur est émise lorsque l’une des trajectoires programmées en définition de géométrie de la poche est erronée. ERREUR 1227: Intersection de profils erronée dans un cycle de poche quelconque avec ilôts Cette erreur peut se produire dans les cas suivants: - Lorsque deux profils dans le plan présentent une section commune (dessin de gauche) - Lorsque les points de début de deux profils du plan principal sont confondus (dessin de droite) Page 62 Chapitre: 11 POCHES EN 2D ET 3D Section: POCHES EN 3D (ERREURS) 12. UTILISATION D’UN PALPEUR La CNC FAGOR 8050 est équipée de deux entrées de palpeur, l’une pour les signaux 5 Vcc de type TTL, l’autre pour signaux 24 Vcc. L’annexe du Manuel d’Installation et de Mise en Service explique comment raccorder les différents types de palpeurs sur ces entrées. Cette commande permet, grâce à l’utilisation de palpeurs, d’exécuter les opérations suivantes: * Programmation de blocs de déplacement avec palpeur, grâce aux fonctions G75/G76. * Exécution, grâce à la programmation de blocs en langage évolué, des différents cycles d’étalonnage des outils et de mesure des pièces. Chapitre: 12 UTILISATIOND’UNPALPEUR Section: Page 1 12.1 DEPLACEMENT AVEC PALPEUR (G75, G76) La fonction G75 permet de programmer des déplacements qui se terminent dès la réception, par la CNC, du signal émis par le palpeur de mesure utilisé. La fonction G76 permet de programmer des déplacements qui se terminent dès que la CNC ne reçoit plus le signal émis par le palpeur de mesure utilisé. Le format de définition des deux fonctions est: G75 X..C ±5.5 G76 X..C ±5.5 A la suite de la fonction désirée G75 ou G76, on programmera le ou les axes désirés, ainsi que les coordonnées de ces axes, qui définiront le point final du déplacement programmé. La machine se déplacera selon la trajectoire programmée, jusqu’à ce qu’elle reçoive (G75) ou cesse de recevoir (G76) le signal du palpeur; à ce moment, la CNC considère que le bloc est terminé, et prend comme position théorique des axes la position réelle qu’ils occupent à ce moment. Si les axes atteignent la position programmée avant de recevoir ou de cesser de recevoir le signal externe du palpeur, la CNC interrompt le déplacement des axes. Ce type de bloc de déplacement avec palpeur est très utile pour mettre au point des programmes de mesure ou de vérification d’outils et de pièces. Les fonctions G75 et G76 sont non-modales et doivent donc être programmées pour chaque déplacement avec palpeur. Tant que la fonction G75 ou G76 est active, la correction d’avance F programmée ne peut pas être modifiée; elle reste fixée à 100%. Les fonctions G75 et G76 sont incompatibles entre elles et avec les fonctions G00, G02, G03, G33, G41 et G42. En outre, dès que l’une d’elles a été exécutée, la CNC suppose la présence des fonctions G01 et G40. Page 2 Chapitre: 12 UTILISATIOND’UNPALPEUR Section: DEPLACEMENTAVEC PALPEUR (G75, G76) 12.2 CYCLES FIXES DE PALPAGE La CNC FAGOR 8050 dispose des cycles fixes de palpage suivants: 1 Cycle fixe d’étalonnage de longueur d’outil. 2 Cycle fixe d’étalonnage du palpeur. 3 Cycle fixe de mesure de surface. 4 Cycle fixe de mesure de coin extérieur. 5 Cycle fixe de mesure de coin intérieur. 6 Cycle fixe de mesure d’angle. 7 Cycle fixe de mesure de coin et d’angle. 8 Cycle fixe de mesure de trou. 9 Cycle fixe de mesure de moyeu. Tous les déplacements de ces cycles fixes de palpage s’exécuteront selon les axes X, Y, Z, le plan de travail devant être constitué de 2 de ces axes (XY, XZ, YZ, YX, ZX, ZY). L’autre axe, qui doit être perpendiculaire à ce plan, devra être sélectionné comme axe longitudinal. Les cycles fixes devront être programmés au moyen de la mnémonique évoluée PROBE, dont le format de programmation est le suivant: (PROBE (expression), (déclaration d’affectation), ...) La mnémonique PROBE appelle le cycle de palpage indiqué grâce à un numéro ou à toute autre expression dont le résultat soit un nombre. Elle permet en outre d’initialiser les paramètres de ce cycle avec les valeurs nécessaires pour l’exécuter, au moyen des déclarations d’affectation. Considérations générales Le cycles fixes de palpage sont non-modaux, et doivent donc être programmés à chaque exécution. Les palpeurs utilisés dans l’exécution de ces cycles sont: * Palpeur situé en un point fixe de la machine, qui permet d’étalonner les outils. * Palpeur situé sur la broche, qui est considéré comme un outil et qui est utilisé dans les différents cycles de mesure. L’exécution d’un cycle fixe de palpage ne modifie pas l’historique des fonctions "G" précédentes, à l’exception des fonctions de compensation de rayon G41 et G42. Chapitre: 12 UTILISATIOND’UNPALPEUR Section: CYCLESFIXESDEPALPAGE Page 3 12.3 CYCLE FIXE D’ÉTALONNAGE DE LONGUEUR D’OUTIL Ce cycle permet d’étalonner la longueur de l’outil sélectionné. A la fin du cycle, la valeur (L) correspondant au correcteur sélectionné est mise à jour dans la table de correcteurs d’outils. Pour exécuter ce cycle, il est nécessaire de disposer d’un palpeur de bureau installé en un point fixe de la machine et dont les faces sont parallèles aux axes X, Y, Z. Sa position est indiquée en coordonnées absolues par rapport au zéro machine, au moyen des paramètres machine généraux: PRBXMIN indique la coordonnée minimum occupée par le palpeur selon l’axe X. PRBXMAX indique la coordonnée maximum occupée par le palpeur selon l’axe X. PRBYMIN indique la coordonnée minimum occupée par le palpeur selon l’axe Y. PRBYMAX indique la coordonnée maximum occupée par le palpeur selon l’axe Y. PRBZMIN indique la coordonnée minimum occupée par le palpeur selon l’axe Z. PRBZMAX indique la coordonnée maximum occupée par le palpeur selon l’axe Z. Z PRBZMAX PRBZMIN Z PRBXMIN PRBXMAX X Y Y X PRBYMAX PRBYMIN PRBXMIN PRBXMAX X S’il s’agit du premier étalonnage de la longueur de l’outil, il est recommandé d’introduire une valeur approximative de sa longueur (L) dans la table de correcteurs. Le format de programmation de ce cycle est le suivant: (PROBE 1, B, I, F) B5.5 Définit la distance de sécurité. Il doit être programmé avec une valeur positive et supérieure à 0. Page 4 Chapitre: 12 UTILISATIOND’UNPALPEUR Section: ÉTALONNAGEDELONGUEUR D’OUTIL I Indique le mode de réalisation du cycle fixe d’étalonnage: 0= 1= Etalonnage de l’outil selon son axe. Etalonnage de l’outil sur son extrêmité. R I0 I1 Si ce paramètre n’est pas programmé, le cycle fixe prend la valeur I0. F5.5 Définit l’avance selon laquelle s’exécutera le déplacement de palpage. La programmation est effectuée en mm/minute ou en pouces/minute. Fonctionnement de base: B Chapitre: 12 UTILISATIOND’UNPALPEUR Section: ÉTALONNAGEDELONGUEUR D’OUTIL Page 5 1.- Mouvement d’approche Déplacement du palpeur en avance rapide (G00) entre le point d’appel du cycle et le point d’approche. Ce point se situe face au point où doit s’effectuer la mesure, à une distance de sécurité (B) de ce point et selon l’axe longitudinal. Le mouvement d’approche est réalisé en deux phases: 1º Déplacement dans le plan principal de travail. 2º Déplacement selon l’axe longitudinal. 2.- Mouvement de palpage Déplacement du palpeur suivant l’axe longitudinal selon l’avance indiquée (F), jusqu’à la réception du signal émis par le palpeur. La distance maximum à parcourir en mouvement de palpage est 2B. Si, après que cette distance ait été parcourue, la CNC ne reçoit pas de signal du palpeur, le code d’erreur correspondant est affiché et les axes stoppent. 3.- Mouvement de retrait Déplacement du palpeur en avance rapide (G00) entre le point de palpage et le point d’appel du cycle. Le mouvement de retrait est réalisé en deux phases: 1º Déplacement suivant l’axe longitudinal jusqu’à la coordonnée du point (sur l’axe) où le cycle a été appelé. 2º Déplacement dans le plan principal de travail, jusqu’au point d’appel du cycle. A la fin du cycle, la CNC aura mis à jour la valeur de (L) dans la table de correcteurs correspondant au correcteur sélectionné, et initialisé la valeur de (K) a 0; elle renvoie également la valeur du paramètre arithmétique général: P299 Erreur détectée. Page 6 Différence entre la longueur mesurée et la longueur affectée dans la table. Chapitre: 12 UTILISATIOND’UNPALPEUR Section: ÉTALONNAGEDELONGUEUR D’OUTIL 12.4 CYCLE FIXE D’ÉTALONNAGE DE PALPEUR Ce cycle permet d’étalonner le palpeur situé sur la broche. Ce palpeur, qui doit d’abord être étalonné en longueur, est celui qui sera utilisé dans les cycles fixes de mesure avec palpeur. Le cycle mesure l’écart de l’axe de la bille du palpeur par rapport à l’axe du porte-outils, l’étalonnage étant réalisé au moyen d’un trou usiné au préalable et dont le centre et les dimensions sont connues. K I Chaque palpeur de mesure utilisé sera traité par la CNC comme un outil de plus. Les champs de la table de correcteurs correspondant à chaque palpeur auront les significations suivantes: R Rayon de la sphère (bille) du palpeur. Cette valeur est introduite manuellement dans la table. L Longueur du palpeur. Cette valeur sera affectée par le cycle d’étalonnage de longueur d’outil. I Ecart de l’axe de la bille du palpeur par rapport à l’axe du porte-outils selon l’axe des abscisses. Cette valeur sera affectée par ce cycle. K Ecart de l’axe de la bille du palpeur par rapport à l’axe du porte-outils selon l’axe des ordonnées. Cette valeur sera affectée par ce cycle. Les phases de l’étalonnage seront les suivantes: 1.- Après consultation des caractéristiques du palpeur, introduction manuelle de la valeur du rayon de la sphère (R) dans le correcteur correspondant. 2.- Après sélection du numéro de l’outil et du correcteur correspondants, exécution du Cycle d’Etalonnage de la longueur de l’outil, avec mise à jour de la valeur de (L) et initialisation de la valeur de (K) à 0. 3.- Exécution du cycle fixe d’étalonnage de palpeur, avec mise à jour des valeurs "I" et "K". Chapitre: 12 UTILISATIOND’UNPALPEUR Section: CYCLEFIXED’ÉTALON-NAGE DEPALPEUR Page 7 Le format de programmation de ce cycle est: (PROBE 2, X, Y, Z, B, J, E, H, F) X±5.5 Coordonnée réelle, selon l’axe X, du centre du trou. Y±5.5 Coordonnée réelle, selon l’axe Y, du centre du trou. Z±5.5 Coordonnée réelle, selon l’axe Z, du centre du trou. B5.5 Définit la distance de sécurité. Doit être programmé avec une valeur positive et supérieure à 0. J5.5 Définit le diamètre réel du trou. Doit être programmé avec une valeur positive et supérieure à 0. E5.5 Définit la distance de retrait du palpeur après le palpage initial. Doit être programmé avec une valeur positive et supérieure à 0. H5.5 Définit l’avance selon laquelle sera exécuté le déplacement de palpage initial. Doit être programmé en mm/minute ou en pouces/minute. F5.5 Définit l’avance selon laquelle sera exécuté le déplacement de palpage. Doit être programmé en mm/minute ou en pouces/minute. Fonctionnement de base: Z 1 Z X Y 4 Y 8 6 2 X Page 8 Chapitre: 12 UTILISATIOND’UNPALPEUR X Section: CYCLEFIXED’ÉTALON-NAGE DEPALPEUR 1.- Mouvement d’approche Déplacement du palpeur en avance rapide (G00) entre le point d’appel du cycle et le centre du trou. Le mouvement d’approche est réalisé en deux phases: 1º Déplacement dans le plan principal de travail. 2º Déplacement selon l’axe longitudinal. 2.- Mouvement de palpage. Ce mouvement se compose de: * Déplacement du palpeur suivant l’axe des ordonnées selon l’avance indiquée (H), jusqu’à la réception du signal émis par le palpeur. La distance maximum de déplacement en palpage est “B+(J/2)”. Si, après avoir parcouru cette distance, la CNC ne reçoit pas le signal du palpeur, elle affiche le code d’erreur correspondant et arrête le déplacement des axes. * Retrait du palpeur en avance rapide (G00) de la distance indiquée en (E). * Déplacement du palpeur suivant l’axe des ordonnées, selon l’avance indiquée (F), jusqu’à la réception du signal émis par le palpeur. 3.- Mouvement de retrait Déplacement du palpeur en avance rapide (G00) entre le point d’exécution du palpage et le centre réel du trou. 4.- Second mouvement de palpage. Identique au précédent. 5.- Mouvement de retrait Déplacement du palpeur en avance rapide (G00) entre le point d’exécution du palpage et le centre réel du trou suivant l’axe des ordonnées. 6.- Troisième mouvement de palpage. Identique aux précédents. Chapitre: 12 UTILISATIOND’UNPALPEUR Section: CYCLEFIXED’ÉTALON-NAGE DEPALPEUR Page 9 7.- Mouvement de retrait Déplacement du palpeur en avance rapide (G00) entre le point d’exécution du palpage et le centre réel du trou. 8.- Quatrième mouvement de palpage. Identique aux précédents. 9.- Mouvement de retrait Ce mouvement se compose de: * Déplacement du palpeur en avance rapide (G00) entre le point d’exécution du palpage et le centre réel du trou. * Déplacement suivant l’axe longitudinal jusqu’à la coordonnée correspondant au point d’appel de cycle sur cet axe. * Déplacement, dans le plan de travail, jusqu’au point d’appel du cycle. A la fin du cycle, la CNC aura modifié, dans la table de correcteurs, les valeurs "I" et "K" correspondant au correcteur sélectionné. Page 10 Chapitre: 12 UTILISATIOND’UNPALPEUR Section: CYCLEFIXED’ÉTALON-NAGE DEPALPEUR 12.5 CYCLE FIXE DE MESURE DE SURFACE On utilisera un palpeur situé dans la broche, qui devra être étalonné au préalable au moyen des cycles fixes: Cycle fixe d’étalonnage de longueur d’outil. Cycle fixe d’étalonnage de palpeur. Ce cycle permet de corriger la valeur du correcteur d’outil qui a été utilisé dans le processus d’usinage de la surface. Cette correction n’est appliquée que lorsque l’erreur de mesure dépasse une valeur programmée. Le format de programmation de ce cycle est le suivant: (PROBE 3, X, Y, Z, B, K, F, C, D, L) X±5.5 Coordonnée théorique, suivant l’axe X, du point sur lequel la mesure est demandée. Y±5.5 Coordonnée théorique, suivant l’axe Y, du point sur lequel la mesure est demandée. Z±5.5 Coordonnée théorique, suivant l’axe Z, du point sur lequel la mesure est demandée. B5.5 Définit la distance de sécurité. Doit être programmé avec une valeur positive et supérieure à 0. Le palpeur devra être situé, par rapport au point à mesurer, à une distance supérieure à cette valeur lors de l’appel du cycle. Chapitre: 12 UTILISATIOND’UNPALPEUR Section: MESUREDESURFACE Page 11 K Définit l’axe avec lequel l’opérateur désire effectuer la mesure de surface; il sera défini par le code suivant: 0 = Avec l’axe des abscisses du plan de travail. 1 = Avec l’axe des ordonnées du plan de travail. 2 = Avec l’axe longitudinal du plan de travail. Si ce paramètre n’est pas programmé, le cycle fixe prend la valeur K0. K2 K1 K0 Z Y X F5.5 Définit l’avance selon laquelle s’exécutera le déplacement de palpage. La programmation est effectuée en mm/minute ou en pouces/minute. C Indique le point où devra se terminer le cycle de palpage. 0 = Retour au point où l’appel du cycle a eu lieu. 1 = Le cycle se terminera sur le point mesuré, l’axe longitudinal reculant jusqu’à la coordonnée correspondant au point où l’appel du cycle a eu lieu. Si ce paramètre n’est pas programmé, le cycle fixe prendra la valeur C0. D4 Définit le numéro du correcteur auquel s’appliquera la correction, après la fin du cycle de mesure. Si ce paramètre n’est pas programmé, ou programmé avec une valeur 0, la CNC supposera que cette correction n’est pas demandée. L5.5 Définit la tolérance qui s’appliquera à l’erreur mesurée. Elle sera programmée en absolu, et le correcteur ne sera corrigé que si l’erreur est supérieure à la valeur fixée. Si aucune valeur n’est programmée, la CNC affectera la valeur 0 à ce paramètre. Page 12 Chapitre: 12 UTILISATIOND’UNPALPEUR Section: MESUREDESURFACE Fonctionnement de base: B B 1.- Mouvement d’approche Déplacement du palpeur en avance rapide (G00) entre le point d’appel du cycle et le point d’approche. Ce point se situe face au point où doit s’effectuer la mesure, à une distance de sécurité (B) de ce point et selon l’axe où s’effectuera le palpage (K). Le mouvement d’approche est réalisé en deux phases: 1º 2º Déplacement dans le plan principal de travail. Déplacement selon l’axe longitudinal. 2.- Mouvement de palpage Déplacement du palpeur suivant l’axe sélectionné (K) selon l’avance indiquée (F), jusqu’à la réception du signal émis par le palpeur. La distance maximum à parcourir en mouvement de palpage est 2B. Si, après que cette distance ait été parcourue, la CNC ne reçoit pas de signal du palpeur, le code d’erreur correspondant est affiché et les axes stoppent. A la fin du palpage, la CNC prend comme position théorique des axes leur position réelle lors de la réception du signal du palpeur. Chapitre: 12 UTILISATIOND’UNPALPEUR Section: MESUREDESURFACE Page 13 3.- Mouvement de retrait Déplacement du palpeur en avance rapide (G00) entre le point de palpage et le point d’appel du cycle. Le mouvement de retrait est réalisé en trois phases: 1º Déplacement suivant l’axe de palpage, jusqu’au point d’approche. 2º Déplacement, selon l’axe longitudinal, jusqu’à la coordonnée (sur cet axe) du point où le cycle a été appelé. 3º Si (C0) a été programmé, le déplacement s’effectue dans le plan de travail principal jusqu’au point d’appel du cycle. A la fin du cycle, la CNC renvoie les valeurs réelles obtenues après la mesure, dans les paramètres arithmétiques généraux suivants: P298 Coordonnée réelle de la surface. P299 Erreur détectée. Différence entre la coordonnée réelle de la surface et la cote théorique programmée. Si Numéro de Correcteur d’Outil (D) a été sélectionné, la CNC modifiera les valeurs de ce correcteur chaque fois que l’erreur de mesure sera égale ou supérieure à la tolérance (L). En fonction de l’axe avec lequel s’effectuera la mesure (K), la correction portera sur la valeur de la longueur ou du rayon: * Si la mesure est exécutée avec l’axe longitudinal au plan de travail, la modification portera sur l’usure de la longueur (K) du correcteur indiqué (D). * Si la mesure est exécutée avec l’un des axes composant le plan de travail, la modification portera sur l’usure du rayon (I) du correcteur indiqué (D). Page 14 Chapitre: 12 UTILISATIOND’UNPALPEUR Section: MESUREDESURFACE 12.6 CYCLE FIXE DE MESURE DE COIN EXTERIEUR On utilisera un palpeur situé dans la broche, qui devra être étalonné au préalable au moyen des cycles fixes: Cycle fixe d’étalonnage de longueur d’outil. Cycle fixe d’étalonnage de palpeur. Le format de programmation de ce cycle est le suivant: (PROBE 4, X, Y, Z, B, F) X±5.5 Coordonnée théorique, suivant l’axe X, du coin à mesurer. Y±5.5 Coordonnée théorique, suivant l’axe Y, du coin à mesurer. Z±5.5 Coordonnée théorique, suivant l’axe Z, du coin à mesurer. Selon le coin de la pièce à mesurer, le palpeur devra se situer dans la zone hachurée (voir la figure) correspondante avant l’appel du cycle. B5.5 Définit la distance de sécurité. Doit être programmé avec une valeur positive et supérieure à 0. Le palpeur devra être situé, par rapport au point à mesurer, à une distance supérieure à cette valeur lors de l’appel du cycle. F5.5 Définit l’avance selon laquelle s’exécutera le déplacement de palpage. La programmation est effectuée en mm/minute ou en pouces/minute. Chapitre: 12 UTILISATIOND’UNPALPEUR Section: MESUREDECOINEXTERIEUR Page 15 Fonctionnement de base: 2 3 1 B 5 6 B 6 B B 1.- Mouvement d’approche Déplacement du palpeur en avance rapide (G00) entre le point d’appel du cycle et le premier point d’approche, situé à une distance (B) de la première face à palper. Le mouvement d’approche est réalisé en deux phases: 1º Déplacement dans le plan principal de travail. 2º Déplacement selon l’axe longitudinal. 2.- Mouvement de palpage Déplacement du palpeur suivant l’axe des abscisses selon l’avance indiquée (F), jusqu’à la réception du signal émis par le palpeur. La distance maximum à parcourir en mouvement de palpage est 2B. Si, après que cette distance ait été parcourue, la CNC ne reçoit pas de signal du palpeur, le code d’erreur correspondant est affiché et les axes stoppent. 3.- Mouvement de retrait Déplacement du palpeur en avance rapide (G00) entre le point de palpage et le premier point d’approche. Page 16 Chapitre: 12 UTILISATIOND’UNPALPEUR Section: MESUREDECOINEXTERIEUR 4.- Second mouvement d’approche Déplacement du palpeur en avance rapide (G00) entre le premier point d’approche et le second. Ce mouvement d’approche se déroule en deux phases: 1º Déplacement selon l’axe des ordonnées. 2º Déplacement selon l’axe des abscisses. 5.- Second mouvement de palpage Déplacement du palpeur suivant l’axe des ordonnées selon l’avance indiquée (F), jusqu’à la réception du signal émis par le palpeur. La distance maximum à parcourir en mouvement de palpage est 2B. Si, après que cette distance ait été parcourue, la CNC ne reçoit pas de signal du palpeur, le code d’erreur correspondant est affiché et les axes stoppent. 6.- Mouvement de retrait Déplacement du palpeur en avance rapide (G00) entre le point du second palpage et le point où le cycle a été appelé. Le mouvement de retrait se déroule en trois phases: 1º Déplacement selon l’axe de palpage jusqu’au second point d’approche. 2º Déplacement, selon l’axe longitudinal, jusqu’à la coordonnée (sur cet axe) du point où le cycle a été appelé. 3º Déplacement dans le plan de travail principal jusqu’au point d’appel du cycle. A la fin du cycle, la CNC renvoie les valeurs réelles obtenues après la mesure, dans les paramètres arithmétiques généraux suivants: P296 Coordonnée réelle du coin selon l’axe des abscisses. P297 Coordonnée réelle du coin selon l’axe des ordonnées. P298 Erreur détectée selon l’axe des abscisses. Différence entre la coordonnée réelle du coin et la cote théorique programmée. P299 Erreur détectée selon l’axe des ordonnées. Différence entre la coordonnée réelle du coin et la cote théorique programmée. Chapitre: 12 UTILISATIOND’UNPALPEUR Section: MESUREDECOINEXTERIEUR Page 17 12.7 CYCLE FIXE DE MESURE DE COIN INTERIEUR On utilisera un palpeur situé dans la broche, qui devra être étalonné au préalable au moyen des cycles fixes: Cycle fixe d’étalonnage de longueur d’outil. Cycle fixe d’étalonnage de palpeur. Le format de programmation de ce cycle est le suivant: (PROBE 5, X, Y, Z, B, F) X±5.5 Coordonnée théorique, suivant l’axe X, du coin à mesurer. Y±5.5 Coordonnée théorique, suivant l’axe Y, du coin à mesurer. Z±5.5 Coordonnée théorique, suivant l’axe Z, du coin à mesurer. Le palpeur devra se situer à l’intérieur de la poche avant l’appel du cycle. B5.5 Définit la distance de sécurité. Doit être programmé avec une valeur positive et supérieure à 0. Le palpeur devra être situé, par rapport au point à mesurer, à une distance supérieure à cette valeur lors de l’appel du cycle. F5.5 Page 18 Définit l’avance selon laquelle s’exécutera le déplacement de palpage. La programmation est effectuée en mm/minute ou en pouces/minute. Chapitre: 12 UTILISATIOND’UNPALPEUR Section: MESUREDECOININTERIEUR Fonctionnement de base: 5 4 B 3 2 5 1 B 1.- Mouvement d’approche Déplacement du palpeur en avance rapide (G00) entre le point d’appel du cycle et le premier point d’approche, situé à une distance (B) des deux faces à palper. Le mouvement d’approche est réalisé en deux phases: 1º Déplacement dans le plan principal de travail. 2º Déplacement selon l’axe longitudinal. 2.- Mouvement de palpage Déplacement du palpeur suivant l’axe des abscisses selon l’avance indiquée (F), jusqu’à la réception du signal émis par le palpeur. La distance maximum à parcourir en mouvement de palpage est 2B. Si, après que cette distance ait été parcourue, la CNC ne reçoit pas de signal du palpeur, le code d’erreur correspondant est affiché et les axes stoppent. 3.- Mouvement de retrait Déplacement du palpeur en avance rapide (G00) entre le point de palpage et le point d’approche. 4.- Second mouvement de palpage Déplacement du palpeur suivant l’axe des ordonnées selon l’avance indiquée (F), jusqu’à la réception du signal émis par le palpeur. La distance maximum à parcourir en mouvement de palpage est 2B. Si, après que cette distance ait été parcourue, la CNC ne reçoit pas de signal du palpeur, le code d’erreur correspondant est affiché et les axes stoppent. Chapitre: 12 UTILISATIOND’UNPALPEUR Section: MESUREDECOININTERIEUR Page 19 5.- Mouvement de retrait Déplacement du palpeur en avance rapide (G00) entre le point du second palpage et le point où le cycle a été appelé. Le mouvement de retrait se déroule en trois phases: 1º Déplacement selon l’axe de palpage jusqu’au point d’approche. 2º Déplacement, selon l’axe longitudinal, jusqu’à la coordonnée (sur cet axe) du point où le cycle a été appelé. 3º Déplacement dans le plan de travail principal jusqu’au point d’appel du cycle. A la fin du cycle, la CNC renvoie les valeurs réelles obtenues après la mesure, dans les paramètres arithmétiques généraux suivants: Page 20 P296 Coordonnée réelle du coin selon l’axe des abscisses. P297 Coordonnée réelle du coin selon l’axe des ordonnées. P298 Erreur détectée selon l’axe des abscisses. Différence entre la coordonnée réelle du coin et la cote théorique programmée. P299 Erreur détectée selon l’axe des ordonnées. Différence entre la coordonnée réelle du coin et la cote théorique programmée. Chapitre: 12 UTILISATIOND’UNPALPEUR Section: MESUREDECOININTERIEUR 12.8 CYCLE FIXE DE MESURE D’ANGLE On utilisera un palpeur situé dans la broche, qui devra être étalonné au préalable au moyen des cycles fixes: Cycle fixe d’étalonnage de longueur d’outil. Cycle fixe d’étalonnage de palpeur. Le format de programmation de ce cycle est le suivant: (PROBE 6, X, Y, Z, B, F) X±5.5 Coordonnée théorique, suivant l’axe X, du sommet de l’angle à mesurer. Y±5.5 Coordonnée théorique, suivant l’axe Y, du sommet de l’angle à mesurer. Z±5.5 Coordonnée théorique, suivant l’axe Z, du sommet de l’angle à mesurer. B5.5 Définit la distance de sécurité. Doit être programmé avec une valeur positive et supérieure à 0. Le palpeur devra être situé, par rapport au point programmé, à une distance supérieure à 2 fois cette valeur lors de l’appel du cycle. F5.5 Définit l’avance selon laquelle s’exécutera le déplacement de palpage. La programmation est effectuée en mm/minute ou en pouces/minute. Chapitre: 12 UTILISATIOND’UNPALPEUR Section: MESURED’ANGLE Page 21 Fonctionnement de base: P295 2 3 5 6 2B 4 6 B B 1.- Mouvement d’approche Déplacement du palpeur en avance rapide (G00) entre le point d’appel du cycle et le premier point d’approche, situé à une distance (B) du sommet programmé et à (2B) de la face à palper. Le mouvement d’approche est réalisé en deux phases: 1º Déplacement dans le plan principal de travail. 2º Déplacement selon l’axe longitudinal. 2.- Mouvement de palpage Déplacement du palpeur suivant l’axe des ordonnées selon l’avance indiquée (F), jusqu’à la réception du signal émis par le palpeur. La distance maximum à parcourir en mouvement de palpage est 3B. Si, après que cette distance ait été parcourue, la CNC ne reçoit pas de signal du palpeur, le code d’erreur correspondant est affiché et les axes stoppent. 3.- Mouvement de retrait Déplacement du palpeur en avance rapide (G00) entre le point de palpage et le premier point d’approche. 4.- Second mouvement d’approche Déplacement du palpeur en avance rapide (G00) entre le premier point d’approche et le second, qui se situe à une distance (B) du premier. Page 22 Chapitre: 12 UTILISATIOND’UNPALPEUR Section: MESURED’ANGLE 5.- Second mouvement de palpage Déplacement du palpeur suivant l’axe des ordonnées selon l’avance indiquée (F), jusqu’à la réception du signal émis par le palpeur. La distance maximum à parcourir en mouvement de palpage est 4B. Si, après que cette distance ait été parcourue, la CNC ne reçoit pas de signal du palpeur, le code d’erreur correspondant est affiché et les axes stoppent. 6.- Mouvement de retrait Déplacement du palpeur en avance rapide (G00) entre le point du second palpage et le point où le cycle a été appelé. Le mouvement de retrait se déroule en trois phases: 1º Déplacement selon l’axe des ordonnées jusqu’au second point d’approche. 2º Déplacement, selon l’axe longitudinal, jusqu’à la coordonnée (sur cet axe) du point où le cycle a été appelé. 3º Déplacement dans le plan de travail principal jusqu’au point d’appel du cycle. A la fin du cycle, la CNC renvoie la valeur réelle obtenue après la mesure, dans le paramètre arithmétique général suivant: P295 Angle d’inclinaison de la pièce par rapport à l’axe des abscisses. Ce cycle permet de mesurer des angles compris entre ±45°. Si l’angle à mesurer est > 45° la CNC visualisera le code d’erreur correspondant. Si l’angle à mesurer est ≤ 45°, le palpeur entrera en collision avec la pièce. Chapitre: 12 UTILISATIOND’UNPALPEUR Section: MESURED’ANGLE Page 23 12.9 CYCLE FIXE DE MESURE DE COIN EXTERIEUR ET D’ANGLE On utilisera un palpeur situé dans la broche, qui devra être étalonné au préalable au moyen des cycles fixes: Cycle fixe d’étalonnage de longueur d’outil. Cycle fixe d’étalonnage de palpeur. Le format de programmation de ce cycle est le suivant: (PROBE 7, X, Y, Z, B, F) X±5.5 Coordonnée théorique, suivant l’axe X, du coin à mesurer. Y±5.5 Coordonnée théorique, suivant l’axe Y, du coin à mesurer. Z±5.5 Coordonnée théorique, suivant l’axe Z, du coin à mesurer. Le coin dépendant de la pièce à mesurer, le palpeur devra se situer dans la zone hachurée (voir la figure) correspondante avant l’appel du cycle. B5.5 Définit la distance de sécurité. Doit être programmé avec une valeur positive et supérieure à 0. Le palpeur devra être situé, par rapport au point programmé, à une distance supérieure à 2 fois cette valeur lors de l’appel du cycle. F5.5 Page 24 Définit l’avance selon laquelle s’exécutera le déplacement de palpage. La programmation est effectuée en mm/minute ou en pouces/minute. Chapitre: 12 UTILISATIOND’UNPALPEUR Section: MESUREDECOINEXTERIEUR ETD’ANGLE Fonctionnement de base: 2 3 B 1 8 9 5 6 2B 9 2B B B 1.- Mouvement d’approche Déplacement du palpeur en avance rapide (G00) entre le point d’appel du cycle et le premier point d’approche, situé à une distance (B) de la première face à palper. Le mouvement d’approche est réalisé en deux phases: 1º Déplacement dans le plan principal de travail. 2º Déplacement selon l’axe longitudinal. 2.- Mouvement de palpage Déplacement du palpeur suivant l’axe des abscisses selon l’avance indiquée (F), jusqu’à la réception du signal émis par le palpeur. La distance maximum à parcourir en mouvement de palpage est 3B. Si, après que cette distance ait été parcourue, la CNC ne reçoit pas de signal du palpeur, le code d’erreur correspondant est affiché et les axes stoppent. 3.- Mouvement de retrait Déplacement du palpeur en avance rapide (G00) entre le point de palpage et le premier point d’approche. Chapitre: 12 UTILISATIOND’UNPALPEUR Section: MESUREDECOINEXTERIEUR ETD’ANGLE Page 25 4.- Second mouvement d’approche Déplacement du palpeur en avance rapide (G00) entre le premier point d’approche et le second, situé à une distance (2B) de la seconde face à palper. Ce mouvement d’approche se déroule en deux phases: 1º Déplacement selon l’axe des ordonnées. 2º Déplacement selon l’axe des abscisses. 5.- Second mouvement de palpage Déplacement du palpeur suivant l’axe des ordonnées selon l’avance indiquée (F), jusqu’à la réception du signal émis par le palpeur. La distance maximum à parcourir en mouvement de palpage est 3B. Si, après que cette distance ait été parcourue, la CNC ne reçoit pas de signal du palpeur, le code d’erreur correspondant est affiché et les axes stoppent. 6.- Mouvement de retrait Déplacement du palpeur en avance rapide (G00) entre le point du palpage et le second point d’approche. 7.- Troisième mouvement d’approche Déplacement du palpeur en avance rapide (G00) entre le second point d’approche et le troisième, qui se situe à une distance (B) du précédent. 8.- Troisième mouvement de palpage Déplacement du palpeur suivant l’axe des ordonnées selon l’avance indiquée (F), jusqu’à la réception du signal émis par le palpeur. La distance maximum à parcourir en mouvement de palpage est 4B. Si, après que cette distance ait été parcourue, la CNC ne reçoit pas de signal du palpeur, le code d’erreur correspondant est affiché et les axes stoppent. Page 26 Chapitre: 12 UTILISATIOND’UNPALPEUR Section: MESUREDECOINEXTERIEUR ETD’ANGLE 9.- Mouvement de retrait Déplacement du palpeur en avance rapide (G00) entre le point du troisième palpage et le point où le cycle a été appelé. Le mouvement de retrait se déroule en trois phases: 1º Déplacement selon l’axe de palpage jusqu’au troisième point d’approche. 2º Déplacement, selon l’axe longitudinal, jusqu’à la coordonnée (sur cet axe) du point où le cycle a été appelé. 3º Déplacement dans le plan de travail principal jusqu’au point d’appel du cycle. A la fin du cycle, la CNC renvoie les valeurs réelles obtenues après la mesure, dans les paramètres arithmétiques généraux suivants: P295 Angle d’inclinaison de la pièce par rapport à l’axe des abscisses. P296 Coordonnée réelle du coin selon l’axe des abscisses. P297 Coordonnée réelle du coin selon l’axe des ordonnées. P298 Erreur détectée selon l’axe des abscisses. Différence entre la coordonnée réelle du coin et la cote théorique programmée. P299 Erreur détectée selon l’axe des ordonnées. Différence entre la coordonnée réelle du coin et la cote théorique programmée. Ce cycle permet de mesurer des angles compris entre ±45°. Si l’angle à mesurer est > 45° la CNC visualisera le code d’erreur correspondant. Si l’angle à mesurer est ≤ 45°, le palpeur entrera en collision avec la pièce. Chapitre: 12 UTILISATIOND’UNPALPEUR Section: MESUREDECOINEXTERIEUR ETD’ANGLE Page 27 12.10 CYCLE FIXE DE MESURE DE TROU On utilisera un palpeur situé dans la broche, qui devra être étalonné au préalable au moyen des cycles fixes: Cycle fixe d’étalonnage de longueur d’outil. Cycle fixe d’étalonnage de palpeur. Le format de programmation de ce cycle est le suivant: (PROBE 8, X, Y, Z, B, J, E, C, H, F) X±5.5 Coordonnée théorique, suivant l’axe X, du centre du trou. Y±5.5 Coordonnée théorique, suivant l’axe Y, du centre du trou. Z±5.5 Coordonnée théorique, suivant l’axe Z, du centre du trou. B5.5 Définit la distance de sécurité. Doit être programmé avec une valeur positive et supérieure à 0. J5.5 Définit le diamètre théorique du trou. Doit être programmé avec une valeur positive et supérieure à 0. Ce cycle permet de mesurer des trous dont le diamètre n’est pas supérieur à (J+B). E5.5 Définit la distance de retrait du palpeur après le palpage initial. Doit être programmé avec une valeur positive et supérieure à 0. C Indique où doit se terminer le cycle de palpage. 0 = Retour au point où le cycle a été appeléo. 1 = Le cycle se terminera au centre réel du trou. Si ce paramètre n’est pas programmé, le cycle prendra la valeur C0 par défaut. H5.5 Définit l’avance selon laquelle s’exécutera le déplacement de palpage initial. La programmation est effectuée en mm/minute ou en pouces/minute. F5.5 Définit l’avance selon laquelle s’exécutera le déplacement de palpage. La programmation est effectuée en mm/minute ou en pouces/minute. Page 28 Chapitre: 12 UTILISATIOND’UNPALPEUR Section: MESUREDETROU Fonctionnement de base: Z 1 Z X Y 4 Y 6 8 2 X X 1.- Mouvement d’approche Déplacement du palpeur en avance rapide (G00) entre le point d’appel du cycle et le centre du trou. Le mouvement d’approche est réalisé en deux phases: 1º Déplacement dans le plan principal de travail. 2º Déplacement selon l’axe longitudinal. Chapitre: 12 UTILISATIOND’UNPALPEUR Section: MESUREDETROU Page 29 2.- Mouvement de palpage. Ce mouvement se compose de: * Déplacement du palpeur suivant l’axe des ordonnées selon l’avance indiquée (H), jusqu’à la réception du signal émis par le palpeur. La distance maximum de déplacement en palpage est “B+(J/2)”. Si, après avoir parcouru cette distance, la CNC ne reçoit pas le signal du palpeur, elle affiche le code d’erreur correspondant et arrête le déplacement des axes. * Retrait du palpeur en avance rapide (G00) de la distance indiquée en (E). * Déplacement du palpeur suivant l’axe des ordonnées, selon l’avance indiquée (F), jusqu’à la réception du signal émis par le palpeur. 3.- Mouvement de retrait Déplacement du palpeur en avance rapide (G00) entre le point d’exécution du palpage et le centre théorique du trou. 4.- Second mouvement de palpage Identique au précédent. 5.- Mouvement de retrait Déplacement du palpeur en avance rapide (G00) entre le point d’exécution du palpage et le centre réel (calculé) du trou suivant l’axe des ordonnées. 6.- Troisième mouvement de palpage Identique aux précédents. 7.- Mouvement de retrait Déplacement du palpeur en avance rapide (G00) entre le point d’exécution du palpage et le centre théorique du trou. Page 30 Chapitre: 12 UTILISATIOND’UNPALPEUR Section: MESUREDETROU 8.- Quatrième mouvement de palpage Identique aux précédents. 9.- Mouvement de retrait Ce mouvement se compose de: * Déplacement du palpeur en avance rapide (G00) entre le point d’exécution du palpage et le centre réel (calculé) du trou. * Si (C0) est programmé, le palpeur se déplace jusqu’au point où le cycle a été appelé. 1º Déplacement suivant l’axe longitudinal jusqu’à la coordonnée correspondant au point d’appel de cycle sur cet axe. 2º Déplacement, dans le plan de travail, jusqu’au point d’appel du cycle. A la fin du cycle, la CNC renvoie les valeurs réelles obtenues après la mesure, dans les paramètres arithmétiques généraux suivants: P294 Diamètre du trou. P295 Erreur de diamètre du trou. Différence entre le diamètre réel et le diamètre programmé. P296 Coordonnée réelle du centre selon l’axe des abscisses. P297 Coordonnée réelle du centre selon l’axe des ordonnées. P298 Erreur détectée selon l’axe des abscisses. Différence entre la coordonnée réelle du centre et la cote théorique programmée. P299 Erreur détectée selon l’axe des ordonnées. Différence entre la coordonnée réelle du centre et la cote théorique programmée. Chapitre: 12 UTILISATIOND’UNPALPEUR Section: MESUREDETROU Page 31 12.11 CYCLE FIXE DE MESURE DE MOYEU On utilisera un palpeur situé dans la broche, qui devra être étalonné au préalable au moyen des cycles fixes: Cycle fixe d’étalonnage de longueur d’outil. Cycle fixe d’étalonnage de palpeur. Le format de programmation de ce cycle est le suivant: (PROBE 9, X, Y, Z, B, J, E, C, H, F) X±5.5 Coordonnée théorique, suivant l’axe X, du centre du moyeu. Y±5.5 Coordonnée théorique, suivant l’axe Y, du centre du moyeu. Z±5.5 Coordonnée théorique, suivant l’axe Z, du centre du moyeu. B5.5 Définit la distance de sécurité. Doit être programmé avec une valeur positive et supérieure à 0. J5.5 Définit le diamètre théorique du moyeu. Doit être programmé avec une valeur positive et supérieure à 0. Ce cycle permet de mesurer des moyeux dont le diamètre n’est pas supérieur à (J+B). E5.5 Définit la distance de retrait du palpeur après le palpage initial. Doit être programmé avec une valeur positive et supérieure à 0. C Indique où doit se terminer le cycle de palpage. 0 = Retour au point où le cycle a été appeléo. 1 = Le cycle se terminera en positionnant le palpeur au centre du moyeu, à une distance (B) de la coordonnée théorique programmée. Si ce paramètre n’est pas programmé, le cycle prendra la valeur C0 par défaut. H5.5 Définit l’avance selon laquelle s’exécutera le déplacement de palpage initial. La programmation est effectuée en mm/minute ou en pouces/minute. F5.5 Définit l’avance selon laquelle s’exécutera le déplacement de palpage. La programmation est effectuée en mm/minute ou en pouces/minute. Page 32 Chapitre: 12 UTILISATIOND’UNPALPEUR Section: MESUREDEMOYEU Fonctionnement de base: 1 6 5 7 Z 2 9 3 Y X Z Z B B 2 B B 5 3 9 7 Y B B X B B 1.- Positionnement au centre du moyeu Déplacement du palpeur en avance rapide (G00) entre le point d’appel du cycle et le centre du moyeu. Le mouvement d’approche est réalisé en deux phases: 1º Déplacement dans le plan principal de travail. 2º Déplacement selon l’axe longitudinal, jusqu’à une distance (B) de la surface programmée. 2.- Déplacement jusqu’au premier point d’approche Ce déplacement du palpeur, qui est exécuté en avance rapide (G00), se compose de: 1º Déplacement selon l’axe des ordonnées. 2º Déplacement de l’axe longitudinal, de la distance (2B). Chapitre: 12 UTILISATIOND’UNPALPEUR Section: MESUREDEMOYEU Page 33 3.- Mouvement de palpage. Ce mouvement se compose de: * Déplacement du palpeur suivant l’axe des ordonnées selon l’avance indiquée (H), jusqu’à la réception du signal émis par le palpeur. La distance maximum de déplacement en palpage est “B+(J/2)”. Si, après avoir parcouru cette distance, la CNC ne reçoit pas le signal du palpeur, elle affiche le code d’erreur correspondant et arrête le déplacement des axes. * Retrait du palpeur en avance rapide (G00) de la distance indiquée en (E). * Déplacement du palpeur suivant l’axe des ordonnées, selon l’avance indiquée (F), jusqu’à la réception du signal émis par le palpeur. 4.- Déplacement jusqu’au second point d’approche Ce déplacement du palpeur, exécuté en avance rapide (G00) se compose de: * Retrait jusqu’au premier point d’approche. * Déplacement jusqu’a une distance (B) par-dessus le moyeu, jusqu’au second point d’approche. 5.- Second mouvement de palpage. Identique au premier. 6.- Déplacement jusqu’au troisième point d’approche Identique au précédent. 7.- Troisième mouvement de palpage. Identique aux précédents. 8.- Déplacement jusqu’au quatrième point d’approche Identique aux précédents. 9.- Quatrième mouvement de palpage. Identique aux précédents. Page 34 Chapitre: 12 UTILISATIOND’UNPALPEUR Section: MESUREDEMOYEU 10.-Mouvement de retrait Ce mouvement se compose de: * Retrait jusqu’au quatrième point d’approche. * Déplacement du palpeur en avance rapide (G00) et jusqu’à une distance (B) pardessus le moyeu, jusqu’au centre réel (calculé) du moyeu. * Si (C0) est programmé, le palpeur se déplace jusqu’au point où le cycle a été appelé. 1º Déplacement suivant l’axe longitudinal jusqu’à la coordonnée correspondant au point d’appel de cycle sur cet axe. 2º Déplacement, dans le plan de travail, jusqu’au point d’appel du cycle. A la fin du cycle, la CNC renvoie les valeurs réelles obtenues après la mesure, dans les paramètres arithmétiques généraux suivants: P294 Diamètre du moyeu. P295 Erreur de diamètre du moyeu. Différence entre le diamèter réel et le diamètre programmé. P296 Coordonnée réelle du centre selon l’axe des abscisses. P297 Coordonnée réelle du centre selon l’axe des ordonnées. P298 Erreur détectée selon l’axe des abscisses. Différence entre la coordonnée réelle du centre et la coordonnée théorique programmée. P299 Erreur détectée selon l’axe des ordonnées. Différence entre la coordonnée réelle du centre et la coordonnée théorique programmée. Chapitre: 12 UTILISATIOND’UNPALPEUR Section: MESUREDEMOYEU Page 35 13. PROGRAMMATION EN LANGAGE DE HAUT NIVEAU La CNC FAGOR 8050 dispose d’une série de variables internes accessibles depuis le programme utilisateur, depuis le programme du PLC ou par ligne DNC. L’accès à ces variables depuis le programme utilisateur est obtenu au moyen de commandes de haut niveau. Chaque variable du système accessible sera référencée par sa mnémonique, et elle se différenciera, selon son utilisation, en variables de lecture et en variable de lecture-écriture. 13.1 DESCRIPTION LEXIQUE Tous les mots constituant le langage de haut niveau de la commande numérique doivent être écrits en majuscules, à l’exception des textes associés, qui peuvent être écrits en majuscules et en minuscules. Les éléments disponibles pour la programmation en haut niveau sont: - Les mots réservés. - Les constantes numériques. - Les symboles Chapitre: 13 PROGRAMMATIONENLANGAGEDEHAUTNIVEAU Section: DESCRIPTIONLEXIQUE Page 1 13.1.1 MOTS RESERVES L’ensemble de mots que la CNC utilise dans la programmation de haut niveau pour donner un nom aux variables du système, aux opérateurs, aux mnémoniques de contrôle, etc. est présenté ci-dessous: ABS BCD CALL CSS DATE DNCCSS DNCSL EFHOLD EXP FEED FUP GE IB KEY LE MCALL MPG NE ODW P PLCC PLCI PLCS POS(X-C) PRGFRO RET SCALE SQRT SZONE TAN TLFR TOL WKEY XOR ACOS BIN CLOCK CUTA DEFLEX DNCERR DNCSSO ELSE AND BLKN CNCFRO CYTIME DEFLEY DNCF DSBLK EQ ARG ASIN ATAN CNCERR CNCSSO COS DEFLEZ DNCFPR DSTOP ERROR DFHOLD DNCFRO DW ESBLK DIST(X-C) DNCS FIRST FZLO(X-C) GOTO IF KEYSRC LOG MDOFF MPLC NOSEA OPEN PAGE PLCCSS PLCM PLCSL POSS PRGN ROTPF SCALE(X-C) SREAL SZUP(X-C) TIME TMZP TOOL WRITE FIX FZONE GS INPUT FLWE(X-C) FZUP(X-C) GT FPREV FRO LONGAX MIRROR MPS NOSEW OPMODE PARTC PLCERR PLCMSG PLCSSO PPOS(X-C) PROBE ROTPS SIN SSO LT MOD MS NOT OR PCALL PLCF PLCO PLCT PRGCSS PRGS ROUND SK SUB MP(X-C) MSG NXTOD ORG(X-C) PI PLCFPR PLCOF(X-C) PORGF PRGF PRGSL RPT SLIMIT SYSTEM MPAS TIMER TMZT TOR TLFD TOD TLFF TOK TLFN TOI ESTOP NXTOOL ORGROT PLANE PLCFRO PLCR PORGS PRGFPR PRGSSO SPEED SZLO(X-C) Les mots qui se terminent par (X-C) indiquent un ensemble de 9 éléments constitués de la racine correspondante, suivie de X, Y, Z, U, V, W, A, B et C. ORG(X-C) -> ORGX, ORGY, ORGZ, ORGU, ORGV, ORGW, ORGA, ORGB, ORGC Les lettres de l’alphabet A-Z sont également des mots réservés, car elles peuvent constituer un mot du langage de haut niveau lorsqu’elles sont utilisées seules. Page 2 Chapitre: 13 PROGRAMMATIONENLANGAGEDEHAUTNIVEAU Section: DESCRIPTIONLEXIQUE 13.1.2 CONSTANTES NUMERIQUES Les blocs programmés en langage de haut niveau autorisent les nombres décimaux ne dépassant pas le format ±6.5 , et les nombres hexadécimaux; dans ce cas, ils doivent être précédés du symbole $, et comporter un maximum de 8 chiffres. L’affectation à une variable d’une constante supérieure au format ±6.5, s’effectuera au moyen de paramètres arirthmétiques, d’expressions arithmétiques, ou de constantes en format hexadécimal. Exemple: Pour affecter la valeur 100000000 à la variable "TIMER" , on peut procéder des façons suivantes: (TIMER (TIMER (P100 (TIMER = $5F5E100) = 10000 * 10000) = 10000 * 10000) = P100) Si la commande fonctionne en métrique (mm), la résolution est de 1/10 de micron, et les chiffres sont programmés selon le format ±5.4 (positif ou négatif, avec 5 chiffres entiers et 4 décimales); si elle fonctionne en pouces, la résolution est égale au 1/100.000 de micron, et les chiffres sont programmés selon le format ±4.5 (positif ou négatif, avec 4 chiffres entiers et 5 décimales). Pour faciliter le travail du programmeur, cette commande admet toujours le format ±5.5 (positif ou négatif, avec 5 chiffres entiers et 5 décimales), et elle ajuste selon besoins chaque nombre en fonction des unités de travail au moment de l’utilisation. 13.1.3 SYMBOLES Les symboles utilisés dans le langage de haut nivea sont: ( )" = + - * / , Chapitre: 13 PROGRAMMATIONENLANGAGEDEHAUTNIVEAU Section: DESCRIPTIONLEXIQUE Page 3 13.2 VARIABLES Les variables internes de la CNC accessibles par le langage de haut niveau sont regroupées en tables et peuvent être de lecture seule ou de lecture/écriture. Un groupe de mnémoniques permet de représenter les divers champs des tables de variables. Pour accéder à un élément de ces tables, il suffit d’indiquer le champ de la table désirée au moyen de la mnémonique correspondante (par exemple TOR), puis l’élément désiré (TOR 3). Les variables dont dispose la CNC 8050 peuvent être classées comme suit: - Paramètres ou variables de caractère général Variables associées aux outils Variables associées aux décalages d’origine Variables associées aux paramètres machine Variables associées aux zones de travail Variables associées aux avances Variables associées aux coordonnées Variables associées à la broche Variables associées à l’automate Variables associées aux paramètres locaux Autres variables Les variables qui accèdent à des valeurs réelles de la CNC interrompent la préparation des blocs, et la CNC attend l’exécution de ce bloc avant de reprendre la préparation des blocs. En conséquence, ce type de variable ne doit être utilisé qu’avec précautions car, si elles sont insérées entre des blocs d’usinage travaillant avec compensation, des profils indésirables risquent d’être produits. Exemple: Les blocs de programme suivants sont exécutés dans une section comportant une compensation G41. ........... ........... N10 X50 Y80 N15 (P100=POSX); Affecte au paramètre P100 la valeur de la coordonnée réelle en X. N20 X50 Y50 N30 X80 Y50 ........... ........... Page 4 Chapitre: 13 PROGRAMMATIONENLANGAGEDEHAUTNIVEAU Section: VARIABLES Le bloc N15 interrompt la préparation des blocs; l’exécution du bloc N10 se terminera donc au point A. Y A 80 N10 N20 50 N30 80 50 X Lorsque l’exécution du bloc N15 est terminée, la CNC reprend la préparation des blocsàa partir du bloc N20. Comme le point suivant correspondant à la trajectoire compensée est le point "B", la CNC déplacera l’outil jusqu’à ce point, en exécutant la trajectoire "A-B". Y A 80 N10 B N20 50 N30 X 50 80 Comme on peut le voir, la trajectoire produite n’est pas la trajectoire désirée; il est donc recommandé d’éviter l’utilisation de ce type de variable dans les sections comportant une compensation. Chapitre: 13 PROGRAMMATIONENLANGAGEDEHAUTNIVEAU Section: VARIABLES Page 5 13.2.1 PARAMETRES OU VARIABLES DE CARACTERE GENERAL La CNC FAGOR 8050 dispose de deux types de variables de caractère général, les paramètres locaux P0-P25 et les paramètres globaux P100-P299. Le programmeur pourra utiliser des variables de caractère général lorsqu’il éditera ses propres programmes. Ensuite, et pendant l’exécution, la CNC remplacera ces variables par les valeurs qui leur sont affectées à un moment donné. Exemple: GP0 XP1 Y100 (IF (P100 P101 EQ P102) GOTO N100) -> G1 X-12.5 Y100 -> (IF (2 5 EQ 12) GOTO N100) L’utilisation de ces variables de caractère général dependra du type de bloc dans lequel elles seront programmées et du canal d’exécution. Dans les blocs programmés en ISO, des paramètres peuvent être associés à tous les champs, G X..C F S T D M. Le numéro d’étiquette de bloc sera défini avec une valeur numérique. Si des paramètres sont utilisés dans des blocs programmés en langage de haut niveau, ils pourront être programmés dans n’importe quelle expression. Les programmes exécutés par le canal utilisateur peuvent comporter n’importe quel paramètre global, mais ne peuvent pas utiliser de paramètres locaux. La CNC mettra à jour la table de paramètres après avoir traité les opérations indiquées dans le bloc en préparation. Cette opération est toujours réalisée avant l’exécution du bloc; pour cette raison, il n’est pas obligatoire que les valeurs indiquées dans la table correspondent à celles du bloc en cours d’exécution. Si le mode Exécution est abandonné après une interruption d’exécution du programme, la CNC met à jour les tables de paramètres avec les valeurs correspondant au bloc qui se trouvait en cours d’exécution. Lorsqu’on accède à la table de paramètres locaux et de paramètres globaux, la valeur affectée à chaque paramètre peut être exprimée en notation décimale (4127.423) ou scientifique (0.23476 E-3). La CNC FAGOR 8050 dispose de déclarations de haut niveau permettant de définir et d’utiliser des sous-routines pouvant être appelées depuis un programme principal ou une autre sous-routine qui peut en appeler une seconde, la seconde pouvant en appeler une troisième, etc.... La CNC limite le nombre d’appels, le nombre de niveaux d’imbrication étant limité à 15. Il est possible d’affecter 26 paramètres locaux (P0-P25) à une sous-routine et ces paramètres, qui sont inconnus des blocs externes à la sous-routine, peuvent être référencés par les blocs qui la composent. La CNC permet d’affecter des paramètres locaux à plus d’une sous-routine, le nombre maximum possible de niveaux d’imbrications de paramètres locaux étant de 6 à l’intérieur des 15 niveaux d’imbrication de sous-routines. Page 6 Chapitre: 13 PROGRAMMATIONENLANGAGEDEHAUTNIVEAU Section: VARIABLESDECARACTERE GENERAL Les paramètres locaux utilisés en langage de haut niveau pourront être définis, soit comme indiqué précédemment, soit au moyen des lettres A-Z, à l’exception de Ñ, de telle sorte que A est égal à P0 et Z à P25. L’exemple suivant présente ces 2 méthodes de définition: (IF ((P0+P1) (IF ((A+B) ∗ P2/P3 ∗ C/D EQ P4) GOTO N100) EQ E) GOTO N100) Si un nom de paramètre local (lettre) est utilisé pour lui affecter une valeur (A au lieu de P0 par exemple), et si l’expression arithmétique est une constante numérique, la déclaration peut être abrégée comme suit: (P0=13.7) -> (A=13.7) -> (A13.7) On n’utilisera les parenthèses qu’avec précautions, car M30 ne signifie pas la même chose que (M30). La CNC interprète (M30) comme une déclaration, et comme M est une autre façon de définir le paramètre P12, cette déclaration sera lue comme (P12=30), et la valeur 30 sera affectée au paramètre P12. Les paramètres globaux (P100-P299) peuvent être utilisés dans tout le programme par n’importe quel bloc, indépendamment de son niveau d’imbrication. Les usinages multiples (G60, G61, G62, G63, G64, G65) et les cycles fixes d’usinage (G69, G81, .... G89) utilisent le sixième niveau d’imbrication de paramètres locaux, quand ils sont actifs. Les cycles fixes d’usinage utilisent le paramètre global P299 pour leurs calculs internes, tandis que les cycles fixes de palpeur emploient les paramètres globaux P294 à P299. Chapitre: 13 PROGRAMMATIONENLANGAGEDEHAUTNIVEAU Section: VARIABLESDECARACTERE GENERAL Page 7 13.2.2 VARIABLES ASSOCIÉES AUX OUTILS Ces variables sont associées la table de correcteurs, à la table d’outils et à la table de magasin d’outils; les valeurs affectées ou lues dans ces champs devront respecter les formats définis pour ces tables. Table de Correcteurs R, L, I, K Sont indiqués en unités actives: Si G70 en pouces. Max. ±3937.00787 Si G71 en millimètres. Max. ±99999.9999 Si axe rotatif, en degrés. Max. ±99999.9999 Table d’Outils: Numéro de correcteur Code de famille 0...NTOFFSET (maximum 255) Si outil normal 0 ≤ n < 200 Si outil spécial 200 ≤ n ≤ 255 0...65535 minutes ou opérations 0...9999999 centièmes de minute ou 99999 opérations Vie nominale Vie réelle Table du magasin d’outils: Contenu de chaque logement du magasin Numéro d’outil 1...NTOOL (maximum 255) 0 Vide -1 Annulé Position de l’outil dans le magasin Numéro de logement 1..NPOCKET (maximum 255) 0 Dans la broche -1 Introuvable -2 A la position de changement Variables de lecture TOOL: Donne le numéro de l’outil actif. (P100=TOOL); Affecte au paramètre P100 le numéro de l’outil actif. Page 8 TOD: Donne le numéro du correcteur actif NXTOOL: Donne le numéro de l’outil suivant, sélectionné mais en attente de l’exécution de M06 pour être actif. NXTOD: Donne le numéro du correcteur correspondant à l’outil suivant, sélectionné mais en attente de l’exécution de M06 pour être actif. TMZPn: Donne la position occupée par l’outil indiqué (n) dans le magasin d’outils. Chapitre: 13 Section: PROGRAMMATIONENLANGAGEDEHAUTNIVEAU VARIABLES ASSOCIÉES AUX OUTILS Variables de lecture et d’écriture TORn: Cette variable permet de lire ou de modifier, dans la table de correcteurs, la valeur affectée au Rayon du correcteur indiqué (n). (P110 = TOR3); Correcteur 3. Affecte au paramètre P110 la valeur R du (TOR3 = P111) ; correcteur 3. Affecte la valeur du paramètre P111 à R du TOLn: Cette variable permet de lire ou de modifier, dans la table de correcteurs, la valeur affectée à la Longueur du correcteur indiqué (n). TOIn: Cette variable permet de lire ou de modifier, dans la table de correcteurs, la valeur affectée à l’usure du rayon (I) du correcteur indiqué (n). TOKn: Cette variable permet de lire ou de modifier, dans la table de correcteurs, la valeur affectée à l’usure de la longueur (K) du correcteur indiqué (n). TLFDn: Cette variable permet de lire ou de modifier, dans la table d’outils, le numéro du correcteur de l’outil indiqué (n). TLFFn: Cette variable permet de lire ou de modifier, dans la table d’outils, le code de famille de l’outil indiqué (n). TLFNn: Cette variable permet de lire ou de modifier, dans la table d’outils, la valeur affectée comme vie nominale de l’outil indiqué (n). TLFRn: Cette variable permet de lire ou de modifier, dans la table d’outils, la valeur de la vie réelle de l’outil indiqué (n). TMZTn: Cette variable permet de lire ou de modifier, dans la table du magasin d’outils, le contenu du logement indiqué (n). Chapitre: 13 Section: PROGRAMMATIONENLANGAGEDEHAUTNIVEAU VARIABLES ASSOCIÉES AUX OUTILS Page 9 13.2.3 VARIABLES ASSOCIÉES AUX DECALAGES D’ORIGINE Ces variables sont associées aux décalages d’origine, et peuvent correspondre aux valeurs de la table ou aux valeurs actuelles sélectionnées par la fonction G92 ou par présélection manuelle en mode JOG. Les décalages d’origine possibles, en plus du décalage supplémentaire indiqué par le PLC, sont G54, G55, G56, G57, G58 et G59. Les valeurs de chaque axe s’expriment en unités actives: Si G70 en pouces. Max. ±3937.00787 Si G71 en millimètres. Max. ±99999.9999 Si axe rotatif en degrés. Max. ±99999.9999 Bien qu’il existe des variables liées à chaque axe, la CNC n’autorise que celles associées aux axes sélectionnés dans la CNC. Par exemple, si la CNC contrôle les axes X, Y, Z, U et B, elle n’admettra, dans le cas de ORG(X-C) que les variables ORGX, ORGY, ORGZ, ORGU et ORGB. Variables de lecture ORG(X-C): Donne la valeur du décalage d’origine actif pour l’axe sélectionné. Le décalage supplémentaire indiqué par le PLC n’est pas compris dans cette valeur. (P100 = ORGX) ; Affecte au paramètre P100 la valeur du décalage d’origine actif pour l’axe X. Cette valeur a pu être sélectionnée manuellement, par la fonction G92, ou par la variable “ORG(XC)n”. PORGF: Donne la coordonnée, par rapport à l’origine des coordonnées cartésiennes, de l’origine des coordonnées polaires selon l’axe des abscisses. PORGS: Donne la coordonnée, par rapport à l’origine des coordonnées cartésiennes, de l’origine des coordonnées polaires selon l’axe des ordonnées. Variables de lecture et d’écriture ORG(X-C)n: Cette variable permet de lire ou de modifier la valeur de l’axe sélectionnée dans la table correspondant au décalage d’origine indiqué (n). (P110 = ORGX 55);Affecte au paramètre P110 la valeur de l’axe X dans la table correspondant au décalage d’origine G55. (ORGY 54 = P111) ; Affecte à l’axe Y, dans la table correspondant au décalage d’origine G54, la valeur du paramètre P111. PLCOF(X-C): Cette variable permet de lire ou de modifier la valeur de l’axe sélectionnée dans la table de décalages d’origine indiquée par le PLC. L’accès à l’une des variables PLCOF(X-C) entraîne l’interruption de la préparation des blocs et l’attente de l’exécution de cette commande avant la reprise de la préparation des blocs. Page 10 Chapitre: 13 PROGRAMMATIONENLANGAGEDEHAUTNIVEAU Section: VARIABLES ASSOCIÉES AUX DECALAGES D’ORIGINE 13.2.4 VARIABLES ASSOCIÉES AUX PARAMETRES MACHINE Ces variables, associées aux paramètres machine, sont des variables de lecture. Pour connaître le format des valeurs données, on consultera le manuel d’installation et de mise en service. Les valeurs 1/0 correspondent aux paramètres définis par YES/NO, +/- et ON/OFF. Les valeurs relatives aux coordonnées et aux avances sont exprimées en unités actives: Si G70 en pouces. Max. ±3937.00787 Si G71 en millimètres. Max. ±99999.9999 Si axe rotatif en degrés. Max. ±99999.9999 Variables de lecture MPGn: Donne la valeur affectée au paramètre machine général indiqué (n). (P110 = MPG8) ; Affecte au paramètre P110 la valeur du paramètre machine général P8 "INCHES"; si les unités actives sont les millimètres, P110=0 et si ces unités sont en pouces, P110=1. MP(X-C)n: Donne la valeur affectée au paramètre machine des axes indiqué (n). (P110 = MPY 1) ; Affecte au paramètre P110 la valeur du paramètre machine P1 de l’axe Y "DFORMAT", qui indique le format employé pour sa visualisation. MPSn: Donne la valeur affectée au paramètre machine de broche indiqué (n). MPASn: Donne la valeur affectée au paramètre machine de broche auxiliaire indiqué (n). MPLCn: Donne la valeur affectée au paramètre machine du PLC indiqué (n). Chapitre: 13 PROGRAMMATIONENLANGAGEDEHAUTNIVEAU Section: VARIABLES ASSOCIÉES AUX PARAMETRES MACHINE Page 11 13.2.5 VARIABLES ASSOCIÉES AUX ZONES DE TRAVAIL Ces variables associées aux zones de travail sont des variables à lecture seulement. Les valeurs des limites sont exprimées en unités actives: Si G70 en pouces. Max. ±3937.00787 Si G71 en millimetres. Max. ±99999.9999 Si axe rotatif en degrés. Max. ±99999.9999 L’état des zones de travail est défini par le code suivant: 0 = Invalidée 1 = Validée comme zone interdite à l’entrée 2 = Validée comme zone interdite à la sortie Variables de lecture FZONE: Donne l’état de la zone de travail 1. (P100=FZONE); Affecte au paramètre P100 l’état de la zone de travail 1. Page 12 SZONE: Devuelve el estado de la zona de trabajo 2. FZLO(X-C): Donne la valeur de la limite inférieure de la zone 1 selon l’axe sélectionné (X-C). FZUP(X-C): Donne la valeur de la limite supérieure de la zone 1 selon l’axe sélectionné (X-C). SZLO(X-C): Donne la valeur de la limite inférieure de la zone 2 selon l’axe sélectionné (X-C). SZUP(X-C): Donne la valeur de la limite supérieure de la zone 2 selon l’axe sélectionné (X-C). Chapitre: 13 Section: PROGRAMMATIONENLANGAGEDEHAUTNIVEAU VARIABLES ASSOCIÉES AUX ZONES DE TRAVAIL 13.2.6 VARIABLES ASSOCIÉES AUX AVANCES Les valeurs des avances sont exprimées en unités actives (pouces/minute ou millimètres/ minute). Les valeurs de Correction (“Override”) de l’avance sont données par un entier entre 0 et 255. Variables de lecture FREAL: Donne l’avance réelle de la CNC, en mm/minute ou pouces/minute. (P100 = FREAL) ; Affecte au paramètre P100 l’avance réelle de la CNC. FEED: Donne l’avance sélectionnée dans la CNC par la fonction G94, en mm/minute ou pouces/minute. Cette avance peut être définie par programme, par le PLC ou par DNC, le choix étant fait par la CNC; la plus prioritaire est celle définie par DNC, et la moins prioritaire celle définie par programme. DNCF: Donne l’avance, en mm/minute ou pouces/minute, sélectionnée par DNC. Une valeur 0 signifie que cette avance n’est pas sélectionnée. PLCF: Donne l’avance, en mm/minute ou pouces/minute, sélectionnée par le PLC. Une valeur 0 signifie que cette avance n’est pas sélectionnée. PRGF: Donne l’avance, en mm/minute ou pouces/minute, sélectionnée par programme. FPREV: Donne l’avance sélectionnée dans la CNC par la fonction G95, en mm/tour ou pouces/tour. Cette avance peut être définie par programme, par le PLC ou par DNC, le choix étant fait par la CNC; la plus prioritaire est celle définie par DNC, et la moins prioritaire celle définie par programme. DNCFPR: Donne l’avance, en mm/tour ou pouces/tour, sélectionnée par DNC. Une valeur 0 signifie que cette avance n’est pas sélectionnée. PLCFPR: Donne l’avance, en mm/tour ou pouces/tour, sélectionnée par le PLC. Une valeur 0 signifie que cette avance n’est pas sélectionnée. PRGFPR: Donne l’avance, en mm/tour ou pouces/tour, sélectionnée par programme. Chapitre: 13 Section: PROGRAMMATIONENLANGAGEDEHAUTNIVEAU VARIABLES ASSOCIÉES AUX AVANCES Page 13 FRO: Donne la Correction (Override (%)) d’avance sélectionnée dans la CNC. Elle est indiquée par un entier entre 0 et "MAXFOVR" (maximum: 255). Ce pourcentage de l’avance peut être défini par programme, par le PLC, par DNC ou depuis le panneau avant; il est sélectionné par la CNC, l’ordre de priorité (du plus au moins prioritaire) étant: par programme, par DNC, par le PLC et depuis le sélecteur. DNCFRO: Donne le pourcentage d’avance sélectionné par DNC. Une valeur 0 signifie qu’il n’est pas sélectionné. PLCFRO: Donne le pourcentage d’avance sélectionné par PLC. Une valeur 0 signifie qu’il n’est pas sélectionné. CNCFRO: Donne le pourcentage d’avance défini par le sélecteur. Variables de lecture et d’écriture PRGFRO: Cette variable permet de lire ou de modifier le pourcentage d’avance sélectionné par programme. Il est indiqué par un entier entre 0 et "MAXFOVR" (maximum: 255). Une valeur 0 signifie qu’il n’est pas sélectionné. (P110 = PRGFRO) ; Affecte au paramètre P110 le pourcentage d’avance sélectionné par programme. (PRGFRO = P111) ; Affecte au pourcentage d’avance sélectionné par programme la valeur du paramètre P111. Page 14 Chapitre: 13 Section: PROGRAMMATIONENLANGAGEDEHAUTNIVEAU VARIABLES ASSOCIÉES AUX AVANCES 13.2.7 VARIABLES ASSOCIÉES AUX COORDONNEES Les valeurs des coordonnées de chaque axe sont exprimées en unités actives: Si G70 en pouces. Max. ±3937.00787 Si G71 en millimètres. Max. ±99999.9999 Si axe rotatif en degrés. Max. ±99999.9999 Variables de lecture PPOS(X-C): Donne la coordonnée théorique programmée de l’axe sélectionné. (P100 = PPOSX) ; Affecte au paramètre P100 la coordonnée théorique programmée de l’axe X. POS(X-C): Donne la coordonnée réelle de l’axe sélectionné, par rapport au zéro machine. TPOS(X-C): Donne la coordonnée théorique (coordonnée réelle + erreur de poursuite) de l’axe sélectionné, par rapport au zéro machine. FLWE(X-C): Donne l’erreur de poursuite de l’axe sélectionné. DEFLEX: DEFLEY: DEFLEZ: Donnent l’écart actuel dont dispose la sonde Renishah SP2 sur chaque axe X, Y, Z. L’accès à l’une des variables POS(X-C), TPOS(X-C), FLWE(XC), DEFLEX, DEFLEY ou DEFLEZ entraîne l’interruption de la préparation des blocs et l’attente de l’exécution de cette commande avant la reprise de la préparation des blocs. Variables de lecture et d’écriture DIST(X-C): Ces variables permettent de lire ou de modifier la distance parcourue par l’axe sélectionné. Cette valeur est accumulative et très utile si l’on désire réaliser une opération dépendant de la distance parcourue par les axes, comme par exemple leur graissage. (P110 = DISTX) ; Affecte au paramètre P110 la distance parcourue par l’axe X. (DISTZ = P111) ; Initialise la variable indiquant la distance parcourue par l’axe Z avec la valeur du paramètre P111. L’accès à l’une des variables DIST(X-C) entraîne l’interruption de la préparation des blocs et l’attente de l’exécution de cette commande avant la reprise de la préparation des blocs. Chapitre: 13 Section: PROGRAMMATIONENLANGAGEDEHAUTNIVEAU VARIABLES ASSOCIÉES AUX COORDONNEES Page 15 13.2.8 VARIABLES ASSOCIÉES A LA BROCHE Dans ces variables associées à la broche, les valeurs de vitesse sont données en tours/minute, et les valeurs de Correcteur (“Override”) de la broche sont données par des entiers entre 0 et 255. Variables de lecture SREAL: Donne la vitesse de rotation réelle de broche en tours/minute. (P100 = SREAL) ; Affecte au paramètre P100 la vitesse de rotation réelle de la broche. L’accès à cette variable entraîne l’interruption de la préparation des blocs et l’attente de l’exécution de cette commande avant la reprise de la préparation des blocs. SPEED: Donne, en tours/minute, la vitesse de rotation de broche sélectionnée dans la CNC. Cette vitesse de rotation peut être définie par programme, par le PLC ou par DNC, le choix étant fait par la CNC; la plus prioritaire est celle définie par DNC, et la moins prioritaire celle définie par programme. DNCS: Donne la vitesse de rotation, en tours/minute, sélectionnée par DNC. Une valeur 0 signifie qu’elle n’est pas sélectionnée. PLCS: Donne la vitesse de rotation, en tours/minute, sélectionnée par le PLC. Une valeur 0 signifie qu’elle n’est pas sélectionnée. PRGS: Donne la vitesse de rotation, en tours/minute, sélectionnée par programme. SSO: Donne la Correction (“Override (%)) de vitesse de rotation de broche sélectionnée dans la CNC. Elle est indiquée par un entier entre 0 et "MAXSOVR" (maximum: 255). Ce pourcentage de vitesse de rotation de broche peut être défini par programme, par le PLC, par DNC ou depuis le panneau avant; il est sélectionné par la CNC, l’ordre de priorité (du plus au moins prioritaire) étant: par programme, par DNC, par le PLC et depuis le panneau avant. DNCSSO: Page 16 Donne le pourcentage de vitesse de rotation de la broche sélectionné par DNC. Une valeur 0 signifie qu’il n’est pas sélectionné. Chapitre: 13 Section: PROGRAMMATIONENLANGAGEDEHAUTNIVEAU VARIABLES ASSOCIÉES A LA BROCHE PLCSSO: Donne le pourcentage de vitesse de rotation de la broche sélectionné par PLC. Une valeur 0 signifie qu’il n’est pas sélectionné. CNCSSO: Donne le pourcentage de vitesse de rotation de la broche sélectionné depuis le panneau avant. SLIMIT: Donne, en tours/minute, la valeur définie pour la limite de vitesse de rotation de broche dans la CNC. Cette limite peut être définie par programme, par le PLC ou par DNC, le choix étant fait par la CNC; la plus prioritaire est celle définie par DNC, et la moins prioritaire celle définie par programme. DNCSL: Donne, en tours/minute, la limite de vitesse de rotation de broche sélectionnée par DNC. Une valeur 0 signifie qu’elle n’est pas sélectionnée. PLCSL: Donne, en tours/minute, la limite de vitesse de rotation de broche sélectionnée par le PLC. Une valeur 0 signifie qu’elle n’est pas sélectionnée. PRGSL: Donne, en tours/minute, la limite de vitesse de rotation de broche sélectionnée par programme. POSS: Renvoie la valeur de la position réelle de la broche, quand elle est en boucle fermée (M19). Cette valeur est indiquée en unités de 0,0001 degré entre ±999999999. RPOSS: Renvoie la valeur de la position réelle de la broche. Cette valeur est indiquée en unités de 0,0001 degré entre 0 et 360°. TPOSS: Renvoie la valeur de la position théorique de la broche. Cette valeur est indiquée en unités de 0,0001 degré entre ±999999999. RTPOSS: Renvoie la valeur de la position théorique de la broche. Cette valeur est indiquée en unités de 0,0001 degré entre 0 et 360°. FLWES: Renvoie l’erreur de poursuite de la broche lorsqu’elle fonctionne en boucle fermée (M19). Lors de l’accès à ces variables (POSS, RPOSS, TPOSS, RTPOSS ou FLWES), la préparation des blocs est interrompue et la CNC attend que cette instruction soit exécutée avant de reprendre la préparation des blocs. Variables de lecture et d’écriture PRGSSO: Cette variable permet de lire ou de modifier le pourcentage de vitesse de rotation de broche sélectionné par programme. Il est indiqué par un entier entre 0 et "MAXSOVR" (maximum: 255). Une valeur 0 signifie qu’il n’est pas sélectionné. (P110 = PRGSSO) ; Affecte au paramètre P110 le pourcentage de vitesse de rotation de broche sélectionné par programme. (PRGSSO = P111) ; Affecte au pourcentage de vitesse de rotation de broche sélectionné par programme la valeur du paramètre P111. Chapitre: 13 Section: PROGRAMMATIONENLANGAGEDEHAUTNIVEAU VARIABLES ASSOCIÉES A LA BROCHE Page 17 13.2.9 VARIABLES ASSOCIÉES A L’AUTOMATE On tiendra compte du fait que l’automate dispose des ressources suivantes: Entrées ...................... (I1 à I256) Sorties ....................... (O1 à O256) Indicateurs ................. (M1 à M5957) Registres .................... (R1 à R256) de 32 bits chacun Temporisateurs .......... (T1 à T256) avec comptage sur 32 bits Compteurs ................. (C1 à C256) avec comptage sur 32 bits L’accès à une variable quelconque permettant de lire ou de modifier l’état d’une ressource du PLC (I, O, M, R, T, C), entraîne l’interruption de la préparation des blocs et l’attente de l’exécution de cette commande avant la reprise de la préparation des blocs. Variables de lecture PLCMSG: Donne le numéro du message d’automate le plus prioritaire actif, qui coïncidera avec celui visualisé à l’écran (1..128). En l’absence de message, la variable est à “0” (P100 = PLCMSG) ; Donne le numéro du message d’automate le plus prioritaire actif. Variables de lecture et d’écriture PLCIn: Cette variable permet de lire ou de modifier 32 entrées de l’automate à partir de l’entrée indiquée (n) La valeur des entrées utilisées par l’armoire électrique ne peut pas être modifiée, car elle est imposée par cette armoire. L’état du reste des entrées peut être modifié. PLCOn: Cette variable permet de lire ou de modifier 32 sorties de l’automate à partir de la sortie indiquée (n) (P110 = PLCO 22) ; Affecte au paramètre P110 la valeur des sorties O22 à O53 (32 sorties) du PLC. (PLCO 22 = $F) ; Affecte la valeur 1 aux sorties O22 à O25 et la valeur 0 aux sorties O26 à O53. Bit Sortie Page 18 31 30 29 28 27 26 25 24 23 22 21 20 6 5 4 3 2 1 0 0 0 0 0 0 0 0 0 0 0 0 0 0 0 0 1 1 1 1 53 52 51 50 49 48 47 46 45 44 43 42 28 27 26 25 24 23 22 PLCMn: Cette variable permet de lire ou de modifier 32 marques de l’automate à partir de la marque indiquée (n) PLCRn: Cette variable permet de lire ou de modifier l’état des 32 bits du registre indiqué (n). PLCTn: Cette variable permet de lire ou de modifier le comptage du temporisateur indiqué (n). PLCCn: Cette variable permet de lire ou de modifier le comptage du compteur indiqué (n). Chapitre: 13 PROGRAMMATIONENLANGAGEDEHAUTNIVEAU Section: VARIABLES ASSOCIÉES A L’AUTOMATE 13.2.10 VARIABLES ASSOCIÉES AUX PARAMETRES LOCAUX La CNC permet d’affecter 26 paramètres locaux (P0-P25) à une sous-routine grâce aux mnémoniques PCALL et MCALL. Ces mnémoniques permettent l’exécution de la sous-routine désirée ainsi que l’initialisation de ses paramètres locaux. Variables de lecture CALLP: Permet de savoir quels paramètres locaux ont été définis et ceux qui ne l’ont pas été dans l’appel de sous-routine par la mnémonique PCALL ou MCALL. Les informations sont données par les 26 bits les moins significatifs (bits 0..25), chacun correspondant au paramètre local portant le même numéro; ainsi, le bit 12 correspond à P12. Chaque bit indiquera si le paramètre local a été défini (=1) ou non (=0). 31 30 29 28 27 26 25 24 23 22 21 20 0 0 0 0 0 0 * * * * * * 6 5 * * * * * * * 4 3 2 1 Exemple: (PCALL 20, P0=20, P2=3, P3=5) ; Appel de la sous-routine 20 .... .... (SUB 20) ; Début de la sous-routine 20 (P100 = CALLP) .... .... Dans le paramètre P100, on obtiendra: 0000 0000 0000 0000 0000 0000 0000 1101 LSB Chapitre: 13 PROGRAMMATIONENLANGAGEDEHAUTNIVEAU Section: VARIABLES ASSOCIÉES AUX PARAMETRES LOCAUX Page 19 0 13.2.11 AUTRES VARIABLES Variables de lecture OPMODE: Donne le code correspondant au mode de fonctionnement sélectionné. 0 = Menu principal 10 11 12 13 = = = = Exécution en automatique Exécution en bloc à bloc MDI en EXECUTION Inspection d’outil 20 21 22 23 24 = = = = = Simulation du déplacement selon la trajectoire théorique Simulation des fonctions G Simulation des fonctions G, M, S et T Simulation avec déplacement dans le plan principal Simulation avec déplacement en rapide 30 31 32 33 34 = = = = = Edition normale Edition utilisateur Edition en TEACH-IN Editeur interactif Editeur de profils 40 41 42 43 44 45 46 47 = = = = = = = = Déplacement en JOG continu Déplacement en JOG incrémental Déplacement avec manivelle électronique Recherche du zéro en MANUEL Présélection de position en MANUEL Mesure d’outil MDI en MANUEL Fonctionnement MANUEL utilisateur 50 51 52 53 54 55 = = = = = = Table des origines Table des correcteurs Table d’outils Table de magasin d’outils Table de paramètres globaux Tables de paramètres locaux 60 = Utilitaires 70 = DNC Page 20 Chapitre: 13 PROGRAMMATIONENLANGAGEDEHAUTNIVEAU Section: AUTRESVARIABLES 80 81 82 83 84 85 86 87 88 = = = = = = = = = Edition des fichiers du PLC Compilation du programme du PLC Contrôle du PLC Messages actifs du PLC Pages actives du PLC Sauvegarde du programme du PLC Rappel du programme du PLC Mode “ressources du PLC utilisées” Statistiques du PLC 90 = Personnalisation 100 101 102 103 104 105 106 = = = = = = = 110 111 112 113 = = = = Table des paramètres machine généraux Tables de paramètres machine des axes Table des paramètres machine de la broche Tablas de parámetros máquina des lignes série Table des paramètres machine du PLC Table de fonctions M Tables de compensation de broche et croisée Diagnostic: configuration Diagnostic: test de matériel Diagnostic: test de mémoire RAM Diagnostic: test de mémoire EPROM (sommes de contrôle) 114 = Diagnostic d’utilisateur PRGN: Donne le numéro de programme en cours d’exécution. Si aucun programme n’est sélectionné, cette variable est à la valeur -1. BLKN: Donne le numéro d’étiquette du dernier bloc exécuté. GSn: Donne l’état de la fonction G indiquée (n). Un 1 indique une fonction active, un 0 indique une fonction inactive. (P120 = GS17) ; Affecte la valeur 1 au paramètre P120 si la fonction G17 est active, et la valeur 0 dans le cas contraire. MSn: Donne l’état de la fonction M indiquée (n), soit 1 si elle est active, et 0 dans le cas contraire. Cette variable donne l’état des fonctions M00, M01, M02, M03, M04, M05, M06, M08, M09, M19, M30, M41, M42, M43, M44 et M45. Chapitre: 13 PROGRAMMATIONENLANGAGEDEHAUTNIVEAU Section: AUTRESVARIABLES Page 21 PLANE: Donne sur 32 bits et en binaire les informations sur l’axe des abscisses (bits 4 à 7) et de l’axe des ordonnées (bits 0 à 3) du plan actif. .... .... .... .... .... .... 7654 3210 LSB Axe des ordonnées Axe des abscisses Les axes sont codifiés sur 4 bits et indiquent le numéro de l’axe (de 1 à 6) suivant l’ordre de programmation. Exemple: Si la CNC contrôle les axes X, Y, Z, U, B, C et si le plan ZX est sélectionné (G18) (P122 = PLANE) affecte la valeur $31 au paramètre P122. 0000 LONGAX: 0000 0000 0000 0000 0000 0011 0001 LSB Donne le numéro (1 à 6) selon l’ordre de programmation correspondant à l’axe longitudinal. Il s’agit de l’axe sélectionné par la fonction G15 ou, à défaut, de l’axe perpendiculaire au plan actif, s’il s’agit du plan XY, ZX ou YZ. Exemple: Si la CNC contrôle les axes X, Y, Z, U, B, C et si l’axe U est sélectionné (P122 = LONGAX) affecte la valeur 4 au paramètre P122. MIRROR: Donne, sur les 6 bits de poids le plus faible d’un groupe de 32 bits, l’état de l’image miroir de chaque axe, soit 1 s’il est actif et 0 dans le cas contraire. LSB Axe 1 Axe 2 Axe 3 Axe 4 Axe 5 Axe 6 Le nom de l’axe correspond au numéro (1 à 6) affecté selon leur ordre de programmation. Exemple: Si la CNC contrôle les axes X, Y, Z, U, B, C on aura Axe1=X, Axe2=Y, Axe3=Z, Axe4=U, Axe5=B, Axe6=C. Page 22 Chapitre: 13 PROGRAMMATIONENLANGAGEDEHAUTNIVEAU Section: AUTRESVARIABLES SCALE: Donne le facteur d’échelle général appliqué. SCALE(X-C): Donne le facteur d’échelle particulier de l’axe indiqué (X-C). ORGROT: Donne l’angle de rotation du système de coordonnées sélectionné en cours par la fonction G73. Sa valeur est indiquée en degrés. Max. ±99999.9999 ROTPF: Donne, par rapport à l’origine des coordonnées cartésiennes, la coordonnée du centre de rotation selon l’axe des abscisses. Sa valeur est donnée en unités actives: Si G70 en pouces. Max. ±3937.00787 Si G71 en millimètres. Max. ±99999.9999 ROTPS: Donne, par rapport à l’origine des coordonnées cartésiennes, la coordonnée du centre de rotation selon l’axe des ordonnées. Sa valeur est donnée en unités actives: Si G70 en pouces. Max. ±3937.00787 Si G71 en millimètres. Max. ±99999.9999 PRBST: Donne l’état du palpeur. 0 = le palpeur n’est pas en contact avec la pièce 1 = le palpeur est en contact avec la pièce L’accès à cette variable entraîne l’interruption de la préparation des blocs et l’attente de l’exécution de cette commande avant la reprise de la préparation des blocs. CLOCK: Donne, en secondes, l’heure indiquée par l’horloge système. Les valeurs possibles sont 0...4294967295 L’accès à cette variable entraîne l’interruption de la préparation des blocs et l’attente de l’exécution de cette commande avant la reprise de la préparation des blocs. TIME: Donne l’heure dans le format heures-minutes-secondes. (P150 = TIME) ; Affecte hh-mm-ss au paramètre P150. Par exemple, s’il est 18h 22m. 34seg. on aura 182234 dans P150. L’accès à cette variable entraîne l’interruption de la préparation des blocs et l’attente de l’exécution de cette commande avant la reprise de la préparation des blocs. DATE: Donne la date dans le format année-mois-jour. (P151 = DATE) ; Affecte année-mois-jour au paramètre P151. Pour le 25 Avril 1992, on aura 920425 dans P151. L’accès à cette variable entraîne l’interruption de la préparation des blocs et l’attente de l’exécution de cette commande avant la reprise de la préparation des blocs. Chapitre: 13 PROGRAMMATIONENLANGAGEDEHAUTNIVEAU Section: AUTRESVARIABLES Page 23 CYTIME: Donne, en centièmes de seconde, la durée d’exécution écoulée de la pièce. Les valeurs possibles sont 0..4294967295 L’accès à cette variable entraîne l’interruption de la préparation des blocs et l’attente de l’exécution de cette commande avant la reprise de la préparation des blocs. FIRST: Indique s’il s’agit de la première exécution d’un programme. Cette variable est à “1” dans l’affirmative, et à “0” par la suite. Est considérée comme première exécution celle qui a lieu: Après la mise sous tension de la CNC Après la frappe des touches "Shift - Reset" Chaque fois qu’un nouveau programme est sélectionné. ANAIn: Donne en volts et dans le format ±1.4 (valeurs ±5 Volts), l’état de l’entrée analogique indiquée (n), le choix étant possible parmi l’une des huit (1..8) entrées analogiques. L’accès à cette variable entraîne l’interruption de la préparation des blocs et l’attente de l’exécution de cette commande avant la reprise de la préparation des blocs. Variables de lecture et d’écriture TIMER: Cette variable permet de lire ou de modifier le temps, en secondes, indiqué par l’horloge validée par le PLC. Lers valeurs possibles sont 0...4294967295. L’accès à cette variable entraîne l’interruption de la préparation des blocs et l’attente de l’exécution de cette commande avant la reprise de la préparation des blocs. PARTC: La CNC dispose d’un compteur de pièces qui s’incrémente à chaque exécution de M30 ou M02 et cette variable permet de lire ou de modifier sa valeur, qui est donnée par un nombre compris entre 0 et 4294967295. L’accès à cette variable entraîne l’interruption de la préparation des blocs et l’attente de l’exécution de cette commande avant la reprise de la préparation des blocs. KEY: Permet de lire le code de la dernière touche acceptée par la CNC. Cette variable peut être utilisée comme variable d’écriture exclusivement, dans un programme de personnalisation (canal utilisateur). L’accès à cette variable entraîne l’interruption de la préparation des blocs et l’attente de l’exécution de cette commande avant la reprise de la préparation des blocs. Page 24 Chapitre: 13 PROGRAMMATIONENLANGAGEDEHAUTNIVEAU Section: AUTRESVARIABLES KEYSRC: Cette variable permet de lire ou de modifier la provenance des touches, les valeurs possibles étant les suivantes: 0 = Clavier 1 = PLC 2 = DNC La CNC n’autorise la modification du contenu de cette variable que si elle est à “0”. ANAOn: Cette variable permet de lire ou de modifier la sortie analogique désirée (n). Sa valeur est exprimée en volts et dans le format ±2.4 (±10 Volts). Les sorties analogiques libres parmi les huit (1..8) dont dispose la CNC peuvent être modifiées, et le code d’erreur correspondant apparaîtra en cas de tentative d’écriture dans une sortie occupée. L’accès à cette variable entraîne l’interruption de la préparation des blocs et l’attente de l’exécution de cette commande avant la reprise de la préparation des blocs. Chapitre: 13 PROGRAMMATIONENLANGAGEDEHAUTNIVEAU Section: AUTRESVARIABLES Page 25 13.3 CONSTANTES Sont définies comme constantes toutes les valeurs fixes ne pouvant pas être modifiées par programme. Sont considérés comme constantes: - 13.4 Les nombres exprimés en système décimal. Les nombres hexadécimaux. La constante PI (π). Les tables et les variables de lecture seule, car leur valeur ne peut pas être modifiée à l’intérieur d’un programme. OPERATEURS Un opérateur est un symbole qui indique les manipulations mathématiques ou logiques à réaliser. La CNC 8050 dispose d’opérateurs arithmétiques, relationnels, logiques, binaires, trigonométriques et d’opérateurs spéciaux. Opérateurs arithmétiques + - : addition. : soustraction, également pour indiquer un nombre négatif. ∗ : multiplication. / : division. MOD : modulo ou reste de la division. EXP : exponentiel. P1=3 + 4 P2=5 - 2 P3= -(2 ∗ 3) P4=2 ∗ 3 P5=9 / 2 P6=7 MOD 4 P7=2 EXP 3 -> P1=7 -> P2=3 -> P3=-6 -> P4=6 -> P5=4.5 -> P6=3 -> P7=8 Opérateurs relationnels EQ NE GT GE LT LE Page 26 : égal. : non-égal. : supérieur à. : supérieur ou égal à. : inférieur à. : inférieur ou égal à. Chapitre: 13 PROGRAMMATIONENLANGAGEDEHAUTNIVEAU Section: CONSTANTES ET OPERATEURS Opérateurs logiques et binaires NOT, OR, AND, XOR: agissent comme des opérateurs logiques entres les conditions, et comme des opérateurs binaires entres les variables et les constantes. IF (FIRST AND GS1 EQ 1) GOTO N100 P5 = (P1 AND (NOT P2 OR P3)) Fonctions trigonométriques SIN : COS : TAN : ASIN : ACOS : ATAN : ARG : sinus. cosinus. tangente. sinus d’arc. cosinus d’arc. tangente d’arc. ARG( x,y ) tangente d’arc y/x. P1=SIN 30 P2=COS 30 P3=TAN 30 P4=ASIN 1 P5=ACOS 1 P6=ATAN 1 P7=ARG(-1,-2) -> -> -> -> -> -> -> P1=0.5 P2=0.8660 P3=0.5773 P4=90 P5=0 P6=45 P7=243.4349 Deux fonctions permettent de calculer la tangente d’arc: ATAN qui donne le résultat entre ± 90º et ARG qui la donne entre 0 et 360º. Autres fonctions ABS : valeur absolue. LOG : logarithme décimal. SQRT : racine carrée. ROUND: arrondi a un entier. FIX : partie entière. FUP : si entier, prend la partie entière. si non, prend la partie entière plus un. BCD : convertit le numéro donné en BCD. P1=ABS -8 P2=LOG 100 P3=SQRT 16 P4=ROUND 5.83 P5=FIX 5.423 P6=FUP 7 P6=FUP 5.423 -> P1=8 -> P2=2 -> P3=4 -> P4=6 -> P5=5 -> P6=7 -> P6=6 P7=BCD 234 ->P7=564 0010 0011 0100 BIN : convertit le numéro donné en binaire. P8=BIN $AB -> P8=171 1010 1011 Les conversions en binaire et en BCD s’effectueront sur 32 bits, le nombre 156 pouvant être représenté dans les formats suivants : Décimal Hexadécimal Binaire BCD 156 9C 0000 0000 0000 0000 0000 0000 1001 1100 0000 0000 0000 0000 0000 0001 0101 0110 Chapitre: 13 PROGRAMMATIONENLANGAGEDEHAUTNIVEAU Section: OPERATEURS Page 27 13.5 EXPRESSIONS Une expression est toute combinaison valide entre opérateurs, constantes et variables. Toutes les expressions doivent être placées entre parenthèses, qui peuvent être omises si l’expression se réduit à un nombre entier. 13.5.1 EXPRESSIONS ARITHMETIQUES Les expressions arithmétiques sont formées en combinant des fonctions et des opérateurs arithmétiques, binaires et trigonométriques avec les constantes et les variables du langage. Le mode de fonctionnement avec ces expressions est défini par les priorités des opérateurs et leur associativité Priorité, de la plus haute à la plus basse NOT, fonctions, - (négatif) EXP,MOD ∗,/ +,- (addition, soustraction) opérateurs relationnels AND,XOR OR Associativité de droite à gauche. de gauche à droite. de gauche à droite. de gauche à droite. de gauche à droite. de gauche à droite. de gauche à droite. Il est commode d’utiliser des parenthèses pour clarifier l’ordre dans lequel s’évalue l’expression. (P3 = P4/P5 - P6 P7 - P8/P9 ) (P3 = (P4/P5)-(P6 P7)-(P8/P9)) L’eploi de parenthèses redondantes ou supplémentaires n’entraîne pas d’erreurs et ne réduit pas la vitesse d’exécution. L’emploi de parenthèses est obligatoire avec les fonctions, sauf si elles s’appliquent à une constante numérique; dans ce cas, elles sont optionnelles. (SIN 45) (SIN (45)) (SIN 10+5) les deux sont valides et équivalentes. équivaut à ((SIN 10)+5). Les expressions peuvent également être utilisées pour référencer les paramètres et les tables: (P100 = P9) (P100 = P(P7)) (P100 = P(P8 + SIN(P8 20))) (P100 = ORGX 55) (P100 = ORGX (12+P9)) (PLCM5008 = PLCM5008 OR 1) ; Sélectionne l’exécution Bloc à Bloc (M5008=1) (PLCM5010 = PLCM5010 AND $FFFFFFFE); Libère Override de l’avance (M5010=0) Page 28 Chapitre: 13 PROGRAMMATIONENLANGAGEDEHAUTNIVEAU Section: EXPRESSIONS 13.5.2 EXPRESSIONS RELATIONELLES Il s’agit d’expressions arithmétiques réunies par des opérateurs relationnels (IF (P8 EQ 12.8) ... ; Analyse si la valeur de P8 est égale à 12.8 (IF (ABS(SIN(P24)) GT SPEED) ... ; Analyse si le sinus est supérieur à la vitesse de broche (IF (CLOCK LT(P9*10.99)) ... ; Analyse si le comptage de l’horloge est inférieur à (P9*10.99) A leur tour, ces conditions peuvent être réunies par des opérateurs logiques. (IF ((P8EQ12.8) OR(ABS(SIN(P24))GT SPEED)) AND (CLOCK LT(PT*10.99)) ... Le résultat de ces expressions est vrai ou faux. Chapitre: 13 PROGRAMMATIONENLANGAGEDEHAUTNIVEAU Section: EXPRESSIONS Page 29 14. DECLARATIONS DE CONTROLE DES PROGRAMMES Les déclarations de contrôle disponibles pour la programmation de haut niveau peuvent être regroupées en: * Déclarations de Programmation, constituées de: Déclarations d’affectation Déclarations de visualisation Déclarations de validation-invalidation Déclarations de contrôle de flux Déclarations de sous-routines Déclarations pour génération de programmes * Déclarations de personnalisation Une seule déclaration devra être programmée par bloc, aucune autre information supplémentaire n’étant autorisée. 14.1 DÉCLARATIONS D’AFFECTATION Il s’agit du type de déclaration le plus simple, qui peut être défini comme: ( destination = expression arithmétique ) Le destinataire choisi peut être un paramètre local ou global, ou une variable de lecture et d’écriture. L’expression arithmétique peut être aussi complexe que nécessaire, ou une simple constante numérique. (P102 = FZLOY) (ORGY 55 = (ORGY 54 + P100)) Dans le cas particulier de l’affectation à un paramètre local au moyen de son nom (A au lieu de P0 par exemple) et si l’expression arithmétique est une constante numérique, la déclaration peut être abrégée comme suit: (P0=13.7) ==> (A=13.7) ==> (A13.7) Il est possible de réaliser jusqu’à 26 affectations à divers destinataires dans un seul bloc, l’ensemble d’affectations vers un seul et même destinataire étant interprêté comme une affectation unique. (P1=P1+P2, P1=P1+P3, P1=P1*P4, P1=P1/P5) équivaut à (P1=(P1+P2+P3)*P4/P5). Les différentes affectations réalisées dans un bloc donné sont séparées par des virgules ",". Chapitre: 14 DECLARATIONSDECONTROLEDESPROGRAMMES Section: DÉCLARATIONS D’AFFECTATION Page 1 14.2 DÉCLARATIONS DE VISUALISATION ( ERREUR nombre entier, "texte d’erreur" ) Cette déclaration interrompt l’exécution du programme et visualise l’erreur indiquée, cette erreur pouvant être sélectionnée comme suit: (ERREUR nombre entier). Visualisera le numéro d’erreur indiqué et le texte associé à ce numéro selon le code d’erreurs de la CNC (s’il existe). (ERREUR nombre entier, "texte de l’erreur"). Visualisera le numéro et le texte de l’erreur indiqués, le texcte devant s’écrire entre guillemets. (ERREUR "texte de l’erreur"). Visualisera exclusivement le texte d’erreur indiqué. Le numéro de l’erreur peut être défini par une constante numérique ou par un paramètre. Si un paramètre local est employé, on devra utiliser sa forme numérique (P0-P25). Exemples de programmation: (ERREUR 5) (ERREUR P100) (ERREUR "Erreur utilisateur") (ERREUR 3, "Erreur utilisateur") (ERREUR P120, "Erreur utilisateur") ( MSG "message" ) Cette déclaration visualise le message figurant entre guillemets. L’écran de la CNC comporte une zone de visualisation des messages DNC ou du programme de l’utilisateur, qui affiche toujours le dernier message reçu, indépendamment de sa provenance. Exemple: (MSG "Vérifier outil") Page 2 Chapitre: 14 DECLARATIONSDECONTROLEDESPROGRAMMES Section: DÉCLARATIONSDE VISUALISATION 14.3 DÉCLARATIONS DE VALIDATION-INVALIDATION ( ESBLK et DSBLK ) A partir de l’exécution de la mnémonique ESBLK, la CNC exécute tous les blocs suivants comme s’il s’agissait d’un bloc unique. Ce traitement en bloc unique reste actif jusqu’à son annulation par l’exécution de la mnémonique DSBLK. De cette façon, si le programme est exécuté en mode BLOC à BLOC, le groupe de blocs se trouvant entre les mnémoniques ESBLK et DSBLK s’exécutera en continu; autrement dit, l’exécution ne s’interrompt pas à la fin d’un bloc, mais passe au bloc suivant. Exemple: G01 X10 Y10 F8000 T1 D1 (ESBLK) G02 X20 Y20 I20 J-10 G01 X40 Y20 G01 X40 Y40 F10000 G01 X20 Y40 F8000 (DSBLK) G01 X10 Y10 M30 ; Début du bloc unique ; Annulation du bloc unique ( ESTOP et DSTOP ) A partir de l’exécution de la mnémonique DSTOP, la CNC invalide la touche Stop ainsi que le signal de Stop provenant de la PLC. Cette invalidation reste active jusqu’à ce que la touche soit validée à nouveau par la mnémonique ESTOP. ( EFHOLD et DFHOLD ) A partir de l’exécution de la mnémonique DFHOLD, la CNC invalide l’entrée de Feed-Hold provenant du PLC. Cette invalidation reste active jusqu’à ce que l’entrée soit validée à nouveau par la mnémonique EFHOLD. Chapitre: 14 DECLARATIONSDECONTROLEDESPROGRAMMES Section: DÉCLARATIONS DE VALIDATION-INVALIDATION Page 3 14.4 DÉCLARATIONS DE CONTROLE DE FLUX ( GOTO N(expression) ) La mnémonique GOTO provoque, à l’intérieur d’un programme donné, un saut au bloc défini au moyen de l’étiquette N(expression). L’exécution du programme continuera après le saut, à partir du bloc indiqué. L’étiquette de saut peut être adressée au moyen d’un numéro ou de toute expression dont le résultat est un nombre. Exemple: N22 G00 X0 Y0 Z0 T2 D4 X10 (GOTO N22) X15 Y20 Y22 Z50 G01 X30 Y40 Z40 F10000 G02 X20 Y40 I-5 J-5 .................. .................. ; Instruction de saut ; Pas d’exécution ; Pas d’exécution ; L’exécution continue dans ce bloc. ( RPT N(expression) , N(expression) ) La mnémonique RPT exécute, à l’intérieur d’un programme donné, la partie du programme située entre les blocs définis par les étiquettes N(expression). Les deux étiquettes peuvent être indiquées par un nombre ou par toute expression dont le résultat est un nombre. La partie de programme sélectionnée grâce aux deux étiquettes doit appartenir au même programme, le bloc initial étant défini en premier, le bloc final ensuite. L’exécution du programme se poursuit par le bloc suivant celui dans lequel la mnémonique RPT a été programmée, après exécution de la partie de programme sélectionnée. Exemple: N10 G00 X10 Z20 G01 X5 G00 Z0 N20 X0 N30 (RPT N10, N20) N3 N40 G01 X20 M30 En arrivant au bloc N30, le programme exécutera 3 fois la section N10-N20. A la fin de l’exécution, il passera au bloc N40. Page 4 Chapitre: 14 DECLARATIONSDECONTROLEDESPROGRAMMES Section: DÉCLARATIONSDE CONTROLEDEFLUX ( IF condition <action1> ELSE <action2> ) Cette instruction analyse la condition donnée, qui devra être une expression relationnelle. Si la condition es certaine (résultat égal à 1), <action1> sera exécuté; dans le cas contraire (résultat égal à 0), <action2> sera exécuté. Exemple: (IF (P8 EQ 12.8) CALL 3 ELSE PCALL 5, A2, B5, D8) Si P8 =12.8 exécute l’instruction (CALL3) Si P8<>12.8 exécute l’instruction (PCALL5, A2, B5, D8) ELSE peut être omis dans l’instruction, c’est-à-dire qu’il suffira de programmer IF condition <action1>. Exemple: (IF (P8 EQ 12.8) CALL 3) <action1> et <action2> peuvent être des expressions ou des déclarations, à l’exception des déclarations IF et SUB. Comme, dans un bloc de haut niveau, les paramètres locaux peuvent être nommés au moyen de lettres, des expressions du type ci-dessous peuvent être obtenues: (IF (E EQ 10) M10) Si la condition selon laquelle le paramètre P5 (E) a une valeur 10 est remplie, la fonction auxiliaire M10 n’est pas exécutée car un bloc de haut niveau ne peut pas disposer de commandes en code ISO. Dans ce cas, M10 représente l’affectation de la valeur 10 au paramètre P12, c’est-à-dire que l’on peut programmer: (IF (E EQ 10) M10) ou Chapitre: 14 DECLARATIONSDECONTROLEDESPROGRAMMES (IF (P5 EQ 10) P12=10) Section: DÉCLARATIONSDE CONTROLEDEFLUX Page 5 14.5 DÉCLARATIONS DE SOUS-ROUTINES Une sous-routine est une partie de programme qui, lorsqu’elle est correctement identifiée, peut être appelée depuis n’importe quel point d’un programme pour être exécutée. Une sous-routine peut être chargée dans la mémoire de la CNC comme un programme indépendant ou comme une partie d’un programme, puis être appelée une ou plusieurs fois depuis différents points d’un programme ou depuis différents programmes. ( SUB nombre entier ) La mnémonique SUB définit comme sous-routine l’ensemble de blocs de programmes programmés à la suite de ce bloc; cette sous-routine est identifiée grâce au nombre entier compris entre 0 et 9999, spécifié ci-dessous. Deux sous-routines portant le même numéro d’identification ne peuvent pas cohabiter dans la mémoire de la CNC, même si elles appartiennent à des programmes différents. ( RET ) La mnémonique RET indique que la sous-routine définie grâce à SUB se termine dans ce bloc. Exemple: (SUB 12) G91 G01 XP0 F5000 YP1 X-P0 Y-P1 (RET) ; Définition de la sous-routine ; Fin de sous-routine ( CALL (expression) ) La mnémonique CALL appelle la sous-routine indiquée au moyen d’un nombre ou de toute expression dont le résultat est un nombre. Comme il est possible d’appeler une sous-routine depuis un programme principal ou une sous-routine, puis une seconde sous-routine depuis la première et une troisième depuis la seconde, etc..., la CNC limite les appels à un maximum de 15 niveaux d’imbrications, chaque niveau pouvant être répêté 9999 fois. Page 6 Chapitre: 14 DECLARATIONSDECONTROLEDESPROGRAMMES Section: DÉCLARATIONS DE SOUSROUTINES (CALL 1) (SUB 1) (SUB 2) (CALL 2) (CALL 3) (RET) (RET) (SUB 3) (RET) Exemple: Z 40 30 X 20 10 10 20 30 40 50 10 20 30 40 50 60 70 80 90 100 Y G90 G00 X30 Y20 Z10 (CALL 10) G90 G00 X60 Y20 Z10 (CALL 10) M30 (SUB 10) G91 G01 X20 F5000 (CALL 11) G91 G01 Y10 (CALL 11) G91 G01 X-20 (CALL 11) G91 G01 Y-10 (CALL 11) (RET) ; Perçage et filetage ; Perçage et filetage ; Perçage et filetage ; Perçage et filetage (SUB 11) G81 G98 G91 Z-8 I-22 F1000 S5000 T1 D1 G84 Z-8 I-22 K15 F500 S2000 T2 D2 G80 (RET) Chapitre: 14 DECLARATIONSDECONTROLEDESPROGRAMMES ; Cycle fixe de perçage ; Cycle fixe de filetage Section: DÉCLARATIONS DE SOUSROUTINES Page 7 (PCALL (expression), (déclaration d’affectation), (déclaration d’affectation), ... ) La mnémonique PCALL appelle la sous-routine indiquée au moyen d’un nombre ou de toute expression dont le résultat est un nombre. Elle permet également d’initialiser jusqu’à 26 paramètres locaux de cette sous-routine. Ces paramètres sont initialisés au moyen des déclarations d’affectation. Exemple: (PCALL 52, A3, B5, C4, P10=20) Dans ce cas, un nouveau niveau d’imbrication de paramètres locaux est généré en plus d’un nouveau niveau d’imbrication de sous-routines, avec un maximum de 6 niveaux d’imbrication de paramètres locaux à l’intérieur des 15 niveaux d’imbrication de sousroutines. Le programme principal et chaque sous-routine se trouvant à un niveau d’imbrication de paramètres disposeront de 26 paramètres locaux (P0-P25). Exemple: Page 8 Chapitre: 14 DECLARATIONSDECONTROLEDESPROGRAMMES Section: DÉCLARATIONS DE SOUSROUTINES G90 G00 X30 Y50 Z0 (PCALL 10, P0=20, P1=10) G90 G00 X60 Y50 Z0 (PCALL 10, P0=10, P1=20) M30 ; ou également (PCALL 10, A20, B10) ; ou également (PCALL 10, A10, B20) (SUB 10) G91 G01 XP0 F5000 (CALL 11) G91 G01 YP1 (CALL 11) G91 G01 X-P0 (CALL 11) G91 G01 Y-P1 (CALL 11) (RET) (SUB 11) G81 G98 G91 Z-8 I-22 F1000 S5000 T1 D1 ; Cycle fixe de perçage G84 Z-8 I-22 K15 F500 S2000 T2 D2 ; Cycle fixe de filetage G80 (RET) (MCALL (expression), (déclaration d’affectation), (déclaration d’affectation), ... ) La mnémonique MCALL permet de conférer le statut de cycle fixe à toute sousroutine définie par l’utilisateur (SUB nombre entier). L’exécution de cette mnémonique est identique à celle de PCALL, mais l’appel est modal, c’est-à-dire que si un bloc comportant un déplacement des axes est programmé à la suite de ce bloc, la sous-routine indiquée s’exécutera après ce déplacement avec les mêmes paramètres d’appel. Si un bloc comportant un déplacement avec un nombre de répétitions tel que X10 N3 est exécuté alors qu’une sous-routine modale est sélectionnée, la CNC exécutera le déplacement (X10) une seule fois, et exécutera ensuite la sous-routine modale autant de fois qu’indiqué par le nombre de répétitions. Si des répétitions de bloc sont sélectionnées, la première exécution de la sous-routine modale sera exécutée avec les paramètres d’appel mis à jour, mais les autres répétitions s’effectueront avec les valeurs actuelles de ces paramètres. Si un bloc contenant la mnémonique MCALL est exécuté alors qu’une sous-routine est sélectionnée comme modale, la sous-routine actuelle perdra sa modalité et la nouvelle sous-routine sélectionnée deviendra modale. Chapitre: 14 DECLARATIONSDECONTROLEDESPROGRAMMES Section: DÉCLARATIONS DE SOUSROUTINES Page 9 ( MDOFF ) La mnémonique MDOFF indique que la modalité acquise par la sous-routine grâce à MCALL s’achève dans ce bloc. L’utilisation de sous-routines modales simplifie la programmation. Exemple: G90 G00 X30 Y50 Z0 (PCALL 10, P0=20, P1=10) G90 G00 X60 Y50 Z0 (PCALL 10, P0=10, P1=20) M30 (SUB 10) G91 G01 XP0 F5000 (MCALL 11) G91 G01 YP1 G91 G01 X-P0 G91 G01 Y-P1 (MDOFF) (RET) (SUB 11) G81 G98 G91 Z-8 I-22 F1000 S5000 T1 D1 G84 Z-8 I-22 K15 F500 S2000 T2 D2 G80 (RET) ( PROBE (expression), (déclaration d’affectation), (déclaration d’affectation), ... ) La mnémonique PROBE appelle le cycle de palpeur indiqué grâce à un nombre ou à toute expression dont le résultat est un nombre. Elle permet également d’initialiser les paramètres locaux de ce cycle au moyen des déclarations d’affectation. Cette mnémonique génère également un nouveau niveau d’imbrication de sousroutines. Page 10 Chapitre: 14 DECLARATIONSDECONTROLEDESPROGRAMMES Section: DÉCLARATIONS DE SOUSROUTINES (DIGIT (expression), (déclaration d’affectation), (déclaration d’affectation), ... ) La mnémonique DIGIT appelle le cycle de numérisation indiqué au moyen d’un nombre ou de toute expression dont le résultat est un nombre. Elle permet en outre d’initialiser les paramètres locaux de ce cycle grâce aux déclarations d’affectation. Les points numérisés sont envoyés au programme (en mémoire ou par DNC) précédemment ouvert grâce aux instructions suivantes: (OPEN P (expression), DNC1/2, A/D, “commentaire de programme”) Cette déclaration génère également un nouveau niveau d’imbrication de sous-routines. (TRACE(expression), (déclaration d’affectation), (déclaration d’affectation), ... ) La mnémonique TRACE appelle le cycle de recopie indiqué au moyen d’un nombre ou de toute expression dont le résultat est un nombre. Elle permet en outre d’initialiser les paramètres locaux de ce cycle grâce aux déclarations d’affectation. Les points numérisés sont envoyés au programme (en mémoire ou par DNC) précédemment ouvert grâce aux instructions suivantes: (OPEN P (expression), DNC1/2, A/D, “commentaire de programme”) Cette déclaration génère également un nouveau niveau d’imbrication de sous-routines. Chapitre: 14 DECLARATIONSDECONTROLEDESPROGRAMMES Section: DÉCLARATIONS DE SOUSROUTINES Page 11 14.5.1 DÉCLARATIONS DE SOUS-ROUTINES D’INTERRUPTION Chaque fois que l’une des entrées logiques générales d’interruption “INT1” (M5024), “INT2” (M5025), “INT3” (M5026) ou “INT4” (M5027) est activée, la CNC suspend provisoirement l’exécution du programme en cours et passe à l’exécution de la sous-routine d’interruption dont le numéro est indiqué dans le paramètre machine général correspondant. Avec INT1 (M5024) celle indiquée par le paramètre INT1SUB (P35) Avec INT2 (M5025) celle indiquée par le paramètre INT2SUB (P36) Avec INT3 (M5026) celle indiquée par le paramètre INT3SUB (P37) Avec INT4 (M5027) celle indiquée par le paramètre INT4SUB (P38) Les sous-routines d’interruption sont définies comme n’importe quelle autre sous-routine, en utilisant les déclarations “(SUB nombre entier)” et “(RET)”. Les sous-routines d’interruption ne changent pas le niveau des paramètres locaux; en conséquence, seuls les paramètres globaux peuvent être utilisés dans ces sous-routines. Dans une sous-routine d’interruption, il est possible d’utiliser la déclaration “(REPOS X, Y, Z, ....)” décrite plus loin. Dès la fin de l’exécution de la sous-routine, la CNC poursuit l’exécution du programme en cours. ( REPOS X, Y, Z, ... ) L’instruction REPOS doit toujours être utilisée dans les sous-routines d’interruption, et elle facilite le repositionnement de la machine au point d’interruption. Lorsque cette instruction est exécutée, la CNC déplace les axes jusqu’au point où l’exécution du programme a été interrompue. A l’intérieur de l’instruction REPOS, on devra indiquer l’ordre dans lequel des axes doivent être déplacés jusqu’au point d’interruption. * Les axes sont déplacés un à la fois. * Seuls les axes à repositionner doivent être définis. * Les axes composant le plan principal de la machine sont déplacés ensemble. Il est inutile de définir les deux axes, puisque la CNC les déplace avec le premier. Le déplacement n’est pas répété lors de la définition du second axe, il est ignoré. Exemple: Le plan principal est composé des axes XY, l’axe longitudinal est l’axe Z et la machine utilise les axes C et W en tant qu’axes auxiliaires. Le premier axe à repositionner est l’axe C, puis les axes XY, et enfin l’axe Z. Les définitions suivantes peuvent être utilisées: (REPOS C, X, Y, Z) (REPOS C, X, Z) (REPOS C, Y, Z) Si, pendant l’exécution d’une sous-routine qui n’a pas été activée par l’une des entrées d’interruption, l’instruction REPOS est détectée, la CNC affiche le code d’erreur correspondant. Page 12 Chapitre: 14 DECLARATIONSDECONTROLEDESPROGRAMMES Section: DÉCLARATIONS DE SOUSROUTINES D’INTERRUPTION 14.6 DÉCLARATIONS PERMETTANT DE GENERER DES PROGRAMMES La CNC FAGOR 8050 permet de générer, depuis un programme en cours d’exécution, un programme qui pourra dépendre des valeurs acquises par le programme pendant son exécution. Cette fonctionnalité est très utile lors de la numérisation de pièces. ( OPEN P(expression), DNC1/2, A/D, "commentaire de programme" ) L’instruction OPEN démarre l’édition d’un programme pièce. Le numéro de ce programme est indiqué au moyen d’un nombre ou de toute expression dont le résultat est un nombre. De tous les champs associés à cette instruction, seuls doivent être renseignés ceux relatifs au numéro du programme, le reste des champs étant optionnel; leur signification est la suivante: DNC1/2 Il est utilisé pour éditer un programme sur un périphérique ou un ordinateur et il indique la ligne série servant aux transmissions (DNC1 ou DNC2). Si ce paramètre n’est pas défini, il est supposé que le programme doit être édité dans la CNC. A/D Il est utilisé lorsque le programme à éditer existe déjà. Le traitement effectué par la CNC dépendra de la valeur affectée à ce paramètre, et sera le suivant: Aucune définition. La CNC affiche un message d’erreur en cas de tentative d’ouverture du programme indiqué. "A" La CNC ajoutera les nouveaux blocs édités au moyen de l’instruction WRITE, à la suite des blocs existants. "D" La CNC effacera le programme existant et comencera l’édition d’un nouveau programme. Commentaire de programme Permet d’associer un texte ou un commentaire au programme à éditer. Ce commentaire sera visualisé plus tard avec le programme dans le répertoire de programmes. ( WRITE <texte du bloc> ) La mnémonique WRITE ajoute à la suite du dernier bloc de programme dont l’édition a été commencée au moyen de l’instruction OPEN P, les informations contenues dans <texte du bloc> comme jn nouveau bloc de programme. Si le langage ISO avec programmation paramétrée est utilisé dans le <texte du bloc>, tous les paramètres (globaux et locaux) sont remplacés par leur valeur numérique actuelle au moment de l’exécution de la mnémonique WRITE. Exemples pour P1=10 et P2=20: (WRITE G1 XP1 YP2 F100) (WRITE (IF (P1 NE P2) P3=P1+P2)) -> G1 X10 Y20 F100 -> (IF (P1 NE P2) P3=P1+P2) Si la mnémonique WRITE est programmée sans avoir programmé au préalable la mnémonique OPEN, la CNC affiche le code d’erreur correspondant, sauf en cas d’édition d’un programme de personnalisation de l’utilisateur; dans ce cas, un nouveau bloc est ajouté au programme à éditer. Chapitre: 14 Section: DECLARATIONSDECONTROLEDESPROGRAMMES DÉCLARATIONS PERMETTANT DE GENERER DES PROGRAMMES Page 13 Exemple de création d’un programme contenant plusieurs points d’une cardioïde dont la formule est: R=B cos (Q/2) Y R Q X B La sous-routine numéro 2 est utilisée, dont les paramètres ont la signification suivante: A o P0 B o P1 C o P2 D o P3 Valeur de l’angle Q Valeur de B Incrément angulaire de calcul Avance des axes L’un des modes utilisation de cet exemple pourrait être: G00 X0 Y0 G93 (PCALL 2, A0, B30, C5, D500) M30 Sous-routine de génération du programme: (SUB 2) (OPEN P12345) ; Commence l’édition du programme P12345 (WRITE FP3) ; Sélectionne l’avance d’usinage N100 (P10=P1 (ABS(COS(P0/2)))) ; Calcule R (WRITE G01 G05 RP10 QP0) ; Bloc de déplacement (P0=P0+P2) ; Nouvel angle (IF (P0 LT 365) GOTO N100) ; Si l'angle est inférieur à 365º, calcule le nouveau point (WRITE M30) ; Bloc de fin de programme (RET) Page 14 Section: Chapitre: 14 DECLARATIONSDECONTROLEDESPROGRAMMES DÉCLARATIONS PERMETTANT DE GENERER DES PROGRAMMES 14.7 DÉCLARATIONS DE PERSONNALISATION Las déclarations de personnalisation ne peuvent être utilisées que dans les programmes de personnalisation réalisés par l’utilisateur. Ces programmes de personnalisation peuvent utiliser les “Déclarations de Programmation” et seront exécutés dans le canal spécial réservé à cet effet; le programme sélectionné dans chaque cas sera indiqué dans les paramètres machine généraux suivants. "USERDPLY" indiquera le programme à exécuter dans le mode Exécution. "USEREDIT" indiquera le programme à exécuter dans le mode Edition. "USERMAN" indiquera le programme à exécuter dans le mode Manuel. "USERDIAG" indiquera le programme à exécuter dans le mode Diagnostic. En plus du niveau actuel, les programmes de personnalisation peuvent disposer de cinq autres niveaux d’imbrication. En outre, les déclarations de personnalisation n’admettent pas les paramètres locaux; il est toutefois possible d’utiliser tous les paramètres globaux pour les définir. ( PAGE (expression) ) La mnémonique PAGE visualise à l’écran le numéro de page indiqué au moyen d’un nombre ou de toute expression dont le résultat est un nombre. Les pages définies par l’utilisateur sont comprises entre la page 0 et la page 255, et elles sont définies depuis le clavier de la CNC dans le mode Personnalisationn comme indiqué dans le manuel de l’utilisateur. Les pages du système sont définies par un nombre supérieur à 1000. Voir l’annexe correspondante. ( SYMBOL (expression 1), (expression 2), (expression 3) ) La mnémonique SYMBOL visualise à l’écran le symbole dont le numéro est indiqué par la valeur de l’expression 1 dès qu’elle est évaluée. Par ailleurs, sa position à l’écran est définie par l’expression 2 (colonne) et par l’expression 3 (rangée). Expression 1, comme expression 2 et expression 3 pourront contenir un nombre ou toute expression dont le résultat est un nombre. La CNC permet de visualiser tout symbole défini par l’utilisateur (0-255) depuis le clavier de la CNC dans le mode personnalisation comme indiqué dans le Manuel de l’utilisateur. Pour le positionner dans la zone de visualisation, il convient de définir les pixels de cette dernière, soit 0-639 pour les colonnes (expression 2) et 0-335 pour les rangées (expression 3). Chapitre: 14 DECLARATIONSDECONTROLEDESPROGRAMMES Section: DÉCLARATIONSDE PERSONNALISATION Page 15 ( IB (expression) = INPUT "texte", format ) La CNC dispose de 26 variables d’entrée de données (IB0-IB25). La mnémonique IB visualise, dans la fenêtre d’entrée de données, le texte indiqué et stocke la donnée introduite par l’utilisateur dans la variable d’entrée au moyen d’un nombre ou de toute expression dont le résultat est un nombre. L’introduction des données ne comporte une attente que si le format des données demandées est programmé. Ce format pourra avoir un signe, une partie entière et une partie décimale. Si le format comporte le signe "-" , il admettra des valeurs positives et négatives; dans le cas contraire, il n’admet que des valeurs positives. La partie entière indique le nombre maximum de chiffres entiers (0-6) désirés. La partie entière indique le nombre maximum de chiffres décimaux (0-5) désirés. Si la mnémonique est programmée sans format numérique, comme par exemple (IB1 = INPUT "texte"), la mnémonique affiche le texte indiqué sans attendre l’introduction des données. ( ODW (expression 1), (expression 2), (expression 3) ) La mnémonique ODW définit et dessine à l’écran une fenêtre blanche de dimensions fixes(1 rangée x 14 colonnes). A chaque fenêtre est associé un numéro indiqué par la valeurde l’expression 1 dès qu’elle est évaluée. En outre, sa position sur l’écran est définie par l’expression 2 (rangée) et l’expression 3 (colonne). Expression 1, comme expression 2 et expression 3 pourront contenir un nombre ou toute expression dont le résultat est un nombre. La CNC permet de définir 26 fenêtres (0-25) et de les positionner dans la zone de visualisation; pour ce faire, elle dispose de 21 rangées (0-20) et de 80 colonnes (0-79). Page 16 Chapitre: 14 DECLARATIONSDECONTROLEDESPROGRAMMES Section: DÉCLARATIONSDE PERSONNALISATION ( DW (expression 1) = (expression 2), DW (expression 3) = (expression 4), ... ) La mnémonique DW visualise dans la fenêtre indiquée par la valeur de l’expression 1, expression 3, .. dès qu’elle est évaluée les données numériques indiquées par l’expression 2, expression 4, .... Expression 1, expression 2, expression 3, .... pourront contenir un nombre ou toute expression dont le résultat est un nombre. L’exemple suivant montre une visualisation dynamique de variables: (ODW 1, 6, 33) ; Définit la fenêtre de données 1 (ODW 2, 14, 33) ; Définit la fenêtre de données 2 N10 (DW1=DATE, DW2=TIME) ; Visualise la daye dans la fenêtre 1 et l’heure dans la 2. (GOTO N10) La CNC permet de visualiser les données en format décimal, hexadécimal et binaire, grâce aux instructions suivantes: (DW1 = 100) Format décimal. Visualise dans la fenêtre 1 la valeur "100". (DWH2 = 100) Format hexadécimal. Visualise dans la fenêtre 2 la valeur "64". (DWB3 = 100) Format binaire. Visualise dans la fenêtre 3 la valeur "01100100". En cas d’emploi de la représentation en binaire (DWB), la visualisation se limite à 8 caractères; la valeur "11111111" s’affiche pour les valeurs supérieures à 255, tandis que la valeur "10000000" s’affiche pour les valeurs inférieures à -127. La CNC permet en outre de visualiser dans la fenêtre demandée le nombre chargé dans l’une des 26 variables d’entrée de données (IB0-IB25). L’exemple suivant montre une demande et une visualisation ultérieure de l’avance des axes: (ODW 3, 4, 60) (IB1=INPUT "Avance des axes: ", 5.4) (DW3=IB1) Chapitre: 14 DECLARATIONSDECONTROLEDESPROGRAMMES ; Définit la fenêtre de données 3 ; Demande de l’avance des axes ; Visualise l’avance dans la fenêtre 3 Section: DÉCLARATIONSDE PERSONNALISATION Page 17 ( SK (expression 1) = "texte 1", (expression 2) = "texte 2", .... ) La mnémonique SK définit et visualise le nouveau menu de touches logiciel indiqué. Chacune des expressions indiquera le numéro de touche logiciel à modifier (1-7, en commençant par la gauche) et les textes à écrire dans ces touches. Expression 1, expression 2, expression 3, .... pourront contenir un nombre ou toute expression dont le résultat est un nombre. Chaque texte autorise un maximum de 20 caractères sur deux lignes de 10 caractères chacune. Si le texte sélectionné comporte moins de 10 caractères, la CNC le centre sur la ligne supérieure, mais s’il a plus de 10 caractères, le centrage doit être réalisé par le programmeur. Exemples: (SK 1="HELP", SK 2="COORDONNEE MAXIMUM") (SK 1="AVANCE", SK 2="COORDONNEE _ _ MAXIMUM_") HELP AVANCE COORDONNEE MAXIMUM COORDONNEE MAXIMUM Attention Si une ou plusieurs touches logiciel sont sélectionnées au moyen de l’expression de haut niveau “SK” pendant qu’un menu par touches logiciel CNC standard est actif, la CNC efface toutes les touches logiciel existantes et n’affiche que les touches sélectionnées. Si une ou plusieurs touches logiciel sont sélectionnées au moyen de l’expression de haut niveau “SK” pendant qu’un menu par touches logiciel utilisateur est actif, la CNC ne remplace que les touches logiciel sélectionnées en laissant les autres sans changement. ( WKEY ) La mnémonique WKEY interrompt l’exécution du programme jusqu’à la frappe d’une touche. La touche frappée sera enregistrée dans la variable KEY. Exemple: ........ ........ (WKEY) ; Attente d’une touche (IF KEY EQ $FC00 GOTO N1000); Si F1 a été frappé, poursuite en N1000 ........ ........ Page 18 Chapitre: 14 DECLARATIONSDECONTROLEDESPROGRAMMES Section: DÉCLARATIONSDE PERSONNALISATION ( WBUF "texte", (expression) ) La déclaration WBUF n’est utilisable que dans le programme de personnalisation devant être exécuté dans le mode Edition. Cette déclaration peut être programmée de deux façons et, dans chaque cas, elle permet: ( WBUF "texte", (expression) ) Elle ajoute au bloc en cours d’édition et dans la fenêtre d’entrée de données le texte et la valeur de l’expression dès qu’elle est évaluée. (Expression) pourra contenir un nombre ou toute expression dont le résultat est un nombre. La programmation de l’expression est optionnelle, mais le texte doit obligatoirement être défini. Si aucun texte n’est souhaité, on programmera "". ( WBUF ) Introduit en mémoire, en ajoutant au programme en cours d’édition et derrière l’emplacement du curseur, le bloc en cours d’édition (écrit au préalable avec les déclarations “(WBUF "texte", (expression))”). Par ailleurs, elle efface la mémoire-tampon d’édition, en l’initialisant pour une nouvelle édition de bloc. Ceci permet à l’utilisateur d’éditer un programme complet sans avoir à quitter le mode édition utilisateur après chaque bloc et à frapper [ENTER] pour le charger en mémoire. Exemple: (WBUF "(PCALL 25, ") (IB1=INPUT "Paramètre A:",-5.4) (WBUF "A=", IB1) (IB2=INPUT "Paramètre B: ", -5.4) (WBUF ", B=", IB2) (WBUF ")") (WBUF ) ............ ............ ; Ajoute au bloc en cours d’édition "(PCALL 25, " ; Demande du paramètre A ; Ajoute au bloc en cours d’édition "A = (valeur introduite)" ; Demande du paramètre B ; Ajoute au bloc en cours d’édition "B=(valeur introduite)" ; Ajoute au bloc en cours d’édition ")" ; Charge en mémoire le bloc édité Après l’exécution de ce programme, on dispose en mémoire d’un bloc de ce type: (PCALL 25, A=23.5, B=-2.25) ( SYSTEM ) La mnémonique SYSTEM met fin à l’exécution du programme de personnalisation utilisateur et renvoie au menu standard correspondant de la CNC. Chapitre: 14 DECLARATIONSDECONTROLEDESPROGRAMMES Section: DÉCLARATIONSDE PERSONNALISATION Page 19 Exemple d’un programme de personnalisation: Le programme de personnalisation suivant doit être sélectionné comme programme utilisateur associé au mode Editeur. Après sélection du mode Editeur et frappe de la touche logiciel UTILISATEUR, ce programme commence à s’exécuter et permet de réaliser une édition assistée des deux cycles utilisateur autorisés. Cette édition est réalisée cycle par cycle et autant de fois que désiré. ; Visualise la page d’édition initiale N0 (PAGE 10) ; Personnalise les touches logiciel d’accès aux divers modes et demande une option N5 (SK 1="CICLO 1",SK 2="CICLO 2",SK 7="SALIR") (WKEY ) (IF KEY EQ $FC00 GOTO N10) (IF KEY EQ $FC01 GOTO N20) (IF KEY EQ $FC06 SYSTEM ELSE GOTO N5) ;Demander une touche ;Cycle 1 ;Cycle 2 ;Sortir ou demander une touche ; CYCLE 1 ; Visualise la page 11 et définit 2 fenêtres de données N10 (PAGE 11) (ODW 1,10,60) (ODW 2,15,60) ;Edition (WBUF "( PCALL 1,") ; Ajoute au bloc en cours d’édition (PCALL 1, (IB 1=INPUT "X:",-6.5) (DW 1=IB1) (WBUF "X",IB1) ; Demande de la valeur de X ; Visualise, dans la fenêtre 1, la valeur introduite ; Ajoute au bloc en cours d’édition X (valeur introduite) (WBUF ",") ; Ajoute au bloc en cours d’édition , (IB 2=INPUT "Y:",-6.5) (DW 2=IB2) (WBUF "Y",IB2) ; Demande de la valeur de Y ; Visualise, dans la fenêtre 2, la valeur introduite ; Ajoute au bloc en cours d’édition Y (valor introducido) (WBUF ")") ; Ajoute au bloc en cours d’édition ) (WBUF ) ; Charge en mémoire le bloc édité. P.e. (PCALL 1, X2, Y3) (GOTO N0) ; CYCLE 2 ; Visualise la page 12 et définit 3 fenêtres de données N20 (PAGE 12) (ODW 1,10,60) (ODW 2,13,60) (ODW 3,16,60) Page 20 Chapitre: 14 DECLARATIONSDECONTROLEDESPROGRAMMES Section: DÉCLARATIONSDE PERSONNALISATION ;Edition (WBUF "( PCALL 2,") ; Ajoute au bloc en cours d’édition (PCALL 2, (IB 1=INPUT "A:",-6.5) (DW 1=IB1) (WBUF "A",IB1) ; Demande de la valeur de A ; Visualise, dans la fenêtre 1, la valeur introduite ; Ajoute au bloc en cours d’édition A (valeur introduite) (WBUF ",") ; Ajoute au bloc en cours d’édition , (IB 2=INPUT "B:",-6.5) (DW 2=IB2) (WBUF "Y",IB2) ; Demande de la valeur de B ; Visualise, dans la fenêtre 2, la valeur introduite ; Ajoute au bloc en cours d’édition B (valeur introduite) (WBUF ",") ; Ajoute au bloc en cours d’édition , (IB 3=INPUT "C:",-6.5) (DW 3=IB3) (WBUF "Y",IB3) ; Demande de la valeur de C ; Visualise, dans la fenêtre 3, la valeur introduite ; Ajoute au bloc en cours d’édition C (valeur introduite) (WBUF ")") ; Ajoute au bloc en cours d’édition ) (WBUF ) ; Charge en mémoire le bloc édité. P.e. (PCALL 2, A3, B1, C3) (GOTO N0) Chapitre: 14 DECLARATIONSDECONTROLEDESPROGRAMMES Section: DÉCLARATIONSDE PERSONNALISATION Page 21 15. CYCLES DE NUMERISATION La CNC FAGOR 8050 dispose des cycles fixes de numérisation suivants: 1 2 Cycle fixe de numérisation en grille. Cycle fixe de numérisation en arc. Les cycles fixes doivent être programmés grâce à l’instruction de haut niveau DIGIT, dont le format de programmation est: (DIGIT (expression), (déclaration d’affectation), ...) Cette déclaration appelle le cycle de numérisation indiqué au moyen d’un nombre ou de toute expression dont le résultat est un nombre. Elle permet également d’initialiser les paramètres de ce cycle avec les valeurs désirées, au moyen des déclarations d’affectation. Considérations générales Tous les déplacements de ces cycles fixes de numérisation s’exécuteront sur les axes X, Y, Z, le plan de travail devant être constitué de 2 de ces axes (XY, XZ, YZ, YX, ZX, ZY). L’autre axe, qui doit être perpendiculaire à ce plan, devra être sélectionné en tant qu’axe longitudinal. Les conditions d’usinage dans lesquelles s’exécutera le cycle de numérisation doivent être sélectionnées avant l’appel de ce cycle. Pendant l’exécution d’un cycle fixe de numérisation, les coordonnées de position de chaque point palpé sont stockées dans un programme. Il est donc nécessaire, avant d’appeler le cycle, d’ouvrir grâce à la déclaration (OPEN P), le programme où les données doivent être introduites. Si, au lieu d’être stockées dans la mémoire de programmes de la CNC, les données sont envoyées vers un périphérique ou un ordinateur par une ligne DNC, cette option devra être indiquée au moment der la définition de la déclaration (OPEN P). Il est recommandé d’indiquer dans le programme ouvert au moyen de la déclaration (OPEN P) les conditions d’usinage selon lesquelles ce programme sera exécuté plus tard. Pour ce faire, on éditera les blocs de programme nécessaires grâce à déclaration (WRITE). A la fin du cycle de palpage, le palpeur se trouve à l’emplacement qu’il occupait avant l’exécution du cycle. L’exécution d’un cycle fixe de palpage ne modifie pas l’historique des fonctions _G_ antérieures. On devra tenir compte du fait que les blocs de programme générés par le cycle fixe sont tous des blocs de positionnement. Si l’on désire mettre fin au programme généré, on devra ajouter un bloc contenant l’une des fonctions de fin de programme M02 ou M30. Chapitre: 15 CYCLESDENUMERISATION Section: Page 1 15.1 CYCLE FIXE DE NUMÉRISATION SUIVANT UNE GRILLE Le format de programmation de ce cycle est le suivant: (DIGIT 1, X, Y, Z, I, J, K, B, C, D, F) J K C (X,Y) B (X,Y,Z) I X±5.5 Coordonnée théorique, selon l’axe des abscisses, du premier point de palpage. Il doit être défini en coordonnées absolues et coïncider avec l’un des coins de la grille. Y±5.5 Coordonnée théorique, selon l’axe des ordonnées, du premier point de palpage. Il doit être défini en coordonnées absolues et coïncider avec l’un des coins de la grille. Z±5.5 Coordonnée théorique, selon l’axe de palpage, sur laquelle le palpeur doit se positionner avant le début de la numérisation. Doit être définie en absolu. Lors de la définition de cette coordonnée, on tiendra compte de la hauteur maximum de la pièce et de la distance de sécurité à conserver par rapport à cette pièce. Page 2 Chapitre: 15 CYCLESDENUMERISATION Section: NUMÉRISATIONSUIVANTUNE GRILLE I±5.5 Définit la profondeur maximum de palpage, et est référencé par rapport à la coordonnée définie dans le paramètre Z. Si une partie de la pièce se trouve hors de cette zone, le cycle fixe ne saisit pas les valeurs de ces points, et poursuit l’exécution du cycle de numérisation sans émettre de message d’erreur. S’il est programmé avec la valeur 0, la CNC affiche le message d’erreur correspondant. J±5.5 Définit la longueur de la grille selon l’axe des abscisses. Le signe positif indique que la grille se situe à la droite du point (X, Y), tandis que le signe négatif indique qu’elle se situe à la gauche de ce même point. K±5.5 Définit la longueur de la grille selon l’axe des ordonnées. Le signe positif indique que la grille se situe au-dessus du point (X, Y), tandis que le signe négatif indique qu’elle se situe au-dessous de ce même point. B 5.5 Définit le pas de numérisation selon l’axe des abscisses. Il doit être programmé avec une valeur positive et supérieure à 0 C±5.5 Définit le pas de numérisation selon l’axe des ordonnées. Si ce paramètre est programmé avec une valeur positive, la numérisation de la grille s’effectue selon l’axe des abscisses; si la valeur est négative, elle s’effectue selon l’axe des ordonnées. C(+) C (-) S’il est programmé avec la valeur 0, la CNC affiche le message d’erreur correspondant. Chapitre: 15 CYCLESDENUMERISATION Section: NUMÉRISATIONSUIVANTUNE GRILLE Page 3 D Indique le mode de “balayage” de la grille, selon la code de définition suivant: 0 = Numérisation dans les deux sens (en zig-zag). 1 = Numérisation toujours dans le même sens. Si aucun code n’est programmé, la CNC prend la valeur D0 par défaut. C(+) D0 C(+) D1 C (-) D0 C (-) D1 F5.5 Définit l’avance selon laquelle doit s’exécuter le déplacement de palpage, en mm/minute ou en pouces/minute. Fonctionnement de base 1.- Le palpeur se positionne sur le point défini grâce aux paramètres X, Y, Z. 2.- Le palpeur se déplace selon l’axe de palpage, jusqu’au contact avec la pièce. 3.- La CNC genèrera un nouveau bloc dans le programme préalablement ouvert au moyen de la déclaration (OPEN P). La position occupée par les axes X, Y, Z sera indiquée dans ce bloc. 4.- Le palpeur effectuera un “suivi” de la pièce selon la trajectoire programmée, en générant un nouveau bloc après palpage de chacun des points programmés. 5.- A la fin du cycle fixe, le palpeur retournera au point de départ. Ce déplacement se compose de: Page 4 * Déplacement du palpeur selon l’axe de palpage jusqu’à la coordonnée indiquée par le paramètre Z. * Déplacement dans le plan principal de travail jusqu’au point de départ du cycle (paramètres X, Y). Chapitre: 15 CYCLESDENUMERISATION Section: NUMÉRISATIONSUIVANTUNE GRILLE 15.2 CYCLE FIXE DE NUMÉRISATION SUIVANT UN ARC Le format de programmation de ce cycle est le suivant: (DIGIT 2, X, Y, Z, I, J, K, A, B, C, F) C C J K B A (X,Y) (X,Y,Z) I Chapitre: 15 CYCLESDENUMERISATION Section: NUMÉRISATIONSUIVANTUN ARC Page 5 X±5.5 Coordonnée théorique, selon l’axe des abscisses, du centre de l’arc. Il doit être défini en coordonnées absolues. Y±5.5 Coordonnée théorique, selon l’axe des ordonnées, du centre de l’arc. Il doit être défini en coordonnées absolues. Z±5.5 Coordonnée théorique, selon l’axe de palpage, sur laquelle le palpeur doit se positionner avant le début de la numérisation. Doit être définie en absolu. Lors de la définition de cette coordonnée, on tiendra compte de la hauteur maximum de la pièce et de la distance de sécurité à conserver par rapport à cette pièce. I±5.5 Définit la profondeur maximum de palpage, et est référencé par rapport à la coordonnée définie dans le paramètre Z. Si une partie de la pièce se trouve hors de cette zone, le cycle fixe ne saisit pas les valeurs de ces points, et poursuit l’exécution du cycle de numérisation sans émettre de message d’erreur. S’il est programmé avec la valeur 0, la CNC affiche le message d’erreur correspondant. J 5.5 Définit le rayon correspondant à l’arc le plus à l’extérieur de la zone à numériser. Ce paramètre doit être programmé avec une valeur positive et supérieure à 0. K 5.5 Définit le rayon correspondant à l’arc le plus à l’intérieur de la zone à numériser. Ce paramètre doit être programmé avec une valeur positive. Si ce paramètre n’est pas programmé, le cycle fixe prendra la valeur K0 par défaut. A 5.5 Définit la position angulaire du premier point à numériser par rapport à l’axe des abscisses. Si ce paramètre n’est pas programmé, le cycle fixe prendra la valeur A0 par défaut. Page 6 Chapitre: 15 CYCLESDENUMERISATION Section: NUMÉRISATIONSUIVANTUN ARC B 5.5 Définit la position angulaire de l’autre extrêmité des arcs par rapport à l’axe des abscisses. Lors de la définition des paramètres A et B, on devra tenir compte du fait que la première trajectoire s’effectue toujours dans le sens anti-horaire. Si un arc est programmé, les déplacements s’effectueront en zig-zag, et si un cercle complet est programmé, les déplacements seront concentriques. Si ce paramètre n’est pas programmé, le cycle fixe prendra la valeur B360 par défaut. Pour effectuer des mesures sur toute la circonférence, on affectera la même valeur aux paramètres A et B, ou ne définira aucun paramètre, le cycle fixe affectant les valeurs A0 et B360. C 5.5 Définit le pas de palpage, c’est-à-dire la distance entre deux points de palpage consécutifs. Cette distance sera celle existant entre deux arcs consécutifs et, en ligne droite, celle séparant deux points consécutifs d’un même arc. Le pas devra être programmé en mm ou en pouces, avec une valeur positive et supérieure à 0. F5.5 Définit l’avance choisie pour le mouvement de palpage. Elle sera programmée en mm/minute ou en pouces/minute. Chapitre: 15 CYCLESDENUMERISATION Section: NUMÉRISATIONSUIVANTUN ARC Page 7 Fonctionnement de base: 1.- Le palpeur se positionne sur le point défini grâce aux paramètres X, Y, Z. 2.- Le palpeur se déplace selon l’axe de palpage, jusqu’au contact avec la pièce. 3.- La CNC genèrera un nouveau bloc dans le programme préalablement ouvert au moyen de la déclaration (OPEN P). La position occupée par les axes X, Y, Z sera indiquée dans ce bloc. 4.- Le palpeur effectuera un “suivi” de la pièce selon la trajectoire programmée, en générant un nouveau bloc après palpage de chacun des points programmés. 5.- A la fin du cycle fixe, le palpeur retournera au point de départ. Ce déplacement se compose de: Page 8 * Déplacement du palpeur selon l’axe de palpage jusqu’à la coordonnée indiquée par le paramètre Z. * Déplacement dans le plan principal de travail jusqu’au point de départ du cycle (paramètres X, Y). Chapitre: 15 CYCLESDENUMERISATION Section: NUMÉRISATIONSUIVANTUN ARC 16. 16.1 COPIE ET NUMERISATION INTRODUCTION La terminologie employée dans ce chapitre est définie ci-dessous: Copie: Le palpeur se déplace selon la trajectoire indiquée, tout en maintenant en permanence la sonde en contact avec la surface du modèle. Copie directe: La copie directe est possible lorsque la machine est équipée d’une broche double pouvant accueillir la sonde de copie et l’outil d’usinage. Le terme de copie directe s’applique lorsque l’outil usine la pièce pendant que la sonde copie le modèle. Ces deux éléments se déplacent simultanément. Numérisation: Cette opération consiste à prendre les coordonnées de la machine pendant la copie de la pièce et à envoyer ces coordonnées au fichier ouvert au préalable au moyen de la déclaration (OPEN P). Avant de numériser le modèle, la fonction Copie (G23) doit toujours être activée, qu’une copie directe soit exécutée ou non. La copie et la numérisation peuvent s’effectuer de deux manières: Manuellement. L’opérateur peut amener le palpeur à la main sur la surface du modèle. Automatiquement. Les déplacements du palpeur sont contrôlés par la CNC et les possibilités sont les suivantes: Activtion d’un des cycles fixes suivants: TRACE TRACE TRACE TRACE TRACE 1 2 3 4 5 Cycle fixe de copie / numérisation en grille. Cycle fixe de copie / numérisation en arc. Cycle fixe de copie / numérisation de profil dans le plan. Cycle fixe de copie / numérisation de profil dans l’espace. Cycle fixe de copie / numérisation par balayage de polygone. Activation des fonctions de copie G23 et de numérisation G24. Dans ce cas, la trajectoire que doit suivre la sonde lors de la copie/numérisation du modèle doit être définie. Les options disponibles sont: Copie / numérisation Unidimensionnelle. Copie / numérisation Bidimensionnelle. Copie / numérisation Tridimensionnelle. Les détails sur tous ces types de copie / numérisation sont donnés ci-dessous. Chapitre: 16 COPIEETNUMERISATION Section: Page INTRODUCTION 1 * Copie / Numérisation Manuelles L’opérateur peut amener le palpeur à la main sur la surface du modèle, le déplacement manuel du palpeur pouvant être limité à 1, 2 ou 3 axes. Ce type de copie permet la prise de points sur le modèle, les passes de copie parallèles, les contournages bi- et tridimensionnels, les opérations d’ébauche, etc. Cette option permet la numérisation du modèle point à point ou en continu. La numérisation en continu est exécutée par la CNC en fonction des valeurs affectées aux paramètres de numérisation, fonction G24. Pour exécuter une numérisation point à point, la fonction G24 doit être définie sans paramètres. La prise de points est réalisée par l’opérateur, par frappe de touche logiciel “PRISE POINT A POINT” ou d’un bouton-poussoir externe. Page 2 Chapitre: 16 COPIEETNUMERISATION Section: INTRODUCTION * Copie / Numérisation unidimensionnelles Ce type de copie est le plus courant. Lors de la définition de la fonction G23, on indiquera quel est l’axe qui, contrôlé par la CNC, effectue le balaage du modèle. La trajectoire que doit suivre la sonde de copie est définie par les deux autres axes, et doit être programmée en code ISO, par déplacement des axes au moyen des touches JOG ou par manivelle électronique. Cette option permet la numérisation du modèle en continu, sous le contrôle de la CNC en fonction des valeurs affectées aux paramètres de numérisation, fonction G24. Exemple: La zone de copie est délimitée entre (X100 Y0) et (X150 Y50), l’axe de palpage étant l’axe Z. G90 G01 X100 Y0 Z80 F1000 (OPEN P234) (WRITE G90 G01 G05 F1000) G23 Z I-10 N1.2 G24 L8 E5 K1 N10 G91 X50 Y5 X-50 N20 Y5 (RPT N10,N20) N4 X50 G25 M30 Chapitre: 16 COPIEETNUMERISATION Programme destinataire des données Active la copie Active la fonction numérisation Définit le déplacement “ “ “ “ “ Désactive la copie e la numérisation Section: Page INTRODUCTION 3 * Copie / Numérisation bidimensionnelles Ces fonctions exécutent un contournage du modèle. Il est nécessaire de définir deux axes qui, contrôlés par la CNC, réalisent le “suivi” du profil. Le contour, qui est défini par la fonction G27, peut être du type fermé (le point initial et final coïncident) ou ouvert (le point initial et final ne coïncident pas). Cette option permet la numérisation du modèle en continu, sous le contrôle de la CNC en fonction des valeurs affectées aux paramètres de numérisation, fonction G24. Exemple de contour fermé: G23 XY I50 J8 N0.8 G24 L8 E5 K1 G27 S0 G25 ;Définition de copie bidimensionnelle ;Définition de la numérisation ;Définition de contour fermé ;Désactive la copie et la numérisation Exemple de contour ouvert: G23 XY I60 J20 N0.8 G24 L8 E5 K1 G27 S0 Q10 R25 J15 K0 G25 Page 4 ;Définition de copie bidimensionnelle ;Définition de la numérisation ;Définition de contour ouvert ;Désactive la copie et la numérisation Chapitre: 16 COPIEETNUMERISATION Section: INTRODUCTION * Copie / Numérisation tridimensionnelles Le suivi du profil est exécuté par les trois axes, qui sont contrôlés par la CNC. Le palpeur doit toujours disposer d’une surface d’appui. La pente maximum de la surface balayée dépend de l’avance en balayage et des déflexions nominales. Plus l’avance en balayage est grande, plus la pente autorisée sera faible. Le contour, qui est défini par la fonction G27, peut être du type fermé (le point initial et final coïncident) ou ouvert (le point initial et final ne coïncident pas). Cette option permet la numérisation du modèle en continu, sous le contrôle de la CNC en fonction des valeurs affectées aux paramètres de numérisation, fonction G24. Exemple de contour fermé: G23 XYZ I8 J50 K75 N0.8 M0.5 G24 L8 E5 K1 G27 S1 G25 ;Définition de copie tridimensionnelle ;Définition de la numérisation ;Définition de contour fermé ;Désactive la copie et la numérisation Exemple de contour ouvert: G23 XYZ I20 J50 K45 N0.8 M0.5 G24 L8 E5 K1 G27 S1 Q80 R40 J25 K0 G25 Chapitre: 16 COPIEETNUMERISATION ;Définition de copie tridimensionnelle ;Définition de la numérisation ;Définition de contour ouvert ;Désactive la copie et la numérisation Section: Page INTRODUCTION 5 * Cycles fixes de copie / numérisation Les cycles fixes de copie / numérisation dont dispose la CNC se basent sur les types de copie présentés précédemment et sont les suivants: TRACE TRACE TRACE TRACE TRACE 1 2 3 4 5 Cycle fixe de copie / numérisation en grille. Cycle fixe de copie / numérisation en arc. Cycle fixe de copie / numérisation de profil dans le plan. Cycle fixe de copie / numérisation de profil dans l’espace. Cycle fixe de copie / numérisation par balayage de polygone. Ces cycles sont programmés au moyen de l’instruction de haut niveau TRACE, le numéro du cycle pouvant être indiqué par un chiffre (1, 2, 3, 4, 5) ou par toute expression dont le résultat est l’un de ces chiffres. Tous ces cycles disposent d’une série de paramètres qui définissent la trajectoire de copie et les conditions d’exécution de la numérisation. Pour n’exécuter que la copie de la pièce (sans numérisation), les paramètres de numérisation doivent être mis à “0”. Pour numériser le modèle, le programme dans lequel les données seront introduites doit être ouvert grâce à l’instruction (OPEN P) avant l’appel du cycle, et les paramètres de numérisation doivent être définis correctement. Page 6 Chapitre: 16 COPIEETNUMERISATION Section: INTRODUCTION 16.1.1 CONSIDERATIONS GENERALES La CNC FAGOR 8050 dispose des fonctions préparatoires suivantes permettant de réaliser la copie / numérisation de pièces: G26 G23 G24 G27 G25 Etalonnage de la sonde de copie Activation de la copie Activation de la numérisation Définition du contour de copie Désactivation de la copie / numérisation Elle dispose également des cycles fixes de copie suivants: TRACE TRACE TRACE TRACE TRACE 1 2 3 4 5 Cycle fixe de copie / numérisation en grille. Cycle fixe de copie / numérisation en arc. Cycle fixe de copie / numérisation de profil dans le plan. Cycle fixe de copie / numérisation de profil dans l’espace. Cycle fixe de copie / numérisation par balayage de polygone. A propos de la copie Pendant la copie du modèle, la CNC ne contrôle que les déplacements des axes X, Y, Z, le plan de travail devant être formé par 2 de ces axes (XY, XZ, YZ, YX, ZX, ZY). L’autre axe doit être perpendiculaire à ce plan, et être sélectionné comme axe longitudinal. La sonde de palpage doit se situer en permanence sur l’axe longitudinal L’opération d’étalonnage de la sonde (G26) doit être exécutée à chaque installation de la sonde de copie sur la machine, à chaque changement ou changement d’orientation du palpeur, et à chaque mise en marche de la CNC. Lorsque la fonction G23 (activation de la copie) a été exécutée, la CNC maintient la sonde en contact avec la surface du modèle, en suivant en permanence la trajectoire sélectionnée. Pour exécuter une copie automatique, on devra définir la trajectoire que doit suivre la sonde de copie au moyen de blocs de programme en code ISO, ou en déplaçant les axes grâce aux touches JOG ou à la manivelle électronique. Pour désactiver la copie activée au moyen de la fonction G23, on exécutera la fonction G25 (désactivation de la copie). Lorsque l’un des cycles de copie / numérisation est exécuté, il n’est pas nécessaire d’exécuter les fonctions G23, G25 ni de définir la trajectoire de copie, puisque c’est le cycle fixe lui-même qui gère ces opérations. Lors de la réalisation d’une copie directe (usinage et copie simultanés), il n’est pas possible de compenser les déflexions de la sonde; le rayon de l’outil d’usinage doit donc être le rayon de la bille du palpeur, moins la déflexion nominale. Exemple: dans le cas de l’utilisation d’une pointe de 9 mm de diamètre avec une déflection maximum de 2 mm, on devra utiliser un outil de 5 mm de diamètre. Chapitre: 16 COPIEETNUMERISATION Section: Page CONSIDERATIONS 7 A propos de la numérisation La numérisation consiste à prendre des coordonnées de la machine pendant la recopie de la pièce, et à envoyer ces coordonées au fichier ouvert au préalable au moyen de la déclaration (OPEN P). Pour pouvoir numériser un modèle, il est nécessaire d’exécuter l’un des cycles de copie / numérisation (TRACE) ou, après avoir activé les fonctions Copie G23 et Numérisation G24, de définir la trajectoire que la sonde doit suivre pour numériser le modèle. La CNC prend des points du modèle en fonction des paramètres indiqués dans la fonction G24 ou, dans le mode JOG, chaque fois que l’utilisateur actionne le poussoir externe ou la touche logiciel correspondante. Pendant la numérisation du modèle, la CNC contrôle uniquement les déplacements des axes X, Y, Z. Les blocs de programme générés ne contiennent donc que des informations sur l’ensemble des axes X, Y, Z ou sur certains. En outre, la CNC tient compte des déflexions de la sonde lorsqu’elle calcule les coordonnées du nouveau point numérisé. La prise de points n’est pas automatique lorsque le palpeur est en recherche de pièce ou décollé de la surface du modèle. Page 8 Chapitre: 16 COPIEETNUMERISATION Section: CONSIDERATIONS 16.2 G26. ETALONNAGE DE LA SONDE DE COPIE Cette fonction exécute un cycle d’étalonnage interne qui permet de compenser un éventuel défaut de parallélisme entre les axes de la sonde de copie et ceux de la machine. Cet étalonnage est recommandé lors de chaque installation de la sonde de copie sur la machine, chaque changement ou changement d’orientation de palpeur et à chaque mise en service de la CNC. Pour étalonner la sonde de copie, on utilisera un parallélépipède dont les faces seront rectifiées et parallèles aux axes de la machine. La sonde de copie est considérée par la CNC comme un outil de plus, auquel un correcteur correctement défini devra être associé (longueur de la sonde et rayon de la bille). Après sélection du correcteur, la sonde de copie, qui doit être installée selon l’axe longitudinal, devra se positionner au-dessus du parallèlépipède (en son centre). Le format de programmation de cette fonction est: G26 S Le paramètre S indique le sens, selon l’axe longitudinal (sur lequel se situe la sonde de copie), suivant lequel la recherche de pièce doit s’effectuer. Les valeurs pouvant être affectées à ce paramètre sont: 0 = Sens négatif 1 = Sens positif Dès que la sonde est en contact avec le parallèlépipède, la CNC la déplace sur sa surface en effectuant des mesures sur les autres faces comme indiqué ci-dessous. Attention: L’avance définie pour ces déplacements doit être sélectionnée avant l’exécution de la fonction G26. Les déviations de la sonde sur chacun des axes X, Y, Z sont stockées intérieurement pour être appliquées par la suite en tant que facteurs de correction chaque fois qu’une copie (G23) ou l’un des cycles de copie TRACE sont exécutés. Chaque fois que l’option de visualisation “Erreur de poursuite” est sélectionnée dans le mode JOG, la CNC affiche dans la partie droite de l’écran et à l’intérieur du cadre réservé aux valeurs de la sonde de copie le facteur de correction appliqué à chaque axe, les déflexions de chaque axe et la déflexion totale. Chapitre: 16 COPIEETNUMERISATION Section: ETALONNAGEDELASONDE DECOPIE Page 9 MANUEL P000662 N..... 11 : 50 : 14 ERREUR DE POURSUITE DEVIATIONS FACTEURS F03000.0000 %100 S00000.0000 %100 T0000 D000 NT0000 ND000 S 0000 RPM G00 G17 G54 PARTC=000000 CYTIME=00:00:00:00 TIMER=000000:00:00 DEPLACEMENT MANUEL EN CONTINU RECHERCE ZERO F1 PRESELECTION F2 MESURE F3 MDI F4 CAP INS UTILISATEUR VISUALISER F5 F6 MM/ POUCES F7 La fonction G26 n’est pas modale et doit donc être programmée à chaque étalonnage de la sonde de copie. La fonction G26 doit être programmée seule dans un bloc. Page 10 Chapitre: 16 COPIEETNUMERISATION Section: ETALONNAGEDELASONDE DECOPIE 16.3 G23. ACTIVATION DE LA COPIE Dès que la fonction Copie G23 est activée, la CNC maintient le palpeur en contact avec la surface du modèle jusqu’à l’annulation de la copie par G25. Lors de la définition de G23, on indiquera la déflexion nominale ou la pression que doit maintenir la sonde lorsqu’elle est en contact avec la surface du modèle. Les types de copie sélectionnables par la fonction G23 sont présentés ci-dessous: * Copie Manuelle. La déflexion de la sonde dépend de la pression exercée par l’utilisateur sur le palpeur. * Copie unidimensionnelle. Il s’agit du type le plus courant, et l’axe exécutant le balayage du modèle doit être défini. Lorsque ce type de copie a été défini, on programmera la trajectoire de copie grâce aux 2 autres axes. * Copie bidimensionnelle. Elle effectue un contournage du modèle, et les deux axes réalisant le suivi du profil doivent être définis. Lorsque ce type de copie a été défini, seuls les déplacement de l’autre axe peuvent être programmés. * Copie tridimensionnelle. Elle effectue un contournage du modèle, et le suivi du profil sera réalisé par les trois axes qui doivent donc être tous définis. Lorsque ce type de copie a été défini, il est impossible de programmer des déplacements pour les axes X, Y, Z. Chapitre: 16 COPIEETNUMERISATION Section: ACTIVATION DE LA COPIE (G23) Page 11 16.3.1 G23. ACTIVATION DE LA COPIE MANUELLE Ce type de copie permet à l’opérateur de déplacer le palpeur à la main sur la surface du modèle à copier. Pendant ce type de copie, la déflexion de la sonde dépend de la pression exercée par l’opérateur sur le palpeur. Il est donc conseillé d’utiliser ce type de copie pour les opérations d’ébauche, ou la fonction de numérisation G24 de façon que la CNC génère un programme compensant la déflexion de la sonde. La copie manuelle doit être sélectionnée dans l’option MDI du mode JOG. Le format de programmation est le suivant: G23 [X] [Y] [Z] X, Y, Z Définissent le ou les axes qui exécuteront le balayage du modèle. Il est possible de définir un, deux ou les trois axes. Si plusieurs axes sont définis, ils doivent être programmés dans l’ordre X, Y, Z. Si aucun axe n’est défini, la CNC prend l’axe longitudinal comme axe de palpage. Le palpeur ne peut être déplacé manuellement que sur les axes définis, les autres axes devant être déplacés au moyen des touches de JOG, par manivelle électronique ou par l’exécution de blocs en mode MDI. Par exemple, si la fonction Copie est activée sous la forme G23 Y Z, le palpeur pourra se déplacer manuellement selon les axes Y, Z. Pour le déplacer selon l’axe X, on peut utiliser les touches de JOG, une manivelle électronique ou des blocs en MDI. Toute tentative de déplacement d’un des axes sélectionnés comme axe de balayage en JOG ou par une manivelle électronique provoque l’émission du message d’erreur correspondant par la CNC. Page 12 Chapitre: 16 COPIEETNUMERISATION Section: ACTIVATION DE LA COPIE MANUELLE(G23) Exemples: G23 X Y Z * Cette option est très intéressante pour exécuter des opérations d’ébauche ou des contournages en 3 dimensions. * L’utilisateur peut déplacer le palpeur manuellement dans tous les sens. * Il est impossible de déplacer les axes X, Y, Z au moyen des touches JOG ou par une manivelle électronique. G23 X Y, G23 X Z , G23 YZ * Cette option permet d’exécuter des contournages bidimensionnels ou des passes de copie parallèles. * L’utilisateur peut déplacer le palpeur manuellement selon les axes sélectionnés (axes Y et Z dans l’exemple de passes de copie parallèles). * Seul l’axe non sélectionné (axe X dans l’exemple de passes de copie parallèles) peut être déplacé grâce aux touches de JOG ou à une manivelle électronique). * Si des passes de copie parallèles doivent être exécutées, le déplacement de l’autre axe doit être commandé par touches JOG ou par une manivelle électronique. G23 X , G23 Y , G23 Z * Cette option permet d’exécuter une prise de données en des points définis du modèle. * L’utilisateur ne peut déplacer le palpeur manuellement que sur l’axe sélectionné. * Les deux autres axes doivent être déplacés au moyen des touches JOG ou d’une manivelle électronique. Chapitre: 16 COPIEETNUMERISATION Section: ACTIVATION DE LA COPIE MANUELLE(G23) Page 13 16.3.2 G23. ACTIVATION DE LA COPIE UNIDIMENSIONNELLE Ce type de copie peut être sélectionné par programme pièce ou dans l’option MDI des modes de fonctionnement Manuel et Automatique. Dès que ce type est activé, la CNC approche la sonde jusqu’à ce qu’elle entre en contact avec le modèle, et elle la maintient en contact avec la surface de ce modèle en suivant en permanence la trajectoire sélectionnée. La trajectoire de copie peut être programmée en code ISO, ou être obtenue par déplacement des axes au moyen des touches JOG ou d’une manivelle électronique. Ne pas oublier que, lorsque ce type de copie est activé, l’axe de balayage ne peut pas être programmé ni déplacé. Toute tentative de déplacement entraîne l’émission du message d’erreur correspondant par la CNC. Le format de programmation est le suivant: G23 [axe] I±5.5 N5.5 [axe] Définit l’axe effectuant le balayage du modèle. Il peut s’agir de l’axe X, Y ou Z. Si aucun axe n’est défini, la CNC prend l’axe longitudinal comme axe de balayage. Les axes non définis doivent être utilisés pour définir la trajectoire de copie, soit en la programmant en code ISO, soit en les déplaçant grâce aux touches JOG ou à la manivelle électronique. I±5.5 Définit la profondeur maximum de copie de l’axe de balayage, par rapport à la position de la sonde au moment de la définition. Si une partie de la pièce se situe hors de cette zone, la copie affectera à l’axe de balayage la coordonnée indiquée par ce paramètre. Page 14 Chapitre: 16 COPIEETNUMERISATION Section: ACTIVATION DE LA COPIE UNIDIMENSIONNELLE (G23) N 5.5 Déflexion nominale. Elle indique la pression exercée par la sonde lorsqu’elle est en contact avec la surface du modèle. La déflexion est définie en unités de travail sélectionnées (mm ou pouces) et sa valeur se situe normalement entre 0,3 mm et 1,5 mm. La qualité de la copie dépend de la déflexion, de l’avance et de la géométrie du modèle. Pour éviter que la sonde ne se détache du modèle, il est conseillé d’utiliser, pour le suivi du profil, une avance égale à 1000 fois la déflexion par minute. Par exemple, pour une déflexion de 1 mm, on choisira une avance de 1 m/min. Exemple d’application aux axes X, Y, Z: Exemple de programmation: La zone de copie est délimitée entre (X100 Y0) et (X150 Y50), le palpage devant s’effectuer selon l’axe Z. G90 G01 X100 Y0 Z80 F1000 G23 Z I-10 N1.2 Active la copie N10 G91 X50 Définit le déplacement Y5 “ X-50 “ N20 Y5 “ (RPT N10,N20) N4 “ X50 “ G25 Désactive la copie M30 Chapitre: 16 COPIEETNUMERISATION Section: Page ACTIVATION DE LA COPIE UNIDIMENSIONNELLE (G23) 15 16.3.3 G23. ACTIVATION DE LA COPIE BIDIMENSIONNELLE Ce type de copie permet d’exécuter des contours bidimensionnels. Il peut être sélectionné par programme pièce ou dans l’option MDI des modes de fonctionnement Manuel et Automatique. Dès que ce type est activé, la CNC déplace la sonde jusqu’au point d’approche (I, J) indiqué dans la définition de la fonction G23. Ensuite, elle approche la sonde jusqu’à ce qu’elle entre en contact avec le modèle suivant les axes sélectionnés et la maintient en contact sur cette surface en suivant en permanence la trajectoire sélectionnée. Ne pas oublier que, lorsque ce type de copie est activé, les axes de balayage ne peuvent être ni programmés ni déplacés. Toute tentative de déplacement d’un de ces axes entraîne l’émission du message d’erreur correspondant par la CNC. La trajectoire de contournage doit être définie par la fonction G27 (définition du contour de copie) décrite dans ce chapitre ou par déplacement de l’axe autre que l’axe de balayage, grâce aux touches JOG ou à une manivelle électronique. Le format de programmation est le suivant: G23 [eje1] [eje2] I±5.5 J±5.5 N5.5 eje1 eje2 Définissent les axes effectuant le balayage du modèle. Deux des trois axes X, Y, Z doivent être définis dans l’ordre indiqué. I±5.5 Définit la coordonnée d’approche de l’axe “1”, par rapport au zéro pièce. J±5.5 Définit la coordonnée d’approche de l’axe “2”, par rapport au zéro pièce. Page 16 Chapitre: 16 COPIEETNUMERISATION Section: ACTIVATION DE LA COPIE BIDIMENSIONNELLE(G23) N 5.5 Déflexion nominale. Elle indique la pression exercée par la sonde lorsqu’elle est en contact avec la surface du modèle. La déflexion est définie en unités de travail sélectionnées (mm ou pouces) et sa valeur se situe normalement entre 0,3 mm et 1,5 mm. La qualité de la copie dépend de la déflexion, de l’avance et de la géométrie du modèle. Pour éviter que la sonde ne se détache du modèle, il est conseillé d’utiliser, pour le suivi du profil, une avance égale à 1000 fois la déflexion par minute. Par exemple, pour une déflexion de 1 mm, on choisira une avance de 1 m/min. Exemples de copie de différents contours: Chapitre: 16 COPIEETNUMERISATION Section: ACTIVATION DE LA COPIE BIDIMENSIONNELLE(G23) Page 17 16.3.4 G23. ACTIVACION DE LA COPIE TRIDIMENSIONNELLE Ce type de copie permet d’exécuter des contournages tridimensionnels. Le palpeur doit toujours disposer d’une surface d’appui. La pente maximum de la surface balayée dépend de l’avance en balayage et des déflexions nominales. Plus l’avance en balayage est grande, plus la pente autorisée sera faiblea. Ce type de copie peut être sélectionné par programme pièce ou dans l’option MDI des modes de fonctionnement Manuel et Automatique. Dès que ce type est activé, la CNC déplace la sonde jusqu’au point d’approche (I, J, K) indiqué dans la définition de la fonction G23. Ensuite, elle approche la sonde jusqu’à ce qu’elle entre en contact avec le modèle et la maintient en contact sur cette surface en suivant en permanence la trajectoire sélectionnée. Ne pas oublier que, lorsque ce type de copie est activé, les axes X, Y, Z ne peuvent être ni programmés ni déplacés. Toute tentative de déplacement d’un de ces axes entraîne l’émission du message d’erreur correspondant par la CNC. La trajectoire de contournage doit être définie par la fonction G27 (définition du contour de copie) décrite dans ce chapitre. Page 18 Chapitre: 16 COPIEETNUMERISATION Section: ACTIVACION DE LA COPIE TRIDIMENSIONNELLE(G23) Le format de programmation est le suivant: G23 X Y Z I±5.5 J±5.5 K±5.5 N5.5 M5.5 X, Y, Z Définissent les axes effectuant le balayage du modèle. Tous les axes doivent être définis, dans l’ordre X, Y, Z I±5.5 Définit la coordonnée d’approche de l’axe “X”, par rapport au zéro pièce. J±5.5 Définit la coordonnée d’approche de l’axe “Y”, par rapport au zéro pièce. K±5.5 Définit la coordonnée d’approche de l’axe “Z”, par rapport au zéro pièce. N 5.5 Déflexion nominale des axes constituant le plan. M 5.5 Déflexion nominale de l’axe longitudinal. Les déflexions N et M indiquent la pression exercée par la sonde lorsqu’elle est en contact avec la surface du modèle. La déflexion est définie en unités de travail sélectionnées (mm ou pouces) et sa valeur se situe normalement entre 0,3 mm et 1,5 mm. La qualité de la copie dépend de la déflexion, de l’avance et de la géométrie du modèle. Pour éviter que la sonde ne se détache du modèle, il est conseillé d’utiliser, pour le suivi du profil, une avance égale à 1000 fois la déflexion par minute. Par exemple, pour une déflexion de 1 mm, on choisira une avance de 1 m/min. Chapitre: 16 COPIEETNUMERISATION Section: ACTIVACION DE LA COPIE TRIDIMENSIONNELLE(G23) Page 19 16.4 G27. DEFINITION DU CONTOUR DE COPIE Chaque fois qu’une copie bidimensionnelle ou tridimensionnelle est activée, le contour de copie doit être défini par la fonction G27. La sonde de palpage commence à se déplacer autour du modèle en restant en contact avec lui, selon le sens indiqué. Il est possible de définir un contour fermé (les points de début et de fin coïncident) ou un contour ouvert (dans lequel les points de début et de fin ne coïncident pas). Exemple de contour fermé: Dans le cas d’un contour ouvert, la fin du contour doit être définie par un segment parallèle aux axes. La copie est terminée lorsque la sonde croise ce segment. Page 20 Chapitre: 16 COPIEETNUMERISATION Section: DEFINITIONDUCONTOURDE COPIE (G27) Le format de programmation est le suivant: G27 S Q±5.5 R±5.5 J5.5 K S Indique le sens du balayage du modèle. 0 = Le palpeur se déplace en laissant le modèle à sa droite. 1 = Le palpeur se déplace en laissant le modèle à sa gauche. Si ce paramètre n’est pas programmé, la CNC prend la valeur S0 par défaut. Q, R±5.5 Ces paramètres doivent être définis lorsqu’un contour ouvert est défini (les points de début et de fin ne coïncident pas). Ils définissent le point de début du segment qui indique la fin du contour, par rapport au zéro pièce. La coordonnée Q correspond à l’axe des abscisses, et la cote R correspond à l’axe des ordonnées. Dans le cas d’un contour fermé (les points de début et de fin coïncident), on ne programmera que G27 S. J 5.5 Ce paramètre doit être défini dans le cas d’un contour ouvert, c’est-à-dire lorsque Q et R ont été définis. Définit la longueur du segment indiquant la fin du contour. K Ce paramètre doit être défini dans le cas d’un contour ouvert, c’est-à-dire lorsque Q et R ont été définis. Il définit la direction et le sens du segment indiquant la fin du contour. 0 1 2 3 = = = = Vers les coordonnées positives de l’axe des abscisses Vers les coordonnées négatives de l’axe des abscisses. Vers les coordonnées positives de l’axe des ordonnées. Vers les coordonnées négatives de l’axe des ordonnées. Si ce paramètre n’est pas programmé, la CNC prendra la valeur K0 par défaut. Chapitre: 16 COPIEETNUMERISATION Section: DEFINITIONDUCONTOURDE COPIE (G27) Page 21 Exemples de programmation bidimensionnelle: Contour bidimensionnel fermé: G23 XY I50 J8 N0.8 G24 L8 E5 K1 G27 S0 G25 ;Définition de copie bidimensionnelle ;Définition de la numérisation ;Définition de contour fermé ;Désactive la copie et la numérisation Contour bidimensionnel ouvert: G23 XY I60 J20 N0.8 G24 L8 E5 K1 G27 S0 Q10 R25 J15 K0 G25 Page 22 ;Définition de copie bidimensionnelle ;Définition de la numérisation ;Définition de contour ouvert ;Désactive la copie et la numérisation Chapitre: 16 COPIEETNUMERISATION Section: DEFINITIONDUCONTOURDE COPIE (G27) Exemples de programmation tridimensionnelle: Contour tridimensionnel fermé: G23 XYZ I8 J50 K75 N0.8 G24 L8 E5 K1 G27 S1 G25 ;Définition de copie tridimensionnelle ;Définition de la numérisation ;Définition de contour fermé ;Désactive la copie et la numérisation Contour tridimensionnel ouvert: G23 XYZ I20 J50 K45 N0.8 M0.5 G24 L8 E5 K1 G27 S1 Q80 R40 J25 K0 G25 Chapitre: 16 COPIEETNUMERISATION ;Définition de copie tridimensionnelle ;Définition de la numérisation ;Définition de contour ouvert ;Désactive la copie et la numérisation Section: DEFINITIONDUCONTOURDE COPIE (G27) Page 23 16.5 G25. DESACTIVATION DE LA COPIE La fonction Copie peut être désactivée comme suit: - Par G25, qui peut être programmé dans n’importe quel bloc. - Par sélection d’un nouveau plan de travail (G16, G17, G18, G19). - Lorsqu’un nouvel axe longitudinal est sélectionné (G15). - Après exécution d’une fin de programme (M02, M30). - Après une URGENCE ou un RESET. Si, lors de la désactivation de la fonction Copie, la fonction Numérisation (G24) est active en même temps que la fonction Copie (G23), la CNC désactivera les deux fonctions. Page 24 Chapitre: 16 COPIEETNUMERISATION Section: DESACTIVATION DE LA COPIE (G25) 16.6 G24. ACTIVATION DE LA NUMERISATION La numérisation consiste à prendre les coordonnées de la machine pendant la copie de la pièce et à envoyer ces coordonnées au fichier ouvert au préalable au moyen de la déclaration (OPEN P). Indépendamment du type de copie utilisé (manuel, unidimensionnel, bidimensionnel ou tridimensionnel), les points numérisés présentent les coordonnées selon les axes X, Y, Z. Il existe deux types de numérisation: la numérisation continue et la numérisation point à point. Numérisation continue. Elle peut être utilisée avec tous les types de copie. Son format de programmation est: G24 L E K La CNC exécute une prise de points du modèle en fonction de la valeur affectée aux paramètres “L” et “E”. Si le paramètre “L” n’est pas programmé, la CNC suppose que la numérisation choisie est du type point à point. Numérisation point à point. Ce type de numérisation n’est utilisable qu’en cas de copie manuelle, c’est-à-dire lorsque l’opérateur amène le palpeur manuellement sur la surface du modèle. Son format de programmation est: G24 K La CNC génère un nouveau point chaque fois que l’utilisateur actionne la touche logiciel “PRISE POINT A POINT”, ou chaque fois que le PLC provoque une transition positive au niveau de l’entrée logique générale “POINT” de la CNC (poussoir externe). Le format de programmation général pour activation de la numérisation est le suivant: G24 L5.5 E5.5 K L 5.5 Indique le pas de balayage, ou distance séparant deux points numérisés successifs. La CNC fournit les coordonnées d’un nouveau point après avoir parcouru, dans l’espace et selon la trajectoire programmée, la distance indiquée par le paramètre “L”. Si ce paramètre n’est pas programmé, la CNC supposera le choix de la numérisation point à point. Chapitre: 16 COPIEETNUMERISATION Section: ACTIVATIONDELA NUMERISATION(G24) Page 25 E 5.5 Indique l’erreur à la corde, ou différence maximum admise entre la surface du modèle et le segment passant par les points mémorisés. Elle est définie en unités de travail sélectionnées (mm ou pouces). Si ce paramètre n’est pas programmé ou s’il est programmé avec une valeur “0”, l’erreur à la corde n’est pas prise en compte et un nouveau point est fourni après que la distance indiquée dans le paramètre “L” ait été parcourue dans l’espace et selon le déplacement programmé. K Indique le format de mémorisation des points numérisés dans le programme sélectionné au moyen de la déclaration (OPEN P). K=0 Format absolu. Tous les points seront programmés en coordonnées absolues (G90) et définis au moyen des axes X, Y et Z. K=1 Format absolu filtré. Tous les points seront programmés en coordonnées absolues (G90), mais seuls les axes dont la position a changé par rapport au point numérisé antérieur sont définis. K=2 Format incrémental filtré. Tous les points seront programmés en coordonnées incrémentales (G91), par rapport au point numérisé précédent. Seuls les axes dont la position a changé par rapport au point numérisé antérieur sont définis. Si ce paramètre n’est pas programmé, le cycle fixe prendra la valeur K0. Concepts de base: * La fonction G24 doit être définie immédiatement avant le bloc où doit commencer la numérisation de la pièce. * Avant d’activer la numérisation (G24), on ouvrira, au moyen de la déclaration “OPEN P”, le programme où seront stockés les points numérisés. Page 26 Chapitre: 16 COPIEETNUMERISATION Section: ACTIVATIONDELA NUMERISATION(G24) Si, au lieu de charger les données dans la mémoire de programmes de la CNC, l’opérateur souhaite les envoyer vers un périphérique ou un ordinateur par ligne DNC, il devra le préciser pendant la définition de la déclaration (OPEN P). Lorsque les transmissions sont réalisées par ligne DNC, si la vitesse de transmission est inférieure à la vitesse de saisie des données, la vitesse de copie est plus lente. * Pendant la numérisation du modèle, la CNC ne contrôle que les déplacements des axes X, Y, Z. Les blocs de programme générés ne contiennent donc que des informations sur un ou plusieurs de ces axes X, Y, Z. * Aucun point n’est généré lorsque le palpeur cherche la pièce ou lorsqu’il s’est détaché de la surface du modèle. * La CNC tient compte des déflexions de la sonde lorsqu’elle calcule les coordonnées du nouveau point numérisé. * Pour désactiver la numérisation, on programmera la fonction G25. La fonction de numérisation est également désactivée lorsque la fonction Copie (G23) est désactivée, par conséquent dans les cas suivants: - Choix d’un nouveau plan de travail (G16, G17, G18, G19). - Choix d’un nouvel axe longitudinal (G15). - Après exécution d’une fin de programme (M02, M30). - Après une URGENCE ou un RESET. Exemple de programmation: G17 G90 G01 X65 Y0 F1000 (OPEN P12345) (WRITE G01 G05 F1000) G23 Z I-10 N1 G24 L8 E5 K1 G1 X100 Y35 “ “ G25 Sélectionne l’axe Z en tant qu’axe longitudinal Positionnement Programme destinataire des données Active la fonction de copie Active la fonction de numérisation Définit le déplacement de copie “ “ Désactive les fonctions de copie et de numérisation M30 Chapitre: 16 COPIEETNUMERISATION Section: ACTIVATIONDELA NUMERISATION(G24) Page 27 16.7 CYCLES FIXES DE COPIE ET DE NUMERISATION Les cycles fixes de copie / numérisation dont dispose la CNC sont basés sur les types de copie ci-dessous, présentés précédemment: TRACE TRACE TRACE TRACE TRACE 1 2 3 4 5 Cycle fixe de copie / numérisation en grille. Cycle fixe de copie / numérisation en arc. Cycle fixe de copie / numérisation de profil dans le plan. Cycle fixe de copie / numérisation de profil dans l’espace/ Cycle fixe de copie / numérisation par balayage de polygone. Ces cycles sont programmés au moyen de l’instruction de haut niveau TRACE, le numéro du cycle pouvant être indiqué par un chiffre (1, 2, 3, 4, 5) ou par toute expression dont l’un de ces chiffres est le résultat. Tous ces cycles disposent d’une série de paramètres qui définissent la trajectoire de la copie et les conditions de la numérisation. Pour n’exécuter que la copie de la pièce (sans numérisation) les paramètres de numérisation doivent être mis à “0”. Pour numériser le modèle, on tiendra compte, après avoir défini correctement les paramètres de numérisation, des éléments suivants: * Avant d’appeler le cycle fixe, on ouvrira le programme devant contenir les données au moyen de la déclaration (OPEN P). * Si au lieu de charger les données dans la mémoire de programmes de la CNC, l’opérateur décide de les envoyer vers un périphérique ou un ordinateur par ligne DNC, il devra l’indiquer lorsqu’il définira la déclaration (OPEN P). * Les blocs du programme générés par le cycle fixe sont tous des blocs de positionnement (G01 X Y Z); il est recommandé d’indiquer dans ce programme les conditions de l’usinage au moyen de la déclaration (WRITE). * A la fin de la numérisation, l’une des fonctions de fin de programme M03 ou M30 doit être générée au moyen de la déclaration (WRITE). A la fin du cycle de palpage, le palpeur se situe à l’emplacement qu’il occupait avant l’exécution du cycle. L’exécution d’un cycle fixe de copie ne modifie pas l’historique des fonctions "G" antérieures. Page 28 Chapitre: 16 COPIEETNUMERISATION Section: CYCLES FIXES DE COPIE ET DE NUMERISATION 16.7.1 CYCLE FIXE DE COPIE SUIVANT UNE GRILLE Le format de programmation de ce cycle est le suivant: (TRACE 1, X, Y, Z, I, J, K, A, C, Q, D, N, L, E, G, H, F) X±5.5 Coordonnée théorique, selon l’axe des abscisses, du premier point de palpage; elle est définie en absolu et doit coïncider avec l’un des coins de la grille. Y±5.5 Coordonnée théorique, selon l’axe des ordonnées, du premier point de palpage; elle est définie en absolu et doit coïncider avec l’un des coins de la grille. Z±5.5 Coordonnée théorique de l’axe de palpage (axe longitudinal), où doit se positionner la sonde avant de commencer la copie. Elle est définie en absolu et doit être séparée du modèle, avec maintien d’une distance de sécurité par rapport à la surface la plus à l’extérieur. I±5.5 Définit la profondeur maximum de copie, par rapport à la coordonnée définie dans le paramètre Z. Si une partie de la pièce se situe hors de cette zone, la copie affecte à l’axe longitudinal la coordonnée absolue correspondant à cette profondeur maximum, et l’exécution du cycle se poursuit sans émission d’un message d’erreur. Si ce paramètre est programmé avec la valeur 0, la CNC affiche le message d’erreur correspondant. Chapitre: 16 COPIEETNUMERISATION Section: CYCLEFIXEDECOPIE SUIVANTUNEGRILLE Page 29 J±5.5 Définit la longueur de la grille selon l’axe des abscisses. Un signe “+” indique que la grille se situe à la droite du point (X, Y), tandis que le signe “-” indique qu’elle est à la gauche de ce point. K±5.5 Définit la longueur de la grille selon l’axe des ordonnées. Un signe “+” indique que la grille se situe au-dessus du point (X, Y), tandis que le signe “-” indique qu’elle est au-dessous de ce point. A 5.5 Définit l’angle de la trajectoire de balayage. Il doit être compris entre 0° (inclus) et 90° (exclus). Si ce paramètre n’est pas programmé, le cycle fixe prend la valeur A0. C±5.5 Définit la distance maintenue entre deux passes de copie. Si ce paramètre est programmé avec le signe “+”, la copie est réalisée selon l’axe des abscisses et la distance est prise sur l’axe des ordonnées. S’il est programmé avec une valeur négative, la copie est réalisée selon l’axe des ordonnées et la distance est prise sur l’axe des abscisses. Si ce paramètre est programmé avec la valeur 0, la CNC affiche le message d’erreur correspondant. Q 5.5 Définit l’angle des trajectoires incrémentales. Il doit être compris entre 0 et 45° (ces deux valeurs comprises). Si l’angle n’est pas programmé ou si une copie unidirectionelle (D=1) est programmée, le cycle fixe prend la valeur Q0. Page 30 Chapitre: 16 COPIEETNUMERISATION Section: CYCLEFIXEDECOPIE SUIVANTUNEGRILLE D Indique le type de trajet sur la grille, au moyen du code suivant: 0 = Copie exécutée dans les deux sens (en zig-zag). 1 = Copie exécutée toujours dans le même sens (unidirectionnel). Si ce paramètre n’est pas programmé, le cycle fixe prend la valeur D0. N 5.5 Déflexion nominale. Elle indique la pression exercée par la sonde lorsqu’elle est en contact avec la surface du modèle. La déflexion est définie en unités de travail sélectionnées (mm ou pouces) et sa valeur se situe normalement entre 0,3 mm et 1,5 mm. La qualité de la copie dépend de la déflexion, de l’avance et de la géométrie du modèle. Pour éviter que la sonde ne se détache du modèle, il est conseillé d’utiliser, pour le suivi du profil, une avance égale à 1000 fois la déflexion par minute. Par exemple, pour une déflexion de 1 mm, on choisira une avance de 1 m/min. Si ce paramètre n’est pas programmé, le cycle fixe applique une déflexion de 1 mm. L 5.5 Ce paramètre doit être défini lorsqu’une numérisation de la pièce doit être effectuée en plus de la copie. Il indique le pas de balayage ou distance entre deux points numérisés. Chapitre: 16 COPIEETNUMERISATION Section: CYCLEFIXEDECOPIE SUIVANTUNEGRILLE Page 31 La CNC maintient la sonde en contact permanent avec la surface du modèle suivant la trajectoire programmée et fournit les coordonnées d’un nouveau point lorsque la distance indiquée dans le paramètre “L” a été parcourue dans l’espace et selon le trajet programmé. Si ce paramètre n’est pas programmé, ou s’il est programmé avec la valeur 0, le cycle fixe suppose que la numérisation de la pièce n’est pas désirée. E 5.5 Ce paramètre doit être défini lorsque l’opérateur désire réaliser la numérisation de la pièce en plus de la copie. Il indique l’erreur à la corde, ou différence maximum admise entre la surface du modèle et le segment passant par les points mémorisés. Elle est définie en unités de travail sélectionnées (mm ou pouces). Si ce paramètre n’est pas programmé ou s’il est programmé avec une valeur “0”, l’erreur à la corde n’est pas prise en compte et un nouveau point est fourni après que la distance indiquée dans le paramètre “L” ait été parcourue dans l’espace et selon le déplacement programmé. G Ce paramètre doit être défini lorsqu’une numérisation de la pièce doit être effectuée en plus de la copie. Il indique le format de mémorisation des points numérisés dans le programme sélectionné au moyen de la déclaration (OPEN P). G=0 Format absolu. Tous les points seront programmés en coordonnées absolues (G90) et définis au moyen des axes X, Y et Z. G=1 Format absolu filtré. Tous les points seront programmés en coordonnées absolues (G90), mais seuls les axes dont la position a changé par rapport au point numérisé antérieur sont définis. Page 32 Chapitre: 16 COPIEETNUMERISATION Section: CYCLEFIXEDECOPIE SUIVANTUNEGRILLE G=2 Format incrémental filtré. Tous les points seront programmés en coordonnées incrémentales (G91), par rapport au point numérisé précédent. Seuls les axes dont la position a changé par rapport au point numérisé antérieur sont définis. Si ce paramètre n’est pas programmé, le cycle fixe prendra la valeur G0. H5.5 Définit l’avance appliquée pour l’exécution des trajectoires incrémentales. Ce paramètre est programmé en mm/minute ou en pouces/minute. Si ce paramètre n’est pas programmé, le cycle fixe prend la valeur F (avance des trajectoires de balayage). F5.5 Définit l’avance appliquée pour l’exécution des trajectoires de balayage. Ce paramètre est programmé en mm/minute ou en pouces/minute. FONCTIONNEMENT DE BASE: 1.- La sonde se positionne sur le point défini par les paramètres X, Y, Z. 2.- La CNC approche la sonde du modèle jusqu’à ce qu’elle entre en contact avec ce dernier. 3.- La sonde est maintenue en contact permanent avec la surface du modèle, et exécute le suivi selon le trajet programmé. Si une numérisation de la pièce a été demandée, (paramètres “L” et “E”), elle génère, pour chaque point numérisé, un nouveau bloc dans le programme ouvert au moyen de la déclaration (OPEN P). 4.- A la fin du cycle fixe, la sonde revient au point de départ. Ce déplacement se compose de: * Déplacement du palpeur selon l’axe de palpage (axe longitudinal) jusqu’à la coordonnée indiquée par le paramètre Z. * Déplacement dans le plan principal de travail jusqu’au point de départ du cycle (paramètres X, Y). Chapitre: 16 COPIEETNUMERISATION Section: CYCLEFIXEDECOPIE SUIVANTUNEGRILLE Page 33 16.7.2 CYCLE FIXE DE COPIE SUIVANT UN ARC Le format de programmation de ce cycle est le suivant: (TRACE 2, X, Y, Z, I, J, K, A, B, C, D, R, N, L, E, G, H, F) X±5.5 Coordonnée théorique, selon l’axe des abscisses, du centre de l’arc; elle est définie en absolu. Y±5.5 Coordonnée théorique, selon l’axe des ordonnées, du centre de l’arc; elle est définie en absolu. Z±5.5 Coordonnée théorique de l’axe de palpage (axe longitudinal), où doit se positionner la sonde avant de commencer la copie. Elle est définie en absolu et doit être séparée du modèle, avec maintien d’une distance de sécurité par rapport à la surface la plus à l’extérieur. I±5.5 Définit la profondeur maximum de copie, par rapport à la coordonnée définie dans le paramètre Z. Si une partie de la pièce se situe hors de cette zone, la copie affecte à l’axe longitudinal la coordonnée absolue correspondant à cette profondeur maximum, et l’exécution du cycle se poursuit sans émission d’un message d’erreur. Page 34 Chapitre: 16 COPIEETNUMERISATION Section: CYCLEFIXEDECOPIE SUIVANT UN ARC Si ce paramètre est programmé avec la valeur 0, la CNC affiche le message d’erreur correspondant. J 5.5 Définit le rayon correspondant à l’arc le plus extérieur à la zone à copier. Ce paramètre doit être programmé avec une valeur positive et supérieure à 0. K 5.5 Définit le rayon correspondant à l’arc le plus à l’intérieur de la zone à copier. Ce paramètre doit être programmé avec une valeur positive. Si ce paramètre n’est pas programmé, le cycle fixe prend la valeur K0. A 5.5 Définit l’angle formé par le point de départ de la copie et l’axe des abscisses. Si ce paramètre n’est pas programmé, le cycle fixe prend la valeur A0. B 5.5 Définit l’angle formé par l’autre extrêmité des arcs et l’axe des abscisses. Si ce paramètre n’est pas programmé, le cycle fixe prend la valeur B360. Si la copie doit concerner toute la circonférence, on affectera la même valeur aux paramètres A et B, ou on n’en définira aucun. Par défaut, le cycle fixe affectera les valeurs A0 et B360. C 5.5 Définit la distance à maintenir entre deux passes de copie. Ce paramètre est programmé en mm ou en pouces dans le cas des trajectoires circulaires (R0), et en degrés dans le cas des trajectoires linéaires (R1). On affectera une valeur positive et supérieure à 0. Chapitre: 16 COPIEETNUMERISATION Section: CYCLEFIXEDECOPIE SUIVANT UN ARC Page 35 D Indique le mode d’exécution des trajectoires de balayage au moyen du code suivant: 0 = Copie exécutée dans les deux sens (en zig-zag). 1 = Copie exécutée toujours dans le même sens (unidirectionnel). Si ce paramètre n’est pas programmé, le cycle fixe prend la valeur 0. R Indique le type de trajectoire de balayage désiré au moyen du code suivant: 0 = Trajectoire circulaire, en suivant l’arc. 1 = Trajectoire linéaire, en suivant le rayon. Si ce paramètre n’est pas programmé, le cycle fixe prend la valeur 0. Exemple de sélection de R0 (trajectoire circulaire): * Lors de la définition des paramètres A et B, on tiendra compte du fait que le premier balayage s’effectue toujours dans le sens anti-horaire. * Le pas C indique la distance linéaire entre deux passes de copie. On programmera ce paramètre en mm ou en pouces. Exemple de sélection de R1 (trajectoire linéaire): * Le pas C indique la distance angulaire entre deux passes de copie. Elle doit être programmée en degrés. * Le paramètre K, qui correspond à l’arc le plus à l’intérieur, peut être programmé avec des valeurs positives ou négatives. * Si R1 D1 (trajectoire linéaire unidirectionnelle) est également sélectionné, le balayage s’effectue toujours du rayon le plus à l’intérieur (K) au rayon le plus à l’extérieur (J). Page 36 Chapitre: 16 COPIEETNUMERISATION Section: CYCLEFIXEDECOPIE SUIVANT UN ARC N 5.5 Déflexion nominale. Elle indique la pression exercée par la sonde lorsqu’elle est en contact avec la surface du modèle. La déflexion est définie en unités de travail sélectionnées (mm ou pouces) et sa valeur se situe normalement entre 0,3 mm et 1,5 mm. La qualité de la copie dépend de la déflexion, de l’avance et de la géométrie du modèle. Pour éviter que la sonde ne se détache du modèle, il est conseillé d’utiliser, pour le suivi du profil, une avance égale à 1000 fois la déflexion par minute. Par exemple, pour une déflexion de 1 mm, on choisira une avance de 1 m/min. Si ce paramètre n’est pas programmé, le cycle fixe applique une déflexion de 1 mm. L 5.5 Ce paramètre doit être défini lorsqu’une numérisation de la pièce doit être effectuée en plus de la copie. Il indique le pas de balayage ou distance entre deux points numérisés. La CNC maintient la sonde en contact permanent avec la surface du modèle suivant la trajectoire programmée et fournit les coordonnées d’un nouveau point lorsque la distance indiquée dans le paramètre “L” a été parcourue dans l’espace et selon le trajet programmé. Si ce paramètre n’est pas programmé, ou s’il est programmé avec la valeur 0, le cycle fixe suppose que la numérisation de la pièce n’est pas désirée. E 5.5 Ce paramètre doit être défini lorsque l’opérateur désire réaliser la numérisation de la pièce en plus de la copie. Il indique l’erreur à la corde, ou différence maximum admise entre la surface du modèle et le segment passant par les points mémorisés. Elle est définie en unités de travail sélectionnées (mm ou pouces). Chapitre: 16 COPIEETNUMERISATION Section: CYCLEFIXEDECOPIE SUIVANT UN ARC Page 37 Si ce paramètre n’est pas programmé ou s’il est programmé avec une valeur “0”, l’erreur à la corde n’est pas prise en compte et un nouveau point est fourni après que la distance indiquée dans le paramètre “L” ait été parcourue dans l’espace et selon le déplacement programmé. G Ce paramètre doit être défini lorsqu’une numérisation de la pièce doit être effectuée en plus de la copie. Il indique le format de mémorisation des points numérisés dans le programme sélectionné au moyen de la déclaration (OPEN P). G=0 Format absolu. Tous les points seront programmés en coordonnées absolues (G90) et définis au moyen des axes X, Y et Z. G=1 Format absolu filtré. Tous les points seront programmés en coordonnées absolues (G90), mais seuls les axes dont la position a changé par rapport au point numérisé antérieur sont définis. G=2 Format incrémental filtré. Tous les points seront programmés en coordonnées incrémentales (G91), par rapport au point numérisé précédent. Seuls les axes dont la position a changé par rapport au point numérisé antérieur sont définis. Si ce paramètre n’est pas programmé, le cycle fixe prendra la valeur G0. H5.5 Page 38 Définit l’avance appliquée pour l’exécution des trajectoires incrémentales. Ce paramètre est programmé en mm/minute ou en pouces/minute. Chapitre: 16 COPIEETNUMERISATION Section: CYCLEFIXEDECOPIE SUIVANT UN ARC Si ce paramètre n’est pas programmé, le cycle fixe prend la valeur F (avance des trajectoires de balayage). F5.5 Définit l’avance appliquée pour l’exécution des trajectoires de balayage. Ce paramètre est programmé en mm/minute ou en pouces/minute. FONCTIONNEMENT DE BASE: 1.- La sonde se positionne sur le point défini par les paramètres X, Y, Z. 2.- La CNC approche la sonde du modèle jusqu’à ce qu’elle entre en contact avec ce dernier. 3.- La sonde est maintenue en contact permanent avec la surface du modèle, et exécute le suivi selon le trajet programmé. Si une numérisation de la pièce a été demandée, (paramètres “L” et “E”), elle génère, pour chaque point numérisé, un nouveau bloc dans le programme ouvert au moyen de la déclaration (OPEN P). 4.- A la fin du cycle fixe, la sonde revient au point de départ. Ce déplacement se compose de: * Déplacement du palpeur selon l’axe de palpage (axe longitudinal) jusqu’à la coordonnée indiquée par le paramètre Z. * Déplacement dans le plan principal de travail jusqu’au point de départ du cycle (paramètres X, Y). Chapitre: 16 COPIEETNUMERISATION Section: CYCLEFIXEDECOPIE SUIVANT UN ARC Page 39 16.7.3 CYCLE FIXE DE COPIE DE PROFIL DANS LE PLAN Le format de programmation de ce cycle est le suivant: (TRACE 3, X, Y, Z, I, D, B, A, C, S, Q, R, J, K, N, L, E, G, H, F) X±5.5 Coordonnée théorique, selon l’axe des abscisses, du point d’approche au modèle; elle est définie en absolu et doit se situer hors du modèle. Y±5.5 Coordonnée théorique, selon l’axe des ordonnées, du point d’approche au modèle; elle est définie en absolu et doit se situer hors du modèle. Z±5.5 Coordonnée théorique de l’axe de palpage (axe longitudinal), où doit se positionner la sonde avant de commencer la copie. Elle est définie en absolu et doit être séparée du modèle, avec maintien d’une distance de sécurité par rapport à la surface la plus à l’extérieur. I±5.5 Coordonnée théorique de l’axe de palpage (axe longitudinal), où doit s’effectuer la dernière passe de copie. D 5.5 Définit, sur l’axe de palpage, (axe longitudinal), la distance entre le point de positionnement de la sonde (paramètre Z) et le plan où doit s’effectuer la première passe de copie. Si ce paramètre n’est pas programmé, la CNC n’exécutera qu’une passe de copie à la hauteur indiquée par le paramètre I. B 5.5 Ce paramètre doit être défini à chaque définition du paramètre D. Définit, sur l’axe de palpage, (axe longitudinal), la distance entre deux passes de copie consécutives. Si ce paramètre est programmé avec une valeur “0”, la CNC émet le message d’erreur correspondant. A Page 40 Indique la direction et le sens que suivra la sonde de copie après s’être positionnée sur le point X Y Z et être descendue dans le plan où sera exécutée la première passe de copie, pour trouver le modèle. Chapitre: 16 COPIEETNUMERISATION Section: CYCLEFIXEDECOPIEDE PROFIL DANS LE PLAN 0 = Vers les coordonnées positives de l’axe des abscisses 1 = Vers les coordonnées négatives de l’axe des abscisses 2 = Vers les coordonnées positives de l’axe des ordonnées 3 = Vers les coordonnées négatives de l’axe des ordonnées Si ce paramètre n’est pas programmé, la CNC prendra la valeur A0. C Ce paramètre est lié au paramètre A. Il indique la distance maximum que pourra parcourir la sonde de palpage pour trouver le modèle. S Indique le sens d’exécution désiré pour le suivi du modèle. 0 = Le palpeur se déplace en laissant le modèle à sa droite 1 = Le palpeur se déplace en laissant le modèle à sa gauche. Si ce paramètre n’est pas programmé, la CNC prendra la valeur S0. Q, R±5.5 Ces paramètres doivent être définis lorsque le contour n’est pas fermé. Ils définissent le point de départ du segment qui indique la fin du contour, et sont pris par rapport au zéro pièce. La coordonnée Q correspond à l’axe des abscisses, la coordonnée R correspond à l’axe des ordonnées. Si ces paramètres ne sont pas définis, la CNC exécute une copie du contour fermé (figure de gauche). Chapitre: 16 COPIEETNUMERISATION Section: CYCLEFIXEDECOPIEDE PROFIL DANS LE PLAN Page 41 J 5.5 Ce paramètre doit être défini lorsque le contour n’est pas fermé, c’est-à-dire lorsque Q et R ont été définis. Il définit la longueur du segment indiquant la fin du contour. S’il n’est pas programmé, la CNC prend une valeur infinie. K Ce paramètre doit être défini lorsque le contour n’est pas fermé, c’est-à-dire lorsque Q et R ont été définis. Il définit la direction et le sens du segment indiquant la fin du contour. 0 1 2 3 = = = = Vers les coordonnées positives de l’axe des abscisses. Vers les coordonnées négatives de l’axe des abscisses. Vers les coordonnées positives de l’axe des ordonnées. Vers les coordonnées négatives de l’axe des ordonnées. Si ce paramètre n’est pas programmé, la CNC prendra la valeur K0. N 5.5 Déflexion nominale. Elle indique la pression exercée par la sonde lorsqu’elle est en contact avec la surface du modèle. La déflexion est définie en unités de travail sélectionnées (mm ou pouces) et sa valeur se situe normalement entre 0,3 mm et 1,5 mm. La qualité de la copie dépend de la déflexion, de l’avance et de la géométrie du modèle. Pour éviter que la sonde ne se détache du modèle, il est conseillé d’utiliser, pour le suivi du profil, une avance égale à 1000 fois la déflexion par minute. Par exemple, pour une déflexion de 1 mm, on choisira une avance de 1 m/min. Si ce paramètre n’est pas programmé, le cycle fixe applique une déflexion de 1 mm. L 5.5 Ce paramètre doit être défini lorsqu’une numérisation de la pièce doit être effectuée en plus de la copie. Il indique le pas de balayage ou distance entre deux points numérisés. La CNC maintient la sonde en contact permanent avec la surface du modèle suivant la trajectoire programmée et fournit les coordonnées d’un nouveau point lorsque la distance indiquée dans le paramètre “L” a été parcourue dans l’espace et selon le trajet programmé. Page 42 Chapitre: 16 COPIEETNUMERISATION Section: CYCLEFIXEDECOPIEDE PROFIL DANS LE PLAN Si ce paramètre n’est pas programmé, ou s’il est programmé avec la valeur 0, le cycle fixe suppose que la numérisation de la pièce n’est pas désirée. E 5.5 Ce paramètre doit être défini lorsque l’opérateur désire réaliser la numérisation de la pièce en plus de la copie. Il indique l’erreur à la corde, ou différence maximum admise entre la surface du modèle et le segment passant par les points mémorisés. Elle est définie en unités de travail sélectionnées (mm ou pouces). Si ce paramètre n’est pas programmé ou s’il est programmé avec une valeur “0”, l’erreur à la corde n’est pas prise en compte et un nouveau point est fourni après que la distance indiquée dans le paramètre “L” ait été parcourue dans l’espace et selon le déplacement programmé. G Ce paramètre doit être défini lorsqu’une numérisation de la pièce doit être effectuée en plus de la copie. Il indique le format de mémorisation des points numérisés dans le programme sélectionné au moyen de la déclaration (OPEN P). G=0 Format absolu. Tous les points seront programmés en coordonnées absolues (G90) et définis au moyen des axes X, Y et Z. G=1 Format absolu filtré. Tous les points seront programmés en coordonnées absolues (G90), mais seuls les axes dont la position a changé par rapport au point numérisé antérieur sont définis. Chapitre: 16 COPIEETNUMERISATION Section: CYCLEFIXEDECOPIEDE PROFIL DANS LE PLAN Page 43 G=2 Format incrémental filtré. Tous les points seront programmés en coordonnées incrémentales (G91), par rapport au point numérisé précédent. Seuls les axes dont la position a changé par rapport au point numérisé antérieur sont définis. Si ce paramètre n’est pas programmé, le cycle fixe prendra la valeur G0. H5.5 Définit l’avance appliquée pour l’exécution des trajectoires incrémentales. Ce paramètre est programmé en mm/minute ou en pouces/minute. Si ce paramètre n’est pas programmé, le cycle fixe prend la valeur F (avance des trajectoires de balayage). F5.5 Définit l’avance appliquée pour l’exécution des trajectoires de balayage. Ce paramètre est programmé en mm/minute ou en pouces/minute. FONCTIONNEMENT DE BASE 1.- La sonde se positionne sur le point défini par les paramètres X, Y, Z. 2.- La CNC approche la sonde du modèle jusqu’à ce qu’elle entre en contact avec ce dernier. 3.- La sonde est maintenue en contact permanent avec la surface du modèle, et exécute le suivi selon le trajet programmé. Si une numérisation de la pièce a été demandée, (paramètres “L” et “E”), elle génère, pour chaque point numérisé, un nouveau bloc dans le programme ouvert au moyen de la déclaration (OPEN P). 4.- A la fin du cycle fixe, la sonde revient au point de départ. Ce déplacement se compose de: * Déplacement du palpeur selon l’axe de palpage (axe longitudinal) jusqu’à la coordonnée indiquée par le paramètre Z. * Déplacement dans le plan principal de travail jusqu’au point de départ du cycle (paramètres X, Y). Page 44 Chapitre: 16 COPIEETNUMERISATION Section: CYCLEFIXEDECOPIEDE PROFIL DANS LE PLAN 16.7.4 CYCLE FIXE DE COPIE DE PROFIL DANS L’ESPACE Le format de programmation de ce cycle est le suivant: (TRACE 4, X, Y, Z, I, A, C, S, Q, R, J, K, M, N, L, E, G, F) X±5.5 Coordonnée théorique, selon l’axe des abscisses, du point d’approche au modèle; elle est définie en absolu et doit se situer hors du modèle. Y±5.5 Coordonnée théorique, selon l’axe des ordonnées, du point d’approche au modèle; elle est définie en absolu et doit se situer hors du modèle. Z±5.5 Coordonnée, suivant l’axe de palpage (axe longitudinal), du point d’approche au modèle; elle est définie en absolu. Elle doit se situer hors et au-dessus du modèle, car le premier déplacement de recherche du modèle s’effectue dans le plan de travail. I±5.5 Définit la profondeur de copie maximum, par rapport à la coordonnée définie dans le paramètre Z. Si une partie de la pièce se situe hors de cette zone, la copie affecte à l’axe longitudinal la coordonnée absolue correspondant à cette profondeur maximum, et l’exécution du cycle se poursuit sans émission d’un message d’erreur. Si ce paramètre est programmé avec la valeur 0, la CNC affiche le message d’erreur correspondant. Chapitre: 16 COPIEETNUMERISATION Section: CYCLEFIXEDECOPIEDE PROFIL DANS L’ESPACE Page 45 A Indique la direction et le sens que suivra la sonde de copie après s’être positionnée sur le point X Y Z, pour trouver le modèle. 0 = Vers les coordonnées positives de l’axe des abscisses 1 = Vers les coordonnées négatives de l’axe des abscisses 2 = Vers les coordonnées positives de l’axe des ordonnées 3 = Vers les coordonnées négatives de l’axe de ordonnées Si ce paramètre n’est pas programmé, la CNC prendra la valeur A0. C Ce paramètre est lié au paramètre A. Il indique la distance maximum que pourra parcourir la sonde de palpage pour trouver le modèle. S Indique le sens d’exécution désiré pour le suivi du modèle. 0 = Le palpeur se déplace en laissant le modèle à sa droite 1 = Le palpeur se déplace en laissant le modèle à sa gauche. Si ce paramètre n’est pas programmé, la CNC prendra la valeur S0. Q, R±5.5 Ces paramètres doivent être définis lorsque le contour n’est pas fermé. Ils définissent le point de départ du segment qui indique la fin du contour, et sont pris par rapport au zéro pièce. La coordonnée Q correspond à l’axe des abscisses, la coordonnée R correspond à l’axe des ordonnées. J 5.5 Ce paramètre doit être défini lorsque le contour n’est pas fermé, c’est-à-dire lorsque Q et R ont été définis. Il définit la longueur du segment indiquant la fin du contour et, s’il n’est pas programmé, la CNC prend une valeur infinie. K Page 46 Ce paramètre doit être défini lorsque le contour n’est pas fermé, c’est-à-dire lorsque Q et R ont été définis. Chapitre: 16 COPIEETNUMERISATION Section: CYCLEFIXEDECOPIEDE PROFIL DANS L’ESPACE Il définit la direction et le sens du segment indiquant la fin du contour. 0 1 2 3 = = = = Vers les coordonnées positives de l’axe des abscisses. Vers les coordonnées négatives de l’axe des abscisses. Vers les coordonnées positives de l’axe des ordonnées. Vers les coordonnées négatives de l’axe des ordonnées. Si ce paramètre n’est pas programmé, la CNC prendra la valeur K0. M 5.5 Déflexion nominale de l’axe longitudinal. Si elle n’est pas programmée, le cycle fixe applique une déflexion de 1 mm. N 5.5 Déflexion nominale des axes formant le plan. Les déflexions N et M indiquent la pression exercée par la sonde lorsqu’elle est en contact avec la surface du modèle. La déflexion est définie en unités de travail sélectionnées (mm ou pouces) et sa valeur se situe normalement entre 0,3 mm et 1,5 mm. La qualité de la copie dépend de la déflexion, de l’avance et de la géométrie du modèle. Pour éviter que la sonde ne se détache du modèle, il est conseillé d’utiliser, pour le suivi du profil, une avance égale à 1000 fois la déflexion par minute. Par exemple, pour une déflexion de 1 mm, on choisira une avance de 1 m/min. Si ce paramètre n’est pas programmé, le cycle fixe applique une déflexion de 1 mm. L 5.5 Ce paramètre doit être défini lorsqu’une numérisation de la pièce doit être effectuée en plus de la copie. Il indique le pas de balayage ou distance entre deux points numérisés. La CNC maintient la sonde en contact permanent avec la surface du modèle suivant la trajectoire programmée et fournit les coordonnées d’un nouveau point lorsque la distance indiquée dans le paramètre “L” a été parcourue dans l’espace et selon le trajet programmé. Si ce paramètre n’est pas programmé, ou s’il est programmé avec la valeur 0, le cycle fixe suppose que la numérisation de la pièce n’est pas désirée. Chapitre: 16 COPIEETNUMERISATION Section: CYCLEFIXEDECOPIEDE PROFIL DANS L’ESPACE Page 47 E 5.5 Ce paramètre doit être défini lorsque l’opérateur désire réaliser la numérisation de la pièce en plus de la copie. Il indique l’erreur à la corde, ou différence maximum admise entre la surface du modèle et le segment passant par les points mémorisés. Elle est définie en unités de travail sélectionnées (mm ou pouces). Si ce paramètre n’est pas programmé ou s’il est programmé avec une valeur “0”, l’erreur à la corde n’est pas prise en compte et un nouveau point est fourni après que la distance indiquée dans le paramètre “L” ait été parcourue dans l’espace et selon le déplacement programmé. G Ce paramètre doit être défini lorsqu’une numérisation de la pièce doit être effectuée en plus de la copie. Il indique le format de mémorisation des points numérisés dans le programme sélectionné au moyen de la déclaration (OPEN P). G=0 Format absolu. Tous les points seront programmés en coordonnées absolues (G90) et définis au moyen des axes X, Y et Z. G=1 Format absolu filtré. Tous les points seront programmés en coordonnées absolues (G90), mais seuls les axes dont la position a changé par rapport au point numérisé antérieur sont définis. G=2 Format incrémental filtré. Tous les points seront programmés en coordonnées incrémentales (G91), par rapport au point numérisé précédent. Seuls les axes dont la position a changé par rapport au point numérisé antérieur sont définis. Si ce paramètre n’est pas programmé, le cycle fixe prendra la valeur G0. F5.5 Page 48 Définit l’avance appliquée pour l’exécution des trajectoires de balayage. Ce paramètre est programmé en mm/minute ou en pouces/minute. Chapitre: 16 COPIEETNUMERISATION Section: CYCLEFIXEDECOPIEDE PROFIL DANS L’ESPACE FONCTIONNEMENT DE BASE: 1.- La sonde se positionne sur le point défini par les paramètres X, Y, Z. 2.- La CNC approche la sonde du modèle jusqu’à ce qu’elle entre en contact avec ce dernier. 3.- La sonde est maintenue en contact permanent avec la surface du modèle, et exécute le suivi selon le trajet programmé. Si une numérisation de la pièce a été demandée, (paramètres “L” et “E”), elle génère, pour chaque point numérisé, un nouveau bloc dans le programme ouvert au moyen de la déclaration (OPEN P). 4.- A la fin du cycle fixe, la sonde revient au point de départ. Ce déplacement se compose de: * Déplacement du palpeur selon l’axe de palpage (axe longitudinal) jusqu’à la coordonnée indiquée par le paramètre Z. * Déplacement dans le plan principal de travail jusqu’au point de départ du cycle (paramètres X, Y). Chapitre: 16 COPIEETNUMERISATION Section: CYCLEFIXEDECOPIEDE PROFIL DANS L’ESPACE Page 49 16.7.5 CYCLE FIXE DE COPIE PAR BALAYAGE DE POLYGONE Cette option permet de délimiter, au moyen d’éléments géométriques simples (sections droites et arcs), la zone à copier. Il est également possible de définir des zones intérieures à cette zone, dans lesquelles aucune copie n’est exécutée. Ces zones portent le nom d’ilôts. Le format de programmation de ce cycle est le suivant: (TRACE 5, A, Z, I, C, D, N, L, E, G, H, F, P, U) A±5.5 Définit l’angle formé par les trajectoires de balayage avec l’axe des abscisses. Si ce paramètre n’est pas programmé, la CNC prendra la valeur A0. Z±5.5 Coordonnée théorique de l’axe de palpage (axe longitudinal), où doit se positionner la sonde avant de commencer la copie. Elle est définie en absolu et doit être séparée du modèle, avec maintien d’une distance de sécurité par rapport à la surface la plus à l’extérieur. I±5.5 Page 50 Définit la profondeur maximum de copie, par rapport à la coordonnée définie dans le paramètre Z. Chapitre: 16 COPIEETNUMERISATION Section: CYCLEFIXEDECOPIEPAR BALAYAGEDEPOLYGONE Si une partie de la pièce se situe hors de cette zone, la copie affecte à l’axe longitudinal la coordonnée absolue correspondant à cette profondeur maximum, et l’exécution du cycle se poursuit sans émission d’un message d’erreur. Si ce paramètre est programmé avec la valeur 0, la CNC affiche le message d’erreur correspondant. C Définit la distance maintenue entre deux passes de copie. Si ce paramètre est programmé avec la valeur 0, la CNC affiche le message d’erreur correspondant. D Indique le type de trajet sur la grille, au moyen du code suivant: 0 = Copie exécutée dans les deux sens (en zig-zag). 1 = Copie exécutée toujours dans le même sens (unidirectionnel). Si ce paramètre n’est pas programmé, le cycle fixe prend la valeur D0. N 5.5 Déflexion nominale. Elle indique la pression exercée par la sonde lorsqu’elle est en contact avec la surface du modèle. La déflexion est définie en unités de travail sélectionnées (mm ou pouces) et sa valeur se situe normalement entre 0,3 mm et 1,5 mm. La qualité de la copie dépend de la déflexion, de l’avance et de la géométrie du modèle. Pour éviter que la sonde ne se détache du modèle, il est conseillé d’utiliser, pour le suivi du profil, une avance égale à 1000 fois la déflexion par minute. Par exemple, pour une déflexion de 1 mm, on choisira une avance de 1 m/min. Si ce paramètre n’est pas programmé, le cycle fixe applique une déflexion de 1 mm. Chapitre: 16 COPIEETNUMERISATION Section: CYCLEFIXEDECOPIEPAR BALAYAGEDEPOLYGONE Page 51 L 5.5 Ce paramètre doit être défini lorsqu’une numérisation de la pièce doit être effectuée en plus de la copie. Il indique le pas de balayage ou distance entre deux points numérisés. La CNC maintient la sonde en contact permanent avec la surface du modèle suivant la trajectoire programmée et fournit les coordonnées d’un nouveau point lorsque la distance indiquée dans le paramètre “L” a été parcourue dans l’espace et selon le trajet programmé. Si ce paramètre n’est pas programmé, ou s’il est programmé avec la valeur 0, le cycle fixe suppose que la numérisation de la pièce n’est pas désirée. E 5.5 Ce paramètre doit être défini lorsque l’opérateur désire réaliser la numérisation de la pièce en plus de la copie. Il indique l’erreur à la corde, ou différence maximum admise entre la surface du modèle et le segment passant par les points mémorisés. Elle est définie en unités de travail sélectionnées (mm ou pouces). Si ce paramètre n’est pas programmé ou s’il est programmé avec une valeur “0”, l’erreur à la corde n’est pas prise en compte et un nouveau point est fourni après que la distance indiquée dans le paramètre “L” ait été parcourue dans l’espace et selon le déplacement programmé. G Ce paramètre doit être défini lorsqu’une numérisation de la pièce doit être effectuée en plus de la copie. Il indique le format de mémorisation des points numérisés dans le programme sélectionné au moyen de la déclaration (OPEN P). Page 52 Chapitre: 16 COPIEETNUMERISATION Section: CYCLEFIXEDECOPIEPAR BALAYAGEDEPOLYGONE G=0 Format absolu. Tous les points seront programmés en coordonnées absolues (G90) et définis au moyen des axes X, Y et Z. G=1 Format absolu filtré. Tous les points seront programmés en coordonnées absolues (G90), mais seuls les axes dont la position a changé par rapport au point numérisé antérieur sont définis. G=2 Format incrémental filtré. Tous les points seront programmés en coordonnées incrémentales (G91), par rapport au point numérisé précédent. Seuls les axes dont la position a changé par rapport au point numérisé antérieur sont définis. Si ce paramètre n’est pas programmé, le cycle fixe prendra la valeur G0. H5.5 Définit l’avance appliquée pour l’exécution des trajectoires incrémentales. Ce paramètre est programmé en mm/minute ou en pouces/minute. Si ce paramètre n’est pas programmé, le cycle fixe prend la valeur F (avance des trajectoires de balayage). F5.5 Définit l’avance appliquée pour l’exécution des trajectoires de balayage. Ce paramètre est programmé en mm/minute ou en pouces/minute. P (0-9999) Définit le numéro d’étiquette du bloc où commence la description géométrique des profils composant la pièce. U (0-9999) Définit le numéro d’étiquette du bloc où se termine la description géométrique des profils composant la pièce. Tous les profils programmés (extérieurs et ilôts) doivent être fermés. Les règles de programmation des profils ainsi que la syntaxe de programmation à utiliser sont exposées en détail plus loin. Chapitre: 16 COPIEETNUMERISATION Section: CYCLEFIXEDECOPIEPAR BALAYAGEDEPOLYGONE Page 53 FONCTIONNEMENT DE BASE: 1.- Après avoir analysé la zone à copier, la CNC calcule le point où doit commencer la copie, et positionne la sonde sur ce point et à la hauteur indiquée par le paramètre Z. 2.- Ensuite, elle approche la sonde du modèle jusqu’à ce qu’elle entre en contact avec ce dernier. 3.- La sonde est maintenue en contact permanent avec la surface du modèle, et exécute le suivi selon le trajet programmé. Si une numérisation de la pièce a été demandée, (paramètres “L” et “E”), elle génère, pour chaque point numérisé, un nouveau bloc dans le programme ouvert au moyen de la déclaration (OPEN P). 4.- A la fin du cycle fixe, la sonde revient au point de départ. Ce déplacement se compose de: * Déplacement du palpeur selon l’axe de palpage (axe longitudinal) jusqu’à la coordonnée indiquée par le paramètre Z. * Déplacement dans le plan principal de travail jusqu’au point de départ du cycle (paramètres X, Y). Page 54 Chapitre: 16 COPIEETNUMERISATION Section: CYCLEFIXEDECOPIEPAR BALAYAGEDEPOLYGONE 16.7.5.1 REGLES DE PROGRAMMATION DES PROFILS La définition des zones à copier et des ilôts ou zones intérieures dans lesquelles la copie n’est pas souhaitée doit s’effectuer selon les règles de programmation suivantes: 1.- Tout type de profil programmé doit être fermé. Les exemples suivants provoquent une erreur de géométrie. 2.- Aucun profil ne doit se recouper lui-même. Les exemples suivants provoquent une erreur de géométrie. 3.- Le premier polygone programmé sera considéré par la CNC comme un profil extérieur ou une zone à copier. Les autres polygones éventuels doivent être intérieurs au précédent et ils indiquent les ilôts ou les zones intérieures dans lesdquelles aucune copie ne doit être exécutée. 4.- Il n’est pas obligatoire de programmer des profils intérieurs. S’ils sont programmés, ils devront se situer entièrement à l’intérieur du profil extérieur. 5.- Il est déconseillé de définir un profil intérieur situé en totalité dans un autre profil intérieur. Dans ce cas, il ne sera tenu compte que du profil le plus extérieur des deux. La CNC vérifie toutes ces règles de géométrie avant de commencer l’exécution du cycle fixe; elle adapte le profil de copie à ces règles et visualise le message d’erreur correspondant en cas de besoin. Chapitre: 16 COPIEETNUMERISATION Section: CYCLEFIXEDECOPIEPAR BALAYAGEDEPOLYGONE Page 55 16.7.5.2 SYNTAXE DE PROGRAMMATION DES PROFILS Le profil extérieur et les profils intérieurs ou ilôts programmés devront être définis au moyen d’éléments géométriques simples (sections droites et arcs). La syntaxe de programmation de profils doit respecter les règles suivantes: 1.- Le bloc de début de la description géométrique doit comporter un numéro d’étiquette. Ce numéro doit être affecté au paramètre “P” lors de la définition du cycle fixe. 2.- On définira d’abord le profil extérieur ou la zone à copier. Aucune fonction n’est à programmer pour indiquer la fin de la définition du profil. La CNC considère que la programmation du profil est terminée lorsque la fonction G00 (indiquant le début d’un nouveau profil) est programmée. 3.- Il est possible de programmer l’un après l’autre tous les profils intérieurs désirés. Tous doivent commencer par la fonction G00 (qui indique le début d’un profil). Attention: On veillera à programmer G01, G02 ou G03 dans le bloc suivant le bloc de définition de début, car G00 est modal. On évite ainsi que la CNC interprète les blocs suivants comme des débuts de nouveaux profils. 4.- Lorsque la définition des profils est terminée, un numéro d’étiquette doit être affecté au dernier bloc programmé. Ce numéro doit être affecté au paramètre “U” lors de la définition du cycle fixe. 5.- Les profils sont décrits comme des trajectoires programmées et peuvent comporter les fonctions suivantes: G01 G02 G03 G06 G08 G09 G36 G39 G53 G70 G71 G90 G91 G93 Interpolation linéaire Interpolation circulaire à droite Interpolation circulaire à gauche Centre de circonférence en coordonnées absolues Circonférence tangente à la trajectoire précédente Circonférence définie par trois points Arrondi aux angles Chanfrein Programmation par rapport au zéro machine Programmation en pouces Programmation en millimètres Programmation absolue Programmation incrémentale Présélection d’origine polaire 6.- Dans la description de profils, la programmation d’images miroir, de facteurs d’échelle, de la rotation du système de coordonnées, de décalages d’origine n’est pas autorisée. 7.- De même, la programmation de blocs en langage de haut niveau tels que sauts, appels de sous-routines ou la programmation paramétrée ne sont pas autorisées. 8.- La programmation d’autres cycles fixes n’est pas autorisée Page 56 Chapitre: 16 COPIEETNUMERISATION Section: CYCLEFIXEDECOPIEPAR BALAYAGEDEPOLYGONE Exemple de programmation: (TRACE 5, A, Z, I, C, D, N, L, E, G, H, F, P400, U500) N400 X-260 Y-190 Z4.5 G1........ ......... G0 X230 Y170 G1........ ......... G0 X-120 Y90 G2........ .......... ; Début du premier extérieur N500 X-120 Y90 ; Fin de description géométrique Chapitre: 16 COPIEETNUMERISATION ; Début d’un profil intérieur ; Début d’un autre profil intérieur Section: CYCLEFIXEDECOPIEPAR BALAYAGEDEPOLYGONE Page 57 ANNEXE A PROGRAMMATION EN CODE ISO Fonction M D V Signification G00 G01 G02 G03 G04 G05 G06 G07 G08 G09 G10 G11 G12 G13 G14 G15 G16 G17 G18 G19 G20 G21 G22 G23 G24 G25 G26 G27 * * * * ? ? * * * * * ? * * * ? * * Transversal rapide Interpolation linéaire Interpolation circulaire (hélicoïdale) à droite Interpolation circulaire (hélicoïdale) à gauche Temporisation/Interruption de la préparation de blocs Arrondi aux angles Centre de circonférence en coordonnées absolues Angle vif Traject. circulaire tangente à une trajectoire précédente Trajectoire circulaire définie par trois points Annulation de l’image-miroir Image-miroir en X Image-miroir en Y Image-miroir en Z Image-miroir dans les directions programmées Sélection de l’axe longitudinal Sélection du plan principal par deux directions Plan principal X-Y et axe longitudinal Z Plan principal Z-X et axe longitudinal Y Plan principal Y-Z et axe longitudinal X Définition des limites inférieures des zones de travail Définition des limites supérieures des zones de travail Validation/invalidation des zones de travail Activation de la copie Activation de la numérisation Désactivation de la copie/numérisation Etalonnage de la sonde de copie Définition du contour de copie 6.1 6.2 6.3 6.3 7.1, 7.2 7.3.1 6.4 7.3.2 6.5 6.6 7.5 7.5 7.5 7.5 7.5 8.2 3.2 3.2 3.2 3.2 3.7.1 3.7.1 3.7.2 16.3 16.6 16.5 16.2 16.4 G33 * * Filetage 6.12 * * * * Arrondi aux angles Entrée tangentielle Sortie tangentielle Chanfrein Annulation de compensation de rayon Compensation de rayon d’outil à gauche Compensation de rayon d’outil à droite Compensation de longueur Annulation de compensation de longueur 6.10 6.8 6.9 6.11 8.1 8.1 8.1 8.2 8.2 Arrondi aux angles contrôlé Analyse par anticipation Déplacement jusqu’à une butée mécanique Programmation par rapport au zéro machine Décalage d’origine absolu 1 Décalage d’origine 2 Décalage d’origine 3 Décalage d’origine 4 Décalage d’origine supplémentaire 1 Décalage d’origine supplémentaire 2 Usinage multiple selon une droite Usinage multiple selon un parallélogramme 7.3.3 7.4 6.13 4.3 4.4.2 4.4.2 4.4.2 4.4.2 4.4.2 4.4.2 10.1 10.2 G36 G37 G38 G39 G40 G41 G42 G43 G44 G50 G51 G52 G53 G54 G55 G56 G57 G58 G59 G60 G61 2 * * * * * * * * * * * * * ? ? * * * * * * * * * * * * * * * * * * ? ? * * * * * * * * * * * * * * * * * * * * * * Section Fonction G62 G63 G64 G65 G66 G67 G68 G69 G70 G71 G72 G73 G74 G75 G76 G77 G78 G79 G80 G81 G82 G83 G84 G85 G86 G87 G88 G89 G90 G91 G92 G93 G94 G95 G96 G97 G98 G99 M * * * * * * * D ? ? V Signification Section * * * * * * * * * Usinage multiple selon une grille Usinage multiple selon une circonférence Usinage multiple selon un arc Usinage programmé au moyen d’une corde d’arc Cycle fixe de poches avec ilôts Opération d’ébauche de poches avec ilôts Opération de finition de poches avec ilôts Cycle fixe de perçage profond à pas variable Programmation en pouces Programmation en millimètres Facteur d’échelle général et particulier Rotation du système de coordonnées Recherche de référence machine Déplacement avec palpeur jusqu’au contact Déplac. avec palpeur jusqu’à l’interruption du contact Couplage électronique d’axes Annulation du couplage électronique d’axes 10.3 10.4 10.5 10.6 11.1 11.3 11.4 9.5.1 3.3 3.3 7.6 7.7 4.2 12.1 12.1 7.8.1 7.8.2 Modification des paramètres d’un cycle fixe Annulation de cycle fixe Cycle fixe de perçage Cycle fixe de perçage avec temporisation Cycle fixe de perçage profond à pas constant Cycle fixe de taraudage Cycle fixe d’alésage de précision Cycle fixe d’alésage avec retrait en G00 Cycle fixe de poche rectangulaire Cycle fixe de poche circulaire Cycle fixe d’alésage avec retrait en G01 Programmation absolue Programmation incrémentale Présél. de coordonnées/Limit. de la vitesse de broche Présélection de l’origine polaire Avance en millimètres (pouces) par minute Avance en millimètres (pouces) par tour Vitesse du point de coupe constante Vitesse constante du centre de l’outil Retour au plan de départ à la fin du cycle fixe Retour au plan de référence à la fin du cycle fixe 9.2.1 9.3 9.5.2 9.5.3 9.5.4 9.5.5 9.5.6 9.5.7 9.5.8 9.5.9 9.5.10 3.4 3.4 4.4.1 4.5 5.2.1 5.2.2 5.3.1 5.3.2 9.5 9.5 * * * * * * * * * * * * * * * * * * * * * * * * * * ? ? * * * * * * * * * ? ? * * * * * * La lettre M signifie MODAL, c’est-à-dire qu’une fois programmée, la fonction G reste active tant qu’une autre fonction G incompatible n’est pas programmée, que M03, M30, URGENCE, RESET n’est pas exécuté ou que la CNC soit éteinte puis rallumée. La lettre D signifie PAR DEFAUT, c’est-à-dire que ces fonctions sont prises en compte par la CNC à la mise sous tension, après l’exécution de M02, M30, ou après une URGENCE ou un RESET. Dans les cas signalés par “?”, il est entendu que l’état PAR DEFAUT de ces fonctions dépend de l’état des paramètres machine généraux de la CNC. La lettre V signifie que la fonction G est visualisée, dans les modes exécution et simulation, avec les conditions selon lesquelles l’usinage est exécuté. 3 ANNEXE B VARIABLES INTERNES DE LA CNC Le symbole R indique que la variable correspondante peut être lue. Le symbole W indique que la variable correspondante peut être modifiée. VARIABLES ASSOCIEES AUX OUTILS Section (13.2.2) 4 Variable CNC PLC DNC TOOL TOD NXTOOL NXTOD TMZPn TLFDn TLFFn TLFNn TLFRn TMZTn TORn TOLn TOIn TOKn TOXn TOZn TOFn TORn TOIn R R R R R R/W R/W R/W R/W R/W R/W R/W R/W R/W R/W R/W R/W R/W R/W R R R R R R/W R/W R/W R/W R/W R/W R/W R/W R/W R/W R/W R/W R/W R/W R R R R - TOKn R/W R/W - NOSEAn NOSEWn CUTAn R/W R/W R/W R/W R/W R/W - Numéro de l’outil actif Numéro du correcteur actif Numéro de l’outil suivant, en attente de M06. Numéro du correcteur de l’outil suivant Position occupée par l’outil (n) dans le magasin. Numéro du correcteur de l’outil indiqué (n) Code de la famille de l’outil indiqué (n) Durée de vie nominale de l’outil indiqué (n) Valeur de durée de vie réelle de l’outil indiqué (n) Contenu de l’emplacement de magasin repéré (n) Rayon (R) du correcteur indiqué (n). Modèle Fraiseuse. Longueur (L) du correcteur indiqué (n). Modèle Fraiseuse. Usure de rayon (I) du correcteur indiqué (n). Modèle Fraiseuse. Usure de longueur (K) du correcteur indiqué (n). Modèle Frais. Longueur selon l’axe X du correcteur indiqué (n). Modèle Tour Longueur selon l’axe Z du correcteur indiqué (n). Modèle Tour Code de forme (F) du correcteur indiqué (n). Modèle Tour Rayon (R) du correcteur indiqué (n). Modèle Tour Usure de longueur selon l’axe X (I) du correcteur indiqué (n). Modèle Tour Usure de longueur selon l’axe Z (I) du correcteur indiqué (n). Modèle Tour Angle de la plaquette de l’outil indiqué. Modèle Tour Largeur de la plaquette de l’outil indiqué. Modèle Tour Angle de coupe de l’outil indiqué. Modèle Tour VARIABLES ASSOCIEES AUX DECALAGES D’ORIGINE Section (13.2.3) Variable CNC PLC DNC ORG(X-C) R R - PORGF R - R PORGS R - R ORG(X-C)n PLCOF(X-C) R/W R/W R/W R/W R R Décalage d’origine actif sur l’axe sélectionné. Le décalage supplémentaire indiqué par le PLC est exclu. Coordonnée, selon l’axe des abscisses, de l’origine des coordonnées polaires Coordonnée, selon l’axe des ordonnées, de l’origine des coordonnées polaires Valeur du décalage d’origine indiqué (n) pour l’axe sélectionné Valeur du décalage d’origine supplémentaire indiqué (PLC) pour l’axe sélectionné. VARIABLES ASSOCIEES AUX PARAMETRES MACHINE Section (13.2.4) Variable MPGn MP(X-C)n MPSn MPSSn MPLCn CNC PLC R R R R R R R R R R DNC - Valeur affectée au paramètre machine général indiqué (n) Valeur affectée au paramètre machine des axes indiqués (n) Valeur affectée au paramètre machine (n) de la broche principale Valeur affectée au paramètre machine (n) de la seconde broche Valeur affectée au paramètre machine du PLC indiqué (n) VARIABLES ASSOCIEES AUX ZONES DE TRAVAIL Section (13.2.5) Variable CNC PLC DNC FZONE FZLO(X-C) FZUP(X-C) SZONE SZLO(X-C) SZUP(X-C) TZONE TZLO(X-C) TZUP(X-C) R R R R R R R R R R/W R/W R/W R/W R/W R/W R/W R/W R/W R R R R R R R R R Etat de la zone de travail 1 Limite inférieure de la Zone 1 selon l’axe sélectionné (X-C) Limite supérieure de la Zone 1 selon l’axe sélectionné (X-C) Etat de la zone de travail 2 Limite inférieure de la Zone 2 selon l’axe sélectionné (X-C) Limite supérieure de la Zone 2 selon l’axe sélectionné (X-C) Etat de la zone de travail 3 Limite inférieure de la Zone 3 selon l’axe sélectionné (X-C) Limite supérieure de la Zone 3 selon l’axe sélectionné (X-C) 5 VARIABLES ASSOCIEES AUX AVANCES Section (13.2.6) Variable FREAL FEED DNCF PLCF PRGF FPREV CNC R R R R R R PLC R R R R/W R R DNC R R R/W R R R DNCFPR PLCFPR PRGFPR FRO PRGFRO DNCFRO PLCFRO CNCFRO R R R R R/W R R R R R/W R R R R R/W R R/W R R R R R/W R R Avance réelle de la CNC, en m/mn ou en pouces/mn Avance active dans la CNC (G94), en mm/mn ou en pouces/mn Avance sélectionnée par DNC Avance sélectionnée par PLC Avance sélectionnée par programme Avance active dans la CNC (G95), en mm/tour ou en pouces/tour Avance sélectionnée par DNC Avance sélectionnée par PLC Avance sélectionnée par programme Pourcentage de correction d’avance actif dans la CNC Pourcentage de correction sélectionné par programme Pourcentage de correction sélectionné par DNC Pourcentage de correction sélectionné parPLC Pourcentage de correction sélectionné depuis le sélecteur VARIABLES ASSOCIEES AUX COORDONNEES Section (13.2.7) Variable 6 CNC PLC DNC PPOS(X-C) POS(X-C) TPOS(X-C) R R R R R R R FLWE(X-C) DEFLEX DEFLEY DEFLEZ DIST(X-C) R R R R R/W R R R R R/W R R R R R Coordonnée théorique programmée Coordonnée réelle de l’axe sélectionné Coordonnée théorique (coordonnée réelle + erreur de poursuite) de l’axe sélectionné Erreur de poursuite de l’axe sélectionné Déflexion du palpeur selon l’axe X. Modèle Fraiseuse Déflexion du palpeur selon l’axe Y. Modèle Fraiseuse Déflexion du palpeur selon l’axe Z. Modèle Fraiseuse Distance parcourue par l’axe sélectionné VARIABLES ASSOCIEES A LA BROCHE Variable CNC PLC DNC SREAL SPEED DNCS PLCS PRGS CSS R R R R R R R R R R/W R R R R R/W R R R DNCCSS PLCCSS PRGCSS R R R R R/W R R/W R R SSO R R R PRGSSO DNCSSO PLCSSO CNCSSO SLIMIT R/W R R R R R R R/W R R R R/W R R R DNCSL PLCSL PRGSL POSS RPOSS TPOSS RTPOSS FLWES R R R R R R R R R R/W R R R R R R R/W R R R R R R R Section (13.2.8) Vitesse de rotation réelle de broche, en tours/minute Vitesse de rotation de broche active dans la CNC Vitesse de rotation sélectionnée par DNC Vitesse de rotation sélectionnée par PLC Vitesse de rotation sélectionnée par programme Vitesse de coupe constante active dans la CNC, en mètres/minute ou en pieds/minute. Modèle Tour Vitesse de coupe constante sélectionnée par DNC. Modèle Tour Vitesse de coupe constante sélectionnée par PLC. Modèle Tour Vitesse de coupe constante sélectionnée par programme. Modèle Tour Pourcentage de correction de vitesse de rotation de broche active dans la CNC. Pourcentage de correction sélectionné par programme. Pourcentage de correction sélectionné par DNC Pourcentage de correction sélectionné par PLC Pourcentage de correction sélectionné depuis le panneau avant Limite de vitesse de rotation de broche active dans la CNC, en tours/minute Limite de vitesse de rotation de broche sélectionnée par DNC. Limite de vitesse de rotation de broche sélectionnée par PLC. Limite de vitesse de rotat. de broche sélect. par programme. Position réelle de la broche (±999999999 en 0.0001°) Position réelle de la broche (entre 0 et 360° en 0.0001°) Position théorique de la broche (±999999999 en 0.0001°) Position théorique de la broche (entre 0 et 360° en 0.0001°) Erreur de poursuite de la broche en boucle fermée (M19), en degrés VARIABLES ASSOCIEES A LA SECONDE BROCHE (Manuel de programmation de tour) Variable CNC PLC DNC SREAL SPEED DNCS PLCS PRGS CSS R R R R R R R R R R/W R R R R R/W R R R DNCCSS PLCCSS PRGCSS SSO PRGSSO DNCSSO PLCSSO CNCSSO SLIMIT R R R R R/W R R R R R R/W R R R R R/W R R R/W R R R R R/W R R R DNCSL PLCSL PRGSL POSS RPOSS TPOSS RTPOSS FLWES R R R R R R R R R R/W R R R R R R R/W R R R R R R R Vitesse de rotation réelle de broche, en tours/minute Vitesse de rotation de broche active dans la CNC Vitesse de rotation sélectionnée par DNC Vitesse de rotation sélectionnée par PLC Vitesse de rotation sélectionnée par programme Vitesse de coupe constante active dans la CNC, en mètres/minute ou en pieds/minute. Modèle Tour Vitesse de coupe constante sélectionnée par DNC. Modèle Tour Vitesse de coupe constante sélectionnée par PLC. Modèle Tour Vitesse de coupe const. sélect. par programme. Modèle Tour Pourcent. de correction de vitesse de broche active dans la CNC. Pourcentage de correction sélectionné par programme. Pourcentage de correction sélectionné par DNC Pourcentage de correction sélectionné par PLC Pourcentage de correction sélectionné depuis le panneau avant Limite de vitesse de rotation de broche active dans la CNC, en tours/minute Limite de vitesse de rotation de broche sélectionnée par DNC. Limite de vitesse de rotation de broche sélectionnée par PLC. Limite de vitesse de rotat. de broche sélect. par programme. Position réelle de la broche (±999999999 en 0.0001°) Position réelle de la broche (entre 0 et 360° en 0.0001°) Position théorique de la broche (±999999999 en 0.0001°) Position théorique de la broche (entre 0 et 360° en 0.0001°) Erreur de poursuite de la broche en boucle fermée (M19), en degrés 7 VARIABLES ASSOCIEES A L’AUTOMATE Variable CNC PLC PLCMSG PLCIn PLCOn PLCMn PLCRn PLCTn PLCCn R R/W R/W R/W R/W R/W R/W - Section (13.2.9) DNC R - Numéro du message d’automate le plus prioritaire actif 32 entrées automate à partir de celle repérée (n) 32 sorties automate à partir de celle repérée (n) 32 marques automate à partir de celle repérée (n) Registre indiqué (n) Comptage du temporisateur indiqué (n) Comptage du compteur indiqué (n) VARIABLES ASSOCIEES AUX PARAMETRES GLOBAUX ET LOCAUX Section (13.2.10) Variable GUP n LUP (a,b) CALLP CNC PLC DNC R R/W R/W - - Paramètre global (P100-P299) indiqué (n) Paramètre local (P0-P25) indiqué (b), du niveau d’imbrication (a) Indique les paramètres locaux qui ont été définis et ceux qui n’ont pas été défini, dans l’appel de sous-routine, par l’instruction PCALL ou MCALL. AUTRES VARIABLES Section (13.2.11) Variable CNC PLC DNC OPMODE PRGN BLKN GSn GGSA GGSB GGSC GGSD MSn GMS PLANE LONGAX R R R R R R R R R R R R R R R R R R R R R R R R R R MIRROR SCALE SCALE(X-C) ORGROT R R R R R R R R R R R R ROTPF ROTPS PRBST CLOCK TIME DATE TIMER CYTIME PARTC FIRST KEY KEYSRC ANAIn ANAOn CNCERR PLCERR DNCERR R R R R R R R/W R R/W R R/W* R/W R R/W - R R R R R/W R R/W R R/W R/W R R/W R R R R R/W R/W R/W R R/W R R/W R/W R R/W R R - Mode de fonctionnement Numéro de programme en cours d’exécution Numéro d’étiquette du dernier bloc exécuté Etat de la fonction G indiquée (n) Etat des fonctions G00 à G24 Etat des fonctions G25 à G49 Etat des fonctions G50 à G74 Etat des fonctions G75 à G99 Etat de la fonction M indiquée (n) Etat des fonctions M (0..6, 8, 9, 19, 30, 41..44) Axes des abscisses et des ordonnées du plan actif Axe auquel s’applique la compensation de longueur (G15) Modèle Fraiseuse Images-miroir actives Facteur d’échelle général appliqué Facteur d’échelle particulier de l’axe indiqué Angle de rotation du système de coordonnées (G73), en degrés. Modèle Fraiseuse Centre de rotation selon l’axe des abscisses. Modèle Fraiseuse Centre de rotation selon l’axe des ordonnées. Modèle Fraiseuse Donne l’état du palpeur Horloge système, en secondes Heure selon le format heures-minutes-secondes Date selon le format année-mois-jour Horloge validée par le PLC, en secondes Temps d’exécution d’une pièce, en centièmes de seconde Compteur de pièces de la CNC Première exécution d’un programme Code créé par touche Origine des touches: 0 = Clavier, 1 = PLC, 2 = DNC Tension, en volts, de l’entrée analogique indiquée (n) Tension, en volts, à appliquer à la sortie analogique indiquée (n) Numéro d’erreur actif dans la CNC Numéro d’erreur actif dans le PLC Numéro d’erreur dans les communications par ligne DNC Attention: La variable “KEY” de la CNC est à écriture (W) seule dans le canal utilisateur. 8 ANNEXE C PROGRAMMATION DE NIVEAU HAUT DECLARATIONS DE VISUALISATION (Section 14.2) (ERROR, nombre entier, “texte d’erreur”) Interrompt l’exécution du programme et visualise l’erreur indiquée. (MSG “message”) Visualise le message indiqué. DECLARATIONS DE VALIDATION-INVALIDATION (Section 14.3) (ESBLK et DSBLK) La CNC exécute tous les blocs entre ESBLK et DSBLK comme s’il s’agissait d’un bloc unique. (ESTOP et DSTOP) Validation (ESTOP) et invalidation (DSTOP) de la touche Stop et du signal Stop externe (PLC) (EFHOLD et DFHOLD) Validation (EFHOLD) et invalidation (DFHOLD) de l’entrée Feed Hold (Arrêt des avances) (PLC) DECLARATIONS DE CONTROLE DE FLUX (Section 14.4) (GOTO N (expression)) Provoque un saut à l’intérieur du programme jusqu’au bloc défini par l’étiquette N(expression). (RPT N(expression), N(expression)) Répète l’exécution de la partie de programme existante entre les deux blocs définis par les étiquettes N(expression). (IF condition <action1> ELSE <action 2>) Analyse la condition donnée, qui devra être une expression relationnelle. Si la condition est vraie (résultat égal à 1), l’<action 1> est exécutée; dans le cas contraire résultat égal à 0), l’<action 2> est exécutée. DECLARATIONS DE SOUS-ROUTINES (SUB nombre entier) Définition de sous-routine (RET) Fin de sous-routine (CALL (expression)) Appel de sous-routine (Section 14.5) (PCALL (expression), (déclaration d’affectation), (déclaration d’affectation), ...) Appel de sousroutine. Permet aussi, grâce aux déclarations d’affectation, d’initialiser jusqu’à 26 paramètres locaux de cette sous-routine. (MCALL (expression), (déclaration d’affectation), (déclaration d’affectation), ...) Identique PCALL, mais transforme la sous-routine indiquée en sous-routine modale. (MDOFF) à Annulation de sous-routine modale. (PROBE (expression), (déclaration d’affectation), (déclaration d’affectation), ...) Exécute un cycle fixe de palpeur, en initialisant ses paramètres au moyen des déclarations d’affectation. (DIGIT (expression), (déclaration d’affectation), (déclaration d’affectation), ...) Exécute un cycle fixe de numérisation, en initialisant ses paramètres au moyen des déclarations d’affectation. (TRACE (expression), (déclaration d’affectation), (déclaration d’affectation), ...) Exécute un cycle fixe de copie, en initialisant ses paramètres au moyen des déclarations d’affectation. (REPOS X, Y, Z, ...) Doit toujours être utilisé dans les sous-routines d’interruption et facilite le repositionnement de la machine sur le point d’interruption. 9 DECLARATIONS PERMETTANT DE GENERER DES PROGRAMMES (Section 14.6) (OPEN P(expression), “commentaire de programme”) Commence l’édition d’un nouveau programme et permet de lui associer un commentaire. (WRITE <texte du bloc>) Ajoute, à la suite du dernier bloc du programme dont l’édition a commencé au moyen de la déclaration OPEN P, les informations contenues dans <texte du bloc> comme un nouveau bloc du programme. DECLARATIONS DE PERSONNALISATION (PAGE (expression)) (Section 14.7) Visualise à l’écran le numéro de page utilisateur (0-255) ou système (1000) indiqué. (SYMBOL (expression1), (expression2), (expression 3)) Visualise à l’écran le symbole (0-255) indiqué par l’expression 1. Son emplacement sur l’écran est définie par l’expression 2 (rangée 0639) et par l’expression 3 (colonne 0-335). (IB (expression) = INPUT “texte”, format) Visualise le texte indiqué dans la fenêtre d’entrée de données et charge dans la variable d’entrée (IBn) la donnée introduite par l’utilisateur. (ODW (expression1), (expression2), (expression 3))Définit et dessine à l’écran une fenêtre de couleur blanche (1 rangée x 14 colonnes). Son emplacement sur l’écran est définie par l’expression 2 (rangée) et par l’expression 3 (colonne). (DW (expression1) = (expression 2), DW (expression 3) = (expression 4), ...) Visualise dans les fenêtres indiquées par la valeur de l’expression 1, 3,..., la donnée numérique indiquée par l’expression 2, 4,... (SK (expression 1) = “texte 1”, (expression 2) = “texte 2”, ....) de touches logiciel indiqué. 10 Définit et visualise le nouveau menu (WKEY) Interrompt l’exécution du programme jusqu’à la frappe d’une touche. (WBUF “texte”, (expression)) Ajoute au bloc en cours d’édition et dans la fenêtre d’entrée de données le texte et la valeur de l’expression après évaluation. (WBUF) Introduit en mémoire le bloc en cours d’édition. Ne peut être utilisé que dans le programme de personnalisation à exécuter dans le mode Edition. (SYSTEM) Met fin à l’exécution du programme de personnalisation de l’utilisateur et revient au menu standard correspondant de la CNC. ANNEXE D CODES CREES PAR TOUCHES La frappe de chaque touche permet de générer jusqu’à quatre codes différents, selon l’état des fonctions SHIFT et CAPS. Par exemple, la frappe de la touche A permet d’obtenir les codes suivants: Hex. $61 $41 $41 $61 Touche Décimal 097 065 065 097 Si aucune fonction n’est active lors de la frappe de A Si la fonction SHIFT est active lors de la frappe de A Si la fonction CAPS est active lors de la frappe de A Si les deux fonctions sont actives lors de la frappe de A Touche Hexadécimal Décimal Hexadécimal Décimal A A+SHIFT A+CAPS A+SHIFT+CAPS $61 $41 $41 $61 097 065 065 097 H H+SHIFT H+CAPS H+SHIFT+CAPS $68 $48 $48 $68 104 072 072 104 B B+SHIFT B+CAPS B+SHIFT+CAPS $62 $42 $42 $62 098 066 066 098 I I+SHIFT I+CAPS I+SHIFT+CAPS $69 $49 $49 $69 105 073 073 105 C C+SHIFT C+CAPS C+SHIFT+CAPS $63 $43 $43 $63 099 067 067 099 J J+SHIFT J+CAPS J+SHIFT+CAPS $6A $4A $4A $6A 106 074 074 106 D D+SHIFT D+CAPS D+SHIFT+CAPS $64 $44 $44 $64 100 068 068 100 K K+SHIFT K+CAPS K+SHIFT+CAPS $6B $4B $4B $6B 107 075 075 107 E E+SHIFT E+CAPS E+SHIFT+CAPS $65 $45 $45 $65 101 069 069 101 L L+SHIFT L+CAPS L+SHIFT+CAPS $6C $4C $4C $6C 108 076 076 108 F F+SHIFT F+CAPS F+SHIFT+CAPS $66 $46 $46 $66 102 070 070 102 M M+SHIFT M+CAPS M+SHIFT+CAPS $6D $4D $4D $6D 109 077 077 109 G G+SHIFT G+CAPS G+SHIFT+CAPS $67 $47 $47 $67 103 071 071 103 N N+SHIFT N+CAPS N+SHIFT+CAPS $6E $4E $4E $6E 110 078 078 110 11 Hexadécimal Décimal U U+SHIFT U+CAPS U+SHIFT+CAPS $75 $55 $55 $75 117 085 085 117 111 079 079 111 V V+SHIFT V+CAPS V+SHIFT+CAPS $76 $56 $56 $76 118 086 086 118 $70 $50 $50 $70 112 080 080 112 W W+SHIFT W+CAPS W+SHIFT+CAPS $77 $57 $57 $77 119 087 087 119 Q Q+SHIFT Q+CAPS Q+SHIFT+CAPS $71 $51 $51 $71 113 081 081 113 X X+SHIFT X+CAPS X+SHIFT+CAPS $78 $58 $58 $78 120 088 088 120 R R+SHIFT R+CAPS R+SHIFT+CAPS $72 $52 $52 $72 114 082 082 114 Y Y+SHIFT Y+CAPS Y+SHIFT+CAPS $79 $59 $59 $79 121 089 089 121 S S+SHIFT S+CAPS S+SHIFT+CAPS $73 $53 $53 $73 115 083 083 115 Z Z+SHIFT Z+CAPS Z+SHIFT+CAPS $7A $5A $5A $7A 122 090 090 122 T T+SHIFT T+CAPS T+SHIFT+CAPS $74 $54 $54 $74 116 084 084 116 SP SP+SHIFT SP+CAPS SP+SHIFT+CAPS $20 $20 $20 $20 032 032 032 032 Touche Hexadécimal Décimal Ñ Ñ+SHIFT Ñ+CAPS Ñ+SHIFT+CAPS $A5 $A4 $A4 $A5 164 165 165 164 O O+SHIFT O+CAPS O+SHIFT+CAPS $6F $4F $4F $6F P P+SHIFT P+CAPS P+SHIFT+CAPS 12 Touche Touche Hexadécimal Décimal 0 +SHIFT +CAPS +SHIFT+CAPS $30 $3B $30 $3B 048 059 048 059 1 +SHIFT +CAPS +SHIFT+CAPS $31 $21 $31 $21 049 033 049 033 “ 2 +SHIFT +CAPS +SHIFT+CAPS $32 $22 $32 $22 050 034 050 034 3 +SHIFT +CAPS +SHIFT+CAPS $33 $27 $33 $27 4 +SHIFT +CAPS +SHIFT+CAPS Hexadécimal Décimal 8 +SHIFT +CAPS +SHIFT+CAPS $38 $29 $38 $29 056 041 056 041 $ 9 +SHIFT +CAPS +SHIFT+CAPS $39 $24 $39 $24 057 036 057 036 . +SHIFT +CAPS +SHIFT+CAPS $2E $3A $2E $3A 046 058 046 058 051 039 051 039 > + +SHIFT +CAPS +SHIFT+CAPS $2B $3E $2B $3E 043 062 043 062 $34 $5B $34 $5B 052 091 052 091 < +SHIFT +CAPS +SHIFT+CAPS $2D $3C $2D $3C 045 060 045 060 5 +SHIFT +CAPS +SHIFT+CAPS $35 $5D $35 $5D 053 093 053 093 ? * +SHIFT +CAPS +SHIFT+CAPS $2A $3F $2A $3F 042 063 042 063 & 6 +SHIFT +CAPS +SHIFT+CAPS $36 $26 $36 $26 054 038 054 038 % / +SHIFT +CAPS +SHIFT+CAPS $2F $25 $2F $25 047 037 047 037 $37 $28 $37 $28 055 040 055 040 # = +SHIFT +CAPS +SHIFT+CAPS $3D $23 $3D $23 061 035 061 035 ; Touche ) ! : , [ ] ( 7 +SHIFT +CAPS +SHIFT+CAPS 13 Touche Hexadécimal Décimal Touche Hexadécimal Décimal ENTER +SHIFT +CAPS +SHIFT+CAPS $0D $0D $0D $0D 013 013 013 013 Page précédente +SHIFT +CAPS +SHIFT+CAPS $FFA5 $FFA5 $FFA5 $FFA5 65445 65445 65445 65445 HELP +SHIFT +CAPS +SHIFT+CAPS $FFF2 $FFF2 $FFF2 $FFF2 65522 65522 65522 65522 Page suivante +SHIFT +CAPS +SHIFT+CAPS $FFAF 65455 $FFA5 65455 RESET +SHIFT +CAPS +SHIFT+CAPS $FFF3 65523 $FFF3 65523 Haut +SHIFT +CAPS +SHIFT+CAPS $FFB0 $FFB1 $FFB0 $FFB1 65456 65457 65456 65457 ESC ESC+SHIFT ESC+CAPS ESC+SHIFT+CAPS $1B $1B $1B $1B 027 027 027 027 Bas +SHIFT +CAPS +SHIFT+CAPS $FFB2 $FFB3 $FFB2 $FFB3 65458 65459 65458 65459 MAIN MENU +SHIFT +CAPS +SHIFT+CAPS $FFF4 $FFF4 $FFF4 $FFF4 65524 65524 65524 65524 Gauche +SHIFT +CAPS +SHIFT+CAPS $FFB4 $FFB5 $FFB4 $FFB5 65460 65461 65460 65461 CL CL+SHIFT CL+CAPS CL+SHIFT+CAPS $FFAD 65453 $FFAD 65453 Droite +SHIFT +CAPS +SHIFT+CAPS $FFB6 $FFB7 $FFB6 $FFB7 65462 65463 65462 65463 INS INS+SHIFT INS+CAPS INS+SHIFT+CAPS $FFAE $FFAE $FFAE $FFAE 65454 65454 65454 65454 14 Touche Hexadécimal Décimal Touche Hexadécimal Décimal F1 F1+SHIFT F1+CAPS F1+SHIFT+CAPS $FC00 $FC00 $FC00 $FC00 64512 64512 64512 64512 Marche +SHIFT +CAPS +SHIFT+CAPS $FFF1 $FFF1 $FFF1 $FFF1 65521 65521 65521 65521 F2 F2+SHIFT F2+CAPS F2+SHIFT+CAPS $FC01 $FC01 $FC01 $FC01 64513 64513 64513 64513 Arrêt +SHIFT +CAPS +SHIFT+CAPS $FFF0 $FFF0 $FFF0 $FFF0 65520 65520 65520 65520 F3 F3+SHIFT F3+CAPS F3+SHIFT+CAPS $FC02 $FC02 $FC02 $FC02 64514 64514 64514 64514 F4 F4+SHIFT F4+CAPS F4+SHIFT+CAPS $FC03 $FC03 $FC03 $FC03 64515 64515 64515 64515 F5 F5+SHIFT F5+CAPS F5+SHIFT+CAPS $FC04 $FC04 $FC04 $FC04 64516 64516 64516 64516 F6 F6+SHIFT F6+CAPS F6+SHIFT+CAPS $FC05 $FC05 $FC05 $FC05 64517 64517 64517 64517 F7 F7+SHIFT F7+CAPS F7+SHIFT+CAPS $FC06 $FC06 $FC06 $FC06 64518 64518 64518 64518 15 ANNEXE E PAGES DU SYSTEME D’AIDE A LA PROGRAMMATION . Ces pages peuvent être visualisées grâce à l’instruction de haut niveau “PAGE”; elles appartiennent toutes au système de la CNC et sont utilisées comme pages d’aide des fonctions respectives. AIDES LEXICOGRAPHIQUES Page 1000 Page 1001 Page 1002 Page 1003 Page 1004 Page 1005 Page 1006 Page 1007 Page 1008 Page 1009 Page 1010 Page 1011 Page 1012 Page 1013 Page 1014 Page 1015 Page 1016 Page 1017 Page 1018 Page 1019 Page 1020 Page 1021 Page 1022 Page 1023 Page 1024 Page 1025 Page 1026 Page 1027 Page 1028 Page 1029 Page 1030 Page 1031 Page 1032 16 Fonctions préparatoires G00-G09 Fonctions préparatoires G10-G19 Fonctions préparatoires G20-G44 Fonctions préparatoires G53-G59 Fonctions préparatoires G60-G69 Fonctions préparatoires G70-G79 Fonctions préparatoires G80-G89 Fonctions préparatoires G90-G99 Fonctions auxiliaires M Fonctions auxiliaires M, avec le symbole de page suivante Coïncide avec la 250 du répertoire si elle existe Coïncide avec la 251 du répertoire si elle existe Coïncide avec la 252 du répertoire si elle existe Coïncide avec la 253 du répertoire si elle existe Coïncide avec la 254 du répertoire si elle existe Coïncide avec la 255 du répertoire si elle existe Dictionnaire du langage de haut niveau (de A à G) Dictionnaire du langage de haut niveau (de H à N) Dictionnaire du langage de haut niveau (de O à S) Dictionnaire du langage de haut niveau (de T à Z) Variables accessibles par niveau haut (1ère partie) Variables accessibles par niveau haut (2ème partie) Variables accessibles par niveau haut (3ème partie) Variables accessibles par niveau haut (4ème partie) Variables accessibles par niveau haut (5ème partie) Variables accessibles par niveau haut (6ème partie) Variables accessibles par niveau haut (7ème partie) Variables accessibles par niveau haut (8ème partie) Variables accessibles par niveau haut (9ème partie) Variables accessibles par niveau haut (10ème partie) Variables accessibles par niveau haut (11ème partie) Variables accessibles par niveau haut (12ème partie) Opérateurs mathématiques AIDES SYNTAXIQUES: LANGAGE ISO Page 1033 Structure d’un bloc de programme Page 1034 Positionnement et interpolation linéaire: G00, G01 (1ère partie) Page 1035 Positionnement et interpolation linéaire: G00, G01 (2ème partie) Page 1036 Interpolation circulaire-hélicoïdale: G02, G03 (1ère partie) Page 1037 Interpolation circulaire-hélicoïdale: G02, G03 (2ème partie) Page 1038 Interpolation circulaire-hélicoïdale: G02, G03 (3ème partie) Page 1039 Trajectoire circulaire tangente: G08 (1ère partie) Page 1040 Trajectoire circulaire tangente: G08 (2ème partie) Page 1041 Trajectoire circulaire définie par 3 points: G09 (1ère partie) Page 1042 Trajectoire circulaire définie par 3 points: G09 (2ème partie) Page 1043 Filetage: G33 Page 1044 Arrondi: G36 Page 1045 Entrée tangentielle: G37 Page 1046 Sortie tangentielle: G38 Page 1047 Chanfrein: G39 Page 1048 Temporisation/interruption de la préparation des blocs: G04, G04K Page 1049 Arête vive, arête arrondie: G07, G05 Page 1050 Image-miroir: G11, G12, G13, G14 Page 1051 Programmation de plans et d’axe longitudinal: G16, G17, G18, G19, G15 Page 1052 Zones de travail: G21, G22 Page 1053 Compensation de rayon: G40, G41, G42 Page 1054 Compensation de longueur: G43, G44 Page 1055 Décalages d’origine Page 1056 Millimètres/pouces G71, G70 Page 1057 Facteur d’échelle: G72 Page 1058 Rotation des coordonnées: G73 Page 1059 Recherche de référence machine: G74 Page 1060 Travail avec palpeur: G75 Page 1061 Couplage électronique des axes: G77, G78 Page 1062 Absolues/incrémentales: G90, G91 Page 1063 Présélection de coordonnées et d’origine polaire: G92, G93 Page 1064 Programmation des avances: G94, G95 Page 1065 Fonctions G associées aux cycles fixes: G79, G80, G98 et G99 Page 1066 Programmation des fonctions auxiliaires: F, S, T et D Page 1067 Programmation des fonctions auxiliaires M AIDES SYNTAXIQUES: TABLES DE CNC Page 1090 Page 1091 Page 1092 Page 1093 Page 1094 Page 1095 Page 1096 Page 1097 Page 1098 Page 1099 Table de correcteurs Table d’outils Table de magasin d’outils Table de fonctions auxiliaires M Table d’origines Table de compensation de vis Table de compensation croisée Table de paramètres machine Table de paramètres utilisateur Table de mots de passe 17 AIDES SYNTAXIQUES: NIVEAU HAUT . Page 1100: Instructions ERROR et MSG Page 1101: Instructions GOTO et RPT Page 1102: Instructions OPEN et WRITE Page 1103: Instructions SUB et RET Page 1104: Instructions CALL, PCALL, MCALL, MDOFF et PROBE Page 1105: Instructions DSBLK, ESBLK, DSTOP, ESTOP, DFHOLD et EFHOLD Page 1106: Instruction IF Page 1107: Blocs d’affectations Page 1108: Expressions mathématiques Page 1109: Instruction PAGE Page 1110: Instruction ODW Page 1111: Instruction DW Page 1112: Instruction IB Page 1113: Instruction SK Page 1114: Instructions WKEY et SYSTEM Page 1115: Instruction KEYSRC Page 1116: Instruction WBUF Page 1117: Instruction SYMBOL AIDES SYNTAXIQUES: CYCLES FIXES Page 1070: Usinage multiple selon une droite: G60 Page 1071: Usinage multiple selon un parallélogramme: G61 Page 1072: Usinage multiple selon une grille: G62 Page 1073: Usinage multiple formant une circonférence: G63 Page 1074: Usinage multiple formant un arc: G64 Page 1075: Usinage programmé au moyen d’une corde d’arc: G65 Page 1076: Cycle fixe de poche avec ilôts: G66 Page 1077: Opération d’ébauche de poche avec ilôts: G67 Page 1078: Opération de finition de poche avec ilôts: G68 Page 1079: Cycle fixe de perçage profond à pas variable: G69 Page 1080: Cycle fixe de perçage: G81 Page 1081: Cycle fixe de perçage avec temporisation: G82 Page 1082: Cycle fixe de perçage profond à pas constant: G83 Page 1083: Cycle fixe de taraudage: G84 Page 1084: Cycle fixe d’alésage de précision: G85 Page 1085: Cycle fixe d’alésage avec retrait en G00: G86 Page 1086: Cycle fixe de poche rectangulaire: G87 Page 1887: Cycle fixe de poche circulaire: G88 Page 1088: Cycle fixe d’alésage avec retrait en G01: G89 18 ">
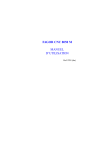
Lien public mis à jour
Le lien public vers votre chat a été mis à jour.