Fisher Contrôleurs pneumatiques et transmetteurs C1 (C1 Pneumatic Controllers and Manuel du propriétaire
PDF
Télécharger
Document
Manuel d'instructions Contrôleurs et transmetteurs C1 D103292X0FR Septembre 2019 Contrôleurs pneumatiques et transmetteurs Fisher™ C1 Table des matières Introduction . . . . . . . . . . . . . . . . . . . . . . . . . . . . . . . . . . . . . . 2 Objet du manuel . . . . . . . . . . . . . . . . . . . . . . . . . . . . . . . . . 2 Description . . . . . . . . . . . . . . . . . . . . . . . . . . . . . . . . . . . . . . 2 Spécifications . . . . . . . . . . . . . . . . . . . . . . . . . . . . . . . . . . . . 2 Services de formation . . . . . . . . . . . . . . . . . . . . . . . . . . . . . 2 Installation . . . . . . . . . . . . . . . . . . . . . . . . . . . . . . . . . . . . . . . . 6 Installation standard . . . . . . . . . . . . . . . . . . . . . . . . . . . . . . 6 Montage sur panneau . . . . . . . . . . . . . . . . . . . . . . . . . . . . . 7 Montage sur paroi . . . . . . . . . . . . . . . . . . . . . . . . . . . . . . . . 7 Montage sur tuyauterie . . . . . . . . . . . . . . . . . . . . . . . . . . . . 7 Montage sur actionneur . . . . . . . . . . . . . . . . . . . . . . . . . . . 7 Raccordements pneumatiques . . . . . . . . . . . . . . . . . . . . . . 9 Pression d'alimentation . . . . . . . . . . . . . . . . . . . . . . . . 9 Pression du procédé . . . . . . . . . . . . . . . . . . . . . . . . . . 10 Event . . . . . . . . . . . . . . . . . . . . . . . . . . . . . . . . . . . . . . . . . . 11 Fonctionnement du contrôleur . . . . . . . . . . . . . . . . . . . . . . 11 Contrôleurs proportionnels uniquement . . . . . . . . . . . . . 11 Réglages . . . . . . . . . . . . . . . . . . . . . . . . . . . . . . . . . . . 11 Réglage : Point de consigne . . . . . . . . . . . . . . . . . 11 Réglage : Bande proportionnelle . . . . . . . . . . . . . 11 Etalonnage : Contrôleurs proportionnels uniquement . . . . . . . . . . . . . . . . . . . . . . . . . . . . . . 12 Mise en service : Contrôleurs proportionnels uniquement . . . . . . . . . . . . . . . . . . . . . . . . . . . . . . 15 Contrôleur proportionnel plus réinitialisation . . . . . . . . . 15 Réglages . . . . . . . . . . . . . . . . . . . . . . . . . . . . . . . . . . . 16 Réglage : Point de consigne . . . . . . . . . . . . . . . . . 16 Réglage : Bande proportionnelle . . . . . . . . . . . . . 16 Réglage : Réinitialisation . . . . . . . . . . . . . . . . . . . . 16 Réglage : Enroulement anti-réinitialisation . . . . . . . . . . . . . . . . . . . . . . . . 17 Etalonnage . . . . . . . . . . . . . . . . . . . . . . . . . . . . . . . . . 17 Etalonnage : Contrôleurs proportionnels plus réinitialisation . . . . . . . . . . . . . . . . . . . . . . . . 17 Etalonnage : Enroulement anti-réinitialisation . . . . . . . . . . . . . . . . . . . . . . . . 19 Mise en service : Contrôleurs proportionnels plus réinitialisation . . . . . . . . . . . . . . . . . . . . . . . . 20 Contrôleurs d'écart différentiel . . . . . . . . . . . . . . . . . . . . . 20 Réglages . . . . . . . . . . . . . . . . . . . . . . . . . . . . . . . . . . . 21 Réglage : Point de consigne . . . . . . . . . . . . . . . . . 21 Réglage : Bande proportionnelle . . . . . . . . . . . . . 21 Etalonnage : Contrôleurs d'écart différentiel . . . . . . . . . . . . . . . . . . . . . . . . . . . . . . . 21 Mise en service : Contrôleurs d'écart différentiel . . . . . . . . . . . . . . . . . . . . . . . . . . . . . . . 23 Fonctionnement du transmetteur . . . . . . . . . . . . . . . . . . . 23 Réglages . . . . . . . . . . . . . . . . . . . . . . . . . . . . . . . . . . . . . . . 23 Réglage : Zéro . . . . . . . . . . . . . . . . . . . . . . . . . . . . . . . 23 Réglage : Etendue . . . . . . . . . . . . . . . . . . . . . . . . . . . 24 www.Fisher.com Figure 1. Contrôleur monté sur arcade ou actionneur à vanne de régulation C1 Fisher W9263-1 Etalonnage : Transmetteurs . . . . . . . . . . . . . . . . . . . . . . . Mise en service : Transmetteurs . . . . . . . . . . . . . . . . . . . . Principe de fonctionnement . . . . . . . . . . . . . . . . . . . . . . . . Contrôleurs proportionnels uniquement . . . . . . . . . . . . . Contrôleurs proportionnels plus réinitialisation . . . . . . . Contrôleurs avec enroulement anti-réinitialisation . . . . Contrôleurs d'écart différentiel . . . . . . . . . . . . . . . . . . . . . Transmetteurs . . . . . . . . . . . . . . . . . . . . . . . . . . . . . . . . . . Maintenance . . . . . . . . . . . . . . . . . . . . . . . . . . . . . . . . . . . . . Remplacement des manomètres . . . . . . . . . . . . . . . . . . . Remplacement du tube de Bourdon . . . . . . . . . . . . . . . . Remplacement du capteur à soufflet . . . . . . . . . . . . . . . . Changement de la vanne de réinitialisation ou proportionnelle . . . . . . . . . . . . . . . . . . . . . . . . . . . . Changement de la soupape de décharge différentielle avec enroulement anti-réinitialisation . . . . . . . . . . . . Changement de l'action . . . . . . . . . . . . . . . . . . . . . . . . . . Conversion d'un contrôleur proportionnel uniquement en un contrôleur d'écart différentiel . . . . . . . . . . . . . . . . . . . . . . . . . . . . . . . Passer à une action directe . . . . . . . . . . . . . . . . . . . . Remplacement du relais . . . . . . . . . . . . . . . . . . . . . . . . . . Changement de la plage du signal de sortie . . . . . . . . . . Commande de pièces détachées . . . . . . . . . . . . . . . . . . . . 24 26 27 27 28 28 28 29 30 30 31 32 33 33 33 33 34 36 37 40 Manuel d'instructions Contrôleurs et transmetteurs C1 D103292X0FR Septembre 2019 Table des matières (suite) Kits de pièces . . . . . . . . . . . . . . . . . . . . . . . . . . . . . . . . . . . . Liste des pièces . . . . . . . . . . . . . . . . . . . . . . . . . . . . . . . . . . . Pièces communes . . . . . . . . . . . . . . . . . . . . . . . . . . . . . . . Pièces pour le montage sur panneau, sur paroi, sur tuyauterie ou sur actionneur . . . . . . . . . . . . . . . . . 41 41 41 50 Introduction Objet du manuel Ce manuel d'instructions fournit des informations relatives à l'installation, au fonctionnement, à la maintenance et aux pièces détachées destinées aux contrôleurs de pression et transmetteurs C1 de Fisher indiqués dans la figure 1. Consulter les manuels d'instructions séparés pour toute information relative à la vanne de régulation, à l'actionneur et aux accessoires. Les personnes effectuant les procédures d'installation, d'exploitation ou de maintenance des contrôleurs de pression et transmetteurs C1 doivent être parfaitement formées et qualifiées aux procédures d'installation, d'exploitation et de maintenance de vannes, d'actionneurs et d'accessoires. Pour éviter des blessures et des dommages matériels, il est important de lire attentivement, assimiler et suivre l'intégralité du contenu de ce manuel, y compris les avertissements et les précautions. Pour toute question relative à ces instructions, contacter un bureau de vente Emerson avant toute intervention. Description Les contrôleurs pneumatiques et transmetteurs C1 utilisent un capteur à soufflet ou à tube de Bourdon pour mesurer la pression manométrique, le vide, la pression tangentielle ou la pression différentielle d'un liquide ou d'un gaz. Le contrôleur ou le transmetteur émet un signal de pression pneumatique qui peut être utilisé pour faire fonctionner un élément de contrôle final, un dispositif indicateur ou d'enregistrement. Sauf indication contraire, toutes les références NACE correspondent aux normes NACE MR0175 / ISO15156 et NACE MR0103. Spécifications Les spécifications des contrôleurs et transmetteurs C1 sont indiquées dans le tableau 1. Le tableau 2 explique les configurations et les options disponibles. Services de formation Pour tout renseignement sur les cours disponibles pour les contrôleurs et transmetteurs C1, ainsi que pour d'autres types de produits, contacter : Emerson Automation Solutions Educational Services - Registration Téléphone : +1-641-754-3771 ou +1-800-338-8158 E-mail : education@emerson.com emerson.com/fishervalvetraining 2 Manuel d'instructions Contrôleurs et transmetteurs C1 D103292X0FR Septembre 2019 Tableau 1. Spécifications Configurations disponibles Connexions d'alimentation et de sortie Voir le tableau 2 Interne de 1/4 NPT Signal d'entrée Conversions courantes de la pression du signal Type : J Pression manométrique, J vide, J pression tangentielle, ou J pression différentielle d'un liquide ou d'un gaz Limites : Voir le tableau 3 ou 4 Voir le tableau 6 Réglage de la bande proportionnelle Pour les contrôleurs proportionnels uniquement : Changement complet de pression de sortie réglable de J 2 % à 100 % de la plage du capteur entre 0,2 et 1,0 bar (3 et 15 psig) ou J 4 % à 100 % de la plage du capteur entre 0,4 et 2,0 bar (6 et 30 psig) Signal de sortie Contrôleurs et transmetteurs proportionnels uniquement ou proportionnels plus réinitialisation : J signal de pression pneumatique 0,2 à 1,0 bar (3 à 15 psig) ou J 0,4 à 2,0 bar (6 à 30 psig) Contrôleurs d'écart différentiel : J 0 à 1,4 bar (0 à 20 psig) ou J signal de pression pneumatique 0 and 2,4 bar (0 and 35 psig) Action : L'action de régulation est réversible sur site entre J action directe (la pression mesurée croissante produit un signal de sortie croissant) et J action inverse (la pression mesurée croissante produit un signal de sortie décroissant). Pour les contrôleurs proportionnels plus réinitialisation : Changement de pression de sortie totale réglable de J 3 % à 100 % de la plage du capteur entre 0,2 et 1,0 bar (3 et 15 psig) ou J 6 % à 100 % de la plage du capteur entre 0,4 et 2,0 bar (6 et 30 psig) Réglage de l'écart différentiel Pour les contrôleurs d'écart différentiel : Changement de pression de sortie totale réglable de 15 % à 100 % de la plage du capteur Spécifications de pression d'alimentation(1) Réglage de la réinitialisation Voir le tableau 5 Pour les contrôleurs proportionnels plus réinitialisation : Réglable de 0,01 à 74 minutes par répétition (100 à 0,01 répétitions par minute) Gaz de pression d'alimentation Air ou gaz naturel Le produit d'alimentation doit être propre, sec et non-corrosif. Selon la norme ISA 7.0.01 Des particules de 40 micromètres au maximum dans le circuit pneumatique sont acceptables. Il est recommandé de procéder à une filtration supplémentaire pour réduire la taille des particules à 5 micromètres. La teneur en lubrifiant ne doit pas dépasser 1 ppm en poids (p/p) ou en volume (vol/vol). La condensation dans l'alimentation d'air doit être minimale. Selon la norme ISO 8573-1 Masse volumique maximale des particules : Classe 7 Teneur en lubrifiant : Classe 3 Point de rosée sous pression : Classe 3 ou au moins 10 °C inférieurs à la température ambiante la plus basse attendue Réglage du zéro (transmetteurs uniquement) Réglable en continu pour le positionnement d'une étendue inférieure à 100 % en tout point sur la plage du capteur Réglage de l'étendue (transmetteurs uniquement) Changement complet de pression de sortie réglable de 6 à 100 % de la plage du capteur Performance Répétabilité : 0,5% de la plage du capteur Zone morte (sauf contrôleurs d'écart différentiel)(4) : 0,1 % de la plage du capteur Réponse en fréquence à 100 % de la bande proportionnelle Sortie vers l'actionneur : Déphasage de 0,7 Hz et 110_ avec un volume de 1 850 cm3 (113 in.3), actionneur à mi-course Sortie vers le soufflet du positionneur : Déphasage de 9 Hz et 130_ avec une sortie de 0,2 à 1,0 bar (3 à 15 psig) vers le soufflet de 33 cm3 (2 in.3) Consommation d'air à régime stable(2,3) 0,2 à 1,0 bar (3 à 15 psig) : 0,08 m3/h normaux (3 scfh) 0,4 à 2,0 bar (6 à 30 psig) : 0,12 m3/h normalisés (4.5 scfh) - suite - 3 Manuel d'instructions Contrôleurs et transmetteurs C1 D103292X0FR Septembre 2019 Tableau 1. Spécifications (suite) changement de température de 28 _C (50 _F) entre -40 et 71 _C (-40 et 160 _F) pour un transmetteur réglé à 100 % de l'étendue de l'échelle Limites de température ambiante de fonctionnement (1) J Construction standard : -40 à 71 _C (-40 à 160 _F) J Construction pour température élevée : -18 à 104 _C (0 à 220 _F) Les options d'enroulement anti-réinitialisation (système de protection contre les surpressions différentielles) et de manomètre de procédé sont uniquement disponibles pour la construction standard Classement de zones dangereuses Conformes aux exigences ATEX Groupe II, Catégorie 2, gaz et poussières Ex h IIC Tx Gb Ex h IIIC Tx Db Si la température de procédé sort de la plage de température ambiante de fonctionnement du contrôleur, la longueur du tube capillaire entre le point du capteur à l'entrée et le procédé du contrôleur peut être réglée afin de protéger le contrôleur de la température de procéd La température de surface maximale (Tx) dépend des conditions de fonctionnement Gaz : T4, T5, T6 Poussière : T85…T104 Influence de la température ambiante de fonctionnement typique Voir la figure 26 pour l'emplacement de la marque ATEX Contrôleur proportionnel uniquement : $3,0 % de l'étendue du signal de sortie pour chaque changement de température de 28 _C (50 _F) entre -40 et 71 _C (-40 et 160 _F) pour un contrôleur réglé à 100 % de la bande proportionnelle Poids approximatif 8,2 kg (18 lb) Déclaration de BPT Contrôleur proportionnel plus réinitialisation : $2,0 % de l'étendue du signal de sortie pour chaque changement de température de 28 _C (50 _F) entre -40 et 71 _C (-40 et 160 _F) pour un contrôleur réglé à 100 % de la bande proportionnelle Fisher Controls International LLC déclare que ce produit est conforme à l'article 4, paragraphe 3, de la Directive sur les équipements sous pression (DESP) 2014/68/EU. Il a été conçu et fabriqué conformément aux Bonne Pratiques Techniques (BPT) et ne peut pas porter la marque CE relative à la DESP. Transmetteurs uniquement : $3,0 % de l'étendue du signal de sortie pour chaque Le produit peut cependant porter la marque CE indiquant la conformité à d'autres directives européennes applicables. 1. Ne pas dépasser les limites de pression/température indiquées dans ce manuel et celles de toute norme ou de tout code applicable. 2. m3/h normalisés : mètres cubes par heure normalisés (m3/h, 0 _C et 1,01325 bar, absolu). Scfh : pied cube standard par heure (Standard cubic feet per hour) (ft3/h, 60 _F et 14.7 psig). 3. Pour convertir le débit de l'air au débit du gaz naturel, multiplier la valeur par 1,29. 4. Un écart différentiel réglable (contrôleurs d'écart différentiel) est équivalent à une zone morte réglable. Tableau 2. Configurations disponibles NUMERO DU TYPE DESCRIPTION Capteur à tube de Bourdon (pression manométrique uniquement) Capteur à soufflet Pression manométrique Pression différentielle Contrôleur proportionnel uniquement Sans enroulement anti-réinitialisation Avec enroulement anti-réinitialisation Contrôleur d'écart différentiel Contrôleur proportionnel plus réinitialisation Transmetteur 4 C1D C1P C1B ----C1D Manuel d'instructions Contrôleurs et transmetteurs C1 D103292X0FR Septembre 2019 Tableau 3. Plage de pression et matériaux du tube de Bourdon LIMITES DE PRESSION STATIQUE MAXIMALE AUTORISEE(3) PLAGES DE PRESSION(1,2) Bar Avec butée de course en option(4) Standard Psig Bar Psig Bar Psig 0 à 2,0 0 à 4,0 0 à 7,0 0 à 14 0 à 20 0 à 40 0 à 70 0 à 30 0 à 60 0 à 100 0 à 200 0 à 300 0 à 600 0 à 1000 2,0 4,0 7,0 14 20 40 70 30 60 100 200 300 600 1000 3,3 6,6 11 19 29 50 83 48 96 160 280 420 720 1200 0 à 100 0 à 200 0 à 350 0 à 550 0 à 700 0 à 1500 0 à 3000 0 à 5000 0 à 8000 0 à 10000 100 200 350 550 700 1500 3000 5000 8000 10000 115 230 380 550 700 1650 3300 5500 8000 10000 MATERIAU(5) Acier inoxydable 316 1. Si le procédé peut passer à une valeur sortant de la plage de fonctionnement du capteur, il est possible d'utiliser un dispositif de protection contre les à-coups de pression et les pulsations disponible dans le commerce, comme un dispositif de protection contre les surpressions. 2. La plage figurant sur le tube de Bourdon peut être indiquée en kPa (1 bar = 100 kPa) 3. Le tube de Bourdon peut être pressurisé jusqu'à la limite indiquée sans dérive permanente du zéro. 4. Avec butée de course réglée à 110 % de la plage. 5. Les tubes de Bourdon sont également disponibles en matériau conforme à la norme NACE. Contacter un bureau de vente Emerson pour plus de renseignements. Tableau 4. Plages de pression et matériaux du soufflet LIMITES DE PRESSION STATIQUE MAXIMALE AUTORISEE(2) Construction en Construction en laiton acier inoxydable Bar Psig Bar Psig PLAGES DE PRESSION(1) Vide Pression tangentielle Pression manométrique Pression positive Pression différentielle(5) 0 à 150 mbar (0 à 60 in. CE) 0 à 340 mbar (0 à 10 in. Hg) 0 à 1,0 bar (0 à 30 in. Hg) 75 mbar vac. à 75 mbar (30 in. CE vac. à 30 in. CE) 500 mbar vac. à 500 mbar (15 in. Hg vac. à 7.5 psig) 1,0 bar vac. à 1,0 bar (30 in. Hg vac. à 15 psig) 0 à 150 mbar (0 à 60 in. CE) 0 à 250 mbar(3) (0 à 100 in. CE) 0 à 350 mbar(4) (0 à 140 in. CE) 0 à 0,35 bar (0 à 5 psig) 0 à 0,5 bar (0 à 7.5 psig) 0 à 0,7 bar (0 à 10 psig) 0 à 1,0 bar (0 à 15 psig) 0 à 1,4 bar (0 à 20 psig) 0 à 2,0 bar (0 à 30 psig) 1,4 2,8 2,8 1,4 2,8 2,8 1,4 1,4 2,8 2,8 2,8 2,8 2,8 2,8 2,8 20 40 40 20 40 40 20 20 40 40 40 40 40 40 40 ----6,9 --6,9 6,9 ------------6,9 --6,9 ----100 --100 100 ------------100 --100 0 à 300 mbar (0 à 80 in. CE) 0 à 0,7 bar (0 à 10 psi) 0 à 1,4 bar (0 à 20 psi) 0 à 2,0 bar (0 à 30 psi) 1,4 2,8 2,8 --- 20 40 40 --- ------6,9 ------100 1. Si le procédé peut passer à une valeur hors de la plage de fonctionnement du capteur, il est possible d'utiliser un dispositif de protection contre les à-coups de pression et les pulsations disponible dans le commerce tel qu'un dispositif de protection contre les surpressions. 2. Le soufflet peut être pressurisé jusqu'à la limite indiquée sans dérive permanente du zéro. 3. Transmetteur uniquement. 4. Sauf transmetteur. 5. La limite de dépassement pour ces éléments de détection est une pression différentielle égale à la limite de pression statique maximale autorisée. Tableau 5. Spécifications de pression d'alimentation 0,2 à 1,0 ou 0 et 1,4 (écart différentiel) Pression d'alimentation en mode de fonctionnement normal(1) 1,4 0,4 à 2,0 ou 0 et 2,4 (écart différentiel) 2,4 2,8 3 à 15 ou 0 et 20 (écart différentiel) 20 40 6 à 30 ou 0 et 35 (écart différentiel) 35 40 Plage de signal de sortie Bar Psig Pression d'alimentation maximale autorisée pour éviter des dégâts internes 2,8 1. Le dépassement de cette pression peut perturber le contrôle. 5 Manuel d'instructions Contrôleurs et transmetteurs C1 D103292X0FR Septembre 2019 Tableau 6. Conversions courantes de la pression du signal Mps kg/cm2 bar kPa Psi 0,02 0,03 0,04 0,05 0,06 0,2 0,3 0,4 0,5 0,6 0,2(2) 0,3 0,4 0,5 0,6 20(1) 35 40(1) 50 60 3 5 6 7 9 0,07 0,08 0,09 0,10 0,12 0,8 0,8 1,0 1,0(3) 1,3 0,8 0,8 1,0 1,0(2) 1,2 75 80 95 100(1) 125 11 12 14 15 18 0,14 0,15 0,17 0,18 0,20 1,4 1,5 1,8 1,9 2,0 1,4 1,5 1,7 1,9 2,0(3) 140 150 170 185 200(1) 20 22 25 27 30 0,22 0,23 0,24 0,34 0,55 2,2 2,3 2,5 3,5 5,6 2,2 2,3 2,4 3,4 5,5 220 230 240 345 550 32 33 35 50 80 0,69 1,03 7,0 10,5 6,9 10,3 690 1035 100 150 1. Valeurs telles que listées dans la norme ANSI/S7.4. 2. Valeurs telles que listées dans la norme CEI 382. 3. Valeurs arrondies afin de correspondre aux valeurs en kPa. Installation AVERTISSEMENT Pour éviter toute blessure ou tout dommage provoqué par la dissipation soudaine de la pression : D Toujours porter des vêtements, des gants et des lunettes de protection lors de toute opération d'installation. D Des blessures ou des dommages matériels peuvent résulter d'un incendie ou d'une explosion si du gaz naturel est utilisé comme produit d'alimentation et que les mesures de prévention appropriées ne sont pas prises. Les mesures préventives nécessaires peuvent comprendre, notamment, l'un des éléments suivants : mise à l'évent déportée de l'unité, réévaluation de la classification des zones dangereuses, assurance d'une ventilation adéquate et élimination de toute source d'inflammation Pour tout renseignement sur la mise à l'évent déportée de ce contrôleur/transmetteur, se reporter à la page 11. D En cas d'installation dans une application existante, consulter aussi l'AVERTISSEMENT au début de la section Maintenance de ce manuel d'instructions. D Consulter l'ingénieur des procédés ou l'ingénieur responsable de la sécurité pour toute autre mesure supplémentaire de protection contre le fluide du procédé. ATTENTION Ne pas utiliser de ruban d'étanchéité sur les raccordements pneumatiques. Cet instrument comporte de petits passages d'écoulement qui peuvent être obstrués par un ruban d'étanchéité détaché. Un produit d'étanchéité pour filetage doit être utilisé pour sceller et lubrifier les raccordements pneumatiques filetés. Installation standard Les instruments sont généralement montés à la verticale, le boîtier/couvercle positionné comme indiqué dans la figure 1. En cas d'installation de l'instrument dans toute autre position, veiller à ce que l'ouverture d'évent indiquée dans la figure 2 soit orientée vers le bas. 6 Manuel d'instructions D103292X0FR Contrôleurs et transmetteurs C1 Septembre 2019 Montage sur panneau Voir la figure 2. Découper un trou dans la surface du panneau selon les dimensions indiquées dans la figure 2. Retirer les vis d'assemblage (n_ 252), les supports (n_ 251) et l'évent (n_ 28). Faire glisser le contrôleur ou le transmetteur dans l'orifice découpé et fixer les supports. Serrer les vis d'assemblages situées au centre de chaque support afin de fixer parfaitement le boîtier contre le panneau. Remettre l'évent en place, à moins qu'un évent déporté ne soit utilisé. Montage sur paroi Voir la figure 2. Percer quatre orifices dans la paroi selon les dimensions indiquées dans la figure 2. Les orifices du support (n_ 251) sont de 8,7 mm (0.3438 in.) de diamètre. Faire sortir la vis d'assemblage située au centre de chaque support. (Les vis sont utilisées pour le montage sur panneau mais pas pour le montage sur paroi.) Si la paroi comporte des tuyaux, percer les orifices en fonction de leur emplacement. La figure 2 indique les emplacements des raccordements des prises de pression à l'arrière du boîtier. Monter le contrôleur au support à l'aide des quatre vis d'assemblage (n_ 252) fournies. Fixer le support à la paroi avec des vis ou des boulons adaptés. Montage sur tuyauterie Voir la figure 2. Utiliser un marteau et un poinçon pour percer les orifices pré-formés indiqués sur la vue arrière de la figure 2. Fixer les bobines d'entretoise (n_ 228) et la plaque de montage (n_ 213) au contrôleur avec les vis d'assemblage, les rondelles de blocage et les écrous (n_ 215, 221 et 216). Fixer le contrôleur à un tuyau de 2 in. (nominal) avec le collier de serrage (n_ 250). Montage sur actionneur Voir la figure 3. Les contrôleurs spécifiés pour le montage sur l'actionneur d'une vanne de régulation sont montés en usine. Si l'instrument est commandé séparément pour une installation sur l'actionneur d'une vanne de régulation, le monter en suivant les instructions ci-dessous. Les pièces de montage pour les différents types et tailles d'actionneurs peuvent varier. Deux montages types d'installation de l'actionneur sont illustrés dans la figure 3 ; voir la liste des pièces requises pour le type et la taille de l'actionneur spécifique. Utiliser un marteau et un poinçon pour percer les orifices préformés indiqués sur la vue arrière de la figure 2. Fixer les bobines d'entretoise (n_ 228) et la plaque de montage (n_ 213) sur le contrôleur avec les vis mécaniques, les rondelles de blocage et les écrous (n_ 215, 221 et 216). Fixer le support de montage sur l'arcade de l'actionneur à l'aide des vis d'assemblage (n_ 222) et des bobines d'entretoise si nécessaire. Le support de montage est fixé sur le boîtier de la membrane de l'actionneur et non pas sur l'arcade sur certains modèles. 7 Manuel d'instructions Contrôleurs et transmetteurs C1 D103292X0FR Septembre 2019 Figure 2. Montage sur panneau, paroi et tuyauterie 180,8 (7.12) 63,5 (2.50) TUYAU DE 2 IN. (NOMINAL) 63,5 (2.50) 65,8 (2.59) 23,1 (0.91) EVENT (N_ 28) ORIFICE PRE-PERFORE 69,1 (2.72) VUE ARRIERE MONTAGE SUR TUYAUTERIE 244,3 (9.62) 215,9 (8.50) 142,7 (5.62) 8,7 (11/32) 218,9 (8.62) ORIFICES DE MONTAGE MONTAGE SUR PANNEAU 8 101,6 (4.00) 14,3 (0.56) R MONTAGE SUR PAROI REMARQUES : 1. TOUS LES RACCORDEMENTS SONT DE 1/4 NPT INTERNE. 2 RACCORDEMENT HAUTE PRESSION POUR LES UNITES A PRESSION DIFFERENTIELLE. 3 RACCORDEMENT BASSE PRESSION POUR LES UNITES A PRESSION DIFFERENTIELLE E1052 ORIFICE PRE-PERFORE DECOUPE POUR LE MONTAGE SUR PANNEAU QUATRE ORIFICES POUR LE MONTAGE SUR PAROI mm (in.) Manuel d'instructions Contrôleurs et transmetteurs C1 D103292X0FR Septembre 2019 Figure 3. Montage sur actionneur REGULATEUR DE PRESSION D'ALIMENTATION REGULATEUR DE PRESSION D'ALIMENTATION GE33947-A GE33946-A ACTIONNEUR ROTATIF ACTIONNEUR LINEAIRE Raccordements pneumatiques AVERTISSEMENT Pour éviter toute blessure ou tout dommage matériel provoqué par la dissipation soudaine de la pression, ne pas installer un des composants du système où les conditions de service peuvent dépasser les valeurs maximales indiquées dans ce manuel. Utiliser des dispositifs de dissipation de la pression tels que requis par le gouvernement ou acceptés par les codes professionnels et selon les bonnes pratiques techniques en usage. ATTENTION Ne pas utiliser de ruban d'étanchéité sur les raccordements pneumatiques. Cet instrument comporte de petits passages d'écoulement qui peuvent être obstrués par un ruban d'étanchéité détaché. Un produit d'étanchéité pour filetage doit être utilisé pour sceller et lubrifier les raccordements pneumatiques filetés. Tous les raccordements pneumatiques des instruments C1 sont des connexions internes de 1/4 NPT. Utiliser un tuyau ou un tube de 6 mm (1/4 in.) ou 10 mm (3/8 in.) pour la tuyauterie d'alimentation et de sortie. Les emplacements des raccordements des prises de pression sont illustrés sur la figure 2. Pression d'alimentation AVERTISSEMENT Un procédé mal contrôlé, associé à un produit d'alimentation de l'instrument qui n'est pas propre, sec, exempt de graisse ou non corrosif, peut provoquer des dommages matériels ou des blessures graves. Bien qu'une utilisation et un entretien régulier d'un filtre qui capte les particules d'un diamètre supérieur à 40 micromètres suffisent dans la plupart des applications, consulter un bureau commercial Emerson et vérifier les normes de qualité du produit d'alimentation des instruments du secteur avant toute utilisation de gaz dangereux ou en cas de doute quant à la quantité de filtration d'air ou la maintenance du filtre. 9 Contrôleurs et transmetteurs C1 Septembre 2019 Manuel d'instructions D103292X0FR La pression d'alimentation doit être fournie sous forme d'air propre, sec et non corrosif, répondant aux exigences de la norme ISA 7.0.01 ou ISO 8573-1. Des particules de 40 micromètres maximum dans le circuit pneumatique sont acceptables. Il est recommandé de procéder à une filtration supplémentaire pour réduire la taille des particules à 5 micromètres. La teneur en lubrifiant ne doit pas dépasser 1 ppm en poids (p/p) ou en volume (vol/vol). La condensation dans l'air d'alimentation doit être minimale. Utiliser un régulateur haute pression de pression d'alimentation pour faire baisser la source de pression de l'alimentation à la pression d'alimentation en mode de fonctionnement normal indiquée dans le tableau 5. Raccorder la pression d'alimentation sur le raccord ALIMENTATION à l'arrière du boîtier. AVERTISSEMENT Pour éviter toute blessure ou tout dommage provoqué par la fuite soudaine de la pression, utiliser un régulateur haute pression pour le fonctionnement du contrôleur ou du transmetteur à partir d'une source haute pression. En cas de fonctionnement du contrôleur ou du transmetteur à partir d'une source haute pression [jusqu'à 138 bar (2000 psig)], utiliser un régulateur haute pression tel que le système d'alimentation d'instrument haute pression Fisher 1367. Pour obtenir des informations sur l'installation, le réglage et la maintenance du système d'alimentation d'instrument haute pression avec protection contre les surpressions 1367, se reporter à son manuel d'instructions, référence D100343X012. Pression du procédé AVERTISSEMENT Pour éviter toute blessure ou tout dommage matériel provoqué par la dissipation soudaine de la pression lors de l'utilisation d'un produit corrosif, vérifier que la tuyauterie et les composants de l'instrument en contact avec le fluide corrosif sont constitués d'un matériau adéquat non corrosif. Voir l'avertissement d'installation au début de cette section. Les raccordements pneumatiques vers le contrôleur dépendent du type de détection de la pression, manométrique ou différentielle. Le capteur des contrôleurs de pression manométrique utilise soit un tube de Bourdon, soit un soufflet, comme indiqué dans le tableau 2. Les contrôleurs de pression différentielle utilisent deux soufflets pour mesurer la pression différentielle. Pour les instruments à pression manométrique : Le bloc de pression de contrôle (n_ 10 dans la figure 22) possède deux raccordements. En fonction de l'application de l'instrument, la pression du procédé peut être raccordée sur le raccordement de CONTROLE à l'arrière du boîtier ou sur le raccordement situé sur le côté gauche du boîtier comme indiqué dans la figure 2. Boucher le raccordement inutilisé. Pour les instruments à pression différentielle : Raccorder la ligne à basse pression sur le raccordement de CONTROLE sur le côté du boîtier et la ligne haute pression sur le raccordement de CONTROLE à l'arrière du boîtier comme indiqué dans la figure 2. Lors de l'installation de la tuyauterie du procédé, suivre les pratiques en usage pour assurer la transmission précise de la pression du procédé vers le contrôleur ou le transmetteur. Selon le besoin, poser des vannes d'étanchéité, des évents, des robinets de purge ou des systèmes d'étanchéité au niveau des conduites sous pression. Si l'instrument est placé de façon telle que les conduites sous pression du procédé adjacentes seront à l'horizontale, les conduites contenant des liquides doivent être inclinées vers le bas tandis que les conduites contenant des gaz doivent être inclinées vers le haut. Ceci minimisera le risque d'air piégé dans le capteur pour les conduites contenant des liquides ou de condensation piégée dans les conduites contenant des gaz. L'inclinaison recommandée est de 83 mm par mètre (1 in. par ft). Si un contrôleur est utilisé conjointement avec une vanne de régulation afin de contrôler la pression de la tuyauterie, raccorder la ligne de pression du procédé sur une section de tuyaux droite à une distance d'environ 10 diamètres de conduite de la vanne, mais à l'écart des courbes, des coudes et des vitesses anormales des fluides. Pour un service de réduction de la pression, la tuyauterie de procédé doit être raccordée en aval de la vanne. Pour un service de décharge de la pression, la tuyauterie de pression du procédé doit être raccordée en amont de la vanne de régulation. Installer une vanne à pointeau sur la tuyauterie de pression du procédé pour réduire les pulsations. 10 Manuel d'instructions D103292X0FR Contrôleurs et transmetteurs C1 Septembre 2019 Event AVERTISSEMENT Un incendie ou une explosion dues à l'accumulation de gaz pouvant entraîner des blessures ou des dommages matériels risque de se produire si un gaz dangereux est utilisé comme produit de pression d'alimentation. L'ensemble boîtier/couvercle de l'instrument n'est pas hermétique et, quand il est placé dans un lieu clos, une conduite d'évent déportée, une ventilation adéquate et les mesures de sécurité nécessaires doivent être appliquées pour éviter l'accumulation de gaz inflammables ou dangereux. Cependant, une tuyauterie à évent déporté ne peut suffire seule à l'évacuation de tous les gaz inflammables et dangereux. La tuyauterie à évent déporté doit être conforme aux codes locaux et régionaux et doit être aussi courte que possible avec un diamètre intérieur adéquat et peu de coudes afin de réduire l'accumulation de pression à l'intérieur du boîtier. ATTENTION Lors de l'installation d'une tuyauterie à évent déporté, veiller à ne pas serrer excessivement la tuyauterie dans le raccord de l'évent. Un serrage excessif endommagerait le filetage dans le raccord. L'évent (n_ 28, figure 2) ou l'extrémité déportée d'une conduite d'évent doit être protégé afin d'éviter la pénétration de matériau étrangers qui pourraient former une obstruction. En cas d'utilisation d'une tuyauterie à évent déporté, utiliser une tuyauterie de 13 mm (1/2 in.). Vérifier régulièrement l'évent pour s'assurer qu'il n'est pas obstrué. Fonctionnement du contrôleur Contrôleurs proportionnels uniquement Cette section décrit les réglages et les procédures nécessaires à l'étalonnage et à la mise en service. L'emplacement des boutons de réglage est indiqué dans la figure 4, sauf indication contraire. Tous les réglages doivent être effectués avec le couvercle de l'instrument ouvert. Une fois les procédures de réglage et d'étalonnage terminées, fermer le couvercle et le verrouiller. Pour mieux comprendre les réglages et le fonctionnement global du contrôleur, se reporter à la section Principe de fonctionnement pour les contrôleurs proportionnels de ce manuel. Se reporter également au schéma dans la figure 13. Réglages Réglage : Point de consigne Tourner le bouton dans le sens horaire pour augmenter le point de consigne et dans le sens antihoraire pour le diminuer. Noter que le réglage du cadran et la pression réelle du procédé peuvent varier de manière significative, en particulier en cas de réglage large de la bande proportionnelle. Réglage : Bande proportionnelle Pour régler la bande proportionnelle, tourner le bouton de réglage de la bande proportionnelle jusqu'à la valeur souhaitée. Le réglage de la bande proportionnelle détermine la quantité de changements de la pression régulée requise pour que la vanne de régulation atteigne sa course complète. Elle peut être réglée de 2 à 100 % pour 0,2 à 1,0 bar (3 à 15 psig) ou 4 à 100 % pour 0,4 à 2,0 bar (6 à 30 psig) de la pression nominale du capteur. 11 Manuel d'instructions Contrôleurs et transmetteurs C1 D103292X0FR Septembre 2019 Etalonnage : Contrôleurs proportionnels uniquement Sauf indication contraire, les emplacements des numéros sont indiqués dans la figure 4. Fournir une source de pression du procédé permettant de stimuler la plage de pression du procédé du contrôleur. Si aucun manomètre de sortie n'a été fourni, installer un manomètre approprié pour l'étalonnage. Figure 4. Emplacements des boutons de réglage des contrôleurs proportionnels uniquement BOUTON DE REGLAGE DE LA PRESSION (N_ 58) CADRAN DE REGLAGE DE LA PRESSION (N_ 6) BOUTON DE REGLAGE DE LA BANDE PROPORTIONNELLE REGLAGE DE L'ETALONNAGE (N_ 36) GE28280-B E1059 VIS DE REGLAGE DE L'ETALONNAGE (N_ 48) PALETTE (N_ 40) BUSE (N_ 54) Connecter une source de pression sur le régulateur de pression d'alimentation et s'assurer que ce dernier fournit la pression d'alimentation correcte au contrôleur. Le contrôleur doit être raccordé en boucle ouverte (boucle ouverte : les changements de pression de sortie du contrôleur doivent être dirigés vers un manomètre et neutralisés). Les procédures suivantes utilisent une plage de pression de sortie de 0,2 à 1,0 bar (3 à 15 psig) en guise d'exemple. Pour une plage de sortie de 0,4 à 2,0 bar (6 à 30 psig), adapter les valeurs de façon appropriée. 1. Terminer les raccordements et fournir une pression du procédé égale à la plage du capteur. 2. Tourner le bouton de réglage de la bande proportionnelle, indiqué dans la figure 4, sur 1,5 (15 % de la bande proportionnelle). 3. Vérifier que les vis d'étalonnage (n_ 48) sont en position de mi-course dans les fentes du dispositif de réglage (n_ 36). En fonction de l'action du contrôleur, suivre une des procédures suivantes. 12 Manuel d'instructions Contrôleurs et transmetteurs C1 D103292X0FR Septembre 2019 Pour les contrôleurs à action inverse : 4. Appliquer une pression d'entrée égale à la borne supérieure de la plage du capteur. 5. Tourner le bouton de réglage de la pression jusqu'à la valeur maximale. 6. Régler la buse (n_ 54) jusqu'à ce que la pression de sortie du contrôleur soit comprise entre 0,6 et 0,7 bar (8 et 10 psig). 7. Appliquer une pression d'entrée égale à la borne inférieure de la plage du capteur. 8. Tourner le bouton de réglage de la pression jusqu'à la valeur minimale. Remarque Lors du réglage de l'étendue à l'étape 9, ne pas tenir compte du manomètre de sortie lors du réglage de l'étalonnage. La variation de la sortie n'offre pas une bonne indication du changement de l'étendue. Lors du déplacement du dispositif de réglage de l'étalonnage, la pression de sortie peut varier dans la direction opposée à la direction attendue. Ainsi, lorsque le dispositif de réglage de l'étalonnage est déplacé afin d'augmenter l'étendue, la pression de sortie peut diminuer. Ignorer cette diminution car, bien que la pression de sortie baisse, l'étendue augmente. La réponse correcte du contrôleur dépend de l'alignement de la buse avec la palette. Lors des réglages de l'étendue, desserrer avec précaution les deux vis du dispositif de réglage de l'étalonnage tout en maintenant le dispositif. Ensuite, déplacer légèrement le dispositif dans la direction requise, à la main ou à l'aide d'un tournevis. Vérifier que la buse est correctement alignée avec la palette et maintenir le dispositif en place lors du serrage des deux vis. 9. Si la pression de sortie n'est pas comprise entre 0,6 et 0,7 bar (8 et 10 psig), régler l'étendue du contrôleur en desserrant les deux vis (n_ 48) et en déplaçant le dispositif de réglage de l'étalonnage (n_ 36) sur une courte distance comme indiqué dans la figure 5. 10. Répéter les étapes 4 à 9 jusqu'à ce que la valeur souhaitée soit atteinte. 11. Effectuer la procédure de mise en service pour les contrôleurs proportionnels. Figure 5. Réglage de l'étendue du contrôleur à action inverse - Contrôleurs proportionnels uniquement SI LA SORTIE EST : SUPERIEURE A 0,6 A 0,7 BAR (8 A 10 PSIG) INFERIEURE A 0,6 A 0,7 BAR (8 A 10 PSIG) DEPLACER LE DISPOSITIF DE REGLAGE VERS LA GAUCHE DEPLACER LE DISPOSITIF DE REGLAGE VERS LA DROITE PALETTE BUSE REMARQUE : SORTIE DE 0,2 A 1,0 BAR (3 A 15 PSIG) INDIQUEE. POUR UNE SORTIE COMPRISE ENTRE 0,4 ET 2,0 BAR (6 ET 30 PSIG), ADAPTER LES VALEURS DE FAÇON APPROPRIEE. A6155-1 13 Manuel d'instructions Contrôleurs et transmetteurs C1 D103292X0FR Septembre 2019 Pour les contrôleurs à action directe : 4. Appliquer une pression d'entrée égale à la borne inférieure de la plage du capteur. 5. Tourner le bouton de réglage de la pression jusqu'à la valeur minimale. 6. Régler la buse (n_ 54) jusqu'à ce que la pression de sortie du contrôleur soit comprise entre 0,6 et 0,7 bar (8 et 10 psig). 7. Appliquer une pression d'entrée égale à la borne supérieure de la plage du capteur. 8. Tourner le bouton de réglage de la pression jusqu'à la valeur maximale. Remarque Lors du réglage de l'étendue à l'étape 9, ne pas tenir compte du manomètre de sortie lors du réglage de l'étalonnage. La variation de la sortie n'offre pas une bonne indication du changement de l'étendue. Lors du déplacement du dispositif de réglage de l'étalonnage, la pression de sortie peut varier dans la direction opposée à la direction attendue. Ainsi, lorsque le dispositif de réglage de l'étalonnage est déplacé afin d'augmenter l'étendue, la pression de sortie peut diminuer. Ignorer cette diminution car, bien que la pression de sortie baisse, l'étendue augmente. La réponse correcte du contrôleur dépend de l'alignement de la buse avec la palette. Lors des réglages de l'étendue, desserrer avec précaution les deux vis du dispositif de réglage de l'étalonnage tout en maintenant le dispositif. Ensuite, déplacer légèrement le dispositif dans la direction requise, à la main ou à l'aide d'un tournevis. Vérifier que la buse est correctement alignée avec la palette et maintenir le dispositif en place lors du serrage des deux vis. 9. Si la pression de sortie n'est pas comprise entre 0,6 et 0,7 bar (8 et 10 psig), régler l'étendue du contrôleur en desserrant les deux vis (n_ 48) et en déplaçant le dispositif de réglage de l'étalonnage (n_ 36) sur une courte distance comme indiqué dans la figure 6. 10. Répéter les étapes 4 à 9 jusqu'à ce que la valeur souhaitée soit atteinte. 11. Effectuer la procédure de mise en service pour les contrôleurs proportionnels. Figure 6. Réglage de l'étendue du contrôleur à action directe - Contrôleurs proportionnels uniquement SI LA SORTIE EST : INFERIEURE A 0,6 A 0,7 BAR (8 A 10 PSIG) SUPERIEURE A 0,6 A 0,7 BAR (8 A 10 PSIG) DEPLACER LE DISPOSITIF DE REGLAGE VERS LA GAUCHE DEPLACER LE DISPOSITIF DE REGLAGE VERS LA DROITE PALETTE BUSE REMARQUE : SORTIE DE 0,2 A 1,0 BAR (3 A 15 PSIG) INDIQUEE. POUR UNE SORTIE COMPRISE ENTRE 0,4 ET 2,0 BAR (6 ET 30 PSIG), ADAPTER LES VALEURS DE FAÇON APPROPRIEE. A6154 14 Manuel d'instructions Contrôleurs et transmetteurs C1 D103292X0FR Septembre 2019 Mise en service : Contrôleurs proportionnels uniquement (Recommandations générales de réglage) Procéder à l'étalonnage du contrôleur avant cette procédure. 1. S'assurer que le régulateur de pression d'alimentation fournit la pression d'alimentation correcte au contrôleur. 2. Tourner le bouton de réglage de la pression jusqu'au point de consigne souhaité. 3. Régler la bande proportionnelle sur 100 % pour les procédés rapides (tels que les pressions ou les débits liquides). Pour les procédés lents (tels que la température), calculer le pourcentage à l'aide de l'équation ci-dessous : Pour les procédés lents, déterminer le réglage initial de la bande proportionnelle en pourcentage à l'aide de l'équation ci-dessous : 2 dépassement permis Etendue de pression 100 % + B.P. Par exemple : 2 ( 0, 14 bar 2, 1 bar 100 % ^ 13 % 2 100 % ^ 13 % 2 psig 30 psig ) Réglage de la bande proportionnelle à 1,3. 4. Action proportionnelle Dérégler le système en tapotant la palette ou en modifiant légèrement le point de consigne et vérifier si le système commence un nouveau cycle. Si ce n'est pas le cas, abaisser alors la bande proportionnelle (augmenter le gain), puis dérégler à nouveau le système. Continuer jusqu'à ce que le système reprenne son cycle. Doubler alors le réglage de la bande proportionnelle. Remarque Le réglage de la bande proportionnelle affecte le point de consigne. Les contrôleurs proportionnels uniquement indiqueront un décalage par rapport au point de consigne en fonction du réglage de la bande proportionnelle et de la demande du procédé. Après le réglage de la bande proportionnelle, remettre le système à zéro en tournant la buse (n_ 54) jusqu'à ce que la pression à régime stable du procédé soit égale à la lecture du cadran de paramètre de la pression. Cette procédure de réglage peut s'avérer trop prudente pour certains systèmes. Vérifier la stabilité du réglage de la bande proportionnelle recommandé en perturbant le système et en surveillant le procédé. Contrôleurs proportionnels plus réinitialisation Cette section décrit les réglages et les procédures nécessaires à l'étalonnage et à la mise en service. L'emplacement des boutons de réglage est indiqué dans la figure 7, sauf indication contraire. Tous les réglages doivent être effectués avec le couvercle de l'instrument ouvert. Une fois les procédures de réglage et d'étalonnage terminées, fermer le couvercle et le verrouiller. Pour mieux comprendre les réglages et le fonctionnement global du contrôleur, se reporter à la section Principe de fonctionnement pour les contrôleurs proportionnels plus réinitialisation de ce manuel. Se reporter également au schéma dans la figure 13. 15 Manuel d'instructions Contrôleurs et transmetteurs C1 D103292X0FR Septembre 2019 Figure 7. Emplacements des boutons de réglage des contrôleurs proportionnels plus réinitialisation BOUTON DE REGLAGE DE LA REINITIALISATION BOUTON DE REGLAGE DE LA PRESSION (N_ 58) CADRAN DE REGLAGE DE LA PRESSION (N_ 6) REGLAGE DE L'ETALONNAGE (N_ 36) GE28281-B E1060 VIS DE REGLAGE (N_ 48) PALETTE (N_ 40) BUSE (N_ 54) BOUTON DE REGLAGE DE LA BANDE PROPORTIONNELLE Réglages Réglage : Point de consigne Tourner le bouton dans le sens horaire pour augmenter le point de consigne et dans le sens antihoraire pour le diminuer. Tourner le bouton jusqu'à ce que l'indicateur pointe vers la valeur du point de consigne souhaité. Le cadran de réglage de la pression indiquera le point de consigne souhaité si le contrôleur est correctement étalonné. Réglage : Bande proportionnelle Pour régler la bande proportionnelle, tourner le bouton de réglage de la bande proportionnelle jusqu'à la valeur souhaitée. Le réglage de la bande proportionnelle détermine la quantité de changements de la pression régulée requise pour que la vanne de régulation atteigne sa course complète. Elle peut être réglée de 3 à 100 % pour 0,2 à 1,0 bar (3 à 15 psig) ou 6 à 100 % pour 0,4 à 2,0 bar (6 à 30 psig) de la pression nominale du capteur. Réglage : Réinitialisation Pour régler l'action de réinitialisation, tourner le bouton dans le sens horaire afin de diminuer le nombre de minutes par répétition. Tourner le bouton dans le sens antihoraire afin d'augmenter le nombre de minutes par répétition Le fait d'augmenter le nombre de minutes par répétition permet une action de réinitialisation plus lente. Le cadran de réglage de la réinitialisation est gradué en minutes par répétition. Par définition, il s'agit du temps en minute requis par l'action de réinitialisation pour produire un changement de sortie égal au changement produit par une action de régulation 16 Manuel d'instructions Contrôleurs et transmetteurs C1 D103292X0FR Septembre 2019 proportionnelle. Il s'agit en fait du temps en minutes requis au contrôleur pour augmenter (ou diminuer) sa pression de sortie par une quantité égale à l'augmentation (ou la diminution) proportionnelle provoquée par un changement du point de consigne ou de la pression du procédé. Réglage : Enroulement anti-réinitialisation La soupape de décharge différentielle montée à l'extérieur peut être installée pour dissiper une augmentation ou une diminution de la pression de sortie. Etalonnage Etalonnage : Contrôleurs proportionnels plus réinitialisation Sauf indication contraire, les emplacements des numéros sont indiqués dans la figure 7. Avant de commencer cette procédure : D Fournir une source de pression du procédé permettant de stimuler la plage de pression du procédé du contrôleur. D Si aucun manomètre de sortie n'a été fourni, installer un manomètre approprié pour l'étalonnage. Le contrôleur doit être raccordé en boucle ouverte (boucle ouverte : les changements de pression de sortie du contrôleur doivent être dirigés vers un manomètre et neutralisés). Remarque Les contrôleurs avec enroulement anti-réinitialisation C1P et C1B sont livrés avec deux joints toriques (n_ 81), un couvercle d'enroulement anti-réinitialisation (n_ 80) et deux vis mécaniques (n_ 82). Utiliser ces pièces à l'étape suivante. 1. Prendre note de la position de la flèche sur le dispositif à enroulement anti-réinitialisation (n_ 190 de la figure 23) pour les contrôleurs avec enroulement anti-réinitialisation C1P et C1B. Retirer le dispositif et poser les deux joints toriques (n_ 81) et le couvercle (n_ 80). Fixer le couvercle à l'aide des deux vis mécaniques (n_ 82) fournies. 2. Connecter la pression d'alimentation régulée sur le contrôleur. Ne pas dépasser la pression normale de fonctionnement indiquée dans le tableau 5. 3. Tourner le bouton de réinitialisation sur 0,01 minute par répétition (réglage le plus rapide). 4. Tourner le bouton de réglage de la bande proportionnelle sur 1,5 (15 % de la bande proportionnelle). 5. Vérifier que les vis d'étalonnage (n_ 48) sont en position de mi-course dans les fentes du dispositif de réglage (n_ 36). En fonction de l'action du contrôleur, suivre une des procédures suivantes. Pour les contrôleurs à action inverse : 6. Appliquer une pression d'entrée égale à la borne supérieure de la plage du capteur. 7. Tourner le bouton de réglage de la pression jusqu'à la valeur maximale. 8. Régler la buse (n_ 54) jusqu'à ce que la pression de sortie du contrôleur soit comprise entre 0,6 et 0,7 bar (8 et 10 psig). 9. Appliquer une pression d'entrée égale à la borne inférieure de la plage du capteur. 10. Tourner le bouton de réglage de la pression jusqu'à la valeur minimale. Remarque Lors du réglage de l'étendue à l'étape 11, ne pas tenir compte du manomètre de sortie lors du réglage de l'étalonnage. La variation de la sortie n'offre pas une bonne indication du changement de l'étendue. Lors du déplacement du dispositif de réglage de 17 Manuel d'instructions Contrôleurs et transmetteurs C1 D103292X0FR Septembre 2019 l'étalonnage, la pression de sortie peut varier dans la direction opposée à la direction attendue. Ainsi, lorsque le dispositif de réglage de l'étalonnage est déplacé afin d'augmenter l'étendue, la pression de sortie peut diminuer. Ignorer cette diminution car, bien que la pression de sortie baisse, l'étendue augmente. La réponse correcte du contrôleur dépend de l'alignement de la buse avec la palette. Lors des réglages de l'étendue, desserrer avec précaution les deux vis du dispositif de réglage de l'étalonnage tout en maintenant le dispositif. Ensuite, déplacer légèrement le dispositif dans la direction requise, à la main ou à l'aide d'un tournevis. Vérifier que la buse est correctement alignée avec la palette et maintenir le dispositif en place lors du serrage des deux vis. 11. Si la pression de sortie n'est pas comprise entre 0,6 et 0,7 bar (8 et 10 psig), régler l'étendue du contrôleur en desserrant les deux vis (n_ 48) et en déplaçant le dispositif de réglage de l'étalonnage (n_ 36) sur une courte distance comme indiqué dans la figure 8. 12. Répéter les étapes 6 à 11 jusqu'à ce que la valeur souhaitée soit atteinte. 13. Pour les contrôleurs avec enroulement anti-réinitialisation C1P et C1B, retirer les deux vis mécaniques, le couvercle d'enroulement anti-réinitialisation et les deux joints toriques mis en place à l'étape 1 de cette procédure. Installer le dispositif à enroulement anti-réinitialisation (n_ 190) avec la flèche pointant dans la direction notée à l'étape 1. 14. Effectuer la procédure de mise en service pour les contrôleurs proportionnels plus réinitialisation. Figure 8. Réglage de l'étendue du contrôleur à action inverse - Contrôleurs proportionnels plus réinitialisation SI LA SORTIE EST : SUPERIEURE A 0,6 A 0,7 BAR (8 A 10 PSIG) INFERIEURE A 0,6 A 0,7 BAR (8 A 10 PSIG) DEPLACER LE DISPOSITIF DE REGLAGE VERS LA GAUCHE DEPLACER LE DISPOSITIF DE REGLAGE VERS LA DROITE PALETTE BUSE REMARQUE : SORTIE DE 0,2 A 1,0 BAR (3 A 15 PSIG) INDIQUEE. POUR UNE SORTIE COMPRISE ENTRE 0,4 ET 2,0 BAR (6 ET 30 PSIG), ADAPTER LES VALEURS DE FAÇON APPROPRIEE. A6155-1 Pour les contrôleurs à action directe : 6. Appliquer une pression d'entrée égale à la borne inférieure de la plage du capteur. 7. Tourner le bouton de réglage de la pression jusqu'à la valeur minimale. 8. Régler la buse (n_ 54) jusqu'à ce que la pression de sortie du contrôleur soit comprise entre 0,6 et 0,7 bar (8 et 10 psig). 9. Appliquer une pression d'entrée égale à la borne supérieure de la plage du capteur. 10. Tourner le bouton de réglage de la pression jusqu'à la valeur maximale. Remarque Lors du réglage de l'étendue à l'étape 11, ne pas tenir compte du manomètre de sortie lors du réglage de l'étalonnage. La variation de la sortie n'offre pas une bonne indication du changement de l'étendue. Lors du déplacement du dispositif de réglage de 18 Manuel d'instructions Contrôleurs et transmetteurs C1 D103292X0FR Septembre 2019 l'étalonnage, la pression de sortie peut varier dans la direction opposée à la direction attendue. Ainsi, lorsque le dispositif de réglage de l'étalonnage est déplacé afin d'augmenter l'étendue, la pression de sortie peut diminuer. Ignorer cette diminution car, bien que la pression de sortie baisse, l'étendue augmente. La réponse correcte du contrôleur dépend de l'alignement de la buse avec la palette. Lors des réglages de l'étendue, desserrer avec précaution les deux vis du dispositif de réglage de l'étalonnage tout en tenant ce dernier en place. Ensuite, déplacer légèrement le dispositif dans la direction requise, à la main ou à l'aide d'un tournevis. Vérifier que la buse est correctement alignée avec la palette et maintenir le dispositif en place lors du serrage des deux vis. 11. Si la pression de sortie n'est pas comprise entre 0,6 et 0,7 bar (8 et 10 psig), régler l'étendue du contrôleur en desserrant les deux vis (n_ 48) et en déplaçant le dispositif de réglage de l'étalonnage (n_ 36) sur une courte distance comme indiqué dans la figure 9. 12. Répéter les étapes 6 à 11 jusqu'à ce que la valeur souhaitée soit atteinte. 13. Pour les contrôleurs avec enroulement anti-réinitialisation C1P et C1B, retirer les deux vis mécaniques, le couvercle d'enroulement anti-réinitialisation et les deux joints toriques mis en place à l'étape 1 de cette procédure. Installer le dispositif à enroulement anti-réinitialisation (n_ 190) avec la flèche pointant dans la direction notée à l'étape 1. 14. Effectuer la procédure de mise en service pour les contrôleurs proportionnels plus réinitialisation. Figure 9. Réglage de l'étendue du contrôleur à action directe - Contrôleurs proportionnels plus réinitialisation SI LA SORTIE EST : INFERIEURE A 0,6 A 0,7 BAR (8 A 10 PSIG) SUPERIEURE A 0,6 A 0,7 BAR (8 A 10 PSIG) DEPLACER LE DISPOSITIF DE REGLAGE VERS LA GAUCHE DEPLACER LE DISPOSITIF DE REGLAGE VERS LA DROITE PALETTE BUSE REMARQUE : SORTIE DE 0,2 A 1,0 BAR (3 A 15 PSIG) INDIQUEE. POUR UNE SORTIE COMPRISE ENTRE 0,4 ET 2,0 BAR (6 ET 30 PSIG), ADAPTER LES VALEURS DE FAÇON APPROPRIEE. A6154 Etalonnage : Enroulement anti-réinitialisation Les contrôleurs dotés d'un enroulement anti-réinitialisation sont équipés d'une soupape de décharge différentielle (figure 23). Cette soupape de décharge est réglée en usine pour dissiper la différence de pression à 0,3 bar (5 psi) entre la pression de réinitialisation du soufflet et la pression proportionnelle du soufflet. Il est possible de régler la soupape pour lui permettre de dissiper la pression entre 0,14 et 0,4 bar (2 et 7 psig). La soupape de décharge peut dissiper la pression de sortie du contrôleur montante ou la pression de sortie du contrôleur descendante. Si la flèche de la soupape de décharge pointe vers le bas du boîtier du contrôleur comme indiqué dans la figure 23, la soupape dissipera une pression de sortie descendante Si la flèche pointe dans la direction opposée, elle dissipera une pression de sortie montante. La soupape peut être retirée et réinstallée avec la flèche pointant dans la direction opposée afin de changer l'action de décharge. 19 Contrôleurs et transmetteurs C1 Manuel d'instructions D103292X0FR Septembre 2019 Mise en service : Contrôleurs proportionnels plus réinitialisation (recommandations générales de réglage) Procéder à l'étalonnage du contrôleur avant cette procédure. 1. S'assurer que le régulateur de pression d'alimentation fournit la pression d'alimentation correcte au contrôleur. 2. Tourner le bouton de réglage de la pression jusqu'au point de consigne souhaité.. 3. Commencer par un réglage de réinitialisation de 0,05 minute par répétition (m/r) pour les procédés rapides, et de 0,5 m/r pour les procédés lents. 4. Régler la bande proportionnelle sur 100 % pour les procédés rapides (par exemple : pour les pressions ou les débits liquides). Pour un procédé lent (tel que la température), calculer le pourcentage à l'aide de l'équation ci-dessous : Pour les procédés lents, déterminer le réglage initial de la bande proportionnelle en pourcentage à l'aide de l'équation ci-dessous : 2 dépassement permis Etendue de pression 100 % + B.P. Par exemple : 2 ( 0, 14 bar 2, 1 bar 100 % ^ 13 % 2 100 % ^ 13 % 2 psig 30 psig ) Réglage de la bande proportionnelle à 1,3. 5. Action proportionnelle : Dérégler le système en tapotant la palette ou en modifiant légèrement le point de consigne et vérifier si le système commence un nouveau cycle. Si ce n'est pas le cas, abaisser alors la bande proportionnelle (augmenter le gain), puis dérégler à nouveau le système. Continuer jusqu'à ce que le système reprenne son cycle. A ce point, doubler le réglage de la bande proportionnelle et commencer le réglage de la réinitialisation. 6. Action de réinitialisation : Dérégler le système. Si le système ne commence pas un nouveau cycle, accélérer la réinitialisation et dérégler une nouvelle fois le système. Continuer jusqu'à ce que le système reprenne son cycle. Lorsque le système commence un nouveau cycle, multiplier la durée de réinitialisation par un facteur de trois (3) puis ralentir la réinitialisation jusqu'à la nouvelle valeur. La réinitialisation est à présent réglée. Cette procédure de réglage peut s'avérer trop prudente pour certains systèmes. Vérifier la stabilité du réglage de la bande proportionnelle et le réglage de la réinitialisation recommandés en perturbant le système et en surveillant le procédé de la façon précédemment décrite. Un contrôle plus strict peut s'avérer souhaitable pour certaines applications. Contrôleurs d'écart différentiel Cette section décrit les réglages et les procédures nécessaire à l'étalonnage et à la mise en service. L'emplacement des boutons de réglage est indiqué dans la figure 4, sauf indication contraire. La sortie de chaque contrôleur est vérifiée en usine avant l'expédition. Pour convertir un contrôleur d'écart différentiel en un contrôleur proportionnel uniquement, ou vice versa, se reporter à la procédure appropriée de la section Maintenance. Si la pression du procédé peut varier au niveau de la plage du capteur (entière ou non) ou au niveau des deux points de commutation souhaités, utiliser la pression du procédé pour l'étalonnage. Dans le cas contraire, fournir une source d'alimentation pour simuler la plage de pression du procédé pour les procédures d'étalonnage. 20 Manuel d'instructions Contrôleurs et transmetteurs C1 D103292X0FR Septembre 2019 Pour mieux comprendre les réglages et le fonctionnement global du contrôleur, se reporter à la section Principe de fonctionnement pour les contrôleurs d'écart différentiel de ce manuel, ainsi qu'aux schémas de la figure 13. Réglages Réglage : Point de consigne L'emplacement du bouton de réglage de la pression détermine l'emplacement de l'écart différentiel au niveau la plage du capteur de pression. Déplacer l'aiguille indicatrice vers la position souhaitée au niveau de laquelle la sortie du contrôleur devrait passer de zéro à la pression d'alimentation totale avec la pression du procédé montante (contrôleurs à action directe) ou avec la pression du procédé descendante (contrôleurs à action inverse). Réglage : Bande proportionnelle Le réglage de la bande proportionnelle indiqué dans la figure 4 détermine la taille de l'écart différentiel. La taille de l'écart différentiel est la différence entre les pressions de procédé au niveau de laquelle la sortie du contrôleur passera de zéro à la pression d'alimentation totale, ou de la pression d'alimentation totale à zéro. La relation entre le réglage du cadran de la bande proportionnelle et la bande proportionnelle est indiquée dans la figure 10. REGLAGE DU BOUTON DE BANDE PROPORTIONNELLE Figure 10. Réglage de l'écart différentiel pour les contrôleurs d'écart différentiel A2202-3 ECART DIFFERENTIEL (% DE LA PLAGE DE L'ELEMENT) Etalonnage : Contrôleurs d'écart différentiel La sortie de chaque contrôleur est vérifiée en usine avant l'expédition de l'unité. Avant de placer le contrôleur à la régulation d'une boucle de procédé, vérifier qu'il est correctement étalonné pour l'application. Le contrôleur doit être raccordé en boucle ouverte (boucle ouverte : les changements de pression de sortie du contrôleur doivent être dirigés vers un manomètre et neutralisés). 1. Convertir de façon temporaire le contrôleur d'écart différentiel en un contrôleur proportionnel uniquement en déconnectant le tube proportionnel (n_ 25, figure 16) de la base de montage. Connecter le tube à l'autre raccord de la base. Retirer l'ensemble de la bande proportionnelle et l'inverser comme indiqué dans la figure 16. Ne pas inverser le bloc d'inversion (n_ 37, figure 16). 2. Inverser de façon temporaire l'ensemble de la bande proportionnelle (voir la figure 17) : a. Placer l'ensemble de la bande proportionnelle (n_ 73) sur 10. b. Dévisser le tendeur du ressort (n_ 65) et retirer le ressort de justesse (n_ 70) et les rondelles (n_ 62). 21 Manuel d'instructions Contrôleurs et transmetteurs C1 D103292X0FR Septembre 2019 c. Détacher le ressort de verrouillage (n_ 72). Retirer l'échelle de l'indicateur (n_ 69) et le bouton de réglage de la bande proportionnelle (n_ 73). d. Retirer la barre de réglage du gain (n_ 63). La retourner de façon à la fixer du côté opposé au ressort en porte-à-faux (n_ 8), comme indiqué dans la figure 16 et la visser. e. Retourner l'échelle de l'indicateur (n_ 69) ; l'assembler au bouton de réglage de la bande proportionnelle (n_ 73). Enfoncer le ressort de verrouillage (n_ 72) jusqu'à ce qu'un déclic se fasse entendre. f. Serrer le tendeur du ressort (n_ 65) avec le ressort de justesse (n_ 70) et les rondelles (n_ 62) jusqu'à ce qu'il butte contre la barre de réglage du gain (n_ 63). g. Tourner le bouton de réglage de la bande proportionnelle sur 10. S'il est impossible de le tourner jusqu'à 10, desserrer le tendeur du ressort (n_ 65). 3. Procéder à l'étalonnage pour les contrôleurs proportionnels uniquement comme indiqué à la page 12 de ce manuel. 4. Une fois l'étalonnage terminé, réinstaller le tube (n_ 25) et l'ensemble de la bande proportionnelle à leurs emplacements d'origine et passer à l'étape 5 de cette procédure. Remarque Une fois le tube (n_ 25) et l'ensemble de la bande proportionnelle remis en place, on remarque un léger décalage de la pression de sortie en raison du passage du soufflet proportionnel au soufflet de réinitialisation et au repositionnement du ressort en porte-à-faux. Procéder à l'étape 6b ci-dessous pour corriger ce décalage. 5. Voir la figure 10 pour déterminer le réglage du cadran de la bande proportionnelle requis pour l'écart différentiel souhaité. Par exemple, on assume qu'un capteur de 0 à 100 psig est utilisé et que le contrôleur doit passer de zéro à une pression d'alimentation totale à 80 psig avec une pression du procédé montante et d'une pression d'alimentation totale à zéro à 20 psig avec une pression du procédé descendante. (Il s'agit d'un contrôleur à action directe.) L'écart différentiel est : 5, 5 bar * 1, 3 bar 6, 9 bar ( 80 psig * 20 psig 100 psig 100 % + 60 % 100 % + 60 % ) Selon la 10, le réglage du cadran de la bande proportionnelle devrait être environ 4,5 ; tourner le bouton de réglage pour atteindre cette valeur. 6. Réglage de la pression du procédé Pour un contrôleur à action directe : a. Tourner le bouton de réglage de la pression afin d'atteindre la pression à laquelle la sortie du contrôleur passe au point de commutation supérieur (de zéro à la pression d'alimentation totale) avec la pression du procédé montante. Dans l'exemple ci-dessus, cette pression est établie à 5,5 bar (80 psig). b. Augmenter la pression vers le capteur tout en surveillant le manomètre de sortie. Avec une pression d'entrée montante, la pression de sortie du contrôleur doit passer de zéro à la pression d'alimentation totale lorsque le point de commutation supérieur est atteint. Remarque Si le point de commutation supérieur est incorrect, régler la buse afin de corriger l'erreur. Répéter l'étape 6b jusqu'à ce que la pression d'entrée et le point de commutation supérieur souhaités soient atteints. 22 Manuel d'instructions Contrôleurs et transmetteurs C1 D103292X0FR Septembre 2019 c. Avec une pression d'entrée descendante, la pression de sortie du contrôleur doit passer de la pression d'alimentation totale à zéro lorsque le point de commutation inférieur est atteint. Les contrôleurs à action inverse produisent une réponse inverse. 7. Modifier la pression du procédé et observer les points de commutation. Augmenter ou diminuer l'écart différentiel en tournant le bouton de réglage de la bande proportionnelle, puis répéter les étapes ci-dessus. Si la pression de sortie est comprise entre les limites mentionnées, se reporter aux procédures de mise en service de cette section. Si la pression de sortie ne peut être réglée entre ces limites, se reporter aux procédures de maintenance. Mise en service : Contrôleurs d'écart différentiel Procéder à l'étalonnage du contrôleur avant cette procédure. 1. S'assurer que le régulateur de pression d'alimentation fournit la pression d'alimentation correcte au contrôleur. 2. Régler la bande proportionnelle afin d'obtenir un écart différentiel correct (voir la figure 10). 3. Si le contrôleur est utilisé conjointement avec une vanne de régulation, ouvrir lentement les vannes d'étanchéité manuelles en amont et en aval et fermer les vannes de dérivation. 4. Pour modifier l'écart différentiel, effectuer les étapes 1 à 5 de la procédure d'étalonnage pour les contrôleurs d'écart différentiel. Fonctionnement du transmetteur Cette section décrit les réglages et les procédures nécessaire à l'étalonnage et à la mise en service. Voir la figure 11 pour l'emplacement des réglages. Tous les réglages doivent être effectués avec le couvercle de l'instrument ouvert. Une fois les procédures de réglage et d'étalonnage terminées, fermer le couvercle et le verrouiller. Pour mieux comprendre les réglages et le fonctionnement global du transmetteur, se reporter à la section Principe de fonctionnement pour les transmetteurs de ce manuel. Se reporter également au schéma dans la figure 13. Réglages Réglage : Zéro Le cadran de réglage de la pression indique ZERO ADJUSTMENT PRESSURE SETTING (réglage du zéro réglage de la pression). Le zéro est situé au centre du cadran et les valeurs de la pression augmentent sur la droite et la gauche du centre comme indiqué dans la figure 11. Pour régler le zéro, tourner aiguille indicatrice sur le cadran de réglage de la pression. En fonction de l'action du transmetteur ou du réglage souhaité, tourner l'aiguille indicatrice dans le sens horaire pour augmenter la pression de sortie ou dans le sens antihoraire pour la diminuer. Pour les transmetteurs à action directe, le réglage du zéro détermine la pression du procédé pour le point auquel le signal de sortie du transmetteur atteindra la limite inférieure de la plage. Les graduations du cadran (n_ 6) offrent des indications approximatives du réglage du zéro du transmetteur. Ne pas se baser uniquement sur le cadran pour procéder aux réglages. Contrôler la pression du procédé et la pression de sortie pour s'assurer que les réglages souhaités sont atteints. 23 Manuel d'instructions Contrôleurs et transmetteurs C1 D103292X0FR Septembre 2019 Figure 11. Emplacements de réglage du transmetteur BOUTON DE REGLAGE DU ZERO (N_ 58) CADRAN DE REGLAGE DE LA PRESSION (N_ 6) VIS DU DISPOSITIF DE REGLAGE DE L'ETALONNAGE (N_ 48) GE34729-B E1061 PALETTE (N_ 40) BOUTON DE REGLAGE DE L'ÉTENDUE BUSE (N_ 54) DISPOSITIF DE REGLAGE DE L'ETALONNAGE (N_ 36) Réglage : Etendue L'étendue est graduée de 0 à 10. Un réglage sur 10 représente une étendue de 100 % de la plage du capteur du procédé. Le transmetteur atteint une précision optimale lorsque l'étendue est de 100 %. Le réglage de l'étendue du transmetteur indiqué dans la figure 11 est le même que le réglage de la bande proportionnelle du contrôleur. Etalonnage : Transmetteurs La sortie de chaque transmetteur est vérifiée en usine avant l'expédition de l'unité. Le transmetteur fournit un signal de sortie proportionnel à la pression appliquée au capteur. La pression de sortie n'a pas d'incidence directe sur la pression du procédé. Le transmetteur est étalonné en usine et ne requiert pas de réglage supplémentaire. Utiliser les procédures d'étalonnage suivantes après le remplacement du capteur ou toute autre procédure de maintenance pouvant altérer l'étalonnage du transmetteur. Les procédures suivantes utilisent une plage de pression de sortie de 0,2 à 1,0 bar (3 à 15 psig) en guise d'exemple. Pour les autres plages de pression de sortie [telles que 0,4 à 2,0 bar (6 à 30 psig)], adapter les valeurs à l'application. 24 Manuel d'instructions Contrôleurs et transmetteurs C1 D103292X0FR Septembre 2019 Fournir une source de pression du procédé permettant de stimuler la plage de pression du procédé du transmetteur. Si aucun manomètre de sortie n'a été fourni, installer un manomètre approprié pour l'étalonnage. Connecter une source de pression sur le régulateur de pression d'alimentation et s'assurer que ce dernier fournit la pression d'alimentation correcte au transmetteur. Remarque Pour plus de stabilité, certaines applications du transmetteur requièrent des volumes supplémentaires à celui du manomètre. Fournir un volume minimum d'environ 25 cm3 (1.5 in.3) ou plus si la stabilité pose un problème. Sauf indication contraire, les emplacements des numéros sont indiqués dans la figure 11. 1. Terminer les raccordements et fournir une pression du procédé égale à la plage du capteur. 2. Tourner le bouton de réglage de l'étendue jusqu'au maximum (100 % sur le cadran). 3. Vérifier que les vis du dispositif de d'étalonnage (n_ 48) sont en position de mi-course dans les fentes du dispositif (n_ 36). En fonction de l'action du transmetteur, appliquer l'une des procédures suivantes. Pour les transmetteurs à action inverse : 4. Tourner le bouton de réglage du zéro sur zéro. 5. Appliquer une pression d'entrée égale à la valeur de la limite supérieure de la plage du capteur. 6. Régler la buse (n_ 57) jusqu'à ce que la pression de sortie du transmetteur atteigne 0,2 bar (3 psig). 7. Régler la pression d'entrée sur zéro. Remarque La réponse correcte du transmetteur dépend de l'alignement de la buse avec la palette. Lors des réglages de l'étendue à l'étape 8, desserrer avec précaution les deux vis du dispositif de réglage de l'étalonnage tout en tenant ce dernier en place. Ensuite, déplacer légèrement le dispositif dans la direction requise, à la main ou à l'aide d'un tournevis. Vérifier que la buse est correctement alignée avec la palette et maintenir le dispositif en place lors du serrage des deux vis. 8. Si la pression de sortie n'est pas égale à 15 psig, régler l'étendue en desserrant les deux vis (n_ 48) et en déplaçant le dispositif de réglage de l'étalonnage (n_ 36) sur une courte distance comme indiqué dans la figure 12. 9. Répéter les étapes 4 à 8 jusqu'à ce que la valeur souhaitée soit atteinte. 10. Effectuer la procédure de mise en service pour les transmetteurs. 25 Manuel d'instructions Contrôleurs et transmetteurs C1 D103292X0FR Septembre 2019 Figure 12. Réglage de l'étendue du transmetteur SI LA SORTIE EST : INFERIEURE A 1,0 BAR (15 PSIG) DEPLACER LE DISPOSITIF VERS LA GAUCHE SUPERIEURE A 1,0 BAR (15 PSIG) DEPLACER LE DISPOSITIF VERS LA DROITE REMARQUE : SORTIE DE 0,2 A 1,0 BAR (3 A 15 PSIG) INDIQUEE. POUR UNE SORTIE COMPRISE ENTRE 0,4 ET 2,0 BAR (6 ET 30 PSIG), ADAPTER LES VALEURS DE FAÇON APPROPRIEE. A6156 Pour les transmetteurs à action directe : 4. Tourner le bouton de réglage du zéro sur zéro. 5. Régler la pression d'entrée sur zéro. 6. Régler la buse (n_ 54) jusqu'à ce que la pression de sortie du transmetteur atteigne 0,2 bar (3 psig). 7. Appliquer une pression d'entrée égale à la borne supérieure de la plage du capteur. Remarque La réponse correcte du transmetteur dépend de l'alignement de la buse avec la palette. Lors des réglages de l'étendue à l'étape 8, desserrer avec précaution les deux vis du dispositif de réglage de l'étalonnage tout en tenant ce dernier en place. Ensuite, déplacer légèrement le dispositif dans la direction requise, à la main ou à l'aide d'un tournevis. Vérifier que la buse est correctement alignée avec la palette et maintenir le dispositif en place lors du serrage des deux vis. 8. Si la pression de sortie n'est pas égale à 15 psig, régler l'étendue en desserrant les deux vis (n_ 48) et en déplaçant le dispositif de réglage de l'étalonnage (n_ 36) sur une courte distance comme indiqué dans la figure 12. 9. Répéter les étapes 4 à 8 jusqu'à ce que la valeur souhaitée soit atteinte. 10. Effectuer la procédure de mise en service pour les transmetteurs. Mise en service : Transmetteurs 1. S'assurer que le régulateur de pression d'alimentation fournit la pression d'alimentation correcte au transmetteur. 2. Se reporter aux procédures d'étalonnage pour les réglages initiaux du transmetteur. 3. Si le transmetteur est utilisé conjointement avec une vanne de régulation, ouvrir lentement les vannes d'étanchéité manuelles en amont et en aval et fermer les vannes de dérivation. 26 Manuel d'instructions Contrôleurs et transmetteurs C1 D103292X0FR Septembre 2019 Principe de fonctionnement Les sections suivantes décrivent le fonctionnement d'un contrôleur ou d'un transmetteur doté d'un capteur à tube de Bourdon. Le fonctionnement est identique à celui d'un instrument utilisant un capteur à soufflet (n_ 71, figure 25), à l'exception que le mouvement du faisceau est formé par l'expansion et la contraction du soufflet ou du soufflet différentiel. Contrôleurs proportionnels uniquement Comme indiqué dans la figure 13, la pression d'alimentation entre dans le relais et passe par l'orifice fixe avant de s'échapper par la buse. La pression de la buse est également enregistrée sur la grande membrane du relais et la pression de pilotage (pression de sortie du contrôleur) est enregistrée sur la petite membrane du relais. Figure 13. Schéma des contrôleurs proportionnels uniquement à action inverse et proportionnels plus réinitialisation PRESSION D'ALIMENTATION CONSTANTE EXTREMITE D'ENTREE DE LA VANNE DE RELAIS PETITE MEMBRANE GRANDE MEMBRANE RESTRICTION EVACUATION BOUTON DE REGLAGE DE LA PRESSION CADRAN DE REGLAGE DE LA PRESSION EXTREMITE D'EVACUATION DU RELAIS SOUFFLET DE REINITIALISATION BOUTON DE REGLAGE DE LA BANDE PROPORTIONNELLE SOUFFLET DE REINITIALISATION TUBE DE BOURDON BUSE PIVOT FIXE VERS L'ELEMENT DE REGLAGE FINAL EVENT FAISCEAU ET PALETTE SOUFFLET PROPORTIONNEL RESSORT EN PORTE-A-FAUX SOUFFLET PROPORTIONNEL VANNE DE REINITIALISATION PRESSION MESUREE CONTROLEUR PROPORTIONNEL PLUS REINITIALISATION CONTROLEUR PROPORTIONNEL UNIQUEMENT PRESSION MESUR PRESSION DE SORTIE PRESSION DE LA BUSE PRESSION DE REINITIALISATION GE23696 GE34724-A E1062 Un changement de la pression du procédé provoque le déplacement du faisceau et de la palette par rapport à la buse en déployant ou contractant l'arc du tube de Bourdon. Une pression montante du procédé avec action directe (ou une pression descendante avec action inverse) produit une restriction au niveau de la buse et de la palette qui augmente la pression sur la grande membrane du relais et ouvre la vanne du relais. La pression d'alimentation additionnelle s'écoule par la chambre du relais pour augmenter la pression de chargement sur l'actionneur de la vanne de régulation. Une pression du procédé descendante avec action directe (ou une pression montante avec action inverse) produit une ouverture au niveau de la buse et de la palette qui laisse s'échapper la pression sur la grande membrane du relais et ouvre la vanne du relais pour laisser s'échapper la pression de sortie du contrôleur de l'actionneur. 27 Contrôleurs et transmetteurs C1 Septembre 2019 Manuel d'instructions D103292X0FR Ce changement de la pression de sortie du contrôleur se répercute sur le soufflet proportionnel, neutralisant le changement de pression dans la buse et égalisant le différentiel de pression de la membrane du relais. La vanne du relais maintient une nouvelle pression de charge en fonction du changement de la pression mesurée. Si le réglage de la bande proportionnelle est au maximum (10), le facteur de rappel du ressort en porte-à-faux situé dans l'ensemble de la bande proportionnelle est faible, ce qui permet un transfert de retour de mouvement supérieur en provenance du soufflet proportionnel afin de changer la pression de sortie. La longueur effective du porte-à-faux étant réduite, le facteur de rappel du ressort augmente, diminuant ainsi le retour de mouvement du soufflet proportionnel. Le réglage du ressort en porte-à-faux à sa longueur maximale résulte en une bande proportionnelle de 100 %. Plus le réglage de la bande proportionnelle est faible, plus la longueur effective du ressort en porte-à-faux est courte. Le facteur de rappel du ressort augmente tandis que sa longueur diminue, ce qui a pour effet de transférer moins de mouvement du soufflet vers le faisceau et la palette pour un changement déterminé de la pression de sortie. Contrôleurs proportionnels plus réinitialisation L'action d'un contrôleur proportionnel plus réinitialisation est similaire à celle d'un contrôleur proportionnel uniquement, à l'exception que le retour de la pression de sortie du contrôleur est connecté à un soufflet de réinitialisation ainsi qu'au soufflet proportionnel comme indiqué sur la droite de la figure 13. La pression du soufflet de réinitialisation augmente tandis que la pression de sortie du contrôleur augmente. L'augmentation de la pression au niveau du soufflet de réinitialisation entraîne le rapprochement du faisceau et de la palette de la buse, ce qui a pour effet une nouvelle augmentation de la pression dans le système. La montée en pression continue jusqu'à ce que la pression régulée soit ramenée au point de consigne. La vanne de réinitialisation peut être réglée pour permettre de varier le délai de la réinitialisation. La fermeture de la vanne de réinitialisation augmente le délai de la réinitialisation. Contrôleurs avec enroulement anti-réinitialisation Lors d'une différence prolongée entre le point de consigne et la variable contrôlée, lors de l'utilisation d'applications de contrôle intermittent (par exemple pour le contrôle de température en lot ou de moniteurs entièrement ouverts pour le contrôle de pression), la réinitialisation place la sortie du contrôleur soit sur zéro, soit sur la pression d'alimentation maximale ; il s'agit de l'enroulement de réinitialisation. Lorsque la variable contrôlée franchit le point de consigne, il existe un délai avant que la sortie du contrôleur ne réponde au changement de la variable contrôlée. L'enroulement de réinitialisation minimise ce délai et permet de rétablir la variable contrôlée au point de consigne plus rapidement et avec un dépassement du point de consigne réduit. Comme indiqué dans la figure 14, un contrôleur proportionnel plus réinitialisation avec enroulement anti-réinitialisation inclut une soupape de décharge différentielle. La soupape est constituée de deux chambres de pression séparées par une membrane à ressort. Pour le contrôleur indiqué dans la figure 14, la pression proportionnelle est rapidement enregistrée sur le côté du ressort de la membrane de la soupape de décharge ainsi que dans le soufflet proportionnel ; la pression de réinitialisation est enregistrée sur le côté opposé à la membrane de la soupape de décharge. Tant que les changements de pression régulée ne sont pas trop rapides pour l'action de réinitialisation et proportionnelle normale, le ressort de la soupape de décharge empêche l'ouverture de la membrane. Cependant, si la pression régulée baisse de façon importante ou rapide, le relais dissipe rapidement de la pression de pilotage au niveau du dispositif de contrôle ainsi qu'au niveau de système proportionnel et du côté du ressort de la membrane de la soupape de décharge. Si cette baisse du côté du ressort de la membrane est supérieure au réglage du ressort de la soupape de décharge, la membrane libère l'orifice de la soupape et permet ainsi à la pression proportionnelle du côté opposé à la membrane de la soupape de se dissiper rapidement dans le soufflet de réinitialisation. Cette action d'enroulement anti-réinitialisation peut également être inversée pour dissiper une pression proportionnelle montante. Contrôleurs d'écart différentiel Avec un contrôleur d'écart différentiel, la pression de contre-réaction ne contrebalance pas le changement de position de la palette comme elle le ferait pour un contrôleur proportionnel uniquement. Par contre, la pression contre-réaction est envoyée vers le soufflet situé sur le côté du faisceau et de la palette opposés à la buse (soufflet proportionnel illustré dans la figure 13). Ensuite, alors que la pression de sortie du contrôleur augmente, la pression de contre-réaction rapproche la palette de la buse afin de continuer à augmenter la pression de sortie du contrôleur. Ce processus se poursuit rapidement jusqu'à ce que la pression de sortie du contrôleur atteigne la limite supérieure de la plage. L'action d'un contrôleur d'écart différentiel est si rapide que la pression de 28 Manuel d'instructions Contrôleurs et transmetteurs C1 D103292X0FR Septembre 2019 sortie passe de zéro au maximum dès que le point de commutation est atteint. Cette action est similaire pour une pression de sortie descendante. Une pression de contre-réaction plus basse réduit la pression du soufflet, ce qui éloigne la palette de la buse. Ceci réduit encore la pression de sortie et ce mécanisme continue jusqu'à ce que la pression de sortie atteigne zéro. Figure 14. Schéma du contrôleur proportionnel plus réinitialisation à action inverse avec enroulement anti-réinitialisation FLECHE VERS LE HAUT - DISSIPE LA PRESSION MONTANTE (SORTIE A ZERO PENDANT L'ARRET) FLECHE VERS LE BAS - DISSIPE LA PRESSION DESCENDANTE (SORTIE A PRESSION D'ALIMENTATION PENDANT L'ARRET) PRESSION D'ALIMENTATION CONSTANTE SOUPAPE DE DECHARGE DIFFERENTIELLE RESTRICTION EVACUATION BOUTON DE REGLAGE DE LA PRESSION CADRAN DE REGLAGE DE LA PRESSION SOUFFLET DE REINITIALISATION BOUTON DE REGLAGE DE LA BANDE PROPORTIONNELLE VERS L'ELEMENT DE REGLAGE FINAL RESSORT EN PORTE-A-FAUX SOUFFLET PROPORTIONNEL VANNE DE REINITIALISATION PRESSION MESUREE PRESSION MESUREE PRESSION DE SORTIE PRESSION DE LA BUSE PRESSION DE REINITIALISATION GE23697-A GE34724-A E1063 Transmetteurs L'action d'un transmetteur pneumatique est similaire à celle d'un contrôleur proportionnel uniquement. La pression de sortie n'ayant pas d'incidence sur la pression du procédé, la pression de sortie du transmetteur est une mesure proportionnelle de la pression du procédé. Le réglage de la bande proportionnelle détermine l'étendue du transmetteur et le mécanisme de réglage de la pression détermine le zéro du transmetteur. 29 Contrôleurs et transmetteurs C1 Septembre 2019 Manuel d'instructions D103292X0FR Maintenance Si l'installation comporte un filtre détendeur 67 de Fisher, ouvrir régulièrement l'orifice de drainage du détendeur pour évacuer toute accumulation d'humidité. Passer également le fil métallique de nettoyage à ressort dans l'orifice du relais. Vérifier l'ouverture de l'évent (n_ 28, figure 2) ou l'ouverture de tuyauterie de l'évent déporté (le cas échéant). Si nécessaire, nettoyer les ouvertures. Les pièces sont sujettes à une usure normale et doivent être inspectées et remplacées, si nécessaire. La fréquence des inspections et des remplacements des pièces dépend des conditions d'utilisation. AVERTISSEMENT Il est nécessaire de mettre le contrôleur hors service afin d'effectuer les procédures de maintenance suivantes. Observer les consignes suivantes pour éviter les blessures et les dommages matériels provoqués par le relâchement de pression ou de fluide de procédé. D Toujours porter des vêtements, des gants et des lunettes de protection. D Prévoir un mode de régulation temporaire du procédé avant de mettre le contrôleur hors service. D Prévoir un moyen de contenir le fluide de procédé avant de retirer tout dispositif de mesure du procédé. D Utiliser une procédure de verrouillage pour être certain que les mesures précédentes restent effectives lors de l'intervention sur l'équipement. D Des blessures ou des dommages matériels peuvent résulter d'un incendie ou d'une explosion si du gaz naturel est utilisé comme produit d'alimentation et que les mesures de prévention appropriées ne sont pas prises. Les mesures préventives nécessaires peuvent comprendre, notamment, un des éléments suivants : mise à l'évent déportée de l'unité, réévaluation de la classification des zones dangereuses, assurance d'une ventilation adéquate et élimination de toute source d'inflammation Pour tout renseignement sur la mise à l'évent déportée de ce contrôleur/transmetteur, se reporter à la page 11. D Consulter l'ingénieur des procédés ou l'ingénieur responsable de la sécurité pour connaître les éventuelles mesures supplémentaires à prendre pour se protéger contre l'exposition au fluide de procédé. Remplacement des manomètres Sauf indication contraire, voir les figures 22 et 23 pour l'emplacement des éléments numérotés. Trois configurations du manomètre sont disponibles pour les unités C1. D Indications de la pression d'alimentation et de sortie D Indications de la pression du procédé et de sortie D Indications de la pression d'alimentation, du procédé et de sortie Un type de manomètre (n_ 2) est utilisé pour les indications de la pression d'alimentation et de sortie lorsque les manomètres sont utilisés dans le boîtier du contrôleur. L'élément n_ 2 est doté d'une tige de raccordement de 1/8 in. adaptée au bossage fileté du manomètre dépassant de la base du relais. Dans certains cas, un manomètre de procédé (n_ 4) couvre la position du manomètre d'alimentation interne. Le manomètre d'alimentation a été retiré et remplacé par un bouchon de conduite (n_ 15). Le bloc de contrôle de la pression (n_ 10) est différent afin d'accommoder une tuyauterie de contrôle différente (n_ 23) avec une prise de pression (n_ 14) pour le manomètre de procédé. Si un manomètre d'alimentation est requis, un manomètre doté d'une tige de raccordement de 1/4 in. (n_ 3) peut être installé sur le régulateur de pression d'alimentation. ATTENTION Avant d'exécuter cette procédure, s'assurer que les manomètres de rechange sont réglés à la plage correcte pour éviter qu'ils ne soient endommagés par une surpression. 30 Manuel d'instructions Contrôleurs et transmetteurs C1 D103292X0FR Septembre 2019 Remarque L'élément n_ 2 est utilisé à la fois comme manomètre d'alimentation et manomètre de sortie pour les unités sans manomètre de procédé. Deux éléments sont requis pour ces unités. L'élément 2 est utilisé comme manomètre de sortie sur les unités dotées d'un manomètre à indicateur de pression du procédé (n_ 4). Un élément est requis pour ces unités. Utiliser l'élément n_ 3 pour obtenir une indication de la pression d'alimentation lorsqu'un manomètre de procédé est installé. Installer l'élément n_ 3 sur le régulateur de pression d'alimentation. 1. Couper la pression d'alimentation et les lignes de procédé vers le contrôleur ou le transmetteur. 2. Retirer le manomètre à remplacer. D Dévisser le manomètre d'alimentation ou de sortie (n_ 2) de la base du relais. D Dévisser le manomètre de procédé (n_ 4) de la prise de procédé (n_ 14). D Dévisser le manomètre d'alimentation (n_ 3) du régulateur de pression d'alimentation. 3. Recouvrir le filetage du manomètre de rechange avec du produit d'étanchéité. 4. Visser le manomètre de rechange sur la base du relais, la prise de procédé ou le régulateur de pression d'alimentation. 5. Vérifier l'absence de fuite en appliquant la pression d'alimentation correcte avec la buse recouverte d'un capuchon afin d'obtenir une pression de sortie totale. Remplacement du tube de Bourdon Sauf indication contraire, voir la figure 24 pour l'emplacement des éléments numérotés. 1. Couper la pression d'alimentation et les lignes de procédé vers le contrôleur ou le transmetteur. 2. Dévisser la vis mécanique (n_ 56) pour déconnecter le lien (n_ 16) et la bague (n_ 31) du faisceau (n_ 39). Ne pas égarer la bague (n_ 31). Les rondelles (n_ 62) de la vis mécanique (n_ 56) sont parfois fournies pour une insertion au niveau du raccord du faisceau (n_ 39) afin de permettre un alignement du lien de raccordement (n_ 16). 3. Débrancher la tuyauterie de contrôle (n_ 23, figure 23). Dévisser les deux vis (n_ 55) et les rondelles (n_ 45) et retirer le tube de Bourdon (n_ 5). 4. Dévisser la vis mécanique (n_ 56) et retirer le lien et la bague (n_ 16 et 31) du tube de Bourdon. Ne pas égarer la bague. 5. Fixer le lien et la bague sur le tube de Bourdon de rechange. 6. Fixer le tube de Bourdon avec deux vis mécaniques et les rondelles (n_ 55 et 45). 7. Raccorder le lien et la bague sur le faisceau (n_ 39). 8. Après avoir branché le lien sur le faisceau, s'assurer que le lien est parallèle au capteur (n_ 5) et au faisceau (n_ 39) afin qu'il n'entre pas en contact avec le capteur du faisceau. La figure 15 illustre un lien de raccordement correctement aligné ; ce dernier n'est pas en contact avec le tube de Bourdon ou avec les rondelles. Lorsque le lien de raccordement est correctement configuré, il se déplace librement lorsqu'ils est touché. Les rondelles (n_ 62) servent de cales pour régler le parallélisme. 9. Vérifier que le faisceau est parallèle au bas du boîtier et que le lien (n_ 16) est sous tension. S'il n'est pas parallèle, desserrer les vis mécaniques (n_ 55), repositionner le tube de Bourdon afin qu'il soit parallèle avec le faisceau et resserrer les vis. 10. En cas d'installation d'un tube de Bourdon avec une plage différente, retirer la vis mécanique et la rondelle (n_ 61 et 60) ainsi que le cadran (n_ 6). Installer un nouveau cadran doté d'un réglage correspondant à la plage du tube de Bourdon. En cas d'utilisation d'un manomètre de procédé optionnel (n_ 4, figure 22), installer un nouveau manomètre doté de la capacité de mesure appropriée. 31 Manuel d'instructions Contrôleurs et transmetteurs C1 D103292X0FR Septembre 2019 Figure 15. Lien de raccordement TUBE DE BOURDON (N_ 5) TUBE DE BOURDON (N_ 5) BAGUE DE LIAISON (N_ 31) RONDELLE (N_ 62) RONDELLE (QTE 2) (N_ 62) BAGUE DE LIAISON (N_ 31) FAISCEAU (N_ 39) LIEN DE RACCORDEMENT EN CONTACT (ALIGNEMENT INCORRECT) LIEN DE RACCORDEMENT (N_ 16) RONDELLE (N_ 62) FAISCEAU (N_ 39) LIEN DE RACCORDEMENT CORRECTEMENT ALIGNE GE37119 LIEN DE RACCORDEMENT (N_ 16) 11. Vérifier qu'aucun raccord ne fuit et que les vis mécaniques du tube de Bourdon sont bien serrées, serrer selon le besoin. Effectuer les procédures d'étalonnage appropriées. Replacement du capteur à soufflet Sauf indication contraire, voir la figure 25 pour l'emplacement des éléments numérotés. 1. Couper la pression d'alimentation et les lignes de procédé vers le contrôleur ou le transmetteur. 2. Déconnecter la tuyauterie de la base de montage (n_ 57) et du dispositif de réglage de l'étalonnage (n_ 36). Déconnecter la tuyauterie qui relie le bloc de pression (n_ 8, figure 22) à l'ensemble du soufflet (n_ 71), situé à l'extrémité du bloc de pression. 3. Dévisser les vis mécaniques (n_ 41, figure 22 ou 23) et retirer le sous-ensemble de détection de la pression du boîtier. 4. Retirer les vis mécaniques et les rondelles de l'arcade du soufflet et (n_ 98 et 99) et déplacer l'arcade du soufflet vers la droite pour pouvoir accéder à la vis du lien. 5. Débrancher le lien (n_ 71M) et la bague (n_ 71L) du faisceau. Ne pas égarer la bague. 6. Desserrer les écrous qui maintiennent l'ensemble du soufflet (n_ 71) et retirer ce dernier de l'arcade du soufflet (n_ 100). 7. Pour le capteur du manomètre (ensemble composé d'un seul soufflet), installer le ressort du soufflet approprié dans l'ensemble du soufflet si la plage du signal d'entrée est modifiée. 8. Installer le nouvel ensemble de soufflet dans l'arcade. 9. Fixer le lien et la bague à l'ensemble de soufflet. Placer l'arcade du soufflet (n_ 100) sur la base de montage (n_ 57) et fixer le lien et la bague sur le faisceau. Visser, sans serrer, les quatre vis mécaniques (n_ 98) avec les rondelles (n_ 99) qui permettent de fixer l'arcade sur la base de montage. Faire glisser l'arcade vers le haut ou le bas selon le besoin afin de positionner le faisceau à l'horizontale, comme indiqué dans la figure 25. Serrer les vis mécaniques. 10. Remplacer le sous-ensemble dans le boîtier et fixer à l'aide des quatre vis mécaniques (n_ 41, figure 22 ou 23). Rebrancher toutes les tuyauteries. 11. En cas d'installation d'un tube de Bourdon avec une plage différente, retirer la vis mécanique et la rondelle (n_ 61 et 60) ainsi que le cadran (n_ 6) et installer un nouveau cadran doté d'un réglage correspondant à la plage du tube de Bourdon. En cas d'utilisation d'un manomètre de procédé optionnel (n_ 4, figure 22), installer un nouveau manomètre doté de la capacité de mesure appropriée. 32 Manuel d'instructions Contrôleurs et transmetteurs C1 D103292X0FR Septembre 2019 12. Vérifier qu'aucun raccord ne fuit et que les vis mécaniques de l'arcade du soufflet sont bien serrées, serrer selon le besoin. Effectuer les procédures d'étalonnage appropriées. Changement de la vanne de réinitialisation 1. Déconnecter la tuyauterie appropriée et retirer l'ensemble de la vanne de restriction de réinitialisation (n_ 256, figure 23) en retirant la vis (n_ 22, non illustrée) de l'arrière du boîtier. Installer l'ensemble de rechange souhaité. 2. Brancher la tuyauterie, vérifier que les raccords ne fuient pas et effectuer les procédures d'étalonnage appropriées. Changement de la soupape de décharge différentielle avec enroulement anti-réinitialisation Voir la figure 24 pour l'emplacement des éléments numérotés. 1. Prendre note de la pression de sortie du contrôleur (zéro ou alimentation) lorsque le procédé est arrêté. 2. Retirer l'ensemble de la soupape de décharge différentielle. 3. Voir la figure 14. Installer la soupape de décharge différentielle avec la flèche positionnée de façon à ce que la valeur de la sortie du contrôleur corresponde à la valeur notée à l'étape 1 lors de l'arrêt du procédé. Changement de l'action Conversion d'un contrôleur proportionnel uniquement en un contrôleur à écart différentiel Il est possible de convertir un contrôleur proportionnel uniquement en un contrôleur d'écart différentiel, ou vice versa, en modifiant la position de la tuyauterie proportionnelle et en inversant l'ensemble de la bande proportionnelle. 1. Isoler le contrôleur ou le transmetteur de la pression du procédé, de régulation et d'alimentation. Dissiper toute pression accumulée dans le contrôleur ou le transmetteur avant de procéder aux étapes suivantes. 2. Déconnecter la tuyauterie proportionnelle (n_ 25, figure 16) de la base de montage (n_ 57, figure 24 ou 25) et la réinstaller dans l'autre prise de la base. Figure 16. Raccordement de la tuyauterie à action directe/inverse pour le contrôleur à écart différentiel TUYAUTERIE PROPORTIONNELLE (N_ 25) TUYAUTERIE PROPORTIONNELLE (N_ 25) TUYAUTERIE DU RELAIS (N_ 24) TUYAUTERIE DU RELAIS (N_ 24) SOUFFLET (N_ 52) PALETTE/VIS (N_ 40 ET 46) POSITION D'ACTION INVERSE BLOC D'INVERSION (N_ 37) ENSEMBLE DE LA BANDE PROPORTIONNELLE POSITIONNEUR A MODE D'ACTION DIRECTE PALETTE/VIS (N_ 40 ET 46) SOUFFLET (N_ 52) ENSEMBLE DE LA BANDE PROPORTIONNELLE BLOC D'INVERSION (N_ 37) ACTION DIRECTE ACTION INVERSE GE34724-B CONTROLEUR A ECART DIFFERENTIEL 33 Contrôleurs et transmetteurs C1 Manuel d'instructions D103292X0FR Septembre 2019 3. Ne pas inverser le bloc d'inversion à moins de convertir également l'action du contrôleur de directe en action inverse (ou vice versa). 4. Inverser l'ensemble de la bande proportionnelle (voir la figure 17) : a. Tourner le bouton de réglage de la bande proportionnelle (n_ 73) jusqu'à 10. b. Dévisser le tendeur du ressort (n_ 65) et retirer le ressort de justesse (n_ 70) et les rondelles (n_ 64). c. Détacher le ressort de verrouillage (n_ 72). Retirer l'échelle de l'indicateur (n_ 69) et le bouton de réglage de la bande proportionnelle (n_ 73). d. Retirer la barre de réglage du gain (n_ 63). La retourner de façon à la fixer du côté opposé au ressort à porte-à-faux (n_ 8), comme indiqué dans la figure 16 et la visser. e. Retourner l'échelle de l'indicateur (n_ 69) ; l'assembler au bouton de réglage de la bande proportionnelle (n_ 73). Enfoncer le ressort de verrouillage (n_ 72) jusqu'à ce qu'un déclic se fasse entendre. f. Serrer le tendeur du ressort (n_ 65) avec le ressort de justesse (n_ 70) et les rondelles (n_ 64) jusqu'à ce qu'il butte contre la barre de réglage du gain (n_ 63). g. Tourner le bouton de réglage de la bande proportionnelle sur 10. S'il est impossible de le tourner jusqu'à 10, desserrer le tendeur du ressort (n_ 63). 5. Vérifier l'absence de fuite avec de l'eau savonneuse. Effectuer la procédure d'étalonnage appropriée. Figure 17. Ensemble de la bande proportionnelle BOUTON DE REGLAGE DE LA BANDE PROPORTIONNELLE (N_ 73) RESSORT DE VERROUILLAGE (N_ 72) VIS MECANIQUE (N_ 56) RESSORT EN PORTE-A-FAUX (N_ 8) ECHELLE DE L'INDICATEUR (N_ 69) ENTRETOISE DE RESSORT (N° 245) VIS MECANIQUE (N_ 74) RESSORT DE JUSTESSE (N_ 70) BARRE DE REGLAGE DU GAIN (N_ 63) RONDELLE (N_ 64) TENDEUR DU RESSORT (N_ 65) GE34725-B Passer à une action directe Suivre les étapes ci-dessous pour passer d'une action inverse (une pression du procédé montante produit une pression de sortie descendante) à une action directe (une pression du procédé descendante produit une pression de sortie montante), ou vice versa. La modification de l'action nécessite également l'inversion des positions du bloc d'inversion, de la bande proportionnelle et des tuyauteries des soufflets. Sauf indication contraire, voir les figures 16, 17, 18, et 21 pour l'emplacement des éléments numérotés. 1. Isoler le contrôleur ou le transmetteur de la pression du procédé, de régulation et d'alimentation. Dissiper toute pression accumulée dans le contrôleur ou le transmetteur avant de procéder à cette procédure. 2. Comme indiqué dans la figure 18, repérer les emplacements de la nouvelle tuyauterie, de l'ensemble de la bande proportionnelle et du bloc d'inversion pour l'action souhaitée. 34 Manuel d'instructions Contrôleurs et transmetteurs C1 D103292X0FR Septembre 2019 Figure 18. Raccordement de la tuyauterie à action directe/inverse pour les contrôleurs proportionnels ou pour le transmetteur TUYAUTERIE PROPORTIONNELLE (N_ 25) TUYAUTERIE DU RELAIS (N_ 24) TUYAUTERIE PROPORTIONNELLE (N_ 25) TUYAUTERIE DU RELAIS (N_ 24) BLOC D'INVERSION (N_ 37) PIQUAGE (N° 54) SOUFFLET (N_ 52) ENSEMBLE DE LA BANDE PROPORTIONNELLE POSITIONNEUR A MODE D'ACTION DIRECTE PALETTE/VIS (N_ 40 ET 46) POSITION D'ACTION INVERSE PALETTE/VIS (N_ 40 ET 46) ENSEMBLE DE LA BANDE PROPORTIONNELLE SOUFFLET (N_ 52) BLOC D'INVERSION (N_ 37) PIQUAGE (N° 54) ACTION DIRECTE ACTION INVERSE POUR MODIFIER L'ACTION DU CONTROLEUR, REPOSITIONNER LA TUBULURE PROPORTIONNELLE, LE BLOC D'INVERSION/PIQUAGE ET LA BANDE PROPORTIONNELLE COMME INDIQUÉ PLUS HAUT GE28263-B CONTROLEUR PROPORTIONNEL UNIQUEMENT OU TRANSMETTEUR VANNE DE REINITIALISATI ON (N_ 256) VANNE DE REINITIALISATION (N_ 256) TUYAUTERIE DE REINITIALISATION TUYAUTERIE DU (N_ 27) RELAIS (N_ 24) TUYAUTERIE DU RELAIS (N_ 24) TUYAUTERIE DE REINITIALISATION (N_ 27) TUYAUTERIE PROPORTIONNELLE (N_ 27) TUYAUTERIE PROPORTIONNELLE (N_ 27) BLOC D'INVERSION (N_ 37) POSITIONNEUR A ENSEMBLE DE LA BANDE MODE D'ACTION PROPORTIONNELLE DIRECTE PALETTE/VIS (N_ 40 ET 46) POSITION D'ACTION INVERSE SOUFFLET (N_ 52) PALETTE/VIS (N_ 40 ET 46) SOUFFLET (N_ 52) ENSEMBLE DE LA BANDE PROPORTIONNELLE BLOC D'INVERSION (N_ 37) GG15992-1 ACTION DIRECTE ACTION INVERSE CONTROLEUR PROPORTIONNEL PLUS REINITIALISATION 3. Repérer les deux soufflets (n_ 52), l'ensemble de la bande proportionnelle (voir la figure 18) et le bloc d'inversion (n_ 37). 4. Déconnecter la tuyauterie (voir la figure 18) : a. Pour un contrôleur proportionnel uniquement ou pour un transmetteur, déconnecter le tube proportionnel (n_ 25) de la base de montage et les brancher sur le côté opposé. b. Pour un contrôleur proportionnel plus réinitialisation, déconnecter le tube proportionnel (n_ 27) et la tuyauterie de réinitialisation (n_ 27) de la base de montage et les brancher sur le côté oppos. 5. Inverser l'ensemble de la bande proportionnelle (voir la figure 17) : a. Tourner le bouton de réglage de la bande proportionnelle (n_ 73) jusqu'à 10. 35 Contrôleurs et transmetteurs C1 Manuel d'instructions Septembre 2019 D103292X0FR b. Dévisser le tendeur du ressort (n_ 65) et retirer le ressort de justesse (n_ 70) ainsi que les rondelles (n_ 64). c. Détacher le ressort de verrouillage (n_ 72). Retirer l'échelle de l'indicateur (n_ 69) et le bouton de réglage de la bande proportionnelle (n_ 73). d. Retirer la barre de réglage du gain (n_ 63). La retourner de façon à la positionner du côté opposé au ressort à porte-à-faux (n_ 8), comme indiqué dans la figure 18 et la fixer à nouveau. e. Retourner l'échelle de l'indicateur (n_ 69, figure 17) ; l'assembler au bouton de réglage de la bande proportionnelle (n_ 73). Enfoncer le ressort de verrouillage (n_ 72) jusqu'à ce qu'un déclic se fasse entendre. f. Serrer le tendeur du ressort (n_ 65) avec le ressort de justesse (n_ 70) et les rondelles (n_ 64) jusqu'à ce qu'il butte contre la barre de réglage du gain (n_ 63). g. Tourner le bouton de réglage de la bande proportionnelle sur 10. S'il est impossible de le tourner, desserrer le tendeur du ressort (n_ 65). 6. Changer l'ensemble du bloc d'inversion (figure 16 ou 18, n_ 37) : a. Retirer la vis d'étanchéité (n_ 49, figure 24 ou 25). Vérifier le joint torique (n_ 77), situé dans le renfoncement sous la tête de la vis d'étanchéité. Remplacer le joint torique si nécessaire. b. Retirer la vis du bloc d'inversion (n_ 50, figure 24 ou 25) et l'ensemble du bloc d'inversion (n_ 37). Vérifier les joints toriques (n_ 77) situés dans le renfoncement sous la tête de la vis du bloc d'inversion et entre l'ensemble du bloc d'inversion et le dispositif de réglage de l'étalonnage (n_ 36). Les remplacer si nécessaire. c. Placer l'ensemble du bloc d'inversion sur le dispositif de réglage de l'étalonnage (n_ 36) avec un joint torique de façon à ce que la buse soit du côté opposé au faisceau (n_ 39) par rapport au côté duquel elle a été retirée. Placer l'orifice du bloc d'inversion dans le dispositif de réglage de l'étalonnage. Poser la vis du bloc d'inversion (n_ 50) avec un joint torique (n_ 77). d. Poser une vis d'étanchéité (n_ 49) avec un joint torique dans l'orifice précédemment occupé par l'ensemble du bloc d'inversion. 7. Vérifier l'absence de fuite avec de l'eau savonneuse. Effectuer les procédures d'étalonnage appropriées. Remplacement du relais Sauf indication contraire, les numéros utilisés dans cette procédure sont indiqués dans la figure 22 ou 23. 1. Couper la pression d'alimentation et la ou les conduites de procédé vers le contrôleur ou le transmetteur. 2. Débrancher la tuyauterie (n_ 24) du relais. 3. Dévisser le manomètre d'alimentation ou de sortie (n_ 3). 4. Pour retirer le relais, dévisser deux vis mécaniques cruciformes (n_ 29, non illustrées) située derrière le relais à l'arrière du boîtier. 5. Retirer le joint d'étanchéité du relais (n_ 19, figure 22). 6. Un nouveau relais peut être installé en tant que pièce de rechange. Continuer avec l'étape suivante s'il s'agit de l'installation d'un nouveau relais. 7. Fixer le relais de rechange et le nouveau joint d'étanchéité du relais en insérant les vis mécaniques par l'arrière du boîtier. Réinstaller le manomètre d'alimentation ou de sortie. 8. Brancher la tuyauterie et vérifier que les raccords ne fuient pas. Effectuer les procédures d'étalonnage appropriées. 36 Manuel d'instructions Contrôleurs et transmetteurs C1 D103292X0FR Septembre 2019 Changement de la plage du signal de sortie Suivre les informations et les procédures suivantes lors du changement de la plage du signal de sortie du contrôleur ou du transmetteur. Suivre la procédure suivante : D Pour un contrôleur ou un transmetteur, utiliser cette procédure pour passer de la plage du signal de sortie de 0,2 à 1,0 bar (3 à 15 psig) à une plage de 0,4 à 2,0 bar (6 à 30 psig) ou vice versa. (voir également la figure 19). D Pour un contrôleur d'écart différentiel, utiliser cette procédure pour passer de la plage du signal de sortie de 0 à 1,4 bar (0 à 20 psig) à la plage de 0 à 2,4 bar (0 à 35 psig) ou vice versa. (voir également la figure 19) D Lors de la modification de la plage de la source de pression d'alimentation, se reporter au tableau 5 pour obtenir les spécifications de pression d'alimentation pour la plage du signal de sortie sélectionnée. Figure 19. Modification de la plage du signal de sortie de 0,2 à 1,0 bar (3 à 15 psig) à la plage de 0,4 à 2,0 bar (6 à 30 psig) ou vice versa RESSORT EN PORTE-A-FAUX (N° 8) RESSORT EN PORTE-A-FAUX (N° 8) ENTRETOISE DE RESSORT (N° 245) ENTRETOISE 1 DE RESSORT (N° 245) 1 RESSORT DE JUSTESSE (N° 70) RONDELLE (N° 64) RESSORT DE JUSTESSE (N° 70) RONDELLE (N° 64) AJUSTEUR DE RESSORT (N° 65) PLAGE DE SORTIE DE 0,2 A 1,0 BAR (3 A 15 PSIG) AJUSTEUR DE RESSORT (N° 65) PLAGE DE SORTIE DE 0,4 A 2.0 BAR (6 A 30 PSIG) REMARQUE 1 INVERSER L'ENTRETOISE DE RESSORT SELON LE BESOIN POUR MODIFIER LA LONGUEUR UTILE DU RESSORT DE JUSTESSE. GG15991-A Modifier également les plaques signalétiques du contrôleur ou du transmetteur afin de prendre la nouvelle plage en compte. Sauf indication contraire, voir la figure 24 ou 25 pour l'emplacement des articles numérotés. 1. Couper la pression d'alimentation et les lignes de procédé vers le contrôleur ou le transmetteur. 2. Déconnecter la tuyauterie de la base de montage (n_ 57) et du dispositif de réglage de l'étalonnage (n_ 36). Déconnecter la tuyauterie qui relie le bloc de pression (n_ 10, figure 22 ou 23) à l'ensemble du tube de Bourdon ou à l'ensemble du soufflet (n_ 5 ou 52), situé à l'extrémité du bloc de pression. 3. Dévisser les vis mécaniques (n_ 41, figure 22 ou 23) et retirer le sous-ensemble du boîtier. 4. Si le contrôleur ou le transmetteur est doté d'un capteur à tube de Bourdon, débrancher ce dernier du faisceau (n_ 39) en retirant la vis (n_ 56). Ne pas égarer la bague (n_ 31). Dévisser les vis mécaniques (n_ 55) et retirer les rondelles et le tube de Bourdon (n_ 45 et 5). 37 Manuel d'instructions Contrôleurs et transmetteurs C1 D103292X0FR Septembre 2019 5. Dévisser les vis du soufflet (n_ 53) de chaque extrémité de la base de montage (n_ 57). Remarque Les vis du soufflet (n_ 53) sont dotées d'un joint torique (n_ 77, figure 20) qui est installé sous leur tête. Retirer le joint torique et en prévoir un de rechange lors du remontage du soufflet. Figure 20. Détail de vis du soufflet JOINT TORIQUE (N_ 77) A6281-1 6. Desserrer le tendeur du ressort (n_ 65). Détacher le ressort de verrouillage (n_ 72, figure 17) et retirer l'échelle de l'indicateur (n_ 69) ainsi que le bouton de réglage de la bande proportionnelle (n_ 73). 7. Comprimer le soufflet (n_ 52) de façon à pouvoir retirer l'extrémité de ce dernier, le faisceau (n_ 39) et le ressort en porte-à-faux (n_ 8) de la base de montage (n_ 57). 8. Dévisser le soufflet (n_ 52) de l'ensemble soufflet/ressort en porte-à-faux. 9. Retirer le ressort en porte-à-faux de l'entretoise (n_ 34). a. Retirer les vis mécaniques du faisceau (figure 21, étape m). b. Retirer les vis mécaniques du ressort en porte-à-faux (figure 21, étape l). c. Retirer la flexion interne (figure 21, étape j) et l'installer sur le nouveau ressort en porte-à-faux. 10. Installer le nouveau ressort en porte-à-faux (n_ 8), reconnecter le faisceau (n_ 39) l'entretoise du faisceau (n_ 34) dans l'ordre inverse des étapes 9a. et 9b. et fixer à nouveau le soufflet à l'ensemble soufflet/ressort en porte-à-faux. 11. Comprimer les soufflets et les installer sur la base de montage (n° 57). Aligner le ressort en porte-à-faux avec la barre de réglage du gain (n° 63). Pour plages de sortie de 0,2 à 1,0 bar (3 à 15 psig) et 0,4 à 2,0 bar (6 à 30 psig) : inverser l'entretoise du ressort (n° 245) comme illustré dans la figure 19. Installer l'ensemble constitué de l'indicateur de course (n° 69) et du bouton de réglage de la bande proportionnelle (n° 73). Attacher le ressort de verrouillage (n° 72) à l'échelle de l'indicateur. 12. Installer le tendeur de ressort (n° 65, figure 17) avec la rondelle (n° 64, figure 17) de chaque côté du ressort de justesse (n° 70, figure 17). Serrer le tendeur du ressort jusqu'à ce qu'il butte contre la barre de réglage du gain (n° 63). 38 Manuel d'instructions Contrôleurs et transmetteurs C1 D103292X0FR Septembre 2019 13. Tourner le bouton de réglage de la bande proportionnelle sur 10. S'il est impossible de le tourner jusqu'à ce point, desserrer le tendeur du ressort (n_ 65). 14. Fixer le soufflet (n_ 52) avec les vis du soufflet (n_ 53), en veillant que la buse (n_ 54) soit centrée sur la palette (n_ 40). 15. Dévisser les manomètres de sortie et d'alimentation (figure 22 ou 23, n_ 2) et installer les nouveaux manomètres avec les plages correctes. 16. Remplacer le sous-ensemble dans le boîtier et fixer à l'aide des vis mécaniques (n_ 41, figure 22 ou 23). Réinstaller le tube de Bourdon s'il a été retiré. Pour ce faire, se reporter à la section Remplacement du tube de Bourdon. Rebrancher toutes les tuyauteries. 17. Vérifier qu'aucun raccord ne fuit et que les vis mécaniques du soufflet sont bien serrées, serrer selon le besoin. Effectuer les procédures d'étalonnage appropriées. Figure 21. Ensemble du faisceau/ressort en porte-à-faux ENTRETOISE DU SOUFFLET (N_ 34) FLEXION INTERNE (N_ 67) FLEXION EXTERNE (N_ 68) VIS MECANIQUE (N_ 51) RESSORT EN PORTE-A-FAUX (N_ 8) VIS MECANIQUE (N_ 51) FAISCEAU (N_ 39) GE34726-B E1068 39 Contrôleurs et transmetteurs C1 Septembre 2019 Manuel d'instructions D103292X0FR Commande de pièces détachées Lors de toute correspondance avec le bureau commercial Emerson à propos du présent équipement, toujours préciser le numéro de série de l'unité. Ce dernier est indiqué sur la plaque signalétique (n_ 22, figure 22). AVERTISSEMENT N'utiliser que des pièces détachées d'origine Fisher. Des composants non fournis par Emerson ne doivent, en aucune circonstance, être utilisés dans un instrument Fisher. L'utilisation de composants non fournis par Emerson peut annuler la garantie, affecter les performances de l'instrument et causer des blessures et des dommages matériels. 40 Manuel d'instructions Contrôleurs et transmetteurs C1 D103292X0FR Septembre 2019 Kits de pièces N_ Description Référence Controller Repair Kits Kit includes Gasket, Relay Gasket, Bellows Frame Gasket, and keys 16, 20, 21, 31, 37, 38, 40, 46, 49, 50, 54, 62, 75, 76, and 77 Remarque Les éléments 71K, 71L et 71M peuvent également s'avérer nécessaires pour la réparation des contrôleurs C1B et C1D. Se reporter à la section Pièces communes pour obtenir les numéros de référence. Remarque L'élément n_ 2 est utilisé à la fois comme manomètre d'alimentation et manomètre de sortie pour les unités sans manomètre de procédé. Deux éléments sont requis pour ces unités. Sur les unités dotées d'un manomètre de pression du procédé (n_ 106), l'élément n_ 2 est utilisé comme manomètre de sortie. Un élément est requis pour ces unités. Utiliser l'élément n_ 3 pour obtenir une indication de la pression d'alimentation lorsqu'un manomètre de procédé est installé. Installer l'élément n_ 3 sur le régulateur de pression d'alimentation. 2* Standard Temperature High Temperature RC100X00L12 RC100X00H12 Relay Replacement Kits Kit includes keys 19 and 29, the replacement relay, and 2 Machine Screws Standard Temperature RRELAYX0L22 High Temperature RRELAYX0H22 Case Assembly Seal Kit Kit includes 3 Manifold Seals, 1 Manifold Cover, and 10 Mounting Screws RC100X00012 C1P Tubing Replacement Kit Kit includes key 23, 24, 25, 26, and 27 RC100XTRK12 Remarque Contacter un bureau de vente Emerson pour des informations sur la commande de pièces détachées. Pièces communes (figures 22, 23, 24 et 25) 1 Description Case and Cover Assembly *Pièces de rechange recommandées Supply and Output Pressure Gauge, w/o process pressure gauge (1/8-inch connecting stem), (2 req'd) Dual scale 0-2.0 kg/cm2 and 0-30 psig 0-4.0 kg/cm2 and 0-60 psig Triple scale 0-2.0 bar, 0-0.2 MPa, and 0-30 psig 0-4.0 bar, 0-0.4 MPa, and 0-60 psig 0-2.0 kg/cm2 and 0-30 psig 0-4.0 kg/cm2 and 0-60 psig 2* Output Pressure Gauge, w/process pressure gauge (1/8-inch connecting stem) Triple scale 0-2.0 bar, 0-0.2 MPa, and 0-30 psig 0-4.0 bar, 0-0.4 MPa, and 0-60 psig 3* Supply Pressure Gauge, w/process pressure gauge (1/4-inch connecting stem) Triple scale 0-2.0 bar, 0-0.2 MPa, and 0-30 psig 0-4.0 bar, 0-0.4 MPa, and 0-60 psig Liste des pièces N_ Description Remarque Les contrôleurs dotés d'un capteur à soufflet utilisent uniquement des manomètres de procédé en acier inoxydable et en laiton à triple échelle de 2,0 bar, 0 à 0,2 MPa et 0 à 0 à 30 psig. Les contrôleurs de pression différentielle n'utilisent pas de manomètre de procédé. 4* Process Pressure Indicator Gauge (use only when specified) Triple scale 0-2.0 bar, 0-0.2 MPa, and 0-30 psig 0-20 bar, 0-2.0 MPa, and 0-300 psig 0-69 bar, 0-6.9 MPa, and 0-1000 psig 41 Manuel d'instructions Contrôleurs et transmetteurs C1 D103292X0FR Septembre 2019 Figure 22. Ensemble C1 de Fisher à action inverse type (se reporter à la figure 26 pour la vue frontale du boîtier et du couvercle) FIL METALLIQUE DE NETTOYAGE A RESSORT RELAIS INDICATION EN OPTION DE PRESSION DU PROCEDE SOUS-ENSEMBLE (N_ INDIQUE DANS LA FIGURE 24 OU 25) REMARQUE : LES ELEMENTS N_ 11, 21 ET 29 NE SONT PAS ILLUSTRES GE34729-B GE31719-A E1069 N_ 5* 6 7 8* 9 10 Description Bourdon Tube Dial Screw (transmitters only) Cantilever Spring 3-15 psi range 6-30 psi range Nameplate Control Pressure Block For gauge pressure instruments w/o process pressure gauge for standard, NACE and oxygen service w/process gauge TRANSMETTEUR N_ Description 11 Plug (not shown) used with gauge pressure only 1 req'd for standard/NACE 2 req'd for oxygen service 12 13 Machine Screw (4 req'd) Lockwasher (4 req'd) 14 Pressure Connection Use w/process gauge Pipe Plug (not shown) Use w/process gauge, not used w/Bourdon tube protector 15 *Pièces de rechange recommandées 42 Manuel d'instructions Contrôleurs et transmetteurs C1 D103292X0FR Septembre 2019 Figure 22. Ensemble C1 de Fisher à action inverse type (suite) (se reporter à la figure 26 pour la vue frontale du boîtier et du couvercle) FIL METALLIQUE DE NETTOYAGE A RESSORT RELAIS SOUS-ENSEMBLE (N_ INDIQUE DANS LA FIGURE 24 OU 25) REMARQUE : LES ELEMENTS N_ 11, 21 ET 29 NE SONT PAS ILLUSTRES GE28280-B E1070 N_ CONTROLEURS PROPORTIONNELS UNIQUEMENT Description 16* Connecting Link(1), Bourdon tube instruments only 16 Connecting Link, Bourdon tube w/optional travel stop 17 N_ Description 20* 21* O-Ring(1) Gasket(1) (not shown) Lockwasher, steel pl (2 req'd) Use w/optional Bourdon tube travel stop 22 Mounting Screw for reset restriction valve 1/4-20 UNC (not shown) 18 Machine Screw, steel pl (2 req'd) Use w/optional Bourdon tube travel stop 23* 19* Relay Gasket(1) Std Temp Hi Temp Control Tubing Assembly For Bourdon tube instruments w/o process pressure gauge Std. Oxygen Service w/process pressure gauge *Pièces de rechange recommandées 1. Cette pièce est incluse dans le kit de réparation du contrôleur. 43 Manuel d'instructions Contrôleurs et transmetteurs C1 D103292X0FR Septembre 2019 Figure 23. Ensemble C1 de Fisher à action inverse type Ensemble proportionnel plus réinitialisation (se reporter à la figure 26 pour la vue frontale du boîtier et du couvercle) FIL METALLIQUE DE NETTOYAGE A RESSORT RELAIS SOUS-ENSEMBLE (N_ INDIQUE DANS LA FIGURE 24 OU 25) REMARQUE : LES ELEMENTS N_ 11, 21 ET 22 NE SONT PAS ILLUSTRES GE28281-B E1071 CONTROLEUR PROPORTIONNEL PLUS REINITIALISATION SANS ENROULEMENT ANTI-REINITIALISATION N_ Description 23* Control Tubing Assembly 24* Relay Tubing Assembly 25* Compensator Tubing 26* 27* Reset Tubing Compensator Tubing (2 req'd) 28 29 30 Vent Ass'y Machine Screw(2) (not shown) (2 req'd) NPT Adaptor, aluminum 31* Link bearing(1) Bourdon tube instruments only (2 req'd) 32 33 Rotary Spring Bellows Stud (not shown) 34 35 36 37 38 Spacer Pressure Set Arm Calibration Adjuster Reversing Block(1) Sleeve(1) N_ Description 39 40 41 42 43 Beam Flapper(1) Machine Screw (4 req'd) Flexure Strip Flexure Strip Washer (2 req'd) 44 45 46 Washer (2 req'd) Washer (2 req'd) Machine Screw(1) 47 48 49 50 51 52* 53 54* 55 56 57 Machine Screw (4 req'd) Machine Screw (2 req'd) Sealing Screw(1) Reversing Block Screw(1) Cap Screw (8 req'd) Reversing Bellows Ass'y (2 req'd) Bellows Screw (2 req'd) Nozzle(1) Machine Screw (2 req'd) Machine Screw (4 req'd) Mounting Base *Pièces de rechange recommandées 1. Cette pièce est incluse dans le kit de réparation du contrôleur. 2. Cette pièce est incluse dans le kit de réparation du relais. 44 Manuel d'instructions Contrôleurs et transmetteurs C1 D103292X0FR Septembre 2019 Figure 23. Ensemble C1 de Fisher à action inverse type Ensemble proportionnel plus réinitialisation (suite) (se reporter à la figure 26 pour la vue frontale du boîtier et du couvercle) FIL METALLIQUE DE NETTOYAGE A RESSORT RELAIS 2 REMARQUES : 1 FLECHE VERS LE BAS - DISSIPE LA PRESSION DESCENDANTE (SORTIE A L'ALIMENTATION A L'ARRET) 2 FLECHE VERS LE HAUT - DISSIPE LA PRESSION MONTANTE (SORTIE A ZERO A L'ARRET). LES N_ 80, 81 ET 82 NE SONT PAS ILLUSTRES GE31718-A E1072 N_ 1 CONTROLEUR PROPORTIONNEL PLUS REINITIALISATION AVEC SOUPAPE DE DECHARGE DIFFERENTIELLE POUR ENROULEMENT ANTI-REINITIALISATION Description 58 59 Knob Knob Spring 60 61 62 Washer Machine Screw Washer(1) (2 req'd) 63 64 Gain Adj Bar Washer 65 Spring Adjustor 66 67* Travel Stop Assembly Use w/optional Bourdon tube travel stop Inner Flexure 68* 69 70 Outer Flexure Indicator Scal Bias Spring N_ 71* Description Gauge Pressure Bellows (input)(3) 0-150 mbar (0-60 inches wc) positive, 0-150 mbar (6-60 inches wc) vacuum, and 75-0-75 mbar (30-0-30 inches wc) compound 0-250 mbar (0-100 inches wc) positive 0-0.35 mbar (0-5 psig) positive and for 0-350 mbar (0-10 inches Hg) vacuum 0-0.5 bar (0-7.5 psig) positive 0-0.7 bar (0-10 psig) positive 0-1.0 bar (0-15 psig) positive, 0-1.0 bar (0-30 inches Hg) vacuum, and 500-0-500 mbar (15-0-7.5 psig) compound 0-1.4 bar (0-20 psig) positive 0-2.0 bar (0-30 psig) positive and 1.0-0-1.0 bar (30-0-15 psig) compound *Pièces de rechange recommandées 1. Cette pièce est incluse dans le kit de réparation du contrôleur. 3. Pour toute commande d'un soufflet (n_ 71) pour la modification de la plage d'un contrôleur de pression manométrique, commander également le ressort du soufflet approprié (n_ 80). Commander également les éléments 101, 102 et 103 si nécessaire. 45 Manuel d'instructions Contrôleurs et transmetteurs C1 D103292X0FR Septembre 2019 Figure 24. Sous-ensemble du contrôleur avec capteur à tube de Bourdon A B C A B A A C GE33918-A VUE A-A SOUS-ENSEMBLE DE LA BUTEE DE COURSE DU TUBE DE BOURDON SECTION A-A SECTION B-B SECTION C-C REMARQUE : LES ELEMENTS N_ 33 ET 74 NE SONT PAS ILLUSTRES. GE26600-C N_ Description 71* Differential-Pressure Bellows (input) 0-200 mbar (0-80 inches wc) 0-0.7 bar (0-10 psi) 0-1.4 bar (0-20 psi) 0-2.0 bar (0-30 psi) 71K Machine Screw(4) bellows sensing instruments only (2 req'd) 71L* Bearing(4) bellows sensing instruments only (2 req'd) 71M* Link(4) bellows sensing instruments only 72* N_ Description 73 74 Proportional Band Adjustment Knob Machine Screw(1) (2 req'd) 75* Gasket(1) (2 req'd) Std Temp High Temp 76* Nozzle O-Ring(1) Std Temp High Temp Lock Spring *Pièces de rechange recommandées 46 1. Cette pièce est incluse dans le kit de réparation du contrôleur. Commander les éléments 101, 102 et 103 si nécessaire. 4. Cette pièce fait partie de l'ensemble du soufflet, n_ 71. Manuel d'instructions Contrôleurs et transmetteurs C1 D103292X0FR Septembre 2019 Figure 25. Sous-ensemble du contrôleur avec manomètre à soufflet ou capteur à soufflet pour pression différentielle A B SECTION A-A A B SECTION B‐B LIAISON (N° 71M) 1 1 VIS (N° 71K) BAGUE (N° 71L) LIAISON (N° 71M) 1 1 VIS (N° 71K) VUE LATERALE DU SOUS-ENSEMBLE AVEC CAPTEUR A SOUFFLET POUR PRESSION MANOMETRIQUE REMARQUES : LES ELEMENTS 33, 46 ET 74 NE SONT PAS ILLUSTRES L'ELEMENT 52 EST LE SOUFFLET DE CONTRE-REACTION 1 LES ELEMENTS 71K, 71L ET 71M NE FONT PAS PARTIE DE L'ENSEMBLE DU SOUFFLET (N° 71) 1 BAGUE (N° 71L) 1 VUE LATERALE DU SOUS-ENSEMBLE AVEC CAPTEUR A SOUFFLET POUR PRESSION DIFFERENTIELLE GE35161-A GE34735-C 47 Manuel d'instructions Contrôleurs et transmetteurs C1 D103292X0FR Septembre 2019 N_ Description N_ 98 Machine Screw (4 req'd) Gauge and differential pressure bellow instruments 99 Washer for Bourdon tube instruments (2 req'd) for bellows sensing instruments (4 req'd) Bellows Yoke use with gauge and differential pressure bellows Remarque Un total de 5 joints toriques (n_ 77) est utilisé. 1 joint torique est utilisé sous la vis d'étanchéité (n_ 49), le second sous la vis du bloc d'inversion (n_ 50), le troisième entre le bloc d'inversion (n_ 52) et le dispositif de réglage de l'étalonnage (n_ 36), le quatrième et le cinquième dans le renfoncement sous la tête de chaque vis du soufflet (n_ 53). Description 100 Remarque Les éléments 78 à 82 sont uniquement utilisés pour les instruments à manomètre à soufflet. 77* O-Ring (5 req'd) Std Temp High Temp Remarque Les éléments 78 à 82 sont uniquement utilisés sur les contrôleurs proportionnels plus réinitialisation. 78 79 80 81* 82 48 Tubing Assembly Tubing Assembly Anti-Reset Windup Cover (not shown) O-Ring (not shown) (2 req'd) Machine screw (not shown) (2 req'd) 101 102 103 Jam Nut Washer Spring seat 104 105 Spring Label, bellows sensing instruments only 190 Anti-Reset Windup Ass'y For Proportional-Plus-Reset Controllers only 245 Spring Spacer 256 Reset Restriction Valve For proportional-plus-reset controllers w/o anti-reset windup For proportional-plus-reset controllers w/ anti-reset windup *Pièces de rechange recommandées Manuel d'instructions Contrôleurs et transmetteurs C1 D103292X0FR Septembre 2019 Figure 26. Vue frontale du boîtier et du couvercle CLAPETS DE COMPRESSION ETIQUETTE DE MODIFICATION D'ACTION (A L'INTERIEUR DU COUVERCLE) SECTION B-B B A GOUPILLE ELASTIQUE (2X) B A MARQUAGE ATEX COUVERCLE BOITIER SECTION A-A GE28278-B E1075-1 49 Manuel d'instructions Contrôleurs et transmetteurs C1 D103292X0FR Septembre 2019 Pièces de montage pour le montage sur panneau, paroi, tuyauterie, actionneur Fisher (figures 2 et 3) N_ Description 213 Mounting Plate For yoke mounting on 470, 472, 513, 656, 657 and 667 For yoke mounting on 480 Vertical For yoke mounting on 1051 and 1052 Size 40, positions 1 and 3 w/switch and Size 60, position 1 w/switch All others For yoke mounting on 1061 Size 30, positions 1 and 3 w/switch and position 1 w/o switch, Size 40, position 1 w/switch and Sizes 80 and 100, position 3 w/o switch All others For pipe stand mounting 215 Machine Screw (specify quantity req'd) 5/16 UNC X 1 inch 5/16 UNC X 1-1/2 inches 5/16 UNC X 2 inches 216 Hex Nut (specify quantity req'd) For filter regulator mounting on 1051, 1052 and 1061 All other types and mountings 220 Mounting Bracket (not shown) For casing mounting and casing-mounted filter regulator on 1051 and 1052 221 222 Rondelle de blocage, acier pl (spécifier la quantité requise) Cap Screw (specify quantity req'd) 5/16 UNC X 3/4 inch 5/16 UNC X 1 inch 5/16 UNC X 1-1/8 inches 5/16 UNC X 1-1/4 inches 5/16 UNC X 1-3/4 inches 5/16 UNC X 2-1/2 inches 3/8 UNF X 1-1/8 inches 223 Cap Screw 1051 and 1052 with either case or yoke mounted regulator and 1061 with yoke mounted regulator (2 req'd) 228 Spacer Spool (specify quantity req'd) 470, 472, 480, 513, 656, 657, 667, pipe stand 1051, 1052 and 1061 50 N_ Description 229 Cap Screw (not shown) (specify quantity req'd) 1051 and 1052 casing-mounted controller 238 Mounting Plate For yoke-mounted filter regulator 1051, 1052 and 1062 sizes 40 and 60 1061 size 30 240 Cap Screw For yoke-mounted filter regulator on 1051 and 1052 sizes 40 and 60 (2 req'd) Spacer Spool For yoke mounted filter regulators on 1051 and 1052 sizes 40 and 60 (2 req'd) Spacer Spool (not shown) For yoke mounting on 1051 and 1052 size 40 (2 req'd) 1061 sizes 30, 80 and 100 (2 req'd) Street Elbow (not shown) For mounting on 470, 472, 480, 513, 656, 657, 667, panel, pipe stand, 1051, 1052 and 1061 w/nipple-mounted filter regulator 241 242 243 244 Pipe Nipple (not shown) For mounting on 470, 472, 480, 513, 656, 657, panel, pipe stand, 1051, 1052 and 1061 w/nipple-mounted filter regulator 250 Clamp For pipe stand mounting (2 req'd) 251 Bracket Assembly For panel or wall mounting (2 req'd) 252 Cap Screw For panel or wall mounting (4 req'd) Remarque Spécifier la quantité de raccords. Connector 1/4 NPT X 1/4 O.D. tubing 1/4 NPT X 3/8 O.D. tubing Elbow 1/4 NPT X 1/4 O.D. tubing 1/4 NPT X 3/8 O.D. Tubing Manuel d'instructions D103292X0FR Contrôleurs et transmetteurs C1 Septembre 2019 51 Contrôleurs et transmetteurs C1 Septembre 2019 Manuel d'instructions D103292X0FR Ni Emerson, ni Emerson Automation Solutions, ni aucune de leurs entités affiliées n'assument quelque responsabilité que ce soit quant au choix, à l'utilisation ou à la maintenance d'un quelconque produit. La responsabilité du choix, de l'utilisation et de l'entretien d'un produit incombe à l'acquéreur et à l'utilisateur final. Fisher est une marque qui appartient à l'une des sociétés de la division commerciale d'Emerson Automation Solutions d'Emerson Electric Co. Emerson Automation Solutions, Emerson et le logo Emerson sont des marques de commerce et de service d'Emerson Electric Co. Toutes les autres marques sont la propriété de leurs propriétaires respectifs. Le contenu de cette publication n'est présenté qu'à titre informatif et bien que les efforts aient été faits pour s'assurer de la véracité des informations présentées, celles-ci ne sauraient être considérées comme une ou des garanties, tacites ou expresses, des produits ou services décrits par les présentes, ni une ou des garanties quant à l'utilisation ou l'applicabilité desdits produits et services. Toutes les ventes sont régies par nos conditions générales, disponibles sur demande. Nous nous réservons le droit de modifier ou d'améliorer la conception ou les spécifications desdits produits à tout moment et sans préavis. Emerson Automation Solutions Marshalltown, Iowa 50158 USA Sorocaba, 18087 Brazil Cernay, 68700 France Dubai, United Arab Emirates Singapore 128461 Singapore www.Fisher.com 522008, 2019 Fisher Controls International LLC. Tous droits réservés. E ">
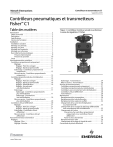
Lien public mis à jour
Le lien public vers votre chat a été mis à jour.