Miller PROHEAT 35 ce Manuel du propriétaire
PDF
Scarica
Documento
OM-271146V/fre 2024-08 Procédés Chauffage par induction Description Source d’alimentation de chauffage par induction ProHeat 35 CE et Modèles Non CE ™ (Pour n de stock 907689 et 907690) Pour des informations sur le produit, des traductions du Manuel de l’utilisateur et bien plus, rendez-vous sur www.MillerWelds.com MANUEL DE L’UTILISATEUR Miller, votre partenaire soudage! Félicitations et merci d’avoir choisi Miller. Dès maintenant, vous pouvez faire votre travail, comme il faut. Nous savons que vous n’avez pas le temps de faire autrement. C’est pourquoi Niels Miller, quand il a commencé à fabriquer les postes à souder à l’arc en 1929, s’efforçait de fournir des produits de qualité supérieure destinés à offrir des performances optimales pendant de longues années. Comme vous, ses clients exigeaient les meilleurs produits disponible sur le marché. Chaque source de soudage Miller bénéficie d'une garantie “sans soucis” Aujourd’hui, la tradition continue grâce aux gens qui fabriquent et vendent les produits Miller. L’engagement de fournir le matériel et le service répondant aux même exigences rigoureuses de qualité et de valeur qu’en 1929 demeure inchangé. Ce manuel de l’utilisateur est destiné à vous aider à profiter le mieux de vos produits Miller. Veuillez prendre le temps de lire les précautions de sécurité. Elles vous aident à vous protéger contre des dangers éventuels au travail. Miller vous permet une installation rapide et l’exploitation facile. Convenablement entretenu, le matériel Miller vous assure des performances fiables pendant de longues années. Si pour toutes raisons, une réparation de l’unité s’avère nécessaire, la section Dépannage vous aidera à faire un diagnostic rapide pour déterminer le problème. Notre réseau de service complet vous permettra alors de le résoudre. Vous trouverez également les informations concernant la garantie et l’entretien spécifiques à votre modèle. Miller Electric fabrique une gamme complète de machines à souder et d’équipements liés au soudage. Pour des renseignements sur les autres produits Miller, adressez-vous à votre distributeur local Miller pour obtenir le catalogue le plus récent sur toute la gamme, ou les feuilles techniques de chaque produit. Pour trouver un concessionnaire ou un agent de service agréé, se rendre sur www.MillerWelds.com ou appeler le 1−800−4−A−Miller. Miller est le premier fabricant de matériel de soudage aux États- Unis à être certifié conforme au système d'assurance du contrôle de la qualité ISO 9001. TABLE DES MATIÈRES SECTION 1 – CONSIGNES DE SÉCURITÉ - LIRE AVANT UTILISATION . . . . . . . . . . . . . . . . . . . . . . . . . . . . . . . . . . . . . . . . . . . . . . . . . . . . . . . . . . . . 1 1-1 Symboles utilisés. . . . . . . . . . . . . . . . . . . . . . . . . . . . . . . . . . . . . . . . . . . . . . . . . . . . . . . . . . . . . . . . . . . . . . . . . . . . . . . . . . . . . . . . . . . . . . . . . . . . 1 1-2 Dangers relatifs au chauffage par induction . . . . . . . . . . . . . . . . . . . . . . . . . . . . . . . . . . . . . . . . . . . . . . . . . . . . . . . . . . . . . . . . . . . . . . . . . . . . . 1 1-3 Symboles de dangers supplémentaires en relation avec l’installation, le fonctionnement et la maintenance . . . . . . . . . . . . . . . . . . . . . . 2 1-4 Proposition californienne 65 Avertissements . . . . . . . . . . . . . . . . . . . . . . . . . . . . . . . . . . . . . . . . . . . . . . . . . . . . . . . . . . . . . . . . . . . . . . . . . . . . 3 1-5 Principales normes de sécurité . . . . . . . . . . . . . . . . . . . . . . . . . . . . . . . . . . . . . . . . . . . . . . . . . . . . . . . . . . . . . . . . . . . . . . . . . . . . . . . . . . . . . . . . 3 1-6 Informations relatives aux CEM . . . . . . . . . . . . . . . . . . . . . . . . . . . . . . . . . . . . . . . . . . . . . . . . . . . . . . . . . . . . . . . . . . . . . . . . . . . . . . . . . . . . . . . 3 SECTION 2 – DÉFINITIONS . . . . . . . . . . . . . . . . . . . . . . . . . . . . . . . . . . . . . . . . . . . . . . . . . . . . . . . . . . . . . . . . . . . . . . . . . . . . . . . . . . . . . . . . . . . . . . . . . . . 5 2-1 Symboles et définitions supplémentaires relatifs à la Sécurité . . . . . . . . . . . . . . . . . . . . . . . . . . . . . . . . . . . . . . . . . . . . . . . . . . . . . . . . . . . . . 5 2-2 Symboles et définitions divers . . . . . . . . . . . . . . . . . . . . . . . . . . . . . . . . . . . . . . . . . . . . . . . . . . . . . . . . . . . . . . . . . . . . . . . . . . . . . . . . . . . . . . . . . 7 SECTION 3 – SPÉCIFICATIONS . . . . . . . . . . . . . . . . . . . . . . . . . . . . . . . . . . . . . . . . . . . . . . . . . . . . . . . . . . . . . . . . . . . . . . . . . . . . . . . . . . . . . . . . . . . . . . . 8 3-1 Emplacement du numéro de série et de la plaque signalétique. . . . . . . . . . . . . . . . . . . . . . . . . . . . . . . . . . . . . . . . . . . . . . . . . . . . . . . . . . . . . 8 3-2 Contrat de licence de logiciel. . . . . . . . . . . . . . . . . . . . . . . . . . . . . . . . . . . . . . . . . . . . . . . . . . . . . . . . . . . . . . . . . . . . . . . . . . . . . . . . . . . . . . . . . . 8 3-3 Informations sur les paramètres et réglages de soudage par défaut . . . . . . . . . . . . . . . . . . . . . . . . . . . . . . . . . . . . . . . . . . . . . . . . . . . . . . . . 8 3-4 Spécifications. . . . . . . . . . . . . . . . . . . . . . . . . . . . . . . . . . . . . . . . . . . . . . . . . . . . . . . . . . . . . . . . . . . . . . . . . . . . . . . . . . . . . . . . . . . . . . . . . . . . . . . 8 3-5 Spécifications environnementales . . . . . . . . . . . . . . . . . . . . . . . . . . . . . . . . . . . . . . . . . . . . . . . . . . . . . . . . . . . . . . . . . . . . . . . . . . . . . . . . . . . . . 8 SECTION 4 – INSTALLATION. . . . . . . . . . . . . . . . . . . . . . . . . . . . . . . . . . . . . . . . . . . . . . . . . . . . . . . . . . . . . . . . . . . . . . . . . . . . . . . . . . . . . . . . . . . . . . . . . 11 4-1 Choix d’un emplacement . . . . . . . . . . . . . . . . . . . . . . . . . . . . . . . . . . . . . . . . . . . . . . . . . . . . . . . . . . . . . . . . . . . . . . . . . . . . . . . . . . . . . . . . . . . . 11 4-2 Dimensions et poids . . . . . . . . . . . . . . . . . . . . . . . . . . . . . . . . . . . . . . . . . . . . . . . . . . . . . . . . . . . . . . . . . . . . . . . . . . . . . . . . . . . . . . . . . . . . . . . . 12 4-3 Guide d’entretien électrique. . . . . . . . . . . . . . . . . . . . . . . . . . . . . . . . . . . . . . . . . . . . . . . . . . . . . . . . . . . . . . . . . . . . . . . . . . . . . . . . . . . . . . . . . . 13 4-4 Connexion de l’alimentation triphasée pour les modèles 460/575Volts . . . . . . . . . . . . . . . . . . . . . . . . . . . . . . . . . . . . . . . . . . . . . . . . . . . . . 14 4-5 Connexion de l’alimentation triphasée pour les modèles 460/575Volts . . . . . . . . . . . . . . . . . . . . . . . . . . . . . . . . . . . . . . . . . . . . . . . . . . . . . 15 4-6 Connexion de l’alimentation triphasée pour les modèles 400/460V IEC et CE . . . . . . . . . . . . . . . . . . . . . . . . . . . . . . . . . . . . . . . . . . . . . . . 16 4-7 Connexion de l’alimentation triphasée pour les modèles 400/460V IEC et CE . . . . . . . . . . . . . . . . . . . . . . . . . . . . . . . . . . . . . . . . . . . . . . . 17 4-8 Raccords du cavalier de liquide de refroidissement. . . . . . . . . . . . . . . . . . . . . . . . . . . . . . . . . . . . . . . . . . . . . . . . . . . . . . . . . . . . . . . . . . . . . . 17 4-9 Connexions de sortie de la source d’alimentation . . . . . . . . . . . . . . . . . . . . . . . . . . . . . . . . . . . . . . . . . . . . . . . . . . . . . . . . . . . . . . . . . . . . . . . 18 4-10 Informations et connexions concernant la prise de commande à distance RC14. . . . . . . . . . . . . . . . . . . . . . . . . . . . . . . . . . . . . . . . . . . . . 19 4-11 Informations relatives à la prise distante 14 . . . . . . . . . . . . . . . . . . . . . . . . . . . . . . . . . . . . . . . . . . . . . . . . . . . . . . . . . . . . . . . . . . . . . . . . . . . . 19 4-12 Informations et connexions concernant la prise d’enregistrement de température RC9 . . . . . . . . . . . . . . . . . . . . . . . . . . . . . . . . . . . . . . . 20 4-13 Informations concernant les broches d’enregistrement de température. . . . . . . . . . . . . . . . . . . . . . . . . . . . . . . . . . . . . . . . . . . . . . . . . . . . . 20 4-14 Protection d’isolation secondaire . . . . . . . . . . . . . . . . . . . . . . . . . . . . . . . . . . . . . . . . . . . . . . . . . . . . . . . . . . . . . . . . . . . . . . . . . . . . . . . . . . . . . 21 4-15 Boîtier duplex de 115VAC et dispositif de protection supplémentaire . . . . . . . . . . . . . . . . . . . . . . . . . . . . . . . . . . . . . . . . . . . . . . . . . . . . . . . 22 4-16 Position des thermocouples. . . . . . . . . . . . . . . . . . . . . . . . . . . . . . . . . . . . . . . . . . . . . . . . . . . . . . . . . . . . . . . . . . . . . . . . . . . . . . . . . . . . . . . . . . 23 4-17 Position des thermocouples (Suite) . . . . . . . . . . . . . . . . . . . . . . . . . . . . . . . . . . . . . . . . . . . . . . . . . . . . . . . . . . . . . . . . . . . . . . . . . . . . . . . . . . . 24 4-18 Fixation des thermocouples soudés . . . . . . . . . . . . . . . . . . . . . . . . . . . . . . . . . . . . . . . . . . . . . . . . . . . . . . . . . . . . . . . . . . . . . . . . . . . . . . . . . . . 25 4-19 Utilisation de capteurs TC de contact. . . . . . . . . . . . . . . . . . . . . . . . . . . . . . . . . . . . . . . . . . . . . . . . . . . . . . . . . . . . . . . . . . . . . . . . . . . . . . . . . . 26 4-20 Utilisation de capteurs de température sans contact . . . . . . . . . . . . . . . . . . . . . . . . . . . . . . . . . . . . . . . . . . . . . . . . . . . . . . . . . . . . . . . . . . . . . 27 SECTION 5 – COMPOSANTS ET COMMANDES. . . . . . . . . . . . . . . . . . . . . . . . . . . . . . . . . . . . . . . . . . . . . . . . . . . . . . . . . . . . . . . . . . . . . . . . . . . . . . . . 28 5-1 Commandes. . . . . . . . . . . . . . . . . . . . . . . . . . . . . . . . . . . . . . . . . . . . . . . . . . . . . . . . . . . . . . . . . . . . . . . . . . . . . . . . . . . . . . . . . . . . . . . . . . . . . . . 28 SECTION 6 – CONFIGURATION ET FONCTIONNEMENT . . . . . . . . . . . . . . . . . . . . . . . . . . . . . . . . . . . . . . . . . . . . . . . . . . . . . . . . . . . . . . . . . . . . . . . . 29 6-1 Équipement de sécurité . . . . . . . . . . . . . . . . . . . . . . . . . . . . . . . . . . . . . . . . . . . . . . . . . . . . . . . . . . . . . . . . . . . . . . . . . . . . . . . . . . . . . . . . . . . . . 29 6-2 Description du système . . . . . . . . . . . . . . . . . . . . . . . . . . . . . . . . . . . . . . . . . . . . . . . . . . . . . . . . . . . . . . . . . . . . . . . . . . . . . . . . . . . . . . . . . . . . . 29 6-3 Directives importantes . . . . . . . . . . . . . . . . . . . . . . . . . . . . . . . . . . . . . . . . . . . . . . . . . . . . . . . . . . . . . . . . . . . . . . . . . . . . . . . . . . . . . . . . . . . . . . 29 6-4 Source d’alimentation/Configuration du système . . . . . . . . . . . . . . . . . . . . . . . . . . . . . . . . . . . . . . . . . . . . . . . . . . . . . . . . . . . . . . . . . . . . . . . . 29 6-5 Programmation . . . . . . . . . . . . . . . . . . . . . . . . . . . . . . . . . . . . . . . . . . . . . . . . . . . . . . . . . . . . . . . . . . . . . . . . . . . . . . . . . . . . . . . . . . . . . . . . . . . . 32 6-6 État de marche. . . . . . . . . . . . . . . . . . . . . . . . . . . . . . . . . . . . . . . . . . . . . . . . . . . . . . . . . . . . . . . . . . . . . . . . . . . . . . . . . . . . . . . . . . . . . . . . . . . . . 41 SECTION 7 – MAINTENANCE & DÉPANNAGE . . . . . . . . . . . . . . . . . . . . . . . . . . . . . . . . . . . . . . . . . . . . . . . . . . . . . . . . . . . . . . . . . . . . . . . . . . . . . . . . . 48 7-1 Maintenance de routine . . . . . . . . . . . . . . . . . . . . . . . . . . . . . . . . . . . . . . . . . . . . . . . . . . . . . . . . . . . . . . . . . . . . . . . . . . . . . . . . . . . . . . . . . . . . . 48 7-2 Équipement de vérification de l’étalonnage. . . . . . . . . . . . . . . . . . . . . . . . . . . . . . . . . . . . . . . . . . . . . . . . . . . . . . . . . . . . . . . . . . . . . . . . . . . . . 49 7-3 Procédure de vérification de l’étalonnage . . . . . . . . . . . . . . . . . . . . . . . . . . . . . . . . . . . . . . . . . . . . . . . . . . . . . . . . . . . . . . . . . . . . . . . . . . . . . . 49 7-4 Servicing Hazards . . . . . . . . . . . . . . . . . . . . . . . . . . . . . . . . . . . . . . . . . . . . . . . . . . . . . . . . . . . . . . . . . . . . . . . . . . . . . . . . . . . . . . . . . . . . . . . . . . 53 SECTION 8 – DIAGNOSTIC ET DÉTECTION DES PANNES . . . . . . . . . . . . . . . . . . . . . . . . . . . . . . . . . . . . . . . . . . . . . . . . . . . . . . . . . . . . . . . . . . . . . . 57 8-1 Indicateurs opérateur à distance. . . . . . . . . . . . . . . . . . . . . . . . . . . . . . . . . . . . . . . . . . . . . . . . . . . . . . . . . . . . . . . . . . . . . . . . . . . . . . . . . . . . . . 57 8-2 Conditions de limites. . . . . . . . . . . . . . . . . . . . . . . . . . . . . . . . . . . . . . . . . . . . . . . . . . . . . . . . . . . . . . . . . . . . . . . . . . . . . . . . . . . . . . . . . . . . . . . . 57 8-3 Codes des conditions de limite . . . . . . . . . . . . . . . . . . . . . . . . . . . . . . . . . . . . . . . . . . . . . . . . . . . . . . . . . . . . . . . . . . . . . . . . . . . . . . . . . . . . . . . 59 8-4 Description et tableaux de dépannage des codes d’erreur. . . . . . . . . . . . . . . . . . . . . . . . . . . . . . . . . . . . . . . . . . . . . . . . . . . . . . . . . . . . . . . . 60 8-5 Tableau de dépannage . . . . . . . . . . . . . . . . . . . . . . . . . . . . . . . . . . . . . . . . . . . . . . . . . . . . . . . . . . . . . . . . . . . . . . . . . . . . . . . . . . . . . . . . . . . . . . 60 SECTION 9 – SCHEMA ELECTRIQUE . . . . . . . . . . . . . . . . . . . . . . . . . . . . . . . . . . . . . . . . . . . . . . . . . . . . . . . . . . . . . . . . . . . . . . . . . . . . . . . . . . . . . . . . . 62 DÉCLARATION DE CONFORMITÉ pour les produits de la Communauté Européenne (marqués CE). MILLER Electric Mfg. LLC, 1635 West Spencer Street, Appleton, WI 54914 États-Unis déclare que le(s) produit(s) identifié(s) dans la présente déclaration est (sont) conforme(s) aux exigences et dispositions essentielles de la ou des directives et normes du comité indiqué. Identification du produit/de l'appareil : Produit ProHeat 35, 400−460V Cooler/ProHeat Heavy Duty Induction Référence 907690 301298 Directives du Conseil et Règlements de la commission : • 2014/35/EU Low voltage • 2014/30/EU Electromagnetic compatibility • 2009/125/EC and regulation 2019/1784 Ecodesign requirements for energy−related products • 2011/65/EU and amendment 2015/863 Restriction of the use of certain hazardous substances in electrical and electronic equipment Normes : • EN IEC 60974−1:2018/AI:2019 Arc welding equipment – Part 1: Welding power sources • EN IEC 60974−2:2019 Arc welding equipment – Part 2: Liquid cooling systems • EN 60974−10:2014/A1:2015 Arc welding equipment – Part 10: Electromagnetic compatibility requirements • EN IEC 63000:2018 – Technical documentation for the assessment of electrical and electronic products with respect to the restriction of hazardous substances Signataire : November 5, 2021 _____________________________________ ___________________________________________ David A. Werba Date de la déclaration MANAGER, PRODUCT DESIGN COMPLIANCE 272703D DECLARATION OF CONFORMITY For United Kingdom (UKCA marked) products. MILLER Electric Mfg. LLC, 1635 West Spencer Street, Appleton, WI 54914 U.S.A. declares that the product(s) identified in this declaration, when used exclusively with MILLER induction heating cables and inductors, conform to the essential requirements and provisions of the stated Regulation(s) and Standard(s). Product/Apparatus Identification: Product ProHeat 35, 400−460V Cooler/ProHeat Heavy Duty Induction Stock Number 907690 301298 Regulations: • • • S.I. 2016/1101 Electrical Equipment (Safety) Regulations 2016 S.I. 2016/1091 Electromagnetic Compatibility Regulations 2016 S.I. 2012/3032 Restriction of the Use of Certain Hazardous Substances in Electrical and Electronic Equipment Regulations 2012 Standards: • • • • EN IEC 60974−1:2018/A1:2019 Arc welding equipment – Part 1 Welding power sources EN IEC 60974−2:2019 Arc welding equipment – Part 2: Liquid cooling systems EN 60974−10:2014/A1:2015 Arc welding equipment – Part 10: Electromagnetic compatibility requirements EN IEC 63000:2018 Technical documentation for the assessment of electrical and electronic products with respect to the restriction of hazardous substances Signatory: November 5, 2021 _____________________________________ ___________________________________________ David A. Werba Date of Declaration MANAGER, PRODUCT DESIGN COMPLIANCE 290552B FICHE TECHNIQUE EMF POUR SOURCE D'ALIMENTATION DE CHAUFFAGE À INDUCTION MILLER Electric Mfg. Co., 1635 Spencer Street, Appleton, WI 54914 États-Unis fournit volontairement les informations suivantes pour aider les employeurs européens à effectuer leurs évaluations pour démontrer leur conformité à la directive 2013/35/UE concernant les obligations minimales en termes de santé et de sécurité en termes d'exposition des employés aux risques que présentent les agents physiques (champs électromagnétiques). Identification du produit/de l'appareil Produit PROHEAT 35, 400-460V (CE) Référence 907690 Récapitulatif des informations de conformité Réglementation en vigueur Directive 2014/35/EU Limites de référence Directive 2013/35/EU, Recommendation 1999/519/EC Normes applicables Aucune ☐ usage grand public Usage prévu ☒ usage professionnel Les effets sensoriels doivent être pris en considération pour l'évaluation du poste de travail ☐ OUI ☒ NON Les effets sanitaires non thermiques doivent être pris en considération pour l'évaluation du poste de travail ☒ OUI ☐ NON Les effets sanitaires thermiques doivent être pris en considération pour l'évaluation du poste de travail ☐ OUI ☒ NON ☒ Les données sont basées sur la capacité maximale de la source d'alimentation (valables sans changement de microprogramme/matériel) ☐ Les données sont basées sur le cas de réglage/programme le plus défavorable (valables seulement jusqu'à la modification des options de réglage/programmes de soudage) ☐ Les données sont basées sur plusieurs réglages/programmes (valables seulement jusqu'à la modification des options de réglage/programmes de soudage) Données EMF pour les effets sanitaires non thermiques Distances d'approche minimales du tuyau/de la spire lorsque les valeurs limites d'exposition EMF ne sont pas dépassées (Indice d'exposition ELV ≤ 1) Partie du corps Puissance émise Tête Tronc Main Cuisse 35 kW 12 cm 14 cm 6 cm 12 cm 25 kW 11 cm 13 cm 4 cm 11 cm 15 kW 9 cm 11 cm 2 cm 9 cm 5 kW 4 cm 6 cm 0 cm 4 cm Distance à laquelle tous les indices VLE d'exposition professionnelle descendent en-dessous de 0,20 (20 %) 30 cm Distance à laquelle tous les indices VLE d'exposition grand public descendent en-dessous de 1,00 (100 %) 56 cm Évaluation réalisée par : 276511-A Mike Madsen Date de réalisation : 2016-03-18 SECTION 1 – CONSIGNES DE SÉCURITÉ - LIRE AVANT UTILISATION Pour écarter les risques de blessure pour vous-même et pour autrui — lire, appliquer et ranger en lieu sûr ces consignes relatives aux précautions de sécurité et au mode opératoire. 1-1. Symboles utilisés DANGER! – Indique une situation dangereuse qui si on l’évite pas peut donner la mort ou des blessures graves. Les dangers possibles sont montrés par les symboles joints ou sont expliqués dans le texte. Indique une situation dangereuse qui si on l’évite pas peut donner la mort ou des blessures graves. Les dangers possibles sont montrés par les symboles joints ou sont expliqués dans le texte. AVIS – Indique des déclarations pas en relation avec des blessures personnelles. Ce groupe de symboles veut dire Avertissement! Attention! DANGER DE CHOC ELECTRIQUE, PIECES EN MOUVEMENT, et PIECES CHAUDES. Reportez-vous aux symboles et aux directives cidessous afin de connaître les mesures à prendre pour éviter tout danger. � Indique des instructions spécifiques. 1-2. Dangers relatifs au chauffage par induction Les symboles représentés ci-dessous sont utilisés dans ce manuel pour attirer l’attention et identifier les dangers possibles. En présence de ce symbole, prendre garde et suivre les instructions afférentes pour éviter tout risque. Les consignes de sécurité présentées ci-après ne font que résumer l’information contenue dans les Normes de sécurité principales. Lire et suivre toutes les Normes de sécurité. L’installation, l’utilisation, l’entretien et les réparations ne doivent être confiés qu’à des personnes qualifiées. Une personne qualifiée est définie comme celle qui, par la possession d’un diplôme reconnu, d’un certificat ou d’un statut professionnel, ou qui, par une connaissance, une formation et une expérience approfondies, a démontré avec succès sa capacité à résoudre les problèmes liés à la tâche, le travail ou le projet et a reçu une formation en sécurité afin de reconnaître et d’éviter les risques inhérents. Au cours de l’utilisation, tenir toute personne à l’écart et plus particulièrement les enfants. UNE DÉCHARGE ÉLECTRIQUE peut entraîner la mort. � Couper l’alimentation d’entrée avant d’installer l’appareil ou d’effectuer l’entretien. Verrouiller ou étiqueter la sortie d’alimentation selon la norme OSHA 29 CFR 1910.147(se reporter aux Principales normes de sécurité). � N’utiliser que des tuyaux de refroidissement non conducteurs ayant une longueur minimale de 457 mm pour garantir l’isolation. � Installer le poste correctement et le mettre à la terre convenablement selon les consignes du manuel de l’opérateur et les normes nationales, provinciales et locales. � Toujours vérifier la mise à la terre — vérifier et assurez-vous que le conducteur de mise à la terre du cordon d’alimentation est bien raccordé à la borne de mise à la terre dans le boîtier de déconnexion ou que la fiche du cordon est raccordée à une prise correctement mise à la terre. � En effectuant les raccordements d’entrée, fixer d’abord le conducteur de mise à la terre approprié et revérifier les connexions. � Les câbles doivent être exempts d’humidité, d’huile et de graisse; protégez-les contre les étincelles et les pièces métalliques chaudes. � Vérifier fréquemment le cordon d’alimentation et le conducteur de mise à la terre afin de s’assurer qu’il n’est pas altéré ou dénudé. Le remplacer immédiatement s’il l’est. Un fil dénudé peut entraîner la mort. Le contact de composants électriques peut provoquer des accidents mortels ou des brûlures graves. Le circuit électrique et les barres collectrices ou les connexions de sortie sont sous tension lorsque l’appareil fonctionne. Le circuit d’alimentation et les circuits internes de la machine sont également sous tension lorsque l’alimentation est sur marche. Des équipements installés ou reliés à la borne de terre de manière incorrecte sont dangereux. � L’équipement doit être hors tension lorsqu’il n’est pas utilisé. � Ne pas toucher aux pièces électriques sous tension. � Ne pas toucher le circuit électrique si l’on est en contact avec la pièce, la terre ou le circuit électrique d’une autre machine. � Protéger toutes les barres collectrices et les raccords de refroidissement pour éviter de les toucher par inadvertance. � Porter des gants isolants et des vêtements de protection secs et sans trous. � S’isoler de la pièce à couper et du sol en utilisant des housses ou des tapis assez grands afin d’éviter tout contact physique avec la pièce à couper ou le sol. � D’autres consignes de sécurité sont nécessaires dans les conditions suivantes : risques électriques dans un environnement humide ou si l’on porte des vêtements mouillés ; sur des structures métalliques telles que sols, grilles ou échafaudages ; en position coincée comme assise, à genoux ou couchée ; ou s’il y a un risque élevé de contact inévitable ou accidentel avec la pièce à souder ou le sol. Dans ces conditions, voir ANSI Z49.1 énuméré dans les normes de sécurité. En outre, ne pas travailler seul ! � Ne stockez pas et n’utilisez pas l’équipement dans de l’eau stagnante. � Ne pas utiliser des câbles usés, endommagés, de grosseur insuffisante ou mal épissés. � Ne pas enrouler les câbles autour du corps. � N’utiliser qu’un matériel en bon état. Réparer ou remplacer sur-lechamp les pièces endommagées. Entretenir l’appareil conformément à ce manuel. � Porter un harnais de sécurité si l’on doit travailler au-dessus du sol. � S’assurer que tous les panneaux et couvercles sont correctement en place. � Utiliser une protection différentielle lors de l’utilisation d’un équipement auxiliaire dans des endroits humides ou mouillés. LES FUMÉES ET LES GAZ peuvent être dangereux. Le chauffage à induction de certains matériaux, adhésifs et flux génère des fumées et des gaz. Leur inhalation peut être dangereuse pour votre santé. OM-271146 Page 1 � Ne pas mettre sa tête au-dessus des vapeurs. Ne pas respirer ces vapeurs. � À l’intérieur, ventiler la zone et/ou utiliser une ventilation forcée au niveau de l’arc pour l’évacuation des fumées et des gaz de soudage. Pour déterminer la bonne ventilation, il est recommandé de procéder à un prélèvement pour la composition et la quantité de fumées et de gaz auxquelles est exposé le personnel. � Si la ventilation est médiocre, porter un respirateur anti-vapeurs approuvé. � Lire et comprendre les fiches de données de sécurité et les instructions du fabricant concernant les adhésifs, les revêtements, les nettoyants, les consommables, les produits de refroidissement, les dégraisseurs, les flux et les métaux. � Travailler dans un espace fermé seulement s’il est bien ventilé ou en portant un respirateur. Demander toujours à un surveillant dûment formé de se tenir à proximité. Des fumées et des gaz provenant du chauffage peuvent déplacer l’air, abaisser le niveau d’oxygène et provoquer des lésions ou des accidents mortels. S’assurer que l’air ambiant ne présente aucun danger. � Ne pas chauffer dans des endroits se trouvant à proximité d’opérations de dégraissage, de nettoyage ou de pulvérisation. La chaleur peut réagir en présence de vapeurs et former des gaz hautement toxiques et irritants. � Ne pas surchauffer des métaux munis d’un revêtement tels que l’acier galvanisé, plaqué au plomb ou au cadmium, à moins que le revêtement ne soit enlevé de la zone chauffée, que la zone soit bien ventilée et, si nécessaire, en portant un respirateur. Les revêtements et tous les métaux contenant ces éléments peuvent dégager des fumées toxiques s’ils sont surchauffés. Voir les informations concernant la température dans les spécifications de revêtement SDS. Risque D’INCENDIE OU D’EXPLOSION. � Ne pas surchauffer les composants. � Attention aux risques d’incendie: tenir un extincteur à proximité. � Stocker des produits inflammables hors de la zone de travail. 1-3. � Ne pas placer l’appareil sur, au-dessus ou à proximité de surfaces inflammables. � Ne pas utiliser l’appareil pour dégeler des tuyaux. � Ne pas installer l’appareil à proximité de produits inflammables. � Ne pas couvrir les protections isolantes refroidies par air avec un matériau pouvant entraîner leur surchauffe. � Ne pas souder là où l’air ambiant pourrait contenir des poussières, gaz ou émanations inflammables (vapeur d’essence, par exemple). � Une fois le travail achevé, assurez-vous qu’il ne reste aucune trace d’étincelles incandescentes ni de flammes. � Utiliser exclusivement des fusibles ou coupe-circuits appropriés. Ne pas augmenter leur puissance; ne pas les ponter. � Lire et comprendre les fiches de données de sécurité et les instructions du fabricant concernant les adhésifs, les revêtements, les nettoyants, les consommables, les produits de refroidissement, les dégraisseurs, les flux et les métaux. � Porter une protection corporelle en cuir ou des vêtements ignifuges (FRC). La protection du corps comporte des vêtements sans huile, comme des gants de cuir, une chemise solide, des pantalons sans revers, des chaussures hautes et une casquette. LE CHAUFFAGE PAR INDUCTION peut provoquer des brûlures. � Ne pas toucher des parties chaudes à mains nues. � Laisser refroidir les composants ou équipements avant de les manipuler. � Ne pas toucher ou manipuler les câbles/enroulements d’induction durant l’opération à moins que l’équipement soit conçu à cet effet comme indiqué dans le manuel d’utilisateur. � Tenir les bijoux et autres objets personnels en métal éloignés de la tête/de l’enroulement pendant le fonctionnement. � Ne pas toucher aux pièces chaudes, utiliser les outils recommandés et porter des gants de soudage et des vêtements épais pour éviter les brûlures. Symboles de dangers supplémentaires en relation avec l’installation, le fonctionnement et la maintenance LA CHUTE DE L’ÉQUIPEMENT peut provoquer des blessures. � Utiliser l’anneau de levage uniquement pour soulever l’appareil, NON PAS les organes de roulement, les bouteilles de gaz ou tout autre accessoire. � Utilisez les procédures correctes et des équipements d’une capacité appropriée pour soulever et supporter l’appareil. � En utilisant des fourches de levage pour déplacer l’unité, s’assurer que les fourches sont suffisamment longues pour dépasser du côté opposé de l’appareil. � Tenir l’équipement (câbles et cordons) à distance des véhicules mobiles lors de toute opération en hauteur. � Suivre les consignes du Manuel des applications pour l’équation de levage NIOSH révisée (Publication Nº94– 110) lors du levage manuelle de pièces ou équipements lourds. DES PIECES DE METAL ou DES SALETES peuvent provoquer des blessures dans les yeux. � Porter des lunettes de sécurité à coques latérales ou un écran facial. OM-271146 Page 2 Les PIÈCES MOBILES peuvent causer des blessures. � S’abstenir de toucher des organes mobiles tels que des ventilateurs. � Maintenir fermés et verrouillés les portes, panneaux, recouvrements et dispositifs de protection. � Lorsque cela est nécessaire pour des travaux d’entretien et de dépannage, faire retirer les portes, panneaux, recouvrements ou dispositifs de protection uniquement par du personnel qualifié. � Remettre les portes, panneaux, recouvrements ou dispositifs de protection quand l’entretien est terminé et avant de rebrancher l’alimentation électrique. Les CHAMPS ÉLECTROMAGNÉTIQUES (CEM) peuvent affecter les implants médicaux. � Les porteurs de stimulateurs cardiaques et autres implants médicaux doivent rester à distance. � Les porteurs d’implants médicaux doivent consulter leur médecin et le fabricant du dispositif avant de s’approcher de la zone où se déroule du soudage à l’arc, du soudage par points, du gougeage, de la découpe plasma ou une opération de chauffage par induction. LE LIQUIDE DE REFROIDISSEMENT CHAUD ET LA VAPEUR peuvent causer des brûlures. � Utiliser des pochettes et des boîtes antistatiques pour stocker, déplacer ou expédier des cartes de circuits imprimes. L’EXPLOSION DE LA BATTERIE peut provoquer des blessures. Si le liquide de refroidissement est en surchauffe, un boyau pourrait se sectionner. � Ne jamais débrancher les deux extrémités du tuyau lorsque l’appareil est installé sur une pièce de travail chaude. � Si le liquide de refroidissement cesse de s’écouler, laisser une extrémité du tuyau branchée pour permettre au liquide de refroidissement chaud de revenir au refroidisseur et dépressuriser. � Ne pas utiliser d’équipement à induction pour charger les batteries ou une batterie d’appoint pour démarrer des véhicules, sauf si celui-ci est doté d’une caractéristique de charge de batterie conçue à cette fin. LE RAYONNEMENT HAUTE FRÉQUENCE (HF) risque de provoquer des interférences. � Pour éviter tout risque de dommage, retirer le tuyau de la pièce de travail chaude. � Effectuer une inspection visuelle des boyaux, cordons et câbles avant chaque utilisation. Ne pas utiliser des boyaux, cordons ou câbles endommagés. � Laissez refroidir avant d’intervenir sur l’équipement. � Le rayonnement haute fréquence (HF) peut provoquer des interférences avec les équipements de radio-navigation et de communication, les services de sécurité et les ordinateurs. LES LIQUIDES SOUS HAUTE PRESSION peuvent provoquer des blessures ou la mort. � Demander seulement à des personnes qualifiées familiarisées avec des équipements électroniques de faire fonctionner l’installation. � Liquide de refroidissement sous haute pression. � L’utilisateur est tenu de faire corriger rapidement par un électricien qualifié les interférences résultant de l’installation. � Libérez la pression avant d’intervenir sur le refroidisseur. � En cas d’injection d’un liquide QUELCONQUE dans la peau ou le corps, consultez immédiatement un médecin. L’EMPLOI EXCESSIF peut SURCHAUFFER L’ÉQUIPEMENT. � Si le FCC signale des interférences, arrêter immédiatement l’appareil. � Effectuer régulièrement le contrôle et l’entretien de l’installation. � Maintenir soigneusement fermés les portes et les panneaux des sources de haute fréquence. LIRE LES INSTRUCTIONS. � Prévoir une période de refroidissement. � Réduire le courant de sortie ou le facteur de marche avant de recommencer le chauffage. � Respecter le cycle opératoire nominal. LES CHARGES ÉLECTROSTATIQUES peuvent endommager les circuits imprimés. � Établir la connexion avec la barrette de terre AVANT de manipuler des cartes ou des pièces. 1-4. section. � N’utiliser que des pièces de remplacement provenant du fabricant. � Effectuer l’installation, l’entretien et toute intervention selon les manuels d’utilisateurs, les normes nationales, provinciales et de l’industrie, ainsi que les codes municipaux. Proposition californienne 65 Avertissements AVERTISSEMENT – Ce produit peut vous exposer à des produits chimiques tels que le plomb, reconnus par l’État de Californie comme cancérigènes et sources de malformations ou d’autres troubles de la reproduction. 1-5. � Lire et appliquer les instructions sur les étiquettes et le Mode d’emploi avant l’installation, l’utilisation ou l’entretien de l’appareil. Lire les informations de sécurité au début du manuel et dans chaque Pour plus d’informations, consulter www.P65Warnings.ca.gov. Principales normes de sécurité Safety in Welding, Cutting, and Allied Processes, American Welding Society standard ANSI Standard Z49.1. Website: www.aws.org. Canadian Electrical Code Part 1, CSA Standard C22.1 from Canadian Standards Association. Website: www.csagroup.org. Safety in Welding, Cutting, and Allied Processes, CSA Standard W117.2 from Canadian Standards Association. Website: www. csagroup.org. Safe Practice For Occupational And Educational Eye And Face Protection, ANSI Standard Z87.1, from American National Standards Institute. Website: safetyequipment.org. OSHA, Occupational Safety and Health Standards for General Industry, Title 29, Code of Federal Regulations (CFR), Part 1910.177 Subpart N, Part 1910 Subpart Q, and Part 1926, Subpart J. Website: www.osha.gov. OSHA Important Note Regarding the ACGIH TLV, Policy Statement on the Uses of TLVs and BEIs. Website: www.osha.gov. National Electrical Code, NFPA Standard 70 from National Fire Protection Association. Website: www.nfpa.org. 1-6. Applications Manual for the Revised NIOSH Lifting Equation from the National Institute for Occupational Safety and Health (NIOSH). Website: www.cdc.gov/NIOSH. IHOM_fre 2024–01 Informations relatives aux CEM Le courant électrique qui traverse tout conducteur génère des champs électromagnétiques (CEM) à certains endroits. Le courant issu d’un soudage à l’arc (et de procédés connexes, y compris le soudage par points, le gougeage, le découpage plasma et les opérations de chauffage par induction) crée un champ électromagnétique (CEM) autour du circuit de soudage. Les champs électromagnétiques OM-271146 Page 3 produits peuvent causer interférence à certains implants médicaux, p. ex. les stimulateurs cardiaques. Des mesures de protection pour les porteurs d’implants médicaux doivent être prises: par exemple, des restrictions d’accès pour les passants ou une évaluation individuelle des risques pour les soudeurs. Tous les soudeurs doivent appliquer les procédures suivantes pour minimiser l’exposition aux CEM provenant du circuit de soudage: 1. Rassembler les câbles en les torsadant ou en les attachant avec du ruban adhésif ou avec une housse. 2. Ne pas se tenir au milieu des câbles de soudage. Disposer les câbles d’un côté et à distance de l’opérateur. 3. Ne pas courber et ne pas entourer les câbles autour de votre corps. 4. Maintenir la tête et le torse aussi loin que possible du matériel du circuit de soudage. 5. Connecter la pince sur la pièce aussi près que possible de la soudure. OM-271146 Page 4 6. Ne pas travailler à proximité d’une source de soudage, ni s’asseoir ou se pencher dessus. 7. Ne pas souder tout en portant la source de soudage ou le dévidoir. Pour des informations supplémentaires relatives au chauffage par induction et à l'exposition aux champs électriques et magnétiques (CEM), se reporter au communiqué suivant: https://www. millerwelds. com/-/media/miller-electric/files/pdf/safety/ bulletins/bulletin-on-induction-heating-and-emf-exposure.pdf En ce qui concerne les implants médicaux : Les porteurs d’implants doivent d’abord consulter leur médecin avant de s’approcher des opérations de soudage à l’arc, de soudage par points, de gougeage, du coupage plasma ou de chauffage par induction. Si le médecin approuve, il est recommandé de suivre les procédures précédentes. Safe37 201 During the first 50 hours of operation keep welding load above 200 amperes. Do not weld below 200 amperes of output. SECTION 2 – DÉFINITIONS Wear dry insulating gloves. Do not touch electrode with bare hand. Do not wear wet or damaged gloves. 2-1. Safe54 2017 Symboles et définitions supplémentaires relatifs à la Sécurité � Certains symboles se trouvent seulement sur les produits CE. Safe2 201 After the first 50 hours of operation, change the engine oil and filter. Avertissement! Attention! Les risques éventuels sont indiqués par ces symboles. Protect yourself from electric shock by insulating yourself from work and ground. Safe55 2012 Safe3 201 Porter des gants isolants secs. Ne pas porter de gants mouillés ou en Wear dry insulating gloves. Do not wear wet or damaged gloves. mauvais état. Protect yourself from electric shock by insulating yourself from work and ground. Safe56 201 Safe4 201 la working prise ou on couper l’alimentation avant toute intervention Disconnect input plug orDébrancher power before Wear dry insulating gloves. Do not touch electrodemachine. (wire) with bare hand. Do not wear wet or damaged gloves. sur l’appareil. Safe5 201 Safe57 201 Induction heating can cause injuryororpar burns fromhot hot items suchas asdes rings, watches, parts. Induction can injury burns from items such rings, watches, orordes parts. Keep yourheating head out ofcause the Le fumes. chauffage induction peut provoquer blessures ou brûInduction heating can cause injury ororor burns from hot items such as rings, watches, ororparts. Induction heating can cause injury burns from hot items such asas rings, watches, parts. Induction heating can cause injury burns from hot items such rings, watches, lures d’objets chauds comme les bagues, montres ou pièces.or parts. Protect yourself from electric shock by insulating yourself from work and ground. Safe74201 20 Safe74 Safe6 201 201 Safe74 Safe74 20 Safe74 2 Safe58 201 Neand pas porter de bijoux ou autres personnels ba-operation. Donot notwear wearmetal metaljewelry jewelry andother othermetal metal personal itemsobjets suchas asrings ringsand andmétalliques, watchesduring during operation. Do personal items such watches Keep your head outjewelry of the fumes Do not wear metal and other metal personal such as rings and watches during operation. gues ou montres pendant leitems fonctionnement. Do not wear metal jewelry and other metal personal items such asas rings and watches during operation. Do not wear metal jewelry and other metal personal items such rings and watches during operation. Safe75201 20 Safe75 Safe75 201 Safe75 20 Safe7 201 Safe75 2 Keep your head out of the fumes. Les étincelles de chauffage par induction peuvent provoquer des inInductionheating heatingsparks sparks cancause cause fire.Do Donot notoverheat overheat partsand and adhesives. Induction can parts adhesives. Ne fire. pas surchauffer pièces et adhésifs. Use forced ventilation orcendies. local exhaust toDo remove the les fumes. Induction heating sparks can cause fire. not overheat parts and adhesives. Induction heating sparks can cause fire. Do not overheat parts and adhesives. Induction heating sparks can cause fire. Do not overheat parts and adhesives. Safe59 201 Safe76201 20 Safe76 Safe76 201 Safe76 20 Safe8 201 Safe76 2 Use forced ventilation or local exhaust to remove the fumes. toute operation. substanceDo inflammable desflammables. opérations de chauffage. Keepflammables flammablesaway awayÉloigner fromheating heating notheat heatnear near Keep from operation. Do not flammables. Use forced ventilation orfrom local exhaust toàremove the fumes. Ne pas chauffer proximité d’une telle substance. Keep flammables away heating operation. Do not heat near flammables. Keep flammables away from heating operation. Do not heat near flammables. Keep flammables away from heating operation. Do not heat near flammables. Safe60 2012 Safe77201 20 Safe77 Safe9 201 201 Safe77 Safe77 20 Safe77 2 Use ventilating fan to remove fumes. Safe61 201 Lesfires. étincelles de chauffage peuvent provoquer des Unready exHeatingsparks sparkscan cancause cause fires. Havea afire fire extinguisher nearby andhave have watchperson readytotouse useit.it. Heating Have extinguisher nearby and aaincendies. watchperson tincteur doit seaatrouver à proximité et un and surveillant doit être prêt àready Heating sparks can cause fires. Have fire extinguisher nearby have a watchperson totouse it.it.it. Heating sparks can cause fires. Have fire extinguisher nearby and have a watchperson ready Heating sparks can cause fires. Have a fire extinguisher nearby and have a watchperson ready touse use s’en servir. Safe78201 20 Safe78 Safe78 Safe78201 20 Safe78 2 Keep flammables away from welding. Do not weld near flammables. Safe62 2012 Il peut êtrehazardous dangereux pour la santéRead de respirer lesSafety fumées de chaufBreathingheating heatingfumes fumes canbe be yourhealth. health. Material Data Sheets(MSDSs) (MSDSs)and and Breathing can hazardous totoyour Read Material Safety Data Sheets fage. Lire les spécifications de sécurité des matériaux et les instrucBreathing heating fumes can be hazardous to your health. Read Material Safety Data Sheets (MSDSs) and Breathing heating fumes can be hazardous to your health. Read Material Safety Data Sheets (MSDSs) and manufacturer’s instructions formaterial material used.to your health. Read Material Safety Data manufacturer’s instructions for used. Breathing heating fumes can be hazardous Sheets (MSDSs) and tions du fabricant concernant le matériel utilisé. manufacturer’s instructions for material used. manufacturer’s instructions for material used. manufacturer’s instructions for material used. Safe79 20 Safe79 201 Safe79201 20 Welding sparks can cause fires. Have a fire extinguisher nearby, and have a watchperson ready to use it.Safe79 Safe79 2 Safe63 2012 Keepyour yourhead headout outofofthe thefumes. fumes. Keep Keep your head out ofofthe fumes. Keep your head out fumes. Keep your head out ofthe the fumes. Safe80201 20 Safe80 Safe80 Safe80201 20 Safe80 2 OM-271146 Page 5 Useforced forcedventilation ventilationororlocal localexhaust exhausttotoremove removethe thefumes. fumes. Use Breathing heating fumes can be Have hazardous to your health. Read and Material Safety Data Sheets (MSDSs) and Welding sparks canfumes causecan fires. a fire extinguisher nearby, haveSafety a watchperson ready to use it. Breathing heating hazardous to to your health. Read Material Data Sheets (MSDSs) and manufacturer’s instructions forbematerial used. Breathing heating fumes can be hazardous your health. Read Material Safety Data Sheets (MSDSs) and manufacturer’s instructions forfor material used. manufacturer’s instructions material used. Safe Safe1 Safe S Do not work on unit if engine is running. Stop engine first. Cutting sparks can fires. Have a fire extinguisher nearby, and have a watchperson ready to use it. Keep your head outcause of the fumes. Maintenir la tête à l’écart des fumées. Keep your head outout of of the fumes. Safe2 Keep your head the fumes. Safe1 Safe Safe S Do not smoke while fueling or if near fuel. Chasser les fumées à l’aide d’un système de ventilation forcée ou Do weld ventilation on drums or containers. Usenot forced or any localclosed exhaust to remove the fumes. système d’extraction local. Use forced ventilation ord’un local exhaust to to remove the fumes. Use forced ventilation or local exhaust remove the fumes. Safe2 Safe Safe Safe7 Safe S Stop engine before fueling. Do cut on drums any closed Usenot ventilating fan toorremove fumes. Chasser lescontainers. fumées à l’aide de ventilations. Use ventilating fanfan to to remove fumes. Use ventilating remove fumes. Safe2 Safe Safe Safe8 Safe S Always wear safety near glasses or goggles during and around heating operations preventou possible injury. Toujours se munir de lunettes ou masques de sécuritétopendant à Do not grip material cutting path. Always wear safety glasses or or goggles during and heating to to prevent possible injury. Always wear safety glasses goggles during and around heating operations prevent possible injury. proximité des opérations dearound chauffage pouroperations éviter les blessures Do not fuel a hot engine.éventuelles. Safe9 Safe Safe Safe S Safe2 1-1. Additional Turn Safety Symbols And Definitions power before disassembling torch. Wearoff either safety glasses or full depending on type of un operation nearby processes. Porter soitgoggles des lunettes de sécurité soit masqueand complet selon le Writer: If necessary, necessary, replace the word “handle” “handle” withon “lifttype eye’. Wear either safety glasses full goggles depending of of operation and nearby processes. Writer: If replace the word with “lift Wear either safety glasses or full goggles depending oneye’. type operation and nearby processes. typeord’opération. Doonly not use useCE oneproducts. handle to to lift lift or or support support unit. unit. Do not one handle Some symbols are found on Safe105 Safe Safe Safe S Use lift eye to lift unit and properly installed accessories only, not gas cylinders. Do not exceed maximumSafe3 lift e Safe3 rating (see Specifications). Do not remove or paint over (cover) the ou label. Ne pas enlever recouvrir l’étiquette de peinture. Warning! Out! There Drive rolls rollsWatch can injure injure fingers.are possible hazards as shown by the symbols. Drive can fingers. Safe2 Safe2 Safe Safe Safe When applied (where failed parts can explode orapplicable) cause otheravec partsles todéchets explode.ménagers. Do notpower discardisproduct applicable) with (si general waste. Ne pas jeter le produit les Equipment déchets d’équipements électriques élecReuse or recycle Waste Réutiliser Electrical ou andrecycler Electronic (WEEE) by disposing at aetdesignated collection troniques les jeter dans operation un conteneur prévu à cet effet. Welding wire wire and and drive drive parts parts are at at(DEEE) weldingetvoltage voltage during operation keep hands and metal objects objects away. away. Safe2 facility. Welding keep hands and are welding during metal Contacter le bureau chargé du recyclage local ou le revendeur local Contact your local recycling or your local distributor for further information. pouroffice de plus amples informations. Safe3 Safe Safe Flying pieces of parts can cause injury. Always wear a face shield when servicing unit. Wear dryrating insulating Do not la touch electrode with bare hand. Do not wear wet or damaged gloves. Consulter plaque signalétique pour les conditions d’alimentation. Consult labelgloves. for input input power requirements. Consult rating label for power requirements. Safe2 Safe Always wear long sleeves and button your collar when servicing unit. Safe3 Safe3 Safe2 Protect yourself from electric shock by insulating yourself from work and ground. Recevoir une formation convenable et lire les Become trained trained and and read read the instructions instructions and labels labels before working working oninstructions machine. et les étiBecome the and before on machine. quettes avant de procéder aux interventions exécutées sur le poste. After taking proper precautions as shown, connect power to unit. Safe Safe Safe Safe2 Protect yourself from electric shock by insulating yourself from work and ground. Connect Green Green Or Or Green/Yellow Green/Yellow grounding grounding conductor conductor to to ground ground terminal terminal first. first. Connect la to prise couper l’alimentation avant toute intervention Connect input input conductors (L1, L2, L2, L3) to lineou terminals. Disconnect input plug orDébrancher power before working on machine. Connect conductors (L1, L3) line terminals. sur l’appareil. Safe Safe3 Safe3 Safe3 OM-271146 Page 6 Disconnect input plug or power before working on machine. Wear hat hat and and safety safety glasses. glasses. Use Use ear ear protection protection and and button button ss Wear collar. Use Use welding welding helmet helmet with with correct correct shade shade of of filter. filter. Wear Wear co co collar. body protection. protection. Safe body Hazardous voltage remains on inputconservent capacitors after turned Les condensateurs d’alimentation une power tensionisdangeoff. Do après not touch fully charged capacitors.Ne Always wait 60 des seconds reuse coupure de l’alimentation. pas toucher condensaafter is turned off Attendre before working on 60 unit, ANDbefore check input ca-on the Become trained and read the instructions working teurspower encore chargés. toujours secondes après coupure pacitor voltage, and be sure it is near 0 before machine or heating. de l’alimentation avant toute intervention surtouching l’appareilany ETparts. vérifier la tension du condensateur d’alimentation et s’assurer qu’elle est proche de 0 avant de toucher des pièces de l’appareil. Safe42 2017 04 Safe85 2012 06 Hazardous voltage remains on input capacitors after power is turned Raccorder le conducteur de mise à la terre vert wait ou jaune/vert à la off. Do not touch fully charged capacitors. Always 5 minutes Connect green or green/yellow grounding conductor to after ground borneisdeturned masse. power off before working on unit, AND check input capacitor terminal. Brancher les conducteurs d’alimentation (L1, L2 et L3) aux bornes de voltage, and be sure it is near 0 before touching any parts. phases.Connect input conductors (L1, L2 And L3) to line terminals. Safe43 2017 04 Safe86 2012 06 = < 60° Always lift and support unit using both handles. Keep angle of lifting device less than 60 degrees. Become trained and the instructions before workingeven on thedoors and winNever use read generator a home or garage, Suivre une formation et lire les inside instructions avant de travaillerif avec la Use a proper cartare to move unit. ordows heating. machine open. machine de chauffage. Safe44 2012 05 2012 07 Safe87 Safe85 2012 06 2-2. � Symboles et définitions divers Certains symboles se trouvent seulement sur les produits CE. Only generator outside and far away from windows, doors, and Connect green or green/yellow grounding conductor to ground Engine fuel plususe flames or sparks can cause fire. terminal. vents. Connect input conductors (L1, L2 And L3) to line terminals. Safe45 2012 05 Safe88 Safe86 2012 06 2012 07 Ampères Courant primaire Pourcentage Remove unit from shipping crate. Remove Owner’s Manual from unit. Never use generator inside a home or garage, even if doors and winFollow instructions to install muffler. Do not use ether or other starting fluids. Using fluids voids warranty. See engine Owner’s Manual. dowsstarting are open. Volts Courant nominal Safe46 2012 à 05 Commande Safe87 2012 07 distance Safe89 2017 04 OnlyOwner’s use generator and far Read Manual.outside Read labels onaway unit. from windows, doors, and Courant Hot alternatif Panneau Tension primaire vents. muffler and exhaust pipe can cause severe burns. Safe47 2012 05 Safe88 2012 07 Safe90 2017 04 Facteur de marche température Tension de links charge Move jumper as shown on inside label to matchHaute input voltage at job site. Include extra length in grounding conductor and connect grounding conductor first. Connect line input conductors as shown on Do not use ether or other starting fluids. Using inside starting fluids voids warranty. See engine Owner’s Manual. label. Double-check all connections, jumper link positions, and Welding, cutting, drilling, or grinding on base can cause fire or explosion. input voltage before applying power. Niveau de Tension Lire les instructions d’alimentation Safe49 2012 05 protection Safe89 2017 04 Safe91 2017 04 www.MillerWelds.com FINITIONS Phase tive ontrol Phase ive sten Arc ing Convertisseur transformateur redresHertz Arrêt Plugged or hoses can cause overheating to the power source seur defilter fréquence torch. Hot muffler and exhaust pipe can cause severeand burns. statique triphasé Do not spray water on CST units. Protection du circuit % Courant d’alimentation nominal maximum Safe90 2017 Safe50 2012 05 04 Marche Safe92 2017 04 Every 100 hours, check and clean filter and check condition of hoses. d’éChauffage par cause fire or explosion. Welding, cutting, drilling, or grinding on base canConsommation Sortie Percent nergie maximale induction Door must be fully open during operation. Increase Augmenter Safe51 2012 05 04 Safe91 2017 Triphasé Safe93 2012 08 Use coolant suggested by the manufacturer. Do not spray water on CST units. Output Branchement au can Drive rolls injure fingers. Welding wire and drive parts are at welding voltage during operation keep hands Safe52 2012 05 secteur and metal objects away. ° Shielded Metal Safe92 2017 04 Safe95 2012 05 Arc Welding Falling unit can cause injury. Do not move or operate unit where it could tip. (SMAW) Door must be fully open during operation. Lift-Arc Operation (GTAW) Safe53 2017 04 OM- Safe93 2012 08 Pulsed Drive rolls can injure fingers. Welding wire and drive parts are at welding voltage during operation OM-271146 Page 7 keep hands OM- SECTION 3 – SPÉCIFICATIONS 3-1. Emplacement du numéro de série et de la plaque signalétique Le numéro de série et la plaque signalétique du générateur se trouvent sur l’avant de l’appareil. La plaque signalétique permet de déterminer l’alimentation électrique requise et/ou la puissance nominale. Pour référence ultérieure, noter le numéro de série dans l’espace prévu à cet effet sur la couverture au dos de ce manuel. 3-2. Contrat de licence de logiciel Le Contrat de licence de l'utilisateur final et tous les avis et conditions de tiers concernant les logiciels tiers se trouvent à l'adresse https://www. millerwelds.com/eula et sont incorporés par référence aux présentes. 3-3. Informations sur les paramètres et réglages de soudage par défaut AVIS – Chaque application de soudage est unique. Bien que certains produits Miller Electric soient conçus pour déterminer et régler par défaut certains paramètres et réglages de soudage typiques en fonction de variables d'application spécifiques et relativement limitées saisies par l'utilisateur final, ces réglages par défaut servent uniquement à des fins de référence ; les résultats de soudage finaux peuvent être affectés par d'autres variables et circonstances spécifiques à l'application. La pertinence de tous les paramètres et réglages doit être évaluée et modifiée par l'utilisateur final selon les besoins, en fonction des exigences spécifiques à l'application. L'utilisateur final est seul responsable de la sélection et de la coordination de l'équipement approprié, de l'adoption ou de l'ajustement des paramètres et réglages de soudage par défaut, ainsi que de la qualité et de la durabilité ultimes de toutes les soudures résultantes. Miller Electric décline expressément toute garantie implicite, y compris toute garantie implicite d'adéquation à un usage particulier. 3-4. Spécifications pas utiliser les informations du tableau de spécifications de l’appareil pour déterminer si une intervention est requise au niveau du cir� Ne cuit électrique. Pour en savoir plus sur le branchement de l’alimentation d’entrée, voir les Sections 4-3, 4-4, et 4-6 � La capacité nominale de cet équipement est assurée jusqu’à une température ambiante de 104 °F (40 °C). Puissance nominale Fréquence de sortie Sortie simple Inductance mutuelle requise Sortie double Ampérage d’entrée en fonction de la puissance nominale, 50 ou 60 Hz, triphasé 400 V 460 V 575 V Dimensions hors tout kVA Poids kW Longueur : 36,75 po. (933 mm) 5 à 30 kHz 3-5. 35 kW à 100% du facteur de marche 35 kW à 100% du facteur de marche 350 A (RMS), 700 V (RMS) 700 A (RMS), 700 V (RMS) 2.5 à 50 μh 60 A 50 A 40 A 39 37 Largeur : 21,75 po. (553 mm) 103 kg Hauteur : 27,5 po. (699 mm) Spécifications environnementales A. Niveau de protection (IP) Niveau de protection (IP) IP23 Le présent matériel est conçu pour une utilisation à l’extérieur. B. Informations sur la Compatibilité Électromagnétique (CEM) L’utilisation de cet équipement de classe A n’est pas prévue dans des lieux résidentiels où l’énergie électrique est fournie par le système d’alimentation public en basse tension. Il peut y avoir des difficultés potentielles pour garantir une compatibilité électromagnétique dans ces zones, du fait de perturbations tant en mode conduit qu’en mode rayonné. Cet équipement est conforme aux normes CEI61000−3−11 et CEI61000−3−12, et peut être relié à des systèmes publics basse tension, à condition que l’impédance Zmax de ces systèmes au point de couplage commun soit inférieur à 33,37mΩ (ou que la puissance de court−circuit Ssc soit supérieure à 112 138 497,99 VA). L’installateur ou l’utilisateur de l’équipement est tenu de s’assurer que l’impédance du système est conforme aux restrictions prévues, si nécessaire en consultant l’opérateur du réseau de distribution. OM-271146 Page 8 Warning! Watch Out! There are possible hazards as shown by the symbols. C. Informations sur l’écoconception de l’UE Safe1 2012 Ne pasapplicable) jeter le produit applicable) Do not discard product (where with (si general waste.avec les déchets ménagers. les Equipment déchets d’équipements électriques élecReuse or recycle Waste Réutiliser Electrical ou andrecycler Electronic (WEEE) by disposing at aetdesignated collection troniques (DEEE) et les jeter dans un conteneur prévu à cet effet. facility. Contacter le bureau chargé du recyclage local ou le revendeur local Contact your local recycling or your local distributor for further information. pouroffice de plus amples informations. Safe37 2017 Matières premières critiques éventuellement présentes en quantités indicatives supérieures à 1 gramme au niveau des composants Composant Cartes de circuits imprimés Wear dry insulating gloves. DoMatière not touch electrode with bare hand. Do not wear wet or damaged gloves. première critique Baryte, bismuth, cobalt, gallium, germanium, hafnium, indium, terres rares lourdes, terres rares légères, niobium, métaux du groupe du platine, scandium, silicium métal, tantale, vanadium Composants en plastique Antimoine, Baryte Composants électriques et électroniques Antimoine, béryllium, magnésium Composants métalliques Protect yourself from electric shock vanadium by insulating yourself from work and ground. Béryllium, cobalt, magnésium, tungstène, Câbles et assemblages de câbles Borate, Antimoine, Baryte, Béryllium, Magnésium Panneaux d’affichage Gallium, indium, terres rares lourdes, terres rares légères, niobium, métaux du groupe du platine, scandium Batteries Spath fluor, terres rares lourdes, terres rares légères, magnésium Protect yourself from electric shock by insulating yourself from work and ground. Safe2 2017 Safe3 2017 Safe4 2017 Disconnect input plug or power before working on machine. Safe5 2017 Keep your head out of the fumes. Safe6 2017 Keep your head out of the fumes Safe7 2017 Use forced ventilation or local exhaust to remove the fumes. Safe8 2012 Use forced ventilation or local exhaust to remove the fumes. Safe9 2012 O OM-271146 Page 9 D. Spécifications de température pour le fonctionnement en climat froid du système de chauffage par induction pour roulements Miller ProHeat 35 ProHeat Stockage Fonctionnement Refroidisseur Câbles de chauffage Stockage Fonctionnement Stockage Fonctionnement \\\\\\\\\\\\\\\\\\\\ \\\\\\\\\\\\\\\\\\\\ \\\\\\\\\\\\\\\\\\\\ \\\\\\\\\\\\\\\\\\\\ \\\\\\\\\\\\\\\\\\\\ \\\\\\\\\\\\\\\\\\\\ \\\\\\\\\\\\\\\\\\\\ \\\\\\\\\\\\\\\\\\\\ \\\\\\\\\\\\\\\\\\\\ \\\\\\\\\\\\\\\\\\\\ \\\\\\\\\\\\\\\\\\\\ \\\\\\\\\\\\\\\\\\\\ \\\\\\\\\\\\\\\\\\\\ \\\\\\\\\\\\\\\\\\\\ \\\\\\\\\\\\\\\\\\\\ \\\\\\\\\\\\\\\\\\\\ \\\\\\\\\\\\\\\\\\\\ \\\\\\\\\\\\\\\\\\\\ \\\\\\\\\\\\\\\\\\\\ \\\\\\\\\\\\\\\\\\\\ \\\\\\\\\\\\\\\\\\\\ \\\\\\\\\\\\\\\\\\\\ \\\\\\\\\\\\\\\\\\\\ \\\\\\\\\\\\\\\\\\\\ \\\\\\\\\\\\\\\\\\\\ \\\\\\\\\\\\\\\\\\\\ \\\\\\\\\\\\\\\\\\\\ \\\\\\\\\\\\\\\\\\\\ \\\\\\\\\\\\\\\\\\\\ \\\\\\\\\\\\\\\\\\\\ \\\\\\\\\\\\\\\\\\\\ \\\\\\\\\\\\\\\\\\\\ \\\\\\\\\\\\\\\\\\\\ \\\\\\\\\\\\\\\\\\\\ \\\\\\\\\\\\\\\\\\\\ \\\\\\\\\\\\\\\\\\\\ \\\\\\\\\\\\\\\\\\\\ \\\\\\\\\\\\\\\\\\\\ \\\\\\\\\\\\\\\\\\\\ \\\\\\\\\\\\\\\\\\\\ \\\\\\\\\\\\\\\\\\\\ \\\\\\\\\\\\\\\\\\\\ \\\\\\\\\\\\\\\\\\\\ \\\\\\\\\\\\\\\\\\\\ \\\\\\\\\\\\\\\\\\\\ \\\\\\\\\\\\\\\\\\\\ \\\\\\\\\\\\\\\\\\\\ \\\\\\\\\\\\\\\\\\\\ \\\\\\\\\\\\\\\\\\\\ \\\\\\\\\\\\\\\\\\\\ °C °F 60 140 55 131 \\\\\\\\\\\\\\\\\\\\ 50 122 \\\\\\\\\\\\\\\\\\\\ 45 113 \\\\\\\\\\\\\\\\\\\\ 40 104 \\\\\\\\\\\\\\\\\\\\ \\\\\\\\\\\\\\\\\\\\ \\\\\\\\\\\\\\\\\\\\ \\\\\\\\\\\\\\\\\\\\ 35 95 \\\\\\\\\\\\\\\\\\\\ \\\\\\\\\\\\\\\\\\\\ \\\\\\\\\\\\\\\\\\\\ 30 86 \\\\\\\\\\\\\\\\\\\\ \\\\\\\\\\\\\\\\\\\\ \\\\\\\\\\\\\\\\\\\\ 25 77 \\\\\\\\\\\\\\\\\\\\ \\\\\\\\\\\\\\\\\\\\ 20 68 \\\\\\\\\\\\\\\\\\\\ 15 59 \\\\\\\\\\\\\\\\\\\\ Rendements réduits au−dessus de 40°C Stockage Fonctionnement Bobine d’induction \\\\\\\\\\\\\\\\\\\\ \\\\\\\\\\\\\\\\\\\\ Rendements réduits au−dessus de 40°C \\\\\\\\\\\\\\\\\\\\ 10 50 \\\\\\\\\\\\\\\\\\\\ \\\\\\\\\\\\\\\\\\\\ \\\\\\\\\\\\\\\\\\\\ \\\\\\\\\\\\\\\\\\\\ \\\\\\\\\\\\\\\\\\\\ \\\\\\\\\\\\\\\\\\\\ \\\\\\\\\\\\\\\\\\\\ \\\\\\\\\\\\\\\\\\\\ 5 41 \\\\\\\\\\\\\\\\\\\\ \\\\\\\\\\\\\\\\\\\\ \\\\\\\\\\\\\\\\\\\\ \\\\\\\\\\\\\\\\\\\\ \\\\\\\\\\\\\\\\\\\\ \\\\\\\\\\\\\\\\\\\\ \\\\\\\\\\\\\\\\\\\\ \\\\\\\\\\\\\\\\\\\\ 0 32 \\\\\\\\\\\\\\\\\\\\ \\\\\\\\\\\\\\\\\\\\ \\\\\\\\\\\\\\\\\\\\ \\\\\\\\\\\\\\\\\\\\ \\\\\\\\\\\\\\\\\\\\ \\\\\\\\\\\\\\\\\\\\ \\\\\\\\\\\\\\\\\\\\ \\\\\\\\\\\\\\\\\\\\ -5 23 \\\\\\\\\\\\\\\\\\\\ \\\\\\\\\\\\\\\\\\\\ \\\\\\\\\\\\\\\\\\\\ \\\\\\\\\\\\\\\\\\\\ \\\\\\\\\\\\\\\\\\\\ \\\\\\\\\\\\\\\\\\\\ \\\\\\\\\\\\\\\\\\\\ \\\\\\\\\\\\\\\\\\\\ -10 14 \\\\\\\\\\\\\\\\\\\\ \\\\\\\\\\\\\\\\\\\\ \\\\\\\\\\\\\\\\\\\\ \\\\\\\\\\\\\\\\\\\\ \\\\\\\\\\\\\\\\\\\\ \\\\\\\\\\\\\\\\\\\\ \\\\\\\\\\\\\\\\\\\\ \\\\\\\\\\\\\\\\\\\\ Alimenter fréquemment le système pour maintenir la température du liquide de refroidissement au dessus de -10°C (14° F). \\\\\\\\\\\\\\\\\\\\ Alimenter fréquemment le système pour maintenir la température du liquide de refroidissement au dessus de -10°C (14° F). \\\\\\\\\\\\\\\\\\\\ Alimenter fréquemment le système pour maintenir la température du liquide de refroidissement au dessus de -10°C (14° F). -15 5 \\\\\\\\\\\\\\\\\\\\ \\\\\\\\\\\\\\\\\\\\ \\\\\\\\\\\\\\\\\\\\ -20 -4 \\\\\\\\\\\\\\\\\\\\ \\\\\\\\\\\\\\\\\\\\ \\\\\\\\\\\\\\\\\\\\ -25 -13 \\\\\\\\\\\\\\\\\\\\ \\\\\\\\\\\\\\\\\\\\ -30 -22 \\\\\\\\\\\\\\\\\\\\ \\\\\\\\\\\\\\\\\\\\ -35 -31 \\\\\\\\\\\\\\\\\\\\ \\\\\\\\\\\\\\\\\\\\ Stocker dans un endroit sec -40 -40 \\\\\\\\\\\\\\\\\\\\ \\\\\\\\\\\\\\\\\\\\ \\\\\\\\\\\\\\\\\\\\ Stocker dans un endroit sec \\\\\\\\\\\\\\\\\\\\ Stocker dans un endroit sec Non recommandé Avec qualifications \\\\\\\\\\\\\\\\\\\\\\\\\\\\\\\\\\\\\\\\\\\\\\\\\\\\\\\\\\\\\\\\\\\\\\\\\\\\\\\\\\\\\\\\\\\\\\\\\\\\\ Fonctionnement normal avec liquide de refroidissement AVIS – La bobine d’induction Rolling Miller ProHeat 35 est conçue pour fonctionner dans des températures allant de −10°C à 60°C (14°F à 140° F). Pour un fonctionnement dans des températures allant de −40°C à -10°C (−40°F à 14°F), veuillez prendre les précautions suivantes pour éviter d’endommager votre équipement : � Connectez les conduites du liquide de refroidissement à la bobine d’induction Rolling une fois qu’elle est sèche, ou lorsque la température ambiante est au dessus de −20°C (−4°F). � Utilisez le refroidisseur de système à induction ProHeat 35 Heavy Duty uniquement aux températures comprises entre −10°C et 40°C (14°F et 104°F) pendant le fonctionnement de la bobine d’induction Rolling/ des conduites du liquide de refroidissement. � Utilisez toujours un liquide de refroidissement Miller (numéro de pièce Miller : 043810). � Le liquide de refroidissement doit couler de façon continue à travers la bobine d’induction Rolling/ les conduites du liquide de refroidissement, et de la puissance doit être appliquée à la bobine d’induction Rolling/ aux conduites du liquide de refroidissement à des intervalles réguliers pour maintenir la température du liquide de refroidissement à au moins −10°C (14°F). � Conservez la bobine d’induction Rolling/ les conduites du liquide de refroidissement dans un endroit sec. Séchez l’unité en utilisant de l’air comprimé à une pression maximale de 40 psi (2,75 bar) pour souffler le liquide de refroidissement hors de la bobine d’induction Rolling et du câble d’alimentation. � Stockez le refroidisseur de système à induction ProHeat 35 Heavy Duty à une température comprise entre −20°C et 55°C (−4°F et 131°F). � Le liquide de refroidissement ne pourra commencer à couler qu’à partir de −10C (14°F). AVIS – Pour un stockage plus froid, le refroidisseur doit être conservé dans un endroit sec. Séchez l’unité en utilisant de l’air comprimé à une pression maximale de 40 psi (2,75 bar) pour souffler le liquide de refroidissement hors des conduites du liquide de refroidissement, des cuves de filtre, de la pompe, de l’indicateur de flux, et de l’échangeur thermique. OM-271146 Page 10 A complete Parts List is available at www.MillerWelds.com Writers: Remember to move unit dimension and weight and rating label location information SECTION to the appropriate sections. 4 – INSTALLATION 4-1. Choix d’un emplacement 1-3. Selecting A Location Mouvement dimension and weight and rating lapropriate sections. Ne pas déplacer ou faire fonctionner l’appareil à un endroit où il pourrait se renverser. Une installation spéciale peut être nécessaire en présence d’essence ou de liquides volatils - voir NEC article 511 ou CEC section 20. 1 1 Anneau de levage 2 Fourches de levage Utiliser l’anneau ou les fourches de levage pour déplacer l’appareil. 2 En cas d’utilisation des fourches de levage, les faire dépasser du côté opposé de l’appareil. 3 Sectionneur 3 Placer le poste près d’une source d’alimentation appropriée. 2 18 in. (460 mm) Emplacement et circulation d’air 3 3 18 po. (460 mm) 18 in. (460 mm) 18 in. (460 mm) 18 po. (460 mm) loc_large 2018-08 18 po. (460 mm) 18 po. (460 mm) loc_large 2018-08 / 803992-B loc_large 2018-08 OMOM-271146 Page 11 4-2. Dimensions et poids � Les dimensions hors tout (A, B et C) incluent l'anneau de levage, les poignées, le matériel etc. Dimensions * A A 27,5 po. (699 mm) B 21,75 po. (553 mm) C 36,75 po. (933 mm) Poids 103 kg B C * Poids nominal pour l’anneau de levage 272 kg (maximale) 803992-B OM-271146 Page 12 4-3. Guide d’entretien électrique Le non-respect des recommandations de ce guide d’entretien électrique entraîne des risques d’électrocution ou d’incendie. Les présentes recommandations sont pour un circuit de dérivation individuel dimensionné pour la puissance nominale et le rapport cyclique d’une source d’alimentation de soudage.Dans les installations de circuits de dérivation individuels, le code électrique national américain (NEC) autorise que la puissance au niveau du logement ou du conducteur soit inférieure à la puissance requise pour le dispositif de protection du circuit. Tous les composants du circuit doivent être physiquement compatibles. Voir NEC articles 210.21, 630.11 et 630.12. L’équipement estampillé CE doit être utilisé uniquement sur un réseau électrique triphasé à quatre fils dont le neutre est relié à la terre. 50 Hz triphasé Tension d’alimentation nominale (V) 60 Hz triphasé 400 460 575 Courant d’alimentation nominal maximum I1max (A) 60 50 40 Courant d’alimentation utile maximumI1eff (A) 60 50 40 Fusibles temporisés 2 70 60 50 Fusibles ordinaires3 90 70 60 214 (74) 213 (65) 333 (101) Taille minimum des conducteurs d’alimentation en AWG (mm2)5 6 (16) 8 (10) 8 (10) Dimension min. du conducteur de terre en AWG (mm2) 5 8 (10) 8 (10) 10 (6) 4 (25) 4(25) 6 (16) Fourni par le client Fourni par le client Fourni par le client Capacité maximum recommandée d’un fusible standard en ampères1 Longueur maximale recommandée du conducteur d’alimentation en pieds (mètres)4 Installation de la conduite Installation du cordon flexible Taille minimum des conducteurs d’alimentation en AWG (mm2)6 Décharge de traction recommandée7 Référence : 2023 National Electrical Code (NEC) (y compris l’article 630) 1 Lorsqu’un disjoncteur est utilisé à la place d’un fusible, sélectionner un disjoncteur avec des courbes temps/intensité comparables à celles du fusible recommandé. 2 Les fusibles temporisés sont de classe UL RK5. Voir UL 248. 3 "Normal" (général – pas de temporisation intentionnelle) fusibles de classe UL "K5" (jusqu’à 60 A compris) et classe UL "H" (65 A et plus). Voir UL 248. 4 Longueur totale maximale des conducteurs d'alimentation en cuivre dans l’ensemble de l’installation, de la conduite et/ou du cordon flexible. 5 Les données sur les conducteurs de cette section précisent la taille des conducteurs (à l’exclusion du câble ou du cordon souple) entre le panneau et l’équipement, conformément au tableau 310.16 du CEN, et sont basées sur les intensités admissibles des conducteurs en cuivre isolés ayant une classe de température de 167°F (75°C) et ne comportant pas plus de trois conducteurs à courant porteur unique dans un chemin de roulement. 6 La taille du conducteur du cordon flexible est basée sur le tableau NEC 400.5(A)(1) pour un câble gainé SOOW 600 V 90°C (194°F) dans une température ambiante de 30°C (86°F). Voir le tableau NEC 310.15(B)(1)(1) pour les facteurs de correction de la température ambiante. Le cordon flexible utilisé pour la connexion au système d’alimentation devra être conforme aux exigences de la norme UL62. 7 Le cas échéant, demandez à une personne qualifiée d’agrandir le trou d’accès dans le panneau de la machine pour accommoder la décharge de traction. OM-271146 Page 13 4-4. Connexion de l’alimentation triphasée pour les modèles 460/575Volts 3 Terre GND/PE 8 7 10 9 4 6 1 4 2 O’s s/ elbrush n_set philips head wrench crescent wrench NGO’s 5 tools/ 6 3 input3 2015-01 / 803994-E 3/8 pouce nutdriver flathead OM-271146 Page 14 philips head chippinghammer wrench crescent wrench 4-5. Connexion de l’alimentation triphasée pour les modèles 460/575Volts L’installation doit être conforme à tous les codes nationaux et locaux faire effectuer cette installation uniquement par des personnes qualifiées. Débrancher et verrouiller ou consigner l’alimentation avant de connecter les conducteurs d’alimentation de l’appareil. Suivre les procédures établies relatives à l’installation et au démontage des dispositifs de verrouillage ou de consigne. Raccorder le câble d’alimentation à la source de soudage d’abord. Toujours raccorder le conducteur vert ou vert et jaune à la borne terre de l’alimentation en premier, et jamais à une borne de phase. � Le circuit de cet appareil adapte automatiquement l’appareil à la tension d’alimentation à laquelle il est raccordé. Vérifier la tension d'alimentation disponible sur le site. Cette unité peut être raccordée à toute alimentation entre 460 ou 575 V AC. Se référer à la plaque signalétique du poste etvérifier la tension disponible sur le site. Sélectionner la section et la longueur des conducteurs selon la guide de service électrique. Les conducteurs doivent correspondre aux codes électriques nationaux et locaux. Le cas échéant, utiliser des cosses correspondant à l’ampérage et modifier la taille du trou. Connexions d’alimentation de la source de soudage 2 Serre-câble (fourniture client) Installer un serre-câble de dimension adaptée à l’appareil et aux conducteurs. Faire passer les conducteurs (le cordon) dans le serre-câble et serrer les vis. 3 Borne de terre de l’appareil 4 Conducteur de mise à la terre vert ouvert et jaune Brancher le conducteur de terre vert ou vert/ jaune à la borne de terre de la soudeuse en premier. 5 Bornes des phases de la source de soudage 6 Conducteurs d’entrée (L1, L2 et L3) 1 Conducteurs d’alimentation (fourni par le client) Raccorder les conducteurs d’alimentation L1 (U), L2 (V) et L3 (W) aux bornes des phases du poste de soudure. Fermer et verrouiller la porte d’accès du poste de soudure. Débranchement de l’alimentation du poste de soudure 7 Sectionneur (interrupteur présenté enposition fermée) 8 Débrancher le dispositif de coupure de ligne de mise à la terre (alimentation) du poste Raccorder d’abord le fil vert ou vert/jaune de mise à la terre à la borne terre du sectionneur. 9 Bornes des phases du sectionneur Brancher les conducteurs d’entrée L1, L2 et L3 sur les bornes des phases du sectionneur. 10 Protection contre les surintensités Sélectionner le type et le calibre de protection contre les surintensités conformément à la guide de service électrique (interrupteur de coupure à fusible illustré). Fermer et fixer la porte sur le sectionneur. Suivre les procédures de verrouillage et deconsigne établies pour la mise en service de l’appareil. OM-271146 Page 15 4-6. Connexion de l’alimentation triphasée pour les modèles 400/460V IEC et CE 3 Terre GND/PE 8 10 7 9 4 6 2 1 6 5 2 NGO’s tools/ 7 9 flathead philips head wrench crescent wrench NGO’s tools/ Input3 2015-01 / 272715-A 5/32 pouce allen_wrench steelbrush 3/8 pouce allen_set nutdriver flathead chippinghammer OM-271146 Page 16 philips head wrench crescent wrench 4-7. Connexion de l’alimentation triphasée pour les modèles 400/460V IEC et CE L’installation doit être conforme à tous les codes nationaux et locaux faire effectuer cette installation uniquement par des personnes qualifiées. Débrancher et verrouiller ou consigner l’alimentation avant de connecter les conducteurs d’alimentation de l’appareil. Suivre les procédures établies relatives à l’installation et au démontage des dispositifs de verrouillage ou de consigne. Raccorder le câble d’alimentation à la source de soudage d’abord. Toujours raccorder le conducteur vert ou vert et jaune à la borne terre de l’alimentation en premier, et jamais à une borne de phase. circuit de cet appareil adapte auto� Lematiquement l’appareil à la tension d’alimentation à laquelle il est raccordé. Vérifier la tension d'alimentation disponible sur le site. Cette unité peut être raccordée à toute alimentation entre 400 ou 460 V AC. Se référer à la plaque signalétique du poste etvérifier la tension disponible sur le site. 1 Conducteurs d’alimentation (fourni par le client) 4-8. Sélectionner la section et la longueur des conducteurs selon la guide de service électrique. Les conducteurs doivent correspondre aux codes électriques nationaux et locaux. Le cas échéant, utiliser des cosses correspondant à l’ampérage et modifier la taille du trou. Connexions d’alimentation de la source de soudage 2 Serre-câble (fourniture client) Installer un serre-câble de dimension adaptée à l’appareil et aux conducteurs. Faire passer les conducteurs (le cordon) dans le serre-câble et serrer les vis. Fermer et verrouiller la porte d’accès du poste de soudure. Débranchement de l’alimentation du poste de soudure 7 Sectionneur (interrupteur présenté enposition fermée) 8 Débrancher le dispositif de coupure de ligne de mise à la terre (alimentation) du poste Raccorder d’abord le fil vert ou vert/jaune de mise à la terre à la borne terre du sectionneur. 9 Bornes des phases du sectionneur 3 Borne de terre de l’appareil 4 Conducteur de mise à la terre vert ouvert et jaune Brancher les conducteurs d’entrée L1, L2 et L3 sur les bornes des phases du sectionneur. Brancher le conducteur de terre vert ou vert/ jaune à la borne de terre de la soudeuse en premier. 10 Protection contre les surintensités 5 Bornes des phases de la source de soudage 6 Conducteurs d’entrée (L1, L2 et L3) Raccorder les conducteurs d’alimentation L1 (U), L2 (V) et L3 (W) aux bornes des phases du poste de soudure. Sélectionner le type et le calibre de protection contre les surintensités conformément à la guide de service électrique (interrupteur de coupure à fusible illustré). Fermer et fixer la porte sur le sectionneur. Suivre les procédures de verrouillage et deconsigne établies pour la mise en service de l’appareil. Raccords du cavalier de liquide de refroidissement 276861-A OM-271146 Page 17 4-9. Connexions de sortie de la source d’alimentation 2 1 Connexion de sortie double refroidie par air 2 1 2 1 4 4 Connexion de sortie double refroidie par liquide 2 2 2 1 5 1 5 4 3 5 Raccordement de sortie simple refroidie par liquide Raccordement de sortie simple refroidie par air 1 3 Ref. 803993-D / Ref. 804217-A 1 2 3 4 5 La vapeur et le liquide de refroidissement chaud peuvent causer des brûlures. Un tuyau peut se rompre lorsque le liquide de refroidissement surchauffe. Ne débranchez jamais les deux extrémités du tuyau lorsqu'il est installé sur une pièce chaude. Si le liquide de refroidissement cesse de s'écouler, laissez une extrémité du tuyau reliée pour permettre au liquide de refroidissement chaud de se refroidir et à la pression de diminuer. Retirez le tuyau de la pièce chaude pour éviter tout dommage. Connecteur de sortie 1 Connecteur de sortie 2 Fiche de protection Câble d’extension refroidi par air Câble d’extension refroidi par liquide Raccordement de sortie simple refroidie par air Ne pas déplacer ou débrancher des câbles lorsque la sortie est active. Connecter les câbles d’extension de sortie refroidis par air aux connecteurs de sortie 1 et 2. OM-271146 Page 18 Connecter le câble d’extension de sortie refroidi par air au connecteur de sortie 1 ou au connecteur de sortie 2. Connecter la fiche de protection au connecteur de sortie restant. Raccordement de sortie simple refroidie par liquide Connecter le câble d’extension de sortie refroidi par liquide au connecteur de sortie 1 ou au connecteur de sortie 2. Connecter la fiche protectrice au connecteur de sortie restant. Connexion de sortie double refroidie par air câbles d’extension doivent être de � Les même longueur: 7,6 m, 15,2 m ou 22,8 m. couvertures doivent être de mê� Les mes dimensions. Connexion de sortie double refroidie par liquide Connecter les câbles d’extension de sortie refroidis par liquide aux connecteurs de sortie 1 et 2. Les câbles d’extension doivent être de même longueur: 3 m, 7,6 m ou 15,2 m. Les câbles de chauffage doivent être de même longueur: 9,1 m, 15,2 m, 24,2 m ou 42,7 m. La longueur totale des câbles d’extension et de chauffage ne doit pas dépasser 110 m. La longueur du câble d’extension est multipliée par deux parce qu’il a un tuyau d’alimentation et un tuyau de retour. Utiliser uniquement les accessoires pour ProHeat fournis par Miller. 4-10. Informations et connexions concernant la prise de commande à distance RC14 2 1 Prise de commande à distance RC14 411) 1 A 2 B 1 C D K L N M E 2 Ergot de positionnement J I 3 Collet fileté H G 4 Fiche Pour brancher la prise, aligner l’ergot de positionnement, insérer la fiche et serrer le collet fileté. AVIS – Utiliser uniquement les accessoires pour ProHeat fournis par Miller. F 3 4 803993-D 4-11. Informations relatives à la prise distante 14 Broche A B +24VDC. Contacteur à distance C D E La fermeture du contact en A rend opérationnel le circuit de commande du contacteur 24VDC. Référence de commande; +10VDC. Commande de sortie à distance G F, J Informations sur la prise Remote 14 Commun du circuit de commande. Signal de commande d’entrée (curseur du potentiomètre ou 0 à +10VDC). Détect. du sens de déplacement. Défaut source d’alimentation H L’absence de fermeture de contact interne entre F et J signale un défaut de la source d’alimentation au dispositif de télécommande (il faut utiliser une source d’alimentation externe). IRMS réservoir 2 (1 volt/10 ampères). I Fréquence réelle du signal de sortie (1V/10kHz). L Puissance moyenne du signal de sortie (1V/10kW). M Mesure à distance Tension efficace du signal de sortie RMS (1V/100V). N Courant efficace total du signal de sortie RMS (1V/100A). K Châssis commun. OM-271146 Page 19 4-12. Informations et connexions concernant la prise d’enregistrement de température RC9 1 1 Prise d’enregistrement de température RC9 (voir Section 4-13) 2 Collet fileté 3 Fiche 2 1 Pour brancher la prise, insérer la fiche et serrer le collet fileté. 2 3 803993-D 4-13. Informations concernant les broches d’enregistrement de température Broche n° Informations concernant la prise 1 Thermocouple n°1 (TC1), signal 0-10volts DC [0V = −46°C, 10V = 816°C] 2 Thermocouple n°2 (TC2), signal 0-10volts DC [0V = −46°C, 10V = 816°C] 3 Thermocouple n°3 (TC3), signal 0-10volt DC [0V = −46°C, 10V = 816°C] 4 Thermocouple n°4 (TC4), signal 0-10volts DC [0V = −46°C, 10V = 816°C] 5 Commun du signal 6 Thermocouple n°5 (TC5), signal 0-10volts DC [0V = −46°C, 10V = 816°C] 7 Thermocouple n°6 (TC6), signal 0-10volts DC [0V = −46°C, 10V = 816°C] 8 Inutilisé 9 Inutilisé 10 Terre du châssis 11 Inutilisé 12 Inutilisé 13 Inutilisé 14 Inutilisé Le calcul de la tension selon la température se fait comme suit : (Tension sortie DC x 155) − 50 = °F (Tension sortie DC x 86,1) − 45.4 = °C L’écran ProHeat doit indiquer ± 6 °F ou ± 3,3 °C. OM-271146 Page 20 4-14. Protection d’isolation secondaire Raccordez les fils de terre fournis entre la pièce et le générateur pour fournir une isolation secondaire adéquate. Pour une sortie unique, un seul fil de terre est requis. Pour une double sortie, utilisez les deux fils de terre. Le circuit d’isolation secondaire coupe automatiquement la sortie du générateur si une condition potentiellement dangereuse existe sur le dispositif de chauffage connecté au générateur (par ex. l’isolation est cassée sur une couverture chauffante ou une bobine de chauffage amène le conducteur à entrer en contact avec la pièce). 1 Prises femelles 2 Fiche Afin de brancher la fiche, alignez la clé avec les ergots, insérez l’extrémité dans la prise femelle et faites tourner la fiche jusqu’à ce qu’elle soit serrée. 3 Poignée 4 Aimant d’isolation secondaire doit � L’aimant être en contact avec du métal nu (exempt de rouille, peinture, graisse etc.). 1 5 Pièce 2 Utilisez la poignée pour placer l’aimant sur la pièce. 6 Couverture chauffante ou bobine de chauffage 7 Espace de 12 pouces L’aimant et la poignée doit être placés à plus de 12 pouces de la couverture chauffante ou de la bobine de chauffage. L’espace est nécessaire pour éviter d’endommager l’aimant. 6 5 7 4 3 803994-E / 272889-A OM-271146 Page 21 4-15. Boîtier duplex de 115VAC et dispositif de protection supplémentaire 1 Prise RC1 monophasée 115VAC 2,5A 2 Dispositif de protection supplémentaire CB1 (2,5A) 1 2 1 CB1 protège la prise RC1 sous 115V contre les surcharges. Si CB1 s’ouvre, RC1 ne fonctionne pas. 2 803993-D OM-271146 Page 22 Le boîtier fournit une puissance auxiliaire nominale de 115VAC utilisée avec l’enregistreur numérique en option. La sortie maximale du boîtier est de 2,5A. 4-16. Position des thermocouples La position des thermocouples est une étape critique de l’opération de traitement thermique. Les thermocouples doivent être placés comme suit pour un contrôle uniforme du chauffage et une surveillance efficace de la durée et de la température : 1 Positionner les thermocouples pour garantir un contrôle de la zone entière à chauffer. � Le code spécifie normalement le nombre de thermocouples utilisés en fonction du diamètre du tube. � Le thermocouple de commande est place dans le plan de soudure (centre de la zone de chauffage). � Le thermocouple est placé en haut du tube dans une configuration standard de jonction tubulaire. Dans d’autres applications, le thermocouple doit être placé au point le plus chaud de la soudure à relaxer. 2 Prendre en compte tous les embouts et autres fixations soudées pouvant servir de dissipateur thermique via la masse métallique ou des points froids causés par la convection ou la conduction thermique, et appliquer des thermocouples supplémentaires. 3 Fixer un thermocouple de secours près des thermocouples de commande. 4 Fixer les thermocouples de façon à assurer l’uniformité de la température aussi bien dans les pièces minces que dans les pièces épaisses. 5 Inspecter physiquement la continuité de tous les thermocouples et les marquer d’un numéro d’identification correspondant à l’entrée de l’enregistreur. 6 Faire correspondre les schémas de la pièce indiquant les diverses positions des thermocouples, des thermocouples de commande, etc. à l’information d’identification de la soudure. 7 Le système comporte des connexions de thermocouples à 3 broches. Six thermocouples peuvent être reliés à la source d’alimentation. � Le système comporte des connecteurs à 3 broches pour l’insertion des câbles d’extension blindés. Les câbles blindés protègent des interférences électriques. 8 Le fil de thermocouple de type K comporte un fil positif et un fil négatif. Le fil positif est marqué en jaune plein ou rayé. Les bornes à vis du connecteur comportent une indication positive ou négative. Respecter la polarité lors du câblage du connecteur. 9 Plusieurs dispositifs utilisant un thermocouple de type K sont compatibles, notamment les sondes TC de contact, le fil TC à souder et les capteurs IR munis d’une sortie de type K. Les capteurs IR avec sorties 4−20 mA sont également compatibles. 10 Le routage du thermocouple de la pièce à la source d’alimentation est décrit ci-dessous. � Un fil de thermocouple de type K (deux fils) est fixé directement à la pièce au moyen d’un élément de fixation de thermocouple (voir la section suivante pour les informations sur la fixation des thermocouples). � L’autre extrémité est insérée dans un connecteur de type K à 2 broches. � Le connecteur à 2 broches est branché à un câble d’extension composite à 3 broches. Le câble d’extension comporte un bloc à six connecteurs femelles à 3 broches. La taille des broches indique le positionnement du connecteur à 2 broches sur l’extension. � Le câble d’extension contient six faisceaux de câble blindé à 3 fils. � Le câble d’extension mâle à 3 broches s’insère dans le connecteur femelle à 3 broches à l’avant de la source d’alimentation. OM-271146 Page 23 4-17. Position des thermocouples (Suite) 1 3 4 2 804320-A En mode contrôle de température, la source d’alimentation doit comporter (au minimum) un thermocouple connecté au boîtier TC1. Si l’on utilise plusieurs thermocouples, il faut utiliser soit les fiches de thermocouples individuelles, soit le câble d’extension des thermocouples. Procéder comme suit pour connecter les thermocouples à la source d’alimentation : OM-271146 Page 24 PAS souder les thermocouples à la � NE pièce tant que le câble des thermocouples est connecté d’alimentation. à la source Mettre la source d’alimentation hors tension. 1 Alimentation 2 Prises des thermocouples 3 Câble d’extension des thermocouples individuels 4 Câble d’extension pour thermocouples multiples Aligner la ou les broches de la fiche à celles de la prise et enfoncer la fiche dans la prise. 4-18. Fixation des thermocouples soudés � NE PAS souder les thermocouples tant qu’ils sont connectés à la source d’alimentation. 1 Fixez les thermocouples en utilisant une unité de fixation de thermocouple (Thermocouple Attachment Unit , TAU) portable. L’unité soude par point le fil du thermocouple directement sur la pièce. Cette méthode de fixation de thermocouple garantit une mesure précise de la température. 2 Nettoyer (limer ou poncer) toutes les écailles ou traces de rouille de la pièce aux endroits où les fils doivent être fixés. 3 Nettoyer l’emplacement de l’aimant principal pour minimiser la résistance. Placer l’aimant aussi près que possible des positions des thermocouples. 4 Retirer 6mm d’isolation des fils des thermocouples. 5 Réglez le contrôle variable de sortie de la TAU à environ 80 %. 6 Saisir l’un des fils dénudés avec la pointe des pinces. pinces ne doivent pas toucher les deux fils du thermocouple en même temps lorsque le dispositif de fixation de thermocouples � Les est sous tension. Les thermocouples seraient alors soudés aux pinces plutôt qu’à la pièce. 7 Le câble du thermocouple K possède un fil positif et un fil négatif. Le fil positif est marqué par du jaune ou des rayures jaunes. Les bornes à vis du connecteur sont marquées comme positive et négative. Veillez à fixer le fil au connecteur en respectant la polarité. 8 Plusieurs dispositifs utilisant un thermocouple de type K sont compatibles, notamment les sondes TC de contact, le fil TC à souder et les capteurs IR munis d'une sortie de type K. Les capteurs IR avec sorties 4-20 mA sont également compatibles. 9 La section suivante décrit l’acheminement du thermocouple depuis la pièce jusqu’au générateur. Bande ou ruban Fils de thermocouple Outils nécessaires : 804322-A OM-271146 Page 25 4-19. Utilisation de capteurs TC de contact 1 Couverture 2 Sonde de température de contact (voir la fiche de documentation du produit) Les thermocouples soudés mentionnés précédemment peuvent être utilisés pour des opérations de préchauffage ou de détensionnement. De tels composants sont habituellement utilisés dans les applications de détensionnement en raison de leur précision et de leur aptitude à supporter des températures élevées. 1 2 Vue de dessus à plat sur la pièce, sous le centre des bobines Vue latérale Ne placez pas le raccord réducteur de la sonde TC sous la couverture de chauffage Lorsque l’on retire la sonde de température de � contact, une baisse de température de courte du- Surface plane rée sera affichée par un enregistreur de température (en cas d’utilisation d’un tel accessoire). La sonde de température de contact peut être branchée au câble prolongateur de thermocouple ou à un câble prolongateur blindé type K de 7,6m*. Chaque sonde nécessite l’un de ces câbles prolongateurs. Surface plane du capteur en contact avec la couverture. Dans les applications de préchauffage, la sonde doit être placée sous la bobine d’induction. Pour que la sonde donne des résultats précis, il faut maintenir son extrémité plate au contact de la surface chauffée. Si des inducteurs refroidies par eau ou par air se chevauchent en un quelconque emplacement de l’installation, il est recommandé de placer une deuxième sonde à cet endroit. AVIS – L’inobservation de ces recommandations risque de conduire à une détérioration de la couverture ou de l’inducteur sous l’effet de la chaleur. Il est possible de vérifier la température de préchauffage au niveau du joint soudé à l’aide de crayons thermochromes. Incorrect TC de contrôle Découpler la ceinture près des extrémités Mise en place d’un capteur TC de contact Placez le capteur entre la couverture et le matériau métallique. Le capteur doit être à plat et bien en contact avec le matériau chauffé. La pointe du capteur doit être positionnée sous la ceinture, peu importe l’endroit mais toujours centré entre les deux fils. Ajouter des TC suppl. près des extrémités 273097-A OM-271146 Page 26 En variante, il est possible d’utiliser une sonde de température de contact dans les applications de préchauffage. Cela permet d’éviter de souder des thermocouples et de déplacer la sonde pendant le processus de préchauffage pour contrôler la température à d’autres emplacements du joint (la température maximale pour les sondes de température de contact est de 260°C). Pour maintenir le capteur TC en place, vous pouvez utiliser une bande (réf. 301 073). AVIS – Si un thermocouple de contact est utilisée avec une couverture refroidie par air, sa position est primordiale. Si la température d’une quelconque partie de la couverture dépasse 200C pendant une durée prolongée, cela endommagera la couverture. D’autres capteurs peuvent être placés aux extrémités de la pièce à protéger de la surchauffe. Si une couverture dépasse d’une extrémité de la pièce ou d’une découpe, il est possible d’ajouter de l’isolant entre la couverture et le matériau métallique. Pour cela, il faut découpler légèrement la bobine, ce qui diminue les courants parasites et la quantité de chaleur produite. AVIS – En cas de chauffage à proximité d’un raccord de soudure, un capteur de contrôle (TC1) doit être placé sous la bobine de chauffage. Un autre capteur peut être positionné au niveau du raccord pour surveiller sa température. Si une couverture est placée à la verticale ou en hauteur, vérifiez que son côté non isolé est en mesure de diffuser la chaleur. Ne posez pas d’isolant, de bois ou autre, sur la couverture. La rétention de chaleur dans la couverture peut l’endommager. 4-20. Utilisation de capteurs de température sans contact Il est important de positionner les capteurs de température sans contact de sorte qu’ils effectuent des mesures au plus proche de la zone chauffée. Cela permet au système de réguler la température de manière constante. Plus la distance entre la zone chauffée et la zone de mesure du capteur est importante, plus la boucle de contrôle fluctuera autour de la température cible. Le point de mesure doit se trouver à 50 mm maximum de la zone chauffée. OM-271146 Page 27 SECTION 5 – COMPOSANTS ET COMMANDES 5-1. Commandes 3 4 5 6 7 10 9 8 11 18 16 17 2 15 14 13 19 12 1 803995-B touche du panneau de � Lorsqu’une commande est enfoncé, le voyant jaune s’allume pour l’activation 1 Interrupteur d’alimentation indiquer 7 LED de fonctionnement du chauffage 14 Touche Paramètre La LED s’allume pour indiquer la sortie de la source est alimentée. Utiliser cette touche pour afficher les paramètres de fonctionnement de la source d’alimentation en temps réel. 8 Touche d’arrêt 15 Touche Refroidisseur Utiliser l’interrupteur pour mettre en marche et arrêter l’alimentation. Utiliser cette touche pour arrêter un processus de chauffage. 2 Afficheurs de température TC1−4 9 Touche Maintien Utiliser cette touche pour activer et désactiver le refroidisseur. Affiche la température des thermocouples 1 à 4. Utiliser cette touche pour maintenir un processus de chauffage. 16 Touche Augmenter 3 LED de contrôle des thermocouples 10 Touche Marche Utiliser cette touche pour augmenter les valeurs dans l’écran de configuration. Les LED indiquent quels thermocouples (1 à 4) sont utilisés pour commander le processus de chauffage. Utiliser cette touche pour lancer un processus de chauffage. 4 LED des sondes de température 11 Touche du curseur Les LED indiquent les unités de mesure de température (°F ou °C). Utiliser la touche pour déplacer le curseur de sélection dans l’afficheur LCD 4 x 40 (élément 18). 5 LED de panne 12 Touche Programme La LED s’allume pour indiquer une condition de panne du système. Utiliser cette touche pour programmer la commande du procédé. 6 LED de limite. 13 Touche d’état de marche La LED s’allume pour indiquer une condition limite du système. Utiliser cette touche pour afficher l’état de fonctionnement en temps réel. OM-271146 Page 28 17 Touche Diminuer Utiliser cete touche pour diminuer les valeurs dans l’écran de programme. 18 Afficheur LCD 4 x 40 Affiche la programmation, l’état de fonctionnement, les paramètres, les conditions de limite et de panne, et le guide de dépannage. 19 Prises d’entrée des thermocouples Utiliser les prises pour les entrées de thermocouples de type K. SECTION 6 – CONFIGURATION ET FONCTIONNEMENT 6-1. Équipement de sécurité NE PAS porter de bagues ou de montres pendant le fonctionnement. 2 1 Se munir des protections suivantes pendant le fonctionnement : 1 Gants d’isolation secs 2 Lunettes avec protections latérales 6-2. Description du système Le système de chauffage par induction ProHeat 35 est compatible avec un refroidissement par air ou par liquide. Selon le type de dispositif de chauffage auquel elle est reliée (à refroidissement par air/liquide ou à bobine d’induction), la source d’alimentation fonctionne et fournit automatiquement la puissance adaptée. Un identifiant spécial incorporé au connecteur du câble d’extension permet à la source d’alimentation de s’autoconfigurer en reconnaissant le type de câbles d’extension fixés à ses connecteurs de sortie. Conçue pour fournir un niveau de sortie unique (jusqu’à 35kW), la source d’alimentation ProHeat 35 comporte deux connecteurs montés sur le panneau qui sont connectés en parallèle à la sortie de la source d’alimentation. La conception permet au système de fonctionner avec un ou deux câbles d’extension. Si l’on utilise un seul câble d’extension, une fiche de protection DOIT être placée sur le connecteur de sortie non utilisé pour que le système puisse fonctionner. Si l’on utilise deux câbles d’extension, ils DOIVENT être tous deux du même type (refroidis par air ou par liquide) pour que le système puisse fonctionner (dans ce cas, on n’utilise pas de fiche de protection). Lorsqu’on utilise deux câbles d’extension et appareils de chauffage avec le système, les longueurs des câbles d’extension et les dispositifs de chauffage DOIVENT être identiques (voir Section 4-9). Le système ProHeat 35 est intelligent dans la mesure où il ajustera automatiquement les niveaux de sortie si les paramètres de fonctionnement internes ou les températures internes atteignent ou dépassent les limites spécifiques déterminées. 6-3. Directives importantes AVIS – Lorsque plusieurs systèmes ProHeat sont utilisés sur la même pièce, maintenez une distance d’au moins 30cm entre les bobines de chaque système. Le ProHeat 35 risque d’être endommagé si cette distance minimale n’est pas respectée. AVIS – Un phénomène de chaleur résiduelle est possible sur certains matériaux ferreux à proximité des câbles de sortie. Pour éviter ceci, éloigner les câbles de sortie des matériaux ferreux. Pour les agencements, des matériaux non-ferreux peuvent être utilisés selon la température de la pièce, comme du «glastic», un plastique à renfort de verre, des panneaux perforés, du bois, du PVC et de la fibre de verre. Si l’usage de matériaux métalliques est nécessaire, veiller à limiter la quantité d’aluminium, de cuivre ou de laiton. 6-4. Source d’alimentation/Configuration du système kW A V Hz Pour accéder à l’écran de configuration du système (System Setup), appuyez simultanément sur les touches Parameters et Program (paramètres) (programme) pour afficher l’écran suivant : Écran de configuration du système 1 Deg Units...:>F SYSTEM SETUP1 Tolerance...: ±25 Max Output..: 35 KW RI Clr Purge: 60s Control Mode: Temp RI Init KW: 0.0KW Pour modifier un paramètre : Appuyez sur la touche Cursor (curseur) pour déplacer le curseur sur le paramètre à modifier. OM-271146 Page 29 Appuyez sur les touches Increase que vous souhaitez régler. (déplacer vers le haut) or Decrease (déplacer vers le bas) pour sélectionner le paramètre Paramètres disponibles : Unités de température : °F / °C Tolérance : de ±5 à 99 en °F (de ±3 à 55 en °C) Mode de commande : Temp / Remote / Time / Manual (température / à distance / durée / manuel) Mode Temp (température) � Valeur kW initiale utilisée en mode bobine d’induction uniquement � Contrôle de la puissance via IR Mode Time (durée) � N’utilise pas la valeur kW initiale � Les capteurs IR surveillent la température mais pas la puissance Mode Remote (à distance) � Même fonctionnement que le mode Manual (manuel) mais à distance � Les capteurs IR surveillent la température mais pas la puissance Mode Manual (manuel) � La valeur kW initiale n’est pas utilisée � Les capteurs IR surveillent la température mais pas la puissance Puissance (kW) initiale de la bobine d’induction : de 0,0 à 35,0 kW Puissance de sortie : de 1 à 35 kW Temps de purge du refroidisseur de la bobine d’induction : de 30 à 240 secondes Unités de température- une fois l’unité sélectionnée, le témoin lumineux correspondant au °F ou au °C s’allumera. � L’unité par défaut est le Fahrenheit (°F). � Le passage du °F au °C entraînera la conversion des valeurs de programme enregistrées : température de rampe, température de palier, vitesse de rampe et tolérance de température. Tolérance- la valeur par défaut est ±25 °F. Mode de commande- Temp (température), Remote (à distance), Power (puissance) pour Time (durée), ou Manual (manuel). Pour plus de détails sur les méthodes de commande, voir la Section 6-5. � Le mode de commande par défaut est Temp (température). Puissance (kW) initiale de la bobine d’induction− la valeur par défaut est 0,0. Le réglage Max dépend du paramètre Max Output. Puissance de sortie− la valeur par défaut est 35 kW. Temps de purge du refroidisseur de la bobine d’induction− la valeur par défaut est 60 secondes. kW A V Hz Appuyez à nouveau sur les touches Parameters raît : (paramètres) et Program Écran de configuration du système 2 TC1,2 Type...:>IR4−20 SYSTEM SETUP2 IR Input Max.: 752 Trvl Detect..: On IR Input Min.: 122 Trvl Speed...: IPM Decouple Fault: On OM-271146 Page 30 (programme) simultanément ; l’écran suivant appa- Réglez la mise à l’échelle appropriée pour le capteur infrarouge. Miller a prévu deux capteurs différents pour la bobine d’induction L’échelle doit être réglée correctement pour afficher les températures appropriées sur l’affichage de la température. Capteur actuel Capteur d’origine Numéro de pièce 283080 265076 Entrée IR Max 400°C (752°F) 400°C (752°F) Entrée IR Min 50°C (122°F) 100°C (212°F) Dates actives 11-06-2018 jusqu’à aujourd’hui 07-21-2015 jusqu’à 11-06-2018 Paramètres disponibles : Type d’entrée : thermocouple K / infrarouge 4−20 mA (TC 3−6 sont fixés au TC K) Entrée IR max. : définir la valeur équivalente du capteur IR (20 mA) Détection des déplacements : marche/arrêt. Fonctionne comme un interrupteur marche/arrêt avec des câbles refroidis par air et par liquide. Se reporter à Tableau 6-2 pour obtenir des informations sur le fonctionnement avec une bobine d’induction. Entrée IR min. : définir la valeur équivalente du capteur IR (4 mA) Vitesse de déplacement en IPM ou CPM (pouces par minute ou centimètres par minute) Erreur de découplage (Decouple Fault) : marche/arrêt L’arrêt de la fonction Decouple Fault (erreur de découplage) permet au système de fonctionner avec des bobines mal accouplées. Cette fonctionnalité est disponible uniquement avec des câbles refroidis par liquide. Le message suivant apparaîtra à chaque démarrage de ProHeat pour vous rappeler que la fonction est désactivée. F73: Decoupled/Open Coil Fault Disabled for Liquid Cooled Cables Only Press (−) to Acknowledge Appuyez sur la touche Decrease (déplacer vers le bas) du panneau avant pour confirmer le message. Si vous utilisez un interrupteur marche/arrêt distant, activez deux fois arrêt/marche en 3 secondes pour confirmer le message. Contraste de l’afficheur - tout en maintenant la touche Cursor (curseur) enfoncée, appuyez sur la touche Increase assombrir ou sur la touche Decrease (augmenter) pour (diminuer) pour réduire le contraste. paramètres de Configuration du système ayant un caractère général, toute modification apportée à la configuration s’appliquera à tous � Les les programmes. d’activation / de désactivation du rétroéclairage a été retirée depuis la version 1.26 du logiciel. Le rétroéclairage est désormais actif � L’option en permanence. OM-271146 Page 31 A. Paramètres par défaut Pour réinitialiser aux paramètres d’usine par défaut, couper la source d’alimentation, et attendre que l’afficheur s’éteint. Rallumer la source d’ali- mentation. Lorsque l’afficheur s’allume, presser et maintenir enfoncé les touches Augmenter et Diminuer Program» s’affichera pour réinitialiser aux paramètres d’usine par défaut. Relâcher les touches Augmenter puyer sur la touche Programme 6-5. . Le message «Press et Diminuer , et ap- . Programmation La programmation permet à l’opérateur de définir un programme pour un procédé de chauffage particulier. Les choix disponibles sont : Température, Distance, Manuel ou Puissance/Durée (Durée). A. Commande fondée sur la température La commande fondée sur la température contrôle le système et le procédé de chauffage en fonction des informations sur la température transmises par les entrées des thermocouples. Le système ne peut fonctionner dans ce mode qu’en présence de thermocouples. Quatre procédés différents sont disponibles en mode fondé sur la température: préchauffage, étuvage, PWHT (traitement thermique après soudage) et programme personnalisé. Appuyer sur la touche Programme pour accéder au mode Programmation. Utiliser la touche Curseur pour déplacer le curseur sur le procédé fondé sur la température désiré, puis appuyer encore sur la touche Programme pour sélectionner le processus. A..1. Préchauffage (Preheat) Le procédé de préchauffage est une méthode simple de chauffage du matériau à une température désirée et à maintenir cette température pour une durée spécifique. Lorsque ce procédé est sélectionné, l’écran suivant apparaît sur l’afficheur LCD : Écran Préchauffage Mode..........: Preheat Control TC...: 1 Temperature: 400 Soak Time...: 01:00:00 La position par défaut du curseur est près de Control TC. Appuyer sur la touche Augmenter et Diminuer pour sélectionner le nombre de thermocouples de commande utilisés pour le programme. Les sélections sont les suivantes: 1, 1,2, 1,2,3, ou 1,2,3,4. TC1 DOIT toujours être un thermocouple de commande. TC2 à TC4 peuvent être utilisés pour commander ou contrôler. Lorsqu’un thermocouple est sélectionné comme commande, la LED adjacente à l’afficheur à sept segments s’allume. Utiliser le bouton Curseur ton Augmenter pour déplacer le curseur sur la sélection désirée (Température ou Durée d’exposition), et appuyer sur le bou- ou Diminuer pour modifier la valeur du paramètre désiré. températures minimale et maximale de préchauffage sont 0 et 1450 F (−18 et 788 C). Les durées d’exposition minimal et maximal sont � Les 0 et 100 heures. Lorsque le système utilise des couvertures refroidies par air, le paramètre de température maximale est 400 F (204 C). Si le paramètre de programme est supérieur à 400 F (204 C), l’écran suivant apparaît sur l’afficheur LCD lorsque le bouton Marche est enfoncé : Écran de message de température maximale Cannot enter Run mode Programmed temperature settings exceed air cooled limits (400 °F, 204 °C) OM-271146 Page 32 A..2. Étuvage Le processus d’étuvage permet à l’opérateur de programmer une température et un durée d’exposition ainsi qu’une vitesse de refroidissement de l’étuvage si nécessaire. Lorsque ce processus est sélectionné, l’écran suivant apparaît sur l’afficheur : Écran Étuvage Mode......: Bake−Out Control TC:>1 Soak Temp.: 600 Soak Time: 01:00:00 Cool Temp.: 200 Cool Rate: 600 °/Hr La position par défaut du curseur est près de Control TC. Appuyer sur la touche Augmenter et Diminuer pour sélectionner le nombre de thermocouples de commande utilisés pour le programme. Les sélections sont les suivantes: 1, 1,2, 1,2,3, ou 1,2,3,4. TC1 DOIT toujours être un thermocouple de commande. TC2 à TC4 peuvent être utilisés pour commander ou contrôler. Lorsqu’un thermocouple est sélectionné comme commande, la LED adjacente à l’afficheur à sept segments s’allume. Utiliser le bouton Curseur pour déplacer le curseur sur la sélection désirée (Température d’exposition, durée d’exposition, Température de refroidissement, ou Vitesse de refroidissement), et appuyer sur le bouton Augmenter du paramètre désiré. ou Diminuer pour modifier la valeur valeurs minimum et maximum de température de palier et de refroidissement pour le recuit sont −18 et 788 C. Les durées minimum et � Les maximum de palier sont 0 et 100 heures ou Durée prolongée. Les vitesses de refroidissement minimum et maximum sont 10 et 9999 /hr. Lorsque le système utilise des couvertures refroidies par air, la température maximale est de 204 C. Si le programme est réglé à plus de 204 C, une pression sur la touche Run (Exécuter) fera apparaître l’écran LCD suivant : Écran de message de température maximale Cannot enter Run mode Programmed temperature settings exceed air cooled limits (400 °F, 204 °C) A..3. PWHT (traitement thermique après soudage) Le processus de traitement thermique après soudage permet à l’opérateur de programmer un traitement thermique après soudage où la température de rampe (croissante ou décroissante) et les vitesses de rampes sont identiques. La sélection de ce processus fait apparaître l’écran suivant sur l’afficheur : Écran PWHT Mode......: PWHT Control TC:>1,2 Ramp Temp.: 200 Ramp Rate: 600 /Hr Soak Temp.: 400 Soak Time: 01:00:00 La position par défaut du curseur est près de Control TC. Appuyer sur la touche Augmenter et Diminuer pour sélectionner le nombre de thermocouples de commande utilisés pour le programme. Les sélections sont les suivantes: 1, 1,2, 1,2,3, ou 1,2,3,4. TC1 DOIT toujours être un thermocouple de commande. TC2 à TC4 peuvent être utilisés pour commander ou contrôler. Lorsqu’un thermocouple est sélectionné comme commande, la LED adjacente à l’afficheur à sept segments s’allume. OM-271146 Page 33 Utiliser le bouton Curseur pour déplacer le curseur sur la sélection désirée (Ramp Temperature, Ramp Rate, Soak Temperature ou Soak Time), et appuyer sur le bouton Augmenter Température d’immersion ou Diminuer pour modifier la valeur du paramètre désiré. Temps d’immersion Taux de rampe Température de rampe Figure 6-1. Paramètres d’étuvage paramètres de température minimale et maximale pour le PWHT sont 0 et 1450F (−18 et 788C). Les vitesses de rampe minimale et � Les maximale sont 10 et 9999F/h (6 et 5555C/h). Les températures d’exposition minimale et maximale sont 0 et 1450 F (−18 et 788 C). Les durées minimum et maximum de palier sont 0 et 100 heures ou Durée prolongée. Lorsque le système utilise des couvertures refroidies par air, le paramètre de température maximale est 400F (204C). Si le paramètre programmé est supérieur à 400F (204C), l’écran suivant apparaît sur l’afficheur LCD lorsque le bouton Marche est enfoncé. Écran de message de température maximale Cannot enter Run mode Programmed temperature settings exceed air cooled limits (400 °F, 204 °C) A..4. Fonctionnement PWHT Lorsqu’un cycle PWHT est démarré, vous pouvez surveiller l’endroit où vous vous trouvez dans le cycle en sélectionnant l’Écran d’état. À partir de là, vous pouvez déterminer dans quel mode vous êtes, quelle est la température cible calculée actuelle du contrôleur de chaleur, et voir le compte à rebours de temporisation d’exposition. Lorsque vous utilisez un seul TC dans la boucle de contrôle, il est chargé du cycle entier. Lorsque vous utilisez 2 à 4 TC, le contrôle de chaleur du ProHeat 35 a les caractéristiques suivantes : � Lors de la montée, de la température de rampe à la température d’exposition, le TC avec la température la plus élevée est le TC qui contrôle. � Dans de nombreuses applications, la température de tous les TC de contrôle reste proche pendant tout le cycle, dans la bande de tolérance programmée (la valeur par défaut est +/- 25°F) du point de consigne. Dans ces cas typiques, l’unité continue du cycle de rampe au cycle d’exposition, et le compte à rebours d’exposition commence. Lorsqu’au point de consigne de la température d’exposition, toutes les températures de TC de contrôle doivent être dans la bande de tolérance avant que le compte à rebord d’exposition ne démarre. Si tous les TC ne sont pas dans la tolérance, le chauffage continue jusqu’à ce que le TC le plus chaud atteigne le point de consigne plus la bande de tolérance. L’unité n’autorise pas de débit au −delà du point de consigne plus la bande de tolérance. Si aucune des températures n’est dans la bande de tolérance, vous avez trois options : 1 Laisser du temps à la chaleur pour qu’elle se conduise à travers le matériau. Cela peut permettre à la zone avec le TC le plus froid de se réchauffer au−dessus du minimum (point de consigne − tolérance) permettant de continuer le cycle d’exposition. 2 Manipuler la bobine au−dessus de la zone chaude, permettant à la zone de refroidir. Pour ce faire, vous devez arrêter le cycle, écarter les spires de la bobine, retirer les spires de la bobine ou retirer la bobine (découplage de la bobine) uniquement sur la zone où se trouve le TC de contrôle chaud. En conséquence, la puissance de débit augmentera légèrement, permettant aux zones plus froides de se réchauffer. 3 Changer la bande de tolérance. Pour ce faire, arrêtez le cycle, entrez dans l’écran de configuration et augmentez le paramètre de tolérance. Reprenez le cycle. Certains codes tels que ASME B31.1 et B31.3 ne permettent pas les réglages de tolérance au−delà de +/- 25°F, alors assurez−vous de vérifier le code ou de vérifier avec vos ingénieurs pour voir si cela est permis. � Lors de la descente de la température d’exposition à la température de rampe, le TC avec la température la plus basse est le TC qui contrôle. � Si la pièce ne peut pas être chauffée à la vitesse demandée (c’est−à−dire en raison de la masse partielle, de la configuration de la bobine, etc.), la température cible affichée par le contrôle de chaleur ne dépassera jamais une différence de 10°F du TC de contrôle. OM-271146 Page 34 A..5. Programme personnalisé (Custom Program) La programmation personnalisée permet à l’opérateur de créer ses propres programmes à étapes multiples, ou des programmes de traitement thermique non symétriques où les vitesses et les températures de chauffage et de refroidissement sont différentes. La sélection de ce programme fait apparaître l’écran suivant sur l’afficheur : � L’écran ci-dessous indique l’utilisation initiale du système. L’utilisation ultérieure fait apparaître le dernier programme utilisé. Écran Programme personnalisé Mode..........: Custom Program Segment.....: >1 Type...........: End Control TC...: 1 La position par défaut du curseur est à côté de Segment. Appuyer sur la touche Augmenter ou Diminuer pour augmenter ou diminuer le nombre de segments, sauf si le type de segment est End (Fin). Dans ce cas, le nombre de segments avancera au segment 1. Utiliser la touche Curseur ou diminuer pour déplacer le curseur sur la sélection désirée (Type or Control TC), et appuyer sur la touche Augmenter pour modifier la valeur du paramètre désiré. Lorsque le curseur est positionné sur la sélection Type, les boutons Augmenter et Diminuer segment sont les suivantes : permettent de modifier le segment en Step, Ramp, Soak, ou End. Les fonctions de chaque type de � Step augmente la température dans l’élément à la puissance du programme complet. La température maximale programmable est 1450°F (788°C). � Ramp augmente ou diminue la température dans la pièce à une vitesse commandée en degrés par heure. La température maximale programmable est 1450°F (788°C) à une vitesse maximale de 9999°F/h (5555°C/h). � Soak maintient la température pendant un laps de temps programmé. Les durées minimale et maximale d’étuvage sont 0 et 100 heures. � La programmation End indique l’achèvement du cycle et la coupure de la puissance de sortie. Fonction Step Lorsque le type de segment est Step, l’écran suivant apparaît sur l’afficheur : Écran Programme personnalisé Mode..........: Custom Program Segment.....: 1 Type...........: > Step Control TC...: 600 Utiliser la touche Curseur Augmenter ou Diminuer pour déplacer le curseur à la position Température et ajuster la température initiale au moyen de la touche . Le programme passe automatiquement au numéro de segment suivant si on appuie de nouveau sur la touche Curseur . Fonction Rampe Lorsque le type de segment est Ramp, l’écran suivant apparaît sur l’afficheur : OM-271146 Page 35 Écran Programme personnalisé Mode.......: Custom Program Segment....: 1 Type.......: Ramp Temperature: 600 Utiliser la touche Curseur menter Ramp Rate: 600 °/Hr pour déplacer le curseur en position Température ou Vitesse de rampe (Ramp Rate) et utiliser la touche Aug- ou Diminuer pour définir la valeur souhaitée. Lorsque le curseur est en position Vitesse de rampe, le programme passe automatiquement au numéro de segment suivant si on appuie de nou- . veau sur la touche Curseur Fonction Maintien (Soak) Lorsque le type de segment est Soak, l’écran suivant apparaît sur l’afficheur : Écran Programme personnalisé Mode..........: Custom Program Segment.....: 1 Type...........: > Soak Soak Time...: 00:01:00 Utiliser la touche Curseur pour déplacer le curseur en position Soak Time et utiliser la touche Augmenter ou Diminuer pour définir la valeur désirée. Lorsque le curseur est en position Soak Time, le programme passe automatiquement au numéro de segment suivant si on appuie de nouveau sur la touche Curseur . Fonction Fin (End) Lorsque le type de segment est End, l’écran suivant apparaît sur l’afficheur : Écran Programme personnalisé Mode..........: Custom Program Segment.....: > 2 Type...........: End Soak Time...: 1 Le seul paramètre modifiable dans un segment End est le nombre de thermocouples sélectionné. Utiliser la touche Curseur pour dépla- cer le curseur en position TC de commande (Control TC). Appuyer sur la touche Augmenter ou Diminuer pour sélectionner le nombre de thermocouples de commandes utilisés dans le programme. Les sélections sont les suivantes: 1, 1,2, 1,2,3, ou 1,2,3,4. TC1 DOIT OM-271146 Page 36 toujours être un thermocouple de commande. TC2 à TC4 peuvent être utilisés pour la commande ou le contrôle. Lorsqu’un thermocouple est sélectionné pour la commande, la LED adjacente à l’affichage à sept segments s’allume. Un programme personnalisé peut comporter jusqu’à 10 segments. Pour consulter les paramètres de programmation, positionner le curseur sur Segment et utiliser la touche Augmenter ou Diminuer pour parcourir les numéros de segments jusqu’au segment End. Lorsqu’un numéro de segment est modifié, les informations de paramétrage du segment apparaissent sur l’afficheur. Exemple de programme à 5 segments Écran Programme personnalisé Mode..........: Custom Program Segment.....: 1 Type...........: >Step Soak Time...: 600 La température augmente de 600 degrés à la puissance du programme complet. Écran Programme personnalisé Mode.......: Custom Program Segment....: 2 Type.......: Ramp Temperature: >1250 Ramp Rate: 600 °/Hr Chauffage commandé à 1250 degrés F à une rampe de 600 degrés par heure. Écran Programme personnalisé Mode..........: Custom Program Segment.....: 3 Type...........: Soak Soak Time...: 00:01:00 Exposition à 1250 degrés F sur une période de 1:00. Écran Programme personnalisé Mode.......: Custom Program Segment....: 4 Type.......: <Ramp Temperature: 600 Ramp Rate: 600 °/Hr Refroidissement commandé à 600 degrés F à une vitesse de 600 degrés par heure. Écran Programme personnalisé Mode..........: Custom Program Segment.....: 5 Type...........: End Soak Time...: 1 Le segment End achève le cycle de traitement thermique. La commande est programmée pour commander le processus au moyen de quatre thermocouples. OM-271146 Page 37 B. Commande à distance La commande à distance permet le contrôle du système depuis un périphérique distant activant ou désactivant la sortie, ainsi que le réglage du niveau de courant souhaité en fonction du réglage maximum de courant de sortie choisi sur l’écran de configuration du système. En mode de commande à distance, le bouton de démarrage sur l’avant du ProHeat 35 est désactivé. Si le mode de commande à distance a été sélectionné dans l’écran de configuration du système, l’écran suivant s’affiche pour la programmation : Mode....: Remote Power..: 0.0 KW Run Time:>00:03:00 Current: 0 A Voltage: 0 V Frequency: 4.5 KHz La durée est le seul paramètre réglable. Les valeurs vont de 0 à 99:59:59. ce mode, la touche Marche sur l’avant de la source ne fonctionne pas. Utiliser la commande à distance pour activer ou désactiver la � Dans sortie. C. Commande Puissance/Durée La commande Puissance/Durée actionne le système et commande la procédure de chauffage à partir de la durée et de la puissance programmées. La puissance augmente pendant toute la durée programmée. Appuyer sur la touche Programme pour accéder au mode de programmation. Utiliser la touche Curseur pour positionner le curseur sur Mode, Segment, Type, Puissance ou Durée. Mode....: Timed Segment: 1 Type...:>Power Level Power..: 0.0 KW Time: 00:00:00 Par défaut, le curseur est placé à côté de Programme. Appuyer sur la touche Augmenter Utiliser la touche Curseur . pour positionner le curseur à l’endroit voulu puis appuyer sur la touche Augmenter pour régler la valeur souhaitée. Sélections possibles chronométrées : Segment : 1 − 10 Type : Niveau de puissance, Pente, Fin Puissance : 0,0 − 35 ................ Durée : 00:00:00 − 99:59:59 ou durée infinie OM-271146 Page 38 ou Diminuer ou Diminuer D. Commande manuelle La commande manuelle permet la programmation d’un niveau de puissance spécifique sur une durée donnée. La sélection de ce processus fait apparaître l’écran suivant sur l’afficheur : Écran de programmation manuelle Mode..........: Manual Power..: 0.0 KW Command...: 0.0 KW Current: 0 A Run Time..: 00:03:00 Voltage: 0 V Frequency: 4.5 KHz Les seules sélections programmables sont Command Power (puissance commandée) et Run Time (durée de marche). La commande peut être réglée pour fournir jusqu’à 35KW (en fonction de la puissance maximale sélectionnée dans l’écran de configuration) pour une période pouvant atteindre 99 heures, 59 minutes, 59 secondes. La puissance de fonctionnement de la source d’alimentation, le courant, la tension, et la fréquence sont indiqués sur le côté droit de l’afficheur. Pour réinitialiser aux paramètres d’usine par défaut, couper la source d’alimentation, et attendre que l’afficheur s’éteint. Rallumer la source d’ali- mentation. Lorsque l’afficheur s’allume, presser et maintenir enfoncé les touches Augmenter et Diminuer Program» s’affichera pour réinitialiser aux paramètres d’usine par défaut. Relâcher les touches Augmenter puyer sur la touche Programme . Le message «Press et Diminuer , et ap- . E. Bobine d’induction : mode de commande Manual (manuel) ou Temp (température) AVIS – Avec une bobine d’induction, un mesurage infrarouge de la température et une détection des déplacements sont fortement recommandés. La bobine d’induction induit jusqu’à 20 kW sur une petite zone. La température d’une pièce peut donc rapidement atteindre plus de 315 C si cette dernière ne se déplace pas assez rapidement. Cela peut endommager la bobine ou la pièce. Le système utilise le capteur de déplacement pour diminuer la puissance de chauffe à mesure que la vitesse de déplacement diminue et interrompre la chauffe dès lors qu’aucun déplacement ne se produit. de déplacement est un instrument sensible qui permet de mesurer des vitesses de déplacement inférieures à un IPM. Une fois � Lequecapteur la pièce cesse de se déplacer, il y a un délai de trois secondes avant que la sortie puisse être à nouveau mise sous tension. Des vibrations produites par des phénomènes tels qu'un mouvement de chariot, d'engrenages, une opération de rectification et de manipulation de la pièce pendant plus de trois secondes peuvent déclencher le capteur et mettre la sortie sous tension. Appuyez toujours sur Stop sur le panneau avant de ProHeat quand la pièce cesse de se déplacer et ce, afin d'éviter que la pièce ne chauffe par inadvertance. Détection des déplacements Le capteur de déplacement peut être monté à gauche ou à droite de la bobine d'induction. Il peut également être installé hors de la bobine, là où la vitesse de déplacement est identique à celle de la bobine. Dans ce cas, un support de 96 mm (L.) x 64 mm (l.) vous permettra de le monter. � Raccordez la ou les bobine(s) d’induction à la source d’alimentation avant la mise sous tension. kW A V Hz Pour accéder à l’écran de configuration du système (System Setup), appuyez simultanément sur les touches Parameters et Program (paramètres) (programme) pour afficher l’écran suivant : � Appuyez sur la touche Cursor (curseur) pour déplacer le curseur sur le paramètre à modifier. Appuyez sur les touches Increase (déplacer vers le haut) ou Decrease (déplacer vers le bas) pour accéder aux paramètres à régler. OM-271146 Page 39 ÉCRAN DE CONFIGURATION DU SYSTÈME 1 Deg Units...:>°F SYSTEM SETUP1 Tolerance...: ±25 Max Output..: 35 KW RI Clr Purge: 60S Control Mode: Temp RI Init KW: 0.0KW Réglez le paramètre Deg Units (unités de température) sur ° F ou ° C suivant le cas. Si nécessaire, définissez la valeur du paramètre Tolerance (tolérance). Réglez le paramètre Control Mode (mode de commande) sur Manual (manuel) ou Temp (température) suivant le cas. Définissez une valeur comprise entre 0,0 et 35,0 kW pour le paramètre Rolling Inductor Initial kW (puissance de démarrage de la bobine d’induction) � La valeur du paramètre Rolling Inductor Initial kW (puissance initiale de la bobine d’induction) peut être augmentée lorsque vous travaillez sur des pièces en série plus grandes. Il est recommandé de définir une valeur kW basse pour chauffer la première pièce. Observez le niveau kW maximal atteint au terme du cycle de chauffe puis réglez la valeur initiale kW à cette valeur, ou à une valeur inférieure. � La valeur du paramètre Max Output kW (puissance maximale en kW) peut être réduite s’agissant de pièces en série plus petites, ce afin de minimiser la puissance de chauffe. � Temps de purge du refroidisseur de la bobine d’induction : de 30 à 240 secondes � Le temps de purge du refroidisseur de la bobine d’induction est de 60 secondes par défaut pour des applications utilisant des câbles de bobine de 18,29 m. Il peut être défini à 30 secondes pour les câbles de bobine standards de 9,14 m. ProHeat doublera automatiquement ce temps si deux bobines d’induction sont raccordées. kW A V Hz Appuyez à nouveau sur les touches Parameters raît : (paramètres) et Program (programme) simultanément ; l’écran suivant appa- ÉCRAN DE CONFIGURATION DU SYSTÈME 2 TC1,2 Type...:>IR4−20 SYSTEM SETUP2 IR Input Max.: 750 Trvl Detect..: On IR Input Min.: 212 Trvl Speed...: IPM Decouple Fault: On Réglez le paramètre Trvl Detect (capteur de déplacement) sur On (marche) si vous utilisez la détection des déplacements. La détection des déplacements est recommandée pour toutes les applications utilisant une bobine d’induction. En effet, elle permet de maintenir une chaleur homogène au niveau de la pièce et elle régule la puissance de chauffe en fonction de la vitesse de déplacement en mode Temp (température). Définissez les valeurs du paramètre Trvl Speed (vitesse de déplacement) selon les besoins. � IPM = Inches Per Minute (pouces par minute) : PI = 3,14159 r = rayon (distance entre le centre de la partie en rotation et la roue de détection des déplacements) s = secondes par rotation. Sens de déplacement r Sens de déplacement r IPM = (2 * PI * r * 60) / s Exemple : pour un tuyau de 24 po. de diamètre, de rayon 12 po. et effectuant une rotation complète en 45 secondes, la formule serait la suivante : IPM = (2 * 3,14159 * 12 * 60) / 45 Tuyau IPM = (4523,9) / 45 IPM = 100,5 la chauffe, la valeur en IPM peut être obtenue à partir � Pendant du menu Run Status (état en marche). OM-271146 Page 40 Bride Appuyez une fois sur la touche Program (programme) pour accéder à l’écran de programmation de la bobine d’induction. Un écran similaire à l’exemple ci−dessous apparaît alors. Écran de programmation de la bobine d’induction Mode....: Manual Power…: 0.0 KW Command.: >0.0 KW Current: 0 A Run Time: 00:03:00 Voltage: 0 V Frequency: 4.5 kHz Branchez une extrémité du câble prolongateur du thermocouple à la prise TC5 de la source d’alimentation et l’autre extrémité à l’arrière de la bobine d’induction. Si deux bobines d’induction fonctionnent sur la même source d’alimentation, branchez un second câble prolongateur de thermocouple entre la seconde bobine et la prise TC6 de la source d’alimentation. pièces doivent être de dimensions et matériau identiques si deux bobines d’induction sont utilisées sur une même source � Les d’alimentation. AVIS – TC5 et TC6 se connectent au thermocouple interne de la bobine d’induction qui surveille les températures internes du noyau de la bobine d’induction. Mesurez la température de la pièce avec des crayons de température, un capteur infrarouge ou des thermocouples à contact à moins de 5 cm de la bobine d’induction. 6-6. État de marche L’état de marche permet de vérifier l’état d’un programme pendant le chauffage en cours. Selon le mode de commande (température ou manuel) et le mode fondé sur la température (Preheat (Préchauffage), Bake-Out (Étuvage), PWHT ou Custom (Personnalisé)), des écrans de styles différents apparaissent sur l’afficheur. L’état de marche ne sert qu’à vérifier le processus et ne permet pas de sélectionner ou de modifier des paramètres. A. Commande fondée sur la température A..1. Écran d’état de marche de préchauffage, d’étuvage et de PWHT Écran d’état de marche Mode.......: Preheat TC5: 77 Target Temp: −−−− TC6: 77 Countdown..: −−:−−:−− TvlIPM(Off): 0 Status.....: Stopped Mode indique le mode de programmation (Préchauffage, Étuvage, PWHT ou Programme personnalisé). Pendant le fonctionnement actif, Target Temp indique la température cible en fonction du programme spécifique, Countdown indique le temps restant dans un segment d’exposition, et Status indique le type de segment du programme (étape, exposition, rampe, maintien ou arrêté). TC5 et TC6 indiquent la température des thermocouples 5 et 6. Cet écran ne sert qu’à vérifier le processus. A..2. Programme personnalisé (non disponible avec une bobine d’induction) Écran d’état de marche Mode.......: Custom Program TC5: 77 Target Temp: −−−− TC6: 77 Countdown..: −−:−−:−− Segment: 1 Status.....: Stopped Mode affiche le mode de programmation (Préchauffage, Cuisson, PWHT ou Programme personnalisé). Pendant le fonctionnement actif, Target Temp indique la température cible en fonction du programme spécifique, Countdown indique le temps restant dans un segment d’exposition, et Status indique le type de segment de programme (étape, exposition, rampe, maintien ou arrêté) du segment actif et son numéro. TC5 et TC6 indiquent la température des thermocouples 5 et 6. Cet écran ne sert qu’à vérifier le processus. OM-271146 Page 41 B. Commande manuelle Écran d’état de marche Mode..........: Manual TC5: 77 Power....: 0.0 KW TC6: 77 Countdown: −−:−−:−− TvlIPM(Off): 0 Status...: Stopped Pendant le fonctionnement actif, Power indique la puissance réelle fournie par la source d’alimentation, Countdown indique le temps restant du cycle de chauffage, et Status indique si le système est en marche ou arrêté. TC5 et TC6 indiquent la température des thermocouples 5 et 6. Cet écran ne sert qu’à vérifier le processus. � Aucune modification n’est possible dans l’écran d’état de marche. Les touches Augmenter et Diminuer sont inactifs. C. Commande à distance Écran d’état de marche Mode.....: Remote TC5: 77 Power....: 0.0 KW TC6: 77 Countdown: 00:00:00 TvlIPM(Off): 0 Status...: Stopped Pendant le fonctionnement actif, Power indique la puissance réelle fournie par la source d’alimentation, Countdown indique le temps restant du cycle de chauffage, et Status indique si le système est en marche ou arrêté. TC5 et TC6 indiquent la température des thermocouples 5 et 6. Cet écran ne sert qu’à vérifier le processus. � Aucune modification n'est possible dans l’écran d’état de marche. Les touches Augmenter et Diminuer sont inactives. D. Commande Puissance/Durée Écran d’état de marche Mode...: Power vs Time TC5: OPEN Segment: 1 TC6: OPEN Type...: −−:−−:−− TvlIPM(Off): 0 Power..: 0.0 KW Type: End Mode affiche le mode de commande. Sont également affichés le segment de programme en cours, le type de segment, le niveau de puissance et le temps restant pour le segment. E. Paramètres Pendant le fonctionnement actif, l’écran Paramètres permet à l’opérateur de vérifier les paramètres de fonctionnement de la sortie de la source d’alimentation. Ces paramètres comprennent la puissance, l’intensité, la tension et la fréquence de sortie. L’écran affiche en outre les températures des thermocouples TC5 et TC6. L’écran Paramètres ne sert qu’à vérifier le processus et ne permet pas de sélectionner ou de modifier des paramètres. Écran Paramètres Power....: 0.2 KW Current..: 20 A OM-271146 Page 42 TC5: OPEN TC6: OPEN Voltage..: 52 V Power Level Frequency: 11.7 KHz Countdown: 00:14:36 F. Refroidisseur (Cooler) Le bouton Cooler sert à activer/désactiver le refroidisseur sur les systèmes utilisant des câbles de sortie refroidis par liquide. Les systèmes utilisant des câbles de sortie refroidis par liquide ne fourniront pas de sortie sans que le refroidisseur soit activé. Si le refroidisseur n’est pas activé avant le lancement d’un cycle de chauffage, il sera automatiquement démarré par le système lorsque le bouton Marche foncé. Le refroidisseur ne s’arrête pas si on appuie sur la touche Arrêt froidisseur sera en- , mais doit être éteint séparément en appuyant sur la touche Re- . Lorsque la sortie de la source d’alimentation est activée, le refroidisseur ne peut pas être arrêté. Si on appuie sur la touche Cooler quand la sortie est sous tension, l’écran suivant apparaît sur l’afficheur: Écran de message du refroidisseur Cooler cannot be turned off while output is on � La touche Refroidisseur est inactif si aucun refroidisseur n’est détecté ou si aucun câble de sortie refroidi par liquide n’est détecté. une bobine d’induction est reliée à la source d’alimentation, le refroidisseur sera purgé pendant une durée définie via le paramètre � Quand RI Clr Purge dans Configuration du système (écran 1), soit généralement 30 à 60 secondes par bobine d’induction, avant que la sortie puisse être activée. G. Fonctionnement en temps réel À chaque première mise en marche de l’appareil, le système effectue une routine de vérification de la communication entre les cartes et traque les défauts d’isolation éventuels. Pendant ces vérifications, tous les afficheurs et LED s’allument et l’écran suivant apparaît sur l’afficheur : Écran de message à l’allumage ProHeat Firmware Revision X.XX Copyright (c) 2005 − 2015 Miller Electric Mfg. Co. X.XX indique le numéro de révision du micrologiciel installé dans l’appareil. Si la routine de vérification détecte une erreur, la LED de panne du système s’éclaire et un écran de message d’erreur apparaît sur l’afficheur. Lorsque la routine de vérification est achevée avec succès, l’interface opérateur devient par défaut : � La LED indicatrice du bouton Arrêt s’éclaire pour indiquer qu’aucun cycle de chauffage n’est en cours. � Les afficheurs de température indiquent la température réelle des TC (thermocouples). Si aucun thermocouple n’est connecté, les afficheurs indiquent OPEN (OUVERT). � Les LED de commande s’éclairent pour indiquer le nombre de TC de commande dans le dernier programme. � Le voyant correspondant à l’unité de température appropriée (°F ou °C) s’éclaire. � L’écran par défaut de l’afficheur est l’état de marche du dernier programme utilisé et la LED indicatrice du bouton d’état de marche s’éclaire. � Les voyants d’état du système ne s’allument pas si aucune condition de panne ou de limite n’est détectée. OM-271146 Page 43 Après avoir achevé la configuration de la procédure programmée désirée (voir Section 6-4), appuyer sur la touche Marche pour initier un cycle de chauffage. Lors d’un lancement de programme, la LED jaune indicatrice du bouton Marche s’éclaire et la LED bleue indicatrice de chauffage en marche s’allume pour prévenir que la bobine est alimentée. Le cycle continuera jusqu’à la fin du programme ou une pres- sion sur la touche Arrêt . Le système comporte une fonction de maintien qui maintiendra la température ou la durée d’exposition de tout programme commandé par tem- pérature actif. Si on appuie sur la touche Maintien mode marche, l’écran suivant apparaît sur l’afficheur: , la fonction Maintien ne sera activée qu’en mode marche. Si le système n’est pas en Écran de message de maintien Must be running to enter Hold mode De plus, lorsque le système fonctionne en mode manuel, la touche Maintien est inactif. Si on appuie sur la touche Maintien quand le système fonctionne en mode manuel, l’écran suivant apparaît sur l’afficheur : Écran de message de maintien Hold mode not available when temperature control is not active Lorsqu’un programme commandé par la température est activé, la touche Maintien active la fonction maintien. En mode maintien, les paramètres du programme en cours peuvent être modifiés. Le cycle continue après avoir appuyé sur la touche Marche . Le changement des paramètres du programme pendant le maintien n’affecte pas le programme original. Les paramètres d’origine sont maintenus pour le cycle de chauffage suivant. Pour modifier un programme en mode marche, appuyer sur la touche Maintien et la LED indicatrice jaune s’allumera, tandis que la LED jaune indicatrice de la touche Marche s’éteindra. En mode maintien, le système conservera la température réelle du thermocouple le plus chaud pendant que le programme est modifié. � Appuyer sur la touche Programme et la LED indicatrice jaune s’allume. L’afficheur change pour indiquer le mode actuel de fonctionnement ou le segment en cours d’un programme personnalisé. � Utiliser la touche Curseur � Appuyer sur la touche Augmenter OM-271146 Page 44 pour déplacer le curseur sur le paramètre à modifier. ou Diminuer pour effectuer les modifications désirées. � Appuyer sur la touche Marche pour reprendre le fonctionnement du programme, ce qui allumera la LED indicatrice jaune et coupe- ra celle de la touche Maintien . Tous les paramètres des programmes (températures, vitesses, durées ou nombre de TC) peuvent être modifiés en mode maintien. Dans un programme personnalisé, les numéros des segments peuvent être modifiés, mais si un segment a déjà été exécuté dans un programme, la modification dans ce segment n’affectera pas la fonction du programme. � Appuyer sur la touche Arrêt pour terminer le programme. H. Caractéristiques de fonctionnement du système La source d’alimentation fournit une sortie de courant alternatif à haute fréquence qui alimente la bobine pour créer un champ magnétique utilisé pour chauffer la pièce. Les caractéristiques de sortie de la source d’alimentation sont fonction de la configuration, du type et du nombre de bobines utilisées comme l’indique le tableau suivant: Tableau 6-1. Caractéristiques de sortie de la source d’alimentation Type de sortie Intensité maximale Tension maximale Plage de fréquence 700 V 5 − 25,7 kHz Voir Remarque 1 700 V 25,7 − 30 kHz 350 A 700 V 5 − 20 kHz Voir Remarque 2 700 V 20 − 30 kHz 350A par sortie/700A au total 700 V 5 − 20 kHz Voir Remarque 2 700 V 20 − 30 kHz 250A par sortie pendant 15 minutes. Au bout de 15 minutes, la puissance Refroidi par air simple et double décroît pour limiter le courant à 150 ampères par sortie pour la suite de l’opération. Refroidi par liquide simple Refroidi par liquide double 300 1: dans la plage de fréquence 25,7 à 30kHz, l’inten� Remarque sité de sortie maximale décroît linéairement de 250 à 175 am- Sortie refroidie par air Intensité maximale par sortie 250 pères par sortie. Indépendamment de la fréquence, après 15 minutes la sortie maximale est réduite à 150 ampères par sortie. 200 150 100 50 0 5 Fréquence (KHz) 25.7 30 OM-271146 Page 45 400 Sortie refroidie par liquide 2: dans la plage de fréquence 20 à 30kHz, la sortie � Remarque maximale décroît linéairement de 350 à 175 ampères par Intensité maximale par sortie 350 sortie. 300 250 200 150 100 50 0 5 Fréquence (KHz) 20 30 Tableau 6-2. Caractéristiques de puissance de la bobine d’induction Configuration Intensité maximale 1 bobine d’induction 300 A 2 bobines d’induction 300 A par bobine La puissance maximale du système étant de 35 kW, la puissance de chaque bobine sera d’environ 17,5 kW, soit une intensité inférieure à 300 A Puissance de sortie max. vs Durée de chauffe La bobine d’induction peut fonctionner en mode Manual (manuel), en mode Temp (température) seulement ou en Mode Temp (température) avec détection des déplacements. Avec une puissance initiale de 0 kW 35.0 Le mode Manual (manuel) fournit une puissance de sortie maximale telle que définie sur l’écran 1 de Configuration du système, au début du cycle. 30.0 25.0 KW 20.0 Au-dessus de 38hsCPM 15.0 En-dessous de 38hsCPM, ou pas 10.0 Détection des déplacements 5.0 0.0 00:00 01:00 02:00 03:00 04:00 Minutes 05:00 06:00 07:00 08:00 Le mode Temp (température) fournit une puissance de sortie à partir de la valeur de puissance initiale RI telle que définie sur l’écran 1 de Configuration du système, au début du cycle. Les courbes de l’illustration augmentent comme indiqué, directement à partir de la valeur de puissance initiale RI. Pour éviter une surchauffe de la pièce, la puissance nominale de sortie est limitée aux vitesses de déplacement inférieures à 38 cm/min. ou lorsqu’ aucune détection des déplacements n’est activée. Quand la détection des déplacements est activée et que les vitesses de déplacement sont supérieures à 38 cm/min., la puissance nominale de sortie est augmentée. Dans les deux cas, la puissance de sortie maximale est limitée à 300 ampères par sortie, ce qui représente environ 20 kW avec une bobine d’induction et 35 kW avec deux bobines d’induction. Ce graphique illustre la vitesse à laquelle la puissance de sortie augmente avec la durée de chauffe. OM-271146 Page 46 Puissance de sortie max. vs Vitesse de déplacement Détection des déplacements activée, la puissance de sortie maximale est déterminée par la vitesse de déplacement, comme illustré. (Pour le mode de commande Temp ou Manual avec détection des déplacements) 35 30 Puis. max. 25 Puis. max. 20 15 10 5 0 0 5 10 15 20 25 30 Vitesse de déplacement (en IPM) OM-271146 Page 47 SECTION 7 – MAINTENANCE & DÉPANNAGE 7-1. Maintenance de routine Débrancher l’alimentation avant d’effectuer des travaux d’entretien. � Effectuer des entretiens plus fréquents s’il est utilisé dans des conditions de service rigoureuses. Tous les jours Calendrier de maintenance Câbles et cordons Prise de fil de protection d'isolement Effectuez un examen visuel de l'état des cordons et câbles. Remplacer cordons et câbles endommagés. Tous les 3 mois Tous les 6 mois Tous les 12 mois � Nettoyer prises en fil de protection d'isolement. � Voir Sections 4-9 et 4-14. Étiquettes Interface opérateur la couche Contacts du connecteur de sortie Fiche de protection Vérifier et remplacer les étiquettes est endommagé. � Nettoyer interface opérateur la couche. � Voir Sections 4-9 et 4-14. Nettoyer contacts du connecteur de sortie. � Voir Sections 4-9 et 4-14. Contrôler intégrité de la fiche de protection. Les remplacer si endommagés. � Voir Sections 4-9 et 4-14. Intérieur du poste Nettoyer intérieur du poste. � Vérifier l’étalonnage de l’unité � Calibrage Voir Sections 7-2 et 7-3. * Travail à confier à un agent d’entretien agréé par l'usine. OM-271146 Page 48 7-2. Équipement de vérification de l’étalonnage 2 1 Équipement l’étalonnage de vérification 3 4 de câbles, connecter le rouge au négatif et le jaune au positif. 1 Calibreur de thermocouple 3 Connecteur mâle 2 broches de type K Calibreur recommandé : Fluke 714 ou équivalent. Connecteur recommandé : Omega Engineering OST-K-M ou équivalent. 2 Mini−connecteur de type K Connecteur recommandé : Fluke 80CK −M ou équivalent. Une longueur de fil de thermocouple de type K est requise. Pour connecter avec des 7-3. 4 Étiquette d’étalonnage Étiquette recommandée QCC306BU ou équivalent. 6 5 : Q −CEES Voltmètres recommandés : multimètre Agilent ou multimètre Hewlett Packard modèle 34401A ou équivalent. Le voltmètre numérique de précision doit pouvoir lire au millième près (0,000). 6 Câble d’interconnexion MILLER Réf. 300168 peut servir à connecter l’Enregistreur à l’alimentation électrique DC. 5 Voltmètre numérique de précision Procédure de vérification de l’étalonnage L’étalonnage devrait être vérifié tous les ans. Utiliser le Certificat d’étalonnage adéquat pour enregistrer les données de l’étalonnage. Une feuille de calcul peut également être utilisée pour enregistrer les données. A. Configuration d’origine 1 2 3 4 5 6 7 8 9 Couper le courant d’alimentation. Faire appel à un technicien qualifié pour connecter l’alimentation primaire au ProHeat 35. Mettre ProHeat 35 sous tension. Appuyer de manière prolongée sur la touche Programme puis appuyer sur Paramètres pour entrer dans le mode de configuration. Appuyer sur la touche Curseur 4 fois pour arriver à la ligne Control Mode. Appuyer sur la touche Diminuer pour passer au mode Manuel, si besoin est. Appuyer sur la touche État de marche. (TC5 et TC6 s’affichent en haut à droite de l’écran.) Laisser l’unité tourner pendant au moins 15 minutes avant de vérifier l’étalonnage. Allumer le calibreur de thermocouple Fluke 714 et le voltmètre numérique de précision. Attendre au moins 15 minutes avant de vérifier l’étalonnage. 10 Vérifiez que TC1 et TC2 sont réglés sur Type K. Voir la Section 6-4 pour des instructions détaillées. B. Vérifier TC Entrée/Sortie 1 Connecter le voltmètre numérique de précision (la tension DC s’affiche au millième près) à RC9, le connecteur supérieur qui se trouve à l’arrière du ProHeat 35. Le fil rouge est branché à la broche 1 et le noir à la broche 5. 2 Régler le calibreur de TC à 382,0 °F ou 194,5 °C et le connecter à l’entrée TC1 à l’avant du ProHeat. 3 Vérifier que la valeur TC affichée est (±3°F) ou (±2°C). La sortie RC9 a une marge de tolérance de (±6°F) ou (±3.3°C). Le voltmètre numérique doit afficher 2,787 Vdc (± 0,038) (2,749 − 2,825). 4 Annoter les valeurs du voltmètre numérique sur le certificat d’étalonnage. Si une feuille de calcul est utilisée, utiliser le calcul suivant. Le calcul de la tension par rapport à la température est le suivant: (Tension sortie DC x 155) − 50 = °F (Tension sortie DC x 86,1) − 45,4 = °C 5 Répéter les étapes 1.−4. pour les entrées TC2 − TC6. Pour l’entrée TC2, brancher le fil rouge du voltmètre numérique de précision sur la broche 2 du RC9. Pour l’entrée TC3, brancher le fil rouge du voltmètre numérique de précision sur la broche 3 du RC9. Pour l’entrée TC4, brancher le fil rouge du voltmètre numérique de précision sur la broche 4 du RC9. Pour l’entrée TC5, brancher le fil rouge du voltmètre numérique de précision sur la broche 6 du RC9. Pour l’entrée TC6, brancher le fil rouge du voltmètre numérique de précision sur la broche 7 du RC9. � TC5 et TC6 s’affichent en haut à droite de l’écran. 6 Répéter les étapes 1.−5. avec le calibreur de TC réglé sur 882,0 °F ou 472,2 °C, vérifier que la valeur de TC affichée est bien (±3°F) ou (± 2° C). La sortie RC9 a une marge de tolérance de (± 6°F) ou (± 3,3°C). Le voltmètre numérique indique 6,013 Vdc (± 0,038) (5,975 − 6,041). OM-271146 Page 49 7 Répéter les étapes 1.−5. avec le calibreur de TC réglé sur 1382,0 °F ou 750 °C, vérifier que la valeur de TC affichée est bien (± 3°F) ou (± 2° C). La sortie RC9 a une marge de tolérance de (± 6°F) ou (± 3.3°C). Le voltmètre numérique indique 9,239 Vdc (± 0,038) (9,201 − 9,277). C. Procédure de finition 1 Si le Mode de commande Température était sélectionnée pour le ProHeat 35, suivre les étapes 7-3-1, les étapes 4.−6. pour le remettre sur Température. 2 Mettre le ProHeat 35 hors tension. 3 Faire appel à un technicien qualifié pour déconnecter l’alimentation primaire. 4 Retirer le voltmètre numérique de précision et le calibreur de TC. 5 Remplir l’étiquette d’étalonnage et l’apposer directement sur l’unité, au−dessus de l’écran TC1. Nº ID. (numéro de série de la carte TC) Vérifier que le numéro de série correspond à la carte de la machine. Par (vos initiales) Date (la date d’aujourd’hui) Prochain étalonnage (date actuelle plus 1 an) 6 Imprimer une copie du certificat à envoyer avec le ProHeat 35. 7 Si les données sont saisies dans une feuille de calcul, enregistrer les données. OM-271146 Page 50 Calibration Date: Re−Calibration Date: A−232171−C 09/09/16 Calibrated Multimeter: Thermocouple Calibrator: Instrumentation Used: CHANNEL 1 CHANNEL 2 CHANNEL 3 CHANNEL 4 CHANNEL 5 CHANNEL 6 PRIMARY STANDARD 382 (°F) Voltage Equivalent Out (V) Temp (°F) PRIMARY STANDARD 1382 (°F) Voltage Equivalent Out (V) Temp (°F) Serial Number: Serial Number: PRIMARY STANDARD 882 (°F) Voltage Equivalent Out (V) Temp (°F) does hereby certify the above instrument was calibrated against standards Company name and meets or exceeds all published specifications. maintained by Company name The accuracy of these standards is directly traceable to the National Institute of Standards and Technology. TCI Serial Number: Certified by: CERTIFICATE OF CALIBRATION VERIFICATION Com pany Nam e Street PO Box City, State, Zip Code D. OM-271146 Page 51 OM-271146 Page 52 Calibration Date: Re−Calibration Date: A−232171−C 09/09/16 Calibrated Multimeter: Thermocouple Calibrator: Instrumentation Used: CHANNEL 1 CHANNEL 2 CHANNEL 3 CHANNEL 4 CHANNEL 5 CHANNEL 6 PRIMARY STANDARD 382 (°F) Voltage Equivalent Out (V) Temp (°F) PRIMARY STANDARD 1382 (°F) Voltage Equivalent Out (V) Temp (°F) Serial Number: Serial Number: PRIMARY STANDARD 882 (°F) Voltage Equivalent Out (V) Temp (°F) does hereby certify the above instrument was calibrated against standards Company name and meets or exceeds all published specifications. maintained by Company name The accuracy of these standards is directly traceable to the National Institute of Standards and Technology. TCI Serial Number: Certified by: CERTIFICATE OF CALIBRATION VERIFICATION Com pany Nam e Street PO Box City, State, Zip Code E. 7-4. Servicing Hazards Les symboles représentés ci-dessous sont utilisés dans ce manuel pour attirer l’attention et identifier les dangers possibles. En présence de ce symbole, prendre garde et suivre les instructions afférentes pour éviter tout risque. L’installation, l’utilisation, l’entretien et les réparations ne doivent être confiés qu’à des personnes qualifiées. Une personne qualifiée est définie comme celle qui, par la possession d’un diplôme reconnu, d’un certificat ou d’un statut professionnel, ou qui, par une connaissance, une formation et une expérience approfondies, a démontré avec succès sa capacité à résoudre les problèmes liés à la tâche, le travail ou le projet et a reçu une formation en sécurité afin de reconnaître et d’éviter les risques inhérents. Pendant les interventions, éloigner toutes les personnes, en particulier les enfants. A. UN CHOC ELECTRIQUE peut tuer. � Ne pas toucher des pièces électriques sous tension. � Couper l’alimentation de induction du dévidoir puis débrancher et verrouiller l’interrupteur de coupure, les coupe-circuits ou retirer la prise ou arrêter le moteur avant d’intervenir sauf si la procédure exige un appareil sous tension. � Ne travaillez pas sur l'équipement avant d'avoir vérifié que le boîtier de la machine n'est pas alimenté. � S’isoler de la terre en se tenant ou en travaillant sur des tapis isolants secs assez grands pour éviter tout contact avec le sol. � Ne pas laisser le poste sous tension sans surveillance. � Si la procédure utilisée nécessite que le poste soit sous tension, ne laisser intervenir que du personnel connaissant et respectant les pratiques de sécurité standard. � Lors du test d’un poste sous tension, n’utiliser que la méthode d’une seule main. Ne pas mettre les deux mains à l’intérieur du poste. Conserver toujours une main à l’extérieur. � Débrancher les conducteurs d’alimentation de la ligne coupée AVANT de déplacer un source d’alimentation de chauffage par induction. Il reste une TENSION DC NON NÉGLIGEABLE dans les sources de soudage onduleur après la mise hors tension de l’alimentation électrique. � Éteignez l'unité, débranchez le courant électrique, et déchargez les condensateurs d’alimentation selon les instructions indiquées dans le manuel avant de toucher les pièces. B. LES CHARGES ÉLECTROSTATIQUES peuvent endommager les circuits imprimés. � Établir la connexion avec la barrette de terre AVANT de manipuler des cartes ou des pièces. � Utiliser des pochettes et des boîtes antistatiques pour stocker, déplacer ou expédier des cartes de circuits imprimes. C. Risque D’INCENDIE OU D’EXPLOSION. � Ne pas placer l’appareil sur, au-dessus ou à proximité de surfaces inflammables. � Ne pas intervenir sur l’appareil à proximité de substances inflammables. OM-271146 Page 53 D. UN ARC ÉLECTRIQUE peut être mortel. Un arc électrique est une décharge rapide et violente d'énergie qui se produit lorsqu'un courant électrique quitte son chemin prévu et saute sur d'autres conducteurs ou sur la masse. Un arc peut être causé par une défaillance électrique (isolation défectueuse, corrosion, poussière), une mauvaise installation, une erreur humaine (disposition inappropriée des outils) et autres facteurs. Les vapeurs conductrices peuvent entretenir l'arc jusqu'à ce que les dispositifs de surintensité ouvrent le circuit. Les personnes dans la portée d'un coup d'arc sont en danger. � Ne pas intervenir sur un équipement sous tension à moins qu'une évaluation des risques de coup d'arc à partir d'un circuit d'alimentation ait été faite par une personne qualifiée et qu'une formation aux pratiques de travail sécuritaires ait été offerte par l'employeur. � Suivre les exigences de la norme NFPA 70E en matière de pratiques de travail sécuritaires et d'équipement de protection individuelle (ÉPI). E. LA PROJECTION DE MÉTAL OU DE SALETÉ peut blesser les yeux. � Porter des lunettes de sécurité avec protections latérales ou un écran facial pour intervenir. � Faire attention à ne pas mettre d’outils, de pièces ou de fils en court-circuit pendant les tests ou l’intervention. F. LE CHAUFFAGE PAR INDUCTION peut provoquer des brûlures. � Ne pas toucher des parties chaudes à mains nues. � Laisser refroidir les composants ou équipements avant de les manipuler. � Ne pas toucher ou manipuler la tête/l’enroulement à induction pendant le fonctionnement. � Tenir les bijoux et autres objets personnels en métal éloignés de la tête/de l’enroulement pendant le fonctionnement. � Ne pas toucher aux pièces chaudes, utiliser les outils recommandés et porter des gants de soudage et des vêtements épais pour éviter les brûlures. G. DES ORGANES QUI EXPLOSENT peuvent provoquer des blessures. � Lors de la mise sous tension des onduleurs, certaines pièces défectueuses peuvent exploser ou provoquer l’explosion d’autres pièces. � Porter toujours un écran facial et des manches longues pour intervenir sur les onduleurs. H. RISQUE D’ÉLECTROCUTION pendant les tests. � Couper l'alimentation la source d’alimentation de chauffage par induction avant de raccorder ou de modifier les raccordements des fils de mesure. � Utiliser au moins un fil de mesure équipé d’un raccordement à ressort comme une pince crocodile. � Lire les instructions des équipements de test. OM-271146 Page 54 I. LA CHUTE DE L’ÉQUIPEMENT peut provoquer des blessures. � Utiliser l’anneau de levage uniquement pour soulever l’appareil, NON PAS les organes de roulement, les bouteilles de gaz ou tout autre accessoire. � Utilisez les procédures correctes et des équipements d’une capacité appropriée pour soulever et supporter l’appareil. � En utilisant des fourches de levage pour déplacer l’unité, s’assurer que les fourches sont suffisamment longues pour dépasser du côté opposé de l’appareil. � Suivre les consignes du Manuel des applications pour l’équation de levage NIOSH révisée (Publication Nº94–110) lors du levage manuelle de pièces ou équipements lourds. J. Les PIÈCES MOBILES peuvent provoquer des blessures. � Rester à l’écart des organes mobiles comme le ventilateur. � Seules des personnes qualifiées sont autorisées à enlever les portes, panneaux, recouvrements ou dispositifs de protection pour effectuer, s’il y a lieu, des travaux d’entretien et de dépannage. � Ne pas approcher les mains, cheveux, vêtements lâches et outils des organes mobiles. � Remettre les portes, panneaux, recouvrements ou dispositifs de protection quand l’entretien est terminé et avant de rebrancher l’alimentation électrique. K. Les CHAMPS ÉLECTROMAGNÉTIQUES (CEM) peuvent affecter les implants médicaux. � Les porteurs de stimulateurs cardiaques et autres implants médicaux doivent rester à distance des zones d’intervention tant qu’ils n’ont pas consulté leur médecin. L. L’EMPLOI EXCESSIF peut SURCHAUFFER L’ÉQUIPEMENT. � Prévoir une période de refroidissement, respecter le cycle opératoire nominal. � Réduire le courant ou le cycle opératoire avant de utiliser les appareils de chauffage par induction. � Ne pas obstruer les passages d’air du poste. OM-271146 Page 55 M. LE RAYONNEMENT HAUTE FRÉQUENCE (H.F.) risque de provoquer des interférences. � Le rayonnement haute fréquence (H.F.) peut provoquer des interférences avec les équipements de radio-navigation et de communication, les services de sécurité et les ordinateurs. � Demander seulement à des personnes qualifiées familiarisées avec des équipements électroniques de faire fonctionner l’installation. � L’utilisateur est tenu de faire corriger rapidement par un électricien qualifié les interférences résultant de l’installation. � Si le FCC signale des interférences, arrêter immédiatement l’appareil. � Effectuer régulièrement le contrôle et l’entretien de l’installation. � Maintenir soigneusement fermés les portes et les panneaux des sources de haute fréquence, maintenir les éclateurs à une distance correcte et utiliser une terre et un blindage pour réduire les interférences éventuelles. N. LIRE LES INSTRUCTIONS. � Utiliser le livret des tests (réf. 150 853) lors des interventions sur ce poste. � Consulter les précautions de sécurité de soudage dans le manuel d’utilisation. � Utiliser exclusivement les pièces de rechange du fabricant. � Lire avec attention et appliquer les instructions sur les étiquettes et le Manuel Technique avant toute installation, utilisation ou entretien de l’unité. Lire les informations de sécurité au début du manuel et dans chaque section. � Effectuer l’installation, la maintenance et l’entretien conformément aux le manuel technique, aux normes de l’industrie et aux codes nationaux, provinciaux et locaux. OM-271146 Page 56 SECTION 8 – DIAGNOSTIC ET DÉTECTION DES PANNES La source d’alimentation ProHeat 35 comporte des fonctionnalités intégrées de détection des pannes qui pourraient se produire pendant le fonctionnement. Ces fonctionnalités sont représentées par la LED de panne, la LED de limite et les écrans de message apparaissant sur l’afficheur LCD du panneau avant. 8-1. Indicateurs opérateur à distance 1 2 3 803995-B 1 LED de panne 2 LED de limite 3 Afficheur LCD 4 x 40 La LED s’allume pour indiquer une condition de panne du système. La LED s’allume pour indiquer une condition limite du système. Affiche la programmation, l’état de fonctionnement, les paramètres, les conditions de panne et de limite et le guide de détection des pannes. 8-2. Conditions de limites Une condition de limite indique que le système a rencontré un thermocouple ouvert ou qu’il est hors de la plage des conditions ou paramètres de fonctionnement optimaux. Si une condition de limite se produit pendant le fonctionnement, la LED jaune de limite clignote pour indiquer un problème. Si l’afficheur LCD représente l’écran État ou Paramètres, un message décrivant la condition de limite concernée sera affiché. Si l’é- cran actif est Programme, appuyer sur la touche Run Status pour afficher la condition de limite. Dans une condition de limite, la source d’alimentation continue à fournir une puissance de sortie, mais la réduit pour se protéger des dommages. Cette situation donne le temps de déterminer la meilleure action pour corriger le problème décrit par le message de limite sur l’afficheur LCD. Deux options sont possibles lorsqu’une condition de limite se produit : � Valider la limite et continuer l’opération. � Arrêter l’opération pour corriger le problème à l’origine de la limite. OM-271146 Page 57 permet de vailder la limite et de continuer l’opération avec le paramétrage existant. Lorsqu’on valide l’état, la LED La touche Diminuer jaune de limite arrêt de clignoter et reste allumée en permanence. L’afficheur LCD retourne à l’écran actif dès que la touche Programme kW A V Hz , Run Status ou Paramètres sont enfoncés. Si une nouvelle condition de limite se produit après la reconnaissance de la première, la LED jaune de limite recommence à clignoter pour indi- quer un nouveau problème. Pour afficher la condition de limite, appuyer sur la touche Run Status le nouveau message de limite et le précédent. pour afficher un message décrivant Pour obtenir des informations supplémentaires à propos de la condition de limite et des suggestions de solutions, appuyer sur la touche Aug- menter pour afficher les solutions possibles en fonction du type de condition de limite. Si l’opérateur détermine que la meilleure solution est d’arrêter l’opération et de proposer les modifications à la configuration pour éliminer la condition de limite, appuyer sur la touche Arrêt . Après avoir effectué les modifications de configuration, appuyer sur la touche Marche OM-271146 Page 58 pour redémarrer le processus. 8-3. Codes des conditions de limite Condition de limite L01: Thermocouple n°1 ouvert Informations complémentaires Vérifier que les sondes de température ne sont pas ouvertes et réparer Passer à la sonde de température de secours L02: Thermocouple n°2 ouvert Vérifier que les sondes de température ne sont pas ouvertes et réparer Passer à la sonde de température de secours L03: Thermocouple n°3 ouvert Vérifier que les sondes de température ne sont pas ouvertes et réparer Passer à la sonde de température de secours L04: Thermocouple n°4 ouvert Vérifier que les sondes de température ne sont pas ouvertes et réparer Passer à la sonde de température de secours L05: Thermocouple n°5 ouvert Vérifier que les sondes de température ne sont pas ouvertes et réparer Passer à la sonde de température de secours L06: Thermocouple n°6 ouvert Vérifier que les sondes de température ne sont pas ouvertes et réparer Passer à la sonde de température de secours L07: Limite de la tension de sortie Resserrer la couverture isolante autour de la surface du tube. Raccourcir le câble d’extension. Augmenter le nombre de spires. L08: Limite de la tension de sortie Augmenter l’espace de la bobine. Raccourcir le câble d’extension. Augmenter l’épaisseur d’isolation. L09: Limite du courant de sortie Resserrer la couverture isolante autour de la surface du tube Augmenter le nombre de spires. L10: Limite du courant de sortie Augmenter l’espace de la bobine. Resserrer le câble sur l’isolant. Contrôler la circulation et le niveau de réfrigérant. L11: Limite de surchauffe du réfrigérant Nettoyer les filtres du réfrigérant et l’échangeur thermique. Augmenter le nombre de spires. Vérifier l’épaisseur d’isolation appropriée. L12: Limite de surchauffe de la source d’alimentation S’assurer que les grilles de ventilation ne sont pas obstruées. Nettoyer les dissipateurs thermiques du tunnel de refroidissement. S’assurer que les connexions de sortie ne sont pas desserrées/ouvertes. L13: Connexion des câbles Vérifier que tous les câbles de sortie sont du même type. Vérifier la connexion de la prise d’admission. Vérifiez l’identification des câbles 1 et 2 sur l’écran de diagnostic DIAG1. L14 : Limite de température d’accessoire – L15 : vitesse de déplacement faible – OM-271146 Page 59 8-4. Description et tableaux de dépannage des codes d’erreur Message sur afficheur LED Type de message Message sur afficheur LCD Message de solution LCD Message du journal d’erreurs LCD ERR COMMS ERROR Internal comm loss: AC lost Cooler (Perte de communication interne : ACM avec le refroidisseur) Press button to clear error (Appuyer sur le bouton pour effacer l’erreur) ACM lost comms from Cooler (L’ACM a perdu la communication avec le refroidisseur) ERR COOLER ERROR Cooler peripheral malfunction (Dysfonctionnement du périphérique du refroidisseur) Cycle power on the power source (Éteindre puis rallumer le poste de soudage). Cooler USART Error (Erreur USART du refroidisseur) ERR COMMS ERROR Internal comm loss: Refroidisseur lost CA (Perte de communication interne : refroidisseur avec l’ACM) Press button to clear error (Appuyer sur le bouton pour effacer l’erreur) Cooler lost comms from ACM (Le refroidisseur a perdu la communication avec l’ACM) ERR COOLSTAL ERROR Cooler Motor Stalled (Moteur du refroidisseur bloqué) Press button to clear error (Appuyer sur le bouton pour effacer l’erreur) Cooler Motor Stalled (Moteur du refroidisseur bloqué) ERR COOLOPEN ERROR Cooler Thermistor Open (Thermistance du refroidisseur ouverte) Press button to clear error (Appuyer sur le bouton pour effacer l’erreur) Cooler Thermistor Open (Thermistance du refroidisseur ouverte) ERR COOLSHRT ERROR Cooler Thermistor Shorted (Thermistance du refroidisseur courtcircuitée) Press button to clear error (Appuyer sur le bouton pour effacer l’erreur) Cooler Thermistor Shorted (Thermistance du refroidisseur courtcircuitée) ERR COOLTEMP ERROR Cooler Over Temperature (Surchauffe du refroidisseur) Press button to clear error (Appuyer sur le bouton pour effacer l’erreur) Cooler Over Temperature (Surchauffe du refroidisseur) ERR COOLFLOW ERROR Cooler Low Flow (Bas débit du refroidisseur) Press button to clear error (Appuyer sur le bouton pour effacer l’erreur) Cooler Low Flow (Bas débit du refroidisseur) 8-5. Tableau de dépannage Panne Le système de refroidissement ne fonctionne pas. Solution S'assurer que l'alimentation du refroidisseur et les câbles de communication depuis l'alimentation sont connectés aux prises du refroidisseur. Contrôler les fusibles d’alimentation ou le disjoncteur, et remplacer ou réarmer, si nécessaire. Demander à un agent d'entretien agréé par l'usine de contrôler le moteur. Pas d'écoulement ou écoulement réduit du liquide de refroidissement. Ajouter du liquide de refoidissement. S'assurer que les tuyaux ou le filtre du liquide de refroidissement ne sont pas obstrués. Nettoyer le filtre ou nettoyer/remplacer les tuyaux si nécessaire. Débrancher la pompe et s’assurer que l’accouplement n’est pas cisaillé. Remplacer l’accouplement, si nécessaire. OM-271146 Page 60 Notes SECTION 9 – SCHEMA ELECTRIQUE Figure 9-1. Schema electrique OM-271146 Page 62 271167-D OM-271146 Page 63 Notes Entrée en vigueur le 1 janvier 2024 (Equipement portant le numéro de série précédé de “NE” ou plus récent) Cette garantie limitée remplace toutes les garanties antérieures de MILLER et exclut toutes les autres garanties expresses ou implicites. GARANTIE LIMITEE - En vertu des conditions générales mentionnées ci-après, Miller Electric Mfg. LLC, Appleton, Wisconsin, garantit aux distributeurs agréés que le nouvel équipement Miller vendu après la date d'entrée en vigueur de cette garantie limitée est libre de tout vice de matériau et de main-d'œuvre au moment de son expédition par Miller. CETTE GARANTIE REMPLACE EXPRESSEMENT TOUTES LES AUTRES GARANTIES EXPRESSES OU IMPLICITES, Y COMPRIS LES GARANTIES DE QUALITE LOYALE ET MARCHANDE ET D'APTITUDE. Au cours des périodes de garantie indiquées ciaprès MILLER s'engage à réparer ou à remplacer tous les composants et pièces défectueuses sous garantie résultant de tels vices de matériau et de main-d'œuvre. Des notifications envoyées en tant que réclamations au titre de la garantie en ligne doivent fournir des descriptions détaillées de la défaillance et des étapes de dépannage mises en œuvre pour déterminer lesdites parties défaillantes. Toutes réclamations au titre de la garantie manquant les informations requises comme il est stipulé dans le Manuel de l'utilisation des services Miller (SOG) pourraient être refusées par Miller. Miller s'engage à répondre aux réclamations au titre de la garantie concernant du matériel éligible énuméré ci-dessous en cas de survenance d'une défaillance de ce genre au cours de ces périodes de garantie répertoriées ci-dessous. La période de garantie commence à courir à partir de la date de livraison de l'équipement à l'acheteur final. 1 Pièces 5 ans — Main-d'œuvre 3 ans � Redresseurs de puissance d'origine, uniquement thyristors, diodes et modules redresseurs discrets en produit non onduler 2 Pièces 4 ans (pas de garantie main-d'œuvre) � Verres de casque ClearLight 2.0 à obscurcissement automatique 3 3 ans — Pièces et main-d'œuvre, sauf spécification � Cellules de casque à teinte automatique (Aucune main d'œuvre) � Systèmes de soudage collaboratifs Copilot � Générateurs/Groupe autonome de soudage (y compris EnPak) (REMARQUE : Moteurs garantis par le fabriquant.) � Sources d’alimentation de laser portable � Produits Insight Welding Intelligence (À l'exception des capteurs externes) � Sources onduleurs � Sources de découpage plasma � Contrôleur de procédé � Dévidoirs semi-automatiques et automatiques � Transformateur/redresseur de puissance 4 2 ans — Pièces et main-d'œuvre � Masques de soudage autoassombrissants (pas de garantie main-d'œuvre) � Extracteurs de fumées - Filtair 215, Séries Capture 5 et Industrial Collector. 5 1 an — Pièces et main-d'œuvre, sauf spécification � Réchauffeur ArcReach � Systèmes de soudage AugmentedArc, LiveArc, et MobileArc � Dispositifs de déplacements automatiques � Pistolets de soudage MIG Bernard BTB refroidis par air (pas de garantie main-d'œuvre) � CoolBelt, Groupe ventilateur de PAPR, écran facial de PAPR (pas de garantie main-d'œuvre) � Sécheur d'air au dessicant � Options non montées en usine (REMARQUE: Ces options sont couvertes pour la durée résiduelle de la garantie de l'équipement sur lequel elles sont installées ou pour une période minimum d'un an -, la période la plus grande étant retenue.) � Commandes au pied RFCS (sauf RFCS-RJ45) � Extracteurs de fumée – Filtair 130, séries MWX et SWX, bras d’aspiration et boîtier de contrôle moteur standard, téléscopiques et ZoneFlow � Torches laser portables (pas de garantie maind'œuvre) � Unités HF � Sources de chauffage par induction, refroidisseurs (REMARQUE : Les enregistreurs numériques sont garantis séparément par le fabricant.) � Capteurs de Insight � Casque de soudage laser (pas de garantie maind'œuvre) � Bancs de charge � Pistolets MDX Series MIG (pas de garantie maind'œuvre) � Moteur de torche Push-pull � Positionneurs et contrôleurs � Racks (Pour loger plusieurs sources d'alimentation) � Organes de roulement/remorques � Pistolets à bobine Spoolmate (pas de garantie maind'œuvre) � Ensembles d'entraînement de fil Subarc � Boîtier et panneaux pour Respirateur à adduction dáir (SAR) � Torches TIG (pas de garantie main-d'œuvre) � Torches Tregaskiss (pas de main-d'oeuvre) � Systèmes de refroidissement par eau � Télécommandes sans fil et récepteurs � Postes de travail/Tables de soudage (pas de garantie main-d'œuvre) � Torches de découpe au plasma XT (pas de garantie main-d'œuvre) 6 6 mois — Pièces � Batteries de type automobile de 12 volts 7 90 jours — Pièces � Kits d'accessoires � Enrouleur automatique et câbles refroidis par air pour réchauffeur ArcReach � Bâches � Enroulements et couvertures, câbles et commandes non électroniques de chauffage par induction � Torches M � Pistolets MIG, torches de soudage à l'arc submergé (SAW) et têtes de surfaçage externes � Commandes à distance et RFCS-RJ45 � Pièces de rechange (pas de main-d'oeuvre) La garantie limitée True Blue ne s'applique pas aux: ® 1. Consommables tels que tubes contact, têtes de coupe, contacteurs, balais, relais, surfaces de poste de travail et rideaux de soudage ou toute pièce dont le remplacement est nécessaire en raison de l'usure normale. (Exception: les balais et les relais sont garantis sur tous les produits entraînés par moteur.) 2. Articles fournis par MILLER, mais fabriqués par des tiers, tels que des moteurs ou des accessoires du commerce. Ces articles sont couverts par la garantie du fabricant, s'il y a lieu. 3. Équipements modifiés par une partie autre que MILLER, ou équipements dont l'installation, le fonctionnement n'ont pas été conformes ou qui ont été utilisés de manière abusive par rapport aux normes industrielles, ou équipements n'ayant pas reçu un entretien nécessaire et raisonnable, ou équipements utilisés pour des besoins sans rapport avec les spécifications du matériel. 4. Défauts causés par un accident, une réparation non autorisée ou un test inadéquat. LES PRODUITS MILLER SONT DESTINÉS À DES UTILISATEURS DU COMMERCE ET DE L'INDUSTRIE FORMÉS ET EXPÉRIMENTÉS DANS L'UTILISATION ET L'ENTRETIEN DE MATÉRIEL DE SOUDAGE. Les seuls recours possibles en cas de réclamation en lien avec la garantie, au choix de Miller, sont : (1) la réparation ; ou (2) le remplacement ; ou, si approuvé par écrit par Miller, (3) le remboursement du coût approuvé au préalable des réparations ou du remplacement dans un centre de services agréé par Miller ; ou (4) le paiement ou les crédits équivalents au prix d'achat (après soustraction d'un montant raisonnable découlant de l'utilisation du produit). Les produits ne peuvent être renvoyés à Miller sans son autorisation écrite. Les expéditions de retour des produits sont à la charge et aux risques du client. Les recours ci-dessus seront mis à disposition à Appleton, WI (États-Unis) ou dans un centre de services agréé par Miller. Le transport et l'expédition seront sous la responsabilité du client. DANS LA MESURE OÙ CELA EST AUTORISÉ PAR LA LOI, LES RECOURS PRÉVUS DANS LES PRÉSENTES SONT LES SEULS ET UNIQUES RECOURS POSSIBLES, QUELLE QUE SOIT LA DOCTRINE JURIDIQUE ENVISAGÉE. EN AUCUN CAS MILLER NE SERA TENU RESPONSABLE POUR DES DOMMAGES DIRECTS, INDIRECTS, SPÉCIAUX, ACCESSOIRES OU CONSÉCUTIFS (COMPRENANT LA PERTE DE BÉNÉFICE), QUELLE QUE SOIT LA DOCTRINE JURIDIQUE ENVISAGÉE. MILLER NE RECONNAÎT AUCUNE GARANTIE NON EXPRESSÉMENT CITÉE DANS LES PRÉSENTES NI GARANTIE IMPLICITE, Y COMPRIS CELLE DE QUALITÉ MARCHANDE OU D'APTITUDE À UN USAGE PARTICULIER. Certains états aux U.S.A. n'autorisent pas de limitations dans la durée de la garantie, ou l'exclusion de dommages accessoire, indirect, particulier ou conséquent, de sorte que la limitation ou l'exclusion précitée ne s'applique pas dans votre cas. Cette garantie prévoit des droits légaux spécifiques, d'autres droits peuvant exister, mais varier d'un état à l'autre. Au Canada, la législation dans certaines provinces prévoit des garanties ou des remèdes supplémentaires autres que ceux spécifiés dans les présentes, et dans la mesure où ils ne sont pas susceptibles d'annulation, les limitations et les exclusions indiquées ci-dessus ne s'appliquent pas. Cette garantie limitée prévoit des droits légaux spécifiques, d'autres droits peuvant exister, mais varier d'une province à l'autre. Vous avez des questions concernant la garantie ? Pour trouver votre distributeur, appelez le 1–800–4–A-Miller Votre distributeur vous offre également Service Vous obtiendrez toujours la réponse rapide et fiable à laquelle vous vous attendez. La plupart des pièces de rechange pour cous être livrées dans les 24 heures. Assistance Vous avez besoin de réponses rapides à vos questions difficiles relatives à la soudure ? L’expertise de votre distributeur et Miller est là pour vous aider, tout au long du processus. Informations propriétaire Veuillez remplir le formulaire ci-dessous et conservez-le dans vos dossiers. Nom du modèle Date d’achate Numéro de série/style (Date du livraison de l’appareil au client d’origine) Distributeur Adresse Service Communiquez avec votre DISTRIBUTEUR ou CENTRE DE SERVICE. Veuillez toujours préciser le NOM DU MODÈLE et le NUMÉRO DE SÉRIE/STYLE. Communiquez avec votre distributeur pour: Consommable Options et accessoires Équipement de protection personnel Conseil et réparation Pièces détachées Formation Manuels techniques (Maintenance et pièces) Miller Electric Mfg. LLC Schémas électriques An Illinois Tool Works Company 1635 West Spencer Street Appleton, WI 54914 USA Manuels de procédés de soudage Pour trouver un concessionnaire ou un agent de service agréé, se rendre sur www.millerwelds.com ou appeler le 1−800−4−A−Miller. Adressez-vous à l’agent de transport en cas Déposer une réclamation de dommages/intéde: rêts pendant l’expédition. Pour toute aide concernant le dépôt et le réglage de réclamations, adressez-vous à votre distributeur et/ou au Service transport du fabricant du matériel. TRADUCTION DES INSTRUCTIONS ORIGINELLES - IMPRIME AUX USA © Miller Electric Mfg. LLC 2024-08 International Headquarters–USA USA Phone: 920-735-4505 USA & Canada FAX: 920-735-4134 International FAX: 920-735-4125 Pour les sites internationaux, visitez www.MillerWelds.com ">
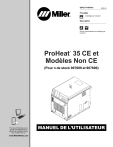
Link pubblico aggiornato
Il link pubblico alla tua chat è stato aggiornato.