Toptech MultiLoad II Mode d'emploi
PDF
Скачать
Документ
1 MultiLoad II Manuel d’utilisation MultiLoad II MultiLoad II SMP MultiLoad II Mobile Part # 6017 Version logiciel interne 3/4.31.14 Novembre 2013 2 Droits d’auteur Copyright © 2006 - 2013 Toptech Systems, Inc. Les informations figurant dans le présent document sont d’ordre confidentiel et propriété de Toptech Systems Inc. Il est interdit d’en copier, reproduire ou transmettre sous quelque forme que ce soit sans l’autorisation expresse écrite de Toptech Systems, Inc. Clause de non-responsabilité Toptech Systems décline toute responsabilité pour tout dommage résultant de l’installation ou de l’utilisation de ses produits. Toptech Systems ne sera responsable d'aucune réclamation, de dommages, de perte de données ou de temps résultant de l’utilisation de ses produits. Toptech Systems, Inc. Fait partie de la Société IDEX Ce logo est une marque déposée de Toptech Systems, Inc. MultiLoad II EXL ™, TMS™, TMS5™, TMS6™, RCU II t™, Toptech MultiLoad II™, MultiLoad II -RCU™, FCM Flow Control Module™ sont des marques de Toptech Systems, Inc. Copyright © 2007-2013 Toptech Systems, Inc. Tous droits réservés. 3 Sommaire CHAPTER 1 AVANT DE COMMENCER ......................................................................................................... 11 A QUI S’ADRESSE CE MANUEL? .................................................................................................................. 11 COMMENT SE PRESENTE CE MANUEL? ........................................................................................................ 11 CONVENTIONS DE DOCUMENTATION ............................................................................................................ 12 1.1.2 CAPTURES D’ECRAN .............................................................................................................................. 12 1.1.3 PROCEDURES ........................................................................................................................................ 12 ALERTES INFORMATIVES ............................................................................................................................ 13 CONVENTIONS TYPOGRAPHIQUES ............................................................................................................... 13 CHAPTER 2 DESCRIPTION DU SYSTEME .................................................................................................... 14 2.1 Vue d’ensemble ..................................................................................................................................... 14 2.2 Vue d’ensemble du Système ................................................................................................................ 15 2.3 Trois Modes de fonctionnement .......................................................................................................... 16 2.3.1 Mode de Commande Locale................................................................................................................ 16 2.3.2 Mode de télécommande ...................................................................................................................... 16 2.3.3 Mode UAP............................................................................................................................................ 16 2.4 Composants du système ...................................................................................................................... 17 2.5 RCU du MultiLoad II............................................................................................................................... 17 2.5.1 Boîtiers RCU disponibles avec le MultiLoad II.................................................................................... 17 2.5.2 Boîtiers RCU disponibles avec le MultiLoad II SMP ............................................................................ 17 2.6 FCM externe (Module de commande de débit) ................................................................................... 18 2.7 FCM II ...................................................................................................................................................... 19 2.8 Carte interne des entrées et sorties (I/O) ............................................................................................ 21 2.9 Carte interne I/O à deux compteurs ..................................................................................................... 22 2.10 Naviguer dans le système: ................................................................................................................... 23 2.10.1 Menus et Ecrans .............................................................................................................................. 23 2.10.2 Modification de Champs et Entrée de Données .............................................................................. 24 2.11 Commutateur de Commande d’Accès ................................................................................................. 26 2.11.1 Commutateurs Programme /poids et mesures (W&M) de type 1 .................................................... 27 2.11.2 Commutateurs Programme / W&M de Type 2 ................................................................................ 28 2.11.3 COMMUTATEURS Programme / W&M de Type 3 ......................................................................... 29 2.11.4 Commutateur Mode Programme / Poids et Mesures DIP ............................................................... 30 2.11.5 2.10.5 Commutateurs Locaux « Program Mode / W&M » .............................................................. 31 allez à Program Mode -> Configuration -> RCU Setup (page vers le bas) ..................................................... 31 2.12 Démarrage .............................................................................................................................................. 32 2.13 Paramètres de Configuration ............................................................................................................... 33 2.14 Outil de Configuration du MultiLoad II ................................................................................................ 33 2.15 Paramètres Usine par Défaut ............................................................................................................... 33 CHAPTER 3 3.1 3.2 3.3 3.4 OUTIL DE CONFIGURATION GUI ............................................................................................. 34 Vue d’ensemble ..................................................................................................................................... 34 Accès depuis le TMS 5 GUI .................................................................................................................. 35 Navigation d’Ecran ................................................................................................................................ 37 Fonctions de Menu ................................................................................................................................ 38 4 3.4.1 Fonctions de Fichier ............................................................................................................................ 38 3.4.2 FONCTION D’EDITION ....................................................................................................................... 38 3.5 Fonctions d’Outil ................................................................................................................................... 39 3.6 Programme de Génération de Tickets de Connaissement (BOL) .................................................... 39 3.6.1 Téléchargement de Registres.............................................................................................................. 39 3.6.2 Télétransmission des Registres .......................................................................................................... 40 3.7 Recharger la Langue ............................................................................................................................. 40 3.7.1 Extraction et Visualisation des Transactions ...................................................................................... 41 3.7.2 Création de connaissements ( BOL) depuis les Transactions ............................................................ 41 3.8 Rapports MultiLoad II ............................................................................................................................ 42 3.8.1 Rapport de Configuration..................................................................................................................... 42 3.8.2 Rapport des Modules de Contrôle du débit ......................................................................................... 43 3.9 Paramètres de Mode Local uniquement.............................................................................................. 44 3.9.1 Invites Chauffeurs ................................................................................................................................ 44 3.9.2 Configuration du Produit ...................................................................................................................... 45 3.9.3 Carte d’Accès Chauffeur ...................................................................................................................... 46 3.9.4 Instructions relatives aux Risques ....................................................................................................... 47 3.10 Autres fonctions d’Outil de Configuration .......................................................................................... 47 3.10.1 Affichage GUI du FCM ..................................................................................................................... 48 3.11 Outils de Configuration des Fenêtres MultiMate ................................................................................ 49 3.11.1 Installation ........................................................................................................................................ 49 3.11.2 Connexion au MultiLoad II ............................................................................................................... 51 3.11.3 Fichier d’Invite de Paramètre de Téléchargement .......................................................................... 54 3.11.4 Création d’un Fichier de Configuration ............................................................................................ 56 3.11.5 Télécharger un Fichier de Configuration depuis un MultiLoad II .................................................... 58 3.11.6 Télétransfert d’un Fichier de Configuration vers un MultiLoad II ..................................................... 59 3.11.7 Mise à jour de l’Image du Logiciel interne dans un MultiLoad II .................................................... 60 CHAPTER 4 CONFIGURATION GÉNÉRALE ................................................................................................. 63 4.1 Vue d’ensemble ..................................................................................................................................... 63 4.2 Réglage des Communications ............................................................................................................. 63 4.3 Réglage du Réseau ................................................................................................................................ 66 4.4 Réglage Général du RCU ...................................................................................................................... 69 4.5 Réglage du RCU ..................................................................................................................................... 72 4.6 Réglage de TRACE ................................................................................................................................ 78 4.7 Installation des Equipements ............................................................................................................... 80 4.7.1 Installation du Quai .............................................................................................................................. 82 4.7.2 Réglage des valeurs prédéfinies ......................................................................................................... 85 4.7.3 Réglage du Compteur .......................................................................................................................... 95 4.7.4 Installation des Composants.............................................................................................................. 105 4.8 Réglage des Alarmes .......................................................................................................................... 111 4.8.1 Réglage Alarme Quai ........................................................................................................................ 114 4.8.2 Réglage des Alarmes Prédéfinies ..................................................................................................... 115 4.8.3 Réglage des Alarmes de Compteurs ................................................................................................. 116 4.8.4 Réglage des Alarmes du Composant ................................................................................................ 118 4.8.5 Réglages des Alarmes Additifs .......................................................................................................... 121 4.9 Définition et Affectation Locale des Produits .................................................................................. 123 4.10 Réglage des Produits .......................................................................................................................... 124 4.11 Définition des composants de Base .................................................................................................. 125 5 4.11.1 Définition des Recettes de Composants de Base ......................................................................... 126 4.11.2 Définition d’un Additif ..................................................................................................................... 127 4.12 Définition des Produits Commercialisables ..................................................................................... 129 4.13 Réglages des Produits Prédéfinis ..................................................................................................... 132 4.13.1 Nom Prédéfini ................................................................................................................................ 132 4.13.2 Affectation de Composants............................................................................................................ 133 4.13.3 Affectation d’Additifs ...................................................................................................................... 134 4.13.4 Affectation de Produits Autorisés .................................................................................................. 135 4.13.5 Ecran de Configuration d’Enregistrement des Produits disponibles à partir de l’Outil de Configuration .................................................................................................................................................. 136 4.13.6 Ecran de Configuration de Recette disponible à partir de l’Outil de Configuration ....................... 136 4.14 ID d'Accès ............................................................................................................................................. 137 4.15 Réglage du Logo du Client ................................................................................................................. 138 4.15.1 Chargement d’un Logo Client Incorpore ........................................................................................ 139 4.15.2 Télétransférer un Logo Client .BMP ............................................................................................. 139 4.16 Date et Heure du Système .................................................................................................................. 140 4.17 Impression ............................................................................................................................................ 141 4.18 Site GPSS ( uniquement ML II Mobile) ............................................................................................... 143 CHAPTER 5 CONTROLE DU DEBIT DU PRODUIT ..................................................................................... 145 5.1 Vue d’ensemble ................................................................................................................................... 145 5.2 Livraison de Produit Unique ............................................................................................................... 146 5.2.1 Haut débit........................................................................................................................................... 148 5.2.2 Déclenchement de la 1ère Etape ...................................................................................................... 148 5.2.3 Déclenchement de la 2ème Etape .................................................................................................... 149 5.2.4 Déclenchement Final ......................................................................................................................... 149 5.2.5 Vannes 2”-3” de Commande Numérique ........................................................................................... 149 5.2.6 Algorithme Adaptatif de Commande Numérique ............................................................................... 150 5.2.7 Vannes à Deux Etapes ...................................................................................................................... 150 5.2.8 Vannes Analogiques .......................................................................................................................... 151 5.3 Mélange Séquentiel (sauf SMP) ........................................................................................................ 152 5.3.1 Configuration du Mélange Séquentiel ............................................................................................... 153 5.4 Mélange Proportionnel (sauf SMP) .................................................................................................... 157 5.4.1 Configuration du Mélange Proportionnel ........................................................................................... 158 5.5 Mélange à Flux Latéral – Side Stream (sauf SMP) ........................................................................... 162 5.5.1 Configuration du Mélangeur à Flux Latéral Simple ........................................................................... 162 5.6 Mélange Hybride (sauf SMP) .............................................................................................................. 164 5.6.1 Flux Latéraux Multiples ...................................................................................................................... 164 5.6.2 Mélange Séquentiel à Flux Latéral .................................................................................................... 166 5.6.3 Mélange Proportionnel à Flux Latéral ................................................................................................ 168 5.7 Test des Compteurs à Flux Latéral (sauf SMP) ............................................................................... 170 5.8 Purge de Conduite (sauf SMP) ........................................................................................................... 171 5.9 Remarques concernant le Mélange Proportionnel (sauf SMP) ....................................................... 174 5.10 Etalonnage par Linéarisation du Coefficient de mesure ................................................................. 176 5.10.1 Coefficient de mesure Unique ....................................................................................................... 179 5.10.2 Règles Relatives aux Facteurs de Mesure .................................................................................... 179 CHAPTER 6 6.1 CONTROLE DES ADDITIFS..................................................................................................... 180 Vue d’ensemble ................................................................................................................................... 180 6 6.2 Cycles de l’Injecteur à Piston ............................................................................................................. 181 6.3 Attribution des Ports d’additifs .......................................................................................................... 182 6.3.1 Affectation des Ports d’Entrée et de Sortie d’Additifs ........................................................................ 182 6.4 Unités d’Additifs .................................................................................................................................. 182 6.5 Méthodes de Commande des Additifs .............................................................................................. 183 6.5.1 Méthode 1 – Piston Uniquement ....................................................................................................... 183 6.5.2 Configuration d’un Additif ” Piston Uniquement”................................................................................ 184 6.5.3 Methode 2 – Piston avec Entrée (Commutateur à Rétrosignal) ........................................................ 185 6.5.4 Configuration d’un Piston avec Entrée d’Additifs .............................................................................. 186 6.5.5 Methode 3 – Entrée du Générateur d’Impulsions .............................................................................. 187 6.5.6 Configuration d’un Additif avec Entrée du Générateur d’Impulsions ................................................. 187 6.5.7 Méthodé 4 – ADDITIF ANALOGIQUE ............................................................................................... 188 6.5.8 Configuration d’un additif analogique ................................................................................................ 188 6.5.9 Methode 5 – Compteur Usuel a Plusieurs Additifs ........................................................................... 189 6.5.10 Vannes d’Arrêt d’Additifs Uniquement ........................................................................................... 191 6.5.11 Configuration d’un Compteur Usuel à Plusieurs Additifs ............................................................... 192 6.6 Réglage Général des Additifs ............................................................................................................. 195 6.7 Etalonnage d’Additifs .......................................................................................................................... 203 6.7.1 Fonction d’Etalonnage d’Additifs ....................................................................................................... 203 6.7.2 Fonction d’Etalonnage Automatique .................................................................................................. 204 6.7.3 Etalonnage d’Additif avec Injecteurs de Type à Piston ..................................................................... 208 6.8 Calcul du Volume ou de l’Injection d’Additif .................................................................................... 209 6.9 Etalonnage d’Additif à Distance ......................................................................................................... 211 6.10 Ecran de Statut d’Additif ..................................................................................................................... 216 6.11 Fonctions de Purge d’Additifs ........................................................................................................... 217 6.11.1 Fonctions de Purge de Base ......................................................................................................... 217 6.11.2 Techniques de Purge de Colorant ................................................................................................. 219 6.11.3 Vannes d’Arrêt de Pompes de Purge ............................................................................................ 220 CHAPTER 7 7.1 7.2 7.3 7.4 Vue d’ensemble ................................................................................................................................... 223 Fonctionnement du Bras Oscillant .................................................................................................... 224 Logique de Relais et de Commutation .............................................................................................. 224 Configuration du Bras Oscillant ........................................................................................................ 226 CHAPTER 8 8.1 8.2 8.3 8.4 8.5 8.6 8.7 8.8 8.9 8.10 8.11 8.12 8.13 REGLAGE ET FONCTIONNEMENT DU BRAS OSCILLANT (SAUF SMP) ........................... 223 DIAGNOSTICS .......................................................................................................................... 228 Vue d’ensemble ................................................................................................................................... 228 Lecteur de Carte (sauf SMP) ............................................................................................................... 229 Lecteur iButton (sauf SMP)................................................................................................................. 231 Essai de Bouclage ............................................................................................................................... 232 Essai de Port Sériel ............................................................................................................................. 234 Essai Réseau ........................................................................................................................................ 236 Essai de Clavier ................................................................................................................................... 238 Essai d’Affichage ................................................................................................................................ 239 Essai Unicode ...................................................................................................................................... 240 Communications FCM ......................................................................................................................... 241 Communications PCM ......................................................................................................................... 242 Statut de l’Etat du FCM ....................................................................................................................... 243 Statut Etat du PCM .............................................................................................................................. 244 7 8.14 8.15 8.16 8.17 8.18 8.19 8.20 8.21 8.22 Diagnostics RCU .................................................................................................................................. 245 Diagnostics du Quai ............................................................................................................................ 246 Diagnostic de Valeurs Prédéfinies ..................................................................................................... 247 Diagnostic du Compteur ..................................................................................................................... 248 Essai de la Vanne de Régulation Numérique ................................................................................... 252 Diagnostic des Composants .............................................................................................................. 255 Diagnostic d’Additifs ........................................................................................................................... 256 Logique Personnalisée ....................................................................................................................... 258 Diagnostic du GPS (uniquement pour le MultiLoad II Mobile) ........................................................ 259 CHAPTER 9 POIDS ET MESURES ............................................................................................................... 260 9.1 Vue d’ensemble ................................................................................................................................... 260 9.1.1 Poids et Mesures ............................................................................................................................... 260 9.2 Restrictions d’Accès aux Paramètres des Poids et Mesures ......................................................... 261 9.3 Journal des Modifications des Poids et Mesures et Sécurité des Paramètres Météorologiques 262 9.4 Fonctions du Coefficient de Correction du Volume ........................................................................ 263 9.5 CALCUL DE LA MASSE ...................................................................................................................... 264 9.5.1 Sortie Nette d'Impulsions ................................................................................................................... 265 9.5.2 Sortie d'Impulsions de masse ............................................................................................................ 265 9.5.3 Livraison Grossière, Nette ou Masse ................................................................................................ 265 9.5.4 Calculateurs VCF Tableau API .......................................................................................................... 265 9.5.5 Affichage du Volume Net et Données Accessoires ........................................................................... 266 9.5.6 API MPMS Chapitre 11.1-2004/ajout à IP 200/04/ajout à ASTM D 1250-04 .................................... 266 9.5.7 Configuration de la température de Correction (CTL) ....................................................................... 266 9.6 Calcul de Livraison Directe du MultiLoad (un seul composant)..................................................... 291 9.7 Calculs de Mélanges Séquentiels du MultiLoad .............................................................................. 293 9.8 Calculs des proportions de Mélange MultiLoad ............................................................................... 296 9.9 Calculs des Mélanges MultiLoad Secondaires ................................................................................. 299 9.10 Calculs Séquentiels MultiLoad avec Mélange Proportionnel ......................................................... 302 9.11 Calculs MultiLoad Sequentiels avec Mélange Secondaire ............................................................. 306 9.12 Calculs MultiLoad de la Proportion pour le Mélange Secondaire .................................................. 310 9.13 Etalonnage de la Température des Compteurs ................................................................................ 313 9.14 Ecart de Température et Calculateur VCF......................................................................................... 315 9.15 Etalonnage de la Pression pour les Compteurs ............................................................................... 317 9.16 Etalonnage de la Densité .................................................................................................................... 319 9.17 Etalonnage de la Densité relative ...................................................................................................... 320 9.18 Etalonnage de la gravité API .............................................................................................................. 321 9.19 Etalonnage BSW1 ................................................................................................................................ 322 9.20 Etalonnage BSW2 ................................................................................................................................ 323 CHAPTER 10 AFFICHAGE ET REQUÊTES ................................................................................................... 325 10.1 Vue d’ensemble ................................................................................................................................... 325 10.2 Visualisation des Alarmes .................................................................................................................. 326 10.3 Visualisation des Totalisateurs .......................................................................................................... 327 10.3.1 Visualisation des Totalisateurs de la Valeur Prédéfinie ................................................................ 328 10.3.2 Visualisation des Totalisateurs de Compteur ................................................................................ 330 10.3.3 Visualisation des Totalisateurs de Composants ............................................................................ 332 10.3.4 Visualisation des Totalisateurs d’Additifs ...................................................................................... 334 10.4 Visualisation des Températures ........................................................................................................ 335 8 10.5 10.6 10.7 10.8 10.9 10.10 10.11 10.12 10.13 10.14 Visualisation des Pressions ............................................................................................................... 336 Visualisation de la Densité ................................................................................................................. 337 Visualisation de la Densité Relative .................................................................................................. 338 Visualisation BSW1 ............................................................................................................................. 339 Visualisation BSW2 ............................................................................................................................. 339 Visualisation de la gravité API........................................................................................................ 340 Visualisation des Transactions ...................................................................................................... 341 Visualisation du Journal des Changements des Poids et Mesures ........................................... 346 Visualisation du Journal des Messages du MultiLoad II ............................................................. 349 Visualisation du journal d’audits du MultiLoad II ......................................................................... 350 CHAPTER 11 11.1 11.2 11.3 11.4 11.5 11.6 11.7 CARTE SD................................................................................................................................. 352 Aperçu................................................................................................................................................... 352 Visualisation des Répertoires/Fichiers ............................................................................................. 353 Chargement Configuration ................................................................................................................. 355 Configuration de la sauvegarde ......................................................................................................... 356 Chargement du Logo........................................................................................................................... 357 Logiciel de chargement....................................................................................................................... 358 Données de diagnostic de Vidange (Dump) ..................................................................................... 359 CHAPTER 12 FONCTIONNEMENT ................................................................................................................. 360 12.1 Vue d’ensemble ................................................................................................................................... 360 12.2 Phases de Fonctionnement ................................................................................................................ 360 12.3 Accès par Carte Chauffeur ou Clavier ............................................................................................... 360 12.4 Fonctionnement de la Commande à Distance .................................................................................. 361 12.4.1 Phase d'Autorisation ...................................................................................................................... 361 12.4.2 Ecran d'Introduction de la Carte .................................................................................................... 361 12.4.3 Valeurs du Statut de Chargement ................................................................................................. 369 12.4.4 Fin de la Phase de Chargement .................................................................................................... 371 12.4.5 Bol Tms .......................................................................................................................................... 371 12.5 Fonctionnement en Mode Local (Autonome) ................................................................................... 371 12.5.1 Base de Données d’Access ID ..................................................................................................... 371 12.5.2 Base de Données des Produits ..................................................................................................... 372 12.5.3 Impression des Tickets de Comptage ........................................................................................... 372 12.5.4 Tâches Diverses ............................................................................................................................ 373 12.5.5 Configuration du MultiLoad II en Mode Local ................................................................................ 374 12.5.6 Fonctionnement en Mode Local .................................................................................................... 374 12.5.7 Autorisation Locale ........................................................................................................................ 375 12.5.8 Ticket de Comptage ....................................................................................................................... 376 12.5.9 Revenir au Mode à Distance ......................................................................................................... 376 12.6 Fonction d’Etalonnage Automatique de Contrôle ............................................................................ 377 12.6.1 Utilisation de la Fonction d’Etalonnage de Contrôle ...................................................................... 378 CHAPTER 13 13.1 13.2 13.3 13.4 13.5 LOGIQUE PERSONNALISÉE .................................................................................................. 383 Vue d’ensemble ................................................................................................................................... 383 Accès du MultiLoad II à la Logique Personnalisée .......................................................................... 384 Accès de l’Outil de Configuration du MultiLoad II à la Logique Personnalisée............................ 384 Rédaction de la Logique Personnalisée ............................................................................................ 385 fonctions en Temps Réel (RT) du MultiLoad II ................................................................................. 387 9 13.6 Fonctions Logiques ............................................................................................................................. 392 CHAPTER 14 14.1 14.2 14.3 14.4 14.5 14.6 14.7 14.8 14.9 14.10 Aperçu................................................................................................................................................... 394 Login ..................................................................................................................................................... 394 Website ................................................................................................................................................. 394 Journal des messages (Message Log) .............................................................................................. 396 W&M Change Log – Journal des changements Poids et Mesures ................................................ 396 Audit Log – Journal des audits .......................................................................................................... 396 Fichiers sur la carte SD ....................................................................................................................... 397 Télétransférer des fichiers vers la carte SD ..................................................................................... 397 Visualisation des Transactions .......................................................................................................... 398 Page Simulateur ............................................................................................................................... 399 CHAPTER 15 15.1 15.2 ASSISTANCE MULTILOAD ..................................................................................................... 401 Aperçu................................................................................................................................................... 401 Comment l’utiliser ............................................................................................................................... 401 CHAPTER 16 16.1 16.2 INTERFACE WEB ..................................................................................................................... 394 HISTORIQUE DES RÉVISIONS DU LOGICIEL ....................................................................... 402 Vue d’ensemble ................................................................................................................................... 402 Changements apportés au Logiciel ................................................................................................... 402 10 Sommaire des Figures Figure 2-1 Modules FCM II ................................................................................................................................... 20 Figure 2-2 Commutateurs Programme / Poids et Mesures de Type 1 ............................................................. 27 Figure 2-3 Interrupteurs de Programme / Poids et Mesures (W&M) de Type 2 ............................................... 28 Figure 2-4 Commutateurs Programme / Poids et Mesures de Type 3 ............................................................. 29 Figure 2.5 Commutateurs de Programme de Carte CPU et Poids et Mesures DIP Rev 1.0 ........................... 30 Figure 3-1 Ecran de Sélection de Fichier .......................................................................................................... 35 Figure 3-2 Menu de Configuration du Quai ....................................................................................................... 36 Figure 3-3 Menu de Configuration du RCU ...................................................................................................... 37 Figure 3-10 Configuration du Menu des Invites .................................................................................................. 44 Figure 3-11 Ecran de Configuration du Produit .................................................................................................. 45 Figure 3-12 Ecran Carte d’Accès ........................................................................................................................ 46 Figure 3-13 Ecran de Configuration des Risques ............................................................................................... 47 Figure 3-14 Graphique des Affectations des Entrées et Sorties ......................................................................... 48 Figure 3-15 Détail des Affectations des Entrées et Sorties ................................................................................ 48 Figure 5-1 Profil du débit ................................................................................................................................. 145 Figure 5-2 Profil des débits pour une Livraison de Produit Unique ................................................................ 146 Figure 5-3 Application Mélange Séquentiel .................................................................................................... 152 Figure 5-4 Application Mélange Proportionnel ................................................................................................ 157 Figure 5-5 Application Flux Latéral Simple ..................................................................................................... 162 Figure 5-6 Configuration Flux Latéral Simple ................................................................................................. 163 Figure 5-7 Application Flux Latéral Multiple .......................................................................................................... 164 Figure 5-8 Configuration Flux Latéraux Multiples ........................................................................................... 165 Figure 5-9 Application Mélange Séquentiel avec Flux Latéraux ..................................................................... 166 Figure 5-10 Configuration de Mélange Séquentiel avec Flux Latéraux ............................................................ 167 Figure 5-11 Application Mélange Proportionnel à Flux Latéral ......................................................................... 168 Figure 5-12 Configuration Mélange Proportionnel à Flux Latéral .................................................................... 169 Figure 5-13 Linéarisation du Coefficient de mesure ........................................................................................ 176 Figure 6-1 Schéma du Cycle du Piston........................................................................................................... 181 Figure 6-2 Injection d’Additifs .......................................................................................................................... 183 Figure 6-3 Vanne d’Injecteur Usuel - Schéma ................................................................................................ 189 Figure 6-4 Schéma Electrique avec Vanne d’Injecteur ................................................................................... 190 Figure.6-5 Schéma avec Vannes d’Arrêt pour l’Injection ................................................................................ 191 Figure 6-6 Schéma Electrique avec Vannes d’Arrêt comme Injecteurs ......................................................... 191 Figure 6-7 Surinjection d’Additifs .................................................................................................................... 199 Figure 6-8 Calcul de Vol/Inj ............................................................................................................................. 210 Figure 6-9 Cycle de purge de base ................................................................................................................. 217 Figure 6-10 Chargement Frontal de Colorant ................................................................................................... 219 Figure 6-11 Injecteur Monobloc et Station de Coloration.................................................................................. 220 Figure 6-12 Compteur d’Additif dans la Trajectoire de Purge ........................................................................... 221 Figure 6-13 Compteur d’Additif et Vanne d’Injecteur dans la Trajectoire de Purge ......................................... 222 Figure 7-1 Configuration du Bras Oscillant ..................................................................................................... 223 Figure 7-2 Socle de Relais FCM du Bras Oscillant ......................................................................................... 225 Figure 10-1 Ecran principal de Fichier de Visualisation des Transactions ....................................................... 341 Figure 12-1 Ecran de Commande des Valeurs Prédéfinies.............................................................................. 366 Chapitre 1 – Avant de commencer CHAPTER 1 11 AVANT DE COMMENCER A QUI S’ADRESSE CE MANUEL? Ce manuel est destiné aux personnes de votre entreprise qui installeront et utiliseront le système de MultiLoad II : les directeurs techniques, administrateurs de système, opérateurs de terminaux, techniciens, les personnes chargées de l’étalonnage du compteur volumétrique et les chauffeurs de l’installation. COMMENT SE PRESENTE CE MANUEL? Le MultiLoad II Utilisateur Manuel est classé d’après les procédures fonctionnelles. Il reflète plus ou moins la structure du menu du MultiLoad II. Chaque chapitre traite d’une procédure unique ou d’un groupe de procédures similaires à effectuer pour installer et utiliser le système en fonction de vos besoins. Le tableau ci-dessous reprend un plan détaillé des informations traitées dans ce manuel. Chapitre 1. Avant de commencer 2. Description du système 3. Outil de configuration GUI 4. Configuration générale 5. Contrôle du débit (débit) du produit 6. Contrôle des additifs 7. Diagnostics 8. Poids et Mesures 9. Affichage et requêtes 10. Opération 11. Logique personnalisée Public Tous Sujets traités Conventions utilisées dans ce manuel. Tous Description du système, modes de fonctionnement local et à distance, composants du système, navigation, entrée des données et démarrage. But, accès, fonctions de menu, navigation et commande locale - uniquement configuration des paramètres. Réglage des communications, réglage du matériel, installation du produit, valeurs prédéfinies, étalonnage des additifs, profils d’accès, date et heure du système. Configuration du contrôle du débit pour une livraison unique de produit et étalonnage. Admin. du système, expert en installation Admin. du système, expert en installation Admin. du système, expert en installation Expert en additifs Configuration pour différents méthodes de commande des additifs: uniquement piston, entrée du générateur d’impulsion, etc. Admin. du système, techniciens, électriciens Test du lecteur de carte; diagnostics pour quai, valeurs prédéfinies, compteurs, composants et additifs. Admin. du système, techniciens Opérateurs Résolution de l’impulsion de comptage, facteurs de mesure / étalonnage, étalonnage de la température Visualisation des valeurs prédéfinies, totalisateurs et températures de compteur. Chauffeurs, opérateurs Phases d’opération, entrée clavier, opérations locales de commande, opération de télécommande, autorisation TMS, RCU ditto. Comment personnaliser l’activation des sorties du FCM en utilisant des expressions de logique booléenne. Admin, analystes, programmeurs Chapitre 1 – Avant de commencer 12 CONVENTIONS DE DOCUMENTATION Les conventions qui suivent sont utilisées tout au long de ce manuel. 1.1.2 CAPTURES D’ECRAN Les données fournies le sont purement à titre d’exemple. 1.1.3 PROCEDURES Les procédures à suivre dans l’ordre sont indiquées étape par étape. En général, le résultat d’une action de l’utilisateur s’affiche à la ligne suivante. Par exemple: 1. A partir du menu de configuration, choisir Equipment Setup. Appuyez sur Enter. Le menu “Equipment Setup” s’affiche. Error! Reference source not found. 2. Sélectionnez si vous désirez tout voir (=ALL) ou un paramètre précis comme par exemple API. Appuyez sur Enter. EQUIPMENT SETUP MENU Bay Preset Meters Components Additives 3. Appuyez sur Next jusqu’à ce que « Compteurs » soit mis en surbrillance. Appuyez sur Enter. L’écran « Compteur Setup » s’affiche: Next Prev Exit Enter Chapitre 1 – Avant de commencer PRE #1 MTR #1 SETUP Flow Control Module#: 0 Side-Stream on Mtr#: 0 Side-Strm on Any Mtr: DISABLD Meter Type: VOL PUL Max Quad Errors: 10 Reset Quad Errors: 10000 Low Flow Alarm Rate: 10 Low Flow Alarm Time: 10.000 Excess Flw Alrm Rate: 800 Minimum Flow Rate: 50 Maximum Flow Rate: 650 Low Flow DB Rate: 40 High Flow DB Rate: 40 1st Stage DB Rate: 40 ALERTES INFORMATIVES Next Prev Exit Enter Le manuel utilise les conventions graphiques suivantes pour attirer l’attention du lecteur sur certains types d’informations: Remarques: informations complémentaires, additionnelles ou “bonnes à savoir” pas vraiment indispensables pour la tâche ou le sujet actuels. Recommandations: avertissent de la possibilité de résultats inattendus quand vous effectuez une action. Elles sont également utilisées pour vous informer de choses importantes à garder à l‘esprit. ! Avertissements: informent des dommages éventuels qui pourraient survenir lorsque vous effectuez ou n’effectuez pas une action particulière. Il faut donc faire attention lorsque vous rencontrez ce symbole ! CONVENTIONS TYPOGRAPHIQUES Les conventions typographiques qui suivent sont utilisées pour au long du manuel. Gras Italique Indique ce que vous devez taper ou le(s) bouton(s) sur le(s)quel(s) vous devez appuyer sur le clavier du RCU du MultiLoad II. Exemple: "Introduire 00000 et appuyez sur la touche Next." Dans les textes de sujet, les parties en italique indiquent un mot-clé du MultiLoad II ou un terme industriel. Exemple: "L’écran représente une liste à choix multiple de la sélection d’articles." L’italique est également utilisée pour l’accentuation. 13 Chapitre 2 –Déscription du système CHAPTER 2 2.1 14 DESCRIPTION DU SYSTEME VUE D’ENSEMBLE Ce chapitre vous présente le système MultiLoad II en définissant ses capacités, en décrivant ses modes de fonctionnement, en identifiant ses principaux composants et en traitant de la navigation de l’interface utilisateur. Les sujets principaux qu’il couvre sont: - Vue d’ensemble du système - Trois modes de fonctionnement - Composants du système - Naviguer dans le système - Commutateur du contrôle d’accès - Démarrage - Outil de configuration MultiLoad II (MultiMate) Chapitre 2 –Déscription du système 2.2 VUE D’ENSEMBLE DU SYSTEME Le MultiLoad II est conçu pour gérer des chargements par travée multiples pour livraison de produits directs ou mélangés. Le système fonctionne en conjonction avec le système Toptech TMS (mode de traitement à distance), en mode local (autonome) ou connecté au nuage (mode UAP). Le MultiLoad II est configuré pour manipuler: 12 bras de chargement par travée 5 mètres par bras de chargement, 6 composants pour le mélange proportionnel. 8 composants par bras de chargement, 8 composants pour le mélange séquentiel. Mélange séquentiel, proportionnel et en dérivation (mélange proportionnel ou non) 16 injecteurs d’additifs par bras de chargement Vannes de commande numériques à 2 étapes, analogiques de 4-20 mA Entrées de température RTD Entrée 4-20 mA pour la densité, la densité relative, la gravité API, la pression, BSW ou proportion d’eau Communications Ethernet Impression Ethernet Le MultiLoad II SMP (configuration unique du compteur) est un ensemble économique destiné à supporter des applications avec compteur unique / bras de chargement unique. Le système peut fonctionner en conjonction avec le système Toptech TMS (mode de traitement à distance), en mode local (autonome) ou en mode UAP (TDS). Le MultiLoad II SMP est configuré pour manipuler : 1 bras de chargement 1 compteur 8 composants (facteurs de compteurs différents pour chaque produit) Pas de mélange. 2 injecteurs d’additif Vannes de commande numériques à 2 étapes, analogiques de 4-20 mA Entrée de température RTD Entrée de 4-20 mA pour la densité, la densité relative, la gravité API, la pression ou BSW Communications Ethernet Impression Ethernet 15 Chapitre 2 –Déscription du système 2.3 TROIS MODES DE FONCTIONNEMENT Le MultiLoad II peut être configuré pour fonctionner en trois modes différents: Mode de commande local (autonome) – Les informations sur les produits et les accès sont enregistrées dans la mémoire non volatile du MultiLoad II. Mode télécommande – Les informations sur les produits et les accès proviennent des bases de données TMS ou d’un autre système informatique à distance. UAP – En interface avec un ordinateur hôte dans le nuage qui a toutes les fonctionnalités TAS de base. 2.3.1 MODE DE COMMANDE LOCALE En mode local, le RCU du MultiLoad II lit la carte de proximité du chauffeur (sauf pour le SMP) ou lui demandera d’introduire son code d’accès. La carte d’accès du chauffeur ou son code personnel et le code PIN doivent correspondre aux données enregistrées dans la base de données de ce chauffeur dans la mémoire non volatile du RCU du MultiLoad II. Quand ces vérifications sont terminées, le MultiLoad II agit sur sa configuration interne des invites supplémentaires. Le MultiLoad II possède 4 invites configurables qui peuvent être présentées au chauffeur. Une fois ces invites d’entrée de données enregistrées, le chargement est autorisé. Les caractéristiques du fonctionnant en mode local sont: - 300 cartes de chauffeur/ profils d’accès et codes PIN associés. - 10.000 archives de transaction complètes avec produits commercialisables, détail des composants et détail des additifs. - 5 invites personnalisables par l’utilisateur avec, pour résultat, des données sauvegardées pour chaque transaction. - 33 recettes de produits par compteur/bras de chargement. - Ticket de comptage - ticket combiné pour tous les levages dans un format configurable par l’utilisateur - Propriétés d’étalonnage du compteur, des additifs et de la température. - Journal des 1.000 dernières modifications de paramètres des poids et mesures. Egalement enregistrés sur la carte SD pendant 90 jours. - Config Change Log des 500 derniers changements de paramètres y compris les paramètres W&M. Egalement enregistrés sur la carte SD pendant 90 jours. 2.3.2 MODE DE TÉLÉCOMMANDE Lorsqu’il est en interface avec un système informatique à distance, le nombre d’enregistrements de chauffeurs, d’invites client et de recettes est virtuellement illimité. 2.3.3 MODE UAP Il s’agit d’une interface avec le nuage. Il a toutes les fonctionnalités de base d’un système TAS dans le nuage. 16 Chapitre 2 –Déscription du système 2.4 COMPOSANTS DU SYSTEME La famille de produits Toptech MultiLoad II est disponible dans les configurations suivantes : MultiLoad II – bras multiple, système de mélange de composants multiple MultiLoad II SMP (configuration unique du compteur) – 1 bras, système de mélange composant unique. Le matériel local se connecte au système par une carte interne des entrées / sorties, plusieurs FCM (modules de commande du débit) externes ou une combinaison des deux. 2.5 RCU DU MULTILOAD II Le bloc de télécommande (RCU) du système MultiLoad II est l’interface du chauffeur avec le système qui effectue toutes les commandes ; il effectue toutes les commandes de processus de haut niveau, contient toutes les informations relatives à la configuration aux totalisateurs et aux journaux des événements. L’interface du chauffeur contient un clavier, un affichage et un lecteur de carte de proximité (sauf pour le SMP). 2.5.1 2.5.2 BOÎTIERS RCU DISPONIBLES AVEC LE MULTILOAD II. Boîtier de division 2 (avec carte entrées / sorties I/O en option) Boîtier lumineux antidéflagrant de division 1/zone 1 (EXL) (avec carte entrées / sorties en option) BOÎTIERS RCU DISPONIBLES AVEC LE MULTILOAD II SMP Boîtier antidéflagrant de division 1/ zone 1 avec carte interne entrées / sorties (sans lecteur de carte) 17 Chapitre 2 –Déscription du système 18 2.6 FCM EXTERNE (MODULE DE COMMANDE DE DEBIT) Le MultiLoad Flow Control Module (FCM) est un appareil du dernier cri qui apporte le maximum de matière de traitement, flexible et modulaire, du contrôle du débit. Le FCM contient son propre microprocesseur pour la commande numérique des soupapes, le comptage des impulsions du compteur et la factorisation, l’injection d’additifs, les permissions de pompe et de compteur, etc. en tant que composant principal du MultiLoad, le FCM fonctionne comme le « preset on a card ». Sa conception hautement modulaire permet de répondre à vos besoins actuels de contrôle de débit et de l’étendre aisément et à peu de frais lorsque vos besoins augmentent. Qu’il s’agisse d’un simple chargement de produit ou de mélange séquentiel, le MultiLoad peut traiter toutes vos exigences en matière de contrôle de débit – maintenant et à l’avenir. Le but premier du FCM est de fournir un contrôle maximal d’une section unique de mesure. Un FCM contrôle une section de mesure. Les FCM peuvent être branchés en réseau pour former des mélanges proportionnels ou séquentiels de composants multiples ou pour une livraison de produit simple sur des bras multiples. Pr ess 'A' key t o Begi n. . . MultiLoad RCU T o p t e c h Sy s t e m s , I n c . Rem ot e Cont r ol Uni t 1 2 3 4 5 6 B Pr evious 7 8 9 C A Abor t 0 CL R D Ent er Next TX M FCM 1 TX M FCM 2 TX FCM 3 M Chapitre 2 –Déscription du système 2.7 FCM II Le module de commande du débit (FCM) fait partie intégrante du système MultiLoad. Le FCM a son propre microprocesseur pour la commande de la vanne numérique/analogue, le comptage des impulsions au compteur et la factorisation, l’injection d’additifs, les permissifs de la pompe et du compteur, les entrées / sorties à but général DC & AC, l’entrée RTD, l’entrée/sortie 4-20 mA, etc. L’utilisation des FCM vous permet d’étendre le contrôle bien au-delà des limites des boîtiers bien chers en métal lourd qui s’accumulent aujourd’hui sur les quais de chargement. Vous pouvez en acheter autant que vous voulez et les disposer là où vous en avez besoin. Leur conception permet de compresser significativement les frais de matériel et d’installation par rapport aux configurations classiques. Si vous devez ajouter une configuration à votre voie de chargement, vous n’êtes pas obligés d’acheter, de câbler et d’installer tout un appareil préconfiguré. Il vous suffit d’accrocher un ou plusieurs de ces modules de commande du débit dans le boîtier du FCM et de le configurer en conséquence. Non seulement le FCM II apporte toutes les fonctionnalités déjà présentes dans les blocs des générations précédentes, mais en plus il introduit toute une série de nouvelles caractéristiques dans un nouvel emballage compact. Construction modulaire – Le FCM II existe en huit variétés (représentées plus loin). Cette construction modulaire simplifie le processus de configuration des FCM selon l’équipement sur les quais de chargements en attribuant à chaque modèle de FCM II la quantité exacte d’entrées/ sorties pour l’objectif recherché. De plus, les FCM II se montent sur un rail DIN et n’ont pas besoin de câblage entre les différents appareils ; les communications 24 Vdc et de séries sont à bus, ce qui simplifie considérablement l’installation et le câblage. Emballage compact - Les FCM II occupent considérablement moins de place que la génération précédente. Le plus petit format fait 1/3 à 1/6 de la taille de l’appareil d’origine, ce qui permet d’augmenter le nombre d’entrées / sorties par boîtier et de monter plusieurs FCM II dans un boîtier antidéflagrant compact. Compatibilité – Le FCM I et le FCM II utilisent le même protocole et coexistent sur le même bus RS-485. En outre, les FCM II sont compatibles avec les générations précédentes de FCM, ce qui leur permet de remplacer des appareils FCM vieillis. De plus, le FCM II est conçu pour fonctionner de la même façon avec tous les produits MultiLoad. FCM II se compose de 8 types différents de modules: 19 Chapitre 2 –Déscription du système 20 4DCIN/4ACOUT: 4 entrées DC (5-30 VDC), 4 sorties AC (85-250 VAC) 6ACIN: 6 entrées AC (90-140 VAC) ou (180-250 VAC) 6ACOUT: 6 sorties AC (85-250 VAC) 6DCIN: 6 entrées DC (5-30 VDC) 6DCOUT: 6 sorties DC (0-30 VDC) ANALOG/4DCIN/4ACOUT: entrée RTD, entrée 4-20 mA, sortie 4-20mA, 4 entrées DC (5-30 VDC), 4 sorties AC (85-250 VAC) Figure 2-1 Modules FCM II Chapitre 2 –Déscription du système 2.8 CARTE INTERNE DES ENTREES ET SORTIES (I/O) Tous les boîtiers RCU peuvent supporter l’installation d’une carte interne entrées /sorties (I/O). La fonctionnalité de base de la carte I/O reflète un FCM externe mais en y ajoutant une entrée de 4-20 mA, une sortie 4-20mA et plusieurs entrées et sorties discrètes supplémentaires. Une seule carte I/O peut permettre de gérer un système. 21 Chapitre 2 –Déscription du système 2.9 22 CARTE INTERNE I/O A DEUX COMPTEURS Tous les boîtiers RCU, y compris le boîtier antidéflagrant SMP division 1 / zone 1 peuvent supporter l’installation d’une carte interne I/O à deux compteurs. La fonctionnalité de base de la carte I/O à 2 compteurs reflète les fonctions de deux FCM externes mais propose plusieurs entrées et sorties supplémentaires par rapport à un FCM. Une carte interne I/O à deux compteurs peut assurer la commande de deux systèmes maximum. 1 5 4 1 1 4 1 5 4 1 1 4 6 1 6 1 4 1 Chapitre 2 –Déscription du système 2.10 23 NAVIGUER DANS LE SYSTEME: Cette section décrit comment naviguer dans le système, sélectionner les valeurs locales, introduire des données et activer ou désactiver des options. Remarque: Toutes les séquences inconnues ou non autorisées d’activations de commutateurs ou de touches sont rejetées et n’ont aucun impact sur le logiciel ou les données de mesure. 2.10.1 MENUS ET ECRANS Le menu principal du MultiLoad II est représenté ci-dessous. A partir de celui-ci, sélectionnez l’une des quatre fonctions principales. M A I N M E N U Configuration Diagnostics Views and Inquiries SD Card Error! Reference source not found.La barre en surbrillance inverse indique la sélection actuelle. Appuyez sur Next pour sélectionner Diagnostics, puis appuyez sur Enter pour aller au menu Diagnostics. Next Prev Exit Enter Error! Reference source not found. Pour les options du menu et les éléments de l’écran des fonctions, appuyez sur la touche Next, ce qui fera bouger la barre de sélection vers le bas ; si vous appuyez sur la touche Prev (Previous), la barre bouge vers le haut. Pour revenir au menu principal, appuyez sur EXIT. Pour retourner à n’importe quel écran précédent, appuyez sur la touche EXIT. Remarque : L’écran du lecteur de carte (Card Reader) peut apparaitre sous forme d’un lecteur iButton selon le mode de lecteur de carte choisi. 2.10.2 MODIFICATION DE CHAMPS ET ENTRÉE DE DONNÉES Tous les champs de MultiLoad II ont été prédéfinis en usine. Il existe deux types de champs, les champs à plusieurs valeurs et les entrées de données. Les champs à plusieurs valeurs offrent plusieurs choix. Parcourez les choix en appuyant sur la touche Enter. Pour les champs d’entrée de données, vous avez besoin d’entrer une valeur se situant dans un intervalle d’application donné. Dans l’exemple ci-dessous, le champ de l’adresse RCU a été mis en exergue. Chapitre 2 –Déscription du système 24 RCU GENERAL SETUP RCU Address: 001 Card Reader Type: DISABLD Remote Processing: StndAln Swing Arm Secondary: DISABLD Password #1: ******* Password #2: ******* Password #3: ******* Password #4: ******* Password #5: ******* Modem Init: AT&F0&B1&C1&D0S0=1 Modem Dial: Host Login: TDSTEST TDSTEST Error! Reference source not found. Terminal Name: Toptech TerminalTruck Number: Next Prev Exit Enter Appuyez sur ENTER pour choisir le champ. Un curseur clignotant vous invite à y entrer une valeur. Next Prev Exit Enter RCU GENERAL SETUP RCU Address: █ Card Reader Type: DISABLD Remote Processing: StndAln Swing Arm Secondary: DISABLD Password #1: ******* Password #2: ******* Password #3: ******* Password #4: ******* Password #5: ******* Modem Init: AT&F0&B1&C1&D0S0=1 Modem Dial: Host Login: TDSTEST TDSTEST TerminalError! Name: Toptechsource Terminal Reference not found. Truck Number: Next Prev Exit Enter Enter Exit Chapitre 2 –Déscription du système 25 Introduisez la nouvelle valeur (ex. 123) et appuyez sur ENTER. La nouvelle valeur s’affiche à l’écran. RCU GENERAL SETUP RCU Address: 123█ Card Reader Type: DISABLD Remote Processing: StndAln Swing Arm Secondary: DISABLD Password #1: ******* Password #2: ******* Password #3: ******* Password #4: ******* Password #5: ******* Modem Init: AT&F275324442=1 Modem Dial: Host Login: TDSTEST TDSTEST Terminal Name: Toptech Terminal Error! Reference source not found. Truck Number: En utilisant le même écran comme exemple, si vous sélectionnez la ligne “Remote Processing “et que vous Next Prev ExitpourEnter appuyez sur ENTER, utilisez les touches NEXT ou PREV basculer entre les valeurs ENABLED et DISABLD, comme illustré ci-dessous. Vous devez ensuite appuyer sur ENTER pour faire valider le choix désiré. Enter Exit RCU GENERAL SETUP RCU Address: 001 Card Reader Type: DISABLD Remote Processing: StndAln Swing Arm Secondary: DISABLD Password #1: ******* Password #2: ******* Password #3: ******* Password #4: ******* Password #5: ******* Modem Init: AT&F0&B1&C1&D0S0=1 Modem Dial: Host Login: TDSTEST TDSTEST Terminal Name: Toptech Terminal Error! Reference source not found. Truck Number: Les paramètres affichés en ROUGE sont des valeurs contrôlées de Poids et de Mesures (W&M). Le Nextpermettre Prev des Exit Enter commutateur W&M doit être actif pour modifications. Tout changement apporté aux mesures contrôlées de poids et mesures doivent être enregistré dans le Journal des Changements de poids et mesures. Chapitre 2 –Déscription du système 26 RCU SETUP Preset Slct Timeout: Pixel Test: Meter Proving Mode: W&M Key FCM#: Program Key FCM#: Startup Keypad Locked: RCU Address: 0 DISABLD DISABLD DISABLD DISABLD DISABLD 001 Error! Reference source not found. Next Prev Exit Enter Dans les écrans de configuration RCU, Trace, Bay, Preset, Component, Meter et Additives, les paramètres surlignés en JAUNE indiquent des valeurs qui ont été modifiées par rapport aux valeurs usine par défaut. 2.11 COMMUTATEUR DE COMMANDE D’ACCES Le MultiLoad II supporte des commutateurs externes de commande d’accès. Ce type de commutateur limite l’accès aux paramètres du mode programme et aux modifications aux poids et mesures (valeurs affichées en rouge). Il existe trois types de commutateurs externes qui peuvent tous être scellés et/ou verrouillés pour éviter d’accéder au mode de programme et de changer des paramètres contrôlés des poids et mesures. Dans “Program Mode”, l’opérateur a accès aux éléments suivants: - paramètres du menu configuration - menu “Diagnostics” et ses fonctions - d’autres procédures administratives, comme par exemple les alarmes d’effacement de niveau élevé. Pour avoir accès au “Program Mode”, l’opérateur de la borne MultiLoad II doit: 1. Placer le commutateur Program Mode en position active. 2. Sur l’écran de départ, introduire son code de sécurité (le code par défaut étant le 000000) et appuyer sur la touche <Next>. Il se peut que vous deviez contacter votre bureau local des Poids et Mesures suite à la rupture du scellé ou la modification de paramètres. Cela ne se fait en général qu’au cours des procédures d’étalonnage des compteurs et de la température du terminal. Chapitre 2 –Déscription du système 2.11.1 27 COMMUTATEURS PROGRAMME /POIDS ET MESURES (W&M) DE TYPE 1 Les commutateurs de type 1 se composent de deux commutateurs externes séparés, l’un pour l’accès au mode programme et l’autre pour l’accès aux changements de poids et mesures. Chaque commutateur dispose d’un clapet externe qui se replie vers le bas qui peut être verrouillé ou scellé avec un fil ou un plomb de sécurité pour empêcher le commutateur de passer en mode actif. Les caches seront clairement marqués “W&M” ou “Program” pour indiquer leur fonction précise. Figure 2-2 Commutateurs Programme / Poids et Mesures de Type 1 Chapitre 2 –Déscription du système 2.11.2 28 COMMUTATEURS PROGRAMME / W&M DE TYPE 2 Les commutateurs de type 2 se composent d’un seul commutateur externe à 3 positions, chacune d’entre elles correspondant à un mode de fonctionnement. Le commutateur a deux clapets pliables externes qui limitent sa rotation comme le montre la figure ci-dessous. Ces clapets peuvent être scellés ou verrouillés avec un fil ou un plomb de sécurité pour empêcher qu’ils ne passent en actif. Ils seront également marqués comme “W&M” ou “Program” pour indiquer leur fonction précise. Figure 2-3 Interrupteurs de Programme / Poids et Mesures (W&M) de Type 2 Chapitre 2 –Déscription du système 2.11.3 29 COMMUTATEURS PROGRAMME / W&M DE TYPE 3 Les commutateurs de type 3 se composent de deux verrous magnétiques externes distincts, l’un pour avoir accès au mode programme, l’autre pour avoir accès aux modifications poids et mesures. L’accès au programme ou aux poids et mesures se fait en retirant le boulon correspondant. Il y a un trou dans chaque boulon pour y passer un fil ou un plomb de sécurité permettant de détecter toute tentative d’accès non autorisé. Les deux boulons ont également un clapet pliable extérieur qui peut être verrouillé pour empêcher que l’on ne retire un boulon. Le clapet doit également être marqué “W&M” ou “Program” pour indiquer la fonction précise de chaque boulon. Figure 2-4 Commutateurs Programme / Poids et Mesures de Type 3 Chapitre 2 –Déscription du système 2.11.4 30 COMMUTATEUR MODE PROGRAMME / POIDS ET MESURES DIP Sur la carte CPU, il y a deux commutateurs DIP (double rangée de broches) permettant de fermer les contacts d’interrupteur « Program Mode / W&M ». S’il n’y a pas de commutateur externe « Program Mode / W&M » installé sur le MultiLoad II, il faut utiliser ces commutateurs DIP sur la carte CPU pour pouvoir accéder au mode programme et au Poids et Mesures (W&M). Les commutateurs sont numérotés de 1 à 4; le n°1 est le plus proche de l’avant du boîtier (en haut de la photo) et le n° 4 vers le fond de celui-ci (bas de la photo). Lorsque le commutateur est en position ON, il est actif. Le commutateur est mis sur ON en le poussant vers la droite et sur OFF en le poussant vers la gauche. Le commutateur n° 3 est celui du mode programme. Le commutateur n°4 est celui de l’accès au Poids et Mesures (W&M). Dans la figure ci-dessous, le commutateur du mode programme est sur actif, contrairement au commutateur W&M. entrée de commutateur est considérée comme active lorsque soit le commutateur DIP OU le Une commutateur externe est actif (ON). Votre inspecteur des Poids et Mesures peut demander à vérifier que le commutateur DIP 4 (celui du bas) est bien en position OFF (poussé vers la gauche) avant de sceller le boîtier MultiLoad II pour s’assurer que les paramètres W&M sont à l’abri de toute fausse manœuvre. Figure 2.5 Commutateurs de Programme de Carte CPU et Poids et Mesures DIP Rev 1.0 Figure 2.6 Programme Rev 2.0 de carte CPU et commutateurs W&M DIP Chapitre 2 –Déscription du système 2.11.5 31 2.10.5 COMMUTATEURS LOCAUX « PROGRAM MODE / W&M » Le MultiLoad II peut également accepter des insertions locales aux commutateurs de mode programme et d’accès aux poids et mesures. Le “W&M Key FCM#” et le “Program Key FCM#” dans la liste des paramètres W&M du RCU (bloc de télécommande) permettent à n’importe quelle position d’entrées/sorties locale de servir de source d’entrée de commutateur. Référez-vous à Poids et Mesures pour de plus amples informations. un commutateur externe est raccordé au MultiLoad II comme commutateur d’accès W&M, il pourra être Sidemandé à l’installateur de sceller le boîtier du commutateur et tous les points de jonction du conduit entre le commutateur et le MultiLoad II pour s’assurer que les paramètres Poids et Mesures ne soient pas modifiés. Consultez les Poids et Mesures locaux pour plus de détails. entrée commutateur sera considérée active si le commutateur externe OU un point I/O configuré est Une actif (ON). Votre inspecteur des Poids et Mesures pourra demander de vérifier le paramètre “W&M Key FCM#” avant de sceller le commutateur Poids et Mesures du MultiLoad II pour s’assurer que ces paramètres sont bien à l’abri de toute fausse manœuvre. - Si aucun commutateur externe W&M n’a été installé, IL FAUT DESACTIVER ce paramètre. - Si un commutateur externe W&M a été installé, ce paramètre DOIT indiquer le port des entrées/sorties I/O local correct. ALLEZ À PROGRAM MODE -> CONFIGURATION -> RCU SETUP (PAGE VERS LE BAS) RCU SETUP Measure on Load Scrn: DISABLD Status Scrn Lockout: ENABLED Load Screen Timeout: 60 Preset Slct Timeout: 0 Pixel Test: DISABLD Meter Proving Mode: DISABLD W&M Key FCM#: DISABLD Program Key FCM#: DISABLD RCU Address: 001 Next Prev Exit Enter Chapitre 2 –Déscription du système 2.12 32 DEMARRAGE Quand vous êtes sorti du mode programme et que vous mettez pour la première fois le RCU du MultiLoad II en route, l’identification du microprocesseur s’affichera pendant quelques secondes. M.u.l.t.i.L.o.a.d. .I.I. . . v3.31.xx ............................Sep xx 2013 Copyright(c) 2013 Toptech Systems, Inc. M.u.l.t.i.L.o.a.d. .S.M.P. . v3.31.xx ............................Sep xx 2013 Copyright(c) 2013 Toptech Systems, Inc. MultiLoad II affichera l’écran d’invites d’accès, indiquant que l’appareil est en mode de fonctionnement. Error! Reference source not found. Error! Reference source not found. Chapitre 2 –Déscription du système 33 Lorsque l’accès au mode programme est autorisé, (voir Commutateur de Commande d’Accès), le personnel agréé peut rentrer dans le mode programme à partir de cet écran en tapant 00000 et en appuyant sur la touche NEXT. Le menu principal s’affiche alors: Error! Reference source not found. Le reste de ce manuel traite des fonctions disponibles à partir du menu principal du MultiLoad II. Pour sortir du menu principal, appuyez sur EXIT. Quand vous êtes sorti de ce menu, le MultiLoad II se réinitialise. L’écran avec bannière MultiLoad II apparaîtra brièvement avec le numéro de version du logiciel interne. 2.13 PARAMETRES DE CONFIGURATION Les écrans de configuration du MultiLoad II contiennent des champs de configuration définissant le système de commande des paramètres. Les paramètres de configuration sont sauvegardés dans la mémoire non volatile du MultiLoad II. 2.14 OUTIL DE CONFIGURATION DU MULTILOAD II MultiLoad II dispose d’une Interface Graphique Utilisateur en option (GUI), outil de configuration permettant de configurer le système à partir d’un PC. Cet outil vous permet de créer et de conserver des fichiers de configuration et de télétransmettre et télécharger ces fichiers entre le PC et le MultiLoad II. Cet outil permet également le chargement de nouvelles images logiciel internes au fur et à mesure qu’elles sont disponibles. Vous trouverez des informations complémentaires sur l’outil de configuration du MultiLoad II au Chapitre 3. 2.15 PARAMETRES USINE PAR DEFAUT S’il s’avérait nécessaire de reparamétrer le MultiLoad II en paramètres usine par défaut, cela peut se faire de la façon suivante : #1. Activez le commutateur poids et mesures W&M (retirez le boulon W&M). #2. Débranchez l’alimentation du MultiLoad II. #3. Commencez par appuyer plusieurs fois sur la touche “CLR” tout en rebranchant le MultiLoad II. #4. Arrêtez de pousser sur la touche “CLR” lorsque vous voyez “Setting Factory Defaults” qui s’affiche. Remarque: Ce reparamétrage aux valeurs par défauts usine sera enregistré dans le journal des poids et mesures. Les totaliseurs, le journal W&M et le “journal légal” ne seront PAS effacés si vous reparamétrez les paramètres par défaut usine. Chapitre 3 –Outil de configuration GUI CHAPTER 3 OUTIL DE CONFIGURATION GUI 3.1 VUE D’ENSEMBLE L’outil de configuration GUI du MultiLoad II se caractérise par une Interface Graphique Utilisateur menant aux fonctions de configuration du MultiLoad II. Plusieurs versions de cet outil ont été écrites pour TMS 5, TMS 6 et Microsoft Windows. Cet outil logiciel peut être utilisé lorsque le MultiLoad II est configuré pour le mode à distance, le mode local (autonome) ou le mode UAP. L’un des avantages majeurs de l’outil de configuration est sa faculté d’enregistrer la configuration pour une unité de MultiLoad II sur un disque dur qui peut être sauvegardé. Si vous perdiez la configuration du MultiLoad II, ou s’il était abîmé, toute la configuration pourrait être récupérée vers le matériel de remplacement en quelques minutes. Autres avantages de l’utilisation de l’ensemble de configuration GUI: Tous les champs de paramètres liés sont affichés sur un seul écran GUI. Possibilité de créer et de gérer de multiples fichiers de configuration. La plupart des tâches de configuration peuvent s’effectuer à partir de la console TMS (en mode à distance) ou depuis un ordinateur isolé. Les modifications de configuration peuvent être télétransmises au MultiLoad II. Les rapports de configuration peuvent être affichés ou imprimés. L’aide sur l’écran et les champs est facilement disponible. 34 Chapitre 3 –Outil de configuration GUI 3.2 35 ACCES DEPUIS LE TMS 5 GUI 1. Depuis le menu principal TMS, sélectionnez: 2. Facility | Facility Configuration Menu | Load Rack Communications | TLC MultiLoad II Configuration. 3. Un écran de configuration vierge apparaît. 4. Ouvrez le menu Fichiers (« File ») sur la barre de menu et choisissez “Open” (ouvrir). 5. Une boîte de dialogue de sélection de fichier s’affiche. Figure 3-1 Ecran de Sélection de Fichier 6. Cliquez sur la flèche du menu déroulant à droite du champ « File Name » (nom de fichier). 7. Sélectionnez le nom de fichier qui apparaît. Ce fichier a été préconfiguré chez Toptech pour votre facilité. Il peut être modifié et vous pouvez créer de nouveaux fichiers de configuration pouvant être téléchargés vers le MultiLoad II. 8. Après avoir sélectionné le fichier de configuration, cliquez sur le bouton “Done” (terminé). Chapitre 3 –Outil de configuration GUI 36 9. L’écran de configuration du niveau du quai apparaît. Figure 3-2 Menu de Configuration du Quai Remarquez que les champs de cet écran correspondent aux champs des paramètres se trouvant sur l’écran de réglage du quai, « Bay Setup » (depuis le menu de réglage de l’équipement « Equipment Setup ») à partir de l’écran de configuration du MultiLoad II. Chapitre 3 –Outil de configuration GUI 3.3 37 NAVIGATION D’ECRAN Si vous avez l’habitude de Windows Explorer ou du système d’aide du TMS, vous savez déjà comment accéder aux écrans d’outil de configuration. Le répertoire d’écran dynamique se trouve sur le côté gauche de chaque écran. Comme vous le voyez ci-dessous, la hiérarchisation des écrans principaux se compose de Quai, FCM et Divers (Bay, FCM, Miscellaneous). Les cases avec le signe + indiquent qu’il existe des niveaux inférieurs. Pour accéder aux écrans de ces niveaux inférieurs, cliquez sur la case +. Figure 3-3 Menu de Configuration du RCU Par exemple, pour accéder aux écrans de configuration dans Bay (quai), cliquez sur la case à côté de Bay. Le second niveau de la hiérarchie s’affiche et le premier écran de l’ensemble est activé, comme représenté cidessus. L’écran de configuration du niveau de RCU s’active. Il se trouve en surbrillance pour montrer où vous vous trouvez dans la hiérarchie des écrans. Remarquez qu’une barre de défilement verticale apparaît à la droite de l’écran, indiquant qu’il y a plus de champs Vous pouvez utiliser cette barre de défilement pour voir ces champs complémentaires ou simplement saisir le bas de l’écran et le tirer vers le bas pour l’allonger. Vous pouvez procéder de la même façon pour des écrans qui ont des champs à droite en les faisant défiler horizontalement ou en redimensionnant l’écran. Les noms de paramètres en rouge sont des paramètres gérés par les Poids et Mesures. Si vous essayez de charger une valeur différente de celle qui est déjà dans MultiLoad II et que le commutateur externe n’est PAS en mode poids et mesure (W&M), ce chargement de paramètre sera refusé par le MultiLoad II. Après chargement, un rapport de toutes les commandes rejetées s’affichera. Les noms de paramètres en bleu sont des paramètres qui ont été modifiés à partir de la valeur par défaut. Dans la plupart des cas, il convient de laisser la plupart des paramètres en valeur par défaut. Le marquage des paramètres qui ont été modifiés à partir des valeurs par défaut est une simple façon de souligner le changement. Remarquez également que la petite case à côté de Quai présente le signe “-“ (moins) signifiant ouvert. Pour fermer ou masquer la hiérarchie de l’écran Quai, cliquez sur la case “moins” (-). Pour accéder à un autre écran, il suffit de cliquer dessus à partir de la hiérarchie graphique. Chapitre 3 –Outil de configuration GUI 3.4 FONCTIONS DE MENU Ci-dessous, de brèves descriptions des fonctions disponibles à partir du menu principal de l'Outil de Configuration. 3.4.1 FONCTIONS DE FICHIER Ci-dessous de brèves descriptions des fonctions disponibles depuis le menu Fichier. New (Nouveau) Crée un nouveau fichier de configuration. Open (Ouvrir) Ouvre un fichier de configuration existant. Save (Enregistrer) Enregistre le fichier de configuration actuellement ouvert. Save As (Enregistrer sous) Enregistre le fichier de configuration actuellement ouvert sous un nouveau nom (et en option, un nouveau répertoire). Close (Fermer) Ferme le fichier actuel configuration. Exit (Quitter) Quitte la fonction de l'Outil de Configuration. 3.4.2 FONCTION D’EDITION La fonction Copie permet à l’utilisateur de copier une configuration prédéfinie vers une autre valeur prédéfinie pour le même quai. Cette caractéristique s’utilise pour les produits du MultiLoad II supportant de multiples bras de chargement et ne s’applique pas au SMP. 38 Chapitre 3 –Outil de configuration GUI 3.5 39 FONCTIONS D’OUTIL Ci-dessous, de brèves descriptions des fonctions disponibles depuis le menu Outil. 3.6 PROGRAMME DE GENERATION DE TICKETS DE CONNAISSEMENT (BOL) Utilisez cette fonction pour générer un ticket de comptage basé sur le fichier actuel de configuration. 3.6.1 TÉLÉCHARGEMENT DE REGISTRES Utilisez cette fonction pour télécharger les paramètres de configuration (contenus dans les registres du RCU du MultiLoad) du RCU MultiLoad ver le TMS. Figure 3.4 Fenêtre de Téléchargement Protocol Type de protocole de valeur prédéfinie : Smith (par défaut), Brooks, DanLoad. LC Name Contrôleur de ligne qui commande l'ouverture du port sériel du MultiLoad II du MultiLoad. Address Adresse du MultiLoad II depuis laquelle les valeurs de paramètres de configuration sont téléchargées. Directory Chemin complet du répertoire où se trouvent où se trouveront les fichiers. File Name Nom du fichier de configuration. Down Load Prompt L’invite de téléchargement indique des informations sur les paramètres configurables de Multiload II. Quand le logiciel interne est mis à jour et que de nouveaux paramètres sont ajoutés, télécharger une invite revient à faire afficher ces nouveaux paramètres dans l’outil de configuration. La langue dans laquelle ces invites apparaissent est également déterminée par le fichier invite. En mettant la langue du mode programme sur la langue souhaitée, puis en téléchargeant le fichier d’invite, vous ferez apparaître toute la description des paramètres de l’outil de configuration MutiLoad II dans la langue sélectionnée. Down Load Registers Les valeurs des paramètres de configuration se trouvent dans des “registres” internes au MultiLoad II. Ces valeurs sont téléchargées vers le fichier de Chapitre 3 –Outil de configuration GUI 40 configuration approprié avant de pouvoir éditer le fichier et de le télétransmettre au MultiLoad II. Disabled RCU Download 3.6.2 while Il est recommandé de contrôler cette case parce qu'elle arrêtera le quai en cours de téléchargement. Si la case n'est pas cochée (vierge), il sera possible pour un chauffeur d’entamer un chargement alors que le téléchargement ou la télétransmission est en cours ! TÉLÉTRANSMISSION DES REGISTRES Utilisez cette fonction pour télétransmettre un fichier de configuration dans le MultiLoad II au niveau de la rampe de chargement. Cette fonction sera généralement utilisée après avoir modifié un fichier de configuration existant ou créé un nouveau fichier de configuration. Télétransmettez ensuite le fichier vers le MultiLoad II approprié. Figure 3.5 Fenêtre de Télétransmission Protocol Type of protocole de communication: Smith (par défaut), Brooks, DanLoad. LC Name Contrôleur de ligne qui contrôle si le port sériel du MultiLoad II est ouvert. Address Adresse du MultiLoad II vers laquelle il faut télétransmettre les valeurs de paramètres de configuration. Directory Chemin complet du répertoire où résidera le fichier de configuration. File Name Nom du fichier de configuration. Disabled RCU Download 3.7 while Il est recommandé de contrôler cette case parce qu'elle arrêtera le quai alors que le télétransfert est en cours. Attention : si la case n'est pas cochée (vierge), il sera possible pour un chauffeur d’entamer un chargement alors que le télétransfert ou le téléchargement est en cours ! RECHARGER LA LANGUE Cette fonction n’est plus utilisée. Chapitre 3 –Outil de configuration GUI 3.7.1 41 EXTRACTION ET VISUALISATION DES TRANSACTIONS Figure 3.6 3.7.2 Fenêtre des Transactions CRÉATION DE CONNAISSEMENTS ( BOL) DEPUIS LES TRANSACTIONS Figure 3.7 Fenêtre des Connaissements (BOL) Chapitre 3 –Outil de configuration GUI 3.8 42 RAPPORTS MULTILOAD II Le progiciel de Configuration GUI du MultiLoad II fournit deux rapports utiles : le rapport de configuration et le rapport des modules de contrôle du débit. Le format, le mécanisme et les options d'affichage du rapport sont identiques à ceux utilisés pour les rapports TMS. Pour de plus amples informations en matière de possibilités et d'options des rapports TMS, prière de se référer au Manuel d'Opérations TMS. Ce rapport contient toutes les informations de configuration de votre système MultiLoad II. 3.8.1 RAPPORT DE CONFIGURATION Ce rapport contient toutes les informations de configuration de votre système MultiLoad II. Figure 3.8 Rapport de Configuration Chapitre 3 –Outil de configuration GUI 3.8.2 43 RAPPORT DES MODULES DE CONTRÔLE DU DÉBIT Le rapport des modules de contrôle du débit se présente sous forme d’une liste exhaustive de toutes les affectations entrées/sorties associée au MultiLoad II. Ces affectations peuvent être sur les FCM externes (sauf SMP) ou sur une carte interne des entrées et sorties en option. Figure 3.9 Rapport des Affectations des Entrées et Sorties Chapitre 3 –Outil de configuration GUI 3.9 44 PARAMETRES DE MODE LOCAL UNIQUEMENT En mode à distance, certaines invites du MultiLoad II sont fournies par le TMS ou d’autres TAS. En mode Local, les valeurs de paramètre doivent être fournies par l'outil de Configuration du MultiLoad II en lieu et place du TMS. Ces “paramètres en local uniquement” sont accessibles dans le groupe "Miscellaneous" (divers) comme dans l'écran représenté ci-dessous. 3.9.1 INVITES CHAUFFEURS Lorsqu'un chauffeur introduit sa carte, il est invité à entrer son numéro de code PIN. Le système lui demande alors le nom du client qui achète le produit et, si d'application, le compte particulier de ce client. Etant donné que cette donnée n’est pas vérifiée par un ordinateur externe, elle doit être spécifiée localement. Figure 3-4 Configuration du Menu des Invites Prompt #1 est la première invite que le chauffeur voit. Elle demande au chauffeur d'introduire le numéro d'identification du propriétaire du produit. L'écran ci-dessous définit l'invite que le chauffeur voit, de même que l'emplacement sur le ticket de comptage où cette information apparaîtra. Sur l'écran représenté, l'invite demande au chauffeur d'entrer l'ID du propriétaire. Quand le chargement est terminé, la valeur introduite par le chauffeur s’affichera en ligne 10, colonne 68 sur le ticket de comptage suivant qui s'imprime. Length of Data Nombre de caractères autorisés pour l'entrée. BOL line Numéro de ligne sur le ticket de comptage / connaissement où le nom du propriétaire du produit apparaît. Pour désactiver, tapez 00. BOL Position Numéro de colonne sur le ticket de comptage / connaissement où le nom du propriétaire du produit apparaît. Pour désactiver, tapez 00. Language#1 L'invite actuelle que le chauffeur verra, dans la langue primaire (Langue A) Exemple : si la langue A est l'anglais, introduisez "Enter Stockholder" (Entrez Propriétaire). Language#2 L'invite actuelle que le chauffeur verra, dans la langue secondaire (Langue B) Exemple: si la langue B est l'espagnol, introduisez Entrada Dueno De Producto (Entrée Propriétaire du Produit). Chapitre 3 –Outil de configuration GUI 45 Prompt#2 est généralement utilisé pour le client. Prompt#3 est généralement utilisé pour le compte. Prompt#4 est généralement utilisé pour l'ID du camion. Prompt #5 est généralement utilisé pour l’ID du camion2. 3.9.2 CONFIGURATION DU PRODUIT Figure 3-5 Ecran de Configuration du Produit Dans Télécommande, les informations concernant le produit sont fournies au MultiLoad II par la base de données Produits du TMS. En mode local, vous devez fournir les données concernant le produit. Product ID Numéro d'identification numérique ou alphanumérique ; jusqu'à 5 caractères. Product Short Name Nom abrégé du produit ; jusqu'à 10 caractères. Product Name Longue description ou long nom du produit ; jusqu'à 25 caractères. Product Index Numéro d'index attribué au produit sélectionné. Hazard Index Jusqu'à cinq risques peuvent être configurés en mode autonome. Allez au menu "Hazard" (risque) pour spécifier les descriptions des risques. Components Si le produit est un mélange, spécifiez les composants de base et leurs pourcentages respectifs. Additives Si le produit inclut un (des) additif(s), spécifiez le pourcentage d'additifs qui doit être injecté dans le produit sélectionné. Par exemple, si la quantité d'additifs injectés doit être de 1% du produit total, tapez 1. Chapitre 3 –Outil de configuration GUI 3.9.3 46 CARTE D’ACCÈS CHAUFFEUR Figure 3-6 Ecran Carte d’Accès Dans « Remote Control » (télécommande), les informations relatives au chauffeur sont fournies par la base de données du TMS. En mode local, vous devez fournir certaines données relatives au chauffeur. Faites-le à l’aide de l’écran de configuration de carte d’accès représenté ici. Index Numéro d'index de la carte sélectionnée. Card No. Numéro de la carte du chauffeur (8 chiffres). PIN No. Numéro d'identification personnel du chauffeur (4 chiffres). Company ID du transporteur pour lequel le chauffeur travaille (2 chiffres). Language Code de la langue qui détermine la langue du texte qui apparaît à l'écran du MultiLoad II lorsque le chauffeur introduit sa carte ou introduit son code. Preset #n Lockout Lorsque cette fonction est activée (ON), le chauffeur ne sera pas autorisé à charger au(x) bras de chargement commandés par la(les) valeur(s) prédéfinie(s) correspondante(s). Dans l'écran d'exemple ci-dessus, le chauffeur ne sera pas autorisé à charger aux valeurs prédéfinies 3, 4, 5 ou 6. Chapitre 3 –Outil de configuration GUI 3.9.4 47 INSTRUCTIONS RELATIVES AUX RISQUES Utilisez l’écran de configuration des registres de risques pour définir jusqu’à cinq avertissements de risque qui seront imprimés sur le ticket de comptage après chargement. Un code de risque peut être attribué à chaque en se servant du champ d’index des risques sur l’écran de configuration des registres de produits. Figure 3-7 Ecran de Configuration des Risques Ne pas utiliser de ponctuation dans ces champs. 3.10 AUTRES FONCTIONS D’OUTIL DE CONFIGURATION Tous les autres écrans d'outil de configuration reflètent la fonctionnalité disponible et accessible depuis le menu de configuration du RCU du MultiLoad II, décrit dans le chapitre suivant. Les écrans d'outil de configuration équivalents sont représentés après chaque section décrivant une zone de configuration : réglage du RCU, valeurs prédéfinies, comptages, composants, additifs, etc. La seule exception concerne l'écran d'affichage du module de contrôle du débit qui permet de voir, en un clin d'œil, comment chaque FCM est configuré. Chaque port d'entrée/sortie I/O est désigné et indique la valeur prédéfinie (Pn), le comptage (Mn), le composant (Cn) ou l'additif (An), comme représenté sur les écrans d'exemple de la page suivante. Le fait de cliquer sur un port d’entrée/sortie I/O affichera les informations détaillées relatives à ce port. Chapitre 3 –Outil de configuration GUI 3.10.1 48 AFFICHAGE GUI DU FCM Figure 3-8 Graphique des Affectations des Entrées et Sorties Pour voir le détail d’un port, cliquez dessus avec le bouton gauche de la souris. Une fenêtre détaillée apparaîtra immédiatement sur la droite de l’écran. Figure 3-9 Détail des Affectations des Entrées et Sorties Chapitre 3 –Outil de configuration GUI 3.11 3.11.1 OUTILS DE CONFIGURATION DES FENETRES MULTIMATE INSTALLATION Le programme d’outil de configuration MultiMate est normalement distribué sous forme de fichier .ZIP. Les instructions ci-dessous décrivent la marche à suivre pour installer et faire fonctionner le logiciel. 1. Extraire le fichier zip . 2. Exécutez setup.exe en suivant soigneusement les instructions. 3. En option: détruisez le fichier MultiLoad_cfg.zip. 4. Exécutez le programme MultiLoad_cfg.exe. La fenêtre programme s’ouvre. 5. Ouvrez le programme sous le fichier de tous les programmes. 6. L’écran suivant apparait : 49 Chapitre 3 –Outil de configuration GUI 50 Chapitre 3 –Outil de configuration GUI 3.11.2 CONNEXION AU MULTILOAD II Connecter au MultiLoad II au moyen DE sériel, tms5/6 ou ackligh: 1. Allez au menu « Communications » et sélectionnez « Connection ». 2. Un nouvel écran apparait. Dans le coin supérieur gauche, appuyez sur le bouton « new connection » 3. Cela enclenchera le « Connection Configuration Wizard ». Suivez les instructions pour créer une connexion au MultiLoad. 51 Chapitre 3 –Outil de configuration GUI 4. Il existe trois façons de connecter Multimate à un dispositif : - Ethernet - Port sériel de votre PC/portable - par votre système Tms5 ou Tms6 Pour sélectionner Ethernet, il faut l’adresse IP du MTL. 52 Chapitre 3 –Outil de configuration GUI 5. La confirmation de l’adresse IP provoque une première vérification du bon fonctionnement de la connexion. De toute façon, la connexion est enregistrée et peut être réutilisée lorsque vous rouvrez Multimate. 53 Chapitre 3 –Outil de configuration GUI 3.11.3 FICHIER D’INVITE DE PARAMÈTRE DE TÉLÉCHARGEMENT Lors de la première installation de l’outil de configuration MultiMate, il n’y a pas de fichier d’invite de paramètre. Ce fichier décrit tous les paramètres pouvant être configurés sur le MultiLoad II. Le fichier d’invite doit être téléchargé depuis le MultiLoad II avant de créer, de télécharger ou d’éditer des fichiers de configuration. Les instructions ci-dessous expliquent la marche à suivre pour télécharger le fichier d’invite de paramètre à partir du MultiLoad II. REMARQUE : La langue des paramètres du fichier d’invites est déterminée par la configuration du mode langue dans le MultiLoadII. 1. Connectez au moyen de la connexion au Multiload que vous venez d’effectuer. (A chaque connexion, MultiMate demandera de rafraichir la liste des invites). 2. Enregistrez le fichier invites sur votre PC ou, si vous en avez un, dans votre système Tms 6 3. Répondez à la question « Reload the prompt file » par « Yes ». Dans ce cas, vous utiliserez immédiatement le nouveau fichier d’invites. Le fichier de configuration est désormais disponible. 54 Chapitre 3 –Outil de configuration GUI 55 Chapitre 3 –Outil de configuration GUI 3.11.4 CRÉATION D’UN FICHIER DE CONFIGURATION Pour créer, éditer et sauvegarder un Fichier de Connexion, il faut que le fichier correct d’invites soit déjà sur votre machine. 1. Dans le rectangle rouge se trouve l’option pour créer un nouveau fichier de configuration. Appuyez dessus pour créer un nouveau fichier. 2. Si vous effectuez une modification dans le fichier de configuration ; tout paramètre ne correspondant pas à la valeur par défaut apparaitra en jaune. 3. Enregistrez le fichier de configuration au moyen du Menu File et de Save. 56 Chapitre 3 –Outil de configuration GUI 4. Le fichier peut être enregistré sur votre PC ou, le cas échéant, sur le serveur TMS6. 57 Chapitre 3 –Outil de configuration GUI 3.11.5 TÉLÉCHARGER UN FICHIER DE CONFIGURATION DEPUIS UN MULTILOAD II Pour télécharger un fichier de configuration depuis un MultiLoad II : 1. Démarrez le programme. 2. Ouvrez une connexion à un dispositif Multiload (invites de téléchargement). 3. Une fois les invites téléchargées, on peut utiliser le bouton éclairé en rouge pour télécharger tous les registres config. 4. Enregistrez le fichier configuration 5. L’écran devrait afficher toute une série de lignes jaunes : le téléchargement s’est bien déroulé. Cela dépend du nombre de paramètres qui ne correspondent pas aux valeurs par défaut. 6. Vous pouvez ensuite rouvrir le fichier en démarrant MultiMate et en allant sur File puis sur Open Menu. 58 Chapitre 3 –Outil de configuration GUI 3.11.6 TÉLÉTRANSFERT D’UN FICHIER DE CONFIGURATION VERS UN MULTILOAD II Pour télétransférer un fichier de configuration vers un MultiLoad II : 1. Démarrez le programme MultiMate. 2. Ouvrez la connexion configurée au dispositif MultiLoad (invites de téléchargement) 3. Après le téléchargement des invites, vous pouvez utiliser le bouton éclairé en rouge pour télétransférer tous les registres config. 4. Ouvrez le fichier configuration qui doit être télétransféré. 5. Dans le coin inférieur droit, une barre de progression apparait. Il faut qu’elle soit remplie à 100% pour être certain que tous les registres ont été correctement télétransférés. 59 Chapitre 3 –Outil de configuration GUI 3.11.7 MISE À JOUR DE L’IMAGE DU LOGICIEL INTERNE DANS UN MULTILOAD II La procédure de mise à jour de l’image du logiciel interne dans un MultiLoad II se passe en deux temps. Tout d’abord, il faut télécharger la nouvelle image du logiciel interne vers le MultiLoad II. Cette étape prend un certain temps mais peut être faite en même temps que des opérations normales de chargement. La seconde étape consiste à mettre à jour la mémoire flash avec la nouvelle image et à redémarrer le système. Cela ne prend que 10 secondes environ mais les opérations de chargement et la communication hôte doivent être interrompues pendant cette opération. Pour mettre à jour l’image du logiciel interne dans un MultiLoad II. 1. Démarrez l’outil Multimate. 2. Créez une nouvelle connetion au dispositif MultiLoadI. 3. Dans le menu des outils (Tools), sélectionnez « Firmware Upgrade ». REMARQUE: Si vous utilisez une connexion sérielle à 115K Baud, le télétransfert du logiciel interne devrait durer 25 minutes. A 56K, il devrait durer 50 minutes. A 9600 Baud, il devrait durer 300 minutes. REMARQUE: Certaines mises à jours de logiciel interne PEUVENT entraîner un retour des paramètres de configuration, et éventuellement des données du totalisateur aux paramètres usine par défaut. Il faut donc absolument télécharger une copie très récente de la configuration actuelle du MultiLoad II avant de mettre le logiciel interne à jour. Les totalisateurs peuvent être remis à zéro. 4. Avant de télétransférer le logiciel, il faut sélectionner le fichier BIN qui doit être télétransféré. 60 Chapitre 3 –Outil de configuration GUI 5. Quand un bon fichier BIN a été sélectionné, l’option télétransfert (Upload) est disponible 6. Télétransfert 7. Quand le télétransfert est terminé, vous serez invité à mettre la mémoire flash à jour : “Update FLASH memory”. 61 Chapitre 3 –Outil de configuration GUI REMARQUE: Si l’accès au commutateur des Poids et Mesures (W&M) n’est pas actif, l’opération flash échouera puisque l’image du logiciel interne est protégée par W&M. 8. Message avertissant que les paramètres pourraient être perdus selon la taille de la mise à niveau du logiciel. 9. Quand vous avez terminé la mise à niveau, il faut réintroduire les paramètres de communication dans le Multiload. 10. Testez la communication au moyen de MultiMate et télétransférez à nouveau la configuration existante. REMARQUE: Le logiciel MultiLoad II interne à 1 bras peut être mis à jour pour la version complète du logiciel interne MultiLoad II 2.29.02 ou une version ultérieure. 62 Chapitre 4 – Configuration Générale CHAPTER 4 4.1 63 CONFIGURATION GÉNÉRALE VUE D’ENSEMBLE Le MultiLoad II est largement configurable, ce qui le rend extrêmement flexible et adaptable à tous vos besoins en matière de modifications des installations. Les fonctions de configuration du MultiLoad II sont disponibles à partir du menu de configuration. Allez à cet écran comme suit: Program Mode -> Configuration L’écran CONFIGURATION MENU s’affiche: Error! Reference source not found. A l’exception du réglage des additifs et des fonctions d’étalonnage, toutes les fonctions et particularités de configuration sont traitées dans ce chapitre dans l’ordre où elles apparaissent dans le menu de configuration. Les fonctions relatives à la configuration des additifs et à l’étalonnage sont reprises séparément plus loin dans ce manuel. 4.2 RÉGLAGE DES COMMUNICATIONS Utilisez la fonction de réglage des communications pour définir les paramètres de communication pour chaque port sériel de communication. Allez sur cet écran comme suit: Program Mode -> Configuration -> Communication L’écran de réglage des communications COMMUNICATION SETUP s’affiche: Error! Reference source not found. Chapitre 4 – Configuration Générale Les trois colonnes correspondent aux trois ports de communications disponibles: Com0, Com1 et Com2. En commençant par Com0, parcourez la liste en modifiant les paramètres de communication si nécessaire. Poussez sur le bouton Enter pour basculer la sélection de chaque champ. Poussez sur le bouton Next pour passer au paramètre suivant. Quand vous avez terminé avec Com0, poursuivez avec Com1 et Com2. Quand tout est terminé, appuyez sur Exit pour sauvegarder les modifications et revenir au menu de configuration. Paramètres Description line 1 – Baud Rate Sélectionnez la vitesse de transmission. Vous avez le choix entre 300, 1200, 2400, 4800, 9600, 19.2 (pour 19,200) 38.4 (pour 38,400), 57.6 (pour 57,600), 115.2 (pour 115,200) et 230 (pour 230,400) bauds. line 2 – Parity Sélectionnez la parité. Choisissez entre None (Aucune), Odd (Impair), et Even (Pair). line 3 – Word size Sélectionnez la taille du mot Possibilités : 7 ou 8. line 4 – Stop bits Sélectionnez le nombre de bits d’arrêt. Possibilités : 1 et 2. line 5 – Tri-State Pour définir les trois états, sélectionnez « Multi » (multiple) ou « Single » (unique). Pour Com0 et Com1, les options sont « Single », « Multi » et « 2-Wire » (2-fils). Com2 est toujours « Single ». Ces trois options sont décrites ci-dessous : Single Faire ce choix si les deux conditions ci-après sont réunies. 1. Seul un MultiLoad II sera branché sur le circuit 2. Il s'agit d'un circuit RS-485 à 4 fils Multi Faire ce choix si les deux conditions ci-après sont réunies 1. Plusieurs MultiLoad II sont branchés sur le circuit 2. Il s'agit d'un circuit RS-485 à 4 fils 2-Wire Faire ce choix lors de l’utilisation d’un circuit RS-485 à 2 fils. Cette sélection autorise une connexion multipoints. Toptech recommande l’utilisation de la méthode "single" à 4 fils autant que possible. La connexion multipoints à 4 ou 2 fils peut ne pas être réalisable pour des installations de grande envergure. 64 Chapitre 4 – Configuration Générale Paramètres Description line 6 – Port Usage Spécifiez comment le port doit être utilisé: Choix possibles: FCM communique avec les FCM externes (sauf SMP) ou une carte interne des entrées/sorties I/O en option valeur par défaut de Com0 Host communique avec un TMS valeur par défaut de Com1 N/A (pas d’application) valeur par défaut de Com2 Print indique le port d’imprimante. Log envoie un message à l’imprimante de série Ethernet permet au serveur (TMS) de communiquer avec le port sériel par Ethernet grâce à l’adresse support se trouvant sur l’écran de réglage du réseau (Network Setup) (de 7000 à 7002) Alibi Log indique le port de journal légal. PTB Alibi indique le port du journal PTB GPS indique le port GPS de protocole NMEA 0183 (mobile ML II uniquement) MASS MTR indique une connexion en série à un ou plusieurs compteurs de masse Si “Print” ou “Alibi Log” est configuré pour être sur COM 2, la ligne de synchronisation CTS DOIT être connectée, faute de quoi un message d’erreur *PRNTR ERR empêchera le chargement. Référez-vous au manuel d’installation pour obtenir des informations sur la connexion du COM 2. Un seul port peut être défini comme FCM, Print. ou Alibi Log, autrement un message apparaîtra - ‘Port usage conflict(s)’ au moment du redémarrage. Si un port est configuré comme GPS, les trois dernières invites à la transaction reprendront les informations relatives à la latitude, la longitude et le nom du site. Il faut sortir du mode programme pour que les nouvelles valeurs prédéfinies puissent fonctionner. Il est possible d’utiliser 2 ports hôtes en même temps, mais le système hôte ne parlera qu’à un seul à la fois! Pour en savoir plus sur la sélection “Message Log »: Affichage et requêtes (Views and Inquiries) 65 Chapitre 4 – Configuration Générale 4.3 66 RÉGLAGE DU RÉSEAU Utilisez la fonction “Network Setup” pour définir les paramètres réseau pour le port Ethernet. Allez à cet écran comme suit: Program Mode -> Configuration -> Network L’écran de réglage du réseau NETWORK SETUP s’affiche: NETWORK SETUP MAC Address: 00:50:c2:60:90:00 Network: DISABLD IP Address: 192.168.0.200 IP Mask: 255.255.255.0 IP Gateway: 192.168.0.1 IP Host: 192.168.0.1 Socket Port: 7734 Modbus Port: 502 Com 0 Port: 7000 Com 1 Port: 7001 Com 2 Port: 7002 Webpage Setup Network Printer Setup WEBPAGE SETUP Next Prev 80 Exit Enter HTTP Port: Admin Password: ******* User Password: ******* Next Prev Exit Enter Chapitre 4 – Configuration Générale 67 NETWORK PRINTER SETUP Printer1 IP: 0.0.0.0 Printer1 Port : 9100 Printer2 IP: 0.0.0.0 Printer2 Port : 9100 Printer Alibi IP: 0.0.0.0 Printer Alibi Port : 9100 Après avoir modifié dans cet écran, il faut sortir du mode programme pour valider les changements. Paramètre Description MAC Address Il s’agit d’un paramètre en lecture seule qui indique l’adresse du matériel MAC du port Ethernet. Ce nombre unique, Exit attribué Enter par l’usine et ne peut être modifié. Nextest Prev Network Active et désactive le port Ethernet. Si le port Ethernet est activé sans qu’un réseau soit connecté, le démarrage peut avoir 10-20 secondes de temporisation pour vérifier la connexion. IP Address Adresse IP statique attribuée au système. Cette valeur doit être communiquée par l’administrateur de réseau local et être unique pour ce réseau. L’adresse dynamique IP (DHCP) n’est pas acceptée. IP Mask Le masque IP sert à définir si une adresse IP se trouve dans le réseau local ou de l’autre côté de la passerelle. Valeur par défaut 255.255.255.0 IP Gateway Adresse IP de la passerelle du réseau utilisée pour accéder aux adresses IP en dehors du réseau local. IP Host Adresse IP du système serveur (TMS). Cette adresse est utilisée pendant le diagnostic réseau pour régler des ICMP sur l’ordinateur serveur. Socket Port Il s’agit d’un paramètre en lecture seule qui indique le numéro de port de l’interface de connexion (7734) que le système serveur (TMS) doit connecter pour établir une connexion en série par le port série. Le type de connexion du connecteur de logiciel est SOCKET_STREAM. Modbus Port Il s’agit d’un paramètre en lecture seule. Il indique le numéro de port de l’interface de connexion (502) que le système PLC doit connecter pour établir une connexion par le port 68ackligh. Il s’agit d’une connexion de type SOCKET_STREAM. Com 0 Port Paramètre en lecture seule qui indique l’adresse de l’interface de connexion que le serveur (TMS) utilisera pour communiquer avec ce port série s’il est configuré comme INTERNET. (7000) Com 1 Port Paramètre en lecture seule qui indique l’adresse d’interface de connexion que le serveur (TMS) utilisera pour communiquer avec le port série s’il est configuré comme INERNET. (7001) Com 2 Port Paramètre en lecture seule qui indique l’adresse de l’interface de connexion que le serveur (TMS) utilisera pour communiquer avec le port série s’il est configuré comme INTERNET. (7002) Chapitre 4 – Configuration Générale 68 Paramètre Description HTTP Port Adresse de l’interface de connexion que les ordinateurs du client utilisent pour contacter le serveur HTTP incorporé. Une valeur de 0 désactive le serveur HPPT. Valeur par défaut: 80 Admin Password Mot de passe pour l’utilisateur Admin qui a droit d’accès à la lecture et l’écriture, autrement dit accès à rcuditto avec clavier et fichiers de télétransfert. Son nom d’utilisateur est “admin” (en minuscules) User Password Mot de passe pour l’utilisateur. L’utilisateur a accès à la lecture, autrement dit accès à rcuditto sans clavier et ne peut pas télétransférer de fichiers. Le nom de l’utilisateur est “user” (en minuscules) Printer1 IP Pour imprimer un ticket sur une imprimante du réseau, encodez l’adresse IP de cette imprimante Printer1 Port Ce port est paramétré sur 9100 (Protocole raw standard) Printer2 IP Pour imprimer un ticket sur une imprimante du réseau, donnez l’adresse IP de cette imprimante. Si les deux imprimantes sont utilisées, nous enverrons une copie à chacune des imprimantes. Si les deux adresses IP sont les mêmes, deux copies sortiront de la même imprimante. Printer2 Port Ce port est paramétré sur 9100 (protocole raw standard) Printer Alibi IP Imprime vers un PC protocole PTB ou une imprimante du réseau Printer Alibi Port Ce port est paramétré sur 9100 (protocole raw standard) Remarque: le mot de passe par défaut pour les deux est Toptech (en minuscules); si on change le mot de passe en utilisant le clavier du MultiLoadMultiLoadII, il doit toujours être en majuscules. Si on le change par l’interface Internet, il peut être en majuscules ou en minuscules. Après avoir activé le réseau et redémarré le MultiLoad II, les deux voyants d’activité à côté de la connexion Ethernet devraient s’enclencher pour indiquer l’activité du réseau et le statut du lien. L’écran de démarrage affichera: M.u.l.t.i.L.o.a.d. .I.I. . . v3.31.xx ............................Sep xx 2013 Copyright(c) 2013 Toptech Systems, Inc. MAC Address: 00:50:c2:60:90:00 IP Address: 192.168.0.200 Net Mask: 255.255.255.0 Broadcast: 192.168.0.255 Gateway: 192.168.0.1 Host: 192.168.0.1 Chapitre 4 – Configuration Générale 69 M.u.l.t.i.L.o.a.d. .S.M.P. . v3.31.xx ............................Sep xx 2013 Copyright(c) 2013 Toptech Systems, Inc. MAC Address: 00:50:c2:60:90:00 IP Address: 192.168.0.200 Net Mask: 255.255.255.0 Broadcast: 192.168.0.255 Gateway: 192.168.0.1 Host: 192.168.0.1 Pour des raisons de sécurité, les informations relatives à l’adresse IP ne s’afficheront que lorsque le réseau est activé pour la première fois et que l’appareil est branché pour la première fois. 4.4 RÉGLAGE GÉNÉRAL DU RCU Utilisez la fonction de réglage général du RCU pour: - Spécifier l’adresse du RCU - Activer ou désactiver le processus à distance par un TMS. - Attribuer des mots de passe pour entrer dans le mode de configuration du MultiLoad II. Dans cet écran, allez à: Program Mode -> Configuration -> RCU General Setup L’écran du réglage général du RCU (RCU General Setup) s’affiche: Error! Reference source not found. L’adresse du RCU est un champ d’entrée des données. Appuyez sur Enter et introduisez la valeur appropriée de l’adresse. Ensuite, appuyez sur Enter pour sauvegarder cette valeur. Le traitement à distance (Remote Processing) est un champ à bascule. Utilisez Next ou Prev pour mettre le champ approprié en surbrillance. Appuyez sur Enter pour accéder au champ, puis sur Next ou Prev pour changer les paramètres. Appuyez sur Enter pour sauvegarder les modifications. Le mot de passe est un champ d’entrée de données. Appuyez sur Enter et introduisez un nouveau mot de passe. Appuyez sur Enter pour sauvegarder la modification. Chapitre 4 – Configuration Générale 70 RCU GENERAL SETUP RCU Address: █ Card Reader Type: DISABLD Remote Mode: StndAln Swing Arm Secondary: DISABLD Password #1: ******* Password #2: ******* Password #3: ******* Password #4: ******* Password #5: ******* Modem Init: AT&F0&B1&C1&D0S0=1 Modem Dial: Host Login: TDSTEST TDSTEST Terminal SPLC: 123456001 Terminal Name: Toptech Terminal Description Enter Exit Adresse du RCU du MultiLoad II. Les valeurs sont 001–099. Paramètres RCU Address Card Reader (Excluding SMP) Type Active ou désactive le lecteur de cartes. Lorsqu’il est activé, les options suivantes sont possibles : BUCKET BUCKET NON CAPTIVE SLOT SLOT NON CAPTIVE iBUTTON BUCKET DUAL NON CAPTIVE (Le mot « dual » signifie que la première carte insérée est celle du chauffeur, n’importe quelle autre carte est utilisée au cours du chargement pour que le système TAS enclenche quelque chose). SLOT DUAL NON CAPTIVE Remote Processing Commande à distance, StndAln (qui représente le mode autonome). D’autres modes sont possibles, comme par exemple, UAP, si nécessaire. Swing Arm Secondary (excluding SMP) Lorsque les bras oscillants sont utilisés, un RCU de quai sera désigné comme le RCU secondaire. Activez ce paramètre pour identifier le RCU comme étant secondaire. Lorsque ce paramètre est désactivé, le RCU sera considéré comme primaire pour le bras oscillant. Si aucun bras oscillant n'est engagé dans le quai, désactivez ce paramètre. Password Mot de passe du mode programme. Il peut y avoir jusqu'à cinq mots de passe composé chacun de sept caractères alphanumériques. Le gestionnaire des terminaux doit affecter un mot de passe à chaque personne/groupe. Par exemple, l’employé #1 a le mot de passe #1. Lorsque cet employé #1 accède au menu des Poids et Mesures (W&M), son code sera repris dans l'historique des changements. Il sera affiché « ID: 1 has Weights & Measurements Menu Access » (ID : 1 a accès au menu des poids et mesures). Tout changement repris dans le journal sera précédé du numéro d’identification (ID#). Modem Dial (Cette fonction n'a pas encore été mise en application) Host Login (Cette fonction n'a pas encore été mise en application) Terminal SPLC Code du terminal SPLC pour le système hôte (par exemple : TDS) Chapitre 4 – Configuration Générale 71 Paramètres Description Terminal Name Introduisez dans ce champ le nom du terminal ou du dépôt. Ce nom sera imprimé sur les enregistrements légaux et les tickets de comptage s'ils ont été activés. Truck Number Paramètre UAP Carrier ID Paramètre UAP TDS Retry Interval Temps en secondes pour que MultiLoad arrive dans le nuage. Seller ID Paramètre UAP Consignee Paramètre UAP BOL Prefix Paramètre UAP Chapitre 4 – Configuration Générale 4.5 RÉGLAGE DU RCU Utilisez la fonction de réglage du RCU (RCU Setup) pour configurer le fonctionnement du RCU du MultiLoad II. Dans cet écran, allez à: Program Mode -> Configuration -> RCU Setup Toutes les valeurs de poids et mesures contrôlées s’affichent en rouge sur l’écran et dans ce manuel. L’écran de réglage du RCU s’affiche: RCU SETUP Reload ROM Lang File: ENABLED Driver Language: ENGLISH ProgramMode Language: ENGLISH Card Reader: DISABLD Prox Card Pull Secs: 3 Processing Mode: StndAln Message Swap Delay: 3 Message Hold Delay: 10 Max GPS Site Distance: 200 Auto Authorize: DISABLD MM/DD/YYY Date: ENABLED Mass Measured Used: POUNDS Load Date From End: ENABLED Measure Used: GALLONS Next Prev Exit En utilisant les descriptions de champ ci-dessous, effectuez tousEnter les changements nécessaires. Lorsque le réglage du RCU est terminé, appuyez sur EXIT pour sauvegarder les modifications et revenir au menu de configuration. Paramètre Reload Lang File Description ROM Si vous activez ce paramètre, l’alarme et les mentions de statut reviendront aux paramètres usine par défaut lors du redémarrage. Driver Language Spécifie la langue: anglais, espagnol portugais, français, allemand, mandarin (ancien et moderne) ou en Thaï affichée pour le chauffeur. Program Language Spécifie la langue: anglais, espagnol, portugais, français, allemand, mandarin (ancien et moderne) ou en Thaï affichée dans le mode programme. Mode 72 Chapitre 4 – Configuration Générale Paramètre Description Card reader MultiLoad Indique si un lecteur de carte a été configuré ou si l’appareil ne peut être utilisé que comme clavier. Sélectionnez le mode de lecteur de carte. BUCKET BUCKET NON CAPTIVE SLOT SLOT NON CAPTIVE iBUTTON BUCKET DUAL NON CAPTIVE SLOT NON CAPTIVE Lorsqu’il est désactivé, le MultiLoad II invite le chauffeur à pousser sur ‘Press Next to Begin” pour se connecter. Ensuite, le chauffeur introduit son numéro de carte et de code PIN. Procédure pour la carte dual : la première carte est la carte de chargement ; pendant le chargement, une seconde carte peut être introduite : elle sera indiquée avec un statut de carte 2 au lieu de 1 qui est réservé à la première carte. La seconde carte peut avoir le même registre de carte R962 (modbus 2900 ... 2979) Prox Card Pull SecsMultiLoad Ce nombre indique le laps de temps en secondes pour retirer la carte avant que le MultiLoad ne mette fin à la transaction. Ce paramètre peut augmenter à partir zéro pour diminuer les effets des interférences électromagnétiques (EMI) générées sur le site. Dans certains cas, les EMI externes peuvent faire croire au MultiLoad II que la carte de proximité a été retirée, ce qui provoque l’interruption prématurée de la transaction. Processing Mode Lorsque ce paramètre est Remote, le MultiLoad II est en mode d’exécution à distance et donc commandé par un MultiLoad. Si le paramètre est Stndaln, le MultiLoad II est en mode local, autonome. Message Delay Swap Nombre de secondes pendant lesquelles un message est retardé avant de basculer à l’invite d’inactivité. L’invite d’inactivité est généralement “For Access, Press Next to Begin” (Pour avoir accès, appuyez sur NEXT pour commencer) ou “For Access, Insert Driver Card”. (Pour avoir accès, insérez la carte de chauffeur). Message Delay Hold Nombre de secondes pendant lesquelles un message est retardé après une commande ESC D. Ce registre n’est utilisé que pour des affichages temporaires par le MultiLoad. Max GPS Distance Site Le produit MultiLoad II Mobile dispose d’une base de données. Chaque site a un nom, une latitude et une longitude. Lorsque le paramètre de distance maximum GPS Site est « nonzero », le MultiLoad enclenche une alarme et empêche le chargement si la position instantanée n’est pas à portée d’un site dans la base de données du site. Auto Authorize Activez ce paramètre pour contourner les invites de sécurité. Ce paramètre est destiné aux opérations autonomes, quand aucun système d'automatisation de terminal n'est utilisé pour fournir une autorisation à distance et lorsque le MultiLoad II est dans un endroit sécurisé. Quand il est activé, le MultiLoad II reste toujours en état "autorisé". L'écran de charge est toujours affiché, permettant à un opérateur de choisir un bras et de commencer à charger sans entrer de données de numéro d'identification (PIN) ou d'identification. L'écran de charge sera affiché à chaque fois que la clé de programme se trouve en position OFF (coupée). Pour entrer en mode programme, activez la clé de programme et appuyez deux fois sur EXIT. Ensuite, suivez la procédure normale pour entrer dans le mode programme. Après être sorti du mode programme, mettez la clé de programme sur OFF pour retourner automatiquement à l'état autorisé. MM/DD/YY Date Quand les dates activées apparaissent sur les tickets sous forme de MM/DD/YY au lieu de DD/MM/YY. Mass Used Unités de mesure de masse du produit pour l’affichage. Ce registre doit être correctement complété lorsque l’on charge par masse. Measure 73 Chapitre 4 – Configuration Générale Paramètre Load End Description date from Date de chargement depuis la fin: signifie que la date de chargement de la transaction est celle de fin du chargement. Par exemple, si une transaction a lieu vers minuit, ce paramètre contrôlera si la date de chargement est la date de commencement ou de fin de la transaction. Measure Used Unités de mesure du produit qui doivent être affichées. Blend Details Gère l’impression et l’archivage des valeurs de transaction, d’additifs, de composants et de compteurs. 0 = pas de valeurs d’additif, de composant ou de compteur 1 = Toutes les valeurs des additifs et des composants. Données du compteur uniquement si les valeurs diffèrent des données du composant. 2 = Toutes les valeurs des additifs, des composants et des compteurs. Compartment Entry S’il est activé, le MultiLoad II demandera au chauffeur une entrée de compartiment pour chaque lot. Ces données du bac sont enregistrées avec la transaction. Print Totalizers Active l’enregistrement des valeurs du totalisateur final dans la transaction pour (P)reset, (M)eter, Component and (A)dditives. Simulation Mode Quand il est activé, ce mode place le MultiLoad en mode Simulation Mode pour une démonstration ou des tests. Dans ce mode, un message clignotant “Simulation Mode” s’affiche sur l’écran de chargement, avertissant l’opérateur qu’une simulation est en cours. Toutes les opérations FCM ou carte I/O des produits et des additives seront simulées dans le logiciel. Il n’y a pas besoin de FCM ou de carte I/O pour ce mode. Config Mins Il s’agit du nombre de minutes pendants lesquelles le mode programme reste en fonction sans aucune frappe de l’utilisateur. Si ce paramètre n’est pas de zéro, le mode d’opération redémarrera quand ce nombre de minutes est écoulé sans qu’il y ait eu de frappe au clavier. Timeout Large Prompts S’il est activé, cela forcera le message inactif de bascule et toutes les invites autonomes (“Enter Access ID”, “Enter PIN”, et toutes les invites personnalisées) à s’afficher en grands caractères. Remarque: les messages de bascule de plus de 20 caractères ne s’afficheront pas en grands caractères. Confirm Starts S’il est activé, l’utilisateur est invité pour la seconde fois à confirmer avant d’entamer le débit. Flow Display Adtv as CCs Permet d’afficher la quantité d’additifs en cc. Désactivez pour afficher les quantités d’additifs en unités de base (gallons ou litres). Display Hundredths Permet d’afficher les centièmes des unités, même quand on se trouve en mode de test de comptage. La résolution du totalisateur et de la transaction est toujours en chiffres ronds lorsque ce paramètre est activé. Use Hundredths Activez-le s’il faut une résolution 1/100 dans l’affichage, le total et l’enregistrement des volumes de transaction. Il forcera le paramètre Display Hundredths (affichage des centièmes). Les écrans View Totalizer et View Transaction afficheront une résolution 1/100. REMARQUE: Quand ce paramètre est activé, l’interface du registre hôte (sériel et Ethernet) renverra les données de volume avec 2 places pour les décimales dans les totalisateurs, les détails de transaction (pas d’additif) et le volume réel livré (commande MRS). Des changements de configuration ou de programme dans le système hôte pourraient s’avérer nécessaires quand on recourt à cette option. Consultez le manuel des communications MultiLoad pour de plus amples informations. W&M Lock Activez ce paramètre sur W&M pour protéger la densité, la densité relative et la gravité API sur le compteur en tant que niveau de composant. De plus, la mise à jour de la communication de ces paramètres est bloquée. Density 74 Chapitre 4 – Configuration Générale Print Ticket Permet à ce paramètre d’imprimer un ticket de comptage à partir du port sériel de l’imprimante. Form Feed After Tckt Ce paramètre sert en même temps que la fonction d’impression du ticket. Si ce paramètre est activé, le MultiLoad II envoie un saut de page après chaque ticket imprimé. Print Ticket PCM Activez ce paramètre pour imprimer un ticket de comptage depuis un module de commande d’imprimante (PCM). Un ticket de comptage est un enregistrement imprimé de la transaction. Après activation de ce paramètre, allez au paramètre “Ticket PCM#” et attribuez un PCM. on Ticket PCM # Ce paramètre désigne le module de commande d’impression (PCM) qui sera utilisé comme port sériel pour envoyer les données du ticket de comptage à une imprimante. Meter Timeout Arch Durée (en secondes) pendant laquelle le MultiLoad II attendra avant que le système serveur ne retrouve les données de chargement en cours avant d’effacer les totaux. Ce paramètre n’est valable que pour le mode à distance. Inactivity Timeout Si aucune activité de débit ou aucune pression de touche ne s'est produite pendant le temps indiqué par ce paramètre, la transaction sera terminée et toutes les livraisons seront archivées. Cette fonction est destinée aux opérations autonomes, lorsqu'il n'y a aucun ordinateur superviseur réglant le temps de transaction. Introduisez zéro pour désactiver cette fonction. La fourchette valable d'entrées est comprise entre 0 et 60 minutes. Ce paramètre ne fonctionnera que si le programme de poids et mesures (W&M) est activé ou s’il on est en mode de test (Proving Mode). Print Msg Log on PCM Permet à ce paramètre d’imprimer un journal des messages à partir d’un module de commande d’impression (PCM). Un journal des messages est un rapport de toutes les activités et de toutes les alarmes sur le MultiLoad II et est essentiellement utilisé pour détecter les pannes. Après activation de ce paramètre, allez au journal des messages PCM# “Message Log PCM#” et attribuez un PCM. Message PCM# Log Ce paramètre désigne le module des commandes d’impression (PCM) qui sera utilisé en tant que port sériel pour envoyer le journal des messages vers une imprimante. No Prox Pull If Flow Lorsque ce paramètre est activé, le fait de retirer la carte de proximité du lecteur captif ne met pas fin à la transaction s’il y a débit. Les mélanges séquentiels se poursuivent jusqu'au bout. Quand les débits s'arrêtent sur tous les bras et que la carte de proximité n'est pas dans le lecteur, la transaction se termine et tous les chargements sont archivés pour la récupération de données. Lorsque ce paramètre est désactivé, tous les chargements sont arrêtés et archivés immédiatement après le retrait de la carte de proximité. Host Timeout Down Durée en secondes pendant laquelle le MultiLoad II attendra avant de se mettre sur HOST DOWN (temps mort serveur coupé) s’il n’a plus reçu de communication du MultiLoad. Ce paramètre ne fonctionne que si le MultiLoad II fonctionne en mode à distance. Host Timeout Wait La durée en secondes pendant laquelle le MultiLoad II attendra avant de se mettre sur HOST DOWN s’il n’a plus reçu de communications du MultiLoad après avoir reçu une commande « FHOSTWAIT ». Ce paramètre ne fonctionne que si le MultiLoad II est en mode à distance. Print Alibi Log on PCM Activez ce paramètre pour imprimer un journal légal depuis un module de commande d’impression (PCM). Un journal d’alibi est un rapport de toutes les transactions enregistrées par le MultiLoad II. Après l’activation de ce paramètre, allez à journal d’alibi <PCM# - “Alibi Log PCM#” et attribuez un PCM. De plus, le débit non autorisé sera imprimé sur une souche. Alibi Log PCM# Ce paramètre désigne le module de commande d’impression (PCM) qui servira de port sériel pour envoyer les données du journal d’alibi vers une imprimante. 75 Chapitre 4 – Configuration Générale Swing Secondary (Excluding MultiLoad) Arm Lorsque des bras oscillants sont utilisés, un RCU de quai sera désigné comme étant le MultiLoad secondaire. Activez ce paramètre pour identifier ce MultiLoad en tant que secondaire. Lorsque ce paramètre est désactivé, le MultiLoad sera considéré comme étant primaire pour les bras oscillants. Si aucun bras oscillant n'est engagé dans le quai, désactivez ce paramètre. Screen Timeout Saver Temps exprimé en secondes pour que l’économiseur l’écran se mette en veille lorsque le MultiLoad II est inactif. Screen Bright Saver Luminosité exprimée en pourcentage qui se manifestera lorsque l’écran de veille s’allume. Min Time Change Secs Min Time Change Secs: avant le début de chaque transaction, le TMS tentera de synchroniser la date et l’heure du MultiLoad II avec celles de l’ordinateur TMS. Le TMS mettra la date et l’heure du MultiLoad II à jour si la différence entre l’heure système du TMS et celle du MultiLoad II est supérieure à la valeur de ce paramètre. Introduisez une valeur en secondes. La date et l’heure du MultiLoad II ne seront pas mises à jour si le commutateur des poids et mesures n’est pas activé. Display volume Quand ce paramètre est activé, la somme de tous les volumes livrés au cours d’une transaction apparaît au bas de l’écran de charge. Le texte “Total Delivered” (total livré) s’affichera immédiatement sous le dernier bras de chargement inscrit à l’écran de charge. Ce total sera remis à zéro lorsque la transaction sera terminée en retirant la carte ou en poussant deux fois sur la touche Exit à l’écran de charge. Load Display Help Aide affichage: lorsque ce drapeau est activé, tous les paramètres de configuration ouvrent un nouvel écran qui donne les valeurs minimum, par défaut, maximum ainsi que la valeur utilisée. Une description de l'aide est également disponible dans la langue de l'installation. Si elle est plus longue que l'écran, vous pouvez faire dérouler le texte. Measure on Load Scrn Activez ce paramètre pour afficher une désignation d'unités qui sera visible à l'Écran de Chargement, adjacent à chaque bras de chargement. Les désignations d'unité sont les suivantes : Gallons = g, Litres = L, Mètres cubes = c, Tonnes = t, Kilogrammes = k, Grammes = G, Livres = p, Barils = B. Status Lockout Scrn Activez ce paramètre pour empêcher le chauffeur ou l'opérateur de voir les écrans de statut. Lorsque ce paramètre est activé, le chauffeur ne pourra voir que deux écrans. L'un est l'écran de charge, qui énumère tous les bras de chargement ou valeurs prédéfinies. L'autre est l'écran de contrôle qui affiche la quantité prédéfinie et la quantité restante du bras de chargement sélectionné. Pour faciliter le diagnostic des pannes, le personnel du terminal peut désactiver temporairement cette fonction en activant le commutateur du programme, ce qui permettra aux techniciens de voir les écrans de statut pendant le chargement, sans changer le paramètre. Load Timeout Screen Ce paramètre renverra l'utilisateur à l'écran de charge après une période spécifiée en secondes. L'écran de charge est l'écran primaire qui affiche tous les bras de chargement ou valeur prédéfinies. Pour faciliter les recherches de diagnostic des pannes, cette fonction est automatiquement désactivée lorsque la clé de programme est activée. Preset Timeout Slct Prédéfinit la fin de sélection. Ce paramètre détermine combien de temps la barre en surbrillance restera active à l'écran de groupe. La barre en surbrillance noire indique quel bras de chargement ou quelle valeur prédéfinie est sélectionné à l'écran de groupe. Si ce paramètre est fixé à zéro, la barre en surbrillance restera toujours affichée sur une des sélections de bras de chargement. S'il est réglé sur une certaine durée exprimée en secondes, la barre disparaîtra à la fin de cette période. Pixel Test Activez ce paramètre s'il est obligatoire d'exécuter un essai d'affichage avant chaque transaction. Lorsque l'essai commence, chaque pixel devient noir pendant 0.75 secondes. Ensuite, blanc pendant 0.75 secondes. Les pixels inopérants apparaîtront sous la forme de petits points contrastants. A la fin des essais, l'écran de charge s'affiche. 76 Chapitre 4 – Configuration Générale Proving Le mode de test de comptage est activé en mode autonome de fourniture d’un seul produit. Les changements aux paramètres poids et mesures (W&M) ne sont pas autorisés sauf si le commutateur W&M est actif. Max Lines on a Ticket Pour le moment, on utilise uniquement ce paramètre en mode UAP. Il définit le nombre de lignes sur chaque ticket imprimé. W&M Key FCM # Permet de connecter un interrupteur externe pour avoir accès en écriture aux paramètres W&M. Mettez ce paramètre sur le FCM et sur Port pour l’entrée où l’interrupteur est fixé. La valeur d’entrée à cet endroit sera Ord avec le statut de l’interrupteur W&M du MultiLoad II. Le diagnostic RCU montrera le statut de cet interrupteur. Program FCM # Key Permet de connecter un interrupteur externe pour avoir accès au mode programme. Mettez ce paramètre sur le FCM et sur Port pour l’entrée où l’interrupteur est fixé. La valeur d’entrée à cet endroit sera Ord avec le statut de l’interrupteur du mode programme du MultiLoad II. Le diagnostic RCU montrera le statut de cet interrupteur. Startup Locked Keypad Quand le MultiLoadII démarre, le clavier est verrouillé ou non verrouillé. Le seul écran où le clavier fonctionne encore est l’écran IDLE. Le menu configuration reste donc accessible. Meter Mode Screen Brightness Luminosité de l’affichage RCU Address Introduisez l’adresse du RCU MultiLoad II sous une forme valable: 001 à 099 sont acceptés. Toptech recommande vivement d’utiliser une adresse 001 pour tous les MultiLoad II. 77 Chapitre 4 – Configuration Générale 4.6 78 RÉGLAGE DE TRACE Utilisez la fonction « TRACE Setup » pour configurer ce que le RCU du MultiLoad II encodera dans le journal des messages. Allez à cet écran de la façon suivante: Program Mode - > Configuration - > TRACE Setup Toutes les valeurs commandées des Poids et Mesures s’affichent en rouge sur l’écran et dans ce manuel. L’écran TRACE Setup affiche ceci: TRACE SETUP Trace Preset Number: 32 Trace Adtv Number: 1 Trace UAP Level: 3 Trace Recipe: DISABLD FCM Trace: ENABLED Trace FCM Number: 32 Trace FCM Assignment: DISABLD Trace Meter Flows: DISABLD Trace Adtv Volume: DISABLD Next Prev Exit Enter Effectuez les changements nécessaires à l’aide des description de champ ci-après. Quand vous aurez terminé le MultiLoad Setup, appuyez sur la touche EXIT pour enregistrer vos modifications et revenir au menu Configuration. Paramètre Description FCM Trace Activez ou désactivez. Ce paramètre sert pour la détection avancée des pannes. Ne le désactivez pas sauf si Toptech Systems Engineering vous le demande Trace Number Preset Trace UAP Level Les paramètres Trace servent à capturer des données supplémentaires à partir du système, données qui seront envoyées au journal des activités tant que cet élément est actif. Ces paramètres doivent avoir une valeur spécifiée pour pouvoir utiliser les paramètres de traçage qui suivent. Introduisez une valeur représentant les valeurs prédéfinies à tester. La valeur 1 est une entrée valable. Ce paramètre sert au diagnostic avancé des pannes. Ne l’activez pas sans instruction de Toptech Systems. Les paramètres servent à capturer des données à partir du système. On enverra des données supplémentaires au journal des événements tant que cette fonction sera activée. Le paramètre doit avoir une valeur spécifiée pour pouvoir utiliser les paramètres Trace qui suivent. Introduisez une valeur représentant le niveau de traçage pour UAP. Les valeurs acceptées vont de 1 à 5. Ce paramètre sert à la détection avancée des pannes. Ne le désactivez pas sans instruction de Toptech Systems. Chapitre 4 – Configuration Générale Trace Recipe Utilisez ce paramètre pour voir comment les mélanges se forment dans MultiLoad II. La composition d’un mélange utilisé pendant les livraisons des valeurs prédéfinies dans « Trace Preset Number » se répercute dans le journal pour analyse. Ce paramètre sert au diagnostic avancé des pannes. Ne l’activez pas sans instruction de Toptech Systems. Trace Number Adtv Utilisez ce paramètre pour préciser l’injecteur en cours de test. On ne peut tracer qu’un seul injecteur à la fois. Commencez par préciser les valeurs prédéfinies de l’injecteur dans «Trace Preset Number ». Introduisez ensuite une valeur représentant l’injecteur en cours de test et activez le paramètre de traçage du volume d’additifs Trace Adtv volume. Ce paramètre sert au diagnostic avancé des pannes. Ne l’activez pas sans instruction de Toptech Systems. Trace Number FCM Utilisez ce paramètre pour préciser un FCM pour analyse. Référez-vous au paramètre Trace FCM Assignment. (Tracer affectation FCM). Remettez ce paramètre à la valeur par défaut value 32 s’il n’est pas utilisé. Ce paramètre sert au diagnostic avancé des pannes. Ne l’activez pas sans instruction de Toptech Systems. Trace FCM Assignment Lorsqu’on introduit la valeur 1 dans un champ de paramètre “Trace FCM Number” et que ce paramètre est activé, les affectations du MultiLoad se reflètent dans le journal des activités pour analyse chaque fois que le MultiLoad II redémarre. Ce paramètre sert au diagnostic avancé des pannes. Ne l’activez pas sans instruction de Toptech Systems. Trace Meter Flows Utilisez ce paramètre pour des échantillons de la vitesse de débit de comptage prélevé dans des valeurs prédéfinies précisées dans Tracer le nombre de valeurs prédéfinies (Trace Preset Number). Les vitesses de débit de comptage sont échantillonnées et copiées dans le journal des activités pour analyse. Les vitesses de débit peuvent ensuite être exportées dans un tableau et mises sous forme de graphiques pour analyse. Les données consignées comprennent le volume total livré, les vitesses de débit de comptage et les états de la vanne numérique. Ce paramètre sert au diagnostic avancé des pannes. Ne l’activez pas sans instruction de Toptech Systems. Trace volume Si ce paramètre est activé, les détails volumétriques de chaque injection seront copiés au journal des activités pour analyse. Utilisez les paramètres « Trace Preset Number » et « Trace Adtv Numbe » pour préciser l’injecteur testé. Ce paramètre sert au diagnostic avancé des pannes. Ne l’activez pas sans instruction de Toptech Systems. Adtv 79 Chapitre 4 – Configuration Générale 4.7 80 INSTALLATION DES EQUIPEMENTS Utilisez les fonctions d’installation pour configurer le quai (Bay) et ses valeurs prédéfinies associées: compteurs, composants et additifs. Sur cet écran, allez à: Program Mode -> Configuration -> Equipment Setup - > Select Parameter Level SELECT PARAMETER LEVEL ALL Input/Output Weights & Measures Flow Control & Rates Blending API Alarms Prev Exit Enter les retrouver facilement. Il se peut que Cette nouvelle sélection regroupe tousNext les paramètres pour pouvoir certains paramètres se trouvent dans plusieurs groupes. Le menu d’installation des équipements s’affiche: EQUIPMENT SETUP MENU Bay Preset Meters Components Additives Next Prev Exit Enter Remarque: Un quai SMP MultiLoad II normal se compose d’un bras de chargement ou “Preset”, d’une vanne principale de comptage/régulation du produit connectée à un composant avec deux additifs maximum. Le tableau ci-dessous montre les liens entre les ports de la carte des entrées et sorties et les affectations fonctionnelles: Sortie AC Port 0 Sortie 1 injection additif Chapitre 4 – Configuration Générale 81 Sortie AC Port 1 Sortie 2 injection additif Sortie AC Port 2 Electro-aimant normalement ouvert Sortie AC Port 3 Electro-aimant normalement fermé Entrée DC Port 4 Canal compteur A Entrée DC Port 5 Canal compteur B (option) Entrée DC Port 6 Entrée 2 compteur additif Entrée DC Port 7 Entrée 1 compteur additif Entrée DC Port 9 Entrée terre Sortie DC Port 10 Sortie DC Port 11 Sortie DC Port 12 Chapitre 4 – Configuration Générale 4.7.1 82 INSTALLATION DU QUAI Utilisez les fonctions d’installation du quai pour configurer toutes les niveaux de quai. Dans cet écran, allez à: Program Mode -> Configuration -> Equipment Setup -> Select Parameter Level - > Bay Setup Toutes les valeurs de poids et mesures contrôlées sont affichées en rouge sur l’écran et dans ce manuel. Le menu d’installation du quai s’affiche: Paramètre Number Bay Presets (Excluding SMP) BAY SETUP Number Bay Presets: 1 Number of FCMs: 1 Number of PCMs: 0 Temps in F: DISABLD Canada API Limits: DISABLD Bay Number: 0 Number External Presets: 0 Output Pulse FCM#: 0 Output Pulse Factor: 10.000 Deadman Mode: NONE Input Deadman FCM#: DISABLD Deadman Stop Timer: 180 Output Deadman FCM#: DISABLD Deadman Warning Timer: 20 Description Next Prev Exit Enter Introduisez le nombre de valeurs prédéfinies « bras de chargement » contrôlées par ce MultiLoad II. Number of FCMs Introduisez le nombre de modules de commande du débit (FCM) reprenant la carte des entrées et sorties I/O qui seront liées à ce quai. Ce nombre sera de 32 maximum (1 sur SMP MultiLoad II. Number of PCMs Introduisez le nombre de modules de commande d’impression (PCM) qui seront raccordés à ce quai. Temps in F Cette sélection indique si les températures sont en Fahrenheit ou en Celsius. Sélectionnez "Enabled" pour choisir Fahrenheit ou "Disabled" pour choisir Celsius. Canada API LImits Si ce paramètre est activé, les tableaux API se serviront de gammes de températures imposées par Measurement Canada. Bay Number Introduisez un numéro que le terminal ou le dépôt utilisera pour identifier le quai (portique). Cette désignation de quai apparaîtra sur les tickets de comptage et les journaux d’alibi. Les entrées valables vont de 000 à 9999. Number External Presets (Excluding SMP) Introduisez le nombre de valeurs prédéfinies qu’un ordinateur hôte affichera à l’écran de chargement du MultiLoad II. Ces valeurs s’afficheront sur un fond vert avec un message “Not Legal for Trade” (non commercialisable légalement). Référez-vous au manuel de communication du MultiLoad II pour de plus amples informations. Chapitre 4 – Configuration Générale 83 Paramètre Description Output Pulse FCM# Ce paramètre active un port de sortie qui fournit une impulsion de sortie représentant le volume fourni. Pour les FCM et les cartes d’entrées/ sorties avec logiciel interne 035 ou antérieur, le port doit toujours être réglé sur 1 pour les FCM et 10 pour les cartes d’entrées/ sorties. Pour les FCM et les cartes entrées/sorties avec logiciel 036 et ultérieur, le port peut être réglé sur 0-5 pour les FCM et sur 10-12 pour les cartes d’entrées/ sorties. Les FCM et les cartes entrées/sorties avec logiciel 038 et ultérieur supportent des sorties d’impulsion à double voie. Activez la sortie d’impulsion double en configurant “Invert” sur ce port. Ce port sera l’impulsion principale, l’impulsion secondaire étant le port contigu suivant (0/1, ½, 2/3, 3/4, 4/5, 10/11, 11/12) sur le FCM ou la carte des entrées/sorties. Remarques: Impulsion de sortie unique limitée à 500 Hz Max. Impulsion de sortie double limitée à 250 Hz Max. Les impulsions de sortie ne sont PAS en temps réel et subissent un temporisation pouvant aller jusqu’à 1 seconde à partir de l’acquisition. Output Pulse Factor Un coefficient peut être appliqué à la sortie d'impulsion pour obtenir la résolution d'impulsion désirée. La résolution d'impulsion peut être configurée de 0.0001 à 50.000 impulsions par unité de mesure. D Deadman Mode None: la fonctionnalité est désactivée ContHld: (Continuous Hold) L’entrée “homme-mort” doit être prédéfinie quand le chargement passe en bas débit, faute de quoi le chargement s’arrête. Pas de préalarme. Hld&Rel: (Hold and Release) maintenir et relâcher. Il faut appuyez en continu sur l’entrée Deadman; Si la pré-alarme se déclenche, il faut relâcher le Deadman (pendant maximum 3 secondes) puis il faut à nouveau appuyer jusqu’à ce que la pré-alarme se réenclenche. Push: (appuyez) Il faut appuyer sur Deadman par intervalles. Il faut appuyer lorsque la pré-alarme est active. Si vous appuyez trop tôt, l’intervalle se remettra à zéro. Input Deadman FCM# C’est le bouton de remise à zéro de l’homme-mort pour recalculer l’intervalle. Deadman Stop Timer Intervalle de l’homme-mort lorsqu’il faut arrêter le chargement, lorsque le bouton de remise à zéro n’a pas été manipulé dans le mode correct. Output FCM# Deadman C’est la sortie de l’homme-mort pour la pré-alarme pour avertir le conducteur que la période d’arrêt de l’homme-mort touche à sa fin. Deadman Timer Warning Heure avant laquelle la minuterie de l’arrêt de l’homme-mort va s’arrêter, ce qui déclenchera également la sortie de la pré-alarme de l’homme-mort. Deadman Bypass Key FCM# Il est possible, sans rentrer dans le mode programme, de désactiver la fonction hommemort avec une touche-contact. Alarm Out FCM# Produit un signal de sortie quand le quai a une alarme active. Ce paramètre sélectionne un port de sortie qui sera attribué pour signaler une alarme non précisée au quai. Authorized FCM# Produit un signal de sortie quand la procédure autorisée est terminée. La sortie reste active jusqu’à ce que la transaction soit terminée. On utilise souvent cette sortie pour signaler le démarrage ou l’arrêt de dispositifs de récupération de vapeur (VRU). Permiss (0-7) FCM# Permet de sélectionner un module de commande de débit (FCM) et un port qui recevra un signal d’entrée. Le signal d’entrée représentera l’état permissif 0-7. Si ce signal n’est pas présent au moment de l’autorisation ou est perdu en cours de livraison, la procédure sera interrompue et une alarme se déclenche au niveau du quai. Permiss Out FCM# Ce paramètre permet de sélectionner un module de commande de débit (FCM) et un port qui émettra un signal de sortie. Le signal représente la perte de l’un ou plusieurs des permissifs quai 0-7. Chapitre 4 – Configuration Générale 84 Réglage de l’homme-mort Le tableau ci-dessous montre quels paramètres il faut configurer pour chaque mode homme-mort. Les champs vierges n’ont aucune influence sur la fonction. Mode homme-mort (Deadman) Entrée Deadman Minuterie d’arrêt Sortie Deadman Minuterie d’avertissement None ContHld X Hld&Rel X X X X Push X X X X Chapitre 4 – Configuration Générale 4.7.2 85 RÉGLAGE DES VALEURS PRÉDÉFINIES Utilisez les fonctions d’installation des valeurs prédéfinies pour configurer les caractéristiques des bras de chargement. Vous trouverez des détails supplémentaires sur la commande de débit au Chapitre 5. Sur cet écran, allez à: Program Mode -> Configuration -> Equipment Setup -> Select Parameter Level - > Preset Toutes les valeurs contrôlées poids et mesures s’affichent en rouge sur l’écran et dans ce manuel. L’écran de réglage des valeurs prédéfinies s’affiche: Paramètre Number of (Excluding SMP) PRE #1 (Preset 001) SETUP Number of Meters: 1 Number of Components: 1 Number of Additives: 0 Sequential Blending: DISABLD Ratio Blending: DISABLD W&M Controlled: DISABLD Proving Flow Rate: 600 Excess Flw Alrm Rate: 1100 Overrun Alarm Vol: 5 Low Flow Start Vol: 50 Low Flow Restart Vol: 15 Low Flow Rate: 150 High Flow Rate: 600 Proving Low Flow Vol: 50 Description Next Prev Exit Enter Meters Introduisez le nombre de débitmètres qui seront attribués au bras de chargement (valeurs prédéfinies). Number of Components Indique le nombre de composants qui passeront par le compteur. Number of additives Indique le nombre d’additifs qui seront attribués au bras de chargement. Ce nombre est de 2 maximum, le minimum étant 0. Blending Type (Excluding SMP) Modes possibles : RATIO (proportionnel) - Active le mélange proportionnel. De multiples débitmètres et des vannes de régulation sont exigés pour le mélange proportionnel. Activez ce paramètre si de multiples débitmètres et vannes de régulations sont attribués au bras de chargement et que vous désirez un mélange proportionnel. SEQ Active le mélange séquentiel. Activez-le si vous utilisez un seul débitmètre dans les valeurs prédéfinies, avec de multiples composants. Pour le chargement d’un seul composant au travers d’un seul débitmètre, il faut désactiver ce paramètre. RAT+SEQ Active les deux options décrites ci-avant. WATERCT Ce mode calcule la quantité d’huile et d’eau. Il faut un réglage à 2 composants et des sondes bsw ou un bsw par défaut. W&M Controlled Active la sélection des paramètres mélange et recette pour que cette valeur prédéfinie soit sous contrôle des Poids et Mesures (W&M). Chapitre 4 – Configuration Générale 86 Paramètre Description Proving Flow Rate Introduisez le débitmètre-cible qui sera utilisé au cours de l’essai. Excess Flw Alrm Rate Ce paramètre définit le débit qui déclenche l’alarme de dépassement de débit. Ce débit est considéré comme excessif s’il dépasse le débit maximum absolu pour le bras oscillant. La valeur de ce paramètre doit être supérieure au paramètre de haut débit dans le menu des valeurs prédéfinies. Overrun Alarm Vol Définit le volume de dépassement qui déclenche l’alarme du volume de dépassement. Il s’agit du volume de produit livré dépassant la quantité de la valeur prédéfinie. Low Flow Start Vol. Après le démarrage initial d’un lot, le débit sera maintenu au niveau du débit-cible jusqu’à ce que le volume de l’amorce ait été livré. Low Flow Restart Vol. En reprenant un lot interrompu, le débit sera maintenu au niveau du débit d’amorce à faible débit jusqu’au réamorçage à faible débit jusqu’à ce que le volume de redémarrage à faible débit ait été livré. Low Flow Rate Ce débit indique le débit cible du faible débit. Ce débit sera maintenu jusqu'à ce que le volume de l'amorce à faible débit ait été livré. Ce taux sera aussi utilisé pour l'étape de réamorçage à faible débit. High Flow Rate Ce paramètre indique le débit-cible du haut débit. Le débit maximum au travers du bras de chargement est déterminé par ce taux. Ce débit sera maintenu jusqu'à ce que la première étape du volume de déclenchement ait été atteint. Proving Low Flow Vol Pendant le processus d'essai, la livraison dans un caisson d'essai commencera à un faible débit, jusqu'à ce que la valeur spécifiée par ce paramètre ait été livrée. Introduisez une valeur qui déterminera le volume qui sera livré à faible débit. En général, le volume d'amorce à faible débit pour une livraison d'essai est inférieur au volume à faible débit d'une livraison normale. Line Flush Vol (Excluding SMP) Spécifiez le volume de produit exigé pour la purge de la section tubulaire qui se trouve entre le débitmètre et la fin du bras de chargement. Lorsque ce paramètre est réglé sur zéro, la fonction de purge de conduite est désactivée. Line Flush Min (Excluding SMP) Spécifiez le volume de purge de conduite qui sera acceptable si le volume de purge de conduite réel n'est pas atteint. Si le volume minimum de purge de conduite n'est pas atteint, l'alarme de purge de ligne s'enclenche. Ce paramètre est destiné à empêcher les alarmes de nuisance en raison de faibles écarts, acceptables, du volume de purge de conduite. Le volume minimal de purge de conduite sera la valeur de purge affichée à l'écran de statut. Cette valeur va en décroissant à mesure que la conduite se purge. Vol Line Flush Comp# (Excluding SMP) Take L.F. from (Excluding SMP) Sélectionnez le composant pour purger la section tubulaire qui se trouve entre le débitmètre et la fin du bras de chargement. Après avoir mesuré le composant de purge de conduite, il reste dans la section tubulaire au-delà du débitmètre quand la quantité de la valeur prédéfinie a été atteinte et le chargement achevé. Le composant de purge n’est pas livré pendant le chargement au cours duquel il a été mesuré mais sera livré lors d'un chargement ultérieur. En effet, le composant de purge est le premier produit dans le camion mais il n'est pas mesuré comme faisant partie de la charge jusqu'à la phase de purge de conduite de la livraison. La fourchette d'entrées est de 1 pour le composant #1 jusqu'à un nombre qui représente le composant de commande le plus élevé configuré pour la valeur prédéfinie. Match Prendre la purge de conduite à partir du composant correspondant. Si un des composants utilisés dans une recette donnée devait être désigné comme étant le composant de purge de conduite indiqué, ce composant de recette serait sous-livré pour s'adapter au volume de purge de conduite à la fin du chargement. La partie sous-livrée est livrée pendant la phase de purge de conduite. Les choix pour ce paramètre sont "Désactiver" ou "Activer". Si ce paramètre est désactivé, la recette choisira de réduire soit le premier composant de la recette, soit le dernier selon ce qui est spécifié par les deux paramètres qui suivent. Chapitre 4 – Configuration Générale 87 Paramètre Description Take L.F. from (Excluding SMP) First Prendre la purge de conduite à partir du premier composant de recette. Si le paramètre "Take Line Flush From Match" est désactivé ou si le composant de purge désigné n'est pas utilisé dans une recette particulière, l'algorithme ressemblera à ce paramètre pour l'instruction indiquant le composant de recette à réduire. Un composant de recette doit être réduit pour s'adapter au volume de purge de conduite. Si ce paramètre est activé, le premier composant de recette sera choisi comme composant à réduire. Si ce paramètre est désactivé, l'algorithme ressemblera au paramètre suivant pour l'instruction : "Take L.F. From Last". Take L.F. from (Excluding SMP) Last Prendre la purge de conduite à partir du dernier composant. Si le paramètre "Take Line Flush From Match" est désactivé ou si le composant de purge désigné n'est pas utilisé dans une recette particulière et si le paramètre "Take L.F. From First" est désactivé, l'algorithme ressemblera à ce paramètre pour l'instruction indiquant le composant de recette à réduire. Un composant de recette doit être réduit pour s'adapter au volume de purge de conduite. Si ce paramètre est activé, le dernier composant de recette sera choisi comme étant le composant à réduire. Ce paramètre ne peut être désactivé si les deux paramètres précédents sont tous deux désactivés. Compute Blend Density Lorsque la densité du niveau du compteur n’est pas définie et que la densité du niveau du composant est définie, si Compute Blend Density est activé, la densité du compteur est calculée par une moyenne pondérée du volume des densités de composant. Si Compute Blend Density n’est pas activé, la densité du compteur est prise à partir de la densité du composant principal Alt. High Flow Rate Le haut débit alternatif peut servir de débit intermédiaire quand le liquide dans le réservoir de purge d’air est tombé à un certain niveau, ce qui nécessite un débit inférieur au débit élevé mais supérieur au débit faible. Mettez ce paramètre sur une valeur inférieure au haut débit mais égale ou supérieure au paramètre de débit faible. Stop Start Delay Ce paramètre garantit qu’un minimum de temps (en secondes) s’écoule entre l’arrêt et le début d’un débit. Si vous accélérez le MultiLoad ou sortez du mode programme, ce temporisateur s’enclenche. Si le chauffeur tente de déclencher le débit en cours de période d’attente, le MultiLoad II enregistre un message stipulant qu’un chauffeur a essayé de lancer le débit au cours de cette période. Les valeurs prédéfinies resteront en condition de démarrage jusqu’à ce que la période de temporisation soit écoulée, puis le débit démarrera normalement. Blend Chk Sart (Excluding SMP) Vol Le volume d'amorce de contrôle du mélange ne s'applique qu'au mélange proportionnel. Quand le volume spécifié dans ce paramètre a été livré, le système commence à vérifier la proportion du mélange. Ce paramètre est destiné à donner, depuis les multiples débitmètres, une occasion au débit de se stabiliser après un démarrage initial depuis le débit zéro. Aucun contrôle de proportion de mélange ou de réglages n'a lieu tant que ce volume n'a pas été livré. Ce réglage doit être configuré supérieur au volume d'amorce à faible débit, de façon à ce que les contrôles puissent commencer après la transition vers le haut débit. Blnd Chk Restart (Excluding SMP) Vol Le volume de réamorçage de contrôle du mélange ne s'applique qu'au mélange proportionnel. Quand le volume spécifié dans ce paramètre a été livré, le système commence à vérifier la proportion du mélange. Ce paramètre est destiné à donner, depuis les multiples débitmètres, une occasion au débit de se stabiliser après un redémarrage depuis le débit zéro. Les contrôles de proportion de mélange ne reprendront pas tant que ce volume n'a pas été livré. Ce réglage doit être configuré supérieur au volume de réamorçage à faible débit, de façon à ce que les contrôles puissent commencer après la transition vers le haut débit. Chapitre 4 – Configuration Générale 88 Paramètre Description Blnd Chk Alarm (Excluding SMP) % Mélange Proportionnel - Blend Check Alarm %. Lorsque la proportion n'est pas dans les limites de tolérance pour le pourcentage indiqué dans ce paramètre, le chargement s'arrête et une alarme OVR BLEND ou UND BLEND apparaît. L'alarme se produit lorsque l'erreur de pourcentage a duré pendant la période indiquée par le paramètre de Temps d’alarme de Contrôle du mélange. Mélange Séquentiel - Dans des applications de mélange séquentiel, ce paramètre peut être utilisé pour donner une alarme quand la composition du mélange n'est pas dans les limites des spécifications au moment de l'achèvement du lot. Si, quand la livraison est terminée et que les totaux sont annulés, la proportion de n'importe quel composant d'un mélange séquentiel est hors spécifications pour la valeur entrée dans ce paramètre, une alarme OVR BLEND ou UND BLEND se déclenche. Blnd Chk Alarm (Excluding SMP) Vol Mélange Proportionnel - Blend Check Alarm volume. Lorsque la proportion n'est pas dans les limites de tolérance par le volume spécifié dans ce paramètre, le chargement s'arrête et une alarme OVR BLEND ou UND BLEND apparaît. L'alarme se produit lorsque l'erreur de volume a duré pendant la période indiquée par le paramètre de temps d’alarme de contrôle du mélange. Mélange Séquentiel - Dans des applications de mélange séquentiel, ce paramètre peut être utilisé pour donner une alarme quand la composition du mélange n'est pas dans les limites des spécifications au moment de l'achèvement du lot. Si, quand la livraison est terminée et que les totaux sont annulés, le volume de n'importe quel composant d'un mélange séquentiel est hors spécifications pour la valeur introduite dans ce paramètre, une alarme OVR BLEND ou UND BLEND se déclenche. Blnd Chk Alarm (Excluding SMP) Time Temps d’alarme de contrôle du mélange ne s'applique qu'au mélange proportionnel. Lorsque la proportion n'est pas dans les limites de tolérance pour la période de temps déterminée par ce paramètre, le chargement s'arrêtera et une alarme de proportion de mélange se déclenchera. Introduisez le temps en secondes. Low Flow Start Percentage Calculez le volume de départ du bas débit à partir de la quantité prédéfinie introduite. On utilise uniquement ce volume s’il est supérieur au paramètre Low Flow Start. Ce volume calculé ne dépassera pas 65,535. La valeur de redémarrage du bas débit ne se calcule pas à l’aide de la valeur prédéfinie. Blnd On Lead (Excluding SMP) Le mélange sur le composant principal ne s'applique qu'au mélange proportionnel et au flux latéral. Activez ce paramètre pour que tous les autres composants suivent à la trace le débit du composant principal. Le composant principal est défini comme le premier composant répertorié dans la recette de produit. La recette de produit est livrée au MultiLoad par des systèmes d'automatisation de terminaux (TAS) comme le TMS5/6. Cette fonction devrait être utilisée lors du mélange de composants visqueux comme l'asphalte. Le composant principal doit être le composant qui est le facteur limitatif dans la réalisation du débit maximal pour le mélange. Le composant principal peut être limité par une pression contradictoire à la pompe, par exemple. (v2.25) Le composant principal peut être défini de trois façons différentes : FIRCOMP: premier composant défini dans la recette HIGPERC: le pourcentage le plus élevé de composants défini dans la recette LOWPERC: le pourcentage le plus bas de composants définis dans la recette Comp. Chapitre 4 – Configuration Générale 89 Paramètre Description Blnd Adj Start (excluding SMP) vol Le volume d'amorce de l’ajustement du mélange ne s'applique qu'au mélange proportionnel. Quand le volume spécifié par ce paramètre a été livré, le système commence à ajuster la proportion du mélange lorsqu'il s'écarte de la tolérance de la quantité indiquée dans le paramètre de pourcentage d'écart d’ajustement du mélange. L'écart doit se produire pendant la période spécifiée par le paramètre de temps d’ajustement du mélange avant tout essai d’ajustement. Ce paramètre est destiné à donner, depuis les multiples débitmètres, une occasion au débit de se stabiliser après un démarrage initial depuis le débit zéro. Aucun ajustement de la proportion du mélange n'a lieu tant que ce volume n'a pas été livré. Ce réglage doit être configuré supérieur au volume d'amorce à faible débit et inférieur au volume d'amorce de contrôle du mélange, de façon à ce que les ajustements puissent commencer après la transition vers le haut débit. Blnd Adj Restart (Excluding SMP) Vol Le volume de réamorçage de l’ajustement du mélange ne s'applique qu'au mélange proportionnel. Quand le volume spécifié par ce paramètre a été livré, le système commence à ajuster la proportion du mélange lorsqu'il s'écarte de la tolérance de la quantité indiquée dans le paramètre de pourcentage d'écart d’ajustement du mélange. L'écart doit avoir lieu pendant la période spécifiée par le paramètre de temps d’ajustement du mélange avant tout essai d’ajustement. Ce paramètre est destiné à donner, depuis les multiples débitmètres, une occasion au débit de se stabiliser après un redémarrage depuis le débit zéro. Aucun ajustement de la proportion du mélange n'a lieu tant que ce volume n'a pas été livré. Ce réglage doit être configuré pour être supérieur au volume de réamorçage à faible débit et inférieur au volume de réamorçage de contrôle du mélange, de façon à ce que les ajustements puissent commencer après la transition vers le haut débit. Blnd Adj Dev % (Excluding SMP) Le pourcentage d'écart de l’ajustement du mélange ne s'applique qu'au mélange proportionnel. Le système commence à ajuster la proportion du mélange lorsqu'il s'écarte de la tolérance de la quantité indiquée dans ce paramètre. L'écart doit se produire pendant la période spécifiée par le paramètre de temps d’ajustement du mélange avant tout essai d’ajustement. Blnd Adj Dev (Excluding SMP) Vol Le volume d'écart de l’ajustement du mélange ne s'applique qu'au mélange proportionnel. Le système commence à ajuster la proportion du mélange lorsqu'il s'écarte de la tolérance du volume indiqué dans ce paramètre. L'écart doit se produire pendant la période spécifiée par le paramètre de Temps d’ajustement du mélange avant tout essai d’ajustement. Blnd Adj Time (Excluding SMP) Période de Temps, en secondes, pendant laquelle un écart dans la tolérance de la proportion du mélange doit se produire pour pouvoir effectuer un ajustement proportionnel. (Voir paramètres Blnd Adj Dev% et Blnd Adj Restart Vol.) Proving Low Flow Rate Le bas débit utilisé au cours du mode d’essai Min Preset volume Volume minimum autorisé de la valeur prédéfinie. Default Preset Volume Dans le mode non-zéro et en fonctionnement autonome cette valeur sera le volume à charger défini par défaut. Si un seul produit est autorisé, il n’y aura pas d’invite. Max Preset volume Volume maximum de la valeur prédéfinie. Auto Batch Authorize Activé : dans le mode de fonctionnement autonome, une transaction est autorisée et le bouton du mode programme est inactif. Le système va essayer d’auto-autoriser le lot. Si le chargement sur ce bras n’est autorisé que pour un seul produit et que le volume prédéfini par défaut n’est pas valable, il n’y aura pas d’invite. Chapitre 4 – Configuration Générale 90 Paramètre Description Delivery in Typ Ce paramètre, lorsque NET est sélectionné, permet d'introduire et de livrer des quantités de valeur prédéfinie en volumes nets. Les CTL et/ou CPL doivent être configurés avant la fin de la livraison nette. Chaque valeur prédéfinie dans le quai peut être configurée indépendamment des autres tant pour la livraison brute que nette. Quand on sélectionne MASS, on autorise l’introduction de quantités prédéfinies en tant que masse et fournies en tant que masse. CTL et/ou CPL doivent être configurés avant d’effectuer la livraison en masse. Chaque valeur prédéfinie pour le quai peut être configurée séparément pour une livraison brute ou nette. De plus, le réglage RCU UOM pour la masse doit être maintenu, faute de quoi une alarme *IFCONFIG retentira. Si ce paramètre est sélectionné sur le type de livraison GROSS, les entrées prédéfinies seront brutes et la livraison sera basée sur des volumes bruts. Blk Valve Open Delay Définissez ce paramètre pour retarder l'ouverture d'une vanne d'arrêt pour une période indiquée en secondes. Quand une vanne d'arrêt d'un niveau prédéfini est utilisée, elle s'ouvrira après cette période. Le temporisateur s’enclenchera au moment où l’on appuie sur le bouton de démarrage. B.V. Open Alarm Time Spécifie une durée en secondes pour permettre à une vanne d'arrêt d'un niveau prédéfini de s'ouvrir. Si la vanne utilise un signal de rétroaction, une alarme se produira si ce signal n'est pas reçu dans le délai spécifié. B.V. Close Alarm Time Spécifie une durée en secondes pour permettre à une vanne d'arrêt d'un niveau prédéfini de se fermer. Si la vanne emploie un signal de rétroaction, une alarme se produira si ce signal n'est pas reçu dans le délai spécifié. Non-Proportional Blending Le mélange non proportionnel est un type de mélange utilisé lorsqu’un certain bras a des mélanges de 5 à 95 %. Au lieu de garder en permanence le mélange non proportionnel dans les spécifications, le mélange sera hors spécifications tout le temps jusqu’à ce que le chargement soit totalement terminé. MultiLoad pré-calculera l’objectif pour tous les composants. Cela fonctionne pour des proportions telles que les mélanges secondaires. Débit des produits: MultiLoad vérifie dans la recette quel est le composant le plus important. Ce composant circulera seul en bas débit. Quand le composant principal passe en haut débit, les autres petits composants démarrent aussi en haut débit. Le haut débit de chaque composant est défini au niveau Composant. Ce débit doit être proche du débit maximum du compteur. Cela veut donc dire qu’en bas débit, on utilise la valeur prédéfinie Low Flow (débit bas) pour le composant principal. Pour le haut débit, le MultiLoad utilise la valeur haut débit au niveau composant pour chaque coposant et ne recherchera pas le haut débit du composant au niveau prédéfini! Ce type de mélange est extrêmement précis parce que les compteurs du plus petit composant ne fonctionnent quasiment qu’en débit maximum et environ au débit minimum du compteur qui est le moins précis. Le premier et le second trips (séries de préréglages) prédéfinis sont utilisés comme avant. La plupart du temps, le volume du premier et du second trips des produits de qualité inférieure sont paramétrés sur zéro. Chapitre 4 – Configuration Générale 91 Paramètre Description Output Pulse FCM# Ce paramètre active une impulsion de sortie représentant le volume fourni par un débitmètre à valeurs prédéfinies. Pour les FCM et les cartes entrée/sorties d’un logiciel internes de 035 ou antérieurs, le port doit toujours être réglé sur 1 pour les FCM et 10 pour les cartes d’entrées/sorties. Pour les FCM et les cartes entrées/sorties de logiciel internes 026 et ultérieurs, le port peut être réglé sur 0-5 pour les FCM et 10-12 pour les cartes entrées/sorties. Les FCM et les carte d’entrées/sorties de logiciel internes 038 et ultérieurs tolèrent des sorties à double impulsion. Activez la sortie à double impulsion en configurant « Invert » sur ce port qui sera l’impulsion principale. L’impulsion secondaire sera le port contigu suivant (0/1, 1/2, 2/3, 3/4, 4/5, 10/11, 11/12) sur le FCM ou la carte d’entrées/sorties. Remarques: Impulsion de sortie simple limitée à 500 Hz Max. Impulsion de sortie double limitée à 250 Hz Max. Les impulsions de sortie ne sont PAS en temps réel et sont décalée de 1 seconde à partir de l’acquisition. Output Pulse Factor Un coefficient peut être appliqué à la sortie d'impulsion pour atteindre la résolution d'impulsion voulue. La résolution d'impulsion peut être configurée de 0.0001 à 50.000 impulsions par volume ou masse d'unité. Output Pulse Typ Sur NET, les impulsions de sortie représentent des volumes nets. CTL et/ou CPL doivent être configurés avant de procéder à des impulsions représentant du volume net. Les impulsions de sortie seront des volumes grossiers si ce paramètre est placé sur GROSS. Si le paramètre est placé sur MASS, la sortie se fera en masse. Il faut que la densité de même que le type UOM de masse soient complétés. Alt. High Flow Start Delay Utilisez ce paramètre pour retarder l’introduction de Alt. High Flow Rate. Le signal Alt. High Flow Rate doit être actif tout le temps, faute de quoi la minuterie se réinitialisera. On utilise surtout ce paramètre pour les détecteurs de bulle. Alt. High Flow Stop Delay Servez-vous de ce paramètre pour retarder la sortie de Alt. High Flow Rate. Il faut que le signal Alt. High Flow Rate Signal ne soit pas actif pendant tout ce temps, faute de quoi la minuterie se réinitialisera. On utilise surtout ce paramètre avec des détecteurs de bulles. Permissive Alarm Time Servez-vous de ce paramètre pour retarder le retentissement d’une alarme permissive. Il faut qu’elle reste inactive tout le temps, faute de quoi la minuterie se réinitialisera. On utilise surtout ce paramètre avec des détecteurs à bulles. Excess Flow Alarm Time Utilisez ce paramètre pour retarder l’alarme de débit excessif pour que celle-ci ne se déclenche pas tout de suite. Cela sert à cacher de brefs poussées de débit que certains compteurs sont à même de traiter. Il est possible d’utiliser deux sondes BSW. Quand la première est hors échelle, on utilisera la seconde. Si la seconde est également hors échelle, on utilisera la BSW par défaut. Si la seconde sonde est désactivée, nous passerons directement de la sonde 1 à la valeur BSW par défaut. BSW1 Sensor Ce paramètre indique qu’on utilise une sonde bsw pour le compteur sélectionné. Activez ce paramètre si la sonde BSW1 est utilisée pour surveiller bsw au compteur. BSW1 Sensor FCM# Introduisez le numéro de FCM pour la sonde BSW1. Introduisez une valeur de 0 pour la carte I/O interne. Default BSW Quand la sonde BSW et désactivée, cette valeur précisera quel BSW il faut utiliser pour le niveau compteur BSW. Si la sonde BSW est désactivée et que la valeur BSW par défaut est de zéro, la valeur instantanée sera toujours zéro. Pas de niveau composant BSW. (La valeur par défaut est la même pour BSW1 et BSW2) Chapitre 4 – Configuration Générale Paramètre 92 Description Alarm Low BSW1 Quand une sonde BSW1 et activée, on peut utiliser ce paramètre pour déclencher une alarme lorsque le BSW1 mesuré passe sous la valeur minimum. Lorsque le BSW1 du produit mesuré tombe sous la valeur introduire dans ce champ, une alarme BSW se déclenche et le chargement s’arrête. Voyez le point sur l’étalonnage BSW pour trouver les instructions de configuration d’une sonde BSW. Alarm High BSW1 Quand une sonde BSW1 est activée, on peut utiliser ce paramètre pour déclencher une alarme lorsque le BSW1 mesuré passe au-dessus d’une valeur maximum. Quand le BSW1 d’un produit mesuré dépasse la valeur introduite dans ce champ, une alarme BSW se déclenche et le chargement s’arrête. Voyez le point sur l’étalonnage BSW pour trouver les instructions de configuration d’une sonde BSW BSW Alarm Time A la valeur par défaut de zéro seconde, les alarmes BSW s’enclenchent automatiquement. On peut y ajouter une petite temporisation en secondes, pour éviter des alarmes intempestives lorsque le BSW est momentanément hors échelle. La minuterie de l’alarme BSW ne s’enclenche que s’il n’y a pas d’alarme BSW active et qu’un lot est autorisé à ce moment-là sur cette valeur prédéfinie. (L’heure d’alarme est la même pour BSW1 et BSW2) BSW1 @ 4mA Introduisez le BSW1 représentant la plus petite valeur BSW1 mesurée par le capteur de mesures. Cette valeur sera égale à 4 mA. BSW1 @ 20mA Introduisez le BSW1 représentant la plus haute valeur BSW1 mesurée par le capteur de mesures. Cette valeur sera égale à 20 mA. BSW1 Offset Ce paramètre permet d’introduire un écart BSW1 pour corriger le BSW indiqué le BSW1 observé. BSW2 Sensor Ce paramètre indique l’utilisation d’une sonde BSW pour le compteur sélectionné. Activez-le si une sonde BSW2 est utilisée pour surveiller BSW sur le débitmètre. BSW2 Sensor FCM# Introduisez le numéro FCM pour la sonde BSW2. Introduisez une valeur de 0 pour la carte I/O interne. Alarm Low BSW2 Quand une sonde BSW2 est activée, on peut utiliser ce paramètre pour déclencher une alarme lorsque le BSW2 mesuré passe sous une valeur minimum. Lorsque le BSW2 du produit mesuré passe sous la valeur introduite dans ce champ, une alarme BSW s’enclenche et le chargement s’arrête. Voyez le point sur l’étalonnage BSW pour trouver les instructions de configuration d’une sonde Alarm High BSW2 Quand une sonde BSW2 est activée, on peut utiliser ce paramètre pour déclencher une alarme lorsque le BSW2 mesuré dépasse une valeur maximum. Lorsque le BSW2 du produit mesuré dépasse la valeur introduite dans ce champ, une alarme BSW se déclenche et le chargement s’arrête. Voyez le point sur l’étalonnage BSW pour trouver les instructions de configuration d’une sonde BSW. BSW2 @ 4mA Introduisez le BSW2 représentant la plus petite valeur BSW2 mesurée par le capteur de mesures. Cette valeur sera égale à 4 mA. BSW2 @ 20mA Introduisez le BSW2 représentant la plus haute valeur de BS2 mesurée par le capteur de mesures. Cette valeur sera égale à 20 mA. BSW2 Offset Ce paramètre permet d’introduire un écart BSW2 pour corriger le BSW2 indiqué pour le BSW2 observé. Oil Density Si le réglage du type de mélange est mis sur coupure d’eau (Watercut) et que nous n’avons pas de sonde BSW ou de valeur par défaut, il faut prendre la densité d’huile et la densité d’eau pour calculer le BSW. Water Density Si le réglage du type de mélange est mis sur coupure d’eau (Watercut) et que nous n’avons pas de sonde BSW ou de valeur par défaut, il faut la densité d’eau et la densité d’huile pour calculer le BSW. Chapitre 4 – Configuration Générale Paramètre 93 Description Remote Clear FCM# Permet de sélectionner un module de commande du débit (FCM) et un port permettant à un interrupteur à distance d’évacuer un lot terminé. Cette option utilisée avec les paramètres Remote Start et Auto Batch Authorize peut s’avérer très utile pour remplir des tonneaux ou pour d’autres opérations multi-lots. Alt. HF Rate FCM# (Excluding SMP) Permet de sélectionner un module de commande de débit (FCM) et un port qui géreront une entrée à partir d’une tête de purgeur d’air ou un autre dispositif. Lorsqu’une impulsion est reçue, le débit passe du haut débit au débit alternatif précisé par le paramètre de débit alternatif que vous trouverez dans les valeurs prédéfinies de poids et mesures. Close Blk Val FCM# Permet la sélection d'un port de sortie qui fournira un signal de sortie pour fermer une vanne d'arrêt de niveau prédéfini. Cette fonction est proposée pour les vannes d'arrêt qui exigent des signaux d'ouverture et de fermeture séparés. Blk Val Status FCM# Le paramètre "Block Valve Status FCM#" permet la sélection d'un port qui recevra un signal d'entrée. Ce signal d'entrée représente l'état de la vanne d'arrêt de niveau prédéfini, indiquant si elle est ouverte ou fermée. Lorsque la vanne d'arrêt est fermée, un contact externe relié à la vanne se ferme, appliquant un signal de statut à l'entrée. Lorsque la vanne d'arrêt est ouverte, le contact externe sera également ouvert, supprimant ainsi le signal de statut de l'entrée. Lorsque la vanne d'arrêt a reçu une commande d'ouverture, l'absence d'un signal à l'entrée indiquera que la vanne a été ouverte. Si le signal "fermé" est toujours présent quand la Durée d'Ouverture de la Vanne d'arrêt s'est écoulée, une alarme d'échec de la vanne d'arrêt se produira. Lorsque la vanne d'arrêt a reçu une commande de fermeture, la présence du signal de statut à l'entrée indiquera que la vanne a été fermée. Si le signal "fermé" n'a pas été détecté quand la Durée de Fermeture de la Vanne d'arrêt s'est écoulée, une alarme d'échec de la vanne d'arrêt se produira. Open Blk Val FCM# Permet la sélection d'un port qui fournira un signal de sortie pour ouvrir une vanne d'arrêt de niveau prédéfini. La vanne d'arrêt de niveau prédéfini reçoit une commande d'ouverture après avoir appuyé sur bouton de démarrage et que la Durée d'Ouverture de la Vanne d'arrêt est écoulée. La vanne reçoit une commande de fermeture pendant lors de l’une des conditions suivantes: fin de lot, alarme quelconque, lorsque le bouton d'Arrêt a été poussé ou si la carte a été retirée du lecteur de cartes. Flow Active FCM# Ce paramètre sélectionne un port qui fournira un signal de sortie pour indiquer que le débit est actif. Lorsque vous poussez sur le bouton de démarrage, le signal devient actif. Le signal sera désactivé à la fin du lot lorsque le bouton d'arrêt est poussé ou si une alarme arrête le débit. Le signal sera réactivé lorsque le bouton de démarrage est poussé suite à soit, une alarme, soit une interruption involontaire du lot. Par défaut, un signal élevé représentera une condition active. Batch Authorized FCM# Ce paramètre sélectionne un port qui fournira un signal de sortie pour indiquer que la valeur prédéfinie est autorisée pour le chargement. Le signal deviendra actif après l'octroi de l'autorisation. Le signal restera actif jusqu'à ce que l'opérateur archive le lot en effaçant les valeurs prédéfinies ou en retirant la carte. Par défaut, un signal élevé représentera une condition active. Remote Start FCM# Ce paramètre permet la sélection d'un port qui sera assigné pour recevoir l'entrée du bouton de démarrage à Distance. Le bouton de démarrage à Distance peut être utilisé pour commencer un chargement depuis un endroit éloigné du MultiLoad II, comme depuis un endroit de chargement supérieur. Le processus d'introduction de carte et de l'entrée de la valeur prédéfinie doit être terminé au niveau du MultiLoad II avant d'activer le débit avec le bouton de démarrage à Distance. Cette fonction peut être utilisée conjointement avec la fonction "Arrêt du compteur". Si le débit est arrêté par "Arrêt du compteur", il peut redémarrer en activant le bouton de démarrage à Distance. Si le débit est arrêté en raison d'une Alarme de faible débit, cette alarme peut être annulée et le débit, redémarre par simple activation du bouton de démarrage à Distance. Chapitre 4 – Configuration Générale 94 Paramètre Description Swing Arm FCM# Si un bras oscillant est configuré pour ces valeurs prédéfinies, introduisez le numéro du module de commande de débit et de port qui recevront les valeurs prédéfinies pour le commutateur de détecteur de bras oscillant. Meter Stop FCM# Sélectionne le port d’entrée qui sera attribué pour détecter le bouton d’arrêt du compteur. Lorsque le commutateur ‘arrêt du compteur est activé, la vanne de régulation du débit se ferme et la pompe de composant s’arrête. Alarm Out FCM# “Alarm Out” émet un signal de sortie sur les valeurs prédéfinies ont une alarme active. Ce paramètre sélectionne le port de sortie qui sera attribué pour signaler une alarme non précisée lors de la définition des valeurs. Authorized FCM# Le FCM autorisé produit un signal de sortie sir les valeurs prédéfinies ont été autorisées pour le débit suite à la connexion d’un chauffeur ou la sélection d’un produit. Permiss FCM# Le paramètre Permiss FCM# permet de sélectionner un port qui recevra un signal d’entrée représentant l’état des valeurs « permissive » prédéfinies. Si le signal n’est pas présent lors de l’autorisation, ou s’il est perdu en cours de livraison, la procédure sera interrompue et une alarme de niveau permissif se produira. Permiss Out FCM# Ce paramètre permet de sélectionner un port qui fournira un signal de sorti représentant la perte des valeurs “permissive” prédéfinies. Chapitre 4 – Configuration Générale 95 RÉGLAGE DU COMPTEUR 4.7.3 Utilisez les fonctions de réglage du compteur pour configurer les caractéristiques pour le comptage d’un produit. Vous trouverez de plus amples détails au Chapitre 5. Les débits de comptage sont configurés dans les poids et mesures : Weights & Measures -> Meter section que vous retrouverez au Chapitre 8. Sur cet écran, allez à: Program Mode -> Configuration -> Equipment Setup -> Select Paramet Level - > Meter Toutes les valeurs contrôlées de poids et mesures s’affichent en rouge sur l’écran et dans le manuel. L’écran de réglage du compteur affiche: Paramètre Flow #t PRE #1 MTR #1 SETUP Flow Control Module#: 0 Side-Stream on Mtr# 0 Side-Strm on Any Mtr# DISABLD Meter Address: 0 Meter Type: VOL PUL Max Quad Errors: 10 Reset Quad Errors: 10000 Low Flow Alarm Rate: 10 Low Flow Alarm Time: 10.000 Excess Flw Alrm Rate: 800 Minimum Flow Rate: 50 Maximum Flow Rate: 650 Low Flow DB Rate: 40 High Flow DB Rate: 40 Next Prev Exit Enter Description Control Module Attribuez un module de contrôle du débit (FCM) au débitmètre du produit sélectionné. i vous utilisez une carte I/O interne, 0 est la seule valeur acceptée. Le port 4 est automatiquement sélectionné comme signal d’entrée du compteur de canal A. Si vous utilisez une entrée de compteur de canal B, il faut la connecter au port 5. Pour activer le canal B, voir au paramètre Poids et Mesures "Quad Check Enable." Les sorties amont et aval de la vanne de régulation numérique sont automatiquement attribués respectivement aux ports 2 et 3. Side Stream on Mtr # (Excluding SMP) Si ce compteur est un compteur de flux latéral, utilisez ce paramètre pour identifier le compteur primaire de courant dans lequel le flux latéral s'écoulera. Voir au chapitre consacré à la configuration latérale pour de plus amples détails. Side-Stream on Any Meter (Excluding SMP) Activez ce paramètre si un compteur de flux latéral doit desservir un bras oscillant de plus d’un débitmètre de transfert fiduciaire. Une application commune est, par exemple, lorsqu’un compteur de flux latéral sert à un bras de mélange proportionnel à deux composants. Toutefois, le compteur de flux latéral ne peut s’écouler qu’au travers d’un débitmètre à la fois. Chapitre 4 – Configuration Générale 96 Paramètre Description Type de compteur Ce paramètre indique que l’entrée d’impulsion est exprimée en unités de masse mais doit être convertie en volume. Tous les affichages et les quantités prédéfinies sont encore toujours exprimés en volume. Les procédures et les données sont configurées à différents niveaux du matériel. En général, les données proviennent du hardware du compteur même et passent au niveau du compteur puis au niveau composant attribué et enfin au niveau des valeurs prédéfinies. En introduisant « Mass Pulse »,les “impulsions en masse”, le niveau compteur peut faire passer des données d’impulsion de procédure et de produits comme masse. Ceci comprend le chargement de la température et de la densité observées. Les données en masse du compteur sont converties en volume quand elles passent du niveau compteur au niveau composant (Vol = Mass * Density). Au niveau composant, le volume brut est converti en volume net et les valeurs, - brut et net – passent au niveau des valeurs prédéfinies. Seul le niveau compteur est capable de traiter efficacement des données en masse et, par conséquent, la plupart des paramètres de vitesse et de volume au niveau composant et au niveau des valeurs prédéfinies passent au niveau compteur pour configurer le matériel de commande du débit (carte des entrées/sorties) pour le chargement. Quand on active l’impulsion en masse”, tous les paramètres de volume et de vitesse se trouvant aux niveaux compteur, composants et valeurs prédéfinies sont exprimés en unités de masse, SAUF LES ELEMENTS SUIVANTS, qui restent en unités de volume : Niveau valeurs prédéfinies: Vitesse d’alarme de dépassement de débit Niveau des valeurs prédéfinies: volume alarme débordement Niveau des valeurs prédéfinies: volume de purge de conduites Niveau des valeurs prédéfinies: volume minimum de purge de conduites Niveau des valeurs prédéfinies: volume minimum des valeurs prédéfinies Niveau des valeurs prédéfinies: volume maximum des valeurs prédéfinies Niveau des valeurs prédéfinies: Coefficient d’impulsion de sortie Niveau Composant: volume alarme débit non autorisé. Niveau Composant: Vitesse d’ouverture de la vanne d’arrêt Niveau Composant: volume nouvel essai de traitement de secours. Volume 4-20mA entrée analogique – un signal de 4-20mA indique le débit. Le coefficient K du compteur permet de convertir ce signal en flux d’impulsion virtuel. Le débit de 4mA et 20mA peut se configurer de même qu’un léger écart et un taux de blocage plus bas. Les facteurs du compteur peuvent s’appliquer pour étalonner le volume. Remarque ; la version du FCM ou de la carte I/O du logiciel 039 ou ultérieure est indispensable pour utiliser une entrée analogique de 4-20mA de type compteur. Entrée Volume Krohne – Une connexion sérielle Modbus au compteur masse indique les valeurs de volume, débit, température et densité. Des écrans supplémentaires de réglage et de diagnostic sont disponibles lorsque cette option est activée. Entrée Volume MicroMotion – une connexion sérielle Modbus au compteur masse MicroMotion indique les valeurs de volume, débit,température et densité. Des écrans supplémentaires de réglage et de diagnostic sont disponibles lorsque cette option est activée. Chapitre 4 – Configuration Générale 97 Paramètre Description Max Quad Errors Ce paramètre n'est valable que lorsque la fonction quadrature a été activée. Introduisez le nombre d'erreurs de quadrature (sécurité d'impulsion) qui déclenche une alarme de quadrature. L'alarme arrêtera le débit. Un débitmètre à double capteur ou un générateur d'impulsions à deux voies, commandé par compteur, est exigé pour utiliser cette fonction. Reset Quad Errors Ce paramètre n'est valable que lorsque la fonction quadrature a été activée. Ce paramètre détermine le nombre d'impulsions qui seront vérifiées en matière d'erreurs. Si aucune erreur de quadrature (sécurité d'impulsion) ne se produit pendant la transmission du nombre d'impulsions déterminées par ce paramètre, le compteur d'erreur de quadrature se réinitialisera de lui-même. Le compteur d'erreur commencera alors à cataloguer les erreurs à partir de zéro. Lorsque le nombre d'erreurs cataloguées dans le compteur dépasse la valeur d'erreurs maximum de quadrature Avant que la quantité d'impulsions établie dans ce paramètre n'ait été transmise, une alarme de quadrature se produira. Low Flow Alarm Rate Spécifie le débit minimum absolu du débitmètre. Lorsque le débit passe sous cette valeur pendant une période spécifiée par le paramètre de temps d’alarme de faible débit, l'alarme de faible débit du compteur s'active. En général, cette valeur est définie sur le plus petit débit du débitmètre tel que publié par le fabricant du compteur. Low Flow Alarm Time Lorsque le débit chute sous le taux d’alarme de faible débit pendant la durée de temps spécifiée dans ce paramètre, cette alarme se déclenche. Excess Flw alarm Rate Spécifie le débit maximum absolu du débitmètre. Lorsque le débit dépasse cette valeur, l'alarme de dépassement du débit s'active. En général, cette valeur est définie sur le plus haut débit du débitmètre tel que publié par le fabricant du compteur. Minimum Flow Rate Introduisez le débit minimum du débitmètre tel que prescrit par le fabricant. Le système ne permettra pas que le débit descende sous cette valeur. Maximum Flow Rate Introduisez le débit maximum du débitmètre tel que prescrit par le fabricant. Le système ne permettra pas que le débit excède cette valeur. Low Flow DB Rate Le faible débit de Zone Morte spécifie la quantité d'erreur de taux qui sera tolérée avant un essai d’ajustement de taux par la vanne de régulation du débit. Si, par exemple, ce paramètre est réglé sur 10 gpm et que le faible débit est réglé sur 100 gpm, la vanne n'essayera pas d'ajuster le débit jusqu'à ce que le faible débit dépasse 110 gpm ou tombe sous 90 gpm. High Flow DB Rate Le haut débit de Zone Morte spécifie la quantité d'erreur de taux qui sera tolérée avant un essai d’ajustement de taux par la vanne de régulation du débit. Si, par exemple, ce paramètre est réglé sur 10 gpm et que le haut débit est réglé sur 1000 gpm, la vanne n'essayera pas d'ajuster le débit jusqu'à ce que le haut débit dépasse 1010 gpm ou tombe sous 990 gpm. 1st Stage DB Rate Le Premier débit de zone Morte du dispositif de déclenchement spécifie la quantité d'erreur de taux tolérée avant un essai d’ajustement de taux par la vanne de régulation du débit. Si, par exemple, ce paramètre est réglé sur 10 gpm et que la zone morte du dispositif de déclenchement est réglée sur 200 gpm, la vanne n'essayera pas d'ajuster le débit jusqu'à ce que la zone morte du dispositif de déclenchement dépasse 210 gpm ou tombe sous 190 gpm. 2nd Le Second débit de zone Morte du dispositif de déclenchement spécifie la quantité d'erreur de taux tolérée avant un essai d’ajustement de taux par la vanne de régulation du débit. Si, par exemple, ce paramètre est réglé sur 10 gpm et que le second débit de zone morte du dispositif de déclenchement est réglé sur 50 gpm, la vanne n'essayera pas d'ajuster le débit jusqu'à ce que le second débit de zone morte du dispositif de déclenchement dépasse 60 gpm ou jusqu'à ce que le premier débit de zone morte du dispositif de déclenchement tombe sous 40 gpm. Stage DB Rate Chapitre 4 – Configuration Générale 98 Paramètre Description Valve Cntl Alrm Time Lorsque la vanne de régulation est incapable de réduire le débit pendant la période spécifiée dans ce paramètre, l'alarme de contrôle de la vanne s'enclenche. Cette alarme arrête le chargement. Le déclenchement répété de cette alarme peut indiquer que la vanne est inerte; un entretien ou une inspection de la vanne peut s’avérer nécessaire. Valve Fault Alrm Vol Lorsque la vanne a reçu une commande de fermeture, l'alarme d'erreur de vanne s'activera si cette fermeture échoue avant que le volume de l'alarme d'erreur de vanne n'ait été livré. Creep Reset Time Le fluage est n'importe quel volume qui traverse le débitmètre lorsqu'une commande de fermeture de vanne est passée. Les volumes de fluage peuvent apparaître lorsque le composant est autorisé ou non autorisé. Ce paramètre permettra au compteur interne du fluage d'être réinitialisé périodiquement pour éviter les alarmes intempestives, en raison de coups de bélier. La réinitialisation périodique de ce compteur interne empêche les petites quantités de fluage de s'accumuler pendant des heures et de déclencher des alarmes trompeuses d'erreur de vanne. Définissez la durée en secondes. Cette fonction ne réinitialise pas le totalisateur de fluage qui s'affiche à l'écran "Meter Views and Inquiries". Ratio Adj P. Factor (Excluding SMP) Facteur proportionnel de correction par ratio. Ce paramètre ne s’applique qu’aux mélanges proportionnels. Ne réglez pas ce paramètre sans avoir consulté l’assistance technique de Toptech. Meter Creep Alrm Vol Introduisez le volume de fluage qui déclenchera une alarme de fluage. Si le volume du fluage spécifié dans ce paramètre s'accumule pendant la période indiquée dans le paramètre de durée de réinitialisation du fluage, une alarme de fluage se produira. Le fluage peut indiquer qu'il y a une petite fuite dans la vanne ou peut provenir d'un coup de bélier excessif. Le fluage signifie que le liquide passe devant le compteur quand la vanne est censée fermée. Flow Scan Time Utilisez ce paramètre pour une commande de débit plus fluide si la résolution d'impulsion du débitmètre est basse. Le temps d'analyse par défaut doit être utilisé si la résolution du débitmètre est de 40 impulsions par gallon ou plus. Si le réglage par défaut est de 0.100 secondes, le FCM échantillonnera le débit 10 fois à chaque seconde. Si les indications ci-dessous ne produisent pas l'effet désiré, incrémentez le paramètre par 0.100 seconde jusqu'à ce que les résultats désirés soient atteints. La fourchette de réglage s'étend de 0.100 à 1.000 secondes. 40 ppg = 0.100 secondes 25 ppg = 0.200 secondes 10 ppg = 0.500 secondes 1 ppg = 1.000 secondes Chapitre 4 – Configuration Générale 99 Paramètre Description Valve Dwell Time Utilisez ce paramètre pour les vannes de régulation numériques avec vannes de contrôle de la vitesse d'ouverture et de fermeture grandes ouvertes. Ce paramètre doit être ajusté lorsque des clapets à bille sont utilisés sur des vannes de régulation numériques pour régler la vitesse d'ouverture et de fermeture. Si la vanne de régulation contient des vannes à pointeau de réglage de vitesse et qu'elle est utilisée pour régler les vitesses d'ouverture et de fermeture de la vanne de régulation, utilisez le réglage par défaut de 1 seconde. A défaut de quoi, référez-vous aux instructions suivantes, basées sur la dimension de la vanne. Vanne de Régulation Numérique de 4” = 0.040- 0.080 secondes Vanne de Régulation Numérique de 3” = 0.030- 0.070 secondes Vanne de Régulation Numérique de 2” = 0.020- 0.040 secondes Lorsque le FCM tente d'ajuster le débit, les électrovannes d'ouverture et de fermeture de la vanne de régulation s'activent. Le temps de pause de la vanne détermine la durée de mise en action de l’électrovanne. Si le temps de pause de la vanne diminue, la mise en action des électrovannes sera de plus en plus courte et rapide. Si la vanne s'ouvre ou se ferme, des étapes plus précises seront nécessaires vers le débit-cible à mesure que le temps de pause de la vanne diminue. Voir à « taux de pause pas de la vanne » ci-après. Valve Dwell Step Rate Ce paramètre s’utilise conjointement au temps de pause de la vanne. Définissez ce paramètre de façon à ce qu’il corresponde à quatre fois le débit de zone morte. Les ajustements importants de la vanne de limitation de course s'effectueront lorsque le débit est loin de la zone morte. A mesure que l'on approche de la zone morte, la vanne commence à faire les ajustements précis prescrits par le temps de pause de la vanne. Les réglages du débit de zone morte se retrouvent sous Configuration/Installation des Équipements/Compteur. Voir à « Temps de Pause du Pas de la Vanne ». Valve Dwell Step Time Définissez cette valeur sur 1.00 lors de l'utilisation des paramètres de Temps de Pause de la Vanne et Taux de Pause du Pas de la Vanne. Adaptive Valve Control S’il est activé, l’algorithme de la vanne de régulation essayera de s’adapter à la vitesse de la vanne, ce qui entraînera des débit-cibles plus précis. Pour utiliser cette fonction: Le temps d’analyse de débit doit être mis sur 0.200 secondes. Le temps de pause de la vanne doit être mis sur 0.030 secondes. Analog Valve Control Activer ce paramètre permet d’utiliser une vanne de régulation analogique de 4-20mA . 4mA est considéré comme complètement fermé et 20mA comme complètement ouvert. 0mA indique qu’il n’y a pas de débit ou que ce n’est pas actif. 4-20mA Increase Step La quantité de mA pour AUGMENTER la sortie analogique après chaque analyse de débit s’avère être INFERIEURE au débit-cible de zone morte. 4-20mA Step La quantité de mA pour DIMINUER la sortie analogique après chaque analyse de débit s’avère être SUPERIEURE au débit-cible de zone morte. Decrease Alarm Réglez ce paramètre pour retarder l’alarme de débit excessif pour que l’alarme n’apparaisse pas immédiatement afin de cacher de petites poussées de débit que certains compteurs sont à même de traiter. Analog Flow Rate @ 4mA Introduisez le débit représenté par un signal de 4mA à partir du capteur de mesures analogiques. Cette valeur est habituellement 0. Vérifiez les documents du compteur analogique ou la configuration pour cette valeur. Analog Flow Rate @ 20mA Introduisez le débit représenté par un signal de 20mA signal à partir du capteur de mesures analogiques du compteur. Cette valeur est habituellement le débit maximum que le compteur peut mesurer. Vérifiez les documents du compteur analogique ou la configuration pour cette valeur. Excess Time Flow 10 0 Chapitre 4 – Configuration Générale Paramètre Description Rate Introduisez n’importe quel écart de débit nécessaire. Tout ajustement de l’étalonnement du débit devrait se faire dans le capteur de mesures du compteur. Utilisez ce paramètre pour effectuer des ajustements si le débit sur le compteur diffère de celui affiché sur le MultiLoad. Analog Flow Rate CutOff Introduisez le débit de blocage. Tout débit mesuré sur le signal 4-20mA signal inférieur à cette valeur sera traité comme un débit zéro. Density Sensor Ce paramètre indique l’utilisation d’une sonde de densité pour le compteur sélectionné. Activez-le si on utilise une sonde de densité pour surveiller la densité au compteur. Density Sensor FCM# Introduisez le numéro de FCM # pour la sonde de densité. Introduisez une valeur de 0 pour la carte I/O interne. Default Density Pour les tableaux API nécessitant une entrée de densité, introduisez ici la valeur qui doit être celle de la densité du composant à 15 C. Utilisez des kg/m³. Lorsque la sonde densité est désactivée, cette valeur précisera la densité qu’il faut utiliser pour la densité au niveau du compteur. Si la sonde de densité est désactivée et que la valeur de densité par défaut est de 0, on utilisera la densité instantanée prévue pour le composant. Si ce compteur est le flux principal d’un mélange flux latéral, on calcule une densité pondérée de mélange à partir des densités du composant du flux principal et latéral. Pour les tableaux API nécessitant une densité, on utilisera la densité au niveau du compteur pour ce calcul. Alarm Low Density Quand un capteur de densité est activé, vous pouvez utiliser ce paramètre pour enclencher une alarme si la densité mesurée tombe sous une valeur minimum. Lorsque la densité du produit mesuré tombe sous la valeur introduite dans ce champ, une alarme de DENSITE se déclenche et le chargement s’arrête. Référez-vous à point relatif à l’étalonnage de la densité pour les directives concernant la configuration d’un capteur de densité. Alarm High Density Quand un capteur de densité est activé, vous pouvez utiliser ce paramètre pour enclencher une alarme si la densité mesurée s’élève au-delà d’une valeur maximum. Lorsque la densité du produit mesuré dépasse la valeur introduite dans ce champ, une alarme de DENSITE se déclenche et le chargement s’arrête. Référez-vous au point concernant l’étalonnage de la densité pour les directives relatives à la configuration d’un capteur de densité. Density Alarm Time Pour une valeur par défaut de zéro seconde, les alarmes de densité se déclenchent instantanément. On peut y ajouter une légère temporisation en secondes pour éviter des déclenchements intempestifs si la densité se trouve temporairement hors échelle. La minuterie de l’alarme densité s’enclenche uniquement si aucune alarme densité n’est active et qu’un lot est autorisé à ce moment-là pour cette valeur prédéfinie. Density @ 4mA Introduisez la densité correspondant à la plus petite valeur de densité mesurée par le capteur de mesures. Cette valeur est de 4 mA. Density @ 20mA Introduisez la densité correspondant à la plus haute valeur de densité mesurée pas le capteur de mesures. Cette valeur est de 20 mA. Density Offset Ce paramètre permet d’introduire un écart de densité pour corriger la densité indiquée par rapport à la densité observée. Pressure Sensor Ce paramètre indique l'utilisation d'un capteur de pression pour le compteur sélectionné. Activez ce paramètre si un capteur de pression est utilisé pour contrôler la pression au débitmètre. Pressure FCM# Introduisez le FCM # pour le capteur de pression. Introduisez la valeur 0 pour la carte interne I/O. Analog Offset Flow Sensor 10 1 Chapitre 4 – Configuration Générale Paramètre Description Default Pressure C’est la pression que le tableau API utilise lorsque le capteur de mesures de pression est en cours d’entretien. N’ajustez cette valeur que s’il est hors service. Revenez à la valeur 999.9 lorsqu’il est remis en service. Alarm Low Pressure Introduisez la pression qui représente la valeur minimale de pression du tableau API en service. Lorsque la pression tombe sous cette valeur, une alarme se produit. Alarm High Pressure Introduisez la pression qui représente la valeur maximale de pression du tableau API en service. Lorsque la pression dépasse cette valeur, une alarme se produit. Pressure Alarm Timer L’alarme pression se déclenche instantanément à une valeur par défaut de zéro seconde. On peut ajouter une légère temporisation en secondes pour éviter un déclenchement intempestif de l’alarme si la pression se trouve temporairement hors échelle. Pressure @ 4mA Introduisez la pression qui représente la valeur de pression la plus basse mesurée par le manomètre. Cette valeur est égale à 4 mA. Pressure @ 20mA Introduisez la pression qui représente la valeur de pression la plus haute mesurée par le manomètre. Cette valeur est égale à 20 mA. Pressure Offset Ce paramètre permet d’introduire une compensation de pression pour corriger la pression indiquée en pression observée. La gamme de compensation s'étend de -3.00 à 3.00 unités. Relative Sensor Density Ce paramètre qu’on utilise une sonde de densité relative pour le compteur sélectionné. Activez-le si on utilise une sonde de densité relative pour surveiller la densité relative au compteur de débit. Relative Density Sensor FCM# Introduisez le numéro de FCM # pour la sonde de densité relative. Introduisez une valeur de 0 pour la carte I/O interne. Default Density Relative Pour les tableaux API nécessitant l’introduction de la densité relative, introduisez cette valeur ici. La valeur devrait être la densité relative du composant à 15 C. Quand la sonde de densité relative est désactivée, cette valeur spécifie la densité relative qu’il faut utiliser pour la densité relative au niveau du compteur. Si la sonde de densité relative est désactivée et que la valeur de la densité relative par défaut est 0, on utilisera la densité relative du composant désigné à ce moment-là. Si ce compteur est le primaire d’un mélange secondaire, on calcule une densité relative pondérée du mélange à partir des densités relatives du composant primaire et secondaire. Pour les tableaux API nécessitant une densité relative, on utilise la densité relative au niveau compteur pour ce calcul. Alarm Low Density Relative Lorsqu’une sonde de densité relative est activée, on peut utiliser ce paramètre pour déclencher une alarme lorsque la densité relative mesurée passe en-dessous d’une valeur minimum. Lorsque la densité relative d’un produit mesure passe sous la valeur introduite dans ce champ, on déclenche une alarme de densité et le chargement s’arrête. Voir le point consacré à l’étalonnage de la densité relative pour les instructions sur la configuration d’une sonde de densité relative. Alarm High Relative Density Lorsqu’une sonde de densité est désactivée, on peut utiliser ce paramètre pour déclencher une alarme lorsque la densité mesurée passe au-dessus de la valeur maximum. Lorsque la densité relative du produit mesuré dépasse la valeur introduite dans ce champ, on déclenche une alarme densité et le chargement s’arrête. Voir le point consacré à l’étalonnage de la densité relative pour les instructions sur la configuration d’une sonde de densité relative. 10 2 Chapitre 4 – Configuration Générale Paramètre Description Relative Density Alarm Time A la valeur par défaut de zéro seconde, des alarmes de densité se déclenchent automatiquement. On peut y ajouter une brève temporisation en secondes pour éviter des alarmes intempestives lorsque la densité relative est momentanément hors échelle. La minuterie de l’alarme de densité relative ne fonctionne que si aucune alarme de densité est active et qu’un lot est autorisé à ce moment-là pour cette valeur prédéfinie. Relative 4mA Density @ Introduisez la densité relative représentant la valeur de densité la plus basse mesurée par le capteur de mesures. Cette valeur est égale à 4 mA. Relative 20mA Density @ Introduisez la densité relative représentant la valeur de densité la plus élevée mesurée par le capteur de mesures. Cette valeur est égale à 20 mA. Relative Density Offset Ce paramètre permet d’introduire un écart de densité relative pour corriger la densité relative indiquée à la densité relative observée. 2% MF Limit Ref La Référence Limite de 2% du Facteur de Mesure est un nombre représentatif des facteurs de mesure obtenus pendant une session d'essai initiale. Introduisez une valeur correspondant à la moyenne de tous les facteurs de mesure obtenus pendant une session d'essai initiale. Les exemples de sessions d'essai initiales sont des essais qui surviennent après réparation ou remplacement d'un compteur. Si, pendant des sessions d'essais successives, un des quatre facteurs de mesure a changé de plus de 2% par rapport à la référence limite, une alarme INVCONFIG se déclenche. Le débitmètre doit être vérifié s'il n'est pas possible d'obtenir un facteur de mesure compris dans les 2 % de la référence. Mettez ce paramètre sur zéro pour désactiver la fonction. Adjacent MF Dev Limt Introduisez une valeur pour limiter les écarts au niveau des facteurs de mesure adjacents. La Limite de Déviation du Facteur de Mesure Adjacent empêchera l’ajustement d'un facteur de mesure qui aboutirait à un écart par rapport à la valeur introduite. Par exemple, on désire limiter l'écart des facteurs de mesure adjacents à 0.25 %. Si un nouveau facteur de mesure a été obtenu pour le facteur #2 de mesure, ce nouveau facteur de mesure ne peut pas dévier de plus d'environ 0.25 % par rapport au facteur # 1 ou facteur #3 de mesure. Si un nouveau facteur de mesure transgressant ce réglage est introduit, une alarme INVCONFIG se produit après la réinitialisation du MultiLoad II. Pour régler la limite à 0.25 %, introduisez une valeur de 0.0025. Le débitmètre doit être vérifié s'il n'est pas possible d'obtenir un facteur de mesure qui ne transgresse pas cette condition. Mettez ce paramètre sur zéro pour désactiver la fonction. Temp Offset Limit Ce paramètre limite la fourchette de compensation de la température pouvant être introduite. La fourchette valable d'entrées va de 1 à 5 degrés. Si, par exemple, la valeur 1 est introduite, le paramètre de compensation de la température ne peut varier de zéro que de 1 degré. Pour une mesure de la température en Celsius, introduisez une valeur de 1. Pour une mesure de la température en Fahrenheit, utilisez une valeur de 3. Alarm Out FCM# La sortie alarme fournit un signal de sortie si le compteur a une alarme active. Ce paramètre sélectionne le port de sortie qui sera attribué pour signaler une alarme spécifique venant du compteur. Authorized FCM# Le FCM autorisé fournit un signal de sortie sur le compteur autorisé à débiter si un chauffeur a introduit sa carte ou si un produit a été sélectionné. Permiss FCM# Autorise la sélection d’un port qui recevra un signal d’entrée. Le signal d’entrée représente l’état d’autorisation du compteur. S’il n’y a pas de signal au moment de l’autorisation ou si le signal se perd au cours de la livraison, la procédure est interrompue et une alarme se déclenche au compteur. Permiss Out FCM# Ce paramètre permet de sélectionner un module de commande du débit (FCM) et un port qui produit un signal de sortie. Le signal représente une perte d’autorisations du compteur. Meter K-factor Le coefficient K représente le nombre d’impulsions produites par unité de volume livré. L’unité de volume représentée par le coefficient K détermine l’unité de volume utilisée dans tous les paramètres qui exigent une spécification du volume. 10 3 Chapitre 4 – Configuration Générale Paramètre Description Quad Check Enable Ce paramètre permet d'activer ou de désactiver le contrôle de la quadrature, également appelé "sécurité d'impulsion". Cette fonction est destinée à vérifier les d'entrées d'impulsion du compteur par la réception de deux entrées du train d'impulsions depuis un débitmètre simple. L'entrée de quadrature doit se faire sur le port 5. L'entrée du compteur primaire doit utiliser le Port 4. Temperature Offset Ce paramètre permet de proposer une compensation de température pour corriger la température indiquée en température observée. La gamme de compensation peut être limitée de 1 à 5 degrés par le biais du paramètre de limite de compensation de la température. Temperature Time À la valeur par défaut de zéro seconde, des alarmes de température se produisent instantanément. Une légère temporisation peut être ajoutée, en secondes pour éviter des alarmes intempestives lorsqu'un module RTD est en train de se synchroniser sur son FCM après récupération suite à une coupure d'alimentation. Alarm Temp Sensor FCM# Quand le type de module de température est de +10, introduisez le FCM # pour le capteur de température. Introduisez la valeur 0 pour la carte interne d’entrées et de sorties. Temperature Sensor Permet d'activer une sonde de température pour ce compteur. Désactivez ce paramètre si la température provient d'une source extérieure au SMP. Voir aussi les paramètres Type de Module de Temp. et FCM# du Capteur de Temp. Default Temperature En cas de panne d'un RTD, la température observée peut être introduite manuellement pour être utilisée par le système jusqu'à ce que le RTD soit réparé. Lors de la panne d'un RTD, une alarme RTD se produit. S'il faut mettre le RTD hors service, désactivez (coupez) le paramètre "Disable RTD" et la clef à la température observée. Lorsque le RTD est remis en service, activez le paramètre RTD. Alarm Low Temp Lorsque la température du produit mesuré chute sous la température spécifiée par ce paramètre, l'alarme de basse de température se déclenche. Introduisez la température en Celsius ou en Fahrenheit. Les unités de température utilisées pour le quai entier sont définies par un paramètre du menu quai. Alarm High Temp Lorsque la température du produit mesuré monte au-dessus de la température spécifiée par ce paramètre, l'alarme de température élevée se déclenche. Introduisez la température en Celsius ou en Fahrenheit. Les unités de température utilisées pour le quai entier sont définies par un paramètre du menu quai. Temp Module Type Introduisez une valeur représentant le type approprié de capteur de température. Pour un réglage normal, prenez 1. Pour le MultiLoad II SMP: 1 – Carte interne entrées/sorties RTD 3 – Carte interne entrées/sorties 4-20mA Pour le MultiLoad II: 0 – FCM externe avec module RTD Opto22 1 – Carte interne entrées/sorties ou FCM externe avec Module RTD Toptech 2 – FCM externe avec module Opto22 4-20mA 3 – Carte interne entrées/sorties 4-20mA Ajoutez +10 à cette valeur pour spécifier un FCM autre que celui auquel le compteur est assigné. Utilisez le FCM# du sonde de température pour spécifier le FCM alternatif. Temperature @ 4mA Quand vous utilisez un capteur de température produisant un signal 4-20 mA, introduisez la température représentée par 4 mA. Temperature @ 20mA Quand vous utilisez un capteur de température produisant un signal 4-20 mA, introduisez la température représentée par 20 mA. 10 4 Chapitre 4 – Configuration Générale Paramètre Description API Gravity Sensor Ce paramètre indique qu’on utilise une sonde de gravité API pour le compteur sélectionné. Activez-le si on en utilise un pour surveiller la gravité API au débitmètre. API Gravity FCM# Introduisez le numéro de FCM pour la sonde de gravité API. Introduisez une valeur de 0 pour la carte I/O interne. Sensor Default API Gravity Pour les tableaux API nécessitant l’introduction de la gravité API, introduisez cette valeur ici. La valeur devrait être la gravité API du composant à 15 C ou à 60 F. Quand la sonde de gravité API est désactivée, cette valeur spécifie la gravité API qui doit être utilisée pour la gravité API au niveau compteur. Si la sonde de gravité API est désactivée et que la valeur de gravité API pa défaut est zéro, on utilise la gravité API du composant désigné à ce moment-là. Si ce compteur est le primaire d’un mélange secondaire, on calcule une gravité API pondérée du mélange à partir de la gravité API du composant primaire et secondaire. Pour les tableaux API nécessitant une gravité API, on utilisera la gravité APi au niveau compteur pour ce calcul. Alarm Low API Gravity Quand une sonde de gravité API est enclenchée, on utilise ce paramètre pour déclencher une alarme lorsque la gravité API mesure passe sous une valeur minimum. Lorsque la gravité API pour le produit mesuré passe sous la valeur introduite dans ce champ, une alarme gravité API s’enclenche et le chargement s’arrête. Voir le point relatif à l’étalonnage de la gravité pour des instructions sur la configuration d’une sonde de gravité API. Alarm Gravity High API Lorsqu’une sonde de gravité API est activée, on peut utiliser ce paramètre pour déclencher une alarme lorsque la gravité API mesurée passe au-dessus d’une valeur maximum. Lorsque la gravité API du produit mesure dépasse la valeur introduite dans ce champ, une alarme gravité API s’enclenche et le chargement s’arrête. Voir le point sur l’étalonnage de la gravité API pour les instructions sur la configuration de la sonde de gravité API. API Gravity Time Alarm A la valeur par défaut de zéro seconde, les alarmes de gravité API s’enclenchent instantanément. On peut ajouter une légère temporisation en secondes pou éviter des alarmes intempestives lorsque la gravité est momentanément hors d’échelle. La minuterie d’alarme de gravité API ne fonctionne que lorsqu’aucune alarme de gravité API est active et qu’un lot est autorisé à ce moment-là pour cette valeur prédéfinie. API Gravity @ 4mA Introduisez la gravité API représentant la valeur de gravité API la plus basse mesurée par le capteur de mesures. Cette valeur est égale à 4mA. API Gravity @ 20mA Introduisez la gravité API représentant la valeur de gravité API la plus élevée mesurée par le capteur de mesures. Cette valeur est égale à 20 mA. API Gravity Offset Ce paramètre permet d’introduire un écart de gravité API pour corriger la gravité API indiquée à la gravité API observée. 10 5 Chapitre 4 – Configuration Générale 4.7.4 INSTALLATION DES COMPOSANTS Utilisez les fonctions d’installation des composants pour configurer les caractéristiques de ce composant. Pour de plus amples détails sur le contrôle du débit, voir au Chapitre 5. Les débits de composants sont configurés dans Weights & Measures -> Components et au Chapitre 8. Dans cet écran, allez à: Program Mode -> Configuration -> Equipment Setup -> Selct Parametr Level - > Components L’écran d’installation des composants s’affiche: Paramètre Meter # PRE #1 CMP #1 (Base 001 ) SETUP Meter#: 1 High Flow Rate: 600 1st Stage Trip Vol: 70 1st Stage Flow Rate: 225 2nd Stage Trip Vol: 20 2nd Stage Flow Rate: 150 Final Trip Vol: 1.15 Final Trip Max Time: 5.000 Final Trip Vol Lock: DISABLD Unauth Flow Alrm Vol: 10 W&M Recipe Percentage: %0.00 BlkValve Open Rate: 0 BlkValve Open Delay: 0 B.V. Open Alrm Time: 10 Action Next Prev Exit Enter Assignez le composant à un débitmètre. High Flow Rate Paramétrez à la même valeur que le haut débit du menu des valeurs prédéfinies. Il peut s’agir d’une valeur différente si la tuyauterie l’exige. 1st Stage Trip Vol Introduisez un volume qui déclenche le début de la phase de déclenchement de la 1ère étape. La phase de déclenchement de la 1ère étape commence lorsque le volume restant de la valeur prédéfinie est égal à la valeur indiquée dans ce paramètre. La phase de déclenchement de la 1ère étape représente la réduction initiale depuis le haut débit jusqu'à la condition "sans débit". Lorsque le volume de déclenchement de la 1ère étape est atteint, la vanne de régulation du débit fait passer le haut débit à un débit spécifié par le paramètre de débit de la 1ère étape. La phase de déclenchement de la 1ère ème étape se termine lorsque la phase de déclenchement de la 2 étape est atteinte. 1st Stage Flow Rate Introduisez le débit-cible pour le débit de la 1ère étape. 2 nd Stage trip Vol Introduisez un volume qui déclenche le début de la phase de déclenchement de la 2 ème étape. La phase de déclenchement de la 2 étape commence lorsque le volume restant de la valeur prédéfinie est égal à la valeur indiquée dans ce paramètre. La phase ème de déclenchement de la 2 étape représente la seconde phase d'une série d’ajustements depuis le haut débit jusqu'à la condition "sans débit". Lorsque le volume ème de déclenchement de la 2 étape est atteint, la vanne de régulation du débit réduit le ère débit depuis le débit de la 1 étape jusqu'à un débit spécifié par le paramètre de débit ème ème de la 2 étape. La phase de déclenchement de la 2 étape se termine lorsqu’on atteint la phase finale de déclenchement. ème 2 nd Stage Flow Rate Introduisez le débit-cible pour le débit de la seconde étape. 10 6 Chapitre 4 – Configuration Générale Paramètre Action Final Trip Vol Introduisez un volume qui compense le temps que prend la vanne de régulation pour se fermer depuis la Phase de déclenchement de la Seconde Étape, dès que la quantité de la valeur prédéfinie est atteinte. Avant d'entrer une valeur pour ce paramètre, réglez la vitesse de fermeture de la vanne de régulation pour obtenir un réglage optimal, en utilisant les procédures fournies par le fabricant de la vanne. Ce paramètre commande la fermeture de la vanne un peu plus tôt pour compenser de petits surpassements uniformes. Ou bien il peut commander la fermeture un peu plus tard pour compenser de petits manquements uniformes. Cet ajustement se fait sur une base volumétrique. Final Trip Max Time L'étape de déclenchement final est la dernière phase de livraison autorisant de débiter le produit. Le paramètre de temps max. de déclenchement final établit la durée, en millisecondes, pendant laquelle cette phase est active. Lorsque le temps spécifié dans ce paramètre s'est écoulé, le débit doit être complètement stoppé. S'il n'y a aucun débit lorsque le temps s’est écoulé, la valeur prédéfinie passe à l'état inactif. Si un débit est toujours détecté, passé cette période, l'alarme de dépassement s'enclenche si le volume d’alarme de dépassement a été dépassé. Final Trip Vol Lock Activez ce paramètre pour empêcher le MultiLoad II d'ajuster d'automatiquement le paramètre de volume de déclenchement final. Lorsque ce paramètre est activé, le MultiLoad II analyse l’état de fermeture de la vanne de régulation et effectue les ajustements éventuellement nécessaires au volume de déclenchement final. W&M Percentage Si ce composant doit avoir le pourcentage de recette sous protection poids et mesures, mettez cette valeur sur la valeur acceptée par les poids et mesures. Lorsque cette valeur n’est pas de zéro, le pourcentage de recette du composant DOIT être égal au pourcentage de recettes des poids et mesures ou bien toutes les tentatives visant à autoriser un lot échoueront et vous lirez le message “W&M Required Composant Pct Not Correct”. (Pourcentage de composant requis par les poids et mesures incorrect) Recipe Unauth Flow Alrm Vol Spécifiez le volume de débit non autorisé qui doit s'accumuler avant qu'une alarme de débit non autorisée ne s'active. Le débit non autorisé se produit lorsque le débitmètre détecte le mouvement du produit avant que la livraison du produit n’a pas été autorisée. Blk Valve Open Rate Utilisez ce paramètre lors de l'utilisation de vannes de sélection de produits hydrauliques, au lieu de vannes motorisées (MOV). Une valeur de zéro désactive cette fonction. Il se peut que des vannes hydrauliques utilisées en amont de la vanne de régulation numérique ne s'ouvrent pas entièrement pendant l'étape de faible débit, en raison d'une faible pression différentielle au travers de la vanne de sélection de produit. Cela peut empêcher l'entrée de statut de la vanne d'arrêt de signaler que la vanne de sélection de produit est ouverte, bien que le débit arrive. Commencez avec une valeur égale au faible débit moins le taux de zone morte (DB) à faible débit. Introduisez cette valeur dans le champ" Block Valve Open Rate". Les alarmes d'ouverture de la vanne d'arrêt ne s'activent pas lorsque le débit est inférieur à cette valeur. Blk Valve Open Delay Définissez ce paramètre pour retarder l'ouverture d'une vanne d'arrêt pour une période spécifiée en secondes. Lorsqu'une vanne d'arrêt est utilisée, elle s'ouvre quand le délai de temporisation est écoulé. Pour le premier composant d'un mélange, la temporisation intervient au moment de pousser sur le bouton de démarrage. Pour les composants suivants, la temporisation commence dès que le débit s’est arrêté pour le composant précédent. Ignorez ce paramètre si les vannes d'arrêt ne sont pas utilisées. B.V. Open Alrm Time Spécifie le temps en secondes pour permettre à la vanne d'arrêt du composant de s'ouvrir. Si une vanne d'arrêt de composant emploie un signal de rétroaction, une alarme se produit si la condition de rétroaction n'est pas satisfaite dans le délai voulu. B.V. Close Alrm Time Spécifie le temps en secondes pour permettre à la vanne d'arrêt du composant de se fermer. Si une vanne d'arrêt de composant emploie un signal de rétroaction, une alarme se produit si la condition de rétroaction n'est pas satisfaite dans le délai voulu. Pump Start Delay Le démarrage de la pompe sera différé du nombre de secondes précisé par ce paramètre. 10 7 Chapitre 4 – Configuration Générale Paramètre Action Pump Stop Delay Une fois le lot terminé, la pompe reste en fonctionnement pendant le nombre de secondes précisé par ce paramètre. Pump Start Alrm Time Ce réglage d’alarme est utilisé conjointement avec une entrée de statut de pompe. Si le signal de statut de pompe n'est pas reçu dans le temps indiqué par ce paramètre, une alarme de statut de pompe se produit. Le temps est spécifié en secondes. Le minutage commence dès que le bouton de démarrage est poussé. Le réglage pour ce paramètre doit dépasser le réglage du temps de temporisation de démarrage de la pompe. Flow Start Delay Retarde l'ouverture de la vanne de régulation du débit pour une durée, exprimée en secondes, spécifiée par ce paramètre. Le temps de temporisation commence lorsque le bouton de démarrage est poussé. Unauth reset Time Ce paramètre est destiné à empêcher les alarmes intempestives de débits non autorisés pour des bras de chargement qui restent généralement inoccupés pendant de longues périodes de temps. Avec le temps, les impulsions perdues peuvent s'accumuler et éventuellement déclencher de fausses alarmes de débits non autorisés dans des bras de chargement inoccupés. La valeur introduite ici détermine combien de fois un compteur d’alarme de débit non autorisé interne est réinitialisé. Le compteur d’alarme de débit non autorisé interne n'est pas visible par l'utilisateur et ne doit pas être confondu avec les totalisateurs de débits non autorisés qui ne sont pas réinitialisés par cette fonction. Ce paramètre réinitialisera le compteur interne périodiquement tel que spécifié par la valeur introduite ici pour empêcher des alarmes intempestives. Introduisez une valeur en secondes. La fourchette d'entrées possible est comprise entre 600 et 65.535 secondes. Fallback Rate Si pendant l'étape à haut débit, le débit se retrouve sous le débit de zone morte à haut débit pendant la période indiquée par le paramètre de temps de repli, l'algorithme de commande retombe au débit spécifié par ce paramètre. Ce paramètre est destiné à être utilisé avec des débitmètres à turbine. Lorsque le haut débit est introuvable, le débit reviendra au débit indiqué qui doit avoir un facteur de mesure éprouvé. Si le débitmètre est un compteur volumétrique (PD), définissez ce paramètre comme zéro et passez en revue le paramètre de temps de repli automatique. Après avoir spécifié un taux de repli automatique pour une application de compteur à turbine, configurez le temps de repli automatique, le temps de réitération de repli automatique et le volume de réitération de repli automatique. Fallback Time Si pendant l'étape à haut débit, le débit se retrouve sous le débit de zone morte à haut débit pendant la période indiquée par ce paramètre, l'algorithme de commande recherche un débit contrôlable. Commencez par une valeur de 3 secondes. Une entrée de zéro seconde désactive la fonction de repli automatique. Fallback Retry Time Après l'obtention d'un débit contrôlable, il est maintenu pendant une période déterminée par le réglage de ce paramètre. En se basant sur l'expiration du temps de réitération de repli automatique, l'algorithme essaie de retrouver le débit-cible. Si le débit cible ne peut être récupéré dans le délai imparti par le paramètre de temps de repli automatique, l'algorithme cherche à nouveau un débit contrôlable. Commencez par une valeur de 45 secondes. Une entrée de zéro seconde désactive la fonction de repli automatique. Fallback Retry volume Ce paramètre annonce à l'algorithme de commande quand il doit arrêter d'essayer de retrouver le débit-cible. Lorsque le volume restant de la charge est égal à la valeur indiquée par ce paramètre, aucune nouvelle tentative n’est engagée. Définissez le ère paramètre sur la même valeur que la 1 étape du volume de déclenchement plus 50 gallons. Une entrée de zéro seconde désactive la fonction de repli automatique. API Table Name Sélectionnez le tableau API voulu pour corriger la température ou la pression de référence pour les volumes de liquides. Mettez ce champ en surbrillance et appuyez sur Enter pour faire défiler les choix possibles. API 54 YG Il faut sélectionner le nom du produit conformément au tableau API 54YG 10 8 Chapitre 4 – Configuration Générale Paramètre Action API BIO On utilise ces tableaux API BIO la Méthode 3 à partir de PTB Community. Sélectionnez le nom du tableau API PTB-BIO combiné à API BIO pour choisir le produit désiré. Formule: V(T) = V0 *{1 + [A1 *(T – T0) + A2 *(T – T0)2 + A3 *(T – T0)3]} V0 = Volume @ base température V(T) = Volume @ température observée T0 = température de base (15° C) T = température observée A1, A2, A3 = coefficients biocarburants API Range Extrapolated S’il est actif, on peut utiliser les valeurs VCF des fourchettes extrapolées des tableaux values pour les calculs CTL et CPL sans déclencher d‘alarme au tableau API. API Gravity Pour les tableaux API qui nécessitent l’introduction d’une valeur de gravité API, introduisez cette valeur ici. La valeur doit correspondre à celle du composant à 60° F. Les unités sont des degrés API. Relative Density Pour les tableaux API qui nécessitent l'entrée d'une densité relative, introduisez cette valeur ici. La valeur doit correspondre à la densité relative du composant à 60 F. Notez qu’il n’y a pas d’unité pour la densité relative. Default Density Pour les tableaux API qui nécessitent l'introduction d'une densité relative, introduisez cette valeur ici. La valeur doit correspondre à la densité relative du composant à 15° C et s’exprime en kg/m³. Lorsque cette valeur n’est pas de zéro, on la reporte comme densité au niveau composant et elle peut servir de densité au niveau compteur si la densité n’est pas définie au niveau compteur. Si la valeur est zéro, on utilise la densité au niveau compteur comme densité au niveau composant. S’il s’agit du composant primaire sur un mélange secondaire, on recalcule une densité à partir de la densité au niveau compteur et de la densité du composant ou du compteur secondaire. Expansion Coef. Pour les tableaux API qui requièrent l'entrée du coefficient d’expansion, introduisez cette valeur ici. La valeur doit être le coefficient d’expansion du composant @ 60F ou 15 C, selon le tableau. Hydrometer Used Activez ce paramètre si un hydromètre est utilisé pour déterminer la gravité ou la densité API. Commodity Type Utilisé uniquement pour les tableaux API X: pas de type, brut, raffiné et lubrifiant Expansion Coef. UOM Uniquement utilisé pour les tableaux API X tables: C ou F Density UOM Uniquement utilisé pour les tableaux API X: kg/m³, gravité API et densité relative Pressure UOM Uniquement utilisé pour les tableaux API X: BAR, PSIG et kPA Reference Temperature On l’utilise pour les tableaux API X et les tableaux éthanol (TEC B40 , TEC B100, TEC E40, TEC E100) Alcohol Percentage On n’utilise cette valeur de pourcentage que pour le tableau brésilien des alcools. Cette valeur sert à déterminer le facteur VCF. API Delay Alarm On utilise ce paramètre pour les quais de déchargement lorsque le dispositif de densité, de gravité ou de densité relative donne une valeur non acceptée parce qu’il y a de l’air dans la ligne. En augmentant ce paramètre en secondes, on peut toutefois continuer le chargement sans déclencher d’alarme. C’est la dernière densité connue qui sera utilisée pour les calculs. 10 9 Chapitre 4 – Configuration Générale Paramètre Action Close Block Vanne FCM# Permet la sélection d'un port qui fournit un signal de sortie pour fermer la vanne d'arrêt du composant. Cette fonction est destinée aux vannes d'arrêt qui exigent des signaux d'ouverture et de fermeture séparés. Blk Val Status FCM# Permet de sélectionner un port qui recevra un signal d'entrée. Le signal d'entrée représentera le statut de la vanne d'arrêt du composant, indiquant si elle est ouverte ou fermée. Lorsque la vanne d'arrêt est fermée, un contact externe lié à la vanne se ferme, appliquant un signal de statut à l'entrée. Lorsque la vanne d'arrêt est ouverte, le contact externe s'ouvrira aussi, supprimant le signal de statut de l'entrée. Lorsque la vanne d'arrêt a reçu une commande d'ouverture, l'absence de signal à l'entrée indique que la vanne s'est ouverte. Si le signal "fermé" est toujours présent lorsque le temps de temporisation de fermeture de la vanne d'arrêt s'est écoulé, une alarme d'échec de vanne d'arrêt se produit. Quand la vanne d’arrêt a reçu l’ordre de se fermer, la présence d’un signal de statut à l’entrée indique que la vanne est fermée. Si le signal « fermé » n’a pas été détecté au moment où le temps de temporisation de fermeture de la vanne d’arrêt s’est écoulé, une alarme d’échec se produit. Open Blk Val FCM# Permet de sélectionner un port qui donne un signal de sortie pour commander la vanne d’arrêt d’un composant. Cette sortie produit un signal d’ouverture de la vanne d’arrêt. Lorsque le MultiLoad II demande à la vanne de se fermer, le signal disparaît. Pump Run FCM# Permet de sélectionner un port qui donne un signal de sortie à un démarreur de pompe. Pump Kill FCM# Permet de sélectionner un port qui donne un signal de sortie pour arrêter la pompe. Le signal de sortie est envoyé pour arrêter la pompe chaque fois qu’il y a alarme d’échec de vanne sans tenir compte de quels autres quais demandent à la pompe de fonctionner. Pump Status FCM# Permet la sélection d'un port qui fournit une entrée pour contrôler la pression de la pompe. Un port auquel a été attribué la fonction de statut de pompe reçoit un signal (élevé ou faible) depuis un capteur de pression lorsque la pression de la pompe a atteint un niveau suffisant. Le paramètre du temps d’alarme du démarrage de la pompe doit être configuré à l’aide de cette fonction. Alarm Out FCM# Donne un signal de sortie si le composant a une alarme active. Ce paramètre sélectionne un port de sortie auquel a été attribué une alarme spécifique du composant. Authorized FCM# Le FCM donne un signal de sortie si le composant a été autorisé à s’écouler parce que le chauffeur a introduit sa carte ou qu’un produit a été sélectionné. Ce paramètre sélectionne un port de sortie chargé de signaler cette condition. Permiss FCM# Permet de sélectionner un port qui recevra un signal d’entrée représentant l’état de la permission du composant. S’il n’y a pas de signal lors de l’autorisation ou si le signal se perd au cours de la livraison, la procédure sera interrompue et une alarme de niveau de permission du composant se produira. Permiss Out FCM# Ce paramètre permet de sélectionner un port qui donne un signal de sortie représentant la perte de permission du composant. Meter Factor #1 Introduisez le facteur de mesure qui a été calculé lors de l'essai du débit du facteur #1 de mesure. Le facteur de mesure est utilisé pour corriger le volume indiqué à l'écran du MultiLoad II de façon à correspondre avec le volume brut observé. Le volume brut observé est généralement déterminé par un dispositif de vérification. Laissez le réglage par défaut de ce paramètre (1.0000) si la linéarisation n'est pas utilisée. Laissez les autres paramètres du facteur de mesure sur leurs réglages par défaut. La fourchette autorisée d'entrées est comprise entre 0.8000 et 1.200. Meter Factor #1 Rate Introduisez le débit utilisé lors de l'essai pour trouver le facteur #1 de Mesure. Il s'agit du premier point de linéarisation. Le facteur #1 de mesure est utilisé pour corriger le volume indiqué pour les débits à partir de zéro jusque et y compris le débit du facteur #1 de mesure. Maintenez le réglage par défaut de ce paramètre (150) si la linéarisation n'est pas utilisée. Maintenez les autres paramètres du facteur de mesure à leurs réglages par défaut. 11 0 Chapitre 4 – Configuration Générale Paramètre Action Meter Factor #2 Introduisez le facteur de mesure calculé lors de l'essai du débit du facteur #2 de mesure. Le facteur de mesure est utilisé pour corriger le volume indiqué à l'écran du MultiLoad II de façon à correspondre avec le volume brut observé. Le volume brut observé est généralement déterminé par un dispositif de vérification. Maintenez le réglage par défaut de ce paramètre (1,0000) si la linéarisation n'est pas utilisée. Maintenez les autres paramètres du facteur de mesure aux réglages par défaut. La fourchette autorisée d'entrées est comprise entre 0,8000 et 1,200. Meter Factor #2 Rate Introduisez le débit utilisé lors de l'essai pour trouver le facteur #2 de mesure. Il s'agit du second point de linéarisation. Lorsque le débit est compris entre le débit du facteur #1 de mesure et le débit du débit du facteur #2 de mesure, le MultiLoad II interpolera un facteur de mesure sur la base du débit actuel. Maintenez le réglage par défaut de ce paramètre (200) si la linéarisation n'est pas utilisée. Maintenez les autres paramètres du facteur de mesure aux réglages par défaut. Meter Factor #3 Introduisez le facteur de mesure lors de l'essai du débit du facteur de mesure #3. Le facteur de mesure est utilisé pour corriger le volume indiqué à l'écran du MultiLoad II de façon à correspondre avec le volume brut observé. Le volume brut observé est généralement déterminé par un dispositif de vérification. Maintenez le réglage par défaut de ce paramètre (1,0000) si ce point de linéarisation n'est pas utilisé. Maintenez les autres paramètres du facteur de mesure aux réglages par défaut. La fourchette autorisée d'entrées est comprise entre 0,8000 et 1,200. Meter Factor #3 Rate Introduisez le débit utilisé lors de l'essai pour trouver le facteur de mesure #3. Il s'agit du troisième point de linéarisation. Lorsque le débit est compris entre le débit du facteur #2 de mesure et le débit du débit du facteur #3 de mesure, le MultiLoad II interpolera un facteur de mesure sur la bse du débit actuel. Maintenez le réglage par défaut de ce paramètre (400) si ce point de linéarisation n'est pas utilisé. Maintenez les autres paramètres du facteur de mesure aux réglages par défaut Meter Factor #4 Introduisez le facteur de mesure calculé lors de l'essai du débit du facteur de mesure #4. Le facteur de mesure est utilisé pour corriger le volume indiqué à l'écran du MultiLoad II de façon à correspondre avec le volume brut observé. Le volume brut observé est généralement déterminé par un dispositif de vérification. Maintenez le réglage par défaut de ce paramètre (1,0000) si ce point de linéarisation n'est pas utilisé. Maintenez les autres paramètres du facteur de mesure aux réglages par défaut. La fourchette autorisée d'entrées est comprise entre 0,8000 et 1,200. Meter Factor #4 Rate Introduisez le débit utilisé lors de l'essai pour trouver le facteur #4 de mesure. Il s'agit du quatrième point de linéarisation. Lorsque le débit est compris entre le débit du facteur #3 de mesure et le débit du débit du facteur #4 de mesure, le MultiLoad II interpolera un facteur de mesure sur la base du débit actuel. Le facteur #4 de mesure sera utilisé pour tous les débits qui dépassent le débit du facteur #4 de mesure. Maintenez le réglage par défaut de ce paramètre (800) si ce point de linéarisation n'est pas utilisé. # Meter Factors Used Introduisez le nombre de facteurs de mesure qui doit être fixé par des vérifications de débitmètre. Pour étalonner un débit simple, introduisez 1 dans ce champ. Les données des champs se rapportant aux facteurs de mesure 2, 3 et 4 seront ignorées. Pour étalonner deux débits, introduisez 2 dans ce champ. Les données se rapportant aux facteurs de mesure 3 et 4 seront ignorées. Pour étalonner trois débits, introduisez 3 dans ce champ. Les données se rapportant au facteur de mesure 4 seront ignorées. Pour étalonner quatre débits, introduisez 4 dans ce champ. 11 1 Chapitre 4 – Configuration Générale 4.8 RÉGLAGE DES ALARMES Utilisez les fonctions de réglage des alarmes pour définir des conditions d’alarme et les permissions aux divers niveaux de configuration: quai, valeur prédéfinie, compteur, composant et additif. Tous les écrans de réglage des alarmes indiqueront qui est autorisé à lever l’alarme et comment il faut le faire. Le tableau ci-après montre ces autorités en ordre croissant de gravité et/ou d’importance. AUTO L’alarme s’efface automatiquement lorsque la condition se résout d’elle-même. DRIVER Le chauffeur peut lever l’alarme. REMOTE L’alarme peut être levée à distance par le système (TMS), PROGRAM L’alarme peut être levée quand le commutateur de programme est activé. W&M L’alarme peut être levée quand le commutateur des poids et mesures (W&M) est activé. Certaines alarmes ne peuvent pas être remises en effacement automatique (Auto Clear). C’est ce qui se passe lorsque l’alarme par défaut n’est pas sur AUTO Clear. Il n’est pas possible de mettre un niveau d’alarme sur W&M ni de changer de paramètres sur une alarme lorsque celle-ci est mise sur W&M, sauf si le commutateur W&M est actif. Les changements apportés dans chacun de ces deux cas seront consignés dans le Journal des Changements W&M. Dans cet écran, allez à: Program Mode -> Configuration -> Alarm Setup L’écran des réglages des alarmes s’affiche: ALARM SETUP MENU Bay Preset Meters Components Additives Next Prev Exit desEnter L’écran des réglages d’alarme du quai s’affiche (les écrans valeurs prédéfinies, compteur, composant et additif sont similaires). Chapitre 4 – Configuration Générale BAY ALARM SETUP *BAY FCM: AUTO *GROUND: AUTO *VRU: AUTO *OVERFILL: AUTO *ESD PERM: AUTO *BAY PERM4: AUTO *BAY PERM5: AUTO *BAY PERM6: AUTO *BAY PERM7: AUTO *ALL STOP: AUTO *BAY PCM: AUTO *PRNTR ERR: AUTO *BALARM 12: DRIVER DRIVERinciter à une alarme après un certain nombre d’alarmes Autre possibilité de réglage*BALARM d’alarme 13: en option: Prevde Exit récurrentes à un autre niveau. Sur l’écranNext de réglage l’alarmeEnter des additifs représenté sous l’alarme de défaut d’injection, le chauffeur sera effaçable pour les trois premières occurrences, mais passera ensuite sur effaçable à distance. Le comptage des occurrences et le retour à l’alarme de départ se réinitialiseront à l’autorisation de transaction suivante. ADDITIVE ALARM SETUP *ADTV FCM: AUTO *ADTV PERM: AUTO *UND ADTV: REMOTE *OVR ADTV: REMOTE *VALVE FLT: PROGRAM *PUMP STAT: DRIVER *INJCT FLT: DRIVER 03x REMOTE AUTHORZ *UNAUTH FL: REMOTE *NO LNFLSH: DRIVER *MTR CREEP: REMOTE *BLK VALVE: DRIVER *AALARM 11: DRIVER DRIVER Le comptage des occurrences*AALARM d’alarme 12: peut être réinitialisé de la façon suivante: *AALARM 13: DRIVER 2 MIN Après 2 minutes de temps réseau continu Next Prev Exit Enter 5 MIN Après 5 minutes de temps réseau continu. 15 MIN Après 15 minutes de temps réseau continu. 30 MIN Après 30 minutes de temps réseau continu. 60 MIN Après 60 minutes de temps réseau continu. 3 HRS Après 3 heures de temps réseau continu. 6 HRS Après 6 heures de temps réseau continu. 12 HRS Après 12 heures de temps réseau continu. 24 HRS Après 24 heures de temps réseau continu. AUTHORZ Jusqu’à ce que la prochaine transaction soit autorisée. CLEAR Quand l’alarme a été levée, 11 2 Chapitre 4 – Configuration Générale Pour les sujets suivants, seul l’écran de réglage des alarmes de quai (Bay Alarm Setup) sera reproduit. Pour modifier une alarme, vous devez appuyer sur ENTER pour entrer dans ALARM DETAIL SETUP SCREEN (écran de réglage des détails alarmes) ADDITIVE ALARM DETAIL SETUP Alarm Name: *ADTV FCM Alarm Level: AUTO Promo Count: 01x Promo Alarm Level: AUTO Promo Reset Mode: CLEAR Alarm to Host: REMOTE FCM Output#: DISABLED Don’t store Alarm: DISABLED Alarme Signification Nom d’alarme MultiLoadC’est le nom de l’alarme. Seules quelques alarmes peuvent être rebaptisées. Next Alarm Level Prev Exit Enter MultiLoadC’est le niveau général de l’alarme et la façon dont il peut être effacé. Si l’alarme n’est pas par défaut eu niveau AUTO, on ne peut jamais la mettre à ce niveau. Promo Count Le nombre de fois que l’alarme doit se produire avant de passer au niveau Promo Alarm Promo Level Alarm MultiLoadIl a en fait les mêmes niveaux que Alarm Level mais on ne s’en sert que lorsqu’on atteint le promo count Promo Mode Reset Indique comment le promocount peut être remis à zéro. Alarm Host Alarm to Host peut être réglé en commande à distance (Remote) signifiant que l’alarme est envoyée à l’hôte. Alarm Local signifie que n’importe quel système hôte pourra la voir. FCM Output# Lorsqu’il est activé, une sortie général du FCM sera envoyée au PLC. Don’t store Alarm Désactive l’enregistrement et l’impression d’une certaine alarme jugée indésirable. Influence Printing Bol, Printing Alibi Log ainsi que l’alarme de stockage. Si la valeur Promo Count est zéro, Promo Alarm level et Promo Rest Mode ne s’afficheront pas. 11 3 Chapitre 4 – Configuration Générale 4.8.1 RÉGLAGE ALARME QUAI Les valeurs par défaut se trouvent dans le colonne de gauche Alarme Signification BAY FCM MultiLoad II a perdu la communication avec la carte I/O ou le FCM. Ce message indique que les fonctions niveau quai sont affectées par l’interruption de communication. L’alarme s’efface automatiquement lorsque la communication avec la carte I/O se rétablit. Vérifiez FCM Com dans le menu Diagnostic pour voir si la carte I/O ou le FCM fonctionne correctement. AUTO BAY PERM 0-7 AUTO Lorsqu’un signal (ou plusieurs signaux) attribué aux permissions quai de 0 à 7 se perd, le chargement s’arrête et un message d’affiche. L’alarme disparaît d’elle-même lorsque le signal en dérangement se rétablit. Le message d’alarme lu par l’opérateur se configure au moyen de l’outil de configuration du MultiLoad dans les alarmes quai. Les noms par défaut sont, entre autres, “*GROUND, *VRU, *OVERFILL, *ESD PERM”. ALL STOP AUTO Cette fonction n’est pas disponible. BAY PCM AUTO Le RCU du MultiLoad II a perdu la communication avec une carte PCM configurée. PRNTR ERR AUTO L’imprimante connectée à un module PCM est victiime d’une erreur (déconnectée, plus de papier, etc.). *GPS_ERROR (ML II Mobile Only) Apparaît si la communication GPS est configurée et que l’une des situations ci-après se présente: - Aucune donnée fixe GPS n’arrive depuis 60 secondes. - “Max GPS Site Distance” est configuré comme valeur non zéro et une transaction est autorisée lorsque la position instantanée n’est à portée d’un site se trouvant dans la base de données GPS du site. - La position actuelle a quitté le site où l’autorisation avait été accordée. AUTO BALARM 13,17-31 DRIVER Affectations des futures alarmes au niveau quai. DEADMAN DRIVER Cette alarme s’enclenche lorsque le chauffeur n’a pas appuyé sur le bouton homme-mort assez vite. FCM Trace Cette alarme apparaît lorsque certains caractéristiques de diagnostic sont activées par l’assistance Toptech. Elle ne devrait pas se produire au cours d’opérations normales. DRIVER POWERFAIL DRIVER Cette alarme apparaît lorsqu’il y a coupure de courant sur le MTL2. 11 4 Chapitre 4 – Configuration Générale RÉGLAGE DES ALARMES PRÉDÉFINIES 4.8.2 Alarme Signification PRE FCM Le MultiLoad II a perdu la communication avec le FCM ou la carte entrées / sorties. Ce message indique que les fonctions de niveau de valeurs prédéfinies sont affectées par l'interruption de la communication. Cette alarme se lève automatiquement lorsque les communications sont rétablies. Vérifiez au menu Diagnostic sous "Comm. FCM" pour déterminer si la carte des entrées / sorties ou le FCM est bien en train de communiquer. AUTO PRE PERM Permissions valeurs prédéfinies. Lorsque le signal de permission de valeurs prédéfinies est perdu, le chargement s'arrête et revient automatiquement lorsque le signal est rétabli. Le message d’alarme qui se manifeste à l'opérateur est configuré par l'Utilitaire de Configuration du MultiLoad, Alarmes de valeurs prédéfinies, Alarme 1. AUTO ARM L’alarme du bras oscillant se manifeste lorsque le bras oscillant n’est pas en position de chargement correcte. Elle se lève automatiquement si le bras oscillant est dans la bonne position. NO LNFLSH (Sauf SMP) Alarme pas de purge de conduite. Elle se manifeste lorsque le volume minimal de la purge de conduite n’a pas été atteinte pour le chargement. Vérifiez sur l’écran de statut la quantité de purge de conduite nécessaire pour que la conduite soit correctement purgée. SWING (Sauf SMP) AUTO AUTO BLK VALVE Alarme de Vanne d'Arrêt. Cette alarme s'active lorsqu'une vanne d'arrêt ne s'est pas ouverte dans le temps dicté par le paramètre de temps d’alarme d'ouverture de la vanne d'arrêt. Cette alarme se produit également si la vanne d'arrêt ne s'est pas fermée dans le temps exigé par le paramètre de temps de l'alarme de fermeture de la vanne d'Arrêt. A chaque fois qu'une vanne d'arrêt n'est pas positionnée correctement, l'alarme s'active. AUTO BAY ALARM AUTO Ce réglage d’alarme doit rester en position Auto Clear. Elle indique que les valeurs prédéfinies ont une alarme active au niveau du quai. COMP ALARM AUTO Ce réglage d’alarme doit rester en position Auto Clear. Elle indique que les valeurs prédéfinies ont une alarme active au niveau des composants. ADD ALARM AUTO Ce réglage d’alarme doit rester en position Auto Clear. Elle indique que les valeurs prédéfinies ont une alarme active au niveau des additifs. MTR STOP Arrêt du compteur. Ce message s'affiche lorsque le bouton d'arrêt du compteur a été poussé. Un bouton d'arrêt externe peut être configuré, en option, pour chaque valeur prédéfinie. Le chauffeur peut annuler l'alarme par défaut et recommencer à charger à tout moment. AUTO OVERRUN L'alarme de dépassement se produit lorsque la quantité livrée a dépassé la quantité prédéfinie par une valeur configurée dans le paramètre d’alarme du volume de dépassement. Cette alarme est destinée à alerter le personnel d’entretien qu'une vanne de régulation peut ne pas se fermer aussi rapidement qu'elle le devrait. Un entretien de cette vanne peut s’avérer nécessaire. Le réglage de cette alarme doit être inférieur à l'alarme d'erreur de vanne, qui est destinée à signaler une erreur de vanne de régulation plus grave. REMOTE EXCESS FL REMOTE L'alarme de débit excessif se produit lorsque le débit qui s'écoule par le bras de chargement a dépassé le débit maximal configuré dans le paramètre de débit excessif. Elle peut également se produire en cas de capteurs de mesures d’impulsions défaillants ou d’interruption de raccordements d’impulsions. 11 5 Chapitre 4 – Configuration Générale Alarme Signification BSW Cette alarme indique que la valeur mesurée par la sonde BSW a dévié de la fourchette spécifiée par les paramètres Alarm Low BSW et Alarm High BSW Parmi les autres causes possibles, citons une sonde déconnectée ou une valeur inappropriée dans le champ BSW par défaut. Allez au menu du mode programme dans Views & Inquiries - > BSW pour lire le BSW instantané. REMOTE PALARM 11-14 DRIVER Affectations ultérieures d’alarmes de niveau prédéfinies. INVCONFIG Cette alarme indique qu'une configuration non valable a été détectée. Des changements inappropriés du facteur de mesure en sont souvent la cause. Lorsque cette alarme se produit, entrez dans le mode de programme et sélectionnez Views & Inquiries -> Message Log (Affichage et Requêtes /Journal des Messages). Le Journal des Messages indiquera la source de l'alarme INVCONFIG. 4.8.3 RÉGLAGE DES ALARMES DE COMPTEURS Alarme Signification MTR FCM Le MultiLoad II a perdu la communication avec la carte des entrées/sorties ou le FCM. Ce message indique que les fonctions de niveau du compteur sont affectées par l'interruption de la communication. Cette alarme s'annule automatiquement lorsque les communications sont rétablies. Vérifiez au menu diagnostic sous "Comm. FCM" si la carte des entrées/sorties ou le FCM est bien en train de communiquer. AUTO MTR PERM Permissions de compteur. Lorsque le signal de permission de compteur est perdu, le chargement s'arrête sur le bras de chargement si le compteur est utilisé. L'alarme s'annule automatiquement lorsque le signal est rétabli. Le message d’alarme qui se manifeste à l'opérateur est configuré par l'Utilitaire de Configuration du MultiLoad II, Alarmes de Compteur, Alarme 1. AUTO FCM CONF Configuration FCM non valable. Cette alarme est le résultat d'une erreur de configuration. Cette erreur est très probablement en rapport avec les débitmètres. Si les débits ne sont pas entrés en ordre croissant, cette alarme se produira. Par exemple, le débit du facteur de mesure #2 doit être plus élevé que celui de mesure #1. Si les facteurs de mesure varient significativement les uns par rapport aux autres, cette alarme peut se produire. Recherchez les erreurs d'entrée des paramètres du facteur du mesure. REMOTE FCM WDT Temporisateur chien de garde du FCM. Cette alarme indique qu'une erreur s'est produite au processeur sur la carte entrées/sorties ou le FCM. Réinitialisez l'alarme et essayez de reprendre l'opération. Si l'alarme se reproduit à plusieurs reprises, il peut être nécessaire de remplacer le la carte des entrées/sorties ou le FCM. Contactez l’assistance technique de Toptech. REMOTE FCM TMOUT Timeout (délai dépassé) FCM. Cette alarme est amorcée par la carte des entrées/sorties ou le FCM s'il ne peut communiquer avec le MultiLoad II. On est obligé de couper l’alimentation des sorties par mesure de sécurité. La carte des entrées/sorties n'initialise cette alarme que lorsqu'il commande activement le débit ou excite les sorties. Le débit sera arrêté sur la carte des entrées/sorties si cette alarme se produit. Lorsque les communications sont rétablies entre la carte des entrées/sorties et le MultiLoad II, il est possible de lever l'alarme et de reprendre les opérations. 11 6 11 7 Chapitre 4 – Configuration Générale Alarme Signification REMOTE VANNE FLT Erreur de vanne. La vanne de régulation a reçu l’ordre de se fermer mais le débit ne s'est pas arrêté. L'alarme s'active lorsque le volume spécifié dans le paramètre de volume d’alarme de l'erreur de vanne a dépassé le compteur, après la commande de fermeture de la vanne. Lorsque l'alarme se produit, les vannes d'arrêt de composant reçoivent une commande de fermeture et la pompe correspondante reçoit une commande d'arrêt. La sortie d'arrêt de la pompe sera activée, si elle est utilisée. Un message de statut d’alarme s'affichera sur les autres bras de chargement qui utilisent la sortie habituelle de fonctionnement de la pompe. Par exemple, si une erreur de vanne se produit sur le bras de chargement#1 (diesel), tous les autres bras de chargement de diesel dans le quai afficheront l'alarme de statut de la pompe et ne pourront pas charger jusqu'à ce qu'il y ait eu une action corrective. Cette alarme peut indiquer que la vanne de régulation nécessite un entretien et indique une situation dangereuse. PROGRAM LOW FLOW Le débit est resté sous l'alarme de faible débit pendant une période indiquée par le paramètre d’alarme de faible débit. La pompe peut s'être arrêtée ou la vanne s'être fermée. Une erreur de générateur d'impulsions du compteur peut également provoquer cette alarme. DRIVER EXCESS FL Débit excessif : Au niveau du débitmètre, cette alarme indique que le débit maximal du débitmètre a été dépassé. Elle peut également se produire avec de mauvais capteurs de mesures d’impulsions ou si les raccordements d’impulsions se sont interrompus. REMOTE Alarme Signification QUAD ENC Erreur de code en quadrature également appelée erreur de sécurité associée aux impulsions. Cette alarme s'applique aux débitmètres qui utilisent des générateurs d'impulsions à double voie. Une des voies du générateur d'impulsion a échoué ou échoue par intermittence. Cette alarme se produit dans de nouvelles installations lorsque la voie A du générateur d'impulsions est reliée à la voie B de ce même générateur et vice versa. Elle se produira également si un débit inverse est détecté. 1. Vérifiez que les générateurs d'impulsions ou préamplificateurs du compteur reçoivent une alimentation électrique. 2. Vérifiez les raccordements du générateur d'impulsions au FCM. 3. Assurez-vous que les voies A et B des générateurs d'impulsion ne sont pas câblées à l’envers. REMOTE DENSITY REMOTE RTD ERROR 4. Recherchez la présence de débit inverse en regardant le totalisateur du compteur (refoulement brut). Cette alarme indique que la valeur mesurée par le capteur de densité ou de densité relative a dévié de la fourchette spécifiée par les paramètres d’alarme de basse densité et d’alarme de haute densité ou les paramètres d’alarme de basse densité relative et de haute densité relative. Parmi les autres causes possibles, citons un capteur débranché ou une valeur inappropriée dans le champ de densité par défaut ou de densité relative par défaut. Allez au menu du mode de programme Views & Inquiries -> Density ou Relative Density pour lire la densité instantanée. Cette alarme indique que la température mesurée par le RTD a dévié de la fourchette établie par les paramètres des alarmes de températures élevées et basses. Parmi les autres causes possibles, citons un détecteur débranché ou un paramètre de type de module de 11 8 Chapitre 4 – Configuration Générale température mal configuré. Allez au menu de mode de programme Views & Inquiries >Temperature ("Affichage & Requêtes/Température") pour d’autres messages de diagnostic. REMOTE VALVE CTL Erreur de la vanne de Régulation - Cette alarme indique que la vanne de régulation n'a pas été capable de maintenir le débit dans la zone morte fixée par le menu compteur. Cette alarme peut indiquer qu'un entretien de la vanne est nécessaire ou que la pression est insuffisante pour commander la vanne. Utilisez l’écran de statuts des composants pour voir si la vanne peut attendre les débit-cibles précisés par le haut débit, le faible débit et les 1ers et 2nds vitesses de déclenchement. Si la vanne fonctionne en position grande ouverte et n’arrive pas au débit-cible, elle est donc sensible aux problèmes de commande engendrés par une pression différentielle faible. Dans ce cas, réduisez le débit-cible ou activez la fonction de secours « Fallback » (repli) dans le menu des composants. REMOTE Cette alarme indique que du volume est passé par le débitmètre alors que la vanne n’avait pas reçu l’ordre de s’ouvrir. Cela peut indiquer une petite fuite ou que des signaux erronés de débit ont été relevés par le système. La quantité de volume qui déclenche l'alarme est configurée dans le paramètre de volume d’alarme de fluage du compteur. Voyez aussi au paramètre Creep reset Time (Temps de Réinitialisation du Fluage). MTR CREEP REMOTE PRES ALRM Cette alarme indique que la pression mesurée par le capteur de mesures de pression a dévié de la fourchette établie par les paramètres d’alarme de haute et de basse pression. Vérifiez le fonctionnement du capteur de mesures. REMOTE Ce message d’alarme indique que la voie A du générateur d'impulsions référencé ne produit pas d’impulsions soit entièrement, soit par intermittence. La voie A du compteur doit être reliée au port 4 du FCM du compteur. Si cette alarme est émise conjointement à l'alarme QUAD CH B, les voies du compteur sont soit raccordées à l’envers, soit il y a refoulement. Référez-vous à l’alarme QUAD ENC. QUAD CHA REMOTE Ce message d’alarme indique que les impulsions venant de la voie B du générateur d'impulsions référencé ne sont pas reçues au port 5 du FCM ou uniquement de façon intermittente. Si elle est émise conjointement à l'alarme QUAD CH A, soit les voies du compteur sont raccordées à l'envers, soit il y a un refoulement. Référez-vous à QUAD ENC. QUAD CHB REMOTE MTR COM AUTO 1. Pas de communication avec le compteur connecté par une ligne de communication GRAVITY Cette alarme indique que la valeur mesurée par la sonde BSW a dévié de la fourchette spécifiée par les paramètres Alarm Low API Gravity et Alarm High API Gravity. Parmi les autres causes possibles, citons une sonde déconnectée ou une valeur inappropriée dans le camp de la gravité API par défaut. Allez au menu du mode programme dans Views & Inquiries - > API Gravity et lisez la gravité API instantanée. REMOTE MALARM 17, 1931 4.8.4 Affectations de futures alarmes au niveau compteur RÉGLAGE DES ALARMES DU COMPOSANT Alarme Signification COMP FCM Le MultiLoad II a perdu la communication avec la carte des entrées/sorties ou le FCM. Ce message indique que les fonctions de niveau du composant sont affectées par l'interruption de la communication. Elle s'annule automatiquement lorsque les communications sont Chapitre 4 – Configuration Générale Alarme Signification rétablies. Vérifiez au menu Diagnostic sous "Comm. FCM" pour déterminer si la carte des entrées/sorties ou le FCM sont bien en train de communiquer. AUTO COMP PERM Permission Composant. Les permissions peuvent être définies pour affecter des composants dans des bras de chargement multi-composants. Lorsque le signal de permission de composant est perdu, le chargement s'arrête sur le bras de chargement si le composant est utilisé. L'alarme se lève automatiquement quand le signal est rétabli. Le message d’alarme qui se manifeste à l'opérateur est configuré par l'Utilitaire de Configuration du MultiLoad, Alarmes de Composants, Alarme 1. AUTO BLK VALVE Alarme de vanne d'arrêt. Cette alarme s'active lorsqu'une vanne d'arrêt ne s'est pas ouverte dans le temps dicté par le paramètre de temps de l'alarme d'ouverture de la vanne d'arrêt. Cette alarme se produit également si la vanne d'arrêt ne s'est pas fermée dans le temps exigé par le paramètre de temps de l'alarme de fermeture de la vanne d'arrêt. A chaque fois qu'une vanne d'arrêt n'est pas positionnée correctement, l'alarme s'active. DRIVER UNAUTH FL REMOTE PUMP STAT Alarme de débit non autorisé - Cette alarme se produit lorsque le débit passe par le compteur lorsque le compteur n'est pas autorisé à charger. Le volume qui déclenche l'alarme est défini par le volume d’alarme du débit non autorisé. L'alarme du statut de la pompe se produit dans deux situations. Le plus généralement, elle survient conjointement avec une alarme d'erreur de vanne. Si une vanne de régulation ne se ferme pas, la sortie correspondante de la pompe sera baissée pour arrêter le débit. L'alarme du statut de la pompe apparaîtra sur tous les bras de chargement du quai qui se servent de la même pompe. Par exemple, si une alarme du statut de la pompe apparaît sur le bras de chargement n° 7 (diesel), elle peut se produire en raison d'une erreur de vanne sur un autre bras diesel sur le même quai. L'alarme du statut de la pompe se produit si on utilise l'entrée du statut de la pompe pour vérifier la pression d'une pompe. Lorsque la pompe perd de la pression, l'alarme de statut de la pompe apparaît sur tous les bras de chargement du quai qui en dépendent. DRIVER MTR ALARM Ce réglage d’alarme doit rester en position "Auto Clear" (Effacement automatique) et indique que le composant a une alarme active au niveau du compteur. AUTO OVR BLEND (excluding SMP) Alarme de "mélange excessif" - Cette alarme se produit lorsqu'un composant d'un mélange proportionnel dépasse les limites de tolérance du pourcentage spécifié par le paramètre de % d’alarme de Contrôle du mélange ou du volume spécifié par le paramètre de volume d’alarme de Contrôle du mélange. Pour les Mélanges Séquentiels, cette alarme se déclenche lorsqu'un lot est supprimé et que le mélange dépasse les limites établies par le pourcentage ou le volume spécifié par les paramètres susmentionnés. DRIVER UND BLEND (Excluding SMP) Alarme "d'insuffisance de mélange" - Cette alarme se produit lorsqu'un composant d'un mélange proportionnel est inférieur aux limites de tolérance du pourcentage spécifié par le paramètre de % d’alarme de contrôle du mélange ou du volume spécifié par le paramètre de volume d’alarme de contrôle du mélange. Pour les mélanges séquentiels, cette alarme se déclenchera lorsqu'un lot est supprimé et que le mélange est inférieur aux limites établies par le pourcentage ou le volume spécifié par les paramètres susmentionnés. DRIVER API TABLE Cette alarme indique que soit, un certain paramètre, soit un tableau CTL, soit un tableau CPL 11 9 Chapitre 4 – Configuration Générale Alarme Signification est hors des limites. Elle peut provenir d'un paramètre de tableau mal configuré ou d'une erreur du capteur de pression ou de température. Lorsque cette alarme se produit, entrez dans le mode de programme et sélectionnez Views & Inquiries/Message Log (Affichage & Requêtes/Journal des Messages). Le Journal des Messages indiquera la valeur prédéfinie et le composant relatifs à l'alarme de tableau API active. Si une alarme de Pression ou RTD se déclenche en plus de l'Alarme de Tableau API, résolvez d'abord le problème de pression et/ou de température. S'il n'y a pas d’alarme de pression ou de température, rentrez dans la section des Poids et Mesures dans le mode de programme. Entrez dans le menu de Compensation de la Température de la Valeur Prédéfinie et du Composant qui présentent l'alarme. Vérifiez les réglages du Coefficient de Gravité, Densité ou d'Expansion. Assurezvous que les réglages sont appropriés au tableau sélectionné. Si une correction de pression est utilisée, vérifiez également ses paramètres dans le menu de compensation de la pression. Vérifiez les paramètres de gravité ou de densité. Assurez-vous que les réglages sont appropriés au tableau sélectionné. DRIVER CALARM 9-31 DRIVER Affectations futures d’alarme de niveau de composants. 12 0 Chapitre 4 – Configuration Générale 4.8.5 RÉGLAGES DES ALARMES ADDITIFS Alarme Signification ADTV FCM Le MultiLoad II a perdu la communication avec la carte des entrées/sorties ou le FCM. Ce message indique que les fonctions de niveau des additifs sont affectées par l'interruption de la communication avec le FCM. Cette alarme se lève automatiquement quand les communications sont rétablies. Vérifiez dans le menu Diagnostic sous "Comm. FCM" pour déterminer si la carte des entrées/sorties ou le FCM sont bien en train de communiquer. AUTO ADTV PERM Permission des additifs. Les permissions peuvent être définies pour affecter des additifs spécifiques dans des bras de chargement pour additifs multiples. Lorsque le signal de permission des additifs est perdu, le chargement s'arrête sur le bras de chargement si l'additif est utilisé. L'alarme se lève automatiquement quand le signal est rétabli. Le message d’alarme qui se manifeste à l'opérateur est configuré par l'Utilitaire de Configuration du MultiLoad, Alarmes Additifs, Alarme 1. AUTO UND ADTV REMOTE Alarme sous-enrichi - Le chargement est arrêté lorsque les additifs sont sous-enrichis par le nombre d'injections spécifié par l'Alarme Sous Enrichi # Inj. OVR ADTV REMOTE Alarme sur-enrichi - Le chargement est arrêté lorsque les additifs sont sur-enrichis par le nombre d'injections spécifié par l'Alarme Sur-enrichi # Inj. VALVE FLT L'erreur de vanne d'additifs se produit lorsque le débit d'additifs continue après la commande de fermeture de l’électrovanne d'injection. Une alarme se produit lorsque le volume spécifié dans le volume de l'alarme de l'erreur de vanne a passé le compteur d'additifs après une commande de fermeture. Les sorties appropriées de la vanne d'arrêt et de la pompe seront baissées pour arrêter le débit. La sortie de suppression de la pompe sera activée, si elle est utilisée. Un message d’alarme du statut de la pompe se produit sur d'autres bras de chargement qui utilisent la sortie habituelle du fonctionnement de la pompe. Par exemple, si une erreur de vanne d'additifs se produit sur un injecteur d'un bras de chargement qui livre l'additif de marque X, tous les autres bras de chargement dans le quai qui délivrent l'additif de cette marque affichent l'alarme du statut de la pompe et ne pourront pas charger jusqu'à ce qu'il y ait eu correction. PROGRAM PUMP STAT DRIVER L'alarme du statut de la pompe des additifs se produit dans deux situations. Le plus généralement, elle survient conjointement avec une alarme d'erreur de vanne. Si une vanne de régulation ne se ferme pas, la sortie correspondante de la pompe sera baissée pour arrêter le débit. L'alarme du statut de la pompe apparaîtra sur tous les bras de chargement du quai qui se servent de la sortie habituelle de fonctionnement de la pompe. Par exemple, si une alarme du statut de la pompe apparaît sur le bras de chargement #7, elle peut se produire en raison d'une erreur de vanne d’additifs sur un autre bras diesel qui se trouve sur le même quai. L'alarme du statut de la pompe se produit également lors de l'utilisation de l'entrée du statut de la pompe pour vérifier la pression d'une pompe. Lorsque la pompe perd de la pression, l'alarme de statut de la pompe apparaît sur tous les bras de chargement du quai qui dépendent de la pompe. 12 1 Chapitre 4 – Configuration Générale Alarme Signification INJCT FLT Cette alarme indique que le MultiLoad II a détecté une panne d'injection. Si un injecteur à piston est utilisé, l'alarme indique la perte de plusieurs injections. La quantité d'injections perdues est spécifiée par le paramètre Max Pstn Missed Inj. D'autres pannes peuvent causer cette alarme: un piston coincé, pannes du distributeur/électrovanne, filtres et injecteurs obstrués. De plus, un interrupteur à lame souple de piston incorrectement ajusté ou cassé peut être source de panne. Dans certains cas, il peut être nécessaire d'augmenter le paramètre de temps maximum de débattement du piston lorsqu'il y a une très faible pression des additifs. Si l'additif est très visqueux ou si un injecteur de volume important est utilisé, il faut peut-être augmenter le temps de débattement du piston. Cela donnera plus de temps à l'injecteur pour achever un cycle d'injection. Si on utilise la méthode de mesure de l'additif, cette alarme signale que le volume-cible d'injection d'additif n'a pas été atteint pendant la période spécifiée par le temps maximum d’injection de l’électrovanne. Dans la plupart des cas, cela signifie qu'une vanne d'additifs est fermée ou que la pompe d'additifs ne démarre pas. D'autres pannes peuvent causer cette alarme: pannes d’électrovannes, filtres bouchés et mauvais fonctionnement du capteur du compteur ou du préamplificateur. Dans certains cas, il peut être nécessaire d'augmenter le temps maximum d’injection de l’électrovanne lorsqu'il s'agit d'un chargement frontal ou d'injecter de grandes quantités d'additifs avant une purge de conduite. Cela donnera plus de temps à l'injecteur pour achever un cycle d'injection. DRIVER UNAUTH FL Alarme de débit non autorisé - Cette alarme se produit lorsqu'un volume d'additifs passe par le compteur et que la livraison n’en est pas autorisée. Le volume du débit qui déclenche l'alarme est défini par le paramètre du volume d’alarme du débit non autorisé. REMOTE NO LNFLSH Pas de purge de conduite. Cette alarme se produit si le chargement est interrompu et que la purge minimum de conduite n'a pas eu l'occasion de se faire. DRIVER MTR CREEP Cette alarme indique qu'une petite quantité de volume est passée par le débitmètre ou le piston. Cela peut signifier qu'il y a une petite fuite ou que des signaux erronés de débit ont été relevés par le système. La quantité de volume qui déclenche l'alarme est configurée dans le paramètre de volume d’alarme de fluage du compteur. Voir aussi le paramètre de temps de réinitialisation du fluage. DRIVER BLK VANNE Alarme de vanne d'arrêt. Cette alarme s'active lorsqu'une vanne d'arrêt d'additifs ne s'est pas ouverte dans le délai prescrit par le paramètre de temps d’alarme d'ouverture de la vanne d'arrêt. Cette alarme se produit également si la vanne d'arrêt ne s'est pas fermée dans le délai prescrit par le paramètre de temps de l'alarme de fermeture de la vanne d'arrêt. Chaque fois qu'une vanne d'arrêt n'est pas positionnée correctement, l'alarme s'active. DRIVER ALARM 11-31 DRIVER Affectations ultérieures d’alarmes au niveau des additifs. 12 2 12 3 Chapitre 4 – Configuration Générale 4.9 DÉFINITION ET AFFECTATION LOCALE DES PRODUITS Les fonctions de réglage des produits servent à: - définir les composants de base, les additifs de base, les produits simples et les produits mélangés pour les installations locales de commande. - affecter des composants, des additifs et/ou des produits autorisés à des valeurs prédéfinies existantes. Toptech recommande de terminer les fonctions de Réglage des Équipements (Quai, valeurs prédéfinies, Compteurs, Composants, Additifs) avant d'utiliser les fonctions de Réglage de Produits. Il faudrait utiliser ces fonctions en mode local autonome uniquement. En mode à distance, les informations relatives au réglage des produits devraient être fournies par le TMS. Pour définir localement les noms et les descriptions des produits, il faut utiliser l’outil de configuration du MultiLoad. Pour cet écran, allez à: Program Mode -> Configuration -> Products Le menu de réglages de produits s’affiche: Error! Reference source not found. Cette série de fonctions permet à l’utilisateur de définir les composants de base, les additifs, les produits commercialisables simples (“Product”) et les produits commercialisables mélangés (“Blnd”) de deux composants de base ou plus, avec ou sans additif(s). Pour des installations MultiLoad II fonctionnant avec un TMS, les informations de réglage des produits se chargent automatiquement par le TMS. Les informations de réglage de produits ne doivent donc pas être configurées manuellement dans le MultiLoad II. Si la communication avec le TMS échoue, ces informations seront immédiatement disponibles pour un fonctionnement autonome. 12 4 Chapitre 4 – Configuration Générale 4.10 RÉGLAGE DES PRODUITS Utilisez cette fonction pour définir vos produits lorsque le MultiLoad II est configuré pour le mode local autonome. Ici, la stratégie est de définir vos composants de base et additifs de base d'abord et de les utiliser, ensuite, en tant que blocs modulaires pour définir les produits. Dans cet écran, allez à: Program Mode -> Configuration -> Products -> Product setup L’écran de réglage des produits s’affiche: Error! Reference source not found. Au départ, vous voyez les produits de base, les additifs de base et les produits commercialisables par défaut. Appuyez sur Enter pour sélectionner le produit à traiter. L’écran d’édition des produits s’affiche: Error! Reference source not found. 12 5 Chapitre 4 – Configuration Générale 4.11 DÉFINITION DES COMPOSANTS DE BASE Dans l’écran exemplifié ci-dessous, un opérateur a complété les valeurs pour créer un composant de base 87 sans plomb. Remarquez que, comme le clavier MultiLoad II SMP ne prend pas les caractères Alpha, les spécifications ou les caractères Alpha des noms de produits DOIVENT être introduits par l’outil de configuration du MultiLoad. Error! Reference source not found. Les consignes sont reprises ci-dessous: 1. Lorsque "Code" est en surbrillance, appuyez sur Enter. 2. Au niveau du curseur, introduisez un code de produit pour le composant de base à définir. Le code peut avoir jusqu'à 6 chiffres. 3. Après introduction du code de produit, appuyez sur Enter. 4. Appuyez sur Next et sélectionnez Long Desc. (description longue). Appuyez sur Enter. 5. Au niveau du curseur, introduisez une longue description pour le composant de base. La description peut avoir 25 caractères maximum. Ce texte apparaîtra à l'écran de commande des valeurs prédéfinies et à l'écran de sélection de produits. 6. Complétez les autres paramètres de définition des produits, comme suit : Short Desc Description sommaire du produit. Maximum 10 caractères. Hazard Idx Le code d’index du danger associé à ce produit. Il fait référence à la mention de danger appropriée à imprimer sur les tickets de comptage. Type Le type de produit : composants de base, additif de base et « non défini ». Dans cet exemple, sélectionnez composant de base. 7. Sélectionnez Edit Product Recipe. L’écran correspondant apparaît. 12 6 Chapitre 4 – Configuration Générale 4.11.1 DÉFINITION DES RECETTES DE COMPOSANTS DE BASE Pour le TMS et MultiLoad II, chaque composant de produit de base doit être 100% pur. La recette du produit d’un composant de base ressemble donc à ceci: Error! Reference source not found. Remarquez sur le pourcentage par défaut est de 100, autrement dit, ce “produit” est 100% pur. Appuyez sur Exit pour revenir à l’écran d’édition de produit. Appuyez sur Exit pour revenir à l’écran de sélection du produit où vous trouverez les composants de base nouvellement créés, tel qu’illustré ci-après : Error! Reference source not found. 12 7 Chapitre 4 – Configuration Générale 4.11.2 DÉFINITION D’UN ADDITIF La définition d’un additif est quasiment la même que pour un composant de base: Sur l’écran de sélection des produits, mettez le produit à éditer en surbrillance. Error! Reference source not found. Appuyez sur Enter et sélectionnez le produit à éditer. L’écran d’édition des produits s’affiche: Remplissez les champs comme pour un composant de base, à une exception près: pour le type, sélectionnez additif de base, comme dans l’exemple ci-après. Error! Reference source not found. 12 8 Chapitre 4 – Configuration Générale Sélectionnez Enter. L’additif de base se définit automatiquement et est pur à 100%. Si vous devez sélectionner l’édition de recette de produits, le nouvel additif de base s’afficherait sur l’écran des recettes de produits, comme ci-après. (Toutefois, normalement, il n’y aurait pas besoin d’aller à l’écran de recettes des produits pour configurer des additifs de base et des composants de produits de base.) Error! Reference source not found. Sélectionnez Exit pour revenir à l’écran de sélection des produits. Continuez à définir les additifs de base si nécessaire. Error! Reference source not found. 12 9 Chapitre 4 – Configuration Générale 4.12 DÉFINITION DES PRODUITS COMMERCIALISABLES Après avoir défini les composants de base et les additifs de base, commencez à définir les produits commercialisables. Le système définit un produit commercialisable simple (Product) comme étant composé de 1 à 8 composants de base et de 0 à 16 additifs. Jusqu'à ce point, l'écran de recette de produit n'a pas été nécessaire, puisque chaque composant de base est automatiquement défini comme 100 % pur. Toutefois, pour définir des produits commercialisables, l'écran de recettes de produits devient essentiel dans la définition de produit. Définir un produit commercialisable simple Dans la séquence suivante, un produit commercialisable simple est créé à partir d'un composant de base simple et d'un certain pourcentage d'additif. Sur l’écran de sélection de produits, mettez le produit à éditer en surbrillance. Error! Reference source not found. Appuyez sur Enter et sélectionnez le produit à éditer. L’écran d’édition des produits s’affiche: Error! Reference source not found. 13 0 Chapitre 4 – Configuration Générale Complétez les champs et pour le type, sélectionnez « Product » comme le montre l’exemple ci-après. Error! Reference source not found. Sélectionnez « Edit Product Recipe ». L’écran de recette de produit s’affiche: Error! Reference source not found. 13 1 Chapitre 4 – Configuration Générale Configurez le composant de base et l’additif de base comme dans l’exemple ci-après. Error! Reference source not found. Quand vous avez terminé, appuyez deux fois sur Exit pour revenir au menu de réglage des produits. 13 2 Chapitre 4 – Configuration Générale 4.13 RÉGLAGES DES PRODUITS PRÉDÉFINIS Utilisez les fonctions de réglage des produits prédéfinis pour - attribuer des composants de base définis à un composant - attribuer des additifs de base définis à un additif. - attribuer des produits commercialisables définis à un réglage produit prédéfini Dans cet écran, allez à: Program Mode -> Configuration -> Products -> Preset Product setup Cet écran de réglage des produits prédéfinis s’affiche : Error! Reference source not found. 4.13.1 NOM PRÉDÉFINI On peut attribuer un nom au prédéfini. Celui-ci sera affiché avant que le chauffeur ne sélectionne un produit. 13 3 Chapitre 4 – Configuration Générale 4.13.2 AFFECTATION DE COMPOSANTS Quand vous avez terminé de définir vos composants de base, cette fonction vous permet d’attribuer au composant physique. L’écran de détection du composant s’affiche alors : Error! Reference source not found. Configurez le composant de base attribué comme le montre l’exemple ci-après : Error! Reference source not found. 13 4 Chapitre 4 – Configuration Générale 4.13.3 AFFECTATION D’ADDITIFS Après avoir défini vos additifs de base, cette fonction vous permet d’affecter à l’additif physique. Quand les définitions sont terminées, l’écran de sélection d’additifs s’affiche : Error! Reference source not found. Configurez l’additif de base attribué comme le montre l’exemple ci-après : Error! Reference source not found. 13 5 Chapitre 4 – Configuration Générale 4.13.4 AFFECTATION DE PRODUITS AUTORISÉS Quand vous avez terminé de définir vos produits commercialisables, utilisez cette fonction pour préciser pour quels produits commercialisables le chargement est autorisé dans ces valeurs prédéfinies. Quand vous avez sélectionné les produits autorisés, l’écran des produits autorisés s’affiche : Error! Reference source not found. Configurez les produits commercialisables autorisés comme le montre l’exemple ci-après: Error! Reference source not found. S’il y a plus d’un produit commercialisable sélectionné, le chauffeur recevra un écran de sélection des produits au cours de l’autorisation. Remarque: Les composants de base (Comp) peuvent également être disponibles pour chargement si vous le désirez. Chapitre 4 – Configuration Générale 4.13.5 ECRAN DE CONFIGURATION D’ENREGISTREMENT DES PRODUITS DISPONIBLES À PARTIR DE L’OUTIL DE CONFIGURATION (Voir également à Local Produit Definition Assignment pour plus d’informations sur cet écran) 4.13.6 ECRAN DE CONFIGURATION DE RECETTE DISPONIBLE À PARTIR DE L’OUTIL DE CONFIGURATION 13 6 Chapitre 4 – Configuration Générale 4.14 ID D'ACCÈS Utilisez la fonction Access ID's pour attribuer des numéros d’identification personnelle (PIN) aux cartes d’accès au MultiLoad II. Vous pouvez stocker un maximum de 300 (0–299) ID d’accès (cartes) dans le système avec leur code PIN associé. Le numéro d’accès peut avoir de 4 à 8 caractères. Dans cet écran, allez à: Program Mode -> Configuration -> Access ID’s L’écran de réglage des ID d’accès s’affiche: A C C E S S I D ' S [000] Card No: 00000111 PIN: 0111 [001] Card No: 00000123 PIN: 0123 [002] Card No: 00000132 PIN: 0132 [003] Card No: <empty> PIN: [004] Card No: <empty> PIN: [005] Card No: <empty> PIN: [006] Card No: <empty> PIN: [007] Card No: <empty> PIN: [008] Card No: <empty> PIN: [009] Card No: <empty> PIN: [010] Card No: <empty> PIN: [011] Card No: <empty> PIN: [012] Card No: <empty> PIN: No: <empty> PIN: Pour chaque carte, appuyez sur [013] Enter etCard introduisez le numéro de carte à l’aide du clavier. Appuyez sur Enter et Next Prev Exit introduisez le numéro PIN correspondant. Appuyez de nouveau Enter sur Enter pour sauvegarder. Ensuite, appuyez sur Next pour sélectionner la ligne suivante et répétez ce qui précède. Après avoir complété la dernière carte sur le premier écran, appuyez sur Next pour passer à l'écran suivant. Remarquez que la barre de sélection se trouve sur la dernière ligne de l'écran de suite ([013]). Appuyez sur Next pour déplacer la barre de sélection vers le sommet de l'écran pour continuer avec la carte suivante par ordre ([014). 13 7 13 8 Chapitre 4 – Configuration Générale 4.15 RÉGLAGE DU LOGO DU CLIENT Quand le MultiLoad II est inactif (aucun chargement autorisé, l’écran affiche un message qui explique au chauffeur la façon d’engager le processus d’autorisation. Press Next to Begin For Access Insert Driver Card For Access Press Next to Begin For Access Insert Driver Card For Access L’affichage alterne entre deux images graphiques - 2 images d’identification du produit - et un logo client configurable (logo client par défaut: celui de “Toptech Systems”) . Il y a deux façons de configurer le logo du client: charger à partir d’un logo de client incorporé ou télétransférer un fichier .bmp du client. 13 9 Chapitre 4 – Configuration Générale 4.15.1 CHARGEMENT D’UN LOGO CLIENT INCORPORE Entrez dans le mode programme, sélectionnez Configuration, puis « Customer Logo Setup ». L’écran de réglage du logo du client s’affiche. CUSTOMER LOGO SETUP Next Prev Exit Enter Le logo du client en cours de chargement s’affiche. Appuyez sur les touches Next et Prev pour voir tous les logos incorporés. Appuyez sur Exit pour revenir au menu de configuration sans changer le logo client chargé. Appuyez sur Enter pour charger le logo client à l’affichage. 4.15.2 TÉLÉTRANSFÉRER UN LOGO CLIENT .BMP Le fichier .BMP avec le logo du client doit être conforme à certains critères pour réussir le télétransfert. A savoir : - Format BMP (Bitmap) 4 bits par pixel (16 couleurs) Hauteur OBLIGATOIRE de 240 pixels. - NOIR (0, 0, 0) Données image non compressées Largeur OBLIGATOIRE de 640 pixels. Maximum 6 couleurs client. A savoir les couleurs (R, G, B) autres que: BLEU (0, 0, 255) ROUGE (255, 0, 0) MAGENTA (255, 0, 255) VERT (0, 255, 0) CYAN (0, 255, 255) JAUNE (255, 255, 0) BLANC (255, 255, 255) Le TMS 5 et le TMS 6 ont un programme utilitaire permettant de télétransférer un fichier .BMP conforme à ces critères vers un MultiLoad II. Pour les applications MultiLoad II autonomes, et RCU II, utilisez l’outil de configuration Multimate le plus récent pour télétransférer un logo client. Sur les cartes CPU version 2.0, on peut également utiliser la carte SD pour télétransférer un fichier BMP de logo. 14 0 Chapitre 4 – Configuration Générale 4.16 DATE ET HEURE DU SYSTÈME Utilisez la fonction Date & Time pour régler la date et l’heure correctes. 1. A partir du menu de configuration, sélectionnez Date & Time. L’écran de réglage de l’horloge (CLOCK SETUP) s’affiche: Error! Reference source not found. 2. Appuyez sur 1 et introduisez la date du jour sous forme YYYYMMDD. Par exemple, introduisez le 8 avril 2003 sous forme 030408. Appuyez sur ENTER pour sauvegarder votre réglage. 3. Appuyez sur 2 et introduisez l’heure correcte sous forme HHMMSS (heures, minutes, secondes). Par exemple, pour 2.30.15’’ de l’après-midi, tapez 143015. Appuyez sur ENTER pour sauvegarder votre réglage. Les modifications aux paramètres de temps et d’heure sont enregistrés dans le journal des modifications des poids et mesures (W&M Change Log). 14 1 Chapitre 4 – Configuration Générale 4.17 IMPRESSION Ce menu est soumis à conditions et n’apparaît que si nous avons configuré une imprimante Alibilog ou une imprimante réseau. P R I N T I N G M E N U Alibilog Labels Hazard Labels Prompts BOL Layout Next Prevl’écran Exitde réglage Enter de l’Alibilog où vous pouvez changer toutes En sélectionnant le premier écran, vous obtiendrez les étiquettes. Prev (Les étiquettes doivent être en majusculesNext dans cet écran)Exit Enter A L I B I L O G S E T U P BAY: Bay: TICKET: Ticket: CARD: Card #: PRESET: Preset: PROD: Prod COMP: Comp ADTV: Adtv GROSS: Gross NET: Net TEMP: Temp PRESS: Press GRAV: Grav RELDEN: RelDen DENSITY: Density En sélectionnant le second menu, à Hazard Next vous Prevarrivez Exit EnterLabels. Ces étiquettes peuvent être reliées à chaque produit. Appuyez sur Enter si vous voulez modifier ces textes. Error! Reference source not found. En sélectionnant le troisième menu, vous arrivez aux invites autonomes. Pour entrer dans l’écran, vous devez sélectionner l’invite que vous désirez modifier. 14 2 Chapitre 4 – Configuration Générale P R O M P T Prompt1 Prompt2 Prompt3 Prompt4 Prompt5 S E T U P Next Exit Prev Enter Sélectionnez l’invite puis vous pourrez introduire la longueur des données, les réglages BOL et les langues selon les paramètres de la carte du chauffeur. these texts. P R O M P T S E T U P D E T A I L Length of Data : 00 BOL Line : 0005 BOL Position: 0050 Language1: Enter Stockholder Language2: Enter Stockholder Language3: Language4: Language5: Language6: Language7: Language8: En sélectionnant le quatrième menu, vous arrivez à l’écran de mise en page du BOL. Vous pouvez changer la position et la ligne. Vous pouvez également effectuer un test d’impression pour vérifier l’alignement. NextvousPrev Exit Print Enter Error! Reference source not found.Si sélectionnez Transaction, un échantillon de transaction sera imprimé pour vérifier l’alignement. 4.18 SITE GPSS ( UNIQUEMENT ML II MOBILE) Utilisez la fonction de réglage du site GPS Site pour introduire un maximum de 4.000 sites agréés dont le nom ne dépasse pas 15 caractères. Un GPS doit être branché et configuré pour utiliser cette option. Cette base de données peut servir à: afficher le nom du site sur la carte affichée. enregistrer la latitude, la longitude et le nom du site dans l’en-tête de la base de données de la transaction locale. en option, susciter une erreur GPS si l’autorisation de transaction n’est pas pour un site de la base de données. Susciter une erreur GPS si la position change après autorisation de la transaction. Dans cet écran, allez à: Program Mode -> Configuration -> GPS Sites L’écran de réglage de sites GPS s’affiche: 14 3 Chapitre 4 – Configuration Générale Error! Reference source not found. Pour chaque site, appuyez sur Enter, puis introduisez le nom du site à l’aide du clavier. Appuyez sur Enter puis introduisez la latitude et la longitude. Appuyez sur Enter pour sauvegarder. Appuyez ensuite sur Next pour sélectionner la ligne suivante et répétez comme expliqué ci-avant. Quand vous avez complété le site sur le premier écran, appuyez sur next pour passer à l’écran suivant. La carte que vous voyez s’affiche : Insert Driver Card For Access Latitude: 28 41.655 N Longitude: 081 21.113 W Speed: 0.0(MPH) Heading: 39 Site: Toptech 22 M Chapitre 4 – Configuration Générale 14 4 Chapitre 5 – Contrôle du debit du produit CHAPTER 5 5.1 145 CONTROLE DU DEBIT DU PRODUIT VUE D’ENSEMBLE Ce chapitre s’attache à la configuration de régulation du débit et analyse les concepts et les procédures relatifs à un contrôle efficace du débit du produit - Livraison de produit à composant unique - Etalonnage par linéarisation du coefficient de mesure Pas Démarrage de flux Faible débit er Haut débit Figure 5-1 ème DéclenDéclen- Déclen- chement chement chement Final 1 Profil du débit 2 Chapitre 5 – Contrôle du debit du produit 5.2 146 LIVRAISON DE PRODUIT UNIQUE Les explications qui suivent concernent un bras de chargement qui charge un composant unique. Il y a cinq étapes au cours de l’écoulement du produit. Démarrage de faible débit Débit élevé ère Déclenchement 1 étape nde Déclenchement 2 étape Déclenchement final La vanne numérique de régulation est le composant clef de la section de comptage. Le MultiLoad II effectue des ajustements à la vanne basée sur base de la rétroaction à partir du débitmètre. Le profil des débits illustré cidessous montre comment chaque étape progresse au cours du chargement. Figure 5-2 Profil des débits pour une Livraison de Produit Unique Le chargement commence à l'étape de démarrage de faible débit. Lorsque vous poussez sur le bouton de démarrage, la vanne de régulation s'ouvre et le débit passe de zéro au débit requis pour le démarrage de faible débit. Tant les électrovannes normalement ouverts (amont) que normalement fermés (aval) de la vanne numérique de régulation sont sous tension, provoquant l'ouverture de la vanne de régulation. S'il y a suffisamment de pression, la vitesse du faible débit est atteinte en quelques secondes. Lorsque le débit s'élève à la vitesse de la zone morte de faible débit, l’électrovanne (aval) normalement fermée de la vanne de régulation se coupe. Cette action ferme la vanne dans la position requise pour maintenir la vitesse souhaitée. L'ouverture de la vanne de régulation peut être retardée par le paramètre de « Flow Start Delay » pour permettre à la pompe d’atteindre le niveau approprié de pression. Le démarrage de la pompe peut être retardé par le « Pump Start Delay » pour permettre aux vannes d’arrêt de s’ouvrir ou de se fermer complètement. Une fois que la vitesse du faible débit a été atteinte, le MultiLoad II ajuste périodiquement la vanne si le débit dérive au-dessus ou au-dessous du débit de la zone morte à faible débit. Les débits de zone morte sont Chapitre 5 – Contrôle du debit du produit 147 configurés à l'écran de réglage du compteur. La durée de l'étape de faible débit est définie par le paramètre de volume de démarrage de faible débit qui se trouve dans l'écran d'installation de réglage des valeurs prédéfinies. Comme le nom de ce paramètre l'indique, la durée de l'étape de démarrage du faible débit est déterminée volumétriquement. Le volume de démarrage du faible débit doit être configuré pour permettre une humidification adéquate du réservoir et empêcher la formation de charge statique. Lorsque le volume de démarrage de faible débit a été livré, l'étape de haut débit commence. Chaque fois qu'un chargement est momentanément arrêté avant la fin puis redémarré, l'étape de démarrage du faible débit reprend. Si un chargement est redémarré au beau milieu du cycle de haut débit, un faible débit sera utilisé au départ et sera plus court que le démarrage de faible débit. Le tableau qui suit énumère les paramètres qui affectent le démarrage du chargement et les propriétés de démarrage de faible débit. Paramètre Réglage par défaut Emplacement de l’écran Low Flow Start volume 50 gallons Réglage des prédéfinies valeurs Low Flow Rate 150 gallons par minute Réglage des prédéfinies valeurs Low Flow DB Rate +/- 40 gallons par minute Réglage du compteur Low Flow Alarm Rate 10 gallons par minute Réglage du compteur Low Flow Alarm Time 10 secondes Réglage du compteur Flow Start Delay 5 secondes Réglage des composants Pump Start Delay 3 secondes Réglage des composants Low Flow Restart volume 15 gallons Réglage des prédéfinies valeurs Pour une description détaillée des paramètres, veuillez vous référer au chapitre 4 traitant de la configuration générale. Chapitre 5 – Contrôle du debit du produit 5.2.1 148 HAUT DÉBIT Lorsque l'étape de haut débit commence, le MultiLoad II met les deux électrovannes de la vanne numérique de régulation sous tension, ce qui permet à la pression de la conduite d'agrandir la partie ouverte de la vanne. Une fois la vitesse du haut débit atteinte, l’électrovanne (aval) normalement fermée sera hors tension. Ceci dans le but de fermer la vanne dans une position qui lui permettra de maintenir le débit souhaité. Des ajustements périodiques sont nécessaires pour la vanne si le débit dérive au-dessus ou au-dessous du débit de la zone morte à haut débit. Les débits de zone morte sont configurés au menu compteur. Le produit continuera à s’écouler à la ère vitesse de haut débit jusqu'à ce que le volume de déclenchement de la 1 étape soit atteint. Le tableau qui suit énumère les paramètres qui affectent les propriétés de l'étape de haut débit. 5.2.2 Paramètre Réglage par défaut Emplacement de l’écran High Flow Rate* 600 gallons par minute Réglage valeurs prédéfinies High Flow DB Rate +/- 40 gallons par minute Réglage compteur Excess Flow Alarm Rate 800 gallons par minute Réglage compteur DÉCLENCHEMENT DE LA 1ÈRE ETAPE ère La phase de déclenchement de la 1 étape commence lorsque le volume restant atteint le volume indiqué par le ère paramètre du volume de déclenchement de la 1 étape, qui se trouve à l'écran de réglage des composants. Cette phase représente la transition initiale à l'approche de la livraison-cible. Lorsque le volume du ère déclenchement de la 1 étape est atteint, le MultiLoad II met hors tension les deux électrovannes et la pression de la conduite réduit l'ouverture de la vanne. Les électrovannes resteront hors tension jusqu'à ce que le débit de ère ère la 1 étape soit atteint. Le débit de la 1 étape est configuré dans le menu des composants. ère Lorsque le débit de déclenchement de la 1 étape est atteint, le MultiLoad II met sous tension l’électrovanne normalement ouverte (amont) pour fermer la vanne dans une position qui lui permettra de maintenir le débit souhaité. Des ajustements périodiques seront apportés à la vanne si le débit dérive au-dessus ou au-dessous du ère débit de la zone morte de déclenchement de la 1 étape. Le produit continuera à s’écouler à la vitesse de ère ème déclenchement de la 1 étape jusqu'à ce que le volume de déclenchement de la 2 étape soit atteint. Paramètre Réglage par défaut Emplacement de l’écran 1st Stage Flow Rate* 225 gallons par minute Réglage composant 1st Stage Trip Volume* 70 gallons Réglage composant 1st Stage DB Rate +/- 40 gallons par minute Réglage compteur Chapitre 5 – Contrôle du debit du produit 5.2.3 149 DÉCLENCHEMENT DE LA 2ÈME ETAPE ème La phase de déclenchement de la 2 étape commence lorsque le volume restant atteint le volume indiqué par le ème paramètre du volume de déclenchement de la 2 étape. Ce paramètre se trouve au menu des composants. Cette phase est la seconde dans une série d’ajustements depuis le haut débit jusqu'à la condition "sans débit". ème Lorsque le volume du déclenchement de la 2 étape est atteint, le MultiLoad II met hors tension les deux électrovannes, ce qui permet à la pression de la conduite de réduire l'ouverture de la vanne. Les électrovannes ème ème resteront hors tension jusqu'à ce que le débit de la 2 étape soit atteint. Le débit de la 2 étape se configure au menu des composants. ème Lorsque le débit de déclenchement de la 2 étape est atteint, le MultiLoad II met sous tension l’électrovanne normalement ouverte (amont) pour fermer la vanne dans une position qui lui permettra de maintenir le débit souhaité. On effectuera des ajustements périodiques à la vanne si le débit dérive au-dessus ou au-dessous du ème débit de la zone morte de déclenchement de la 2 étape. Le produit continuera à s’écouler à la vitesse de ème déclenchement de la 2 étape jusqu'à ce que le volume de déclenchement final soit atteint. 5.2.4 Paramètre Réglage par défaut Emplacement de l’écran 2nd Stage Flow Rate 150 gallons par minute Réglage Composant 2nd Stage Trip Volume 20 gallons Réglage Composant 2nd Stage DB Rate +/- 40 gallons par minute Réglage Compteur DÉCLENCHEMENT FINAL L'étape du déclenchement final est la dernière phase de livraison autorisant le débit de produit. Lorsque le temps indiqué dans le paramètre de temps maximum de déclenchement final s'est écoulé, le débit doit être complètement arrêté. Lorsque le temps maximum de déclenchement final s’est écoulé, la valeur prédéfinie passe à l'état inoccupé (« idle »). Si le débit est toujours détecté passé cette période et si le volume d’alarme de dépassement a été dépassé, l'alarme de dépassement se déclenche. Le paramètre de volume de déclenchement final commande la fermeture de la vanne avant d'atteindre la quantité de la valeur prédéfinie pour compenser de petits dépassements uniformes de livraison. Cet ajustement est fait volumétriquement. Par exemple, si la vanne livre systématiquement 1,50 unités volumétriques de plus que la quantité prédéfinie, introduisez 1.50 pour ce paramètre. Les paramètres de déclenchement final se trouvent à l'écran de réglage des composants. 5.2.5 Paramètre Réglage par défaut Emplacement de l’écran Final Trip volume 1.15 gallons Réglage Composant Final Trip Maximum Time 500 millisecondes Réglage Composant Overrun Alarm volume 20 gallons Réglage valeurs prédéfinies VANNES 2”-3” DE COMMANDE NUMÉRIQUE Quand vous avez effectué les ajustements de la vanne de régulation numérique et du pointeau, la commande de vanne numérique n’est plus un problème. Mais avec de petites vannes numériques de 2”-3” ou des vannes sans pointeau, celles-ci ont tendance à réagir très vite, ce qui provoque parfois un dépassement constant du débitcible. On peut observer ce phénomène quand la vanne n’arrive pas à se bloquer sur un débit régulier alors que les électrovannes continuent à clignoter au cours du chargement. Pour éviter ce problème, on peut configurer un autre algorithme de débit permettant d’éliminer le dépassement et de réduire les valeurs de zone morte de débit en effectuant les ajustements par petites étapes. Si vous changez la durée d’inactivité de l’électrovanne (Valve Dwell Time), cela permet au logiciel de régler la vitesse de la vanne de la même façon qu’un pointeau ajuste la vitesse d’une vanne. Chapitre 5 – Contrôle du debit du produit 150 Le MultiLoad peut être configuré à l’aide de l’algorithmealgorithme de la vanne alternative de commande numérique comme indiqué ci-après : Allez à: Program Mode->Configuration->Equipment Setup et configurez les paramètres suivants : Paramètre Réglage Emplacement de l’écran Flow Scan Time 0.200 Secondes Réglage Compteur Valve Dwell Time 0.060 Secondes Réglage Compteur Pour accélérer l’ajustement, faites passer le temps d’inactivité de la vanne (Valve Dwell Time) de 0,005 à 0,170 secondes maximum. Pour ralentir l’ajustement, faites descendre le temps d’inactivé de la vanne de 0,005 à 0,030 secondes minimum. 5.2.6 ALGORITHME ADAPTATIF DE COMMANDE NUMÉRIQUE Pour affiner la précision des débit-cibles, un algorithme adaptatif de commande numérique a été créé pour noter la vitesse d’ajustement de la vanne de régulation numérique selon le débit et l’état de la vanne. Une fois ce débitcible verrouillé, les nouveaux ajustements s’effectueront jusqu’à ce que le débit instantané tombe en dehors de la zone morte cible. Pour les versions de cartes des entrées et sorties I/O 037 et ultérieures, le MultiLoad II peut se configurer pour utiliser cet algorithme adaptatif de commande numérique en procédant comme suit : Allez à: Program Mode->Configuration->Equipment Setup et configurez les paramètres suivants : 5.2.7 Paramètre Réglage Emplacement de l’écran Flow Scan Time 0.200 secondes Réglage Compteur Adaptive Valve Control ACTIVE Réglage Compteur VANNES À DEUX ETAPES Les vannes à deux étapes ressemblent aux vannes à commande numérique car elles fonctionnent aussi avec des électrovannes normalement ouvertes (NO) ou normalement fermées (NC). Cette vanne à deux étapes ne donne toutefois que deux débits : bas et haut. Le MultiLoad peut utiliser les vannes à deux étapes si la configuration est appropriée, à savoir: Allez à: Program Mode->Configuration->Equipment Setup et configurez les paramètres suivants: Réglage Compteurs Composants Low Flow Rate: 5000 Zone morte bas débit: 4999 Haut débit: 9999 High Flow Rate: 9999 Zone morte débit 1ère étape: 4999 Débit 1ère étape: 5000 Alarme de dépassement de débit: > Max débit anticipé Débit 2ème étape Trip Vol: 0 Temps de repli: 0 Chapitre 5 – Contrôle du debit du produit 5.2.8 151 VANNES ANALOGIQUES Les vannes analogiques sont des vannes de commande fonctionnant avec un signal de 4-20mA indiquant l’ouverture proportionnelle de la vanne. Un signal analogique < ou = à 4mA provoque la fermeture complète de vanne (0%). Un signal analogique > ou = à 20mA provoque l’ouverture complète de vanne (100%). Un signal analogique compris entre 4mA et 20mA provoque une ouverture de vanne de 0% à 100%. En soi, une vanne analogique ne vise pas un débit et le signal de commande de débit doit donc être adapté par le MultiLoad pour viser le profil de débit. Avec les versions du FCM ou de la carte des entrées et sorties I/O 037 et ultérieures, le MultiLoad peut se servir de vannes analogiques si la configuration suivante est effectuée correctement : Allez à: Program Mode->Configuration->Equipment Setup et configurez les paramètres suivants : Paramètre Réglage Emplacement de l’écran Flow Scan Time 0,200 secondes Réglage Compteur Analog Valve Control ACTIVE Réglage Compteur 4-20mA Increase Step 0.080 mA Réglage Compteur 4-20mA Decrease Step 0.800 mA Réglage Compteur Pour modifier la vitesse des modifications positives de débit, modifiez « 4-20mA Increase Step ». Pour modifier la vitesse des modifications négatives de débit, modifiez « 4-20mA Decrease Step ». Chapitre 5 – Contrôle du debit du produit 5.3 152 MELANGE SEQUENTIEL (SAUF SMP) Regular P Comp #1 BV T1 M1 Premium P CV Comp #2 Figure 5-3 BV Application Mélange Séquentiel La fonction de mélange séquentiel est utilisée en chargeant deux à huit (2 - 8) composants ensemble dans un compartiment pour en faire un produit simple. Généralement, les composants sont livrés un par un, par un même bras de chargement, au moyen d'un débitmètre et d'une vanne numérique de régulation. Les vannes d'arrêt, qui servent de vannes de sélection de composants, doivent être utilisées pour assurer le chargement du composant approprié dans l'ordre adéquat. Ces vannes peuvent être motorisées (MOV) ou manuelles. Dans les deux cas, un signal de statut de vanne d'arrêt ou de rétroaction peut être employé pour vérifier si les vannes sont dans la bonne position à tout moment du chargement. La séquence de commande du profil des débits utilisée en mélange séquentiel est très similaire à la séquence utilisée pour le chargement d'un produit unique. La séquence se répète pour chaque composant utilisé dans la recette du produit. Le premier composant du mélange passe par plusieurs cycles au travers des phases suivantes : Démarrage du faible débit Haut débit Déclenchement de la 1ère étape Déclenchement de la 2ème étape Déclenchement final Le chargement commence à l'étape de démarrage de faible débit. Lorsqu’on appuie sur le bouton de démarrage, la vanne de régulation s'ouvre et le débit passe de zéro au débit requis pour le démarrage de faible débit. Les électrovannes normalement ouvertes (NO) et normalement fermées (NC) de la vanne numérique de régulation sont tous mises sous tension, provoquant l'ouverture de la vanne de régulation. S'il y a suffisamment de pression, la vitesse du faible débit est atteinte en quelques secondes. Lorsque le débit s'élève à la vitesse de la zone morte de faible débit, l’électrovanne (NC) normalement fermée de la vanne de régulation se coupe. Cette action ferme la vanne dans la position requise pour maintenir la vitesse souhaitée. L'ouverture initiale de la vanne de régulation peut être retardée par le paramètre de retard de démarrage de la pompe et/ou le paramètre de retard de rédémarrage du débit. Le retard optionnel de démarrage de la pompe permet à la pompe d’atteindre le niveau approprié de pression. La vanne de régulation s'ouvre dès que le temps de retard de démarrage de la pompe s’est écoulé, si le paramètre de retard de démarrage du débit est réglé sur zéro. Autrement, l'ouverture de la vanne de régulation sera une nouvelle fois retardée de la période de temps spécifiée par le paramètre de retard de démarrage du débit. Ces paramètres se trouvent au menu Composants. Une fois la vitesse du faible débit atteinte, le module de contrôle du débit effectue des ajustements périodiques à la vanne si le débit dérive au-dessus ou au-dessous du débit de la zone morte à faible débit. Les débits de zone morte sont configurés à l'écran de réglage du compteur. La durée de l'étape de faible débit est définie par le paramètre de volume de démarrage de faible débit. Ce paramètre se trouve sur l'écran d'Installation de réglage des valeurs prédéfinies. Comme le nom de ce paramètre l'indique, la durée de l'étape de démarrage du faible débit est déterminée volumétriquement. Le volume de démarrage du faible débit doit être configuré pour permettre une humidification adéquate du réservoir pour empêcher la formation de charge statique. Lorsque le volume de démarrage de faible débit a été livré, l'étape de haut débit peut commencer. Quand des composants suivants démarrent, le réservoir a déjà été humidifié. Il n’est donc pas nécessaire de rester au débit de démarrage du faible débit aussi longtemps que pour le premier composant. Les composants qui suivent le premier composant commencent à être chargés à la vitesse de démarrage de faible débit jusqu'à livraison du volume indiqué par le paramètre de redémarrage de faible débit. Le débit de produit des composants suivants peut être retardé par le paramètre de retard de démarrage de la pompe et par le paramètre de retard de Chapitre 5 – Contrôle du debit du produit 153 démarrage du débit comme décrit pour le premier composant. Ces paramètres doivent être configurés individuellement pour chaque composant affecté à la valeur prédéfinie (bras de chargement). 5.3.1 CONFIGURATION DU MÉLANGE SÉQUENTIEL La configuration d'un bras de chargement/d'une valeur prédéfinie pour le mélange séquentiel implique la définition d’un certain nombre de paramètres de configuration au niveau des valeurs prédéfinies, compteur et composants. Réglage des Valeurs Prédéfinies (Preset) Configurez la valeur prédéfinie ou le bras de chargement pour le mélange séquentiel en indiquant le nombre de débitmètres affectés à la valeur prédéfinie. En général, pour des mélangeurs séquentiels, on utilise un débitmètre et une vanne de régulation. Il est possible d'utiliser cinq compteurs maximum. On suppose que s’il a plus d'un compteur, il y aura plusieurs sections de comptage indépendantes avec une vanne propre à chaque compteur. Error! Reference source not found. Après avoir établi le nombre de débitmètres affectés à la valeur prédéfinie, indiquez le nombre des composants qui seront livrés par le bras de chargement. Activez le paramètre de mélange séquentiel. Pour plusieurs sections de comptage, le paramètre de mélange proportionnel peut également être activé si certaines recettes utilisent la livraison proportionnelle. Le faible débit et le haut débit sont fixés dans le menu des Poids et Mesures/Valeur Prédéfinie. Les volumes de démarrage et de redémarrage de faible débit sont également spécifiés sur cet écran. Ces paramètres sont introduits pour définir le profil des débits. Paramètre Réglage par défaut Low Flow Start volume 50 gallons Low Flow Restart volume 15 gallons Low Flow Rate 150 gallons par minute High Flow Rate 600 gallons par minute Chapitre 5 – Contrôle du debit du produit 154 Réglage du Compteur La phase suivante de configuration du mélange séquentiel se passe au niveau du compteur sur l’écran de réglage du compteur. PRE #1 MTR #1 SETUP Flow Control Module#: 0 Side-Stream on Mtr# 0 Side-Strm on Any Mtr# DISABLD Meter Address: 0 Meter Type: VOL PUL Max Quad Errors: 10 Reset Quad Errors: 10000 Low Flow Alarm Rate: 10 Low Flow Alarm Time: 10.000 Excess Flw Alrm Rate: 800 Minimum Flow Rate: 50 Maximum Flow Rate: 650 Low Flow DB Rate: 40 High de Flow DB Rate: Introduisez le numéro du Module Contrôle du débit qui recevra l'entrée de 40 débitmètre. Possibilités : de 0 à 31. Le numéro d'un FCM est déterminé par Next l'adresse de communication du module. L'adresse est déterminée par le Prev Exit Enter réglage du micro-interrupteur (DIP) (S1) placé sur le FCM. La position du micro-interrupteur indique un zéro binaire quand il est en position désactivée (OFF) ; un binaire "un" est représenté par un commutateur en position ON (actif). La voie A du signal du débitmètre est toujours sur le port 4 du module de commande du débit sélectionné. Si le signal de la voie B est utilisé pour la sécurité d'impulsion, cette entrée est toujours connectée au port 5. Si la voie B n'est pas utilisée, le port 5 peut être affecté à certaines autres fonctions d'E/S. Le port 2 est automatiquement affecté à l’électrovanne normalement ouvert de la vanne de régulation. Le port 3 est utilisé pour le signal d’électrovanne normalement fermé de la vanne de régulation. Les débits de zone morte pour les étapes de débit sont configurés sur cet écran. Aucun ajustement de vanne ne sera tenté lorsque le débit se trouve en zone morte. Chaque fois que le débit dérive hors zone morte, la vanne effectue des ajustements pour le replacer dans les limites de la zone morte. Si plusieurs compteurs sont affectés à la valeur prédéfinie, recommencez pour tous les autres compteurs. Paramètre Réglage par défaut Flow Control Module # 0 1st Stage Dead Band Rate 40 gallons par minute 2nd Stage Dead Band Rate 40 gallons par minute Chapitre 5 – Contrôle du debit du produit Réglage des Composants Les paramètres de composants relatifs au mélange séquentiel se trouvent dans l’écran de réglage des composants illustré ci-après. Faites défiler l’écran pour voir les champs de paramètres supplémentaires. PRE #1 CMP #1 (Base 001 ) SETUP Meter#: 1 High Flow Rate: 600 1st Stage Trip Volume: 70 1st Stage Flow Rate: 225 2nd Stage Trip Volume: 20 2nd Stage Flow Rate: 150 Final Trip Vol: 1.15 Final Trip Max Time: 5.000 Final Trip Vol Lock: DISABLD Unauth Flow Alrm Vol: 10 W&M Recipe Percentage: %0.00 BlkValve Open Rate: 0 BlkValve Open Delay: 0 Open Alrm Time: 10 on utilise un débitmètre pour Configurez le composant #1.B.V. Affectez le composant au compteur #1. En général, Next Prev Exità unEnter les mélangeurs séquentiels. Si plus d'un compteur est affecté mélangeur, affectez le composant au numéro de compteur approprié. Affectez la sortie qui indique à la vanne d'arrêt de s'ouvrir. Si d'application, affectez un signal de sortie pour forcer la fermeture de la vanne d'arrêt. Un signal optionnel de statut de la vanne d'arrêt peut être configuré. Affectez un point d'entrée pour recevoir le signal de rétroaction. Les signaux d'entrée et de sortie de la vanne d'arrêt peuvent être assignés à n'importe quel port. Pour le FCM I, assurez-vous que le module Opto est approprié au type de tension utilisée. Les temps d'ouverture et de fermeture de la vanne d'arrêt peuvent être configurés. Si le signal approprié de statut de la vanne d'arrêt n'est pas reçu pendant le temps spécifié, le chargement s’arrête pour cause d’erreur de la vanne d'arrêt. L'affectation du port de démarrage de la pompe pour le composant est configurée sur cet écran. De plus, il y a une sortie d'arrêt de la pompe qui peut être attribuée pour fournir un signal de coupure de l'alimentation de la pompe. Il existe également une option pour configurer un signal de statut de la pompe permettant de vérifier le bon fonctionnement de celle-ci. Les signaux d'entrée et de sortie relatifs à la pompe peuvent être affectés à n'importe quel module de contrôle du débit. Les paramètres “1st Stage Trip” et “2nd Stage Trip” sont définis à l’écran “W&M Setup”. Introduisez le volume et le débit définis dans “1st Stage Trip” et “2nd Stage Trip” . 155 Chapitre 5 – Contrôle du debit du produit 156 S’il y a plus d’un composant affecté à la valeur prédéfinie, répétez cette procédure pour les autres composants. Paramètre Réglage par défaut Meter # 1 1st Stage Trip volume 70 gallons 1st Stage Trip Flow Rate 225 gallons par minute 2nd Stage Trip volume 20 gallons 2nd Stage Trip Flow Rate 150 gallons par minute Pump Run FCM# Désactivé Pump Kill FCM# Désactivé Pump Status FCM# Désactivé Block Valve Open FCM# Désactivé Block Valve Close FCM# Désactivé Block Valve Status FCM# Désactivé Pour une description détaillée des paramètres, veuillez vous référer au chapitre consacré aux configurations générales et plus particulièrement au “Réglage des Composants”. Chapitre 5 – Contrôle du debit du produit 5.4 157 MELANGE PROPORTIONNEL (SAUF SMP) Regular T1 P Comp #1 P Comp #2 Premium M1 CV M2 CV T2 Figure 5-4 Application Mélange Proportionnel Pour effectuer un mélange proportionnel, deux à cinq sections de comptage doivent être créées pour livrer chaque composant par un bras de chargement simple. Chaque section de comptage se compose d'un débitmètre et d'une vanne de régulation. Le MultiLoad livre simultanément à chacun des composants de la recette. Le MultiLoad tente de maintenir la proportion totale du mélange dans la fourchette établie par le pourcentage de déviation de l’ajustement du mélange tout au long du chargement. Pendant l'étape de démarrage du faible débit, le débit combiné de toutes les sections de comptage est contrôlé pour maintenir le débit configuré pour le paramètre de la vitesse de démarrage du faible débit. Le faible débit pour chaque composant est déterminé par la proportion de ce composant dans un mélange donné. Par exemple, un mélange à deux composants d’un rapport de 50/50 produit des débits égaux dans les compteurs pendant l'étape de démarrage du faible débit. Le faible débit au travers de chaque compteur équivaut à 50 % de la vitesse de démarrage du faible débit. Le débit résultant de n'importe quel compteur ne peut pas transgresser le taux spécifié dans le paramètre de débit minimal. Le message "Invalid Recipe" (recette non acceptée) s'affiche avant le chargement si cette limite est dépassée. Une valeur de débit minimal du compteur est configurée dans le menu du compteur pour chaque débitmètre affecté à la valeur prédéfinie. Au moment des transitions de chargement vers le haut débit, le débit de chaque compteur utilisé dans le mélange augmente proportionnellement pour atteindre le haut débit. Le débit de chaque compteur est exprimé en pourcentage du haut débit. Le débit provenant de n'importe quel compteur ne peut pas transgresser le taux spécifié dans le paramètre de débit maximal. Le message "Recette Invalide" s'affiche avant de charger si cette limite est transgressée. Une valeur de débit maximal du compteur est configurée dans le menu du compteur pour chaque débitmètre affecté à la valeur prédéfinie. Chaque composant utilisé dans une recette donnée assure la transition vers la phase de déclenchement de la ère ère ère 1 étape lorsqu'il atteint le volume de déclenchement de la 1 étape. Le volume de déclenchement de la 1 étape est configuré dans le menu des composants pour chaque composant affecté à la valeur prédéfinie. Chaque ère composant atteint probablement le volume de déclenchement de la 1 étape à des moments légèrement ère différents. Les débits de chaque compteur descendent au taux indiqué dans le débit de déclenchement de la 1 étape. Le MultiLoad maintient tous les débits proportionnellement les uns par rapport aux autres lorsqu'ils sont ère dans la phase de déclenchement de la 1 étape. Le débit combiné ne dépasse pas le haut débit, mais peut ère dépasser le taux de n'importe quel débit individuel de déclenchement de la 1 étape. ère Après la phase de déclenchement de la 1 étape de chaque composant, celui-ci assure la transition vers la ème ème phase de déclenchement de la 2 étape lorsqu'il atteint le volume de déclenchement de la 2 étape. Le ème volume de déclenchement de la 2 étape est configuré dans le menu des composants pour chaque composant ème assigné à la valeur prédéfinie. Chaque composant atteint probablement le volume de déclenchement de la 2 étape à des moments légèrement différents. Les débits de chaque mètre compteur descendent au taux spécifié ème dans le débit de déclenchement de la 2 étape. Le MultiLoad maintient tous les débits proportionnellement les ème uns par rapport aux autres lorsqu'ils sont dans la phase de déclenchement de la 2 étape. Le débit combiné ne dépasse pas le haut débit, mais il peut dépasser le taux de n'importe quel débit individuel de déclenchement de la ème 2 étape. Quand un composant a accompli ses exigences en matière de chargement, sa vanne de régulation se ferme. Chaque composant termine probablement à des moments légèrement différents. Chapitre 5 – Contrôle du debit du produit 5.4.1 158 CONFIGURATION DU MÉLANGE PROPORTIONNEL Réglage des Valeurs Prédéfinies La configuration de la Valeur Prédéfinie pour le mélange Proportionnel s'effectue sur l'écran de Réglage des Valeurs Prédéfinies, affiché ci-dessous. Configurez la valeur prédéfinie ou le bras de chargement pour le mélange séquentiel en indiquant le nombre de débitmètres affectés à la valeur prédéfinie. En général, pour des mélangeurs proportionnels, on utilise deux sections de comptage. Il est possible d'utiliser cinq sections de comptage maximum. Indiquez le nombre des composants qui seront livrés par le bras de chargement. PRE #1 (Preset 001) SETUP Number of Meters: 1 Number of Components: 1 Number of Additives: 0 Sequential Blending: DISABLD Ratio Blending: ENABLED W&M Controlled: DISABLD Proving Flow Rate: 600 Excess Flw Alrm Rate: 1100 Overrun Alarm Vol: 5 Low Flow Start Vol: 50 Low Flow Restart Vol: 15 Low Flow Rate: 150 High Flow Rate: 600 Proving Low Flow Vol: 50 Activez le paramètre de mélange proportionnel. Le mélange séquentiel peut également être effectué sur le même Next Prev Exit Enter bras de chargement si les vannes (d'arrêt) de sélection de produit sont employées. L'étape suivante consiste à configurer les paramètres de contrôle du mélange. PRE #1 (Preset 001) SETUP Line Flush Vol: 0 Line Flush Min Vol: 0 Line Flush Comp#: 0 Take L.F. from Match: ENABLED Take L.F. from First: DISABLD Take L.F. from Last: DISABLD Alt. High Flow Rate: 600 Stop Start Delay: 0 Blnd Chk Start Vol: 60 Blnd Chk Restart Vol: 10 Blnd Chk Alarm %: %5.00 Blnd Chk Alarm Vol: 25 Blnd Chk Alarm Time: 10 Blnd On Lead Comp: DISABLD Next Prev Exit Enter Chapitre 5 – Contrôle du debit du produit 159 Les paramètres de contrôle du mélange indiquent au contrôleur quand commencer à vérifier la proportion du mélange pour se conformer aux tolérances de la recette. Les volumes de démarrage du contrôle du mélange et de redémarrage du contrôle du mélange sont destinés à empêcher les contrôles pendant des transitions d'étape de débit, comme le démarrage de faible débit. Toptech recommande de définir ces paramètres de façon à empêcher de contrôler le mélange jusqu'à ce que le débit soit stabilisé sur le haut débit. Lorsque ces volumes de transition sont dépassés, le chargement s'arrête si le pourcentage proportionnel chute hors pourcentage d’alarme de contrôle du mélange. La proportion doit être hors tolérance pour la période spécifiée au temps d’alarme de contrôle du mélange. L'alarme peut aussi être activée suite à une erreur volumétrique plutôt qu'une erreur de pourcentage à l’aide du paramètre de volume d’alarme de contrôle du mélange. Paramètre Réglage par défaut Blend Check Start Volume 60 gallons Blend Check Restart Volume 10 gallons Blend Check Alarm % 5% Blend Check Alarm Volume 25 gallons Blend Check Alarm Time 10 secondes Les prochains paramètres à configurer sont les paramètres d’ajustement de mélange. Sur base des contrôles du mélange, les ajustements de mélange s’effectuent en fonction de la configuration de ces paramètres. Le contrôleur essaie toujours de maintenir le mélange dans le pourcentage dicté par le pourcentage de déviation d’ajustement du mélange. Aucune tentative d’ajustement n’a lieu tant que les volumes de démarrage ou de redémarrage de l’ajustement du mélange ne sont pas passés. Le pourcentage de déviation de l’ajustement du mélange ou le volume de déviation de l’ajustement du mélange doit être dépassé pour la période spécifiée par le temps d’ajustement avant de procéder à un ajustement. Les volumes de démarrage et de redémarrage d’ajustement du mélange doivent être définis à des valeurs inférieures aux valeurs définies, respectivement pour les volumes de démarrage et de redémarrage de contrôle du mélange. Paramètre Réglage par défaut Blend Adjust Start Volume 60 gallons Blend Adjust Restart Volume 10 gallons Blend Adjust Deviation % 1% Blend Adjust Deviation Volume 5 gallons Blend Adjust Time 5 secondes Pour des descriptions détaillées des paramètres, se référer au chapitre Configuration, sujet “Réglage des Valeurs Prédéfinies”. Chapitre 5 – Contrôle du debit du produit 160 Réglage du Compteur Il faut configurer les paramètres du compteur pour chaque débitmètre. Sélectionnez la valeur prédéfinie et le compteur appropriés. Sur l'écran de réglage du compteur, introduisez le numéro du module de contrôle du débit qui reçoit l'entrée du débitmètre. Les entrées acceptées sont comprises entre 0 et 31. Le numéro du FCM est déterminé par l'adresse de communication du module. L'adresse est définie par le réglage du micro-interrupteur (DIP) (S1) placé sur le FCM. La position du micro-interrupteur indique un zéro binaire quand il est en position désactivée (OFF) ; un binaire "un" est représenté par un commutateur en position ON (actif). La voie A du signal du débitmètre est toujours sur le port 4 du module de contrôle du débit sélectionné. Si le signal de la voie B est utilisé pour la sécurité d'impulsion, cette entrée est toujours connectée au port 5. Si la voie B n'est pas utilisée, le port 5 peut être affecté à certaines autres fonctions d'E/S. Le port 2 est automatiquement affecté à l’électrovanne normalement ouverte de la vanne de régulation. Le port 3 est utilisé pour le signal d’électrovanne en aval de la vanne de régulation. PRE #1 MTR #1 SETUP Flow Control Module#: 0 Side-Stream on Mtr# 0 Side-Strm on Any Mtr# DISABLD Meter Address: 0 Meter Type: VOL PUL Max Quad Errors: 10 Reset Quad Errors: 10000 Low Flow Alarm Rate: 10 Low Flow Alarm Time: 10.000 Excess Flw Alrm Rate: 800 Minimum Flow Rate: 50 Maximum Flow Rate: 650 Low Flow DB Rate: 40 High 40de réglage du compteur. Aucun Les débits de zone morte pour lesFlow étapesDBdeRate: débit sont configurés sur l'écran ajustement de vanne ne peut être tenté lorsque le débit se trouve en zone morte. A chaque fois que le débit Next Prev Exit Enter dérive hors zone morte, la vanne effectue des ajustements pour replacer le débit dans les limites de la zone morte. Si plusieurs compteurs sont affectés à la valeur prédéfinie, répétez ce processus pour tous les autres compteurs. On retrouve deux paramètres proportionnels-séquentiels complémentaires à l'écran de réglage du compteur. Le facteur proportionnel de correction par ratio et celui de correction par ratio sont configurés en usine. Ces paramètres ne peuvent pas être ajustés sans consulter Toptech Systems. Paramètre Réglage par défaut Flow Control Module # 0 1st Stage Dead Band Rate 40 gallons par minute 2nd Stage Dead Band Rate 40 gallons par minute Chapitre 5 – Contrôle du debit du produit 161 Réglage des Composants Pour le mélange proportionnel, chaque composant doit avoir son compteur. Attribuez le composant #1 au compteur #1. Attribuez le composant #2 au compteur #2, et ainsi de suite. Error! Reference source not found. L'affectation du port de démarrage de la pompe pour le composant est également configurée sur cet écran. De plus, il y a une sortie de suppression de la pompe qui peut être affectée pour fournir un signal de coupure de l'alimentation de la pompe. Il existe également une option pour configurer un signal de statut de la pompe pour en vérifier le bon fonctionnement. Les signaux d'entrée et de sortie relatifs à la pompe peuvent être affectés à n'importe quel module de contrôle du débit. Les paramètres 1st Stage Trip et 2nd Stage Trip sont également définis sur ce écran. Introduisez le volume et le ère nde débit définis dans le déclenchement de 1 et 2 étapes. Paramètre Réglage par défaut 1st Stage Trip Volume 70 gallons 1st Stage Trip Flow Rate 225 gallons par minute 2nd Stage Trip Volume 20 gallons 2nd Stage Trip Flow Rate 150 gallons par minute Pump Run FCM# Désactivé Pump Kill FCM# Désactivé Pump Status FCM# Désactivé Pour de plus amples renseignements sur les paramètres, veuillez vous référer à la configuration générale et plus particulièrement au chapitre consacré au réglage des composants - “Component Setup.” Chapitre 5 – Contrôle du debit du produit 162 MÉLANGE À FLUX LATÉRAL – SIDE STREAM (SAUF SMP) 5.5 Regular T1 P Comp #1 Ethanol M1 CV T2 P Comp #2 Figure 5-5 M2 CV Application Flux Latéral Simple Le mélange à flux latéral est similaire au mélange proportionnel en ce sens que deux ou plusieurs composants sont livrés simultanément pour terminer un mélange. Chaque composant incorpore sa propre vanne de régulation et son propre débitmètre. Dans une configuration à flux latéral, un(des) composant(s) mineur(s) est(sont) injecté(s) en amont du débitmètre du composant majeur (compteur primaire). Le débit dans le compteur primaire s'écoule à la vitesse dictée par le paramètre de haut débit au niveau de la valeur prédéfinie. Le débit du composant à flux latéral suit à la trace le débit du compteur primaire. Le flux latéral cherche à maintenir ce débit sur une proportion préprogrammée du débit commandée par la vanne ou le compteur primaire. Le compteur primaire mesure les composants principaux et mineurs mélangés. 5.5.1 CONFIGURATION DU MÉLANGEUR À FLUX LATÉRAL SIMPLE Pour configurer un bras de chargement en mélangeur à flux latéral, commencez au niveau de la valeur prédéfinie. A ce niveau, définissez le nombre de débitmètres et de composants (liquides) qui seront livrés par le bras de chargement. Un maximum de cinq débitmètres et de huit composants peuvent être affectés à un même bras de chargement. Activez le paramètre de mélange proportionnel au niveau de la valeur prédéfinie. Pour la configuration au niveau du compteur, les valeurs par défaut sont généralement utilisées pour le compteur primaire (Compteur 1). En configurant les paramètres pour le Compteur 2, introduisez une valeur au paramètre Meter# activé flux latéral. En introduisant une valeur de "1" pour ce paramètre, le Compteur 2 est désigné comme flux latéral du compteur 1. Il sera probablement nécessaire d'ajuster les débits et la zone morte du compteur 2, puisque le compteur de flux latéral est généralement plus petit que le compteur de flux primaire. Référez-vous au tableau pour les réglages suggérés. Les paramètres des débits maximum et minimum pour le compteur 2 devront également être ajustés pour répondre aux spécifications du fabricant de débitmètres. Pour la configuration au niveau du composant, les composants sont affectés à un compteur particulier, au moyen du paramètre Meter#. En se référant au schéma de la Figure 5.2, le composant 1 est affecté au compteur 1 et le composant 2 au compteur 2. Chapitre 5 – Contrôle du debit du produit 163 Valeur Prédéfinie Compteur (Compteur 2) Composants 1 & 2 Paramètre d'Affectation du “Meter#” au Composant-àCompteu" Nombre de Compteurs : 2 Flux latéral sur le Compteur # =1 Composant 1 : Compteur# = 1 Nombre de Composants : 2 Vitesse ZM Faible débit 10 gpm Composant 2 : Compteur# = 2 Mélange Proport. : activé Vitesse ZM haut débit 10 gpm Mélange Séq. : désactivé Débit ZM 1 ère Débit ZM 2 ème étape 10 gpm étape 10 gpm Débit Minimum 5 gpm Débit Maximum 100 gpm Poids et Mesures - Compteurs Débit Minimum 5 gpm Débit Maximum 100 gpm Figure 5-6 Configuration Flux Latéral Simple Chapitre 5 – Contrôle du debit du produit 5.6 164 MELANGE HYBRIDE (SAUF SMP) L’architecture du MultiLoad permet des schémas de mélange hybrides où il peut y avoir plusieurs flux latéraux ou plusieurs composants importants passant par le flux primaire. 5.6.1 FLUX LATÉRAUX MULTIPLES Puisqu'il est possible d'affecter cinq débitmètres à un bras de chargement, on peut avoir plusieurs débits latéraux servant un compteur primaire. Pour ce faire, il faut désigner des compteurs comme compteurs de flux latéraux lors de la configuration au niveau du compteur. T1 P Comp #1 M1 CV T2 P Comp #2 M2 CV T3 P Comp #3 M3 CV Figure 5-7 Application Flux Latéral Multiple Chapitre 5 – Contrôle du debit du produit 165 Le tableau qui suit identifie les paramètres de configuration nécessaires pour le schéma de la Figure 5.3. Le Compteur#2 et le Compteur#3 sont désignés comme compteurs de débit latéraux du compteur#1. Quatre compteurs de débit latéraux peuvent potentiellement être affectés à ce bras de chargement. Valeur Prédéfinie Compteur (Compteur #2) Compteur (Compteur #3) Composants 1-3 Paramètre d'Affectation du “Compteur#” au "Composant-à-Compteur" Nombre de Compteur : 3 Flux latéral sur le Compteur # = 1 Flux latéral sur le Compteur # = 1 Composant 1 : Compteur #=1 Nombre Composants : 3 de Vitesse ZM débit 10 gpm Faible Vitesse ZM Faible débit 10 gpm Composant 2 : Compteur #=2 Composant 3 : Compteur #=3 Mélange activé Proport. : Vitesse ZM débit 10 gpm haut Vitesse ZM débit 10 gpm haut Mélange désactivé Séq. : Débit ZM 1 10 gpm ère étape Débit ZM 1 10 gpm ère étape ème étape Débit ZM 2 10 gpm ème étape Débit ZM 2 10 gpm Débit gpm Minimum 5 Débit Maximum 100 gpm Débit gpm Minimum Débit Maximum 100 gpm Poids et Mesures Compteur #2 Poids et Mesures Compteur #3 Débit Minimum 5 gpm Débit Minimum 5 gpm Débit Maximum 100 gpm Débit Maximum 100 gpm Figure 5-8 5 Configuration Flux Latéraux Multiples Chapitre 5 – Contrôle du debit du produit 5.6.2 166 MÉLANGE SÉQUENTIEL À FLUX LATÉRAL Le mélange séquentiel avec un composant à flux latéral est un schéma de mélange hybride. Comme chaque composant est livré à tour de rôle par le flux primaire, un composant mineur sera mélangé dans le flux primaire, en amont du débitmètre primaire. Regular P Comp #1 BV T1 M1 Premium P CV Comp #2 BV Ethanol T2 P Comp #3 Figure 5-9 M2 CV Application Mélange Séquentiel avec Flux Latéraux Au niveau de la valeur prédéfinie, définissez le nombre de débitmètres et de composants (liquides) livrés au bras de chargement. Dans cet exemple, il y a deux débitmètres et trois composants. Activez les paramètres de mélange proportionnel de mélange séquentiel au niveau de la valeur prédéfinie. Pour la configuration au niveau du compteur, les valeurs par défaut sont généralement utilisées pour le compteur primaire (Compteur 1). En configurant les paramètres pour le Compteur 2, introduisez une valeur au paramètre Compteur# Activé Flux latéral. En introduisant une valeur de "1" pour ce paramètre, le Compteur 2 est désigné comme flux latéral du compteur 1. Il faudra probablement ajuster les débits de zone morte du compteur 2, puisque le compteur à flux latéral est généralement plus petit que le compteur de flux primaire. Référez-vous au tableau pour les réglages suggérés. Les paramètres des débits maximum et minimum pour le Compteur 2 devront également être ajustés pour répondre aux spécifications du fabricant de débitmètres. Pour la configuration au niveau du composant, les composants sont affectés à un compteur particulier, au moyen du paramètre Compteur#. En se référant au schéma de la Figure 5.4, le Composant 1 et le Composant 2 sont affectés au Compteur 1 et le Composant 3 au Compteur 2. Chapitre 5 – Contrôle du debit du produit 167 Valeur Prédéfinie Compteur (Compteur 2) Composants 1-3 Paramètre d'Affectation du “Compteur#” au "Composant-àCompteur" Nombre de Compteurs : 2 Flux latéral sur le Compteur # = 1 Composant 1 : Compteur # = 1 Nombre de Composants : 2 Vitesse ZM Faible débit 10 gpm Composant 2 : Compteur # = 1 Mélange Proport. : Activé Vitesse ZM haut débit 10 gpm Composant 3 : Compteur # = 2 Mélange Séq. : Activé Débit ZM 1 ère Débit ZM 2 ème étape 10 gpm étape 10 gpm Poids et Mesures - Compteur #2 Débit Minimum 5 gpm Débit Maximum 100 gpm Figure 5-10 Configuration de Mélange Séquentiel avec Flux Latéraux Au niveau composant, les affectations E/S peuvent être introduites pour les pompes de produit et les vannes de sélection de produits (vannes d’arrêt), etc. Chapitre 5 – Contrôle du debit du produit 5.6.3 168 MÉLANGE PROPORTIONNEL À FLUX LATÉRAL Des compteurs de flux latéraux peuvent être ajoutés aux sections de comptage d'un bras de chargement de mélange proportionnel. Un flux latéral peut être configuré pour servir un des flux primaires d'un bras de chargement proportionnel. Un flux latéral peut être configuré pour servir plusieurs flux d'un bras de chargement proportionnel. De multiples flux latéraux peuvent être affectés à un bras de mélange proportionnel. Jusqu'à cinq débitmètres peuvent être affectés à un bras de chargement, indépendamment de la fonction du compteur (compteur de flux latéral ou primaire). Regular T1 P M1 CV M2 CV BV Comp #1 Premium T2 P BV Comp #2 Ethanol T3 P C #3 Figure 5-11 M3 CV Application Mélange Proportionnel à Flux Latéral L'exemple montre un compteur de flux latéral servant deux composants primaires d'un mélangeur proportionnel. Le compteur de flux latéral ne s'écoule que dans un flux primaire pendant un lot donné. Au cas où deux flux primaires sont utilisés dans un mélange, le compteur de flux latéral ne continue à s'écouler que par un seul flux primaire. Au niveau de la valeur prédéfinie, définissez le nombre de débitmètres et de composants (liquides) livrés au bras de chargement. Dans cet exemple, il y a trois débitmètres et trois composants. Activez le paramètre de mélange proportionnel au niveau de la valeur prédéfinie. Pour la configuration au niveau du compteur, les valeurs par défaut sont généralement utilisées pour les compteurs primaires (Compteur 1 et Compteur 2). En configurant les paramètres pour le Compteur 3, introduisez une valeur au paramètre « Side-Stream On Meter# ». En entrant une valeur de "1" pour ce paramètre, le Compteur 3 est désigné comme flux latéral du compteur 1. S'il est nécessaire de passer par d'un flux primaire, activez également le paramètre "Side-Stream on Any Meter » (flux latéral sur n'importe quel compteur) depuis la configuration du compteur 3. Cela permet au compteur de flux latéral de s'écouler par un autre flux primaire si le Compteur 1 ne sert pas dans le mélange. Le compteur de flux latéral s'échappe en principe toujours par le compteur 1 lorsque celui-ci est utilisé dans un mélange vu les réglages du paramètre de Compteur # de flux latéral activé (Side-Stream On Meter#). Il faudra probablement ajuster les débits de zone morte du compteur 3, puisque le compteur de flux latéral est généralement plus petit que les compteurs de débit primaire. Référez-vous au tableau pour les réglages suggérés. Les paramètres des débits maximum et minimum pour le compteur 3 devront également être ajustés pour répondre aux spécifications du fabricant de débitmètres. Chapitre 5 – Contrôle du debit du produit 169 Pour la configuration au niveau du composant, les composants sont affectés à un compteur particulier, au moyen du paramètre Meter #. En se référant au schéma de la Figure 5.5, le Composant 1 est affecté au Compteur 1, le Composant 2 est affecté au Compteur 2 et le Composant 3 au Compteur 3. Valeur Prédéfinie Compteur (Compteur 3) Composants 1-3 Paramètre d'Affectation du “Compteur#” au "Composant-àCompteur" Nombre de Compteurs : 3 Flux latéral sur le Compteur # = 1 Composant 1 : Compteur # = 1 Nombre de Composants : 3 Flux latéral sur n'importe quel Compteur : Activé Composant 2 : Compteur # = 2 Mélange Proport. : Activé Vitesse ZM Faible débit 10 gpm Composant 3 : Compteur # = 3 Mélange Séq. : Désactivé Vitesse ZM haut débit 10 gpm Débit ZM 1 ère étape 10 gpm Débit ZM 2 ème étape 10 gpm Poids et Mesures – Compteur 3 Débit minimum 5 gpm Débit maximum 100 gpm Figure 5-12 Configuration Mélange Proportionnel à Flux Latéral Au niveau des composants, les affectations d'E/S peuvent être effectuées pour les pompes de produits, etc. Les vannes de sélection de produits (BV) utilisées dans cet exemple ne sont toutefois pas configurées à la section "Composants". Elles fonctionnent selon un sous-programme sur mesure de l’utilisateur. Le sous-programme ciaprès peut être utilisé pour diriger le composant de flux latéral dans le débit du compteur 2, lorsque le Compteur 1 n'est pas utilisé dans un mélange. La logique personnalisée est configurée à partir du menu Configuration/Custom Logic. Les lignes 000 à 005 commandent l'ouverture de la BV, lorsque le compteur 1/composant 1 est utilisé dans le mélange. Si les deux compteurs (1 et 2) sont utilisés pour faire un mélange, le flux latéral se règle par défaut sur le compteur 1. Les lignes 006 à 011 commandent l'ouverture de BV2 lorsque le compteur 1/composant 1 n'est pas utilisé dans un mélange. 000 P01 M03 Side-Stream on Mtr 001 Set Value = 1 002 [000] Equals [001] 003 P01 C03 Open BV 004 [002] AND [003] 005 FCM OUTPUT XX.Y = [004] 006 P01 M03 Side-Stream on Mtr 007 Set Value = 2 008 [006] Equals [007] 009 P01 C03 Open BV 010 [008] AND [009] 011 FCM OUTPUT XX.Y = [010] Remarque: XX = FCM#, Y = FCM port#, P01 = valeur prédéfinie #1, M03 = compteur #3, C03 = composant #3 Chapitre 5 – Contrôle du debit du produit 5.7 TEST DES COMPTEURS A FLUX LATERAL (SAUF SMP) On suppose que les raccordements d'essai sont utilisés pour ponter le compteur primaire et la vanne de façon à ce que le liquide s'écoule par le compteur à flux latéral dans un caisson d'étalonnage. Avant de tester un compteur de flux latéral, effectuez les modifications de configuration suivantes : Pour les versions du logiciel antérieures à 3.28.21 : 1. Entrez dans le Mode de Programme 2. Allez au menu Configuration/Equipment Setup/Meter. Sélectionnez la valeur prédéfinie appropriée. 3. Sélectionnez le compteur du flux latéral approprié. Il s'agit, en général, du compteur 2. 4. Recherchez le paramètre “Side-Stream on MTR# ” (flux latéral sur compteur #). Changez ce paramètre et mettez-le sur 0. 5. Sortez du mode de programme en appuyant sur la touche EXIT six fois. 6. Entamez la procédure d’essai. 7. A la fin de la procédure, retournez au mode de programme et redéfinissez le paramètre du flux latéral sur Meter # aux réglages d'origine. La valeur est généralement de 1. Pour les versions du logiciel à partir de 3.28.21 : Les changements de configuration ci-avant ne sont pas nécessaires pour autant que l’hôte ait indiqué qu’il s’agit d’un test de transaction ou que le mode test compteur a été activé dans Configuration - > RCU Setup. 170 Chapitre 5 – Contrôle du debit du produit 5.8 171 PURGE DE CONDUITE (SAUF SMP) Les bras de chargement qui manipulent des composants multiples ont souvent besoin de préparer la conduite avec un composant spécifique à la fin du chargement. Si la conduite n'est pas purgée à la fin d'un chargement, la section du tuyau entre le débitmètre et l'extrémité du bras de chargement contiendra le dernier composant livré, ce qui peut ne pas convenir au chargement suivant. La fonction de purge de conduite est conçue pour préparer la conduite avec le composant choisi à la fin de chaque chargement. Ce composant choisi est appelé « Line flush Component » - En français : Composant de Purge de Conduite. La première étape dans la purge de conduite consiste à déterminer le volume de liquide contenu entre la fin du débitmètre et la fin du bras de chargement. Le MultiLoad retire ce volume de la quantité prédéfinie et arrête le chargement d'un composant non purgeant lorsque la quantité restante est égale au volume de purge de conduite. Le composant de la purge de conduite se mesure alors pour correspondre à la quantité prédéfinie. Ensuite, il reste dans la section de la conduite au-delà du débitmètre. Le composant de la purge de conduite n'est pas livré pendant le chargement dans lequel il a été mesuré mais lors d'un chargement ultérieur. En effet, il s’agit du premier produit mis dans le camion, mais il n'est pas mesuré comme faisant partie du chargement avant l'étape de purge de conduite à la fin du chargement. La seconde étape décide du volume minimum de la purge de conduite. Ce paramètre est destiné à éviter des alarmes intempestives si le volume réellement purgé dans un chargement n'est pas exactement égal au volume de la purge de conduite. La valeur du volume minimum de la purge de conduite doit être inférieure au volume de la purge de conduite mais doit représenter un volume de purge acceptable. La valeur du volume minimum de la purge de conduite s’affiche à l'écran de statut pendant le chargement puisque lors de la purge, la valeur va descendre à zéro. Si une purge ne répond pas au volume minimum, une alarme de purge de conduite se déclenche. La quantité du volume de purge nécessaire pour correspondre au volume minimum de purge de conduite s'affiche. Cette information aide le personnel du site à décider de l'action corrective opportune. La dernière étape consiste à identifier le composant pour purger la conduite à la fin de chaque chargement. Introduisez une valeur numérique représentant le composant de purge dans le paramètre du Component # de la purge de conduite. Les paramètres dont question dans cette section, se retrouvent à l'écran de Réglage des Valeurs Prédéfinies représenté ci-après : PRE #1 (Preset 001) SETUP Line Flush Vol: 0 Line Flush Min Vol: 0 Line Flush Comp#: 0 Take L.F. from Match: ENABLED Take L.F. from First: DISABLD Take L.F. from Last: DISABLD Alf. High Delay: 0 Stop Start Delay: 0 Blnd Chk Start Vol: 60 Blnd Chk Restart Vol: 10 Blnd Chk Alarm %: %5.00 Blnd Chk Alarm Vol: 25 Blnd Chk Alarm Time: 10 Blnd On Lead Comp: DISABLD Next Prev Exit Enter Chaque fois que le composant de purge est livré en dehors d'une étape de purge, la purge minimale requise à l'écran de statut revient à zéro, puisque le volume minimum de purge de conduite est terminé. Ce registre monte immédiatement à la valeur de volume minimum de purge de conduite dès qu’un composant non-purgé est lancé dans la conduite. Prenons l'exemple d'un mélange séquentiel où le composant #1 est le composant de purge mais le chargement est interrompu en cours de livraison; ni le composant #2 ni la purge ne sont livrés. Bien que Chapitre 5 – Contrôle du debit du produit 172 techniquement, la purge n’ait pas eu lieu, la fonction de purge ne produit pas d’alarme puisqu'elle sait que la conduite est remplie de composant #1 qui s'avère être le composant de purge. L'alarme ne s'active pas à condition que la purge minimale requise soit présente pendant le chargement du composant #1. Pour désactiver la fonction de purge de conduite, mettez à zéro les valeurs des trois premiers paramètres du tableau ci-dessous. Les autres paramètres de purge sont associés au mélange. Paramètre Réglage par défaut Emplacement de l’écran Line Flush volume 0 gallon Réglage des prédéfinies valeurs Line Flush Minimum volume 0 gallon Réglage des prédéfinies valeurs Line Flush Component # 0 (aucun composant sélectionné) Réglage des prédéfinies valeurs Take Line Flush From Match Activé Réglage des prédéfinies valeurs Take Line Flush From First Désactivé Réglage des prédéfinies valeurs Take Line Flush From Last Désactivé Réglage des prédéfinies valeurs Purge de Conduite et Mélange En mélangeant des composants multiples dans un bras de chargement, un des composants de produit doit être diminué d’un volume égal au volume de purge de conduite. Il y a trois paramètres de purge de conduite qui peuvent être configurés pour déterminer le composant qui sera diminué. Le MultiLoad II considére chaque paramètre dans l'ordre où il apparaît dans le tableau ci-dessus. Si les conditions du premier paramètre ne parviennent pas à déterminer quel paramètre diminuer, le paramètre suivant est pris en compte, et ainsi de suite. Le premier paramètre de décision est « Take Line flush From Match » (Effectuer Purge de Conduite Depuis le Composant Correspondant). Ce paramètre, s'il est activé, charge le MultiLoad de déterminer si le composant de purge est utilisé dans le produit. Si tel est le cas, il diminue ce composant de la quantité du volume de purge de conduite. Le déficit s’ajuste au cours de la purge de conduite. Si le composant de purge n'est pas utilisé dans la recette de produit ou si le paramètre est désactivé, le MultiLoad se base sur le paramètre suivant. Le deuxième paramètre de décision est « Take Line Flush From First » (Effectuer Purge de Conduite Depuis le Premier Composant). Cette décision est prise en compte si le paramètre précédent est désactivé ou si la décision précédente n'a pas été appliquée. Si ce paramètre est activé, le MultiLoad diminue le premier composant dans la recette; le premier composant est diminué du volume de purge de conduite. Si ce paramètre est désactivé, le MultiLoad compte sur le troisième paramètre de décision. Le troisième paramètre de décision est « Take Line Flush From Last » (Effectuer Purge de Conduite Depuis le Dernier Composant). Ce paramètre doit être activé si les deux paramètres précédents sont désactivés. Le MultiLoad retire le volume de purge de conduite du dernier composant dans la recette. La quantité prédéfinie correspond au composant de purge de conduite dans l'étape de purge de conduite. Chapitre 5 – Contrôle du debit du produit 173 Exemple Le tableau suivant montre comment un chargement de 1000 gallons est influencé par chacun des paramètres de décision. Le produit est un mélange 60/40. Le composant #1 représente 60 % du total et le composant #2, 40 % du total. Le composant de purge de conduite est le composant #1. Le volume de purge de conduite est de 100 gallons. Composant # Proportion désirée Quantité livrée Option de Purge 1 600 500 Effectuer Purge depuis le Composant Correspondant 2 400 400 Exemple 1 Purge Total Prédéfini 100 1000 1000 1 600 500 2 400 400 Le Composant de Purge de Conduite est le composant #1 Exemple 2 Purge Total Prédéfini 100 1000 1000 1 600 600 2 400 300 Effectuer Purge depuis le Premier Composant Le Composant de Purge de Conduite est le composant #1 Exemple 3 Purge Total Prédéfini 100 1000 Effectuer Purge depuis le Dernier Composant Le Composant de Purge de Conduite est le composant #1 1000 Dans l'exemple 1, l'utilisation de "Effectuer la Purge de Conduite depuis le Composant Correspondant" aboutit à un mélange de 60/40. Le premier composant diminue de 100 gallons mais est ajusté à la fin du chargement puisque le premier composant est également le composant de purge. L'exemple 2 produit des résultats identiques. Le MultiLoad réduit le premier composant dans la recette de produit. Il arrive que ce premier composant soit le composant de purge. Dans l'exemple 3, en exécutant "Effectuer la Purge de Conduite depuis le Dernier Composant", la proportion résultante de produit est de 70/30. Le dernier composant (le composant #2) est réduit de 100 gallons et la quantité prédéfinie est atteinte par le composant de purge, le composant #1. Le résultat désiré de 60/40 aurait été atteint dans ce cas si le composant #2 avait été désigné comme Composant de Purge de Conduite. Chapitre 5 – Contrôle du debit du produit 5.9 REMARQUES CONCERNANT LE MELANGE PROPORTIONNEL (SAUF SMP) Lors d'un mélange proportionnel, tous les composants de la recette du produit s'écoulent simultanément. A chaque mélange proportionnel, une condition de purge apparaît à l'écran de statut, puisqu'il y a un mélange de composants dans la conduite. Avant d’entamer un chargement de mélange proportionnel, l'algorithme décide quel composant doit être réduit. Lorsque la quantité prédéfinie restante est égale au volume de purge de conduite, le débit de tous les composants mélangés s'arrête. Commence alors l'étape de purge où seul le composant de purge de conduite s'écoule. Tous les composants qui ne sont pas des composants de purge dans la recette de produit doivent avoir livré leurs volumes exigés à ce moment-là. Lorsque les mélanges sont interrompus avant que la purge n’ait lieu ou que le volume minimum de purge de conduite n'ait été livré, l'alarme de purge de conduite se déclenche. Le volume d'erreur de purge s'affiche à l'écran de statut. Si la purge participe au mélange proportionnel, le réglage du % d’alarme de contrôle du mélange peut empêcher le chargement d'une certaine quantité parce que l'on a forcé le mélange à se trouver temporairement hors spécification avant d’entamer la phase de purge. Cette décision se prend avant d’entamer le chargement. 174 Chapitre 5 – Contrôle du debit du produit 175 Exemple Le pourcentage d’alarme de contrôle du mélange est défini à 5 % et une valeur prédéfinie de 1000 gallons est sélectionnée pour un chargement à 60/40 dans lequel le composant #2 est le composant de purge. Le volume de purge est de 100 gallons. Les 600 gallons du composant #1 doivent être complètement livrés au moment où la purge des 100 derniers gallons commence. Lorsque le débit s'arrête pour commencer la phase de purge et avant d’entamer la purge, la proportion sera de 600/300, ce qui provoque une erreur de 6.7 % jusqu'à ce que la purge commence. Le chargement s'arrête parce que la spécification du mélange n’a pas été respectée. Pour livrer des chargements de 1000 gallons dans ce cas, le réglage du pourcentage d’alarme de contrôle du mélange doit être relâché à 7 %. Veuillez vous référer à la section concernant le mélange proportionnel, dans ce chapitre, pour les détails de configuration. La fonction de purge pour charger un produit simple à partir d'une valeur prédéfinie de mélange proportionnel fonctionne de la même façon que lorsque le chargement est dirigé par une recette séquentielle. Le tableau suivant montre comment un chargement de 1000 gallons est influencé par chacun des paramètres de décision. Le composant #1 représente 60 % du total et le composant #2, 40 % du total. Le composant de purge de conduite est le composant #2. Le volume de purge de conduite est de 100 gallons. Livraison de purges de conduite pour diverses options de purges de conduite – Mélange proportionnel Composant # Proportion désirée Quantité livrée Option de purge 1 600 600 Take Flush from Matching Component 2 400 300 Exemple 1 Purge (flush) Total prédéfini 100 1000 1000 1 600 500 2 400 400 Flush component #2 Exemple 2 Purge Total prédéfini 100 1000 1000 1 600 600 2 400 300 Take Flush From First Component Flush component #2 Exemple 3 Purge Total prédéfini 100 1000 Take Flush From Last Component Flush component #2 1000 Dans l'exemple 2, en exécutant " Take Flush From First Component " (exécuter la purge à partir du premier composant), la proportion résultante de produit est de 50/50, puisque le composant non-purgeant a été réduit (le component #1). Dans ce cas, le résultat désiré de 60/40 aurait été atteint si le composant #1 avait été désigné comme composant de purge de conduite. Chapitre 5 – Contrôle du debit du produit 5.10 176 ETALONNAGE PAR LINEARISATION DU COEFFICIENT DE MESURE Les facteurs de mesure sont fixés pendant les essais du débitmètre en comparant le volume observé au volume indiqué à l'écran du MultiLoad II. Etant donné que le MultiLoad II accumule les impulsions d'un débitmètre, il les divise par le coefficient K pour obtenir un volume de stock brut. Les facteurs de mesure sont utilisés pour le volume de stock brut pour que le volume indiqué à l'écran du MultiLoad II corresponde au volume observé pendant les essais du débitmètre. Les facteurs de mesure peuvent varier significativement à des débits différents. C’est pourquoi les facteurs de mesure sont fixés pour deux ou plusieurs débits pour améliorer la précision d’une série de débits. La linéarisation du coefficient de mesure permet au MultiLoad II d'interpoler un coefficient de mesure lorsque le produit s'écoule entre deux débits aux facteurs de mesure bien établis. Lorsque le produit est livré, le coefficient de mesure est continuellement appliqué au volume de stock brut pour afficher le volume brut. Le coefficient de mesure qui est appliqué au volume de stock brut change lorsque le débit varie entre deux débits établis. MF#4 M e t e MF#1 r F a c t o r MF#3 MF#2 MFR#1 MFR#2 MFR#3 Meter Factor (Flow) Rate Figure 5-13 Linéarisation du Coefficient de mesure MFR#4 Chapitre 5 – Contrôle du debit du produit 177 Configuration du Coefficient de mesure Les facteurs de mesure sont accessibles dans le mode de Programme depuis le menu Configuration > Equipment Setup ci-dessous. Si des composants multiples sont livrés par un même compteur, les facteurs de mesure doivent être fixés pour chaque composant. C’est particulièrement important si les caractéristiques physiques des composants, comme la densité et la viscosité, sont sujettes à d'importantes variations. Les facteurs de mesure et débits des facteurs de mesure sont les champs de paramètres qui seront introduits. Ces champs sont protégés par les "Poids et Mesures". Quand on introduit les valeurs à l’aide du clavier MultiLoad II, il faut d’abord activer le commutateur des poids et mesures pour pouvoir changer cette valeur. A partir du menu Configuration->Equipment Setup, sélectionnez « Components ». EQUIPMENT SETUP MENU Bay Preset Meters Components Additives L’écran de réglage des composants s’affiche: Next Prev Exit Enter PRE #1 CMP #1 (Base 001 Meter Factor #1: Meter Factor #1 Rate: Meter Factor #2: Meter Factor #2 Rate: Meter Factor #3: Meter Factor #3 Rate: Meter Factor #4: Meter Factor #4 Rate: # Meter Factors Used: Next Prev Exit ) SETUP 1.0000 150 1.0000 200 1.0000 400 1.0000 800 4 Enter Si deux débits de coefficient de mesure doivent être fixés, le débit le plus bas doit être le débit du coefficient de mesure#1. Introduisez "Meter Factor #1" dans le champ approprié. Introduisez le débit utilisé pour déterminer le coefficient de mesure dans le champ "Meter Factor#1 Rate". En s'écoulant entre zéro et le débit du coefficient de mesure#1, le coefficient de mesure#1 s'applique au volume de stock brut. Le second coefficient de mesure doit être introduit dans le champ "Meter Factor#2". Introduisez le débit utilisé pour déterminer le coefficient de mesure dans le champ "Meter Factor #2 Rate". En s'écoulant entre le débit du Chapitre 5 – Contrôle du debit du produit coefficient de mesure#1 et le débit du coefficient de mesure#2, un coefficient de mesure interpolé sera appliqué au volume de stock brut. Le coefficient de mesure interpolé est une valeur qui se trouve quelque part entre le débit du coefficient de mesure #1 et le débit du coefficient de mesure #2. Si le débit est supérieur au débit du coefficient de mesure #*2, le coefficient de mesure qui est appliqué au volume de stock brut est compris entre le coefficient de mesure#2 et le coefficient de mesure#3. Si le coefficient de mesure#3 est fixé, assurez-vous que le débit du coefficient de mesure#3 est supérieur au débit du coefficient de mesure#2. Si aucun coefficient de mesure n'a été fixé pour le coefficient de mesure#3, introduisez le coefficient de mesure établi pour le plus haut débit testé. Assurez-vous que le débit du coefficient de mesure#4 est supérieur au débit du coefficient de mesure#3. Si un coefficient de mesure est fixé pour le coefficient de mesure#3 et le coefficient de mesure#4 et que le flux du produit dépasse le débit du coefficient de mesure#4, ce coefficient de mesure#4 sera appliqué au volume de stock brut pour tous les débits qui dépassent le débit du coefficient de mesure#4. Si aucun coefficient de mesure n'a été fixé pour le coefficient de mesure#4, introduisez le coefficient de mesure établi pour le plus haut débit testé. Introduisez le nombre réel de facteurs de mesure configurés (1-4) dans le paramètre # Meter Factors Used. 178 Chapitre 5 – Contrôle du debit du produit 179 COEFFICIENT DE MESURE UNIQUE 5.10.1 Vous pouvez utiliser un coefficient de mesure unique en introduisant la même valeur de coefficient de mesure dans les quatre paramètres de coefficient de mesure. Toutefois, les débits des facteurs de mesure doivent avoir des valeurs différentes. Exemple Meter Factor #1 1.0451 Meter Factor #1 Rate 150 Meter Factor #2 1.0451 Meter Factor #2 Rate 400 Meter Factor #3 1.0451 Meter Factor #3 Rate 600 Meter Factor #4 1.0451 Meter Factor #4 Rate 800 RÈGLES RELATIVES AUX FACTEURS DE MESURE 5.10.2 - Si les conditions suivantes ne sont pas remplies, il y aura une alarme de conflit de FCM au moment du flux Les débits des facteurs de mesure doivent toujours suivre la règle suivante: Débit MF#1 < débit MF#2 < débit MF#3 < débit MF#4 - Les débits de facteurs doivent toujours respecter la restriction suivante : 0,8000 < coefficient de mesure< 1,2000 # Meter Factors Used- Introduisez le nombre de facteurs de mesure fixé pour le composant pour éviter les erreurs de configuration et les alarmes de conflits de FCM que ces erreurs pourraient provoquer. Chapitre 6 – Contrôle des additifs CHAPTER 6 6.1 180 CONTROLE DES ADDITIFS VUE D’ENSEMBLE Le contrôle sophistiqué des additifs fait partie intégrante du MultiLoad II. Comme cette commande est intégrée dans le MultiLoad II, il n'est pas nécessaire d'ajouter de dispositifs discrets de commande d'additifs ni d’interfaces au système d'automatisation du terminal. 16 injecteurs maximum peuvent être assignés à n'importe quel bras de chargement sur un MultiLoad II. Les taux d'injection des additifs sont introduits dans le MultiLoad II sous forme de pourcentage de la recette du produit total. Par exemple, si le taux d'injection des additifs est de 0,5000 gallon d'additifs par 1.000 gallons de produit, le pourcentage d'additif dans la recette de produit sera de 0,0500 %. Une fois que ce nombre est défini, n'importe quel volume d'injection (volume d’additifs par injection) peut être programmé dans le MultiLoad II s’il se situe dans les limites mécaniques de l'injecteur. Le MultiLoad II ajuste la fréquence des injections pour maintenir le pourcentage correct d'additifs. Ce chapitre décrit les dispositifs et les fonctions d'additifs du MultiLoad II. Veuillez relire les sujets qui traitent des caractéristiques communes à toutes les méthodes d'additifs avant d'étudier les méthodes individuelles. Les quatre méthodes d'additifs traitées dans ce chapitre sont : Piston uniquement (cylindre calibré) Piston avec entrée (cylindre calibré avec commutateur à rétrosignal) Entrée de l’électrovanne & du générateur d’impulsions (uniquement compteur d'additifs) Compteur usuel pour additifs multiples Pompe/vanne analogique avec commande boucle PID Toptech recommande la méthode de l’électrovanne et du générateur d’impulsions parce qu'elle donne directement tous les totalisateurs de commande et l'étalonnage des additifs. Cette méthode évite également l'utilisation d'un équipement d'injection des additifs basé sur un microprocesseur, économisant ainsi des frais considérables en formation et en entretien des systèmes d'additifs. Ce chapitre décrit aussi les dispositions d'étalonnage des additifs disponibles pour le MultiLoad II. Chapitre 6 – Contrôle des additifs 6.2 181 CYCLES DE L’INJECTEUR A PISTON Le temps de manœuvre du piston est un paramètre configuré pour toutes les méthodes de type de piston. Le temps de manœuvre est le temps que prend le piston pour achever une moitié de cycle. Notez qu'il ne s'agit pas d'une valeur calculée mais de la valeur déterminée par le temps que prend le piston pour un demi-cycle. Quand une injection est amorcée, le système suppose que le piston s'est déplacé jusqu'à son point d'extension maximal lorsque le temps de manœuvre s’est écoulé. Le signal d'injection est alors supprimé et le piston commence à revenir à sa position de départ. Le temps nécessaire pour ce faire est aussi, en théorie, égal au temps de manœuvre du piston. Le système ne tente pas d’autre injection jusqu'à ce que le temps de manœuvre de retour ne soit écoulé. Le piston doit revenir à sa position de départ avant la fin de cette période. Veuillez vous référer à la Figure 6. 1 ci-dessous. Inject (Launch) Piston @ Max Travel (1/2 Cycle Complete) Return (Throw Time Expires) on st Pi Tr av el Piston Cycle Graph Pi st on n ur et R Piston Switch High IDLE Figure 6-1 Throw Time Expired. Injection Complete Piston Switch High Throw Time Schéma du Cycle du Piston Throw Time IDLE Chapitre 6 – Contrôle des additifs 6.3 182 ATTRIBUTION DES PORTS D’ADDITIFS Dans la plupart des méthodes d'additifs, il faut une sortie d'additifs (signal d'injection) et une entrée d'additifs. Lorsqu'un additif est configuré, il faut l'assigner à un port FCM qui sert pour la sortie d'additifs (signal d'injection). Choix possibles pour les numéros acceptables de ports FCM : 0, 1, 2 et 3 sur un FCM externe. Le port de sortie choisi décide quel port utiliser pour l'entrée. Par exemple, si le Port 0 est choisi comme Port# FCM, la sortie se trouve sur le port 0 et l'entrée correspondante sur le port 7. Ci-dessous, un tableau des affectations possibles des ports. Avec la méthode "Piston Uniquement", il n'y a aucun signal d'entrée d'additif à contrôler. Toutefois, le port d'entrée qui correspond au port de sortie choisi sert de port d'additif. Ce port est hors service et ne peut être utilisé pour aucune autre fonction. AFFECTATION DES PORTS D’ENTRÉE ET DE SORTIE D’ADDITIFS 6.3.1 Port de sortie Port d’entrée Injecteur #1 0 7 Injecteur #2 1 6 Injecteur #3 (sauf SMP) 2 5 Injecteur #4 (sauf SMP) 3 4 6.4 UNITES D’ADDITIFS Des totaux d'additifs peuvent être affichés en une ou deux unités : en centimètre-cubes (cc) ou en millièmes de gallon (1/1000 gal.). Le paramètre pour choisir les unités voulues pour les additifs, « Display Adtv as CC » (Afficher Add. en cc) est disponible depuis l'écran de réglage du MultiLoad II. Lorsque cette fonction est activée, tous les écrans relatifs aux additifs affichent des totaux d'additifs en centimètre-cubes (cc). Si elle est désactivée, les totaux d'additifs sont affichés en millièmes d’unité de volume. Les unités d'additifs sont affichées en millièmes d'unités volumétriques ou de masse utilisés par les composants principaux. Par exemple, si le coefficient k du compteur de produit est en impulsions par litre, les unités d'additifs sont présentées en millièmes de litre. L'option d’affichage des additifs en centimètre-cubes n'est valable que lorsque les débitmètres du produit sont enregistrés en impulsions par gallon. Chapitre 6 – Contrôle des additifs 6.5 6.5.1 183 METHODES DE COMMANDE DES ADDITIFS MÉTHODE 1 – PISTON UNIQUEMENT La méthode "Piston Uniquement" est destinée à l'utilisation d'un injecteur de type à piston avec cylindre calibré. Cette méthode ne vérifie pas la livraison des additifs mais appelle simplement une injection si la demande d'additifs s'accumule. Une injection se produit dès que la livraison de produit est suffisante pour créer la demande d'un volume d'additifs égal à la moitié d'une injection (Figure 6.2). Le volume d'injection est déterminé par le paramètre "Volume par Injection". Si l'injection réussit, une injection complète est livrée avant que la demande n'ait atteint une injection complète. Le totalisateur d'additif livré est incrémenté d'un plein volume d'injection quand le piston a eu le temps de revenir à sa position de départ. Le paramètre de temps de manœuvre du piston détermine quand le système s'attend à ce que le cycle d'injection soit achevé. (Voir Figure 6. 1). Additive Recipe % (Programmed) Additive Volume Additiv e Inj ection Graph 2 Inject Vol. 1/2 Inject Surplus Right On 1 Inject Vol. 1/2 Inj Vol. 1/2 Inject Deficit exists: Injection Initiated 0 Product Delivered Figure 6-2 Injection d’Additifs Une alarme d'additifs est possible avec cette méthode. Bien qu'il n'y ait pas vérification de la livraison d'additifs avec cette méthode, le système vérifie toutefois le totalisateur des additifs livrés par rapport au totalisateur de recette (cible). Une alarme d'insuffisance d'additifs peut se produire si l'additif a été configuré pour une cible qu'il n’est pas capable d’atteindre. Avec ce dispositif, une alarme d'additifs indique que le rythme de livraison dépasse les capacités physiques de l'injecteur ou que la cible de proportion des additifs est irréaliste. Une alarme peut se produire si le paramètre de temps de manœuvre du piston est réglé pour une durée excessive. La configuration du temps de manœuvre retarde les nouvelles injections pour permettre le temps nécessaire à la course du piston. Si c’est trop long, certaines proportions pourraient ne pas être atteintes en raison des limitations d'action du piston. Chapitre 6 – Contrôle des additifs 6.5.2 184 CONFIGURATION D’UN ADDITIF ” PISTON UNIQUEMENT” Ce sujet traite de la configuration minimale pour qu'un additif opère avec cette méthode. La configuration de ces paramètres est obligatoire. Accédez au mode de programme en utilisant l'outil de configuration du MultiLoad II ou le clavier du bloc de télécommande. Depuis le menu de configuration, sélectionnez la valeur prédéfinie et l'additif désiré. Additive Enable Activez ce paramètre Flow Control Module # Mettez cette valeur sur FCM # où l’additif est branché. Mettez cette valeur à zéro pour la carte interne des entrées et sorties. FCM Port # Sélectionnez le port utilisé pour la sortie d’injection de l’additif. Remarque: une sortie d’additif correspondante est automatiquement attribuée. Référez-vous à la description des affectations de port d’additifs ci-dessus. Additive volume Per Injection Introduisez le volume du cylindre dans l’unité ad hoc. Les unités ou le volume sont configurés en CC ou en millièmes de gallon. Piston Throw Time Introduisez le temps nécessaire en secondes pour que le piston fasse une moitié de cycle d’injection. Les autres paramètres qui s'appliquent à cette méthode d'additifs sont facultatifs. Ils servent à régler les alarmes, les sorties de la pompe et les entrées autorisées. Certains de ces paramètres règlent la livraison d’additifs aux différentes étapes du cycle de chargement. Tous les écrans de configuration des additifs et les descriptions des paramètres se trouvent au point consacré au « Réglage Général des Additifs » ci-après. Le tableau des paramètres pour les méthodes d'additifs identifie les paramètres qui s'appliquent à cette méthode. Chapitre 6 – Contrôle des additifs 6.5.3 METHODE 2 – PISTON AVEC ENTRÉE (COMMUTATEUR À RÉTROSIGNAL) Cette méthode est destinée à l'utilisation d'un injecteur de type à piston avec un cylindre étalonné. Une disposition a été prise pour recevoir un signal de rétroaction qui vérifie que le piston a été lancé et qu'il est revenu à sa position de départ. Une injection se produit dès qu'il y a suffisamment de produit livré pour créer la demande d'un volume d'additifs égal à la moitié d'une injection. Le volume d'injection est déterminé par le paramètre "Volume par Injection". Si l'injection réussit, une injection complète aura été livrée avant que la demande n'ait atteint une pleine injection. Le totalisateur d'additif livré est incrémenté d'un plein volume d'injection dès que le piston a eu le temps de revenir à sa position de départ et que le signal approprié de rétroaction a été reçu au niveau du port d'entrée d'additif. Le paramètre de temps de manœuvre du piston détermine quand le système s'attend à ce que le cycle d'injection soit achevé. Référez-vous à la Figure 6. 1 pour illustration. Lorsqu'une injection est commandée, le piston doit quitter sa position de départ avant que le temps de manœuvre ne soit écoulé. L'entrée du piston (commutateur à rétrosignal) devrait indiquer un changement d'état lorsque le piston a été lancé. L'état par défaut est "haut" lorsque le piston se trouve en position de départ et passe sur "bas" lorsque les courses du piston l'éloignent de son siège. Si le signal d'entrée du piston passe sur "bas" avant que le temps de manœuvre ne soit écoulé, le programmateur du temps de manœuvre est réinitialisé, mettant en attente la commande de retour du piston. Si l'état ne change pas pendant le temps de manœuvre, le système enregistre, en interne, une injection manquée. Le chargement peut être programmé de façon à déclencher une alarme après l'enregistrement d'un certain nombre d'injections manquées. Lorsque le temps de manœuvre s'est écoulé, le signal de sortie d'additifs (injection) est supprimé, permettant au piston de revenir à la position de départ. Après la suppression du signal de sortie, le programmateur du temps de manœuvre redémarre. Le piston doit revenir à la position de départ avant que le temps de manœuvre ne se soit écoulé. Si les pistons retournent en position de départ avant la fin du temps de manœuvre, l'état change et passe sur " haut". Le système suppose ainsi que l'injection a réussi et incrémente le totalisateur d'additifs de la quantité spécifiée dans le paramètre "Volume par Injection". Si le signal n'est pas passé sur "haut" avant la fin du temps de manœuvre, une injection manquée est enregistrée en interne. Le système tente immédiatement une nouvelle injection en supposant que la tentative précédente n'a livré aucun additif. Quand le nombre d'injections manquées équivaut à la valeur entrée pour le paramètre "Max Pstn Missed Inj" (Max. d'Injections Manquées Piston), une alarme d'erreur d'injection se produit et le chargement s'arrête. Si le piston est revenu à sa position de départ, comme défini par le signal de rétroaction, le piston est placé en attente jusqu'à ce qu'un autre signal d'injection vienne du port de sortie d'additifs. Un autre signal de commande d'injection est envoyé à l'injecteur lorsque la demande d'additifs, basée sur la livraison de produits, atteint 50 % d'un volume d'injection. 185 Chapitre 6 – Contrôle des additifs 6.5.4 186 CONFIGURATION D’UN PISTON AVEC ENTRÉE D’ADDITIFS Ce sujet traite de la configuration minimale nécessaire pour qu’un additif fonctionne avec cette méthode. La configuration des paramètres suivants est obligatoire. A l’aide de l’outil de configuration du MultiLoad II ou le clavier de la télécommande dans le mode de programme, sélectionnez la valeur prédéfinie et l’additif désiré. Paramètre Action Additive Enable Activez ce paramètre Additive FCM# Mettez cette valeur au FCM # où l’additif est branché. Mettez cette valeur à zéro pour la carte interne des entrées et sorties. FCM Port # Sélectionnez le port pour la sortie du signal d’injection. Remarque: un port d’entrée d’additif correspondant sera automatiquement assigné. Référezvous à la description de l’affectation des ports d’additifs ci-avant. Additive Type Activez cette valeur sur PstnNFB si l’entrée piston est normalement élevée (Normal Feedback). Mettez sur PstnIFB si l’entrée piston est normalement basse (Inverted Feedback). Additive Injection Volume Piston Throw Time Per Introduisez le volume du cylindre dans l’unité ad hoc. Introduisez le temps nécessaire en secondes pour que le piston puisse achever une moitié de cycle d’injection. Les autres paramètres qui s'appliquent à cette méthode d'additifs sont facultatifs. Ils servent à régler les alarmes, les sorties de la pompe et les entrées autorisées. Certains de ces paramètres influencent la livraison d’additif aux différents stades du cycle de chargement. Tous les écrans de configuration des additifs et les descriptions des paramètres se trouvent à la section : "Réglage Général des Additifs' ci-après. Le tableau des "Paramètres pour les Méthodes d'Additifs" identifie les paramètres qui s'appliquent à cette méthode. Chapitre 6 – Contrôle des additifs 6.5.5 187 METHODE 3 – ENTRÉE DU GÉNÉRATEUR D’IMPULSIONS Cette méthode suppose qu'un dispositif de mesure du débit évalue la quantité d'additifs qui rentre dans le flux de produit. Cela présuppose qu’il n’y a pas de piston ou de cylindre et que le port de sortie d’additif commande une électrovanne qui commande l’apport d’additif. Au lieu d'incrémenter le totalisateur d'additifs à chaque injection ou au moment de la réception d'un signal de rétroaction, cette fonction met à jour les totalisateurs d'additifs sur base du débit mesuré. Puisque les limitations physiques d'un injecteur à piston/cylindre sont éliminées, le paramètre de temps de manœuvre n'est pas pertinent. Toutefois, le paramètre du volume par injection est toujours valable. Le paramètre du volume par injection définit un rythme-cible mais le système effectue une injection, si nécessaire, pour éliminer un déficit. Le paramètre d’impulsion de la fermeture de l'électrovanne" ne s'applique qu'à la méthode d'additifs d'entrée du générateur d’impulsions. Son but est de compenser la vitesse finale de l'électrovanne, qui peut permettre des surlivraisons uniformes (non cumulés). La compensation se fait sur la base d'impulsions plutôt que sur base volumétrique. Cette fonction est destinée à éliminer d’autres surlivraisons et cela, en supposant que des ajustements mécaniques à la vitesse finale de l'électrovanne aient déjà été effectués. La quantité de surplus d'impulsions provenant de l'action de la vanne peut être établie en effectuant l'essai d'étalonnage d'additif ou le test de diagnostic d'additifs. La quantité d'excès d'impulsions données pour chaque injection d'essai peut être observée. Lorsque le nombre d'impulsions en surplus est établi, introduisez-le dans ce paramètre pour réduire le dépassement. (Voir à "Etalonnage des Additifs" plus loin pour de plus amples détails.) 6.5.6 CONFIGURATION D’UN ADDITIF AVEC ENTRÉE DU GÉNÉRATEUR D’IMPULSIONS Ce sujet traite de la configuration minimale pour un additif avec cette méthode. La configuration des paramètres suivants est obligatoire. Pour ce faire, utiliser l'outil de configuration du MultiLoad II ou le clavier de la télécommande dans le mode programme. Sélectionnez la valeur prédéfinie et l'additif désiré. Additive Enable Activez ce paramètre Flow Control Module# Mettez cette valeur sur le FCM # où l’additif est branché. Mettez cette valeur sur zéro pour la carte interne des E/S FCM Port # Sélectionnez le port servant de sortie d’injection de l’additif. Remarque: Un port d’entrée d’additif correspondant est automatiquement attribué. Référez-vous à la description de l’attribution de port d’additif ci-avant. Additive Type Mettez cette valeur sur SolnMtr. Le Multiload donne ordre à la vanne électromagnétique d’injecter et de mesurer les impulsions Additive Volume per Injections Introduisez le volume d’injection avec les unités appropriées Throw Time Pas d’application Additive Meter K-Factor Introduisez le facteur K du compteur d’additif en impulsions par gallon. Les autres paramètre d’application pour cette méthode d’additif sont en option. On les utilise pour régler les entrées d’alarme, de pompe et les permissions. Certains autres paramètres influencent la façon dont l’additif est fourni à différentes étapes du cycle de chargement. Les écrans de configurations « All Additives » et les descriptions des paramètres se trouvent à la section suivante (Réglage général des additifs). Le tableau “Parameters for Additive Methods” énumère les paramètres s’appliquant à cette méthode. Chapitre 6 – Contrôle des additifs 6.5.7 188 MÉTHODÉ 4 – ADDITIF ANALOGIQUE Cette configuration présume la présence d’un dispositif de mesure du débit de la quantité d’additif entrant dans le flux de produit, qu’il n’y a pas de piston/cylindre et que le port de sortie d’additif (4 – 20mA) commande un pilote de pompe qui gère la livraison d’additif. Au lieu d’incrémenter le totalisateur d’additif à chaque injection ou à la réception d’un signal de feedback, cette fonction met à jour les totalisateurs d’additifs basés sur le débit mesuré. Puisque les limites physiques de l’injecteur à piston/cylindre sont éliminées, le paramètre « Throw Time » n’a plus de sens. Par contre, le paramètre « Volume Per Injection » reste valable. Ce paramètre fixe le rythme auquel le système injecte, si nécessaire, afin d’éliminer tout déficit. Pour mieux commander le pilote de la pompe, une boucle PID a été implémentée. Les trois paramètres peuvent être modifiés pour arriver à un fonctionnement régulier de la pompe au cours du chargement. Le paramètre Solenoid Shut Pulses ne s’applique qu’à la méthode d’additifs par entrée d’impulsions ‘Pulser Input”. Le nombre de dépassements d’impulsions dus à l’action de l’électrovanne peut être déterminé en effectuant le test d’étalonnage d’additifs ou l’injection d’essai de diagnostic additifs. Le nombre d’impulsions superflues pour chaque injection d’essai peut être observé. Lorsque le nombre d’impulsions de dépassement est déterminé, introduisez le nombre dans ce paramètre pour réduire davantage ce dépassement. (Voir au point consacré à l’étalonnage d’additifs plus loin dans ce chapitre) 6.5.8 CONFIGURATION D’UN ADDITIF ANALOGIQUE Ce point décrit la configuration minimum nécessaire pour faire fonctionner un additif par cette méthode. Il faut absolument configurer les paramètres suivants. Vous pouvez le faire grâce à l’outil de configuration du MultiLoad II ou le clavier MultiLoad dans le mode “Program”. Sélectionnez la valeur prédéfinie et l’additif désiré. Additive Enable Activez ce paramètre Flow control module # Mettez cette valeur sur le n° FCM # où l’additif est connecté. Mettez cette valeur à zéro pour la carte I/O interne. Il doit toujours y avoir un débit fcm2 car c’est le seul FCM à sortie analogique. FCM Port # Sélectionnez le port servant à la sortie d’injection d’additif. Remarque: Un port additif correspondant sera automatiquement attribué. Référez-vous à l’attribution de port d’additif ci-avant Additive Type Mettez sur valeur sur ‘AnlgMtr’. Le Multiload choisit la vitesse de pompe adéquate pour injecter l’additif en continu dans la ligne principale. L’impulsion de l’additif nous fournit un feedback. Additive Volume Per Injection Introduisez le volume d’injection dans l’unité appropriée. Piston Throw Time Ce paramètre n’est pas d’application. Additive Compteur K-Factor Introduisez le coefficient K du compteur d’additifs en impulsions par gallon. Les autres paramètres de cette méthode d’additifs sont facultatifs. Ils servent au réglage d’alarmes, aux sorties de pompes et aux entrées autorisées. Certains paramètres influencent la livraison d’additif à des moments divers du cycle de chargement. Tous les écrans de configuration d’additifs et les descriptions de paramètres se trouvent dans le point « réglage général des additifs » ci-après. Le tableau des paramètres pour les méthodes d’additifs reprend les paramètres qui s’appliquent à cette méthode. Chapitre 6 – Contrôle des additifs 6.5.9 189 METHODE 5 – COMPTEUR USUEL A PLUSIEURS ADDITIFS La méthode 5 permet de livrer de plusieurs additifs par injecteur centré. L'injecteur doit utiliser un compteur d'additifs avec sortie pulsée vers un FCM (Module de Contrôle de Flux). Cette méthode de mesure d'additifs est une extension de la démarche "Entrée d'Impulsion" (Méthode 3). Les principes décrits pour la méthode 3 s'appliquent également à celle-ci. Un maximum de 16 additifs (2 additifs sur SMP) peut être acheminé au travers d'un injecteur simple. Indépendamment de la configuration, 16 additifs maximum peuvent être assignés à chaque bras de chargement; un seul additif peut être livré par l'injecteur centré pendant un même chargement. L'algorithme du compteur usuel a été conçu pour deux configurations hydrauliques: un programme utilise une vanne d'injecteur et des vannes d'arrêt d'additif. Le second programme ne se sert que de vannes d'arrêt d'additif. Add #1 Add #2 Additive Block Valve Add #1 M Additive Meter Injector Valve Figure 6-3 Vanne d’Injecteur Usuel - Schéma Dans le schéma ci-dessus, les électrovannes d'arrêt d'additif servent à sélectionner l'additif à livrer. Une de ces vannes s'ouvre lorsqu’on pousse sur le bouton de démarrage. Il se ferme lorsque la quantité d'additifs nécessaire pour l'entièreté du chargement a été livrée. Pendant le chargement, la valve d'injecteur d'additif s'ouvre et se ferme régulièrement pour injecter l'additif dans le flux de produit. La valve d'injecteur d'additif s’ouvre suffisamment longtemps pour livrer la quantité spécifiée par le paramètre du volume d'additif par injection. Chapitre 6 – Contrôle des additifs 190 Le schéma qui suit illustre le rapport électrique entre les sorties du Module de Contrôle de Flux (FCM) et les électrovannes. Les sorties du FCM sont représentées par des commutateurs dans le diagramme. Pendant un chargement, une seule sortie de la vanne d'arrêt d'additif est active. La sortie reste active, alimentant l’électroaimant correspondant pour la durée du chargement. La sortie d'Injection d'additif se ferme et s'ouvre au gré des besoins des injections, alimentant et ré-alimentant l’électro-aimant d'injection. L1 L2 Additive Injection Output Figure 6-4 Injector Valve Solenoid Additive Block Valve Output-Add #1 Additive Block Valve Solenoid-Add #1 Additive Block Valve Output-Add #2 Additive Block Valve Solenoid-Add #2 Schéma Electrique avec Vanne d’Injecteur Chapitre 6 – Contrôle des additifs 191 VANNES D’ARRÊT D’ADDITIFS UNIQUEMENT 6.5.10 Add #1 Add #2 Additive Block Valve Add #1 M Figure.6-5 Additive Meter Schéma avec Vannes d’Arrêt pour l’Injection Dans le schéma ci-dessus, les électrovannes d'arrêt d'additifs servent à sélectionner l'additif à livrer. Contrairement au schéma précédent, on n’utilise pas de vanne d’injecteur d'additif. Pendant un chargement, la vanne d'arrêt d'additif de l'additif sélectionné ne s'ouvre que lors de la commande d'une injection. Ceci se fait en raccordant la sortie de la vanne d'arrêt d'additifs en série avec la sortie d'injection d'additifs. Voir le schéma ciaprès. Pendant un chargement, la sortie de la vanne d'arrêt d'additifs sélectionnée est active à tout moment. La sortie d'injection d'additifs termine régulièrement le circuit, alimentant l’électro-aimant de la vanne d'arrêt d'additifs à chaque commande d'injection. L1 L2 Additive Injection Output Figure 6-6 Additive Block Valve Output-Add #1 Additive Block Valve Solenoid-Add #1 Additive Block Valve Output-Add #2 Additive Block Valve Solenoid-Add #2 Schéma Electrique avec Vannes d’Arrêt comme Injecteurs Chapitre 6 – Contrôle des additifs 192 CONFIGURATION D’UN COMPTEUR USUEL À PLUSIEURS ADDITIFS 6.5.11 Ce sujet traite de la configuration minimale exigée pour un additif avec cette méthode. La configuration des paramètres suivants est obligatoire. Pour ce faire, utilisez l’outil de configuration E/S II ou le clavier de la télécommande dans le mode de programme. Ces paramètres sont configurés pour chaque additif assigné à l'injecteur centré. Additive Enable Désactivez ce paramètre Flow Control Module # Mettez cette valeur sur le FCM # où l’additif est branché. Mettez cette valeur à zéro pour la carte interne des entrées et sorties. FCM Port # Sélectionnez le port pour la sortie d’injection d’additif. Remarque: un port d’entrée d’additifs correspondant est automatiquement attribué. Référezvous à la description des attributions de ports d’additifs ci-avant. Additive Type SolnMtr/anlgMtr Piston Throw Time Ce paramètre n’est pas d’application Additive Meter K-Factor Introduisez le facteur K du compteur d’additifs en impulsions par gallon. Open Block Valve FCM# Attribuez un port de sortie offrant une sortie pour une vanne d’arrêt d’additif qui servira à la sélection des additifs. Les autres paramètres qui s'appliquent à cette méthode d'additifs sont facultatifs. Ils servent à régler les alarmes, les sorties de la pompe et les entrées autorisées. Certains de ces paramètres règlent la livraison de l’additif aux différents stades du cycle de chargement. Tous les écrans de configuration des additifs et les descriptions des paramètres se trouvent au point suivant : "Réglage Général des Additifs'. Le tableau des paramètres pour les méthodes d'additifs identifie les paramètres qui s'appliquent à cette méthode. Tous les paramètres d'additifs ne s’appliquent pas à toutes les méthodes de livraison des additifs. Le tableau qui suit montre les paramètres s'appliquant à chacune des quatre méthodes possibles. "Oui" indique qu’il s'applique à la méthode d'additif. "Non" indique qu’il ne s'applique pas à cette méthode. Piston seulement w/entrée piston Impulsions seulement Compteur habituel Analogique Add. Enable Activé* Activé* Activé* Activé* Activé* Add. FCM# Oui* Oui* Oui* Oui* Oui* FCM Port (output) Oui* Oui* Oui* Oui* Oui* (4 – 20mA) W&M Controlled Oui Oui Oui Oui Oui Upstream Valve Oui Oui Oui Oui Oui Additive Type Pstn PstnNFB/PstnIF B SolnMtr SolnMtr/AnlgM tr AnlgMtr Additive P Factor Non Non Non Non Oui Additive I Time NOon Non Non Non Oui Additive D Time Non Non Non Non Oui Block Chapitre 6 – Contrôle des additifs 193 Piston seulement w/entrée piston Impulsions seulement Compteur habituel Analogique Sol. Shut Pulses Non Non Oui Oui Non Shutoff Vol. End Oui Oui Oui Oui Oui Last Inj. Vol. End Oui Oui Oui Oui Oui Line Flush Min. Vol. Oui Oui Oui Oui Oui W&M Recipe Percentage Oui Oui Oui Oui Oui Add. Vol per Inj. Oui* Oui* Oui* Oui* Oui Vol./Inj. Cal factor Oui Oui Non Non Oui Add. K-Factor Non Non Oui* Oui* Oui Add. Meter Factor Non Non Oui Oui Oui Max Pstn Missed Inj Non Oui Non Non Non Max Solenoid Inj Time Non Non Oui Oui Oui Under Add. Inj # Oui Oui Oui Oui Oui Over Add. Inj. # Oui Oui Oui Oui Oui Check Add. Tol. Oui Oui Oui Oui Oui UA Flow Alm Vol Non Oui Oui Oui Oui Valve Fault Vol. Non Oui Oui Oui Oui Over Inject Vol. Oui Oui Oui Oui Oui Creep Time Reset Non Non Oui Oui Oui Unauth Time Reset Non Non Oui Oui Oui Max Pstn Throw Time Oui* Oui* Non Non Non Pump Status Alm. Oui Oui Oui Oui Oui Meter Creep Alm. Vol Non Non Oui Oui Oui Remote Calibrate Oui Oui Oui Oui Oui Chapitre 6 – Contrôle des additifs 194 Piston seulement W/Entrée Piston Impulsion seulement Compteur habituel Analogique BV Open Time Alrm Oui Oui Oui Oui Oui BV Close Time Alrm Oui Oui Oui Oui Oui Pump Stop Delay Oui Oui Oui Oui Oui Flush Pump Run Time Oui Oui Oui Oui Oui Meter Flushed Non Non Oui Oui Oui Solenoid Flushed Non Non Oui Oui Oui W&M Alarm Promo Count Non Oui Oui Oui Oui W&M Alarm Reset Mode Non Oui Oui Oui Oui Flush Pump Run FCM# Oui Oui Oui Oui Oui Close FCM# Val Oui Oui Oui Oui Oui Status Oui Oui Oui Oui Oui Val Oui Oui Oui Oui* Oui Test Button FCM# Oui Oui Oui Oui Oui Pump Run FCM# Oui Oui Oui Oui Oui Pump Kill FCM# Oui Oui Oui Oui Oui Pump Stat FCM# Oui Oui Oui Oui Oui Alarm Out FCM# Oui Oui Oui Oui Oui Authorized FCM# Oui Oui Oui Oui Oui Permiss FCM# Oui Oui Oui Oui Oui Permiss FCM# Oui Oui Oui Oui Oui Blk Blk Val FCM# Open FCM# Blk Out * Configuration obligatoire de ce paramètre Chapitre 6 – Contrôle des additifs 6.6 195 REGLAGE GENERAL DES ADDITIFS 1. A partir du mode de programme, sélectionnez "Configuration" | Equipment Setup. 2. A partir du menu de réglage des équipements, sélectionnez Additives. Le menu de sélection des valeurs prédéfinies s'affiche. 3. Sélectionnez une valeur prédéfinie. L'écran de sélection des additifs – # valeurs prédéfinies s'affiche. 4. Sélectionnez un additif. L'écran de réglage des additifs s'affiche. Paramètre PRE #1 ADTV #1 (Adtv 001 Additive Enable: Flow Control Module#: FCM Port#: W&M Controlled: Upstream Block Valve: Additive Type: Additive P Factor: Additive I Time: Additive D Time: Solenoid Shut Pulses: Shutoff Vol From End: Last Inj Vol From End: Line Flush Min Vol: Assigned Component: Description Additive Enable Active et désactive l’additif sélectionné Flow Module# Mettez cette valeur sur le FCM # où l’additif est branché Mettez cette valeur à zéro pour la carte interne des entrées et sorties Next Control Prev Exit ) SETUP DISABLD 0 0 DISABLD DISABLD SolnMtr 1.000 3.000 0.000 0 0 20 0 0 Enter Chapitre 6 – Contrôle des additifs 196 Paramètre Description FCM Port# Choisissez le port de signal (sortie) d'injection d'additif pour l'additif sélectionné. Possibilités de 0 à 3 (de 0 à 1 sur SMP). Ce choix de port détermine automatiquement un port sur le même FCM comme entrée du compteur d'additif ou comme signal de rétroaction d'additif. La liste qui suit montre la correspondance entre l’entrée de compteur d'additif/entrée de rétroaction d'injecteur et le port d'additif. Port d'Additif Entrée de Compteur d'Additif /Rétroaction d'Injecteur Port de sortie Port d’entrée Injecteur #1 0 7 Injecteur #2 1 6 Injecteur #3 (sauf SMP) 2 5 Injecteur #4 (sauf SMP) 3 4 Par exemple, si le Port d'Additif #0 est choisi, l’électro-aimant d'additif est alimenté par la sortie du port 0 et le signal d'entrée du compteur d'additif est attendu au port 7. Si un cylindre étalonné est utilisé sans compteur d'additif, un signal de rétroaction peut être envoyé au port 7 pour vérifier que le piston a bien terminé le cycle d'injection. Active la sélection de paramètres d’additifs pour cet additif contrôlé par les Poids et Mesures. W&M Controlled Block Activez ce paramètre si la vanne de blocage d’additifs est en amont de l’injecteur. Lorsqu’il est activé, la vanne de blocage d’additifs restera ouverte pendant l’étalonnage d’additif. Additive P Factor gain proportionnel pour la boucle PID (ne s’applique qu’au type d’additif à vanne analogique) Additive I Time Gain intégral pour la boucle PID (ne s’applique qu’au type d’additif à vanne analogique) Additive D Time Terme dérivé pour la boucle PID (ne s’applique qu’au type d’additif à vanne analogique) Additive Type Choisissez le type de commande d’additif parmi les éléments suivants : SolnMtr : vanne électromagnétique avec compteur PstnNFB : piston à feedback normal PstnIFC : piston à feedback inversé Pstn : piston sans feedback AnlgMtr : vanne analogique avec compteur à commande PID Solenoid Shut Pulses Ce paramètre ne s'applique qu'à la méthode d'additif "Générateur d'Impulsions". Son but est de compenser la vitesse finale de l'électrovanne, qui peut permettre des surlivraisons uniformes. La compensation se fait sur la base d'impulsions plutôt que sur une base volumétrique. Cette fonction est destinée à éliminer les autres surlivraisons en supposant que des ajustements mécaniques à la vitesse finale de l'électrovanne ont déjà été effectués. La quantité de surplus d'impulsions générées par l'action de la vanne peut être déterminée en exécutant le test d’étalonnage d'additif ou le test de diagnostic d'additifs. La quantité d'excès d'impulsions pour chaque injection d'essai peut être observée. Lorsque le nombre d'impulsions en surplus est établi, introduisez-le dans ce paramètre pour éliminer le dépassement. Upstream Valve Chapitre 6 – Contrôle des additifs 197 Paramètre Description Shutoff Vol From End La livraison de l'additif s'arrête lorsque la quantité prédéfinie indiquée par ce paramètre est atteinte. Introduisez une valeur numérique dans les unités de volume des composants de base. Quand la quantité restante du chargement atteint le volume spécifié dans ce paramètre, la livraison de l'additif sélectionné cesse, indépendamment de la quantité de demande d'additif restant. Cela permet en général à l'additif de s'écouler depuis le bras de chargement au moment où la livraison de produit est terminée. Si on désire une injection d'additif pour l'ensemble de la livraison, introduisez zéro pour ce paramètre. Voir les descriptions des paramètres liés intitulés "Volume de la dernière injection depuis la fin" et "Volume minimum de purge de conduite". Last Inj Vol From End Volume de la dernière injection depuis la fin. Ce paramètre spécifie quand la dernière injection doit se produire pour pouvoir livrer le volume approprié d'additifs sur base de la quantité prédéfinie. Avec ce paramètre, il est possible de purger le bras de chargement d'additif comme décrit dans le paramètre "Shutoff Vol From End" tout en maintenant toujours une proportion additif/produit appropriée pendant quasi toute la livraison. Quand la dernière injection est amorcée, la demande d'additif restant est livrée le plus vite possible avant que le " Shutoff Vol From End" ne soit atteint. Exemple : Nous avons une quantité prédéfinie de 1000 gallons et nous voulons que la livraison de l'additif soit terminée au moment où nous atteignons les 50 derniers gallons du lot pour purger le bras de chargement d'additif. Le paramètre " Shutoff Vol From End" est réglé sur 50 gallons, commandant ainsi la fin de la livraison de l'additif à ce stade. Si nous réglons le paramètre du volume de la dernière injection depuis la fin sur 100 gallons, l'additif es injecté à un débit qui assure une proportion appropriée d'additif à tout moment avant que les 100 derniers gallons ne soient livrés. Si le lot est interrompu à 500 gallons, le chauffeur obtient un chargement correct d'additif. Lorsque le lot atteint la marque finale de 100 gallons, le système sait qu'il doit livrer l'additif restant avant d’arriver à la marque finale de 50 gallons. Le taux d'injection augmente considérablement pour respecter les conditions de chargement. Par conséquent, le lot est suralimenté en additif pour un court laps de temps pendant la livraison des 100 derniers gallons. Lorsque le dernier gallon a été livré, le lot est correctement chargé en additif. Même si la purge de conduite des additifs n'est pas une obligation, il est recommandé de régler ce paramètre sur la valeur par défaut de 20 gallons, ce qui garantira une livraison précise d'additif. Line Flush Min Vol Le volume minimum de purge de conduite spécifie le volume de la purge de conduite du produit pour purger de manière satisfaisante l'additif du bras de chargement. Introduisez la valeur dans l'unité volumétrique utilisée par le débitmètre du produit. A la fin de la livraison de l'additif, le volume entré dans ce paramètre doit passer par le débitmètre du produit. Si le volume indiqué à ce paramètre n'est pas livré lorsque les critères de chargement d'additif sont atteints, une alarme de purge se produit. Introduisez zéro dans ce paramètre pour désactiver la fonction. Cette fonction n'a rien à voir avec les réglages des paramètres de purge qui se trouvent au menu des valeurs prédéfinies. Assigned Component Composant attribué: si on injecte un additif dans un composant d’un mélange séquentiel, tout le volume d’additif de ce lot doit être livré lorsque ce composant est en train d’être débité. Ce paramètre spécifie, en dehors du non-zéro, que l’additif ne peut passer que lorsque le composant spécifié est débité. W&M Percentage Pourcentage Poids et Mesures. Si cet additif doit avoir le pourcentage de recette protégé par les Poids et Mesures, mettez cette valeur sur la valeur acceptée par les Poids et Mesures. Si cette valeur est de non-zéro, le pourcentage de recette d’additif DOIT être égal au pourcentage de recette des Poids et Mesures ou bien toute tentative d’autorisation de lot échouera et vous lirez un message : “W&M Required Additive Pct Not Correct” (pourcentage d’additif exigé par les Poids et Mesures incorrect) Recipe Chapitre 6 – Contrôle des additifs Paramètre Additive Vol Chk 198 Description Start Quantité de produit principal qui doit passer avant de démarrer la vérification de la recette. Ce paramètre s’utilise ave Additive Tol Percentage Additive Vol/Inject Le paramètre "Volume d'Additif par Injection" s'applique à toutes les méthodes d'additif. Quand vous utilisez un système à piston, avec ou sans rétroaction, introduisez le volume du cylindre étalonné comme prescrit par le fabricant ou le service d'étalonnage. Si la méthode d'additif implique un piston et un générateur d'impulsions de débit d'additif, introduisez la dimension du cylindre. Si on utilise un générateur d'impulsions de débit d'additif, introduisez le volume de l'additif désiré pour chaque injection. Introduisez la valeur dans les mêmes unités de volume que le coefficient K du débitmètre du produit principal. N’utilisez par les CC. Vol/Inject Cal Factor Ce facteur corrige le volume du cylindre calibré sur le volume brut réellement mesuré au cours du processus d'étalonnage d'additif. Si un compteur d'additif est impliqué, avec ou sans système à piston, réglez le paramètre sur 1,0000. Additive Percentage Tol Ce paramètre permet de vérifier en fonction du pourcentage d’additif. Il s’utilise en combinaison avec Additive Chk Start Vol. Il s’agit de la quantité de produit principal qui doit passer avant de démarrer la vérification de la recette. L’additif par volume d’injection continuera à fonctionner en même temps si nécessaire Additive Mtr K-Factor Introduisez le coefficient K du débitmètre d'additif. Ce paramètre s'applique si un débitmètre d'additif avec ou sans injecteur à piston est utilisé. Introduisez la valeur avec les mêmes unités de volume que le coefficient K du débitmètre du produit principal. N’utilisez par les CC. Additive Meter Factor Il s'agit du coefficient de mesure pour le débitmètre d'additif utilisé pour corriger les résultats mesurés jusqu'au volume observé d'additif obtenu au cours de l'étalonnage du compteur d'additif. Max Pstn Missed Inj Utilisez le paramètre d’injections maximum manquées avec la méthode de piston avec entrée de la livraison d'additif. Introduisez le nombre d'injections à piston qui peuvent être manquées avant que le système ne lance une alarme d'erreur d'injection. L'alarme est levée si la quantité spécifiée d'injections manquées se produit juste après ou si la quantité d'injections manquées s'accumule avant livraison de la quantité prédéfinie. MaxSolenoid Inj Time Ce paramètre de temps maximum de l’électrovanne d’injection définit le temps d’ouverture de l'électrovanne pendant une injection. Si aucune impulsion n'est reçue dans la période de temps spécifiée, une alarme INJCT FLT (erreur d'injection) se produit. Il faudra peut-être vérifier le fonctionnement du générateur d’impulsions. Introduisez une durée en millisecondes. Si les injections durent plus longtemps que le réglage par défaut de ce paramètre, il faut augmenter le temps de façon à ce qu'il soit supérieur au temps d'injection standard. Il faudra peut-être augmenter la valeur par défaut en cas de chargement frontal d'additif ou si la purge des conduites exige une injection finale plus importante. Under Add Alrm # Inj # alarmes d'insuffisance d'additifs des injections. Lorsque le produit n'est pas suffisamment enrichi d'additif selon le nombre d'injections spécifiées par ce paramètre, une alarme d'additif se produit et la livraison s'arrête. Le volume de chaque injection est déterminé au paramètre "Vol/Inj Additive". Over Add Alrm # Inj # alarmes d'excédent d'additifs d’injection. Lorsque le produit est suralimenté en additif selon le nombre d'injections spécifiées par ce paramètre, une alarme d'additif se produit et la livraison s'arrête. Le volume de chaque injection est déterminé au paramètre "Vol/Inj Additive". Chapitre 6 – Contrôle des additifs 199 Paramètre Description Check Add Tol Time Définissez le contrôle de la limite de temps de tolérance d'additif pour donner suffisamment de temps au système pour récupérer d'une condition d'alarme d'insuffisance ou d'excédent d'additif. Si le réglage de cette valeur est trop bas, le système reste en état d'alarme jusqu'à ce que l'erreur d'additif soit résolue de façon à rester dans les limites du nombre d'injections spécifiées par les paramètres d'alarme d'additifs. Introduisez une valeur en unités de temps (secondes). Unauth Flow Alrm Vol Spécifiez le volume de débit non autorisé d'additif qui doit s'accumuler avant l’activation d’une alarme de débit non autorisé d'additifs. Ce paramètre ne s'applique pas aux méthodes sans générateurs d'impulsions. Valve Fault Alrm Vol Spécifiez le volume de débit d'additif qui devra s'accumuler avant qu'une alarme d'erreur de vanne d'additifs ne se déclenche. L'alarme se produit quand l'utilisation d'un additif est autorisée et qu'il s'écoule sans que le système n'ait commandé ce débit. C'est la seule condition d'alarme qui provoque l'arrêt de la pompe d'additif. Ce paramètre ne s'applique pas aux méthodes sans générateurs d'impulsions. Over Inject Vol Ce paramètre vise à assurer que la livraison d’additif soit à l’avance chaque fois qu’un chargement échoue. Au démarrage du chargement il y aura immédiatement un certain nombre d’injections dépendant du nombre introduit pour ce paramètre. Si on introduit la valeur 1, il y aura une seule injection dès que l’on pousse sur Start. Au cours du reste du chargement, un surplus d’une injection se maintient. Quand le chargement est terminé, le volume d’additif livré équivaut à 100% du volume spécifié, plus le volume d’une injection. Si on doit mettre fin prématurément au chargement, la quantité correcte d’additif aura donc été livrée, plus un volume de 0,5 à 1 injection. Entrées acceptables de1,0 à 65. Voir figure 6.7. Effective Additive O ffset Additive Volume 3 Inject Vol. 1 Injection Surplus Additive Recipe % (Programmed) 2 Inject Vol. Additiv e Ov er Inj ection Graph 1 Inject Vol. 1/2 Inj Vol. 1/2 Inject Surplus exists: Injection Initiated 0 Product Volume Delivered Figure 6-7 Surinjection d’Additifs Chapitre 6 – Contrôle des additifs 200 Paramètre Description Creep Reset Time Par fluage du compteur d'additif, on entend n'importe quel volume qui passe par le compteur d'additif lorsqu'il y a commande de fermeture de vanne. Des volumes de fluage peuvent se présenter lorsque l'additif est autorisé ou non autorisé (voir la description du paramètre de temps de réinitialisation non autorisé). On peut s'attendre à une faible quantité de fluage en raison de chocs dans la conduite. Le débit ne s’enclenche pas nécessairement, mais un léger mouvement du compteur en raison du choc de conduite peut le faire percevoir comme tel au système. Avec le temps, le volume de fluage accumulé peut passer à une valeur occasionnant une alarme (fluage du compteur ou erreur de vanne). Pour éviter les alarmes intempestives, cette valeur accumulée doit être réinitialisée périodiquement. Le paramètre temps de réinitialisation du fluage fixe l'intervalle de réinitialisation en secondes. Si le volume du fluage du compteur spécifié dans le volume d'alarme du fluage du compteur se produit pendant la période de temps fixée par ce paramètre, une alarme de fluage du compteur s'active. Cette fonction ne réinitialise pas le totalisateur de fluage observable sur l'écran "Additive Views & Inquiry". Unauth Reset Time Temps de réinitialisation (débit) non autorisé: le débit non autorisé d'additif est n'importe quel volume qui passe au travers du compteur d'additif lorsque l'additif n'est pas autorisé. On peut s'attendre à une faible quantité de détection du flux non autorisé en raison de chocs dans la conduite. Le flux ne se produit pas nécessairement, mais un léger mouvement du compteur en raison du choc de conduite peut le faire percevoir comme tel au système. Avec le temps, le volume non autorisé accumulé peut atteindre une valeur provoquant une alarme (flux non autorisé). Pour éviter les alarmes inutiles, cette valeur accumulée doit être réinitialisée périodiquement. Le paramètre de temps de réinitialisation non autorisé fixe l'intervalle de réinitialisation en secondes. Si le volume du débit non autorisé spécifié dans le paramètre de volume du débit non autorisé se produit pendant la période de temps fixée par ce paramètre, une alarme de débit non autorisé s'active. Cette fonction ne réinitialise pas le totalisateur de débit non autorisé dans l'écran "Additive Views & Inquiries". Max Piston Throw Time Lorsqu’on utilise des injecteurs à piston, ce paramètre indique à la logique de commande des additifs le temps nécessaire pour permettre à l'injecteur d'achever sa course d'injection. Pump Start Alrm Time Si un signal de statut de pompe n'a pas été reçu depuis la pompe d'additif pendant la période de temps indiquée par ce paramètre, l'alarme de statut de la pompe de l'additif s'active. Introduisez le temps en secondes. Pour désactiver cette alarme, introduisez zéro. Meter Creep Alrm Vol Introduisez le volume du fluage du compteur qui déclenche une alarme de fluage de compteur. Si le volume du fluage du compteur indiqué à ce paramètre s'accumule pendant la période de temps indiquée au paramètre de temps de réinitialisation du fluage, une alarme de fluage du compteur se produit. Le fluage du compteur peut indiquer qu'il y a une petite fuite dans la vanne ou peut être le résultat d'un choc de conduite excessif. Le fluage du compteur signifie que le liquide passe devant le compteur alors que la vanne est supposée fermée. Remote Calibration Activez ce paramètre si l'additif sélectionné doit être actif sur la liste de sélection de l'étalonnage d'additif à distance. Ce paramètre n'est pertinent que si la fonction d'étalonnage d'additif à distance doit être utilisée et que des boutons de contrôle à distance ont été installés. B.V. Open Alrm Time Temps d'alarme d’ouverture de la vanne d'arrêt. Ce paramètre précise le temps, en secondes, pour que la vanne d'arrêt de l'additif s'ouvre. Si une vanne d'arrêt d'additif utilise un signal de rétroaction, une alarme se produit si cette exigence n'est pas satisfaite pendant cette période de temps. Si un signal de rétroaction n'est pas utilisé et si la valeur de ce paramètre dépasse zéro, l'ouverture de la vanne d'arrêt est retardée jusqu'à ce que le temps d'alarme d'ouverture de la vanne d'arrêt se soit écoulé. Chapitre 6 – Contrôle des additifs 201 Paramètre Description BV Close Alrm Time Spécifie le temps, en secondes, pour que la vanne d'arrêt de l'additif se ferme. Si cette vanne utilise un signal de rétroaction, une alarme se produit si ce critère n'est pas satisfait sur cette période de temps. Pump Stop Delay Introduisez le temps, en secondes, pendant lequel la pompe d'additif doit continuer à fonctionner après la fin du lot. Lorsque ce paramètre est fixé à zéro seconde, la pompe continue à fonctionner jusqu'à ce que le lot s'achève. Pour la plupart des configurations, la livraison d'additif se termine avant le lot de façon à concilier un débit d'additif de la conduite de produits. Si plusieurs bras de chargement effectuent une demande au niveau du contact de la pompe d'additif, ce contact reste actif tant qu'un bras de charge appelle cet additif. Flush Pump Run Time Le signal de la pompe de purge sert à faire fonctionner une pompe qui rince l'orifice d'une vanne d'arrêt. La vanne d'arrêt et la pompe de purge sont généralement utilisées pour des applications à colorant rouge. Le signal de pompe de purge s'enclenche lorsque la quantité nécessaire de colorant a été livrée et que la commande de fermeture de la vanne d'arrêt est passée. La pompe de purge fonctionne pendant toute la durée spécifiée par ce paramètre. Introduisez une valeur en secondes. Meter Flushed Ce paramètre doit être activé si le compteur d'additif se trouve sur le parcours de la purge. Lorsqu'il est activé, les impulsions du compteur d'additif sont ignorées pendant une période spécifiée au paramètre du temps de fonctionnement de la pompe de purge". Consultez le manuel de l’utilisateur pour de plus amples détails en matière d'exécution de la purge d'additif sur ce type de configuration. Voyez aussi la description du paramètre d’électro-aimant purgé. Solenoid Flushed Ce paramètre doit être activé si la valve d'injecteur d'additif se trouve sur le parcours de la purge. La valve d'injecteur d'additif est maintenue ouverte pendant une période spécifiée par le paramètre du temps de fonctionnement pompe de purge. Consultez le manuel de l’utilisateur pour de plus amples détails en matière d'exécution de la purge d'additif sur ce type de configuration. W&M Count Alarm Promo Si cet additif doit être annulé au niveau des Poids et Mesures, en mettant cette valeur sur “non-zéro”, vous passez outre de la valeur configurée dans les réglages d’alarme d’additif. W&M Mode Alarm Reset Si le compte W&M Alarm Promo Count est de non-zéro, la valeur de cet additif est supérieure à celle de la configuration du réglage de l’alarme des additifs. Flush Pump Run FCM# Ce paramètre permet de sélectionner un port de sortie donnant un signal de sortie qui active la pompe de purge. Close Blk Val FCM# #FCM fermeture de la vanne d'arrêt. Ce paramètre permet la sélection d'un FCM et du port qui produit un signal de sortie pour fermer la vanne d'arrêt d'un additif. Cette commande de fermeture de la vanne se produit lorsque la quantité restante du chargement atteint la valeur indiquée au paramètre du volume de fermeture depuis la fin (Shutoff volume From End) pour permettre à l'additif ou au colorant de s'écouler depuis la conduite. Chapitre 6 – Contrôle des additifs 202 Paramètre Description Blk Val Status FCM# #FCM statut de la vanne d'arrêt. Ce paramètre permet la sélection d'un port qui recevra un signal d'entrée. Le signal d'entrée représente le statut de la vanne d'arrêt d'additif, indiquant si elle est ouverte ou fermée. Lorsque la vanne d'arrêt est fermée, un contact externe attaché à la valve se ferme, donnant un signal de statut à l'entrée. Lorsque la vanne d'arrêt est ouverte, le contact externe est également ouvert, supprimant le signal de statut de l'entrée. Lorsque la vanne d'arrêt a reçu une commande d'ouverture, l'absence d'un signal à l'entrée indique que la vanne s'est ouverte. Si le signal "fermé" (closed) est toujours présent quand le retard d'ouverture de la vanne d'arrêt s'est écoulé, une alarme d'erreur de vanne d'arrêt se produit. Lorsque la vanne d'arrêt a reçu une commande de fermeture, la présence du signal de statut à l'entrée indique que la vanne s'est fermée. Si le signal "fermé" n'a pas été détecté au moment où le retard d'ouverture de la vanne d'arrêt s'est écoulé, une alarme d'erreur de vanne d'arrêt s’enclenche. Open Blk Val FCM# #FCM ouverture de la vanne d'arrêt. Ce paramètre permet la sélection d'un port qui produit un signal de sortie pour ouvrir la vanne d'arrêt d'un additif. Cette sortie donne un signal d’ouverture de la vanne d'arrêt dès que le bouton de démarrage a été poussé. Le signal se supprime lorsque la quantité restante du chargement atteint la valeur indiquée au paramètre du volume de fermeture depuis la fin (Shutoff volume From End) pour permettre à la vanne de se fermer et à l'additif ou au colorant de s'écouler depuis la conduite. Lorsque le MultiLoad II commande à la vanne de se fermer, le signal d'ouverture de la vanne d'arrêt disparaît. Test Button FCM# Ce paramètre permet de sélectionner un port recevant un signal d’entrée pour le bouton de test d’injection utilisé pendant l’étalonnage. Pump Run FCM# Permet de sélectionner un port donnant un signal de sortie pour enclencher la pompe d’additif. Pump Kill FCM# Permet la sélection d'un port qui donne un signal de sortie pour arrêter la pompe d'additif. Le signal d'arrêt de la pompe n'est actif que lorsque le système subit une alarme d'erreur de vanne d'additif. Pump Status FCM# Permet la sélection d'un port qui accepte un signal d'entrée, signal qui vérifie si la pompe d'additif fonctionne ou pas. Si ce signal est absent pendant la période indiquée au paramètre du temps d'alarme du statut de la pompe, une alarme du statut de la pompe de l'additif se produit. Alarm Out FCM# Donne un signal de sortie si l'additif possède une alarme active. Ce paramètre sélectionne le port de sortie attribué pour signaler une condition d'alarme de niveau d'additif. Authorized FCM# Donne un signal de sortie si le débit de l'additif a été autorisé par l'insertion de la carte du chauffeur. Ce paramètre sélectionne le port de sortie attribué pour signaler la condition. Permiss FCM# Le paramètre d’autorisation FCM# permet de sélectionner un port recevant un signal d’entrée représentant l’état d’autorisation de l’additif. S’il n’y a pas de signal au moment de l’autorisation ou s’il est perdu en cours de livraison, la procédure est interrompue et une alarme de niveau d’additif autorisé se déclenche. Permiss Out FCM# Ce paramètre permet de sélectionner un port qui produit un signal de sortie indiquant que toutes les exigences de permissions d'additifs sont en ordre. Chapitre 6 – Contrôle des additifs 6.7 203 ETALONNAGE D’ADDITIFS Deux méthodes d'étalonnage d'additif sont disponibles avec le MultiLoad II : "additive Cal.", qui s'adresse à un additif à la fois, et "Remote Calibration" (étalonnage à distance), qui permet le réglage simultané de plusieurs additifs pour l'étalonnage. La fonction d'étalonnage à distance est traitée au point suivant la fonction d'étalonnage standard. 6.7.1 FONCTION D’ETALONNAGE D’ADDITIFS La fonction d'étalon(nage) standard permet à l'utilisateur d'étalonner un additif à la fois. Les injections d'essai peuvent être amorcées par un bouton-poussoir facultatif installé sur le panneau d'additif ou en appuyant sur un bouton du clavier du MultiLoad II. Pour utiliser un bouton-poussoir, configurez le FCM # du bouton de test du paramètre d’additif pour indiquer le port d’entrée connecté au bouton-poussoir. Si le paramètre #FCM Test Button est désactivé, le système s’attend à ce que l’on pousse sur un bouton du clavier du MultiLoad II. Pour entamer la procédure d’étalonnage de l’additif: 1. A partir du menu de configuration, sélectionnez Additive Cal. 2. L’écran de sélection des valeurs prédéfinies s’affiche. 3. Sélectionnez l’additif désiré. Error! Reference source not found. Chapitre 6 – Contrôle des additifs 204 4. L’écran d’étalonnage de l’additif s’affiche pour l’additif sélectionné: Error! Reference source not found. 6.7.2 FONCTION D’ETALONNAGE AUTOMATIQUE L’écran ci-après illustre les débitmètres standards d’additifs. Les écrans pour les compteurs de type piston sont légèrement différents. La séquence présente des injections amorcées au MultiLoad II. 1. A partir de l’écran d’étalonnage des additifs, sélectionnez Automatic Calibration Function. 2. L’écran de l’étalonnage des additifs s’affiche. Error! Reference source not found. (Remarque: si le bouton d’essai est activé, le texte ‘Hold Test Button To Inject Now!’ (Maintenez le bouton d’essai pour injecter maintenant) apparait au lieu de ‘Press NEXT Key to Inject Now!’ (Appuyez sur la touche pour injecter maintenant !) 3. Placez le verre de mesure pour recueillir les injections d’additif et ouvrez le port de test sur l’injecteur. 4. Appuyez sur NEXT ou sur le bouton d’essai. 5. La première injection est faite. Chapitre 6 – Contrôle des additifs 205 6. Le nombre d’impulsion s’affiche ainsi que le volume débité, en gallons et en CC (entre parenthèses). Error! Reference source not found. 7. Repoussez sur la touche NEXT pour provoquer une nouvelle injection. Continuez à injecter jusqu’à ce que le volume dans le verre soit suffisant pour que vous puissiez lire la mesure. Error! Reference source not found. 8. Enregistrez le volume recueilli dans le verre. 9. Appuyez sur EXIT. Chapitre 6 – Contrôle des additifs 206 10. Un message ‘Please Wait’ (Attendez S.V.P.) s’affiche brièvement, suivi de l’écran ci-dessous: PRE #1 ADTV #1 (Adtv 001 ) CALIBRATE Delivered Vol: 0.100( 379cc) [1]Beaker Vol: 0.000000 [2]Beaker Vol CCs: 0.000 Meter Pulses: 261 Additive Mtr K-Factr: 2600 11. Pour introduire le volume recueilli dans le verre en millièmes de gallons, appuyez sur 1. Exit 12. Pour introduire le volume recueilli dans le verre en CC, appuyez sur 2 (comme ci-dessous). PRE #1 ADTV #1 (Adtv 001 ) CALIBRATE Delivered Vol: 0.100( 379cc) [1]Beaker Vol: 0.000000 [2]Beaker Vol CCs: █ Meter Pulses: 261 Additive Mtr K-Factr: 2600 Exit Chapitre 6 – Contrôle des additifs 207 13. A l’invite _ , introduisez le volume d’additif recueilli dans le verre puis appuyez sur Enter. (Dans l’exemple ci-après, on a introduit la valeur 405) Error! Reference source not found. La valeur « Beaker Vol » (volume verre) reflète le volume dans le verre en millième de gallon et le nouveau facteur de compteur d’additif s’affiche sur la dernière ligne. 14. 14. Appuyez sur Enter pour sauvegarder le nouveau facteur de compteur d’additif. 15. Ceci vous ramène à l’écran d’étalonnage des additifs (Additive Calibrate) qui affiche le nouveau facteur de compteur d’additifs. Error! Reference source not found. Ce nouveau facteur est maintenant fonctionnel. 16. Appuyez sur EXIT pour sortir de l’écran d’étalonnage des additifs. Tous les volumes d’additifs livrés au cours du processus d’étalonnage s’ajoutent au Unauthorized Totalizer” de l’additif testé. Chapitre 6 – Contrôle des additifs 208 ETALONNAGE D’ADDITIF AVEC INJECTEURS DE TYPE À PISTON 6.7.3 Error! Reference source not found. Comme indiqué précédemment, les écrans d‘étalonnage pour les injecteurs de type à piston sont légèrement différents des écrans utilisés pour les injecteurs de débitmètre d’additifs. La procédure est toutefois pareille. Error! Reference source not found. Voici un écran-type pour un injecteur de type piston après étalonnage. Remarquez que les trois derniers champs (Piston Cycles, Additive Vol/Inject et Vol/Inject Cal Factr) sont spécifiques au type de piston ou d’injecteur. Paramètre Description Beaker Vol Volume recueilli dans le verre affiché en millième de gallon. Beaker Vol CCs Volume recueilli dans le verre affiché en cc. Piston Cycles Nombre de courses de piston utilisées pour l’étalonnage. Additive Vol/Inject Le paramètre du volume d'additif par injection s’applique à toutes les méthodes d'additif. S’il s’agit d’un système à piston, avec ou sans rétroaction, introduisez le volume du cylindre étalonné comme spécifié par le fabricant ou le service d'étalonnage. Lorsque la méthode d'additif implique un piston et un générateur d'impulsion à débitmètre, introduisez le volume du cylindre. Vol/Inject Factr Cal Ce facteur corrige le volume du cylindre calibré au volume brut mesuré réellement au cours de l’étalonnage d'additif. Si un compteur d'additif est impliqué, avec ou sans système à piston, réglez le paramètre sur 1,0000. Chapitre 6 – Contrôle des additifs 6.8 209 CALCUL DU VOLUME OU DE L’INJECTION D’ADDITIF Cette fonction est accessible depuis l'écran d'étalonnage d'additif. La fonction est en fait un calculateur qui peut aider l'utilisateur à déterminer l'étendue optimale du volume/injection sur base de données connues telles que le pourcentage de la recette d'additif. Les calculs servent à trouver une quantité de volume/injection qui ne force pas l'injecteur ou n’occasionne pas de minutage d’injections trop écartées les unes des autres. Le calcul qui en résulte pour le volume/injection peut être automatiquement introduit pour être utilisé par le système. Le réglage du volume par injection détermine la fréquence des injections. Si le réglage du volume par injection est trop bas, l'injecteur fonctionne trop fort. Si les injections sont trop espacées, il s’agit d’un réglage trop important du volume par injection, ce qui peut affaiblir la proportion instantanée d'additif/produit. 1. Pour utiliser cette fonction, mettez “Calculate Additive Vol/Inject” en surbrillance et appuyez sur Enter. PRE #1 ADTV #1 (Adtv 001 ) CALIBRATE Automatic Calibration Function Review Last Calibration Data Calculate Additive Vol/Inject Additive Vol/Inject: 0.0200 Additive Mtr K-Factr: 2600 Additive Mtr Factor: 1.0000 2. L’écran suivant s’affiche: Next Prev 001 Exit ) Enter PRE #1 ADTV #1 (Adtv CALCULATE [1]Additive Percentage: [2]Additive Vol Per 1000: [3]Additive Vol Per 1000: cc [4]Additive Pacing Rate: 40.0 Additive Vol/Inject: Additive Vol/Inject: cc Enter=Save Exit 3. Si vous connaissez le pourcentage de la recette d’additif, appuyez sur le bouton 1 et introduisez le pourcentage. Les valeurs calculées apparaissent dans les autres champs. Chapitre 6 – Contrôle des additifs 210 Dans l’exemple, on a introduit un pourcentage de 0,05. Le second champ montre le volume d’additif généré par un chargement de 1000 unités de volume. PRE #1 ADTV #1 (Adtv 001 ) CALCULATE [1]Additive Percentage: 0.05000 [2]Additive Vol Per 1000: 0.5000 [3]Additive Vol Per 1000: 1892cc [4]Additive Pacing Rate: 40.0 Additive Vol/Inject: 0.02000 Additive Vol/Inject: 75.71cc FigureEnter=Save 6-8 CalculExit de Vol/Inj Le troisième champ montre combien de centimètres cubes d'additif sont livrés dans 1000 gallons. Ce champ n'est valable que si le produit principal est livré en gallons. Le quatrième champ montre le rythme qui en résulte, c’est-à-dire le nombre de fois qu'une injection se produit sur base du pourcentage de la recette qui a été introduit. Dans l'exemple, une injection se produit toutes les 40 unités de volume livré. Si la livraison est en gallons, la valeur 40 entraîne souvent un taux d'injection agréable et modéré. Avec d'autres unités que les gallons, introduisez une mesure équivalant à 40 gallons dans le champ du rythme. Le calcul du vol/injection devrait fournir un taux d'injection modéré. Après le rythme, vient le volume calculé par injection. Cette valeur doit être utilisée au moment de la configuration de l'additif. Appuyez sur Enter pour valider cette valeur pour l'additif sélectionné. PRE #1 ADTV #1 (DYE )CALCULATE [1]Additive Percentage: 0.05000 [2]Additive Vol Per 1000: 0.5000 [3]Additive Vol Per 1000: 1892cc [4]Additive Pacing Rate: 40.0 Additive Vol/Inject: 0.02000 Additive Vol/Inject: 75.71cc Enter=Save Exit Chapitre 6 – Contrôle des additifs 6.9 211 ETALONNAGE D’ADDITIF A DISTANCE La fonction d’étalonnage d’additif à distance permet au technicien de sélectionner à l'avance tous les additifs évalués lors d'une session d'étalonnage. Les injecteurs peuvent être évalués les uns après les autres sans devoir revenir au MultiLoad II pour introduire les données. Les volumes observés d'additif sont introduits en une fois quand tous les échantillons ont été mesurés et enregistrés. Les injections doivent être amorcées à l’aide des bouton-poussoirs sur les panneaux d'additif. Pour assigner un bouton-poussoir qui se trouve sur le panneau d'additif, allez au menu d'additif et sélectionnez "#FCM Test Button". Sélectionnez un port d'entrée qui assigne le bouton-poussoir au port FCM. Cela doit se faire pour chaque additif évalué avec la fonction d’étalonnage d’additif à distance. 1. Pour entamer la procédure d'étalonnage, entrez dans le mode de programme et sélectionnez "Configuration" à partir du menu principal. 2. Sélectionnez Remote Adtv Cal et poussez sur Enter. C O N F I G U R A T I O N Communication Network RCU General Setup RCU Setup Equipment Setup Alarm Setup Products Additive Cal. Remote Adtv Cal. Access ID's Custom Logic Customer Logo Setup M E N U 3. Le menu “Remote Additive Calibration” s’affiche: Next Prev Exit Enter 4. Mettez « Select additives » en surbrillance et appuyez sur Enter. REMOTE ADDITIVE CALIBRATION Select Additives Collect Samples Check Delivered Next Prev Exit Enter Chapitre 6 – Contrôle des additifs 212 5. L’écran de sélection des additifs s’affiche. SELECT ADDITIVES FOR REMOTE CALIBRATION P#1 A#1 Adtv 001 P#1 A#2 Adtv 002 : : ENABLED ENABLED Prev Exit 6. Sélectionnez les additifs à tester dansNext la session en cours. ! Enter Si plusieurs additifs sont attribués au même bouton de test, assurez-vous qu’un seul est activé; sinon, les autres pourraient injecter quand vous poussez sur ce bouton. 7. Appuyez sur EXIT quand vous avez sélectionné tous les additifs désirés. Vous revenez alors au menu de calibrage des additifs à distance. 8. Sélectionnez ‘Collect Samples’ (Récolte d’échantillons). REMOTE ADDITIVE CALIBRATION Select Additives Collect Samples Check Delivered 9. Le technicien est invité à retirer la clé du programme pour verrouiller le clavier du MultiLoad II (facultatif). En entrant dans cet écran, tous les additifs activés au stade précédent sont maintenant prêts pour l’étalonnage. Next Prev Exit et Enter Les contacts de pompe d’additifs appropriés sont activés le restent jusqu’à ce que vous sortiez de l’écran. Chapitre 6 – Contrôle des additifs 213 Error! Reference source not found. 10. Choisissez un des additifs activés à évaluer. L'ordre d'évaluation importe peu. Placez un récipient au premier point d'essai pour recueillir l'additif injecté. Poussez le bouton-poussoir d'essai une fois par injection désirée. Par exemple, s’il faut cinq injections pour recueillir un volume mesurable, poussez et maintenez le boutonpoussoir d'essai enfoncé jusqu'à ce que la cinquième injection commence. 11. Lorsque vous avez recueilli assez d'additif, enregistrez les résultats mesurés. Continuez avec l'additif suivant. Placez un récipient au point d'essai de l'additif suivant à évaluer et utilisez le bouton-poussoir d'essai de cet injecteur pour recueillir un échantillon mesurable. Enregistrez les résultats. Continuez à recueillir des échantillons et à enregistrer les résultats jusqu'à ce que tous les injecteurs d'additifs aient été évalués. Il n'est pas nécessaire d'évaluer tous les additifs qui ont été activés à l'étape "Sélection d'Additifs". 12. Après avoir testé tous les injecteurs, retournez au MultiLoad II et débloquez son clavier avec la clef de programme, si nécessaire. Poussez sur la touche de Exit pour continuer. Error! Reference source not found. Chapitre 6 – Contrôle des additifs 214 13. Dans le menu d’étalonnage à distance des additifs, sélectionnez l’option de contrôle de livraison « Check Delivered ». L’écran de contrôle d’additif livré “Check Delivered Additive” s’affiche: CHECK DELIVERED ADDITIVE P#1 A#1 Adtv 001 0.100( 379cc) P#1 A#2 Adtv 002 (None Delivered) Next Prev Exit Enter 14. Le volume mesuré par chaque injecteur s’affiche. Sélectionnez un des additifs testés. L’écran de détail des additifs sélectionnés s’affiche. PRE #1 ADTV #1 (Adtv 001 ) CALIBRATE Delivered Vol: 0.100( 379cc) [1]Beaker Vol: 0.000000 [2]Beaker Vol CCs: 0.000 Meter Pulses: 261 Additive Mtr K-Factr: 2600 Exit Chapitre 6 – Contrôle des additifs 215 15. Appuyez sur 2 et encodez la quantité mesurée d’additif recueilli en CC puis appuyez sur Enter (dans l’exemple ci-dessous, nous utilisons 405 CC). PRE #1 ADTV #1 (Adtv 001 ) CALIBRATE Delivered Vol: 0.100( 379cc) [1]Beaker Vol: 0.106990 [2]Beaker Vol CCs: 405.000 Meter Pulses: 261 Additive Mtr K-Factr: 2600 New Additive Mtr Factor: 1.0658 Enter=Save Exit 16. Un nouveau coefficient de mesure d’additifs (ou un nouveau facteur d’étalonnage pour le cylindre de type à piston) se calcule automatiquement. Les valeurs sur l’écran changent et reflètent le volume recueilli réel. 17. Appuyez sur Enter pour activer le nouveau facteur et revenez à l’écran de contrôle des additifs livrés où vous sélectionnez un autre additif à étalonner. 18. Quand tous les additifs ont été étalonnés, appuyez sur la touche Exit jusqu’à ce que vous sortiez du mode programme. Le/s nouveau(x) facteur(s) de mesure d’additif ou le(s) nouveau(x) facteur(s) d’étalonnage du cylindre est/sont maintenant fonctionnel(s). Tous les volumes d’additifs livrés au cours de la procédure d’étalonnage s’ajoutent au totalisateur non autorisé d’additif d’essai. Chapitre 6 – Contrôle des additifs 6.10 216 ECRAN DE STATUT D’ADDITIF Pendant l'opération, un écran de statut de l'additif est disponible pour chaque valeur prédéfinie. L'écran de Statut d'Additif, tel que représenté ci-dessous, montre tous les additifs associés à la valeur prédéfinie. Les additifs assignés à une valeur prédéfinie mais non utilisés pour la livraison en cours sont étiquetés "INACTIVE". Les additifs utilisés pour la livraison en cours sont étiquetés "READY" ‘(prêt). Lorsqu'une injection est commandée, cette indication se change en "INJECTING" (injection en cours) pendant un cycle d'injection. La colonne "RECIPE" (recette) conserve un total cumulé instantané de quantité d'additif dans le lot. La colonne "DEL" montre la quantité d'additif réellement livrée. Error! Reference source not found. Chapitre 6 – Contrôle des additifs 6.11 217 FONCTIONS DE PURGE D’ADDITIFS En général, plusieurs marques différentes d'additifs sont livrées par un bras de chargement simple. C'est pourquoi, la conduite principale de produit doit être purgée de ses additifs quand le chargement est terminé. La purge peut tout simplement se résumer à arrêter l’injection à un certain point du chargement et autoriser le produit restant à rincer la conduite d'additif à la fin de la livraison. Une autre méthode consiste à utiliser des pompes et vannes de purge pour les applications qui exigent une purge, telles que les opérations avec du colorant rouge. Le MultiLoad II possède des fonctions complémentaires permettant d’adapter le matériel qui a été conçu pour ces applications. 6.11.1 FONCTIONS DE PURGE DE BASE Pour purger la conduite, il est possible de programmer l'arrêt des injections d'additif à un volume de lot prédéterminé, permettant ainsi au volume restant dans le chargement de faire sortir l'additif demeurant dans la ère conduite. Souvent, il suffit d'arrêter la livraison d'additif à la 1 étape de déclenchement du cycle de livraison puisque le volume de chargement restant à ces étapes de déclenchement dépasse souvent le volume présent entre le point d'injection additif et la fin du bras de chargement. Trois paramètres doivent être configurés pour régler une purge d'un additif simple. Figure 6-9 Cycle de purge de base Volume Dernière Injection Depuis la Fin =200 gal. 600 Volume Cible d’Additif Taux du Flux (gpm) Vol. 1ère Etape de Déclenchement 200 gal. Volume d’Arrêt Depuis la Fin =150 gal. lum Vo 100 e it if dd d’A é livr dé Vol. Purge Min =150 gal. 1000 500 200 Volume de Chargement restant (gal.) 0 Chapitre 6 – Contrôle des additifs Last Injection volume From End - Volume de la Dernière Injection Depuis la Fin - Ce paramètre avertit le système qu'il s'approche d'un point où tout l'additif doit être livré pour le chargement. Déterminez le volume ère présent entre le point d'injection et la fin du bras de chargement. Si le volume de la 1 étape de déclenchement correspond à plusieurs fois le volume qui existe entre le point d'injection et la fin du bras de chargement, ère introduisez une valeur égale au volume de la 1 étape de déclenchement. Lorsque le volume restant dans le chargement est égal au volume de la dernière injection depuis la fin, le système commence son injection finale pour terminer la demande en additif du chargement. Ce paramètre doit être réglé sur un nombre plus élevé que le volume spécifié au paramètre Shutoff Volume From End (volume d’arrêt depuis la fin). Shutoff volume From End - Volume d'Arrêt Depuis la Fin - Lorsque le volume restant dans le chargement atteint la valeur introduite pour « Shutoff Volume From End », la livraison d'additif cesse, indépendamment de la demande restante. Si c paramètre est fixé à 150 gallons, la livraison d'additif s'arrête lorsqu'il y aura 150 gallons à livrer. Le volume de produit restant débarrassera la conduite des restes d’additif. Line Flush Min Vol – Vol. Min Purge de Conduite - Réglez ce paramètre pour garantir la livraison du volume minimum exigé de purge. Si le chargement est interrompu avant qu’une quantité suffisante de produit n’ait purgé la conduite, une alarme de purge s'active, prévenant ainsi que la purge n’est peut-être pas suffisante. Presque tout au long du cycle de livraison, la proportion additif/produit se trouve dans les limites de la recette spécifiée. Lorsque l'injection finale se produit, avant d'atteindre le volume spécifié au paramètre " Shutoff Volume From End ", le chargement est légèrement suralimenté. Au moment où le chargement est terminé, la proportion additif/produit a atteint sa cible. 218 Chapitre 6 – Contrôle des additifs 6.11.2 219 TECHNIQUES DE PURGE DE COLORANT Chargement Frontal de Colorant Le cycle de purge peut être optimisé en injectant toute la demande en colorant du chargement au tout début du cycle de livraison. La purge se produit pour la majorité du chargement ; le chargement est suralimenté pendant quasi toute la livraison. Le Volume de la Dernière Injection Depuis la Fin peut être réglé sur un nombre égal à la quantité prédéfinie maximale autorisée pour que l'injection finale se produise dès que le lot a commencé. Le Volume d'Arrêt Depuis la Fin doit être réglé sur un volume inférieur au Volume de la Dernière Injection Depuis la Fin. Il peut être nécessaire de faire plusieurs essais avec cette valeur. Trouvez une gamme de volume qui donne assez de temps pour pouvoir livrer tout le colorant nécessaire. Envisageons l'exemple du schéma ci-dessous. Le Volume de la Dernière Injection Depuis la Fin est réglé sur 1000 gallons. Dans un lot de 1000 gallons, le colorant commence son injection finale immédiatement. Puisque le Volume d'Arrêt de l'additif est réglé sur 700 gallons, le volume entier de colorant exigé pour un lot de 1000 gallons doit être livré lors de la livraison des 300 premiers gallons. Cet exemple correspond peut-être à la réalité, selon la quantité de la recette et les caractéristiques hydrauliques du système. Le volume restant du chargement peut être utilisé pour rincer la conduite. Le volume minimal de purge peut être étendu à 700 gallons ou moins. Si le chargement est interrompu avant que la quantité minimale de volume de purge ne soit passée, une alarme de purge d'additif se produit. Shutoff Volume From End=700 gal. 600 Additive Target Volume Flow Rate (gpm) Additive Volume Delivered Last Injection Volume From End=1000 gal. 100 Min Flush Vol=700 gal. 1000 500 200 Remaining Load Volume (gal.) Figure 6-10 Chargement Frontal de Colorant 0 Chapitre 6 – Contrôle des additifs 6.11.3 220 VANNES D’ARRÊT DE POMPES DE PURGE Il existe dans le MultiLoad II une fonction permettant les vannes d’arrêt d’additifs et/ou les pompes de purge. Les vannes d'arrêt sont montées en aval du compteur d'additif et de la vanne d’injecteur. Le compteur d'additif et la vanne d’injecteur sont souvent intégrés dans un ensemble monobloc. La vanne d'arrêt se trouve en aval de l'ensemble monobloc et sert de sécurité contre les fuites de colorant dans l'ensemble, lorsque le système est au repos. La vanne d'arrêt s'ouvre quand on pousse sur le bouton de démarrage du MultiLoad II. La vanne d'arrêt se ferme dès que le volume spécifié au paramètre du volume d'arrêt depuis la fin est atteint. Les pompes de purge ont été conçues pour empêcher le colorant de coller à l'orifice de sortie de la vanne d'arrêt. Après l'injection finale et la fermeture de la vanne, la pompe de purge se déclenche pendant une période préprogrammée. La pompe de purge fait circuler le produit par l'orifice de la vanne d'arrêt, délogeant ainsi le colorant résiduel. Block Valve Red Dye Dye Pump M Mono-block Assembly P Flush Pump Product Flow P Dye-Point Assembly Figure 6-11 Injecteur Monobloc et Station de Coloration Pour configurer une vanne d’arrêt, recherchez le paramètre "Open Blk Val FCM#" dans la section relative aux additifs. Assignez un FCM et un port pour exécuter cette fonction. Pour les vannes qui nécessitent un signal de fermeture séparé et/ou un signal de statut de vanne, des ports peuvent également être assignés à ces fonctions. Pour configurer une pompe de purge, recherchez le paramètre Flush Pump Run FCM# pour y assigner un port. Déterminez le temps nécessaire pour une purge correcte et introduisez cette valeur, en secondes, dans le paramètre Flush Pump Run Time (temps de fonctionnement de la pompe de purge). Chapitre 6 – Contrôle des additifs 221 Systèmes de Purge à Vannes d’arrêt Multiples sur un Compteur d’Additifs Simple Si le compteur d'additif se trouve sur la trajectoire de la purge, il générera des impulsions pendant la phase de purge lorsque la livraison de l'additif est arrêtée. Dans un tel cas, activez le paramètre "Meter Flushed". Les impulsions du compteur seront dès lors ignorées pendant toute la phase de purge. Référez-vous au schéma. Add #1 Add #2 Additive Block Valve Add #1 P M Flush Pump Figure 6-12 Compteur d’Additif dans la Trajectoire de Purge Chapitre 6 – Contrôle des additifs 222 Si la vanne d'injecteur se trouve dans la trajectoire de la purge, comme dans le schéma ci-dessous, elle devra rester ouverte pendant la phase de purge. Dans ce cas, activez le paramètre "Solenoid Flushed". La vanne d'injecteur restera alors ouverte pendant la phase de purge. Add #1 Add #2 Additive Block Valve Add #1 P M Additive Meter Flush Pump Injector Valve Figure 6-13 Compteur d’Additif et Vanne d’Injecteur dans la Trajectoire de Purge Chapitre 7 – Réglage et fonctionnement du bras oscillant CHAPTER 7 (SAUF SMP) 223 REGLAGE ET FONCTIONNEMENT DU BRAS OSCILLANT VUE D’ENSEMBLE 7.1 Remarque: si le MultiLoad II SMP, il n’est pas possible de faire fonctionner le bras oscillant. Un bras oscillant est monté sur un îlot et peut tirer vers n'importe lequel des deux quais adjacents à l'îlot. Sur le MultiLoad II, on peut monter un maximum de 12 bras oscillants assignés à un quai. Un quai peut avoir n'importe quelle combinaison de bras de chargement fixes et oscillants, pourvu que le nombre total de bras de chargement par quai ne dépasse pas 12. Les deux quais desservis par un bras oscillant auront chacun un MultiLoad II. Les entrées et sorties associées à un débitmètre de bras oscillant et une vanne de régulation doivent se trouver sur des Modules de Contrôle du Flux communs au MultiLoad II des deux quais. Le FCM reçoit l'entrée du débitmètre et fait fonctionner la vanne de régulation ; il communique avec les RCU des deux quais, mais pas simultanément. Un interrupteur détecteur de bras oscillant et un relais sont utilisés pour établir une bonne liaison de communication entre le(s) FMC du bras oscillant et le RCU MultiLoad II du quai sélectionné. Chaque bras oscillant utilise deux interrupteurs détecteurs et un relais de commutation. Veuillez vous référer à la Figure 7.1. RCU-Bay 1 Primary RCU-Bay 2 Secondary Pr ess 'A' key t o Begi n. . . Pr ess 'A' key t o Begi n. . . To pt ec h Sy s t e m s , I nc . To pt ec h Sy s t e m s , Remot e Cont rol Uni t I nc . Remot e Cont rol Uni t 1 4 7 2 5 3 A Next 6 B 8 9 C Abor t 0 CL R D Ent er 1 2 3 4 5 6 B Pr evious 7 8 9 C Abor t 0 CL R D A Ent er Next Pr evious FCM 0 FCM 0 +24 vdc Swing Arm Detector Switch Bay 2 Swing Arm Detector Switch Bay 1 4-Wire RS-485 4-Wire RS-485 +24 vdc 14 1 9 2 10 3 11 4 12 13 Relay Coil +19.2-26.4 vdc 4-Wire RS-485 FCM 1 4-Wire RS-485 Swing Arm FCMs Figure 7-1 6 11 7 12 8 4-Wire RS-485 FCM 2 FCM 3 5 N.O. Relay Contacts Secondary Bay 4-Wire RS-485 N.C. Relay Contacts Primary Bay 9 10 FCM 3 Configuration du Bras Oscillant Chapitre 7 – Réglage et fonctionnement du bras oscillant 7.2 FONCTIONNEMENT DU BRAS OSCILLANT Quand un bras oscillant est présent et autorisé sur un quai, le MultiLoad II de ce quai l'affiche comme étant "Inactive". Les bras de chargement qui sont à l'état inactif sont des bras prêts à être utilisés. En regardant l'écran de chargement du MultiLoad II de l'autre quai, une alarme de bras oscillant sera affichée dans la colonne de statut du bras oscillant absent. L'alarme de bras oscillant ne peut être effacée et ne s'annule pas tant que le bras oscillant n’est pas revenu dans le quai et que sa présence n’a pas été détectée par le MultiLoad II. Quand un bras oscillant est absent d'un quai, tous les autres bras de chargement de ce quai peuvent être utilisés normalement. Un bras oscillant peut être renvoyé vers un quai sans que cela n'affecte en rien une transaction en cours. Par exemple, un chauffeur peut introduire sa carte dans un quai alors qu'un bras oscillant est utilisé au quai opposé. En outre, le chargement sur les autres bras de chargement du quai peut commencer sans la présence des bras oscillants d'un quai. Un bras oscillant absent peut être amené dans le quai à n'importe quel moment de la transaction. Lorsqu'un bras oscillant est renvoyé vers un quai alors qu'une transaction est en cours, l'alarme du bras oscillant est annulée automatiquement et son statut passera sur inactif. Dès ce moment, un produit peut être sélectionné et le chargement peut commencer comme pour n'importe quel bras de chargement du quai. De même, un bras oscillant peut être retiré d'un quai à n'importe quel moment en cours de transaction. Si le lot d'un bras oscillant s’arrête avant la livraison de la quantité prédéfinie et que le bras oscillant est retiré du quai, on considère le lot sur ce bras comme étant terminé. Si le bras est renvoyé vers le quai alors que la transaction est toujours en cours, il n’est pas possible de terminer le lot interrompu. Lorsque le bras retourne vers le quai, le statut indique que le lot est terminé. Ce lot doit être annulé en appuyant sur le bouton CLR avant qu'un autre lot ne puisse commencer sur ce bras. Si la transaction est terminée (retrait de la carte) sans le renvoi du bras et sans annulation manuelle du lot, ce lot est archivé avec tous les autres lots arrivés au quai pendant la transaction. 7.3 LOGIQUE DE RELAIS ET DE COMMUTATION Quand un bras oscillant est retiré d'un quai, le(s) FCM du bras oscillant(s) est/sont enlevé(s) du circuit de communication du RCU du MultiLoad II /FCM de ce quai. Normalement, lorsqu'un FCM n'arrive pas à communiquer avec un bloc de télécommande, une alarme d'échec de communication FCM se produit. Toutefois, puisque le(s) FCM est(sont) associé(s) à un bras oscillant, il se peut que ces FCMS perdent le circuit de communication de temps à autre. S'il se produit un réel échec de communication FCM dû à des circuits ouverts de courant ou une panne de la carte FCM, l'échec sera détecté par le RCU du MultiLoad II sur lequel se trouve l'interrupteur détecteur du bras oscillant actif. Le quai avec l'interrupteur détecteur du bras oscillant actif est supposé voir tous les FCM associés au bras oscillant. Lorsqu'un bras oscillant est en position neutre, les deux interrupteurs détecteurs du bras oscillant sont ouverts et la bobine relais coupée. Lorsque la bobine relais est coupée, les contacts normalement fermés (N.C.) relient les FCM du bras oscillant au RCU du MultiLoad II primaire. Puisque le bras oscillant est en position neutre et qu'aucun interrupteur détecteur de bras oscillant n'est fermé, les RCU du MultiLoad II primaire et secondaire affichent des alarmes de bras oscillant. Le déplacement du bras oscillant dans le quai primaire entraîne la fermeture de l'interrupteur détecteur du bras oscillant de ce quai, indiquant au RCU du MultiLoad II primaire que le bras oscillant est présent. La bobine relais reste coupée et les contacts N.C. continuent à relier les FCM du bras oscillant au RCU du MultiLoad II primaire. La fermeture de l'interrupteur détecteur du bras oscillant entraîne l'annulation de l'alarme du bras oscillant dans la RCU du MultiLoad II primaire. Le déplacement du bras oscillant dans le quai secondaire entraîne la fermeture de l'interrupteur détecteur du bras oscillant du quai secondaire. Le RCU du MultiLoad II secondaire s'attend alors à communiquer avec les FCM du bras oscillant. La fermeture de l'interrupteur détecteur du bras oscillant du quai secondaire active la bobine relais. Les contacts de relais normalement ouverts (NO) dans le quai secondaire se ferment, reliant les FCM du bras oscillant au circuit de communication du RCU du MultiLoad II secondaire. Les contacts NC du quai primaire sont ouverts puisque la bobine relais est activée, coupant la liaison de télécommunication entre les FCM du bras oscillant et le RCU du MultiLoad II primaire. 224 Chapitre 7 – Réglage et fonctionnement du bras oscillant 225 Broche de relais FCM quai primaire FCM bras oscillant FCM quai secondaire 1 J3-4 (TDB) X X 2 J3-3 (TDA) X X 3 J3-2 (RDB) X X 4 J3-1 (RDA) X X 5 X X J3-4 (TDB) 6 X X J3-3 (TDA) 7 X X J3-2 (RDB) 8 X X J3-1 (RDA) 9 X J3-4 (TDB) X 10 X J3-3 (TDA) X 11 X J3-2 (RDB) X 12 X J3-1 (RDA) X Bobine relais 13 X X standard Bobine relais 14 X X +24 VDC or 115 VAC par interrupteur bras oscillant 9 12 13 14 1 4 5 8 Relay Socket Swing Arm FCMs Communication Switching Relay Socket-Square D- Part # 8501NR45 Relay-Square D-Part # 8501RSD34V53 Figure 7-2 Socle de Relais FCM du Bras Oscillant Chapitre 7 – Réglage et fonctionnement du bras oscillant 7.4 CONFIGURATION DU BRAS OSCILLANT Exécutez les étapes suivantes pour configurer deux quais partageant un ou plusieurs bras oscillants. Désignez un des RCU du MultiLoad II de quai qui deviendra le RCU secondaire du bras oscillant. Peu importe le RCU choisi comme secondaire. Pour rendre un RCU secondaire, allez vers le RCU désigné et entrez dans le mode de programme. Sélectionnez le menu de configuration puis RCU Setup. Dans le menu de réglage du RCU, recherchez le paramètre Swing Arm Secondary (Bras Oscillant Secondaire). Activez-le puis quittez le mode de programme. Il nest pas nécessaire de régler à nouveau ce paramètre si des bras oscillants complémentaires doivent être ajoutés à un quai à l'avenir. Allez au RCU primaire et assurez-vous que le paramètre du bras oscillant secondaire est désactivé. Choisissez un des RCU du MultiLoad II de quai à configurer. Peu importe le quai qui est configuré en premier lieu. Dans le cas présent, configurons d'abord le RCU du MultiLoad II primaire. Entrez dans le mode de programme du RCU primaire. Sélectionnez le menu de Configuration puis Equipment Setup (réglage de l'équipement). Entrez dans le menu des valeurs prédéfinies. Sélectionnez une valeur prédéfinie qui sera configurée comme un bras oscillant. Dans le menu des valeurs prédéfinies, recherchez le paramètre Swing Arm #FCM. Appuyez sur Enter. Appuyez sur Next pour activer le paramètre. Introduisez un numéro qui représente le Module de contrôle du débit (FCM) qui contiendra le port d'entrée pour l'interrupteur détecteur du bras oscillant du quai. FCM choisi ne peut pas être un FCM consacré aux fonctions du bras oscillant ; il doit Le s'agir d'un FCM raccordé à un RCU du MultiLoad II simple. premier FCM sur le circuit de télécommunication (FCM 0) ne peut pas être un FCM de Le bras oscillant. Après avoir introduit un #FCM, introduisez un numéro qui représente le port d'entrée qui recevra le signal de l'interrupteur détecteur. Sélectionnez n'importe quel port disponible. Au besoin, configurez d'autres paramètres du menu valeurs prédéfinies. Toutes les assignations d'E/S au niveau des valeurs prédéfinies devront être attribuées à un des FCM du bras oscillant qui se trouve sur le circuit de télécommunication du RCU du MultiLoad II commun. Autrement, la même fonction d'E/S devra être configurée sur les deux RCU du MultiLoad II. Notez les assignations du port du FCM du bras oscillant, puisqu'elles seront utilisées dans le RCU du MultiLoad II secondaire. Quittez le menu des valeurs prédéfinies et retournez au menu d'installation d'équipement. Sélectionnez et rentrez dans le menu compteur. Sélectionnez la valeur prédéfinie assignée au bras oscillant configuré. Sélectionnez le Compteur #1. Le premier paramètre est le # du Module de contrôle du débit. Introduisez un numéro qui représente le FCM utilisé pour faire fonctionner la vanne régulation du bras oscillant et contrôler l'entrée du débitmètre du bras oscillant. Les ports 2 et 3 sont réservés, respectivement, pour les sorties amont et aval de l’électro-aimant. Le port 4 est réservé à l’entrée A d'impulsion de débitmètre. Le port 5 est disponible pour l'entrée B d'impulsions de débitmètre ou pour toute autre fonction associée au bras oscillant. Tous les autres ports inutilisés sur ce FCM doivent être réservés à l'utilisation exclusive de ce bras oscillant puisque le FCM ne sera pas disponible tout le temps pour chaque quai. Configurez d'autres paramètres nécessaires du menu compteur. Toutes les assignations d'E/S effectuées au niveau des compteurs devront être attribuées à un des FCM du bras oscillant qui se trouve sur le circuit de télécommunication du RCU du MultiLoad II commun. Autrement, la même fonction d'E/S devra être configurée sur les deux RCU du MultiLoad II. Notez les assignations du port du FCM du bras oscillant, puisqu'elles seront utilisées dans l'autre RCU du MultiLoad II secondaire. Quittez le menu compteur et retournez au menu d'installation d'équipement. Configurez les paramètres au niveau des composants pour le bras oscillant. Lorsque les pompes de composants du bras oscillant sont communes aux autres bras de chargement du quai, le statut et le fonctionnement de la pompe doivent être affectés à des FCM consacrés à un seul RCU du MultiLoad II. Cela signifie que les affectations d'E/S relatives à la pompe doivent être configurées sur les deux RCU du MultiLoad II. Toutefois, si une pompe de composants n'est nécessaire que pour le bras oscillant, il peut être plus efficace d'assigner les E/S relatives à la pompe aux ports FCM du bras oscillant. Le statut de la vanne d’arrêt et de l'ouverture de la vanne 226 Chapitre 7 – Réglage et fonctionnement du bras oscillant d’arrêt doit être affecté aux ports FCM du bras oscillant qui se trouveront sur le circuit de communication commun du RCU du MultiLoad II. Configurez les paramètres au niveau des additifs pour le bras oscillant. Le port de sortie qui signale l'injection et le port d'entrée qui reçoit les rétroactions de l'injecteur doivent être assignés à un FCM du bras oscillant. Configurez le paramètre # du module de contrôle du débit, introduisez un nombre qui représente un FCM du bras oscillant. Configurez le paramètre # du Port FCM sur un port disponible du FCM du bras oscillant. Consultez la section consacrée au réglage général des additifs au Chapitre 6 du Manuel de l'Utilisateur pour de plus amples instructions sur le choix du port d'additifs. Les boutons d'essai d'additifs utilisés pour l'étalonnage doivent également être assignés à un FCM du bras oscillant. Lorsque les pompes d'additif du bras oscillant sont communes aux autres bras de chargement du quai, le statut et le fonctionnement de la pompe doivent être affectés à des FCM consacrés à un seul RCU du MultiLoad II. Cela signifie que les affectations doivent être configurées sur les deux RCU. Toutefois, si une pompe d'additifs n'est nécessaire que pour le bras oscillant, il peut être plus efficace d'assigner les E/S relatives à la pompe au FCM du bras oscillant. Lorsque la configuration du RCU primaire est terminée, configurez les bras de chargement du RCU secondaire. Pour configurer les bras oscillants de l'unité secondaire, utilisez le même FCM et les mêmes attributions de port que pour le bras oscillant du quai primaire. ne faut pas qu’un bras oscillant dans le quai secondaire se serve du même numéro de valeur Ilprédéfinie que le quai primaire. Par exemple, si un bras oscillant a été assigné à la valeur prédéfinie #1 dans le quai primaire, ce même bras oscillant peut être assigné à la valeur prédéfinie #2 dans le quai secondaire. Pour le bras oscillant du quai secondaire, utilisez le même FCM et les mêmes attributions de port que le quai primaire. effectuer un essai de compteur, les facteurs de mesure résultants doivent être introduits Pour dans les deux RCU du MultiLoad II du quai. Pour configurer les quais de bras oscillants, n’activez PAS les fanions de bras oscillants dans TMS. Les quais de bras oscillants du MultiLoad II sont considérés comme des quais indépendants par TMS. 227 Chapitre 8 – Diagnostics CHAPTER 8 8.1 228 DIAGNOSTICS VUE D’ENSEMBLE Le MultiLoad II fournit des outils intégrés de diagnostic qui permettent à vos techniciens ou électriciens d'isoler les problèmes de câblage ou de matériel lors de divers essais. Les principales fonctions de diagnostic disponibles depuis le Menu Diagnostics et décrites dans ce chapitre sont : Error! Reference source not found. Card Reader (sauf SMP) Essai lecteur de carte. COM Loopback Teste les ports de communication de et vers le serveur (TMS) Network Test Teste la connexion réseau de et vers le serveur (TMS) Keypad Teste les différentes touches du clavier Display Teste le fonctionnement de l’affichage Unicode Teste le police de caractère de l’affichage FCM Com Communique le statut entre la carte E/S et les FCM PCM Com Communique le statut entre les PCM FCM Health Enregistre le nombre de temps morts et de communications perdues pour la carte E/S et les FCM. PCM Health Enregistre le nombre de temps morts et de communications perdues pour les PCMs. RCU Affiche/modifie les E/S au niveau du RCU, y compris le statut du commutateur à clé du programme et des poids et mesures. Bay Affiche/modifie les E/S au niveau du quai Preset Affiche/modifie les E/S au niveau des valeurs prédéfinies. Meters Affiche/modifie les E/S au niveau du compteur. Components Affiche/modifie les E/S/ au niveau des composants Additives Affiche/modifie les E/S au niveau des additifs Custom Logic Teste l’exécution de la logique personnalisée GPS Affiche le statut instantané détaillé du GPS. Ces fonctions sont étudiées dans leur ordre d’apparition au menu diagnostic. Chapitre 8 – Diagnostics 8.2 229 LECTEUR DE CARTE (SAUF SMP) Remarque: Si le MultiLoad II est un SMP ou ne possède pas d’installation pour lecteur de carte, ce test n’est pas d’application. Utilisez la fonction « Card reader » pour vérifier le fonctionnement du lecteur de carte et la carte de chauffeur. A partir du menu de diagnostic, sélectionnez Card Reader. Error! Reference source not found. L’écran Card Reader Test (test de lecteur de carte) s’affiche. Insérez une carte dans le lecteur et l’écran effectue une mise à jour après chaque lecteur de carte. Error! Reference source not found. Les données de diagnostic enregistrées sont: - Good Reads – Bonnes lectures – Nombre de lectures réussies de la carte. Cette valeur s’incrémente environ toutes les secondes quand une carte est insérée. - Card Pulls – Retraits de carte – Nombre de retraits de cartes du lecteur - Parity, LRC, Timeouts – Parité, LRC, Temps morts – Nombre d’occurrences d’une erreur de lecture particulière. Ces valeurs devraient rester à 0. - Pour les cartes de proximité HID 26-bit, 0=yy=0000000=xxxxxxxx=01 – Numéro de carte lu sur cette carte où yy représente le numéro de l’installation (00-99) et xxxxxxxx le numéro de la carte (00000000-00065535). - Pour les cartes de proximité HID 26-bit Corporate 1000, 0=yyyy=00000=xxxxxxxx=01 – Numéro de carte lu sur cette carte où yyyy représente le numéro de l’installation (00-4095) et xxxxxxxx le numéro de carte (00000000-01048575). Chapitre 8 – Diagnostics Pour les cartes de proximité formatées HID 37-bit H10320 , 0=yy=0000000=xxxxxxxx=01 – Numéro de carte lue par le lecteur où yy est le numéro de l’installation (Toujours 00) et xxxxxxxx le numéro de carte (00000000-99999999). A la lecture d’une carte TWIC, le test de lecteur de carte s’affiche. - - Error! Reference source not found. Les données de diagnostic enregistrées sont: 1111,2222,333333,4,5,6666666666788889 – TWIC Card FASC- Numéro lu sur la carte et où 1111 = Code de l’agence 2222 = Code du système 333333 = Numéro de légitimation 4 = Portée de la légitimation 5 = Légitimation individuelle 6666666666 = Identifiant de la personne (Utilisé comme numéro de carte dans la base de données « Access ID ») 7 = Catégorie organisationnelle 8888 = Identifiant organisationnel 9 = Association de la personne ou de l’organisme 230 Chapitre 8 – Diagnostics 8.3 231 LECTEUR IBUTTON (SAUF SMP) Remarque : Si le MultiLoad II est un SMP ou qu’il n’est pas muni d’un iButton, ce test n’est pas d’application. Utilisez la fonction iButton pour vérifier le fonctionnement de l’iButton et une carte chauffeur. A partir du menu DIAGNOSTICS, sélectionnez iButton Reader. D I A G N O S T I C S M E N U iButton Reader Meters COM Loopback Components Serial Ports Additives Network Test Custom Logic Keypad Display Unicode FCM Com PCM Com FCM Health PCM Health RCU Bay Preset Next Prev Exit Enter L’écran iButton Reader Test apparaît. Quand vous avez placé un iButton sur le lecteur, l’écran se remettra à jour à chaque lecture de l’iButton. iBUTTON DIAGNOSTICS Read Count: 00005 iButton ID: 000032AF532 Exit Clear Chapitre 8 – Diagnostics 8.4 232 ESSAI DE BOUCLAGE L’essai de bouclage - Loopback Test – sert à deux choses: - tester les capacités de transmission et de réception du port COM serveur sur le MultiLoad II. repérer les problèmes de communication entre le MultiLoad II et le serveur (TMS).A partir du menu DIAGNOSTIC MENU, choisissez COM Loopback (bouclage COM). Error! Reference source not found. L’écran d’essai de bouclage s’affiche: Error! Reference source not found. Chapitre 8 – Diagnostics Utilisation du bouclage pour évaluer la communication entre le RCU du MultiLoad et l'ordinateur TAS : 1. Poussez sur la touche 1 pour faire basculer Loopback sur ON. 2. Une fois sur ON, appuyez sur n'importe quelle touche sur le clavier du MultiLoad II pour faire transmettre ce caractère au port de série assigné au serveur. 3. Si les transmissions ne sont pas reçues par l'ordinateur TMS ou le coupleur optoélectronique, vérifiez que le MultiLoad II est capable de transmettre des données. Les utilisateurs TMS peuvent faire fonctionner l'utilitaire TMSLCOMM en mode de bouclage pour déterminer si les caractères sont reçus par l'ordinateur. Ou bien: le bouclage peut être défini pour transmettre un message de “test” en continu.. Appuyez sur la touche 1 pour faire basculer l'essai de bouclage sur AUTO. Utilisation du bouclage pour évaluer les capacités de transmission du MultiLoad II: 1. Au port de série du MultiLoad II, débranchez le câble de communication et court-circuitez les bornes suivantes: a. RS232 – RX to TX (ou) b. RS485 - RDA to TDA, RDB to TDB 2. Lorsque le bouclage est activé (ON), appuyez sur n'importe quelle touche du clavier du MultiLoad II pour faire apparaître ce caractère à l'écran du MultiLoad II, indiquant que le bouclage a réussi. Si le caractère n'apparaît pas à l'écran, le Port de Comm est peut-être mauvais. Quand l’essai est terminé, appuyez sur la touche 1 pour faire basculer le test de bouclage sur OFF. Mode automatique: En poussant une nouvelle fois sur la touche 1, vous vous retrouvez en mode automatique. Lorsque le mode automatique est activé (On) : a) La chaîne de caractères “TESTING…” est envoyée du port sériel hôte toutes les secondes. b) Chaque caractère reçu sur le port sériel hôte s'affiche à l'écran du MultiLoad II. 233 Chapitre 8 – Diagnostics 8.5 234 ESSAI DE PORT SERIEL L’essai de port sériel sert à vérifier le matériel du port sériel du MultiLoad II. Ce test offre au personnel d’entretien une méthode pour faire le bulletin de santé du port sériel avant de le renvoyer pour réparation chez Toptech. A partir du menu DIAGNOSTIC, sélectionnez Serial Ports. Error! Reference source not found. L’écran d’introduction de l’essai de port sériel s’affiche: Error! Reference source not found. Remarque: Pour effectuer cet essai, il faut placer un câble spécial de bouclage avec les connections reprises ci-dessus. Sans ce câble, l’essai échoue. Chapitre 8 – Diagnostics 235 Quand le câble est installé, appuyez sur Enter. L’écran d’essai du port sériel s’affiche et l’essai démarre. Error! Reference source not found. Appuyez sur Exit pour terminer l’essai. Chapitre 8 – Diagnostics 8.6 236 ESSAI RESEAU L’essai réseau sert à vérifier ou repérer la connexion du réseau entre le MultiLoad II et le serveur (TMS): A partir du menu DIAGNOSTICS, sélectionnez Network. Error! Reference source not found. L’écran d’introduction d’essai réseau s’affiche: Error! Reference source not found. Chapitre 8 – Diagnostics 237 Appuyez sur Enter. L’écran d’essai réseau s’affiche et l’essai démarre. Error! Reference source not found. Appuyez sur Exit pour terminer le test. Chapitre 8 – Diagnostics 8.7 238 ESSAI DE CLAVIER L’essai de clavier permet de vérifier le fonctionnement du clavier en testant les différentes touches. 1. A partir du menu DIAGNOSTICS, sélectionnez Keypad. D I A G N O S T I C S M E N U Card Reader Meters COM Loopback Components Serial Ports Additives Network Test Custom Logic Keypad Display Unicode FCM Com PCM Com FCM Health PCM Health RCU Bay Preset Next Prev Exit Enter 2. L’écran de test de clavier s’affiche. 3. Type: 1234567890 KEYPAD TEST Checksum Errors: 00000 Firmware Ver: 000 Heartbeat: Received: 59478 Missed: 00000 Keys Pressed: 1234567890 Exit CLeaR 4. Appuyez sur une touche que vous croyez défectueuse. 5. Si une touche fonctionne convenablement, le caractère s’affiche sur l’écran de diagnostic chaque fois qu’on appuie dessus. Si le caractère d’une touche n’apparaît pas sur l’écran quand on appuie dessus, ou apparaît plusieurs fois, il faut remplacer le clavier. 6. S’il y a un chiffre dans “Checksum Errors” ou dans “Missed”, il y a probablement un problème de clavier. Chapitre 8 – Diagnostics 8.8 239 ESSAI D’AFFICHAGE Utilisez cette fonction pour tester l’affichage du MultiLoad II. 1. A partir du menu Diagnostics, sélectionnez Display. D I A G N O S T I C S M E N U Card Reader Meters COM Loopback Components Serial Ports Additives Network Test Custom Logic Keypad Display Unicode FCM Com PCM Com FCM Health PCM Health RCU Bay Preset Next Prev Exit Enter 2. L’écran de test d’affichage apparaît: l’écran est testé par une barre de couleur, un test de signal de couleur rouge, un test de signal de couleur verte, un test signal de couleur bleu et plusieurs tests de polices de caractère. Si une couleur manque ou qu’un caractère s’affiche mal, il y a probablement un problème à l’affichage ou au câble d’affichage. Error! Reference source not found. 3. Appuyez sur Next ou Prev pour circuler manuellement à travers l’essai d’affichage. Appuyez sur Exit pour terminer l’essai. Chapitre 8 – Diagnostics 8.9 240 ESSAI UNICODE Utilisez cette fonction pour étudier les polices de caractères acceptées par Unicode. 4. A partir du menu Diagnostics, sélectionnez Unicode. Error! Reference source not found. 5. L’écran d’essai Unicode apparaît et se positionne sur la série de caractères Hiragana Unicode. U+4E00:一丁丂七丄丅丆万丈三上下丌不与丏 U+4E10:丐丑丒专且丕世丗丘丙业丛东丝丞丟 U+4E20:丠両丢丣两严並丧丨丩个丫丬中丮丯 U+4E30:丰丱串丳临丵丶丷丸丹为主丼丽举丿 U+4E40:乀乁乂乃乄久乆乇么义乊之乌乍乎乏 U+4E50:乐乑乒乓乔乕乖乗乘乙乚乛乜九乞也 U+4E60:习乡乢乣乤乥书乧乨乩乪乫乬乭乮乯 U+4E70:买乱乲乳乴乵乶乷乸乹乺乻乼乽乾乿 U+4E80:亀亁亂亃亄亅了亇予争亊事二亍于亏 U+4E90:亐云互亓五井亖亗亘亙亚些亜亝亞亟 U+4EA0:亠亡亢亣交亥亦产亨亩亪享京亭亮亯 U+4EB0:亰亱亲亳亴亵亶亷亸亹人亻亼亽亾亿 U+4EC0:什仁仂仃仄仅仆仇仈仉今介仌仍从仏 U+4ED0:仐仑仒仓仔仕他仗付仙仚仛仜仝仞仟 U+4EE0:仠仡仢代令以仦仧仨仩仪仫们仭仮仯 U+4EF0:仰仱仲仳仴仵件价仸仹仺任仼份仾仿 6. Appuyez sur Next or Prev pour avancer ou reculer dans les points de code Unicode. Appuyez sur Exit pour terminer l’essai. Chapitre 8 – Diagnostics 8.10 241 COMMUNICATIONS FCM Utilisez cette fonction pour déterminer si la carte interne des entrées et sorties ainsi que les FCM externes communiquent bien avec le MultiLoad II. 1. A partir du menu Diagnostics, sélectionnez FCM Com. Error! Reference source not found. 2. L’écran de diagnostic FCM COM s’affiche: Error! Reference source not found. 3. Une carte des entrées/sorties ou un FCM qui ne communique pas affiche ERR. 4. Quand les communications sont rétablies, le message d’erreur se change en OK. Chapitre 8 – Diagnostics 8.11 242 COMMUNICATIONS PCM Utilisez cette fonction pour déterminer sur un PCM communique bien avec le MultiLoad II. 1. A partir du menu Diagnostics, sélectionnez PCM Com. D I A G N O S T I C S M E N U Card Reader Meters COM Loopback Components Serial Ports Additives Network Test Custom Logic Keypad Display Unicode FCM Com PCM Com FCM Health PCM Health RCU Bay Preset Next Prev Exit Enter 2. L’écran de diagnostic PCM COM s’affiche: 004 FCM COM DIAGNOSTICS 00-Ok Exit 3. Un PCM qui ne communique pas bien affiche ERR. 4. Quand les communications sont rétablies, le message ERR se change en OK. Chapitre 8 – Diagnostics 8.12 243 STATUT DE L’ETAT DU FCM La fonction de statut de l’état du FCM peut servir à repérer des erreurs intermittentes de communication entre le MultiLoad II et la carte interne E/S » ou des FCM externes. 1. A partir du menu Diagnostics, sélectionnez FCM Health. Error! Reference source not found. 2. L’écran de statut “FCM Health” s’affiche: FCM# 00 VIEW FCM HEALTH STATS Timeouts Com Lost Ver 000000000 000000000 036 CLeaR Next Prev Exit 3. Après réparation, appuyez sur la touche CLR pour réinitialiser les totalisateurs. Puis revenez à cet écran pour vérifier si la réparation est bonne. FCM# Numéro du module de contrôle du débit. La carte I/O 1-Meter est 00 et 00 et 01 pour le 2-Meter. Timeouts Un temps mort se produit lorsque le RCU ne reçoit pas de réponse de la carte interne des E/S ou d’un FCM externe après interrogation. Le MultiLoad II interprète trois temps morts consécutifs comme des pertes de communication avec le FCM externe ou la carte interne des E/S. Le totalisateur de temps morts s'incrémente à chaque temps mort. Com Lost Le totalisateur Com Lost s’incrémente à chaque série de trois temps morts consécutifs. Ver Affirme le numéro de révision du programme local ou Err si les communications avec la carte interne des E/S ou le FCM externe sont perdues à ce moment-là. Chapitre 8 – Diagnostics 8.13 244 STATUT ETAT DU PCM La fonction de statut d’état du PCM peut servir à repérer des problèmes de communication intermittente entre le MultiLoad II et un PCM. 1. A partir du menu Diagnostics, sélectionnez PCM Health. Error! Reference source not found. 2. L’écran de statut de l’état du PCM s’affiche: PCM# 00 VIEW PCM HEALTH STATS Timeouts Com Lost Ver 000000000 000000000 001 CLeaR Next Prev Exit 4. Après réparation, appuyez sur la touche CLR pour réinitialiser les totalisateurs puis revenez à l’écran pour vérifier que la réparation a bien eu lieu. PCM# Numéro du module de commande de débit. Timeouts Un temps mort se produit lorsque le MultiLoad II ne reçoit pas de réponse d'un PCM après voir interrogé les PCM. Il interprète trois temps morts consécutifs comme perte de communications avec le PCM. Le totalisateur de temps morts s'incrémente à chaque temps mort. Com Lost Le totalisateur Com Lost s’incrémente après trois temps morts consécutifs. Ver Affiche le numéro de révision local ou Err si les communications avec le PCM sont momentanément suspendues. Chapitre 8 – Diagnostics 8.14 245 DIAGNOSTICS RCU L’écran de diagnostics RCU affiche l’état du commutateur de programme MultiLoad II et des commutateurs des Poids et Mesures. 1. A partir du menu Diagnostics, sélectionnez RCU. 2. L’écran de diagnostics RCU s’affiche: D I A G N O S T I C S M E N U Card Reader Meters COM Loopback Components Serial Ports Additives Network Test Custom Logic Keypad Display Unicode FCM Com PCM Com FCM Health PCM Health RCU Bay Preset Next Prev Exit Enter Le nouveau logiciel affichera également le tension de la batterie, la tension compensée en température et la température intérieure du MultiLoad2. Il affichera également le niveau restant de la batterie. RCU DIAGNOSTICS Program Key -ON W&M Key -ON Battery @ 31C 3.30V Battery 100% Pwr 09/10/13 14:02 Pgm 09/10/13 14:02 Exit Battery 3.30V @ 31C Donne la température observée ainsi que la tension mesurée. La température s’affiche en F ou C selon que le quai a été configuré ou non en Fahrenheit. Battery 100% Capacité restant de batterie avant qu’elle ne doive être remplacée Pwr Mentionne la date et l’heure où l’alimentation a été connectée pour la dernière fois. Pgm Mentionne la date et l’heure de dernière utilisation en mode programme. Remarque: Lors de la première mise sous tension, les deux paramètres sont identiques (Pwr = Pgm)! Chapitre 8 – Diagnostics 8.15 246 DIAGNOSTICS DU QUAI Utilisez la fonction de diagnostic de quai « Bay Diagnostics » pour établir si: - Les permissions de quai sont activées (ON) ou désactivées (OFF). - Les sorties de permission non valable de quai (Permissive-Out), autorisé (Authorized) et d’alarme de sortie (Alarm Out) peuvent être activées ou désactivées à partir de cet écran en appuyant sur le chiffre conrrespondant à la fonction. 1. A partir du menu Diagnostics, sélectionnez RCU. Error! Reference source not found. 2. L’écran de diagnostics de quai s’affiche: seules les entrées et sorties configurées s’affichent. Error! Reference source not found. Chapitre 8 – Diagnostics 8.16 247 DIAGNOSTIC DE VALEURS PREDEFINIES Le diagnostic des valeurs prédéfinies permet au technicien ou à l’électricien de délimiter le problème en affichant ce qui est activé ou non. - Le statut des entrées peut être visualisé comme ON ou OFF (ouvert ou fermé). - Les sorties peuvent être activées ou désactivées à partir de cet écran en poussant sur le chiffre correspondant à la fonction. 1. A partir du menu Diagnostics, sélectionnez Preset. D I A G N O S T I C S M E N U Card Reader Meters COM Loopback Components Serial Ports Additives Network Test Custom Logic Keypad Display Unicode FCM Com PCM Com FCM Health PCM Health RCU Bay Preset Next Prev Exit Enter 2. L’écran de diagnostic des valeurs prédéfinies affiche: seules les entrées et sorties configurées apparaissent à l’écran. PRE #1 (Preset 001) DIAGNOSTICS Permissive -OFF [1]PermissOut -ON [2]Authorized -OFF [3]Alarm Out -ON Meter Stop -OFF Remote Start-OFF [4]Batch Auth -OFF [5]Flow Active -OFF [6]Opn Bk Val -OFF [7]Cls Bk Val -ON Bk Val Status-OFF [8]OutPulse 20 Exit Chapitre 8 – Diagnostics 8.17 248 DIAGNOSTIC DU COMPTEUR Le diagnostic du compteur permet à votre technicien ou électricien de diagnostiquer les problèmes électriques ou de matériel en évaluant le câblage et la commande du MultiLoad II vers les dispositifs extérieurs comme les vannes de régulation numériques, les débitmètres et les systèmes à autorisation. - les statuts d’entrée peuvent être visualisés comme ON (ouvert) ou OFF (fermé) - les sorties peuvent être activées ou désactivées à partir de cet écran en appuyant sur le chiffre correspondant à cette fonction. 1. A partir du menu Diagnostics Menu, sélectionnez Meters. D I A G N O S T I C S M E N U Card Reader Meters COM Loopback Components Serial Ports Additives Network Test Custom Logic Keypad Display Unicode FCM Com PCM Com FCM Health PCM Health RCU Bay Preset Next Prev Exit Enter 2. Après avoir sélectionné le compteur, l’écran de diagnostic compteur s’affiche: seules les entrées et sorties configurées apparaissent. PRE #1 MTR #1 DIAGNOSTICS Permissive -OFF [1]PermissOut -ON [2]Authorized -OFF [3]Alarm Out -OFF [4]Upstrm Val -OFF [5]Dnstrm Val -OFF [6]OPN/CLS Test Del Pulses0 Del Vol0.00 Input mA- +00.000 Rate0 Exit Si le compteur est configuré pour accepter une sortie de vanne analogique, l’écran suivant d’affiche: Chapitre 8 – Diagnostics 249 PRE #1 MTR #1 DIAGNOSTICS Permissive -OFF [1]PermissOut -ON [2]Authorized -OFF [3]Alarm Out -OFF [4]Set Output 0 mA [5]Set Output 4 mA [6]Set Output 12 mA [7]Set Output 20 mA [8]Output mA 00.000 Del Pulses0 Del Vol0.00 Rate0 Exit Upstrm Val Met l’électrovanne amont sous tension ou hors tension Dnstrm Val Met l’électrovanne aval sous tension ou hors tension OPN/CLS Test Enclenche un essai automatique de mesure de la vitesse d’ouverture et de fermeture de la vanne de régulation. Set Output xx mA Mettez la sortie du pilote mA sur xx Output mA xx.xxxx Affichez ou mettez la sortie du pilote que xx.xxxx Input mA Signal 420mA du compteur utilisé (uniquement pour entrée compteur analogique) Del Pulses Nombre d’impulsions reçues au compteur Del Volume Volume livré au compteur Rate Débit instantané En activant "Upstrm Val" et "Dnstrm Val" simultanément, vous ouvrez la vanne de régulation numérique, ce qui peut produire un débit (si les pompes, vannes d'arrêt et états de casse sèche sont réglés correctement). ! ! Si on utilise la sortie mA avec une valeur supérieure à 4mA, la vanne de régulation numérique s’ouvre, ce qui peut produire un débit (si les pompes, vannes d’arrêt et états de casse sèche sont réglés correctement). Chapitre 8 – Diagnostics 250 Si le compteur et configuré comme compteur de masse Krohne, l’écran suivant apparaît: Error! Reference source not found. PRE #1 MTR #1 KROHNE DIAGNOSTICS Mass Flow: 0.000000kg/Min Volume Flow: 0.000000USGal/Min Density: 1.050000kg/m3 Temperature: 22.991680C Mass Total: -0.002545kg Volume Total: -0.670395USGal [1]Communications [2]Sensor Info [3]General Setup [4]Zero Calibration [5]Density Calibration [6]Service Page [7]Register Access [8]Service Register Access Exit Mass Flow Débit instantané pour le flux de masse configuré. Volume Flow Débit instantané pour le débit de volume configuré. Density Densité instantanée dans la densité configurée. Temperature température instantanée dans la température configurée Mass Total Masse total de produit débité depuis que le compteur de masse a été mis sous tension Volume Total Volume total de produit débité depuis que le compteur de masse a été mis sous tension. Chapitre 8 – Diagnostics 251 Si le compteur est configuré comme un compteur de masse Micro Motion, l’écran suivant apparaît: PRE #1 MTR #1 MICRO MOTION METER Mass Flow Rate: Mass Total: xxxxx.xx kg/hr xxxxxxxxx.xx kg Volume Flow Rate: xxxx.xx l/hr Volume Total: xxxxxxxxx.xx l Temperature: Density: xxxx.xx C xx.xxxxxx [1]Broadcast Address Set #01:OFF [2]Perform Flowmeter Zeroing:OFF [3]Perform Totalizer Reset: OFF Exit Upstrm Val Connecte ou déconnecte l’électrovanne amont Dnstrm Val Connecte ou déconnecte l’électrovanne aval OPN/CLS Test Enclenche un test automatisé qui mesure la vitesse d’ouverture de de fermeture de la vanne de commande Set Output xx mA Mettez la sortie du pilote mA sur xx. Output mA xx.xxxx Affichez ou mettez la sortie du pilote mA sur xx.xxxx. Del Pulses Nombre d’impulsions compteur reçues Del Volume Volume livré compteur Input mA- Signal 4-20mA instantané du compteur (Uniquement entrée compteur analogue). Rate Débit instantané. Chapitre 8 – Diagnostics 8.18 252 ESSAI DE LA VANNE DE REGULATION NUMERIQUE Le MultiLoad II comporte un essai d’ouverture et de fermeture de vanne à l’écran de diagnostic du compteur. Cet essai ouvre automatiquement la vanne de régulation numérique jusqu'à ce que le haut débit soit atteint. Ensuite, la vanne de régulation numérique reçoit une commande de fermeture. Les temps d'ouverture et de fermeture sont mesurés et affichés pour servir d'assistance au réglage du contrôle de vitesse. ! Pour effectuer l'essai, le liquide doit s'écouler par la vanne. C'est pourquoi, un réceptacle approprié destiné à recevoir le flux de produit doit être prévu. Assurez-vous qu'il y a assez de place dans le réceptacle pour recevoir les débits d'essai. Chaque essai déverse environ 50 gallons avec une vanne de régulation fonctionnant correctement. Conservez un journal des totaux livrés pour chaque essai. Les volumes livrés sont classés comme débit non autorisé. ! Au lancer de l'essai, le débit passera immédiatement au haut débit, sans phase de démarrage à faible débit. Consultez les procédures de sécurité du terminal pour charger l'hydrocarbure dans un réservoir vide. ! Soyez prêt à interrompre manuellement le débit, par exemple avec un frein à main, si la vanne fonctionne mal ou s’il faut faire des réglages. Appuyez sur n’importe quelle touche pour annuler l’essai. La procédure suivante peut être utilisée pour déterminer les vitesses d'ouverture et de fermeture de la vanne de régulation numérique. 1. Sur le MultiLoad II, entrez dans le mode Programme et sélectionnez le menu Diagnostic. 2. Mettez la pompe du composant désiré sous tension: a. A partir de l'écran des Diagnostics, sélectionnez Components. b. Sélectionnez la valeur prédéfinie qui est à l'essai. Sélectionnez le composant désiré pour la vanne à l'essai. c. Poussez sur le numéro qui correspond au fonctionnement de la pompe. Cela devrait faire démarrer la pompe si l'alimentation de tous les appareils intermédiaires, comme les PLC, est branchée. Selon la configuration du site, il faut peut-être ouvrir la vanne d'arrêt des composants. Au besoin, appuyez sur le numéro qui correspond à "Opn Blk Val". d. Poussez sur la touche Enter pour passer au menu du diagnostic du compteur. 1. 3. Lancez l’essai: a. A l'écran de diagnostic du compteur (voir page suivante), assurez-vous que tout a été préparé pour accueillir le débit de produit. Appuyez sur le numéro qui correspond à l'essai OPN/CLS ; l'écran indique que les électro-aimants en amont et en aval sont sous tension (ON). Le produit commence à s'écouler; les impulsions et le volume commencent à s'accumuler, comme indiqué à l'écran de diagnostic. Chapitre 8 – Diagnostics 253 PRE #1 MTR #1 DIAGNOSTICS Permissive -OFF [1]PermissOut -ON [2]Authorized -OFF [3]Alarm Out -OFF [4]Upstrm Val -ON [5]Dnstrm Val -ON [6]DNSUPSDel Pulses46 Del Vol0.90 Gross Rate23 Exit b. Le débit commence à s’élever à partir de zéro, comme indiqué à l'écran de diagnostic. Le débit continue à augmenter jusqu'au haut débit. c. Dès que le haut débit est atteint, les deux électro-aimants se coupent automatiquement et leurs vannes reviennent à leur état normal. L'électrovanne en amont revient en position ouverte et l'électrovanne en aval, en position fermée. Lorsque le débit est retombé à zéro, l'essai est terminé. PRE #1 MTR #1 DIAGNOSTICS Permissive -OFF [1]PermissOut -ON [2]Authorized -OFF [3]Alarm Out -OFF [4]Upstrm Val -OFF [5]Dnstrm Val -OFF [6]DNS-19.4UPS- 2.7 Del Pulses2840 Del Vol56.80 Gross Rate0 Exit ! La vanne reste ouverte jusqu'à ce que le haut débit soit atteint. Si le haut débit ne peut être obtenu, arrêtez le débit en appuyant sur n'importe quelle touche. Déterminez pourquoi le haut débit ne peut être atteint avant de reprendre l'essai. Chapitre 8 – Diagnostics 4. Lisez les temps d’ouverture et de fermeture a) DNS: Les chiffres à droite de cet élément indiquent la vitesse d’ouverture en secondes. Il faut viser audelà de 10 secondes mais en-dessous de 20 secondes. Le pointeau aval réglera ce temps. Fermez pour augmenter le temps et ouvrez pour le diminuer. b) UPS: Les chiffres à droite de cet élément indiquent la vitesse de fermeture en secondes. Il faut viser plus de 1,5 secondes mais moins de 2,5 secondes Le pointeau amont règle ce temps. Fermez pour augmenter le temps et ouvrez pour le diminuer. Il peut être souhaitable de répéter l'étape n°3 à plusieurs reprises pour obtenir une moyenne. Un total cumulé du volume délivré sera retenu si la touche Exit n'est pas activée pendant les essais. 5. Vérifiez si les vitesses d'ouverture et de fermeture tombent bien dans la fourchette des valeurs recommandées par le fabricant de vannes. Si les temps d'ouverture et de fermeture appropriés sont atteints, quittez le mode de diagnostic et effectuez une séquence de chargement typique pour évaluer la performance du débit. Si la valeur chute en dehors de ces limites, faire un réglage d'¼ de tour comme décrit ci-dessous. Répétez les étapes 3 à 5 pour atteindre les vitesses désirées. a. Augmentez la vitesse de fermeture - S'il faut augmenter la vitesse de fermeture (UPS), faites tourner le pointeau de la vitesse de fermeture d'¼ de tour dans le sens inverse des aiguilles d’une montre (CCW). Il s'agit du pointeau du côté amont du bloc. b. Diminuez la vitesse de fermeture - S'il faut diminuer la vitesse de fermeture (UPS), faites tourner le pointeau de la vitesse de fermeture d'¼ de tour dans le sens des aiguilles d’une montre (CW). Il s'agit du pointeau du côté amont du bloc. c. Augmentez la vitesse d'ouverture - S'il faut augmenter la vitesse d'ouverture (DNS), faites tourner le pointeau de la vitesse d'ouverture, d'¼ de tour dans le sens inverses des aiguilles d’une montre (CCW). Il s'agit du pointeau du côté aval du bloc. d. Diminuez la vitesse d'ouverture - S'il faut diminuer la vitesse d'ouverture (DNS), faites tourner le pointeau de la vitesse d'ouverture d'¼ de tour dans le sens des aiguilles d’une montre (CW). Il s'agit du pointeau du côté aval du bloc. 6. Arrêtez la pompe - Pour arrêter la pompe et fermer la vanne d'arrêt, poussez sur Exit pour obtenir l'écran de diagnostic. a. A partir de l'écran de diagnostic, sélectionnez Components. b. Sélectionnez la valeur prédéfinie qui est à l'essai. Sélectionnez le composant désiré pour la vanne à l'essai. c. Poussez sur le numéro qui correspond au fonctionnement de la pompe pour l’arrêter. Selon la configuration du site, il peut être nécessaire de fermer la vanne d'arrêt du composant. Au besoin, poussez sur le numéro qui correspond à Opn Blk Val. d. Poussez sur Exit jusqu'au redémarrage du MultiLoad II (sortie du mode de programme). Remarque: Si vous redémarrez (sortie du mode programme) sans arrêter la pompe ou fermer la vanne d’arrêt, ces appareils se coupent automatiquement. 254 Chapitre 8 – Diagnostics 8.19 255 DIAGNOSTIC DES COMPOSANTS Le diagnostic des composants permet au technicien ou à l’électricien de diagnostiquer les problèmes de câblage ou d’équipement en testant le câblage et les commandes partant du MultiLoad II vers les périphériques tels que vannes d’arrêt, statut/fonctionnement de pompe et autorisations. - les statuts d’entrée peuvent être visualisés comme ON (ouvert) ou OFF (fermé). - Les sorties peuvent être activées ou désactivées à partir de cet écran en poussant sur le chiffre correspondant à cette fonction. 1. A partir du menu Diagnostics, sélectionnez Components. Error! Reference source not found. 2. Après la sélection du composant, l’écran de diagnostic des composants s’affiche. Seules les entrées et sorties configurées apparaissent à l’écran Error! Reference source not found. Pour voir les diagnostics du compteur associés à ce composant, appuyez sur Enter. Si vous allez au diagnostic compteur à partir de cet écran, vous pouvez commander les vannes après le démarrage des pompes et l’ouverture des vannes d’arrêt. Chapitre 8 – Diagnostics 8.20 256 DIAGNOSTIC D’ADDITIFS Le diagnostic d’additifs permet au technicien ou à l’électricien de diagnostiquer les problèmes de câblage ou d’équipement en testant le câblage et les commandes à partir du MultiLoad II vers les périphériques tels que vannes d’arrêt, fonctionnement: statut de la pompe, entrées et sorties d’injecteur et autorisations. - Les statuts d’entrée peuvent être visualisés comme ON (ouverts) ou OFF (fermés). 1. A Les sorties peuvent être activées ou désactivées à partir de cet écran en poussant sur le chiffre correspondant à la fonction. partir du menu Diagnostics Menu, sélectionnez Additives. D I A G N O S T I C S M E N U Card Reader Meters COM Loopback Components Serial Ports Additives Network Test Custom Logic Keypad Display Unicode FCM Com PCM Com FCM Health PCM Health RCU Bay Preset Next Prev Exit Enter 2. Après la sélection de l’additif, l’écran de diagnostic de l’additif s’affiche. Seules les entrées et sorties configurées apparaissent à l’écran s’il ne s’agit pas d’additifs analogiques PRE #1 ADTV #1 DIAGNOSTICS Permissive -OFF Del Pulses0 [1]PermissOut -ON Del Volume0 [2]Authorized -OFF [3]Alarm Out -OFF Feedback -OFF Test Button -OFF [4]Pump Run -OFF [5]Pump Kill -OFF Pump Status -OFF [6]Flush Pump -OFF [7]Opn Bk Val -OFF [8]Cls Bk Val -ON Bk Val Status-OFF [9]Del Pulses0 Exit Si l’additif analogique est configuré, l’écran suivant apparaît. On peut y commander la vitesse de pompe avec la sortie analogique. Chapitre 8 – Diagnostics 257 PRE #1 ADTV #1 DIAGNOSTICS Permissive -OFF Del Pulses0 [1]PermissOut -ON Del Volume0 [2]Authorized -OFF [9]Set Output 0mA [3]Alarm Out -OFF[10]Set Output 4mA Feedback -OFF[11]Set Output 12mA Test Button -OFF[12]Set Output 20mA [4]Pump Run -OFF[13]Output mA 00.000 [5]Pump Kill -OFF Pump Status -OFF [6]Flush Pump -OFF [7]Opn Bk Val -OFF [8]Cls Bk Val -ON Bk Val Status-OFF Exit Chapitre 8 – Diagnostics 258 Feedback Lit le signal de rétroaction qui vérifie que le piston a été lancé et est revenu à sa position de départ. Test Button Lit le signal de bouton d’essai (Cf. Additive Calibration au Chapitre 6.) Pump Run Active ou désactive un signal de sortie vers un démarreur de pompe d'additif. La sortie de la pompe d'additif reste sous tension jusqu'à ce que le chargement soit achevé, à moins qu'une alarme d'erreur de vanne ne se produise. Pump Kill Active ou désactive un signal de sortie pour arrêter la pompe d'additif. Le signal Pump Kill ne s'active que lorsque le système subit une alarme d’erreur de vanne d’additif. Pump Status Lit le signal du statut de pompe qui indique si la pompe d'additif fonctionne ou pas. Si ce signal est absent pendant la période indiquée au paramètre de temps d'alarme du statut de pompe, l'alarme du statut de pompe de l'additif s'enclenche. [x]Del Pulses Démarre une injection. Le nombre d’impulsions au compteur d’additifs attendu pour cette injection apparaît sur la droite. Del Pulses Nombre d’impulsions d’additif reçues depuis le compteur d’additifs. Del volume Volume total d’additif injecté. 8.21 LOGIQUE PERSONNALISEE La fonction de diagnostic de logique personnalisée sert à n'importe quels outils de diagnostic ou de fonctions personnalisées exigées par votre société ou votre terminal. Si, à un moment donné, vous voulez inclure le diagnostic personnalisé, prière de contacter le département "Account Management" de Toptech. La fonction de diagnostic Custom Logic est analysée plus loin dans ce manuel de l’utilisateur. Chapitre 8 – Diagnostics 8.22 259 DIAGNOSTIC DU GPS (UNIQUEMENT POUR LE MULTILOAD II MOBILE) Le diagnostic de GPS affiche le statut instantané détaillé des GPS branchés. D I A G N O S T I C S M E N U UTC Date: 15/9/08 UTC Time: 18:11:52 Latitude: 28 41.655 N Longitude: 081 21.112 W Altitude: 52.8 M Speed: 0.0(MPH) 0.0(KPH) Heading: 104 Site: Toptech 27 M Prn: 19 7 13 27 3 23 11 6 8 28 16 51 Rx: 22 28 36 26 13 39 23 22 20 19 14 27 Fix: ** ** ** ** ** ** ** ** Next Prev Exit Enter UTC Date Date du Temps Universel coordonné (UTC) enregistrée par le GPS. UTC Time Heure du Temps Universel Coordonné (UTC) enregistré par le GPS. Latitude Latitude instantanée enregistrée par le GPS. Longitude Longitude instantanée enregistrée par le GPS. Altitude Altitude instantanée au-dessus du niveau de la mer enregistrée par le GPS. Heading Cap instantané enregistré par le GPS. Remarque: cette valeur est calculée par le mouvement et non par l’orientation du véhicule. Site S’il est configuré, enregistre le nom et la distance du site par rapport à la position instantanée. Prn Le code PRN du bruit pseudo-aléatoire enregistré pour chaque signal d’engin spatial (SV) reçu par le GPS. Rx La puissance du signal reçu pour chaque signal SV reçu. Plus ce nombre est élevé, plus le signal est fort. Fix Comme le GPS l’a enregistré, le “**” indique que le signal Sv correspondant est utilisé pour calculer la localisation de la position instantanée. Chapitre 9 – Poids et Mesures CHAPTER 9 9.1 9.1.1 260 POIDS ET MESURES VUE D’ENSEMBLE POIDS ET MESURES Le commutateur à clef ou la prise des Poids et Mesures peut être scellé ou verrouillé, empêchant ainsi l'accès aux paramètres des Poids et Mesures. Tous les paramètres protégés s’affichent en rouge sur la télécommande du MultiLoad. Il se peut que vous deviez contacter votre bureau local des Poids et Mesures après avoir brisé les scellés et modifié les paramètres. Cela ne se produit normalement que pendant les essais de compteur ou les procédures d'étalonnage de température du terminal. Chapitre 9 – Poids et Mesures RESTRICTIONS D’ACCÈS AUX PARAMÈTRES DES POIDS ET MESURES 9.2 MultiLoad II utilise trois méthodes d’accès en écriture aux paramètres de Poids et Mesures (W&M). Introduction manuelle de paramètres W&M par le clavier du MultiLoad II. Télétransfert à distance de paramètres par la liaison sérielle ou le lien Ethernet sur le MultiLoad II. Chargement des paramètres par une carte mémoire SD sur le Multiload II (uniquement sur tableau CPU rev 2.0). Quoiqu’il en soit, tous les accès en écriture aux paramètres W&M sont refusés à moins que le commutateur ou la prise des Poids et Mesures ne soit en position d’accès aux paramètres. Pour effectuer un télétransfert de paramètres météorologiques à distance, le commutateur ou la prise W&M DOIT être en position d’accès aux Poids et Mesures, faute de quoi toutes les tentatives à distance de modifications de ces paramètres sont refusées. Le boîtier du MultiLoad II dispose d’un endroit où placer un plomb pour empêcher de toucher à l’intérieur du MultiLoad II pour accéder aux branchements locaux, au CPU, à la mémoire de configuration ou à l’électronique des commutateurs. Ce plomb permet de voir directement s’il y a eu tentative d’accès. Le Multiload II utilise deux méthodes différentes pour mettre à jour les logiciels : - Télétranfert à distance d’une nouvelle image du logiciel par la liaison sérielle ou le lien Ethernet sur le MultiLoad II. - Télétransfert d’une nouvelle image du logiciel par une carte mémoire SD sur le Multiload II (uniquement sur tableau CPU rev 2.0). Toute tentative de mise à jour du logiciel local du MultiLoad sera rejetée à moins que le commutateur ou la prise des Poids et Mesures ne soit en position d’accès. Pour effectuer une mise à jour à distance du logiciel local, le commutateur ou la prise W&M DOIT être en position d’accès aux Poids et Mesures, faute de quoi toutes les tentatives à distance de mise à jour seront refusées. Les changements de paramètres W&M ou mises à jour de logiciel sont enregistrés dans le journal des modifications des Poids et Mesures. On peut avoir un maximum de 5 mots de passe pour y accéder; chaque mot de passe a une particularité qui le rattache à un opérateur particulier. Le MultiLoad II peut accepter un mode de programme et/ou des commutateurs de mode Poids et Mesures fournis par un client à distance. Dans ce cas, le client est responsable du respect de toutes les consignes relatives au plombage de ces commutateurs externes et du câblage exigé par les autorités météorologiques locales. 261 Chapitre 9 – Poids et Mesures 262 9.3 JOURNAL DES MODIFICATIONS DES POIDS ET MESURES ET SÉCURITÉ DES PARAMÈTRES MÉTÉOROLOGIQUES Les 1.000 derniers changements apportés aux Poids et Mesures sont enregistrés dans la mémoire non volatile (NVRAM) du MultiLoad II. L'accès en écriture à ces registres est limité par un logiciel. Lorsque toutes les conditions sont réunies pour changer un paramètre W&M, une écriture simple n'est autorisée qu'après création d'une nouvelle entrée dans le journal des modifications des W&M, journal qui enregistre les informations suivantes pour les modifications aux paramètres : Date Heure Nom du paramètre Numéro de l'événement Identifiant Valeur prédéfinie affectée (bras de chargement) Débitmètre affecté Composant affecté Valeur précédente Nouvelle valeur Le journal des modifications des W&M est stocké dans la NVRAM du MultiLoad et ne peut être ni édité ni modifié. Chapitre 9 – Poids et Mesures 9.4 FONCTIONS DU COEFFICIENT DE CORRECTION DU VOLUME Le MultiLoad II peut calculer des volumes nets. Dans le cas qui nous occupe, le volume net représente le volume brut corrigé à une température de référence et/ou une tension de vapeur. Le volume net est calculé en multipliant le volume brut par un coefficient de correction de volume (VCF). Dans les applications MultiLoad II, le VCF est le produit de deux coefficients différents: le coefficient de correction de la température du liquide (CTL) et le coefficient de correction de la pression du liquide (CPL). Les fonctions CTL et CPL peuvent être activées simultanément ou séparément. VCF = CTL x CPL Le volume grossier est le volume brut multiplié par un facteur de mesure (MF). Le volume brut représente les impulsions non pondérées du compteur divisées par le coefficient K du débitmètre. Les unités du coefficient K sont des impulsions par unité de volume. Par exemple, le coefficient K nominal d'un débitmètre à turbine de 3 pouces est de 50 impulsions/gallon. La séquence ci-dessous peut être utilisée pour concevoir la façon d'utiliser les impulsions d'un débitmètre pour déterminer le volume grossier, le volume brut et le volume net. Volume brut = Impulsions/coefficient K ou volume brut = (Impulsions) x (1/coefficient K) Volume grossier = Volume brut x MF Volume net = volume grossier x VCF Calcul du CTL - Les tableaux établis par l'Institut Américain du Pétrole (l'API) servent à donner le coefficient de correction de la température du Liquide (CTL). Le MultiLoad calcule le CTL conformément à la Norme API 2540. Le CTL sert à corriger le volume grossier pour un volume à une température de référence. Après l'application du CTL au volume grossier, le volume net résultant représente la zone que le volume grossier occuperait s'il avait été mesuré à la température de référence. Les tableaux API sélectionnés sont disponibles dans le MultiLoad II pour utilisation avec des liquides et à des températures de référence spécifiques. Les calculs se servent tous de deux variables : l'Alpha du liquide et la Température Delta du liquide. L'Alpha est le coefficient d’expansion du liquide. La Température Delta est la différence entre la température mesurée du liquide et la température de référence. Les tableaux API employés utilisent les températures de référence de 60°F ou 15°C. Quelques tableaux API calculent l'Alpha sur base de la température du liquide et de la gravité API du liquide. La gravité API est une valeur introduite par l'utilisateur et qui dépend du type de liquide à mesurer. D'autres tableaux API calculent l'Alpha sur base de la température du liquide et de la densité relative du liquide. Toutefois, d'autres tableaux calculent l'Alpha sur base de la température du liquide et de la densité du liquide. La densité du liquide, comme la gravité API, dépend du type de liquide à mesurer. Dans les tableaux "C", l'Alpha est introduit par l'utilisateur. Calcul du CPL - Le coefficient de correction de la pression du liquide (CPL) sert à corriger le volume grossier pour un volume à la tension de vapeur du liquide. Après l'application du CPL au volume grossier, le volume net résultant représente la zone que le liquide occuperait s'il était à sa tension de vapeur. Le calcul pour le CPL implique trois variables : la pression instantanée du liquide, la tension de vapeur du liquide et le coefficient F du liquide. La tension du courant est la pression du liquide. C’est une variable mesurée et il faudra utiliser un capteur de pression pour fournir des informations sur la pression au module de commande du débit (FCM) sous forme d’un signal 4-20 mA. La tension de vapeur est la pression à laquelle le liquide se transforme en vapeur à la température liquide instantanée. On parle parfois de la tension de vapeur comme étant la pression d’équilibre et le point d’ébullition. On utilise TP-15 pour déterminer la tension de vapeur. Le facteur F est le facteur de compressibilité du liquide. On le calcule au moyen des tableaux API 11.2.1 et 11.2.2. 263 Chapitre 9 – Poids et Mesures 9.5 264 CALCUL DE LA MASSE Le Multiload II sert à aussi à calculer la masse. Pour ce faire, la masse est définie comme le volume net connecté à une densité. Cette masse se calcule en multipliant le volume net par une densité. On peut utiliser 3 types différents de densités : 1/ Densité 2/ Densité relative 3/ Gravité API La densité utilisée dans la formule de la masse suit la règle ci-après : Si on sélectionne un tableau API, celui-ci détermine la densité Si on ne sélectionne pas de tableau API, les règles suivantes s’appliquent : Vérifiez s’il n’y a pas de défaut de densité ou de densité relative ou de gravité API Si ce n’est pas le cas : Vérifiez s’il n’y a pas de capteur de compteur activé pour la densité, la densité relative ou gravité API Si ce n’est pas le cas : Vérifiez s’il y a une densité de compteur par défaut ou une densité relative ou une gravité API la On utilise la formule suivante lorsque l’on a une densité par défaut, une densité relative ou une gravité API : masse = volume net x densité On utilise la formule suivante pour mesurer la densité observée : masse = volume net x densité Remarque : Le kilogramme air changera de -1.1 pour les produits d’une densité inférieure à 996.6 ; entre 996.6 et 1663.5, on utilise un changement de densité de -1.0 et tout ce qui dépasse 1663.5 sera de -0.9. Chapitre 9 – Poids et Mesures 9.5.1 SORTIE NETTE D'IMPULSIONS Il est possible de produire une sortie nette d'impulsions. Un coefficient peut être appliqué à la sortie nette d'impulsions de façon à obtenir la résolution voulue des impulsions. La configuration possible de la résolution des impulsions va de 0,001 à 50,000 impulsions par volume d'unité. Les paramètres de configuration de la sortie nette d'impulsions se trouvent au menu Valeurs Prédéfinies. 9.5.2 SORTIE D'IMPULSIONS DE MASSE Il est possible de produire une sortie d’impulsions de masse. On peut appliquer un facteur à la sortie d’impulsions nette pour arriver à la résolution d’impulsions souhaitée. La résolution d’impulsions peut se configurer de 0.001 à 50.000 impulsions par unité de volume. Le paramètre de configuration de l’impulsion de sortie de masse se trouve dans le menu des valeurs prédéfinies. 9.5.3 LIVRAISON GROSSIÈRE, NETTE OU MASSE Chaque bras de chargement peut être configuré de façon à livrer soit en volume grossier, soit en volume net, soit en masse. Si une valeur prédéfinie est configurée pour livrer en quantités grossières, les quantités de cette valeur sont introduites en grossier. Une valeur prédéfinie configurée pour livrer en volume net accepte des quantités de valeurs prédéfinies en volume net. Des valeurs prédéfinies qui sont configurées pour livrer en masse accepteront des quantités prédéfinies en masse. Chaque valeur prédéfinie dans le quai peut être configurée indépendamment des autres pour une livraison grossière, nette ou en masse. La fonction "Type de Livraison" se trouve dans le menu Poids et Mesure/Valeurs prédéfinies. 9.5.4 CALCULATEURS VCF TABLEAU API Dans les menus de configuration des fonctions du tableau API, il est possible d'entrer des valeurs d'essai de variables utilisées pour calculer les coefficients. Par exemple, en utilisant un tableau CTL qui repose sur une densité ou une gravité introduite par l'utilisateur et une température mesurée, une température d'essai peut être introduite pour déterminer le CTL qui serait calculé à cette température et gravité. De même, les tableaux utilisés conjointement avec le CPL, permettent l'introduction de températures et de pressions d'essai pour déterminer le CPL qui en découle. Le menu de configuration et le calculateur pour le CTL se trouvent dans « Weights & Measures/API TABLE » dans le mode de programme. Le menu de configuration et le calculateur pour le CPL se trouvent dans Weights & Measures/API TABLE dans le mode programme. Si des données d'essai valables (température et pression) sont comprises dans la fourchette du tableau API sélectionné, la ligne inférieure affiche Calculated VCF. Dans certains cas, la ligne inférieure peut afficher un Vcf extrapolé. Cela signifie que le tableau donne un coefficient qui n'a pas été obtenu par l'expérimentation mais qui provient d’une zone d’extrapolation du tableau, comme recommandé par API. Lorsque les données d'essai et la gravité dépassent la fourchette recommandée du tableau choisi, la ligne inférieure affiche " API Input Data Out of Range" (Données d'entrée API hors limite) ! La température, la densité et la pression ne sont pas utilisées par le tableau API lorsque le produit est débité. La gravité introduite est une valeur utilisée par le tableau en cours de fonctionnement. 265 Chapitre 9 – Poids et Mesures AFFICHAGE DU VOLUME NET ET DONNÉES ACCESSOIRES 9.5.5 Chaque fois que la fonction CTL ou CPL est activée pour une valeur prédéfinie (bras de chargement), le volume net peut être visualisé à l'écran de détail des composants, écran secondaire de l'écran de statut du composant. L'écran de détail des composants de la valeur prédéfinie affiche aussi les CTL et CPL instantanés. De plus, l'écran de statut du composant affiche une des variables suivantes, adaptées au tableau API sélectionné: gravité API, densité, densité relative ou coefficient d’expansion. Si la fonction "Delivery in Net" est désactivée, les volumes à l'écran de chargement et commande de la valeur définie sont des valeurs brutes. En activant la fonction de livraison en net, les volumes à l'écran de chargement et de commande de la valeur prédéfinie seront des valeurs nettes. Les quantités de la valeur prédéfinie sont alors introduites comme étant des quantités nettes et la livraison se fait en volume net. L'écran de commande de la valeur prédéfinie affiche un message indiquant les unités de volume et la température de référence avec volume corrigé. L'écran de détail du composant est accessible depuis l'écran de statut du composant. Un écran de détail du composant est visible pour chaque composant qui est repris à l'écran de statut. A partir de l'écran de statut du composant, appuyez sur le numéro qui correspond au composant. Le menu Views and Inquiry (Affichage et Requêtes) permet l'observation des températures et des pressions instantanées, y compris les compensations, sans affecter la sécurité des Poids & Mesures. Pour visualiser une température ou une pression, rentrez dans le mode de programme et sélectionnez le menu Views and Inquiry à partir du menu principal de configuration. Choisissez la température ou la pression désirée. Ensuite, sélectionnez le bras de chargement voulu et le débitmètre associé. API MPMS CHAPITRE 11.1-2004/AJOUT À IP 200/04/AJOUT À ASTM D 1250-04 9.5.6 Le logiciel Multiload II version 4.31.04 supporte l’API MPMS Chapitre 11.1-2004/ajout à IP 200/040 ajout à ASTM D 1250-04, référencé ci-après comme la norme 2004. Parmi les avantages par rapport à la norme 1980, citons une touche supplémentaire de précision et de correction à des températures de référence arbitraires ou à la gravité. On peut utiliser ces méthodes pour recréer des coefficients de correction à la manière des tableaux d’historique en introduisant les données appropriées. CONFIGURATION DE LA TEMPÉRATURE DE CORRECTION (CTL) 9.5.7 Le logiciel MultiLoad II supporte différents tableaux de mesures de pétrole utilisés pour produire un CTL. La sélection du tableau approprié dépend du type de produit, des unités de densité de la mesure utilisée et de la température à laquelle le volume sera corrigé. Rentrez dans le mode de programme et sélectionnez View and Inquiries. A partir de là, sélectionnez Temp. Comp. Choisissez la valeur prédéfinie puis le composant désiré. Chaque composant d'une valeur prédéfinie donnée doit être configuré séparément pour le CTL. 1. Sélection du tableau API CTL Mettez ce champ en surbrillance et appuyez sur Enter pour faire défiler les choix. Quand vous voyez le tableau désiré, appuyez sur Next pour avancer au champ suivant. Voici ci-dessous une liste des options du tableau API et des conditions d’utilisation. Si le mot NMI s’y trouve en rouge, cela signifie que le tableau est approuvé pour être utilisé pour MID. 266 Chapitre 9 – Poids et Mesures 267 Tableau Description ASTM 12501980 Table 6A Ce tableau donne les coefficients CTL pour la correction des volumes de pétrole brut à des températures observées de 60 F. Utilisez ce tableau si les conditions ci-après sont réunies. Le liquide est du pétrole brut La gravité API à 60 F est connue La température de référence est de 60 F Après avoir sélectionné ce tableau, introduisez la gravité API du liquide à 60 F. La fourchette de validité de gravité va de 0 à 100° API. Les températures d'essai peuvent être introduites dans cet écran qui calcule un CTL sur base de la température d'essai et de la gravité API. La température d'essai et le CTL calculé ne servent que de points de référence et ne sont pas utilisés dans des calculs pendant les opérations. Chapitre 9 – Poids et Mesures 268 Tableau Description ASTM12501980 Table 6B Ce tableau fournit les coefficients CTL pour la correction des volumes d’essence à des températures observées de 60 F. Utilisez ce tableau si les conditions ci-après sont réunies. Le liquide est un produit raffiné La gravité API à 60 F est connue La température de référence est de 60 F Sélectionnez ce tableau puis introduisez la gravité API du liquide à 60 F. La fourchette de validité de la gravité API va de 0 à 85° API. On peut introduire des tests de température dans cet écran qui calcule un CTL sur la base de la température d'essai et de la gravité API. La température d'essai et le CTL calculé ne servent que de points de référence et ne sont pas utilisés dans des calculs pendant les opérations. ASTM12501980 Table 6C Ce tableau donne les coefficients CTL pour la correction des volumes de produits pétroliers à des températures observées de 60 F. Utilisez-le si les conditions ci-après sont réunies : ASTM12501980 Table 6D Ce tableau fournit les coefficients CTL pour la correction des volumes d'huiles de graissage à des températures observées de 60 F. Utilisez-le si les conditions ci-après sont réunies. Le liquide est un produit raffiné ou du pétrole brut Le coefficient d’expansion à 60 F est connu La température de référence est de 60 F Sélectionnez ce tableau puis introduisez le coefficient d’expansion thermique (alpha) du liquide à 60 F. La fourchette de validité d’alpha s'étend de 0,000270 à 0.000930. Toutefois, l’Alpha peut être introduit dans cet écran sous la forme 270-930. On peut introduire des températures d’essai. La température d'essai et le CTL calculé ne servent que de points de référence et ne sont pas utilisés dans des calculs pendant les opérations. Le liquide est une huile de graissage La gravité API à 60 F est connue La température de référence est de 60 F Sélectionnez ce tableau puis introduisez la gravité API du liquide à 60 F. La fourchette de validité de la gravité API va de -10 à 45° API. Les températures d'essai peuvent être introduites dans cet écran qui calcule un CTL sur base de la température d'essai et de la gravité API. La température d'essai et le CTL calculé ne servent que de points de référence et ne sont pas utilisés dans des calculs pendant les opérations. ASTM12501980 Table 23E Ce tableau fournit la densité à 60° F pour des hydrocarbures légers à une température et une densité observées. Utilisez ce tableau si les conditions ci-après sont réunies : Table Description ASTM12501980 Table 24A Ce tableau fournit des coefficients CTL pour corriger des volumes de pétrole brut à des températures observées de 60 F. Utilisez ce tableau si les conditions ciaprès sont réunies: Le liquide est du gaz naturel liquide (NGL) ou du LPG (propane) La température et la densité instantanées doivent être disponibles La densité relative à 60° F est inconnue La température de référence est de 60° F. Les températures et les densités d’essai peuvent être introduites dans cet écran qui calcule la densité corrigée à la température et à la densité d'essai. La température d'essai, la densité et la densité corrigée calculés à 60° F ne servent que de points de référence et ne sont pas utilisés dans des calculs pendant les opérations. REMARQUE : Ce tableau ne fournira pas de valeur CTL, mais il peut être utilisé par d’autres tableaux. Le liquide est du pétrole brut Chapitre 9 – Poids et Mesures La densité relative à 60 F est connue La température de référence est de 60 F Sélectionnez ce tableau, puis introduisez la densité relative du liquide à 60 F. La densité relative peut varier de 0.6110 à 1.0760. On peut introduire des températures d’essai sur cet écran qui calculera un CTL basé sur la température d’essai et la densité relative. La température d’essai et le CTL calculé sont donnés à titre indicatif et ne seront pas utilisés pour des calculs pendant les opérations. ASTM12501980 Table 24B Ce tableau fournit les coefficients CTL pour corriger des volumes d’essence à des températures observées de 60 F. Utilisez-le si les conditions suivantes sont réunies: le liquide est un produit raffiné la densité relative à 60 F est connue la température de référence est de 60 F Sélectionnez ce tableau, puis introduisez la densité relative du liquide à 60 F. La densité relative peut varier de 0.6535 à 1.0760. On peut introduire des températures d’essai sur cet écran qui calculera un CTL basé sur la température d’essai et la densité relative. La température d’essai et le CTL calculé sont donnés à titre indicatif et ne seront pas utilisés pour des calculs pendant les opérations. ASTM12501980 Table 24E Ce tableau fournit des coefficients CTL pour corriger des volumes d’hydrocarbures légers à des températures observées de 60 F. Utilisez-le si les conditions ci-après sont remplies : le liquide est du NGL ou du LPG (propane) la densité relative à 60 F est connue la température de référence est de 60 F Sélectionnez le tableau puis introduisez la densité relative du liquide à 60 F. La densité relative peut varier de 0.3500 à 0.6880. On peut introduire des températures d’essai sur cet écran qui calculera un CTL basé sur la température d’essai et la densité relative. La température d’essai et le CTL calculé sont fournis à titre indicatif et ne seront pas utilisés pour des calculs pendant les opérations. ASTM12501980 Table 53B NMI Ce tableau sert à corriger une densité observée à la température observée à 15 C. Lorsqu’il est activé, la densité corrigée s’utilise automatiquement dans le tableau 54B, qui fournit les coefficients CTL pour corriger des volumes d’essence à des températures observées de 15 C. Utilisez-le si les conditions ci-après sont réunies : le liquide est un produit raffiné la densité observée doit être corrigée à 15 C et utilisée dans le tableau 54B la température de référence est de 15 C Sélectionnez ce tableau, puis introduisez la densité du liquide à la température observée. La densité peut varier de 653 à 1075 kg/m³. On peut introduire des températures d’essai sur cet écran qui calculera un CTL basé sur la température d’essai et la densité. La température d’essai et le CTL calculé sont donnés à titre indicatif et ne seront pas utilisés dans des calculs pendant les opérations. 269 Chapitre 9 – Poids et Mesures 270 Tableau Description ASTM12501980Table 54 Ce tableau donne les coefficients CTL pour la correction des volumes de pétrole brut à des températures observées de 15 C. Utilisez-le si les conditions ci-après sont réunies : NMI ASTM 1250-1980 Table 54A NMI ASTM1250-1980 Table 54B Le liquide est du pétrole brut La densité à 15 C est connue La température de référence est de 15 C Sélectionnez ce tableau puis introduisez la densité du liquide à 15 C. La fourchette de validité de la densité va de 500 à 600 kg/m³. Les températures d'essai peuvent être introduites dans cet écran qui calculera un CTL sur base de la température d'essai et de la densité. La température d'essai et le CTL calculé ne servent que de points de référence et ne sont pas utilisés dans des calculs pendant les opérations. Ce tableau donne les coefficients CTL pour la correction des volumes de pétrole brut à des températures observées de 15 C. Utilisez-le si les conditions ci-après sont réunies : Le liquide est du pétrole brut La densité à 15 C est connue La température de référence est de 15 C Sélectionnez ce tableau puis introduisez la densité du liquide à 15 C. La fourchette de validité de la densité va de 610 à 1075 kg/m³. Les températures d'essai peuvent être introduites dans cet écran qui calcule un CTL sur base de la température d'essai et de la densité. La température d'essai et le CTL calculé ne servent que de points de référence et ne sont pas utilisés dans des calculs pendant les opérations. REMARQUE: L’activation des paramètres de quai “Canada API Limits” rabaisse la fourchette de température à -40 conformément au Measurement Canada Bulletin: V18-E rev.3 1999-09-19 section 270. Ce tableau donne les coefficients CTL pour la correction des volumes d'essence à une température observée de 15 C. Utilisez-le si les conditions ci-après sont réunies : Le liquide est un produit raffiné La densité à 15 C est connue (utilisez le tableau 53B si vous utilisez la densité à la température observée) La température de référence est de 15 C NMI Sélectionnez ce tableau puis introduisez la densité du liquide à 15 C. La fourchette de validité de la densité va de 653 à 1075 kg/m³. Des températures d'essai peuvent être introduites dans cet écran qui calculera un CTL sur base de la température d'essai et de la densité. La température d'essai et le CTL calculé ne servent que de points de référence et ne seront pas utilisés dans des calculs pendant les opérations. REMARQUE: L’activation des paramètres de quai “Canada API Limits” rabaisse la fourchette de température à -40 conformément au Measurement Canada Bulletin: V18-E rev.3 1999-09-19 section 270. ASTM1250-1980 Table 54C Ce tableau fournit les coefficients CTL pour la correction des produits pétroliers à une température observée de 15 C. Utilisez-le si les conditions ci-après sont réunies : NMI Le liquide est un produit raffiné ou du pétrole brut Le coefficient d’expansion à 15 C est connu La température de référence est de 15 C Sélectionnez ce tableau puis introduisez le coefficient d’expansion thermique (alpha) du liquide à 15 C. La fourchette de validité de l'alpha va de 0,000486 à 0,001674. Toutefois, l'alpha sera introduit sous forme 486-1674. Des températures d'essai Chapitre 9 – Poids et Mesures 271 peuvent être introduites dans cet écran qui calcule un CTL sur base de la température d'essai et l'alpha. La température d'essai et le CTL calculé ne servent que de points de référence et ne sont pas utilisés dans des calculs pendant les opérations. REMARQUE: L’activation des paramètres de quai “Canada API Limits” rabaisse la fourchette de température à -40 conformément au Measurement Canada Bulletin: V18-E rev.3 1999-09-19 section 270. ASTM12501980 Table 54D Ce tableau fournit les coefficients CTL pour la correction des huiles de graissage à une température observée de 15 C. Utilisez-le si les conditions ci-après sont réunies : NMI Le liquide est une huile de graissage Le coefficient d’expansion à 15 C est connu La température de référence est de 15 C Sélectionnez ce tableau puis introduisez la densité du liquide à 15 C. La fourchette de validité de la densité va de 800 à 1064 kg/m³. Des températures d'essai peuvent être introduites dans cet écran qui calcule un CTL sur base de la température d'essai et de la densité. La température d'essai et le CTL calculé ne servent que de points de référence et ne sont pas utilisés dans des calculs pendant les opérations. REMARQUE: L’activation des paramètres de quai “Canada API Limits” rabaisse la fourchette de température à -40 conformément au Measurement Canada Bulletin: V-18-E rev.3 1999-09-19 section 270. Chapitre 9 – Poids et Mesures ASTM12501980 Table 54AG Germany 272 Ce tableau fournit des coefficients CTL pour corriger des volumes de pétrole brut à des températures observées de 15 C. Utilisez-le si les conditions suivantes sont réunies: - le liquide est du pétrole brut - la densité à 15 C est connue - la température de référence est de 15 C Sélectionnez ce tableau puis introduisez la densité du liquide à 15 C. La densité peut varier de 610 à 1075 kg/m³. Des températures d’essai peuvent être introduites sur cet écran qui calculera un CTL basé sur la température d’essai et la densité. La température d’essai et le CTL calculé sont donnés à titre indicatif et ne seront pas utilisés dans des calculs pendant les opérations. NMI Densité (610,5 à 778,5) (779,0 à 824,0) (824,5 à 1 075,0) ASTM12501980 Table 54BG Germany Ce tableau fournit des coefficients CTL pour corriger des volumes d’essence à des températures observées de 15 C. Utilisez-le si les conditions suivantes sont réunies: Température −18 à 95 −18 à 125 −18 à 150 le liquide est un produit raffiné la densité à 15 C est connue la température de référence est de 15 C Sélectionnez ce tableau, puis introduisez la densité du liquide à 15 C. La densité peut varier de 600 à 1200 kg/m³. Des températures d’essai peuvent être introduites sur cet écran qui calculera un CTL basé sur la température d’essai et la densité. La température d’essai et le CTL calculé sont donnés à titre indicatif et ne seront pas utilisés dans des calculs pendant les opérations. . Densité 600,0 à 770,4 770,5 à 778,5 778,6 à 787,5 787,6 à 824,0 824,1 à 838,5 838,6 à 1 200,0 NMI ASTM12501980 Table 54CG Germany NMI Température -18 à 95 −18 à 95 −18 à 125 −18 à 125 −18 à 150 −18 à 150 Ce tableau fournit des coefficients CTL pour corriger des volumes de produits pétroliers à des températures observées de 15 C. Utilisez-le si les conditions suivantes sont réunies : le liquide est un produit raffiné ou du pétrole brut le coefficient d’expansion à 15 C est connu la température de référence est de 15 C Sélectionnez ce tableau puis introduisez le coefficient d’expansion thermique (alpha) du liquide à 15 C. L’alpha peut varier de 0.000486 à 0.001674. L’alpha sera toutefois introduit sous forme 486-1674. Des températures d’essai peuvent être introduites sur cet écran qui calculera un CTL basé sur la température d’essai et l’alpha. La température d’essai et le CTL calculé sont donnés à titre indicatif et ne seront pas utilisés dans des calculs pendant les opérations. Expansion 0,000 486 à 0,000 918 0,000 919 à 0,000 954 0,000 955 à 0,001 674 ASTM1250- Température -18 à 150 −18 à 125 −18 à 95 Ce tableau fournit des coefficients CTL pour corriger les volumes d’huile de graissage à des Chapitre 9 – Poids et Mesures 1980 Table 54DG Germany NMI températures observées de 15° C. Utilisez-le si les conditions suivantes sont réunies : le liquide est une huile de graissage la densité à 15 C est connue la température de référence est de 15 C. Sélectionnez ce tableau puis introduisez la densité du liquide à 15° C. La densité peut varier de 750 à 1164 kg/m³. Des températures d’essai peuvent être introduites sur cet écran qui calculera un CTL basé sur la température d’essai et la densité. La température d’essai et le CTL calculé sont donnés à titre indicatif et ne seront pas utilisés pendant les opérations. Densité 750,0 à 1 164,0 ASTM12501980 Table 54XG Germany ASTM12501980 Table 54YG Germany Température -18 à 170 Ce tableau fournit des coefficients CTL pour corriger des volumes de gaz et de bitumes à des températures observées de 15 C. Utilisez-le si les conditions suivantes sont réunies : le liquide est un gaz ou un bitume la densité à 15 C est connue la température de référence est de 15 C La température d’essai et le CTL calculé sont donnés à titre indicatif et ne seront pas utilisés pour des calculs pendant les opérations. Densité 500,0 à 650,0 950,0 à 1200,0 NMI 273 Température -50 à 50 0 à 250 Ce tableau fournit des coefficients CTL pour corriger des volumes de produits chimiques à des températures observées de 15 C. Utilisez-le si les conditions suivantes sont réunies : le liquide est un produit chimique la densité à 15 C est connue la température de référence est de 15 C Alpha et le coefficient K sont connus. Ces coefficients sont sélectionnés dans le MultiloadII à l’aide du paramètre YG nom du produit. La température d’essai et le CTL calculés sont donnés à titre indicatif et ne seront pas utilisés dans des calculs pendant les opérations. Nom du produit Coefficient thermique Constante K Densité 15 C Fourchette de température C Alpha 15 C Propane 0.002850 1.55 507.6 -10 à 40 Propène 0.003095 1.36 523.1 -10 à 40 Butane 0.001900 0.80 584.5 -10 à 40 Isobutane 0.002130 1.00 563.0 -10 à 40 Isobutène 0.002060 1.45 600.1 -10 à 40 Cis-But-2-en 0.001900 0.80 627.0 -10 à 40 Trans-But-2-en 0.001910 1.33 610.1 -10 à 40 But-1-en 0.001955 1.30 602.1 -10 à 40 But-1,3-dien 0.001972 0.80 627.7 -10 à 40 Méthanol 0.001155 -0.38 796.1 0 à 40 Éthanol 0.001078 0.86 793.5 -20 à 40 Chapitre 9 – Poids et Mesures NMI ASTM12501980 E Tableau 59 274 Isopropanol 0.001027 0.93 789.1 0 à 30 Isobutanol 0.000923 0.82 805.6 0 à 30 MTBE 0.001413 0.95 745.6 0 à 30 TAME 0.001204 1.72 775.0 15 à 30 Benzol 0.001188 0.68 884.2 0 à 30 Toluol 0.001060 0.73 871.6 0 à 30 o-Xylol 0.000954 0.78 884.3 0 à 40 m-Xylol 0.000983 1.03 868.4 0 à 30 p-Xylol 0.000990 1.30 865.3 15 à 40 Ce tableau fournit la densité à 20° C pour des hydrocarbures légers à la température et la densité observées. Utilisez-le si les conditions ci-après sont réunies : Le liquide est de NGL ou du LPG (propane) La température et la densité instantanée est connue La densité relative à 20° C n’est pas connue La température de référence est de 20 C. Des températures d'essai peuvent être introduites dans cet écran qui calcule la densité corrigée à la température et la densité d’essai. La température d'essai, la densité et la densité calculée corrigée à 20° ne servent que de points de référence et ne sont pas utilisés dans des calculs pendant les opérations. La valeur CTL est calculée sous la forme CTL = densité observée / densité corrigée à 20°C. NMI ASTM12501980 TABLE 60o __________ ASTM12501980 Table 901A Ce tableau donne la densité à 20° C pour les hydrocarbures légers à la température et la densité observées. _____________________________________________________________ Il s’agit de la correction du volume basée sur le tableau pour les alcools/biocarburants (Brésil). Norme de référence : ABNT NBR 5992 pour l‘éthanol (901A). C’est au-delà de la densité API 20 du produit à 60° (API60) et de la température du produit en degré F. Chapitre 9 – Poids et Mesures Table TEC 275 Ce tableau donne les coefficients CTL pour la correction de l'éthanol à une température observée de 15 C ou 60 F. Utilisez-le si les conditions ci-après sont réunies: Le liquide est de l'éthanol Le coefficient d’expansion à 15 C ou 60 F est connu La température de référence est de 15 C ou 60 F. Sélectionnez ce tableau puis introduisez le coefficient d’expansion du liquide à 15 C ou 60 F. Des températures d'essai peuvent être introduites dans cet écran qui calcule un CTL sur base de la température d'essai et du coefficient d’expansion. La température d'essai et le CTL calculé ne servent que de points de référence et ne sont pas utilisés dans des calculs pendant les opérations. Table TEC ETH US Ce tableau donne les coefficients CTL pour la correction de l'éthanol à une température observée de 15 C ou 60 F. Utilisez-le si les conditions ci-après sont réunies : Le liquide est de l'éthanol Le coefficient d’expansion à 15 C ou 60 F n'est pas connu La température de référence est de 15 C ou 60 F. Les températures d'essai peuvent être introduites dans cet écran qui calcule un CTL sur base de la température d'essai et du coefficient d’expansion. La température d'essai et le CTL calculé ne servent que de points de référence et ne sont pas utilisés dans des calculs pendant les opérations. Table TEC ETH B100 Ce tableau donne les coefficients CTL pour la correction de l'éthanol à une température observée de 15 C ou 60 F. Utilisez-le si les conditions ci-après sont réunies : NMI Le liquide est de l'éthanol Le coefficient d’expansion à 15 C ou 60 F n'est pas connu La température de référence est de 15 C ou 60 F. (doit êtremaintenu sous le niveau du composant !) Le coefficient de densité est fixé à 0.84*10E-3. Les températures d'essai peuvent être introduites dans cet écran qui calcule un CTL sur base de la température d'essai et du coefficient d’expansion. La température d'essai et le CTL calculé ne servent que de points de référence et ne sont pas utilisés dans des calculs pendant les opérations. Remarque : Le mélange va de B0 à B100 Table TEC ETH B40 Ce tableau fournit les coefficients CTL pour la correction des volumes d’éthanol aux températures observées à 15 C ou 60 F. Utilisez-le si les conditions suivantes sont réunies: NMI le liquide est de l’éthanol le coefficient d’expansion à 15 C ou 60 F n’est pas connu la température de référence est de 15 C ou 60 F (doit être maintenue sous le niveau du composant!) Chapitre 9 – Poids et Mesures 276 Le coefficient de densité est fixé à 0.84*10E-3 Les températures d’essai peuvent être introduites sur cet écran qui calculera un CTL basé sur la température d’essai et le coefficient d’expansion. La température d’essai et le CTL calculé sont donnés à titre indicatif et ne seront pas utilisés dans les calculs pendant les opérations. REMARQUE: le mélange varie de B0 à B40 Table TEC ETH E40 Ce tableau fournit les coefficients CTL pour la correction des volumes d’éthanol aux températures observées à 15 C ou 60 F. le liquide est de l’éthanol NMI le coefficient d’expansion à 15 C ou 60 F n’est pas connu la température de référence est de 15 C ou 60 F (doit être maintenue sous le niveau du composant!) Le coefficient de densité est de 1.27*10E-3 Des températures d’essai peuvent être introduites sur cet écran qui calculera un CTL basé sur la température d’essai et le coefficient d’expansion. La température d’essai et le CTL calculé sont donnés à titre indicatif et ne seront pas utilisés dans les calculs pendant les opérations. REMARQUE: le mélange varie de E0 à E40 Table PTBBIO Ce tableau API BIO sert pour la Méthode3 à partir de PTB Community. Sélectionner le tableau PTBBIO table combiné à API BIO pour choisir le produit désiré. Formule: V(T) = V0 *{1 + [A1 *(T – T0) + A2 *(T – T0)2 + A3 *(T – T0)3]} V0 = Volume @ température de base V(T) = Volume @ température observée T0 = Température de base (15° C) T = Température observée A1, A2, A3 = coefficients biocarburants Type de produit A1 A2 A3 Densité de référence E5 1.2422 x 10-3 9.1811 x 10-7 5.3906 x 10-9 738.858 E10 - - - 741.447 Chapitre 9 – Poids et Mesures 277 1.2415 x 10-3 9.8712 x 10-7 6.6333 x 10-9 E80 1.1129 x 10-3 6.5049 x 10-7 8.8556 x 10-9 781.410 E85 1.1023 x 10-3 6.0110 x 10-7 8.7249 x 10-9 784.549 E100 1.0720 x 10-3 4.5474 x 10-7 8.3383 x 10-9 793.949 Pétrole 1.2361 x 10-3 6.7788 x 10-7 3.8516 x 10-9 733.919 Diesel 8.2239 x 10-4 5.1745 x 10-8 1.3703 x 10-9 844.615 B5 RME 8.2261 x 10-4 5.5270 x 10-8 1.3289 x 10-9 846.439 B7 RME 8.2258 x 10-4 5.4729 x 10-8 1.3921 x 10-9 847.171 B100 RME 8.2330 x 10-4 1.4698 x 10-7 1.6545 x 10-9 883.314 B5 SME 8.1922 x 10-4 2.9212 x 10-8 1.0385 x 10-9 846.486 B7 SME 8.1925 x 10-4 3.1305 x 10-8 1.0918 x 10-9 847.253 B100 SME 8.2132 x 10-4 1.0329 x 10-7 1.0793 x 10-9 885.229 RME: esther méthyl d’huile de colza SME: esther méthyl d’huile de soja Chapitre 9 – Poids et Mesures 278 Table TEC ETH E 100 Ce tableau fournit des coefficients CTL pour la correction des volumes d’éthanol à des températures observées de 15 C ou 60 F. Utilisez ce tableau si les conditions suivantes sont réunies: le liquide est de l’éthanol le coefficient d’expansion à 15 C ou 60 F n’est pas connu La température de référence est de 15 C ou 60 F (doit être maintenue sous le niveau du composant!) Le coefficient de densité est de 1.1427*10E-3 Des températures d’essai peuvent être introduites sur cet écran qui calculera un CTL basé sur la température d’essai et le coefficient d’expansion. La température d’essai et le CTL calculé sont donnés à titre indicatif et ne seront pas utilisés dans les calculs pendant les opérations. NMI REMARQUE: le mélange varie de E60 à E100 Ce tableau fournit des coefficients CTL pour la correction des volumes d’éthanol à des températures observées à 20 C. Utilisez ce tableau si les conditions suivantes sont réunies: TABLE ETH BRAZIL Le liquide est de l’alcool Le pourcentage d’alcool est connu La température instantanée est disponible. Des températures d’essai peuvent être introduites sur cet écran qui calculera un CTL basé sur la température d’essai et le pourcentage d’alcool. La température d’essai et le CTL calculé sont donnés à titre indicatif et ne seront pas utilisés dans les calculs pendant les opérations. La densité corrigée à 20 degrés sera calculée et enregistrée Ce tableau fournit des coefficients CTL pour la correction des volumes d’hydrocarbures à des températures observées à 20 C. Utilisez ce tableau si les conditions suivantes sont réunies: TABLE HYDRO BRAZIL Le liquide est de l’alcool la température instantanée et la densité à 20 C sont disponibles. Des températures d’essai peuvent être introduites sur cet écran qui calculera un CTL basé sur la température d’essai et la densité. La température d’essai et le CTL calculé sont donnés à titre indicatif et ne seront pas utilisés dans les calculs pendant les opérations. Produit Min Temp Max Temp Min Dens20 Max Dens20 LPG -50 75 498 700 Essence -25 75 700 800 Diesel, Lubrifiants -25 125 800 900 Pétrole brut, huiles lourdes, … 0 200 900 1200 La densité corrigée au degré observé sera calculée et enregistrée. Chapitre 9 – Poids et Mesures ASTM 12502004 Table 5A Ce tableau fournit la gravité API à 60 F température observée pour le pétrole brut et la gravité API. Utilisez ce tableau si les conditions suivantes sont réunies: Le liquide est du pétrole brut La température instantanée et la gravité API sont connues NMI La gravité API à 60 F est inconnue ASTM 12502004 Table 5B Ce tableau fournit la gravité API à 60 F pour des produits raffinés à la température observée et la gravité API. Utilisez ce tableau si les conditions suivantes sont réunies: NMI Le liquide est un produit raffiné La température instantanée et la gravité API sont connues La gravité API à 60 F est inconnue ASTM12502004 Table 5D Ce tableau fournit la gravité API à 60 F de l’huile de graissage à la température observée et à la gravité API. Utilisez ce tableau si les conditions suivantes sont réunies: Le liquide est de l’huile de graissage La température instantanée et la gravité API sont connues NMI La gravité API à 60 F est inconnue ASTM12502004 Table 5X Ce tableau fournit la gravité API d’un produit pétrolier à des températures observées et à la gravité API. Ce tableau permet de spécifier le produit mesuré, la température de référence et les unités de mesure de densité, de pression et de température. ASTM12502004 Table 6A Ce tableau fournit des coefficients CTL pour la correction des volumes de pétrole brut à des températures observées à 60 F, par la méthode décrite au chapitre 11.1.6.1 de la norme 2004. Utilisez ce tableau si les conditions suivantes sont réunies: NMI ASTM12502004 Table 6B NMI ASTM12502004 Table 6C NMI Le liquide est un produit raffiné La gravité API à 60 F est connue La température de référence est de 60 F Ce tableau fournit des coefficients CTL pour la correction des volumes de produits pétroliers liquides à des températures observées à 60 F, par la méthode décrite au chapitre 11.1.6.1 de la norme 2004. Utilisez ce tableau si les conditions suivantes sont réunies : Le liquide est un produit raffiné ou du pétrole brut Le coefficient d’expansion à 60 F est connu La température de référence est de 60 F Ce tableau fournit des coefficients CTL pour la correction des volumes d’huile de graissage à des températures observées à 60 F, par la méthode décrite au chapitre 11.1.6.1 de la norme 2004. Utilisez ce tableau si les conditions suivantes sont réunies : ASTM12502004 Table 6D NMI Le liquide est du pétrole brut La gravité API à 60 F est connue La température de référence est de 60 F Ce tableau fournit des coefficients CTL pour la correction des volumes d’essence à des températures observées à 60 F, par la méthode décrite au chapitre 11.1.6.1 de la norme 2004. Utilisez ce tableau si les conditions suivantes sont réunies: Le liquide est de l’huile de graissage La gravité API à 60 F est connue La température de référence est de 60 F 279 Chapitre 9 – Poids et Mesures 280 ASTM1250-2004 Table 6X Ce tableau fournit des coefficients CTL pour la correction des volumes de produits pétroliers à des températures observées. Ce tableau permet de spécifier le produit mesuré, le coefficient d’expansion, la température de référence ainsi que les unités de mesure de densité, de pression et de température. ASTM1250-2004 Table 24A Ce tableau fournit des coefficients CTL pour la correction des volumes de pétrole brut à des températures observées à 60 F, par la méthode décrite au chapitre 11.1.6.1 de la norme 2004. Utilisez ce tableau si les conditions suivantes sont réunies: La température de référence est de 60 F NMI ASTM1250-2004 Table 24B ASTM1250-2004 Table 24C ASTM1250-2004 Table 24D NMI Ce tableau fournit des coefficients CTL pour la correction des volumes d’essence à des températures observées à 60 F, par la méthode décrite au chapitre 11.1.6.1 de la norme 2004. Utilisez ce tableau si les conditions suivantes sont réunies: Le liquide est un produit raffiné La densité à 60 F est connue La température de référence est de 60 F NMI NMI Le liquide est du pétrole brut La densité relative à 60 F est connue ASTM1250-2007 Table 24E Ce tableau fournit des coefficients CTL pour la correction des volumes de produits pétroliers liquides à des températures observées à 60 F, par la méthode décrite au chapitre 11.1.6.1 de la norme 2004. Utilisez ce tableau si les conditions suivantes sont réunies. Le liquide est un produit raffiné ou du pétrole brut Le coefficient d’expansion à 60 F est connu La température de référence est de 60 F Ce tableau fournit des coefficients CTL pour la correction des volumes d’huiles de graissage à des températures observées à 60 F, par la méthode décrite au chapitre 11.1.6.1 de la norme 2004. Utilisez ce tableau si les conditions suivantes sont réunies: Le liquide est une huile de graissage La densité relative à 60 F est connue La température de référence est de 60 F Ce tableau fournit des coefficients CTL pour la correction des volumes d’hydrocarbures légers à des températures observées à 60 F. Utilisez ce tableau si les conditions suivantes sont réunies: Le liquide est du NGL ou du LPG (propane) La densité relative à 60 F est connue La température de référence est de 60 F Sélectionnez ce tableau puis introduisez la densité relative du liquide à 60 F. La densité relative peut varier de 0.3500 à 0.6880. Des températures d’essai peuvent être introduites sur cet écran qui calculera un CTL basé sur la température d’essai et la densité relative. La température d’essai et le CTL calculé sont donnés à titre indicatif et ne seront pas utilisés dans les calculs pendant les opérations. ASTM1250-2004 Table 24X Ce tableau fournit les coefficients CPL d’un produit pétrolier à des températures observées et à la densité relative. Ce tableau permet de spécifier le produit mesuré, la température de référence et les unités de mesure de densité, de pression et de température ASTM1250-2004 Table 23A Ce tableau fournit la valeur de la densité relative à 60 F du pétrole brut à la température et la densité observées. Utilisez ce tableau si les conditions suivantes sont réunies: Chapitre 9 – Poids et Mesures NMI ASTM1250-2004 Table 23B NMI 281 Le liquide est du pétrole brut. La température instantanée et la densité sont disponibles. La densité relative à 60 F est inconnue La température de référence est de 60 F Ce tableau fournit la valeur de la densité relative à 60 F des essences à la température et la densité observées. Utilisez ce tableau si les conditions suivantes sont réunies: Le liquide est un produit raffiné. La température instantanée et la densité sont disponibles La densité relative à 60 F est inconnue La température de référence est de 60 F ASTM1250-2004 Table 23D NMI Ce tableau fournit la valeur de la densité relative à 60 F des huiles de graissage à la densité et la température observées. Utilisez ce tableau si les conditions suivantes sont réunies: Le liquide est de l’huile de graissage. La température instantanée et la densité sont disponibles. La densité relative at 60 F est inconnue La température de référence est de 60 F ASTM1250-2007 Table 23E Ce tableau fournit la densité à 60 F d’hydrocarbures légers à la densité et la température observées. Utilisez ce tableau si les conditions suivantes sont réunies: Le liquide est du NGL ou du LPG (propane) La température instantanée et la densité sont disponibles. La densité relative à 60 F est inconnue La température de référence est de 60 F Des températures d’essai et des densités peuvent être introduites sur cet écran qui calculera la densité corrigée à la température d’essai et la densité. La température d’essai, la densité et la densité corrigée calculée à 60 F sont données à titre indicatif et ne seront pas utilisées dans les calculs pendant les opérations. REMARQUE: ce tableau ne donnera pas de valeur CTL mais il peut être utilisé par d’autres tableaux ASTM1250-2004 Table 23X Ce tableau fournit la densité relative d’un produit pétrolier à une densité et une température observées. Ce tableau permet de spécifier le produit mesuré, la température de référence et les unités de mesure de densité, de pression et de température. ASTM1250-2004 Table 54A Ce tableau fournit des coefficients CTL pour la correction des volumes de pétrole brut à des températures observées à 15 C. Utilisez ce tableau si les conditions suivantes sont réunies: Le liquide est de pétrole brut La densité à 15 C est connue La température de référence est de 15 C NMI Sélectionnez ce tableau et introduisez la densité du liquide à 15 C. La densité peut varier de 610 à1075 kg/m³. Des températures d’essai peuvent être introduites sur cet écran qui calculera un CTL basé sur la température d’essai et la densité. La température d’essai et le CTL calculé sont donnés à titre indicatif et ne seront pas utilisés dans les calculs pendant les opérations. ASTM1250-2004 Table 54B Ce tableau fournit des coefficients CTL pour la correction des volumes d’essence à des températures observées à 15 C. Utilisez ce tableau si les conditions suivantes sont réunies: Le liquide est un produit raffiné La densité à 15 C est connue La température de référence est de 15 C NMI Sélectionnez ce tableau et introduisez la densité du liquide à 15 C. La densité peut varier de 653 à1075 kg/m³. Des températures d’essai peuvent être introduites sur cet écran qui calculera un CTL basé sur la température d’essai et la densité. La température d’essai et le CTL calculé sont donnés à titre indicatif et ne seront pas utilisés dans les calculs pendant les opérations. ASTM1250-2004 Ce tableau fournit des coefficients CTL pour la correction des volumes de produits pétroliers liquides Chapitre 9 – Poids et Mesures Table 54C 282 à des températures observées à 15 C. Utilisez ce tableau si les conditions suivantes sont réunies: Le liquide est un produit raffiné ou du pétrole brut Le coefficient d’expansion à 15 C est connu La température de référence est de 15 C NMI Sélectionnez ce tableau et introduisez le coefficient d’expansion thermique (alpha) du liquide à 15 C. L’apha peut varier de 0.000486 à 0.001674. Toutefois, l’alpha sera introduit sous la forme 486-1674. Des températures d’essai peuvent être introduites sur cet écran qui calculera un CTL basé sur la température d’essai et l’alpha. La température d’essai et le CTL calculé sont donnés à titre indicatif et ne seront pas utilisés dans les calculs pendant les opérations. ASTM1250-2004 Table 54D Ce tableau fournit des coefficients CTL pour la correction des volumes d’huiles de graissage à des températures observées à 15 C. Utilisez ce tableau si les conditions suivantes sont réunies: Le liquide est de l’huile de graissage La densité à 15 C est connue La température de référence est de 15 C NMI Sélectionnez ce tableau et introduisez la densité du liquide à 15 C. La densité peut varier de 800 à 1064 kg/m³. Des températures d’essai peuvent être introduites sur cet écran qui calculera un CTL basé sur la température d’essai et la densité. La température d’essai et le CTL calculé sont donnés à titre indicatif et ne seront pas utilisés dans les calculs pendant les opérations. ASTM1250-2007 Table 54E Ce tableau fournit des coefficients CTL pour la correction des volumes d’hydrocarbures légers à des températures observées à 15 C. Utilisez ce tableau si les conditions suivantes sont réunies: Le liquide est du NGL ou du LPG (propane) La densité at 15 C est connue La température de référence est de 15 C Sélectionnez ce tableau et introduisez la densité du liquide à 15 C. La densité peut varier de 350 à 688. Des températures d’essai peuvent être introduites sur cet écran qui calculera un CTL basé sur la température d’essai et la densité. La température d’essai et le CTL calculé sont donnés à titre indicatif et ne seront pas utilisés dans les calculs pendant les opérations. ASTM1250-2004 Table 60A Ce tableau fournit des coefficients CTL pour la correction des volumes de pétrole brut à des températures observées à 20 C. Utilisez ce tableau si les conditions suivantes sont réunies: Le liquide est de pétrole brut La densité at 20 C est connue La température de référence est de 20 C Sélectionnez ce tableau et introduisez la densité du liquide à 20 C. La densité peut varier de 610 à1075 kg/m³. Des températures d’essai peuvent être introduites sur cet écran qui calculera un CTL basé sur la température d’essai et la densité. La température d’essai et le CTL calculé sont donnés à titre indicatif et ne seront pas utilisés dans les calculs pendant les opérations. NMI ASTM1250-2004 Table 60B Ce tableau fournit des coefficients CTL pour la correction des volumes d’essence à des températures observées à 20 C. Utilisez ce tableau si les conditions suivantes sont réunies: Le liquide est un produit raffiné La densité à 20 C est connue La température de référence est de 20 C NMI Sélectionnez ce tableau et introduisez la densité du liquide at 20 C. La densité peut varier de 653 à1075 kg/m³. Des températures d’essai peuvent être introduites sur cet écran qui calculera un CTL basé sur la température d’essai et la densité. La température d’essai et le CTL calculé sont donnés à titre indicatif et ne seront pas utilisés dans les calculs pendant les opérations. ASTM1250-2004 Table 60C Ce tableau fournit des coefficients CTL pour la correction des volumes de produits pétroliers liquides à des températures observées à 20 C. Utilisez ce tableau si les conditions suivantes sont réunies: Le liquide est un produit raffiné ou du pétrole brut Le coefficient d’expansion à 20 C est connu Chapitre 9 – Poids et Mesures 283 La température de référence est de 20 C Sélectionnez ce tableau et introduisez le coefficient d’expansion thermique (alpha) du liquide à 20 C. L’alpha peut varier de 0.000486 à 0.001674. Toutefois on introduira l’alpha sous la forme 486-1674. Des températures d’essai peuvent être introduites sur cet écran qui calculera un CTL basé sur la température d’essai et l’alpha. La température d’essai et le CTL calculé sont donnés à titre indicatif et ne seront pas utilisés dans les calculs pendant les opérations. NMI ASTM1250-2004 Table 60D Ce tableau fournit des coefficients CTL pour la correction des volumes d’huiles de graissage à des températures observées à 20 C. Utilisez ce tableau si les conditions suivantes sont réunies: Le liquide est de l’huile de graissage La densité à 20 C est connue La température de référence est de 20 C NMI Sélectionnez ce tableau et introduisez la densité du liquide à 20 C. La densité peut varier de 800 à 1064 kg/m³. Des températures d’essai peuvent être introduites sur cet écran qui calculera un CTL basé sur la température d’essai et la densité. La température d’essai et le CTL calculé sont donnés à titre indicatif et ne seront pas utilisés dans les calculs pendant les opérations. ASTM1250-2007 Table 60E Ce tableau fournit des coefficients CTL pour la correction des volumes d’hydrocarbures légers à des températures observées à 20 C. Utilisez ce tableau si les conditions suivantes sont réunies: Le liquide est du NGL ou du LPG (propane) La densité à 20 C est conne La température de référence est de 20 C Sélectionnez ce tableau et introduisez la densité du liquide à 20 C. La densité peut varier de 350 à 688. Des températures d’essai peuvent être introduites sur cet écran qui calculera un CTL basé sur la température d’essai et la densité. La température d’essai et le CTL calculé sont donnés à titre indicatif et ne seront pas utilisés dans les calculs pendant les opérations. ASTM1250-2004 Table 60X Ce tableau fournit les coefficients CTL d’un produit pétrolier à des températures et une densité observées. Ce tableau permet de spécifier le produit mesuré, la température de référence et les unités de mesure de densité, de pression et de température. ASTM1250-2004 Table 53A Ce tableau sert à corriger la densité à la température observée pour la densité à 15 C. Lorsqu’il est activé, la densité corrigée est automatique utilisée dans le tableau 54B, qui fournit des coefficients CTL pour corriger des volumes d’essence à des températures observées à 15 C. Utilisez ce tableau si les conditions suivantes sont réunies: Le liquide est du pétrole brut La densité observée doit être corrigée à 15 C et utilisée au tableau 54B La température de référence est de 15 C Sélectionnez ce tableau et introduisez la densité du liquide à la température observée. La densité peut varier de 610 à 1075 kg/m³. Des températures d’essai peuvent être introduites sur cet écran qui calculera un CTL basé sur la température d’essai et la densité. La température d’essai et le CTL calculé sont donnés à titre indicatif et ne seront pas utilisés dans les calculs pendant les opérations. ASTM1250-2004 Table 53B Ce tableau sert à corriger la densité observée à la température pour une densité à 15 C. Lorsque ce tableau est activé, la densité corrigée est automatiquement utilisée dans le tableau 54B, qui fournit des coefficients CTL pour corriger des volumes d’essence à des températures observées à 15 C. Utilisez ce tableau si les conditions suivantes sont réunies: Le liquide est un produit raffiné NMI La densité observée doit être corrigée à 15 C et utilisée au tableau 54B NMI La température de référence est de 15 C Sélectionnez ce tableau et introduisez la densité du liquide à la température observée. La densité peut varier de 653 à 1075 kg/m³. Des températures d’essai peuvent être introduites sur cet écran qui calculera un CTL basé sur la température d’essai et la densité. La température d’essai et le CTL calculé sont donnés à titre indicatif et ne seront pas utilisés dans les calculs pendant les opérations. Chapitre 9 – Poids et Mesures ASTM1250-2004 Table 53D 284 Ce tableau sert à corriger la densité observée à la température observée à une densité de 15 C. Lorsque ce tableau est activé, la densité corrigée est automatiquement utilisés au tableau 54B, qui fournit des coefficients CTL pour corriger des volumes d’essence à des températures observées à 15 C. Utilisez ce tableau si les conditions suivantes sont réunies: Le liquide est de l’huile de graissage La densité doit être corrigée à 15 C et utilisée au tableau 54B NMI La température de référence est de 15 C Sélectionnez ce tableau et introduisez la densité du liquide à la température observée. La densité peut varier de 800 à 1064 kg/m³. Des températures d’essai peuvent être introduites sur cet écran qui calculera un CTL basé sur la température d’essai et la densité. La température d’essai et le CTL calculé sont donnés à titre indicatif et ne seront pas utilisés dans les calculs pendant les opérations. ASTM1250-2007 Table 53E Ce tableau fournit la densité à 15 C pour des hydrocarbures légers à une densité et une température observées. Utilisez ce tableau si les conditions suivantes sont réunies: Le liquide est du NGL ou du LPG (propane) La température instantanée et la densité sont disponibles. La densité à 15 C est inconnue La température de référence est de 15 C Des températures et des densités d’essai peuvent être introduites sur cet écran qui calculera la densité corrigée à la température et la densité d’essai. La température d’essai, la densité et la densité corrigée calculée à 60 F sont données à titre indicatif et ne seront pas utilisées dans les calculs pendant les opérations. REMARQUE : Ce tableau ne fournit pas de valeur mais il peut être utilisé par d’autres tableaux. ASTM1250-2004 Table 59A Ce tableau sert à corriger la densité observée à la température observée à 20 C. Lorsqu’il est activé, la densité corrigée est automatiquement utilisée au tableau 54B, qui fournit des coefficients CTL pour corriger des volumes d’essence à des températures observées à 20 C. Utilisez ce tableau si les conditions suivantes sont réunies: Le liquide est du pétrole brut La densité observée doit être corrigée à 20 C et utilisée au tableau 54B La température de référence est de 20 C Sélectionnez ce tableau et introduisez la densité du liquide à la température observée. La densité peut varier de 610 à 1075 kg/m³. Des températures d’essai peuvent être introduites sur cet écran qui calculera un CTL basé sur la température d’essai et la densité. La température d’essai et le CTL calculé sont donnés à titre indicatif et ne seront pas utilisés dans les calculs pendant les opérations. ASTM1250-2004 Table 59B Ce tableau sert à corriger la densité à la température observée à 20 C. Quand il est activé, la densité corrigée est automatiquement utilisée au tableau 54B, qui fournit des coefficients CTL pour corriger des d’essence à des températures observées à 20 C. Utilisez ce tableau si les conditions suivantes sont réunies: Le liquide est un produit raffiné La densité observée est corrigée à 20 C et utilisée au tableau 54B La température de référence est de 20 C Sélectionnez ce tableau et introduisez la densité du liquide à la température observée. La densité peut varier de 653 à 1075 kg/m³. Des températures d’essai peuvent être introduites sur cet écran qui calculera un CTL basé sur la température d’essai et la densité. La température d’essai et le CTL calculé sont donnés à titre indicatif et ne seront pas utilisés dans les calculs pendant les opérations. ASTM1250-2004 Table 59D Ce tableau sert à corriger la densité observée à la température observée à 20 C. Lorsqu’il est activé, la densité est automatiquement utilisée au tableau 54B, qui fournit des coefficients CTL pour corriger des volumes d’essence à des températures observées à 20 C. Utilisez ce tableau si les conditions suivantes sont réunies: NMI NMI Le liquide est de l’huile de graissage La densité observée doit être corrigée à 20 C et utilisée au tableau 54B Chapitre 9 – Poids et Mesures 285 La température de référence est de 20 C Sélectionnez ce tableau et introduisez la densité du liquide à la température observée. La densité peut varier de 800 à 1064 kg/m³. Des températures d’essai peuvent être introduites sur cet écran qui calculera un CTL basé sur la température d’essai et la densité. La température d’essai et le CTL calculé sont donnés à titre indicatif et ne seront pas utilisés dans les calculs pendant les opérations. ASTM1250-2007 Table 59E Ce tableau fournit la densité à 20 C pour des hydrocarbures légers à une température et une densité observées. Utilisez ce tableau si les conditions suivantes sont réunies: Le liquide est du NGL ou du LPG (propane) La température instantanée et la densité sont disponibles. La densité à 20 C est inconnue La température de référence est de 20 C Des températures d’essai et des densités peuvent être introduites sur cet écran qui calculera la densité corrigée à la température et la densité d’essai. La température d’essai, la densité et la densité corrigée calculée à 20 C sont données à titre indicatif et ne seront pas utilisées dans les calculs pendant les opérations. REMARQUE: Ce tableau ne fournira pas de valeur CTL mais il pourra être utilisé par d’autres tableaux ASTM1250-2004 Table 59X Ce tableau fournit la densité de base d’un produit pétrolier à des températures et des densités observées. Ce tableau permet de spécifier le produit mesuré, la température de référence et les unités de mesure de densité, de pression et de température OIML6 Ce tableau sert à calculer le pourcentage de la masse d’alcool à une température et une densité observées. Lorsqu’il est activé, le coefficient CTL contiendra la quantité d’alcool. De cette façon, le volume net affiché sur chaque écran est le volume d’alcool dans le produit. NMI Le liquide est un produit raffiné La densité observée est utilisée dans le tableau OIML6 La température observée est utilisée Après avoir sélectionné ce tableau, la densité n’a pas de plage ; seul le contrôle de la température est permis entre -20 et + 40 degrés. Des températures d’essai peuvent être introduites sur cet écran qui calculera un CTL basé sur la température d’essai et la densité. La température d’essai et le CTL calculé sont donnés à titre indicatif et ne seront pas utilisés dans les calculs pendant les opérations. Ce tableau sert à calculer le volume du pourcentage d’alcool à une densité et une température observées. Lorsqu’il est activé, le coefficient CTL contient la quantité d’alcool. De cette façon, le volume net qui s’affiche sur chaque écran est le volume d’alcool dans le produit. OIML7 Le liquide est un produit raffiné La densité observée est utilisée au tableau OIML7 La température observée est utilisée Après avoir sélectionné ce tableau, la densité n’a pas de plage ; seul le contrôle de la température est permis entre -20 et + 40 degrés. Des températures d’essai peuvent être introduites sur cet écran qui calculera un CTL basé sur la température d’essai et la densité. La température d’essai et le CTL calculé sont donnés à titre indicatif et ne seront pas utilisés dans les calculs pendant les opérations. Chapitre 9 – Poids et Mesures 2. Configuration de la mesure de la température Les tableaux API utilisés dans le MultiLoad II exigent une température observée qui est celle du liquide au moment de la mesure. La température observée peut être contrôlée en continu au moyen d'une sonde de température à résistance (RTD) ou un transmetteur de température de 4-20 mA. Vous pouvez également introduire manuellement une température par défaut. 3. Configuration d’une sonde de température a) Reliez la sonde de température au tableau interne E/S ou à un FCM externe (module de commande du débit). Consultez les schémas électriques dans le manuel d’installation. b) Etalonnez la température. c) Entrez dans le mode de programme du Multiload II. Sélectionnez le menu Configuration/equipment Setup Meters. Puis, la valeur prédéfinie et le compteur appropriés. d) Activez le paramètre "Sonde de température". Ce paramètre doit déjà être activé si l'étape d'étalonnage de la température a déjà été effectuée. e) Recherchez le paramètre "Default temperature" et configurez-le sur 999,9. Ne pas ajuster cette valeur à moins que le RTD ne soit en cours d’entretien. f) Recherchez le paramètre Temp Module Type. Introduisez une valeur représentant le type approprié de sonde de température: Pour MultiLoad II SMP: 1 – Carte E/S interne RTD 3 – Carte E/S interne 4-20mA Pour MultiLoad II: 0 – FCM l externe avec module Opto22 RTD 1 – Carte E/S interne RTD ou FCM l avec module Toptech RTD ou FCM ll RTD 2 – FCM l externe avec module Opto22 4-20mA 3 – Carte E/S interne 4-20mA ou FCM ll 4-20 mA externe. Si le module de température est sur un FCM différent de son compteur, ajoutez 10 aux valeurs ci-dessus. g) Recherchez le paramètre "Alarm High Temp". (Ce paramètre se trouve au menu "Configuration/Equipment Setup/Meter Menu) et introduisez la température qui représente la limite supérieure de température du tableau API utilisé. h) Recherchez le paramètre Alarm Low Temp (alarme de température basse). Il se trouve au menu Configuration/Setup Equipment/Meter. Introduisez la température représentant la limite de température inférieure du tableau API utilisé. 4. Configuration de la température par défaut 286 Chapitre 9 – Poids et Mesures Lorsque la sonde de température est à l’entretien, la température observée peut être introduite manuellement pour être utilisée par le tableau API. a. Entrez dans le mode de programme du MultiLoad II. Sélectionnez le menu Configuration, Equipment Setup/Meters. Puis, la valeur prédéfinie et le compteur appropriés. b. Recherchez le paramètre "Temperature Sensor". Placez ce paramètre sur "Disabled". c. Recherchez le paramètre "Default Température". Introduisez la température observée sur le débitmètre. d. Lorsque la sonde de température est remise en service, réactivez le paramètre "Temperature Sensor" et remettez la température par défaut sur 999,9. 5. Configuration des Mesures de Densité Pour les tableaux API qui utilisent la densité, une valeur de densité peut être introduite manuellement ou mesurée au cours du chargement. Des valeurs manuelles de densité sont introduites par l'utilisateur lorsque le tableau API approprié est activé. Pour utiliser la lecture en direct des densités depuis un densitomètre (4-20 mA) et corriger le volume, utilisez la procédure ci-après : a. Raccordez le transmetteur de densité à n'importe quel module de commande du débit disponible (FCM). Utilisez n'importe quel port analogique. Consultez les schémas électriques des transmetteurs dans le manuel d’installation. b. Entrez dans le mode de programme du MultiLoad II. Sélectionnez le menu Configuration, Equipment Setup/Meters. Puis, la valeur prédéfinie et le compteur appropriés. c. Recherchez le paramètre "Density Sensor" et activez-le. d. Recherchez le paramètre "Density Sensor » et introduisez 0. e. Recherchez le paramètre "La densité à 4 mA". Introduisez la densité représentant la valeur minimale de densité mesurée par le transmetteur. Cette valeur sera égale à 4 mA. f. Recherchez le paramètre "density @ 20 mA". Introduisez la densité représentant la valeur maximale de densité mesurée par le transmetteur. Cette valeur sera égale à 20 mA. g. Appuyez sur la touche "Exit" pour afficher le menu principal. Rentrez dans le menu Configuration/ Equipment/ Setup/Component. Sélectionnez la valeur prédéfinie et le composant appropriés. h. Recherchez le paramètre d’alarme de basse densité. Introduisez une valeur de densité représentant la limite inférieure de densité du tableau API utilisé. i. Recherchez le paramètre d’alarme de haute densité. Introduisez une valeur de densité correspondant à la limite supérieure de densité du tableau API utilisé. j. Etalonnez la densité relative. 6. Configuration de la mesure de densité relative Pour les tableaux API qui utilisent la densité relative, on peut introduire manuellement une valeur de densité relative ou mesurer une densité relative au cours du chargement. L’utilisateur introduit les valeurs de densité relatives manuelles lorsque le tableau API approprié est activé. Pour utiliser les données de densité relatives en direct à partir d’un densitomètre (4-20 mA) pour corriger un volume, suivez la procédure ci-après. a) Connectez le transmetteur de densité relative à n’importe quel module de commande du débit (FCM) disponible. Utilisez n’importe quel port analogique libre. Consultez les diagrammes de câblage du transmetteur dans le guide d’installation. b) Introduisez le mode de programme au MultiLoad II. Sélectionnez le menu Configuration, Equipment Setup, Meters puis sélectionnez la valeur prédéfinie et le composant adéquats. c) Trouvez le paramètre appelé Relative Density Sensor et activez-le. d) Trouvez le paramètre appelé Relative Density Sensor FCM# et introduisez un zéro. 287 Chapitre 9 – Poids et Mesures e) Trouvez le paramètre appelé Relative Density @ 4 mA. Introduisez la densité relative qui représentera la densité relative la plus basse mesurée par le transmetteur. Cette valeur sera égale à 4 mA. f) Trouvez le paramètre appelé Relative Density @ 20 mA. Introduisez la densité relative qui représentera la valeur de densité la plus élevée mesurée par le transmetteur. Celle valeur sera égale à 20 mA. g) Appuyez sur la touche EXIT jusqu’à ce que le menu principal apparaisse. Introduisez le menu Configuration/Equipment Setup/Component. Sélectionnez la valeur prédéfinie et le composant appropriés. h) Trouvez le paramètre appelé Alarm Low Relative Density. Introduisez une valeur de densité relative représentant la limite inférieure de densité relative du tableau API utilisé. i) Trouvez le paramètre appelé Alarm High Relative Density. Introduisez une valeur de densité relative représentant la imite de densité relative supérieur du tableau API utilisé. j) Etalonnez la densité relative. 7. Configuration de la Correction de Pression (CPL) Le CPL est surtout utilisé pour des applications au propane. Rentrez dans le mode programme et sélectionnez le menu « Views and Inquiries » dans lequel vous sélectionnez « Pressure Comp. ». Sélectionnez la valeur prédéfinie et le composant. a) Sélectionnez le tableau API CPL Mettez ce champ en surbrillance et appuyez sur Enter pour voir le menu déroulant. Quand vous avez trouvé le tableau désiré, appuyez sur Next pour passer au champ suivant. Vous trouverez ci-après une liste des options de tableaux API ainsi que leurs modalités d’utilisation. 288 Chapitre 9 – Poids et Mesures Table 11.2.2- 289 Ce tableau donne les coefficients CTL de correction des volumes d'hydrocarbures légers à une pression observée et la température du liquide est à la tension de vapeur. Utilisez-le si les conditions ci-après sont réunies : Le liquide est du liquide de gaz naturel ou du GPL (propane) La densité relative à 60 F est connue La température de référence est de 60 F Sélectionnez ce tableau puis introduisez la densité relative du liquide à 60° F. La fourchette de validité de la densité relative va de 0,350 à 0,637. Les températures et pressions d'essai peuvent être introduites dans cet écran qui calcule un CTL sur base de la température d'essai, la pression d'essai et de la densité relative. La température d'essai, la pression d'essai et le CTL calculé ne servent que de points de référence et ne sont pas utilisés dans des calculs pendant les opérations. Table 11.2.2M Ce tableau donne les coefficients CTL de correction des volumes d'hydrocarbures légers à une pression observée et la température pour le volume existant lorsque le liquide est à sa tension de vapeur. Utilisez-le si les conditions ci-après sont réunies: Le liquide est du liquide de gaz naturel (NLG) ou du GPL (propane) La densité relative à 15 C est connue La température de référence est de 15 C Sélectionnez ce tableau puis introduisez la densité relative du liquide à 15° C. La fourchette de validité de la densité relative va de 350 à 637 kg/m³. Les températures et pressions d'essai peuvent être introduites dans cet écran qui calcule un CTL sur base de la température d'essai, la pression d'essai et de la densité relative. La température d'essai, la pression d'essai et le CTL calculé ne servent que de points de référence et ne sont pas utilisés dans des calculs pendant les opérations. 8. Configuration d’une Sonde de Pression a) b) Raccordez le transducteur de pression à la carte des entrées et sorties. Utilisez n’importe quel port d’entrée analogique. Consultez les schémas de câblage dans le manuel d’installation. Effectuez l'étalonnage de la pression. c) Entrez dans le mode de programme du MultiLoad II et sélectionnez le Weights & Measures/Meters. Puis, la valeur prédéfinie et le compteur appropriés. d) Recherchez le paramètre « Pressure Sensor ». Normalement, il est déjà activé si l’étalonnage de la pression a déjà eu lieu. e) Recherchez le paramètre de pression par défaut. Configurez-le sur 999,9. N’ajustez pas cette valeur à moins que le transducteur de pression ne soit en cours d’entretien. la menu f) Recherchez le paramètre de pression à 4 mA. Introduisez représentant la valeur minimale de densité mesurée par la sonde. pression g) Recherchez le paramètre de pression à 20 mA. Introduisez la pression représentant la valeur maximale de pression mesurée par la sonde. Chapitre 9 – Poids et Mesures h) i) 290 Appuyez sur Exit pour afficher le menu principal. Rentrez dans le menu Configuration/ Equipment/Setup/Meter. Sélectionnez la valeur prédéfinie et compteur appropriés. Recherchez le paramètre d’alarme de basse pression. Introduisez une de pression représentant la limite inférieure de pression du tableau API utilisé. le valeur Recherchez le paramètre d’alarme de haute pression. Introduisez la pression représentant la limite supérieure de pression du tableau API utilisé. 9. Configuration de la Pression par Défaut Lorsque le transducteur de pression est à l’entretien, la pression observée peut être introduite manuellement pour être utilisée par le tableau API. j) a. Entrez dans le mode de programme du MultiLoad II. Sélectionnez le menu Weights & Measures/Meters. Puis, la valeur prédéfinie et le compteur appropriés. b. Recherchez le paramètre de la sonde de pression et désactivez-le. c. Recherchez le paramètre de pression par défaut et introduisez la pression observée sur le débitmètre. d. Lorsque le transducteur de pression est remis en service, réactivez le paramètre du transducteur de pression et remettez la pression par défaut sur 999,9. Chapitre 9 – Poids et Mesures 9.6 291 CALCUL DE LIVRAISON DIRECTE DU MULTILOAD (UN SEUL COMPOSANT) Regular T1 P Comp #1 M1 CV Les valeurs du niveau du compteur sont les suivantes: Gm = M1 Tm = T1 Dm = D1 ou Dr Nm = Gm * VCFr(Tm,Dm) Mm = >Nm * Dr OU Mm = Gm * Dm Où: Gm = volume brut chargé pour le compteur M1 = volume brut enregistré par le compteur M1 Tm = température pour le compteur T1 = température moyenne pondérée du volume enregistré par la sonde T1 Dm = densité pour le compteur D1 = densité moyenne du volume mesuré OU spécifié pour le compteur M1 Dr = densité spécifiée pour le composant Regular Nm = volume net chargé pour le compteur VCFr = tableau de correction API pour la Regular Mm = masse chargée pour le compteur Les valeurs du produit Regular (niveau composant) sont rapportées de la façon suivante: Gr = Gm Tr = Tm Dr = Dr’ OU Dm Nr = Nm Mr = Mm Où: Gr = volume grossier chargé pour le composant Regular Tr = température du composant Regular Dr = densité du composant Regular Chapitre 9 – Poids et Mesures Dr’ = densité spécifiée pour le composant Regular Nr = volume net chargé pour le composant Regular Mr = masse chargée pour le composant Regular Les valeurs du produit commercialisable (niveau valeur prédéfinie) sont enregistrées de la façon suivante: Gb = Gm Tb = Tm Db = Dm Nb = Nm Mb = Mm Où: Gb = volume grossier chargé du mélange Tb = température du mélange Db = densité du mélange Nb = volume net de mélange chargé Mb = masse chargée pour le mélange La pression et la gravité se traitent de la même manière que la température et la densité. 292 Chapitre 9 – Poids et Mesures 293 9.7 CALCULS DE MÉLANGES SÉQUENTIELS DU MULTILOAD Regular P Comp #1 BV T1 M1 Premium P CV Comp #2 BV Les valeurs du compteur (niveau compteur) s’enregistrent de la manière suivante: Grm = M1 Trm = T1 Drm = D1 oOUDr Nrm= Grm*VCFr(Trm, Drm) Mrm = Nrm * Dr OU Mrm = Grm * Dm Où: Grm = volume grossier chargé pour le compteur Regular M1 = volume grossier enregistré par le compteur M1 au cours du débit de Regular Trm = température pour le compteur Regular T1 = température moyenne pondérée du volume enregistrée par la sonde T1 au cours du débit de Regular Drm = densité pour le compteur Regular D1 = densité moyenne pondérée du volume mesurée au cours du débit de Regular OU spécifiée pour le compteur M1 Dr = densité spécifiée pour le composant Regular Nrm = volume net chargé pour le compteur Regular VCFr = tableau de correction API pour la Regular Mrm = masse chargée pour le compteur Regular Les valeurs du produit Regular (niveau composant) sont enregistrées comme suit: Gr = Grm Tr = Trm Dr = Dr’ OU Drm Nr = Nrm Mr = Mrm Où: Gr = volume grossier chargé pour le composant Regular Tr = température pour le composant Regular Dr = densité pour le composant Regular Dr’ = densité spécifiée pour le composant Regular Nr = volume net chargé pour le composant Regular Chapitre 9 – Poids et Mesures Mr = masse chargée pour le composant Regular Les valeurs du compteur Premium (niveau compteur) sont enregistrées comme suit : Gpm = M1 Tpm = T1 Dpm = D1 OU Dp Npm = Gpm*VCFp(Tpm,Dpm) Mpm = Npm * Dpm OU Mpm = Gpm * Dpm Où: Gpm = volume grossier chargé pour le compteur Premium M1 = volume grossier enregistré par le compteur M1 au cours du débit de Premium Tpm = température pour le compteur Premium T1 = température moyenne pondérée du volume enregistrée par la sonde T1 au cours du débit de Premium Dpm = densité pour le compteur Premium D1 = densité moyenne pondérée du volume cours du débit de Premium OU spécifiée pour le compteur M1 Dp = densité spécifiée pour le composant Premium Npm = volume net chargé pour le compteur Premium VCFp = tableau de correction API pour la Premium Mpm = masse chargée pour le compteur Premium Les valeurs du produit Premium (niveau Composant) sont enregistrées comme suit: Gp = Gpm Tp = Tpm Dp = Dp’ OU Dpm Np = Npm Mp = Mpm Où: Gp = volume grossier chargé pour le composant Premium Tp = température pour le composant Premium Dp = densité pour le composant Premium Dp’ = densité spécifiée pour le composant Premium Np = volume net chargé pour le composant Premium Mp = masse chargée pour le composant Premium Les valeurs pour la Premium (niveau composant) sont enregistrées de la manière suivante: Gp = Gpm Tp = Tpm Dp = Dp’ OU Dpm Np = Npm Mp = Mpm 294 Chapitre 9 – Poids et Mesures Où: 295 Gp = volume brut chargé pour le composant Premium Tp = température pour le composant Premium Dp = densité pour le composant Premium Dp’ = densité spécifiée pour le composant Premium Np = volume net chargé pour le composant Premium Mp = masse chargée pour le composant Premium Les valeurs pour les produits mélangés (niveau des valeurs prédéfinies) sont enregistrées de la manière suivante: Gb = Gr + Gp Tb = ((Tr*Gr) + (Tp*Gp)) / Gb Db = ((Dr*Gr) + (Dp*Gp))/Gb Nb = Nr + Np Mb = Mr + Mp Où: (valeur à ne pas utiliser dans le commerce) (valeur à ne pas utiliser dans le commerce) (valeur à ne pas utiliser dans le commerce) Gb = volume brut chargé pour le mélange Tb = température pour le mélange ((Tr*Gr) + (Tp*Gp)) / Gb est la température pondérée du volume pour le mélange Db = densité pour le mélange ((Dr*Gr) + (Dp*Gp))/Gb = densité pondérée du volume pour le mélange Nb = volume net chargé pour le mélange Mb = masse chargée pour le mélange La pression et la gravité sont traitées de la même manière que la température et la densité. Chapitre 9 – Poids et Mesures 9.8 296 CALCULS DES PROPORTIONS DE MÉLANGE MULTILOAD Regular T1 P Comp #1 P Comp #2 Premium M1 CV M2 CV T2 Les valeurs pour le compteur Regular (niveau compteur) sont enregistrées comme suit: Grm = M1 Trm = T1 Drm = D1 OU Dr Nrm = Grm*VCFr(Trm,Drm) Mrm = Nrm * Dr OU Mrm = Grm * Dm Où: Grm = volume grossier chargé pour le compteur Regular M1 = volume grossier enregistré par le compteur M1 Trm = température pour le compteur Regular T1 = température moyenne pondérée du volume enregistrée par la sonde T1 Drm = densité pour le compteur Regular D1 = densité moyenne pondérée du volume mesurée OU spécifiée pour le compteur M1 Dr = densité spécifiée pour le composant Regular Nrm = volume net chargé pour le compteur Regular VCFr = tableau de correction API pour la Regular Mrm = mase chargée pour le compteur Regular Les valeurs du produit Regular (niveau composant) sont enregistrées comme suit: Gr = Grm Tr = Trm Dr = Dr’ OU Drm Nr = Nrm Mr = Mrm Où: Gr = volume grossier chargé pour le composant Regular Tr = température pour le composant Regular Dr = densité pour le composant Regular Chapitre 9 – Poids et Mesures 297 Dr’ = densité spécifiée pour le composant Regular Nr = volume net chargé pour le composant Regular Mr = masse chargée pour le composant Regular Les valeurs pour le compteur Premium (niveau compteur) sont enregistrées comme suit: Gpm = M2 Tpm = T2 Dpm = D2 OU Dp Npm = Gpm*VCFp(Tpm,Dpm) Mpm = Npm * Dpm OU Mpm = Gpm * Dpm Où: Gpm = volume grossier chargé pour le compteur Premium M2 = volume grossier enregistré par le compteur M2 Tpm = température pour le compteur Premium T2 = température moyenne pondérée volume enregistrée par la sonde T2 Dpm = densité pour le compteur Premium D2 = densité moyenne pondérée du volume mesurée OU spécifiée pour le compteur M2 Dp = densité spécifiée pour le composant Premium Npm = volume net chargé pour le compteur Premium VCFp = tableau de correction API pour la Premium Mpm = masse chargée pour le compteur Premium Les valeurs pour le produit Premium (niveau composant) sont enregistrées comme suit: Gp = Gpm Tp = Tpm Dp = Dp’ OU Dpm Np = Npm Mp = Mpm Où: Gp = volume grossier chargé pour le composant Premium Tp = température pour le composant Premium Dp = densité pour le composant Premium Dp’ = densité spécifiée pour le composant Premium Np = volume net chargé pour le composant Premium Mp = masse chargée pour le composant Premium Les valeurs du produit mélangé (niveau valeurs prédéfinies) sont enregistrées comme suit: Gb = Gr + Gp Tb = ((Tr*Gr) + (Tp*Gp) / Gb Db = ((Dr*Gr) + (Dp*Gp)) / Gb Nb = Nr + Np Mb = Mr + Mp (valeur à ne pas utiliser dans le commerce) (valeur à ne pas utiliser dans le commerce) (valeur à ne pas utiliser dans le commerce) Chapitre 9 – Poids et Mesures Où: 298 Gb = volume grossier chargé pour le mélange Tb = température pour le mélange ((Tr*Gr) + (Tp*Gp))/Gb = température pondérée volume pour le mélange Db = densité pour le mélange ((Dr*Gr) + (Dp*Gp)) / Gb = densité pondérée du volume pour le mélange Nb = volume net chargé pour le mélange Mb = masse chargée pour le mélange La pression et la gravité sont traitées de la même façon que la température et la densité. Chapitre 9 – Poids et Mesures 9.9 299 CALCULS DES MÉLANGES MULTILOAD SECONDAIRES (Regular primaire, Éthanol secondaire) Regular T1 P Ethanol M1 CV T2 P M2 CV Les valeurs du compteur de mélange (niveau compteur) sont enregistrées de la manière suivante : Gbm = M1 Tbm = T1 Dbm = D1 OU ((De*Ge) + (Dr*Gr))/ Gb Nbm = Gbm*VcFr(Tbm,Dbm) Mbm= Nbm * D1 OU Mbm = Gbm * Dbm Où : Gbm = produit grossier chargée pour le compteur mélange M1 = volume grossier enregistré par le compteur M1 Tbm = température pour le compteur de mélange T1 = température moyenne pondérée volume enregistrée par la sonde T1 Dbm = densité pour le compteur mélange D1 = densité moyenne pondérée du volume mesurée OU spécifiée pour le compteur M1 ((De * Ge) + (Dr * Gr)) / Gbm = densité pondérée du volume pour le mélange (cf Paramètre prédéfini de niveau Compute Blend Density) Nbm = volume net chargé pour le compteur de mélange VCFr = tableau de correction API pour la Regular Mbm = masse chargée pour le compteur mélange Les valeurs pour le produit de mélange (niveau valeurs prédéfinies) sont enregistrées de la manière suivante : Gb = Gbm Tb = Tbm Db = Dbm Nb = Nbm Mb = Mbm Où : Gb = volume grossier pour le mélange Chapitre 9 – Poids et Mesures 300 Tb = température pour le mélange Db = densité pour le mélange Nb = volume net chargé pour le mélange Mb = masse chargée pour le mélange Les valeurs du compteur d’éthanol (niveau compteur) sont enregistrées de la façon suivante: Gem = M2 (valeur à ne pas utiliser dans le commerce) Tem = T2 (valeur à ne pas utiliser dans le commerce) Dem = D2 OU De Nem=Gem*VCFe(Tem,Dem) (valeur à ne pas utiliser dans le commerce) Mem=Nem * D2 OU Mem=Gem * Dem (valeur à ne pas utiliser dans le commerce) Où: Gem = volume grossier chargé pour le compteur d’éthanol M2 = volume grossier enregistré par le compteur M2 Tem = température pour le compteur d’éthanol T2 = température moyenne pondérée du volume enregistrée par la sonde T2 D2 = densité moyenne pondérée du volume mesurée OU spécifiée par le compteur M2 De = densité spécifiée pour le composant d’éthanol Nem = volume net chargé pour le compteur d’éthanol VCFe = tableau de correction API pour l’éthanol Mem = masse chargée pour le compteur d’éthanol Les valeurs du produit éthanol (niveau composant) sont enregistrées de la manière suivante: Ge = Gem Te = Tem De = De’ Ne = Nem Me = Mem Où: (valeur à ne pas utiliser dans le commerce) (valeur à ne pas utiliser dans le commerce) OU Dem (valeur à ne pas utiliser dans le commerce) (valeur à ne pas utiliser dans le commerce) Ge = volume grossier chargé pour le composant d’éthanol Te = température pour le composant d’éthanol De = densité pour le composant d’éthanol De’ = densité spécifiée pour le composant d’éthanol Ne = volume net chargé pour le composant d’éthanol Me = masse chargée pour le composant d’éthanol Les valeurs du produit Regular (niveau composant) sont enregistrées de la manière suivante: Gr = Gbm-Ge Tr = ((Tbm * Gbm) – (Te * Ge)) / Gr Dr = Dr’ OU Dr = ((Dbm * Gbm) – (De * Ge)) / Gr Nr = Nbm-Ne Mr = Mbm-Me (valeur à ne pas utiliser dans le commerce) (valeur à ne pas utiliser dans le commerce) (valeur à ne pas utiliser dans le commerce) (valeur à ne pas utiliser dans le commerce) (valeur à ne pas utiliser dans le commerce) Chapitre 9 – Poids et Mesures Où: Gr = volume grossier chargé pour le composant Regular Gbm-Ge = différence de volume grossier chargé entre le mélange et l’éthanol Tr = température pour le composant Regular ((Tbm * Gbm) – (Te * Ge)) / Gr = température moyenne recalculée pour le composant Regular Dr = densité pour le composant Regular Dr’ = densité spécifiée pour le composant Regular ((Dbm * Gbm) – (De * Ge)) / Gr = densité moyenne recalculée pour le composant Regular (voir Paramètre prédéfini de niveau Compute Blend Density) Nr = volume net chargé pour le composant Regular Nbm-Ne = différence en volume net entre le volume net du mélange et le volume net d’éthanol Mr = masse chargée pour le composant Regular Mbm-Me = différence de masse entre la masse du mélange et la masse d’éthanol La pression et la gravité sont traitées de la même manière que la température et la densité. 301 Chapitre 9 – Poids et Mesures 9.10 302 CALCULS SÉQUENTIELS MULTILOAD AVEC MÉLANGE PROPORTIONNEL (Primaires séquentiels Regular/Premium, mélange proportionnel Éthanol) Regular P Comp #1 BV T1 M1 CV M2 CV Premium P Comp #2 BV Ethanol T2 P Comp #3 Les valeurs pour la Regular (niveau compteur) sont enregistrées de la manière suivante: Grm = M1 Trm = T1 Nrm = Grm*VCFr(Trm, Drm) Mrm = Nrm * Drm OU Mrm = Grm * D1 Où: Grm = volume brut chargé pour le compteur Regular M1 = volume brut enregistré par le compteur M1 au cours du débit de Regular Trm = température pour le compteur Regular T1 = température enregistrée par la sonde T1 au cours du débit de Regular Drm = densité pour le compteur Regular D1 = densité moyenne pondérée du volume mesurée au cours du débit de Regular OU spécifiée pour le compteur M1 Dr = densité spécifiée pour le composant de Regular Nrm = volume net chargé pour le compteur de Regular VCFr = tableau de correction API pour la Regular Mrm = masse chargée pour le compteur de Regular Les valeurs du produit Regular (niveau composant) ont été enregistrées de la manière suivante: Gr = Grm Chapitre 9 – Poids et Mesures Tr = Trm Dr = Dr’ OU Drm Nr = Nrm Mr = Mrm Où: Gr = volume grossier chargé pour le composant de Regular Tr = température pour le composant de Regular Dr = densité pour le composant de Regular Dr’= densité spécifiée pour le composant de Regular Nr = volume net chargé pour le composant de Regular Mr = masse chargée pour le composant de Regular Les valeurs du compteur de Premium (niveau compteur) ont été enregistrées de la manière suivante: Gpm = M1 Tpm = T1 Dpm = D1 OU Dp Npm = Gpm*VCFp(Tpm,Dpm) Mpm = Npm * Dpm OU Mpm=Gpm * D1 Où: Gpm = volume grossier chargé pour le compteur Premium M1 = volume grossier enregistrée par le compteur M1 au cours du débit de Premium Tpm = température pour le compteur Premium T1 = température moyenne pondérée du volume enregistrée par la sonde T1 au cours du débit de Premium Dpm = densité pour le compteur Premium D1 = densité moyenne pondérée du volume mesurée au cours du débit de Premium OU spécifiée par le compteur M1 Dp = densité spécifiée pour le composant Premium Npm = volume net chargé pour le compteur Premium VCFp = tableau de correction API pour le Premium Mpm = masse chargée pour le compteur Premium Les valeurs pour le produit Premium (niveau composant) ont été enregistrées de la manière suivante : Gp = Gpm Tp = Tpm Dp = Dp’ OU Dpm Np = Npm Mp = Mpm Où: Gp = volume grossier chargé pour le composant Premium Tp = température pour le composant Premium Dp = densité pour le composant Premium Dp’ = densité spécifiée pour le composant Premium Np = volume net chargé pour le composant Premium 303 Chapitre 9 – Poids et Mesures Mp = masse chargée pour le composant Premium Les valeurs pour le compteur éthanol (niveau compteur) ont été enregistrées de la manière suivante: Gem = M2 Tem = T2 Dem = D2 OU De Nem = Gem*VCFe(Tem,Dem) Mem = Nem * Dem OU Mem = Gem * D2 Où: Gem = volume grossier chargé pour le compteur d’éthanol M2 = volume grossier enregistré par le compteur M2 Tem = température pour le compteur d’éthanol T2 = température moyenne pondérée du volume enregistrée par la sonde T2 Dem = densité pour le compteur d’éthanol D2 = densité moyenne pondérée du volume mesurée OU spécifiée pour le compteur M2 De = densité spécifiée pour le composant d’éthanol Nem = volume net chargé pour le compteur d’éthanol VCFe = tableau de correction API pour l’éthanol Mem = masse chargée pour le compteur d’éthanol Les valeurs du produit Ethanol (niveau composant) ont été enregistrées de la manière suivante: Ge = Gem Te = Tem De = De’ OU Dem Ne = Nem Me = Mem Où: Ge = volume grossier chargé pour le composant d’éthanol Te = température pour le composant d’éthanol De = densité pour le composant d’éthanol De’ = densité spécifiée pour le composant d’éthanol Ne = volume net volume chargé pour le composant d’éthanol Me = masse chargée pour le composant d’éthanol Les valeurs du produit de mélange (niveau valeurs prédéfinies) ont été enregistrées de la manière suivante: Gb = Gr + Gp + Ge (valeur à ne pas utiliser dans le commerce) Tb = ((Tr*Gr) + (Tp*Gp) + (Te*Ge)) / Gb (valeur à ne pas utiliser dans le commerce) Db = ((Dr*Gr) + (Dp*Gp) + (De*Ge)) / Gb (valeur à ne pas utiliser dans le commerce) Nb = Nr + Np + Ne Mb = Mr + Mp + Me Où: Gb = volume grossier chargé pour le mélange Tb = température pour le mélange ((Tr*Gr) + (Tp*Gp) + (Te*Ge)) / Gb = température pondérée pour le volume pour le mélange 304 Chapitre 9 – Poids et Mesures Db = densité pour le mélange ((Dr*Gr) + (Dp*Gp) + (De*Ge)) / Gb = densité pondérée du volume pour le mélange Nb = volume net chargé pour le mélange Mb = masse chargée pour le mélange La pression et la gravité sont traitées de la même manière que la température et la densité. 305 Chapitre 9 – Poids et Mesures 9.11 306 CALCULS MULTILOAD SEQUENTIELS AVEC MÉLANGE SECONDAIRE (Primaires séquentiel Regular/Premium, éthanol secondaire) Regular P Comp #1 BV T1 M1 Premium P CV Comp #2 BV Ethanol T2 P M2 CV Les valeurs du compteur Regular/Ethanol (niveau compteur) ont été enregistrées de la manière suivante: Grem = M1 Trem = T1 Drem = D1 OU ((Dr * (Grem - Ge)) + (De * Ge)) / Grem Nrem = Grem*VCFr(Trem,Drem) Mrem = Nrem * Drem OU Mrem=Grem * D1 Où: Grem = volume grossier chargé pour le compteur Regular/Ethanol M1 = volume grossier enregistré par le compteur M1 au cours du débit de Regular/Ethanol Trem = température pour le compteur Regular/éthanol T1 = température moyenne pondérée pour le volume enregistrée par la sonde T1 au cours du débit Regular/Ethanol Drem = densité pour le compteur Regular/éthanol D1 = densité moyenne pondérée du volume mesurée au cours du débit de Regular/Ethanol OU spécifiée pour le compteur M1 ((Dr * (Grem - Ge)) + (De * Ge)) / Grem = densité moyenne pondérée du volume pour Regular/Ethanol (voir paramètre de niveau prédéfini pour Compute Blend Density)) Dr = densité spécifiée pour le composant Regular De = densité spécifiée pour le composant Ethanol Nrem = volume net chargé pour le compteur Regular/Ethanol VCFr = tableau de correction API pour la Regular Mrem = masse chargée pour le compteur de Regular/Ethanol Chapitre 9 – Poids et Mesures Les valeurs du compteur de Premium/Ethanol (niveau compteur) ont été enregistrées de la manière suivante: Gpem = M1 Tpem = T1 Dpem = D1 OU ((Dp * (Gpem - Ge)) + (De * Ge)) / Gpem Npem = Gpem*VCFp(Tpem,Dpem) Mpem = Npem * Dpem OU Mpem=Gpem * D1 Où: Gpem = volume grossier chargé pour le compteur de Premium/Ethanol M1 = volume grossier enregistré par le compteur M1 au cours du débit de Premium/Ethanol Tpem = température pour le compteur de Premium/Ethanol T1 = température moyenne pondérée du volume enregistrée par la sonde T1 au cours du débit de Premium/Ethanol Dpem = densité pour le compteur de Premium/Ethanol D1 = densité moyenne pondérée du volume mesurée au cours du débit de Premium/Ethanol OU spécifiée pour le compteur M1 ((Dp * (Gpem - Ge)) + (De * Ge)) / Gpem = densité moyenne pondérée du volume pour le Premium/Ethanol (voir paramètre de niveau prédéfini pour Compute Blend Density)) Dp = densité spécifiée pour le composant Premium De = densité spécifiée pour le composant Ethanol Npem = volume net chargé pour le compteur de Premium/Ethanol VCFp = tableau de correction API pour la Regular Mpem = masse chargée pour le compteur de Premium/Ethanol Les valeurs de produits mélangés (niveau valeurs prédéfinies) ont été enregistrées de la manière suivante: Gb = Grem + Gpem (valeur à ne pas utiliser dans le commerce) Tb = ((Trem*Grem) + (Tpem*Gpem)) / Gb (valeur à ne pas utiliser dans le commerce) Db = ((Drem*Grem) + (Dpem*Gpem) / Gb (valeur à ne pas utiliser dans le commerce) Nb = Nrem + Npem Mb = Mrem + Mpem Où: Gb = volume grossier chargé pour le mélange Tb = température pour le mélange ((Trem*Grem) + (Tpem*Gpem)) / Gb = température pondérée du volume pour le mélange Db = densité pour le mélange ((Drem*Grem) + (Dpem*Gpem) / Gb = densité pondérée du volume pour le mélange Nb = volume net chargé pour le mélange Mb = masse chargée pour le mélange Les valeurs du compteur d’éthanol (niveau compteur) ont été enregistrées de la manière suivante: 307 Chapitre 9 – Poids et Mesures 308 Gem = M2 (valeur à ne pas utiliser dans le commerce) Tem = T2 (valeur à ne pas utiliser dans le commerce) Dem = D2 OU De Nem = Gem*VCFe(Tem,Dem) (valeur à ne pas utiliser dans le commerce) Mem = Nem * Dem OR Mem = Gem * D1 (valeur à ne pas utiliser dans le commerce) Où: Gem = volume grossier chargé pour le compteur d’éthanol M2 = Volume grossier enregistré par le compteur M2 Tem = température pour le compteur d’éthanol T2 = température moyenne pondérée du volume enregistrée par la sonde T2 Dem = densité pour le compteur d’éthanol D2 = densité moyenne pondérée du volume mesurée OU spécifiée pour le compteur M2 De = densité spécifiée pour le composant Ethanol Nem = volume net chargé pour le compteur d’éthanol VCFe = tableau de correction API pour l’éthanol Mem = masse chargée pour le compteur d’éthanol Les valeurs du produit Ethanol (niveau composant) ont été enregistrées de la manière suivante: Ge = Gem Te = Tem De = De’ OU Dem Ne = Nem Me = Mem Où: (valeur à ne pas utiliser dans le commerce) (valeur à ne pas utiliser dans le commerce) (valeur à ne pas utiliser dans le commerce) (valeur à ne pas utiliser dans le commerce) Ge = volume grossier chargé pour le composant Ethanol Te = température pour le composant Ethanol De = densité pour le composant Ethanol De’ = densité spécifiée pour le composant Ethanol Ne = volume net chargé pour le composant Ethanol Me = masse chargée pour le composant Ethanol Les valeurs du produit Regular (niveau composant) values ont été enregistrées de la manière suivante: Gr = Grem-Ger (valeur à ne pas utiliser dans le commerce) T = ((Trem * Grem) – (Ter * Ger)) / Gr (valeur à ne pas utiliser dans le commerce) Dr = Dr’ OU Dr = ((Drem * Grem) – (Der * Ger)) / Gr (valeur à ne pas utiliser dans le commerce) Nr = Nrem-Ner (valeur à ne pas utiliser dans le commerce) Mr = Mrem-Mer (valeur à ne pas utiliser dans le commerce) Où: Gr = volume grossier chargé pour le composant Regular Ger = volume grossier chargé pour le composant Ethanol au cours du débit de Regular/Ethanol Tr = température pour le composant Regular Chapitre 9 – Poids et Mesures 309 Ter = température moyenne pondérée du volume pour le composant Ethanol au cours du débit de Regular/Ethanol ((Trem * Grem) – (Ter * Ger)) / Gr = température moyenne recalculée pour le composant Regular Dr = densité pour le composant Regular Dr’ = densité spécifiée pour le composant Regular Der = densité moyenne pondérée du volume pour le composant Ethanol au cours du débit de Regular/Ethanol ((Drem * Grem) – (Der * Ger)) / Gr = densité moyenne recalculée pour le composant Regular (voir paramètre de niveau prédéfini pour Compute Blend Density)) Nr = volume net chargé pour le composant Regular Ner = volume net chargé pour le composant Ethanol au cours du débit de Regular/Ethanol Mr = masse chargée pour le composant Regular Mer = masse chargée pour le composant Ethanol au cours du débit de Regular/Ethanol Les valeurs du produit Premium (niveau composant) ont été enregistrées de la manière suivante: Gp = Gpem-Gep Tp = ((Tpem * Gpem) – (Tep * Gep)) / Gp commerce) Dp = Dp’ OU Dp = ((Dpem * Gpem) – (Dep * Gep)) / Gp commerce) Np = Npem-Nep Mp = Mpem-Mep Où: (valeur à ne pas utiliser dans le commerce) (valeur à ne pas utiliser dans le (valeur à ne pas utiliser dans le (valeur à ne pas utiliser dans le commerce) (valeur à ne pas utiliser dans le commerce) Gp = volume grossier chargé pour le composant Premium Gep =Volume grossier chargé pour le composant Ethanol au cours du débit de Premium/Ethanol Tp = température pour le composant Premium Tep = température moyenne pondérée du volume pour le composant Ethanol au cours du débit de Premium/Ethanol ((Tpem * Gpem) – (Tep * Gep)) / Gp = température moyenne recalculée pour le composant Premium Dp = densité pour le composant Premium Dp’ = densité spécifiée pour le composant Premium Dep = densité moyenne pondérée du volume pour le composant Ethanol au cours du débit de Premium/Ethanol ((Dpem * Gpem) – (Dep * Gep)) / Gp = densité moyenne recalculée pour le composant Premium (voir paramètre de niveau prédéfini pour Compute Blend Density)) Np = volume net chargé pour le composant Premium Nep = volume net chargé pour le composant Ethanol au cours du débit de Premium/Ethanol Mp = masse chargée pour le composant Premium Mep = masse chargée pour le composant Ethanol au cours du débit de Premium/Ethanol La pression et la gravité sont traitées de la même manière que la température et la densité. Chapitre 9 – Poids et Mesures 9.12 310 CALCULS MULTILOAD DE LA PROPORTION POUR LE MÉLANGE SECONDAIRE (Proportions Regular/Premium primaires, Éthanol secondaire sur la Regular) Regular T1 P Comp #1 Premium M1 CV M2 CV T2 P Comp #2 Ethanol T3 P Comp #3 M3 CV Les valeurs du compteur Regular/Ethanol (niveau compteur) ont été enregistrées de la manière suivante: Grem = M1 Trem = T1 Drem = D1 OU ((De * Ge) + (Dr * Gr)) / Gb Nrem = Grem*VCFr(Trem,Drem) Mrem = Nrem * Drem OU Mrem = Grem * D1 Où: Grem = volume grossier chargé pour le compteur de Regular/Ethanol M1 = volume grossier enregistré par le compteur M1 Trem = température pour le compteur Regular/éthanol T1 = température moyenne pondérée du volume enregistrée par la sonde T1 Drem = densité pour le compteur Regular/éthanol D1 = densité moyenne pondérée de volume mesurée OU spécifiée pour le compteur M1 ((De * Ge) + (Dr * Gr)) / Grem = densité pondérée du volume pour le mélange de Regular/éthanol (voir paramètre de niveau des valeurs prédéfinies Compute Blend Density) Nrem = volume net chargé pour le compteur de Regular/Ethanol VCFr = tableau de correction API pour la Regular Mrem = masse chargée pour le compteur de Regular/éthanol Chapitre 9 – Poids et Mesures Les valeurs du compteur de Premium (niveau compteur) ont été enregistrées de la manière suivante: Gpm = M2 Tpm = T2 Dpm = D2 OU Dp Npm = Gpm*VCFp(Tpm,Dpm) Mpm = Npm * Dpm OU Mpm=Gpm * D2 Où: Gpm = volume grossier chargé pour le compteur de Premium M2 = volume grossier enregistré par le compteur M2 Tpm =T température pour le compteur de Premium T2 = température moyenne pondérée du volume enregistrée par la sonde T2 Dpm = densité pour le compteur de Premium D2 = densité moyenne pondérée du volume mesurée OU spécifiée pour le compteur M2 Dp = densité spécifiée pour le composant Premium Npm = volume net chargé pour le compteur de Premium VCFp = tableau de correction API pour le Premium Mpm = masse chargée pour le compteur Premium Les valeurs de produit mélangé (niveau valeurs prédéfinies) ont été enregistrées de la manière suivante: Gb = Grem + Gpm (valeur à ne pas utiliser dans le commerce) Tb = ((Trem*Grem) + (Tpm*Gpm)) / Gb (valeur à ne pas utiliser dans le commerce) Db = ((Drem*Grem) + (Dpm*Gpm)) / Gb (valeur à ne pas utiliser dans le commerce) Nb = Nrem + Npem Mb = Mrem + Mpem Où: Gb = volume grossier chargé pour le mélange Tb = température pour le mélange ((Trem*Grem) + (Tpm*Gpm)) / Gb = température pondérée du volume pour le mélange Db = densité pour le mélange ((Drem*Grem) + (Dpm*Gpm)) / Gb = densité pondérée du volume pour le mélange Nb = volume net chargé pour le mélange Mb = masse chargée pour le mélange Les valeurs du compteur d’éthanol (niveau compteur) ont été enregistrées de la manière suivante: Gem = M3 (valeur à ne pas utiliser dans le commerce) Tem = T3 (valeur à ne pas utiliser dans le commerce) Dem = D3 OU De Nem = Gem*VCFe(Tem,Dem) (valeur à ne pas utiliser dans le commerce) Mem = Nem * Dem OU Mem=Gem * D2 (valeur à ne pas utiliser dans le commerce) Où: Gem = volume grossier chargé pour le compteur d’éthanol M3 = volume grossier enregistrée par le compteur M3 311 Chapitre 9 – Poids et Mesures 312 Tem = température pour le compteur d’éthanol T3 = température moyenne pondérée du volume enregistrée par la sonde T3 Dem = densité pour le compteur d’éthanol D3 = densité moyenne du volume mesurée OU spécifiée pour le compteur M3 De = densité spécifiée pour le composant Ethanol Nem = volume net chargé pour le compteur d’éthanol VCFe = tableau de correction API pour l’éthanol Mem = masse chargée pour le compteur d’éthanol Les valeurs du produit Ethanol (niveau compteur) ont été enregistrées de la manière suivante: Ge = Gem Te = Tem De = De’ OU Dem Ne = Nem Me = Mem Où: (valeur à ne pas utiliser dans le commerce) (valeur à ne pas utiliser dans le commerce) (valeur à ne pas utiliser dans le commerce) (valeur à ne pas utiliser dans le commerce) Ge = volume grossier chargé pour le composant Ethanol Te = température pour le composant Ethanol De = densité pour le composant Ethanol De’ = densité spécifiée pour le composant Ethanol Ne = volume net chargé pour le composant Ethanol Me = masse chargée pour le composant Ethanol Les valeurs du produit Regular (niveau composant) ont été enregistrées de la manière suivante: Gr = Grem-Ge Tr = ((Trem * Grem) – (Te * Ge)) / Gr Dr = Dr’ OU Dr = ((Drem * Grem) – (De * Ge)) / Gr Nr = Nrem-Ne Mr = Mrem-Me Où: (valeur à ne pas utiliser dans le commerce) (valeur à ne pas utiliser dans le commerce) (valeur à ne pas utiliser dans le commerce) (valeur à ne pas utiliser dans le commerce) (valeur à ne pas utiliser dans le commerce) Gr = volume grossier chargé pour le composant Regular Grem-Ge = différence du volume grossier chargé entre le mélange et l’éthanol Tr = température pour le composant Regular ((Trem * Grem) – (Te * Ge)) / Gr = température moyenne recalculée pour le composant Regular Dr = densité pour le composant Regular Dr’ = densité spécifiée pour le composant Regular ((Drem * Grem) – (De * Ge)) / Gr = densité moyenne recalculée pour le composant Regular (voir paramètre de niveau des valeurs prédéfinies Compute Blend Density) Nr = volume net chargé pour le composant Regular Nrem-Ne = différence en volume net entre le volume net de mélange et le volume net d’éthanol Mr = masse chargée pour le composant Regular Mrem-Me = différence de masse entre la masse du mélange et la masse d’éthanol Chapitre 9 – Poids et Mesures 313 Les valeurs du produit Premium (niveau composant) ont été enregistrées de la manière suivante: Gp = Gpm Tp = Tpm Dp = Dp’ OU Dpm Np = Npm Mp = Mpm Où: Gp = volume grossier chargé pour le composant Premium Tp = température pour le composant Premium Dp = densité pour le composant Premium Dp’ = densité spécifiée pour le composant Premium Np = volume net chargé pour le composant Premium Mp = masse chargée pour le composant Premium La pression et la gravité sont traitées de la même façon que la température et la densité. 9.13 ETALONNAGE DE LA TEMPÉRATURE DES COMPTEURS Utilisez l’écran Temperature pour étalonner la température d’un compteur. 1. A partir du menu Views and Inquiries, sélectionnez Température. Sélectionnez la valeur prédéfinie et le compteur. L’écran de la température s’affiche. Error! Reference source not found. - 2. Si la température observée diffère de la température inchangée affichée, vous avez deux possibilités: Appuyez sur 1 et introduisez l’écart observé (la différence entre Temp Unadjusted et Temp Adjusted). Ou bien appuyez sur 2 et introduisez la température observée dans le champ Temp Adjusted : l’écart de température (Temp Offset) se calcule automatiquement et s’affiche. Error! Reference source not found. Utilisez les touches +/- pour basculer entre le signe moins (–) et le signe plus (+). L’écart de température ne peut dépasser + ou - 3 degrés. Si vous introduisez une valeur supérieure à 3 dans ce champ, elle se changera automatiquement en "3" et la température ne s’ajustera que par + ou - 3 degrés. De même, en introduisant une température observée supérieure à la valeur de Temp. Unadjusted de 3 degrés, l’écart ne changera que de 3 degrés. Paramètre Description Chapitre 9 – Poids et Mesures 314 Temp Unadjusted Affiche la température en temps réel du détecteur de température de résistance. Temp Offset Affiche la valeur de l’écart instantané de température, autrement dit, la différence entre la valeur Temp Unadjusted et la valeur Temp Adjusted (température observée). Temp Adjusted Affiche la température observée suite à l’application de l’écart de température. Chapitre 9 – Poids et Mesures 9.14 315 ECART DE TEMPÉRATURE ET CALCULATEUR VCF Utilisez la fonction Temp(erature) Comp(ensation) pour configurer un tableau API pour corriger le volume pour la température du liquide (CTL) et corriger celui de la pression du liquide (CPL). Cet écran permet également d’introduire une température d’essai pour calculer un CTL basé sur plusieurs températures. Quand on introduit une température d’essai, un VCF se calcule et s’affiche. La température d’essai n’a pas d’influence sur le fonctionnement normal. 1. A partir du menu Views & Inquiries, sélectionnez Temp Comp. Sélectionnez la valeur prédéfinie et le composant ; l’écran de réglage du tableau VCF s’affiche. PRE #1 CMP #1 VCF TABLE SETUP API Name:ASTM1250-2004 Table 6B Test Temp: +0.00C Test API Gravity: +0.0 Calculated VCF: 1.0203 Calculated CTL: 1.0203 Calculated CPL: 1.0000 2. Mettez la ligne du nom du tableau API VCF en surbrillance et appuyez sur ENTER. 3. Appuyez sur les touches Next ou Previous pour faire défiler les choix du tableau API. Appuyez sur ENTER pour sélectionner le tableau voulu. Deux champs de paramètres s’ajoutent à l’écran: l’un est API Test Temp; l’autre dépend du tableau API que vous avez sélectionné. Next Prev Exit Enter 4. Introduisez une valeur de température d’essai dans le champ Test Temp. Cette valeur sert à calculer un VCF dans le bas de l’écran pour information. La valeur introduite n’influence pas les calculs nets au cours d’un fonctionnement normal. Introduisez une valeur de zéro jusqu’à ce que les autres données soient introduites. 5. Selon le tableau API sélectionné, l’invite suivante vous demande de choisir entre la gravité, la densité ou un coefficient d’expansion. Quand l’utilisateur introduit une valeur, le VCF calculé se modifie. Si vous lisez “API Input Data Out of Range!” sur la dernière ligne, il se peut que la valeur introduite ne soit pas acceptée pour le tableau API que vous avez sélectionné. 6. Quand vous avez introduit la gravité, la densité ou un coefficient d’expansion, la configuration de VCF est terminée et vous pouvez introduire plusieurs températures, densités et densités relatives d’essai pour voir quel VCF serait utilisé si la température du liquide avait la même valeur. Paramètre Description API Name Sélectionnez le tableau API voulu pour corriger les volumes de liquide à une température de référence. Mettez le champ en surbrillance et appuyez sur Enter pour faire défiler les choix possibles. Test Temp Introduisez une température dans ce champ. La température introduite n’aura pas d’impact sur la mesure réelle. Chapitre 9 – Poids et Mesures 316 Paramètre Description Test Density or Test relative Density or Test API Gravity Introduisez une densité, une densité relative ou une gravité API d’essai dans ce champ. La valeur introduite ici n’influencera pas la mesure réelle. API Gravity/Expansi on Coefficient Un de ces champs apparait en fonction du tableau API choisi. Introduisez la valeur nécessaire dans ce champ. Elle servira à calculer le VCF au cours du fonctionnement. Calculated VCF La valeur de ce champ dépend de la température d’essai API et des données du champ précedent (densité, gravité ou coefficient d’expansion). Ce VCF calculé est donné à titre d’information et n’a pas d’impact sur la mesure réelle VCF = CTL * CPL. Calculated CTL La valeur de ce champ provient de la température d’essai API et des données du champ précédent (densité, gravité ou coefficient d’expansion). Ce VCF n’est calculé que pour information et n’a pas d’impact sur la mesure réelle. La valeur dans ce champ provient de la température d’esssai API et des données du champ précédent (pression). Ce VCF n’est calculé que pour information et n’influencera pas la mesure réelle. Calculated CPL Corrected Density Relative Ce champ apparait selon le tableau API sélectionné. La valeur montre la densité relative corrigée. Corrected Density Ce champ apparait selon le tableau API sélectionné. La valeur montre la densité corrigée. Corrected Gravity Ce champ apparait selon le tableau API sélectionné. La valeur montre la gravité corrigée. Chapitre 9 – Poids et Mesures 9.15 317 ETALONNAGE DE LA PRESSION POUR LES COMPTEURS Utilisez l’écran de la pression (Pressure) pour étalonner la pression d’un compteur. 1. Dans le menu des affichages et requêtes (Views & Inquiries), choisissez Pressure. Sélectionnez la valeur prédéfinie et le compteur : l’écran de la pression s’affiche. Error! Reference source not found. 2. Si la pression observée diffère de la pression inchangée affichée, vous avez deux possibilités: - Appuyez sur 1 et introduisez l’écart observé (autrement dit, la différence entre la pression inchangée Pressure Unadjusted et la pression ajustée Pressure Adjusted). Ou bien appuyez sur 2 et introduisez la pression observée dans le champ Pressure Adjusted et l’écart de pression (Pressure Offset) se calcule et s’affiche automatiquement. Error! Reference source not found. Utilisez les touches +/- pour basculer entre un signe moins (–) et un signe plus (+). Paramètre Description Pressure Unadjusted Affiche la pression en temps réel Pressure Offset Affiche la valeur d’écart de la pression, autrement dit la différence entre la valeur de la pression inchangée Pressure Unadjusted et la valeur de pression ajustée Pressure Adjusted (pression observée). Pressure Adjusted Affiche la pression observée suite à l’application de l’écart de pression. Chapitre 9 – Poids et Mesures 318 Error! Reference source not found. 9.16 ETALONNAGE DE LA DENSITÉ Utilisez l’écran La densité pour étalonner la densité d’un compteur. 1. Dans le menu Views & Inquiries, sélectionnez La densité. Sélectionnez ensuite la valeur prédéfinie et le compteur. L’écran de densité apparait : Error! Reference source not found. 2. Si la densité observée diffère de la densité ajustée qui s’affiche, il y a deux possibilités: Soit vous appuyez sur 1 et vous introduisez l’écart observé (autrement dit, la différence entreDensity Unadjusted et Density Adjusted). Soit vous appuyez sur 2 et vous introduisez la densité observée dans le champ La Density Adjusted et l’écart de densité se calcule et s’affiche automatiquement (Density Offset). - Error! Reference source not found. Utilisez les touches +/- key pour basculer entre un signe moins (–) et un signe plus (+). Paramètre Description Density Unadjusted Affiche la densité en temps réel Density Offset Affiche la valeur d’écart de la densité instantanée, autrement dit la différence entre la valeur de densité inchangée Density Unadjusted et la valeur de densité ajustée Density Adjusted (densité observée). Density Adjusted Affiche la densité observée provenant de l’application de l’écart de densité. 9.17 ETALONNAGE DE LA DENSITÉ RELATIVE Utilisez l’écran de la densité relative pour étalonner la densité relative d’un compteur. 3. A partir du menu Views & Inquiries, sélectionnez Relative Density. Sélectionnez les valeurs prédéfinies et le compteur et l’écran de la densité relative apparait: PRE #1 MTR #1 RELATIVE DENSITY Relative Density Unadjusted:+0.5000 [1]Relative Density Offset: +0.0000 [2]Relative Density Adjusted: +0.5000 Next Prev Exit Chapitre 9 – Poids et Mesures 319 4. Si la densité relative observée diffère de la densité relative non ajustée, vous avez deux possibilités: - soit vous appuyez sur 1 et vous introduisez l’écart observé (c’est à dire la différence entre la densité relative non ajustée et la densité relative ajustée). soit vous appuyez sur 2 et vous introduisez la densité observée dans le champ de la densité relative observée. Dans ce cas, l’écart de densité relative se calculera et s’affichera automatiquement. PRE #1 MTR #1 DENSITY Relative Density Unadjusted:+0.5000 [1]Relative Density Offset: +█ [2]Relative Density Adjusted: +0.5000 Utilisez la touche +/pour Enter basculer d’un +/Exitsigne moins (–) à un signe plus (+) dans l’écart. Paramètre Description Relative Unadjusted Density Affiche la densité relative en temps réel. Relative Offset Density Affiche la valeur de l’écart de la densité relative instantanée, à savoir la différence entre la valeur de la densité relative non ajustée et celle de la densité relative ajustée (densité relative observée). Relative Adjusted Density Affiche la densité relative observée provenant de l’application de l’écart de densité relative. 9.18 ETALONNAGE DE LA GRAVITÉ API Utilisez l’écran de gravité API pour étalonner la gravité API d’un compteur. 5. A partir du menu Views & Inquiries, sélectionnez API Gravity. Sélectionnez les valeurs prédéfinies et le compteur et l’écran de la gravité API apparait: Chapitre 9 – Poids et Mesures 320 PRE #1 MTR #1 API GRAVITY API Gravity Unadjusted: [1]API Gravity Offset: [2]API Gravity Adjusted: +100.5 +0.0 +100.50 6. Si la gravité API observée diffère de la gravité API non ajustée, vous avez deux possibilités: - Soit vous appuyez sur 1 et vous introduisez l’écart observé (c’est à dire la différence entre la gravité API Next Prev Exit non ajustée et la gravité API ajustée). Soit vous appuyez sur 2 et vous introduisez la gravité observée dans le champ de la gravité API ajustée. Dans ce cas, l’écart de gravité API se calcule et s’affiche automatiquement. PRE #1 MTR #1 API GRAVITY API Gravity Unadjusted: +1000.5 [1]API Gravity Offset: +█ [2]API Gravity Adjusted: +100.5 Utilisez la touche +/pour Enter basculer entre +/Exit un signe moins (–) et un signe plus (+) dans l’écart. Paramètre Description API GravityUnadjusted Affiche la densité relative en temps réel API Gravity Offset Affiche la valeur de l’écart de la gravité API instantanée, à savoir la différence entre la valeur de la gravité API non ajustée et celle de la gravité API ajustée (densité relative observée). API Gravity Adjusted Affiche la gravité API observée provenant de l’application de l’écart de gravité API. 9.19 ETALONNAGE BSW1 Utilisez l’écran BSW pour étalonner la densité relative pour un compteur. Chapitre 9 – Poids et Mesures 321 7. A partir du menu Views & Inquiries, sélectionnez BSW1. Sélectionnez les valeurs prédéfinies et le compteur et l’écran BSW1 apparait: PRE #1 MTR #1 BSW1 BSW1 Unadjusted: [1]BSW1 Offset: [2]BSW1 Adjusted: +50.5% + 0.0% +50.5% 8. Si le BSW1 diffère du BSW1 non ajusté affiché, vous avez deux possibilités: Next Prev Exit - Soit vous appuyez sur 1 et vous introduisez l’écart observé (c’est à dire la différence entre le BSW1 non ajusté et le BSW1 ajusté). - Soit vous appuyez sur 2 et vous introduisez le BSW1 observé dans le champ. Dans ce cas, l’écart de BSW1 se calcule et s’affiche automatiquement. PRE #1 MTR #1 BSW1 BSW1 Unadjusted: [1]BSW1 Offset: [2]BSW1 Adjusted: +50.5% + 0.0% +50.5% Utilisez la touche +/- pour basculer entre un signe moins (–) et un signe plus (+) dans l’écart. Next Prev Exit Paramètre Description BSW1 Unadjusted Affiche BSW1 en temps réel. BSW1 Offset Affiche la valeur de l’écart BSW1 instantané, à savoir la différence entre le BSW1 non ajusté et le BSW1 ajusté (BSW1 observé). BSW1 Adjusted Affiche le BSW1 provenant de l’application de l’écart de BSW1. 9.20 ETALONNAGE BSW2 Utilisez l’écran BSW pour calibrer la densité relative pour un compteur. Chapitre 9 – Poids et Mesures 322 9. A partir du menu Views & Inquiries, sélectionnez BSW2. Sélectionnez les valeurs prédéfinies et le compteur et l’écran BSW2 apparait: PRE #1 MTR #1 BSW2 BSW2 Unadjusted: [1]BSW2 Offset: [2]BSW2 Adjusted: +50.5% + 0.0% +50.5% 10. Si le BSW2 observé est différent du BSW2 non ajusté qui s’affiche, vous avez deux possibilités: - Soit vous appuyez sur 1 et vous introduisez dans l’écart observé (c’est à dire la différence entre le BSW2 Next Prev Exit non ajusté et le BSW2 ajusté). Soit vous appuyez sur 2 et vous introduisez dans le BSW2 observé dans le champ BSW2 ajusté. Dans ce cas, l’écart BSW2 se calcule et s’affiche automatiquement. PRE #1 MTR #1 BSW2 BSW2 Unadjusted: [1]BSW2 Offset: [2]BSW2 Adjusted: +50.5% +█ % +50.5% Utilisez la touche +/pour Enter basculer entre +/Exit un signe moins (–) et un signe plus (+) dans l’écart. Paramètre Description BSW2 Unadjusted Affiche BSW2 en temps réel. BSW2 Offset Affiche la valeur de l’écart BSW2 instantané, à savoir la différence entre la valeur BSW2 non ajustée et la valeur BSW2 ajustée (BSW2 observé). BSW2Adjusted Affiche le BSW2 observé provenant de l’application de l’écart BSW2. Chapitre 10 – Affichage et requêtes CHAPTER 10 10.1 323 AFFICHAGE ET REQUÊTES VUE D’ENSEMBLE Le MultiLoad II fournit des fonctions de requêtes disponibles à partir du menu Views and Inquiry représenté cidessous VIEWS AND INQUIRY MENU Alarms Audit Log Totalizers Temperature Pressure Density Relative Density BSW1 BSW2API Gravity Temp Comp Mass Calc Pressure Comp Transactions W&M Change Log Message Log Next Prev Exit Enter Next Prev Exit Enter Chapitre 10 – Affichage et requêtes 10.2 324 VISUALISATION DES ALARMES Dans le menu Views and Inquiry, sélectionnez Alarms. L’écran de visualisation des alarmes s’affiche. Error! Reference source not found. Les alarmes répertoriées, précédées d'un retrait, sont associées à la valeur prédéfinie reprise au-dessus d'elles. Si le message d'alarme est plus long que ce que l'affichage de l'écran permet, il sera renvoyé à la ligne suivante. Pour annuler toutes les alarmes actives, appuyez sur la touche CLR. Toutefois, certaines alarmes, telles que RTD ERROR, ne s'annulent pas avant que la condition n'ait été corrigée. Chapitre 10 – Affichage et requêtes 10.3 325 VISUALISATION DES TOTALISATEURS Dans le menu Views and Inquiry, sélectionnez Totalizers. Le menu de visualisation des totalisateurs s’affiche. Il est possible d’atteindre directement cet écran en combinant le code 4448 avec NEXT. Error! Reference source not found. Chapitre 10 – Affichage et requêtes 10.3.1 326 VISUALISATION DES TOTALISATEURS DE LA VALEUR PRÉDÉFINIE Dans le menu « View Totalizers », sélectionnez « Presets », puis la valeur définie que vous désirez voir et l’écran de visualisation des totalisateurs de la valeur prédéfinie s’affiche. PRE #1 (Preset 001) TOTALIZERS Total Gross:000000631 (000000631) Total Net :000000631 (000000631) Total Mass :000000631 (000000631) Authorized Gross:000000631 (000000631) Authorized Net :000000631 (000000631) Authorized Mass :000000631 (000000631) Unauthorized Gross:000000000 (000000000) Unauthorized Net :000000000 (000000000) Unauthorized Mass :000000000 (000000000) PRE #1 (Preset 001) TOTALIZERS CLeaR Next Prev Exit Total Gross:0000006.31 0000006.31 Total Net :0000006.31 0000006.31 Total Mass :0000006.31 0000006.31 Authorized Gross:0000006.31 0000006.31 Authorized Net :0000006.31 0000006.31 Authorized Mass :0000006.31 0000006.31 Unauthorized Gross:0000000.00 0000000.00 Unauthorized Net :0000000.00 0000000.00 Unauthorized Mass :0000000.00 0000000.00 CLeaR Next Prev Exit Description des paramètres Total Gross Volume brut total par la valeur prédéfinie (bras de chargement). Total Net Volume total net par les valeurs prédéfinies (bras de chargement) Total Mass Masse totale par la valeur prédéfinie Authorized Gross Volume brut total autorisé par la valeur prédéfinie (bras de chargement). Authorized Net Volume net total autorisé par la valeur prédéfinie (bras de chargement). Authorized Mass Masse totale autorisée par la valeur prédéfinie (bras de chargement) Unauthorized Gross Volume brut total non autorisé par la valeur prédéfinie (bras de chargement) Chapitre 10 – Affichage et requêtes Unauthorized Net Volume net total non autorisé par la valeur prédéfinie chargement). 327 (bras de Remarques: Les nombres de volume affichés sont des nombres entiers ou à une résolution de 1/100 selon le réglage utilisé pour le paramètre RCU W&M « Use Hundredths » . Les numéros à gauche indiquent des volumes dans des totalisateurs sans remise à zéro. Les numéros à droite indiquent des volumes dans des totalisateurs réinitialisables. Utilisez la touche CLR pour remettre les totalisateurs réinitialisables à zéro. Chapitre 10 – Affichage et requêtes 10.3.2 328 VISUALISATION DES TOTALISATEURS DE COMPTEUR Dans le menu View Totalizers, sélectionnez Meters, puis la valeur prédéfinie et le compteur. L’écran de visualisation des totalisateurs de compteur s’affiche. PRE #1 MTR #1 TOTALIZERS Total Gross:000000631 (000000631) Authorized Gross:000000631 (000000631) Unauthorized Gross:000000000 (000000000) Meter Creep Gross:000000000 (000000000) Backflow Gross:000000000 (000000000) PRE #1 MTR TOTALIZERS CLeaR Next#1 Prev Exit Total Gross:0000006.31 0000006.31 Authorized Gross:0000006.31 0000006.31 Unauthorized Gross:0000000.00 0000000.00 Meter Creep Gross:0000000.00 0000000.00 Backflow Gross:0000000.00 0000000.00 Description des paramètres CLeaR Next Prev Exit Total Gross Volume brut total au travers du débitmètre Authorized Gross Volume brut total autorisé au travers du débitmètre Unauthorized Gross Volume brut total non autorisé à travers le débitmètre. Meter Creep Gross Quantité brute de volume désignée en tant que fluage du compteur. Les volumes de fluage de compteur sont de faibles quantités de volume désignées par le compteur lorsque le débit est censé être à l'arrêt. Le fluage de compteur peut être occasionné par une petite fuite, un choc excessif dans la conduite ou des interférences Chapitre 10 – Affichage et requêtes électromagnétiques. Backflow Gross Le volume brut total qui s'est écoulé par l'arrière au travers du compteur. Cela ne peut être détecté qu'avec des débitmètres à double capteur . Remarques: Les nombres affichés pour le volume sont des nombres entiers ou avec une résolution de 1/100 selon le réglage utilisé pour le paramètre RCU W&M « Use Hundredths ». Les numéros à gauche indiquent des volumes dans des totalisateurs sans remise à zéro. Les numéros à droite indiquent des volumes dans des totalisateurs réinitialisables. Utilisez la touche CLR pour remettre les totalisateurs réinitialisables à zéro . 329 Chapitre 10 – Affichage et requêtes 10.3.3 330 VISUALISATION DES TOTALISATEURS DE COMPOSANTS Dans le menu View Totalizers, sélectionnez Components, puis la valeur prédéfinie et le composant. L’écran de visualisation des totalisateurs de composants s’affiche. PRE #1 CMP #1 (Base 001 ) TOTALIZERS Total Gross:000000631 (000000631) Total Net :000000631 (000000631) Total Mass :000000631 (000000631) Authorized Gross:000000631 (000000631) Authorized Net :000000631 (000000631) Authorized Mass :000000631 (000000631) Unauthorized Gross:000000000 (000000000) Unauthorized Net :000000000 (000000000) Unauthorized Mass :000000000 (000000000) CLeaR Next Prev Exit PRE #1 CMP #1 (Base 001 ) TOTALIZERS Total Gross:0000006.31 0000006.31 Total Net :0000006.31 0000006.31 Total Mass :0000006.31 0000006.31 Authorized Gross:0000006.31 0000006.31 Authorized Net :0000006.31 0000006.31 Authorized Mass :0000006.31 0000006.31 Unauthorized Gross:0000000.00 0000000.00 Unauthorized Net :0000000.00 0000000.00 Unauthorized Mass :0000000.00 0000000.00 CLeaR Next Prev Exit Description des paramètres Total Gross Volume brut total de composant livré. Total Net Volume net total de composant livré. Total Mass Masse totale de composant livré. Authorized Gross Volume brut total autorisé du composant livré. Authorized Net Volume net total autorisé du composant livré. Chapitre 10 – Affichage et requêtes Authorized Mass Masse totale autorisée de composant livré Unauthorized Gross Volume brut total non autorisé du composant livré. Unauthorized Net Volume net total non autorisé du composant livré. Unauthorized Mass Masse totale non autorisée de composant livré. Remarques: Les nombres affichés pour le volume sont des nombres entiers ou avec une résolution de 1/100 selon le réglage utilisé pour le paramètre RCU W&M « Use Hundredths ». Les numéros à gauche indiquent des volumes dans des totalisateurs sans remise à zéro. Les numéros à droite indiquent des volumes dans des totalisateurs réinitialisables. Utilisez la touche CLR pour remettre les totalisateurs réinitialisables à zéro . 331 Chapitre 10 – Affichage et requêtes 332 VISUALISATION DES TOTALISATEURS D’ADDITIFS 10.3.4 Dans le menu View Totalizers, sélectionnez Additives puis la valeur prédéfinie et l’additif. L’écran de visualisation de totalisateurs d’additifs s’affiche. PRE #1 ADTV #1 (Adtv 001 ) TOTALIZERS Total Gross:000000000 (000000000) Authorized Gross:000000000 (000000000) Unauthorized Gross:000000000 (000000000) Meter Creep Gross:000000000 (000000000) CLeaR Next Prev Exit Description des paramètres: Total Gross Volume brut total au travers du compteur d’additifs. Authorized Gross Volume brut total autorisé au travers du compteur d’additifs. Unauthorized Gross Volume brut total non autorisé au travers du compteur d’additifs. Meter Creep Gross Quantité brute de volume désignée comme fluage du compteur. Les volumes de fluage de compteur sont de faibles quantités de volume désignées par le compteur lorsque le flux est censé être à l'arrêt. Le fluage de compteur peut être occasionné par une petite fuite, un choc excessif dans la conduite ou des interférences électromagnétiques. Remarque: èmes Les nombres sont indiqués en 1/1000 à droite du nombre le moins significatif. d'unité de mesure. La virgule est tacite à trois positions Les nombres à gauche indiquent les volumes dans les totalisateurs non réinitialisables. Les nombres à droite indiquent les volumes dans les totalisateurs réinitialisables. Utilisez la touche CLR pour remettre les totalisateurs réinitialisables à zéro. Chapitre 10 – Affichage et requêtes 10.4 333 VISUALISATION DES TEMPÉRATURES Dans le menu Views and Inquiry, sélectionnez Temperature, puis la valeur prédéfinie et le compteur. L’écran de visualisation des températures s’affiche. PRE #1 MTR #1 TEMPERATURE Temperature Unadjusted: [1]Temperature Offset: [2]Temperature Adjusted: Status Ok Next Prev +42.27C +0.00C +42.27C Exit Description des paramètres: Temp Unadjusted Affiche la température en temps réel du capteur de température à résistance. Temp Offset Affiche la valeur de compensation instantanée de la température, à savoir la différence entre la valeur Temp Unadjusted et celle de Temp Adjusted (température observée). Temp Adjusted Affiche la température observée obtenue par la composation de température. Chapitre 10 – Affichage et requêtes 10.5 334 VISUALISATION DES PRESSIONS Dans le menu Views and Inquiry, sélectionnez Pressure puis la valeur prédéfinie et le compteur. L’écran de visualisation des pressions s’affiche. PRE #1 MTR #1 PRESSURE Pressure Unadjusted: [1]Pressure Offset: [2]Pressure Adjusted: Next Prev 25.00 +0.00 25.00 Exit Description des paramètres: Pression Unadjusted Affiche la pression en temps réel Pression Offset Affiche la valeur de compensation de la pression, autrement dit, la différence entre la valeur de la pression inchangée et celle de la pression ajustée (pression observée). Pression Adjusted Affiche la pression observée suite à l’application de la compensation de pression. Chapitre 10 – Affichage et requêtes 10.6 335 VISUALISATION DE LA DENSITÉ Dans le menu Views and Inquiry, sélectionnez Density, puis la valeur prédéfinie et le compteur. L’écran de la densité s’affiche. PRE #1 MTR #1 DENSITY Density Unadjusted: [1]Density Offset: [2]Density Adjusted: Next Prev +500.0 +0.0 +500.0 Exit Description des paramètres: Paramètre Description Density Unadjusted Affiche la densité en temps réel. Density Offset Affiche la valeur de compensation de la densité instantanée, à savoir la différence entre la valeur de la densité inchangée et celle de la densité ajustée (densité observée). Density Adjusted Affiche la densité observée suite à l’application de la compensation de densité. Chapitre 10 – Affichage et requêtes 10.7 336 VISUALISATION DE LA DENSITÉ RELATIVE Dans le menu Views and Inquiry, sélectionnez Relative Density, puis la valeur prédéfinie et le compteur. L’écran de la densité relative s’affiche. PRE #1 MTR #1 RELATIVE DENSITY Relative Density Unadjusted:+0.5000 [1]Relative Density Offset: +0.0000 [2]Relative Density Adjusted: +0.5000 Next Prev Exit Description des paramètres: Paramètre Description Relative Unadjusted Density Affiche la densité relative en temps réel. Relative Offset Density Affiche la valeur de compensation de la densité relative instantanée, à savoir la différence entre la valeur de la densité relative inchangée et celle de la densité relative ajustée (densité relative observée). Relative Adjusted Density Affiche la densité relative observée suite à l’application de la compensation de densité relative. Chapitre 10 – Affichage et requêtes 10.8 337 VISUALISATION BSW1 A partir du menu Views and Inquiry, sélectionnez BSW1. Sélectionnez la valeur prédéfinie et le compteur et l’écran BSW1 s’affiche: PRE #1 MTR #1 BSW1 BSW1 Unadjusted: [1]BSW1 Offset: [2]BSW1 Adjusted: Next Prev +050.0 +0.0 +050.0 Exit Description des paramètres: Paramètre Description BSW1 Unadjusted Affiche BSW1 en temps réel BSW1 Offset Affiche la valeur de l’écrat BSW1 instantané, à savoir la différence entre la valeur non ajustée BSW1 et la valeur ajustée BSW1 (densité relative observée). BSW1 Adjusted Affiche le BSW1 observé provenant de l’application de l’écart BSW1. 10.9 VISUALISATION BSW2 A partir du menu Views and Inquiry, sélectionnez BSW2. Sélectionnez la valeur prédéfinie et le compteur et l’écran BSW2 apparaît: PRE #1 MTR #1 BSW2 BSW2 Unadjusted: [1]BSW2 Offset: [2]BSW2 Adjusted: Next Prev +050.0 +0.0 +050.0 Exit Chapitre 10 – Affichage et requêtes 338 Description des paramètres: Parameter Description BSW2 Unadjusted Affiche BSW2 en temps réel. BSW2 Offset Affiche la valeur de l’écart BSW2 instantané, à savoir la différence entre la valeur non ajustée BSW2 et la valeur ajustée BSW2 (densité relative observée). BSW2 Adjusted Affiche le BSW2 observé provenant de l’application de l’écart BSW2. 10.10 VISUALISATION DE LA GRAVITÉ API A partir du menu Views and Inquiry, sélectionnez la gravité API. Sélectionnez la valeur prédéfinie et le compteur et l’écran de gravité API apparaît: PRE #1 MTR #1 API GRAVITY Api Gravity Unadjusted: [1] Api Gravity Offset: [2] Api Gravity Adjusted: +500.0 +0.0 +500.0 Description des paramètres: Next Paramètre Api Unadjusted Prev Exit Description Gravity Affiche la gravité API en temps réel. Api Gravity Offset Affiche la valeur de l’écart de gravité API instantanée, à savoir la différence entre la valeur non ajustée de la gravité API et la valeur ajustée de la gravité API (densité relative observée). Api Gravity Adjusted Affiche la gravité API observée provenant de l’application de l’écart de gravité API. Chapitre 10 – Affichage et requêtes 339 10.11 VISUALISATION DES TRANSACTIONS Utilisez la fonction de requête des transactions pour visualiser les transactions de chargement du ticket de connaissement (Bill of Lading - BOL). Il est également possible d’atteindre directement cet écran de visualisation par le code 4447 combiné à NEXT. Sélectionnez Transactions dans le menu Views & Inquiry. L’écran de visualisation des transactions s’affiche: BOL# CARD# CMPY DATE START STOP 0003 00000132 00 03/23 00:27 00:31 0002 00000132 00 03/23 00:26 00:27 0001 00000132 00 09/12 08:38 08:39 Next Prev Exit Enter Les transactions en cours sont reprises sur l’écran qui s’affiche: Description des champs: BOL# Numéro du ticket de connaissement (BOL) CARD# Numéro de la carte chauffeur CMPY Numéro ID de la société. ID à deux chiffres associé à une carte chauffeur. Utilisé en mode autonome uniquement. DATE Date de chargement START Heure de début de chargement STOP Heure de fin du chargement Sélectionnez une transaction pour visualiser plus en détails. L’écran View Transaction Header apparaît: VIEW TRANSACTION HEADER Bol#: 0003 Card#: 00000132 Company: 00 Date: 03/23 Start: 00:27 #Details: 2 Stop: 00:31 Prompts: Toptech (5M) 28 41.646 N 081 21.119 W 2=Print Transactions xxxx-yyyy 1=Print Transaction Next Prev Exit Enter=Details Figure 10-1 Ecran principal de Fichier de Visualisation des Transactions Chapitre 10 – Affichage et requêtes 340 #Details Indique le nombre de lignes de détails pour cette transaction. Prompts Invites configurables en option: Stockholder ID, Customer ID, Account ID, and Trailer ID., (uniquement sur le ML II Mobile). Lors de la configuration de la communication GPS, les invites 3 et 4 reprennent la latitude et la longitude au moment de l’autorisation. Lors de la configuration de “Max GPS Site Distance”, l’invite #2 reprend le nom du site et la distance par rapport à celui-ci. Si un port COM est défini comme PRINT, “1=Print Transaction” s’affiche. Si vous tapez ‘1’, vous imprimez la transaction sélectionnée. “2=Print Transactions xxxx-yyyy” à la visualisation d’une seconde transaction. xxxx-yyyy est le numéro de Bol des deux dernières transactions visualisées ; il indique l’éventail de transactions à imprimer. Tapez ‘2’ pour imprimer l’éventail de transactions sélectionnées. S’il s’agit d’une réimpression de la transaction, la transaction imprimée porte la mention “Duplicate” (copie). Appuyez sur Enter pour visualiser le détail des données de cette transaction (produits, brut, net, temp., etc.). L’écran de détail des transactions s’affiche: VIEW TRANSACTION DETAILS FOR BOL# 0003 Pr T Prod Gross Net Temp 01 1 PRD001 499.54 499.54 042.3C 01 2 BAS001 499.54 499.54 042.3C Next Prev Exit VIEW TRANSACTION DETAILS FOR BOL# 0003 Pr T Prod Gross Net Temp 01 1 PRD001 499 499 042.3C 01 2 BAS001 499 499 042.3C Next Prev Exit Chapitre 10 – Affichage et requêtes 341 (Résolution 1/100 si le paramètre « Une Hundredths » du RCU W&M est activé) Pr Numéro prédéfini (toujours 1 sur le MultiLoad II SMP). Typ Type de produit: 1 = recette de produits commercialisables; 2 = composant; 3 = additif ; 4 = compteur ; 5 = totalisateur valeurs définies ; 6 = totalisateur compteurs ; 7 = totalisateur composants ; 8 = totalisateur additifs Prod ID du produit. Gross Volume brut Net Volume net. Temp Température. Dens Densité/Densité relative/Gravité. CP Numéro de compartiment. VIEW TRANSACTION DETAILS FOR BOL# 0003 Pr T Prod Gross Net Temp 01 1 PRD001 499.54 499.54 042.3C 01 2 BAS001 499.54 499.54 042.3C Next Prev Exit Enter Tout lot pour lequel une alarme s’est déclenchée en cours de livraison pour laquelle la précision pourrait être contestée sera marqué en surbrillance ROUGE. Sélectionnez un lot et appuyez sur Enter pour visualiser les détails. Chapitre 10 – Affichage et requêtes 342 VIEW TRANSACTION DETAIL DETAILS Bol#: 00001 Detail#: 00001 Batch#: 0000005 Preset: 01 Component: 01 Type: Preset Product: PRD001 Alarm: No Gross: 499.54 Net: 499.54 Mass: 0.0 Temperature: +28.5 Pressure: +0.0 BSW: +0.0 VCF(None): 1.0000 CTL: 1.0000 CPL: 1.0000 Next Prev Exit Enter Bol# Numéro de séquence BOL à partir de MultiLoadII Detail Nombre de détails d’une transaction (1 à 99) Batch# Numéro de séquence du numéro de lot à partir de MultiLoadII; pour chaque lot chargé, le nombre sera augmenté de 1 Preset Valeur prédéfinie ou bras utilisé au cours du chargement Component Composant chargé Type Type de produit 1 = recette produit commercialisable; 2 = Composant; 3 = additif; 4 = compteur; 5 = totalisateur valeurs prédéfinies; 6 = totalisateur compteurs; 7 = totalisateur composants; 8 = totalisateur additifs Product Nom du produit (commercialisable, composant, additif) Alarm Indique s’il y a eu alarme pour cette transaction Gross Volume brut Net Volume net Mass Masse Temperature Température du chargement Pressure Pression du chargement BSW Eau sédiment en dépôt (pourcentage %) Density Densité du chargement Relative Density Densité relative du chargement API Gravity Gravité API du chargement API Table Nom du tableau API utilisé pour ce lot Vcf Coefficient Vcf utilisé au cours du chargement Ctl Coefficient de correction de la température Cpl Coefficient de correction de la pression Chapitre 10 – Affichage et requêtes 343 MultiLoad enregistre par lot les alarmes qui se sont produites au cours du chargement pour tous les niveaux d’alarme à l’exception du niveau quai. Sélectionnez l’alarme et appuyez sur Enter pour visualiser les détails d’alarmes. VIEW TRANSACTION ALARM DETAILS Preset 1 No Alarms Next Prev Exit Vous verrez ainsi tous les niveaux d’alarmes pour les valeurs prédéfinies, les compteurs, les composants et les additifs. Chapitre 10 – Affichage et requêtes 344 10.12 VISUALISATION DU JOURNAL DES CHANGEMENTS DES POIDS ET MESURES Sélectionnez W&M Change Log dans le menu Views & Inquiry (Affichage et Requête). Le journal des changements des poids et mesures (W&M Change Log) s’affiche. Si une imprimante sérielle ou réseau est configurée, il est possible d’imprimer le journal W&M sur l’imprimante configurée. VIEW WEIGHTS & MEASURES CHANGE LOG View Print Next Prev Exit Enter Si vous sélectionnez le View Mode, le journal W&M s’affiche : VIEW WEIGHTS & MEASURES CHANGE LOG Ref:00003 Pre:01 Cmp:01 None ->TAB59E Id:1 07/03/23 10:58 API CTL Table Name Ref:00002 Pre:01 Mtr:01 DISABLD-> ENABLED Id:1 07/03/23 10:56 Temperature Sensor Ref:00001 Id:1 07/03/23 10:54 Has W&M Access Next Prev Exit L'entrée la plus récente s’affiche en haut de l'écran. Pour voir les entrées antérieures, appuyez sur la touche Next et faites les défiler. Remarque: Pour revenir rapidement à l'entrée la plus récente, appuyez sur Exit et resélectionnez l'option visualisation. Impression du Journal des Changements P & M - Sélectionnez "Print" pour imprimer le journal. Une imprimante sérielle doit être raccordée au Port de Communication 2 du MultiLoad II. Ce port doit être Chapitre 10 – Affichage et requêtes configuré en tant qu'imprimante à l’écran de réglage de la communication pour pouvoir imprimer le Journal des Changements des P & M. Chaque événement comporte deux lignes de données. La première ligne reprend: 1. le numéro de référence - Jusqu'à 1.000 entrées sont conservées dans le journal. Après l'enregistrement de ces 1000 entrées, la plus ancienne est abandonnée. Aucun numéro de référence ne se répète tant que les 65.535 événements ne sont pas dans le journal. 2. l'identification de la valeur prédéfinie - Ce champ décrit la valeur prédéfinie (bras de chargement) pertinente pour cet événement. Cette valeur est toujours 1 sur le MultiLoad II SMP. Exemple : Pre:01 indique qu'un événement s'est produit et qu'il concerne le bras de chargement 1. La désignation numérique qui suit le préfixe "Pre" est une désignation arbitraire de l'ingénieur des installations et qui se décide lors de la configuration du système. 3. l'identification du composant ou du compteur - Ce champ indique qu'un changement au niveau du composant ou au niveau du compteur a été introduit. Puisque plusieurs composants (liquides) ou compteurs peuvent être assignés à un même bras de chargement, un indicateur numérique identifie le composant ou le compteur du bras de chargement dont il s’agit. Des changements de niveau des composants peuvent inclure des réglages tels que configurations des facteurs de mesure, débits et VCF. Les changements au niveau des compteurs peuvent inclure des réglages tels que des configurations de température et de pression. Ce champ indique CMP:xx pour un changement au composant ou MTR:xx pour un changement au compteur. La désignation numérique qui suit les préfixes Cmp ou Mtr est une désignation arbitraire de l'ingénieur des installations et qui se décide lors de la configuration du système. 4. le changement de la valeur du paramètre - Ce champ indique la valeur précédente du paramètre suivie de la nouvelle valeur. Par exemple : 2.400->2.500 indique que la valeur a été modifiée: de 2.400, elle est passée à 2.500. La seconde ligne de données reprend : 1. le numéro d'identification - Ce champ comporte une désignation numérique qui identifie l'individu qui a occasionné l'événement. Jusqu'à cinq mots de passe individuels peuvent être attribués au personnel autorisé. Si la valeur dans ce champ est de 1, cela signifie que la personne qui possède le mot de passe numéro 1 a provoqué l'événement. Si la valeur dans ce champ est la lettre C, cela signifie que les changements de paramètre ont été effectués par l'ordinateur à distance. Les changements aux paramètres protégés ne peuvent être effectués par l'ordinateur à distance sauf si le commutateur à clef des Poids et Mesures a été activé. L'attribution des mots de passe est configurée dans le menu d'installation générale du RCU dans le menu configuration. 2. la date - Ce champ indique la date de changement de paramètre. 3. l'heure - Ce champ indique l'heure de changement de paramètre. 4. le nom du paramètre - Ce champ identifie le paramètre changé qui a provoqué l'événement. 345 Chapitre 10 – Affichage et requêtes 346 VIEW WEIGHTS & MEASURES CHANGE LOG Ref:00003 Pre:01 Cmp:01 None ->TAB59E Id:1 07/03/23 10:58 API CTL Table Name Ref:00002 Pre:01 Mtr:01 DISABLD-> ENABLED Id:1 07/03/23 10:56 Temperature Sensor Ref:00001 Id:1 07/03/23 10:54 Has W&M Access Next Prev Exit Supposons que la toute dernière entrée soit l’événement 00003. Il indique que pour la valeur prédéfinie 1 (bras de chargement), le tableau API CTL du composant 1 est passé de « None » (aucun) au tableau 59E. Ce changement s’est produit le 23 mars 2007 à 10:58. Chaque paire de lignes constitue un message en soi. Le Journal des Messages peut être envoyé à une imprimante sérielle. Allez dans "Communications" et définissez COM2 comme imprimante avant d’entrer dans l’écran de visualisation du Journal des Changements des Poids et Mesures (View Weights & Measures Change Log). Vous pouvez visualiser et imprimer à partir du Journal des Changements des Poids et Mesures sans rentrer dans le mode programme, en tapant 4449 NEXT. Le menu View Totalizers peut se visualiser et s’imprimer sans entrer dans le mode programme en tapant 4448 NEXT Le menu View Transactions peut se visualiser et s’imprimer sans entrer dans le mode programme en tapant 4447 NEXT Chapitre 10 – Affichage et requêtes 347 10.13 VISUALISATION DU JOURNAL DES MESSAGES DU MULTILOAD II Le journal des messages du MultiLoad II est un relevé des activités en temps réel. Toutes les occurrences et annulations d'alarme ainsi que d’autres événements y sont répertoriés avec la date et heure. Des événements particuliers occasionnent également l'enregistrement des valeurs du totalisateur. A partir du menu Affichage et Requêtes, sélectionnez Message Log (Journal des Messages). L'écran de Visualisation du Journal des Messages s'affiche. VIEW MESSAGE LOG 13:32:14 PROGRAM MODE ENTERED 13:32:11 Transaction Done 13:32:11 Preset 1, Batch Cleared 13:25:01 Preset 1, Flow Stopping at 500. 13:23:14 Preset 1, Flow Starting at 0. 13:23:13 Preset 1, Batch Authorized prod=PRD001 vol=500 13:23:10 Transaction Stand-Alone Authorized for 132 Next Prev Exit Chaque paire de lignes constitue un message en soi mentionnant l’heure de journalisation. La toute dernière entrée s’affiche en haut de l’écran. Pour visualiser des entrées plus anciennes, appuyez sur la touche Next pour faire défiler les entrées antérieures. Chapitre 10 – Affichage et requêtes 348 10.14 VISUALISATION DU JOURNAL D’AUDITS DU MULTILOAD II Le Config Change Log du MultiLoad II est un journal en temps réel. Tout changement de configuration aux niveaux RCU, quai, valeurs prédéfinies, compteur, composant, additifs et trace y sont répertoriés. A partir du menu Views and Inquiry, sélectionnez Audit Log. L’écran View Audit Log s’affiche: VIEW AUDIT LOG Ref:00003 Pre:01 Cmp:01 None ->TAB59E Id:1 07/03/23 10:58 API CTL Table Name Ref:00002 Pre:01 Mtr:01 DISABLD-> ENABLED Id:1 07/03/23 10:56 Temperature Sensor Ref:00001 Next Prev Exit Chaque paire de ligne constitue un message complet avec l’heure d’insertion au journal. La mention la plus récente s’affiche en haut de l’écran. Pour visualiser des mentions plus anciennes, appuyez sur Next pour les voir défiler. Première ligne: 1. Reference Number- Le journal peut collationner jusqu’à 1.000 mentions, puis il laissera tomber la mention la plus ancienne. Aucun numéro de référence ne se répète tant qu’il n’y a pas 65.535 événements dans le journal. 2. Preset Identification- Ce champ décrit la valeur prédéfinie (bras de chargement) correspondant à cet événement. Cette valeur sera toujours égale à 1 sur le MultiLoad II SMP. Exemple: Pre:01 indique qu’un événement s’est produit sur le bras de chargement n° 1. La désignation numérique qui suit le préfixe PRE est arbitrairement choisie par le technicien des installations. Elle est définie lors de la configuration du système. 3. Component or Meter Identification- Ce champ indique qu’il y a eu modification au niveau d’un composant. Etant donné qu’un bras de chargement peut avoir des composants (liquides) ou des compteurs multiples qui lui sont affectés, une indication numérique identifie quels sont les composants ou les compteurs référencés. Des modifications au niveau composant peuvent concerner des réglages tels que la configuration des coefficients de compteur, des débits et de la VCF. Des modifications au niveau compteur peuvent concerner des réglages tels que la température ou la pression. Ce champ indique CMP:xx pour un événement rapportant une modification de composant ou MTR:xx pour un événement rapportant une modification de compteur. La désignation numérique qui suit les préfixes Cmp or Mtr est arbitrairement choisie par le technicien des installations. Elle est définie lors de la configuration du système. 4. Parameter Value Change- Ce champ indique la valeur du paramètre précédent suivie de la nouvelle valeur. Par exemple, 2400->2500 indique que la valeur est passée de 2400 à 2500. Chapitre 10 – Affichage et requêtes Seconde ligne: La seconde ligne comprend les données suivantes: 1. Identification Number- Ce champ contient une désignation numérique identifiant qui a provoqué l’événement. On peut y attribuer un maximum de 5 mots de passe individuels pour du personnel agréé. Si la valeur dans ce champ est de 1, cela signifie que la personne ayant le mot de passe 1 a provoqué la mention de l’événement dans le journal. Si la valeur introduite dans ce champ est C, cela signifie que les modifications ont été introduites à distance par le port de communication. Il est impossible d’effectuer des modifications à distance pour des paramètres protégés sauf si le commutateur de la touche Weights & Measures a été activé. L’attribution des mots de passe se fait dans le menu General Setup menu RCU par le menu de configuration. 2. Date- Ce champ indique la date de changement du paramètre. 3. Time- Ce champ indique l’heure de changement du paramètre. 4. Parameter Name- Ce champ identifie le paramètre modifié qui a provoqué l’événement. 349 Chapitre 11 – Carte SD 350 CHAPTER 11 11.1 CARTE SD APERÇU Sur les tableaux CPU du MultiLoad II fabriqués après 1/1/2011 se trouve une fente pour la carte SD au-dessus de la carte du processeur qui permet le chargement et la sauvegarde rapides des fichiers de configuration de même que le chargement de fichiers logo clients et les mises à jours du logiciel. La version 4.xx.xx du logiciel MultiLoadII propose un menu des fonctions de la carte SD accessible à partir du menu principal représenté ciaprès: SD CARD MENU View Dir/Files Load Configuration Save Configuration Load Logo Load Firmware Dump Diagnostic Data Next Prev Exit Enter Il faut insérer une carte SD formatée dans la fente prévue pur la carte SD sur le tableau CPU avant de sélectionner l’une des options au-dessus, faute de quoi un message “Not Accessible” s’affiche. REMARQUE: Les listes de fichiers ne proposent que les extensions de fichier associées (*.mlc , *.bin or *.bmp). Chapitre 11 – Carte SD 351 11.2 VISUALISATION DES RÉPERTOIRES/FICHIERS A partir du menu de la carte SD, sélectionnez View Dir/Files. L’écran View Dir/Files affiche des fichiers (en noir) et des répertoires (en bleu) sur la carte SD. A partir de là, vous pouvez créer et naviguer dans les répertoires. Vous pouvez également en rebaptiser ou en supprimer. View Dir/Files FileName1.bin Configuration 1.mlc Directory1 2013_09_23_ML_LOG Directory2 [new directory] Next Prev Exit Enter CLeaR Pour atteindre un répertoire, il suffit de la sélectionner dans le menu. Sélectionnez le “..” quand vous êtes dans le répertoire pour en ressortir. View Dir/Files . .. Filename1.txt Filename2.bin Directory1_2 [new directory] Next Prev Exit Enter CLeaR Chapitre 11 – Carte SD 352 Pour rebaptiser un fichier, sélectionnez-le dans le menu puis introduisez le nouveau nom de fichier et appuyez sur ENTER. N’ajoutez pas l’extension quand vous créez le nouveau nom: elle s’ajoute automatiquement. View Dir/Files FileName1.bin Configuration 1.mlc Directory1 2013_09_23_ML_LOG Directory2 FileName2.txt [new directory] Next Prev Exit Enter CLeaR Vous devez être à l’intérieur d’un répertoire pour pouvoir le rebaptiser. Lorsque vous y êtes, sélectionnez le “.”, introduisez le nouveau nom puis appuyez sur ENTER. View Dir/Files . .. Filename1.txt Filename2.bin Directory1_2 [new directory] Next Prev Exit Enter CLeaR Chapitre 11 – Carte SD 353 11.3 CHARGEMENT CONFIGURATION A partir du menu SD Card, sélectionnez Load Configuration. L’écran de configuration du chargement affiche les fichiers sur la carte SD. Load Configuration Configuration 1.mlc Configuration 2.mlc Next Prev Exit Enter CLeaR Sélectionnez le fichier de configuration à charger. Le nombre de paramètres acceptés ou refusés apparaît. Des paramètres peuvent être refusés s’ils sont hors échelle ou s’ils tentent de modifier un paramètre W&M protégé sans que la touche W&M ne soit activée. Load Configuration Configuration 1.mlc Configuration 2.mlc Next Prev Exit Enter CLeaR Chapitre 11 – Carte SD 354 11.4 CONFIGURATION DE LA SAUVEGARDE A partir du menu de la carte SD, sélectionnez Save Configuration. L’écran de configuration de la sauvegarde affiche les fichiers sur la carte SD. Save Configuration Configuration 1.mlc Configuration 2.mlc [new file] [new directory] Next Prev Exit Enter CLeaR Sélectionnez le fichier de configuration ou créez un nouveau fichier pour sauvegarder la configuration. Save Configuration Configuration 1.mlc Configuration 2.mlc [new file] [new directory] Next Prev Exit Enter CLeaR Chapitre 11 – Carte SD 355 11.5 CHARGEMENT DU LOGO A partir du menu de la carte SD, sélectionnez Load Logo. L’écran Load Logo affiche les fichiers sur la carte SD. Load Logo Customer Logo.bmp Next Prev Exit Enter CLeaR Sélectionnez le fichier de logo à charger. Il faut absolument avoir un fichier BMP d’une résolution de 640x240x16 couleurs. ous les formats de fichier ou questions relatives aux couleurs s’affichent s’il n’y a pas moyen de charger le fichier. Il est conseillé de créer le fichier logo avec le programme MultiMate. Lorsque le fichier est chargé, l’écran suivant apparaît: Load Configuration Configuration 1.mlc Configuration 2.mlc Next Prev Exit Enter CLeaR Chapitre 11 – Carte SD 356 11.6 LOGICIEL DE CHARGEMENT A partir du menu de la carte SD, sélectionnez Load Firmware. L’écran du logiciel de chargement affiche les fichiers sur la carte SD. Load Firmware 20100101_ML_4_30_01.bin Next Prev Exit Enter CLeaR Sélectionnez le fichier de logiciel à charger. Le commutateur W&M doit être actif et l’image du fichier du logiciel sera vérifiée avant d’être acceptée et chargée dans la mémoire flash. Load Configuration Configuration 1.mlc Configuration 2.mlc Next Prev Exit Enter CLeaR Chapitre 11 – Carte SD 357 11.7 DONNÉES DE DIAGNOSTIC DE VIDANGE (DUMP) A partir du menu de la carte SD, sélectionnez Dump Diagnostic Data. L’écran Dump Diagnostic Data vous invite à appuyez sur Enter avant de continuer. DIAGNOSTIC DATA DUMP Press Enter To Continue... Exit Assurez-vous qu’il y a bien une carte SD insérée dans le MultiLoad et appuyez sur Enter. La mention NVRAM et FLASH s’inscrit sur la carte SD sous la forme NVRAM.BIN et FLASH.BIN. Envoyez les fichiers à l’assistance Toptech pour analyse. DIAGNOSTIC DATA DUMP Dumping data to SD. DO NOT REMOVE POWER Dumping NVRAM...Done. Dumping FLASH...Done. Success! Exit Chapitre 12 – Fonctionnement 358 CHAPTER 12 12.1 FONCTIONNEMENT VUE D’ENSEMBLE Ce chapitre traite des deux méthodes de fonctionnement du MultiLoad II: la commande à distance (télécommande) et la commande locale. Dans Remote Control, le MultiLoad II se repose sur le TMS pour traiter toutes les tâches d’entrées de données chauffeur ainsi que l’autorisation des produits. Dans Local Control, le MultiLoad II traite des tâches d’entrées de données chauffeur et de leur validation par la configuration interne ainsi que des listes de validation enregistrées. Sur le MultiLoad II Sur le MultiLoad II SMP PRE PRODUCT >1 Preset 001 2 Preset 002 SET 0 0 DEL 0 0 STATUS IDLE IDLE Preset 001 IDLE PRESET: 0 0 DELIVER: Next Prev ExitLoad Enter=Pick GALLONS ExitLoad Enter=Preset (Une résolution 1/100 s’affiche lorsque le paramètre « use Hundredths RCU W&M » est activé) 12.2 PHASES DE FONCTIONNEMENT Il existe quatre phases importantes de fonctionnement pour le MultiLoad II : Phase 1 – Autorisation Phase 2 – Valeur prédéfinie Phase 3 – Chargement Phase 4 – Fin du chargement 12.3 ACCÈS PAR CARTE CHAUFFEUR OU CLAVIER Pour entamer le processus d’autorisation, le MultiLoad II RCU lit la carte de proximité du chauffeur (sauf pour le SMP) ou demande au chauffeur d’entrée un code d’accès. Ensuite, le chauffeur doit introduire un code PIN. Chapitre 12 – Fonctionnement 12.4 359 FONCTIONNEMENT DE LA COMMANDE À DISTANCE La séquence suivante donne des instructions détaillées au chauffeur pour utiliser le MultiLoad en mode à distance à savoir un hôte (TMS) ainsi que des informations "d'arrière-plan" pertinentes pour l'administrateur du système. 12.4.1 Pour activer le fonctionnement à distance, il faut activer le paramètre de Remote Processing (traitement à distance) à l'écran d'installation générale du RCU (accessible par le menu configuration). PHASE D'AUTORISATION En mode à distance, le processus d'autorisation est plus étendu qu'en mode local. Avant d’autoriser un chargement, le TMS peut proposer plusieurs invites au chauffeur, entre autres: camion, remorque, propriétaire, client, compte, numéro PO, numéro d'édition, etc. Avant d’autoriser un lot, l’hôte (TMS) peut proposer plusieurs invites au chauffeur, entre autres : produit, quantité, compartiment. L’hôte peut contrôler les données fournies et les affectations avant de télétransférer la recette du produit et d’autoriser le lot. A la réception de l'autorisation de lot données par le TMS, le MultiLoad II demande au chauffeur de confirmer le début (Confirm Start) en appuyant une nouvelle fois la touche Enter pour commencer à débiter. 12.4.2 ECRAN D'INTRODUCTION DE LA CARTE Lorsque le MultiLoad II est en « Operation Mode », l'écran d'introduction de la carte s'affiche. Sur le MultiLoad II For Access Press Next to Begin Sur le MultiLoad II SMP For Access Insert Driver Card Chapitre 12 – Fonctionnement 360 Après avoir introduit la carte de chauffeur ou en appuyant sur Next pour introduire un numéro d’identification chauffeur, celui-ci est invité à introduire son code PIN. Enter PIN Number:***█ Il se peut qu’on demande au chauffeur d’autres renseignements comme, par exemple, d’identifier sa remorque (« Trailer »). Ensuite, l’écran de sélection du client s’affiche: Select Customer Number:█ 0000001 ABC OIL 0000002 SHIPCO 0000003 XYZ HEATING 0000004 VANCE SHIPPING Next Prev Exit Enter Le chauffeur peut soit choisir le client à partir de la liste de sélection, soit introduire le client à l'invite. Dans les deux cas, appuyez sur Enter. Si le client que vous avez choisi possède au moins un compte défini, l'écran de sélection du compte s'affiche (voir ci-dessous). Si le client que vous avez choisi n'a aucun compte défini, passez directement à l'écran de confirmation. Chapitre 12 – Fonctionnement 361 Select Account Number:█ 0000001 ABC ACCOUNT ONE 0000002 ABC ACCOUNT TWO 0000003 ABC ACCOUNT THREE Next Prev Exit Enter Sélectionnez le compte ou introduisez le numéro de compte à l’invite. L’écran de confirmation de chargement s’affiche : Error! Reference source not found. Si les renseignements ne sont pas corrects, appuyez sur Prev pour revenir à l’écran de sélection du client (Customer Selection). S’ils sont corrects, appuyez sur Enter pour passer à l’écran de chargement. Chapitre 12 – Fonctionnement 362 Sur le MultiLoad II PRE PRODUCT >1 Preset 001 2 Preset 002 SET 0 0 Sur le MultiLoad II SMP DEL 0 0 STATUS IDLE IDLE Preset 001 IDLE PRESET: 0 0 DELIVER: GALLONS ExitLoad Enter=Preset Next Prev ExitLoad Enter=Pick (Une résolution 1/100 s’affiche lorsque le paramètre « use Hundredths RCU W&M » est activé) Sélectionnez un bras de chargement et appuyez sur Enter pour définir le produit à charger. L’écran de la valeur définie du produit s’affiche: S’il est possible de charger plusieurs produits, vous pouvez le faire sur cet écran. PRESET SCREEN PRODUCT: Low Sulfur Diesel PRESET QUANTITY: █ Enter Preset Quantity; Press Enter Chapitre 12 – Fonctionnement 363 Le chauffeur introduit alors le volume à charger (par exemple 5000) et appuie sur Enter. Error! Reference source not found. Appuyez sur Enter pour obtenir l’autorisation de chargement. Error! Reference source not found. Chapitre 12 – Fonctionnement 364 Un message PLEASE WAIT (Attendez, S.V.P.) s’affiche brièvement dans l’attente de l’autorisation. Error! Reference source not found. Ensuite, l’écran de chargement se réaffiche. Sur le MultiLoad II Sur MultiLoad II SMP Error! Reference source not found. Error! Reference source not found. Figure 12-1 Ecran de Commande des Valeurs Prédéfinies (Une résolution 1/100 s’affiche lorsque le paramètre « use Hundredths RCU W&M » est activé) Chapitre 12 – Fonctionnement Appuyez sur Enter pour entamer le chargement. Sur le MultiLoad II Sur le MultiLoad II SMP Error! Reference source not found. Error! Reference source not found. Le chargement démarre et vous voyez le statut changer au fur et à mesure de la quantité livrée. Lorsque le chargement est terminé, le statut indique terminé (COMPLETE) et la quantité livrée doit normalement être celle qui avait été introduite. Sur le MultiLoad II Sur le MultiLoad II SMP Error! Reference source not found. Error! Reference source not found. 365 Chapitre 12 – Fonctionnement 366 Sur le MultiLoad II 12:07 PRESET 01 CONTROL SCREEN PRODUCT: Default Product 001 STATUS: STOPPED PRESET: DELIVER: 1000 0 GALLONS 0% ++++++ + + + + + + ++++++ Gross Tot. : 000000099 Net Tot. : 000000099 Mass Tot. : 000000099 09/10/2013 17:05 Next Prev ExitLoad Enter=Pick Le temps réel s’affiche dans le coin supérieur gauche à l’écran de chargement pour tous les dispositifs sauf le SMP. Chapitre 12 – Fonctionnement 367 12.4.3 VALEURS DU STATUT DE CHARGEMENT *Alarm Une ou plusieurs alarmes actuellement actives sur le bras. Tous les noms d’alarmes sont précédés d’une astérisque (* ). Unauth Le bras de chargement n’est pas disponible à l’autorisation. Idle Le bras de chargement est disponible à l’autorisation. Stopped Le bras de chargement est autorisé mais aucun produit n’est débité. Starting Le bras de chargement est en train d’entamer le débit. Low Flow Après le démarrage d’un lot, le débit se maintient à faible débit jusqu’à ce que le volume de démarrage de faible débit ait été livré. High Flow Ce taux spécifie le débit-cible à faible débit et est maintenu jusqu’à ce que le volume de déclenchement de la 1ère étape soit atteint. st 1 Trip 2 nd Trip Complete La phase de déclenchement de la 1ère étape commence lorsque le volume restant de la valeur prédéfinie est égal à la valeur indiquée par le paramètre du volume de déclenchement de la 1ère étape. Cette phase représente la diminution initiale depuis le haut débit jusqu'à la condition "sans débit". Lorsque le volume de déclenchement de la 1ère étape est atteint, la vanne de régulation du flux réduit le débit depuis le haut débit jusqu'à un débit spécifié par le paramètre de débit de la 1ère étape. La phase de déclenchement de la 1ère étape se termine lorsque la ème phase de déclenchement de la 2 étape est atteinte. ème La phase de déclenchement de la 2 étape commence lorsque le volume restant de la valeur prédéfinie est égal à la valeur indiquée dans ce paramètre. Cette phase est la seconde d'une série d'ajustements depuis le haut débit jusqu'à la condition "sans débit". Lorsque le volume de ème déclenchement de la 2 étape est atteint, la vanne de régulation du flux réduit le débit depuis ère ème le débit de la 1 étape jusqu'à un débit spécifié par le paramètre de débit de la 2 étape. La ème phase de déclenchement de la 2 étape se termine lorsque la phase de déclenchement final est atteinte. Chargement terminé. Pour de plus amples informations sur les paramètres décrits ci-dessus, consultez le Chapitre 5 – Contrôle du Débit du Produit. Visualisation du Statut Détails de Chargement L’accès chauffeur à ces écrans peut se bloquer à l’aide du paramètre de verrouillage de l’écran de statut Status Screen Lockout se trouvant à l’écran d’installation du RCU, à partir du menu de configuration. Appuyez sur les touches Next et Prev pour aller aux écrans de détails de chargement: Chapitre 12 – Fonctionnement 368 Dans l’écran de chargement Load, appuyez sur Next. L’écran de statut de la valeur prédéfinie s’affiche. Error! Reference source not found. Appuyez sur la touche Next et l’écran de statut du composant s’affiche. Error! Reference source not found. Appuyez sur la touche Next et l’écran des additifs s’affiche. Error! Reference source not found. Appuyez sur la touche Next pour revenir à l’écran de chargement. Chapitre 12 – Fonctionnement 12.4.4 369 FIN DE LA PHASE DE CHARGEMENT Pour terminer un chargement, le chauffeur retire sa carte ou appuie deux fois sur la touche Exit à l’écran de chargement. Quand le débit est totalement arrêté, le MultiLoad II rassemble et archive toutes les informations relatives à la transaction et les enregistre dans sa base de données des transactions. La transaction est donc terminée. Remarque: Au démarrage du MultiLoad II et de la version SMP 2.29.02, l’archivage de la transaction enregistre les 10.000 dernières transactions. Celles-ci peuvent être consultées ou imprimées en mode programme. Les anciennes transactions sont détruites dans leur ordre d’entrée. 12.4.5 BOL TMS Le TMS extrait toutes les données de chargement et génère le ticket de connaissement (Bol). Pour plus d’informations sur la fonction RCU Ditto, consultez le Manuel de l’Utilisateur du TMS. 12.5 FONCTIONNEMENT EN MODE LOCAL (AUTONOME) Dans le mode de commande local (autonome), les informations d'accès et de produit sont enregistrées dans la mémoire non volatile du MultiLoad II. (En mode de commande à distance, les informations d'accès et de produit proviennent des bases de données TMS.) En mode local, le MultiLoad II invite le chauffeur à introduire un code PIN (numéro d'identification personnel) après vérification de la carte chauffeur ou de l'ID d'Accès. Ce code PIN doit correspondre au code PIN du tableau chauffeur enregistré dans la base de données de la mémoire non volatile du MultiLoad II. Une fois le code PIN vérifié, le MultiLoad II affiche d’autres invites chauffeur (configurables par l'utilisateur), sur base de sa configuration interne (configurable par l'utilisateur). Jusqu'à 4 invites configurables peuvent être présentées au chauffeur. Une fois que le chauffeur à répondu, le MultiLoad II autorise un chargement. Avant le fonctionnement en mode local, il faut définir deux bases de données dans le MultiLoad II: une base de données des cartes chauffeur et une base de données des produits. 12.5.1 BASE DE DONNÉES D’ACCESS ID La base de données des cartes chauffeur contient le numéro de carte et le code PIN de chaque chauffeur. Jusqu'à 300 cartes chauffeur peuvent être entrées dans le MultiLoad II. Il y a deux façons d'entrer ces données. Entrez les données de la carte chauffeur manuellement par le panneau frontal du MultiLoad II. Entrez les données de la carte chauffeur manuellement par l'outil de configuration du MultiLoad II et téléchargezles dans le MultiLoad II. (Consultez la procédure dans les registres de téléchargement) Remarque : Actuellement, il n'y a pas de support pour l'importation/l'exportation de ces données vers/depuis les fichiers de données. De même, il n'y a aucune méthode pour obtenir des données actuelles de base de données chauffeur fournies par le TMS vers le MultiLoad II. Aucun agent, client ou autres informations de type "Compte" n’est stocké dans le MultiLoad II. Les chauffeurs peuvent être invités à entrer ces informations pour une transaction, mais aucun nom ou adresse de client n'est enregistrée dans le MultiLoad en tant que configuration. Il n’y a pas de validation des données fournies par le chauffeur. Chapitre 12 – Fonctionnement 370 BASE DE DONNÉES DES PRODUITS 12.5.2 La base de données des produits se subdivise en cinq catégories. définitions des produits de base - affectations des composants de base - définitions des produits commercialisables - valeur prédéfinie des produits autorisés - affectations des additifs de base - Chaque catégorie peut être introduite manuellement dans le MultiLoad II ou avec son outil de configuration, mais ces informations sont automatiquement écrasées par le TMS chaque fois que le quai démarre avec les affectations de produits configurées dans le TMS. Remarquez que tous les produits énumérés sont disponibles pour tous les chauffeurs en mode local. IMPRESSION DES TICKETS DE COMPTAGE 12.5.3 S’il faut imprimer les tickets de comptage, connectez une imprimante sérielle directement au Com 2 du MultiLoad II. Après quoi, les paramètres COM corrects et l'option IMPRESSION (Print) doivent être sélectionnés dans « Configuration | Communication Setup ». Un format par défaut de ticket de comptage est enregistré dans le MultiLoad II. Il peut être reconfiguré sans modification logicielle, mais pas manuellement par le MultiLoad II ou son outil de configuration. Prière de contacter Toptech pour la reconfiguration du format du ticket de comptage. Les avertissements de danger peuvent également être configurés par produit. Sur le MultiLoad II Mobile, le ticket a été configuré par défaut à un petit format de 4.5” de large avec tous les noms de paramètre alignés à gauche. La latitude, la longitude et le nom du site de l’autorisation apparaissent sur ce ticket par défaut. On peut raccorder plusieurs appareils MultiLoad à une même imprimante sérielle. Comme les connexions du RS232 du MultiLoad sont du type « Multidrop », il est possible de brancher le port RS232 COM 2 de plusieurs MultiLoad II sur une imprimante commune. Les connexions sérielles sont les suivantes: SMP #1 COMM2 TB5 SMP #2 COMM2 TB5 1 RX 2 CTS 3 4 TX GND PRINTER 1 RX 2 CTS 3 TX 4 1 3 4 GND 5 5 DSR 5 DSR 6 DCD 6 DSD RTS 7 RTS DTR 8 DTR 7 8 6 20 7 RTS DSR CTS Chapitre 12 – Fonctionnement Le signal DTR de l’imprimante doit fournir le statut de celle-ci (occupé, en ligne, plus de papier, erreur, etc.) Le MultiLoad gère son entrée CTS de façon à informer de toute erreur de statut de l’imprimante. Lorsque le COM 2 est mis en mode Multi, le MultiLoad gère la ligne RTS pour déterminer quand l’imprimante est utilisée par un autre appareil MultiLoad II. Si le MultiLoad veut gérer l’imprimante, il doit modifier le statut d’un signal appelé DCD et le faire passer de haut en bas. 12.5.4 TÂCHES DIVERSES Toute source d’énergie, tous signaux, permissions ou blocages qui ne sont pas fournis ou contrôlés directement par le MultiLoad II devront être court-circuités ou passer en opération manuelle. Par exemple, si une permission vers le MultiLoad II ou une pompe d'additifs ou une pompe de produit est commandée par un PLC qui reçoit les commandes depuis le TMS plutôt que le MultiLoad II, ces pompes ne démarrent pas automatiquement en mode autonome parce que le TMS et le PLC ne sont pas informés du statut du MultiLoad II (en fonctionnement autonome). 371 Chapitre 12 – Fonctionnement 12.5.5 372 CONFIGURATION DU MULTILOAD II EN MODE LOCAL Si le MultiLoad II est configuré pour fonctionner en mode à distance, c'est-à-dire avec un TMS, il ne faut modifier qu'un seul paramètre de configuration pour fonctionner en mode autonome. Rentrez dans le mode de programme, configuration, puis RCU General Setup (Installation Générale du RCU). L'écran d'Installation Générale du RCU s'affiche. RCU GENERAL SETUP RCU Address: 001 Card Reader DISABLED Remote Processing: StndAln Swing Arm Secondary DISABLED Password #1: ******* Password #2: ******* Password #3: ******* Password #4: ******* Password #5: ******* Modem Init: AT&F0&B1&C1&D0S0=1 Modem Dial: Host Login: TDSTEST TDSTEST Terminal Name: Toptech Terminal Truck Number: Next Prev Exit Enter Sélectionnez Remote Processing et appuyez sur Enter. ENABLED (activé) passe sur DISABLED (désactivé) et le MultiLoad II passe en mode local autonome. 12.5.6 FONCTIONNEMENT EN MODE LOCAL Le fonctionnement en mode local autonome est quasiment identique au mode à distance, sauf que, en mode local, le chauffeur doit introduire le propriétaire du produit et les ID client à l’invite (autrefois géré par l’outil de configuration). Autrement dit, il n’y a pas de listes de sélection de comptes en mode local. Chapitre 12 – Fonctionnement 12.5.7 373 AUTORISATION LOCALE Comme indiqué plus haut, en mode local, le MultiLoad II invite le chauffeur à introduire un code PIN après vérification de la carte chauffeur. Ce code PIN doit correspondre au code PIN du tableau chauffeur enregistré dans la base de données de la mémoire non volatile du MultiLoad II. Une fois le code PIN vérifié, le MultiLoad II agit selon une configuration interne des invites complémentaires. Le MultiLoad II dispose d’un maximum de quatre invites configurables à présenter au chauffeur. Quand le chauffeur y a répondu, le MultiLoad II autorise le chargement. Les invites chauffeur sont définies au moyen de la fonction "Miscellaneous" (divers) dans l'outil de configuration. Le chauffeur ne voit que les invites que vous avez définies. Par exemple, si vous définissez Prompt 1 (invite 1) pour inviter le chauffeur à introduire l'ID de l'expéditeur, le chauffeur voit l'écran suivant. Error! Reference source not found. Quand le chauffeur introduit l’ID de l’expéditeur et appuie sur Enter, la seconde invite personnalisée s’affiche : Enter Account:█ Chapitre 12 – Fonctionnement 374 Le chauffeur introduit le numéro de compte et appuie sur Enter. S’il s’agit des seules invites définies, l’écran suivant vu par le chauffeur est l’écran de sélection dechargement. Sur le MultiLoad II Sur le MultiLoad II SMP Error! Reference source not found. Error! Reference source not found. A partir de là, le fonctionnement est identique à celui du mode à distance. Toutefois, lorsque le chargement est terminé et que le chauffeur retire sa carte, ce n’est pas le TMS qui imprime le ticket de connaissement (BoL), mais c’est le MultiLoad II qui imprime un ticket de comptage. 12.5.8 TICKET DE COMPTAGE S’il est configuré pour ce faire, le MultiLoad II imprime un ticket de comptage pour l’ensemble de la transaction. 12.5.9 REVENIR AU MODE À DISTANCE Pour revenir au mode à distance, rentrez dans le mode programme et sélectionnez Configuration, RCU General Setup. L’écran d’installation générale du RCU s’affiche. Error! Reference source not found. Sélectionnez Remote Processing et appuyez sur Enter. DISABLED (désactivé) se transforme en ENABLED (activé) et le MultiLoad II passe en mode à distance. Chapitre 12 – Fonctionnement 12.6 375 FONCTION D’ETALONNAGE AUTOMATIQUE DE CONTRÔLE Cette fonction est conçue pour l’étalonnage de débitmètres effectué en livrant un volume prédéterminé dans un réservoir statique et étalonné. Lorsqu'un étalonnage de contrôle est amorcé, des débits et volumes de livraison peuvent être sélectionnés et exécutés, sans entrer dans le mode de programme et sans modifier le profil du débit utilisé pour les opérations quotidiennes. Lorsque la livraison est terminée, l'opérateur-vérificateur est invité à introduire le volume observé dans le réservoir étalonné. Un nouveau facteur de mesure pour ce débit d'essai se calcule et est introduit dans la configuration du MultiLoad II, s'il est approuvé par l'opérateur. Déterminer le nombre de débits d’essai - Le nombre de débits à étalonner doit être défini pendant l'installation initiale du MultiLoad II. Déterminez le nombre de débits à étalonner. En mode programme, entrez dans le menu des Poids et Mesures et sélectionnez les composants. Faites défiler le menu et sélectionnez le paramètre # Meter Factors Used nombre de facteurs de mesure utilisés). Introduisez ce chiffre pour étalonner le compteur pour le composant sélectionné. Les possibilités valables vont de 1 à 4. Etablir des débits de facteur de mesure - Introduisez les taux qui devront être étalonnés. En mode programme, entrez dans le menu des Poids et Mesures et sélectionnez les composants. Parcourez le menu et sélectionnez Meter Factor #1 Rate (débit du facteur de mesure #1). Introduisez le premier débit d’étalonnage. Si l’étalonnage doit être effectué pour deux débits, introduisez le deuxième débit dans le champ de débit du facteur de mesure 2. Vous pouvez introduire maximum quatre débits d’étalonnage. Chapitre 12 – Fonctionnement 12.6.1 376 UTILISATION DE LA FONCTION D’ETALONNAGE DE CONTRÔLE 1. Activez le commutateur des Poids et Mesures (Weights and Measures). En mode autonome, allez à Program Mode->Configuration->RCU Setup et activez le paramètre Meter Proving Mode. En mode à distance, l’hôte soit envoyer un ordre « MPT » (transaction de test compteur) au MultiLoad. 2. Autorisez une seule transaction de produit sur le MultiLoad II. (Il ne peut pas s’agir d’un mélange). 3. Appuyez sur Enter et introduisez une valeur prédéfinie de volume correspondant au volume à livrer dans le réservoir d’essai. 4. Appuyez sur Enter pour autoriser la quantité prédéfinie. 5. Après autorisation, l’opérateur passe à l’écran Meter Proving Preconfiguration où il met le champ du débit en surbrillance (Flow Rate). PRE #1 (Preset 001) CMP #1 (LS DIESEL ) Meter Proving Preconfiguration Proving Rate M.F. M.F .Flow Rate: 150 150 1.0000 Low Flow Vol: 50 200 1.0000 Low Flow Rate: 60 400 1.0000 Prover 800 1.0000 Exp Coeff: 0.000000000 Next Prev Exit Enter (Remarque: Le commutateur des Poids et Mesures DOIT être actif pour pouvoir modifier le débit et les paramètres M.F.). 6. Appuyez sur Enter pour faire défiler les débits d’essai fixés lors de l’installation préliminaire. Appuyez sur Next quand vous avez trouvé le débit désiré. Remarque: Si les débits ne sont plus appropriés, vous pouvez les changer à condition de vous conformer aux instructions ci-après. 7. Dans le champ de volume à faible débit, appuyez sur Enter pour introduire le volume à livrer à faible débit. Appuyez sur Next pour passer au champ suivant. 8. Dans le champ Low Flow Rate, appuyez sur Enter pour introduire le débit. Appuyez sur Next pour passer au champ suivant. 9. Dans le champ du coefficient d’expansion, appuyez sur Enter pour introduire le coefficient d’expansion du réservoir d’essai. (Consultez les valeurs dans le tableau ci-après). Si vous ignorez cette valeur, laissez sur zéro. Appuyez sur Next pour passer au champ taux (Rate). Chapitre 12 – Fonctionnement 377 Matériel d’Etalonnage Coefficient d’Expansion Inox (Seraphin) 0.00004770/°C Inox (Seraphin) 0.00002650/°F 304 SS 0.00005184/°C 304 SS 0.00002880/°F 316 SS 0.00004536/°C 316 SS 0.00002520/°F 10. Au point "Taux", vous trouverez les débits définis pour de fins de calibrage de contrôle. Si ces taux ne sont plus appropriés, c’est là que vous pouvez les modifier. Appuyez sur Enter pour changer le débit d’étalonnage de contrôle ou sur Next pour avancer jusqu'au champ du facteur de mesure (MF) du taux. S'il s'avère nécessaire de changer le taux, le facteur de mesure (MF) correspondant doit être changé en 1,0000. Si un taux et/ou un Facteur de Mesure (MF) a été modifié, il faut revenir au champ du Débit et de sélectionner le nouveau taux. Utilisez la touche "Prev" pour retourner au champ du Débit. Appuyez sur Enter jusqu'à ce que le nouveau taux apparaisse. Passez à l'étape suivante. 11. Le champ MF montre le facteur de mesure instantané pour le débit affiché à gauche du champ. Il ne doit pas être changé par l'utilisateur à cet endroit, sauf si vous devez utiliser un nouveau débit, comme décrit à l'étape précédente. 12. Le fait de pousser sur "Next" amène l'utilisateur aux autres taux et facteurs de mesure. Pour retourner à n'importe quel champ précédent, appuyez sur Prev. Sur le MultiLoad II Sur le MultiLoad II SMP PRE PRODUCT >1 LS Diesel 2 Preset 002 SET 1000 0 DEL 0 0 STATUS STOPPED IDLE Low Sulfur Diesel STOPPED PRESET: 1000 0 DELIVER: Next Prev ExitLoad Enter=Pick GALLONS ExitLoad Clear=Preset Enter=Start 13. Quand la pré-configuration de l’étalonnage du compteur est terminée, appuyez sur Exit pour passer à l’écran de commande des valeurs prédéfinies. Chapitre 12 – Fonctionnement 378 14. Appuyez sur Enter pour entamer l’étalonnage de contrôle et l’écran de statut des valeurs prédéfinies apparaît. PRESET 01 STATUS SCREEN Low Sulfur Diesel LOW FLOW GROSS NET PRESET: 1000 REMAIN: 996 DELIVER: 3.90 3.90 TOTAL: 4 PRODUCT: STATUS: TEMPERATURE: PRESSURE: DENSITY: BSW: FLOW RATE: 24.00C 0.00 0.0 0.00 59 Next Prev Exit Stop 15.Quand la quantité prédéfinie a été livrée, appuyez sur Next pour passer à l’écran de résultats de l’étalonnage de contrôle du compteur. PRE #1 (Preset 001) CMP #1 (LS DIESEL ) Meter Proving Results (1 of 4) Prover Volume: 1001.10 Prover Temperature #1: 20.00 Prover Temperature #2: 21.00 Prover Temperature #3: Prover Temperature #4: Next Prev Exit Enter 16.Le champ de Volume Etalon (Prover Volume) doit être mis en surbrillance. Appuyez sur Enter et introduisez le volume observé dans le réservoir d'essai. 17. Appuyez sur Next pour avancer jusqu'au champ Prover Temp. #1. Si des lectures de la température étalon sont disponibles, appuyez sur Enter et introduisez la température observée sur le premier thermomètre. Appuyez sur Next pour avancer jusqu'au champ de température suivant. Chapitre 12 – Fonctionnement 379 18. Introduisez les températures comme à l'étape précédente. Ensuite, appuyez sur Next pour avancer jusqu'à l'écran des résultats d’étalonnage de contrôle du compteur #2. Si aucune température n'est entrée, appuyez sur Next jusqu'à ce que l'écran des résultats de l’étalonnage de contrôle du compteur 2 apparaisse. PRE #1 (Preset 001) CMP #1 (LS DIESEL ) Meter Proving Results (2 of 4) Prover Volume: 1001.10 Prover Avg Temp: 20.50 Prover Correction Factor: 1.000000000 Prover Corrected Vol: 1001.10 Next Prev Exit 19. L'écran des résultats de l’étalonnage de contrôle du compteur présente les données suivantes entrées par l'opérateur : volume observé, moyenne des températures d'essai et facteur de correction de l'étalon. Le volume corrigé de l'étalon est calculé et affiché à partir de ces données. Aucune entrée ne se fait sur cet écran. Appuyez sur Next pour avancer jusqu'à l'écran des résultats de l’étalonnage de contrôle du compteur 3. PRE #1 (Preset 001) CMP #1 (LS DIESEL ) Meter Proving Results (3 of 4) Prover Corrected Vol: 1001.10 Metered Volume: 999.64 Correction Factor: 1.0014605 Next Prev Exit Chapitre 12 – Fonctionnement 380 20.L'écran des résultats de l’étalonnage de contrôle du compteur 3 affiche le volume corrigé de l'étalon, le volume mesuré et le facteur de correction calculés à partir de toutes les données introduites par l'opérateur. Aucune entrée n'est faite à cet écran. Appuyez sur Next pour avancer à l'écran des résultats d’étalonnage de contrôle du compteur 4. PRE #1 (Preset 001) CMP #1 (LS DIESEL ) Meter Proving Results (4 of 4) Proving Rate M.F. Flow Rate: 150 150 1.0000 Old MF: 1.0000 200 1.0000 New MF: 1.0015 400 1.0000 Apply New Meter Factor 800 1.0000 Next Prev Exit Enter (Remarque: Le commutateur Weights & Measures DOIT être actif pour modifier les paramètres « Rate » et « M.F. ».) 21. Le débit d’étalonnage de contrôle, l'ancien facteur de mesure et le nouveau facteur de mesure s'affichent à l'écran des résultats de l’étalonnage de contrôle du compteur 4. a. Pour accepter le nouveau facteur de mesure, appuyez sur Enter. Il se programme automatiquement dans le système pour un débit d’étalonnage de contrôle approprié. Ensuite, appuyez sur Exit pour retourner à l'écran de commande de la valeur prédéfinie. Si d'autres étalonnages de contrôle doivent être effectués, annulez la valeur prédéfinie et sélectionnez un nouveau produit. Répétez le processus en commençant à l'étape 4. Vous pouvez également effectuer manuellement des modifications à MF et Rates en appuyant sur la touche suivante. b. Si l’étalonnage de contrôle doit être interrompu, appuyez sur Exit. L'ancien facteur de mesure reste en vigueur. Pour retourner à l'écran de contrôle de la valeur prédéfinie, appuyez sur Exit dans cet écran. Le lot peut être annulé et d'autres étalonnages de contrôle peuvent être entamés à partir de l'écran de contrôle de la valeur prédéfinie. 22. Lorsque tous les étalonnages sont terminés, Appuyez deux fois sur Exit pour mettre fin à la transaction. Chapitre 13 – Logique Personnalisée CHAPTER 13 13.1 381 LOGIQUE PERSONNALISÉE VUE D’ENSEMBLE Custom Logic (Logique Personnalisée) s’ajoute à la programmation normale de base du MultiLoad II. Le MultiLoad II peut ainsi effectuer de nombreuses tâches de mise en séquence simple des entrées et sorties pour lesquels on aurait besoin d’un PLC supplémentaire. Pour configurer la logique personnalisée, il faut établir une liste des instructions logiques permettant de lire les entrées FCM, les éléments internes du MultiLoad II (quai et lot autorisés, fonctionnement de la pompe, etc.), d’effectuer des opérations logiques (logique AND, OR, etc.) et de gérer les sorties FCM. Chapitre 13 – Logique Personnalisée 13.2 ACCÈS DU MULTILOAD II À LA LOGIQUE PERSONNALISÉE Pour rentrer dans la configuration personnalisée à partir du clavier du MultiLoad II, rentrez dans le mode programme et sélectionnez Configuration, puis Custom Logic. L’écran de logique personnalisée Custom Logic s’affiche. Error! Reference source not found. 13.3 ACCÈS DE L’OUTIL DE CONFIGURATION DU MULTILOAD II À LA LOGIQUE PERSONNALISÉE Vous trouverez la logique personnalisée au point «Miscellaneous » (divers) dans l’utilitaire de configuration du MultiLoad II. 382 Chapitre 13 – Logique Personnalisée 13.4 RÉDACTION DE LA LOGIQUE PERSONNALISÉE Chaque ligne de la routine de logique personnalisée se compose à l’aide de certains ou des cinq champs de l'écran de la Logique Personnalisé. Les champs "Index" et "Type" sont toujours utilisés. Trois champs qui suivent le champ "Type" sont définis par la fonction sélectionnée au champ "Type". Pour créer une ligne de logique personnalisée, introduisez un numéro d'index dans le champ "Index". La première ligne introduite est 000. Ensuite, sélectionnez une fonction à partir du champ "Type". Les fonctions sont soit des fonctions standard du MultiLoad II, soit des opérations Booléennes. Après avoir choisi une fonction "Type", définissez les trois champs suivants. Lorsqu'une ligne de logique personnalisée est terminée, elle s’ajoute à la liste des logiques personnalisées lorsque le bouton Add/Update (Ajouter/Mettre à Jour) est sélectionné. Deux fonctions de la logique personnalisée sont mises en surbrillance : Le paramètre INTERNAL INPUT permet de configurer directement des permissions de configuration dans les lignes de logique personnalisée. Le paramètre EXTERNAL OUTPUT permet à un système de communication externe de mettre à jour la valeur pourune ligne particulière de la logique personnalisée. INDEX : Ce champ numérote chaque ligne de logique. En créant la première ligne, utilisez l'index 000. Numérotez les lignes suivantes de façon consécutive. TYPE : Il y a deux classes d'éléments pour sélectionner ce champ : l'élément sélectionné est soit une fonction du MultiLoad II, comme une sortie d'alarme, soit une opération booléenne. Les opérations du MultiLoad II sont définies en temps réel (RT) et les opérations booléennes sont identifiées par des opérations spécifiques mathématiques ou de logique, comme ADD (ajouter), SUBSTRACT (soustraire), NOR, AND, etc. REAL TIME: Les opérations en temps réel (RT) représentent des fonctions existantes du MultiLoad II. Les fonctions sont assignées à divers niveaux hiérarchiques du MultiLoad II: RCU, Quai, Valeur Prédéfinie, Compteur, Composant et Additif. Après la sélection d'une fonction en temps réel, il faut spécifier la valeur prédéfinie pertinente ainsi qu’un compteur, un composant ou un additif spécifique. L'exemple ci-avant utilise la fonction "Alarm Out". Cette fonction particulière est définie au niveau du compteur dans le MultiLoad II. Chaque fois qu'une alarme relative à un compteur spécifique est déclenchée par le MultiLoad II, une sortie peut être activée. Dans cet exemple , on désire profiter de la logique "Alarm Out" 383 Chapitre 13 – Logique Personnalisée du MultiLoad II pour prendre certaines décisions, plutôt que d'activer une sortie FCM basée sur une condition "Alarm Out" au niveau du compteur. Une invite en temps réel au niveau du compteur, appelée "Alarm Out" a été sélectionnée. Après avoir sélectionné cette invite, le programmeur doit indiquer à quelle valeur prédéfinie (bras de chargement) il est fait référence. Dans l'exemple, la valeur prédéfinie 1 est sélectionnée pour l'index 000. Puisque que la fonction "Alarm Out" concerne le compteur, le compteur spécifique à la valeur prédéfinie doit être identifié (Le SMP n’a qu’un seul compteur ce sera donc toujours le 1). 384 Chapitre 13 – Logique Personnalisée BOOLEAN OPERATION: Lorsqu'un fonctionnementbooléen, comme OR, est sélectionné dans le champ TYPE, il s’applique à deux lignes dans la liste de logique personnalisée. Les lignes auxquelles ce fonctionnement s'adresse peuvent être spécifiées dans les deux champs après le champ "Type". La figure 4 montre comment ce fonctionnement s'applique à l'index 000 et l'index 001. Dans l'exemple, on désire activer une lampe-témoin chaque fois qu'une condition d'alarme se déclenche au niveau d’un compteur ou d’un composant. Toutes les "Alarm Out" compteurs et composants sont, en fin de compte, ORed : quand tous les bras fonctionnent normalement, une haute tension est disponible à la sortie assignée. Lorsqu’un des bras se met en alarme, la sortie de haute tension chute et la lampe-témoin d'alarme s'allume. La toute dernière ligne (Index 003) attribue un port de sortie FCM qu’il faut ouvrir ou fermer selon le résultat affiché par l’index 002. la sortie est disponible sur la carte interne des entrées et sorties ou le FCM externe, le port 1 par exemple. Les sélections “Custom Logic” pour le champ TYPE sont énumérées ci-après. Il y a actuellement 28 possibilités. Chacun d’eux peut devoir préciser un certain nombre de champs supplémentaires. 13.5 FONCTIONS EN TEMPS RÉEL (RT) DU MULTILOAD II 1. Inutilisé – Vous le sélectionnez pour laisser une ligne d’index vierge. 2. FCM Input Port: recherchez un port d’entrée. a. FCM #: spécifiez un numéro de FCM (0 pour la carte E/S) b. FCM Input Port # : spécifiez un numéro de port FCM 3. FCM Output Port : Activez une sortie FCM. a. FCM #: spécifiez un numéro FCM (0 pour la carte E/S) b. FCM Output Port # : spécifiez un numéro de port de sortie FCM c. Logique personnalisée: La sortie est activée selon l’état de la ligne d’index référencée par ce champ. 4. RCU Real Time (RT) - Temps Réel RCU a. RCU Real Time Prompt - Invite Temps Réel RCU 385 Chapitre 13 – Logique Personnalisée i. ii. iii. iv. Proving Mode - Indique si le RCU est en Mode d'Essai. W&M Key - Indique si la touche des P&M est active Program Key - Indique si la Touche Programme est active Card Inserted - Indique si une carte à bande magnétique ou de proximité a été détectée par le lecteur de carte. v. Time – Indique l’heure en heures et minutes pour ce jour vi. Date – Indique l’année, le mois et le jour (YYMMDD) instantanés pour le MutliLoad. 5. Bay Real Time (RT) - Temps Réel Quai a. Bay Real Time Prompt - Invite Temps Réel Quai i. Clearing Errors - Indique que des alarmes opérationnelles sont annulées. Ce processus peut être amorcé à distance ou localement. ii. Diagnostic Mode - Indique quand l'opérateur est entré dans un écran de diagnostique. iii. All Stop - Indique quand le bouton TOUT ARRETER a été pressé. iv. Alarm Out - Indique quand une alarme au niveau du Quai, comme une permission, a été enfreinte. v. Authorized - Indique quand un chauffeur a terminée avec succès le processus d'autorisation et est prêt à charger. vi. Permissive Out - Indique que toutes les permissions au niveau du quai sont satisfaites. vii. Permissive 0-7 - Contrôle l'état des permissions 0-7. viii. Deadman Input – (pour réinitialiser la minuterie du l’homme-mort) ix. deadman Output (pour donner une pré-alarme homme-mort) x. deadman Bypass (pour contourner la fonction homme-ort) xi. Total Volume (volume fourni par tout le quai) 6. Preset Real Time (RT) - Temps Réel Valeur Prédéfinie a. Preset Real Time Prompt - Invite Temps Réel Valeur Prédéfinie i. Authorized - Indique quand un chauffeur est autorisé à utiliser une valeur prédéfinie particulière (bras de chargement). ii. Flow Active - Indique quand un flux est actif sur une valeur prédéfinie particulière. iii. Batch Authorized - Indique quand un TMS a examiné la quantité de la valeur prédéfinie et les informations de sélection de produit et a autorisé la livraison du lot. iv. Load Complete - Indique quand un groupe a été achevé sur un bras de chargement particulier. v. Clearing Errors - Indique que des alarmes opérationnelles sont annulées sur une valeur prédéfinie particulière. Ce processus peut être amorcé à distance ou localement. vi. Clearing Load - Indique que le lot a été archivé dans une valeur prédéfinie particulière. Un chauffeur annule un lot en pressant le bouton CLR avant de sélectionner le produit suivant à charger ou en retirant la carte pour finir l'entièreté de la transaction. vii. Open Block Valve - Indique une commande d'ouverture de la Vanne d'Arrêt au niveau de la Valeur Prédéfinie. viii. Block Valve Status - Indique la réception du statut de la Vanne d'Arrêt au niveau de la Valeur Prédéfinie. ix. Close Block Valve - Indique une commande de fermeture de la Vanne d'Arrêt au niveau de la Valeur Prédéfinie. x. Remote Start - Indique que le bouton de Démarrage à Distance d'une Valeur Prédéfinie particulière a été pressé. xi. Swing Arm - Indique que le bras oscillant d'une Valeur Prédéfinie particulière est actif (dans le quai). xii. Meter Stop - Indique que le bouton d'Arrêt du Compteur d'une Valeur Prédéfinie particulière a été pressé. 386 Chapitre 13 – Logique Personnalisée 387 xiii. Alarm Out - Indique qu'une alarme au niveau d'une valeur prédéfinie est active. xiv. Permissive - Indique qu'une permission au niveau d'une valeur prédéfinie est active. xv. Permissive Out - Indique que toutes les permissions au niveau des valeurs prédéfinies sont en ordre. xvi. Preset State (High Flow, Low Flow,….) FST_IDLE = 0, FST_LOW_FLOW = 1, FST_HIGH_FLOW = 2, FST_FIRST_TRIP = 3, FST_SECOND_TRIP = 4, FST_FINAL_TRIP =5 xvii. Quantité prédéfinie fournie en gros (valeur définie en nombres entiers) xviii. Quantité prédéfinie fournie en net (valeur définie en nombres entiers) xix. Quandtité prédéfinie livrée en masse (valeur définie en nombres entiers) xx. Pourcentage fourni (valeur en centièmes, deux chiffres après le point des décimales) xxi. Volume restant (valeur définie en nombres entiers) xxii. Débit brut (valeur définie en nombres entiers) xxiii. Température (valeur en centièmes, deux chiffres après le point des décimales) xxiv. Pression (valeur en centièmes, deux chiffres après le point des décimales) xxv. Densité (valeur en dixièmes, un chiffre après le point des décimales) xxvi. Densité relative ( valeur définie en /10.000èmes, 4 chiffres après le point des décimales) xxvii. Gravité API (valeur en dixièmes, un chiffre après le point des décimales) xxviii. BSW (valeur en centièmes, deux chiffres après le point des décimales) b. Preset Number - Utiliser ce champ pour spécifier une Valeur Prédéfinie particulière (bras de chargement). 7. Component Real Time (RT) - Temps Réel Composant a. Component Real Time Prompt - Invite Temps Réel Composant i. Clearing Errors - Indique qu'une alarme au niveau du composant est annulée pour un composant particulier. ii. Clearing Batch - Indique qu'un composant particulier est annulé et archivé. iii. Pump Run - Indique qu'une pompe d'un composant particulier a reçu une commande de fonctionnement. iv. Pump Kill - Indique qu'un signal d'arrêt de la pompe a été reçu pour un composant particulier. v. Pump Status - Indique qu'un signal de statut de la pompe est en ordre pour un composant particulier. vi. Open Block Valve - Indique une commande d'ouverture de la vanne d'arrêt pour un composant particulier. vii. Block Valve Status - Indique la réception du statut de la vanne d'arrêt à partir d'un composant particulier viii. Close Block Valve - Indique une commande de fermeture de la vanne d'arrêt pour un composant particulier. Chapitre 13 – Logique Personnalisée 388 ix. Alarm Out - Indique qu'une alarme au niveau du composant, tel que le statut de la vanne d'arrêt, est active pour un composant particulier. x. Authorized - Indique quand un chauffeur est autorisé à utiliser un composant particulier. xi. Permissive - Indique qu'une permission au niveau du composant est active. xii. Permissive Out - Indique que toutes les permissions au niveau des composants sont en ordre satisfaites. xiii. Comp State(High Flow, Low Flow,…..) FST_IDLE = 0, FST_LOW_FLOW = 1, FST_HIGH_FLOW = 2, FST_FIRST_TRIP = 3, FST_SECOND_TRIP = 4, FST_FINAL_TRIP =5 xiv. Gross Deliverd Preset Quantity (valeur réfinie en nombre entier) xv. Net Delivered Preset Quantity (valeur réfinie en nombre entier) xvi. Mass Delivered Preset Quantity (valeur réfinie en nombre entier) xvii. Gross Flow Rate (valeur réfinie en nombre entier) xviii. Temperature (value is in hundreths defined meaning two numbers after the decimal point) xix. Pressure (valeur définie en centièmes; 2 chiffres après le point des décimales) xx. Density (valeur définie en dixièmes; 1 chiffre après le point des décimales) xxi. Relative Density (valeur définie en dix millièmes; 4 chiffres après le point des décimales) xxii. Api Gravity (valeur définie en dixièmes; 1 chiffre après le point des décimales) b. Preset Number - Utilisez ce champ pour spécifier une valeur prédéfinie particulière (bras de chargement). c. Component Number - Spécifiez le composant. Il peut y avoir jusqu'à 8 composants assignés à une valeur prédéfinie. 8. Meter Real Time (RT) - Temps Réel Compteur a. Meter Real Time Prompt - Invite Temps Réel Compteur i. Clearing Errors - Indique qu'une alarme au niveau du compteur est annulée pour un débitmètre particulier. ii. Clearing Totals - Indique que le total des lots est annulé pour un débitmètre particulier. iii. Alarm Out - Indique qu'une alarme au niveau du compteur, comme par exemple le faible débit, est active. iv. Authorized - Indique qu'un débitmètre particulier peut être utilisé. v. Permissive - Indique qu'une permission alarme au niveau du compteur est active. vi. Permissive Out - Indique que toutes les permissions au niveau des compteurs sont en ordre. vii. Side-Stream on meter - Indique qu'un débitmètre particulier est un compteur de flux latéral et que son utilisation est autorisée pour le lot. Comp State(High Flow, Low Flow,…..) FST_IDLE = 0, FST_LOW_FLOW = 1, FST_HIGH_FLOW = 2, Chapitre 13 – Logique Personnalisée 389 FST_FIRST_TRIP = 3, FST_SECOND_TRIP = 4, FST_FINAL_TRIP =5 viii. Gross Deliverd Preset Quantity (valeur définie en nombre entier) ix. Net Delivered Preset Quantity (valeur définie en nombre entier) x. Mass Delivered Preset Quantity (valeur définie en nombre entier) xi. Gross Flow Rate (valeur définie en nombre entier) xii. Temperature (valeur définie en centièmes; 2 chiffres après le point des décimales) xiii. Pressure (valeur définie en centièmes; 2 chiffres après le point des décimales) xiv. Density (valeur définie en dixièmes; 1 chiffre après le point des décimales) xv. Relative Density (valeur définie en dix millièmes; 4 chiffres après le point des décimales) xvi. Api Gravity (valeur définie en dixièmes; 1 chiffre après le point des décimales) b. Preset Number - Utilisez ce champ pour spécifier une valeur prédéfinie particulière (bras de chargement). c. Meter Number-Spécifier le compteur. Il peut y avoir jusqu'à 6 débitmètres assignés à une valeur prédéfinie. 9. Additive Real Time (RT) - Temps Réel Additif a. Additive Real Time Prompts - Invite Temps Réel Additif i. Clearing Errors - Indique qu'une alarme au niveau de l'additif est annulée pour un additif particulier ii. Clearing Batch - Indique le que les totaux d'additifs d'un injecteur particulier sont archivés. iii. Test Button - Indique que le bouton d'essai utilisé dans l'étalonnage de l'injecteur a été utilisé pour un injecteur particulier. iv. Pump Run - Indique qu'une pompe d'un additif particulier a reçu une commande de fonctionnement. v. Pump Kill - Indique qu'un signal d'arrêt de la pompe a été reçu pour un additif particulier. vi. Pump Status - Indique qu'un signal de statut de la pompe est en ordre pour un additif particulier. Open Block Valve - Indique une commande d'ouverture de la vanne d'arrêt pour un additif particulier. vii. Open Block Valves – Indique qu’une vanne de blocage a reçu l’ordre d’ouvrir un additif particulier. viii. Block Valve Status - Indique la réception du statut de la vanne d'arrêt à partir d'un additif particulier. ix. Flush Pump Run - Indique qu'une pompe de purge d'un additif particulier a reçu une commande de fonctionnement. x. Close Block Valve - Indique une commande de fermeture de la vanne d'arrêt pour un additif particulier. xi. Alarm Out - Indique qu'une alarme au niveau de l'additif, tel qu’une panne d'injecteur, est active pour un additif particulier. xii. Authorized - Indique quand un chauffeur est autorisé à utiliser un additif particulier. xiii. Permissive - Indique qu'une permission au niveau de l'additif a été reçue. xiv. Permissive Out - Indique que toutes les permissions au niveau des additifs sont en ordre. xv. Gross Delivered (valeur définie en nombres entiers) xvi. Additive Percentage (valeur en centièmes ; deux chiffres après le point des décimales) Chapitre 13 – Logique Personnalisée 390 b. Preset Number - Utilisez ce champ pour spécifier une valeur prédéfinie particulière (bras de chargement). c. Additive Number- Spécifiez l'injecteur. Il peut y avoir jusqu'à 16 injecteurs assignés à une valeur prédéfinie. 13.6 FONCTIONS LOGIQUES 1. Always False (toujours faux) 11. SUBTRACT (soustraire) 2. always True (toujours vrai) a. Logique personnalisée 3. Assign (assigner) b. Logique personnalisée a. Logique personnalisée 4. Not (ne pas) a. Logique personnalisée 5. AND (et) 12. MULTIPLY (multiplier) a. Logique personnalisée b. Logique personnalisée 13. DIVIDE (diviser) a. Logique personnalisée a. Logique personnalisée b. Logique personnalisée b. Logique personnalisée 6. NAND 14. SET VALUE (définir une valeur) a. Logique personnalisée a. Value b. Logique personnalisée 15. EQUAL (égal) 7. OR (ou) a. Logique personnalisée b. Logique personnalisée 8. NOR (ni) a. Logique personnalisée b. Logique personnalisée 9. EOR a. Logique personnalisée b. Logique personnalisée 10. ADD (ajouter) a. Logique personnalisée b. Logique personnalisée a. Logique personnalisée b. Logique personnalisée 16. LESS THAN (plus petit que) a. Logique personnalisée b. Logique personnalisée 17. GREATER THAN (plus grand que) a. Logique personnalisée b. Logique personnalisée 18. LESS THAN OR EQUAL (plus petit que ou égal) a. Logique personnalisée b. Logique personnalisée 19. GREATER THAN OR EQUAL (plus grand que ou égal) a. Logique personnalisée b. Logique personnalisée 20. START DELAY (départ différé) 21. STOP DELAY (départ arrêté) a. Index logique personnalisée a. Index logique personnalisée b. Index logique personnalisée b. Index logique personnalisée 22. BEACON (Continues Pulse) – BALISE (impulsions continues) 23. PULSE (Single Pulse) IMPULSION (impulsion unique) Chapitre 13 – Logique Personnalisée 391 a. Index logique personnalisée (On time) moment de l’impulsion) a. Index logique personnalisée (Au b. Index logique personnalisée (Off time) (Trigger for the Pulse) b. Index logique personnalisée 24. ANALOG IN 25. ANALOG OUT a. Index logique personnalisée a. Index logique personnalisée b. Index logique personnalisée b. Index logique personnalisée 26. RTD 27. BAY ALARM (alarme quai) a. Index logique personnalisée a. Index logique personnalisée b. Index logique personnalisée b. Index logique personnalisée 28. PRESET ALARM (alarme valeurs prédéfinies) 29. METER ALARM (alarme compteur) a. Index logique personnalisée a. Index logique personnalisée b. Index logique personnalisée b. Index logique personnalisée 30. ADDITIVE ALARM a. Index logique personnalisée b. Index logique personnalisée 32. EXTERNAL INPUT (entrée externe) 31. INTERNAL INPUT (entrée interne) Chapitre 14 – Interface Web 392 CHAPTER 14 14.1 INTERFACE WEB APERÇU Le MultiLoadII est désormais muni d’une interface Internet fournissant les informations suivantes: Rcu Ditto (Visualisation de l’affichage dans le champ) Message Log (Journalisation normale du MultiLoadII) W&M Change Log (Journal des Poids et Mesures pour paramètres modifiés) Files (Il est possible de voir tous les fichiers sur la carte SD et de les télécharger) Upload File (Il est possible de télétransférer des fichiers ou des logiciels distants du dispositif) Simulator Page (Sur cette page, vous pouvez déclencher des entrées et des sorties) 14.2 LOGIN Quand vous allez sur l’adresse IP du dispositif, l’écran suivant apparaît: 14.3 WEBSITE Site Internet du MultiLoadII Quand vous ouvrez le serveur rcuditto, vous pouvez visualiser ce que le pilote fait et le clavier à distance vous permet d’intervenir avec le pilote. Chapitre 14 – Interface Web Remarque: Le clavier n’est disponible que lorsque l’utilisateur est en train de journaliser avec l’utilisateur admin. 393 Chapitre 14 – Interface Web 14.4 394 JOURNAL DES MESSAGES (MESSAGE LOG) Montre l’ensemble des journalisations de chaque événement dans le MultiLoadII. 14.5 W&M CHANGE LOG – JOURNAL DES CHANGEMENTS POIDS ET MESURES Montre toutes les journalisations des Poids et Mesures de chaque modification de paramètre W&M dans le MultiLoadII. 14.6 AUDIT LOG – JOURNAL DES AUDITS Donne toutes les modifications de paramètres du MultiLoadII. Allez sur Audit Log Screen pour des informations complémentaires. Chapitre 14 – Interface Web 14.7 395 FICHIERS SUR LA CARTE SD Vous pouvez voir tous les fichiers de la carte SD à distance. Vous pouvez cliquer sur les fichiers du journal et les ouvrir dans l’interface pour vous penchez sur un problème si nécessaire. 14.8 TÉLÉTRANSFÉRER DES FICHIERS VERS LA CARTE SD Pour télétransférer des fichiers à distance sur le MultiLoad et même pour envoyer le fichier logiciel au dispositif. Chapitre 14 – Interface Web 14.9 396 VISUALISATION DES TRANSACTIONS Vous pouvez visualiser les 10.000 dernières transactions sur l’interface du MultiLoadII. Ouvrir une transaction pour avoir tous les détails du chargement: Chapitre 14 – Interface Web 14.10 PAGE SIMULATEUR La page Internet montre ce qu’il est possible de forcer pour chaque FCM. Dans certains conditions, telles que la quadrature, les ports 2 et 3 seront masqués. Cette page permet de tester n’importe quel scénario à partir de l’overrun (surcharge) pour des permissions qui manqueraient en cours de chargement. 397 Chapitre 14 – Interface Web 398 Chapitre 15 – Assistance MultiLoad CHAPTER 15 15.1 399 ASSISTANCE MULTILOAD APERÇU Le MultiLoad dispose désormais d’une assistance intégrée qui explique chaque paramètre de l’écran MultiLoadII. 15.2 COMMENT L’UTILISER Allez à RCU SETUP -> Parameter Display. Activez ce paramètre. Error! Reference source not found. Cet écran donne la valeur configurée réelle et peut être modifié en appuyant sur ENTER. En outre, cet écran permet de montrer les valeurs minimum, par défaut et maximum. En mettant le paramètre en surbrillance et en appuyant sur ENTER, vous copiez cette valeur dans les valeurs de configuration (config Value). Ci-dessous, une description de l’assistance pour le paramètre. Si l’écran est trop petit, vous pouvez mettre le texte en surbrillance et faire dérouler jusqu’au bas de la description. Chapitre 16 – Historique des révisions du logiciel CHAPTER 16 16.1 HISTORIQUE DES RÉVISIONS DU LOGICIEL VUE D’ENSEMBLE Ce résumé des révisions vous donne un aperçu des différentes versions de logiciels locaux. Certains commentaires peuvent faire référence à des essais internes, des essais en usine ou des routines d’étalonnage, des versions du simulateur qui n’auront pas nécessairement un impact pour les utilisateurs du MultiLoad mais sont considérés comme partie intégrante de l’historique de révision du logiciel. 16.2 CHANGEMENTS APPORTÉS AU LOGICIEL 08/30/06 ML, ML1, SMP 3.26 WJP (released to QA and production) MultiLoad 1 Version 2.26 ported to MultiLoad II platform. Added customer logos. Added Kanji character sets. VGA (RCU) and QVGA (QRCU) support added. Ethernet support added. Support for FCMs with I/O board and 4-20ma functionality added. Added remote firmware upload (up to 16 MB). Added factory tests. 09/08/06 ML, ML1, SMP 3.26 WJP (released to QA and production) Added support for DIP, config(Program Mode) and W&M switches. Hardcoded legacy “all_stop” switch off. Removed legacy “all stop” configuration parameters. Added check to verify that the W&M switch is active before allowing firmware flash update. Changed default value Temp Module type from 0 (FCM 1 RTD) to 1 (FCM II and FCM I Toptech module). 09/12/06 ML, ML1, SMP 3.26 WJP Updated Ethernet default values to 192.168.0.200, 255.255.255.0, 192.168.0.1, 192.168.0.1 for factory tests. 09/18/06 ML, ML1, SMP 3.26 WJP (released to QA and production) Corrected bug in keypad driver that could cause application code to lockup. Increased ml_terminal protocol buffer size from 655 to 2048 characters for processing longer messages. Added ability to upload a new firmware image with various packet sizes. 09/22/06 ML, ML1, SMP 3.26 WJP Corrected font size on Meter Proving Screens for SMP. 11/02/06 ML, ML1, SMP 3.26 WJP Added Factory Menu for use in testing. Added reboot support inside factory test functiona. Added ML, ML1 and SMP product logos and updated display logic to alternate between product logo and customer logo. Set default value logo display to 1st graphic (toptech globe). Fixed bug in Serial Port Test routine to restore the previous port parameter when exiting the test. Added a factory I/O board calibration screen. Updated flash routines to keep interrupts enabled during flash programming. 400 Chapitre 16 – Historique des révisions du logiciel 401 Added additive calibration logic to prevent block valve from opening unless injector is shaired. Added a flush volume reset after calibration to prevent flush alarm. Updated clock setup to show time/date in real time. 11/03/06 ML, ML1, SMP 3.26 WJP Added interface to use 4-20mA input on I/O Board or FCM II for Pressure and Density Inputs. Added screensaver backlight control logic to dim backlight when idle. Added a new parameter, R046-screensaver_seconds with a default value of 10 minutes. Added a new parameter, R047-screensaver_brightness_pct with a default value of 50.00%. 11/06/06 ML, ML1, SMP 3.26 WJP (released to production) 11/17/06 2.27 WJP CAR #226 - Add service to background tasks in close_transaction_header to allow COM and prevent the WDT from causing a reboot while processing transactions with a very large number of details (>100). 11/21/06 2.27 WJP (released) CAR #233 - Force all “unused”/”future use” parameters to zero, and log when a parameter change occurs. CAR #234 - Correct time edit position on the screen. 11/29/06 2.27 WJP (released to measurement canada) (Req. of Measurement Canada) Added vapor pressure to component status display. (Req. of Measurement Canada) Added bay configuration parameter "Canada API Limits" to extend low temps down to -40C on tables 54A, 54B (54BC removed), 54C, 54D. Corrected bug in conversion from 4-20ma to pressure or temperature that caused value to loop around. (Req. of Measurement Canada) Limit 4-20mA pressure input to 0 to 4000 Kpa/PSI, instead of the 9999. Extend pressure offset from +/- 3.00 to +/- 30.00 Kpa/PSI. (Req. of Measurement Canada) Changed the stand alone BOL to include "(Net) volume corrected to Vapour Pressure 15C" instead of "Net values corrected to 15C". (Req. of Measurement Canada) Changed the preset control screen to include "GALLONS volume corrected to 60 F" instead of "GALLONS corrected to 60 F". Fixed bug with uninitialized new_hazidx in ticket printing routine that caused application to halt. 01/05/07 WJP Changed SMP normal fonts from 20 col to 40 col. prompting as well as host driven prompts. This includes all stand alone 01/18/07 WJP Added component_current_temp_hunds, component_current_press_hunds and component_current_density_tenths to real time structure. 01/18/07 3.27.01 WJP Added minor version number to firmware version. xx.yy.zz Updated boot screen to display minor version number and firmware build date. Added UTF-8 terminal support. Updated R000 to include minor version number. Updated ditto register to return utf8 characters if displayed. Extend picklist register to handle UTF8 characters. Chapitre 16 – Historique des révisions du logiciel Added Unicode diagnostic screen to view available CJK characters. Updated firmware version to 3.27.01 02/01/07 3.27.02 WJP Program Mode key switch no longer enables displaying 1/100s vol. Added RCU Setup parameter to enable or disable displaying 1/100s vol. W&M key switch no longer automatically enters proving mode when in stand alone mode. Added RCU parameter to enable or disable automatic proving mode when in stand alone mode. When in proving mode, 1/100s vol are still displayed. Proving mode can be entered when W&M key not active, but parameter changes can not be made. Added component_current_temp_hund, component_current_pressure_hund and component_current_density_tenths options to the MRS command. Corrected bug of unassigned meter variable that caused component status screen to lockup SMP. Display current_temperature instead of batch temperature on component status screen. Updated firmware version to 3.27.02 02/05/07 3.27.03 WJP Moved density sensor configuration from component level to meter level for meter mass calculations. Kept optional default value density at the component level. Any non-zero value overrides value from meter level. Removed "density_error" from component level alarms. Replaced the obsolete "fcm_permissive" with "density_alarm" in the meter level alarms. Removed the unused meter level calculation of "gross_remain_hund". Updated ctl_densitygravity() to return batch_density when no API table selected. Updated the weighted temperature/pressure/density routine to provide more accuracy (less rounding). Slowed down the FCM polling from open loop to 4 polls per second. Updated transaction to always record the density in the transaction. Updated PTB alibi transaction log logic to correctly record symbol for PTB_APPROVED_SPECIFICATION when density_sensor is disabled, OR an overriding density is specified at the component level configuration. Added meter level configuration "pulse_in_mass" to enable the conversion of meter level mass pulses to component level volume. Added MSS command for SMP, similar to the MRS command but only returns 1 component instead of 8, 1 meter instead of 4, and 2 additives instead of 16. Added new query_3 value with bits to return meter level values Meter_Batch_Gross_Del_Whole (Mass) and Meter_Gross_Flow_Rate (Mass Flow). Updated Preset Status Screen to Display Current Temperature/Pressure/Density when flowing and Batch Temperature/Pressure/Density when stopped. Updated Component Status Screen to Display Current Temperature/Pressure/Density when flowing or zero delivered and Batch Temperature/Pressure/Density when stopped. Included Component Status Screen on the Next/Prev Screen Loop. Removed pressing # on Component Screen to enter Component Status Screen. (In prep for keyless program alarm clearing) Added Mass Section to the Component Status Screen showing Target, Delivered and Rate when Pulses In Mass is configured. Updated Component Status Screen to always show Temperature/Pressure/Density. Moved Unicode Display from Factory Menu to Diagnostic Menu. Updated firmware version to 3.27.03. Updated database version to 3.27.03 for RCU Setup Database, Real Time Database, and Equipment Database. 402 Chapitre 16 – Historique des révisions du logiciel Updated Makefile to build qml and qml1 images for use with QVGA displays. 03/02/07 3.27.04 WJP Added multilingual support all DRIVER and program mode screens (except meter calibration screens and MAC address configuration screen). Added "DRIVER Language", R008, and "Program Mode Language", R009, RCU level parameters to select the language. Added the format type of 21 of "Language" type (0=English, 1=Spanish). Configuration parameter lengths have been increased from 20 to 30 characters. All levels of configuration screens are wider now to accommodate forign languages. Configuration prompts will be returned in the language specified by "Program Mode Language" parameter. Configuration parameters descriptions, ranges and default values, as well as status and key prompts have been moved into ROM. Updates to language prompt registers u000-099, u101xxx, u102xxx, u103xxx, u104xxx no longer supported. Removed all configurable prompt registers, 700xxx, except ones used by TMS for overseas customers (70000x-70004x, 70007x, 70019x, 70020x, 70028x, 70035x). Removed 701(status) and 705(additive status) label registers. Removed 720(key prompt) label registers. Alarm Label registers (R7100xx-R7140xx) will return the alarms in the language specified by "Program Mode Language". Alarm Labels registers (U7100xx-U7140xx) will only update the labels on permissives (U711001-711008, U712001, U712001, U713001, U714001). API tables 23E 'a', 59E 'b' have been added to support correction to 20C. Moved integer front end of API table 24E to a separate routine to allow 23E and 59E to access the 24E floating point calculations without rounding. Corrected Table 24E start point. Correction did not effect 24E calculations. API tables can now return corrected_relative_density and corrected_density. Default value configurable prompts are now disabled. Preset status and component status formatting has changed to accommodate forign languages. Updated W&M change log to trace parameter index, and not memory index to parameter, to handle ROM placement of parameters. Updated firmware version to 3.27.04. Updated database version to 3.27.04 for RCU Setup Database, Real Time Database, and Equipment Database and W&M Log & Totalizer Database. 03/02/07 3.27.05 WJP (released to QA for testing) Marked parameters not releavent to the SMP builds to be NA. All NA parameters are reset to the default value value on bootup. A message is logged when this occurs. Updated code so that writes to NA registers returns an invalid parameter code. Added "W&M Key FCM#" and "Program Key FCM#" as RCU level parameters for external connection of W&M and program switches. Status of these inputs are ORed with internal inputs/DIP switches and can be viewed on the RCU Diagnostic screen. Incorporated final review of all Spanish Translations. Added MultiLingual Product Graphic capability with English and Spanish versions for the ML II, ML II 1-Arm, MultiLoad II SMP graphics. Corrected SMP bug when the program key was not active and the Load Screen Timeout occurs, the screen would stop updating and keypad would stop functioning until a end transaction signal was received. Updated firmware version to 3.27.05. Updated database version to 3.27.05 for Equipment Database. Per PEMEX, Calculation of CTL from Table 59E is calculated as CTL = Measured_Density / Corrected Density from API Table 59E. 403 Chapitre 16 – Historique des révisions du logiciel 03/23/07 3.27.06 WJP (released to QA for testing) Corrected bug in transaction archive not recording the ending time. Corrected design in transaction archive that omitted storing the year in the date. Removed unused datestr and timestr from RCU Setup Database. Removed unused Report Time, Detailed Report, and Auto Report from RCU Setup Parameters. Marked the Preset Select Timeout RCU Setup Parameter as NA on SMP builds. Fixed bug where all RCU level NA parameters were logged as being reset to default values on every startup. Added debug precompiler directive label LOG_TERMINAL_CLEAN to assist with capturing screen shots for manuals. Corrected bug that prevented the polling of the program and W&M switch when system marked as not configured. Corrected bug that caused corruption of preset batch temp/pressure/density values. Updated firmware version to 3.27.06. Updated database version to 3.27.06 for RCU Setup Database. 03/27/07 3.27.07 WJP (released to Pemex) Bug in 3.27.00-3.27.06 firmware checked Version instead of Product ID on firmware uploads. Added dummy version strings to firmware image to allow uploading by 3.27.00-2.27.06 firmware. Updated firmware version to 3.27.07. 04/05/07 3.27.08 WJP (released) Fixed bug in custom logic port selection screen where "Select..." was displayed instead of "Port #x" in picklist. Updated firmware version to 3.27.08. 06/27/07 3.28.01 WJP (released to QA) Per Measurement Canada changed Side Stream Blend Logic as: Back calculation of main product stream component temperature is no longer done. Blend meter temperature/pressure/density is passed back to the main product stream component level. Blend meter temperature/pressure/density is passed up to preset level and side stream temperature/pressure/density is not passed up to prset level Blend meter volume is passed up to preset values and side stream volume is not passed up to the preset values. API table listed for the main product stream is applied to the gross blend meter volume and is passed up to preset values level CR - Offloading Air Eliminator High flow control functionality. Added two new parameters "Alt. High Flow Rate" and "Alt. H.F. Rate FCM#" to change to an alternate high flow rate when a status input changes. This change is intended for single product delivery without blend. Updated real time database version to 3.28.01. Updated firmware version to 3.28.01. 07/18/07 3.28.02 WJP (released to Measurement Canada) (Req. of Measurement Canada) Updated Ticket to include an "*" by any values not measured for trade. Updated default value stand alone ticket definitions to properly format ticket with "*"s. Added preset and component status bit to indicate when "gross value measured for trade". For Preset, when "gross value measured for trade" is not set, Temperature, Pressure, Density, and Gross volume may not be used for trade. Net volume may only 404 Chapitre 16 – Historique des révisions du logiciel be used for trade when MultiLoad is applying an API table to convert gross to net for all components. For Component, when "gross value measured for trade" is not set, Temperature, Pressure, Density, Gross volume and Net volume may not be used for trade. Updated firmware version to 3.28.02 (bug, still at 3.28.01). 07/23/07 3.28.02 (bug, still at 3.28.01) WJP (released to QA) Corrected placement of Measured for Trade Flag in Transaction Database. Updated transaction database version to 3.28.02. 08/06/07 3.28.02 WJP (released to QA) Corrected firmware version from 3.28.01 to 3.28.02. 08/07/07 3.28.02 WJP (released to QA) Corrected the retrieval of Gravity, Rel. Density, and Exp. Coeff at the preset values in MRS and transaction archive to use component with most volume delivered (value not directly measured and not valid for trade, no averaging done). 08/14/07 3.28.03 WJP (released to QA) Updated dates to support 4 digit years per CR xxxx. Since hardware clock only supports two digit years, any year outside the range 2005-2099 will be displayed as zeros (0000). Printed tickets, Alibi Log, and Clock Setup Screens updated to display 4 digits. Updated transaction archive database version to 3.28.03. Updated firmware version to 3.28.03. 08/20/07 3.28.03 WJP (released to TTE) Updated "MM/DD/YY Date:" parameter name. 10/16/07 3.28.04 GLP (released to QA) Corrected bug in network socket RX task that did not close connection after a timeout. Explicit close from server is often not sent. Updated firmware version to 3.28.04. 11/02/07 3.28.05 WJP (released to QA) Incorporated the Portuguese Language. Updated firmware version to 3.28.05. 11/26/07 3.28.05 WJP (released to QA) Replaced "No" with "#" in Portuguese Language. Added the ability to send serial messages from ethernet ports through the serial ports (Term Server). Added communication type 5=Etherenet Passthrough Port to Register 091-093. Added communication type "Ethernet" to the Communcation Setup Screen. Added listing the COM0, COM1 and COM2 socket ports on the Network Setup Screen. Removed checking on startup for the configuration of a host communication port. Updated firmware version to 3.28.05. 11/27/07 3.28.06 GLP Implemented alphanumeric data entry capability for the EXL keyboard. Updated firmware version to 3.28.06. 01/09/08 3.28.07 WJP Updated firmware version to 3.28.07. Increased latest FCM version number from 17 to 34 for FCM II release. Large Prompts parameter was added to the RCU setup. Updated large prompt logic to only control prompts. ECO2007-058 405 Chapitre 16 – Historique des révisions du logiciel Increased the number of components in SMP builds from 1 to 8 to support multiple meter factors for ECO2007-58. Number of Components parameter added back into SMP builds. ECO2008-001 Moved all flow rate parameters out of W&M control, except meter min and max flow rates. TMS can change these values when a batch is not authorized. Preset - Low Flow Rate Preset - High Flow Rate Preset - Alt. High Flow Rate Component - High Flow Rate Component - 1st Stage Trip Vol Component - 1st Stage Flow Rate Component - 2nd Stage Trip Vol Component - 2nd Stage Flow Rate ECO2008-002 Added ability to lock down additive calibration data and recipe percentage under W&M protection. New parameters added. Additive - W&M Recipe Percentage Additive - W&M Additive Vol/Inject Additive - W&M Vol/Inject Cal Factr Additive - W&M Additive Mtr K-Factr Additive - W&M Additive Mtr Factor ECO2008-003 Added the ability to connect an Alibi Log to a Serial Port. Added a communication port type of Alibi Log. RTS and DTS are always driven active. Data will only be transmitted when DCD, DSR and CTS signals are active. If DCD, DSR or CTS remain inactive for 5 seconds or more, a printer alarm will be raised. Printer must be in hardware handshake mode, DTR used for pacing. Also added printer flow control and alarming to ticket printing. ECO2008-004 Added interface to allow TMS to display other preset volumes, seperate from ML values on the load screen. Values will be maintained in a different color to clearly establish them as “not legally relevant” and should not be used for trade. Added new bay parameter "Number External Presets" to specify how many external presets should be displayed. All external presets are displayed in a different color with a message indicating "Not Legal for Trade". Added R/U401 register to update displayed external preset data. When an external preset is selected, the MultiLoad state will go to a 'a'-'h' matching the preset number. MAMppp - can be sent by the host to return to the load screen when done driving the screen. ECO2008-007 Added ability to reprint any ticket or range of tickets from the transaction archive. A serial port must be configured as connected to a printer. When viewing the header of a transaction in Views & Inquiry -> Transactions a footer prompt of "1=Print Transaction" now appears instructing how to print the transaction. After viewing two different transactions, a footer prompt of "2=Print Transactions xxxx-yyyy" now appears instructing how to print the selected range of transactions. Transactions that have been printed before, will be marked as Duplicates on the ticket. (W&M requirement) 406 Chapitre 16 – Historique des révisions du logiciel 407 Note: Per ECO2008-003, hardware handshake and alarming has also been added. (W&M requirement). This will require that customers properly wire the DTR and other handshake signals to the RCU or a printer alarm will be raised and prevent loading. 01/26/08 3.28.07 WJP (sent to QA for testing) Corrected bug that caused meter level alarms not to clear when leaving factory calibration/analog calibration menu. 01/29/08 3.28.07 WJP (sent to QA for testing) Corrected bug that caused unknown RTD value on powerups and other errors. 03/13/08 2.28.07 WJP Corrected bug to properly handle and return negative API gravity. Updated transaction retrival, MRS, and ticket printing. 03/17/08 3.28.08 WJP Corrected network RX task to properly handle abnormal socket terminations from WINSOCK that return -1 from the socket read(). Bug caused SMP/ML to lockup when a WINSOCK host application abnormally terminated. Added ml_fcm2_tester binary output and functions to perform all digital and analog FCM2 testing and calibration. Corrected display of 6 digit integers on the configuration screens (min/max preset value). Added ability to use Temperature Module Type 3 to use 4-20mA on I/O Board or FCM II Analog Board for Temperature Input. Updated firmware version to 3.28.08. 03/19/08 3.28.08 WJP (QA approved and released) Added Toptech 4-20mA status status line on the V&I -> View Temperature screen. 04/04/08 3.28.09 WJP (Beta Release to D.H. to solve field blend issue) Corrected signed/unsigned compares in ml_fcm_config.c causing blend to race out of tolerance and alarm. 04/16/08 3.28.09 WJP (37 bit prox cards) Updated card reader code to support HID 37 bit H10320 formatted cards (facility code = 0). 05/07/08 3.28.09 WJP Added Decal and Terquimsa customer logos for TTE. 06/03/08 3.28.09 WJP Corrected bug in limit checking 1st and 2nd trip flow rates that allowed negative target rates to ramp up flow beyond excess rate. Corrected bug in computing lower BD rate that caused valve to "hunt" when lower limit went negative. 06/22/08 3.28.10 WJP Added customer supplied TransMontaigne2 logo. Corrected bug in reading IP address information on the serial port. Moved the Date & Time setup from the W&M Menu to the Configuration Menu. are still logged in the W&M change log. Updated FCM 2 tester code to use fast polling. Updated FCM 2 tester code to display DC power output status. Updated firmware version to 3.28.10. Changes Chapitre 16 – Historique des révisions du logiciel 06/26/08 3.28.10 WJP Fixed bug that caused the output pulse configuration to incorrectly reserve port 1 (on IO boards should be port 10) and raise a configuration alarm when anything else was assigned to the port. Since output pulse can be on port 1 (fcm) or 10 (io board), and it is not known what board is attached do not report output pulse assignment conflicts. 07/17/08 3.28.10 WJP Added ml_gps.c to build to support GPS opérations. To support the building of a linux ML simulator task, Updated Makefile to build a linux ml_sim executable. SIMULATE precompiler definition will be used to enable simulation code. SIMULATE will exclude MAC address viewing and modification. SIMULATE will include a driver to display the virtual display on the screen. SIMULATE will include FEXIT command to save NVRAM and terminate application. SIMULATE will include command line switches to supporting enabling the terminal display, keypad, device address and device socket port. 07/28/08 3.28.11 WJP (released to Measurement Canada) Updated firmware version to 3.28.11. 08/27/08 3.28.12 WJP (released to G.R.) Correct bug in U133 that prevented access to FCM ports over 7. Corrected bug in uploadable logo size on SMP that prevented uploading new customer logos. Updated firmware version to 3.28.12. 09/5/08 3.28.12 WJP Updated makefile to build new MultiLoad II Mobile application. Added new "MultiLoad II Mobile" product identification graphic. R000 will respond with "MultiLoad Mobl" to identify MultiLoad II Mobile product. The following are specific only to the MultiLoad II Mobile product. Added GPS sélection in Communication Setup display. Setup default value serial configuration to have GPS on COM1 and Printer on COM2. Added GPS Diagnostic screen under the Diagnostics Menu. Added GPS Site Database to store up to 4,000 site names with Lat/Log position. Added GPS Site Setup screen under the Configuration Menu. Added new RCU level parameter "Max GPS Site Distance". The current position must be within this number of meters of a site in the GPS Site Database. If this number is zero, location verification is not performed. Added new "*GPS Err" alarm. Alarm raised when no GPS fix data arrives for 60 seconds. Also raised when a transaction is authorized and the authorization position is not at a site in the GPS Site Database or the current position has moved from the site where authorization was obtained. Updated logic to place Site Name, Latitude and Longitude information into the last three transaction prompt champs. Updated duplicate ticket message will appear on left margin for small ticket size. Setup default value ticket configuration for a small ticket size with Site, Latitude, and Longitude information. Updated idle screen to display Latitude, Longitude, Speed, Heading, and Site Name. 408 Chapitre 16 – Historique des révisions du logiciel Updated Transaction Archive Header Screen to display entire length of 4 prompts to show Lat and Long infomration. Added new meter level parameters "Density Alarm Time" and "Pressure Alarm Time" to provide a time that the value must be out of spec before raising the alarm. Same logic as the "Temperature Alarm Time" parameter. Updated density calculations to handle values larger then 1200.0. Expanded range from 1200.0 to 9999.9 for Meter Level Default value Density, Density Alarm High, and Density Alarm Low. Expanded range from 1200.0 to 9999.9 for Component Level Default value Density. Expanded range from 1200.0 to 4000.0 for Meter Level Density @ 4mA and Density @ 20mA. Updated RCU Setup Database version to 3.28.12. Updated Real Time Database version to 3.28.12. Added PetroPlus Logo for TTE. Updated firmware version to 3.28.12. 09/5/08 3.28.12 WJP Added support for MultiClass PIV-200 card reader to read TWIC cards returning the card FASC-N. Updated card reader logic to support TWIC card reads. Added W&M_CLEAR alarm level that only allow clearing of alarm when W&M switch is active. Added wm_clear_errors bit to bay, preset, component, meter and additive status (MRS command). Added promotion_count, promoted alarm level, and alarm_count_reset_mode to the alarm configuration. When an alarm occurs promotion_count number of times, the alarm level is changed to the promoted alarm level. When the alarm_count_reset_mode condition is met, the alarm count is reset and the alarm is returned to the base alarm level. Reset modes can be on transaction authorization, successful alarm clearing, or a delay of time from minutes to days of up system time. Power cycling a system will restart the time required to return an alarm to the base level. Attempts to set non-autoclearable alarms to autoclear will result in the alarm being set to driver clearable (ie. low_flow alarm). Added new configuration format type, ALARM_COUNT_RESET_MODE. Updated Alarm Configuration Registers 710-714 to support new parameters, but still accept updates in the old format. On U710-714 attempts to set non-autoclearable alarms to autoclear will result in the alarm being set to DRIVER clearable (ie. low_flow alarm). Added alarm count to "alarm raised" log message when promotion count is configured. Added Additive W&M controlled parameters "W&M Inj Flt Promo Count" and "W&M Inj Flt Reset Mode" to override registers for alarm promotion to WM_CLEAR on particular additives. Added W&M logging to alarm level changes when old or new alarm levels are WM_CLEAR. Updated Configuration->Alarm, to support the new Alarm Configurations. Updated Views->W&M Change Log, to display the new Alarm Configuration Changes. Updated R912 W&M Change Log to support new W&M Alarm Configuraiton Changes. Removed legacy R030,U030-Card Length Register. Removed legacy R031,U031-Card Offset Register. Increased size of R962-Card Data from 40 characters to 80. 409 Chapitre 16 – Historique des révisions du logiciel Updated Diagnostics->Card Reader to report new Card Data Format Error. The following are specific only to the MultiLoad II Mobile product. Added R/U650 to support reading or writing the GPS database. Added R140 to support reading the current Latitude/Longitude position. Added R141 to support reading the current load Latitude/Longitude/Site Index. Increased transaction count from 200 to 900 transactions and increased the transaction detail count from 1750 to 3500. Added new additive W&M comfigurations R/U104054-W&M Inj Flt Promo Count and R/U104055-W&M Inj Flt Reset Mode to add W&M promotions to particular additives. Updated Equipment Configuration Database version to 3.28.12. Moved placement of NVRAM6 Alibi Log to after NVRAM3. Updated init code to verify no overlap between NVRAM structures. 09/17/08 3.28.12 WJP Updated R071-074, Network Address Configurations, to be left justified. Corrected Alarm log messages to indicate Alarm Count. Added log message to indicate when Alarm Count is cleared. Updated Set Factory Default values to also reset GPS site Database. Corrected data formatting on Access IDs and Alarm Setup screens. Added "W&M Access Denied" message on Alarms Setup screens. Corrected formatting on R140 and R114, GPS data register. Corrected formatting on R650, GPS Site Database register. Left justified alarm name in R710-R714. 10/31/08 2.28.12 WJP (Released) Added buffer clear to prevent old message data from bring processed with new incomplete commands. Installed default value company name from ML Mobile small format ticket. 10/01/08 3.28.13 WJP Removed legacy FCM trace logging. Problem with prompt display on view transaction header Added code to increase the number of supported fcm ports from x to 39 ports. Added code to increase the number of supported fcm pulse output ports from 1 to 6 ports. Removed bay.output_pulse_enabled parameter. Changed bay.output_pulse_fcm_number to output_pulse_fcm_address to include port. Changed bay.output_pulses_per_volume to output_pulses_per_volume_thous with 3 implied decimal places to deliver less then one pulse per unit. Removed preset.output_pulse_enabled parameter. Changed preset.output_pulse_fcm_number to output_pulse_fcm_address to include port. Changed preset.output_pulses_per_volume to output_pulses_per_volume_thous with 3 implied decimal places to deliver less then one pulse per unit. Added pulse output to the bay diagnostics screen. Updated R133/U133 to support up to 39 ports. Removed unused disp_bstat structure from real_time_database. Increased latest known FCM version to 036. Per Measurement Canada, whole number totals on ticket must always add up. Updated Preset and Load whole unit totals to sum component whole totals, and not fractional parts, per Measurement Canada Requirement. Updated Component side stream back calculation to difference whole totals, and not fractional parts, per Measurement Canada Requirement. 410 Chapitre 16 – Historique des révisions du logiciel Added "*" on ticket total line to indicate if totals are or are not a sum of fortrade preset values, per Measurement Canada Requirement. Updated RCU Setup Database version to 3.28.13. Updated Real Time Database version to 3.28.13. Updated Equipment Configuration Database version to 3.28.13. Updated firmware version to 3.28.13. 10/25/08 3.28.13 WJP Introduced beta MODBUS register interface. 11/12/08 3.28_13 WJP Updated Card Reader Logic to support 26-bit, Corporate 1000 formatted cards. Corporate 1000 reads are returned to the Host system as 0=%04u=00000=%08u=01. Added ability to build a stand alone serial Opto-Iso II tester firmware build. Corrected bug with MRCA Request Component Alarms command returning invalid data. Was using indicated component as preset index. Updated FCM II factory tests to be event based instead of time based to increase reliability and speed of test. Updated FCM II factory tests to support AC expander and Relay expander boards. 12/05/08 3.28_13 WJP Released full MODBUS protocol and register interface as described in the MultiLoad Communication Manual. Updated card reader logic to only accept TWIC card reads if two consecutive reads indicate only one card is in the reader. Updated card reader logic to force a card out for approx 2 seconds when TWIC cards are swapped. Add logic to keep current card during power cycle. 12/08/08 3.28_13 WJP (Released to QA) 12/19/08 3.28.13 WJP (Special Build, on ML Moble Units) Corrected Pulse Output Port Logic to also accept port 10 on Ver<036 FCMs and I/O Boards. Added back in logic to check fcm port assignment conflicts on Pulse Output Ports. Increased GPS Site Database to 22,000 sites. Added Default value Site List to MLM for Special Build Updated GPS site search to break up search processing over several calls. Corrected Database Overlap Checking startup logic. Updated simulation startup usage to display keymapping and notes. 12/30/08 3.28.14 WJP (released to QA for testing) Bug Fix: In certain side stream configurations and conditions (explained below), the MultiLoad firmware did not correctly calculate one or more Component Net volumes. "For Trade" Values and Calculations (Niveau des valeurs prédéfinies Gross and Net volumes) were not effected. Only "Not for Trade" or "For Inventory Only" Values and Calculations (Component Level Net volumes) were effected. Problem limited to the previous version of firmware 3.29.11-3.29.13. Problem limited to configurations where more then one main component shared the same side stream component. For instance, Reg and Prem components sharing a ethanol side stream. Problem limited to recipes that included flowing both of these main components sequentially in the same blend. For instance, Reg flow with Ethanol side stream, followed by Prem flow with Ethanol side stream. Problem limited to the calculation of the Net Component volumes calculated for any main components with a common side stream that flow after the first main 411 Chapitre 16 – Historique des révisions du logiciel component with the common side stream in the blend. For instance, the Premium component in the previous exemple. Main Component Net volume error on effected components would always be an understatement in the amount of side stream net volume that flowed during the previous main components with the common side stream. Corrected placement of "*" when performing a sequential or ratio blend with a side stream. Updated application of API VCF and meter calibration to perform rounded calculations. Updated firmware version to 3.28.14 1/13/08 3.28.16 WJP (released to QA for testing) Corrected placment of "*" on additive net on printed ticket. Corrected titles on factory Optical Isolator Test. Updated firmware version to 3.28.16 1/22/09 3.28.16 WJP (released to Measurement Canada for testing) Added Meter Net/Gross to Component Status Screen. Added Transaction Detail Record for Component Meter (Per Measurement Canada Requirement). Updated transaction database and transaction printing to support type 4 details. Changed transacction database version to 3.28.16. Kept firmware version the same since 3.28.16 was not released to production or outside Toptech. 1/28/09 3.28.16 WJP Added Analog Test/No Cal function to FCM 2 Factory Test. 1/30/09 3.28.16 WJP (Released) Corrected bug in reading Modbus register 4180 (Preset Batch Rate). On FCM II Factory Calibration function, increased threshold on missed COM messages to avoid restarting calibration over again when FCM updates internal EEPROM after a successful calibration. 3/4/09 3.28.17 WJP (released) Corrected bug in TEC and TEC-ETH API tables where temp/10 was being delivered to the calculation. Corrected bug in TEC and TEC-ETH API tables where temp > ref_temp, calculation would always produce grossly invalid value. Added Preset Configuration Parameter "Stop Start Delay" to prevent stop and start within x time to eliminate concern with Rogue Smith Pulsers. Set parameter to 45 seconds to prevent Rogue Smith Pulsers from activating alternate operating mode Do not raise an alarm, just start flow after delay expires. Log message when driver attempts to start flow within this time pour later analysis/tracking. Updated Real Time Database version to 3.28.17. Updated firmware version to 3.28.17. 2/26/09 3.29.01 WJP Updated PetroPlus logo per customer supplied graphic. To support dynamic Configuration Parameters that may change from general to W&M controlled parameters, all W&M parameterrs have been moved into general areas and the W&M Menu has been removed. All W&M controlled parameters are now displayed in red and are still protected from modification via the external W&M switch. Screens include RCU Setup, Bay Setup, Preset Setup, Component Setup, Additive Setup, Additive Calibration, Meter 412 Chapitre 16 – Historique des révisions du logiciel Proving, View Temperature, View Density, View Pressure, Temperature Comp, Pressure Comp. Alarm Setup Updated PickList routines to support attributed (color sélection) of items in the list. Moved all W&M Equipment Configurations back under Equipment Configurations. Moved Temperature, Pressure and Density Calibration functions to the Temperature, Pressure and Density View Screens. Moved Temperature Comp and Pressure Comp screens from the W&M Menu to the View and Inquiry Menu. Updated Alarm setup screen to display Alarm configurations under W&M control as Red and restrict saving changes with W&M switch active. Added new configuration parameter level of CONDITIONAL to indicate parameters that can be switched into or out of W&M control. Added Preset Configuration Parameter "W&M Controlled" that adds W&M write protection via screen and remote register access (inc. Modbus) to certain parameters. Changed level of "Blnd Chk Alarm %", "Blnd Chk Alarm Vol", "Blnd Chk Alarm Time" to CONDITIONAL. Added Additive Configuration Parameter "W&M Controlled" that adds W&M write protection via screen and remote access to certain parameters. Changed level of "Additive Vol/Inject", "Vol/Inject Cal Factor", "Additive Mtr K-Factr", "Additive Mtr Factor", "Max Pstn Missed Inj", "Under Add Alrm # Inj", "Over Add Alrm # Inj", "Check Add Tol Time", "Over Inj Vol" level to CONDITIONAL. Removed Additive Configuration Parameters "W&M Vol per Inject", "W&M Vol factor", "W&M Pulses per vol", "W&M Pulse Factor" since no longer needed. Added Component Configuration Parameter "W&M Recipe Percentage" to enforce delivery. Corrected Meter Proving Screen Meter Factor data entry data column alignment. Updated Equipment Configuration Database version to 3.29.01. Added printer multidrop capability to Ticket Printing. Added printer multidrop capability to Alibi Log Printing. Added ability to multi-drop several MultiLoads on to a single printer using RS232 on COM2. Connections must be as follows: ML#1 ML#n Serial Printer RX<-------------RX<--------------------TX CTS<------------CTS<-------------------DTR TX------------->TX-------------------->RX GND-------------GND--------------------GND DSR-DTR DSR-DTR RTS-CTS-DSR RTS-DCD<------->RTS-DCD DCD Added more discrete control of the Transmitter Enable to support having multiple MultiLoads connected to a single printer. Dropped monitoring of DSR or DCD for printer status. CTS indicates printer status. Added Meter Configuration Parameters "Adaptive Valve Control", "Analog Valve Control", "4-20mA Increase Step", "4-20mA Decrease Step" to support analog valve control. Allow ports 2 & 3 to be used as general IO when Analog Valve control is enabled. Increased latest known FCM version to 037. On FCM_TESTER and ISO_TESTER build, allow entry into factory menu. Updated FCM2 Analog Calibration to ignore COM timeouts when setting calibration values during test. Was causing test to sometimes restart when FCM was writing to EPROM and not communicating. Updated FCM2 Analog RTD/mA Calibration to perform 3 tests then stop. 413 Chapitre 16 – Historique des révisions du logiciel Updated FCM2 Analog RTD/mA Check to perform 1 test then stop. Added Legacy ACR test to Factory Menu. Expanded Configuration Prompts Register, r100-104, to return a max of 90 bytes and a default value of 30 bytes (instead of 20 bytes) to support UTF-8 worst case. Increased size of Alarm Names storage to handle UTF-8 characters. Expanded Alarm Configuration Registers, R/U710-714, to return 30, instead of 10 bytes to support UTF-8 worst case. Expanded Modbus Alarm Configuration Registers, 2500-2599, to return 15, instead of 10 bytes to support UTF-8. Updated Alarm Setup Screen to properly display UTF-8 strings. Updated RCU Setup Database version to 3.29.01. Added W&M logging of firmware updates by monitoring the current firmware type, version and build date on startup (Canada & US W&M req.). Added W&M logging of when any database is reset to factory default values. Expanded W&M Log Register, R912, to support Firmware Updates and Factory Default value events. Updated View W&M Log to support Firmware Updates and Factory Default value events. Updated start_clock() to immediately poll RTC for current date/time at startup to prevent W&M and Relevé des activitéss from reporting 00/00/00 00:00:00. Updated W&M Log and Totalizer Database version to 3.29.01. Added lcd_driver code to read the LCD device ID from display color lines. Binary set of 10K pull down resistors on Blue color lines identify LCD display model connected. 0x0000 = 8.4 VGA with limited 50-100% on backlight dimming, no pull down resistors on color lines. 0x0001 = 8.4 VGA with full 0-100% on backlight dimming, 10K Pull Down on Display Board Blue 1 (LSB) color line. Corrected bug in Output Pulse Port processing where specification of port 10 would not send pulses to IO board. Workaround was previously to specify port 1 for port 10 on IO boards. Removed qml, qml1, qmlm targets from the Makefile build script. Updated firmware version to 3.29.01. 4/6/09 3.29.01 WJP (released for testing) Corrected alarm count to allow up to promo count alarm clears before promoting to new level on next alarm. Previously promoted on promo count alarm occurance. Moved Blend Check Start Vol and Blend Check Restart Vol under Conditional W&M control. Corrected U600 register to correctly parse both 0, 8 and 16 lockout bits on stand along card database. 8/5/09 3.29.02 WJP Correct bug in card reader code that prevented correct identification of some corporate 1000 HID cards. Updated simulation display terminal code to display utf-8 unicode and text foreground/background colors. Added "Toptech Product ID French" graphic screens. Added "Total Oil" and various other customer logo graphic screens. Replaced "Toptech Global Solutions" with "Toptech Systems" graphic screen. Updated "MultiLoad" (English, Spanish, French) product ID graphic screens. 414 Chapitre 16 – Historique des révisions du logiciel Updated code to bring in product ID graphics as raw files in /rcutlc4/bmp directory instead of compiled C const structs. Updated U/R 990 and 991 registers to work with new .raw file method. Removed ml1 (MultiLoad 1-Arm) target from the Makefile build script. Updated ML package firmware to contain 1-Arm product id string to allow legacy 1Arm firmware to upgrade to this and later full MultiLoad versions. Updated simulation get_ticks() to not log warnings about non-monotonic system timer jitter on Lunux. Updated simulation to work with backspace key for clear. Corrected bug in Diagnostic Display Unicode where rolling backwards would attempt to display code point 0xffffffff. Updated firmware version from 2.29.01 to 3.29.02. Updated product recipe register to support 6 additives. Updated Modbus 2200..2271 interface to support 6 additives in a recipe. Updated R/U500 to support 4 and 6 additives in a recipe. Added French language prompts. Include Additive Under_add and Over_add alarms under conditional W&M control. Renamed additive cofig parameters "wm_inj_fault_promo_count/reset_mode" as "wm_alarm_promo_count/reset_mode". Added logic to handle alarm promotion and clearing for Under_add and Over Add alarms. Changed "Max Solenoid Injection Time" from General to Conditional W&M control. Added support to store up to 10,000 transactions. Updated Transaction Archive Database version to 3.29.02. Moved transaction storage from NVRAM to last 10 MB of program flash memory. Max storage size based on 10,000 transactions, 20 details per transaction and max clear block size at program startup. Tickets numbers are 1-9999 inclusive. Removed sidx from header record, and hidx from detail record. Updated FBOL (find first transaction for a specified date) to work with large transaction database. Updated factory default values to clear all transactions and transaction flash blocks. Will loose COM during operation. To greatly reduce possibility of a missed COM message while erasing a flash block, added support on reboot to verify at least 256K of flash transaction storage is available. Added powerup text when unlocking transaction flash blocks to explain new powerup delay. Added "TRACE_ARCHIVE" ifdef to allow logging of storage actions and locations for debugging. Setup AUTOLOAD when tracing archive to load one 10-15 gal preset for each transaction to quickly load the entire transaction archive (30-40 Hrs). Updated modbus 7810..7916 interface to read expanded transaction archive. Updated R800 to read expanded transaction archive. Added ability to send dual output pulse. For dual pulse, FCM_2 or IO_BOARD version must be 38 or greater. Indicate use of dual pulse by turning on invert flag on output FCM port configuration parameter. Second pulse will always be on the next port, 0/1, 1/2, 2/3, 3/4, 4/5, 10/11, 11/12 Note: Single Output Limited to 500 Hz, Dual Pulse Output Limited to 250 Hz. Note: As before, output pulses are not real time and delayed approx. 1 second. Added logic to only allow resetting to factory default values when W&M key active and on a powerup. ML Simulator Updates: Updated simulation to display log messages to console. Added exit code to restore proper terminal functionality when closing the program. 415 Chapitre 16 – Historique des révisions du logiciel Added digital control valve state into meter_trace as 0=close, 50=lock, 100=open. Corrected bug in 1-Arm and SMP products where preset level alarms could not be manually cleared from preset control and preset status screens. In FCM2_TESTER build, added I/O board digital output, digital input, analog cal, and analog test functions. Updated FCM 2 Analog Tester to correctly exit RTD calibration mode. Updated "4-20mA Input" to more descriptive "Observed 4-20mA". Display yellow background on parameters changed from the default value on RCU, Bay, Preset, Component, Meter and Additive configuration screens. Added "Id:X" to R912 W&M Log Register to include an Id with each W&M change logged by TMS. Updated R912 register to contain the ID of person that performed that change. Updated View W&M log to have the ability to print a W&M log. Added new terminal esc sequences for: Added <esc>G command to set Foreground/Background text colors Updated <esc>J and <esc>K to clear to EOL and EOS with color and size attributes. Added <esc>d command to Draw Customer Logo Added <esc>e command to Draw Graphics Bitmap Added <esc>g command to Fill Graphics Box with Color Corrected API Table TEC-ETH to correctly apply TEC values. Was off by *10 on the application of the TEC. Corrected spelling of Component in the W&M change log. Corrected TTE reported bug in Modbus 7000 register not resetting HOSTUP timer. Corrected new bug that prevented printing tickets after a load. Corrected new bug that caused line to not increment when printing details. Corrected bug sending a UTF8 character instead of extended ascii to the ticket printer. 10/30/09 3.29.02 WJP Corrected bug in ticket printing where line-feed character was not printing after each line. Corrected communications ports wrong factory default values. Corrected bug in display type checking. Caused some legacy displays to dim too much with the screen saver enabled. Added ability autodetect display type and support QVGA. SMP will default to QVGA for unknown displays. ML will default to VGA for unknown displays. Added identification of display id #0000 for legacy 8.4" displays. Corrected bug that prevented alibi log printing on multidropped configurations. 11/02/09 3.29.02 WJP (released to QA) 11/11/09 3.29.02 WJP Added card reader ability into SMP firmware, but defaults to disabled. 11/16/09 3.29.02 WJP Added ability in view transaction archive details to display batches that have the alarm flag set in red. Added Batch_Alarm preset status bit (on MRS command) to latch any preset alarm to be reported on transactions. 11/20/09 3.29.03 WJP Updated SMP graphic to high resolution version. To support adding back in card reader for SMP Div 2, also added back in Prox Card Pull Secs and No Prox Pull If Flow parameters. Corrected bug that prevented dual pulse output from working on port 2/3. 416 Chapitre 16 – Historique des révisions du logiciel Updated preset, meter and component totalizers to accept and view volume in whole units or hundredths. Updated backflow totalizer logic to capture 100s without dropping percision across whole numbers. Added new W&M RCU Setup parameter "Use Hundredths", R030, to enable display, recording, and totalizing in hundredths. Added support to transaction archive and alibi log for viewing or printing whole units or hundredths. Updated Transaction Detail view screen to display whole units or hundredths. Corrected ticket printing of leading zeros on temperature, pressure and density. Updated Serial and Modbus interface for totalizers, transaction archive to return implied two decimal places when the "Use Hundredths" parameter (R030) is enabled. Updated firmware version to 3.29.03. 12/14/09 3.29.04 WJP Added API tables 60o and 901A for TTE. Updated firmware version to 3.29.04. 12/15/09 3.29.05 WJP (merge with atmel development) Updated firmware version to 3.29.05 12/16/09 3.29.04 WJP Correct remote picklist processing to setup default colors when picklist is written. Bug caused picklist items to appear with black foreground and black background when host displayed a picklist. Problem would only occur between powerup and first time entering program mode. Once program mode was entered, picklist would display correctly. Picklist would always appear on RCU ditto even when displayed items were black. 2/23/10 3.29.06 WJP (Beta Release to Sam Yu) In MAC address setup, allow specification of most resent IEEE assigned MAC address block. Include NanoSleep() call in linux simulator build to prevent idle task starvation. Updated firmware version to 3.29.06 Added Chinese language to product. Started adding eMail support. Todo: add registers for email settings. Increased configuration prompt string from 30 to 45 bytes (max 30 ASCII characters or 15 UTF-8 characters 3-byte each). Increased language prompt string from 40 to 60 bytes (max 40 ASCII characters or 20 UTF-8 characters 3-byte each). Added HTTP server. Added, for now, engligh product graphics for portuguese and chinese. 4/14/10 Added conoco Farmington density alarm timeout modification for air in line. Only time timeout when not in alarm and authorized to allow time for correct density to be read. 4/30/10 3.29.06 WJP (ILTA Demo) ILTA Mass Meter Demo Code Updated Krohne meter diagnostics to include more registers. Update FCM control logic to deal with mass meter flow with on/off valve for demo. 5/5/10 3.29.20 WJP (release to QA) Merge of parallel development streams back into one!!! Added Mardarin language. 417 Chapitre 16 – Historique des révisions du logiciel Changed all variable flags from char to int to improve efficiency. Changed all string usage of "unsigned char" to "char" for compiler compatability. Started email functionality development. Updated serial routines to use integer instead of character configuration parameters. Added web server functionality. Added routines to get and set ethernet MAC address for new and old processor. Added ML_Mass build for demo of Krohne meter at ILTA. Density alarm, 4-20mA values outside 4-20 are to be treated as an error and density set to zero. Added time delay on density alarms. Added code to support uploading new firmware on new processor. Added ablity to support 3 host connections at the same time. Corrected simulation build processor utilization bug by adding nanosleep call. Changed firmware version to 3.29.20. Changed all database versions (except NR3-W&M & Totalizers) to 3.29.20. 5/17/10 3.29.20 WJP (release to QA) Added Factory Test function to verify the installation of OptoFCMs firmware in FCM I and FCM II. 5/18/10 WJP Rev 9.26.20 Corrected web display of W&M Log and Event Log. Increased latest known FCM version to 038. 5/21/10 WJP Rev 9.26.20 Corrected bug that prevented multidropped alibi log printing from releasing the control line. 6/7/10 WJP No Changes 7/26/10 WJP Added W&M protected parameter to enable FCM simulation for demo and debug purposes. "Simulation Mode" is displayed on loading screen Updated all logo code to use .c const struct inclusion in place of binary files for bitmaps. Minor changes to remove Keil compiler warnings messages. Currected bug in standalong card processing when searching for 2nd occurance of the same card number with a different PIN. Moved AT91SAM9G45 modbus code to use PXA255 super-switch. Corrected modbus extended services command execution bug where command execution would occur at the completion of any write to the ESR, not just at the write of the last register. ESR changed from unsigned char to char to eliminate compiler warning. Added start_alt_high_flow_rate and end_alt_high_flow_rate parameters to delay entry into and exit from alt high flow for use with the LC bubble detector. Added preset Permissive Alarm Time parameter to delay the occurance of a Permissive Alarm for use with the LC bubble detector. Added additive Upstream Block Valve parameter to allow the automatic opening of the additive block valve during additive calibration. Added logic to allow the delivery of a single side stream component for meter calibration while in proving mode. Added logic to mark side stream component as complete when main meter is complete to prevent side stream from running on when main stream stops. 9/10/10 WJP 418 Chapitre 16 – Historique des révisions du logiciel Continued debugging of Atmel routines for Card Reader, Real Time Clock, Flash Memory, LCD Driver, Serial Ports, Network. No impact to existing PXA255 code. Rewrite and simplify ExL Alphanumeric Entry code. Updated software ID to be different for PXA255 vs Atmel builds to prevent upload image swap. Added start of hardware watchdog timer at startup. Updated software major number for new platform builds. Disabled much of the email WIP code. 9/17/10 WJP Added ability to accept analog flow meter inputs. Added signed_div1000 and meter_input_type to configuration parameter types. Changed "Pulse in Mass" meter configuration parameter to "Meter Type". Added several "Analog Meter Input" parameters for @4mA Rate, @20mA Rate, Rate Offset, and Cutoff Rate. When Meter Type is Volume Analog Input, ports 4 and 5 can be used for other functions. Updated meter diagnostic screen to display Input mA. Corrected Mandarin LOW FLOW and HIGH FLOW text. Increased latest known FCM version to 039. Added R/U998 to read/update bitmap cache data area (16MB 0x00000000-0x00ffffff). Added T`hrcwhoooooooo command to display graphics from the cached bitmap data area. Changed firmware version to 3.29.21. Changed equipment database version to 3.29.21. 10/7/10 WJP Added a blue screen exception handler that will display the type of fault, address of fault and all register values. 12/9/10 3/4.30.00 WJP Switched to eCos RTOS for Atmel processor (same OS as xScale uses). Removed all references to IAR and Keil compilers and RTOS. Added Atmel Exception Handler Blue Screen. Added CN GPS tracking demo code. Added 200 gps position log. Added compiler switches for GPS_SITE_DATABASE and GPS_POSITION_LOG. Replaced Modem Sign On configuration parameter with Host Sign On. (Language Conversions needed) Added TDS 3PO interface routines. In process: Adding Krohne and Micromotion functionality Removed ILTA Mass Meter demo code. Added Mass Meter Real Time Status Registers. Added VOLUME_KROHNE(3) and VOLUME_MICROMOTION(4) to meter type enumeration. Added MASS MTR to the Communication Setup port type. Added Mass Meter Diagnostics to Meter Diagnostic Screen. Corrected bug where the input of UNSIGNED_DIV1000 formatted parameters accepted the selection of a sign. Removed workaround to force state to idle when powerup and a transaction is completing. Addws SD Card Functions. Added SD Card selection to the Views and Inquiries Menu. Changed firmware version to 3/4.30.00. Changed real time database version to 3.30.00. 12/20/10 3/4.30.00 WJP 419 Chapitre 16 – Historique des révisions du logiciel Added new Calculations for Shell Canada and Measurement Canada V18. For Side Stream Calculations: When a default density value is supplied or measured at the meter level, this density value is accepted as the meter density and is applied to API calculations on the received meter volumes. When a default density value is not supplied or measured at the meter level, a blend weighted density is calculated from the component densities and is accepted as the meter density and is applied to API calculations on the received meter volumes. When a default density value is supplied at the component level, this density value is accepted as the component density. When a default density value is not supplied at the component level, a back calculated density is calculated and is accepted as the component density. Meter sampled temperature continues to be used for the API calculation on the received meter volumes. The meter temperature/density can still be viewed on the Component Status Screen next to the calculated CTL/CPL values. The meter temperature/density, gross and calculated net volumes still appear on the meter line of the printed ticket. Main component temperature is once again back calculated to keep back end accounting systems happy. The component temperature/density, gross and net volumes appear on the component line of the printed ticket and are marked not for custody transfer. A host system that queries for real time component level values will be supplied with the same component temperature/density, gross and net volumes that appear on the component line of the printed ticket. A host system that queries for real time component meter level values will be supplied with the meter temperature/density, gross and net volumes that appear on the meter line of the printed ticket. A host system that queries for the transaction archive information will be supplied with all same meter and component information that is on the printed ticket. Setup Component and Meter Temperature/Pressure/Density real time component data. Setup Component and Meter Gravity/Density get routines. API routines always use Meter Temperature/Pressure/Density from the real time component data. Transaction Component Data always contains component Temperature/Pressure/Density from the real time component data. Transaction Meter Data always contains meter Temperature/Pressure/Density from the real time meter data. MRS command component data returns component Temperature/Pressure/Density from the real time component data. Modbus 4756..5331 register, contains component Temperature/Pressure/Density from the real time component data. Component Meter Screen displays the meter Temperature/Pressure/Density from the real time component data. Renamed RCU parameter "Print Blend Components" to "Print Blend Details". When set to 2, all meter records will be archived and printed. 1/5/10 3/4.30.00 WJP On Simulation builds, send transaction to display. Move NR3 by 0x1000 bytes to prevent overlap. Updated MRS and MSS commands to support configuration bits to return meter level parameters. Added meter level pressure/temperature/density to the component status screen. Followup: Check meter detail print logic on ml_main:2050. Followup: Add Modbus registers for meter level gross/net/temp/press/density. 420 Chapitre 16 – Historique des révisions du logiciel 2/3/11 WJP Transacton archive lockup issue resolved. After a card out on 3.29.xx firmware, there was a slight possibility of the following issues occurring: - Lockup on preset screen while displaying a status of clearing on one or more arms. - Lockup on transaction complete screen. - Real time clock updates stop. - Loss of serial or Ethernet communication. - Loss of keypad operation. Upon power cycle after the issue: - Lockup on preset screen display with status as blank or clearing on one or more arms. - Lockup on blank white screen. - Real time clock stuck at 00/00/00 00:00:00. - Factory defaults were required to regain control. - Multiple power cycle operations to regain real time clock operations. Root Cause: - Operating System flash routines were flushing and disabling the CPU cache with both the scheduler and interrupts enabled. - If a task switch or interrupt occurred while flushing the cache, but before disabling the cache, DRAM memory updates were lost. - When this occurred, one of more tasks would stop running, the system could lock up or the system state would become invalid. Solution: - Disable CPU cache in the MMU at startup for the flash memory area. - Use application flash routines that do not modify CPU cache states. - Added check for all presets complete to end transaction in case previous end transaction was interrupted. - Remove background processing in end transaction routine to prevent recursion with previous change. Build now links with pxa255-rcu-lib-romram-net-11 with cache disabled on flash address space. Use application flash routines for firmware and transaction updates. (Verify firmware update functionality) For PXA255, Flash block unlock routine checks lock status before unlocking flash blocks. Transaction archive blocks are left unlocked. Corrected issue with reading transaction details on the Modbus interface. Restored ability to remotely modify time without an active W&M switch (changes are W&M logged) Updated copyright date. 2/8/11 WJP Increased the number of allowable additives in a recipe from 6 to 12. Changed firmware version to 3/4.31.00. Realigned all NVRAM structures for new fields (totalizers will not be preserved from previous versions) Changed all NVRAM DBASE versions to 3.31.00. Added ability to place compartment number on standalone ticket. Added column position to R203 command. (MultiMate update needed) Adjusted default ticket to display compartment number and also have room for totalizer widths. Added remote clear input to clear batch on external input. (No Flow, No Alarm, Load Complete) remote_clear bit added to preset status. Added new Preset configuration parameter, "Remote Clear FCM#". 421 Chapitre 16 – Historique des révisions du logiciel Added ability to read a live relative density. Density error will be reported for a density or relative density error. Added new Meter configuration parameters to support live Relative Density input: "Relative Density Sensor Enabled" "Relative Density Sensor FCM#" "Default Relative Density" "Alarm Low Relative Density" "Alarm High Relative Density" "Relative Density Alarm Time" "Relative Density at 4mA" "Relative Density at 20mA" "Relative Density Offset" Added new Component configuration parameter, "Default Relative Density". Relative Density weighting calculations are the same as Density Calculations. Added ability for API functions to use live Relative Density. Added ability to read component current relative density in MRS command. Added ability to read component meter current relative density in MRS command. Updated preset and component status screens to display relative density. Added ability to read component current relative density from Modbus register 6292 ... 6483. View Relative Density Screen (modify offset) added to Views and Inquiries. Updated API table setup screen to handle test Relative Densities. Corrected bug where if entry into program mode followed PIN input, caused "***" to appear when entering numbers in program mode. Updated view transaction to display density instead of pressure. Updated view transaction to display totalizers stored in transactions. Updated view transaction to display no net, temperature or density for additives. Removed dates and line number from message log display to increase the display from 57 to 71 characters. Added ability to include ending totalizers in a transactions. Added new configuration format type TOTALIZER_SELECTION=25. (MultiMate update needed) Added new RCU configuration parameter, "Print Totalizers" to select what totalizers (PMCA) should be included in a transaction and alibi log. Increased the max number of Transaction Details from 99 to 999. Added optional extension to R800 register to support reading details over 99. Added blank line between each preset totalizer groups printed on ticket. Added new Preset configuration parameter, "Default Preset" to automatically enter a preset quantity. Updated preset prompt routine to skip preset if default preset is specified. Added new Meter configuration parameter, "Meter Address" to specify the Modbus address of a serially connected mass meter. Added new W&M Component configuration parameter, "API Extrapolated Range" to allow the use of API tables in the extrapolated ranges. Updated proving mode to always use proving low flow rate and proving low flow volume. Corrected bug in Preset Net Totalizer not correctly showing preset net volume with side stream. Component 1 Net was also impacted, but transaction volumes were not affected. For meter creep on an unauthorized batch, preset product code is now "CREEP " instead of "000000" (first product). Product description on ticket displayed at "MeterCreep". Updated ticket printing routine to print product code from transaction and not the currently loaded product list. Updated set clock routines and serial interface to return an error when values are out of range. Increased range of low flow alarm time from 65.535 seconds to 999.999 seconds. 422 Chapitre 16 – Historique des révisions du logiciel Added new Preset configuration parameter, "Auto Batch Authorize" to support auto batch authorizations when product and volume are already specified and program key off in standalone mode. 2/10/11 WJP (release) Added BP Customer Logo. 2/21/11 WJP (release to QA) Updated 4449 inspection mode to directly access W&M change log (bypassing views & inquery menu). Corrected bug with density and relative input density format in the Temp Comp screen. 2/24/11 WJP (release to QA) For AT91SAM9G45 flash, added ability to properly handle top boot flash (first 100 boards shipped). May cause later transactions not to be written to flash. Correct bug in handling NO_TRANSACTION state after firmware upgrade causing a blank screen on first startup. Corrected bug where if back calculating density or relative density for a main component of a side stream, logic was only looking at the side stream meter density. Logic now also checks side stream component density. Added safety check for max number of transaction details on loops. 4/8/11 WJP Rev 3/4.31.01 WJP (release) Updated vsprintf() calls to handle null return strings. Corrected DMA buffer alignment issue on Atmel CPU boards that caused some serial messages to be corrupted and old messages to be reprocessed a second time. Updated Diagnostic Serial Port Test to also perform full duplex tests. Changed firmware version to 3/4.31.01. 5/4/11 WJP Rev 3/4.31.02 WJP Added Preset level configuration parameter "Compute Blend Density". When meter level density is not defined and component level density is defined, if Compute Blend Density is enabled, the meter density is computed by a volume weighted average of the component densities. if Compute Blend Density is not enabled, then meter density is taken from the main component density. Changed firmware version to 3/4.31.02. 6/2/11 WJP Corrected bug in Component Net Totalizer. On side stream blends it was possible that the side stream volume would clear before the main component cleared. This would cause the component totalizer to bump up by the side stream amount. This bug did not impact any volumes reported on the transaction. 6/27/11 WJP To prevent a false API_TABLE alarm when side stream flow is ahead of main product stream, only call API calculation when component batch_gross_del_hund_signed > 0. 6/2/11 WJP Added Analog Valve 4-20mA output controls to Meter Diagnostics screen. 7/1/11 WJP Added hardware toggle of COM 2 DTR and RTS signals on startup with TX enabled to sync outputs and inputs with optical isolator. 7/5/11 WJP 423 Chapitre 16 – Historique des révisions du logiciel Added clear of API table alarm when exiting the program mode - temp comp screen. 7/5/11 WJP (release) Corrected Web RCU Ditto processing of the stop key. 7/19/11 WJP Added Preset, Component and Additive product names to the alibi log. 7/19/11 WJP Added new configuration W&M protection type of CONDITIONAL_DENSITY. Added new configuration parameter "W&M Density Lock", that will conditionally move default density, default relative density and API gravity parameters under W&M protection. 7/26/11 MSH For CN Builds, added truck_no, carrier_id, tds_retry_interval, seller_id, consignee parameters. No register access. For CN Builds, added comments, is_manual_bol, transaction_id and cosignee to transaction archive header. TDS access only. No register or print access. 7/28/11 WJP Added Boot Screen and R000 extension to identify custom built firmware. 8/9/11 WJP Corrected "ReprintTicket" prompt to only reprint ticket on Next keypress, not Enter keypress. 8/23/11 WJP Added clear of entire nvram DB blocks to avoid config problems when switching between build types. Added check for struct size exceeding block size. Added start and end dates to transaction headers for use with TDS records. Updated Transaction Archive database version. Updated GPS, GPS_SITE_DATABASE and GPS_POSITION_LOG compiler switches. 8/24/11 WJP Added TDS_INTERFACE precompiler switch for selective inclusion. Updated support for CONFAR_BUILD and CN_BUILD precompiler switches. Removed MULTILOAD_MOBILE_BUILD precompiler switch and logos. Increased SOFTWARE_BUILD_ID size from 15 to 25 characters (R000 and boot screen display). For CONFAR_BUILDs, added LAT,LONG and WELL NAME to TDS transaction comments. 8/24/11 WJP Bumped position log from 200 records to 500 records. Increased GPS database block size from 512K to 1M. Cleaned up GPS data on Idle Screen to allow for GPS_SITE_DATABASE and GPS_POSITION_LOG at the same time. 8/24/11 WJP Clean up RCU Setup Screen for selective inclusion of TDS_INTERFACE prameters. 8/26/11 WJP Added automatic selection of Conoco Logo on CONFAR builds. 9/9/11 WJP 424 Chapitre 16 – Historique des révisions du logiciel Correct display of Load Volume on the Main Preset Screen to display Hundredsths if Use_Hundredths is enabled. Added printing of Average Load Temperature if the Load Totals are displayed directly under the transaction details (tot_gpos=99 and tot_glin=99). 9/9/11 MSH Added support for two-meter I/O board automated test rig. Changed prompting sequence to use Driver Language setting in RCU Setup rather than language bit in card database. 10/3/11 MSH Added vehicle ID as prompted in transload to truck scenario to transaction sent to TDS. Added "BOL Prefix" configurable to RCU General Setup for CN builds. Prefix is user adjustable and is prepended to ticket number when sent to TDS. 10/4/11 WJP Added ASTM1240-2004 tables. Added the following configuration types: COMMODITY_TYPE = 28, EXP_COEF_UOM_TYPE = 29, DENSITY_UOM_TYPE = 30, PRESSURE_UOM_TYPE = 31 With the following assignments: #define COMMODITY_TYPE_NONE 0 #define COMMODITY_TYPE_CRUDE 1 #define COMMODITY_TYPE_REFINE 2 #define COMMODITY_TYPE_LUBRIC 3 #define EXP_COEF_UOM_TYPE_FAHRENHEIT 1 #define EXP_COEF_UOM_TYPE_DEGREES 2 #define DENSITY_UOM_TYPE_KG 1 #define DENSITY_UOM_TYPE_API 2 #define DENSITY_UOM_TYPE_REL 3 #define PRESSURE_UOM_TYPE_PSIG 1 #define PRESSURE_UOM_TYPE_KPA 2 #define PRESSURE_UOM_TYPE_BAR 3 Added the following W&M Component configuration parameters: commodity_type; /* 103048 */ \ exp_coef_uom; /* 103049 */ \ density_uom; /* 103050 */ \ pressure_uom; /* 103051 */ \ reference_temp; /* 103052 */ \ Added ability to selectively display these parameters on the Temp Comp screen. Updated Makefile to include: ml_api_2004_5.c ml_api_2004_6.c Added the ASTM 2004 table types. Changed equipment database version to 3.30.03. Added long table name for display. Increased CTL table count from 21 to 48. Added ability to display and use 5 decimal place VCFs. Component Status Screen 4 and 5 digit CTLs. Increased API table name size on the API Table Setup Screens TODO: Need to update USE flags for 2004 tables. TODO: Need to return correct density types for transaction. TODO: Need to retest all 2004 tables. TODO: Need to address CTPL values. 425 Chapitre 16 – Historique des révisions du logiciel 10/14/11 MSH Added option to SD card menu to dump diagnostic data to SD, including contents of NVRAM and flash transaction archive. Fixed improper BOL number when packing transactions. Changed order of operations in TDS task, so that any pending transactions will be sent first. 10/17/11 MSH Filter tankcar list by terminal ID. Sort Vendor BOLs by BOL number. 10/17/11 WJP Added new configuration parameter (U075) of http_port to allow using alternate ports or complete disabling (http_port = 0) the http service. This value defaults to 80 (enabled). On simulation firmware builds, http port is stilll +1000 of the specified host port. Updated CTL Setup screen to correctly display needed parameters for 2004 tables. Updated logic to return density, rel density, gravity, etc. when no table is selected. Limited "Local Databases" on Diagnostics to only CN builds. 10/20/11 WJP Updated 2004 tables to only include needed parameters. 10/21/11 MSH Changed TDS task to only reset the task if in an idle/error state. 10/21/11 WJP Added new 2004 api "X" tables. 10/25/11 WJP Removed legacy touch I/O from Makefile. More debugging on 2004 API tables. Corrected format of Density/Rel Density/Exp Coeff/API Gravity on stand alone tickets and in the transaction viewer. Removed compartment from the transaction viewer. 10/28/11 WJP More updates for API tables. Replaced CTL and CPL with VCF on screens. Replaced CTL and CPL table configuration with VCF table configuration. Replaced Temp Comp and Press Comp setup screens with API Table setup screen. Moved 11.2.2M to API table 54. Moved 11.2.2 to API table 24e. CPL calculation done when pressure is not zero. Added 2004 11.2.1 and 2004 11.2.1M tables. 10/31/11 WJP Added Expansion Coefficient and VCF to transaction details. Added printing expansion coefficient and VCF to alibi log. Added new alibi log label for VCF (U706018). Added ticket exp_coeff_pos and vcf_pos (U203) for printing these values on the printed ticket (defaults to not printing). Added sign to the Gravity Display on the alibi log and transaction detail screen. Added display of Corrected Gravity to Meter Status Screen, API Diagnostic Screen. Correct display of Expansion Coefficient in alibi log. 426 Chapitre 16 – Historique des révisions du logiciel 427 11/3/11 WJP Add format checking to all printf and scanf type application functions. 11/3/11 WJP Added densitygravity_type and corrected_densitygravity_type to the transaction detail for proper formatting of the densitygravity value. Update sprintfexp() to return number of characters written to string. 11/4/11 MSH Added Thai translations. 11/7/11 MSH Fixed TDS routines to close connection when our local databases are full. should keep the records queued on TDS. This 11/9/11 WJP Added transaction detail detail screen to view all transaction detail details. 11/10/11 MSH Added local database browser for CN builds. Located under Program mode\Diagnostics\Local Databases. Increased size of local database for vendor BOL storage on CN builds. Changed size of database for vendor storage per suggestions from PM. New values are 1400 vendor BOLs, 20 vendors. Still 75Klocomotives. 11/15/11 WJP In API TABLE_2004_53A, the corrected density is now properly reported. The parameter name "API Table Name" was shortened to simply "API Table" to allow room to display whole 25 character table name. Updated all API TABLE_2004_??X tables to report the configured reference temperature. Updated all API TABLE_2004 to limit message logging unless in api table setup screen. On transaction viewer: Corrected displayed density index to start at 1. Corrected displayed preset, component, meter and additive index to start at 1. Only display temp and pressure on preset, component and meter details. Updated "Dens" field name to "D/G/RD" Corrected previous page opeartions on detail picklist display. Changed firmware version to 3/4.31.04. 11/18/11 MSH Added new bay level alarm to CN/CONFAR builds, "DB ERROR" which will be set when the local database is full. 11/16/11 WJP Increased min/default/max preset range from 999,999 to 9,999,999. Updated default ticket layouts to handle 7 characters for gross and net values. Updated alibi log to handle 7 characters for gross and net values. Added preset name to alibi log (NMI Req). Updated configuration output routines to display 7 characters on UNSIGNED_INT and ZP_UNSIGNED_INT types. Updated transaction detail screen, and transaction detail details screen to handle 7 characters for gross and net values. Corrected alignment issues and ####### overflow indication on additive volume. Check against xpos values that could cause lockups on ticket printing of invalid ticket configurations. Chapitre 16 – Historique des révisions du logiciel 11/28/11 WJP Corrected recently introduced bug in computing a VCF from the CTP and CPL for 1980s tables. 11/29/11 WJP Added API Tables 54AG, 54BG, 54CG, and 54DG; 12/17/11 WJP When reading a configuration from an SD Card, any rejected commands are added to the message log. 12/21/11 MSH Add Vendor Term ID to Transloading operations. 01/03/12 MSH Merge fix from 3/4.31.01 branch Fix issue where printing tickets longer than 60 lines cause the firmware to crash. Added range checking to ticket configuration paraemters (R200-R206). Increased bspool buffer from 60 lines to 120 lines (2 pages). Added safe bspool write routines to prevent writing outside bspool area. Added 1 extra line for safety in case any items on the last line wrap to the next line. 01/04/12 WJP Added PTB Alibi Log Capability Added PTB Alibi Log Port to Serial Port Selections Com port type updated with the followig assignments: 6 = ALIBI LOG TEXT PORT 7 = MASS METER PORT 8 = GPS PORT (not selectable on screen without GPS capability) 9 = ALIBI LOG PTB PORT PTB Alibi Log port also checks handshake lines on COM2. Multidrop supported on COM2 RS232 connections. Will poll PTB printer every 15 seconds and report a printer error if no response from PTB printer. 1/12/12 WJP Removed degree symbol from AlibiLog output. Corrected PTB Alibi Log multidrop functionality. Added two pad characters for PTB Alibi Log output. 1/17/12 WJP Added ability to inject additive using an analog valve/pump using a PID loop control. Added additive PID loop variables to the bstat struct. Added logging of PID values when Additive Trace is enabled in RCU Setup. Replaced Piston Injector Used parameter with Additive Type enumeration with the following assignments: ADDITIVE_TYPE_SOLENOID_WITH_METER 0 ADDITIVE_TYPE_PISTON_WITH_NORM_FEEDBACK 1 ADDITIVE_TYPE_PISTON_WITH_INV_FEEDBACK 2 ADDITIVE_TYPE_PISTON_WITH_NO_FEEDBACK 3 ADDITIVE_TYPE_ANALOG_VALVE_WITH_METER 4 Removed Pulse Input Used, Piston Input Used, and Feedback Stats Inverted parameters. Added Additive PID P Factor, I Time, and D Time parameters. Updated Additive Diagnostics to support new injector type. 428 Chapitre 16 – Historique des révisions du logiciel Updated Meter Diagnostics new Analog Output logic. Updated Additive FCM Configuration routines to support new additive type. Need to retest all additive types, injecting, diagnostics and calibrations. Updated analog valve output logic to support additive analog valve. Need to retest meter diagnostic screen with analog valve output. Need to add check for misconfiguration of Analog Valves or Additive Analog Valves attempting to use the same 4-20mA output. 01/19/12 WJP Updated the terminal text command, Esc K (Clear EOL) and esc (Clear EOS) to use the current character attributes unless one is specified using the esc G command. 01/22/12 WJP Added new configuration parameter type, API_PRODUCT_TABLE_NAME_TYPE. API_PRODUCT_TABLE_NO_PRODUCT 0 API_PRODUCT_TABLE_PROPAN 1 API_PRODUCT_TABLE_PROPYLEN 2 API_PRODUCT_TABLE_BUTAN 3 API_PRODUCT_TABLE_ISOBUTAN 4 API_PRODUCT_TABLE_ISOBUTEN 5 API_PRODUCT_TABLE_CISBUT2EN 6 API_PRODUCT_TABLE_TRANSBUT2EN 7 API_PRODUCT_TABLE_BUT1EN 8 API_PRODUCT_TABLE_BUTA13DIEN 9 API_PRODUCT_TABLE_METHANOL 10 API_PRODUCT_TABLE_ETHANOL 11 API_PRODUCT_TABLE_ISOPROPANOL 12 API_PRODUCT_TABLE_ISOBUTANOL 13 API_PRODUCT_TABLE_MTBE 14 API_PRODUCT_TABLE_TAME 15 API_PRODUCT_TABLE_BENZOL 16 API_PRODUCT_TABLE_TOLUOL 17 API_PRODUCT_TABLE_OXYLOL 18 API_PRODUCT_TABLE_MXYLOL 19 API_PRODUCT_TABLE_PXYLOL 20 Added new component configuration parameter API X Products. Added API tables 54XG and 54YG. 01/27/12 WJP Changed API_PRODUCT_TABLE_NAME_TYPE to API_54YG_PRODUCT_TYPE. Changed api_product_table_name to api_54yg_product. Renamed configruation parameter "API X PRODUCTS" to "API 54YG Product". Added API tables: TABLE_TEC_ETH_US = 'G', TABLE_TEC_ETH_B100 = 200, TABLE_TEC_ETH_B40 = 201, TABLE_TEC_ETH_E40 = 202, TABLE_TEC_ETH_E100 = 203 Removed tec_eth() function. Updated tec() function to accept base temp and expansion coefficient. Updated TEC_ETH_xxx calls to use updated tec() function and handle both C and F temperature units. Corrected value placement bug in ticket where gross position was used for the net value position for placing the measurement character. Added api_54yg_product to api setup screen. For tables that support both Def F and Deg C (TEC and Ethanol), added logic to correctly display the correct units and the reference temperature selected. 429 Chapitre 16 – Historique des révisions du logiciel 02/15/12 WJP Corrected FCM analog additive simulation. Corrected API 54XG table implementation before release. Corrected analog additive 4-20mA output scaling and log messages. Updated software copyright year. Corrected scaling and update bug in meter and additive analog output diagnostic screens. 02/21/12 WJP Updated the following API table defs for integration with new TMS5 bay code. TABLE_54CG = 'K', TABLE_54XG = 'L', TABLE_54YG = 'O', 02/21/12 WJP Increased Message Log from 100 to 750 messages. For non-PXA255 builds, added ability to save 90 days of message log files to the SD Card. Each day will be saved into a seperate file in the root directory. Attempts to save to the SD Card will be aborted after 5 consective failed attempts to save to the SD Card. On startup or after a reboot, Savnig to teh SD card will resume. For UAP or CN builds, added ability to send message log lines to TDS. Added internal reference number to all log messages. 02/22/12 WJP Updated transaction processing to store any authorized component or additive in transaction, even if flow volume is zero. Corrected recent bug with additive normal piston switch feedback, incorrectly configuring the FCM version 14 or greater for inverted piston switch input. On R910 message log register, max two digit counter to 99 for values over two digits. 02/24/12 WJP Now storing the target additive volume in the net field of the additive transaction detail record. Updated the view transaction archive screen to display the additive target and delivered volume. Updated the view transaction archive screen to display the currently configured VCF table for each component. 2/28/12 WJP Added additive target volume and percent deviation to Alibi Log output. 3/3/12 WJP Added log file cleanup and resync when writes to the SD Card are interrupted (power cycle). TODO: Delete oldest log file when freespace is limited. TODO: Develop design on time zones on time sync updates from TDS. 3/6/12 MSH Added support in web server for download of files from SD card. Added logging of user input/selections during prompting sequence. CN builds: Added download of CN specific databases, including locomotives, vendors, vendor BOLs, and drivers. 3/18/12 WJP For UAP Builds, increase BOL max lines from 80 to 4 pages (66*4). 430 Chapitre 16 – Historique des révisions du logiciel For SIMULATION builds, added \r to diagnostic output for new cygwin terminal. Corrected minor compiler warnings. For UAP Builds, added LUA script processing for multipage BOL generation. 4/9/12 MSH Added archiving of Lua chunks to flash along with transaction in UAP builds. Changed logic of TDS thread to allow processing of lower priority tasks even if higher priority tasks fail. 4/13/12 Added Modem init string to General Setup screen. UAP development: Replaced Modem Init String and Modem Dial String with Terminal ID and Bay ID. (Modem parameters to be dropped when UAP included in all ML Builds) Replaced meter_type field with disabled on the preset table. Added supplier number to UAP terminal_profile and preset_authorized_products tables. Added processing of UAP disabled fields in Bay, Meter and Preset tables. Added handeling of compartment required fields on Bay and TerminalProfile tables.. Added LUA parsing of bay_id and term(inal)_id configuration parameters into LUA. Added lookup and error handling for terminal_profile and bay table records. Updated UAP product authorizations to use terminal supplier number. Updated LUA goto, find and product authorization logging. Added logic to exclude saleable products from preset authorized products is the base components or additives are not present on the additive. Added logic to abort LUA processing when a LUA script error occurs. 4/21/12 WJP UAP Development: Updated simulation build of network_get_mac_address() to get MAC address of host PC. Removed Terminal ID and Bay ID from configuration and from prompt script startup variables. Added LUA mac_address startup variable. Changed prompt script to look for the Bay record by using the device IP adderess. Added device address to the "Bay not Found" MessageDenied. Added tds_client to Driver find. Curreted bug where no pin required, would skip Driver validation. Added tds_client and term_id to Carrier picklist and find. Renamed PromptVehicle to PromptTruck. Added tds_client to Truck find. Added tds_client to Trailer find. Added ability to find on five fields. Correct bug in find routines where search would be aborted if first record was greater than search record. 4/23/12 MSH Beta release to QA UAP Development: Add support for card reader when in UAP mode. Added ability to clear records in individual/all databases. Updated transaction payload for communication with TDS. BOL reprint logic added to prompting sequence. 4/25/12 MSH Fix issue where ML would hang/reboot in multidrop and miswired/not connected. 431 Chapitre 16 – Historique des révisions du logiciel 5/8/12 WJP Corrected bug where loss of only the RX line from an FCM will prevent flow termination and droping of all outputs after 6 seconds. Updated FCM, PCM and Krohne Mass Meter polling logic to wait 8 seconds before retrying after lost communications. This will ensure that any FCM flowing product or with outputs on will stop flow and drop all outputs. 5/10/12 WJP Removed CTS check on PTB Alibi Log Printers. 5/15/12 MSH CN builds: Addressed ISS_2045 "Vehicle not archived with transaction" which affected transload to truck operations 5/16/12 WJP Added RCU configuration parameter Trace UAP Level (0=minimal logging, 1=, 2=, 3=, 4=inc low level logic, 5=inc low level com). Added low level logging to the UAP product authorization processing. 5/16/12 WJP Added Disabled field to UAP TDSClientProducts struct (to be removed again). Fixed issue where UAP local database edits did not mark DB as dirty. Corrected null error issue with UAP AuthorizeTransaction() when using Prox Cards. Bug with UAP Update Saleable Products where Prod ID was checked as Prod Type. Added UAP Preset Authorized Products functionalty to include all saleable and base products when no records are present in the PAP table. 5/17/12 WJP Removed Disabled field from UAP TDSClientProducts struct. 5/18/12 WJP Updated UAP processing of TDSClientProducts component percent field to contain a decimal point in 000.0000 format. 6/1/12 WJP Updated UAP processing of UAP meter_type field to use P(Product) and A(Additive) instead of C(Component) and A(Additive). Updated UAP processing of UAP prod_type field to use 1(Product) and 2,3,4(Additive) instead of C(Component), A(Additive) and S(Saleable). 06/11/12 WJP Added seperate monitoring per port of non_toptech_host connections. 06/29/12 MSH UAP - Updated base product process to use comp_add_id rather than meter_id when assigning products/components to meters. 07/03/12 MSH Added two new passwords: 4448 to jump to the view totalizers menu (for transmontagne), and 4447 to jump to the view transactions screen (for CN). 07/05/12 WJP Added prototypes to ml_pm_view.h to remove compiler warnings. Corrected var naming of uap_comp_add_id. Corrected additive volume in uap transaction record to include three decimal places. 432 Chapitre 16 – Historique des révisions du logiciel 07/09/12 MSH Version number increased to 3/4.31.06 in anticipation of release. 07/10/12 MSH Revert changes to authorization process relating to Meter table. Remove comp_add_id from Meter table. 07/24/12 MSH Revert changes made to PWM value for display ID 0x02. Add new display ID 0x03 for MultiLoad Mobile display. Add setting for max brightness (register 80). 7/27/2012 WJP Update MRS gross and net volumes (excluding preset volume whole), to return volumes in hunds when use_hunds configuration parameter is set. 8/15/2012 WJP Added compiler switch in ml_functions.c to Record or Playback keypresses for demos and automated testing. 8/21/2012 WJP Added SD CARD menu to simulation builds. Fix possible NULL pointer when saving configuration to the SD card. Added compiler switch to supply demo or simple UAP test data when clearing local database. 8/21/2012 WJP Added compiler switch to include UAP Enterprise BOL. 8/21/2012 WJP Updated Ticket prompting script to display the ticket prompt number, 1..10. Updated Ticket prompting script to verify ticket number is a valid number and greater than 0. 8/21/2012 WJP Updated Ticket prompting script to verify ticket number is not negative. 8/23/2012 WJP Replaced Mandarin with Simplified Chinese and added Traditional Chinese. 8/24/2012 WJP Appended Bay Number to Preset Number on Alibi Log per Germany requirement. 8/26/2012 WJP Updated the functionality on the Message log and W&M Log web pages. Corrected bug that prevented the Next/Prev page buttons on the bottom of the page from working on some web browsers. Buttons shifting around made it difficult to quickly page thru. Updated logic to keep all buttons visible. Added First and Last buttons to quickly move to the first or last page. Added 25, 50, 100 buttons to allow displaying more records per page. Increased default number of lines shown from 15 to 25. Added Transaction Log Summary Page Same functionality and feel as the Message Log and W&M Log pages, including the same buttons and starting on the last page to view the most recent transaction. Clicking on a transaction will drive to the detail screen for that transaction. Added LUA Data to transaction detail (for UAP) to show all additional record data also stored with transaction. 433 Chapitre 16 – Historique des révisions du logiciel 434 Added Next and Prev buttons to the transaction detail screen to step into other transaction without returning to the Transaction Log Summary page. 8/31/2012 WJP Added ability to UAP firmware to read the BOL script from the SD Card for customer/site custom BOL formats. On startup, bol_script.LUA is read from the root directory of the SD card. bol_scripts directory has been created in Perforce to maintain controlled version control and history of custom BOLs developed. If a bol_script.LUA file is not present, the default_bol_script in the source code (moved to ml_db.c) will be used. 9/21/2012 MSH Added German translation. Added Comfort Energy logo. 10/4/2012 MSH Fix for display on SMP EXL. Was broken by 07/24/12 build. 10/11/2012 PS Add EOD report for Shell. Report triggered by "FEODLOG" command from host. Prints totalizers per preset/meter/component to Alibi Log. 10/12/2012 MSH Add Meter Creep voucher. 10/16/2012 MSH Tweaks to Unauth Flow voucher: formatting, net volume. Change to how we handle meter creep/unauthorized flow. We will no longer generate a ticket for the meter creep. We will print a Unauth Flow (meter creep) voucher for all unauthorized flow regardless of whether drive is carded in or not. 10/25/2012 MSH Added new web server based on Mongoose open source web server. Ported existing ML pages over to new web server. Added authentication for web pages. Both an "admin" (read-write) and "user" (read-only) user. Added file upload to SD card. 11/01/2012 PS Fix the MAX_API_TABLES count Comment out the 1122 Pressure tables 11/01/2012 PS Added ability that Multimate and other systems can download the picklist possibilities via the r300 prompt register 11/01/2012 PS Increase 4 times the alibilog 11/01/2012 PS Fix alignment issue on Gross Totalizers EOD-Report (FEODLOG-command) 11/01/2012 PS German prompt fix Chapitre 16 – Historique des révisions du logiciel 11/01/2012 PS Changed revision to 3/4.31.07 and for nvram alibilog 11/02/2012 PS Add ability of EOD-Report to trigger via modbus 11/04/2012 WJP Added RCU general configuratuion parameter (R/U076) Ethernet HTTP "admin" Password (default "toptech") Added RCU general configuratuion parameter (R/U077) Ethernet HTTP "user" Password (default "toptech") 11/06/2012 PS Integrated a Low Flow Proving Rate, so during proving another low flow rate can be giving instead of using the preset low flow rate 11/6/2012 Corrected bug in UAP script with respect to picklist paging. PickListHandle() calls in the prompt script must NOT have commands following it on the same line. 11/7/2012 WJP Corrected UAP bug where a blank driver PIN was still prompted for when pin_req was not "N". Updated UAP LUA script error processing to display message as well as writing it into the message log. Correct web file upload naming to correctly deal with windows "\"s in filenames. 11/7/2012 PSFix transaction viewer via web-interface. Values were not reflected correctly. Density, Relative, Pressure, possible hundredths mode, Alarm, Measurement approved 11/9/2012 PS Remove Time of UAP R000 register 11/13/2012 WJP Corrected UAP bug that caused TDS transactions and BOLs to omit data fields when special characters, for example ""(quotes), appeared in the UAP database values. 11/19/2012 PS fix bug in reading via modbus relative density add new functionality of BSW real-time analog input , all parameters, transactionviewer also store value, alibilog , ticketbuilder, reading live BSW via MRS, modbus functional, bsw can be back-calculated blending add new functionality of API Gravity real-time analog input, all parameters, reading live API Gravity via MRS, modbus functional, api gravity can be backcalculated blending add new functionality to simulate analog input each fcm number will bump the current with 300mA 435 Chapitre 16 – Historique des révisions du logiciel changed meter screens logic that only 1 density type is shown at a time: api gravity or relative density or density changed sd_card routine that we store all parameters even if higher than 100 registers changed boot config check that we check more than 100 registers for each level added BSW into UAP build 11/19/2012 PS added change that prompts higher than 100 can be read. r-command 11/20/2012 PS API Table function has now a Test API Gravity instead of using the real API Gravity. No W&M key needs to be turned on Added on the MRS command for BSW and API Gravity the average of meter and component level Merge display denstiy_type routine to one routine. 11/21/2012 PS Fix issue on ticket printer that only on the total amount the hundreths digit was missing for gross and net 11/26/2012 PS Added ability to store alarms by batch into transaction for preset, meter, component and additive level Added ability to view batch alarms in transaction viewer and webpage transactionviewer Added ability to print the alarms by batch on the alibilog printer Fixed bug that webtransaction viewer would never show type 4 meter level 11/26/2012 PS Fix language german for product screen and layout 11/28/2012 PS Fix language german for Network screen alignment for counts was wrong 11/28/2012 PS UAP fix ticket number tracelog messages , always a diff of 1 UAP fix during tds send of transaction, could clear transaction LUA data 11/28/2012 PS UAP fix that stack doesn't overflow when checking transactions view web interface 11/29/2012 PS Enhance German language on Main Meter Screens 12/03/2012 PS Fix Color selection on the MultiLoad screen was not working 100% 12/04/2012 PS Delete ENTERPRISE BOL out of tds routine and made a seperate bol script 12/04/2012 PS Enhance Meter trace for analog valves (only for FCM2 not IO-boards),also limit between 0 and 24mA 13/04/2012 PS Enhance the SD-Card menu 436 Chapitre 16 – Historique des révisions du logiciel Each Menu will only show the files with the correct extension to prevent selecting invalid files Web-interface will still show all files on the sd-card 12/7/2012 WJP Include UAP functionality into standard MultiLoad firmware builds. Remove ability to build special UAP MultiLoad builds. Remove ability to build ml_uap_sim from the Makefile. Remove UAP special build label. Correct #ifdef TDS_INTERFACE/#endif alignments in source. Correct size of returned LUA Data in web transaction viewer. On ml_tds_3op and ml_db, added ability to selectivly start or stop tasks. Updated database viewer to return if ml_db has not started. Corrected UAP BOL duplicate label to use transaction_printed_bit_table. Only include Local Databases item on Program Mode Menu when Processing Mode is set to UAP. Delay processing first TDS_3PO call (1 minute) until after the ml_db has started (5 seconds) 12/09/2012 PS Change default Meter Archive timeout and host down timeout from 30 to 120 seconds 13/12/2012 PS UAP Fix when driver and card number are not equal then reprint doesn't work, because database has driver number, reprint search on card number UAP Fix alignment issue on Reprint Prompt 12/17/2012 PS New enhancement Low Flow Start Volume Based on Percentage 12/17/2012 PS Enhancement on UAP ticket number Webpage, TransactionViewer and BOLs 12/17/2012 PS Enhancement on UAP ticket date change be change to MM/DD/YY or DD/MM/YY 12/19/2012 WJP - Release to Customer Correct Print_Blend_Details so when: 0 - Exclude components, additives and meters. 1 - Include components, additives and meters(only when meters are needed). 2 - Include components, additives and meters(always include meters, even when not needed). Updated Low Flow Start Volume to use the greater or either the configured Low Flow Start Volume or the computed Low Flow Start Volume by Percentage. Low Flow Restart Volume always uses the configured Low Flow Restart Volume. 12/24/2012 PS Enhance Network Menu combining parameters under a new webpage menu Add new Network Printer Menu 12/25/2012 PS Enhance modbus interface that all transaction values are readable api_expansion_coef_tenths corrected_densitygravity volume_correction_factor bsw_hund alibilog_alarm 437 Chapitre 16 – Historique des révisions du logiciel 12/26/2012 PS Restrict low flow start volume to 65535 when using low flow percentage 12/29/2012 PS New feature deadman with input and output signal, deadman interval timer, deadman warning timer. 3 modes: Continuous push, Continuous push with scheduled periodic release, Scheduled periodic releases. All signals are added to the Bay Diagnostic screen. New alarm added *DEADMAN. 01/01/2013 PS New feature FKEYPADON and FKEYPADOFF, this gives the capability to disable the keypad. Stop button will still work to ensure driver can always stop the load Also the Idle and the Menu screen are not keypad locked Modbus commands added Reg 7008 and 7009 Copyright changed to 2013 01/02/2013 PS Enhancement Default startup mode if keypad is locked or unlocked 01/02/2013 WJP Added the ability for bol printing on ethernet printers. 01/03/2012 PS Add Bsw to Webinterface Transaction View 01/04/2013 PS Changed UNAUTH FLOW voucher that we take alibilog labels for GROSS and NET, also remove approval chars 01/11/2013 PS Added new bio ethanol API tables PTB Method 3 , for Products E5, E10, E80, E85, E100, Benzin/Petrol, Diesel, B5 RME, B7 RME, B100RME, B5 SME , B7 SME, B100SME. Corrected Density 15degrees has a fixed value for BIO components Added picklist routines and read register for Multimate 01/12/2013 PS Enhancement UNAUTH FLOW Voucher will use the real-time unauth totalizer amount instead of the clear amount on the component level. This is to ensure the full amount is always on the alibilog. 01/15/2013 PS Added rollover check to unauthorized flow voucher New feature non-proportional ratio and side-stream blending, the component max flow rate will be used to determin the high flow The main component (highest percentage) which flow in low flow all other component wait until the high flow start is reached. Blend check is only done at the end of the load load, during the load the product is never in spec only at the end. Fallback and flush feature are still working in the non-proportional enhancements. 01/16/2013 PS Added Time on Main Loading Screen for all devices except SMP 438 Chapitre 16 – Historique des révisions du logiciel 01/29/2013 PS Added Alcohol Table Brazil NBR 5992 01/30/2013 PS Fix double use of RCU Registers 79 and 80 Change firmware number to x.31.09 SD-card will save register 78, 79 and 80 Changed equipment database version to 3.31.09. 01/31/2013 PS Added Hydrocarbon Table Brazil (LPG, Gasoline, Diesel, Lubes, Crude, Asfalt and heavy oils) 01/31/2013 PS Enhance sd card filelists to only display select extensions (.bmp, .mlc, .bin) ignoring extension case. Release 3/4.31.09 02/04/2013 PS Enhancement of Deadman with bypass key, to disable deadman function without going into program mode 02/11/2013 PS Added API alarm timeout so, alarm would not raise after x time. Vcf stays the last known value Changed version number to x.31.10 02/15/2013 PS Enhance UAP that Product Message is after each the product/component line Swapped UAP Bol City line with Phone number line Fix UAP Bol when more than 1 page, cursor would not follow the end of copy line 02/21/2013 WJP Trim CRs and LFs from BOL script to prevent TDS communications from hanging on message_log lines with CRs. 02/22/2013 PS Enhancement of the Alarm Screens Added new functionality that each status alarm (bay,preset,meter,component,additive) can be hidden for any remote system. 2/26/2013 WJP Added Driver Routines to read NVRAM Battery Monitor Voltage and Temperature. Added Battery Monitor Service Routine to Check Battery Voltage every 24 hours. 2/26/2013 PS Added new alarm routine which give all 32 bit alarm states. New communication commands are added Bay(MRBA32),Preset(MRPA32, MRPA), Meter(MRMA32), Comp(MRCA32), Add(MRAA32). 03/01/2013 PS Enhancement of new Menu Level under Equipment Setup for settings up the MultiLoadII 439 Chapitre 16 – Historique des révisions du logiciel 03/02/2013 PS Add Deadman functionality also to Custom Logic 03/06/2013 PS Enhancement on payload transaction to UAP. Added BSW and Pressure to the transaction file. 03/07/2013 PS Enhancement of Custom Logic supports now Temperature, BSW, Gravity, Relative Density, Density, Pressure, Volumes Enhancement of Custom Logic supports now Timers Start and Stop Delay. 03/07/2013 WJP Added display of Battery Voltage and Temperature on RCU Diagnostics screen (only if CPU board supports the feature). 03/08/2013 PS Enhancement of Register800 to always transaction read of api_expansion_coef_tenths, corrected_densitygravity, volume_correction_factor, bsw_hund, alibilog_alarm 03/08/2013 PS Added Bay Number to the Web-Interface 03/11/2013 PS Fix Ticket Print: Measure used was on totalizer line correct for gross , but incorrect for net. Also allow totalizer to be shown with max value of 999999999 Fix Measure used for Additive Totalizer Line was missing 03/12/2013 PS Added in Custom Logic the State for Preset,Meter,Component (High Flow, Low Flow, ....) Added in Custom Logic under Rcu Real Time Parameters the Date and Time value 03/12/2013 WJP Corrected bug on SMP firmware builds where the editing of parameters on the RCU General screen edited the wrong parameter. 03/12/2013 WJP Update TDS 3po checksum routine to stop converting all incomming and outgoing data to upper case. 03/18/2013 WJP Corrected bug (may have been created on 5/17/2011) in processing and prompting for PIN numbers when processing mode is set to Stand-Alone. 03/19/2013 WJP Added ability to support two different serial ports set to host mode. 03/21/2013 WJP 440 Chapitre 16 – Historique des révisions du logiciel 441 Added MRTDpppddd command to directly read the specified preset, archived after clearing each batch. transaction details, for a 03/29/2013 WJP Added Batch Number (1-9,999,999) to the transaction archive details. Added printing BSW on UAP tickets (previously missing). Added printing Batch Number on UAP tickets. Added printing Batch Numer on Stand Alone tickets. Added new LUA command, SetDetailBatchNumberPos(), to BOL script processing. Added SetDetailBswPos() and SetDetailBatchNumberPos() to default BOL script. Added Batch Number to transaction details in the MRTDppp and R800 commands. Added Batch Number to the Transaction Viewer Screen. Added Stand Alone Batch Number ticket position to R203. Added R006 command to read the current (last assigned) Batch Number. Added Batch Number to the Web Server Transaction Detail Viewer. 03/29/2013 PS Adding new transaction alibilog label BATCH and adding batch number to the alibilog 04/02/2013 PS Transaction to UAP had always spaces in po_number changed to get it from account record 04/04/2013 PS Change batch number from bay level to preset level. Added batch number to unauth flow voucher, which will have also a different batch number. (Transaction will be not stored) 04/05/2013 PS Add batch_number to the modbus protocol so it can be read out of the transaction 04/05/2013 PS Add new features to Custom Logic Beacon: Pulse generator, variable ON and OFF time Pulse: Single Puls on a high input trigger and variable ON time 04/10/2013 Found many issues with language selection in MultiLoad. This impacted displaying the correct language and footers with some stand alone, UAP and host configurations. Incorrectly referencing the driver_language for the stand alone driver card database instead of program_mode_language. Picklist footers in 5 program mode UAP database screens Picklist footers in 5 diagnostic screens. Incorrectly referencing the default_alt_langauge instead of the currently selected driver langauge. Host commanded picklist footers. Chapitre 16 – Historique des révisions du logiciel Incorrectly referencing the driver_language configuration parameter instead of the currently selected driver language. Messages for Authorizing Transaction, Completing Transaction, Transaction Done, Transaction Cancelled, Authorized to Load, Please Wait, and Keypad Locked. TDS connection staus messages, GPS messages, Reprint Ticket, CN Prompts, and all Meter Screens. Language on the Idle Screen Logo images. UAP authorization picklists. Incorrectly only referencing the driver language for the stand alone driver card database instead of the currently selected driver_language. Uploaded host messages for Please Wait, Insert Card, Remove Card, Invalid Card, Press Any Key for Access, and System Unavailable. Custom Stand Alone Prompts. On display of the card in screen, current driver language was being set to the default_alt_language instead of the driver_language configuration parameter. Updated native and modbus protocols to update the currently selected driver language when the driver_language configuration parameter is updated. Since language does not exist in the UAP driver database, update the currently selected driver language to the driver_language configuration parameter for UAP driver authorization. Removed the default_alt_language configuration parameter. Host bay code needs to be updated to: 1. Once a driver card is read and the driver language is known, update the R008 register (driver language) with the driver language using the following index mapping table. (ie. tms language 45 is german, converts to index 4 in ML) #define LANGUAGE_ENGLISH 0 #define LANGUAGE_SPANISH 1 #define LANGUAGE_PORTUGUESE 2 #define LANGUAGE_FRENCH 3 #define LANGUAGE_GERMAN 4 #define LANGUAGE_SIMPLIFIED_CHINESE 5 #define LANGUAGE_TRADITIONAL_CHINESE 6 #define LANGUAGE_THAI 7 2. Keep the current operation of reading the TMS language prompt database at language index 0 and writing this prompt into R700xx0 registers for older MultiLoad firmware. 3. Read the TMS language prompt database for the selected driver language (ie. tms language 45 is german) and write this prompt into R700xxl where l is the same index that was written into R008 (ie. 4 for german). 4. Update the R008 register (driver language) with the default driver language once the driver transaction is done or cancelled. 04/07/2013 PS Fixed update Custom Logic via ml_terminal or ml_modbus Added to fcm_control logic for mass level Added Mass to the transaction archive details. Added printing mass on UAP tickets. Added printing mass on Stand Alone tickets. Added new LUA command, SetDetailMassNumberPos(), to BOL script processing. Added SetDetailMassPos() to default BOL script. 442 Chapitre 16 – Historique des révisions du logiciel Added Mass to transaction details in the MRTDppp and R800 commands. Added Mass to the Transaction Viewer Screen. Added MRS command to read the current mass. Added Mass to the Web Server Transaction Detail Viewer. Added Mass to Alibilog only saleable product(will not print when Mass is ZERO) Added new mass totalizer to Totalizer Screen Added new register R114 to read real-time Mass Totalizers Added real-time preset gross/net/mass totalizers to CONTROL SCREEN Added new mass_measured_used_type on RCU Level Added new mass_measured_used_type to r133 Register Added new alibilog labels for mass Added new ml_weight.c Added Mass on Preset Screen Added Mass on Component Screen Enhanced Deliver in Net Parameter to Deliver_type (Gross or Net or Mass) Added new deliver_type to r133 Register Added new message on Preset Screen (Volume_unit) corrected to (Mass_Unit) Added all previous change for Mass also in hundreths mode Added routine to go from weight_to_net and net_to_gross Added routine to go from measured_unit to mass_measured_unit (mass units in the measured_unit are out of scope) Updated all Meter_Type for volume and mass totalizer calculations Added Date to the Preset Control Screen (Mode DD/MM/YYYY or MM/DD/YYYY) Fixed bug for alibilog when in hundreths mode that the decimal points would be not converted to comma only saleable level Moved Time on Preset COntrol Screen next to the date value Enhancement on EOD-Report include now also Mass Totalizers and Thruput Fixed bug in EOD-Report if more than 1 meter per arm was assigned , report would loop multiple times Added new thruput totalizers (auth + unauth volume) for Gross, Net, Mass Added Mass calculations when using online density/relative/API Gravity instead of using - Mass = (Net * Dens) we will use Mass = (Gross * Dens) Added DINISO rounding routines for weight When not loading in hundreths net and mass gets calculate from whole values Added new Mass Calculator Screen (starts from Net volume to Mass) Added Mass to Custom Logic Preset and Component Level Added missing net hundreths level to clear reset (component level) 4/17/2013 WJP Fixed bug in UAP bol processing where sometimes the header lines would not get copied to other pages. Corrected bug in UAP BOL default script where one detail line on the start of new pages was lost. Updated UAP BOL default script to add a dividing line under the column headers and after all column data to help readability. Updated UAP BOL default script to keep all footer lines on the same page. 443 Chapitre 16 – Historique des révisions du logiciel 444 4/18/2013 WJP Global rename of “thruput” totalizer to "alibilog_daily_gross_del". With mass delivery as an option, clarify some global fields across source files: Global rename batch_volume_del to batch_del. Global rename volume_preset_whole to preset_whole. Global rename load_volume_del to load_del. Global rename batch_volume_ to batch_. 4/22/2013 WJP Increased resolution of transaction temperature from tenths to hundredths. Updated view transactions and web transaction viewer to display temperature in hundredths. Added temperature in hundredths to the end of the R800 and MRTD commands as %05d (implied 2 decimal digits). Kept existing transaction temperature reads in tenths for backward compatibility. Kept existing TDS transaction detail temperature field in tenths for backward compatibility. 04/24/2013 PS Store Mass Totalizers for each loaded Batch Added to Transaction Viewer the Mass Totalizer Added to Webinterface the Mass Totalizer Fixed Hundrehts totalizers in Webinterface would show whole totalizers Added Mass Totalizers to Alibi Log Added to Unauthorized flow voucher the mass value Added to Ticket Printer in Standalone the mass totalizers (not for UAP) 04/25/2013 PS Added check when delivery type is mass that the mass measure used cannot be NONE Added check when delivery type is net or mass that the measure used cannot be NONE 04/27/2013 WJP Updated U700 so language index 0 is used before any other language indexes (1..MAX_LANG) to maintain backwards compatability. Added new card_reader_types to support non-captive card readers and ibutton readers. Added new U700 strings to support "Swipe Card" and "Touch iButton" messages. 04/28/2013 PS Added iButton routine to read the iButton Reader, also updated the firmware v003. Added new diagnostic screen to see ibutton reader data, with read counter. Added iButton animation on the IDLE Screen keypad 04/28/2013 WJP Added support and card reader types for noncaptive card readers (India Req.). Chapitre 16 – Historique des révisions du logiciel Changed Driver Card Number from an Integer to a String for iButton Support. Manual entry of Card Numbers (Access ID setup and Card Reader Disabled) zero pads numbers. UAP, TMS and MultiMate uploads of Driver Card Number data should be zero padded before uploading. UAP, TMS and MultiMate should be updated to support alphanumerics (hex) data for ibutton support. TMS needs to be updated to support the following card reader types for MultiLoad/SMP: #define CARD_READER_TYPE_DISABLED 0 #define CARD_READER_TYPE_BUCKET_CAPTIVE 1 #define CARD_READER_TYPE_BUCKET_NONCAPTIVE 2 #define CARD_READER_TYPE_SLOT_CAPTIVE 3 #define CARD_READER_TYPE_SLOT_NONCAPTIVE 4 #define CARD_READER_TYPE_IBUTTON 5 04/29/2013 PS Increased firmware number to x.31.11 for Mass changes 05/01/2013 PS Added Raizen Logo 05/03/2013 PS Added new feature that prompts1 to 4 can be used in custom logic (remark entry value will stay, until next driver enter new value) Added new feature that Alibilog can print all 5 prompts when they are not blank, prompts can contain any data. Also added 5 new alibilog labels for the 5 prompts, default names are Stockholder,Customer,Account,Destination,Driver. 05/04/2013 PS Added new fifth standalone Prompt, updated all protocols, can be also used on standalone BOL. Enhancement all prompts are getting clear at the end of the load, only in standalone mode. Added new feature that output pulse on Preset Level can also be Mass 05/06/2013 WJP Update UAP Set_Max_Preset() routine to ignore limit when Max Load Qty from TDS is 0 or blank. 05/9/2013 WJP Added debug code to assist with incorporating new TFT displays. Added TEST_NEW_DISPLAY precompiler flag to force display of the display diagnostic screen on powerup. Added a screen to adjust and apply changes to the display parameters when the TEST_NEW_DISPLAY precompiler flag is defined. 05/11/2013 PS 445 Chapitre 16 – Historique des révisions du logiciel Enhancement of Custom Logic added analog in , analog out and RTD input for only FCM2. Added also to modbus as other protocols. Added to Diagnostic Mode. Added check if analog output is already used by meter level for valve control. 05/14/2013 PS Added Canexus Logo Added Alarm Ouput for each alarm on global alarm level 05/15/2013 PS Enhancement on Custom Logic: Each Alarm Level Bay, Preset, Meter, Component and Additive can be used for a certain/specific Bay, Preset, Meter, Component and Additive. Also added this to all communication protocols as modbus. 05/16/2013 PS Added 2 new API tables for Alcohol, these tables use temperature and density as an input and will give the alcohol percentage of the product. 05/17/2013 PS Change German Ethanol table from temperature hundreths to tenths mode. Added totalizers to UAP Bol. 05/18/2013 PS Added new feature to mask the storage of an alarm. Results in tot storing, printing the alarm. Update communication protocols. 05/18/2013 PS Added density air for less then 996.6 (1.1 kg/m3), range 996.6 to 1663.5 (1.0 kg/m3) and greater then 1663.5 (0.9 kg/m3) 05/30/2013 WJP Added simulation control web page to allow: Change meter simulation between Auto, Force Flow and Hold Flow. Change additive simulation between Auto, Force Flow and Hold Flow. Change input port simulation between Auto, Force On and Hold Off. 05/30/2013 WJP Added CTL and CPL display on the component status screen and api table setup screen. Update CN code to work with previous card_id parameter change. 06/15/2013 WJP Corrected Weighted Average Routine for Temp, Density, Rel. Density, Pressure, Gravity, BSW where negative values were always computed as one least significant unit lower than actual at the component level (-0.01 temp for example) and two 446 Chapitre 16 – Historique des révisions du logiciel least significant units lower than actual at the preset level (-0.02 temp for example). 06/23/2013 WJP Remove not batch_complete check from remote_clear input processing. Added DEBUG_VOLUME and MEMORY_FILL test code. 07/02/2013 PS Start new build x.31.12 For the creation of type 4 transaction record: When loading in whole we only will generate a type4 transaction if the whole value has a difference When loading in hundredths we will only check the hundredths difference Added also Net_whole and gross_hunds value for checking. 07/03/2013 PS Enhancement that API 5X, 6X, 23X, 24X and 59/60X also support expansion coef factor. 07/08/2013 PS Enhancement split Vcf into Ctl and Cpl for modbus, and all other protocols Change Web-Interface and transaction viewer in MTL2 to show both values Make these 2 new values available for Standalone Bol and for UAP Bol Add this two values to the MRTD command. Fix bug extra white line between net and mass totalizer on Web Interface page Fix bug that Vcf didn't check API-TABLE to show the correct decimal place Added Ctl, Cpl and Vcf to the MRS command Added the Vcf , Ctl and Cpl to the Custom Logic 07/09/2013 WJP Reset Preset Load Totals at Transaction Authorization. 07/13/2013 PS Added Modbus TCP/IP Protocol on port 502 Added Phase 1 Alibilog Screen and Bol Position Screen Restrict send Modbus Command to 1000 Registers (instead of 32768) 07/16/2013 PS Phase 2 Bol Position Screen make it possible to print bol sample to verify configuration 07/24/2013 PS Enhance the webpage transaction viewer will not show anymore ctl,cpl and ctpl for saleable product Enhance the webpage simulation page if additive excists we don't show the same port again Enhance the webpage so that when we have a meter connected to the fcm it does not show 2 times port 4 Enhance the webpage so that when we have a meter with quadrature we don't show 2 times port 5 Enhance transaction viewer don't show exp coef. or corrected density/gravity/relative when not applicable 07/25/2013 PS New enhancement additive tolerance percentage if used, additive check by injection size can be still used at the same time. 447 Chapitre 16 – Historique des révisions du logiciel Added excess flow timer for preset and meter level, if timer zero fcm does the check if timer used MTL2 will do the check. Added Additive volume start check so before we will not check the additive injection combined with additive tolerance check Fixed relative sensor enabled in the W&M menu 08/02/2013 PS Added support for printing W&M Logs to Network Printers 08/05/2013 WJP Corrected check_fcm_analog_assignment() to allow multiple additives on the same preset to share the same analog output. 08/08/2013 PS Fix problem with non-proportional blending, that we allow straight loading of the second product. 08/19/2013 WJP Added saving/restoring of TDS/UAP configuration parameters (R106000-R106005) when saving/restoring ML configurations to/from the SD card. 08/27/2013 WJP Updated firmware version to 4.31.13. Added BUCKET_DUAL_NONCAPTIVE and SLOT_DUAL_NONCAPTIVE card reader types. Card_Inserted status will now return a '2' when a second card has been read while a transaction is active. Card_Inserted status will return to a '1' when the first card has been read again while a transaction is active. R962 (and modbus 2900..2979) will return the first card data when Card_Inserted is a '1', and the second card data then Card_Inserted is a '2'. Reading a third card while the Card_Inserted status is a '2', will only update the R962 register to the card data of the third card. The Card_Inserted status of '2' will remain unchanged. Update NR database version to 3.31.13. 08/28/2013 PS Added in RCU Diagnostic the Hardware and Software Reboot Date and Time. Date can be shown as MM/DD/YYYY or DD/MM/YYYY. Fix standalone dual card processing. 08/29/2013 PS Added new Bay *POWERFAIL Alarm. Added this alarm to the Custom Logic Alarm Section. Moved update hardware boot time, so it will be only updated when we have a real hardware reboot. 08/29/2013 TF Added new CTS/DTR test. Added this test to the Serial Port Test section. 09/01/2013 PS Enhancement change ratio and sequential register to 1 register picklist. Added picklist to Multimate communication protocol. Rename all references to blending_type. Enhancement that any configuration inputs can also be linked straight to the custom logic parameter. Update all communication protocol to read and write the new register option Updated display routine to support custom logic linking 448 Chapitre 16 – Historique des révisions du logiciel Split FCM_ADDRESS in FCM_ADDRESS_OUTPUT and FCM_ADDRESS_INPUT Enhancement of the Mass Calculation Screen: Added Measured Used and Mass Measuered Used to the selection screen 09/03/2013 PS PHASE1: Moved BSW from meter level to preset level, this includes communcitation (smith to modbus), BSW removed from component screen, added a second BSW to support two ranges of inputs, calculations, view and inquire BSW1 and 2 screen. Enhancement add full logic to support 2 BSW values at the same time, includes also diagnostic purpose, only one of the two will be available at the communication level. PHASE2: Add watercut formula and make the call to it. 09/04/2013 PS Enhancement let fcm output configuration parameters link to custom logic with the internal input value. Enhancement let external communication systems send values to MTL2, which can be linked to custom logic with the external input value. Update communication protocols so external systems can write via all protocols to custom_logic_values. 09/05/2013 PS Enhancement of all input and output configuration permissives so they can be inverted, instead of doing this in custom logic. Fix that custom logic parameter set_value can it also can be updated with a negative value over communication. Fix in Access ID Screen the check if a driver record is empty. 09/06/2013 PS Enhancement move trace configuration under new menu and register 108. Added new trace menu screen, with out of range checking at boot up. Added storage of these value on the sd-card. Added register 108 to all protocols, not modbus. Rename all trace references in the code. 09/09/2013 TF Added the ability to view, rename, create, and delete a file or directory on the SD Card. Fix when going in and out of directores shows the proper page and cursor placement. Fix when renaming or saving a file only pressing the ENTER key will actually save the file. 09/09/2013 PS Fix to show in the webpage rcudittoscreen the sign > and <. 09/11/2013 PS Phase2: Enhancement add correct battery voltage to the RCU Diagnostic screen. 09/20/2013 PS Phase3: Added serial flash storage of total off time as a check value. Added battery capacity calculations. Adjustment on compensation voltage and temperature reading. 09/23/2013 TF 449 Chapitre 16 – Historique des révisions du logiciel Added a conformation screen when setting factory defaults on powerup using the CLR key that asks the user to press '1234' to continue. If any other key (except the CLR key) is pressed, then setting factory defaults is aborted. 09/25/2013 TF Chinese language configuration prompt translations have been updated. Fix W&M log software version number display. Update preset current temperature to be set to zero if no flow. Previously was last flowing blended temp. Fixed modbus register 955 Driver Name both read and write were misaligned. 10/2/2013 WJP Added Facilty Code to UAP Terminal Profile database. Updated UAP script to verify card facility code if a facility code is specified in the Terminal Profile. 10/3/2013 PS In Meter Proving Mode the Minimum Preset Qty will be not checked, the Maximum Preset is still checked. 10/7/2013 TF Fix display of a filename in the SD card screens. Now it will only display as much of the path as possible on one line. Previously was wrapping it around to subsequent lines. 10/7/2013 PS Removed Fcm-Trace Alarm under Bay Level and custom logic, because was not in use anymore. Rewrite Real Time Alarms under Custom Logic so we see the same alarm names as under Alarm Setup. Also all 32 Alarms are now available. 10/8/2013 TF Fix renaming of SD card filename with an extension. If an extension is longer than 20 characters user must re-enter it in manually. 10/8/2013 PS Added in Factory Menu reset Capacity for Battery. Added in Factory Menu check for Voltage and Temperature. 10/9/2013 PS Fix: Default Processing Mode Invalid was out of range in the build. Fix: If changing a custom logic line from one to another type we need clear the previous setting. Fix: In Additive Calibration Screen range check for vol_per_injection was not working. Fix: Command P enable picklist w/len, that the range is between 0 and Max Columns. Fix: DB routings out of range checking. Remove net approval char for additive totalizer Fix: Simulation Webpage should show unsigned values instead of signed. Fix: Mass Calculator Volume is unsigned instead of signed. Fix: Logmsg in prompt.c file are signed instead of unsigned. Fix: Multimate response for picklist values. 10/10/2013 PS Fix: CN Bol Date range check was allowing zero. 450 Chapitre 16 – Historique des révisions du logiciel 10/13/2013 WJP Updated Auto Batch authorize to work when current screen is load, control or any status screen. Updated Auto Batch authorize to not switch to the control screen when a remote start is configured. Corrected bug in Auto authorization where multiple presets running auth authorization at the same time would not work. 10/15/2013 WJP Updated UAP TDS record download to space fill if the record received from TDS is smaller than the record size defined in the database table. 10/25/2013 PS Increased version number to x.31.14 Enhancement of Custom Logic: Ability to read any configuration parameter Rcu, Bay, Preset, Meter, Component and Additive Level. Ability to write any configuration parameter Rcu, Bay, Preset, Meter, Component and Additive Level. But if it is a W&M parameter, the W&M bolt needs to be out, otherwise no update is possible. FCM Output Value in Diagnostic will only show a 0 or 1. Added Groups in Custom Logic to easier find functions. Timer, Alarm, Config Read, Config Write, Operations Groups. Added new custom_logic values to all protocols as also modbus. 10/26/2013 PS Added W&M ID for Custom Logic "L", so if a W&M parameter gets updated via Custom Logic it will log this in the W&M Log. Custom Logic can only update W&M config if the W&M bolt is not inserted! 10/27/2013 PS Enhancement NEW Hazard screen gives the ability to change the hazards on the MultiLoad Screen. 10/28/2013 PS Added all 2007 API E-tables Gas Products. 10/31/2013 WJP Fixed startup issue where if power was removed during the initialization of the MultiLoad hardware, the previous state could be lost, preventing a currently active transaction at the time of initial power failure to not be restored correctly. This could cause loss of the currently active transaction data. Fixed bug where after firmware upgrade, ML could get stuck in load screen until a factory reset was done. Corrected CN bug where a missing transaction data would prevent ML from sending any further data packets to TDS causing a communcation loss. 11/01/2013 PS Enhancement Printing Menu has now also option to change the standalone prompts. 11/4/2013 TF Added CRC checksum to firmware image. Added startup CRC checksum verification against stored firmware flash image on startup. Added CRC checksum verification before loading new firmware image into flash (if it contains a checksum). 451 Chapitre 16 – Historique des révisions du logiciel 11/04/2013 PS Adding the VSX Database to UAP. TODO: Logic of VSX/VSE. Removed battery calculation for compenstation and removed displaying this value. 11/08/2013 PS Added new help screen with description for Rcu, Bay, Preset, Meter, Component, Additive and Trace level. Also added value, minimum, default and maximum value to screen. When selecting min, default or max value this value will be copied into config value. Enhanced code for multilangual support. 11/18/2013 PS Help supports English, French and Portuguese. Added audit trail logging. New screen to see the last 500 changes and added the ability to store these change to the SD-Card by day. Also purge older audit logs after 90 days on the sd-card. Screens as all communication protocols will go into audit trail if level is mentioned below. Following levels are going into the audit trail: Rcu,Bay,Preset,Meter,Component,Additive,Trace. Excluding the General Setup registers and Communication setting registers. Added support to see Audit Trail on Webpage. Added R913 register to support reading of audit trail real-time. Added in Custom Logic the state of the RCU. Fix: RCU Setup screen the language selection puts the cursor on the next line. 11/19/2013 PS Added FCLEARAUDIT to clear the config change log. 452 ">
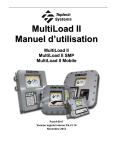
Публичная ссылка обновлена
Публичная ссылка на ваш чат обновлена.