Pfeiffer GSD 350 OmniStar/ThermoStar - Gas Analysis System Mode d'emploi
PDF
Scarica
Documento
MANUEL DE L'UTILISATEUR FR Traduction d'original GSD 350 OMNISTAR ∣ THERMOSTAR Système d’analyse du gaz Cher client, Nous vous remercions d’avoir opté pour un produit Pfeiffer Vacuum. Votre nouveau système d’analyse du gaz est conçu pour vous donner entière satisfaction pour votre application, de par sa conception rigoureuse et son parfait fonctionnement. La marque Pfeiffer Vacuum, synonyme de techniques du vide performantes, se décline en une gamme exhaustive et variée de produits de grande qualité, assortis d’un service client irréprochable. Forts de cette expérience pratique étendue, nous avons compilé une multitude d’informations qui peuvent contribuer à une implémentation efficace et à votre sécurité personnelle. Sachant que notre produit doit vous permettre d’éviter des arrêts de production coûteux, nous sommes confiants qu’il pourra vous offrir une solution pour une implémentation efficace et fiable de votre application individuelle. Veuillez lire ce manuel de l'utilisateur avant de mettre votre produit en service pour la première fois. Si vous avez des questions ou suggestions, n’hésitez pas à nous contacter par e-mail à l’adresse info@pfeiffer-vacuum.de. Vous trouverez d’autres manuels de l'utilisateur de Pfeiffer Vacuum dans le Centre de téléchargement sur notre site Internet. Exclusion de responsabilité Ce manuel d'instructions décrit tous les modèles et variantes de votre produit. Noter que votre produit peut ne pas être équipé de toutes les fonctionnalités décrites dans ce manuel. Pfeiffer Vacuum adapte constamment ses produits sans préavis. Veuillez noter que le manuel d'utilisation en ligne peut différer du document imprimé, fourni avec votre produit. D'autre part, Pfeiffer Vacuum n'assume aucune responsabilité pour les dommages résultant d'une utilisation contraire à l'usage prévu, ou d'une utilisation définie comme mauvaise utilisation prévisible. Droits d’auteur (Copyright) Ce document est la propriété intellectuelle de Pfeiffer Vacuum et tous les contenus de ce document sont protégés par le droit d'auteur. Ils ne peuvent être copiés, modifiés, reproduits ou publiés sans l'autorisation écrite préalable de Pfeiffer Vacuum. Nous nous réservons le droit de modifier les données techniques et les informations contenues dans ce document. 2/122 Table des matières Table des matières 1 A propos de ce manuel 1.1 Validité 1.1.1 Documents applicables 1.1.2 Variantes 1.2 Groupe cible 1.3 Conventions 1.3.1 Instructions dans le texte 1.3.2 Pictogrammes 1.3.3 Autocollants sur le produit 1.3.4 Orientation gauche/droite 1.3.5 Abréviations 1.4 Justificatif de marque 10 10 10 11 12 12 12 12 13 14 14 15 2 Sécurité 2.1 Consignes générales de sécurité 2.2 Consignes de sécurité 2.3 Mesures de sécurité 2.4 Limites d’utilisation du produit 2.5 Utilisation conforme 2.6 Utilisation incorrecte envisageable 2.7 Qualification personnelle 2.7.1 Garantir la qualification du personnel 2.7.2 Qualification du personnel pour la maintenance et la réparation 2.7.3 Formation avancée avec Pfeiffer Vacuum 16 16 16 19 20 20 21 21 21 22 22 3 Description du produit 3.1 Description fonctionnelle 3.1.1 OmniStar 3.1.2 ThermoStar 3.1.3 Version pour gaz corrosifs 3.2 Commandes et indicateurs 3.2.1 Version avec écran 3.2.2 Version sans écran 3.3 Configuration de l’unité 3.3.1 Instrument fondamental 3.3.2 Zone de connexion 3.3.3 Système d’admission de gaz 3.3.4 Unité de calibration 3.3.5 Système côté vide élevé 3.3.6 Système de vide primaire 3.3.7 Système de purge de gaz neutre 3.3.8 Unité d’analyse de gaz 3.3.9 Chauffage et isolation 3.3.10Composants électroniques 3.4 Identification du produit 3.5 Volume de livraison 23 23 23 24 24 24 24 25 26 26 26 27 28 29 29 30 30 31 33 34 34 4 Transport et stockage 4.1 Transport du produit 4.2 Stockage du produit 36 36 37 5 Installation 5.1 Assurer la ventilation 5.2 Retrait de la protection pour le transport de la pompe à membrane 5.3 Établissement de la connexion Ethernet 5.4 Raccordement de la conduite d’échappement 38 38 38 39 39 3/122 Table des matières 4/122 5.4.1 Sectionnement du tuyau de gaz d'échappement 5.4.2 Raccordement du tuyau de gaz d’échappement 5.5 Raccordement de la conduite de purge de gaz neutre 5.5.1 Sectionnement du tuyau de purge de gaz neutre 5.5.2 Raccordement de la conduite de purge de gaz neutre 5.6 Raccordement du capillaire 5.6.1 Raccordement du capillaire en acier inoxydable OmniStar 5.6.2 Raccordement du capillaire ThermoStar quartz 5.7 Adaptation de la position du tuyau flexible de capillaire 5.8 Établissement d’une connexion au réseau 5.8.1 Adresses IP 5.8.2 Sous-réseaux 5.8.3 Changement d’adresse IP de la GSD 350 5.8.4 Modification de l’adresse IP de l’ordinateur hôte 5.9 Raccordement de la terre fonctionnelle 5.10 Raccordement de l’alimentation électrique 5.11 Installation du logiciel PV MassSpec 39 40 40 40 41 41 42 42 43 43 44 45 45 46 47 48 48 6 Interfaces et connexions 6.1 Alimentation 6.2 Borne de connexion de terre 6.3 Connexion « User I/O » 6.4 Connexion « AUX IO » 6.5 Connexion Ethernet (LAN) 49 49 49 49 51 52 7 Mise en service 7.1 Activation de l’unité 7.2 Démarrage du système de pompage 53 53 53 8 Fonctionnement via l’affichage 8.1 Écran « Tableau de bord » 8.2 Structure du menu avec les fonctions 8.3 Menu « Info » 8.4 Menu « Réglages » 8.4.1 Création et édition des recettes de mesure 8.4.2 Ajustement des unités de chauffage 8.4.3 Ajustage des capteurs 8.4.4 Modification des réglages de l’utilisateur 8.4.5 Réglage des fonctions de démarrage automatique 8.4.6 Réglage des paramètres réseau 8.4.7 Réinitialisation de l'unité aux réglages initiaux 8.4.8 Sous-menu « Maintenance » 8.5 Menu « Messages » 8.6 Menu « Commande » 8.6.1 Pompage du système de vide 8.6.2 Ventilation du système à vide 8.6.3 Activation et désactivation des dispositifs de chauffage 8.6.4 Ouverture et fermeture de l’admission de gaz (Omnistar) 8.6.5 Étuvage de l’enceinte à vide 8.6.6 Activation et désactivation de l’émission 8.6.7 Activation et désactivation du multiplicateur d’électrons 8.6.8 Ouverture et fermeture de la vanne de calibration 8.7 Menu « Mesure » 55 55 56 58 58 59 61 62 63 63 64 64 65 65 66 67 67 68 68 69 69 70 70 70 9 Mise hors service 72 10 Maintenance 10.1 Opérations de maintenance et intervalles de maintenance 10.2 Maintenance de l’instrument fondamental 10.2.1Retrait/fixation du couvercle de l’admission de gaz 73 73 75 76 Table des matières 10.2.2Retrait/fixation des couvercles sur le côté 10.2.3Retrait/fixation du couvercle de carter 10.2.4Nettoyage des pièces de carter 10.2.5Nettoyage des écrans de protection sur les ventilateurs 10.3 Maintenance du système de vide élevé 10.3.1Remplacement du réservoir de fluide d’exploitation sur la pompe turbomoléculaire 10.3.2Remplacement de la vanne de ventilation 10.4 Maintenance du système de vide primaire 10.4.1Remplacement de la pompe à membrane 10.4.2Remplacement de la membrane de la pompe à membrane 10.5 Maintenance de l’unité d’analyse de gaz 10.5.1Maintenance de l’analyseur QMA 250 M 10.5.2Maintenance de la jauge de pression totale 10.6 Maintenance du système d’admission de gaz sur Omnistar 10.6.1Retrait de la bride de l’admission de gaz 10.6.2Remplacement de l’orifice 10.6.3Remplacement du diffuseur de gaz intérieur et de l’orifice 10.6.4Installation de la bride d’aspiration de gaz 10.7 Maintenance du système d’admission de gaz sur ThermoStar 10.7.1Retrait de la bride de l’admission de gaz 10.7.2Remplacement de l’orifice 10.7.3Remplacement du diffuseur de gaz intérieur et de l’orifice 10.7.4Installation de la bride d’aspiration de gaz 10.8 Entretien du capillaire 10.8.1Réduction de la longueur des capillarités en acier inoxydable 10.8.2Remplacement du capillaire en acier inoxydable 10.8.3Découpage à longueur des capillarités en quartz 10.8.4Remplacement du capillaire en quartz 10.9 Maintenance des unités de chauffage 10.9.1Remplacez le tube capillaire 10.9.2Maintenance du chauffage de l’admission de gaz 10.9.3Entretien du chauffage de l’enceinte à vide 10.10 Entretien des composants électroniques 10.10. Remplacement de l’affichage 1 10.10. Remplacement de l'injecteur PoE 2 10.10. Remplacement de la platine principale 3 10.10. Remplacement de l'unité de courant 4 10.10. Remplacement de l’unité électronique QME 250 5 10.10. Remplacement de l’unité de commande électronique TC 110 sur la 6 pompe turbomoléculaire 10.11 Maintenance de l’unité de calibration 10.11. Appoint en fluide de calibration 1 10.11. Remplacement de la vanne de calibration 2 10.12 Opérations de maintenance additionnelles pour la version pour gaz corrosif 10.12. Remplacement de la vanne de la purge de gaz 1 10.12. Remplacement du régulateur de pression manuel 2 10.12. Remplacement du manocontacteur numérique 3 76 77 78 79 80 80 81 81 81 83 84 84 86 87 88 89 89 90 91 92 93 94 95 95 96 97 98 99 100 100 100 100 100 100 101 101 101 101 102 102 102 103 103 103 103 103 5/122 Table des matières 6/122 11 Dépannage 104 12 Expédition 108 13 Recyclage et mise au rebut 13.1 Informations générales sur la mise au rebut 13.2 Élimination du système d’analyse du gaz 109 109 109 14 Solutions de service de Pfeiffer Vacuum 110 15 Pièces de rechange 112 16 Outil spécial 115 17 Accessoires 17.1 Informations sur les accessoires 17.2 Commande d’accessoires 116 116 116 18 Caractéristiques techniques et dimensions 18.1 Généralités 18.2 Fiche technique 18.3 Dimensions 117 117 117 119 Certification 120 Déclaration de conformité 121 Liste des tableaux Liste des tableaux Tab. 1: Tab. 2: Tab. 3: Tab. 4: Tab. 5: Tab. 6: Tab. 7: Tab. 8: Tab. 9: Tab. 10: Tab. 11: Tab. 12: Tab. 13: Tab. 14: Tab. 15: Tab. 16: Tab. 17: Tab. 18: Tab. 19: Tab. 20: Tab. 21: Tab. 22: Documents applicables Variantes Caractéristiques des variantes Abréviations employées Conditions ambiantes autorisées Symboles et couleurs des icônes d’état et de composant LED d’état et leur signification Dispositifs de chauffage sur l’unité Exemples de sous-réseaux État de la connexion Ethernet Structure du menu avec les fonctions Opérations de maintenance et intervalles de maintenance Sensibilité déterminée du spectromètre de masse Dépannage Pièces de rechange et composants, maintenance niveau 1 Couleurs et dimensions du tuyau flexible Composants des raccords pour tuyau flexible Outil spécial Accessoires Tableau de conversion : unités de pression Tableau de conversion : unités de débit de gaz Fiche technique 11 11 12 14 20 25 26 31 45 52 57 75 85 107 113 113 114 115 116 117 117 119 7/122 Liste des figures Liste des figures Fig. 1: Fig. 2: Fig. 3: Fig. 4: Fig. 5: Fig. 6: Fig. 7: Fig. 8: Fig. 9: Fig. 10: Fig. 11: Fig. 12: Fig. 13: Fig. 14: Fig. 15: Fig. 16: Fig. 17: Fig. 18: Fig. 19: Fig. 20: Fig. 21: Fig. 22: Fig. 23: Fig. 24: Fig. 25: Fig. 26: Fig. 27: Fig. 28: Fig. 29: Fig. 30: Fig. 31: Fig. 32: Fig. 33: Fig. 34: Fig. 35: Fig. 36: Fig. 37: Fig. 38: Fig. 39: Fig. 40: Fig. 41: Fig. 42: Fig. 43: Fig. 44: Fig. 45: Fig. 46: Fig. 47: Fig. 48: Fig. 49: Fig. 50: Fig. 51: Fig. 52: Fig. 53: Fig. 54: 8/122 Position des autocollants sur le produit Diagramme du vide de l’OmniStar Diagramme du vide du ThermoStar Alimentation supplémentaire en purge de gaz neutre dans la version pour gaz corrosif Écran d’affichage avec touches opérateur Éléments du carter Panneau de connexion avec interfaces et connexions Systèmes d’admission de gaz Unité de calibration en admission de gaz Pompe à membrane Système de purge de gaz neutre Composants de l’unité d’analyse de gaz Chauffage et isolation de l’enceinte à vide Chauffage de l’admission de gaz Chauffage du capillaire Composants électroniques Équipement de montage pour analyseur QMA 250 Outil spécial pour l’orifice du système d’admission de gaz Aide au montage du support de gaz de calibration Protection pour le transport de la pompe à membrane Distances latérales minimum de l’unité Protection pour le transport de la pompe à membrane Sectionnement du tuyau de gaz d'échappement Raccordement du tuyau de gaz d’échappement Sectionnement du tuyau de purge de gaz neutre Raccordement de la conduite de purge de gaz neutre Raccordement du capillaire Position du tuyau flexible capillaire à la livraison Changement de l’adresse IP de la GSD 350 via l’interface Web Raccordement pour la terre fonctionnelle Connexion d'alimentation électrique avec fiche CEI 320 C13 Branchement secteur avec interrupteur principal et fusible Connexion « USER I/O » Connexion « AUX IO » Connexion Ethernet (LAN) Écran « Tableau de bord » après démarrage du programme Écran de « commande » Écran « Tableau de bord » Exemple de réglage de paramètre Sous-menu « Recettes » Recette de mesure pour le mode de mesure « Scan du spectre » Recette de mesure pour le mode de mesure « Masses sélectionnées » Recette de mesure pour le mode de mesure « Masses sélectionnées – Spécial » Mode de trempage de l’enceinte à vide Sous-menu « Réglages de l’utilisateur » Sous-menu « Démarrage automatique » Sous-menu « Réseau » Sous-menu « Factory settings » Exemple de message d’anomalie Exemple de messages anciens Menu « Commande » Sélection de la recette Retrait/fixation du couvercle de l’admission de gaz Retrait/fixation des couvercles sur le côté 13 23 24 24 25 26 27 28 29 29 30 31 32 33 33 34 35 35 35 36 38 38 39 40 40 41 42 43 46 47 48 49 50 52 52 53 54 56 58 59 60 60 61 62 63 63 64 65 65 66 67 71 76 77 Liste des figures Fig. 55: Fig. 56: Fig. 57: Fig. 58: Fig. 59: Fig. 60: Fig. 61: Fig. 62: Fig. 63: Fig. 64: Fig. 65: Fig. 66: Fig. 67: Fig. 68: Fig. 69: Fig. 70: Fig. 71: Fig. 72: Fig. 73: Fig. 74: Fig. 75: Fig. 76: Fig. 77: Fig. 78: Fig. 79: Retrait/fixation du couvercle de carter Face inférieure de l’unité Remplacement de la pompe à membrane Raccordement et retrait du tuyau de gaz d’échappement et d’admission Spectromètre de masse quadripôle PrismaPro Gorge sur l’analyseur Jauge de pression totale sur l’unité d’analyse de gaz Pièces du diffuseur de gaz interne sur l’Omnistar Démontage du bloc de vannes Diffuseur de gaz environ 1–2 mm derrière l’extrémité du manchon céramique Pièces du diffuseur de gaz interne sur ThermoStar Retrait de la bride de l’admission de gaz Diffuseur de gaz environ 1–2 mm derrière l’extrémité du manchon céramique Longueur du capillaire en acier inoxydable avec raccord à vis à collier de serrage Entaillage et cassage du capillaire en acier inoxydable Raccord à collier de serrage pour capillaire en acier inoxydable Entaillage et cassage du capillaire de quartz Raccord à vis avant du capillaire en quartz Remplacement de l’affichage Unité de calibration Clé à écrou pour couvercle de carter de pompe turbomoléculaire Jauge de centrage pour QMA Aide au montage du support de gaz de calibration Adaptateur de tube capillaire Dimensions 78 80 82 82 84 85 86 87 88 90 92 93 94 96 96 97 98 99 101 102 115 115 115 116 119 9/122 A propos de ce manuel 1 A propos de ce manuel IMPORTANT Bien lire avant d'utiliser le produit. Conserver ce manuel pour une future utilisation. 1.1 Validité Ce document décrit la fonction des produits de la liste suivante et contient les informations les plus importantes pour une utilisation sécurisée. La description est rédigée conformément aux directives en vigueur. Les informations contenues dans ce document correspondent à l'état de développement actuel des produits. Le document conserve sa validité à condition que le client n'apporte aucune modification au produit. 1.1.1 Documents applicables Désignation Document Manuel de l’utilisateur « GSD 350 OmniStar/ThermoStar » Fonctionnement via l’interface Web et PV MassSpec DA 0106 Manuel de l’utilisateur « Spectromètre de masse quadripole » QMG 250 PrismaPro BG 6001 Guide de démarrage rapide « Spectromètre de masse quadripole » QMG 250 PrismaPro BG 6003 Manuel de l’utilisateur « Pompe à membrane » MVP 010-3 DC PU 0071 Manuel de l’utilisateur « Pompe turbomoléculaire » HiPace 80 PT 0208 Informations supplémentaires « Pompe turbomoléculaire » SplitFlow 80 PT 0635 Manuel de l’utilisateur « Unité de commande électronique » TC 110 PT 0204 Manuel de l’utilisateur « Manomètre de pression totale » Jauge à cathode froide/Pirani DigiLine MPT 200 AR PG 0025 Informations supplémentaires « Relais analogique » Jauge DigiLine PG 0029 Manuel de l’utilisateur « Mini vanne équerre » 1) EVI 005 M BP 5120 Manuel de l’utilisateur pour « Vanne de remise à l’air » PT 0228 Manuel de l’utilisateur « Vanne de la purge de gaz » 2) PT 0229 Documentation du logiciel PV MassSpec (partie du logiciel) Fiche technique de sécurité 3) Perfluorotributylamine (PFTBA) - 1) 10/122 Uniquement pour la version avec unité de calibration 2) uniquement pour la version pour gaz corrosifs 3) Uniquement pour la version avec unité de calibration A propos de ce manuel Désignation Document Manuel de l’utilisateur « Manocontacteur numérique » 4) OM_ZSE_ISE30A_OML0003 (SMC) Déclaration de conformité (composante de ces instructions) Tab. 1: Documents applicables Vous trouverez ces documents dans le Centre de téléchargement Pfeiffer Vacuum. 1.1.2 Variantes Ce document s’applique à tous les produits avec les références suivantes : Variante Version Analyseur avec filament chauffé Admission de gaz Domaine de masse Affichage PT Q8 = OmniStar 0 = Standard GSD 350 O 1 = Gaz corrosif GSD 350 O C 1 = Ir-Y2O3 (unité de calibration) 2 = Ir-Y2O3 151 = Quartz / 1 m / chauffage à 200 °C 1 = 100 u 2 = 200 u 3 = 300 u 0 = oui 1 = non 1 = 100 u 2 = 200 u 3 = 300 u 0 = oui 1 = non 5 = W (unité de calibration) 6=W 152 = Quartz / 2 m / chauffage à 200 °C 153 = Quartz / 1 m / chauffage à 350 °C 161 = Acier inoxydable/ sans tube capillaire 171 = Acier inoxydable / 1 m / chauffage 200 °C 172 = Acier inoxydable / 2 m / chauffage 200 °C 173 = Acier inoxydable / 1 m / chauffage 350 °C PT Q9 = ThermoStar 0 = Standard GSD 350 T 1 = Gaz corrosif GSD 350 T C 1 = Ir-Y2O3 (unité de calibration) 2 = Ir-Y2O3 5 = W (unité de calibration) 6=W 101 = Quartz/sans tube capillaire 111 = Quartz / 1 m / chauffage à 200 °C 112 = Quartz / 2 m / chauffage à 200 °C 113 = Quartz / 1 m / chauffage à 350 °C Tab. 2: Variantes Exemple de décomposition de la référence PT Q80 217 110 ● ● ● ● Version Omnistar Version standard Analyseur avec filament chauffé en Ir-Y2O3, sans unité de calibration Admission de gaz avec chauffage jusqu’à 200 °C et capillaire en acier inoxydable d’une longueur de 1 m ● Domaine de masse jusqu’à 100 u ● Version avec écran Caractéristiques OmniStar Capillaire Acier inoxydable (OD = 1/16", ID = 0,12 mm) ou Quartz (OD 0,23", ID = 0,14 mm) Écran d’admission de gaz Platine 4) ThermoStar uniquement pour la version pour gaz corrosifs 11/122 A propos de ce manuel Caractéristiques OmniStar ThermoStar Admission de gaz Commande par 2 vannes Ouvert en continu Options ● Chauffage jusqu’à 200 °C ou 350 °C ● Version pour gaz corrosif avec raccord de la purge de gaz neutre ● Unité de calibration pour calibration de l’échelle de masse (Fluide de calibration pour calibration de la masse : PFTBA) Tab. 3: Caractéristiques des variantes Vous trouverez le numéro de la pièce sur la plaque signalétique du produit. Pfeiffer Vacuum se réserve le droit d'apporter des modifications techniques sans préavis. Les figures de ce document ne sont pas à l’échelle. Les dimensions sont indiquées en mm, sauf avis contraire. 1.2 Groupe cible Ce manuel d'utilisation s’adresse à toutes les personnes en charge ● ● ● ● ● ● du transport, de l'installation, de la commande et de l'utilisation, de la mise hors service, de la maintenance et du nettoyage, du stockage et du recyclage du produit. Les opérations décrites dans ce document doivent uniquement être effectuées par un personnel doté de la formation technique nécessaire (personnel qualifié), ou ayant suivi une formation correspondante de Pfeiffer Vacuum. 1.3 Conventions 1.3.1 Instructions dans le texte Les instructions figurant dans ce document sont présentées selon une structure précise. Les actions à réaliser sont soit uniques, soit en plusieurs étapes. Action unique Un symbole en forme de triangle signale une activité à effectuer en une seule étape. ► Il s'agit d’une étape unique. Action en plusieurs étapes Une liste numérotée indique une action comportant plusieurs étapes à effectuer dans l'ordre chronologique. 1. Étape 1 2. Étape 2 3. ... 1.3.2 Pictogrammes Les pictogrammes utilisés dans ce document indiquent des informations utiles. Remarque Conseil 12/122 A propos de ce manuel Portez des gants de laboratoire Contrôlez visuellement 1.3.3 Autocollants sur le produit Cette section décrit tous les autocollants sur le produit ainsi que leurs significations. Plaque signalétique (exemple) Plaque signalétique de l’unité. D-35614 Asslar Mod. P/N S/N Input GSD 350 PT Q.. ... ... ... Made in Germany 2022/02 Sceau de garantie Le produit est scellé, départ d’usine. L’endommagement ou le retrait d’un sceau de garantie rend tout recours en garantie caduque. warranty seal Avertissement, surface chaude Cet autocollant met en garde contre les risques de blessure liés aux hautes températures à la suite d’un contact sans protection pendant le fonctionnement. Autocollant VSM Cet autocollant contient des liens vers la gestion de service virtuel Dreebit. www.vsm-cloud.com 1 2 4 3 2 Fig. 1: Position des autocollants sur le produit 1 Autocollant « Avertissement - surface chaude » 5) 2 Sceau de garantie 5) 3 4 Autocollant VSM Plaque signalétique Uniquement pour chauffage du capillaire jusqu’à 350 °C 13/122 A propos de ce manuel 1.3.4 Orientation gauche/droite L’orientation gauche et droite est donnée à partir du point de vue de l’opérateur de l’affichage. 1.3.5 Abréviations Abréviation Explication OD Diamètre extérieur AI Entrée analogique AO Sortie analogique ATEX Zones présentant un risque d’atmosphère explosive (atmosphères explosives) C/B Croisement (type de source d’ions) DCU Appareil de commande et d’affichage DHCP Protocole de communication pour l’attribution de la configuration du réseau (Dynamic Host Communication Protocol) DI Entrée numérique DO Sortie numérique EM Multiplicateur d’électrons EPDM Caoutchouc éthylène-propylène-diène monomère, groupe M FIL Filament chauffé FKM Caoutchouc fluoré ID Diamètre intérieur IP Protocole Internet IQS Norme pour les connecteurs mâle-femelle dans la technique du vide Ir-Y2O3 Iridium recouvert d’oxyde d’yttrium (Y2O3) (Ir) MVP Pompe à vide à membrane NBR Caoutchouc butadiène-nitrile MSL Niveau moyen de la mer PA Polyamide PE Polyéthylène PFTBA Liquide incolore pour le calibration des masses (perfluorotributylamine) PID Régulateur proportionnel, intégral, dérivé PoE Alimentation électrique par câble Ethernet (Power over Ethernet) PT100 Résistance de mesure platine avec résistance de dérivation de 100 Ohm PTFE Polymère de fluor et de carbone (polytétrafluoroéthylène) Tuyau flexible en PUN Tuyau flexible polyuréthane calibré externe PV Pfeiffer Vacuum PVC Chlorure de polyvinyle PWM Type de modulation (impulsion avec modulation) dans laquelle une variable technique, par ex. la tension électrique, varie entre 2 valeurs. RJ-45 Connecteur mâle-femelle normalisé pour le câblage de télécommunication (jack normalisé) sccm Centimètres cube standard par minute comme unité d’une quantité définie de débit de gaz par unité de temps sous des conditions standard slpm Litres standard par minute comme unité d’une quantité définie de débit de gaz par unité de temps sous des conditions standard VLAN Réseau local virtuel VSM Logiciel basé sur le Cloud pour la gestion des composants et des systèmes de vide, et pour la planification de procédés de service (gestion virtuelle de services) W Tungstène Tab. 4: 14/122 Abréviations employées A propos de ce manuel 1.4 Justificatif de marque ● Windows® et Internet Explorer® sont des marques déposées de Microsoft Corporation. ● OmniStar®, ThermoStar® et PrismaPro® sont des marques déposées de Pfeiffer Vacuum GmbH. ● Swagelok® est une marque de commerce déposée de la société Swagelok. 15/122 Sécurité 2 Sécurité 2.1 Consignes générales de sécurité Dans le présent document, 4 niveaux de risques et 1 niveau de consignes sont identifiés comme suit : DANGER Danger direct et imminent Caractérise un danger direct et imminent entraînant un accident grave voire mortel. ► Instruction à suivre pour éviter la situation de danger AVERTISSEMENT Danger potentiellement imminent Caractérise un danger imminent qui peut entraîner un accident grave voire mortel. ► Instruction à suivre pour éviter la situation de danger ATTENTION Danger potentiellement imminent Caractérise un danger imminent qui peut entraîner des blessures légères. ► Instruction à suivre pour éviter la situation de danger AVIS Obligation ou signalement Signale une pratique qui peut occasionner des dégâts matériels sans risque potentiel de blessure physique. ► Instruction à suivre pour éviter les dégâts matériels Consignes, conseils ou exemples désignent des informations importantes concernant le produit ou le présent document. 2.2 Consignes de sécurité Consignes de sécurité selon les étapes de la vie du produit Toutes les consignes de sécurité de ce document sont basées sur les résultats d’une évaluation des risques. Pfeiffer Vacuum a pris en compte toutes les étapes pertinentes de la vie du produit. Risques lors du transport AVERTISSEMENT Danger de blessures graves en cas de chute d’objets La chute d’objets peut entraîner des blessures sur les membres, voire même des fractures osseuses. ► Soyez particulièrement vigilant lors du transport manuel du produit. ► Ne pas empiler le produit. ► Portez un équipement de protection, tel que des chaussures de sécurité. 16/122 Sécurité AVERTISSEMENT Risque de blessure lors du levage de charges lourdes Le produit est lourd ; il peut peser jusqu’à 26 kg, selon la version. Une personne soulevant le produit sans aide et de manière incorrecte risque de se blesser. ► Faites toujours appel à 2 personnes pour soulever le produit à deux mains. ► Prenez toujours les mesures de sécurité requises (portez par ex. des gants de protection). ► Respectez la réglementation locale. ► Conforme aux instructions pour un transport en toute sécurité. Risques lors de l’installation DANGER Danger de mort en cas d’électrocution Une mise à la terre inappropriée ou incorrecte de l’unité entraîne une tension sensible aux contacts au niveau du boîtier. Lors de la connexion, des courants de fuite plus élevés vont déclencher un choc électrique potentiellement mortel. ► Avant l’installation, contrôlez que les conducteurs d’alimentation ne sont pas sous tension. ► Acheminez le câble électrique conformément aux dispositions locales en vigueur. ► Assurez-vous que les valeurs de tension et de fréquence locales correspondent aux spécifications de la plaque signalétique. ► Veillez à ce que le câble d’alimentation et la rallonge soient conformes aux exigences de double isolation entre la tension d’entrée et la tension de sortie, conformément aux normes CEI 61010 et CEI 60950. ► N'utilisez qu’un câble d'alimentation à 3 broches et une rallonge disposant d'une mise à la terre correcte (conducteur mis à la terre). ► Ne branchez la fiche électrique que dans une prise disposant d'un contact de mise à la terre. ► Afin de garantir la protection de la mise à la terre, il convient de toujours brancher le câble électrique avant tous les autres. DANGER Électrocution en raison de l’absence de conducteur de protection interne Le conducteur de protection interne est fixé au logement. Une unité sans conducteur de protection interne peut présenter un danger de mort en cas de dysfonctionnement. ► Ne tournez pas ou ne débloquez pas le conducteur de protection interne. Risques pendant le fonctionnement DANGER Choc électrique dû à la pénétration d’humidité dans l’unité La pénétration d’eau dans l’unité cause des blessures aux personnes par chocs électriques. ► Utilisez seulement l’unité dans un environnement sec. ► Utilisez l’unité à l’écart de tout fluide ou source d’humidité. ► Ne mettez pas en circuit l’unité si du fluide a pénétré à l’intérieur de celle-ci. Au lieu de cela, contactez Pfeiffer Vacuum Service. ► Déconnectez toujours l’alimentation électrique avant de nettoyer l’unité. AVERTISSEMENT Risque de brûlure sur les surfaces chaudes Pendant le fonctionnement, les températures montent très haut (> 50 °C) sur les surfaces de contact des composants de chauffage et sur l’admission de gaz. Il existe un risque de brûlure. ► Prenez les mesures requises pour prévenir tout contact avec les pièces chaudes. ► Apposez des signaux d’avertissement. ► Veillez à ce que le produit se soit refroidi avant d’intervenir dessus. ► Portez des gants de protection (conformément à EN 420). 17/122 Sécurité AVERTISSEMENT Risque d’empoisonnement dû à la substance de processus toxique s’échappant de la conduite d’échappement Lorsqu’elle fonctionne sans conduite de refoulement, la pompe à vide rejette les gaz et vapeurs de refoulement dans l’air. Risque de blessure et de mort dû à l’empoisonnement par les substances de processus toxiques. ► Respecter la réglementation en vigueur concernant le traitement des substances de processus toxiques. ► Évacuer les substances de processus toxiques en toute sécurité par une conduite de refoulement. ► Employer des moyens de filtration appropriés pour séparer les substances de processus toxiques. ATTENTION Risques sanitaires et environnementaux dus aux de gaz de procédé utilisés Les gaz utilisés (gaz de procédé) constituent un risque sanitaire et environnemental. ► Contrôler l'étanchéité des branchements avant de laisser le gaz de procédé pénétrer dans le système. ► Veiller à ce que le système des gaz d'échappement soit compatible avec les gaz injectés. ► Tenir compte des interactions potentielles entre les matériaux et les gaz de procédé. ► Respecter les directives en vigueur lors de la manipulation de gaz utilisés. ► Respecter les mesures de protection. Risques pendant la maintenance DANGER Danger de mort par électrocution L'appareil présente des tensions élevées. Danger de mort en cas de contact avec des éléments sous tension. La mise en service de l'appareil alors qu'il est visiblement endommagé implique un danger de mort. ► Toute intervention sur l'appareil ouvert doit être confiée à un personnel spécialisé et qualifié. ► Avant d'exécuter une installation ou une opération de maintenance, arrêtez l'appareil et déconnectez-le de l'alimentation électrique. ► N’ouvrez jamais l'appareil lorsqu'il est branché à une source d'alimentation électrique. ► Prenez les mesures nécessaires pour éviter toute réactivation involontaire ou non autorisée. ► Ne faites jamais fonctionner un appareil ouvert ou défectueux. ► Prenez les mesures nécessaires pour empêcher l'utilisation accidentelle d'un appareil défectueux. ► Protégez l'appareil contre l'humidité. AVERTISSEMENT Risque de brûlure sur les surfaces chaudes Pendant le fonctionnement, les températures montent très haut (> 50 °C) sur les surfaces de contact des composants de chauffage et sur l’admission de gaz. Il existe un risque de brûlure. ► Prenez les mesures requises pour prévenir tout contact avec les pièces chaudes. ► Apposez des signaux d’avertissement. ► Veillez à ce que le produit se soit refroidi avant d’intervenir dessus. ► Portez des gants de protection (conformément à EN 420). 18/122 Sécurité AVERTISSEMENT Risques pour la santé dus aux agents nettoyants Les détergents utilisés peuvent nuire à la santé et causer un empoisonnement, des allergies, une irritation de la peau, des brûlures chimiques ou endommager les voies respiratoires. ► Respectez les réglementations en vigueur pour la manipulation des agents nettoyants. ► Respectez les mesures de sécurité concernant la manipulation et la mise au rebut des agents nettoyants. ► Attention aux réactions potentielles avec les matériaux du produit. AVERTISSEMENT Risque d’intoxication dû à des composants ou appareils contaminés par des substances toxiques Les substances de procédé toxiques contaminent certaines pièces matérielles. Pendant les opérations de maintenance, tout contact avec ces substances toxiques présente un risque pour la santé. L’élimination illégale de substances toxiques nuit à l’environnement. ► Respecter les précautions de sécurité adéquates et éviter les risques sanitaires ou environnementaux dus aux substances de procédé toxiques. ► Décontaminer les pièces concernées avant d’exécuter des opérations de maintenance. ► Porter des équipements de protection individuelle. ATTENTION Risque de blessure par éclatement du capillaire en quartz Les capillaires au quartz éclatent en cas d’utilisation non conforme. Risque de grave blessure aux yeux lié à la projection d'éclats. ► N’exercez pas de force en entaillant le capillaire en quartz. ► Portez des lunettes de protection. Risques liés à l’expédition AVERTISSEMENT Risque d’empoisonnement par produits contaminés L’expédition de produits contenant des substances dangereuses pour leur maintenance ou réparation implique un risque pour la santé et l’ sécurité du personnel de maintenance. ► Conforme aux instructions pour une distribution en toute sécurité. Risques pendant la mise au rebut AVERTISSEMENT Risque d’intoxication dû à des composants ou appareils contaminés par des substances toxiques Les substances de procédé toxiques contaminent certaines pièces matérielles. Pendant les opérations de maintenance, tout contact avec ces substances toxiques présente un risque pour la santé. L’élimination illégale de substances toxiques nuit à l’environnement. ► Respecter les précautions de sécurité adéquates et éviter les risques sanitaires ou environnementaux dus aux substances de procédé toxiques. ► Décontaminer les pièces concernées avant d’exécuter des opérations de maintenance. ► Porter des équipements de protection individuelle. 2.3 Mesures de sécurité Le produit est conçu sur la base des technologies les plus récentes et des règles techniques de sécurité reconnues. Cependant, une utilisation incorrecte peut présenter un risque de blessure ou un danger de mort pour l'opérateur et toute autre personne, ainsi qu'un risque de dommages matériels sur le produit et autres. 19/122 Sécurité Obligation de fournir des informations sur les dangers potentiels Le propriétaire du produit ou l’utilisateur est dans l’obligation d’informer l’ensemble du personnel opérateur des dangers inhérents à ce produit. Chaque personne en charge de l’installation, du fonctionnement ou de la maintenance du produit doit lire, comprendre et respecter les sections de sécurité de ce document. Violation de la conformité en cas de modifications sur le produit La déclaration de conformité du fabricant n'est plus valide si l'utilisateur modifie le produit d'origine ou installe un équipement supplémentaire ● Après l'installation dans un système, l'exploitant est tenu de vérifier et de réévaluer, le cas échéant, la conformité de l'ensemble du système dans le contexte des directives européennes applicables avant de mettre en service ce système. Mesures de sécurité générales lors de la manipulation du produit ► Respectez toutes les dispositions de sécurité et de prévention des accidents en vigueur. ► Contrôlez régulièrement que toutes les mesures de sécurité sont respectées. ► Les consignes de sécurité doivent être transmises aux autres utilisateurs. ► N'exposez aucune partie du corps au vide. ► Assurez toujours un raccordement sûr au conducteur de terre (PE). ► Ne débranchez jamais les fiches de raccordement en cours de fonctionnement. ► Respectez les procédures d’arrêt ci-dessus. ► Tenez les conduites et les câbles éloignés des surfaces chaudes (> 70 °C). ► N'effectuez pas vous-même de conversions ou de modifications de l'appareil. ► Consultez le degré de protection de l’unité avant son installation ou fonctionnement dans d’autres environnements. ► Mettez en place des équipements de protection adaptés contre tout contact physique si la température de surface dépasse 70 °C. ► Il convient de toujours s'informer d'éventuelles contaminations avant de commencer à travailler. 2.4 Limites d’utilisation du produit Emplacement de l’installation protégé des intempéries (espace intérieur) Altitude de l’installation 2 000 m max. Humidité rel. de l’air max. 80 %, à T <31°C, jusqu’à max. 50 % à T <40°C Classe de protection I Catégorie de surtension II Degré de protection admissible IP30 Degré de pollution 2 Température ambiante 10 °C à 40 °C Tab. 5: 2.5 Conditions ambiantes autorisées Utilisation conforme Le système d’analyse du gaz est utilisé pour le contrôle manuel ou l’analyse automatique des gaz non corrosifs et non inflammables. La version pour gaz corrosifs du système d’analyse du gaz est compatible avec les applications spécifiques pour gaz corrosifs. ► L'installation, l'utilisation et l'entretien du produit doivent être exécutés exclusivement conformément au manuel de l'utilisateur. ► Conforme aux limites d'application. ► Observez la fiche technique. ► Contactez Pfeiffer Vacuum pour demander conseil sur les gaz corrosifs ou inflammables. 20/122 Sécurité 2.6 Utilisation incorrecte envisageable Toute utilisation incorrecte du produit invalide les réclamations de garantie et de responsabilité. Toute utilisation non conforme à l’objectif du produit, qu’elle soit intentionnelle ou non, est considérée comme abusive, en particulier : ● Utilisation hors des limites mécaniques et électriques d’application ● Utilisation avec des substances corrosives ou inflammables, si cette utilisation n’est pas explicitement autorisée ● Fonctionnement dans les zones potentiellement explosives 6) ● Fonctionnement dans des environnements susceptibles de contenir des mélanges gazeux explosifs. ● Fonctionnement à l’extérieur ● Utilisation suite à des modifications techniques (à l’intérieur ou à l’extérieur du produit) ● Utilisation d’accessoires ou de pièces de rechange non listés dans ces instructions 2.7 Qualification personnelle L'utilisation décrite dans ce document doit être confiée à des personnes disposant des qualifications professionnelles adéquates et de l'expérience nécessaire ou qui ont suivi la formation requise dispensée par Pfeiffer Vacuum. Formation du personnel 1. Former le personnel technique sur le produit. 2. Ne laisser le personnel à former travailler avec et sur le produit que sous la supervision d'un personnel qualifié. 3. Seul un personnel technique formé est autorisé à travailler avec le produit. 4. Avant de commencer à travailler, s'assurer que le personnel engagé a lu et compris ce mode d'emploi et tous les documents pertinents, en particulier les informations relatives à la sécurité, à l'entretien et à la réparation. 2.7.1 Garantir la qualification du personnel Spécialistes des travaux mécaniques Seuls des spécialistes qualifiés peuvent effectuer des travaux mécaniques. Selon la définition de ce document, les spécialistes sont des personnes responsables de la construction, de l'installation mécanique, de la recherche de pannes et de la maintenance du produit, et disposant des qualifications suivantes : ● Compétences dans le domaine mécanique conformément aux régulations nationales en vigueur ● Connaissance de cette documentation Spécialisation dans les travaux d'ingénierie électriques Seul un électricien qualifié peut effectuer des travaux d'ingénierie électriques. Selon la définition de ce document, les électriciens sont des personnes responsables de l'installation électrique, de la mise en service, de la recherche de pannes et de la maintenance du produit, et disposant des qualifications suivantes : ● Compétences dans le domaine de l'ingénierie électrique conformément aux régulations nationales en vigueur ● Connaissance de cette documentation De plus, ces personnes doivent être familiarisées avec les réglementations et la législation en matière de sécurité en vigueur, ainsi que les normes, directives et lois mentionnées dans cette documentation. Les personnes mentionnées ci-dessus doivent avoir obtenu expressément l'autorisation d'utilisation afin de mettre en service, de programmer, de configurer, de marquer et de mettre à la terre les appareils, systèmes et circuits conformément aux standards technologiques en matière de sécurité. Personnes qualifiées Seules les personnes spécialement formées peuvent effectuer toutes les opérations relatives au transport, à l'entreposage, à l'utilisation et à la mise au rebut. Ce type de formation doit garantir que ces personnes sont capables d'exécuter correctement les activités et opérations requises, et en toute sécurité. 6) Le système d’analyse du gaz n’est pas à l’épreuve des explosions, dans le sens de la norme ATEX. 21/122 Sécurité 2.7.2 Qualification du personnel pour la maintenance et la réparation Formations avancées Pfeiffer Vacuum propose des formations avancées pour les niveaux de maintenance 2 et 3. Les personnes adéquatement qualifiées sont : ● Maintenance de niveau 1 ─ Client (spécialiste formé) ● Maintenance de niveau 2 ─ Client avec formation technique ─ Technicien de maintenance Pfeiffer Vacuum ● Maintenance de niveau 3 ─ Client avec formation à l'entretien Pfeiffer Vacuum ─ Technicien de maintenance Pfeiffer Vacuum 2.7.3 Formation avancée avec Pfeiffer Vacuum Pour une utilisation optimale et sans problème de ce produit, Pfeiffer Vacuum propose une gamme complète de cours et de formations techniques. Pour plus de précisions, contacter le service de formation technique Pfeiffer Vacuum. 22/122 Description du produit 3 Description du produit 3.1 Description fonctionnelle Le GSD 350 peut analyser différents composants de gaz simultanément. Le gaz à analyser passe à travers un capillaire pour atteindre le spectromètre de masse qui fonctionne dans un vide. Le spectromètre de masse ionise une partie du gaz et sépare et détecte les différents composants du gaz à partir de leur différent rapport masse/charge. Les différents systèmes d’entrée de gaz OmniStar et ThermoStar réduisent la pression du gaz à analyser de 1000 hPa à la pression de travail du spectromètre de masse. L’unité d’analyse de gaz, le vide élevé et le système d’acheminement du gaz sont les mêmes dans les versions OmniStar et ThermoStar. 3.1.1 OmniStar 14 15 1 2 4 5 3 6 7 10 13 8 12 11 Fig. 2: 1 2 3 4 5 6 7 8 9 Diagramme du vide de l’OmniStar Analyseur QMA 250 M Chauffage de récipient Source d’ions Vanne de débitmètre (V1) vers la source d’ions Chauffage de l’admission de gaz Capillaire en acier inoxydable avec chauffage Vanne Split-flow (V2) Vanne d’isolement EVI 005 M sur l’unité de calibration 9 10 11 12 13 14 15 Unité de calibration (en option) Pompe à membrane Raccord de gaz d’échappement Pompe turbomoléculaire Vanne de ventilation Unité électronique QME 250 Jauge de pression totale 23/122 Description du produit 3.1.2 ThermoStar 1 2 3 13 12 4 5 8 6 11 9 7 10 Fig. 3: 1 2 3 4 5 6 7 3.1.3 Diagramme du vide du ThermoStar Analyseur QMA 250 M Source d’ions Chauffage de récipient Chauffage de l’admission de gaz Capillaire en quartz avec chauffage Vanne d’isolement EVI 005 M sur l’unité de calibration Unité de calibration (en option) 8 9 10 11 12 13 Pompe turbomoléculaire Pompe à membrane Raccord de gaz d’échappement Vanne de ventilation Unité électronique QME 250 Jauge de pression totale Version pour gaz corrosifs 1 9 8 7 5 6 P 2 4 Fig. 4: 1 2 3 4 5 3 Alimentation supplémentaire en purge de gaz neutre dans la version pour gaz corrosif Raccordement à l’enceinte à vide Raccord de gaz d’échappement Vanne d’étranglement Vanne de retenue Manocontacteur numérique avec jauge de pression 3.2 Commandes et indicateurs 3.2.1 Version avec écran 6 7 8 9 Vanne de la purge de gaz Raccord de la purge de gaz neutre Régulateur de pression manuel Vanne de ventilation L’écran tactile 7" est situé en face avant de l’unité et peut être retiré du carter via les 2 rainures de dégagements sur le côté. Le champ opérateur et les touches opérateur sont sensibles au contexte et 24/122 Description du produit changent afin de refléter les fonctions de l’écran. Les fonctions indisponibles sont grisées. Sur l’écran « Messages », les niveaux de message inactifs sont aussi affichés comme des boutons gris. Messages d’avertissement ou de défaut En cas de message d’anomalie ou d’avertissement, un triangle d’avertissement apparaît en haut à droite de l’affichage. Le triangle d’avertissement est susceptible d’apparaître sur l’ensemble des écrans de menu. Appuyez sur le triangle d’avertissement ou le bouton « Messages » pour afficher l’aperçu du message. 8 1 2 7 6 6 5 Fig. 5: 3 Écran d’affichage avec touches opérateur 1 Barre de titre avec le nom du menu 2 Triangle d’avertissement en cas d’avertissement ou de message d’anomalie 3 Réglages de l’utilisateur 4 Champ opérateur inactif à l’écran (grisé) 5 Icône d’état Symbole 6 7 Icône de composant Commandes 8 9 Champ opérateur actif à l’écran Lien vers le tableau de bord Signification Couleur Vert clair Activé, état de marche atteint Vert foncé Activé, état de marche pas encore atteint Gris clair Non activé Gris foncé En cours de désactivation, état de désactivation pas encore atteint Coche sur l’icône d’état état stable, état final d’activation ou de désactivation atteint Arc tournant dans l’icône d’état Fonction lancée ou stoppée, état final pas encore atteint Tab. 6: 3.2.2 4 Symboles et couleurs des icônes d’état et de composant Version sans écran Diverses LED indiquent l’état des différents systèmes sur le modèle dépourvu d’écran. La commande se fait uniquement via l’interface Web. LED Fonction Description 0 Puissance La LED indique l’état de l’alimentation électrique. Lorsqu’elle est allumée, l’unité est sous tension. 1 Vide prêt La LED clignote pendant la mise en route des pompes à vide ; elle reste allumée fixe dès que la pompe à vide est évacuée et le système est opérationnel pour effectuer une mesure. 2 Erreur Message d’erreur générale 3 Chauffage La LED s’allume lorsque les unités de chauffage sont mises en marche. 25/122 Description du produit LED Fonction Description 4 Filament chauffé La LED s’allume en présence d’un flux dans le filament. 5 Purge La LED s’allume lorsque le raccordement à la purge de gaz neutre est établie ; elle clignote lorsque la surveillance de la purge de gaz neutre est shuntée (uniquement pour les travaux de maintenance). Tab. 7: LED d’état et leur signification 3.3 Configuration de l’unité 3.3.1 Instrument fondamental L’instrument fondamental est constitué d’un châssis et de couvercle amovibles. Pour la ventilation, le GSD 350 est équipé de : ● 2 ouvertures de ventilation, avec ventilateurs sur les côtés ● Ouvertures de ventilation en haut et en bas de l’affichage amovible 2 1 3 12 11 8 5 9 10 Fig. 6: 3.3.2 4 6 7 Éléments du carter 1 Couvercle de carter 2, 3 Panneau de connexion en option pour le tube capillaire chauffé 4 Ouverture de ventilation (admission) 8 9 Ouverture de ventilation (sortie) Capot latéral (de droite) 10 5 Capot latéral (de gauche) 11 6 7 Cadre, châssis Zone de connexion 12 Panneau de connexion pour le tube capillaire chauffé (position à la livraison) Affichage de contact 7" (Alternative : affichage à LED sans écran) Couvercle de l’admission de gaz Zone de connexion Le panneau de connexion contient toutes les interfaces et connexions de l’unité. 26/122 warranty seal warranty seal Description du produit www.vsm-cloud.com D-35614 Asslar Mod. GSD 350 P/N PT Q.. ... S/N ... Input ... Made in Germany 2022/02 1 2 8 Fig. 7: 3.3.3 7 6 5 4 3 Panneau de connexion avec interfaces et connexions 1 Raccord de terre (terre fonctionnelle) 5 2 Alimentation avec interrupteur de mise sous tension 3 Raccord de gaz d’échappement 4 Raccord de la purge de gaz neutre 8) 6 7 8 Manocontacteur numérique pour purge de gaz neutre 7) Connexion Ethernet (RJ-45) Connexion « USER IO » Connexion « AUX IO » Système d’admission de gaz Le diffuseur de gaz vers la source d’ions est vissé sur les systèmes d’admission d’admission de gaz de l’OmniStar et du ThermoStar. Le diffuseur de gaz retient l’orifice et dirige le flux de gaz réduit vers la chambre de formation de la source d’ions. La douille en céramique agit comme isolant électrique. Un ressort à pression comprime la douille en céramique contre la chambre de formation de la source d’ions. Système d’admission de gaz (OmniStar) Lorsque l’admission de gaz est ouverte, un volume de 1 à 2 sccm du gaz à analyser reflue par le capillaire en acier inoxydable vers l’unité de vanne. Par l’intermédiaire de l’étage de réduction de pression, constitué du capillaire et d’un orifice devant le diffuseur de gaz, le gaz à analyser atteint le spectromètre de masse sans démixtion. Le capillaire en acier inoxydable est situé dans un tube capillaire, qui peut être chauffé à 200 °C, voire à 350 °C en option. Quand le chauffage du capillaire est activé, le chauffage d’admission est aussi activé et l’admission de gaz est automatiquement chauffée. Les effets de la condensation dans les gaz à analyser peuvent être évités par l’augmentation de la température. Les vannes permettent l’interruption du flux de gaz d’échantillon. L’orifice encastré permet à une petite fraction du flux de gaz de pénétrer dans l’enceinte à vide. Le flux de gaz résiduel atteint l’aspiration intermédiaire de la pompe turbomoléculaire. Quand l’admission de gaz et les vannes Split-flow sont fermées, le flux de gaz dans l’enceinte à vide est nul. Ceci permet de déterminer le bruit de fond de l’enceinte à vide avec le spectromètre de masse et de la soustraire des mesures ultérieures, si nécessaire. La non linéarité du spectromètre de masse peut nuire à la haute précision des mesures. La pénétration d’un gaz très propre (gaz zéro) permet de déterminer avec précision le bruit de fond du spectromètre de masse, même à la pression de travail (environ 1 × 10-5 hPa). Le gaz zéro doit être injecté dans les mêmes conditions de pression que pour le gaz à analyser. Système d’admission de gaz (ThermoStar) 1 à 2 sccm du gaz à analyser passe par l’étage de réduction de pression, constitué du capillaire et d’un orifice dans le diffuseur de gaz, pour atteindre le spectromètre de masse sans démixtion. Le capillaire en quartz est situé dans un tube capillaire, qui peut être chauffé à 200 °C, voire à 350 °C en option. Quand le chauffage du capillaire est activé, le chauffage d’admission est aussi activé et l’admission de gaz est donc chauffée. Les effets de la condensation dans les gaz à analyser peuvent être évités par l’augmentation de la température. Le capillaire en quartz se termine à 1 à 2mm avant l’orifice. Cela signifie qu’une partie du gaz sortant du capillaire en quartz atteint le spectromètre de masse sans impact sur les parois dans l’étage de réduction de la pression. Ceci est important pour identifier de faibles concentrations de gaz réactifs, car ceux-ci ne doivent pas entrer en contact avec l’acier inoxydable. Le flux de gaz ne peut pas être séparé de l’enceinte à vide avec le spectromètre de masse quand cette variante d’admission de gaz est utilisée. Ceci signifie que le bruit de fond de l’enceinte à vide et le spectromè- 7) uniquement pour la version pour gaz corrosifs 8) uniquement pour la version pour gaz corrosifs 27/122 Description du produit tre de masse ne peut pas être déterminé et ajusté. Si c’est nécessaire, la pénétration d’un gaz très propre (gaz zéro) permet de déterminer avec précision le bruit de fond du spectromètre de masse, même à la pression de travail (environ 1 × 10-5 hPa). Le gaz zéro doit être injecté dans les mêmes conditions de pression que pour le gaz à analyser. 1 8 7 2 6 5 4 3 Fig. 8: 1 2 3 4 3.3.4 Systèmes d’admission de gaz Admission de gaz Thermostat Enceinte à vide Pompe turbomoléculaire Aspiration intermédiaire de la pompe turbomoléculaire 5 6 7 8 Bride de raccordement Admission de gaz Omnistar Vanne de débitmètre Vanne Split-flow Unité de calibration L’unité de calibration optionnelle permet la calibration de ’échelle de masse et de la résolution du spectromètre de masse dans le domaine de masse haut (> 200 u). Un récipient collecteur en verre avec de la perfluortributylamine (PFTBA) sert de fluide de calibration et est inséré dans l’enceinte à vide via un orifice et une vanne d’isolement. L’enceinte à vide est raccordée sur le côté, via une bride DN 40 CF sur la face avant. La vanne d’isolement sur l’unité de calibration peut être ouverte et fermée via la commande du GSD 350. Perfluorotributylamine (PFTBA) dans le signal de fond Le PFTBA présente l'inconvénient de laisser des traces dans le signal de fond de l'unité longtemps après la fermeture de la vanne de calibration. Si cela interfère avec l'analyse des gaz prévue, Pfeiffer Vacuum recommande l’étuvage de l’enceinte à vide après le calibration avec le PFTBA. 28/122 Description du produit 1 2 3 4 Fig. 9: Unité de calibration en admission de gaz 1 Admission de gaz 2 Tube en acier inoxydable 1/8 po 3.3.5 3 4 Vanne d’isolement EVI 005 M Récipient collecteur en verre pour le fluide de calibration PFTBA Système côté vide élevé La pompe turbomoléculaire fonctionne selon le principe SplitFlow et maintient une pression de fonctionnement < 5 × 10-5 hPa dans l’enceinte à vide avec l’admission de gaz ouverte. La pompe turbomoléculaire prend en charge la majorité du gaz qui s'écoule via le capillaire par aspiration intermédiaire. 3.3.6 Système de vide primaire La pompe à membrane établit le vide primaire requis pour faire tourner la pompe turbomoléculaire. Le branchement au raccord de vide primaire (filetage 1/4") sur la pompe turbomoléculaire se fait par un tuyau flexible de raccordement. Pour une élimination spécifique du gaz pompé, la pompe à membrane est dotée d’une conduite d’échappement qui vous pouvez relier à une conduite locale d’évacuation du gaz ou acheminer hors du laboratoire. Bruit croissant de la pompe à membrane La vitesse de rotation de la pompe à membrane est automatiquement adaptée aux différents états de marche de la GSD 350. Ceci peut entraîner différents bruits croissants. Changement de la fréquence de la pompe avec émission active Vous pouvez changer la fréquence de la pompe à membrane pour des mesures sensibles avec les spectromètre de masse et l’émission active. Ceci vous permet de réduire au minimum l’influence sur le signal de mesure. Pour une description détaillée, se reporter au document DA0106 « Fonctionnement via interface Web et PV MassSpec ». Fig. 10: Pompe à membrane 29/122 Description du produit 3.3.7 Système de purge de gaz neutre Sur la version pour gaz corrosif, la purge de gaz neutre protège les paliers de la pompe turbomoléculaire et assure que le gaz corrosif est évacué vers la pompe à membrane sous une forme diluée. Cela améliore la durée de vie de la pompe à membrane et empêche la condensation des vapeurs dans la pompe à membrane. La version de gaz corrosif est dotée d’un régulateur de pression interne réglé en usine qui utilise un rhéomètre pour assurer un flux adéquat de purge de gaz neutre. Une faible fraction de la purge de gaz neutre atteint la vanne de purge de gaz neutre et de ventilation de la pompe turbomoléculaire via un diviseur de débit. La fraction principale de la purge de gaz neutre, environ 300 sccm, s’écoule directement vers le raccord de gaz d’échappement. Si un conduit d’échappement ou un épurateur est raccordé, il ne doit pas y avoir de surpression au niveau du raccordement des gaz d’échappement. Objet du manocontacteur numérique : ● fournir un indicateur visuel de la pression de la purge de gaz neutre interne (2 à 16 kPa de surpression) en aval du régulateur de pression ● émettre un signal qui déclenche la procédure d’arrêt si la pression de la purge de gaz neutre dépasse ou tombe en dessous de la plage autorisée Concentrations de gaz admissibles Pour calculer la toxicité de la purge de gaz neutre, on part du principe que la purge de gaz neutre dilue les concentrations des gaz d’admission par un facteur > 100. 1 2 3 4 5 6 15 7 14 13 12 11 9 8 1 Tuyau flexible entre la pompe à membrane et la pompe turbomoléculaire 2 Pompe à membrane 9 Raccord de la purge de gaz neutre 10 3 Tuyau flexible de gaz d’échappement de la pompe à membrane 4 Vanne de retenue d’étranglement 5 Tuyau vers le raccord de gaz d’échappement 6 Vanne de retenue 7 Régulateur de pression manuel 8 Raccord de gaz d’échappement 11 Manocontacteur numérique avec jauge de pression Tuyau vers la vanne de la purge de gaz 12 13 14 15 Tuyau flexible de la purge de gaz neutre Tuyau vers la vanne de ventilation Vanne de la purge de gaz Vanne de ventilation 10 Fig. 11: 3.3.8 Système de purge de gaz neutre Unité d’analyse de gaz Principe fonctionnel du spectromètre de masse Le principe fonctionnel du spectromètre de masse PrismaPro est décrit dans le manuel de l’utilisateur correspondant. 30/122 Description du produit Le spectromètre de masse analyse la petite fraction de gaz à analyser pénétrant dans l’enceinte à vide via l’orifice. Quand l’émission est activée, l’unité d’analyse de gaz peut déterminer la pression dans l’enceinte à vide de façon autonome et l’afficher dans le logiciel PV MassSpec. L’unité d’analyse de gaz a aussi une jauge de pression totale sur l’enceinte à vide qui permet une mesure du vide dans le domaine de pression allant de 1000 à 5 × 10-9 hPa indépendamment du spectromètre de masse. La pression totale mesurée peut être lue sur l’affichage, l’UI Web et dans le logiciel PV MassSpec. 1 4 10 2 9 3 4 5 8 7 Fig. 12: 3.3.9 6 Composants de l’unité d’analyse de gaz 1 Jauge de pression totale 2 Unité électronique QME 250 3 Capteur de température 6 7 8 4 Cartouche de chauffage dans l’enceinte à vide 5 Vanne de la purge de gaz sur la version pour gaz corrosif 9 Vanne de ventilation Pompe turbomoléculaire Aspiration intermédiaire de la pompe turbomoléculaire Source d’ions pour analyseur QMA 250 M 10 Enceinte à vide Chauffage et isolation AVERTISSEMENT Risque de brûlure sur les surfaces chaudes Pendant le fonctionnement, les températures montent très haut (> 50 °C) sur les surfaces de contact des composants de chauffage et sur l’admission de gaz. Il existe un risque de brûlure. ► Prenez les mesures requises pour prévenir tout contact avec les pièces chaudes. ► Apposez des signaux d’avertissement. ► Veillez à ce que le produit se soit refroidi avant d’intervenir dessus. ► Portez des gants de protection (conformément à EN 420). Les dispositifs de chauffage de l’unité peuvent être totalement contrôlées via le contrôleur de l’unité. Type Température (max.) Température (réglable) Chauffage du capillaire (200 °C) 200 °C 80 à 200 °C Chauffage du capillaire (350 °C) 350 °C 80 à 350 °C Chauffage de l’admission de gaz 100 °C Réglé automatiquement Chauffage de récipient 130 °C 40 à 130 °C Tab. 8: Dispositifs de chauffage sur l’unité 31/122 Description du produit Chauffage de récipient (étuvage) L’étuvage réduit les gaz de condensation adhérant à la surface de l’enceinte à vide. Cela conduit à une pression totale plus faible dans l’enceinte à vide, et à un signal de fond plus faible pendant les mesures. La quantité d’eau est ainsi réduite dans le système de vide. Caractéristiques de chauffage de récipient ● L’enceinte à vide dispose de 2 cartouches de chauffage. ● Vous pouvez enlever l’isolation de l’enceinte à vide et le raccord angulaire. ● Vous pouvez sélectionner la durée de l’étuvage de 1 à 24 h. La valeur standard pour l’étuvage est de 4 heures. ● Vous pouvez annuler à tout moment le processus d’étuvage via la commande sur l’unité. ● Vous pouvez sélectionner une température entre 100 et 130 °C. La valeur standard de la température est de 120 °C. 5 4 1 2 3 Fig. 13: Chauffage et isolation de l’enceinte à vide 1,3 Cartouches de chauffage de récipient 2 Capteur de température 4 5 Isolation (coudée) Isolation de l’enceinte à vide Chauffage de l’admission de gaz Caractéristiques du chauffage de l’admission de gaz ● Les admissions de gaz OmniStar et ThermoStar ont une plaque de conducteur thermique avec un coussin de chauffage et une douille isolante. ● La version Omnistar a aussi une cartouche de chauffage dans le bloc de vannes. ● Le chauffage de l’admission de gaz est toujours activé et désactivé parallèlement au chauffage du capillaire. ● La GSD 350 ajuste automatiquement la température de l’admission de gaz. Vous ne pouvez pas ajuster la température de chauffage de l’admission de gaz. 32/122 Description du produit 1 2 3 6 Fig. 14: 5 4 Chauffage de l’admission de gaz 1 Chauffage du capillaire dans le tube capillaire 4 2 Douille isolante du couvercle de l’admission de gaz 3 Couvercle de l’admission de gaz 5 Coussin de chauffage (collé à la plaque de conducteur thermique) Plaque de conducteur thermique 6 Douille isolante de paroi arrière Chauffage du capillaire Le capillaire est situé dans un tube capillaire flexible avec un chauffage à résistance. Vous pouvez chauffer le capillaire à 200 °C ou 350 °C. La valeur standard de la température du chauffage de capillaire est 120 °C. En fonction du réglage de la température et de la variante de tube capillaire, des températures > 70 °C sont possibles sur la surface du tube capillaire. 5 6 7 1 2 3 4 Fig. 15: 3.3.10 Chauffage du capillaire 1 Serpentin de chauffage 2 Élément d’isolement 4 5+6 3 Guide de capillaire pour la variante à 200 °C : Tuyau flexible en PTFE pour la variante à 350 °C : Tube en acier inoxydable 7 Capteur de température PT100 Raccordement électrique pour le chauffage Élément de fixation sur l’unité Composants électroniques Unité électronique QME 250 L’unité électronique QME 250 est montée sur l’analyseur QMA 250 M et contient les interfaces du spectromètre de masse. La QME 250 fournit toutes les tensions requises pour le fonctionnement de l’analyseur QMA 250 et prépare les courants d’ions mesurés au traitement ultérieur. Unité de commande électronique TC 110 L’unité de commande électronique TC 110 est un composant permanent de la pompe turbomoléculaire. Le rôle de l’unité de commande électronique est d’entraîner, de surveiller et de commander l’ensemble de la pompe turbomoléculaire. Unité de commande électronique de pompe à membrane L’unité de commande électronique est un composant permanent de la pompe à membrane. L’unité de commande électronique sert à surveiller et à contrôler toute la pompe à membrane. Unité de courant L’alimentation électrique étendue alimente en tension tous les composants du GSD 350. Affichage Commande le GSD 350 et interroge les fonctions via l’affichage. 33/122 Description du produit Injecteur PoE L’injecteur PoE alimente l’affichage en courant. Platine principale La platine principale est située sur la plaque de base du châssis et remplit les fonctions suivantes : ● ● ● ● ● ● ● Serveur VLAN pour la communication entre le spectromètre de masse et l’affichage Commande de la pompe turbomoléculaire et de la pompe à membrane Commande des vannes d’admission de l’OmniStar Commande de la vanne de gaz de calibration de la GSD 350 avec unité de calibration Contrôle du chauffage en boucle ouverte et fermée Commande du ventilateur pour la température du carter Interfaces externes 2 1 7 6 3 4 5 Fig. 16: 1 2 3 4 3.4 Composants électroniques Unité de courant Affichage Injecteur PoE Unité de commande électronique de pompe à membrane 5 6 7 Carte superviseur Unité électronique QME 250 Unité de commande électronique TC 110 Identification du produit Toutes les données de la plaque signalétique sont nécessaires pour identifier assurément le produit pour toute communication avec Pfeiffer Vacuum. 1. Relever les données sur la plaque signalétique produit. 2. Enregistrer ces données. 3. Toutes les caractéristiques de la plaque signalétique doivent toujours être disponibles. 3.5 Volume de livraison Le volume de livraison inclut les pièces suivantes : ● GSD 350 OmniStar/ThermoStar ● Matériel d’installation et petites pièces ─ Clé mâle coudée pour vis à six pans creux, WAF 2, WAF 2,5 et WAF 3 ─ Clé plate métrique, WAF 8, WAF 10 (2x) et WAF 14 ─ Clé plate à unités impériales, WAF 5/16", WAF 3/8" et WAF 9/16" 34/122 Description du produit ─ ─ ─ ─ ─ ─ ● ● ● ● Clé à douille à deux côtés pour la source d’ions Outil spécial pour l’orifice du système d’admission de gaz Équipement de montage pour analyseur QMA 250 2 joints toriques en FKM, 9,25 × 1,78 mm et 18,77 × 1,78 mm 2 fusibles lents, 10 A pour OmniStar avec capillaire en acier surfin seulement ○ Clé à fourche pour douille hexagonale, TX20 ○ Jeu de colliers de serrage pour tube 1/16" (5 pièces) ─ pour ThermoStar ou GSD 350 avec capillaire au quartz seulement ○ Jeu de joints pour capillaire 250 µm (virole) (5 pièces) ─ Uniquement pour les versions avec unité de calibration ○ Aide au montage du support de gaz de calibration Protection pour le transport, pour l’analyseur QMA 250 M Câble Ethernet, 3 m de long, rouge Câble de secteur Manuel de l’utilisateur ─ GSD 350 OmniStar/ThermoStar ─ Composants (voir chapitre « Documents applicables », page 10) Fig. 17: Équipement de montage pour analyseur QMA 250 Fig. 18: Outil spécial pour l’orifice du système d’admission de gaz Fig. 19: Aide au montage du support de gaz de calibration Déballage du produit et contrôle du contenu de la livraison 1. Déballer le produit. 2. Déposez les sécurités et les protections pour le transport, etc. 3. Rangez les sécurités et les protections pour le transport dans un endroit sûr. 4. Vérifier que toutes les pièces sont présentes. 5. Contrôler qu'aucune pièce n'a été endommagée. 35/122 Transport et stockage 4 Transport et stockage AVERTISSEMENT Risque de blessure lors du levage de charges lourdes Le produit est lourd ; il peut peser jusqu’à 26 kg, selon la version. Une personne soulevant le produit sans aide et de manière incorrecte risque de se blesser. ► Faites toujours appel à 2 personnes pour soulever le produit à deux mains. ► Prenez toujours les mesures de sécurité requises (portez par ex. des gants de protection). ► Respectez la réglementation locale. ► Conforme aux instructions pour un transport en toute sécurité. AVERTISSEMENT Danger de blessures graves en cas de chute d’objets La chute d’objets peut entraîner des blessures sur les membres, voire même des fractures osseuses. ► Soyez particulièrement vigilant lors du transport manuel du produit. ► Ne pas empiler le produit. ► Portez un équipement de protection, tel que des chaussures de sécurité. 4.1 Transport du produit AVIS Dégâts causés par un transport incorrect Un transport dans un emballage incorrect ou la non-installation de tous les verrous de transport peut endommager le produit. ► Conforme aux instructions pour un transport en toute sécurité. Emballage Nous recommandons de conserver l’emballage de transport et de protection d’origine. 2 1 Fig. 20: Protection pour le transport de la pompe à membrane 1 Protection pour le transport de la pompe à membrane 2 Patte Informations générales sur le transport en toute sécurité 1. Prenez en compte le poids du produit. 2. Dans la mesure du possible, transportez ou expédiez toujours le produit dans son emballage d’origine. 3. Utilisez toujours un emballage compact qui protège le produit des chocs. 36/122 Transport et stockage 4. Installez toujours l’ensemble de la protection pour le transport avant le transport. 5. Retirez le cache de protection existant seulement juste avant l’installation. Installation de la protection pour le transport de la pompe à membrane 1. Soulevez légèrement le côté gauche de la GSD 350. 2. Vissez complètement dans la protection pour le transport. 4.2 Stockage du produit AVIS Risque de détériorations causées par un entreposage incorrect Un entreposage incorrect provoquera des dégâts sur le produit. ► Conforme aux instructions pour un entreposage en toute sécurité. Emballage Nous recommandons de stocker le produit dans son emballage d'origine. Stocker le produit en toute sécurité ► Conservez le produit dans un endroit frais, sec et sans poussière, où il n’est pas soumis à des chocs ni à des vibrations mécaniques. ► Utilisez toujours un emballage compact qui protège le produit des chocs. ► Dans la mesure du possible, stockez le produit dans son emballage d’origine. ► Stockez les composants électroniques dans un emballage antistatique. ► Maintenez la température d’entreposage admissible. ► Évitez les fortes variations de températures ambiantes. ► Évitez un taux d’humidité élevé dans l’air. ► Fermez les raccords avec les bouchons de protection d’origine. ► Protégez le produit avec les protections de transport d’origine (si disponibles). 37/122 Installation 5 Installation 5.1 Assurer la ventilation AVIS Dégâts causés par surchauffe La température ambiante ne doit pas excéder la température de service admissible de l'appareil. ► Veillez à assurer une bonne circulation de l'air lors de l'installation de l'appareil. ► Si nécessaire, contrôlez et nettoyez régulièrement le filtre à air installé. Fig. 21: Distances latérales minimum de l’unité Procédure 1. Gardez toujours une zone > 25 mm propre autour de l’unité. 2. Si vous installez l’unité dans une armoire : ● Veillez à ce que l’armoire soit assez grande. ● Veillez à ce que l’armoire assure suffisamment d'aération par le ventilateur installé dans l’unité. 5.2 Retrait de la protection pour le transport de la pompe à membrane 2 1 Fig. 22: Protection pour le transport de la pompe à membrane 1 Protection pour le transport de la pompe à membrane 38/122 2 Patte Installation Procédé La protection pour le transport est située au-dessous de la GSD 350. Pfeiffer Vacuum a marqué la protection pour le transport avec une patte au départ usine. 1. Installez l’unité GSD 350 à l’emplacement d’utilisation. 2. Soulevez légèrement le côté gauche de la GSD 350 pour accéder sous l’unité. 3. Dévissez complètement la protection pour le transport. 4. Conservez la protection pour le transport dans un endroit sûr. 5.3 Établissement de la connexion Ethernet Vous avez besoin d'une connexion Ethernet appropriée pour faire fonctionner le GSD 350 via l’interface web ou le logiciel PV MassSpec en utilisant un PC (ordinateur hôte) ou un réseau. Raccordement du câble Ethernet ► Reliez le câble Ethernet fourni au GSD 350 et au PC. Les deux LED dans la prise RJ-45 indiquent le statut de l’interface (voir chapitre « Connexion Ethernet (LAN) », page 52). 5.4 Raccordement de la conduite d’échappement AVERTISSEMENT Risque d’empoisonnement dû à la substance de processus toxique s’échappant de la conduite d’échappement Lorsqu’elle fonctionne sans conduite de refoulement, la pompe à vide rejette les gaz et vapeurs de refoulement dans l’air. Risque de blessure et de mort dû à l’empoisonnement par les substances de processus toxiques. ► Respecter la réglementation en vigueur concernant le traitement des substances de processus toxiques. ► Évacuer les substances de processus toxiques en toute sécurité par une conduite de refoulement. ► Employer des moyens de filtration appropriés pour séparer les substances de processus toxiques. 5.4.1 Sectionnement du tuyau de gaz d'échappement Outil nécessaire ● Cutter à flexible Équipement nécessaire ● Tuyau flexible PE (Ø extérieur = 6 mm) Fig. 23: Sectionnement du tuyau de gaz d'échappement Procédure 1. Vous devez prendre beaucoup de précautions pour la coupe du tuyau flexible de gaz d'échappement. – Le tuyau flexible de gaz d'échappement ne doit pas être déformé, éraflé ou fendillé. 2. Coupez proprement le tuyau flexible de gaz d'échappement : ● à la longueur requise ● aux bons angles 39/122 Installation 5.4.2 Raccordement du tuyau de gaz d’échappement Condition préalable ● Conduite d'échappement non pressurisée Équipement nécessaire ● Tuyau d’échappement PE (Ø extérieur = 6 mm) ● en option : connecteurs mâle-femelle IQS ou Schott supplémentaires Connecteurs mâle-femelle IQS Les connecteurs mâle-femelle IQS ont 2 points de pression : Griffe de maintien et joint. Le tuyau flexible est correctement raccordé lorsque les deux points de pression sont passés. 2 1 Fig. 24: Raccordement du tuyau de gaz d’échappement 1 Bague de déblocage 2 Tuyau flexible Raccordement du tuyau de gaz d’échappement 1. Raccordez le tuyau de gaz d’échappement au raccord de gaz d’échappement sur l’unité. 2. Raccordez une conduite d’échappement à l’unité si vous utilisez cette dernière avec des substances corrosives. 3. Respectez la réglementation locale en vigueur concernant le traitement des gaz de processus. 5.5 Raccordement de la conduite de purge de gaz neutre 5.5.1 Sectionnement du tuyau de purge de gaz neutre Outil nécessaire ● Cutter à flexible Équipement nécessaire ● Tuyau flexible PE (Ø extérieur = 4 mm) Fig. 25: Sectionnement du tuyau de purge de gaz neutre Procédure 1. Vous devez prendre beaucoup de précautions pour la coupe du tuyau flexible de purge de gaz neutre. – Le tuyau flexible de purge de gaz neutre ne doit pas être déformé, éraflé ou fendillé. 2. Coupez proprement le tuyau flexible de purge de gaz neutre : ● à la longueur requise ● aux bons angles 40/122 Installation 5.5.2 Raccordement de la conduite de purge de gaz neutre Condition préalable ● Conduites de purge de gaz et d'échappement non pressurisées Équipement nécessaire ● Tuyau de purge de gaz neutre PE (Ø extérieur = 4 mm) ● en option : connecteurs mâle-femelle IQS ou Schott supplémentaires Connecteurs mâle-femelle IQS Les connecteurs mâle-femelle IQS ont 2 points de pression : Griffe de maintien et joint. Le tuyau flexible est correctement raccordé lorsque les deux points de pression sont passés. 2 1 Fig. 26: Raccordement de la conduite de purge de gaz neutre 1 Bague de déblocage 2 Tuyau flexible Raccordement du tuyau de purge de gaz neutre 1. Installez un système de réduction de pression si vous attendez un dépassement de la plage de pression autorisée pour la purge de gaz neutre. – L’unité ne dispose pas de sa propre vanne d’isolement de purge de gaz neutre. 2. Reliez le tuyau de purge de gaz neutre au raccord de la purge de gaz neutre sur l’unité. 3. Respectez la réglementation locale en vigueur concernant le traitement des gaz de processus. 5.6 Raccordement du capillaire AVIS Endommagement du système d’échantillonnage Une manipulation incorrecte du capillaire peut endommager le système d’échantillonnage de l'unité. ► Tenez compte du rayon de courbure. ● Tuyau capillaire 200 °C : ≥ 50 mm ● Tuyau capillaire 350 °C : ≥ 200 mm ► N’isolez pas en plus le chauffage du capillaire. ► Ne couvrez pas en plus le chauffage du capillaire. ► N’exposez pas le capillaire à une chaleur supplémentaire, par ex. d'une bride chauffée. 41/122 Installation AVIS Défaillance due à la contamination et à la détérioration Tout contact à mains nues avec les appareils ou les composants augmente le taux de désorption et entraîne des mesures incorrectes. La saleté (p. ex. poussières, traces de doigts, etc.) et les dégâts nuisent au fonctionnement. ► Portez toujours des gants de laboratoire propres, non pelucheux et sans poudre pour les travaux sur les installations ultra-vide ou à vide élevé. ► Utilisez uniquement des outils propres. ► Vérifiez que les brides de raccordement sont sans graisse. ► Retirez les obturateurs de protection et les couvercles de protection des brides et des raccordements uniquement lorsque cela est nécessaire. ► Effectuez toutes les opérations dans un espace bien éclairé. Adaptateur de tube capillaire comme accessoire Un adaptateur de tube capillaire est disponible comme accessoire pour raccorder correctement le tube capillaire. 2 1 Fig. 27: Raccordement du capillaire 1 Bande adhésive 5.6.1 2 Exemple de sécurisation d’un tuyau capillaire Raccordement du capillaire en acier inoxydable OmniStar Procédure 1. Retirez la bande adhésive du capillaire en acier inoxydable. 2. Attachez le capillaire en acier inoxydable sur le point de mesure. 3. Utilisez l’adaptateur de tube capillaire en acier inoxydable de la gamme d’accessoires Pfeiffer Vacuum. 4. Fixez le tube capillaire. 5. Serrez le tube capillaire dans la zone solide et fixe à l’avant uniquement. 5.6.2 Raccordement du capillaire ThermoStar quartz Procédure 1. Retirez la bande adhésive du capillaire en quartz. 2. Si nécessaire, tirez le capillaire en quartz ou insérez-le pour atteindre le point de mesure. – Pour cela, retirez le capot de l’admission de gaz (voir chapitre « Retrait/fixation du couvercle de l’admission de gaz », page 76). 3. Attachez le capillaire en quartz sur le point de mesure. 4. Utilisez l’adaptateur de tube capillaire en acier inoxydable de la gamme d’accessoires Pfeiffer Vacuum. 5. Fixez le tube capillaire. 6. Serrez le tube capillaire dans la zone solide et fixe à l’avant uniquement. 42/122 Installation 5.7 Adaptation de la position du tuyau flexible de capillaire AVERTISSEMENT Risque de brûlure sur les surfaces chaudes Pendant le fonctionnement, les températures montent très haut (> 50 °C) sur les surfaces de contact des composants de chauffage et sur l’admission de gaz. Il existe un risque de brûlure. ► Prenez les mesures requises pour prévenir tout contact avec les pièces chaudes. ► Apposez des signaux d’avertissement. ► Veillez à ce que le produit se soit refroidi avant d’intervenir dessus. ► Portez des gants de protection (conformément à EN 420). Pour optimiser le positionnement du tube capillaire pour des applications spécifiques, 3 positions du tuyau flexible capillaire sont possibles. Pfeiffer Vacuum fournit la GSD 350 avec le tuyau flexible de capillaire sur le côté droit. Des bouchons borgnes viennent obturer les deux positions non utilisées. Conditions préalables ● GSD 350 désactivée ● Couvercle d’admission de gaz retiré Outils nécessaires ● Clé mâle coudée pour vis à six pans creux, WAF 2 1 2 3 Fig. 28: Position du tuyau flexible capillaire à la livraison 1 Bouchon borgne, à gauche 2 Bouchon borgne, en haut 3 Tuyau flexible capillaire avec bouchon borgne, à droite Procédure 1. Dévissez les 3 vis à tête conique et le bouchon borgne au niveau de la nouvelle position du tube capillaire. 2. Dévissez les 3 vis à tête conique et le capuchon avec le tube capillaire. 3. Retirez soigneusement le capuchon avec le tube capillaire de sorte à pouvoir guider le capillaire et le câble à travers la fente du boîtier. – Le capillaire peut rester à demeure sur l’entrée. 4. Serrez le capuchon avec le tube capillaire sur la nouvelle position du tube capillaire, à l’aide des 3 vis à tête conique. 5. Obturez la position précédente du tube capillaire avec le bouchon borgne et les 3 vis à tête conique. 5.8 Établissement d’une connexion au réseau Une connexion réseau correspondante est nécessaire pour le fonctionnement de GSD 350 via l’interface web ou du logiciel PV MassSpec à l’aide d’un PC (ordinateur de pilotage) ou via un réseau. 43/122 Installation ● Adresses IP Un réseau utilise des adresses IP comme moyen d’identification des unités individuelles. Les adresses IP sont uniques au sein d’un réseau, mais ne sont pas universelles. Cela signifie qu’une seule unité dans un réseau peut avoir une certaine adresse IP, mais 2 unités dans des réseaux séparés peuvent avoir la même adresse IP. Les paragraphes suivants donnent des informations sur certains réseaux généraux disponibles pouvant avoir un effet sur la connexion GDS 350 (voir chapitre « Réglage des paramètres réseau », page 64). Procédure ► Réglez l’adresse IP du GSD 350. ► Réglez l’adresse IP du PC (ordinateur hôte) que vous utilisez. ► Définissez un sous-réseau. 5.8.1 Adresses IP AVIS Les adresses IP entrent en conflit en cas de raccordement de plusieurs unités Pfeiffer Vacuum fournit à chaque GSD 350 la même adresse IP par défaut. Si vous souhaitez connecter plusieurs unités GSD 350, gardez à l’esprit que leurs adresses IP ne sont pas uniques au départ La connexion simultanée de plusieurs GSD 350 avec une adresse IP standard identique entraîne des conflits d'adresse IP dans le réseau. ► Modifiez l'adresse IP des unités que vous voulez connecter dans le réseau. ► Dans la mesure du possible, utilisez des adresses IP statiques. ► Connectez ensuite les unités à un réseau. Utilisation des adresses IP Pfeiffer Vacuum recommande d’utiliser des adresses IP statiques pour le GSD 350. Réservez un bloc d'adresses IP statiques et vérifiez que ces adresses IP réservées sont interdites sur le serveur DHCP (hôte). Cela évitera tout conflit avec des doublons d'adresses IP. Si vous connectez le GSD 350 à un réseau local existant, vous aurez besoin d’une adresse IP statique pour chaque GSD 350 installé. Consultez votre administrateur réseau pour qu’il attribue les différentes adresses IP. Les adresses IP statiques protègent contre la perte de données. Le logiciel PV MassSpec et l’interface web utilisent l'adresse IP du GSD 350 pour identifier chaque GSD 350 connecté. L’adresse IP du GSD 350 ne doit pas changer pendant le fonctionnement. Avec DHCP, l’hôte peut générer une nouvelle adresse IP à chaque connexion et reconnexion du GSD 350. DHCP peut également modifier automatiquement l’adresse IP en cas de conflit d’adresse IP sur le réseau. Si l’adresse IP du GSD 350 est modifiée par accident pendant l’acquisition des données, l’interface web et le logiciel PV MassSpec ne sont pas automatiquement reconnectés au GSD 350, dans la mesure où le logiciel PV MassSpec ne reconnaît pas l’adresse IP nouvellement attribuée. Il en résulte une rupture de communication et de données. Les adresses IP statiques changent seulement si l’adresse IP est modifiée manuellement, ce qui contribue à protéger le GSD 350 contre les pertes de communication et de données. Adresse IP standard pour le GSD 350 ● Préfixe réseau : 192.168.1.xxx ● Adresse IP : 192.168.1.100 Le GSD 350 utilise des adresses IP IPv4. Les adresses IP IPv4 sont composées de 32 bit en notation décimale pointée. Elles sont constituées de quatre numéros décimaux, séparés chacun de 0 à 255 par des points, par exemple : 192.168.1.100. Chaque numéro représente un octet. En principe, les adresses IP contiennent un préfixe réseau et un protocole hôte. 44/122 Installation Réglage des adresses IP ► Recommandation : utilisez des adresses IP statiques. – Vous pouvez régler et modifier manuellement les adresses IP statiques. ► N’utilisez pas d’adresses IP dynamiques. – Un hôte (DHCP) règle automatiquement ces adresses IP ► Une alternative à la modification de l’adresse IP du consiste à modifier l’adresse IP de l’ordinateur hôte, afin de permettre la communication entre l’ordinateur hôte et l’unité . 5.8.2 Sous-réseaux Masque de sous-réseau standard pour GSD 350 ● Masque de sous-réseau : 255.255.255.0 Un sous-réseau est une sous-division logique visuelle d’un réseau IP. Le fait de diviser un réseau IP en plusieurs sous-réseaux est désigné par sous-réseautage. Le sous-réseautage définit la partie de l’adresse IP qui est utilisée comme préfixe de réseau pour toutes les adresses IP au sein d’un sousréseau. Cette opération est effectuée par le masque de sous-réseau. Exemple 1 Exemple 2 Exemple 3 Adresse IP 192.168.1.104 192.168.1.105 192.168.1.150 Masque de sous-réseau 255.255.255.0 255.255.0.0 255.255.255.192 Préfixe réseau 192.168.1.0 192.168.0.0 192.168.1.128 Protocole hôte 0.0.0.104 0.0.1.105 0.0.0.22 Tab. 9: Exemples de sous-réseaux Le masque de sous-réseau définit quel octet doit être utilisé par l’adresse IP comme préfixe réseau. Pour permettre à 2 unités réseau de communiquer, les unités réseau doivent être dans le même sousréseau. Cela implique que non seulement, ils doivent être connectés au même réseau internet, mais également qu’ils doivent avoir le même préfixe réseau. 5.8.3 Changement d’adresse IP de la GSD 350 Manuel de l'utilisateur pour l’interface web et le logiciel PV MassSpec Des informations sur l'utilisation du GSD 350 via l'interface web et PV MassSpec sont disponibles dans le manuel de l'utilisateur en annexe, sous le numéro de document DA 0106. Adresses IP dans la gamme 192.168.2.xxx Les adresses IP dans la gamme 192.168.2.xxx sont réservées aux services internes. Ces adresses IP ne peuvent pas être utilisées. 45/122 Installation Fig. 29: Changement de l’adresse IP de la GSD 350 via l’interface Web Procédé ► Utilisation de l’affichage pour modifier l’adresse IP de l’unité (voir chapitre « Réglage des paramètres réseau », page 64). ► Utilisation de l’interface Web pour modifier l’adresse IP de l’unité. 5.8.4 Modification de l’adresse IP de l’ordinateur hôte Droits d’administrateur Les étapes suivantes sont valables pour le système d’exploitation Windows 10. Toute modification de l’adresse IP de l’ordinateur hôte nécessite des droits d’administrateur. Contactez votre administrateur système le cas échéant. Adresse IP par défaut 192.168.1.100 Par défaut, l'adresse IP de l’unité est 192.168.1.100. Vous ne pouvez pas l’utiliser ici. Rétablissement de la valeur par défaut de l’adresse IP Effectuez toutes les étapes depuis le début et remplacez à nouveau les propriétés IPv4 par les valeurs standards pour régler l’adresse IP sur la valeur standard. Procédure 1. Appuyez sur le bouton Démarrage dans la barre des tâche. 2. Appuyez sur Réglages. – La fenêtre Réglages s'ouvre. 3. Cliquez sur Réseau & Internet. 4. Cliquez sur Sans fil. 5. Sélectionnez Gestion des réseaux connus. 6. Sélectionnez le réseau dont vous souhaitez modifier les réglages. 7. Sélectionnez Propriétés. 8. Sous Attribution IP, sélectionnez l'option Édition. 9. Sous Édition réglages IP, sélectionnez l'option Manuel. 10. Activez IPv4. 11. Saisissez l’adresse IP, la longueur du préfixe de sous-réseau et les réglages pour l’adresse IP. – Ne modifiez pas la passerelle. – GSD 350 avec adresse IP par défaut : Utilisez 192.168.1.xxx comme adresse IP :, et 255.255.255.0 comme longueur de préfixe de sous-réseau. – « xxx » ne doit pas correspondre à 100 dans l’adresse IP. 46/122 Installation 12. Sélectionnez Sauvegarder. – L’adresse IP de votre ordinateur est alors réglée sur l’adresse IP manuelle sélectionnée. 13. Fermez toutes les fenêtres de réglages ouvertes. Raccordement de la terre fonctionnelle DANGER Danger de mort en cas d’électrocution Une mise à la terre inappropriée ou incorrecte de l’unité entraîne une tension sensible aux contacts au niveau du boîtier. Lors de la connexion, des courants de fuite plus élevés vont déclencher un choc électrique potentiellement mortel. ► Avant l’installation, contrôlez que les conducteurs d’alimentation ne sont pas sous tension. ► Acheminez le câble électrique conformément aux dispositions locales en vigueur. ► Assurez-vous que les valeurs de tension et de fréquence locales correspondent aux spécifications de la plaque signalétique. ► Veillez à ce que le câble d’alimentation et la rallonge soient conformes aux exigences de double isolation entre la tension d’entrée et la tension de sortie, conformément aux normes CEI 61010 et CEI 60950. ► N'utilisez qu’un câble d'alimentation à 3 broches et une rallonge disposant d'une mise à la terre correcte (conducteur mis à la terre). ► Ne branchez la fiche électrique que dans une prise disposant d'un contact de mise à la terre. ► Afin de garantir la protection de la mise à la terre, il convient de toujours brancher le câble électrique avant tous les autres. DANGER Électrocution en raison de l’absence de conducteur de protection interne Le conducteur de protection interne est fixé au logement. Une unité sans conducteur de protection interne peut présenter un danger de mort en cas de dysfonctionnement. ► Ne tournez pas ou ne débloquez pas le conducteur de protection interne. warranty seal warranty seal 5.9 www.vsm-cloud.com D-35614 Asslar Mod. GSD 350 P/N PT Q.. ... S/N ... Input ... Made in Germany 2022/02 1 Fig. 30: Raccordement pour la terre fonctionnelle 1 Raccordement pour la terre fonctionnelle (vis M5) Procédure ► Si nécessaire, utilisez la vis M5 pour raccorder l’unité à la terre de référence du système via un conducteur de protection par exemple. 47/122 Installation 5.10 Raccordement de l’alimentation électrique DANGER Danger de mort en cas d’électrocution Une mise à la terre inappropriée ou incorrecte de l’unité entraîne une tension sensible aux contacts au niveau du boîtier. Lors de la connexion, des courants de fuite plus élevés vont déclencher un choc électrique potentiellement mortel. ► Avant l’installation, contrôlez que les conducteurs d’alimentation ne sont pas sous tension. ► Acheminez le câble électrique conformément aux dispositions locales en vigueur. ► Assurez-vous que les valeurs de tension et de fréquence locales correspondent aux spécifications de la plaque signalétique. ► Veillez à ce que le câble d’alimentation et la rallonge soient conformes aux exigences de double isolation entre la tension d’entrée et la tension de sortie, conformément aux normes CEI 61010 et CEI 60950. ► N'utilisez qu’un câble d'alimentation à 3 broches et une rallonge disposant d'une mise à la terre correcte (conducteur mis à la terre). ► Ne branchez la fiche électrique que dans une prise disposant d'un contact de mise à la terre. ► Afin de garantir la protection de la mise à la terre, il convient de toujours brancher le câble électrique avant tous les autres. Fig. 31: Connexion d'alimentation électrique avec fiche CEI 320 C13 Raccordement du câble d’alimentation électrique 1. Raccordez le câble d’alimentation à la prise de branchement du secteur. 2. Raccordez le connecteur du câble d’alimentation dans une prise adaptée. 5.11 Installation du logiciel PV MassSpec Les opérations de mesure analytique exigeantes et les applications dans lesquelles les valeurs mesurées doivent être enregistrées nécessitent un fonctionnement direct de PrismaPro intégré dans le GSD 350 à l’aide du logiciel PV MassSpec. Le logiciel PV MassSpec est utilisé pour paramétrer le PrismaPro et pour créer, ouvrir et démarrer des recettes de mesure. Tous les autres paramètres et toutes les autres fonctions de l’unité GSD 350 peuvent encore être commandés via l’affichage ou l’interface web. Manuel de l'utilisateur pour l’interface web et le logiciel PV MassSpec Des informations sur l'utilisation du GSD 350 via l'interface web et PV MassSpec sont disponibles dans le manuel de l'utilisateur en annexe, sous le numéro de document DA 0106. 48/122 Interfaces et connexions 6 Interfaces et connexions Le GSD 350 dispose d’une interface Ethernet pour la communication et de 2 connexions entrée/sortie (I/O), User I/O et AUX I/O, permettant au GSD 350 d’échanger des informations avec les appareils périphériques du client. 6.1 Alimentation La prise de branchement secteur avec l’interrupteur principal et le fusible est située dans le panneau de connexion de l’unité. Le câble de secteur nécessaire est compris dans la livraison. 4 1 2 3 Fig. 32: Branchement secteur avec interrupteur principal et fusible 1 Interrupteur principal 2 Fusible 6.2 3 4 Prise de branchement secteur (IEC 320 C14) Câble de secteur avec fiche de l’appareil froid C13 Borne de connexion de terre DANGER Électrocution en raison de l’absence de conducteur de protection interne Le conducteur de protection interne est fixé au logement. Une unité sans conducteur de protection interne peut présenter un danger de mort en cas de dysfonctionnement. ► Ne tournez pas ou ne débloquez pas le conducteur de protection interne. L’unité dispose de 2 conducteurs de protection : ● Le conducteur de protection interne est situé sous l’unité de courant. ● Le raccord vers la terre fonctionnelle est situé dans e panneau de connexion de l’unité. 6.3 Connexion « User I/O » AVIS Défaillance des branchements électriques causée par des influences perturbatrices externes Les influences externes parasites liées aux émissions électromagnétiques entraînent des pannes de l’unité et des dommages matériels. Pfeiffer Vacuum recommande vivement le câblage des entrées analogiques (+) et (-) avec des paires torsadées. ► Un câble blindé doit être utilisé pour la comptabilité électromagnétique (CEM). ► Évitez les influences externes de parasitage. ► Raccordez le blindage au boîtier de raccordement. ► Laissez l’autre extrémité ouverte ou reliez-la à la terre afin d’éliminer les courants de boucle de terre. La connexion « USER I/O » fournit une interface pour les entrées et les sorties numériques et analogiques. Entrée numérique L’entrée numérique est hautement active. Une résistance de rappel configure l’entrée sur haut en interne. Vous pouvez régler l’entrée sur bas via un contact ou un transistor vers la terre. En cas d’utilisation 49/122 Interfaces et connexions avec le logiciel PV MassSpec, vous pouvez visualiser l’état de cette entrée ou l’utiliser pour la recette ou la commande séquentielle. ● Nombre total de canaux : 1 ● Connexion « consommateur I/O » : DI1 Sortie relais Vous pouvez réglez la sortie relais (24 V CA/CC, 1 A) via la sortie numérique DO8. Le contact normalement ouvert se trouve sur la broche 3 et le contact de référence sur la broche 4. ● Nombre total de canaux : 1 ● Connexion « consommateur I/O » : DO8 Entrées analogiques Les entrées analogiques sont des entrées différentielles pour la gamme -10 à +10 V. Le logiciel PV MassSpec enregistre les signaux d’entrée analogique ou contrôle les séquences de programme. ● ● ● ● Nombre total de canaux : 2 Connexion « consommateur I/O » : AI1 – AI2 Impédance d’entrée : 50 kΩ Taux d’échantillonnage : 14 bit Sortie analogique Les sorties analogiques permettent de sortir des tensions dans la gamme de 0 à 10 V. ● ● ● ● Nombre total de canaux : 2 Connexion « consommateur I/O » : AO0 – AO1 Impédance de sortie : 100 Ω Taux d’échantillonnage : 16 bit Relais d’état du système La connexion « USER I/O » inclut un relais indiquant l’état de la GSD 350. Quand le système est dans l’état prêt pour la mesure (prêt pour le vide), le contact de travail est fermé. Cela indique que l’unité est prête pour la mesure. ● Connexion « consommateur I/O » : broche 13 (relais contact inverseur, COM) ● Connexion « consommateur I/O » : broche 14 (relais contact normalement ouvert, NO) ● Connexion « consommateur I/O » : broche 15 (relais contact normalement fermé, NC) Fig. 33: 1 → 15 → 8 9 Connexion « USER I/O » 1 2 3 4 Masse (GND) Entrée numérique DI1 Relais contact inverseur DO8 Relais contact normalement ouvert DO8 5 Entrée analogique AI2 (-) 6 Entrée analogique AI2 (+) 9 10 11 12 Terre analogique (PrismaPro EXT I/O) Masse (GND) Sortie analogique AO1 Sortie analogique AO0 13 14 7 Entrée analogique AI1 (-) 15 Relais contact inverseur (système de pompage) Relais contact normalement ouvert (système de pompage) Relais contact normalement fermé (système de pompage) 8 Entrée analogique AI1 (+) 50/122 Interfaces et connexions 6.4 Connexion « AUX IO » AVIS Défaillance des branchements électriques causée par des influences perturbatrices externes Les influences externes parasites liées aux émissions électromagnétiques entraînent des pannes de l’unité et des dommages matériels. Pfeiffer Vacuum recommande vivement le câblage des entrées analogiques (+) et (-) avec des paires torsadées. ► Un câble blindé doit être utilisé pour la comptabilité électromagnétique (CEM). ► Évitez les influences externes de parasitage. ► Raccordez le blindage au boîtier de raccordement. ► Laissez l’autre extrémité ouverte ou reliez-la à la terre afin d’éliminer les courants de boucle de terre. La connexion « AUX I/O » fournit une interface supplémentaire pour les entrées et les sorties numériques et analogiques. Entrées numériques Les entrées numériques sont hautement actives. Le logiciel PV MassSpec vous permet de régler les actions activées par les entrées numériques sur bas actif. Une résistance de rappel configure ces entrées en interne sur +24 V. Les entrées peuvent être réglées sur bas via un contact ou sur la masse via un transistor. En cas d’utilisation avec le logiciel PV MassSpec, l’état des entrées numériques peut être visualisé ou utilisé pour la commande séquentielle. ● Nombre total de canaux : 3 ● Connexion « AUX IO » : DI13 – DI15 Sorties numériques Les sorties numériques sont des collecteurs ouverts et peuvent chacune supporter une charge max. de 200 mA. En cas d’utilisation avec le logiciel PV MassSpec, vous pouvez régler les sorties numériques de façon permanente ou en fonction des courants, de l'état des unités et de l'état de la séquence. Si vous activez la sortie, la sortie commute de la haute tension (> 20 V) sur 0 V. ● Nombre total de canaux : 6 ● Connexion « AUX IO » : DO2 – DO7 Entrées analogiques Les entrées analogiques sont des entrées différentielles pour la plage -10 à +10 V. En cas d’utilisation avec le logiciel PV MassSpec, vous pouvez enregistrer simultanément les signaux d’entrée analogique ou contrôler les séquences de programme. ● ● ● ● Nombre total de canaux : 3 Connexion « AUX IO » : AI3 – AI5 Impédance d’entrée : 50 kΩ Taux d’échantillonnage : 16 bit Sortie analogique Les sorties analogiques permettent la sortie de tensions dans la gamme de 0 à 10 V. En cas d’utilisation avec le logiciel PV MassSpec, les courants d'ions des masses individuelles peuvent être convertis dans les tensions de sortie correspondantes à l’aide d’un configurateur, puis être sorties. ● ● ● ● Nombre total de canaux : 2 Connexion « AUX IO » : AO2 – AO3 Impédance de sortie : 100 Ω Taux d’échantillonnage : 16 bit 51/122 Interfaces et connexions Fig. 34: 1 2 3 4 5 6 7 8 9 10 11 12 13 6.5 1 → 25 → 13 14 Connexion « AUX IO » Sortie analogique AO2 Terre analogique Entrée analogique AI3 (-) Entrée analogique AI4 (-) Entrée analogique AI5 (-) Terre analogique Entrée numérique DI13 Entrée numérique DI15 24 V Sortie numérique DO3 Sortie numérique DO5 Sortie numérique DO7 Terre ou masse numérique 14 15 16 17 18 19 20 21 22 23 24 25 Sortie analogique AO3 Terre ou masse numérique Entrée analogique AI3 (+) Entrée analogique AI4 (+) Entrée analogique AI5 (+) Terre ou masse numérique Entrée numérique DI14 Terre ou masse numérique Sortie numérique DO2 Sortie numérique DO4 Sortie numérique DO6 non attribué Connexion Ethernet (LAN) La connexion Ethernet permet une communication directe avec l'appareil par le biais d'un ordinateur. RJ-45 1 8 green yellow Fig. 35: Connexion Ethernet (LAN) 1 Transmission de données (TD+) 2 Transmission de données (TD-) 3 Réception de données (RD+) 6 4, 5, 7, 8 LED État Signification Verte (lien) allumée Connexion de l'équipement présente éteinte Connexion de l'équipement absente allumée (clignotement) Transmission de données en cours éteinte Aucune transmission de données/absence de connexion Jaune (activité) Tab. 10: 52/122 État de la connexion Ethernet Réception de données (RD-) Non utilisé Mise en service 7 Mise en service AVIS Une forte vibration endommage la pompe turbomoléculaire De fortes vibrations en cours de fonctionnement et après la mise à l’arrêt peuvent endommager la pompe turbomoléculaire. ► Évitez les chocs et les vibrations en cours de fonctionnement, par exemple en roulant sur les câbles ou les seuils de porte. ► Évitez toute vibration dans les 5 minutes suivant la mise hors circuit du système. 7.1 Activation de l’unité Fig. 36: Écran « Tableau de bord » après démarrage du programme Procédé 1. Activez l’interrupteur principal. – L’unité démarre. Une fois que l’électronique et l'interrupteur VLAN interne ont démarré, le système est opérationnel et peut être piloté à l’aide de l’écran ou de l’interface Web. 2. Configurez la langue si nécessaire (voir chapitre « Modification des réglages de l’utilisateur », page 63). 3. Démarrez le système de pompage. 4. Avant la mesure, notez le temps de stabilisation de la jauge de pression totale de 5 à 10 minutes. 7.2 Démarrage du système de pompage Exigences relatives à la disponibilité opérationnelle de mesure (vide prêt) ● Pression< 5 × 10-5 hPa ● Vitesse de rotation de la pompe turbomoléculaire > 1 200 Hz ● Courant à pleine charge de la pompe turbomoléculaire < 2 A 53/122 Mise en service Fig. 37: Écran de « commande » Pompage du système de vide 1. Basculez sur l’écran « Control ». 2. Appuyez sur le bouton « Pump down » (voir chapitre « Pompage du système de vide », page 67). L'unité peut exécuter la mesure. 54/122 Fonctionnement via l’affichage 8 Fonctionnement via l’affichage Manuel de l'utilisateur pour l’interface web et le logiciel PV MassSpec Des informations sur l'utilisation du GSD 350 via l'interface web et PV MassSpec sont disponibles dans le manuel de l'utilisateur en annexe, sous le numéro de document DA 0106. Le GSD 350 peut fonctionner via l’affichage ou l’interface web. Sur les variantes sans affichage, seule l’interface web est utilisée pour le fonctionnement. Exécution de mesures sur spectromètre de masse Trois types de mesures sur spectromètre de masse sont possibles. ► Effectuez les mesures sur spectromètre de masse selon l’une des 3 méthodes suivantes. ► Utilisez le logiciel PV MassSpec. – Les données de mesure ne peuvent être sauvegardées que si vous utilisez le logiciel PV MassSpec. ► Utilisez l’affichage. – Vous ne pouvez pas sauvegarder les données de mesure via l'affichage. ► Utilisez l’interface web. – Vous ne pouvez pas sauvegarder les données de mesure via l'interface web. Exécution de mesures analytiques complexes ► Utilisez le logiciel PV MassSpec. Navigation entre les écrans et les menus Les fonctions de l’unité sont associées à différents écrans et menus. ► Actionnez les boutons correspondants sur l’affichage pour naviguer entre les écrans et les fonctions. – Les touches indisponibles ou les réglages inactifs dans le menu Messages sont grisés. ► Appuyez sur le bouton « Suivant » pour passer à la page suivante du menu et visualiser plus de fonctions. ► Actionnez le bouton « Retour » pour revenir au niveau précédent dans l’arborescence du menu. 8.1 Écran « Tableau de bord » Le premier écran qui apparaît après le démarrage du programme est le « Tableau de bord ». Toutes les fonctions et informations peuvent être affichées directement ou indirectement à partir d’ici. Pour plus d’informations sur les commandes et les affichages, voir : (voir chapitre « Commandes et indicateurs », page 24) 55/122 Fonctionnement via l’affichage 2 1 6 3 5 4 Fig. 38: Écran « Tableau de bord » 1 Valeur actuelle de la pression dans l’enceinte à vide 2 Triangle d’avertissement en cas d’avertissement ou de message d’anomalie 3 Réglages de l’utilisateur 4 État du système 8.2 5 6 État du chauffage État du système de vide 7 Lien vers le tableau de bord Structure du menu avec les fonctions Menu Info (voir page 58) Sous-programmes, fonctions et informations 1er niveau 2e niveau Pompes à vide Pompe à membrane Pompe turbomoléculaire Capteurs Jauges Capteur de purge de gaz neutre Vannes Vanne de débitmètre (V1) Vanne Split-flow (V2) Vanne de calibration Unités de chauffage Capillaire Admission de gaz Enceinte à vide DMD Heures de fonctionnement, versions de micrologiciel, etc. Réseau DHCP Adresse IP Passerelle Masque de sous-réseau Ventilateur Ventilateur aspiration Ventilateur sortie de pompe 56/122 Fonctionnement via l’affichage Menu Sous-programmes, fonctions et informations Réglages (voir page 58) 1er niveau 2e niveau Recettes Créer une nouvelle recette Recettes par défaut pour l’air Unités de chauffage Capillaire Admission de gaz Enceinte à vide Capteurs Jauges Capteur de purge de gaz neutre Réglages de l’utilisateur Nom de l’utilisateur Rouleau Langue Unité de pression Unité de température Date Démarrage automatique Vide Chauffage Admission de gaz Réseau DHCP Adresse IP Passerelle Masque de sous-réseau Réglages usine Reset à l’état de livraison Service 9) Pompes à vide Capteurs Vannes Unités de chauffage DMD Ventilateur Messages (voir page 65) Messages actifs : historique et confirmation Contenu, historique, filtre des erreurs, avertissements, infos (filtres inactifs grisés) Commande (voir page 66) Refoulement (vers) - Ventilation - Marche/arrêt du chauffage - Mesure (voir page 70) Tab. 11: Vanne de débitmètre ouverte/fermée 10) - Marche/arrêt de l’étuvage - Marche/arrêt émission - Marche/arrêt du multiplicateur d’électrons - Ouvrir/fermer la vanne de calibration 11) - Sélection de la recette - Structure du menu avec les fonctions 9) Disponible uniquement pour le personnel de maintenance après identification 10) Uniquement pour OmniStar 11) uniquement avec l’unité de calibration en option 57/122 Fonctionnement via l’affichage 8.3 Menu « Info » Le menu « Info » affiche le statut actuel et les réglages des paramètres des composants du système. Les réglages ne peuvent pas être modifiés dans le menu « Info ». ● ● ● ● ● ● ● 8.4 Pompes à vide Capteurs Clapets Unités de chauffage Système GSD Réseau Ventilateur Menu « Réglages » AVIS Dommages matériels dus à des modifications non intentionnelles dans le menu Service Des modifications incorrectes ans le menu Service rendent les fonctions de l’unité inutilisables et endommagent l’unité et ses composants. Le menu Service est réservé au Pfeiffer Vacuum Service et n’est accessible qu’après s’être identifié. ► Contactez Pfeiffer Vacuum Service. Le menu « Réglages » contient les fonctions et les sous-menus suivants : ● Sous-menu « Recettes » ─ Création, édition et suppression des recettes de mesure ● Sous-menu « Chauffage » ─ Spécifiez les températures de point de consigne pour le chauffage et réglez le mode de chauffage de récipient ● Sous-menu « Capteurs » ─ Ajustage des capteurs ● Sous-menu « Réglages de l’utilisateur » ─ Modification des réglages de l’utilisateur ● Sous-menu « Démarrage automatique » ─ Réglage des fonctions de démarrage automatique ● Sous-menu « Réseau » ─ Réglage du réseau ● Sous-menu « Réglages initiaux » ─ Réinitialisation des réglages initiaux ● Sous-menu « Maintenance » ─ Fonctions de maintenance 12) 1 2 Fig. 39: Exemple de réglage de paramètre 1 Symbole de l’interrupteur (désactivé) 12) 58/122 2 Valeur numérique modifiable Disponible uniquement pour le personnel de maintenance après identification Fonctionnement via l’affichage Utilisation d’un interrupteur pour modifier les paramètres 1. Naviguez vers le paramètre souhaité. 2. Appuyez sur le symbole de l’interrupteur pour basculer ce dernier. 3. Appuyez sur le bouton « Save » pour enregistrer les modifications. ou Appuyez sur le bouton « Back » pour annuler les modifications. 4. Effectuez les autres modifications, si nécessaire. Saisie des valeurs des paramètres 1. Naviguez vers le paramètre souhaité. 2. Appuyez sur le champ des paramètres. – Un champ de saisie numérique apparaît. 3. Saisissez la valeur souhaitée. – Pour les valeurs en-dehors de la plage de valeurs autorisée, le GSD 350 adopte automatiquement la valeur la plus haute ou la plus basse autorisée. 4. Appuyez sur le bouton « Save » pour enregistrer les modifications. ou Appuyez sur le bouton « Back » pour annuler les modifications. 5. Effectuez les autres modifications, si nécessaire. 8.4.1 Création et édition des recettes de mesure Fig. 40: Sous-menu « Recettes » Vous pouvez sélectionner, modifier ou effacer des recettes de mesure existantes dans le sous-menu « Recettes ». Les recettes de mesure suivantes sont prédéfinies : ● Recette de mesure pour un scan (par défaut SCAN AIR) ● Recette de mesure pour mesurer diverses masses sur une période donnée (par défaut Masses sélectionnées Air) 59/122 Fonctionnement via l’affichage Fig. 41: Recette de mesure pour le mode de mesure « Scan du spectre » Édition de la recette de mesure pour le mode de mesure « Scan du spectre » 1. Appuyez sur le bouton « New recipe ». 2. Saisissez un nom pour la recette de mesure. 3. Sélectionnez le mode de mesure « Spectrum Scan ». 4. Définissez le domaine de masse en saisissant la masse de départ et la masse finale (FromAMU et ToAMU). 5. Définissez le nombre de points de mesure par masse (PointsPerAMU). 6. Définissez le temps de mesure pour un point de masse (dwell). 7. Appuyez sur « Save » pour sauvegarder la recette de mesure sous le nom saisi. ou Appuyez sur « Back » pour annuler l’entrée actuelle. ou Appuyez sur « Delete » pour supprimer la recette de mesure actuelle. Fig. 42: 60/122 Recette de mesure pour le mode de mesure « Masses sélectionnées » Fonctionnement via l’affichage Fig. 43: Recette de mesure pour le mode de mesure « Masses sélectionnées – Spécial » Édition de la recette de mesure pour le mode de mesure « Masses sélectionnées » 1. Appuyez sur le bouton « Nouvelle recette ». 2. Saisissez un nom pour la recette de mesure. 3. Sélectionnez le mode de mesure « Masses sélectionnées ». 4. Sélectionnez l’affichage pour une masse ou valeur spéciale (p. ex. valeur de la pression). 5. Définissez le temps de mesure pour une masse (dwell). 6. Définissez les nombres de masse individuels (masse : nn) que vous voulez que le GSD 350 enregistre et affiche sur la durée. 7. Appuyez sur le bouton « Nouvelle ligne » pour ajouter des nombres de masse supplémentaires. 8. Appuyez sur le bouton « Supprimer » pour supprimer les nombres de masse individuels. 9. Appuyez sur « Enregistrer » pour sauvegarder la recette de mesure sous le nom saisi. ou Appuyez sur « Retour » pour annuler l’entrée actuelle. ou Appuyez sur « Supprimer » pour supprimer la recette de mesure actuelle. 8.4.2 Ajustement des unités de chauffage Protection contre les surchauffes des unités de chauffage Toutes les unités de chauffage sont protégées contre la surchauffe. En cas de déviation par rapport à la température nominale, la GSD 350 émet un avertissement. Dans certaines conditions, ceci peut aussi se produire quand la température ambiante est basse. L’avertissement disparaît dès que la température de chauffage est à nouveau dans la gamme prévue. Si la GSD 350 mesure une température inadmissible, le chauffage est désactivé. Il peut être réactivé dès que la cause a été éliminée. Les paramètres de réglage du chauffage (températures nominales) sont affichées dans le sous-menu « Heating ». Unités de chauffage ● Chauffage de l’admission de gaz ● Chauffage du capillaire ● Chauffage de l’enceinte à vide 61/122 Fonctionnement via l’affichage Fig. 44: Mode de trempage de l’enceinte à vide En principe, le GSD 350 ne chauffe pas l’enceinte à vide pendant une opération de mesure. Pour certaines mesures analytiques, vous pouvez activer le « Tempering mode » dans le sous-menu « Vacuum chamber ». Lorsque le mode de trempageest activé, le GSD 350 chauffe toujours l’enceinte à vide à la température nominale réglée lorsque le GSD 350 met en marche le chauffage capillaire. Activation du mode tempérage de l’enceinte à vide 1. Utilisation du mode tempérage pour certaines mesures analytiques. 2. Dans le menu « Heating », appuyez sur le bouton « Vacuum chamber ». 3. Ajustez la température nominale pour le « Tempering set temperature ». 4. Activez le mode tempérage. 8.4.3 Ajustage des capteurs Les paramètres courants du capteur sont affichés dans le sous-menu « Capteurs ». Capteurs ● Jauges Le système ignore l’activation/désactivation du capteur et les erreurs de capteur ● Capteur de purge de gaz neutre (seulement sur la version pour gaz corrosifs) Ignore les erreurs de capteur Recommandations pour les manomètres de pression totale ► Dans la mesure du possible, laissez les manomètres de pression totale en marche tout le temps, pour assurer une protection des filaments chauffés et des pompes à vide du GSD 350. ► Coupez temporairement le manomètre de pression totale avec la fonction « Marche/arrêt capteur », si cela est requis pour certaines tâches d’analyse spécifiques. ► Désactivez la fonction d’arrêt du GSD 350 pour le manomètre de pression totale, avec la fonction « Ignorer l’erreur du capteur » afin de pouvoir poursuivre les mesures en cours si le manomètre de pression totale est désactivé ou défectueux. ► N’utilisez pas la fonction de désactivation plus longtemps que nécessaire. ► Remplacez immédiatement le manomètre pour pression totale dès qu’il s’avère défectueux. Recommandations pour le capteur de purge de gaz neutre ► Dans la mesure du possible, laissez le capteur de purge de gaz neutre en marche tout le temps, pour assurer une protection des pompes à vide du GSD 350. ► Utilisez la fonction "Ignorer l’erreur du capteur" pour désactiver temporairement la surveillance de la purge de gaz neutre afin de réduire la consommation de la purge de gaz neutre pour les tâches de mesure où le GSD 350 n’est pas exposé à des gaz corrosifs ou à des mélanges de gaz condensables. ► N’utilisez pas la fonction de désactivation plus longtemps que nécessaire. 62/122 Fonctionnement via l’affichage 8.4.4 Modification des réglages de l’utilisateur Fig. 45: Sous-menu « Réglages de l’utilisateur » Vous pouvez changer d’unité de variables physiques de pression et de température dans le menu Navigation dans le sous-menu « Réglages de l’utilisateur ». Vous pouvez également définir la langue, la date et l’heure. État de livraison ● Pression : hPa ● Température : °C Langues disponibles ● Anglais (par défaut) ● Allemand Réglage de l’heure et de la date 1. Appuyez sur la date et l'heure à l'écran. 2. Régler la date. 3. Régler l’heure. 4. Sélectionnez « Save » pour confirmer les réglages. 8.4.5 Réglage des fonctions de démarrage automatique Fig. 46: Sous-menu « Démarrage automatique » Dans le sous-menu « Démarrage automatique », vous pouvez définir les fonctions du GSD 350 devant démarrer automatiquement après la mise en marche. Fonctions de démarrage automatique ● Vide Démarre la pompe à vide ● Chauffage Monte le chauffage du capillaire jusqu’au point de consigne ● Admission Ouvrir la vanne d’entrée (OmniStar seulement) 63/122 Fonctionnement via l’affichage Vide requis dans l’enceinte à vide Les fonctions de démarrage automatique « Chauffage » et « Admission de gaz » sont disponibles uniquement en combinaison avec la fonction de démarrage automatique « Vide », car le vide requis doit avoir été établi dans l’enceinte à vide pour ces fonctions de démarrage automatique. 8.4.6 Réglage des paramètres réseau Fig. 47: Sous-menu « Réseau » Vous pouvez définir les paramètres réseau du GSD 350 dans le sous-menu « Réseau ». Le GSD 350 doit être redémarré pour l’activation des nouveaux paramètres réseau. Pour le fonctionnement avec un ordinateur de mesure, la GSD 350 nécessite une adresse IP statique. Paramètres réseau ● ● ● ● DHCP Adresse IP Passerelle Masque de sous-réseau Ne pas désactiver dans l’état évacué Ne désactivez pas la GSD 350 dans l’état évacué. Réglage de l’adresse IP pour le GSD 350 1. Saisissez la nouvelle adresse IP statique. – L’adresse IP 192.168.2.xxx est réservée pour les services internes et ne peut pas être sélectionnée. 2. Saisissez le nouveau masque de sous-réseau, si nécessaire. 3. Appuyez sur le bouton « Enregistrer ». 4. Attendez l’invite à la mise hors circuit du GSD 350. 5. Arrêtez l’unité. 6. Réactivez l’unité après > 20 secondes. Vous trouverez le GSD 350 dans les nouveaux réglages. 8.4.7 Réinitialisation de l'unité aux réglages initiaux Les réglages modifiés sont perdus Cette fonction vous permet de faire un reset de tous les paramètres réglés/modifiés par l’utilisateur et de charger toutes les valeurs par défaut (réglages-usine). Tous les réglages modifiés sont perdus en cas de remise à zéro sur les réglages usine. Vous ne pouvez pas annuler cette fonction. L’adresse IP affectée et les recettes de mesure sont conservées. 64/122 Fonctionnement via l’affichage Fig. 48: Sous-menu « Factory settings » Vous pouvez rétablir tous les réglages du GSD 350 sur les réglages initiaux, dans le sous-menu « Factory settings ». Procédure 1. Activez l'interrupteur « Reset to as-delivered condition ». 2. Confirmez l'invite de sécurité en actionnant le bouton « Save ». ou Actionnez le bouton « Back » pour conserver les paramètres actuels. 8.4.8 Sous-menu « Maintenance » AVIS Dommages matériels dus à des modifications non intentionnelles dans le menu Service Des modifications incorrectes ans le menu Service rendent les fonctions de l’unité inutilisables et endommagent l’unité et ses composants. Le menu Service est réservé au Pfeiffer Vacuum Service et n’est accessible qu’après s’être identifié. ► Contactez Pfeiffer Vacuum Service. ● ● ● ● ● ● 8.5 Pompes à vide Capteurs Vannes Unités de chauffage DMD Ventilateur Menu « Messages » Le menu « Messages » affiche les messages d’avertissement et de dysfonctionnement actuels de l’unité. Fig. 49: Exemple de message d’anomalie 65/122 Fonctionnement via l’affichage Fig. 50: Exemple de messages anciens Accès aux messages d’avertissement et de dysfonctionnement ► Basculez dans le menu « Messages » ou appuyez sur le triangle d’avertissement. – Les messages d’avertissement et de dysfonctionnement apparaissent. ► Effleurez le bouton « Historique » pour accéder aux anciens messages. ► Effleurez le bouton « Historique » pour appliquer les filtres. 8.6 Menu « Commande » Le menu « Commande » affiche le diagramme du vide du système et ses paramètres essentiels. Le menu dispose des fonctions suivantes selon l’état de marche de l’unité et le type d’unité : ● ● ● ● ● ● Pompage / ventilation du système de vide Activation / désactivation du capillaire et du chauffage à l’entrée Activation / désactivation du chauffage de récipient (étuvage) Ouverture / fermeture de l’admission de gaz (OmniStar) Activation / désactivation de l’émission (filament chauffé) Activation / désactivation du multiplicateur d’électrons Des explications sur le diagramme du vide sont disponibles ici : (voir chapitre « Description fonctionnelle », page 23) 66/122 Fonctionnement via l’affichage 1 3 2 Fig. 51: Menu « Commande » 1 Pression dans l’enceinte à vide (manomètre de pression totale) 2 Vitesse de rotation de la pompe turbomoléculaire 8.6.1 3 État du filament chauffé du spectromètre de masse et du multiplicateur d’électrons Pompage du système de vide Condition préalable ● GSD 350 prête pour l’utilisation Procédé 1. Basculez dans le menu « Commande ». 2. Appuyez sur le bouton « Pompage ». Séquence ● ● ● ● Le GSD 350 passe de l’état « Ventilé » à l’état « Pompage ». La vanne de ventilation se coupe. La pompe à membrane démarre et évacue le système de vide. Après avoir atteint la valeur seuil (10 hPa), la pompe turbomoléculaire accélère jusqu’à la vitesse de rotation finale de 1500 Hz. ● Au bout de quelques minutes, le système de vide atteint une pression < 5×10-5 hPa. ● La GSD 350 est maintenant prête pour la mesure (vide prêt) 8.6.2 Ventilation du système à vide Conditions préalables ● Mesures en cours terminées (voir chapitre « Menu « Mesure » », page 70) ● Le filament chauffé sur le multiplicateur d’électrons est coupé (voir chapitre « Menu « Commande » », page 66). Procédé 1. Basculez dans le menu « Commande ». 2. Désactivez le multiplicateur d’électrons secondaire et l’émission. 3. Appuyez sur le bouton « Ventiler ». Séquence ● Le GSD 350 passe de l’état « Vide » à l’état « Ventilé ». ● Un timer interne est activé si l’émission était encore activée 15 minutes maximum avant la ventilation. Le timer permet au filament chauffé de refroidir avant de ventiler l’enceinte à vide. Le timer est réglé sur 15 minutes ; il s’agit du laps de temps réglé après coupure de l’émission. Si l’émis- 67/122 Fonctionnement via l’affichage sion était encore activée au moment du démarrage de la « Ventilation », le timer démarre à 15 minutes. Le temps restant du timer est affiché en haut à droite de l’écran. ● Une fois le temps du timer écoulé, la pompe à membrane s’arrête ainsi que la pompe turbomoléculaire. ─ En dessous de la vitesse de rotation de la ventilation (750 Hz), la vanne de ventilation permet de ventiler la pompe turbomoléculaire et l’enceinte à vide. ─ La vanne de ventilation et la vanne de la purge de gaz (pour la version de gaz corrosif) restent ouvertes. 8.6.3 Activation et désactivation des dispositifs de chauffage Chauffage passif de l’enceinte à vide Après l’activation, le chauffage de l’admission de gaz chauffe aussi passivement l’enceinte à vide jusqu’à ce que la température de compensation soit atteinte, car l’admission de gaz et l’enceinte à vide sont raccordées ensemble. Condition préalable ● GSD 350 prête pour la mesure (vide prêt) Activation du chauffage 1. Basculez dans le menu « Commande ». 2. Actionnez le bouton « Chauffage activé ». Séquence d’activation ● Le GSD 350 active le chauffage du capillaire et le chauffage de l’admission de gaz. ● Une commande PID régule chaque circuit de chauffage avec les paramètres de commande correspondants pour atteindre la température de consigne requise(± 5 °C). Coupure du chauffage 1. Basculez dans le menu « Commande ». 2. Actionnez le bouton « Chauffage désactivé ». Séquence de désactivation ● Le GSD 350 désactive le chauffage du capillaire et le chauffage de l’admission de gaz. ● À partir d’une valeur seuil de ≤ 40 °C, l’état « Chauffage désactivé » est atteint. 8.6.4 Ouverture et fermeture de l’admission de gaz (Omnistar) Condition préalable ● GSD 350 prête pour la mesure (vide prêt) Ouverture de l’admission de gaz 1. Recommandation : Désactivez le filament chauffé lors de l’ouverture de la vanne. 2. Basculez dans le menu « Commande ». 3. Appuyez sur le bouton « Ouvrir la vanne d’admission ». Séquence d’ouverture ● La pompe à membrane augmente sa vitesse de rotation. ● La vanne de Split-flow V2 s’ouvre et se ferme plusieurs fois brièvement dans un intervalle défini afin d’éviter des montée de pression non admissibles. ● La vanne de Split-flow V2 reste ouverte une fois le dernier intervalle dépassé. ● La vanne de débitmètre V1 s’ouvre après un retard de 4 secondes. ● Une commande PWM maintient alors les deux vannes ouvertes, pour maintenir un faible débit dans le serpentin, pour des raisons thermiques. ● La pompe à membrane réduit à nouveau sa vitesse de rotation sur 30 Hz. Fermeture de l’admission de gaz 1. Basculez dans le menu « Commande ». 2. Appuyez sur le bouton « Fermer la vanne d’admission ». Séquence de fermeture ● La vanne de débitmètre V1 se ferme. ● La vanne Split-flow V2 se ferme. 68/122 Fonctionnement via l’affichage 8.6.5 Étuvage de l’enceinte à vide Une fois le timer écoulé, l’étuvage est automatiquement désactivé, ou alors l’utilisateur peut sélectionner la fonction « Étuvage désactivé ». Condition préalable ● GSD 350 prête pour la mesure (vide prêt) Étuvage de l’enceinte à vide 1. Recommandation : Pendant l’étuvage, désactivez le multiplicateur d’électrons et activez l’émission des filaments chauffés. 2. Recommandation : Fermez les vannes d’entrée avant l’étuvage (OmniStar). 3. Basculez dans le menu « Commande ». 4. Actionnez le bouton « Étuvage activé ». Séquence d’étuvage ● La GSD 350 passe de l’état « Étuvage désactivé » à l’état « Étuvage activé ». ● La GSD 350 active les cartouches de chauffage de récipient. ─ Une commande PID régule le circuit de chauffage avec les paramètres de commande correspondants pour atteindre la température de consigne requise (par défaut = 120 °C, réglable entre 100 °C et 130 °C) ─ La GSD 350 désactive le chauffage s’il y a un risque de température supérieure à la normale dans l’unité. L’affichage notifie cet état de fait. ● Le timer démarre (valeur standard : 4 h). ─ Une fois le timer écoulé (entre 1 et 24 heures), l’étuvage est automatiquement désactivé. Fin de l'étuvage de l’enceinte à vide 1. Basculez dans le menu « Control ». 2. Actionnez le bouton « Bake out off ». Séquence de fin de processus ● La GSD 350 passe de l’état « Étuvage activé » à l’état « Étuvage désactivé ». ● La GSD 350 désactive les cartouches de chauffage de récipient. ─ À partir d’une valeur seuil de ≤ 40 °C, l’état « Refroidi » est atteint. 8.6.6 Activation et désactivation de l’émission Des dysfonctionnements ou des conditions non admissibles se traduisent par une désactivation automatique de l’émission. Condition préalable ● GSD 350 prête pour la mesure (vide prêt) Activation de l’émission 1. Basculez dans le menu « Control ». 2. Actionner le bouton « Emission on ». Séquence d’activation ● La GSD 350 active l’émission du filament chauffé. ● La GSD 350 maintient un courant d’émission constant sur le filament chauffé, avec une surveillance permanente. Lorsque la pression dans l’enceinte à vide est excessive, le courant du filament chauffé devient trop élevé, ou les variations d’émissions sont trop accentuées ; l’émission est automatiquement coupée. Désactivation de l’émission 1. Basculez dans le menu « Control ». 2. Actionnez le bouton « Emission off ». Séquence de désactivation ● La GSD 350 désactive l’émission du filament chauffé. 69/122 Fonctionnement via l’affichage 8.6.7 Activation et désactivation du multiplicateur d’électrons Des dysfonctionnements ou des conditions non admissibles se traduisent par une désactivation automatique du multiplicateur d’électrons. Si l’émission du filament est coupée manuellement ou automatiquement, le multiplicateur d’électrons est également coupé automatiquement. Conditions préalables ● GSD 350 prête pour la mesure (vide prêt) ● Émission activée Activation du multiplicateur d'électrons 1. Basculez dans le menu « Control ». 2. Actionnez le bouton « EM on ». Séquence d’activation ● La GSD 350 active le multiplicateur d’électrons. Désactivation du multiplicateur d'électrons 1. Basculez dans le menu « Control ». 2. Actionnez le bouton « EM off ». Séquence de désactivation ● La GSD 350 désactive le multiplicateur d’électrons. 8.6.8 Ouverture et fermeture de la vanne de calibration La vanne de calibration est disponible uniquement sur les variantes du GSD 350 avec une unité de calibration. Condition préalable ● GSD 350 prête pour la mesure (vide prêt) Ouverture de la vanne de calibration 1. Recommandation : Pour éviter d’exposer le filament chauffé à une montée de pression inutile, ouvrez seulement la vanne de calibration quand l’émission est désactivée. 2. Attendez que la pression dans l’enceinte à vide soit inférieure à 1 × 10-5 hPa avant d’activer le filament chauffé. 3. Basculez dans le menu « Commande ». 4. Appuyez sur le bouton « Ouvrir la vanne de calibration ». 5. Calibrez l’échelle de masse du spectromètre de masse. Séquence d’ouverture ● La vanne de calibration ouvre pour lancer un cycle. ● Le fluide de calibration circule dans l’enceinte à vide avec le spectromètre de masse. Fermeture de la vanne de calibration 1. Basculez dans le menu « Control ». 2. Appuyez sur le bouton « Shut calibration valve ». Séquence de fermeture ● La vanne de calibration se ferme. 8.7 Menu « Mesure » Le menu dispose des fonctions suivantes selon l’état de marche de l’unité : ● ouverture et démarrage des recettes de mesure existantes ● État à la livraison : scan de masse (par défaut SCAN AIR / scan du spectre) ou mesure des masses individuelles (par défaut masses d’air sélectionnées / masses sélectionnées) 70/122 Fonctionnement via l’affichage Fig. 52: Sélection de la recette Lancement de la mesure 1. Dans le menu « Control », activez le filament chauffé et, si nécessaire, le multiplicateur d'électrons. 2. Dans le menu « Measure », actionnez le bouton « Start ». 3. Si nécessaire, permutez l’affichage entre linéaire et logarithmique. Arrêt de la mesure 1. Dans le menu « Measure », actionnez le bouton « Stop ». 2. Dans le menu « Control », désactivez le filament chauffé et, si nécessaire, le multiplicateur d'électrons. 71/122 Mise hors service 9 Mise hors service AVIS Une forte vibration endommage la pompe turbomoléculaire De fortes vibrations en cours de fonctionnement et après la mise à l’arrêt peuvent endommager la pompe turbomoléculaire. ► Évitez les chocs et les vibrations en cours de fonctionnement, par exemple en roulant sur les câbles ou les seuils de porte. ► Évitez toute vibration dans les 5 minutes suivant la mise hors circuit du système. AVIS Dommages matériels résultants de l’interruption de l'alimentation électrique pendant le fonctionnement Débrancher la prise d’alimentation ou couper l’interrupteur principal en secteur de fonctionnement peut fortement solliciter le filament chauffé et réduire sa durée de vie si l’unité est sous vide et l’émission activée. Le filament chauffé risque d’être irrémédiablement détruit. ► Veillez à toujours mettre correctement l’unité hors service. ► Mettez l’unité hors service avant de débrancher la prise secteur. Protection du filament chauffé Afin de protéger le filament chauffé, la pompe turbomoléculaire se coupe 15 minutes après la coupure du filament chauffé au plus tôt. L’opération de ventilation actuelle, celle du système, démarre lorsque la pompe turbomoléculaire atteint une vitesse de rotation de 750 Hz. Recommandations pour les gaz corrosifs et les mélanges de gaz condensables 1. Laissez passer de l'air sec ou un gaz inerte par le capillaire. 2. Laissez le GSD 350 fonctionner encore pendant environ 30 minutes pour évacuer hors du système les résidus de gaz corrosifs et de gaz condensables. Désactivation de l’unité 1. Désactivez l’EM du spectromètre de masse (voir chapitre « Activation et désactivation du multiplicateur d’électrons », page 70). 2. Désactivez l’émission du spectromètre de masse (voir chapitre « Activation et désactivation de l’émission », page 69). 3. Ventilez le système de vide pour le désactiver (voir chapitre « Ventilation du système à vide », page 67). 4. Patientez jusqu’à ce que le GSD 350 ventile le système et coupe les pompes à vide. 5. Arrêtez l’alimentation de purge de gaz neutre (version de gaz corrosif). 6. Coupez l’interrupteur principal sur l’unité. 7. Débranchez le câble d’alimentation de l’alimentation. Débranchement du tuyau de gaz d’échappement 1. Appuyez fermement des deux côtés sur la bague de déverrouillage pour la descendre au niveau de la pièce de raccordement du gaz d’échappement afin d’ouvrir uniformément les griffes de maintien et d’éviter tout rayure sur le tuyau de gaz d’échappement. 2. Tirez le tuyau de gaz d’échappement à la verticale pour le sortir de la pièce de raccordement du gaz d’échappement sur l’unité. Déconnexion du tuyau flexible de purge de gaz neutre 1. Veillez à ce que la conduite de purge de gaz neutre ne soit pas sous pression. 2. Appuyez fermement des deux côtés sur la bague de déverrouillage pour la descendre au niveau de la pièce de raccordement afin d’ouvrir uniformément les griffes de maintien et d’éviter tout rayure sur le tuyau de purge de gaz neutre. 3. Tirez le tuyau de purge de gaz neutre à la verticale pour le sortir de la pièce de raccordement sur l’unité. 72/122 Maintenance 10 Maintenance AVERTISSEMENT Risque d’intoxication dû à des composants ou appareils contaminés par des substances toxiques Les substances de procédé toxiques contaminent certaines pièces matérielles. Pendant les opérations de maintenance, tout contact avec ces substances toxiques présente un risque pour la santé. L’élimination illégale de substances toxiques nuit à l’environnement. ► Respecter les précautions de sécurité adéquates et éviter les risques sanitaires ou environnementaux dus aux substances de procédé toxiques. ► Décontaminer les pièces concernées avant d’exécuter des opérations de maintenance. ► Porter des équipements de protection individuelle. Maintenance dans le Centre de service Pfeiffer Vacuum Pfeiffer Vacuum propose une gamme complète de services de maintenance pour tous les produits. Pfeiffer Vacuum recommande : Contacter un Centre de service Pfeiffer Vacuum pour organiser la maintenance de produits et de composants défectueux. Maintenance dans le Centre de service Pfeiffer Vacuum Pfeiffer Vacuum recommande : Contacter le Centre de service Pfeiffer Vacuum local pour organiser la maintenance de produits et de composants défectueux. Demande de garantie Ouvrir l’appareil pendant la période de garantie ou endommager/supprimer le sceau de garantie annulera la garantie. Les sceaux de garantie sont fixés sur l’unité de manière à ce que vous puissiez ouvrir les pièces suivantes de la GSD 350 sans enlever le sceau de garantie : ● Admission de gaz ● Réservoir du fluide d’exploitation de la pompe turbomoléculaire ● Ouverture de service du fluide de calibration (PFTBA) Contactez le Centre de service Pfeiffer Vacuum en cas d’intervalle de maintenance raccourcis lié au processus. Commencer par lire intégralement les sections Lire intégralement la section consacrée aux instructions de travail avant de commencer à travailler. 10.1 Opérations de maintenance et intervalles de maintenance Remarques relatives aux intervalles de maintenance Les durées des intervalles de maintenance dépendent fortement des conditions de procédé ; elles concernent les opérations avec des gaz de nettoyage et des gaz inertes. L’utilisation de gaz de processus corrosifs peut réduire considérablement les intervalles de maintenance. ● En cas de charges extrêmes ou de procédés spécifiques, consultez Pfeiffer Vacuum Service pour déterminer des intervalles de maintenance plus courts. Vous pouvez procéder vous-même à des travaux de maintenance au niveau de maintenance 1. Nous recommandons de faire appel à Pfeiffer Vacuum Service pour les travaux de maintenance du niveau de maintenance 2 et du niveau de maintenance 3 (révision). Si les intervalles de maintenance recensés ci-dessous sont dépassés ou si l’intervention est mal exécutée, aucune réclamation de garantie ou de responsabilité ne sera acceptée de la part de Pfeiffer Vacuum. Ces consignes s’appliquent aussi s’il ne s’agit pas de pièces de rechange d’origine. 73/122 Maintenance Groupe de composants, module et action Intervalle Niveau de maintenance Pièces de rechange/jeu de pièces de rechange Remplacer les vis du carter en cas de perte 1 Vis du carter Nettoyer les pièces du carter Si nécessaire 1 - Remplacer le couvercle de l’admission de gaz Si nécessaire 1 Couvercle de l’admission de gaz Remplacer le couvercle sur le côté Si nécessaire 1 Couvercle sur le côté Remplacer le couvercle de carter Si nécessaire 1 Couvercle de carter Remplacer l’aire de connexion du tuyau flexible de capillaire Si nécessaire 1 Zone de connexion Nettoyer la grille de protection sur le ventilateur Si contaminé 1 - Remplacer le joint cuivre sur le raccord à bride DN 40 CF Toujours lorsque le raccord à bride CF est ouvert 1 Joint cuivre Remplacer le réservoir du fluide d’exploitation sur la pompe turbomoléculaire 4 ans 1 Réservoir du fluide d’exploitation Remplacer les roulements de la pompe turbomoléculaire 4 ans 2 - Remplacement de la pompe à membrane Si nécessaire 1 Pompe à membrane Remplacement de la membrane de la pompe à membrane après 15 000 heures de fonctionnement 1 Kit de révision Installez/démontez l’analyseur QMA 250 M Si nécessaire 1 - Remplacez le filament chauffé (en tungstène) Si nécessaire Après défaillance du premier des 2 filaments chauffés 1 Unité de filaments chauffés 1 Unité de filaments chauffés Remplacer la source d’ions (filaments chauffés en tungstène) Si contaminé 1 Source d’ions Remplacer la source d’ions (filaments chauffés Ir-Y2O3) Si contaminé 1 Source d’ions Remplacer le capteur sur le manomètre de pression totale Si contaminé 1 Capteur Remplacer le manomètre de pression totale en cas de défaut 1 Jauge de pression totale Installez/déposez l’admission de gaz (Omnistar) Si nécessaire 2 - Remplacez l’admission de gaz (Omnistar) Si nécessaire 2 Admission de gaz Installez/déposez l’admission de gaz (Thermostat) Si nécessaire 2 - Remplacez l’admission de gaz (Thermostat) Si nécessaire 2 Admission de gaz Remplacez l’orifice (Omnistar) En cas de bouchon 2 Écran Remplacez l’orifice (ThermoStar) En cas de bouchon 2 Remplacez l’orifice et le diffuseur de gaz interne (Omnistar) Si nécessaire 2 Remplacer l’orifice et le diffuseur de gaz interne (ThermoStar) Si nécessaire 2 Réduction de la longueur des capillarités en acier inoxydable En cas de bouchon 1 - Remplacement du capillaire en acier inoxydable En cas de bouchon 1 Capillaire Joints de capillaire Instrument fondamental Système côté vide élevé Système de vide primaire Unité d’analyse de gaz Remplacer le filament chauffé (Ir-Y2O3) Système d’admission de gaz Jeu de pièces de rechange Capillaire 74/122 Maintenance Groupe de composants, module et action Intervalle Niveau de maintenance Pièces de rechange/jeu de pièces de rechange Découpage à longueur des capillarités en quartz En cas de bouchon 1 - Remplacement du capillaire en quartz En cas de bouchon 1 Capillaire Joints de capillaire en cas de défaut 1 Affichage de contact 7" Si nécessaire 2 Fluide de calibration (PFTBA) Composants électroniques Remplacement de l’affichage Unité de calibration (option) Faire l’appoint de fluide de calibration (PFTBA) Tab. 12: 10.2 Opérations de maintenance et intervalles de maintenance Maintenance de l’instrument fondamental DANGER Danger de mort par électrocution L'appareil présente des tensions élevées. Danger de mort en cas de contact avec des éléments sous tension. La mise en service de l'appareil alors qu'il est visiblement endommagé implique un danger de mort. ► Toute intervention sur l'appareil ouvert doit être confiée à un personnel spécialisé et qualifié. ► Avant d'exécuter une installation ou une opération de maintenance, arrêtez l'appareil et déconnectez-le de l'alimentation électrique. ► N’ouvrez jamais l'appareil lorsqu'il est branché à une source d'alimentation électrique. ► Prenez les mesures nécessaires pour éviter toute réactivation involontaire ou non autorisée. ► Ne faites jamais fonctionner un appareil ouvert ou défectueux. ► Prenez les mesures nécessaires pour empêcher l'utilisation accidentelle d'un appareil défectueux. ► Protégez l'appareil contre l'humidité. AVERTISSEMENT Risque de brûlure sur les surfaces chaudes Pendant le fonctionnement, les températures montent très haut (> 50 °C) sur les surfaces de contact des composants de chauffage et sur l’admission de gaz. Il existe un risque de brûlure. ► Prenez les mesures requises pour prévenir tout contact avec les pièces chaudes. ► Apposez des signaux d’avertissement. ► Veillez à ce que le produit se soit refroidi avant d’intervenir dessus. ► Portez des gants de protection (conformément à EN 420). 75/122 Maintenance 10.2.1 Retrait/fixation du couvercle de l’admission de gaz 2 1 Fig. 53: Retrait/fixation du couvercle de l’admission de gaz 1 Couvercle de l’admission de gaz 2 Vis à six pans creux intérieurs (M3) Conditions préalables ● GSD 350 désactivée ● Câble d’alimentation débranché Outils nécessaires ● Clé mâle coudée pour vis à six pans creux, WAF 2 Retrait du couvercle de l’admission de gaz 1. Desserrez les vis à six pans creux intérieurs sur le couvercle de l’admission de gaz, sur le châssis. 2. Retirez avec précaution le couvercle de l’admission de gaz par l’avant. 3. Desserrez les éléments de fixation en Velcro du capot de séparation. 4. Retirez le capot de séparation de l’admission de gaz. Fixation du couvercle d’admission de gaz 1. Placez le capot de séparation sur l’admission de gaz. 2. Fixez les éléments de fixation en Velcro du capot de séparation. 3. Posez le couvercle de l’admission de gaz sur le châssis. 4. Fixez le couvercle de l’admission de gaz sur le châssis à l’aide des vis à six pans creux intérieurs. 10.2.2 Retrait/fixation des couvercles sur le côté Ne retirez pas le couvercle de l’admission de gaz Il est inutile de retirer le couvercle de l’admission de gaz pour enlever les capots latéraux. Demande de garantie Ouvrir l’appareil pendant la période de garantie ou endommager/supprimer le sceau de garantie annulera la garantie. Les sceaux de garantie sont fixés sur l’unité de manière à ce que vous puissiez ouvrir les pièces suivantes de la GSD 350 sans enlever le sceau de garantie : ● Admission de gaz ● Réservoir du fluide d’exploitation de la pompe turbomoléculaire ● Ouverture de service du fluide de calibration (PFTBA) Contactez le Centre de service Pfeiffer Vacuum en cas d’intervalle de maintenance raccourcis lié au processus. 76/122 Maintenance 2 1 3 3 Fig. 54: Retrait/fixation des couvercles sur le côté 1 Capot latéral de droite 2 Capot latéral de gauche 3 Vis à six pans creux intérieurs (2×M3) Conditions préalables ● GSD 350 désactivée ● Câble d’alimentation débranché Outils nécessaires ● Clé mâle coudée pour vis à six pans creux, WAF 2 Retrait des capots latéraux 1. Desserrez et retirez les vis à six pans creux intérieurs sur le capot latéral du châssis. 2. Retirez avec précaution le capot latéral par l’arrière. – Faites attention aux sangles de montage sur le capot latéral. 3. Desserrez le connecteur mâle-femelle du câble de terre, sur le capot latéral. Fixation des capots latéraux 1. Fixez le connecteur mâle-femelle du câble de terre sur le capot latéral. 2. Montez prudemment le capot latéral depuis l’arrière. – Faites attention aux sangles de montage sur le capot latéral. 3. Serrez les vis à six pans creux intérieure du capot latéral sur le châssis. 10.2.3 Retrait/fixation du couvercle de carter Demande de garantie Ouvrir l’appareil pendant la période de garantie ou endommager/supprimer le sceau de garantie annulera la garantie. Les sceaux de garantie sont fixés sur l’unité de manière à ce que vous puissiez ouvrir les pièces suivantes de la GSD 350 sans enlever le sceau de garantie : ● Admission de gaz ● Réservoir du fluide d’exploitation de la pompe turbomoléculaire ● Ouverture de service du fluide de calibration (PFTBA) Contactez le Centre de service Pfeiffer Vacuum en cas d’intervalle de maintenance raccourcis lié au processus. Conditions préalables ● GSD 350 désactivée ● Câble d’alimentation débranché ● Capots latéraux retirés 77/122 Maintenance Outils nécessaires ● Clé mâle coudée pour vis à six pans creux, WAF 2 1 2 2 Fig. 55: Retrait/fixation du couvercle de carter 1 Couvercle de carter 2 Vis à six pans creux intérieurs (2×M3) Dépose du couvercle de carter 1. Desserrez les vis à six pans creux intérieurs sur le couvercle de carter, sur le châssis. 2. Retirez le couvercle de carter avec précaution, en tirant vers le haut. 3. Desserrez le connecteur mâle-femelle du câble de terre, sur le couvercle de carter. Fixation du couvercle de carter 1. Fixez le connecteur mâle-femelle du câble de terre sur le couvercle de carter. 2. Montez prudemment le couvercle de carter depuis le haut. 3. Serrez les vis à six pans creux intérieurs du couvercle de carter sur le châssis. 10.2.4 Nettoyage des pièces de carter DANGER Choc électrique dû à la pénétration d’humidité dans l’unité La pénétration d’eau dans l’unité cause des blessures aux personnes par chocs électriques. ► Utilisez seulement l’unité dans un environnement sec. ► Utilisez l’unité à l’écart de tout fluide ou source d’humidité. ► Ne mettez pas en circuit l’unité si du fluide a pénétré à l’intérieur de celle-ci. Au lieu de cela, contactez Pfeiffer Vacuum Service. ► Déconnectez toujours l’alimentation électrique avant de nettoyer l’unité. AVERTISSEMENT Risques pour la santé dus aux agents nettoyants Les détergents utilisés peuvent nuire à la santé et causer un empoisonnement, des allergies, une irritation de la peau, des brûlures chimiques ou endommager les voies respiratoires. ► Respectez les réglementations en vigueur pour la manipulation des agents nettoyants. ► Respectez les mesures de sécurité concernant la manipulation et la mise au rebut des agents nettoyants. ► Attention aux réactions potentielles avec les matériaux du produit. 78/122 Maintenance AVIS Dégâts causés par la pénétration d'humidité La pénétration d'humidité, sous la forme de condensation ou d'égouttement, endommage l'appareil. ► Protéger l'appareil contre la pénétration de l'humidité. ► L'appareil ne peut être utilisé que dans un environnement propre et sec. ► L'appareil doit être utilisé à distance de tout liquide et source d'humidité. ► Des précautions spécifiques doivent être prises en cas de risque d'égouttement d'eau. ► Ne pas allumer l'appareil si un liquide y a pénétré. Contacter le Centre de service Pfeiffer Vacuum. AVIS Dégâts provoqués par des agents nettoyants inadaptés L'usage d'agents nettoyants inadaptés endommage le produit. ► Ne pas utiliser de solvants qui endommageraient sa surface. ► Ne pas utiliser d'agents nettoyants agressifs ou abrasifs. Conditions préalables ● GSD 350 mis hors circuit ● Câble d’alimentation débranché Consommables nécessaires ● Détergent à nettoyer (détergent doux, par exemple) ● Chiffon (propre, doux, non pelucheux) ● Air comprimé Exigences relatives à l’air comprimé ─ ─ ─ ─ Exempt d’huile Sec Sans particules > 30 μm < 2 bar de surpression Nettoyage des pièces de carter 1. Utilisez un chiffon doux humide pour nettoyer l’extérieur de l’habillage. 2. Laissez sécher les surfaces complètement après le nettoyage. 3. Éliminez les couches de poussière à l’intérieur en les soufflant prudemment à l’air comprimé. 10.2.5 Nettoyage des écrans de protection sur les ventilateurs Intervalle de nettoyage Définissez l'intervalle de nettoyage par des inspection visuelles et en fonction du dégagement de poussière sur site. De manière générale, il suffit d’aspirer occasionnellement l’écran de protection à travers les ouvertures de ventilation en utilisant un aspirateur. Conditions préalables ● GSD 350 à l’arrêt ● Câble d’alimentation débranché ● Capots latéraux retirés Équipement requis ● Aspirateur Procédé 1. Nettoyez la grille de protection dès qu’une couche est visible et avant que la circulation de l’air voir tombe au-dessous du niveau requis. 2. Tenez fermement le ventilateur pour éviter l’induction de courant sur le ventilateur. 3. Utilisez un aspirateur pour éliminer la poussière sur la grille de protection. 79/122 Maintenance 10.3 Maintenance du système de vide élevé 10.3.1 laire Remplacement du réservoir de fluide d’exploitation sur la pompe turbomolécuAVERTISSEMENT Risque d’empoisonnement par les vapeurs toxiques L’inflammation et le chauffage de fluide d’exploitation synthétique forment des vapeurs toxiques. Risque d’empoisonnement en cas d’inhalation. ► Respecter les consignes et précautions d’application. ► Tenir les produits à base de tabac à l’écart du fluide d’exploitation. Conditions préalables ● ● ● ● GSD 350 désactivée Câble d’alimentation débranché Système de vide à l’arrêt et mis à l’air à la pression atmosphérique Couvercles sur le côté installés Outils nécessaires ● Tournevis, 4 mm Outils spéciaux demandés ● Clé pour couvercle de carter (référence PV M40 813) Équipement nécessaire ● Réservoir du fluide d’exploitation (référence PM 143 740 -T) 1 Fig. 56: Face inférieure de l’unité 1 Couvercle de carter sur la pompe turbomoléculaire Procédé 1. Installez la protection pour le transport de la pompe à membrane. (voir chapitre « Transport et stockage », page 36) 2. Positionnez le GSD 350 avec précaution sur le côté. 3. Ouvrez le couvercle de carter de la pompe turbomoléculaire à l’aide d’une clé à fourche spéciale pour le couvercle de carter. 4. Remplacez le réservoir du fluide d’exploitation et les tiges Poroplast en suivant les instructions du manuel de l’utilisateur de la pompe turbomoléculaire. 5. Fermez le couvercle de carter de la pompe turbomoléculaire à l’aide d’une clé à fourche spéciale pour le couvercle de carter. 6. Redressez le GSD 350 avec précaution. 7. Retirez la protection pour le transport de la pompe à membrane. (voir chapitre « Retrait de la protection pour le transport de la pompe à membrane », page 38) 80/122 Maintenance 10.3.2 Remplacement de la vanne de ventilation Pfeiffer Vacuum Service prend en charge le remplacement. ► Contactez Pfeiffer Vacuum Service. 10.4 Maintenance du système de vide primaire 10.4.1 Remplacement de la pompe à membrane Conditions préalables ● ● ● ● ● GSD 350 désactivée Câble d’alimentation débranché Pompe turbomoléculaire à l’arrêt Capots latéraux retirés Couvercle de carter retiré Outils nécessaires ● Clé à fourche, WAF 7 ● Clé mâle coudée pour vis à six pans creux, WAF 3 ● Tournevis cruciforme Instrument nécessaire ● Appareil de commande DCU 110, DCU 180 ou DCU 310 avec câble de raccordement Pièce de rechange requise ● Pompe à membrane MVP 010-3 DC (référence PK T05 072) 81/122 Maintenance 1 2 14 3 4 13 5 12 11 10 9 8 6 7 Fig. 57: 1 2 3 4 5 6 7 Remplacement de la pompe à membrane Boulon six pans M4×10 (4×) Disques de blocage (4×) Borne du raccord de terre Vis à tête hexagonale M4×12 (2×) Disques de blocage (2×) Patte de protection pour le transport Protection pour le transport 8 9 10 11 12 13 14 Amortisseur de vibrations à ressorts (4×) Ressort de compression (4×) Plaque de fixation Écrou (4×) Support de pompe à membrane Vis à épaulement Pompe à membrane 2 1 Fig. 58: Raccordement et retrait du tuyau de gaz d’échappement et d’admission 1 Bague de déblocage 2 Tuyau flexible Retrait de la pompe à membrane 1. Fixez la protection pour le transport sur la pompe à membrane. 2. Détachez le tuyau flexible de gaz d’échappement de la pompe à membrane. 3. Détachez le tuyau flexible d’admission de la pompe à membrane. 4. Desserrez les vis de blocage sur le connecteur D-Sub de la pompe à membrane. 82/122 Maintenance 5. Débranchez le connecteur D-Sub sur la pompe à membrane. 6. Desserrez le raccord de terre sur la pompe à membrane. 7. Dévissez les vis à six pans creux avec les rondelles du support de pompe à membrane. 8. Retirez la pompe à membrane et son support de la plaque de fixation, en tournant doucement. 9. Desserrez les vis à six pans creux et les rondelles sur la pompe à membrane. 10. Séparez le support de pompe à membrane et la pompe à membrane. 11. Dévissez la vis à épaulement de la plaque de fixation. 12. Desserrez les écrous et retirez la plaque de fixation. 13. Détachez les ressorts de compression et amortisseurs de vibrations à ressorts du carter de la GSD 350. Réglage de l’adresse RS-485 de la nouvelle pompe à membrane ► Définissez l’adresse RS485 de la nouvelle pompe à membrane sur une valeur de « 10 » à l’aide d’une DCU 110/180/310 et du câble de connexion approprié. Installation de la pompe à membrane 1. Fixez les ressorts de compression et les amortisseurs de vibrations à ressorts sur le carter de la GSD 350. 2. Fixez la plaque de fixation en position à l’aide des écrous. 3. Vissez la vis à épaulement dans la plaque de fixation. 4. Utilisez les boulons six pans et les rondelles pour fixer le support de la pompe à membrane sur la pompe à membrane. 5. Positionnez la pompe à membrane avec le support de pompe à membrane sur la plaque de fixation. 6. Vissez les vis à six pans creux avec les rondelles sur le support de pompe à membrane. 7. Fixez le raccord de terre sur la pompe à membrane. 8. Connectez le connecteur Sub D. 9. Fixez les vis de verrouillage du connecteur Sub D sur la pompe à membrane. 10. Insérez le tuyau flexible d’entrée dans la pompe à membrane. – Faites attention à la bonne position côté aspiration. 11. Insérez le tuyau flexible de gaz d’échappement dans la pompe à membrane. – Faites attention à la bonne position sur le côté gaz d’échappement. 12. Si nécessaire, retirez la protection pour le transport de la pompe à membrane. 10.4.2 Remplacement de la membrane de la pompe à membrane La durée de vie courante des membranes et des vannes est de 15 000 heures de fonctionnement, à vitesse nominale, dans des conditions de fonctionnement propres et avec le GSD 350 analysant uniquement des gaz inertes. Conditions préalables ● ● ● ● ● ● GSD 350 désactivée Câble d’alimentation débranché Système de vide à l’arrêt et mis à l’air à la pression atmosphérique Capots latéraux retirés Couvercle de carter retiré Pompe à membrane enlevée du GSD 350 Équipement nécessaire ● Ensemble de révision (référence PU E22 030 -T) Procédure 1. Remplacez les membranes et les vannes au plus tard après 15 000 heures de fonctionnement. 2. Remplacez les membranes et les vannes en suivant les instructions du manuel de l’utilisateur de la pompe à membrane. 83/122 Maintenance 10.5 Maintenance de l’unité d’analyse de gaz 10.5.1 Maintenance de l’analyseur QMA 250 M AVIS Défaillance liée à la contamination et à la détérioration Tout contact à mains nues avec les appareils ou les composants augmente le taux de désorption et entraîne des mesures incorrectes. La saleté (p. ex. poussières, traces de doigts, etc.) et les dégâts nuisent au fonctionnement. ► Lors de l’assemblage et de la maintenance sur les systèmes à vide élevé ou à ultra-vide, veiller à toujours porter des gants de laboratoire propres, non pelucheux et sans poudre. ► Utilisez uniquement des outils propres. ► Vérifiez que les brides de raccordement sont sans graisse. ► Enlevez les obturateurs de protection et les couvercles protecteurs des brides et des raccordements uniquement lorsque cela est nécessaire. ► Enlevez la protection pour le transport de l’analyseur seulement lorsque cela est nécessaire. ► Effectuez toutes les opérations dans un espace bien éclairé. Manuel de l’utilisateur du spectromètre de masse Les informations relatives au démontage et au montage de l’unité électronique (QME) et de l’analyseur (QMA) sont disponibles dans le manuel de l’utilisateur du spectromètre de masse PrismaPro. Centrage de la source d’ions Une source d’ions décentrée va affecter les performances de mesure du spectromètre de masse et entraîner un vieillissement prématuré des filaments chauffés. Conditions préalables ● ● ● ● ● ● GSD 350 désactivée Câble d’alimentation débranché Pompe turbomoléculaire à l’arrêt Capots latéraux retirés Couvercle de carter retiré Admission de gaz retirée (pour réinstallation du QMA) Outils nécessaires ● 2 clés à fourche, WAF 10 Accessoires requis ● Équipement de montage pour analyseur QMA 250 ● Jauge de centrage pour QMA (disponible comme outil spécial) 4 3 2 1 Fig. 59: Spectromètre de masse quadripôle PrismaPro 1 Analyseur QMA 250 M 2 Bride 84/122 3 4 Collier de serrage Unité électronique QME 250 Maintenance 1 Fig. 60: Gorge sur l’analyseur 1 Gorge sur l’analyseur Détermination de la sensibilité du spectromètre de masse Si vous constatez une perte de sensibilité de la mesure, la cause peut être une diminution du gain du multiplicateur d’électrons intégré (EM) ou la contamination de la source d’ions. Dans ce cas, Pfeiffer Vacuum recommande de déterminer la sensibilité du spectromètre de masse avec le multiplicateur d’électrons à l’arrêt, c.à.d. uniquement avec le détecteur Faraday. 1. Déterminez la sensibilité du spectromètre de masse avec le détecteur Faraday. 2. Laissez l’air circuler dans le système via l’entrée du capillaire. 3. Ajoutez les courants d’ions (pics maximums) des 8 à 10 pics les plus élevés. 4. Calculez le courant d’ions total par rapport à la pression totale (se reporter au tableau). – Cela vous donne une bonne approximation de la sensibilité en A/hPa. La valeur doit être > 4 × 10-5 A/hPa. 5. Compensez l’usure du multiplicateur d’électrons en réglant une tension plus élevée de l’amplificateur. Valeur -6 < 5 × 10 A/hPa -6 > 5 × 10 A/hPa Tab. 13: Cause de perte de sensibilité Action corrective Contamination de la source d’ions Remplacez la source d’ions. Filament chauffé en fin de vie Remplacez le filament chauffé. Usure du multiplicateur d’électrons Augmentez la tension de l’amplificateur. Sensibilité déterminée du spectromètre de masse Remplacement des filaments chauffés Si l’un des filaments chauffés est défectueux, la mesure peut continuer temporairement avec le deuxième filament chauffé. ► Recommandation : Remplacez les deux filaments chauffés dès que possible en cas de défaillance d’un filament chauffé. ► Vérifiez également l’état de la source d’ions. – En cas de forte contamination de la source d’ions, Pfeiffer Vacuum recommande le remplacement de l’ensemble de la source d’ions. Effectuer la maintenance de l’analyseur 1. Débranchez tous les câbles de raccordement sur la platine frontale de l’unité électronique QME 250. 2. Retirez le collier de serrage noir sur l’unité électronique et dégagez l’unité électronique de l’analyseur. 3. Retirez le raccord à bride entre l’analyseur et l’enceinte à vide. 4. Sortez avec précaution l’analyseur de l’enceinte à vide. 5. Insérez l’analyseur dans l’équipement de montage avec la bride pointant vers le bas. 6. Exécutez les opérations de maintenance requises sur l’analyseur, en suivant le manuel de l’utilisateur du spectromètre de masse : ● Remplacer l’unité de filament chauffé, ou ● Remplacer la source d’ions 7. Positionnez l’analyseur avec un nouveau joint cuivre plaqué argent dans le vide. – Prenez garde à ce que la gorge sur l’analyseur soit bien orientée (« position à 9h ») sur la bride de passage. 85/122 Maintenance 8. Serrez l’analyseur de manière à ce que la source d’ions reste positionnée au centre dans la bride. 9. Positionnez l’unité électronique sur l’analyseur. – La gorge dans l’analyseur doit s’engager dans la patte sur l’unité électronique. 10. Serrez le collier de serrage noir sur l’unité électronique. 11. Branchez tous les câbles de raccordement sur la platine frontale de l’unité électronique QME 250. 10.5.2 Maintenance de la jauge de pression totale Durée d’allumage de la cathode froide à basses pressions Si vous désactivez la jauge dans le mode « Ignorer erreurs capteur », un certain temps va se passer avant que la GSD 350 affiche des valeurs de pression valides quand elle est réactivée. Conditions préalables ● ● ● ● ● GSD 350 désactivée Câble d’alimentation débranché Système de vide à l’arrêt et mis à l’air à la pression atmosphérique Capots latéraux retirés Couvercle de carter retiré Outils nécessaires ● 2 clés plates, WAF 10 (non-magnétiques) Pièces de rechange requises ● Joint cuivre, (DN 40 CF, plaqué argent) (référence 490DFL040-S-G-S5) ● Pour le remplacement de l’insert de capteur : Capteur (référence PT 120 212 -T) ● Pour le remplacement du manomètre de pression totale : Manomètre de pression totale (référence : PT R40 351) 1 2 3 4 5 6 7 8 10 9 Fig. 61: 1 2 3 4 5 Jauge de pression totale sur l’unité d’analyse de gaz Raccord angulaire avec coussin d’isolation (non illustré) Écrous six pans Rondelles Bride CF Joint cuivre 6 7 8 9 10 Rondelles Boulons six pans Jauge de pression totale Écrou six pans Vis moletée Procédure 1. Retirez le matelas isolant autour du raccord angulaire et de la bride de manomètre. 2. Desserrez les câbles de raccordement sur le manomètre. 3. Ouvrez le raccord à bride entre le manomètre et le raccord angulaire et retirez le manomètre. 4. Remplacez l’insert de capteur sur le manomètre en suivant le manuel de l’utilisateur du manomètre, ou utilisez un nouveau manomètre. 5. Si vous utilisez un nouveau manomètre : Sur le sélecteur d’adresse du manomètre, définissez l’adresse sur une valeur de « 1 ». 86/122 Maintenance 6. Installez la jauge sur le raccord angulaire à l’aide d’un nouveau joint cuivre plaqué argent. 7. Mettez le matelas isolant en place autour du raccord angulaire et la bride de manomètre. 8. Connectez les câbles de raccordement au manomètre. 10.6 Maintenance du système d’admission de gaz sur Omnistar AVIS Défaillance due à la contamination et à la détérioration Tout contact à mains nues avec les appareils ou les composants augmente le taux de désorption et entraîne des mesures incorrectes. La saleté (p. ex. poussières, traces de doigts, etc.) et les dégâts nuisent au fonctionnement. ► Portez toujours des gants de laboratoire propres, non pelucheux et sans poudre pour les travaux sur les installations ultra-vide ou à vide élevé. ► Utilisez uniquement des outils propres. ► Vérifiez que les brides de raccordement sont sans graisse. ► Retirez les obturateurs de protection et les couvercles de protection des brides et des raccordements uniquement lorsque cela est nécessaire. ► Effectuez toutes les opérations dans un espace bien éclairé. Découpage à longueur ou remplacement du capillaire en acier inoxydable Découpez à la longueur le capillaire en acier inoxydable ou remplacez d’abord le capillaire en acier inoxydable. Remplacez seulement l’orifice si le travail sur le capillaire en acier inoxydable n’a pas permis d’atteindre les résultats escomptés. Si la pression dans la GSD 350 n’augmente pas ou augmente seulement très peu après l’ouverture de la vanne de débitmètre (la pression reste < 1 × 10-6 hPa), alors le capillaire ou l’orifice d’admission de gaz est probablement partiellement ou complètement bloqué. La probabilité d’un capillaire bloqué est supérieure à celle d’un orifice bloqué. 6 4 5 3 2 1 Fig. 62: Pièces du diffuseur de gaz interne sur l’Omnistar 1 Douille en céramique 2 Ressort de compression 3 Diffuseur de gaz 4 5 6 Joint torique, intérieur Joint torique, extérieur Écran 87/122 Maintenance 10.6.1 Retrait de la bride de l’admission de gaz AVIS Destruction de la pompe turbomoléculaire en raison d'un diffuseur de gaz interne incomplet Si la douille en céramique, le ressort de pression ou l'un des deux joints toriques du diffuseur de gaz intérieur sont absents, la mise en service du GSD 350 entraîne la destruction de la pompe turbomoléculaire. ► Veillez à ce que le diffuseur de gaz interne soit complet. ► Veillez à ce que le ressort de compression et la douille en céramique soient bien en place sur le diffuseur de gaz. ► Retirez les pièces manquantes de l’enceinte à vide avant de redémarrer le GSD 350. Conditions préalables ● ● ● ● ● GSD 350 désactivée Câble d’alimentation débranché Système de vide à l’arrêt et mis à l’air à la pression atmosphérique Couvercle d’admission de gaz retiré Douille de séparation retirée Outils nécessaires ● ● ● ● Clé hexagonale, WAF 2,5 Clé plate, WAF 5/16" Clé plate, WAF 9/16" Clé plate, WAF 14 1 2 12 3 4 10 5 6 9 11 8 Fig. 63: 1 2 3 4 5 6 7 7 Démontage du bloc de vannes Vanne de débitmètre Capteur de température Disque de serrage Vis à tête arrondie Disques de blocage (2×) Vis à six pans creux intérieurs (2×) Vis à six pans creux intérieurs 8 9 10 11 12 13 Disque de serrage Cartouche de chauffage Raccord à vis du capillaire Bloc de vannes Vanne Split-flow Bride de raccordement Procédé 1. Desserrez les écrous sur les bobines des deux vannes. 2. Tirez sur la plaque de conducteur thermique pour la sortir du bloc de vannes et placez-la sur la GSD 350. 3. Retirez les bobines des corps des deux vannes. 4. Ouvrez le raccord à vis du capillaire sur le bloc de valves à l’aide de la clé plate et tirez sur le capillaire en acier inoxydable pour le sortir. 5. Desserrez la rondelle et la vis à tête arrondie du capteur de température. 6. Retirez le capteur de température. 7. Desserrez la rondelle de serrage et la vis à six pans creux de la cartouche de chauffage. 88/122 Maintenance 8. Tirez sur la cartouche de chauffage pour la sortir du bloc de vannes. 9. Desserrez les rondelles de serrage et les vis à six pans creux sur le bloc de vannes. 10. Tirez sur le bloc de vannes avec précaution vers l’avant pour le sortir de la bride de raccordement. 11. Veillez à ce que le diffuseur de gaz interne soit complet. Compléter le travail nécessaire suivant ► Complétez le travail supplémentaire nécessaire : – Remplacer l’orifice – Remplacer le diffuseur de gaz intérieur et l’orifice – Remplacer l’admission de gaz complète 10.6.2 Remplacement de l’orifice Conditions préalables ● ● ● ● GSD 350 désactivée Câble d’alimentation débranché Système de vide à l’arrêt et mis à l’air à la pression atmosphérique Admission de gaz déposée Outils nécessaires ● Outil spécial pour l’orifice du système d’admission de gaz ● Clé plate pour diffuseur de gaz, WAF 8 Pièce de rechange requise ● Orifice, 50 μm (référence BK212576) Procédé 1. Dévissez et retirez le diffuseur de gaz sur le bloc de vannes. 2. Tournez l’admission de gaz de sorte à pouvoir dégager l’orifice. 3. Percez manuellement l’orifice avec un outil spécial et sortez l’orifice du bloc de vanne si l’orifice reste coincé. 4. Si l’orifice ne peut pas être desserré avec l’outil spécial, tapez doucement l’admission de gaz sur une surface non dure pour le faire tomber. 5. Positionnez le nouvel orifice sur le diffuseur de gaz en l’orientant correctement de manière à ce que le côté mat soit visible quand vous regardez dans le trou. 6. Avec une clé à écrou, serrez à la main le diffuseur de gaz dans le bloc de vannes. 10.6.3 Remplacement du diffuseur de gaz intérieur et de l’orifice Conditions préalables ● ● ● ● GSD 350 désactivée Câble d’alimentation débranché Système de vide à l’arrêt et mis à l’air à la pression atmosphérique Admission de gaz déposée Outils nécessaires ● Outil spécial pour l’orifice du système d’admission de gaz ● Clé plate pour diffuseur de gaz, WAF 8 Accessoires requis ● Papier propre Pièces de rechange requises ● Lot de pièces de rechange (référence PT 167 014 -T) 89/122 Maintenance 1 2 3 Fig. 64: Diffuseur de gaz environ 1–2 mm derrière l’extrémité du manchon céramique 1 Douille en céramique 2 Ressort de compression 3 Diffuseur de gaz Procédé 1. Dévissez et retirez le diffuseur de gaz sur le bloc de vannes. 2. Tournez l’admission de gaz de sorte à dégager l’orifice. 3. Percez manuellement l’orifice avec un outil spécial et sortez l’orifice du bloc de vanne si l’orifice reste coincé. 4. Si l’orifice ne peut pas être desserré avec l’outil spécial, tapez doucement l’admission de gaz sur une surface non dure pour le faire tomber. 5. Remplacez le diffuseur de gaz, l’anneau de compression et la douille en céramique. 6. Poussez le ressort sur le manchon céramique. 7. Poussez le ressort et le manchon céramique sur le diffuseur de gaz. 8. Vérifiez que le diffuseur de gaz est situé à environ 1–2 mm derrière l’extrémité du manchon céramique. 9. Poussez le manchon céramique sur un morceau de papier propre et vérifiez que le ressort du diffuseur de gaz agit en compression et que le frottement est faible. 10. Positionnez le nouvel orifice sur le diffuseur de gaz en l’orientant correctement de manière à ce que le côté mat soit visible quand vous regardez dans le trou. 11. Avec une clé à écrou, serrez à la main le diffuseur de gaz dans le bloc de vannes. 10.6.4 Installation de la bride d’aspiration de gaz AVIS Destruction de la pompe turbomoléculaire en raison d'un diffuseur de gaz interne incomplet Si la douille en céramique, le ressort de pression ou l'un des deux joints toriques du diffuseur de gaz intérieur sont absents, la mise en service du GSD 350 entraîne la destruction de la pompe turbomoléculaire. ► Veillez à ce que le diffuseur de gaz interne soit complet. ► Veillez à ce que le ressort de compression et la douille en céramique soient bien en place sur le diffuseur de gaz. ► Retirez les pièces manquantes de l’enceinte à vide avant de redémarrer le GSD 350. Conditions préalables ● ● ● ● ● ● ● 90/122 GSD 350 désactivée Câble d’alimentation débranché Système de vide à l’arrêt et mis à l’air à la pression atmosphérique Couvercle d’admission de gaz retiré Douille de séparation retirée Admission de gaz déposée Capillarités en acier inoxydable éventuellement installées sur le bloc de vannes Maintenance Outils nécessaires ● ● ● ● Clé mâle coudée pour vis à six pans creux, WAF 2,5 Clé plate, WAF 5/16" Clé plate, WAF 9/16" Clé plate, WAF 14 pour vannes Procédé 1. Contrôlez l’assise du ressort de compression et de la douille en céramique. 2. Centrez avec précaution et insérez le bloc de vannes dans la bride de raccordement sur l’enceinte à vide. – Le dernier centimètre de guidage de gaz est directement dans le spectromètre de masse. 3. Fixez les rondelles de serrage et les vis à six pans creux sur le bloc de vannes. 4. Poussez la cartouche de chauffage dans le bloc de vannes. 5. Fixez la rondelle de serrage et la vis à six pans creux de la cartouche de chauffage. 6. Fixez le capteur de température avec la rondelle de serrage et la vis à tête arrondie. 7. Enfoncez à nouveau le capillaire en acier inoxydable dans le tube capillaire. 8. Placez les bobines sur les corps des deux vannes. 9. Boulonnez les bobines à un angle de 90°. 10. Veillez à ce que ce tout corresponde bien. 11. Poussez la plaque de conducteur thermique sous le bloc de vannes dans l’admission de gaz. 12. Montez le chapeau isolant sur le carter de l’admission de gaz. 10.7 Maintenance du système d’admission de gaz sur ThermoStar AVIS Défaillance due à la contamination et à la détérioration Tout contact à mains nues avec les appareils ou les composants augmente le taux de désorption et entraîne des mesures incorrectes. La saleté (p. ex. poussières, traces de doigts, etc.) et les dégâts nuisent au fonctionnement. ► Portez toujours des gants de laboratoire propres, non pelucheux et sans poudre pour les travaux sur les installations ultra-vide ou à vide élevé. ► Utilisez uniquement des outils propres. ► Vérifiez que les brides de raccordement sont sans graisse. ► Retirez les obturateurs de protection et les couvercles de protection des brides et des raccordements uniquement lorsque cela est nécessaire. ► Effectuez toutes les opérations dans un espace bien éclairé. Réduisez d’abord la longueur ou remplacez le capillaire en quartz Pfeiffer Vacuum recommande d’abord de réduire la longueur ou de remplacer le capillaire quart, et de ne remplacer l’orifice que si les opérations sur le capillaire quartz ne donnent pas les résultats escomptés. Si la pression dans la GSD 350 est toujours < 1 × 10-6 hPa malgré la pression atmosphérique sur l’admission de gaz, alors le capillaire ou l’orifice d’admission est probablement partiellement ou complètement bloqué. La probabilité d’un capillaire bloqué est supérieure à celle d’un orifice bloqué. 91/122 Maintenance 5 4 6 3 2 1 Fig. 65: Pièces du diffuseur de gaz interne sur ThermoStar 1 Douille en céramique 2 Ressort de compression 3 Diffuseur de gaz 10.7.1 4 5 6 Écran Joint torique, intérieur Joint torique, extérieur Retrait de la bride de l’admission de gaz AVIS Destruction de la pompe turbomoléculaire en raison d'un diffuseur de gaz interne incomplet Si la douille en céramique, le ressort de pression ou l'un des deux joints toriques du diffuseur de gaz intérieur sont absents, la mise en service du GSD 350 entraîne la destruction de la pompe turbomoléculaire. ► Veillez à ce que le diffuseur de gaz interne soit complet. ► Veillez à ce que le ressort de compression et la douille en céramique soient bien en place sur le diffuseur de gaz. ► Retirez les pièces manquantes de l’enceinte à vide avant de redémarrer le GSD 350. Conditions préalables ● ● ● ● ● GSD 350 désactivée Câble d’alimentation débranché Système de vide à l’arrêt et mis à l’air à la pression atmosphérique Couvercle d’admission de gaz retiré Douille de séparation retirée Outils nécessaires ● ● ● ● 92/122 Clé mâle coudée pour vis à six pans creux, WAF 2,5 Clé à fourche, WAF 5,5 Clé plate, WAF 1/4" Clé plate, WAF 3/8" Maintenance 1 2 3 4 8 7 6 5 Fig. 66: 1 2 3 4 Retrait de la bride de l’admission de gaz Disques de blocage (2×) Vis à six pans creux intérieurs (2×) Vis à tête arrondie Capteur de température 5 6 7 8 Borne de connexion Raccord à vis du capillaire Bride d’aspiration de gaz Bride de raccordement Procédé 1. Retirez le chapeau isolant sur le carter de l’admission de gaz. 2. Tirez sur la plaque de conducteur thermique pour la sortir et placez-la sur la GSD 350. 3. Ouvrez le raccord à vis du capillaire sur la bride d’aspiration et sortez le capillaire en quartz. 4. Desserrez la vis à tête arrondie et le collier du capteur de température. 5. Retirez le capteur de température. 6. Fixez les deux vis à six pans creux et les rondelles sur la bride d’aspiration de gaz. 7. Tirez sur la bride d’aspiration de gaz avec précaution vers l’avant pour la sortir de la bride de raccordement. 8. Veillez à ce que le diffuseur de gaz interne soit complet. Compléter le travail nécessaire suivant ► Complétez le travail supplémentaire nécessaire : – Remplacer l’orifice – Remplacer le diffuseur de gaz intérieur et l’orifice – Remplacer l’admission de gaz complète 10.7.2 Remplacement de l’orifice Conditions préalables ● ● ● ● GSD 350 désactivée Câble d’alimentation débranché Système de vide à l’arrêt et mis à l’air à la pression atmosphérique Admission de gaz déposée Outils nécessaires ● Outil spécial pour l’orifice du système d’admission de gaz ● Clé plate pour diffuseur de gaz, WAF 8 ● Mandrin pour orifice, diamètre 1,5 mm, longueur 40 mm Pièce de rechange requise ● Orifice, 50 μm (référence BK212576) Procédé 1. Dévissez et retirez le diffuseur de gaz sur la bride d’aspiration de gaz. 2. Tournez l’admission de gaz de sorte à pouvoir dégager l’orifice. 3. Avec un mandrin fin, poussez sur l’orifice pour le sortir du côté capillaire. 4. Contrôlez si l’orifice peut être réutilisé. 5. Percez manuellement l’orifice avec un outil spécial et sortez l’orifice du bloc de vanne si l’orifice reste coincé. 93/122 Maintenance 6. Si l’orifice ne peut pas être desserré avec l’outil spécial, tapez doucement l’admission de gaz sur une surface non dure pour le faire tomber. 7. Positionnez le nouvel orifice sur le diffuseur de gaz en l’orientant correctement de manière à ce que le côté mat soit visible quand vous regardez dans le trou. 8. Avec la clé plate, serrez à la main le diffuseur de gaz dans la bride d’aspiration de gaz. 10.7.3 Remplacement du diffuseur de gaz intérieur et de l’orifice Conditions préalables ● ● ● ● GSD 350 désactivée Câble d’alimentation débranché Système de vide à l’arrêt et mis à l’air à la pression atmosphérique Admission de gaz déposée Outils nécessaires ● Outil spécial pour l’orifice du système d’admission de gaz ● Clé plate pour diffuseur de gaz, WAF 8 Accessoires requis ● Papier propre Pièces de rechange requises ● Lot de pièces de rechange (référence PT 167 014 -T) 1 2 3 Fig. 67: Diffuseur de gaz environ 1–2 mm derrière l’extrémité du manchon céramique 1 Douille en céramique 2 Ressort de compression 3 Diffuseur de gaz Procédé 1. Dévissez et retirez le diffuseur de gaz sur la bride d’aspiration de gaz. 2. Tournez l’admission de gaz de sorte à dégager l’orifice. 3. Percez manuellement l’orifice avec un outil spécial et sortez l’orifice du bloc de vanne si l’orifice reste coincé. 4. Si l’orifice ne peut pas être desserré avec l’outil spécial, tapez doucement l’admission de gaz sur une surface non dure pour le faire tomber. 5. Remplacez le diffuseur de gaz, l’anneau de compression et la douille en céramique. 6. Poussez le ressort sur le manchon céramique. 7. Poussez le ressort et le manchon céramique sur le diffuseur de gaz. 8. Vérifiez que le diffuseur de gaz est situé à environ 1–2 mm derrière l’extrémité du manchon céramique. 9. Poussez le manchon céramique sur un morceau de papier propre et vérifiez que le ressort du diffuseur de gaz agit en compression et que le frottement est faible. 10. Positionnez le nouvel orifice sur le diffuseur de gaz en l’orientant correctement de manière à ce que le côté mat soit visible quand vous regardez dans le trou. 11. Avec la clé plate, serrez à la main le diffuseur de gaz dans la bride d’aspiration de gaz. 94/122 Maintenance 10.7.4 Installation de la bride d’aspiration de gaz AVIS Destruction de la pompe turbomoléculaire en raison d'un diffuseur de gaz interne incomplet Si la douille en céramique, le ressort de pression ou l'un des deux joints toriques du diffuseur de gaz intérieur sont absents, la mise en service du GSD 350 entraîne la destruction de la pompe turbomoléculaire. ► Veillez à ce que le diffuseur de gaz interne soit complet. ► Veillez à ce que le ressort de compression et la douille en céramique soient bien en place sur le diffuseur de gaz. ► Retirez les pièces manquantes de l’enceinte à vide avant de redémarrer le GSD 350. Conditions préalables ● ● ● ● ● ● ● GSD 350 désactivée Câble d’alimentation débranché Système de vide à l’arrêt et mis à l’air à la pression atmosphérique Couvercle d’admission de gaz retiré Douille de séparation retirée Admission de gaz déposée Capillaire quartz éventuellement assemblé sur la bride d’aspiration de gaz Outils nécessaires ● ● ● ● Clé mâle coudée pour vis à six pans creux, WAF 2,5 Clé à fourche, WAF 5,5 Clé plate, WAF 1/4" Clé plate, WAF 3/8" Procédé 1. Contrôlez l’assise du ressort de compression et de la douille en céramique. 2. Insérez prudemment la bride d’aspiration de gaz dans la bride de raccordement sur l’enceinte à vide. 3. Serrez les deux vis à six pans creux et les rondelles sur la bride d’aspiration de gaz. 4. Enfoncez à nouveau le capillaire en quartz dans le tube capillaire. 5. Poussez le collier sur le raccord à vis du milieu de l’admission de gaz. 6. Fixez le capteur de température sur le collier avec la vis à tête arrondie. 7. Poussez dans la plaque du conducteur thermique. 8. Montez le chapeau isolant sur le carter de l’admission de gaz. 10.8 Entretien du capillaire Utilisez uniquement les capillarités d’origine parmi les accessoires Le capillaire fait partie de l’étage de réduction et est nécessaire pour atteindre la pression de travail du spectromètre de masse. Utilisez uniquement les capillarités d’origine parmi les accessoires Pfeiffer Vacuum. Contactez Pfeiffer Vacuum Service si vous avez des questions. Réduction ou remplacement du capillaire Pfeiffer Vacuum recommande d’abord de réduire la longueur ou de remplacer le capillaire, et de ne remplacer l’orifice que si les opérations sur le capillaire ne donnent pas les résultats escomptés. Lorsque la pression totale escomptée n’est pas atteinte dans le GSD 350 et que la pression total reste à < 1 × 10-6 hPa avec l’admission de gaz ouverte (OmniStar), on peut supposer que soit le capillaire, soit l’orifice sur l’admission de gaz, est partiellement ou intégralement bloqué. La probabilité d’un capillaire bloqué est supérieure à celle d’un orifice bloqué. 95/122 Maintenance 10.8.1 Réduction de la longueur des capillarités en acier inoxydable Longueur nécessaire des capillarités en acier inoxydable Longueur du capillaire = longueur du tube capillaire + 15 cm + longueur requise au point de mesure Le capillaire fait partie du système de réduction de pression. Un capillaire dont la longueur dépasse 2 m peut entraîner des pressions plus basses dans l’enceinte à vide. Un blocage potentiel des capillarités en acier inoxydable survient souvent dans la zone avant côté atmosphère des capillarités en acier inoxydable. Découpez à longueur les capillarités en acier inoxydable pour éliminer le blocage. Conditions préalables ● Capillaire en acier inoxydable déconnecté du point de mesure ● Longueur du capillaire en acier inoxydable encore suffisante après réduction Outils nécessaires ● Tube ou cutter de capillaire (1/16") lime coupante 3 2 1 Fig. 68: Longueur du capillaire en acier inoxydable avec raccord à vis à collier de serrage 1 Capillaire en acier inoxydable 2 Raccord à vis à collier de serrage ≈1 Fig. 69: 0m 3 Joint capillaire (virole) m Entaillage et cassage du capillaire en acier inoxydable Sectionnement du capillaire en acier inoxydable avec le tube ou les cutters de capillaire 1. Tirez le capillaire en acier inoxydable suffisamment pour le sortir du tube de capillaire. 2. Coupez le capillaire en acier inoxydable avec le tube ou les cutters de capillaire. Sectionnement du capillaire en acier inoxydable avec une lime 1. Tirez le capillaire en acier inoxydable suffisamment pour le sortir du tube de capillaire. 2. Entaillez avec précaution le capillaire en acier inoxydable en deux endroits opposés. – Entailles = profondeur max. 0,5 mm 3. Pliez avec précaution le capillaire en acier inoxydable jusqu’à ce qu’il se rompe au niveau des entailles. Mise en service de l’unité 1. Démarrez le système de pompage. 2. Attendez pendant le temps d’accélération de la pompe turbomoléculaire (environ 5 minutes). 96/122 Maintenance Contrôle de la pression dans l’enceinte à vide 1. Contrôlez la pression dans l’enceinte à vide. – La pression affichée doit être de ≥ 1 × 10-6 hPa avec la vanne de débitmètre ouverte. 2. Si la pression affichée est < 1 × 10-6 hPa, les causes suivantes sont possibles : – Capillaire en acier inoxydable bouché sur toute sa longueur (voir chapitre « Remplacement du capillaire en acier inoxydable », page 97) – Écran bloqué (voir chapitre « Remplacement de l’orifice », page 89) ou (voir chapitre « Remplacement du diffuseur de gaz intérieur et de l’orifice », page 89) – Capillaire en acier inoxydable trop long – Diamètre du capillaire trop petit 10.8.2 Remplacement du capillaire en acier inoxydable Conditions préalables ● ● ● ● ● ● GSD 350 désactivée Câble d’alimentation débranché Système de vide à l’arrêt et mis à l’air à la pression atmosphérique Capillaire en acier inoxydable déconnecté du point de mesure Couvercle d’admission de gaz retiré Douille de séparation retirée Outils nécessaires ● Clé plate, WAF 9/16" ● Clé plate, WAF 5/16" ● Tube ou cutter de capillaire (1/16") lime coupante Pièces de rechange requises ● Capillaire en acier inoxydable (référence PT 167 060 -T) ● Joints de capillaire (référence PT 167 017 -T) 5 1 Fig. 70: 2 3 4 Raccord à collier de serrage pour capillaire en acier inoxydable 1 Adaptateur 2 Écrou 3 Collier de serrage avant 4 5 Collier de serrage arrière Capillaire en acier inoxydable 97/122 Maintenance Procédé 1. Découpez à la longueur les capillarités en acier inoxydable. – Longueur du capillaire = longueur du tube capillaire + 15 cm + longueur requise au point de mesure 2. Ouvrez le raccord à chapeau de serrage de refroidissement. 3. Retirez l’ancien capillaire en acier inoxydable. 4. Enfilez le raccords à chapeau de serrage et un nouveau joint capillaire sur le nouveau capillaire en acier inoxydable sectionné. 5. Enfilez le capillaire en acier inoxydable, avec le joint capillaire et le raccord à chapeau de serrage, dans le raccord fileté sur le bloc de vannes. 6. Vissez légèrement le raccord à chapeau de serrage, de sorte que les capillaires en acier inoxydable puissent continuer de bouger. 7. Poussez le capillaire en acier inoxydable jusqu’en butée. 8. Ramenez le capillaire en acier inoxydable d’1 ou 2 mm en arrière. 9. Serrez le raccords à chapeau de serrage avec les clés à fourche. 10. Enfilez avec précaution l’extrémité libre du capillaire en acier inoxydable dans le tube capillaire. 10.8.3 Découpage à longueur des capillarités en quartz ATTENTION Risque de blessure par éclatement du capillaire en quartz Les capillaires au quartz éclatent en cas d’utilisation non conforme. Risque de grave blessure aux yeux lié à la projection d'éclats. ► N’exercez pas de force en entaillant le capillaire en quartz. ► Portez des lunettes de protection. Longueur nécessaire des capillarités en quartz Longueur du capillaire = longueur du tube capillaire + 30 cm + longueur requise au point de mesure Un blocage potentiel des capillarités en quartz survient souvent dans la zone avant côté atmosphère des capillarités en quartz. Découpez à longueur les capillarités en quartz pour éliminer le blocage. Conditions préalables ● Capillaire en quartz déconnecté du point de mesure ● Longueur du capillaire en quartz encore suffisante après réduction Outils nécessaires ● Outil de coupe du capillaire ≈1 Fig. 71: 0m m Entaillage et cassage du capillaire de quartz Sectionnement du capillaire en quartz 1. Tirez le capillaire en quartz suffisamment pour le sortir du tube de capillaire. 2. Entaillez avec précaution le capillaire en quartz, sans forcer. 3. Rompez avec précaution le capillaire en quartz à l’endroit entaillé précédemment. 98/122 Maintenance Mise en service de l’unité 1. Démarrez le système de pompage. 2. Attendez pendant le temps d’accélération de la pompe turbomoléculaire (environ 5 minutes). Contrôle de la pression dans l’enceinte à vide 1. Contrôlez la pression dans l’enceinte à vide. – La pression affichée doit être de ≥ 1 × 10-6 hPa. 2. Si la pression affichée est < 1 × 10-6 hPa, les causes suivantes sont possibles : – Capillaire en quartz bouché sur toute sa longueur (voir chapitre « Remplacement du capillaire en quartz », page 99) – Écran bloqué (voir chapitre « Remplacement de l’orifice », page 93) ou (voir chapitre « Remplacement du diffuseur de gaz intérieur et de l’orifice », page 94) 10.8.4 Remplacement du capillaire en quartz Conditions préalables ● ● ● ● ● ● GSD 350 désactivée Câble d’alimentation débranché Système de vide à l’arrêt et mis à l’air à la pression atmosphérique Capillaire en quartz déconnecté du point de mesure Couvercle d’admission de gaz retiré Douille de séparation retirée Outils nécessaires ● Clé plate, WAF 1/4" ● Clé plate, WAF 3/8" ● Outil de coupe du capillaire Pièces de rechange requises ● Capillaire en quartz (référence B1975082EC) ● Joints de capillaire (référence PT 167 015 -T) Ne desserrez pas le raccord à vis arrière Vous ne devez pas ouvrir le raccord à vis arrière sur la bride d’aspiration de gaz. Pour remplacer le capillaire, ouvrez seulement le raccord à vis avant. 1 2 4 5 6 7 8 3 Fig. 72: 1 2 3 4 Raccord à vis avant du capillaire en quartz Capteur de température Vis à tête arrondie Borne de connexion Raccord à vis arrière 5 6 7 8 Vis de pression Joint (virole) Vis de pression Capillaire en quartz Procédé 1. Découpez à la longueur les capillarités en quartz. – Longueur du capillaire = longueur du tube capillaire + 30 cm + longueur requise au point de mesure 2. Desserrez la vie à tête arrondie. 3. Retirez le capteur de température et le collier. 4. Desserrez la vie de pression. 5. Retirez l’ancien capillaire en quartz. 99/122 Maintenance 6. Poussez la vis de pression et un nouveau joint capillaire sur le nouveau capillaire en quartz découpé à longueur. – Distance entre l’extrémité du capillaire et la virole = env. 25 mm 7. Poussez le capillaire en quartz, avec le joint capillaire et la vis de pression sur le raccord à vis arrière sur la bride d’aspiration de gaz. 8. Poussez le capillaire en quartz jusqu’en butée. 9. Ramenez le capillaire en quartz de 1 ou 2 mm en arrière. 10. Serrez la vis de pression avec les clés plates. 11. Enfilez avec précaution l’extrémité libre du capillaire en quartz dans le tube capillaire. 12. Fixez le capteur de température et le collier avec la vis à tête arrondie. 10.9 Maintenance des unités de chauffage AVERTISSEMENT Risque de brûlure sur les surfaces chaudes Pendant le fonctionnement, les températures montent très haut (> 50 °C) sur les surfaces de contact des composants de chauffage et sur l’admission de gaz. Il existe un risque de brûlure. ► Prenez les mesures requises pour prévenir tout contact avec les pièces chaudes. ► Apposez des signaux d’avertissement. ► Veillez à ce que le produit se soit refroidi avant d’intervenir dessus. ► Portez des gants de protection (conformément à EN 420). 10.9.1 Remplacez le tube capillaire Pfeiffer Vacuum Service prend en charge le remplacement. ► Contactez Pfeiffer Vacuum Service. 10.9.2 Maintenance du chauffage de l’admission de gaz Si le GSD 350 a un défaut dans le chauffage de l’admission de gaz, remplacez le chauffage et/ou le capteur de température. Pfeiffer Vacuum Service prend en charge le remplacement. ► Contactez Pfeiffer Vacuum Service. 10.9.3 Entretien du chauffage de l’enceinte à vide Lorsque la température dans l’enceinte à vide n’atteint pas la température définie lors de l’étuvage, même après un laps de temps prolongé, ou si le GSD 350 notifie une défaillance du chauffage de l’enceinte à vide, remplacez le chauffage et/ou le capteur de température concerné. Pfeiffer Vacuum Service prend en charge le remplacement. ► Contactez Pfeiffer Vacuum Service. 10.10 Entretien des composants électroniques Tous les composants électroniques sur le GSD 350 sont sans entretien. Vous devez remplacer tous les composants électroniques défectueux. 10.10.1 Remplacement de l’affichage Conditions préalables ● GSD 350 désactivée ● Câble d’alimentation débranché ● Système de vide à l’arrêt et mis à l’air à la pression atmosphérique Outils nécessaires ● Tournevis cruciforme 100/122 Maintenance Pièce de rechange requise ● Affichage de contact 7" (référence PT 167 025) Afficher la tension d’alimentation L'injecteur PoE du GSD 350 alimente l'écran en tension via le câble de raccordement. Ne connectez pas d’autres composants Ethernet à ce câble de raccordement. 2 1 3 Fig. 73: Remplacement de l’affichage 1 Vis à tête conique (2×) 2 Élément de fixation du câble 3 Affichage Procédure 1. Retirez avec précaution l’affichage du GSD 350. 2. A l’arrière de l’affichage, desserrez les vis à tête conique sur les éléments de fixation. 3. Déconnectez le câble de raccordement sur l’affichage. 4. Branchez le câble de raccordement au nouvel affichage. 5. A l’arrière de l’affichage, serrez les vis à tête conique sur les éléments de fixation. 6. Placez l’affichage dans le GSD 350. Pendant la phase d’accélération, le GSD 350 synchronise automatiquement l’affichage avec la configuration du GSD 350. 10.10.2 Remplacement de l'injecteur PoE Pfeiffer Vacuum Service prend en charge le remplacement. ► Contactez Pfeiffer Vacuum Service. 10.10.3 Remplacement de la platine principale Pfeiffer Vacuum Service prend en charge le remplacement. ► Contactez Pfeiffer Vacuum Service. 10.10.4 Remplacement de l'unité de courant Pfeiffer Vacuum Service prend en charge le remplacement. ► Contactez Pfeiffer Vacuum Service. 10.10.5 Remplacement de l’unité électronique QME 250 Pfeiffer Vacuum Service prend en charge le remplacement. ► Contactez Pfeiffer Vacuum Service. 101/122 Maintenance 10.10.6 Remplacement de l’unité de commande électronique TC 110 sur la pompe turbomoléculaire Pfeiffer Vacuum Service prend en charge le remplacement. ► Contactez Pfeiffer Vacuum Service. 10.11 Maintenance de l’unité de calibration 10.11.1 Appoint en fluide de calibration Conditions préalables ● GSD 350 désactivée ● Câble d’alimentation débranché ● Système de vide à l’arrêt et mis à l’air à la pression atmosphérique Outils nécessaires ● Clé mâle coudée pour vis à six pans creux, WAF 2,5 ● Aide au montage du support de gaz de calibration Consommables requis ● Fluide de calibration (PFTBA) (référence PT 167 031) 1 2 3 4 5 6 7 8 10 9 Fig. 74: 1 2 3 4 5 102/122 Unité de calibration Vanne d’isolement EVI 005 M Joint Écran Joint Récipient collecteur 6 7 8 9 10 Raccord à vis Crochet Écrou six pans Couvercle Vis à tête conique (3×) Maintenance Personne supplémentaire pour l’assistance Pour cette étape, vous devez tirer la GSD 350 à environ 17 cm du bord de la table pour pouvoir ouvrir le couvercle de la base du carter de la GSD 350. Pfeiffer Vacuum recommande de vous faire assister par une autre personne pour éviter que la GSD 350 glisse pendant cette étape. Procédé 1. Tirez la GSD 350 vers l’avant de manière à ce qu’elle dépasse d’environ 17 cm du bord de la table. 2. Desserrez les vis à tête conique de la base du carter. 3. Retirez le couvercle. 4. Desserrez le raccord à vis au-dessus du récipient collecteur avec l’aide au montage. 5. Tirez le récipient collecteur vers le bas pour le détacher de la vanne d’isolement. – Attention aux joints et à l’orifice. 6. Remplissez le récipient collecteur avec le fluide de calibration. 7. Installez le récipient collecteur sur la vanne d’isolement avec l’aide au montage. – Attention aux joints et à l’orifice. 8. Fixez à la main le raccord à vis. 9. Fixez le couvercle sur la base du carter avec la vis à tête conique. 10.11.2 Remplacement de la vanne de calibration Pfeiffer Vacuum Service prend en charge le remplacement. ► Contactez Pfeiffer Vacuum Service. 10.12 Opérations de maintenance additionnelles pour la version pour gaz corrosif 10.12.1 Remplacement de la vanne de la purge de gaz Pfeiffer Vacuum Service prend en charge le remplacement. ► Contactez Pfeiffer Vacuum Service. 10.12.2 Remplacement du régulateur de pression manuel Pfeiffer Vacuum Service prend en charge le remplacement et l’ajustage. ► Contactez Pfeiffer Vacuum Service. 10.12.3 Remplacement du manocontacteur numérique Réglage par défaut du manocontacteur Ne modifiez pas ce réglage par défaut. Pfeiffer Vacuum a réglé par défaut le manocontacteur. Pfeiffer Vacuum Service prend en charge le remplacement. ► Contactez Pfeiffer Vacuum Service. 103/122 Dépannage 11 Dépannage Notes sur la gestion des dysfonctionnement dans les menus d’aide Pour de plus amples informations sur les messages d’anomalie et le dépannage lors de l’utilisation de l’appareil via l’interface Web ou lors de l’utilisation du logiciel PV MassSpec, se référer aux menus d’aide correspondants. Problème Cause possible Action corrective L’écran reste noir après sa mise en route. Absence d’alimentation sur le module Vérifiez l’alimentation et le câble de secteur. Fusibles secteur (2×10 AT) défaillants Remplacez les fusibles secteur. Câble de l’écran mal branché Contrôlez le connecteur mâle-femelle sur l’affichage et sur le PoE dans la GSD 350. Câble d’alimentation électrique entre le PoE et la carte superviseur détaché Contrôlez le connecteur mâle-femelle du câble d’alimentation électrique entre le PoE et la carte superviseur. Le temps d’accélération n’est pas écoulé Patientez jusqu’à la fin du temps d’accélération d’environ 60 secondes. L’unité a été désactivée, puis réactivée trop rapidement 1. Arrêtez l’unité. 2. Patientez 15 secondes. 3. Réactivez l’unité. Câble Ethernet entre le PoE et la carte superviseur détaché Contrôlez le connecteur mâle-femelle du câble Ethernet entre le PoE et la carte superviseur. Connexion du câble desserrée Contrôlez le connecteur mâle-femelle sur la pompe à membrane et sur la carte superviseur. Pompe à membrane défectueuse Effectuez l’entretien de la pompe à membrane ou remplacez la pompe à membrane. Pression de la purge de gaz neutre insuffisante (pour la version pour gaz corrosif) Contrôlez l’alimentation de la purge de gaz neutre. Après l’instruction de réglage « Pomper », la pompe à membrane ne parvient pas à atteindre la vitesse de rotation nominale (l’icône reste en vert foncé). Pompe à membrane défectueuse Effectuez l’entretien de la pompe à membrane ou remplacez la pompe à membrane. Après l’instruction de réglage « Refouler », la pompe turbomoléculaire ne parvient pas à démarrer (l’icône reste en gris clair). Activation du vide à 10 hPa pas encore atteinte Patientez jusqu’à la fin du pompage pour le vide primaire (cible < 60 s). Condensats dans la pompe à membrane 1. Démontez et nettoyez la pompe à membrane. 2. Séchez les éléments de la pompe à membrane. Pompe à membrane défectueuse Effectuez l’entretien de la pompe à membrane ou remplacez la pompe à membrane. Connexion du câble desserrée Contrôlez le connecteur mâle-femelle sur l’unité de commande électronique et sur la carte superviseur. Pompe turbomoléculaire défaillante Remplacez la pompe turbomoléculaire. Après l’activation, l’écran de démarrage "tableau de bord" n’apparaît pas. Après l’instruction de réglage « Refouler », la pompe à membrane ne parvient pas à démarrer (l’icône reste en gris clair). 104/122 Dépannage Problème Cause possible Action corrective Après l’instruction de réglage « Refouler », la pompe turbomoléculaire ne parvient pas à atteindre la vitesse de rotation nominale (l’icône reste en vert foncé). Le temps d’accélération de la pompe turbomoléculaire n’est pas écoulé Patientez jusqu’à la fin du temps d’accélération < 8 minutes. Pression d’entrée trop élevée (seulement pour Thermostat) Réduisez la pression du côté entrée du capillaire à < 1 200 hPa. Non étanchéité Contrôlez le joint capillaire dans la zone d’admission de gaz. Pression de vide primaire trop haute Contrôlez l’étanchéité du raccord à vide de la pompe à membrane/ pompe turbomoléculaire. Température excessive 1. Vérifiez les ventilateurs. 2. Effectuez la maintenance de la pompe à membrane. Connexion du câble desserrée Contrôlez le connecteur mâle-femelle sur la pompe à membrane et sur la carte superviseur. Pompe à membrane défectueuse Effectuez l’entretien de la pompe à membrane ou remplacez la pompe à membrane. Température excessive 1. Vérifiez les ventilateurs. 2. Effectuez la maintenance de la pompe turbomoléculaire. Pression d’entrée trop élevée Réduisez la pression du côté entrée du capillaire à < 1 200 hPa. Non étanchéité Contrôlez le joint capillaire dans la zone d’admission de gaz. Pression de vide primaire trop haute Contrôlez l’étanchéité du raccord à vide de la pompe à membrane/ pompe turbomoléculaire. Condensats dans la pompe à membrane 1. Démontez et nettoyez la pompe à membrane. 2. Séchez les éléments de la pompe à membrane. Pompe à membrane défectueuse Effectuez l’entretien de la pompe à membrane ou remplacez la pompe à membrane. Température excessive 1. Vérifiez les ventilateurs. 2. Nettoyez les grilles de protection sur les ventilateurs. 3. Maintenez la température ambiante admissible. La pompe à membrane s’arrête. La pompe turbomoléculaire se désactive. Les deux pompes à vide sont mises hors circuit et le système est automatiquement coupé. Pression de la purge de gaz neutre insuffisante (pour la version pour gaz corrosif) Contrôlez l’alimentation de la purge de gaz neutre. 105/122 Dépannage Problème Cause possible Action corrective La pression dans l’enceinte à vide avec la fermeture de la vanne de débitmètre est > 1 × 10-7 hPa (seulement pour OmniStar). Le système n’est pas en route depuis longtemps Continuez le pompage. Humidité excessive dans le système à vide Étuvez l’enceinte à vide. Vanne d’entrée non étanche Remplacez le bloc de vannes. Pression de vide primaire trop haute Contrôlez l’étanchéité du raccord à vide de la pompe à membrane/ pompe turbomoléculaire. Condensats dans la pompe à membrane 1. Démontez et nettoyez la pompe à membrane. 2. Séchez les éléments de la pompe à membrane. Pompe à membrane défectueuse Effectuez l’entretien de la pompe à membrane ou remplacez la pompe à membrane. Pression d’entrée trop élevée Réduisez la pression du côté entrée du capillaire à < 1 200 hPa. Non étanchéité Contrôlez le joint capillaire dans la zone d’admission de gaz. Humidité excessive dans le système à vide Étuvez l’enceinte à vide. Pression de vide primaire trop haute Contrôlez l’étanchéité du raccord à vide de la pompe à membrane/ pompe turbomoléculaire. Condensats dans la pompe à membrane 1. Démontez et nettoyez la pompe à membrane. 2. Séchez les éléments de la pompe à membrane. Pompe à membrane défectueuse Effectuez l’entretien de la pompe à membrane ou remplacez la pompe à membrane. Vanne Split-flow contaminée (OmniStar uniquement) Remplacez le bloc de vannes. Vanne Split-flow défectueuse (OmniStar uniquement) Remplacez le bloc de vannes. Jauge de pression totale polluée Nettoyez la jauge de pression totale. Jauge pour pression totale défectueuse Remplacez la jauge de pression totale. Pression d’entrée insuffisante Augmentez la pression du côté entrée du capillaire. Capillaire bloqué Découpez à longueur le capillaire ou remplacez-le. Orifice bloqué Remplacez l’orifice. Temporisation pour le passage de la vanne pas encore écoulée Patientez jusqu’à la fin de la temporisation < 15 secondes. La vanne de débitmètre n’est pas contrôlée. Contrôlez le connecteur mâle-femelle sur la vanne de débitmètre et sur la carte superviseur. Vanne de débitmètre contaminée Remplacez le bloc de vannes. Vanne de débitmètre défectueuse Remplacez le bloc de vannes. La pression dans l’enceinte à vide est trop haute (> 3 × 10-5 hPa) (pour ThermoStar et/ou OmniStar avec vanne de débitmètre ouverte). Pression excessive dans l’enceinte à vide (> 1 × 10-3 hPa). La pression dans l’enceinte à vide est trop basse (< 1 × 10-6 hPa) (pour ThermoStar et/ou OmniStar avec vanne de débitmètre ouverte). La vanne de débitmètre ne s’ouvre pas (OmniStar uniquement) 106/122 Dépannage Problème Cause possible Action corrective Pas de pic de masse visible dans la plage > 200 u lors de la calibration de l’échelle de masse (version avec unité de calibration) Sensibilité trop basse du spectromètre de masse Lire le manuel de l’utilisateur du spectromètre de masse pour de plus amples informations. Stock de fluide de calibration insuffisant Faites l’appoint en fluide de calibration. La vanne d’isolement sur l’unité de calibration n’est pas contrôlée. Contrôlez le connecteur mâle-femelle sur la vanne d’isolement et sur la carte superviseur. Vanne d’isolement sur l’unité de calibration polluée Remplacez la vanne d’isolement sur l’unité de calibration. La vanne d’isolement sur l’unité de calibration est défectueuse Remplacez la vanne d’isolement sur l’unité de calibration. Erreur pendant la mesure Erreur du spectromètre de masse Lire le manuel de l’utilisateur du spectromètre de masse pour de plus amples informations. Sensibilité de mesure insuffisante Réglages incorrects du spectromètre de masse Lire le manuel de l’utilisateur du spectromètre de masse pour de plus amples informations. Forme de pic médiocre Réglages incorrects du spectromètre de masse Lire le manuel de l’utilisateur du spectromètre de masse pour de plus amples informations. Niveau de bruit élevé Réglages incorrects du spectromètre de masse Lire le manuel de l’utilisateur du spectromètre de masse pour de plus amples informations. Après l’instruction de réglage « Ventiler », les pompes à vide continuent de fonctionner et le système n’est pas ventilé. Temporisation pour la ventilation pas encore écoulée Patientez jusqu’à la fin de la temporisation < 15 minutes. (Temps affiché en haut à droite de l’écran.) A l’issue de l’instruction de réglage « Ventilation », la vanne de ventilation ne parvient pas à s’ouvrir. Vitesse de rotation de la pompe turbomoléculaire encore > 750 Hz Attendez que la vitesse de rotation de la pompe turbomoléculaire est < 750 Hz. La vanne de ventilation n’est pas contrôlée. Contrôlez le connecteur mâle-femelle sur la vanne de ventilation et sur la carte superviseur. Vanne de ventilation polluée Remplacez la vanne de ventilation. Vanne de ventilation défectueuse Remplacez la vanne de ventilation. Tab. 14: Dépannage 107/122 Expédition 12 Expédition AVERTISSEMENT Risque d’empoisonnement par produits contaminés L’expédition de produits contenant des substances dangereuses pour leur maintenance ou réparation implique un risque pour la santé et l’ sécurité du personnel de maintenance. ► Conforme aux instructions pour une distribution en toute sécurité. Décontamination payante Pfeiffer Vacuum décontamine les produits qui ne sont pas clairement déclarés comme « Sans contaminants », à votre charge. Expédier le produit en toute sécurité ► L’expédition de produits microbiologiques, explosibles ou ayant subi une contamination radioactive est interdite. ► Respecter les consignes d’expédition des pays et des sociétés de transport impliqués. ► Les risques potentiels doivent être mis en évidence sur la face extérieure de l’emballage. ► Téléchargez les explications sur la contamination en vous connectant à Pfeiffer Vacuum Service. ► Toujours joindre une déclaration de contamination dûment remplie. 108/122 Recyclage et mise au rebut 13 Recyclage et mise au rebut AVERTISSEMENT Risque d’intoxication dû à des composants ou appareils contaminés par des substances toxiques Les substances de procédé toxiques contaminent certaines pièces matérielles. Pendant les opérations de maintenance, tout contact avec ces substances toxiques présente un risque pour la santé. L’élimination illégale de substances toxiques nuit à l’environnement. ► Respecter les précautions de sécurité adéquates et éviter les risques sanitaires ou environnementaux dus aux substances de procédé toxiques. ► Décontaminer les pièces concernées avant d’exécuter des opérations de maintenance. ► Porter des équipements de protection individuelle. Protection de l’environnement Vous devez mettre au rebut le produit et ses composants conformément aux directives applicables pour la protection des personnes, de l’environnement et de la nature. ● Contribuez à la réduction du gaspillage des ressources naturelles. ● Évitez toute contamination. Protection de l'environnement La mise au rebut du produit ou de ses composants doit être réalisée conformément aux réglementations en vigueur pour ce qui concerne la protection de l’environnement et la santé des personnes, ceci afin de réduire le gaspillage des ressources naturelles et prévenir de la pollution. 13.1 Informations générales sur la mise au rebut Les produits Pfeiffer Vacuum contiennent des matériaux recyclables. ► Mettez au rebut nos produits en séparant : – Fer – Aluminium – Cuivre – Matière synthétique – Composants électroniques – Huiles et graisses, sans solvant ► Observez les mesures de sécurité spéciales pour la mise au rebut de : – Fluoroélastomères (FKM) – Composants potentiellement contaminés en contact avec le fluide de procédé 13.2 Élimination du système d’analyse du gaz Les systèmes d’analyse du gaz Pfeiffer Vacuum contiennent des matériaux recyclables. 1. Démontez les éléments du boîtier. 2. Démontez tous les composants individuels. 3. Démontez les composants électroniques. 4. Décontaminez les composants qui entrent en contact avec les gaz de procédé. 5. Séparez les composants en matériaux recyclables. 6. Recyclez les composants non contaminés. 7. Mettez au rebut le produit ou les composants de façon sûre en conformité avec toutes les directives applicables. 109/122 Solutions de service de Pfeiffer Vacuum 14 Solutions de service de Pfeiffer Vacuum Nous offrons un service de première classe Une longue durée de vie des composants du vide, associée à des temps d’arrêt réduits, sont ce que vous attendez clairement de nous. Nous répondons à vos besoins par des produits efficaces et un service d’exception. Nous nous efforçons de perfectionner en permanence notre compétence clé, à savoir le service liés aux composants du vide. Et notre service est loin d’être terminé une fois que vous avez acheté votre produit Pfeiffer Vacuum. Il ne démarre souvent qu’à partir de là. Dans la qualité Pfeiffer Vacuum reconnue, bien évidemment. Nos ingénieurs commerciaux et techniciens de service professionnels sont à votre disposition pour vous assurer un soutien pratique dans le monde entier. Pfeiffer Vacuum offre une gamme complète de services, allant des pièces de rechange d’origine aux accords de service. Profitez du service Pfeiffer Vacuum Qu'il s’agisse du service préventif sur place de notre service sur site, du remplacement rapide par des produits de rechange comme neufs ou de la réparation dans un centre de service proche de chez vous ; vous disposez d'une variété d’options pour maintenir la disponibilité de votre équipement. Vous trouverez des informations détaillées ainsi que les adresses sur notre site web dans la section Pfeiffer Vacuum Service. Des conseils sur la solution optimale sont disponibles auprès de votre interlocuteur Pfeiffer Vacuum. Pour un déroulement rapide et efficace de la procédure de service, nous recommandons de suivre les étapes suivantes : 1. Télécharger les modèles de formulaire actuels. ─ Déclaration de demande de service ─ Demande de service ─ Déclaration de contamination a) Démonter tous les accessoires et les conserver (toutes les pièces externes montées telles que la vanne, le filtre d’arrivée, etc.). b) Vidanger le fluide d'exploitation / lubrifiant si nécessaire. c) Vidanger le fluide de refroidissement si nécessaire. 2. Remplir la demande de service et la déclaration de contamination. ANFORDERUNG SERVICE ERKLÄRUNG KONTAMINIERUNG 3. Envoyer les formulaires par e-mail, fax ou par courrier à votre centre de service local. 4. Vous recevrez une réponse de Pfeiffer Vacuum. Envoi de produits contaminés Aucune unité ne sera acceptée si elle est contaminée par des substances micro-biologiques, explosives ou radioactives. Si les produits sont contaminés ou si la déclaration de contamination est manquante, Pfeiffer Vacuum contactera le client avant de démarrer la maintenance. Par ailleurs, selon le produit et le niveau de contamination, des frais de décontamination supplémentaires peuvent être facturés. 110/122 Solutions de service de Pfeiffer Vacuum 5. Préparer le produit pour le transport conformément aux détails contenus dans la déclaration de contamination. a) Neutraliser le produit avec de l’azote ou de l’air sec. b) Fermer toutes les ouvertures avec des obturateurs étanches à l’air. c) Sceller le produit dans un film de protection approprié. d) Emballer le produit dans des conteneurs de transport stables appropriés uniquement. e) Respecter les conditions de transport en vigueur. ERKLÄRUNG KONTAMINIERUNG 6. Joindre la déclaration de contamination sur l’extérieur de l’emballage. 7. Envoyer ensuite le produit à votre centre de service local. 8. Vous recevrez un message de confirmation / un devis de la part de Pfeiffer Vacuum. Pour toutes les demandes de service, nos Conditions générales de vente et de livraison ainsi que nos Conditions générales de réparation et de maintenance sont appliquées aux équipements et composants du vide. 111/122 Pièces de rechange 15 Pièces de rechange Commande de pièces de rechange ► Vous devez vous munir du numéro de pièce ainsi que des informations complémentaires sur la plaque signalétique. ► Installez uniquement des pièces détachées d'origine. Désignation Référence Description/contenu de la livraison Couvercle de carter PT 167 000 - Couvercle de l’admission de gaz PT 167 005 - Couvercle sur le côté, OmniStar PT 167 003 gauche PT 167 004 droit PT 167 001 gauche PT 167 002 droit Aire de connexion du tuyau flexible de capillaire PT 167 007 Couvercle avec alésage PT 167 006 Couvercle sans alésage Vis du carter PT 167 065 -T Ensemble (10 pcs) 490DFL040-S-G-S5 DN 40 CF (ensemble de 10 pcs) PT 167 016 -T OmniStar Insert de bride avec vannes, orifice 50 µm, 2 joints toriques et diffuseur de gaz interne, sans capillaire en acier inoxydable PT 167 013 -T ThermoStar Insert de bride, orifice 50 µm, 2 joints toriques et diffuseur de gaz interne, sans capillaire en quartz Jeu de pièces de rechange PT 167 014 -T OmniStar et ThermoStar 2 joints toriques, orifice de 50 µm, diffuseur de gaz, ressort de compression Écran BK212576 OmniStar et ThermoStar 50 μm Capillaire PT 167 060 Acier inoxydable, 1/16", 0,12 mm × 5 m B1975082EC Quartz, 0,23", 0,14 mm × 5 m PT 167 017 -T Joints de capillaire (viroles) pour capillaire en acier inoxydable (ensemble de 10 pcs) PT 167 015 -T Joints de capillaire (viroles) pour capillaires en quartz (ensemble de 10 pcs) PT 167 031 En flacon de 5 ml Pompe à membrane PK T05 072 Pompe à membrane MVP 010-3 DC Kit de révision PU E22 030 -T Membranes et vannes Jauge de pression totale PT R40 351 -A Jauge de remplacement MPT 200 AR Capteur PT 120 212 -T Capteur MPT, DN 40 CF Structure et éléments du carter Couvercle sur le côté, ThermoStar Raccords à bride Joint cuivre Admission de gaz et capillarités Admission de gaz Joints de capillaire Unité de calibration Fluide de calibration (PFTBA) Pompe à membrane Jauge de pression totale Analyseur PrismaPro QMA 250 M avec source d’ions spéciale 112/122 Pièces de rechange Désignation Référence Description/contenu de la livraison Analyseur PT M25 451 1 – 100 u, avec source d’ions croisés, unité filament chauffé tungstène et EM PT M25 452 1 – 100 u, avec source d’ions croisés, unité filament chauffé Ir-Y2O3 et EM PT M25 453 1 – 200 u, avec source d’ions croisés, unité filament chauffé tungstène et EM PT M25 454 1 – 200 u, avec source d’ions croisés, unité filament chauffé Ir-Y2O3 et EM PT M25 455 1 – 300 u, avec source d’ions croisés, unité filament chauffé tungstène et EM PT M25 456 1 – 300 u, avec source d’ions croisés, unité filament chauffé Ir-Y2O3 et EM PT 163 291 Source d’ions avec 2 filaments chauffés en tungstène PT 163 292 Source d’ions avec 2 filaments chauffés Ir-Y2O3 PT 163 331 Unité de filaments chauffés en tungstène avec 2 filaments chauffés PT 163 332 Unité de filaments chauffés Ir-Y2O3avec 2 filaments chauffés PT 160 010 - PM 143 740 -T Réservoir du fluide d’exploitation avec tiges capillaires Vanne de la purge de gaz PM Z01 310 A - Raccord de gaz d’échappement PT 167 011 Raccord de gaz d’échappement, 6 mm, pour assemblage dans paroi de carter PT 167 025 Module d’affichage, sans câbles Source d’ions Unité de filaments chauffés Protection pour le transport Pompe turbomoléculaire Réservoir du fluide d’exploitation Système de purge de gaz neutre Affichage Affichage de contact 7" Tab. 15: Pièces de rechange et composants, maintenance niveau 1 Les tuyaux flexibles sur la GSD 350 sont constitués de tuyau flexible PUN à calibration externe. Système Couleur Diamètre Longueur requise Connexion Vide Bleu 8 × 5 mm 170 mm, bobiné Pompe à membrane et pompe turbomoléculaire Gaz d’échappement Noir 6 × 4 mm 120 mm Régulateur de pression et dilution du gaz de refoulement 500 mm Air d’échappement de la pompe à membrane (standard) 45 mm Pièce intermédiaire (pièce Y) et raccord d’échappement 400 mm Air d’échappement de la pompe à membrane (version de gaz corrosif) 140 mm Raccord de la purge de gaz neutre et régulateur de pression 120 mm Régulateur de pression et vanne de retenue 570 mm Raccord de la purge de gaz neutre et pompe turbomoléculaire 740 mm Raccord de mise à l’air et pompe turbomoléculaire Transparent Purge de gaz neutre/purge Tab. 16: Transparent 4 × 2,5 mm Couleurs et dimensions du tuyau flexible 113/122 Pièces de rechange Description Nombre par GSD 350 Référence (Tempel) Raccord à connecteur angulaire, long, filetage 1/8", 8 mm 1 IQSLL 188 G Raccord à bouchon angulaire, filetage 1/8", 4 mm 4 IQSL 184 GL Raccord à connecteur angulaire, long, filetage 1/4", 8 mm 1 IQSLL 148 G Raccord à connecteur angulaire, long, filetage 1/8", 6 mm 2 IQSLL 186 G Connecteur à distributeur multiple, 4x, R 1/8", 4 mm 1 IQSLV4 184 Raccord à connecteur Schott, 4 mm 1 IQSS 40 Raccord à connecteur Schott, 6 mm 1 IQSS 60 Raccord à connecteur Y, 6 mm -6 mm 1 IQSY 60 Raccord à connecteur angulaire Y, filetage E/S 1/8", 6 mm 1 IQSYTF 186 G Vanne de retenue, 6 mm 1 AK2000-F01 Silencieux, filetage 1/8" 1 U 18 Régulateur de pression ARX21-F01 1 OT-SMC005811 Contacteur : Tempel Hydraulik & Reinigungstechnik Schwarze Kiefern 12 09633 Halsbrücke OT Tuttendorf Page Web d’accueil et boutique en ligne Tab. 17: 114/122 Composants des raccords pour tuyau flexible Outil spécial 16 Outil spécial Désignation Référence Usage Clé à écrou pour couvercle de carter de pompe turbomoléculaire PV M40 813 (voir chapitre « Remplacement du réservoir de fluide d’exploitation sur la pompe turbomoléculaire », page 80) Jauge de centrage pour QMA PT 167 082 (voir chapitre « Maintenance de l’analyseur QMA 250 M », page 84) Aide au montage du support de gaz de calibration PT 167 081 (voir chapitre « Appoint en fluide de calibration », page 102) Tab. 18: Outil spécial Fig. 75: Clé à écrou pour couvercle de carter de pompe turbomoléculaire Fig. 76: Jauge de centrage pour QMA Fig. 77: Aide au montage du support de gaz de calibration 115/122 Accessoires 17 Accessoires Vous trouverez sur notre site Internet la gamme des accessoires ThermoStar et OmniStar. 17.1 Informations sur les accessoires Adaptateur de tube capillaire L’adaptateur de tube capillaire est utilisé pour raccorder correctement le tube capillaire. Fig. 78: 17.2 Commande d’accessoires Description Référence Adaptateur de tube capillaire PT 167 070 -T Tab. 19: 116/122 Adaptateur de tube capillaire Accessoires Caractéristiques techniques et dimensions 18 Caractéristiques techniques et dimensions 18.1 Généralités mbar bar Pa hPa kPa Torr | mm Hg 100 1 0,1 0,75 1 · 10 1,000 100 1 · 10 1 0,01 1 · 10 7.5 · 10-3 1 1 · 10-3 100 1 0,1 0,75 kPa 10 0,01 1,000 10 1 7,5 Torr | mm Hg 1,33 1,33 · 10-3 133,32 1,33 0,133 1 mbar 1 1 · 10 bar 1,000 1 Pa 0,01 hPa -3 5 -5 1 Pa = 1 N/m Tab. 20: 750 -3 2 Tableau de conversion : unités de pression mbar l/s mbar l/s Pa m3/s sccm Torr l/s atm cm3/s 1 0,1 59,2 0,75 0,987 592 7,5 10 3 Pa m /s sccm 1 Torr l/s 3 atm cm /s Tab. 21: 9,87 1.69 · 10 1.69 · 10 1 1,33 0,133 78,9 1 1,32 1,01 0,101 59,8 0,76 1 -2 -3 -2 1,27 · 10 1.67 · 10-2 Tableau de conversion : unités de débit de gaz 18.2 Fiche technique Configuration (domaine de masse) 1 à 100 u 1 à 200 u 1 à 300 u Type PrismaPro QMG 250 M1 PrismaPro QMG 250 M2 PrismaPro QMG 250 M3 Détecteur C-SEM Source d’ions Crossbeam (C/B) Nombre de filaments chauffés 2 Spectromètre de masse quadripôle Performance du capteur en fonction du domaine de masse13) Limites de détection minimales (C-SEM) < 100 ppb < 1 ppm < 10 ppm Quantité de masse voisine(40/41) < 10 ppm < 20 ppm < 50 ppm Repos Réglable de 1 ms/u à 16 s/u Admission de gaz/gaz de procédé Type OmniStar : avec vanne d’entrée ThermoStar : ouvert en permanence Pression de gaz échantillon, max. 1 200 hPa Débit de gaz 1 à 2 sccm Contaminants Grandeur des particules ≤ 1 μm Commande de vanne (OmniStar) Via affichage en couleur 7" ou interface Web Capillaire Matière OmniStar : quartz ou acier inoxydable ThermoStar : Quartz Longueur 1 m (2 m également disponible) 13) Les spécifications du domaine de masse s’appliquent seulement aux gaz/espèces sans interférence. 117/122 Caractéristiques techniques et dimensions Configuration (domaine de masse) 1 à 100 u 1 à 200 u Diamètre OmniStar : OD = 1/16", ID = 0,12 mm ThermoStar : OD = 0,23 mm, ID = 0,14 mm Température de fonctionnement du capillaire 200 °C (350 °C également disponible) 1 à 300 u Gaz d’échappement Pression admissible ≤ pression atmosphérique Connexion Connecteurs mâle-femelle IQS, 6 mm Tuyau flexible PE (Ø extérieur = 6 mm) Purge de gaz neutre (version de gaz corrosif) Gaz de pressurisation Gaz inerte, azote ou argon recommandé Pression 5 000 à 7 000 hPa Débit de gaz 300 sccm env. Impuretés ≤ 100 ppm oxygène Connexion Connecteurs mâle-femelle IQS, 4 mm Tuyau flexible PE (Ø extérieur = 4 mm) Unité de calibration (option) Fluide pour calibration de la masse PFTBA Conditions ambiantes Température de transport et stockage -20 à 55 °C Température de service 10 à 40 °C Humidité relative de l’air max. 80 % jusqu’à 31 °C, diminution linéaire jusqu’à 50 % à 40 °C Lieu de mise en place Intérieur, étanche à l’eau Altitude de l’installation ≤ 2 000 m au-dessus du niveau de la mer Classe de protection I Catégorie de surtension II Degré de protection IP30 Degré de pollution 2 Matériaux côté vide Capillaire Acier inoxydable, verre en quartz (selon la version) Admission de gaz Acier inoxydable, FKM, PTFE (capillaire en quartz seulement) Écran Platine/Iridium Enceinte à vide Aluminium/acier inoxydable, PTFE, cuivre, argent Analyseur Acier inoxydable, cuivre, argent, or, verre de quart, céramique Filament chauffé Ir-Y2O3 ou W Pompe turbomoléculaire Aluminium, acier inoxydable, résine époxy, lubrifiant Pompe à membrane EPDM, aluminium, PVC, laiton, polyamide Jauge de pression totale Tungstène, acier inoxydable, nickel, molybdène, verre Alimentation Tension 100 à 240 V AC Fréquence 50-60 Hz Puissance absorbée 830 W Fusible secteur 2× 10 A (lent) Interfaces utilisateur Fonctionnement Via affichage de contact 7” ou interface Web Logiciel PV MassSpec Transfert de données Ethernet TCP/IP Caractéristiques de la pompe Disponibilité opérationnelle Après 10 minutes Temps de mise hors circuit 15 minutes Commande utilisateur 118/122 Caractéristiques techniques et dimensions Configuration (domaine de masse) 1 à 100 u 1 à 200 u 1 à 300 u Entrées analogiques 5× ±10 V, résolution 14 et 16 bit Entrées numériques 4× nominal +24 V Sorties analogiques 4× 0 à 10 V, Imax = 10 mA, résolution 16 bit Sorties numériques 6× collecteurs ouverts, nominal 24 V, Imax = 200 mA Nombre de relais 2 Tension d’enclenchement des relais 24 V CA/CC Courant de commutation des relais 1A Relais pour le statut du système de pompage Connexion « consommateur I/O » : Broches 13, 14 et 15 Connecteur multiple USER I/O : 15 broches, D-Sub AUX I/O : 25 broches, D-Sub Niveau de bruit < 50 dB en fonctionnement maximum Poids 23 kg à 26 kg (en fonction de la version respective) Tab. 22: Fiche technique 18.3 Dimensions 274 358 50 216 Dimensions en mm. 60 615 Fig. 79: Dimensions 119/122 The product GSD 350 OmniStar/ThermoStar - conforms to the UL standards UL 61010-1:2012 R4.16 Safety requirements for electrical equipment for measurement, control and laboratory use Part 1: General requirements TÜV Rheinland C US UL 61010-2-010:2014 Safety requirements for electrical equipment for measurement, control and laboratory use Part 2-010: Particular requirements for laboratory equipment for the heating of materials - is certified to the CAN/CSA standards CAN/CSA No. 61010-1:2012 + GI1 + GI2 (R2017) Safety requirements for electrical equipment for measurement, control and laboratory use Part 1: General requirements CAN/CSA No. 61010-2-010:2014 Safety requirements for electrical equipment for measurement, control and laboratory use Part 2-010: Particular requirements for laboratory equipment for the heating of materials - conforms to the following rules and regulations FCC, Title 47 CFR, Part 15, Subpart B Telecommunication - Radio Frequency Devices - Unintentional Radiators Déclaration de conformité Déclaration pour produit(s) du type : Système d’analyse de gaz GSD 350 OmniStar GSD 350 ThermoStar Par la présente, nous déclarons que le produit cité est conforme aux Directives européennes suivantes. Compatibilité électromagnétique 2014/30/UE Limitation de l’utilisation de certaines matières dangereuses 2011/65/UE Limitation de l’utilisation de certaines matières dangereuses, directive déléguée 2015/863/UE Normes harmonisées et normes et spécifications nationales appliquées : IEC 61010-1:2010+A1 IEC 61010-2-010:2019 EN ISO 12100:2010 EN 61326-1:2013 EN 55011:2009 + A1:2011 EN 61000-3-2:2014 EN 61000-3-3:2013 IEC 60529:1989 + A1:1999 + A2:2013 Signature: Pfeiffer Vacuum GmbH Berliner Straße 43 35614 Asslar Allemagne (Daniel Sälzer) Directeur général Asslar, 2022-03-09 *DA0105* ed. B - Date 2208 - P/N:DA0105BFR ">
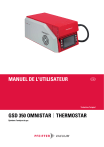
Link pubblico aggiornato
Il link pubblico alla tua chat è stato aggiornato.