Schneider Electric TeSys T LTMR Contrôleur de gestion de moteur Mode d'emploi
PDF
Télécharger
Document
TeSys™ T LTMR Contrôleur de gestion des moteurs Manuel d’installation 06/2022 DOCA0128FR-02 www.se.com Mentions légales La marque Schneider Electric et toutes les marques de commerce de Schneider Electric SE et de ses filiales mentionnées dans ce guide sont la propriété de Schneider Electric SE ou de ses filiales. Toutes les autres marques peuvent être des marques de commerce de leurs propriétaires respectifs. Ce guide et son contenu sont protégés par les lois sur la propriété intellectuelle applicables et sont fournis à titre d'information uniquement. Aucune partie de ce guide ne peut être reproduite ou transmise sous quelque forme ou par quelque moyen que ce soit (électronique, mécanique, photocopie, enregistrement ou autre), à quelque fin que ce soit, sans l'autorisation écrite préalable de Schneider Electric. Schneider Electric n'accorde aucun droit ni aucune licence d'utilisation commerciale de ce guide ou de son contenu, sauf dans le cadre d'une licence non exclusive et personnelle, pour le consulter tel quel. Les produits et équipements Schneider Electric doivent être installés, utilisés et entretenus uniquement par le personnel qualifié. Les normes, spécifications et conceptions sont susceptibles d'être modifiées à tout moment. Les informations contenues dans ce guide peuvent faire l'objet de modifications sans préavis. Dans la mesure permise par la loi applicable, Schneider Electric et ses filiales déclinent toute responsabilité en cas d'erreurs ou d'omissions dans le contenu informatif du présent document ou pour toute conséquence résultant de l'utilisation des informations qu'il contient. Contrôleur de gestion des moteurs Table des matières Catégories de dangers et symboles spéciaux ........................................5 Remarque importante .................................................................................5 À propos de ce manuel ..............................................................................6 Présentation du système de gestion de moteur TeSys T......................9 Présentation du système de gestion de moteur TeSys T ................................9 Installation ..................................................................................................10 Principes généraux...................................................................................10 Dimensions .............................................................................................. 11 Assemblage .............................................................................................13 Montage ..................................................................................................15 Câblage - Généralités ...............................................................................18 Câblage : transformateurs de courant (TC) .................................................23 Câblage des transformateurs de courant de fuite à la terre...........................26 Câblage : capteurs de température ............................................................28 Câblage - Alimentation..............................................................................29 Câblage - Entrées logiques .......................................................................31 Câblage - Sorties logiques ........................................................................36 Connexion à un système HMI ....................................................................37 Mise en service .........................................................................................43 Présentation.............................................................................................43 Première mise sous tension ......................................................................45 Paramètres requis et optionnels ................................................................46 Paramètres du courant pleine charge (FLC - Full Load Current) ...................47 Vérification du câblage du système ............................................................49 Vérification de la configuration ...................................................................51 Maintenance ..............................................................................................52 Détection des problèmes...........................................................................52 Dépannage ..............................................................................................53 Maintenance préventive ............................................................................55 Remplacement d’un contrôleur LTMR et d’un module d’extension LTME.......................................................................................................58 Alarmes et déclenchements de communication...........................................59 Paramètres configurables........................................................................62 Paramètres principaux ..............................................................................62 Contrôle...................................................................................................63 Communication ........................................................................................65 Thermique ...............................................................................................66 Courant ...................................................................................................67 Tension....................................................................................................69 Puissance ................................................................................................71 HMI .........................................................................................................72 Schémas de câblage ................................................................................74 Schémas de câblage au format IEC ...........................................................74 Schémas de câblage en mode Surcharge.............................................75 Schémas de câblage en mode Indépendant..........................................79 Schémas de câblage en mode Inverse .................................................81 Schémas de câblage étoile-triangle en mode 2 étapes...........................83 DOCA0128FR-02 3 Contrôleur de gestion des moteurs Schémas de câblage de résistance primaire en mode 2 étapes ..............85 Schémas de câblage d’autotransformateur en mode 2 étapes................87 Schémas de câblage en mode Dahlander 2 vitesses .............................89 Schémas de câblage de changement de polarité en mode 2 vitesses..............................................................................................92 Schémas de câblage au format NEMA .......................................................94 Schémas de câblage en mode Surcharge.............................................95 Schémas de câblage en mode Indépendant..........................................99 Schémas de câblage en mode Inverse ............................................... 101 Schémas de câblage étoile-triangle en mode 2 étapes......................... 103 Schémas de câblage de résistance primaire en mode 2 étapes ............ 105 Schémas de câblage d’autotransformateur en mode 2 étapes.............. 107 Schémas de câblage en mode deux vitesses : enroulement simple (pôle conséquent) ............................................................................. 109 Schémas de câblage en mode deux vitesses : enroulement séparé ............................................................................................. 111 Glossaire .................................................................................................. 113 Index ......................................................................................................... 117 4 DOCA0128FR-02 Catégories de dangers et symboles spéciaux Contrôleur de gestion des moteurs Catégories de dangers et symboles spéciaux Lisez attentivement ces instructions et examinez le matériel pour vous familiariser avec l'appareil avant de tenter de l'installer, de le faire fonctionner, de le réparer ou d'assurer sa maintenance. Les messages spéciaux suivants peuvent apparaître dans les présentes directives ou sur l'appareil pour avertir l'utilisateur de dangers potentiels ou pour attirer l'attention sur des informations qui clarifient ou simplifient une procédure. L'ajout d'un de ces symboles à une étiquette de sécurité « Danger » ou « Avertissement » indique qu'il existe un danger électrique qui entraînera des blessures si les instructions ne sont pas respectées. Ce symbole est le symbole d'alerte de sécurité. Il sert à vous avertir d'un danger de blessures corporelles. Respectez scrupuleusement les consignes de sécurité associées à ce symbole pour éviter de vous blesser ou de mettre votre vie en danger. DANGER DANGER indique un danger immédiat qui, s'il n'est pas évité, entraînera la mort ou des blessures graves. AVERTISSEMENT AVERTISSEMENT indique un danger potentiel qui, s'il n'est pas évité, pourrait entraîner la mort ou des blessures graves. MISE EN GARDE MISE EN GARDE indique un danger potentiel qui, s'il n'est pas évité, pourrait entraîner des blessures légères ou de gravité moyenne. AVIS AVIS concerne des questions non liées à des blessures corporelles. NOTE: Fournit des renseignements complémentaires pour clarifier ou simplifier une procédure. Remarque importante L’installation, l’utilisation, la réparation et la maintenance des équipements électriques doivent être assurées par du personnel qualifié uniquement. Schneider Electric décline toute responsabilité quant aux conséquences de l’utilisation de ce matériel. Une personne qualifiée est une personne disposant de compétences et de connaissances dans le domaine de la construction, de l'installation et du fonctionnement des équipements électriques, et ayant suivi une formation en sécurité leur permettant d'identifier et d'éviter les risques encourus. DOCA0128FR-02 5 Contrôleur de gestion des moteurs À propos de ce manuel À propos de ce manuel Objectif du document Ce guide décrit le contrôleur de gestion de moteur TeSys™ T LTMR et le module d'extension LTME. Objectif de ce manuel : • Décrire et expliquer les fonctions de contrôle, de protection et de surveillance du contrôleur LTMR et du module d’extension LTME. • Fournir les informations nécessaires à la mise en œuvre et à la prise en charge d’une solution répondant au mieux aux exigences de votre application. Ce manuel décrit les quatre principales conditions de la réussite de la mise en œuvre du système : • Installation du contrôleur LTMR et du module d’extension LTME. • Mise en service du contrôleur LTMR par le réglage des paramètres essentiels. • Utilisation du contrôleur LTMR et du module d’extension LTME, avec et sans systèmes d’interface HMI (homme-machine) supplémentaires. • Maintenance du contrôleur LTMR et du module d’extension LTME. Ce document s’adresse : • aux ingénieurs d’études, • aux intégrateurs système, • aux opérateurs système, • aux techniciens de maintenance. Champ d'application Ce manuel est valide pour tous les contrôleurs LTMR. La disponibilité de certaines fonctions dépend de la version du logiciel du contrôleur et du protocole de communication utilisé. Documents à consulter 6 Titre de documentation Description Référence TeSys T LTMR - Contrôleur de gestion des moteurs - Guide utilisateur Ce guide présente les produits TeSys T et décrit les principales fonctions du contrôleur de gestion des moteurs TeSys T LTMR et du module d’extension LTME. DOCA0127EN TeSys T LTMR - Contrôleur de gestion des moteurs - Guide de communication Ethernet Ce guide décrit la version du protocole réseau Ethernet utilisée avec le contrôleur de gestion de moteur TeSys T LTMR. DOCA0129EN TeSys T LTMR - Contrôleur de gestion des moteurs - Guide de communication Modbus Ce guide décrit la version du protocole réseau Modbus utilisée avec le contrôleur de gestion de moteur TeSys T LTMR. DOCA0130EN TeSys T LTMR - Contrôleur de gestion de moteur - Guide de communication PROFIBUS DP Ce guide décrit la version du protocole réseau PROFIBUS DP utilisée avec le contrôleur de gestion de moteur TeSys T LTMR. DOCA0131EN TeSys T LTMR - Contrôleur de gestion de moteur - Guide de communication CANopen Ce guide décrit la version du protocole réseau CANopen pour le contrôleur de gestion de moteur TeSys T LTMR. DOCA0132EN DOCA0128FR-02 À propos de ce manuel DOCA0128FR-02 Contrôleur de gestion des moteurs Titre de documentation Description Référence TeSys T LTMR - Contrôleur de gestion de moteur - Guide de communication DeviceNet Ce guide décrit la version du protocole réseau DeviceNet pour le contrôleur de gestion de moteur TeSys T LTMR. DOCA0133EN TeSys® T LTM CU - Unité de contrôle opérateur - Manuel d'utilisation Ce manuel décrit comment installer, configurer et utiliser l'unité de contrôle opérateur TeSys T LTMCU 1639581EN Compact Display Units - Magelis XBT N/XBT R - User Manual Ce manuel décrit les caractéristiques et la présentation des terminaux XBT N/XBT R. 1681029EN TeSys T LTMR Ethernet/IP with a Third-Party PLC - Quick Start Guide Ce guide est le document de référence pour configurer et raccorder le TeSys T et l'automate programmable industriel (API) AllenBradley. DOCA0119EN TeSys T LTM R Modbus - Motor Management Controller - Quick Start Guide Ce guide utilise un exemple d’application pour décrire la procédure permettant d’installer, de configurer et d’utiliser TeSys T sur le réseau Modbus. 1639572EN TeSys T LTM R Profibus-DP - Motor Management Controller - Quick Start Guide Ce guide utilise un exemple d’application pour décrire la procédure permettant d’installer, de configurer et d’utiliser TeSys T sur le réseau PROFIBUS-DP. 1639573EN TeSys T LTM R CANopen - Motor Management Controller - Quick Start Guide Ce guide utilise un exemple d’application pour décrire la procédure permettant d’installer, de configurer et d’utiliser TeSys T sur le réseau CANopen. 1639574EN TeSys T LTM R DeviceNet - Motor Management Controller - Quick Start Guide Ce guide utilise un exemple d’application pour décrire la procédure permettant d’installer, de configurer et d’utiliser TeSys T sur le réseau DeviceNet. 1639575EN Compatibilité électromagnétique Consignes d'installation pratique Ce guide fournit des informations sur la compatibilité électromagnétique. DEG999EN TeSys T LTM R•• - Instruction de service Ce document décrit le montage et le raccordement du contrôleur de gestion de moteur TeSys T LTMR. AAV7709901 TeSys T LTM E•• - Instruction de service Ce document décrit le montage et le raccordement du contrôleur de gestion de moteur TeSys T LTME. AAV7950501 Magelis - Terminaux compacts XBT N/R/RT - Instruction de service Ce document décrit le montage et la connexion des terminaux Magelis XBT-N. 1681014 TeSys T LTM CU• - Instruction de service Ce document décrit le montage et le raccordement du contrôleur de gestion de l’unité de contrôle TeSys T LTMCU. AAV6665701 TeSys T DTM pour le conteneur FDT - Aide en ligne L’aide en ligne décrit TeSys T DTM et l’éditeur de programme utilisateur de TeSys T DTM qui permet de personnaliser les fonctions de contrôle du système de gestion de moteur TeSys T. 1672614EN TCSMCNAM3M002P Convertisseur USBRS485 - Instruction de service Ce guide décrit le câble de configuration entre l'ordinateur et le TeSys T : USB-RS485 BBV28000 Electrical Installation Guide (version Wiki) Le but de Guide d’installation électrique (et maintenant Wiki) est d'aider les ingénieurs et techniciens en électricité à concevoir des installations électriques conformes à la norme IEC60364 ou à d'autres normes en vigueur. www.electricalinstallation.org 7 Contrôleur de gestion des moteurs À propos de ce manuel Vous pouvez télécharger ces publications techniques ainsi que d'autres informations techniques à partir de notre site Web : www.se.com. Marques commerciales Toutes les marques appartiennent à Schneider Electric Industries SAS ou à ses filiales. 8 DOCA0128FR-02 Présentation du système de gestion de moteur TeSys T Contrôleur de gestion des moteurs Présentation du système de gestion de moteur TeSys T Vue d’ensemble Ce chapitre présente le système de gestion de moteur TeSys T, ainsi que les équipements qui l'accompagnent. Présentation du système de gestion de moteur TeSys T Fonction du produit Le système de gestion de moteur TeSys T offre des fonctions de protection, de contrôle et de surveillance pour les moteurs à induction AC monophasés et triphasés. Le système est flexible, modulaire, et peut être configuré pour répondre aux exigences de l’industrie. Ce système est conçu pour satisfaire les exigences des systèmes de protection intégrés en termes de communications ouvertes et d’architecture globale. Des capteurs haute précision et la protection intégrale du moteur à semiconducteur garantissent une meilleure utilisation du moteur. Des fonctions de surveillance complètes permettent d’analyser les conditions de fonctionnement du moteur et améliorent la réactivité afin d’éviter l’immobilisation du système. Le système propose également des fonctions de diagnostic et de statistiques, ainsi que des déclenchements et des alarmes configurables afin de mieux anticiper la maintenance des composants. Il fournit enfin des données permettant d’améliorer en permanence le système dans son ensemble. Pour plus d’informations sur le produit, consultez le document TeSys T LTMR Motor Management Controller User Guide. DOCA0128FR-02 9 Contrôleur de gestion des moteurs Installation Installation Présentation Ce chapitre présente l'installation physique, ainsi que l'assemblage du contrôleur LTMR et du module d'extension LTME. Il explique également comment connecter et câbler le bloc du bornier de terminal de contrôleur, notamment le câblage du port de communication dans une armoire ou sur un tableau de distribution. DANGER RISQUE D'ELECTROCUTION, D'EXPLOSION OU D'ARC ELECTRIQUE • Mettez l'équipement hors tension avant toute opération. • Portez un équipement de protection individuelle adapté et respectez les consignes de sécurité électrique courantes. Le non-respect de ces instructions provoquera la mort ou des blessures graves. AVERTISSEMENT FONCTIONNEMENT IMPRÉVU DE L'ÉQUIPEMENT • L’application de ce produit nécessite des compétences en conception et programmation de systèmes de contrôle. Seules les personnes possédant ces compétences doivent être autorisées à programmer et à utiliser ce produit. • Respectez la réglementation locale et nationale en matière de sécurité. • Respectez toutes les règles de compatibilité électromagnétique décrites dans ce guide. • Respectez toutes les règles d’installation et de câblage décrites dans ce guide. Le non-respect de ces instructions peut provoquer la mort, des blessures graves ou des dommages matériels. AVERTISSEMENT : Ce produit peut vous exposer à des agents chimiques, y compris du plomb et des composés à base de plomb, identifiés par l'État de Californie comme pouvant causer le cancer et des malformations congénitales ou autres troubles de l'appareil reproducteur. Pour plus d'informations, consultez le site www.P65Warnings.ca.gov. Principes généraux Introduction à la sécurité fonctionnelle Le système de gestion de moteur TeSys T est une composante de l’architecture générale. Pour fournir une sécurité fonctionnelle, certains risques doivent être analysés, par exemple : • Risques fonctionnels globaux • Risques de panne informatique ou logicielle • Risques électromagnétiques sur l’environnement Pour réduire les risques électromagnétiques sur l’environnement, les règles d’installation et de câblage doivent être respectées. Pour plus d’informations sur les émissions électromagnétiques, consultez Electrical Installation Guide, section ElectroMagnetic Compatibility (Compatibilité électromagnétique), version Wiki disponible en anglais uniquement sur www. electrical-installation.org. 10 DOCA0128FR-02 Installation Contrôleur de gestion des moteurs Règles d’installation Principales règles d’installation à respecter pour permettre le fonctionnement correct du LTMR : • • • Règles d’installation des composants : ◦ Association du contrôleur LTMR au module d’extension LTME ◦ Installation dans un tableau de distribution tel que : Okken, Blokset ou autre. Règles, page 18 de câblage du contrôleur LTMR : ◦ Câblage du système d’alimentation électrique ◦ Câblage des E/S : câblage d’entrée logique et câblage de sortie logique Règles de câblage du réseau de communication Règles d’installation dans un tableau de distribution L’installation du contrôleur LTMR dans le tiroir amovible d’un tableau de distribution présente des contraintes spécifiques au type de tableau de distribution : • Pour l’installation du contrôleur LTMR dans un tableau de distribution Schneider Electric Okken, voir le manuel Okken Communications Cabling & Wiring Guide (Guide de câblage et de raccordement de communications Okken), (disponible sur demande). • Pour l’installation du contrôleur LTMR dans un tableau de distribution Schneider Electric Blokset, voir le manuel Blokset Communications Cabling & Wiring Guide (Guide de câblage et de raccordement de communications Blokset), (disponible sur demande). • Pour l’installation du contrôleur LTMR dans d’autres types de tableaux de distribution, suivez les instructions de compatibilité électromagnétique spécifiques du présent manuel et consultez les instructions spécifiques relatives à votre type de tableau de distribution. Dimensions Vue d’ensemble Cette section présente les dimensions du contrôleur LTMR et du module d’extension LTME, ainsi que l’espace à prévoir autour des deux appareils. Les dimensions, fournies en millimètres et en pouces, s’appliquent à tous les modèles LTMR et LTME. DOCA0128FR-02 11 Contrôleur de gestion des moteurs Installation Dimensions du contrôleur LTMR NOTE: la hauteur du contrôleur peut être plus élevée avec d’autres bornes de branchement. Dimensions du module d’extension LTME Dégagement à prévoir Pour la compatibilité électromagnétique (CEM), il est recommandé d’installer un contacteur à une distance de plus de 5 cm (1,97 in.) du contrôleur LTMR et du module d’extension LTME. La température ambiante maximale pour le contrôleur dépend du dégagement autour de celui-ci. Ces valeurs sont indiquées dans le tableau ci-dessous. 12 DOCA0128FR-02 Installation Contrôleur de gestion des moteurs Assemblage Vue d’ensemble Cette section décrit la façon d’assembler le contrôleur LTMR et le module d’extension LTME dans un tableau de distribution. DOCA0128FR-02 13 Contrôleur de gestion des moteurs Installation Raccordement du contrôleur LTMR et du module d’extension LTME Il est conseillé de monter le contrôleur LTMR et son module d’extension LTME côte à côte, le module d’extension LTME à gauche du contrôleur LTMR et de les relier grâce au cavalier de raccordement LTMCC004 (1). S’il est impossible de monter le contrôleur LTMR et son module d’extension LTME côte à côté : 14 • Utilisez uniquement des câbles blindés LTM9CEXP03 (2) ou des câbles LTM9CEXP10 (3) pour les connecter. • Mettez à la terre le câble blindé. • Séparez les câbles de connexion LTM9CEXP•• de tous les autres câbles d’alimentation ou de commande pour éviter les perturbations électromagnétiques. DOCA0128FR-02 Installation Contrôleur de gestion des moteurs Exemple de montage dans un tiroir amovible de tableau de distribution A1, A2 Alimentation du contrôleur LTMR B1, B2 Alimentation dédiée aux sorties logiques Montage Présentation Cette section décrit le montage du contrôleur LTMR et du module d’extension LTME sur un rail DIN, une plaque de fixation pleine ou une plaque de fixation perforée (appelée plaque TE), par exemple, une plaque Telequick™. Elle décrit également les accessoires nécessaires pour le montage et le démontage de chaque élément. Rappel : Le contrôleur LTMR et son module d'extension LTME doivent être montés côte à côte, avec le module d’extension LTME du côté gauche du contrôleur LTMR, et reliés par le cavalier de connexion LTMCC004Assemblage, page 13. Montage sur rail DIN Vous pouvez installer le contrôleur et le module d'extension sur un rail DIN de 35 mm (1,38 in.), d'une épaisseur de 1,35 mm (0,05 in.) et 0,75 mm (0,02 in.). Une fois montés, les pieds de montage du contrôleur ne s'étendent pas au-delà des dimensions du contrôleur, page 12. Pour monter le contrôleur : DOCA0128FR-02 15 Contrôleur de gestion des moteurs Installation Étape Action 1 Deux attaches pour rail DIN sont situées à l'arrière du contrôleur. Placez l'attache supérieure dans le rail DIN. 2 Appuyez le contrôleur contre le rail DIN jusqu'à ce que l'attache inférieure s'y accroche. Le contrôleur est ainsi fixé sur le rail. Retrait d’un rail DIN Pour retirer le contrôleur d'un rail DIN : Étape Action 1 A l'aide d'un tournevis, abaissez le mécanisme de verrouillage blanc afin de libérer le contrôleur. 2 Soulevez le contrôleur pour le dégager du rail DIN. Installation sur une plaque de montage pleine Vous pouvez monter le contrôleur et le module d’extension sur une plaque de montage métallique, en utilisant des vis autotaraudeuses en acier ST2.9 (quatre pour le contrôleur et deux pour le module d’extension). L'épaisseur de la plaque de montage ne doit pas dépasser 7 mm (0.275 in.). Une fois montés, les pieds de montage du contrôleur peuvent dépasser les dimensions du contrôleur, page 12 de 8mm (0,3 in.) dans les deux directions. Pour installer le contrôleur et le module d'extension sur une plaque de montage : Étape Action 1 Repérez les quatre trous de montage situés à chaque coin du contrôleur et les deux trous de montage du module d’extension. 2 Positionnez le contrôleur et le module d'extension sur la plaque de montage en veillant à laisser un dégagement suffisantDimensions, page 11. 16 DOCA0128FR-02 Installation Contrôleur de gestion des moteurs Étape Action 3 Insérez les six vis autotaraudeuses. 4 A l'aide d'un tournevis, serrez chaque vis et fixez le contrôleur et le module d'extension à leur emplacement. Couple de serrage : 1 N•m (8.8 lb-in). Montage sur une platine TE Vous pouvez monter le contrôleur et le module d'extension sur une platine TE, telle qu'une platine Telequick, en utilisant 6 attaches de montage (AF1 EA4). Une fois montés, les pieds de montage du contrôleur peuvent dépasser les dimensions du contrôleur, page 12 de 8mm (0,3 in.) dans les deux directions. Pour monter le contrôleur sur une platine Telequick : Étape Action 1 Fixez les six attaches de montage à la platine Telequick, comme indiqué sur le schéma ci-dessous. Le bord arrondi doit être orienté vers le haut pour les attaches supérieures et vers le bas pour les attaches inférieures. 2 Positionnez le contrôleur et le module d'extension sur les attaches en alignant leurs trous sur ceux des attaches. Insérez les vis dans les trous et serrez-les légèrement. 3 Lorsque le contrôleur et le module d'extension sont correctement placés, serrez les vis inférieures, puis les vis supérieures à l'aide d'un tournevis. Couple de serrage : 1 N•m (8.8 lb-in). DOCA0128FR-02 17 Contrôleur de gestion des moteurs Installation Position de fonctionnement Vous pouvez installer le contrôleur et le module d'extension selon un angle de 90° (perpendiculaire) par rapport au plan de montage vertical normal. Câblage - Généralités Présentation Le câblage de chaque pièce du contrôleur LTMR et du module d'extension LTME est décrit en détail avec ses spécificités : • Câblage des transformateurs de courant, page 23. • Câblage des transformateurs de courant de fuite à la terre, page 26. • Câblage des capteurs de température, page 28. • Câblage d'alimentation électrique, page 29. • Câblage des entrées logiques, page 31. • Câblage des sorties logiques, page 36. • Câblage des transformateurs de tension sur le module d'extension LTME. Le câblage du port de communication dépend du protocole de communication (voir le guide de communication relatif au protocole utilisé). Règles de câblage Les règles de raccordement doivent être respectées afin de réduire les perturbations électromagnétiques susceptibles d’affecter le comportement du contrôleur LTMR : 18 • Gardez une distance maximale entre le câble de communication et les câbles d'alimentation et/ou de commande (minimum 30 cm ou 11,8 pouces). • Croisez différents types de câbles à angles droits si nécessaire. • Ne pas plier ou endommager les câbles. Le rayon de courbure minimal est de 10 fois le diamètre du câble. • Évitez les angles aigus des chemins ou de passage du câble. DOCA0128FR-02 Installation Contrôleur de gestion des moteurs • Utilisez des câbles blindés pour raccorder les transformateurs de courant de fuite à la terre : ◦ Le câble blindé doit être connecté à un dispositif de mise à la terre aux deux extrémités. ◦ La connexion du câble blindé à la mise à la terre doit être la plus courte possible. ◦ Connectez tous les blindages si nécessaire. ◦ Exécutez la mise à la terre du blindage avec un collier. • Ajoutez des filtres sur les bobines du contacteur de tous les contacteurs et les relais. • Placez le câble le long de la plaque de mise à la terre autour du tiroir amovible. Pour obtenir plus d'informations, reportez-vous au Electrical Installation Guide (Manuel d'installation électrique) (disponible en anglais uniquement), chapitre ElectroMagnetic Compatibility (EMC) (Comptabilité électromagnétique (CEM)). Exemple de schéma de câblage : Le LTMR contrôle un moteur triphasé Le schéma suivant illustre le câblage du contrôleur LTMR et de son module d'extension LTME qui permettent de contrôler un moteur triphasé en mode indépendant à trois fils (impulsion) : A1, A2 alimentation électrique du contrôleur LTMR B1, B2 Alimentation dédiée aux sorties logiques DOCA0128FR-02 19 Contrôleur de gestion des moteurs Installation Exemple de schéma de câblage : Le LTMR contrôle un moteur monophasé Le schéma suivant illustre le câblage du contrôleur LTMR et de son module d'extension LTME, qui permettent de contrôler un moteur monophasé en mode indépendant à trois fils (impulsion) : A1, A2 alimentation électrique du contrôleur LTMR B1, B2 Alimentation dédiée aux sorties logiques Borniers enfichables et brochage du contrôleur LTMR Voici la description des borniers enfichables et du brochage du contrôleur LTMR : 20 DOCA0128FR-02 Installation Contrôleur de gestion des moteurs Bornier Broche Description Bornier de la tension de contrôle, des entrées logiques et de la source commune A1 Entrée de tension d'alimentation (+ / ∼) A2 La borne négative de l’alimentation pour les modèles CC ou la borne secondaire reliée à la terre d’un transformateur d’alimentation de contrôle pour les modèles CA (– / ∼) I.1 Entrée logique 1 I.2 Entrée logique 2 I.3 Entrée logique 3 I.4 Entrée logique 4 I.5 Entrée logique 5 I.6 Entrée logique 6 C Point commun des entrées 97–98 Contact NO 95–96 Contact NF Borniers de sortie logique O.4 Remarque : Les contacts 97– 98 et 95– 96 se trouvent sur le même relais. Ainsi, l’état ouvert/ fermé d’une paire de contacts est toujours contraire à l’état de l’autre paire. Borniers de sortie logique O.1 à O.3 13–14 Contact NO - sortie logique 1 23–24 Contact NO - sortie logique 2 33–34 Contact NO - sortie logique 3 Le contrôleur LTMR est dotés des bornes enfichables et des affectations de broches suivantes pour différents protocoles de communication : Protocole de communication Bornier Broche Description Ethernet Entrée de courant de fuite à la terre et entrée du capteur de température Z1–Z2 Connexion du transformateur de courant de fuite à la terre externe T1–T2 Connexion pour capteurs de température du moteur Z1–Z2 Connexion du transformateur de courant de fuite à la terre externe T1–T2 Connexion du dispositif de détection de température du moteur intégré S Blindage ou broche FE de PROFIBUS DP A Transfert des données négatif (RD-/TD-) B Transfert des données positif (RD+/TD+) DGND Broche de terre de données VP Broche d’alimentation Z1–Z2 Connexion du transformateur de courant de fuite à la terre externe T1–T2 Connexion du dispositif de détection de température du moteur intégré V- Broche commune CANopen CAN.L Broche CAN.L (bas dominant) S Broche blindée CANopen CAN.H Broche CAN.H (haut dominant) V+ Alimentation externe CANopen) PROFIBUS DP CANopen DOCA0128FR-02 Entrée déclenchement du courant de fuite à la terre, entrée du capteur de température et bornes de l’automate programmable Entrée déclenchement du courant de fuite à la terre, entrée du capteur de température et bornes de l’automate programmable 21 Contrôleur de gestion des moteurs Installation Protocole de communication Bornier Broche Description DeviceNet Entrée déclenchement du courant de fuite à la terre, entrée du capteur de température et bornes de l’automate programmable Z1–Z2 Connexion du transformateur de courant de fuite à la terre externe T1–T2 Connexion du dispositif de détection de température du moteur intégré V– Broche commune DeviceNet CAN.L Broche DeviceNet CAN.L (bas dominant) S Broche blindée DeviceNet CAN.H Broche DeviceNet CAN.H (haut dominant) V+ Broche d'alimentation externe DeviceNet Bornier enfichable et brochage du contrôleur d'extension LTME Voici la description des borniers enfichables et du brochage du module d'extension LTME : Bornier Broche Description Entrées de tension LV1 Tension de phase de l’entrée 1 LV2 Tension de phase de l’entrée 2 LV3 Tension de phase de l’entrée 3 I.7 Entrée logique n° 7 C7 Commun pour I.7 I.8 Entrée logique n° I.8 C8 Commun pour I.8 I.9 Entrée logique n° I.9 C9 Commun pour I.9 I.10 Entrée logique n° I.10 C10 Commun pour I.10 Entrées logiques et bornes communes Caractéristiques du câblage des bornes Les bornes du contrôleur LTMR et du module d'extension LTME ont les mêmes caractéristiques. Les borniers sont dotés d’une isolation nominale de 320 VCA. Le tableau ci-dessous présente les caractéristiques des câbles pouvant être utilisés pour connecter les bornes : Type de câble Câble souple (multibrin) Câble rigide Câble souple (multibrin) avec extrémités isolées Câble souple (multibrin) avec extrémités non isolées 22 Nb de conducteurs Section du conducteur mm² AWG Un conducteur 0,2...2,5 24...14 Deux conducteurs 0,2...1,5 24...16 Un conducteur 0,2...2,5 24...14 Deux conducteurs 0,2...1,0 24...18 Un conducteur 0,25 à 2,5 24...14 Deux conducteurs 0,5...1,5 20...16 Un conducteur 0,25 à 2,5 24...14 Deux conducteurs 0,2...1,0 24...18 DOCA0128FR-02 Installation Contrôleur de gestion des moteurs Le tableau ci-dessous décrit les caractéristiques des bornes : Pas 5,08 mm 0,2 in. Couple de serrage 0,5 à 0,6 N•m 5 lb-in Tournevis plat 3 mm 0,10 in. Câblage : transformateurs de courant (TC) Vue d’ensemble Le contrôleur LTMR comporte trois ouvertures TC par lesquelles vous pouvez faire passer les conducteurs du moteur vers les connexions de charge des contacteurs. Ces ouvertures permettent de brancher le contrôleur de quatre façons différentes, selon la tension et le modèle de contrôleur : • Câblage TC interne par les ouvertures • Câblage TC interne avec plusieurs passages • Câblage TC charge externe Cette rubrique décrit ces options. Câblage TC interne par les ouvertures Les schémas suivants présentent le câblage type par les ouvertures TC pour les moteurs triphasés ou monophasés : DOCA0128FR-02 23 Contrôleur de gestion des moteurs Installation Câblage TC interne avec plusieurs passages Le contrôleur peut physiquement accepter au maximum cinq passages de fils de 2,5 mm² (14 AWG) via les ouvertures TC. Trois autres ouvertures, situées sous les ouvertures TC, peuvent physiquement accepter des boucles de quatre fils. Définissez le paramètre TC charge - nombre de passages afin de compter le nombre de passages des câbles moteur dans les ouvertures TC et afficher ainsi les mesures de courant exactes. Pour plus d’informations, consultez la rubrique Paramètres du transformateur de courant de charge, page 63. Le schéma suivant présente le câblage type avec deux passages (une boucle) : Pour déterminer l’intensité totale traversant les capteurs de courant internes, multipliez l’intensité par le nombre de passages des câbles moteur dans les ouvertures CT. L’ajout de passages permet : • d’augmenter l’intensité mesurée par les capteurs de courant internes à un niveau détectable par le contrôleur, ou • d’obtenir une mesure plus exacte des capteurs de courant internes. Nous vous recommandons de choisir un contrôleur avec une plage de valeurs FLC qui tienne compte du courant de pleine charge du moteur FLC. Si, malgré tout, le courant de pleine charge (FLC) du moteur est inférieur à la plage FLC du contrôleur, plusieurs passages peuvent permettre d’augmenter le niveau d’intensité détecté par les capteurs de courant internes à un niveau décelable par le contrôleur. Ainsi, si vous utilisez un contrôleur avec une plage FLC de 5 à 100 A et que le courant de pleine charge du moteur (FLC) est de 3 A, le contrôleur ne peut pas détecter correctement le courant. Dans ce cas, vous avez la possibilité de passer deux fois le câblage d’alimentation dans les capteurs de courant internes du contrôleur, élevant alors leur détection à 6 A (2 passages x 3 A), un niveau d’intensité satisfaisant à la plage FLC du contrôleur. Pour plus d’informations sur les types de contrôleur, consultez le document TeSys T LTMR - Contrôleur de gestion de moteur - Guide utilisateur. 24 DOCA0128FR-02 Installation Contrôleur de gestion des moteurs Câblage TC charge externe Le contrôleur peut accepter des signaux secondaires de 1 A et 5 A en provenance de transformateurs de courant externes. Le modèle de contrôleur recommandé pour ces intensités est le modèle 0,4 à 8 A. Utilisez plusieurs passages dans les ouvertures CT du contrôleur si nécessaire. Les CTs externes sont caractérisés par un rapport de transformation. Le rapport du TC externe est le rapport entre le courant d’entrée moteur et le courant de sortie du TC. Pour permettre au contrôleur d’ajuster la plage FLC et d’afficher le courant de phase réel, définissez les paramètres suivants : • CT charge - primaire (premier nombre du rapport CT) • CT charge - secondaire (second nombre du rapport CT) • CT charge - nombre de passages (nombre de passages des câbles de sortie CT dans les ouvertures CT internes du contrôleur). Pour plus d’informations, consultez la rubrique Paramètres du transformateur du courant de charge, page 63. Le schéma suivant présente le câblage avec CTs externe : Pour plus d’informations sur les caractéristiques des TC externes, consultez le document TeSys T LTMR - Contrôleur de gestion de moteur - Guide utilisateur. Câblage TC en présence d’un entraînement à vitesse variable Lorsque le moteur est contrôlé par un entraînement à vitesse variable (VSD) : DOCA0128FR-02 25 Contrôleur de gestion des moteurs Installation • Les transformateurs de courant (externe ou interne) doivent être montés en amont de l’entraînement à vitesse variable, et pas entre l’entraînement à vitesse variable et le moteur. Les transformateurs de courant (TC) ne peuvent pas être placés entre les sorties du variateur et le moteur car le variateur peut produire des fréquences fondamentales en dehors de la plage 47 - 63 Hz. • Des pièges doivent être montés sur les trois phases, entre les transformateurs (interne ou externe), et l’entraînement à vitesse variable, pour réduire les harmoniques de démarrage progressif et les perturbations de tension générées par l’entraînement à vitesse variable. Câblage des transformateurs de courant de fuite à la terre Installation du transformateur de courant de fuite à la terre Le schéma qui suit représente une installation de contrôleur LTMR classique utilisant un transformateur de courant de fuite à la terre (GFCT) : 26 DOCA0128FR-02 Installation Contrôleur de gestion des moteurs Les GFCTs sont caractérisés par un rapport de transformation. Le rapport du GFCT est le rapport entre le courant de fuite à la terre de déclenchement et le courant de sortie. Pour permettre au contrôleur de mesurer correctement le courant réel de déclenchement à la terre qui circule dans le circuit, définissez les paramètres suivants : • CT primaire de courant de fuite à la terre (le premier chiffre du rapport GFCT) • CT secondaire de courant de fuite à la terre (le second chiffre du rapport GFCT) Pour une description des caractéristiques du GFCT, consultez le document TeSys T LTMR - Contrôleur de gestion des moteurs - Guide de l’utilisateur. Câblage du transformateur de courant de fuite à la terre Le transformateur de courant de fuite à la terre externe (GFCT) doit être connecté aux bornes du contrôleur LTMR Z1 et Z2 à l’aide d’un câble blindé à paire torsadée. Le blindage doit être connecté à la terre aux deux extrémités par le biais de raccordements les plus courts possibles. DOCA0128FR-02 27 Contrôleur de gestion des moteurs Installation Câblage : capteurs de température Capteurs de température Le contrôleur LTMR comporte deux bornes dédiées à la protection des capteurs de température du moteur : T1 et T2. Ces bornes transmettent la température mesurée par les résistances détectrices de température (RTD). Parmi les types de capteurs de température moteur existants, il est possible d’utiliser l’un des capteurs suivants : • PTC binaire • PT100 • PTC analogique • NTC analogique Pour plus d’informations sur les capteurs de température, consultez le document TeSys T LTMR - Contrôleur de gestion de moteur - Guide utilisateur. Câblage du capteur de température Le tableau suivant indique les longueurs de câble maximales pour l’ensemble de détection de température : Calibre de fil 0,5 mm2 (AWG 20) 0,75 mm2 (AWG 18) 1,5 mm2 (AWG 16) 2,5 mm2 (AWG 14) Longueur maximale du câble 220 m (656 ft) 300 m (985 ft) 400 m (1312 ft) 600 m (1970 ft) Utilisez un câble à paires torsadées non blindé pour connecter le contrôleur au capteur de température. Pour que le contrôleur mesure correctement la résistance de l’ensemble de détection de température, vous devez mesurer la résistance du câble à paire torsadée et l’ajouter à la résistance souhaitée en protection. Cette méthode permet de compenser la résistance du fil. 28 DOCA0128FR-02 Installation Contrôleur de gestion des moteurs Le schéma qui suit montre le câblage du contrôleur LTMR et le capteur de température d’un moteur monophasé : Pour plus d’informations sur le câblage, voir Câblage - Généralités, page 18 Câblage - Alimentation Vue d’ensemble La tension d’alimentation du contrôleur LTMR peut être : • 24 VCC ou • 100-240 VCA Le tableau qui suit présente le contrôleur LTMR et les règles d’association du module d’extension LTME : LTMR•••BD (VCC) LTMR•••FM (VCA) LTME•••BD (VCC) X X LTME•••FM (VCA) – X X Association autorisée – Association non autorisée Alimentation CC Une alimentation 24 VCC est nécessaire pour fournir : • un ou plusieurs contrôleurs LTMR incluant les entrées logiques du ou des contrôleurs LTMR, • les entrées logiques du ou des modules d’extension LTME Une alimentation 24 VCC supplémentaire est nécessaire pour alimenter : • les sorties logiques de contrôleur LTMR, • d’autres unités L’alimentation CC du contrôleur LTMR doit présenter les caractéristiques suivantes : DOCA0128FR-02 29 Contrôleur de gestion des moteurs Installation • Convertisseur CA/CC. • Isolation galvanique entrée CA / sortie CC : 4 kVac minimum à 50 Hz. • Tension en entrée : 240 VCA (+15 % / -20 %). • Tension en sortie : 24 VCC (+/-10 %). Les systèmes d’alimentation Schneider Electric ABL8RPS24••• suivants sont recommandés : Référence Tension en entrée Courant/tension en sortie Nombre maximal de contrôleurs LTMR fournis ABL8RPS24100 200 - 500 VCA 24 VCC/10 A 24 ABL8RPS24050 200 - 500 VCA 24 VCC/5 A 12 ABL8RPS24030 200 - 500 VCA 24 VCC/3 A 8 Alimentation électrique CA Une alimentation électrique CA/CA ou onduleur (UPS) dédiée est nécessaire pour fournir : • un ou plusieurs contrôleurs LTMR incluant les entrées logiques du ou des contrôleurs LTMR, • les entrées logiques du ou des modules d’extension LTME Une alimentation CA ou CC supplémentaire est nécessaire pour fournir : • les sorties logiques de contrôleur LTMR, • d’autres unités L’alimentation CA ou l’onduleur (UPS) du contrôleur LTMR doit présenter les caractéristiques suivantes : 30 • Transformateur d’isolation • Tension en sortie : 115 ou 230 VCA (+15 % / -20 %). ◦ Une tension de sortie de 115 VCA est conseillée. ◦ Avec une tension en sortie de 230 VCA, un filtre externe LTM9F supplémentaire peut être nécessaire. • Puissance adaptée au nombre de contrôleurs LTMR (plusieurs alimentations CA sont conseillées). • Un onduleur (UPS) est obligatoire si la tension est instable et n’est pas conforme aux spécifications de la norme EN 50160. DOCA0128FR-02 Installation Contrôleur de gestion des moteurs Alimentation en réseau chaîné Si la même alimentation (CA ou CC) est utilisée pour alimenter plusieurs contrôleurs LTMR, il est conseillé de fermer la boucle : • pour éviter les coupures, • pour réduire la perte de tension due à des câbles longs. Câblage - Entrées logiques Vue d’ensemble 10 entrées logiques maximum sont fournies : DOCA0128FR-02 • Six entrées logiques sur le contrôleur LTMR, alimenté en interne par LTMR • Quatre entrées logiques sur le module d’extension LTME, alimenté de façon indépendante 31 Contrôleur de gestion des moteurs Installation Entrées logiques du contrôleur LTMR Le contrôleur LTMR comporte six entrées logiques : • disponibles via des bornes de branchement sur site I.1 à I.6 • alimentées en interne par la tension de contrôle du contrôleur LTMR (la tension en entrée est la même que celle de la tension d’alimentation du contrôleur.) • isolées des entrées du module d’extension LTME Les trois bornes communes (C) du contrôleur LTMR sont raccordées à la tension de contrôle A1 via un filtre interne, comme indiqué dans les exemples de schéma de câblage, page 18. AVIS RISQUE DE DESTRUCTION DES ENTRÉES LOGIQUES • Raccordez les entrées du contrôleur LTMR en utilisant les trois bornes communes (C) connectées à la tension de contrôle A1 via un filtre interne. • Ne connectez pas la borne (C) commune aux entrées de tension de contrôle A1 ou A2. Le non-respect de ces instructions peut provoquer des dommages matériels. Pour plus d’informations, consultez la section Câblage de l’alimentation, page 29 et les spécifications techniques du contrôleur LTMR dans le document TeSys T LTMR - Contrôleur de gestion de moteur - Guide utilisateur. Entrées logiques du module d’extension LTME Les quatre entrées logiques du module d’extension LTME (I.7 - I.10) ne sont pas alimentées par la tension de contrôle du contrôleur LTMR. Pour plus d’informations, consultez les spécifications techniques du contrôleur LTME et la section Câblage de l’alimentation dans le document TeSys T LTMR Contrôleur de gestion de moteur - Guide utilisateur, page 29. Réglages des entrées CA du contrôleur Le contrôleur LTMR utilise des filtres numériques pour obtenir un signal CA correct au niveau des entrées. Pour des résultats plus précis, ce filtre peut être configuré par le registre de réglage des entrées CA de contrôleur définissant la tension d’alimentation et activant la fonction interne de filtrage d’adaptation. Connexion des entrées logiques AVIS FONCTIONNEMENT IMPREVU DE L’APPAREIL • Installez un relais intermédiaire pour les entrées longue distance. • Séparez le câble de contrôle du câble d’alimentation. • Utilisez un contact sec sur les entrées LTMR. • Respectez les recommandations indiquées dans cette section. Le non respect de ces consignes peut provoquer un arrêt imprévu du moteur. 32 DOCA0128FR-02 Installation Contrôleur de gestion des moteurs Trois types de connexion sont possibles : • Connexion directe à toutes les informations des entrées logiques issues du tableau de distribution. • Connexion par relais intermédiaire de toutes les informations des entrées logiques issues de l’extérieur du tableau de distribution et raccordées principalement à de longues lignes. L’utilisation de relais intermédiaires réduisent les perturbations électromagnétiques sur le contrôleur LTMR et accroît la fiabilité des informations. • Connexion sans relais intermédiaires pour les entrées logiques courte distance. Pour les applications d’E/S TeSys T, seuls les contacts secs libres de potentiel peuvent être utilisés. Sinon, du courant peut être fourni au capteur ou au dispositif et affecter l’état des E/S. Interférences inductives Si des câbles de contrôle et d’alimentation sont parallèles et à proximité sur une distance de plus de 100 m (328 ft), une tension induite peut être générée et provoquer le blocage du relais. Il est fortement recommandé de séparer les câbles de contrôle et d’alimentation de 50 cm (1,64 ft) ou bien d’utiliser une plaque de séparation. Pour limiter la tension induite en CA, il est possible d’ajouter une résistance de blocage en parallèle au relais intermédiaire. Distance maximale sans relais intermédiaire Voici la distance maximale autorisée sans relais intermédiaire : Calibre de fil 1 mm2 (AWG 18) 1,5 mm2 (AWG 16) 2 mm2 (AWG 14) 2,5 mm2 (AWG 14) Distance maximale des fils 210 m (689 ft) 182 m (597 ft) 163 m (535 ft) 149 m (489 ft) Cependant, étant donné la variabilité des installations, il est fortement recommandé d’utiliser des relais intermédiaires si la longueur des câbles de contrôle est supérieure à 100 m (328 ft). Relais intermédiaire recommandé Les relais intermédiaires doivent présenter les caractéristiques suivantes : • Relais électromécanique avec isolation minimum 2,5 kVCA. • Contact auto-nettoyant ou faible intensité (I < 5 mA). • Installés sur le tableau de distribution aussi près que possible du contrôleur LTMR • Tension de circuit de commande CA ou CC, fournie par un dispositif d'alimentation électrique distinct (fournie par la même alimentation que le contrôleur LTMR, pour respecter l'isolation galvanique). Si les distances entre le processus et le contrôleur LTMR sont importantes, les relais intermédiaires avec tension de circuit de commande CC sont recommandés. Le module de protection est obligatoire sur les relais intermédiaires et ce, afin d’éviter les surtensions. Les relais intermédiaires Schneider Electric RSB1 suivants sont recommandés : DOCA0128FR-02 33 Contrôleur de gestion des moteurs Installation Référence Tension du circuit de commande Module de protection RSB1A120•D 6, 12, 24, 48, 60, 110 VCC Diode RZM040W RSB1A120•7 24, 48 VCA Circuit RC RZM041BN7 RSB1A120•7 120, 220, 230, 240 VCA Circuit RC RZM041FU7 Utilisation de relais intermédiaires CC Les relais intermédiaires CC sont recommandés, car les distances de câblage de commande du relais peut être longue. Tension de relais RSB1 CC 24 VCC 48 VCC 110 VCC Distance maximale pour les fils en parallèle sans écran métallique 3 000 m (10 000 ft) 3 000 m (10 000 ft) 3 000 m (10 000 ft) Distance maximale pour les fils en parallèle avec écran métallique 3 000 m (10 000 ft) 3 000 m (10 000 ft) 3 000 m (10 000 ft) Le schéma ci-dessous représente un exemple d’utilisation de relais intermédiaires CC : Utilisation de relais intermédiaires CA L’utilisation d’un relais intermédiaire CA est permise sur de courtes distances si une tension CA est obligatoire. Tension de relais RSB1 CA 24 VCA 48 VCA 120 VCA 230/240 VCA Distance maximale pour les fils en parallèle sans écran métallique 3 000 m (10 000 ft) 1 650 m (5 500 ft) 170 m (550 ft) 50 m (165 ft) Distance maximale pour les fils en parallèle avec écran métallique 2 620 m (8 600 ft) 930 m (3 000 ft) 96 m (315 ft) 30 m (100 ft) 34 DOCA0128FR-02 Installation Contrôleur de gestion des moteurs Le schéma qui suit représente un exemple d’utilisation de relais intermédiaires CA : Utilisation de relais intermédiaires CA avec un redresseur L’utilisation d’un relais intermédiaire CA avec un redresseur est conseillée sur les longues distances si la tension CA est obligatoire. Ajoutez un redresseur composé de diodes de 1 A/1 000 V pour commander un relais intermédiaire CA. Ainsi, le courant CA rectifié circule dans le câble de commande lorsque le commutateur de la partie continue est fermé. Le temps de désactivation du relais augmente avec la capacitance parasite (câble long) car la capacitance réduit l’inductance de la bobine. Le composant équivalent est en général une résistance qui augmente le temps de désactivation. Plus la tension est élevée, plus le phénomène est important. Tension de relais RSB1 CA 24 VCA 48 VCA 120 VCA 230/240 VCA Distance maximale pour les fils en parallèle sans écran métallique 3 000 m (10 000 ft) 3 000 m (10 000 ft) 3 000 m (10 000 ft) 3 000 m (10 000 ft) Distance maximale pour les fils en parallèle avec écran métallique 3 000 m (10 000 ft) 3 000 m (10 000 ft) 3 000 m (10 000 ft) 3 000 m (10 000 ft) DOCA0128FR-02 35 Contrôleur de gestion des moteurs Installation Le schéma ci-dessous représente un exemple d’utilisation de relais intermédiaires CA avec un redresseur : Câblage - Sorties logiques Vue d’ensemble Les quatre sorties logiques du contrôleur LTMR sont des sorties de relais. Les sorties de relais commandent le moteur géré par le contrôleur LTMR. Description des quatre sorties de relais sur le contrôleur LTMR : • Trois sorties relais unipolaires et unidirectionnelles (SPST, NO) • Une sortie relais bipolaire et unidirectionnelle (DPST, NC+NO) Relais intermédiaires de sortie Lorsqu’une sortie commande un contacteur, un relais intermédiaire peut être requis en fonction de la tension de la bobine et de la puissance requise par le contacteur utilisé. 36 DOCA0128FR-02 Installation Contrôleur de gestion des moteurs Les schémas ci-dessous représentent le câblage du système avec et sans relais intermédiaire KA1 : B1, B2 Alimentation dédiée aux sorties logiques Caractéristiques des sorties logiques du contrôleur LTMR : • Tension d’isolement nominale : 300 V • Charge thermique nominale AC : 250 VCA / 5 A • Charge thermique nominale DC : 30 VCA / 5 A • Calibre AC 15 : 480 VA, 500 000 opérations, Ie max = 2 A • Calibre DC 13 : 30 W, 500 000 opérations, Ie max = 1,25 A Si la sortie logique du contrôleur LTMR ne peut pas contrôler directement le contacteur, un relais intermédiaire est requis. Le module de protection est obligatoire sur les relais intermédiaires, afin d’éviter les surtensions. Contacteurs recommandés Les tableaux de l’annexe qui donnent les références et les caractéristiques des contacteurs Schneider Electric indiquent si un relais intermédiaire est ou non requis Pour plus d’informations sur les contacteurs recommandés, voir le document TeSys T LTMR - Contrôleur de gestion de moteur - Guide utilisateur. Connexion à un système HMI Présentation Cette section explique comment connecter le contrôleur LTMR à un système HMI, tel que Magelis XBT ou TeSys T LTMCU, ou à un PC exécutant SoMove avec TeSys T DTM. Le système HMI doit être connecté au port RJ45 du contrôleur LTMR ou au port d’interface HMI (RJ45) du module d’extension LTME. Le système XBT HMI Magelis doit être alimenté séparément. Connectez-le à un contrôleur en mode Un à plusieurs. DOCA0128FR-02 37 Contrôleur de gestion des moteurs Installation Règles de câblage Les règles de câblage doivent être respectées afin de réduire les perturbations électromagnétiques sur le fonctionnement du contrôleur LTMR : La liste exhaustive des règles de câblage est fournie dans les recommandations générales, page 18. AVIS FONCTIONNEMENT IMPRÉVU DE L'ÉQUIPEMENT Utilisez des câbles Schneider Electric standard. Le non-respect de ces instructions peut provoquer des dommages matériels. Raccordement à un système HMI Magelis XBT en mode Un à plusieurs Le schéma ci-dessous montre une connexion Un à plusieurs entre le système HMI Magelis XBTN410 et jusqu’à huit contrôleurs avec ou sans module d’extension LTME : 1 Unité IHM Magelis XBTN410 2 Câble de connexion Magelis XBTZ938 3 Boîtes de dérivation en TVW3 A8 306 TF•• 4 Câble blindé avec deux connecteurs RJ45 VW3 A8 306 R•• 5 Terminaison de ligne VW3 A8 306 R 6 Contrôleur LTMR 7 Module d'extension LTME 38 DOCA0128FR-02 Installation Contrôleur de gestion des moteurs Raccordement à une unité IHM TeSys T LTMCU Les schémas ci-dessous représentent l’unité IHM TeSys T LTMCU raccordée au contrôleur LTMR avec ou sans module d’extension LTME : 1 Unité de commande opérateur LTMCU 2 Collier de mise à la terre 3 Câble de raccordement à l'unité IHM LTM9CU•• 4 Contrôleur LTMR 5 Module d'extension LTME Raccordement à un système HMI générique Connectez le contrôleur LTMR et le module d’extension à un système HMI de votre choix en utilisant un câble blindé pour le bus Modbus, référence TSX CSA •••. Broches de port RJ45 qui permettent de connecter le port HMI du contrôleur LTMR ou du module d’extension LTME : Connexions RJ45 : N° broche Signal Description 1 Réservé Ne pas connecter 2 Réservé Ne pas connecter 3 – Non connecté 4 D1 ou D(B) Communication entre l’HMI et le contrôleur LTMR 5 D0 ou D(A) Communication entre l’HMI et le contrôleur LTMR 6 Réservé Ne pas connecter 7 VP Alimentation électrique de +7 VCC (100 mA) fournie par le contrôleur LTMR 8 Commun Commun signal et alimentation DOCA0128FR-02 39 Contrôleur de gestion des moteurs Installation Connexion à un PC exécutant SoMove avec TeSys T DTM en mode Un à plusieurs via le port HMI Les schémas ci-dessous représentent une connexion Un à un entre un PC exécutant le logiciel SoMove avec TeSys T DTM, et le port HMI du contrôleur LTMR avec et sans module d’extension LTME et le LTMCU : 1 PC exécutant SoMove avec la TeSys T DTM 2 Câble Modbus TCSMCNAM3M0 USB/RJ45 3 Contrôleur LTMR 4 Module d'extension LTME 1 PC exécutant SoMove avec la TeSys T DTM 2 Kit de câblage TCSMCNAM3M002P 3 Contrôleur LTMR 4 Module d'extension LTME 5 Unité de commande opérateur LTMCU 6 Collier de mise à la terre 7 Câble de raccordement à l'unité LTM9CU•• HMI 40 DOCA0128FR-02 Installation Contrôleur de gestion des moteurs Connexion à un PC exécutant SoMove avec TeSys T DTM en mode Un à plusieurs via le port réseau Ethernet LTMR Les schémas ci-dessous représentent une connexion Un à un entre un PC exécutant le logiciel SoMove avec TeSys T DTM, et l’un des deux ports réseau du contrôleur Ethernet LTMR avec et sans module d’extension LTME et le LTMCU : 1 PC exécutant SoMove avec la TeSys T DTM 2 Câble Ethernet blindé ou à paire torsadée non blindé de catégorie 5 3 Contrôleur Ethernet LTMR 4 Module d'extension LTME 1 PC exécutant SoMove avec la TeSys T DTM 2 Câble Ethernet blindé ou à paire torsadée non blindé de catégorie 5 3 Contrôleur Ethernet LTMR 4 Module d'extension LTME 5 Unité de commande opérateur LTMCU 6 Collier de mise à la terre 7 Câble de raccordement à l'unité LTM9CU•• HMI Si le LTMCU est connecté à un PC, le LTMCU devient passif et n’est pas utilisable pour afficher des informations. Connexion à un PC exécutant SoMove avec TeSys T DTM en mode Un à plusieurs Le schéma ci-dessous représente une connexion Un à plusieurs entre un PC exécutant SoMove avec TeSys T DTM et jusqu’à huit contrôleurs (avec ou sans module d’extension LTME) : DOCA0128FR-02 41 Contrôleur de gestion des moteurs Installation 1 PC exécutant SoMove avec la TeSys T DTM 2 Kit de câblage TCSMCNAM3M002P 3 Boîtes de dérivation en T VW3 A8 306 TF•• comprenant un câble blindé avec deux connecteurs RJ45 4 Câble blindé avec 2 connecteurs RJ45 VW3 A8 306 R•• 5 Terminaison de ligne VW3 A8 306 R 6 Contrôleur LTMR 7 Module d'extension LTME NOTE: Pour le protocole de communication Modbus, cette connexion requiert la configuration de différentes adresses de communication HMI. La configuration d’usine de l’adresse du port HMI est 1. Accessoires de raccordement Le tableau suivant répertorie les accessoires de raccordement pour les systèmes HMI tels que XBT Magelis : Désignation Description Référence Boîtes de dérivation T Boîte avec deux connecteurs femelles RJ45 pour un câble principal et un câble intégré de 0,3 m (1 pi) avec connecteur mâle RJ45 pour la dérivation VW3 A8 306 TF03 Boîte avec deux connecteurs femelles RJ45 pour un câble principal et un câble intégré de 1 m (3,2 pi) avec connecteur mâle RJ45 pour la dérivation VW3 A8 306 TF10 Terminaison de ligne pour le connecteur RJ45 R = 120 Ω VW3 A8 306 R Câble de connexion Magelis Longueur = 2,5 m (8,2 ft) XBTZ938 (Magelis XBTN410 uniquement) Connecteur SUB-D 25 points pour raccordement au système Magelis® XBT Kit de câble Longueur = 2,5 m (8,2 ft) TCSMCNAM3M002P Convertisseur USB vers RS 485 Câbles de communication Câble de connexion de système HMI 42 Longueur = 0,3 m (1 ft) VW3 A8 306 R03 Longueur = 1 m (3,2 ft) VW3 A8 306 R10 Longueur = 3 m (3,2 ft) VW3 A8 306 R30 Longueur = 1 m (3,2 ft) LTM9CU10 Longueur = 3 m (9,6 ft) LTM9CU30 DOCA0128FR-02 Mise en service Contrôleur de gestion des moteurs Mise en service Vue d’ensemble Ce chapitre présente la mise en service du contrôleur LTMR et du module d’extension LTME. Présentation Présentation La mise en service doit être réalisée après l’installation physique du contrôleur LTMR, du module d’extension LTME et d’autres équipements. Etapes du processus de mise en service : • Initialisation des équipements installés et • Configuration des paramètres du contrôleur LTMR requis pour le fonctionnement du contrôleur LTMR, du module d’extension LTME et des autres équipements du système. La personne réalisant la mise en service doit bien connaître les équipements matériels du système, ainsi que leur mode d’installation et leur utilisation dans le cadre de l’application souhaitée. Exemples d’équipements : • Moteur • Transformateurs de tension • Transformateurs de courant de charge externe • Transformateurs de courant de fuite à la terre • Réseau de communication Les spécifications de ces produits fournissent les informations de paramétrage requises. Il est nécessaire de comprendre comment sera utilisé le contrôleur LTMR afin de configurer les fonctions de protection, de surveillance et de contrôle nécessaires pour l’application. Pour plus d’informations sur la configuration des paramètres de protection et de contrôle, consultez le document TeSys T LTMR - Contrôleur de gestion de moteur - Guide utilisateur. Pour plus d’informations sur la configuration du réseau de communication, consultez • TeSys T LTMR Ethernet - Guide de communication • TeSys T LTMR Modbus - Guide de communication • TeSys T LTMR PROFIBUS DP - Guide de communication • TeSys T LTMR CANopen - Guide de communication • TeSys T LTMR - Guide de communication DeviceNet Initialisation Le contrôleur LTMR est prêt à être initialisé une fois que l’installation matérielle est terminée. Pour initialiser le contrôleur LTMR : DOCA0128FR-02 • Vérifiez que la commande de contrôle du moteur est OFF • Démarrez le contrôleur LTMR 43 Contrôleur de gestion des moteurs Mise en service ATTENTION INITIALISATION INCORRECTE Déconnectez l’alimentation du moteur avant de procéder à l’initialisation du contrôleur LTMR. Le non-respect de ces instructions peut provoquer des blessures ou des dommages matériels. Ni le contrôleur LTMR, ni le module d’extension LTME ne nécessitent une configuration matérielle supplémentaire (par exemple, pour régler des cadrans ou des commutateurs DIP) pour leur initialisation. Une fois mis sous tension pour la première fois, le contrôleur LTMR passe en état initial et est prêt pour la mise en service. Outils de configuration Identifiez la source de contrôle de la configuration, ainsi que l’outil de configuration, avant de configurer les paramètres. Le contrôleur LTMR et le module d’extension LTME peuvent être configurés localement, via un système HMI, ou à distance via la connexion réseau. La mise en service du contrôleur LTMR peut s’effectuer grâce à : • Une unité de contrôle opérateur LTMCU • Un PC exécutant SoMove avec TeSys T DTM • Un automate connecté au contrôleur LTMR via le port réseau Les paramètres suivants identifient la source de contrôle de la configuration : Paramètre Permet d’utiliser cet outil Réglage usine Configuration - par clavier HMI Unité de contrôle opérateur TeSys T LTMCU Activé Configuration - par logiciel PC PC exécutant SoMove avec TeSys T DTM Activé Configuration - par port réseau Port réseau (PLC ou PC exécutant SoMove avec TeSys T DTM) Activé Cette section décrit la mise en service réalisée à l’aide de l’unité de contrôle opérateur LTMCU ou du logiciel SoMove avec TeSys T DTM.. Processus de mise en service Le processus de mise en service reste identique, quel que soit l’outil de configuration choisi. Ce processus se compose des étapes suivantes : Etape Description Première mise sous tension Le contrôleur LTMR est initialisé et devient prêt pour la configuration des paramètres. Configuration des réglages requis Configurez ces paramètres afin que le contrôleur LTMR quitte son état d’initialisation. Le contrôleur LTMR est prêt à fonctionner. Configuration des réglages optionnels Configurez ces paramètres afin de pouvoir utiliser les fonctions du contrôleur LTMR requises pour l’application. Vérification matérielle Vérifiez le câblage du matériel. Vérification de la configuration Vérifiez que les réglages des paramètres sont corrects. 44 DOCA0128FR-02 Mise en service Contrôleur de gestion des moteurs Première mise sous tension Vue d’ensemble Première mise sous tension décrit l’opération consistant à faire circuler le courant dans : • un nouveau contrôleur LTMR ou • un contrôleur LTMR qui a été mis en service précédemment, mais dont les paramètres ont été rétablis sur leurs réglages usine, suite à : ◦ l’exécution de la commande Effacement - général ou ◦ une mise à niveau logicielle Lors de la première mise sous tension, le contrôleur LTMR se trouve à l’état verrouillé et non configuré (l’état « initialisation ») et le paramètre Contrôleur configuration système requise est activé. Le contrôleur LTMR quitte cet état uniquement après la configuration de certains paramètres (les paramètres « requis »). Une fois la mise en service effectuée, le contrôleur LTMR n’est plus verrouillé et est prêt à fonctionner. Pour plus d’informations sur les état de fonctionnement, consultez le document TeSys T LTMR - Contrôleur de gestion de moteur - Guide utilisateur. Première mise sous tension avec l’unité LTMCU LTMCULors de l’utilisation d’une unité de contrôle opérateur, la configuration des paramètres dans Menu > First Setup permet de désactiver le paramètre Contrôleur - configuration système requise et d’amener le contrôleur LTMR à quitter l’état d’initialisation. La première fois que le contrôleur LTMR est mis sous tension à sa sortie d’usine, l’écran de l’unité de contrôle opérateur LTMCULCD affiche automatiquement le menu First Setup, avec une liste de paramètres devant être immédiatement configurés : Cliquez sur OK. Dès que tous les paramètres sont définis, le dernier élément de menu qui apparaît est End Config : Cliquez sur OK. DOCA0128FR-02 45 Contrôleur de gestion des moteurs Mise en service Cliquez sur Yes pour enregistrer la configuration. Une fois la configuration enregistrée, le menu First Setup ne s’affiche plus. Pour accéder à nouveau à ce menu de première configuration, envoyez une commande Clear All au produit. Pour plus d’informations, consultez le document TeSys T LTMCU - Unité de contrôle opérateur - Guide utilisateur. Première mise sous tension avec l’unité SoMove avec TeSys T DTM En cas d’utilisation de SoMove avec TeSys T DTM pour définir tous les paramètres, à la première mise sous tension du contrôleur LTMR, le paramètre contrôleur - configuration système requise est activé et peut être effacé de deux façons : • En mode déconnecté, en cliquant sur Communication > Stocker sur périphérique pour télécharger les fichiers de configuration • En mode connecté, en cliquant sur Périphérique > commande > quitter la configuration une fois tous les paramètres définis Les deux commandes sortent le contrôleur LTMR de l’état d’initialisation. Paramètres requis et optionnels Introduction En plus des paramètres requis, vous pouvez configurer des paramètres facultatifs, lors du premier démarrage ou ultérieurement. Dans l’HMI du LTMCU Dans l’HMI LTMCU, les paramètres requis et optionnels se trouvent dans les cinq sous-menus du Menu. Dans SoMove avec TeSys T DTM Dans SoMove avec TeSys T DTM, les paramètres requis et optionnels sont des éléments de l’arborescence dans l’onglet Liste des paramètres. 46 DOCA0128FR-02 Mise en service Contrôleur de gestion des moteurs Paramètres du courant pleine charge (FLC - Full Load Current) Définition du courant pleine charge (FLC) Le courant de pleine charge (FLC) représente le courant de pleine charge réel du moteur étant protégé par le contrôleur LTMR. Le courant FLC est une caractéristique du moteur, que l’on peut trouver sur la plaque du moteur. De nombreux paramètres de protection sont définis comme des multiples de la valeur du courant FLC. Le courant FLC peut être défini du courant de pleine charge minimal (FLCmin) au courant de pleine charge maximal (FLCmax). Des exemples de réglage du courant FLC sont détaillés ci-dessous. Autres définitions TC charge - rapport = TC charge - primaire / (TC charge - secondaire * Passages) Courant - maximum du capteur = Courant - plage maximum * TC charge rapport La plage de courant maximum est indiquée sur la référence commerciale du contrôleur LTMR. Elle est stockée en unités de 0,1 A et peut avoir l’une des valeurs suivantes : 8,0 ; 27,0 ou 100,0 A Le courant de coupure du contacteur est stocké en unités de 0,1 A et est défini par l’utilisateur entre 1,0 et 1000,0 A . Le courant pleine charge maximum (FLCmax) correspond à la valeur la plus basse entre le courant maximum du capteur et le courant de coupure du contacteur. FLCmin = Courant maximum du capteur / 20 (valeur arrondie au centième d’ampère le plus proche.) Le courant pleine charge minimum (FLCmin) est stocké en interne en unités de 0,01 A. NOTE: • La modification du courant de coupure du contacteur et/ou du TC charge - rapport modifie la valeur du courant FLC. • Ne définissez pas de valeur FLC inférieure à la valeur FLCmin. Conversion d’ampères en paramètres FLC Les valeurs FLC sont stockées sous la forme d’un pourcentage de FLCmax FLC (en %) = FLC (en A) / FLCmax NOTE: Les valeurs FLC doivent être exprimées en pourcentage de la valeur FLCmax (résolution de 1 %). Si vous entrez une valeur non autorisée, le contrôleur LTMR l’arrondit à la valeur autorisée la plus proche. Par exemple, sur une unité de 0,4 à 8 A, la valeur entre les FLC est de 0,08 A. Si vous définissez une valeur FLC de 0,43 A, le contrôleur LTMR l’arrondit à 0,4 A. Exemple 1 (sans TC externe) Données : • DOCA0128FR-02 FLC (en A) = 0,43 A 47 Contrôleur de gestion des moteurs Mise en service • Courant plage maximum = 8,0 A • TC charge primaire = 1 • TC charge secondaire = 1 • Passages = 1 • Contacteur courant de coupure = 810,0 A Paramètres calculés sur la base d’un passage : • TC charge - rapport = TC charge - primaire / (TC charge - secondaire * Passages) = 1 / (1 * 1) = 1,0 • Courant - maximum du capteur = Courant - plage maximum * TC charge rapport = 8,0 * 1,0 = 8,0 A • FLCmax = min. (Courant - maximum du capteur, Contacteur - courant de coupure) = min. (8,0 ; 810,0) = 8,0 A • FLCmin = Courant - maximum du capteur / 20 = 8,0 / 20 = 0,40 A • FLC (in %) = FLC (en A) / FLCmax = 0,43 / 8,0 = 5 % Exemple 2 (sans TC externe, plusieurs passages) Données : • FLC (en A) = 0,43 A • Courant plage maximum = 8,0 A • TC charge primaire = 1 • TC charge secondaire = 1 • Passages = 5 • Contacteur courant de coupure = 810,0 A Paramètres calculés sur la base de cinq passages : • TC charge - rapport = TC charge - primaire / (TC charge - secondaire * Passages) = 1 / (1 * 5) = 0,2 • Courant - maximum du capteur = Courant - plage maximum * TC charge rapport = 8,0 * 0,2 = 1,6 A • FLCmax = min. (Courant - maximum du capteur, Contacteur - courant de coupure) = min. (1,6 ; 810,0) = 1,6 A • FLCmin = Courant - maximum du capteur / 20 = 1,6 / 20 = 0,08 A • FLC (in %) = FLC (en A) / FLCmax = 0,43 / 1,6 = 27 % Exemple 3 (TC externes, courant de coupure du contacteur réduit) Données : • FLC (en A) = 135 A • Courant plage maximum = 8,0 A • TC charge primaire = 200 • TC charge secondaire = 1 • Passages = 1 • Contacteur - courant de coupure = 150,0 A Paramètres calculés sur la base d’un passage : 48 • TC charge - rapport = TC charge - primaire / (TC charge - secondaire * Passages) = 200 / (1 * 1) = 200.0 • Courant - maximum du capteur = Courant - plage maximum * TC charge rapport = 8,0 * 200,0 = 1 600,0 A DOCA0128FR-02 Mise en service Contrôleur de gestion des moteurs • FLCmax = min. (Courant - maximum du capteur, Contacteur - courant de coupure) = min. (1600,0 ; 150,0) = 150,0 A • FLCmin = Courant - maximum du capteur / 20 = 1 600,0 / 20 = 80,0 A • FLC (in %) = FLC (en A) / FLCmax = 135 / 150,0 = 90 % Vérification du câblage du système Présentation Une fois tous les paramètres requis et optionnels configurés, vérifiez le câblage de votre système, qui peut inclure : • Câblage d’alimentation du moteur • Câblage du contrôleur LTMR • Câblage du transformateur de courant externe • Câblage de diagnostic • Câblage I/O Câblage d’alimentation du moteur Pour vérifier le câblage de l’alimentation du moteur, contrôlez les éléments suivants : Elément à contrôler Action Plaque d’identification du moteur Vérifiez que le moteur génère un courant et une tension compris dans les plages acceptées par le contrôleur LTMR. Schéma de câblage d’alimentation Vérifiez visuellement que le câblage réel correspond à ce qui est décrit sur le schéma de câblage de l’alimentation. Liste des déclenchements et des alarmes dans SoMove avec le TeSys T DTM ou l'affichage LCD de l’IHM Recherchez les alarmes ou les déclenchements suivants : La liste de tous les paramètres ou des paramètres en lecture seule dans le logiciel SoMove avec TeSys T DTM ou sur l’affichage déroulant de l’unité HMI. • Surcharge en puissance • Sous-charge en puissance • Sur-facteur de puissance • Sous-facteur de puissance Recherchez des valeurs inhabituelles pour les paramètres suivants : • Puissance active • Puissance réactive • Facteur de puissance Câblage du circuit de contrôle Pour vérifier le câblage du circuit de contrôle, contrôlez les éléments suivants : Elément à contrôler Action Schéma de câblage de contrôle Vérifiez visuellement que le câblage réel correspond à ce qui est décrit sur le schéma de câblage du contrôle. Voyant Power du contrôleur LTMR Si le voyant est éteint, il est possible que le contrôleur LTMR ne reçoive aucune alimentation. Voyant HMI du contrôleur LTMR Si le voyant est éteint, il est possible que le contrôleur LTMR ne communique pas avec le LTMCU ou le PC running SoMove Voyant Power du module d’extension LTME Si le voyant est éteint, il est possible que le module d’extension LTME ne reçoive aucune alimentation. DOCA0128FR-02 49 Contrôleur de gestion des moteurs Mise en service Câblage du transformateur de courant Vérifiez le câblage du transformateur de courant de charge et, si l’application inclut des transformateurs de courant de charge externes, vérifiez également les éléments suivants : Elément à contrôler Action Schéma de câblage du TC externe Vérifiez visuellement que le câblage réel correspond à ce qui est décrit sur le schéma de câblage. Le réglage des paramètres TC charge suivants à l’aide du logiciel SoMove avec TeSys T DTM : Vérifiez que le paramètre TC charge - rapport, ou la combinaison des paramètres TC charge - primaire et TC charge - secondaire, correspond au rapport TC de charge souhaité. • TC charge - rapport • TC charge - primaire • TC charge - secondaire Vérifiez visuellement que le paramètre TC charge - nombre de passages correspond au nombre de passages du câblage à travers les ouvertures du TC intégré au contrôleur LTMR. • TC charge - nombre de passages Le réglage des paramètres de moteur de charge suivants à l’aide du logiciel SoMove avec TeSys T DTM : • Moteur - nombre de phases Le réglage du paramètre de moteur de charge ci-dessous en utilisant SoMove avec TeSys T DTM ou l’écran LCD de l’unité HMI : • Vérifiez visuellement que le moteur et le contrôleur LTMR sont câblés conformément au nombre de phases défini dans le paramètre Moteur nombre de phases. Dans le cas d’un moteur triphasé, vérifiez visuellement que la séquence de câblage de phases correspond au réglage du paramètre Moteur séquence des phases. Moteur - séquence des phases Câblage de diagnostic Vérifiez le câblage de tout capteur de température du moteur ou de tout transformateur de courant à la terre externe, si l’application comporte ces dispositifs, en examinant les éléments suivants : Elément à contrôler Action Le schéma de câblage Vérifiez visuellement que le câblage réel correspond à ce qui est décrit sur le schéma de câblage. Spécifications du TC de terre externe Vérifiez que la combinaison des paramètres TC terre - primaire et TC terre - secondaire correspond au rapport TC terre souhaité. - et Le réglage des paramètres TC de fuite suivants à l’aide du logiciel SoMove avec TeSys T DTM : • TC terre - primaire • TC terre - secondaire Spécifications du capteur de température du moteur Vérifiez que le capteur de température du moteur utilisé correspond au type de capteur défini dans le paramètre Capteur température moteur. - et Le réglage du paramètre suivant en utilisant le logiciel SoMove avec TeSys T DTM ou l’écran LCD de l’unité HMI : • Capteur de température du moteur Câblage des E/S Vérifiez le câblage de toutes les connexions I/O en examinant les éléments suivants : Elément à contrôler Action Le schéma de câblage Vérifiez visuellement que le câblage réel correspond à ce qui est décrit sur le schéma de câblage. Les touches AUX1 (Run 1), AUX2 (Run 2) et Stop de l’unité HMI Vérifiez que chaque commande exécute la fonction de démarrage ou d’arrêt souhaitée, lorsque le contrôle s’effectue via le bornier ou le port de l’HMI. - et - 50 DOCA0128FR-02 Mise en service Contrôleur de gestion des moteurs Elément à contrôler Action Le réglage du paramètre suivant en utilisant SoMove avec TeSys T DTM ou l’écran LCD de l’unité HMI : • Contrôle - sélection du canal local Touche Reset de l’unité HMI Vérifiez que l’HMI peut commander un réarmement manuel en cas de déclenchement, lorsque le contrôle est défini sur le mode manuel. - et Le réglage du paramètre suivant en utilisant le logiciel SoMove avec TeSys T DTM ou l’écran LCD de l’unité HMI : • Réarmement du déclenchement par surcharge thermique Automate (PLC), si le contrôleur LTMR est connecté à un réseau Vérifiez que l’automate (PLC) peut commander les fonctions souhaitées de démarrage, d’arrêt et de réarmement à distance. - et Le réglage du paramètre suivant en utilisant SoMove avec TeSys T DTM ou l’écran LCD de l’unité HMI : • Réarmement du déclenchement par surcharge thermique Vérification de la configuration Présentation La dernière étape du processus de mise en service consiste à vérifier que tous les paramètres configurables utilisés dans l’application sont correctement configurés. Lors de l’exécution de cette tâche, une liste principale de tous les paramètres à configurer et des paramètres souhaités est requise. Il est indispensable de comparer cette aux valeurs réelles des paramètres configurés. Traitement La vérification des réglages des paramètres comporte trois étapes : • Transférez le fichier de configuration du contrôleur LTMR vers le PC exécutant SoMove avec TeSys T DTM. Vous pouvez ainsi consulter les valeurs des paramètres du contrôleur LTMR. Pour plus d’informations sur le transfert de fichiers du contrôleur LTMR vers un PC, consultez l’aide en ligne du conteneur TeSys T DTM pour SoMove FDT. • Comparez la liste principale des paramètres et réglages souhaités aux réglages équivalents situés dans l’onglet Liste des paramètres dans SoMove avec TeSys T DTM. SoMove peut se trouver dans l’onglet Liste des paramètres, la liste de paramètres Modifiés. C’est un moyen rapide de voir les paramètres définis. • Modifiez les paramètres de configuration souhaités. Pour ce faire, vous pouvez utiliser : ◦ Le logiciel SoMove avec TeSys T DTM , puis télécharger le fichier modifié de votre PC vers le contrôleur LTMR. Pour plus d’informations sur le transfert de fichiers du PC vers le contrôleur LTMR, consultez l’aide en ligne du conteneur TeSys T DTM pour SoMove FDT. ◦ DOCA0128FR-02 ou sur l’HMI LTMCU : pour modifier les paramètres dans le Menu, accédez aux paramètres des sous-menus et apportez les changements souhaités. 51 Contrôleur de gestion des moteurs Maintenance Maintenance Vue d’ensemble Cette section décrit les fonctions de maintenance et d’auto-diagnostic du contrôleur LTMR et du module d’extension. AVERTISSEMENT FONCTIONNEMENT IMPREVU DE L’APPAREIL L’application de ce produit nécessite des compétences en conception et programmation de systèmes de contrôle. Seules les personnes ayant acquis ces compétences doivent être autorisées à programmer, installer, modifier et à appliquer ce produit. Respectez la réglementation locale et nationale en matière de sécurité. Le non-respect de ces instructions peut provoquer la mort, des blessures graves ou des dommages matériels. Détection des problèmes Présentation Le contrôleur LTMR et le module d’extension effectuent des autodiagnostics au démarrage et pendant le fonctionnement. Les problèmes avec le contrôleur LTMR ou le module d’extension peuvent être détectés à l’aide : • des voyants Alarm et Power situés sur le contrôleur LTMR • des voyants d’entrée et Power sur le module d’extension • Écran LCD de l’unité IHM Magelis XBTN410 ou une unité de contrôle opérateur TeSys T LTMCU connectée au port IHM du contrôleur LTMR, ou • SoMove avec TeSys T DTM exécuté sur un PC connecté au port HMI du contrôleur LTMR Voyants des équipements Les voyants situés sur le contrôleur LTMR et le module d’extension indiquent les problèmes suivants : Voyant LTMR Voyant LTME Problème Puissance Alarme Alarme PLC Puissance Désactivé Rouge fixe - - Déclenchement interne Activé Rouge fixe - - Déclenchement de protection Activé Rouge clignotant (2 fois par seconde) - - Alarme de protection Activé Rouge clignotant (5 fois par seconde) - - Délestage ou cycle rapide Activé - - Rouge fixe Déclenchement interne 52 DOCA0128FR-02 Maintenance Contrôleur de gestion des moteurs Système HMI Magelis XBT L’IHM Magelis XBTN410 affiche automatiquement des informations sur un déclenchement ou une alarme, notamment sur les alarmes et déclenchements d’autodiagnostic du contrôleur LTMR. Pour plus d’informations sur l’affichage des déclenchements et des alarmes en utilisant l’IHM dans une configuration Un à plusieurs, consultez la section Gestion des déclenchements dans le document TeSys T LTMR - Contrôleur de gestion des moteurs - Guide de l’utilisateur. Unité de contrôle opérateur LTMCU L’unité de contrôle opérateur TeSys T LTMCU affiche automatiquement des informations sur un déclenchement ou une alarme. Pour plus d’informations, consultez la rubrique Affichage des déclenchements et des alarmes dans le document TeSys T LTMCU - Unité de contrôle opérateur Guide de l’utilisateur. SoMove avec le TeSys T DTM Le logiciel SoMove avec TeSys T DTM affiche un tableau visuel des déclenchements et alarmes actifs, notamment les déclenchements et alarmes d'autodiagnostic du contrôleur LTMR, lorsque ces déclenchements surviennent. Pour plus d’informations sur l’affichage des déclenchements et alarmes actifs, consultez l’Aide en ligne du conteneur TeSys T DTM pour SoMove FDT. Dépannage Tests d’autodiagnostic Le contrôleur LTMR exécute des tests d’autodiagnostic à la mise sous tension et pendant le fonctionnement. Ces tests, les erreurs qu’ils détectent et les mesures nécessaires à prendre en réponse à un problème, sont décrits ci-dessous : DOCA0128FR-02 53 Contrôleur de gestion des moteurs Maintenance Type Erreur détectée Action Déclenchements internes majeurs Déclenchement par température interne Ce déclenchement indique une alarme à 80 °C, un déclenchement mineur à 85 °C et un déclenchement majeur à 100 °C. Pour réduire la température ambiante, procédez comme suit : • Ajoutez un ventilateur auxiliaire • Remontez le contrôleur LTMR et le module d’extension afin de laisser un plus grand dégagement autour de l’ensemble. Si la situation persiste : 1 Coupez et rétablissez l’alimentation. 2 Patientez 30 s. 3 Si le déclenchement persiste, remplacez le contrôleur LTMR. Défaut détecté par l'UC Erreur de checksum de programme Ces déclenchements indiquent une défaillance du matériel. Exécutez les étapes suivantes : 1 Coupez et rétablissez l’alimentation. 2 Patientez 30 s. Déclenchement du test de RAM 3 Si le déclenchement persiste, remplacez le contrôleur LTMR. Débordement de pile Débordement négatif de pile Temporisation du chien de garde Déclenchements internes mineurs Déclenchement par configuration invalide Déclenchement de checksum de configuration (EEROM) Indique soit un mauvais checksum (erreur de checksum de configuration), soit un bon checksum, mais des données fausses (déclenchement par configuration invalide). Dans les deux cas, une défaillance du matériel en est à l’origine. Exécutez les étapes suivantes : 1 Redémarrez et patientez 30 s. 2 Réinitialisez les paramètres de configuration aux réglages usine. 3 Si le déclenchement persiste, remplacez le contrôleur LTMR. Erreurs détectées lors du diagnostic Détection d’une défaillance interne des communications réseau Ces déclenchements indiquent une défaillance du matériel. Exécutez les étapes suivantes : 1 Redémarrez et patientez 30 s. Déclenchement par dépassement des limites d’A/ N 2 Si le déclenchement persiste, remplacez le contrôleur LTMR. Vérification de la commande de démarrage Indique que l’appareil a détecté la présence ou l’absence d’un courant de moteur différent de l’état attendu. Vérifiez les éléments suivants : Test de la commande d’arrêt • • Vérification de l’arrêt du moteur Vérification du fonctionnement du moteur Sorties relais Ensemble du câblage, notamment : ◦ Circuit de commande, y compris tous les équipements électromécaniques ◦ Circuit d’alimentation, y compris tous les composants ◦ Câblage TC charge Une fois toutes les vérifications terminées : 1 Réarmez le déclenchement. 2 Si le défaut persiste, redémarrez et patientez 30 s. 3 Si le déclenchement persiste, remplacez le contrôleur LTMR. 54 DOCA0128FR-02 Maintenance Contrôleur de gestion des moteurs Type Erreur détectée Action Déclenchements de câblage/ configuration Déclenchement par inversion des transformateurs de courant Corrigez la polarité des transformateurs de courant. Assurez-vous que : • Tous les TC externes sont orientés dans le même sens • Tous les câblages TC charge passent à travers les ouvertures dans le même sens Une fois la vérification terminée : 1 Procédez à un réarmement du déclenchement. 2 Si le défaut persiste, redémarrez et patientez 30 s. 3 Si le déclenchement persiste, remplacez le contrôleur LTMR. Déclenchement par inversion de courant/tension de phase Déclenchement par configuration de phase Vérifiez : • que les câbles des raccordements L1, L2 et L3 ne sont pas croisés ; • le réglage du paramètre moteur - séquence des phases (ABC par rapport à ACB) ; Une fois toutes les vérifications terminées : 1 Procédez à un réarmement du déclenchement. 2 Si le défaut persiste, redémarrez et patientez 30 s. 3 Si le déclenchement persiste, remplacez le contrôleur LTMR. Déclenchement par connexion PTC Vérifiez que : • court-circuit ou circuit ouvert dans le câblage du capteur de température du moteur • type de capteur de température du moteur incorrect • configuration des paramètres de l’équipement sélectionné incorrecte Une fois toutes les vérifications terminées : 1 Procédez à un réarmement du déclenchement. 2 Si le défaut persiste, redémarrez et patientez 30 s. 3 Si le déclenchement persiste, remplacez le contrôleur LTMR. Déclenchement par perte de tension de phase Vérifiez que : • câblage incorrect (par exemple des terminaisons desserrées) • des fusibles ont sauté • des fils sont coupés • moteur monophasé configuré pour un fonctionnement triphasé • moteur monophasé non raccordé via les ouvertures du TC de charge A et C • Perte de la source d’alimentation (par exemple, l’alimentation principale). Une fois toutes les vérifications terminées : 1 Procédez à un réarmement du déclenchement. 2 Si le défaut persiste, redémarrez et patientez 30 s. 3 Si le déclenchement persiste, remplacez le contrôleur LTMR. Maintenance préventive Présentation Les mesures de protection suivantes doivent être effectuées entre les principales vérifications système, afin de permettre la maintenance de votre système ainsi que sa protection contre les déclenchements logiciels et matériels irrémédiables : DOCA0128FR-02 • l’examen continu des statistiques de fonctionnement ; • l’enregistrement des paramètres de configuration du contrôleur LTMR dans un fichier de sauvegarde ; • la maintenance de l’environnement du contrôleur LTMR ; • l’exécution périodique d’un autotest du contrôleur LTMR ; • la vérification de l’horloge interne du contrôleur LTMR pour garantir la précision. 55 Contrôleur de gestion des moteurs Maintenance Statistiques Le contrôleur LTMR collecte les types d’information suivants : • Données de tension, de courant, d’alimentation, de température, d’E/S et de déclenchement, en temps réel. • Nombre de déclenchements, par type de défaut, survenus depuis la dernière mise sous tension. • Historique horodaté de l’état du contrôleur LTMR, qui affiche les mesures de la tension, du courant, de l’alimentation et de la température, au moment où chacun des 5 derniers déclenchements sont survenus. Utilisez le logiciel SoMove avec TeSys T DTM, une IHM Magelis XBTN410, ou une unité d’opérateur de commande TeSys T LTMCU pour accéder à ces statistiques et les consulter. Analysez ces informations pour déterminer si l’enregistrement actuel des opérations signale un problème. Paramètres de configuration En cas de déclenchement irréparable du contrôleur LTMR, vous pouvez rapidement restaurer les paramètres de configuration si vous les avez enregistrés dans un fichier. Lorsque le contrôleur LTMR est configuré pour la première fois (et chaque fois que les paramètres de configuration sont modifiés), utilisez le logiciel SoMove avec TeSys T DTM pour enregistrer les réglages des paramètres dans un fichier. Pour enregistrer un fichier de configuration : • Sélectionnez Fichier > Enregistrer sous.... Pour restaurer le fichier de configuration enregistré : 1. Ouvrez le fichier enregistré : Sélectionnez Fichier > Ouvrir (puis parcourez les fichiers). 2. Téléchargez le fichier de configuration vers le nouveau contrôleur. 3. Sélectionnez Communication > Transférer dans l’appareil. Environnement Comme tout autre équipement électronique, le contrôleur LTMR est affecté par son environnement physique. Assurez-vous que l’environnement est convivial en prenant des mesures préventives logiques, notamment : • en programmant des examens périodiques des blocs batterie, des fusibles, des blocs prise, des piles, des parasurtenseurs et des alimentations. • En gardant propres le contrôleur LTMR, le panneau et tous les équipements. Un flux d’air libre empêchera l’accumulation de poussière, propice aux conditions de court-circuit. • En restant vigilant pour éviter le risque de radiations électromagnétiques produites par d’autres équipements. Assurez-vous qu’aucun équipement ne provoque d’interférences électromagnétiques avec le contrôleur LTMR. Autotest avec le moteur coupé Exécutez un autotest soit : 56 • en maintenant enfoncé le bouton Test/Reset situé sur la face du contrôleur LTMR pendant 3 à 15 secondes • Commande des menus via l'affichage du LTMCU • En définissant le paramètre de Commande d’autotest (Registre 704.5). DOCA0128FR-02 Maintenance Contrôleur de gestion des moteurs Pour indiquer que l’autotest est en cours, tous les voyants d’état (IHM, alimentation, alarme, annulation, automate programmable) sont allumés et les relais de sortie sont ouverts. Un autotest peut être exécuté seulement si : • Il n’y a pas de déclenchement, • Le paramètre d’activation de l’autotest est défini (réglages usine). Le contrôleur LTMR exécute les vérifications suivantes pendant un autotest : • une vérification de chien de garde ; • une vérification de la mémoire RAM ; • Contrôle de la constante de temps de la mémoire thermique • Un test de module d’extension LTME (s’il est connecté à un module d’extension) • Un test de communication interne • Test voyants : tous les voyants sont éteints, puis chaque voyant s’allume dans l’ordre : • ◦ Voyant d’activité de communication HMI ◦ Voyant d'alimentation ◦ Voyant Fallback (repli) ◦ Voyant d’activité de communication d’automate Test du relais de sortie : ouvre tous les relais En cas d’échec de l’un des tests, le LTMR signale un déclenchement interne mineur. En cas de mesure de courant à l’une des étapes de l’autotest, le contrôleur LTMR active immédiatement un Déclenchement d’autotest. À la fin du test, si aucune erreur n’est détectée, tous les voyants demeurent allumés et les relais de sortie demeurent ouverts jusqu’à ce que le bouton de réinitialisation soit activé ou que l’alimentation soit coupée et rétablie. Durant l’autotest du contrôleur LTMR, la chaîne « autotest » s’affiche sur l’HMI. Autotest avec moteur allumé Exécutez un autotest soit : • en maintenant enfoncé le bouton Test/Reset situé sur la face du contrôleur LTMR pendant 3 à 15 secondes • Commande des menus via l'affichage du LTMCU • En définissant le paramètre de Commande d’autotest (Registre 704.5). Lorsque le moteur est allumé, le fait d’exécuter un autotest simule un déclenchement thermique qui permet de vérifier si la sortie logique O.4 fonctionne correctement. Cela déclenche un déclenchement de surcharge thermique. Pendant un autotest, le contrôleur LTMR définit le paramètre de Commande d’autotest sur 1. À la fin de l’autotest, ce paramètre est réinitialisé à 0. Horloge interne Pour garantir un enregistrement précis des déclenchements, assurez-vous de maintenir l'horloge interne du contrôleur LTMR. L’horodatage du contrôleur LTMR marque tous les défauts, à l’aide de la valeur stockée dans le paramètre Date et heure. DOCA0128FR-02 57 Contrôleur de gestion des moteurs Maintenance La précision de l’horloge interne est de +/- 1 seconde par heure. Si l’alimentation est appliquée en continu pendant un an, la précision de l’horloge interne est de +/- 30 minutes par an. Si l’alimentation est désactivée pendant 30 minutes ou moins, le contrôleur LTMR conserve ses paramètres d’horloge interne, avec une précision de +/- 2 minutes. Si l’alimentation est désactivée pendant plus de 30 minutes, le contrôleur LTMR réinitialise son horloge interne à l’heure où l’alimentation a été coupée. Remplacement d’un contrôleur LTMR et d’un module d’extension LTME Présentation Les points à prendre en compte à l’avance lors du remplacement du contrôleur LTMR ou d’un module d'extension LTME sont les suivants : • Le modèle de l’équipement de remplacement est-il le même que l’original ? • Les paramètres de configuration du contrôleur LTMR ont-ils été enregistrés et sont-ils disponibles pour être transférés vers l’équipement de remplacement ? Assurez-vous que le moteur est arrêté avant de remplacer le contrôleur LTMR ou le module d’extension LTME. Remplacement du contrôleur LTMR Il faut envisager le remplacement d’un contrôleur LTMR : • si les paramètres du contrôleur LTMR sont configurés initialement et • chaque fois qu'un ou plusieurs de ses paramètres sont reconfigurés par la suite. Comme les valeurs des paramètres peuvent ne pas être accessibles lorsque le contrôleur LTMR est remplacé, par exemple, en cas de défaillance de l’équipement, vous devez créer un enregistrement de ces valeurs chaque fois qu’elles sont définies. SoMove avec TeSys T DTM, tous les paramètres configurés de contrôleur LTMR, excepté la date et l’heure peuvent être enregistrés dans un fichier. Une fois enregistrés, vous pouvez utiliser SoMove avec TeSys T DTM pour transférer ces paramètres soit vers le contrôleur LTM R d’origine, soit vers son remplaçant. NOTE: Seuls les paramètres configurés sont enregistrés. Les données statistiques historiques ne sont pas enregistrées et par conséquent ne peuvent pas être appliquées à un contrôleur LTMR de remplacement. Pour plus d’informations sur la façon d’utiliser le logiciel SoMove pour créer, enregistrer et transférer les fichiers des paramètres de configuration, reportezvous à l’Aide en ligne de SoMove. Remplacement du module d’extension Il est primordial de remplacer le module d’extension LTME par le même modèle (24 VCC ou 110 - 240 VCA) que l’original. 58 DOCA0128FR-02 Maintenance Contrôleur de gestion des moteurs Mise hors service des équipements Le contrôleur LTMR et le module d’extension LTME contiennent des circuits électroniques qui nécessitent un traitement particulier à la fin de leur vie utile. Lors de la mise hors service d’un équipement, assurez-vous de respecter toutes les pratiques, réglementations et lois en vigueur. Alarmes et déclenchements de communication Présentation Les déclenchements et les alarmes de communication sont gérés de manière standard, comme tous les autres types de déclenchement et d’alarmes. La présence d’un déclenchement est signalée par plusieurs indicateurs : • État des voyants : ◦ Sur les contrôleurs Ethernet LTMR : 3 voyants sont dédiés à la communication, 1 voyant STS et 2 voyants LK/ACT, un pour chaque connecteur de port réseau. ◦ Sur les contrôleurs Modbus LTMR : 1 voyant dédié à la communication, PLC Comm. ◦ Sur les contrôleurs LMTR PROFIBUS DP : 1 voyant dédié à la communication, BF. ◦ Sur les contrôleurs LTMR CANopen : 1 voyant dédié à la communication, Status. ◦ Sur les contrôleurs LTMR DeviceNet : 1 voyant dédié à la communication du MNS. • Etat des relais de sortie • Alarme • Message(s) affiché(s) sur l’écran de l’HMI • Présence d’un code d’exception (un compte-rendu de l’automate, par exemple). Perte de communication avec l’automate Une perte de communication est gérée de la même manière que les autres déclenchements. Le contrôleur LTMR surveille la communication avec l’automate. A l’aide d’un temps d’inactivité du réseau réglable (temporisation), la fonction de chien de garde du contrôleur LTMR peut signaler une perte de réseau (chien de garde du firmware). NOTE: La temporisation n’est pas définie dans le contrôleur LTMR PROFIBUS DP, mais au niveau primaire du PROFIBUS DP. Si le PROFIBUS DP primaire permet la modification de cette temporisation, sa valeur doit être transmise par l’unité primaire au contrôleur LTMR PROFIBUS DP. En cas de perte de réseau, le contrôleur LTMR peut-être configuré afin d’exécuter certaines actions. Celles-ci dépendent du mode de contrôle sous lequel le contrôleur LTMR fonctionnait avant la perte de réseau. Si la communication automate-contrôleur LTMR est perdue alors que le contrôleur LTMR est en mode de contrôle Réseau, le contrôleur LTMR passe en état de repli. Si la communication automate-contrôleur LTMR est perdue alors que le contrôleur LTMR est en mode de contrôle Local, puis passe en mode de contrôle Réseau, le contrôleur LTMR passe en état de repli. DOCA0128FR-02 59 Contrôleur de gestion des moteurs Maintenance Si la communication automate-contrôleur LTMR est restaurée alors que le mode de contrôle est défini sur Réseau, le contrôleur LTMR quitte l’état de repli. Si le mode de contrôle passe en Local, le contrôleur LTMR quitte l’état de repli, quel que soit l’état des communications automate-contrôleur. Le tableau ci-dessous définit les actions possibles que le contrôleur LTMR peut exécuter pendant une perte de communication et que l’utilisateur peut sélectionner lors de la configuration du contrôleur LTMR. Actions lors d’une perte de communication en mode Réseau : Mode de contrôle de sortie du contrôleur LTMR avant la perte de réseau Actions possibles du contrôleur LTMR après perte de réseau automatecontrôleur LTMR Bornier et contrôle HMI Possibilités de contrôle des déclenchements et des alarmes : Contrôle Réseau • Aucun signal • Activer une alarme • Activer un déclenchement • Activer un déclenchement et une alarme Possibilités de contrôle des déclenchements et des alarmes : • Aucun signal • Activer une alarme • Activer un déclenchement • Activer un déclenchement et une alarme • Le fonctionnement des relais LO1 et LO2 dépend du mode de contrôle du moteur et de la stratégie de repli choisis. Perte de communication avec l’HMI Le contrôleur LTMR surveille la communication avec tous les ports HMI recommandés. A l’aide d’un temps d’inactivité du réseau fixe (temporisation), la fonction de chien de garde du contrôleur LTMR peut indiquer une perte de réseau. En cas de perte de communication, le contrôleur LTMR peut-être configuré afin d’exécuter certaines actions. Celles-ci dépendent du mode de contrôle sous lequel le contrôleur LTMR fonctionnait avant la perte de communication. Si la communication HMI-contrôleur est perdue alors que le contrôleur LTMR est en mode de contrôle HMI, le contrôleur LTMR passe en état de repli. Si la communication HMI-contrôleur LTMR est perdue alors que le contrôleur LTMR n’est pas en mode de contrôle HMI, puis passe en mode de contrôle HMI, le contrôleur LTMR passe en état de repli. Si la communication HMI-contrôleur est restaurée alors que le mode de contrôle est défini sur HMI, le contrôleur LTMR quitte l’état de repli. Si le mode de contrôle passe en mode Bornier ou Réseau, le contrôleur LTMR quitte l’état de repli, quel que soit l’état des communications HMI-contrôleur. Le tableau ci-dessous définit les actions possibles que le contrôleur LTMR peut exécuter lors d’une perte de communication. Sélectionnez l’une de ces actions lors de la configuration du contrôleur LTMR. 60 DOCA0128FR-02 Maintenance Contrôleur de gestion des moteurs Mode de contrôle de sortie du contrôleur LTMR avant la perte HMI Actions possibles du contrôleur LTMR après perte HMI-contrôleur LTMR Bornier et contrôle réseau Possibilités de contrôle des déclenchements et des alarmes : Contrôle HMI • Aucun signal • Activer une alarme • Activer un déclenchement • Activer un déclenchement et une alarme Possibilités de contrôle des déclenchements et des alarmes : • Aucun signal • Activer une alarme • Activer un déclenchement • Activer un déclenchement et une alarme • Le fonctionnement des relais LO1 et LO2 dépend du mode de contrôle du moteur et de la stratégie de repli choisis. NOTE: Pour plus d’informations sur la perte de communication et la stratégie de repli, consultez la section Condition de repli de la rubrique décrivant la Perte de communication du document TeSys T LTMR - Contrôleur de gestion de moteur - Guide utilisateur. DOCA0128FR-02 61 Contrôleur de gestion des moteurs Paramètres configurables Paramètres configurables Présentation Les paramètres configurables du contrôleur LTMR et du module d'extension LTME sont décrits ci-dessous. La séquence de configuration des paramètres dépend de l’outil de configuration utilisé, soit une unité HMI, soit le logiciel SoMove avec TeSys T DTM. Les paramètres sont regroupés en fonction de l’onglet Liste de paramètres de TeSys T DTM. Pour vous aider à trouver la liaison avec les tables de variables dans le chapitre Utilisation, chaque paramètre possède un numéro de registre correspondant. AVERTISSEMENT RISQUE DE CONFIGURATION ET FONCTIONNEMENT IMPREVUS Lorsque vous modifiez des paramètres du contrôleur LTMR : • Soyez particulièrement prudent si vous modifiez les paramètres alors que le moteur tourne. • Désactivez le contrôle réseau du contrôleur LTMR afin d’éviter une configuration et un fonctionnement imprévus des paramètres. Le non-respect de ces instructions peut provoquer la mort, des blessures graves ou des dommages matériels. Paramètres principaux Phases Paramètre Phases moteur Plage de réglage • Moteur triphasé • Moteur monophasé Réglage usine Moteur triphasé Mode de fonctionnement Paramètre Mode de fonctionnement moteur Moteur en configuration étoile-triangle Plage de réglage • Surcharge - 2 fils • Surcharge - 3 fils • Indépendant - 2 fils • Indépendant - 3 fils • Inverse - 2 fils • Inverse - 3 fils • Deux étapes 2 fils • Deux étapes 3 fils • Deux vitesses - 2 fils • Deux vitesses - 3 fils • Personnalisé 0 = désactivé Réglage usine Indépendant - 3 fils 0 1 = activé 62 DOCA0128FR-02 Paramètres configurables Contrôleur de gestion des moteurs Contacteur Paramètre Plage de réglage Réglage usine Contacteur - courant de coupure De 1 à 1 000 A par incréments de 1 A 810 A Moteur Paramètre Plage de réglage Réglage usine Moteur - tension nominale 110 à 690 V 400 V Puissance nominale du moteur 0.134...1339.866 HP 10,05 HP Puissance nominale du moteur 0,1 à 999,9 kW par incréments de 0,1 kW 7,5 kW Moteur - ventilateur auxiliaire • Désactiver • Activer Désactiver Rapport de courant à pleine charge du moteur (FLC1) 5...100 % du courant de pleine charge maximal par incréments de 1 % 5 % du courant de pleine charge maximal Moteur - courant à pleine charge – – Moteur - rapport du courant à pleine charge - haute vitesse (FLC2) 5...100 % du courant de pleine charge maximal par incréments de 1 % 5 % du courant de pleine charge maximal Moteur - haute vitesse - courant à pleine charge (FLC2) 0...100 A par incréments de 1 A 5A Transformateur de courant de charge Paramètre Plage de réglage Réglage usine TC charge - primaire De 1 à 65 535 par incréments de 1 1 TC charge - secondaire De 1 à 500 par incréments de 1 1 TC de charge à passages multiples De 1 à 100 passages par incréments de 1 1 Transformateur de courant de fuite à la terre Paramètre Mode Courant à la terre Plage de réglage • Interne • Externe Réglage usine Interne TC terre - primaire De 1 à 65 535 par incréments de 1 1 TC terre - secondaire De 1 à 65 535 par incréments de 1 1 Contrôle Mode de fonctionnement Paramètre Plage de réglage Réglage usine Contrôle - mode de transition Marche/Arrêt Désactivé Moteur - temporisation transition 0...999,9 s 1s DOCA0128FR-02 63 Contrôleur de gestion des moteurs Paramètres configurables Paramètre Plage de réglage Réglage usine Moteur - seuil étape 1 à 2 De 20 à 800 % de courant de pleine charge par incréments de 1 % 150 % du courant FLC Moteur - temporisation étape 1 à 2 0,1...999,9 s 5s Entrées/Sorties Paramètre Configuration des entrées logiques CA du contrôleur Activation de l’entrée logique 3 pour l’état externe prêt Plage de réglage • Inconnu • Inférieur à 170 V 50 Hz • Inférieur à 170 V 60Hz • Supérieur à 170 V 50 Hz • Supérieur à 170 V 60Hz • Désactiver • Activer Réglage usine Inconnu Désactiver Cycle rapide Paramètre Plage de réglage Réglage usine Cycle rapide - temporisation verrouillage De 0 s à 9999 s par incréments de 1 s 0s Contrôle local/distant Paramètre Contrôle - sélection du canal distant Plage de réglage • Réseau • Bornier • HMI • Bornier • HMI • A-coups • Sans à-coups Contrôle - activation des boutons de commande locale/à distance • Désactiver • Activer Contrôle - mode de défaut local/à distance • A distance • Local • Activer • Désactiver • Activer • Désactiver Contrôle - sélection du canal local Contrôle - mode de transfert Désactivation de la touche d’arrêt de l’IHM Désactivation de l’arrêt sur le bornier Réglage usine Réseau Bornier A-coups Désactiver A distance Désactiver Désactiver Diagnostic Paramètre Plage de réglage Activation du déclenchement de diagnostic • • Activer Activation de l’alarme de diagnostic • Désactiver • Activer 64 Désactiver Réglage usine Activer Activer DOCA0128FR-02 Paramètres configurables Contrôleur de gestion des moteurs Paramètre Plage de réglage Activation du déclenchement de câblage Moteur - séquence des phases • Désactiver • Activer • A-B-C • A-C-B Réglage usine Activer A-B-C Déclenchement et alarme Paramètre Plage de réglage Mode de réarmement du déclenchement • Manuel ou HMI • A distance par réseau • Automatique Réglage usine Manuel ou HMI Réarmement automatique - réglage tentatives groupe 1 0 = manuel, 1, 2, 3, 4, 5 = nombre illimité de tentatives de réarmement 5 Réarmement automatique groupe 1 - temporisation De 0 s à 9 999 s par incréments de 1 s 480 s Réarmement automatique - réglage tentatives groupe 2 0 = manuel, 1, 2, 3, 4, 5 = nombre illimité de tentatives de réarmement 0 Réarmement automatique groupe 2 - temporisation De 0 s à 9999 s par incréments de 1 s 1 200 s Réarmement automatique - réglage tentatives groupe 3 0 = manuel, 1, 2, 3, 4, 5 = nombre illimité de tentatives de réarmement 0 Réarmement automatique groupe 3 - temporisation De 0 s à 9999 s par incréments de 1 s 60 s Communication Configuration du contrôle des ports réseau et du repli Pour plus d’informations sur les paramètres de configuration du réseau de communication, consultez • TeSys T LTMR Ethernet - Guide de communication • TeSys T LTMR Modbus - Guide de communication • TeSys T LTMR PROFIBUS DP - Guide de communication • TeSys T LTMR CANopen - Guide de communication • TeSys T LTMR - Guide de communication DeviceNet Port HMI Paramètre Plage de réglage Réglage usine Port IHM - réglage adresse 1...247 1 Port IHM - réglage vitesse en bauds Port IHM - réglage parité Port IHM - réglage endian Réglage de repli du port HMI DOCA0128FR-02 • 4 800 • 9 600 • 19 200 • Auto détection • Néant • Paire • LSW first (little endian) • MSW first (big endian) • Suspendre LO1 LO2 • Exécution (2 étapes) ou désactivé 19 200 bits/s Paire MSW first (big endian) LO1, LO2 off 65 Contrôleur de gestion des moteurs Paramètre Port IHM - activation du déclenchement Port IHM - activation de l’alarme Activation de la configuration via l’IHM Activation de la configuration via le clavier de l'IHM Paramètres configurables Plage de réglage • LO1, LO2 off • LO1, LO2 activé (ovl, ind, cust) ou désactivé • LO1 activé ou désactivé (2 étapes) • LO2 activé ou désactivé (2 étapes) • Désactiver • Activer • Désactiver • Activer • Interdit • Autorisé • Interdit • Autorisé Réglage usine Désactiver Désactiver Autorisé Autorisé Thermique Surcharge thermique Paramètre Mode Surcharge thermique Moteur - classe de déclenchement Activation du déclenchement par surcharge thermique Seuil de réarmement du déclenchement par surcharge thermique Activation de l’alarme de surcharge thermique Plage de réglage • Défini • Inversion thermique • Classe de moteur 5 • Classe de moteur 10 • Classe de moteur 15 • Classe de moteur 20 • Classe de moteur 25 • Classe de moteur 30 • Désactiver • Activer 35...95 % par incréments de 1 % • Désactiver • Activer Réglage usine Inversion thermique Classe de moteur 5 Activer 75 % Activer Seuil d’alarme de surcharge thermique 10..100 % par incréments de 1 % 85 % Temporisation de déclenchement de démarrage long De 1 s à 200 s par incréments de 1 s 10 s Activation du déclenchement par surcharge thermique Temporisation définie du déclenchement par surcharge thermique Activation de l’alarme de surcharge thermique 66 • Désactiver • Activer De 1 s à 300 s par incréments de 1 s • Désactiver • Activer Activer 10 s Activer DOCA0128FR-02 Paramètres configurables Contrôleur de gestion des moteurs Température moteur Paramètres Type de capteur de température moteur Activation du déclenchement du capteur de température moteur Plage de réglages • Néant • PTC binaire • PT100 • PTC analogique • NTC analogique • Désactiver • Activer Réglage usine Néant Désactiver Seuil de déclenchement du capteur de température moteur 20 à 6 500 Ω 20 Ω Seuil de déclenchement du capteur de température moteur (en degrés) 0...200 °C 0℃ Activation de l’alarme du capteur de température moteur • Désactiver • Activer Désactiver Seuil d’alarme du capteur de température moteur 20 à 6 500 Ω 20 Ω Seuil d’alarme du capteur de température moteur (en degrés) 0...200 °C 0℃ Courant Courant de terre Paramètres Plage de réglages Courant à la terre désactivé lors du démarrage du moteur Activation du déclenchement par courant à la terre • Non • Oui • Désactiver • Activer Réglage usine Non Activer Seuil interne de déclenchement par courant à la terre De 20 à 500 % du courant FLCmin par incréments de 1 % 30 % du courant FLCmin Temporisation interne du déclenchement par courant à la terre De 0,5 s à 25 s par incréments de 0,1 s 1s Seuil externe de déclenchement par courant à la terre De 0,02 à 20 °A par incréments de 0,01 A 1A Temporisation externe du déclenchement par courant à la terre De 0,1 s à 25 s par incréments de 0,01 s 0,5 s Activation de l’alarme de courant à la terre • Désactiver • Activer Activer Seuil interne de l’alarme de courant à la terre De 50 à 500 % du courant FLCmin par incréments de 1 % 50 % du courant FLCmin Seuil externe de l’alarme de courant à la terre De 0,02 à 20 °A par incréments de 0,01 A 1A Phases Paramètres Activation du déclenchement par déséquilibre de courant de phase Seuil de déclenchement par déséquilibre de courant de phase DOCA0128FR-02 Plage de réglages • Désactiver • Activer De 10 à 70 % par incréments de 1 % Réglage usine Activer 10 % 67 Contrôleur de gestion des moteurs Paramètres configurables Paramètres Plage de réglages Réglage usine Démarrage de la temporisation du déclenchement par déséquilibre de courant de phase De 0,2 s à 20 s par incréments de 0,1 s 0,7 s Temporisation de déclenchement par déséquilibre de courant de phase De 0,2 s à 20 s par incréments de 0,1 s 5s Activation de l’alarme de déséquilibre de courant de phase Seuil de l’alarme de déséquilibre de courant de phase Activation du déclenchement par perte de courant de phase Temporisation de perte de courant de phase Activation de l’alarme de perte de courant de phase Activation du déclenchement par inversion du courant de phase • Désactiver • Activer De 10 à 70 % par incréments de 1 % • Désactiver • Activer De 0,1 s à 30 s par incréments de 0,1 s • Désactiver • Activer • Désactiver • Activer Désactiver 10 % Activer 3s Activer Désactiver Démarrage long Paramètres Activation du déclenchement de démarrage long Plage de réglages • Désactiver • Activer Réglage usine Activer Seuil de déclenchement de démarrage long De 100 à 800 % de courant de pleine charge par incréments de 1 % 100 % du courant FLC Temporisation de déclenchement de démarrage long De 1 s à 200 s par incréments de 1 s 10 s Blocage Paramètres Activation du déclenchement par blocage Plage de réglages • Désactiver • Activer Réglage usine Activer Seuil de déclenchement de blocage De 100 à 800 % de courant de pleine charge par incréments de 1 % 200 % du courant FLC Temporisation de déclenchement de blocage De 1 s à 30 s par incréments de 1 s 5s Activation de l'alarme de blocage Seuil d’alarme de blocage • Désactiver • Activer De 100 à 800 % de courant de pleine charge par incréments de 1 % Désactiver 200 % du courant FLC Sous-intensité Paramètres Activation du déclenchement par sous-intensité Plage de réglages • Désactiver • Activer Réglage usine Désactiver Seuil de déclenchement par sous-intensité De 30 à 100 % de courant de pleine charge par incréments de 1 % 50 % du courant FLC Temporisation du déclenchement par sous-intensité De 1 s à 200 s par incréments de 1 s 10 s 68 DOCA0128FR-02 Paramètres configurables Paramètres Contrôleur de gestion des moteurs Plage de réglages Activation de l’alarme de sous-intensité Seuil de l’alarme de sous-intensité • Désactiver • Activer De 30 à 100 % de courant de pleine charge par incréments de 1 % Réglage usine Désactiver 50 % du courant FLC Surintensité Paramètres Plage de réglages Activation du déclenchement par surintensité • Désactiver • Activer Réglage usine Désactiver Seuil de déclenchement par surintensité De 20 à 800 % de courant de pleine charge par incréments de 1 % 200 % du courant FLC Temporisation du déclenchement par surintensité De 1 s à 250 s par incréments de 1 s 10 s Activation de l’alarme de surintensité Seuil de l’alarme de surintensité • Désactiver • Activer De 20 à 800 % de courant de pleine charge par incréments de 1 % Désactiver 200 % du courant FLC Tension Phases Paramètres Activation du déclenchement par déséquilibre de tension de phase Plage de réglages • Désactiver • Activer Réglage usine Désactiver Seuil de déclenchement par déséquilibre de tension de phase De 3 à 15 % du déséquilibre calculé par incréments de 1 % Déséquilibre 10 % Temporisation du déclenchement par déséquilibre de tension de phase pendant le démarrage De 0,2 s à 20 s par incréments de 1 s 0,7 s Temporisation de déclenchement par déséquilibre de tension de phase pendant le moteur en marche De 0,2 s à 20 s par incréments de 1 s 2s Activation de l’alarme de déséquilibre de tension de phase Seuil de l’alarme de déséquilibre de tension de phase Activation du déclenchement par perte de tension de phase Temporisation du déclenchement par perte de tension de phase Activation de l’alarme de perte de tension de phase Activation de la perte par inversion de la tension de phase DOCA0128FR-02 • Désactiver • Activer De 3 à 15 % du déséquilibre calculé par incréments de 1 % • Désactiver • Activer De 0,1 s à 30 s par incréments de 0,1 s • Désactiver • Activer • Désactiver • Activer Désactiver Déséquilibre 10 % Désactiver 3s Désactiver Désactiver 69 Contrôleur de gestion des moteurs Paramètres configurables Sous-tension Paramètres Plage de réglages Activation du déclenchement par sous-intensité • Désactiver • Activer Réglage usine Désactiver Seuil de déclenchement par sous-tension De 70 à 99 % de la tension nominale du moteur par incréments de 1 % 85 % de la tension nominale du moteur Temporisation du déclenchement par sous-tension De 0,2 s à 25 s par incréments de 0,1 s 3s Activation de l’alarme de sous-tension Seuil de l’alarme de sous-tension • Désactiver • Activer De 70 à 99 % de la tension nominale du moteur par incréments de 1 % Désactiver 85 % de la tension nominale du moteur Surtension Paramètres Plage de réglages Activation du déclenchement par surtension • Désactiver • Activer Réglage usine Désactiver Seuil de déclenchement par surtension De 101 à 115 % de la tension nominale du moteur par incréments de 1 % 110 % de la tension nominale du moteur Temporisation du déclenchement par surtension De 0,2 s à 25 s par incréments de 0,1 s 3s Activation de l’alarme de surtension Seuil de l’alarme de surtension • Désactiver • Activer De 101 à 115 % de la tension nominale du moteur par incréments de 1 % Désactiver 110 % de la tension nominale du moteur Creux de tension Paramètres Mode Creux de tension Plage de réglages • Néant • Délestage • Redémarrage automatique Réglage usine Néant Seuil du creux de tension De 50 à 115 % de la tension nominale du moteur par incréments de 1 % 65 % de la tension nominale du moteur Temporisation d'activation du délestage De 1 s à 9999 s par incréments de 1 s 10 s Seuil de redémarrage du mode Creux de tension De 65 à 115 % de la tension nominale du moteur par incréments de 1 % 90 % de la tension nominale du moteur Temporisation redémarrage du mode Creux de tension De 0 s à 9999 s par incréments de 1 s 2s Seuil du creux de tension De 50 à 115 % de la tension nominale du moteur par incréments de 1 % 65 % de la tension nominale du moteur Seuil de redémarrage du mode Creux de tension De 65 à 115 % de la tension nominale du moteur par incréments de 1 % 90 % de la tension nominale du moteur Temporisation redémarrage du mode Creux de tension De 0 s à 9999 s par incréments de 1 s 2s Temporisation du redémarrage automatique immédiat De 0 s à 0,4 s par incréments de 0,1 s 0,2 s Temporisation du redémarrage automatique différé De 0 s à 301 s par incréments de 1 s 4s 70 DOCA0128FR-02 Paramètres configurables Contrôleur de gestion des moteurs Puissance Sous-charge en puissance Paramètres Activation du déclenchement par sous-charge en puissance Plage de réglages • Désactiver • Activer Réglage usine Désactiver Seuil de déclenchement par sous-charge en puissance De 20 à 800 % de la puissance nominale du moteur par incréments de 1 % 20 % de la tension nominale du moteur Temporisation du déclenchement par sous-charge en puissance De 1 s à 100 s par incréments de 1 s 60 s Activation de l’alarme de sous-charge en puissance Seuil de l’alarme de sous-charge en puissance • Désactiver • Activer De 20 à 800 % de la puissance nominale du moteur par incréments de 1 % Désactiver 30 % de la tension nominale du moteur Surcharge en puissance Paramètres Activation du déclenchement par surcharge en puissance Plage de réglages • Désactiver • Activer Réglage usine Désactiver Seuil de déclenchement par surcharge en puissance De 20 à 800 % de la puissance nominale du moteur par incréments de 1 % 150 % de la tension nominale du moteur Temporisation du déclenchement par surcharge en puissance De 1 s à 100 s par incréments de 1 s 60 s Activation de l’alarme par surcharge en puissance Seuil de l’alarme de surcharge en puissance • Désactiver • Activer Désactiver De 20 à 800 % de la puissance nominale du moteur par incréments de 1 % 150 % de la tension nominale du moteur Plage de réglages Réglage usine Sous-facteur de puissance Paramètres Activation du déclenchement par sous-facteur de puissance • Désactiver • Activer Désactiver Seuil de déclenchement par sous-facteur de puissance De 0 à 1 par incréments de 0,01 0,6 Temporisation du déclenchement par sous-facteur de puissance De 1 s à 25 s par incréments de 0,1 s 10 s Activation de l’alarme de sous-facteur de puissance Seuil de l’alarme de sous-facteur de puissance • Désactiver • Activer De 0 à 1 par incréments de 0,01 Désactiver 0,6 Sur-facteur de puissance Paramètres Activation du déclenchement par sur-facteur de puissance Seuil de déclenchement par sur-facteur de puissance DOCA0128FR-02 Plage de réglages • Désactiver • Activer De 0 à 1 par incréments de 0,01 Réglage usine Désactiver 0,9 71 Contrôleur de gestion des moteurs Paramètres configurables Paramètres Plage de réglages Réglage usine Temporisation du déclenchement par sous-facteur de puissance De 1 s à 25 s par incréments de 0,1 s 10 s Activation de l’alarme de sur-facteur de puissance Seuil de l’alarme de sur-facteur de puissance • Désactiver • Activer De 0 à 1 par incréments de 0,01 Désactiver 0,9 HMI Affichage HMI Paramètre Plage de réglages Réglage usine Affichage HMI - sélection langue – English HMI - réglage contraste affichage 0...255 127 HMI - réglage luminosité affichage 0...255 127 HMI - couleur voyant état moteur • Rouge • Vert Rouge Clavier HMI Paramètre validation boutons distants local Arrêt - désactivation HMI Plage de réglages • Désactiver • Activer • Oui • Non Réglage usine Désactiver Non Vue de défilement écran HMI Paramètre Affichage HMI - état moteur Affichage HMI - date Affichage HMI - heure Affichage HMI - durée de fonctionnement Affichage HMI - nombre de démarrages par heure Affichage HMI - état E/S Ecran HMI - mode contrôle Affichage HMI - capacité thermique Affichage HMI - capacité thermique restante 72 Plage de réglages • Masqué • Affiché • Masqué • Affiché • Masqué • Affiché • Masqué • Affiché • Masqué • Affiché • Masqué • Affiché • Masqué • Affiché • Masqué • Affiché • Masqué • Affiché Réglage usine Masqué Masqué Masqué Masqué Masqué Masqué Masqué Masqué Masqué DOCA0128FR-02 Paramètres configurables Paramètre Affichage HMI - délai de déclenchement Affichage HMI - capteur température moteur Affichage HMI - température moteur en degrés CF Affichage HMI - courant moyen Affichage HMI - courant L1 Affichage HMI - courant L2 Affichage HMI - courant L3 Affichage HMI - rapport courant moyen Affichage HMI - rapport courant L1 Affichage HMI - rapport courant L2 Affichage HMI - rapport courant L3 Affichage HMI - déséquilibre courant phase Affichage HMI - courant de terre Affichage HMI - statistiques démarrage Affichage HMI - tension moyenne Affichage HMI - tension L1L2 Affichage HMI - tension L2L3 Affichage HMI - tension L3L1 Affichage HMI - déséquilibre tension phase Affichage HMI - fréquence Affichage HMI - facteur de puissance Affichage HMI - puissance active Affichage HMI - puissance réactive Affichage HMI - puissance consommée DOCA0128FR-02 Contrôleur de gestion des moteurs Plage de réglages • Masqué • Affiché • Masqué • Affiché • °C • °F • Masqué • Affiché • Masqué • Affiché • Masqué • Affiché • Masqué • Affiché • Masqué • Affiché • Masqué • Affiché • Masqué • Affiché • Masqué • Affiché • Masqué • Affiché • Masqué • Affiché • Masqué • Affiché • Masqué • Affiché • Masqué • Affiché • Masqué • Affiché • Masqué • Affiché • Masqué • Affiché • Masqué • Affiché • Masqué • Affiché • Masqué • Affiché • Masqué • Affiché • Masqué • Affiché Réglage usine Masqué Masqué °C Affiché Masqué Masqué Masqué Masqué Masqué Masqué Masqué Masqué Masqué Masqué Masqué Masqué Masqué Masqué Masqué Masqué Masqué Masqué Masqué Masqué 73 Contrôleur de gestion des moteurs Schémas de câblage Schémas de câblage Présentation Les schémas de câblage du contrôleur LTMR en mode de fonctionnement peuvent être au format IEC ou NEMA. DANGER RISQUE D'ELECTROCUTION, D'EXPLOSION OU D'ARC ELECTRIQUE • Mettez l'équipement hors tension avant toute opération. • Portez un équipement de protection individuelle adapté et respectez les consignes de sécurité électrique courantes. Le non-respect de ces instructions provoquera la mort ou des blessures graves. AVIS RISQUE DE DESTRUCTION DES ENTRÉES LOGIQUES • Raccordez les entrées du contrôleur LTMR en utilisant les trois bornes communes (C) connectées à la tension de contrôle A1 via un filtre interne. • Ne connectez pas la borne (C) commune aux entrées de tension de contrôle A1 ou A2. Le non-respect de ces instructions peut provoquer des dommages matériels. Schémas de câblage au format IEC Présentation Cette section contient les schémas de câblage correspondant aux cinq modes de fonctionnement préconfigurés : Surcharge Surveillance de la charge du moteur lorsque le contrôle (marche/arrêt) de celle-ci est assuré par un mécanisme autre que le contrôleur. Indépendant Applications de démarrage direct comprenant un moteur à 1 sens de marche, fonctionnant à la tension maximale (pleine tension) Inverse Applications de démarrage direct comprenant un moteur à 2 sens de marche, fonctionnant à la tension maximale (pleine tension) Deux étapes Applications de démarrage de moteur à tension réduite, notamment : Deux vitesses • les configurations étoile-triangle ; • les résistances primaires de transition ouverte ; • les autotransformateurs de transition ouverte. Les applications à 2 vitesses pour les types de moteurs suivants : • Dahlander (pôle conséquent) • à commutateur de polarité Chaque application est décrite individuellement, avec : 74 DOCA0128FR-02 Schémas de câblage Contrôleur de gestion des moteurs Un schéma d’ensemble de l’application Contrôle Bornier à 3 fils (par impulsion) (incluant l’alimentation et le contrôle) Trois schémas partiels Contrôle Bornier à 2 fils (maintenus) (variantes de câblage d’entrée logique de contrôle) Contrôle Bornier à 3 fils (par impulsion) fonctionnant en mode de contrôle Réseau Contrôle Bornier à 2 fils (maintenus) fonctionnant en mode de contrôle Réseau Schémas de câblage en mode Surcharge Schéma d’application avec contrôle Bornier 3 fils (par impulsion) Le schéma d’application suivant présente un câblage de contrôle Bornier à 3 fils (par impulsion) : DOCA0128FR-02 75 Contrôleur de gestion des moteurs Schémas de câblage Schéma d’application avec contrôle Bornier 2 fils (maintenus) Le schéma d’application suivant présente un câblage de contrôle Bornier à 2 fils (maintenus) : 76 DOCA0128FR-02 Schémas de câblage Contrôleur de gestion des moteurs Schéma d’application avec contrôle Bornier à 3 fils (par impulsion) fonctionnant en mode de contrôle Réseau Le schéma d’application suivant présente un câblage de contrôle Bornier à 3 fils (par impulsion) fonctionnant en mode de contrôle Réseau : N Réseau TS Bornier DOCA0128FR-02 77 Contrôleur de gestion des moteurs Schémas de câblage Schéma d’application avec contrôle Bornier à 2 fils (maintenus) fonctionnant en mode de contrôle Réseau Le schéma d’application suivant présente un câblage de contrôle Bornier à 2 fils (maintenus) fonctionnant en mode de contrôle Réseau : N Réseau TS Bornier 78 DOCA0128FR-02 Schémas de câblage Contrôleur de gestion des moteurs Schémas de câblage en mode Indépendant Schéma d’application avec contrôle Bornier 3 fils (par impulsion) Le schéma d’application suivant présente un câblage de contrôle Bornier à 3 fils (par impulsion) : Schéma d’application avec contrôle Bornier 2 fils (maintenus) Le schéma d’application suivant présente un câblage de contrôle Bornier à 2 fils (maintenus) : DOCA0128FR-02 79 Contrôleur de gestion des moteurs Schémas de câblage Schéma d’application avec contrôle Bornier à 3 fils (par impulsion) fonctionnant en mode de contrôle Réseau Le schéma d’application suivant présente un câblage de contrôle Bornier à 3 fils (par impulsion) fonctionnant en mode de contrôle Réseau : L Contrôle Bornier O Arrêt N Contrôle Réseau Schéma d’application avec contrôle Bornier à 2 fils (maintenus) fonctionnant en mode de contrôle Réseau Le schéma d’application suivant présente un câblage de contrôle Bornier à 2 fils (maintenus) fonctionnant en mode de contrôle Réseau : L Contrôle Bornier O Arrêt N Contrôle Réseau 80 DOCA0128FR-02 Schémas de câblage Contrôleur de gestion des moteurs Schémas de câblage en mode Inverse Schéma d’application avec contrôle Bornier 3 fils (par impulsion) Le schéma d’application suivant présente un câblage de contrôle Bornier à 3 fils (par impulsion) : Start FW Passe en marche directe Start RV Passe en marche inverse 1 Les contacts de verrouillage NC KM1 et KM2 ne sont pas obligatoires, car le contrôleur verrouille électroniquement les sorties O.1 et O.2. Schéma d’application avec contrôle Bornier 2 fils (maintenus) Le schéma d’application suivant présente un câblage de contrôle Bornier à 2 fils (maintenus) : FW Marche directe O Arrêt RV Marche inverse DOCA0128FR-02 81 Contrôleur de gestion des moteurs Schémas de câblage Schéma d’application avec contrôle Bornier à 3 fils (par impulsion) fonctionnant en mode de contrôle Réseau Le schéma d’application suivant présente un câblage de contrôle Bornier à 3 fils (par impulsion) fonctionnant en mode de contrôle Réseau : L Contrôle Bornier O Arrêt N Contrôle Réseau Start FW Passe en marche directe Start RV Passe en marche inverse Schéma d’application avec contrôle Bornier à 2 fils (maintenus) fonctionnant en mode de contrôle Réseau Le schéma d’application suivant présente un câblage de contrôle Bornier à 2 fils (maintenus) fonctionnant en mode de contrôle Réseau : L Contrôle Bornier O Arrêt N Contrôle Réseau FW Marche directe RV Marche inverse 82 DOCA0128FR-02 Schémas de câblage Contrôleur de gestion des moteurs Schémas de câblage étoile-triangle en mode 2 étapes Schéma d’application avec contrôle Bornier 3 fils (par impulsion) Le schéma d’application suivant présente un câblage de contrôle Bornier à 3 fils (par impulsion) : 1 Les contacts de verrouillage NC KM1 et KM3 ne sont pas obligatoires, car le contrôleur verrouille électroniquement les sorties O.1 et O.2. Schéma d’application avec contrôle Bornier 2 fils (maintenus) Le schéma d’application suivant présente un câblage de contrôle Bornier à 2 fils (maintenus) : DOCA0128FR-02 83 Contrôleur de gestion des moteurs Schémas de câblage Schéma d’application avec contrôle Bornier à 3 fils (par impulsion) fonctionnant en mode de contrôle Réseau Le schéma d’application suivant présente un câblage de contrôle Bornier à 3 fils (par impulsion) fonctionnant en mode de contrôle Réseau : L Contrôle Bornier O Arrêt N Contrôle Réseau Schéma d’application avec contrôle Bornier à 2 fils (maintenus) fonctionnant en mode de contrôle Réseau Le schéma d’application suivant présente un câblage de contrôle Bornier à 2 fils (maintenus) fonctionnant en mode de contrôle Réseau : L Contrôle Bornier O Arrêt N Contrôle Réseau 84 DOCA0128FR-02 Schémas de câblage Contrôleur de gestion des moteurs Schémas de câblage de résistance primaire en mode 2 étapes Schéma d’application avec contrôle Bornier 3 fils (par impulsion) Le schéma d’application suivant présente un câblage de contrôle Bornier à 3 fils (par impulsion) : Schéma d’application avec contrôle Bornier 2 fils (maintenus) Le schéma d’application suivant présente un câblage de contrôle Bornier à 2 fils (maintenus) : DOCA0128FR-02 85 Contrôleur de gestion des moteurs Schémas de câblage Schéma d’application avec contrôle Bornier à 3 fils (par impulsion) fonctionnant en mode de contrôle Réseau Le schéma d’application suivant présente un câblage de contrôle Bornier à 3 fils (par impulsion) fonctionnant en mode de contrôle Réseau : L Contrôle Bornier O Arrêt N Contrôle Réseau Schéma d’application avec contrôle Bornier à 2 fils (maintenus) fonctionnant en mode de contrôle Réseau Le schéma d’application suivant présente un câblage de contrôle Bornier à 2 fils (maintenus) fonctionnant en mode de contrôle Réseau : L Contrôle Bornier O Arrêt N Contrôle Réseau 86 DOCA0128FR-02 Schémas de câblage Contrôleur de gestion des moteurs Schémas de câblage d’autotransformateur en mode 2 étapes Schéma d’application avec contrôle Bornier 3 fils (par impulsion) Le schéma d’application suivant présente un câblage de contrôle Bornier à 3 fils (par impulsion) : 1 Les contacts de verrouillage NC KM1 et KM3 ne sont pas obligatoires, car le contrôleur verrouille électroniquement les sorties O.1 et O.2. Schéma d’application avec contrôle Bornier 2 fils (maintenus) Le schéma d’application suivant présente un câblage de contrôle Bornier à 2 fils (maintenus) : DOCA0128FR-02 87 Contrôleur de gestion des moteurs Schémas de câblage Schéma d’application avec contrôle Bornier à 3 fils (par impulsion) fonctionnant en mode de contrôle Réseau Le schéma d’application suivant présente un câblage de contrôle Bornier à 3 fils (par impulsion) fonctionnant en mode de contrôle Réseau : L Contrôle Bornier O Arrêt N Contrôle Réseau Schéma d’application avec contrôle Bornier à 2 fils (maintenus) fonctionnant en mode de contrôle Réseau Le schéma d’application suivant présente un câblage de contrôle Bornier à 2 fils (maintenus) fonctionnant en mode de contrôle Réseau : L Contrôle Bornier O Arrêt N Contrôle Réseau 88 DOCA0128FR-02 Schémas de câblage Contrôleur de gestion des moteurs Schémas de câblage en mode Dahlander 2 vitesses Schéma d’application avec contrôle Bornier 3 fils (par impulsion) Le schéma d’application suivant présente un câblage de contrôle Bornier à 3 fils (par impulsion) : LS Vitesse 1 HS Vitesse 2 1 Dans une application Dahlander, vous devez faire passer deux jeux de câbles à travers les ouvertures du transformateur de courant (TC). Vous pouvez également placer le contrôleur en amont des contacteurs. Dans ce cas et si le moteur Dahlander est utilisé en mode couple variable, tous les câbles en aval doivent être de même taille. 2 Les contacts de verrouillage NC KM1 et KM2 ne sont pas obligatoires, car le contrôleur verrouille électroniquement les sorties O.1 et O.2. DOCA0128FR-02 89 Contrôleur de gestion des moteurs Schémas de câblage Schéma d’application avec contrôle Bornier 2 fils (maintenus) Le schéma d’application suivant présente un câblage de contrôle Bornier à 2 fils (maintenus) : LS Vitesse 1 O Arrêt HS Vitesse 2 Schéma d’application avec contrôle Bornier à 3 fils (par impulsion) fonctionnant en mode de contrôle Réseau Le schéma d’application suivant présente un câblage de contrôle Bornier à 3 fils (par impulsion) fonctionnant en mode de contrôle Réseau : L Contrôle Bornier O Arrêt N Contrôle Réseau LS Vitesse 1 HS Vitesse 2 90 DOCA0128FR-02 Schémas de câblage Contrôleur de gestion des moteurs Schéma d’application avec contrôle Bornier à 2 fils (maintenus) fonctionnant en mode de contrôle Réseau Le schéma d’application suivant présente un câblage de contrôle Bornier à 2 fils (maintenus) fonctionnant en mode de contrôle Réseau : L Contrôle Bornier O Arrêt N Contrôle Réseau LS Vitesse 1 HS Vitesse 2 DOCA0128FR-02 91 Contrôleur de gestion des moteurs Schémas de câblage Schémas de câblage de changement de polarité en mode 2 vitesses Schéma d’application avec contrôle Bornier 3 fils (par impulsion) Le schéma d’application suivant présente un câblage de contrôle Bornier à 3 fils (par impulsion) : LS Vitesse 1 HS Vitesse 2 1 Dans une application avec changement de polarité, vous devez faire passer deux jeux de câbles à travers les ouvertures du transformateur de courant (TC). Vous pouvez également placer le contrôleur en amont des contacteurs. Dans ce cas, tous les câbles en aval des contacteurs doivent être de même taille. 2 Les contacts de verrouillage NC KM1 et KM2 ne sont pas obligatoires, car le firmware du contrôleur verrouille les sorties O.1 et O.2. 92 DOCA0128FR-02 Schémas de câblage Contrôleur de gestion des moteurs Schéma d’application avec contrôle Bornier 2 fils (maintenus) Le schéma d’application suivant présente un câblage de contrôle Bornier à 2 fils (maintenus) : LS Vitesse 1 O Arrêt HS Vitesse 2 Schéma d’application avec contrôle Bornier à 3 fils (par impulsion) fonctionnant en mode de contrôle Réseau Le schéma d’application suivant présente un câblage de contrôle Bornier à 3 fils (par impulsion) fonctionnant en mode de contrôle Réseau : L Contrôle Bornier O Arrêt N Contrôle Réseau Start LS Démarrage à la vitesse 1 Start HS Démarrage à la vitesse 2 DOCA0128FR-02 93 Contrôleur de gestion des moteurs Schémas de câblage Schéma d’application avec contrôle Bornier à 2 fils (maintenus) fonctionnant en mode de contrôle Réseau Le schéma d’application suivant présente un câblage de contrôle Bornier à 2 fils (maintenus) fonctionnant en mode de contrôle Réseau : L Contrôle Bornier O Arrêt N Contrôle Réseau LS Vitesse 1 HS Vitesse 2 Schémas de câblage au format NEMA Présentation Cette section contient les schémas de câblage correspondant aux cinq modes de fonctionnement préconfigurés : Surcharge Surveillance de la charge du moteur lorsque le contrôle (marche/arrêt) de celle-ci est assuré par un mécanisme autre que le contrôleur. Indépendant Applications de démarrage direct comprenant un moteur à 1 sens de marche, fonctionnant à la tension maximale (pleine tension) Inverse Applications de démarrage direct comprenant un moteur à 2 sens de marche, fonctionnant à la tension maximale (pleine tension) Deux étapes Applications de démarrage de moteur à tension réduite, notamment : Deux vitesses • les configurations étoile-triangle ; • les résistances primaires de transition ouverte ; • les autotransformateurs de transition ouverte. Les applications à 2 vitesses pour les types de moteurs suivants : • Dahlander (pôle conséquent) • à commutateur de polarité Chaque application est décrite individuellement, avec : Un schéma d’ensemble de l’application Contrôle Bornier à 3 fils (par impulsion) (incluant l’alimentation et le contrôle) Trois schémas partiels Contrôle Bornier à 2 fils (maintenus) (variantes de câblage d’entrée logique de contrôle) Contrôle Bornier à 3 fils (par impulsion) fonctionnant en mode de contrôle Réseau Contrôle Bornier à 2 fils (maintenus) fonctionnant en mode de contrôle Réseau 94 DOCA0128FR-02 Schémas de câblage Contrôleur de gestion des moteurs Schémas de câblage en mode Surcharge Schéma d’application avec contrôle Bornier 3 fils (par impulsion) Le schéma d’application suivant présente un câblage de contrôle Bornier à 3 fils (par impulsion) : DOCA0128FR-02 95 Contrôleur de gestion des moteurs Schémas de câblage Schéma d’application avec contrôle Bornier 2 fils (maintenus) Le schéma d’application suivant présente un câblage de contrôle Bornier à 2 fils (maintenus) : 96 DOCA0128FR-02 Schémas de câblage Contrôleur de gestion des moteurs Schéma d’application avec contrôle Bornier à 3 fils (par impulsion) fonctionnant en mode de contrôle Réseau Le schéma d’application suivant présente un câblage de contrôle Bornier à 3 fils (par impulsion) fonctionnant en mode de contrôle Réseau : H Manuel (contrôle Bornier) O Arrêt A Automatique (contrôle Réseau) DOCA0128FR-02 97 Contrôleur de gestion des moteurs Schémas de câblage Schéma d’application avec contrôle Bornier à 2 fils (maintenus) fonctionnant en mode de contrôle Réseau Le schéma d’application suivant présente un câblage de contrôle Bornier à 2 fils (maintenus) fonctionnant en mode de contrôle Réseau : H Manuel (contrôle Bornier) O Arrêt A Automatique (contrôle Réseau) 98 DOCA0128FR-02 Schémas de câblage Contrôleur de gestion des moteurs Schémas de câblage en mode Indépendant Schéma d’application avec contrôle Bornier 3 fils (par impulsion) Le schéma d’application suivant présente un câblage de contrôle Bornier à 3 fils (par impulsion) : Schéma d’application avec contrôle Bornier 2 fils (maintenus) Le schéma d’application suivant présente un câblage de contrôle Bornier à 2 fils (maintenus) : DOCA0128FR-02 99 Contrôleur de gestion des moteurs Schémas de câblage Schéma d’application avec contrôle Bornier à 3 fils (par impulsion) fonctionnant en mode de contrôle Réseau Le schéma d’application suivant présente un câblage de contrôle Bornier à 3 fils (par impulsion) fonctionnant en mode de contrôle Réseau : H Manuel (contrôle Bornier) O Arrêt A Automatique (contrôle Réseau) Schéma d’application avec contrôle Bornier à 2 fils (maintenus) fonctionnant en mode de contrôle Réseau Le schéma d’application suivant présente un câblage de contrôle Bornier à 2 fils (maintenus) fonctionnant en mode de contrôle Réseau : H Manuel (contrôle Bornier) O Arrêt A Automatique (contrôle Réseau) 100 DOCA0128FR-02 Schémas de câblage Contrôleur de gestion des moteurs Schémas de câblage en mode Inverse Schéma d’application avec contrôle Bornier 3 fils (par impulsion) Le schéma d’application suivant présente un câblage de contrôle Bornier à 3 fils (par impulsion) : F Marche directe R Marche inverse Schéma d’application avec contrôle Bornier 2 fils (maintenus) Le schéma d’application suivant présente un câblage de contrôle Bornier à 2 fils (maintenus) : F Marche directe O Arrêt R Marche inverse DOCA0128FR-02 101 Contrôleur de gestion des moteurs Schémas de câblage Schéma d’application avec contrôle Bornier à 3 fils (par impulsion) fonctionnant en mode de contrôle Réseau Le schéma d’application suivant présente un câblage de contrôle Bornier à 3 fils (par impulsion) fonctionnant en mode de contrôle Réseau : F Marche directe R Marche inverse H Manuel (contrôle Bornier) O Arrêt A Automatique (contrôle Réseau) Schéma d’application avec contrôle Bornier à 2 fils (maintenus) fonctionnant en mode de contrôle Réseau Le schéma d’application suivant présente un câblage de contrôle Bornier à 2 fils (maintenus) fonctionnant en mode de contrôle Réseau : F Marche directe R Marche inverse H Manuel (contrôle Bornier) O Arrêt A Automatique (contrôle Réseau) 102 DOCA0128FR-02 Schémas de câblage Contrôleur de gestion des moteurs Schémas de câblage étoile-triangle en mode 2 étapes Schéma d’application avec contrôle Bornier 3 fils (par impulsion) Le schéma d’application suivant présente un câblage de contrôle Bornier à 3 fils (par impulsion) : Schéma d’application avec contrôle Bornier 2 fils (maintenus) Le schéma d’application suivant présente un câblage de contrôle Bornier à 2 fils (maintenus) : DOCA0128FR-02 103 Contrôleur de gestion des moteurs Schémas de câblage Schéma d’application avec contrôle Bornier à 3 fils (par impulsion) fonctionnant en mode de contrôle Réseau Le schéma d’application suivant présente un câblage de contrôle Bornier à 3 fils (par impulsion) fonctionnant en mode de contrôle Réseau : H Manuel (contrôle Bornier) O Arrêt A Automatique (contrôle Réseau) Schéma d’application avec contrôle Bornier à 2 fils (maintenus) fonctionnant en mode de contrôle Réseau Le schéma d’application suivant présente un câblage de contrôle Bornier à 2 fils (maintenus) fonctionnant en mode de contrôle Réseau : H Manuel (contrôle Bornier) O Arrêt A Automatique (contrôle Réseau) 104 DOCA0128FR-02 Schémas de câblage Contrôleur de gestion des moteurs Schémas de câblage de résistance primaire en mode 2 étapes Schéma d’application avec contrôle Bornier 3 fils (par impulsion) Le schéma d’application suivant présente un câblage de contrôle Bornier à 3 fils (par impulsion) : Schéma d’application avec contrôle Bornier 2 fils (maintenus) Le schéma d’application suivant présente un câblage de contrôle Bornier à 2 fils (maintenus) : DOCA0128FR-02 105 Contrôleur de gestion des moteurs Schémas de câblage Schéma d’application avec contrôle Bornier à 3 fils (par impulsion) fonctionnant en mode de contrôle Réseau Le schéma d’application suivant présente un câblage de contrôle Bornier à 3 fils (par impulsion) fonctionnant en mode de contrôle Réseau : H Manuel (contrôle Bornier) O Arrêt A Automatique (contrôle Réseau) Schéma d’application avec contrôle Bornier à 2 fils (maintenus) fonctionnant en mode de contrôle Réseau Le schéma d’application suivant présente un câblage de contrôle Bornier à 2 fils (maintenus) fonctionnant en mode de contrôle Réseau : H Manuel (contrôle Bornier) O Arrêt A Automatique (contrôle Réseau) 106 DOCA0128FR-02 Schémas de câblage Contrôleur de gestion des moteurs Schémas de câblage d’autotransformateur en mode 2 étapes Schéma d’application avec contrôle Bornier 3 fils (par impulsion) Le schéma d’application suivant présente un câblage de contrôle Bornier à 3 fils (par impulsion) : Schéma d’application avec contrôle Bornier 2 fils (maintenus) Le schéma d’application suivant présente un câblage de contrôle Bornier à 2 fils (maintenus) : DOCA0128FR-02 107 Contrôleur de gestion des moteurs Schémas de câblage Schéma d’application avec contrôle Bornier à 3 fils (par impulsion) fonctionnant en mode de contrôle Réseau Le schéma d’application suivant présente un câblage de contrôle Bornier à 3 fils (par impulsion) fonctionnant en mode de contrôle Réseau : H Manuel (contrôle Bornier) O Arrêt A Automatique (contrôle Réseau) Schéma d’application avec contrôle Bornier à 2 fils (maintenus) fonctionnant en mode de contrôle Réseau Le schéma d’application suivant présente un câblage de contrôle Bornier à 2 fils (maintenus) fonctionnant en mode de contrôle Réseau : H Manuel (contrôle Bornier) O Arrêt A Automatique (contrôle Réseau) 108 DOCA0128FR-02 Schémas de câblage Contrôleur de gestion des moteurs Schémas de câblage en mode deux vitesses : enroulement simple (pôle conséquent) Schéma d’application avec contrôle Bornier 3 fils (par impulsion) Le schéma d’application suivant présente un câblage de contrôle Bornier à 3 fils (par impulsion) : L Vitesse 1 H Vitesse 2 Schéma d’application avec contrôle Bornier 2 fils (maintenus) Le schéma d’application suivant présente un câblage de contrôle Bornier à 2 fils (maintenus) : L Vitesse 1 O Arrêt H Vitesse 2 DOCA0128FR-02 109 Contrôleur de gestion des moteurs Schémas de câblage Schéma d’application avec contrôle Bornier à 3 fils (par impulsion) fonctionnant en mode de contrôle Réseau Le schéma d’application suivant présente un câblage de contrôle Bornier à 3 fils (par impulsion) fonctionnant en mode de contrôle Réseau : LS Vitesse 1 HS Vitesse 2 H Manuel (contrôle Bornier) O Arrêt A Automatique (contrôle Réseau) Schéma d’application avec contrôle Bornier à 2 fils (maintenus) fonctionnant en mode de contrôle Réseau Le schéma d’application suivant présente un câblage de contrôle Bornier à 2 fils (maintenus) fonctionnant en mode de contrôle Réseau : LS Vitesse 1 HS Vitesse 2 H Manuel (contrôle Bornier) O Arrêt A Automatique (contrôle Réseau) 110 DOCA0128FR-02 Schémas de câblage Contrôleur de gestion des moteurs Schémas de câblage en mode deux vitesses : enroulement séparé Schéma d’application avec contrôle Bornier 3 fils (par impulsion) Le schéma d’application suivant présente un câblage de contrôle Bornier à 3 fils (par impulsion) : L Vitesse 1 H Vitesse 2 Schéma d’application avec contrôle Bornier 2 fils (maintenus) Le schéma d’application suivant présente un câblage de contrôle Bornier à 2 fils (maintenus) : L Vitesse 1 O Arrêt H Vitesse 2 DOCA0128FR-02 111 Contrôleur de gestion des moteurs Schémas de câblage Schéma d’application avec contrôle Bornier à 3 fils (par impulsion) fonctionnant en mode de contrôle Réseau Le schéma d’application suivant présente un câblage de contrôle Bornier à 3 fils (par impulsion) fonctionnant en mode de contrôle Réseau : LS Vitesse 1 HS Vitesse 2 H Manuel (contrôle Bornier) O Arrêt A Automatique (contrôle Réseau) Schéma d’application avec contrôle Bornier à 2 fils (maintenus) fonctionnant en mode de contrôle Réseau Le schéma d’application suivant présente un câblage de contrôle Bornier à 2 fils (maintenus) fonctionnant en mode de contrôle Réseau : LS Vitesse 1 HS Vitesse 2 H Manuel (contrôle Bornier) O Arrêt A Automatique (contrôle Réseau) 112 DOCA0128FR-02 Contrôleur de gestion des moteurs Glossaire A analogique: Décrit des entrées (de température, par exemple) ou des sorties (telles que la vitesse du moteur) pouvant être définies sur une plage de valeurs. Par opposition à ToR. AUTOMATE: Automate programmable industriel. B Bipolaire unidirectionnel: bipolaire unidirectionnel. Commutateur qui connecte ou déconnecte deux conducteurs dans un circuit à une seule dérivation. Un commutateur bipolaire unidirectionnel (DPST) possède quatre bornes et équivaut à deux commutateurs unipolaires unidirectionnels contrôlés par un seul mécanisme, comme schématisé ci-dessous : C CANopen: Protocole industriel standard ouvert utilisé sur le bus de communication interne. Ce protocole permet la connexion de tout périphérique CANopen standard au bus îlot. D DeviceNet: DeviceNet est un protocole réseau de bas niveau orienté connexion reposant sur le protocole CAN, un système de bus série sans couche d’application définie. DeviceNet spécifie donc une couche pour l’application industrielle du protocole CAN. DIN: Deutsches Institut für Normung. Organisation européenne qui gère la création et le maintien des normes techniques et dimensionnelles. E équipement: Au sens le plus large, tout appareil électrique qui peut être ajouté à un réseau. Plus spécifiquement, un appareil électronique programmable (automate, contrôleur numérique ou robot, par exemple) ou une carte E/S. EtherNet/IP: (Ethernet Industrial Protocol) est un protocole d’application industrielle basé sur les protocoles TCP/IP et CIP. Il est principalement utilisé sur les réseaux automatisés. Il définit les équipements réseaux sous forme d’objets et permet la communication entre le système de contrôle industriel et ses composants (contrôleurs, automates programmables, systèmes I/O) DOCA0128FR-02 113 Contrôleur de gestion des moteurs F facteur de puissance: Egalement appelé cosinus phi (ou ϕ), le facteur de puissance représente la valeur absolue du rapport de la puissance active sur la puissance apparente dans les systèmes électriques CA. FLC1: Rapport du courant de pleine charge du moteur. Paramétrage FLC pour les moteurs une vitesse ou vitesse réduite. FLC2: Rapport courant pleine charge vitesse 2 du moteur. Paramétrage FLC pour les moteurs grande vitesse. FLC: courant de pleine charge. Egalement appelé courant nominal. Courant tiré par le moteur à tension et à la charge nominales. Le contrôleur LTMR comporte deux paramètres FLC : FLC1 (moteur - rapport courant pleine charge) et FLC2 (moteur - rapport courant pleine charge de moteur vitesse 2), chacun défini sur un pourcentage de FLC max. FLCmax: Courant de pleine charge maximal, paramètre de courant de crête FLCmin: Courant de pleine charge minimal. Plus petite quantité de courant moteur acceptée par le contrôleur LTMR. Cette valeur est déterminée par le modèle de contrôleur LTMR. H hystérésis: Valeur, additionnée aux paramètres de seuil inférieur ou soustraite des paramètres de seuil supérieur, qui retarde la réponse du contrôleur LTMR, avant qu'il n'arrête de mesurer la durée des déclenchements et des alarmes. I inversion thermique: Type de TCC où le délai de déclenchement initial est déterminé par un modèle thermique du moteur et varie lorsque la quantité mesurée change (le courant, par exemple). Par opposition à temps défini. M Modbus: Modbus est le nom du protocole de communication série maître-esclave/clientserveur développé par Modicon (désormais Schneider Automation, Inc.) en 1979, devenu depuis un protocole réseau standard des automatismes industriels. N NTC analogique: Type de RTD. NTC: Coefficient de température négatif. Caractéristique d’une thermistance (résistance à sensibilité thermique) dont la résistance dépend de sa température : sa résistance augmente si la température diminue, et inversement. 114 DOCA0128FR-02 Contrôleur de gestion des moteurs P PROFIBUS DP: Système de bus ouvert utilisant un réseau électrique basé sur une ligne à 2 fils blindée ou un réseau optique basé sur un câble en fibre optique. PT100: Type de RTD. PTC analogique: Type de RTD. PTC binaire: Type de RTD. PTC: Coefficient de température positif. Caractéristique d’une thermistance (résistance à sensibilité thermique) dont la résistance s’accroît avec l’augmentation de la température, et diminue avec la réduction de la température. puissance active: Egalement appelée puissance réelle, la puissance active est la quantité d’énergie électrique produite, transférée ou utilisée. Mesurée en watts (W), elle est souvent exprimée en kilowatts (kW) ou en mégawatts (MW). puissance apparente: Produit du courant et de la tension, la puissance apparente comprend à la fois la puissance active et la puissance réactive. Mesurée en voltampères, elle est souvent exprimée en kilovoltampères (kVA) ou mégavoltampères (MVA). puissance nominale: Puissance nominale du moteur. Paramètre pour la puissance produite par le moteur à tension et courant nominaux. R Rail DIN: Rail de montage en acier conçu selon les normes DIN (généralement de 35 mm de largeur). Il permet une meilleure fixation des équipements électriques IEC, notamment du module d’extension et du contrôleur LTMR. Son système d’enclenchement s’oppose aux montages à vis sur panneau de commande qui requièrent de percer et de tarauder des trous. réglage endian (big endian): big endian signifie que l’octet ou le mot de poids fort du nombre est stocké en mémoire au niveau de l’adresse la plus basse, et l’octet ou le mot de poids faible au niveau de l’adresse la plus haute (côté fort en premier). réglage endian (little endian): little endian signifie que l’octet ou le mot de poids faible du nombre est stocké en mémoire au niveau de l’adresse la plus basse, et l’octet ou le mot de poids fort au niveau de l’adresse la plus haute (côté faible en premier). rms: Valeur efficace. Méthode de calcul du courant alternatif ou de la tension alternative. Etant donné que le courant alternatif et la tension alternative sont bidirectionnels, la moyenne arithmétique de CA est toujours égale à 0. DOCA0128FR-02 115 Contrôleur de gestion des moteurs RTD: résistance détectrice de température. Thermistance (thermorésistance) utilisée pour mesurer la température du moteur. Nécessaire à la fonction de protection du moteur Capteur température moteur du contrôleur LTMR. T TCC: caractéristique de la courbe de déclenchement. Type de retard employé pour stopper le flux de courant en réponse à une condition de déclenchement. Comme c’est le cas pour le contrôleur LTMR, tous les retards de déclenchement des fonctions de protection du moteur sont à temps défini, à l’exception de la fonction de surcharge thermique qui présente également des retards de déclenchement à inversion thermique. TC: Transformateur de courant. temps de réarmement: Délai entre le changement soudain de quantité mesurée (par exemple, le courant) et la commutation de la sortie relais. temps défini ;: Type de TCC ou de TVC où le retard de déclenchement initial reste constant et ne varie pas lorsque la quantité mesurée change (le courant, par exemple). Contraire avec inversion thermique. tension nominale: Tension nominale du moteur. Paramètre pour la tension nominale. ToR: Décrit des entrées (des commutateurs, par exemple) ou des sorties (telles que des bobines) qui peuvent uniquement être en position ouverte ou fermée. Par opposition à analogique. TVC: caractéristique de déclenchement en tension. Type de retard employé pour déclencher en tension en réponse à une condition de déclenchement. Comme c’est le cas pour le contrôleur LTMR et le module d’extension, tous les TVC sont à temps défini. 116 DOCA0128FR-02 Contrôleur de gestion des moteurs Index A affichage capacité thermique.............................................72 capacité thermique restante................................72 courant de terre .................................................73 courant L1 .........................................................73 courant L2 .........................................................73 courant L3 .........................................................73 courant moyen...................................................73 date ..................................................................72 délai de déclenchement......................................73 dernier démarrage .............................................73 déséquilibre courant phase .................................73 déséquilibre tension phase .................................73 durée de fonctionnement ....................................72 entrées/sorties...................................................72 état moteur ........................................................72 facteur de puissance ..........................................73 fréquence ..........................................................73 heure ................................................................72 mode de contrôle ...............................................72 nombre de démarrages par heure .......................72 puissance active ................................................73 puissance consommée.......................................73 puissance réactive .............................................73 rapport courant L1..............................................73 rapport courant L2..............................................73 rapport courant L3..............................................73 rapport courant moyen .......................................73 température en °C ou en °F ................................73 température moteur............................................73 tension L1L2......................................................73 tension L2L3......................................................73 tension L3L1......................................................73 tension moyenne ...............................................73 affichage HMI réglage contraste ...............................................72 réglage luminosité..............................................72 sélection langue.................................................72 arrêt désactivation touche ..........................................72 Auto-test......................................................... 56–57 activer ...............................................................57 B blocage activer alarme ....................................................68 seuil d'alarme ....................................................68 seuil de déclenchement ......................................68 temporisation de déclenchement.........................68 validation déclenchement ...................................68 bornier désactivation de l’arrêt sur le bornier ...................64 C câblage Moteur - séquence des phases ...........................65 validation déclenchement ...................................65 commande effacement général ............................................45 commande locale réglage du canal ................................................64 DOCA0128FR-02 Commande locale/à distance Activation des touches........................................64 désactivation de la touche d’arrêt ........................64 mode de transfert...............................................64 Mode par défaut.................................................64 config via Activation du port réseau de l’IHM .......................44 clavier de l'HMI - activer......................................44 outil de conception HMI - activer..........................44 configuration de la communication activation via l’outil de conception........................66 activation via le clavier de l’IHM...........................66 contacteur - courant de coupure .............................63 contrôle distant réglage du canal ................................................64 sélection du canal ..............................................72 contrôleur configuration système requise.............................45 courant de terre activer alarme ....................................................67 désactiver au démarrage du moteur ....................67 miroir ................................................................63 validation déclenchement ...................................67 courant de terre externe seuil d'alarme ....................................................67 seuil de déclenchement ......................................67 temporisation de déclenchement.........................67 courant de terre interne seuil d'alarme ....................................................67 seuil de déclenchement ......................................67 temporisation de déclenchement.........................67 creux de tension miroir ................................................................70 seuil ..................................................................70 seuil de redémarrage .........................................70 temporisation de redémarrage ............................70 D de vidage Auto-test ...........................................................57 déclenchement - mode de réarmement ...................65 délestage timeout (ou temporisation) ..................................70 démarrage long seuil de déclenchement ......................................68 temporisation de déclenchement.........................68 validation déclenchement ...................................68 déséquilibre courant phase activer alarme ....................................................68 seuil d'alarme ....................................................68 seuil de déclenchement ......................................67 temporisation de déclenchement au démarrage ...68 temporisation de déclenchement en marche ........68 validation déclenchement ...................................67 déséquilibre tension phase activer alarme ....................................................69 seuil d'alarme ....................................................69 seuil de déclenchement ......................................69 temporisation de déclenchement au démarrage ...69 temporisation de déclenchement en marche ........69 validation déclenchement ...................................69 Diagnostic activer alarme ....................................................64 validation déclenchement ...................................64 117 Contrôleur de gestion des moteurs E entrée logique Entrée logique 3 pour l’état externe prêt...............64 entrées/sorties configuration des entrées logiques CA.................64 F FLCmax ...............................................................47 FLCmin ................................................................47 H HMI - couleur voyant état moteur ............................72 horloge interne ......................................................57 horodatage ...........................................................57 I introduction.............................................................9 inversion courant phase validation déclenchement ...................................68 inversion de tension de phase validation déclenchement ...................................69 M maintenance .........................................................52 dépannage ........................................................53 détection des problèmes.....................................52 maintenance préventive.........................................55 Environnement ..................................................56 Paramètres de configuration ...............................56 statistiques ........................................................56 mise en route première mise sous tension ................................45 mise en service introduction .......................................................43 Vérifier la configuration.......................................51 vérifiez le câblage ..............................................49 moteur courant à pleine charge ......................................63 courant à pleine charge - haute vitesse................63 Cycle rapide - temporisation de verrouillage .........64 étoile-triangle.....................................................62 Mode de fonctionnement ....................................62 Mode de transition .............................................63 Nombre des phases ...........................................62 puissance nominale ...........................................63 rapport courant pleine charge .............................63 rapport de courant à pleine charge - haute vitesse.............................................................63 seuil étape 1 à 2.................................................64 Temporisation de la transition..............................63 temporisation étape 1 à 2 ...................................64 tension nominale................................................63 P paramètres Configurable......................................................62 paramètres du courant pleine charge ......................47 paramètres FLC ....................................................47 perte courant phase activer alarme ....................................................68 temporisation de déclenchement.........................68 118 validation déclenchement ...................................68 perte tension phase activer alarme ....................................................69 temporisation de déclenchement.........................69 validation déclenchement ...................................69 Port HMI activer alarme ....................................................66 réglage adresse .................................................65 réglage de l’action de repli ..................................65 réglage de la parité ............................................65 réglage endian...................................................65 réglage vitesse de transmission ..........................65 validation déclenchement ...................................66 première mise sous tension....................................45 R réarmement automatique du déclenchement temporisation groupe 1.......................................65 temporisation groupe 2.......................................65 temporisation groupe 3.......................................65 tentatives groupe 1.............................................65 tentatives groupe 2.............................................65 tentatives groupe 3.............................................65 redémarrage automatique temporisation de redémarrage immédiat ..............70 temporisation du redémarrage différé ..................70 Remplacement Contrôleur LTMR ...............................................58 module d'extension ............................................58 S sous-charge en puissance activer alarme ....................................................71 seuil d'alarme ....................................................71 seuil de déclenchement ......................................71 temporisation de déclenchement.........................71 validation déclenchement ...................................71 sous-facteur de puissance activer alarme ....................................................71 seuil d'alarme ....................................................71 seuil de déclenchement ......................................71 temporisation de déclenchement.........................71 validation déclenchement ...................................71 sous-intensité activer alarme ....................................................69 seuil d'alarme ....................................................69 seuil de déclenchement ......................................68 temporisation de déclenchement.........................68 validation déclenchement ...................................68 sous-tension activer alarme ....................................................70 seuil d'alarme ....................................................70 seuil de déclenchement ......................................70 temporisation de déclenchement.........................70 validation déclenchement ...................................70 sur-facteur de puissance activer alarme ....................................................72 seuil d'alarme ....................................................72 temporisation de déclenchement.........................72 validation déclenchement ...................................71 surcharge en puissance activer alarme ....................................................71 seuil d'alarme ....................................................71 seuil de déclenchement ......................................71 temporisation de déclenchement.........................71 validation déclenchement ...................................71 DOCA0128FR-02 Contrôleur de gestion des moteurs surcharge thermique activer alarme ....................................................66 classe de moteur................................................66 déclenchement - seuil de réarmement .................66 miroir ................................................................66 seuil d'alarme ....................................................66 temporisation de déclenchement.........................66 validation déclenchement ...................................66 surintensité activer alarme ....................................................69 seuil d'alarme ....................................................69 seuil de déclenchement ......................................69 temporisation de déclenchement.........................69 validation déclenchement ...................................69 surtension activer alarme ....................................................70 seuil d'alarme ....................................................70 seuil de déclenchement ......................................70 temporisation de déclenchement.........................70 validation déclenchement ...................................70 T température moteur activer alarme ....................................................67 seuil d'alarme °C................................................67 seuil d'alarme Ω .................................................67 seuil de déclenchement Ω...................................67 seuil du capteur °C.............................................67 type de capteur ..................................................67 validation déclenchement ...................................67 temps défini ; temporisation de déclenchement du démarrage long.................................................................66 TeSys T système de gestion de moteur ..............................9 transformateur de courant de charge nombre de passages..........................................63 primaire.............................................................63 secondaire ........................................................63 transformateur de courant de fuite à la terre primaire.............................................................63 secondaire ........................................................63 DOCA0128FR-02 119 Schneider Electric 800 Federal Street Andover, MA 01810 États-Unis 888–778–2733 www.se.com Les normes, spécifications et conceptions pouvant changer de temps à autre, veuillez demander la confirmation des informations figurant dans cette publication. © 2017 – 2022 Schneider Electric. Tous droits réservés. DOCA0128FR-02 ">
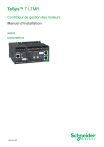
Lien public mis à jour
Le lien public vers votre chat a été mis à jour.