Guide d’application
pour nos produits de collage et d’étanchéité employés en construction et réparation navale
Table des matières
1 - Introduction
2 - Panorama des produits de la gamme Sika Marine et de leurs applications
3 - Introduction à la technique du collage souple
3.1 - Bénéfices liés à l’utilisation des colles et mastics souples Sikaflex
®
3.2 - Principes de durcissement des colles et mastics d’étanchéité
3.3 - Conception des joints
3.4 - Préparation des surfaces
3.5 - Application d’un primaire
3.6 - Conditions générales d’application
3.7 - Application des Sikaflex
®
3.8 - Les différentes étapes de la polymérisation
4 - Instructions relatives à la mise en oeuvre des produits de la gamme Sika Marine
4.1 - Ragréage, collage et calfatage de ponts en teck
4.2 - Collage d’éléments en bois
4.3 - Collage de revêtements de pont antidérapants
4.4 - Pose et étanchéité d’éléments d’accastillage
4.5 - Collage de listons et défenses
4.6 - Liaison pont-coque
4.7 - Liaison coque-quille
4.8 - Collage des flybridges
4.9 - Collage et étanchéité des verres organiques
4.10 - Collage et étanchéité du verre minéral
4.11 - Collage des anodes sacrificielles
4.12 - Collage de panneaux décoratifs et plans de travail
4.13 - Collage de panneaux de pont et ponts à motifs
4.14 - Etanchéité des zones très exposées aux UV
4.15 - Collage de cloisons intérieures légères
4.16 - Collage de plaques antidérapantes en salle des machines
4.17 - Calfatage de bordés à franc-bord en bois
5 - Informations complémentaires
5.1 - Remarques relatives aux substrats
5.2 - Tableau de consommation
5.3 - Dégraissants et primaires pour Sikaflex
®
5.4 - Propriétés physiques des Sikaflex
®
Marine
5.5 - Préparations de surfaces
48
50
51
52
54
39
42
46
47
32
34
36
38
18
26
28
30
55
56
59
60
61
62
7
13
14
15
16
9
10
11
12
17
3
5
Introduction
3
De nos jours, les méthodes et les produits d’assemblage n’ont plus rien à voir avec ce qui existait au début de la révolution industrielle.
Les adhésifs souples par leur grande facilité d'emploi et la haute qualité du résultat final obtenu, ont permis de réelles avancées technologiques en matière de collage et d’étanchéité.
Historiquement, le calfatage des ponts est l’application qui, en construction navale, a subi la plus grande évolution.
Les anciens cordons de chanvre ou de coton trempés dans du goudron, ont été remplacés par des matériaux élastomères.
Ces produits ont été choisis par les chantiers du monde entier car ils permettent
à la fois de réaliser des joints d’étanchéité et d’assembler des matériaux, identiques ou différents.
Nos colles-mastics de première qualité : la garantie d’un joint parfaitement étanche
Les adhésifs utilisés en construction navale doivent permettre d’éviter la corrosion des métaux et d’absorber les contraintes produites par l'assemblage de matériaux différents, ce qui est impossible avec les techniques de fixation rigides telles que le soudage, le rivetage ou le vissage.
L'adhésif doit pouvoir s'adapter et résister aux déformations engendrées par les différents coefficients de dilatation des matériaux utilisés ainsi qu'aux contraintes spécifiques liées aux conditions d'utilisation. Le joint doit être correctement conçu et appliqué, afin que ni les substrats, ni l’adhésif, ni les interfaces ne soient endommagés en service.
Le collage souple permet d'assembler et d'étancher dans le respect des contraintes évoquées ci-dessus ; mais également d'assurer l’isolation acoustique et thermique.
Les produits de la gamme Sika Marine, colles et mastics polyuréthanne monocomposant assurent la double fonction de collage et d'étanchéité garantissant la résistance à long terme de l’assemblage et, par là même, un joint d'étanchéité résistant, durable et totalement imperméable.
Ce manuel d'utilisation est le fruit de notre longue expérience du collage souple de matériaux soumis aux conditions climatiques les plus dures et aux contraintes de compression et de dilatation qui leur sont associées.
Avant d’envisager l’utilisation de la technique du collage souple, il est important de comprendre que celle-ci impose de respecter des procédures bien définies.
Chaque étape doit être correctement réalisée pour atteindre le résultat final désiré.
Les différentes opérations sont généralement simples mais aucune ne doit être négligée.
C’est pourquoi nous vous conseillons de vous référer à ce manuel avant toute application. Lire plus particulièrement les chapitres consacrés aux instructions de mise en œuvre et à l’utilisation des agents d’adhérence et primaires Sika.
Panorama
des produits de la gamme Sika Marine et de leurs applications
5
Les colles et mastics d'étanchéité
Sikaflex
® sont largement utilisés dans la construction d'un grand nombre de navires et de structures maritimes, du yacht de plaisance au paquebot de ligne, du chalutier au supertanker, du canoë à la plate-forme pétrolière. Les systèmes polyuréthanne de collage et d’étanchéité
Sikaflex
® permettent de réaliser des assemblages souples, parfaitement étanches et résistants entre un grand nombre de matériaux et peuvent être utilisés en toute confiance au-dessus comme au-dessous (sous certaines conditions) de la ligne de flottaison. C'est dans cette optique que la majorité des produits de la gamme Sika Marine a été approuvée par les organismes certificateurs et autorisée à porter la " barre à roues "
¤
.
Sikaflex
®
-290 DC
¤
Le Sikaflex
®
-290 DC est une colle-mastic polyuréthanne monocomposant qui possède une excellente résistance aux UV et peut être poncé pour assurer une finition parfaite. Il a été spécifiquement conçu pour le calfatage des ponts en teck.
Sikaflex
®
-291 ¤
Le Sikaflex
®
-291 est une colle-mastic polyuréthanne monocomposant bas module. Ce produit polyvalent est employé pour tous types d’étanchéité.
Sikaflex
®
-292
¤
Le Sikaflex
®
-292 est une colle polyuréthanne monocomposant moyen module destinée aux applications de collage structural. Il est utilisé dans de nombreuses applications comme le collage des cadènes, la liaison coque-pont, la fixation d’éléments d’accastillage sur la coque et l’assemblage des rails de fargues.
Sikaflex
®
-295 UV ¤
Le Sikaflex
®
-295 UV est une colle polyuréthanne monocomposant hautes performances à polymérisation rapide, présentant une excellente résistance aux
UV, destinée au collage et à l'étanchéité des fenêtres et des hublots. Le
Sikaflex
®
-295 UV est adapté au collage de tous types de verre organique (PC,
PMMA).
Sikaflex
®
-296
¤
Le Sikaflex
®
-296 est une colle polyur-
éthanne monocomposant haut module
à polymérisation rapide, pour le collage des fenêtres et des hublots. Le Sikaflex
®
-
296 est adapté au collage de tous les types de verre minéral ainsi qu’aux opérations d’étanchéité extérieure en raison de sa très bonne tenue aux UV.
Sikaflex
®
-298 ¤
Le Sikaflex
®
-298 est une colle-mastic monocomposant spatulable aux remarquables propriétés adhésives. Ce produit peut être facilement étalé et possède un temps ouvert important qui convient aux grandes surfaces de travail.
Sikaflex
®
-852 FR
¤
Le Sikaflex
®
-852 FR est une colle-mastic polyuréthanne monocomposant qui possède d’excellentes propriétés de réaction au feu (auto extinguible).
SikaTransfloor
®
-352 SL ¤
Le SikaTransfloor
®
-352 SL est un produit bi-composant à base de polyuréthanne, utilisé pour le ragréage des ponts avant collage du teck.
Lloyd’s Register, Det Norske Veritas,
Rina, Germanische Lloyd, American Bureau of
Shipping, Bureau Veritas, USPH, etc,
Introduction
à la technique du collage souple
7
Les colles sont de plus en plus souvent utilisées dans les opérations d'assemblage, et cette constatation n'est nulle part aussi évidente qu'en construction navale.
Le remplacement total ou partiel des fixations mécaniques par des collages se révèle très avantageux en termes de durabilité, de légèreté, d'aérodynamisme, de design et de longévité.
La simplicité, la tolérance et la facilité d'application et d'utilisation des systèmes
Sikaflex
®
Marine, associées à leur élasticité permanente après polymérisation, les rendent idéalement adaptés à la construction de navires, de yachts, de ferries, de paquebots de croisière et même de plates-formes offshore.
Les systèmes de collage souple Sikaflex
® contribuent à la diminution des concentrations de contraintes, réduisent la transmission des bruits et aident à l'élimination des problèmes de corrosion et d’étanchéité.
Les systèmes de collage Sikaflex
® ont permis une approche totalement nouvelle des assemblages en construction navale.
Leur grande facilité d'application permet de réduire les délais de production.
Grâce à leurs caractéristiques adaptables, ces systèmes de collage et d'étanchéité constituent une technologie d'assemblage fiable convenant à une très large gamme d'applications.
Les systèmes de collage souple et d'étanchéité offrent une liberté maximale aux concepteurs et architectes navals.
Les Sikaflex
® sont conditionnés de manière à réduire le plus possible les déchets et les gaspillages, répondant ainsi aux normes actuelles de production
écologique et économique.
Sika assure le suivi de ses produits et de leur utilisation en vous fournissant assistance et conseils techniques.
En raison de l'utilisation croissante des systèmes de collage souple et d'étanchéité en construction navale, les chantiers de réparation ne peuvent plus ignorer la technologie et l'utilisation correcte des systèmes Sika.
Ce manuel est conçu pour les professionnels impliqués dans la conception, les spécifications, la construction et la maintenance des navires et bateaux de plaisance. Il fournit des informations pratiques sur les applications les plus courantes dans ce secteur.
Pour toute information complémentaire, veuillez contacter votre représentant local Sika.
3.1 Bénéfices liés à l’utilisation des colles et mastics souples Sikaflex
®
Voici quelques-uns des nombreux avantages liés à l’utilisation des systèmes Sikaflex
® de collage souple et d'étanchéité :
Liberté de conception accrue
Assemblage de matériaux semblables ou différents
Assemblage d'éléments pré-peints
Compensation des différences de dilatation thermique
Amortissement des bruits et des vibrations
Suppression des pics de contrainte
Grande résistance aux forces de pelage et de cisaillement
Excellente résistance à l'arrachement
Tolérances de fabrication plus larges des pièces à assembler
Prévention du risque de corrosion galvanique des métaux
Gains de poids, réduction des coûts
Suppression des joints spéciaux et garnitures d'étanchéité sur mesure
Assemblage et étanchéité réalisables en une seule opération
Rhéologies adaptées aux applications : produits auto-nivelants à très thixotropes
Systèmes monocomposant polymérisant à l'humidité
Systèmes à polymérisation rapide, pour une résistance initiale élevée et une manipulation rapide des assemblages
Pas de déformation des métaux
(comme ce peut être le cas avec la soudure, etc.)
Pas d’endommagement des substrats ou revêtements, à la différence des techniques de soudage, de per-
çage ou de rivetage
Possibilité de mise en peinture des joints
Souplesse accrue des procédés de fabrication
Grande durabilité pour une plus longue utilisation
Haute résistance aux UV
Résistance prouvée à l'eau de mer et aux conditions climatiques extrêmes
Haute résistance aux chocs
9
3.2 Principes de durcissement des colles et mastics d’étanchéité
Les colles et mastics d'étanchéité Sika sont des matériaux réactifs qui présentent de bonnes affinités avec les autres surfaces. Leur fonction est de mouiller les surfaces en épousant la forme des reliefs, puis de se transformer en un solide, créant un lien physique et chimique avec le substrat. Les colles et mastics d'étanchéité Sika Marine présentent à l’état frais diverses consistances (produits fluides auto-nivelants ou produits pâteux thixotropes), et se transforment après polymérisation en élastomères plus ou moins souples suivant le produit utilisé (le choix dépendant du type d’application et de la résistance recherchée).
La capacité d'une colle ou d'un mastic
à mouiller une surface est un facteur essentiel à l’obtention d'un joint de qualité. Le durcissement peut être le résultat d'un mécanisme physique, d’une réaction chimique ou d'une combinaison de ces deux types de facteurs.
Exemples de mécanismes de durcissement :
Durcissement par séchage de la colle
Evaporation de l'humidité ou des solvants contenus dans la colle
(surfaces ouvertes et / ou substrats poreux).
Par exemple : colle acrylique en phase aqueuse.
(SikaColl
®
-4659/03)
Durcissement par refroidissement d’une colle fondue appliquée à chaud
L'assemblage est maintenu le temps nécessaire à la solidification de la colle par refroidissement.
Colle thermofusible ou Hotmelt.
(SikaMelt
®)
)
Durcissement par dosage et mélange de deux composants réagissant chimiquement l’un sur l’autre
Les deux éléments réactifs de la colle sont mélangés, le joint est appliqué et l’assemblage maintenu jusqu'à obtention de la résistance nécessaire à la manipulation.
Par exemple : résine époxy ou système polyuréthanne bi-composant.
(SikaTransfloor
®
-352 SL)
Durcissement par réaction chimique d’une colle monocomposant avec l’humidité contenue dans l’air ambiant
La colle est appliquée et l’assemblage maintenu jusqu’à ce que la réaction avec l’humidité ait permis de développer la résistance nécessaire à la manipulation.
Par exemple : système polyuréthanne monocomposant Sikaflex
®
.
3.3 Conception des joints
Pour bien concevoir un joint, il est impératif de connaître les réponses aux questions suivantes :
Quels sont les matériaux à coller ?
Quelles sont les propriétés mécaniques des substrats ?
Quelles sont les préparations de surface (mécaniques ou chimiques) nécessaires ou possibles sur ces substrats ?
Exemples de forces
Cisaillement
Traction
A quels niveaux de contrainte (en continu et pics occasionnels) le joint sera-t-il soumis ?
Quel aspect final le joint doit-il présenter (quelle est la finition prévue) ?
Quelle résistance le joint doit-il opposer aux agressions chimiques ?
Quelle résistance le joint doit-il opposer aux rayons UV ou en température ?
Une fois en service, les joints de colle peuvent être soumis à des forces variées
(voir croquis).
La résistance d'un joint dépend principalement de la surface d'encollage, de la résistance propre à la colle et de la répartition des forces dans le joint. Un joint mal conçu peut favoriser les concentrations de contraintes sur le joint lui-même ainsi que sur les substrats qu'il assemble : ces contraintes peuvent à leur tour entraîner une défaillance prématurée du joint.
Compression
Torsion
Pelage
Note : Les forces de pelage sont extrêmement destructrices : il convient donc de les éviter dès la conception.
Exemple :
Pour garantir la longévité d’un assemblage dans les conditions extrêmes de navigation en mer, il est essentiel de concevoir convenablement le joint, en tenant compte de l'aspect pratique de l'application ainsi que de la géométrie de l'assemblage.
Nous donnons ici des informations générales sur la conception des joints. Pour des recommandations plus spécifiques, n'hésitez pas à contacter le représentant local Sika qui pourra apporter une solution aux demandes particulières que vous lui soumettrez.
Exemples de joints
Particulièrement adapté pour résister aux forces de cisaillement.
Particulièrement adapté pour résister aux forces de traction et/ou compression.
On accroît la résistance aux forces de traction / compression en augmentant la surface de section du collage.
Le biseautage est un autre moyen d'augmenter la surface de collage, mais qui est peu adapté aux collages souples.
11
3.4 Préparation des surfaces
Une bonne préparation des surfaces est l’élément clé d'un collage réussi. Dans la plupart des cas, l’utilisation des produits de la gamme Sika Marine nécessite un simple nettoyage des surfaces.
Toutefois, lorsque les surfaces présentent une faible cohésion, sont contaminées ou pour augmenter les performances du collage, une préparation plus poussée est nécessaire pour obtenir un joint parfait. On prêtera plus particulièrement attention à la présence de poussières, de graisses et huiles, de résidus de pétrole, de rouille, et de peinture écaillée sur les surfaces à encoller.
Le pré-traitement sélectionné dépendra du type de substrat (métal, matière plastique, peinture, bois, etc.), des contraintes appliquées en service au produit fini, du degré de détérioration des surfaces et des caractéristiques propres à chaque configuration de mise en oeuvre.
Vous trouverez dans ce manuel des renseignements détaillés pour chaque application, ainsi qu'un tableau récapitulatif des principaux pré-traitements en fin d'ouvrage.
Vous pouvez également demander des informations complémentaires à votre représentant local Sika.
Nettoyage mécanique
Une préparation mécanique sera nécessaire dans certains cas : présence par exemple de corrosion, de couches de faible cohésion en surface ou de dégradations superficielles ( revêtements de surface abîmés mais présentant encore une bonne adhérence). L'importance du nettoyage sera fonction du type de surface et du degré de dégradation. Parmi les techniques de nettoyage, citons l'utilisation de tampons abrasifs en nylon, de papier de verre ou de toile émeri, de paille de fer, de disques de ponçage ou le sablage, à sec ou non. Après ces traitements mécaniques, on devra éventuellement envisager un nettoyage complémentaire à l’aide de dégraissants.
Dépoussiérage, dégraissage
Si vous dépoussiérez une surface en soufflant de l'air comprimé, veillez à utiliser un filtre pour ôter tous les résidus d'huile ou de graisse qui pourraient être contenus dans l’air. Pour le dépoussiérage, préférez les aspirateurs. Toutes les surfaces non poreuses doivent être nettoyées avant application du Sikaflex
®
.
N'utiliser que les produits de nettoyage recommandés par Sika
®
. Les solvants, comme le White-Spirit ne sont pas conseillés car ils contiennent des résidus qui peuvent par la suite réduire l’adhérence.
N'utilisez que des chiffons propres et nonpelucheux, et remplacez-les fréquemment pour éviter que les salissures enlevées dans un premier temps ne soient redéposées sur les surfaces. Les substrats nettoyés doivent être parfaitement secs avant de passer à l’étape suivante.
Note : Certains dégraissants, comme le
Sika
®
Cleaner-205, ne doivent pas être utilisés sur des substrats poreux car des solvants non-évaporés pourraient avoir une action néfaste sur la polymérisation du Sikaflex
®
.
Les solvants à base d'alcool empêchent la polymérisation des colles et mastics
à base de polyuréthanne.
Autres traitements
Certains substrats – polyéthylène (PE), polypropylène (PP) ou polyoxyméthylène
(POM) – requièrent un traitement de surface plus élaboré comme un décapage
à l'acide ou une décharge électrique pour permettre une bonne adhérence. Dans ces cas, contactez votre représentant local Sika pour obtenir les conseils nécessaires.
3.5 Application d’un primaire
Peu de surfaces sont idéales pour le collage : l'application d'un primaire est un moyen de transformer le substrat de manière chimique et/ou physique, en un terrain parfaitement adapté au collage, renforçant ainsi l’adhérence à long terme.
Le moyen le plus simple pour créer ce terrain propice consiste à appliquer sur les surfaces un promoteur d’adhérence
(comme le Sika
®
Activateur), qui réagit avec le matériau pour accroître son pouvoir réactif et la mouillabilité de la colle.
Les surfaces particulièrement poreuses et/ou rugueuses nécessitent l'application d'un primaire filmogène pour égaliser la surface et permettre une meilleure adhérence du joint de colle.
Dans certains cas, les primaires filmogènes évitent également que les plastifiants et autres agents de texture présents dans la colle à l’état frais soient absorbés par le substrat, ce qui pourrait entraîner une décoloration ou des problèmes de crazing (PC, PMMA...).
Laissez toujours soigneusement sécher les primaires avant d'appliquer la colle
Sikaflex
®
. Si vous avez attendu trop longtemps après l'application d'un primaire, les surfaces concernées doivent être réactivées. Les temps de séchage minimaux et maximaux sont donnés dans ce manuel et récapitulés en fin d’ouvrage.
Les surfaces traitées doivent être protégées de toute contamination – poussières et salissures, graisses, vapeur, humidité, etc. – jusqu'à l’application de la colle.
Veuillez noter que les flacons de primaire doivent être agités avant l'emploi. Veillez
à bien les reboucher après utilisation.
13
3.6 Conditions générales d’application
Préparation et planification
Une préparation et une planification soignées des opérations garantiront une application sans problème et sans surprise. Il est essentiel de commencer par identifier les matériaux utilisés et analyser leur aspect de surface pour choisir la colle qui convient et la méthode de préparation adéquate. Les agents de démoulage, les composants non-stabilisés ou volatiles etc., influent sur la qualité de l’adhérence du joint final. En cas de doute, nous recommandons fortement de procéder à des essais préliminaires et d'effectuer des tests de compatibilité en contactant votre représentant local Sika.
L'atelier
L'atelier doit être propre et bien organisé, convenablement éclairé et bien ventilé.
Ces conditions sont essentielles pour réaliser un travail de qualité dans des conditions de confort optimales. Pour l’application des primaires et des colles, la température ambiante doit être comprise entre +5°C et +35°C (idéalement entre
+15°C et +25°C). La zone dédiée au nettoyage général et aux opérations d'abrasion doit être distincte de la zone d'application des primaires et des colles.
Veillez à ce que chaque poste de travail dispose du matériel nécessaire et qu'il soit possible de protéger convenablement les surfaces si nécessaire.
Préparation : liste de contrôle
Poste de travail propre, stable ; matériel de marquage pour délimiter la zone de collage sur les substrats
Pistolet à air comprimé avec filtre à huile ou aspirateur pour éliminer les poussières des surfaces à coller
Papier de nettoyage ou chiffon propre et non-pelucheux
Pinceau brosse ou tampon feutre neuf pour chaque type et chaque application de primaire
Bande de masquage douce, nonabsorbante, sans silicone et résistante au déchirement
Gants de travail
Ventilation adéquate
Collage : liste de contrôle
Pistolet à air comprimé ou manuel fiable
Régulateur de pression sur le pistolet à air comprimé pour régler le débit d'extrusion de la colle
Outil pour ouvrir l’emballage de la colle
Couteau tranchant pour tailler la buse
Cales d'espacement souples, d’une dureté Shore comparable à celle de la colle ou du mastic Sikaflex
®
à employer, pour garantir une épaisseur correcte du joint
Outils de maintien (serre-joints, lest) des pièces assemblées pour éviter qu'elles ne glissent
Spatules pour retirer la colle en excédent
Sika
®
Remover-208 pour éliminer les résidus de colle non polymérisée
Sika
®
Tooling Agent N pour lisser les joints de Sikaflex
®
3.7 Application des Sikaflex
®
Les colles et mastics d'étanchéité
Sikaflex
® sont proposés dans des viscosités différentes – du produit spatulable jusqu'aux pâtes très thixotropes – le choix de la viscosité dépendant de l'application. Ces produits sont conditionnés en cartouches, recharges souples, tonnelets et fûts. Ils peuvent être appliqués
à l’aide de pistolets manuels, pneumatiques ou électriques et, pour les tonnelets et fûts, à l'aide de systèmes de pompage hydrauliques ou pneumatiques spécialement conçus.
Le choix du matériel dépend de la fréquence, du type et de l'environnement de l'application. Les longs joints continus – par exemple pour coller des gates ou pour des applications d’assemblage du pont à la coque – demandent une main sûre et expérimentée. Les pistolets pneumatiques ou électriques sont dans ce cas une aide certaine pour obtenir une distribution uniforme et extruder les Sikaflex
®
à haute viscosité comme par exemple le Sikaflex
®
-296 ou le
Sikaflex
®
-292.
La forme et la découpe de la buse interviennent de façon importante dans la réalisation d'un joint correct. Pour une étanchéité bord à bord, coupez la buse en biseau de sorte que la dimension de l'ouverture convienne à la taille du joint.
Les joints profonds doivent être remplis en commençant par le fond pour éviter l’emprisonnement de bulles d'air. Si besoin est, masquez les abords de la zone de collage avec un ruban de masquage que vous retirerez immédiatement après application de la colle pour une finition impeccable.
Pour les applications de collage faisant intervenir des produits thixotropes, nous recommandons d’appliquer la colle sous forme de cordons triangulaires : ces cordons se déforment et s'écrasent sous l'effet de la pression lors de l’assemblage des pièces pour former un joint de colle plat et uniforme, qui garantit la plus grande zone de contact entre la colle et les supports.
Exemples de découpe des buses pour différents types d’application :
Buse originale
Buse coupée pour cordon rond
Section en V pour cordon triangulaire
15
3.8 Les différentes étapes de la polymérisation
Les colles et mastics polyuréthanne monocomposant Sikaflex
® poly- mérisent sous l’action de l’humidité contenue dans l’air pour former un élastomère. Ces produits possèdent d'excellentes propriétés d’adhérence et développent une résistance mécanique
élevée une fois la polymérisation achevée.
La réaction chimique de polymérisation des polyuréthannes monocomposant
Sikaflex
® nécessite quelques précautions en matière de délai de manipulation des assemblages et de temps de polymérisation.
Délai de manipulation de l’assemblage
Le délai avant manipulation et le délai avant mise en service dépendent des contraintes appliquées, mais aussi de la diffusion de l'humidité depuis l’extérieur jusqu’au cœur du cordon de
Sikaflex
®
. La vitesse de polymérisation et la montée en résistance peuvent varier de manière significative en fonction de la conception du joint, de la porosité du ou des substrats, de l'hygrométrie absolue de l'air, de la température ambiante et de la température du substrat.
Le délai avant manipulation des assemblages et le temps nécessaire à la polymérisation peuvent varier en fonction des efforts que le joint doit supporter et de la configuration de l’assemblage.
Temps de polymérisation
Le temps de polymérisation est la durée nécessaire à la colle pour polymériser jusqu'à obtention de la résistance maximale de l’assemblage.
Temps ouvert
Le temps ouvert est la période qui s’écoule entre l’application de la colle et l’affichage du second support à assembler.
Ce temps est toujours inférieur au temps de formation de peau. Le temps ouvert des Sikaflex
® varie en fonction du type de colle choisi et des conditions atmosphériques.
Un joint bien conçu permet à l'humidité de diffuser depuis toutes les faces du joint et contribue à l'optimisation des temps de production. Sika a en outre mis au point des systèmes spécifiques permettant de réduire les temps de polymérisation et d’accroître la productivité.
Consultez votre représentant local Sika.
Courbe de polymérisation type
0 2 4 6 8 10
Durée (en jours)
23°C, 50% HR
10°C, 50% HR
H
2
O
H
2
O H
2
O
H
2
O H
2
O H
2
O
Instructions
relatives à la mise en oeuvre des produits de la gamme Sika Marine
17
4.1 Ragréage, collage et calfatage de ponts en teck
Description de l'application
Le teck, matériau noble, est utilisé depuis des centaines d'années dans la construction de ponts de navires et de bateaux car il est imputrescible. En plus de renforcer la structure du pont proprement dit, le teck contribue à l'isolation thermique des cabines intérieures, par temps froid comme par temps chaud.
Mais la meilleure raison de posséder un pont en teck reste sans doute l’aspect luxueux qu’il confère à un navire et qu’aucun autre matériau ne peut égaler.
L'installation de ce matériau très esthétique nécessite néanmoins beaucoup de soins. Il faut en effet éviter toute stagnation ou fuite d'eau qui pourrait causer des dommages sévères tels que traces disgracieuses sur la coque, dégradation des éléments en bois et corrosion des parties métalliques. Une étanchéité parfaite est donc essentielle. Le teck n'est en outre pas un matériau constant : les teneurs en huiles, en graisses et en résine, ainsi que la porosité peuvent être très différentes d'un bois à l'autre, en fonction de son âge et de son origine. Les instructions de mise en œuvre qui suivent détaillent les procédures à respecter pour le ragréage, le collage et le calfatage de ponts revêtus de teck avec les produits Sika. Le respect de ces procédures vous permettra d'obtenir un pont parfaitement étanche pendant des années. Par ailleurs, l'utilisation du
Sikaflex
®
-290 DC, confèrera à votre pont, même mouillé, des propriétés antidérapantes.
Conditions générales
Les meilleurs résultats sont obtenus à une température constante ou décroissante, comprise entre +5°C et +25°C avec une hygrométrie ambiante inférieure
à 75%.
Pendant toute l'opération, et plus particulièrement pendant le calfatage proprement dit, protégez impérativement les surfaces de travail de la pluie et de l'exposition directe au soleil.
Après application des produits Sika pour les ponts en teck, les surfaces doivent
être protégées des intempéries pendant une durée minimum de 8 heures.
Pour la réussite de l'opération, il est important de travailler dans un espace convenablement organisé et bien ventilé.
Qualité du bois
Les lattes de teck doivent être taillées dans la longueur, anneaux annuels verticaux.
La teneur en humidité au cœur du bois ne doit pas dépasser 12% : une humidité initiale trop importante peut provoquer un retrait excessif des différentes lattes de teck dans une atmosphère plus sèche, engendrant ainsi des tensions importantes sur le joint de Sikaflex
®
-290 DC et pouvant entraîner sa rupture.
Les lattes
Les lattes de teck sont disponibles dans des dimensions et des qualités différentes. Dans leur forme la plus simple, les lattes sont symétriques (A). La souplesse du Sikaflex
®
-290 DC permet de compenser les dilatations et retraits liés aux variations de température et d’hygrométrie. Il est également possible, en principe, d'utiliser des lattes de teck asymétriques (B) avec une rainure de séparation d'un seul côté. Toutefois, le dimensionnement et l'application du fond de joint demandent davantage de soin.
A
B
Instructions pour le ragréage, le collage et le calfatage de ponts en teck
Les lattes de teck sont en général posées sur un pont en acier, aluminium, bois, contreplaqué ou polyester. Si le pont présente des irrégularités, les substrats doivent être ragréés pour éviter toute accumulation d'eau sous le teck (source de corrosion). En raison de leur mode d'assemblage (soudure), les ponts en acier et aluminium nécessitent un ragréage quasi-systématique. Avant cette opération, les substrats doivent être convenablement préparés (voir ci-contre).
Le ragréage s'effectue avec le
SikaTransfloor
®
-352 SL, un système polyuréthanne bi-composant auto-lissant
à polymérisation rapide qui présente d'excellentes qualités d'adhérence sur les surfaces apprêtées avec le Sika
®
Icosit ZP
Primer et permet de récupérer les différences de niveau du pont.
Le pont doit être protégé de tout contact avec l'eau, et ce pendant l'ensemble des opérations de préparation du pont, mélange du produit, application, ainsi que pendant toute la durée de la polymérisation. Il convient également de prendre en compte le point de rosée, afin d'éviter toute condensation sur le pont.
Préparation des substrats avant ragréage
Ponts en aluminium ou en acier (y compris revêtus d’un primaire atelier)
Acier : la surface à coller doit être sablée à SA 2,5 conformément à la norme
DIN 55928 partie 4.
Aluminium : Poncer légèrement la surface à coller.
Dépoussiérer consciencieusement les substrats.
Dégraisser la surface à coller avec le Sika
®
Cleaner-205.
Temps de séchage : minimum 10 minutes - maximum 2 heures
Appliquer une couche régulière de Sika
®
Icosit ZP Primer sur toute la surface
(Fig. A) à l'aide d'un pinceau ou d'un rouleau propre à raison de 200 g / m
2.
Temps de séchage :
10°C mini 4 h – maxi 24 h
20°C mini 3 h – maxi 24 h
30°C mini 2 h – maxi 14 h
Protéger de toute salissure. Si nécessaire, nettoyer à l'eau et laisser sécher complètement avant de passer à l'étape suivante
Note
Disponibilité des produits
Les besoins en système de ragréage
SikaTransfloor
®
-352 SL et Sika
®
Icosit ZP
Primer étant peu fréquents, en particulier sur les bateaux de plaisance, ces produits ne sont pas tenus en stock par Sika
France, mais fabriqués à la demande.
Nous consulter pour les délais de livraison sur ces 2 produits.
Fig. A
Ragréage du pont
Le SikaTransfloor
®
-352 SL est un produit de ragréage qui forme une couche légère et isolante (isolation phonique) sur laquelle il est possible de coller sans primaire les lattes de teck avec le Sikaflex
®
-
298.
Le ragréage n'est pas nécessaire si le pont présente des différences de niveau inférieures à 1-1.5 mm. Si aucun ragréage n'est nécessaire, consultez les recommandations suivantes sur la préparation des substrats et continuez avec l'application de la colle.
Dans le cas contraire, pendant le temps qui sépare la polymérisation du produit de ragréage et l'application de la colle, la surface du SikaTransfloor
®
-352 SL doit
être protégée de toute salissure : traces de pas, poussière, graisses, huiles, etc.
En cas de salissure apparente, recommencez la procédure de nettoyage à l'aide d'un nettoyant à l'eau et attendre un séchage complet.
Poncer la surface du SikaTransfloor
®
-352
SL et aspirer les poussières avant d'appliquer le Sikaflex
®
-298.
19
Fig. A
Fig. B
1 - Soudure
2 - SikaTransfloor
®
-352 SL
3 - Pont métallique
4 - Icosit
®
ZP Primer
1
Ajouter le composant B du SikaTransfloor
®
-352 SL au composant A préalablement remué. Mélanger au mélangeur mécanique à vitesse moyenne pendant 3 minutes pour éviter l’emprisonnement d’air. Transvaser le produit obtenu dans un autre fût en raclant les bords et le fond, puis mélanger encore une minute avant de faire couler le produit sur le pont (fig. A, B et C). Ne jamais appliquer directement sur le pont le produit restant dans le fond du seau : transvaser ce qui reste de produit dans le seau de préparation suivant, etc.
Etaler le SikaTransfloor
®
-352 SL mélangé sur le pont à l’aide d’une spatule plate ou crantée de manière à obtenir une épaisseur dépassant légèrement le point le plus élevé du pont en aluminium ou en acier (Fig. D). Ne pas appliquer le produit en couche supérieure à 30 mm ni sur des ponts dont l’inclinaison est supérieure à
3°. Si cela est nécessaire, procéder en plusieurs opérations consécutives jusqu'au ragréage désiré. Un ponçage suivi d'un dépoussiérage est recommandé entre chaque couche.
Conditions climatiques de travail : entre +10°C et +35°C et hygrométrie ambiante
75% max.
Temps de séchage : on peut marcher sur le revêtement 24 heures après la pose, et commencer l'étape suivante.
La présence de gouttes d'eau ou de condensation sur le pont préparé entraînera des pertes d'adhésion. Respecter le point de rosée entre la phase de préparation de surface et l'application du SikaTransfloor
®
-352 SL.
3
2
4
Fig. C
Fig. D
Préparation des substrats avant collage des lattes de teck
Ponts ragréés avec le SikaTransfloor
®
-352 SL
Poncer légèrement la zone à coller et aspirer les poussières.
Nettoyer le support avec le Sika
®
Cleaner-205 et un chiffon ou un papier sec, propre, non-pelucheux et régulièrement renouvelé .
Temps de séchage : minimum 10 minutes - maximum 2 heures
Ponts GRP (Plastique renforcé fibres de verre)
Commencer par nettoyer les surfaces très souillées à l'aide d'un solvant pur (Sika
®
Remover-208) pour retirer les traces les plus importantes.
Poncer légèrement la zone à coller avec un papier de verre très fin. Aspirer les poussières.
Nettoyer le support avec le Sika
®
Cleaner-205 et un chiffon ou un papier sec, propre, non-pelucheux et régulièrement renouvelé .
Temps de séchage : minimum 10 minutes - maximum 2 heures
Appliquer une couche mince et régulière de Sika
®
Primaire-206 G+P ou de Sika
®
Primaire-
215 à l'aide d'un pinceau propre ou d'un tampon applicateur en feutre (Fig. A).
Temps de séchage : minimum 30 minutes - maximum 24 heures
Ponts en bois, contre-plaqué etc., et planches de teck
Poncer la surface de collage sur le pont avec un papier de verre 80/100 et aspirer les poussières.
Appliquer une couche mince et régulière de Sika
®
Primaire-290 DC à l'aide d'un pinceau propre ou d'un tampon applicateur en feutre (Fig. B).
Temps de séchage : minimum 60 minutes - maximum 24 heures
Fig. A
Fig. B
21
Collage des lattes de teck
Les lattes seront positionnées à sec afin de repérer leur emplacement. Le système de fixation temporaire devra être déterminé avant de retirer les lattes et d'appliquer sur celles-ci une couche mince et régulière de Sika
®
Primaire-290 DC. Respecter un temps de séchage minimum d'une heure avant de coller les lattes sur le pont.
Fig. A
Appliquer le Sikaflex
®
-298 sur la surface préalablement préparée et répartir le produit sur la zone à couvrir à l'aide d'une spatule crantée (dents de 3 à 5 x 5 mm).
La quantité à appliquer dépend de la régularité de la surface. Veiller à réaliser un film continu de 2 mm d’épaisseur de Sikaflex
®
-298 pour éviter tout risque de pénétration d'eau sous le pont en teck (Fig. A et B).
Les lattes de teck doivent être mises en place avec précision dans les 20 à 30 minutes (à 20°C) qui suivent l’application de la colle et fermement pressées. Pour cette raison, nous recommandons fortement de n'appliquer la colle que sur une surface limitée qu'il sera possible de recouvrir dans le temps imparti (Fig. C).
Utiliser des serre-joints, du lest ou des vis (à retirer après la prise de la colle) pour assurer un contact parfait entre les lattes et la colle, et maintenir les lattes en place le temps nécessaire à la prise de la colle. Vous pouvez également, pour les petits panneaux préfabriqués, utiliser la méthode de presse par le vide.
Le délai de maintien à l'aide de fixations temporaires dépend de la température, de l'humidité ambiante et du niveau de pression exercé sur les lattes. A titre d'exemple, des lattes posées à plat ne nécessitent que 12 heures de maintien si la température est supérieure à 18°C.
Les panneaux atteignent leur capacité de charge maximale après 24 heures environ, et les fixations temporaires peuvent alors être retirées en toute sécurité.
Les traces de Sikaflex
® non-polymérisé peuvent être enlevées des supports non poreux et du matériel à l'aide du Sika
®
Remover-208. Ne jamais utiliser de dégraissant, ni le Sika
®
Cleaner-205 pour cette tâche. Sur le bois, laisser les résidus de
Sikaflex
® polymériser complètement, puis les enlever mécaniquement.
Fig. B
Fig. C Fig. D Fig. E
Calfatage des ponts en teck
Suivant sa forme et sa fabrication, un pont peut être soumis à des mouvements importants. Ceci vaut également pour les ponts en acier où les lattes sont boulonnées, en particulier lors de la construction du bateau. Lorsqu'il est appliqué correctement, le Sikaflex
®
-290 DC peut contenir des mouvements allant jusqu'à
10% de la largeur moyenne du joint (1 mm de mouvement pour un joint de 10 mm de large). Ce coefficient doit être pris en compte dès le début des travaux. Le bois brut quant à lui subit des déformations en raison, non seulement des variations de températures, mais surtout des variations dans sa teneur en humidité.
Un bois sec a une teneur en humidité inférieure à 12%. En service, la teneur en humidité d'un pont de bateau en bois brut peut varier entre 5% et 20 %. Des difficultés considérables apparaissent lorsqu'un bois insuffisamment sec est utilisé dans la construction d'un pont. Les bois utilisés doivent avoir une teneur en humidité inférieure à 12% pour éviter un retrait excessif du bois en service.
L'épaisseur des lattes de teck sera idéalement comprise entre 6 et 22 mm. Des lattes plus fines tendent à se recourber sous l'effet de la chaleur et de l'humidité, induisant sur le haut du joint de calfatage une déformation supérieure aux 10% préconisés. Ceci peut causer une dégradation rapide du calfatage et de l'adhérence du joint sur le bois. Pour éviter ce phénomène, la latte devra être collée sur toute sa surface avec le Sikaflex
®
-298.
Le teck sera idéalement coupé dans le sens radial pour minimiser les distorsions et le retrait.
La largeur de la rainure doit impérativement être fonction de sa profondeur et de la largeur de la latte. Nous donnons page suivante les recommandations correspondantes. Si vos dimensions sont incompatibles avec nos propres recommandations, veuillez contacter votre représentant local Sika.
Préparation des rainures
L'application d'un primaire sur les lattes est une étape essentielle du procédé de calfatage avec le Sikaflex
®
-290 DC. La qualité finale du joint peut être grandement affectée – de même que la durée de vie du pont – si les recommandations ne sont pas expressément respectées. L'application du primaire peut commencer après le nettoyage et le dégraissage soignés des lattes de teck.
Pour obtenir une adhérence durable du Sikaflex
®
-290 DC sur les bords des joints, ceux-ci doivent être méticuleusement préparés. Toute substance étrangère doit être éliminée et les rainures doivent être propres et sèches avant l'application du primaire. Pour de meilleurs résultats, utiliser un aspirateur industriel haute puissance. Ne pas employer d'appareil pneumatique à moins qu'il ne soit
équipé d'un filtre séparateur d'huile car le teck absorbe facilement les graisses. Il est fortement recommandé de procéder à un dégraissage des faces de la rainure
à l'aide d'un chiffon non-pelucheux imbibé d'acétone ou de MEC (Méthyl Ethyl
Cétone). Le chiffon sera remplacé régulièrement pour éviter de souiller de nouveau les surfaces propres. Attendre 10 minutes pour que le produit s'évapore naturellement. Attention : ces solvants sont inflammables et les précautions nécessaires doivent être prises.
Appliquer une couche fine et continue de Sika
®
Primaire-290 DC sur les côtés des rainures, à l'aide d'un pinceau ou d'un spray. Veiller à bien recouvrir la totalité des surfaces, en passant le pinceau d'avant en arrière. Le Sika
®
Primaire-290 DC est un primaire filmogène : la couche appliquée doit briller légèrement, même lorsque le produit est sec. Températures de travail +5°C à +35°C, hygrométrie ambiante
75 % max. (Fig. D).
Temps de séchage : minimum 60 minutes - maximum 24 heures.
Protéger la zone traitée avec le primaire de la poussière et de la pluie, et laisser sécher la couche de primaire une heure au moins avant de commencer le calfatage proprement dit. Les deux opérations, apprêt et calfatage, ne doivent pas être séparées de plus de 24 heures : une fois ce délai écoulé, il faudra appliquer une nouvelle couche de primaire. Ne pas laisser le primaire s’accumuler dans le fond de joint, ceci pouvant générer des phénomènes de bullage.
Application du fond de joint
Le Sikaflex
®
-290 DC est conçu pour absorber les mouvements latéraux des lattes de teck lorsqu'elles se dilatent ou se rétractent sous l'effet des variations climatiques ou de la teneur en eau du bois. Pour permettre au pont de "bouger", il est impératif d'éviter à tout prix le collage de la partie basse de la rainure. Pour cela, un fond de joint est appliqué au fond de la rainure dès que le primaire est sec
(Fig. E).
Retrait tangentiel en % pour une variation de 1% de la teneur en humidité
Teck de 0.24 à 0.3 %
Retrait radial en % pour une variation de
1% de la teneur en humidité
de 0.13 à 0.18 %
Pour des joints soumis à des déformations importantes, consulter nos services techniques
23
Application du Sikaflex
®
-290 DC
¤
Dès que le primaire est sec et que le fond de joint a été mis en place, le calfatage peut commencer.
Avant d’entreprendre le travail, vérifier que la température du bois ne dépasse pas
25 °C. Par ailleurs, la température ambiante pendant l'application doit rester constante ou décroître lentement, elle sera idéalement comprise entre +5°C et +25 °C.
Appliquer le Sikaflex
®
-290 DC en veillant à ne pas laisser d'air dans la rainure.
Pour cela placer l’extrémité de la buse au contact du fond de la rainure et maintenir le pistolet à un angle de 60 à 90 °. Utiliser uniquement un pistolet manuel ou un pistolet pneumatique à piston. Tirer la buse pour que le joint se forme derrière elle en veillant à conserver un mouvement régulier (Fig. A).
Après application du Sikaflex
®
-290 DC et avant la formation de peau, retirer l'excédent de produit de la surface du pont à l'aide d'une spatule souple maintenue à
45° : cette opération permet de s'assurer que la rainure est parfaitement remplie.
Protéger l’ensemble de la surface à calfater avant, pendant, et durant les 8 heures qui suivent le calfatage de la pluie et du rayonnement solaire. Ne pas utiliser le matériau excédentaire tiré à la spatule pour remplir les rainures.
Après 7 jours, le Sikaflex
®
-290 DC est prêt pour le ponçage.
Largeur de la latte
(mm) (in)
35
45
50
75
100
125
4
5
2
3
1
3
/
8
1
3
/
4
Largeur du joint
(mm) (in)
4
4 à 5
5 à 6
8
10
12
5
/
32
5
/
32
–
3
/
16
3
/
16
–
1
/
4
5
/
16
13
/
32
2
/
3
Profondeur du joint
(mm) (in)
6
7
4 à 5
6
8
10
3
/
16
–
1
/
4
1
/
4
1
/
4
9
/
32
5
/
16
13
/
32
Ponçage
Après 7 jours de polymérisation, le pont peut être poncé. Pour un résultat optimum, utiliser une ponceuse industrielle.
Nous recommandons de commencer le ponçage avec un grain moyen (80) avant de continuer avec un grain plus fin (120 ou plus). Utilisez de préférence une ponceuse à bande ou une ponceuse vibrante. Poncez toujours dans le sens du bois (Fig. B).
Note
Les ponts en teck préfabriqués se présentent souvent sous forme de panneaux multicouches, c'est-à-dire d'un support en bois sur lequel a été collée une fine couche de teck. Les pores des différentes essences de bois sont de tailles et de structures différentes, et le produit de calfatage n'est pas toujours en mesure de les remplir et d'évacuer les poches d'air. En conséquence, des bulles peuvent apparaître à la surface du joint pendant l'opération. Pour éviter la formation de ces bulles d'air, nous recommandons de lisser les joints à l'aide d'une spatule flexible tirée à un angle de 45° : vous pourrez ainsi faire sortir l'air des pores et obtenir un joint parfait après polymérisation.
Fig. A
Fig. B
Finition et entretien
Le teck non traité prend en vieillissant une teinte naturelle gris argent qui n’a pas d’influence sur les propriétés mécaniques ou physiques du bois.
Compte tenu de la résistance naturelle du teck (bois imputrescible), l’utilisation de peintures ou de revêtements de protection n’est ni nécessaire, ni recommandée.
Les peintures et les laques sont des revêtements décoratifs qui, appliqués sur les ponts en teck, forment en séchant un film continu (lattes et joints). Certaines peintures ne sèchent pas correctement au contact des produits de calfatage et laissent ainsi la surface collante. Avec le temps, la plupart des peintures s’écaillent le long du joint. Ce phénomène qui nuit à l’apparence du pont peut créer des fissures le long des joints.
Si toutefois une vitrification est envisagée, il convient d’être très prudent sur le choix du produit utilisé et de respecter les règles suivantes :
Ne jamais vitrifier tant que le
Sikaflex
®
-290 DC n’est pas parfaitement polymérisé. Nous recommandons d’attendre au moins un mois entre la pose du Sikaflex
®
-290 DC et celle d’un produit de vitrification.
et le nettoyage du teck, il nous est impossible de fournir des recommandations exhaustives pour chaque dénomination commerciale. C’est pourquoi nous nous limiterons ici à donner des conseils d’utilisation de la gamme d'entretien Sika
Marine, dont la compatibilité avec le
Sikaflex
®
-290 DC a été testée dans nos laboratoires.
Sika
®
Teak Oil
Cette huile de protection et d'entretien ne doit jamais être appliquée en plein soleil et nous recommandons de ne la laisser agir que quelques minutes et d'essuyer l'huile en excès sur le bois et les joints.
Sika
®
Teak Cleaner et
Sika
®
Teak Brightener
Les nettoyants et ravivants pour le teck contiennent des additifs qui peuvent attaquer le produit de calfatage et le bois.
C'est pourquoi il est impératif de ne pas laisser agir ces produits trop longtemps
(2 à 3 minutes pour le Cleaner, 5 minutes pour le Brightener), et de rincer abondamment le pont à l'eau douce dans les
15 minutes qui suivent l'application du produit.
La compatibilité du produit doit être
évaluée sur une petite zone avant toute application générale.
Au vu de l’extrême diversité des produits commercialisés pour la protection
Note :
Lors de l'application de ces 3 produits, les surfaces adjacentes (gel coat et autres matériaux) doivent être protégées, et d'éventuelles éclaboussures immédiatement nettoyées.
Les salissures importantes peuvent être enlevées en frottant avec une éponge dure. L’utilisation de nettoyeurs hautepression n’est pas recommandée, l’eau sous pression enlevant des écailles de bois et pouvant détruire le joint de calfatage.
Pendant les périodes de chaleur ou de sécheresse prolongées, les ponts en teck devront être mouillés régulièrement pour
éviter que le bois ne se dessèche complètement. Une perte d’humidité excessive amène un retrait important du bois qui peut, dans des conditions défavorables (et particulièrement lorsque les recommandations Sika en matière de dimensionnement des joints n’ont pas été respectées) amener un vieillissement prématuré ou une rupture du joint.
Les produits d'entretien Sika Marine protègent et embellissent les ponts en teck neufs ou anciens. Ces produits peuvent
également être utilisés pour entretenir la beauté naturelle d'autres essences de bois employées au-dessus de la ligne de flottaison.
Conseils d'utilisation
Porter des gants en caoutchouc et des lunettes de protection,
Bien agiter les bidons avant ouverture,
Assurer une bonne ventilation des lieux confinés (intérieur du bateau),
Tester la compatibilité du produit sur une petite surface avant de procéder au traitement complet,
Lire attentivement les instructions de mise en œuvre détaillées dans notre brochure " Sika Marine, Système d'entretien des ponts en teck ".
25
4.2 Collage d’éléments en bois
Description de l'application
Sur les yachts et les navires de plaisance comme sur les grands paquebots de ligne, les escaliers, les échelles de descente et les rampes sont souvent fabriqués à partir de bois tropicaux durs, choisis pour leur longévité et leur beauté. La fixation mécanique de ces bois peut réduire leur longévité et altérer leur aspect, en raison de l'infiltration d'humidité par les trous de perçage. Il est donc préférable de coller ces pièces. L'absence de perçage prévient les infiltrations et l’endommagement du bois, ce qui est particulièrement important pour les échelles.
Par ailleurs, le collage offre d'autres avantages. La couche de colle contribue à amortir les bruits de pas et autres vibrations. Il est possible de conserver l'intégrité des surfaces peintes sans perdre la protection contre la corrosion, et d'éliminer les conséquences délétères d'une
éventuelle infiltration d'eau dans le GRP.
Préparation des substrats
Bois non traités (teck, acajou)
Poncer la surface à coller avec un papier de verre 80/100 et aspirer les poussières.
Appliquer une couche mince et régulière de Sika
®
Primaire-290 DC à l'aide d'un pinceau propre ou d'un tampon applicateur en feutre.
Temps de séchage : minimum 60 minutes - maximum 24 heures
GRP
Commencer par nettoyer les surfaces très souillées à l'aide d'un solvant pur (Sika
®
Remover - 208) pour retirer les traces les plus importantes.
Poncer légèrement la zone à coller avec un papier de verre très fin (80/100).
Aspirer les poussières.
Nettoyer le substrat avec le Sika
®
Cleaner-205 et un chiffon ou un papier sec, propre, non-pelucheux et régulièrement renouvelé.
Temps de séchage : minimum 10 minutes - maximum 2 heures.
Appliquer une couche mince et régulière de Sika
®
Primaire-206 G+P, de Sika
®
Primaire-210 T ou de Sika
®
Primaire-215 à l'aide d'un pinceau propre ou d'un tampon applicateur en feutre.
Temps de séchage : minimum 30 minutes - maximum 24 heures.
Acier inoxydable (échelles par exemple)
Commencer par nettoyer les surfaces très souillées à l'aide d'un solvant pur (Sika
®
Remover - 208) pour retirer les traces les plus importantes.
Poncer légèrement la zone à coller avec un tampon Scotch-Brite très fin. Aspirer les poussières.
Nettoyer le substrat avec le Sika
®
Cleaner-205 et un chiffon ou un papier sec, propre, non-pelucheux et régulièrement renouvelé.
Temps de séchage : minimum 10 minutes - maximum 2 heures.
Appliquer une couche mince et régulière de Sika
®
Primaire-210 T à l'aide d'un pinceau propre ou d'un tampon applicateur en feutre.
Temps de séchage : minimum 60 minutes - maximum 24 heures.
Bois, aluminium ou acier recouvert d'une laque bi-composant
Nettoyer le substrat avec le Sika
®
Cleaner-205 et un chiffon ou un papier sec, propre, non-pelucheux et régulièrement renouvelé.
Temps de séchage : minimum 10 minutes - maximum 2 heures.
Pour la préparation d'autres substrats, consultez le tableau d'utilisation des primaires en fin d’ouvrage.
Application du Sikaflex
®
-292
¤
Positionner des cales d'espacement d’une épaisseur de 2 mm, et d’une dureté
Shore A de 50 (ne surtout pas les fixer avec une colle cyanoacrylate).
Appliquer le Sikaflex
®
-292 sur toute la surface de collage. Sur de grandes surfaces, le Sikaflex
®
-292 peut être appliqué à l’aide d’une spatule crantée (dents 4 x 4 mm).
Assembler les composants dans les 20 minutes qui suivent l'application de la colle.
Maintenir les pièces en place à l'aide d’instruments appropriés (serre-joints, etc.) pour comprimer la colle jusqu'à la hauteur des cales d'espacement. Enlever l'excès de colle sur tout le pourtour du joint à l'aide d'une spatule souple.
Note : La pression exercée ne doit pas être excessive. Si vous utilisez des vis comme fixations complémentaires, serrez-les suffisamment pour maintenir, mais pas davantage, jusqu'à ce que la colle ait pris. Attendez 24 heures avant de serrer définitivement.
Les traces de Sikaflex
® non-polymérisé peuvent être enlevées à l'aide du Sika
®
Remover-208. N'utiliser sous aucun prétexte un agent de nettoyage, ni le Sika
®
Cleaner-205 pour cette tâche.
Les fixations temporaires (serre-joints, etc.) peuvent être retirées après 12 heures.
La résistance et la dureté finales sont atteintes après 7 jours.
Important :
Consultez les notices techniques et les fiches de sécurité Sika qui sont à votre disposition auprès de votre représentant local Sika.
27
4.3 Collage de revêtements de pont antidérapants
Description de l'application
Les revêtements de pont ou les tapis en résine de synthèse offrent une surface antidérapante sûre ainsi qu'un moyen de protection contre les chocs et les fuites.
L'utilisation d'une colle polyuréthanne maximise l'efficacité de ces revêtements, en facilite l'installation et garantit une finition professionnelle.
Les marques de revêtements de ponts les plus couramment utilisées sont :
T B S
Anti-slide
Treadmaster
Lay Tech
Polygrip
Nautoflex
Norament
Marine Deck 2000
Floormaster
Gates Rubber Co
Les colles polyuréthanne monocomposant donnent d'excellents résultats avec tous ces produits. Leur mise en place est simple, et les performances à long terme de la colle utilisée offrent un grand nombre d'avantages.
Note : Compte tenu de la grande vari-
été de revêtements de pont existant sur le marché, il est toujours recommandé de procéder à un test pour vérifier la bonne tenue du collage.
Préparation des substrats
Ponts GRP
Commencer par nettoyer les surfaces très souillées à l'aide d'un solvant pur (Sika
®
Remover-208) pour retirer les traces les plus importantes.
Poncer légèrement la zone de collage avec un papier de verre très fin (Scotch-
Brite M 600). Aspirer les poussières.
Nettoyer le substrat avec le Sika
®
Cleaner-205 et un chiffon ou un papier sec, propre, non-pelucheux et régulièrement renouvelé.
Temps de séchage : minimum 10 minutes - maximum 2 heures.
Ponts en bois
Poncer la surface à coller avec un papier de verre 80/100 et aspirer les poussières.
Appliquer une couche mince et régulière de Sika
®
Primaire-290 DC à l'aide d'un pinceau propre ou d'un tampon applicateur en feutre.
Temps de séchage : minimum 60 minutes - maximum 24 heures
Ponts en aluminium recouverts d'une laque bi-composant
Nettoyer le substrat avec le Sika
®
Cleaner-205 et un chiffon ou un papier sec, propre, non-pelucheux et régulièrement renouvelé.
Temps de séchage : minimum 10 minutes - maximum 2 heures
Pour la préparation d'autres substrats, consultez le tableau d'utilisation des primaires en fin d’ouvrage.
Revêtement de pont
Le revêtement doit être débarrassé de tout apprêt de finition ainsi que de tout autre agent utilisé au cours de sa production. Utiliser du MEC (Méthyl Ethyl
Cétone), ou tout autre solvant approprié et recommandé par le fabricant. Effectuer un test sur une petite surface pour vérifier que le substrat n'est pas affecté par le solvant.
Pour les revêtements non poreux, nettoyer la face à coller avec le Sika
®
Cleaner-
205 et un chiffon ou un papier sec, propre, non-pelucheux et régulièrement renouvelé.
Temps de séchage : minimum 10 minutes – maximum 2 heures
Dans le cas de revêtements présentant une structure poreuse ouverte ou une armature tissée, il suffit simplement de vérifier que la surface à coller soit correctement dépoussiérée.
Application de la colle (Sikaflex
®
-291
¤
ou Sikaflex
®
-298
¤
)
Surfaces horizontales : Sikaflex
®
-298 / Surfaces inclinées : Sikaflex
®
-291
Appliquer la colle sur la surface préalablement préparée et répartir sur la zone à recouvrir à l'aide d'une spatule à dents triangulaires (2mm). La couche doit atteindre une épaisseur comprise entre 0,5 et 1 mm.
Positionner le revêtement dans les 30 minutes qui suivent l'application de la colle : pour cette raison, nous recommandons fortement de n'appliquer la colle que sur une surface limitée qu'il sera possible de recouvrir dans le temps imparti.
Une fois le revêtement en place, passer un rouleau de caoutchouc du centre vers les bords pour expulser les bulles d'air emprisonnées et repousser la colle excédentaire vers les bords où elle sera enlevée. Ce marouflage est indispensable pour enlever toutes les éventuelles bulles d'air sous le revêtement.
Note : si le revêtement est placé en tension, les bords doivent être maintenus ou correctement lestés.
Les traces de Sikaflex
® non-polymérisé peuvent être enlevées à l'aide du Sika
®
Remover-208. N'utiliser sous aucun prétexte un agent de nettoyage, ni le Sika
®
Cleaner-205 pour cette tâche.
Important : Consultez les notices techniques et fiches de sécurité Sika qui sont à
votre disposition auprès de votre représentant local Sika.
29
4.4 Pose et étanchéité d’éléments d’accastillage
Description de l'application
Tous les éléments d’accastillage doivent
être solidement fixés et parfaitement
étanches. Certains d’entre eux peuvent
également être soumis à des contraintes ou des forces de torsion très importantes.
Les joints mal réalisés peuvent favoriser la corrosion des métaux, l'osmose ou les fuites d'eau, et finir par occasionner des dégâts sérieux aux équipements et aux garnitures intérieures.
Pose et étanchéité d’éléments soumis
à de fortes contraintes mécaniques
Les équipements de pont comme les cadènes, les winchs et les guindeaux, doivent absorber des contraintes dynamiques très importantes. Pour ce type d'application, utilisez un produit hautes performances, comme le Sikaflex
®
-292, et complétez par des fixations mécaniques.
Pose et étanchéité d’éléments soumis
à de faibles contraintes mécaniques
Les équipements de pont comme les ventilateurs, les panneaux d'écoutilles, etc., doivent être fixés de manière à ne pas laisser entrer l'eau mais ne sont pas soumis à des forces de traction importantes. Ces équipements peuvent être efficacement posés et étanchés avec le seul Sikaflex
®
-291.
Préparation des substrats
Ponts de bois
Poncer la surface à coller avec un papier de verre 80/100. Aspirer les poussières.
Appliquer une couche mince et régulière de Sika
®
Primaire-290 DC à l'aide d'un pinceau propre ou d'un tampon applicateur en feutre.
Temps de séchage : minimum 60 minutes - maximum 24 heures
Ponts en aluminium (peints)
Nettoyer le substrat avec le Sika
®
Cleaner-205 et un chiffon ou un papier sec, propre, non-pelucheux et régulièrement renouvelé.
Temps de séchage : minimum 10 minutes - maximum 2 heures
Eléments en bronze, en cuivre ou en acier inoxydable
Nettoyer le substrat avec le Sika
®
Cleaner-205 et un chiffon ou un papier sec, propre, non-pelucheux et régulièrement renouvelé.
Temps de séchage : minimum 10 minutes - maximum 2 heures
Appliquer une couche mince et régulière de Sika
®
Primaire-210 T à l'aide d'un pinceau propre ou d'un tampon applicateur en feutre.
Temps de séchage : minimum 60 minutes – maximum 24 heures.
Eléments en aluminium
Poncer légèrement la surface de contact avec un tampon abrasif très fin (Scotch-
Brite M 600).
Nettoyer le substrat avec le Sika
®
Cleaner-205 et un chiffon ou un papier sec, propre, non-pelucheux et régulièrement renouvelé.
Temps de séchage : minimum 10 minutes - maximum 2 heures
Appliquer une couche mince et régulière de Sika
®
Primaire-210 T à l'aide d'un pinceau propre ou d'un tampon applicateur en feutre.
Temps de séchage : minimum 60 minutes - maximum 24 heures
Pour la préparation d'autres substrats, consultez le tableau d'utilisation des primaires en fin d’ouvrage.
Application de la colle (Sikaflex
®
-292
¤
ou Sikaflex
®
-291
¤
)
La colle doit être appliquée sur le pont et dans les trous de vissage en cordons d'épaisseur suffisante. Positionner ensuite la pièce à coller en appuyant fortement.
Les vis de fixation doivent être suffisamment serrées pour amener l'assise de la pièce au contact des rondelles d'espacement, mais pas davantage.
Attendez 24 heures avant le serrage définitif. Utilisez une spatule en plastique pour éliminer la colle en excédent.
Les traces de Sikaflex
® non-polymérisé peuvent être enlevées à l'aide du
Sika
®
Remover-208. N'utiliser sous aucun prétexte un agent de nettoyage, ni le Sika
®
Cleaner-205 pour cette tâche.
Important : Consultez les notices techniques et les fiches de sécurité Sika qui
sont à votre disposition auprès de votre représentant local Sika.
Remarque importante :
Il est absolument essentiel que la colle ne soit pas expulsée de la surface de collage par le serrage des vis. Pour éviter ce phénomène, utilisez des rondelles de
1 mm d'épaisseur environ enfilées sur les vis et qui serviront de cales d'espacement. Pensez également à remplir les trous de mastic avant de mettre les vis en place.
Surélever de cette manière l'élément collé de 2 à 3 mm par rapport au pont facilite
également sa dépose ultérieure : il suffira alors de glisser une lame ou un fil à couper entre l’élément et le pont pour couper le joint de colle.
31
4.5 Collage de listons et défenses
Description de l'application
Les listons et défenses sont destinés à protéger la coque des chocs (appontements, abordages...). Ils agissent comme des tampons qui absorbent les chocs et les frottements : plus ils sont souples et mieux ils remplissent leur fonction.
La capacité d'absorption des chocs d'un liston est grandement améliorée par l'utilisation d'un joint de colle souple : la protection conférée à la coque est ainsi maximale.
Préparation des substrats
Coques en GRP
Commencer par nettoyer les surfaces très souillées à l'aide d'un solvant pur (Sika
®
Remover-208) pour retirer les traces les plus importantes.
Poncer légèrement la zone de contact avec un papier de verre très fin. Aspirer les poussières.
Nettoyer le substrat avec le Sika
®
Cleaner-205 et un chiffon ou un papier sec, propre, non-pelucheux et régulièrement renouvelé.
Temps de séchage : minimum 10 minutes - maximum 2 heures.
Appliquer une couche mince et régulière de Sika
®
Primaire-206 G+P ou de Sika
®
Primaire-215 à l'aide d'un pinceau propre ou d'un tampon applicateur en feutre.
Temps de séchage : minimum 30 minutes - maximum 24 heures.
Coques en aluminium ou en acier avec peinture de finition (laque bi-composant)
Nettoyer le substrat avec le Sika
®
Cleaner-205 et un chiffon ou un papier sec, propre, non-pelucheux et régulièrement renouvelé.
Temps de séchage : minimum 10 minutes - maximum 2 heures.
Les listons en bois, en PVC ou en polyuréthanne peuvent être collés sur la coque avec le Sikaflex
®
-292 (autres matières, nous consulter). Le joint souple ainsi formé contribue à absorber l'essentiel des contraintes de cisaillement et de traction auxquelles sont soumis les listons au moment d'accoster ou d'appareiller.
Dans le cas où les listons sont fixés avec des vis, on obtient un effet analogue en remplissant le profil avec du Sikaflex
®
-
291, un mastic d'étanchéité polyuréthanne d'une grande souplesse. En plus d'absorber les forces de torsion, le
Sikaflex
®
-291 permet également d’étancher les trous de vis et d'éviter les infiltrations d'eau ou de poussière entre le liston et la coque.
Listons en bois
Poncer la surface de collage avec un papier de verre 80/100. Aspirer les poussières.
Appliquer une couche mince et régulière de Sika
®
Primaire-290 DC à l'aide d'un pinceau propre ou d'un tampon applicateur en feutre.
Temps de séchage : minimum 60 minutes - maximum 24 heures.
Listons en PVC ou en polyuréthanne moulé
La face à coller du liston ne doit plus porter de trace des produits de démoulage ni d'aucune autre substance chimique. Toute trace de ces produits doit être éliminée avant de poursuivre l'opération.
Poncer la face à coller de la bande de frottement avec un papier de verre gros grain (60/80) pour strier la surface.
Nettoyer le substrat avec le Sika
®
Cleaner-205 et un chiffon ou un papier sec, propre, non-pelucheux et régulièrement renouvelé.
Temps de séchage : minimum 10 minutes - maximum 2 heures
Remarque importante : Si vous ignorez de quel matériau est composée votre bande
de frottement, contactez votre fournisseur.
Application de la colle (Sikaflex
®
-292
¤
ou Sikaflex
®
-291
¤
)
Positionner des cales d'espacement d’une épaisseur de 2 mm et d’une dureté shore A d’environ 50 (ne surtout pas les fixer avec une colle cyanoacrylate).
Appliquer le Sikaflex
®
-292 (ou le Sikaflex
®
-291 si vous utilisez des vis en complément de fixation) en un cordon triangulaire de 8 mm x 10 mm sur l'ensemble de la zone à coller.
Assembler les composants dans les 20 minutes qui suivent l'application de la colle.
Presser pour positionner le liston, soit directement sur la coque, soit dans le profil prévu. Maintenir les pièces en place à l'aide d’instruments appropriés (serrejoints, etc.) en attendant que la colle durcisse. Si le liston doit être également fixé de manière mécanique, remplir de colle les trous correspondants.
Les traces de Sikaflex
® non-polymérisé peuvent être enlevées à l'aide du Sika
®
Remover-208. N'utiliser sous aucun prétexte un agent de nettoyage, ni le Sika
®
Cleaner-205 pour cette tâche.
Les fixations temporaires (serre-joints, etc.) peuvent être retirées après 24 heures.
La résistance et la dureté finales sont atteintes après 7 jours.
Important : Consultez les notices techniques et les fiches de sécurité Sika qui
sont à votre disposition auprès de votre représentant local Sika.
33
4.6 Liaison pont-coque
Introduction
En construction navale de bateaux en
GRP, l'une des options est de concevoir une unité pont-coque monobloc. Une autre option consiste à fabriquer séparément pont et coque, puis à assembler les deux éléments à un stade ultérieur du process. Chaque option a ses avantages et ses inconvénients. Toutefois, dès lors que l'on choisit de fabriquer séparément les deux éléments, il convient d'envisager une méthode d'assemblage sûre et
économique.
Description de l'application
Le collage avec un Sikaflex
® est le moyen le plus simple et le plus élégant pour compenser les différences de tolérances de fabrication entre la coque et le pont. L'assemblage des deux éléments (GRP/GRP ou assemblage mixte d'aluminium et de GRP) ne requiert en effet alors qu'un minimum de fixations mécaniques.
Le collage offre de nombreux avantages dans ce type d'application. Il permet d'éviter les opérations pénibles de stratification du GRP et, grâce aux propriétés de remplissage des interstices des colles souples, autorise de plus grandes tolérances de fabrication pour les coques et les ponts moulés. Le joint de colle absorbe les forces de torsion et les impacts, et garantit simultanément une parfaite étanchéité.
Préparation des substrats
Aluminium
Commencer par nettoyer les surfaces très souillées à l'aide d'un solvant pur
(Sika
®
Remover-208) pour retirer les traces les plus importantes.
Poncer légèrement la zone de contact avec un papier de verre très fin. Aspirer les poussières.
Nettoyer le substrat avec le Sika
®
Cleaner-205 et un chiffon ou un papier sec, propre, non-pelucheux et régulièrement renouvelé.
Temps de séchage : minimum 10 minutes - maximum 2 heures.
Appliquer une couche mince et régulière de Sika
®
Primaire-210 T à l'aide d'un pinceau propre ou d'un tampon applicateur en feutre.
Temps de séchage : minimum 60 minutes - maximum 24 heures.
GRP
Commencer par nettoyer les surfaces très souillées à l'aide d'un solvant pur
(Sika
®
Remover-208) pour retirer les traces les plus importantes.
Poncer légèrement la zone de contact avec un papier de verre très fin ou un tampon Scotch-Brite. Aspirer les poussières.
Nettoyer le substrat avec le Sika
®
Cleaner-205 et un chiffon ou un papier sec, propre, non-pelucheux et régulièrement renouvelé.
Temps de séchage : minimum 10 minutes - maximum 2 heures
Appliquer une couche mince et régulière de Sika
®
Primaire-206 G+P ou de
Sika
®
Primaire-215 à l'aide d'un pinceau propre ou d'un tampon applicateur en feutre.
Temps de séchage : minimum 30 minutes - maximum 24 heures.
Fig. A
Fig. B
Fig. C
Fig. D
Application de la colle
Il est absolument essentiel de vérifier la précision de l'ajustement avant d'appliquer la colle afin de ne pas avoir à séparer les pièces assemblées.
Positionner des cales d'espacement ; épaisseur 4 mm, dureté shore A de 50 environ (ne surtout pas les fixer avec une colle cyanoacrylate). Les cales peuvent également être mises en place et pressées dans le joint de colle une fois celui-ci appliqué.
Appliquer le Sikaflex
®
-292 (Fig A) ou un système Sikaflex Boosté sur toute la périphérie de la coque. Le cordon de colle doit être appliqué en continu autour de toutes les découpes et de tous les orifices libres (montants de ponts, tuyaux, cadènes, par exemple) pour garantir l'intégrité du joint d’étanchéité
(Fig. B).
Assembler les composants dans les 20 minutes qui suivent l'application de la colle (Fig. C et D).
Serrer les pièces pour comprimer la colle jusqu'à l'épaisseur des cales d'espacement à l'aide d’instruments de serrage appropriés (serre-joints, etc.).
Les fixations temporaires (serre-joints, etc.) peuvent être retirées après 24 heures.
La résistance et la dureté finales sont atteintes après 7 jours.
Les traces de Sikaflex
® non-polymérisé peuvent être enlevées à l'aide du Sika
®
Remover-208. N'utiliser sous aucun prétexte un agent de nettoyage, ni le Sika
®
Cleaner-205 pour cette tâche.
Important : Consultez les notices techniques et les fiches de sécurité Sika qui
sont à votre disposition auprès de votre représentant local Sika.
35
4.7 Liaison coque-quille
Description de l'application
Le joint entre la quille et la coque est soumis à de très fortes contraintes, particulièrement lorsque le navire est sous voile ou qu'il s'échoue.
Pour résister à ces contraintes, ce joint doit être conçu et réalisé avec le plus grand soin.
Ce joint est en outre particulièrement prédisposé aux fuites qui se manifestent par des traînées de rouille sur la quille visibles lorsque le navire est mis en cale sèche.
Important : Les zones d'encollage de
la quille doivent également être préparées avec le Sika
®
Cleaner-205. Pour les quilles en plomb, la zone de contact doit en outre recevoir une couche de peinture protectrice à base de résine époxy bicomposant.
Temps de séchage : 24 heures minimum.
Préparation des substrats
Coques en aluminium
Commencer par nettoyer les surfaces très souillées à l'aide d'un solvant pur (Sika
®
Remover-208) pour retirer les traces les plus importantes.
Poncer légèrement la zone de contact avec un papier de verre très fin. Aspirer les poussières.
Nettoyer le substrat avec le Sika
®
Cleaner-205 et un chiffon ou un papier sec, propre, non-pelucheux et régulièrement renouvelé.
Temps de séchage : minimum 10 minutes - maximum 2 heures.
Appliquer une couche mince et régulière de Sika
®
Primaire-210 T à l'aide d'un pinceau propre ou d'un tampon applicateur en feutre.
Temps de séchage : minimum 60 minutes - maximum 24 heures.
Coques en GRP
Commencer par nettoyer les surfaces très souillées à l'aide d'un solvant pur (Sika
®
Remover-208) pour retirer les traces les plus importantes.
Poncer légèrement la zone de contact avec un papier de verre très fin. Aspirer les poussières.
Nettoyer le substrat avec le Sika
®
Cleaner-205 et un chiffon ou un papier sec, propre, non-pelucheux et régulièrement renouvelé.
Temps de séchage : minimum 10 minutes - maximum 2 heures.
Appliquer une couche mince et régulière de Sika
®
Primaire-206 G+P ou de Sika
®
Primaire-215 à l'aide d'un pinceau propre ou d'un tampon applicateur en feutre.
Temps de séchage : minimum 30 minutes – maximum 24 heures.
Etanchéité du propulseur d’étrave
Coques en bois
Poncer la surface de contact de la coque avec un papier de verre 80/100 et aspirer les poussières.
Appliquer une couche mince et régulière de Sika
®
Primaire-290 DC à l'aide d'un pinceau propre ou d'un tampon applicateur en feutre.
Temps de séchage : minimum 60 minutes - maximum 24 heures.
Coques en acier avec couche de protection anticorrosion bi-composant
Nettoyer le substrat avec le Sika
®
Cleaner-205 et un chiffon ou un papier sec, propre, non-pelucheux et régulièrement renouvelé.
Temps de séchage : minimum 10 minutes - maximum 2 heures.
Pour la préparation d'autres substrats, consultez le tableau d'utilisation des primaires en fin d’ouvrage.
Application du Sikaflex
®
-292
¤
Positionner des cales d'espacement d’une épaisseur de 10 mm, et d’une dureté shore A de 50 environ (ne surtout pas fixer les cales avec une colle cyanoacrylate).
Appliquer le Sikaflex
®
-292 en cordons triangulaires de 20 mm à 25 mm de hauteur.
Chaque cordon doit former une bande continue et fermée. Les orifices de vissage doivent être traités de la même façon.
Mettre la quille en place, en respectant soigneusement le temps ouvert du
Sikaflex
®
-292, et visser les boulons de la quille jusqu'à toucher les cales d'espacement. La colle expulsée lors du serrage peut être lissée.
Après 3 ou 4 jours, les boulons de la quille peuvent être serrés à leur couple définitif. La pression supplémentaire ainsi appliquée à la colle donne au joint entre la coque et la quille la rigidité de torsion nécessaire. Une fois la colle parfaitement durcie, le joint peut être peint à l'aide de n'importe quelle peinture anti-fouling de bonne qualité. Le joint de colle absorbe les tensions dynamiques qui se créent à cet endroit du navire, et assure une parfaite étanchéité entre la coque et la quille.
Les traces de Sikaflex
® non-polymérisé peuvent être enlevées à l'aide du Sika
®
Remover-208. N'utiliser sous aucun prétexte un agent de nettoyage, ni le Sika
®
Cleaner-205 pour cette tâche.
Important : Consultez les notices techniques et les fiches de sécurité Sika qui sont
à votre disposition auprès de votre représentant local Sika.
37
4.8 Collage des flybridges
De nombreux yachts modernes sont désormais équipés d'un flybridge. Les méthodes traditionnelles de fixation – fixations mécaniques ou colles rigides – concentrent les contraintes en un ou plusieurs points fixes, pouvant engendrer des fissures dans le substrat. Ces fissures favorisent les infiltrations d'eau et les dégâts qui y sont liés.
La fixation des flybridges à l'aide de colles souples permet une distribution uniforme des contraintes tout en optimisant la résistance à l'impact et aux effets d'usure.
Préparation des substrats
GRP
Commencer par nettoyer les surfaces très souillées à l'aide d'un solvant pur (Sika
®
Remover-208) pour retirer les traces les plus importantes.
Poncer légèrement la zone à coller avec un papier de verre très fin. Aspirer les poussières.
Nettoyer le substrat avec le Sika
®
Cleaner-205 et un chiffon ou un papier sec, propre, non-pelucheux et régulièrement renouvelé.
Temps de séchage : minimum 10 minutes - maximum 2 heures.
Appliquer une couche mince et régulière de Sika
®
Primaire-206 G+P ou de Sika
®
Primaire-215 à l'aide d'un pinceau propre ou d'un tampon applicateur en feutre.
Important : Consultez les notices tech-
niques et les fiches de sécurité Sika qui sont à votre disposition auprès de votre représentant local Sika.
Temps de séchage : minimum 30 minutes - maximum 24 heures.
Fig. A
Application du Sikaflex
®
-292
¤
Positionner des cales d'espacement souples de 3 mm d’épaisseur, et d’une dureté shore A de 50 environ (ne surtout pas fixer les cales avec une colle cyanoacrylate).
Appliquer le Sikaflex
®
-292 en un cordon triangulaire de 8 mm x 10 mm sur l'ensemble de la périphérie du flybridge. En fonction de l’importance des charges à supporter, un second cordon de colle peut être nécessaire. (Fig. A)
Assembler les composants dans les 20 minutes qui suivent l'application de la colle.
Maintenir les pièces en place à l'aide d’instruments appropriés (serre-joints, etc.) pour comprimer la colle jusqu'à la hauteur des cales d'espacement.
Les traces de Sikaflex
® non-polymérisé peuvent être enlevées à l'aide du Sika
®
Remover-208. N'utiliser sous aucun prétexte un agent de nettoyage, ni le Sika
®
Cleaner-205 pour cette tâche.
Les fixations temporaires (serre-joints, etc.) peuvent être retirées après 12 heures.
La résistance et la dureté finales sont atteintes après 7 jours.
4.9 Collage et étanchéité des verres organiques
Description de l'application
La plupart des vitrages organiques (plastiques) utilisés dans la construction navale appartiennent soit à la catégorie des feuilles acryliques transparentes
(PMMA) plus connues sous leurs noms commerciaux comme "Perspex" ou
"Plexiglas" soit à la famille des polycarbonates (PC) commercialisés sous les noms " Makrolon " ou " Lexan ".
Tous les vitrages organiques possèdent des caractéristiques qui doivent être correctement prises en compte pour garantir une installation et un collage convenables. D'une manière générale, les vitrages organiques mal posés peuvent
être sujets à des phénomènes de crazing (fendillement), risque encore augmenté par l'utilisation de certaines colles ou primaires.
Les vitrages organiques possèdent un coefficient de dilatation thermique supérieur à celui des verres minéraux. Pour cette raison, il convient lors de la conception d’ouvrants en verre organique, de prévoir un espace de 10 mm minimum sur toute la périphérie entre le dormant et le panneau pour permettre les dilatations thermiques. Pour les mêmes raisons, les trous doivent être percés à un diamètre supérieur à celui des vis utilisées.
Pour réduire le risque de crazing, les feuilles de verre organique plates doivent
être installées totalement à plat, elles ne doivent pas être contraintes à prendre une forme courbe au moyen de fixations mécaniques. Si la conception exige l'utilisation de panneaux courbés, les vitrages devront être fabriqués sur mesure et convenablement thermoformés par un fabricant spécialisé pour garantir un montage sans contrainte interne.
Les variétés de vitrages organiques sont nombreuses : c’est pourquoi nous vous recommandons de bien vérifier que le produit choisi est compatible avec l'utilisation du Sikaflex
®
-295 UV. Pour tout renseignement complémentaire, contactez votre représentant local Sika.
Epaisseur minimale du joint de colle
OK
1
4
Epaisseur du joint insuffisante
0 0,5 1 1,5
Plus grande dimension du vitrage (m)
2
5
3
2
1 - Cadre
2 - Vitrage
3 - Sikaflex
®
-295 UV (collage)
4 - Sikaflex
®
-295 UV (étanchéité)
5 - Ruban de protection UV Sika
®
39
Préparation des substrats
Cadre GRP
Poncer légèrement la zone de contact avec un papier de verre très fin. Aspirer les poussières.
Nettoyer le substrat avec le Sika
®
Cleaner-205 et un chiffon ou un papier sec, propre, non-pelucheux et régulièrement renouvelé.
Temps de séchage : minimum 10 minutes - maximum 2 heures.
Appliquer une couche mince et régulière de Sika
®
Primaire-206 G+P, de Sika
®
Primaire-215 ou de Sika
®
Primaire-209 N à l'aide d'un pinceau propre ou d'un tampon applicateur en feutre.
Temps de séchage : minimum 30 minutes - maximum 24 heures
Cadre aluminium anodisé
Nettoyer avec le Sika
®
Cleaner-205 et un chiffon ou un papier sec, propre, nonpelucheux et régulièrement renouvelé.
Temps de séchage : minimum 10 minutes - maximum 2 heures.
Appliquer une couche mince et régulière de Sika
®
Primaire-210 T à l'aide d'un pinceau propre ou d'un tampon applicateur en feutre.
Temps de séchage : minimum 60 minutes - maximum 24 heures.
Cadre en bois ou en aluminium recouvert d'une laque bi-composant
Nettoyer le substrat avec le Sika
®
Cleaner-205 et un chiffon ou un papier sec, propre, non-pelucheux et régulièrement renouvelé.
Temps de séchage : minimum 10 minutes - maximum 2 heures.
Vitrage PMMA / PC
Protéger le périmètre de la zone à coller à l'aide d'un ruban de masquage. Poncer légèrement la surface à encoller avec un papier de verre ou un tampon Scotch-
Brite.
Nettoyer le substrat avec le Sika
®
Cleaner-205 et un chiffon ou un papier sec, propre, non-pelucheux et régulièrement renouvelé.
Temps de séchage : minimum 10 minutes - maximum 2 heures.
Appliquer une couche mince et régulière de Sika
®
Primaire-209 N à l'aide d'un pinceau propre ou d'un tampon applicateur en feutre.
Temps de séchage : minimum 30 minutes - maximum 24 heures.
Pour la préparation d'autres substrats, consultez le tableau d'utilisation des primaires en fin d’ouvrage.
Application du Sikaflex
®
-295 UV
¤
Positionner des cales d'espacement. L'épaisseur des cales doit être choisie en fonction de la taille du vitrage (voir diagramme p.39) ; dureté Shore A approximative 30. Ne surtout pas fixer les cales avec une colle cyanoacrylate. Les cales ne doivent pas altérer la continuité du joint de colle. Pour ce faire, elles peuvent être placées de part et d'autre du cordon.
Appliquer le Sikaflex
®
-295 UV sur le cadre ou sur le vitrage, en formant à l’aide d’une buse triangulaire un cordon de 10 mm de large au moins.
Assembler les composants dans les 20 minutes qui suivent l'application de la colle.
Pour éviter que le panneau ne glisse, placer des cales supplémentaires (bois ou plastique) sur le rebord inférieur au moment de la mise en place du vitrage ; ces cales seront retirées après polymérisation. L'espace entre le vitrage et le rebord doit être de 10 mm au moins.
Les traces de Sikaflex
® non-polymérisé peuvent être enlevées à l'aide du Sika
®
Remover-208. N'utiliser sous aucun prétexte un agent de nettoyage, ni le Sika
®
Cleaner-205 pour cette tâche.
Les cales et fixations temporaires (serre-joints, etc.) peuvent être retirées après 24 heures. Après ce délai, l'espace entre le rebord et le panneau de vitrage peut être comblé avec du Sikaflex
®
-295 UV. Pour cette opération, il est essentiel d'attendre la polymérisation complète de la colle vitrage. Le joint d'étanchéité peut être lissé avec le Sika
®
Tooling Agent N. Cette opération doit être réalisée avant que le joint n'ait formé sa peau.
Conformément à nos recommandations, appliquer le ruban de protection Sika
®
UV
Shielding Tape pour protéger le joint.
Important : Consultez les notices techniques et les fiches de sécurité Sika qui
sont à votre disposition auprès de votre représentant local Sika.
Protection du joint
Comme les verres minéraux traditionnels, les panneaux de vitrage organique ne mettent généralement pas le joint de colle
à l'abri des rayons UV. Pour cette raison, le joint doit être protégé à l'aide de l'une des méthodes décrites ici :
Vitrage organique à faible transmission (< 0,5 %) des rayons UV
Bande de recouvrement (métallique ou autre) extérieure de dimension adéquate
Ruban de protection Sika
®
UV
Shielding Tape de dimension adéquate
Etanchéité en périphérie du vitrage
En général, les joints de finition en périphérie du vitrage sont réalisés avec des produits Sikaflex
®
. La préparation des surfaces est identique à celle nécessaire à un collage. L’étanchéification des bordures permet de prévenir l'accumulation d’eau sur ou à proximité du joint de colle, tout en améliorant la finition. Veiller à remplir complètement l'espace entre le vitrage et le cadre, sans laisser de vide entre le joint de colle et le joint d'étanchéité. La largeur minimale des joints de
Sikaflex
®
-295 UV sur des panneaux de vitrage organique est donnée par le diagramme ci-dessous.
Recommandations minimales pour la protection du joint contre les rayons ultraviolets d
d = épaisseur de la fenêtre
3
O = recouvrement
2
Règle Sika
O = 2 x d
Exemple : si d = 8 mm, le recouvrement doit au moins être égal à 16 mm
1
1 - Protection UV
2 - Sikaflex
®
-295 UV
3 - Vitrage
Largeur minimale du joint d’étanchéité ok trop petit
0 1 2 3
Plus grande dimension de la fenêtre (m)
41
4.10 Collage et étanchéité du verre minéral
Description de l'application
Le collage du verre minéral – verre de sécurité trempé – dans un cadre, sur la coque ou sur le pont, exige une connaissance détaillée des paramètres à prendre en compte.
Il est essentiel que le verre remplisse toutes les exigences et soit conforme aux normes qui réglementent ce type d’application. Pour les double-vitrages, la cohérence du procédé de collage est primordiale : utilisez des colles Sikaflex
® pour l’ensemble de l’application.
Nous recommandons d'utiliser des vitrages spécifiquement développés pour la construction navale, tels que par exemple le Formglas Spezial (H.J Tilse GmbH et Schiffstechnik).
Le joint de colle polyuréthanne doit toujours être protégé contre les rayons UV.
Plusieurs solutions sont envisageables pour assurer cette protection (voir paragraphe protection du joint de colle page
45).
Autres méthodes, consulter votre représentant local Sika.
Note : Respectez toujours les régle-
mentations locales et nationales en vigueur dans la construction navale.
Dimensionnement des joints de collage et d’étanchéité
Les dimensions du joint de colle et sa géométrie doivent respecter les règles de calcul Sika. Les mesures suivantes sont préconisées lorsque les mouvements du pont sont négligeables. Dans tous les cas, les recommandations des sociétés de classification doivent être respectées.
Vitrage minéral : Largeur du joint d’étanchéité ok ok trop petit
0 1 2 3
Plus grande dimension de la fenêtre (m)
Vitrage minéral : Epaisseur du joint de colle
Aluminium
Acier
trop petit
0 1 2 3
Plus grande dimension du verre (m)
Largeur du joint
Largeur du joint
Largeur du joint de colle
(de 12 mm à 20 mm)
Epaisseur du joint de colle
Fig. A
1
2
5
Solution 1
1 - Verre minéral
2- Revêtement céramique
3 - Sikaflex
®
-296
4 - Primaire sur cadre
5 - Sika
®
Primaire-206 G+P
4
3
1
Préparation des substrats
Vitrage avec bordure en céramique noire - Solution 1
Appliquer le Sika
®
Activateur en fine pellicule et en une seule fois à l'aide d'un chiffon propre ou d'un papier absorbant non pelucheux. Essuyer immédiatement les excès de produit à l'aide d'un nouveau chiffon propre ou d'un papier absorbant non pelucheux (Fig. A).
Temps de séchage : minimum 10 minutes - maximum 2 heures.
Appliquer une couche mince et régulière de Sika
®
Primaire-206 G+P sur la tranche du vitrage, à l'aide d'un pinceau propre ou d'un tampon applicateur en feutre.
Temps de séchage : minimum 30 minutes - maximum 24 heures.
Si la transmission lumineuse de la bordure céramique noire est supérieure à
0.01%, compléter la préparation ci-dessus par l'application d'une couche mince et régulière de Sika
®
Primaire-206 G+P sur la bordure céramique.
Temps de séchage : minimum 30 minutes - maximum 24 heures.
Vitrage + protection périphérique extérieure - Solution 2
Appliquer le Sika
®
Activateur en fine pellicule et en une seule fois à l'aide d'un chiffon propre ou d'un papier absorbant non pelucheux. Essuyer immédiatement les excès de produit à l'aide d'un nouveau chiffon propre ou d'un papier absorbant non pelucheux.
Temps de séchage : minimum 10 minutes - maximum 2 heures.
Pour la préparation du cadre, consultez le tableau d'utilisation des primaires en fin d’ouvrage.
4
3
2
Solution 2
1 - Verre minéral
2 - Sikaflex
®
-296
3 - Primaire sur cadre
4 - Protection périphérique
43
Application de la colle (Sikaflex
®
-296
¤
)
Positionner les cales d'espacement. L'épaisseur des cales doit être au minimum de 5 mm (voir diagramme p. 42) ; dureté Shore A approximative 30. Ne surtout pas fixer les cales avec une colle cyanoacrylate. Les cales ne doivent pas altérer la continuité du joint de colle. Pour ce faire, elles peuvent être placées de part et d'autre du cordon.
Appliquer le Sikaflex
®
-296 sur le rebord du cadre ou sur le verre, à l’aide d’une buse triangulaire en déposant un joint de 12 mm minimum.
Assembler les composants dans les 20 minutes qui suivent l'application de la colle.
Pour éviter que le panneau ne glisse (essentiellement dans le cas de panneaux verticaux), placer des cales (bois ou plastique) supplémentaires sur le rebord inférieur pendant l'installation ; ces cales seront retirées après polymérisation. Nous recommandons 10 mm minimum d'espace entre le vitrage et le rebord.
Les traces de Sikaflex
® non-polymérisé peuvent être enlevées à l'aide du Sika
®
Remover-208. N'utiliser sous aucun prétexte un agent de nettoyage, ni le Sika
®
Cleaner-205 pour cette tâche.
Les cales et fixations temporaires (serre-joints, etc) peuvent être retirées après 24 heures. Après ce délai, l'espace entre le rebord et le panneau peut être comblé avec le Sikaflex
®
-296 (Fig. A) ou le Sikaflex
®
-295 UV. Pour cette opération, il est essentiel d'attendre la polymérisation complète de la colle vitrage. Veiller à remplir complètement l'espace entre le vitrage et le cadre, sans laisser de vide entre le joint de colle et le joint d'étanchéité. Le joint d'étanchéité peut être lissé avec le
Sika
®
Tooling Agent N. Cette opération doit être réalisée avant que le joint n'ait formé sa peau.
Le navire peut être remis en service après une semaine.
Important : Consultez les notices techniques et les fiches de sécurité Sika qui
sont à votre disposition auprès de votre représentant local Sika.
Fig. A
Protection du joint de colle
Les verres minéraux ne mettent généralement pas le joint de colle à l'abri des rayons UV. Pour cette raison, le joint doit
être protégé à l'aide de l'une des méthodes décrites ici :
Protection périphérique extérieure
(bande de recouvrement plastique ou métallique ; ruban de protection Sika
®
UV Shielding Tape) de dimension adéquate (voir règle ci-dessous)
Sérigraphie céramique noire en bordure de vitrage complétée par l'application du Sika
®
Primaire-
206 G+P :
- Sur la tranche du vitrage uniquement, si la transmission lumineuse de la céramique est inférieure à
0.01%
- Sur la tranche et sur la sérigraphie céramique (zone de collage), si la transmission lumineuse de celleci est supérieure à 0.01%.
Recommandations minimales pour la protection du joint contre les rayons ultraviolets d
d = épaisseur de la fenêtre
3
O = recouvrement
2
Règle Sika
O = 2 x d
Exemple : si d = 8 mm, le recouvrement doit au moins être égal à 16 mm
1
1 - Protection UV
2 - Sikaflex
®
-296
3 - Fenêtre
45
4.11 Collage des anodes sacrificielles
Description de l'application
Les anodes sacrificielles sont des blocs de métal brut fixés sur les coques en acier pour réduire les effets de la corrosion galvanique. Ils sont fixés mécaniquement de l'intérieur sur la coque. Pour
éviter toute infiltration d'eau, il est impératif de réaliser un joint d’étanchéité à l'extérieur. Le Sikaflex
®
-291 est pour cela un produit idéal.
Préparation des substrats
Coque en acier
Nettoyer le substrat avec le Sika
®
Cleaner-205 et un chiffon ou un papier sec, propre, non-pelucheux et régulièrement renouvelé.
Temps de séchage : minimum 10 minutes - maximum 2 heures.
Note : Compte-tenu de la grande variété de substrats envisageables, il est
conseillé de consulter le tableau d'utilisation des primaires en fin d’ouvrage.
Application du Sikaflex
®
-291
¤
Appliquer le Sikaflex
®
-291 autour du trou et du boulon en un mince cordon autour des arêtes de la fixation lorsque celle-ci est vissée à fond dans sa position finale. Le mastic superflu expulsé au serrage peut être retiré à l'aide d'une spatule en plastique.
Les traces de Sikaflex
® non-polymérisé peuvent être enlevées à l'aide du Sika
®
Remover-208. N'utiliser sous aucun prétexte un agent de nettoyage, ni le Sika
®
Cleaner-205 pour cette tâche.
4.12 Collage de panneaux décoratifs et plans de travail
Description de l'application
De nombreux matériaux modernes ou traditionnels – miroirs, Avonite
®
, Corian
®
, etc. – sont utilisés pour la décoration intérieure des bateaux. Ces panneaux peuvent être utilisés pour des raisons purement esthétiques ou servir de véritables plans de travail, en cuisine par exemple. Dans tous les cas, le collage souple est une méthode de fixation simple et durable, qui ne présente pas les inconvénients esthétiques des fixations mécaniques.
Préparation des substrats
En raison de la grande diversité des matériaux – panneaux, plans de travail et substrats – veuillez consulter le tableau d'utilisation des primaires en fin d’ouvrage pour le travail de préparation des surfaces.
Application de la colle (Sikaflex
®
-292
¤
, Sikaflex
®
-298
¤
ou Sikaflex
®
-291
¤
)
Panneaux verticaux
Positionner des cales d'espacement : épaisseur usuelle 3 mm ; dureté Shore A approximative 50. Ne surtout pas fixer les cales avec une colle cyanoacrylate.
Appliquer le Sikaflex
®
-292 en cordons triangulaires parallèles distants de 60 mm environ, dimensions 8 mm x 10 mm.
Assembler les composants dans les 20 minutes qui suivent l'application de la colle.
Si nécessaire, les panneaux peuvent être maintenus en position pendant le temps de polymérisation par des serre-joints ou des étais de soutènement.
Les traces de Sikaflex
® non-polymérisé peuvent être enlevées à l'aide du Sika
®
Remover-208. N'utiliser sous aucun prétexte un agent de nettoyage, ni le Sika
®
Cleaner-205 pour cette tâche.
Les éléments de fixation temporaire peuvent être retirés après 24 heures.
La résistance et la dureté finales sont atteintes après 7 jours.
Panneaux horizontaux
Surfaces planes : Sikaflex
®
-298. Surfaces inclinées : Sikaflex
®
-291
Appliquer la colle sur la surface préalablement préparée et répartir sur toute la zone à coller à l'aide d'une spatule crantée (crans triangulaires de 4 mm).
L'épaisseur de la couche dépend des irrégularités de surface à rattraper (usuellement entre 1 et 2 mm).
Les panneaux doivent être positionnés avec précision avant que la colle n’ait formé sa peau ; presser fermement en position pour chasser les bulles d'air.
Utiliser des serre-joints, du lest ou des vis – à retirer après la prise de la colle – pour maintenir le panneau le temps nécessaire au durcissement de la colle. Vous pouvez également, si cela est possible, utiliser la méthode de presse par le vide.
Les panneaux atteignent leur capacité de charge maximale après 24 heures environ, et les éléments de fixation temporaire peuvent alors être retirés. Dans le cas de substrats étanches à la vapeur d'eau, pulvériser un fin brouillard d'eau (environ
10 g/m²) sur la surface du Sikaflex
®
-298 pour accélérer la polymérisation.
Important : Consultez les notices techniques et les fiches de sécurité Sika qui
sont à votre disposition auprès de votre représentant local Sika.
1
4
3
2
1 - Support
2 - Panneau décoratif
3 - Sikaflex
®
-298
4 - Sikaflex
®
-291
1
2
3
4
1 - Support
2 - Cale d'espacement
3 - Sikaflex
®
-292
4 - Panneau décoratif
47
4.13 Collage de panneaux de pont et ponts à motifs
Description de l'application
Sur les bateaux modernes, la partie du pont qui est en bois se compose souvent de panneaux préfabriqués posés sur une structure rigide : cette méthode est en général choisie pour des raisons économiques.
On utilise généralement des panneaux de contreplaqué marine sur lesquels sont collées des lattes de teck ou de pin d'Oregon. On trouve également des panneaux composés de lattes de teck maintenues ensemble par plusieurs couches de feuilles de fibre de verre imprégnées de résine époxy. Les panneaux sont disponibles en dimensions standards ou en sections de pont coupées et usinées sur mesure à partir d'un modèle.
D'autres panneaux préfabriqués sont constitués de planches de teck reliées entre elles par des joints élastomères sans support de contreplaqué.
Les colles polyuréthanne monocomposant Sikaflex
® sont la solution idéale pour le collage de ces panneaux sur un pont.
Elles sont résistantes à l'eau de mer, possèdent d'excellentes propriétés de remplissage des interstices et ne nécessitent aucune fixation mécanique complémentaire. Une fois la polymérisation terminée, le joint de colle extrêmement résistant, demeure indéfiniment souple et imperméable.
Grâce à ses qualités d'étanchéité, la colle, qui est appliquée sur la totalité de la surface du pont, se comporte comme une "peau" complémentaire qui protège le pont contre les attaques des éléments.
Comme les vis et les boulons sont inutiles, il n'est pas nécessaire de percer des trous par lesquels l'eau pourrait s'infiltrer et provoquer des dégâts.
Préparation des substrats
Ponts GRP (Plastique renforcé fibres de verre)
Commencer par nettoyer les surfaces très souillées à l'aide d'un solvant pur (Sika
®
Remover-208) pour retirer les traces les plus importantes.
Poncer légèrement la zone de collage avec un papier de verre très fin. Aspirer les poussières.
Nettoyer le substrat avec le Sika
®
Cleaner-205 et un chiffon ou un papier sec, propre, non-pelucheux et régulièrement renouvelé.
Temps de séchage : minimum 10 minutes - maximum 2 heures.
Appliquer une couche mince et régulière de Sika
®
Primaire-206 G+P ou de Sika
®
Primaire-215 à l'aide d'un pinceau propre ou d'un tampon applicateur en feutre.
Temps de séchage : minimum 30 minutes – maximum 24 heures.
Ponts en bois
Poncer la surface de collage avec un papier de verre 80/100 et aspirer les poussières.
Appliquer une couche mince et régulière de Sika
®
Primaire-290 DC à l'aide d'un pinceau propre ou d'un tampon applicateur en feutre.
Temps de séchage : minimum 60 minutes – maximum 24 heures.
Ponts en aluminium ou en acier, recouverts d'une laque bi-composant
Nettoyer le substrat avec le Sika
®
Cleaner-205 et un chiffon ou un papier sec, propre, non-pelucheux et régulièrement renouvelé.
Temps de séchage : minimum 10 minutes - maximum 2 heures.
Panneaux de ponts revêtus époxy
Commencer par nettoyer les surfaces très souillées à l'aide d'un solvant pur (Sika
®
Remover-208) pour retirer les traces les plus importantes.
Poncer légèrement la zone de collage avec un papier de verre très fin. Aspirer les poussières.
Nettoyer le substrat avec le Sika
®
Cleaner-205 et un chiffon ou un papier sec, propre, non-pelucheux et régulièrement renouvelé.
Temps de séchage : minimum 10 minutes - maximum 2 heures.
Appliquer une couche mince et régulière de Sika
®
Primaire-215 à l'aide d'un pinceau propre ou d'un tampon applicateur en feutre.
Temps de séchage : minimum 30 minutes - maximum 24 heures.
3
1
1 - Sikaflex
®
-290 DC
2 - Panneau de pont à motifs
3 - Sikaflex
®
-298 ou Sikaflex
®
-291
4 - Pont
4
2
Application de la colle (Sikaflex
®
-298
¤
ou Sikaflex
®
-291
¤
)
Surfaces planes : Sikaflex
®
-298. Surfaces inclinées : Sikaflex
®
-291.
Appliquer la colle sur la surface préalablement préparée et répartir sur toute la zone à coller à l'aide d'une spatule crantée (crans triangulaires de 4 mm).
L'épaisseur de la couche dépend des irrégularités de surface à rattraper
(usuellement entre 1 et 2 mm, correspondant à 1 - 2 litres de colle par m²).
Les panneaux de pont doivent être positionnés avec précision avant que la colle n’ait formé sa peau ; presser fermement en position.
Utiliser des serre-joints, du lest ou des vis – à retirer après la prise de la colle
– pour maintenir les panneaux le temps nécessaire au durcissement de la colle. Vous pouvez également, si cela est possible, utiliser la méthode de presse par le vide.
Les traces de Sikaflex
® non-polymérisé peuvent être enlevées à l'aide du Sika
®
Remover-208. N'utiliser sous aucun prétexte un agent de nettoyage, ni le Sika
®
Cleaner-205 pour cette tâche.
Les panneaux atteignent leur capacité de charge maximale après 24 heures environ, et les éléments de fixation temporaire peuvent alors être retirés.
Important : Consultez les notices techniques et les fiches de sécurité Sika qui
sont à votre disposition auprès de votre représentant local Sika.
49
4.14 Etanchéité des zones très exposées aux UV
Description de l'application
Sur tous les bateaux de plaisance modernes, il est essentiel de rendre étanche l’ensemble des assemblages sans pour autant sacrifier l'esthétique de la finition.
Les systèmes polyuréthanne monocomposant Sikaflex
® représentent une solution hautes performances pour l’étanchéité : en raison de leurs excellentes qualités d'adhérence sur des supports très variés, ces systèmes offrent souplesse et étanchéité permanentes, ainsi qu’une résistance à la corrosion.
Les colles et mastics d'étanchéité polyuréthanne présentent toutefois une certaine sensibilité aux rayons UV. Après des périodes prolongées d'exposition, le joint peut se dégrader en surface et présenter de fines craquelures. Ces effets purement superficiels n'ont aucune incidence sur les propriétés d’adhérence et d'étanchéité du mastic. Toutefois, si le joint doit conserver durablement une finition soignée, il est préférable d'opter pour un polyuréthanne spécialement conçu pour résister aux UV.
Le Sikaflex
®
-295 UV, disponible en noir ou en blanc, offre une excellente résistance aux rayonnements solaires ainsi qu'à l'eau de mer. Par ailleurs, le
Sikaflex
®
-295 UV blanc possède de remarquables propriétés anti-jaunissement.
Le Sikaflex
®
-295 UV est donc particulièrement adapté à la réalisation de joints d’étanchéité sur les éléments d’accastillage de pont, les panneaux d'écoutille, les rebords de hublots, etc.
Note : Ces instructions ne concernent
pas les situations où les rayons ultraviolets sont susceptibles de s'attaquer directement aux surfaces de collage, c’est-
à-dire dans le cas de substrats transparents. Veuillez consulter les instructions spécifiques à ce type d'application.
Le Sikaflex
®
-295 UV ne convient pas non plus au calfatage des ponts en teck.
Préparation des substrats
Bois
Poncer la surface de contact avec la coque avec un papier de verre 80/100 et aspirer les poussières.
Appliquer une couche mince et régulière de Sika
®
Primaire-290 DC à l'aide d'un pinceau propre ou d'un tampon applicateur en feutre.
Temps de séchage : minimum 60 minutes - maximum 24 heures.
Aluminium, acier inox, peinture à base acrylique ou polyuréthanne
Nettoyer le substrat avec le Sika
®
Cleaner-205 et un chiffon ou un papier sec, propre, non-pelucheux et régulièrement renouvelé.
GRP
Temps de séchage : minimum 10 minutes - maximum 2 heures.
Poncer légèrement la zone de contact avec un papier de verre très fin. Aspirer les poussières.
Nettoyer le substrat avec le Sika
®
Cleaner-205 et un chiffon ou un papier sec, propre, non-pelucheux et régulièrement renouvelé.
Temps de séchage : minimum 10 minutes - maximum 2 heures.
Appliquer une couche mince et régulière de Sika
®
Primaire-206 G+P ou de Sika
®
Primaire-215 à l'aide d'un pinceau propre ou d'un tampon applicateur en feutre.
Temps de séchage : minimum 30 minutes - maximum 24 heures.
Autres substrats, consultez le tableau d'utilisation des primaires en fin d’ouvrage.
Application du Sikaflex
®
-295 UV
¤
Le Sikaflex
®
-295 UV doit être appliqué en un cordon suffisamment large tout en prenant soin d'éviter d'emprisonner des bulles d'air. Les excès de produit expulsés au serrage peuvent être retirés à l'aide d'une spatule en plastique. Le joint d'étanchéité peut être lissé avec le
Sika
®
Tooling Agent N. Cette opération doit être réalisée avant que le joint n'ait formé sa peau.
Les traces de Sikaflex
® non-polymérisé peuvent être enlevées à l'aide du Sika
®
Remover-208. N'utiliser sous aucun prétexte un agent de nettoyage, ni le Sika
®
Cleaner-205 pour cette tâche.
Important : Consultez les notices techniques et les fiches de données de sécurité
Sika qui sont à votre disposition auprès de votre représentant local Sika.
4.15 Collage de cloisons intérieures légères
Description de l'application
Les cloisons intérieures sont généralement de type panneaux sandwich, constitués de peaux en bois et d’une âme en mousse polyuréthanne ou nid d’abeille.
A bord, elles permettent de délimiter et d'insonoriser des espaces comme les cabines et les remises, sans alourdir le navire.
En raison de la faible densité de l’âme, les cloisons légères ne peuvent pas être fixées de manière mécanique à la structure de la coque, comme les panneaux de contreplaqué traditionnels. Le collage de ces cloisons avec le Sikaflex
®
-292 est la solution la mieux adaptée, par ailleurs recommandée par les fabricants de panneaux légers.
4
3
Préparation des substrats
Coques GRP
Commencer par nettoyer les surfaces très souillées à l'aide d'un solvant pur (Sika
®
Remover-208) pour retirer les traces les plus importantes.
Poncer légèrement la zone de collage avec un papier de verre très fin. Aspirer les poussières.
Nettoyer le substrat avec le Sika
®
Cleaner-205 et un chiffon ou un papier sec, propre, non-pelucheux et régulièrement renouvelé.
Temps de séchage : minimum 10 minutes - maximum 2 heures.
Appliquer une couche mince et régulière de Sika
®
Primaire-206 G+P ou de Sika
®
Primaire-215 à l'aide d'un pinceau propre ou d'un tampon applicateur en feutre.
Temps de séchage : minimum 30 minutes - maximum 24 heures.
1 - Cloison
2 - Garniture
3 - Sikaflex
®
-292
4 - Support
1
2
Coques en bois et cloisons
Poncer la surface de collage avec un papier de verre 80/100 et aspirer les poussières.
Appliquer une couche mince et régulière de Sika
®
Primaire-290 DC à l'aide d'un pinceau propre ou d'un tampon applicateur en feutre.
Temps de séchage : minimum 60 minutes - maximum 24 heures.
Pour la préparation d'autres substrats, consultez le tableau d'utilisation des primaires en fin d’ouvrage.
Application du Sikaflex
®
-292
¤
Présentez les panneaux à sec pour vérifier la précision de l'ajustement et des dimensions. Positionner des cales d'espacement souples (épaisseur 3 mm, dureté Shore A 50). Ne surtout pas fixer les cales avec une colle cyanoacrylate.
Appliquer le Sikaflex
®
-292 sur la face appropriée en un cordon triangulaire de
8 mm x 10 mm.
Assembler les composants dans les 20 minutes qui suivent l'application de la colle.
Maintenir les pièces en place à l'aide d’instruments appropriés (serre-joints, supports, etc.).
Les traces de Sikaflex
® non-polymérisé peuvent être enlevées à l'aide du Sika
®
Remover-208. N'utiliser sous aucun prétexte un agent de nettoyage, ni le Sika
®
Cleaner-205 pour cette tâche.
Les éléments de fixation temporaire peuvent être retirés après 24 heures.
Important : Consultez les notices techniques et les fiches de sécurité Sika qui sont
à votre disposition auprès de votre représentant local Sika.
51
4.16 Collage de plaques antidérapantes en salle des machines
Description de l'application
Les plaques antidérapantes utilisées dans les salles des machines ou dans les remises techniques sont souvent rivetées ou fixées mécaniquement au sol. Dans ces pièces où les vibrations sont naturellement fortes, ces fixations finissent par se desceller, ce qui demande généralement des travaux de réparation importants. Le collage de ces plaques permet une meilleure distribution des forces, et supprime ainsi la nécessité des réparations. Par ailleurs, la fixation et l'étanchéité s'effectuent en une seule opération.
Préparation des substrats
Sols GRP
Commencer par nettoyer les surfaces très souillées à l'aide d'un solvant pur (Sika
®
Remover-208) pour retirer les traces les plus importantes.
Poncer légèrement la zone de collage avec un papier de verre très fin. Aspirer les poussières.
Nettoyer le substrat avec le Sika
®
Cleaner-205 et un chiffon ou un papier sec, propre, non-pelucheux et régulièrement renouvelé.
Temps de séchage : minimum 10 minutes - maximum 2 heures.
Appliquer une couche mince et régulière de Sika
®
Primaire-206 G+P ou de Sika
®
Primaire-215 à l'aide d'un pinceau propre ou d'un tampon applicateur en feutre.
Temps de séchage : minimum 30 minutes - maximum 24 heures.
Sols acier
Nettoyer mécaniquement la surface par sablage (SA 1,5). Aspirer les poussières.
Nettoyer le substrat avec le Sika
®
Remover-208
Appliquer une couche régulière de Sika - Icosit
®
ZP Primer ( primaire anticorrosion bi-composant).
Temps de séchage : minimum 3 heures – maximum 14 heures.
Plaques antidérapantes en aluminium
Poncer légèrement la zone de collage avec un papier de verre très fin. Aspirer les poussières.
Nettoyer le substrat avec le Sika
®
Cleaner-205 et un chiffon ou un papier sec, propre, non-pelucheux et régulièrement renouvelé.
Temps de séchage : minimum 10 minutes - maximum 2 heures.
Appliquer une couche mince et régulière de Sika
®
Primaire-210 T à l'aide d'un pinceau propre ou d'un tampon applicateur en feutre.
Temps de séchage : minimum 60 minutes - maximum 24 heures.
Pour la préparation d'autres substrats, consultez le tableau d'utilisation des primaires en fin d’ouvrage.
Application du Sikaflex
®
-292
¤
Positionner des cales d'espacement (épaisseur 4 mm, dureté Shore A 50).
Les cales peuvent être noyées dans la colle pendant l'application. Ne surtout pas fixer les cales avec une colle cyanoacrylate.
Appliquer le Sikaflex
®
-292 en cordons parallèles triangulaires de 8 mm x 10 mm.
Epaisseur minimum du joint 4 mm.
Assembler les composants dans les 20 minutes qui suivent l'application de la colle.
Presser les pièces à l'aide de lest ou de tout autre accessoire, jusqu'à la hauteur des cales d'espacement.
Les traces de Sikaflex
® non-polymérisé peuvent être enlevées à l'aide du Sika
®
Remover-208. N'utiliser sous aucun prétexte un agent de nettoyage, ni le Sika
®
Cleaner-205 pour cette tâche.
Attendre 24 heures avant de marcher sur les éléments collés.
Important : Consultez les notices techniques et les fiches de sécurité Sika qui sont
à votre disposition auprès de votre représentant local Sika.
1
3
2
1 - Plaque antidérapante
2 - Sikaflex
®
-292
3 - Structure du sol
53
4.17 Calfatage de bordés à franc-bord en bois
Description de l'application
La technique traditionnelle de construction de bateaux en bois consistait à découper et à assembler les bordés de manière à ce que l'espace entre chaque latte ainsi que l'espace aux points de jonction avec la proue et la poupe puissent être calfatés de l'extérieur. Les lattes étaient chanfreinées de manière à présenter en face extérieure une gorge en V qui était ensuite calfatée pour rendre la coque totalement étanche. Après mise en forme des lattes, refroidissement, séchage puis fixation sur les membrures, l'opération de calfatage proprement dite pouvait commencer. On insérait d'abord une cordelette ou torsade de coton dans les interstices, pour forcer les joints à s'écarter légèrement. Ces derniers étaient ensuite remplis avec du brai en dessous de la ligne de flottaison, et avec un mastic
à base d'huile de lin au-dessus de cette même ligne. L'étanchéité totale de la coque était garantie dès la mise à l'eau du bateau, par un léger gonflement des bordés permettant d'assurer une pression sur les joints.
Les peintures actuelles n'étant pas compatibles avec le brai ou les autres matériaux bitumineux, il est nécessaire, lorsque l'on entreprend la restauration d'un vieux bateau en bois, d'utiliser un autre produit de calfatage. Les Sikaflex
®
Marine se sont révélés parfaitement adaptés à cette application, et peuvent être poncés et peints sans aucun problème.
L'acajou et le chêne sont les 2 essences les plus rencontrées pour la fabrication de coques en bois. Les instructions qui suivent restent néanmoins valables pour les autres essences utilisées en construction navale.
Les bordés à calfater doivent être sains.
Remplacer les lattes détériorées ou pourries. Les lattes doivent également être sèches. Pour ce faire, le bateau doit être mis à l'abri sur un quai couvert et aéré pendant 8 jours minimum. Les fissures importantes (5 mm ou plus) sur les lattes doivent êtres comblées pour garantir la rigidité de la coque. On pourra combler ces fissures en collant des bandes de bois et en les ponçant jusqu'à affleurement de la coque.
Retirer ensuite toute trace de l'ancien produit de calfatage en veillant à ne pas en-
Préparation des rainures
dommager ni déplacer le coton en fond de gorge.
L'utilisation de solvants n'est pas suffisante pour éliminer tous les résidus de l'ancien joint de calfatage. Un nettoyage mécanique, en particulier des bords du joint qui doivent être parfaitement propres, est nécessaire pour s'assurer qu'aucun corps gras (goudron, brai…) ne vienne perturber l'adhésion du joint de Sikaflex
®
.
Lorsque le bateau est mis à l'eau, l'expansion des bordés comprime le joint de
Sikaflex
®
, assurant une étanchéité parfaite de la coque. Les joints de calfatage présentent en outre une élasticité suffisante pour absorber les mouvements de torsion auxquels la coque sera soumise en mer.
Appliquer une première couche fine et continue de Sika
®
Primaire-290 DC sur les côtés des rainures, à l'aide d'un pinceau. Veiller à bien recouvrir la totalité des surfaces, en passant le pinceau d'avant en arrière. Laisser sécher 12 heures en protégeant la zone traitée de la poussière et de la pluie. Appliquer une seconde couche de Sika
®
Primaire-290 DC. Laisser sécher 2 heures minimum.
Application du Sikaflex
®
-291
¤
ou Sikaflex
®
-290 DC
¤
Le produit de calfatage sera appliqué dans la même journée que la seconde couche de primaire. Appliquer le Sikaflex
®
-291 ou le Sikaflex
®
-290 DC dans la rainure. Veiller à bien remplir le joint en poussant le produit avec un couteau ou une spatule.
Nettoyer immédiatement les excès de Sikaflex non polymérisé avec le Sika
®
Remover-208.
Dans des conditions standards, la coque peut être poncée après 5 à 7 jours. Si la profondeur du joint est supérieure à 15 mm et/ou si la température ambiante est inférieure à 15°C, le mastic polymérisera plus lentement et le délai à respecter avant ponçage sera plus long.
La coque peut ensuite être peinte. L'utilisation de peintures polyuréthanne bi-composant ou époxy bi-composant ne nécessite pas de test préliminaire. Des tests de compatibilité avec le mastic sont par contre recommandés pour les peintures monocomposant à base de résine synthétique ou peintures alkyde.
Il est préférable d'utiliser des peintures souples afin d'éviter le fendillement du film sous l'action des mouvements du joint.
Informations complémentaires
55
5.1 Remarques relatives aux substrats
Généralités
Les substrats doivent être propres et dénués de poussière, de salissure, de pétrole, de graisse comme de tout autre contaminant. Les surfaces sales, corrodées ou dégradées doivent être nettoyées.
Mise en peinture
Les produits Sikaflex
® peuvent être recouverts par la plupart des peintures usuelles (à l'exception des peintures base alkyde). Les meilleurs résultats s'obtiennent après polymérisation complète de la colle ou du mastic. Toutefois, s'il est nécessaire de peindre avant le séchage complet, nous recommandons de procéder systématiquement à un test de compatibilité. Notez que les peintures rigides s'opposent aux mouvements des joints et peuvent ainsi se craqueler.
Surfaces revêtues, peintures et vernis
Il est indispensable de procéder à des essais de collage sur les surfaces enduites. En règle générale, les systèmes réactifs nécessitant une cuisson (peintures en poudre) ou à réaction de polyaddition (enduits époxy ou PUR) sont compatibles avec les produits Sikaflex
®
.
Les peintures et les vernis base alkyde sont déconseillés. Les systèmes à base de polyvinyle butyrale (PVB), d'ester de résine époxy ainsi que les autres peintures monocomposant non-réactives à séchage à l'air donnent des collages moins résistants mais restent en général compatibles, du moins physiquement, avec nos mastics d'étanchéité. En revanche, et selon les forces appliquées au substrat, ces systèmes sont souvent moins compatibles avec nos colles.
Veuillez noter que les additifs qui agissent sur la surface des peintures ou des vernis – comme les agents de vitrification, les silicones, les antifongiques, etc.
– peuvent diminuer l'adhérence des colles et des mastics sur les peintures.
Verre et autres substrats transparents
Si vous utilisez un substrat transparent qui laisse la lumière du soleil parvenir directement jusqu'à la surface de colle, il est nécessaire de prévoir une protection supplémentaire contre les rayons UV.
Vous pouvez choisir entre : une bande de recouvrement périphérique extérieure plastique ou métallique ; une bordure céramique périphérique sérigraphiée – sur les verres minéraux – qui offrira une barrière suffisante contre les UV (transmission lumineuse <0.01%) ; un ruban de masquage noir ou blanc comme le Sika
®
UV Shielding Tape.
Pour chacune des solutions présentées ci-dessus, il conviendra de calculer le recouvrement nécessaire pour tenir compte des effets de réfraction.
En cas de doute, n'hésitez pas à consulter votre représentant local Sika.
Plastiques renforcés fibres de verre
(GRP)
En général, le GRP est un thermodur à base de résine polyester insaturée (UP), d'une résine époxy (EP) ou d'une résine polyuréthanne (PUR). Les GRP-UP
(communément appelés Polyester) fraîchement produits peuvent contenir des monomères de styrène résiduels : comme la réaction chimique n'est pas terminée, le substrat peut continuer à se rétracter et re-larguer du styrène. Seules les pièces en GRP "âgé" ou post-polymérisé peuvent être collées. La partie lisse – face gel-coat – du GRP peut contenir des agents de démoulage qui empêcheront tout collage efficace : ces résidus doivent être éliminés. La partie rugueuse des panneaux de GRP contient parfois des paraffines qui servent d'additif pour le séchage à l'air. Si le collage doit s'effectuer de ce côté, poncez soigneusement cette face du panneau, nettoyez avec le Sika
®
Cleaner-205 et passez une couche de Sika
®
Primaire-206
G+P ou de Sika
®
Primaire-215. Les feuillets minces et transparents ou faiblement colorés de GRP sont perméables aux
UV : consultez la section sur le verre et autres substrats transparents.
Plastiques
Certains matériaux plastiques comme le polyéthylène et le polypropylène, ne peuvent être collés qu’après avoir subi des traitements physico-chimiques : flammage, plasma, oxydation chimique. En raison de la diversité des compositions chimiques et de la présence d'agents internes ou externes de démoulage dans la plupart des composés chimiques, il est impossible de fournir des recommandations de collage pour chacun de ces produits. Nous vous recommandons de contacter votre représentant local
Sika. En effectuant des tests sur les différents matériaux pour déterminer la préparation la mieux appropriée à l'usage prévu, nous serons en mesure de vous conseiller avec précision.
Aluminium
L'aluminium et ses alliages se présentent sous forme de barres, de feuilles, de panneaux, de profilés et de moulages. La préparation dépend du produit
Sikaflex
® utilisé. Pour les pièces en aluminium traité – anodisé ou peint – un nettoyage avec le Sika
®
Cleaner-205 est souvent la seule préparation nécessaire avant le collage.
Acier galvanisé
La galvanisation de l'acier peut s'effectuer par : métallisation à chaud au pistolet, ou zingage électrolytique, ou immersion à chaud.
Dans les deux premiers cas, le métal de base est clairement défini et la composition de surface est relativement constante, alors que la finition de surface de la troisième méthode n'est généralement pas constante, et il convient de vérifier régulièrement la qualité des propriétés d'adhésion. Nous recommandons fortement d'effectuer des tests préalables.
57
Services Sika
Sika offre à ses clients une assistance technique et commerciale complète directement ou par l'intermédiaire de son réseau mondial de distributeurs spécialistes. Pour des renseignements plus détaillés, contactez votre représentant local Sika.
Les adresses des différentes sociétés
Sika dans le monde sont disponibles sur le site internet : www.industry.sika.fr
Manipulation et stockage
Les produits Sika doivent être entreposés et utilisés en respectant les bonnes pratiques d'hygiène et conformément
à la réglementation en vigueur. Il est de la responsabilité de notre client d'effectuer une évaluation fiable et suffisante des risques qu'entraîne l'utilisation de nos produits. Respectez les conseils de manutention qui figurent sur les emballages des produits Sika. Vous trouverez des conseils et des recommandations supplémentaires concernant la sécurité, les équipements de protection, les premiers soins, la mise au rebut, etc. sur les fiches de sécurité des produits, accessibles sur le site internet : www.industry.sika.fr.
Important
Les informations contenues dans ce document, et en particulier les recommandations relatives à l’application et à l’utilisation finale des produits Sika, sont fournies en toute bonne foi et se fondent sur la connaissance et l’expérience que la Société Sika a acquises à ce jour de ses produits lorsqu’ils ont été convenablement stockés, manipulés et appliqués dans des conditions normales. En pratique, les différences entre matériaux, substrats et conditions spécifiques sur site sont telles que ces informations ou toute recommandation écrite ou conseil donné n’impliquent aucune garantie de qualité marchande autre que la garantie légale contre les vices cachés. Nos services sont à votre disposition pour toute précision complémentaire.
Notre responsabilité ne saurait d’aucune manière être engagée dans l’hypothèse d’une application non conforme à nos renseignements. Les droits de propriété détenus par des tiers doivent impérativement être respectés. Toutes les commandes sont acceptées sous réserve de nos Conditions de Vente et de Livraison en vigueur. Les utilisateurs doivent impérativement consulter la version la plus récente de la fiche technique correspondant au produit concerné, qui leur sera remise sur demande.
Veuillez contacter votre représentant local Sika pour la mise à jour des informations disponibles. Les notices techniques Sika sont régulièrement mises
à jour ; nos clients sont ainsi appelés à vérifier qu'ils possèdent bien la version la plus récente.
5.2 Tableau de consommation
Produit
Sika
®
Activateur
Sika
®
Cleaner-205
Sika
®
Primaire-206 G+P
Sika
®
Primaire-209 N
Sika
®
Primaire-210 T
Sika
®
Primaire-215
Sika
®
Primaire-290 DC
250
1 000
250
1 000
250
250
250
1 000
250
1 000
250
1 000
Conditionnement
(ml)
Quantité nécessaire par m
2
(ml)
40
40
150
150
150
150
150
Surface traitée par conditionnement
(m
2
)
Longueur traitée par conditionnement sur la base d’un joint de
30 mm de large
(mètres linéaires)
6.25
25.00
6.25
25.00
1.60
50
1.60
1.60
6.60
1.60
6.60
1.60
6.60
50
50
200
50
200
50
200
Dimension des joints de calfatage avec le Sikaflex
®
-290 DC
4 x 5 mm
6 x 5mm
8 x 5mm
10 x 5mm
10 x 8mm
Couverture par conditionnement
(mètres linéaires) cartouche de 310ml recharge de 600ml
16
12
8
6
3
30
20
15
12
6
Epaisseur de
Sikaflex
®
-298
(mm)
2
4
Quantité nécessaire
(l/m
2
)
2
4
Nombre de conditionnements de
600 ml nécessaires pour couvrir 1 m
2
3
6
59
5.3 Dégraissants et primaires pour Sikaflex
®
5.4 Propriétés physiques des Sikaflex
®
Marine
61
5.5 Préparations de surfaces
Aluminium
(AlMg3)
Supports
Colles et mastics recommandés
Sikaflex
®
-291
Sikaflex
®
-292
Sikaflex
®
-295 UV
Sikaflex
®
-296
Sikaflex
®
-298
Préparation
Poncer légèrement la surface avec un tampon abrasif très fin (Scotch-Brite M 600)
Aspirer les poussières
Nettoyer la surface avec le Sika
®
Cleaner-205 et un chiffon ou un papier sec, propre, non pelucheux et régulièrement renouvelé
Temps de séchage* : minimum 10 minutes - maximum 2 heures
Appliquer une couche fine et régulière de Sika
®
Primaire-210 T à l’aide d’un pinceau propre
Temps de séchage : minimum 60 minutes - maximum 24 heures
Aluminium anodisé
Acier, métaux non ferreux, acier galvanisé
Sikaflex
®
-291
Sikaflex
®
-292
Sikaflex
®
-295 UV
Sikaflex
®
-296
Sikaflex
®
-298
Appliquer un primaire bi-composant type époxy suivant les instructions du fabricant
(ex : Sika
®
Icosit ZP Primer)
Laisser sécher 24 heures
Nettoyer les surfaces avec le Sika
®
Remover-208
Important : Procéder à des tests d’adhérence au préalable ou contacter nos services techniques
Acier inoxydable
Sikaflex
®
-291
Sikaflex
®
-292
Sikaflex
®
-295 UV
Sikaflex
®
-296
Sikaflex
®
-298
Nettoyer la surface avec le Sika
®
Cleaner-205 et un chiffon ou un papier sec, propre, non pelucheux et régulièrement renouvelé
Temps de séchage* : minimum 10 minutes - maximum 2 heures
Remarque : Certaines surfaces en aluminium anodisé présentent des poussières de laques ou de peintures. Procéder à des tests préliminaires.
Sikaflex
®
-291
Sikaflex
®
-292
Sikaflex
®
-295 UV
Sikaflex
®
-296
Sikaflex
®
-298
Nettoyer la surface avec le Sika
®
Cleaner-205 ou le Sika
®
Activateur et un chiffon ou un papier sec, propre, non pelucheux et régulièrement renouvelé
Temps de séchage* : minimum 10 minutes - maximum 2 heures
Remarque : Dans le cas de surfaces rugueuses ou d’applications de collage, suivre le mode opératoire de l’aluminium.
Verre minéral avec sérigraphie
Sikaflex
®
-296 Se référer aux instructions du collage de vitrage minéral en page 42, tout en observant les précautions suivantes :
- Transmission lumineuse < 0,01 % (verre trempé) ou <0,02 % (verre feuilleté), appliquer une couche de Sika
®
Activateur
- Si la transmission lumineuse est supérieure à ces valeurs, appliquer une couche de
Sika
®
Primaire-206 G+P après le Sika
®
Activateur.
PMMA / PC
(Plexiglas,
Polycarbonate)
Sikaflex
®
-295 UV La préparation de surface et la procédure d’assemblage doivent respecter les instructions du constructeur.
Nettoyer la surface avec le Sika
®
Cleaner-205 et un chiffon ou un papier sec, propre, non pelucheux et régulièrement renouvelé
Temps de séchage* : minimum 10 minutes - maximum 2 heures
Appliquer une couche fine et régulière de Sika
®
Primaire-209 N à l’aide d’un pinceau propre
Temps de séchage* : minimum 30 minutes - maximum 24 heures
Supports
ABS / PVC
Colles et mastics recommandés
Sikaflex
®
-291
Sikaflex
®
-292
Sikaflex
®
-295 UV
Sikaflex
®
-296
Sikaflex
®
-298
Préparation
Nettoyer la surface avec le Sika
®
Cleaner-205 et un chiffon ou un papier sec, propre, non pelucheux et régulièrement renouvelé
Temps de séchage* : minimum 10 minutes - maximum 2 heures
Appliquer une couche de Sika
®
Primaire-215 à l’aide d’un pinceau propre
Temps de séchage* : minimum 30 minutes - maximum 24 heures
Polyester renforcé fibres de verre (GRP)
Sikaflex
®
-291
Sikaflex
®
-292
Sikaflex
®
-295 UV
Sikaflex
®
-296
Sikaflex
®
-298
Côté fibres :
Poncer la surface à l’aide d’un papier de verre (grain 80)
Suivre ensuite la méthode d’application pour le gel coat (excepté le ponçage)
Côté gel coat :
Poncer la surface avec un tampon abrasif très fin (Scotch-Brite M 600)
Aspirer les poussières
Nettoyer la surface avec le Sika
®
Cleaner-205 et un chiffon ou un papier sec, propre, non pelucheux et régulièrement renouvelé
Temps de séchage* : minimum 10 minutes - maximum 2 heures
Appliquer une couche fine et régulière de Sika
®
Primaire-215 à l’aide d’un pinceau propre
Temps de séchage* : minimum 30 minutes - maximum 24 heures
Remarque : Les panneaux de GRP translucides exposés aux rayons UV doivent être protégés à l’aide d’un ruban de masquage (type Sika
®
UV Shielding Tape) ou d’une peinture opaque.
Peintures acryliques et PUR
Sikaflex
®
-291
Sikaflex
®
-292
Sikaflex
®
-295 UV
Sikaflex
®
-296
Sikaflex
®
-298
Nettoyer la surface avec le Sika
®
Cleaner-205, le Sika
®
Activateur ou le Sika
®
Remover-
208
Respecter le temps de séchage approprié
Remarque : Face aux nombreuses compositions chimiques des peintures, nous recommandons de procéder à des tests préliminaires.
Bois non traité
Sikaflex
®
-291
Sikaflex
®
-292
Sikaflex
®
-295 UV
Sikaflex
®
-296
Sikaflex
®
-298
Eliminer toute poussière
Appliquer une couche de Sika
®
Primaire-290 DC à l’aide d’un pinceau
Temps de séchage* : minimum 30 minutes - maximum 24 heures
Remarques :
Bois peint : suivre le mode opératoire indiqué pour les peintures acryliques et PUR
Bois imprégné : doit préalablement être poncé et nettoyé
Procéder à des tests préliminaires
* à 23°C et 50 % HR
Important : les temps de séchage sont fonction de la température et de l’humidité
63
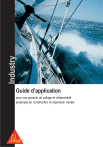
Enlace público actualizado
El enlace público a tu chat ha sido actualizado.