Instruções de operação | Cleaver-Brooks Hawk 1000 Boiler Mode d'emploi
PDF
Descarregar
Documento
Hawk 1000 Commande de chaudière Manuel d’utilisation 750-366 07/2013 À L’ATTENTION DE : Propriétaires, opérateurs et/ou personnel d’entretien Ce manuel d’utilisation présente des informations qui aideront à faire fonctionner et entretenir correctement le matériel. Veiller à étudier son contenu avec attention. L’appareil offrira un fonctionnement fiable et durable si les instructions d’exploitation et d’entretien sont respectées comme il se doit. Ne jamais tenter de faire fonctionner l’appareil avoir d’avoir une connaissance approfondie de ses principes de fonctionnement et de tous ses composants. Le propriétaire a la responsabilité de former et de conseiller non seulement son personnel, mais aussi le personnel des entreprises chargées de l’entretien, de la réparation ou de l’exploitation de l’équipement, sur tous les aspects qui concernent la sécurité. L’équipement Cleaver-Brooks est conçu et fabriqué de façon à offrir une grande durabilité et un excellent fonctionnement. Les dispositifs électriques et mécaniques fournis dans le cadre de l’appareil sont choisis sur la base de leurs capacités établies de fonctionnement; toutefois, des procédures d’exploitation et d’entretien appropriées doivent être suivies en tout temps. Les fonctionnalités « automatiques » intégrées au système ne déchargent l’exploitant d’aucune de ses responsabilités. Ces fonctionnalités éliminent simplement certaines tâches répétitives et permettent de consacrer plus de temps au bon entretien de l’équipement. La responsabilité de l’exploitation et l’entretien corrects de l’équipement incombe exclusivement à l’exploitant. Aucune quantité d’instructions écrites ne peut remplacer la réflexion et le raisonnement intelligents et l’objectif de ce manuel n’est pas de décharger le personnel d’exploitation de la responsabilité de faire fonctionner l’équipement de façon correcte. Néanmoins, une très bonne compréhension de ce manuel est nécessaire avant de tenter de faire fonctionner, d’entretenir et de réparer cet équipement. Les commandes d’exploitation fonctionnent de façon fiable pendant de longues durées et nous avons constaté que certains exploitants deviennent négligents dans leurs contrôles quotidiens ou mensuels, présumant qu’un fonctionnement normal continuera indéfiniment. Les problèmes de fonctionnement des commandes se traduisent par une exploitation peu économique et par des dommages et, le plus souvent, on constate que ces problèmes sont directement liés à un manque de soin et à des insuffisances de contrôle et d’entretien. L’exploitation de cet équipement par le propriétaire ou par son personnel d’exploitation doit être conforme avec toutes les exigences et règlements de sa compagnie d’assurance et/ou des autres autorités compétentes. En cas de conflit ou incompatibilité entre ces exigences et les mises en garde ou instructions aux présentes, communiquer avec Cleaver-Brooks avant de poursuivre. Cleaver-Brooks HAWK 1000 Commande de chaudière Manuel d’utilisation Veuillez adresser vos bons de commande de manuels de rechange à votre représentant Cleaver-Brooks agréé local. Manuel réf. 750-366 07/2013 TABLE DES MATIÈRES Section 1 Généralités Introduction .................................................................................. 1-2 Description du système .................................................................. 1-3 Caractéristiques du système Hawk 1000 .......................................... 1-4 Sécurité et diagnostic ..................................................................... 1-5 Entrées et sorties ............................................................................ 1-6 Section 2 Éléments du système Vue d’ensemble .............................................................................. 2-2 Unité principale ............................................................................. 2-2 Interface homme-machine (IHM) ..................................................... 2-3 Communications ........................................................................... 2-4 Entrées de capteurs ....................................................................... 2-6 Section 3 Vérification du matériel Vérification des éléments du pupitre de commande ............................ 3-2 Vérification des actionneurs Modbus ................................................ 3-7 Section 4 Configuration du système Introduction ................................................................................. 4-2 Menu principal ............................................................................. 4-2 Vue d’ensemble de la chaudière ..................................................... 4-3 Configuration du système .............................................................. 4-4 Section 5 Mise en service Mise en service des actionneurs . . . . . . . . . . . . . . . . . . . . . . . . . . . 5-2 Réglage de la combustion - Positionnement parallèle . . . . . . . . . . . . . 5-4 Réglage de la combustion - Positionnement monopoint . . . . . . . . . . . 5-8 Réglage de la combustion - Bas/haut/bas . . . . . . . . . . . . . . . . . . . . . 5-8 Écran d’allure de chauffe . . . . . . . . . . . . . . . . . . . . . . . . . . . . . . . . 5-9 Alarmes et limites . . . . . . . . . . . . . . . . . . . . . . . . . . . . . . . . . . . . . 5-11 Points de consigne . . . . . . . . . . . . . . . . . . . . . . . . . . . . . . . . . . . . 5-13 O2 Trim . . . . . . . . . . . . . . . . . . . . . . . . . . . . . . . . . . . . . . . . . . . . 5-15 Données de VFD . . . . . . . . . . . . . . . . . . . . . . . . . . . . . . . . . . . . . . 5-16 Configuration Ethernet . . . . . . . . . . . . . . . . . . . . . . . . . . . . . . . . . . 5-16 Avance/retard avec deux chaudières . . . . . . . . . . . . . . . . . . . . . . . . 5-17 Routine de protection contre les chocs thermiques . . . . . . . . . . . . . 5-18 Section 6 Diagnostics et dépannage Contrôle et diagnostics du système . . . . . . . . . . . . . . . . . . . . . . . . . 6-2 État de la PLC . . . . . . . . . . . . . . . . . . . . . . . . . . . . . . . . . . . . . . . 6-4 Section 7 Nomenclature des pièces Nomenclature des pièces . . . . . . . . . . . . . . . . . . . . . . . . . . . . . . . . 7-1 Section 1 Généralités Introduction . . . . . . . . . . . . . . . . . . . . . . . . . . . . . . . . . . . . . . . . . . . . . . . . 1-2 Description du système . . . . . . . . . . . . . . . . . . . . . . . . . . . . . . . . . . . . . . . . 1-3 Caractéristiques du système Hawk 1000 . . . . . . . . . . . . . . . . . . . . . . . . . . . . 1-4 Sécurité et diagnostic . . . . . . . . . . . . . . . . . . . . . . . . . . . . . . . . . . . . . . . . . . 1-5 Gestion du brûleur . . . . . . . . . . . . . . . . . . . . . . . . . . . . . . . . . . . . . 1-5 Commandes de la chaudière . . . . . . . . . . . . . . . . . . . . . . . . . . . . . . 1-5 Entrées et sorties . . . . . . . . . . . . . . . . . . . . . . . . . . . . . . . . . . . . . . . . . . . . . 1-6 www.cleaverbrooks.com Section 1 — Généralités Hawk 1000 1.1 Introduction Le HAWK 1000 de Cleaver-Brooks est un système exclusif de commande et gestion de chaudière conçu spécifiquement pour intégrer les fonctions d’une commande programmable de chaudière et d’un système de gestion de brûleur, ainsi que d’autres commandes d’exploitation de chaudière et accessoires. Le système HAWK 1000 comporte une interface homme-machine (IHM) graphique conviviale qui afficher les paramètres de chaudière, les messages d’erreur et l’historique des alarmes, en plus de donner accès aux fonctions de configuration et de commande de chaudière. Figure 1-1. Écran de vue d’ensemble de chaudière Figure 1-2. Configuration typique du tableau 1-2 Réf. 750-366 Hawk 1000 Section 1 — Généralités 1.2 Description du système Le système de commande de chaudière HAWK 1000 permet de réguler l’allure de chauffe de façon à maintenir la pression de vapeur (ou la température d’une alimentation d’eau chaude) à sa valeur de consigne. Le ou les organes de commande finaux sont modulés par l’intermédiaire d’un réseau de communication Modbus afin d’assurer le maintien d’un mélange combustible/air optimal sur tout la plage de chauffe. Le système Hawk 1000 est compatible avec deux types de combustible. Chaque type de combustible peut être utilisé dans trois modes possibles : combustion monopoint, combustion parallèle et BAS-HAUT-BAS (mazout n° 2 seulement). Dans les systèmes parallèles, la commande Hawk 1000 peut également commander un registre de recirculation des gaz brûlés (FGR). La Hawk 1000 peut être contrôlée par les systèmes d’automatisation du bâtiment ou de l’usine via un convertisseur de protocole CB-PT. En outre, les communications EtherNet/Internet permettent le contrôle à distance du système de commande de chaudière Hawk 1000 (logiciels et/ou matériel supplémentaires requis). La commande HAWK 1000 peut être utilisée sur la majorité des types de chaudières à vapeur et à eau chaude, notamment les chaudières Firetube (tubes de fumées), à tubes d’eau industrielles et à tubes d’eau commerciales. En plus de l’installation sur des chaudières neuves, la HAWK 1000 peut être ajoutée lors de la rénovation de chaudières existantes. Pour plus de détails, appeler le représentant agréé Cleaver-Brooks local. Consulter les manuels Cleaver-Brooks suivants pour plus d’informations sur l’exploitation et l’entretien d’options système particulières : Level Master - 750-281 Convertisseur de protocole CB-PT, convertisseur de protocole à serveur Web CB-PTWS - 750-325 Commande de brûleur CB120E - 750-264 Commande de brûleur CB780E - 750-234 Entraînements à vitesse variable (VSD) - 750-198 Régulateur d’excès d’air O2 Trim - 750-224 Réf. 750-366 1-3 Section 1 — Généralités Hawk 1000 1.3 Caractéristiques du système Hawk 1000 • Commande des séquences de démarrage et d’arrêt du brûleur et contrôle de la flamme et des verrouillages • Compatible avec les commandes de brûleur et détecteurs de flamme CB780E et CB120E • La commande de chaudière contrôle et affiche les paramètres liés à la chaudière (pression ou température d’exploitation, température de cheminée, température de l’eau dans l’enveloppe, % O2, etc.) • Interface homme-machine (IHM) à clavier/écran tactile couleur de 4 pouces • Régulation optimisée de l’allure de chauffe de la chaudière • Indication et historique des alarmes/erreurs -- indication de première défaillance avec horodatage et affichage dans l’ordre chronologique • Possibilité de deux points de consigne • Protection contre les chocs thermiques (comprend séquence de préchauffage, maintien d’une allure minimale et mode d’arrêt à chaud) • Entrée utilisable pour l’UNE quelconque des fonctionnalités suivantes : modulation à distance, point de consigne à distance ou interface de niveau d’eau Level Master • Entrée utilisable pour l’UNE quelconque des fonctionnalités suivantes : température d’eau (vapeur) • Réinitialisation de la température de retour ou extérieure (chaudières à eau chaude) • Modulation à distance par communication (EtherNet) • Consigne à distance par communication (EtherNet) • Calcul du rendement de la chaudière • Coupure assurée à l’allure minimale • Asservissement externe avec des dispositifs auxiliaires (registre/obturateur d’air, pompes de circulation, etc.) • Alarme de température élevée des gaz brûlés et mise à l’arrêt • Capacité intégrée d’avance/retard à deux chaudières (point de consigne local) • Communications EtherNet • Trois modes de combustion : monopoint, parallèle ou HAUT-BAS-HAUT • Fonction de retour à la commande de veilleuse (nécessite la commande de brûleur CB120E) • Permet la commande d’un registre de recirculation des gaz brûlés (FGR) • Permet la commande d’un deuxième actionneur de combustible gazeux (deux combustibles gazeux) • Logiciel de serveur OPC pour l’interface avec le système d’automatisation du bâtiment/de l’usine • Logiciel de contrôle à distance • Contrôle de l’O2 et régulation de l’excès d’O2 (en option) • Entraînement à vitesse variable (VSD) sur le ventilateur d’air de combustion (avec dérivation) (en option) • Contrôle de la température de l’air de combustion (en option) 1-4 Réf. 750-366 Hawk 1000 Section 1 — Généralités 1.4 Sécurité et diagnostic 1.4.1 Gestion du brûleur • Utilise la commande de brûleur CB780E ou CB120E • Communique avec la commande programmable (PLC) via Modbus • État, erreurs et diagnostics de la commande de brûleur affichés sur l’IHM ou sur la commande de brûleur montée sur pupitre • Contrôle de l’état de la flamme au moyen d’un détecteur de flamme IR ou UV Figure 1-3. CB 780E Figure 1-4. Écran de commande de brûleur 1.4.2 Commandes de chaudière • Commandes d’exploitation et de modulation • Contrôle l’arrêt pour bas niveau d’eau • Contrôle la borne d’alarme de la commande de brûleur • Le relais de limite sans réactivation se désactivent en cas d’erreurs système ou défaillances de la PLC • Alarmes pour signal d’entrée de transmetteur hors limites • Diagnostic des erreurs de communication Modbus d’actionneurs • Écrans de configuration et de réglage du système protégés par mot de passe • Gestion des alarmes incorporée dans l’IHM montée sur porte • Protection par mot de passe des programmes de la commande programmable • Fonction d’arrêt pour défaillance de l’entraînement à fréquence variable (VFD) Figure 1-5. Hawk 1000 - Menu principal Réf. 750-366 1-5 1-6 E. ana. S. ana. I1/13 I1/14 I1/15 O1/0 O1/1 Alarme auxiliaire 1 Alarme auxiliaire 2 Alarme auxiliaire 3 Réservé * Prêt pour avance/retard * Réservé pour des ajouts futurs Total Compteur haute vit. (NON UTILISÉ) Connecteur 3 O2/1 I2/3 Niveau d’eau (vap) / Mod. dist. / Pt cons. dist. O2/0 I2/2 Temp. eau (vap) / Temp. ext. (eau) / Temp retour (eau) Allure de chauffe I2/1 Temp. gaz brûlés Commande VSD I2/0 Press. vap. (vap.) / Temp. alim. (eau) O1/2-O1/15 I1/12 Libre Libre(s) I1/11 I1/7 Pression air d’atomisation I1/10 I1/6 Contacteur tiroir mazout Air de combustion haut I1/5 Haute pression combustible 2 Dérivation VSD I1/4 Basse pression combustible 2 I1/8 I1/3 Hte press. combustible 1/hte temp. mazout I1/9 I1/2 Basse press. combustible 1/basse temp. mazout Eau élevée (vap.) ou cont. débit (eau) I1/1 ALWCO Pression air de combustion I1/0 Commande limite haute 16 1 1 1 1 1 1 1 1 1 1 1 1 1 1 1 1 16 14 1 1 4 1 1 1 1 2 1 1 Conn. 4 S. num. E/S intégrée I/O - Connecteur 1 à 3 E. num. 1769 SM2 Brone combustible ppal Borne veilleuse ALFCO Asservisst démarr. dispos. ext. (FAD) Prêt à démarre / Limites fermées Forcer allure minimale État VSD État analyseur O2 (Yokogawa) Purge Borne souffleur I5/15 Interrupteur de brûleur I5/14 Chaud. avc. / Sél. mod. dist. / Sél. consigne I5/13 Alarme eau basse I5/12 Borne alarme de commande de brûleur I5/11 Combustible 2 sélectionné I5/10 Combustible 1 sélectionné I5/9 I5/8 I5/7 I5/6 I5/5 I5/4 I5/3 I5/2 I5/1 I5/0 Connecteur 5 1769 IA16 Entrée numérique 1 16 1 1 1 1 1 1 1 1 1 1 1 1 1 1 1 O6/7 Ouvrir vanne 1 mazout allure max O6/6 Sonnerie d’alarme O6/5 Vérif. allure maximale / Ouvrir vanne 2 mazout allure max O6/4 Retour à la veilleuse (Fireye CB120E seulement) O6/3 Vérifier allure minimale O6/2 Limite non-réactivation (NRLR) O6/1 Démarr. dispositif ext. (FAD) O6/0 Limite réactivation (RLR) Connecteur 6 1769 OW8I Sortie numérique isolée 8 1 1 1 1 1 1 1 1 I7/3 Réservé * I7/2 Temp. air comb. I7/1 Signal O2 I7/0 Retour VSD Connecteur 7 1769 IF4 Entrée analogique (en option avec O2, VSD ou Temp. air comb.) 4 1 1 1 1 1.5 Entrées et sorties Processeur 1769-L24ER-QBFC1B - Connecteur 0 Section 1 — Généralités Hawk 1000 Réf. 750-366 Section 2 Éléments du système Vue d’ensemble . . . . . . . . . . . . . . . . . . . . . . . . . . . . . . . . . . . . . . . . . . . . . . 2-2 Unité principale . . . . . . . . . . . . . . . . . . . . . . . . . . . . . . . . . . . . . . . . . . . . . . 2-2 Interface homme-machine (IHM) . . . . . . . . . . . . . . . . . . . . . . . . . . . . . . . . . 2-3 Communications . . . . . . . . . . . . . . . . . . . . . . . . . . . . . . . . . . . . . . . . . . . . . 2-4 Modbus . . . . . . . . . . . . . . . . . . . . . . . . . . . . . . . . . . . . . . . . . . . . 2-4 Ethernet . . . . . . . . . . . . . . . . . . . . . . . . . . . . . . . . . . . . . . . . . . . . 2-5 USB . . . . . . . . . . . . . . . . . . . . . . . . . . . . . . . . . . . . . . . . . . . . . . 2-5 Entrées de capteurs . . . . . . . . . . . . . . . . . . . . . . . . . . . . . . . . . . . . . . . . . . . 2-6 Systèmes à vapeur. . . . . . . . . . . . . . . . . . . . . . . . . . . . . . . . . . . . . 2-6 Systèmes à eau chaude . . . . . . . . . . . . . . . . . . . . . . . . . . . . . . . . . 2-6 www.cleaverbrooks.com Section 2 — Éléments du système Hawk 1000 2.1 Vue d’ensemble Les principaux éléments du système de commande de chaudière HAWK 1000 sont la commande programmable (PLC), l’interface homme-machine (IHM) à écran tactile et la commande de sécurité du brûleur. Le système comporte également des alimentations électriques 24 Vcc et divers relais et disjoncteurs. 1 1a 6 1b 2 3 4 5 7 8 9 Figure 2-1. Tableau du Hawk 1000 1. Unité principale 1a. Commande programmable L24ER (PLC) 1b. E/S intégrée 2. Module de communication Modbus SM2 3. Entrées numériques 4. Sorties numériques 5. Entrées analogiques (en option) 6. Commande de brûleur 7. Alimentations électriques 8. Disjoncteurs, relais, fusibles, etc. 9. Commande ALWCO La commande de chaudière HAWK 1000 est préprogrammée à l’usine pour fonctionner avec la majorité des chaudières à tubes de fumée et à tubes d’eau Cleaver-Brooks, mais restent faciles à configurer pour toute chaudière particulière. Le programme de commande la chaudière est protégé par mot de passe, assurant l’inviolabilité du système de commande. L’IHM à écran tactile permet un accès convivial aux fonctions de régulation de l’allure de chauffe, aux diagnostics de la chaudière et à l’historique des alarmes, ainsi qu’aux paramètres d’exploitation associés. La gestion du brûleur est assurée par la commande de brûleur éprouvée CB780E ou, en option, CB120E. 2.2 Unité principale L’unité principale est constituée du processeur (CPU), qui contient la programmation et la configuration de la commande de chaudière, et des modules d’E/S intégrés, qui consistent en des entrées discrètes, des sorties discrètes et des entrées analogiques. La programmation est protégée par mot de passe à l’usine. Le module SM2 assure les communications Modbus entre la PLC et les autres périphériques. 2-2 Réf. 750-366 Hawk 1000 Section 2 — Éléments du système L’alimentation électrique aliment l’unité principale et les modules d’E/S. Le reste de la baie de PLC est utilisé pour les modules d’entrées et de sorties discrètes et pour le module d’entrée analogique (en option). Les modules d’E/S servent à envoyer et à recevoir des signaux de commande et de communication vers/depuis les autres parties du système. Connecteur Module 0 Processeur 1769-L24ER-QBFC1B 1 2 UNITÉ Entrées/sorties analogiques intégrées PRINCIPALE 3 Compteur haute vitesse intégré 4 Module Modbus SM2 5 Module d’entrée numérique 6 Module de sortie de relais 7 Module d’entrée analogique (4 can. – en option) Entrées/sorties discrètes intégrées Une terminaison à droite est requise pour compléter le bus de communication modulaire. Elle se pose sur le côté droit du dernier module de la baie. Une module d’entrée analogique en option peut être ajouté à la PLC pour offrir des fonctionnalités supplémentaires. Types de signaux DISCRETS et ANALOGIQUES Les entrées/sorties discrètes sont utilisées pour les signaux ne connaissant que deux états possibles (marche/arrêt, ouvrir/fermer, etc.). L’état d’entrée est représenté par un bit (0 ou 1) dans le programme de commande. Exemple : Chaudière prête (oui/non) Les signaux analogiques peuvent prendre presque une infinité de valeurs au sein de l’intervalle de courant d’entrée/sortie analogique fixé de 4 à 20 mA. La PLC du Hawk 1000 convertit cette valeur de courant en une plage de grandeur physique. Exemple : Pression de vapeur (0 à 150 PSI) REMARQUE : Le programme de la PLC suppose que chaque périphérique est placé sur un connecteur particulier. Les commandes HAWK 1000 ne fonctionnent pas si tous les périphériques ne sont pas installés et configurés comme il se doit. 2.3 Interface homme-machine (IHM) L’IHM affiche de façon concise de nombreux paramètres de la chaudière et offre une navigation facile par menus pour la configuration des paramètres du système, le réglage de la combustion, le contrôle des processus de la chaudière et la gestion et l’annonce des alarmes du système. L’IHM communique avec la PLC via Ethernet et est alimentée par une alimentation électrique 24 Vcc montée sur rail DIN. Réf. 750-366 2-3 Section 2 — Éléments du système Hawk 1000 Figure 2-2. Écran d’allure de chauffe 2.4 Communications 2.4.1 Modbus Modbus est un protocole série ouvert utilisé par le système HAWK 1000 pour envoyer et recevoir les commandes de contrôle, les données de position et les données de diagnostic entre la PLC et les périphériques connectés. Les communications Modbus sont gérées par le module SM2 situé à droite de l’unité principale dans le connecteur 4. Les périphériques HAWK 1000 communiquant à l’aide du Modbus sont la commande de sécurité du brûleur et les actionneurs de combustible, d’air et de recirculation des gaz brûlés (FGR). Le réseau de communication Modbus permet la transmission des informations d’état et d’erreur du système de commande de brûleur et leur affichage sur l’écran de l’IHM, en plus de son utilisation pour les données de commande, de retour et d’erreur des actionneurs. Figure 2-3. Module Modbus SM2 2-4 Réf. 750-366 Hawk 1000 Section 2 — Éléments du système 2.4.2 Ethernet Le système HAWK 1000 utilise Ethernet pour plusieurs fonctions de communication : • Communication entre la PLC et l’IHM. Le câble Ethernet reliant la PLC et l’IHM peut être de type droit ou croisé. • Raccordement du système de commande de chaudière à une infrastructure existante, par ex. au réseau local (LAN) de l’établissement • Intégration avec un système d’automatisation de bâtiment/usine (BAS) • Contrôle à distance du système de commande de chaudière par l’intermédiaire du réseau étendu (WAN) du client ou par l’Internet • Raccordement d’un ordinateur portable à des fins de diagnostic L’Ethernet/IP est également utilisé pour les fonctions de commande. Des commandes de chaudière individuelles peuvent être mises en réseau pour permettre la commande en avance/retard, avec une interface de système d’automatisation unique pour de multiples systèmes de chaudières. 8 00 08 A0+ A0- Z0+ Z0- 03 11 A1+ A1- 04 12 B1+ B1- 05 13 Z1+ Z1- 06 14 COM COM 0 1 +V +V OUT OUT 0 2 OUT 0UT 1 3 NC NC COM COM 00 08 01 09 02 10 03 11 04 12 00:00:BC:2E:69:F6 05 13 06 14 07 15 COM COM 0 1 DC OUT +24VDC +24VDC COM COM 1 IN IN OUT OUT 0 0 2 FUSE 2 FUSE 3 OK OK 3 B0+ B0- 02 10 +V +V PORT USB DC INPUT HSC 07 15 A0 B0 Z0 A0 B0 Z0 A1 B1 Z1 A1 B1 Z1 1 DC IN 01 09 PORT 2 DC INPUT 2 3 4 5 6 7 1 2 3 4 5 6 7 10 11 12 13 14 15 9 10 11 12 13 14 15 2 3 4 5 6 7 1 2 3 4 5 6 7 10 11 12 13 14 15 9 10 11 12 13 14 15 HIGH SPEED HIGH SPEED COUNTER COUNTER 1 0 9 8 1 0 9 8 DC OUTPUT 8 0 DC OUTPUT 24VDC SOURCE 0 24VDC SINK\ SOURCE L24ER QBFC1B 24VDC SOURCE PORT 1 24VDC SINK\ SOURCE 2.4.3 USB La communication USB s’utilise pour raccorder un ordinateur portable à des fins de diagnostic. V in 0+ I in 0+ V/I in 0CJC + V in 2+ I in 2+ V/I in 2V in 3+ CJC inI - 3+ V V/I in in 1+ 3I V/I in in 1+ 1V V OUT OUT 0+ 1+ I I OUT in 0+ 1+ COM COM ANALOG FG FG Ports Ethernet (bas de l’unité principale) Figure 2-4. Ports de communication L24ER Réf. 750-366 2-5 Section 2 — Éléments du système Hawk 1000 2.5 Entrées de capteurs La table suivante indique les capteurs proposés de série et en option pour les systèmes à vapeur (ST) et pour les systèmes à eau chaude (HW) : Capteur Pression de vapeur Tempér. gaz brûlés Température d’eau Niveau d’eau Tempér. alimentation Tempér. extérieure Température retour Système ST ST et HW ST ST HW HW HW De série Oui Oui Oui En option Oui Oui Oui Oui Tous les systèmes utilisent des sondes RTD avec un transmetteur pour produire la sortie 4-20 mA de mesure de la température. 2.5.1 Systèmes à vapeur Pression de vapeur : c’est la principale entrée de capteur vers la commande HAWK 1000 dans un système à vapeur. Elle transmet au contrôleur un signal de variable de processus de 4-20 mA utilisé pour réguler l’allure de chauffe et les limites opératoires. Température des gaz brûlés : ce signal est utilisé pour les alarmes et arrêts en cas de température des gaz brûlés élevée. Il sert également dans les calculs de rendement de la chaudière. Température d’eau (obligatoire sur les chaudières à vapeur) : cette sonde mesure la température de l’eau dans l’enveloppe de chaudière et s’utilise pour la protection contre les chocs thermiques dans les chaudières à vapeur. L’emplacement standard de la sonde thermométrique est un raccord de 1/2 po NPT sur l’axe médian du côté droit de l’enveloppe de chaudière. Si cet emplacement n’est pas disponible, il est possible de se servir d’un raccord d’arrivée d’eau inutilisé. Niveau d’eau : ce capteur est FACULTATIF, mais doit être un CB Level Master. 2.5.2 Systèmes à eau chaude Température d’alimentation : c’est la principale entrée de capteur vers la commande HAWK 1000 dans un système à eau chaude. Elle transmet au contrôleur un signal de variable de processus de 4-20mA utilisé pour réguler l’allure de chauffe et les limites opératoires. Température extérieure : ce signal est utilisé dans les systèmes à eau chaude équipés de l’option de recalage sur la température extérieure. Température de retour : s’utilise dans les systèmes à eau chaude comportant l’option de température de retour et à des fins de surveillance seulement. REMARQUE : Les sondes de température extérieure et de température de retour utilisent la même entrée. L’une ou l’autre peut être utilisée avec la commande Hawk 1000, mais pas les deux à la fois. 2-6 Réf. 750-366 Section 3 Vérification du matériel Vérification des éléments du pupitre de commande . . . . . . . . . . . . . . . . . . 3-2 Loquets de rails DIN et leviers de verrouillage de modules d’extension d’E/S . . . . . . . . . . . . . . . . . . . . . . . . . . . . . . . 3-2 Terminaisons de câblages in-situ et de tableau . . . . . . . . . . . . . . 3-3 Commutateurs DIP de module SM2 . . . . . . . . . . . . . . . . . . . . . 3-3 Adresse Modbus et débit en baud de la commande de brûleur CB780E . . . . . . . . . . . . . . . . . . . . . . . . . . . . . . . . . . . . . 3-4 Adresse Modbus et débit en baud de la commande de brûleur CB120E . . . . . . . . . . . . . . . . . . . . . . . . . . . . . . . . . . . . . 3-6 Commutateur de PLC . . . . . . . . . . . . . . . . . . . . . . . . . . . . . . . 3-7 Vérification des actionneurs Modbus . . . . . . . . . . . . . . . . . . . . . . . . . . . . 3-7 Fixation . . . . . . . . . . . . . . . . . . . . . . . . . . . . . . . . . . . . . . . . . 3-7 Raccordements électriques . . . . . . . . . . . . . . . . . . . . . . . . . . . . 3-7 Attribution de l’adresse de nœud Modbus . . . . . . . . . . . . . . . . . 3-9 Voyant d’alimentation / communication . . . . . . . . . . . . . . . . . . . 3-10 Activation manuelle de l’actionneur . . . . . . . . . . . . . . . . . . . . . . 3-11 www.cleaverbrooks.com Section 3 — Vérification du matériel Hawk 1000 ! Important L’unité principale et les modules d’extension ne sont pas conçus pour être déposés et mis en place sous tension. Lorsque le système de commande programmable (PLC) est sous tension, toute interruption de la connexion entre l’alimentation électrique et l’unité principale (c.-à-d. dépose de l’alimentation électrique, de l’unité principale ou d’un module d’extension) a pour effacer la mémoire du processeur, y compris le programme de l’utilisateur. Veiller à s’assurer que l’alimentation électrique est COUPÉE avant de déposer ou de mettre en place un quelconque élément de PLC. 3.1 Vérification des éléments du pupitre de commande Cette section couvre la vérification initiale du système à effectuer préalablement à la configuration et à la mise en service du système au moyen des menus de l’IHM. Il est nécessaire de vérifier que tous les composants intégrés et tout le câblage d’interconnexion sont solidement en place. Les vibrations et les secousses durant le transport et l’installation peuvent avoir desserré certains composants ou bornes de câblage. Il est de bonne pratique de vérifier le bon état et le serrage de tous les composants avant la mise sous tension initiale du système. Tout câblage d’asservissement externe et de signal à distance doit également être raccordé à la commande de chaudière. 3.1.1 Loquets de rails DIN et leviers de verrouillage de modules d’extension d’E/S Avant la mise sous tension initiale du système de commande, vérifier que tous les loquets de rails DIN et leviers de verrouillage de modules d’extension sont en place (voir Figure 3-1 et Figure 3-2). Figure 3-1. Loquets de rail DIN Figure 3-2. Leviers de verrouillage de modules d’extension d’E/S Les leviers de verrouillage de module doivent tous être fermement engagés vers la gauche. 3-2 Réf. 750-366 Hawk 1000 Section 3 — Vérification du matériel 3.1.2 Terminaisons de câblages in-situ et de tableau Vérifier que tous les raccordements de câblage d’usine sont bien serrés et que les terminaisons de câblage in-situ sont solidement en place. Figure 3-3. Vérifier tous les câblages et raccordements 3.1.3 Commutateurs DIP de module SM2 Vérifier que le réglage des commutateurs DIP de module SM2 correspond à l’illustration ci-dessous (commutateur du haut à gauche, commutateur du bas à droite). Réglage des commutateurs DIP : haut à g., bas à dr. Figure 3-4. Réglage des commutateurs DIP de module SM2 Réf. 750-366 3-3 Section 3 — Vérification du matériel Hawk 1000 3.1.4 Adresse Modbus et débit en bauds de la commande de brûleur - CB780E L’adresse de nœud Modbus de la CB780E doit être 05 et son débit en bauds 9600. Ces réglages se font à l’aide de l’affichage à touches 780E. Appuyer sur les trois touches de gauche du module d’affichage pendant une seconde puis les relâcher. DISPLAY Setup (Configuration AFFICHAGE) s’affiche. Appuyer simultanément sur les deux touches ENTER. Appuyer sur la touche fléchée Bas jusqu’à afficher MB ADDRESS. Appuyer simultanément sur les touches ENTER. Appuyer deux fois sur la touche fléchée Bas. Régler l’adresse Modbus sur 05 à l’aide des touches fléchées Haut et Bas. Appuyer simultanément sur les touches ENTER. 3-4 Réf. 750-366 Hawk 1000 Section 3 — Vérification du matériel Appuyer sur la touche fléchée Bas pour valider. Appuyer sur la touche fléchée Bas jusqu’à afficher MB BAUD. Appuyer simultanément sur les touches ENTER. Appuyer sur la touche fléchée Bas pour sélectionner. À l’aide des touches fléchées Haut et Bas, sélectionner 9600. Appuyer simultanément sur les touches ENTER. Réf. 750-366 3-5 Section 3 — Vérification du matériel Hawk 1000 Appuyer sur la touche fléchée Bas pour valider. Appuyer simultanément sur les touches ENTER. Appuyer sur la touche fléchée Haut pour quitter. 3.1.5 Adresse Modbus et débit en baud de la commande de brûleur - CB120E La CB120E comporte une capacité Modbus intégrée; pour permettre les communications, le débit en bauds et l’adresse de nœud ModBus doivent être correctement configurés. Pour la vérification de ces paramètres, la CB120E doit être en marche. Appuyer sur la touche <BACK> (Précédent) ou <NEXT> (Suivant) sur l’afficheur de la CB120E jusqu’à afficher PROGRAM SETUP> (Paramètres du programme). 3-6 Réf. 750-366 Hawk 1000 Section 3 — Vérification du matériel Appuyer sur la touche <MODE> puis sur <NEXT> jusqu’à afficher BAUD RATE (Débit en bauds). Appuyer sur la touche <MDFY> (Modifier) et utiliser la touche <BACK> ou <NEXT> pour sélectionner 4800. Appuyer sur <MDFY> pour valider. Appuyer sur la touche <NEXT> jusqu’à afficher UNIT ADDRESS # (N° d’adresse d’unité). Pour modifier l’adresse de l’unité, utiliser la touche <BACK> ou <NEXT> jusqu’à afficher 5. Appuyer sur <MDFY> pour valider. Appuyer sur <MODE> pour quitter le menu. 3.1.6 Commutateur de PLC Vérifier que le commutateur de PLC est en position RUN (Marche). La chaudière ne fonctionne pas si le commutateur est en position PROG. La chaudière s’arrête immédiatement si le commutateur est placé en position PROG. Le commutateur doit être en position PROG et l’interrupteur de brûleur en position OFF avant que le programme de la PLC puisse être copié sur une carte SD vide au format de dossier Logix. Le commutateur peut être en position PROG ou RUN durant la copie d’un programme de PLC depuis une carte SD contenant un dossier Logix. Aucun autre fichier ne doit être présent sur la carte SD. 3.2 Vérification des actionneurs Modbus 3.2.1 Fixation Fixer l’actionneur au moyen de vis traversant le support de fixation et vissées dans la face de l’actionneur. S’assurer que la surface de fixation repose solidement à plat contre le support de fixation. La sortie d’arbre de l’actionneur doit être raccordée à l’arbre de la vanne au moyen d’un accouplement adapté. L’accouplement doit être fixé avec des vis de calage et immobilisé ou bloqué en place au moyen d’une clavette. Il est conseillé de laisser la sortie d’arbre de l’actionneur découplée de l’arbre de la vanne (ou du levier de registre) jusqu’à ce que l’adresse Modbus de l’actionneur soit correctement configurée, que le câblage soit vérifié et que le sens de rotation d’ouverture de la vanne ou du registre soit établi. 3.2.2 Raccordements électriques Les actionneurs comportent un raccordement de câble entrant (depuis l’actionneur précédent ou le pupitre Hawk) et un raccordement de câble sortant (vers l’actionneur suivant). Les connecteurs de câble et les fiches de raccordement sont rainurés pour assurer le bon alignement des broches. Pour raccorder le câble, aligner les broches et la rainure et enfoncer la fiche. Tourner le collier fileté dans le sens horaire pour serrer le câble. Attacher les câbles en évitant qu’ils puissent être pincés ou entraver les mouvements mécaniques des dispositifs actionnés. Dans certaines installations, la réglementation et autres normes peuvent exiger un câblage direct (sans connecteurs) des actionneurs. Voir Figure 3-7. Réf. 750-366 3-7 Section 3 — Vérification du matériel Hawk 1000 MODULE MODBUS SM2 CONNECTEUR 1 ALIMENTATION ÉLECTRIQUE ANALOGIQUE (24 Vcc) CÂBLE 5 CONDUCTEURS VERS ACTIONNEUR D’AIR (ADRESSE 1) JAUNE/VERT Figure 3-5. Câblage du SM2 vers les actionneurs MODULE MODBUS SM2 CONNECTEUR 1 ACTIONNEURS MODBUS À CÂBLAGE DIRECT ALIMENTATION ÉLECTRIQUE ANALOGIQUE VUE CÔTÉ FEMELLE TYPIQUE DE TOUS LES CONNECTEURS (ADRESSE 2) (ADRESSE 1) NOIR BRUN BRUN BRUN BLEU BLEU JAUNE/VERT BRUN BLEU BLEU VERT/JAUNE BLEU BLANC BLANC VERT VERT/JAUNE VERT BRUN BLEU BLANC BLANC BLANC CÂBLE 5 CONDUCTEURS BRUN BLANC VERT VERT/JAUNE NOIR NOIR CÂBLE 5 CONDUCTEURS BLEU BLANC (ADRESSE 7) NOIR NOIR CÂBLE 5 CONDUCTEURS BRUN ACTIONNEUR FGR (ADRESSE 5) NOIR NOIR CÂBLE 5 CONDUCTEURS ACT. 1 COMB. 2 ACT. 1 COMB. 1 VERS ACTIONNEUR D’AIR (24 Vcc) VERT VERT/JAUNE VERT VERT VERT/JAUNE VERT VERT/JAUNE VERT/JAUNE Figure 3-6. Actionneurs en guirlande avec fiches de connexion 3-8 Réf. 750-366 Hawk 1000 Section 3 — Vérification du matériel ACTIONNEURS MODBUS À CÂBLAGE DIRECT (ADRESSE 2) (ADRESSE 1) CÂBLE 5 CONDUCTEURS ACT. 1 COMB. 2 ACT. 1 COMB. 1 VERS ACTIONNEUR D’AIR CÂBLE 5 CONDUCTEURS VERT/JAUNE (ADRESSE 7) (ADRESSE 5) CÂBLE 5 CONDUCTEURS VERT/JAUNE VERT/JAUNE ACTIONNEUR FGR CÂBLE 5 CONDUCTEURS VERT/JAUNE VERT/JAUNE VERT/JAUNE VERT/JAUNE VUE DE L’ACTIONNEUR SANS COUVERCLE Figure 3-7. Actionneurs en guirlande à câblage direct 3.2.3 Attribution de l’adresse de nœud Modbus Les actionneurs doivent avoir des adresses de nœud Modbus uniques. L’adresse du nœud se règle au moyen d’un commutateur de type tournant situé sur la plaque frontale de l’actionneur. Tourner ce sélecteur jusqu’à l’adresse souhaitée à l’aide d’un petit tournevis plat. Réf. 750-366 3-9 Section 3 — Vérification du matériel Hawk 1000 Sélecteur tournant réglage de l’adresse de nœud Voyant d’alimentation/ communication Figure 3-8. Actionneur Modbus Une fois que l’adresse de nœud est réglée, l’actionneur peut être mis sous tension. L’actionneur doit passer par un cycle de marche avant qu’une nouvelle adresse de nœud soit validée par l’actionneur. Table des adresses de nœud d’actionneur : Actionneur Actionneur d’air Actionneur combustible 1 2e actionneur combustible 1 Actionneur combustible 2 2e actionneur combustible 2 Actionneur FGR Adresse 1 2 3 5 6 7 3.2.4 Voyant d’alimentation / communication Chaque actionneur comporte un voyant d’alimentation / communication. Ce voyant présente trois états possibles : Éteint - vérifier que l’alimentation 24 Vcc est présente. Le voyant est également éteint si le bouton-poussoir de rotation horaire ou antihoraire est enfoncé. Allumé en continu - alimentation électrique présente mais aucune commande en provenance de la PLC. C’est l’état normal d’un actionneur non sollicité par la PLC, tel que l’actionneur du combustible 2 lorsque le sélecteur de combustible est réglé sur le combustible 1, par ex. Clignotement rapide - l’actionneur répond aux commandes de la PLC et renvoie des données de position. 3-10 Réf. 750-366 Hawk 1000 Section 3 — Vérification du matériel 3.2.5 Activation manuelle de l’actionneur Appuyer sur l’un des deux boutons rouges situés sur l’actionneur pour le faire tourner dans le sens horaire ou antihoraire (Figure 3-9). L’un des boutons rouges faire tourner l’arbre de l’actionneur dans le sens horaire, l’autre le faire tourner dans le sens inverse. Le servomoteur s’arrête automatiquement lorsqu’il arrive en bout de course. L’activation manuelle des actionneurs doit se faire uniquement lorsque la vanne de combustible principale est fermée. L’activation manuelle des actionneurs alors que la vanne de combustible principale est ouverte génère une erreur. Lorsqu’on relâche le bouton-poussoir manuel, la PLC commande automatiquement la mise en position des actionneurs; par conséquent, ces boutons ne doivent pas être utilisés durant la mise en service, mais uniquement en tant qu’outil de dépannage. L’écran d’étalonnage des actionneurs dans l’IHM comporte des boutons d’ouverture / fermeture. Veiller à utiliser ces boutons lors de l’étalonnage des actionneurs. Le sens de rotation (horaire ou antihoraire) de l’arbre d’actionneur se détermine lorsqu’on l’observe comme sur la Figure 3-9. Sens antihoraire Sens horaire Figure 3-9. Boutons-poussoirs manuels de l’actionneur Réf. 750-366 3-11 Section 3 — Vérification du matériel 3-12 Hawk 1000 Réf. 750-366 Section 4 Configuration du système Introduction . . . . . . . . . . . . . . . . . . . . . . . . . . . . . . . . . . . . . . . . . . . . . 4-2 Menu principal . . . . . . . . . . . . . . . . . . . . . . . . . . . . . . . . . . . . . . . . . . . 4-2 Vue d’ensemble de la chaudière . . . . . . . . . . . . . . . . . . . . . . . . . . . . . . . 4-3 Configuration du système . . . . . . . . . . . . . . . . . . . . . . . . . . . . . . . . . . . . 4-4 Fluide caloporteur et type de chaudière . . . . . . . . . . . . . . . . . . . 4-6 Configuration du combustible . . . . . . . . . . . . . . . . . . . . . . . . . . 4-11 Système de surveillance de flamme . . . . . . . . . . . . . . . . . . . . . . 4-12 Entrées analogiques . . . . . . . . . . . . . . . . . . . . . . . . . . . . . . . . . 4-13 Modulation à distance/consigne à distance . . . . . . . . . . . . . . . . . 4-15 Sélection des actionneurs . . . . . . . . . . . . . . . . . . . . . . . . . . . . . 4-17 Entraînement à fréquence variable . . . . . . . . . . . . . . . . . . . . . . . 4-18 Options . . . . . . . . . . . . . . . . . . . . . . . . . . . . . . . . . . . . . . . . . 4-19 Récapitulatif de la configuration . . . . . . . . . . . . . . . . . . . . . . . . 4-23 www.cleaverbrooks.com Section 4 — Configuration du système Hawk 1000 4.1 Introduction La commande Hawk 1000 est équipée d’une interface homme-machine (IHM) à écran tactile couleur de 4 pouces. L’IHM et l’affichage de la commande de brûleur constituent les points d’interface pour le contrôle et la commande de la chaudière par l’opérateur et pour la configuration et la mise en service du système par le technicien d’entretien. Cette section décrit les écrans de l’IHM et leurs fonctions. Pour plus de renseignements sur la commande de brûleur (système de surveillance de flamme), consulter l’une des publications CB suivantes : Commande de brûleur CB120E - 750-264 Commande de brûleur CB780E - 750-234 Figure 4-1. Écran d’allure de chauffe Un bouton gris sur l’IHM indique qu’un mot de passe est nécessaire avant que la saisie par l’utilisateur soit admissible. La commande Hawk 1000 comporte trois niveaux de sécurité : Operator (opérateur), Service (maintenance) et Factory (usine). Le fait d’appuyer sur un bouton-poussoir gris ouvre la fenêtre d’ouverture de session. 4.2 Menu principal Le menu principal (Figure 4-2) est le premier écran qui s’affiche lors de la mise sous tension du système. L’en-tête au sommet de l’écran affiche la date et l’heure courantes, l’état de connexion utilisateur, un bouton de déconnexion (Logout) et une sonnerie d’alarme en présence d’une alarme. Le reste de l’écran contient des boutons de navigation. Lors de la première mise sous tension du système (Figure 4-3), le bouton <System Config>* (Configuration système) comporte la mention « System Config Required » (Configuration système requise). L’écran indique « Commissioning Not Done » (Mise en service non effectuée) tant que la configuration initiale et la mise en service ne sont pas achevées. On notera que certains boutons de l’écran ne sont pas encore disponibles. *Dans ce manuel, les boutons de l’écran de l’IHM sont identifiés par l’intitulé du bouton placé entre chevrons, suivi d’une traduction entre parenthèses, par ex.<Main> (Principal). 4-2 Réf. 750-366 Hawk 1000 Section 4 — Configuration du système Figure 4-2. Menu principal (tous les boutons possibles) Figure 4-3. Menu principal (démarrage initial) 4.3 Vue d’ensemble de la chaudière L’écran de vue d’ensemble de la chaudière (Figure 4-4) constitue le point d’interface principal pour l’opérateur. L’objet principal de cet écran est la surveillance de l’état actuel de la chaudière. Réf. 750-366 4-3 Section 4 — Configuration du système Hawk 1000 Flextube Firetube Modèle 4/5 Figure 4-4. Vue d’ensemble de la chaudière 4.4 Configuration du système La première étape de mise en service de la chaudière consiste à configurer les options du système de commande. Dans l’écran principal, appuyer sur <System Config> (Configuration système). Un message de mise en garde s’affiche : Appuyer de nouveau sur <System Config>; un écran de mise en garde finale s’affiche : Figure 4-5. Avertissement 1 4-4 Réf. 750-366 Hawk 1000 Section 4 — Configuration du système Figure 4-6. Avertissement 2 Appuyer sur <Next> (Suivant) pour poursuivre. Les paramètres suivants sont configurables depuis le mode de configuration du système : • Fluide caloporteur - vapeur ou eau chaude • Type de chaudière - Firetube, Flextube ou M4/M5 • Consigne de la soupape de sûreté • Niveau de NOx (ppm) • Nombre de combustibles • Combustible 1 - Type de combustible • Combustible 1 - Type de commande (parallèle ou monopoint) • Combustible 1 - Marge de réglage • Combustible 2 - Type de combustible • Combustible 2 - Type de commande (parallèle, monopoint ou bas-haut) • Combustible 2 - Marge de réglage • Sélection du système de surveillance de flamme • Retour à la veilleuse (CB120E seulement) • Sélection du signal de retour à la veilleuse (CB120E seulement) • Entrée analogique I:2.2 • Entrée analogique I:2.3 • Modulation à distance/sélection du signal de consigne • Sélection du double point de consigne • Sélection des actionneurs • Sélection de l’option VFD (nécessite un module d’entrée analogique supplémentaire sur le connecteur 7) • Sélection de l’option de dérivation de VFD • Analyseur d’O2 (lorsque cette option est sélectionnée, le type d’analyseur doit être spécifié - nécessite un module d’entrée analogique supplémentaire sur le connecteur 7) • O2 Trim • Option de mise à l’arrêt pour O2 bas • Sélection de l’option d’arrêt à chaud • Sélection de l’option de température d’air de combustion (nécessite un module d’entrée analogique supplémentaire sur le connecteur 7) • Sélection de l’option Level Master (chaudière à vapeur) • Température de retour d’eau (eau chaude seulement) • Sélection du recalage sur la température extérieure (eau chaude seulement) • Graphisme sélectionnable de l’écran de vue d’ensemble - chaudière Firetube, Flextube ou M4/M5 Réf. 750-366 4-5 Section 4 — Configuration du système Hawk 1000 On notera que si un paramètre de configuration est marqué d’une astérisque, la modification de sa valeur a pour effet d’effacer les courbes de combustion. ! Attention L’accès au mode de configuration du système alors que la chaudière est en marche déclenche une mise à l’arrêt de sécurité. Les mises à l’arrêt répétées ou intempestives peuvent entraîner une défaillance prématurée du matériel. ! Attention L’accès aux écrans suivants doit être réservé à du personnel qualifié. Ne jamais sélectionner des paramètres alors que la chaudière est en marche. Remarque : La chaudière ne démarre pas lorsqu’on est dans l’écran de configuration du système. Remarque : L’allure de chauffe passe en mode manuel lors de l’accès à l’écran de configuration du système. 4.4.1 Fluide caloporteur et type de chaudière La première étape de la procédure de configuration est la sélection du fluide caloporteur et du type de chaudière. Figure 4-7. Sélection du fluide caloporteur et du type de chaudière Chaque fois qu’un bouton gris s’affiche, un nom d’utilisateur et un mot de passe sont requis pour les saisies de l’utilisateur. Appuyer sur <Boiler Media> (Fluide caloporteur) ou sur <Boiler Type> (type de chaudière) pour accéder à l’écran suivant : 4-6 Réf. 750-366 Hawk 1000 Section 4 — Configuration du système Appuyer sur <User> (Utilisateur) ou sur <Password> (Mot de passe) pour ouvrir un clavier alphanumérique. Utiliser ce clavier (ou le clavier matériel de l’IHM) pour entrer le nom d’utilisateur et le mot de passe. Un clavier USB peut également être utilisé. Taper le mot de passe (nom d’utilisateur) suivi de la touche d’entrée . Lorsqu’un nom d’utilisateur et un mot de passe valides sont entrés, l’écran suivant s’affiche : Réf. 750-366 4-7 Section 4 — Configuration du système Hawk 1000 Figure 4-8. Configuration du système Dans cet exemple, le type de chaudière sélectionné est « Firetube » (tubes de fumée). Après la sélection du fluide caloporteur (vapeur ou eau chaude), des boutons supplémentaires s’affichent à l’écran. La sélection de « Steam » (Vapeur) affiche les boutons d’étendue du transmetteur de vapeur, de consigne de la soupape de sûreté et de niveau de NOx. Pour changer les valeurs par défaut, appuyer sur le bouton souhaité et un clavier s’affiche pour permettre la saisie par l’utilisateur. La sélection du type de chaudière et du fluide caloporteur fait afficher le bouton <Next> (Suivant), qui permet de passer à l’écran de configuration suivant. L’utilisateur doit être connecté au niveau d’accès par mot de passe approprié pour modifier des données de configuration. Si un utilisateur ne disposant pas de droits d’accès suffisants essaie de changer des données de configuration, une fenêtre de saisie de mot passe s’affiche. Figure 4-9. Fluide caloporteur sélectionné 4-8 Réf. 750-366 Hawk 1000 Section 4 — Configuration du système Si un nom d’utilisateur et un mot de passe valides sont entrés, l’opérateur est autorisé à modifier les données. L’état actuel de connexion utilisateur est visible dans le coin supérieur droit de chaque écran. La couleur du bouton-poussoir indique aussi si l’utilisateur dispose de droits d’accès suffisants. Appuyer sur le bouton de la valeur à modifier pour faire apparaître un clavier numérique, qui permet de saisir la nouvelle valeur. On notera que la plage de valeurs admissibles est indiquée au sommet du clavier numérique. Une valeur hors limites s’affiche en rouge et doit être remplacée par une valeur admissible. Entrer la valeur souhaitée et appuyer sur la touche Entrée (Enter). Si la valeur est admissible, elle est acceptée et le clavier disparaît. On notera que toutes les valeurs peuvent être saisies depuis l’écran tactile ou du clavier de l’IHM. Les valeurs numériques peuvent être saisies ici ou depuis le clavier numérique qui s’affiche à l’écran Clavier à l’écran Valeur non valable Fluide caloporteur Sous Boiler Media (Fluide caloporteur), sélectionner Steam (Vapeur) ou Hot Water (Eau chaude) en fonction du type de système. Type de chaudière Le choix du type de chaudière (Boiler Type) permet d’afficher la représentation graphique correcte dans l’écran de vue d’ensemble de la chaudière. Les trois choix de type de chaudière sont : Firetube, Flextube et M4/M5. Le type de chaudière s’utilise aussi pour fixer des limites maximales pour la saisie des paramètres de consigne de la soupape de sûreté (vapeur) ou de température nominale maximale (eau chaude). Consigne max. soupape de sûreté Firetube 400 psi Flextube 250 psi M4/M5 600 psi Température nominale maximale (eau chaude) Tous types = entre 93 à 204 °C (200 et 400 °F) Réf. 750-366 4-9 Section 4 — Configuration du système Hawk 1000 Consigne de soupape de sûreté (vapeur) Avec une chaudière à vapeur, la valeur de consigne de la soupape de sûreté doit correspondre au réglage de pression de la ou des soupapes de sûreté sur la chaudière. ! Avertissement Ce paramètre est essentiel au bon fonctionnement de la chaudière. Une valeur incorrecte peut produire un fonctionnement dangereux. Une chaudière à eau chaude est configurée de façon semblable. La température nominale maximale de la chaudière doit être saisie. Cette valeur ne doit pas dépasser la température maximale théorique de la chaudière. La valeur par défaut pour les chaudières à eau chaude est 121 °C (250 °F). Consulter le représentant Cleaver-Brooks local si la température nominale maximale de la chaudière utilisée n’est pas connue. Étendue du transmetteur de vapeur Le paramètre d’étendue de la plage du transmetteur de vapeur est ajustable. Cette valeur (Steam Transmitter Span) ne peut pas être inférieure à la valeur de consigne de la soupape de sûreté (Safety Valve Setpoint) ni supérieure à 1000. Au départ, le paramètre d’étendue du transmetteur de vapeur est affecté d’une valeur par défaut : Consigne soupape de sûreté 15,0 psi ou moins 15,1 à 150,0 150,1 à 300,0 300,1 à 500,0 500,1 à 600,0 Étendue transmetteur vapeur 15,0 150,0 300,0 500,0 600,0 Dans les systèmes à eau chaude, l’échelle du transmetteur de température n’est pas modifiable. Le transmetteur utilisé doit être compatible avec la plage requise : Si la température nominale max. est > 121 °C (250 °F), alors le transmetteur de température d’alimentation est réglé sur 10 à 149 °C (50 à 300 °F). Si la température nominale max. = 121 °C (250 °F) ou plus, alors le transmetteur de température d’alimentation est réglé sur 10 à 260 °C (50 à 500 °F). Niveau de NOx (ppm) Entrer le niveau de NOx (NOx Level) pour l’installation considérée. Le niveau de NOx peut être compris entre 5 et 150 ppm et est affecté d’une valeur initiale de 60,0 ppm. Remarque : Sur les chaudières à vapeur, si le niveau de NOx est inférieur à 60,0 ppm, les options de consigne à distance et de double point de consigne ne sont pas disponibles. Une fois que tous les paramètres configurables de cet écrans sont affectés de valeurs admissibles, le bouton <Next> (Suivant) s’affiche pour permettre de poursuivre la configuration du système. L’écran suivant est la configuration du combustible, où le nombre et les types de combustibles, la marge de réglage et la méthode de régulation de la combustion sont sélectionnés. 4-10 Réf. 750-366 Hawk 1000 Section 4 — Configuration du système 4.4.2 Configuration du combustible Figure 4-10. Configuration du combustible Nombre de combustibles Entrer le nombre de combustibles pour l’installation considérée. Les valeurs possibles sont 1 ou 2. La méthode de régulation Haut/bas doit IMPÉRATIVEMENT être combustible 2. Type de combustible 1/combustible 2 Sélectionner le type de combustible pour chaque combustible utilisé. Appuyer sur le bouton <Fuel Type> (Type de combustible) pour afficher un sélecteur. Les flèches haut/bas peuvent être utilisées pour sélectionner le combustible correct. Appuyer sur la touche d’entrée pour accepter la sélection. Marge de réglage du combustible 1/combustible 2 Entrer la marge de réglage (Turndown) pour chaque combustible de l’application considérée. Cette valeur entre dans les calculs de rendement du brûleur - elle est sans effet sur la marge de réglage effective du brûleur. Le taux de marge de réglage est établi durant la mise en service du brûleur par un technicien qualifié. Réf. 750-366 4-11 Section 4 — Configuration du système Hawk 1000 Méthode de régulation du combustible 1/combustible 2 Sélectionner le type de méthode de régulation pour chaque combustible de l’installation considérée. Les valeurs admissibles pour le combustible 1 (Fuel 1 Control Method) sont Parallel Position (positionnement parallèle) ou Single Point (positionnement monopoint). Les valeurs admissibles pour le combustible 2 (Fuel 2 Control Method) sont Parallel Position, Single Point ou Low/High (bas/haut). Remarque - Le positionnement monopoint ne peut pas être sélectionné en conjonction avec le positionnement parallèle. Une fois que la configuration du combustible est terminée, appuyer sur <Next> (Suivant) pour passer à la configuration du système de surveillance de flamme. 4.4.3 Système de surveillance de flamme Figure 4-11. Écran du système de surveillance de flamme (FSG) Système de surveillance de flamme Sélectionner le type de système de surveillance de flamme utilisé pour l’installation considérée. Les systèmes CB780E et CB120E sont les deux choix possibles pour la commande Hawk 1000. Si CB120E est sélectionné, l’option de retour à la veilleuse (RTP) est disponible (non disponible sur le CB780E). Retour à la veilleuse Pour sélectionner l’option de retour à la veilleuse, appuyer sur le bouton <Revert to Pilot> (Retour à la veilleuse) de façon à afficher « Yes » (Oui) dans le bouton. Si cette option est sélectionnée, il y a deux manières de lancer une séquence de retour à la veilleuse - par variable de processus (pression de vapeur/température d’eau) ou par entrée numérique. Si la variable de processus est sélectionnée, le point de consigne du retour à la veilleuse doit être saisi depuis l’écran de point de consigne - pour plus de détails, voir Section 5.7 - Points de consigne. Si l’entrée numérique est sélectionnée, la fonction de retour à la veilleuse est déclenchée lorsque l’entrée discrète I:5.7 ALFCO passe à l’état bas (Off). 4-12 Réf. 750-366 Hawk 1000 Section 4 — Configuration du système ! Attention Les modes de retour à la veilleuse doivent être déterminés sur le terrain après analyse détaillée des conditions de charge qui nécessitent l’utilisation de ces modes de fonctionnement. Veiller à éviter tout redémarrage inutile et dommages à la chaudière. 4.4.4 Entrées analogiques Figure 4-12. Entrées analogiques (vapeur) Entrée analogique I:2.2 Pour les systèmes à vapeur, l’entrée analogique I:2.2 doit impérativement être la Water Temp (Température d’eau). Pour les systèmes à eau chaude, les choix d’entrée analogique I:2.2 sont None (Aucune), Outdoor Temp (Température extérieure) et Return Temp (Température de retour). Réf. 750-366 4-13 Section 4 — Configuration du système Hawk 1000 Figure 4-13. Entrées analogiques (eau chaude) Entrée analogique I:2.3 Pour les systèmes à vapeur, les choix d’entrée analogique I:2.3 sont None (Aucune), Water Level (Niveau d’eau), Remote Modulation (Modulation à distance) et Remote Set Point (Consigne à distance). Si est sélectionné, le capteur utilisé pour mesurer le niveau d’eau doit impérativement être le Level Master. L’entrée Consigne à distance n’est pas disponible sur les chaudières à faible émission < 60 ppm. 750-281 Level Master Pour les systèmes à eau chaude, les choix d’entrée analogique I:2.3 sont Aucune, Modulation à distance et Consigne à distance. Si l’entrée analogique I:2.3 est utilisée pour la modulation à distance ou la consigne à distance, alors les options de modulation à distance et de point de consigne à distance par une connexion de communication ne sont pas disponibles. 4-14 Réf. 750-366 Hawk 1000 Section 4 — Configuration du système 4.4.5 Modulation à distance/consigne à distance Les signaux pour la modulation à distance ou la consigne à distance peuvent être fournis soit par une entrée analogique, soit directement à la PLC par une connexion de communication (Ethernet). Figure 4-14. Modulation/consigne à dist. par communication Modulation à distance par entrée analogique Cela configure la commande de chaudière pour recevoir un signal extérieur de 4-20 mA sur l’entrée I:2.3 pour commander l’allure de chauffe de la chaudière. Le signal est sur une échelle de 0 à 100%, (4 mA = allure minimale et 20 mA = allure maximale). Sélection du signal de modulation à distance par entrée analogique L’utilisateur a le choix entre l’IHM et l’entrée numérique pour activer la modulation à distance. Sélectionner <Digital Input> (Entrée numérique) si un autre système de commande doit activer la modulation à distance au moyen d’un signal d’entrée par contact isolé (120 Vca) sur l’entrée numérique I:5.14. Lorsque cette entrée est désactivée, la commande de chaudière revient en mode de commande locale de l’allure de chauffe. Si le mode de modulation à distance doit être activé manuellement, sélectionner <HMI> (IHM). La modulation à distance peut alors être activée en appuyant sur le bouton <Remote> (à distance) dans l’écran d’allure de chauffe. Si la PLC détecte un mauvais signal analogique, une alarme « Remote Modulation Signal Failure » (Défaillance du signal de modulation à distance) s’active et l’allure de chauffe revient au réglage LOCAL de l’IHM. Réf. 750-366 4-15 Section 4 — Configuration du système Hawk 1000 Figure 4-15. Sélection du signal de modulation à distance Modulation à distance par communication Cela configure la commande de chaudière pour recevoir un signal de modulation à distance directement par une connexion de communication (Ethernet). Les unités de modulation s’étendent de 0 à 100%. L’intégrité de la communication est déterminée par un signal de battement de cœur entre le système de commande et le système de gestion de bâtiment. Si une défaillance de communication est détectée, un message d’alarme « Remote Communications Failed » (Défaillance de communication à distance) s’affiche sur l’IHM et la modulation revient au réglage LOCAL de l’IHM. Consigne à distance par entrée analogique Cela configure la commande de chaudière pour recevoir un signal extérieur de 4-20 mA sur l’entrée I:2.3 pour faire varier le point de consigne de la chaudière. Remarque : La consigne à distance n’est pas permise sur les chaudières à vapeur de faible émission. Si la consigne à distance est sélectionnée, le signal analogique peut être converti en grandeur physique dans l’écran des alarmes et limites en fixant les valeurs d’échelle de consigne à distance (zéro et étendue) du signal 4-20 mA externe. Sélection du signal de consigne à distance par entrée analogique L’utilisateur a le choix entre l’IHM et l’entrée numérique pour activer la consigne à distance. Sélectionner <Digital Input> (Entrée numérique) si un autre système de commande doit activer la consigne à distance au moyen d’un signal d’entrée par contact isolé (120 Vca) sur l’entrée numérique I:5.14. Lorsque cette entrée est désactivée, la commande de chaudière revient en mode de commande locale du point de consigne. Si le mode de consigne à distance doit être activé manuellement, sélectionner <HMI Input> (Entrée IHM). La consigne à distance peut alors être activée en appuyant sur le bouton <Remote> (à distance) dans l’écran d’allure de chauffe. Si la PLC détecte un mauvais signal analogique, une alarme « Remote Setpoint Signal Failure » (Défaillance du signal de consigne à distance) s’active et le point de consigne revient au réglage LOCAL de l’IHM. Consigne à distance par communication Cela configure la commande de chaudière pour recevoir un signal de consigne à distance directement par une connexion de communication (Ethernet). La valeur de consigne est fournie en unité physique. L’intégrité de 4-16 Réf. 750-366 Hawk 1000 Section 4 — Configuration du système la communication est déterminée par un signal de battement de cœur entre le système de commande et le système de gestion de bâtiment. Si une défaillance de communication est détectée, un message d’alarme « Remote Communications Failed » (Défaillance de communication à distance) s’affiche sur l’IHM et le point de consigne revient au réglage LOCAL de l’IHM. ! Avertissement La commande à distance du point de consigne ne doit pas être utilisée sur certains systèmes de chaudière à faible émission. Les chaudières à faible émission peuvent être sensibles à la modification des valeurs de consigne d’exploitation. Consulter le représentant Cleaver-Brooks pour déterminer si la commande à distance du point de consigne est permise sur la chaudière considérée. Le non-respect de ces mesures de précaution peut entraîner des dégâts matériels, des blessures corporelles graves, voire la mort. Double point de consigne La commande par double point de consigne, souvent qualifiée de baisse de régime nocturne, permet à la commande de chaudière de basculer facilement du point de consigne principal (consigne 1) au point de consigne de bas régime (consigne 2). La consigne 1 est le point de consigne principal de la commande et constitue l’unique point de consigne disponible si l’option de double point de consigne n’est pas permissible (voir ci-dessous). La baisse de régime peut être déclenchée manuellement (depuis l’écran d’allure de chauffe de l’IHM) ou à distance (par l’activation d’un signal d’entrée par contact isolé de 120 Vca) sur l’entrée numérique I:5.14. Appuyer sur le bouton à droite de « Dual Set Point Selection By » (Sélection du double point de consigne par » pour alterner entre <HMI Input> (Entrée IHM) et <Digital Input> (Entrée numérique). L’option de double point de consigne n’est pas permise lorsque les options de modulation à distance ou de consigne à distance sont activées. Sélectionner <Yes> (Oui) pour Dual Setpoint pour activer la commande par double point de consigne. Cette option n’est pas permise sur les chaudières à vapeur à faible émission (<60 ppm). ! Avertissement La commande à double point de consigne ne doit pas être utilisée sur certains systèmes de chaudière à faible émission. Les chaudières à faible émission peuvent être sensibles à la modification des valeurs de consigne d’exploitation. Consulter le représentant Cleaver-Brooks pour déterminer si la commande à double point de consigne est permise sur la chaudière considérée. Le non-respect de ces mesures de précaution peut entraîner des dégâts matériels, des blessures corporelles graves, voire la mort. 4.4.6 Sélection des actionneurs Actionneur de recirculation des gaz brûlés (FGR) L’actionneur FGR doit être sélectionné (Yes) si le système en est équipé. Cet actionneur est disponible uniquement pour la commande à positionnement parallèle. Réf. 750-366 4-17 Section 4 — Configuration du système Hawk 1000 Actionneur 2 du combustible 1 Le paramètre Fuel 1 Actuator 2 doit être sélectionné (Yes) si le système est équipé de cet actionneur. Cet actionneur est disponible uniquement pour la commande à positionnement parallèle. Actionneur 2 du combustible 2 Le paramètre Fuel 2 Actuator 2 doit être sélectionné (Yes) si le système est équipé de cet actionneur. Cet actionneur est disponible uniquement pour la commande à positionnement parallèle. Figure 4-16. Sélection des actionneurs 4.4.7 Entraînement à fréquence variable (VFD) Type de VFD Sélectionner le type de VFD qui convient pour l’installation considérée. Les choix possibles sont None (Aucun), PowerFlex et Other Mfg (Autre marque). Sélectionner <PowerFlex> si le système est équipé de l’entraînement PowerFlex 400, PowerFlex 70 Enhanced ou PowerFlex 700 Vector. Tous ces types d’entraînement utilisent une commande et un retour de 4-20 mA. Dérivation de VFD Sélectionner l’option VFD Bypass (Yes) si l’installation considérée comporte une dérivation de VFD. Une courbe air/combustible doit être configurée pour chaque combustible pour le mode de dérivation. La dérivation de VFD permet au système de chaudière de maintenir le moteur de ventilateur en marche même si l’entraînement à fréquence variable est supprimé de la boucle pour une raison quelconque. 4-18 Réf. 750-366 Hawk 1000 Section 4 — Configuration du système Figure 4-17. Écran de VFD Entraînement à fréquence variable pour le ventilateur d’air de combustion Les entraînements à fréquence variable (VFD) présentent de nombreux avantages en termes de réduction des coûts énergétiques et d’extension de la durée de service des équipements mécaniques. L’entraînement à fréquence variable (VFD) en option régule la vitesse du moteur de ventilateur d’air de combustion aux fins d’améliorer le rendement de la chaudière et de réduire sa consommation électrique. 4.4.8 Options Analyseur d’oxygène L’analyseur d’oxygène (O2) permet de surveiller la concentration d’oxygène dans les gaz brûlés. L’analyseur d’O2 transmet un signal analogique à la commande. Ce signal d’O2 est utilisé pour les alarmes pour O2 bas, la mise à l’arrêt pour O2 bas et les calculs de rendement de la chaudière. La concentration d’O2 est affichée dans les écrans d’allure de chauffe et de vue d’ensemble de la chaudière. Figure 4-18. Analyseur d’O2 O2 Trim Réf. 750-366 4-19 Section 4 — Configuration du système Hawk 1000 La régulation de l’excès d’O2, ou O2 Trim, fait partie intégrante du système HAWK 1000. Cette fonction offre un contrôle supplémentaire des taux de mélange combustible/air dans l’éventualité de conditions atmosphériques défavorables ou de fluctuations du pouvoir calorifique du combustible. L’IHM comporte un écran O2 Trim qui affiche la concentration reélle d’O2 et les points de consigne d’O2. Cet écran permet l’affichage et l’étalonnage de la sonde d’oxygène Cleaver Brooks (CB) ainsi que l’ajustement des gains PID. L’écran de régulation de l’oxygène dans les gaz brûlés est accessible depuis l’écran principal. Figure 4-19. Écran de régulation d’O2 des gaz brûlés Mise à l’arrêt pour O2 bas La mise à l’arrêt pour O2 bas (Low O2 Shutdown) est une fonction qui permet d’arrêter la chaudière si la concentration d’O2 devient trop basse. Elle peut être activée ou désactivée en faisant alterner la valeur de « O2 Shutdown » (dans l’écran de configuration du système) entre <Yes> (Oui) et <No> (Non). Si elle est activée, le point de consigne et la durée de retard de la mise à arrêt pour O2 bas peuvent être ajustés depuis l’écran des alarmes et limites. Arrêt à chaud La fonction d’arrêt à chaud (Hot Standby) maintient l’eau dans la chaudière à une température minimale lorsqu’il n’y a aucune demande. Lorsqu’elle est active, la chaudière reste à son allure de chauffe minimale et s’allume et s’éteint en fonction du point de consigne de température d’eau de la fonction d’arrêt à chaud. Cette température de consigne est configurée dans l’écran des points de consigne (Setpoints) accessible depuis l’écran principal. La fonction d’arrêt à chaud s’active et se désactive en appuyant sur le bouton Hot Standby pour alterner entre <Yes> (Oui) et <No> (Non). Les écrans d’allure de chauffe et de vue d’ensemble de la chaudière indiquent si la chaudière est en mode d’arrêt à chaud. L’arrêt à chaud peut être démarré manuellement en appuyant sur <Force Hot Standby> (Forcer arrêt à chaud) sur l’écran d’allure de chauffe. La chaudière reste alors dans ce mode jusqu’à ce que ce bouton soit à nouveau enfoncé. Pour en savoir plus sur l’arrêt à chaud, voir Section 5 - Mise en service. 4-20 Réf. 750-366 Hawk 1000 Section 4 — Configuration du système Vue d’ensemble - Arrêt à chaud Forcer l’arrêt à chaud Figure 4-20. Arrêt à chaud Recalage sur la température extérieure (modèles à eau chaude seulement) Lorsque l’option Recalage sur la température extérieure (Outdoor Temperature Reset) est sélectionnée, une correction est appliquée au point de consigne d’exploitation en fonction de la température extérieure. Un transmetteur de température extérieure est requis sur l’entrée analogique 2.2 pour cette fonctionnalité. Lorsque la température extérieure est sélectionnée pour l’entrée analogique 2.2, la température extérieure est affichée dans l’écran de vue d’ensemble de la chaudière. Figure 4-21. Options Lorsque la fonction de recalage sur l’extérieur est sélectionnée, les points de consigne de température extérieure et de température de l’eau doivent être saisis depuis l’écran des points de consigne (voir Section 5.7 - Points de consigne) une fois la configuration du système terminée. Température de l’air de combustion La sonde de température de l’air de combustion transmet un signal de 4-20 mA à la commande. Le signal de température de l’air de combustion est utilisé dans les calculs de rendement de la chaudière et est affiché dans l’écran de vue d’ensemble de la chaudière. Un module d’entrée analogique est requis (connecteur 7). Réf. 750-366 4-21 Section 4 — Configuration du système Hawk 1000 Informations sur la chaudière Le nom du client, l’ID de la chaudière et le numéro de série de la chaudière peuvent être saisis dans le système. Ces renseignements sont affichés dans l’écran d’information système. Pour saisir ces informations, appuyer sur le bouton d’affichage de texte sous la description. Cela affiche un clavier alphanumérique. Figure 4-22. Informations sur la chaudière Une fois que les renseignements sont saisis, appuyer sur le bouton de retour chariot. L’ID de chaudière et le numéro de série sont limités à 20 caractères chacun, espaces compris. Si un pupitre Master Panel est utilisé dans le système, le nom du client, l’ID de chaudière et le numéro de série de la chaudière doivent être saisis une deuxième fois pour qu’ils apparaissent sur l’IHM Master Panel. Alarmes auxiliaires 1 à 3 Si le système comporte des alarmes auxiliaires, le texte qui s’affiche lorsque l’alarme est déclenchée peut être entré dans le système. Pour saisir ces informations, appuyer sur le bouton d’affichage de texte sous la description. Cela affiche un clavier alphanumérique. Une fois que les renseignements sont saisis, appuyer sur le bouton de retour chariot. Les textes d’alarme auxiliaire sont limités à 20 caractères chacun, espaces compris. L’alarme auxiliaire 1 doit être raccordée à l’entrée 13 du connecteur 1 L’alarme auxiliaire 2 doit être raccordée à l’entrée 14 du connecteur 1 L’alarme auxiliaire 3 doit être raccordée à l’entrée 15 du connecteur 1 Exemple : Si le texte entré pour l’alarme auxiliaire 1 est « Bas débit d’eau » et que l’entrée discrète I:1.13 est à l’état haut (On), le message affiché par l’IHM pour l’alarme auxiliaire 1 est « Aux 1 - Bas débit d’eau ». 4-22 Réf. 750-366 Hawk 1000 Section 4 — Configuration du système Figure 4-23. Entrées auxiliaires 4.4.9 Récapitulatif de la configuration Une fois que les paramètres de configuration du système ont été définis, ils peuvent être passés en revue dans les écrans récapitulatifs de la configuration du système. Remarque : Le bouton <Confirm Options> (Confirmer les options) n’est visible que s’il s’agit d’une nouvelle configuration du système ou qu’un paramètre de configuration du système marqué d’une astérisque a été modifié. Page 1 Page 2 Figure 4-24. Récapitulatif de la configuration Pour terminer la configuration du système, appuyer sur le bouton <Confirm Options> dans l’écran récapitulatif des options. Les paramètres de configuration peuvent être changés après l’installation de la commande HAWK 1000. Toutefois, pour nombre d’options, du matériel supplémentaire est nécessaire pour que la fonction soit utilisable. Voir le matériel nécessaire dans la section Nomenclature des pièces. Réf. 750-366 4-23 Section 5 Mise en service Mise en service des actionneurs . . . . . . . . . . . . . . . . . . . . . . . . . . . . . . . . . . . . . . . . . . . . . . 5-2 Réglage de la combustion - Positionnement parallèle . . . . . . . . . . . . . . . . . . . . . . . . . . . . . . . . 5-4 Enregistrer la purge . . . . . . . . . . . . . . . . . . . . . . . . . . . . . . . . . . . . . . . . . . . . . . 5-5 Enregistrer l’allumage . . . . . . . . . . . . . . . . . . . . . . . . . . . . . . . . . . . . . . . . . . . . . 5-6 Définir la courbe de combustion . . . . . . . . . . . . . . . . . . . . . . . . . . . . . . . . . . . . . 5-7 Réglage de la combustion - Positionnement monopoint . . . . . . . . . . . . . . . . . . . . . . . . . . . . . . 5-8 VFD ou O2 Trim . . . . . . . . . . . . . . . . . . . . . . . . . . . . . . . . . . . . . . . . . . . . . . . . 5-8 Sans VFD ni O2 Trim . . . . . . . . . . . . . . . . . . . . . . . . . . . . . . . . . . . . . . . . . . . . . 5-8 Réglage de la combustion - Bas/haut/bas . . . . . . . . . . . . . . . . . . . . . . . . . . . . . . . . . . . . . . . . 5-8 Écran d’allure de chauffe . . . . . . . . . . . . . . . . . . . . . . . . . . . . . . . . . . . . . . . . . . . . . . . . . . . 5-9 Alarmes et limites . . . . . . . . . . . . . . . . . . . . . . . . . . . . . . . . . . . . . . . . . . . . . . . . . . . . . . . . 5-11 O2 bas . . . . . . . . . . . . . . . . . . . . . . . . . . . . . . . . . . . . . . . . . . . . . . . . . . . . . . . 5-11 Pression de vapeur basse . . . . . . . . . . . . . . . . . . . . . . . . . . . . . . . . . . . . . . . . . . 5-11 Limiteur de taux de modulation, correction O2 max., arrêt à distance via communications . . . . . . . . . . . . . . . . . . . . . . . . . . . . . . . . . . . . . . . . . 5-12 Maintien en cas de basse température des gaz brûlés . . . . . . . . . . . . . . . . . . . . . . 5-12 Points de consigne . . . . . . . . . . . . . . . . . . . . . . . . . . . . . . . . . . . . . . . . . . . . . . . . . . . . . . . . 5-13 Point de consigne d’exploitation . . . . . . . . . . . . . . . . . . . . . . . . . . . . . . . . . . . . . . 5-13 Recalage sur la température extérieure (eau chaude seulement) . . . . . . . . . . . . . . . . 5-13 Retour à la veilleuse (CB 120E seulement) . . . . . . . . . . . . . . . . . . . . . . . . . . . . . . 5-14 O2 Trim . . . . . . . . . . . . . . . . . . . . . . . . . . . . . . . . . . . . . . . . . . . . . . . . . . . . . . . . . . . . . . . 5-15 Données de VFD . . . . . . . . . . . . . . . . . . . . . . . . . . . . . . . . . . . . . . . . . . . . . . . . . . . . . . . . . 5-16 Configuration Ethernet . . . . . . . . . . . . . . . . . . . . . . . . . . . . . . . . . . . . . . . . . . . . . . . . . . . . . 5-16 Avance/retard avec deux chaudières . . . . . . . . . . . . . . . . . . . . . . . . . . . . . . . . . . . . . . . . . . . . 5-17 Routine de protection contre les chocs thermiques . . . . . . . . . . . . . . . . . . . . . . . . . . . . . . . . . 5-18 www.cleaverbrooks.com Section 5 — Mise en service Hawk 1000 5.1 Mise en service des actionneurs Une fois que la configuration du système est terminée, le bouton <Calibrate Actuators> (Étalonner actionneurs) s’affiche sur l’écran principal avec la mention « Required » (Requis). Figure 5-1. Étalonnage des actionneurs requis Appuyer sur <Calibrate Actuators> pour accéder à l’écran de mise en service des actionneurs, où les actionneurs d’air, de combustible et recirculation des gaz brûlés peuvent être sélectionnés individuellement pour être mis en service. Sur cet écran, appuyer sur <Commission Actuator> (Mise en service actionneur) pour l’actionneur souhaité et lire l’écran de mise en garde qui suit. Dans cet exemple, il s’agit de la mise en service de l’actionneur d’air. Écran de mise en service d’actionneur Avertissement Figure 5-2. Mise en service d’actionneur REMARQUE : Toutes les courbes de combustion préalablement enregistrées pour le combustible actuel seront effacées au début du processus de mise en service de l’actionneur. Appuyer sur <Enable Air Actuator Commissioning> (Activer mise en service d’actionneur d’air) sur l’écran de mise en garde pour poursuivre. Sélectionner d’abord le sens de rotation de l’arbre d’actionneur. Il s’agit du sens de rotation pour ouvrir l’actionneur vu depuis la carte de circuit d’actionneur (ou le capot de la carte de circuit). 5-2 Part No. 750-366 Hawk 1000 Section 5 — Mise en service Figure 5-3. Rotation de l’actionneur Le sens de rotation par défaut est le sens antihoraire (CCW) pour l’air et tous les combustibles et le sens horaire (CW) pour la recirculation des gaz brûlés (FGR). Cet écran indique aussi le couple nominal (Torque Rating) de l’actionneur (lu par la PLC via Modbus). Appuyer sur <Next> (Suivant) après avoir confirmé le sens de rotation de l’actionneur. Enregistrer ensuite les positions ouverte et fermée de l’actionneur. À l’aide des boutons <Actuator Close/Open> (Ouvrir/fermer actionneur), amener l’actionneur en position totalement ouverte ou fermée (l’une ou l’autre position peut être enregistrée en premier). L’actionneur étant complètement ouvert (fermé), appuyer sur <Store Open/Close> (Enregistrer ouvert/fermé). Figure 5-4. Course de l’actionneur Remarque : Une rotation antihoraire (CCW) signifie que la position fermée est supérieure à la position ouverte. Une rotation horaire (CW) signifie que la position ouverte est supérieure à la position fermée. L’unité d’affichage de la position de l’actionneur est le degré x 10. La plage admissible est de 0 à 1100 unités (0 à 110 degrés). Les positions ouverte et fermée doivent être séparées de plus de 100 unités (10 degrés). Si cette condition n’est pas satisfaite, cela produit une erreur de type « Configuration Invalid » (Configuration non valable) et l’actionneur doit être reconfiguré. Lorsque des valeurs valables ont été saisies, le bouton <Save Air Actuator Configuration> (Enregistrer configuration d’actionneur d’air) s’affiche. Appuyer dessus pour valider les valeurs puis appuyer sur <Next Actuator> (Actionneur suivant) et répéter les étapes ci-dessus. Part No. 750-366 5-3 Section 5 — Mise en service Hawk 1000 Données non valables Enregistrer les données Figure 5-5. Confirmer l’étalonnage de l’actionneur 5.2 Réglage de la combustion - Positionnement parallèle Une fois que les actionneurs du combustible actuellement sélectionné sont étalonnés, le bouton <Set Combustion> (Régler la combustion) est accessible sur l’écran principal. Pour démarrer la procédure, appuyer sur <Set Combustion> et respecter la mise en garde qui s’affiche (accès réservé aux personnes compétentes). Écran principal Avertissement Figure 5-6. Début du réglage de la combustion Appuyer sur <I READ THE WARNING - I AM QUALIFIED> (J’ai lu l’avertissement - Je suit qualifié) pour poursuivre. Un autre écran de mise en garde s’affiche, informant l’utilisateur que le relais de limite d’exploitation de la chaudière sera désactivé durant le réglage de la combustion. Appuyer sur <Confirm Combustion Setup> (Confirmer le réglage de combustion) pour poursuivre. 2e avertissement 5-4 Part No. 750-366 Hawk 1000 Section 5 — Mise en service 5.2.1 Enregistrer la purge La première étape est d’enregistrer la position de purge. Un écran d’aide est prévu pour guider l’utilisateur durant l’enregistrement des positions de purge (et d’allumage) : Figure 5-7. Aide pour purge/allumage Pour que la position de purge soit valable, l’actionneur d’air doit être ouvert à plus de 80%. Pour positionner les actionneurs lors du réglage de la combustion, appuyer d’abord sur le bouton de l’actionneur souhaité dans l’écran de réglage de la combustion. Appuyer sur pour ajuster l’actionneur Figure 5-8. Réglage de la combustion Utiliser ensuite les boutons <Dec> (Diminuer) et <Inc> (Augmenter) pour amener l’actionneur d’air jusqu’à la position souhaitée. Part No. 750-366 5-5 Section 5 — Mise en service Hawk 1000 Figure 5-9. Ajuster l’actionneur Une fois la position de purge réglée, appuyer sur <Store Purge> (Enregistrer purger). À l’invite « Store Current Values? » (Enregistrer les valeurs actuelles?), appuyer de nouveau sur <Store Purge> pour confirmer ou sur <Cancel> (Annuler) pour réajuster. Figure 5-10. Enregistrer la purge Remarque : S’il y a un entraînement à fréquence variable (VFD), la valeur de purge de VFD est automatiquement fixée sur 100%. 5.2.2 Enregistrer l’allumage Une fois que la position de purge est réglée, le bouton <Store Lightoff> (Enregistrer allumage) est accessible sur l’écran de réglage de la combustion. Après avoir placé les actionneurs dans la position d’allumage, appuyer sur <Store Lightoff>. Une invite de confirmation s’affiche comme lors de l’enregistrement de la position de purge. Une fois que la purge et l’allumage sont tous deux définis, le bouton <Curve Setup> (Définir la courbe). Toutes les valeurs sauf celles du VFD doivent être inférieures à 25% pour pouvoir valider l’allumage. 5-6 Part No. 750-366 Hawk 1000 Section 5 — Mise en service Figure 5-11. Enregistrer l’allumage 5.2.3 Définir la courbe de combustion Un écran d’aide est prévu pour guider l’utilisateur durant l’opération de définition de la courbe de combustion : Figure 5-12. Aide pour le réglage de la combustion Pour définir la courbe de combustion, le brûleur doit être en marche. Si toutes les conditions préalables au démarrage de la chaudière sont satisfaites, le bouton-poussoir <Burner Start> (Démarrage brûleur) s’affiche sur l’écran de réglage de la combustion. Appuyer sur <Burner Start>; la séquence de purge s’exécute puis les actionneurs reviennent à leur position d’allumage. Appuyer sur <Lightoff> (Allumage). La séquence de surveillance de flamme exécute l’essai de veilleuse et de flamme principale puis le brûleur s’allume. Les actionneurs peuvent à présent être mis en position pour le premier point de référence. • 8 points au minimum doivent être enregistrés pour que la courbe soit valable (maximum admissible de 16 points). • Il n’est pas possible de sauter des points. • Les valeurs pour l’actionneur d’air et de combustible 1 doivent être supérieures aux valeurs précédentes pour qu’un point valable soit enregistré. • Appuyer sur <New Profile> (Nouveau profil) à tout moment pour effacer la courbe actuelle. • Une fois que la courbe de combustion est définie (8 points valables en mémoire), le bouton <Firing Rate> (Allure de chauffe) s’affiche à la place du bouton <Main> (Principal). Part No. 750-366 5-7 Section 5 — Mise en service Hawk 1000 • Appuyer sur <Pt Adv Enable> (Activer défilement de points) permet de se déplacer sur la courbe de combustion à l’aide de <Next> (Suivant) et <Prev> (Précédent) sans déplacer les actionneurs. Lorsque le défilement de points est désactivé, les actionneurs se déplacent jusqu’aux positions du point actuellement sélectionné. Figure 5-13. Courbe de combustion terminée 5.3 Réglage de la combustion - Positionnement monopoint 5.3.1 VFD ou O2 Trim Si VFD ou O2 Trim est sélectionné, le réglage de combustion est identique au positionnement parallèle, sauf que seul l’actionneur d’air est activé. Une minimum de 8 points est requis pour la courbe de combustion, jusqu’à un maximum de 16 points. 5.3.2 Sans VFD ni O2 Trim La courbe de combustion consiste en 2 points. Seul l’actionneur d’air est activé. Le point 1 correspond à l’allure minimale, le point 2 à l’allure maximale. 5.4 Réglage de la combustion - Bas/haut/bas Le mode de combustion bas/haut/bas n’est proposée que sur les chaudières Cleaver-Brooks modèle 4 et modèle 5. Le mode bas/haut/bas n’est proposé que pour le mazout (en tant que combustible 2). La courbe de combustion consiste en 2 points; seul l’actionneur d’air est activé. Le point 1 correspond à l’allure minimale, le point 2 à l’allure maximale. Un écran d’affichage/réglage des points de consigne est prévu à cet effet. Figure 5-14. Afficher/régler les points de consigne 5-8 Part No. 750-366 Hawk 1000 Section 5 — Mise en service Dans le mode de combustion bas/haut/bas, l’allure de chauffe de la chaudière est soit 0%, soit 100%. Les vannes de mazout s’ouvrent et se ferme en fonction du pourcentage de retour de l’actionneur d’air. Les points de consigne d’allure maximale et d’allure minimale sont limités par les points Marche chaudière et Arrêt chaudière. Lorsque la pression de vapeur est supérieure au point d’allure minimale, l’allure de chauffe passe à 0%. Lorsque la pression de vapeur est inférieure au point d’allure maximale, l’allure de chauffe passe à 100%. 5.5 Écran d’allure de chauffe Depuis l’écran d’allure de chauffe, il est possible d’alterner entre les modes d’exploitation manuelle et automatique des commandes de la chaudière. Si <Manual> (Manuel) est sélectionné, les actionneurs restent dans leurs positions actuelles jusqu’à ce qu’ils soient déplacés manuellement par l’opérateur à l’aides des boutons <Decrease> et <Increase> (Augmenter et Diminuer) sous Control Output (Sortie de commande). Figure 5-15. En mode automatique, la sortie de commande dépend de la demande; la position des actionneurs varie conformément à la courbe de combustion active. En mode automatique, la chaudière peut être placée de force à son allure minimale au moyen d’un signal de 120 Vca appliqué à l’entrée numérique I:5.4. La chaudière reste à son allure minimale jusqu’à la suppression de ce signal. Figure 5-16. L’écran d’allure de chauffe permet également la sélection du mode de point de consigne à distance ou de modulation à distance pour permettre l’interface avec un système de gestion de bâtiment ou autre système de commande. Part No. 750-366 5-9 Section 5 — Mise en service Hawk 1000 Figure 5-17. Dans l’éventualité d’un signal distant incorrect, un message d’alarme s’affiche à l’écran et la commande revient en mode Local/Auto. Le bouton <Adjust Gains> (Ajuster les gains) donne accès à l’ajustement PID du système. Les valeurs par défaut sont les suivantes : P=5, I=5, D=0. Figure 5-18. Ajuster les gains <Adjust Setpoint> (Ajuster le point de consigne) permet l’ajustement du point de consigne 1 et du point de consigne 2 (configuration à deux points de consigne). Figure 5-19. Ajuster le point de consigne <View Actuator> (Afficher les actionneurs) montre les valeurs de point de consigne et de retour pour tous actionneurs configurés. 5-10 Part No. 750-366 Hawk 1000 Section 5 — Mise en service Figure 5-20. Afficher les actionneurs Le bouton <Manipulate Actuators> (Manipuler les actionneurs) permet aux actionneurs de déplacer les actionneurs de 0 à 100% de l’allure de chauffe pour vérifier qu’ils se positionnent correctement à l’allure de chauffe actuelle. Pour utiliser cette fonctionnalité, l’interrupteur du brûleur doit être sur OFF (Arrêt) et l’allure de chauffe doit être en mode MANUEL. Durant la manipulation des actionneurs, la sortie et l’allure de chauffe ne sont pas limitées. 5.6 Alarmes et limites Les alarmes à paramètres configurables et les limites d’allure de chauffe/de consigne peuvent être modifiées depuis cet écran. Les paramètres configurables sont les suivants : 5.6.1 O2 bas Sélectionner les points Alarm (Alarme), Shutdown (Arrêt) et Alarm Delay (Retard d’alarme) sous Low O2 (O2 bas). L’alarme Low O2 n’est disponible qu’avec la sélection d’un analyseur d’O2. L’arrêt n’est disponible que s’il est sélectionné dans le menu de configuration. 5.6.2 Pression de vapeur basse Sélectionner Alarm Setpoint (Consigne d’alarme) et Audible Yes/No (Sonore Oui/non) sous Low Steam Pressure (Pression de vapeur basse). Un avertisseur ou une sonnerie d’alarme doit être disponible pour les alarmes sonores. Figure 5-21. Alarmes et limites O2 bas Figure 5-22. Alarmes et limites - Pression de vapeur basse Part No. 750-366 5-11 Section 5 — Mise en service Hawk 1000 5.6.3 Limiteur de taux de modulation, correction O2 max., arrêt à distance via communications Modulation Rate Limiter (Limiteur du taux de modulation) permet d’augmenter/diminuer le taux de variation de la sortie d’allure de chauffe. La valeur saisie correspond au nombre de secondes nécessaire à la sortie de commande pour passer de 0 à 100%. Maximum O2 Trim Correction (Correction maximale d’O2 Trim) est la valeur dont l’actionneur d’air et le VFD peuvent être corrigés en plus ou en moins (+/- 10% maximum). Remote Shutdown by Communications (Arrêt à distance via communications) permet de commander le démarrage et l’arrêt de la chaudière à distance. Si cette fonction est activée, le paramètre <On Comms Failure Shutdown Boiler?> (Arrêt de chaudière sur défaillance de communication?) définit ce que fait la chaudière en cas de défaillance des communications à distance (mise à l’arrêt ou maintien du dernier état). 5.6.4 Maintien en cas de basse température des gaz brûlés Cette option n’est disponible qu’avec la recirculation des gaz brûlés (FGR). Elle permet de choisir entre le maintien de la FGR seule (20 ppm ou moins) ou de la FGR et de l’allure de chauffe. La valeur « FGR Posn w/ Low Stk Temp » (Position FGR à basse tempér. gaz brûlés) doit être fixée pour chaque courbe de combustion (4 au maximum) et doit être inférieure au point d’allure minimale de FGR. Si l’option Stack Low Temp Hold est activée (Enable/Yes) et que la température des gaz brûlés est inférieure à la valeur de consigne « Stack Low Temp Hold / Set Point », la chaudière est autorisée à moduler alors que l’actionneur de FGR est amené à la position « FGR Posn w/Low Stk Temp ». Lorsque la température des gaz brûlés passe au-dessus du point de consigne et y reste pendant la durée « Delay Seconds » (Retard en secondes), la FGR est libérée et revient à la position commandée par l’allure de chauffe. 5-12 Part No. 750-366 Hawk 1000 Section 5 — Mise en service 5.7 Points de consigne 5.7.1 Point de consigne d’exploitation Figure 5-23. Point de consigne d’exploitation Cet écran permet de définir le point de consigne et le différentiel de marche/arrêt pour la pression de vapeur (température d’eau). Si deux points de consigne sont sélectionnés, le point de consigne d’exploitation 2 peut être saisi depuis l’IHM, mais les point On/Off (Marche/arrêt) sont calculés à l’aide du même dP/dT que le point de consigne 1. Set Point = point de consigne d’exploitation de pression de vapeur (température d’eau) On Point (Point de marche) = point de consigne + (On dP% x point de consigne)/100. Les valeurs admissibles pour On dP% vont de -50% à Off dP%. Off Point (Point d’arrêt) = point de consigne + (Off dP% x point de consigne)/100. Les valeurs admissibles pour Off dP% vont de On dP% à une valeur calculée telle que la valeur Off Point ne soit pas supérieure à la valeur de consigne de la soupape de sûreté. 5.7.2 Recalage sur la température extérieure (eau chaude seulement) Si l’option Outdoor Temperature Reset (Recalage température extérieure) a été sélectionnée durant la configuration du système, les points de consigne souhaités doivent être entrés ici. Figure 5-24. Écran de recalage sur la température extérieure Lorsqu’elle est activée, l’option Hot Standby (Arrêt à chaud) déclenche la chaudière si la température de l’eau de l’enveloppe chute de 2,75 °C (5 °F) en dessous de la valeur « Hot Standby Temp » (Temp. d’arrêt à chaud). La chaudière fonctionne alors à son allure minimale jusqu’à ce que la température de l’eau de l’enveloppe Part No. 750-366 5-13 Section 5 — Mise en service Hawk 1000 atteint la valeur « Hot Standby Temp », puis la chaudière s’éteint. L’entrée I:5.7 ALFCO doit être à l’état bas (Off) pour démarrer l’arrêt à chaud. L’arrêt à chaud peut être démarré manuellement en appuyant sur <Force Hot Standby> (Forcer arrêt à chaud) sur l’écran d’allure de chauffe. COURBE DE RECALAGE SUR L’EXTÉRIEUR La consigne est une fonction linéaire de la température extérieure. La plage du transmetteur de température extérieure est la suivante : 4 mA = -45,5 °C (-50 °F), 20 mA = 482,2 °C (900 °F). Dans cet exemple : Limite inf. plage temp. ext. = 0 °F Limite sup. plage consigne = 200 °F Limite sup. plage temp. ext. = 60 °F Limite inf. plage consigne = 180 °F 205 200 195 Consigne 190 185 180 Température extérieure 175 -60 -40 -20 0 20 40 60 80 Figure 5-25. Courbe de recalage sur la température extérieure 5.7.3 Retour à la veilleuse (CB 120E seulement) L’option de retour à la veilleuse, ou RTP (Revert to Pilot), réduit les cycles de marche par l’élimination de la séquence de purge. Lorsque la fonction RTP est démarrée, la chaudière revient à son allure minimale, la sortie O:6.4 est activée et le signale RTP est envoyé au système de surveillance de flamme (FSG). La séquence RTP est gérée par le FSG : la veilleuse est activée puis, après confirmation d’allumage de la veilleuse, la vanne de gaz principale est désactivée et la chaudière reste en mode de veilleuse. Lors du retour de la demande ou si l’entrée numérique J:5.7 est à l’état haut (On), la vanne de gaz principale est activée. Lorsque la RTP est activée, un indicateur « Rev to Pilot » s’affiche sur les écrans de vue d’ensemble et d’allure de chauffe. Démarrage par variable de processus Si l’option de démarrage par variable de processus (Initiate by Process Variable) est sélectionnée, la fonction de retour à la veilleuse (RTP) est démarrée lorsque la pression de vapeur est supérieure ou égale à la valeur « Revert to Pilot Pressure » (pression RTP) et désactivée lorsque la pression de vapeur est inférieure à la valeur « On Point » (point de marche) de la chaudière. Revert to Pilot Pressure = Off Point (point d’arrêt) - (Revert to Pilot dP% x Off Point) [garantit que le réglage de RTP est toujours inférieur ou égal au point d’arrêt de la chaudière]. 5-14 Part No. 750-366 Hawk 1000 Section 5 — Mise en service La pression RTP (Revert to Pilot Pressure) doit être supérieure à la fois à la consigne d’exploitation (Setpoint) et au point de marche (On Point) de la chaudière. Figure 5-26. Retour à la veilleuse Démarrage par entrée numérique Si l’option de démarrage par entrée numérique (Initiate by Digital Input) est sélectionnée, l’écran ci-dessus ne s’affiche pas; la fonction RTP est démarrée lorsque l’entrée numérique I:5.7 ALFCO est à l’état bas (Off). 5.8 O2 Trim Si l’option O2 Trim (régulation de l’excès d’O2) est sélectionnée et qu’un analyseur spécifié durant la configuration du système, le bouton <Flue Gas O2 Control> (Régulation O2 de gaz brûlés) s’affiche sur l’écran principal. Figure 5-27. La régulation de l’excès d’O2 s’effectue au moyen de l’actionneur d’air, pour par l’entraînement à fréquence variable (VFD) le cas échéant (si le VFD est en dérivation, l’actionneur d’air est utilisé). Un mode d’exploitation manuel est prévu à des fins d’essai et de diagnostic. L’analyseur d’oxygène CB doit être étalonné lors de la mise sous tension ou s’il s’est écoulé une semaine depuis le dernier étalonnage. Si l’analyseur Yokogawa est utilisé, la PLC attend un signal « Capteur OK » de l’analyseur à l’entrée I:5.2. Une fois que le capteur O2 est étalonné ou que l’entrée « Capteur OK » est activée, le point de consigne d’O2 est défini lors de la définition des courbes de combustion. La régulation d’O2 est assurée par une commande PID. Les valeurs peuvent être modifiées en appuyant sur <Adjust Gains> (Ajuster les gains). Les gains par défaut sont P=3, I=5 et D=0. Part No. 750-366 5-15 Section 5 — Mise en service Hawk 1000 5.9 Données de VFD Sur les systèmes à VFD, le bouton <Drive Data> (Données de l’entraînement) commande l’affichage d’un écran en lecture seule indiquant les valeurs de sortie et de retour du VFD, les consignes de limite basse, limite haute et allumage et la fréquence de marche actuelle. 5.10 Configuration Ethernet Des chaudières multiples sur un même réseau Ethernet nécessitent des adresses IP uniques. Pour modifier la configuration d’une chaudière, appuyer sur le champ souhaité dans la zone « Set New Ethernet Configuration » (Définir nouvelle configuration Ethernet). Si l’utilisateur est connecté au niveau de privilège correct, un clavier numérique s’affiche. Saisir la nouvelle valeur puis appuyer sur la touche Enter (ou utilise le clavier PV+). Pour finir, aller à <Set Enet Config> (Définir config. Ethernet) et, à l’invite « Set PLC Ethernet Port Configuration? » (Définir la configuration de port Ethernet de PLC?), appuyer sur <Yes> (Oui). Figure 5-28. Après avoir défini une nouvelle configuration Ethernet, la communication entre l’IHM et la PLC sera perdue et doit être rétablie depuis l’IHM. Pour plus de renseignements, voir la « Procédure de chargement et de configuration d’un PV+ » (sur le portail CB). 5-16 Part No. 750-366 Hawk 1000 Section 5 — Mise en service 5.11 Avance/retard avec deux chaudières La commande Hawk 1000 utilise deux points de consigne pour réaliser une commande « avance/retard » dans un schéma de commande à deux chaudières. Les points de consigne reposent sur la pression de vapeur locale de chaque chaudière (pour les chaudières à vapeur). La chaudière « principale » comporte un commutateur de sélection qui assigne le statut d’avance ou de retard à chacune des deux chaudières. Il y a deux contacts pour le sélecteur à deux positions. L’option de double point de consigne par entrée numérique doit être sélectionnée lors de la configuration du système. Le premier contact sert à fournir une entrée numérique à la PLC de la chaudière n°1 (I:5/14) pour désigner cette chaudière en tant que chaudière principale. Le deuxième contact du sélecteur sert à fournir une entrée numérique à la PLC de la chaudière n°2 (I:5/14) pour désigner cette chaudière en tant que chaudière principale. Lorsque l’entrée est activée, le point de consigne 2 est sélectionné. Le point de consigne 2 est utilisé pour le fonctionnement de la chaudière lorsqu’elle est sélectionnée en tant qu’unité « retard ». Cette sélection définit laquelle des chaudières doit utiliser le point de consigne 1 et laquelle le point de consigne 2. Les deux chaudières démarrent et s’arrêtent alors en fonction de ces points de consigne. Les valeurs de consigne sont définies dans l’écran de pupitre. Il est important que le point de consigne 1 soit supérieur au point de consigne 2. La commande Hawk 1000, toutefois, n’offre pas de modulation en unisson. La Hawk 1000 n’utilise pas de transmetteur de pression de vapeur (ou de température d’eau chaude) de collecteur pour les commandes en avance/retard, mais uniquement le transmetteur de pression de vapeur (ou de température d’eau chaude) locale sur la chaudière. Figure 5-29. Double point de consigne, sélection du double point de consigne Chaudière n°1 Avance Chaudière n°2 Avance Chaudière n°1 120 Vca Chaudière n°1 I5/14 Chaudière n°2 120 Vca Chaudière n°2 I5/14 Figure 5-30. Câblage avance/retard à 2 chaudières, typique Part No. 750-366 5-17 Section 5 — Mise en service Hawk 1000 5.12 Routine de protection contre les chocs thermiques Chaudières à vapeur La protection contre les chocs thermiques est activée lorsque la température réelle de l’eau est inférieure à 60% de la température de saturation au point de consigne. La limite maximale de CV pour PID repose sur la température de l’eau et est déterminée par un générateur de fonction. Si la chaudière est en mode de protection contre les chocs thermiques, que la condition de retour à la modulation hors FSG est vraie et que la température de l’eau est supérieure au réglage de température de coupure de l’arrêt à chaud (Hot Standby)*, alors la temporisation de priorité sur la protection contre les chocs thermiques est activée. Cette temporisation est réglée sur 126 secondes. Le bit de fin de cette temporisation remet la temporisation à zéro et augmente d’une unité le compteur de priorité de chocs thermiques. La valeur cumulée du compteur est comparée à la sortie du générateur de fonction et la plus élevée des deux valeurs est choisie en tant que limite maximale pour CV. Chaque fois que l’échelon de choc thermique devient vrai, la sortie du générateur de fonction est affectée de la valeur cumulée du compteur. La routine de protection contre les chocs thermiques est désactivée lorsque le température de l’eau chaude atteint 90% de la température de saturation au point de consigne. Elle n’est pas activée avant que la température chute en dessous de 60% avec la borne de vanne de combustible désexcitée. Si la vanne de combustible a été désexcitée pendant plus de 8 heures, la protection contre les chocs thermiques s’active. Chaudières à eau chaude La protection contre les chocs thermiques est activée lorsque la température réelle de l’eau est inférieure à la température minimale (66 °C/150 °F pour Firetube, 49 °C/120 °F pour FLX). La limite maximale de CV pour PID repose sur la température de l’eau et est déterminée par un générateur de fonction. Si la chaudière est en mode de protection contre les chocs thermiques, que la condition de retour à la modulation hors FSG est vraie et que la température de l’eau est supérieure au réglage de température de coupure de l’arrêt à chaud (Hot Standby)*, alors la temporisation de priorité sur la protection contre les chocs thermiques est activée. Cette temporisation est réglée sur 60 secondes. Le bit de fin de cette temporisation remet la temporisation à zéro et augmente d’une unité le compteur de priorité de chocs thermiques. La valeur cumulée du compteur est comparée à la sortie du générateur de fonction et la plus élevée des deux valeurs est choisie en tant que limite maximale pour CV. Chaque fois que l’échelon de choc thermique devient vrai, la sortie du générateur de fonction est affectée de la valeur cumulée du compteur. La routine de protection contre les chocs thermiques est désactivée lorsque le température de l’eau chaude atteint 90% du point de consigne. Elle n’est pas activée avant que la température chute en dessous de la température minimale avec la borne de vanne de combustible désexcitée. Si la vanne de combustible a été désexcitée pendant plus de 8 heures, la protection contre les chocs thermiques s’active. *Si la vanne de combustible est activée pendant plus de 1 heure (vapeur) ou de 10 minutes (eau chaude) et que la température de l’eau est toujours inférieure au réglage de la température d’arrêt à chaud. L’allure de chauffe commence à augmenter progressivement comme décrit. 5-18 Part No. 750-366 Section 6 Diagnostics et dépannage Contrôle et diagnostics du système . . . . . . . . . . . . . . . . . . . . . . . . . . . . . 6-2 Vue d’ensemble de la chaudière . . . . . . . . . . . . . . . . . . . . . . . . 6-2 Commande de brûleur . . . . . . . . . . . . . . . . . . . . . . . . . . . . . . . 6-2 Informations sur le système . . . . . . . . . . . . . . . . . . . . . . . . . . . 6-3 Informations sur la PLC . . . . . . . . . . . . . . . . . . . . . . . . . . . . . . 6-3 Écrans de diagnostic . . . . . . . . . . . . . . . . . . . . . . . . . . . . . . . . 6-4 État de la PLC . . . . . . . . . . . . . . . . . . . . . . . . . . . . . . . . . . . . . . . . . . . . 6-4 www.cleaverbrooks.com Section 6 — Diagnostics et dépannage Hawk 1000 6.1 Contrôle et diagnostics du système 6.1.1 Vue d’ensemble de la chaudière La commande Hawk 1000 comporte diverses fonctionnalités de contrôle des performances du système et de diagnostic des problèmes. L’écran de vue d’ensemble de la chaudière, accessible depuis l’écran principal, affiche les données d’exploitation principales de la chaudière. Figure 6-1. Écran de vue d’ensemble 6.1.2 Commande de brûleur L’écran de commande de brûleur fournit des données relatives au système de surveillance de flamme installé (CB780 ou CB120). Commande de brûleur - CB780 Commande de brûleur - CB120 Figure 6-2. Écrans de commande de brûleur On y voit l’état du système de surveillance de flamme, ainsi que l’état des entrées qui permettent le démarrage de la chaudière. Les entrées d’état de surveillance de flamme et de chaudière suivantes sont affichées dans l’écran de commande de brûleur : Interrupteur de brûleur - (Burner Sw) Indique la position de l’interrupteur de brûleur. Demande - (Load Demand) Lors du démarrage de la chaudière, il y a une demande si la pression (vapeur) ou température (eau chaude) du système est inférieure à la consigne de marche. Lorsque la pression/température 6-2 Part No. 750-366 Hawk 1000 Section 6 — Diagnostics et dépannage du système dépasse la consigne d’arrêt, l’écran affiche « No Demand » (Pas de demande). Lorsque la pression/ température du système passe en dessous de la consigne de marche, « Load Demand » s’affiche à nouveau. Limites - (Limits OK) Ceci est une indication de l’état des asservissements courants dans la chaudière. Asservissement externe - (Ext Interlk) Entrée de retour d’un asservissement externe. En présence d’une demande et si l’interrupteur et les contacteurs de limite du brûleur sont fermés, la commande HAWK 1000 comporte des contacts isolés (2,5 A sous 125 Vca) pour la sortie vers un dispositif asservis externe (registre d’air extérieur, pompe de circulation, par ex.). La chaudière démarre une fois que l’asservissement externe est confirmé. Remarque : L’asservissement externe doit être court-circuité s’il n’est pas utilisé. ALFCO - Assured Low Fire Cut-Off (Coupure assurée à l’allure minimale). Un contact démarrage-arrêt isolé externe peut être prévu pour mettre la chaudière à l’arrêt. Ce contact amène la chaudière à son allure minimale préalablement à la mise à l’arrêt. Remarque : L’entrée ALFCO doit être court-circuitée si elle n’est pas utilisée. 6.1.3 Informations sur le système Appuyer sur <System Information> (Informations sur le système) depuis l’écran principal pour y accéder. Cet écran présente des informations d’identification de la chaudière, les programmes actuellement chargés pour la PLC et l’IHM, la durée et les cycles écoulés depuis le dernier démarrage et les données d’adresse de réseau. Figure 6-3. Informations sur le système 6.1.4 Informations sur la PLC Figure 6-4. Informations sur la PLC Part No. 750-366 6-3 Section 6 — Diagnostics et dépannage Hawk 1000 Cet écran reproduit les voyants d’état de la L24 et affiche en plus la version courante du firmware de PLC, le numéro de série et la position du commutateur à clé de la PLC. 6.1.5 Écrans de diagnostic Appuyer sur <Diagnostic> dans l’écran principal pour accéder à l’écran de diagnostic. Sélectionner un élément de l’écran pour afficher une vue détaillée du programme logique correspondant. Les éléments en vert sont à l’état VRAI, ceux en blanc à l’état FAUX. Figure 6-5. Écran de diagnostic 6.2 État de la PLC La L24E comporte une série de voyants multi-états pour indiquer l’état d’exploitation et les activités de communication du système de commande. Voir les tables ci-dessous. Table 1: Voyants d’état de la PLC Indicateur État DESCRIPTION RUN Éteint La commande est en mode de programmation ou d’essai. FORCE I/O 6-4 Vert La commande est en mode de marche. Éteint Aucune balise ne contient de valeur d’E/S assignée de force. L’assignation forcée des E/S est inactive (désactivée). Jaune L’assignation forcée des E/S est active (activée). Des valeurs d’E/S assignées de force peuvent ou non être présentes. Jaune clignotant Une ou plusieurs adresses d’entrée ou de sortie ont été affectées de force à l’état haut (On) ou bas (Off) mais l’assignation forcée n’a pas été activée. Éteint La commande ne contient pas de projet. Vert La commande communique avec tous les périphériques de sa configuration d’E/S. Vert clignotant Un ou plusieurs périphériques de la configuration d’E/S de la commande ne répondent pas. Rouge clignotant Le système est dans l’une des situations suivantes : • La commande ne communique avec aucun des périphériques. • Une erreur s’est produite dans la PLC. Part No. 750-366 Hawk 1000 Section 6 — Diagnostics et dépannage Table 1: Voyants d’état de la PLC (Suite) OK Éteint Pas d’alimentation électrique. Vert La commande est OK. Vert clignotant La commande est en train d’enregistrer un projet ou de charger un projet depuis la carte SD. Rouge La commande a détecté une erreur majeure non récupérable et a effacé le projet de la mémoire. Rouge clignotant L’une des situations suivantes : • Le firmware de la commande doit être mis à jour. • Une erreur majeure récupérable s’est produite dans la commande. • Une erreur majeure non récupérable s’est produite dans la commande et a effacé le programme de la mémoire. • Une mise à jour du firmware de la commande est en cours. Vert pâle à rouge Enregistrement dans une mémoire Flash lors de la mise à l’arrêt. Table 2: Voyants de communication de la PLC Indicateur État DESCRIPTION État du réseau Ethernet (NS) Éteint Le port n’est pas initialisé; il n’a pas d’adresse IP et fonctionne en mode BOOTP ou DHCP. Vert Le port a une adresse IP et les connexions CIP sont établies. État des liaisons Ethernet (LINK 1/ LINK 2) État d’activité de la carte SD (SD) Part No. 750-366 Vert clignotant Le port a une adresse IP mais aucune connexion CIP n’est établie. Rouge Le port a détecté que l’adresse IP attribuée est déjà utilisée. Rouge/vert clignotant Le port exécute sa séquence d’autocontrôle de démarrage. Éteint Le système est dans l’une des situations suivantes : • Pas de liaison. • Port désactivé par l’administrateur. • Port désactivé parce qu’un état d’erreur d’anneau rapide a été détecté (LINK2). Vert Le système est dans l’une des situations suivantes : • Une liaison de 100 Mbits/s (semi-duplex ou duplex intégral) existe, pas d’activité. • Une liaison de 10 Mbits/s (semi-duplex ou duplex intégral) existe, pas d’activité. • Le réseau en anneau fonctionne normalement et la PLC est le superviseur actif. • Le réseau en anneau a rencontré une rare erreur partielle de réseau et la PLC est le superviseur actif. Vert clignotant Le système est dans l’une des situations suivantes : • Une liaison de 100 Mbits/s existe et il y a une activité. • Une liaison de 10 Mbits/s existe et il y a une activité. Éteint Il n’y a aucune activité vers la carte SD. Vert clignotant Lecture ou écriture sur la carte SD par la commande. Rouge clignotant La carte SD ne comporte pas de système de fichier correct. 6-5 Section 6 — Diagnostics et dépannage 6-6 Hawk 1000 Part No. 750-366 Section 7 Nomenclature des pièces PLC, E/S, IHM Qté Référence 1 880-06082-000 Description 1 833-10039-000 Processeur de PLC 1 833-10040-000 Écran tactile compact PV+ 4 pouces avec (étiquette 118-04514-000 comprise) 1 833-02842-000 Module d’entrée numérique 1 833-02872-000 Module de relais 1 833-03099-000 Module Modbus SM2 2 826-00111-000 Câble Ethernet 1 832-02404-000 Alimentation électrique 120 W, (pour PLC, PV+ et entrées analogiques) 1 832-02037-000 Alimentation électrique 50 W (pour Modbus), utiliser 120 W pour actionneur 50 Nm 1 848-01623-000 Armoire 60 x 30 x 10, sans ouverture défonçable (les conversions utilisent une taille différente) 1 983-00083-000 6A 1 836-00620-000 Qté 1 (ajouter un autre si un réchauffeur pour mazout n° 6 est requis) 1 118-03173-000 4 po x 16 po 1 001-01476-000 Orion, OA109-12POT/DIN 1 817-00239-000 Sonnerie d’alarme Kit Hawk 1000 - à commander en tant que kit complet seulement ACTIONNEURS Qté Référence 1 945-00259-000 Description Modbus FX04-1, 3 pi-lb (4 Nm) (pour vannes de combustible et FGR, sauf applications à couple élevé) 1 945-00260-000 Modbus FX20-1, 15 pi-lb (20 Nm) (pour registre d’air de combustion, sauf applications à couple élevé) 1 945-00261-000 Modbus FX50-1, 37 pi-lb (50 Nm) 600 po 826-00205-000 Câble 5 conducteurs, 18 AWG 826-00206-000 Connecteur femelle droit, raccord vissé de 7/8 po - Deux requis par actionneur www.cleaverbrooks.com Section 7 — Nomenclature des pièces Hawk 1000 DIVERS Qté Référence 1 833-02835-000 Description Module d’entrée de courant analogique 1769-IF4 (requis pour option O2 Trim, VFD ou Temp. air de combustion) 1 833-10116-000 Routeur appareils Ethernet 9300-ENA 1 817-05166-000 Sonde de température 8 po, -50 à 900 °F 1 833-09181-000 Commutateur Ethernet, Rockwell Stratix 5 ports, 1783-US05T 1 833-09163-000 Commutateur Ethernet, Rockwell Stratix 8 ports, 1783-US08T 1 817-05166-000 Sonde de température 8 po, -50 à 900 °F 1 008-02998-000 Monture de transmetteur de recalage extérieur 1 836-00627-000 Kit complet - Sélecteur gaz mazout 1 Système de surveillance de flamme (FSG) Qté Description CB-780E avec kit scanneur IR 1 833-03517-000 Programmateur CB-780E 1 833-02725-000 Support inférieur de câblage 1 833-03495-000 Amplificateur infrarouge 1 833-02730-000 Carte de temporisation de purge 1 817-04133-000 Scanneur IR 817-1742 880-02118-000 CB-780E avec kit scanneur UV 833-03517-000 Programmateur CB-780E 1 833-02725-000 Support de câblage 1 833-02724-000 Amplificateur UV 1 833-02730-000 Carte de temporisation de purge 1 817-01743-000 Détecteur de flamme UV 1 7-2 Référence 880-02117-000 880-02097-000 CB-780E avec kit scanneur IR 1 833-03708-000 Châssis/amplificateur 1 833-03153-000 Support de câblage ouverte avec bornier 1 833-03143-000 Programmateur 1 833-03151-000 Affichage 1 833-03516-000 Câble de communication ED-512, longueur 4 pieds 1 817-01933-000 Scanneur IR 817-2261 880-02096-000 CB-780E avec kit scanneur UV 1 833-03135-000 Châssis/amplificateur 1 833-03153-000 Support de câblage ouverte avec bornier 1 833-03143-000 Programmateur 1 833-03151-000 Affichage 1 833-03516-000 Câble de communication ED-512, longueur 4 pieds 1 817-02262-000 Détecteur UV Part No. 750-366 Hawk 1000 Section 7 — Nomenclature des pièces TRANSMETTEURS DE VAPEUR Qté Référence 1 817-04866-000 Description E&H PMC131-A22F1Q4H 1 817-00001-000 E&H PMC131-A22F1Q4N 1 817-04867-000 E&H PMC131-A22F1Q4R 1 817-04868-000 E&H PMC131-A22F1Q4S 1 817-04869-000 E&H PMC131-A22F1Q4T 1 817-04873-000 PMP51-1CQW9/0 (comprend une vanne d’isolement) 1 817-00002-000 PMP51-1R5E5/0 (vanne d’isolement comprise) 1 817-04874-000 PMP51-1JAN0/0 (vanne d’isolement comprise) 1 817-04875-000 PMP51-E9K7/115 (vanne d’isolement comprise) 1 817-04876-000 PMP51-E9K7/101 (préciser la plage) (vanne comprise) 1 817-04877-000 PMP51-E9K7/139 (préciser la plage) (vanne comprise) 1 817-04878-000 PMP51-E9K7/125 (préciser la plage) (vanne comprise) 1 817-09768-000 PMP51-E9K7/142 (vanne d’isolement comprise) 1 817-05167-000 E&H, TH13-1A13X1BBA1AK, NON HART, puits thermo. 2,5 po, -50 à 900 °F 1 817-05166-000 E&H, TH11-B8CBBA1AK4, NON HART, sonde 8 po, -50 à 900 °F Transmetteurs de vapeur (en option) EAU CHAUDE Qté Référence 1 817-09776-000 Sonde thermo. 4,5 po, plage +50 à 300 °F Description 1 817-09777-000 Sonde thermo. 4,5 po, plage -50 à 900 °F 1 817-09778-000 Sonde thermo. 4,5 po, plage +50 à 500 °F 1 817-09777-000 Sonde thermo. 4,5 po, plage -50 à 900 °F O2 TRIM Qté Référence Description 1 985-00130-000 1 656-07576-000 1 817-05166-000 E&H, TH11-B8CBBA1AK4, NON HART, sonde 8 po, -50 à 900 °F Mesure O2 seulement ou Air Trim Sonde et analyseur O2 622-00027-000 Mesure O2 seulement ou Air Trim 1 880-01847-000 Contrôleur ECM avec capteur large bande NTK et faisceau de câble 1 817-05166-000 E&H, TH11-B8CBBA1AK4, NON HART, sonde 8 po, -50 à 900 °F 1 040-00735-000 Boîtier de sonde d’échantillonnage d’O2 1 832-02404-00 Alimentation électrique O2 Trim 120 W Part No. 750-366 7-3 Section 7 — Nomenclature des pièces 7-4 Hawk 1000 Part No. 750-366 ">
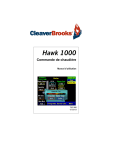
Link público atualizado
O link público para o seu chat foi atualizado.